McQuay MWMV Specifications
Add to my manuals
27 Pages
McQuay MWMV is a high-efficiency vertical water source heat pump that provides both cooling and heating, making it an ideal choice for residential, commercial, and industrial applications. With its whisper-quiet operation, easy installation, and user-friendly features, the MWMV offers a comfortable and energy-efficient solution for year-round climate control.
advertisement
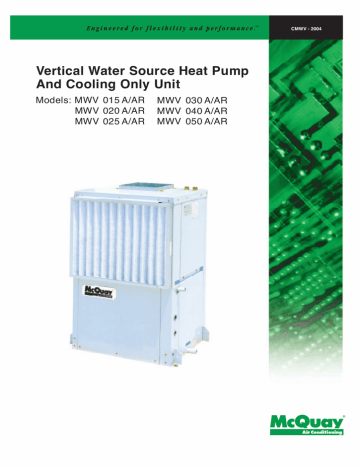
Vertical Water Source Heat Pump
And Cooling Only Unit
Models: MWV 015 A/AR
MWV 020 A/AR
MWV 025 A/AR
MWV 030 A/AR
MWV 040 A/AR
MWV 050 A/AR
CMWV - 2004
Contents
Features ......................................................................................................................... 2
Specification ............................................................................................................. 3- 4
Operating Limits ............................................................................................................ 5
Water Loop System Diagram........................................................................................ 6
Performance Tables ............................................................................................... 7 - 12
Dimensions Table ....................................................................................................... 13
Wiring Diagrams .................................................................................................. 14 - 16
Transportation and Storage ....................................................................................... 17
Installation ............................................................................................................ 17 - 22
Start-Up ....................................................................................................................... 23
Maintenance................................................................................................................. 24
Troubleshooting ................................................................................................... 24 - 25
Note: Installation and maintenance are to be performed only by qualified personnel who are familiar with local codes and regulations, and experienced with this type of equipment,
Caution: Sharp edges and coil surfaces are a potential injury hazard. Avoid contact with them.
Warning: Moving machinery and electrical power hazards. May cause severe personal injury or death.
Disconnect and lock off power before servicing equipment.
"McQuay" is a registered trademark of McQuay International. All rights reserved throughout the world.
2003 McQuay International
"Bulletin illustrations cover the general appearance of McQuay International products at the time of publication and we reserve the right to make changes in design and construction at any time without notice."
Page 1
Features
High Energy efficiency
The unit has high efficiency as the high energy/effect ratio and a Max. COP of 4.2 as well as saving the running cost due to water as cooling and heating media.
Whisper- Quiet Operation
Solid casing, special sound absorbing and thermal insulation material, separated fan and compressor as well as the special noise reduction for compressor ensure an effective noise control for the whole set.
Easy and flexible installation
The physical size of the unit is specially designed for space saving. It is therefore offering greatest flexibility in selecting installation location.
Service and Maintenance Friendly
The unique structure design: small and compact structure with many overhaul doors and high/low pressure overhaul valve which helps overhauling and maintenance.
Also, Tube in tube heater exchanger specially designed for water loop heat pump set which reduces pipe block and ensures a longer use life and a higher thermal conductivity.
Microcomputer Remote Control
The microcomputer remote control has following functions:
Five optional operation modes (heat/cool/dry/fan/auto)
Fan speed can be set at high, medium, low and automatic.
Sleep mode automatically increase set temperature since temperature is lower at night thus achieving healthy sleep.
Microcomputer controlled thermostat precisely controls room temperature resulting in energy saving and increases comfort.
Hot start and hot keep mode do not supply air for 30 sec. After deicing as well as initial operation of heating mode. This prevents cold draft and maintains the indoor comfort.
Timer on/off can be preset for the maximum of 15 hours.
A wide Operating Scope
All products of AWV series have adopted air compressors with world famous brands.
The operating scopes are:
Water temperature: (a) Cooling 13-40 ℃ (b) Heating: 10-32 ℃
This series of types are applicable for residential, shopping complex, hotels and industries.
