- No category
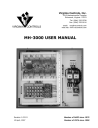
advertisement
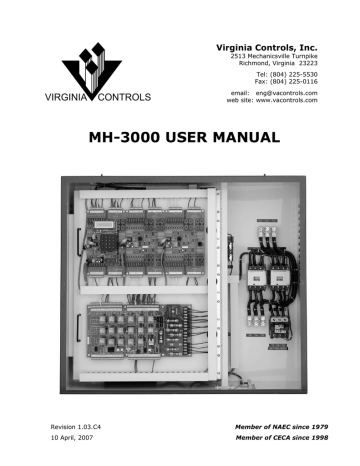
Virginia Controls, Inc.
2513 Mechanicsville Turnpike
Richmond, Virginia 23223
Tel: (804) 225-5530
Fax: (804) 225-0116 email: [email protected] web site: www.vacontrols.com
VIRGINIA CONTROLS
MH-3000 USER MANUAL
Revision 1.03.C4
10 April, 2007
Member of NAEC since 1979
Member of CECA since 1998
VCI -- MH-3000 User Manual (Rev 1_03C4)
TABLE OF CONTENTS
1.
PRE-INSTALLATION INSTRUCTIONS AND
NOTES.................................................................... 1
General Notes ...........................................................1
Important Precautions And Notes .................................1
2.
CONTROLLER INSTALLATION AND WIRING . 3
Controller Installation .................................................3
2.1.1 Controller Location Selection and Environment........................ 3
2.1.2 Controller Grounding........................................................... 4
Car and Hoistway Wiring.............................................4
2.2.1 Floor Switches.................................................................... 4
2.2.2 Car Top Selector................................................................. 5
2.2.3 Leveling Switches................................................................ 5
2.2.4 Terminal Landing Normal Slowdown Switches ......................... 5
2.2.5 Terminal Landing Normal Limit Switches ................................ 5
2.2.6 Terminal Landing Final Limit Switches.................................... 6
2.2.7 Emergency Terminal Landing Limit Switch.............................. 6
2.2.8 Hoistway Access Zone Switches ............................................ 6
2.2.9 Door Open and Close Limit Switches...................................... 6
Machine Room Wiring .................................................7
2.3.1 Incoming Power ................................................................. 7
2.3.2 Grounding ......................................................................... 7
2.3.3 Pump Motor Wiring ............................................................. 8
2.3.4 Wye-Delta Run Contact Wiring.............................................. 8
3.
START-UP INSTRUCTIONS............................ 9
Before Applying Power................................................9
3.1.1 Power and Grounding .......................................................... 9
3.1.2 Input/Output Wiring............................................................ 9
Applying Power........................................................ 10
3.2.1 Motor Rotation ................................................................. 10
MH-3000 User Manual Page I
Temporary Run Connections...................................... 10
4.
FINAL ADJUSTMENTS ................................. 12
Inspection Operation ................................................ 12
Floor Position and Slowdown ..................................... 13
Position Indicators ................................................... 13
Independent Service ................................................ 13
Car and Hall Calls .................................................... 14
Door Operation........................................................ 14
Fire Service............................................................. 15
Failure Timers ......................................................... 15
4.8.1 Stuck Button Timer ........................................................... 15
4.8.2 Running Timers ................................................................ 15
Field Adjustable Features .......................................... 16
Zoned Duplex Operation ........................................... 16
4.10.1 Common Circuits .............................................................. 16
4.10.2 Next Car.......................................................................... 16
4.10.3 Car Start ......................................................................... 17
4.10.4 Homing ........................................................................... 17
4.10.5 Communication ................................................................ 18
Zoned Group Operation ............................................ 18
4.11.1 Common Circuits .............................................................. 18
4.11.2 Homing ........................................................................... 19
4.11.3 Communication ................................................................ 19
4.11.4 Car Controller Settings ...................................................... 20
4.11.4.1 Dispatch Failure Calls .................................................. 20
4.11.4.2 Car Homing ............................................................... 20
4.11.5 Dispatch Controller Settings ............................................... 20
4.11.5.1 Zone Code Settings .................................................... 20
4.11.6 Dispatch Traffic Programs .................................................. 21
5.
HARDWARE DESCRIPTION ......................... 22
MH-3000 User Manual Page II
Transformers .......................................................... 22
Fuses ..................................................................... 23
12VDC Power Supply................................................ 24
Safety Interface Board.............................................. 24
5.4.1 MH4................................................................................ 25
5.4.2 MH5................................................................................ 25
5.4.3 Phase Monitor .................................................................. 26
5.4.4 Digiset Timer ................................................................... 27
5.4.5 Bypass Switches............................................................... 27
5.4.6 Inspection Switches .......................................................... 28
5.4.7 Connections ..................................................................... 28
Microprocessor ........................................................ 29
5.5.1 CPU ................................................................................ 29
5.5.1.1 CPU Battery............................................................... 30
5.5.1.2 LED Description.......................................................... 31
5.5.1.3 Reset Button.............................................................. 32
5.5.1.4 CPU Connectors ......................................................... 33
5.5.1.5 S2 Slide Switch .......................................................... 35
5.5.2 Input/Output Boards ......................................................... 36
5.5.2.1 Addressing ................................................................ 38
5.5.2.2 Terminal Wiring.......................................................... 38
5.5.2.3 Input/Output LEDs...................................................... 39
5.5.2.4 Board Status LED ....................................................... 39
5.5.2.5 I/O Bus Communication Connectors .............................. 40
5.5.2.6 Programming Connector .............................................. 40
5.5.2.7 Power Connector ........................................................ 40
5.5.2.8 Jumper Blocks............................................................ 41
Motor Control .......................................................... 42
5.6.1 Across-the-line Starting..................................................... 42
5.6.2 Wye-Delta Starting ........................................................... 43
5.6.3 Solid-State Starting .......................................................... 44
B.O.R.I.S................................................................ 45
6.
MH-3000 SCREENS AND DIAGNOSTICS ...... 46
Run Mode ............................................................... 46
6.1.1 Run Mode Screens ............................................................ 46
6.1.1.1 Banner Screen ........................................................... 47
MH-3000 User Manual Page III
6.1.2 Show I/O Status............................................................... 48
6.1.2.1 Moving Around in I/O Status Screen.............................. 48
6.1.3 Show Fault Log................................................................. 48
6.1.3.1 Typical Fault Screen.................................................... 49
6.1.3.2 Fault Number............................................................. 49
6.1.3.3 Fault Time Stamp ....................................................... 49
6.1.3.4 Fault Code................................................................. 50
6.1.3.5 Fault Log Status Signals .............................................. 56
6.1.3.6 Moving Around in the Fault Log .................................... 59
6.1.3.7 LED Description in "Show Fault Log" Mode ..................... 59
6.1.3.8 Historical Log ............................................................. 59
6.1.4 Show Internal Memory ...................................................... 61
6.1.4.1 Moving Around in the Internal Memory .......................... 62
6.1.4.2 LED Description in "Show Internal Memory" Mode ........... 62
6.1.4.3 Changing values in the “Show Internal Memory” Mode..... 63
6.1.5 Show Car Status............................................................... 63
6.1.5.1 Messages Displayed on the “Car Status” Screen.............. 64
6.1.5.2 Messages Displayed on the “Dispatcher Status” Screen.... 67
6.1.6 Go To Set-Up Mode........................................................... 67
6.1.7 Effect of Diagnostic Modes on Scan Time.............................. 68
Set-Up Mode ........................................................... 69
6.2.1 How to Enter Set-Up Mode ................................................. 69
6.2.2 How to Exit Set-Up Mode ................................................... 69
6.2.3 Set-Up Mode Screens ........................................................ 69
6.2.4 Reset Settings.................................................................. 70
6.2.5 Change Settings ............................................................... 71
6.2.5.1 Description of Settings ................................................ 72
6.2.5.2 Numerical Settings ..................................................... 72
6.2.5.3 Bit Features ............................................................... 74
6.2.5.4 Timers ...................................................................... 75
6.2.5.5 Custom Timers........................................................... 75
6.2.5.6 Tenth of a Second Timers ............................................ 75
6.2.5.7 One Second Timers..................................................... 76
6.2.5.8 Ten Second Timers ..................................................... 78
6.2.5.9 Description of Bit Feature Settings ................................ 78
6.2.6 Change Features .............................................................. 85
6.2.6.1 Description of Features................................................ 86
6.2.7 Show Fault Log................................................................. 87
6.2.8 Show Internal Memory ...................................................... 87
6.2.9 Set the Time .................................................................... 88
6.2.10 Enter Password ................................................................ 89
6.2.11 Test I/O Boards ................................................................ 89
MH-3000 User Manual Page IV
7.
CONTROLLER NOMENCLATURE ................... 91
8.
PARTS LIST ................................................ 92
9.
TROUBLESHOOTING SUGGESTIONS ........... 94
Locating Faults ........................................................ 94
9.1.1 Troubleshooting I/O Board Communication Problems ............. 95
I/O Board Replacement ............................................ 96
Factory Assistance ................................................... 96
Changes for Program Revisions.................................. 96
9.4.1 Program Revision 2D......................................................... 96
9.4.2 Program Revision 3A ......................................................... 97
9.4.3 Program Revision 3B ......................................................... 97
9.4.4 Program Revision 3C ......................................................... 97
10.
CONTROLLER MAINTENANCE...................... 98
Periodic Maintenance................................................ 98
Parts Replacement ................................................... 98
10.2.1 CPU Exchange .................................................................. 98
10.2.2 EPROM Memory Chip Exchange........................................... 99
10.2.3 Input/Output Board Exchange ............................................ 99
11.
FREQUENTLY ASKED QUESTIONS ............. 101
Questions on Field Devices ...................................... 101
Questions on the Controller ..................................... 101
INDEX
MH-3000 User Manual Page V
1. Pre-Installation Instructions and Notes
1.1 General Notes
It is strongly recommend that you read this manual carefully before proceeding with the installation.
Important information is highlighted by the headings WARNING, CAUTION, or NOTE.
These words are defined as follows:
WARNING - Warnings are used to indicate instructions which, if not followed correctly, will probably result in personal injury or substantial damage to equipment.
CAUTION - Cautions are used to indicate instructions or information which, if not observed, may result in some damage to equipment if care is not taken.
NOTE - Notes are used to indicate instructions or information which are especially helpful in understanding and operating the equipment, and which will usually speed up the installation process.
1.2 Important Precautions And Notes
The following general rules and safety precautions must be observed for safe and reliable operation of your system.
WARNING: If you need to change the EPROM program chip on the
CPU board, make sure you read the instructions and know exactly how to install the new chip. Plugging the EPROM chip in upside-down may damage the chip. Static electricity can damage the EPROM, so avoid touching the pins on the chip, and ground yourself (by touching the controller cabinet) before touching the chip or the controller. Do not expose the EPROM program chip to bright light, and do not remove the label over the EPROM program chip window.
WARNING: The elevator controller must be installed by experienced field installation personnel. The field installation personnel must know and follow all the rules and regulations pertaining to the safe installation and running of elevators. Additional information for specific devices (such as the valves, door operator, etc.) is the responsibility of the manufacturers of those devices.
WARNING: This equipment is designed and built to comply with ANSI
A17.1, ASME A17.5 and CAN/CSA B44.1 and must be installed by a qualified contractor. It is the responsibility of the contractor to make sure that the final installation complies with all applicable local, state and national codes, and is installed safely.
MH-3000 User Manual Page 1
WARNING: The 3 phase AC power supply to this equipment must come from a fused disconnect switch or circuit breaker which is sized in accordance with all applicable national, state and local electrical codes, in order to provide the necessary branch circuit protection for the controller and motor. Incorrect motor branch circuit protection may create a hazardous condition.
WARNING: Proper grounding is vital for the safe operation of your system. Bring the ground wire to the ground stud that is labeled
"GND" or "G". You must choose the proper conductor size. See national electrical code article 250-95, or the related local applicable code.
Pay special attention to points highlighted in this manner. They are of special consideration and are frequently overlooked.
MH-3000 User Manual Page 2
2. Controller Installation and Wiring
2.1 Controller Installation
2.1.1 Controller Location Selection and Environment
Mount the controller in a location that provides:
• adequate support for the weight of the controller,
• adequate lighting for installation and maintenance,
• convenient access for the routing of required conduits and cables,
• convenient access to other devices in the machine room,
• a minimum of vibration (supply additional bracing or reinforcement if required).
For improved controller reliability:
• Keep the machine room clean.
• Do not install the controller in a dusty area.
• Do not install the controller in a carpeted area, or area where static electricity is a problem.
• Keep room temperature between 0°C to 50°C (32°F to 122°F), and 95% noncondensing relative humidity. Extended high temperatures will shorten the life of electronic components. Provide adequate ventilation or air-conditioning as required if necessary.
• Avoid condensation on the equipment. Keep the controller away from sources of condensation and water (such as open windows) as these can create a hazardous condition and can damage the equipment.
• Do not install the controller in a hazardous location and where excessive amounts of vapors or chemical fumes may be present. A NEMA 4 or NEMA 12 rated enclosure can be provided if necessary.
• Make sure power line fluctuations are within ±10%.
• High levels of radio frequency emissions may cause interference with the controller microprocessor, and produce unexpected results. This could be caused by hand-held communications devices used near the controller.
• Long term operation of the controller without the door or cover in place is not recommended.
MH-3000 User Manual Page 3
2.1.2 Controller Grounding
Grounding of the controller must conform to all applicable codes. Proper grounding is essential to the safe operation of the equipment. It will also reduce the likelihood of noise-induced problems, which could include CPU crashes, or I/O communication errors.
• The grounding wire should be sized per the applicable codes.
• Connect the ground to a good building ground, such as the structural steel of the building, or a cold water pipe.
2.2 Car and Hoistway Wiring
Review the schematics and field wiring diagrams before attempting to hook up the controller.
2.2.1 Floor Switches
The Floor Switches, if used, are normally open contacts that should close under each of the following conditions:
1. the car is at the slowdown point above the floor, OR
2. the car is at the slowdown point below the floor, OR
3. the car is at the floor (optional), OR
4. the car is between the up and down slowdown points of that landing (optional).
Conditions (1) and (2) are required to change the floor relays and initiate slowdown.
Condition (3) is required at the terminal landings, but is optional at the intermediate landings.
Condition (4) is optional.
There are many acceptable methods of providing the floor switch signals, such as by having a single Floor Switch at floor level, and an adjustable length cam on the car, or by having two Floor Switches per floor, and a fixed length cam on the car. The Floor Switches may be mounted on the car if they are in separate rows. It is recommended that the method used allow for separate adjustment of the up and down slowdown distances.
NOTE: Recommended slowdown distance is about 6" for every 25fpm of car speed, for speeds of up to 200fpm. Minimum recommended target length for the floor switches is 1".
If there are short floors, refer to the schematic for special instructions, if required.
NOTE: The terminal landing Floor Switches must be maintained while the car is within door zone of the terminal landing.
MH-3000 User Manual Page 4
2.2.2 Car Top Selector
The pulsing-type Car Top Selector provides Floor Change/Slowdown signals and Leveling signals, as shown on the car top selector sheet in the schematic. The signals should be a normally open contact that closes as described below.
1. UP SLOWDOWN closes at the Slowdown distance below the floor.
2. DOWN SLOWDOWN closes at the Slowdown distance above the floor.
3. UP and DOWN LEVEL, and DOOR ZONE/LOW LEVEL. (See "Leveling Sws")
NOTE: Recommended slowdown distance is about 6" for every 25fpm of car speed, for speeds of up to 200fpm. Minimum recommended target length for the floor switches is 1".
An extra reset target is required at each terminal landing, as shown on the schematic, so that the Up Slowdown Switch is closed when the car is in the leveling zone at the top landing, and the Down Slowdown Switch is closed when the car is in the leveling zone at the bottom landing. These targets are used to reset the floor position at the terminal landings.
2.2.3 Leveling Switches
The Up Level Switch is a normally open contact that closes when the car is in the leveling zone below the floor, and the Down Level Switch is a normally open contact that closes when the car is in the leveling zone above the floor. Adjust the distance between the Up Level
Switch and the Down Level Switch to be equal to the length of the leveling vane/target plus the desired Dead Zone distance (usually 1/4" to 1/2"). The actual length of the leveling target is not critical (except in some short floor situations) and is usually 6-10". Position the leveling vane/target so that when the car is floor level the Up and Down Leveling Switches are centered around the vane/target, and both switches are open.
The Door Zone Switch is a switch (or switches) activated by the leveling vane/target when the car is within 3" of floor level. If the leveling vane/target is 6" long, then only one switch is required, mounted between the Up and Down Leveling Switches, otherwise two switches wired in series should be provided.
2.2.4 Terminal Landing Normal Slowdown Switches
The Terminal Landing Normal Slowdown Limit Switch is a normally closed contact that opens when the car is closer to a terminal landing than the minimum slowdown distance. It will prevent the car from running into the terminal landing at full speed. It should be adjusted to open approximately one inch beyond the point where the normal slowdown (from the floor switches or the car top selector) is initiated.
2.2.5 Terminal Landing Normal Limit Switches
The Terminal Landing Normal Limit Switch (sometimes called a Directional Limit
Switch) is a normally closed contact that opens when the car has traveled 1" past floor level at a terminal landing. The car should not be on the Terminal Landing
Normal Limit Switch when the car is floor level at the terminal landing. The Limit
MH-3000 User Manual Page 5
Switch will prevent the car from traveling further away from the normal area of car travel, but allows the car to run back towards the normal area of car travel.
2.2.6 Terminal Landing Final Limit Switches
The Terminal Landing Final Limit Switch, where required by code, is a normally closed contact that opens when the car has gone a considerable distance beyond floor level at a terminal landing. It will prevent any further movement of the car in either direction. Consult the applicable codes for the proper setting of this switch.
2.2.7 Emergency Terminal Landing Limit Switch
The Emergency Terminal Landing Slowdown Switch should be installed as required by the applicable codes. It is a normally closed contact that opens after the car has gone beyond the Terminal Landing Normal Limit Switch.
2.2.8 Hoistway Access Zone Switches
The Hoistway Access Limit Switches limit the motion of the car on Hoistway Access, by disabling the car if it moves away from the access floor. Install the zone switches to stop the car from running down if the top of the car goes below floor level at the top access floor, and to stop the car from running up if the car goes above the second floor while on
Hoistway Access at the bottom floor.
2.2.9 Door Open and Close Limit Switches
The Door Open Limit Switch is open when the doors are fully open, and closed at all other times. It will de-energize the door open relays in the door operator when the doors have opened fully.
The Door Close limit Switch is open when the doors are fully closed, and closed at all other times. It will de-energize the door close relays in the door operator when the doors have closed fully.
NOTE: Many problems in operation can be attributed to failures in the Door
Open or Close Limit Switches (including long door times, improper door operation on Fire Service, inability to go on to or to clear Fire Service, etc.)
Always check the Door Open and Close Limit Switches if unusual operation of the elevator is observed.
NOTE: It is recommended that the Door Close Limit Switch be adjusted so that, as the doors are closing, the Car Door Contact closes before the Door
Close Limit opens. Consult the Door Operator Manufacturer's installation instructions for further details on the adjustment of the doors.
NOTE: 2000 (or later) code compliant controllers will not run without the
Door Close Limit operation properly.
NOTE: If a solid state door operator unit is being used, check the appropriate schematics to see if any changes are required on the actual operator. These may include changing resistors in the operator, and adding a diode for proper open and close torque.
MH-3000 User Manual Page 6
2.3 Machine Room Wiring
Mount the controller firmly and install all required conduits before wiring the controller.
Note where duct has been provided in the controller for customer access, before deciding where to locate conduit openings.
WARNING: Do not allow any metal shavings to get into relays or contactors, or in or behind the electronic components, as these could cause serious damage to personnel or the equipment.
2.3.1 Incoming Power
WARNING: THE 3 PHASE AC POWER SUPPLY TO THIS EQUIPMENT
MUST COME FROM A FUSED DISCONNECT SWITCH OR CIRCUIT
BREAKER WHICH IS SIZED IN ACCORDANCE WITH ALL APPLICABLE
NATIONAL, STATE AND LOCAL ELECTRICAL CODES, IN ORDER TO
PROVIDE THE NECESSARY BRANCH CIRCUIT PROTECTION FOR THE
CONTROLLER AND MOTOR. INCORRECT MOTOR BRANCH CIRCUIT
PROTECTION MAY CREATE A HAZARDOUS CONDITION.
Incoming AC power wiring should be done by a qualified and licensed electrician, using the appropriate size wires for the installation. Consider the motor size and type of starter, and also the length of wire required from the main power distribution center in determining the proper wire size.
Proper branch circuit protection and disconnect device(s) must be provided, as required by applicable local, state and national codes.
2.3.2 Grounding
WARNING: PROPER GROUNDING IS VITAL FOR THE SAFE
OPERATION OF YOUR SYSTEM. BRING THE GROUND WIRE TO THE
GROUND STUD THAT IS LABELED "GND" OR "G". YOU MUST CHOOSE
THE PROPER CONDUCTOR SIZE AND MINIMIZE THE RESISTANCE TO
GROUND BY USING SHORTEST POSSIBLE ROUTING. SEE NATIONAL
ELECTRICAL CODE ARTICLE 250-95, OR THE RELATED LOCAL
APPLICABLE CODE.
Proper grounding is vital for the safe operation of your system, and will also reduce the likelihood of noise-induced problems, which could include CPU crashes, or I/O communication errors.
• The grounding wire should be sized per the applicable codes.
• Connect the ground to a good building ground, such as the structural steel of the building, or a cold water pipe.
• Connect the ground on the controller to the stud labeled "GND" or the terminal "G", as shown on the controller schematic.
MH-3000 User Manual Page 7
2.3.3 Pump Motor Wiring
Connect the pump motor as shown on sheet S of the schematic.
If an Across-the-Line starter is used, then the motor leads will connect to the starter overload.
If a Wye-Delta starter is used, then the motor leads will connect to the bottom of the overload, and to terminals T4,T5,T6. See the schematic for specific connection details.
2.3.4 Wye-Delta Run Contact Wiring
If a Wye-Delta starter is used, an auxiliary contact of the RU contactor may be connected in series with the up valves, to prevent the car from starting to run up until the motor is in the Delta mode. If this is not desired, then jump the contact. This will allow the valves to be energized as soon as the pump motor starts.
If a Soft-Start is used, the Up-to-Speed signal is used in a similar way.
MH-3000 User Manual Page 8
3. Start-Up Instructions
If it is desired to run the car temporarily, during construction, refer to the Temporary
Run Connections section. Otherwise proceed through each of these steps and checks before applying power.
3.1 Before Applying Power
The system has been programmed and tested for the specific elevator system. Refer to the MH-3000 Setting sheet in the as-built schematic for default factory settings and features.
3.1.1 Power and Grounding
WARNING: Confirm that the voltage of the incoming power matches the controller before applying power to the controller.
Check the system for improper grounds before applying power to the controller.
With the power off, remove the fuses from the secondary of the main control circuit transformer ("CCXF"). Check the safety circuit (terminals 1 through 6, and 14, 16, 18, 19) for grounds.
NOTE: A meter will read a short through the windings of the main control circuit transformer and/or any power supplies.
With the fuses still removed, apply power to the controller, and verify that the voltage at the secondary of the main control circuit transformer ("CCXF") is 110-125VAC.
3.1.2 Input/Output Wiring
NOTE: The input/output boards are equipped with quick disconnect terminal blocks. During the initial installation, you may want to remove the terminal blocks, hook up your field wires to the terminal blocks, test the field wiring for no shorts to ground or hot (terminal 1) before plugging these terminals back into the I/O boards.
With the power off, and the fuses removed, check each input point for grounds, as described in the section Power and Grounding. If a ground is observed, check the schematic to determine if this is correct (it usually is NOT!).
With the power off check each output for grounds, also check for shorts to the hot side
(terminal 1). Note that some field devices, such as buzzers, will have very low resistance.
WARNING: Each output point should be isolated from ground and the hot side.
MH-3000 User Manual Page 9
3.2 Applying Power
Remove all fuses before applying power. Reinsert the fuses, one circuit at a time, checking each circuit before adding the next.
It is recommended that you start up the controller in Inspection mode, which can be done by opening the Inspection Switch, or removing the field wire(s) from terminal 23.
WARNING: The field wire in terminal 23 is HOT. If it is removed, make sure it is insulated and labeled. Reconnect it when the car is to be taken off Inspection Operation.
3.2.1 Motor Rotation
Check that the motor is rotating in the proper direction by turning on the power, then briefly pushing in the motor starter ("PM" on across-the-line installations, "STR" on Wye-
Delta installations). Observe the direction of rotation of the motor, and if it is incorrect, reverse any two of the main power leads at the main line disconnect.
If a Reverse Phase relay is provided, check that the OK light is on when power is applied to it. If it is not, then reverse any on the two wires connected to the A,B,C terminals.
3.3 Temporary Run Connections
The following diagram show how the car may be run on temporary service, before the controller is fully installed.
FROM MAIN FUSES, OR DISCONNECT
TRANSFORMER
“CCXF”
See Sht#S for the connection diagram for the Pump Motor and Incoming Power.
