- Home
- Domestic appliances
- Sewing & ironing
- Sewing machines
- Artisan Home Furniture
- Toro-3000
- User manual
Artisan Home Furniture TORO-3000 Spare Parts & Instruction Manual
Add to my manuals
36 Pages
The Artisan Home Furniture Toro-3000 is a heavy-duty cylinder bed lockstitch compound needle feed walking foot stitching machine, suitable for saddle stitching, tacking, shoes, boots, saddle bags, and harnesses. It features adjustable stitch length from 0 to 11 mm, a maximum sewing speed of 800 stitches per minute, and the ability to use a wide range of thread sizes from Z-69 to 415 and #00 to #6 cord.
advertisement
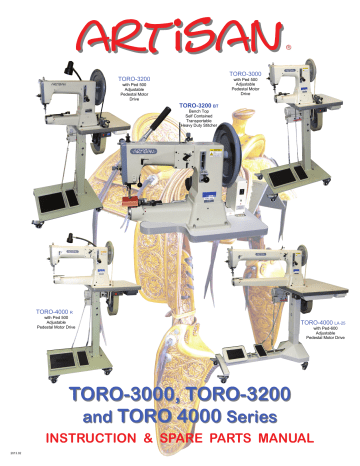
TORO-3200 with Ped 500
Adjustable
Pedestal Motor
Drive
TORO-3200
BT
Bench Top
Self Contained
Transportable
Heavy Duty Stitcher
TORO-3000 with Ped 500
Adjustable
Pedestal Motor
Drive
TORO-4000
R with Ped 500
Adjustable
Pedestal Motor Drive
TORO-4000
LA-25 with Ped-600
Adjustable
Pedestal Motor Drive
2013.02
TORO 3000, TORO
and
TORO 4000
3200
TORO 4000
Series
INSTRUCTION & SPARE PARTS MANUAL
I. Operating Instructions
B. Specifications
3.
1. CLEANING
LUBRICATION.
3.
3.
4.
HOW
6.
7. HOW TO THREAD THE MACHINE 6 and 32
9. THREAD TENSION
10. THREAD SPRING
7.
7.
11. ADJUSTING THE PRESSER FOOT PRESSURE 8.
FEED ADJUSTMENT
FOOT
8.
HEIGHT
SHUTTLE
FEED
16.
TIMING ADJUSTMENTS 9, 9
A
, 9
B
, 10, 11, 12.
II. Spare Parts List
1. COVER
3. NEEDLE BAR & UPPER FEED COMPONENTS
4. COMPONENTS
18, 19.
21.
HOOK
7.
28, 29.
ADDITIONAL INSTRUCTIONS FOR
TORO-3200 BT and TORO 4000 BT
Located on Pages 33 and 35
We Strive to Continuously Improve our Machinery. Specifications and features are constantly being updated.
Your New TORO Stitcher may look slightly different then as shown in this pamphlet.
2.
artisan
u
TORO-3000, TORO-3200 and TORO-4000
Extra Heavy Duty Cylinder Bed Lockstitch Compound
Needle Feed Walking Foot Stitching Machines.
CAUTION
…..
READ BEFORE OPERATING
THIS MACHINE...
1. Lubricate the Stitcher before operating!
2. Confirm you are plugging the electric motor into the correct rated voltage.
3. Confirm the machine and motor are turning over in a counter-clockwise rotation.
4. Your Artisan TORO machine is normally set up with an SR-2 speed reducer/transmission to controll your stitching speeds and to add additional torque to drive the needle into heavy leathers and fabrics at slow operating speeds.
5. After operating the machine for more than 25 days, if desired, the top stitching speed may be increased to a maximum speed of 800 spm.
6. Keep your hands and all clothing away from the machine when pushing the button to turn the electric motor on.
7. Switch on the Servo Motor and check for the
LED light to illuminate.
