4. HOW TO USE THE POINT TABLE. Mitsubishi Electric MR-JE-_A SERVO AMPLIFIER
Add to My manuals396 Pages
advertisement
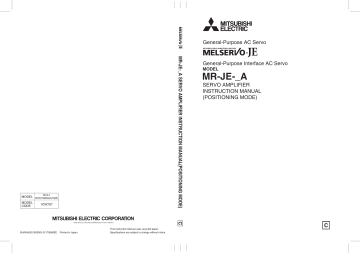
4. HOW TO USE THE POINT TABLE
4. HOW TO USE THE POINT TABLE
The following items are the same as MR-JE-_A servo amplifiers. For details, refer to each section indicated in the detailed explanation field. "MR-JE-_A" means "MR-JE-_A Servo Amplifier Instruction Manual".
Switching power on for the first time MR-JE-_A section 4.1
POINT
For the mark detection function (Current position latch), refer to section 6.2.2.
For the mark detection function (Interrupt positioning), refer to section 6.2.3.
There are the following restrictions on the number of gear teeth on machine side
([Pr. PA06 Number of gear teeth on machine side]) and the servo motor speed
(N).
When CMX ≤ 2000, N < 3076.7 r/min
When CMX > 2000, N < (3276.7 - CMX)/10 r/min
When the servo motor is operated at a servo motor speed higher than the limit value, [AL. E3 Absolute position counter warning] will occur.
4 - 1
4. HOW TO USE THE POINT TABLE
4.1 Startup
WARNING
When executing a test run, follow the notice and procedures in this instruction manual. Otherwise, it may cause a malfunction, damage to the machine, or injury.
Do not operate the switches with wet hands. Otherwise, it may cause an electric shock.
CAUTION
Before starting operation, check the parameters. Improper settings may cause some machines to operate unexpectedly.
The servo amplifier heat sink, regenerative resistor, servo motor, etc., may be hot while the power is on and for some time after power-off. Take safety measures such as providing covers to avoid accidentally touching them by hands and parts such as cables.
During operation, never touch the rotor of the servo motor. Otherwise, it may cause injury.
Before wiring, switch operation, etc., eliminate static electricity. Otherwise, it may cause a malfunction.
4.1.1 Power on and off procedures
When the servo amplifier is powered on for the first time, the control mode is set to position control mode.
(Refer to section 4.2.1 of "MR-JE-_A Servo Amplifier Instruction Manual".)
This section provides a case where the servo amplifier is powered on after setting the positioning mode.
(1) Power-on
Switch the power on in the following procedure. Always follow this procedure at power-on.
1) Switch off SON (Servo-on).
2) Make sure that ST1 (Forward rotation start) and ST2 (Reverse rotation start) are off.
3) Turn on the power.
The display shows "PoS" and 2 s later shows data.
(2) Power-off
1) Switch off ST1 (Forward rotation start) and ST2 (Reverse rotation start).
2) Switch off SON (Servo-on).
3) Shut off the power.
4 - 2
4. HOW TO USE THE POINT TABLE
4.1.2 Stop
Turn off SON (Servo-on) after the servo motor has stopped, and then switch the power off.
If any of the following situations occurs, the servo amplifier suspends and stops the operation of the servo motor.
Refer to section 3.10 of "MR-JE-_A Servo Amplifier Instruction Manual" for the servo motor with an electromagnetic brake.
Switch off SON (Servo-on).
Alarm occurrence
EM2 (Forced stop 2) off
The base circuit is shut off, and the servo motor coasts.
The servo motor decelerates to a stop. With some alarms; however, the dynamic brake operates to stop the servo motor. (Refer to chapter 8. (Note))
The servo motor decelerates to a stop with the command. [AL. E6 Servo forced stop warning] occurs. Refer to section 2.3 for EM1.
LSP (Forward rotation stroke end) off or LSN The servo motor stops immediately and will be servo locked. Operation in the
(Reverse rotation stroke end) off opposite direction is possible.
Note. Only a list of alarms and warnings is listed in chapter 8. Refer to "MELSERVO-JE Servo Amplifier Instruction Manual
(Troubleshooting)" for details of alarms and warnings.
4 - 3
4. HOW TO USE THE POINT TABLE
4.1.3 Test operation
Before starting an actual operation, perform a test operation to make sure that the machine operates normally.
Refer to section 4.1 for how to power on and off the servo amplifier.
Test operation of the servo motor alone in JOG operation of test operation mode
In this step, confirm that the servo amplifier and the servo motor operate normally.
With the servo motor disconnected from the machine, use the test operation mode and check whether the servo motor rotates correctly at the slowest speed. For the test operation mode, refer to section 3.1.8 and 3.1.9 in this manual, and section 4.5.9 of "MR-JE-_A Servo Amplifier Instruction Manual".
Manual operation of the servo motor alone in test operation mode
In this step, confirm that the servo motor rotates correctly at the slowest speed in the manual operation mode.
Make sure that the servo motor rotates in the following procedure.
1) Switch on EM2 (Forced stop 2) and SON (Servo-on). When the servo amplifier is in a servo-on status, RD (Ready) switches on.
2) Switch on LSP (Forward rotation stroke end) and LSN (Reverse rotation stroke end).
3) When MD0 (Operation mode selection 1) is switched off from the
Test operation with the servo motor and machine connected
Automatic operation using the point table controller and ST1 (Forward rotation start) or ST2 (Reverse rotation start) is switched on in the manual operation mode, the servo motor starts rotating. Set a low speed to the point table at first, operate the servo motor, and check the rotation direction of the servo motor, etc. If the servo motor does not operate in the intended direction, check the input signal.
In this step, connect the servo motor with the machine and confirm that the machine operates normally with the commands from the controller.
Make sure that the servo motor rotates in the following procedure.
1) Switch on EM2 (Forced stop 2) and SON (Servo-on). When the servo amplifier is in a servo-on status, RD (Ready) switches on.
2) Switch on LSP (Forward rotation stroke end) and LSN (Reverse rotation stroke end).
3) When MD0 (Operation mode selection 1) is switched off from the controller and ST1 (Forward rotation start) or ST2 (Reverse rotation start) is switched on in the manual operation mode, the servo motor starts rotating. Set a low speed to the point table at first, operate the servo motor, and check the rotation direction of the machine, etc. If the servo motor does not operate in the intended direction, check the input signal. In the status display, check for any problems of the servo motor speed, load ratio, etc.
Check automatic operation from the controller.
4 - 4
4. HOW TO USE THE POINT TABLE
4.1.4 Parameter setting
POINT
The following encoder cables are of four-wire type. When using any of these encoder cables, set [Pr. PC22] to "1 _ _ _" to select the four-wire type. Incorrect setting will result in [AL. 16 Encoder initial communication error 1].
MR-EKCBL30M-L
MR-EKCBL30M-H
MR-EKCBL40M-H
MR-EKCBL50M-H
Assign the following output devices to the CN1-23 pin with [Pr. PD24].
CN1-23: ZP (Home position return completion)
When you use the servo in the point table method, set [Pr. PA01] to "_ _ _ 6" (Positioning mode (point table method)). In the point table method, the servo can be used by merely changing the basic setting parameters
([Pr. PA _ _ ]) and the positioning control parameters ([Pr. PT _ _ ]) mainly.
As necessary, set other parameters.
The following table shows the necessary setting of [Pr. PA _ _ ] and [Pr. PT _ _ ] in the point table method.
Operation mode selection item Parameter setting Input device setting
Operation mode
[Pr. PA01] [Pr. PT04]
MD0
(Note 1)
DI0 to DI4
(Note 1, 2)
Automatic operation mode in point table method
Manual operation mode
Home position return mode
Each positioning operation
Varying-speed operation
Automatic continuous operation
JOG operation
Manual pulse generator operation
Dog type
Automatic continuous positioning operation
Count type
Data set type
Stopper type
Home position ignorance (servoon position as home position)
Dog type rear end reference
Count type front end reference
Dog cradle type
Dog type last Z-phase reference
Dog type front end reference
Dogless Z-phase reference
_ _ _ 6
_ _ _ 0
_ _ _ 1
_ _ _ 2
_ _ _ 3
_ _ _ 4
_ _ _ 5
_ _ _ 6
_ _ _ 7
_ _ _ 8
_ _ _ 9
_ _ _ A
On
Set the point table
No. (Refer to section
4.2.1 (2) (b).)
Off
Note 1. MD0: Operation mode selection 1, DI0 to DI4: Point table No. selection 1 to Point table No. selection 5
2. DI4 is available only with the communication function. This device cannot be assigned as an input signal.
4 - 5
4. HOW TO USE THE POINT TABLE
4.1.5 Point table setting
Set the data for operation to the point table. The following shows the items to be set.
Position data
Servo motor speed
Set the position data for movement.
Set the command speed of the servo motor for execution of positioning.
Acceleration time constant
Deceleration time constant
M code
Set the acceleration time constant.
Set the deceleration time constant.
Dwell Set the waiting time when performing automatic continuous operation.
Auxiliary function Set when performing automatic continuous operation.
The first digit and the second digit of the M code are outputted in 4-bit binary respectively.
M code will be available in the future.
Refer to section 4.2.2 for details of the point table.
4.1.6 Actual operation
Start actual operation after confirmation of normal operation by test operation and completion of the corresponding parameter settings.
4.1.7 Troubleshooting at start-up
CAUTION
Never adjust or change the parameter values extremely as it will make operation unstable.
POINT
Using MR Configurator2, you can refer to the reason for rotation failure, etc.
The following faults may occur at start-up. If any of such faults occurs, take the corresponding action.
"MR-JE-_A" means "MR-JE-_A Servo Amplifier Instruction Manual".
Fault
The 7-segment LED display does not turn on.
The 7-segment LED display blinks.
Alarm occurs.
Not solved even if CN1, CN2, and
CN3 connectors are disconnected.
1. Power supply voltage fault
2. The servo amplifier is malfunctioning.
Solved when CN1 connector is disconnected.
Solved when CN2 connector is disconnected.
Power supply of CN1 cabling is shorted.
1. Power supply of encoder cabling is shorted.
2. Encoder is malfunctioning.
Solved when CN3 connector is disconnected.
Power supply of CN3 cabling is shorted.
Refer to chapter 8 and remove the cause.
2 Switch on SON
(Servo-on).
Alarm occurs.
Servo motor shaft is not servo-locked.
(Servo motor shaft is free.)
Refer to chapter 8 and remove the cause.
1. Check the display to see if the servo amplifier is ready to operate.
2. Check the external I/O signal indication (section 3.1.7) to see if SON (Servo-on) is on.
1. SON (Servo-on) is not input.
(wiring mistake)
2. 24 V DC power is not supplied to DICOM.
Chapter 8
(Note)
Chapter 8
(Note)
Section
3.1.7
4 - 6
4. HOW TO USE THE POINT TABLE
Fault
3 Perform a home position return.
4 Switch on ST1
(Forward rotation start) or ST2
(Reverse rotation start).
Servo motor does not rotate.
The home position return is not completed.
Servo motor does not rotate. fluctuations) are large at low speed.
Check the on/off status of the input signal with the external I/O signal display. (Refer to section
3.1.7.)
Check [Pr. PA11 Forward rotation torque limit] and [Pr.
PA12 Reverse rotation torque limit].
When TLA (Analog torque limit) is usable, check the input voltage on the status display.
Check the on/off status of input signal DOG with the external I/O signal display. (Refer to section
3.1.7.)
Check the on/off status of the input signal with the external I/O signal display (section 3.1.7).
LSP, LSN, and ST1 are off.
Torque limit level is too low for the load torque.
Torque limit level is too low for the load torque.
The proximity dog is set incorrectly.
LSP, LSN, and ST2 are off.
Check [Pr. PA11 Forward rotation torque limit] and [Pr. PA12
Reverse rotation torque limit].
Torque limit level is too low for the load torque.
When TLA (Analog torque limit) is usable, check the input voltage on the status display.
Torque limit level is too low for the load torque.
Gain adjustment fault Make gain adjustment in the following procedure.
1. Increase the auto tuning response level.
2. Repeat acceleration and deceleration several times to complete auto tuning.
Large load inertia moment causes the servo motor shaft to
If the servo motor may be driven with safety, repeat acceleration and deceleration three times or
Gain adjustment fault oscillate side to side. more to complete the auto tuning.
Note. Only a list of alarms and warnings is listed in chapter 8. Refer to "MELSERVO-JE Servo Amplifier Instruction Manual
(Troubleshooting)" for details of alarms and warnings.
Section
3.1.7
Section
7.2.1
Section
3.1.2
Section
3.1.7
Section
3.1.7
Section
7.2.1
Section
3.1.2
MR-JE-_A
Chapter 6
MR-JE-_A
Chapter 6
4 - 7
4. HOW TO USE THE POINT TABLE
4.2 Automatic operation mode
4.2.1 Automatic operation mode
(1) Command method
Set point tables in advance, and select any point table by using an input signal or RS-422/RS-485 communication. Start the operation using ST1 (Forward rotation start) or ST2 (Reverse rotation start).
Absolute value command method and incremental value command method are available in automatic operation mode.
(a) Absolute value command method
As position data, set the target address to be reached.
1) mm, inch, and pulse unit
Setting range: -999999 to 999999 [×10 STM μ m] (STM = Feed length multiplication [Pr. PT03])
-999999 to 999999 [×10 (STM-4) inch] (STM = Feed length multiplication [Pr. PT03])
-999999 to 999999 [pulse]
-999999 999999
Setting range of the position data
[×10 STM μ m] / [×10 (STM-4) inch] / [pulse]
2) Degree unit
Set the target position by indicating the CCW direction with a "+" sign and the CW direction with a
"-" sign.
In the absolute value command method, the rotation direction can be specified with a "+" or "-" sign.
An example of setting is shown below.
0
(-360)
Coordinate system in degrees
The coordinate is determined by referring to the position
90
(-270)
Setting range of the position data
[degree]
270
(-90) of 0 degree.
+ direction: 0 → 90 → 180 → 270 → 0
- direction: 0 → -90 → -180 → -270 → -360
The positions of 270 degrees and -90 degrees are the same.
The positions of 0 degree, 360 degrees and -360 degrees are the same.
180
(-180)
The travel direction to the target position is set with [Pr. PT03].
[Pr. PT03] setting
_ 0 _ _
_ 1 _ _
Servo motor rotation direction
The servo motor rotates to the target position in a direction specified with a sign of the position data.
