advertisement
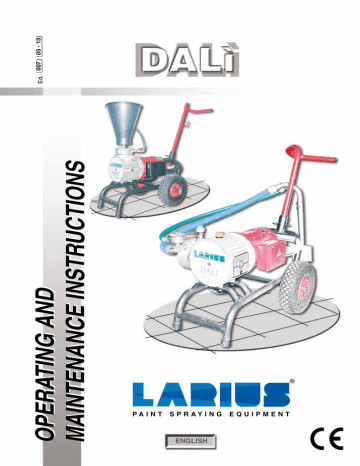
P A I N T S P R A Y I N G E Q U I P M E N T
ENGLISH
Due to a constant product improvement programme, the factory reserves the right to modify technical details mentioned in this manual without prior notice.
This manual is to be considered as an English language translation of the original manual in Italian.
The manufacturer shall bear no responsibility for any damages or inconveniences that may arise due to the incorrect translation of the instructions contained within the original manual in Italian.
DALì
F
G
H
I
D
E
A
B
C
INTRODUCTION ................................................p.1
WORKING PRINCIPLE ......................................p.2
TECHNICAL DATA .............................................p.2
DESCRIPTION OF THE EQUIPMENT ..............p.3
TRANSPORT AND UNPACKING ......................p.4
SAFETY RULES .................................................p.4
SETTING-UP ......................................................p.5
WORKING ..........................................................p.8
CLEANING AT THE END OF THE WORK ........p.9
ROUTINE MAINTENANCE ................................p.10
S
T
U
L
M
N
O
P
Q
WARNING PLATE ..............................................p.11
PROBLEMS AND SOLUTIONS .........................p.12
CORRECT PROCEDURE OF DECOMPRESSION ......p.13
COMPLETE HYDRAULIC BODY .......................p.14
DALÌ PETROL - DALÌ LINER ..............................p.16
COMPLETE COLOUR BODY ............................p.18
HIGH PRESSURE GUN "AT 250" ......................p.21
SUCTION SYSTEM ............................................p.22
TROLLEY ...........................................................p.23
ACCESSORIES ..................................................p.25
Read this operator’s manual carefully before using the equipment. An improper use of this machine can cause injuries to people or things.
It indicates an accident risk or serious damage to equipment if this warning is not followed.
It indicates a fire or explosion risk if this warning is not followed.
It is obligatory to wear suitable clothing as gloves, goggles and face shield.
It indicates important recommendations about disposal andrecycling process of products in accordance with the environmental regulations.
WE ADVISE THE USE OF THIS EQUIPMENT ONLY BY PROFESSIONAL OPERATORS.
ONLY USE THIS MACHINE FOR USAGE SPECIFICALLY MENTIONED IN THIS MANUAL.
Thank you for choosing a LARIUS S.R.L. product. As well as the product purchased, you will receive a range of support services enabling you to achieve the results desired, quickly and professionally.
1
DALì
A
WORKING PRINCIPLE
The LARIUS DALÍ unit is defined as an “electric diaphragm pump”. An electric diaphragm pump is used for high pressure paint spraying without air (known as “airless”).
The pump is powered by an electric (internal combustion) motor coupled with a cam shaft. The shaft acts on the hydraulic piston as it pumps oil from the hydraulic case and sends the suction diaphragm into fibrillation. When the diaphragm moves, it creates
B
TECHNICAL DATA
a vacuum. The product is sucked up, pushed towards the pump outlet and sent to the guns through the flexible hose . A hydraulic valve on the hydraulic case head allows setting and checking the pressure of the paint product at the pump outlet. A second hydraulic safety valve to avoid over-pressure, ensures total equipment reliability.
DALÌ
SUPPLY (single-phase, Three-phase internal combustion supply, petrol-diesel)*
MOTOR POWER Mono-threephase
Internal combustion
MAX. WORKING PRESSURE
MAX. DELIVERY
MATERIAL OUTLET
WEIGHT
LEVEL OF THE SOUND PRESSURE
LENGTH
WIDTH
MAXIMUM HEIGHT
MINIMUM HEIGHT
220V 50Hz / 110V 60Hz
380V 50Hz
1,1 kW
3 HP
200 bar 2900 psi
4 L/min
M16 x 1,5 (M)
38 Kg
≤ 65dB(A)
(
A) 1100 mm
(
B) 500 mm
(
C) 1000 mm
(
C1) 710 mm
*Available on request with special voltages
PARTS OF THE PUMP IN CONTACT WITH THE MATERIAL Stainless Steel AISI 420B, Teflon, Aluminium.
