9. Service. Agilent Technologies 85330A, Multiple Channel Controller 85330A, 54503A
Add to my manuals
166 Pages
Agilent Technologies 54503A is a powerful, flexible instrument designed for high-performance applications. It is the ideal solution for testing and characterization of electronic devices, materials, and systems. With its advanced features and capabilities, the 54503A can help you to improve your productivity and accuracy. Here are just a few of the things that you can do with the 54503A:
- Generate, measure, and analyze electrical signals
- Characterize electronic components and devices
- Test and debug circuits and systems
- Perform research and development The 54503A is a versatile instrument that can be used in a wide variety of applications. It is the perfect tool for engineers, scientists, and technicians who need a powerful and reliable instrument for their testing and measurement needs.
advertisement
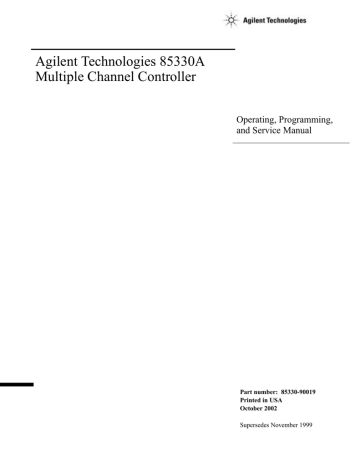
9
Introduction
CAUTION
Service
Service
This chapter explains the following topics:
•
Theory of Operation (how the multiple channel switching system works)
•
Recommended Test Equipment (the equipment required for servicing these instruments)
•
Service
❍
Troubleshooting (how to determine which part of the system is faulty)
❍
Replaceable Parts (how to identify and order parts)
❍
❍
❍
Assembly/Disassembly (how to remove and replace failed assemblies)
Adjustments (how to make any adjustments or settings required)
Preventive Maintenance (what service should be done as a preventive)
The assemblies used in the multiple channel controller system are static sensitive. Use anti-static techniques when performing the following procedures. For example, wear an anti-static ground strap and work at a station equipped with an anti-static mat.
85330A Multiple Channel Controller 9-1
NOTE
Service
Theory of Operation
Theory of Operation
The 85330A multiple channel controller was designed as a high-speed, real-time controller for the 8530A microwave receiver. The 85330A controls external solid-state transmit and receive switches and allows for asynchronous TTL communications to the receiver, the RF and LO sources, and other remote 85330As. It is implemented using a standard VXI mainframe and has a downloadable software driver that provides the controllers with their own GPIB command set for control, setup, and initiating runtime sequences.
A diagram of the entire system is shown in the
Block Diagram,” next. All of the connections from the 85330-60002 card’s
rear panel to other instruments are optional and may be different for each system, depending on the system’s requirements from the 85330A.
A receiver may use the STOP SWEEP line, if the RCVR READY line is not available.
The 85330A was implemented using an Agilent 75000 Series B VXI mainframe. A special VXI card was developed to handle the necessary control and timing requirements. This card is driven by a standard VXI parallel interface card (Digital I/O card.) A downloadable software driver was developed to provide fast runtime control of the measurement system.
9-2 85330A Multiple Channel Controller
GPIB
Service
Theory of Operation
The 85330-60002 card contains the TTL trigger and ready lines that interface to the 8530A microwave receiver, the RF source, and the LO source. The communication to the switch control unit is through sets of parallel twisted-pair wires and bias wires. These wires enable placement of the switches next to the transmit and receive devices. This minimizes the RF path lengths to the external mixer modules and therefore decreases the amount of RF losses.
Configuration of the 85330A is achieved by sending a series of GPIB commands to the mainframe prior to the runtime. To initiate the runtime sequence, a GPIB command is issued to the controller, or, the controller begins the measurement sequence, or waits for a trigger signal to the
EVENT TRIG to begin the sequence. For the latter, the controller repeats the sequence for each trigger sent to the EVENT TRIG.
Figure 9-2 shows the timing sequence of a typical measurement using the
85330A.
Table 9-1 on page 9-6 shows the time required for each trigger
shown in
Figure 9-2 . This measurement not only controls a transmit and
receive switch, but may optionally control the RF and LO sources for high speed frequency switching during the measurement. Upon receiving a trigger from the Positioner Controller or other trigger source, the 85330A issues the receiver trigger, waits for the receiver ready line, asserts the next set of switch states, waits for the switches to settle, and issues the receiver another trigger. To change frequency, the 85330A triggers the RF and LO sources and waits for the source ready lines before proceeding to the next set of switch states.
