- Computers & electronics
- Computer components
- System components
- Motherboards
- Digi
- ConnectCore 9P 9750 Module 16MB SDRAM, 32MB Flash
- User manual
Digi ConnectCore 9P 9750 Module 16MB SDRAM, 32MB Flash User manual
Add to my manuals
47 Pages
The Digi ConnectCore 9P 9750 Module 16MB SDRAM, 32MB Flash is a compact and powerful embedded system module designed for a wide range of industrial and commercial applications. It features a 32-bit ARM926EJ-S core processor with speeds up to 200MHz, providing high performance and low power consumption. The module includes 16MB of SDRAM and 32MB of NAND Flash memory, allowing for ample storage and smooth operation of various applications. With its rich set of connectivity options, including 10/100 Mbps Ethernet, USB 2.
advertisement
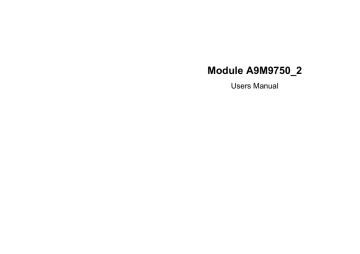
Module A9M9750_2
Users Manual
Module A9M9750_2
Copyright 2005:
FS Forth-Systeme GmbH
Postfach 1103, 79200 Breisach, Germany
Release of Document: April 05, 2005
Filename: UM_Module_A9M9750_2.doc
Author:
Program Version
Karl Rudolf
All rights reserved. No part of this document may be copied or reproduced in any form or by any means without the prior written consent of FS Forth-Systeme
GmbH.
2
Module A9M9750_2
2005-04-05 (V1.00) KR: Initial Version derived from Spec A9M9750_2 Module
3
Module A9M9750_2
Table of Contents
1. Revision History ............................................................................................. 3
2. Introduction .................................................................................................... 6
2.1. Benefits of the ModARM9 Concept ...................................................... 6
2.2. Common Features ............................................................................... 6
2.3. Differences between A9M9750_1 and A9M9750_2 Modules ............... 7
2.4. Planned and realised Variants for A9M9750_2 Module ........................ 8
3. A9M9750 Features......................................................................................... 9
3.1. Size 60 x 44 mm .................................................................................. 9
3.2. 2 x 120-pin connectors......................................................................... 9
3.3. NS9750 CPU on the A9M9750_2 Module ............................................ 9
3.4. Configuration Pins CPU ..................................................................... 10
3.5. Configuration Pins Module ................................................................. 15
3.6. Clock Generation ............................................................................... 18
3.7. Serial Boot EEPROM, Boot SPI Channel Settings ............................. 21
3.8. Chip Selects, Memory Map ................................................................ 21
3.9. NAND Flash ....................................................................................... 23
3.10.16/32/64 MBytes SDRAM .................................................................. 25
3.11.50 GPIO Pins (multiplexed with other Functions)............................... 27
3.12.PCI/CardBus Port .............................................................................. 30
3.13.10/100Mbps Ethernet Port ................................................................. 31
3.14.USB 2.0 full and low speed Host and Device Controller..................... 31
3.15.UART Channels................................................................................. 31
3.16.SPI Channels..................................................................................... 31
3.17.Calculation of Baudrates.................................................................... 32
3.18.I²C Bus .............................................................................................. 34
3.19.LCD Controller (STN & TFT).............................................................. 36
3.20.Serial EEPROM for storing Configuration Parameters ....................... 36
3.21.RTC................................................................................................... 36
3.22.JTAG, Boundary Scan ....................................................................... 36
3.23.Single 3.3V Power Supply ................................................................. 38
3.24.Power Sequencing on A9M9750_2 Module ....................................... 38
3.25.Voltage Supervision and RESET Generation..................................... 39
4. Bootloader.................................................................................................... 40
4
Module A9M9750_2
5. Software .......................................................................................................40
6. Mechanics ....................................................................................................42
6.1. Extended Module................................................................................44
7. Known Faults and Limitations .......................................................................46
7.1. USB Pins are not 5V tolerant ..............................................................46
7.2. Timing Bug in IIC Stage ......................................................................46
7.3. PLL Clock Generation instable............................................................46
8. Appendix.......................................................................................................47
8.1. Pinning Module ...................................................................................47
8.2. Pinning Module on A9MVali Validation Board .....................................47
8.3. Pinning Module on A9M9750DEV Development Board ......................47
5
Module A9M9750_2
There are now a number of interesting ARM9-based SoC solutions available on the market. These chips are usually designed for particular market segments, which implies a departure from the “one-size-fits-all” philosophy for the modules.
To accommodate this, the ModARM9 concept foresees more than one ARM9based module, with the modules having a common subset of functions. One, or two, of these modules will become a standard product at FS Forth, the others will be custom designs. The first standard module, based on the NetSilicon NS9750, is called the A9M9750.
The 1 st silicon of the NS9750 had a lot of bugs; some of these needed hardware work arounds extending the 1 st A9M9750_0 modules size about 8mm on the long side.
With the announcement of the 2 nd silicon NS9750_A1 most of the important bugs are fixed; all new modules A9M9750_X have the original size of 60X44mm.
Due to the fact of PLL instabilities in the 2 nd silicon the module A9M9750_2 was necessary with changed generators for system and USB clock.
2.1. Benefits of the ModARM9 Concept
One of the problems constantly faced at any design house involved in custom designs is how to re-use the work done in previous designs. The ModARM9 concept is designed to help address this by expanding the common set of tools available to the design engineers. For example, an evaluation board will be designed which is the same for all modules. This will allow the “common features” of a new module to be tested quickly. If the new module is a custom design, then the customer’s base board must be used to test all the peripherals available on the module. This will allow custom designs to be offered at a more attractive price than previously possible.
Below are the common features of this module, which will be covered in further detail later in the document.
• ARM9 core with MMU
6
• Size 60mm x 44mm with 240-pin connector
• SDRAM 16MB – 256MB
• NAND Flash 32MB – 256MB
• 2..4 serial RS232 interfaces
• Host or device USB interface, USB2.0 compliant
• 10/100Mbps Ethernet interface
• I²C interface, 100KHz and 400KHz
Module A9M9750_2
This means that approx. 150 pins of the connector are reserved for the above functionality, the others are free for module-specific functions.
2.3. Differences between A9M9750_1 and A9M9750_2 Modules
The NS9750_A1 chips has still an important bug: System frequencies are instable if system and USB clock is generated by crystal circuits. Stable clocks are ensured only when both clocks are made by oscillators. This information was distributed by NetSilicon when the A9M9750_1 redesign was finished. So another redesign was necessary ending in the module A9M9750_2.
Differences in detail:
1. System clock 29.4912MHz now made with oscillator
2. USB clock 48MHz now made with oscillator
3. RSTIN# directly connected to U13 pin 7 (MR#).
4. Pull up resistor R34 from RSTIN# to +3.3V added.
7
Module A9M9750_2
2.4. Planned and realised Variants for A9M9750_2 Module
Modules using CPU A1 chips with working PLL will have at least two speed and temperature variants:
1. CPU speed 199.0656MHz, 0..70° temperature range. Realised: V01/0364 with 32M NAND Flash and 16M SDRAM, V02/0380 with 32M NAND Flash and 64M SDRAM
2. CPU speed 162.5MHz, -40..+85° temperature range. Not realised in the moment
Maybe a PCI host and client version of each variant will be created, which have different parts in the PCI block populated.
