Bandit SG-40 Operating & Parts Manual
Add to my manuals
92 Pages
Bandit SG-40 is a professional-grade stump grinder designed for efficient and safe stump removal. Its powerful engine, robust construction, and advanced features make it an ideal choice for landscapers, arborists, and homeowners alike.
The SG-40 is equipped with a heavy-duty cutter head that can grind stumps up to 12 inches in diameter, making it suitable for a wide range of stump removal tasks. The hydraulic lift system provides effortless height adjustment, allowing you to easily maneuver the grinder over uneven terrain and stumps of various heights.
With its intuitive controls and safety features, the Bandit SG-40 is easy to operate and maintain, ensuring a productive and safe work environment.
advertisement
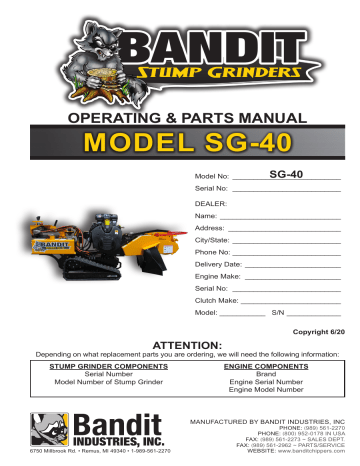
OPERATING & PARTS MANUAL
MODEL SG-40
Serial No: __________________________
DEALER:
Name: _____________________________
Address: ___________________________
City/State: __________________________
Phone No: __________________________
Delivery Date: _______________________
Engine Make: _______________________
Serial No: __________________________
Clutch Make: ________________________
Model: ___________ S/N _____________
Copyright 6/20
ATTENTION:
Depending on what replacement parts you are ordering, we will need the following information:
STUMP GRINDER COMPONENTS
Serial Number
Model Number of Stump Grinder
ENGINE COMPONENTS
Brand
Engine Serial Number
Engine Model Number
6750 Millbrook Rd. • Remus, MI 49340 • 1-989-561-2270
MANUFACTURED BY BANDIT INDUSTRIES, INC
PHONE: ( 989 ) 561-2270
PHONE: ( 800 ) 952-0178 IN USA
FAX: ( 989 ) 561-2273 ~ SALES DEPT.
FAX: ( 989 ) 561-2962 ~ PARTS/SERVICE
WEBSITE: www.banditchippers.com
CALIFORNIA PROPOSITION 65
!
WARNING
!
ADVERTENCIA
Breathing diesel engine exhaust exposes you to
chemicals known to the
State of California to cause cancer and birth defects or other reproductive harm.
Respirar gases de escape de diesel le expone a
qu Í micos conocidos por el estado de California como causales de cáncer y defectos congénitos u otros daños reproductivos.
• Always start and
operate the engine in a
well-ventilated area.
• If in an enclosed area, vent the exhaust to the outside.
• Do not modify or tamper with the exhaust system.
• Do not idle the engine
except as necessary.
• Siempre encienda y opere el
•
For more information go to: www.P65warnings.ca.gov/diesel
motor en áreas bien ventiladas.
• Si está en un área cerrada,
ventile escape hacia el exterior.
No modifi que ni altere el
sistema de escape.
• No deje el motor en ralent ser que sea necesario.
Í a no
Para mayor informaci Ó n visite: www.P65warnings.ca.gov/diesel
SPW-46 8/18
!
!
WARNING
ADVERTENCIA
Cancer and
Reproductive
Harm
Cáncer y daño
reproductivo
www.P65warnings.ca.gov
SPW-47 8/18
WARRANTY VALIDATION FORM
(STUMP GRINDER)
IMPORTANT - WARRANTY WILL BE DEEMED NULL AND
VOID IF THIS FORM IS NOT FILLED OUT COMPLETELY AND
ACCURATELY AND RETURNED TO THE CUSTOMER DATA
DEPARTMENT WITHIN 10 DAYS OF EQUIPMENT DELIVERY
PURCHASER / OWNER INFORMATION:
Customer Data Department
6750 Millbrook Road
Remus, MI, USA 49340
Phone: (800) 952-0178 in USA
Phone: (989) 561-2270
Fax: (989) 561-2273
Website: www.banditchippers.com
Company Name __________________________________ Contact Name _____________________
Mailing/Street Address _______________________________________ City _______________________
State ___________________ Zip Code _______ Country ______________ Telephone Number ( __ ) ________
E-mail ____________________________ Machine Model No. _______ Date Put Into Service ______
Machine Serial No. ____________________ Machine Work Order No. ________ Machine Hours _______
Engine Make _________________ Engine Serial No. __________________ Machine Color _______
DEALER / SELLER INFORMATION:
Dealer/Seller Name _______________________________ Contact Name _____________________
Mailing/Street Address _______________________________________ City _______________________
State ___________________ Zip Code _______ Country ______________ Telephone Number ( __ ) ________
1. _____ The customer has received instruction and fully understands all operational, safety and maintenance requirements of the equipment.
2. _____ The customer has received instruction and fully understands that everyone within 100 feet of the machine must wear proper personal safety equipment including hard hat, face shield, safety glass, gloves, ear protection and/or other items per OSHA and ANSI requirements.
3. _____ The customer has received instruction and fully understands the equipment maintenance schedules and procedures.
The customer understands that it is their responsibility to perform scheduled maintenance that includes periodic relief valve
adjustments,retighteningallfastenersasneeded,periodiccleaningofflowdivider,clutchandbeltadjustments,andotheritems.
4. _____ The customer has received instruction and fully understands not to reach near the cutter head with hands or feet ortobelocatedneardebrisfieldwithenginerunning.
5. _____ The customer has received instruction and fully understands that the operators must always be located within easy reach of all control and shut down devices.
6. _____ The customer has received instruction and fully understands to not start grinding a stump without checking for power lines, water lines, sewer lines, phone lines, etc.
7. _____ The customer has received instruction and fully understands the purpose of and how to operate the shut down/shut-offdevices,andwillnotattempttooverrideanysafetydevicesorguards.
8. _____ The customer has received instruction and fully understands that before performing any maintenance on the machine the ignition key must be removed, the cables must be completely disconnected from the battery, the cutter head must have come to a complete stop, and the cutter head lock must be installed. The customer understands they must allow the necessary time for the cutter head to come to a complete stop before opening the cutter head guard or start any maintenance or service procedures. If applicable the customer has received instruction and fully understands the purpose of the beltshield inspection hole and that they are never to attempt any maintenance or service procedures until visually confirmingthebeltshavecometoacompletestop.
9. _____ The customer has received instruction and fully understands the machine is not to be operated without the factory approved cutter head guard in place, the machine is not to be operated with any type of make shift cutter head guard, and the machine is not to be operated under any circumstances with the cutter guard open or unsecured.
10. _____ The customer has reviewed and fully understands limited warranty, and all written and visual instructions.
11. _____ The customer has received instruction and fully understands that warranty will not apply if the machine is operated with replacement parts or equipment not manufactured or recommended by Bandit Industries, Inc.
12. _____ The customer has received, been advised, and understands the manuals, and the Safety/Service video supplied with the grinder. A video is supplied for equipment models as available.
13. _____ All Danger, Warning and Operational decals are properly displayed on equipment and fully understood by customer.
14. _____ The customer has been instructed, understands, and agrees that all potential operators must: See the supplied video, be instructed on all the Danger, Warning and Operational decals, read the manual and follow the procedures.
I have inspected this equipment and find it in correct working condition. To the best of my knowledge, the customer and his/her personnel are aware of, and agree to the above procedures.
Signed: ________________________________________________________ Date: ______________
(Dealer Representative)
The equipment has been thoroughly checked by the above named dealer representative, and I am satisfied with his/her instructions. I have also read, understand, and agree to reverse side of page.
Signed: ________________________________________________________ Date: ______________
Copyright 2/17 FORM #WV-124
(Customer)
Copyright 2/17 FORM #Q-112
TO BE RETURNED AFTER THIRTY (30)
DAYS OF OPERATION
DATE PURCHASE: ______________________
MODEL: ________________________________
Please return to: Customer Data Department
6750 Millbrook Road
Remus, MI 49340
SERIAL NUMBER: _______________________
DEALER NAME: ________________________
Phone: (800) 952-0178 in USA
Phone: (989) 561-2270
Fax: (989) 561-2273
Website: www.banditchippers.com
_______________________________________
STUMP GRINDER QUALITY REPORT
All of the employees that build your equipment strive to manufacturer the very best quality product on themarket.Wewouldappreciateyoureffortsinlettingusknowhowwearedoing.
Wewouldlikeyoutooperateyourmachineforthirty(30)daysandthenfilloutthisquestionnaireandmailittous.
This will help us to keep producing a good product and improving our products through your recommendations.
1. Did your machine perform to your expectations? _______________________________________
2. Was the machine delivered on schedule? _____________________________________________
3. Wasthepaintcolorandfinishtoyoursatisfaction?______________________________________
4. Was machine equipment as ordered? ________________________________________________
5. Did all welds appear to be high quality? ______________________________________________
6. Was the overall machine to your liking? ______________________________________________
7. What problems have you experienced? ______________________________________________
8. Have any components regularly loosened that caused problems? __________________________
9. Does the hydraulic system seem to have adequate power? ______________________________
10. Is the machine manufactured to accommodate service in an adequate manner? If not, please explain:
_______________________________________________________________________________
11. General comments and/or suggestions: ________________________________________________
_______________________________________________________________________________
_______________________________________________________________________________
12. Would you like to be contacted concerning more of our equipment? ________________________
YOUR COMPANY: ________________________________
NAME: __________________________________________
ADDRESS: ______________________________________
CITY: ___________________________________________
STATE & ZIP: _____________________________________
PHONE: ( ____ ) _________________________________
E-MAIL: _________________________________________
1
MODEL SG-40
TABLE OF CONTENTS
TABLE OF CONTENTS
Serial Number Locations ...........................................................................................5
Safety Procedures ......................................................................................................6
Equipment Specifications
........................................................................................10
Controls .....................................................................................................................11
Machine Operation ...................................................................................................14
Transportation Procedures......................................................................................16
Maintenance ..............................................................................................................18
Hydraulics .................................................................................................................29
Replacement Parts ...................................................................................................33
Decals .................................................................................................................34
Engine Side ........................................................................................................36
Cutter Wheel Side ..............................................................................................38
Green Teeth Cutter Wheel .................................................................................40
New River “Revolution” Cutter Wheel .............................................................41
Frame ..................................................................................................................42
Swing Out Console ............................................................................................44
Fuel & Hydraulic Tank........................................................................................46
Service Record .........................................................................................................48
Ogura Clutch Manual ...............................................................................................49
Bandit
MODEL SG-40 SERIAL NUMBER LOCATIONS
TYPICAL SERIAL NUMBER AND/OR
WORK ORDER NUMBER LOCATIONS
1
2
1. Serial Number on top of frame near the
bulkheads or between the tracks on the frame.
2. Work Order Number on top of frame near the
bulkheads or between the tracks on the frame.
NOTICE
The engine information is located on the
engine block.
5
Bandit
MODEL SG-40 SAFETY PROCEDURES
INTRODUCTION
The purpose of this manual is to provide the user withspecificationsandproceduresfortheoperation,
maintenance and repair of this BANDIT product. As with any piece of equipment, safety should always be a constant thought while the machine is being operated, serviced or stored. In order to highlight this
consideration, the material which addresses safety is proceeded by the following signal words:
DANGER
DANGER indicates a hazardous situation which, if not avoided, WILL result in death or serious injury
(contains white letters on red background).