8. Always switch off the motor when finished sewing. Never leave the motor running while away from the machine.
9. Always switch off the motor before changing needles or adjusting the sewing machine.
10. The machine is a fine tool, not a toy. Do not let children operate the sewing machine.
SPECIFICATIONS
USAGE
SEWING SPEEDS
STITCH LENGTH
Saddle Stitching, Tack, Shoes,
Boots, Saddle Bags, Harness.
Normal up to 600 spm.
Max. 800 spm.
0 to 11 mm
NEEDLE
NEEDLE DIAMETER
Schmetz 794 D or 794 S for
Leather. For fabric 794
# 110 to 250
# 18 to 27
THREAD Z-69 to 415
# 00 to # 6 cord
STITCH ADGUSTING Sliding Lever with Reverse PRESSER FOOT LIFT By Hand Lifter 15 mm
By Foot Lifter 25 mm
TORO-3200
THREAD TAKE-UP
SYSTEM
Cam type thread take-up lever
NEEDLE BAR
STROKE
56 mm
LUBRICATION
MOTOR
Manual Lubrication with
Sewing Machine Oil
Electronic Servo.
3.
1.
Normal stitching operation causes dust, lint, and dirt to build up around the moving parts of your TORO-3000, 3200 and 4000. Periodically clean around all the moving parts of the machine. Pay special attention to keeping the shuttle, shuttle race, and throat plate area clean.
Simply wipe off the build-up with a clean cloth or blow off the dirt with compressed air.
2.
TORO-4000 P
Lubricate these five points through the front inspection cover.
Your new artisan u
TORO-3000 and 4000 was thoroughly lubricated at our factory. However please re-lubricate the machine before putting the new stitcher into service.
The TORO-3000 and 4000 requires lubrication at the above points on a regular basis. Artisan recommends that the machine is oiled about every 7 to 12 hours of actual usage.
We suggest the best time to oil the machine is at the end of your work day. When you begin to use the machine the next time, simply wipe off the excess oil and the dirt or lint at the same time.
4.
4.
3.
4.
SWITCH OFF THE MOTOR BEFORE REMOVING
OR INSERTING A NEEDLE
Artisan recommends that you use only “SCHMETZ” brand Needles.
For Leather use size; 794 D, 794 S, 794 LR
For Canvas, Nylon and Fabrics use size: 794
1. Turn the hand wheel counter-clockwise and raise the needle bar to its highest position.
2. Loosen the needle set screw # (1) remove the old needle and insert a new needle #2 into the needle bar. Push it up into the hole as far as it will go.
3. Remember to locate the needle scarf # (A) towards the hand wheel and the long groove of the needle to the left side.
4. Securely tighten the needle set screw # (1).
1. Turn the handwheel counter-clockwise until the needle reaches
its lowest position.
2. Place your open left hand under the Shuttle area to catch the bobbin.
3. Depressing the retaining latch #(1) will open the bobbin case.
4. Remove the bobbin being careful to leave the light weight beehive shaped bobbin push spring inside the bobbin case.
5. of a TORO-3200 and TORO-4000
5.
5.
6.
1. Pull approximately 3 to 4 inches of thread off the bobbin
and insert the new bobbin into the bobbin case so that
when turning the bobbin turns counter-clockwise.
2. Pass the thread through the slot # (A) of the bobbin case
and pull the thread until the thread passes under the
bobbin thread tension adjusting spring and rests in the
groove as pictured.
3. Leave at least 3to 5 inches of thread remaining and
hanging out beyond the bobbin case.
4. Turn the handwheel counter-clockwise, with the needle
threaded one revolution, and the bobbin thread will be
pulled up through the needle plate.
7.
A.
C.
D.
( See Back Page for Greater Detail )
B.
ar-
F.
F.
E.
G.
H.
I.
6.
1. Place your spool of thread on the “thread stand” mounted to the rear of your machines table top. Normally located on the right hand rear corner of the sewing machines table top.
2. Pull some thread off the spool and thread it though the eyelet
directly over the spool on the upper horizontal lever of the
thread stand.
