Centurion BENINCA IT24N Installation Instructions Manual
Add to My manuals48 Pages
Centurion BENINCA IT24N is an underground swing gate operator ideal for domestic and light-industrial applications. It offers smooth acceleration, safe protection against crushing, and critical power failure protection. Features include standard, pedestrian, and free-exit opening modes, auto-close, open and closed end-of-travel limits, infrared safety beam input, status LED output, solenoid lock drive, pillar light control, holiday lockout, and battery low protection.
advertisement
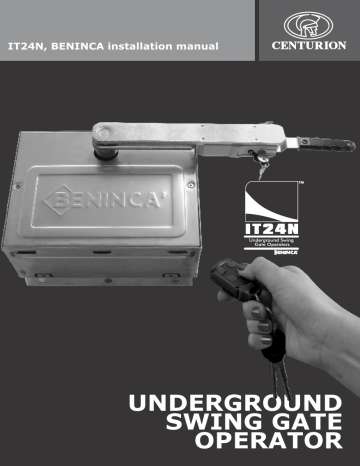
IT24N, BENINCA installation manual
I T 2 4 N
UNDERGROUND
SWING GATE
OPERATOR
Company Profile
1986
In-house
R & D development team
1990 1995 1999
Manufacture to international quality standard
ISO 9001:2008
100% testing of products
Competent after-sales technical support
Sales and support throughout
Southern Africa and over
50 countries worldwide
CENTURION SYSTEMS (Pty) Ltd. reserves the right to make changes to the products described in this manual without notice and without obligation of CENTURION SYSTEMS (Pty) Ltd. to notify any persons of any such revisions or changes. Additionally, CENTURION SYSTEMS
(Pty) Ltd. makes no representations or warranties with respect to this manual.
No part of this document may be copied, stored in a retrieval system or transmitted in any form or by any means electronic, mechanical, optical or photographic, without the express prior written consent of CENTURION SYSTEMS (Pty) Ltd.
Contents
Mechanical setup
Electrical setup
Commissioning and handover
IMPORTANT SAFETY INSTRUCTIONS page 1 page 2 page 2 page 3
1. Declaration of conformity
2. General description page 5 page 6
Fuse protection
4. Icons used in this manual
5. Product identification page 9 page 10
6. Required tools and equipment
7. Preparation of site page 11 page 12
8. Cabling requirements page 13
9. Operator installation page 15
10. Electrical setup page 23
11. Wiring diagram for safety beams page 25
12. Wiring diagram for other accessories page 26
13. Wiring diagram for motors and open limits page 27
14. Controller features page 32
15. Description of terminal functions page 35
16. Diagnostics
18. Installation handover
Diagnostic LEDs
Gate status LED
17. Manual release operation page 37 page 37 page 38 page 39 page 40
Mechanical setup
These abbreviated instructions are for the experienced installer who needs a checklist to get a standard installation up and running in the minimum of time.
Detailed installation features and functions are referred to later in this manual.
Gather required tools and equipment page 11
Heed necessary site considerations page 12
Check cabling requirements
Install foundation box page 13 page 15
Install motor and link to gate page 18
Set limit switches and /or fit mechanical endstops page 21 page 1
Electrical setup
Mount controller enclosure and connect all wiring
Commissioning and handover
Commission system
Carry out professional handover to client page 2
IMPORTANT
Safety Instructions
ATTENTION
To ensure the safety of people, it is important that you read all the following instructions. Incorrect installation or incorrect use of the product could cause serious harm to people.
The installer, being either professional or DIY, is the last person on the site who can ensure that the operator is safely installed, and that the whole system can be operated safely.
Warnings for the installer
CAREFULLY READ AND FOLLOW ALL INSTRUCTIONS
before beginning to install the product.
All installation, repair, and service work to this product must be carried out by a suitably qualified person
This appliance is not intended for use by persons (including children) with reduced physical, sensory or mental capabilities, or lack of experience and knowledge, unless they have been given
* person responsible for their safety
Do not activate your gate opener unless you can see it and can determine that its area of travel is clear of people, pets, or other obstructions
NO ONE MAY CROSS THE PATH OF A MOVING GATE.
Always keep people and objects away from the gate and its area of travel
NEVER LET CHILDREN OPERATE OR PLAY WITH THE GATE
CONTROLS
Secure all easily accessed gate opener controls in order to prevent unauthorized use of the gate
Do not in any way modify the components of the automated system
Do not install the equipment in an explosive atmosphere: the presence of flammable gasses or fumes is a serious danger to safety
Before attempting any work on the system, cut electrical power to the operator and disconnect the batteries
The mains power supply of the automated system must be fitted with an all-pole switch with contact opening distance of 3mm or greater.
