- Home
- Do-It-Yourself tools
- Power tools
- Power fine-spray systems
- MULTIQUIP
- Sander FM9
- Operation manual
advertisement
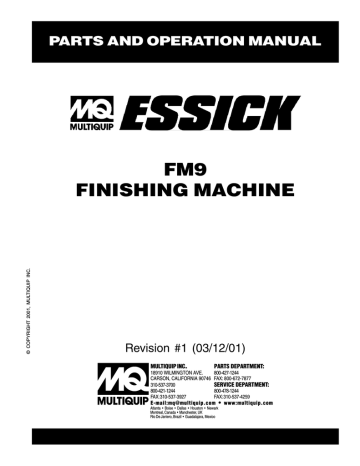
FM-9 — OPERATIONS
SAFETY
1. Do not operate or service this equipment before reading the operating and maintenance instruction manual.
2. Do not operate this equipment unless all guards and safety devices are attached and in place.
3. Stop engine when leaving equipment.
4. Block unit when parking on a slope.
5. Maintain this equipment in safe operating condition at all times.
6. Caution must be exercised while servicing this equipment.
Rotating and moving parts can cause injury if contacted.
7. Stop engine before adding fuel or oil. Never spray water over the engine or electrical motor.
8. Keep all inexperienced and unauthorized people away from equipment at all times.
9. Unauthorized equipment modifications will void all warranties.
10. Run transmission in reverse gear to relieve back pressure before disconnecting gun or hoses.
11. Screen must be on hopper at all times machine is in operation.
12. Stop engine before putting hands in hopper.
13. Wear safety eye glasses at all times when working around machine or material lines.
14. Electrical operated machines refer to supplemental FM5E-
I safety/operating instructions
OPERATING INSTRUCTIONS
Connect the air lines from the machine to the air control block mounted on the nozzle. One air line runs from the air compressor outlet on the machine to the inlet on the control block next to the sleeve valve. This line has air blowing out of it when the compressor is running. The other air line runs from the sleeve valve on the control block to the throttle cylinder inlet on the machine.
In operation, the compressor furnishes air to the control block.
The valve located on the front of the block is for the adjustment of atomized air which is used for the spraying of material. The sleeve valve operates the throttle cylinder on the engine. When the sleeve valve is in the closed position, air pressure is applied to the cylinder and the engine will speed up to the preset governed speed. When the sleeve valve is in the open position, air pressure is released from the spring loaded throttle cylinder and the engine will return to idle speed.
Before starting engine, check oil levels in engine crankcase, transmission and compressor. Place volume control lever
(transmission lever) in the position for the desired speed to be used. Turn the throttle control air valve, located on the spray gun, to the “off position.
After mixing the material, lubricate the pump and hose by pouring a few gallons of water into the hopper. Adjust the air pressure to approximately 20 lbs. and turn the throttle control air valve to
“on” position.
Continue to pump out the water until it reaches the level of the pump. Then fill the hopper half full with the material to be sprayed.
After the remaining water in the hose has been pumped out and material appears at the nozzle, point nozzle into hopper and make final air adjustments. With final adjustments made, turn air valve off.
GENERAL
The essick model FM9 plastering machine is in a class by itself.
Its main functions are that of a standard finishing machine: Mainly applying acoustical ceilings, exterior dash stucco finish and inside sand finish, as well as fireproofing steel beams. Although it was not designed to be used in place of a high-volume base coat plastering machine, it may be used to apply inside brown and it is capable of applying a half-sand, half-vermiculite mix at a very practical rate, which is satisfactory for some jobs.
This machine is equipped with a transmission having 3 forward speeds plus a reverse gear and is powered by a 9.2 hp engine, which also drives a heavy-duty twin-cylinder air compressor.
Although the procedure for mixing and applying the materials varies with each material being sprayed, the following procedure applies to all the materials mentioned above.
CAUTION: Never turn off pump until material appears at nozzle.
This may cause separation of the material, which would clog up pump and hose.
Fill hopper and carry nozzle and hose to spraying area. Turn air valve”on” and proceed to spray, working a pattern. Always overlap the spray, but never hold the gun still in an attempt to fill a void or defect.