WARNING
It is the responsibility of the owner or employer to ensure that the operator is trained and practices safe operation while using and servicing the machine. It is also the owner’s responsibility to
provide and follow a regularly scheduled preventative maintenance and repair program on the product, using only factory approved replacement parts. Any unapprovedrepairsormodificationsmaynotonly damage the machine and its performance, but could result in severe personal injury. Unapproved repairs or modifications will void warranty and eliminate manufacturer of any liability claims. Consult the equipment manufacturer with any questions.
WARNING
WARNING indicates a hazardous situation which, if not avoided, COULD result in death or serious injury (contains black letters on orange background).
CAUTION
CAUTION indicates a hazardous situation which, if not avoided, COULD result in minor or moderate injury (contains black letters on yellow background).
Each machine is shipped with a manual, a customer’s check sheet on the product, and any
available parts & service manuals on component parts not produced by this manufacturer. Additional copies of these manuals and check sheets can be purchased from the manufacturer, or through the dealer. Engine parts, service and maintenance manuals MUST be purchased through the engine manufacturer or their dealer.
NOTICE
NOTICE indicates information considered important, but not hazard related (contains white italic letters on blue background).
NOTICE
The producer of this Bandit product reserves therighttomakeanymodificationsorrevisionsto thedesignorspecificationsofitsmachinewithout advance notice. The producer also reserves the right to change machine and part prices as needed without advance notice.
SAFETY INSTRUCTIONS
SAFETY INSTRUCTIONS indicate general instructions relative to safe work practices and reminders of proper safety procedures (contains white italic letters on green background).
The equipment is designed and manufactured in accordance with the latest product industry
standards. This alone does not prevent injury. It is the operator’s responsibility to use good judgement and follow the warnings and instructions as indicated in this manual, on the machine and follow all safety
standards per ANSI and OSHA instructions.
WARNING
Improper use of the product can result in severe personal injury. Personnel using the equipment must bequalified,trainedandfamiliarwiththeoperating procedures as defined in this manual, prior to operating the product.
6/20 6
MODEL SG-40 SAFETY PROCEDURES
WARNING
Before operating the machine, you must have all
potential operators read and follow manuals and decals, watch the video and follow the guidelines.
Read and follow all the instructions in this
manual thoroughly. Your safety is dependent on your knowledge of how to operate and maintain this
machine. You may obtain additional copies of this manual from your Bandit Dealer.
Always be cautious and careful when operating your equipment.
This equipment is intended for use by adults who have been properly trained and are physically
capable of operating the machine safely. Never
allow minors to operate this machine. Never operate anymachinewhileundertheinfluenceofdrugsor
alcohol. Never operate equipment that is in need of repair or adjustment. Keep children, bystanders and animals clear of working area.
There must be at least two qualified and trained operators at the work site. They must be
positioned in safe working locations, following safety
procedures and instructions, and aware of each
others whereabouts. There must, also, be at least two people on site during maintenance and service procedures in case an accident should occur.
This machine is equipped with safety decals, guards and designs for your protection.
Accidents are typically caused by making mistakes. The operator does not read the manual, overlooks safety decals, or fails to use lockouts provided for their safety. This occurs after the operator has become familiar with the machine.
The operator is very cautious in the initial start up and operation because they do not understand the machine.
NOTICE
Before starting the machine, take a minute to check a few things. The machine should be in an area restricted from people passing by. This area around the machine must be free of all objects that can obstruct your movement when working with the machine. The machine should be checked for loose tools or foreign objects. All tools not in use should be secured in a tool box.
must at all times be located within easy reachofallcontrolandshut-offdeviceswhentheunit is running. They must be attentive and prepared to activate the devices.
DANGER
Torn or loose clothing is more likely to get caught in moving machinery parts. Keep such items as long hair, shirt sleeves, and shirt tails properly contained.
Avoid wearing necklaces, rings, watches, and especially neckties while operating this machinery.
Wear all personal protection equipment (PPE) and follow all safety standards per ANSI and OSHA
instructions. Examples of equipment: hard hat, face shield, safety glasses, gloves, ear protection, high visibility vest, and steel toe boots. Do not wear
gauntletorsecuredfitgloves.Alwayskeepafully charged fire extinguisher with the machine while
operating or servicing the machine. Failure to do this will cause severe injury or death.
DANGER
Do not go near the rotating cutter wheel for any reason. Do not go near the cutter wheel while the engine is running or the cutter wheel is coasting to a stop. Contact with a rotating cutter wheel will result in severe injury or death.
Avoid moving parts. Keep hands, feet, and clothing away from power driven parts. Keep all guards and shields in place and properly secured. Contact with moving parts will result in severe injury or death.
Never sit, stand, lay, climb or ride anywhere on this machine while it is running, operating, or in transit.
You will be injured.
Do not start the engine with the clutch or cutter wheel engaged. Any debris may become a dangerous projectile. Contact with the rotating cutter wheel will result in serious injury or death.
Do not operate this machine indoors. Exhaust fumes can be fatal.
Never refuel while the machine is running. Never refuel in the shop or building. Always refuel in a well ventilatedarea,awayfromsparksoropenflames.
Do not smoke while refueling. Extinguish all smoking materials. Wipe up all spilled fuel before restarting the engine.
Keep hands clear of all pinch points. Failure to do this will result in serious injury or death.
7
Bandit
MODEL SG-40 SAFETY PROCEDURES
SAFETY PROCEDURES
Do not start to grind a stump unless you are
completely sure there are not any utility lines in the area above or below the ground level where you are grinding. Always contact the utility locating service in your area or local utility companies to mark underground utility lines. Failure to do so will result in severe injury or death.
DANGER
Make sure everyone is clear of machine before moving the machine. Stay clear of undercarriage travel system when the machine is moving. Contact with the undercarriage travel system will cause severe injury or death.
WARNING
Do not work on the machine if the engine is running with the clutch or cutter wheel disengaged.
Severe injury or death may occur if the cutter wheel was engaged.
Donotgonearorin-linewiththedebrisfieldof the stump grinder while in operation. While grinding stumps,thechipsandportionsofthestumpflyfrom the cutter wheel and can cause severe injury.
For optimum performance, the stump should be cut with the portion of the cutter wheel shown below. Never undercut the stump. Undercutting the stump may cause severe kickback, vibration and component damage. Never cut the stump from the top. The cutter wheel will throw debris up and toward the operator, instead of down and under the machine.
Do not go near hydraulic leaks. High pressure oil easily punctures skin causing serious injury, gangrene,ordeath.Avoidburnsfromfluid.Hotfluid under pressure can cause severe burns. Do not use fingers,skin,orbarehandstocheckforleaks.Use anobjectsuchasapieceofcardboardtofindleaks.
Lower load or relieve hydraulic pressure before looseningfittings.Relieveallpressureinthesystem before disconnecting the lines, hoses, or performing other work. Allow system to cool down to ambient temperature before opening any coolant or hydraulic oil system.
Clean machine of all debris. Do not leave this machine unattended until all potential fire debris is removed, no fire or smoldering exists, and hot spots are cold. The engine creates many hot spots
including: exhaust manifold, exhaust, turbo (if equipped),etc.Removeallflammabledebrissuch as wood, chips, leaves, oils, fuels, etc. from engine exhaust, engine turbo (if equipped), beside, around, and under engine, around and under tanks, inside belt shields and guards, inside battery and tool boxes, inside cabinets (if equipped), and anywhere
materialscollect.AlwayskeepseveraltypeA:B:Cfire
extinguishers operational and on the job at all times.
Before performing maintenance on the machine remove all debris, oil, grease, water, snow, ice, etc. from all machine surfaces.
90°
CUTTING AREA
Do not touch hot machine surfaces. The machine surfaces may be hot due to the machine operating recently or the machine setting in the sunlight.
Contact with hot machine surfaces may cause severe injury.
Never grind materials that might contain wires, stones, nails, or other metal objects which may
damage the teeth. Damaged teeth and foreign objects may become dangerous projectiles and can cause severe injury or death. Remove all foreign objects from stump grinding area.
Sparks can occur if cutter teeth strike rocks, metal, or other hard objects. Do not use in high or very high firehazardseverityzones.
Operation of this equipment may create sparks thatcanstartfiresarounddryvegetation.Aspark arrester may be required. The operator should
contactlocalfireagenciesforlawsorregulations relatingtofirepreventionrequirements.
6/20 8
25° MAX.
MODEL SG-40 SAFETY PROCEDURES
SAFETY PROCEDURES
Maximum Slope Grade
Ascending or Descending Slope
25° MAX.
100 FT. (30.5 m)
WARNING
Do not attempt to operate the machine on an ascending or descending slope of more than 25° or
46% or a side slope of more than 17° or 30%, it is dangerous and could be fatal. This is the maximum slope grade the machine can be operated on if the hydraulic system, self propelled undercarriage, and engine are running at maximum performance and good traction is sustained.
46 FT.
(14 m)
(46%)
Use extreme caution when traveling over non-level surfaces. This machine can tip over or tip backwards on non-level surfaces. You will cause engine damage, machine damage and possible personal injury or death.
17° MAX.
Side Slope The machine should never be parked on a slope at any time. The machine can coast or creep causing
equipment damage and/or personal injury.
17° MAX.
30 FT.
(9.1 m)
(30%)
100 FT. (30.5 m)
Diagram shows percentage to degree of slope.
Percentage is in vertical feet for every 100 horizontal feet.
NOTICE
Do not attempt to start the engine or engage the cutter wheel on this machine if the cutter wheel is jammed or frozen in place. If you do, you will damage the cutter wheel drive system, which will not be covered under warranty and will cost you down time and money.
Engage and disengage the cutter wheel at idle.
Failure to do this will damage the cutter wheel drive system.
Keep the machine in good condition. Be sure the
machine is in good operating condition and that all
safety devices, including guards and shields are
installed and functioning properly. Visually inspect the machine daily before starting the machine.
Refer to the “Daily Start Up & Maintenance”. Do not makeanymodificationstoyourequipmentunless specificallyrecommendedorrequestedbyBandit
Industries Inc.
Any increase from the specified maximum
operating angles may cause loss of lubrication function and damage the engine.
Do not continue to operate the machine if the cutter wheel stalls. Immediately lift cutter wheel out of the stump, dirt, etc. and start again with less bite.
Prolonged cutter wheel stall will ruin the cutter wheel drivesystem,creatingextremeheatandpossiblefire hazard.
SAFETY INSTRUCTIONS
Before attempting any type of maintenance,
disengage clutch or cutter wheel engagement, wait for the cutter wheel to come to a complete stop, turn offengine,removetheignitionkey,makesurethe ignition key is in your possession, disconnect the battery, and install the cutter wheel lock pin.
