- Sports & recreation
- Camping, tourism & outdoor
- Above ground pools
- Above ground pool accessories
- Waterco
- Turbotemp 400HD
- Installation and Operation Manual
advertisement
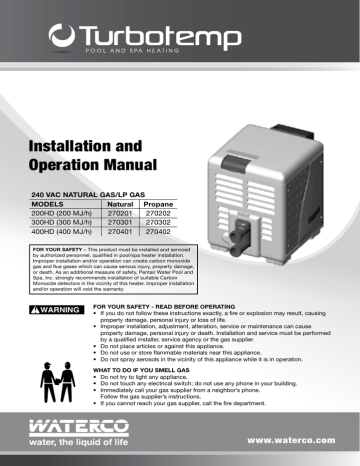
Installation and
Operation Manual
240 VAC NATURAL GAS/LP GAS
MODELS Natural Propane
200HD (200 MJ/h)
300HD (300 MJ/h)
400HD (400 MJ/h)
270201
270301
270401
270202
270302
270402
FOR YOUR SAFETY – This product must be installed and serviced by authorized personnel, qualified in pool/spa heater installation.
Improper installation and/or operation can create carbon monoxide gas and flue gases which can cause serious injury, property damage, or death. As an additional measure of safety, Pentair Water Pool and
Spa, Inc. strongly recommends installation of suitable Carbon
Monoxide detectors in the vicinity of this heater. Improper installation and/or operation will void the warranty.
!
WARNING
FOR YOUR SAFETY - READ BEFORE OPERATING
• If you do not follow these instructions exactly, a fire or explosion may result, causing property damage, personal injury or loss of life.
• Improper installation, adjustment, alteration, service or maintenance can cause property damage, personal injury or death. Installation and service must be performed by a qualified installer, service agency or the gas supplier.
• Do not place articles or against this appliance.
• Do not use or store flammable materials near this appliance.
• Do not spray aerosols in the vicinity of this appliance while it is in operation.
WHAT TO DO IF YOU SMELL GAS
• Do not try to light any appliance.
• Do not touch any electrical switch; do not use any phone in your building.
• Immediately call your gas supplier from a neighbor’s phone.
Follow the gas supplier’s instructions.
• If you cannot reach your gas supplier, call the fire department.
www.waterco.com
Section 1. Heater Identification ............... 2
Information (HIN)
Heater Data Rating Plate ......................... 2
Section 2. Introduction ............................ 3
Important Notices ...................................... 3
Warranty Information ................................. 4
Code Requirements ................................... 4
Consumer Information and ........................ 5
Safety Information
General Specifications ............................... 8
Section 3. Installation .............................. 9
Heater Description ...................................... 9
Sequence of Operation .............................. 10
Putting the Heater into Service .................. 10
Specifications ............................................ 11
Plumbing Connections ............................... 12
Valves ......................................................... 12
Manual By-Pass ......................................... 12
Water Connections ..................................... 13
Below Pool Installation ............................... 13
Gas Connections ........................................ 14
Gas Pipe Sizing .......................................... 15
Sediment Trap/Drip Leg .............................. 15
Testing Gas Leaks and Gas Pressure ......... 15
Gas Pressure Requirements ....................... 16
Outdoor Installation / ................................. 16
Heater Clearances
Indoor Venting—General Requirements ..... 18
Heater Clearances / Outside Vent Removal
Combustion Air Supply / Corrosive ............ 20
Vapors and Possible Causes
Vent Installation (Indoor Installation or ........ 21
Outdoor Shelter) - Vertical Venting
Horizontal or Vertical Venting - Using ......... 24
Single-Wall Stainless Gas Vent
Connecting Single-Wall Stainless ............... 25
Steel Vent to the Heater
Horizontal or Vertical Venting Flexible ....... 28
Duct (Flex-Vent)
Corrosive Vapors and Possible Causes ...... 28
Control Panel Indexing ............................... 29
Final Installation Check .............................. 29
Electrical Connections ............................... 29
Fireman’s Switch Connection/ ................... 30
Remote Control Connections
Turbotemp Wiring Diagram / ...................... 32
Electrical Schematic Ladder Diagram
Section 4. Operation ................................ 34
Basic System Operation / HSI ................... 34
(Hot-Surface Ignition) Lighting/Operation
Operating Instructions ............................... 35
To Turn Off Gas to Appliance ..................... 36
Safety Controls (Air Flow Switch / .............. 37
Water Pressure Switch / Hight Limits /
Operation of Ignitiion Module)
Operating the Control Panel / .................... 38
Temperature Setting / Maximum
Temperature Set Point
Section 5. Troubleshooting ...................... 40
Initial Troubleshooting and ......................... 40
Troubleshooting Chart
Heater Will Not Fire Troubleshooting .......... 41
(A, B, C, D)
LED Diagnostics ......................................... 45
(AGS, AFS, HLS, PS Thermistor)
Burner / Heat Exchanger Troubleshooting .. 47
Section 6. Maintenance ............................ 48
Care and Maintenance ............................... 48
Pressure Relief Valve .................................. 49
After Start-Up ............................................. 49
Spring, Fall (Autumn) and ........................... 49
Winter Operation
Maintaining Pool Temperature / .................. 51
Energy Saving Tips
Chemical Balance ....................................... 51
Replacement Parts ..................................... 54
Section 1. Heater Identification Information
I pg 02
HEATER IDENTIFICATION INFORMATION (HIN)
To identify the heater, see the data rating plate on the inner front panel of the heater. There are two designators for each heater, one is the Model Number and the other is the Heater
Identification Number (HIN).
Heater Identification Number (HIN)
The following example simplifies the identification system:
1. MT : Turbotemp
2. Model Size : (200, 300 or 400) : Input rating (Mega Joule [MJ]/hr)
3. Construction : (HD = Heavy Duty Model)
4. Fuel Type : (LP = Propane gas or N = Natural gas)
H. I. N.
HEATER IDENTIFICATION NUMBER
ID DESIGNATOR FOR WATERCO WATER POOL & SPA TURBOTEMP HEATERS
Example:
1 2
MT 300
3
HD
4
N
FUEL TYPE =
N = NATURAL GAS
LP = PROPANE GAS
HD = HEAVY DUTY MODEL
MODEL SIZE = MJ INPUT = Mega Joule [MJ] / HR
200 (200[MJ]/ HR), 300 (300[MJ]/ HR) or 400 (400[MJ] /HR)
MT = TURBOTEMP
HEATER DATA RATING PLATE
The heater data rating plate is located on the inner front panel of the heater. To access the data rating plate, unbolt and remove the side door access panel as shown below.
Heater Data Rating Plate Location
Top Panel
Door
Access
Panel
Door
Access Panel
INTRODUCTION
Turbotemp (Australia) Pool and Spa Heater
Congratulations on your purchase of a Turbotemp high performance heating system. Proper installation and service of your new heating system and correct chemical maintenance of the water will ensure years of enjoyment. The Turbotemp is a compact, lightweight, efficient, induced-draft, gas fired high performance pool and spa heater that can be directly connected to schedule 40 PVC pipe. The Turbotemp also comes equipped with the Pentair Water Pool and
Spa® multifunction temperature controller which shows, at a glance, the proper functioning of the heater. All Turbotemp heaters are designed with a direct ignition device, HSI (hot-surface ignition), which eliminates the need for a standing pilot. The Turbotemp requires an external power source (240 VAC 50 Hz) to operate.
SPECIAL INSTRUCTIONS TO OWNER: Retain this manual for future reference. This instruction manual provides operating instructions, installation and service information for the Turbotemp high performance heater. The information in this manual applies to all Turbotemp models.
READ
AND REVIEW THIS MANUAL COMPLETELY, it is very important that the owner/installer read and understand the section covering installation instructions, and recognize the local and state codes before installing the Turbotemp. Its use will reduce service calls and chance of injury and will lengthen product life. History and experience has shown that most heater damage is caused by improper installation practices.
IMPORTANT NOTICES
THIS PRODUCT MUST BE INSTALLED AND SERVICED BY A PROFESSIONAL SERVICE
TECHNICIAN, QUALIFIED IN POOL HEATER INSTALLATION.
For the installer and operator of the Turbotemp pool and spa heater: The manufacturer’s warranty may be void if, for any reason, the heater is improperly installed and/or operated. Be sure to follow the instructions set forth in this manual. If you need more information or if you have any questions regarding to this pool heater, please contact.
Waterco Limited - Offices Australia
NSW - Sydney (HEAD OFFICE)
Tel : +61 2 9898 8686
QLD - Brisbane
Tel : +61 7 3299 9900
VIC/ TAS - Melbourne
Tel : +61 3 9764 1211
SA/ NT - Adelaide
Tel : +61 8 8244 6000
WA - Perth
Tel : +61 8 9273 1900
Waterco (NZ) Limited
Auckland, New Zealand
Tel : +64 9 525 7570
Section 2. Introduction
I pg 04
WARRANTY INFORMATION
The Turbotemp pool heater is sold with a limited factory warranty.
Specific details are described
in the Waterco Warranty Terms and Conditions booklet included with the product.
Waterco pool and spa’s high standards of excellence include a policy of continuous product improvement resulting in your state-of-the-art heater. We reserve the right to make improvements which change the specifications of the heater without incurring an obligation to update the current heater equipment.
These heaters are designed for the heating of chlorine, bromine or salt system swimming pools and spas or in non-stationary installations, and should never be employed for use as space heating boilers or general purpose water heaters. The manufacturer’s warranty may be void if, for any reason, the heater is improperly installed and/or operated. Be sure to follow the instructions set forth in this manual.
!
CAUTION
OPERATING THIS HEATER CONTINUOUSLY AT WATER TEMPERATURE BELOW 20°C.
WILL CAUSE HARMFUL CONDENSATION AND WILL DAMAGE THE HEATER AND VOID
THE WARRANTY. Do not use the heater to protect pools or spas from freezing if the final maintenance temperature desired is below 20°C., as this will cause condensation related problems.
CODE REQUIREMENTS
Installation must be in accordance with the following:
• Manufacturer’s Installation Instructions
• AS/NZS 5601.1 for Gas Installations
• Local Gas Fitting Regulations,
• Municipal Building Codes,
• S.A.A. Wiring Code,
• Local Electrical Regulations
• Any other statutory regulations
!
DANGER
CARBON MONOXIDE GAS IS DEADLY – Exhaust from this pool heater contains toxic levels of carbon monoxide, a dangerous, poisonous gas you cannot see or smell.
CONSUMER INFORMATION AND SAFETY
!
WARNING
The U.S. Consumer Product Safety Commission warns that carbon monoxide is an
“invisible killer”. Carbon monoxide is a colorless and odorless gas.
1. Carbon monoxide is produced by burning fuel, including natural gas and propane.
2. Proper installation, operation and maintenance of fuel-burning appliances in the home is the most important factor in reducing carbon monoxide poisoning.
3. Be sure that fuel burning appliances such as heaters are installed by professionals according to manufacturer’s instructions and codes.
4. Always follow the manufacturer’s directions for safe operation.
5. Have the heating system (including vents) inspected and serviced annually by a trained service technician.
6. Examine vents regularly for improper connections, visible cracks, rust or stains.
7. Install battery-operated carbon monoxide alarms. The alarms should be certified to the requirements of the most recent UL, IAS, CSA and IAPMO standard for carbon monoxide alarms. Test carbon monoxide alarms regularly and replace dead batteries.
!
WARNING
The U.S. Consumer Product Safety Commission warns that elevated water temperature can be hazardous. See below for water temperature guidelines before setting temperature.
1. Spa or hot tub water temperatures should never exceed 40° C. A temperature of 37° C. is considered safe for a healthy adult. Special caution is suggested for young children.
Prolonged immersion in hot water can induce hyperthermia.
2. Drinking of alcoholic beverages before or during spa or hot tub use can cause drowsiness which could lead to unconsciousness and subsequently result in drowning.
3. Pregnant women beware! Soaking in water above 37° C. can cause fetal damage during the first three months of pregnancy (resulting in the birth of a brain-damaged or deformed child).
Pregnant women should stick to the 37° C. maximum rule.
4. Before entering the spa or hot tub, the user should check the water temperature with an accurate thermometer. Spa or hot tub thermostats may err in regulating water temperatures by as much as -15° C.
5. Persons with a medical history of heart disease, circulatory problems, diabetes or blood pressure problems should obtain their physician’s advice before using spas or hot tubs.
6. Persons taking medication which induce drowsiness, such as tranquilizers, antihistamines or anticoagulants should not use spas or hot tubs.
!
WARNING
Should overheating occur or the gas supply fail to shut off, turn off the manual gas control valve to the heater. Do not use this heater if any part has been under water.
Immediately call a qualified service technician to inspect the heater and to replace any part of control system and gas control which has been under water.
Section 2. Introduction
I pg 06
SAFETY INFORMATION
The Turbotemp pool heaters are designed and manufactured to provide many years of safe and reliable service when installed, operated and maintained according to the information in this manual. Throughout the manual, safety warnings and cautions are identified by the
“ “symbol. Be sure to read and comply with all of the warnings and cautions.
!
DANGER
CARBON MONOXIDE GAS IS DEADLY
• • READ OWNERS MANUAL COMPLETELY BEFORE OPERATING. • •
THIS PRODUCT MUST BE INSTALLED AND SERVICED BY A
PROFESSIONAL SERVICE TECHNICIAN, QUALIFIED IN POOL HEATER
INSTALLATION. Some jurisdictions require that installers be licensed. Check with your local building authority about contractor licensing requirements.
Improper installation and/or operation could create carbon monoxide gas and flue gases which could cause serious injury or death. Improper installation and/or operation will void the warranty.
Exhaust from this pool heater contains carbon monoxide, a dangerous, poisonous gas you cannot see or smell. Symptoms of carbon monoxide exposure or poisoning include dizziness, headache, nausea, weakness, sleepiness, muscular twitching, vomiting and inability to think clearly. IF YOU
EXPERIENCE ANY OF THE ABOVE SYMPTOMS, IMMEDIATELY TURN
OFF THE POOL HEATER, LEAVE THE VICINITY OF THE POOL OR SPA
AND GET INTO FRESH AIR IMMEDIATELY. THE POOL HEATER MUST BE
THOROUGHLY TESTED BY A GAS PROFESSIONAL BEFORE RESUMING
OPERATION.
EXCESSIVE CARBON MONOXIDE EXPOSURE CAN CAUSE BRAIN
DAMAGE OR DEATH.
Install this pool heater far from open windows, doors, vents and other openings, see page 16 for minimum distances.
Waterco strongly recommends that all vents, pipes and exhaust systems be initially and periodically tested for proper operation. This testing can be accomplished by using a hand-held carbon monoxide meter and/or by consulting with a gas professional. Pool heaters must be used in conjunction with carbon monoxide detectors installed near the pool heater. The carbon monoxide detectors must be periodically inspected for proper operation so as to insure continued safety. Broken or malfunctioning carbon monoxide detectors must be replaced immediately.
!
WARNING
This heater is equipped with an unconventional gas control valve that
is factory set with a manifold pressure of 11 ± 5 Pa. Improper installation, adjustment, alteration, service or maintenance can cause property damage, personal injury or loss of life. Installation or service must be performed by a qualified installer, service agency or the gas supplier. If this control is replaced, it must be replaced with an identical control.
