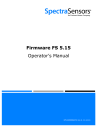
advertisement
▼
Scroll to page 2
of 128
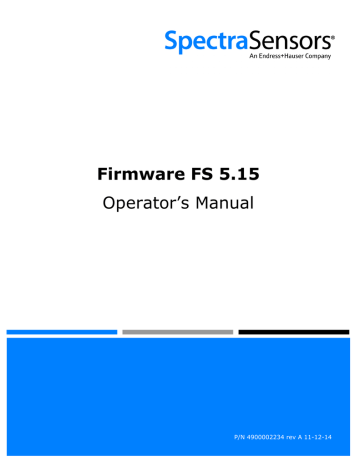
Firmware FS 5.15 Operator’s Manual P/N 4900002234 rev A 11-12-14 Firmware FS 5.15 Operator’s Manual Products of 11027 Arrow Route Rancho Cucamonga, CA 91730 Tel: 800.619.2861 Fax: 909.948.4100 www.spectrasensors.com Copyright © 2014 SpectraSensors, Inc. No part of this manual may be reproduced in whole or in part without the express written permission of SpectraSensors, Inc. SpectraSensors reserves the right to change product design and specifications at any time without prior notice. Revision History Revision Engineering Order Date A EO15903 11/12/14 TABLE OF CONTENTS List of Figures . . . . . . . . . . . . . . . . . . . . . . . . . . . . . . . . . . . . . . . . . . . . . . .v List of Tables . . . . . . . . . . . . . . . . . . . . . . . . . . . . . . . . . . . . . . . . . . . . . . vii 1: Introduction Who Should Read This Manual . . . . General Note Icons . . . . . . . . . Conventions Used in this Manual SpectraSensors Overview . . . . . . . . . . . . . . . . . . . . . . . . . . . . . . . . . . . . . . . . . . . . . . . . . . . . . . . . . . . . . . . . . . . . . . . . . . . . . . . . . . . . . . . . . . . . . . . . . . . . . . . . . . . . . . . . . . . . . . . . . . . . . . . . . . . . . . . 1-1 1-1 1-1 1-2 Firmware Version . . . . . . . . . . . . . . . . . . . . . . Powering Up the Analyzer . . . . . . . . . . . . . . . . To power up the analyzer . . . . . . . . . . . . . . Powering Down the Analyzer . . . . . . . . . . . . . . To power down the analyzer . . . . . . . . . . . . Operating the Analyzer from the Keypad . . . . . . Modes Defined . . . . . . . . . . . . . . . . . . . . . . . . Mode 1: (Normal Mode) . . . . . . . . . . . . . . . Mode 2: (Set Parameter Mode) . . . . . . . . . . Mode 3: (Scrubber Life Data) . . . . . . . . . . . Mode 4: (System Diagnostic Parameters) . . . Mode 5: (Analog Output Test Mode). . . . . . . Mode 6: (Diagnostic Data Download) . . . . . . Mode 7: (Measure Port1 Mode) . . . . . . . . . . Mode 8: (Measure Port2 Mode) . . . . . . . . . . Mode 9: (Recall Validation Results) . . . . . . . Mode TEST: (Analog Input Test Mode) . . . . . Configuring the Analyzer at Start-Up . . . . . . . . . Parameter Setting/Checking Procedure: . . . . Changing Measurement and Control Parameters . To change parameters in Mode 2 . . . . . . . . . Measurement and Control Parameters Defined . . 2 Way Com Port . . . . . . . . . . . . . . . . . . . . 4-20 mA Alarm Action . . . . . . . . . . . . . . . . 4-20 mA Val Action . . . . . . . . . . . . . . . . . . AI 4 mA Value . . . . . . . . . . . . . . . . . . . . . . AI 20 mA Value . . . . . . . . . . . . . . . . . . . . . AI Pressure Input. . . . . . . . . . . . . . . . . . . . AO 4 mA Value . . . . . . . . . . . . . . . . . . . . . AO 20 mA Value . . . . . . . . . . . . . . . . . . . . AO 4-20 mA Test . . . . . . . . . . . . . . . . . . . . Baud Rate . . . . . . . . . . . . . . . . . . . . . . . . . Calculate Dew Point . . . . . . . . . . . . . . . . . . Cancel Val Alarms . . . . . . . . . . . . . . . . . . . Concentration Unit . . . . . . . . . . . . . . . . . . . Custom Precision . . . . . . . . . . . . . . . . . . . . Daily Validation . . . . . . . . . . . . . . . . . . . . . Dew Point Method . . . . . . . . . . . . . . . . . . . DO Alarm Setup. . . . . . . . . . . . . . . . . . . . . General Alarm DO . . . . . . . . . . . . . . . . . . . High Alarm Setpoint . . . . . . . . . . . . . . . . . . Keypad Watchdog . . . . . . . . . . . . . . . . . . . . . . . . . . . . . . . . . . . . . . . . . . . . . . . . . . . . . . . . . . . . . . . . . . . . . . . . . . . . . . . . . . . . . . . . . . . . . . . . . . . . . . . . . . . . . . . . . . . . . . . . . . . . . . . . . . . . . . . . . . . . . . . . . . . . . . . . . . . . . . . . . . . . . . . . . . . . . . . . . . . . . . . . . . . . . . . . . . . . . . . . . . . . . . . . . . . . . . . . . . . . . . . . . . . . . . . . . . . . . . . . . . . . . . . . . . . . . . . . . . . . . . . . . . . . . . . . . . . . . . . . . . . . . . . . . . . . . . . . . . . . . . . . . . . . . . . . . . . . . . . . . . . . . . . . . . . . . . . . . . . . . . . . . . . . . . . . . . . . . . . . . . . . . . . . . . . . . . . . . . . . . . . . . . . . . . . . . . . . . . . . . . . . . . . . . . . . . . . . . . . . . . . . . . . . . . . . . . . . . . . . . . . . . . . . . . . . . . . . . . . . . . . . . . . . . . . . . . . . . . . . . . . . . . . . . . . . . . . . . . . . . . . . . . . . . . . . . . . . . . . . . . . . . . . . . . . . . . . . . . . . . . . . . . . . . . . . . . . . . . . . . . . . . . . . . . . . . . . . . . . . . . . . . . . . . . . . . . . . . . . . . . . . . . . . . . . . . . . . . . . . . . . . . . . . . . . . . . . . . . . . . . . . . . . . . . . . . . . . . . . . . . . . . . . . . . . . . . . . . . . . . . . . . . . . . . . . . . . . . . . . . . . . . . . . . . . . . . . . . . . . . . . . . . . . . . . . . . . . . . . . . . . . . . . . . . . . . . . . . . . . . . . . . . . . . . . . . . . . . . . . . . . . . . . . . . . . . . . . . . . . . . . . . . . . . . . . . . . . . . . . . . . . . . . . . . . . . . . . . . . . . . . . . . . . . . . . . . . . . . . . . . . . . . . . . . . . . . . . . . . . . . . . . . . . . . . . . . . . . . . . . . . . . . . . . . . . . . . . . . . . . . . . . . . . . . . . . . . . . . . . . . . . 2-1 . 2-1 . 2-1 . 2-3 . 2-3 . 2-3 . 2-4 . 2-5 . 2-5 . 2-5 . 2-6 . 2-7 . 2-7 . 2-7 . 2-8 . 2-8 2-10 2-10 2-10 2-11 2-15 2-15 2-16 2-16 2-16 2-17 2-17 2-17 2-17 2-18 2-18 2-18 2-19 2-19 2-19 2-20 2-20 2-20 2-21 2-22 2-23 2-23 2: Operating the Analyzer Operator’s Manual i FS 5.15 Firmware Logger Rate . . . . . . . . . . . . . . . . . . . . . . . . . . . . . . . . Low Alarm Setpoint . . . . . . . . . . . . . . . . . . . . . . . . . . . Modbus Address . . . . . . . . . . . . . . . . . . . . . . . . . . . . . Modbus Mode . . . . . . . . . . . . . . . . . . . . . . . . . . . . . . . New Scrub Installed . . . . . . . . . . . . . . . . . . . . . . . . . . . Operator Parameter01 to Operator Parameter20 . . . . . . . Operator Password . . . . . . . . . . . . . . . . . . . . . . . . . . . Peak Tracking . . . . . . . . . . . . . . . . . . . . . . . . . . . . . . . Pipeline Pressure . . . . . . . . . . . . . . . . . . . . . . . . . . . . . Pressure Unit. . . . . . . . . . . . . . . . . . . . . . . . . . . . . . . . Process Purge Time . . . . . . . . . . . . . . . . . . . . . . . . . . . Rapid Change Monitor . . . . . . . . . . . . . . . . . . . . . . . . . RATA (Relative Accuracy Test Audit) . . . . . . . . . . . . . . . RATA Multiplier . . . . . . . . . . . . . . . . . . . . . . . . . . . . . . RATA Offset . . . . . . . . . . . . . . . . . . . . . . . . . . . . . . . . Set Time - Day . . . . . . . . . . . . . . . . . . . . . . . . . . . . . . Set Time - Hour . . . . . . . . . . . . . . . . . . . . . . . . . . . . . . Set Time - Minute . . . . . . . . . . . . . . . . . . . . . . . . . . . . Set Time - Month . . . . . . . . . . . . . . . . . . . . . . . . . . . . . Set Time - Year . . . . . . . . . . . . . . . . . . . . . . . . . . . . . . Start Validation . . . . . . . . . . . . . . . . . . . . . . . . . . . . . . Temperature Unit. . . . . . . . . . . . . . . . . . . . . . . . . . . . . Update RATA . . . . . . . . . . . . . . . . . . . . . . . . . . . . . . . . Val 1 Concentration . . . . . . . . . . . . . . . . . . . . . . . . . . . Val 2 Concentration . . . . . . . . . . . . . . . . . . . . . . . . . . . Val Attempts . . . . . . . . . . . . . . . . . . . . . . . . . . . . . . . . Val Auto DumpSpectrm . . . . . . . . . . . . . . . . . . . . . . . . Val Duration . . . . . . . . . . . . . . . . . . . . . . . . . . . . . . . . Validation Allowance. . . . . . . . . . . . . . . . . . . . . . . . . . . Val Interval . . . . . . . . . . . . . . . . . . . . . . . . . . . . . . . . . Val Perm Constant Kp. . . . . . . . . . . . . . . . . . . . . . . . . . Val Perm Rate Rp. . . . . . . . . . . . . . . . . . . . . . . . . . . . . Val Purge Period . . . . . . . . . . . . . . . . . . . . . . . . . . . . . Val Start Time . . . . . . . . . . . . . . . . . . . . . . . . . . . . . . . Zero Val Tolerance . . . . . . . . . . . . . . . . . . . . . . . . . . . . Adjusting Analyzer Reading to Match Specific Standard(s) To perform the calculation: . . . . . . . . . . . . . . . . . . . . . . To adjust the analyzer reading: . . . . . . . . . . . . . . . . . . . Application Examples . . . . . . . . . . . . . . . . . . . . . . . . . . Manual Dual Validation . . . . . . . . . . . . . . . . . . . . . . Semi-Automatic Single or Dual Validation . . . . . . . . . Automatic Single or Dual Validation . . . . . . . . . . . . . Scaling and Calibrating the Current Loop Signal . . . . . . . . . . To scale the current loop signal . . . . . . . . . . . . . . . . . . . Warnings . . . . . . . . . . . . . . . . . . . . . . . . . . . . . . . . . . . . . Alarms. . . . . . . . . . . . . . . . . . . . . . . . . . . . . . . . . . . . . . . System Faults . . . . . . . . . . . . . . . . . . . . . . . . . . . . . . . User Alarms . . . . . . . . . . . . . . . . . . . . . . . . . . . . . . . . Historical Alarm Flag . . . . . . . . . . . . . . . . . . . . . . . . . . Assignable Alarm . . . . . . . . . . . . . . . . . . . . . . . . . . . . . Validating the Analyzer . . . . . . . . . . . . . . . . . . . . . . . . . . . To validate automatically . . . . . . . . . . . . . . . . . . . . . . . To validate semi-automatically . . . . . . . . . . . . . . . . . . . To validate manually: . . . . . . . . . . . . . . . . . . . . . . . . . . Calibrating the Analyzer. . . . . . . . . . . . . . . . . . . . . . . . . . . . . . . . . . . . . . . . . . . . . . . . . . . . . . . . . . . . . . . . . . . . . . . . . . . . . . . . . . . . . . . . . . . . . . . . . . . . . . . . . . . . . . . . . . . . . . . . . . . . . . . . . . . . . . . . . . . . . . . . . . . . . . . . . . . . . . . . . . . . . . . . . . . . . . . . . . . . . . . . . . . . . . . . . . . . . . . . . . . . . . . . . . . . . . . . . . . . . . . . . . . . . . . . . . . . . . . . . . . . . . . . . . . . . . . . . . . . . . . . . . . . . . . . . . . . . . . . . . . . . . . . . . . . . . . . . . . . . . . . . . . . . . . . . . . . . . . . . . . . . . . . . . . . . . . . . . . . . . . . . . . . . . . . . . . . . . . . . . . . . . . . . . . . . . . . . . . . . . . . . . . . . . . . . . . . . . . . . . . . . . . . . . . . . . . . . . . . . . . . . . . . . . . . . . . . . . . . . . . . . . . . . . . . . . . . . . . . . . . . . . . . . . . . . . . . . . . . . . . . . . . . . . . . . . . . . . . . . . . . . . . . . . . . . . . . . . . . . . . . . . . . . . . . . . . . . . . . . . . . . . . . . . . . . . . . . . . . . . . . . . . . . . . . . . . . . . . . . . . . . . . . . . . . . . . . . . . . . . . . . . . . . . . . . . . . . . . . . . . . . . . . . . . . . . . . . . . . . . . . . . . . . . . . . . . . . . . . . . . . . . . . . . . . . . . . . . . . . . . . . . . . . . . . . . . . . . . . . . . . . . . . . . . . . . . . . . . . . . . . . . . . . . . . . . . . . . . . . . 2-23 2-24 2-24 2-24 2-25 2-25 2-27 2-27 2-28 2-28 2-28 2-28 2-29 2-29 2-29 2-30 2-30 2-30 2-30 2-31 2-31 2-31 2-31 2-32 2-32 2-33 2-33 2-33 2-34 2-34 2-34 2-35 2-35 2-36 2-36 2-36 2-37 2-38 2-38 2-38 2-39 2-40 2-40 2-41 2-41 2-42 2-43 2-45 2-45 2-47 2-47 2-47 2-47 2-48 2-49 3: Serial Port Communications Receiving Serial Data (Customer Port Output) . . . . . . . . . . . . . . . . . . . . . . . . . 3-1 To launch HyperTerminal . . . . . . . . . . . . . . . . . . . . . . . . . . . . . . . . . . . . . 3-1 Mode 1 Data String . . . . . . . . . . . . . . . . . . . . . . . . . . . . . . . . . . . . . . . 3-1 ii 4900002234 rev. A 11-12-14 Table of Contents To capture and save data from the serial port . To read diagnostic data with HyperTerminal . . Mode 6 Data . . . . . . . . . . . . . . . . . . . . . Viewing Diagnostic Data with Microsoft Excel . . . . To import the data file into Excel . . . . . . . . . . Modbus Communications Protocol . . . . . . . . . . . . Framing/Protocol . . . . . . . . . . . . . . . . . . . . . Functions . . . . . . . . . . . . . . . . . . . . . . . . . . Addressing . . . . . . . . . . . . . . . . . . . . . . . . . Reading/Writing in Daniel Modbus Mode . . . . . Reading/Writing in Gould Modbus Mode . . . . . Endianness . . . . . . . . . . . . . . . . . . . . . . . . . To enable Modbus communications . . . . . . . . Modbus Accessible Parameter Definitions. . . . . . . . . . . . . . . . . . . . . . . . . . . . . . . . . . . . . . . . . . . . . . . . . . . . . . . . . . . . . . . . . . . . . . . . . . . . . . . . . . . . . . . . . . . . . . . . . . . . . . . . . . . . . . . . . . . . . . . . . . . . . . . . . . . . . . . . . . . . . . . . . . . . . . . . . . . . . . . . . . . . . . . . . . . . . . . . . . . . . . . . . . . . . . . . . . . . . . . . . . . . . . . . . . . . . . . . . . . . . . . . . . . . . . . . . . . . . . . . . . . . . . . . . . . . . . . . . . . . . . . . . . . . . . . . . . . . . . . . . . . . . . . . . . . . . . . . . 3-5 . 3-5 . 3-6 . 3-8 . 3-8 3-12 3-12 3-13 3-13 3-13 3-13 3-14 3-14 3-20 4: Ethernet Communications Configuring the Built-in Ethernet Port . . . . . . . . . . . . . . . . . . . . . . . . . . . . . . . 4-1 To configure the built-in Ethernet port . . . . . . . . . . . . . . . . . . . . . . . . . . . . 4-1 General Information for Configuring Ethernet . . . . . . . . . . . . . . . . . . . . . . . . . . 4-2 5: Validation of Trace Moisture Measurements Validation Methods . . . . . . . . . . . . . . . . . . . . . . . . . . . . . . . . . . . Permeation Validation for Trace Moisture Analyzers (0-10 ppm H2O) Setting the Kp Value . . . . . . . . . . . . . . . . . . . . . . . . . . . . . . . Recalculating the System Constant Kp . . . . . . . . . . . . . . . . . . . To recalculate the system constant . . . . . . . . . . . . . . . . . . . Validation of Trace Moisture or Ammonia Measurements Using Permeation Devices. . . . . . . . . . . . . . . . . . . . . . . . . . . . . . . . . . . . . . . . . . . . . . . . . . . . . . . . . . . . . . . . . . . . . . . . . . . . . . . 5-1 5-2 5-3 5-3 5-3 . . . . . . . . . 5-4 Appendix A: Water Correlation Water Content . . . . . . . . . . . . . . . . . . . . . Dew Point . . . . . . . . . . . . . . . . . . . . . . . . Dew Point Conversion. . . . . . . . . . . . . . Raoult’s Law. . . . . . . . . . . . . . . . . . Arden Buck Equations . . . . . . . . . . . ASTM1. . . . . . . . . . . . . . . . . . . . . . ASTM2. . . . . . . . . . . . . . . . . . . . . . ISO . . . . . . . . . . . . . . . . . . . . . . . . Method Comparisons for Natural Gas . . . The Arden Buck Method Comparison . References . . . . . . . . . . . . . . . . . . . . . . . . . . . . . . . . . . . . . . . . . . . . . . . . . . . . . . . . . . . . . . . . . . . . . . . . . . . . . . . . . . . . . . . . . . . . . . . . . . . . . . . . . . . . . . . . . . . . . . . . . . . . . . . . . . . . . . . . . . . . . . . . . . . . . . . . . . . . . . . . . . . . . . . . . . . . . . . . . . . . . . . . . . . . . . . . . . . . . . . . . . . . . . . . . . . . . . . . . . . . . . . . . . . . . . . . . . . . . . . . . . . . . . . . . . . . . . . . . . . . . . . . . . . . . . . . . . . . . . . . . . . . . . . . . . . . . . . . . . . . A-1 . A-2 . A-2 . A-2 . A-3 . A-3 . A-3 . A-4 . A-9 A-13 A-14 Appendix B: Troubleshooting Excessive Sampling Gas Temperatures and Pressures . Peak Tracking Reset Procedure . . . . . . . . . . . . . . . . . To reset the Peak Tracking function . . . . . . . . . . . Instrument Problems. . . . . . . . . . . . . . . . . . . . . . . . Service Contact . . . . . . . . . . . . . . . . . . . . . . . . . . . Customer Service. . . . . . . . . . . . . . . . . . . . . . . Return Material Authorization . . . . . . . . . . . . . . . Disclaimers . . . . . . . . . . . . . . . . . . . . . . . . . . . . . . Warranty . . . . . . . . . . . . . . . . . . . . . . . . . . . . . . . . . . . . . . . . . . . . . . . . . . . B-1 . . . . . . . . . . . . . . . . . . . B-1 . . . . . . . . . . . . . . . . . . . B-1 . . . . . . . . . . . . . . . . . . . B-2 . . . . . . . . . . . . . . . . . . . B-4 . . . . . . . . . . . . . . . . . . . B-4 . . . . . . . . . . . . . . . . . . . B-5 . . . . . . . . . . . . . . . . . . . B-5 . . . . . . . . . . . . . . . . . . . B-5 Index . . . . . . . . . . . . . . . . . . . . . . . . . . . . . . . . . . . . . . . . . . . . . . . . Index -1 Operator’s Manual iii FS 5.15 Firmware THIS PAGE INTENTIONALLY LEFT BLANK iv 4900002234 rev. A 11-12-14 LIST OF FIGURES Figure 2–1. Figure 2–2. Analyzer keypad . . . . . . . . . . . . . . . . . . . . . . . . . . . . . . . . . . . . 2-4 LCD display with alarm code visible indicating Pressure Low Alarm fault . . . . . . . . . . . . . . . . . . . . . . . . . . . . . 2-45 Figure Figure Figure Figure Figure Figure Figure Figure Figure Figure Figure Figure Connection Description window . . . . . . . . . . . Connect To window . . . . . . . . . . . . . . . . . . . . COM Properties window . . . . . . . . . . . . . . . . . Hyperterminal window with streaming data . . . Sample diagnostic data output . . . . . . . . . . . . Opening a data file in Excel . . . . . . . . . . . . . . Setting data type in Text Import Wizard . . . . . Setting Tab and Space as delimiters . . . . . . . . Highlighting imported data for plotting in Excel Chart Wizard - Step 1 window . . . . . . . . . . . . Data file plot in Excel . . . . . . . . . . . . . . . . . . Format Data Series window . . . . . . . . . . . . . . 3–1. 3–2. 3–3. 3–4. 3–5. 3–6. 3–7. 3–8. 3–9. 3–10. 3–11. 3–12. . . . . . . . . . . . . . . . . . . . . . . . . . . . . . . . . . . . . . . . . . . . . . . . . . . . . . . . . . . . . . . . . . . . . . . . . . . . . . . . . . . . . . . . . . . . . . . . . . . . . . . . . . . . . . . . . . . . . . . . . . . . . . . . . . . . . . . . . . . . . . . . . . . . . . . . . . . . . . 3-2 . 3-2 . 3-3 . 3-3 . 3-7 . 3-9 . 3-9 3-10 3-10 3-11 3-11 3-12 Figure 5–1. Figure 5–2. Schematic of permeation tube . . . . . . . . . . . . . . . . . . . . . . . . . . 5-4 Typical sample system for differential measurement with permeation tube validation capability . . . . . . . . . . . . . . . . . . 5-5 Figure A–1. Comparison of calculation results for ASTM1 [8], ASTM2 [9] and ISO [10] methods with experimental data from the GERG report [14] for mixture NG1 . . . . . . . . . . . . . . . . . . . . . . . . . Comparison of calculation results for ASTM1 [8], ASTM2 [9] and ISO [10] methods with experimental data from the GERG report [14] for mixture NG3 . . . . . . . . . . . . . . . . . . . . . . . . . Comparison of calculation results for ASTM1 [8], ASTM2 [9] and ISO [10] methods with experimental data from the GERG report [14] for mixture NG4 . . . . . . . . . . . . . . . . . . . . . . . . . Comparison of calculation results for ASTM1 [8], ASTM2 [9] and ISO [10] methods with experimental data from the GERG report [14] for mixture NG7 . . . . . . . . . . . . . . . . . . . . . . . . . Courses of measured water contents at 60 bar for natural gas mixtures NG1, NG3, NG4 and NG7 . . . . . . . . . . . . . . . . . Figure A–2. Figure A–3. Figure A–4. Figure A–5. Operator’s Manual . . A-10 . . A-10 . . A-11 . . A-11 . . A-13 v FS 5.15 Firmware THIS PAGE INTENTIONALLY LEFT BLANK vi 4900002234 rev. A 11-12-14 LIST Table Table Table Table 2–1. 2–2. 2–3. 2–4. OF TABLES Typical values for parameter setpoints. Assignable Alarm functionality . . . . . . Operator Parameters . . . . . . . . . . . . . LCD display alarm codes . . . . . . . . . . . . . . . . . . . . . . . . . . . . . . . . . . . . . . . . . . . . . . . . . . . . . . . . . . . . . . . . . . . . . . . . . . . . . . . . . . . . . . 2-11 2-21 2-26 2-45 Table 3–1. Table 3–2. Table 3–3. Modbus register map. . . . . . . . . . . . . . . . . . . . . . . . . . . . . . . . 3-15 Status flags . . . . . . . . . . . . . . . . . . . . . . . . . . . . . . . . . . . . . . 3-26 ASCII Character Map. . . . . . . . . . . . . . . . . . . . . . . . . . . . . . . . 3-28 Table Table Table Table Table Table Common reference conditions . . . . . . . . . . . . . . . . Gas composition [14] . . . . . . . . . . . . . . . . . . . . . . Coefficients for Eq. (15) [14] . . . . . . . . . . . . . . . . . Binary interaction parameters [14] . . . . . . . . . . . . . Experimental gas compositions [14] . . . . . . . . . . . . Range of composition applicable to ISO method [10] A–1. A–2. A-3. A–4. A–5. A–6. Table B–1. . . . . . . . . . . . . . . . . . . . . . . . . . . . . . . . . . . . . . . . . . . . . . . . . . . . . . . . A-2 . A-5 . A-6 . A-7 A-12 A-14 Potential instrument problems and their solutions. . . . . . . . . . . . . B-3 Operator’s Manual vii FS 5.15 Firmware THIS PAGE INTENTIONALLY LEFT BLANK viii 4900002234 rev. A 11-12-14 1 - INTRODUCTION This SpectraSensors analyzer was shipped with SpectraSensors’ FS 5.15 Firmware. This firmware version provides users with the features and functions to operate the tunable diode laser (TDL) analyzer. This manual was designed to provide the user with an overview of the FS 5.15 firmware functionality. The information contained in this manual is divided into the following sections: • • • Operations Serial Communication Firmware Troubleshooting Who Should Read This Manual This manual should be read and referenced by anyone operating or having direct contact with the analyzer. General Note Icons Instructional icons are provided in this manual to alert the user of important information and valuable tips. The following symbols and associated information can be found throughout the manual. General notes and important information concerning the installation and operation of the analyzer. Failure to follow all directions may result in malfunction of the analyzer. INVISIBLE LASER RADIATION - Avoid exposure to beam. Class 3b Radiation Product. Refer servicing to the manufacturerqualified personnel. Warning statement for hazardous voltage. Contact may cause electric shock or burn. Turn off and lock out system before servicing. Conventions Used in this Manual In addition to the symbols and instructional information, this manual is created with “hot links” to enable the user to quickly navigate between different Operator’s Manual 1–1 FS 5.15 Firmware sections within the manual. and to other manuals. These links are identified by a pointing finger cursor when rolling over the text. Simply click on the link to navigate to the associated reference. SpectraSensors Overview SpectraSensors, Inc. is a leading manufacturer of technologically advanced electro-optical gas analyzers for the industrial process, gas distribution and environmental monitoring markets. Headquartered in Houston, Texas, SpectraSensors was incorporated in 1999 as a spin-off of the NASA/Caltech Jet Propulsion Laboratory (JPL) for the purpose of commercializing space-proven measurement technologies initially developed at JPL. 1–2 4900002234 rev. A 11-12-14 2 - OPERATING THE ANALYZER The analyzer is designed to be a stationary measuring device. It should be securely mounted during normal operation. The laser housing labels on the flanges of the sample cell warn about exposure to laser radiation inside. Never open the sample cell unless directed to do so by a service representative and the analyzer power is turned off. The optical head has a seal and “WARNING” sticker to prevent inadvertent tampering with the device. Do not attempt to compromise the seal of the optical head assembly. Doing so will result in loss of device sensitivity and inaccurate measurement data. Repairs can then only be performed by the factory and are not covered under warranty. Firmware Version Each SpectraSensors analyzer operates based on its own version of firmware. The firmware version for each analyzer is listed in the system calibration report, and displays upon start-up of the analyzer. The operation instructions provided in this chapter are intended for the FS 5.15 firmware version. Powering Up the Analyzer After mounting the analyzer, connecting the power wires, connecting the gas lines, connecting the (optional) output signal wires and checking for leaks, you are ready to power up the analyzer. Refer to the figures for the analyzer electronic control boards in the Hardware Manual for locating fuses. If you need to replace a fuse, use only the same type and rating of fuse as the original as listed in the analyzer fuse specifications table in the Hardware Manual. To power up the analyzer: 1. Power up the analyzer by energizing the circuit to the analyzer. 