CAUTION: Never run the pump dry, as this causes rapid pump wear or damage.
ESSICK FM9 — PARTS & OPERATION MANUAL — REV. #1 (03/12/01) — PAGE 7
FM-9 — OPERATIONS
CLEANING OF MACHINE
At the end of the day, or when changing from one material to another, the machine should be washed out. It is also suggested that when pumping quick setting materials to wash out machine and hoses approximately every 4 hours.
To clean the hopper and pump parts, run transmission in reverse gear to relieve back pressure in hose, turn off engine, remove spray gun and disconnect material hose. Remove pipe plug at bottom of hopper, drain, and wash down the remaining material with water. Replace plug.
After the material has been washed out of the hopper, the hose can be cleaned by disconnecting the material hose from the machine and removing the spray gun. Roll up a wet sponge and place it into the material hose, reconnect the hose to pump fitting, fill hopper half full with water and start machine.Pump enough water through hose to push sponge through entire length of hose. After sponge is pumped out, turn off engine and remove drain plug from hopper to drain remaining water. Repeat the sponge process if necessary.
Wash out spray gun, nozzle and orifices. Hose down screens and the outside of the machine.
Note: When washing down the outside of the machine, be sure the rubber boot is in place over the transmission lever pivot.
This prevents water from entering the transmission. Clean and oil all threads and joints.
MIXING AND APPLYING VARIOUS MATERIAL
The surface to be sprayed should be thoroughly dry. Do not wet before applying dash coat. Use either a 1/4" or 3/8" orifice. Be sure a soft rubber stator tube is used, as soft rubber will resist abrasives. After material is mixed, proceed as explained in the operating instructions. Adjust volume at low speed and air pressure to 20-25 lbs. If a second coat is to be applied, be sure that the surface appears dry to the eye before application or it will dry spotty and show a different shade of color.
SIMULATED ACOUSTIC CEILINGS
In many areas prepared materials are available for simulated acoustic ceilings. In areas where prepared materials are not available and where a contractor prefers to mix his own, the following mix makes a satisfactory texture.
100 lbs. — Gypsum
6 cu. ft. — Vermiculite or perlite
Mix the above materials thoroughly so the aggregate does not separate when in hopper. This mix should be of heavier consistency than exterior dash, but still wet enough to pass through a 3/8" screen.
If the material aggregate is made of vermiculite, use the hard rubber stator. If the material is made of perlite, the soft rubber stator should be installed. By using a 3/8" orifice and adjusting the volume at second speed and the air pressure to 20-25 lbs. A very satisfactory pattern can be obtained.
EXTERIOR DASH STUCCO
In areas where this type of finish is popular, a prepared machine mix is available which requires only the addition of water.
however, some contractors prefer to mix their own material. The following is considered a very satisfactory machine mix:
Since the finished appearance depends on the condition of the original surface, it is suggested that any obvious defects, such as ridges or holes, should be repaired with a hand trowel also, the ceiling should BE scraped with a floor or wall scraper prior to spraying the first coat.
200 lbs. — Silica sand mo. 20
50 to 60 lbs. — Hydrated lime
100 lbs. — Plastic cement
2 to 3 lbs. — Zonolite finish aggregate
Color may be added as desired, but should be measured for uniformity.
Care should be taken when spraying the ceilings to fill the angles well. This can be achieved by pointing the nozzle directly into the angle, thereby spraying on the wall as well as on the ceiling.
The overspray on the wall can be quickly removed by using the same scraper mentioned above.
The above materials must be thoroughly mixed and of a thin consistency, similar to a hand dash coat mix.
You will find that a better job can be accomplished if two coats are applied. But before applying the second coat, an inspection of the surface should be made and any defects should be repaired with a small trowel. After the inspection, the second coat can be immediately applied.
PAGE 8 — ESSICK FM9 — PARTS & OPERATION MANUAL — REV. #1 (03/12/01)
FM-9 — OPERATIONS
FULL ACOUSTIC CEILINGS AND FIREPROOFING UNDER
STEEL DECK
There are a number of various acoustic materials available, all of which can be pumped through this machine. Some of these materials are made from vermiculite and others from perlite.