8
Module A9M9750_2
3.1. Size 60 x 44 mm
The A9M9750 module has a size of 60 X 44 mm.
3.2. 2 x 120-pin connectors
Two 120-pin connectors on the long side of the module allow accessing most signals of the NetSilicon NS9750 CPU. An optional extension with another two
60-pin connectors is planned. This will extend the length of the module from
60mm to approximately 95mm.
Pin-compatible in power supply and main port functions to other ModARM9 modules.
3.3. NS9750 CPU on the A9M9750_2 Module
NS9750 CPU has a 32-bit ARM926EJ-S core. Further details see Hardware
Reference 9000624c.pdf. NetSilicon has planned to support two temperature ranges:
• 0..70°C with 200MHz CPU clock
• -40..+85°C with 162.5MHz CPU clock
9
Module A9M9750_2
3.4. Configuration Pins CPU
Several pins allow configuration of the CPU before booting. CPU pins have weak pull ups (value range is 15..300K) for a default configuration. Most pins do not have configuration options, some are connected for internal configuration on the module; some others allow external configuration via external connector pins.
The configuration state is latched 5 system crystal clock cycles after the rising edge of the PWRGOOD signal at the RESET# input of the CPU (5 * 1 /
(29.4912.* 10E6 = 169.5ns)
CPU
Pin
RTCK
Data Sheet of NS9750
Function
PCIAC (PCI Arbiter
Configuration)
0 = External PCI Arbiter
1 = Internal PCI Arbiter
RESET_D
ONE
CONF0
BOOTDS (Boot Mode)
0 = Boot from SPI
EEPROM
1 = Boot from Flash/ROM
CS1LEP (Chip select 1 byte lane enable polarity
Bootstrap Select)
0 = BEx# function
1 = WEx# function
CONF0 is inverted
CONF1
CONF2
CARDBSEL (CardBus
Mode Bootstrap Select)
0 = CardBus mode
1 = PCI mode
MEMRDSEL (Memory
Interface read mode
Bootstrap Select)
0 = Command delayed mode
1 = Clock delayed mode
CONF4,3 CS1DWSEL (Chip Select 1
Usage on Module
PU/PD external configu rable external pin name
Comment
PD 2k2 optional
PD 2k2 no no no internal PCI arbiter on PCI host version, external
PCI arbiter on PCI device version; pin
RTCK is not provided on module
RSTOUT# Boot mode default from serial SPI
EEPROM
-
-
PD 2k2
no yes no no no
HCONF3 default PCI mode, can be changed externally with pin
HCONF3 no always command delayed mode, clock delayed mode does not work no
Set to WEx# function. Not relevant on module.
default 32bit.
10
Data Sheet of NS9750
Data width bootstrap select)
00 = 16 bits
01 = 8 bits
10 = reserved
11 = 32 bits
GPIO2,0 PLL_FS(1:0) (PLL
Frequency divider select)
00 = 4
01 = 8
10 = 1
11 = 2 (default)
GPIO2 inverted, GPIO0 not inverted
GPIO17,1
2,10,8,4
PLL_ND(4:0) (PLL multiplier
= ND+1) b11010 = 26 decimal
PLL multiplier default 27
GPIO10, 4 inverted
5 PD
2K2 optional
GPIO19
GPIO24,2
0
GPIO36
GPIO37
GPIO44
PLLBP (PLL bypass)
0 = PLL bypassed
1 = PLL not bypassed
GPIO19 is inverted
PLL_IS(1:0) (PLL charge pump current ND)
00 = ND0..3
01 = ND4..7
10 = ND8..15
11 = ND16..31 (default)
MODVERS0 (LSB Module
Version)
MODVERS1 (MSB Module
Version)
GPIO37 GPIO36
0 1 V2.0, CPU
PLL ok
ENDSEL (Endian mode)
0 = Big endian
1 = Little endian
PD 2k2 optional
-
PD 2k2 optional
PD 2k2
PD 2k2 optional
Module A9M9750_2
Usage on Module
Not relevant on module, as we do always boot from
SPI EEPROM no GPIO0 =
TXDB or
SPI_DOB,
GPIO2 =
RTSB# config. pins on module n. c.
no no no
GPIO4 =
DTRB#
GPIO8 =
TXDA or
SPI_DOA
GPIO10 =
RTSA#
GPIO12 =
DTRA#
GPIO17 =
USB
Power
Relay
GPIO19 =
LCDHSY
NC
GPIO20 =
LCD_CLK
GPIO24 =
LCDD0 pins on module n.
c.
no no no
GPIO36 =
LCDD12
GPIO37 =
LCDD13
GPIO36 left open
GPIO37 PD
GPIO44 =
TXDD or
SPI_DOD resistor not populated sets to little endian.
11
Module A9M9750_2
Data Sheet of NS9750
GPIO44 is inverted
GPIO49 CS1POLSEL (Chip select 1 polarity)
0 = Active high
1 = Active low
GPIO49 is inverted
PU 10k
Usage on Module no -
SPI Boot does not work in big endian mode (?)
Not relevant on module, as we do always boot from
SPI EEPROM.
Used as FR/B#.
PU 10k is at
NAND-Flash.
32 of the 50 GPIO pins allow user specific configurations. They are latched in the
GEN_ID register with the rising edge of RESET# (address 0xA0900210).
Bit GEN_ID GPIO
GPIO49
Configuratio n usage
CS1POLSEL
Configuration
Protection ext. usage
27
26
25
24
31
30
29
28
23
22
21
20
GPIO48
GPIO47
GPIO46
GPIO45
GPIO44
GPIO43
GPIO42
GPIO41
GPIO40
GPIO39
GPIO38
GPIO37
GPIO36
GPIO35
GPIO34
GPIO33
GPIO32
GPIO31
GPIO30
ENDSEL
SCONF3
SCONF2
SCONF1
SCONF0
MOD_VER1
MOD_VER0 yes yes yes yes yes yes yes no (NAND
FR/B#)
DMA1_REQ
LCDD23
LCDD22
LCDD21
LCDD20
LCDD19
LCDD18
LCDD17
LCDD16
LCDD15
LCDD14
LCDD13
LCDD12
LCDD11
LCDD10
LCDD9
LCDD8
LCDD7
LCDD6
12
Bit GEN_ID
19
18
17
16
15
14
13
12
11
10
9
8
7
6
5
4
3
2
GPIO14
GPIO13
GPIO12
GPIO11
GPIO10
GPIO9
GPIO8
GPIO7
GPIO6
GPIO5
GPIO4
GPIO
GPIO29
GPIO28
GPIO27
GPIO26
GPIO25
GPIO24
GPIO23
GPIO22
GPIO21
GPIO20
GPIO19
GPIO18
GPIO17
GPIO16
GPIO15
Configuratio n usage
PLL_IS1
PLL_IS0
PLLBP
PLL_ND4
PLL_ND3
PLL_ND2
PLL_ND1
PLL_ND0
Module A9M9750_2
Configuration
Protection yes yes yes yes yes yes yes yes ext. usage
LCDD5
LCDD4
LCDD3
LCDD2
LCDD1
LCDD0
LCD_LEND
LCD_BIAS_D_
EN
LCD_VFSYNC
LCD_CLK
LCD_HSYNC
LCD_PWREN
USB_PWRREL
USB_OVCUR
DCDA#,
SPI_ENA#
RIA#,
SPI_CLKA
DSRA# (used as RTC_INT#)
DTRA#
GPIO11
GPIO10
(RTSA#)
RXDA,
SPIA_DI
TXDA,
SPIA_DO
DCDB#,
SPIB_EN#
RIB#,
SPIB_CLK
DSRB#
DTRB#
13
Module A9M9750_2
Bit GEN_ID
1
0
GPIO
GPIO3
GPIO2
GPIO1
GPIO0
Configuratio n usage
PLL_FS1
Configuration
Protection yes
PLL_FS0 yes ext. usage
CTSB#
RTSB#
RXDB,
SPIB_DI
TXDB,
SPIB_DO
The GPIO configuration pins marked as protected are separated from the external connector pins with an analog switch when RESET# active or their output signal is buffered. So external signal connections cannot change the preset hardware configurations on the module or external configuration pins. The switched port lines have 10K pull ups when open to prevent floating. signals.
