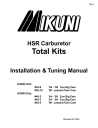
advertisement
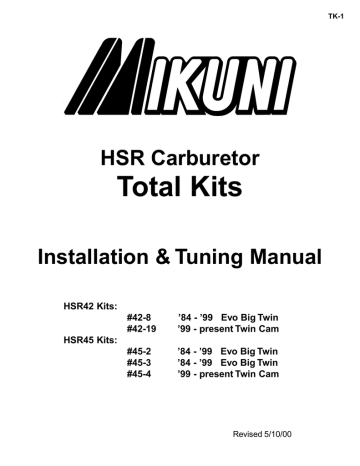
HSR Carburetor
Total Kits
Installation & Tuning Manual
HSR42 Kits:
HSR45 Kits:
#42-8 ’84 - ’99 Evo Big Twin
#42-19 ’99 - present Twin Cam
#45-2 ’84 - ’99 Evo Big Twin
#45-3 ’84 - ’99 Evo Big Twin
#45-4 ’99 - present Twin Cam
Revised 5/10/00
TK-1
TK-2
Total Kit Installation
The HSR series carburetors are precise yet durable instruments; however, like any other piece of fine equipment, they require correct installation and reasonable care to assure optimum performance and long life. Extra time spent during installation will pay off in both short and long term performance and reliability.
This Mikuni HSR carburetor kit is designed to be a bolt-on application, and as such, is set-up and jetted properly for many applications. However, since many Harley-Davidson motors are highly modified, re-tuning may sometimes be necessary. We include the Tuning Section for that purpose.
NOTE: Carburetor Kits not designated as C.A.R.B. exempt, are not legal for motor vehicles operated on public highways in the state of California, or in any other states and countries where similar laws apply.
Application:
This installation manual applies to 1340 Evo Big Twin and Twin Cam models
Required Tools:
These are the tools typically required to remove the stock carburetor and install the HSR carburetor kit.
1. Allen wrenches, 1/8”, 5/32”, 1/4” & 5/16”
5. Slotted and #2 Phillips screwdriver
2. Standard wrenches, 3/8”, 1/2”, 9/16”, 11/16”, 3/4”
3. Small adjustable wrench
4. Diagonal cutters (dykes)
6. Blue Loctite or equivalent
7. T25 Torx (’96–present)
8. Shop manual (for your model).
Notes, Cautions and Warnings
Statements in this manual preceded by these words are very important:
NOTE
Gives helpful information that can make a job easie r.
CAUTION
Indicates a possibility of damage to vehicle if instructions are not followed.
WARNING
Indicates a possibility of personal injury or vehicle damage if instructions are not followed.
Please:
Read these instructions carefully before you begin installation of your HSR kit. All procedures should be followed exactly as described in this manual, paying particular attention to the following:
WARNING
1. Mikuni HSR series carburetors require the use of a push/pull throttle assembly to assure positive closing of the throttle valve. The high vacuum encountered, as well as dirt ingested into the carburetor when running without an air filter may hinder the throttle valve from closing promptly.
2. The throttle cables should be routed freely (without sharp bends) between the throttle twist grip and the carburetor.
The throttle cables should not be pinched by the installed fuel tank, nor should they be pinched, pulled or restricted by the motorcycle bodywork and/or the fork assembly when it is turned through the full range of motion.
3. Gasoline is extremely flammable and is explosive under certain conditions. Before attempting to install or service your Mikuni carburetor, follow these fire safety procedures: a.
Make sure your work area is well ventilated and free from any source of flame or sparks, i.e. , appliances with pilot lights, such as water heaters, clothes dryers, space heaters, etc.
b.
Never look directly into the bore of the carburetor while the engine is running as injury may result from possible backfire.
CAUTION
A moderate level of mechanical skill is required to install this carburetor kit. After reading these instructions, if you have any doubts, we recommend that you have a professional install it for you. If you install the kit yourself, we recommend that you also use the applicable shop manual for your motorcycle.
NOTE
The Mikuni intake manifold, included in these kits, requires the flanges and seals from a ’90 and later “Big Twin.” If you do not have these parts, you will need to to get them from a Harley-
Davidson dealer. The required part numbers are:
1. 27009-86A Flange 1 ea.
2. 27010-86A Flange 1 ea.
3. 26995-86C Seal 2 ea.
TK-3
Disassembly:
1.
Disconnect the battery ground wire from the battery.
2.
Turn the fuel petcock to the “OFF” position.
3.
Elevate the rear of the fuel tank for better access to the carburetor area.
4.