The servo motor rotates from the current position to the target position in the shorter direction.
If the distances from the current position to the target position are the same for CCW and CW, the servo motor rotates in the CCW direction.
4 - 8
4. HOW TO USE THE POINT TABLE a) When using the Rotation direction specifying ([Pr. PT03] = "_ 0 _ _")
When the position data of 270.000 degrees is specified, the servo motor rotates in the CCW direction.
Target position
(270)
Current position
When the position data of -90.000 degrees is specified, the servo motor rotates in the CW direction.
Target position
(-90)
Current position
When the position data of -360.000 degrees is specified, the servo motor rotates in the CW direction. (A)
When the position data of 360.000 degrees or 0 degree is specified, the servo motor rotates in the CCW direction. (B)
Target position
(-360)
(B)
(A)
Current position
4 - 9
4. HOW TO USE THE POINT TABLE b) When using the shortest rotation specification ( [Pr. PT03] = _ 1 _ _)
When the position data of 270.000 degrees is specified, the servo motor rotates in the CCW direction.
Target position
(270)
Current position
When the position data of -90.000 degrees is specified, the servo motor rotates in the CCW direction.
Target position
(-90)
Current position
If the position data of 270.000 degrees is specified when the current position is at 90, the distances in the CCW and CW are the same. In such a case, the servo motor rotates in the
CCW direction.
Current position
(90)
Target position
(270)
4 - 10
4. HOW TO USE THE POINT TABLE
(b) Incremental value command method
As position data, set the travel distance from the current address to the target address.
1) mm, inch, and pulse unit
Setting range: 0 to 999999 [×10 STM μ m] (STM = Feed length multiplication [Pr. PT03])
0 to 999999 [×10 (STM-4) inch] (STM = Feed length multiplication [Pr. PT03])
0 to 999999 [pulse]
Current address Target address
Position data = |Target address - Current address|
2) Degree unit
Current address
80 degrees
0 degree
Position data = Target address - Current address
Here, Travel distance = -170 degrees
Target address
270 degrees
4 - 11
4. HOW TO USE THE POINT TABLE
(2) Point table
(a) Point table setting
1 to 31 point tables can be set. To use point table No. 4 to 31, enable DI2 (Point table No. selection
3) to DI4 (Point table No. selection 5) with "Device Setting" on MR Configurator2.
Set point tables using MR Configurator2 or the operation section of the servo amplifier.
The following table lists what to set. Refer to section 4.2.2 for details of the settings.
Position data
Servo motor speed
Set the position data for movement.
Set the command speed of the servo motor for execution of positioning.
Acceleration time constant
M code
Set the acceleration time constant.
Deceleration time constant
Dwell
Set the deceleration time constant.
Set the waiting time when performing automatic continuous operation.
Auxiliary function Set when performing automatic continuous operation.
The first digit and the second digit of the M code are outputted in 4-bit binary respectively.
M code will be available in the future.
(b) Selection of point tables
Using the input signal or the communication function, select the point table No. with the communication command from the controller such as a personal computer.
The following table lists the point table No. selected in response to the input signal and the communication command.
However, when using the input signal to select the point table No., you can only use point table No. 1 to 3 in the initial status.
To use point table No. 4 to 31, enable DI2 (Point table No. selection 3) to DI4 (Point table No. selection 5) with "Device Setting" on MR Configurator2.
When using the communication function to select the point table No., refer to chapter 10.
Input signal (Note 1)
DI4
(Note 2)
Selected point table No.
0 0 0 0 1
0 0 0 1 0
0 0 0 1 1
0 0 1 0 0
1 1 1 1 0
1 1 1 1 1
1
2
3
4
30
31
Note 1. 0: Off
1: On
2. DI4 is available only with the communication function. This device cannot be assigned as an input signal.
4 - 12
4. HOW TO USE THE POINT TABLE
4.2.2 Automatic operation using point table
(1) Absolute value command method
This method allows to select absolute value command or incremental value command with the auxiliary function of the point table.
(a) Point table
Set the point table values using MR Configurator2 or the operation section.
Set the position data, servo motor speed, acceleration time constant, deceleration time constant, dwell, auxiliary function, and M code to the point table.
To use the point table with the absolute value command method, set "0", "1", "8", or "9" to the auxiliary function. To use the point table with the incremental value command method, set "2", "3",
"10", or "11" to the auxiliary function.
When you set a value outside the setting range to the point table, the set value will be clamped with the maximum or minimum value. If the value becomes out of the range because of the changes in the command unit or the connected servo motor, [AL. 37] will occur.
Servo motor speed
0 to permissible speed
10
10
STM
(STM-4)
μ m
inch
10 -3 degree pulse
(Note 2) r/min
Description
(1) When using this point table with the absolute value command method
Set the target address (absolute value).
The teaching function is also available for setting this value.
(2) When using this point table with the incremental value command method
Set the travel distance. A "-" sign indicates a reverse rotation command.
The teaching function is not available. When teaching is executed, the setting will not be completed.
Set the command speed of the servo motor for execution of positioning.
The setting value must be the permissible instantaneous speed or less of the servo motor used.
Acceleration time constant 0 to 20000
Deceleration time constant 0 to 20000 ms ms
Set a time for the servo motor to reach the rated speed.
Set a time for the servo motor to stop from the rated speed.
Dwell
Auxiliary function
0 to 20000
0 to 3, 8 to 11 ms
Set the dwell.
To disable the dwell, set "0" or "2" to the auxiliary function.
To perform a continuous operation, set "1", "3", "8", "9", "10", or "11" to the auxiliary function and "0" to the dwell.
When the dwell is set, a positioning of the next point table will be started after the positioning of the selected data is completed, and the set dwell has elapsed.
Set the auxiliary function.
(1) When using this point table with the absolute value command method
0: Executes automatic operation for a selected point table.
1: Executes automatic continuous operation without stopping for the next point table.
8: Executes automatic continuous operation without stopping for the point table selected at the start.
9: Executes automatic continuous operation without stopping for the point table No. 1.
(2) When using this point table with the incremental value command method
2: Executes automatic operation for a selected point table.
3: Executes automatic continuous operation without stopping for the next point table.
10: Executes automatic continuous operation without stopping for the point table selected at the start.
11: Executes automatic continuous operation without stopping for the point table No. 1.
When an opposite rotation direction is set, the servo motor rotates in the opposite direction after smoothing zero (command output) is confirmed.
Setting "1" or "3" to point table No. 31 results in an error.
For details, refer to (3) (b) in this section.
M code 0 to 99
Outputs the first digit and the second digit of the M code in 4-bit binary respectively.
M code will be available in the future.
Note. The setting range of the position data in degrees is -360.000 to 360.000. When the unit of the position data is μ m or inch, the location of the decimal point is changed according to the STM setting.
4 - 13
4. HOW TO USE THE POINT TABLE
(b) Parameter setting
Set the following parameters to perform automatic operation.
1) Command method selection ([Pr. PT01])
Select the absolute value command method as shown below.
[Pr. PT01]
0
Absolute value command method
2) Rotation direction selection ([Pr. PA14])
Select the servo motor rotation direction when ST1 (Forward rotation start) is switched on.
[Pr. PA14] setting
0
1
Servo motor rotation direction when ST1
(Forward rotation start) is switched on
CCW rotation with + position data
CW rotation with - position data
CW rotation with + position data
CCW rotation with - position data
CCW
CW
Set the unit of the position data.
[Pr. PT01] setting
_ 0 _ _
_ 1 _ _
_ 2 _ _
_ 3 _ _
Position data unit mm inch degree pulse
4) Feed length multiplication ([Pr. PT03])
Set the feed length multiplication factor (STM) of the position data.
[Pr. PT03] setting
Position data input range
[mm] [degree] (Note 1) [pulse] (Note 1)
_ _ _ 0 - 999.999 to + 999.999 - 99.9999 to + 99.9999
_ _ _ 1
_ _ _ 2
- 9999.99 to + 9999.99
- 99999.9 to + 99999.9
- 999.999 to + 999.999
- 9999.99 to + 9999.99
- 360.000 to + 360.000
(Note 2)
_ _ _ 3 - 999999 to + 999999 - 99999.9 to + 99999.9
Note 1. The feed length multiplication setting ([Pr. PT03]) is not applied to the unit multiplication factor.
- 999999 to + 999999
Adjust the unit multiplication factor in the electronic gear setting ([Pr. PA06] and [Pr. PA07]).
2. The "-" sign has different meanings under the absolute value command method and the incremental value command method.
Refer to section 4.2.1 for details.
4 - 14
4. HOW TO USE THE POINT TABLE
(c) Operation
Selecting DI0 to DI4 for the point table and switching on ST1 starts positioning to the position data at the set speed, acceleration time constant and deceleration time constant. At this time, ST2 (Reverse rotation start) is disabled.
Item Device to be used
Automatic operation mode selection MD0 (Operation mode selection 1)
Point table selection
Start
DI0 (Point table No. selection 1)
DI1 (Point table No. selection 2)
DI2 (Point table No. selection 3)
DI3 (Point table No. selection 4)
DI4 (Point table No. selection 5)
ST1 (Forward rotation start)
Setting
Switch on MD0.
Refer to section 4.2.1 (2) (b).
Switch on ST1 to start.
(2) Incremental value command method
(a) Point table
Set the point table values using MR Configurator2 or the operation section.
Set the position data, servo motor speed, acceleration time constant, deceleration time constant, dwell, auxiliary function, and M code to the point table.
When you set a value outside the setting range to the point table, the set value will be clamped with the maximum or minimum value. If the value becomes out of the range because of the changes in the command unit or the connected servo motor, [AL. 37] will occur.
Description
Position data 0 to 999999 (Note)
Servo motor speed
0 to permissible speed
×10 STM μ m
×10 (STM-4) inch
×10 -3 degree pulse r/min
Set the travel distance.
The teaching function is not available. When teaching is executed, the setting will not be completed.
The unit can be changed by [Pr. PT03] (Feed length multiplication).
Set the command speed of the servo motor for execution of positioning.
The setting value must be the permissible instantaneous speed or less of the servo motor used.
Acceleration time constant
Deceleration time constant
0 to 20000
0 to 20000 ms ms
Set a time for the servo motor to reach the rated speed.
Set a time for the servo motor to stop from the rated speed.
Dwell
Auxiliary function
0 to 20000
0, 1, 8, 9 ms
Set the dwell.
To disable the dwell, set "0" to the auxiliary function.
To perform varying-speed operation, set "1", "8" or "9" to the auxiliary function and "0" to the dwell.
When the dwell is set, a positioning of the next point table will be started after the positioning of the selected data is completed, and the set dwell has elapsed.
Set the auxiliary function.
0: Executes automatic operation for a selected point table.
1: Executes automatic continuous operation without stopping for the next point table.
8: Executes automatic continuous operation without stopping for the point table selected at the start.
9: Executes automatic continuous operation without stopping for the point table No. 1.
Setting "1" to point table No. 31 results in an error.
For details, refer to (3) (b) in this section.
M code 0 to 99
Outputs the first digit and the second digit of the M code in 4-bit binary respectively.
M code will be available in the future.
Note. The setting range of the position data in degrees is 0 to 999.999. When the unit of the position data is μ m or inch, the location of the decimal point is changed according to the STM setting.
4 - 15
4. HOW TO USE THE POINT TABLE
(b) Parameter setting
Set the following parameters to perform automatic operation.
1) Command method selection ([Pr. PT01])
Select the incremental value command method as shown below.
[Pr. PT01]
1
Incremental value command method
2) Rotation direction selection ([Pr. PA14])
Select the servo motor rotation direction when ST1 (Forward rotation start) or ST2 (Reverse rotation start) is switched on.
[Pr. PA14] setting
0
1
Servo motor rotation direction
ST1 (Forward rotation start) ST2 (Reverse rotation start)
CCW rotation (address increase)
CW rotation (address increase)
CW rotation (address decrease)
CCW rotation (address decrease)
ST1: on
CCW
CW
ST2: on
[Pr. PA14]: 0
Set the unit of the position data.
[Pr. PT01] setting
_ 0 _ _
_ 1 _ _
_ 2 _ _
_ 3 _ _
Position data unit mm inch degree pulse
4) Feed length multiplication ([Pr. PT03])
Set the feed length multiplication factor (STM) of the position data.
Position data input range
[Pr. PT03] setting
_ _ _ 0
_ _ _ 1
_ _ _ 2
0 to + 999.999
0 to + 9999.99
0 to + 99999.9
0 to + 99.9999
0 to + 999.999
0 to + 9999.99
0 to + 999.999
_ _ _ 3 0 to + 999999 0 to + 99999.9
Note. The feed length multiplication setting ([Pr. PT03]) is not applied to the unit multiplication factor.
Adjust the unit multiplication factor in the electronic gear setting ([Pr. PA06] and [Pr. PA07]).
ST2: on
CCW
CW
ST1: on
[Pr. PA14]: 1
[pulse] (Note)
0 to + 999999
4 - 16
4. HOW TO USE THE POINT TABLE
(c) Operation
Selecting DI0 to DI4 for the point table and switching on ST1 starts a forward rotation of the motor over the travel distance of the position data at the set speed, acceleration time constant and deceleration time constant.
Switching on ST2 starts a reverse rotation of the motor in accordance with the values set to the selected point table.
When the positioning operation is performed consecutively with the incremental value command method, the servo motor rotates in the same direction only.
To change the travel direction during the continuous operation, perform the operation with the absolute value command method.
Item Device to be used Setting
Automatic operation mode selection MD0 (Operation mode selection 1) Switch on MD0.
Point table selection
Start
DI0 (Point table No. selection 1)
DI1 (Point table No. selection 2)
DI2 (Point table No. selection 3)
DI3 (Point table No. selection 4)
DI4 (Point table No. selection 5)
ST1 (Forward rotation start)
ST2 (Reverse rotation start)
Refer to section 4.2.1 (2) (b).
Switch on ST1 to start.
Switch on ST2 to start.
4 - 17
4. HOW TO USE THE POINT TABLE
(3) Automatic operation timing chart
(a) Automatic individual positioning operation
1) Absolute value command method ([Pr. PT01] = _ _ _ 0)
While the servo motor is stopped under servo-on state, switching on ST1 (Forward rotation start) starts the automatic positioning operation.