Switching time at the rising edge of PWRGOOD is delayed about 200ns
(configuration is latched 5 system crystal clock cycles after the rising edge of
PWRGOOD in the CPU). Using not protected pins for configuration purposes is possible, if the major load is the configuration resistor.
RTCK is not connected to external and has no switching logic. RSTOUT# is generated from RESET_DONE & PWRGOOD. So RESET_DONE cannot be loaded externally.
Another three configuration pins on the CPU are used for internal tests from
NetSilicon and to switch from normal mode to ARM/JTAG debug or boundary scan mode. Switching is done with the configuration pins DEBUG_EN# and
OCD_EN# described in the next chapter.
PLLTST#
(AF21)
1
1
1
BISTEN#
(AD20)
0
1
0
SCANEN#
(AE21)
0
0
0 normal
Mode
Debug enable
Boundary Scan enable
14
Module A9M9750_2
3.5. Configuration Pins Module
Module configuration pins change either hardware configurations on the module
(HCONF0..3) or they are user specific and can be read in the GEN_ID register
(SCONF0..3).
Signal name
DEBUG_EN#
FWP#
OCD_EN#
CONF1
GPIO38
GPIO39
GPIO40
Function PU/
PD external pin name
PU 10K HCONF0
Comment
CPU Mode Select
0 = Disconnects TRST# and PWRGOOD for
JTAG and Boundary scandebug mode
1 = TRST# and
PWRGOOD connected for normal mode (default) internal NAND flash write protect
0 = write protect active
1 = no write protect
JTAG / Boundary Scan function selection
0 = ARM Debug Mode,
BISTEN# set to high
1 = Boundary Scan
Mode, BISTEN# set to low (default)
CARDBSEL (CardBus
Mode Bootstrap Select)
0 = CardBus mode
1 = PCI mode
User defined software configuration pin, can be read in GEN ID register bit 28, default high
User defined software configuration pin, can be read in GEN ID register bit 29, default high
User defined software configuration pin, can be
PU 10K HCONF1
PU 10K HCONF2 Select JTAG mode,
DEBUG_EN# has to be low too
HCONF3 default PCI mode,
SCONF0
SCONF1
SCONF2 can be changed externally with pin
HCONF3 read Bit 28
GEN_ID read Bit 29
GEN_ID read Bit 30
GEN_ID
15
Module A9M9750_2
Signal name Function
GPIO41 read in GEN ID register bit 30, default high
User defined software configuration pin, can be read in GEN ID register bit 31, default high
PU/
PD external pin name
Comment
SCONF3 read Bit 31
GEN_ID
16
Module A9M9750_2
Recommended Combinations of DEBUG_EN# and OCD_EN#:
HCONF0 HCONF2 Mode Comments
OFF
ON
OFF
ON
OFF
OFF
ON
ON
Normal mode
Debug mode ok ok not recommended, may hang avoid
OCD mode ok
17
Module A9M9750_2
Different clocks will have to be generated for the module in the CPU:
1. Input clock at X1 (C8) 29.4912 MHz with PLL multiplied to 398.1312 MHz
(*27 /2).
2. CPU clock 199.0656 MHz (or 162.5 or 125 MHz depending on CPU version).
Multiplied input clock divided by 2. These frequencies are the default values set by strapping pins. PLL Multiplier and divider vaues can be changed at runtime by software; a 4ms RESET allows PLL to lock, usage needs cold/warmstart detection in the software.
3. AHB clock 99.5328 MHz (81.25, 62.5 MHz). Multiplied input clock divided by
4.
4. BBUS clock 49.7664 MHz (40.625, 31.25 MHz). Multiplied input clock divided by 8.
5. PCI clock internally is fixed to input clock divided by 14, (14, 12, 10 or 8 are strapping options). For other frequencies an external clock source connected to PCI_CLK_IN (AB24) has to be used.
6. LCD clock by either dividing input clock (by 4, 8, 16, or 32) or using an external clock source connected to LCDCLOCK (J2).
7. External clock CLKOUT. NS9750 has no dedicated external clock pin.
CLKOUT3 from the memory controller is used to generate an external clock of half CPU clock (99.5328MHz or 81.25MHz or 62.5MHz). This clock is buffered with a clock buffer with 4ns slew rates allowing up to 50mA output currents @ 3.3V.
Oscillators, PLL settings and resulting frequencies:
Oscillator
PLL_ND(4:0), PLL Multiplier
Unit Modules with
200MHz CPU
(0..70°)
MHz
-
29,4912
0b11111, 27
Modules with
162.5MHz CPU
(-40..+85°):
29,4912
0b10000, 22
18
PLL_FS(1:0), PLL divider
PLL_IS(1:0), value
VCO output (= Oscillator * PLL
Multiplier) resulting PLL clock (= VCO /
PLL Divider)
CPU clock (= PLL /2)
AHB, SDRAM and external clock (= CPU /2)
BBUS clock (= AHB /2)
UART Baud Rate Clock
X1_SYS_CLK/M internal PCI clock
Module A9M9750_2
Unit Modules with
200MHz CPU
(0..70°)
-
-
MHz
0b11, 2
796,2624
Modules with
162.5MHz CPU
(-40..+85°):
0b11, 2
0b11, ND16..31 0b11, ND16..31
648,8064
MHz
MHz
MHz
398,1312
199,0656
99,5328
324,4032
162,2016
81,1008
MHz
MHz
MHz
49,7664
14,4560
28,4379
40,5504
14,4560
32,4403
19
Module A9M9750_2
Summary Clock Frequencies on Module:
Oscillator
PLL_ND(4:0), PLL Multiplier
PLL_FS(1:0), PLL divider
PLL_IS(1:0), value resulting PLL clock
CPU clock
AHB, SDRAM and external clock
BBUS clock
UART Baud Rate Clock BBus
PCI clock
LCD clock
29.4912MHz
11111, 27, CPU PLL active
11, 2, CPU PLL active
11, ND16..31, CPU PLL active
398.1312
199.0656
99.5328
49.7664
49.7664
33.33MHz with external oscillator
99.5328MHz, 49.7668MHz,
24,8834MHz or 12,4417MHz
SDRAM_CLKOUT0 feeds the SDRAM. A 2 nd signal path with the same length as the connection between CPU and SDRAM is coupled to the feedback input
SDRAM_CLKIN0. SDM_CLKOUT0 and SDM_CLKIN0 are decoupled with a 22R resistor each. The feedback inputs SDRAM_CLK1..3 are grounded.