Although we do not make any recommendations as to which is the better acoustic material, we do point out the fact that perlite is very abrasive and will cause rapid pump wear whereas, vermiculite will give longer pump life.
Only water needs to be added to ready-prepared materials. Some manufacturers suggest the correct amount of water in the instructions on the bag. However, if no instructions are available, the material should be mixed to a consistency thinner than. that of a mixture for hand application. I.E., thin enough so that only about i0 percent of the material will be retained on a 1/2" screen when it is poured into the hopper of the machine.
After the material is mixed, proceed as explained in the operating instructions. Use either a 3/8", 7/16" or 1/2" orifice, depending on the desired texture. Use the same size hopper screen as the size of the orifice that is going to be used. Use 3/8" screen with 7/16" orifice. Use a hard rubber stator with vermiculite and a soft rubber stator with perlite. By adjusting the volume to second speed and the air pressure to 15-20 lbs, a good yardage can be obtained in small areas. However, in larger areas it may be desirable to operate at full volume.
The application of full acoustic is very similar to that of simulated acoustic, except that successive coats can be applied until proper thickness is obtained. For application procedure refer to
“simulated acoustic ceilings” paragraph.
DRYWALL MIX APPLICATION
The FM9 works quite satisfactorily for applying drywall texture mixes such as: Spatter, orange peel, fog, sand finish, as well as simulated acoustic textures. In addition, it can be used for application of mastics, sealants, emulsions, glazes, roofingfinishes, sealers, water base paints, and cement paints.
BROWN COAT
As previously stated, the ESSICK MODEL FM9 plastering machine is not designed to do the work of a large base coat machine. Although it is not recommended, due to the rapid wear on the rotor and stator tube, it can apply brown coat and scratch material at a rate fast enough to be practical for some jobs.
When the machine is to be used for the application of brown or scratch material we recommend that the following suggestions be taken into consideration to aid the machine in pumping and also to obtain better results.
Install on machine, if not presently equipped, a soft rubber stator, a “hi volume” rotor and a 1-1/2" pump outlet fitting. Refer to “hi volume” instructions for changing of rotor and stator.
Use, if possible, a 400675 browning nozzle with a 5/8" orifice for outside brown and scratch and a 1/2" orifice for inside brown.
The length of 1-1/2" hose should not exceed 100 ft. With hoses and nozzle attached adjust the air pressure to approximately 20 p.s.i. and set machine at full volume.
The following is a satisfactory brown coat mix:
FIREPROOFING STEEL BEAMS
Consult the building specifications regarding the type of material to be used. Normally, for fireproofing metal lath wrapped steel beams, the mixture consists of one sack of either perlite or vermiculite and one sack of gypsum. These materials should be mixed to a consistency thinner than that for hand application and sprayed approximately 1" thick with an application. If a greater volume is desired, it is recommended to use a 1-1/2" hose with the machine at full volume. Note: The shorter the hose length, the greater the volume obtained.
Use the hard rubber stator with vermiculite and the soft rubber stator with perlite. It is also suggested that the largest size air jet be used in the nozzle and a 7/16" or 1/2" orifice. With the air pressure at minimum (approximately 10 PSI).
This is a very difficult operation and the operator’s technique will improve with experience. The majority of experienced operators prefer to use a short nozzle for better maneuvering around steel beams.
1-1/2 cu. ft. — Vermiculite
1-1/2 cu. ft. — Sand
1 Sack gypsum
Note: The best results are obtained by not using over 50 percent sand aggregate.
The mixing procedure should be as follows: Put approximately
10 gallons of water in the mixer and add 1-1/2 cu. ft.of vermiculite.
This allows the vermiculite to absorb sufficient water. Add one sack of gypsum (machine application type) and shovel in 1-1/2 cu. ft. of sand (approximately eleven no. 2 shovels). additional water should be added at this time.
It is difficult to predetermine the amount of water, as there are several variations possible. The amount of water is critical and experience will allow the operator to deterhine the correct amount.
ESSICK FM9 — PARTS & OPERATION MANUAL — REV. #1 (03/12/01) — PAGE 9
FM-9 — OPERATIONS
MAINTENANCE OF MACHINE
ENGINE
Refer to engine manufacturer’s maintenance manual for lubrication, adjustments and maintenance. Under extremely dusty working conditions special attention should be given to air and oil filters and crankcase breather.