Use of a 5A thermal breaker with all-pole circuit break is recommended
Make sure that an earth leakage circuit breaker with a threshold of
30mA is fitted upstream of the system page 3
Never short circuit the battery and do not try to recharge the batteries with power supply units other than that supplied with the product, or by Centurion Systems
Make sure that the earthing system is correctly constructed, and that all metal parts of the system are suitably earthed
Safety devices must be fitted to the installation to guard against mechanical movement risks, such as crushing, dragging and shearing
It is recommended that at least one warning indicator light be fitted to every system
Always fit the warning signs visibly to the inside and outside of the gate
The installer must explain and demonstrate the manual operation of the gate in case of an emergency, and must hand the User Guide over to the user
Explain these safety instructions to all persons authorized to use this gate, and be sure that they understand the hazards associated with automated gates
Do not leave packing materials (plastic, polystyrene, etc.) within reach of children as such materials are potential sources of danger
Dispose of all waste products like packaging materials, worn out batteries, etc. according to local regulations
Always check the obstruction detection system, and safety devices for correct operation
Centurion Systems does not accept any liability caused by improper use of the product, or for use other than that for which the automated system was intended
This product was designed and built strictly for the use indicated in this documentation. Any other use, not expressly indicated here, could compromise the service life/operation of the product and/or be a source of danger page 4
1. Declaration of conformity
Manufacturer:
Address:
Automatismi Benincà spA
Via Capitello, 45 - 36066 Sandrigo (VI) - Italia
Herewith declares that: the operator for hinged gates model DU.IT24N
is intended to be incorpored into machinery or to be assembled with other machinery to constitute
machinery covered by Directive 89/392 EEC, as amended;
does therefore not in every respect comply with the provisions of this Directive; does comply with the provisions of the following other EEC Directives:
Direttiva compatibilità elettromagnetica 89/336/CEE, 93/68/CEE.
and that:
the following (parts/clauses of) harmonized standards have been applied:
EN 55022, EN 61000-3-2, EN 61000-3-3, EN 50082-1.
And furthermore declares that it is not allowed to put the machinery into service until the machinery into which it is to be incorporated or of which it is to be a component has been found and declared to be in conformity with the provisions of Directive 89/392/EEC and with national implementing legislation, i.e. as a whole, including the machinery referred to in this declaration.
Benincà Luigi, Responsabile legale.
Sndrigo, 10/01/2005.
page 5
2. General description
The
IT24, Beninca
is an underground swing gate operator designed for domestic and lightindustrial applications where the operator is hidden from view. It is also useful in applications where the gate swings hard up against its side wall leaving absolutely no space to mount a traditional above-the-ground unit.
The operator consists of a high-torque 24V DC motor coupled to a double-stage worm reduction gearbox housed inside a steel foundation box. The assembly is mounted flush with the ground, up against the gate support pillar, directly under the gate hinges. Its output drive arm extends upwards from the operator linking with a drive shoe that is welded to the underside of the gate.
The drive arm, drive shoe and operator cover plate are the only parts that are visible. The gate is supported by the operator with the bottom gate hinge removed. Only the top hinge is left to stabilize the top of the gate.
To ensure rigid closing of the gate in the closed position, end-of-travel mechanical endstops must be installed. In addition, if the gate leaf is wider than 2.5m, an electric lock must be fitted, and on any width if maximum security is required.
The internal mechanical limit switches can be used to stop the gates in the open position, the alternative being mechanical endstops.
A Manual Override with key release is incorporated into the drive arm assembly.
The operators are battery driven via the CP77/24V dual motor controller, which supports a host of useful features in addition to providing smooth acceleration of the motors on start-up, safe protection against crushing and critical power failure protection.