Page 2
Specifications
MODEL
COOLING CAPACITY
HEATING CAPACITY
MWV015A MWV015AR MWV020A MWV020AR MWV025A MWV025AR
Btu/h 14330 19110 23890
Btu/h
COOLING W
- 15360 - 20478 - 25600
4200 5600 7000
POWER INPUT
HEATING W - 4500 - 6000 - 7500
POWER SOURCE
EER
COP
ROW / FIN PER INCH
FACE AREA
FAN
AIR FLOW
WATER FLOW
V/Ph/Hz 220 - 240 / 1 / 50 220 - 240 / 1 / 50 220 - 240 / 1 / 50
4.2 3.5 3.9 m 2
W
3 / 14 3 / 14 3 / 12
0.183 0.183 0.267
103 215 191 POWER INPUT
Depth mm 178 178 254
Width mm 178 178 203
CFM 440 600 740
L/s
GPM
L/s
208 283 347
3.48 4.44 5.7
0.222 0.305 0.361
WATER PRESSURE DROP
WATER CONNECTIONS mH
2
O
FPT
CONNECTIONS I.D. mm 19.05
OPERATING kg
WEIGHT
SHIPPING kg
Rated in accordance with ANSI/ARI Standard 320-1998
MODEL
93 95 115
MWV030A MWV030AR MWV040A MWV040AR MWV050A MWV050AR
COOLING CAPACITY Btu/h 30720 37540 47780
HEATING CAPACITY
1.3 1.5 1.7
3/4
POWER INPUT
POWER SOURCE
EER
COP
Btu/h
V/Ph/Hz
- 34130 - 42660 - 52900
COOLING W 9000 11000 14000
HEATING W - 10000 - 12500 - 15500
220 - 240 / 1 / 50 380 - 415 / 3 / 50 380 - 415 / 3 / 50
3.7 - -
- 3.7 - -
ROW / FIN PER INCH
FACE AREA
FAN
AIR FLOW
WATER FLOW
WATER PRESSURE DROP
WATER CONNECTIONS m 2
W
3 / 13 3 / 14 3 / 14
0.267 0.315 0.315
261 275 473 POWER INPUT
Depth mm 254 254 254
Width mm 203 254 254
CFM
L/s
GPM
L/s mH
2
O
FPT
940 1176 1470
444 555 694
6.97 - -
0.222 0.305 0.361
2 2.5 3.5
3/4
CONNECTIONS I.D. mm 19.05
OPERATING kg 125 - -
WEIGHT
SHIPPING Kg 160 - -
Rated in accordance with ANSI/ARI Standard 320-1998
Notes:
1. a) EER = Energy Efficiency Ratio b) COP = Coefficient of Performance c) L/s = Liters per second
2. Nominal cooling and heating capacity are based on the conditions below: a) Cooling Capacity is based on 26.7°C (80°F) (DB), 19.4°C (67°F) (WB) entering air temp and 29.6°C (85°F)entering, 35°C (95°F) leaving water temp。 b) Heating Capacity is based on 21.1°C (70°F) (DB) entering air temp and 21.1°C (70°F) entering water temp。
3. All specifications are subjected to change by manufacture without prior notice.
Page 3
Airflow Correction Factors
Total Cooling Capillary
Sensible Cooling Capillary kW -Cooling
Total Heat Of Rejection
Total Heating Capillary kW -Heating
Percent of Nominal Airflow
0.972 0.982 0.994 1.000 1.007 1.010 1.013
0.926 0.948 0.974 1.000 1.027 1.055 1.066
0.977 0.984 0.993 1.000 1.011 1.018 1.028
0.975 0.983 0.991 1.000 1.008 1.015 1.018
0.967 0.978 0.990 1.000 1.009 1.017 1.024
1.009 1.006 1.003 1.000 0.997 0.995 0.993
Total Heat Of Absorption 0.967 0.976 0.989 1.000 1.010 1.019 1.025
Fan Performance Table
50 cycle, 220volts, single phase (includes allowance for dry coil, and no filter)
MODEL
MWV015A/AR
MWV020A/AR
MWV025A/AR
MWV030A/AR
FAN
SPEED
HI
LOW
HI
LOW
EXTERNAL STATIC PRESSURE (Pa)
30 50 80 100 120 150 170
208 - -
139
283
197
-
-
-
-
-
-
HI 404 400 385 375 350 269 -
LOW 324 317 294 284 275 208 -
HI 484 483 461 457 453 420 -
LOW 354 358 352 345 338 302 -
MWV040A/AR
HI
MWV050A/AR
LOW
Electrical Data
The electrical data is based at 220V~/50Hz and 380V/3N/50Hz
MODEL
MWV015A/AR
MWV020A/AR
MWV025A/AR
MWV030A/AR
MWV040A/AR
MWV050A/AR
HI 703 667 619 576 542 453 -
LOW 542 531 498 472 435 353 -
694
500
Power Compressor
Motor
Voltage Hz Phase RLA LRA FLA
220/240 50 1 6.1 26 0.5
220/240 50 1 8.6 34
220/240 50 1 10.2 47
220/240 50 1 13 54
380/415 50 3 4.8 42
380/415 50 3 7 42
1
0.85
1.15
1.3
3.6
Total
Unit FLA
Voltage
Range
5.2 187~264
Max.
Circuit
Ampacity
6
- 187~264 -
9.8 187~264 12.1
13.1 187~264 18.8
5.8 342~456 7.8
- 342~456 -
Max.
Fuse
Size
15
-
20
25
15
-
Page 4
Operating Limits
Air limits °C (Sl units)
Min. Ambient Air
Normal Ambient Air
Cooling Heating
19.4 21
Note:
Max. Ambient Air
Min. Entering Air (1)&(2)
Normal Entering Air, DB/WB
Max. Entering Air, DB/WB
(1)&(2)
Water enthalpy °C (Sl units)
2. Max and min values may not be
19.4 21 combined. If one value is at max or
26.7/19.4 21 min, the other two conditions may not exceed the normal condition.
35/21.7 26.7
Cooling Heating
Min. Entering Water (1)&(2)
Normal Entering Water
13 10
29.4 21
Max. Entering Water (1)&(2) 40 32
Environment
This equipment is designed for indoor installation only. Sheltered locations such as attics, garages, etc., generally will not provide sufficient protection against extremes in temperature and/or humidity, and equipment performance, reliability, and service life may be adversely affected.
Power supply
A voltage variation of ±10% of nameplate utilization voltage is acceptable. Three-phase system unbalance shall not exceed 2%.
Operating voltages
220-240V~/50Hz ---------------------------------------------------------------------------- 198V min., 264V max.