Figure 9-2 85330A Timing Sequence of a Typical Measurement
85330A Multiple Channel Controller 9-5
Service
Theory of Operation
Trigger
EVENT TRIGGER
MEAS BUSY
RCVR TRIG
RCVR READY:
Switch Settling
Receiver Measurement
SWITCH PORT 1
SWITCH PORT 2
SRC 1 TRIG
SRC 2 TRIG
Frequency switching
SRC 1 READY
SRC 2 READY
Table 9-1 Timing Sequence Trigger Widths
Width
1
µ s
≤ t ev
≤1 ms
Description
Trigger width dependent on trigger source
Dependent on measurement time of 85330A
1
µ s
≤ t rc
≤3 µ s
Default 2
µ s typ.
≥
200
µ s
Variable
Variable
10
µ s
≤ t sr1
≤14 µ s
10
µ s
≤ t sr2
≤14 µ s typ
≥5
ms typ 1
µ s typ 1
µ s
Set by 85330 command- RUNT:SWIT:DEL
Dependent on measurement time of 8530A
Dependent on RCVR TRIG and RCVR READY lines
Dependent on RCVR TRIG and RCVR READY lines
Dependent on frequency switching time of source
Trigger width dependent on trigger source
Trigger width dependent on trigger source
For large systems, the distance between the transmitters and receiver may exceed the physical capabilities of a single controller. For these applications, multiple controllers can be used. The REMOTE1 and REMOTE2 provide the communications between controllers via two balanced twisted-pair wires, similar to RS-422. In defining the runtime parameters, the event sequence is also defined which enables the controllers to operate in unison via these wires.
The AUX POWER IN allows for use of an external
±
12 Vdc power supply to be used if the VXI mainframe can not supply the required power for a large switching system, or to compensate for local control cable losses, or special switch voltages. The AUX 1 and AUX 2 outputs can provide a user-controllable TTL line for special applications.
The 85330-60002 card communicates with the switch control units via the
SWITCH PORT1 and SWITCH PORT2 connectors. These SCUs decode the switching control signals and provide bias for the Switches. The physical connection of a switch control module is accomplished using one of the two independent output ports on the 85330-60002 card. The separate ports provide the cabling requirements for remote switches to the transmit and receive sites. The cascading feature provides for building switch trees, or simultaneous switching into multiple RF channels.
Switch control units can be individually addressed for independent control, or can share the same address for simultaneous switching or tree configurations. Each module has two bits of unit-address decode and six bits
9-6 85330A Multiple Channel Controller
Service
Theory of Operation of channel-address decode. The six channel-address bits allow unique addressing for switches up to a 64 throw switch.
For the detailed theory of operation for the E1301B VXI mainframe, see the
Service chapter in the Agilent E1301B Service Manual.
85330A Multiple Channel Controller 9-7
Service
Recommended Test Equipment
Recommended Test Equipment
Table 9-2 lists the equipment that is mandatory when servicing the multiple
channel controller and switches. Other equipment can be substituted if it meets or exceeds the requirements for the tests, or the requirements specified below.
Table 9-2 Required Test Equipment
1
1
1
1
Qty
1
1
3
1
1
1
1
1
1
1
Item
Downloadable Driver Disk
Multimeter
±
20 Vdc, digital
Digital Oscilloscope (1 MHz Single-shot Band Width)
Tee Adapter (BNC male to female, female)
Cable (BNC male to male 122 cm)
Network Analyzer System
3
50 MHz to 40 GHz
4
,
5
90 dB dynamic range
Plotter or Printer
6
Torque Wrench 2.4/3.5 mm (8 in-lb)
TORX Driver T-8
TORX Driver T-10
TORX Driver T-15
Posidriv No.1
Posidriv No.2
Soldering Iron
Agilent Part or Model Number
85330-10016
2
E2377A
54501A
1250-0781
8120-1840
8722C Option 003
HP 7550A+ or LaserJet
8710-1765
7
8710-1673
8710-1284
8710-1816
8710-0899
8710-0900
Use
I, T, P
P, T
P, T
P, T
P, T
P, T
P
P, T, I, O
T
T
T
T
T
T
1
1. O = Operation
P = Performance Verification
A = Adjustments
T = Troubleshooting
I = Installation
2. Included with the 85330A shipment.
3. System must include vector network analyzer, test port cables, and calibration kit.
4. A 50 MHz to 26.5 GHz network analyzer may be used if the 3.5 mm adapters are used with the microwave switches.
5. If a network analyzer is used with a frequency range less than the switches, then the performance verification will only be valid over the frequency range of the network analyzer.
6. Plotter or printer must connect to the network analyzer and oscilloscope for test documentation.
7. Use this wrench for any 2.4/3.5/SMA mm connections in the procedure.
9-8 85330A Multiple Channel Controller
CAUTION
CAUTION
NOTE
Service
Service
Service
The assemblies used in the multiple channel controller system are static sensitive. Use anti-static techniques when performing the following procedures. For example, wear an anti-static ground strap and work at a station equipped with an anti-static mat.
Do not disconnect or remove any boards from the mainframe unless the mainframe is unplugged. Some boards contain devices that can be damaged if the board is removed when the power is on. Several components, including
MOS devices, can be damaged by electrostatic discharge. Use a proper ESD workstation when servicing this instrument.