20
Module A9M9750_2
3.7. Serial Boot EEPROM, Boot SPI Channel Settings
Connected to SPI channel B (GPIO0->SI, GPIO1-> SO, GPIO6->SCK, GPIO7-
>CS#) is a serial SPI EEPROM 8Kx8 containing initialization values and boot program. It is loaded after end of RESET# low into the SDRAM, if configuration line RESET_DONE is pulled low at the rising edge of RESET# (default on module). The module has to be in little endian mode; a CPU bug prevents booting via SPI EEPROM in big endian mode.
To allow external usage of the SPI channel after boot the SPI chip select is divided into an internal and an external SPI chip select. Activation internal chip select SPIB_INT# while RESET_DONE low; activation external chip select
SPI_ENB# with RESET_DONE high.
3.8. Chip Selects, Memory Map
NS9750 CPU provides 8 chip selects divided in 4 channels for dynamic RAMs and 4 static chip selects. Every chip select has a 256MB range. Below the whole memory map of the NS9750 chip:
Name Pin Address Range
SDM_CS0# E1 0x00000000..0x0FFFFFFF
SDM_CS1# F2 0x10000000..0x1FFFFFFF
SDM_CS2# G3 0x20000000..0x2FFFFFFF
SDM_CS3# F1 0x30000000..0x3FFFFFFF
EXT_CS0# B10 0x40000000..0x4FFFFFFF
EXT_CS1# C10 0x50000000..0x5FFFFFFF
EXT_CS2#
EXT_CS3#
B9
C9
0x60000000..0x6FFFFFFF
0x70000000..0x7FFFFFFF
PCI
BBus -
0x80000000..0x8FFFFFFF
0x90000000..0x9FFFFFFF
Size
[Mbyte]
256
256
256
256
256
256
256
256
256
256
Usage
SDRAM bank 0 n. c.
n. c.
n. c.
external,
CS0#
NAND-
Flash external,
CS2# external,
CS3#
PCI memory
BBus memory
Comments
1 st
bank on module
Program
Memory
21
Module A9M9750_2
PCI
PCI
PCI
PCI
Bridge reserved
Ethernet
Memory
LCD
System reserved
-
-
-
-
-
-
-
-
-
-
0xA0000000..0xA00FFFFF
0xA0100000..0xA01FFFFF
0xA0200000..0xA02FFFFF
0xA0300000..0xA03FFFFF
0xA0400000..0xA04FFFFF
0xA0500000..0xA05FFFFF
0xA0600000..0xA06FFFFF
0xA0700000..0xA07FFFFF
0xA0800000..0xA08FFFFF
0xA0900000..0xA09FFFFF
0XA0A00000..0xFFFFFFFF
1
1
1
PCI IO
PCI
Configur ation
Address
PCI
Configur ation
Data
1
1
1
PCI
Arbiter
BBus to
AHB
Bridge reserved
Ethernet
Commun ication
Module
1
1 r
Memory
Controlle
LCD r
Controlle
System 1
Control
Module
1536 reserved
22
Module A9M9750_2
A9M9750 has 32Mx8, 64Mx8 or 128Mx8 NAND Flash onboard. Optionally greater sizes can be populated (depending on availability). The NS9750 does limit the address range of a single chip select to 256MByte, but this is not relevant for NAND Flash, as the interface to the NAND flash needs always 32 kByte here due to usage of A13, 14 for address and command control.
The NAND flash is accessed with EXT_CS1#. The chip can be write protected externally with the signal FWP#.
Timing considerations (assumes 99.5328MHz AHB and 49.7664MHz BBus clock):
Static memory controller has a clock of 99.5328MHz = 10.048ns per clock cycle.
The AHB memory controller needs 5 cycles (50ns) for every sequence from start to the activation of the memories address, data and control signals. This timing overhead occurs once per single operation and when running burst cycles. The read or write cycle has a minimum time of one cycle (10ns). The static memory controller allows different adjustments for the memory timings:
Values in the registers of static CS1 (verified with module w 199MHz CPU clock),
HCLK = 99.5328MHz = 10.048ns per cycle:
Chip Select 1 Configuration
MEM_StConfig1: 0x80 = no write protect, write buffer disabled, extended wait disabled, BEx# used, chip select low active, bus width 8bit
Write Enable Delay
MEM_StWaitWen1: 0x1 = 2 HCLK cycles; CS setup is 0ns
Output Enable Delay
MEM_StWaitOen1: 0x3 = 3 HCLK cycles; data setup is 20ns
Length OE in non page mode, Delay 1 st read in page mode
23
Module A9M9750_2
MEM_StWaitRd1: 0x8 = 9 HCLK cycles; OE width is 60ns. Important: Length
OE is value from this register minus value in MEM_StWaitOen
Delay next read in page mode
MEM_StWaitpage1: 0x6 = 8 HCLK cycles; data rate is 50ns
Delay write
MEM_StWaitWr1: 0x5 = 6 HCLK cycles; min write length is 45ns
Delay between data direction change
MEM_StWaitTurn1: 0x7 = 7 HCLK cycles; delay between WE high and RD low is
60ns
24
Module A9M9750_2
3.10. 16/32/64 MBytes SDRAM
One SDRAM bank is available. It is connected to CS4# (SDM_CS0#). CS5#
(SDM_CS1#), CS6# (SDM_CS2#) and CS7# (SDM_CS3#) are lost. The module does not provide external SDRAM connection.
A9M9750 has 4MX32 (16 MByte) or 16MX32 (64 MByte) SDRAM onboard.
Larger chips can be populated (depending on availability), the highest address connected is A12. Range of chip select is 256M.