9
Bandit
MODEL SG-40 EQUIPMENT SPECIFICATIONS
EQUIPMENT SPECIFICATIONS
Approximate Dimensions & Weights
(Dimensions & Weights will vary depending on optional equipment)
SG-40
Height
Length
Width
Weight
Cutter Wheel Height
Cutter Wheel Depth
Cutter Wheel Swing
Cutter Wheel Diameter
Number of Teeth
Fuel Tank Capacity
Hydraulic Tank Capacity
48” (1.2 m)
101” (2.5 m)
29” (0.7 m)
1600 lbs. (726kg)
22” (0.6 m)
12” (0.3 m)
47” (1.2 m)
18” (0.5 m)
8
7 gal. (26L)
7 gal. (26L)
6/20 10
MODEL SG-40
MACHINE ORIENTATION REFERENCE
CONTROLS
BACK
RIGHT
LEFT
FRONT
11
Bandit
MODEL SG-40 CONTROLS
ENGINE OPERATING SPEEDS
NOTICE
Refer to the Completion/Check Sheet, that is shipped with the machine for the correct engine RPM. If needed, contact your local dealer or Bandit Industries.
Some Current Engine Types Maximum RPM
Kohler CH980 38 Hp EFI 3600
CONTROLS & COMPONENTS
4
5
6
7
8
# Control
1 Cutter Wheel Up/Down & Swing Left/Right
2
3
Left Track Forward/Reverse
Right Track Forward/Reverse
Emergency Stop Button
CutterWheelOn/OffSwitch
Swing Out Console Lock
Tach/Hour Meter
Swing Speed Control
12
13
14
15
16
#
9
10
11
Control
Ignition Switch
Throttle Up/Down Lever
Level Gauge
Hydraulic Tank
Fuel Tank
Cutter Wheel
Cutter Wheel Teeth
Cutter Wheel Bar
16
14
15
12
8
11
10
9
4
13
5
3
2 1
7
6
6/20 12
MODEL SG-40 CONTROLS
CONTROLS
1. A. Cutter Wheel Up/Down: Tomovethecutterwheelup;pullthejoystickonthevalvebanktowardsthebackof themachine.Tomovethecutterwheeldown;pushthejoystickonthevalvebanktowardsthefrontofthemachine.
B. Swing Left/Right: Tomovethecutterwheeltotheleft;pushthejoystickonthevalvebanktowards theleftsideofthemachine.Tomovethecutterwheeltotheright;pushthejoystickonthevalvebank towards the right side of the machine.
2. Left Track Forward/Reverse: Tomovethelefttrackforward;pushthehandleonthevalvebanklabelled
“L.TrackForward”towardsthefrontofthemachine.Toreversethelefttrack;pullthehandleonthevalve bank labelled “L. Track Reverse” towards the back of the machine.
3. Right Track Forward/Reverse: Tomovetherighttrackforward;pushthehandleonthevalvebank labelled“R.TrackForward”towardsthefrontofthemachine.Toreversetherighttrack;pullthehandle on the valve bank labelled “R. Track Reverse” towards the back of the machine.
4. Emergency Stop Button: When the emergency stop button is pressed the entire machine will shut down.
The cutter wheel will not stop immediately stop, it will coast to a stop.
5. Cutter Wheel On/Off Switch: Before turning the cutter wheel on, make sure the engine is at low idle.
Flip the switch to the “On” position, then throttle the machine up.
6. Swing Out Console Lock: To change the swing out position, pull the swing out console lock handle towards the back of the machine and move the console swing arm to the left or right side, and release the handle. Continue to move the console swing arm until it locks into place.
7. Tach/Hour Meter: The tach/hour meter keeps track of the amount of hours on the machine.
8. Swing Speed Control: To control the swing speed so the swing speed is increased, loosen the swing speed valve. To control the swing speed so the swing speed in decreased, tighten the swing speed valve.
9. Ignition Switch: To start the machine, insert the ignition key, and turn towards the front of the machine.
Toturnthemachineoff,turnthekeytothebackofthemachine,andremovethekey.
10. Throttle Up/Down Lever: To throttle the machine up move the lever to the high RPM symbol. To throttle the machine down move the low RPM symbol.
NOTICE
Refertoenginemanufacturer’smanualforspecific engine controls and operation.
13
Bandit
MODEL SG-40 MACHINE OPERATION
MACHINE OPERATION
DANGER
Do not start to grind a stump unless you are
completely sure there are not any utility lines in the area above or below the ground level where you are grinding. Always contact the utility locating service in your area or local utility companies to mark underground utility lines.
NOTICE
The stump must be cut as low to the ground as possible to reduce the amount of grinding material, debris,andlessenthechanceofflyingdebrisinthe work area.
DO NOT operate machine with extremely worn or broken teeth.
Keep clear of cutting wheel, moving machine parts andgrinderdebrisfield.
WARNING
Wear all personal protective equipment per ANSI,
OSHA and manuals.
DO NOT operate machine without a full set of teeth. Operating the machine without a full set of teeth can cause excessive vibration and premature bearing failure.
Use only original equipment manufacturer’s teeth.
The use of any other aftermarket teeth may cause damage or premature failure to the drive train.
1. Before starting the machine check all fluids, and follow all daily maintenance procedures.
2. Make sure the lock pin is not in the frame lock hole or the cutter wheel lock hole.
3. Start the engine.
4. Test the following controls to make sure they function properly.
a. Swing Left/Right b. Cutter Wheel Up/Down c. Travel Forward/Reverse
5. Make sure the machine is at low idle.
6. Engage the cutter wheel.
7. Throttle the machine up to ensure the cutter wheel rotates properly (if the cutter wheel does not rotate properly shut the machine down and diagnose the issue).
8. Throttle the machine down.
9. Disengage the cutter wheel.
10. Throttle the machine up.
11. Movethemachinetothefirststump.
12. Raise the cutter wheel above the stump.
13. Swing the cutter wheel all the way to the left and to the right to ensure there are no obstructions.
14. Make sure the cutter wheel is positioned on the right side of the stump.
15. Throttle the machine down.
16. Engage the cutter wheel.
17. Throttle the machine up.
18. Lower the cutter wheel to the stump and make a few light passes at the stump to get a feel for the cutting action.
19. Gradually increase the cutting action and work away at the stump by swinging the cutter wheel left-to-right-to-left through the stump in a side-to-side motion. The cutting actions should besmoothandeffortless.Ifitisnoteitherback the machine up or lift the cutter wheel up to take a smaller bite.
20. Continue cutting the stump by adjusting the cutter wheel progressively lower until the stump is cut well below ground level.
21. Raise the cutter wheel above the ground.
22. Swing the cutter wheel back to the right side of the stump.
23. Move the machine closer to the stump for the next series of passes and continue cutting.
24. Repeat steps 19 through 23 until the stump has been fully removed.
25. If working with a large stump, you may need to reposition the machine in order to fully remove the stump.
26. Repeat steps 8 through 25 until all required stumps are removed.
27. When all stumps are removed, return the cutter wheel to the center position
28. Insert the lock pin in the frame lock hole.
29. Load the machine according to the instructions in the Transportation Procedures.
6/20 14
MODEL SG-40 MACHINE OPERATION
MACHINE OPERATION
If the grinding material starts to interfere with the machine operation, follow the steps below before removing any grinding material. Never remove any grinding material with cutter wheel running. Contact with a rotating cutter wheel will result in serious bodily injury or death.
1. Disengage the cutter wheel.
2. Position the machine away from the stump.
3. Before attempting any type of maintenance, disengage clutch or cutter wheel engagement, wait for the
cutterwheeltocometoacompletestop,turnoffengine,removetheignitionkey,makesuretheignition key is in your possession, install the cutter wheel lock pin, wait 2 minutes then disconnect the battery.
4. Clear the grinding material away from the stump.
5. Start the machine and reposition it at the stump before engaging the cutter wheel.
CUTTING AREA
DANGER
For optimum performance, the stump should be cut with the portion of the cutter wheel shown below. Never undercut the stump. Undercutting the stump may cause severe kickback, vibration and component damage.
Never cut the stump from the top. The cutter wheel will throw debris up and toward the operator, instead of down and under the machine.
15
90°
CUTTING AREA
Bandit
MODEL SG-40 TRANSPORTATION PROCEDURES
LOADING & UNLOADING
WARNING
BEFORE LOADING OR UNLOADING THE MACHINE, INSPECT AND CONFIRM THE FOLLOWING
STEPS: When loading or unloading the self-propelled machine on the trailer, use care and caution. The maneuvering of the equipment must be slow, smooth, and intentional, not fast and jerky.
1. Make sure the trailer and towing vehicle are parked on a flat surface. They must be stable on the surface with the brakes locked and/or the wheels chocked to avoid unwanted movement.
2. Position the loading ramps or loading gate securely between the trailer and the ground level. Have them located so that they are in line with the tires or tracks of the machine when it moves.
3. Remove and store the chains and binders used for transporting.
4. Before loading or unloading the machine remove all debris, oil, grease, water, snow, ice, etc. from all trailer surface and loading ramp.
5. Confirmthattherearenotanyobstaclesonthe trailer bed, around the trailer that may cause restricted movement of the machine or the operator.
6. The only person in the area should be the one that is operating the machine controls, and they should be very experienced with the controls on this machine.
7. If you are on streets, roads or public areas, position the warning cones etc, per your company’s safety policy.
8. Check and make sure the frame lock pin is installed correctly. If the frame lock pin is not installed correctly, start up the machine and raise or lower the frame until the frame lock holes line up and install the frame lock pin.
9. Loadorunloadthemachineonoroffthetrailer.
10. Follow the trailer manufacturer's recommendations for the amount of weight on the tongue or hitch according to the total machine package weight to correctly position the machine on the trailer bed.
11. Align the machine with the trailer bed, and the loading ramps. The only equipment movement shouldbeslowly,straightonorstraightoffthe trailer.
12. With the engine and the machine at as low of speed as possible, move the machine toward the ramp system. Make sure the alignment is correct throughout the travel and the cutter wheel clears obstacles as it is going up or down the ramp system.
13. Properly secure the equipment and the area to avoid any possible accidents or dangers.
14. The trailer should be constructed with appropriate chain down positions for the specificsizedmachine.Youmusthavebinders that will withstand the strain of the machine trying to move while it is being transported.
15. The loading ramps or loading gate of the trailer must be constructed to withstand the weight and forces involved in loading and unloading the machine.
6/20 16
MODEL SG-40 TRANSPORTATION PROCEDURES
TRANSPORTATION PROCEDURES
BEFORE TRANSPORTING THE MACHINE, INSPECT AND CONFIRM THE FOLLOWING STEPS
1. The trailer must have a cargo weight rating capacity for the weight of the stump grinder.
The combined weight of the trailer and the stump grinder can not exceed the load capacity of the tires, axles, hitch coupler system or the
GVWR (Gross Vehicle Weight Rating) of the trailer.
2. The towing vehicle must be rated for and have the towing capabilities to haul the stump grinder package ( includes the stump grinder and a trailer). The towing vehicle must be mechanically sound and capable of handling the towing job.
3. The hitch on the towing vehicle and the coupler on the trailer must match in size, type, and needed capacity.
4. Make sure both the towing hitch and the coupler are in good mechanical and wear condition, that they are joined together securely, and the coupler/hitch is locked in place.
5. The safety chains must have the correct capacity for the equipment being towed.
6. The safety chains are crossed under the coupler/hitch then securely attached to the towing vehicle. The safety chains are long enough to not restrict the turning movement, but short enough to not drag on the road.
7. The electrical plug-in on the towing vehicle and the trailer must be wired for the same functions and they fit securely together. The plug-in wire is long enough to not restrict the turning movement, but short enough to not drag on the road. The trailer must have a lighting system and braking system to match and perform correctly offthetowingvehiclessystem.Youmustmeet the Federal and your States’ Department of
Transportation Code of Regulations concerning lights, brakes, and highway transit.