Do not attempt to adjust the gas flow by adjusting the regulator setting.
!
WARNING
Risk of fire or explosion from incorrect fuel use or faulty fuel conversion.
Do not try to run a heater set up for natural gas on propane gas or vice versa. Only qualified service technicians should attempt to convert heater from one fuel to the other. Do not attempt to alter the rated input or type of gas by changing the orifice. If it is necessary to convert to a different type of gas, consult your Waterco dealer. Serious malfunction of the burner can occur which may result in loss of life. Any additions, changes, or conversions required in order for the appliance to satisfactorily meet the application needs must be made by a Waterco dealer or other qualified agency using factory specified and approved parts. The heater is available for use with natural gas or LP (propane) gas only. It is not designed to operate with any other fuels. Refer to the nameplate for the type of gas the heater is equipped to use.
• Use heater only with the fuel for which it is designed.
• If a fuel conversion is necessary, refer this work to a qualified service technician or gas supplier before putting the heater into operation.
!
WARNING
Risk of fire or explosion from flammable vapors. Do not store gasoline, cleaning fluids, varnishes, paints, or other volatile flammable liquids near heater.
!
WARNING
Risk of explosion if unit is installed near propane gas storage. Propane
(LP) gas is heavier than air. Consult local codes and fire protection authorities about specific installation requirements and restrictions. Locate the heater away from propane gas storage and filling equipment as specified by the
Standard for the Storage and Handling of Liquefied Petroleum Gases (latest edition).
!
WARNING
Risk of fire. Do not place articles on, near or against the heater.
!
WARNING
Vent
Cover
Risk of burn hazard. To reduce the risk of injury, do not touch the side heater vent cover when the heater is operating. Side heater vent covers are HOT and can burn when touched causing personal injury. Do not allow children to play on or around heater or associated equipment.
!
WARNING
Risk of asphyxiation if exhaust is not correctly vented. Follow venting
instructions exactly when installing heater. Do not use a drafthood with this heater, as the exhaust is under pressure from the burner blower and a draft hood will allow exhaust fumes to blow into the room housing the heater. The heater is supplied with an integral venting system for outdoor installation.
Section 2. Introduction
I pg 08
!
CAUTION
Label all wires prior to disconnection when servicing controls. Wiring errors can cause improper and dangerous operation. Wiring errors can also destroy the control board.
• Connect heater to 240 Volt, 50 Hz., Single Phase power only.
• Verify proper operation after servicing.
• Do not allow children to play on or around heater or associated equipment.
• Never allow children to use the pool or spa without adult supervision.
• Read and follow other safety information contained in this manual prior to operating this pool heater.
GENERAL SPECIFICATIONS
NOTICE:
• Combustion air contaminated by corrosive chemical fumes can damage the heater and will void the warranty.
• The Combination Gas Control Valve on this heater differs from most appliance gas controls.
If it must be replaced, for safety reasons replace it only with an identical gas control.
• The access door panels must be in place to provide proper ventilation. Do not operate the heater for more than five (5) minutes with the access door panels removed.
• This heater is design certified by IAPMO as complying with the Standard for Gas Fired Pool
Heaters, and is intended for use in heating fresh water swimming pools or spas.
• The heater is designed for the heating of chlorine, bromine or salt system swimming pools and spas. It should NOT be used as a space heating boiler, or general purpose water heater.
The heater requires an external 240 VAC single-phase electric power source.
• The heater should be located in an area where leakage of the heater or connections will not result in damage to the area adjacent to the heater or to the structure. When such locations cannot be avoided, it is recommended that a suitable drain pan, adequately drained, be installed under the heater. The pan must not restrict air flow.
• The heater may not be installed within 3.5M (11.5 ft.) of the inside surface of a pool or spa unless it is separated by a solid fence, wall or other permanent barrier.
INSTALLATION INSTRUCTIONS
THIS PRODUCT MUST BE INSTALLED AND SERVICED BY A PROFESSIONAL SERVICE
TECHNICIAN, QUALIFIED IN POOL HEATER INSTALLATION.
Waterco strongly recommends that all vents, pipes and exhaust systems be initially and periodically tested for proper operation. This testing can be accomplished by using a handheld carbon monoxide meter and/or by consulting with a gas professional.
Pool heaters must be used in conjunction with carbon monoxide detectors installed near the pool heater. The carbon monoxide detectors must be periodically inspected for proper operation so as to insure continued safety. Broken or malfunctioning carbon monoxide detectors must be replaced immediately.
HEATER DESCRIPTION
Figure 1 is a diagram of the heater showing how it operates. Precisely matched orifice plates meter the air and gas into the mixer. The blower draws the air and gas through the mixer and forces it into the burner’s flame holder. A sealed heat exchanger surrounds the flame holder, discharging exhaust gases out the flue.
Five (5) cm PVC water piping connects directly to the manifold/ header on the heat exchanger using 5 cm PVC slip unions provided with the heater. The outer manifold remains cool; no heat sinks are required. A thermal regulator and an internal bypass regulate the water flow through the heat exchanger to maintain the correct outlet temperature. The heater operator control panel board assembly is located on top of the heater.
Inlet
(Cold
Water)
Air
Mixer
Blower
Outlet
(Mixed
Water)
Burner
Figure 1.
Heating Coils
Section 3. Installation
I pg 10
SEQUENCE OF OPERATION
An electronic temperature sensing thermistor in the manifold adapter inlet controls the heater operation. When the inlet water temperature drops below the temperature set on the
operating
control, the burner controller supplies power to the combustion air blower through a series of safety interlocks. The interlocks consist of: above 53° C (127° F), and
automatic gas shut-off (AGS) switch, which opens if the heat exchanger outlet temperature goes above 60° C (140° F).
• the reaches 249° C (480° F).
• the
goes above 55° C (131° F), and....
inlet temperature control switch, which opens if the inlet temperature goes above
45° C (110° F).
The air flow switch (AFS) senses the pressure drop across the air metering orifice. As soon as there is sufficient air flow, the AFS closes, closing the circuit to the
hot surface igniter (HSI), which ignites the fuel mixture. On a call for heat, the blower and HSI are energized. In about 20 seconds, the gas valve opens and ignition occurs. The HSI then switches to a sensing mode and monitors the flame.
The heater is equipped with a digital operating control that enables the user to pre-set the desired pool and spa water temperatures. The control enables the user to select between pool and spa heating, and features a digital display that indicates the water temperature.
PUTTING THE HEATER INTO SERVICE
If the heater is installed below the level of the pool, or more than 0.6 meters (2 feet) above pool level, the pressure switch setting should be adjusted. See “WATER PRESSURE SWITCH” in the “SAFETY CONTROLS Section” (page 32) and the “CAUTION” under “BELOW POOL
INSTALLATION Section” (page 12).
Before putting the heater into service for the first time, follow the instructions under “BEFORE
START-UP” (page 30) in the front of this manual. Check for proper operation of the heater by following the steps under “OPERATION INSTRUCTIONS.”
Damage to equipment caused by improper installation or repair will void the warranty.
SPECIFICATIONS
These installation instructions are designed for use by qualified personnel only, trained especially for installation of this type of heating equipment and related components. Some states require installation and repair by licensed personnel. If this applies in your state, be sure your contractor bears the appropriate license. See Figure 2 for Outdoor Installations.
DIMENSIONS IN CENTIMETERS & INCHES
58.5 cm
(23.02")
71.5 cm
(28.15")
82.8 cm
(32.61")
53.3 cm
(21.0")
40.6 cm
(16")
FRONT
ELECTRICAL
CONDUIT PORT
TOP
EXHAUST SIDE
40.6 cm
(16.0")
57.7 cm
(22.7")
71.6 cm
(28.2")
Figure 2.
PLUMBING SIDE
14.2 cm
(5.6")
25.7 cm
(10.13")
Section 3. Installation
I pg 12
PLUMBING CONNECTIONS
The Turbotemp heater has the unique capability of direct schedule 40
PVC plumbing connections. A set of bulkhead fittings is included with the
Turbotemp to insure conformity with
Waterco’s recommended PVC plumbing procedure. Other plumbing connections can be used. See Figure 3 for plumbing connections.
POOL
HEATER
MANUAL
BY-PASS
TO
POOL
GATE
VALVE
FILTER
PUMP
Figure 3.
FROM POOL
!
CAUTION
Before operating the heater on a new installation, turn on the circulation pump and bleed all the air from the filter using the air relief valve on top of the filter. Water should flow freely through the heater. Do not operate the heater unless water in the pool/spa is at the proper level. If a manual by-pass is installed, temporarily close it to insure that all air is purged from the heater.
VALVES
When any equipment is located below the surface of the pool or spa, valves should be placed in the circulation piping system to isolate the equipment from the pool or spa. Check valves are recommended to prevent back-siphoning. Backsiphoning is most likely to occur when the pump stops, creating a pressure-suction differential. Do NOT sanitize the pool by putting chlorine tablets or sticks into the skimmer(s). When the pump is off, this will cause a high concentration of chlorine to enter the heater, which could cause corrosion damage to the heat exchanger.
!
CAUTION
Exercise care when installing chemical feeders so as to not allow back siphoning of chemical into the heater, filters or pump. When chemical feeders are installed in the circulation of the piping system, make sure the feeder outlet line is down stream of the heater, and is equipped with a positive seal noncorrosive “Check Valve”, (P/N
R172288), between the feeder and heater.
MANUAL BY-PASS
( WATER FLOW RATE)
Where the water flow rate exceeds the maximum 454 LPM, a manual bypass should be installed and adjusted. After installing the valve, adjust the valve to bring the flow rate within the acceptable range.
Then remove the valve handle or lock it in place to avoid tampering.
See Figure 4.
Table 1.
Model Min. LPM (GPM) Max. LPM (GPM) *
200
300
76 (20)
114 (30)
454 (120)
454 (120)
400 152 (40) 454 (120)
*Do not exceed the maximum recommended flow rate for the connecting piping.
See page 32 for Pressure Relief Valve Installations.
Cool water
Warm water out
1. Set Manual
By-Pass Valve.
2. Remove Handle.
Outlet to pool
Figure 4.
Inlet to heater
WATER CONNECTIONS
The heater requires proper water flow and pressure for its operation. See Figure 5 for the recommended installation. The filter pump discharges to the filter, the filter discharges to the heater, and the heater discharges directly to the pool or spa.
A manual bypass valve should be installed across the heater when the pump flow exceeds
454 LPM (120 GPM). See “WATER FLOW RATE” on page 11 - Table 1 for setting of the manual by-pass valve.
Make sure that the outlet plumbing from the heater contains no shut-off valves or other flow restrictions that could prevent flow through the heater (except for below pool as noted below,
Figure 5.
or winterizing valves where needed). To switch flow between the pool and spa, use a diverter valve. Do not use any valve that can shut off the flow. Do not use a shut-off valve to isolate the heater unless it is below the level of the pool or spa. Install the chemical feeder downstream of the heater. Install a chemical resistant one-way check valve between the heater and the chemical feeder to prevent back-siphoning through the heater when the pump is off.
NOTICE: If the heater is plumbed in backwards, it will cycle continuously. Make sure piping from filter is not reversed when installing heater.
Connect the heater directly to 5 cm PVC pipe, using the integral unions provided. Heat sinks are not required. The low thermal mass of the heater will prevent overheating of the piping connected to the pump even if the heater shuts down unexpectedly.
Occasionally a two-speed pump will not develop enough pressure on the low speed to operate the heater. In this case, run the pump at high speed only to operate the heater. If this does not solve the problem, do not try to run the heater. Instead, correct the installation.
Do not operate the heater while an automatic pool cleaner is also operating. If the circulation pump suction is plugged (for example by leaves), there may not be adequate flow to the heater.
Do not rely on the pressure switch in this case.
Local codes may require the installation of a pressure relief valve (PRV), see page 50 for
“PRESSURE RELIEF INSTRUCTIONS”.
BELOW POOL INSTALLATION
If the heater is below water level, the pressure switch must be adjusted. This adjustment must be done by a qualified service technician.
See following CAUTION before installation.
!
CAUTION
BELOW OR ABOVE POOL INSTALLATION
The water pressure switch is set in the factory at 21 kPa (± 5 kPa). This setting is for a heater installed at pool level. If the heater is to be installed more than 0.3 m above or below, the water pressure switch must be adjusted by a qualified service technician.
See page 36, Figure 28.
Section 3. Installation
I pg 14
FLOW SWITCH
If the heater is installed more than 1.5 m above the pool or more than 1.2 m below the pool level, you will be beyond the limits of the pressure switch and a flow switch must be installed. Locate and install the flow switch externally on the outlet piping from the heater, as close as possible to the heater. Connect the flow switch wires in place of the water pressure switch wires.
GAS CONNECTIONS
GAS LINE INSTALLATIONS
The gas supply must be installed in accordance with the Gas Installation Code, AS/NZS 5601.1, as applicable and all applicable local codes.
Before installing the gas line, be sure to check which gas the heater has been designed to burn.
This is important because different types of gas require different gas pipe sizes. The rating plate on the heater will indicate which gas the heater is designed to burn. Table 2 below shows the recommended gas inlet pipe sizes required for the distance from the gas meter to the heater.
The table is for natural gas at a specific gravity of .65 and propane at a specific gravity of 1.55.
When sizing gas lines, calculate 0.9 additional meters of straight pipe for every elbow used.
When installing the gas line, avoid getting dirt, grease or other foreign material in the pipe as this may cause damage to the gas valve, which may result in heater failure.
The gas meter should be checked to make sure that it will supply enough gas to the heater and any other appliances that may be used on the same meter. Insufficient gas supply will cause the heater to operate below its designed performance or not at all. The gas line from the meter will usually be of a larger size than the gas valve supplied with the heater. Therefore a reduction of the connecting gas pipe will be necessary. Make this reduction as close to the heater as possible. Gas supply companies are increasingly supplying natural gas to new installations with 2.75 kPa; this means if the gas pressure is not adjusted to the correct working pressure, the heater will be over gassed and cause serious damage within minutes. This damage is not covered under the heater warranty.
Install a manual shut-off valve that conforms with Type 1 or Type 2 as per AG201 and/or AS4617 standards, and a sediment trap/drip leg and union located outside the heater panels, see Figure
6. Do not use a restrictive gas cock.
The heater and any other gas appliances must be disconnected from the gas supply piping system during any pressure testing on that system, (greater than 6.0 kPa). The heater and its gas connection must be leak tested before placing the heater in operation.
Do not use flame
to test the gas line. Use soapy water or another nonflammable method.
NOTE
A manual main shut-off valve must be installed externally to the heater.
!
WARNING
DO NOT INSTALL THE GAS LINE UNION INSIDE THE HEATER CABINET. THIS WILL
VOID YOUR WARRANTY.
GAS PIPE SIZING
Heater Size
200
300
400
0 to 15 m
Distance from the Meter
16 to 30 m 31 to 60 m
25 mm 32 mm 32 mm
32 mm
32 mm
32 mm
40 mm
40 mm
50 mm
Table 2.
