- Home
- Do-It-Yourself tools
- Power tools
- Paint Sprayer
- Australian Pump Industries
- Aussie Super Indy
- Datasheet
Datasheet | Australian Pump Industries Aussie Super Indy Technical data
Add to my manuals
16 Pages
Australian Pump Industries Aussie Super Indy
The Aussie Super Indy is a high-performance centrifugal pump designed for a wide range of applications, including:
- Water transfer: The Super Indy can quickly and efficiently transfer water from one location to another, making it ideal for tasks such as filling pools, emptying flooded areas, and irrigating gardens.
- Dewatering: The Super Indy can be used to remove water from flooded areas, such as basements, garages, and construction sites.
- Firefighting: The Super Indy can be used to fight fires by delivering a powerful stream of water to the affected area.
advertisement
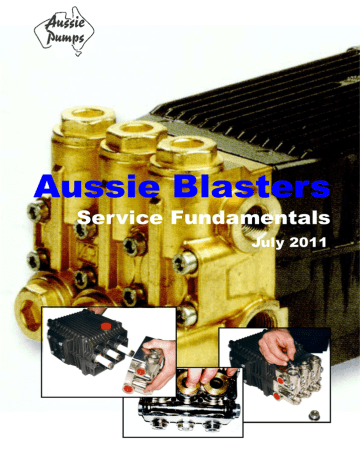
Aussie Blasters
Service Fundamentals
July 2011
2
INTRODUCTION
This manual was developed as a basic guide to understanding the operation and requirements, installation and servicing of Aussie Pumps
>Big Berty= Bertolini positive displacement pumps.
High pressure cleaning equipment is a potentially hazardous undertaking and can cause injury and property damage. It must be installed and repaired in accordance with the manufacturer
=s instructions. Recommended OH&S safety practices must be observed at all times.
Australian Pump Industries does not assume liability or responsibility for the design or operation of a customer
=s high pressure system.
CONTENTS
Introduction ..................................................................................................................................3
Typical operation and requirement .....................................................................................4
Pressure....................................................................................................................4
Flow ..........................................................................................................................4
Detergent Injection ....................................................................................................4
Hot water/steam systems..........................................................................................3
Designing your system.........................................................................................................5
Pump selection..........................................................................................................5
Motor/engine selection ..............................................................................................5
Spray tip selection guide......................................................................................................6
Determining spray tip size .........................................................................................6
Drive System .......................................................................................................................6
Other components ...............................................................................................................7
Inlet side components ...............................................................................................8
Outlet side components ............................................................................................8
Installation of components ...................................................................................................8
Troubleshooting ...................................................................................................................9
Service guidelines..............................................................................................................10
Valve assemblies ....................................................................................................10
Removing manifold head ........................................................................................10
Replacing plungers .................................................................................................11
Replacing V-packings .............................................................................................12
Pressure cleaner test set ........................................................................................13
Pressure setting instructions - engine drive.....................................................14
- electric drive ....................................................15
Change up to Big Berty
- the Quality Change Out
3
TYPICAL OPERATION AND REQUIREMENTS
Pressure
The pressure produced in a pressure washer system is the result of forcing a known volume of water through a known orifice size (spray tip).
This pressure is measured in bar or pounds per square inch (psi). and the development of dangerously high pressure.
Note: Failure to install correct unloader valve or regulator device could result in serious injury and property damage.
Chemical injection
Flow
In a pressure washer system the flow produced is determined by the speed that the pump shaft is rotated (rpm). The faster the shaft is rotated the higher the output volume. This water flow is measured in litres per minute.
Nozzle Orifice
Setting unloader valves for the required pressure of the machine depends entirely on the correct nozzle selection. The correct nozzle orifice can be selected to suit any specific pressure/flow combination using the chart on page 5.
Cleaning chemicals or detergents may be introduced into either the inbound or outbound flow of water. An inbound chemical injector uses the pump =s ability to draw or suck fluid in to introduce a chemical into the water flow. An upstream injector allows chemicals to be applied to the surface to be cleaned at normal high water pressures. As any chemicals introduced upstream pass through the pump body, care must be taken to ensure the chemicals are compatible with the pump =s construction material and components, such as seals.
Operators should be conscious that nozzle wear will create a drop in pressure and an apparent malfunction of the machine. The abrasive nature of water and the subsequent wear enlarges the orifice in the nozzle. The larger the orifice, the less pressure and the more danger of subsequent machine malfunction through unloader failure.