A
B
2
A
B
DALì
C
DESCRIPTION OF THE EQUIPMENT
17
16
14
15
8
13
9
10
2 3
7
11
12
2
4
5
3
6
1
4 10
POS.
7
8
5
6
9
3
4
1
2
Description
Carriage
Electric / combustion motor
High pressure manometer
Setting valve
Hydraulic oil filling cap
Hydraulic body
Colour body
Suction and recirculation tube
High pressure feed tube
POS.
14
15
16
17
10
11
12
13
Description
LARIUS AT 250 gun
Fast clean
Tools box
Recirculation valve
Recirculation pipe connection
Feed tube connection
Adjustable handle
Tank (for "vertical Dalì" version)
3
DALì
D
TRANSPORT AND
UNPACKING
• The packed parts should be handled as indicated in the symbols and markings on the outside of the packing.
• Before installing the equipment, ensure that the area to be used is large enough for such purposes, is properly lit and has a clean, smooth floor surface.
• The user is responsible for the operations of unloading and handling and should use the maximum care so as not to damage the individual parts or injure anyone.
To perform the unloading operation, use only qualified and trained personnel (truck and crane operators, etc.) and also suitable hoisting equipment for the weight of the installation or its parts.
Follow carefully all the safety rules.
The personnel must be equipped with the necessary safety clothing.
• The manufacturer will not be responsible for the unloading operations and transport to the workplace of the machine.
E
SAFETY RULES
THE BEHAVIOUR OF THE EMPLOYEES SHALL STRICTLY
COMPLY WITH THE ACCIDENT PREVENTION AND
ALSO ENVIRONMENTAL REGULATIONS IN FORCE IN
THE COUNTRY WHERE THE PLANT IS INSTALLED AND
USED.
Read carefully and entirely the following instructions before using the product. Please save these instructions in a safe place.
The unauthorised tampering/replacement of one or more parts composing the machine, the use of accessories, tools, expendable materials other than those recommended by the Manufacturer can be a danger of accident.
The Manufacturer will be relieved from tort and criminal liability.
• KEEP YOUR WORK PLACE CLEAN AND TIDY. DISORDER
WHERE YOU ARE WORKING CREATES A POTENTIAL
RISK OF ACCIDENTS.
• ALWAYS KEEP PROPER BALANCE AVOIDING UNUSUAL
STANCE.
• BEFORE USING THE TOOL, ENSURE THERE ARE NOT
DAMAGED PARTS AND THE MACHINE CAN WORK PRO-
PERLY.
• Check the packing is undamaged on receipt of the equipment. Unpack the machine and verify if there has been any damage due to transportation.
In case of damage, call immediately LARIUS and the
Shipping Agent. All the notices about possible damage or anomalies must arrive timely within 8 days at least from the date of receipt of the plant through Registered Letter to the Shipping Agent and to LARIUS.
• The disposal of packaging materials is a customer’s competence and must be performed in accordance with the regulations in force in the country where the plant is installed and used.It is nevertheless sound practice to recycle packaging materials in an environment-friendly manner as much as possible.
• ALWAYS FOLLOW THE INSTRUCTIONS ABOUT SAFETY
AND THE REGULATIONS IN FORCE.
• KEEP THOSE WHO ARE NOT RESPONSIBLE FOR THE
EQUIPMENT OUT OF THE WORK AREA.
• NEVER EXCEED THE MAXIMUM WORKING PRESSURE
INDICATED.
•
NEVER POINT THE SPRAY GUN AT YOURSELVES OR AT
OTHER PEOPLE. THE CONTACT WITH THE CASTING CAN
CAUSE SERIOUS INJURIES.
• IN CASE OF INJURIES CAUSED BY THE GUN CASTING,
SEEK IMMEDIATE MEDICAL ADVICE SPECIFYING THE
TYPE OF THE PRODUCT INJECTED. NEVER UNDER-
VALUE A WOUND CAUSED BY THE INJECTION OF A
FLUID.
• ALWAYS DISCONNECT THE SUPPLY AND RELEASE THE
PRESSURE IN THE CIRCUIT BEFORE PERFORMING ANY
CHECK OR PART REPLACEMENT OF THE EQUIPMENT.
•
THE EMPLOYER SHALL TRAIN ITS EMPLOYEES
ABOUT ALL THOSE RISKS STEMMING FROM ACCI-
DENTS, ABOUT THE USE OF SAFETY DEVICES FOR
THEIR OWN SAFETY AND ABOUT THE GENERAL
RULES FOR ACCIDENT PREVENTION IN COMPLIAN-
CE WITH INTERNATIONAL REGULATIONS AND WITH
THE LAWS OF THE COUNTRY WHERE THE PLANT
IS USED.