SEDIMENT TRAP/DRIP LEG
Install a sediment trap/drip leg and union located outside the heater panels in accordance with National code requirements. Do not use a restrictive gas cock. The sediment trap/drip leg shall be either a tee fitting with a capped nipple in the bottom outlet which can be removed for cleaning, as illustrated in Figure 6, or an other device recognized as an effective sediment trap/drip leg. All gas piping should be tested after installation in accordance with local codes.
Figure 6.
TESTING GAS LEAKS AND GAS PRESSURE
Before operating the heater, the heater and its gas connections must be leak tested. Do NOT use an open flame to test for leaks. Test all gas connections for leaks with soapy water.
The gas valve must be completely disconnected from the gas supply piping system during any pressure testing of that system at test pressures in excess of 6.0 kPa (.87 psig).
TESTING THE GAS PRESSURE THROUGH THE COMBINATION GAS CONTROL VALVE
!
WARNING
Risk of fire and explosion. Alteration, service, or maintenance of the Combination Gas
Control Valve can lead to fire or explosion, causing loss of life, personal injury, and/or property damage. DO NOT ATTEMPT TO ADJUST THE GAS CONTROL VALVE.
These instructions are for the use of qualified service technicians only!
1. Shut off the gas supply to the heater.
2. Loosen the small screw inside the pressure tap as shown in Figure 7.
3. Connect the manometer hose.
4. Open the gas supply to the heater.
5. Turn on the heater.
6. Take the gas pressure reading.
7. Turn off the heater.
Section 3. Installation
I pg 16
8. Shut off the gas supply to the heater.
9. Disconnect the manometer hose.
10. Tighten the small screw inside the pressure tap.
11. Open the gas supply to the heater.
12. Verify that the seal connection in the pressure tap is closed by testing for leaks with soapy water.
Note: If the pressure reading is out of range,
(see Table 3), regulate the incoming gas pressure.
INLET GAS PRESSURE REQUIREMENTS
Gas Pressure
Natural Gas
Propane Gas
Minimum
1.0 kPa
2.5 kPa
Maximum
6.0 kPa
6.0 kPa
NOTE: The minimum value approved for input adjustment.
Do not exceed the maximum supply pressure.
All readings must be taken while heater is operating. Any adjustments or readings made while heater is off will result in performance problems.
Table 3.
Figure 7.
OUTDOOR INSTALLATION (Australia)
For heaters located outdoors, using the built-in stackless venting system.
!
DANGER
CARBON MONOXIDE GAS IS DEADLY – Exhaust from this pool heater contains carbon monoxide, a dangerous, poisonous gas you cannot see or smell. Symptoms of carbon monoxide exposure or poisoning include dizziness, headache, nausea, weakness, sleepiness, muscular twitching, vomiting and inability to think clearly. IF YOU EXPERIENCE
ANY OF THE ABOVE SYMPTOMS, IMMEDIATELY TURN OFF THE POOL HEATER, LEAVE
THE VICINITY OF THE POOL OR SPA AND GET INTO FRESH AIR IMMEDIATELY. THE
POOL HEATER MUST BE THOROUGHLY TESTED BY A GAS PROFESSIONAL BEFORE
RESUMING OPERATION.
EXCESSIVE CARBON MONOXIDE EXPOSURE CAN CAUSE BRAIN DAMAGE OR
DEATH.
!
WARNING
Risk of explosion if a unit burning propane gas is installed in a pit or other low spot.
Propane is heavier than air. Do not install the heater using propane in pits or other locations where gas might collect. Consult your local building code officials to determine installation requirements and specific installation restrictions of the heater relative to propane storage tanks and filling equipment. Installation must meet the requirements for the Standard for the
Storage and Handling of Liquid Petroleum Gases. Consult local codes and fire protection authorities about specific installation restrictions.
OUTDOOR INSTALLATION (Australia)
Locate the heater in an open, unroofed area and on a level surface that is protected from drainage or run-off. Install the heater in an area where leaves or other debris will not collect on or around the heater.
BASE FOR USE ON
COMBUSTIBLE FLOORS
Figure 8.
It is recommended that a non-combustible base be a platform under the heater constructed of hollow masonry blocks, not less than 100 millimeters (mm) thick (laid with ends unsealed and joints matched for air circulation). Cover blocks with 0.75 mm (min.) galvanized sheet metal, see Figure 8.
To avoid damage to the electronic components in the heater, take care to prevent prolonged exposure to driving sources of water (such as lawn sprinklers, heavy roof runoff, hoses, etc.).
Avoid operation in persistent, extreme, moist or salty environments.
In extreme weather, shut down the heater and disconnect the power to it until the weather has moderated. In areas subject to hurricanes or very high winds, purchase the Bolt Down
Bracket Kit, P/N 460738, see Figure 9.
SHEET
METAL
BLOCKS
152.4 mm Min.
152.4 mm Min.
Hollow masonry blocks, not less than 100 mm thick, (laid with ends unsealed and joints matched for air circulation). Cover blocks with
0.75 mm (min.) galvanized sheet metal.
Figure 9.
HEATER CLEARANCES – OUTDOOR
IMPORTANT!
• In an outdoor installation it is important to ensure water is diverted from overhanging eves with a proper gutter/ drainage system. The heater must be set on a level foundation for proper drainage.
• This unit shall not be operated outdoors at temperatures below -7˚C.
If the heater is located under a roof or deck overhang, there must be at least 1 meter (3 ft.) of clearance between the bottom of the overhang and the top of the heater exhaust vent, see
Figure 10. If the heater is under a roof or deck overhang, the space around the heater must be open on three sides.
For minimum exhaust vent clearances for building openings, see below Figure 11.
Orient the heater for convenient access to the water connections and the gas and electrical connections.
Check local building codes for setback (property line) requirements.
1 meter (3 ft.) or more
Figure 10.
Section 3. Installation
I pg 18
!
CAUTION
If installing the heater next to or near an air conditioning unit or a heat pump, allow a minimum of 91.4 cm (36 in.) between the air conditioning unit and the heater.
Figure 11.
!
WARNING
Risk of fire and explosion. Do not spray aerosols in the vicinity of the heater while it is in operation. Chemicals should not be stored near the heater installation. Combustion air can be contaminated by corrosive chemical fumes which can damage the heater and will void the warranty.
INDOOR VENTING — General Requirements
NOTE: REMOVE OR COVER “OUTDOOR ONLY” LABEL LOCATED ON HEATER OUTSIDE
PANEL WITH “INDOOR INSTALLATION” LABEL (P/N 474275) INCLUDED IN ACCESSORY
BAG (P/N 473607).
INDOOR INSTALLATION
(SEE INSTALLATION GUIDE FOR CORRECT PLACEMENT OF THIS LABEL)
P/N 474275
If you are considering connecting this heater to a pre-existing vent system, make sure that the vent system meets the appropriate venting requirements as given in this manual on pages 17-
28. If not, replace the vent system. DO NOT use a draft hood with this heater. The Turbotemp heaters are capable of a 270-degree discharge rotation and with a vent gas temperature less than 204° C (400° F). The total length of the horizontal run must not exceed the length that is listed in Table 7, Page 24.
HEATER CLEARANCES — General Requirements
INDOOR INSTALLATION AND OUTDOOR SHELTER
The following clearances must be maintained from the nearest walls: (See Figure 12 and Figure
12a)
TOP .............................. 15 cm. (6 in)
EXHAUST SIDE ......... 15 cm (6 in.)
HEADER SIDE ........... 15 cm (6 in.)
DOOR PANELS* ........ 15 cm (6 in.)
Note (*) For service access it is advisable to allow for sufficient clearance on at least one door panel. The heater is designed for installation on combustible flooring. For installation on carpeting, the heater must be mounted on a metal or wood panel that extends at least three inches (10cm) beyond the base of the heater. If the heater is installed in a closet or alcove, the entire floor shall be covered by the panel. On an outdoor shelter installation, the exhaust discharges into a vent pipe. Orient the heater so that the vent pipe does not interfere with adjustment of the operating controls. The control panel located on the top panel can be rotated to any of the three sides of the heater for easy access. However, the control panel must not be located on the side where the vent is located.
Chimney or Gas Vent
(*) For service access, it is advisable to allow for sufficient clearance on at least one door panel.
15 cm (6 in)
Vent Cap and
Riser Furnished by Installer
Outlet Air
Opening
15 cm* (6 in)
15 cm (6 in)
15 cm*
(6 in)
Side
Wall Vent
Heater
Inlet Air
Opening
15 cm (6 in)
Figure 12.
Figure 12a.
OUTSIDE VENT COVER REMOVAL
The heater is supplied from the factory with a built-in stackless outside vent for outdoor installation. Remove the outside vent cover for outdoor shelter installation.
Section 3. Installation
I pg 20
COMBUSTION AIR SUPPLY
For indoor installation, the heater location must provide sufficient air supply for proper combustion and ventilation of the surrounding area
(in accordance with AS/NZS 5601.1).
The minimum requirements for the air supply specify that the room in which a heater is installed should be provided with two permanent air supply openings; one within 30 cm (12 in) of the ceiling, the other within 30 cm (12in) of the floor for combustion air, in accordance with the AS/
NZS 5601.1 as applicable, and any local codes that may apply. These openings shall directly, or through duct, connect to outdoor air.
Waterco Limited does not recommend indoor installations that do not provide combustion air from outside the building.
Air Supply Requirement Guide for Turbotemp Heaters
Model
200
300
400
Minimum Net Free Open Area for Each Opening*
(Square Inches/Centimeters)
All Air From Inside Building
Combustion Vent
200 sq. in.
1290 sq. cm.
200 sq. in.
1290 sq. cm.
All Air From Outside Building
Combustion Vent
50 sq. in.
323 sq. cm.
50 sq. in.
323 sq. cm.
325 sq. in.
2097 sq. cm.
325 sq. in.
2097 sq. cm.
80 sq. in.
516 sq. cm.
80 sq. in.
516 sq. cm.
400 sq. in.
2580 sq. cm.
400 sq. in.
2580 sq. cm.
100 sq. in.
645 sq. cm.
100 sq. in.
645 sq. cm.
* Area indicated is for one of two openings; one at floor level and one at the ceiling.
Table 4.
Combustion 3 in. PVC Pipe
Inlet Air Intake Duct Requirements*
Combustion Air Intake 3 in. Pipe
(Vertical or Horizontal)
No. of 90° Elbows
0
Maximum Length in Feet (M)
70 ft. (21.3 M)
1
2
58 ft. (17.7 M)
46 ft. (14.0 M)
3
4
34 ft. (10.4 M)
22 ft. ( 6.7 M)
!
WARNING
DO NOT USE PVC PIPE FOR FLUE EXHAUST VENT. FLUE EXHAUST VENT
TEMPERATURES CAN BE IN EXCESS OF 400° F. FLUE EXHAUST VENT
MUST BE
CATEGORY I or CATEGORY III METAL VENT.
Note (*) Combustion Air Intake Duct Connection Kit (Part Number 6844326) for all Turbotemp heater models can be purchased separately. See page 52 for parts list.
Section 3. Installation
I pg 22
NOTE
Each 90-degree elbow reduces the maximum horizontal PVC air intake duct run by 3.6 metres and each 45-degree elbow in the PVC air intake duct run reduces the maximum run by 1.8 metres. See the Table 5 above for the maximum lengths using 90-degree elbows.
Corrosive Vapors and Possible Causes
Area
Chlorinated swimming pools and spas
New construction and remodeling areas
Beauty parlors
Refrigeration plants or various industrial finishing and processing plants
Dry cleaning and laundry areas
Likely Contaminants
Pool or spa cleaning chemicals. Acids, such as hydrochloric or muriatic acid.
Glues and cements, construction adhesives, paints, varnishes, and paint and varnish strippers. Waxes and cleaners containing calcium or sodium chloride.
Permanent wave solutions, bleaches, aerosol cans containing chlorocarbons or fluorocarbons.
Refrigerants, acids, glues and cements, construction adhesives.
Bleaches, detergents, or laundry soaps containing chlorine.
Waxes and cleaners containing chlorine, calcium or sodium chloride.
Table 5.
!
CAUTION
Chemicals should not be stored near the heater installation. Combustion air can be contaminated by corrosive chemical fumes which can void the warranty.
VENT INSTALLATION –
INDOOR INSTALLATION OR OUTDOOR SHELTER
Flueing must be in accordance with AS/NZS 5601.1
Always vent the heater to the outdoors, see Note*.
• Vent it vertically using double wall vent
connector pipe.
NOTE *: Vent must be at least 2.4 m (8 ft) away from nearest vertical surface. Vents extending 1.5 m (5 ft) or more above the roof must be braced or guyed. Consult your local code officials for detailed information.
Locate the heater so as to minimize the length of horizontal venting and the number of vent elbows required. Horizontal vent runs must slope to allow exhaust condensate to drain and it is recommended to have a condensate drain as described in the venting installation instructions.
VERTICAL VENTING
(See Figures 12 and 14)
Vent the heater vertically in a system in accordance with AS/NZS 5601.1 and local codes. Double-wall vent connector is recommended; however single-wall pipe is allowed in some circumstances. Consult your local code official for detailed information. Do not use a draft hood with this heater.
To connect a double wall metal gas vent to the heater, order the appropriate Metal Flue Collar from the chart below:
1. See Table 6 to determine allowable vent sizes for your heater.
Metal Flue Collar
100 mm x 150 mm (4” x 6”)
100 mm x 200 mm (4” x 8”)
Table 6.
Part No.
684431106
684431108
Figure 13.
NOTICE: Table 6 is for installations in which the total lateral vent length (that is, the horizontal distance from the flue collar to the main vertical portion of the vent) is less than half the total vent height (the vertical distance from the flue collar to the vent termination) and which have three or less elbows in the system. For vent lenghts greater than 16 m (52.5 ft), only one elbow is allowed. See Table 6a below for details.
Read “VERTICAL VENTING” before using this table.
Section 3. Installation
I pg 24
Table 6.
– Permitted Minimum and Maximum Vent Heights By Size and Heater Model
Vent Size
Double-Wall Vent with Double-Wall Connector in Meters (Feet)
Model 200
Height min./max.
Model 300
Height min./max.
Model 400
Height min./max.
150 mm (6 in.) 1.8 m (6 ft.) / 22 m (72 ft.) 9 m (30 ft.) / 22 m (72 ft.) Not Suitable
200 mm (8 in.) 1.8 m (6 ft.) / 22 m (72 ft.) 1.8 m (6 ft.) / 22 m (72 ft.) 2.4 m (8 ft.) / 22 m (72 ft.)
Double-Wall Vent with Single-Wall Connector in Meters (Feet)
Vent Size
150 mm (6 in.)
Model 200
Height min./max.
1.8 m (6 ft.) / 4.6 m (15 ft.)
Model 300
Height min./max.
Not Suitable
Model 400
Height min./max.
Not Suitable
200 mm (8 in.) Not Suitable 1.8 m (6 ft.) / 6 m (20 ft.) 2.4 m (8 ft.) / 6 m (20 ft.)
Table 6a.
– Maximum Number of Elbows per Vent Lengths
Maximum
Elbows
Allowed
3
2
1
Maximum Number of Elbows per Vent Lengths
[C]
Total Vent Length
(C=A+B)
[A]
Horizontal Maximum
Vent Length
[B]
Vertical Vent Length
2m (6.6 ft.)