8. The break-away actuator (if equipped) that is installed on the trailer correctly works and is appropriately attached to the towing vehicle.
9. All lights and brakes on the trailer must correctly function when activated by the systems in the towing vehicle.
10. The tires must be checked for cuts or damaged rims, air pressure is correct, and the axle lug nuts have been checked for correct torque
(refer to trailer manual).
11. When the stump grinder is on the trailer, the trailer must have the right load capacity, with the stump grinder positioned on the trailer for the correct weight distribution (follow the trailer manufacturer’s recommendations for the amount of weight on the tongue or hitch according to the total stump grinder package weight), the stump grinder brakes, if equipped, are locked, the cutter wheel is raised off the trailer bed with the lock pin installed, and the stump grinder is securely bound down to the trailer bed per your States binding requirements.
12. Any loose debris, tools or parts must be cleared offorareputaway.
13. Make sure to close and secure any of the following if equipped: tool box, battery box, engine cowl doors and side panels, radiator debris screens, inspection doors, cabinet doors, housing covers, tank caps and covers, vise, etc.
14. Make sure the load ramps are securely stored for transport.
15. Make sure the stump grinder’s engine is not running, the ignition key is in your possession, and all controls are stored correctly and locked in place for transport.
16. The stump grinder package must be hauled level and the towing vehicle must be sized to handle hitch weight and towing weight. The towing vehicle or the combination of towing package must have enough braking capacity to meet the Federal and your State Department of Transportation
requirements.
17. The stump grinder package is now ready for transport. Make sure to obey all local regulation and laws regarding the transporting of this type of stump grinder.
18. Do not drive too fast for road conditions or exceed speed regulations for equipment towing.
17
Bandit
MODEL SG-40 MAINTENANCE
MACHINE ORIENTATION REFERENCE
BACK
RIGHT
LEFT
FRONT
6/20 18
MODEL SG-40
What to Check
Safety decals
Safety equipment
Loose bolts, nuts parts or components
Safety guards
Cutter wheel, pockets, pocket bolts, & teeth
Grease cutter wheel bearings
Grease jack shaft bearings
Clear debris from beltshields
Adjust belt tension/ alignement
Hydraulic oil level
Fluid leaks
Hydraulic control valves
Fuel level
Engine oil & coolant level
Cooling fan & debris screen
Air cleaner & precleaner
Track Assembly
Safety procedures reviewed
Grease cylinder lug pins
Steel friction areas
Set screws in bearings
Grease swing spindle assembly
Grinder bearings & sheaves
Bearing lock collars
Hydraulic function pressure
Hydraulicoilfilter
Inspect swing spindle assembly
Dismantle & repack swing spindle assembly
Swing out console pivot
Fuel tank
Hydraulic oil
Hydraulic suction screen
X
X
X
X
X
X
X
X
X
Daily
(10 hrs.)
X
X
MAINTENANCE
How often to check
Weekly
(50 hrs.)
Monthly
(200 hrs.)
Quarterly
(500 hrs.)
X
X
X
X
X
X
X
X
X
X
X
X
X
X
X
X
MAINTENANCE
Yearly
(2000 hrs.)
Procedure
Page #
ü
20
20
20
20
20, 24
Semi Yearly
(1000 hrs.)
X
X
X
X
20
20
20
21
21
21
21
21
21
34
25
21
21
21
21
26 - 27
20
20
20
20
20
21
21
21
21
21
19
REMEMBER TO CHECK EVERYTHING ON THE CHECKLIST!
Bandit
MODEL SG-40 MAINTENANCE
BOLT TORQUE CHART
(THESE TORQUES ARE BASED ON DRY, CLEAN THREADS)
DESCRIPTION
Cutter Wheel Green Tooth Pocket Bolts
Cutter Wheel Green Tooth Nut
Cutter Wheel Sheave Bushing
Jack Shaft Sheave Bushing - Cutter Wheel Side
Jack Shaft Sheave Bushing - Engine Side
Engine Sheave Bushing
Hydraulic Pump Sheave Bushing
Cutter Wheel Bearing Bolts
Cutter Wheel Bearing Set Screws
Track Drive Sprocket
BOLT SIZE TORQUE (FT.-LBS.) TORQUE (Nm)
5/8” - 18 NF
7/16” - 14 NC
3/8” - 16 NC
3/8” - 16 NC
5/16” - 18 NC
3/8” - 16 NC
3/8” - 16 NC
5/8” - 11 NC
1/2” - 20 Lug Nut
180
35
30
30
15
30
30
80
14
90
Before tightening bolts be sure you have the correct size bolt for the correct amount of torque.
Use only factory approved teeth and hardware.
244
47
41
41
20
41
41
108
19
122
DAILY MAINTENANCE
SAFETY DECAL & CONTROL GAUGES
Replace any missing or damaged decals and/or any gauges (if equipped) in the control panel.
SAFETY EQUIPMENT
Check for proper operation. Repair or replace as
needed.
LOOSE BOLTS, NUTS, PARTS OR
COMPONENTS
Check entire machine for any loose parts or
components. Check for loose nuts or bolts. Torque, tighten, or replace any of the loose components. See page20forspecificbolttorques.
SAFETY GUARDS
Check to make sure all guards are in place and
installed correctly. Make sure they are secure.
CUTTER WHEEL, POCKETS, POCKET
BOLTS AND TEETH FOR WEAR
GREASE JACK SHAFT BEARINGS
Use an EP-2 Lithium type grease only for all
bearings. Purge jack shaft bearings with grease.
You can not over grease these bearings. This type of bearing is designed with a relief system that will not allow over greasing. In other words, you can not hurt the bearing seals by pumping in too much grease. Most of the failures related to bearings are diagnosed as “Contamination”. Contamination is caused by improper lubrication. Wipe off excess grease. Excessive grease will attract dirt.
CLEAN DEBRIS FROM BELTSHIELDS
Inspect the drive side beltshield and the cutter wheel beltshield for debris and clean out any chips.
HYDRAULIC OIL LEVEL
The hydraulic oil reservoir tank level should always remain at 7/8 full. Remember to check DAILY to avoid excessive heat build up.
Check for elongated bolt holes, secure welds, torqued bolts, excessive wear, and impact cracks.
Check the condition of cutter teeth, pockets, and hardware. Rotate cutter teeth to keep them sharp.
Replace if necessary. All cutter wheel pockets must be factory approved. Pocket bolts must be replaced after a maximum of 5 rotations/changes to ensure safe clamping ability.
GREASE CUTTER WHEEL BEARINGS
FLUID LEAKS
Inspect for any oil, fuel, hydraulic oil, or engine coolantleaks.Checkallhoses,fittings,lines,and tanks. DO NOT use fingers or skin to check for
hydraulic leaks. Repair or replace any damaged or leaking components.
HYDRAULIC CONTROL VALVES
Inspect all hydraulic control valves and ensure they operate smoothly and shift correctly.
Use an EP-2 Lithium type grease only for all
bearings. Purge cutter wheel bearings with grease.
You can not over grease these bearings. This type of bearing is designed with a relief system that will not allow over greasing. In other words, you can not hurt the bearing seals by pumping in too much grease. Most of the failures related to bearings are diagnosed as “Contamination”. Contamination is caused by improper lubrication. Wipe off excess grease. Excessive grease will attract dirt.
FUEL LEVEL
Check the fuel level, running out and repriming is timeconsuming.Donotoverfill,andyoumustleave fuel expansion space in the top of the tank.
ENGINE OIL & COOLANT LEVEL
Follow the engine manufacturer manual
recommendationsforfluidlevels.You MUST follow specificENGINEMFG.manualrecommendations for radiator coolant, additives, lubrication, correct engine speed, ETC.
6/20 20
MODEL SG-40 MAINTENANCE
DAILY MAINTENANCE
COOLING FAN & DEBRIS SCREEN
Refer to the engine manufacturer’s manual.
Clean cooling fan, shroud on air cooled engines, and the debris screen (if equipped). Improper service, maintenance, or neglect will cause overheating problems and/or engine failure.
AIR CLEANER & PRECLEANER
Clean or replace element following engine
manual recommendations. Also, check and clean the vacuator valve.
REVIEW ALL SAFETY PROCEDURES ON
DECALS, FROM MANUAL, & FROM VIDEO
WEEKLY MAINTENANCE
GREASE CYLINDER LUG PIN BUSHING
Grease cylinder lug pin bushings with 1 to 2 shots ofEP-2Lithiumtypegrease.Wipeoffexcessgrease.
Excessive grease will attract dirt.
CUTTER WHEEL BEARING LOCK
COLLARS
Check set screws in cutter wheel and jack shaft bearings for tightness.
ALL STEEL FRICTION AREAS
Lubricate all steel friction areas including , but not limited to pivoting, hinged, sliding, rotating areas on the machine (i.e. cutter wheel guard, control box doors, etc.).
MONTHLY MAINTENANCE
GREASE SWING SPINDLE ASSEMBLY
Grease cylinder lug pin bushings with 2 to 3 shots ofEP-2Lithiumtypegrease.Wipeoffexcessgrease.
Excessive grease will attract dirt.
JACK SHAFT BEARING LOCK COLLARS
Check and retighten bearing lock collars to correct torque.
GRINDER BEARINGS & SHEAVES
Check and retighten all bearing bolts and belt sheave bushings to correct torque.
HYDRAULIC FUNCTION PRESSURE
Check, reset and maintain all hydraulic function pressure settings to a maximum of the specified
PSI (bar). This will give you the best performance from the hydraulic system.
QUARTERLY
MAINTENANCE
HYDRAULIC OIL FILTER
Replacehydraulicoilfilterafterthefirst10hours ofoperation.Usea10Micronfilter.Afterthefirst change, replace oil filter every 3 months or 400 hours. Located in the hydraulic tank
INSPECT SWING SPINDLE ASSEMBLY
Remove the swing spindle access cover and inspect the grease. If grease is contaminated, dismantle and repack the grease according to the
“Dismantle & Repack Swing Spindle Assembly” instructions in the Semi Yearly section.
FUEL TANK
Drain and clean the fuel tank yearly.
SEMI YEARLY
MAINTENANCE
DISMANTLE & REPACK SWING SPINDLE
ASSEMBLY
Remove the swing spindle access cover, inspect and clean the swing spindle bearings, cups, and seals. Replace seals if ever removed. Replace bearings and cups as needed. Grease the bearings with an EP-2 Lithium type grease. Remove rubber plug and pump grease into E-Z Lube zerk until all of the old grease is pumped out of the dust cap. Wipe offexcessgrease. Excessive grease will attract dirt.
YEARLY MAINTENANCE
SWING OUT CONSOLE PIVOT
Grease swing out console pivot once every year
1 to 2 shots with an EP-2 Lithium type grease. Wipe offexcessgrease. Excessive grease will attract dirt.
HYDRAULIC OIL
Change hydraulic oil and flush the hydraulic reservoir tank.
HYDRAULIC SUCTION SCREEN
Change hydraulic suction screen yearly or every
2000 hours.