• NEVER MODIFY ANY PART IN THE EQUIPMENT. CHECK
REGULARLY THE COMPONENTS OF THE SYSTEM.
REPLACE THE PARTS DAMAGED OR WORN.
• TIGHTEN AND CHECK ALL THE FITTINGS FOR
4
DALì
CONNECTION BETWEEN PUMP, FLEXIBLE HOSE AND
SPRAY GUN BEFORE USING THE EQUIPMENT.
• ALWAYS USE THE FLEXIBLE HOSE SUPPLIED WITH
STANDARD KIT. THE USE OF ANY ACCESSORIES OR
TOOLING OTHER THAN THOSE RECOMMENDED IN
THIS MANUAL, MAY CAUSE DAMAGE OR INJURE THE
OPERATOR.
• THE FLUID CONTAINED IN THE FLEXIBLE HOSE CAN
BE VERY DANGEROUS. HANDLE THE FLEXIBLE HOSE
CAREFULLY. DO NOT PULL THE FLEXIBLE HOSE TO
MOVE THE EQUIPMENT. NEVER USE A DAMAGED OR
A REPAIRED FLEXIBLE HOSE.
The high speed of travel of the product in the hose can create static electricity through discharges and sparks. It is suggested to earth the equipment.
The pump is earthed through the earth cable of the supply.
The gun is earthed through the high pressure flexible hose.
All the conductors near the work area must be earthed.
Electrical safety precautions
• Check the "ON/OFF" switch is on the "OFF" position before
• connecting the cable to the mains.
Never carry a plugged-in equipment.
• Disconnect the equipment before storing it and before performing any maintenance operation or replacing of accessories.
• Do not carry the equipment neither unplug it by pulling the electric cable.
Protect the cable from heat, oil and sharp edges.
• When the tool is used outdoors, use only an extension cable suited for outdoor use and so marked.
Never attempt to tamper with the calibre of instruments.
• NEVER SPRAY OVER FLAMMABLE PRODUCTS OR
SOLVENTS IN CLOSED PLACES.
• NEVER USE THE TOOLING IN PRESENCE OF POTEN-
TIALLY EXPLOSIVE GAS.
• Take care when the pumping rod is moving.
Stop the machine whenever someone is within its vicinity.
• Repairs of the electrical equipment should only be carried out by skilled personnel, otherwise considerabledanger to the user may result.
Always check the product is compatible with the materials composing the equipment (pump, spray gun, flexible hose and accessories) with which it can come into contact. Never use paints or
If these products come into contact with aluminium parts can provoke dangerous chemical reactions with risk of corrosion and explosion.
solvents containing Halogen Hydrocarbons
(as the Methylene Chloride).
F
SETTING-UP
CONNECTION OF THE FLEXIBLE HOSE TO THE GUN
• Connect the high pressure flexible hose to the pump and to the gun, ensuring to tighten the fittings (the use of two
wrenches is suggested).
NEVER use sealants on fittings’ threads.
• It is recommended to use the hose provided with the standard kit (ref. 35017).
NEVER use a damaged or a repaired flexible hose.
CHECK ON POWER SUPPLY
• Check the plant is earthed.
IF THE PRODUCT TO BE USED IS TOXIC, AVOID INHALATION
AND CONTACT BY USING PROTECTION GLOVES, GOGGLES
AND PROPER FACE SHIELDS.
TAKE PROPER SAFETY MEASURES FOR THE PROTECTION
OF HEARING IN CASE OF WORK NEAR THE PLANT.
5
DALì
•
Check the mains voltage corresponds to the equipment’s rating (
F1).
F1
Should anyone use an extension cable between the tooling and the socket, it must have the same characteristics as the cable supplied (minimum diameter of the wire 2.5 mm
2
) with a maximum length of 50 mt. Higher lengths and lower diameters can provoke excessive voltage falls and also an anomalous working of the equipment.
CONNECTION OF THE TOOLING TO THE POWER SUPPLY
• Check the ON/OFF switch (
F3) is on the "OFF" position (0) before connecting the cable to the mains.
• Place the pressure control knob (
F4) on the “MIN” position
(turn counterclockwise).
•
The supply cable (
F2) is provided without plug.
Use a plug which guarantees the plant earthing.
Only a technician or a skilled person should perform the connection of the plug to the electric cable.