3m (9.8 ft.)
4m (13.1 ft.)
5m (16.4 ft.)
6m (19.7 ft.)
7m (23 ft.)
8m (26.2 ft.)
9m (29.5 ft.)
10m (32.8 ft.)
11m (36.1 ft.)
12m (39.4 ft.)
13m (42.6 ft.)
14m (45.9 ft.)
15m (49.2 ft.)
16m (52.5 ft.)
17m (55.8 ft.)
18m (59 ft.)
19m (62.3 ft.)
20m (65.6 ft.)
21m (68.9 ft.)
22m (72.2 ft.)
0.67m (2.2 ft.)
1m (3.3 ft.)
1.33m (4.4 ft.)
1.67m (5.5 ft.)
2m (6.6 ft.)
2.33m (7.6 ft.)
2.67m (8.8 ft)
3m (9.8 ft.)
3.33m (10.9 ft.)
3.67m (12 ft.)
4m (13.1 ft.)
4.33m (14.2 ft.)
4.67m (15.3 ft ft.)
5m (16.4 ft.)
5.33m (17.5 ft.)
5.67m (18.6 ft.)
6m (19.7 ft)
6.33m (20.8 ft.)
6.67m (21.9 ft.)
7m (23 ft.)
7.33m (24 ft.)
1.33m (4.4 ft.)
2m (6.6 ft.)
2.67m (8.8 ft.)
3.33m (10.9 ft.)
4m (13.1 ft.)
4.67m (15.3 ft.)
5.33m (17.5 ft.)
6m (19.7 ft.)
6.67m (21.9 ft.)
7.33m (24 ft.)
8m (26.2 ft.)
8.67m (28.4 ft.)
9.33m (30.6 ft.)
10m (32.8 ft.)
10.67m (35 ft.)
11.33m (37.2 ft.)
12m (39.4 ft.)
12.67m (41.6 ft.)
13.33m (43.7 ft.)
14m (45.9 ft.)
14.67m (48.1 ft.)
2. Install the metal Flue Collar in the Vent
Body of the heater (located under the outside vent cover). Fasten the metal
Flue Collar to the Vent Body with two #10 sheet metal screws. Use high temperature silicone RTV to seal the Flue Collar to the
Vent Body. Before connecting the metal
Flue Collar to the Vent Body, wet a clean cloth or paper towel with isopropyl alcohol
(rubbing alcohol) and vigorously wipe the socket of the Vent Body. Immediately wipe the cleaned surfaces dry with a clean cloth or paper towel. Repeat for the exterior of the 100 mm (4”) end of the metal Flue
Collar. Attach the metal Flue Collar to the
Vent Body using the RTV supplied with the kit, following the vent manufacturer’s instructions (included with kit).
3. Attach the vent pipe to the metal Flue Collar with sheet-metal screws.
!
WARNING
Risk of fire or asphyxiation if vent is not assembled according to manufacturer’s instructions or if vent parts from different
manufacturers are mixed. Vent parts from different manufacturers ARE NOT interchangeable. Mixing parts from more than one manufacturer may cause leaks or damage to vent. When assembling a vent, pick one manufacturer and be sure that all vent parts come from that manufacturer and are specified by the manufacturer for your system. Follow manufacturer’s instructions, local code requirements and
AS/NZS 5601.1 standards carefully during assembly and installation.
Figure 14. – Typical Metal Vent Pipe
Installation (Vertical Venting)
4. Install vent pipe so that it can expand and contract freely as the temperature changes. Support the vent pipe according to applicable codes and the vent manufacturer’s instructions. Pipe support must allow the vent pipe free movement out and back, from side to side, or up and down as necessary, without putting a strain on the heater or vent body. Slope horizontal pipe down to condensate trap at least 2 cm per meter (1/4 in per foot). Install approved condensate drains at low points where condensate might collect. Plumb condensate drains to a drain through hard piping or high temperature tubing such as silicone rubber or EPDM rubber – do not use vinyl or other low temperature tubing. Follow drain manufacturer’s installation instructions.
Section 3. Installation
I pg 26
5. Use approved fire stop for floor and ceiling penetrations. Use approved thimble for wall penetrations. Use a approved roof flashing, roof jack, or roof thimble for all roof penetrations.
Do not fill the space around the vent (that is, the clear air space in the thimble or fire stop) with insulation. The roof opening must be located so that the vent is vertical.
6.
Do not run the heater vent into a common vent with any other appliance.
!
WARNING
Fire Hazard. Do not vent the heater directly into a masonry chimney. Installation into a masonry chimney must use a chimney liner which must meet AS/NZS 5601.1 standards and all local code requirements.
!
WARNING
Risk of fire, carbon monoxide poisoning, or asphyxiation. It is recommended to use a
CO Monitor and Fire Alarm in rooms that contain gas fired appliances.
NOTE
After installation, installer must check for correct and safe operation of the heater.
HORIZONTAL OR VERTICAL VENTING - USING SINGLE-WALL STAINLESS GAS VENT
(See Figures 15, 16 & 17)
Vent the heater either horizontally or vertically using an optional vent adapter of the 150 mm (6 in) special gas approved stainless steel vent pipes. Installation must be in accordance with all local codes and ordinances/or the latest edition of the AS/NZS 5601.1 standards and/or local codes. The heater, when installed, must be electrically grounded and bonded in accordance with local codes. Do not use a draft hood with this heater. Install the vent according to the vent manufacturer’s detailed instructions. Note: Keep a 150 cm (6 in) minimum clearance between the vent pipe and combustible surfaces. Follow the vent manufacturer’s instructions and code requirements. Do not place any insulating materials around the vent or inside the required clear air space surrounding the vent. See Table 7 for maximum permissible vent lengths.
NOTE
The allowable vent runs for each vent pipe diameter are different and can not be exceeded.
150 mm (6 in.) Special Gas Vent
(Vertical or Horizontal)*
No. of 90° Elbows Maximum Length in Feet (M)
0 11.6 m (38 ft.)
Each 90-degree elbow reduces the maximum horizontal vent run by 3.6 m
(12 feet) and each 45-degree elbow in the vent run reduces the maximum vent run by 1.8 m (6 feet). See the Table 7 for the maximum vent lengths using 90° elbows.
1 8 m (26 ft.)
*Minimum vent length is 0.34M (1 ft.) or in accordance with vent manufacturer’s instruction, and local and national codes. Horizontal vents 1 m (3 in) or less in length do not require a condensate tee, but must slope down toward the outlet at 2 cm to the meter (1/4 in / ft.) to allow condensate to drain.
Table 7.
NOTE
It is recommended that vent runs over 5.4 m (18 feet) may need to be insulated to reduce condensation related problems and/or the use of a condensate trap in the vent run close to the heater may be necessary in certain installations such as cold climates. Horizontal vents 1 m (3 feet) or less in length do not require a condensate tee. The Turbotemp heater is suitable for throughthe-wall venting.
Flue gases may escape into the dwelling with any cracks or loose joints in the vent pipe, or
improper vent installation. The vent pipe must be of a sealed-seam construction and for operating temperatures less than 204° C (400°F). Vent pipe construction will be of AS/NZS
5601.1 approved non-corrosive material, such as stainless steel. A condensate trap may be needed. The use of “Approved” thimbles, roof jacks and/or side vent terminals are required; and the proper clearances to combustible materials must be maintained in accordance with type of vent pipe employed—in the absence of a clearance recommendation by the vent pipe manufacturer, the requirements of the Uniform Mechanical Code should be met. The ventilation
air requirements for the Turbotemp heater can be found on page 20. It is recommended that vent runs over 5.4 M (18 ft) may need to be insulated to reduce condensation related problems and/or the use of a condensate trap in the vent run close to the heater may be necessary in certain installations such as cold climates. Horizontal vents 1 M (3 ft) or less in length do not require a condensate tee. The Turbotemp heater is suitable for through-the-wall venting.
NOTE
After installation, installer must check for correct and safe operation of the heater.
CONNECTING SINGLE-WALL STAINLESS STEEL VENT TO THE HEATER
Metallic:
1. Order an optional appliance adapter kit, (Waterco offers optional appliance adapter kits, call
our Customer Service dept.):
- Part No. 6844320 150mm Flexible Duct Exhaust Double Wall Metal
2. Remove the outside vent cover.
3. Install the Appliance Adapter in the Vent Body of the heater (located under the outside Vent
Cover). Before connecting the Appliance Adapter to the Vent Body, wet a clean cloth or paper towel with isopropyl alcohol (rubbing alcohol) and vigorously wipe the socket of the
Vent Body. Immediately wipe the cleaned surfaces dry with a clean cloth or paper towel.
Repeat for the exterior of the heater end of the Appliance Adapter. Attach the appliance adapter to the vent body using the adhesive specified by the vent manufacturer, following the vent manufacturer’s instructions.
!
WARNING
Risk of carbon monoxide poisoning if adapter is improperly attached. Mechanical connections (such as screws) can cause cracking and leaks in the adapter. Do NOT drill holes or use screws to connect the appliance adapter to the heater vent body. Attach with manufacturer’s specified adhesive.
!
WARNING
Risk of fire or asphyxiation if vent is not assembled according to manufacturer’s
instructions or if vent parts from different manufacturers are mixed. Vent parts from different manufacturers ARE NOT interchangeable. Mixing parts from more than one manufacturer may cause leaks or damage to vent. When installing a vent, pick one manufacturer and be sure that all vent parts come from that manufacturer and are specified by the manufacturer for your system. Follow manufacturer’s instructions and local and AS/
NZS 5601.1 requirements carefully during assembly and installation.
Section 3. Installation
I pg 28
4. Install vent pipe so that it can expand and contract freely as the temperature changes.
Support the vent pipe according to applicable codes and vent manufacturer’s instructions.
Pipe support must allow the vent pipe free movement out and back, from side to side, or up and down as necessary, without putting a strain on the heater or vent body. It is recommended to slope the horizontal pipe down to condensate trap at least 2cm/M (1/4 in per foot). Install “Approved” condensate drains at low points where condensate might collect. Plumb condensate drains to a drain through hard piping or high-temperature tubing such as silicone rubber or EPDM rubber – do not use vinyl or other low temperature tubing.
Follow drain manufacturer’s installation instructions.
5. Use an “Approved” firestop for floor and ceiling penetrations. Use an “Approved” thimble for wall penetrations. Use an “Approved” roof flashing, roof jack, or roof thimble for all roof penetrations. Do not fill the space around the vent (that is, the clear air space in the thimble or firestop) with insulation. The roof opening must be located so that the vent is vertical.
6. Vent Termination – Vertical (See Figures 14, 15 and 16), for height of vent termination above the roof. Use an “Approved” vent terminal specified by local and national codes and your manufacturer’s instructions. A roof termination must be vertical.
7. Make sure entire installation is sealed according to approved standard.
Chimney or Gas Vent Chimney or Gas Vent
Vent Cap and
Riser Furnished by Installer
Vent Cap and
Riser Furnished by Installer
Outlet Air
Opening
Outlet Air Opening
Side
Wall Vent
Figure 15.
Heater
Inlet Air
Opening
Side
Wall Vent
Vent
Termination
0.3 M (1 in) Minimum above sn ow or finished grade
(whichever is higher)
Forced Air
Inlet
Figure 17.
1.2 M (4 in) Min.
1.2 M (4 in) Min.
1.2 M (4 in) Min.
Vent
Termination
0.3 M (1 in) Min.
1.2 M
(4 in)
Min.
Gas Meter r hor izontal distance to exhaust opening is less than 3.3 M (10 ft).
Heater
Inlet Air Opening
Figure 16.
Max. 304 mm (12 in)
Min. 76 mm (3 in)
Vent
Termination
At least 2.1 M (7 in) above grade adjacent to public walkways
8.
Vent Termination – Horizontal
The terminal must be located (See Figure 17):
• at least 76 mm (3 in) and at most 304 mm (12 in) out from the wall (see Figure 18), following the vent manufacturer’s instructions
• at least 304 mm (12 in) above finished grade or the normally expected snow accumulation level, whichever is higher
• at least 1.2 M (4 ft) below or horizontally from, or 0.3 M (1 ft) above, any doors or windows or gravity air inlet to a building
• at least 0.9 M (3 ft) above any forced air inlet located within 3 M (10 ft)
• at least 1.2 M (4 ft) horizontally from electric meters, gas meters, regulators and relief equipment
• at least 2.1M (7 ft) above grade adjacent to walkways or similar traffic areas.
The terminal must be located (See Figure 17):
• at least 3.3M (10 ft) from any opening into a building
• at least 0.3 M (12 in) above finished grade or the normally expected snow accumulation level, whichever is higher
• at least 1.2 M (4 ft) horizontally from electric meters, gas meters, regulators and relief equipment
• at least 2.1 M (7 ft) above grade adjacent to walkways or similar traffic areas
Allow at least 1 M (3 ft) vertical clearance over vent termination when terminating under an overhang or deck.
Avoid corners or alcoves where snow or wind could have an effect. Exhaust may affect shrubbery and some building materials. Keep shrubbery away from termination. To prevent staining or deterioration, sealing or shielding exposed surfaces may be required.
Metal
Vent
Body
Metal Special
Gas Vent requires
Appliance
Adapter
Support weight of pipe
Condensate
Tee
Condensate drain w/Trap
(Optional)
Figure 18.
Slope at least
(2 cm per Meter)
1/4" per foot down towards condensate drain
Approved
Termina l
12" (30.5 cm) Max.
3" (7.6 cm) Min.,
Clearance
!
WARNING
Fire Hazard. Do not run the heater vent into a common vent with any other appliance. Do not run the Special Gas Vent into, through, or within any active vent such as a factory built or masonry chimney.
NOTE: After installation, installer must check for correct and safe operation of the heater
Section 3. Installation
I pg 30
HORIZONTAL OR VERTICAL VENTING FLEXIBLE DUCT (FLEX-VENT)
(See Figures 15, 16, 17 & 19)
Table 8.
NOTE: THE ALLOWABLE VENT RUNS
FOR EACH VENT PIPE DIAMETER
ARE DIFFERENT AND CAN NOT BE
EXCEEDED.
It is recommended that vent runs over
No. of 90° Bends Maximum Length in Feet (M)
0
1
150 mm (6 in.) Flex-Vent
(Vertical or Horizontal)*
11.6 m (38 ft.)
8 m (26 ft.)
5.4 m (18 ft) may need to be insulated to reduce condensation related problems and/or the use of a condensate trap in
*Minimum vent length is 0.34M (1 ft.) or in accordance with vent manufacturer’s instruction, and local and national codes. Horizontal vents 1 m (3 in) or less in length do not the vent run close to the heater may be necessary in certain installations such as cold climates. Horizontal vents 1 m
(3 feet) or less in length do not require a condensate tee. The Turbotemp heater is suitable for through-the-wall venting.
See Table 8 for maximum permissible
Flexible Vent lengths.
require a condensate tee, but must slope down toward the outlet at 2 cm to the meter (1/4 in / ft.) to allow condensate to drain.
** Radius minimum to be 110 mm (4.33 in) as shown in
Figure 19.
Flexible Vent
Section
Figure 19.
!
CAUTION
Do NOT combine exhaust vent pipes to a common exhaust vent in multiple unit installations. Run separate vent pipes.