Remove the coil, horn or other devices on the left hand side of the engine to allow free access to the intake manifold bolts.
5.
Remove the complete air cleaner assembly, including the backing plate.
6.
Disconnect any vacuum hoses and the fuel hose from the stock carburetor.
7.
Disconnect the choke cable from the frame.
8.
Remove the stock carburetor.
9.
Evo: remove the stock manifold.
10. Twin Cam: unplug MAP sensor, remove manifold and then remove the MAP sensor from the manifold.
Installation:
Intake Manifold:
Twin Cam only: Install MAP sensor in Mikuni manifold.
1.
Attach the Mikuni manifold to the engine. Align the manifold before tightening the bolts. The flange surface of the Mikuni manifold should be parallel with the front of the engine’s cam cover. Use a level or angle meter to check this. Tighten the manifold bolts.
2.
Attach the rubber flange to the Mikuni manifold with the 5/16”x3/4” bolts and washers.
NOTE
To ease installation, use liqiud detergent to lubricate the manifold seals.
Choke:
Evo:
We recommend that you use the Mikuni choke cable that is furnished with the carburetor. However, you can use the stock Harley cable (’90–’99 models only) if you follow the Twin Cam choke cable instructions.
Twin Cam:
1.
Remove the Harley choke cable from the stock carb.
2.
Remove the Harley spring and plunger from the
Harley choke cable.
3. Remove the Mikuni spring and plunger from the
Mikuni carburetor.
5.
Install the Mikuni spring and plunger onto the Harley choke cable. Change nothing else; be sure to use the Harley plastic nut, not the Mikuni nut.
6.
Install the new assembly into the Mikuni. Be careful to only gently tighten the plastic nut.
Figure 1: Harley nut with Mikuni spring & plunger
Figure 2: Choke cable adjustments
NOTE
An optional choke cable mounting bracket is included in the
Evo kits for custom installations.
Throttle Cables:
Note: The HSR carburetor uses the same cables that fit the stock CV (constant velocity) carburetor Harley-
Davidson has been using since 1990.
However, if your Harley is fitted with some other carburetor, you may need to purchase a set of cables designed for the late CV-type stock carburetor. Be sure to get cables made for your bike’s model year.
1. Route the throttle cables with large radius curves and
so that they do not interfere with other components.
2. Screw the cable adjusters together to make them as short as possible.
3. Connect the “close” cable first (see Figure 3).
4. Install the “open” cable next (see Figure 3).
5. Adjust the opening cable until the slide can be opened fully. Snug the adjuster lock nut.
6. Turn the handlebar to the right and adjust the throttle free-play with the closing cable adjuster to approximately 1/8” (see Figure 4).
CAUTION
1. The control cables must not pull tight when the handlebar is turned fully left and right. Also, be sure that the cables clear the fork stops at the steering head so they are not pinched when the handlebar is turned.
2. It is important to check for adequate clearance between the cable elbows and the gas tank when the handlebar is turned from lock to lock.
WARNING
There must be some free play at all handlebar positions to avoid binding in the throttle cables.
TK-4
Figure 3: Cable installation guide
Figure 4: Throttle free-play
Cable Lube:
Remove upper throttle housing and inject half the cable lube in each cable.
Figure 5: Cable lube procedure
CAUTION
Cable lubrication is important. Dry cables can result in sticky throttle action, slow return to idle and excess cable wear.
Air Cleaner and Breather:
Use the supplied brackets, breather kit parts, O-rings, bolts & washers as required. See illustrations below.
Evo Engines:
’84-’91: Use 2 ea. 5/16”x3/4” bolts, washers and O-rings.
’92: Use 2 ea. ½”x ¾” bolts and flat washers.
’93-’99: Add the included breather assembly (KHS-020).
TwinCam: Use 5/16” flat washers and nuts together with the KHS-030 breather kit (KHS-030).
1. Loosely attach the brackets and/or breather parts to the cylinder heads with the appropriate hardware.
2. Remove the rubber stud protectors from the Mikuni air filter and place the two backing plates on the studs.
Position the air filter up to the carburetor while aligning the brackets with the filter studs. Once the filter is in place, tighten the filter clamp. Then, secure the filter to the brackets with the enclosed 5/16” nuts and flat washers (see Figure 9).
3. Cut out the thin membranes in the back of the filter and insert the plastic elbows. Use the 5/16” i.d. hose to connect the elbows to the breather fittings.