F3
F2
6
F4
WASHING OF THE NEW EQUIPMENT
• The equipment has already been adjusted at our factory with light mineral oil left inside the pumping group as protection.
Therefore, wash with diluent before sucking the product.
DALì
•
•
Lift the suction pipe and dip it into the solvent tank (
Ensure the gun (
F6) is without nozzle.
F5).
• Point the gun at a container keeping the trigger pressed (so
as to drain the oil inside) till a clean solvent comes out. Now, release the trigger.
• Remove the suction pipe and take away the solvent tank.
F5
• Point the gun at the solvent tank and press the trigger so as to recover the residual solvent.
• As the pump idles, press the ON/OFF switch (
F8) on the position "
OFF" (0) to stop the tooling.
F6
• Open the re-circulation tap (
F7).
Turn the unit ON-OFF switch (
F8) on the "ON" position (I).
F7
Absolutely avoid to spray solvents indoors. In addition, it is recommended to keep away from the pump in order to avoid the contact between the solvent fumes and the electric motor.
• Now the machine is ready. Should you use water paints, besides the solvent wash, a wash with soapy and then clean water is suggested.
• Insert the gun trigger lock and assemble the nozzle.
I
I
F8
• Rotate the pressure setting knob (
F9) slightly clockwise so that the machine operates at minimum power.
PREPARATION OF THE PAINT
• Make sure the product is suitable to be used with a spray gun.
• Mix and filter the product before using it. For filtration, use
CLOSE-MESH (ref.214) and LARGE-MESH (ref.215) LA-
RIUS METEX braids.
Make sure the product to be used is compatible with the materials employed for manufacturing the equipment (stainless steel and aluminium).
Because of that, please contact the supplier of the product.
Never use products containing halogen hydrocarbons (as
methylene chloride). If these products come into contact with aluminium parts of the equipment, can provoke dangerous chemical reactions with risk of explosion.
F9
7
DALì
G
WORKING
G3
G2
G1 G4
START OF THE PAINTING OPERATIONS
• Use the tooling after performing all the SETTING UP operations above described.
• Dip the suction pipe ( G1) into the product tank.
• Open the re-circulation valve ( G2).
• Press the ON/OFF switch of the equipment and turn a little the pressure control knob ( G3) clockwise, so as the machine works at the idle speed.
• Make sure the product recycles from the return tube (
G4).
• Close the re-circulation valve.
• At this point the machine will continue to suck the paint product until the delivery hose is completely full. Afterwards, the product will re-circulate automatically.
SPRAY ADJUSTMENT
• Slowly turn clockwise the pressure control knob to reach the pressure value in order to ensure a good atomization of the product.
• An irregular and marked spray on the sides indicates a low working pressure. On the contrary, a too high pressure causes a high fog (“overspray”) and waste of product.
• In order to avoid overthickness of paint, let the gun advance sideways (right-left) when spraying.
• Always paint with regular parallel bands coats.
• Keep a safety and constant distance between the gun and the support to be painted and also keep yourselves perpendicular to it.
NEVER point the spray gun at yourselves or at other people. The contact with the casting can use serious injuries. In case of injuries caused by the gun casting, seek immediate medical advice specifying the type of the product injected.
The drain valve is a safety valve too. When working at the maximum pressure available, releasing the gun trigger sudden increases of pressure can occur. In this case, the drain valve opens automatically eliminating part of the product from the recirculating tube. Then it closes so as to go back to the first working conditions.
8
H
CLEANING AT THE END WORK
• Reduce pressure to the minimum (turn counterclockwise the
pressure control knob (
H1) ).
DALì
H2
H1
• Press the ON/OFF switch ( H2) placed on the box of the electric motor, to stop the equipment.
• Make sure the solvent recycles the washing fluid from the return tube ( H4).
H4
• First release the residual pressure from the gun by holding it pointed down towards the paint container, then open the re-circulation valve ( H3).
H3
H5
• Close the re-circulation valve ( H5) .
• Point the gun at the product tank and, keeping the trigger pressed, release the remaining product till a clean solvent comes out. Now, release the trigger.
• Lift again the suction pipe and remove the solvent tank.
•
• Lift the suction pipe and replace the product tank with that of the solvent (ensure it is compatible with the product being
used).
• Now point the gun at the solvent tank and press the trigger so as to recover the residual solvent.
• Unscrew the gun nozzle (do not forget to clean it with sol-
vent!).
•
As the pump starts idling, press the ON/OFF switch to stop the equipment.
Turn the ON-OFF switch (H2) on the ON position and rotate the pressure setting knob (H1) slightly clockwise.