380-415V/3N/50Hz ---------------------------------------------------------------------------- 342V min., 456V max.
Additional information (initial start-up only)
Standard conditions are guaranteed to start and operate in an ambient temperature of 5°C, with entering air at 5°C, with entering water at 21°C, with both air and water at the flow rates used in the ARI Standard 320-
86 rating test, for initial start-up in winter.
Note: This is not a normal or continuous operating condition. It is assumed that such a start-up is for the
purpose of bringing the building space up to occupancy temperature.
Page 5
Water Loop System Diagram
expansion tank water supply cooling tower air vent valve thermometer water pump boiler filter flow switch filter thermometer flow switch
AWV unit drain valve
AWV unit
ACC indoor unit
AWSC outdoor unit
Page 6
Performance Tables
Model: MWV 015A/AR
Water
Flow
(m 3 /h)
E.W.T
( o C)
Air Flow: 760m 3 /h Electrical Characteristics: 220V / 1Ph / 50Hz
COOLING HEATING
O.W.T ( o
C) E.A.T C) Capacity (W) E.A.T ( o
(W)
0.82 10 -
19.4/13.9 5002 16 4119
26.7/19.4 5204 21 4160
35/21.7 5308 27 4243
19.4/13.9 4856 16 4246
26.7/19.4 5028 21 4311
35/21.7 5129 27 4397
19.4/13.9 4715 16 4378
26.7/19.4 4858 21 4467
35/21.7 4955 27 4556
19.4/13.9 4578 16 4509
26.7/19.4 4694 21 4623
35/21.7 4788 27 4716
19.4/13.9 4444 16 4644
26.7/19.4 4535 21 4785
35/21.7 4626 27 4881
19.4/13.9 4311 16 4784
26.7/19.4 4376 21 4953
35/21.7 4464 27 5052
19.4/13.9 4182 - -
26.7/19.4 4223 -
35/21.7 4308 -
-
-
19.4/13.9 4056 -
26.7/19.4 4075 -
35/21.7 4157 -
-
-
-
E.A.T = Entering Air Temperature E.W.T = Entering Water Temperature
O.W.T = Leaving Water Temperature
Page 7
Model: MWV 020A/AR
Water
Flow
(m
3
/h)
E.W.T
( o
C)
Air Flow: 1020m 3 /h Electrical Characteristics: 220V / 1Ph / 50Hz
COOLING HEATING
O.W.T ( o C) E.A.T C) Capacity (W) E.A.T ( o (W)
1.1 10 -
E.W.T = Entering Water Temperature
O.W.T = Leaving Water Temperature
19.4/13.9 6177 16 5532
26.7/19.4 6426 21 5587
35/21.7 6555 27 5699
19.4/13.9 5997 16 5704
26.7/19.4 6209 21 5790
35/21.7 6333 27 5906
19.4/13.9 5822 16 5880
26.7/19.4 5999 21 6000
35/21.7 6119 27 6120
19.4/13.9 5653 16 6056
26.7/19.4 5796 21 6210
35/21.7 5912 27 6334
19.4/13.9 5488 16 6238
26.7/19.4 5600 21 6427
35/21.7 5712 27 6556
19.4/13.9 5323 16 6425
26.7/19.4 5404 21 6652
35/21.7 5512 27 6785
19.4/13.9 5164 - -
26.7/19.4 5215 -
35/21.7 5319 -
19.4/13.9 5009 -
26.7/19.4 5032 -
35/21.7 5133 -
-
-
-
-
-
E.A.T = Entering Air Temperature
Page 8
Model: MWV 025A/AR
Water
Flow
(m
3
/h)
E.W.T
( o
C)
Air Flow: 1200m 3 /h Electrical Characteristics: 220V / 1Ph / 50Hz
COOLING HEATING
O.W.T ( o C) E.A.T C) Capacity (W) E.A.T ( o (W)
1.32 10 -
E.W.T = Entering Water Temperature
O.W.T = Leaving Water Temperature
19.4/13.9 7721 16 6916
26.7/19.4 8033 21 6984
35/21.7 8193 27 7124
19.4/13.9 7496 16 7130
26.7/19.4 7761 21 7238
35/21.7 7916 27 7382
19.4/13.9 7278 16 7350
26.7/19.4 7499 21 7500
35/21.7 7649 27 7650
19.4/13.9 7066 16 7571