TRANSMISSION
The transmission has 3 speeds forward plus one reverse and is totally enclosed with all gears running in oil. Shifting to the forward and reverse speeds is similar to that of an automobile. See diagram.
The reverse gear can be used to relieve the back pressure whenever the hose or pump becomes clogged.
Note: Gears should only be shifted when engine is idling.
If at any time it is difficult to shift gears, it is because the gears are meeting at flat points and realignment can be fired by speeding up the engine and returning it to idle.
The oil level plug, filter plug and drain plug are located on the side of the transmission. Use SAE 90 oil and check monthly.
ROTOR AND STATOR
Both the rotor and stator parts are subjected to wear. It is difficult to say just how long a stator or rotor will last, as this depends on various conditions under which the machine is operated. The abrasive type materials will cause the most wear. Therefore, to prolong the life of the pump, the stator tubes are made of two types of rubber: A soft rubber stator for use with abrasive aggregates, such as sand or perlite and a hard rubber stator for use with non-abrasive aggregates. It is not necessary to replace both the rotor and stator at the same time, as a rotor will normally last through approximately 3 stator tubes.
To prevent excessive wear of the pump, the following precautions should be taken.
1. Do not use long hoses. Use as short a hose as feasible.
2. Avoid the use of extremely stiff materials. They reduce the volume.
3. Ensure sufficient “fat” for lubrication by not having the mixes too “lean”.
4. Never allow the hopper to run out of material with the pump operating.
5. Turn stator tube end for end about twice during its life.
COMPRESSOR
Refer to compressor manufacturer’s maintenance manual for lubrication, adjustments and maintenance.
CLUTCH
The clutch is a centrifugal type clutch and is fully automatic. It is set at the factory to start engaging at 1600 r.p.m. and is fully engaged at 1700 r.p.m. It is ineffective at engine idle speed of
1550 r.p.m. Do not idle engine for prolonged periods of time, as it may overheat. Also, be sure engine does not idle at a higher speed, as this will wear the automatic, clutch.
ROTOR AND INSTALLATION
Lubricate the inside of the stator tube and the rotor with a liquid detergent or soap (oil will deteriorate the rubber). This will make the rotor slide into the stator tube with very little pressure.
The fit between the stator and rotor has to be very tight and may be difficult to achieve when these parts are assembled without lubrication.
It is normally difficult to operate the machine in second or third gear with the “hi volume” pump until approximately one days run of material has passed through the newly installed pump. This is due to the fact that the rotor must smooth itself out. The rotor and stator have to be very tight in the machine, as well as the clamp around the stator tube.
Upon installing the soft rubber pump you will find that the fit between the rotor and stator is not quite as tight as on the hard rubber pump. With lubricant in the pump (water or material) you should be able to run the machine in second or third gear from the beginning.
PAGE 10 — ESSICK FM9 — PARTS & OPERATION MANUAL — REV. #1 (03/12/01)
FM-9 — OPERATIONS
PACKING GLAND ADJUSTMENT
Near the transmission and welded to the bottom side of the hopper is a packing box with special rubberized packing. A split packing gland is located on the outside of the hopper. By tightening this gland the packing in the box is compressed to keep moisture from leaking out around the shaft.
It is necessary on new units for the packing to be compressed several times before it sets properly around the drive shaft. This must be done when the unit is put into operation for the first time as well as each time a complete new set of packings are installed.
The following is a suggested procedure of maintenance:
DRIVE SHAFT ALIGNMENT
If at any time the transmission is disassembled from its mounting base then caution should be taken that on reassembly the drive shaft is in alignment with transmission. to check alignment let drive shaft with packing and packing gland installed, rest free.
Place transmission onto base.If mounting holes in drive shaft and transmission do not line up without any pressure or force being applied then it is necessary to place shims beneath transmission until required height is obtained.
BREAK-IN
Tighten evenly approximately 100 in. pounds torque) the two nuts located on packing gland. These nuts should be tight but not so tight as to seize or bind the shaft. Do this twice a day for the first 5 days of running time.