• In case of long storage, we recommend you to suck and to leave light mineral oil inside the pumping group and the flexible hose.
Follow the washing procedure before using again the equipment.
9
DALì
I
ROUTINE MAINTENANCE
TOP UP HYDRAULIC OIL
With each start up, check the hydraulic oil level by looking through the gauge ( I1) on the side of the hydraulic body. If necessary, use
“AGIP OSO 46 type hydraulic oil” to top up the level.
CLEANING THE COMPRESSION VALVE
When the compression valve (
I3) must be removed, clean it with specific solvents depending on the type of paint used and refit all parts by inverting the removal order.
I3
I1
Assemble the components in the correct order.
RELEASE THE SUCTION VALVE
REPLACING HYDRAULIC OIL
If the pump malfunctions, release the suction valve fitted on the head of the pump in the following way:
After operating for 100 hours, replace the oil in the pump;
• Discharge the waste oil through the
plug (I4) fitted at the bottom of the pump casing.
• Remove the suction hose fitting and release the valve by inserting a rigid rod ( I2) with a diameter of no more than 15 mm.
• Clean the seals on the cap and replace it if worn.
• Remove and clean the filter ( I5) on the side of the pump casing; if necessary, replace the filter and the respective seals.
I2
• Clean and, if necessary, replace the worn seals (I5).
• Replace the plug (I4).
• Fill the pump with the recommended oil until it reaches the maximum level.
• Then, substitute the oil every 250 hours.
10
I5
I4
CLEANING THE MOTOR COOLING FAN GUARD
Clean the motor cooling fan protection guard (
I6) periodically to ensure the best cooling.
DALì
I6
L
WARNING PLATE
Apparecchi per verniciatura
Paint spraying units
ATTENZIONE
UTILIZZARE GRUPPI ELETTROGENI
CON ALTERNATORE ASINCRONO
http: www.larius.com
WARNING
USE POWER UNITS WITH
ASYNCHRONOUS ALTERNATOR
e-mail [email protected]
11
DALì
M
PROBLEMS AND SOLUTIONS
Problem
Cause
Solution
•
The equipment does not start
• Lack of voltage;
• Considerable drops in mains voltage;
• ON-OFF switch disconnected;
• Check the correct connection to the power supply;
• Check the extension cable;
• Ensure the ON-OFF switch is on the
“ON” position and turn clockwise the pressure control knob;
• Setting valve faulty pressure;
• Verify and replace it, if necessary;
• Breakdown of motor electric control box;
• The product is solidified inside the pump;
• Verify and replace it, if necessary;
• Open the drain valve to release pressure in the circuit and stop the machine. Remove the compression valve and clean it;
•
The equipment does not suck the product
• Suction filter clogged;
• Suction filter too fine;
•
The equipment suck but does not reach the pressure desired
• The equipment sucks air;
• Lack of product;
• The equipment sucks air;
• The drain valve is open;
• Suction or delivery valve dirty;
• Clean or replace it;
• Replace it with a larger-mesh filter
(with very dense products, remove
the filter);
• Check the suction pipe;
• Add the product;
• Check the suction pipe;
• Close the drain valve;
• Disassemble the colour body group;
•
When pressing the trigger, the pressure lowers considerably
• Nozzle too big or worn;
• The product is too dense;
• The filter of the gun-butt is too fine;
• Replace it with a smaller one;
• Dilute the product, if possible;
• Replace it with a larger-mesh filter;
•
The pressure is normal but the product is not atomized.
Leakage from the seal-tightening screw
• The nozzle is partially clogged;
• The product is too dense;
• The filter of the gun-butt is too fine;
•
The atomization is imperfect
• The nozzle is worn;
• Clean or replace it;
• Dilute the product, if possible;
• Replace it with a larger-mesh filter;
• Replace it;
Always close the air compressed supply and unload the plant pressure before performing any check or replacement of pump parts (see "correct procedure of decompression").
12
DALì
N
CORRECT PROCEDURE OF DECOMPRESSION
• Insert the gun clamp ( N1).
• Move the ON/OFF switch ( N2) to the OFF position (0) to stop the equipment.
• Set the valve ( N3) at its minimum pressure setting (turn anticlockwise).
N1
• Disconnect the power supply cable ( N4).
N2
N3
N5
N4
• Release the gun clamp ( N5). Point the gun at the tank of the product and press the trigger to release pressure. At the end of the operation, insert the gun clamp.
• Open the re-circulation valve ( N6) to release residual pressure.
