- Home
- Home security & automation
- Gate Opener
- Automatic Solutions
- ASA 550L I
- Installation and Maintenance Manual
Automatic Solutions ASA 550L I Installation and Maintenance Manual
Add to My manuals16 Pages
Automatic Solutions 750L I Range is a heavy-duty sliding gate operator designed for industrial and commercial applications. It features a powerful motor that can handle gates weighing up to 750 kilograms and a maximum length of 12 meters. The operator is equipped with a variable speed drive that allows for smooth and controlled gate movement, and it also has a built-in safety clutch to protect the gate and operator from damage in the event of an obstruction.
advertisement
▼
Scroll to page 2
of
16
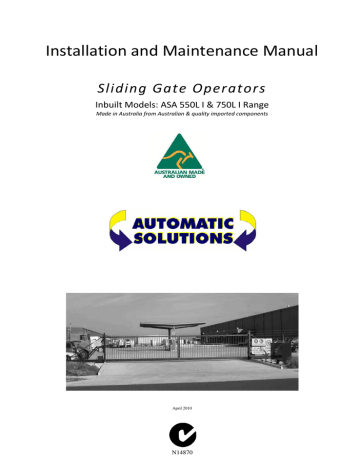
Installation and Maintenance Manual Sliding Gate Operators Inbuilt Models: ASA 550L I & 750L I Range Made in Australia from Australian & quality imported components April 2010 N14870 Abbreviated Installation Instructions (For those who don't have time!) Sliding Gate Operators ASA 550, 750 “L” Range Made in Australia from Australian & quality imported components Place operator in correct position (Pinion wheel to be parallel to the gate and stepped out to allow for width of rack once it is mounted onto the gate frame). Mark out fixings and fix operator to the concrete pad. Fix rack to the gate frame keeping 1mm-2mm clearance between the rack teeth and Pinion wheel Once the rack is fixed move the gate and sight the rack moving over the pinion wheel, check that most of the pinion wheel meshes with the rack. Make sure rack runs freely over the pinion wheel, any tights spots should be corrected by adjusting the rack height. Check the operator is firmly bolted down to the concrete pad. Ensure stops are installed on the gate for the fully closed and fully open positions. Connect required P.E Beams. Adjust Limits to actuate prior to gate end positions. Connect Power supply. Turn on Power. To commission the gate, move the gate approximately 1m from the fully open position and tighten the knurled wheel (Clockwise) engaging the clutch assembly Press the opening button located under the dip switches to begin opening cycle, Ensure the direction the gate travels is in accordance with the opening and closing status LED’s, if not reverse two of the motor wires at the inverter terminals. Inverter settings can be adjusted via the keypad i.e. Opening speed, closing speed and ramp times. Automation settings operating modes are able to be adjusted via the CB6 board, refer to manual for further instructions Once Inverter settings are appropriately set proceed to fine adjust the Limits for required operation CONTENTS Abbreviated Installation Instructions Page 2-3 Section 1 Safety Precautions Page 5 Section 2 Wiring Requirements Page 6 Section 3 Installation Page 6-10 Electrical Cabling Mechanical Installation Electrical Connections CB6 Control Board Variable Speed Drive Unit Commissioning Section 4 Manual Release Instructions Section 5 Maintenance Page 11 Section 6 Warranty Page 12 Annexure Control Board Layout for Inverter Controls Schematic Wiring Diagram Page 10 1. SAFETY PRECAUTIONS WARNING! FAILURE TO FOLLO LOW THESE SAFETY PRECAUTIONS AND INS NSTALLATION INSTRUCTIONS COULD RESULT IN INJURY OR DEATH AND/OR DAMAGE TO P PROPERTY AND EQUIPMENT. Appropriately licensed and competen etent personnel only should install the automation equ equipment. The operators are designed specifica ically to open and close sliding gates or doors and sh should not be used for any other purpose. Before commencing installation,, read through this installation manual. Check that the operator and controls ols are in new condition and have not been damaged ed iin transit. Check the gate or door and its associ ociated support posts and walls to protect against shea hearing, compression and other various traps aps which could cause serious injury or death. Takee in into consideration the general installation and surround nding environment. Check the gateposts or mounting str structure has the necessary strength and rigidity to su support the operator and the load of the opening ng and closing gate motion. CAUTION! Always incorporate the appropria riate Photo Electric Cells, Induction Loops and an any other safety devices to protect both equipment ent and personnel. Extra caution should be employ loyed when using operator in auto close mode. Display any necessary signs to indica dicate any danger areas and automatic operation of th the gate or door. The operators are not designed to be u used in any hazardous areas or areas subject to flo flooding etc. All electrical connections and wiring ing must be performed with AS/NZS 3000-2007 ass tthe guidelines. (Or its counterpart for