110 mm (4.33 in)
Radius Minimum
MINIMUM FLEX BEND RADIUS
NOTE: KEEP A 150 CM (6 IN) MINIMUM CLEARANCE BETWEEN THE VENT PIPE AND
COMBUSTIBLE SURFACES. FOLLOW THE VENT MANUFACTURER’S INSTRUCTIONS
AND CODE REQUIREMENTS.
Each 90° bend reduces the maximum horizontal vent run by 3.6 m (12 feet) and each 45° bend in the vent run reduces the maximum vent run by 1.8 m (6 feet). See Table 8 for the maximum vent length using one 90° bend.
NOTE
After installation, installer must check for correct and safe operation of the heater.
Corrosive Vapors and Possible Causes
Area
Chlorinated swimming pools and spas
Table 5.
Likely Contaminants
Pool or spa cleaning chemicals. Acids, such as hydrochloric or muriatic acid.
New construction and remodeling areas
Beauty parlors
Glues and cements, construction adhesives, paints, varnishes, and paint and varnish strippers. Waxes and cleaners containing calcium or sodium chloride.
Permanent wave solutions, bleaches, aerosol cans containing chlorocarbons or fluorocarbons.
Refrigeration plants or various industrial finishing and processing plants
Refrigerants, acids, glues and cements, construction adhesives.
Dry cleaning and laundry areas Bleaches, detergents, or laundry soaps containing chlorine.
Waxes and cleaners containing chlorine, calcium or sodium chloride.
CONTROL PANEL INDEXING
On an outdoor shelter installation, the exhaust discharges into a vent pipe. Orient the heater so that the vent pipe does not interfere with adjustment of the operating controls. The control panel located on the top panel can be rotated to any of the three sides of the heater for easy access, see Figure 20.
1. Remove the bolts from the door panels. Remove both door access panels.
2. Remove the four corner screws that secure the top panel.
Lift the top panel upward to remove the top panel.
3. Rotate the top panel to the desired position located at 90° angles. Note that the control panel must NOT be located on the side where the vent is located.
4. Replace the top panel down onto the side panels. Be sure that there are no wires caught under the panel.
5. Secure the top panel using the four corner screws.
6. Reattach the door access panels.
Top Panel
Door
Access Panel
Door
Access
Panel
Figure 20.
FINAL INSTALLATION CHECK
After installation, the installer MUST test and check that the heater is operating and functioning properly.
Some building codes require that the heater be anchored to the equipment pad or platform to withstand high wind pressures created during hurricanes. A Bolt Down Bracket Kit, P/N 460738, is available with anchor clamps designed to hold the unit to the equipment pad in high wind conditions, see Figure 21. Installation of the anchor clamps are recommended in all installations.
Figure 21.
ELECTRICAL CONNECTIONS
Electrical Rating 50 Hz 240 Volts AC, single phase
The heater is supplied with a 240V VAC, 10 AMP, 50 Hz power cord (AS/NZS 3112) approved for outdoor use. The power cord wire is 3 x 16 AWG (3 x 10 mm2).
!
CAUTION
This heater is designed to operate at 240 VAC. It is not recommended to be connected to OR operate on 208 VAC.
NOTE
• If any of the original wiring supplied with this heater must be replaced, installer must supply (No.
18 AWG, 600V, 105° C. U.L. approved AWM low energy stranded) copper wire or it’s equivalent.
Section 3. Installation
I pg 32
Please read the boxes headed “IMPORTANT! READ ME FIRST!” on pages 40 and 44 before proceeding.
1. All wiring must be in accordance with all applicable codes and
must be wired by a licensed electrician to AS3000 Wiring rules.
2. The heater, when installed, must be electrically grounded and bonded in accordance with local codes or, in the absence of local codes, with the National
Electrical Standards. A bonding lug is provided on the outside of the panel under the vent for this purpose.
3. Electrical power circuits to the pool heater must follow local codes and National
Electrical Standards.
4. All wiring between the heater and devices not attached to it, or between separate devices which are installed in the field, must be “Type T” wire rated for 35°C rise.
5.
The filter pump should run continuously when the heater is on, and for at least 15
minutes after the heater turns off. Any switches in the pump circuit (including circuit breakers) that can disconnect the pump must also disconnect the heater.
AC Plug
240 Volt
Figure 22.
including protective devices, into a grounded line. The heater is not sensitive to polarity.
Use the provided waterproof wire nuts when connecting the power supply.
A time clock controlling the filter pump should have a low-voltage Fireman’s Switch that switches off the heater at least 15 minutes before shutting off the pump.
CONNECTION OF FIREMAN’S SWITCH OR REMOTE CONTACT
!
CAUTION
This heater is designed to operate at 240 VAC. It is not recommended to be connected to OR operate on a 208 VAC.
REMOTE CONTROL CONNECTIONS
1. Switch off power to heater at main circuit breaker panel.
2. Unbolt and remove the access door panels.
3. Open control box cover (see Figure 23).
4a. To connect a 2-Wire Control (such as the Pentair Water Pool and Spa IntelliTouch™ or
EasyTouch™) or a timer:
- Remove the factory installed jumper from the Fireman’s Switch terminals.
- Connect wires between the Fireman’s Switch terminals on the heater and the relay.
Connect wires from the controller or timer to the Fireman’s Switch. Controller, timer or relay should be sized to handle 24VAC at 0.5 Amp (because it will be completing the 24VAC control board circuit on the heater as shown in Figure 24). DO NOT apply line voltage to the Fireman’s
Switch terminals. Use 18 gauge wire with a minimum 1.2 mm
(3/64 in.) thick insulation rated for a temperature rise of at least
105° C.
- Knock-outs are provided to route the wires through the bottom of the control box and past the junction box.
4b. To connect a 3-Wire Control:
- Connect wires between the control board terminals on the heater and the external relays, as shown in Figure
25 on page 32. Use at least 2 relays per heater, to allow for an “OFF setting” on each heater mode. Select relays that can handle logic level switching. DO NOT apply line voltage to control board terminals.
- Move jumper (as shown in Figure 25 on page 28) to enable external control and to disable the heater membrane pad’s “Pool
ON” and “Spa ON” buttons (the “OFF” key on the membrane pad remains functional).
- Knock-outs are provided to route the wires through the bottom and the top of the control box and past the junction box.
5. Close control box cover.
6. Re-install the access door panels.
To control heaters that are operated in parallel, connect wiring at same locations on heater as
2-Wire or 3-Wire Control. It is imperative that each control circuit is isolated from the other control circuits, to avoid that current will flow from one heater to another through the control circuits.
NOTICE: The fuse for the Fireman’s Switch is a
1.25 Amp 31.75 mm x 6.35 mm fast blow fuse, which is commonly available.
Figure 23.
Figure 24.
Section 3. Installation
I pg 34
TURBOTEMP WIRING DIAGRAM
(3-WIRE SYSTEM)
CONNECTION DIAGRAM
Inlet Temperature Control Switch and AGS Switch
Stack Flue Sensor
Gas Valve
Y/W
Y
W
W
R
R
BL
BL
O
O
O
O
PR
PR
Air Flow Switch
Extra Switch 1
Hi-Limit Switch
Pressure Switch
PS
HLS
ES1
AFS
TH IND GND
OPERATING CONTROL
MEMBRANE PAD
CONNECTION
AGS
SFS
GAS
JMP3
1
External Control Interface Circuit Disabled,
Heater Membrane Pad Enabled
JMP
Spa Line
Common Line
External Control Interface
W
1
BK
Pool Line
J6
Y
Y/R
Y
BR
BR
Y
Y
Y
Y/BL
Y/O
Y/W
Y
NA/LP
Models Only
JMP
F1 F2
24
VAC
DIAGNOSTIC INDICATOR
IGNITION CONTROL
MODULE
1
External Control Interface Circuit
Enabled, "Pool On" and "Spa On"
Keys Disabled. "OFF" Key on
Membrane Pad Remains Functional.
S1
240
S1/
120 L1
L2 S2 TH IND VALGND
GY GY BK GY
Y/W
Y/O
Y/BL
Y/R
120 VAC
IGNITER
Y/W
GND
Plug –12 pin
240V – Red
BK
GY
O
BK
BK
BK
1
GY
W
R
GY
12 Position
Receptacle
Y
BK
W W
BK
Y
R
Line 1
JUNCTION BOX
BR
Line 2
Ground
BL
G/Y
GND
BL
NOTICE: Touching any 24VAC wire, including the Fireman's Switch wire, to the 240V terminal while the heater is connected to line power will immediately destroy the control board and void the warranty.
G
GND
BL
R
L1
F1
BLOWER
Y
Y/W
Y/O
Y/BL
Y/R
Y Y Y Y
Y
24 VAC
SEC
Y
Y
FL
BK
W
O
W
TRAN S
L2
BM
R R W
TURBOTEMP ELECTRICAL SCHEMATIC LADDER DIAGRAM
L1
LADDER DIAGRAM
240
VAC
L2
L1 S1
IGNITER
S2 L2
F1
24 VAC
F2
240
VAC
BLOWER
GND
CLASS II
TRANSFORMER
24 VAC
OPERATING
CONTROL
24 VAC
GND
24V
COM NO
LOGIC
WATER
PRESSURE
SWITCH
HI
LIMIT
SWITCH
AIR
FLOW
SWITCH
TH
IND
VAL
AGS
SWITCH
INLET TEMPERATURE
CONTROL SWITCH
GAS VALVE
THERMISTOR
SENSOR
STACK FLUE
SENSOR
NOTES:
1.)
L1 L2 F1 F2 S1 24 VAC
2. )
3. )
S2 GND IND VAL AND TH
ARE CONNECTED ON THE IGNITION MODULE.
PIN AND SOCKET CONNECTOR.
IF ANY OF THE ORIGINAL WIRES AS SUPPLIED
WITH THE APPLIANCE MUST BE REPLACED,
THEY MUST BE REPLACED WITH TYPE 105° C
OR ITS EQUIVALENT.
Figure 26.
Section 4. Operation
I pg 36
OPERATION INSTRUCTIONS
BASIC SYSTEM OPERATION
Start pump, make sure the pump is running and is primed, to close the water pressure
switch and supply power to heater. Be sure the pool and/or spa is properly filled with water.
Follow the Lighting/Operating instructions below.
TURBOTEMP HSI ELECTRONIC IGNITION LIGHTING/OPERATION
FOR YOUR SAFETY: READ BEFORE LIGHTING
!
WARNING
If you do not follow these instructions exactly, a fire or explosion may result causing property damage, personal injury or loss of life.
Do not attempt to light the heater if you suspect a gas leak. Lighting the heater can result in a fire or explosion which can cause personal injury, death, and property damage.
START-UP AND OPERATION
START-UP AND SHUTDOWN INSTRUCTIONS ARE ON THE LABEL ATTACHED TO THE
COVER OF THE APPLIANCE CONTROL BOX.
BEFORE START-UP
A. This appliance does not have a pilot. It is equipped with an ignition device which automatically lights the burners. Do not try to light the burners by hand.
B.
BEFORE OPERATING, smell all around the appliance area for gas. Be sure to smell next to the floor because some gas is heavier than air and will settle on the floor.
WHAT TO DO IF YOU SMELL GAS
– Do not try to light any appliance.
– Do not touch any electrical switch; do not use any phone in your building.
– Immediately call your gas supplier from a neighbor’s phone.
Follow the gas supplier’s instructions.
– If you cannot reach your gas supplier, call the Fire Department.
C. Use only your hand to turn the gas control on or off. Never use tools. If you cannot change the ON/OFF setting by hand, don’t try to repair it, call a qualified service technician. Forced or attempted repair may result in a fire or explosion.
D. Do not use this heater if any part has been under water. Immediately call a qualified service technician to inspect the heater and to replace any part of the control system and any gas control which has been under water.
E. Do not operate the pool heater unless the pool or spa is properly filled with water.
F. Before operating the appliance for the first time or after it has been off for an extended time, perform the following checklist:
1. Remove debris or other articles from inside the heater and the area around the heater and its exhaust vent. Make sure the ventilation openings are clear of debris or obstruction. For installations in an enclosed space, make sure openings for combustion and ventilation air are unobstructed.
2. Keep heater area clear and free from combustibles, flammable liquids and chemicals.
3. Check that all water connections are tight.
4. Water must be flowing through the heater during operation. Make sure that pool/spa is filled with water and have pump operating. Check that water flow is unobstructed from the appliance. When operating for the first time or after an extended shut-down, run filter pump for several minutes to clear all air from the system.
OPERATING INSTRUCTIONS
1. STOP! Read the safety information on (page 34).
External Manual
Shut-off Valve
2. Set both pool and spa thermostats to the lowest settings.
3. Turn off all electric power to the appliance.
4. This appliance does not have a pilot. It is equipped with an ignition device which automatically lights the burner. Do not try to light the burner by hand.
5. Turn off the outside external manual shut-off gas valve, see Figure 27.
Figure 27.
6. Wait five (5) minutes to clear out any gas. If you then smell gas, STOP! Follow “B” in the
“Before Start-up” instructions (page 34). If you don’t smell gas, go to the next step.
7. Turn on the outside external manual shut-off gas valve, see Figure 27.
8. Set 3-way valves on inlet and outlet to pool or spa, as appropriate.
9. Turn on all electric power to the appliance.
10. Press either the POOL ON or SPA ON button switch on the operating control.
11. Set the thermostat to desired setting (NOTICE: Setpoint must be above actual water temperature or burner will not fire). See “OPERATING the CONTROL PANEL”.
12. The blower should come on immediately, and after about 20 seconds, the burner should fire. When operating for the first time, the burner may not fire on the first try because of air in the gas line. If it does not fire at first, push the OFF switch, wait five minutes, and again push the POOL or SPA ON switch. The burner should fire after about 20 seconds. You may have to repeat this until all of the air has cleared the gas line.
13. The burner should fire until the pool/spa temperature reaches the desired temperature set on the thermostat. The blower will continue to run for about 45 seconds after the burner shuts off. If any of the safety interlocks should open during burner operation, the burner shuts off immediately, but the blower continues to run for about 45 seconds. Should overheating occur or the gas supply fail to shut off, turn off the manual gas control valve to the appliance.
Section 4. Operation
I pg 38
14. If the appliance will not operate, follow the instructions below “TO TURN OFF GAS TO THE
APPLIANCE”, and call your service technician or gas supplier.
15. If the electrical power is lost while the heater is running, the heater will retain all program settings and the unit will come back to it’s original mode and settings once the power is restored.
TO TURN OFF GAS TO APPLIANCE
1. Press the OFF button on operating control.
2. Switch off all electric power to the unit.
3. Turn off the outside external manual shut-off gas valve, see Figure 27.
SAFETY CONTROLS
AIR FLOW SWITCH (AFS)
The air flow switch, (see Figure 28), is a safety device used to insure that the combustion air blower (fan) is operating and has been designed to monitor the vacuum (negative) pressure within the blower housing. The air flow switch is factory set and is connected upstream of the ignition module. The ignition module does not operate unless the air pressure switch and all safety switches are closed.
Air Flow Switch
Figure 28.
WATER PRESSURE SWITCH
!
WARNING
Hazardous pressure. Do not bypass the Water Pressure
Switch or render it inoperable.