4. Use the enclosed cover screw to attach the Mikuni air cleaner cover to the air filter.
Hose Routing:
1. Use the small hose clamps to secure the fuel hose to the petcock and the carburetor. The screw clamp goes on the petcock end and the spring clamp attaches to the carburetor end.
2. Evo: Attach the V.O.E.S. (Vacuum Operated Electronic
Switch) hose to the carburetor.
NOTE: If required, a 9” piece of vacuum hose is included in this kit
3. Twin Cam: Attach the petcock vacuum hose to the carburetor.
(see illustration in tuning section of this manual for the location of the fitting on the carb.).
4. Route the overflow hose from the bottom of the
float bowl to below the engine. Do not connect this
hose to any other hoses.
CAUTION
If you are not using the V.O.E.S., be sure that you cap off the vacuum fitting on the carburetor (refer to page TM8).
NOTE
You may have some hoses remaining after your installation.
Since this is a performance application only, some hoses and related hardware may no longer be required.
Starting:
Re-connect the battery and re-assemble the remainder of the motorcycle. Turn the petcock on and start the engine as you normally would. After it is warm, set the idle to the recommended 1,000 to 1,100 rpm. To learn more about adjusting your HSR carburetor, refer to the “Tuning the
HSR” section of this manual.
NOTE
Inspect and, if necessary, clean the air filter every 5,000 miles. The K&N brand filter supplied with this kit is very effective. It filters extremely small particles out yet does not substantially interfere with air flow into the engine. When you clean the filter, be sure to follow the cleaning instructions included with this kit.
Figure 8: ’93 – ’99 Evo breather (KHS-020)
Figure 6: Air cleaner assembly guide
Figure 7: ’84 – ’92 breather installation
Figure 9: Twin Cam breather (KHS-030)
Notes
TK-5
TK-6
Twin Cam: 42-19, 45-4
Part# Description Qty
.
TM42-6
TM45-2
HS42/012
HS42/012-300
HS42/02-250-CHR
HS42/061-45TC
HS42/062-42
HS42/062-45
KHS-030
N100.604-155
N100.604-165
N100.604-170
N100.604-180
RS36/28
RS36/47
TMX/002-32
Z70/042
Z70/045
Z70/05512
Z70/146
HS42/073
Carburetor
Carburetor
Air Filter, 2.5”
Air Filter, 3”
42-19, 45-4
1
1
1
1
Cover A/C (Chrome) 1 1
Manifold
Rubber Flange
Rubber Flange
Breather Kit
Main Jet
Main Jet
Main Jet
Main Jet
Nut, 5/16”
Plate, Back
Hose Clamp
Flat Washer, 5/16”
Hose Clamp
Hose, Fuel
Cable Tie
Cable Lube
1 1
1
1
1
1
1
1
1
2 2
2 2
1 1
2 2
1 1
1 1
4 4
1 1
Note: The 45-3 Kit does not include a manifold. Otherwise, it is identical to the 45-2 Kit.
Kit Contents:
Evo: 42-8, 45-2
Part# Description Qty
TM42-6
TM45-2
HS42/012
HS42/012-300
HS42/019
Carburetor
Carburetor
Air Filter, 2.5”
Air Filter, 3”
42-8, 45-2
Bracket, Air Filter
1
1
1
1
2 2
HS42/021-250-CHR Cover A/C 1 1
HS42/034
HS42/037
O-ring
Bolt, ½”-13 x 1”
4 4
2 2
HS42/038
HS42/061-45
HS42/062-42
HS42/062-45
½” Washer
Manifold
Rubber Flange
Rubber Flange
2 2
1 1
1
1
KHS-020
N100.604-155
N100.604-165
N100.604-170
N100.604-180
RS36/02-17
RS36/23
RS36/27-075
Breather Kit
Main Jet
Main Jet
Main Jet
Main Jet
Hose Clamp
Choke Bracket
Bolt, 5/16” x ¾”
1
1
1
1
1
1 1
1 1
4 4
RS36/28
RS36/3609
RS36/37
RS36/47
RS36/54
TMX/002-32
Z70/042
Z70/045
Z70/05512
Z70/146
990-662-002
HS42/073
Nut, 5/16”
Screw, Cover
Hose Clamp
Hose, Fuel
Cable Tie, 7-1/2”
Choke Cble Assy
Cable Lube
2 2
Hose, 3/16” x 9” 1 1
Elbow, Plastic, 3/8” 2 2
Plate, Back 2 2
1 1
1 1
Flat Washer, 5/16” 6 6
Hose Clamp 1 1
1 1
4 4
1 1
1 1
Tuning Manual
For
HSR42/45 CARBURETORS
Revised 5/10/00
TM-1
TM-2
Tu n i n g the HSR
Your Mikuni HSR is fitted with the tuning parts we found to work with the great majority of engine performance modifications. However, the large number of differing exhaust systems and cams available makes it impossible to accommodate all possible combinations with one carburetor set-up. Your HSR will almost certainly run correctly on your engine without exchanging any parts. But, if it doesn’t, you may alter its tuning to suit your engine’s needs by following this guide.