3. Pass the thread directly through the first thread guide # (A)
Pull the thread over the top of the tension disks in a clockwise
fashion and make certain that the thread slips between the two
tension disks of the upper auxiliary tension assembly # (B).
4. Then place the thread back through the thread guide # (A).
5. Pull enough thread down and pass it through the middle thread wire guide # (C).
6. Wind the thread in a counter-clockwise direction around the main thread tension roller # (D) two complete revolutions and again back through the same thread guide
slightly to the right of the main tension #
# (C).
7. Then, pass the thread through the check spring #
(C).
(E) , located
8. Pull additional thread up and pass it through the eyelet of the
“Take-up” lever # (F) from the left side to the right side.
9. Then pull more thread down and pass the thread through the
mid thread guide # (G) to the left side of the screw.
10. Continue through the lower casting thread guide # (H).
11. Then through the Needle Bar thread guide # (I).
12. Lastly, pass the thread through the eye of the needle from the
left side of the needle to the right side of the needle towards
the handwheel. About 7 or 8 inches of thread should extend
beyond the needle.
Make one counter-clockwise revolution of the handwheel and pick
6. up the bobbin thread above the needle plate.
Please Hold the Bobbin and Needle Thread taughtly in one hand while beginning to stitch the first two or three stitches.
Then release and trim the excess thread.
8.
9.
Aux. Tension
Looser (B)
Tighter (A)
10.
To Adjust the Stitch Length
1. Turn the adjuster nut # (1) counter-clockwise and push the
handle in a downward direction for a longer stitch length.
1. For a shorter stitch length raise the handle and then turn the adjuster nut # (1) to lock in the handle.
2. A zero stitch length is in the middle of the slot.
The longest stitch length is at the bottom of the slot
located below #11 stamped on the face of the guide.
4. Pull the handle upwards to stitch in reverse. When the
forward stitch length and the adjuster nut are set correctly,
the machine will sew in an equal distant reverse stitch length.
5. To correctly back stitch in the same needle penetration holes; stop the machine with the needle down, then raise the needle approximately 1/4” upwards, pull the reverse handle all the way up, then make several stitches in reverse.
6. To sew forward, push the handle all the way down and sew.
Main
Tension
Adjusting the Needle Thread Tension: a. Turn the nut on the end of the Aux.
Tension shaft in a clockwise direction to increase thread tension in small amounts # (A) b. Rotate the nut counter-clockwise to decrease the thread tension. # (B) c. For a greater amount of thread tension rotate the nut on the main tension device in a clockwise direction. To loosen rotate the nut counter clockwise.
If you have thread loops on the bottom side of your work, tighten the main tension. If the thread knot is on the top side of the work loosen the main tension. For minor adjustments adjust with the aux. tension.
Adjusting the Bobbin Thread Tension: a. Loosen the locking set screw # (1) with a small screw driver. b. Turn the spring tension adjusting screw # c. Turn the adjusting screw #
(2) clockwise for greater thread tension.
(2) counter-clockwise to decrease the thread tension.
Normally one does not need to re-adjust the bobbin case thread tension unless one changes the sewing thread to a very small diameter or size.
The Standard stroke of the thread take up spring, commonly called the check spring # (1) is from
8 to 10 mm or about 3/8”.
Normally the stroke or spring tension does not require re-adjustment.
7.
11.
12.
1. The outside presser foot pressure is adjusted by
loosening nut # (3).
2. To increase the holding capacity of the Outside presser foot, turn the regulator # (1) clockwise.
3. To reduce the holding pressure, turn the regulator
Counter-clockwise. Be care not to fully unscrew the
regulator. It is spring loaded and will “pop” out.
4. Tighten the locking nut # (3).
The standard height of the presser foot regulator
from the casting to the top of the regulator screw is about 5/8” to 3/4”.
# (1)
For Leather Stitching: The Feed Dog used in artisan models
TORO-3000, 3200 & 4000 R is smooth, without teeth so not to damage your leather. The TORO-4000 LA-25 and TORO 4000 P may use a different system.
For Fabric Stitching: All models should use a course tooth feed dog.