other countries tries outside of Australia and New Zealand) WARNING! ELECTRICITY CAN KILL LL The manufacturer of the automation on equipment is not responsible for the damage which ich may be caused to either the operator, gate or doorr an and any other person or equipment when: o Wrong or poor installationn ppractices were performed. o No or inadequate safety dev evices were used. o Either the surrounding struct ucture or the gate or door strength and rigidity was as nnot sufficient for the task in hand. o Inefficient locking devicess w were employed. o Poor maintenance on the eq equipment. o Any other circumstances be beyond the manufacturers control. Isolate power before attempting any maintenance, qualified personnel only to carry ou out maintenance Only original spare parts are to bee uused should there be a requirement for them. Keep loose clothing and hands clear ear of the gate whilst in operation or potentially able le to be operated. The installer should provide all info formation concerning the use of the automation equi uipment as well as instructions regarding the manual ov override and maintenance procedures to the users of the system. 2. WIRING REQUIREMENTS 240v 10A non-earth leakage protected power supply where operator is mounted. Low voltage cables from operator for access control. (Shielded cable if over 8m runs). 3. INSTALLATION DETAILS After reading the previous sections in this manual, and having checked for suitable installation, proceed as follows:Electrical Cabling A suitably rated Isolator and 240v power supply should be available near to where the gate operator is to be mounted. The following diagrams will provide measurements for the positioning of conduits and the appropriate position for mounting the operator whether a GDS 550-450LI or a GDS 750-630LI. Mechanical Installation Ensure gate rolls easily and has been installed in a manner where there is no excessive friction or binding occurring. A concrete base approximately 600mm long x 300 wide x 300mm deep should be laid where the gate operator is to be located. IMPORTANT ensure there are gate stops firmly installed in the fully open and closed positions. These stops need to be engineered and installed such that they will be strong enough to stop the gate should the limits fail at any time. Remove the gate operator cover and position mounting plate and operator in approximate mounting location. Use the rack to locate the operator the correct distance away from the gate rail (finer adjustment can be made after). Dynabolt or chemical anchor the bottom mounting plate to the concrete mounting pad using 12 x 100mm fixings. Unscrew anticlockwise the manual disconnect knurled knob so the drive gear free wheels. Fix the rack to the gate rail ensuring there is approximately 1mm - 2mm gap between the meshing of the teeth of the rack and the drive gear (no more). Move the gate by hand from one end to the other while checking that the rack is meshing correctly with the drive gear on the operator. Check also that the rack is centred around the middle of the teeth on the drive cog – tighten the mounting plate nuts. Electrical Connections Connect a non earth leakage protected 10A 240v supply to Din Rail terminals labelled A & N, Connect earth to the earth Din Rail terminal. Conduits for power & control need to preferably come up through the base plate 'knockout'. Connections to Control Board Units are pre-wired Control Inputs The P.E, OPN and STP inputs require a normally closed switch contact and therefore should be shorted to the COM terminal if not used. This is done via bridging links already on the circuit board (bottom left corner) The CLS, OSC and PED inputs require a normally open switch contact and therefore should be left unconnected if not used. All the switch inputs of this control board including the limit switch inputs require a switch contact only. Do not connect any switches which provide a voltage to the control board as this will damage the control board. If the desired inputs are 12/24v or has long wiring associated with it use an IM-1 module to isolate it from the control board’s input. The IM-1 is available from the manufacturer. Powering Accessories Accessories which require a 24v AC supply can be powered from the transformer output used to power the control board via the isolated 24v AC supply which is connected to the DIN rail terminals as labelled. However, the transformer’s current capacity must be checked to allow for the extra power required by the accessories. Never use the supply connected to the 24v AC supply control board terminals to power any accessory as this can interfere with the control boards operation. (Blue Wires) Locks & Lights Use the lock output terminals on the din