21
Bandit
MODEL SG-40 MAINTENANCE
PAINT & DECAL CARE
PAINT CARE
To help keep up the appearance of your Bandit equipment and reduce the possibility of surface rust follow these steps:
DECAL CARE
Decals located on your Bandit equipment contain useful information to assist you in operating your
equipment safely. The safety decals are shown and explained in this section along with decal locations.
1. The machine should be washed by hand with waterforthefirst30dayswhenthepaintisfresh.
Afterwards, the machine should be washed on a regular basis with an automotive wash soap
(not degreaser) and then rinsed thoroughly.
2. Do not pressure wash sensitive areas like: decals, gauges, electronic devices, near chips in the paint, etc. If a pressure washer is used afterthefirst3monthsafterpainting,beaware they are capable of extreme pressures and can damagepaintfinishes.Also,onlyuse1500to
2000 psi with a round pattern nozzle (not a pin point or knife style nozzle) and hold the gun/wand a minimum of 24” (0.6 m) away from the machine.
3. Always wash the machine immediately upon delivery , when the machine is new.
4. If shipping or towing the machine in conditions that include road salt/brine, any other ice melt or dust control products, always wash the machine immediately upon arrival or at the end of the work day.
5. Park the machine inside or under a roof when not in use.
6. Donotallowfuel,antifreeze,DEFfluid,orany othermotorfluidtosetonthemachine.Remove immediately.
7. If a stone chip, paint scratch, or paint crack occurs - it should be repaired immediately.
Simply sand the edges of the damaged paint area,maskoffthesurroundingarea,andapply primer and paint to the dry, clean, and warm area.
This will keep the damaged area from spreading or getting worse.
8. If you are unable to sand and mask the area, there are containers of primer and paint available. A small brush can be used to touch up the area after it is cleaned, dry, and warmed.
Also, primer and most colors of paint are available in aerosol spray cans.
9. Keepgoodmudflapsontowingtruckstoreduce stone chips.
10. Use an automotive wax on a regular basis after thefirst3monthsafterpainting.
It is very important that all decals remain in place and in good condition on your machine. Please follow the care and instructions given below.
1. You should use soap and water to keep your decals clean. Never use mineral spirits or any other abrasive cleaners.
2. Immediately replace any missing or damaged decals. The location the decal is going to be
applied to must be clean and dry, and at least
40°F (5°C) before applying decal.
3. When the need arises to replace a machine component with a decal attached, be sure and replace the decal.
4. Replacement decals are available, and can be purchased from the manufacturer or your
Bandit Dealer.
5. Peel back about half of the backer paper on the decal.Positionitontheflat,dry,cleansurfaceso itissmoothandsecure.Peelofftheremainder of the backer paper as you continue to stick the
decal on the surface.
6. Rub decal from the center outward to remove air bubbles and to secure contact.
7. English/Spanish decals are typically standard.
Other foreign language decals are available and may be purchased. Mail translated decals required to Bandit Industries, Inc.
6/20 22
MODEL SG-40 MAINTENANCE
# DESCRIPTION
1 Jack Shaft Bearings
2 Cutter Wheel Bearings
3 Cylinder Lug Pin Bushings
5 Swing Spindle Assembly
6 Swing Out Console Pivot
LUBRICATION CHART
CHECK
DAY WEEK MONTH PROCEDURE
X Purgebearingsdaily-wipeoffexcess
X
X
X
Purgebearingsdaily-wipeoffexcess
1-2shotsofgrease-wipeoffexcess
Lubricate (i.e. cutter wheel guard, control box doors, etc.)
X 2-3shotsofgrease-wipeoffexcess
Yearly 1-2shotsofgrease-wipeoffexcess
Arightanglegreasefittingmayneedtobeusedtogreasesomeofthelubrication points.Thistypeofgreasefittingcanbeobtainedfrommostlocalautomotive parts stores.
3
3
2
1
6
5
1
2
3
3
NOTICE
23
Use as a reference only, locations may vary depending on options or component manufacturer.
Lubrication point instructions are described on the machine, in the Lubrication & Coolant
Section and Maintenance Section of this manual, or component manufacturer’s manual.
Bandit
MODEL SG-40 MAINTENANCE
CUTTER WHEEL
SAFETY INSTRUCTIONS
Before attempting any type of maintenance,
disengage clutch or cutter wheel engagement, wait for the cutter wheel to come to a complete stop, turn offengine,removetheignitionkey,makesurethe ignition key is in your possession, disconnect the battery, and install the cutter wheel lock pin.
NOTICE
DO NOT operate machine with extremely worn or broken teeth.
DO NOT operate machine without a full set of teeth. Operating the machine without a full set of teeth can cause excessive vibration and premature bearing failure.
DANGER
DO NOT go near the rotating cutter head for any reason. DO NOT go near the cutter head while the engine is running or the cutter head is coasting to a stop. Contact with a rotating cutter head will result in serious bodily injury or death.
Use only original equipment manufacturer’s teeth.
The use of any other aftermarket teeth may cause damage or premature failure to the drive train.
A locking pin is provided to hold the cutter wheel in position during tooth removal and reinstallation.
Locking pin will only lock on outer teeth.
Never use hand on cutter wheel to hold in place while changing teeth. Be sure to remove locking pin before operating the machine.
GREEN TEETH MAINTENANCE
See Page 40 for Cutter Wheel Setup & Part Numbers
Inspect pockets, teeth and bolts for damage and
replace as required.
When replacing pockets, always replace new
pockets across from each other (180°) in order to prevent vibration.
Replacement teeth must be carbide tipped and of like design as provided with the machine.
Use anti-seize on threads to help prevent bolts from “freezing up” in cutter wheel pockets.
When replacing complete set of teeth, be sure to
duplicate original factory tooth arrangement, with the carbide tip facing the cutter wheel rotation. Typically a
1/2” socket is required to change or torque the teeth.
Seepage20fortorquespecifications.
When the tooth has 1/16” of wear on the carbide tip, it is time to rotate or replace the tooth.
6/20 24
MODEL SG-40 MAINTENANCE
TRACK TENSION
SAFETY INSTRUCTIONS
Before attempting any type of maintenance,
disengage clutch or cutter wheel engagement, wait for the cutter wheel to come to a complete stop, turn offengine,removetheignitionkey,makesurethe ignition key is in your possession, disconnect the battery, and install the cutter wheel lock pin.
DANGER
Avoid moving parts. Keep hands, feet, and clothing away from power driven parts. Keep all guards and shields in place and properly secured.
Keep hands clear of pinch points.
1. Measurethedeflectionwith40-50lbs.(18.1-
22.7kg)offorcewith1/2”deflection.
2. If the deflection is not 1/2” tighten or loosen the nuts on the adjuster bolt (shown in green in Figure 1). Note: you will need to adjust the adjuster bolt on the opposite side of the track.
3. Check the tension again and adjust as needed.
Figure 1
1/2”(12.7mm)deflectionat
40 - 50 lbs. (18.1 - 22.7 kg) of force.
25
Adjuster Nuts
NOTICE
Make sure the distance on the track roller adjuster bolt is the same on both sides of each track.
Same distance on both sides
Bandit
MODEL SG-40 MAINTENANCE
BELT TENSION
SAFETY INSTRUCTIONS
Before attempting any type of maintenance,
disengage clutch or cutter wheel engagement, wait for the cutter wheel to come to a complete stop, turn offengine,removetheignitionkey,makesurethe ignition key is in your possession, disconnect the battery, and install the cutter wheel lock pin.
NOTICE
Do not over tighten the hydraulic pump belt. For best results use a good belt tension tester. Most all pump failures result from too much side load on the pump shaft. Too much belt tension is very easy to detect inside a failed pump. Pumps with this condition will not be covered under warranty.
DANGER
Keep hands clear of pinch points.
DO NOT IGNORE THIS MAINTENANCE RULE
New belts stretch very soon and must be adjusted several times in the first few hours of operation.
Adjust after one hour of operation, then every four hours until the belts quit stretching.
GENERAL RULES FOR TENSIONING
1. Checktensioningduringthefirst2through48 hours of run-in operation especially.
2. Over tensioning or under tensioning shortens belt and bearing life.
3. Keep belts free from foreign materials that may cause the belt to slip.
4. Make V-drive inspection on a periodic basis.
Never use belt dressing as this will damage the belt and cause early failure.
5. Belts should never be forced over the sheave.
Allow enough room for belts to slip on.
6. Always make sure sheaves are aligned properly.
CUTTER WHEEL BELT
1. Follow all pre maintenance shut down procedures.
2. Remove the cutter wheel side beltshield.
3. Locate the center of the belt span between the jack shaft sheave and the cutter wheel sheave.
4. Push up on the bottom side of the cutter wheel belt (highlighted in blue in Figure 1) with a double barrel belt tension gauge until the belt hasdeflected7/16”(11.1mm).
5. Record the push force. The force should be 27 lbs. (12.2 kg) for a used belt or 32 lbs. (14.5 kg) for a new belt.
6. Adjust the belt tension if the force falls out of this range.
CUTTER WHEEL BELT ADJUSTMENT
1. Follow all pre maintenance shut down procedures.
2. Remove the cutter wheel side beltshield.
3. Loosen the tensioner bolts (shown in green in
Figure 1).
4. Loosen or tighten the adjuster bolt (highlighted purple in Figure 1) to achieve the correct tension.
5. Tighten the tensioner bolts (shown in green in
Figure 1).
6. Once the correct tension is achieved, reinstall the cutter wheel beltshield.
The idler sheave moves up as the adjuster bolt & nut are tightened.
6/20
Thedeflectionmustbe27lbs.(12.2kg)at7/16”
(11.1mm)forausedbelt;or32lbs.(14.5)at7/16”
(11.1 mm) for a new belt
26
MODEL SG-40 MAINTENANCE
BELT TENSION
ENGINE BELT
1. Follow all pre maintenance shut down procedures.
2. Remove the engine side beltshield.
3. Locate the center of the belt span between the jack shaft sheave and the engine sheave.
4. Push up on the bottom side of the engine belt with a double barrel belt tension gauge until the belthasdeflected1/4”(6.4mm).
5. Record the push force. The force should be 16 lbs. (7.3 kg) for a used belt or 17.5 lbs. (7.9 kg) for a new belt.
6. Adjust the belt tension if the force falls out of this range.
ENGINE BELT ADJUSTMENT
1. Follow all pre maintenance shut down procedures.
2. Remove the engine side beltshield.
3. Loosen all four tensioner plate bolts (shown in green in Figure 1).
4. Loosen or tighten the adjuster bolt (shown in blue in Figure 1) to achieve the correct tension.
5. Tighten all four tensioner plate bolts (shown in green in Figure 1).
6. Once the correct tension is achieved, reinstall the engine beltshield.
PUMP DRIVE BELT
1. Locate the center of the span between sheaves.
2. Push or pull down on the belt until the belt has deflected3/16”(4.8mm).
3. Record push or pull down force. The force should be 4.7 - 5 lbs (2.1 - 2.3 kg) for a used belt or
5.5 lbs (2.5 kg) for a new belt.
4. Adjust the belt tension if the force falls outside of this range.
5. If adjustment is needed, loosen both pump mount bolts.
6. Adjust the pump to achieve the required force anddeflection
7. Tighten the pump mount bolts.
PUMP BELT ADJUSTMENT
1. Follow all pre maintenance shut down procedures.
2. Remove the engine side beltshield.
3. Loosen the pump bolts (shown in green in Figure 1).
4. Loosen or tighten the pump adjuster bolt (shown in orange in Figure 1) to achieve the correct tension.
5. Tighten the pump bolts (highlighted green in
Figure 1).