The following shows a timing chart.
MD0
(Operation mode selection 1)
SON (Servo-on)
ST1
(Forward rotation start)
ST2
(Reverse rotation start)
ON
OFF
ON
OFF
ON
OFF
ON
OFF
(Note 1)
3 ms or longer
5 ms or longer
3 ms or longer
5 ms or longer
Point table No.
1
3 ms or shorter
2
Servo motor speed
Forward rotation
0 r/min
Reverse rotation
INP (In-position)
CPO (Rough match)
MEND
(Travel completion)
PT0 (Point table No.
output 1) to PT4 (Point table No. output 5)
(Note 2)
ON
OFF
ON
OFF
ON
OFF
RD (Ready)
ALM (Malfunction)
ON
OFF
ON
OFF
M code output (Note 3)
Point table No. 1
1
Point table No. 2
M code of point table No. 1
2
Note 1. The detection of external input signals is delayed by the set time in the input filter setting of [Pr. PD29].
Considering the output signal sequence from the controller and signal variations due to hardware, configure a sequence that changes the point table selection earlier.
2. For MR-JE-_A servo amplifiers, up to four points of DO are available; therefore, PT0 to PT4 cannot be outputted simultaneously.
3. M code will be available in the future.
4 - 18
4. HOW TO USE THE POINT TABLE
2) Absolute value command method ([Pr. PT01] = _ _ _ 1)
While the servo motor is stopped under servo-on state, switching on ST1 (Forward rotation start) or ST2 (Reverse rotation start) starts the automatic positioning operation.
The following shows a timing chart.
MD0
(Operation mode selection 1)
SON (Servo-on)
ST1
(Forward rotation start)
ST2
(Reverse rotation start)
ON
OFF
ON
OFF
ON
OFF
ON
OFF
(Note 1)
3 ms or longer
5 ms or longer 3 ms or longer
Point table No.
1
3 ms or shorter
5 ms or longer
2
Servo motor speed
Forward rotation
0 r/min
Reverse rotation
Point table No. 1
Point table No. 2
INP (In-position)
CPO (Rough match)
MEND
(Travel completion)
PT0 (Point table No.
output 1) to PT4 (Point table No. output 5)
(Note 2)
ON
OFF
ON
OFF
ON
OFF
RD (Ready)
ALM (Malfunction)
ON
OFF
ON
OFF
M code output (Note 3)
1
M code of point table No. 1
2
Note 1. The detection of external input signals is delayed by the set time in the input filter setting of [Pr. PD29].
Considering the output signal sequence from the controller and signal variations due to hardware, configure a sequence that changes the point table selection earlier.
2. For MR-JE-_A servo amplifiers, up to four points of DO are available; therefore, PT0 to PT4 cannot be outputted simultaneously.
3. M code will be available in the future.
4 - 19
4. HOW TO USE THE POINT TABLE
(b) Automatic continuous positioning operation
By merely selecting a point table and switching on ST1 (Forward rotation start) or ST2 (Reverse rotation start), the operation can be performed in accordance with the point tables having consecutive numbers.
1) Absolute value command method ([Pr. PT01] = _ _ _ 0)
By specifying the absolute value command or the incremental value command in the auxiliary function of the point table, the automatic continuous operation can be performed.
The following shows how to set.
Dwell
1 or more
Point table setting
Auxiliary function
When the position data is absolute value When the position data is incremental value
1 3
Point table
No. a) Positioning in a single direction
The following shows an operation example with the set values listed in the table below.
In this example, point table No. 1 and No. 3 are set to the absolute value command method, and point table No. 2 the incremental value command method.
Position data
[10 STM μ m]
Servo motor speed [r/min]
Acceleration time constant
[ms]
Deceleration time constant
[ms]
Dwell [ms]
Auxiliary function
M code
(Note 2)
Note 1. Always set "0" or "2" to the auxiliary function of the last point table of the consecutive point tables.
0: When using the point table with the absolute value command method
2: When using the point table with the incremental value command method
2. M code will be available in the future.
Acceleration/deceleration time constant of point table No. 1
Acceleration/deceleration time constant of point table No. 2 Acceleration/deceleration time constant of point table No. 3
Servo motor speed
Forward rotation
0 r/min
Reverse rotation
Speed
(3000)
Dwell time
100 ms
Speed
(2000)
5.00
Speed (1000)
Dwell time
200 ms
Position address
0 5.00
10.00
15.00
15
Selected point table No.
ST1
(Forward rotation start)
ON
OFF
PT0 (Point table No. output 1) to PT4 (Point table No. output 5)
(Note 1)
M code output (Note 2)
1
Note 1. For MR-JE-_A servo amplifiers, up to four points of DO are available; therefore, PT0 to PT4 cannot be outputted simultaneously.
2. M code will be available in the future.
1
05
4 - 20
4. HOW TO USE THE POINT TABLE
Point table
No. b) Positioning in the reverse direction midway
The following shows an operation example with the set values listed in the table below.
In this example, point table No. 1 and No. 3 are set to the absolute value command method, and point table No. 2 the incremental value command method.
Position data
[10 STM μ m]
Servo motor speed [r/min]
Acceleration time constant
[ms]
Deceleration time constant
[ms]
Dwell [ms]
Auxiliary function
M code
(Note 2)
Position address
0
15
Note. 1. Always set "0" or "2" to the auxiliary function of the last point table of the consecutive point tables.
0: When using the point table with the absolute value command method
2: When using the point table with the incremental value command method
2. M code will be available in the future.
Acceleration/deceleration time constant of point table No. 1
Acceleration/deceleration time constant of point table
No. 2
Servo motor speed
Forward rotation
0 r/min
Reverse rotation
Speed
(3000)
Dwell time
100 ms
5.00
Speed
(2000)
Dwell time
200 ms
Speed (1000)
7.00
Acceleration/deceleration time constant of point table No. 3
8.00
12.00
Selected point table No.
ST1
(Forward rotation start)
ON
OFF
PT0 (Point table No. output 1) to PT4 (Point table No. output 5)
(Note 1)
M code output (Note 2)
1
1
05
Note 1. For MR-JE-_A servo amplifiers, up to four points of DO are available; therefore, PT0 to PT4 cannot be outputted simultaneously.
2. M code will be available in the future.
4 - 21
4. HOW TO USE THE POINT TABLE
Point table
No. c) Position data in degrees
The following shows an operation example with the set values listed in the table below.
In this example, point table No. 1, No. 2, and No. 4 are set to the absolute value command method, and point table No. 3 the incremental value command method.
Position data
[degree]
Servo motor speed [r/min]
Acceleration time constant
[ms]
Deceleration time constant
[ms]
Dwell [ms]
Auxiliary function
M code
(Note 2)
2 150
20
Note 1. Always set "0" or "2" to the auxiliary function of the last point table of the consecutive point tables.
0: When using the point table with the absolute value command method
2: When using the point table with the incremental value command method
2. M code will be available in the future.
0
40
(-320)
0
120
(-240)
40
(-320)
0
230
120
(-240)
70
(-290)
0
Servo motor speed
Forward rotation
0 r/min
Reverse rotation
170
(-190)
Point table No. 1
Point table No. 3
Point table No. 2
Selected point table No.
ST1
(Forward rotation start)
ON
OFF
PT0 (Point table No. output 1) to PT4 (Point table No. output 5)
(Note 1)
M code output (Note 2)
1
170
(-190)
Point table No. 4
1
05
Note 1. For MR-JE-_A servo amplifiers, up to four points of DO are available; therefore, PT0 to PT4 cannot be outputted simultaneously.
2. M code will be available in the future.
4 - 22
4. HOW TO USE THE POINT TABLE
2) Incremental value command method ([Pr. PT01] = _ _ _ 1)
The position data of the incremental value command method is the sum of the position data of consecutive point tables.
The following shows how to set.
Point table setting
1 or more 1
Point table
No. a) Positioning in a single direction
The following shows an operation example with the set values listed in the table below.
Position data
[10 STM μ m]
Servo motor speed [r/min]
Acceleration time constant
[ms]
Deceleration time constant
[ms]
Dwell [ms]
Auxiliary function
M code
(Note 2)
15
Note 1. Always set "0" to the auxiliary function of the last point table among the consecutive point tables.
2. M code will be available in the future.
Acceleration/deceleration time constant of point table No. 1
Acceleration/deceleration time constant of point table No. 2
Acceleration/deceleration time constant of point table No. 3
Speed
(2000) Speed (1000)
Servo motor speed
Forward rotation
0 r/min
Reverse rotation
Speed
(3000)
6.00
3.00
Position address
0 5.00
11.00
14.00
Selected point table No.
ST1
(Forward rotation start)
(Note 1)
ON
OFF
PT0 (Point table No. output 1) to PT4 (Point table No. output 5)
(Note 2)
M code output (Note 3)
1
Note 1. Switching on ST2 (Reverse rotation start) starts positioning in the reverse rotation direction.
2. For MR-JE-_A servo amplifiers, up to four points of DO are available; therefore, PT0 to PT4 cannot be outputted simultaneously.
3. M code will be available in the future.
1
05
4 - 23
4. HOW TO USE THE POINT TABLE
Point table
No. b) Position data in degrees
The following shows an operation example with the set values listed in the table below.
Position data
[degree]
Servo motor speed [r/min]
Acceleration time constant
[ms]
Deceleration time constant
[ms]
Dwell [ms]
Auxiliary function
M code
(Note 2)
0 (Note 1) 15
Note 1. Always set "0" or "2" to the auxiliary function of the last point table of the consecutive point tables.
0: When using the point table with the absolute value command method
2: When using the point table with the incremental value command method
2. M code will be available in the future.
0
Servo motor speed
Selected point table No.
Forward rotation
0 r/min
Reverse rotation
ST1
(Forward rotation start)
ON
OFF
PT0 (Point table No. output 1) to PT4 (Point table No. output 5)
(Note 1)
M code output (Note 2)
120
Point table
No. 1
120
(-240)
60 90
180
(-180)
Point table
No. 2
Point table No. 1
Point table No. 2
Point table
No. 3
270
(-90)
Point table No. 3
1
1
05
Note 1. For MR-JE-_A servo amplifiers, up to four points of DO are available; therefore, PT0 to PT4 cannot be outputted simultaneously.
2. M code will be available in the future.
4 - 24
4. HOW TO USE THE POINT TABLE
(c) Varying-speed operation
By setting the auxiliary function of the point table, the servo motor speed during positioning can be changed. Point tables are used by the number of the set speed.
1) Absolute value command method ([Pr. PT01] = _ _ _ 0)
Set "1" or "3" to the auxiliary function to execute the positioning at the speed set in the following point table.
At this time, the position data selected at start is enabled, and the acceleration/deceleration time constant set in the next and subsequent point tables is disabled.
By setting "1" or "3" to sub functions until point table No. 30, the operation can be performed at maximum 31 speeds.
Always set "0" or "2" to the auxiliary function of the last point table.
To perform varying-speed operation, always set "0" to the dwell.
Setting "1" or more enables the automatic continuous positioning operation.
The following table shows an example of setting.
Point table No. Dwell [ms] (Note 1) Auxiliary function Varying-speed operation
1 0 1
3 Disabled 0 (Note 2)
4 0 3
6 Disabled
Note 1. Always set "0".
2 (Note 2) consecutive point tables.
4 - 25
4. HOW TO USE THE POINT TABLE
Point table
No. a) Positioning in a single direction
The following shows an operation example with the set values listed in the table below.
In this example, point table No. 1 and No. 3 are set to the absolute value command method, and point table No. 2 the incremental value command method.
Position data
[10 STM μ m]
Servo motor speed [r/min]
Acceleration time constant
[ms]
Deceleration time constant
[ms]
Dwell [ms]
(Note 1)
Auxiliary function
M code
(Note 3)
2000 Disabled
Disabled 2 (Note 2)
Note 1. Always set "0".
0: When using the point table with the absolute value command method
2: When using the point table with the incremental value command method
3. M code will be available in the future.
Acceleration time constant
(100) of point table No. 1
Speed
(2000)
Deceleration time constant
(150) of point table No. 1
Speed
(1000)
Servo motor speed
Forward rotation
0 r/min
Reverse rotation
Speed
(3000)
Position address
0 5.00
3.00
8.00
10.00
6.00
20
Speed
(500)
16.00
Selected point table No.
ST1
(Forward rotation start)
ON
OFF
PT0 (Point table No. output 1) to PT4 (Point table No. output 5)
(Note 1)
M code output (Note 2)
1
1
05
Note 1. For MR-JE-_A servo amplifiers, up to four points of DO are available; therefore, PT0 to PT4 cannot be outputted simultaneously.
2. M code will be available in the future.
4 - 26
4. HOW TO USE THE POINT TABLE
Point table
No. b) Positioning in the reverse direction midway
The following shows an operation example with the set values listed in the table below.
In this example, point table No. 1 and No. 3 are set to the absolute value command method, and point table No. 2 the incremental value command method.
Position data
[10 STM μ m]
Servo motor speed [r/min]
Acceleration time constant
[ms]
Deceleration time constant
[ms]
Dwell [ms]
(Note 1)
Auxiliary function
M code
(Note 3)
2000
15
Note 1. Always set "0".
0: When using the point table with the absolute value command method
2: When using the point table with the incremental value command method
3. M code will be available in the future.
Acceleration time constant of point table No. 1 (100)
Deceleration time constant of point table No. 1 (150)
Servo motor speed
Forward rotation
0 r/min
Reverse rotation
Position address
0
Speed
(3000)
5.00
Speed
(2000)
7.00
8.00
Speed (1000)
Acceleration time constant of point table No. 1 (100)
12.00
Selected point table No.
ST1
(Forward rotation start)
ON
OFF
PT0 (Point table No. output 1) to PT4 (Point table No. output 5)
(Note 1)
M code output (Note 2)
1
1
05
Note 1. For MR-JE-_A servo amplifiers, up to four points of DO are available; therefore, PT0 to PT4 cannot be outputted simultaneously.
2. M code will be available in the future.
4 - 27
4. HOW TO USE THE POINT TABLE
2) Absolute value command method ([Pr. PT01] = _ _ _ 1)
Setting "1" to the auxiliary function executes positioning at the speed set in the following point table.
At this time, the position data selected at start is enabled, and the acceleration/deceleration time constant set in the next and subsequent point tables is disabled.