2. For systems with a heated enclosure, confirm that the sample system enclosure is heated to approximately the specified temperature by observing the temperature reading on the door mounted thermometer. Operator’s Manual 2–1 FS 5.15 Firmware For systems with heated enclosures, a Temperature too Low or Temperature too High fault will activate the General Fault Alarm when the enclosure temperature is more than 5 °C above or below the specified temperature. Once the enclosure has reached the specified temperature, reset the General Fault Alarm (see “To change parameters in Mode 2” on page 2-15). 3. The system goes through an initialization period while showing the firmware version on the bottom line until the LCD displays the Normal Mode screen. 4. Enable Peak Tracking following the procedure outlined in “Changing Measurement and Control Parameters” on page 2-11. 5. Three to four minutes are required for the analyzer to establish reference spectra before displaying a reading. 6. After initialization and establishment of reference spectra, the LCD displays four lines, the third of which is blank. <NORMAL MODE> H2S: 5.036 ppmv P: 954.4mb T: 76.1F The measurements displayed are: • ANA: Refers to the concentration in the sample cell (in units) of the analyte/component selected in Mode 2. • P: Pressure in the sample cell (in units) selected in Mode 2. • T: Temperature in the sample cell (in units) selected in Mode 2. 7. Continuous updates of the measurement parameters displaying on the LCD indicates that the analyzer is operating normally. Definitions for the acronyms displayed on the LCD are given in the section “Modes Defined” on page 2-4. 2–2 4900002234 rev. A 11-12-14 Operating the Analyzer Powering Down the Analyzer It may be necessary to power down the analyzer for problem solving or maintenance reasons. An approved switch or circuit breaker rated for 15 amps should have been installed and clearly marked as the disconnecting device for the analyzer. To power down the analyzer: 1. Switch off the power to the analyzer using the switch or circuit breaker designated as the disconnection device for the equipment. 2. If the analyzer is going to be shut down for a short period of time for routine maintenance, isolate the analyzer from the sample conditioning system (SCS). Refer to the appropriate Hardware or SCS Manual. 3. If the analyzer is going to be shut down for a long period of time, follow the procedure for isolating the process sample tap for longterm shutdown (in the Hardware or SCS Manual) or contact SpectraSensors’ technical support group. It is recommended to also disconnect the power completely from the analyzer to prevent potential damage from lightning strikes. Operating the Analyzer from the Keypad The keypad enables the operator to modify measurement units, adjust operational parameters, and perform diagnostics. During normal operation, the LCD continuously displays the measured component’s concentration, sample cell temperature, and sample cell pressure. The SpectraSensors keypad is shown in Figure 2–1. To activate any functions on the keypad, press the mode key # followed by a number on the keypad to specify a mode. You must press the # key before pressing a number or function key to trigger a response from the keypad. When you press the # key, the word MODE displays on the LCD. If the keypad watchdog is enabled, a countdown timer will begin when MODE displays. If the countdown expires and no buttons have been pressed, the analyzer will automatically revert to Mode 1. The * key functions as the “Enter” key. When in Mode 2, always press * after entering a value using the keypad (unless the entry was made in error). Pressing the * key stores the displayed parameter value and cycles the LCD to the next parameter. If you do make an error, press the * key followed by the TEST key, and then the * key to return to the parameter and enter the correct value. Operator’s Manual 2–3 FS 5.15 Firmware Figure 2–1 Analyzer keypad Modes Defined Use the keypad to access the following modes by pressing the # key first followed by a number (1, 2, 3, 4, 5, 6, 7, 8 or 9) to activate a mode. The following section explains each mode and the corresponding information that displays on the LCD. When the # key is pressed, measurement will be suspended until the new mode is established, The only modes that produce measurements are Mode 1, Mode 6, Mode 7 or Mode 8. Every time the # key is pressed, the analyzer requires three to four minutes time upon returning to Mode 1, Mode 6, Mode 7 or Mode 8 to re-establish reference spectra before displaying a reading. 2–4 4900002234 rev. A 11-12-14 Operating the Analyzer Mode 1: (Normal Mode) Mode 1 continuously displays updated measurements. Press the # key followed by the 1 key. # + 1 <NORMAL MODE> H2S: 5.036 ppmv P: 954.4mb T: 76.1F The measurements displayed are: • ANA: Refers to the concentration in the sample cell (in units) of the analyte/component selected in Mode 2. • • P: Pressure in the sample cell in units selected in Mode 2. T: Temperature in the sample cell in units selected in Mode 2. Mode 2: (Set Parameter Mode) Mode 2 enables user to view and change measurement parameters. Follow the procedure under “Changing Measurement and Control Parameters” on page 2-11 for viewing and changing any of the parameters. Mode 3: (Scrubber Life Data) Displays the predicted remaining scrubber/dryer percent capacity and number of days remaining of service. Press the # key followed by the 3 key. # + 3 <SCRUBBER LIFE MODE> Scrubber Life Data: Life left: 98.3% Days left: 531 The New Scrubber Alarm fault will activate the General Alarm Fault when the scrubber/dryer capacity is predicted to be 5% or less, or when the value for days left reaches 0. Refer to the Hardware Manual for information on servicing the scrubber. Operator’s Manual 2–5 FS 5.15 Firmware Mode 4: (System Diagnostic Parameters) Mode 4 displays system diagnostic data. These values may be useful when troubleshooting the system. Press the # key followed by the 4 key. # T D: P D: DCD: Fit: 50.7 954 2674 0.98 + 4 W: 50.6 C W: 1103mb W: 2672 Mid:60.24 While in this mode the analyzer suspends measurement until you return to Mode 1, Mode 6, Mode 7 or Mode 8. The diagnostic parameters displayed are: 2–6 • DryTemp (T D): Shows the temperature in the measurement cell when scrubbed sample gas is flowing through it. • WetTemp (W): Shows the temperature in the measurement cell when normal sample gas is flowing through it. • DryPressure (P D): Shows the pressure in the measurement cell when scrubbed sample gas is flowing through it. • WetPressure (W): Shows the pressure in the measurement cell when normal sample gas is flowing through it. • DryDC (DC D): Shows the magnitude of the DC laser power in the measurement cell when scrubbed sample gas is flowing through it. Acceptable values are between 800 and 3300. A number below or above this range will trigger a Laser Power too Low or Laser Power too High, respectively (see “Alarms” on page 2-42) indicating that either the optics need to be cleaned or there is an alignment problem. • WetDC (W): Shows the magnitude of the DC laser power in the measurement cell when normal sample gas is flowing through it. Acceptable values are between 800 and 3300. A number below or above this range will trigger a Laser Power too Low or Laser Power too High, respectively (see “Alarms” on page 2-42) indicating that either the optics need to be cleaned or there is an alignment problem. • • Fit: The measure of “goodness of fit” for the last measurement point. Mid: The laser current set point after adjustment by the peaktracking software. 4900002234 rev. A 11-12-14 Operating the Analyzer Mode 5: (Analog Output Test Mode) Mode 5 is used to turn on the 4-20 mA current loop output (at the current set with the 4-20 mA Test parameter) for test and calibration purposes. Press the # key followed by the 5 key. # + 5 <TEST 4-20MA MODE> 4-20 mA output is at 0.0% or 4.0mA Returning to Mode 1 re-establishes normal 4-20 mA current loop operation. Mode 6: (Diagnostic Data Download) Mode 6 is used to transfer diagnostic data to the serial port and read the individual data points of both the DC and 2f spectra that the instrument analyzes to calculate the gas concentration. Viewing these data can be helpful in diagnosing problems with the analyzer. Press the # key followed by the 6 key. # + 6 <DUMP SPECTRUM MODE> Index: 0 Cycle: 1 of 10 The data points, along with intermediate calculation results, are output to the serial port whenever Mode 6 is selected. Mode 7: (Measure Port1 Mode) Mode 7 switches the analyzer to measure validation 1 gas supply. Press the # key followed by the 7 key. # + 7 <MEASURE PORT1 MODE> Validation 1 Passed ANA: 4.0256ppmv Returning to Mode 1 re-establishes normal operation measuring process gas. Operator’s Manual 2–7 FS 5.15 Firmware Mode 8: (Measure Port2 Mode) Mode 8 switches the analyzer to measure validation 2 gas supply. Press the # key followed by the 8 key. # + 8 <MEASURE PORT2 MODE> Validation 2 Passed ANA: 4.0256ppmv Returning to Mode 1 re-establishes normal operation measuring process gas. Mode 9: (Recall Validation Results) Mode 9 recalls the measured value from the last autovalidation cycle on units with autovalidation capability. Press the # key followed by the 9 key. # + 9 For systems not set up for a validation, the following screen displays: <VALIDATION RESULTS> No Validations Are Defined For systems set up for a single validation, the following screens may be displayed: 1. If an automatic validation or Mode 7 has not yet been processed: <VALIDATION RESULTS> Date: 14-10-17 13:00 1: NO DATA 2. If an automatic validation or Mode 7 has been processed: <VALIDATION RESULTS> Date: 14-10-17 13:00 1:P 1000.00ppmv Rng:1000.0 to 1000.0 2–8 4900002234 rev. A 11-12-14 Operating the Analyzer Definitions for the displayed parameters are as follows: • Date: Displays the time of the last validation. • 1: Represents validation, i.e., Validation 1. • P or F: Indicates ‘Pass’ or ‘Fail’ for the validation result. • 1000.00ppmv: The concentration of the last validation result in the user’s selected engineering units. If the value is from a Mode 7 validation, then it is the average validation value for the time period during which the Mode 7 was run. • Rng:1000.0 to 1000.0: The minimum and maximum concentration value, in the user’s selected engineering units, during the last validation time period. For systems set up for dual validation, the following screens may be displayed: 1. If an automatic validation or Mode 7 or Mode 8 has not yet been processed: <VALIDATION RESULTS> Date: 14-10-17 13:00 1:NO DATA 2:NO DATA 2. If an automatic validation, Mode 7 or Mode 8 has been processed: <VALIDATION RESULTS> Date: 14-10-17 13:00 1:P 1000.00ppmv 2:P 1000.00ppmv Definitions for the displayed parameters are as follows: • Date: Displays the time of the last validation. • 1 or 2: Represents validation, i.e., Validation 1 or Validation 2. • P or F: Indicates ‘Pass’ or ‘Fail’ for the validation result. Operator’s Manual 2–9 FS 5.15 Firmware • 1000.00ppmv: The concentration of the last validation result in the user’s selected engineering units. If the value is from a Mode 7 or Mode 8 validation, then it is the average validation value for the time period during which the Mode 7 or Mode 8 was run. Mode TEST: (Analog Input Test Mode) Mode Test is used to view a real-time reading of the 4-20 mA analog input state, as well as its current raw and scaled values for test and calibration purposes. In this mode, the analyzer functions normally, as in Mode 1, except that the LCD (display) shows the 4-20 mA analog input signal instead of the current concentration, temperature and pressure. Press the # key followed by the TEST key. # + TEST <NORMAL MODE> 4-20mA input is ON 4095 or 68948 mb Configuring the Analyzer at Start-Up SpectraSensors analyzers are pre-programmed at the factory with most parameters set to default values, which are suitable for most applications. There are a few parameters that should be set by the end user. SpectraSensors recommends checking all the parameters at start-up. Parameter Setting/Checking Procedure: 1. After the analyzer has been installed and start up has been completed, press Mode 2 (#2) from the analyzer keypad and enter password 3142. 2. Press the * key repeatedly to scroll through the parameters and verify the settings. The firmware default parameter settings are reflected in Table 2–1. 2–10 4900002234 rev. A 11-12-14 Operating the Analyzer 1. Peak Tracking set = 1 (P1). Peak Tracking may be turned off at the factory prior to shipment to prevent the peak tracking algorithm from shifting the spectrum during initial warm-up of the unit. Once the unit is installed in the field and the cell temperature has stabilized (typically after 5 hours minimum), the Peak Tracking should be turned on and left on at all times. 2. Set remaining parameters as desired for the specific analyzer application. Refer to Table 2–1. 3. After the analyzer is configured, allow the system to run for 24 hours and then clear all alarms. a. b. c. Press Mode 2 (#2) from the analyzer keypad and enter password 3142. Set the General Alarm DO parameter to 2. Set the Cancel Val Alarms parameter to 1. Changing Measurement and Control Parameters In Mode 2, all of the pertinent measurement and control parameters can be viewed and changed. Refer to Table 2–1 for a list of parameters and value range. The parameters are listed in the order viewed during Mode 2 operation. Table 2–1 Typical values for parameter setpoints Parameter Setting Function Notes Contact SpectraSensors before resetting this parameter. Refer to “Service Contact” on page B-4. Process Purge Time 1 - 10000 Default = 60 Sets the purge time before process measurements and after a validation. Logger Rate 1–1000 readings Default = 16 Sets the number of measurements included in the running average. Rapid Change Monitor 0, 1 Default = 0 Sets the dynamic logger rate based on the concentration of rate change. Temperature Unit 0 or 1 Default = 0 Sets the display unit for temperature. Pressure Unit 0, 1, 2, or 3 Default = 0 Sets the display unit for pressure. Concentration Unit 0-8 Default = 0 Sets the display unit for concentration. Custom Precision 0-5 Default = 2 Sets the number of viewable digits to the right of the decimal point. Operator’s Manual Check for all analyzers. Set per customer preference. 2–11 FS 5.15 Firmware Table 2-1 Typical values for parameter setpoints (Continued) Parameter Setting Function Notes RATA (Relative Accuracy Test Audit) 0 or 1 Default = 0 Enables or disables adjustment factors. RATA Multiplier -1.E+06 to 1.E+06 Default = 1 Slope adjustment factor. RATA Offset -1.E+06 to 1.E+06 Default = 0 Offset adjustment factor. Update RATA 0 or 1 Default = 0 Updates RATA Multiplier and RATA Offset to automatically calculated values. Peak Tracking 0, 1 or 2 Default = 0 Sets peak tracking capability to off, on or reset for the system. Set to ‘1’ after process flow is established and analyzer is warm. New Scrub Installed 0 or 1 Default =0 Resets scrubber/dryer lifetime monitor. Keypad Watchdog 0 - 10000 Sets the time in seconds before the MODE screen automatically reverts to Normal Mode. Contact SpectraSensors before resetting this parameter. Refer to “Service Contact” on page B-4. Default = 10 Set Time - Hour 0 - 23 Default = 0 Sets the current hour. Set Time - Minute 0 - 59 Default = 0 Sets the current minute. Set Time - Day 1 - 31 Default = 0 Sets the present day. Set Time - Month 1 - 12 Default = 1 Sets the present month. Set Time - Year 2006-2144 Default = 2012 Sets the present year. General Alarm DO 0, 1, 2 Default = 0 Sets the general fault alarm to be latching, non-latching or reset. DO Alarm Setup 0 - 4.3E+09 Default = 8192 Sets the functionality of the Assignable Alarm digital output. Low Alarm Setpoint -1.0E-06 to 1.0E+06 Default = -10000 Sets the concentration low alarm threshold in ppmv or moisture dew point. High Alarm Setpoint -1.0E-06 to 1.0E+06 Default = 10000 Sets the concentration high alarm threshold in ppmv or moisture dew point. AO 4-20 mA Test 0 - 100.0 Default = 0 Sets the 4-20 mA output to a percentage of full scale. 2–12 Refer to “Adjusting Analyzer Reading to Match Specific Standard(s)” on page 2-36. Check for all analyzers. Set per customer preference. After analyzer is configured press ‘2’ to reset. Parameter will return to previous setting. Check for all analyzers. Set per customer preference. 4900002234 rev. A 11-12-14 Operating the Analyzer Table 2-1 Typical values for parameter setpoints (Continued) Parameter Setting Function Notes 4-20 mA Alarm Action 0, 1, 2 or 3 Default = 0 Sets the current loop state upon alarm condition. AO 4 mA Value -1.0E-06 to 1.0E+06 Default = 0 Sets ppmv or moisture dew point value corresponding to 4 mA current loop z output. AO 20 mA Value -1.0E-06 to 1.0E+06 Default = Full scale Sets ppmv or moisture dew point value corresponding to 20 mA current loop output. Calculate Dew Point 0, 1 or 2 Default = 0 Enables the dew point calculation and controls its output. Dew Point Method 0, 1, 2 or 3 Default = 0 Type of dew point calculation. Pipeline Pressure 0-500000 Default = 1000 Pressure used for dew point calculation. AI Pressure Input 0 or 1 Default = 0 Controls analog input of pipeline pressure. AI 4 mA Value 0-500000 Default = 0 Analog input 4 mA value. AI 20 mA Value 0-500000 Default = 100000 Analog input 20 mA value. Modbus Address User Set, 0-250 Default = 1 Sets the address for the analyzer. Modbus Mode 0, 1, or 2 Default = 0 Sets type of Modbus protocol. 2 Way Com Port 0, 1, 2, 3 Default = 11 Sets the port that allows twoway communications. Baud Rate 0, 1, 2, 3 or 4 Default = 3 Sets the baud rate for the customer port. Val Purge Period 1 - 4000 Default = 60 Sets the amount of time (in seconds) for validation gas to purge the system. Set for standard validation only, not permeation validation. Val Duration 0 - 8000 Default = 240 Sets the duration (in seconds) of the validation routine. Val Attempts 1 - 8000 Default = 2 Sets the number of validations to be attempted before signaling failure. These parameters apply to permeation validation only. Refer to “Service Contact” on page B-4. Val 1 Concentration 0-Full Scale Default = 4 Sets concentration of validation gas supply #1. Operator’s Manual Check for all analyzers. Set per customer preference. Check for all analyzers. Set per customer preference. Check for all analyzers. Set per customer preference. 2–13 FS 5.15 Firmware Table 2-1 Typical values for parameter setpoints (Continued) Parameter Setting Function Notes Val 2 Concentration 0-Full Scale Default = 4 Sets concentration of validation gas supply #2. Set for standard validation only, not permeation validation. Validation Allowance 1-100 Default = 100 Sets acceptable deviation (in %) for validation. Check for all analyzers. Set for customer preference. Zero Val Tolerance 0 - 2000 Default = 1 Sets maximum acceptable zero measurement reading during validation routine. Set for standard validation only, not permeation validation. Daily Validation 0 or 1 Default = 0 Turns daily autovalidation on or off. Val Interval 1 - 400 Default = 1 Interval (in days) between validation cycles. Val Start Time 0 - 23 Default = 8 Sets the hour of the day for. validation. Start Validation 0 or 1 Default = 0 Initiates validation cycle. 4-20 mA Val Action 0 or 1 Default = 0 Sets the current loop mode during validation. Val Perm Constant Kp 0-1000000 Default = 0 Sets the system constant for the permeation tube devices. Val Perm Rate Rp 0-1000000 Default = 0 Sets the calibrated permeation rate for the permeation tube. Cancel Val Alarms 0 or 1 Default = 0 Resets the validation alarms and relays. After analyzer is configured press ‘1’ to reset. Parameter will return to default setting. Val Auto DumpSpectrm 0 or 1 Default =0 Sets the analyzer to dump spectrum information during a validation measurement. Contact SpectraSensors before resetting this parameter. Refer to “Service Contact” on page B-4. Operator Parameter01 to Operator Parameter20 Parameter Index Default: 0 Parameter setup for Operator Parameter section. Refer to Table 2–3. Check for all analyzers. Set for customer preference. 2–14 Check for all analyzers. Set for customer preference. Contact SpectraSensors before resetting this parameter. Refer to “Service Contact” on page B-4. 4900002234 rev. A 11-12-14 Operating the Analyzer To change parameters in Mode 2 1. Press the # key followed by the 2 key. # + 2 <SET PARAMETER MODE> Enter password: FS 5.15-XXXX The LCD prompts for a numeric password. 2. To enter the Customer Parameter section where complete access is provided to all customer parameters, enter the user password (3142) on the keypad. To enter the Operator Parameter section where a user definable set of customer parameters resides, enter the operator password as defined in the Operator Password parameter. Then press the * key to enter the number. <SET PARAMETER MODE> Process Purge Time 60 Enter a value (secs) 3. Starting with the first parameter that displays, enter a new value and/or press the * key to store the value and cycle to the next parameter. 4. When finished changing or viewing the measurement and control parameters, press the # key followed by the 1 key to return to Mode 1 and normal operation. The scroll direction can be reversed by pressing the TEST key followed by the * key. Measurement and Control Parameters Defined The definitions for the measurement and control parameters are shown below in alphabetical order for easy reference. Refer to Table 2–1 to review order listed during Mode 2 configuration. Operator’s Manual 2–15 FS 5.15 Firmware 2 Way Com Port The 2 Way Com Port parameter sets the port that allows two-way communications, including Modbus and the diagnostic protocol. Enter 0 to turn off two-way communications, 1 for the customer port, 2 for the service port, or 3 for the Ethernet port (if applicable). <SET PARAMETER MODE> 2 Way Com Port 1 0:Off1:Cus2:Ser3:Eth The customer port baud rate is set from the Baud Rate parameter with 8 data bits, 1 stop bit, and no parity. The service port baud rate is 115200 with 8 data bits, 1 stop bit, and no parity. If the Ethernet port is available, refer to “Configuring the Built-in Ethernet Port” on page 4-1 for setup information. 