Water
Pressure
Switch
The water pressure switch, (see Figure 29). If the water flow is restricted, the water pressure switch may prevent the burner from firing and cause the “Service System” light to go on. If the light remains on after the filter has been serviced, have a qualified service technician check the system.
For deck-level heater installations, the Water Pressure Switch is factory set at 20.6 kPa (3.00 psi).
NOTE: See, Below Pool Level
Installation instructions on page 13. If the pressure switch is .3M
(1 ft.) below or above the pool water level, reset the switch so that
Figure 29.
it is open when the pump is off and closed when the pump is running. Turn the star-wheel on the switch clockwise ( ) to raise setting (heater below the pool) and counterclockwise ( ) to lower the setting (heater above the pool – see Figure 30. Test the switch after resetting.
NOTICE: When the heater is mounted more than 1.5M (5 ft.) above or 1.2M (4 ft.) below the deck level, a Pressure Switch is no longer adequate. A Flow Switch must be installed instead.
NOTICE: Heater operation with incorrect Pressure Switch setting may cause operation with no water flow. Operation of the heater without sufficient water flow may severely damage it and
will void the warranty.
Turn star wheel clockwise to raise pressure set point if pressure switch is more than 1.2M (4 ft.) below water level
A reference scale is on the back of pressure switch
Star Wheel
Turn star wheel counterclockwise to lower pressure set point if pressure switch is more than 1.5M (5 ft.) above water level
Figure 30.
HIGH LIMITS
A “High Limit”, is a safety device that opens the electrical circuit and shuts off the heater based on a water temperature set point within the “High Limit Device”. The Turbotemp series of heaters contains two (2) high limit devices which are located on the main inlet /outlet header.
Diagnostic LED
1 Flash - Lockout
2 Flashes - Air Flow Fault
4 Flashes - Erroneous Flame
OPERATION OF IGNITION MODULE
The Ignition Module, (see Figure 31), is microprocessor based and operates on 24VAC supplied by the transformer. The control utilizes a microprocessor to continually and safely monitor, analyze, and control the proper operation of the gas flame holder. The module with the presence of the flame sensor, using flame rectification, allows the heater to operate.
Flame Current
Check Point
Figure 31.
Section 4. Operation
I pg 40
OPERATING THE CONTROL PANEL
The five operating switches are:
POOL ON Press this button to govern heater operation by the pool temperature
setting.
SPA ON Press this button to govern heater operation by the spa temperature
setting.
HEATER OFF
TEMP
TEMP
Press this button to switch off the heater.
Press this button to raise the temperature setting.
Press this button to lower the temperature setting.
To toggle the display between degrees Centigrade (°C) and degrees Fahrenheit (°F):
Figure 32.
1. Turn the Operating Control OFF.
2. Press TEMP or TEMP for 5 seconds. The display will flash once and change modes
(°C to °F or vice versa).
3. Turn the Operating Control ON.
When either the
TEMP or TEMP buttons are depressed, the digital display will indicate the temperature setting. After five seconds, the display will return to the actual pool/spa temperature.
In addition to the digital temperature display, there are five indicator lights:
The POOL ON light indicates that the pool water temperature is governing operation of the heater.
The SPA ON light indicates that the spa water temperature is governing operation of the heater.
The
HEATING light comes on and stays on when the burner is firing. This light should be on whenever the burner is on. It blinks when the heater is calling for heat but not firing. If this light is on but the burner fails to come on, one of the “service” lights should come on, indicating a fault in the system.
The SERVICE SYSTEM light indicates that there is insufficient water flow to the heater. If the pump is operating, this usually indicates that the filter and/or skimmers should be cleaned
(some filters may require back-washing). If the light remains on after the filter/skimmers have been serviced, the system should be checked by a qualified service technician.
The
SERVICE HEATER light indicates a fault in the heater or its controls. If this light comes on, shut down the heater (See “TO TURN OFF GAS TO THE APPLIANCE” on page 36), and have a qualified service technician check the system.
!
WARNING
Risk of explosion or fire causing burns or death if safety interlocks are disabled. DO
NOT attempt to operate heater when SERVICE HEATER light is on or if blower or burner will not start. Instead, follow instructions under “To Switch Off Gas to the Appliance,” and call a qualified service technician to repair unit.
TEMPERATURE SETTING
The heater comes factory set at 25.6° C (78° F). for the pool mode and 37.8° C (100° F). for the spa mode. Using the up and down arrows, you can set the pool/spa thermostats to a minimum temperature of 18.3° C (65° F.), or a maximum of 40° C (104° F). If you desire to heat only one body of water, the thermostat is capable of an off mode. As an example, if you only wish to heat the spa and not the pool, simply depress and hold the pool down arrow, and the thermostat will lower its setting to 18.3° C (65° F.) then go to an off mode. See below to change the heater’s
factory set temperature settings.
MAXIMUM TEMPERATURE SET POINT
1. Unbolt and remove the door panels (see Figure
33).
2. Access the control panel board on the underside of the top cover. Locate the yellow button on the corner of the control board.
3. Push the Max. Temp. Set Point button on the back of the control board (see Figure 34).
Top Panel
The following sequence should happen:
A. The unit turns on and the POOL ON light will turn on.
B. Press the TEMP or TEMP pad (on
TOP of the panel) to set maximum pool temperature.
C. Wait up to 30 seconds; the POOL ON light will turn off and the
SPA ON light will turn on.
To override the time delay, push the
Max.
Temp. Set Point button again.
D. Press the TEMP or TEMP button on the control panel and set maximum spa temperature to 40°C (104° F) or less.
E. Wait up to 30 seconds; the SPA ON light will turn off and the unit will shut down.
To override the time delay, push the
Max.
Temp. Set Point button again.
4. Reinstall the access door panels.
Door
Access Panel
S1
Door
Access
Panel
Figure 33.
S1
Figure 34.
Section 5. Troubleshooting
I pg 42
TROUBLESHOOTING INSTRUCTION
Initial Troubleshooting
Only qualified, trained service technicians with appropriate test equipment should service the heater. Remember that all parts of the system affect heater operation. Before starting this troubleshooting procedure, make sure that the pump is running correctly, that there are no blockages in the system, that the valves are correctly set and that the time clock is correctly set and is running.
IMPORTANT! READ ME FIRST!
READ THE FOLLOWING CAREFULLY:
1. Check the line voltage to your heater. This heater operartes on 240 Volts AC.
2. Remove the covers and check the 12-pin plug in the back of the control box.
The plug must match the voltage in the heater circuit.
3. If the 12-pin plug is not plugged into the back of the control box, plug in the
RED 240 volt plug.
Start here for directions to specific Troubleshooting Chart
Is green “POOL” or “SPA”
LED “on”?
YES
NO
Go to chart “HEATER WILL
NOT FIRE - A”
(Page 41)
Is red “SERVICE SYSTEM”
LED “on”?
NO
Is red “SERVICE HEATER”
LED “on”?
YES
YES
Are any red diagnostic
LED’s on back of board (AGS, AFS,
SFS, HLS, PS or
THERMISTOR) “on”
NO
YES
Go to chart “HEATER WILL
NOT FIRE - B”
(Page 42)
Go to specific safety switch troubleshooting chart
(Pages 45 and 46)
NO
Turn off power to heater for about 5 seconds, and turn back on. Make sure temperature setting is above water temperature. Wait one minute.
Do any diagnostic LED’s on back of board (AGS, AFS, SFS,
HLS, PS, or THERMISTOR) come “on” and stay on?
NOTICE: Any or all of the diagnostic LED’s may come
“on” momentarily when you turn on the power to the heater.
YES
NO
Does red “SERVICE
HEATER” LED come
“on”
YES
Go to chart ‘HEATER WILL
NOT FIRE -C”
(Page 43)
NO
Verify that water temperature setting is above water temperature reading. If it is, and heater either will not fire or no red
LED’s come “on”, replace Control Board.
!
WARNING
Hazardous voltage. Can shock, burn or kill.
Disconnect power before servicing any components.
!
WARNING
Fire and Explosion hazard. Do not jumper switch terminals to remedy a failed safety switch.
Heater Will Not Fire - A
Start
Is green “SPA” or
“POOL” LED “on”
YES
Check that the 12-pin plug is installed (red
240V)
NO
NO
YES
YES
Depress “POOL” or “SPA” ON button on Membrane Pad.
Does “POOL” or “SPA” LED come on?
NO
Check for line voltage to heater.
If plug is not installed:
Install the
240V plug in
120V circuit: Replace transformer, control board and ignition control module (see "HEATER
WILL NOT FIRE-C and
-D", Pages 38 and 39).
Check fuse and all other 24V components for damage.
YES
Check for 24 VAC at secondary of Transformer.
NO
Check for Line Voltage between L1 and L2 terminals on Terminal Board.
YES
Check for Line Voltage at
Transformer primary pins.
White connects to Pin 3 on
Transformer, Black to Pin 2,
Orange to Pin 1.
240V: check Pin1 to Pin 3.
YES
NO
NO
NO
YES
YES
YES
NO
Jumper Fireman’s Switch at
Terminal Board and depress
“POOL” or “SPA” ON button on membrane pad. Does “SPA” or
“POOL” LED come “on”?
NO
Leaving jumper in place, check for 24 VAC between
Fireman’s Switch terminals and ground.
Remove jumper. Check ribbon cable connection between
Membrane Pad and J6 on
Control Board. Depress
“POOL” or “SPA” On pad again. Does “POOL” or “SPA”
LED come on?
Jumper pins 6 and 5 on J6 of
Control Board. Does “SPA”
LED come on?
Jumper pins 6 and 4 on J6 of
Control Board. Does “POOL”
LED come on?
NO
YES
YES
NO
GO TO
“HEATER WILLNOT FIRE - B”
Page 37
Heater should fire on demand for heat.
Restore power to heater.
Check wiring connections between power supply and
Junction Box and between
Junction Box and Terminal
Board; restore continuity.
Check wiring connections between Terminal Board and
Transformer primary and restore continuity.
Replace Transformer.
Check Fireman’s Switch circuit connections (time clock, wiring, external controller relay).
Remove jumper. Check wiring between Transformer and J7 terminals on Control Board and between J7 and
Fireman’s Switch on Terminal
Board, check fuse, and restore continuity.
Heater should fire on demand for heat.
Replace Membrane Pad.
Replace Control Board.
Section 5. Troubleshooting
I pg 44
Heater Will Not Fire - B
Start
Is red “SERVICE
HEATER” LED “on”
NO
YES
CONTINUE
Is red “SERVICE SYSTEM”
LED on?
NO
YES
Verify that pump is on, filter is not blocked, and the water flow is above the minimum requirement.
YES
With pump running, adjust
Water Pressure Switch to lower pressure until ‘SERVICE
SYSTEM” LED goes out. Then verify that “SERVICE SYSTEM”
LED goes on with pump off.
NO
YES
NO
Check that water pressure is within the adjustment range of the Pressure Switch (0-35 kPa).
NO
YES
Verify that switch wiring is OK and Pressure Switch port is not blocked, and replace water Pressure Switch.
Check whether any of the red diagnostic LED’s on back of board (AGS, AFS, SFS,
HLS or PS) are “on”
NO
GO TO
“HEATER WILLNOT FIRE - C”
Page 38
YES
Increase POOL/SPA temperature setting on
Membrane Pad above actual water temperature. Heater should fire on demand for heat.
If not, and no other red LED’s light, replace Control Board.
Service pump/filter and eliminate other flow obstructions.
Heater should fire on call for heat. Re-verify that water flow is above minimum requirement.
Minimum Flow Requirements
Model
175
200
250
300
400
Flow
76 LPM (20 gal/min)
76 LPM (20 gal/min)
95 LPM (25 gal/min)
114 LPM (30 gal/min)
151 LPM (40 gal/min)
If water pressure is outside of adjustment range that will open switch with pump off and close switch with pump on, replace with flow switch set above minimum flow requirement.
Minimum Flow Requirements
Model
175
200
250
300
400
Flow
76 LPM (20 gal/min)
76 LPM (20 gal/min)
95 LPM (25 gal/min)
114 LPM (30 gal/min)
151 LPM (40 gal/min)
Go to “Diagnostic LED’s”,
(Pages 45 and 46)
Heater Will Not Fire - C
Start
Is “SERVICE HEATER” LED
“on”?
YES
If any red diagnostic LED’s
(AGS, AFS, SFS, HLS, PS, or
THERMISTOR) come “on”, go to to Pages 45 and 46.
CONTINUE
Did burner fire at all?
YES
Go to “BURNER
TROUBLESHOOTING”
(Page 47)
NO
NO
stay on?
NO
Turn off power to heater for 5 seconds, and turn back on.
Make sure temperature setting is above water temperature.
Wait one minute.
Does heater fire and
YES
NO
Go to “INITIAL
TROUBLESHOOTING”
Continue to observe heater for several minutes. Cycle heater on and off several times.
Observe for delayed or rough ignition, poor combustion, premature extinction of flame, evidence of boiling, or operation of any diagnostic
LED. Go to pertinent troubleshooting section if any malfunction is observed.
Replace Control Board.
Go to “HEATER WILL NOT
FIRE-D” (Page 44)
YES
Did Blower come on?
YES
Verify that gas is flowing to burner during ignition try. Observe gas meter for movement during ignition try (wait for about 30 seconds after calling for heat).
Replace Ignition Control
Module.
NO
Check for 24 VAC between
VAL and GND terminals on
Ignition Control Module.
SEE NOTE 2.
YES
Check for 24 VAC between
VAL and GND terminals on
Control Board. SEE NOTE 2.
NO
Fix wiring between VAL and
GND terminals of Ignition
Control Module and Control
Board.
YES
YES
Check for 24 VAC between TH and GND terminals on Ignition
Control Module.
SEE NOTE 1.
NO
Check for 24 VAC between TH and GND terminals on Control
Board. SEE NOTE 1.
Check for 24 VAC between GAS terminals on Control
Board. SEE NOTE 2.
NO
Replace Control
Board.
YES
NO
YES
NO
NO
Verify that gas supply is open all the way to Gas Valve, and
Gas Valve is set at “on” position.
Check for 24 VAC to Gas
Valve terminals during ignition try. (Voltage appears about 24 seconds after call for heat).
SEE NOTE 2.
YES
Replace Gas Valve with identical part.
Fix wiring between TH and
GND terminals of Ignition
Control Module and Control
Board.
Replace Control Board.
Fix wiring between GAS terminals on Control Board and Gas Valve.
NOTE 1 : Voltage appears immediately after call for heat, and may be on for only about
30 seconds.
NOTE 2 : Voltage appears about
24 seconds after call for heat, and may be on for only about
7 seconds.
Section 5. Troubleshooting
I pg 46
Heater Will Not Fire - D
IMPORTANT! READ ME FIRST!
IMPORTANT! READ ME FIRST!!
If your heater is correctly connected to 240 Volts AC, the Ignition Control Module (ICM) will convert the
240VAC to an intermittent pulse to the ignitor. Digital meters don’t read this type of signal well. (An analog meter will give a better reading than a digital meter). If the ICM is bad, your voltmeter will read either 0
VAC or 240 VAC. If your ICM is good, your meter will read some voltage between 0 and 240 VAC. Exactly what reading you get will depend on the meter, but with a good ICM, the reading won’t be 0 VAC or 240
VAC, but somewhere in between.