Some exhaust system designs strongly interfere with carburetor tuning. For instance, it is very difficult to get smooth and responsive carburetion through the entire rpm range with straight pipes and completely open exhausts. In addition, very small volume, small diameter mufflers are often ‘seen’ by the engine as straight pipes and present the same tuning difficulties.
Very long duration cams often cause relatively poor running below about 3,000 rpm, depending upon the individual cam’s intake valve closing point. Such cams cause reverse airflow out the mouth of the carburetor
(often called: “reversion” or “stand-off”) that can be mistaken for a carburetor tuning problem.
Harley-Davidson Screamin’ Eagle performance parts are proven and predictable. If you have any doubts about a particular exhaust system, air cleaner or ignition, you may substitute the standard Harley Screamin’ Eagle parts as a “reality check.”
When re-tuning is required, it usually involves small alterations to the idle and/or main system. The following paragraphs supply enough detail information to make such changes an easy matter for an experienced mechanic.
Finally, please note that there is simply no point in attempting to tune any carburetor unless the engine is sound and in a good state of tune. If you have any doubts about the general condition of your engine, have it checked by your dealer or an experienced mechanic before attempting to fine-tune your new Mikuni carburetor.
AIR LEAKS:
We have found that a certain percentage of Harley-
Davidson Evo and Twin Cam engines have minor air leaks between the manifold and heads. The leaks affect air/fuel mixtures at low throttle settings and can be troublesome at idle. For best performance, it is important that you test for such leaks and eliminate them if any are found.
It is easy to test for intake manifold air leaks: With the engine warm and idling, spray WD-40 around the junctions of the manifold, carb and heads. If the engine changes from its steady idle, if it surges, misses, etc then there is an air leak that must be corrected if the engine is to run its best.
Because of the frequency of air leaks, we recommend that you replace all three manifold seals when you install your new Mikuni carburetor. These parts are available from any Harley dealer.
If you lubricate the seals just before installation, they will seat more smoothly and are less likely to develop leaks. Liquid dish detergent works well. WD40 is also a good choice but evaporates quickly.
It is important that the manifold be aligned before the lubricant sets or evaporates. Otherwise, the parts may stick to the seals, which, in turn, can cause leaks when the parts are moved into alignment.
NOTE
For the quickest and most accurate results when fine-tuning your HSR, we recommend using “witness” marks on the throttle grip and throttle housing. Use masking tape on the grip and an indicator mark on the throttle housing. Mark the tape in ¼ throttle increments from idle to full throttle. You can then identify the throttle opening where a tuning change may be required and then adjust the correct tuning components.
Figure: T1
HSR TUNING SYSTEMS:
The HSR42 carburetor is divided into four interdependent systems:
1. The choke system
2. The idle system
3. The main system
4. The accelerator pump system
Each of these systems has its major effects in a different throttle range. While there may be some overlap, each system can generally be treated as though it is completely responsible for its range of throttle settings.
Three of the systems have replaceable components that allow fine-tuning should the need arise.
TM-3
THE CHOKE SYSTEM:
The choke system’s purpose is to provide the rich air/ fuel mixture an engine needs to start and run reliably when it is cold. There are no replaceable tuning parts in the HSR42/45 choke mechanism.
The choke is designed to work correctly with the throttle closed. Opening the throttle stops the action of the choke.
NOTE
Make sure that the stock Harley-Davidson choke cable is fully seated in the metal elbow at the carburetor end of the cable assembly (see installation instructions). Harley
‘s cable is stiff and can fail to fully seat in the elbow. This condition results in poor mileage and a poor idle.
The Mikuni choke cable is more flexible and less likely to jamb. Still, it is best to check to be sure the cable is installed correctly.
TUNING THE IDLE SYSTEM: (idle – 1/8 throttle)
The HSR42/45 idle system has two tunable components: the air screw and the pilot jet. The air screw’s purpose is to fine-tune the idle mixture. The pilot jet controls the total amount of fuel passing through the idle system. It can be changed to make larger adjustments to the idle mixture strength.