Timing considerations (assumes 99.5328MHz SDRAM and 49.7664MHz BBus clock, usage of 1MX32X4 75ns SDRAM with CAS latency of 2 and 100MHz
SDRAM clock). Recommended register settings:
1. Control Register (0xA070 0000): set to 0x1 (normal mode, reset address mirror, enable memory controller)
2. Status Register (0xA070 0004): read only
3. Configuration Register (0xA070 0008): set to 0x0 (clock ratio 1:1, little endian mode)
4. Dynamic Memory Control Register (0xA070 0020): set to 0x3, memory clock enabled
5. Dynamic Memory Refresh Timer register (0xA070 0024): set to 0x63 (16µs refresh time with 100MHz SDRAM clock
6. Dynamic Memory Read Configuration Register (0xA070 0028): set to 0x1, command delayed strategy, clock not delayed (modify only Bit0,1; min 0x1, max 0x3)
7. Dynamic Memory Precharge Command Period Register (0xA070 0030): set to 0x1 = 2 clock cycles; TRP=20ns, (modify only bit0:3)
8. Dynamic Memory Active to Precharge Command Period Register (0xA070
0034): set to 0x4 = 5 clock cycles; TRAS=45ns, (modify only bit0:3)
9. Dynamic Memory Self-refresh Exit Time Register (0xA070 0038): set to 0xF
= 0x10 clock cycles; TSREX=???, (modify only bit0:3)
25
Module A9M9750_2
10. Dynamic Memory Last Data Out to Active Time Register (0xA070 003C): set to 0x1 = 2 clock cycles; TAPR=???ns (modify only bit0:3)
11. Dynamic Memory Last Data In to Active Command Time Register (0xA070
0040): set to 0x5 = 6 clock cycles; TDAL or TAPW=40ns, (modify only bit0:3)
12. Dynamic Memory Write Recovery Time Register (0xA070 0044): set to 0x0 =
1 clock cycle; TWR or TDPL or TRWL or TAPW=10ns, (modify only bit0:3)
13. Dynamic Memory Active to Active Command Period Register (0xA070 0048): set to 0x6 = 7 clock cycles; TRC=65ns, (modify only bit0:3)
14. Dynamic Memory Auto Refresh Period Register (0xA070 004C): set to 0x6 =
7 clock cycles; TRFC=???ns, (modify only bit0:4)
15. Dynamic Memory Exit Self-refresh Register (0xA070 0050): set to 0x1F =
0x20 clock cycles; TXSR=???, (modify only bit0:4)
16. Dynamic Memory Active Bank A to Active Bank B Time Register (0xA070
0054): set to 0x1 = 2 clock cycles; TRRD=15ns, (modify only bit0:3)
17. Dynamic Memory Load Mode Register to Active Command Register (0xA070
0058): set to 0x1 = 2 clock cycles; TMRD=???ns, (modify only bit0:3)
18. Dynamic Memory Configuration 0 Register ((0xA070 0100): set for 1MX32X4 to 0x00084500 = buffers enabled, 32-bit extended bus high performance address mapping, 128Mb (4MX32), 4 banks, 12 rows, 8 columns, (modify only bits 20, 14, 12:07)
19. Dynamic Memory RAS and CAS Delay 0 Register (0xA070 104): set to
0x203 = 3 RAS, 2CAS; (modify only bits 0:1 (RAS) and 8:9 (CAS))
20. System Control Dynamic Memory Base Register 4 (0xA090 01D0): set to
0x00000000 = Start Adress 0; (modify only bits31:12)
21. System Control Dynamic Memory Mask Register 4 (0xA090 01D4): set to
0xF0000000 = Range 256MByte (0x00000000 - 0x0FFFFFFF); (modify only bits31:12)
26
Module A9M9750_2
3.11. 50 GPIO Pins (multiplexed with other Functions)
NS9750 has 50 GPIO pins. All pins are multiplexed with other functions (UART,
SPI, USB, DMA, parallel port IEEE1284, LCD port, timers, interrupt inputs).
Using a pin as GPIO means always to give up another functionality.
Port
Name,
Functio n 03
(default at power up)
Alternate
Function
00, UART
Alternate
Function
00, misc.
Alternate
Function 01
Alternate
Function 02
On Module default used as
GPIO0
GPIO1
GPIO2
GPIO3
GPIO4
GPIO5
GPIO6
GPIO7
GPIO8
GPIO9
TXDB
RXDB
RTSB#
CTSB#
DTRB#
DSRB#
RIB#,
RXCLKB
DCDB#,
TXCLKB
TXDA
RXDA
SPI_Boot_
DO and
SPIB_DO
SPI_Boot_
DI and
SPIB_DI
SPI_Boot_
CLK and
SPIB_CLK
SPI Boot
CE# and
SPIB_CE#
DMA0
DONE dupe
DMA0 REQ.
Dupe
Timer 1 dupe
IRQ0
TXDB,
SPI_Boot_DO or external
SPIB_DO
RXDB,
SPI_Boot_DI or external
SPIB_SI
Timer 0 DMA1 ACK RTSB#, DMA
1284 ACK DMA0 REQ CTSB#, DMA
1284 BUSY DMA0
DONE
DTRB#
1284 ERR DMA0 ACK DSRB#, DMA
1284 P_JAM Timer 7 dupe
DMA0 Ack dupe
IRQ1
RIB#,
SPI_Boot_CL
K or external
SPIB_CLK
DCDB#,
SPI_Boot_CE
# or external
SPIB_CE#
SPIA_DO Reserved
SPIA_ DI Reserved
Reserved TXDA, SPI A
Timer 8 dupe
RXDA, SPI A
27
Module A9M9750_2
Port
Name,
Functio n 03
(default at power up)
Alternate
Function
00, UART
Alternate
Function
00, misc.
Alternate
Function 01
Alternate
Function 02
On Module default used as
GPIO10
GPIO11
GPIO12
GPIO13
RTSA#
CTSA#
DTRA#
DSRA#
GPIO20 DTRC#
GPIO21 DSRC#
Reserved
IRQ2 dupe
Reserved
IRQ0 dupe
Reserved
Timer 0 dupe
Reserved
Timer 10 dupe
Reserved GPIO14
GPIO15 DCDA#,
TXCLKA
GPIO16
RIA#,
RXCLKA
GPIO17
GPIO18
GPIO19
GPIO22 RIC#,
RXCLKC
GPIO23 DCDC#,
TXCLKC
GPIO24 DTRD#
SPIA_CLK
SPIA_EN#
Timer 1
Timer 2 Timer 2
USB
Overcurren t
USB
Power
Relay
Ethernet
CAM
Reject
Ethernet
CAM
Reject
1284 P_JAM dupe
Reserved
LCD
PWREN
Timer 11 dupe
Reserved
IRQ3 dupe
LCD HSYNC DMA1 ACK
SPIC_CLK
SPIC_ EN#
LCD CLK
LCD
VFSYNC
LCD
BIAS_D_EN
LCD
LINE_END
LCDD0
Reserved
Reserved
Reserved
Timer 14 dupe
Reserved
RTSA#
CTSA#
GPIO12
GPIO13, used as RTC_INT#
RIA#, SPI A
DCDA#, SPI
A
USB
USB
LCD
LCD
LCD
LCD
LCD
LCD
LCD
28
Module A9M9750_2
Port
Name,
Functio n 03
(default at power up)
Alternate
Function
00, UART
Alternate
Function
00, misc.