Summary of features supported by the CP77/24V controller
Modes of Operation:
Standard only
Pedestrian Opening
Free-exit Opening
Autoclose, selectable via ON/OFF switch and closing time adjustable
Open and closed end-of-travel limits
Infrared safety beam input for gates when closing
A status LED output to indicate the gate status remotely
Solenoid lock drive output with load capacity up to 2A
Pillar Light Control
Holiday Lockout
Battery Low Protection
Leaf delay – must be ordered with specific plug-in microcontrollers page 6
3. Specifications
Gearbox and DC motor assembly
300
220
112
350
200
* Output drive arm, mechanical release and drive shoe not shown
All dimensions shown in millimeters
FIGURE 1. GEARBOX AND MOTOR DIMENSIONS
Foundation box
152
98
All dimensions shown in millimeters
214
294
364
FIGURE 2. FOUNDATION DIMENSIONS
page 7
Technical specifications
Input voltage
Motor voltage
Motor power supply
Battery charger
Current consumption (mains)
Current consumption (motor at rated load)
Current consumption
(controller and receiver only - standby)
Operator output torque - maximum
Typical gate opening time (90° opening)
Operator reversible / irreversible
Manual Override
Maximum number of operations per day
Duty cycle - mains present
Operations in standby
With 7Ah battery
Half day
One day
With 40Ah battery
Half day
One day
Collision sensing
Operating temperature range
Gearbox housing protection
Receiver type
Mass of unit packed
Operator
Foundation box
Controller housing
Packaging dimensions
Operator
Foundation box
Controller housing
220V AC ± 10%, 50Hz
24V DC
Battery driven (standard capacity - 2 x 7Ah)
500mA @ 27.5V DC
60mA
5A
70mA
70mA
360Nm
15-23 seconds
Irreversible
Key release
200
50%
26
19
155
149
Electronic
-15°C to +50°C
IP67
External
11.6kg
8.6kg
4kg (excludes batteries)
350 x 150 x 200mm
400 x 400 x 250mm
480 x 320 x 150mm
Can operate off a solar supply, consult Centurion Systems for assistance
Can increase battery capacity for longer standby times
Based on 25°C ambient temperature and unit not in direct sunlight
Based on an output torque of less than 50% of maximum
Based on double kit excluding infrared safety beams page 8
Allowable gate mass
Leaf width
Leaf mass
External electric lock must be fitted
2.0m
550kg
2.5m
500kg
3.0m
450kg
3.5m
400kg
4.0m
350kg
Allowable wind loading
Leaf width
2.0m
Maximum wind speed
(1.8m high gate, 25% coverage)
80km/h
Maximum wind speed
(1.8m high gate, 100% coverage)
45km/h
Assumes collision sensitivity set to low
2.5m
65km/h
3.0m
50km/h
3.5m
40km/h
4.0m
35km/h
35km/h 30km/h 25km/h 20km/h
Fuse protection
The following protection fuses are provided on the system:
Item
Main controller
Master motor circuit
Slave motor circuit
Light circuit
Auxiliary supply
Type
5 x 20mm
5 x 20mm
5 x 20mm
5 x 20mm
Charger
Mains input 5 x 20mm
Rating
20A slow blow
20A slow blow
3A fast blow
3A fast blow
250mA fast blow
4. Icons used in this manual
This icon indicates tips and other information that could be useful during the installation.
This icon indicates warning, caution or attention! Please take special note of critical aspects that MUST be adhered to in order to prevent injury.
This icon denotes variations and other aspects that should be considered during installation.
page 9
5. Product identification
1. Drive shoe
2. Drive assembly ball bearing
3. Output drive arm
4. Linkage arm
5. Gearbox output shaft and secondary stage wormwheel gear
6. Gearbox housing bottom cover plate
7. Operator drive safety cap
8. Foundation box
9. Manual release mechanism
10. Gearbox drive arm
11. 24V DC motor and sealing O ring
12. Gearbox housing
13. Foundation box cover plate
14. Secondary stage wormwheel shaft assembly
15. Foundation box cover fixing bracket
16. End-of-travel limit switches page 10
6. Required tools and equipment
Allan key – 5mm
Crimping tool and pin lugs
Duct tape
Electric drilling equipment
Hacksaw
Hammer
Measuring tape
Pick
Pliers
Ratchet and extension with a 7mm and 19mm socket
Screwdriver – 3.5mm flat; large star; small star
Side cutters
Spade
Spanner – 17mm and 10mm
Spirit level
Vice grips
Welding equipment page 11
7. Preparation of site
General considerations for the installation
Always recommend the fitment of additional safety equipment such as safety edges and safety beams, for additional protection against entrapment or other mechanical risks
Check that no pipes or electrical cables are in the way of the intended installation
Check that it is possible to mount the foundation box directly beneath the gate hard up against the support pillar noting that the output shaft is vertically below the centerline of the hinges
Check that it is possible to remove the bottom hinge and allow the gate to be supported by the operator
Check that there is a sufficient gap between the underside of the gate and the ground to accommodate the operator drive arm and drive shoe with the operator mounted flush with the ground
Check the fixing of the drive shoe to the underside of the gate. With steel gates the shoe can be welded. With a wooden gate, the shoe will have to be bolted to the gate
Check for loose, sandy soil as the soil may require a larger concrete foundation to securely support and locate the foundation box
Check that adequate draining can be provided for the foundation box
If the swing gate leaf is longer than 2.5mm, ensure that a lock can be fitted
End-of-travel mechanical endstops must be fitted for the gate in the closed position
Should any welding or modifications to the gate be required, this should be done prior to the
Beninca
operator being installed
Install the gate operator only if:
It will not pose a hazard to the public
There is sufficient clearance to a roadway and/or public thoroughfares
The installation will meet all municipal and/or local authority requirements once completed
The gate mass, leaf width, allowable wind loading and application is within the operator specifications (refer to the specification tables)
The gate is in good working order, meaning:
That it swings freely;
Does not move on its own if left in any position;
Each gate leaf is strong and rigid
It can be installed to have sufficient clearance between moving parts when opening and closing to reduce the risk of personal injury and entrapment
Pushbuttons or key switches, when required, can be positioned so that the gate is in line of sight of the operator page 12
8. Cabling requirements
FIGURE 4. CABLING REQUIREMENTS
Legend
2
1a. 220V AC mains cable via double pole mains isolator switch (3 core LNE 1.5mm
SWA ) or
1b. Low voltage cable from transformer (34V secondary @ 800mA) to battery charger
(2 core + earth 1.5mm² Norsk )
2. Motor cables (2 core + earth 1.5mm², 2 core 0.5mm², multi-stranded)
3. Optional intercom, cable from control box to dwelling ( n1
@
4. Optional intercom, cable from control box to entry panel ( n2 0.5mm² multi-stranded)
5. Optional infrared safety beams (3 core 0.5mm² multi-stranded)
7a.Optional pedestrian keyswitch (2 core 0.5mm² multi-stranded) or
7b.Optional keypad (3 core 0.5mm² multi-stranded)
9. Optional pillar lights (3 core LNE SWA , size according to power requirements)
11.Optional electric lock (2 core 0.5mm²) page 13
All cables must be routed in conduit unless underground cable is being used
Mains isolator must be less than 1m from the operator
Safety beams are always recommended page 14
9. Operator installation
To simplify the installation process, it is recommended that the existing gate is removed from the pillar before proceeding.