4-20 mA Alarm Action The 4-20 mA Alarm Option determines the current loop state upon an alarm condition. Enter 0 for no action, 1 for the current loop to assume a low state upon an alarm condition, 2 for the current loop to assume a high state upon an alarm condition, or 3 for the current loop to track and hold the current state upon an alarm condition. <SET PARAMETER MODE> 4-20mA Alarm Action 0 0:None 1:L 2:H 3:T&H 4-20 mA Val Action The 4-20 mA Val Action parameter sets the operation mode of the 4-20 mA current loop during validation cycles. Enter 0 for the current loop to track and hold the last process measurement or 1 for the current loop to continue to output the analyzer measurements during the validation cycle. <SET PARAMETER MODE> 4-20 mA Val Action 0 0:Hold 1:Measure 2–16 4900002234 rev. A 11-12-14 Operating the Analyzer AI 4 mA Value The AI 4 mA Value parameter sets the pipeline pressure (in mbar) corresponding to a 4 mA current loop input. <SET PARAMETER MODE> AI 4 mA Value 0.00000 Enter a value (mb) AI 20 mA Value The AI 20 mA Value parameter sets the pipeline pressure (in mbar) corresponding to a 20 mA current loop input. <SET PARAMETER MODE> AI 20 mA Value 100000.00000 Enter a value (mb) AI Pressure Input The AI Pressure Input parameter enables or disables usage of a live pipeline pressure via the analog input for the calculation and display of dew point temperature. There are two choices: 0 to turn the analog pressure input off, and 1 to turn it on. If this parameter is disabled, then a fixed pipeline pressure must be entered through the Pipeline Pressure parameter. <SET PARAMETER MODE> AI Pressure Input 0 0:Disable 1:Enable AO 4 mA Value The AO 4 mA Value parameter sets the concentration (in ppmv) or dew point temperature (in degrees Celsius or Fahrenheit), depending on whether dew point temperature calculation and display are enabled (i.e., the Calculate Dew Point parameter set equal to 1), corresponding to a 4 mA current loop output. <SET PARAMETER MODE> AO 4 mA Value 0.00000 ppmv or DewPoint F/C Operator’s Manual 2–17 FS 5.15 Firmware AO 20 mA Value The AO 20 mA Value parameter sets the concentration (in ppmv) or dew point temperature (in degrees Celsius or Fahrenheit), depending on whether dew point temperature calculation and display are enabled (i.e., the Calculate Dew Point parameter set equal to 1), corresponding to a 20 mA current loop output. <SET PARAMETER MODE> AO 20 mA Value 20.00000 ppmv or DewPoint F/C AO 4-20 mA Test The AO 20 mA Test parameter sets the output of the current loop when in Mode 5 for testing and calibration purposes. The value entered represents a percent of scale value where zero equals 4 mA and full scale equals 20 mA. Thus, the current loop output, I, is given by I = R 20mA – 4mA + 4mA , where R is the AO 4-20 mA Test parameter value. <SET PARAMETER MODE> AO 4-20 mA Test 0.00000 Enter a value (%) Baud Rate The Baud Rate parameter sets the baud rate for the customer RS-232 port. Enter 0 for 19200, 1 for 38400, 2 for 57600, or 3 for 115200, or 4 for 9600 baud rate. The other settings for this port are 8 data bits, 1 stop bit, no parity and no hardware flow control. <SET PARAMETER MODE> Baud Rate 3 0:19 1:38 2:57 3:115 Make sure that the COM port used is set for the same baud rate as the analyzer. 2–18 4900002234 rev. A 11-12-14 Operating the Analyzer Calculate Dew Point The Calculate Dew Point parameter enables or disables the calculation and display of dew point temperature. There are three choices: 0 to turn the calculation and display of dew point temperature off, 1 to allow the dew point to be output on the LCD and on the analog output (setup of the AO 4 mA and 20 mA values is required), and 2 to allow the dew point to be output on the LCD only. <SET PARAMETER MODE> Calculate Dew Point 0 0:Off 1:lcd&AO 2:lcd Cancel Val Alarms The Cancel Val Alarms parameter cancels the validation alarm and resets all validation flags once activated. Entering 1 cancels the alarm. Once the action is complete the parameter automatically reverts to 0. <SET PARAMETER MODE> Cancel Val Alarms 0 1:Cancel Concentration Unit The Concentration Unit parameter designates the options for measured concentration, which include: • • • • • • • • • 0 for ppmv 1 for lb/MMscf [MMscf =million standard cubic feet (15.6 °C, 101.325 kPa)] 2 for % 3 for mg/Nm3 [Nm3 = normal cubic meters (15.6 °C, 101.325 kPa)] 4 for ppmw 5 for ppbv 6 for ppbw 7 for grains/100scf 8 for custom display units and conversion factor (user EU Tag Part 1 and 2 as defined by Modbus registers 45203 and 45205) <SET PARAMETER MODE> Concentration Unit 0 0:ppm 1:lbs 2:% 3:mg Operator’s Manual 2–19 FS 5.15 Firmware If the display units are correct but the conversion factor is not correct for the application, a custom conversion factor can be defined using Modbus. To set a custom conversion factor, first choose the correct display units (based on the Concentration Unit parameter) and then define the conversion factor for the associated display units using Modbus. If the Modbus register is set to 0 then the default conversion factor is used. However, if it is set to a value greater than 0, then that value is used as the conversion factor. If a correct concentration unit option for the display units does not exist, then a custom display unit and conversion can be created using Modbus. To set a custom display unit, select option 8 for the Concentration Unit parameter. Next define the ASCII display text and associated conversion factor using Modbus. Custom Precision The Custom Precision parameter sets the number of viewable digits to the right of the decimal point. The total number of digits the analyzer can display at any one time is 6. Therefore, when the size of the value plus the Custom Precision exceeds 6 the number of digits to the right of the decimal point will be reduced accordingly. <SET PARAMETER MODE> Custom Precision 2 Enter a value Daily Validation The Daily Validation parameter enables or disables the time of day autovalidation feature. When enabled, an autovalidation cycle is initiated every ‘X’ day (where ‘X’ is defined by Val Interval) at the time of day established by Val Start Time. Enter 0 to turn the feature off or 1 to turn the feature on. <SET PARAMETER MODE> Daily Validation 0 0:Disable 1:Enable Dew Point Method The Dew Point Method parameter sets the type of industry standard dew point calculation to be performed when Calculate Dew Point is enabled. Enter 0 for ISO 18453:2006, 1 for the ASTM 1142-95 Eq. (1), 2 for the ASTM 1142- 2–20 4900002234 rev. A 11-12-14 Operating the Analyzer 95 Eq. (2), or 3 for the Arden Buck method. Refer to Appendix A for further information on the dew point calculation methods. <SET PARAMETER MODE> Dew Point Method 0 0:ISO1:AS12:AS23:AB DO Alarm Setup The DO Alarm Setup parameter sets the functionality of the Assignable Alarm. Add together the hexadecimal values according to Table 2–2 for each fault chosen to trigger the Assignable Alarm. Convert the resulting hexadecimal value to a decimal value and enter the number for normally deactivated relay functionality. Add ‘1’ to the resulting decimal value to switch to normally activated functionality. <SET PARAMETER MODE> DO Alarm Setup 8192 Enter decimal value For example, the hexadecimal value of 0002000 converts to decimal value of 8192, which when entered results in a normally deactivated relay triggered by the Concentra High Alarm. Entering a value of 8193 would result in a normally activated relay (fail safe) triggered by the Concentra High Alarm. To enable the relay to be triggered by the New Scrubber Alarm as well, the two hexadecimal values 0002000 and 8000000 are added to give 8002000, which converts to a decimal value of 134225920. Table 2–2 Assignable Alarm functionality Bit Decimal Hex Value 0 1 00000001 Power Fail (Always Activated) 1 2 00000002 Any alarm active 2 4 00000004 Laser Power Low Alrm 3 8 00000008 Laser Powr High Alrm 4 16 00000010 Laser Zero Low Alarm 5 32 00000020 Laser Zero High Alrm 6 64 00000040 Laser Curnt Low Alrm 7 128 00000080 Laser Curnt High Alrm Operator’s Manual Alarm Functionality 2–21 FS 5.15 Firmware Table 2-2 Assignable Alarm functionality (Continued) Bit Decimal Hex Value Alarm Functionality 8 256 00000100 Pressure Low Alarm 9 512 00000200 Pressure High Alarm 10 1024 00000400 Temp Low Alarm 11 2048 00000800 Temp High Alarm 12 4096 00001000 Concentra Low Alarm 13 8192 00002000 Concentra High Alarm 14 16384 00004000 PeakTk Restart Alarm 15 32768 00008000 Fitting Restart Alrm 16 65536 00010000 RampAdj Restart Alarm 17 131072 00020000 Not Used 18 262144 00040000 Not Used 19 524288 00080000 Flow Switch Alarm 20 1048576 00100000 Val 1 Fail Alarm 21 2097152 00200000 Val 2 Fail Alarm 22 4194304 00400000 Not Used 23 8388608 00800000 Not Used 24 16777216 01000000 DeltaDC Restart Alrm 25 33554432 02000000 DeltaT Restart Alarm 26 67108864 04000000 Dry Pressure Alarm 27 134217728 08000000 New Scrubber Alarm 28 268435456 10000000 R2 Restart Alarm 29 536870912 20000000 R3 Restart Alarm 30 1073741824 40000000 Pressure Restart Alarm 31 2147483648 80000000 Low Purge Rate Alarm General Alarm DO The General Alarm DO sets the operation of the general alarm relay digital output when a General Fault Alarm occurs. The relay is normally energized making it fail-safe for detection of not only alarms, but also power failures. Enter 0 to make the relay latching, which means any General Fault Alarm will de-energize the relay and keep it de-energized even if the alarm condition clears. It takes a reset of the relay using this parameter to return the relay to ‘normal’ state. Enter a 1 to make the relay non-latching, which means any general fault alarm will de-energize the relay; however, when the alarm 2–22 4900002234 rev. A 11-12-14 Operating the Analyzer condition clears, the relay will automatically reset to its normal state. Enter a 2 to reset the relay and any active alarms to the ‘normal’ state. After the relay resets, this parameter will automatically revert to the setting from before the reset was initiated. <SET PARAMETER MODE> General Alarm DO 0 0:L 1:NonL 2:Reset High Alarm Setpoint The High Alarm Setpoint parameter determines the concentration threshold above which the Concentra High Alarm fault will be triggered (see “Alarms” on page 2-42). The value entered is compared to the moving average over the number of measurement points set by the Logger Rate. To be turned off, the setpoint must have a value greater than the maximum range of the analyzer or maximum dew point. <SET PARAMETER MODE> High Alarm Setpoint 0.00000 ppmv or DewPoint F/C Keypad Watchdog The Keypad Watchdog parameter sets the allowable time (in seconds) that the analyzer can be on the MODE screen and the Mode 2 (Set Parameter Mode) password screen before automatically reverting to Mode 1 (Normal Mode). Setting this parameter to a value less than five (5) will disable this feature. If it is set for greater than or equal to five (5), then the value represents the number of seconds before the analyzer reverts to Normal Mode. <SET PARAMETER MODE> Keypad Watchdog 60 <5:Off >=5:Secs Logger Rate The Logger Rate parameter sets the number of measurements included in the running average. The display and the current loop output will each have a value Operator’s Manual 2–23 FS 5.15 Firmware representing the running average of the concentration over a number of measurements equal to Logger Rate. <SET PARAMETER MODE> Logger Rate 16 Enter a value Low Alarm Setpoint The Low Alarm Setpoint parameter determines the concentration threshold below which the Concentra Low Alarm fault will be triggered (see “Alarms” on page 2-42). The value entered is compared to the moving average over the number of measurement points set by the Logger Rate. To be turned off, the setpoint must have a value less than the minimum range of the analyzer or minimum dew point. <SET PARAMETER MODE> Low Alarm Setpoint 0.00000 ppmv or DewPoint F/C Modbus Address The Modbus Address parameter sets the analyzer address when the analyzer is used as a Modbus slave device. Addresses from 1 to 250 can be used. <SET PARAMETER MODE> Modbus Address 1 Enter node (1-250) Modbus Mode The Modbus Mode parameter sets the communications protocol for the port selected by the 2 Way Com Port parameter. There are three choices: 0 for turning the Modbus capabilities off and defaulting to generic serial output as described in “Receiving Serial Data (Customer Port Output)” on page 3-1 (the ports not designated for two-way communications will also output the generic serial output); 1 for enabling the analyzer to respond to Gould Modbus 2–24 4900002234 rev. A 11-12-14 Operating the Analyzer RTU function codes 3, 6 and 16; and 2 for enabling the analyzer to respond to Daniel Modbus RTU function codes 3, 6 and 16. <SET PARAMETER MODE> Modbus Mode 0 0:Off 1:GMR 2:DMR New Scrub Installed The New Scrub Installed parameter resets the scrubber/dryer alarm once activated, and the scrubber/dryer lifetime monitor. The New Scrubber Alarm fault will activate the General Fault Alarm when the scrubber/dryer capacity is predicted to be 5% or less, or when the scrubber days of service remaining reaches 0 days (refer to the Hardware Manual for information on servicing the scrubber). Once the scrubber/dryer is replaced, enter 1 to reset the scrubber/dryer alarm and lifetime monitor. <SET PARAMETER MODE> New Scrub Installed 0 1:Yes Operator Parameter01 to Operator Parameter20 These parameters enable the setup of the Operator Parameter section. A parameter index may be entered for each parameter to be displayed when the analyzer is in the Operator Parameter section. Refer to Table 2–3. Entering 0 (zero) will prevent a parameter from being displayed. To access the Operator Parameter section: 1. From the analyzer keypad, press the # key followed by the 2 key to enter Mode 2. 2. Enter the Operator Password as defined in the Operator Password parameter and press the * key. Refer to the section called “Operator Password” on page 2-27 for more information. Operator’s Manual 2–25 FS 5.15 Firmware Only those parameters with a parameter index indicated will be displayed. If none of the 20 parameters have an index defined, the following screen will display while in Operator Parameter section. <SET PARAMETER MODE> No Operator parameters defined. Press MODE to exit. <SET PARAMETER MODE> Operator Parameter01 0 Enter a parameter # Table 2–3 Parameter Operator Parameters Index Parameter Index Process Purge Time 33 Calculate Dew Point 186 Logger Rate 34 Dew Point Method 187 Rapid Change Monitor 35 Pipeline Pressure 200 Temperature Unit 52 AI Pressure Input 201 Pressure Unit 53 AI 4 mA Value 202 Concentration Unit 30 AI 20 mA Value 203 Custom Precision 54 Modbus Address 205 RATA 84 Modbus Mode 206 RATA Multiplier 85 2 Way Com Port 207 RATA Offset 86 Baud Rate 208 Update RATA 87 Val Purge Period 231 Peak Tracking 88 Val Duration 236 New Scrub Installed 165 Val Attempts 237 Keypad Watchdog 171 Val 1 Concentration 238 Set Time - Hour 172 Val 2 Concentration 239 Set Time - Minute 173 Validation Allowance 240 Set Time - Day 174 Zero Val Tolerance 241 Set Time - Month 175 Daily Validation 242 Set Time - Year 176 Val Interval 243 2–26 4900002234 rev. A 11-12-14 Operating the Analyzer Table 2-3 Operator Parameters (Continued) Parameter Index Parameter Index General Alarm DO 177 Val Start Time 244 DO Alarm Setup 178 Start Validation 245 Low Alarm Setpoint 179 4-20 mA Val Action 247 High Alarm Setpoint 180 ValPerm Constant Kp 262 AO 4-20 mA Test 182 ValPerm Rate Rp 263 4-20 mA Alarm Action 183 Cancel Val Alarms 264 AO 4 mA Value 184 Val Auto DumpSpectrm 265 AO 20 mA Value 185 Operator Password 266 Operator Password The Operator Password parameter enables or disables a password requirement for entering the Operator Parameter section. Enter 0 for a password to disable a password requirement, or a positive value (up to four digits) to require a password. If 0 is used, accessing the Operator Parameter section requires only pressing the # key followed by the 2 key (to enter Mode 2), and then pressing the * key (without entering a password) to display the first parameter. <SET PARAMETER MODE> Operator Password 0 0:No p/w >0:p/w Peak Tracking The Peak Tracking parameter enables a software utility that periodically adjusts the laser current to keep the absorption peak of the measured component at a known location. There are three choices: 0 for no peak tracking, 1 for peak tracking (default) and 2 for resetting the peak to its factory default setting. Selecting 2 will return the current analyzer midpoint to the factory default midpoint, and then automatically revert the parameter value to its setting before the reset was initiated. In most cases, the peak tracking should be set to 1 for on. <SET PARAMETER MODE> Peak Tracking 1 0:Off 1:On 2:Rst Operator’s Manual 2–27 FS 5.15 Firmware Pipeline Pressure The Pipeline Pressure parameter sets the pipeline pressure (in mbar) in the current dew point calculation or, if enabled, displays the current pipeline pressure input through the AI Pressure Input. <SET PARAMETER MODE> Pipeline Pressure 10000.00000 Enter a value (mb) Pressure Unit The Pressure Unit parameter designates the display units for the measured absolute pressure in the cell. There are four choices: 0 for millibar, 1 for Torr, 2 for kPa, and 3 for PSIA. <SET PARAMETER MODE> Pressure Unit 0 0:mb1:Torr2:kPa3:psi Process Purge Time The Process Purge Time sets the time in seconds that the analyzer will purge the system with process gas before starting a dry cycle when switching to the process stream after a validation. <SET PARAMETER MODE> Process Purge Time 60 Enter a value (secs) Rapid Change Monitor The Rapid Change Monitor parameter enables or disables the dynamic logger rate based on the concentration rate of change. Enter 0 to turn the feature off or 1 to turn the feature on. <SET PARAMETER MODE> Rapid Change Monitor 0 0:Disable 1:Enable 2–28 4900002234 rev. A 11-12-14 Operating the Analyzer RATA (Relative Accuracy Test Audit) The RATA parameter enables or disables user definable values that allow adjustment (without affecting the factory calibration) of the analyzer reading in the field [see “Adjusting Analyzer Reading to Match Specific Standard(s)” on page 2-36]. <SET PARAMETER MODE> RATA 0 0:Disable 1:Enable RATA Multiplier The RATA Multiplier parameter is a user definable value that enables adjustment (without affecting the factory calibration) of the analyzer response (or slope) in the field [see “Adjusting Analyzer Reading to Match Specific Standard(s)” on page 2-36]. <SET PARAMETER MODE> RATA Multiplier 1.00000 Enter a value RATA Offset The RATA Offset parameter is a user definable value that enables adjustment (without affecting the factory calibration) of the analyzer offset in the field [see “Adjusting Analyzer Reading to Match Specific Standard(s)” on page 2-36]. <SET PARAMETER MODE> RATA Offset 0.00000 Enter a value Operator’s Manual 2–29 FS 5.15 Firmware Set Time - Day The Set Time - Day parameter sets the current day for the clock driving daily validations. <SET PARAMETER MODE> Set Time - Day 17 Enter a value (DD) Set Time - Hour The Set Time - Hour parameter sets the current hour for the clock driving daily validations. <SET PARAMETER MODE> Set Time - Hour 7 Enter a value (0-23) Set Time - Minute The Set Time - Minute parameter sets the current minute for the clock driving daily validations. <SET PARAMETER MODE> Set Time - Minute 5 Enter a value (0-59) Set Time - Month The Set Time - Month parameter sets the current month for the clock driving daily validations. <SET PARAMETER MODE> Set Time - Month 10 Enter a value (MM) 2–30 4900002234 rev. A 11-12-14 Operating the Analyzer Set Time - Year The Set Time - Year parameter sets the current year for the clock driving daily validations. <SET PARAMETER MODE> Set Time - Year 2014 Enter a value (YYYY) Start Validation The Start Validation parameter initiates the validation cycle. After the cycle begins, this parameter automatically reverts to 0. <SET PARAMETER MODE> Start Validation 0 1:Start Temperature Unit The Temperature Unit parameter designates the display units for the measured cell temperature. There are two choices: 0 for degrees Celsius and 1 for Fahrenheit. The default value is the standard unit of measurement in the region the analyzer is being used. <SET PARAMETER MODE> Temperature Unit 0 0:C 1:F Update RATA The Update RATA parameter is used to update the RATA Multiplier and RATA Offset parameters with the latest automatically calculated values. Each time an automatic, semi-automatic, manual Mode 7 or manual Mode 8 validation is completed, a new RATA Multiplier and RATA Offset will be calculated. This parameter displays the current RATA Multiplier and RATA Offset in the left column of the display as defined in their respective parameter descriptions. In the right column, the newly calculated values are displayed. To Operator’s Manual 2–31 FS 5.15 Firmware accept and use the newly calculated values, enter 1. These values will be invoked when pressing the MODE button while exiting Mode 2. <SET Mult: Ofst: 0 PARAMETER MODE> 1.00 New: 1.00 0.00 New: 0.00 1: Update RATA Refer to the section called “Adjusting Analyzer Reading to Match Specific Standard(s)” on page 2-36 for more information. Val 1 Concentration The Val 1 Concentration parameter sets the concentration value of validation gas supply #1. The analyzer can be configured for a zero gas by setting this parameter to 0.0 and then setting the Zero Val Tolerance to the maximum acceptable reading. Otherwise, set this parameter to the concentration value of the validation gas supply and set Validation Allowance to the allowable variation range (±%). <SET PARAMETER MODE> Val 1 Concentration 4.00000 0:ZeroGas >0:ppmvVal When procuring a gas standard, make sure the background gas is that specified or a mix that closely resembles the contents of the process stream and have the gas standard certified to better than the specified precision of the analyzer, if possible. Val 2 Concentration The Val 2 Concentration parameter sets the concentration value of validation gas supply #2. The analyzer can be configured for a zero gas by setting this parameter to 0.0 and then setting the Zero Val Tolerance to the maximum acceptable reading. Otherwise, set this parameter to the concentration value 2–32 4900002234 rev. A 11-12-14 Operating the Analyzer of the validation gas supply and set Validation Allowance to the allowable variation range (±%). <SET PARAMETER MODE> Val 2 Concentration 16.0000 0:ZeroGas >0:ppmvVal When procuring a gas standard, make sure the background gas is that specified or a mix that closely resembles the contents of the process stream and have the gas standard certified to better than the specified precision of the analyzer, if possible. Val Attempts The Val Attempts parameter sets the maximum number of failures of the analyzer to measure the validation gas within the set tolerances (see Zero Val Tolerance and Validation Allowance) before stopping the autovalidation sequence and triggering a Validation Fail Alarm. <SET PARAMETER MODE> Val Attempts 2 Enter a value Val Auto DumpSpectrm The Val Auto DumpSpectrm parameter determines whether a Mode 6 dump automatically occurs after each validation measurement. There are two choices: 0 to turn the automatic data dump during validation off, and 1 to turn it on. <SET PARAMETER MODE> Val Auto DumpSpectrm 0 0:Disable 1:Enable Val Duration The Val Duration parameter sets the total number of seconds a validation cycle will run. Actual validation measurement time is equal to Val Duration minus Val Purge Period minus the time required to get the first measurement Operator’s Manual 2–33 FS 5.15 Firmware value. Thus, Val Duration must be set to a value greater than the sum of these components. <SET PARAMETER MODE> Val Duration 240 Enter a value (secs) Validation Allowance The Validation Allowance parameter sets the tolerance (%) for validation measurements when Val 1 Concentration or Val 2 Concentration is set to a value greater than 0. <SET PARAMETER MODE> Validation Allowance 100.00000 % of Val Concentratn Val Interval The Val Interval parameter sets the number of days between autovalidation cycles. The next scheduled validation cycle would occur in Val Interval days at the Val Start Time. <SET PARAMETER MODE> Val Interval 1 Enter a value (days) Val Perm Constant Kp The Val Perm Constant Kp parameter is used for permeation validation devices and defines the system constant (Kp), which is determined at the factory at the time of calibration. The permeation device can be replaced with another permeation device with a different permeation rate, and the correct new permeation concentration will be calculated by the analyzer software using the system constant. The Kp will be constant over the life of the analyzer provided the temperature, sample flow rate and pressure of the system are not changed from the factory settings. If the system constant needs to be reset, 2–34 4900002234 rev. A 11-12-14 Operating the Analyzer refer to “Recalculating the System Constant Kp” on page 5-3 for details on recalculating the system constant. <SET PARAMETER MODE> Val Perm Constant Kp 0.24 0:Off >0:System Cons Val Perm Rate Rp The Val Perm Rate Rp parameter is used for permeation validation devices and defines the permeation rate in ng/min, referenced on the permeation device certification. This certification is valid for a period of one year; however, the permeation device may be used longer than this period if a factory certified validation concentration is not required. When the validation concentration begins