It is assumed that the person performing the service tests understands how to operate the multiple channel controller and the specified test equipment.
Equipment settings—other than those used for the multiple channel controller—are stated in general terms. For example, a test might require that a voltage of +5 Vdc be measured, however the Digital Multimeter instructions as to mode and range would not be specified and the operator would be expected to set that control and any other controls as required to obtain a measurement. It is also assumed that the technician will select the cables, adapters, and probes required to complete the test setups illustrated in this section.
85330A Multiple Channel Controller 9-9
Service
Troubleshooting
Troubleshooting
Troubleshooting the
System
Troubleshooting the
Multiple Channel
Controller
NOTE
An understanding of how the 85330A system operates is required before undertaking the troubleshooting of this system. Please read
This system may be broken down into four parts: multiple channel controller
(mainframe), switch control unit, RF switch, and cables. In order to determine which part of the system is not working correctly, a performance verification may be run. For more information, see
Turn ON Self Check
The following screen should appear when you turn the 85330A ON.
Select an instrument._
SYSTEM 85330A IBASIC (see note below)
IBASIC is present only if the IBASIC option is installed.
If you see this display, go on to the next troubleshooting section. If you do
not see this display, load the 85330A downloadable driver files as explained in
Multiple Channel Controller
Run the test
“Verifying the Multiple Channel Controller” on page 2-6 .
VXI Mainframe
For troubleshooting information on the E1301B VXI mainframe, see the
Service chapter in the Agilent E1301B Service Manual. There are a couple of VXI mainframe self tests that can be used, as well as the command *TST?.
85330-60002 Card
The multiple channel controller tests, shown above, will check this plug-in card.
To check the SWITCH PORT1 and SWITCH PORT2 output connector, refer to
Table 9-3 on page 9-11 for each control line function. Use a digital scope
or a logic analyzer to monitor these lines.
9-10 85330A Multiple Channel Controller
Service
Troubleshooting
Table 9-3 SWITCH PORT 1/2 Connector Pinout
11
12
13
9
0
7
8
5
6
3
4
1
2
D-Type
Connector Pins
Function
Bit 6 HI
Bit 6 LO
Bit 7 HI
Bit 7 LO
+
12 Vdc
+
12 Vdc
GND
GND
GND
Bit 0 HI
Bit 0 LO
Bit 1 HI
Bit 1 LO
22
23
20
21
24
25
18
19
16
17
D-Type
Connector Pins
14
15
Function
Bit 2 HI
Bit 2 LO
Bit 3 HI
Bit 3 LO
Bit 4 HI
Bit 4 LO
Bit 5 HI
Bit 5 LO
+
12 Vdc
−
12 Vdc
GND
GND
Troubleshooting the
Switch Control Unit
Run the test
“Verifying the Switch Control Unit” on page 2-12 .
NOTE Check to make sure that the serial number prefixes of the Switch Control
Unit and RF switch match. They are produced at the factory this way. It is acceptable to use switches and SCUs with different serial numbers. But if there is a problem, it may be because a newer switch is used with an older
SCU, or an older switch is used with a newer SCU.
Run the test
“Verifying the RF Switches” on page 2-13.
Troubleshooting the
RF Switch
Troubleshooting the
Cables
The cables will be checked during “Verifying the Switch Control Unit” and
“Verifying the RF Switches” tests in
Chapter 2, “Performance Verification.”
If a cable is suspected, use a voltmeter to check continuity between the connectors on each end of the cable. See
Table 9-4 on page 9-12 for the
wiring information for each set of cables.
85330A Multiple Channel Controller 9-11
Service
Troubleshooting
85383A Local Control Cable
Use
Table 9-4 to check each connector pin for continuity.
Table 9-4 85383A Connector Wiring Table
1
2
D-Type
Connector Pins
5
6
3
4
9
10
7
8
11
12
13
1. nc = No Connection
P
N
J
M
H
B
D
E
L nc
1
F
A
C
Circular
Connector Pins
22
23
20
21
24
25
18
19
16
17
D-Type
Connector Pins
14
15
V a
U
Z
W b
T
Y
S
X
K
R
Circular
Connector Pins
85383B Expansion Cable
This cable has the same connector type on each end—one end male and the other female. Each pin on one connector will have continuity with the same pin on the other end. Remember that each pin on one connector will be on the opposite side of the connector face on the other connector (they are mirror images of each other).
85384A Switch Driver Cable
This cable has the same connector on each end, and each pin on one connector will have continuity with the same pin on the other end.
85385A Remote Trigger Cable
This cable has the same connector on each end, but is wired to cross-connect the inputs and outputs from the multiple channel controller. See
for more information.