Foundation box installation
As the foundation box is liable to fill with water during rainfall, it is critical that an adequate drainage system is prepared.
Refer to step 9.
1. Determine the correct position for the foundation box, i.e.
standard
or
inside
.
Standard mounting configurations
Inside mounting configurations
FIGURE 5. STANDARD MOUNTING CONFIGURATIONS
FIGURE 6. INSIDE MOUNTING CONFIGURATIONS
page 15
2. Dig a hole for the foundation box - the size of the hole being adequate to securely anchor the foundation box taking into consideration:
Weight of the gate resting on the foundation box
Condition of the soil around the foundation box
3. Cast the base of the hole in a quick-drying concrete, ensuring the base is level and that the foundation box when inserted into position, will be flush with the ground.
4. Fold the two anchor tabs at 45° away from the base of the foundation box just prior to inserting it into the hole. page 16
FIGURE 9
5. Cover the drainage holes on the inside with duct tape.
6. Insert the
foundation box
into the hole.
Ensure the box is placed in a horizontal position, with the casing pivot at exactly 90° to the base, and perfectly aligned with the gate's hinge.
7. Lay a 30mm PVC conduit through the cable hole – the conduit must be routed back to the controller housing.
8. Complete casting the foundation box by filling in around the sides with concrete.
page 17
FIGURE 10
Line of gate hinges
Seal between casing and conduit
To controller
Cable conduit
Casing pivot
Horizontal and flush with ground
FIGURE 11
FIGURE 12
9. As soon as the previous step is completed, determine the position on either side of the foundation box to which the drainage holes will lead. Prepare drainage shafts as follows:
Dig drainage shafts next to the concrete foundation adjacent to the drainage holes of the foundation box
Shaft dimensions are approximately -
200mm diameter x 500mm deep
10. Before the concrete has completely set remove the duct tape from the drainage holes and carefully core through the side wall of the concrete foundation into the drainage shaft.
11. Ensure that there is a slope in the coring between the drainage hole and the shaft so that water will be able to drain away.
12. Fill the drainage shafts with crushed stone or pebbles.
Motor and gate assembly
1. Remove the bottom hinge from the gate – only one hinge on each gate is required, with the drive unit itself serving the purpose of the bottom hinge.
Remove bottom hinge
page 18
Foundation box
Drainage hole
Drainage hole
200mm diameter and 500mm deep
FIGURE 13
FIGURE 14
FIGURE 15
2. Assemble the
drive arm
onto the
gearbox
just above the
limit switch cam disc
, firmly tightening the cap screw to a maximum torque of 45Nm.
FIGURE 16
3. Orientate the gearbox and motor assembly according to the mounting configuration
(standard or inside). Lower the motor into the
foundation box
onto the mounting bolts in the base of the box and tighten in position using the M10 nylon nuts supplied.
page 19
FIGURE 17
4. Join the
linkage arm
to the
drive arm
.
FIGURE 18
5. Pre-assemble the
drive assembly
consisting of the
operator output drive arm
,
drive shoe
and
manual release mechanism.
6. Weld this to the underside of the gate frame, ensuring that the pivot on this assembly is
perfectly aligned
with the top hinge of the gate.
Align the top hinge with the pivot.
page 20
FIGURE 19
FIGURE 20
7. Re-install the gate ensuring that the
drive assembly ball bearing
is placed in the cup of the foundation box pivot before lowering the
drive assembly
onto the pivot.
FIGURE 21
8. Join the
linkage arm
together with the
drive assembly
, as mentioned in point four on the pervious page.
FIGURE 22
Limit switches and mechanical endstops
Closed endstop
1. It is necessary to mount a solid mechanical endstop into the ground. Ensure that the gate leaves stop firmly up against the stop and are perfectly aligned with each other in the closed position.