to drop steadily, the permeation device must be replaced. When replacing the device, the Val Perm Rate Rp must also be updated. For instruction on replacing the permeation device, refer to the section called “Validation of Trace Moisture Measurements” in the sample conditioning system (SCS) chapter or manual. <SET PARAMETER MODE> Val Perm Rate Rp 0.33 0:Off >0:ng/min Val Purge Period The Val Purge Period parameter sets the number of seconds the analyzer will purge the system with validation gas before starting a dry cycle upon validation initiation. Because validation gas may be introduced into the system at various distances from the analyzer, adjustment of the Val Purge Period parameter is necessary to optimize the time the validation gas is allowed to purge through the transport tubing before the analyzer makes a validation measurement. Optimization of the Val Purge Period parameter ensures an accurate measurement of the validation gas while minimizing gas consumption. <SET PARAMETER MODE> Val Purge Period 60 Enter a value (secs) Operator’s Manual 2–35 FS 5.15 Firmware Val Start Time The Val Start Time parameter sets the hour of the day for the daily autovalidation to begin. <SET PARAMETER MODE> Val Start Time 8 Hour of day (0-23) Zero Val Tolerance The Zero Val Tolerance parameter is used to set the maximum acceptable reading when validating with zero gas. To configure the analyzer for zero gas set the parameter Val 1 Concentration or Val 2 Concentration to 0.0. <SET PARAMETER MODE> Zero Val Tolerance 1.00000 Enter a value (ppmv) Adjusting Analyzer Reading to Match Specific Standard(s) In some instances, the user may wish to adjust the analyzer reading to match the concentration (or concentrations) of a specific standard (or standards). The RATA Multiplier and RATA Offset parameters are used to adjust the analyzer output in the field without affecting the factory calibration. Both parameters are used when samples from two different concentration standards are available, whereas only the RATA Multiplier parameter is used when a non-zero gas sample from only one concentration standard is available. If using a zero gas sample from only one concentration standard, then only the RATA Offset parameter should be calculated. The value of the RATA Multiplier parameter, S, is determined by C2 – C1 S = ------------------- , A2 – A1 where C1 is the certified concentration of standard No. 1, C2 is the certified concentration of standard No. 2, A1 is the measured concentration (analyzer reading) of standard No. 1 without any RATA adjustment, and A2 is the measured concentration (analyzer reading) of standard No. 2 without any RATA adjustment. The RATA Offset parameter, O, is determined by O = C1 – S A1 , 2–36 4900002234 rev. A 11-12-14 Operating the Analyzer where S can be 1 when a sample from only one concentration standard is available. For a non-zero single concentration standard RATA Multiplier parameter, S is determined by S = (C1 - O) / where O can be zero, if desired. After an automatic, semi-automatic, manual Mode 7 or manual Mode 8 validation completes, the analyzer automatically calculates new RATA Multiplier and RATA Offset values. These values are based on the number of validations that the analyzer is configured to accept and the type of validation used. To perform this calculation, the most recent validation result(s) will be used. These calculations are based on the average measurement values during the validation, which can be viewed from the Mode 9 display. These values are not constrained by the measurement range of the analyzer, which will ensure accurate RATA Multiplier and RATA Offset values are calculated. To perform the calculation: If RATA is enabled, the current RATA Multiplier and RATA Offset values must be removed from the measured Validation 1 and/or Validation 2 concentration values. Depending on the number of validations, or the validation type, one of the following scenarios occur: • If using a non-permeation single validation system with a zero gas as the standard, then a new RATA Offset is calculated leaving the RATA Multiplier at its previous value. • If using a non-permeation single validation system with a non-zero gas as the standard, then a new RATA Multiplier is calculated leaving the RATA Offset at its previous value. • If using a permeation-based single validation system, then a new RATA Multiplier is calculated and the RATA Offset is left at its previous value. • If using a dual validation system, then both a new RATA Multiplier and RATA Offset are calculated. Operator’s Manual 2–37 FS 5.15 Firmware To adjust the analyzer reading: 1. Validate the analyzer using one or two concentration standards (refer to “Validating the Analyzer” on page 2-47). SpectraSensors recommends validating the analyzer using only the analyte mixed in the validation gas specified on the analyzer calibration certificate. A bottle of test gas with certified concentrations of approximately 20% and 80% of full scale are recommended for a two point validation. For a single point validation, a bottle with a certified concentration of approximately 50% of full scale should be used. When procuring a gas standard, make sure the background gas is that specified or a mix that closely resembles the contents of the process stream and have the gas standard certified to better than the specified precision of the analyzer, if possible. 2. Enter Mode 2 by pressing the # key followed by the 2 key. The LCD prompts for a numeric password. 3. Enter the user password (3142) on the keypad, then press the * key. 4. View the newly calculated RATA Multiplier and RATA Offset parameters from the Update RATA parameter or calculate the RATA Multiplier and/or RATA Offset parameter(s) manually using the equations above. 5. Follow the procedure under “To change parameters in Mode 2” on page 2-15 to enter the new values. Confirm the new values by re-measuring the bottle(s) of test gas. RATA values are also applied to the validation measurements. If RATA free validation values are required, the RATA parameter must be disabled before running the validation. Application Examples Manual Dual Validation Two standards are used in this example, Validation 1 and Validation 2, which are manually introduced into the analyzer. Mode 7 and Mode 8 are used to run these standards. 1. Configure the Operator Parameter01 to Operator Parameter20 with the Operator Password set to 0 and one parameter. 2–38 4900002234 rev. A 11-12-14 Operating the Analyzer • Configure Update RATA by setting Operator Parameter01 to 87. Other parameters can be added, if desired. 2. Introduce Validation 1 and press # followed by the 7 key (to enter Mode 7) to allow Validation 1 to run for the desired amount of time. 3. Introduce Validation 2 and press # followed by the 8 key (to enter Mode 8) to allow validation to run for the desired amount of time. 4. Press the # key followed by the 2 key (to enter Mode 2) and then the * key. 5. View the newly calculated RATA values, and if desired, set Update RATA to 1 accept the changes. Leave the setting at 0 to reject the changes and start over. 6. Re-run steps 2 and 3. 7. Press the # key followed by the 9 key (to enter Mode 9) to verify the validation results and confirm that new RATA values are operating correctly. 8. Press the # key followed by the 1 key (to enter Mode 1) to return to Normal Mode. Semi-Automatic Single or Dual Validation In this scenario, either one or two standards (Validation 1 and/or Validation 2) are used, which are automatically introduced and controlled by the analyzer. Typically, the validation is initiated locally by the user or while the user is present by initiating the Start Validation parameter or the Start Validation digital input. 1. Configure the Operator Parameter01 to Operator Parameter20 with the Operator Password set to 0 and two parameters. • Configure Start Validation by setting Operator Parameter01 to 245. • Configure Update RATA by setting Operator Parameter02 to 87. Other parameters can be added, if desired. 2. Press the # key followed by the 2 key (to enter Mode 2) and then press the * key. 3. Set the Start Validation parameter to 1 and then press the * key followed by the # and the 1 key to allow the validation to start. Allow the validation sequence to complete. 4. Press the # key followed by the 2 key (to enter Mode 2) and then press the * key twice. Operator’s Manual 2–39 FS 5.15 Firmware 5. View the newly calculated RATA values, and if desired, set Update RATA to 1 to accept the changes. Leave the setting at 0 to reject the changes and start over. 6. Re-run steps 2 through 4. 7. Press the # key followed by the 9 key (to enter Mode 9) to verify the validation results and confirm that new RATA values are operating correctly 8. Press the # key followed by the 1 key (to enter Mode 1) to return to Normal Mode. Automatic Single or Dual Validation Either one or two standards can be used for automatic single or dual validation; Validation 1 and/or Validation 2, which are automatically introduced and controlled by the analyzer. The validation is automatically initiated based on the hour of the day and is controlled by the Val Start Time, Daily Validation and Val Interval parameters. Validation can also be initiated remotely using the Start Validation parameter or the Start Validation digital input. 1. Configure the Operator Parameter01 to Operator Parameter20 with the Operator Password set to 0 and one parameter. • Configure Update RATA by setting Operator Parameter01 to 87. Other parameters can be added, if desired. 2. Press the # key followed by the 9 key (to enter Mode 9) to verify the validation results. 3. Press the # key followed by the 2 key (to enter Mode 2) and then press the * key. 4. View the newly calculated RATA values, and if desired, set Update RATA to 1 to accept the changes. Leave the setting at 0 to reject the changes and start over. 5. Press the # key followed by the 1 key (to enter Mode 1) to return to Normal Mode. Scaling and Calibrating the Current Loop Signal The 4-20 mA current loop signals are most conveniently scaled and calibrated at the receiving end (RTU, flow computer, etc.). The 4-20 mA current loop is factory set as the source unless otherwise specified. Contact your sales representative if a change is required. 2–40 4900002234 rev. A 11-12-14 Operating the Analyzer To scale the receiver’s output, the analyzer’s current loop output is forced to 4 mA (0%) and 20 mA (100%) using the 4-20 mA Test parameter. The receiver is adjusted to read “0” and “Full Scale,” respectively. Be sure to work in a non-hazardous area while handling any electrical connector. To scale the current loop signal: 1. Make sure the current loop is connected and the receiver is set for the analyzer to source the current. 2. Set the AO 4-20 mA Test parameter to 0% (see Table 2–1). 3. Enter Mode 5 by pressing the # key followed by the 5 key to force the loop current to 4 mA. 4. Adjust the receiver calibration control to read the appropriate value. A current loop output of 4 mA represents the value set in AO 4 mA Value. 5. Set the 4-20 mA Test parameter to 100%. 6. Enter Mode 5 by pressing the # key followed by the 5 key to force the loop current to 20 mA. 7. Adjust the receiver calibration controls for the appropriate value. A current loop output of 20 mA represents the value set in AO 20 mA Value. 8. If needed, repeat steps 2-7 to obtain an accurate calibration over the range. 9. After obtaining an accurate calibration of the current loop receiver, press the # key followed by the 1 key to return to Normal Mode. Every time the # key is pressed, the analyzer requires three to four minutes time upon returning to Mode 1, Mode 6, Mode 7 or Mode 8 to re-establish reference spectra before displaying a reading. Warnings Warning messages appear on the front panel LCD and are transmitted via RS232. Changes in flow conditions such as composition, temperature or pressure since the last scrubber/dryer cycle may produce a warning. Warnings may trigger a system re-start beginning with a fresh scrubber/dryer cycle. Warnings may include one or more of the following: Operator’s Manual 2–41 FS 5.15 Firmware • Dry P out of range: This warning occurs when the pressure in the sample cell during a dry cycle is out of range indicating that the scrubber/dryer may be clogged. • Delta T out of range: This warning occurs when the difference between the measured cell temperature during a wet cycle and the previous dry cycle is out of range. • Delta P out of range: This warning occurs when the difference between the measured cell pressure during a wet cycle and previous dry cycle is out of range. • DCdelta out of range: This warning occurs when the difference between the measured cell DC power during a wet cycle and previous dry cycle is out of range. • Fitting out of range: This warning occurs when the system is unable to adequately fit a curve to the measured signal typically as a result of too much noise in the signal or an unexpected gas mixture in the measurement cell. • R2 out of range: This warning occurs when reference 2 is out of range, typically as a result of too much of the gas component found in the measurement cell. • R3 out of range: This warning occurs when reference 3 is out of range, typically as a result of too much of the gas component found in the measurement cell. • Unable to do validation: This warning occurs if using a permeation validation system with the Daily Validation feature and the current analyzer concentration is beyond an allowable threshold. It is designed to protect the dryer from high concentrations, which can shorten its life cycle. This does not apply to validations that are initiated by the digital input, Mode 7, Mode 8 or Mode 2 Start Validation parameter. • Wet Peak Tracking/Dry Peak Tracking: This warning indicates when a peak tracking correction has occurred. • Ramp Adjust: This warning indicates when a ramp adjustment correction has occurred. Alarms The analyzer is equipped with three dry contact relays that indicate a system fault or alarm state, the General Fault Alarm relay, the user Assignable Alarm relay and the Validation Fail Alarm relay. Refer to the system drawings for this analyzer for relay assignments. In addition, alarm and fault messages appear on the front panel LCD and are transmitted via RS-232. 2–42 4900002234 rev. A 11-12-14 Operating the Analyzer System Faults The General Fault Alarm is triggered by system faults that cause the General Fault Alarm relay to be activated and the current loop to respond according to the 4-20mA Alarm Option setting. Once activated, the General Fault Alarm can be reset via the General Alarm DO parameter (see “Changing Measurement and Control Parameters” on page 2-11). System faults include one or more of the following: • DeltaDC Restart Alrm: This fault occurs when the number of consecutive system restarts caused by a difference between the measured DC signal during a wet cycle and the previous dry cycle exceeds a pre-set limit. • DeltaT Restart Alarm: This fault occurs when the number of consecutive system restarts caused by a difference between the measured cell temperature during a wet cycle and the previous dry cycle exceeds a pre-set limit. • Dry Pressure Restart Alarm: This fault occurs when the number of consecutive system restarts caused by an out of range dry pressure value exceeds a pre-set limit. • Fitting Restart Alarm: This fault occurs when the number of consecutive system restarts caused by the system’s inability to adequately fit a curve to the measured signal exceeds a pre-set limit. • Flow Switch Alarm: This fault occurs on systems with a digital input flow switch enabled and the digital input triggers the alarm state. • Laser Curnt Low Alrm: This fault occurs when the laser current goes below the minimum allowable indicating a potential problem with the laser. • Lasr Curnt High Alrm: This fault occurs when the laser current goes above the maximum allowable indicating a potential problem with the laser. • Laser Power High Alrm: This fault occurs when the DC signal is saturated typically as a result of the absence of absorbing gas in the sample cell. • Laser Power Low Alrm: This fault occurs when the DC signal becomes too weak for a reliable measurement typically as a result of mirror contamination. • Laser Zero High Alarm: This fault occurs if the detector signal value is above the set normal range when the laser is turned off. • Laser Zero Low Alarm: This fault occurs if the detector signal value is below the set normal range when the laser is turned off. • Low Purge Rate Alrm: This fault occurs when the scrubber/dryer is unable to remove the analyte being measured at a quick enough rate typically due to scrubber/dryer saturation. Operator’s Manual 2–43 FS 5.15 Firmware • New Scrubber Alarm: This fault occurs when the internal scrubber/dryer monitor signals that a new scrubber/dryer is necessary. • PeakTk Restart Alarm: This fault occurs when the number of consecutive system restarts caused by a peak tracking correction exceeds a pre-set limit. • Pressure High Alarm: This fault occurs when the pressure in the sample cell exceeds the specified maximum operating pressure. • Pressure Low Alarm: This fault occurs when the pressure in the sample cell is below the specified minimum operating pressure. • Pressure Restart Alarm: This fault occurs when the number of consecutive system restarts caused by a difference between the measured cell pressure during a wet cycle and the previous dry cycle exceeds a pre-set limit. • R2 Restart Alarm: This fault occurs when the number of consecutive system restarts caused when reference 2 is out of range, typically as a result of too much of the gas component found in the measurement cell. • R3 Restart Alarm: This fault occurs when the number of consecutive system restarts caused when reference 3 is out of range, typically as a result of too much of the gas component found in the measurement cell. • Ramp Adjust Restart Alarm: This fault occurs when the number of consecutive system restarts caused by a ramp adjustment exceeds a pre-set limit. • Temp High Alarm: This fault occurs when the temperature in the measurement cell exceeds the specified maximum operating temperature. • Temp Low Alarm: This fault occurs when the temperature in the measurement cell is below the specified minimum operating temperature. For systems with heated enclosures, a Temperature too Low or Temperature too High fault will activate the General Fault Alarm when the enclosure temperature is more than 5 C above or below the specified temperature (refer to the system specifications for this analyzer located in the Hardware Manual). Once the enclosure has reached the specified temperature, reset the General Fault Alarm (see “Changing Measurement and Control Parameters” on page 2-11). • 2–44 Validation 1 Failed/Validation 2 Failed Alarm: An additional alarm for systems equipped with autovalidation that is triggered when the measured concentration of the validation 1 or 2 gas does not agree with the user defined allowable limits. These alarms also trigger the Validation Fail dry contact relay. Refer to “Validation 4900002234 rev. A 11-12-14 Operating the Analyzer Allowance” on page 2-34. Once activated, the Validation Fail Alarm must be manually reset via the Cancel Val Alarms parameter (see “Cancel Val Alarms” on page 2-19). See Appendix B for recommendations and solutions to common firmware problems resulting in a system fault. User Alarms User alarms are generated based on measurement readings and their relation to Mode 2 parameter settings. They include the following: • Concentra High Alarm: This fault occurs when the measured concentration is above the limit set with the High Alarm Setpoint parameter (see “High Alarm Setpoint” on page 2-23). • Concentra Low Alarm: This fault occurs when the measured concentration is below the set limit with the Low Alarm Setpoint (see “Low Alarm Setpoint” on page 2-24). Historical Alarm Flag A Historical Alarm Flag code will also display on the LCD, as shown in Figure 2–2, and remain until the alarm is reset. ALARM CODE <NORMAL MODE 0000004> H2S: 5.036 ppmv P: 954.4mb T: 76.1F Figure 2–2 LCD display with alarm code visible indicating Pressure Low Alarm fault Table 2–4 lists the potential alarm codes and corresponding fault conditions. In the event of multiple alarms, the hexadecimal code from each alarm is added together to yield the Historical Alarm Flag code. For example, a Historical Alarm Flag code of 00C04 indicates that three alarms have occurred: 00004 Laser Power Low Alrm, 00400 Temp Low Alarm, and 00800 Temp High Alarm, where ‘C’ represents ‘12’ in hexadecimal notation. Table 2–4 Hex Value LCD display alarm codes Fault Condition 00000001 General fault condition exists or happened in the past 00000002 General fault condition exists (any alarm is active) 00000004 Laser Power Low Alrm Operator’s Manual 2–45 FS 5.15 Firmware Table 2-4 LCD display alarm codes (Continued) Hex Value 2–46 Fault Condition 00000008 Laser Powr High Alrm 00000010 Laser Zero Low Alarm 00000020 Laser Zero High Alrm 00000040 Laser Curnt Low Alrm 00000080 Lasr Curnt High Alrm 00000100 Pressure Low Alarm 00000200 Pressure High Alarm 00000400 Temp Low Alarm 00000800 Temp High Alarm 00001000 Concentra Low Alarm 00002000 Concentra High Alarm 00004000 PeakTk Restart Alarm 00008000 Fitting Restart Alrm 00010000 RampAdj Restart Alarm 00020000 Not Used 00040000 Not Used 00080000 Flow Switch Alarm 00100000 Validation Fail Alarm 1 00200000 Validation Fail Alarm 2 00400000 Not Used 00800000 Not Used 01000000 DeltaDC Restart Alrm 02000000 DeltaT Restart Alarm 04000000 Dry Pressure Alarm 08000000 New Scrubber Alarm 10000000 R2 Restart Alarm 20000000 R3 Restart Alarm 40000000 Pressure Restart Alarm 80000000 Low Purge Rate Alrm 4900002234 rev. A 11-12-14 Operating the Analyzer Assignable Alarm The functionality of the Assignable Alarm is determined by the DO Alarm Setup parameter set in Mode 2 according to Table 2–2. For example, the Assignable Alarm can be configured as a Concentra High Alarm or Concentra Low Alarm that is triggered when the measured concentration is above or below, respectively, the level set in Mode 2. A high concentration causes the Assignable Alarm relays to be activated and the message “Concentration High” to appear on the LCD. Validating the Analyzer Validation of the analyzer using an appropriate gas standard is automatically conducted at each Val Interval period at the Val Start Time, semiautomatically when initiated via the Validation DI or the Start Validation parameter, or manually by accessing Mode 7 or Mode 8. If using a permeation validation system with the Daily Validation feature, and the current analyzer concentration is beyond an allowable threshold, the analyzer will output a warning message of “Unable to do validation,” activate the Validation Fail alarm and not conduct the validation. The system is designed to protect the dryer from high concentrations, which can shorten its life cycle. This does not apply to validations that are initiated by the digital input Mode 7, Mode 8 or Mode 2 - Start Validation parameter. To validate automatically: 1. Verify that the validation gas source(s) has been properly installed and/or connected. 2. If necessary, set the current time, date, desired validation hour and validation interval (see Table 2–1 for parameter default values). 3. Set the Daily Validation parameter to 1. The analyzer should run a validation cycle at the number of days and hour set by Val Interval and the Val Start Time parameter. To validate semi-automatically: 1. Verify that the validation gas source(s) has been properly installed and/or connected. Operator’s Manual 2–47 FS 5.15 Firmware 2. Initiate a validation cycle by closing the contacts connected to the Validation DI input or by setting the Start Validation parameter to 1. The keypad is disabled when Validation DI is active. To validate manually: If the 4-20 mA Val Action parameter is set to 1, the 4-20 mA signal will output validation measurements and the appropriate relay (Val #1 Active or Val #2 Active) will be activated. During the automatic or semi-automatic validation, if the concentration measured does not fall within the allowable limits for the number of times defined by the Val Attempts parameter (see “Validation Allowance” on page 2-34), the Validation Fail Alarm relay will activate. Once activated, the Validation Fail Alarm must be manually canceled (see “Cancel Val Alarms” on page 2-19). Initiating a new automatic, semi-automatic or manual validation will clear the Validation Fail Alarm so that the new validation can determine its state. Once the validation completes, the analyzer requires three to four minutes upon returning to Mode 1 to re-establish reference spectra before displaying a reading. 