FUSE
(CHECK SCHEMATIC FOR
PROPER FUSE)
(115VAC)
MOTOR
THERMAL
OVERLOAD
(IF USED)
CHASSIS
SAFETY
DEVICES
TEMPORARY
RUN BUTTONS
RUN UP
18X
TO CONTROLLER
MOTOR STARTER
CIRCUITS.
(SEE SHT#S)
35
UP VALVE
35
NOTE: Disconnect controller wires from the bottom of the fuse. Mark and insulate wire(s).
DOWN
115VAC VALVE COILS
DOWN VALVE
WARNING: NO SAFETY DEVICES ARE SHOWN. CONNECT ANY SAFETY
DEVICES AVAILABLE IN SERIES WITH THE RUN BUTTONS, AND USE
EXTREME CAUTION WHEN OPERATING THE CAR.
MH-3000 User Manual Page 10
See the schematic for the pump motor wiring, incoming power wiring and any special requirements.
If the system uses a Soft-Start, then additional connections will be required to make sure the starter energizes. Remove control wires from the starter terminals listed below and temporarily connect them to the bottom of the hot fuse (see previous diagram).
For Allen-Bradley SMC Soft-Starters, terminal “97” on the starter must have 115VAC to allow the fault circuit to operate properly.
For Siemens/Nordic Soft-Starters, terminals “1” and “9” on the starter must have
115VAC.
NOTE: The valves are not connected to the controller, but directly to the run buttons.
It is recommended that the wire(s) from the bottom of the fuse be disconnected, marked, and insulated, to prevent any power being sent to the normal controller circuits.
When the car is sufficiently completed to allow it to be run from the inspection station, reconnect all field devices as shown on the controller schematic field sheets. Reconnect the controller wire(s) to the bottom of the fuse (see previous connection diagram).
NOTE: Switch 3 on the CPU Slide Switch S2 is a Redundancy Defeat. If this is turned ON, then this will prevent a fault from the Redundancy checks, or a
Door Zone Fault. This can be used during initial installation to allow the car to be run without generating these faults. As a reminder to turn the defeat off after installation, the Fire Buzzer will be enabled.
MH-3000 User Manual Page 11
4. Final Adjustments
When the controller is ready to be run in automatic, it is recommended that EITHER a factory reset be performed OR the values of the settings and features be verified. If the program is custom (the job number will be in the bottom line of the banner) then a factory reset is recommended. If the job is not custom (the bottom line of the banner will start with a letter), all the values and settings for the job must be re-entered if a factory reset is done. Refer to the section Reset Settings, or the Frequently Asked Question - How Do I
Reset All Settings and Features Back to the Original Values.
A factory reset can be done by:
1. Turning off the power;
2. Put the car on inspection;
3. Jump terminals 1 to 21 and 1 to 22;
4. Turn on the power for 15 seconds;
5. Turn off the power, and remove the jumpers, and continue as normal.
Alternatively, the keypad can be used. Press Nxt until the menu item "Go to Setup
Menu" is displayed, then press Ent 3 times. (The screen will show a warning, then go to the Setup Menu, where the first item is Reset (factory) Settings). The password “911” should be entered when requested. Press Esc to return the elevator to service.
As the wiring is completed, the following modes of operation can be checked and used.
4.1 Inspection Operation
To run the car on Inspection Operation, the safety string (including the door contacts, terminal landing normal slowdowns, normals and finals) should be operational.
The Doors Closed and Gate Closed inputs on the I/O board should be on.
The Inspection Input should be de-energized.
Pressing the Up Run and Run (or Enable) Buttons will cause the Up Direction output to come on.
If the Doors Closed input is on, the Up Run outputs for the motor and the valves will energize, and the car will run up.
(Down direction is similar)
NOTE: If Hoistway Access is used to get on top of the car, then the doors will be open when Top of Car Inspection is initiated. In this case, the doors will close when the Up (or Down) Run and Run (or Enable) buttons are pressed.
If it is required that the doors should only operate manually on Inspection, then the Bit Feature to “Disable Door Close on Inspection” should be enabled.
In this case the doors must be closed manually or by means of the Door Close button on the Door Operator (if provided).
MH-3000 User Manual Page 12
NOTE: If 2000 (or later) Code and the MH5 board is provided, then the controller is expecting terminal 3 to go low when the Inspection Run Buttons are not being pressed. If a temporary run station is being used that is not wired as shown on the schematics, then the controller will show a fault if terminal 3 does not go low when the car stops. The redundancy fault can be temporarily defeated by turning Switch 3 on the CPU Slide Switch S2 to the
ON position. This will also turn on the Fire Buzzer output, as a reminder to turn off the defeat when the car is ready for full operation.
4.2 Floor Position and Slowdown
The program is in EPROM (Electrically Programmable Read Only Memory). The floor relays and fire service relays are maintained in the microprocessor RAM memory and are held through power loss by a battery on the CPU board. The floor relays may need to be reset when the controller is initially installed. This will be accomplished when the elevator hits any floor switch. With a pulsing type selector, the floor position is reset at either terminal landing when a slowdown switch and a leveling switch are energized at the same time.
NOTE: If floor switches are used, they should be maintained at the terminal landings, so that they are energized whenever the car is in the slowdown zone at that landing.
Make your final adjustments for the slowdown targets. All slowdown distances should be equal.
If a pulsing selector arrangement is used, remember to install the reset targets at the terminal landings.
4.3 Position Indicators
Verify that the floor position changes properly as the car goes past each landing. Floor change should take place at the slowdown point before each landing.
If the Position Indicator does not match the actual car position, run the car to a terminal landing reset target (with pulsing selector only).
4.4 Independent Service
Independent Service is useful for final tune-up of the car. Initiate Independent Service by turning on the Independent Service Switch in the car, or by jumping the Independent
Service Switch input.
On Independent Service, the hall calls will be canceled. The car will run from car calls only, and will park with the doors open. To close the doors, jump terminal 1 to terminal 28
("Door Close Button" input). This jumper may be left on, if desired, so that the car may be run by jumping the desired car call input.
MH-3000 User Manual Page 13
NOTE: To run the car from the machine room, without the doors opening, turn off the DOL Cutout Switch located on the MH4 or MH5 printed circuit board. This will de-energize the Door Open Limit Sw Input, and prevent the doors from opening.
NOTE: If the car does not run, verify that no door protective device (Door
Open Button, Safety Edge, Electric Eye, Infra-red Curtain) is holding the doors open. Verify that the car is not stuck in leveling. Verify that the Door
Contacts input is energized and the Door Close Limit input is de-energized.
4.5 Car and Hall Calls
To observe the operation of the car and hall calls, the system must be in automatic operation (LED D1 on the CPU board should be on.) Verify that all car and hall calls work.
NOTE: On DUPLEX systems the doors must be allowed to operate for the calls to be canceled properly.
Each call will be canceled when the car initiates slowdown for the call, or when the doors start to re-open for the call if the car is already at the floor.
If both hall calls are entered at an intermediate landing, and no other calls are in the system, the doors will close after answering one of the calls, then re-open in response to the other call.
4.6 Door Operation
Verify that any required changes to the door operator, as shown on the door operator drawings, have been made correctly.
Check the Door Open and Close Limits for proper operation.
If the doors attempt to open for too long, the open cycle will be stopped. The car will then respond to other calls, and try to open the doors again.
If the doors fail to close properly within a preset time, the doors will re-open, and try to close again. If the doors closed, but the car does not run in response to a call, the doors will re-cycle, and the car will try again.
For very slow doors, the Door Stuck Timer, which initiates the Door Open and Door Close
Fail, as described above, may need to be increased. It is normally set at 15 seconds.
If Nudging Operation is activated, the Electric Eye will be disabled when the Nudging
Timer has tripped AND the doors are fully open. If the nudging timer trips while the doors are closing, the Nudging Buzzer will turn on, and the Electric Eye will remain active. If the doors do reopen fully, then the Electric Eye will be cut out. The Safety Edge Input remains active on nudging.
MH-3000 User Manual Page 14
4.7 Fire Service
Fire Service Phase 1 may be initiated by turning off a Smoke Sensor input, or by energizing the Hall Fire Switch "On" input.
Confirm that the car returns to the correct Main and Alternate landings.
Confirm that the car operates as required on Car Fire Service (Phase 2) operation.
NOTE: To reset Hall Fire Service (Phase 1), most codes require the Bypass input be energized. To disable Hall Fire Service, jump the Hall Bypass input on. On 2000 (or later) Fire Code, Fire Service (Phase 1) is reset when the Hall
Fire Switch is turned from Bypass to Off.
NOTE: If Car Fire Service (Phase 2) appears to be operating incorrectly, check the Door Open and Close Limits for proper operation. Most codes require that the doors be fully open before allowing a change in the mode of operation on Car Fire Service. Most codes require that Hall Fire Service
(Phase 1) be in effect for the car to return automatically to the main fire landing when the Car Fire Switch is turned to the off position.
4.8 Failure Timers
4.8.1 Stuck Button Timer
If a car or hall call button remains on for an adjustable time, and other calls are registered, the stuck button call will be ignored, and the car will answer the other call(s).
The car will return to the stuck button call as it answers other calls, and the stuck button timer sequence will be repeated.
4.8.2 Running Timers
If the car runs up for an adjustable time, without changing floors, then low oil/shutdown operation will be initiated. The Shutdown LED on the CPU will come on. The Shutdown could be caused by a low oil level; a problem with the motor starter circuit(s); or a problem with the up valve circuit(s). The car will stop running up, then return to the lowest landing and cycle the doors. It will then be shut down, with only the Door Open Button and door re-opening devices being operational. The fault can be reset by cycling the Main Line
Disconnect Switch, or by putting the car on "Inspection" then back to "Automatic".
NOTE: If a Reverse Phase Relay or Emergency Power circuitry is supplied, these will also initiate a shutdown signal if the inputs are not energized.
If the car stops between floors, it will run down until it energizes the Door Zone Input, or a Leveling Switch Input. This prevents the car from parking between floors. If the car runs down for over 10 minutes while looking for a floor, it will stop, and return to normal operation.
MH-3000 User Manual Page 15
4.9 Field Adjustable Features
Refer to the section on changing Settings and Features to see the features that are adjustable.
The controller is usually set up for the specific job when it is shipped from Virginia
Controls. It is recommended that the "Reset Settings" sequence be performed, or the settings and features be checked, when the controller is first powered up. This sequence is described in the section Reset Settings, or in the Frequently Asked Questions - How Do I
Reset All Settings and Features Back to the Original Values.
The settings or features that most often need adjustment are the door times, and fire service return floors.
4.10 Zoned Duplex Operation
The Duplex System will keep one car at the Main Dispatch Landing, as the Lobby Car, and allow the other car, or the Free Car, to stop at it's last call. The Lobby Car will answer calls in the Low Zone, and the Free Car will answer all other calls. The Lobby Car may leave the lobby to assist the Free Car under various load conditions as described below under
Start Control. The "Low Zone" is an adjustable group of landings but the factory preset value is normally the Lobby/Main landing and any landings below the Lobby/Main landing.
All other landings are in the "Upper Zone". If a car is "Next" in a zone, then it will answer calls in that zone, otherwise it will answer calls in the other zone. If both cars are in service, a car will always be homed to the Main Lobby level.
4.10.1 Common Circuits
Several circuits need to be energized when either car is on. These include the Hall Calls,
Fire Service, and some other circuits that may be required for a particular job (such as
Emergency Power, Hospital Service, etc.). These circuits get their power from either car by means of the VR (Voltage) relay. (See the schematic.)
Install each car separately. The Hall Calls and Hall Fire signals may be wired to either car, then cross-connected to the other car.
WARNING: Be careful not to mix the power supplies from one car with the other car. Signals that are common to both controllers must be connected to a common supply, as shown on the schematic.
WARNING: The controller is fed from multiple power supplies.
Dangerous voltage levels may still be present if only one car is turn off.
4.10.2 Next Car
A "Next Car" is selected for the Low Zone and the Upper Zone. This car will be assigned hall calls in the respective zone. The other car may answer calls in a zone where it is not
"Next", but it will not normally be sent to calls outside its zone.
MH-3000 User Manual Page 16
4.10.3 Car Start
The Car START feature controls when the car will respond to registered Hall Calls by controlling the internal direction circuits. When the START circuit is energized the car will immediately begin to respond to Hall Calls. There is a separate start circuit for the Low
Zone and the Upper Zone. A car will always respond to Car Calls immediately.
The START circuit is energized if ANY of the following conditions are true:
1. The car is Next in that zone.
2. The car is in the other zone, and is NOT next in that zone. (This means that both cars are in the other zone, so the car that is not next in the other zone will be pulled into this zone.)
3. The call(s) in this zone have been registered for a preset time. (This allows the other car to help in heavy traffic situations.)
4. The car is not in normal group operation.
5. The other car is not in normal group operation.
6. The other car has a call behind it.
7. Emergency Power is activated, and this car is assigned to run.
4.10.4 Homing
If there are no cars at the Main Dispatch landing, the "Next" car in the Low Zone will home, or return, to the Main Dispatch Landing. If there is no "Next Car" in the Low Zone, then the first available car will home to the Lobby. If desired, the "Free" car can be set up to home to a specific (adjustable) landing in the upper zone, or to home to the Main landing. (See the separate description on Feature Adjustments.)
A car will home if the following conditions have been met for 10 seconds:
1. The car is in group operation (not on Inspection, Independent Service, Fire Service,
Load Weighing etc.).
2. The Stop Switch is not thrown.
3. The car is not stuck.
4. The doors are closed.
5. The car is not at the Main Dispatch Landing.
6. The car is not running.
7. The other car is in group operation.
8. The other car is not next in the Low Zone.
9. The other car is not running down.
10. The other car is not homing.
MH-3000 User Manual Page 17
4.10.5 Communication
Confirm that the termination jumpers have been installed to connect the termination resistors. These are two small jumpers just below the Group Communication Connector block in the upper left corner of the CPU. (Refer to the diagram of the CPU)
Connect the communication cable (twisted pair in shield) from the Group Communication
Connector block of one car to the other car. The drain wire (or shield if no drain wire) should be connected to the “G” (ground) terminal of the Group Communication Connector block on one car only. See picture on page 26.
When both cars are in operation, the LED D4 should flash repeatedly. This indicates the two CPUs are communicating properly.
If LED D4 is not flashing, check the communication cable, the termination jumpers, and the grounding. If these look OK, but the CPUs are not communicating, do a factory reset on both cars. Memory location 3188 shows the number of successful communications (it should be constantly changing when both cars are operating) and memory location 3189 shows the number of bad communication attempts (this should be 0). (Note: These memory locations are subject to change.) LED D4 is also affected by the I/O communications.
4.11 Zoned Group Operation
The Zoned Group System uses one MH3000 controller for each car, and one MH3000 controller as a Dispatcher. The Dispatcher receives all hall calls, and allocates them to the cars. The car controllers provide status information back to the Dispatcher to allow the optimum allocation of hall calls.
The Dispatcher will home the cars, giving priority to the Main Landing, and putting the other cars in empty zones as the cars become available. The number of zones is equal to the number of cars. Each zone will have a car selected as the “Next” car in that zone. As hall calls are entered, the “Next” car for the zone that the hall call is in will be assigned the call. If another car is moving through the zone, or is at the floor where the call was registered, then it will be assigned the call. Any car can cancel a hall call if it answers the call.
If a zone is empty, then an idle car will be sent to that zone. If a call is registered in an empty zone, a car in an adjacent zone will be assigned the call.
4.11.1 Common Circuits
Power for the hall call circuits is provided by a separate fused disconnect that powers the
Dispatcher. Power for the Fire Service circuits is taken from the Dispatcher or from one of the car controllers, as indicated on the schematic, depending on which controller has power.
This allows these critical circuits to be powered under all circumstances.
Install each car separately. The Hall Calls and Hall Fire signals are wired to the
Dispatcher.
WARNING: Be careful not to mix the power supplies from one controller with another. Refer to the schematic.
MH-3000 User Manual Page 18
WARNING: The controllers have circuits that are fed from multiple power supplies. Dangerous voltage levels may still be present even if the disconnect for a particular car is turned off.
4.11.2 Homing
The Dispatcher will home cars to empty zones, giving priority to the Main Landing.
Automatic homing can be overridden by forcing one or more cars to home to a specific floor.
This can be done by enabling the Homing feature on the desired car(s). It is recommended that automatic homing be used unless there are special requirements that necessitate changing the homing operation.
A car will not home if it not in automatic (group) operation, if there are car calls registered, or if the doors are open.
4.11.3 Communication
Confirm that the termination jumpers have been installed to connect the termination resistors. These are two small jumpers just below the Group Communication Connector block in the upper left corner of the CPU. (Refer to the diagram of the CPU)
Connect the communication cable (twisted pair in shield) from the Group Communication
Connector block of one car to the next car, forming a daisy chain that connects all the controllers together. The cars should NOT be connected in a “star” format. Refer to the schematic for a diagram of the correct connections. The order of the cars in the daisy chain is not important. The drain wire (or shield if no drain wire) should be connected to the “G”
(ground) terminal of the Group Communication Connector block at one end only. See the diagram on the schematic.
When a car and Dispatcher are in operation, the LED D4 on the car should flash repeatedly. (If LED D4 is ON, then there is a problem with one of the Input/Output boards.) This indicates the car controller is communicating with the Dispatcher. The LED D4 on the Dispatcher will flash if all cars are communicating properly. The status screen on the
Dispatcher will show which cars are communicating. The top left of the screen will read
“Comm=”. The letters following this message indicate the corresponding car is communicating with the dispatch. For example, if the display shows “Comm=A C “ then cars
A and C are communicating, but cars B and D are not.
If the Dispatcher is not communicating with one of the cars, check the communication cables, the termination jumpers, and the grounding. If these look OK, but the CPUs are not communicating, do a factory reset on the car(s) and Dispatcher. Look at the memory locations in the table below to check the communications.
Address Description
Addresses on the Dispatcher
3186 Increases every time the Dispatch successfully communicates with car A
318E Increases every time the Dispatch successfully communicates with car B
3196 Increases every time the Dispatch successfully communicates with car C
319E Increases every time the Dispatch successfully communicates with car D
31BA Increases every time the Dispatch fails to communicate with any car
Addresses on the Car Controllers
3190 Increases every time the car successfully communicates with the Dispatcher
3191 Increases every time the car fails to communicate with the Dispatcher
MH-3000 User Manual Page 19
Also confirm that the car number setting for each of the car controllers is correct. This is the third setting under “Settings” in the set up menu, as shown on the MH-3000 Settings sheet in the schematic. On the Dispatcher, check that the “Number of Cars” setting is correct.
If none of the communication counters listed above are increasing, then the controller is not trying to communicate. Cycle the power to that controller (or press the “Reset” button on that CPU) to restart the communication.
4.11.4 Car Controller Settings
Refer to the MH-3000 Settings sheet in the schematic for the settings and features available for each job.
4.11.4.1 Dispatch Failure Calls
The “Dispatch Failure Calls” setting is unique to Group car controllers. If the communication with the Dispatch fails, then this setting allows car calls to be registered automatically, to provide service to the building. The default setting is to enter the Main
Landing Car Call only. This will cause the car to return to the Main Landing and wait with its door open. It will continue to respond to car calls normally.
4.11.4.2 Car Homing
The car can be forced to home to either the Dispatch Landing or the Alternate Home
Landing. This will override the automatic homing from the Dispatcher. It is recommended that the Dispatch be allowed to home the cars, and that forced homing be left off.
4.11.5 Dispatch Controller Settings
Settings in the Dispatcher are changed in the same way as on the car controllers, as described in this manual in the section on Settings and Features. There are some settings that are unique to the Dispatcher, that allow it to be tailored to the building requirements.
These settings are normally set to the optimum values in the factory, so they should not normally need to be changed.
Refer to the MH-3000 Settings sheet in the schematic for settings and features that are provided on each installation.
Refer to this manual under the section on Settings and Features for the normal settings and features that are provided on Group controllers. These include parameters that affect the selection of traffic programs.
4.11.5.1 Zone Code Settings
Each landing must be assigned to one zone only. There should be the same number of zones as there are cars, unless there are fewer landings than cars.
It is best if the zones are contiguous, that is that they contain consecutive landings with no breaks in between. For example, do not set Zone 1 as landings 1 and 3 with Zone 2 as
Landing 2.
MH-3000 User Manual Page 20
4.11.6 Dispatch Traffic Programs
The Dispatcher will monitor hall calls and traffic patterns to determine the best mode for meeting the current demand for service. It will initiate Up Heavy, Down Heavy or Heavy programs as required. There are some adjustments that affect how these programs are triggered.
Heavy Program will be initiated if the total number of Up and Down Hall Calls exceeds the adjustable trip value (Setting = # of Calls for Heavy).
Down Heavy Program is initiated if the number of Down Hall Calls minus the number of
Up Hall Calls exceeds the adjustable trip value (Setting = # of Calls for Down Heavy).
If a car leaves the Main Landing with more than the number of Car Calls set by the adjustable trip value (Setting = # of Car Calls for Up Heavy) it initiates the Up Heavy trip time. If an Up Hall Call is registered during this adjustable time (setting = Hold Time for Up
Heavy for Car), then Up Heavy is initiated. Up Heavy will be extended for an adjustable time
(setting = Hold Time for Up Heavy for Group) after a car leaves the Main Landing loaded.
Up Heavy is also held for an adjustable time (setting = Hold Up Heavy after Hall Call) after the Main Landing Up Hall Call has been answered. So, if no cars leave the Main Landing loaded, and the Main Landing Up Hall Call is not registered the Up Heavy program will time out.
Inputs are normally provided to initiate these programs manually. These can be connected to a time clock, if desired, to initiate the program at certain times of the day.
The programs will affect homing, and which calls are assigned to which cars, including assigning calls to cars that are not selected as being the “Next” car in a zone, or are in a different zone.
Forcing the Dispatcher into a traffic program when there is not sufficient demand to justify it may cause the cars to chase each other. Consequently it is recommended that the system be allowed to automatically select the best traffic pattern.
If the Main Landing Up Hall Call is registered and there are multiple cars at the Main
Landing, the cars that are not selected as the “Next” car will not be given the call immediately. The delay allows the “Next” car to respond to the call, so that all the cars do not open their doors for one call. This delay is listed “Main Ldg Call Delay” on the MH-3000
Settings sheet.
If a hall call has been registered for longer than an adjustable time (setting = Hall Call
Help Time), then the call will be assigned to additional cars.
MH-3000 User Manual Page 21
5. Hardware Description
The controller consists of the Microprocessor system, Power Supply section, and Relay
Interface.
The Microprocessor system consists of the Central Processor Board (CPU), which has the microprocessor central processing unit, the EPROM memory chip, and the appropriate hardware to communicate to the LCD display, Keypad, and Input/Output boards.
The program is in EPROM (Electrically Programmable Read Only Memory). The floor position and fire service functions are maintained in battery backed RAM memory. The floor position may need to be reset when the controller is initially installed.
The Power Supply section includes the required transformers and fuses to power the
Microprocessor system and the Relay Interface.
The Relay Interface includes the required relays and contactors to interface the field signals and devices to the microprocessor. This usually includes a printed circuit board for normal signals, as well as other relays or contactors for signals required for each specific job.
5.1 Transformers
“CCXF” is the Control Circuit Transformer. This will provide the controller with 115VAC.
The primary connections will vary depending on the Building Power. See the schematic for sizing and wiring information.
“DOXF” or “DXF” are the Door Circuit Transformer(s). The size and quantity of these transformers will depend on the type of doors used. See the schematic for sizing and wiring information.
MH-3000 User Manual Page 22
5.2 Fuses
The fuse type and rating is shown on the schematic.
NOTE: Only replace fuses with fuses of the same type and rating.
MH-3000 User Manual Page 23
5.3 12VDC Power Supply
The 12VDC Power Supply supplies 12VDC for the microprocessor.
The Power Supply has onboard circuit protection. If the output is shorted, the output will be turned off.
If the Power Supply output is 0 volts, remove the load from the
Power Supply, then measure the output again.
If the output is now 12VDC, check the load to make sure it is not shorted.
NOTE: Output voltages below 12VDC may cause erratic operation.
5.4 Safety Interface Board
The Safety Relay Interface may be provided as a printed circuit board, or as discrete surface mounted relays, or a combination of both.
The Safety Relay Interface provides interface signals to the Motor Starter, Valves, Door
Operator, and Safety String.
Refer to the pictures below to see which type of interface is used.
MH-3000 User Manual Page 24
5.4.1 MH4
5.4.2 MH5
MH-3000 User Manual Page 25
5.4.3 Phase Monitor
The unit provides protection for the pump motor by continuously measuring the voltage of each of the three phases using a microcomputer circuit designed to sense under and over voltage, voltage unbalance, phase loss and phase reversal.
A trip delay is provided to prevent nuisance tripping.
A restart delay is provided to prevent short cycling after a momentary power outage.
Upon application of line voltage, the restart delay begins. The output relay is deenergized during restart delay and the LED flashes green.
Under normal conditions, the output energizes and the LED glows green after the restart delay.
Under voltage, over voltage and voltage unbalance must be sensed for a continuous trip delay period before the output is deenergized. The output will not de-energize if the fault is corrected during the trip delay.
The LED flashes red during the trip delay, then glows red when the output is de-energized.
The restart delay begins as soon as the output relay de-energizes. If the restart delay is completed when the fault is corrected, the output relay will energize immediately.