By setting "1" to sub functions until point table No. 30, the operation can be performed at maximum 31 speeds.
Always set "0" to the auxiliary function of the last point table.
To perform varying-speed operation, always set "0" to the dwell.
Setting "1" or more enables the automatic continuous positioning operation.
The following table shows an example of setting.
Point table No. Dwell [ms] (Note 1) Auxiliary function Varying-speed operation
1 0 1
3 Disabled 0 (Note 2)
4 0 1
6 Disabled
Note 1. Always set "0".
2. consecutive point tables.
0 (Note 2)
Point table
No.
The following shows an operation example with the set values listed in the table below.
Position data
[10 STM μ m]
Servo motor speed [r/min]
Acceleration time constant
[ms]
Deceleration time constant
[ms]
Dwell [ms]
(Note 1)
Auxiliary function
M code
(Note 3)
Note 1. Always set "0".
2000
1000
Disabled 0 (Note 2) 20
3. M code will be available in the future.
4 - 28
4. HOW TO USE THE POINT TABLE
Acceleration time constant of point table No. 1 (100)
Servo motor speed
Forward rotation
0 r/min
Reverse rotation
Speed
(3000)
Speed
(2000)
Deceleration time constant of point table No. 1 (150)
Speed
(1000)
Position address
0
5.00
5.00
3.00
2.00
8.00
10.00
6.00
Speed
(500)
16.00
Selected point table No.
ST1
(Forward rotation start)
ON
OFF
PT0 (Point table No. output 1) to PT4 (Point table No. output 5)
(Note 1)
M code output (Note 2)
1
1
05
Note 1. For MR-JE-_A servo amplifiers, up to four points of DO are available; therefore, PT0 to PT4 cannot be outputted simultaneously.
2. M code will be available in the future.
(d) Automatic repeat positioning operation
By setting the auxiliary function of the point table, the operation pattern of the set point table No. can be returned to, and the positioning operation can be performed repeatedly.
1) Absolute value command method ([Pr. PT01] = _ _ _ 0)
Setting "8" or "10" to the auxiliary function performs an automatic continuous operation or a varying-speed operation until that point table, and after the completion of positioning, performs the operation again from the operation pattern of the point table No. used at start-up.
Setting "9" or "11" to the auxiliary function performs an automatic continuous operation or a varying-speed operation until that point table, and after the completion of positioning, performs the operation again from the operation pattern of point table No. 1. a) Automatic repeat positioning operation by absolute value command method
Example 1. Operations when "8" is set to the auxiliary function of point table No. 4
Point table
No.
Position data
[10 STM μ m]
Servo motor speed [r/min]
Acceleration time constant
[ms]
Deceleration time constant
[ms]
Dwell [ms]
Auxiliary function
M code
(Note)
Note. M code will be available in the future.
4 - 29
4. HOW TO USE THE POINT TABLE
Operation sequence
1) Starting with point table No. 2
2) Executing point table No. 3
3) Executing point table No. 4
4) Executing again point table No. 2 used at start-up when "8" is set to the auxiliary function of point table No. 4
5) Repeating the above execution in the sequence of 2) to 3) to 4) to 2) to 3) to 4)
Point table No. 2 Point table No. 3
1)
2)
Servo motor speed
Forward rotation
0 r/min
Reverse rotation
Speed
(3000)
Speed
(2000)
Point table No. 4
3)
Speed (1000)
Speed
(3000)
4)
Point table No. 2
5.00
Position address
0 5.00
10.00
15.00
Selected point table No.
ST1
(Forward rotation start)
ON
OFF
PT0 (Point table No. output 1) to PT4 (Point table No. output 5)
(Note 1)
M code output (Note 1, 2)
2
Note 1. PT0 to PT4 and M code are not outputted in automatic continuous operation.
2. M code will be available in the future.
Point table
No.
Example 2. Operations when "9" is set to the auxiliary function of point table No. 3
Position data
[10 STM μ m]
Servo motor speed [r/min]
Acceleration time constant
[ms]
Deceleration time constant
[ms]
Dwell [ms]
Auxiliary function
M code
(Note)
Note. M code will be available in the future.
4 - 30
4. HOW TO USE THE POINT TABLE
Operation sequence
1) Starting with point table No. 2
2) Executing point table No. 3
3) Executing point table No. 1 when "9" is set to the auxiliary function of point table No. 3
4) Repeating the above execution in the sequence of 1) to 2) to 3) to 1) to 2) to 3)
Point table No. 2
Point table No. 3
Servo motor speed
Forward rotation
0 r/min
Reverse rotation
1)
Speed
(2000)
2)
Speed (1000)
Speed
(3000)
3)
Point table No. 1
5.00
Position address
0 5.00
15.00
Selected point table No.
ST1
(Forward rotation start)
ON
OFF
PT0 (Point table No. output 1) to PT4 (Point table No. output 5)
(Note 1)
M code output (Note 1, 2)
2
Note 1. PT0 to PT4 and M code are not outputted in automatic continuous operation.
2. M code will be available in the future. b) Automatic repeat positioning operation by incremental value command method
Example 1. Operations when "10" is set to the auxiliary function of point table No. 4
Point table
No.
Position data
[10 STM μ m]
Servo motor speed [r/min]
Acceleration time constant
[ms]
Deceleration time constant
[ms]
Dwell [ms]
Auxiliary function
M code
(Note)
1 4.00 1500 200 100 150 1 01
Note. M code will be available in the future.
4 - 31
4. HOW TO USE THE POINT TABLE
Servo motor speed
Operation sequence
1) Starting with point table No. 2
2) Executing point table No. 3
3) Executing point table No. 4
4) Executing again point table No. 2 used at start-up when "10" is set to the auxiliary function of point table No. 4
5) Repeating the above execution in the sequence of 1) to 2) to 3) to 4) to 2) to 3) to 4)
Point table No. 2 Point table No. 3 Point table No. 2
Forward rotation
0 r/min
Reverse rotation
1)
Speed
(3000)
2)
Speed
(2000)
Point table No. 4
3)
Speed (1000)
Speed
(2000)
Speed
(3000)
4)
2)
Point table No. 3
5.00
5.00
5.00
Position address
0 5.00
10.00
15.00
Selected point table No.
ST1
(Forward rotation start)
ON
OFF
PT0 (Point table No. output 1) to PT4 (Point table No. output 5)
(Note 1)
M code output (Note 1, 2)
2
Note 1. PT0 to PT4 and M code are not outputted in automatic continuous operation.
2. M code will be available in the future.
Example 2. Operations when "11" is set to the auxiliary function of point table No. 3
Point table
No.
Position data
[10 STM μ m]
Servo motor speed [r/min]
Acceleration time constant
[ms]
Deceleration time constant
[ms]
Dwell [ms]
Auxiliary function
M code
(Note)
Note. M code will be available in the future.
4 - 32
4. HOW TO USE THE POINT TABLE
Servo motor speed
Operation sequence
1) Starting with point table No. 2
2) Executing point table No. 3
3) Executing point table No. 1 when "11" is set to the auxiliary function of point table No. 3
4) Repeating the above execution in the sequence of 1) to 2) to 3) to 1) to 2) to 3)
Point table No. 2 Point table No. 1
Forward rotation
0 r/min
Reverse rotation
Speed
(2000)
1)
Point table No. 3
2)
Speed (1000)
Speed
(2000)
1)
Speed
(3000)
3)
Point table No. 2
5.00
5.00
Position address
0 10.00
15.00
Selected point table No.
ST1
(Forward rotation start)
ON
OFF
PT0 (Point table No. output 1) to PT4 (Point table No. output 5)
(Note 1)
M code output (Note 1, 2)
2
Note 1. PT0 to PT4 and M code are not outputted in automatic continuous operation.
2. M code will be available in the future. c) Varying-speed operation by absolute value command method
Example. Operations when "8" is set to the auxiliary function of point table No. 3
Point table
No.
Position data
[10 STM μ m]
Servo motor speed [r/min]
Acceleration time constant
[ms]
Deceleration time constant
[ms]
Dwell [ms]
Auxiliary function
M code
(Note)
Note. M code will be available in the future.
4 - 33
4. HOW TO USE THE POINT TABLE
Operation sequence
1) Starting with point table No. 1
2) Varying the speed and executing point table No. 2
3) Varying the speed and executing point table No. 3
4) Executing point table No. 1 used at start-up in CW direction when "8" is set to the auxiliary function of point table No. 3
5) Repeating the above execution in the sequence of 1) to 2) to 3) to 4) to 2) to 3) to 4)
Servo motor speed
Acceleration time constant of point table No. 1 (100)
1)
Forward rotation
0 r/min
Reverse rotation
Speed
(3000)
Point table No. 1
Deceleration time constant of point table No. 1 (150)
Point table No. 2
Point table No. 3
2)
Speed
(2000) Speed (1000)
3)
Speed
(3000) 4)
Position address
0
Deceleration time constant of point table No. 1 (150)
5.00
5.00
10.00
Acceleration time constant of point table No. 1 (100)
15.00
Selected point table No.
ST1
(Forward rotation start)
ON
OFF
PT0 (Point table No. output 1) to PT4 (Point table No. output 5)
(Note 1)
M code output (Note 1, 2)
1
Note 1. PT0 to PT4 and M code are not outputted in automatic continuous operation.
2. M code will be available in the future.
Point table
No. d) Varying-speed operation by incremental value command method
Example. Operations when "10" is set to the auxiliary function of point table No. 3
Position data
[10 STM μ m]
Servo motor speed [r/min]
Acceleration time constant
[ms]
Deceleration time constant
[ms]
Dwell [ms]
Auxiliary function
M code
(Note)
Note. M code will be available in the future.
4 - 34
4. HOW TO USE THE POINT TABLE
Servo motor speed
Operation sequence
1) Starting with point table No. 1
2) Varying the speed and executing point table No. 2
3) Varying the speed and executing point table No. 3
4) Varying the speed, and executing point table No. 1 when "10" is set to the auxiliary function of point table No. 3
5) Repeating the above execution in the sequence of 1) to 2) to 3) to 4) to 2) to 3) to 4)
Acceleration time constant of point table No. 1 (100)
Deceleration time constant of point table No. 1 (150)
Point table No. 1
Point table No. 2
Point table No. 3
Forward rotation
0 r/min
Reverse rotation
1)
Speed
(3000)
Point table No. 1
2)
Speed
(2000)
Deceleration time constant of point table No. 1 (150)
Speed (1000)
Speed
(2000)
3)
2)
Speed
(3000)
4)
5.00
Point table No. 2
5.00
Acceleration time constant of point table No. 1 (100)
5.00
Position address
0 5.00
10.00
15.00
Selected point table No.
ST1
(Forward rotation start)
ON
OFF
PT0 (Point table No. output 1) to PT4 (Point table No. output 5)
(Note 1)
M code output (Note 1, 2)
1
Note 1. PT0 to PT4 and M code are not outputted in automatic continuous operation.
2. M code will be available in the future.
2) Absolute value command method ([Pr. PT01] = _ _ _ 1)
Setting "8" to the auxiliary function performs automatic continuous operation or varying-speed operation until that point table, and after the completion of positioning, performs the operation again from the operation pattern of the set point table.
Setting "9" to the auxiliary function performs automatic continuous operation or varying-speed operation until that point table, and after the completion of positioning, performs the operation again from the operation pattern of point table No. 1. b) Automatic repeat positioning operation by incremental value command method
Example 1. Operations when "8" is set to the auxiliary function of point table No. 3
Point table
No.
Position data
[10 STM μ m]
Servo motor speed [r/min]
Acceleration time constant
[ms]
Deceleration time constant
[ms]
Dwell [ms]
Auxiliary function
M code
(Note)
Note. M code will be available in the future.
4 - 35
4. HOW TO USE THE POINT TABLE
Servo motor speed
Operation sequence
1) Starting with point table No. 2
2) Executing point table No. 3
3) Executing again point table No. 2 used at start-up when "8" is set to the auxiliary function of point table No. 3
4) Repeating the above execution in the sequence of 1) to 2) to 3) to 2) to 3)
Point table No. 2
3)
Forward rotation
0 r/min
Reverse rotation
1)
Speed
(3000)
2)
Speed
(2000)
Speed
(3000)
2)
Speed
(2000)
5.00
Point table No. 3
6.00
5.00
Position address
0 5.00
11.00
16.00
Selected point table No.
ST1
(Forward rotation start)
ON
OFF
PT0 (Point table No. output 1) to PT4 (Point table No. output 5)
(Note 1)
M code output (Note 1, 2)
2
Note 1. PT0 to PT4 and M code are not outputted in automatic continuous operation.
2. M code will be available in the future.
Example 2. Operations when "9" is set to the auxiliary function of point table No. 2
Point table
No.
Position data
[10 STM μ m]
Servo motor speed [r/min]
Acceleration time constant
[ms]
Deceleration time constant
[ms]
Dwell [ms]
Auxiliary function
M code
(Note)
1 5.00 3000 100 150 100 1 05
2 6.00 2000 150 200 200 9 10
Note. M code will be available in the future.
4 - 36
4. HOW TO USE THE POINT TABLE
Servo motor speed
Operation sequence
1) Starting with point table No. 2
2) Executing point table No. 1 when "9" is set to the auxiliary function of point table No. 2
3) Repeating the above execution in the sequence of 1) to 2) to 1) to 2)
Point table No. 1
Forward rotation
0 r/min
Reverse rotation
1)
Speed
(2000)
Point table No. 2
6.00
2)
Speed
(3000)
5.00
1)
Speed
(2000)
6.00
2)
Speed
(3000)
Position address
0 6.00
11.00
17.00
Selected point table No.
ST1
(Forward rotation start)
ON
OFF
PT0 (Point table No. output 1) to PT4 (Point table No. output 5)
(Note 1)
M code output (Note 1, 2)
2
Note 1. PT0 to PT4 and M code are not outputted in automatic continuous operation.
2. M code will be available in the future. b) Varying-speed operation by incremental value command method
Example. Operations when "8" is set to the auxiliary function of point table No. 2
Point table
No.
Position data
[10 STM μ m]
Servo motor speed [r/min]
Acceleration time constant
[ms]
Deceleration time constant
[ms]
Dwell [ms]
Auxiliary function
M code
(Note)
1 5.00 3000 100 150 0 1 05
Note. M code will be available in the future.