The air mixture screw is set at two turns out from the factory. This is the position we have found to be right most of the time. If the screw position has been altered, gently bottom it and re-open it two full turns.
Next, ride the bike until its engine reaches normal operating temperature. This may require several miles at highway speeds.
With the motorcycle vertical and the engine idling near 1,000 rpm, adjust the air mixture screw in slowly until the idle either slows or becomes irregular, then begin turning the screw out until the engine again slows or again begins to idle irregularly. Count the number of turns between the two positions. Set the air screw midway between these too-rich and too-lean positions.
Use the Idle Adjuster Screw to re-set the idle speed.
If the engine starts to get too hot during the adjustment procedure, the resulting idle mixture will probably be on the lean side of correct. If you have a large fan, use it while adjusting the mixture. If you do not have one, you may need to take time out for a short ride to cool the engine back to normal temperature.
NOTE
1.
If the best idle is achieved with the air screw less than one turn out, the pilot jet is too small and should be exchanged for a larger one.
2.
If the engine speed does not slow after two-and-a-half turns out, the pilot jet is too large and should be exchanged for a smaller one.
Figure: T2
TUNING THE MAIN SYSTEM
JET NEEDLE (1/8 – 1/4 throttle)
The straight diameter portion of the jet needle controls the mixture from just above idle to approximately ¼ throttle. If the mixture is too rich or too lean in this throttle range, the needle will need to be exchanged for a larger or smaller one. HSR jet needles are available in four sizes.
Only the diameter of the straight part of the four jet needles differ. The richest is the “-95” and “-98” is leanest.
LEAN CONDITION:
If the needle is too lean (large in diameter), part throttle acceleration will be flat. There may also be some detonation during part throttle acceleration from low rpm, (although this may have other causes). A lean needle also results in an abnormally slow warm-up.
If any of these conditions exist, install a one-size smaller needle and compare the performance
RICH CONDITION:
While a black, sooty spark plug is a sure sign of richness; there are more subtle signs. If your engine responds crisply at low throttle openings when it is cold, chances are the needle is one size smaller than it needs to be. This assumes, of course, that the idle mixture is correctly tuned.
Poor fuel mileage is another sign of an over-rich condition.
Because of the way most of us ride our Harleys, that richness is usually the result of a jet needle that is too small (rich). The color of the end of the exhausts is a sign of mixture strength. Dark gray with some black is normal for today’s lead-free gasolines.
TM-4
JET NEEDLE (1/4 - 3/4 throttle)
The tapered portion of the jet needle begins to rise out of the needle jet at about ¼ throttle. From that point until the main jet takes over near ¾ throttle, the jet needle taper is the main influence on mixture strength.
When testing, consider the rpm effects of any accessory cam you may have installed. Long duration cams tend to perform poorly below some critical minimum rpm. If you attempt to test below this rpm, the engine may seem soft, flat and unresponsive. No carburetor can compensate for the engine being “off the cam.”
All jet needle and main jet testing should be done with the engine near the middle of its rpm range, but high enough to be “on the cam.” With the engine at operating temperature, accelerate at ½ throttle in third or fourth gear.
LEAN CONDITION:
If acceleration seems soft or flat and the engine is slow to respond when the throttle is quickly opened from the ½ to the ¾ position, the mixture is too lean. Raise the needle one notch and repeat the test (refer to page: TM6).
RICH CONDITION:
If acceleration is crisp but the engine hesitates or staggers as the throttle is quickly shut down from ¾ to ½ throttle, the mixture is too rich. Lower the needle one notch and repeat the test. The needle will be correct when acceleration is crisp at mid-rpm yet the engine does not load up during throttle shut down.
NOTE
See the “How To” section at the back of this manual for jet needle adjustment and removal procedures.
WARNING
Please do not disassemble the throttle lever linkage. It is not normally necessary to remove the bolt to change position of the jet needle. However, if you do remove the throttle shaft bolt, be certain that you:
1. Apply a drop of blue Loctite TM to the threads.
2. Torque the bolt to 18in./lb.
3. Replace the tab washer and bend it up until it is flush
against one of the bolt head flats.
MAIN JET: ¾ — full throttle
The main jet controls fuel flow from ¾ to full throttle.
It is the last you need tune and is the easiest to get right.
METHOD ONE:
An accurate method for choosing the correct main jet is to accelerate at full throttle between two points and note the speed at the second point.
1. Select markers that are far enough apart so the engine gains about 2,000 rpm (in third or fourth gear) between the two.
2. When you pass the first marker, quickly roll the throttle fully open and note the speed as you pass the second marker.