The output relay will not energize if a fault or phase reversal is sensed as the three phase voltage is applied. The LED alternately flashes green then red if a phase reversal is sensed.
Reset is automatic upon correction of a fault.
The technical characteristics of the phase monitor can be determined from the part number as follows:
Example: TVM 460A 10 0.5S 3S
Restart Delay
Trip Delay
Voltage Unbalance %
Line Voltage
Series
MH-3000 User Manual Page 26
5.4.4 Digiset Timer
This unit is a universal voltage solid-state timer that will operate from 19 VAC up to
265 VAC and from 10 VDC up to 120 VDC.
Any time period between 0.1 second and
102.3 seconds is available in 0.1 second increments and can be set with the dip switch.
Application of input voltage to the timer starts the time delay. At the end of the delay period, the load is energized. To reset, remove the input voltage to the timer.
To select a time period, simply add up the selected switches in the “ON” position for the total time delay in seconds.
This timer provides a delay in the Up Run circuit.
5.4.5 Bypass Switches
(MH-4 Board version shown)
The Bypass Switches bypass either the Car Door
Contact(s) or the Hall Door Contacts, as required by the appropriate codes. They may only be used on
Inspection Operation.
The code requires using these switches to run the car on Top of Car Inspection with the doors open, instead of putting jumpers around the Door
Contacts.
Moving either of these switches to the Bypass position will force the car onto Inspection Operation.
WARNING: Use extreme caution with these switches, and always make sure it is safe to operate the car with these switches closed.
NOTE: The Bypass Switches can be permanently removed by popping the cover off the switch and removing the working parts from the inside of the switch. This may be necessary if local codes do not allow the switches to be used. If they are removed in this way, it is not normally possible to re-install the switches.
MH-3000 User Manual Page 27
5.4.6 Inspection Switches
(MH-4 Board version shown)
The Inspection Switches allow the elevator to be run on Inspection, in accord with the appropriate codes.
NOTE: The Controller Inspection Buttons are not active when on Car Top
Inspection.
To operate the car, slide the “S3 Inspection Sw” to “INSP”, then press the “RUN” and
“UP” or “RUN” and “DOWN” buttons together.
WARNING: Use extreme caution when operating the car from the machine room. Make sure it is safe to move the car.
5.4.7 Connections
The top terminal strip(s) of the Safety Interface Board is generally used for factory connections.
The bottom terminal strip(s) are provided for field connections.
MH-3000 User Manual Page 28
5.5 Microprocessor
5.5.1 CPU
12VDC
Power
Supply
LCD Display
CPU
Reset Button
Status
LEDs
Termination
Jumpers
Group
Communication
Connector
Keypad
I/O Board
Communication
Connector
Battery S2 Slide Sws
EPROM
Socket
MH-3000 User Manual Page 29
LCD CONNECTOR
CPU RESET BUTTON
LCD DISPLAY
D1
D2
D3
D4
D5
LEDs
TERMINATION JUMPERS
(DUPLEX ONLY)
MOUNTING HOLES (4)
COMMUNICATION
CONNECTOR
INPUT/OUTPUT
BUS CONNECTOR
+
-
G
CPU
KEYPAD CONNECTOR
KEYPAD (DASHED)
MOUNTED OVER CPU
BATTERY
S2 SLIDE SWS
12VDC INCOMING
POWER CONNECTOR
+
-
+
EPROM
EPROM SOCKET, LEAVE
EMPTY HOLES AT LEFT
The Central Processing Unit (CPU) board contains the hardware that controls the inputs and outputs which control the elevator. This section describes the major components on the board, and the function of the connectors and LEDs.
5.5.1.1 CPU Battery
The CPU battery maintains the Real Time Clock, and also the status of key parameters and functions in the RAM memory. The battery life is approximately 5 years.
WARNING: Replace the battery with RENATA 3V Lithium battery, Part
No. CR2032 Only. Use of another battery may present a risk of Fire or Explosion.
MH-3000 User Manual Page 30
WARNING: Orient the battery properly in the battery holder. The positive side of the battery is marked on the battery, and faces towards the power connector and away from the EPROM socket.
WARNING: Do not use a metal (or conducting) device to remove or install the battery.
To replace the battery, remove the old battery by gently pushing the top of the battery towards the EPROM socket, until it is clear of the black housing, and then slide it out of the socket. Insert the new battery by sliding the edge under the metal retaining finger, then aligning it in the black housing. Be careful not to short out the battery. Dispose of the old battery properly – do NOT incinerate the battery.
5.5.1.2 LED Description
There are five LEDs located at the upper right edge of the CPU board.
D1 – Automatic Operation
D2 – Fire Service
D3 - Shutdown
D4 – Communication Error
D5 - Watchdog
The function of these LEDs during normal monitoring is noted on the schematic. The normal description for these LEDs is as follows:
D1 "Automatic Operation". This LED should be lit during normal operation. It will go out when the car is on Inspection Service, Independent Service, Fire Service, Low Oil
Shutdown, or any other mode that will cause the car to ignore Hall Calls.
D2 "Fire Service". This LED should be off during normal operation. It will be lit if the car is on Fire Service Phase 1 (Hall) or Phase 2 (Car).
D3 "Shutdown". This LED should be off during normal operation. It will be lit if the Up
Run timer indicated the car has been running up for a preset adjustable time without passing a floor. This could be caused by a low oil level; a problem with the motor starter circuit(s); or a problem with the up valve circuit(s). The car will stop running up, then return to the lowest landing and cycle the doors. It will then be shut down, with only the Door Open Button and door re-opening devices being operational. The fault can be reset by cycling the Main Line Disconnect Switch, or by putting the car on "Inspection" then back to "Automatic".
NOTE: If a Reverse Phase Relay or Emergency Power circuitry is supplied, these will also initiate a shutdown signal if the inputs are not energized.
D4 “Communication Error”. This LED should be off during normal operation on a
Simplex. It will be lit if the CPU has failed to communicate properly with an
Input/Output board. This could be caused by a loose or faulty cable between the
MH-3000 User Manual Page 31
boards, improper addressing of the I/O board(s) (see the section on I/O board addressing), or incorrect setting of the number of I/O boards in the CPU (see the section on adjustable settings). Refer to the section on I/O Boards for a description of the communication Status LED on the I/O Board.
On Duplex or Group systems, the LED also monitors the communication with the other CPU. It will flash if the communication with the other car(s) is operating normally. If the LED stays off, then the communication has failed (see the section under Duplexing, Communication). If the LED stays on, then either the Group communication has failed, or the communication to the I/O boards has failed, as described above. Check the LEDs on the I/O boards to determine if they are communicating properly, then check the BADCOMM address as described in the
Duplex Communication section.
D5 "Watchdog". This LED will flash regularly (about once per second) if the CPU is operating properly. NOTE: The LED will flash every 10 seconds if the car is not in the run mode. If the LED stops flashing, reset the CPU by cycling the Main Line
Disconnect Switch, or pressing the Reset Button on the CPU.
NOTE: If the diagnostic mode is changed to monitor the Internal Memory, or the Setup Mode is selected, then the operation of the LEDs will change, as described in the appropriate sections.
5.5.1.3 Reset Button
The Reset Button is located just below the LCD Display.
It is used to reset the CPU if a lockup occurs (such as if LED D5 stops flashing when in the normal operating mode).
Pressing this Reset Button is
NOT the same as doing a factory reset.
The Reset Button restarts the CPU just as if the power had been cycled; whereas a factory reset will reset the settings and features to the factory default values.
WARNING: Pressing the Reset Button will reset the CPU, causing all outputs to be turned off and the car to stop immediately.
NOTE: The Reset Button should not normally need to be used.
MH-3000 User Manual Page 32
5.5.1.4 CPU Connectors
5.5.1.4.1 Duplex Communication Connector
The Duplex Communication Connector is a terminal block located on the left side of the CPU board.
A shielded twisted pair is used to connect the two CPU boards together. The shield is connected to the CPU board mounting screw (which is grounded) at ONE END
OF THE CABLE ONLY. The termination jumpers next to the connector are factory installed on duplex systems.
5.5.1.4.2 LCD Display Connector
The LCD Display Connector is located at the top left of the CPU board.
The LCD display is mounted directly on the connector. The LCD display can be removed for replacement. If it is removed, then set switch 1 on the Slide Switch S2 to the OFF position before turning the power back on. This will ensure the CPU does not try to write to the LCD screen while it is removed. It is recommended that the LCD display AND the
Keypad be removed together, since if the LCD display only is removed, and the keypad is activated, the CPU will probably lock up. Make sure the power is turned OFF before removing either the keypad or the LCD display.
5.5.1.4.3 Keypad Connector
The connector for the Keypad is located behind the keypad. The connector is an 8pin connector. If the keypad is removed, make sure the connector is lined up properly when replacing the keypad. Make sure the power is OFF when removing or installing the keypad.
MH-3000 User Manual Page 33
5.5.1.4.4 Incoming Power Connector
The Incoming Power Connector is a terminal block located in the bottom left corner of the CPU board.
The incoming power is 12VDC from the power supply located near the CPU.
If the CPU board is replaced, the incoming power wires must be connected to the correct terminals. The upper terminal is "+" and the lower terminal is "-". The connector is shaped so that the mating terminal plug can not be inserted upside down.
5.5.1.4.5 Input/Output Bus Connector
The Input/Output Bus Connector is on the left of the CPU board.
An RJ45 style cable is used to connect to the first I/O board.
The other I/O boards are connected to each other using a daisy chain method, with the CPU connecting to the I/O COMM IN of board #1, then the I/O COMM OUT of board
#1 connects to I/O COMM IN of board #2, and so on for all I/O boards.
MH-3000 User Manual Page 34
5.5.1.5 S2 Slide Switch
The S2 Slide Switch is used to set various operating modes or features in the CPU. It is located on the lower right of the CPU board, just above the program chip.
Currently only the first and third switch are used. If the other switches are assigned a particular function, this will be indicated on the paperwork for the particular job.
5.5.1.5.1 Switch 1 on S2 Slide Switch
If switch 1 is ON, then the LCD Display will show the “Car Status” screen on power up.
If switch 1 is OFF, then the LCD Display will be blank on power up. To activate the display and show the “Car Status” screen, press any key. This mode should be used if the
LCD is to be removed for any reason. It is recommended that if the LCD Display is removed that you also remove the keypad, since pressing a key with the LCD removed could lock up the CPU as it attempts to write to the LCD Display.
5.5.1.5.2 Switch 3 on S2 Slide Switch
Switch 3 on the CPU Slide Switch S2 is a Redundancy Defeat. If this is turned ON, then this will prevent a fault from the Redundancy checks, or a Door Zone Fault. This can be used during initial installation to allow the car to be run without generating these faults. As a reminder to turn the defeat off after installation, the Fire Buzzer will be enabled.
If switch 3 on the CPU Slide Switch is OFF, then the Redundancy Faults will function as normal.
MH-3000 User Manual Page 35
5.5.2 Input/Output Boards
Refer to the picture or diagram of the IO boards shown below to identify the key components.
Removable
Terminals
Commons
I/O numbers
Programming
Port
Input LEDs with number below LED
I/O Comm
Connector (IN)
Status LED
12VDC
Incoming
Power
Input LEDs with number above LED number
LED
Address
Switches
I/O
Communication number
LED
MH-3000 User Manual Page 36
TYPICAL I/O BOARD
Jumper Block 1-8
Input LEDs 1-8
Programming
Connector
I/O Co mmunication
Bus IN Connector
Status LED
12VDC Power
Connector
Input LEDs 9-16
Jump er Block 9-16
Terminals
C1234C5678
C1234C5678
12345678
9 11 13 15
10 12 14 16
9 11 C 14 16
12345678
9 11 13 15
10 12 14 16
9 11 C 14 16
Commons
Terminals
Output Relays 1-8
Output LEDs 1-8
Address Sw Block
I/O Communication Bus
OUT Connector
Output LEDs 9-16
Output Relays 9-16
C 10 12 13 15 C 10 12 13 15
Commons
Input/Output boards are used to connect the CPU with the field devices. All inputs
(unless otherwise stated) are 115VAC, and outputs (unless otherwise stated) are dry relay contacts.
The boards are available as 16-Input and 16-Output boards, or 16-Input and no outputs.
All inputs and outputs have individual LED indicators.
Wiring is done to the removable terminal blocks at the top and bottom of the I/O boards.
Fuses are provided externally, not on the I/O boards.
MH-3000 User Manual Page 37
5.5.2.1 Addressing
Each Input/Output board is given a unique address by means of the Address Switch Block on the right of the board, next to the I/O COMM OUT Connector. The first board connected to the CPU is address 1, the next is address 2, and so on. The numbering is consecutive, and no numbers are skipped. To set the address, refer to the chart below. ON indicates the switch is set to the right,
OFF indicates the switch is set to the left, as indicated on the switch itself.
Picture at right shows DIP Sw. 1 to the right, and all the others to the left, which is the address for Board 1, as shown in the table below.
Board # Sw. 1 Sw. 2 Sw. 3 Sw. 4 Board # Sw. 1 Sw. 2 Sw. 3 Sw. 4
1 ON OFF OFF OFF 5 ON OFF ON OFF
2 OFF ON OFF OFF
4 OFF OFF ON OFF
6 OFF ON ON OFF
7 ON ON ON OFF
8 OFF OFF OFF ON
NOTE: If a board is replaced, the board must be set up with the SAME
ADDRESS as the board it was replacing. The address of each I/O point is determined by the Board Number (1 through 8), then the Point Number (1 through 16). The board number is used in the “Show I/O” screen to indicate which board is being monitored.
5.5.2.2 Terminal Wiring
Wiring to Inputs 1-8 is at the TOP LEFT of the I/O board, wiring to the Outputs 1-8 is at the TOP RIGHT of the I/O board. Wiring to Inputs 9-16 is at the BOTTOM LEFT of the I/O board, wiring to the Outputs 9-16 is at the BOTTOM RIGHT of the I/O board.
The terminal blocks are removable, so BEFORE power is applied, remove the terminal blocks and check for grounds at the terminal blocks.
Note also the location of the COMMONS, as shown on the schematic. The far left terminal is the common for the four I/O points to its immediate right, and the sixth terminal from the left is the common for the four I/O points to its immediate right.
WARNING: Be very careful not to jump to a common when you intended to jump to an input or output, as this could damage the controller or other equipment.
Ty pical I/O Board Terminal Block Layout
Com 1 2 3 4 Com 5 6 7 8
MH-3000 User Manual Page 38
5.5.2.3 Input/Output LEDs
Each Input and Output point has its own LED indicator. These are located towards the center of the board, and are on the low voltage/CPU side of the optical isolator in the I/O circuitry.
5.5.2.3.1 Input/Output Naming Conventions
Each Input or Output is mapped to a specific address in the CPU. The address of each
Input/Output point is based both on the address of the board and on the location of the point on the board.
The address of each I/O point is determined by the Board Address (1 through 8) and the
Point Number (1 through 16). This address is used in the Monitor I/O Menu to show the I/O status.
The Board Address is set by the Address Switch Block S1, as described above. The point number is 1 to 8 starting from the left, for the top group, and 9-16 starting from the left, for the bottom group. The point numbers are silk-screened on the board adjacent to the actual LEDs for each point. The LEDs have a “D” number silk-screened next to the LED.
This is a component identifier, and does not correspond to their address. The address number is the slightly larger number between the LED and its resistor. Each LED point number corresponds to the point number by the terminal blocks.
5.5.2.4 Board Status LED
The Status LED located next to the I/O COMM IN connector shows the status of the board. It will flash regularly, and the number of flashes indicates its mode of operation.
Flashes Mode of Operation
Two
Three
Communication Failure. The board is not communicating with the CPU. This could be because the CPU is in Setup
Mode, or a cable is defective or disconnected.
Bad Address. Check the Address
Switches.
Four
Bad Data. Check the cables. Noise is probably being induced in the wiring.
MH-3000 User Manual Page 39
5.5.2.5 I/O Bus Communication Connectors
The connector on the left of the I/O board is for the
I/O bus from the CPU board.
It is connected in a daisy chain from the CPU to the
I/O boards. The I/O COMM OUT on the CPU is cabled to the I/O COMM IN of the first I/O board. The I/O COMM
OUT of that board connects to the I/O COMM IN of the next board, and so on.
The addresses of the boards must correspond to their position in the daisy chain.
5.5.2.6 Programming Connector
This connector is used to program the microprocessor on the I/O board. It is not used once the I/O board is programmed.
5.5.2.7 Power Connector
This connector supplies 12VDC to the I/O board.
MH-3000 User Manual Page 40
5.5.2.8 Jumper Blocks
Two sets of jumper blocks are provided in the upper middle, and lower middle of the board. They allow the inputs and outputs to be jumped together.
The silk-screening by the jumpers indicates which points are connected to which pins.
Putting a jumper block on two horizontally adjacent pins is the same as putting a jumper from the output point to the same numbered input point.
For example, a jumper placed on the pins labeled “3” would jump input point 3 to output point 3.
WARNING: When an input and output are jumped together, always connect the field wiring to the OUTPUT terminal. Do NOT connect the field wiring to the Input terminal, as this could overload the wiring on the board.
Inputs and outputs are normally connected together on the car and hall call buttons and lights.
NOTE: If a board is replaced, the board must be set up with the SAME JUMPERS as the board it was replacing.
MH-3000 User Manual Page 41
5.6 Motor Control
A wide variety of motor starting options are available. Please consult the as-built schematics to determine the exact starting configuration.
5.6.1 Across-the-line Starting
Connect Building
Supply Power
Here
Auxiliary Contacts
Contactor
Electronic
Overload
Connect Motor
Leads Here
MH-3000 User Manual Page 42
5.6.2 Wye-Delta Starting
Connect Building
Supply Power
Here
Run Contactor
Start Contactor
Mechanical
Interlock
Overload
Relay
Connect Motor
Leads Here
MH-3000 User Manual Page 43
5.6.3 Solid-State Starting
Connect Building
Supply Power
Here
Fault Contactor
Connect Motor
Leads Here
MH-3000 User Manual Page 44
5.7 B.O.R.I.S.
BORIS is a fast transfer line-interactive uninterruptible power supply. It is designed to prevent blackouts, brownouts, sags, swells and surges from reaching the protected load under normal conditions. It filters out small utility line fluctuations and isolates the protected load from large disturbances by internally disconnecting from the utility line, while supplying power from its internal batteries until the utility line returns to normal.
While operating on battery, an internal alarm will intermittently beep. The ON/TEST button may be pressed to silence the alarm.
If the line utility does not return and the battery continues to power the protected load, a low battery shutdown may occur.
Advance warning of a low battery condition begins approximately two minutes before the final shutdown. This alarm will be a continuous beeping sound and cannot be silenced. Normally this condition should not occur
(if batteries were previously charged fully) due to remote shutdown capability of BORIS and
Virginia Controls’ controller.
Special features include surge protection; EMI/RFI filtering, high and low voltage correction (without draining batteries), as well as automatic battery testing during power up and every 14 days thereafter. User-replaceable batteries can be replaced without having to remove power from the loads.
For installation instructions and operation details, consult the Battery Operated Rescue
Initiation System Operating Manual. A copy of this manual can be obtained from our web site at www.vacontrols.com or by calling our office at (800)296-2140.
MH-3000 User Manual Page 45
6. MH-3000 Screens and Diagnostics
6.1 Run Mode
When the controller is powered up, or the Reset Button is pushed, the microprocessor will be in the Run Mode. In this mode the microprocessor will allow the Inputs and Outputs to operate properly, and the elevator to run. (The only other mode is the Setup Mode, as described below. In the Setup Mode the elevator is shutdown, and all outputs are turned off.)
Several diagnostic screens are available in the Run Mode, and each is accessed by scrolling through the selections until the desired item is located, and Ent is pressed.
The display will show either the “Car Status” screen or a blank screen, depending on the setting of S2 switch 1 on the CPU. If S2 switch 1 is ON then the “Car Status” screen will be displayed, and if S2 switch 1 is OFF then the screen will be blank until a key is pressed. It will then show the “Car Status” screen.
Press Esc to return to the Run Mode menu screens.
Pressing Nxt or Prv will scroll through the available screens in the Run Mode. To select a display, press Nxt or Prv to show the desired item, then press Ent to show the desired screen.
6.1.1 Run Mode Screens
The screens available in the Run Mode are:
1. Show I/O Status
2. Show Fault Log
3. Show Internal Memory
4. Show Car Status
5. Go to Set-Up Mode
Refer to the diagram shown below to see how to navigate from one screen to another.
The normal procedure is to press Nxt to go to the menu item for the desired screen, then press Ent to access that screen.
Press Esc to return to the Screen Selection Menu.
The “Car Status” screen is displayed after a power up, or when leaving the Banner
Screen, or Setup Screen.
MH-3000 User Manual Page 46
(BLANK SCREEN)
VA CONTROLS
(BANNER SCREEN)
RUN MODE SCREENS
From Setup Mode
To “Go to Setup Menu”, (see below)
Press ENTER to
SHOW CAR STATUS
Press ENTER to
SHOW INT MEMORY
AUTO PwrOk
2 UP CLSD
0400 00 00 00 00
0404 00 00 00 00
Note: LCD will display
Car Status Screen or
Blank Screen on start up, depending on the setting of S2 switch 1.
Press ENTER to
SHOW FAULT LOG
01 09:40 FLTCODE
2 0000 0000 0000
Note: Press “.” to show the current time.
Press ENTER to
SHOW I/O STATUS
Press ENTER to
GO TO SETUP MENU
INPUTS 0000 0000
Board1 0000 0000
Warning: PROGRAM
& CAR WILL STOP!
Virginia Controls
MAIN SETUP MENU
To “Show Car Status”,
(see above)
To Setup Mode
= Press “Nxt”
= Press “Prv”
= Press “Ent”
= Press “Esc”
The normal sequence is to press “Nxt” to select the desired menu item.
Press “Ent” to use the menu item.
Press “Esc” when you are finished.
6.1.1.1 Banner Screen
A "Banner” screen showing the program information is available. This is accessed by pressing Esc from the Run Mode. A sample banner screen is shown here.
VaControls011207
12345.1.DS3CA04.
The "Banner” screen shows "VaControls" on the top line, followed by a code showing the date code for the program in the format MMDDYY (in the example above this is “011207” for January 12th, 2007). The code on the bottom line shows the Virginia Controls Job
Number (in the example above this is “12345”), the program revision number (in the example above this is “1”), and the code for the base program (In the example above this is
“DS3CA04”). Older programs may have a different format, such as having the date on the bottom line, and the base program code on the top line.
The controller displays the "Car Status" screen when the "Banner" screen is exited.
MH-3000 User Manual Page 47
6.1.2 Show I/O Status
The "Show I/O Status" display allows the screen to display the status of the Inputs or
Outputs on one board. This display is useful for checking the integrity of the I/O boards and the communications between the CPU board and the I/O boards. The display should agree with the corresponding LEDs on the I/O boards.
The board number corresponds to the address set by the Address Switches on each I/O board. The top left shows whether inputs or outputs are being monitored, and the bottom left shows the board number being displayed.
INPUTS 0011 0010
Board2 0100 0110
The right side shows the status of the inputs or outputs. The status will be a "1" if the signal is on, or a "0" if the signal is off. The order of the bits corresponds to the order of the LEDs on the I/O board, that is, the top left bit corresponds to Point 1, top right is point
8, bottom left is point 9 and bottom right is point 16. In the example above, the Inputs on
Board # 2 are being monitored, and points 3,4,7 (top line) and points 10,14,15 (bottom line) are all on.
If an I/O Fault is showing on the Status Screen, and the data on the Show I/O Screen matches the I/O boards, then the checksum in the communication is incorrect. This will cause the CPU to ignore the data, and not pass it to the main program. To determine which board is causing the communication failure, refer to the section on troubleshooting suggestions for I/O board faults.
6.1.2.1 Moving Around in I/O Status Screen
Press Nxt or Prv to scroll through the I/O.
Press Aux to toggle between Inputs and Outputs.
Press Esc to return to the Run Mode menu screens.
The keys 0 - 9 , . and Ent are not used in this mode.
6.1.3 Show Fault Log
The “Show Fault Log” screen allows the controller fault log to be viewed. This log shows the fault number, the time stamp of the fault, the fault code, and critical data when the fault occurred, including the floor position of the car and the status of certain key signals.
As shown in the description of the faults below, some of the faults logged are not faults, but events that are useful to know in the maintenance and operation of the elevator.
The controller stores the last 63 faults in battery backed RAM memory.
When a new fault occurs, all the existing faults are moved down to the next fault location, and fault 63 is erased. The most recent fault is stored in fault location 00, and the order of the faults in the fault log is the order in which the faults were logged, with the most recent faults at the top of the fault log table.
MH-3000 User Manual Page 48
If a new fault is logged while viewing the fault log, the screen is not changed, it will continue to show the old fault. This allows the fault data to be viewed if several faults are logged rapidly. To refresh the screen, and show the current fault in that fault location, press Ent.
NOTE: All faults will be cleared when a Factory Reset is performed.