To adjust the height of the feed dog:
Either of the two methods are possible.
1. Open the bobbin case to reveal the feed dog attaching screw.
2. Loosen quired. the
3. Re-tighten the fed dog attaching screw.
OR a second method is to do the following:
3. Loosen and remove the two screws and small springs # (1) that hold the oscillating shuttle/bobbin case in place.
4. Remove the shuttle race and bobbin case from the casting and reveal the feed dog attaching screw.
5. Remove the Feed Dog attaching screw and Feed Dog to
install any of the following except the standard needle plate.
Slotted Needle Plate (A) #43332 Stirrup Needle Plate (B) #43333
Holster Needle Plate (C) #43334 Standard Needle Plate (D) #43337
Fabric Feed Dog w/teeth (E) 211-63400
Leather Needle Plate (F) 43337-L
Leather Smooth Feed Dog (G) 21163400-L
C.
F.
A. G.
8.
B. D.
E.
Needle
Needle
Guard Shuttle Hook
Point
Shuttle Hook
Race Carrier
Frame
Shuttle Hook
Assembly with Bobbin Case
A. Complete Oscillating Shuttle
Hook Assembly with Bobbin Case.
B. Shuttle Hook Point.
C. Bobbin Thread Tension
Adjusting Screw.
D. Bobbin Thread Tension Adjusting
Locking Set Screw.
E. Bobbin Thread Tension Spring.
F. Bobbin Case.
G. Bobbin Case Opener Latch.
A.
D.
F.
G.
Photos Not To Scale. For Representation Purposes Only.
Page 9
Shuttle Hook
Driver
B.
C.
E.
Shuttle Hook
Point
B.
Needle
Guard
Shuttle Hook Point to the Needle Relationship as viewed from behind the needle on the rear left side, and from left to right.
Shuttle Hook
Point
B.
Shuttle Hook
Point
B.
Shuttle Hook
Race
C.
Needle
Needle
Guard
Shuttle Hook Point to the Needle Relationship as viewed from behind the needle and from the right to left side.
Bobbin Case
Opener Latch
G.
Shuttle Hook
Driver
E.
SHUTTLE TO NEEDLE RELATIONSHIP:
Correctly Timing the Needle with the motor switched off.
Set the Stitch Length Lever to the “0” Position. Then turn the Handwheel in a counter-clockwise rotation and raise the needle bar from “Bottom-Dead-Center”, the lowest position, up 4 mm or 5/32. The Shuttle Hook Point should now be directly behind and in the center of the Needle just above eye of the needle.
At 4 mm up, the measurement from the bottom of the needle clamp to the top of the standard needle plate
#
43337 should be at 31 mm or 1-7/32”.
Page 10
To Adjust the height of the walking feet:
(6) and move the lever # (7) up to
Decrease the walking foot height. (B)
2. Move the lever # (7) down in slotted bracket # (8)
to Increase the walking foot height. (A)
3. Tighten the nut # (6) after completing the adjustment.
14. ADJUSTING THE NEEDLE-TO-SHUTTLE RELATIONSHIP
Fig. 14-1
Needle End
Fig. 14-2
C.
D.
Shuttle
Hook
B.
E.
Oscillating
Shuttle Hook
Driver
A.
Thread Cast-off Area.
Normal timing adjustment of the shuttle hook.
1. Turn the handwheel counter-clockwise until the
oscillating shuttle hook is positioned to the fullest
most left position of its travel with the needle at the
“Bottom-Dead-Center” of its travel (fully down).
2. The point of the oscillating shuttle hook
steel shuttle hook race # (C).
# (B).
should then be equal to 1 mm with the end of the
See Pages 9 and 10.
To Adjust the position of the oscillating shuttle hook.
1. Open the front inspection plate cover; located under
the stitch length regulator lever on the front of the
TORO machines’ casting.
2. Insert a 6 mm Allen wrench into the adjusting screw
#
(2) and loosen the screw slightly. It is very T IGHT !