26.7/19.4 7245 21 7763
35/21.7 7390 27 7918
19.4/13.9 6860 16 7798
26.7/19.4 7000 21 8034
35/21.7 7140 27 8195
19.4/13.9 6654 16 8032
26.7/19.4 6755 21 8315
35/21.7 6890 27 8482
19.4/13.9 6455 - -
26.7/19.4 6519 -
35/21.7 6649 -
19.4/13.9 6261 -
26.7/19.4 6290 -
35/21.7 6416 -
-
-
-
-
-
E.A.T = Entering Air Temperature
Page 9
Model: MWV 030A/AR
Water
Flow
(m
3
/h)
E.W.T
( o
C)
Air Flow: 1650m 3 /h Electrical Characteristics: 220V / 1Ph / 50Hz
COOLING HEATING
O.W.T ( o C) E.A.T C) Capacity (W) E.A.T ( o (W)
1.59 10 -
E.W.T = Entering Water Temperature
O.W.T = Leaving Water Temperature
19.4/13.9 9927 16 9221
26.7/19.4 10328 21 9312
35/21.7 10534 27 9498
19.4/13.9 9638 16 9506
26.7/19.4 9978 21 9650
35/21.7 10178 27 9843
19.4/13.9 9357 16 9800
26.7/19.4 9641 21 10000
35/21.7 9834 27 10200
19.4/13.9 9085 16 10094
26.7/19.4 9315 21 10350
35/21.7 9501 27 10557
19.4/13.9 8820 16 10397
26.7/19.4 9000 21 10712
35/21.7 9180 27 10926
19.4/13.9 8555 16 10709
26.7/19.4 8685 21 11087
35/21.7 8859 27 11309
19.4/13.9 8299 - -
26.7/19.4 8381 -
35/21.7 8549 -
19.4/13.9 8050 -
26.7/19.4 8088 -
35/21.7 8249 -
-
-
-
-
-
E.A.T = Entering Air Temperature
Page 10
Model: MWV 040A/AR
Water
Flow
(m
3
/h)
E.W.T
( o
C)
Air Flow: 1950m 3 /h Electrical Characteristics: 380V / 3Ph / 50Hz
COOLING HEATING
O.W.T ( o C) E.A.T C) Capacity (W) E.A.T ( o (W)
1.92 10 -
E.W.T = Entering Water Temperature
O.W.T = Leaving Water Temperature
19.4/13.9 12133 16 11526
26.7/19.4 12623 21 11640
35/21.7 12875 27 11873
19.4/13.9 11780 16 11883
26.7/19.4 12196 21 12063
35/21.7 12440 27 12304
19.4/13.9 11437 16 12250
26.7/19.4 11783 21 12500
35/21.7 12019 27 12750
19.4/13.9 11103 16 12618
26.7/19.4 11385 21 12938
35/21.7 11613 27 13196
19.4/13.9 10780 16 12996
26.7/19.4 11000 21 13390
35/21.7 11220 27 13658
19.4/13.9 10457 16 13386
26.7/19.4 10615 21 13859
35/21.7 10827 27 14136
19.4/13.9 10143 - -
26.7/19.4 10243 -
35/21.7 10448 -
19.4/13.9 9839 -
26.7/19.4 9885 -
35/21.7 10083 -
-
-
-
-
-
E.A.T = Entering Air Temperature
Page 11
Model: MWV 050A/AR
Water
Flow
(m
3
/h)
E.W.T
( o
C)
Air Flow: 2500m 3 /h Electrical Characteristics: 380V / 3Ph / 50Hz
COOLING HEATING
O.W.T ( o C) E.A.T C) Capacity (W) E.A.T ( o (W)
2.3 10 -
E.W.T = Entering Water Temperature
O.W.T = Leaving Water Temperature
19.4/13.9 14890 16 13831
26.7/19.4 15492 21 13968
35/21.7 15801 27 14248
19.4/13.9 14457 16 14259
26.7/19.4 14968 21 14475
35/21.7 15267 27 14765
19.4/13.9 14036 16 14700
26.7/19.4 14462 21 15000
35/21.7 14751 27 15300
19.4/13.9 13627 16 15141
26.7/19.4 13973 21 15525
35/21.7 14252 27 15836
19.4/13.9 13230 16 15595
26.7/19.4 13500 21 16068
35/21.7 13770 27 16390
19.4/13.9 12833 16 16063
26.7/19.4 13028 21 16631
35/21.7 13288 27 16963
19.4/13.9 12448 - -
26.7/19.4 12572 -
35/21.7 12823 -
19.4/13.9 12075 -
26.7/19.4 12132 -
35/21.7 12374 -
-
-
-
-
-
E.A.T = Entering Air Temperature
Page 12
Dimensions Data
All dimensions are approximate. Certified drawings available upon request.