6. Once the correct tension is achieved, reinstall the engine beltshield.
SINGLE BARREL GAUGE
(UP TO 30 lbs.) 900-1919-23
DOUBLE BARREL GAUGE
(UP TO 66 lbs.) 900-1917-02
View behind pump sheave
Pump bolts
(QTY 2)
Tensioner plate bolts
(QTY 4)
27
Engine Belt adjuster bolt
Pump Belt adjuster bolt
Thedeflectionmustbe4.7-5lbs.(2.1-2.3kg)at
3/16”(4.8mm)forausedbelt;or5.5lbs.(2.5kg)at
7/16” (4.8 mm) for a new belt
Thedeflectionmustbe16lbs.(7.3kg)offorceat
1/4”(6.4mm)forausedbelt;or17.5lbs.(7.9kg)of force at 1/4” (6.4 mm) for a new belt
Bandit
MODEL SG-40 MAINTENANCE
TROUBLE SHOOTING
Engine will not start (See engine manufacturer’s manual for more information)
Cutter wheel vibration.
Cutter wheel throwing teeth.
grease.
PROBLEM
Breaking teeth.
Cutter wheel stops turning.
Belt squeal.
Belt jumping off.
Roar in machine when cutter wheel is engaged.
Bearing will not take
POSSIBLE CAUSE SOLUTION
Loose ground cable.
Loose hot cable.
Dead battery.
Cutter wheel was engaged before the machine was started.
Emergency stop activated.
Tooth missing.
Pocket out of balance.
Do not mix new & worn out teeth.
Improper tooth arrangement.
Do not mix new & worn out teeth.
Bad pocket.
Belt guards rubbing on cutter wheel shaft.
Cutter wheel bearings going bad.
Clean and tighten.
Clean and tighten.
Recharge or replace.
Makesuretheignitionswitchisoff, disengage cutter wheel and restart the machine.
Pull or twist the emergency stop to deactivate.
Replace missing teeth.
Always replace pockets in pairs across from each other.
Install correctly with like pairs of teeth directly across from each other.
Replace pocket.
Clean pocket and replace teeth.
Always replace pockets in pairs Dirt in pocket.
Operator hitting rocks.
Cutter wheel belt loose or broke.
across from each other.
Avoid rocks, stones, etc.
Adjust or replace.
Debris wedged around cutter wheel.
Clean out debris.
Belt tension too loose.
Belt out of alignment.
Engaging or disengaging belt at high engine RPM.
Belt tensioners are too loose.
Sheaves out of alignment.
Tighten or replace.
Align sheaves.
Engage/disengage belts at low engine speed or replace.
Adjust belt tension. Refer to belt tension of the maintenance section.
Make sure sheaves are aligned properly.
Repositionguardsoffofshafts.
Replace bearings.
Greasefittingclogged. Replace.
6/20 28
MODEL SG-40 HYDRAULICS
HYDRAULICS
SAFETY INSTRUCTIONS
Before attempting any type of maintenance,
disengage clutch or cutter wheel engagement, wait for the cutter wheel to come to a complete stop, turn offengine,removetheignitionkey,makesurethe ignition key is in your possession, disconnect the battery, and install the cutter wheel lock pin.
WARNING
Do not go near hydraulic leaks. High pressure oil easily punctures skin causing serious injury,
gangrene, or death.Avoid burns from fluid. Hot fluidunderpressurecancausesevereburns.Do not use fingers or skin to check for leaks. Lower load or relieve hydraulic pressure before loosening fittings. Relieve all pressure in the system before
disconnecting the lines, hoses, or performing other work.Useapieceofcardboardtofindleaks.Never use your bare hands. Allow system to cool down to ambient temperature before opening any coolant or hydraulic oil system.
It is very important after you have operated a new machine for approximately an hour to shut down the machineandrecheckallhydraulicfittings.Relieveall pressure and retighten as needed.
WARNING
Do not operate this machine unless all hydraulic control devices operate properly. They must function, shift and position smoothly and accurately at all times. Faulty controls can cause personal injury.
NOTICE
Some equipment and components including fluid engagement clutches (PTO’s) have their own lubrication requirements. Consult their manufacturer’s manual for that information.
After the initial start-up of the machine and after anyreplacementofhydrauliccomponents,fittings and hoses must be re-checked for leaks and clearances.
When returning hydraulic components for warranty make sure to box up all warranted parts to avoid additional damage while shipping.
Do not disassemble any hydraulic components which are to be warrantied. Anything which has been disassembled or tampered with will not be warrantied. Items being returned must be clean. All hydraulic components must have all hosing ports plugged. Failure to plug ports will allow debris to enter components which will void warranty.
In cold weather situations let your hydraulic system idle for approximately 15 minutes to allow the system to warm up to operating temperature.
Thismachineisequippedwithaveryefficient,simplehydraulicsystem.Eachcomponentiscapableof withstandingaspecifiedpressureandstilloperateforaverylongtime.
If the simple rules mentioned below are followed, the hydraulic components will last for years:
• Avoid hydraulic pump cavitation. Low oil levels or cold start-ups will cause the hydraulic pump to cavitate. Cavitation will ruin the pump and possibly the entire hydraulic system. Cavitation only has to happen once. This will start the pump on its way to ruin. Allow hydraulic system to turn slowly for several minutes in cold weather in order for hydraulic system to warm up. Cavitation is not covered under warranty.
• Keep hydraulic oil clean. Dirty oil will cause
excessive wear and loss of hydraulic power.
• Replace the hydraulic oil filter(s) after first 10 hours and with each 400 hours of operation or 3 months.
• Replace hydraulic oil & suction screen(s) at least onceyearly.Thisisalsoaverygoodtimetoflushand clean the tank. Replace hydraulic oil immediately if it is contaminated or looks “milky”. See “Hydraulic
Oil Requirements”.
• If the machine’s hydraulic system is kept clean and the hydraulic pressures are not increased beyond the specifiedpressure,themaximumuseandlifeshould be received from the hydraulic system.
• If a problem is encountered, it will more than likely be located in the relief valve or something as simple asbeltsorclutchslipping,checkthesefirst.
• Donotclosethehydraulicshut-offvalveformore than3to4seconds.Hydraulicshut-offvalvehandle must be completely turned on (in line with hose) at all times unless checking hydraulic pressure. Pressure gauge should be safely stored and installed only when checking pressure. Follow above instructions or this will cause unwarranted damage to the hydraulic components.
• Never close the ball valves on the hydraulic tank suction ports (if equipped) while the machine is running, this will ruin the hydraulic pump and
components.
29
Bandit
MODEL SG-40 HYDRAULICS
HYDRAULIC FLUID REQUIREMENTS
This machine is equipped with “Petro-Canada
HydrexXV”hydraulicfluidanditisrecommendedto be replaced with the same. “Petro-Canada Hydrex
XV”isanallseasonhydraulicfluid.Thisisapremium performance, long life anti-wear, hydraulic fluid, designed for all season use in heavy duty hydraulic systems. “Petro-Canada Hydrex XV” allows year round use under wide extremes of temperature. It allows the hydraulic system to start at temperatures as low as -40°C/-40°F, under no load conditions and it improves lubrication of hydraulic components at high operating temperatures. It will also help protect against hydraulic failures during the wide temperature swings of spring and fall.
Multi Viscosity motor oils are not recommended to mix with “Petro-Canada Hydrex XV” hydraulic oil. AW oils may mix with “Petro-Canada Hydrex
XV” hydraulic oil.The following are specifications and authorizations of compatible oils. Only a high quality anti-wear (AW) hydraulic oil containing foam, corrosion, rust and oxidation inhibitors should be used. This viscosity grade depends on the oil temperature in service, based on the climate and operating conditions.
Alternative hydraulic oils are available, but they do not equal the performance or longevity of the “Hydrex
XV” oil. Consult the following information supplied by the oil distributor.
Viscosity Index
Hydrex XV ISO 22, AW ISO 32, AW ISO 46, AW ISO 68, AW ISO 100, AW
245
Cold Start-up °C (°F) -40 (-40)
110
-37 (-29)
110
-31 (-14)
104
-26 (-3)
106
-22 (16)
102
-16 (24)
CELSIUS (°C) -40 -20 -18 -13 -5 0 1 7 15 25 35 45 55 65 75 85 95
FAHRENHEIT (°F) -40 4 0 9 23 32 34 45 59 77 95 113 131 149 167 185 203
ANTI-WEAR ISO 100
ANTI-WEAR ISO 68
ANTI-WEAR ISO 46
ANTI-WEAR ISO 32
ANTI-WEAR ISO 22
PETRO-CANADA HYDREX XV
NOTICE
The above chart is a suggested guide for viscosity of hydraulic fluids at start up ambient
temperature. The load, demand, and cleanliness oftheequipmentwillaffectactualoiltemperatures which can increase dramatically above ambient air temperatures during operation. The actual viscosity needed is based on oil temperature during operation and not air temperature. Compare your fluidspecificationswiththespecificationsbelow to verify compliance.
Hydraulic fluids vary in their resistance to oxidation at elevated temperatures, their ability to protect against metal-to-metal contact under increasing temperature, and their ability to separate water from the fluid. Viscosity is temperature dependent. Fluids with high viscosity-index (VI) will thin out slower at higher temperature and thicken slower at colder temperatures allowing awideroperatingrange.Chooseafluidthathas test results in these areas for best results.
Based on the varying temperatures of the area where Bandit equipment is used, and the high demand and loads placed on this equipment,
Bandit has filled each hydraulic system with
Petro-Canada’s Hydrex XV All Season Hydraulic
Fluid for maximum protection and performance.
Whenchoosingahydraulicfluid-thesemaximum andminimumspecificationsmustbemet :
Minimum Viscosity during operation = 12 cSt
Maximum No-Load Viscosity at start-up = 2000 cSt
Go to: lubricants.petro-canada.com and click on “Contact Us” then click “Request
AQuote”tofindyournearestPetro-Canadadealer.
6/20 30
MODEL SG-40 HYDRAULICS
HYDRAULICS
TYPICAL HYDRAULIC RELIEF
PRESSURE SETTINGS
(Approximate, For Reference Only,
Engine At Full RPM)
NOTICE
Do not under any circumstances over-set these relief pressures, it will cause damage to component parts and hydraulic parts.
CHECKING HYDRAULIC
PRESSURE
The relief valve is typically located internally in the valve bank. Do not adjust the relief valves above the
specifiedpsi(bar).Thereliefvalvesystemisasimple spring tension design but small pieces of debris can stick the valve partially open which weakens the hydraulic power. The relief as well as hydraulic oil, and suction screen must be kept clean.
Thesetypicalhydraulicflowsandreliefpressure settings are with the engine at full RPM. All settings are subject to change.
After the initial start-up of the machine and after anyreplacementofhydrauliccomponents,fittings and hoses must be re-checked for leaks and clearances.
Equipment
Model
Track Drive
PSI (bar)
Swing Setting - Right
PSI (bar)
Swing Setting - Left
PSI (bar)
Cutter Wheel Up / Down
PSI (bar)
SG-40
2950
(203)
1000
(68)
1200
(82)
1800
(124)
SWING LEFT/RIGHT &
CUTTER WHEEL UP/DOWN
PROCEDURE
1. Makesureallthecontrolsareintheoffposition.
2. Install pressure gauge into the test port, see below.
3. Start engine and adjust engine to full throttle.
4. Engage the control lever or switch so that the
cylinder of the function that needs to be checked, bottoms out and then read the pressure gauge.