3. Fully loosen the Allen screw and rotate the shuttle
hook either clockwise or counter-clockwise to align
the shuttle hook correctly as shown in Fig. 14-1.
4. Remember to firmly tighten the Allen screw #
you have accomplished the adjustment.
(2) when
Front of Machine
Right Side
Hand Wheel
Shuttle Hook
Point
At a 4 mm rise of the
Needle bar from the lowest position.
Set Hook point to center of the needle.
4 mm
Needle Bar Height Setting: 27 mm
Bottom-Dead-Center or Lowest point of Needle Clamp to the top of the Throat Plate.
31 mm
Fig. 14-3
11.
To adjust the needle bar height and timing relationship:
1. Set the stitch length lever to the “0” position.
2. Turn the handwheel counter-clockwise until the needle
bar is at its lowest position (bottom-dead-center).
3. Continue turning the handwheel in a counter-clockwise
rotation and raise the needle bar up exactly 4 mm or
approximately 5/32” up from “bottom-dead-center”.
The point of the shuttle hook # (3) should exactly
bisect the center of the needle, and be approximately
in the center of the needle, just above the eye of the
needle and at the bottom 1/3 of the needle scarf.
This adjustment is crucial to form a proper stitch.
4. At this point, the bottom of the needle bar should be exactly 31mm or 1-7/32” above the top surface of the standard needle plate
#
43337.
Hand
Wheel
Side
Fig. 14-4
At a 4 mm rise of the
Needle bar from the lowest position.
Set Hook point to center of the needle.
Fig. 14-5
Fig. 14-6
Fig. 14-7
The Clearance between the
Shuttle Hook Point and the
Needle should be about the thickness of a piece of paper.
0.25mm to 0.35 mm
Upper Rear
Inspection Cover
The Shuttle Hook Point should be in the center of the needle and aprox.
2 mm above the top of the eye of the needle.
2 mm
Adjusting the Needle to Shuttle Position
1. Loosen the small Allen head screw # 6.
Then lightly snug the screw.
2. Loosen the two 6 mm Allen head screws # 5.
3. With the stitch length lever set to the “0” position, turn
the hand wheel in a counter-clockwise rotation and place
the needle bar to the “Bottom-Dead-Center” position.
At this point align Allen Screw # 6 to the 9:00 O’clock
position and in the same plane as the line “D”
shown in Fig. 14-4.
4. Tighten the small Allen screw # 6
5. Firmly tighten the larger Allen screws equally.
First a little pressure on the right side screw. Then about
the same pressure on the left side screw.
Repeat this procedure in three or four steps until the two
screws are TIGHT.
Setting the Height of the Needle Bar
Set the needle bar height on the TORO-3000, 3200,
4000R or 4000 P as shown in Fig 14-5 at
#
(A).
The point of the shuttle hook should be set to the center
of the needle after the needle rises up 4 mm from the
“Bottom-Dead-Center” position .
To adjust the Height of the Needle Bar
Method 1
1. Turn the Handwheel in a counter-clockwise rotation
until the shuttle hook point is aligned with the center
of the needle.
2. Loosen Screws # 7 in Fig. 14-6.
3. Move the Needle Bar in an up or down fashion to align
the needle to the position in Fig. 14-5
4. Firmly tighten the 2 screws # 7 Fig. 14-6.
Method 2
1. Turn the Handwheel in a counter-clockwise rotation until
Needle is at “Bottom-Dead-Center”.
Screws 7 in Fig. 14-6.
3. Align the needle so that the bottom of the needles eye is just above the “Needle Guard” shown on page 9
B
with enough room for the thread to pass through the needle eye.
4. Firmly tighten the 2 screws # 7 Fig. 14-6.
Front/Back Needle to Shuttle Clearance
The clearance between the needle SCARF (recess) and the point of the shuttle hook is set at the factory between 0.25 mm and 0.35 mm depending on the diameter of the needle used.
Clearance should not normally require adjustment. However, several optional Spacer Plates shown on page 24 with part number reference # 6-44 are available for purchase if desired.