Non-shutdown faults can be prevented from being logged, if desired. See the list of Adjustable Features on sheet “MH-3000 Settings”. One of the Bit Features will be labeled “Disable Non-Shutdown Faults in the Fault Log”. Turn this feature on to disable non-shutdown faults. This may be useful if you are trying to track down a specific fault, and you do not want the fault log to contain minor faults. Refer to the section on Changing
Features for instructions on settings the proper Bit Feature to disable non-shutdown faults.
6.1.3.1 Typical Fault Screen
This is the “Fault Log” screen layout, showing a typical fault message:
Fault Time Stamp
Fault Number
Fault Log Status Signals
01 09:40 FLTCODE
2 1100 0011 0010
Fault Code
Fault Log Status Signals
6.1.3.2 Fault Number
“01” is the fault number, shown on the top left of the “Fault Log” screen. It is a hexadecimal number from 00 to 3E (decimal 62), with 00 being the most recent fault.
Press Nxt to scroll through the fault log, showing the next older fault. Press Prv to show the next most recent fault. You can press 0 to jump to the most recent fault (fault 00).
6.1.3.3 Fault Time Stamp
“09:40” is the time stamp for the fault, shown in the middle of the top line of the “Fault
Log” screen. The time is displayed in 24hour format. The time stamp is accurate to within
10 minutes, so if the fault time is 09:40, as shown above, then the fault occurred between
9:40 and 9:49.
NOTE: Faults that happen within 10 minutes of each other may log the same time. The fault # will indicate the order of occurrence.
If the real time clock is set correctly, then this will be the time of the fault.
NOTE: To set the clock, refer to the section on setting the time under MH-
3000 Screens and Diagnostics/Set-Up Mode/Set the Time.
To verify that the real time clock is set, press . to display the current time and date as shown here. Press Ent to return to the fault log.
MH-3000 User Manual Page 49
CURRENT TIME
13:23 11/13/01
6.1.3.4 Fault Code
“FLTCODE” is the code for the fault, shown on the top right of the “Fault Log” screen. It is an alphanumeric designation up to 7 characters that indicates what the fault was. The following fault codes are standard.
NOTE: If a code is shown that is not in this list, check the paperwork for your specific job to determine the meaning of the code, and the cause of the fault.
Non-shutdown faults can be prevented from being logged, if desired. See the list of
Adjustable Features on sheet “MH-3000 Settings”. One of the Bit Features will be labeled
“Disable Non-Shutdown Faults in the Fault Log”. Turn this feature on to disable nonshutdown faults. This may be useful if you are trying to track down a specific fault, and you do not want the fault log to contain minor faults.
Refer to the section on Changing Features for instructions on settings the proper Bit
Feature to disable non-shutdown faults. Disabling non-shutdown faults will prevent faults
TDOPEN, TDCLOSE, TDOPN-R, TDCLO-R, CARSTUK, DRCONTS, OUT-DZ, COMMFLT, FIRE,
MRSMOKE, SHUNT, FLOOD from being logged.
A Typical Fault Log Screen is shown here:
Fault Number
03 09:40 BAD PWR
2 1100 0101 0010
Car position at the time of the fault
Time of the fault
Fault Code – see the tables below for a full description
Car status at the time of the fault – see the tables below for a full description
MH-3000 User Manual Page 50
ROLLOVR This code is logged every 24 hours, to indicate the faults after this point are from the previous day. The data displayed on the bottom line is not the car status.
The month and date for the following faults are shown on the left, and the number of days without faults is shown on the lower right. For example, the screen below indicates that fault 23 is a rollover, so that fault 24 and older faults occurred on
11/13 and fault 22 and earlier faults occurred on 11/14.
23 00:00 ROLLOVR
11/13 0
Several consecutive rollover faults will be combined into one rollover fault, and the number on the lower right will indicate how many additional rollovers were combined, indicating there were no faults for that many additional days.
23 00:00 ROLLOVR
11/13 2
24 09:30 LOW OIL
3 0110 1001 0000
25 00:00 ROLLOVR
11/07 5
For example, if faults 23, 24 and 25 were as shown above, this indicates a rollover code 25 was combined with five more (on 11/08 to 11/12) so that no faults occurred between 11/08 and 11/12, and fault 24 occurred on 11/13, since that is the date of the next earliest rollover.
LOW OIL
NOTE: If the power is off when a rollover would have occurred (at midnight) then no rollover code will be logged. If power is left on, then the date of any fault is the date shown on the most recent
(lower fault number) rollover code.
Running Shutdown Timer. The car ran for the time specified by the "Shutdown
Time" setting without passing a floor. Note that the time is reset every time the car passes a floor. The car will stop and return to the bottom landing (or the Main
Landing if the appropriate feature is set). It is reset by cycling power or cycling the Inspection Switch. The probable causes are: (1) Low oil, (2) Up valve(s) did not operate properly, (3) Pump did not operate properly. Other possible causes include any situation that prevents the car from running up (such as a bad output for the Up Run; loose wire in the valve coil circuit; bad contact in the Up Normal
Switch, etc.) or prevents the car from changing floors (such as a failure in the
Selector Slowdown Switches).
Check that the setting of the shutdown timer is long enough for the car to run between floors. The normal shutdown timer setting is 25 seconds.
MH-3000 User Manual Page 51
TDOPEN Door Open Fault. The Door Open Limit Switch failed to open after the doors had been opening for the time specified by the "Door Fault" setting. The probable causes are: (1) Door Open Limit Switch failure, (2) door operator failure, (3) door control circuitry failure, This fault can be disabled on Manual Door systems.
TDCLOSE Door Close Fault. The doors failed to close properly when they were parking, or when the car was ready to run for the next call. This fault will not be caused by keeping the doors open through the normal means (Door Open Button, Safety
Edge, Infra-red Unit, etc.), but only if the doors should be closing but were not able to close. The probable causes are: (1) Door Close Limit Switch failure, (2)
Door Contacts failure, (3) door operator failure, (4) door control circuit failure.
TDOPN-R Rear Door Open Fault. This is the same as fault TDOPEN, except it is for the rear door. This fault is only used on elevators with selective open doors (with a front and rear door at the same landing). This fault can be disabled on Manual Door systems.
TDCLO-R Rear Door Close Fault. This is the same as fault TDCLOSE, except it is for the rear door. This fault is only used on elevators with selective open doors (with a front and rear door at the same landing).
CARSTUK Car Stuck Fault. The car was held at a floor for the time set by the "Car Stuck
Time" setting, without running. This may be caused by a stuck button, or just by a passenger holding the car.
BAD PWR Bad Power. The Reverse Phase input or the BORIS input (Battery Backup) or the
Emergency Power input was off.
DRCONTS Door Contact Fault. The Door Contact Input turned off while the car was running.
This fault could be caused by the car tipping a door contact, or another of the devices in the safety string. It could also be caused by a failure of the "DC" Door
Contact relay.
OUT-DZ Door Zone Fault. The car stopped between floors. This is normal when the car is being taken off Inspection Service. This fault will usually be seen with fault 08, since the car will usually stop outside the door zone if the safety string is broken.
COMMFLT Communication Failure on Duplex. This will occur when the power on the other car is turned off, or the other car fails to communicate properly for 5 seconds.
Check the communication cable, and the termination jumpers, which are located by the communication cable terminal strip.
DRCHECK Door Check Fault. The Car or Hall Door Contacts Input was on (indicating the doors are closed) while the Door Close Limit was on (indicating the doors are open). This check is performed when the doors are fully open (Door Open Limit is off) and the car is not on a Leveling Switch. The car will be held with the doors open until the Door Contacts input goes off. The Car Door and Hall Door Contacts are both checked independently. If this fault is not caused by a jumper on the
Door Contacts, then check the Car and Hall Door Contacts very carefully, and check the wiring to the Door Contact Inputs and Door Close Limit Input.
MH-3000 User Manual Page 52
LEV SWS Leveling Switch Fault. Both Leveling Switch Inputs are on. This will shut the car down. Check the Leveling Switches to make sure one of them has not stuck. The switches must be adjusted so that only one leveling switch is energized at a time.
Then check the wiring for shorts. Cycle the power, or put the car on Inspection to clear the fault. In some short floor situations, there may be an overlap of the leveling switches between the floors. In this case special programming will allow an overlap without causing a fault.
FIRE
MRSMOKE The Machine Room or Shaftway Fire Sensors were initiated. This signal is required by the 1998 ANSI code, and will start the Fire Light flashing. It must be reset by turning the Hall Fire Switch to “Bypass”.
SHUNT
Fire Service Phase 1 or Phase 2 was initiated. This does not indicate a fault in the controller operation. Note: If Fire Service is not provided, or it is desired to bypass Fire Service during initial installation, then jump the Hall Fire Switch
Bypass Position Input.
DZFAULT
RED-FLT
The Shunt Trip Input was initiated. The car will stop at the next floor, and open its doors. An output will then come on that can be used to initiate the Shunt Trip
Breaker, and turn power off to the controller.
The Door Zone Switch was energized when the car was running Fast Speed or when the car was slowing down and before it hit an Up or Down Leveling Switch.
The car will shut down when it stops at the next landing.
There are several situations that can give this fault that may not seem to be a problem with the Door Zone Switch, but which ultimately the MH3000 sees as the
Door Zone Input being on when it should not be. In most cases the FSU or FSD relay did not energize properly on a floor-to-floor run. These situations include:
- The Level Lockout Timer is too short. It must be long enough for the FSU or
FSD relays to energize and cut out the Door Zone Input. This timer should be long enough to allow RU to energize, but not longer than the travel time from one floor to the next.
– The “RU” contact is series with the Up valves is energizing too late, preventing the FSU relay from cuting out the Door Zone Input.
– The UL or DL inputs are failing.
– There is a failure in the Up or Down Normal Limit Sw, or Pressure Switch, or RU contact, preventing FSU or FSD from energizing to cut out the Door Zone Input.
– There is a loose wire or bad connection on terminal 6, 14, 14X, 16, 16X, 21 or
22 which is preventing FSU or FSD from energizing properly.
Non-Running Redundancy Fault. The Redundancy Monitoring input(s) did not match the corresponding output(s). The normal signals monitored are the ESB output and ESB input. If the output, relay or input fails, then this fault will be logged, and the car will shut down. On program version 3A, dated March 2005 and later, this fault is replaced by the Redundancy Faults (RED-???) shown below.
RUN-FLT Running Redundancy Fault. The Redundancy Monitoring input(s) did not match the corresponding output(s). The normal signals monitored are the RUN, UP
LEVEL and DOWN LEVEL inputs and the PUMP output. If an output, relay or input fails, then this fault will be logged, and the car will shut down. On program version 3A, dated March 2005 and later, this fault is replaced by the Redundancy
Faults (RED-???) shown below.
MH-3000 User Manual Page 53
FSRELAY
RED-ESB
RED-RUN
RED-SAF
FS Relay Fault. The car attempted to run floor to floor 20 times, but did not make a floor change. This is normally caused by the FS relay failing to cut out the leveling switches, so that the car cannot leave the floor. When this fault is detected, the fault will be logged, and the car will shut down.
Redundancy Fault in the ESB Emergency Stop Sw Bypass circuit. The input that monitors the Emergency Stop Switch Bypass function indicated the Emergency
Stop Switch was bypassed when it should not have been. Check the ESB relay, or
ESB monitoring input, and its associated wiring. The car will shut down at the next stop. The fault is reset by cycling power to the controller.
This fault can be disabled by turning on Switch 3 on the CPU Slide Switch S2.
This also turns on the Fire Buzzer output, as a reminder to turn off the defeat.
Redundancy Fault in the running or leveling circuits.
Controllers using the MH5 printed circuit board – The Door Contact Bypass circuit monitoring point (LV) was energized when it should not have been, OR the Soft
Start Run signal (UTS, if used) was still on after the car stopped, OR the Pump run input (RUN) was still off after the car stopped. Check the external circuits for stuck relays (UL, DL, DZ, LV, LVX, STR, RU) or a stuck input.
Controllers using the MH4 printed circuit board or separate relays – The Run input
(RUN) did not match the Up or Down Level inputs and/or the Run input was still on after the car has stopped. Check the external circuits for stuck relays (UL, DL,
STR, RU) or a stuck input.
Cycle the power to reset the fault.
NOTE: The Fault Log Status Signals for this redundancy fault are custom, to help determine the cause of the fault. Refer to the section that describes the Fault Log Status Signals for a description of the signals.
This fault can be disabled by turning on Switch 3 on the CPU Slide Switch S2.
This also turns on the Fire Buzzer output, as a reminder to turn off the defeat.
Redundancy Fault in the Safety Circuit. The condition of the Door Fault Monitor input (DFM) was not correct, OR the Car Gate Input (5) or Door Contacts Input
(5X) was not correct. This may be caused by temporary jumpers added during initial installation, or a short in the Safety Circuit. Check the Safety Circuit for jumpers, or short circuits. Cycle the power to reset the fault.
NOTE: The Fault Log Status Signals for this redundancy fault are custom, to help determine the cause of the fault. Refer to the section that describes the Fault Log Status Signals for a description of the signals.
This fault can be disabled by turning on Switch 3 on the CPU Slide Switch S2.
This also turns on the Fire Buzzer output, as a reminder to turn off the defeat.
MH-3000 User Manual Page 54
RED-INS
OIL SW.
FLOOD
FAULT18
FAULT19
IOFLT??
Comm A
Comm B
Comm C
Comm D
(OTHER)
Redundancy Fault in the Inspection Door Bypass circuits. One of the inputs that monitors the circuits that bypass the Door Contacts on Inspection or Access operation was closed when the car was not on Inspection or Access, or terminal 4 was not hot. Check the Door Contact circuit for jumpers or shorts. Cycle the power to reset the fault.
NOTE: The Fault Log Status Signals for this redundancy fault are custom, to help determine the cause of the fault. Refer to the section that describes the Fault Log Status Signals for a description of the signals.
This fault can be disabled by turning on Switch 3 on the CPU Slide Switch S2.
This also turns on the Fire Buzzer output, as a reminder to turn off the defeat.
Low Oil Switch Fault. The Low Oil Switch closed. The car will return to the lowest landing and shut down. To reset the fault, cycle the power to the controller.
Flood Switch tripped. This will shut the car down at the designated Flood landing.
The Flood Landing is the second landing by default, but can be changed to the third landing or the top landing by setting the appropriate bit feature. Flood operation is cancelled when the Flood Switch input goes low.
This is a custom fault reserved for future use. If it used on a specific job, it will be described on the “MH-3000 Settings” sheet in the schematic.
This is a custom fault reserved for future use. If it used on a specific job, it will be described on the “MH-3000 Settings” sheet in the schematic.
I/O Board Fault. The I/O boards did not communicate properly with the CPU. The two numbers after “IOFLT” indicate which boards failed. Refer to the table shown below to determine which board or boards have failed. To check Board 8, see the notes in the troubleshooting section. Check the Address Switches for all boards.
Check the setting in the CPU for the number of I/O Boards. Check the cables between boards.
NOTE: If the boards NEVER communicate, a fault will not be logged, since the fault is ignored during power up. The fault is only logged if the boards were communicating properly and then stopped.
Communication with the car A or B or C or D failed. This fault is only seen on a
Group Dispatcher. This fault will occur if the power to the car is turned off, or the car fails to communicate properly for 5 seconds. Check the communication cable, and the termination jumpers, which are located by the communication cable terminal strip. Refer also to the Zoned Group Operation section and
Communication Troubleshooting section for further help.
Other Fault Codes may occasionally be provided on specific jobs. If this is the case, then refer to the additional documentation for that job to see what the codes and descriptions are for those faults.
MH-3000 User Manual Page 55
I/O BOARD FAULT TABLE
Right
Number
Board1
Board2
Board3
Board4
Right
Number
Board1
Board2
Board3
Board4
Left
Number
Board5
Board6
Board7
Left
Number
Board5
Board6
Board7 x0 x1 x2 x3 x4 x5 x6 x7
OK Fault OK Fault OK Fault OK Fault
OK OK OK OK Fault Fault Fault Fault
OK OK OK OK OK OK OK OK
x8 x9 xA xB xC xD xE xF
OK Fault OK Fault OK Fault OK Fault
OK OK OK OK Fault Fault Fault Fault
Fault Fault Fault Fault Fault Fault Fault Fault
0x 1x 2x 3x 4x 5x 6x 7x
OK Fault OK Fault OK Fault OK Fault
OK OK OK OK Fault Fault Fault Fault
8x 9x Ax Bx Cx Dx Ex Fx
OK Fault OK Fault OK Fault OK Fault
OK OK OK OK Fault Fault Fault Fault
6.1.3.5 Fault Log Status Signals
The bottom row of the “Fault Log” screen shows the car position and the status of key signals that help determine what the car was doing when the fault occurred. The car position is a number between 1 and 9, and every other value is either 1 (the signal was on) or 0 (the signal was off).
On Group Dispatchers the bottom line of the Fault Log shows the date of the fault only.
To match the description with the location of each signal, the values in the screen below have been replaced with letters, but in the actual log they would be 1’s and 0’s, as shown in the sample screen at the top of this section. Match the letter shown in the sample screen below with the table below, to determine the description of that signal.
NOTE: The Fault Status Signals are the same for all faults EXCEPT for the
Redundancy Faults RED-RUN, RED-SAF, and RED-INS. Refer to the tables below for the description of the signals for those faults.
01 09:40 FLTCODE
P ABCD EFGH IJKL
Refer to the correct table below, depending on the fault.
MH-3000 User Manual Page 56
SIGNAL
P
A
B
C
D
E
F
G
H
I
J
K
L
DESCRIPTION for STANDARD FAULTS
The car floor position when the fault occurred. The number will be between 1 and
9, with 1 indicating the bottom floor, 2 the second floor, etc. If the value is 9, then the car did not have a floor position.
The last direction the car ran. 1 = Up, 0 = Down.
The last direction selected (as shown by the direction indicators). 1 = Up, 0 =
Down.
The car was running. 1 = Yes, 0 = No.
The car was running fast speed. 1 = Yes, 0 = No.
The car was running between floors (not re-leveling). 1 = Yes, 0 = No.
The Door Contacts Input was On. 1 = Yes, 0 = No.
The Door Close Limit Input was On. (With selective doors, this indicates either Door
Close Limit was On, that is, one or both of the doors was open). 1 = Yes (door open), 0 = No (door closed).
The Door Open Limit Input was On. (With selective doors, this indicates both Door
Open Limits were On, that is, neither door was full open). 1 = Yes (door not fully open), 0 = No (fully open).
Up Level Input was On. 1 = Yes, 0 = No.
Down Level Input was On. 1 = Yes, 0 = No.
Car was in the Door Zone. 1 = Yes, 0 = No.
“LV” Input (monitors the contacts in parallel with the Door Contacts, in the Safety
String) was On. 1 = Yes, 0 = No.
B
C
D
E
F
G
SIGNAL
P
A
DESCRIPTION for RED-RUN FAULT
The car floor position when the fault occurred. The number will be between 1 and
9, with 1 indicating the bottom floor, 2 the second floor, etc. If the value is 9, then the car did not have a floor position.
Full Redundancy was Enabled. 1 = Yes, 0 = No. This determines which redundancy checks are performed, and which inputs are expected.
Input “RUN” was On. 1 = Yes, 0 = No.
Input “UTS” was On. 1 = Yes, 0 = No.
The car had stopped running up. 1 = Yes, 0 = No.
A custom redundancy input was On. 1 = Yes, 0 = No. This is not normally used.
The Door Contacts Input was On. 1 = Yes, 0 = No.
The Door Close Limit Input was On. (With selective doors, this indicates either Door
Close Limit was On, that is, one or both of the doors was open). 1 = Yes (door open), 0 = No (door closed).
MH-3000 User Manual Page 57
SIGNAL
H
I
J
K
L
DESCRIPTION for RED-RUN FAULT
The Door Open Limit Input was On. (With selective doors, this indicates both Door
Open Limits were On, that is, neither door was full open). 1 = Yes (door not fully open), 0 = No (fully open).
Up Level Input was On. 1 = Yes, 0 = No.
Down Level Input was On. 1 = Yes, 0 = No.
Car was in the Door Zone. 1 = Yes, 0 = No.
“LV” Input (monitors the contacts in parallel with the Door Contacts, in the Safety
String) was On. 1 = Yes, 0 = No.
A
B
C
D
E
F
G
SIGNAL
P
H
I
J
K
L
DESCRIPTION for RED-SAF FAULT
The car floor position when the fault occurred. The number will be between 1 and
9, with 1 indicating the bottom floor, 2 the second floor, etc. If the value is 9, then the car did not have a floor position.
The Emergency Stop Switch Input was On. 1 = Yes, 0 = No.
Input “DFM” was On. 1 = Yes, 0 = No. This should match output DF (signal C).
Output “DF” was On. 1 = Yes, 0 = No. This should be match input DFM (signal B).
Input “5B” was On. 1 = Yes, 0 = No.
Input “5” was On. 1 = Yes, 0 = No.
The Door Contacts Input was On. 1 = Yes, 0 = No.
The Door Close Limit Input was On. (With selective doors, this indicates either Door
Close Limit was On, that is, one or both of the doors was open). 1 = Yes (door open), 0 = No (door closed).
The Door Open Limit Input was On. (With selective doors, this indicates both Door
Open Limits were On, that is, neither door was full open). 1 = Yes (door not fully open), 0 = No (fully open).
Up Level Input was On. 1 = Yes, 0 = No.
Down Level Input was On. 1 = Yes, 0 = No.
Car was in the Door Zone. 1 = Yes, 0 = No.
“LV” Input (monitors the contacts in parallel with the Door Contacts, in the Safety
String) was On. 1 = Yes, 0 = No.
SIGNAL
P
A
DESCRIPTION for RED-INS FAULT
The car floor position when the fault occurred. The number will be between 1 and
9, with 1 indicating the bottom floor, 2 the second floor, etc. If the value is 9, then the car did not have a floor position.
The Emergency Stop Switch Input was On. 1 = Yes, 0 = No.
MH-3000 User Manual Page 58
SIGNAL
B
C
D
E
F
G
H
I
J
K
L
DESCRIPTION for RED-INS FAULT
Input “INS” was On. 1 = Yes, 0 = No.
Input “IN6” was On. 1 = Yes, 0 = No. This should be “0”
Input “IN9” was On. 1 = Yes, 0 = No. This should be “0”
Input “4A” was On. 1 = Yes, 0 = No. This should be “0”
Input “5A” was On. 1 = Yes, 0 = No. This should be “0”
Input “5G” was On. 1 = Yes, 0 = No. This should be “0”
The Door Open Limit Input was On. (With selective doors, this indicates both Door
Open Limits were On, that is, neither door was full open). 1 = Yes (door not fully open), 0 = No (fully open).
On SAPB/SBC this indicates Input “5H” was On. 1 = Yes, 0 = No. This should be
“0”
Up Level Input was On. 1 = Yes, 0 = No.
On SAPB/SBC this indicates Input “INC” was On. 1 = Yes, 0 = No. This should be
“0”
Down Level Input was On. 1 = Yes, 0 = No.
Car was in the Door Zone. 1 = Yes, 0 = No.
“LV” Input (monitors the contacts in parallel with the Door Contacts, in the Safety
String) was On. 1 = Yes, 0 = No.
6.1.3.6 Moving Around in the Fault Log
Press Nxt or Prv to scroll through the Fault Log.
Press Aux to jump to the “Show Internal Memory” screen.
Press Ent to refresh the display.
Press Esc to return to the Run Mode menu screens.
Press . to show the current time.
Press 0 to jump to the first fault.
The keys 1 - 9 are not used in this mode.
6.1.3.7 LED Description in "Show Fault Log" Mode
The LEDs D1, D2, D3, D4 change operation in the Show Fault Log Mode. They now show the status of the fault being viewed, in the same manner as the LEDs work in the Shown
Internal Memory mode.
6.1.3.8 Historical Log
The Historical Log contains the number of faults, floor to floor runs, and door operations over a specific time period. They are counted and stored in memory addresses $0520 to
$052F, along with the starting date of the log, according to the following list.
MH-3000 User Manual Page 59
Address Description
$0520
$0521
Month of start of current historical log
Date of start of current historical log
$0522
$0523
$0524
$0525
Number of Faults, Characters 1 and 2
Number of Faults, Characters 3 and 4
Number of Floor to Floor Runs, Characters 1 and 2
Number of Floor to Floor Runs, Characters 3 and 4
$0526
$0527
$0528
$0529
$052A
$052B
$052C
$052D
$052E
$052F
Number of Door Cycles, Characters 1 and 2
Number of Door Cycles, Characters 3 and 4
Month of start of previous historical log
Date of start of previous historical log
Number of Faults in previous log, Characters 1 and 2
Number of Faults in previous log, Characters 3 and 4
Number of Floor to Floor Runs in previous log, Characters 1 and 2
Number of Floor to Floor Runs in previous log, Characters 3 and 4
Number of Door Cycles in previous log, Characters 1 and 2
Number of Door Cycles in previous log, Characters 3 and 4
The number of faults, runs and door cycles are shown in two registers each, to allow the maximum number recorded to be over 65000.
To view the data, use the “Show Internal Memory" function to show address $0520. A sample screen is shown below.
Address of
Fault Log
Month of start of current log
Date of start of current log
Number of Faults since the start of this log
0520 05 11 00 14
0524 13 5F 16 19
Number of Runs since the start of this log
Number of Door Cycles since the start of this log
The number of faults, runs and door cycles are in hexadecimal. You can use the table below to convert the value to decimal.