4 - 37
4. HOW TO USE THE POINT TABLE
Servo motor speed
Operation sequence
1) Starting with point table No. 1
2) Varying the speed and executing point table No. 2
3) Executing again point table No. 1 used at start-up when "8" is set to the auxiliary function of point table No. 2
4) Repeating the above execution in the sequence of 1) to 2) to 3) to 2) to 3)
Point table No. 1
3)
Forward rotation
0 r/min
Reverse rotation
1)
Speed
(3000)
2)
Speed
(2000)
Speed
(3000)
2)
Speed
(2000)
5.00
Point table No. 2
6.00
5.00
Position address
0 5.00
11.00
16.00
Selected point table No.
ST1
(Forward rotation start)
ON
OFF
PT0 (Point table No. output 1) to PT4 (Point table No. output 5)
(Note 1)
M code output (Note 1, 2)
1
Note 1. PT0 to PT4 and M code are not outputted in automatic continuous operation.
2. M code will be available in the future.
4 - 38
4. HOW TO USE THE POINT TABLE
(e) Temporary stop/restart
When TSTP (Temporary stop/restart) is switched on during automatic operation, the servo motor decelerates with the deceleration time constant of the point table being executed, and then stops temporarily.
Switching on TSTP (Temporary stop/restart) again starts the servo motor rotation for the remaining travel distance.
During a temporary stop, ST1 (Forward rotation start) or ST2 (Reverse rotation start) does not function even if it is switched on.
When any of the following conditions is satisfied during a temporary stop, the travel remaining distance is cleared.
The operation mode is switched from the automatic mode to the manual mode.
The servo motor enters the servo-off status.
The clear signal is input.
The temporary stop/restart input does not function during a home position return or JOG operation.
The temporary stop/restart input functions in the following states.
Operation status
During a stop
During acceleration
At a constant speed
During deceleration
During a temporary stop
Automatic operation
Manual operation
Home position return
Pause
Pause
Restart
1) When the servo motor is rotating
Acceleration time constant of point table No. n
Deceleration time constant of point table No. n
Servo motor speed
Forward rotation
0 r/min
Reverse rotation
Point table
ST1 (Forward rotation start) or
ST2 (Reverse rotation start)
TSTP (Temporary stop/restart)
PUS (Temporary stop)
CPO (Rough match)
INP (In-position)
ON
OFF
ON
OFF
MEND (Travel completion)
PT0 (Point table No. output 1) to PT4 (Point table No. output 5)
(Note)
ON
OFF
ON
OFF
ON
OFF
ON
OFF
No. n
Remaining distance
No. n
Note. For MR-JE-_A servo amplifiers, up to four points of DO are available; therefore, PT0 to PT4 cannot be outputted simultaneously.
4 - 39
4. HOW TO USE THE POINT TABLE
2) During dwell
Servo motor speed
Forward rotation
0 r/min
Reverse rotation
Point table
ST1 (Forward rotation start) or
ST2 (Reverse rotation start)
TSTP (Temporary stop/restart)
PUS (Temporary stop)
ON
OFF
ON
OFF
ON
OFF
CPO (Rough match)
INP (In-position)
ON
OFF
ON
OFF
MEND (Travel completion)
PT0 (Point table No. output 1) to PT4 (Point table No. output 5)
(Note)
ON
OFF
Point table No. n ta
Dwell = ta + tb tb
Point table No. n + 1
No. n
No. n
Note. For MR-JE-_A servo amplifiers, up to four points of DO are available; therefore, PT0 to PT4 cannot be outputted simultaneously.
(f) Suspension of automatic operation
To suspend the automatic operation or change the operation pattern, stop the servo motor with
TSTP (Temporary stop/restart), switch off MD0 (Operation mode selection 1), and then set the mode to the manual mode. The travel remaining distance is cleared.
Point table No. n
Remaining distance
Servo motor speed
Forward rotation
0 r/min
Reverse rotation
Point table No.
ST1 (Forward rotation start) or
ST2 (Reverse rotation start)
PUS (Temporary stop)
ON
OFF
ON
OFF
TSTP (Temporary stop/restart)
MD0 (Operation mode selection)
ON
OFF
ON
OFF
No. n
Remaining distance clear
4 - 40
4. HOW TO USE THE POINT TABLE
(g) Using a control unit of "degree"
1) Current position/command position address
The current position/command position address is of ring-address type.
359.999
359.999
0 0 0
2) Software limit activation/deactivation setting
POINT
After changing the "+" or "-" sign of an axis with the software limit activation setting, perform a home position return.
When activating the software limit in an incremental system, perform a home position return after power-on. a) Setting range
When the unit is set to "degree", the setting range of the software limit is from 0 degree (lower limit) to 359.999 degrees (upper limit).
When you set a value other than 0 degree to 359.999 degrees in [Pr. PT15] to [Pr. PT18], the set value is converted as follows. (It will be clamped between 0 degree and 359.999 degrees.)
Software limit value
360.000 degrees to 999.999 degrees
-0.001 degrees to -359.999 degrees
-360.000 degrees to -999.999 degrees
After conversion
The remainder of the set value divided by 360
The sum of the set value and 360
The sum of 360 and the quotient of the set value divided by 360 b) When the software limit is enabled
Set the software limit - ([Pr. PT17] and [Pr. PT18]) for the start position and the software limit +
([Pr. PT15] and [Pr. PT16]) for the end position.
The movable range is the section from - to + in the CCW direction.
0 0
CCW CCW
315 315
Section A
90 90
Section B
Set the movable range of section A as follows:
Software limit - … 315.000 degrees
Software limit + … 90.000 degrees
Set the movable range of section B as follows:
Software limit - … 90.000 degrees
Software limit + … 315.000 degrees
4 - 41
4. HOW TO USE THE POINT TABLE c) When the software limit is disabled
When deactivating the software limit, set the same values to the software limit - ([Pr. PT17] and [Pr. PT18]) and the software limit + ([Pr. PT15] and [Pr. PT16]).
Control can be performed independently of the software limit setting.
3) Position range output enabling/disabling setting a) Setting range
When the unit is set to "degree", the setting range of the position range output is from 0 degree
(lower limit) to 359.999 degrees (upper limit).
When you set a value other than 0 degree to 359.999 degrees in [Pr. PT19] to [Pr. PT22], the set value is converted as follows. (It will be clamped between 0 degree and 359.999 degrees.)
Position range output address After conversion
360.000 degrees to 999.999 degrees The remainder of the set value divided by 360
-0.001 degrees to -359.999 degrees
-360.000 degrees to -999.999 degrees
The sum of the set value and 360
The sum of 360 and the quotient of the set value divided by 360 b) Effective setting of position range output
Set the position range output address - ([Pr. PT21] and [Pr. PT22]) for the start position and the position range output address + ([Pr. PT19] and [Pr. PT20]) for the target position.
The movable range is the section from - to + in the CCW direction.
0 0
CCW CCW
315 315
Section A
90 90
Section B
Set the movable range of section A as follows:
Position range output address - … 315.000 degrees
Position range output address + … 90.000 degrees
Set the movable range of section B as follows:
Position range output address - … 90.000 degrees
Position range output address + … 315.000 degrees
4 - 42
4. HOW TO USE THE POINT TABLE
4.3 Manual operation mode
For the machine adjustment, home position adjustment, and others, positioning to any point is possible using the JOG operation or the manual pulse generator.
4.3.1 JOG operation
(1) Setting
According to the purpose of use, set input devices and parameters as shown below. In this case, DI0
(Point table No. selection 1) to DI4 (Point table No. selection 5) are disabled.
Item Device/parameter to be used Setting
Manual operation mode selection
MD0 (Operation mode selection 1)
Servo motor rotation direction [Pr. PA14]
Switch off MD0.
Refer to (2) in this section.
Set the servo motor speed.
Acceleration time constant/Deceleration time constant
Point table No. 1
The acceleration/deceleration time constant of point table No. 1 is used.
(2) Servo motor rotation direction
[Pr. PA14] setting
Servo motor rotation direction
ST1 (Forward rotation start) on ST2 (Reverse rotation start) on
1 CW rotation CCW rotation
ST1: on
CCW
ST2: on
CCW
CW
ST2: on
[Pr. PA14]: 0
CW
ST1: on
[Pr. PA14]: 1
(3) Operation
Switching on ST1 (Forward rotation start) performs the operation at the JOG speed set by a parameter and the acceleration/deceleration constant of point table No. 1. For the rotation direction, refer to (2) of this section. Switching on ST2 (Reverse rotation start) starts the rotation in the reverse direction of ST1
(Forward rotation start).
Simultaneously switching on or off ST1 (Forward rotation start) and ST2 (Reverse rotation start) stops the operation.
4 - 43
4. HOW TO USE THE POINT TABLE
(4) Timing chart
SON (Servo-on)
RD (Ready)
ON
OFF
ON
OFF
ALM (Malfunction)
ON
OFF
MD0
(Operation mode selection 1)
ON
OFF
MEND
(Travel completion)
CPO (Rough match)
ON
OFF
ON
OFF
Servo motor speed
80 ms
Forward rotation
0 r/min
Reverse rotation
ST1
(Forward rotation direction)
ST2
(Reverse rotation direction)
ON
OFF
ON
OFF
Forward rotation JOG
Reverse rotation JOG
4 - 44
4. HOW TO USE THE POINT TABLE
4.3.2 Manual pulse generator operation
(1) Setting
POINT
To enhance noise tolerance, set "_ 2_ _" to [Pr. PA13] when the command pulse frequency is 500 kpulses/s or less, or set "_3_ _" to [Pr. PA13] when the command pulse frequency is 200 kpulses/s or less.
According to the purpose of use, set input devices and parameters as shown below. In this case, DI0
(Point table No. selection 1) to DI4 (Point table No. selection 5) are disabled.
Item
Manual operation mode selection
Device/parameter to be used
MD0 (Operation mode selection 1) Switch off MD0.
Setting
Manual pulse generator multiplication
[Pr. PT03]
Set the multiplication factor for the pulses generated from the manual pulse generator.
For details, refer to (3) in this section.
Refer to (2) in this section. Servo motor rotation direction [Pr. PA14]
Command input pulse train input form
Pulse train filter selection
[Pr. PA13]
[Pr. PA13]
(2) Servo motor rotation direction
[Pr. PA14] setting
Set "_ _ _ 2" (A/B-phase pulse train).
Set other than "0" and "1".
Servo motor rotation direction
Manual pulse generator operation: forward rotation
Manual pulse generator operation: reverse rotation
1 CW rotation CCW rotation
Forward rotation
CCW
CW
4 - 45
4. HOW TO USE THE POINT TABLE
(3) Manual pulse generator multiplication
(a) Using the input signals (devices) for setting
In "Device setting" of MR Configurator2, set TP0 (Pulse generator multiplication 1) and TP1 (Pulse generator multiplication 2) to input signals.
TP1 (Pulse generator multiplication 2)
(Note)
TP0 (Pulse generator multiplication 1)
(Note)
Servo motor rotation multiplication factor for manual pulse generator rotation amount
Travel distance
0 0 [Pr. PT03] setting enabled
0 1
1 0 10 0.01
Note. 0: Off
1: On
(b) Using the parameter for setting
Using [Pr. PT03], set the servo motor rotation multiplication to the rotation amount of the manual pulse generator.
Travel distance
[Pr. PT03] setting
Servo motor rotation multiplication to manual pulse generator rotation amount
_ _ 0 _
_ _ 1 _
_ _ 2 _
1 time
10 times
100 times
0.001
(4) Operation
Turning the manual pulse generator rotates the servo motor. For the rotation direction of the servo motor, refer to (2) in this section. When you turn the manual pulse generator during a JOG operation, the commands inputted from the manual pulse generator are adjusted by the commands of JOG operation.
4.4 Home position return mode
POINT
Before performing the home position return, make sure that the limit switch operates.
Check the home position return direction. An incorrect setting will cause a reverse running.
Check the input polarity of the proximity dog. Otherwise, it may cause an unexpected operation.
4 - 46
4. HOW TO USE THE POINT TABLE
4.4.1 Outline of home position return
A home position return is performed to match the command coordinates with the machine coordinates. The home position return is required every time the input power is on.
This section shows the home position return methods of the servo amplifier. Select the optimum method according to the configuration and uses of the machine.
This servo amplifier has the home position return automatic retract function. When the machine stops beyond or on a proximity dog, this function automatically moves the machine back to the proper position to perform the home position return. Manual operation with JOG operation, etc. is unnecessary.
(1) Home position return types
Select the optimum home position return type according to the machine type or others.
Dog type
Count type
Type
Data set type
Stopper type
Deceleration starts from the front end of the proximity dog. A position of the first Z-phase signal after the rear end is passed or a position moved by the home position shift amount from the Z-phase signal is set as the home position.
Home position return method Feature
Typical home position return method using a proximity dog
The repeatability of the home position return is high.
The machine is less loaded.
Use this when the width of the proximity dog can be set equal to or greater than the deceleration distance of the servo motor.
Deceleration starts from the front end of the proximity dog. After the proximity dog is passed, the motor travels the specified travel distance. Then, the position specified by the first Z-phase signal, or the position of the first Z-phase signal shifted by the home position shift distance is used as the home position.
An arbitrary position is set as the home position.
This is a home position return method using a proximity dog.
Use this to minimize the length of the proximity dog.
A workpiece is pressed against a mechanical stopper, and the position where it is stopped is set as the home position.
No proximity dog is required.
Since the workpiece collides with the mechanical stopper, the home position return speed must be low enough.
The strength of the machine and stopper must be increased.
Home position ignorance
(servo-on position as home position)
Servo-on position is set as the home position.
Dog type rear end reference
Count type front end reference
Dog cradle type
Dog type last Z-phase reference
Dog type front end reference
Dogless Z-phase reference
Deceleration starts from the front end of the proximity dog. After the rear end is passed, the position is shifted by the travel distance after proximity dog and the home position shift distance. The position after the shifts is set as the home position.
Deceleration starts from the front end of the proximity dog. A position moved by the moving amount after the proximity dog and the home position shift amount is set as the home position.
After the front end of the proximity dog is detected, the position specified by the first Z-phase signal is used as the home position.
After the front end of the proximity dog is detected, the position is shifted away from the proximity dog in the reverse direction. Then, the position specified by the first Z-phase signal or the position of the first Z-phase signal shifted by the home position shift distance is used as the home position.