rail to switch the 12 volts to an electric lock (if fitted). The load switched by the lock output terminals must not exceed 30V A.C / D.C @ 5Amps. If a electro magnetic lock is used, change one wire on the control board lock output to the normally closed output. Use the light relay module (if fitted) to switch the applied voltage to a light. The load switched by the light relay module must not exceed 240V A.C / 30V D.C @ 10 Amps. MODE SELECTION Using the mode selection dip-switches select the desired operating modes. Note the times associated with the parameters marked with an * can be changed. The auto-close times can be changed using the procedure in the following section. See the instruction manual for details on how to change the other parameters. See the detailed instruction manual for details on how to change the other parameters. Position 1 SYNCHRONISING DELAY OFF - No delay ON - Motor 1 starts to open 2 seconds* before Motor 2 and Motor 2 starts to close 2 seconds* before Motor 1. Position 2 PULSE LOCK OUTPUT OFF - Lock output is activated for the entire motor drive cycle. ON - Lock output pulses for 0.3 seconds* at the start of each drive cycle. Position 3 LIGHT OUTPUTS WARNING OFF - Optional light module controls a light with timer which turns light off after 60seconds*. ON - Optional light module controls a warning light which activates whenever motors are on. Position 4 SWIPE MODE (OSC INPUT) OFF - OSC input terminal has standard Open, Close, Stop action. ON - OSC input terminal will only open the door/gate. The input also resets the P.E triggered auto-close mode so that the P.E input will need to be triggered again before a P.E autoclose cycle will be initiated. Position 5 M 2 OUTPUTS STATUS OFF - The M2 output controls second motor ON - The M2 output controls status lights Position 6 P.E STOPS CLOSE CYCLE OFF - Activating the P.E input while motors are closing causes the motors to reverse. ON - Activating the P.E input while motors are closing causes the motors to stop but not reverse. Position 7 P.E STOPS OPEN CYCLE OFF - Activating the P.E input while motors are opening is ignored by the controller. ON - Activating the P.E input while motors are opening causes the motors to stop. Position 8 P.E TRIGGERED AUTO-CLS OFF - Not selected ON - Selects the P.E triggered auto-close mode which causes the motors to auto-close if the P.E input is activated then released. (Auto-close delay time is 0 seconds*) Position 9 PEDESTRIAN AUTO-CLS OFF - No pedestrian access auto-close ON - Selects auto-close in the pedestrian access mode. (Auto-close delay time is 15 seconds*) Position 10 STANDARD AUTO-CLS OFF - Not selected ON - Selects standard auto-close mode which will close the motors after fully opening. (Auto-close delay time is 30 seconds*) Setting Cycle Timers & Auto Close Times The control board has pre-set cycle times which are used to set the maximum time the controller will drive the motors in the open and closed directions. The pre-programmed time for the open and close cycle timer’s is 60 seconds. The control board also has a pre-set pedestrian access time of 5 seconds which is intended to open the motor connected to M1 output only part way. If these default times do not suit your needs simply use the procedure below to adjust them. Note the same procedure can be used to adjust the auto-close times. 1. Place the slide switch into the “set” position 2. Adjust the timer’s value by pressing and holding the required push button for the desired time. 3. Repeat step 2 for the next timer (if desired). 4. Place the slide switch back into the “RUN” position. 5. Test operation. Make sure that the slide switch is placed back into the “RUN” position before testing the new timer value. As you can see the procedure used to set each timer’s value is the same only the push button used changes. Each push button is clearly labelled underneath as to which timer’s value it sets. Note when setting the OPEN, CLOSE and PEDESTRIAN cycle times the controller will drive the motors as if a “real” cycle is being executed. The difference being that the motors will stop as soon as the button is released or the limit switches are reached. The OPN status LED on the control board will flash at 1 second intervals to assist setting times. Note when setting the OPEN and CLOSE cycle times when limit switches are used, release the push button a few seconds after the limit switch cuts motor power. This allows for the motors to slow down over the life of the operators without the need to adjust again. Variable Speed Drive Unit The variable speed drive unit will, ramp up the speed of the operator and then ramp down prior to closing. It must be remembered that the limit switches are to be set in a position