Match the first hex character in the value to the decimal equivalent in the first two columns in the table; match the second character to the value in the next two columns; etc.
Then add up the decimal equivalents for all the values to get the decimal value.
In the example shown above, the number of faults is “0014”(hex). Using the table, this is
0 (1st char hex) = 0 (decimal equivalent from 1st two columns)
0 (2nd char hex) = 0 (decimal equivalent from 2nd1st two columns)
1 (3rd char hex) = 16 (decimal equivalent from 3rd two columns)
4 (4th char hex) = 4 (decimal equivalent from 4th two columns)
0014(hex) = 0+0+16+4 = 20(decimal).
The number of runs is “135F”(hex), which is 4096+768+80+15=4959(dec)
The number of door cycles is “1619”(hex), which is 4096+1536+16+9=5657(dec)
MH-3000 User Manual Page 60
After the number of days set in address $0401 (default is 60) the values from the current
Historical Log (addresses $0520-0527) are moved to the Previous Log (addresses $0528-
052F) and the current log is cleared out. The current date is loaded into the start addresses for the new current historical log.
Table to determine the Decimal Value of a 4-digit Hexadecimal number.
1st Character 2nd Character 3rd Character 4th Character
Hex Decimal Hex Decimal Hex Decimal Hex Decimal
0 0 0 0 0 0 0 0
1 4096 1 256 1 16 1 1
2 8192 2 512 2 32 2 2
3 12288 3 768 3 48 3 3
4 16384 4 1024 4 64 4 4
5 20480 5 1280 5 80 5 5
6 24576 6 1536 6 96 6 6
7 28672 7 1792 7 112 7 7
8 32768 8 2048 8 128 8 8
9 36864 9 2304 9 144 9 9
A 40960 A 2560 A 160 A 10
B 45056 B 2816 B 176 B 11
C 49152 C 3072 C 192 C 12
D 53248 D 3328 D 208 D 13
E 57344 E 3584 E 224 E 14
F 61440 F 3840 F 240 F 15
6.1.4 Show Internal Memory
The "Show Internal Memory" screen (abbreviated to "Show Int. Memory" on the LCD display) shows the contents of the internal memory. This can be used to check the status of internal registers, to show the operation of the system.
When this display is selected, the display will show five numbers on each row. The left number in each row is a 4-digit hexadecimal number showing the memory address of the number immediately to its right. The memory is 8-bit, so the 4 pairs of numbers on the right show the contents of each of four consecutive memory addresses in hexadecimal format. A “$” before a number indicates the number is in hexadecimal not decimal. All memory addresses are hexadecimal, and the contents will be shown in hexadecimal.
Contents of Memory Address shown at top left ($1024)
Contents of next Memory
Address ($1025)
Contents of next Memory
Address ($1026)
Memory Address of top left value
1024 FF 00 2D 14
Contents of next Memory
Address ($1027)
Memory Address of bottom left value 1028 00 FF 00 10
Contents of next four
Memory Addresses ($1028,
$1029, $102A, $102B)
MH-3000 User Manual Page 61
For example, if the display reads "1024 FF 00 2D 14", as shown above, then the top left number "1024" shows the address of the first value; the contents of address "1024" is "FF"; the contents of address "1025" is "00"; the contents of address "1026" is "2D"; and the contents of address "1027" is "14" (with each value being shown in hexadecimal).
NOTE: For addresses that show an ON or OFF condition, "00" is OFF, and "FF" is ON.
6.1.4.1 Moving Around in the Internal Memory
Press Nxt to increase the addresses being displayed by 4.
Press Prv to decrease the addresses being displayed by 4.
Ç1000 Ç100 Ç10 Ç4
Press 3 to increase the addresses being displayed by 10(Hex).
Press 6 to decrease the addresses being displayed by 10(Hex).
Press 2 to increase the addresses being displayed by 100(Hex).
Press 5 to decrease the addresses being displayed by 100(Hex).
È1000 È100
Press 1 to increase the addresses being displayed by 1000(Hex).
Press 4 to decrease the addresses being displayed by 1000(Hex).
È10 È4
Ç1
Press Aux to increase the addresses being shown by 1.
Press Esc to return to the menu screens.
6.1.4.2 LED Description in "Show Internal Memory" Mode
The LEDs D1, D2, D3, D4 change operation in the Show Internal Memory Mode. They now show the status of the top 4 words being displayed.
Specifically, D1 shows the status of the 1st bit of the top left word being displayed; D2 shows the status of the 2nd bit of the 2nd left word being displayed; D3 shows the status of the 3rd bit of the 3rd top left word being displayed; and D4 shows the status of the 4th bit of the 4th top left word being displayed.
This allows the LEDs to show rapid changes in the status of internal memory, that the
LCD display would not be quick enough to respond to.
MH-3000 User Manual Page 62
6.1.4.3 Changing values in the “Show Internal Memory” Mode
If the password has been entered, it is possible to change data in the Show Internal
Memory mode.
WARNING: Changing data could cause unexpected and dangerous results. Do not do this unless you are fully aware of the value that needs to be changed, and how to change it. Take all necessary precautions to prevent an unsafe condition, such as disconnecting the terminal blocks from the outputs, removing the appropriate fuses, or opening the appropriate safety circuits.
Use the normal keys to navigate to the memory location that is to be changed, as shown in “Moving Around” above. You can only change the value that is in the top left of the display. For example, if the top line of the display shows “2012 04 37 82 34” then memory location 2012 can be changed from its current value of 04.
To change a value, press . (the top left character will flash briefly) then press one of the following keys:
Press Nxt to increase the addresses being displayed by 1.
Press Prv to decrease the addresses being displayed by 1.
Press 3 to increase the addresses being displayed by 4.
Press 6 to decrease the addresses being displayed by 4.
Press 2 to increase the addresses being displayed by 10(Hex).
Press 5 to decrease the addresses being displayed by 10(Hex).
Press 1 to increase the addresses being displayed by 40(Hex).
Press 4 to decrease the addresses being displayed by 40(Hex).
Press 8 to enter a value of (“FF”(Hex) minus the old value).
Press 9 to enter a value of “FF”(Hex).
Press 0 to enter a value of “0”.
Press 7 or Aux or . or Ent to leave the value unchanged
Press Esc to return to the menu screens.
6.1.5 Show Car Status
The “Show Car Status” screen displays the car status. Each area of the screen will display one of several messages that allow the user to see what the elevator is doing. The only key that is active in this screen is the Esc key, which returns to the menu selection screens. Leaving the “Car Status” screen on the LCD will slow the scan time down very slightly, since writing to the LCD is a fairly slow process. The writing is done while the I/O boards are being polled, so there is little overall impact on scan time. Consequently it is
MH-3000 User Manual Page 63
acceptable to leave the “Car Status” screen on the LCD, thus allowing a technician to quickly see a fault without having to scroll to that screen.
6.1.5.1 Messages Displayed on the “Car Status” Screen
Each area of the screen will display one of several messages. The numbers in the sample screen below indicate the message areas. Each group of numbers will be replaced by the appropriate message, depending on the status of the car.
Message 1
Message 2
Message 3
Message 4
111 222222333333
4 55 66 7777 888
Message 8
Message 5
Message 6
Message 7
Message # 1 will be replaced with one of the following messages:
1. “INS” – the car is on Inspection Operation.
2. “MEC” – the car is on Medical Emergency in the car, or EMT (Emergency Medical
Technician Service) in the car.
3. “IDS” – the car is on Independent Service.
4. “MEH” – the car is responding to a Medical Emergency Call from the Hall, or an EMT call from the Hall.
5. “ATT” – the car is on Attendant Service.
6. “(no message)” – the car is not on one of the special operations shown above.
Message # 2 will be replaced with one of the following messages:
1. “SHUNT” – the Shunt Trip input is enabled. The car will stop at the next landing, open its doors, and shutdown.
2. “SMOKE” – the Machine Room/Shaftway Fire detectors Input is energized.
3. “FIRE2 ” – the car is on Fire Service Phase 2 (car).
4. “FIRE1 ” – the car is on Fire Service Phase 1 (hall).
5. “FLOOD ” – the car is on Flood Operation.
6. “LowOil” – the car has tripped the Low Oil/Up Run timer.
7. “LevSws” – both of the Leveling Switches are on at the same time.
8. “RedESB” – a Redundancy Fault in the ESB Emergency Stop Sw Bypass circuit has been detected. The input that monitors the Emergency Stop Switch Bypass function indicated the Emergency Stop Switch was bypassed when it should not have been. The car will shut down at the next stop. Check the ESB relay, or ESB monitoring input, and its associated wiring. Cycle the power to reset the fault.
MH-3000 User Manual Page 64
9. “RedRUN” – a Redundancy Fault in the running or leveling circuits has been detected.
The car will shut down at the next stop. Cycle the power to reset the fault.
Controllers using the MH5 printed circuit board – The Door Contact Bypass circuit monitoring point (LV) was energized when it should not have been, OR the Soft Start
Run signal (UTS, if used) was still on after the car stopped, OR the Pump run input
(RUN) was still off after the car stopped. Check the external circuits for stuck relays
(UL, DL, DZ, LV, LVX, STR, RU) or a stuck input.
Controllers using the MH4 printed circuit board or separate relays – The Run input (RUN) did not match the Up or Down Level inputs and/or the Run input was still on after the car has stopped. Check the external circuits for stuck relays (UL, DL, STR, RU) or a stuck input.
10. “RedSAF” – a Redundancy Fault in the Safety Circuit has been detected. The car will shut down at the next stop. The condition of the Door Fault Monitor input (DFM) was not correct, OR the Car Gate Input (5) or Door Contacts Input (5X) was not correct.
This may be caused by temporary jumpers added during initial installation, or a short in the Safety Circuit. Cycle the power to reset the fault.
11. “RedINS” – a Redundancy Fault in the Inspection Door Bypass circuits has been detected. The car will shut down at the next stop. One of the inputs that monitors the circuits that bypass the Door Contacts on Inspection or Access operation was closed when the car was not on Inspection or Access, or terminal 4 was not hot. Check the
Door Contact circuit for jumpers or shorts. Cycle the power to reset the fault.
12. “DZFlt” – a Door Zone Fault was detected. The Door Zone input was on while the car was running fast speed, OR the Door Zone input came on before an Up or Down Level
Switch came on. Check the Door Zone Switch.
13. “OutDZ” – the car has stopped outside the Door Zone.
14. “OilVis” – the car is on Oil Viscosity Operation. The car will return to the lowest landing, and turn on the pump, but not the valves.
15. “ Auto ” – the car is in automatic operation. It will respond to car and hall calls.
16. “ NoHC ” – the car is not answering Hall Calls. This may be caused by Inspection,
Independent Service, Fire Service, Medical Emergency Service, Shutdown, Door Check
Fault. The cause is usually shown in one of the other status messages.
Message # 3 will be replaced with one of the following messages:
1. “BadPwr” – the Reverse Phase Input or the BORIS Input (Battery Backup) or the
Emergency Power Input is off.
2. “ LOSw ” – the Low Oil Switch Input is on.
3. “ JackR” – the car is in Jack Resynch Mode. It will run down past the bottom landing, to compress the jack fully.
4. “ SHTDN” – the car is in shutdown.
5. “ PwrOK” – none of the other faults exist. The car is on normal power, and not on shutdown.
Message # 4 will be replaced with one of the following messages:
MH-3000 User Manual Page 65
1. The car position will be shown as a number between 1 and 8, with 1 as the bottom landing.
2. If the floor position is not known (such as on initial installation) then message #4 will show “?”.
Message # 5 will be replaced with one of the following messages:
1. “UP” – the car is running up.
2. “DN” – the car is running down.
3. “DC” – the doors closed input is on.
4. “DO” – the doors closed input is off. The car cannot run.
Message # 6 will be replaced with one of the following messages:
1. “UL” – the car is leveling up.
2. “DL” – the car is leveling down.
3. “DZ” – the car is in the Door Zone.
4. “FS” – the car is running fast speed.
5. “SS” – the car is running slow speed.
6. “(no message)” – the car is not running, and it is not in the door zone.
If the appropriate fault exists, Message # 7 and #8 will be replaced with one of the following messages:
1. “IO-FAULT” – the communication with one or more of the I/O boards has failed.
2. “DrChkFLT” – the Door Closed Input is on, and the Door Closed Limit is on, indicating the Door Contacts have been jumped.
3. “DrLmtFLT” – the Door Open Limit and the Door Close Limit are both off.
4. If none of these three faults are present, then messages # 7 and # 8 will show the door status as shown below.
Message # 7 will be replaced with one of the following messages:
1. “OPNG” – the doors are opening.
2. “CLSG” – the doors are closing. This is also displayed when the car is running, and the
Door Close output is on.
3. “OPEN” – the doors are fully open.
4. “CLSD” – the doors are fully closed.
5. “STOP” – the doors have stopped and are not fully open or fully closed.
Message # 8 will be replaced with one of the following messages:
1. “NUD” – Nudging Operation has been initiated.
MH-3000 User Manual Page 66
2. “TDO” – the Door Open Timer has tripped. The doors failed to open fully in the preset time.
3. “TDC” – the Door Close Timer has tripped. The doors failed to close fully in the preset time.
4. “TEE” – the Electric Eye Cutout Timer has tripped. The Electric Eye Input will be cut out.
5. “(no message)” – none of the four conditions above are present.
6.1.5.2 Messages Displayed on the “Dispatcher Status” Screen
The top left of the screen shows the communication status for each car. The letter for each car will be visible if the Dispatcher is communicating with that car. The top right of the screen shows any error messages. The bottom left shows the basic status of the cars and thir position. Each area of the screen will display one of several messages. The numbers in the sample screen below indicate the message areas. Each group of numbers will be replaced by the appropriate message, depending on the status of the car.
Message 1
Message 2
Comm=ABCD2222222
Auto=A1 B1 C1 D1
Message 3
Message # 1 shows which car or cars are communicating with the Dispatcher. If a car is communicating the letter for that car will be visible. For example, “Comm=A.C.“ indicates the Dispatcher is communicating with cars A and C only.
Message # 2 will be replaced with one of the following messages:
1. “IO.Flt” – the communication with one or more of the I/O boards has failed.
2. “FIRE” – the system is on Fire Service.
3. “Em.Pwr” – the system is on Emergency Power.
4. “(blank)” – the Dispatcher is operating normally.
Message # 3 shows whether car A is in group operation and what floor each car is at. If the car is in group operation then the letter for the car will be visible, otherwise there will be a period there instead. The number after the car letter shows which landing the car is at.
For example “A2 .1 C3 .2” indicates that car A is in group operation at the 2nd landing, car
B is out of group at the 1st landing, car C is in group at the 3rd landing and car D is out of group at the 2nd landing.
6.1.6 Go To Set-Up Mode
This selection allows the controller to be taken out of normal operation, and put in the
Set-up Mode, so that features and settings may be changed.
When Ent is pressed at this selection, a warning screen will be displayed, indicating that the controller will stop.
If Ent is pressed again, then the controller will turn off all outputs and the controller will go into the Set-up Mode. A banner will be displayed for 1 second indicating the Set-up
Mode has been entered. The first selection of the Set-up Menu will then be displayed.
MH-3000 User Manual Page 67
If any other key is pressed from the warning screen, the controller will return to the Run
Mode, and the controller will continue operating as normal.
LED D5 will flash every 10 seconds in the Set-up Mode, indicating that the CPU is still running normally.
6.1.7 Effect of Diagnostic Modes on Scan Time
The microprocessor scan time is very fast, with each scan taking about 7 milliseconds.
Servicing the LCD display is one of the more time consuming tasks that the microprocessor does, so when the LCD display needs to be updated regularly, the microprocessor must slow down to allow it to accept the data. Consequently, the scan time is slower when in the
"Show I/O Status" and "Show Internal Memory" Modes, than when displaying other screens.
The car will still operate normally, but it is recommended that the display not be left in those modes when those screens are not specifically being used. The LCD can be left showing the “Show Car Status” screen, since this updates the screen while the I/O is being polled, consequently the impact on the scan time is minimal.
With program version 3A, dated March 2005, the scan time has been optimized for IO communication, so the impact on scan time is minimal no matter what screen is being viewed.
MH-3000 User Manual Page 68
6.2 Set-Up Mode
6.2.1 How to Enter Set-Up Mode
In the Run Mode, press Nxt until the selection "Go To Setup Menu" is shown, then press
Ent.
Press Ent when the "Warning" message is displayed.
WARNING: The elevator will stop immediately and be completely shut down, as all outputs will be turned off when the Set-up Mode is entered.
The LEDs D1-D4 are not updated in the Setup Mode, so they will remain in their last state. LED D5 will flash once every 10 seconds, to indicate the CPU is not locked up.
6.2.2 How to Exit Set-Up Mode
Press Esc from the Set-up Menu to return to the Run Mode. The controller will start running again, and will be in the Show Car Status Mode. LED D5 will start flashing about once a second, indicating the CPU is scanning. LEDs D1-D4 will revert to their normal operation.
Note: It may be necessary to press Esc to exit a sub-menu and return to the
Set-up Menu, before going back to the Run Mode.
6.2.3 Set-Up Mode Screens
The following Menu items are available in the Set-up Mode:
1. Reset Settings.
2. Change Settings.
3. Change Features.
4. Show Fault Log.
5. Show Internal Memory.
6. Set The Time.
7. Enter Password.
8. Test I/O Boards.
MH-3000 User Manual Page 69
Virginia Controls
MAIN SETUP MENU
To Run Mode,
Car Status Screen
SETUP MODE SCREENS
To CHANGE SETTINGS, (see below)
Press ENTER to
RESET SETTINGS
ALL SETTINGS
HAVE BEEN RESET
Press ENTER to
TEST I/O BOARD
WARNING: TEST
ACTIVATES RELAYS
= Press “Nxt”
= Press “Prv”
= Press “Ent”
= Press “Esc”
The normal sequence is to press “Nxt” to select the desired menu item.
Press “Ent” to use the menu item.
Press “Esc” when you are finished.
Press ENTER to
ENTER PASSWORD
Press ENTER to
SET THE TIME
Press ENTER to
SHOW INT MEMORY
Press ENTER to
SHOW FAULT LOG
ENTER PASSWORD
(Enter the Time
and Date)
0400 00 00 00 00
0404 00 00 00 00
01 09:40 FLTCODE
2 1100 0011 0010
WARNING:
IN SETUP MODE,
THE CAR IS SHUT DOWN.
Press ENTER to
CHANGE FEATURES
(Display and Change
Adjustable Features)
Press ENTER to
CHANGE SETTINGS
(Display and Change
Adjustable Settings)
To RESET SETTINGS, (see above)
Press the Nxt or Prv keys to move through the Set-up Menu to the desired item, then press Ent to select the menu item.
6.2.4 Reset Settings
This selection allows all settings and features to be reset to the factory values that are stored in the EPROM. This should be done on initial installation, and is recommended if the operation of the car seems strange. (See the warning below.)
Press Ent to reset all settings and features to the values programmed from the factory.
After pressing Ent the password entry screen will be shown. This prevents accidentally resetting the default values. The password must be entered each time the Reset Settings is attempted. Enter the password “911” then press Ent to reset all settings and features to the factory default. Press Esc to exit without resetting the settings and features. If the job is a standard job, then the specific settings and features for your job must be entered after doing a factory reset. (See the warning note below)
Press Nxt or Prv to move to another item in the Set-up Menu.
Press Esc to return to the Run Mode.
MH-3000 User Manual Page 70
NOTE: An internal memory check is done on each power up. So if a corrupted memory is detected, a factory reset will be done automatically.
WARNING: On standard jobs, the factory reset will return the settings and features to a generic default. The actual settings and values for the specific job must now be entered to customize the job for the particular application. To determine if a particular controller has a standard program, go to the banner screen. If the value in the lower left of the screen is the Virginia Controls Job Number, then the chip is specific for that job, and a factory reset will load the values for that job. If the value is not the job number, (it will start with a letter) then the program is a standard, and the actual values for the job need to be entered. These values are provided with the controller in the schematic, and are based on the requirements of the job, as conveyed to Virginia Controls.
A factory reset can also be done without the keypad as follows:
1. Turn off the power
2. Turn the Inspection Switch to "Inspection" (or remove the field wire from terminal
23)
3. Jump terminals 1 to 21 and 22 (Up and Down Level Switch Inputs)
4. Turn the power back on for 10 seconds. Inputs 1 and 2 on Board 1 should both be
ON, and Input 3 on Board 1 should be OFF.
5. Turn off the power
6. Remove all jumpers and put the car back on normal operation.
6.2.5 Change Settings
Use this selection to change the settings described below. Each setting contains a value from 0 to 255. As you scroll through the settings, the current value will be displayed. A new value may be entered over the old value, as desired.
NOTE: The Password “911” is required to gain access to this menu selection, unless the password has already been entered in another sequence.
Press Nxt to go to the next setting, without changing the current setting.
Press Prv to go to the previous setting, without changing the current setting.
Press a numeric key ( 0 - 9 ) to enter a new value. (The decimal point key . is not used)
Press Ent after entering a new value to load the new value into memory. (The message
“VALUE SAVED!” is displayed for 1 second, indicating the new entry has been accepted, then the display will show the setting and the new value) If Nxt, Prv or Esc is pressed after entering a new value, the new value will NOT be stored in memory.
Press Esc to go back to the Setup Menu.
MH-3000 User Manual Page 71
If an incorrect value is entered, press Esc to clear the value before it is accepted, then enter the correct value; or press Nxt or Prv to move to the next setting. If the value was already entered, by pressing Ent, then press Nxt or Prv to return to the incorrect setting, enter the proper value, and press Ent.
6.2.5.1 Description of Settings
Refer to the sheet MH-3000 Settings in the schematic to see the settings and features provided for each particular job. The Settings listed here are standard (NOTE: a value of 0 to 255 can be entered unless otherwise stated).
6.2.5.2 Numerical Settings
• Number of I/O Boards - (Display shows "NUM.OF IO BOARDS") This is the number of
Input and Output Boards that the CPU will address, and is a value between 1 and 8. If a value out of this range is entered, then a default value of 2 will be entered when the car is put back into the Run Mode.
• Number of Landings - (Display shows "NUMBER OF LDGS") This is the number of landings that the controller can serve, and is a value between 2 and 8. If the controller is set up to serve future landings, then this value can be used to temporarily cut off future upper landings. This value also determines which floor the controller will reset to when a top landing reset is initiated with a pulsing selector.
• Car Number (GROUP CAR CONTROLLER ONLY) - (Display shows "CAR ID. NUMBER")
This is the identification number for this car. It is used in the communication to the
Dispatcher, and is a number between 1 and 4. The number assigned to each car in the group MUST be different. The car assigned id # 1 will show up on the Dispatcher as car
A; id # 2 is car B; id # 3 is car C; id # 4 is car D. You should not normally change this value as it has been assigned in the factory. If you do change it, make sure that two cars do not end up with the same id number.
• Number of Cars (GROUP DISPATCHER ONLY) - (Display shows "NUMBER OF CARS")
This is the number of cars is in the group.
• Main Fire Landing - (Display shows "MAIN FIRE LDG") This is the number corresponding to the Main Fire Landing, and is a number between 1 and 8. The value set is based on the bottom floor being "1", the 2nd floor is "2" etc., even if this does not match the building designations.
CAUTION: If it is set to a value greater than the number of landings served, the car will go to the top landing, but it will not open its doors.
• Alternate Fire Landing - (Display shows "ALT. FIRE LDG") This is the number corresponding to the Alternate Fire Landing, and is a number between 1 and 8. The value set is based on the bottom floor being "1", the 2nd floor is "2" etc., even if this does not match the building designations.
CAUTION: If it is set to a value greater than the number of landings served, the car will go to the top landing, but it will not open its doors.
• Home Landing (SIMPLEX ONLY) - (Display shows "HOME LANDING") This is the home landing for a simplex car. The car can be selected to home to this landing, if desired.
This value can be set to any valid landing, as determined by the number of landings setting.
MH-3000 User Manual Page 72
• Dispatch Landing (DUPLEX and GROUP ONLY) - (Display shows "DISPATCH LDG")
This is the dispatch landing for duplex or group systems. One car will always home here. This value can be set to any valid landing, as determined by the number of landings setting.
• Upper Home Landing (DUPLEX ONLY) - (Display shows "UPPER HOME LDG") This is the home landing for the free car in a duplex system. The free car can be selected to home to this landing, if desired. This value should be set to be inside the upper zone, as determined by the Low Zone assignments shown later in the features settings.
• Alternate Home Landing (GROUP CAR CONTROLLERS ONLY) - (Display shows "ALT.
HOME LDG") This is the alternate home landing for the car car. The car can be forced to home to this landing, if desired. This value can be set to any valid landing, as determined by the number of landings setting.
• Front Door Code - (Display shows "FRONT DOOR CODE") This is a binary coded value used to select which front openings are enabled. Each bit corresponds to a landing. If the bit for a landing is on, then the front doors at that landing will be enabled. Use the chart shown in the schematic to determine the proper value. Add up the value for each floor to determine the total value for this setting. A value of “255” will enable the front doors at all floors.