Starting from the front end of the proximity dog, the position is shifted by the travel distance after proximity dog and the home position shift distance. The position after the shifts is used as the home position.
The position specified by the first Z-phase signal, or the position of the first Z-phase signal shifted by the home position shift distance is used as the home position.
The Z-phase signal is not required.
The Z-phase signal is not required.
The Z-phase signal is not required.
4 - 47
4. HOW TO USE THE POINT TABLE
(2) Parameters for home position return
To perform the home position return, set each parameter as follows.
(a) Select the home position return type with [Pr. PT04 Home position return type].
0
[Pr. PT04]
0 0
Home position return method
0: Dog type (rear-end detection Z-phase reference)
1: Count type (front-end detection Z-phase reference)
2: Data set type
3: Stopper type
4: Home position ignorance (servo-on position as home position)
5: Dog type (rear-end detection, rear-end reference)
6: Count type (front-end detection, front-end reference)
7: Dog cradle type
8: Dog type (front-end detection, Z-phase reference)
9: Dog type (front-end detection, front-end reference)
A: Dogless type (Z-phase reference)
(b) Select the starting direction for the home position return with [Pr. PT04 Home position return type].
Setting "0" starts the home position return in a direction of increasing the address from the current position. Setting "1" starts the home position return in a direction of decreasing the address from the current position.
0
[Pr. PT04]
0 0
Home position return direction
0: Address increasing direction
1: Address decreasing direction
(c) Select the polarity where the proximity dog is detected with the DOG (Proximity dog) polarity selection of [Pr. PT29 Function selection T-3].
Setting "0" detects a proximity dog when DOG (Proximity dog) is switched off. Setting "1" detects a proximity dog when DOG (Proximity dog) is switched on.
0
[Pr. PT29]
0 0
DOG (Proximity dog) polarity selection
0: Detection with off
1: Detection with on
4 - 48
4. HOW TO USE THE POINT TABLE
4.4.2 Dog type home position return
This is a home position return method using a proximity dog. Deceleration starts at the front end of the proximity dog. After the rear end is passed, the position specified by the first Z-phase signal, or the position of the first Z-phase signal shifted by the specified home position shift distance is used as the home position.
(1) Device/parameter
Set input devices and parameters as follows.
Item Device/parameter to be used Setting
Switch on MD0.
Home position return mode selection
MD0 (Operation mode selection 1)
DI0 (Point table No. selection 1) to
DI4 (Point table No. selection 5)
Switch off DI0 to DI4.
Dog type home position return
Home position return direction
[Pr. PT04]
[Pr. PT04]
_ _ _ 0: Select the dog type.
Dog input polarity [Pr. PT29]
Home position return speed [Pr. PT05]
Creep speed [Pr. PT06]
Home position shift distance [Pr. PT07]
Refer to section 4.4.1 (2) to select the home position return direction.
Refer to section 4.4.1 (2) to select the proximity dog input polarity.
Set the rotation speed specified until a dog is detected.
Set the rotation speed specified after a dog is detected.
Set this item to shift the home position, which is specified by the first Z-phase signal after the rear end of a proximity dog is passed.
Acceleration time constant/Deceleration time constant
Home position return position data
Point table No. 1
[Pr. PT08]
The acceleration/deceleration time constant of point table No. 1 is used.
Set the current position at the home position return completion.
(2) Length of the proximity dog
To generate the Z-phase signal of the servo motor during the detection of DOG (Proximity dog), set the length of the proximity dog that satisfies equations (4.1) and (4.2).
L
1
≥
V
60
• td
2
··············································································································· (4.1)
L
1
: Length of the proximity dog
V: Home position return speed [mm/min] td: Deceleration time [s]
L
2
≥ 2 • ∆ S ··················································································································· (4.2)
L
2
: Length of the proximity dog
∆ S: Travel distance per servo motor revolution [mm]
4 - 49
4. HOW TO USE THE POINT TABLE
(3) Timing chart
MD0
(Operation mode selection 1)
MEND
(Travel completion)
CPO (Rough match)
ZP
(Home position return completion)
ON
OFF
ON
OFF
ON
OFF
ON
OFF
Servo motor speed
Forward rotation
0 r/min
Reverse rotation
Acceleration time constant
Home position return speed
Deceleration time constant
Creep speed
3 ms or shorter td
Proximity dog
Home position shift distance
Home position
Home position return position data
Z-phase
DOG (Proximity dog)
ST1
(Forward rotation start)
ST2
(Reverse rotation start)
ON
OFF
ON
OFF
ON
OFF
ON
OFF
5 ms or longer
The setting value of [Pr. PT08 Home position return position data] is used as the position address at the home position return completion.
(4) Adjustment
For the dog type home position return, adjust the setting so that the Z-phase signal is always generated during the detection of a dog. Make an adjustment so that the rear end of DOG (Proximity dog) is positioned almost at the center between the positions specified by a Z-phase signal and the next Zphase signal.
The generation position of the Z-phase signal can be checked with "Position within one-revolution" of
"Status display" on MR Configurator2.
0 Resolution/2 0
Servo motor Z-phase
Proximity dog
4 - 50
4. HOW TO USE THE POINT TABLE
4.4.3 Count type home position return
For the count type home position return, after the front end of a proximity dog is detected, the position is shifted by the distance set in [Pr. PT09 Travel distance after proximity dog]. Then, the position specified by the first Z-phase signal is used as the home position. Therefore, when the on-time of DOG (Proximity dog) is
10 ms or more, the length of the proximity dog has no restrictions. When the required proximity dog length for using the dog type home position return cannot be reserved, or when DOG (Proximity dog) is entered electrically from the controller or the like, use the count type home position return.
(1) Device/parameter
Set input devices and parameters as follows.
Item Device/parameter to be used Setting
Switch on MD0.
Home position return mode selection
MD0 (Operation mode selection 1)
DI0 (Point table No. selection 1) to
DI4 (Point table No. selection 5)
Switch off DI0 to DI4.
Count type home position return
Home position return direction
[Pr. PT04]
[Pr. PT04]
_ _ _ 0: Select the count type.
Dog input polarity [Pr. PT29]
Home position return speed [Pr. PT05]
Creep speed [Pr. PT06]
Home position shift distance [Pr. PT07]
Refer to section 4.4.1 (2) to select the home position return direction.
Refer to section 4.4.1 (2) to select the dog input polarity.
Set the rotation speed specified until a dog is detected.
Set the rotation speed specified after a dog is detected.
After the front end of a proximity dog is passed, the position is shifted by the travel distance and then is specified by the first Zphase signal. Set this item to shift the position of the first Z-phase signal.
Set the travel distance specified after the front end of the proximity dog is passed.
Travel distance after proximity dog
Acceleration time constant/Deceleration time constant
Home position return position data
[Pr. PT09]
Point table No. 1
[Pr. PT08]
The acceleration/deceleration time constant of point table No. 1 is used.
Set the current position at the home position return completion.
4 - 51
4. HOW TO USE THE POINT TABLE
(2) Timing chart
MD0
(Operation mode selection 1)
MEND
(Travel completion)
CPO (Rough match)
ZP
(Home position return completion)
Servo motor speed
ON
OFF
ON
OFF
ON
OFF
ON
OFF
Forward rotation
0 r/min
Reverse rotation
Acceleration time constant
Home position return speed
Deceleration time constant
Creep speed
3 ms or shorter
Proximity dog
Home position return position data
Travel distance after proximity dog
Home position shift distance
Home position
Z-phase
DOG (Proximity dog)
ST1
(Forward rotation start)
ST2
(Reverse rotation start)
ON
OFF
ON
OFF
ON
OFF
ON
OFF
5 ms or longer
The setting value of [Pr. PT08 Home position return position data] is used as the position address at the home position return completion.
4 - 52
4. HOW TO USE THE POINT TABLE
4.4.4 Data set type home position return
To set an arbitrary position as the home position, use the data set type home position return. The JOG operation, the manual pulse generator operation, and others can be used for the travel. The data set type home position return can be performed at servo-on only.
(1) Device/parameter
Set input devices and parameters as follows.
Item Device/parameter to be used Setting
Switch on MD0.
Home position return mode selection
MD0 (Operation mode selection 1)
DI0 (Point table No. selection 1) to
DI4 (Point table No. selection 5)
Switch off DI0 to DI4.
Data set type home position return
Home position return position data
[Pr. PT04]
[Pr. PT08]
_ _ _ 2: Select the data set type.
Set the current position at the home position return completion.
(2) Timing chart
SON (Servo-on)
MD0
(Operation mode selection 1)
MEND
(Travel completion)
CPO (Rough match)
ZP
(Home position return completion)
ON
OFF
ON
OFF
ON
OFF
ON
OFF
ON
OFF
Home position return position data Servo motor speed
Forward rotation
0 r/min
Reverse rotation
ST1
(Forward rotation start)
ST2
(Reverse rotation start)
ON
OFF
ON
OFF
3 ms or shorter
5 ms or longer
Travel to home position Execution of data set type home position return
The setting value of [Pr. PT08 Home position return position data] is used as the position address at the home position return completion.
4 - 53
4. HOW TO USE THE POINT TABLE
4.4.5 Stopper type home position return
For the stopper type home position return, the home position is set where the workpiece is pressed against the stopper of the machine by using the JOG operation, the manual pulse generator operation, or others.
(1) Device/parameter
Set input devices and parameters as follows.
Item Device/parameter to be used Setting
Switch on MD0.
Home position return mode selection
MD0 (Operation mode selection 1)
DI0 (Point table No. selection 1) to
DI4 (Point table No. selection 5)
Switch off DI0 to DI4.
Stopper type home position return
Home position return direction
[Pr. PT04]
[Pr. PT04]
_ _ _ 3: Select the stopper type.
Home position return speed [Pr. PT05]
Stopper time
Stopper type home position return torque limit value
Acceleration time constant of home position return
Home position return position data
[Pr. PT10]
[Pr. PT11]
Point table No. 1
[Pr. PT08]
Refer to section 4.4.1 (2) to select the home position return direction.
Set the rotation speed until the workpiece is pressed against the mechanical stopper.
Set the time from when the home position data is obtained after the workpiece is pressed against the stopper until when ZP
(home position return completion) is outputted.
Set the servo motor torque limit value when executing the stopper type home position return.
The acceleration/deceleration time constant of point table No. 1. is used.
Set the current position when the home position return is complete.
4 - 54
4. HOW TO USE THE POINT TABLE
(2) Timing chart
MD0
(Operation mode selection 1)
MEND
(Travel completion)
CPO (Rough match)
ZP
(Home position return completion)
Servo motor speed
ON
OFF
ON
OFF
ON
OFF
ON
OFF
Forward rotation
0 r/min
Reverse rotation
Acceleration time constant
ST1
(Forward rotation start)
ST2
(Reverse rotation start)
TLC (Limiting torque)
ON
OFF
ON
OFF
ON
OFF
Torque limit value [Pr. PC35]
Home position return speed
3 ms or shorter
5 ms or longer
Stopper time
[Pr. PT11] (Note 1)
Home position return position data
Stopper
(Note 2)
[Pr. PC35]
Note 1. The following torque limits are enabled.
Input device (0: off, 1: on)
TL1 TL
0 0
0 1
TLA
1 0
Pr. PC35
Pr. PC35
1 1
TLA
Limit value status
> Pr. PT11
>
<
>
Pr. PT11
Pr. PT11
Pr. PT11
Enabled torque limit value
Pr. PT11
TLA
Pr. PT11
Pr. PC35
Pr. PT11
TLA
2. TLC turns on when a generated torque reaches a value set with any of [Pr. PA11 Forward rotation torque limit], [Pr. PA12
Reverse rotation torque limit], or [Pr. PC35 Internal torque limit 2].
The setting value of [Pr. PT08 Home position return position data] is used as the position address at the home position return completion.
4 - 55
4. HOW TO USE THE POINT TABLE
4.4.6 Home position ignorance (servo-on position as home position)
POINT
When you perform this home position return, it is unnecessary to switch to the home position return mode.
Servo-on position is set as the home position.
(1) Device/parameter
Set input devices and parameters as follows.
Item Parameter to be used
Home position ignorance
Home position return position data
[Pr. PT04]
[Pr. PT08]
(2) Timing chart
SON (Servo-on)
RD (Ready)
ON
OFF
ON
OFF
MEND
(Travel completion)
ON
OFF
CPO
(Rough match)
ZP
(Home position return completion)
ON
OFF
ON
OFF
Setting
_ _ _ 4: Select the home position ignorance.
Set the current position when the home position return is complete.
Home position return position data
Servo motor speed
Forward rotation
0 r/min
Reverse rotation
The setting value of [Pr. PT08 Home position return position data] is used as the position address at the home position return completion.
4 - 56
4. HOW TO USE THE POINT TABLE
4.4.7 Dog type rear end reference home position return
POINT
This home position return method depends on the timing of reading DOG
(Proximity dog) that has detected the rear end of a proximity dog. Therefore, when a home position return is performed at a creep speed of 100 r/min, the home position has an error of 200 pulses (for HG series servo motor). The higher the creep speed, the greater the error of the home position.
Deceleration starts from the front end of a proximity dog. After the rear end is passed, the position is shifted by the travel distance after proximity dog and the home position shift distance. The position after the shifts is set as the home position. The home position return is available independently of the Z-phase signal.
Changing the creep speed may change the home position.
(1) Device/parameter
Set input devices and parameters as follows.
Item Device/parameter to be used Setting
Switch on MD0.
Home position return mode selection
MD0 (Operation mode selection 1)
DI0 (Point table No. selection 1) to
DI4 (Point table No. selection 5)
Switch off DI0 to DI4.
Dog type rear end reference home position return
Home position return direction
Dog input polarity
Creep speed
[Pr. PT04]
[Pr. PT04]
[Pr. PT29]
Home position return speed [Pr. PT05]
[Pr. PT06]
Home position shift distance [Pr. PT07]
[Pr. PT09]
_ _ _ 5: Select the dog type (rear end detection/rear end reference).
Refer to section 4.4.1 (2) to select the home position return direction.
Refer to section 4.4.1 (2) to select the dog input polarity.
Set the rotation speed specified until a dog is detected.
Set the rotation speed specified after a dog is detected.
Set this to shift the home position, which is specified after the rear end of a proximity dog is passed.
Set the travel distance after the rear end of a proximity dog is passed.