12.
13.
15.
794 (D or S) NM 200, # 25 Needle
The above adjustments are for stitching normal fabrics and do not
apply to stitching heavy leathers for the TORO-3000 or 4000 R.
Leather machines are specially adjusted for each application.
The standard adjustments are only a starting point.
14.
16.
1. The thread breaks or tends to fray and
then break.
1. A burr, cut, ruffness, or other imperfection was created on the needle plate, shuttle, shuttle race or presser foot by a broken or damaged needle.
1. Clean off and remove the flaw with a fine
India stone or other abrasive.
2. Loosen the upper thread tension.
3. Always use a good quality pre-lubricated left
2. Needle thread tension excessively tight.
3. Poor quality or incorrect thread size.
4. Machine is out of synchronization.
5. Excessive needle heat build-up. twist sewing thread like “Rice” brand threads.
4. Check and if necessary re-time the machine.
5. Add an additional silicone thread lubrication system to your machine.
6. Replace your needle with a new “Schmetz” brand quality sewing needle.
Skipped Stitches
3. Improper thread tension,
irregular looking
stitches, or excessive
bobbin thread tension.
1. The needle is too far away from the shuttle hook point.
2. The shuttle hook timing is set too fast or too slow in relationship to the needle.
3. The leather or fabric “jumps” up with the
Needle. (called flagging)
4. Bent needle, dull point, or improper needle
diameter size for the leather sewn.
5. The check spring tension is too hard or too soft.
6. The check spring travel is too long or too short for the fabric sewn.
7. The needle has overheated, lost temper or is dull or worn out.
8. Excessive thread fraying or wear.
1. See Chapter 14, Adjusting the Needle-to-Shuttle
Relationship.
2. See Chapter 14, Adjusting the Needle-to-Shuttle
Relationship.
3. Tighten the presser bar adjuster screw.
4. Replace with a new and correctly sized needle.
5. Decrease the check tension.
6. Adjust the check spring travel for the weight of the
fabric or leather being sewn.
7. Replace the needle with a Schmetz brand # 794 Needle
Inferior quality needles cause problems.
8. Replace poor quality thread with RICE or Artisan
“Premium Performance Leather Stitching Thread”
from Artisan Sewing Supplies. 888 838 1408
1. Worn out thread guides.
2. The bobbin jams.
3. Weak bobbin thread tension.
4. Bobbin thread is wound to tightly.
5. Bobbin thread showing on top of fabric or leather
6. Loops showing on the bottom of the leather or
Fabric.
1. Repair the guide or replace with a new thread guide.
2. The bobbin may be bent or otherwise damaged.
Replace the bobbin.
3. Tighten the bobbin thread tension, Chapter 9
4. Loosen the tension on the bobbin winder
5. Loosen the Needle Thread Tension, Chapter 9
6. Tighten the needle thread tension, Chapter 9
4. Excessive Thread Abrasion
5. Stitches are out of line
or do not track straight.
1. Worn out or Incorrect needle size
1. Incorrect point for the leather being sewn.
2. Dull or blunt needle point.
1. Replace the Needle
1. Replace your needle with one with the correct
cutting point for the type of leather being sewn.
Read and understand the Schmetz Leather Needle
Pamphlet available from Artisan 888 838 1408
6. The bobbin thread
tension will not adjust.
1. Lint or debris trapped under the bobbin case
spring tension.
1. Remove the bobbin case spring and clean out the
Debris.
7. The v-belt from the
SR-2 speed controller is
slipping or the hand
wheel does not turn
when the motor is
fully engaged
1. The v-belt has stretched.
2. The v–belt is worn out
3. The machine is jammed.
When in doubt….
Call artisan
u
for Help! 888-838 1408
15.
1. Lower the SR-2 Speed controller.
Make the belt tension tighter.