DIMENSIONS
UNIT SIZE
015 & 020
025 & 030
40 inch mm inch mm inch mm inch mm inch mm inch mm
CONNECTIO
NS (FPT)
23.15 588 22.24 565 38.58 980 8.2 208 9.1 232 1.2 30
26.18 665 23.46 596 42.56 1081 11.3 287 10.5 267 1.2 30
30.12 765 24.25 616 48.82 1240 11.3 287 13.1 334 1.2 30
3/4
3/4
1
1 50 30.12 765 26.22 666 48.82 1240 11.3 287 13.1 334 1.2 30
Optional Return Air Duct Filter
Standard 1” (21mm)
UNIT SIZE
A B C inch mm inch mm inch mm
015 & 020 21.85 555 17 432 1 21
025 & 030
UNIT SIZE
24.6 625 20.75 527 1 21
040 & 050 28.2 725 20.75 527 1 21
Optional 2” (51mm)
A B C inch mm inch mm inch mm
015 & 020 21.85 555 17 432 2 51
025 & 030 24.6 625 20.75 527 2 51
040 & 050 28.2 725 20.75 527 2 51
Page 13
Wiring Diagrams
Model: MWV 015 / 020A
M ODEL:AWV015A/020A
RETURN AI R TEMP. SENSOR
WATER TEMP. SENSOR
COI L TEMP. SENSOR
( SLM)
LI NE CONTROLLER
TRANSFORMER
G/ R
L N
LP: LOW PRESSURE SWITCH
HP: HI GH PRESSURE SWITCH
FSW: FLOW SWITCH
FM: FAN MOTOR
CM: COMPRESSOR
C1, C2: CAPACI TOR
Model: MWV 015 / 020 AR
M ODEL:AWV015AR/020AR
( SLM)
WIRE CONTROLLER
RETURN AI R TEMP. SENSOR
WATER TEMP. SENSOR
COI L TEMP. SENSOR
G/ Y
R
C
CM
S
C1
G/ Y
FM
C2
BLUE
TRANSFORMER
BLUE
L N
Y/ G
LP: LOW PRESSURE SWITCH
HP: HI GH PRESSUR SWITCH
FSW: FLOW WATER SWITCH
FM: FAN MOTOR
CM: COMPRESSOR
4WV: 4 WAY VALVE C1, C2: CAPACI TOR
Y/ G
R
C
CM
S
Y/ G
FM
C1
BLUE
C2
BLUE
Page 14
Model: MWV 025 / 030 A
( SLM)
WIRE CONTROLLER
RETURN AI R TEMP. SENSOR
WATER TEMP. SENSOR
COI L TEMP. SENSOR
红
TRANSFORMER
L N
RED
BLUE
L2
L1
L3
KM1
T1
T3
T2
Y/ G
LP: LOW PRESSURE SWITCH
HP: HI GH PRESSURE SWITCH
FSW: FLOW WATER SWITCH
FM: FAN MOTOR
CM: COMPRESSOR
C1, C2: CAPACI TOR
Model: MWV 025 / 030 AR
MODEL:AWV025AR/030AR
( SLM)
WIRE CONTROLLER
RETURN AI R TEMP. SENSOR
WATER TEMP. SENSOR
COI L TEMP. SENSOR
RED
Y/ G
C
R
CM
S
KM1
Y/ G
FM
C1 C2
BLUE
TRANSFORMER
BLUE
L N
RED
BLUE
L1
L2
L3
KM1
T1
T3
T2
Y/ G
Y/ G
R
C
CM
S
KM1
Y/ G
FM
C1 C2
BLUE
LP: LOW PRESSURE SWITCH
HP: HI GH PRESSUR SWITCH
FSW:FLOW WATER SWITCH
FM: FAN MOTOR
CM: COMPRESSOR
4WV: 4 WAY VALVE C1, C2: CAPACI TOR
BLUE
Page 15
Model: MWV 040 / 050 A
M O D E L : A W V 0 4 0 A / 0 5 0 A
C M
Y/ G
RETURN AI R TEMP. SENSOR
WATER TEMP. SENSOR
COI L TEMP. SENSOR
RED
WI RE CONTROLLER
( SLM)
R S T N
Y/ G
LP: LOW PRESSUR SWI TCH
HP: HI GH PRESSUR SWI TCH
FSW: FLOW WATER SWI TCH
Model: MWV 040 / 050 AR
FM: FAN MOTOR
CM: COMPRESSOR
C: CAPACI TOR
DB3- A: PHASE PROTECTOR
TRANSFORMER
BLACK
RED
Y/ G
F M
BLACK
C
BLACK
DB3- A
71
BLACK
81 OL
BROWN
Page 16
Transportation and Storage
Upon receipt of the equipment, check the carton for visible damage. Make a notation on the shipper's delivery ticket before signing. If there is any evidence of rough handing, the cartons should be opened at once to check for concealed damage, If any damage is found, notify the carrier within 48 hours to establish your claim and request their inspection and a report. The Warranty Claims Department should then be contacted.
Don't stand or transport the machine on their sides, For storing, each carton is marked with "up-arrows.
In the event that elevator transfer makes horizontal positioning unavoidable, absolutely insure that the machine is in the normal upright position for at least 24 hours before operating.
Temporary storage at the joist must be indoors, completely shields from rain, snow, etc. High or Low temperature naturally associated with weather pattern will not harm the conditioners. Excessively high temperature of 160°F (60ºC) may deteriorate certain plastic materials and cause permanent damage. In addition, the solid-state circuit boards may experience operating problems.
Installation
General
1. To prevent damage, this equipment should not be operated for supplementary heating and cooling during the construction period.
2. Inspect the carton for any specific tagging numbers as requested by the installing contactor. At this time the voltage, phase and capacity should be checked against the plans.
3. Check the unit sizes against the plans to be sure that the unit will be installed in the correct location.
4. Before installation, check the available closet dimension versus the dimensions of the unit.
5. Pay attention to the location and routing of water piping, and electrical wiring. The locations of these items are clearly marked on submittal drawings.
6. The installing contractor will find it beneficial to confer with piping, sheet metal, ceiling and electrical foreman together before installing any conditioners.
Unit location
1. Locate the unit in an area that allows for easy removal of the filter and access panels, and has enough space for service personnel to perform maintenance of repair. Provide sufficient room to make water, electrical and duct connections.
2. The contractor should make sure that access has provided including clearance for duct collars and fittings at water and electrical connections.
3. Allow adequate room around the unit for a condensate trap.
4. The unit can be installed in an equipment room. However, closet installations are more common for small vertical type units. Generally, the unit is located in the corner of a closet with the non-ducted, return air facing 90° to the door and the major access panels facing the door (Figure A). Alternatively, the unit can have a ducted return air with the opening facing the door and the major access panels facing 90° to the door (Figure B).