9-12 85330A Multiple Channel Controller
Table 9-5 85385A Wiring
6
7
4
5
2
3
Connector 1
1
8
9
1. nc = No Connection
8
9
4
5
6
7
2
3
Connector 2
1 tx/rx tx/rx rx/tx rx/tx
Function nc
1 nc
1 shield nc
1 nc
1
Service
Troubleshooting
85330A Multiple Channel Controller 9-13
Service
Replaceable Parts
Replaceable Parts
This section contains information for ordering replaceable parts for the multiple channel switch system. The replaceable parts include major assemblies and chassis hardware.
Parts List Description
The following tables show the location and identification of replaceable parts. The list provides the following information:
1. Reference designator: identifies the part in the accompanying figure.
2. Agilent part number.
3. Part quantity as shown in the corresponding figure. (There may or may not be more of the same part elsewhere in the instrument.)
4. Part description, and identifying or functional name.
Ordering Information
To order a part, quote the Agilent part number, indicate the quantity required, and address the order to the nearest Agilent office.
To order a part that is not listed in the replaceable parts lists, include the instrument model number, complete serial number, the description and function of the part, and the number of parts required. Address the order to the nearest Agilent office.
Replaceable Parts
The multiple channel switch controller system consists of the following modules: mainframe and plug-in cards, switch control unit, RF switch, and interconnect cables. For information on replaceable parts for each module, see each of the following sections.
9-14 85330A Multiple Channel Controller
Service
Replaceable Parts
Figure 9-3 85330A System Identification Diagram
85330A Multiple Channel Controller 9-15
Mainframe, Plug-in
Cards
Service
Replaceable Parts
The mainframe consists of a E1301B VXI mainframe. For information of replaceable parts for this mainframe, see the “Replaceable Parts” chapter of the Agilent E1301B Service Manual.
Table 9-6 85330A Mainframe Replacement Parts
W1
F1
F2
F3
F4
A2
A3
U2
Reference
Designator
A1
Description
VXI Mainframe
Digital I/O Card for VXI Size B
85330-60002 Card
A3U2 PAL for 85330A standard
A3U2 PAL for 85330A H30
A2-A3 Ribbon Cable Assembly 0.45 m
Fuse 1A 125Vfor
+
5 Vdc int. bias
Fuse 4A 125V for
+
12 Vdc ext. bias
Fuse 1A 125V for
−
12 Vdc ext. bias
Fuse 3A 250V for 115 Vac operation
Downloadable Driver Disk, rev A.03.00
Rack mount kit without handles (Option 908)
Rack mount kit with handles (Option 913)
Agilent 85330A Operating and Service
Manual
E1301B Users Manual
E1301B Service Manual
E1330A/B Users Manual
E1330A/B Service Manual
Part Number
E1301B (Option 010)
E1330B
85330-60002
85330-80013
85330-80014
85330-60013
2110-0047
2110-0476
2110-0047
2110-0043
85330-10016
5062-3978
5962-3984
85330-90019
E1300-90005
E1300-90015
E1330-90004
E1330-90012
Qty.
1
1
1
1
1
2
1
1
1
9-16 85330A Multiple Channel Controller
Service
Replaceable Parts
Switch Control Unit
Table 9-7 85331/2 Switch Control Unit Replacement Parts
Reference
Designator
A5
A6
W6
2
3
Description
Address Decoder Module
Switch Driver Module
A5-A6 Ribbon Cable Assembly: if one A6 module -
If two or three A6 modules -
Screw M4 FH #2 Phillips: one driver module M45 two driver modules M80 three driver modules M110 -
Lid
Lid Label:
Standard -
Special -
Special -
Light Pipe
Light Pipe Shrink Tubing
Gasket Seal
Part Number
85331-60051
85331-60052
85331-60016
85331-60027
0515-2424
0515-2425
0515-2423
85331-20011
85331-80018
85331- 80019
85331-80020
85331-20005
0890-0029
0905-1154
Qty
1
1, 2, 3
1
4
1
1
9
1
1 per module
RF Switch
Table 9-8 85331/2 Switch Replacement Parts
Reference
Designator
A4
Description
A4
85331A 2P Switch 0.045 to 40 GHz (NEW)
(EXCHANGE)
85332A 4P Switch 0.045 to 40 GHz (NEW)
(EXCHANGE)
Part Number
85331-60031
85331-69031
85332-60001
85332-69001
Qty
1
1
85330A Multiple Channel Controller 9-17
Service
Replaceable Parts
Interconnect Cables
Table 9-9 Replacement Interconnect Cables for 85330/31/32
Reference
Designator
W2
Description Part Number
85383A Local Control Cable:
Option 002, 2 meters length -
Option 005, 5 meters length -
Option 010, 10 meters length -
Option 020, 20 meters length -
Option 030, 30 meters length -
Option 040, 40 meters length -
Option 050, 50 meters length -
85330-60020
85330-60018
85330-60019
85330-60011
85330-60023
85330-60024
85330-60021
W3 85383B Expansion Control Cable:
0.5 meters length 85331-60011
W4 85384A Switch Driver Cable:
Option 001, 1 meters length -
Option 002, 2 meters length -
Option 005, 5 meters length -
Option 010, 10 meters length -
85385A Remote Trigger Cable
1
85331-60025
85331-60026
85331-60021
85331-60022
W5
1. There is no replacement cable available. Cable must be repaired, instead of replaced.
9-18 85330A Multiple Channel Controller
CAUTION
Mainframe
NOTE
Service
Assembly and Disassembly
Assembly and Disassembly
The assemblies used in the multiple channel controller system are static sensitive. Use anti-static techniques when performing the following procedures. For example, wear an anti-static ground strap and work at a station equipped with an anti-static mat.