MAINTAIN
The packing should be lubricated daily with two shots of a good grade of waterproof grease. The grease fitting located on the drive line between the packing gland and the transmission is provided for this purpose. Daily lubrication will prolong the life of the packing.
After break-in period, tighten nuts at least once a week unless there are signs of leakage around shaft, (periodic checks for this is suggested) then tighten at once.
When all take-up on gland has been used, loosen packing gland, coat new packing ring and drive shaft with a generous amount of a good grade of waterproof grease, insert packing, and continue to maintain as noted above.
REPLACING AND ADJUSTING THE BELTS
For adjusting the belts on the countershaft pulleys the unit is equipped with belt tighteners. The belts can be tightened by turning the set screws on the counter shaft risers. When adjusting the belts, both sides must be equally adjusted. the belts should be fairly tight.
To adjust the compressor belts, loosen the compressor mounting bolts and slide the compressor until belt is tight. Note: This belt should not be as tight as the ones on the countershaft.
To replace the countershaft belts, loosen the set screws in the bearing collars and slide the shaft out until the belts can be removed. However, it may be necessary (due to the bearings freezing to the shaft) to remove the two bolts on the bearing bracket at each end and slide out the shaft and bearings. When installing a new belt, readjustment will be necessary. After a few hours of operation check the adjustment of the new belt as there is generally a certain amount of initial stretch.
COUNTERSHAFT BEARINGS
The countershaft supports are equipped with double-sealed ball bearings. These bearings are pre-lubricated at the factory and require no additional lubrication.
NEW PACKING
At such a time when old packing is to be completely replaced, coat shaft and packing generously with a good grade of waterproof grease and insert packing rings. Tighten packing gland nuts to approximately 150 in. pounds torque to seat packing, then back off nuts so drive shaft is not bound, but not less than
100 in. pounds torque on the nuts. Then follow procedure outlined above.
SLOW-DOWN DEVICE
A slow-down device is located on the countershaft riser. This device is actuated by air, which is controlled by the air valve on the spray gun. When the air valve is “on,” the shaft of the slowdown device is extended and thereby allows engine to reach the set governed speed. When the valve is turned “off,” the shaft retracts and the engine idles at preset speed.
The governed engine speed is set at the factory at 3000 r.p.m.
less volume can be attained by readjusting the governed speed.
However, the speed should not be adjusted to less than 2000 r.p.m. (about 5 notches on the throttle control lever).
ESSICK FM9 — PARTS & OPERATION MANUAL — REV. #1 (03/12/01) — PAGE 11
FM-9 — OPERATIONS
AIR SYSTEM
An air pulsation chamber is located on the left side of the unit.
The air is supplied to the chamber from the compressor. The chamber is eouipped with an air pressure gauge and a safety valve. The safety valve is set at the factory at approximately 60 lbs.
HI-VOLUME PUMP
An outstanding feature of the ESSICK MODEL FM9 finishing machine is that two different size pumps may be used, which tremendously increases its versatility. A more powerful engine and transmission are designed into this unit and a hi-volume pump is furnished as standard. A lo-volume pump is offered as an optional item. This pump consists of two parts: A smaller rotor and a smaller stator, which, in turn, may be used when a lower volume of material is required.
The installation of this pump is very easy because all parts are interchangeable. It is only necessary to remove the rotor pin, which fastens the rotor to the connecting rod located at the bottom of the material hopper, and then thread out the stator tube with the rotor encased, and install the lo-volume pump in the same manner. The installation is made easier by threading the rotor into the stator tube prior to starting assembly.
Fireproofing is one application where the hi-volume pump is of great advantage. Competitive machines available for fireproofing are twice the price of this versatile machine. Another purpose for which the machine can be employed is the application of browncoat. The hi-volume pump will apply approximately 14 sacks of gypsum hardwall material per hour.
To obtain maximum volume we suggest not to use more than 75 feet of 1-1/2" hose (actual pump volume is slightly under 2 c.f.m.).