• Rear Door Code - (Display shows "REAR DOOR CODE ") This is a binary coded value used to select which rear openings are enabled. Each bit corresponds to a landing. If the bit for a landing is on, then the rear doors at that landing will be enabled. Use the chart in the schematic to determine the proper value. Add up the value for each floor to determine the total value for this setting. A value of “0” will disable the rear doors at all floors.
• Low Zone Code (DUPLEX ONLY) – (Display shows “LOW ZONE CODE”) This value determines which floors are in the Low Zone. The floors will normally be served by the
Lobby car, other floors will normally be served by the Free car. Each bit corresponds to a landing. If the bit for a landing is on, then that floor is in the Low Zone. Use the chart shown in the schematic to determine the proper value. Add up the value for each floor to determine the total value for this setting. A value of “3” will set the Low Zone as the bottom two floors.
• Dispatch Fail Calls (GROUP CAR CONTROLLERS ONLY) - (Display shows "DISP. FAIL
CALLS") This sets the car calls that are entered automatically whenever the car loses communication with the Dispatcher. If no calls are set, the car will park at the last landing served with its doors open if the communication fails. Each bit corresponds to a landing. If the bit for a landing is on, then a call will be entered at that floor. Use the chart shown in the schematic to determine the proper value. Add up the value for each floor to determine the total value for this setting.
• Zone 1 Code (GROUP DISPATCHER ONLY) - (Display shows "ZONE 1 CODE") This is the code to set the landings in Zone 1. Each bit corresponds to a landing. If the bit for a landing is on, then that floor is in Zone 1. Use the chart shown in the schematic to determine the proper value. Add up the value for each floor to determine the total value for this setting. A value of “3” will set Zone 1 as the bottom two floors. Each landing must be assigned to one and only one zone.
• Zone 2 Code (GROUP DISPATCHER ONLY) - (Display shows "ZONE 2 CODE") This is the code to set the landings in Zone 2. Each bit corresponds to a landing. If the bit for a landing is on, then that floor is this Zone. Use the chart in the schematic to determine the proper value. Each landing must be assigned to one and only one zone.
MH-3000 User Manual Page 73
• Zone 3 Code (GROUP DISPATCHER ONLY) - (Display shows "ZONE 3 CODE") This is the code to set the landings in Zone 3. Each bit corresponds to a landing. If the bit for a landing is on, then that floor is this Zone. Use the chart in the schematic to determine the proper value. Each landing must be assigned to one and only one zone.
• Zone 4 Code (GROUP DISPATCHER ONLY) - (Display shows "ZONE 4 CODE") This is the code to set the landings in Zone 4. Each bit corresponds to a landing. If the bit for a landing is on, then that floor is this Zone. Use the chart in the schematic to determine the proper value. Each landing must be assigned to one and only one zone.
• Number of Hall Calls to Initiate Heavy Program (GROUP DISPATCHER ONLY) -
(Display shows "# CALLS = HEAVY") This is the number of Hall Calls that must be entered to initiate the Heavy Traffic Program. This will affect the assignment of calls and the homing scheme. See the section on Zoned Group Operation for a more complete description of the traffic programs.
• Number of Hall Calls to Initiate Down Heavy Program (GROUP DISPATCHER ONLY)
- (Display shows "# CALLS=DN HEAVY") When the number of Down Hall Calls minus the number of Up Hall Calls exceeds this value then the Down Heavy Traffic Program is initiated. This will affect the assignment of calls and the homing scheme. See the section on Zoned Group Operation for a more complete description of the traffic programs.
• Number of Car Calls to Initiate Up Heavy Program (GROUP DISPATCHER ONLY) -
(Display shows "#CAR CALLS=UPHVY") This is the number of Car Calls that must be entered as a car leaves the lower landings to initiate the Up Heavy Traffic Program. This will affect the assignment of calls and the homing scheme. See the section on Zoned
Group Operation for a more complete description of the traffic programs.
6.2.5.3 Bit Features
The Bit Features are multiple features combined into several settings. Each setting consists of 8 features that can be turned on or off individually. Refer to the sheet MH-3000
Settings in the schematic for a breakdown of each setting. A description of the standard features that may be part of the Bit Features are listed in a following section, after the standard settings.
• Bit Features # 1 - (Display shows "BIT FEATURES # 1") This is a binary coded value used to select various features as shown in the chart in the schematic on the MH-3000
SETTINGS sheet. Each bit corresponds to a different feature. If the bit for a feature is on, then that feature is enabled. Use the chart shonw in the schematic to determine the proper value. Add up the value for all the features that should be enabled to determine the total value for this setting.
• Bit Features # 2 - (Display shows "BIT FEATURES # 2") Similar to Bit Features #1.
• Bit Features # 3 - (Display shows "BIT FEATURES # 3") Similar to Bit Features #1.
• Bit Features # 4 - (Display shows "BIT FEATURES # 4") Similar to Bit Features #1.
• Bit Features # 5 - (Display shows "BIT FEATURES # 5") Similar to Bit Features #1.
• Bit Features # 6 - (Display shows "BIT FEATURES # 6") Similar to Bit Features #1.
• Bit Features # 7 - (Display shows "BIT FEATURES # 7") Similar to Bit Features #1.
• Bit Features # 8 - (Display shows "BIT FEATURES # 8") Similar to Bit Features #1.
• Bit Features # 9 - (Display shows "BIT FEATURES # 9") Similar to Bit Features #1.
• Bit Features # 10 - (Display shows "BIT FEATURES # 10") Similar to Bit Features #1.
MH-3000 User Manual Page 74
6.2.5.4 Timers
The Timers are divided into groups based on whether the preset trip time is in tenths of a second, seconds or tens of seconds. In each case the preset range is 0 to 255.
6.2.5.5 Custom Timers
The following timers are custom. If they are assigned to a specific function then this will be described in the schematic. The time base for these timers is not predefined. These values may also be used for non-timing functions.
• Auto Jack Re-Sync Time - (This timer uses one of the Custom Timers. Check the schematic to see which timer is used) The Jack Re-synchronization will be repeated at this interval automatically. Automatic Jack Re-Sync can be disabled, if desired. Note:
This value is in DAYS. This timer is only used with the Jack Resynchronization feature.
• Jack Re-Sync Counter Register - (This timer uses one of the Custom Timers. Check the schematic to see which timer is used) This value is used internally, and shows the number of days since the last Jack Re-Sync. Do NOT adjust this value. This timer is only used with the Jack Resynchronization feature.
• Custom Time #0.1 – (Display shows “CUSTOM TIME #0.1”) This is a reserved value that is not assigned, but may be assigned a function for a specific job. The time base for this timer is not preset, and may change depending on its use. Refer to the Settings sheet in the schematic to see if and how this setting is used.
• Custom Time #0.2 – (Display shows “CUSTOM TIME #0.2”) Similar to Custom Time
#0.1.
• Custom Time #0.3 – (Display shows “CUSTOM TIME #0.3”) Similar to Custom Time
#0.1.
• Custom Time #0.4 – (Display shows “CUSTOM TIME #0.4”) Similar to Custom Time
#0.1.
• Custom Time #0.5 – (Display shows “CUSTOM TIME #0.5”) Similar to Custom Time
#0.1.
6.2.5.6 Tenth of a Second Timers
The following settings are for timers. The timer values are in tenths of a second.
• Door Time, Hall (in tenths of a second) - (Display shows "DOOR TIME, HALL") This is the time in tenths of a second, that the doors will remain open, after they have opened fully, when the car has stopped in response to a hall call. After this time, the doors will start to close.
NOTE: If a car call is entered while the doors are open, the door time will be reduced to the "Door Time, Car" setting. If the Door Close Button is pressed while the doors are open, the door time will be reduced to the "Door Time,
Short" setting. This setting is normally 50, for a time of 5 seconds.
• Door Time, Car (in tenths of a second) - (Display shows "DOOR TIME, CAR") This is the time in tenths of a second, that the doors will remain open, after they have opened fully, when the car has stopped in response to a car call only. After this time, the doors will start to close.
MH-3000 User Manual Page 75
NOTE: If a car call is entered, or the Door Close Button is pressed, while the doors are open, the door time will be reduced to the "Door Time, Short" setting. This normal setting is 20, for a time of 2 seconds.
• Door Time, Short (in tenths of a second) - (Display shows "DOOR TIME, SHORT") This is the time in tenths of a second, that the doors will remain open, after they have opened fully, when the doors have reopened in response to a Door Open Button/Safety edge/Electric Eye/Infra-red Curtain, and no hall call is entered. After this time, the doors will start to close. The normal setting is 10, for a time of 1 second.
• Leveling Lockout/Cutout Time (in tenths of a second) - (Display shows "LEVELING
LOCKOUT") This is the time in tenths of a second that the leveling switches are cut out after the start of a floor to floor run. It allows the external relays to energize and lock out the leveling switches externally. The time must be long enough for the external fast speed relays to cut out the Leveling Switches. Note that the fast speed relays may be delayed by the Run contact or Soft Start contact in series with the Up Normal. If this delay is longer than 2 seconds, then this time might need to be increased to avoid a
Door Zone Fault when the car starts. The normal setting is 20, for a time of 2 seconds.
• Back Call Delay (DUPLEX ONLY) (in tenths of a second) - (Display shows "BACK CALL
DELAY") This is the time in tenths of a second that the back call signal will be delayed before letting the other car respond to calls behind this car. The normal setting is 10, for a time of 1 second.
• Up Main Landing Hall Call Delay (GROUP DISPATCHER ONLY) (in tenths of a second)
- (Display shows "UP MAIN LDG DLAY") This is the time in tenths of a second that the
Up Main Landing Hall Call must be registered before it is given to a car that is not “Next” at the Main Landing. The normal setting is 10, for a time of 1 second.
• Delay Before Stop Jack Re-Sync - (This timer uses one of the Custom Timers. Check the schematic to see which timer is used) The Jack Re-synchronization operation is stopped when the Jack Collapsed Switch Input (if used) has been energized for this time. The delay allows the jack to be fully synchronized. This value is only used with the
Jack Resynchronization feature.
• Custom Time #1.1 (in tenths of a second) - (Display shows "CUSTOM TIME #1.1")
This is a reserved value that is not assigned, but may be assigned a function for a specific job.
• Custom Time #1.2 (in tenths of a second) - (Display shows "CUSTOM TIME #1.2")
See Custom Time # 1.1
• Custom Time #1.3 (in tenths of a second) - (Display shows "CUSTOM TIME #1.3")
See Custom Time # 1.1
6.2.5.7 One Second Timers
The following settings are for timers. The timer values are in seconds.
• Shutdown Time (in seconds) - (Display shows "SHUTDOWN TIME") If the car runs up without passing a floor for this time, then shutdown will be initiated. The car will stop, and run down to the bottom landing, and cycle its doors. It will then be shut down. The car can be returned to service by cycling the Inspection Switch, or the Main Line
Disconnect Sw. The normal setting is 25 seconds.
• Door Nudging Time (in seconds) - (Display shows "NUDGING TIME") This is the time delay before initiating door close nudging, if that feature is provided. A call must be registered, and the car must be in automatic operation. The timer is reset when the
MH-3000 User Manual Page 76
doors get fully closed, or when the car starts a floor to floor run. The normal setting is
25 seconds.
• Electric Eye Cutout Time (in seconds) - (Display shows "EYE CUTOUT TIME") This is the time delay before cutting out the Electric Eye Input, after it has been continuously energized. It is reset when the car runs to the next floor. The normal setting is 20 seconds.
• Homing Delay Time (in seconds) - (Display shows "HOMING DELAY") This is the delay before homing a car to the home landing, after it has answered all calls, and is sitting with its doors closed. The normal setting is 10 seconds.
• Car Stuck Time (in seconds) - (Display shows "CAR STUCK TIME") This is the time delay before calls at the same landing as the car are disabled, so that the car can answer other registered calls. This operates as a stuck button timer. The normal setting is 15 seconds.
• Door Stuck Time (in seconds) - (Display shows "DOOR STUCK TIME") This is the time delay before stopping a door open or close cycle. The normal setting is 20 seconds
• Door Stuck Reset Time (in seconds) - (Display shows "DOOR RESET TIME") This is the time that the doors are held open after failing to close properly, before retrying to close. The normal setting is 10 seconds.
• Delay Before Canceling Independent Service on Fire Service - (Display shows
"KILL IDS ON EFS1") This is the time delay before Independent Service is cut out, when
Fire Service Phase 1 is initiated. This feature can be modified by the Bit Features described above that determine if and when Independent Service is cut out on Fire
Service. The normal setting is 30 seconds.
• Door Close Delay Time on Fire Service (in seconds) - (Display shows "DR CLOSE ON
FIRE") This is the delay before closing the doors after the car has returned to the designated fire landing and the car is in shutdown. This is required on 2000 (or later)
Fire Code. The normal setting is 30 seconds.
• Call Help Time (DUPLEX AND GROUP DISPATCHER ONLY) (in seconds) - (Display shows "CALL HELP TIME") This is the amount of time a hall call can be registered before the other car not assigned this call will respond to the call. The normal setting is 30 seconds.
• Non Interference Time (SAPB ONLY) (in seconds) - (Display shows “NON
INTERFERENCE”) This is the time that the In Use Light will remain on after the car has answered a call and cycled its doors. Hall Call Buttons will be disabled during this time.
The normal setting is 6 seconds.
• Home Delay to Main Ldg (GROUP DISPATCHER ONLY) (in seconds) - (Display shows
"HOME TO MAIN") This is the delay before homing a car to the Main Dispatch Landing.
• Home Delay to Other Ldgs (GROUP DISPATCHER ONLY) (in seconds) - (Display shows
"HOME TO OTHERS") This is the delay before homing a car to any landing other then the Main Dispatch Landing.
• Hold Up Heavy from Hall Call (GROUP DISPATCHER ONLY) (in seconds) - (Display shows "HOLD UPHVY HALL") This is the length of time that the Main Landing Up Hall
Call must be off to cancel the Up Heavy traffic program.
• Hold Up Heavy from Car (GROUP DISPATCHER ONLY) (in seconds) - (Display shows
"HOLD UPHVY CAR") This is the length of time that the car holds the Up Heavy
Initiation signal after it leaves the lower landings with an Up Heavy demand.
MH-3000 User Manual Page 77
• Hold Up Heavy from Group (GROUP DISPATCHER ONLY) (in seconds) - (Display shows "HOLD UPHVY GROUP") This is the length of time that the Dispatcher will hold Up
Heavy after all cars have dropped their Up Heavy Initiation signal.
• Maximum Down Run Time On Jack Re-Sync - (This timer uses one of the Custom
Timers. Check the schematic to see which timer is used) The Jack Re-synchronization operation is stopped when the car has been running down at the bottom landing for this time. This allows the car to return to service if the Jack Collapsed Switch Input fails or is not provided. This value is only used with the Jack Resynchronization feature.
• Custom Time #2.1 (in seconds) - (Display shows "CUSTOM TIME #2.1") This is a reserved value that is not assigned, but may be assigned a function for a specific job.
• Custom Time #2.2 (in seconds) - (Display shows "CUSTOM TIME #2.2") See Custom
Time # 2.1
• Custom Time #2.3 (in seconds) - (Display shows "CUSTOM TIME #2.3") See Custom
Time # 2.1
6.2.5.8 Ten Second Timers
The following settings are for timers. The timer values are in tens of seconds.
• Position Indicator Cutout Time (in tens of seconds) - (Display shows "PI CUT OUT
TIME ") This is the time delay before turning off the Position Indicators, after the car has become idle. If the doors are opened, or the car starts in response to a call, then the Position Indicators will turn on again. The normal setting is 30, for a time of 300 seconds or 5 minutes. To keep the PI’s on at all times, enter a value of “0” for the
Cutout Time.
• Custom Time #3.1 (in tens of seconds) - (Display shows "CUSTOM TIME #3.1") This is a reserved value that is not assigned, but may be assigned a function for a specific job.
• Custom Time #3.2 (in tens of seconds) - (Display shows "CUSTOM TIME #3.2") See
Custom Time # 3.1
• Custom Time #3.3 (in tens of seconds) - (Display shows "CUSTOM TIME #3.3") See
Custom Time # 3.1
Some installations require specific settings or features that are not included in the standard program. In this case, a separate sheet (or sheets) will be provided that describe the operation of these settings or features, and what the factory default settings are.
6.2.5.9 Description of Bit Feature Settings
The following features are combined into the Bit Features 1 through 10. Refer to the sheet MH-3000 Settings in the schematic to see the settings and features provided for each particular job. The following Settings are standard.
• Disable Fire Service – Turn this feature on to disable Fire Service. This feature should be turned on if Fire Service is not provided. It may also be turned on during initial installation, if the Smoke Sensors or Fire Switches have not yet been installed.
• Enable 2000 ANSI Fire Code – Turn this feature on to enable 2000 or 2004 National
Fire Code. The default code is 1998 Fire Code.
• Enable New York Fire Code – Turn this feature on to enable New York Fire Code.
MH-3000 User Manual Page 78
• Enable 2001 Chicago Fire Code – Turn this feature on to enable 2001 Chicago Fire
Code
• Enable 1998 Chicago Fire Code – Turn this feature on to enable 1998 Chicago Fire
Code
• Use 2 Inputs for 1998 Chicago Fire Code – Turn this feature on to use 2 inputs for the Fire Inputs for Chicago 1998 Fire Code.
• Enable Canadian Fire Code – Turn this feature on to enable 1998 Canadian B44 Fire
Code
• Enable Bldg Fire Sw for 2000 Fire Code – Turn this feature on to enable the Remote
Fire Sw on 2000 Fire Code. The input for this feature must have been assigned for this feature to work properly.
• Kill Independent immediately on Fire Service – Turn this feature on to allow Fire
Service to override Independent Service immediately.
• No Timed Kill of Independent on Fire Service – Turn this feature on to prevent Fire
Service from overriding Independent Service. Independent Service must be turned off or the doors closed by the operator to allow the car to run on Fire Service.
• Never kill Indep. on Fire Service – Turn this feature on to prevent Fire Service from overriding Independent Service. Independent Service must be turned off to allow the car to run on Fire Service.
• Main Fire Landing at Rear Opening – Turn this feature on to use the rear opening at the designated fire opening, instead of the front opening. If there is only one opening at the designated fire landing, then this feature will have no effect.
• Alternate Fire Landing at Rear Opening – Turn this feature on to use the rear opening at the alternate fire opening, instead of the front opening. If there is only one opening at the alternate fire landing, then this feature will have no effect.
• Disable Shunt Trip on Fire Service Phase 2 – Turn this feature on to disable Shunt
Trip operation when the car is on Fire Service Phase 2.
• Enable Shunt Trip on Inspection – Turn this feature on to enable Shunt Trip operation when the car is on Inspection.
• Disable ECReturn Latch on 2000 Fire Code – Turn this feature on to disable the holding circuit on Fire Service Phase 2 Return on 2000 (or later) Code. This allows the
Return mode to be cancelled by turning the Fire Switch to the “On” position. Check the appropriate code to see if this is required or allowed.
• Enable Pulsing Selector (off=Floor Sws) – Turn this feature on to enable a pulsing floor selector, rather than individual Floor Switches. With a pulsing arrangement, there is an up or a down pulse to change floors. Additionally at the terminal landings, enabling the up pulse input and the door zone input will reset to the top landing, while energizing the down pulse and door zone will reset the floor position to the bottom landing.
• Enable Separate Call I/O (4 Wire Calls) – Turn this feature on to enable separate wiring for the inputs and outputs for the car and hall calls. If this feature is disabled then the car and hall call inputs are connected to the corresponding outputs.
• Enable Door Check Feature – Turn this feature on to enable the Door Check feature.
This allows the status of the Car Door and the Hall Doors to be checked according to the appropriate codes.
MH-3000 User Manual Page 79
• Enable Redundancy Fault Checking – Turn this feature on to enable 2000 (or later) code redundancy fault checking. This enables the redundancy fault timers, and checks the leveling inputs and running inputs for stuck relays or contacts, according to the 2000
(or later) code.
• Use Car Lantern outputs for Hall Lanterns – Turn this feature on to use the Car
Lantern outputs as Hall Lanterns. If there are only two landings, then the Hall Lanterns can be connected directly to the Car Lantern outputs. If there are more than two landings, then additional external relays are needed to enable the appropriate lantern at each floor.
• Do Not Run On Fire Service and BORIS – Turn this feature on to prevent the car from running if Fire Service is enabled while on battery backup operation.
• Do Not Run on Fire Service and Shutdown – Turn this feature on to prevent the car from running if Fire Service is enabled while on shutdown. If this feature is not enabled the car will be allowed to run down on Fire Serviec and shutdown.
• Allow Stop at Upper Floor on Shutdown – Turn this feature on to allow the car to stop at an upper floor on shutdown if it is the main floor. Check with the appropriate codes to see if this is allowed or required.
• Enable CKO on Independent – Turn this feature on to energize the CKO Car Call
Cutout Override output on Independent Service. This will allow car calls to be registered without the use of access keys.
• Fire Sensors are Normally Open Inputs – Turn this feature on if the Smoke Sensor inputs are normally open on normal operation, and close when a fire is detected. The default is to use Smoke Sensors that are closed on normal operation and open when a fire is detected.
• Dir Indicators show actual direction on Attend. – Turn this feature on to make the
Attendant Direction Indicators show the direction that the car will run next. If this feature is not enabled then they will show whether there are calls registered in either direction. For example, with this feature off, and the car at an intermediate floor with calls above and below the car, then both Attendant Direction Indicators would be on, since there are calls above and below the car. If the feature was enabled, then the indicators woul be the same as the normal Direction Indicators, and only one indicator would be on, depending on which direction had actually been selected.
• Med Emerg Buzzer on Independent only – Turn this feature on to change the operation of the Medical Emergency Buzzer output. With the feature disabled (factory default) the buzzer will come on while the car is returning to the Medical Emergency floor in response to the hall Medical Emergency Switch. If the feature is enabled, the buzzer will come on if the car is on Independent Service and a hall Medical Emergency
Switch is turned on. This alerts the operator to release the car.
• Enable Full Redundancy Fault Checking – Turn this feature on to enable
Redundancy Fault checking with the MH5 board. This enables additional inputs used to check critical circuits. The inputs for this feature must have been assigned for this feature to work properly.
NOTE: Switch 3 on the CPU Dip Switches is a Redundancy Defeat. If this is turned ON, then this will prevent a fault from the Redundancy checks, or a
Door Zone Fault. The Fire Buzzer will be turned on to remind you to turn off the Redundancy Defeat after installation.
MH-3000 User Manual Page 80
• Always Enable DOB at Front Openings – Turn this feature on to allow the Front Door
Open Button to always open the doors at selective openings (where there is a front and rear opening at the same landing). With this feature disabled, the doors must have been opened, or still be open, for the Door Open Button to operate. This allows a measure of security at these landings.
• Always Enable DOB at Rear Openings – Turn this feature on to allow the Rear Door
Open Button to always open the doors at selective openings (where there is a front and rear opening at the same landing). With this feature disabled, the doors must have been opened, or still be open, for the Door Open Button to operate. This allows a measure of security at these landings.
• Disable Non-Shutdown Faults in the Fault Log – Turn this feature on to disable faults from being logged into the Fault Log that are not shutdown faults. This keeps the fault log clear of non-essential faults. The following faults will not be logged if this feature is enabled: TDOPEN, TDCLOSE, TDOPN-R, TDCLO-R, CARSTUK, DRCONTS, OUT-
DZ, COMMFLT, FIRE, MRSMOKE, SHUNT, FLOOD
• Flood Return Ldg is 3 (not 2) – Turn this feature on to make the car return to the third landing from the bottom if Flood Service is initiated. The default floor is the second floor from the bottom.
• Flood Return Ldg is Top Ldg (not 2) – Turn this feature on to make the car return to the top landing if Flood Service is initiated. The default floor is the second floor from the bottom.
• Flood overrides Independent, Attendant, Med Emerg – Turn this feature on to allow Flood Service to override Independent Service, Attendant Operation and Medical
Emergency Operation. If this feature is not enabled, then the car will remain under the control of the operator if the Flood Service input is energized.
• Flood overrides Shutdown (Low Oil, Rev. Phase, etc) – Turn this feature on to allow Flood Service to override shutdown functions that would normally return the car to the bottom landing. The car will still not be able to run up, but Flood Service will remain in effect even though a shutdown feature is in effect.
• Do Not Run on Flood and BORIS – Turn this feature on to prevent the car from running if Flood Service and BORIS Battery Backup operation are initiated at the same time.
• Do Not Run Down Below Main on Flood and Shutdown – Turn this feature on to prevent the car from running if it is at or below the Main Floor and the car is on Flood
Service and Shutdown Operation.
• Fire Service Overrides Flood Operation – Turn this feature on to allow Fire Service to override Flood Service. The car will return to the Main Fire Floor, even if that is the bottom landing.
• Flood Operation Overrides Hall Fire Service – Turn this feature on to allow Flood
Service to override Fire Service, and cause the car to leave the bottom landing, even if that is the designated Fire landing. If this feature is not set, then whichever feature
(Fire Service or Flood Service) is initiated first will take precedence.
• Enable Car To Lobby Input – Turn on to enable the Car To Lobby Shutdown inputs.
The input for this feature must have been assigned for this feature to work properly.
• Enable ES Input – Turn on to enable the ES (Emergency Stop Switch) Input. This is normally used on a Duplex, or with MH5 Monitoring. The input for this feature must have been assigned for this feature to work properly.