1. Verify that the validation gas source(s) has been properly installed and/or connected. 2. Initiate validation measurements by pressing the # key followed by the 7 key (Mode 7) or the # key followed by the 8 key (Mode 8) for a dual validation system. 3. Once validation measurements are complete, press the # key followed by the 1 key (Mode 1) to return to Normal Mode and stop the validation. SpectraSensors recommends validating the analyzer using only the analyte mixed in the validation gas specified on the analyzer calibration report. A bottle of test gas with a certified concentration representing 50% of full scale) for single validation systems), or bottles representing 20% and 80% of full scale (for dual validation systems) are recommended. When procuring a gas standard, make sure the background gas is that specified or a mix that closely resembles the contents of the process stream and have the gas standard certified to better than the specified precision of the analyzer, if possible. 2–48 4900002234 rev. A 11-12-14 Operating the Analyzer Calibrating the Analyzer Calibrating the analyzer is typically not required under normal circumstances. SpectraSensors calibrates each analyzer to a National Institute of Standards and Technology (NIST) traceable standard before shipping the unit to the end user. Because SpectraSensors analyzers use a non-contact form of measurement, they are relatively insensitive to contamination, quite rugged and virtually maintenance free ensuring years of reliable service. Operator’s Manual 2–49 FS 5.15 Firmware THIS PAGE INTENTIONALLY LEFT BLANK 2–50 4900002234 rev. A 11-12-14 3 - SERIAL PORT COMMUNICATIONS Receiving Serial Data (Customer Port Output) When the Modbus Mode parameter is set to 0, the analyzer is configured to transfer a string of data from the analyzer to a serial device via the customer port output. The receiving device is typically a computer terminal running HyperTerminal, which is a program included with Microsoft® Windows® 95, 98, and XP that enables serial communication and the viewing, capturing and storage of serial port data and messages. To launch HyperTerminal: 1. On your Windows desktop, click Start followed by Run (usually located in the lower right side of the Start Menu). 2. Type Hypertrm.exe and hit Return to launch HyperTerminal. For faster access to HyperTerminal, save a HyperTerminal shortcut to the desktop. 3. Once HyperTerminal is activated, the Connection Description window appears, as shown in Figure 3–1. Type in a Filename (where the terminal session settings will be stored for future recall) and click on any icon. Click OK. 4. The Connect To window appears prompting for a connection, as shown in Figure 3–2. Click the Menu Arrow under Connect Using to view the choices. 5. Click on the appropriate port to which your analyzer is connected (COM1, COM2, COM3, etc.) as established under “To connect the signal and alarm cables” in the Hardware Manual. Click OK. 6. Once the port is chosen, the COM Properties window appears. Make sure the COM properties for the port selected reflect those shown in Figure 3–3 (19200 baud or as set in Mode 2, 8 data bits, 1 stop bit, no parity, and no flow control). 7. Click OK to establish the connection. Mode 1 Data String Once connected, the data will start streaming through the Hyperterminal Window as shown in Figure 3–4. Operator’s Manual 3–1 FS 5.15 Firmware Figure 3–1 Connection Description window Figure 3–2 Connect To window 3–2 4900002234 rev. A 11-12-14 Serial Port Communications Figure 3–3 COM Properties window Refer to data output headings in Figure 3–5; reading left to right Figure 3–4 Hyperterminal window with streaming data Operator’s Manual 3–3 FS 5.15 Firmware The data string is tab delimited (each row starting with a tab) forming 23 columns in the following order: 3–4 • • • Date: Current date (in MM:DD:YY). • Wet Temp (C): Current temperature (C) of the gas sample when normal sample gas is flowing. • Wet Pressure (mb): Current pressure (mb) of the gas sample when normal sample gas is flowing. • Dry Temp: Current temperature (0.0 for non-differential units) of the gas sample (in selected engineering units) when scrubbed sample gas is flowing. • Dry Pressure: Current pressure (0.0 for non-differential units) of the gas sample (in selected engineering units) when scrubbed sample is flowing. • Fit Residue: Value ranging from 0 to 1 indicating how well the measured spectrum fits the referenced spectrum, where 1 represents a perfect match. • Fit Ratio: Ratio of the measured spectrum versus the Reference 1 spectrum. • Dry DC: Signal level (laser intensity in counts, 0.0 for nondifferential units) at the high end of the current ramp during the dry cycle. • Wet DC: Signal level at the high end of the current ramp during the wet cycle. • • • Peak Index: Peak index of the measured spectrum. • Val Flg: Indicates current stream being measured (0 = Process, 1 = Val 1, 2 = Val 2). • Process Path Flg: Calculation path (reference spectra) used for the concentration calculation (0 = Process Reference Spectra, 1 = Validation Reference Spectra). • Current Midpoint: Current midpoint that the analyzer is using, including any peak tracking adjustments. • Fit Ratio 2: Ratio of the measured spectrum versus the Reference 2 spectrum, where a value of 0 indicates that the Reference 2 spectrum was not used in the calculation of concentration. Time: Current time (in HH:MM:SS). Concentration (ppmv): Current measured analyte/component concentration (ppmv). Ref Index: Peak index used for reference. Index Difference: Difference between measured and reference peak indices, where a value other than 0 indicates peak tracking is functioning. 4900002234 rev. A 11-12-14 Serial Port Communications • Fit Ratio 3: Ratio of the measured spectrum versus the Reference 3 spectrum, where a value of 0 indicates that the Reference 3 spectrum was not used in the calculation of concentration. • Fit Ratio 4: Ratio of the measured spectrum versus the Reference 4 spectrum, where a value of 0 indicates that the Reference 4 spectrum was not used in the calculation of concentration. • Fit Ratio 5: Ratio of the measured spectrum versus the Reference 5 spectrum, where a value of 0 indicates that the Reference 5 spectrum was not used in the calculation of concentration. • Fit Ratio Dry: Ratio of the measured spectrum versus the Reference Dry spectrum, where a value of 0 indicates that the Reference Dry spectrum was not used in the calculation of concentration. • Fit Ratio Dry-1: Ratio of the measured spectrum versus the Reference Dry spectrum shifted by 1 index value, where a value of 0 indicates that the Reference Dry spectrum shifted by 1 index value was not used in the calculation of concentration. • Alarm Flags: Value representing the status of each individual alarm in the analyzer, as listed in Table 2–2. Any alarm messages will be transmitted along with the data string and will appear in a separate row. The number of seconds between each line of data output should be the # Spectrum Average number set in Mode 2 divided by 4. The factory default setting of 16 for # Spectrum Average results in a line of output each 4 seconds. To capture and save data from the serial port: 1. To save the data from the serial port, use the Transfer/Capture Text function and enter the Filename to where you would like to store the captured data. 2. To stop the capture of the serial data, click on Transfer/Capture Text/Stop. To read diagnostic data with HyperTerminal: 1. Before entering Mode 6, make sure the serial port on the computer used for serial communication is connected to the analyzer and the output stream is showing on the screen as described under “To launch HyperTerminal” on page 3-1. 2. To save the data from the serial port, use the Transfer/Capture Text function and enter the Filename to where you would like to store the captured data. Operator’s Manual 3–5 FS 5.15 Firmware 3. Once capturing is in place, enter Mode 6 by pressing # key followed by the 6 key. # + 6 <DUMP SPECTRUM MODE> Index: 0 Cycle: 1 of 10 The index shown on the LCD display counts by 50’s from 0 to 511. The analyzer will repetitively output this information until the # button is pressed or the number of cycles completes. At the end of the data dump, the screen will display: MODE 4. Press the # key followed by the 1 key to return to Mode 1. 5. Once normal operation resumes, stop the capture of the serial data. To stop the capture of the serial data, click on Transfer/Capture Text/Stop. The resulting data file contains the downloaded data as shown in Figure 3–5. Mode 6 Data The 20 columns of tab delimited data in the file resulting from a Mode 6 data dump are labeled as follows: 3–6 • • • • • • • Index: Index value of points on spectrum scan curve. • 2f Wet: Wet AC spectrum of sample gas. DC Dry: Dry DC spectrum of sample gas. DC Dry Ref 1: Reference 1 dry DC spectrum. DC Wet: Wet DC spectrum of sample gas. DC Wet Ref 1: Reference 1 wet DC spectrum. 2f Dry: Dry AC spectrum of sample gas. 2f Dry Ref 1 Pdry/Pwet: Reference 1 dry AC spectrum based on dry pressure. 4900002234 rev. A 11-12-14 Operator’s Manual Serial Port Communications 3–7 Figure 3–5 Sample diagnostic data output FS 5.15 Firmware • 2f Wet Ref 1 Pwet: Reference 1 wet AC spectrum based on wet pressure. • • • • • • • • • 2f: AC spectrum of sample gas. • 2f Wet Ref Val Pwet: Reference Validation wet AC spectrum based on wet pressure. • 2f Composite: Recreated AC spectrum based on the reference curve fitting ratios. Ref 1: Reference 1 AC spectrum. Ref 2: Reference 2 AC spectrum. Ref 3: Reference 3 AC spectrum. Ref 4: Reference 4 AC spectrum. Ref 0: Reference 0 AC spectrum. Ref 0 RT: Reference 0 real-time AC spectrum. Ref Val: Reference Validation AC spectrum. 2f Dry Ref Val Pdry/Pwet: Reference Validation dry AC spectrum based on dry pressure. Viewing Diagnostic Data with Microsoft Excel A spreadsheet program such as Microsoft Excel can import the data collected in the Mode 6 data dump for viewing and plotting. To import the data file into Excel: 1. In Excel, click Open and choose the name of the spectrum file saved while in Mode 6. Be sure to select All Files (*.*) under Files of type: while searching, as shown in Figure 3–6. 2. The Text Import Wizard should open. Choose the Delimited option and click Next, as shown in Figure 3–7. 3. Under Delimiters, choose the Tab and Space options, check the Treat Consecutive Delimiters as One box, as shown in Figure 3–8, and then click Finish to display the spreadsheet. The first few lines look like the normal serial output data received before the Mode 6 command was entered. Look for the three columns of numbers at the bottom of the file. 4. Click on the upper right cell of the three columns, as shown in Figure 3–9. Hold the Shift key down while pressing the End key followed by the Down Arrow key to highlight the third column. Keep holding down the Shift key and press the End key followed by the Left Arrow key to select the three columns by 512 rows. 3–8 4900002234 rev. A 11-12-14 Serial Port Communications Figure 3–6 Opening a data file in Excel Figure 3–7 Setting data type in Text Import Wizard Operator’s Manual 3–9 FS 5.15 Firmware Figure 3–8 Setting Tab and Space as delimiters Figure 3–9 Highlighting imported data for plotting in Excel 5. Click the Chart Wizard button on the Task Bar. The Chart Wizard should open, as shown in Figure 3–10. 3–10 4900002234 rev. A 11-12-14 Serial Port Communications Figure 3–10 Chart Wizard - Step 1 window 6. Choose the X-Y (Scatter) chart type and the Smoothed Lines Without Markers sub-type. Click Finish to display a graph of the spectrum, as shown in Figure 3–11. 3000 250 2500 200 2000 150 100 1500 50 1000 0 500 -50 0 -500 0 Figure 3–11 7. Series1 Series2 200 400 -100 600-150 Data file plot in Excel If the 2f curve appears flat, double click on it to get to the Format Data Series Window, as shown in Figure 3–12. Select the Axis tab, and select Plot Series on Secondary Axis. Click OK to rescale the plot. Operator’s Manual 3–11 FS 5.15 Firmware Figure 3–12 Format Data Series window Modbus Communications Protocol Modbus is a serial communications protocol published by Modicon in 1979 for use with its programmable logic controllers (PLCs). It has become a de facto standard communications protocol in industry, and is now the most commonly available means of connecting industrial electronic devices. Modbus is used extensively in lieu of other communications protocols because it is openly published and royalty-free, relatively easy to deploy, and capable of moving raw bits or words without placing many restrictions on vendors. Modbus enables communication between many devices connected to the same network, for example, a supervisory computer with a remote terminal unit (RTU) in supervisory control and data acquisition (SCADA) systems. The SpectraSensors analyzer acts as a slave in a master/slave(s) network of devices. It can receive queries from a master and send responses back using either Gould Modbus RTU protocol or Daniel Extended Modbus RTU protocol. Framing/Protocol The transmission mode used to communicate is either Gould Modbus RTU or Daniel Modbus RTU with port parameters 9600 to 115200 (baud rate), 8 (data bits), 1 (stop bit), no (parity), and none (flow control/handshake). The transmission mode is set by the user via the Modbus Mode parameter (see “To change parameters in Mode 2” on page 2-15). Note that the 3–12 4900002234 rev. A 11-12-14 Serial Port Communications generic serial output (HyperTerminal) is disabled if either Gould or Daniel Modbus is selected. Functions Available functions are 0x03 (read holding registers), 0x06 (write to a single register), 0x10 (write to multiple registers), and 0x2B (read device identification). Addressing The analyzer's Modbus slave node address can be in the range of 0-250 with the default being 1. All analyzers will respond to an address of 0, so this address can be used to interrogate a single unit when its address is unknown or to determine its address. See Table 3–1 on page 3–15 for register definitions for both Gould and Daniel Modbus modes. Be aware that for Gould Modbus the table follows the convention of identifying the register with an offset of 40001. Therefore, the actual value transmitted in the starting register field of the command is the listed register value minus 40001 (e.g., register 47001 is addressed as 7000). Reading/Writing in Daniel Modbus Mode Daniel Modbus supports three types of registers: short integer, long integer and floating point. Each “short integer” register is two bytes in length and will contain an integer value. Each “long integer” register is four bytes in length and will contain an integer value and each “floating point” register is four bytes in length and will contain a floating point value. Reading/Writing in Gould Modbus Mode Gould Modbus supports three types of variable data, short integer, long integer and floating point, but all registers are addressed as word (two byte) registers. A “short integer” value is contained in one register whereas a “long integer” or “floating point” value requires two contiguous registers. The registers are defined as Read or Read/Write. Use caution when writing to registers as changing the value of a writable register may affect the calibration of the analyzer. An appropriate password must be downloaded to the password register prior to writing to most registers. The User Level 1 (L1) user password 3142 will allow access to those registers which have been pre-defined as user configurable. Other writable registers can only be downloaded or changed by SpectraSensors support personnel using a User Level 2 (L2) password. Operator’s Manual 3–13 FS 5.15 Firmware Endianness Endianness, often referred to as byte order, is the ordering of individually addressable sub-units (words, bytes, or even bits) within a longer data word. Byte orders with the most versus least significant byte first are called bigendian and little-endian, respectively. In SpectraSensors analyzers, all bytes are stored big-endian. Thus, for floating point and long-integer data types, the byte order will look like: HighWord-HighByte HighWord-LowByte LowWord-HighByte LowWord-LowByte Note that floating point values follow the IEEE Standard for Floating-Point Arithmetic (IEEE 754-2008). To enable Modbus communications: 1. Confirm that the serial cable has been properly connected (see “Connecting the Signals and Alarms” in the Hardware Manual). 2. Power up the analyzer (see “Powering Up the Analyzer” on page 2-1). 3. Enter Mode 2 by pressing the # key followed by the 2 key. <SET PARAMETER MODE> Enter password: FS 5.15-XXXX The LCD prompts for a numeric password. Enter the user password (3142) on the keypad, then press the * key to enter the number to enter Mode 2 (Set Parameter Mode). <SET PARAMETER MODE> Process Purge Time 60 Enter a value(secs) 4. Press the * key repeatedly until the Modbus Address parameter is displayed. <SET PARAMETER MODE> Modbus Address 1 Enter node (1-250) 3–14 4900002234 rev. A 11-12-14 Serial Port Communications 5. Enter the desired Modbus Address and press the * key to store the value and cycle to the Modbus Mode parameter. <SET PARAMETER MODE> Modbus Mode 0 0:Off 1:GMR 2:DMR 6. Enter the desired Modbus Mode and press the * key to store the value (see “To change parameters in Mode 2” on page 2-15). 7. Enter the 2 Way Com Port assignment and press the * key to store the value. <SET PARAMETER MODE> 2 Way Com Port 1 0:Off1:Cus2:Ser3:Eth 8. Press the # key followed by the 1 key to return to Mode 1.The analyzer is now ready to receive Modbus queries. Table 3–1 Modbus register map Parameter Daniel Reg. Gould Reg. Data Type Action Min. Max. Concentration Process 7001 47001 Float Read - - Temperature 7002 47003 Float Read - - Pressure 7003 47005 Float Read - - Concentration ppmv 7004 47007 Float Read - - Wet Temp C 7005 47009 Float Read - - Wet Pressure mb 7006 47011 Float Read - - Fit Residue 7007 47013 Float Read - - Current Midpoint 7008 47015 Float Read - - Dew Point 7009 47017 Float Read - - DC Level 7010 47019 Float Read - - Zero Level 7011 47021 Float Read - - 4-20 mA Output Value 7012 47023 Float Read - - 4-20 mA Input Value 7013 47025 Float Read - - RATA Mult Proposed 7014 47027 Float Read - - RATA Offset Proposed 7015 47029 Float Read - - Operator’s Manual 3–15 FS 5.15 Firmware Table 3-1 Modbus register map (Continued) Daniel Reg. Gould Reg. Data Type Action Min. Max. Conc Process ppmv 7016 47031 Float Read - - Concentration 7017 47033 Float Read - - Val Date 7026 47051 Float Read - - Val Time 7027 47053 Float Read - - Val 1 Value 7028 47055 Float Read - - Val 2 Value 7029 47057 Float Read - - Val 1 Value ppmv 7030 47059 Float Read - - Val 2 Value ppmv 7031 47061 Float Read - - Val 1 Avg Value 7032 47063 Float Read - - Val 1 Avg Value ppmv 7033 47065 Float Read - - Val 1 Min Value ppmv 7034 47067 Float Read - - Val 1 Max Value ppmv 7035 47069 Float Read - - Val 2 Avg Value 7036 47071 Float Read - - Val 2 Avg Value ppmv 7037 47073 Float Read - - Val 2 Min Value ppmv 7038 47075 Float Read - - Val 2 Max Value ppmv 7039 47077 Float Read - - Dry Temp C 7041 47081 Float Read - - Dry Pressure mb 7042 47083 Float Read - - Dry DC Level 7043 47085 Float Read - - Scrubber Life Left 7044 47087 Float Read - - Common Weight 7051 47101 Float Read - - Fitting Ratio 7052 47103 Float Read - - Fitting Ratio 2 7053 47105 Float Read - - Fitting Ratio 3 7054 47107 Float Read - - Fitting Ratio 4 7055 47109 Float Read - - Fitting Ratio 5 7056 47111 Float Read - - Fitting Ratio Dry 7057 47113 Float Read - - Fitting Ratio Dry-1 7058 47115 Float Read - - Cross Shift 7060 47119 Float Read - - Peak Track Index 7061 47121 Float Read - - Peak Index Ref 7062 47123 Float Read - - Peak Track Index Dry 7091 47181 Float Read - - Parameter 3–16 4900002234 rev. A 11-12-14 Serial Port Communications Table 3-1 Modbus register map (Continued) Daniel Reg. Gould Reg. Data Type Action Min. Max. Peak Index Ref Dry 7092 47183 Float Read - - RATA Multiplier 7101 47201 Float R/W L1 -1.00E+06 1.00E+06 RATA Offset 7102 47203 Float R/W L1 -1.00E+06 1.00E+06 Low Alarm Setpoint 7103 47205 Float R/W L1 -1.00E+06 1.00E+06 High Alarm Setpoint 7104 47207 Float R/W L1 -1.00E+06 1.00E+06 AO 4 mA Value 7105 47209 Float R/W L1 0 1.00E+05 AO 20 mA Value 7106 47211 Float R/W L1 0 1.00E+05 AO 4-20 mA Test 7107 47213 Float R/W L1 0 100 AI 4 mA Value 7108 47215 Float R/W L1 0 499999 AI 20 mA Value 7109 47217 Float R/W L1 0 499999 Val 1 Concentration 7110 47219 Float R/W L1 0 1.00E+06 Val 2 Concentration 7111 47221 Float R/W L1 0 1.00E+06 Validation Allowance 7112 47223 Float R/W L1 0 100 Zero Val Tolerance 7113 47225 Float R/W L1 0 1.00E+06 Pipeline Pressure 7125 47249 Float R/W L1 5000 499999 Methane 7126 47251 Float R/W L1 0 1 Ethane 7127 47253 Float R/W L1 0 1 Nitrogen 7128 47255 Float R/W L1 0 1 Carbon Dioxide 7129 47257 Float R/W L1 0 1 Propane 7130 47259 Float R/W L1 0 1 I-Butane 7131 47261 Float R/W L1 0 1 N-Butane 7132 47263 Float R/W L1 0 1 Neo-Pentane 7133 47265 Float R/W L1 0 1 I-Pentane 7134 47267 Float R/W L1 0 1 N-Pentane 7135 47269 Float R/W L1 0 1 Hexane 7136 47271 Float R/W L1 0 1 ppmv ConvFactor 00 7139 47277 Float R/W L1 0 1.00E+06 lb ConvFactor 01 7140 47279 Float R/W L1 0 1.00E+06 % ConvFactor 02 7141 47281 Float R/W L1 0 1.00E+06 mg ConvFactor 03 7142 47283 Float R/W L1 0 1.00E+06 ppmw ConvFactor 04 7143 47285 Float R/W L1 0 1.00E+06 ppbv ConvFactor 05 7144 47287 Float R/W L1 0 1.00E+06 Parameter Operator’s Manual 3–17 FS 5.15 Firmware Table 3-1 Modbus register map (Continued) Daniel Reg. Gould Reg. Data Type Action Min. Max. ppbw ConvFactor 06 7145 47289 Float R/W L1 0 1.00E+06 grn ConvFactor 07 7146 47291 Float R/W L1 0 1.00E+06 user ConvFactor 08 7147 47293 Float R/W L1 0 1.00E+06 Val Perm Constant Kp 7212 47423 Float R/W L1 0 1.00E+06 Val Perm Rate Rp 7213 47425 Float R/W L1 0 1.00E+06 Alarm Flags 5001 45001 Long Read - - Status Flags 5002 45003 Long Read - - DO Alarm Setup 5101 45201 Long R/W L1 0 4.29E+09 user EU Tag Part 1 5102 45203 Long R/W L1 0 4.29E+09 user EU Tag Part 2 5103 45205 Long R/W L1 0 4.29E+09 Serial Date 3001 43001 Integer Read - - Serial Number 3002 43002 Integer Read - - Scrubber Days Left 3081 43081 Integer Read - - Current 2F Flag 3103 43103 Integer Read - - Logger Rate 3202 43202 Integer R/W L1 1 1000 4-20 mA Alarm Action 3204 43204 Integer R/W L1 0 3 Temperature Unit 3205 43205 Integer R/W L1 0 1 Pressure Unit 3206 43206 Integer R/W L1 0 3 Concentration Unit 3207 43207 Integer R/W L1 0 8 Modbus Address 3208 43208 Integer R/W L1 0 250 Modbus Mode 3209 43209 Integer R/W L1 0 2 AI Pressure Input 3210 43210 Integer R/W L1 0 1 RATA 3211 43211 Integer R/W L1 0 1 New Scrub Installed 3212 43212 Integer R/W L1 0 1 General Alarm DO 3213 43213 Integer R/W L1 0 2 Baud Rate 3214 43214 Integer R/W L1 0 4 Set Time - Year 3215 43215 Integer R/W L1 2007 2143 Set Time - Month 3216 43216 Integer R/W L1 1 12 Set Time - Day 3217 43217 Integer R/W L1 1 31 Set Time - Hour 3218 43218 Integer R/W L1 0 23 Set Time - Minute 3219 43219 Integer R/W L1 0 59 Cancel Val Alarms 3220 43220 Integer R/W L1 0 1 Parameter 3–18 4900002234 rev. A 11-12-14 Serial Port Communications Table 3-1 Modbus register map (Continued) Daniel Reg. Gould Reg. Data Type Action Min. Max. Daily Validation 3221 43221 Integer R/W L1 0 1 Val Start Time 3222 43222 Integer R/W L1 0 23 Val Interval 3223 43223 Integer R/W L1 1 400 Start Validation 3224 43224 Integer R/W L1 0 1 Val Purge Period 3225 43225 Integer R/W L1 0 4000 Val Duration 3226 43226 Integer R/W L1 0 8000 Val Attempts 3227 43227 Integer R/W L1 1 8000 4-20 mA Val Action 3228 43228 Integer R/W L1 0 1 Val Auto DumpSpectrm 3230 43230 Integer R/W L1 0 1 Update RATA 3231 43231 Integer R/W L1 0 1 Stream Switch ID 3232 43232 Integer R/W L1 0 10 Stream Switch 3233 43233 Integer R/W L1 0 1 Conversion Type 3251 43251 Integer R/W L1 0 1 Calculate Dew Point 3252 43252 Integer R/W L1 0 2 Dew Point Method 3253 43253 Integer R/W L1 0 3 2 Way Com Port 3365 43365 Integer R/W L1 0 3 Keypad Watchdog 3368 43368 Integer R/W L1 0 9999 Rapid Change Monitor 3402 43402 Integer R/W L1 0 1 Process Purge Time 3408 43408 Integer R/W L1 60 9999 Custom Precision 3413 43413 Integer R/W L1 0 5 Peak Tracking 3419 43419 Integer R/W L1 0 2 Operator Password 3501 43501 Integer R/W L1 0 9999 Operator Parameter01 3502 43502 Integer R/W L1 0 286 Operator Parameter02 3503 43503 Integer R/W L1 0 286 Operator Parameter03 3504 43504 Integer R/W L1 0 286 Operator Parameter04 3505 43505 Integer R/W L1 0 286 Operator Parameter05 3506 43506 Integer R/W L1 0 286 Operator Parameter06 3507 43507 Integer R/W L1 0 286 Operator Parameter07 3508 43508 Integer R/W L1 0 286 Operator Parameter08 3509 43509 Integer R/W L1 0 286 Operator Parameter09 3510 43510 Integer R/W L1 0 286 Parameter Operator’s Manual 3–19 FS 5.15 Firmware Table 3-1 Modbus register map (Continued) Parameter Daniel Reg. Gould Reg. Data Type Action Min. Max. Operator Parameter10 3511 43511 Integer R/W L1 0 286 Operator Parameter11 3512 43512 Integer R/W L1 0 286 Operator Parameter12 3513 43513 Integer R/W L1 0 286 Operator Parameter13 3514 43514 Integer R/W L1 0 286 Operator Parameter14 3515 43515 Integer R/W L1 0 286 Operator Parameter15 3516 43516 Integer R/W L1 0 286 Operator Parameter16 3517 43517 Integer R/W L1 0 286 Operator Parameter17 3518 43518 Integer R/W L1 0 286 Operator Parameter18 3519 43519 Integer R/W L1 0 286 Operator Parameter19 3520 43520 Integer R/W L1 0 286 Operator Parameter20 3521 43521 Integer R/W L1 0 286 Password 4999 44999 Integer R/W L0 0 9999 Modbus Accessible Parameter Definitions For definitions of the Modbus accessible parameters shown in “Modbus register map” on page 3-15, see below. For more detailed information, refer to “Measurement and Control Parameters Defined” on page 2-15. 