An outbound or downstream type of chemical injector uses the venturi system to draw chemical into the water stream. This type of injector requires low pressure to activate chemical flow.
Low pressure is achieved by enlarging the outlet orifice by changing to a larger spray tip or by an adjustable nozzle.
There are advantages to using a downstream injector:
Further information on this subject is covered in the Nozzle Selection Guide section.
Operation
1. Fewer pump component parts are exposed to the cleaning chemicals which may extend system life.
The pump which is motor driven draws water in through a series of inlet check valves as the plungers move back. As the plungers move forward the inlet valves close, forcing the water to travel through a series of outlet check valves and to the pump outlet.
2. The operator can control the flow of chemicals by changing the system pressure at the nozzle.
3. Applying the chemical at lower pressure is more economical as less chemical bounces off the work surface.
Hot water/steam cleaners
When the water exits the pump the direction of flow is controlled by means of an unloader or regulating valve. A positive displacement pump is always delivering a certain volume of water whether the spray outlet is open or closed so a device is needed to control the direction of flow.
This device allows the spray to exit through the spray gun or redirecting (by-passing) the flow back to the inlet of the pump if the gun is closed.
As a safety device at least one pressure relief valve must be installed in the outbound side of the pump to protect against component failure
Heated pressure washers and steam cleaners increase the ability of high pressure water flow to break down dirt and grease. The cleaning action of most detergents is also increased. Units incorporating a boiler are very complex and potentially more hazardous than cold water systems. Design of these systems requires many more additional components and should be designed by qualified professionals with a thorough knowledge of fuels, heat transfers, etc.
4
TYPICAL PRESSURE WASHER SYSTEM
DESIGNING YOUR SYSTEM
Pump selection
The heart of any pressure washer system is your Aussie Pumps >Big Berty= Bertolini pump.
Choose the pump that
=s right for your work demands. Higher pressure is not necessarily best. To much pressure and flow will cause unnecessary wear on your pressure system.
In addition, damage to the objects and surfaces to be cleaned could result.
Never exceed the maximum pressures or rotation speed stated in the Technical Data.
Refer to the Technical Data for the correct rpm required.
DRIVE SYSTEM
There are three common methods of driving or connecting the pump and motor/engine. Direct drive and gear reduction drive require special components that are matched to the pump and to the motor/engine as well as other technical considerations. The third is belt drive. Belt drive is considered inefficient (belt slip) and can
Motor/engine Selection
The size of the motor required is determined by the flow (litres/minute) and the pressure
(bar/psi) desired.
Ensure that a petrol engine runs fast enough to supply the required horsepower but do not exceed the engine manufacturer =s specifications.
Consult pump and engine manufacturer
=s technical guidelines. have negative OH&S ramifications.
5
NOZZLE SELECTION GUIDE
DETERMINING SPRAY TIP SIZE
6
As stated earlier the outlet pressure is determined by ejecting a known volume of water through a spray tip. The size of this tip is an important factor of efficient pressure cleaner performance. A tip that is too large may produce insufficient pressure. A tip that is too small may cause over high pressures causing damage to the pump and other system components.
your own pump. The correct spray tip for the result you require must not exceed 90% of the high flow.
Example: 2030 psi at 11 litres per minute, calculate 90% of flow value = 035 nozzle.
Aussie Laser Tip Nozzles are available in various sizes and spray angles. It is advisable to keep a selection different sized and angled spray tips handy for different cleaning applications.
Refer to the above chart to select the correct nozzle size for your application.
Firstly, ascertain the output flow of your pump from the technical data. Then find the pressure (psi) you require and read down the column until you reach the output closest to
Nozzles are also available with an adjustable spray angle (see Aussie >Vario-Zoom= nozzles for domestic and commercial pressure cleaners.
Big Berties are Bonza!
SELECTING REMAINING COMPONENT
Inlet side components
Inlet filter - It is important to install a water filter on the intake line to remove and impurities or solids in the water. This will increase the operating life of your system and reduce problems.
A 60-120 mesh screen filter is recommended to stop foreign matter clogging valves and orifices, scratching internals, abrading packing and wearing the components.