5. Adjust relief if necessary. Turn the relief clockwise to increase pressure and counter- clockwise to decrease the pressure.
RIGHT & LEFT TRACK
PROCEDURE
1. Makesureallthecontrolsareintheoffposition.
2. Swing the console to the right side, and place a drip pan below.
3. Unhook the Right Track B-Port hose and plug itoff.
4. Install pressure gauge into the test port, see below.
5. Start engine and adjust engine to full throttle.
6. Engage the Right Track in the forward position and read the pressure gauge.
7. Adjust relief if necessary. Turn the relief clockwise to increase pressure and counter- clockwise to decrease the pressure.
31
Track
Relief
Cutter Head Swing Left/Right &
Cutter Head Up/Down Relief
Unhook this hose andplugitoff
Insert Pressure
Check Gauge Here
Bandit
MODEL SG-40 HYDRAULICS
HYDRAULIC SYSTEM TROUBLE SHOOTING
SAFETY INSTRUCTIONS
Before attempting any type of maintenance,
disengage clutch or cutter wheel engagement, wait for the cutter wheel to come to a complete stop, turn offengine,removetheignitionkey,makesurethe ignition key is in your possession, disconnect the battery, and install the cutter wheel lock pin.
PROBLEM
Hydraulic oil very hot, causing system to operate slowly.
Hydraulic system loss of power.
Swing cylinder loss of power.
POSSIBLE CAUSE
Low oil level.
Worn pump.
Poor oil quality.
Damaged hose.
Oilsuctionscreenorfilterplugged
Binding
Low oil level.
Poor oil quality.
Bad cylinder.
Bad pump.
Relief stuck open.
Bad cylinder.
Bad pump.
Relief stuck open.
Cutter wheel does not stay in up position, creeps down.
Bad cylinder
SOLUTION
Fill 7/8 full minimum.
Replace.
Replace.
Replace.
Replace.
Binding
Fill 7/8 full minimum.
Replace.
Repair or replace.
Replace.
Clean or replace.
Repair or replace.
Replace.
Clean or replace.
Repair or replace.
NOTICE
In cold weather situations, let the hydraulic system idle for approximately 15 minutes to allow the system to warm up to operating temperature. Running cold oil through the hydrostatic motor can raise the case drain pressures and damage the shaft seals.
When returning hydraulic components for warranty make sure to box up all warranted parts to avoid additional damage while shipping. Do not disassemble any hydraulic components which are to be warranted.
Anything which has been disassembled or tampered with will not be warranted. Items being returned must be clean. All hydraulic components must have all hosing ports plugged. Failure to plug ports will allow debris to enter components which will void warranty.
6/20 32
MODEL SG-40 REPLACEMENT PARTS
REPLACEMENT PARTS
Depending on what replacement parts you are ordering the following information will be needed:
GRINDER COMPONENTS
Serial Number
Model Number of Grinder
ENGINE COMPONENTS
Brand
Engine Serial Number
Engine Spec. Number
NOTICE
All nuts, bolts, washers, and many other components can be ordered by physical description.
NOTICE
Some of the components shown in this section are for optional equipment and may not apply to every machine.
NOTICE
Bandit Industries Inc. reserves the right to make changes in models, size, design, installations and
applicationsonanypartwithoutnotification.
MACHINE ORIENTATION REFERENCE
BACK
RIGHT
FRONT
33
LEFT
Bandit
MODEL SG-40 REPLACEMENT PARTS
DECALS
Decal locations may vary, these are general locations.
3,20,
21,22
6,13,26,
27,31,35,
36,39
1
23
33
12,29,37
25
6
6/20
2,9,
12,14
15,19
6
1,4,
12
8,17,
28,30 24
5,7,10
32,38
11,16
34
18
23
34
MODEL SG-40
4
5
6
7
8
#
1
2
3
9
Decal
SPD-02
SPD-20
SPD-22
SPD-28
SPD-30
SPD-36
SPD-38
SPD-39
SPD-63
10 SPD-69
11 ID-67
12 INST-12
13 INST-53
14 INST-73
15 INST-74
16 INST-81
17 INST-101
18 INST-111
19 INST-112
20 INST-180
21 INST-365
22 INST-366
Description
Moving Parts...
Flying Objects Stand Clear...
Emergency Shut Down Only
Do Not Insert Fingers...
Do Not Sit, Stand, Lay, Climb...
...Debris Field...
Do Not Entangle Feet...
Do Not Operate...
Do Not Go Near Cutter
Wheel...
Do Not Start to Grind...
Bandit Industries Inc...USA
Grease Daily
Hydraulic Oil...Hydrex XV
Cutterhead Lock Hole
Cutterhead Lock Pin
Swing Speed Controls
Canada Engine Decal
Frame Lock Hole
Frame Lock Pin
CutterWheelOn/Off
Joystick Functions
Swing Out Console Lock
23 INST-393 Grease Weekly - Double Arrow
DECALS
# Decal
24 INST-395
25 INST-446
26 N-02
27 SPN-06
28
29
30
N-33
N-71
N-72
31 SPW-01
32 SPW-03
33 SPW-04
34 SPW-08
35 SPW-28
36 SPW-43
37 SPW-47
38 OL-274
39 OL-313
40 900-8918-09
Description
Grease Yearly
Grease Monthly 2-3 Pumps
Maintain Lubrication...
Decal Maintenance...
Engine Oil Lubrication...
Break-In
Patents...
Service Required Under
Beltshield
Do Not Go Near Oil Leaks...
Gasoline Fuel Only
Frozen Battery Can Explode
Wear Personal Protection...
...Fire Hazard...
Do Not Attempt...Slope More
Than...
Proposition 65...
Gasoline Only
Hydraulic Fluid Only
Bandit Model SG-40 Logo &
Safety Decal Kit -
English/Spanish
41 900-8918-34 Bandit Model SG-40 Logo &
NOTICE
Modificationsand/oradditionsofdecalstothislist will happen. Consult dealer or manufacturer for most current decal package.
35
NOTICE
Some decals are for optional equipment. Decal locations may vary, these are general locations. If any decals become damaged, replace immediately.
Bandit
MODEL SG-40
ENGINE SIDE
32
REPLACEMENT PARTS
33
18
19
20
21
26
22
23
24
25
27
30
28
31
29
10
8
15
12
13
14
11
12 17
16
9
6/20
5
4
2
1
2
3
3
1
6
3
3
4
5
7
36
MODEL SG-40
# Part Number
1 208-3000-90
2 900-1923-27
3 900-4916-70
4 900-1923-25
5 900-4913-92
6 208-3000-43
7 208-2000-53
8 900-7900-10
9 900-3982-38
10 208-2000-58
ENGINE SIDE
Description
Pivot Bearing Cap
Flange Bushing
Pivot Bearing Cap Bolt -
1/2”-13NC x 2 3/4” SHCS
Jack Shaft Bearing
Jack Shaft Bearing Bolt -
3/8”-16NC x 1 1/4” Serrated Flange Bolt
Jack Shaft
Beltshield Backer
Rubber Grommet
Hydraulic Pump
Hydraulic Pump Adjuster
11 900-4906-60
900-4905-88
900-4910-97
12 900-1924-78
3/8”-16NC x 3” Hex Head Bolt
3/8”-16NC Lock Nut
Nord Lock Washer
5/16” Mill Carb Washer
13 900-1924-62
Pump & Engine Sheave
Pump Sheave Bushing
14 900-1924-79 Engine to Hydraulic Drive Belt
15 208-2000-59
16 900-1924-50
Clutch Pin Arm
Engine Sheave Bushing
REPLACEMENT PARTS
# Part Number
17 001-3007-05
Description
Key for Engine Sheave
18 900-1924-55 Engine to Jack Shaft Drive Belt
19 208-3001-10
Clutch Spacer
20 001-3007-04
21 900-6912-24
22 208-3000-71
23 208-3000-89
24 900-6970-04
(Between Clutch & Engine Sheave)
Key for Clutch
Clutch
Clutch Spacer
(Between Clutch & Sheaves)
Clutch Fan Spacer
Clutch Fan
Clutch Fan Bolt -
25 900-4917-99
5/8”-18NF x 3 1/2”
26 208-2000-56 Clutch Belt Tensioner Plate
27 208-1000-36
28 900-4910-41
29 900-1924-54
30 200-300087
Clutch Drive Idler
Clutch Drive Idler Bolt
Jack Shaft Sheave
Key for Jack Shaft Sheave
31 900-1924-31 Jack Shaft Sheave Bushing
32 208-2000-54 Beltshield Cover
33 904-0009-82 Grease Zerk Access Cover
NOTICE
Parts may not be exactly as shown.
37
NOTICE
Nuts, bolts, washers, and all other components can be ordered by physical description.
Bandit
MODEL SG-40
30
31
CUTTER WHEEL SIDE
REPLACEMENT PARTS
27
29
20
28
21
27
25
26
22
23
24
15
32
37 35
1
33
37
34
36
11
12
2
3
4
5
6
7
5 10
18
17
17 18
16
14
13
19
15
8
9
5
6/20 38
MODEL SG-40
CUTTER WHEEL SIDE
# Part Number
1 208-2000-35
Description
Beltshield Cover
2 900-1908-36 Belt
3 900-1924-28 Jack Shaft Sheave Bushing
4 200-300087
Key for Jack Shaft Sheave
Bushing
# Part Number
19 208-3001-43
REPLACEMENT PARTS
Description
Cutter Wheel Bar Linkage
208-2000-32 Cutter Wheel Frame Weldment
21 900-4906-84 Cutter Wheel Shaft Nut
6 900-4906-98
7 900-1926-33
Sheave
Bolt for Idler Bushing
Idler Sheave Bushing
8 900-1903-13 Cutter Wheel Sheave Bushing
10 208-3001-57
11 208-3000-43
900-4910-68
Bushing
12 208-2000-33
13 208-2000-34 Idler Sheave Tensioner Plate
14
900-4906-56
15 900-1924-11
Dust Cover
Jack Shaft
Beltshield Backer
16 208-2000-28 Cutter Wheel Bar Assembly
17 208-2000-18
18 900-1924-80
Idler Sheave Adjuster Bolt
Nut for Idler Sheave Adjuster
Bolt
Cutter Wheel Bearing
Cutter Wheel Bar Mount
Cutter Wheel Bar Mount
Bushing
40 - 41
23 208-3000-35
24 900-4906-73
25 955-300086
26 900-7900-96
27 208-3000-26
28 900-3941-35
29 208-2000-52
Cutter Wheel Assembly
Cutter Wheel Shaft
Cutter Wheel Shaft Bolt
Lock Pin
Lock Pin Rubber Handle
Lift Cylinder Pin
Lift Cylinder
Pivot Assembly
30 900-1902-42 Bushing for Swing Cylinder
31 900-3958-80
32 208-2000-37
33 208-2000-36
34 208-3001-53
Swing Cylinder
Chip Pan - Right Side
Chip Pan - Left Side
Chip Curtain - Large
35 208-3001-55 Chip Curtain Strap - Right Side
36 208-3001-54 Chip Curtain Strap - Left Side
37 208-3001-56 Chip Curtain - Small
NOTICE
Parts may not be exactly as shown.