Start
Gas flows during ignition try, but burner does not fire.
YES
Check voltage across igniter leads; OK?
NO
Replace Ignition
Control Module.
NO
YES
Go back to chart “HEATER WILL
NOT FIRE-C” (Page 44).
Check gas pressure. OK?
NO
Increase gas flow into heater:
• Replace gas line with larger line;
• Replace regulator;
• Replace meter; or
• All of the above.
YES
Replace HSI Igniter.
Diagnostic LED’s: AGS, AFS, HLS, PS, THERMISTOR
AGS or HLS "on"
Replace High Limit
Switch (HLS) or
Automatic Gas
Shutoff (AGS)
CONTINUE
YES
Verify that water flow rate is above minimum required for heater.
YES
Verify that inlet water temperature is below 45° C.
If problem persists, verify proper operation of Internal Bypass Valve and Thermal Governor, and check for Heat Exchanger blockage.
AFS "on"
NO
NO
Service pump and filter to restore proper flow. After servicing, verify proper operation of Pressure Switch (PS).
Replace thermistor or Control
Board to correct overheating.
PS "on"
Verify that wiring is
OK and pressure tap is not blocked. Replace Pressure Switch
CONTINUE
Verify that water flow rate is above minimum required for heater.
NO
Service pump and filter to restore proper flow.
YES
CONTINUE
Adjust Water Pressure Switch to close with pump running and open with pump off.
YES
Replace Blower.
Verify that wires BM and F1 are correctly connected at the terminal strip (see
Heater Connection
Diagram, Page 28).
YES
YES
YES
NO
Does Blower operate?
NO
Disconnect Blower and check for line voltage between pins
1 and 3 of Blower Connector on ignition try.
NO
Check for 24 VAC between
24 VAC and GND terminals on Ignition Control Module on ignition try. Check that IND wire is correctly connected.
NO
Verify correct connection of wiring between
24 VAC and IND terminals on
Ignition Control Module and
Control Board, and replace
Control Board.
Verify that there is no blockage in Blower intake, Heat
Exchanger, and exhaust.
Verify correct connection of wiring and that pressure taps to AFS are OK.
Verify that vinyl tubing to AFS and Blower is not misrouted, kinked, disconnected, or punctured.
Replace Air Flow Switch
(AFS).
If problem persists, replace
Blower.
Connect correctly and retry.
Does Blower start?
Disconnect wires F1 and F2 from Ignition
Control Module and short them together.
Does Blower come on?
YES
NO
NO
NO
Replace Blower. Does Blower start on ignition try?
Replace Ignition Control
Module.
THERMISTOR "on"
Verify Thermistor wiring. If
OK, replace Thermistor.
CAUTION
Do not jumper a safety switch to remedy a failed switch.
NOTE: ES1 is a spare and should be jumpered.
Section 5. Troubleshooting
I pg 48
Diagnostic LED’s: SFS
SFS "on"
Heater starts and runs OK, but temperature of exhaust climbs to 204°–260°C in
3-5 minutes.
NO
Heater starts after several tries, exhaust temperature stays below 121.1 °C.
OR
Heater doesn’t start at all
(exhaust stays cold).
YES
Check Heat Exchanger
Coil for leaks, liming, soot, or low flow.
YES
Check Thermal
Regulator: Open at
48.9°C?
NO
YES
NO
Correct problem;
Heater should fire.
NO
YES
Check Thermal-Regulator:
Seats correctly?
NO
(HD)
Replace Heater
Membrane Pad.
DONE
Replace Heater
Control Board.
DONE
Check pressure and volume of fuel supply
OK
Disconnect the sensor and check continuity across its terminals. Resistance should be 3.5-4.0 megaohms.
= open circuit;
0 = shorted.
Does sensor check OK?
NOT OK
NO
Correct Fuel Supply, reset
Heater and retry. Heater should fire correctly.
NO
Replace Stack Flue Sensor
DONE
Reset power to Heater and retry. Heater should fire.
NO
YES
YES
Check continuity in wiring harness between Control
Board and Probe.
Continuity OK?
NO
Check the J3 and J6 connectors for corrosion/ looseness on the male pins.
YES
Clean/tighten pins as needed.
DONE
Reset power to Heater and retry. Heater should fire.
NO
NO
Repeat checks on fuel supply, Thermal Regulator, check for correct orifices, etc.
YES
Does the Digital
Temperature Display show
Error Code “E05” or “E06”?
NO
(Basic)
Reset power to Heater and retry. Heater should fire.
NO
Check Heat Exchanger Coil for leaks, liming, soot, or low flow.
Replace Heater Control Board.
DONE
Reset power to Heater and retry. Heater should fire.
NO
Replace Heater Membrane Pad.
DONE
Reset power to Heater and retry. Heater should fire.
Burner Troubleshooting
SYMPTOM
Loud, high-pitched whine
CAUSE
Flame is too rich.
Flame is “fluttery .”
Exhaust may have acrid smell or burner may fail to stay lit.
Combustion appears normal, but flame does not stay lit.
Flame is too lean.
Flame current is not being sensed.
REMEDY
Verify pressure tap between gas valve and blower inlet.
Verify that the gas regulator setting is 11 ±
5 Pa.
Contact a qualified technician or service agency to replace the gas orifice.
Verify that the gas regulator setting is 11 ±
5 Pa.
Contact a qualified technician or service agency to replace the gas orifice.
Check for wet or damaged igniter with low resistance to ground. Replacewith new igniter.
Verify burner flameholder is properly grounded.
Replace Ignition Control Module.
Heat Exchanger Troubleshooting
SYMPTOM
Boiling in heat exchanger. May be accompanied by
“bumping” sounds.
CAUSE
Low water flow to heater.
Heat exchanger plugged.
Bypass valve stuck open.
Thermal governor stuck closed.
Sweating.
Thermal governor failed.
REMEDY
Service pump and or filter.
Service heat exchanger. Correct water chemistry.
Service bypass valve.
Replacethermal governor.
Replacethermal governor.
Section 6. Maintenance
I pg 50
MAINTENANCE INSTRUCTIONS
CARE AND MAINTENANCE
!
WARNING
Risk of fire or explosion from flammable vapors. Do not store gasoline, cleaning fluids, varnishes, paints, or other volatile flammable liquids near heater or in the same room with heater.
The following maintenance is recommended every six months and at the start of every swimming season:
1. Inspect the heater panels and venting system to make sure that there are no obstructions to the flow of ventilating air or burner exhaust.
2. Keep the area in and around the heater clear and free from combustible materials, gasoline and other flammable vapors and corrosive liquids.
3. If applicable, test the operation of the pressure relief valve by lifting the valve lever. (See below for “PRESSURE RELIEF VALVE” instructions.)
4. Test for proper operation of the pressure switch. (See “WATER PRESSURE SWITCH” for testing instructions.)
5. Check pipe and fittings for cracks or breaks. The combustion air blower is permanently lubricated, and does not require periodic lubrication. The burner does not require maintenance or adjustment by the user. Call a qualified service technician if you suspect that the burner may require maintenance.
DE-LIMING THE HEATER
!
WARNING
Working with muriatic acid can be dangerous. When cleaning elements always wear rubber gloves and eye protection. Add acid to water, do not add water to acid. Splashing or spilling acid can cause severe personal injury and/or property damage.
Should a heater require de-liming, this may be accomplished by circulating a solution of 30%
Muriatic Acid. This process should only be performed by a person of sufficient skill. The heater
MUST be disconnected from the pool plumbing, gas plumbing, and electric. The heater may be placed on its side with the water manifold “up”. The diluted muriatic acid may be recirculated until visible bubbles are no longer produced. Before being restored to service, the heater water ways should be completely rinsed with regular tap water.
PRESSURE RELIEF VALVE
Local codes may require installation of a pressure relief valve (PRV). Purchase separately and install a 19 mm pressure relief valve complying with the local Plumbing
Codes, having a capacity equal to the Mega Joule (MJ/hr) rating of the heater. The relief pressure of the valve MUST
NOT EXCEED 344 kPa.
The relief valve must be installed vertically. To install the valve, use a 19 mm x 5 mm brass nipple at the manifold, the two brass elbows and nipples are (user supplied), as illustrated in Figure 35. No valve is allowed to be placed between the manifold adapter and the relief valve.
To avoid water damage or scalding from operation of the relief valve, install a drain pipe in the outlet of the pressure relief valve that will direct water discharging from the valve to a safe place for disposal. Do not install any reducing couplings or valves in the drain pipe. The drain pipe must be installed so as to allow complete drainage from the valve and drain line.
The relief valve should be tested at least once a year by lifting the valve lever.
Drill thru the NPT Port, then use a 19 mm Brass Nipple and
Elbow (user supplied) for a
PRV Installation.
Figure 35.
!
WARNING
Explosion hazard. Any heater installed with restrictive devices in the piping system downstream from the heater, (including check valves, isolation valves, flow nozzles, or therapeutic pool valving), must have a relief valve installed as described above.
AFTER START-UP
CHECKING WATER FLOW
!
WARNING
Fire or flooding hazard. If the unit overheats and the burner fails to shut off, follow instructions under “To Turn Off Gas to the Appliance”, page 36, and call a qualified service technician to repair unit.
After start-up, the outlet water pipe should feel slightly warmer than the inlet pipe. If it feels hot, or if you hear the water in the heater boiling, there may not be enough water flow to the appliance. Make sure that the filter is not plugged. If water temperature remains high but the unit continues to operate, turn off the appliance and call your service technician.
SPRING AND FALL OPERATION
If the pool is only used occasionally, lower the pool thermostat to 20° C (68° F) and leave the heater on. This will keep the pool and the surrounding ground warm enough so that the heater should restore the pool to a comfortable temperature within about one day.
Section 6. Maintenance
I pg 52
WINTER OPERATION
!
CAUTION
Operating this heater continuously at water temperatures below 20° C (68° F.) will cause harmful condensation and will damage the heater and void the warranty.
• If the heater has been drained for freezing condition, do NOT turn “ON” until the system is circulating water.
• Water trapped in the heat exchanger can result in freeze damage to the exchanger or headers. Freeze damage is specifically not covered by the warranty.
• When starting the heater for the swimming season with a water temperature below
10° C (50° F), the heater may be used to heat the water; however, make sure that the heater operates continuously until the water temperature reaches the heater’s minimum setting of 20° C (68° F). During cold weather, if there is no danger of freezing, operate the filter pump continuously even if the heater is not operating.
If air temperatures are expected to drop below freezing 0° C (32° F), shut down the heater and winterize it.
For outdoor heaters in freezing climates, shut the heater down and drain it for winter as follows:
1. Turn off electrical supply to the heater and pump.
2. Close the external manual shut-off gas valve (located outside the heater).
3. In colder climates where they may be required, open drain cock located on the bottom of the manifold adapter, and drain the heat exchanger and manifold adapter completely. If heater is below pool water level, be sure to close isolation valves to prevent draining the pool (isolation valves are not required and should not be used on heaters installed above pool water level except when needed for winterizing valves). Assist the draining by blowing out the heat exchanger through the pressure switch fitting with low pressure compressed air
(less than 35 kPa or 5 PSI).
!
WARNING
Explosion hazard. Purging the system with compressed air can cause components to explode, with risk of severe injury or death to anyone nearby. Use only a low pressure (below
35 kPa or 5 PSI), high volume blower when air purging the heater, pump, filter, or piping.
4. Remove the Water Pressure Switch. Plug the port in the manifold to prevent bugs and dirt from getting into the manifold.
5. Drain the plastic inlet/outlet manifold through the outlet pipe. If the pipe does not drain naturally to the pool, install a drain cock in the outlet pipe to drain the manifold.
6. Cover air inlet grate with a plastic bag to prevent bugs, leaves, etc., from getting into the heater.
NOTICE: Water trapped in the heater can cause freeze damage. Allowing the heater to freeze voids the warranty.
To return the heater to service after winterizing:
1. Close drain cock and fittings.
2. Before starting the heater, circulate water through the heater for several minutes until all air noises stop. See also “BEFORE START-UP” (page 34) and “CARE AND MAINTENANCE”
(page 48).
(See additional notes under Important Notices in Introduction.)
MAINTAINING POOL TEMPERATURE
To maintain pool temperature, make sure that the heater switch and valving are reset to pool settings after using the spa.
ENERGY SAVING TIPS
1. Keep the pool or spa covered when not in use. This will reduce heating costs, reduce water evaporation, conserve chemicals and reduce load on the filtering system.
2. Reduce pool thermostat to 26° C (78° F) or lower; reduce spa temperature to 38° C (100° F).
This is accepted as being the most healthy temperature for swimming by the American Red
Cross.
3. Use a time clock to start the filter pump at 6 a.m. or later. The swimming pool loses less heat after daybreak.
4. For pools used only on weekends, lower the thermostat setting by -12° C to -9° C (10° F to 15° F) during the week to reduce heat loss. A properly sized heater will restore normal temperature within one day.
5. Turn the heater off when the pool will not be used for an extended period.
6. Follow a regular program of preventive maintenance for the heater each new swimming season. Check operation of the heater and its controls.
CHEMICAL BALANCE
POOL AND SPA WATER
Your Waterco pool heater was designed specifically for your spa or pool and will give you many years of trouble-free service, provided you keep your water chemistry in proper condition.
Water chemistry should follow good swimming pool water chemistry practices. When using a chlorinator, install it down stream from the heater and at a lower level than the heater outlet.
Install a corrosion resistant positive seal “Check Valve”, (P/N R172288), between the heater and the chlorinator to prevent concentrated chemicals from back-siphoning into the heater. Backsiphoning is most likely to occur when the pump stops, creating a pressure-suction differential.
Do NOT sanitize the pool by putting chlorine tablets or sticks into the skimmer(s). When the pump is off, this will cause a high concentration of chlorine to enter the heater, which could cause corrosion damage to the heat exchanger.
Three major items that can cause problems with your pool heater are: improper pH, disinfectant residual, and total alkalinity. These items, if not kept properly balanced, can shorten the life of the heater and cause permanent damage.
!
CAUTION
Heat exchanger damage resulting from chemical imbalance is not covered by the warranty.
Section 6. Maintenance
I pg 54
WHAT A DISINFECTANT DOES
Two pool guests you do not want are algae and bacteria. To get rid of them and make pool water sanitary for swimming - as well as to improve the water’s taste, odor and clarity - some sort of disinfectant must be used.
Chlorine and bromine are universally approved by health authorities and are accepted disinfecting agents for bacteria control.
WHAT IS A DISINFECTANT RESIDUAL?
When you add chlorine or bromine to the pool water, a portion of the disinfectant will be consumed in the process of destroying bacteria, algae and other oxidizable materials. The disinfectant remaining is called chlorine residual or bromine residual. You can determine the disinfectant residual of your pool water with a reliable test kit, available from your local pool supply store.
You must maintain a disinfectant residual level adequate enough to assure a continuous kill of bacteria or virus introduced into pool water by swimmers, through the air, from dust, rain or other sources.