FIGURE 23
Gate lock
2. For greater security and if the gate leaf is wider than 2.5m, it is recommended that a gate lock is fitted together with the mechanical endstops to fully secure the gates in the closed position.
page 21
Open endstop
3. It is possible to use the internal limit switch to stop the gates in the open position.
4. Alternatively mechanical endstops can be used, mounted where each leaf swings to, in the open position.
5. The
limit switch disc
should already have been mounted onto the motor’s output shaft at an earlier stage.
6. Assemble the microswitch group in either of the positions available, depending on the type of installation.
7. Only one of the two microswitches provided will be used.
Microswitch group
FIGURE 24
8. Determine which microswitch will be activated when the gate opens.
9. Select the
common
and
normally-open
terminals of this microswitch to be connected to the controller:
Black
– Common
Blue
– Normally-open: use
Red
– Normally-closed: ignore
10. Adjust the open limit switch by loosening the screw and then moving the disc until the open microswitch is triggered in the desired position.
11. Close the foundation box by adding the cover plate, and securing it to the box via the cover fixing brackets.
Cover plate
Fixing brackets
Foundation box
page 22
Fixing screws
FIGURE 25
10. Electrical setup
1. Always check that the circuit breaker in the electrical panel is in the OFF position, and that all high voltage circuits (more than 42.4V) are completely isolated from the mains supply before doing any work.
2. Ensure that all low voltage systems (less than 42.4V) are suitably protected from damage, by disconnecting all sources of power such as chargers and batteries before doing any work.
3. All electrical work must be carried out according to the requirements of all applicable local electrical codes. (It is recommended that a licensed electrical contractor perform such work.)
Secure control box to wall
1. Secure control box to the wall using the most appropriate means.
Be sure to position the wall box so as not to cause any hazards during and after the installation.
Preferably mount the wall box:
• Out of direct sunlight
• At a comfortable working height
• Away from garden sprinklers etc.
• To allow easy access even when the
gate is open
FIGURE 26
Connect all wiring
2. Connect all cables as required to the control card and battery charger, according to the wiring diagrams under Section 10, 11 and 12.
Radio receiver
FIGURE 27
page 23
3. Ensure that both the controller and the charger are effectively earthed for improved lightning protection.
• Earth system at the gate using a copper earth spike.
• Ensure that the system is connected to ESCOM or main earth.
FIGURE 28
FIGURE 28
4. Check that the charger is connected to the controller.
Ignore the fact that the terminals 15 and 16 are marked 15V on the control card. The model CP77/24V is modified for a 30V AC supply.
FIGURE 29
page 24
11.
Wiring diagram for safety beams
Receiver beam outside
-
C
N/O
N/C
Receiver beam inside
-
Transmitter beam inside
Transmitter beam outside
FIGURE 30
Although this terminal is marked as 12V the controller is modified to supply 24V DC
Although these terminals are marked as 15V the controller is modified to be supplied by 30V AC page 25
12.
Wiring diagram for other accessories
Radio receiver
PED
TRIGGER
FRX
(Note 1)
STATUS LED
Gate lock
(Note 2)
(Note 3)
Battery
Pillar light
220V
AC
L
N
FIGURE 31
1. Connect a single pole, single throw switch between terminal 5 and common for external autoclose, or select switch 1 “ON”
2. Fit IN4007 “freewheeling” diode across lock - anode connected to positive - lock must operate off a 24V DC supply
3. Signal common terminals denoted “C” on the CP77 are identical (either terminal, or both can be used) page 26
13.
Wiring diagram for motors and
open limits
Although this terminal is marked as 12V the controller is modified to supply 24V DC
FIGURE 32
Although these terminals are marked as 15V the controller is modified to be supplied by 30V AC
Only connect the limit switch that will be activated in the open position page 27
5. Check that the 24V battery supply is connected to the controller.
Ensure that the battery polarity is correct.
6. Switch on the mains supply (via isolator).
7. Check that the
green
charger LED on the controller lights up.
Control card setup
8. Select dipswitch settings to give required
Mode of Operation.
page 28
9. If Autoclose has been selected, set Autoclose timer potentiometer to suit. Clockwise increases time (range 5-30 seconds).
It is always recommended to have infrared safety beams fitted when using the Autoclose feature.
Set motor polarity
10. Identify status LED, which will give information on gate status, whether gate is open, closed, etc.
11. Set the polarity of each motor by triggering the control card, making sure that the gate direction for each leaf corresponds with the status LED.
12. Swap motor wires on the control card to give correct motor rotation.
FIGURE 36
FIGURE 37
FIGURE 38
page 29
Collision sensitivity adjustment
13. Adjust the sensitivity on the controller such that the gate(s) will open and close reliably, but not cause damage to persons or objects in the path of the gate(s).