3–20 • % ConvFactor 02: Sets a custom conversion factor when the parameter Concentration Unit = 2 (%) and this value is greater than 0.0. When it is equal to 0.0, the default conversion factor is used. • 2 Way Com Port: Sets the port that allows two-way communications, including Modbus and the diagnostic protocol. • 4-20 mA Alarm Action: Determines the current loop state upon an alarm condition. • 4-20 mA Input Value: The current value of the 4-20 mA input for pipeline pressure in mA’s. • 4-20 mA Output Value: The current value of the 4-20 mA output for concentration in mA’s. • 4-20 mA Val Action: Sets the operation mode of the 4-20 mA current loop during validation cycles. • AI 4 mA Value: Sets the pipeline pressure (in mbar) corresponding to a 4 mA current loop input. • AI 20 mA Value: Sets the pipeline pressure (in mbar) corresponding to a 20 mA current loop input. 4900002234 rev. A 11-12-14 Serial Port Communications • AI Pressure Input: Enables or disables the analog input pipeline pressure capability. • AO 4mA Value: Sets the concentration (in ppmv) or dew point temperature (in degrees Celsius or Fahrenheit) corresponding to a 4 mA current loop output. • AO 20mA Value: Sets the concentration (in ppmv) or dew point temperature (in degrees Celsius or Fahrenheit) corresponding to a 20 mA current loop output. • AO 4-20 mA Test: Sets the 4-20 mA output to a percentage of full scale when in Mode 5. • Alarm Flags: Long integer register identifying the current status of each individual alarm in the analyzer, as shown in Table 2–4. • • Baud Rate: Sets the baud rate for the customer port. • • Cancel Val Alarms: Cancels all validation alarms once activated. • Common Weight: Ratio of the measured spectrum that did not match a reference spectrum. • Concentration: Current measured (live) analyte concentration (process or validation) in selected engineering units. • Concentration ppmv: Current measured (live) analyte concentration (process or validation) in parts per million by volume (ppmv). • Concentration Process: Measured analyte concentration (process or validation) of last process reading in selected engineering units. • Conc Process ppmv: Measured analyte concentration of last process reading in parts per million by volume (ppmv). • Concentration Unit: Sets the display units for the measured concentration. • Conversion Type: Sets the type of relations (ideal or real gas) used in the dew point calculation [0 for ideal gas relations or 1 for real gas relations (Z calculated using Peng-Robinson EOS)]. For a full description of the conversions, see “Water Correlation” on page A-1. • Cross Shift: The amount of shift applied to match the measured spectrum to the reference spectrum when using Cross Correlation. • Current 2F Flag: Displays the current scrubber protection usage level: 0 = standard protection (used for non-differential units), 1 = mid protection, 2 = high protection, 3 = max protection (no usage). Calculate Dew Point: Enables the calculation of the dew point value and controls where the value will be output. Carbon Dioxide: Sets the mole fraction of carbon dioxide in the dry gas mixture that is used when calculating the dew point temperature per ISO 18453:2006. The default value corresponds to natural gas mixture NG3 of Table A–5 on page A–12. Operator’s Manual 3–21 FS 5.15 Firmware 3–22 • Current Midpoint: Current midpoint that the analyzer is using, including any peak tracking adjustments. • Custom Precision: Sets the number of viewable digits to the right of the decimal point. • • • Daily Validation: Enables or disables the autovalidation feature. • Dew Point Method: Sets the type of dew point calculation to be performed when Calculate Dew Point is enabled. • • DO Alarm Setup: Sets the functionality of the Assignable Alarm. • Dry Pressure mb: Current measured dry pressure of the gas sample in millibar (mb) • Dry Temp C: Current measured dry temperature of the gas sample in degrees in Celsius. • Ethane: Sets the mole fraction of ethane in the dry gas mixture used when calculating the dew point temperature per ISO 18453:2006. The default value corresponds to natural gas mixture NG3 of Table A–5 on page A–12. • Fit Residue: Value ranging from 0 to 1 indicating how well the measured spectrum fit the referenced spectrum, where 1 represents a perfect match. • Fitting Ratio: Ratio of the measured spectrum versus the Reference 1 or Validation spectrum. • Fitting Ratio 2: Ratio of the measured spectrum versus the Reference 2 spectrum, where a value of 0 indicates that the Reference 2 spectrum was not used in the calculation of concentration. • Fitting Ratio 3: Ratio of the measured spectrum versus the Reference 3 spectrum, where a value of 0 indicates that the Reference 3 spectrum was not used in the calculation of concentration. • Fitting Ratio 4: Ratio of the measured spectrum versus the Reference 4 spectrum, where a value of 0 indicates that the Reference 4 spectrum was not used in the calculation of concentration. • Fitting Ratio 5: Ratio of the measured spectrum versus the Reference 5 spectrum, where a value of 0 indicates that the Reference 5 spectrum was not used in the calculation of concentration. DC Level: Signal level at the high end of the current ramp. Dew Point: Measured analyte concentration of last process reading as a moisture dew point. Dry DC Level: Signal level at the high end of the current ramp during the dry cycle. 4900002234 rev. A 11-12-14 Serial Port Communications • Fitting Ratio Dry: Ratio of the measured spectrum versus the Reference Dry spectrum, where a value of 0 indicates that the Reference Dry spectrum was not used in the calculation of concentration. • Fitting Ratio Dry-1: Ratio of the measured spectrum versus the Reference Dry spectrum shifted by 1 index value, where a value of 0 indicates that the Reference Dry spectrum shifted by 1 index value was not used in the calculation of concentration. • General Alarm DO: Sets the operation of the general alarm relay digital output when a general fault alarm occurs. • grn ConvFactor 07: Sets a custom conversion factor when the parameter Concentration Unit = 7 (grains/100scf) and this value is greater than 0.0. The default conversion factor is used when it is equal to 0.0. • High Alarm Setpoint: Determines the concentration threshold above which the Concentra High Alarm will be triggered. • Hexane: Sets the mole fraction of hexane in the dry gas mixture used when calculating the dew point temperature per ISO 18453:2006. The default value corresponds to natural gas mixture NG3 of Table A–5 on page A–12. • I-Butane: Sets the mole fraction of i-butane in the dry gas mixture used when calculating the dew point temperature per ISO 18453:2006. The default value corresponds to natural gas mixture NG3 of Table A–5 on page A–12. • I-Pentane: Sets the mole fraction of i-pentane in the dry gas mixture used when calculating the dew point temperature per ISO 18453:2006. The default value corresponds to natural gas mixture NG3 of Table A–5 on page A–12. • Keypad Watchdog: Sets the allowable time (in seconds) that the analyzer can be on the MODE screen and the Mode 2 (Set Parameter Mode) password screen before automatically reverting to Mode 1 (Normal Mode). • lb ConvFactor 01: Sets a custom conversion factor when the parameter Concentration Unit = 1 (lbs/MMscf) and this value is greater than 0.0. The default conversion factor is used when it is equal to 0.0. • Logger Rate: Sets the number of measurements included in the running average. • Low Alarm Setpoint: Determines the concentration threshold below which the Concentra Low Alarm will be triggered. • Methane: Sets the mole fraction of methane in the dry gas mixture used when calculating the dew point temperature per ISO 18453:2006. The default value corresponds to natural gas mixture NG3 of Table A–5 on page A–12. Operator’s Manual 3–23 FS 5.15 Firmware 3–24 • mg ConvFactor 03: Sets a custom conversion factor when the parameter Concentration Unit = 3 (mg/Nm3) and this value is greater than 0.0. The default conversion factor is used when it is equal to 0.0. • Modbus Address: Sets the analyzer address when the analyzer is used as a Modbus slave device. • Modbus Mode: Sets the communications protocol for the port selected by the 2 Way Com Port parameter. • N-Butane: Sets the mole fraction of n-butane in the dry gas mixture used when calculating the dew point temperature per ISO 18453:2006. The default value corresponds to natural gas mixture NG3 of Table A–5 on page A–12. • N-Pentane: Sets the mole fraction of n-pentane in the dry gas mixture used when calculating the dew point temperature per ISO 18453:2006. The default value corresponds to natural gas mixture NG3 of Table A–5 on page A–12. • Neo-Pentane: Sets the mole fraction of neo-pentane in the dry gas mixture used when calculating the dew point temperature per ISO 18453:2006. The default value corresponds to natural gas mixture NG3 of Table A–5 on page A–12. • New Scrub Installed: Resets the scrubber/dryer alarm once activated, and the scrubber/dryer lifetime monitor. • Nitrogen: Sets the mole fraction of nitrogen in the dry gas mixture used when calculating the dew point temperature per ISO 18453:2006. The default value corresponds to natural gas mixture NG3 of Table A–5 on page A–12. • Operator Parameter01 - Operator Parameter20: Parameter indices for parameters to be viewed through the Operator Parameter section. • Operator Password: Sets a password for the Operator Parameter section. • Password: Required to access the system to download (i.e., change) register settings. • • Peak Index Ref: Peak index used for reference. • • Peak Track Index: Peak index of the measured spectrum. • Peak Tracking: A software utility that periodically adjusts the laser current to keep the absorption peak of the measured component at a known location. Peak Index Ref Dry: Peak index (0.0 for non-differential units) used for reference from the last scrubber cycle. Peak Track Index Dry: Peak index (0.0 for non-differential units) of the measured spectrum from the last scrubber cycle. 4900002234 rev. A 11-12-14 Serial Port Communications • Pipeline Pressure: Sets the pipeline pressure (in mbar) in the current dew point calculation or, if enabled, displays the current pipeline pressure input through the AI Pressure Input. • ppbv ConvFactor 05: Sets a custom conversion factor when the parameter Concentration Unit = 5 (ppbv) and this value is greater than 0.0. When it is equal to 0.0, the default conversion factor is used. • ppbw ConvFactor 06: Sets a custom conversion factor when the parameter Concentration Unit = 6 (ppbw) and this value is greater than 0.0. When it is equal to 0.0, the default conversion factor is used. • ppmv ConvFactor 00: Sets a custom conversion factor when the parameter Concentration Unit = 0 (ppmv) and this value is greater than 0.0. The default conversion factor is used when it is equal to 0.0. • ppmw ConvFactor 04: Sets a custom conversion factor when the parameter Concentration Unit = 4 (ppmw) and this value is greater than 0.0. The default conversion factor is used when it is equal to 0.0. • Pressure: Current measured (live) wet pressure reading of the gas sample in selected engineering units. • Pressure Unit: Designates the display units for the measured absolute pressure in the cell. • Propane: Sets the mole fraction of propane in the dry gas mixture used when calculating the dew point temperature per ISO 18453:2006. The default value corresponds to natural gas mixture NG3 of Table A–5 on page A–12. • Process Purge Time: Sets the time in seconds that the analyzer will purge the system with process gas before starting a dry cycle when switching to the process stream after a validation. • Rapid Change Monitor: Enables or disables the dynamic logger rate based on the concentration rate of change. • RATA: Enables or disables user definable values that allow adjustment (without affecting the factory calibration) of the analyzer reading in the field. • RATA Multiplier: User definable value that enables adjustment (without affecting the factory calibration) of the analyzer response (or slope) in the field. • RATA Mult Proposed: The latest proposed RATA multiplier value calculated based on the last validation run. • RATA Offset: User definable value that enables adjustment (without affecting the factory calibration) of the analyzer offset in the field. • RATA Offset Proposed: The latest proposed RATA offset value calculated based on the last validation run. Operator’s Manual 3–25 FS 5.15 Firmware • Scrubber Days Left: The remaining scrubber life in days. A fresh scrubber will start at a predetermined number of days and will count down to 0. • Scrubber Life Left: The remaining scrubber life in percentage. A fresh scrubber will start at 100% and will decline to 0% when fully exhausted. • • • Serial Date: Date the analyzer was calibrated. • Set Time - Hour: Sets the current hour for the clock driving daily validations. • Set Time - Minute: Sets the current minute for the clock driving daily validations. • Set Time - Month: Sets the current month for the clock driving daily validations. • Set Time - Year: Sets the current year for the clock driving daily validations. • • Start Validation: Initiates the validation cycle. Serial Number: Serial number of the analyzer. Set Time - Day: Sets the current day for the clock driving daily validations. Status Flags: Long integer register identifying the occurrence of various events in the analyzer, as shown in Table 3–2. Table 3–2 Status flags • 3–26 Bit Hex Value 0 00001 Current measurement valid (wet cycle active) 1 00002 Wet purging complete, wet measurement in progress 2 00004 Wet purging in progress 3 00008 Dry purging complete, dry measurement in progress 4 00010 Dry purging in progress 5 00020 Validation Mode 6 00040 Validation Flag 1 7 00080 Validation Flag 2 8 00100 Validation 1 Fail Flag 9 00200 Validation 2 Fail Flag Status Stream Switch ID: The stream ID that matches the stream being switched to by the Stream Switch parameter. 4900002234 rev. A 11-12-14 Serial Port Communications • Stream Switch: If the current value is ‘0’, then setting to ‘1’ allows a stream switch to occur by starting the analyzer's Process Purge Time followed by a scrubber cycle. The value will remain at ‘1’ until the first concentration value is output at which point it will return to ‘0’. If the current value is ‘1’, then this value does not accept any changes. • Temperature: Current measured (live) wet temperature of the gas sample in selected engineering units. • Temperature Unit: Designates the display units for the measured cell temperature. • Update RATA: When set to ‘1’ stores the latest proposed RATA multiplier and offset values in the RATA Multiplier and RATA Offset parameters, respectively. • user ConvFactor 08: Sets a custom conversion factor when the parameter Concentration Unit = 8 (user EU Tag Part 1 and 2) and this value is greater than 0.0. The default conversion factor is used when it is equal to 0.0. • user EU Tag Part 1: Sets a custom engineering unit tag name for the beginning four ASCII characters. For example: A is ASCII hex value 41, so AAAA would be 41414141, which would be 1,094,795,585 in decimal format. Refer to Table 3–3. • user EU Tag Part 2: Sets a custom engineering unit tag name for the last four ASCII characters. For example: A is ASCII hex value 41, so AAAA would be 41414141, which would be 1,094,795,585 in decimal format. Refer to Table 3–3. Operator’s Manual 3–27 FS 5.15 Firmware Table 3–3 ASCII Character Map To find the hexadecimal value in Table 3–3, first find the character needed in the table. Trace to the reference number in the column header (c) at the top of the table, then to the row to the left (r) to create the value (cr). For example, locate the ‘A’ in the table. The ‘A’ corresponds with the value (4) in the column header at the top of the table. Next, follow the row in which ‘A’ is present to the value at the left of the table (1). Combined, these create the hexadecimal value of 41. 3–28 • Val 1 Concentration: Sets the concentration value of validation gas supply #1. • Val 2 Concentration: Sets the concentration value of validation gas supply #2. 4900002234 rev. A 11-12-14 Serial Port Communications • Val 1 Value: Measured analyte concentration of last validation 1 reading in selected engineering units. • Val 2 Value: Measured analyte concentration of last validation 2 reading in selected engineering units. • Val 1 Value ppmv: Measured analyte concentration of last validation 1 reading in parts per million by volume (ppmv) • Val 2 Value ppmv: Measured analyte concentration of last validation 2 reading in parts per million by volume (ppmv) • Val 1 Avg Value: Average analyte concentration of last Validation 1 measurement period in selected engineering units. • Val 2 Avg Value: Average analyte concentration of last Validation 2 measurement period in selected engineering units. • Val 1 Avg Value ppmv: Average analyte concentration of last Validation 1 measurement period in parts per million by volume (ppmv). • Val 2 Avg Value ppmv: Average analyte concentration of last Validation 2 measurement period in parts per million by volume (ppmv). • Val 1 Min Value ppmv: Minimum analyte concentration of last Validation 1 measurement period in parts per million by volume (ppmv). • Val 2 Min Value ppmv: Minimum analyte concentration of last Validation 2 measurement period in parts per million by volume (ppmv). • Val 1 Max Value ppmv: Maximum analyte concentration of last Validation 1 measurement period in parts per million by volume (ppmv). • Val 2 Max Value ppmv: Maximum analyte concentration of last Validation 2 measurement period in parts per million by volume (ppmv). • Val Attempts: Sets the maximum number of failures of the analyzer to measure the validation gas within the set tolerances before stopping the autovalidation sequence and triggering a Validation Fail Alarm. • Val Auto DumpSpectrm: Determines whether a Mode 6 dump automatically occurs after each validation measurement. • • Val Date: Date of the last validation. • Val Duration: Sets the total number of seconds a validation cycle will run. Validation Allowance: Sets the tolerance (%) for validation measurements when Val 1 Concentration or Val 2 Concentration is set to a value greater than 0. Operator’s Manual 3–29 FS 5.15 Firmware 3–30 • Val Interval: Sets the number of days between autovalidation cycles. • Val Perm Constant Kp: Sets the system constant that is determined at the factory at the time of calibration. • Val Perm Rate Rp: Sets the permeation rate in ng/min referenced on the certification for the permeation device. • Val Purge Period: Sets the number of seconds the analyzer will purge the system with validation gas before starting a dry cycle upon validation initiation. • Val Start Time: Sets the hour of the day for the daily autovalidation to begin. • • Val Time: Time of the last validation. • Wet Temp C: Current measured (live) temperature of the gas sample in degrees Celsius. • • Zero Level: Signal level when the laser is turned off. Wet Pressure mb: Current measured (live) wet pressure reading of the gas sample in millibar (mb). Zero Val Tolerance: Used to set the maximum acceptable reading when validating with zero gas. 4900002234 rev. A 11-12-14 4 - ETHERNET COMMUNICATIONS Configuring the Built-in Ethernet Port The built-in Ethernet port must be properly configured to communicate on a network with a serial device. The Ethernet port has been factory set as follows: • • • IP Address: 192.168.000.001 Telnet (Set-up) Port: 9999 Serial Data Port: 10001 The configuration is stored in nonvolatile memory and is retained without power. The configuration can be changed at any time. If the IP address or any other setting needs to be changed, the Ethernet port Setup Mode can be accessed using a Telnet connection to configure the port locally or over the network. To configure the built-in Ethernet port:• 1. From your computer Windows desktop, click Start followed by Run (usually located in the lower right side of the Start Menu). 2. Type the following command: telnet 192.168.000.001 9999 3. Click OK to establish a Telnet connection. The following message appears: MAC address XXXXXXXXXXXX (E.g., 00204A808BE8) Software version V6.3.0.3RC3 (061110) (Version may vary by system) Press Enter for Setup Mode 4. To enter Setup Mode, press Enter within 5 seconds. The configuration settings display, followed by the Change Setup menu. Change Setup: 0 Server 1 Channel 1 5 Expert 6 Security 7 Defaults 8 Exit without save 9 Save and exit Your choice ? 5. Select an option on the menu by entering the number of the option in the “Your choice?” field and pressing Enter. The two menus recommended for review are “0 Server” and “1 Channel 1”. Bypass the other options listed in the menu. Operator’s Manual 4–1 FS 5.15 Firmware 6. After selecting “0” for Server setup, confirm each value and press Enter. Under the “0 Server” option, the most commonly changed parameters include the IP Address and Port No, however, these are not required to be changed. Please confirm with Service before changing any other parameters. 7. For “1 Channel 1,” confirm the current value and press Enter. No parameters under this option need to be changed. Parameters that should never be changed under “1 Channel 1” include: • Baudrate (230400)? • I/F Mode (4C)? • Flow (00)? 8. When finished, save the new configuration by pressing 9 (Save and exit) and Enter. The port will reboot after the configuration has been stored. All other Parameters should be left at default values unless the user is knowledgeable about configuring Ethernet. General Information for Configuring Ethernet For more information on configuring your computer for Ethernet connection, please refer to the Lantronix websites below. 