which initiates the ramp down time. Therefore, the limit switches need to operate much sooner than when there is no variable speed drive unit. The accelerate and decelerate times have been set in the factory for the normal installation but can be changed if necessary. Similarly, the speed that the gate operates at has also been set but can be changed (up to approx 70Hz). NOTE changing the speed will change the position the gate will end up in its fully closed and open position. (Unless limit switch cams are also adjusted accordingly). Accelerate time (FN01) 5 sec Decelerate time (FN02) 2.5 sec Closing Speed (FN08) 40Hz Running Frequency 60Hz To change accelerate time: Press DSP/FUN button Use arrows to select FN01 Press DATA/ENT Use arrows to select new time Press DATA/ENT Press DSP/FUN To change decelerate time: as above except select FN02 To change closing speed: as above except select FN08. If opening speed and closing speed is to be the same, remove wire link between REV and SP1 terminals on invertor. To change opening speed of operator: when display is flashing and showing Hz, use arrows to raise or lower the Hz figure. NOTE frequency upper limit has been set to 70Hz and lower limit 30Hz. Commissioning Position the gate halfway and tighten knurled knob at back of slider, very firmly, by hand so gate will drive. Power up board and with gate in the half way position, press transmitter or manual control switch so operator drives gate. The first pulse will always open gate, green LED will flash (top right hand corner) if it does not, then reverse 2 of the motor wires. Check which limit switch stops gate in each direction and adjust cams so gate will stop in the fully open and closed positions. Limit switches should not switch off the gates too soon (before reaching the stops) and conversely not too late, so the torque limiter is operating. Tighten torque limiter knurled knob. Set open & closed travel time. Check that all safety devices work as designed and the electromagnetic lock holds the gate firmly closed (if fitted). Install cover using screws provided in the front and sides to hold cover firm. Provide full details to the owner concerning the operation and relevant maintenance and disconnect details. 4. M ANUAL R ELEASE I NSTRUCTIONS Should the power fail or for some other reason the gate does not operate in the normal motorised manner, manual disconnection can be achieved by:Turn power off to the control box and isolate. By using the key, unlock the door on the back of the cover. Turn the large knob anticlockwise which will release the drive Manually slide open the gate. 5. M AINTENANCE D ETAILSS WARNING! Failure to maintain equipment may result d eq equipment ult in injury or death and/or damage to property and Recommended maintenance to be perfor formed on the operator and gate are as follows:Operator performs over 150 cy cycles a day each month Operator performs between 10 100-150 cycles a day every 2 month Operator performs between 50 50-99 cycles a day every 4 months Operator performs between 20 20-49 cycles a day every 6 months Operator performs under 20 cy cycles a day every 12 months Date: ................................................................ .............................................................. Site Name:................................................................ ................................................................................................ .......................................................... Site Address: ................................................................ ................................................................................................ ...................................................... Before commencing maintenance on the ooperator, isolate the electrical supply to ensure op operator will not run inadvertently. Gate rolls freely................................ ................................................................................................ ............................................... Gate guide rollers in good ccondition................................................................ ............................................... Gate stops in good condition ion........................................................................................... ........................... Gate rack is tight & correct ct cclearances between pinion wheel & rack ........................... Gate track is not damaged ................................ ............................................................................................... ............................... Gate operator mounting bolt olts right ................................................................ ................................................. No oil leaks from gearboxes es ........................................................................................... ........................... Gearbox mounting bolts/nut uts tight................................................................ .................................................. Inside operator and controll bbox clean ................................................................ ............................................. ‘Baygon’ Surface Spray aro round operator and control box (not on electroni nics) ............. All electrical connections tig tight........................................................................................ ........................ Limit Switches operate in ap appropriate positions............................................................. ............................. External safety devices work ork effectively / cleaned ......................................................... ......................... Electromagnetic lock, if fitte itted, operates correctly and is clean ................................ ...................................... Gearbox self locking i.e. sea seal needs replacing? .............................................................. .............................. General operation i.e. speed ed, auto close etc normal........................................................ ........................ Comments................................................................ ................................................................................................ ............................................ ................................................................ ............................................................................................................................. ............................. ................................................................ ............................................................................................................................. ............................. Service performed by ................................ .......................................................................................................................... .......................................................... 6. W ARRANTY a. Gate Drive Systems Australia warrants that the goods manufactured by it shall be free from defect in manufacture for a period of 12 months from the date of invoice. Should any fault occur within that period as a result of faulty workmanship or materials, Gate Drive Systems Australia will make all necessary repairs, or at its discretion replace the product at no charge to the Customer except for freight. The appropriate Serial Number must be quoted for all warranty claims. b. For the goods not manufactured by Gate Drive Systems Australia, we shall pass on the manufacturer’s warranty to the Customer from the date of invoice. It is the manufacturer’s discretion to repair or replace goods deemed to be defective as a result of faulty workmanship or materials. c. All goods must be returned to Gate Drive Systems Australia or its representative for inspection or testing to assess if a claim is justified. It is the responsibility and at the cost of the Customer, to return the goods for inspection and freight costs are the responsibility of the Customer. d. The warranty is negated and will not apply in the following circumstances:i. If no proof of date of purchase can be produced. ii. If the product has been used in a manner beyond its design parameters. iii. If the product is tampered with or repaired by personnel not authorised to do so. iv. In respect of loss or damage caused by rough treatment. v. If the product is not used and maintained in accordance with instructions or recommendations listed in this Installation and Maintenance Manual. vi. In respect of loss or damage caused by an Act of God or any other cause not within the manufacturers control. e. Goods returned under warranty for repair or testing will incur a charge to be fixed by the manufacturer if no fault is found. f. The Customer shall bear freight charges for returning the goods for inspection and for the delivery of any replacement or repaired product from a justified warranty claim. g. Save for the express conditions and warranties herein contained all other conditions or warranties (whether as the quality, fitness for purpose or any other matter) expressed or implied by statute, common law, equity, trade custom, usage or otherwise are hereby expressly excluded provided that nothing in these terms and conditions shall exclude or limit any breach or condition implied by law, the exclusion or limitation of which is not permitted by law. Single Controls Dual Controls CONTROL BOARD LAYOUT FOR INVERTER CONTROLS FIG. 4 1. 