MH-3000 User Manual Page 81
• Disable DISC Input (BORIS is not used) – Turn on to disable BORIS operation.
• Enable Shunt Trip Feature – Turn on to enable the Shunt Trip feature. The input and output for this feature must have been assigned for this feature to work properly. This feature can be turned off to disable the Shunt Trip if it was supplied, but is not required.
Shunt Trip operation can be accomplished externally to the controller, if desired.
• Enable Low Oil Switch Feature – Turn on to enable the Low Oil Sw feature. The input for this feature must have been assigned for this feature to work properly. This feature can be turned off to disable the Low Oil Sw if it was supplied, but is not required.
• Enable Oil Viscosity Feature – Turn on to enable Oil Viscosity operation. The input for this feature must have been assigned for this feature to work properly. This feature can be turned off to disable the Oil Viscosity feature if it was supplied, but is not required.
• Enable Rear Door Open Output – Turn on to enable the Rear Door Open output at point 8 on the first output board.
• Enable RD (RearDoor) Output – Turn on to enable the RD output at point 8 on the first output board. This is used with front and rear doors only.
• Enable 1UL - 4DL Hall Lantern Outputs – Turn on to enable specific Hall Lantern outputs. The outputs for this feature must have been assigned for this feature to work properly.
• Enable Nudging Output – Turn on to enable the Nudging Output. This is not required for Nudging Operation, as the Nudging Buzzer output is the only output specifically required. The output for this feature must have been assigned for this feature to work properly.
• Enable CKO Output – Turn on to enable the CKO, Car Call Cutout Override, output.
The output for this feature must have been assigned for this feature to work properly.
• Enable PI Blanking Fire Output – Turn on to use the Fire Light output as a Position
Indicator Blanking output.
• Disable Door Close on Inspection – Turn on to prevent the Door Close output from energizing on Inspection. This would require the doors to be closed manually. If this feature is left disabled, the Door Close output will energize when the operator attempts to run the car on Inspection.
• Enable False Down Leveling on Car Fire Service – Turn on to allow the car to False
Down Level when it stops between floors, on Fire Service Phase 2. False Down Level is used to return a car to a landing if it stops outside the door zone. The default is to disable False Down Leveling on Fire Service Phase 2, so that the car will only run when a car call is registered. If this feature is enabled and the car is on Fire Service Phase 2, and the Stop Switch has been opened then closed, then a car call button must be pressed to initiate False Down Level.
• Enable Flashing Hall Fire Light – Turn on to make the Hall Fire Light flash if the
Machine Room Smoke Sensor has tripped. By default the car Fire Light will flash, but not the hall Fire Light.
• Disable Automatic Timed Jack Re-Synch - Enable this bit feature to stop the automatic Jack Re-synchronization. The Jack Re-synchronization will only operate when the Jack Out-of-Synchronization Input turns on, if used. This feature is only used with the Jack Resynchronization feature.
MH-3000 User Manual Page 82
• Do Jack Re-Synchronization When Inspection Sw Is Cycled - Enable this bit feature to initiate the automatic Jack Re-synchronization whenever the Inspection
Switch is turned from Inspection to Normal. This feature is only used with the Jack
Resynchronization feature.
• Enable Jack Out Of Synchronization Input - Enable this bit feature to allow Jack Resynchronization to be initiated by the Jack Out Of Sync Input. This feature is only used with the Jack Resynchronization feature.
Features used on Duplex controllers only
• Elev A Select (A=ON, B=OFF) – Turn this feature on to select this car as Elevator A.
This allows the cars of a Duplex system to coordinate Emergency Power and Duplexing functions.
• Only this car serves Front Calls at Ldg 1 – Turn this feature on if the other car in the duplex does not serve this opening, but this car does.
• Only this car serves Front Calls at Ldg 2 – Turn this feature on if the other car in the duplex does not serve this opening, but this car does.
• Only this car serves Front Calls at Ldg 3 – Turn this feature on if the other car in the duplex does not serve this opening, but this car does.
• Only this car serves Front Calls at Ldg 4 – Turn this feature on if the other car in the duplex does not serve this opening, but this car does.
• Only this car serves Front Calls at Ldg 5 – Turn this feature on if the other car in the duplex does not serve this opening, but this car does.
• Only this car serves Front Calls at Ldg 6 – Turn this feature on if the other car in the duplex does not serve this opening, but this car does.
• Only this car serves Front Calls at Ldg 7 – Turn this feature on if the other car in the duplex does not serve this opening, but this car does.
• Only this car serves Front Calls at Ldg 8 – Turn this feature on if the other car in the duplex does not serve this opening, but this car does.
• Only this car serves Rear Calls at Ldg 1 – Turn this feature on if the other car in the duplex does not serve this opening, but this car does.
• Only this car serves Rear Calls at Ldg 2 – Turn this feature on if the other car in the duplex does not serve this opening, but this car does.
• Only this car serves Rear Calls at Ldg 3 – Turn this feature on if the other car in the duplex does not serve this opening, but this car does.
• Only this car serves Rear Calls at Ldg 4 – Turn this feature on if the other car in the duplex does not serve this opening, but this car does.
• Only this car serves Rear Calls at Ldg 5 – Turn this feature on if the other car in the duplex does not serve this opening, but this car does.
• Only this car serves Rear Calls at Ldg 6 – Turn this feature on if the other car in the duplex does not serve this opening, but this car does.
• Only this car serves Rear Calls at Ldg 7 – Turn this feature on if the other car in the duplex does not serve this opening, but this car does.
MH-3000 User Manual Page 83
• Only this car serves Rear Calls at Ldg 8 – Turn this feature on if the other car in the duplex does not serve this opening, but this car does.
Features used with Single Automatic Pushbutton controllers only
• Enable Single Button Collective Operation – Turn this feature on to enable Single
Button Collective operation instead of Single Automatic Pushbutton operation. Single
Button Collective allows multiple calls to be entered, with calls being answered in sequence as the car reaches them. Single Automatic Pushbutton operation only allows one calls at a time.
• Enable Door Auto Close – Turn this feature on to enable the Automatic Door Close outputs. The Door Close outputs and the appropriate external interface circuits for the
Door Operator must be provided for this feature to work. Unless additional features affecting the Door Close output are energized, the Automatic Door Close output will be energized on Fire Service Phase 1 (Hall) to close the doors and allow the car to return to the designated landing.
• Enable Door Auto Close from Car Buttons – Turn this feature on to allow the automatic Door Close output to be energized when a Car Call Button is pressed.
• Enable Door Auto Close from Hall Buttons – Turn this feature on to allow the automatic Door Close output to be energized when a Hall Call Button is pressed.
• Drop ESB with Door Open Limit – Turn this feature on to de-energize the ESB Stop
Switch Bypass output when the car has returned to the designated landing and opened the doors.
• Drop MF Output on Fire 2000 Code – Turn this feature on to allow the MF output to de-energize if the car has returned to the designated fire landing, and is on shutdown.
With 2000 (or later) Fire Code, the doors should close under these circumstances.
• Enable Shunt with Door Open Limit – Turn this feature on to enable the Shunt Trip output when the Door Open Limit indicates the doors are open. If this feature is disabled, the Shunt Trip output will come on shortly after the car stops, even if the doors have not opened. This feature should only be enabled if there are power operated doors that also have a Door Open Limit signal connected to the controller.
• Enable Timed Door Open Fault in Fault Log – Turn this feature on to enable the
TDOPEN fault in the Fault Log. This feature should only be enabled with power operated doors. If it is enabled with manual doors, then a fault will be logged every time the car stops and the doors are not opened.
• Enable Door Reopen for Courion Doors – Turn this feature on to enable the ECH signal to the power operated doors when the car is on Fire Service and the Car Fire Sw is turned from the Off position back to Hold or On. This is used with Courion door operators to reopen the doors.
Features used with Triplex controllers only
• DISPATCH FAILURE CALLS
• Run to 1st Ldg on Dispatch Failure – Turn this feature on to make the car run to this landing if it loses communication with the dispatcher. Set the desired calls to allow the cars to provide service to the building if the dispatcher fails. The car will park with its doors open if it has no registered calls, and the communication has failed.
MH-3000 User Manual Page 84
• Run to 2nd Ldg on Dispatch Failure – Turn this feature on to make the car run to this landing if it loses communication with the dispatcher.
• Run to 3rd Ldg on Dispatch Failure – Turn this feature on to make the car run to this landing if it loses communication with the dispatcher.
• Run to 4th Ldg on Dispatch Failure – Turn this feature on to make the car run to this landing if it loses communication with the dispatcher.
• Run to 5th Ldg on Dispatch Failure – Turn this feature on to make the car run to this landing if it loses communication with the dispatcher.
• Run to 6th Ldg on Dispatch Failure – Turn this feature on to make the car run to this landing if it loses communication with the dispatcher.
• Run to 7th Ldg on Dispatch Failure – Turn this feature on to make the car run to this landing if it loses communication with the dispatcher.
• Run to 8th Ldg on Dispatch Failure – Turn this feature on to make the car run to this landing if it loses communication with the dispatcher.
• Enable Emergency Power – Turn this feature on to enable Emergency Power operation.
• Disable Fire Light on Fire Service Phase 2 – Turn this feature on to prevent a car on
Fire Service Phase 2 from keeping the Dispatcher Fire Light on.
• Zone1 (not Zone3) answers empty Zone2 – Turn this feature on to allow a car in
Zone 1 to answer a hall call in Zone 2 if there is no car in Zone 2. If this feature is off, then a car from Zone 3 will be given the call.
• Enable Car A – Turn this feature on to enable Car A.
• Enable Car B – Turn this feature on to enable Car B.
• Enable Car C – Turn this feature on to enable Car C.
• Enable Car D – Turn this feature on to enable Car D.
6.2.6 Change Features
Use this selection to change the features described below. Each feature is either on
(value of 255) or off (value of 0). As you scroll through the features, the feature will be shown as enabled (ON) or disabled (OFF). The feature may be changed by pressing Aux to select the desired operation (on/enabled or off/disabled), then press Ent to store the value.
NOTE: The Password “911” is required to gain access to this menu selection, unless the password has already been entered during another sequence.
Press Nxt to go to the next feature, without changing the current feature.
Press Prv to go to the previous feature, without changing the current feature.
Press Aux to toggle the feature between on/enabled or off/disabled.
(The keys 0 - 9 and . are not used)
Press Ent after selecting a new value to load the new value into memory. (The message
“VALUE SAVED!” is displayed for 1 second, to indicate the new value has been accepted.) If
MH-3000 User Manual Page 85
Nxt, Prv or Esc is pressed after entering a new value, the new value will NOT be stored in memory.
Press Esc to go back to the Setup Menu.
6.2.6.1 Description of Features
Refer to the sheet MH-3000 Settings in the schematic to see the settings and features provided for each particular job. Some features may be incorporated into the Bit Features that are listed under the Settings heading. The features that are most likely to require changing are included in the Features heading. The following features are standard (All features are normally off/disabled, unless otherwise specified):
• No Shortened Door Time - (Display shows "NO SHORTDOORTIME") Normally the door time will be shortened by the Door Open Button/Safety Edge/Electric Eye/Infra-red
Curtain. Enable this feature to prevent these devices from shortening the door time.
This is normally required in nursing homes, where the passengers need more time to enter the car. The Door Close Button will still shorten the door time.
• Timed Electric Eye Cutout - (Display shows "TIMED EYE CUTOUT") Enable this feature to allow the Electric Eye input to be disabled after the preset time (see the setting above for the delay before cutting out the Electric Eye). This feature is often provided in the Electric Eye unit itself.
• Door Nudging - (Display shows "DOOR NUDGING") Enable this feature to activate door close nudging. Nudging will be initiated if a call is registered and the doors have been prevented from closing for the preset Door Nudging time. The Electric Eye will be disabled, the Nudging Buzzer will come on, and the Nudging Output will come on if the
Electric Eye input is energized. This means the door will only close at slow speed if the
Electric Eye is blocked.
NOTE: Door Nudging operation requires an optional Nudging Buzzer output and Reduced Speed Door Closing output.
• One Stroke Down Lanterns - (Display shows "1 STROKE DN LANT") The lanterns are normally provided with two strokes for the down direction. Enable this feature to provide only one stroke for the down direction.
• Slow Speed on Inspection - (Display shows "SLOW ON INSPECT") Enable this feature to run slow speed on Inspection. This is normally required if the car speed is 125fpm or above.
• Proximity Detector - (Display shows "PROXIMITY DETECT") Enable this feature if a
Proximity Detector (such as an infra-red curtain) is used. Enabling this feature will cause the Safety Edge input to be disabled on Fire Service, and the Door Nudging feature to be initiated while the doors are closing on Fire Service. The Proximity
Detector may be connected to the Safety Edge Input or the Electric Eye Input, as desired. (The Electric Eye Input is subject to the Timed Electric Eye Cutout and
Nudging, whereas the Safety Edge Input is not.)
NOTE: Door Nudging operation requires an optional Nudging Buzzer output and Reduced Speed Door Closing output.
• Short Floor - (Display shows "SHORT FLOORS") The Short Floor selection applies to installations with Floor Switches or Pulsing Switches where the floor height is less than twice the slowdown distance, but more than the slowdown distance plus the leveling
MH-3000 User Manual Page 86
zone. If Floor Switches are used, then the Short Floor Setting should be enabled if the
Floor Switches overlap at any floor. If Pulsing Switches are used, then the Short Floor
Setting should be enabled if the top of any Up target is BELOW the bottom of the Down target for the floor below. With Floor Switches or a Pulsing Selector, if the slowdown overlaps the leveling zone of the adjacent floor, then special short floor circuitry is required, and this setting will not normally apply. (Check for specific instructions for the job.)
• Enable Homing - (Display shows "ENABLE HOMING" on Simplex, or "HOME #2 TO
MAIN" on Duplex) Enable this feature to enable the homing feature on a Simplex. This will cause the car to home to the Home Landing, when it has been idle for the adjustable
Homing delay time.
NOTE: On a Duplex, one car will always home to the Dispatch Main Landing, and, if this feature is set, then the FREE car will also home to the Dispatch
Main Landing.
• Enable Free Car Homing (Duplex Only) - (Display shows "HOME TO HI ZONE") Enable this feature to home the free car to the Upper Home Landing. If this is not set, then the car will remain where it last stopped.
• Enable Homing to Dispatch Landing (Group Car Controllers Only) - (Display shows
"HOME TO DISP.LDG") Enable this feature to force this car to home to the Dispatch
Landing.
• Enable Homing to Alternate Home Landing (Group Car Controllers Only) - (Display shows "HOME TO ALT.HOME") Enable this feature to force this car to home to the
Alternate Home Landing.
• Home All Cars to the Dispatch Landing (Group Dispatcher Only) - (Display shows
"HOME ALL TO MAIN") Enable this feature to home all cars to the Dispatch Landing.
Some installations require specific settings or features that are not included in the standard program. In this case, a separate sheet (or sheets) will be provided that describe the operation of these settings or features, and what the factory default settings are.
Normally, special features are included in the Bit Features settings, not under the Features.
6.2.7 Show Fault Log
This selection is the same as the Show Fault Log in the Run Mode section. The screen shows the fault log, which consists of the last 63 faults and events recorded by the controller. The controller will not log faults in the Setup Mode, but existing faults can be viewed.
Refer to the descriptions in the Show Fault Log section in the Run Mode for a full description of the operation when viewing this screen, and for a description of the fault codes displayed.
6.2.8 Show Internal Memory
This selection is the same as the Show Internal Memory in the Run Mode section. The screen shows the contents of the internal memory. This can be used to check the status of internal registers, to show the operation of the system. Keep in mind that in the Setup
Mode, the car is stopped, and all Inputs and Outputs are off.
MH-3000 User Manual Page 87
If the password has not been entered in another screen, then when this screen is selected, the “Password Entry” screen will be displayed. If the password (“911”) is entered correctly, then the internal memory can be changed. If it is not entered correctly, then the memory can still be viewed, but cannot be changed.
Refer to the descriptions in the Show Internal Memory section in the Run Mode for a full description of the operation when viewing this screen.
6.2.9 Set the Time
This screen allows the real time clock to be set up. When this selection is made, the current time is displayed, showing the time in 24hour format, and the month, date, and year.
CURRENT TIME
12:22 11/13/01
If these are correct, then press Esc to return to the Setup Menu.
If you want to change the time and/or date, then press any other key to continue with the next menu item.
You will be prompted to enter the year (00-99), month (1-12), date (1-31), hour (0-23), and minute (0-59).
ENTER YEAR 00-99
01
In each case, press Ent to accept the current value, or enter the correct value then press
Ent.
If an incorrect value is entered, just enter the correct value again, and press Ent. If you press Esc during this sequence, then the time and date will not be updated, and the display will return to the setup menu.
After all the data has been entered, the screen will display the new time and date, with the prompt “Enter to accept”.
ENTER TO ACCEPT
12:23 11/13/01
Press Ent to accept the values. At this point the new time and date will be accepted, and the seconds value will be set to zero. If you press Esc, then you will return to the setup menu without entering the new time and date.
The battery is required to keep the real time clock running when power is turned off.
Consequently, the real time clock will need to be reset when the battery is changed.
MH-3000 User Manual Page 88
6.2.10 Enter Password
A common password is provided for all controllers. This common password is "911". The password is required when changing a setting (such as Door Time, Fire Return Landing, etc.) or a feature (such as Fire Service Code, Front and Rear Door selections, etc.).
The password can be entered from the Setup Menu, as described below. Each time the
Setup Menu is entered, the password access is cleared, so the password must be entered again. If the password is required for a menu item, a “Password Entry” screen will be displayed. Just press "911" then Ent to access the menu item.
From the “Enter Password” menu item, press Ent to show the “Password Entry” screen.
Enter the password, “911”, then press Ent.
A message will briefly be displayed indicating whether the password was correct or not.
The display will then move back to the Setup Menu.
If the password has been successfully entered, and it is desired to restore password protection, so that the password must be re-entered to gain access to the protected menu items, select the "Enter Password" menu item and enter an incorrect password. Password protection is also restored whenever the controller goes from the Run Mode to the Setup
Mode.
The password can be entered by pressing the 7 key when the display is activated from the blank screen (after a power cycle), or when the "VA.CONTROLS" banner is displayed
(after pressings Esc from the Run Mode menus). This allows the password to be entered without stopping the controller.
The password can be given to all authorized personnel, that is those who would need to change settings or features on the controller.
WARNING: It is recommended that the password NOT be written on the prints, or controller itself, as this would allow anyone to access settings and features that could cause damage to personnel or equipment.
WARNING: Use great care in changing settings and features, as this may cause unexpected operation. Make sure you understand the consequences of any changes before making them.
6.2.11 Test I/O Boards
This selection allows specific outputs to be turned on as desired, so that they can be tested for proper operation.
This selection is password protected. The password must be entered each time this menu item is selected, even if the password has been correctly entered before. The generic password "911" may be used. This prevents unauthorized personnel from activating this feature, and also prevents accidentally entering this feature.
After pressing Ent to select this item, enter the password “911” and then press Ent.
The LCD screen will display "'Ent' = START TEST, OTHER KEY = QUIT". Press the Ent key to start the test feature, or press any other key to return to the setup menu.
MH-3000 User Manual Page 89
WARNING: When the test feature is activated, outputs may be turned on that may cause the car to move, the doors to operate and other signals to come on. It is the operator’s responsibility to make sure an unsafe condition does not exist. Take any and all the necessary precautions to prevent a dangerous situation.
This could include
• unplugging the terminal blocks on the output boards (this is strongly recommended),
• removing the fuses in the output circuits,
• opening the appropriate safety devices.
While the test feature is activated, each input that is on will turn on the corresponding output on the same board (Input Point 1 will turn on Output Point 1; Input Point 2 will turn on Output Point 2 etc.). This allows the inputs and outputs to be tested by jumping the desired input on, and verifying that the proper output comes on. Note: The outputs are updated once every tenth of a second, so there may be a slight delay in turning on the output after the input has been energized.
WARNING: Be very careful when jumping the inputs on. Make sure you do not jump to the common on the input terminal strips. This will blow a fuse, and could damage the input board components. The input commons are the first and sixth terminals from the left on the input terminal strip (see the schematic).
While the outputs are being tested, a meter can be used to verify that each output is actually coming on.
The test will be stopped, and the outputs turned off, when any key is pressed.
MH-3000 User Manual Page 90
7. Controller Nomenclature
PMP
RU
SP1-5
STR
TRU
TRUP
UL
VR
LIST
ITEM NO
C DOOR CLOSE RELAY (in MODSS on top of the car, if used) A5
DL
DOLX
DZ
DOWN LEVEL RELAY (on Printed Circuit board)
DOOR CHECK RELAY (on Printed Circuit board)
DOOR ZONE RELAY (on Printed Circuit board)
A1
A1
A1
ESB
FSD
FSU
IAS1-2
INS
O
PM
EMERGENCY STOP SWITCH BY-PASS RELAY (on Printed Circuit board)
FAST SPEED DOWN RUN RELAY (on Printed Circuit board)
FAST SPEED UP RUN RELAY (on Printed Circuit board)
INSPECTION ACCESS RELAYS (on Printed Circuit board)
INSPECTION RELAY (on Printed Circuit board)
DOOR OPEN RELAY (in MODSS on top of the car, if used)
STARTER (ACROSS THE LINE START)
A1
A1
A1
A1
A1
A5
B4/B7
PUMP MOTOR PILOT RELAY (110VDC) (on Printed Circuit board)
MOTOR RUN CONTACTOR (WYE-DELTA START)
SPARE RELAYS (Function varies per job) (on Printed Circuit board)
MOTOR START CONTACTOR (WYE-DELTA START)
WYE-DELTA MOTOR RUN RELAY (WYE-DELTA START) (on Printed Circuit board)
WYE-DELTA MOTOR RUN TIMER (WYE-DELTA START) (on Printed Circuit board)
UP LEVEL RELAY (on Printed Circuit board)
VOLTAGE RELAY (OPTIONAL) (on Printed Circuit board)
A2
B1/B6
A1
B1/B6
A1
A4
A1
A1
MH-3000 User Manual Page 91
8. Parts List
B1
B2
B3
B4
B5
B6
B7
RELAYS
A1
A2
A3
4PDT, 120VAC, PLUG-IN RELAY
4PDT, 110VDC, PLUG-IN RELAY
SURFACE MOUNT RELAY SOCKET
A4
A5
TIMER, 0-102.3 SECONDS
3PDT, 120VAC, PLUG-IN RELAY
CONTACTORS, STARTERS, OVERLOAD
Y-D REVERSING CONTACTOR (NEMA)
3 POLE THERMAL OVERLOAD (NEMA)
ACROSS-THE-LINE STARTER (NEMA)
HEATERS FOR 3 POLE OVERLOAD (NEMA)
Y-D REVERSING CONTACTOR (IEC)
ACROSS-THE-LINE STARTER (IEC)
3 POLE OVERLOAD (IEC)
C1
TRANSFORMERS, FUSES, TERMINALS
460-230-208/230-115, (600VA & 300VA)
C2 250V INSTANTANEOUS FUSE
Idec or equivalent
Idec or equivalent
P&B
AIRTRONICS
P&B or equivalent
SQD
SQD
SQD
SQD
SQD/Telemechanique
SQD/Telemechanique
SQD/Telemechanique
RU4S-A110
RU4S-D110
27E894
THCU102S3E
KUP-14A35
S__0__V02
SE0____
S__0__V02
(Types: B, CC, DD)
LC2-____G6
LC1-____G6
LR____
C4
C5
C6
TRACK FOR 250V FUSEHOLDERS
3 POLE TERMINAL, 600V, 50AMP
MOUNTING TRACK FOR TERMINALS
MICRO-PROCESSOR
MICROPROCESSOR CPU BOARD D1
D3 KEYPAD
SQD 9070K____D48
BUSSMAN TYPE BAF
CURTIS PW1F
CURTIS
CURTIS
SW192
3PSWT
CURTIS SW192
V.C. MH3000-CPU
V.C. MH3000-16IO
MISCELLANEOUS COMPONENTS & HARDWARE
E1
E2
PRINTED CIRCUIT BOARD
PHASE MONITOR (208V / 230V / 460V)
MH-3000 User Manual
V.C.
SSAC
MH-4
TVM____A100.5S3S
Page 92
E3
E4
E5
E6
1"W X 2"H DUCT
1"W X 3"H DUCT
1"W DUCT COVER
1"W DUCT MOUNTING CLIPS
TAYLOR
TAYLOR
TAYLOR
TAYLOR
V.C.
91020
91030
99010
08010
(SIZE)
V.C. (SIZE)
All parts are commercially available from the manufacturer, or from Virginia Controls Inc.
(ask for the Parts Department or send an email to [email protected]). Parts are subject to change without notice. Consult Virginia Controls, Inc., for current pricing information. Non-standard material is identified on the schematic.
MH-3000 User Manual Page 93
9. Troubleshooting Suggestions
Troubleshooting is similar to any other controller, and has several features to speed up determining the cause of any problem. No special knowledge of the operation of the microprocessor is required to be able to troubleshoot it.
A safety relay interface is provided to prevent dangerous operation due to a failure of the microprocessor. It is possible that the microprocessor may turn on an output point, yet the field safety switches may prevent the associated device from energizing.