For assembly and disassembly information on the E1301B VXI mainframe, see the Service chapter in the E1301B Service Manual.
Disassembly
1. Turn OFF the ac power switch and remove ac power cable.
2. Loosen the six screws on the E1330 and 85330-60002 card assemblies.
3. Gently slide out both cards together.
4. Remove the ribbon cables from each board by pushing the locking tabs out of the way on each connector and lifting the ribbon connector out of the board connector.
Assembly
1. Make sure that the ac power switch is turned OFF and remove the ac power cable.
2. Ensure that the E1330B card is properly configured. Refer to
Card Configuration” on page 9-20 for more information.
3. Ensure that the 85330-60002 card is properly configured. Refer to
“E1330 Card Configuration” on page 9-20 for more information.
4. Fold the two ribbon cables like a fan.
5. Connect a ribbon cable to each panel connector on the E1330 with the ribbon cable pointed down.
6. Place the E1330 card on top of the 85330-60002 card.
7. Connect the other end of each ribbon cable to the circuit board connector P2 and P3 on the 85330-60002 card.
The cables should not be twisted or cross each other. They should lay flat between the two cards. Make sure that all four connectors are properly seated.
85330A Multiple Channel Controller 9-19
E1330 Card
Configuration
85330-60002 Card
Configuration
NOTE
Service
Assembly and Disassembly
8. Place the E1330 card on top of the 85330-60002 card and slide them into the mainframe.
9. Tighten all six screws.
Before installing a new E1330 card, make sure that it is configured correctly for the system that it will be installed in.
1. The LADDR (logical address) or SW1 should be set to:
Bit
Set
7
1
6
0
5
0
4
1
3
0
2
0
1
0
0
0
This sets the secondary GPIB address to 144. (The secondary address is the logical address divided by 8, which is 18.)
2. IRQ jumpers JM15 and JM16 are both set to position 1.
3. PULL UP MODE jumpers J51, J52, J53, and J54 are ENABLED.
4. FLG COMBINE jumpers should be empty, NO JUMPERS NEEDED.
Before installing a new 85330-60002 card, make sure that it is configured correctly for the system that it will be installed in.
1. Note that sockets J8, J9, and J10 are not normally used.
2. Insure that the correct fuses are installed in F1, F2, and F3. Refer to
Table 9-6 on page 9-16 for a list of these fuses.
3. Insure that the correct U2 PAL is installed. Refer to
correct part number.
4. Make sure that the card is set correctly for the system’s trigger (either positive or negative edged triggering).
Most positioner controllers put out a positive edged trigger, but most other trigger sources use a negative edged trigger. The default triggering is positive edged. To configure the triggering, refer to
Negative-Edge Event Triggers” on page 9-22 .
5. Make sure that the correct jumpers are set for internal or external dc bias. This sets the source of the RF switch dc bias (internal for a small number of switches, or external for a large number of switches.) The default is internally powered. To configure the power, see
“Switching from the Internal to External Power Supply” on page 9-24 .
9-20 85330A Multiple Channel Controller
Switch Control Unit
CAUTION
Service
Assembly and Disassembly
Disassembly
1. Remove the Local Control cable and Switch Drive cable.
2. Remove the four screws from the lid of the Switch Control Unit.
3. Pull the unit apart.
Be careful not to damage the gasket seal in each module.
4. Remove the ribbon cable from the Drive module and the Decoder module.
5. Do not change any switch settings in any of the modules!
Assembly
1. If you are installing a new Decoder or Driver module, the switches S1 and S2 must be set correctly. If you are replacing a module, set the switches for the same setting as the old module. If you are unsure, here arte the factory default settings:
❍
❍
The Decoder module switches are normally factory set to “all closed” for S1 and S2.
The Driver module switches are normally factory set to “all closed” for S1 and S2.
2. Check PAL U2 and U3 in sockets XU2 and XU3 on the Driver module.
The module should contain both PALs, unless there is more than one driver module. If the SCU has more than one driver module, then only the first (bottom) should have both XU2 and XU3 filled with a PAL. Any modules after the first should only have PAL U2 installed. Remove PAL
U3 from socket XU3 for these modules.