2. 3. 4. 5. 6. 7. 8. 9. 10. 11. 12. 13. 14. 15. 16. Mode Selection and Adjustment Protection Fuse Inverter Input Terminals Motor 1 Drive Output Terminals for Inverter Motor 2 Drive Output Terminals for Inverter Motor 1 Limit Switch Inputs Motor 2 Limit Switch Inputs Terminals for Isolated 24vAC Supply for Limit Switch and Control Inputs Pedestrian Access Control Input Open/Stop/Close Control Input Close Control Input Stop Control Input Open Control Input Photoelectric Safety Beam Input Com mon Terminal for Inputs [9] Thru [14]. Control Input Harness Connector 17. 18. 19. 20. 21. 22. 23. 24. 25. 26. 27. 28. 29. 30. Electric Lock Control Terminals Terminals for 24vAC Supply for Control Logic Plug In Rec eiver's Antenna Terminals With Optional Shield Connector for Plug-In Receiver (no t shown) Firmware Version Label Light Control Relay Interface Connector Inp ut Status L.E.Ds. Stop Input Jumper Open Input Jumper PE Beam Input Jumper M2 Close Limit Jumper M2 Open Limit Jumper M1 Close Limit Jumper M1 Open Limit Jumper SELF INSTALL - NEED TECHNICAL ASSISTANCE? OPTION 1: DIRECT WITH THE SERVICE DESK QUICKEST AND MOST EFFECTIVE METHOD Submit your enquiry direct with the service desk at [email protected] The service desk has the most experienced staff in Australia to help with your problem but they need your help. Describe your problem in detail and as clearly as possible. Don t forget to include a telephone number. Be certain to detail which model or models of you are working with. Send photos of the installation they love photos. The people at the service desk are good but they are even better when they can see the installation. Send photos of the overall scene so they can see the entire installation. Also send photos of the wiring to the control board and any other part of the installation you think is relevant. Send video if appropriate. Smartphone s these days take remarkably good video in small file sizes which can be emailed in a moment. If your problem needs a video to show the issue please feel free to send it. NOTE: THIS IS BY FAR THE FASTEST AND MOST SUCCESFUL WAY TO SOLVE YOUR PROBLEM PHOTOS AND VIDEOS ARE THE NEXT BEST THING TO BEING THERE OPTION 2: LODGE YOUR ENQUIRY LOCALLY - SLOWER BUT CAN STILL BE EFFECTIVE Make contact with the store of purchase. Branch staffs are typically not technicians and dependent on their length of service will have varying degrees of technical knowledge. If they cannot help however they will certainly either source help locally from their technicians or make contact with the service technicians on your behalf. OPTION 3: SERVICE CALL WITH AUTOMATIC SOLUTIONS TECHNICIAN SLOWEST METHOD If you fall within the local branch service area it may be possible to book a local technician to look at your installation. Wait times will vary dependent on local workloads. The cost is a service fee which includes the first half hour and the hourly rate thereafter. If any Automatic Solutions provided parts are found to be defective and within warranty these will be provided free of charge. (NOTE: If you suspect that any parts are defective and within warranty you may wish to consider option 4) A note on this option: If you decide on this option you will be asked to sign an authorisation to proceed which will provide legal authority and payment security. This form has three options available of which only the first two are available to you. The third option is for warranty repairs only for full install customers. Self install customers requiring warranty only service need to refer to option four below. IMPORTANT: IN SHORT THIS OPTION WILL INCUR CHARGES OPTION 4: RETURN THE PRODUCT IF BELIEVED TO BE FAULTY As a self install customer who has purchased product if you believe the product to be faulty rather than an installation or site problem you have the option of returning the product for evaluation and to exercise your right to a replacement, repair or refund as applicable. All returned product is forwarded immediately to the service technicians for evaluation and response. There are two main methods available to return product Direct to the service centre this is the quickest method as it cuts out the branch delay Via the branch of purchase slower because of the delay at the branch When choosing this option you need to complete a product return form. This form gives you all the information on procedure involved and where to send to. These are available at the branch of purchase, can be emailed to you (contact your branch), or available here - http://automaticsolutions.com.au/page/warranty.php
advertisement
Related manuals
advertisement