3. The jet that gives the highest speed is the correct one. This method is simple but effective.
METHOD TWO:
1. The best method is to use a dynamometer. The main jet than produces the most power is the correct one. If two jets deliver the same power, use the smaller one.
TUNING THE ACCELERATOR PUMP:
The accelerator pump has two adjustments and one replaceable tuning part, the accelerator pump
nozzle, that can be adjusted or changed to refine the performance of the accelerator pump system.
The accelerator pump injects a metered and adjustable amount of fuel into the engine when the throttle is opened from or near its closed position.
The beginning point of the pump stroke is adjusted with screw #1 on the white plastic pump lever. To start the pump sooner (smaller throttle opening), back the screw out. To start it later, turn the screw in.
The end of the accelerator pump stroke is adjusted by screw #2 located on top of the carburetor just behind the pump lever. Best performance is generally achieved when the pump stroke ends before 2/3 throttle.
The accelerator pump nozzle size (#50, #60 or #70) determines the rate at which fuel is delivered to the throat of the carburetor. A larger nozzle delivers fuel at a higher rate than a smaller nozzle.
Figure: T3
TM-5
4. If a jet or passage does become plugged, use only carburetor cleaner and compressed air. DO NOT push a drill or any other object through the jet or passage to clean them.
FLOAT LEVEL ADJUSTMENT:
1. Invert the carburetor and remove the float bowl.
2. The float assembly’s actuator tab should just contact the Needle Valve assembly when the bottom of the float is 18mm from the carburetor bottom surface as shown.
3. Bend the actuator tab to adjust float level.
Figure T4: Accelerator Pump Adjusters
STANDARD SETTINGS & ADJUSTMENTS:
The standard nozzle size is #70. If the engine seems to run too rich when the throttle is first opened the nozzle may be too large and the fuel delivery rate too high. In this case, fit a smaller nozzle.
The #1 screw is normally adjusted to establish
a gap of about 2mm (about the thickness of a nickel) between the white plastic lever and pump rod end. If there is a hesitation just off idle, reduce the gap.
The #2 screw is normally adjusted to stop the pump action at about 2/3 throttle. If you tend to accelerate from low speeds in a tall gear, you may need to adjust the pump for a longer stroke. If you tend to downshift before accelerating from low speeds and/or have a lighter bike then you might consider shortening the pump stroke.
NOTE
For best results, the accelerator pump nozzle should be pointed directly at the jet needle. The nozzle is held in place by the friction of an O-ring and can be turned easily with a pair of long nosed pliers. Nozzle adjustment should be made with a minimum of pump strokes to avoid flooding the engine.
SERVICING:
There are few moving parts in the HSR series carburetors and they do not require frequent servicing.
However, here are a few suggestions that, if followed, will assure good performance season after season.
1.
If the motorcycle is to be stored for any length of time, the carburetor float bowl should be drained.
2.
The float bowl drain plug (main jet access) should be removed periodically and cleaned of any sediment that may have accumulated during long periods of use.
3.
DO NOT drill or modify any part of this carburetor for any reason, as the result will surely be more problems.
Figure T5: Float Level
NOTE
Check the condition of the float bowl O-ring. If it is worn or does not not fit in the groove correctly, replace it.
MIKUNI OR SCREAMIN’ EAGLE AIR FILTER:
Mikuni, Screamin’ Eagle and many others are made by
K&N and do not need frequent cleaning. A cleaning interval of once a year or 5,000 miles is often enough.
However, if you ride in very dusty conditions, clean the filter when it is obviously dirty over 50% or more of its surface.
1. Tap the element to dislodge embedded dirt; then gently brush with a soft bristle brush.
2. Roll the filter element in a large shallow pan of K&N air filter cleaner (Simple Green, 409, etc) with the depth set to ¼ of a pleat. Remove immediately and let sit for approximately 10 minutes. IMPORTANT: Do not use gasoline or cleaning solvent to wash the filter element, as this will damage the filter.
TM-6
3.
Rinse the element with low-pressure water. Always flush from the inside of the filter out to ensure that dirt is washed out of the filter and not into it. IMPOR-
TANT: Air dry only; do not use compressed air.
4.
After the filter is completely dry, re-oil sparingly.
Apply K&N filter oil with one pass per pleat. Wait 10 minutes and re-oil any white spots.
HOW TO REMOVE & REPLACE :
JET NEEDLE:
1.
Back out the idle speed adjuster five or six turns to ensure that the throttle valve is fully bottomed.
2.
Remove the three top cover screws and remove the cover.