3. Make sure that the gasket seal is properly installed in each module housing.
4. Install the A5-A6 ribbon cable as follows: a.
Plug the 16 pin connector into the decoder board socket J3.
b.
Plug the 14 pin connector into the decoder board socket J4.
c.
Insert the free end of the cable with the 30-pin connector through the large notch in the driver board from the bottom.
d. Lower the Driver module onto the Decoder module, pulling the ribbon cable through the opening.
e.
Plug the 30 pin connector into the driver board socket J1.
f.
Pull the excess length of the ribbon cable up from the Decoder module into the Driver module. Fold the excess length of the cable over the top of the driver board.
85330A Multiple Channel Controller 9-21
Service
Adjustments
5. Place the lid (including the light pipes) onto the Driver module housing.
6. Screw the lid onto the housing. Tighten to about 7 in-lbs to insure that the SCU is environmentally sealed.
Adjustments
Selecting Positive or
Negative-Edge Event
Triggers
There are no adjustments that can be made in the mainframe, Digital I/O card, or the RF switch. Any other adjustments, or settings, that may be performed due to a part replacement or service, is shown below.
85330-60002 Card
By default, the positive-edge of the EVENT TRIG line starts the measurement on the 85330-60002 card. If this card is replaced, the EVENT
TRIG line may be required to be changed to a negative-edge trigger. To change this, perform the following procedure.
CAUTION This device contains devices that are sensitive to static discharge. When you remove the cover of this device, observe static safety precautions:
•
Place the unit on a grounded anti-static mat.
•
Wear a grounded wrist strap, or
•
Foot straps are only acceptable if you wear one on each foot, and if you are standing on a grounded floor mat.
See
9-22 85330A Multiple Channel Controller
Service
Adjustments
Figure 9-4 Positive/Negative-Edge EVENT TRIG jumpers
1. Remove the two screws that hold the E1330B board in place.
2. Remove the four screws that hold the 85330-60002 board in place.
3. Pull out the two boards at the same time. You can do this by pulling each one out a little at a time, until they are both removed. Place the boards on an anti-static surface.
Standard positive-edge operation is set at the factory by jumpering E9 and E10 together.
4. To select negative-edge operation, move the jumper across E9 and E8.
5. Reinstall the boards and screws.
Selecting the Multiple
Channel Controller’s
GPIB Address
The factory default setting of the GPIB address is 9. To view the GPIB address:
Press [Select Instr] {SYSTEM} {GPIB} {READ}
To change the current GPIB address:
1. Press [Select Instr] {SYSTEM} {GPIB} {SET} .
2. Enter the new address and press [Return] .
85330A Multiple Channel Controller 9-23
Switching from the
Internal to External
Power Supply
Service
Adjustments
This set of jumpers sets the 85330-60002 card to use in the internal VXI power supply to bias the remote RF switches and Switch Control Units, or to use the AUX POWER IN connector to bias the switches and SCUs. The internal power supply is used when there is few SCUs and RF switches. The
AUX POWER IN is used when there are a large number of switches and
SCUs, or if the switches require a special dc voltage, or to compensate for losses in a long Local Control Cable. The default is the internal power supply.
To set these jumpers, perform the following on the 85330-60002 card. This card must be removed before changing this switch. Refer to
Disassembly” on page 9-19 for information on removing the card.
1. Locate the jumpers W1 and W2 near the rear panel of the 85330-60002.
They will be next to the AUX POWER IN connector.
2. To set the card to the internal supply, the W1 jumper should go from
+12V to INT, and the W2 jumper should go from
−
12V to INT.
3. To set the card to the AUX POWER IN supply, the W1 jumper should go from +12V to AUX, and the W2 jumper should go from
−
12V to AUX.
Table 9-10 AUX Power In Connector Pinouts (as looking at rear of 85330-60002)
Pin 10
−
12 V
Pin 5
−
GND
Pin 9
+
12 V
Pin 4
+
GND
Pin 8
+
12 V
Pin 3
+
GND
Pin 7
+
12 V
Pin 2
+
GND
Pin 6
+
12 V
Pin 1
+
GND
Required Mating Connector
A Molex Mini-Fit Jr model 5557 (Molex p/n 39-01-2105) receptacle is required. At least three wire crimp terminals are required: 4.2 mm Pitch
Mini-Fit Family Terminal-crimp, Female model 5556 (Molex p/n
39-00-0059).
9-24 85330A Multiple Channel Controller
Service
Preventive Maintenance
Preventive Maintenance
Preventive maintenance for the multiple channel controller consists of cleaning various parts of the mainframe. The switch control unit and switches do not require preventive maintenance. Agilent recommends a twelve month interval between cleaning. However, cleaning intervals are mostly dependent upon where the mainframe is used. The mainframe should be cleaned more often if it is used in a dusty, or very humid area.
To perform the preventive maintenance, refer to the mainframe, Agilent
E1301B, Service Manual. The maintenance instructions are in the Operating
Instructions chapter.