N6
WARNING :
If the equipment is still under pressure after performing the operations above described because of the nozzle or the flexible hose clogged, proceed as follows:
• Loosen very slowly the gun nozzle.
• Release the clamp.
• Point the gun at the container of the product and press the trigger to release pressure.
• Loosen very slowly the fitting of connection from the flexible hose to the gun.
• Clean or replace the flexible hose and the nozzle.
13
O
COMPLETE HYDRAULIC BODY
DALì
14
DALì
Pos.
1C
-
2**
3**
4
1A
-
1B
-
Code
32019
32022
32021
32020
96031
32024
32108
32108
81020
18906
32026
32027
32029
18908
18907
32041
33010
33010
18910
32018
32033
91026
33002/3
18937
33002/1
18936
31125
18925
-
18926
-
18924
-
18901
Description
Electric motor mono-phase 220V
50Hz complete
Electric motor mono-phase 110V
60Hz complete
Electric motor three-phases 380V
50Hz complete
Hydraulic body
Cylinder liner
Piston insert
Nut
Spring
Oil distributor
Diaphragm
Diaphragm insert
Bearing
Elastic ring
Bushing
Bearing
Cover
Screw
OR
Cover
Check nut
Piston
Spring
Spring cap
Elastic ring
Screw
Washer
Plug
Plug
Washer
Washer
Identification plate 220V 50Hz
Pos.
23
24
21
22
17
18**
19
20
25
25V*
26
26V*
27
15
16
13
14
9
10**
11**
12
* Only in the vertical configuration
**Pos. 2-3-10-11-18 spare supplied complete (recommended) - Ref. 18952
*
Code
18929
18938
32032
5059
18567
91915
18946
32014
32017/1C
12475
12461
32010
258
32012
18928
18947
81009
18919
33005
18903
32150
-
32017
32017/2
32016
32155
18931
18932
18933
34020
32007
32108
81012
18909/1
51
52
53*
54*
50
50
48
49
55*
56
46
47
44
45
42
43
40
41
-
39
37
38
35
36
33
34
31
32
29
30
27
28
27
27
Description
Identification plate 110V 60Hz
Petrol identification plate
Identification plate 380V 50Hz
Rivet
Oil inspection window
Plug
Spline
Corteco
Eccentric flywheel
Dowel
Tab
Washer
Nut
Complete pressure regulation valve
Knob
Spring
Retainer
Valve body
OR
Dowel
Oil filter assembly
Filter
Copper washer
Filter sieve 60 MESH
OR
Motor condenser 220V 50Hz
Motor condenser 110V 60Hz
Switch
Screw
Washer
Screw
Ball
Dowel
15
P
DALÌ PETROL - DALÌ LINER
DALì
16
DALì
22
21
26
27
23
24
20
24
25
27
28
C
D
Code
34009
96031
18262
18263
8385
18265
18919
42255
18266
34008
18260
,
18340
.
18347
4415
18261
Pos.
10
11
8
9
12
6
7
4
5
A
.
B+C+D
,
B+C
1
2
3
Description
Complete gearbox – petrol membrane version
Complete gearbox kit – Dalì petrol version with trolley
Complete Dalì liner kit
Motor
Flange motor
Washer
Screw
Pinion
Washer
Screw
Toothed bell
Tab
Bearing
Gearbox cone
Screw
Pos.
25
26
27
28
29
21
22
23
24
17
18
19
20
13
14
15
16
Code
18254
81107
18942
52017
32024
34008
95156
81033
95158
7059
18267
18344
95114
18268
81009
18269
18264
Description
Bearing
Screw
Washer
Hydraulic flange
Dowel
Reduction
Plating guard
Fixing plate
Vibration damper
Threaded pin
Nut
Washer
Screw
Screw
Washer
Nut
Screw
17
29
28
Q
COMPLETE COLOUR BODY
VERTICAL VERSION
DALì
33
32
31
30
1
35
13
12
34
14
23
22
21
20
19
18
17
16
15
11
25
26
27
36
24
3
2
4
5
6
7
8
9
10
18
Code
53006/1
33031
33032
33011
33005
33004
33017
33018
18951
33033
33026
33027/2
33027/1
33028
33029
33019
33020/1
33020
Pos.
15
16
13
14
17
18
11
12
9
10
7
8
5
6
3
4
1
2
Description
Vertical colour body
Valve assembly
Gasket
Ball seat
Valve housing
Ball
Spring seat
Spring
Gas-ring
Check nut
Union
Washer
Screw
Complete valve body
Gas-ring
Conical shutter
Spear valve seat
Valve body
DALì
Code
18614
33013
35101
35103
35006
35007
35008
55000
33021
33022
33023
33024
33025
18922
33012
18569
95284
4011
Pos.