14. The motor will just stop when the gate(s) hits an obstruction while opening or closing.
15. There are two sensitivity potentiometers on the CP77/24V controller. The left-hand potentiometer is used to set the sensitivity of both the master and slave gate(s) when opening. The right-hand potentiometer is used when the gate(s) are closing.
16. Start with the potentiometers set to a midway position.
17. Trigger the gate(s) and when the gate(s) have traveled approximately halfway through the opening or closing movement, obstruct the gate(s) noting the effort required to stop them.
page 30
FIGURE 41
18. Adjust the respective potentiometer depending on whether the gate was opening or closing, clockwise if the gate stopped too easily or anti-clockwise if the gate was hard to stop.
FIGURE 42
page 31
14. Controller features
Inherent safety features
Safety (Collision sensitivity)
If the gate is obstructed, the internal collision circuitry will activate the gate whether opening or closing to just stop.
The response of the system to a collision will vary according to the sensitivity level that has been set. There are two potentiometers, one for setting the gates while opening and the second while closing.
Clockwise adjustment reduces the sensitivity and increases the push force.
Collision count
A counter monitors the number of collisions that the gate experiences before the gate reaches the fully closed position. If the value exceeds a preset value of four, the controller shuts down
for a period of two minutes. A valid trigger received after this shut-down period will reset the
system.
As an indication, the status LED will flash four times every two seconds. The multiple collision
fault indication will continue to flash indefinitely or until a valid trigger has been received.
Selectable features
Autoclose
Autoclose status
The Autoclose feature when turned on, has the function of automatically closing the gate after an adjustable autoclose time.
Autoclose time
A potentiometer is provided on the controller to adjust the Autoclose time between five and thirty seconds.
Autoclose override
It is possible for the user to temporarily turn off Autoclose. To activate Autoclose override,
press
and hold
the button of the remote or the gate intercom (any device connected to the TRG
input) for at least three seconds. Release the button. The gate will open fully and stay open.
The gate response will be to start opening on the first TRG trigger, and then to stop as soon as the Autoclose override feature is activated. On clearing of the TRG input, the gate will continue opening until fully open. The Autoclose feature is now off and the gate will remain open indefinitely.
The next signal received on TRG will clear the Autoclose override feature, close the gate, and set the Autoclose feature back to normal.
Input features
Gate trigger - Modes of Operation (TRG)
The CP77 supports three Modes of Operation:
Standard, Condominium
and
PIRAC
.
However, the gate motors rely on a mechanical endstop to stop the gate in the closed position and the controller must be set so that they shut off when the gates reach these limits. This limits the system to STANDARD Mode of Operation.
page 32
Standard Mode via gate trigger
When stationary, a trigger impulse on TRG will cause the gate to either open or close. While the gate is moving, a trigger impulse on TRG will stop the gate. A third impulse on TRG will cause the gate to reverse its direction of travel, i.e. the action is
start
-
stop
-
reverse
.
Pedestrian Opening (PED)
This feature is associated with the PED input on the controller. When activating this input, the system will open the master gate only to the pedestrian open position (fixed width opening of approximately one metre) and then automatically close after a preset pedestrian Autoclose time of five seconds. If activation of the PED input is maintained, the gate will remain open, and when de-activated the gate will close after the pedestrian Autoclose time.
Free-exit input (SP2)
The Free-exit facility is activated by using the dedicated input to the control card marked SP2.
The Free-exit facility allows for easy exit of vehicles from a townhouse or parking lot. When driving through the free-exit beam or over an inductive loop the controller will automatically open the gate. The free-exit beam facility will only open the gate and therefore the Autoclose facility, described earlier, must be enabled to close the gate.
Holiday Lockout (SP1)
When this feature is enabled using typically a latching device connected between this input and
COM, all inputs that can operate the gate are inhibited. The feature is designed so that even if it is enabled while the gate is moving or in the open position, it will only activate when the gate is back in the closed position.
For instance this ensures that while the property is left unattended for extended periods of time, a would-be intruder cannot try and tamper with any of the inputs such as the intercom gate release button, pedestrian keyswitches / keypads to operate the gate. It also automatically disables any free-exit devices such as underground loops, etc.
Infrared safety beams (IRB)
External safety/detection devices are necessary to sense the presence of a person or vehicle moving through the entrance and ensure that the gate cannot be closed onto the obstruction.
By comparison, the inherent safety mechanism described earlier, relies on the gate hitting the obstruction before reacting.
An infrared safety beam is ideal in domestic installations and will accommodate a multitude of potential obstructions such as people, vehicles and pets. However, in industrial applications with mainly vehicles, large and small, moving through the entrance, an underground loop can be a more reliable detection device.
With the gate in the open position and the detection device activated, the gate cannot be closed.
If the gate is already closing when the detection device is activated, the gate will immediately stop and re-open. If the gate is closed or opening and the detection device is activated, the signal from the device will be ignored.