85330A Multiple Channel Controller 9-25
Service
Preventive Maintenance
9-26 85330A Multiple Channel Controller
advertisement
* Your assessment is very important for improving the workof artificial intelligence, which forms the content of this project
Key Features
- Single-channel, 20-MHz arbitrary waveform generator
- Built-in function generator with 13 standard waveforms
- Arbitrary waveform storage and recall
- Built-in counter/timer
- GPIB and RS-232 interfaces
- Easy-to-use front panel and software
- Compact and portable
- Affordable
Related manuals
Frequently Answers and Questions
What is the frequency range of the 54503A?
What is the maximum output voltage of the 54503A?
What types of waveforms can the 54503A generate?
How many channels does the 54503A have?
What is the maximum sample rate of the 54503A?
advertisement
Table of contents
- 1 Title Page
- 3 What You’ll Find in This Manual…
- 4 Warranty
- 4 Certification
- 4 Documentation Warranty
- 4 Assistance
- 5 Service and Support
- 6 Safety and Regulatory Information
- 7 Safety Earth Ground
- 7 Before Applying Power
- 9 Manufacturers Declaration
- 9 Sound Emmisions
- 11 Typeface Conventions
- 13 Contents
- 19 1. Installation
- 19 Installation at a Glance
- 20 Preparing the Main Antenna Measurement System
- 20 Installing the Agilent 85330A Multiple Channel Controller
- 20 Choosing the Proper Configuration
- 24 Checking Operation of the Multiple Channel Controller
- 24 Loading the Driver from a Personal Computer
- 26 Viewing or Changing the GPIB Address of the Multiple Channel Controller
- 26 Selecting Positive or Negative-Edge Event Triggers
- 28 Installing the Switch Control Units and Switches
- 28 Mounting the SCU and RF Switch
- 28 Switch Control Unit Configuration Switches
- 31 2. Performance Verification
- 31 In This Chapter
- 31 Description
- 32 Recommended Equipment
- 33 Performance Verification Test
- 33 Setting Up the Equipment
- 33 85330 System
- 34 Digital Oscilloscope
- 35 Network Analyzer
- 35 Cables
- 35 Calibration
- 35 Save Setup
- 36 Verifying the Multiple Channel Controller
- 36 Turn-On
- 36 Voltage Check
- 37 Inputs/Outputs
- 37 Output Trigger Test
- 38 Pulse Receive and Cycle Test
- 39 Counter Pulse Delay Test
- 41 Measurement Busy Signal and Pulse Width Test
- 42 Verifying the Switch Control Unit
- 43 Verifying the RF Switches
- 43 Switch Setup
- 44 RF Performance Tests
- 45 Verifying Remote Ports 1 and 2
- 45 Jumpers
- 47 AUX 1 and AUX 2
- 47 Pulse Test
- 47 Measuring Pulses from AUX 1 or AUX 2
- 48 AUX 1 and AUX 2 Output Voltage Test
- 48 When Finished with All Tests
- 49 3. Operator’s Check
- 49 Purpose
- 49 Procedure
- 51 4. General Information
- 51 In This Chapter
- 52 Product Description
- 52 In-depth Information
- 53 Manual Operation
- 53 Automated Operation
- 54 Preparing the 85330A to Control the System
- 54 Special Systems
- 54 Switch Components
- 55 The Downloadable Driver
- 55 System Interface
- 55 Required Equipment
- 55 Cables
- 57 PIN Switches
- 58 Supplied Equipment and Software
- 59 85330A Multiple Channel Controller Characteristics
- 59 Environmental Limits
- 60 Ventilation Requirements
- 60 Dimensions
- 61 Front Panel Features
- 61 Need More Information
- 62 Rear Panel Features
- 65 85330A Compatibility
- 65 Compatible Receivers
- 65 Compatible LO Sources
- 65 Compatible RF Sources
- 67 5. Manual Operation
- 67 In This Chapter
- 68 To Use the Front Panel
- 68 About the Softkeys Menus
- 68 Utility Keys
- 69 Softkey Map
- 70 To View or Change the 85330’s GPIB Address
- 70 Viewing GPIB Address
- 70 Changing the GPIB Address
- 71 To Close Any Switch in the System (to select a channel)
- 71 More about Switch Addresses
- 72 To Change the TTL State of AUX 1 or AUX 2
- 72 To View the Most Recent Error Message
- 72 To View the Revision of the Downloaded Driver
- 73 To View Custom Option Number (If Applicable)
- 73 To Manually Send Trigger Pulses
- 73 To Perform Service Functions
- 75 6. Programming
- 75 In This Chapter
- 75 GPIB Addresses
- 75 Long and Short Command Syntax
- 76 Definition of Terms
- 77 To Choose a Measurement Configuration
- 78 CW Measurement Configuration
- 78 Description
- 78 To Use this Configuration
- 79 Single Source Multiple-Frequency Configuration
- 79 Description
- 79 To Use this Configuration
- 81 Dual Source Multiple-Frequency Measurements
- 81 8530A Control of Sources
- 81 Description
- 81 To Use this Configuration
- 82 Fast Source Control
- 82 Description
- 82 To Use this Configuration
- 83 To Use Direct Control
- 83 Selecting a Channel
- 86 To Use Run-Time Control Mode
- 86 Setup of the 85330A Multiple Channel Controller
- 86 Event Triggering
- 86 Number of Frequency Points
- 86 Number of Angular Increments (Events)
- 86 List of Switch States
- 87 Switch Settling Time
- 87 TTL Trigger and Ready Timeouts
- 88 Using More than One Controller
- 88 Starting Run-Time Mode
- 88 Run-Time Measurement Sequence
- 92 Run-Time Measurement Sequence for Multiple Controllers
- 92 Using IMM vs. TTL Trigger for Source 1
- 95 Programming Examples
- 95 Example 1
- 99 Example 2
- 103 Example 3
- 108 85330A Error Messages
- 111 7. Remote Programming Command Reference
- 111 Command Syntax
- 111 Common Command Format
- 111 Standard Command Format
- 113 Common Commands
- 113 *CLS
- 113 Syntax
- 113 Example
- 113 *IDN?