4–2 • XPort Direct+ Demonstration Kit: http://www.lantronix.com/pdf/XPort-Direct-Plus_QS.pdf • Lantronix Downloads and Documentation: http://www.lantronix.com/support/downloads/?p=XPORTDIRECTPL S 4900002234 rev. A 11-12-14 5 - VALIDATION OF TRACE MOISTURE MEASUREMENTS The information contained in this chapter is provided for systems designed to detect moisture. Please disregard if this does not apply to your analyzer configuration. The permeation rate and resultant water content of the validation flow have been carefully calibrated at the factory (refer to the system drawings for the calibrated output of the validation flow). DO NOT adjust the pressure regulator, flow controllers or temperature of the sample conditioning system or the calibration of the validation flow will be lost. If you suspect the settings of the sample conditioning system have been altered, contact your factory sales representative. Validation Methods SpectraSensors uses one of two methods to validate low moisture measurements; a permeation validation system and a dynamic dilution. Permeation validation systems provide a convenient and reliable method of validating the performance of the analyzer, without the need for elaborate blending systems and certified standards that might be impossible to obtain in the field. The analyzer accuracy and repeatability is not based on, certified or tested using the installed permeation device, however. SpectraSensors has found that permeation devices generally do not generate more stable, repeatable or accurate trace moisture mixes than the dynamic dilution stations used in our factory to calibrate the analyzer. In a dynamic dilution, a certified blend of gas can be diluted using precision flow controllers to produce the desired concentration of trace moisture in the actual sample gas. Operator’s Manual 5–1 FS 5.15 Firmware Permeation Validation for Trace Moisture Analyzers (0-10 ppm H2O) The analyzer accuracy and repeatability is not based on, certified or tested using the installed permeation device. SpectraSensors has found that permeation devices generally do not generate more stable, repeatable or accurate trace moisture mixtures than the dynamic dilution stations used in our factory to calibrate the analyzer. Permeation validation systems do provide a convenient and reliable method of validating the performance of the analyzer, without the need for elaborate blending systems and certified standards that might be impossible to obtain in the field. The concentration measured during calibration, Cp, is related to the certified permeation rate of the device, Rp, by a system constant, Kp, using the equation: Kp = Cp/Rp This equation requires that the following conditions be met: • Sample temperature is stable and equal to the temperature at calibration • • Sample flow is stable and equal to the flow at calibration Sample pressure at the permeation device is stable and equal to the pressure at calibration Due to the required conditions, the sample flow pressure regulator, flow control valve and back pressure regulator are factory set and should not be adjusted in the field. The flow components in the sample system are marked with red tags and the message: FACTORY SET - DO NOT FIELD ADJUST. The components have been set to give the required flow rate at the conditions described in the drawings provided with the analyzer. Changing any of these settings voids the certification of the permeation system and changes the measured concentration during validation. The sample flow flowmeters are NOT intended to be used for setting the flows in the field. The measurement accuracy of the flowmeters is not sufficient to reproduce the factory flow rates in the event the flow rates are inadvertently changed or require a change. 5–2 4900002234 rev. A 11-12-14 Validation of Trace Moisture Measurements Setting the Kp Value The system constant Kp is determined at the factory when the analyzer is calibrated. Using the system constant, the permeation device can be replaced with another permeation device using a different permeation rate, and the correct new permeation concentration will be calculated by the analyzer software. The system constant Kp will be consistent over the life of the analyzer provided the temperature, sample flow rate and pressure of the system are not changed from the factory settings. Recalculating the System Constant Kp Use the procedure in this section to recalculate the system constant Kp in the field when the following conditions have occurred: • The pressure or flow control devices in the sample system are inadvertently changed • The sample background composition differs greatly from that specified for factory calibration To recalculate the system constant In some cases it may not be possible to reproduce the correct validation concentration Cp. In such cases, the system constant will need to be recalculated using the following procedure. DO NOT CHANGE ANY OTHER PARAMETER. Doing so may cause the analyzer to stop functioning or provide an inaccurate measurement. To recalculate the system constant Kp, the analyzer must be reading a correct and accurate value within the measured range. Contact the SpectraSensors Service department if there is any reason to believe the analyzer is not working correctly or making an accurate measurement. Verify that the analyzer and permeation device have stabilized. Allow a minimum of 8 hours, preferably overnight, before beginning this procedure. 1. Press #7 and allow the analyzer to validate for at least one hour before proceeding. 2. Calculate the average (mean) validation measurement value Cp. 3. Calculate the new Kp (Kp = Cp/Rp). 4. Calculate the Standard Deviation of the mean Cp 5. Calculate the Validation Allowance as 3 /Cp * 100. Operator’s Manual 5–3 FS 5.15 Firmware 6. Press #2, enter the password and press the * key. 7. Continue pressing the * key until the Validation Allowance parameter displays. 8. Enter the Validation Allowance calculated above and press the * key. 9. Continue pressing the * key until the Val Perm Constant Kp parameter displays, and enter the new Kp calculated above. 10. Enter the new Kp calculated above and press the * key. 11. Press #1 to return to Normal Mode. 12. Press #7 to ensure that the analyzer will continue to provide the correct Validation Concentration +/- the Validation Allowance. Validation of Trace Moisture or Ammonia Measurements Using Permeation Devices For trace moisture systems, SpectraSensors employs a patented G-CAL permeation tube. The permeation device is designed to continuously release a fixed rate of analyte, approximately 2018NG/M, at 50C. Refer to Figure 5–1 for a schematic diagram of the permeation tube. The analyte released is continuously mixed with the dry process gas at 3000 sccm during validation mode (refer to “Mode 7: (Measure Port1 Mode)” on page 2-7). This will result in a calibration mixture of Cp in parts per million (ppm) by volume, as long as return pressure is at atmospheric pressure. Figure 5–1 Schematic of permeation tube The permeation device connects to a “T” assembly between port 6 and 3 of the six-way valve (refer to Figure 5–2). During normal operating conditions, a portion of the process gas return from the sample cell flows through one end of the “T” and carries the excess moisture or analyte released from the permeation assembly back to vent. When the system is switched to validation (refer to “Mode 7: (Measure Port1 Mode)” on page 2-7), the six-way valve changes positions allowing the dry process gas (flowing at 3000 sccm) through the “T” in the opposite direction, carrying the mixed gas into the sample cell. 5–4 4900002234 rev. A 11-12-14 Validation of Trace Moisture Measurements Flow shown in the ’OFF’ position Permeation Tube Sample Supply Dryer Sample Return Figure 5–2 Typical sample system for differential measurement with permeation tube validation capability The concentration of pollutant obtained in ppm by volume may be computed using the following formula: C = KxP ----------F Operator’s Manual K (Water) = 1.358 5–5 FS 5.15 Firmware where: • • • C = concentration of ppm in volume F = carrier gas flow rate in ML/minute at 1atm and 25C P = permeation rate of the G-CAL assembly in nanograms/minute at the temperature of the G-CAL (environment temperature) The entire flow system is maintained at constant elevated temperature (typically 50 to 60°C).The constant temperature not only minimizes species adsorption/desorption and prevents condensation, but in combination with the regulated sample supply pressure and controlled flow rates, ensures a constant mixture of Cp in parts per million (ppm) by volume. The entire analyzer system is calibrated for operation at the enclosure temperature and sample flow rate specified. Measurements should be considered valid only when the enclosure is at the specified temperature and sample flow rate. After opening the sample system enclosure door to check settings, allow at least 1 to 2 hours for the temperature to re-stabilize before validating. To replace the permeation device, refer to the SCS Overview Manual for instructions. 5–6 4900002234 rev. A 11-12-14 Appendix A: Water Correlation Water Content In the context of gas analyzers, water content refers to the concentration of water vapor in the gaseous phase. Water content is typically stated as mole, mass or volume fraction, which are independent of a reference state, or as mass of water per volume of gas, which is dependent on a reference state. For relatively low water content, the mole fraction of water in the gaseous phase (yw) is typically given in dimensionless form as parts per million (ppm), nw y w = ------------------ 106 [ppm] , nw + nm (1) where nw is the number of moles of water, nm is the number of moles of the “dry” mixture. For mass and volume fraction, the units would be ppm(m) and ppm(v) or ppmv, respectively. In the event the water content is extremely low, parts per billion (ppb) or even parts per trillion (ppt) may be used. Water content expressed as mass of water per volume of gas is typically given in milligrams per normal cubic meter (mg/Nm3), where the letter “N” indicates normal reference conditions (typically 0°C and 1atm), or pounds per million standard cubic feet (lb/MMscf), where “s” indicates standard reference conditions (typically 60°F and 1atm). As shown in Table A–1, the definition of reference conditions varies considerably, and thus, should be specified explicitly when using units dependent on a reference state. Here, normal reference conditions are P N = 101325Pa and T N = 273.15K. The conversion of water content (WC) from mole fraction to mass per volume of gas (mg/Nm3) is given by, yw Mw PN WC = -------------- ----------------- [mg/Nm3] , 1 – y w Z N RT N (2) where Mw is the molecular weight of water (18015.2 mg/mol), TN is the temperature at normal reference conditions (K), PN is the pressure at normal reference conditions (Pa), ZN is the compressibility of the “dry” gas mixture at normal reference conditions, and R is the universal gas constant (8.3145 J/molK). For perfect gases, Z N = 1 and yw WC = ------------- 803745 [mg/Nm3] . 1 – yw Operator’s Manual (3) A–1 FS 5.15 Firmware Table A–1 Common reference conditions T (K) P (Pa) Organization 273.15 100000 International Union of Pure and Applied Chemistry (IUPAC) [1] 288.15 101325 International Organization for Standardization (ISO) [2] 298.15 100000 National Bureau of Standards (NBS) [3] 288.71 100000 Society of Petroleum Engineers (SPE) [4] 293.15 101325 National Institute of Standards and Technology (NIST) 288.71 101560 Organization of the Petroleum Exporting Countries (OPEC) [5] 288.71 101325 Occupational Safety and Health Administration (OSHEA) [6] Dew Point In some instances, it is desired to express the water content in terms of the water “dew point” for the gas mixture. The water dew point of a gas is the temperature at which the gas is saturated with water at a given pressure. Saturation implies that the water vapor is in equilibrium with water in the liquid or solid phase (depending on which is present). When water vapor is in equilibrium with the solid (ice) phase, the dew point is often referred to as the “frost point.” Dew Point Conversion Various correlations and standards have been developed (some based on Raoult’s law) that are currently used in natural gas practice for converting from water dew point temperature to water content, such as ASTM 1142-95 (2006) [8], Bukacek [9], the Arden Buck method and ISO 18453:2006 [10]. Raoult’s Law Assuming ideal gas behavior, the simplest thermodynamically based equation for calculating water content at the dew point temperature is based on Raoult’s law [7] y w P = x w P wsat T , (4) where yw is the mole fraction of water in the vapor phase, P is the total pressure, xw is the mole fraction of water in the liquid phase, and P wsat is the saturation (vapor) pressure of pure water at the dew point temperature T. Assuming the liquid phase is pure water, i.e., there is negligible gas solubility, x w = 1 and we get P wsat T y w = ----------------P A–2 . (5) 4900002234 rev. A 11-12-14 Water Correlation Expressions of this type do not take into account the composition of the gas mixture. Although Eq. (5) is of limited utility because of the simplifying assumptions on which it is based, such as perfect gas behavior, reasonable estimates of water content can be obtained for pressures up to 0.4MPa, above which real gas effects become significant. Arden Buck Equations The Arden Buck equations are a group of empirical correlations that relate the saturation vapor pressure to temperature for moist air at close to atmospheric pressure. The curve fits have been optimized for more accuracy than the Goff–Gratch equation in the range −80 to 50°C. [11] Arden Buck equations are not typically used for natural gas applications; however, results are comparable at near atmospheric pressures. A set of several equations were developed, each of which is applicable in a different situation. Enhancements to the method were published in 1996.[12] A humidity conversion software (HCONL), developed by Buck Research Instruments LLC, is commonly used as a simple tool that easily converts any humidity parameter to any other humidity units. ASTM1 ASTM 1142-95 (2006) includes two correlations, the first of which (referred to here as ASTM1) is a variation of Eq. (5) that expresses the water content in terms of the weight of saturated water vapor, or [8] 6 Pb T WC = w 10 ------ ----P Tb , (6) where WC is the water content (lb/MMscf) at reference conditions Tb (R) and Pb (psia), w is the weight of saturated water vapor (lb/ft3), P is the pressure at which the dew point was determined (psia), and T is the observed dew point temperature (R). The reciprocal of w, or the specific volume of saturated water vapor (ft3/lb), is listed as a function of temperature in Table 1 of ASTM 114295 (2006) for temperatures ranging from 0°F to 100°F. Though not explicit in temperature due to the temperature dependence of w, given the water content, the corresponding dew point temperature can be solved for iteratively. ASTM2 Bukacek proposed a relatively simple modified Raoult’s law approach where the water content of sweet gas is calculated using the ideal expression of Eq. (5) supplemented by a deviation factor [9], Operator’s Manual A–3 FS 5.15 Firmware P wsat WC = 760.4 --------- + 0.016016B P , (7) where WC is the water content (g/Nm3), P wsat is the saturation vapor pressure of pure water (MPa), P is the total pressure of the system (MPa), and B is given by, – 1713.66 log B = ---------------------- + 6.69449 T , (8) where T is the dew point temperature (K). The saturation vapor pressure can be calculated using [13] Tc P wsat ln --------- = ----- – 7.85823 + 1.83991 1.5 – 11.7811 3 Pc T , (9) + 22.6705 3.5 – 1539393 4 + 1.77516 7.5 where T is the temperature (K), Tc is the critical temperature of water (647.14K), Pc is the critical pressure of water (22.064MPa), and = 1 – T T c . A simplified version of Eq. (7) A WC = --- + B P , (10) (referred to here as ASTM2) is included in ASTM 1142-95 (2006) with coefficients A and B (referenced to T b = 520 R and P b = 14.7 psia) listed as a function of temperature in Table 2 for dew point temperatures ranging from –40°F to 440°F. Though not explicit in temperature due to the temperature dependence of A and B, given the water content, the corresponding dew point temperature can be solved for iteratively. Although conveniently simplistic, neither ASTM method takes into account the actual gas composition. In addition, the range of data made available for the specific volume of saturated water vapor (ASTM1) or for the coefficients A and B (ASTM2) is somewhat limited. ISO Perhaps the most rigorous method to date is that of ISO 18453:2006. Based on an extensive study conducted by Groupe Europeen de Recherches Gazieres (GERG) [14], the ISO method uses an equation of state (EOS) approach to calculate water content from water dew point temperature. The semi-empirical Peng-Robinson (P-R) cubic EOS with repulsive and attractive terms has been found to adequately reproduce the behavior of fluids in the gas and liquid phase with the same equation. The P-R EOS for a pure component explicit in P is given by [15] RT aT P T ,V = ------------ – ---------------------------------V – b V 2 + 2bV – b 2 A–4 . (11) 4900002234 rev. A 11-12-14 Water Correlation The coefficients are defined as RT c b = 0.07780 --------Pc (12) and 2 2 0.45724R T c a T = ---------------------------------- T r Pc , (13) where T r = T T c is the reduced temperature and T r is a non-dimensional function of the reduced temperature 12 Tr = 1 + 1 – Tr 2 , (14) 2 where = 0.37464 + 1.54226 – 0.26992 is a substance-specific constant generalized using the acentric factor . Values for the critical pressure, critical temperature and acentric factor are listed in Table A–2. Table A–2 Gas composition [14] i Pc (MPa) Tc (K) Water (H2O) 1 22.064 647.14 0.34437 Methane (CH4) 2 4.599 190.55 0.01140 Ethane (C2H6) 3 4.872 305.33 0.09909 Nitrogen (N2) 4 3.399 126.26 0.03593 Carbon Dioxide (CO2) 5 7.386 304.21 0.22394 Propane (C3H8) 6 4.246 369.85 0.15611 i-Butane (C4H10) 7 3.640 407.85 0.18465 n-Butane (C4H10) 8 3.784 425.14 0.19777 neo-Pentane (C5H12) 9 3.196 433.75 0.19528 i-Pentane (C5H12) 10 3.370 460.39 0.22606 n-Pentane (C5H12) 11 3.364 469.69 0.24983 Hexane/C6+ (C6H14) 12 3.020 507.85 0.29600 Component Operator’s Manual A–5 FS 5.15 Firmware For water specifically, the -function takes a different form in order to accurately reproduce the water vapor pressure over ice as well as liquid [14] 12 Tr = 1 + A1 1 – Tr 12 4 2 12 2 + A2 1 – Tr + A3 1 – Tr , (15) where the coefficients, listed in Table A-3, take on different values depending on whether the temperature is above or below freezing. Table A-3 Coefficients for Eq. (15) [14] Coefficient 223.15 T273.16K 273.16T313.15K A1 0.106025 0.905436 A2 2.683845 -0.213781 A3 -4.75638 0.26005 Application of an equation of state to a mixture requires substituting mixture parameters for those of the pure component. The mixture parameters are related to pure component parameters by means of the mixing rules [16] nc nc xi xj aij T am T = (16) i = 1j = 1 and nc bm = xi bi , (17) i=1 where nc is the number of components in the mixture. The mole fraction of each component, x i , serves as a weight factor and the cross coefficients a ij T of the a -term a ij T = a i T a j T 1 – k ij T (18) are corrected with a temperature-dependent binary interaction parameter [14] T k ij T = k ij 0 + k ij 1 ---------------- – 1 273.15 , (19) where the coefficients k ij 0 and k ij 1 , listed in Table A–4, are typically determined by fitting vapor-liquid equilibrium data of binary mixtures with k ij = k ji and k ii = k jj = 0 . A–6 4900002234 rev. A 11-12-14 Water Correlation Table A–4 Binary interaction parameters [14] i Component i j Component j k ij 0 k ij 1 1 Water 2 Methane 0.6510 -1.3850 1 Water 3 Ethane 0.6350 -0.9300 1 Water 4 Nitrogen 0.4800 0 1 Water 5 Carbon Dioxide 0.1840 0.2360 1 Water 6 Propane 0.5300 0 1 Water 7 i-Butane 0.6900 0 1 Water 8 n-Butane 0.5000 0 1 Water 9 neo-Pentane 0.5000 0 1 Water 10 i-Pentane 0.6900 0 1 Water 11 n-Pentane 0.5000 0 1 Water 12 Hexane/C6+ 0.5000 0 2 Methane 3 Ethane -0.0026 0 2 Methane 4 Nitrogen 0.0311 0 2 Methane 5 Carbon Dioxide 0.0919 0 2 Methane 6 Propane 0.0140 0 2 Methane 7 i-Butane 0.0133 0 2 Methane 8 n-Butane 0.0230 0 2 Methane 9 neo-Pentane 0.0422 0 2 Methane 10 i-Pentane 0.0256 0 2 Methane 11 n-Pentane 0.0180 0 2 Methane 12 Hexane/C6+ -0.0056 0 3 Ethane 4 Nitrogen 0.0515 0 3 Ethane 5 Carbon Dioxide 0.1322 0 3 Ethane 6 Propane 0.0011 0 3 Ethane 7 i-Butane -0.0067 0 3 Ethane 8 n-Butane 0.0096 0 3 Ethane 9 neo-Pentane 0.0230 0 3 Ethane 10 i-Pentane 0.0160 0 3 Ethane 11 n-Pentane 0.0078 0 3 Ethane 12 Hexane/C6+ -0.0100 0 Operator’s Manual A–7 FS 5.15 Firmware Table A-4 Binary interaction parameters [14] (Continued) A–8 i Component i j Component j k ij 0 k ij 1 4 Nitrogen 5 Carbon Dioxide -0.0170 0 4 Nitrogen 6 Propane 0.0852 0 4 Nitrogen 7 i-Butane 0.1033 0 4 Nitrogen 8 n-Butane 0.0800 0 4 Nitrogen 9 neo-Pentane 0.0930 0 4 Nitrogen 10 i-Pentane 0.0922 0 4 Nitrogen 11 n-Pentane 0.1000 0 4 Nitrogen 12 Hexane/C6+ 0.1496 0 5 Carbon Dioxide 6 Propane 0.1241 0 5 Carbon Dioxide 7 i-Butane 0.1200 0 5 Carbon Dioxide 8 n-Butane 0.1333 0 5 Carbon Dioxide 9 neo-Pentane 0.1260 0 5 Carbon Dioxide 10 i-Pentane 0.1219 0 5 Carbon Dioxide 11 n-Pentane 0.1222 0 5 Carbon Dioxide 12 Hexane/C6+ 0.1100 0 6 Propane 7 i-Butane -0.0078 0 6 Propane 8 n-Butane 0.0033 0 6 Propane 9 neo-Pentane 0 0 6 Propane 10 i-Pentane 0.0111 0 6 Propane 11 n-Pentane 0.0267 0 6 Propane 12 Hexane/C6+ 0.0007 0 7 i-Butane 8 n-Butane -0.0004 0 7 i-Butane 9 neo-Pentane 0 0 7 i-Butane 10 i-Pentane 0 0 7 i-Butane 11 n-Pentane 0 0 7 i-Butane 12 Hexane/C6+ 0 0 8 n-Butane 9 neo-Pentane 0 0 8 n-Butane 10 i-Pentane 0 0 8 n-Butane 11 n-Pentane 0.0174 0 8 n-Butane 12 Hexane/C6+ -0.0056 0 9 neo-Pentane 10 i-Pentane 0 0 9 neo-Pentane 11 n-Pentane 0 0 9 neo-Pentane 12 Hexane/C6+ 0 0 10 i-Pentane 11 n-Pentane 0.0600 0 10 i-Pentane 12 Hexane/C6+ 0 0 11 n-Pentane 12 Hexane/C6+ 0 0 4900002234 rev. A 11-12-14 Water Correlation An equilibrium condition for each component can be derived in terms of the fugacity coefficient [17] l v i xi = i yi , (20) l where i is the fugacity coefficient of component i in the liquid phase, x i is the v mole fraction of component i in the liquid phase, i is the fugacity coefficient of component i in the gaseous phase, and y i is the mole fraction of component i in the gaseous phase. For the PR-EOS, the fugacity coefficient is defined as [17] bi ln i = ------ Z – 1 – ln Z – B * bm Z + B* 1 + 2 A* b 2 ai T – ----------------- -----i- – -------------------- x j a i T 1 – k ij ln ------------------------------------am T 2 2B * b m Z + B* 1 – 2 j , (21) 2 where Z is the compressibility factor for the mixture, A * = a m T P RT and B * = b m P RT . The compressibility factor is calculated from an equivalent form of Eq. (10) implicit in the compressibility factor [17] 3 2 2 2 3 Z – 1 – B * Z + A * – 2B * – 3B * Z – A * B * + B * + B * = 0 . (22) Given the mole fractions of the components of the gaseous mixture, y i , the dew point temperature is solved for iteratively by means of successive substitution using the following procedure: 1. Guess T. l v 2. Estimate the initial equilibrium ratios K i = i i using the Wilson –1 approximation K i = P c P exp 5.373 1 + i 1 – T r i [18]. i 3. Estimate the initial liquid mole fractions x i = y i K i . v 4. Calculate Z using Eq. (22) and i using Eq. (20) with the vapor mole fractions, y i . l 5. Calculate Z using Eq. (22) and i using Eq. (20) with the liquid mole fractions, x i . v l 6. Recalculate the liquid mole fractions x i' = x i i i . 7. Repeat steps 5 & 6 until x i' – x i 0 . 8. Adjust T and repeat steps 2-7 until xi' 1 . i Method Comparisons for Natural Gas Measured dew point temperatures versus water content from the GERG report [14] for two pressures, 5bar and 100bar, are shown in Figure A–1, Figure A–2, Figure A–3 and Figure A–4 along with calculated results using the ASTM1, Operator’s Manual A–9 FS 5.15 Firmware ASTM2 and ISO methods described above. The gas mixtures NG1, NG3, NG4 and NG7 are specified in Table A–5. 