33
34
31
32
35
36
29
30
27
28
25
26
23
24
21
22
19
20
Description
Shutter guide
Spring
Washer
Nut
Seal sleeve
Recirculation valve assembly
Washer
Elbow
Cock
Tank assembly
Tank
Close filter
Large filter
Spring ring
Cover
Recirculation tube
Union
Union
19
DALì
HORIZONTAL VERSION
10
9
4
3
8
7
6
5
2
26
25
11
28
27
25
24
12
13
14
23
22
21
20
19
Code
33031
33032
33011
33005
33004
33017
18915
33033
33026
33027/2
33027/1
33028
33029
53006
Pos.
12
13
14
10
11
8
9
6
7
4
5
1
2
3
Description
Standard colour body
Valve assembly
Gasket
Ball seat
Valve housing
Ball
Spring seat
Spring
Gas-ring
Plug
Union
Washer
Screw
Complete valve body
18
17
16
15
Code
33018
33019
33020/1
33020
33021
33022
33023
33024
33025
18922
33012
33013
33015
95284
Pos.
26
27
28
22
23
24
25
18
19
20
21
15
16
17
Description
Gas-ring
Conical shutter
Spear valve seat
Valve body
Shutter guide
Spring
Washer
Nut
Seal sleeve
Recirculation valve assembly
Washer
Cock
Union
Union
1
20
DALì
R
HIGH PRESSURE GUN "AT 250"
A 2 3
1
4
7
8
9
10
5
6g
6a
6h
6b
6c
6d
6e
11
6f
6g
6b
6h
6a
12
13
14
15
16
Components Pos. 5 - 11023 - Linkage
11005/3 Ball
11204/1
11205/2
Ball housing
Spring
11205/4
11205/5
11205/6
11205/7
Linkage
Sleeve
Ring sleeve
Bushing
Pos.
A
1
2
3
4
5
6
6a
6b
6c
6d
6e
6f
Code
See table*
18270
18280
11004
11006 +
11032
11203
11008
11010
11011
11009
11012
11013
11034/1
Description
Nozzle Super Fast Clean
Body Super Fast Clean
Gasket Super Fast Clean
Sleeve
Safety for hand +
3 screws TSP 3x8
Complete linkage
Trigger gun
Safety lever
Brake washer
Trigger
Pin
Pin
Pin
21
Pos.
12
13
14
15
16
10
11
8
9
6g
6h
7
Code
11027
11016
11206
11207
11208
11209
11020
-
11018
11017
32010
11015
11155
Description
Nut M3
Washer
Gun body
Spinet
Plate
Self-locking nut M5
Copper gasket
Filter
Handgrip
Spring
Copper gasket
Articulated joints M16x1,5
Articulated joints 1/4”
S
SUCTION SYSTEMS
DALì
3
4
2
1
Pos.
2
3
-
1
4
Code
85009
85010
16609
18096
85012
Description
Suction systems
Suction tube
Recirculation tube
Spring
Filter of suction
22
DALì
T
TROLLEY
ELECTRIC MOTOR
1
2
1
7
6
5
3
4
9
Code
18911
95159
18912
18914
18902
18913
37218
91047
12454
12473
Pos.
6
7
4
5
8
9
2
3
1
-
Description
Trolley assembly
Plug
Handle
Bushing
Split pin
Trolley frame
Pneumatic wheel
Washer
Feet
Plug
23
8
DALì
COMBUSTION MOTOR
1
3
8
2
Pos.