2. Replace the v– belt
3. Clean out the foreign blockage. Perhaps a small piece of thread is trapped in the shuttle raceway.
1/4” to 3/8”
SR-2 Pulley
SUGGESTED
REFERENCE GUIDE FOR
artisan
u
TORO 3000, 3200, 4000
R
, 4000
P
LEATHER STITCHING MACHINES
Recommended Schmetz brand Needle
#
794
1. Sewing on Thin Leathers of less than 8 oz. or up to1/8”:
Use Schmetz brand Needles number 794 D or S, NM:160 Size 23, Canu 53:20MF1.
“D” is a Triangle Leather Point and “S” is a Spear Point for leather.
Under normal conditions the “D” points will last longer and the “S” point needles have a shorter
life span but will make a straighter stitch.
We recommend using thread sizes 69, 138, or 207. Size 277 might be to heavy.
The same size thread as in the needle or one size smaller for the bobbin thread will give you more yield from the bobbin.
2. Stitching Leathers from 8 oz. to 12 oz or from 1/8” to 3/16”:
Use Schmetz brand Needles number 794 D or S, NM:160 or 180, Size 23 or 24, Canu 53:20MF1.
“D” is a Triangle Leather Point and “S” is a Spear Point for leather.
We recommend using thread sizes 138, 207, or 277 and either the same size thread as in the needle or one or two sizes smaller thread in bobbin is recommended.
3. Leather from 12 oz to 16 oz., 3/16'” to 5/16”:
Use Schmetz brand Needles number 794 D or S, NM:180 or 200, Size 24 or 25, Canu 53:20MF1.
We recommend using thread sizes 207, 277, or 346 and either same size thread as in the needle or one or two sizes smaller thread in bobbin for additional yield.
4. When stitching multiple plies of Leather beyond 7/16,” we recommend the use of Schmetz brand
794 “D” point needle of at least a diameter of # 25 (200). Any size thread may be used. However, the use of 207,
277, or 346 is recommended in the needle and one or two sizes smaller thread in the bobbin.
NOTE:
Your Bobbin Thread tension will require readjustment when using smaller thread diameters such as size 69 or 138 in the bobbin.
SADDLE SKIRTING: 794 D # 25 (200) Needle
Thread 277 or 346 in the Needle
138, 207, OR 277 in the Bobbin
HOLSTERS: 794 D # 25 (200) NEEDLE
Thread 207 or 277 in the Needle
138, 207 or 277 in the Bobbin
CHAPS: 794 S # 24 (180) Needle
138 or 207 in the Needle
HARNESS: 794 D
Thread 207, 277, or 346 in the Needle
138, 207 or 277 in the Bobbin
SHEATHS: 794 D
#
#
24 (180) or #
24 (180) or #
25 (200) Needle
25 (200) Needle
Thread 207, 277, or 346 in the Needle
138, 207, 277 in the Bobbin
BELTS: 794 D # 24 (180) Needle
Thread 138 or 207 in the Needle
138 or 207 in the Bobbin
PURSES: 794 D # 24 (180) Needle
138 or 207 in the Needle
138 or 207 in the Bobbin
MENUS, CHECKBOOKS, BOOK JACKETS, etc
Round Point Needles 794 # 22 (140)
138 or 207 in the Bobbin
NOTE:
Thread 69 or 138 in the Needle and Bobbin.
Change your needle to a non leather point needle when stitching fabrics other than leather. artisan recommends using a Schmetz brand # 794 size 22, 23, or 24 needle on Canvas, Upholstery Fabrics, or Webbing.
For Stitching “Bio-Plastics” use a needle 2 diameters larger than for leather. You must replace the leather presser feet, feed dog and needle plate with a “Blanket Set” for stitching on other than leather. artisan strongly recommends replacing your needle every 8 to 10 hours of actual stitching!
Leather Point Needles are like “knives”. They get dull and require replacement.
Cutting point needles create significant heat going through heavy leather. Needles lose their temper (hardening) with heat and that leads to bending or broken needles. A broken needle may cause damage to your machine.
The potential damage to both your project and your machine will far outweigh the approximately $ 1.
00
Cost of replacing a damaged needle. Think of it a affordable preventative maintenance.