3.
Loosen the Allen screw located on the slide
(long 2.5mm Allen wrench).
4.
Swing the clip aside.
5.
With the slide bottomed, remove the jet needle.
You may use a long-nose pliers or tweezers for this. Be sure to save the small plastic washer under the jet needle clip.
6.
To reassemble, reverse steps 1. through 5. Be sure to snug the Allen screw and replace the plastic washer under the jet needle clip.
HOW TO ADJUST:
JET NEEDLE CLIP:
1.
Remove the jet needle per previous instructions.
2.
Place the open end of the jet needle clip against a hard surface.
3.
Cover the clip area with your hand (to prevent loss of the clip) and press the needle down to snap the clip off the needle.
4.
Place the clip in the desired groove on the needle.
5.
Place the clip against the hard surface with the open end up.
6.
Again cover the clip area with your hand and press down on the needle to snap the clip into place.
MAIN JET:
1.
Turn the fuel petcock to the OFF position.
2.
Use an 11/16” or 17mm wrench to loosen & remove the drain bolt.
3.
Use a good fitting slot type screwdriver to remove the main jet.
4.
Reverse steps 1 through 3 to replace the main jet.
The jet need only be hand-tight; do not over tighten.
PILOT JET:
1.
Turn the fuel petcock to the off position.
2.
Remove the four screws retaining the float bowl (#2
Phillips). Remove the float bowl.
3.
Use a good fitting slot type screwdriver to remove the pilot jet.
4.
To reinstall the pilot jet, Reverse steps 1 through 3.
Start the jet by hand, as the threads are small and relatively fragile. Do not over tighten; snug is enough.
ACCELERATOR PUMP NOZZLE:
1. Turn the fuel petcock to the OFF position.
2. Remove the four screws retaining the float bowl (#2
Phillips). Remove the float bowl.
3. Use your finger to push the nozzle out of the throat of the carburetor (see exploded view).
4. Push in new nozzle/O-ring assembly. Aim the nozzle toward the jet needle.
5. Re-install the float bowl.
6. Turn the fuel petcock on and work the throttle several times to prime the accelerator pump.
7. Use long-nose pliers to turn the nozzle until the fuel stream points to the middle of the carburetor throat.
TM-7
TM-8
TM-9
TM-10
TROUBLE SHOOTING GUIDE:
OVERFLOW: Fuel runs out of carburetor through overflow tube on bottom of float bowl, from vent fitting on side of carburetor or from body/float bowl junction.
Foreign matter around fuel needle valve & seat:
Includes paint flakes, rust or bits of fuel hose.
Stock or clogged tank vent:
Factory one-way tank vents can cause pressure in tank. Clogged tank vent can result in fuel starvation.
Deteriorated gasoline causing sticking fuel needle valve.
Loose float bowl or damaged float bowl packing.
mileage. Highly tuned engines often require leaner jet needles as do motorcycles operating at high altitude.
Stock or clogged tank vent:
Factory one-way tank vents can cause pressure in tank. Clogged tank vent can result in fuel starvation.
Air leak:
It is common that Evo series engines have intake manifold air leaks. An air leak can lead to a lean running condition and even detonation at part throttle.
Loose jets:
A loose main jet can result in an overly rich mixture.
POOR FUEL ECONOMY (at normal cruise speeds):
Mikuni installations normally deliver fuel economy very close to that of the completely stock Harley.
Choke cable routing:
The choke cable must be fully bottomed in the metal elbow (at carburetor end). There must be some perceptible free-play in the choke knob.
Stock or clogged tank vent:
Many current stock Harley tank vents do not allow gasses to leave the tank and pressure may develop from engine heat. Open the vent to allow two-way air flow. Clogged tank vent can result in fuel starvation if the vent valve becomes stuck or partially blocked.
Fuel/Air mixtures:
Incorrect jet needle or pilot jet for tuning set-up or altitude. The speed range in which mileage is usually recorded is controlled by the straight portion of the jet needle and pilot jet. The needle taper and main jet size seldom have an effect at normal cruising speeds.
Loose jets:
A loose pilot or main jet can affect fuel mileage.
POOR IDLE:
Irregular idle speed, too rich or too lean.
It is common for Evo series engines to have intake manifold air leaks. Air leaks result in an irregular idle that does not respond to mixture screw adjustment.
Idle mixture adjustment:
The pilot air adjusting screw is not adjusted correctly resulting in a too rich or too lean idle mixture setting
(see p. TM3).
Incorrect pilot jet:
A jet that is too large or too small.
