Functional Verification Tests. Allen-Bradley Rockwell Automation 1734-AENT
Add to my manuals
114 Pages
advertisement
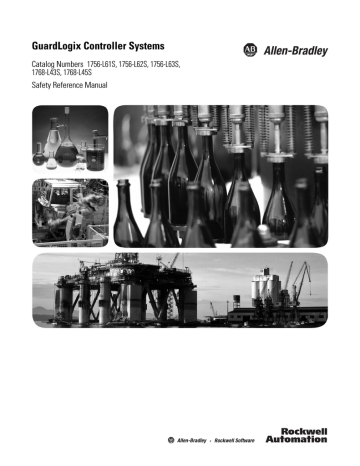
Chapter 1 Safety Integrity Level (SIL) Concept
The TÜV Rheinland has approved GuardLogix controller systems for use in safety-related applications up to SIL 3, in which the de-energized state is considered to be the safe state. All of the examples related to I/O included in this manual are based on achieving de-energization as the safe state for typical Machine Safety and Emergency Shutdown (ESD) Systems.
IMPORTANT
The system user is responsible for:
• the set-up, SIL rating, and validation of any sensors or actuators connected to the GuardLogix system.
• project management and functional testing.
• access control to the safety system, including password handling.
• programming the application software and the device configurations in accordance with the information in this safety reference manual and the GuardLogix Controllers User Manual, publication 1756-UM020 , or the 1768 Compact GuardLogix
Controllers User Manual publication 1768-UM002 .
When applying Functional Safety, restrict access to qualified, authorized personnel who are trained and experienced. The safety-lock function, with passwords, is provided in RSLogix 5000 software.
For information on using the safety-lock feature, refer to the
GuardLogix Controllers User Manual, publication 1756-UM020 or the
1768 Compact GuardLogix Controllers User Manual publication
1768-UM002 .
Functional Verification
Tests
IEC 61508 requires the user to perform various functional verification tests of the equipment used in the system. Functional verification tests are performed at user-defined times. For example, functional verification test intervals can be once a year, once every 15 years, or whatever timeframe is appropriate.
GuardLogix controllers have a functional verification test interval of up to 20 years. Other components of the system, such as Safety I/O modules, sensors, and actuators may have shorter functional verification test intervals. The controller should be included in the functional verification testing of the other components in the safety system.
IMPORTANT
Your specific applications determine the timeframe for the functional verification test interval. However this is mainly related to Safety I/O modules and field instrumentation.
For more information on the requirements of a functional verification
test, see Project Verification Test on pages 57
14 Publication 1756-RM093F-EN-P - January 2010
advertisement
* Your assessment is very important for improving the workof artificial intelligence, which forms the content of this project
Related manuals
advertisement
Table of contents
- 9 Introduction
- 9 About This Publication
- 9 Who Should Use This Publication
- 10 Understanding Terminology
- 11 Additional Resources
- 13 Introduction
- 13 SIL 3 Certification
- 14 Functional Verification Tests
- 15 GuardLogix Architecture for SIL 3 Applications
- 16 GuardLogix System Components
- 18 GuardLogix Certifications
- 19 GuardLogix PFD and PFH Specifications
- 20 Safety Integrity Level (SIL) Compliance Distribution and Weight
- 21 System Reaction Time
- 22 Contact Information If Device Failure Occurs
- 23 Introduction
- 23 1756 GuardLogix Controller Hardware
- 25 1768 Compact GuardLogix Controller Hardware
- 25 CIP Safety Protocol
- 25 Safety I/O
- 26 Communication Bridges
- 28 Programming Overview
- 29 Introduction
- 29 Overview
- 29 Typical Safety Functions of CIP Safety I/O Modules
- 31 Reaction Time
- 31 Safety Considerations for CIP Safety I/O Modules
- 35 Introduction
- 35 The Routable CIP Safety Control System
- 38 Considerations for Assigning the Safety Network Number (SNN)
- 41 Introduction
- 41 Differentiate Between Standard and Safety
- 42 SIL 2 Safety Applications
- 47 SIL3 Safety – the Safety Task
- 49 Safety Programs
- 50 Safety Routines
- 50 Safety Tags
- 52 Additional Resources
- 53 Introduction
- 53 Safety Concept Assumptions
- 53 Basics of Application Development and Testing
- 54 Commissioning Life Cycle
- 61 Downloading the Safety Application Program
- 61 Uploading the Safety Application Program
- 61 Online Editing
- 62 Storing and Loading a Project from Nonvolatile Memory
- 62 Force Data
- 63 Inhibit a Module
- 63 Editing Your Safety Application
- 67 Introduction
- 67 Monitoring System Status
- 74 GuardLogix System Faults
- 77 Introduction
- 77 Safety Application Instructions
- 79 Metal Form Safety Application Instructions
- 80 Safety Instructions
- 81 Additional Resources
- 83 Introduction
- 83 Creating and Using a Safety Add-On Instruction
- 88 Additional Resources
- 89 Introduction
- 89 System Reaction Time
- 89 Logix System Reaction Time
- 95 Introduction
- 96 Checklist for GuardLogix Controller System
- 97 Checklist for Safety Inputs
- 98 Checklist for Safety Outputs
- 99 Checklist for Developing a Safety Application Program
- 101 Introduction
- 101 GuardLogix Controller and Guard I/O Safety Data
- 102 PFD Values
- 102 PFH Values
- 109 Numerics
- 109 A
- 109 C
- 109 D
- 109 E
- 110 F
- 110 G
- 110 H
- 110 I
- 110 L
- 110 M
- 110 N
- 110 O
- 110 P
- 111 Q
- 111 R
- 111 S
- 112 T
- 112 U