For example, if the up run output energizes, but the up normal switch is open, then the up run valve(s) will not energize.
9.1 Locating Faults
Once the system has been installed, and is running properly, the most common problem will be the failure of an external device. The first step in locating the cause is to determine whether the fault is in the microprocessor or whether it is in the external wiring.
For example, if a position indicator light is not lit, check the output module for the appropriate output point to determine if the microprocessor is trying to turn the light on or not. If the output light is on, then confirm that there is voltage at the module terminal. If there is voltage at the module terminal, then the problem is external to the microprocessor.
It could be in the wiring to the position indicator, or perhaps the position indicator light has burned out. Similarly with input points, check that the input module light is on, that there is power at the terminal, and if not then the problem is external.
If it is determined that the problem is with the microprocessor, then the next step is to determine if the problem is in the hardware or the software. Using the keypad, press Nxt to display the "Show I/O Status" menu item. Press Ent. The screen will show the address on the top line and the I/O status on the bottom line. Press Nxt or Prv to show the desired
I/O address, and see if the CPU is responding by showing the correct status of the I/O points. If it is not, then the fault is probably with the I/O hardware; if it is on, then the fault is probably with the software.
If an input or output board fails, it may be possible to temporarily replace that defective board with another board that is used for non-essential functions (such as call register lights), thus providing elevator service while a replacement board is being obtained. See the section on I/O Board Replacement for further information.
If this does not correct the problem, the power supply or the CPU module could be faulty.
If the CPU fails, it will probably stop flashing LED D5. The CPU and I/O modules can be affected by high transient surges in the power supply, such as the building being hit by lightning. This may damage the CPU, or alter the contents of the program. Proper grounding will protect the controller from most of these problems.
MH-3000 User Manual Page 94
9.1.1 Troubleshooting I/O Board Communication Problems
If the IOFAULT error message is shown on the Status Screen, there are several ways to determine which board is causing the fault.
The communication light on the I/O board will usually indicate the problem. The normal status is for that light to blink once. If it blinks 2 or more times then the board is detecting an error in the communication it is receiving, as described in the section on I/O Boards,
Board Status LED.
Additionally the CPU can be monitored to check its communication with the I/O boards.
Address 0051 and 0052 should both be 00, but will show a code corresponding to the board that is not communicating with the CPU. Using the SHOW INT MEMORY screen, navigate to address 0050, then check the value in 0051 (refer to the example shown below with address 0051 in bold).
0050 04 03 03 04
0054 00 00 00 00
In the example shown here, a fault code “03” is seen in 0051. This indicates there is a communication problem with boards 1 and 2. Refer to the chart below for the codes for the board faults. The top section shows the boards for the right code number, and the bottom section shows the codes for the left code number.
Right
Number
Board1
Board2
Board3
Board4
Left
Number
Board5
Board6
Board7
Board8 x0 x1 x2 x3 x4 x5 x6 x7 x8 x9 xA xB xC xD xE xF
OK Fault OK Fault OK Fault OK Fault OK Fault OK Fault OK Fault OK Fault
0x 1x 2x 3x 4x 5x 6x 7x 8x 9x Ax Bx Cx Dx Ex Fx
OK Fault OK Fault OK Fault OK Fault OK Fault OK Fault OK Fault OK Fault
Also addresses 0048 to 004F show the communication attempts to each of the boards.
Refer to the sample shown below.
0048 F* F* 0* 00
004C 00 00 00 00
If a board is not communicating properly, the left number corresponding to the board will be “F” or “E”. The right number will change very quickly. If the board is communicating properly, the left number will be “0” or “1”, and the right number will be changing quickly.
If the CPU is not attempting to communicate to a board, the value will stay at “00”. In the
MH-3000 User Manual Page 95
example above, the CPU is attempting to communicate with boards 1, 2, and 3. Board 3 is communicating properly, but boards 1 and 2 are not. The “*” in the example above indicate numbers that are changing quickly.
Address 051E counts the number of failed IO board communication attempts. This should be 0, as shown in the sample below. (Address 051C is 2E, address 051D is E0 and address 051E is 00)
051C 2E E0 00 00
0520 00 00 00 00
If there are intermittent problems, such as noise causing communication errors, then this value will gradually increase. Check the addressing of the boards, and that all cables are fitted properly. Also check the grounding of the controller. See the section Show Internal
Memory for instructions on viewing internal memory addresses.
9.2 I/O Board Replacement
WARNING: When replacing a board, the Address Switch setting on the new board must be set to match the old board.
To replace an I/O board, TURN THE POWER OFF. Unplug all the terminal blocks at the top and bottom of the board. Unplug the Power Connector and the I/O Bus Connectors.
Remove the screws holding the board in place. Install the new module by reversing the above steps.
9.3 Factory Assistance
IMPORTANT: IF TROUBLESHOOTING ASSISTANCE IS REQUIRED FROM VIRGINIA
CONTROLS, GET THE FOLLOWING INFORMATION BEFORE CALLING (ADDITIONAL
TROUBLESHOOTING INSTRUCTIONS MAY BE GIVEN, DEPENDING ON THE NATURE OF THE
PROBLEM):
• THE VIRGINIA CONTROLS DRAWING NUMBER (located at the bottom right of the schematic).
• AN EXACT DESCRIPTION OF THE PROBLEM.
• THE STATUS OF ALL THE INPUT AND OUTPUT POINTS.
• THE STATUS OF THE LIGHTS ON THE CPU.
9.4 Changes for Program Revisions
The following section lists the changes that are included in program revision.
9.4.1 Program Revision 2D
Approximate Date of implementation – 10/16/2003
The following changes were incorporated:
MH-3000 User Manual Page 96
• Minor changes to Fire Service, especially with 2000 (or later) Code.
• Door Security feature added for systems with Selective Opening doors, including the ability to defeat the security by means of the “Always Enable DOB at Front/Rear
Openings” features.
• Non-Interference and In Use Light operation was changed on Single Automatic
Pushbutton systems.
9.4.2 Program Revision 3A
Approximate Date of implementation – 03/26/2005
The following changes were incorporated:
• Minor changes to Fire Service, especially with 2000 Code.
• Added Flood Service as a standard feature and on the Status Screen and Fault Log.
• Address 051E shows the number of IO Communication failures.
• Non-shutdown faults can be kept out of the Fault Log.
• Added Oil Sw, Red-ESB, Red-RUN, Red-SAF, Red-INS Faults to Fault Log.
• Door Contacts are timed to prevent bouncing the contacts on start.
• A Barrier Free Gong output is now available.
• Several new settings and features are added as shown on the Settings sheet.
9.4.3 Program Revision 3B
Approximate Date of implementation – 05/1/2005
The following changes were incorporated:
• Redundancy Faults were given specific Fault Codes and Status Screen Messages.
• The Fault Status Codes in the Fault Log were customized for Redundancy Faults.
• The Rollover Fault code was modified so that consecutive Rollovers would be combined into one fault, with the number of fault free days shown on the lower right.
9.4.4 Program Revision 3C
Approximate Date of implementation – 05/10/2005
The following changes were incorporated:
• The Historical Log was relocated and updated. A time stamp was added to the
Historical Log.
Minor Revision – 3C03. Approximate Date of implementation – 05/30/2006
The following changes were incorporated:
• The operation was updated for 2004 Fire Code, with changes to call cancellation and
False Down Leveling on Fire Service Phase 2.
MH-3000 User Manual Page 97
10. Controller Maintenance
WARNING: MAKE SURE THE POWER IS OFF BEFORE CONNECTING OR
DISCONNECTING ANY CONNECTORS, ADDRESS JUMPERS OR CABLES
ON THE CPU OR I/O BOARDS.
10.1 Periodic Maintenance
WARNING: Turn off the power before touching the terminals or wiring.
Check that all wires are tight, and properly located in the terminals. Make sure no stray stands of wire are sticking out of the terminal strips.
Check the Motor Starter contacts and Door Operator contacts (if provided) for wear.
Make sure all relays are fully seated in their sockets.
If any varistors are provided in parallel with inductive loads (such as the Valve Solenoids or Motor Starter) check that they are physically sound. Look for signs of burn marks.
Replace it if it looks damaged.
Check the CPU battery. This can be done by cycling the power, then checking to make sure the onboard clock is still correct. To check the time, press Nxt until the display shows
“Press ENTER to SHOW FAULT LOG”. Then press Ent, then press . to show the current time. If the date had been set, and it now shows the date as 01/01/00 then the battery is dead. Change the battery and set the time.
Keep the controller clean and dry. Power supplies and processor chips in particular should be keep clean of dust and other debris. Keeping the machine room itself clean will help keep the controller clean.
10.2 Parts Replacement
10.2.1 CPU Exchange
To swap out the CPU board:
1. Turn off the power to the controller.
2. Note the location of all cables and wires. It is recommended that all cables and wires be marked so that they can be returned to the correct terminal or connector, and be oriented properly.
3. Unplug the incoming power wiring connector from the bottom left terminal block.
4. Unplug the duplex communication connector from the duplex connector (if used).
5. Unplug the I/O Bus Connector.
6. Remove the four screws holding the CPU board in place.
MH-3000 User Manual Page 98
7. Remove the CPU board.
8. Install the new CPU board in the reverse order.
9. If the new CPU was not provided with an EPROM Program Chip, then carefully remove the chip from the old CPU and install it in the new CPU as described under EPROM
Memory Chip Exchange below.
10.2.2 EPROM Memory Chip Exchange
WARNING: IF YOU NEED TO CHANGE THE EPROM PROGRAM CHIP ON
THE CPU BOARD, MAKE SURE YOU READ THE INSTRUCTIONS AND
KNOW EXACTLY HOW TO INSTALL THE NEW CHIP. PLUGGING THE
EPROM IN UPSIDE-DOWN MAY DAMAGE YOUR CHIP. STATIC
ELECTRICITY CAN DAMAGE THE EPROM, SO AVOID TOUCHING THE
PINS ON THE CHIP, AND GROUND YOURSELF (BY TOUCHING THE
CONTROLLER CABINET) BEFORE TOUCHING THE CHIP OR THE
CONTROLLER. DO NOT EXPOSE THE EPROM PROGRAM CHIP TO
BRIGHT LIGHT, AND DO NOT REMOVE THE LABEL OVER THE EPROM
PROGRAM CHIP WINDOW.
To exchange the EPROM memory chip on the CPU board:
1. Turn off power to the controller.
2. Using a small screwdriver, or other appropriate tool, pry out the old EPROM chip by inserting the screwdriver between the chip and its socket from the right side. Gradually work the chip out, trying to avoid swinging it out, which would bend the pins at one end, but rather prying it straight out by working the screwdriver under the chip.
3. Insert the new EPROM chip by orienting it properly, so that the notch is at the left, to match the socket, and all the pins line up with the socket. LEAVE TWO EMPTY HOLES
AT THE LEFT END OF THE CHIP (the end next to the notch). It should not be necessary to use force to insert the EPROM chip, but apply slight sideways pressure to line up the rows of pins with the holes in the socket, if necessary, then evenly press the EPROM chip into place.
Notch
EPROM Chip Positioning
4. Do not apply power until the orientation of the chip has been checked. Also verify that
ALL pins are properly in the socket, and that none of them have been bent out of place.
10.2.3 Input/Output Board Exchange
To exchange on I/O board:
1. Change the Address Switches on the new I/O board to match the board it will replace.
2. Turn off the power to the controller.
MH-3000 User Manual Page 99
3. Unplug all the removable I/O terminal strips from the top and bottom of the I/O board.
It is not usually necessary to mark the terminal blocks, since the wiring will normally hold them in the proper place so that it is obvious which block goes where. If there is any doubt about their location, then mark the terminal blocks to show where they should be re-installed.
4. Unplug the I/O Bus Connectors and power connector.
5. Remove the screws holding the I/O board in place.
6. Install the new I/O board by reversing the previous steps.
MH-3000 User Manual Page 100
11. Frequently Asked Questions
Suggestions for other Frequently Asked Questions are welcomed. Please submit them to
Chris Wilson at Virginia Controls.
11.1 Questions on Field Devices
Q. Are the Reset Targets necessary when using a pulsing selector?
Yes.
The reset targets are required at the terminal landings, as shown on the car top selector installation sheet, to establish or reset the floor position at the terminal landings.
Q. Why are Two Position Indicators energized at the same time?
With Floor Switches, if there is an overlap of the slowdown targets, or a Floor Switch sticks on, then when the car hits a new Floor Switch, all floors that have a Floor Switch input energized will be turned on.
If the problem happens intermittently, it is probably caused by a sticking Floor Switch. If it happens regularly at a particular floor, there is probably an overlap between Floor
Switches. In this case, either separate the Floor Switches (or targets) so there is no overlap, or turn on the "Short Floor" feature, described above in the features section.
Q. The doors do not operate properly on Fire Service
Check the Door Open and Door Close Limit Switches for proper operation. Most problems with Fire Service are a result of one or both of these switches not operating properly. Also check to make sure the correct Fire Code has been selected in the Adjustable
Settings and Features. Refer to the schematic adjustment sheet.
11.2 Questions on the Controller
Q. How Do I Reset All Settings and Features Back to the Original Values?
1. With the controller running normally, press Nxt repeatedly until the menu item shows
"GO TO SETUP MENU".
2. Press Ent. The display will show a warning message. Make sure the car is stopped before continuing.
3. Press Ent. The display will show you have entered the Setup Mode, then display the
"RESET SETTINGS" menu item.
MH-3000 User Manual Page 101
4. Press Ent to reset all settings to the factory defaults.
5. Press Esc to return the controller to normal operation.
NOTE: If the program is a standard program, then the settings for the specific job must be re-entered.
Q. How do I determine if I have a standard program?
1. Go to the Banner screen, by pressing Esc until the top line of the display shows
“VA.CONTROLS” at the left.
2. If the text on the lower left is the job number, then the program is NOT standard. It has been set up for the particular job.
3. If the text on the lower left starts with letters “D” or “E” (such as “DAS” “DDS” “DES”
“DSS” “ES” “ED”) then the program is standard. If a factory reset is performed, the standard default values will be loaded. Check the schematic for the particular values for your installation, and change the values as required. Usually the values that are custom for a particular job are shown in BOLD, so these values must be changed, but the other values should be checked.
Q. How do I check the current values of the settings and features?
1. Go to the Setup Menu.
2. Select the menu item "Change Settings", and press Ent, then enter the password,
“911”.
3. Scroll through the settings by pressing Nxt. The settings will not be changed unless a new value is entered and then Ent is pressed.
4. Press Esc then Nxt to go to the "Change Features" menu item.
5. Press Ent, then enter the password, and press Ent.
6. Press Nxt to scroll through the features. The features will not be changed unless you press Aux then Ent.
7. Press Esc twice to return to normal operation (Run Mode).
Q. Why is the LCD Display blank?
The LCD Display goes blank after the CPU resets if S2 switch 1 is in the OFF position.
This will happen when the power to the CPU is cycled, or when the Reset Button on the CPU board is pressed.
Press any key to activate the screen.
If the screen does not activate, the problem could be with the Keypad (momentarily touch pins 1 (far left) and 8 (far right) on the top of the keypad connector to simulate pushing a key) or the CPU (check that LED D5 is flashing), or the LCD Display.
MH-3000 User Manual Page 102
Q. Why is the Fire Buzzer output On but the car is not on Fire Service?
Switch 3 on the CPU Slide Switch S2 is in the ON position.
This switch disables the Redundancy Faults. This may be useful during initial installation, and the Fire Buzzer is turned on to remind you to turn off this feature after installation.
Slide the switch down to enable Redundancy Faults.
Q. How can I get the latest version of the Manual?
The latest version of this Manual is available online at www.vacontrols.com
. Go to the
“Support” section, and download the MH-3000 manual in pdf format.
Q. Do I need schematics (or prints) to work on the controls?
Each control system built by Virginia Controls is custom designed for each installation.
Though there are some strong similarities between similar jobs, it is strongly recommended that you have accurate prints/schematics before working on any of our control systems.
We require the job number for any installation before we can offer practical help with any problems on that installation, so that we can refer to the actual prints for that job.
MH-3000 User Manual Page 103
INDEX
Flood · 55, 64, 81, 97
A
Access · 6
Addressing · 38
Adjustable Features · 16
G
Grounding · 2, 4, 7, 9
B
Banner Screen · 47
Battery · 30, 65, 98
Bit Features · 49, 50, 74, 78
Bypass Switches · 27
H
Hexadecimal Conversion Table · 61
Historical Log · 59
Homing · 17, 19, 77, 87
Humidity · 3
C
Calls · 14, 16, 17, 18, 31, 65
Car Start · 17
CAUTION · 1, 72
Code · 50, 73, 88, 101
Communication · 18, 19, 33, 39, 40, 52,
95
CPU · 7, 18, 19, 22, 29, 30, 31, 32, 33,
39, 68, 92, 94, 98
I
I/O Fault · 55
I/O Status · 48
Independent · 13, 17, 31, 64, 65, 77
Inspection · 10, 12, 15, 17, 31, 51, 52,
53, 64, 65, 71, 76, 86
Internal Memory · 32, 59, 61, 62, 63, 68,
69, 87
IO Fault · 66, 67, 95
D
Diagnostic · 68
Display · 33, 35, 72, 76, 86, 87, 102, 103
Door Operation · 14
Duplex · 16, 18, 32, 33, 52, 87
J
Jumper · 41
K
Keypad · 22, 33, 102
E
EPROM · 1, 22, 31, 70, 99
L
LED · 14, 15, 18, 19, 31, 32, 37, 39, 59,
62, 68, 69, 94, 95, 102
Low Oil Switch · 55, 65, 82
F
Factory Reset · 12
Failure Timers · 15
Fault Code · 50
Fault Log · 48, 49, 50, 56, 59, 69, 87
Features · 16, 69, 74, 77, 85, 86, 101,
102
Fire Service · 6, 15, 16, 17, 31, 53, 64,
65, 77, 80, 86, 88, 101
M
Maintenance · 98
MH-3000 User Manual Page 104
N
Next Car · 16, 17
Noise · 96
Nomenclature · 91
NOTE · 1, 4, 6, 9, 11, 13, 14, 15, 23, 24,
32, 49, 51, 56, 62, 69, 71, 72, 75, 76,
80, 85, 102
P
Parts List · 92
Parts Replacement · 98
Password · 69, 71, 85, 87, 88, 89
Position Indicators · 13
R
Redundancy · 53, 54, 55, 56, 57, 64, 65,
79, 80, 97
Reset Button · 32, 46, 102
Revision · 96, 97
Rotation · 10
Run Mode · 46, 47, 48, 59, 68, 69, 70,
72, 87, 89, 102
Running Timers · 15
S
S2 Slide Sw · 33, 35, 46, 102
Selector · 5, 86
Settings · 16, 69, 70, 71, 72, 75, 78, 86,
101, 102
Set-Up Mode · 67, 69
Start-Up · 9
Status · 32, 35, 39, 46, 47, 48, 56, 63,
64, 67, 68, 69, 94, 95
Stuck Button · 15
Switches · 5, 6, 39, 48, 53, 55, 64, 86,
99, 101
Floor · 4
Leveling · 5, 15, 52, 53, 64, 76
Limit · 5, 6, 14, 52, 57, 58, 59, 66, 101
Slowdown · 5, 6, 13
Zone · 5, 6, 15, 16, 52, 53, 57, 58, 59, 65,
66, 73
T
Temperature · 3
Temporary · 9, 10
Terminal Wiring · 38
Test · 89
Time · 30, 49, 69, 88
Troubleshooting · 94, 95
W
WARNING · 1, 7, 9, 10, 16, 18, 27, 28,
30, 31, 32, 38, 41, 63, 69, 71, 89, 90,
96, 98, 99
Watchdog · 32
MH-3000 User Manual Page 105
advertisement
Related manuals
advertisement
Table of contents
- 8 Pre-Installation Instructions and Notes
- 8 General Notes
- 8 Important Precautions And Notes
- 10 Controller Installation and Wiring
- 10 Controller Installation
- 10 Controller Location Selection and Environment
- 11 Controller Grounding
- 11 Car and Hoistway Wiring
- 11 Floor Switches
- 12 Car Top Selector
- 12 Leveling Switches
- 12 Terminal Landing Normal Slowdown Switches
- 12 Terminal Landing Normal Limit Switches
- 13 Terminal Landing Final Limit Switches
- 13 Emergency Terminal Landing Limit Switch
- 13 Hoistway Access Zone Switches
- 13 Door Open and Close Limit Switches
- 14 Machine Room Wiring
- 14 Incoming Power
- 14 Grounding
- 15 Pump Motor Wiring
- 15 Wye-Delta Run Contact Wiring
- 16 Start-Up Instructions
- 16 Before Applying Power
- 16 Power and Grounding
- 16 Input/Output Wiring
- 17 Applying Power
- 17 Motor Rotation
- 17 Temporary Run Connections
- 19 Final Adjustments
- 19 Inspection Operation
- 20 Floor Position and Slowdown
- 20 Position Indicators
- 20 Independent Service
- 21 Car and Hall Calls
- 21 Door Operation
- 22 Fire Service
- 22 Failure Timers
- 22 Stuck Button Timer
- 22 Running Timers
- 23 Field Adjustable Features
- 23 Zoned Duplex Operation
- 23 Common Circuits
- 23 Next Car
- 24 Car Start
- 24 Homing
- 25 Communication
- 25 Zoned Group Operation
- 25 Common Circuits
- 26 Homing
- 26 Communication
- 27 Car Controller Settings
- 27 Dispatch Failure Calls
- 27 Car Homing
- 27 Dispatch Controller Settings
- 27 Zone Code Settings
- 28 Dispatch Traffic Programs
- 29 Hardware Description
- 29 Transformers
- 30 Fuses
- 31 12VDC Power Supply
- 31 Safety Interface Board
- 32 MH4
- 32 MH5
- 33 Phase Monitor
- 34 Digiset Timer
- 34 Bypass Switches
- 35 Inspection Switches
- 35 Connections
- 36 Microprocessor
- 36 CPU
- 37 CPU Battery
- 38 LED Description
- 39 Reset Button
- 40 CPU Connectors
- 40 Duplex Communication Connector
- 40 LCD Display Connector
- 40 Keypad Connector
- 41 Incoming Power Connector
- 41 Input/Output Bus Connector
- 42 S2 Slide Switch
- 42 Switch 1 on S2 Slide Switch
- 42 Switch 3 on S2 Slide Switch
- 43 Input/Output Boards
- 45 Addressing
- 45 Terminal Wiring
- 46 Input/Output LEDs
- 46 Input/Output Naming Conventions
- 46 Board Status LED
- 47 I/O Bus Communication Connectors
- 47 Programming Connector
- 47 Power Connector
- 48 Jumper Blocks
- 49 Motor Control
- 49 Across-the-line Starting
- 50 Wye-Delta Starting
- 51 Solid-State Starting
- 52 B.O.R.I.S.
- 53 MH-3000 Screens and Diagnostics
- 53 Run Mode
- 53 Run Mode Screens
- 54 Banner Screen
- 55 Show I/O Status
- 55 Moving Around in I/O Status Screen
- 55 Show Fault Log
- 56 Typical Fault Screen
- 56 Fault Number
- 56 Fault Time Stamp
- 57 Fault Code
- 63 Fault Log Status Signals
- 66 Moving Around in the Fault Log
- 66 LED Description in "Show Fault Log" Mode
- 66 Historical Log
- 68 Show Internal Memory
- 69 Moving Around in the Internal Memory
- 69 LED Description in "Show Internal Memory" Mode
- 70 Changing values in the “Show Internal Memory” Mod
- 70 Show Car Status
- 71 Messages Displayed on the “Car Status” Screen
- 74 Messages Displayed on the “Dispatcher Status” Scr
- 74 Go To Set-Up Mode
- 75 Effect of Diagnostic Modes on Scan Time
- 76 Set-Up Mode
- 76 How to Enter Set-Up Mode
- 76 How to Exit Set-Up Mode
- 76 Set-Up Mode Screens
- 77 Reset Settings
- 78 Change Settings
- 79 Description of Settings
- 79 Numerical Settings
- 81 Bit Features
- 82 Timers
- 82 Custom Timers
- 82 Tenth of a Second Timers
- 83 One Second Timers
- 85 Ten Second Timers
- 85 Description of Bit Feature Settings
- 92 Change Features
- 93 Description of Features
- 94 Show Fault Log
- 94 Show Internal Memory
- 95 Set the Time
- 96 Enter Password
- 96 Test I/O Boards
- 98 Controller Nomenclature
- 99 Parts List
- 101 Troubleshooting Suggestions
- 101 Locating Faults
- 102 Troubleshooting I/O Board Communication Problems
- 103 I/O Board Replacement
- 103 Factory Assistance
- 103 Changes for Program Revisions
- 103 Program Revision 2D
- 104 Program Revision 3A
- 104 Program Revision 3B
- 104 Program Revision 3C
- 105 Controller Maintenance
- 105 Periodic Maintenance
- 105 Parts Replacement
- 105 CPU Exchange
- 106 EPROM Memory Chip Exchange
- 106 Input/Output Board Exchange
- 108 Frequently Asked Questions
- 108 Questions on Field Devices
- 108 Questions on the Controller