Similarly, if the Autoclose feature is selected, the gate will remain open while the detection device is activated. The moment the detection device is cleared the gate will only close after the preset autoclose time has expired. page 33
Outputs with associated features
Gate status LED (LED)
External gate status indicator. This output provides a low current drive to light up a LED which can be used to indicate the gate status remotely.
For instance if the gate is not visible from the intercom handset inside the house, which is used to communicate with a visitor at the gate and operate the gate, an LED fitted to the intercom, wired to the LED output on the gate controller, will give the necessary feedback about the status of the gate.
Courtesy (Pillar) light (LIGHT/LIGHT)
This feature is associated with the LIGHT connections on the controller.
The pillar light circuit has multiple functions:
It operates as a courtesy light and switches on for a preset timed period of two minutes every time the gate is activated
Pillar Light Control (LIT): It can be turned on permanently by making a contact via a single pole, single throw switch connected between LIT and COM
Auxiliary wallbox card
An LED interface, which provides three inputs for switching LEDs, is included with the kit
A typical use would be to connect the controller’s status LED to the interface, and in so doing ensuring that you are always aware of your gate’s movements. It is also a handy notification system for power failures, multiple collisions, etc.
In addition, there is an optional anti-tamper switch which can be connected to a third party alarm. Should the cover be lifted without first deactivating the alarm, the buzzer will sound warning residents that the device is being tampered with
If a 12 V DC buzzer is used, it can be powered directly from the controller’s 12V output, eliminating the need for an additional power supply
The external indicator is connected between LIT and COM
CP77
N/C contact to third party alarm system
From external source
(5V - 12V DC)
(Alarm systems etc.)
(Negative of external system should be connected to COM of controller) page 34
15. Description of terminal functions
PED
SP1
TRG
SP2
ACL
LIT
LED
IRB
MLO
MLC
Pedestrian Opening input
. (A normally-open potential-free input).
Momentarily connecting this input to COM will cause the master gate to open to the pedestrian open position. For more information refer to the pedestrian feature under Section 13.
Holiday Lockout
. (This is a potential-free, latching input). For as long as a connection between this input and COM is maintained the controller will behave normally. But, when this connection to COM is broken all inputs are inhibited. For more information refer to the Holiday Lockout feature under
Section 14.
Trigger input
. (A normally-open potential-free input). Momentarily connecting this input to COM will cause the gate to open or close depending on the operating mode selected. For more information refer to the gate trigger feature under Section 14.
Free-exit input
. (A normally-open potential-free input). Momentarily connecting this input to COM will cause a gate which is closed, or closing, to open or re-open. If the gate is open, or opening, the signal has no effect other than to reset the Autoclose timer (if selected). Free-exit (FRX) never initiates a closing cycle. The only way to close a gate, if only the FRX input is used, is to activate the Autoclose feature on the controller.
Allow external activation of the Autoclose facility. (This is a potential-free, latching input). Using the switch to make a contact between this input and
COM, will cause the Autoclose feature to be switched on. Breaking the contact will disable the feature.
The dipswitch on the controller, which can also be used for enabling the Autoclose feature, must remain switched off in order for the external switch to operate.
Activates the P
illar Light output
. (This is a potential-free, latching input).
Using the switch to make a contact between this input and COM, will cause the
light
relay to energize. Breaking the contact will de-energise the relay.
External gate status indicator
. (A low current output signal.) An output terminal which provides a low current drive (approx. 4,5V DC, 20mA) to a
LED which can be used to indicate the gate status remotely. If more than three LEDs are required it is necessary to fit the CP78 Multi-LED driver card. For more details on the feedback about the status of the gate provided by the status LED refer to Section 16.
Closing edge safety input
. (A normally-open potential-free input). When this connection is made it will prevent the gate from closing if it is stationary, and will stop and reverse the gate if it is closing. This input has no effect if the gate is opening.
Open limit contact for master motor
. The contact must be normallyopen. The contact is wired between this point and common.
Closed limit contact for master motor
. The contact must be normallyopen. The contact is wired between this point and common. Not used if a closed mechanical endstop is used to stop the gate.
page 35
SLO
SLC
12V
Open limit contact for slave motor
. The contact must be normally-open.
The contact is wired between this point and common.
Closed limit contact for slave motor
. The contact must be normallyopen. The contact is wired between this point and common. Not used if a closed mechanical endstop is used to stop the gate.
Auxiliary supply for external accessories such as radio receivers, safety beams, etc. This is a 24V DC supply, maximum current 1.5A.
Ignore the fact that the control card is marked 12V. The model
CP77/24V is modified for a 24V output.
SOL
15V/15V
Solenoid strike
. A solenoid strike lock can be connected between 24V and
SOL. Note that the maximum current draw allowed for the lock is 2A.
Should the solenoid lock exceed this current rating it is necessary to use an interposing relay. If fitting a magnetic lock an interposing relay must be fitted to facilitate a normally-closed contact to drive the lock.