7
8
5
6
3
4
1
2
Code
12355
12454
12710
37218
91047
84007
12711
12473
Description
Trolley assembly
Foot
Trolley base
Pneumatic wheel
Elastic washer
Split pin
Trolley handle
Plug
24
7
6
4
5
U
ACCESSORIES
DALì
Art. 11250: AT 250 1/4"
Art. 11200: AT 250 M16x1,5
Code 270: FILTER 100 MESH
Code 271: FILTER 60 MESH
PISTON GUNSTOCK FILTERS
Code 11039: Green (30M) - Code 11038: White (60M)
Code 11037: Yellow (100M) - Code 11019: Red (200M)
Code 147: HIGH PRESSURE GAUGE M16x1,5
Code 150: HIGH PRESSURE GAUGE GJ 1/4"
Code 85014: FILTER 40 MESH - Code 85012: FILTER 20 MESH
Code 37215: FILTER 40 MESH inox - Code 37216: FILTER 20 MESH inox
MANUAL GUN LX-T
Code 14310: NOZZLE 4 mm
Code 14311: NOZZLE 6 mm
Code 14312: NOZZLE 8 mm
25
DALì
HIGH PRESSURE HOSE 3/8" - M16x1,5 max pressure 425 bar
Code 18063: 7,5 mt
Code 18064: 10 mt
Code 18065: 15 mt
ANTISTATIC HOSE 3/16" - M16x1,5 max pressure 210 bar
Code 6164: 5 mt
Code 55050: 7,5 mt
Code 35018: 10 mt
SUPER FAST-CLEAN
ANTIPULSATIONS 1/4" - M16x1,5 max pressure 250 bar
Code 35013: 5 mt
Code 35014: 7,5 mt
Code 35017: 10 mt
Code 18026: 15 mt
SUPER FAST-CLEAN TIP
SFC07-20
SFC07-40
SFC09-20
SFC09-40
SFC11-20
SFC11-40
SFC13-20
SFC13-40
SFC13-60
SFC15-20
SFC15-40
SFC15-60
SFC17-20
SFC17-40
SFC17-60
SFC19-20
SFC19-40
Nozzles code
SFC19-60
SFC21-20
SFC21-40
SFC21-60
SFC23-20
SFC23-40
SFC23-60
SFC25-20
SFC25-40
SFC25-60
SFC27-20
SFC27-40
SFC27-60
SFC27-80
SFC29-20
SFC29-40
SFC29-60
SFC29-80
SFC31-40
SFC31-60
SFC31-80
SFC33-40
SFC33-60
SFC33-80
SFC39-40
SFC39-60
SFC39-80
SFC43-40
SFC43-60
SFC43-80
SFC51-40
SFC51-60
SFC51-80
Code 18280: GASKET
Code 18270: SUPER FAST-CLEAN base UE 11/16x16
26
DALì
GUN EXTENSION
Art. 153: cm 30 -Art. 153: cm 40
Art. 155: cm 60 - Art. 158: cm 80 - Art. 156: cm 100
PLA 1/4”
+ BASE SUPER
FAST-CLEAN
Art. K11420-K11425-K11430: cm 130-180-240
PLA M16x1,5
+ BASE SUPER
FAST-CLEAN
Art. K11421-K11426-K11431: cm 130-180-240
Art. 16780: TELESCOPIC PAINT ROLLER complete with: n. 1
Roller with extra-long fiber n. 1 Roller with long fiber n. 1 Roller with medium fiber
Flexible hose mt. 2 3/16 " M16x1,5
MX 750
MX 1000 E
MX 1100 E
Code 217550: MX 750 - Code 217560: MX 1000 E - Code 217570: MX 1100 E
27
Code 18241: GRAVITY HOPPER 50 lt
DALÌ VERSIONS
DALì
HORIZONTAL WITHOUT ACCESSORIES
Ref. 18900: 220V / 50 Hz
Ref. 18920: 110V / 60 Hz
Ref. 18955: 380V / 50 Hz
Ref. 18956: Petrol
HORIZONTAL WITH ACCESSORIES
Ref. 18957: 220V / 50 Hz
Ref. 18958: 110V / 60 Hz
Ref. 18959: 380V / 50 Hz
Ref. 18960: Petrol
VERTICAL WITHOUT ACCESSORIES
Ref. 18961: 220V / 50 Hz
Ref. 18962: 110V / 60 Hz
Ref. 18963: 380V / 50 Hz
Ref. 18964: Petrol
VERTICAL WITH ACCESSORIES
Ref. 18965: 220V / 50 Hz
Ref. 18966: 110V / 60 Hz
Ref. 18967: 380V / 50 Hz
Ref. 18968: Petrol
28
PAINT SPRAYING EQUIPMENT
L’innovazione.
Quella vera.
AIRLESS DIAPHRAGM PUMPS
VIKING
Rif. 18741
MIRO'
Rif. 21500
MANUFACTURER:
23801 CALOLZIOCORTE - LECCO - ITALY - Via Antonio Stoppani, 21
Tel. (39) 0341/62.11.52 - Fax (39) 0341/62.12.43
E-mail: [email protected] - Internet http://www.larius.com
DIRECT LINE
CUSTOMERS TECHNICAL SERVICE
Tel. (39) 0341/621256
Fax (39) 0341/621234
GIOTTO
Rif. 12450
advertisement
Related manuals
advertisement