5. It is recommended that the unit be located on top of a vibration absorbing material such as
rubber or carpet to reduce any vibration.
6. If optional field installed controls are required (boilerless systems), space must be provided for the enclosure to mount around the corner from the electrical entrances. Do not locate the side of the unit too close to a wall.
Page 17
Typical closet installation with louver door return & with ducted return
Duct and attenuation
Discharge ductwork is normally used with these conditioners. Return air ductwork may also be required, but will require field installation of a 1" or 2" (21 or 51mm) return air duct collar/ filter rack kit.
The discharge duct system will normally consist of a flexible connector at the unit, a non-insulation piece of the full duct size, a short run of duct, an elbow without vanes, and a trunk duct teeing into a branch circuit with discharge diffusers as shown in FIGURE C.
The transition piece must not have an angle greater than 30 ° or severer loss of air performance can result.
Do not connect the full duct size to the unit without using a transition down to the size of the discharge collar on the unit. With metal duct material, the sides only of the elbow and entirebranch duct should be internally lined with acoustic insulation for sound attenuation. Glass fiber duct board material is more absorbing and may permit omission of the flexible connector.
The ductwork should be laid out so that there is no line of sight between the conditioner discharge and the distribution diffusers.
Return air ducts can be brought in through a wall grille and then to the unit. The return duct system will normally consist of a flexible connector at the unit and a trunk duct to the return air grille. With metal duct material, the return air duct should be internally lined with acoustic insulation for sound attenuation. Glass fiber duct board material is more absorbing and may permit omission of the fiexible connector.
Return air ductwork to the unit requires the optional 2" (51mm) return air duct collar/filter rack kit. The kit can be installed for face side or bottom filter removal. The flexible connector can then be attached to the 1"
(25mm) duct collar.
Don't use sheet metal screws directly into the unit cabinet for connection of supply or return air ductwork, especially return air ductwork which can puncture the drain pan or the air coil.
Page 18
Ventilation Air
Outside air may be required for ventilation. The temperature of the ventilation air must be controlled so that mixture of outside air and return air entering the conditioner does not exceed application limits. It is also general practice to close off the ventilation air system during unoccupied periods (night setback).
The ventilation air system is generally a separate building subsystem with distribution ductwork. Simple introduction of the outside air into each return air plenum chamber reasonably close to the conditioner air inlet is not only adequate, but also recommended. Do not duct outside air directly to the conditioner inlet.
Provide sufficient distance for thorough mixing of outside and return air.
General
1. Be sure the available power is the same voltage and phase as that shown on the unit serial plate. Line and low voltage wiring must be done in accordance with local codes or the National Electrical Code, whichever is applicable.
2. Apply correct line voltage to the unit. Two 7/8" (22mm) holes are supplied on the side of the unit. A disconnect switch near the unit is repaired by code. Power to the unit must be sized correctly and have time delay (dual element) fuses or a HACR circuit breaker for branch circuit overcurrent protection. See the nameplate for correct ratings.
220-240 Volt operation and 50 cycle units
All 220-240 volt single and three-phase units are factory wired for 220 and 380 volt operation. For 240-volt operation, the line voltage tap on the 18-volt transformer must be changed. Disconnect and cap the red lead wire and interchange it with the orange lead wire on the primary of the 18-volt transformer. Three-phase 50 cycle units require a neutral wire for 220-240/1/50 power.
Fan speed change
All units have three-speed fan motors (HI, MID, LOW) and are shipped for HI, MID & LOW speeds operation.
On unit sizes 015 though 050, each fan motor is supplied with a 6-pin terminal block mounted on the fan motor.
Page 19
Piping
1. All units are recommended to be connected to supply and return piping in a two-pipe reverse return configuration. A reverse return system is inherently self-balancing and requires only trim balancing where multiple quantities of units with different flow and pressure drop characteristics are connected to the same loop. A simple way to check for proper water balance is to take a differential temperature reading across the water connections. To insure proper water flow, the differential should be 10°F (5℃) to 14°F (8℃). A direct return system may also be made to word acceptably, but proper water flow balancing is more difficult to achieve and maintain.
2. The piping can be steel, copper or PVC.
3. Supply and return run outs are usually connected to the unit by short lengths of high pressure flexible hose which are sound attenuates for both unit operating noise and hydraulic pumping noise. One end of the hose should have a swivel fitting to facilitate removal for service. Hard piping can also be brought directly to the unit although it is not recommended since no vibration or noise attenuation can be accomplished. The hard piping must have unions to facilitate unit removal. See FIGURE D for typical piping setup.
4. Supply and return shutoff valves are required at each conditioner. The return valve is used for balancing and should have a "memory stop" so that it can always be closed off but can only be reopened to the proper position for the flow required.
5. No unit should be connected to the supply and return piping until the water system has been cleaned and flushed completely. After the cleaning and flushing has taken place, the initial connection should have all valves wide open in preparation for water system flushing.
6. Condensate piping can be steel, copper or PVC. Each unit is supplied with a 3/4" (19.05mm) ODM copper stub.
7. The condensate disposal piping must have a trap and the piping must be pitched away from the unit not less than 1/4" inch per foot (20mm per meter). Generally, the condensate trap is made of copper. See
FIGURE E. A piece of vinyl hoses from the trap to the drain line is used for simple removal. A complete copper or PVC condensate system can also be used. Union fittings in the copper lines should be applied to facilitate removal.