10 4 Water Content [mg/Nm3] Natural Gas NG1 10 3 P=5 bar P=100 bar 10 2 ASTM1 ASTM2 ISO GERG Meas. 10 1 250 300 350 Temperature [K] Figure A–1 Comparison of calculation results for ASTM1 [8], ASTM2 [9] and ISO [10] methods with experimental data from the GERG report [14] for mixture NG1 10 4 Water Content [mg/Nm3] Natural Gas NG3 10 3 P=5 bar P=100 bar 10 2 ASTM1 ASTM2 ISO GERG Meas. 10 1 250 300 350 Temperature [K] Figure A–2 Comparison of calculation results for ASTM1 [8], ASTM2 [9] and ISO [10] methods with experimental data from the GERG report [14] for mixture NG3 A–10 4900002234 rev. A 11-12-14 Water Correlation 10 4 Water Content [mg/Nm3] Natural Gas NG4 10 3 P=5 bar P=100 bar 10 2 ASTM1 ASTM2 ISO GERG Meas. 10 1 250 300 350 Temperature [K] Figure A–3 Comparison of calculation results for ASTM1 [8], ASTM2 [9] and ISO [10] methods with experimental data from the GERG report [14] for mixture NG4 10 4 Water Content [mg/Nm3] Natural Gas NG7 10 3 10 2 ASTM1 ASTM2 ISO GERG Meas. 10 1 250 300 350 Temperature [K] Figure A–4 Comparison of calculation results for ASTM1 [8], ASTM2 [9] and ISO [10] methods with experimental data from the GERG report [14] for mixture NG7 Operator’s Manual A–11 FS 5.15 Firmware Table A–5 Experimental gas compositions [14] Component NG1 NG3 NG4 NG7 Methane (CH4) 0.98210 0.88204 0.86483 0.70148 Ethane (C2H6) 0.00564 0.08360 0.06203 0.02520 Nitrogen (N2) 0.00840 0.00912 0.04871 0.01499 Carbon Dioxide (CO2) 0.00109 0.00000 0.00167 0.25126 Propane (C3H8) 0.00189 0.01763 0.01552 0.00394 i-Butane (C4H10) 0.00029 0.00293 0.00214 0.00067 n-Butane (C4H10) 0.00038 0.00441 0.00315 0.00074 neo-Pentane (C5H12) 0.00001 0.00003 0.00002 0.00003 i-Pentane (C5H12) 0.00007 0.00020 0.00061 0.00029 n-Pentane (C5H12) 0.00006 0.00004 0.00067 0.00022 Hexane/C6+ (C6H14) 0.00007 0.00000 0.00064 0.00118 The ASTM1 method agrees well with the experimental data at low pressure (5 bar) but deviates significantly at higher pressure (100 bar), especially at higher temperatures where the calculated dew points are always too high. Given that the ASTM1 method is based on ideal gas assumptions, it is expected that real gas behavior typical of the higher pressures would not be sufficiently reproduced. Being of similar origin as the ASTM1 method, the ASTM2 method exhibits similar behavior, albeit with even less agreement, especially at lower temperatures where the calculated dew points are always too low (with the exception of the CO2-rich NG7 mixture at high pressure). Thus, if water content calculated by the ASTM2 method is used to control a drying process, water condensation may occur due to prematurely reaching the prescribed dew point. Discrepancies between the two ASTM methods is most likely due to the fact that data for a simple binary methane-water system was used in the development of the ASTM2 method [9]. The experimental water content data for the mixtures NG1, NG3, NG4 and NG7 at 60 bar are summarized in Figure A–5. Relative deviations between the courses tend to increase with decreasing dew point temperature. These deviations (~5K between NG4 and NG7 at 34mg/Nm3) illustrate the importance of accounting for the gas composition, especially when performing calculations with low water content at moderate to high pressure. Of the three methods discussed, only the ISO method takes into account the actual gas composition. A–12 4900002234 rev. A 11-12-14 Water Correlation 10 3 Water Content [mg/Nm3] P=60 bar 10 2 NG1 NG3 NG4 NG7 10 1 250 260 270 280 290 300 Temperature [K] Figure A–5 Courses of measured water contents at 60 bar for natural gas mixtures NG1, NG3, NG4 and NG7 The ISO method is applicable to natural gas mixtures with compositions within the limits listed in Table A–6. Dew point temperatures calculated from water contents were validated to be generally within ±2K for pressures 0.5≤P≤10MPa and dew point temperatures 258.15≤T≤278.15K [14]. Due to the solid thermodynamic basis on which the method was developed, an extended working range of 0.1≤P≤30MPa and 223.15≤T≤313.15K is also considered valid [10]. Beyond the extended working range, however, the uncertainty in calculated dew point temperature is unknown. In summary, for moderate to high water contents at low pressures, all three correlations produce acceptable results. Although somewhat more difficult to implement, the ISO method is arguably the more accurate of the methods (especially for low water contents and high pressures) and provides a great deal more range and flexibility. The Arden Buck Method Comparison The Arden Buck method was developed for air at near-atmospheric pressure and can be used for air and nitrogen backgrounds. The Arden Buck method can be used as an approximation of dew point in natural gas streams with very high levels of methane and inert gases, but as heavier hydrocarbons and CO2 concentrations increase, the Arden Buck method is unable to compensate for the interaction of the various molecules. Errors as high as 10C will be reported in typical natural gas streams at typical pipeline pressures. Therefore, the use of the Arden Buck method should generally be avoided for natural gas streams. Operator’s Manual A–13 FS 5.15 Firmware Table A–6 Range of composition applicable to ISO method [10] Compound mol % Methane (CH4) ≥40.0 Ethane (C2H6) ≤20.0 Nitrogen (N2) ≤55.0 Carbon Dioxide (CO2) ≤30.0 Propane (C3H8) ≤4.5 i-Butane (C4H10) ≤1.5 n-Butane (C4H10) ≤1.5 neo-Pentane (C5H12) ≤1.5 i-Pentane (C5H12) ≤1.5 n-Pentane (C5H12) ≤1.5 Hexane/C6+ (C6H14) ≤1.5 References [1] McNaught, A. D. and Wilkinson, A., eds., Compendium of Chemical Terminology: IUPAC Recommendations (2nd Edition), Blackwell Science, Malden, MA, 1997. [2] ISO 13443: Natural Gas – Standard Reference Conditions, International Organization for Standardization, Geneva, Switzerland, 1996. [3] Wagman, D. D., Evans, W. H., Parker, V. B., Schumm, R. H., Halow, I., S Bailey, S. M., Churney, K. L. and Nuttall, R. L., “The NBS Tables of Chemical Thermodynamic Properties,” J. Phys. Chem. Ref. Data, Vol. 11, Suppl. 2, 1982. [4] The SI Metric System of Units and SPE Metric Standard, Society of Petroleum Engineers of AIME, Richardson, TX, 1984. [5] Ibrahim, O. ed., Annual Statistical Bulletin, Organization of the Petroleum Exporting Countries, Vienna, Austria, 2008. [6] “Storage and Handling of Liquefied Petroleum Gases,” 29 CFR-Labor, Chapter XVII, Part 1910, Sect. 1910.110 and 1910.111, 1993. [7] Prausnitz, J. M., Molecular Thermodynamics of Fluid-Phase Equilibria, Prentice-Hall, Inc., Englewood Cliffs, New Jersey, 1969. [8] ASTM D 1142-95: Standard Test Method for Water Vapor Content of Gaseous Fuels by Measurement of Dew Point Temperature, ASTM International, West Conshohocken, Pennsylvania, 2006. A–14 4900002234 rev. A 11-12-14 Water Correlation [9] Bukacek, R. F., “Equilibrium Moisture Content of Natural Gases,” Research Bulletin 8, Institute of Gas Technology, 1955. [10] ISO 18453: Natural Gas-Correlation between Water Content and Water Dew Point, International Organization for Standardization, Geneva, Switzerland, 2006. [11] Buck, A. L. (1981), “New equations for computing vapor pressure and enhancement factor”, J. Appl. Meteorol. 20: 1527–1532 [12] Buck Research Instruments, LLC, “Model CR-1A Hygrometer with Autofill Operating Manual”, Appendix 1: Humidity Conversion Equations, May 2012. [13] Saul, A. and Wagner, W., “International Equations for the Saturation Properties of Ordinary Water Substance,” J Phys Chem Ref Data, 16:893-901, 1987. [14] Oellrich, L. R. and Althaus, K., “Relationship between Water Content and Water Dew Point keeping in consideration the Gas Composition in the Field of Natural Gas,” GERG Technical Monograph TM14, Verein Deutscher Ingenieure, Duesseldorf, 2000. [15] Peng, D. Y. and Robinson, D. B., “A New Two-Constant Equation of State,” Ind. Eng. Chem. Fundam., 15(1):59-64, 1976. [16] Copeman, T. W. and Mathias, P. M., “Recent Mixing Rules for Equations of State,” in Chao, K. C. ed., Equation of State: Theories and Applications, ACS Symposium Series 300:352-370, 1986. [17] Reid, R. C., Prausnitz, J. M. and Poling, B. E., The Properties of Liquids and Gases (4th Edition), McGraw-Hill Book Company, New York, New York, 1987. [18] Wilson, G., “A Modified Redlich-Kwong Equation of State Applicable to General Physical Data Calculations,” Paper No. 15C, 65th AIChE National meeting, May, 1968. [19] Avila, S., Blanco, S. T., Valesco, I., Rauzy, E. and Otin, S., “Thermodynamic Properties of Synthetic Natural Gases Part 4. Dew Point Curves of Synthetic Natural Gases and their Mixtures with Water: Measurement and Correlation,” Fluid Phase Equilibria 202:399-412, 2002. Operator’s Manual A–15 FS 5.15 Firmware THIS PAGE IS INTENTIONALLY LEFT BLANK A–16 4900002234 rev. A 11-12-14 Appendix B: Troubleshooting This section presents recommendations and solutions such as excessive sampling gas temperatures and pressures, and reset procedures. If your analyzer does not appear to be hampered by one of these related problems, refer to Table B–1 at the end of this chapter before contacting SpectraSensors for service. Excessive Sampling Gas Temperatures and Pressures The embedded software is designed to produce accurate measurements only within the allowable cell operating range (refer to the calibration report or system drawings). The cell temperature operating range for analyzers that are equipped with heated enclosures is equal to the enclosure temperature setpoint ±5 °C. Pressures and temperatures outside this range will trigger a Pressure Low Alarm, Pressure High Alarm, Temp Low Alarm, or Temp High Alarm fault. If the pressure, temperature, or any other readings on the LCD appear suspect, they should be checked against the specifications (refer to the calibration report or system drawings). Peak Tracking Reset Procedure The analyzer’s software is equipped with a peak tracking function that keeps the laser scan centered on the absorption peak. Under some circumstances, the peak tracking function can get lost and lock onto the wrong peak. If the PeakTk Restart Alarm is displayed, the peak tracking function should be reset. To reset the Peak Tracking function: 1. Press the # key followed by the 2 key. <SET PARAMETER MODE> Enter password: FS 5.15-XXXX Operator’s Manual B–1 FS 5.15 Firmware The LCD prompts for a numeric password. Enter the user password (3142) on the keypad, then press the * key to enter the number to enter Mode 2. <SET PARAMETER MODE> Process Purge Time 60 Enter a value (secs) 2. Starting with the first parameter that displays, press the * key to cycle through the screens until the Peak Tracking parameter displays. <SET PARAMETER MODE> Peak Tracking 1 0:Off 1:On 2:Rst 3. Press 2 (RST or Reset) followed by the * key. The peak tracking function will return the current analyzer midpoint to the factory default midpoint, and then automatically revert the parameter value to its setting before the reset was initiated. In most cases, the peak tracking should be set to 1 for on. 4. Press the * key to cycle through the screens until the General Alarm DO parameter displays. <SET PARAMETER MODE> General Alarm DO 2 0:L 1:NonL 2:Reset 5. Press 2 (RESET) followed by the * key. The General Fault relay and any active alarms will be reset to the ‘Normal’ state. After the relay resets, this parameter will automatically revert to the setting before the reset was initiated. 6. Press the mode key # followed by 1 to return to Mode 1 (Normal Mode). Instrument Problems If the instrument does not appear to be hampered by issues described in this chapter, refer to Table B–1 before contacting your sales representative for service. B–2 4900002234 rev. A 11-12-14 Troubleshooting Table B–1 Potential instrument problems and their solutions Symptom Response Non-Operation (at start up) Refer to the Hardware Manual. Non-Operation (after start up) Contact a factory sales representative for service information. Laser Power Low Alrm Press # 6 to capture diagnostic data and send the file to SpectraSensors. Refer to the Hardware Manual. Pressure Low Alarm or Pressure High Alarm fault Refer to the Hardware Manual. Temp Low Alarm or Temp High Alarm fault Refer to the Hardware Manual. Front panel display is not lit and no characters appear Refer to the Hardware Manual. Strange characters appear on front panel display Refer to the Hardware Manual. Pressing keys on front panel do not have specified effect Refer to the Hardware Manual. System stuck in Fit Delta Exceeds Limit restart for greater than 30 minutes Contact a factory sales representative for service information. Not getting enough flow to the sample cell Refer to the Hardware Manual. No reading on device connected to current loop Refer to the Hardware Manual. Current loop is stuck at 4 mA or 20 mA Check display for error message. If alarm has been triggered, reset the alarm. Refer to the Hardware Manual. Reading seems to always be high by a fixed amount Capture diagnostic data and send the file to SpectraSensors (see “To read diagnostic data with HyperTerminal” on page 3-5). Reading seems to always be high by a fixed percentage Capture diagnostic data and send the file to SpectraSensors (see “To read diagnostic data with HyperTerminal” on page 3-5). Check that Peak Tracking is enabled (see “To change parameters in Mode 2” on page 2-15). Operator’s Manual B–3 FS 5.15 Firmware Table B-1 Potential instrument problems and their solutions (Continued) Symptom Response Reading displays 0.0 or seems relatively low Capture diagnostic data and send the file to SpectraSensors (see “To read diagnostic data with HyperTerminal” on page 3-5). Reading is erratic or seems incorrect Refer to the Hardware Manual to check for contamination in the sample system. Capture diagnostic data and send the file to SpectraSensors (see “To read diagnostic data with HyperTerminal” on page 3-5). Reading goes to “0” If 4-20 mA Alarm Action is set to 1, look on display for an error message (see “To change parameters in Mode 2” on page 2-15). Refer to the Hardware Manual. Reading goes to full scale If 4-20 mA Alarm Action is set to 2, look on display for an error message (see “To change parameters in Mode 2” on page 2-15). Refer to the Hardware Manual. Serial output is displaying garbled data Refer to the Hardware Manual. Serial output is providing no data Refer to the Hardware Manual. LCD does not update. Unit is locked up for more than 5 minutes. Refer to the Hardware Manual. Service Contact If the troubleshooting solutions do not resolve the problem, contact customer service. To return the unit for service or replacement, refer to "Return Material Authorization". Customer Service 4333 W Sam Houston Pkwy N, Suite 100 Houston, TX 77043-1223 For SpectraSensors North America Service: Phone: (800) 619-2861, and press 2 for Service Fax: (713) 856-6623 E-mail: [email protected] B–4 4900002234 rev. A 11-12-14 Troubleshooting For SpectraSensors International Service, please contact the SpectraSensors distributor in your area, or contact: Phone: (713) 466-3172, and press 2 for Service Fax: (713) 856-6623 E-mail: [email protected] Return Material Authorization If it is necessary to return the analyzer, obtain a Return Materials Authorization (RMA) Number from Customer Service before shipping to the factory. Your service representative can determine whether the analyzer can be serviced on site or should be returned to the factory. All returns should be shipped to: 11027 Arrow Rte. Rancho Cucamonga, CA 91730-4866 (909) 948-4100 Disclaimers SpectraSensors accepts no responsibility for consequential damages arising from the use of this equipment. Liability is limited to replacement and/or repair of defective components. This manual contains information protected by copyright. No part of this guide may be photocopied or reproduced in any form without prior written consent from SpectraSensors. Warranty The manufacturer warrants the items delivered shall be free from defects (latent and patent) in material and workmanship for a period of one year after delivery to the Buyer. The Buyer’s sole and exclusive remedy under this warranty shall be limited to repair or replacement. Defective goods must be returned to the manufacturer and/or its distributor for valid warranty claims. This warranty shall become inapplicable in instances where the items have been misused or otherwise subjected to negligence by the Buyer. Notwithstanding any other provision of this contract, no other warranties, whether statutory or arising by operation of law, expressed or implied, including but not limited to those of merchantability or fitness for particular purpose, shall apply to the goods or services hereunder, other than the repair and replacement warranty above. Seller shall in no event be liable to Buyer or any third party for any damage, injury or loss, including loss of use or any direct or indirect incidental or consequential damages of any kind. Operator’s Manual B–5 FS 5.15 Firmware THIS PAGE INTENTIONALLY LEFT BLANK B–6 4900002234 rev. A 11-12-14 INDEX 4-20 mA current loop 2–40 A Acentric factor A–5 Alarms 2–42 General Fault Alarm 2–2, 2–43, 2–44 System Faults 2–43 User Alarms 2–45 Concentra High Alarm 2–23, 2–45 Concentra Low Alarm 2–45 Validation 1 Failed/Validation 2 Failed Alarm 2–44 Validation Fail Alarm 2–48 B Background gas 2–32, 2–33, 2–38, 2–48 C Calibrating the analyzer 2–49 Cautions 1–1 COM properties 3–1, 3–3 Concentration 2–3, 2–7, 2–24 Contamination 2–49 Critical pressure A–4 Critical temperature A–4 Current loop 2–23 Calibrating 2–40 Current loop receiver 2–41 Customer Port Output 3–1 D Data Diagnostic 2–6, 2–7, 3–7 Data string 3–4 Dew point temperature A–2 E Energizing the circuit 2–1 Ethernet port IP Address 4–1 Serial Data Port 4–1 Setup Mode 4–1 Operator’s Manual Telnet Port 4–1 Ethernet port (Built-in) 4–1 Excessive sampling gas pressure B–1 Excessive sampling gas temperature B–1 F Faults DeltaDC Restart Alrm 2–43 DeltaT Restart Alarm 2–43 Fit Restart Alarm 2–43 Flow Switch Alarm 2–43 Laser Curnt High Alrm 2–43 Laser Curnt Low Alrm 2–43 Laser Power High 2–43 Laser Power Low 2–43 Laser Power Low Alrm B–3 Laser Zero High Alarm 2–43 Laser Zero Low Alarm 2–43 Low Purge Rate Alrm 2–43 New Scrubber Alarm 2–44 PeakTk Restart Alarm 2–44, B–1 Pressure High Alarm 2–44, B–1, B–3 Pressure Low Alarm B–1, B–3 Pressure too Low 2–44 R2 Restart Alarm 2–44 R3 Restart Alarm 2–44 Temp High Alarm 2–44, B–1, B–3 Temp Low Alarm 2–44, B–1, B–3 Temperature too High 2–2, 2–44 Temperature too Low 2–2, 2–44 Faults/Alarms Assignable Alarm 2–21, 2–47, 3–22 Concentra High Alarm 2–21, 2–22, 2–46, 2–47 Concentra Low Alarm 2–22, 2–47 DeltaDC Restart Alrm 2–22 DeltaT Restart Alarm 2–22, 2–46 Dry Pressure Alarm 2–22, 2–46 Fitting Restart Alrm 2–22, 2–46 Flow Switch Alarm 2–22 Flow Switch Alarm 1 2–46 General Fault Alarm 2–22, 2–25 Historical Alarm Flag Codes 2–45 Laser Curnt Low Alrm 2–21, 2–46 Laser Power Low Alrm 2–21, 2–45 Laser Powr High Alrm 2–21, 2–46 Laser Zero High Alrm 2–21, 2–46 Laser Zero Low Alrm 2–21, 2–46 Index–1 FS 5.15 Firmware Lasr Curnt High Alrm 2–21, 2–46 Low Purge Rate Alarm 2–22 Low Purge Rate Alrm 2–46 Need New Scrubber! 2–21 New Scrubber Alarm 2–22, 2–46 PeakTk Restart Alarm 2–22, 2–46 Pressure High Alarm 2–22, 2–46 Pressure Low Alarm 2–22, 2–45, 2–46 Pressure Restart Alarm 2–22, 2–46 R2 Reset Alarm 2–46 R2 Restart Alarm 2–22 R3 Restart Alarm 2–22, 2–46 RampAdj Restart Alarm 2–22, 2–46 Temp High Alarm 2–22, 2–45, 2–46 Temp Low Alarm 2–22, 2–45, 2–46 Val 1 Fail Alarm 2–22 Val 2 Fail Alarm 2–22 Validation Fail Alarm 2–33, 3–29 Validation Fail Alarm 1 2–46 Validation Fail Alarm 2 2–46 G Gas solubility A–2 Gas standard 2–47 HyperTerminal 3–1 I Ideal gas A–2 Initialization period 2–2 Installation B–1 Intermediate calculation 2–7 K Keypad 2–3 L LCD display 2–2 Liquid phase A–2 M Mass fraction A–1 Measurement parameters 2–2 Measurement units 2–3 Microsoft Excel 3–8 Modbus communications 3–12 Index–2 Framing/protocol 3–12 Modes Mode ^ (Normal Mode) 3–6 Mode 1 (Normal Mode) 2–5, 3–6, 3–15, B–2 Mode 2 (Set Parameter Mode) 2–5, 2–7, 2–47, 3–1, 3–5, 3–14, B–2 Mode 2, Change Parameters (Set Parameter Mode) 2–15 Mode 3 (Scrubber Life Data) 2–7 Mode 3 Not Used 2–5 Mode 4 (Set Parameter Mode) 2–6 Mode 4 (System Diagnostic Parameters) 2–6 Mode 5 (Analog Output Test Mode) 2–7 Mode 5 (Set Parameter Mode) 2–7 Mode 6 (Diagnostic Data Download) 2–7, 2–33, 3–5, 3–6, 3–8, 3–29, B–3 Mode 6 (Set Parameter Mode) 2–7 Mode 7 (Measure Port1 Mode) 2–7, 2–47 Mode 8 (Measure Port2 Mode) 2–47 Mode 8 (Not Used) 2–8 Mode 9 (Recall Validation Results) 2–8 Mode TEST (Analog Input Test Mode) 2–10 Modes and functions 2–4 Molecular weight A–1 N National Institute of Standards and Technology 2–49 Normal cubic meter A–1 Normal reference conditions A–1 P Parameters Diagnostic Alarm Flags 3–5 Concentration (ppmv) 3–4 Current Midpoint 3–4 Dry DC 3–4 Dry Pressure 3–4 Dry Temp 3–4 DryDC 2–6 DryPressure 2–6 DryTemp 2–6 Fit 2–6 Fit Ratio 3–4 4900002234 rev. A 11-12-14 Index Fit Ratio 2 3–4 Fit Ratio 3 3–5 Fit Ratio 4 3–5 Fit Ratio 5 3–5 Fit Ratio Dry 3–5 Fit Ratio Dry-1 3–5 Fit Residue 3–4 Index Difference 3–4 Mid 2–6 Peak Index 3–4 Process Path Fig 3–4 Ref Index 3–4 Val Fig 3–4 Wet DC 3–4 Wet Temp (C) 3–4 WetDC 2–6 WetPressure 2–6 WetPressure (mb) 3–4 WetTemp 2–6 Input Concentration Unit 2–19 Custom Precision 2–20 DO Alarm Setup 2–21, 2–47 New Scrub Installed 2–25 Operator Parameter01 to Operator Parameter20 2–25 Operator Password 2–27 Update RATA 2–31 Val Attempts 2–33 Val Duration 2–33 Val Purge Period 2–35 Validation Allowance 2–33 Zero Val Tolerance 2–33, 2–36 Measurement and control 2–11 # Spectrum Average 3–5 2 Way Com Port 2–16, 3–15 4-20 mA Alarm Action B–4 4-20 mA Alarm Option 2–16 4-20 mA Test 2–7, 2–41 4-20 mA Val Action 2–16, 2–48 4-20mA Alarm Option 2–16, 2–17, 2–18, 2–43 AI 20 mA Value 2–17 AI 4 mA Value 2–17 AI Pressure Input 2–17 AO 20 mA Test 2–18 AO 20 mA Value 2–18 AO 4 mA Value 2–17 AO 4-20 mA Test 2–41 Baud Rate 2–18 Calculate Dew Point 2–17 Calculate DewPoint 2–19 Cancel Scrub Alarm 2–30 Cancel Val Alarms 2–19, 2–45 Daily Validation 2–20, 2–47 Operator’s Manual General Alarm DO 2–22, 2–43, B–2 High Alarm Setpoint 2–23 Keypad Watchdog 2–23 Logger Rate 2–23, 2–24 Low Alarm Setpoint 2–24 Modbus Address 2–24, 3–14, 3–15 Modbus Mode 2–24, 3–1, 3–12, 3–15 Peak Tracking 2–27, B–2 Pipeline Pressure 2–17, 2–28 Pressure Unit 2–28 Process Purge Time 2–28 Rapid Change Monitor 2–28 RATA 2–29 RATA Multiplier 2–29, 2–36 RATA Offset 2–29 Set Time - Day 2–30 Set Time - Hour 2–30 Set Time - Minute 2–30 Set Time - Month 2–30 Set Time - Year 2–31 Start Validation 2–31, 2–47, 2–48 Temperature Unit 2–31 Val 1 Concentration 2–32, 2–34, 3–29 Val 2 Concentration 2–32, 2–34, 3–29 Val Attempts 2–48 Val Auto DumpSpectrm 2–33 Val Interval 2–34, 2–47 Val Perm Constant Kp 2–34 Val Perm Constant Rp 2–35 Val Start Time 2–20, 2–36, 2–47 Validation Allowance 2–32, 2–34 Zero Val Tolerance 2–32 Password 2–15, 2–38, 3–14, B–2 PeakTk 2–44 Permeation Devices 5–4 Powering down the analyzer 2–3 Powering up the analyzer 2–1 R Raoult’s law A–2, A–3 Recommendations and solutions to common problems 2–45 Reference state A–1 Return materials authorization (RMA) number B–5 Index–3 FS 5.15 Firmware S Sample cell pressure 2–3 Sample cell temperature 2–3 Saturated water vapor A–3 Saturation A–2 Saturation vapor pressure A–4 Saving data from the serial port 3–5 Scroll direction 2–15 Serial port 3–5 Service contact B–4 Spectra 2f 2–7, 3–11 DC 2–7 System Faults Pressure Restart Alarm 2–44 T Temperature 2–3 U V Validation 2–47, 2–49 Validation source 2–32 Vapor phase A–2 Volume fraction A–1 W Warnings DCdelta out of range 2–42 Delta P out of range 2–42 Delta T out of range 2–42 Dry P out of range 2–42 Fit Delta Exceeds Limit B–3 Fitting out of range 2–42 General 1–1 Peak Tracking 2–42 R2 out of range 2–42 R3 out of range 2–42 Unable to do validation 2–42 Water content A–1, A–3 Water dew point A–2 Units 2–31 Concentration 2–19 Pressure 2–28 Temperature 2–31 Index–4 4900002234 rev. A 11-12-14
advertisement
* Your assessment is very important for improving the workof artificial intelligence, which forms the content of this project
Related manuals
advertisement