16.
Spare Parts
List
artisan
TORO-3000,
TORO-3200 and
TORO-4000 u
17.
1. FRAME AND COVER COMPONENTS
18.
2. MAIN SHAFT COMPONENTS
19.
Page 20.
18.
69
A.
21.
4. PRESSER BAR COMPONENTS
22.
4.
OUTSIDE PRESSER FOOT WITH TEETH FOR FABRICS
A . 43423
B. 43424
C.
43425
D. 43426
E. 43405
F. 43406
G. 43424S
H. 43425S
Center Grover Leather Presser Foot
Left Side Leather Presser Foot
Right Side Leather Presser Foot
Double Toe Leather Presser Foot
Double Toe Presser Foot with Teeth for Fabric or Webbing (aka Blanket)
Center Presser Foot with Teeth for Fabric or Webbing (aka Blanket)
Short Toe, Left Side Leather Presser Foot
Short Toe, Right Side Leather Presser Foot
E
D
B C
G
A page 23.
H
F
24.
5.
25.
6. Hook Driving Shaft Components
H.
G.
A
E.
F.
C
B
D
Shuttle Hook Parts
184
Locking Set Screw.
164
Thread Tension Adjusting
Screw.
C. GW 113
Thread Tension Spring.
D. GW 114
Bobbin Push-out Spring.
E. GN
Bobbin Case Body.
F. GN 112
Shuttle Body.
G. GW 112
Bobbin Case Opening Spring.
H. GN 114
Bobbin Case Body
Latch.
I. GS 120
Bobbin Case Body Latch
Screw.
26.
6.
OSCILLATING SHUTTLE HOOK
SPACER
27.
28.
7.
29.
8. BOBBIN WINDER AND THREAD GUIDE COMPONENTS
30.
8.
31.
32.
1.
TORO-3000 Bobbin Winder Instructions:
1. Place the bobbin on the spindle. Align the small pin on the spindle
with the hole or slot in the bobbin.
2. Insert the thread into the eye above the bobbin winder tension.
3. Pull the thread between the two tension discs in a clockwise fashion.
4. Continue pulling the thread over to the bobbin and place the thread through the small hole on the right side of the bobbin and thread it from the inside of the bobbin to the outside of the bobbin.
Leave about 3 or 4 inches outside the bobbin. Trim the excess after the
bobbin is wound.
5. Push the Latch up against the center of the bobbin.
6. Operate the machine and the bobbin will begin to fill.
Several bobbins can be wound while the machine is in operation.
If the thread is wound too loosely, tighten the tension nut, if too tight, loosen the nut.
33.
34.
artisan
u
TORO-3200 BT and TORO-4000 BT
A
artisan
u
TORO-3000, 3200 and 4000 T
HREADING
B
H
B
C
D
G
E
F
C
Insert the thread through the upper wire thread guide ( A ) , then around the top tension (auxiliary tension) in a clockwise rotation between the 2 disks, one revolution and back up to the same wire thread guide ( A ).
Bring the thread down and insert it into the main tension thread guide ( B ) as shown. Then wind your thread in a counter-clockwise rotation 2 full revolutions around the main tension rotary disk, and then back up through the same thread guide ( B ) a second time.
Next pass the thread through the hole in the “check spring” ( C ) . Then pull the thread up and pass it through the hole in the take-up lever ( D ) from the left side to right hand side. The lever moves up and down. Then pass the thread down and through the left side of lower middle thread guide ( E ).
Next pass the thread through the lower wire thread guide ( F ) and through the thread guide hole in the bottom of the needle bar ( G ).
Lastly pass the thread through the eye of the needle ( H ) from the left to to right side towards the hand wheel.
Always leave about 6 to 10 inches of thread beyond the needle.
Remember to hold the bobbin and needle threads tightly while stitching the first few stitches.
See Page 6 for Another View of
Correct Threading Instructions
36.
advertisement
* Your assessment is very important for improving the workof artificial intelligence, which forms the content of this project