Page 20
FI GURE E
1 1/ 2"
( 38mm)
1 1/ 2"
( 38mm)
1/ 4" PER FOOT
( 20mm PER METER)
8. No point in the drain system may be above the drain connection of any unit.
9. Automatic flow controlled devices must not be installed prior to system cleaning and flushing.
10. A high point of the piping system must be vented.
11. Check local code for the need for dielectric
Flexible Hose
Since hose may change in length from +2% to –4% under the surge of high pressure, it is necessary to provide sufficient slack for expansion contraction (see Figure F).
Cleaning and Flushing System
WRONG
RI GHT
FI GURE F
1. Prior to first operation of any conditioner, the water circulating system must be cleaned and flushed of all construction dirt and debris.
If the conditioners are equipped with water shut off valves, either electric or pressure operated, the supply and return run outs must be connected together at each conditioner location. This will prevent the introduction of dirt into the unit. Additionally, pressure operated valves only open when the compressor is operation.
2. The system should be filled at the city water makeup connection with all air vents open. After filling, vents should be closed.
The contractor should start main circulator with pressure reducing valve makeup open. Vents should be checked in sequence to bleed off any trapped air to assure circulation through all components of the system.
Power to the heat rejecter unit should be off, and the supplementary heat control set at 80°F (27℃).
While circulating water, the contractor should check and repair any leaks in the piping. Drain at the
lowest point(s) in the system should be opened for initial flush and blow-down, making sure city water
fill are set to make up water at the same rate. Check the pressure gauge at pump suction and manually adjust the makeup to hold the same positive steady pressure both before and after opening the drain valves. Flush should continue for at least two hours, or longer if required, to see clear, clean drain water.
Page 21
3. Supplemental heater and circulator pump should be shut off. All drains and vents should be opened to completely drain down the system. Short circuited supply and return runouts should now be connected to the conditioner supply and return connections. Teflon tape is recommended over pipe dope for pipe dope for pipe thread connections. Do not use sealers at the swivel flare connections of hoses.
4. Trisodium phosphate was formerly recommended as a cleaning agent during flushing. However, many states and localities ban the introduction of phosphates into their sewage systems. The current recommendation is to simply flush linger with warm 80°F (27℃) water.
5. Refill the system with clean water. Test the litmus paper for acidity, and treat as required to leave the water slightly alkaline (pH 7.5 to 8.5). The specified percentage of antifreeze may also be added at this time. Use commercial grade antifreeze designed for HVAC systems only. Do not use automotive
grade antifreeze.
6. Set the system control and alarm panel heat add setpoint to 70°F (21℃) and the heat rejection setpoint to 85°F (29℃). Supply power to all motors and start the circulating pumps. After full flow has been established through all components including the heat rejecter (regardless of season) and air vented and loop temperatures stabilized, each of the conditioners will be ready for check test and start-up and for air and water balancing.
Page 22
Start-Up
1. Open all valves to full open position and turn on power to the conditioners.
2. Set thermostat for "Fan Only" operation by selecting "Off " at the system switch and "On" at the fan switch. If "Auto" fan operation were selected, the fan would cycle with the compressor. Check for proper air delivery.
3. All units have three-speed motors.
4. Set thermostat to "Cool". Many conditioners have time delays which protect the compressor against short cycling. After a few minutes of operation, check the discharge grilles for cool air delivery. Measure the temperature difference between entering and leaving water. It should be approximately 11/2 times greater than the heating mode temperature difference. For example, if the cooling temperature difference is 15°F (8℃), the heating temperature difference should have been 12°F (5℃).
Without automatic flow control valves, a cooling temperature difference of 10°F to 14°F (5℃ to 8℃) is about right. Adjust the combination shutoff/balancing valve in the return line to a water flow rate which will result in the 10°F to 14°F (5℃ to 8℃) difference.
5. Set thermostat to "Heat ". Set system switch to the "Auto " position and depress the heat setting to the warmest selection. Some conditioners have built-in time delays which prevent the compressor from immediately starting. With most control schemes, the fan will start immediately. After a few minutes of compressor operation, check for warm air delivery at discharge grille. If this is a "cold building" start-up, leave unit running until return air to the unit is at least 65°F (18℃).
Measure the temperature difference between entering and leaving air and entering and leaving water.
With entering water of 60°F to 80°F (16℃ to 27℃), leaving water should be 6°F to 12°F(3.3℃ to 6.7℃) cooler, and the air temperature rise through the machine should not exceed 35°F(19℃). If the air temperature exceeds 35°F(19℃), the airflow rate is probably inadequate.
If the water temperature difference is less than 6°F (3.3℃), the water flow rate is excessive. If the water temperature difference exceeds 12°F (6.7℃), then the water flow rate is inadequate.
6. Check the elevation and cleanliness of the condensate line. If the air is too dry for sufficient dehumidification, slowly pour enough water into the condensate pan to ensure proper drainage.
7. If the conditioner does not operate, the following points should be checked: a. Is proper voltage being supplied to the machine? b. Is the proper type of thermostat being used? c. Is the wiring to the thermostat correct?