Loose jets:
A loose pilot or main jet can affect idle performance.
POOR PART-THROTTLE (1/8–1/4) PERFORMANCE
OR MILEAGE:
Overly rich or lean at normal cruise speeds, detonation at part-throttle.
Choke cable routing: (see p. TM3)
Incorrect jet needle:
A too-rich or too-lean jet needle for engine tuning set-up or for operating altitude can cause poor
POOR FULL-THROTTLE PERFORMANCE: Detonation, flat acceleration, misfiring.
Clogged tank vent:
Factory one-way tank vents (located in the tank cap on most models) sometimes fail to allow enough air into the tank to replace fuel flow at high throttle openings.
The result is a partial vacuum and fuel starvation.
Fuel flow restriction:
Clogged fuel filter or fuel petcock screen (located inside tank) can result in fuel starvation.
Incorrect main jet size:
A too large or too small main jet can lead to poor power output.
Clogged main jet:
A partially clogged main jet may allow enough fuel flow for part-throttle operation and yet starve the engine at full throttle.
Dirty air filter:
Stock air filters can become dirty enough to restrict air flow and power output.
BACKFIRE THROUGH CARBURETOR:
When the engine is cold only (choke off):
This can be considered normal. A cold engine does not vaporize fuel completely which can result in an overlylean mixture and backfiring through the carburetor.
Long duration cams:
Cams with late intake valve closing points encourage backfiring at low rpm.
Exhaust systems:
Some very open or incorrectly designed exhaust systems encourage backfiring. Stock length and diameter header pipes together with typical small slipons, like those furnished by Harley-Davidson, typically do not have this problem.
Incorrect accelerator pump adjustment:
If the accelerator pump adjustment is set to start too late, backfiring may occur due to an overly lean mixture just off idle.
BACKFIRING IN EXHAUST SYSTEM when the throttle is closed, especially noticeable from high rpm, is not caused by lean mixtures, although lean mixtures can contribute to its intensity. This is a normal condition when using high performance exhaust systems.
TM-11
Open exhaust system:
High performance mufflers with large exit area or lowrestriction baffles.
Air leak in exhaust system: Air entering at the junction of the header pipes and mufflers can cause popping upon decceleration.
Ignition failure: Out-of-time ignition together with misfiring may lead to loud backfiring. Such backfiring usually occurs irregularly and at large throttle openings.
HSR Accessories
Optional Tuning Components and
Accessories for HSR Carburetors
These parts may be ordered through your local Mikuni dealer
Low & High Speed Jets:
VM28/486-(Size)
Pilot (Idle to ¼), increments of 2.5
(Standard: 25, normal range: 20 to 35)
N100.604 – (Size)
Main (¾ to Full Throttle), increments of 2.5
(Standard: 160, normal range: 150 to 180
Jet Needles (Mid-Range: 1/8 to 3/4)
HSR42 HSR45
Richer J8-8DDY01 – 95 J8-8CFYO2-95
Richer J8-8DDY01 – 96
Standard J8-8DDY01 – 97
Leaner J8-8DDY01 – 98
J8-8CFYO2-96
J8-8CFYO2-97
J8-8CFYO2-98
Standard HSR42 Jet Needle straight diameter is 2.97 mm.
This portion of the needle affects tuning from idle to approximately ¼ throttle opening.
Accelerator Pump Nozzles
Leaner
Std. for Sportster kits
Std. for Big Twins
TM42/11–50
TM42/11–60
TM42/11–70
Mikuni Jet Kit
Jet Tuning Service Kit for HSR42/45 . . . ……….. KHS–025
Jet Kit Contains: 18–Main Jets (2 each 150 thru 170)
10–Pilot Jets (2 each 22.5 thru 35)
3–Needles (1 each –95, –96, –97)
2–#60 Pump Nozzle
4–Needle E-Ring Clips & Washers
1–Plastic Box
HSR42/45 Carburetor Rebuild Kit
Carb Rebuild Kit . . . . . . . . . . . . . . ………….....….KHS–016
See exploded view drawing for kit contents.
Short Idle Screw
Idle Adjuster Screw (Short) . . . …………….... 990-605-065
(See item #59a in exploded view of carb.)
NOTE
Do not modify idle screw or any of its component pieces. If the screw is removed, be sure it is re-installed with the components in place as illustrated in exploded view.
TM-12
Mikuni American Corporation
8910 Mikuni Avenue
Northridge, CA
91324-3496
advertisement
* Your assessment is very important for improving the workof artificial intelligence, which forms the content of this project