It is wise to test pool water regularly. Never allow chlorine residual to drop below 0.6 ppm (parts per million). The minimum level for effective chlorine or bromine residual is 1.4 ppm.
pH - The term pH refers to the acid/alkaline balance of water expressed on a numerical scale from 0 to 14. A test kit for measuring pH balance of your pool water is available from your local pool supply store; see Table 10.
Muriatic Acid has a pH of about 0. Pure water is 7 (neutral). Weak Lye solution have a pH of 13-14.
RULE: 7.4 to 7.6 is a desirable pH range. It is essential to maintain correct pH, see Table 10.
If pH becomes too high (over alkaline), it has these effects:
1. Greatly lowers the ability of chlorine to destroy bacteria and algae.
2. Water becomes cloudy.
3. There is more danger of scale formation on the plaster or in the heat exchanger tubing.
4. Filter elements may become blocked.
If pH is too low (over acid) the following conditions may occur:
1. Excessive eye burn or skin irritation.
2. Etching of the plaster.
3. Corrosion of metal fixtures in the filtration and recirculation system, which may create brown, blue, green, or sometimes almost black stains on the plaster.
4. Corrosion of copper tubes in the heater, which may cause leaks.
5. If you have a sand and gravel filter, the alum used as a filter aid may dissolve and pass through the filter.
CAUTION: Do not test for pH when the chlorine residual is 3.0 ppm or higher, or bromine residual is 6.0 ppm or higher. See your local pool supply store for help in properly balancing your water chemistry.
RULE: Chemicals that are acid lower pH. Chemicals that are alkaline raise pH.
ALKALINITY High or Low:
“Total alkalinity” is a measurement of the total amount of alkaline chemicals in the water, and control pH to a great degree. (It is not the same as pH which refers merely to the relative alkalinity/acidity balance.) Your pool water’s total alkalinity should be 100 - 140 ppm to permit easier pH control.
A total alkalinity test is simple to perform with a reliable test kit. You will need to test about once a week and make proper adjustments until alkalinity is in the proper range. Then, test only once every month or so to be sure it is being maintained. See your local pool dealer for help in properly balancing the water chemistry.
WATER CHEMISTRY PARAMETERS
Disinfectant levels
Free Chlorine, ppm
Combined Chlorine, ppm
Bromine, ppm
Other Sanitizers
Table 10.
Minimum
1.0
None
2.0
Ideal
2.0 - 4.0
None
4 - 6
Maximum
5.0
0.2
10.0
Levels not established. Consult local health department before use.
Chemical Values
pH
Total Alkalinity (Buffering), ppm as
CaCO3
Total Dissolved Solids, ppm
7.2
60
N/A
7.4 - 7.6
80 - 100
N/A
7.8
180
Calcium Hardness, ppm, as CaCO3
Heavy Metals
Biological Values
Algae
Bacteria
150
None
None
None
200 - 400
None
None
None
1,500 ppm >
TDS at startup*
500 - 1,000
None
None
Refer to Local
Code
NOTICE: Failure to adhere to the listed water chemistry parameters may result in premature failure of the heat exchanger and will
void the warranty.
*Start-up TDS includes source water TDS and any other inorganic salt added at start-up.
Section 6. Maintenance
I pg 56
TURBOTEMP REPLACEMENT PARTS
For complete
Electrical System parts breakdown
(Key Nos. 1 through 4), see Page 44.
3
7
2
5
6
1
9
For complete
Burner System parts breakdown
(Key Nos. 5 through 7), see Page 42.
8
4
For complete
Water System parts breakdown
(Key Nos. 8 through 9), see Page 43.
Repair Parts are available from your Pentair dealer.
If your dealer cannot supply you, call Customer Support
If your dealer cannot supply you. Call Customer Support.
TURBOTEMP REPLACEMENT PARTS
CLAMP LID TUB DESIGN
Lid Nut/Washer (9x)
Combustion
Chamber
Gasket
For heaters manufactured between
1/12/2009 and 10/31/2013
(clamp lid tub design)
Note: Kits also include Clamp
Assembly, O-Ring and Silicon Tube
(see page 49)
Section 6. Maintenance
I pg 58
TURBOTEMP REPLACEMENT PARTS
REPAIR PARTS – BURNER SYSTEM
•
8
9
10
11
12
13
•
14
15
6
7
•
5
•
Key
No.
3
4
1
2
•
•
•
•
Part
Description
Gas Valve Assembly [Australia]
19 mm Union
Gas Orifice
Gas Orifice O-Ring
Gas Orifice Kit – NG (Incl. Key Nos. 3 and 4)†
Gas Orifice Kit – Propane (Incl. Key Nos. 3 and 4)†
NG to Propane Conversion Kit
(Incl. Key Nos. 3 and 4)†
Propane to NG Conversion Kit
(Incl. Key Nos. 3 and 4)†
Air Blower [50 Hz]
Air Orifice Kit (Includes Key Nos. 6 and 7)
Air Orifice
Air Orifice Grill
Blower/Adapter Plate Gasket Kit
(Includes Key Nos. 8, 9, 10, 12)
Flameholder Kit (Includes
Key Nos. 10, 11, 12, 13 and on 300 & 400
Models Only - Flameholder Insert)
Blower/Adapter Plate Gasket
Blower Adapter Plate
Flameholder/Adapter Plate Gasket
Flameholder Assembly
Flameholder/Combustion Chamber Gasket***
Flameholder Insulation Cap
Flameholder Insert
Condensate Evaporator Plate
One Piece Metal Chamber/Combustion Chamber
Assembly
Qty.
1
1
1
1
1
1
1
1
1
1
1
1
2
1
1
1
200NA
200LP
474133Z
38404-4097S
474136
474139
474142
474145
474104Z
474107Z
77707-0011
77707-0202
Model
300NA
300LP
474133Z
38404-4097S
474135
474138
474141
474144
474104Z
474106Z
77707-0011
77707-0203
1 474095** 474095**
474957 474957*
400NA
400LP
474133Z
38404-4097S
474134
474137
474140
474143
474104z
474105Z
77707-0011
77707-0204
474095**
474957*
•
16
17
18
19
•
20
•
21
Insulation Kit (Includes Key Nos. 13, 14, 16, 17, 18 and 19)
Bottom Outer Insulation Blanket***
25.4 mm Bottom Inner Insulation
25.4 mm Top Insulation
Top Outer Insulation Blanket***
Lower Enclosure Insulation
One Piece Metal Elbow/Combustion Chamber
Cover Assembly
Combustion Chamber Gasket
Metal Vent Cover Assembly
1
1
1
1
1
77707-0008 77707-0008 77707-0008
42001-0074S 42001-0074S 42001-0074S
474958* 474094** 474958* 474094** 474958* 474094**
474952* 474201** 474952* 474201** 474952* 474201**
474172Z 474172Z 474172Z
22
26
27
28
23
24
25
Heater Top
Side Panel {Service Panel}
Side Panel {Manifold}
Heater Bottom
Side Panel {Flue Stack}
J-Box Cover
Screw Kit, Panel
1
1
1
1
1
1
1
42002-0034Z
42002-0039Z
42002-0033Z
42002-0031Z
42002-0032Z
42002-0041Z
474292
42002-0034Z
42002-0039Z
42002-0033Z
42002-0031Z
42002-0032Z
42002-0041Z
474292
(*) For heaters manufactured after 10/31/2013 (new 9-bolt tub design)
(**) For heaters manufactured between 1/12/2009 and 10/31/2013 (clamp lid tub design).
Note: Kits also include Clamp Assembly,O-Ring and Silicon Tube.
(***) Not available separately
(†)
Not included with heater. Order separately.
42002-0034Z
42002-0039Z
42002-0033Z
42002-0031Z
42002-0032Z
42002-0041Z
474292
TURBOTEMP REPLACEMENT PARTS
1
3
4
5
6
7
8
2
9
10
11
12
13
14
15
16
17
18
19
22
2
11
12
13
14
7
8
9
10
•
5
3
4
6
Key
No.
1
15
19
20
21
22
16
17
•
18
21
20
REPAIR PARTS – WATER SYSTEM
Part
Description
Tube Sheet Coil Assembly Kit ( HD Series)
(Includes Key No.3)
Manifold Kit (Includes Key Nos. 3-14, 21, and
Key Nos. 5-7, 17 in “Electrical System”, Page 51
Coil/Tubesheet Sealing O-Ring Kit
Manifold Bottom Plate
Manifold O-Ring
O-Ring Kit (Incl. Key Nos. 3, 5)
Manifold Insert*
Manifold Baffle Plate
Manifold Bypass Valve
Water Pressure Switch
Manifold
5/16" Washer, S.S.
5/16"-18 x 2-3/4" Hex Cap Screw
Connector Tube O-Ring
Connector Tube Kit (Includes 1 Connector Tube and 1 O-Ring)
Thermal Regulator Kit
(Incl. Key Nos. 16, 17, 18, 19 and Spring Clip)
Thermal Regulator (Includes Spring Clip)
Thermal Regulator Spring
Thermal Regulator Cap O-Ring
Thermal Regulator Spring Clip
Thermal Regulator Cap
Drain Plug
3/4" Pipe Plug
Pressure Relief Valve (Recommended -
Purchase Separately)
Qty.
1
1
1
1
1
1
1
1
1
1
1
1
10
10
2
1
( )
1
1
1
1
1
2
1
200NA
200LP
474062
474391
77707-0117(6)
77707-0120
42001-0060S
77707-0017
77707-0010
38000-0007S
35505-1313
U178-920P
U78-60ZPS
38674-0719
Model
300NA
300LP
474064
474392
77707-0118(10)
77707-0120
42001-0060S
77707-0017
77707-0010
38000-0007S
35505-1313
U178-920P
U78-60ZPS
38674-0719
400NA
400LP
474065
474392
77707-0119(12)
77707-0120
42001-0060S
77707-0017
77707-0010
38000-0007S
35505-1313
U178-920P
U78-60ZPS
38674-0719
•
* Not available separately.
Not illustrated.
Section 6. Maintenance
I pg 60
TURBOTEMP REPLACEMENT PARTS
15
1
14
13
10
11
12
16
2
3
4
17
5
9
8
7
6
Key
No.
Part
Description
REPAIR PARTS – ELECTRICAL SYSTEM
QTY.
200NA
200LP
Model
300NA
300LP
400NA
400LP
1 Heater Display Cover 1 42002-0035 42002-0035 42002-0035
2 Igniter Bracket 1 42001-0030S 42001-0030S 42001-0030S
3 Igniter/Igniter Gasket Kit Incl. Key Nos. 3 and 4)
4 Igniter Gasket
1 77707-0054 77707-0054 77707-0054
1 42001-0066S 42001-0066S 42001-0066S
5 Automatic Gas Shutoff Switch (AGS)
6 High Limit Switch
1 42002-0025S 42002-0025S 42002-0025S
1 474171Z 474171Z 474171Z
7 Thermistor 1 42001-0053S 42001-0053S 42001-0053S
8 Terminal Board 1 42001-0056S 42001-0056S 42001-0056S
9 Fireman’s Switch Fuse (31.75mm X 6.35 mm) 1 32850-0099 32850-0099 32850-0099
10 Fenwal Ignition Control Module 1 474103Z 474103Z 474103Z
11 Transformer, 120/240V 1 42001-0107S 42001-0107S 42001-0107S
12 Air Flow Switch 1 42001-0061S 42001-0061S 42001-0061S
13 Control Board Kit (NA, LP Series) 1 42002-0007S 42002-0007S 42002-0007S
• Heater Wiring Harness 1 474163Z 474163Z 474163Z
14 Heater, Top 1 42002-0034Z 42002-0034Z 42002-0034Z
15 Membrane Pad (NA, LP Series) 1 472610Z 472610Z 472610Z
16 Stack Flue Sensor 1 42002-0024S 42002-0024S 42002-0024S
17 Inlet Temperature Control Switch 1 474363Z 474363Z 474363Z
OFFICES - AUSTRALIA
NSW - Sydney
(HEAD OFFICE)
Tel : +61 2 9898 8686
VIC/ TAS - Melbourne
Tel : +61 3 9764 1211
WA - Perth
Tel : +61 8 9273 1900
QLD - Brisbane
Tel : +61 7 3299 9900
SA/ NT - Adelaide
Tel : +61 8 8244 6000
ACT Distributor
Tel : +61 2 6280 6476
OFFICES - OVERSEAS
Waterco USA
Augusta, USA
Tel : +1 706 793 7291
Waterco Canada
Longueuil, Qc, Canada
Tel : +1 450 748 1421
Waterco (Europe) Limited
Sittingbourne, Kent. UK
Tel : +44(0) 1795 521 733
Waterco France
SAINT PRIEST, France
Tel : +33 (0)4 72 79 33 30
Waterco (NZ) Limited
Auckland, New Zealand
Tel : +64 9 525 7570
Waterco (C) Limited
Guangzhou, China
Tel : +8620 3222 2180
Waterco (Far East) Sdn. Bhd.
Selangor, Malaysia
Tel : +60 3 6145 6000
PT Waterco Indonesia
Jakarta, Indonesia
Tel : +62 21 4585 1481
Waterco International Pte Ltd
Singapore
Tel : +65 6344 2378
Waterco Limited ABN 62 002 070 733
ZZM1439_02/2014
advertisement
* Your assessment is very important for improving the workof artificial intelligence, which forms the content of this project
Related manuals
advertisement
Table of contents
- 3 Section 1. Heater Identification
- 3 Heater Data Rating Plate
- 4 Section 2. Introduction
- 4 Important Notices
- 5 Warranty Information
- 5 Code Requirements
- 6 Consumer Information and
- 9 General Specifications
- 10 Section 3. Installation
- 10 Heater Description
- 11 Sequence of Operation
- 11 Putting the Heater into Service
- 12 Specifications
- 13 Plumbing Connections
- 13 Valves
- 13 Manual By-Pass
- 14 Water Connections
- 14 Below Pool Installation
- 15 Gas Connections
- 16 Gas Pipe Sizing
- 16 Sediment Trap/Drip Leg
- 16 Testing Gas Leaks and Gas Pressure
- 17 Gas Pressure Requirements
- 17 Outdoor Installation
- 19 Indoor Venting—General Requirements
- 21 Combustion Air Supply / Corrosive
- 22 Vent Installation (Indoor Installation or
- 25 Horizontal or Vertical Venting - Using
- 26 Connecting Single-Wall Stainless
- 29 Horizontal or Vertical Venting Flexible
- 29 Corrosive Vapors and Possible Causes
- 30 Control Panel Indexing
- 30 Final Installation Check
- 30 Electrical Connections
- 31 Fireman’s Switch Connection
- 33 Turbotemp Wiring Diagram
- 35 Section 4. Operation
- 35 Basic System Operation / HSI
- 36 Operating Instructions
- 37 To Turn Off Gas to Appliance
- 38 Safety Controls (Air Flow Switch
- 39 Operating the Control Panel
- 41 Section 5. Troubleshooting
- 41 Initial Troubleshooting and
- 42 Heater Will Not Fire Troubleshooting
- 46 LED Diagnostics
- 49 Section 6. Maintenance
- 49 Care and Maintenance
- 50 Pressure Relief Valve
- 50 After Start-Up
- 50 Spring, Fall (Autumn) and
- 52 Maintaining Pool Temperature
- 52 Chemical Balance
- 55 Replacement Parts