Travel distance after proximity dog
Acceleration time constant/deceleration time constant of home position return
Home position return position data
Point table No. 1
[Pr. PT08]
The acceleration/deceleration time constant of point table No. 1 is used.
Set the current position when the home position return is complete.
4 - 57
4. HOW TO USE THE POINT TABLE
(2) Timing chart
MD0
(Operation mode selection 1)
MEND
(Travel completion)
CPO (Rough match)
ZP
(Home position return completion)
ON
OFF
ON
OFF
ON
OFF
ON
OFF
Servo motor speed
Forward rotation
0 r/min
Reverse rotation
Acceleration time constant
Home position return speed
Deceleration time constant
Creep speed
3 ms or shorter
Proximity dog
Travel distance after proximity dog
+
Home position shift distance
Home position return position data
DOG (Proximity dog)
ST1
(Forward rotation start)
ST2
(Reverse rotation start)
ON
OFF
ON
OFF
ON
OFF
5 ms or longer
The setting value of [Pr. PT08 Home position return position data] is used as the position address at the home position return completion.
4 - 58
4. HOW TO USE THE POINT TABLE
4.4.8 Count type front end reference home position return
POINT
This home position return method depends on the timing of reading DOG
(Proximity dog) that has detected the front end of a proximity dog. Therefore, when a home position return is performed with the creep speed of 100 r/min, the home position has an error of 200 pulses (for HG series servo motor). The higher the creep speed, the greater the error of the home position.
After the front end of a proximity dog is detected, if a home position return ends without reaching the creep speed, [AL. 90.2] occurs. Set the travel distance after proximity dog and the home position shift distance enough for deceleration from the home position return speed to the creep speed.
Deceleration starts from the front end of a proximity dog. The position is shifted by the travel distance after proximity dog and the home position shift distance. The position after the shifts is set as the home position.
The home position return is available independently of the Z-phase signal. Changing the creep speed may change the home position.
(1) Device/parameter
Set input devices and parameters as follows.
Item Device/parameter to be used Setting
Switch on MD0.
Home position return mode selection
MD0 (Operation mode selection 1)
DI0 (Point table No. selection 1) to
DI4 (Point table No. selection 5)
Switch off DI0 to DI4.
Count type front end reference home position return
Home position return direction
[Pr. PT04]
[Pr. PT04]
_ _ _ 6: Select the count type (front end detection/front end reference).
Dog input polarity [Pr. PT29]
Home position return speed [Pr. PT05]
Creep speed [Pr. PT06]
Home position shift distance [Pr. PT07]
Refer to section 4.4.1 (2) to select the home position return direction.
Refer to section 4.4.1 (2) to select the dog input polarity.
Set the rotation speed specified until a dog is detected.
Set the rotation speed specified after a dog is detected.
Set this to shift the home position, which is specified after the front end of a proximity dog is passed.
Set the travel distance specified after the front end of the proximity dog is passed.
Travel distance after proximity dog
Acceleration time constant/deceleration time constant of home position return
Home position return position data
[Pr. PT09]
Point table No. 1
[Pr. PT08]
The acceleration/deceleration time constant of point table No. 1 is used.
Set the current position when the home position return is complete.
4 - 59
4. HOW TO USE THE POINT TABLE
(2) Timing chart
MD0
(Operation mode selection 1)
MEND
(Travel completion)
CPO (Rough match)
ZP
(Home position return completion)
ON
OFF
ON
OFF
ON
OFF
ON
OFF
Servo motor speed
Forward rotation
0 r/min
Reverse rotation
Acceleration time constant
Home position return speed
Deceleration time constant
Creep speed
3 ms or shorter
Travel distance after proximity dog
+
Home position shift distance
Home position return position data
Proximity dog
DOG (Proximity dog)
ST1
(Forward rotation start)
ST2
(Reverse rotation start)
ON
OFF
ON
OFF
ON
OFF
5 ms or longer
The setting value of [Pr. PT08 Home position return position data] is used as the position address at the home position return completion.
4 - 60
4. HOW TO USE THE POINT TABLE
4.4.9 Dog cradle type home position return
A position, which is specified by the first Z-phase signal after the front end of a proximity dog is detected, is set as the home position.
(1) Device/parameter
Set input devices and parameters as follows.
Item Device/parameter to be used Setting
Home position return mode selection
MD0 (Operation mode selection 1)
DI0 (Point table No. selection 1) to
DI4 (Point table No. selection 5)
Switch on MD0.
Switch off DI0 to DI4.
Dog cradle type home position return
Home position return direction
[Pr. PT04]
[Pr. PT04]
_ _ _ 7: Select the dog cradle type.
Dog input polarity [Pr. PT29]
Home position return speed [Pr. PT05]
Creep speed [Pr. PT06]
Home position shift distance [Pr. PT07]
Refer to section 4.4.1 (2) to select the home position return direction.
Refer to section 4.4.1 (2) to select the dog input polarity.
Set the rotation speed specified until a dog is detected.
Set the rotation speed specified after a dog is detected.
Set this to shift the home position, which is specified by the Z-phase signal.
Acceleration time constant/deceleration time constant of home position return
Home position return position data
(2) Timing chart
Point table No. 1
[Pr. PT08]
The acceleration/deceleration time constant of point table No. 1 is used.
Set the current position when the home position return is complete.
MD0
(Operation mode selection 1)
MEND
(Travel completion)
CPO (Rough match)
ZP
(Home position return completion)
ON
OFF
ON
OFF
ON
OFF
ON
OFF
Servo motor speed
Forward rotation
0 r/min
Reverse rotation
Acceleration time constant Deceleration time constant
Home position return speed
Creep speed
3 ms or shorter
Proximity dog
Home position shift distance
Home position return position data
Z-phase
DOG (Proximity dog)
ST1
(Forward rotation start)
ST2
(Reverse rotation start)
ON
OFF
ON
OFF
ON
OFF
ON
OFF
5 ms or longer
The setting value of [Pr. PT08 Home position return position data] is used as the position address at the home position return completion.
4 - 61
4. HOW TO USE THE POINT TABLE
4.4.10 Dog type last Z-phase reference home position return
After the front end of a proximity dog is detected, the position is shifted away from the proximity dog at the creep speed in the reverse direction and then specified by the first Z-phase signal. The position of the first Zphase signal is set as the home position.
(1) Device/parameter
Set input devices and parameters as follows.
Item Device/parameter to be used Setting
Switch on MD0.
Home position return mode selection
MD0 (Operation mode selection 1)
DI0 (Point table No. selection 1) to
DI4 (Point table No. selection 5)
Switch off DI0 to DI4.
Dog type last Z-phase reference home position return
Home position return direction
[Pr. PT04]
[Pr. PT04]
_ _ _ 8: Select the dog type last Z-phase reference.
Dog input polarity [Pr. PT29]
Home position return speed [Pr. PT05]
Creep speed [Pr. PT06]
Home position shift distance [Pr. PT07]
Refer to section 4.4.1 (2) to select the home position return direction.
Refer to section 4.4.1 (2) to select the dog input polarity.
Set the rotation speed specified until a dog is detected.
Set the rotation speed specified after a dog is detected.
Set this item to shift the home position, which is specified by the Z-phase signal.
Acceleration time constant/deceleration time constant of home position return
Home position return position data
Point table No. 1
[Pr. PT08]
The acceleration/deceleration time constant of point table No. 1 is used.
Set the current position when the home position return is complete.
4 - 62
4. HOW TO USE THE POINT TABLE
(2) Timing chart
MD0
(Operation mode selection 1)
MEND
(Travel completion)
CPO (Rough match)
ZP
(Home position return completion)
ON
OFF
ON
OFF
ON
OFF
ON
OFF
Acceleration time constant
Home position return speed
Deceleration time constant
Home position return position data
Servo motor speed
Forward rotation
0 r/min
Reverse rotation 3 ms or shorter
Home position shift distance
Creep speed
Proximity dog
Z-phase
DOG (Proximity dog)
ST1
(Forward rotation start)
ST2
(Reverse rotation start)
ON
OFF
ON
OFF
ON
OFF
ON
OFF
5 ms or longer
The setting value of [Pr. PT08 Home position return position data] is used as the position address at the home position return completion.
4 - 63
4. HOW TO USE THE POINT TABLE
4.4.11 Dog type front end reference home position return type
POINT
This home position return method depends on the timing of reading DOG
(Proximity dog) that has detected the front end of a proximity dog. Therefore, when a home position return is performed at a creep speed of 100 r/min, the home position has an error of 200 pulses (for HG series servo motor). The higher the creep speed, the greater the error of the home position.
A position, which is shifted by the travel distance after proximity dog and the home position shift distance from the front end of a proximity dog, is set as the home position.
The home position return is available independently of the Z-phase signal. Changing the creep speed may change the home position.
(1) Device/parameter
Set input devices and parameters as follows.
Item Device/parameter to be used Setting
Switch on MD0.
Home position return mode selection
MD0 (Operation mode selection 1)
DI0 (Point table No. selection 1) to
DI4 (Point table No. selection 5)
Switch off DI0 to DI4.
Dog type front end reference home position return
Home position return direction
Dog input polarity
[Pr. PT04]
[Pr. PT04]
[Pr. PT29]
Home position return speed [Pr. PT05]
Creep speed [Pr. PT06]
Home position shift distance [Pr. PT07]
_ _ _ 9: Select the dog type front end reference.
Refer to section 4.4.1 (2) to select the home position return direction.
Refer to section 4.4.1 (2) to select the dog input polarity.
Set the rotation speed specified until a dog is detected.
Set the rotation speed specified after a dog is detected.
Set this to shift the home position, which is specified by the Z-phase signal.
Acceleration time constant/deceleration time constant of home position return
Home position return position data
Point table No. 1
[Pr. PT08]
The acceleration/deceleration time constant of point table No. 1 is used.
Set the current position when the home position return is complete.
4 - 64
4. HOW TO USE THE POINT TABLE
(2) Timing chart
MD0
(Operation mode selection 1)
MEND
(Travel completion)
ON
OFF
ON
OFF
CPO (Rough match)
ZP
(Home position return completion)
Servo motor speed
ON
OFF
ON
OFF
Forward rotation
0 r/min
Reverse rotation
Acceleration time constant
Home position return speed
Deceleration time constant
Travel distance after proximity dog
+
Home position shift distance
Home position return position data
3 ms or shorter
Creep speed
Proximity dog
DOG (Proximity dog)
ST1
(Forward rotation start)
ST2
(Reverse rotation start)
ON
OFF
ON
OFF
ON
OFF
5 ms or longer
The setting value of [Pr. PT08 Home position return position data] is used as the position address at the home position return completion.
4 - 65
4. HOW TO USE THE POINT TABLE
4.4.12 Dogless Z-phase reference home position return type
A position, which is shifted to by the home position shift distance from a position specified by the Z-phase pulse right after the start of the home position return, is set as the home position.
(1) Device/parameter
Set input devices and parameters as follows.
Item Device/parameter to be used Setting
Switch on MD0.
Home position return mode selection
MD0 (Operation mode selection 1)
DI0 (Point table No. selection 1) to
DI4 (Point table No. selection 5)
Switch off DI0 to DI4.
Dogless Z-phase reference home position return
Home position return direction
[Pr. PT04]
[Pr. PT04]
Home position return speed [Pr. PT05]
Creep speed [Pr. PT06]
Home position shift distance [Pr. PT07]
_ _ _ A: Select the dogless type (Z-phase reference).
Refer to section 4.4.1 (2) to select the home position return direction.
Set the rotation speed specified until the Zphase is detected.
Set the rotation speed specified after the Zphase is detected.
Set this to shift the home position, which is specified by the Z-phase signal.
Acceleration time constant/deceleration time constant of home position return
Home position return position data
Point table No. 1
[Pr. PT08]
The acceleration/deceleration time constant of point table No. 1 is used.
Set the current position when the home position return is complete.
(2) Timing chart
MD0
(Operation mode selection 1)
MEND
(Travel completion)
CPO
(Rough match)
ZP
(Home position return completion)
ON
OFF
ON
OFF
ON
OFF
ON
OFF
Acceleration time constant
Home position return speed
Deceleration time constant
Home position return position data
Servo motor speed
Forward rotation
0 r/min
Reverse rotation 3 ms or shorter
Creep speed
Home position shift distance
Z-phase
ST1
(Forward rotation start)
ST2
(Reverse rotation start)
ON
OFF
ON
OFF
ON
OFF
5 ms or longer
The setting value of [Pr. PT08 Home position return position data] is used as the position address at the home position return completion.
4 - 66
4. HOW TO USE THE POINT TABLE
4.4.13 Automatic retract function used for the home position return
For a home position return using a proximity dog, if the home position return starts from or beyond the proximity dog, this function executes the home position return after the position is shifted back to where the home position return is possible.
(1) When the current position is on the proximity dog
When the current position is on the proximity dog, the position is shifted back automatically to execute the home position return.
Home position return direction Proximity dog
Servo motor speed 0 r/min
Reverse rotation
After the position shifts to the position before the proximity dog, the home position return starts from here.
Note. The software limit cannot be used instead of LSP (Forward stroke end) and LSN (Reverse stroke end).
Home position return start position
(2) When the current position is beyond the proximity dog
The position is shifted in a direction of the home position return. When LSP (Forward rotation stroke end) or LSN (Reverse rotation stroke end) is detected, the position is shifted back automatically. The position will be shifted passing the proximity dog, and the travel will stop. The home position return will be restarted from that position. If the proximity dog is not detected, the travel stops at LSP or LSN on the opposite side, and [AL. 90 Home position return incomplete warning] occurs.
Home position return direction Proximity dog
LSP (Forward rotation stroke end) or
LSN (Reverse rotation stroke end) (Note)
Servo motor speed
Forward rotation
0 r/min
Reverse rotation
Home position return start position
After the position shifts to the position before the proximity dog, the home position return starts from here.
4 - 67
4. HOW TO USE THE POINT TABLE
4.4.14 Automatic positioning to home position function
POINT
The automatic positioning to the home position cannot be performed from outside the setting range of position data. In this case, perform the home position return again using the home position return.
If the home position is fixed by returning to the home position after the power-on, this function enables a high-speed automatic positioning to the home position. For the absolute position detection system, the home position return is unnecessary after the power-on.
If the automatic positioning to the home position is executed without completing the home position return,
[AL. 90.1] will occur.
After the power-on, perform the home position return in advance.