Alternate
Function 01
Alternate
Function 02
GPIO25
GPIO26
GPIO27 DCDD#,
TXCLKD
GPIO28
RID#,
RXCLKD
SPID_CLK
SPID_ EN#
GPIO29
GPIO30
GPIO31
GPIO32
GPIO33
GPIO34
GPIO35
GPIO36
DSRD#
GPIO37
GPIO38
GPIO39
GPIO40
GPIO41
TXDC
RXDC
GPIO42 RTSC#
GPIO43 CTSC#
GPIO44
GPIO45
GPIO46
TXDD
RXDD
RTSD#
LCDD1
LCDD2
LCDD3
Timer 15 dupe
Timer 3
Timer 4
Ext IRQ 1 dupe
Timer 5
Timer 6
Timer 7
LCDD4
LCDD5
LCDD6
LCDD7
EXT IRQ 2 1284 D0
Timer 8
Timer 9
Timer 10
Reserved
Reserved
Reserved
Reserved
1284 D1
1284 D2
1284 D3
1284 D4
1284 D5
1284 D6
1284 D7
IRQ3
Timer 11
Timer 12
Timer 13
1284
PER_ONLIN
E
1284 STRB
1284 ALFD
LCDD8 dupe
LCDD9 dupe
LCDD10 dupe
LCDD11 dupe
LCDD8
LCDD9
LCDD10
LCDD11
LCDD12
LCDD13
LCDD14
LCDD15
LCDD16
LCDD17
LCDD18
LCDD19
LCDD20
LCDD21
LCDD22
On Module default used as
LCD
LCD
LCD
LCD
LCD
LCD
LCD
LCD
LCD
LCD
LCD
LCD
LCD
LCD
LCD
LCD
LCD
LCD
LCD
LCD
LCD
LCD
29
Module A9M9750_2
Port
Name,
Functio n 03
(default at power up)
Alternate
Function
00, UART
GPIO47 CTSD#
GPIO48
GPIO49
Alternate
Function
00, misc.
Alternate
Function 01
Alternate
Function 02
On Module default used as
Timer 14
Timer 15
1284 INIT
1284 P_SEL DMA1 REQ
1284
P_LOG
LCDD23
DMA1
DONE
LCD
DMA
R/B# NAND-
Flash
3.12. PCI/CardBus Port
All address, data and control signals are provided to connect a PCI or CardBus interface compliant to PCI specification 2.1 and 2.2 protocol. All module signals are not buffered; clock buffering, clock distribution and casually necessary buffers for other PCI signals have to be added on the application board. If no internal PCI clock is used, the PCI clock has to be generated externally too.
PCI_CLKIN and PCI_CLKOUT have series resistors populated with 0R in the moment between CPU and connector; these two signals can be shorted near the
CPU optionally on the module.
Generation PCI clock see clock chapter.
Pull up resistors on the module are provided for PCI_GNT1..3#, PCI_REQ1..3#,
PCI_INTA..D#, PCI_PERR#, PCI_SERR#, PCI_STOP#, PCI_DEVSEL#,
PCI_IRDY#, PCI_TRDY# and PCI_FRAME#.
PCI_CENTRAL_RSC# pin is default low (internal pull down), the internal PCI resources and the internal PCI arbiter of the NS9750 active (RTCK high). This is the PCI host version. PCI_IDSEL is connected via series resistor on the module to PCI_AD11 (NS9750 must be PCI device0). The PCI_IDSEL line of an external
PCI Connector has to be connected to PCI_AD signal >11 (for example, connected to PCI_AD13 the connector is configured as PCI device 2).
30
Module A9M9750_2
If external arbiter and no internal resources selected (PCI_CENTRAL_RSC# high and RTCK low), no pull up resistors are populated (PCI device version).
PCI_IDSEL is controlled by the external host, the series resistor on the module not populated.
3.13. 10/100Mbps Ethernet Port
The module has a MII PHY chip on board. Adress selection is set to 1. The transmit signals TPOP and TPON from the PHY are neither decoupled nor terminated on the module. The receive signals TPIP and TPIN are capacitively coupled with 220pF to the PHY. They have an AC-termination to Gnd with 49R9 from each signal. AC coupling with 100nF to Gnd. Signals for link and speed
LEDs are provided. No transformer, Ethernet connector or indication LEDs are on the module, these parts have to be provided by the base board. PHY clock of
25MHz is generated in the PHY chip with a 25MHz crystal.
3.14. USB 2.0 full and low speed Host and Device Controller
The USB section of the NS9750 CPU provides USB+ and USB- signals and two
USB control signals (USB_PWR and USB_OVCURR). All external configuration for a USB device or a USB host interface has to be made on the base board.
48MHz USB clock is generated on the module with a 48MHz crystal in fundamental configuration.
3.15. UART Channels
Up to 4 UART channels with all handshake signals are provided (channels
A=GPIO8..15, B=GPIO0..7, C=GPIO20..23 & GPIO40..43, D=GPIO24..27 &
GPIO44..47). They can be used in asynchronous mode as UART. Baud rates are supported up to 1.8MHz in asynchronous mode.
3.16. SPI Channels
SPI channel B (GPIO0,1,6,7) is connected to the serial 8Kx8 SPI EEPROM U23 when RSTOUT# asserted. The EEPROM contains the boot program and the initial SDRAM parameters for booting via SPI. Usage of this channel at runtime is provided by deconnecting the boot EEPROM with the deassertion of RSTOUT#
31
Module A9M9750_2 using 4 switches. The other SPI channels can be used free if not used in UART mode or blocked by other GPIO usage.
3.17. Calculation of Baudrates
Baud rate generators in the NS9750 have different clock sources selectable:
1. X1_SYS_OSC/M. It is the frequency of the input crystal divided by M. M depends on the multiplier settings PLL_ND of the PLL. M = 2 at PLL_ND
>=19 decimal (14.7456MHz with 29.4912MHz crystal) or M = 4 at PLL_ND <
19 decimal (7.3728MHz). Cannot be used with PLL bypassed.
2. BCLK. For 199.0656MHz CPU is BCLK = 49.7668MHz. Only internal source when PLL bypassed.
3. External receive clock from GPIO pins.
4. External transmit clock from GPIO pins.
These values can be the same for modules with and without used CPU PLL, when BBus is used as clock source.
UM = UART mode, either 8, 16, 32. Normally 16 taken.
M = input clock divider, 2 for ND > 19
0 <= N <= 16383 decimal for baud rate generator count
General calculation formula divider N for clock source 1:
N = ((X1_SYS_OSC / M) / (UM * Baudrate)) – 1 simplifies for X1_SYS_OSC/2 = 14.7456MHz to
N = (921600 / Baudrate) – 1 and for X1_SYS_OSC/4 = 7.3728MHz to
32
Module A9M9750_2
N = (460800 / Baudrate) – 1
Example for 38400 Bd: N = (460800/38400) – 1 = 11, error 0%
General calculation formula divider N for clock source 2:
N = (BCLK / (UM * Baudrate)) - 1 simplifies for 49.7664MHz to
N = (3110400 / Baudrate) – 1
Example for 38400 Bd: N = (3110400/38400) – 1 = 80, error 0%
Simplifies for 40.5504MHz to
N = (2,534400 / Baudrate) – 1
Example for 38400Bd N = (2.534400 / 38400) – 1 = 65, error 0%
33
Module A9M9750_2
Count values vs. Baud Rate Clock:
Baud Rate N, X1_SYS/2 =
14.7456MHz,
(Error) [%]
N, X1_SYS/4
= 7.3728MHz,
(Error) [%]
N, BBus =
49.7664MHz,
(Error), [%]
75
150
300
600
1200
2400
4800
7200
9600
14400
19200
28800
38400
57600
115200
230400
460800
921600
1843200
12287, (-)
6143, (-)
3071, (-)
1535, (-)
767, (-)
383, (-)
191, (-)
127, (-)
95, (-)
63, (-)
47, (-)
31, (-)
23, (-)
15, (-)
7, (-)
3, (-)
1, (-)
0, (-)
-
6143, (-)
3071, (-)
1535, (-)
767, (-)
383, (-)
191, (-)
95, (-)
63, (-)
47, (-)
31, (-)
23, (-)
15, (-)
11, (-)
7, (-)
3, (-)
1, (-)
0, (-)
-
-
-
-
10367, (-)
5183, (-)
2591, (-)
1295, (-)
647, (-)
431, (-)
323, (-)
215, (-)
161, (-)
107, (-)
80, (-)
53, (-)
26, (-)
13, (+3.846)
6, (-3.846)
-
-
N, BBus =
40.5504MHz,
(Error) [%]
-
-
8447, (-)
4223, (-)
2111, (-)
1055, (-)
527, (-)
353, (+0.18)
263, (-)
176, (+0.18)
131, (-)
87, (+0.749)
65, (-)
43, (+0.749)
21
10
5, (+10.824)
CPUs using PLL on modules with 200MHz and 162.5MHz will use the values from column 1 allowing baud rates from 75..921600Bd. A 125MHz CPU will have a PLL multiplier ND = 17 resulting in a X1_SYS/4 clock source. This module will use column 2 resulting in a baud rate from 75..460800Bd.