39
NOTICE
Nuts, bolts, washers, and all other components can be ordered by physical description.
Bandit
MODEL SG-40 REPLACEMENT PARTS
GREEN TEETH CUTTER WHEEL
4
3
3
4
2
2
5
4
6
6
4
5
2
2
5
4
6
6
4
5
2
2
3
4
4
3
2
2
6/20 40
MODEL SG-40 REPLACEMENT PARTS
GREEN TEETH CUTTER WHEEL
# Part Number
1 208-1000-05
2
900-9926-71
900-9937-58
Description
Green Teeth Cutter Wheel
Assembly (Includes 7)
WearSharp Tooth
WearSharp Tooth Nut
900-9937-59 WearSharp Tooth Nut Spacer
# Part Number Description
3 900-9907-42 Pocket Bolt (Without Spacers)
4 900-9907-86 Angle Pocket
5 900-9916-03 Pocket Bolt (With Spacers)
6 900-9938-57
7 900-9938-33
Pocket Spacer
8 Tooth Kit
41
Bandit
MODEL SG-40
FRAME
REPLACEMENT PARTS
12
11
7
13
10
6
5
1
2
2
4 3
2
3
4
2
1
5
6
7
8
9
2
6/20
2
2
3
4
2
4
3
42
MODEL SG-40
FRAME
# Part Number
1 900-5914-89
2 900-5914-27
3 900-4923-96
Description
Rubber Track
Track Roller
Track Roller Adjuster Bolt
Track Roller Adjuster
Track Roller Adjuster Nut
5 208-3002-25 Track Drive Sprocket
6 208-3002-19 Track Drive Motor Mount Plate
7 900-3978-18
8 208-3002-23
9 208-3002-64
10 208-3001-86
11 900-4909-41
12 208-3001-13
Track Drive Motor
Drive Motor Access Cover
Pivot Access Cover
Pivot Hub Plate
Pivot Hub Nut
Bulkhead Plate
REPLACEMENT PARTS
# Part Number
208-1000-29
13
900-5917-63
900-5917-71
900-5917-72
900-4914-00
900-5911-75
900-6916-90
Description
Spindle & Hub Assembly
Hub Kit Only
Jam Nut
Cup & Stud Outer Hud
Cone Nut
Spindle Nut Retainer
Dust Seal
900-5905-30
900-1919-46
Dust Cap
Inner/Outer Bearing
900-5911-97 Outer Bearing Cone
900-5911-13 Rubber Plug for Grease Cap
900-5912-70 “D” Washer
NOTICE
Parts may not be exactly as shown.
43
NOTICE
Nuts, bolts, washers, and all other components can be ordered by physical description.
Bandit
MODEL SG-40
16
19
15
SWING OUT CONSOLE
REPLACEMENT PARTS
6
4
3
2
5
7
7
8
9
10
14
1
13
17
11
12
18
6/20 44
MODEL SG-40
SWING OUT CONSOLE
# Part Number
1 208-2000-12
Description
Swing Out Arm Assembly
2 900-2931-47 Emergency Stop
3 900-2910-93 CutterWheelOn/OffSwitch
4 900-2903-76 Hour Meter
5 208-2000-14 Swing Out Arm Lock Handle
# Part Number
900-5912-79
900-5915-82
11
900-5911-99
Lock Handle
7 996-3007-25 Swing Out Arm Lock Linkage
8 208-3000-60 Swing Out Arm Lock Pin
9 900-4923-40 Swing Out Arm Lock Spring Pin
10 900-4923-61 Swing Out Arm Lock Spring
REPLACEMENT PARTS
Description
Swing Out Arm Spindle
Grease Cap for Spindle
Inner & Outer Bearing for
Spindle
Spindle
010-060-00 Inner & Outer Seal for Spindle
12 208-2000-13
13 208-3000-68
14 900-9910-28
15 208-3001-01
16 208-3001-00
17 208-3000-66
18 900-6911-34
19 900-3981-98
Swing Out Arm Lock Plate
Tank Spacer Cover
Manual Holder
Swing Out Arm Slide
Swing Out Arm Support
Battery Strap
Battery
Hydraulic Valve
NOTICE
Parts may not be exactly as shown.
45
NOTICE
Nuts, bolts, washers, and all other components can be ordered by physical description.
Bandit
MODEL SG-40 REPLACEMENT PARTS
FUEL & HYDRAULIC TANK
4
3
6
9
10
8
11
12
7
5
13
14
2
5 1
6/20 46
MODEL SG-40
# Part Number
2
208-2000-10
900-3951-31
900-3951-32
900-3994-62
3 900-3988-07
4 900-3900-44
5 900-3921-01
6 900-3944-78
7 900-3980-29
REPLACEMENT PARTS
FUEL & HYDRAULIC TANK
Description
Hydraulic Tank Assembly
Hydraulic Tank Weldment
Hydraulic Filter Assembly
Hydraulic Filter Only
Hydraulic Filter Cap Only
Locking Fill Cap - Hydraulic
Tank Only
Sight Gauge
Drain Plug
Tank Strainer
Tank Clean-Out Cover
# Part Number
8 208-1000-08
208-2000-09
Description
Fuel Tank Assembly
(Includes 9 - 14)
Fuel Tank Weldment
900-3909-03 Drop Pipe
10 900-3936-69 1/4” NPT 90° Fuel Return Line
11 900-3988-32
Locking Fill Cap - Fuel Tank
Only
12 900-2929-09
13 900-6910-94
14 900-3967-53
8” Sight Gauge
Cannister Clamp
Carbon Canister
NOTICE
Parts may not be exactly as shown.
47
NOTICE
Nuts, bolts, washers, and all other components can be ordered by physical description.
Bandit
MODEL SG-40
DATE
SERVICE RECORD
DESCRIPTION
SERVICE RECORD
AMOUNT
6/20 48
MODEL SG-40 OGURA CLUTCH MANUAL
49
PTO Clutch/Brake
Installation and Maintenance
Bandit
MODEL SG-40 OGURA CLUTCH MANUAL
6/20 50
MODEL SG-40 OGURA CLUTCH MANUAL
51
Bandit
MODEL SG-40 OGURA CLUTCH MANUAL
6/20 52
MODEL SG-40 OGURA CLUTCH MANUAL
53
Bandit
MODEL SG-40 OGURA CLUTCH MANUAL
6/20
always mounted
54
MODEL SG-40 OGURA CLUTCH MANUAL
55
Minimum shaft length
Bandit
MODEL SG-40 OGURA CLUTCH MANUAL
6/20 56
MODEL SG-40 OGURA CLUTCH MANUAL
57
Engine shaft needs
Bandit
MODEL SG-40 OGURA CLUTCH MANUAL
6/20
Engine shaft needs to be tapped
58
MODEL SG-40 OGURA CLUTCH MANUAL
59
be short enough that pulley bearing carrier
Bandit
MODEL SG-40 OGURA CLUTCH MANUAL
6/20 60
MODEL SG-40 OGURA CLUTCH MANUAL
61
Bandit
MODEL SG-40 OGURA CLUTCH MANUAL
6/20
are set at fa either clockwise or counter- clockwise
62
MODEL SG-40 OGURA CLUTCH MANUAL
63
Springs should operate in tension and not
Bandit
MODEL SG-40 OGURA CLUTCH MANUAL
6/20
PTO backing plate only needs to withstand
64
MODEL SG-40 OGURA CLUTCH MANUAL
65
Bandit
MODEL SG-40 OGURA CLUTCH MANUAL
6/20 66
MODEL SG-40 OGURA CLUTCH MANUAL
67
Bandit
MODEL SG-40 OGURA CLUTCH MANUAL
6/20 68
MODEL SG-40 OGURA CLUTCH MANUAL
69
Bandit
MODEL SG-40 OGURA CLUTCH MANUAL
6/20
Set key in shaft keyway if required (some clutches have internal key)
70
MODEL SG-40 OGURA CLUTCH MANUAL
71
Pulley must not contact radius of shaft shoulder
Pulley must sit against shoulder face, otherwise center
Bandit
MODEL SG-40 OGURA CLUTCH MANUAL
6/20
If clutch requires key, key way on shaft, then damage bearing races
72
MODEL SG-40 OGURA CLUTCH MANUAL
73
Bandit
MODEL SG-40 OGURA CLUTCH MANUAL
6/20 74
MODEL SG-40 OGURA CLUTCH MANUAL
75
Center bolt tightening torque is based on bolt grade adhesive should be used
Bandit
MODEL SG-40 OGURA CLUTCH MANUAL
6/20 76
MODEL SG-40 OGURA CLUTCH MANUAL
77
Bandit
MODEL SG-40 OGURA CLUTCH MANUAL
6/20 78
MODEL SG-40 OGURA CLUTCH MANUAL
79
Bandit
MODEL SG-40 OGURA CLUTCH MANUAL
6/20 80
MODEL SG-40 OGURA CLUTCH MANUAL
81
Most clutch parts do not require maintenance
Bandit
MODEL SG-40 OGURA CLUTCH MANUAL
6/20
All Ogura one-piece clutches are adjusted at factory (no initial adjustment required) As adjustable clutches wear, they can
82
MODEL SG-40 OGURA CLUTCH MANUAL
83
If clutch fails to pull in or will not continue
Bandit
MODEL SG-40 OGURA CLUTCH MANUAL
6/20
Identify clutch model from label located There are three inspection slots on br Place feeler gauge in slot between armature and rotor Slowly tighten brake nut until armature and
84
MODEL SG-40 OGURA CLUTCH MANUAL
85
Almost all Ogura clutches use 24UNF brake (for reference only: feeler gauge is still required)
Bandit
MODEL SG-40 OGURA CLUTCH MANUAL
6/20 86
MODEL SG-40 OGURA CLUTCH MANUAL
87
Bandit
MODEL SG-40 OGURA CLUTCH MANUAL
6/20
increase cycle life between adjustments
88
MODEL SG-40 OGURA CLUTCH MANUAL
89
If there is contact, back off brake nuts and retry until there is no contact
Bandit
MODEL SG-40 OGURA CLUTCH MANUAL
6/20 90
advertisement
* Your assessment is very important for improving the workof artificial intelligence, which forms the content of this project
Key Features
- Powerful engine for efficient stump grinding
- Heavy-duty cutter head can grind stumps up to 12 inches in diameter
- Hydraulic lift system for effortless height adjustment
- Intuitive controls and safety features for ease of operation and maintenance
Related manuals
Frequently Answers and Questions
What is the maximum stump diameter that the Bandit SG-40 can grind?
How does the hydraulic lift system benefit the user?
What safety features are included on the Bandit SG-40?
advertisement
Table of contents
- 7 Serial Number Locations
- 8 Safety Procedures
- 13 Controls
- 16 Machine Operation
- 18 Transportation Procedures
- 20 Maintenance
- 31 Hydraulics
- 35 Replacement Parts
- 36 Decals
- 38 Engine Side
- 40 Cutter Wheel Side
- 42 Green Teeth Cutter Wheel
- 43 New River “Revolution” Cutter Wheel
- 44 Frame
- 46 Swing Out Console
- 48 Fuel & Hydraulic Tank
- 50 Service Record
- 51 Ogura Clutch Manual