Set input devices and parameters as follows.
Item Device/parameter to be used Setting
Switch on MD0.
Home position return mode selection
MD0 (Operation mode selection 1)
DI0 (Point table No. selection 1) to
DI4 (Point table No. selection 5)
Switch off DI0 to DI4.
Home position return speed [Pr. PT05]
Set the servo motor speed to travel to the home position.
Acceleration time constant/deceleration time constant of home position return
Home position return direction
Point table No. 1
[Pr. PT04]
The acceleration/deceleration time constant of point table No. 1 is used.
Set the rotation direction in degrees.
Set the home position return speed of the automatic positioning to home position function with [Pr. PT05].
The data of point table No. 1 is used for acceleration/deceleration time constants. Switching on ST2
(Reverse rotation start) enables high-speed automatic return.
Set the rotation direction with home position return direction of [Pr. PT04] when the unit is set to degree.
MD0 (Operation mode selection 1)
ON
OFF
Acceleration time constant
Home position return speed Deceleration time constant
Servo motor speed
Forward rotation
0 r/min
Reverse rotation
ST1 (Forward rotation start)
ST2 (Reverse rotation start)
ON
OFF
ON
OFF
3 ms or shorter
5 ms or longer
Home position
4 - 68
4. HOW TO USE THE POINT TABLE
4.5 Roll feed mode using the roll feed display function
The roll feed display function changes the display method of the current position and the command position in the status monitor.
By using the roll feed display function, the servo amplifier can be used in the roll feed mode. The roll feed mode is compatible with the incremental system. Additionally, the feed speed can be changed by the override function during an operation. Refer to section 2.4 for details.
(1) Parameter setting
No. Name Setting digit Setting item Setting value Setting
PT26 Current position/command position display selection fraction clear selection
_ _ x _
_ _ _ x
Current position/command position display selection
Electronic gear fraction clear selection
_ _ 1 _
_ _ _ 1
Select the roll feed display.
Clear a fraction of the previous command by the electronic gear at start of the automatic operation. Always set "_ _ _ 1" (enabled) in the electronic gear fraction clear.
(2) Roll feed display function
When the roll feed display function is used, the status display of the current position and the command position at start will be 0.
INP (In-position)
Servo motor speed
ST1
(Forward rotation start)
ON
OFF
Forward rotation
0 r/min
Reverse rotation
ON
OFF
TSTP
(Temporary stop/restart)
CR (Clear)
ON
OFF
ON
OFF
Display of current/ command position
0 10.00
8.00
0 8.00
0
Remaining distance clear
5.90
0
Quick stop by
CR input
Remaining distance clear
6.50
Starting renews the display from 0.
A point table whose feed length is set to
8 is selected.
The temporary stop position is displayed.
Remaining distance clear will not change the display.
Next starting renews the display from 0.
(3) Position data unit
The display unit is expressed in the unit set in [Pr. PT26], and the feed length multiplication is expressed in the unit set in [Pr. PT03].
When the unit is set in degrees, the roll feed display function is disabled.
Refer to section 4.2.2 for details.
(4) Operation method
Only the status display of the current position and command position changes. The operation method is the same as each operation mode.
Operation mode Detailed explanation
Automatic operation
Manual operation
Automatic operation using the point table Section 4.2.2
JOG operation Section 4.3.1
Manual pulse generator operation
Home position return mode
Section 4.3.2
Section 4.4
4 - 69
4. HOW TO USE THE POINT TABLE
4.6 Point table setting method
The following shows the setting method of point tables using MR Configurator2.
4.6.1 Setting procedure
Click "Positioning-data" in the menu bar, and click "Point Table" in the menu.
The following window will be displayed.
(i) (l) (m) (c) (d) (e)
(h)
(f)
(j)
(k)
(g) (a) (b) (n)
(1) Writing point table data (a)
Select changed point table data, and click "Selected Items Write" to write the changed point table data to the servo amplifier.
(2) Writing all point table data (b)
Click "Write All" to write all the point table data to the servo amplifier.
(3) Reading all point table data (c)
Click "Read" to read all the point table data from the servo amplifier and display them.
4 - 70
4. HOW TO USE THE POINT TABLE
(4) Initial setting of point table data (d)
Click "Set to default" to initialize all the data of point table No. 1 to 31. This function also initializes data currently being edited.
(5) Verifying point table data (e)
Click "Verify" to verify all the data displayed and data of the servo amplifier.
(6) Detailed setting of point table data (f)
Click "Detailed Setting" to change position data range and unit in the point table window. Refer to section 4.6.2 for details.
(7) Single-step feed (g)
Click "Single-step Feed" to perform the single-step feed test operation. Refer to section 3.1.9 for details.
(8) Copy and paste of point table data (h)
Click "Copy" to copy the selected point table data. Click "Paste" to paste the copied point table data.
(9) Inserting point table data (i)
Click "Insert" to insert a block before the selected point table No. The selected block and later will be shifted down by one. The selected point table No. and lower rows will be shifted down one by one.
Click "Delete" to delete the selected block of the point table No. The selected block and later will be shifted up by one.
After selecting the data to be changed, enter a new value, and click "Enter". You can change the displayed range and unit with "(6) Detailed setting of point table data" in this section.
(12) Reading point table data (l)
Click "Open" to read the point table data.
Click "Save As" to save the point table data.
Click "Update Project" to update the point table data to a project.
4 - 71
4. HOW TO USE THE POINT TABLE
4.6.2 Detailed setting window
The position data range and unit can be changed with the detailed setting in the point table window. For the position data range and unit of [Pr. PT01] setting, refer to section 4.2.2. To reflect the setting for the corresponding parameter, click "Update Project" in the point table window.
1)
2)
3)
(1) Command method selection (PT01 *CTY): 1)
Select either the absolute position command method or the incremental value command method.
(2) Others
(a) Feed length multiplication parameter setting STM (PT03 *FTY): 2)
Select a feed length multiplication from 1/10/100/1000.
(b) Position data unit setting (PT01 *CTY): 3)
Select a unit of position data from mm/inch/degree/pulse. When degree or pulse is selected for the unit, the setting of feed length multiplication will be disabled.
4 - 72
advertisement
Related manuals
advertisement
Table of contents
- 2 Safety Instructions
- 8 DISPOSAL OF WASTE
- 8 Compliance with global standards
- 8 About the manual
- 8 Cables used for wiring
- 9 U.S. customary units
- 10 CONTENTS
- 14 1. FUNCTIONS AND CONFIGURATION
- 14 1.1 For proper use of the positioning mode
- 15 1.2 Positioning mode specification list
- 17 1.3 Function list
- 20 1.4 Configuration including peripheral equipment
- 22 2. SIGNALS AND WIRING
- 24 2.1 I/O signal connection example
- 28 2.2 Connectors and pin assignment
- 32 2.3 Signal (device) explanations
- 44 2.4 Analog override
- 46 2.5 Internal connection diagram
- 48 2.6 Power-on sequence
- 50 3. DISPLAY AND OPERATION SECTIONS
- 50 3.1 MR-JE-_A
- 50 3.1.1 Display flowchart
- 52 3.1.2 Status display mode
- 57 3.1.3 Diagnostic mode
- 60 3.1.4 Alarm mode
- 62 3.1.5 Point table setting
- 66 3.1.6 Parameter mode
- 68 3.1.7 External I/O signal display
- 69 3.1.8 Output signal (DO) forced output
- 70 3.1.9 Single-step feed
- 72 3.1.10 Teaching function
- 74 4. HOW TO USE THE POINT TABLE
- 75 4.1 Startup
- 75 4.1.1 Power on and off procedures
- 76 4.1.2 Stop
- 77 4.1.3 Test operation
- 78 4.1.4 Parameter setting
- 79 4.1.5 Point table setting
- 79 4.1.6 Actual operation
- 79 4.1.7 Troubleshooting at start-up
- 81 4.2 Automatic operation mode
- 81 4.2.1 Automatic operation mode
- 86 4.2.2 Automatic operation using point table
- 116 4.3 Manual operation mode
- 116 4.3.1 JOG operation
- 118 4.3.2 Manual pulse generator operation
- 119 4.4 Home position return mode
- 120 4.4.1 Outline of home position return
- 122 4.4.2 Dog type home position return
- 124 4.4.3 Count type home position return
- 126 4.4.4 Data set type home position return
- 127 4.4.5 Stopper type home position return
- 129 4.4.6 Home position ignorance (servo-on position as home position)
- 130 4.4.7 Dog type rear end reference home position return
- 132 4.4.8 Count type front end reference home position return
- 134 4.4.9 Dog cradle type home position return
- 135 4.4.10 Dog type last Z-phase reference home position return
- 137 4.4.11 Dog type front end reference home position return type
- 139 4.4.12 Dogless Z-phase reference home position return type
- 140 4.4.13 Automatic retract function used for the home position return
- 141 4.4.14 Automatic positioning to home position function
- 142 4.5 Roll feed mode using the roll feed display function
- 143 4.6 Point table setting method
- 143 4.6.1 Setting procedure
- 145 4.6.2 Detailed setting window
- 146 5. HOW TO USE THE PROGRAM
- 146 5.1 Startup
- 147 5.1.1 Power on and off procedures
- 147 5.1.2 Stop
- 148 5.1.3 Test operation
- 149 5.1.4 Parameter setting
- 150 5.1.5 Actual operation
- 150 5.1.6 Troubleshooting at start-up
- 151 5.2 Program operation method
- 151 5.2.1 Program operation method
- 152 5.2.2 Program language
- 175 5.2.3 Basic settings of signals and parameters
- 177 5.2.4 Timing chart of the program operation
- 179 5.3 Manual operation mode
- 179 5.3.1 JOG operation
- 180 5.3.2 Manual pulse generator operation
- 182 5.4 Home position return mode
- 182 5.4.1 Outline of home position return
- 185 5.4.2 Dog type home position return
- 187 5.4.3 Count type home position return
- 189 5.4.4 Data set type home position return
- 190 5.4.5 Stopper type home position return
- 191 5.4.6 Home position ignorance (servo-on position as home position)
- 192 5.4.7 Dog type rear end reference home position return
- 194 5.4.8 Count type front end reference home position return
- 196 5.4.9 Dog cradle type home position return
- 198 5.4.10 Dog type last Z-phase reference home position return
- 200 5.4.11 Dog type front end reference home position return type
- 202 5.4.12 Dogless Z-phase reference home position return type
- 203 5.4.13 Automatic retract function used for the home position return
- 204 5.5 Serial communication operation
- 204 5.5.1 Positioning operation using the program
- 205 5.5.2 Multi-drop method (RS-422 communication)
- 206 5.5.3 Group specification
- 208 5.6 Incremental value command method
- 209 5.7 Roll feed mode using the roll feed display function
- 210 5.8 Program setting method
- 210 5.8.1 Setting procedure
- 211 5.8.2 Window for program edit
- 212 5.8.3 Indirect addressing window
- 214 6. APPLICATION OF FUNCTIONS
- 214 6.1 Simple cam function
- 214 6.1.1 Outline of simple cam function
- 215 6.1.2 Simple cam function block
- 216 6.1.3 Simple cam specification list
- 217 6.1.4 Control of simple cam function
- 218 6.1.5 Operation in combination with the simple cam
- 220 6.1.6 Setting list
- 221 6.1.7 Data to be used with simple cam function
- 239 6.1.8 Function block diagram for displaying state of simple cam control
- 240 6.1.9 Operation
- 250 6.1.10 Cam No. setting method
- 251 6.1.11 Stop operation of cam control
- 253 6.1.12 Restart operation of cam control
- 254 6.1.13 Cam axis position at cam control switching
- 261 6.1.14 Clutch
- 263 6.1.15 Cam position compensation target position
- 264 6.1.16 Cam position compensation time constant
- 265 6.2 Mark detection
- 265 6.2.1 Current position latch function
- 271 6.2.2 Interrupt positioning function
- 276 7. PARAMETERS
- 276 7.1 Parameter list
- 277 7.1.1 Basic setting parameters ([Pr. PA_ _ ])
- 278 7.1.2 Gain/filter setting parameters ([Pr. PB_ _ ])
- 280 7.1.3 Extension setting parameters ([Pr. PC_ _ ])
- 282 7.1.4 I/O setting parameters ([Pr. PD_ _ ])
- 284 7.1.5 Extension setting 2 parameters ([Pr. PE_ _ ])
- 286 7.1.6 Extension setting 3 parameters ([Pr. PF_ _ ])
- 288 7.1.7 Positioning control parameters ([Pr. PT_ _ ])
- 290 7.2 Detailed list of parameters
- 290 7.2.1 Basic setting parameters ([Pr. PA_ _ ])
- 300 7.2.2 Gain/filter setting parameters ([Pr. PB_ _ ])
- 312 7.2.3 Extension setting parameters ([Pr. PC_ _ ])
- 322 7.2.4 I/O setting parameters ([Pr. PD_ _ ])
- 332 7.2.5 Extension setting 2 parameters ([Pr. PE_ _ ])
- 333 7.2.6 Extension setting 3 parameters ([Pr. PF_ _ ])
- 335 7.2.7 Positioning control parameters ([Pr. PT_ _ ])
- 344 7.3 How to set the electronic gear
- 345 7.4 Software limit
- 346 7.5 Stop method for LSP (Forward rotation stroke end) off or LSN (Reverse rotation stroke end) off
- 347 7.6 Stop method at software limit detection
- 348 8. TROUBLESHOOTING
- 348 8.1 Explanations of the lists
- 349 8.2 Alarm list
- 353 8.3 Warning list
- 356 9. OPTIONS AND PERIPHERAL EQUIPMENT
- 357 9.1 MR-HDP01 manual pulse generator
- 360 10. COMMUNICATION FUNCTION (MITSUBISHI ELECTRIC GENERAL-PURPOSE AC SERVO PROTOCOL)
- 360 10.1 Command and data No. list
- 361 10.1.1 Reading command
- 369 10.1.2 Writing commands
- 373 10.2 Detailed explanations of commands
- 373 10.2.1 External I/O signal status (DIO diagnosis)
- 378 10.2.2 Input device on/off
- 379 10.2.3 Input device on/off (for test operation)
- 380 10.2.4 Test operation mode
- 382 10.2.5 Output signal pin on/off (output signal (DO) forced output)
- 383 10.2.6 Point table
- 392 REVISIONS
- 395 Warranty