8. If the conditioner operates but stops after a brief period, check for: a. Is there proper airflow?Check for dirty filter, incorrect ductwork. b. Is there proper water flow rate within temperature limits?Check water backflush unit if dirt clogged.
9. Check the unit for vibrating refrigerant piping, fan wheels, etc.
10. Do not lubricate the fan motor as it is prelubricated at the factory.
Page 23
Maintenance
1. Normal maintenance on all conditioners is generally limited to filter changes. Lubrication of the fan motor is not required.
2. Filter changes are required at regular intervals. The time period between changes will depend upon the project requirements. Some applications such as motels produce a lot of lint from carpeting and linen changes. It is suggested that the filter be checked at 60-day intervals for the first year until experience is acquired. If light cannot be seen through the filter when held up to sunlight or a bright light, it should be changed. A more critical standard may be desirable.
3. The condensate drain pan should be checked annually and cleaned and flushed as required.
4. Recording of performance measurements of volts, amps, and water temperature differences (both heating and cooling) is recommended. A comparison of logged data with start-up and other annual data is useful as an indicator of general equipment condition.
5. Periodic lockouts always are caused by air or water problems. The lockout (shutdown) of the conditioner is a normal protective result. Check for dirt in the water system, water flow rates, water temperatures, airflow rates (may be dirty filter), and air temperatures. If the lockout occurs in the morning following a return from night setback, entering air below machine limits may be the cause.
Troubleshooting
Should a major problem develop, refer to the following information for possible cause and corrective steps:
Neither fan nor compressor run
1. The fuse may be blown or the circuit breaker is open. Check electrical circuits and motor windings for shorts or grounds. Investigate for possible overloading. Replace fuse or reset circuit breakers after fault is corrected.
2. Wires may be loose or broken. Replace or tighten.
3. Supply voltage may be too low. Check it with the power company.
4. Control system may be faulty. Check thermostat for correct wiring and check 24-volt transformer for burnout.
Fan operates but compressor does not capacitor.
2. Wires may be loose or broken. Replace or tighten.
3. The high pressure may have tripped due to: a) Fouled or plugged condenser ;
b) Lack of or no condenser water ;
c) Too warm condenser water ; d) Not enough airflow over the coil due to dirty filters; e) Coil or fan motor failure.
4. The low temperature switch may have tripped due to:
a) Fouled or plugged condenser ;
b) Lack of or no condenser water ;
c) Too warm condenser water ;
d) Not enough airflow over the coil due to dirty filters ;
e) Coil or fan motor failure ;
5. Check thermostat setting, calibration and wiring.
6. The compressor overload protection is open. If the compressor dome is extremely hot, the overload will not reset until cooled down. If the overload is external, replace it. If the overload is internal, replace the compressor.
7. The internal winding of the compressor motor may be grounded to the compressor shell. If so, replace the compressor.
8. The compressor winding may be open. Check continuity with ohmmeter. If the winding is open, replace the compressor.
Page 24
Compressor attempts to start but doesn’t
2. Check for defective compressor by making resistance check on winding.
3. Check
Compressor runs in short cycle
1. Check thermostat mounting and location.
2. Check all relays, relaying and contacts.
3. Check capacitor.
4. Check high pressure switch.
5. Check low temperature switch.
6. See if reversing valve has not fully shifted to either side.
Insufficient cooling or heating
1. Check thermostat for improper location.
2. Airflow may be insufficient. Check and clean the filter.
3. The reversing valve may be defective, creating a bypass of refrigerant. If the unit will heat, check the reversing valve coil.
4. Check capillary tubes for possible restriction of refrigerant flow.
5. Check for restriction in water flow.
Insufficient water flow through condenser
1. Check to see that valves are open all the way.
2. Check for air in lines.
3. Check circulating pumps.
Water drips from conditioner
1. Check for plugged condensate drain.
2. Check for dirty filter.
3. Check to see if condensate drain runs uphill.
4. See if blower motor is up to speed.
5. Check for loose or mispositioned blower.
6. Are drains properly trapped?
Noisy unit operation
1. Check for fan wheel hitting the housing. Adjust for clearance.
2. Check for bent fan wheel. Replace if damaged.
3. Check for loose fan wheel on shaft. Tighten.
4. Make sure compressor is floating free on its isolator mounts.
5. Check for tubing touching compressor other surface. Readjust tubing by bending slightly.
6. Check screws on panels. Tighten.
7. Check for chattering or humming in the contactor relays due to low voltage or a defective holding coil. Replace component.
8. Check water balance to unit for proper water flow rate.
Page 25
©2003 McQuay International +1 (800) 432-1342 www.mcquay.com
REGISTERED
ISO 9002
S&E
advertisement
* Your assessment is very important for improving the workof artificial intelligence, which forms the content of this project
Related manuals
Frequently Answers and Questions
What is the maximum cooling capacity of the McQuay MWMV unit?
What is the maximum heating capacity of the McQuay MWMV unit?
What are the minimum and maximum voltage ranges for the McQuay MWMV unit?
How many phases does the McQuay MWMV unit operate on?
What is the minimum ambient air temperature for the McQuay MWMV unit to operate in?
What is the maximum ambient air temperature for the McQuay MWMV unit to operate in?
What is the minimum entering water temperature for the McQuay MWMV unit to operate in?
What is the maximum entering water temperature for the McQuay MWMV unit to operate in?
advertisement