Column 3 or 4 is used when PLL bypassed or CPU clock never changes in the application.
3.18. I²C Bus
34
Module A9M9750_2
This bus (SCL, SDA) is connected on the module to a serial EEPROM with I²C interface on device address 0xA0, 0xA1. Device address 0xD0, 0xD1 connects to an RTC on board. All other addresses can be used externally.
Due to a timing bug in the I²C state machine the maximum clock frequency in slow mode should be 50KHz and 200KHz in fast mode. Otherwise minimum setup time for the target can be violated (SDA changes after half low time of SCK instead of shortly after falling edge, so setup time for data is 2.5µs @ 100KHz and 612.5ns @ 400KHz).
Important: Use only 3.3V devices!
35
Module A9M9750_2
3.19. LCD Controller (STN & TFT)
An LCD interface for STN or TFT LCD’s is provided with up to 24 data lines and
6 control lines. Usage for LCD disables serial ports C, D and most GPIOs.
The module provides the full LCD interface: 24 data lines LCCD0..23
(GPIO24..47) and 6 control lines GPIO18..23.
This interface allows connection of most TFT and STN monchrome and color
LCDs. Details see NS9750 hardware user manual.
3.20. Serial EEPROM for storing Configuration Parameters
The nonvolatile storage of parameters like MAC address etc. is supported with a serial 8Kx8 EEPROM (24LC64 or similar) connected to the I²C bus at device address 0xA0, 0xA1.
3.21. RTC
An RTC (MAXIM/DALLAS DS1337 in µSOP8 case) on the module is connected to the I²C bus (device address 0xD0, 0xD1). It has its own 32.768KHz clock crystal. Power is taken from 3.3V when provided, otherwise from V
RTC
fed by an external battery. An interrupt line (GPIO13) is connected to the RTC; it can be opened by depopulating a resistor.
3.22. JTAG, Boundary Scan
NS9750 support JTAG and boundary scan with the signals TCK, TMS, TDI, TDO and TRST#. The signal RTCK is not connected to external. It is only used on the module for PCI arbiter selection.
Selection between normal mode and debug mode is done with the external signal DEBUG_EN# (HCONF0). Selection between ARM debug mode and boundary scan mode is done with the signal OCD_EN# (HCONF2). See table below:
DEBUG_EN#
1
OCD_EN# Mode
1 normal
Comments
36
DEBUG_EN#
1
0
0
Module A9M9750_2
OCD_EN#
0
1
0
Mode not recommended
ARM debug
Boundary Scan
Comments
Boundary Scan possible here too, but TRST# is connected with SRST#, system may hang
37
Module A9M9750_2
3.23. Single 3.3V Power Supply
The module has 3.3V_IN supply pins. VLIO pins are connected to 3.3V_IN too for the A9M9750_2 module. These signals have EMI filters near the connector to suppress emission of the module.
Internal voltages:
1.5V core voltage with up to 700mA will be converted by a switching regulator to keep losses small. This regulator is connected to VLIO.
Worst case power consumption of the NS9750 is at full operation with 200MHz clock 1.05W for the core (1.5V, about 700mA) and 0.65W for the I/O ring (3.3V, about 200mA). In “sleep mode” power consumption decreases to 170..350mW
(120..240mA) for the core and 10..90mW (3..30mA) for the I/O ring depending on the ports used for wake up.
3.24. Power Sequencing on A9M9750_2 Module
Power-up and power-down behavior recommended by NetSilicon and TOSHIBA for the NS9750 (Power up: core voltage will be first to rise; I/O voltage +3.3V will ramp up in <100ms, when core voltage rises over 80% of its nominal value;
Power down: I/O voltage will ramp down in < 100ms, when core voltage falls below 80%) will be ensured by hardware.
The sequencing circuit is realised with two comparators, a variable delay and a
FET switch TPS2022 U18 between 3.3V_IN and +3.3V on the module. The 1 st comparator TLV3012 U12 with a 3.0V threshold supervizes 3.3V_IN. Its output becomes true, if 3.3V_IN > 3.0V. The 2 nd comparator TLC7701 U16 supervizes
+1.5V core voltage. When +1.5V core voltage > 1.3V, the output becomes true. If both signals are true a delay of about 20..40ms starts. Delay time is settable with a capacitor at U15. After this time output RES goes low and 3.3V_IN are connected to +3.3V with the FET switch U18 with a ramp up time of < 20ms.
Output RES# goes high; it is connected as PWREN to the external connector of the module. The outputs of U16 change their state immediately, when either
3.3V_IN < 3.0V or +1.5V < 1.2V. So the +3.3V on the module is switched off immediately and ramps down in a few ms.
38
Module A9M9750_2
3.25. Voltage Supervision and RESET Generation
Voltage supervision and RESET# generation is done for 1.5V core and 3.3V I/O voltage by a triple voltage supervisor with RESET# TPS3307-18. External or manual RESET# control is done by connecting RSTIN# to ground. The push pull
RESET# output with 470R series resistor is connected to the PWRGOOD signal.
3.3V is supervised with SENSE1 and SENSE2, 1.5V with SENSE3. MR# is connected to RSTIN# for manual RESET control. An optional pull up 10K increases the current out of RSTIN# to at least 330µA when connected to Gnd.
39
Module A9M9750_2
4. Bootloader
Every module is delivered with a bootloader (UBOOT) pre-installed in NAND
Flash. The bootloader is capable of booting the Operating System from NAND
Flash, via a serial port or via Ethernet. Parameters can be passed to the kernel from the bootloader.
Some requirements:
• Calculation of Baudrates, Timer-Values depends on the different possible clock sources:
PLL active
BASE_CLK
[MHz]
Yes 398.1312
CPU_CLK
[MHz]
199.0656
Yes 324.4032
Yes 250.6752
162.2016
125.3376
comment
BASE_CLK = 29.4912 MHz * (ND+1) /2
BASE_CLK = 29.4912 MHz * 27 /2
The PLLNDSW bits must be taken into account for calculating baudrates and timer values.