Input from charger transformer for battery charger circuit. 28-32V AC mains, approximately 30V AC.
Ignore the fact that the control card is marked 15V. The model
CP77/24V is modified for a 30V AC input.
LIGHT
COM/COM
SLAVE/
SLAVE
Pillar light connection
. These two terminals provide a normally-open potential-free contact, which is generally used to switch on a Pillar Light
(Courtesy Light). This contact is fuse-protected – 5A. The contact is activated for a period of two minutes each time the gate is operated. Using the LIT input referred to above, the
light
contacts can be energized independently of the operation of the gate.
The
common
termination point. All trigger signals, etc. have their return path to one of the COM terminals.
Motor output – connects to the
blue
and
brown
slave motor wires.
BATTERY+
Negative 24V battery connection.(Battery terminal normally indicated as - or
black
)
Two 12V batteries, wired in series, must be used in this circuit.
BATTERY-
Positive 24V battery connection.(Battery terminal normally indicated as + or
red
).
MASTER/
MASTER
Motor output – connects to the
blue
and
brown
master motor wires.
page 36
16. Diagnostics
Diagnostic LEDs
The CP77 controller has a series of diagnostic LEDs which indicate the state of the inputs.
PED - red
On when the pedestrian signal is present
SP1 - red
On when the LCK/STP input is activated
TRG - red
On when a trigger signal is present
SP2 - red
On when a free-exit signal is present
ACL - red
On when Autoclose is activated
LIT - red
On when the Pillar Light Control is activated
IRB - red
On when the closing beam is activated
MLO - red
On when master limit switch in the open position is activated
MLC - red
On when master limit switch in the closed position is activated
SLO - red
On when slave limit switch in the open position is activated
SLC - red
On when slave limit switch in the closed position is activated
FIGURE 43
page 37
Gate status LED
Status - red
This LED indicates the state of the gate as per table below
Off
On
Continuous slow flash
Continuous fast flash
Gate is closed
Gate is partially or fully open
Gate is opening
Gate is closing
One flash every two seconds Pillar light override is activated
Two flashes every two seconds No mains present
Three flashes every two seconds Battery voltage is low
Four flashes every two seconds Multiple collisions have occurred
FIGURE 44
page 38
17. Manual release operation
Hinge open dust flap
1. Hinge open the dust flap, insert key into lock and give 1/8 turn clockwise.
Insert key and turn
Dust flap
FIGURE 45
2. Pull manual release sideways to disengage gate leaf from operator.
If an external lock is fitted this must also be released.
Pull manual release handle sideways
3. To re-engage gate leaf, swing handle back to centre position, re-engage lock and remove key. Swing leaf and re-engage with drive arm assembly.
Remember to refit dust cap over lock.
FIGURE 46
page 39
18. Installation handover
Once the installation has been successfully completed and tested, it is important for the installer to explain the operation and safety requirements of the system.
NEVER ASSUME THE USER KNOWS HOW TO SAFELY OPERATE AN AUTOMATED GATE!
Even if the user has used one before, it does not mean he knows how to SAFELY operate it. Make sure that the user fully understands the following safety requirements before finally handing over the site.
The following needs to be understood by the user:
How to operate the manual release mechanism (Show them how by demonstration)
How the obstruction detection and all other safety features work (Show them how by demonstration)
All the safety considerations associated with operating an automated gate. The user must also understand that he/she is responsible for explaining these safety instructions to all other users of the automated system
Do not activate the gate operator unless you can see it and can determine that its area of travel is clear of people, pets, or other obstructions
NO ONE MAY CROSS THE PATH OF A MOVING GATE. Always keep people and objects away from the gate and its area of travel
NEVER LET CHILDREN OPERATE OR PLAY WITH THE GATE CONTROLS, and do not allow children or pets near the gate area
Be careful with moving parts and avoid close proximity to areas where fingers or hands could be pinched
Secure all easily accessed gate operator controls in order to prevent unauthorized use of the gate
Keep the automated gate system properly maintained, and ensure that all working areas are free of debris and other objects that could affect the gate operation and safety
On a monthly basis, check the obstruction detection system and safety devices for correct operation
All repair and service work to this product must be done by a suitably qualified person
This product was designed and built strictly for the use indicated in this documentation. Any other use, not expressly indicated here, could compromise the good condition/operation of the product and/or be a source of danger!
Centurion Systems (Pty) Ltd. does not accept any liability caused by improper use, of the product, or for use other than that for which the automated system was designed
.
page 40
Notes
Notes
Notes
Notes
Sharecall 0860-CENTURION (0860 236 887)
Head Office: +27 11 699 2400
Sharecall Technical Support 0861 003 123 or
+27 11 699 2481 from 07h00 to 18h00 (GMT+2)
(Sharecall numbers applicable when dialed from within South Africa only)
0.07.A.0064_22072013
www.centsys.com
advertisement
Related manuals
advertisement