PARTS LIST AND OPERATING INSTRUCTIONS
MODEL FM5E- I
THIS IS A SUPPLEMENT TO THE FM9 OPERATING AND
MAINTENANCE INSTRUCTIONS
READ BOTH SETS OF INSTRUCTIONS BEFORE
OPERATING THIS MACHINE
CAUTION: This machine uses high voltages that can be dangerous and cause injury. Only qualified electricians should install power supplies or service the electrical components. Power supply must be in accordance with local electrical codes and of adequate size to avoid the possibility of overheating the motors due to low voltage. Supply line must be at least No. 8 gauge wire and capable of delivering 35 amperes at 240 volts to control panel of machine. When cleaning, never spray water on the electric motor. Do not operate machine in standing water.
COMPRESSOR MOTOR - The 1H.P. compressor motor is operated by a manual ON-OFF switch on the control panel.
PUMP MOTOR - The 5 H.P. pump motor is operated by a magnetic starter switch. The magnetic starter is equipped with an overload heater for motor protection.
A 240-volt system of switches and relays is used to control the magnetic starter. It is protected by a circuit breaker with a reset button in the door of the starter box
The air control sleeve valve on the nozzle is the master link in the system. Connect the air line from the air compressor outlet to the inlet on the control block next to the sleeve valve. This line has air blowing out of it when the compressor is running. The other air line runs from the sleeve valve to the pressure switch inlet on the machine.
In operation, the sleeve valve operates the pressure switch. When the sleeve valve is in the CLOSED position, air pressure is applied to the pressure switch. This closes the switch and starts the pump motor. When the sleeve valve is in the OPEN position, air pressure is released from the pressure switch. This opens the switch and stops the pump motor. The pump cannot be operated without the air controls and air lines. This is a safety feature for the gun operator and must not be bypassed in any way.
An AUTO-OFF-HAND switch is located on the door of the starter box. Turning the switch to OFF overrides the sleeve valve control and stops the pump. Turning the switch back to AUTO or HAND returns control to the sleeve valve. This switch must never be wired to turn the pump on without air pressure from the sleeve valve to the pressure switch.
R E F
1
D E S C R I P T I O N S E R I A L N O
P A
N
R
O .
T
9 3 9 3 0 3
Q T Y .
1
2
3
4
5
6
7
8
9
1 0
1 1
1 2
1 3
1 4
P U M P – 5 H .
P .
C O M P R E
1
S S
1 /
O R
2 H
M
.
P .
O T O R –
C O M P R E S S O R
M O T O R S U P P O
A N
R T
D
A I R H O S
P R E S
E –
S U R
C O U P L I N G
E S W I T C H
T O
C A B A S S E M B L Y
P U L L Y – P U M P M O T O R
P U L L E Y
P U M P
B U S H I N H
M O T O R
–
P U L L E Y
C O M P R E S S O R
-
M O T O R
P R E S S U R E S W I T C H
F L A N G E D C O N N E C T O R
I N L E T
C O N N E C T O R B O D Y
M A
W I T
G N
H O
E T I C
U T O
S
V
T
E
A
R
R T E R
L O A D
H E A T E R
C O N T A C T O R S W I T C H
O V E R L O A D H E A T E R
9 3 9 0 6 9
4 0 2 7 2 1
4 0 1 5 1 1
4 0 2 7 1 7
9 0 1 2 6 8
9 0 1 4 5 5
9 0 1 1 0 9
9 4 0 0 1 4
9 4 0 0 5 4
9 4 0 0 5 3
9 4 0 6 4 1
9 4 0 0 0 8
9 4 0 2 4 1
1
1
1
1
1
1
1
1
1
1
1
1
1
PAGE 12 — ESSICK FM9 — PARTS & OPERATION MANUAL — REV. #1 (03/12/01)
advertisement
* Your assessment is very important for improving the workof artificial intelligence, which forms the content of this project
Related manuals
advertisement
Table of contents
- 3 Here's How to Get Help
- 4 Table Of Contents
- 5 Parts Ordering Procedures
- 6 Rules For Safe Operation
- 7 Operations
- 13 Specifications
- 14 Explanation Of Codes In Remarks Column
- 15 Suggested Spare Parts
- 16 Cab Assembly
- 18 Automatic Clutch Assembly
- 20 Transmission Assembly
- 24 Browning Nozzle
- 26 Finishing Nozzle
- 28 Terms and Conditions Of Sale — Parts