- 113 Default
- 113 Syntax
- 113 Example
- 114 *OPC?
- 114 Syntax
- 114 Example
- 114 *RST
- 114 Default
- 114 Syntax
- 114 Example
- 115 Standard Command Reference
- 115 ROUTe
- 115 Subsystem Command Syntax
- 115 ROUTe:CLOSe
- 115 Default
- 115 Syntax
- 115 Example
- 116 ROUTe:CONTrol
- 116 Default
- 116 Syntax
- 116 Example
- 116 ROUTe:DELay
- 116 Default
- 116 Syntax
- 116 Example
- 117 RUNTime
- 118 RUNTime:CONTroller
- 118 Default
- 118 Syntax
- 118 Example
- 118 RUNTime:EVENt:COUNt
- 118 Default
- 118 Syntax
- 118 Example
- 119 RUNTime:EVENt:TRIGger
- 119 TTL Mode
- 119 IMM Mode
- 119 Default
- 119 Syntax
- 119 Example
- 120 RUNTime:INITiate:IMM
- 120 Default
- 120 Syntax
- 120 Example
- 120 RUNTime:SOURce:COUNt
- 120 Default
- 120 Syntax
- 120 Example
- 121 RUNTime:SOURce:SOURCE1:TRIGger
- 121 Default
- 121 Syntax
- 121 Example
- 121 RUNTime:SOURce:SOURCE2:TRIGger
- 121 Default
- 121 Syntax
- 121 Example
- 122 RUNTime:SWITch:DELay
- 122 Default
- 122 Syntax
- 122 Example
- 123 RUNTime:SWITch:SCAN
- 123 Default
- 123 Syntax
- 123 Example
- 124 RUNTime:SWITch:TRIGger
- 124 Default
- 124 Syntax
- 124 Example
- 125 RUNTime:TIMEout:EVENt
- 125 Default
- 125 Syntax
- 125 Example
- 125 RUNTime:TIMEout:RECeiver
- 125 Default
- 125 Syntax
- 125 Example
- 126 RUNTime:TIMEout:REMote
- 126 Default
- 126 Syntax
- 126 Example
- 126 RUNTime:TIMEout:SOURce
- 126 Default
- 126 Syntax
- 126 Example
- 126 SYSTem
- 127 SYSTem:ERRor?
- 127 Default
- 127 Syntax
- 127 Example
- 129 8. In Case of Difficulty
- 129 The 85330A Does Not Show the Main Menu When Turned ON
- 131 9. Service
- 131 Introduction
- 132 Theory of Operation
- 137 Recommended Test Equipment
- 138 Service
- 139 Troubleshooting
- 139 Troubleshooting the System
- 139 Troubleshooting the Multiple Channel Controller
- 140 Troubleshooting the Switch Control Unit
- 140 Troubleshooting the RF Switch
- 140 Troubleshooting the Cables
- 143 Replaceable Parts
- 143 Parts List Description
- 143 Ordering Information
- 143 Replaceable Parts
- 145 Mainframe, Plug-in Cards
- 146 Switch Control Unit
- 146 RF Switch
- 147 Interconnect Cables
- 148 Assembly and Disassembly
- 148 Mainframe
- 149 E1330 Card Configuration
- 149 85330-60002 Card Configuration
- 150 Switch Control Unit
- 151 Adjustments
- 151 Selecting Positive or Negative-Edge Event Triggers
- 152 Selecting the Multiple Channel Controller’s GPIB Address
- 153 Switching from the Internal to External Power Supply
- 154 Preventive Maintenance
- 156 10. Accessory Documentation
- 158 Glossary
- 164 Index