BASE_CLK = 29.4912 MHz * (ND+1) /
FS
BASE_CLK = 29.4912 MHz * 22 /2
The PLLNDSW bits must be taken into account for calculating baudrates and timer values.
BASE_CLK = 29.4912 MHz * (ND+1) /
FS
BASE_CLK = 29.4912 MHz * 17 /2
The PLLNDSW bits must be taken into account for calculating baudrates and timer values.
• Bootloader is able to update the bootloader itself.
5. Software
40
Module A9M9750_2
The ARM926 core in the NS9750 contains an MMU thus allowing Operating
Systems such as Linux and Windows CE to be supported. Board Support
Packages for Windows CE .net 4.2 and Linux, using kernel 2.6.x, are in development. Other Operating Systems can be supported on request.
41
Module A9M9750_2
6. Mechanics
The module size is defined to 60 x 44mm. Two holes, for M2 screws, catercornered, are provided to enable fixing of the module on the base board.
Two board-to-board connectors are used on the module. Depending on the counterpart on the base board, different distances between module and base board can be realized. The minimum distance is 5mm.
Therefore, the height of the parts mounted on the bottom side of the module should not exceed 2.5mm. The height of the parts mounted at the top side should not exceed 4.1mm.
Board-to-Board Module Connector X1, X2
Distance h No. of Pins Qty Supplier Order No.
5 mm
6 mm 120 2 AMP
Berg
177983-5
61082-121000
7 mm
8 mm
Base Board Connector X1, X2
No. Of Supplier Order No.
Pins
120
120
AMP
Berg
AMP
Berg
177984-5
61083-
121000
179029-5
61083-
122000
120
120
AMP
Berg
AMP
Berg
179030-5
61083-
123000
179031-5
61083-
124000
42
Mechanical Drawing from TOP View:
1
X1
Module A9M9750_2
Ø 2.2 (2x)
2.4
3.9
1
X2
56.1
57.6
60
43
Module A9M9750_2
Mechanical Drawing from Side View:
28.4
The size of h depends on the board-to-board connectors.
The size between the board-to-board connectors is measured from pad to pad.
For further modules in the ModARM9 family, it might be necessary to have some additional hardware placed on the module, which will need more signal lines connected between module and base board than currently available. To meet these future requirements, an extended board was defined, which has two additional board-to-board connectors with 60 pins each.
The size of the extended module is defined as 92 x 44mm. Two holes, for M2 screws, catercornered, are provided to enable fixing of the module on the base board.
44
Board-to-Board
Distance h
5 mm
No. of
Pins
Module Connector X3, X4
Qty Supplier Order No.
60 2 AMP
Berg
177983-2
61082-061009
Base Board Connector X3, X4
No. Of Pins Supplier Order No.
60 AMP
Berg
177984-2
61083-
061009
6 mm
7 mm
8 mm
60
60
60
Module A9M9750_2
AMP
Berg
AMP
Berg
AMP
Berg
179029-2
61083-
062009
179030-2
61083-
063009
179031-2
61083-
064009
45
Module A9M9750_2
7. Known Faults and Limitations
7.1. USB Pins are not 5V tolerant
As all pins of the NS9750 the USB data pins are not 5V tolerant. To overcome this problem there is a protection circuit on the NetSilicon evaluation board.
Fix: Adding protection circuit on the base board (VALI, DEV). Realised on
A9M9750_1 in the moment.
7.2. Timing Bug in IIC Stage
A timing bug reduces setup and hold times for IIC_SDA signals to half low time of IIC_SCK.
Workaround: Use half maximum frequency, i. e. 50KHz in slow mode and
200KHz in fast mode.
7.3. PLL Clock Generation instable
NS9750A1 CPU may produce frequency shifts on the memory clock, if used at low temperatures and supply voltages at the upper limit.
Workaround: feeding system and USB clock with oscillators eliminates this bug.
A9M9750_2 modules have oscillators for system and USB clock.
46
Module A9M9750_2
8. Appendix
A detailed pin description is available named “Pin_Description_A9M9750_X.pdf” or “*.doc”.
8.2. Pinning Module on A9MVali Validation Board
This pinning is included in the specification of the validation board:
“A9MVali_X.doc” or “*.pdf”.
8.3. Pinning Module on A9M9750DEV Development Board
This pinning is included in the specification of the development board:
“Spec_Devkit_A9M9750_A9M9360_X.doc” or “*.pdf”.
47
advertisement
* Your assessment is very important for improving the workof artificial intelligence, which forms the content of this project
Related manuals
Frequently Answers and Questions
What is the default configuration of the PCI Arbiter?
How can I boot the device from SPI?
How can I boot the device from Flash/ROM?
What is the default configuration of the Chip Select Multiplexer?
Can I use CS0 for NOR Flash?
What is the default configuration of the Byte Lane Multiplexer?
Can I use BL0 for the NAND Flash?
advertisement
Table of contents
- 2 Module A9M
- 3 1. Revision History
- 6 2. Introduction
- 6 2.1. Benefits of the ModARM9 Concept
- 6 2.2. Common Features
- 7 2.3. Differences between A9M9750_1 and A9M9750_2 Modules
- 8 2.4. Planned and realised Variants for A9M9750_2 Module
- 9 3. A9M9750 Features
- 9 3.1. Size 60 x 44 mm
- 9 3.2. 2 x 120-pin connectors
- 9 3.3. NS9750 CPU on the A9M9750_2 Module
- 10 3.4. Configuration Pins CPU
- 15 3.5. Configuration Pins Module
- 18 3.6. Clock Generation
- 21 3.7. Serial Boot EEPROM, Boot SPI Channel Settings
- 21 3.8. Chip Selects, Memory Map
- 23 3.9. NAND Flash
- 25 3.10.16/32/64 MBytes SDRAM
- 27 3.11.50 GPIO Pins (multiplexed with other Functions)
- 30 3.12.PCI/CardBus Port
- 31 3.13.10/100Mbps Ethernet Port
- 31 3.14.USB 2.0 full and low speed Host and Device Controller
- 31 3.15.UART Channels
- 31 3.16.SPI Channels
- 32 3.17.Calculation of Baudrates
- 34 3.18.I²C Bus
- 36 3.19.LCD Controller (STN & TFT)
- 36 3.20.Serial EEPROM for storing Configuration Parameters
- 36 3.21.RTC
- 36 3.22.JTAG, Boundary Scan
- 38 3.23.Single 3.3V Power Supply
- 38 3.24.Power Sequencing on A9M9750_2 Module
- 39 3.25.Voltage Supervision and RESET Generation
- 40 4. Bootloader
- 2 Module A9M
- 40 5. Software
- 42 6. Mechanics
- 44 6.1. Extended Module
- 46 7. Known Faults and Limitations
- 46 7.1. USB Pins are not 5V tolerant
- 46 7.2. Timing Bug in IIC Stage
- 46 7.3. PLL Clock Generation instable
- 47 8. Appendix
- 47 8.1. Pinning Module
- 47 8.2. Pinning Module on A9MVali Validation Board
- 47 8.3. Pinning Module on A9M9750DEV Development Board