By-pass provision - The unloader valve or regulator redirects the water flow back into the pump if the orifice is closed, i.e. the gun trigger is released. An inlet water holding tank must be installed to accept this redirected flow.
Thermal relief valve - This is a device which is temperature operated. The sensor opens the valve and dumps water when a predetermined temperature is reached. Water recirculated by the unloader valve will heat up after a certain time and if this over heated water passes through the pump it may damage the pump =s internals necessitating costly repairs.
Upstream detergent injector - This device uses the pump to introduce the detergent into the water stream before it enters the pump.
This type of injector is not recommended for harsh or corrosive chemicals as passage through the pump may damage internal components.
Pressure reducing valve - If the water supply entering the pump is above the maximum inlet pressure specified in the Technical Data a pressure reducing valve must be installed for proper and safe pump operation.
Check valve - A check valve is installed to prevent any chemicals or detergents being back-flushed into the water supply. Local water supply authority regulations must be observed.
An alternative to a check valve is the use of a holding tank to collect any back flush. Ensure that you do not exceed the negative pressure rating of the pump.
BIG BERTIES BOUNCE THE OTHERS!
Outlet side components
Unloader or regulator valve - This device prevents a build up of water pressure in the system. It is necessary for operator safety and for system protection. When the gun is opened the water is allowed to flow into the outlet hose.
If the gun is closed the water flow is directed back into the inlet side of the pump. Installation of unloader valves must be carried out strictly in accordance with the manufacturer =s instructions.
It should be checked and serviced regularly.
The unloader valve should be mounted as close to the pump outlet as possible. Do not use any hose between the unloader valve and the pump outlet.
Pressure relief valve - This valve prevents a dangerous build up of pressure in the system. It is necessary for operator safety and for system protection. This valve will open and dump water if the system becomes over pressurized due to any component failure.
Installation of pressure relief valves must be carried out strictly in accordance with the manufacturer =s instructions and should be checked and serviced regularly.
Pulsation dampener - This device smooths pulsations caused by the pump itself and to absorb pressure spikes when the gun is closed suddenly. A duplex pump may require a pulsation dampener because of pulsation not experienced in a triplex pump. Long runs of hose may generate a hammer effect which a pulsation dampener may soften or prevent.
Pressure gauge - This displays the operating pressure and not only allows the operator to determine peak performance, but also may indicate any deficiencies occurring within the system. For instance, a decrease in system pressure may indicated a worn spray tip; an increase in pressure may suggest a blockage in the system or a faulty unloader valve.
Select a gauge that is:
- liquid filled to absorb pressure fluctations;
- installed with a restriction orifice to avoid pressure spike damage;
- appropriate for your system =s normal pressure range.
7
8
Downstream injector - This component introduces a detergent downstream of the pump.
The size of the injector must be selected taking into account the pump pressure. Refer to the injector manufacturer for technical data. If the injector is too small a large pressure drop will result causing a high concentration of detergent.
If the injector is too large it will be unable to create sufficient suction to pick up any detergent.
Downstream injectors require low pressure to activate the chemical flow. Approximately 200psi is sufficient. A double nozzle or lance enable both a low pressure and high pressure spray tip to be mounted. This allows the detergent to be applied at low pressure and conveniently removed at higher pressure. An adjustable nozzle may also be used to the same effect.
High pressure hose - Ensure that high pressure hose in your system is compatible with any chemicals you may be using.
Do not use hose clamps to secure the hose as they may be dislodged under pressure. Snap couplings are safer and also more convenient for the operator. Check couplings regularly for leaks and replace if necessary with Aussie brass snap couplings rated to 4060psi. For super high pressure applications we recommend Aussie >H=
Series ST couplings rated to 5200psi.
Avoid an unnecessarily long high pressure hose to prevent pressure accumulation when releasing the gun trigger and to minimise operating pressure loss.
Spray gun - The gun must be selected to withstand operating pressure, volume, temperature and chemicals in the system. A professional gun should be selected such as
Aussie Series. The gun selected should also be comfortable to use to reduce operator fatigue.
INSTALLING YOUR COMPONENTS
Install all components according to manufacturer =s recommendations to ensure operator safety, to avoid property damage and to ensure efficient system operation.
Any plumbing and component parts must be the same size or larger than the inlet and outlet of the pump. The thread sizes are a guide to the required sizes of plumbing for correct water flow.
Mount the motor/engine so that the rotation of the pump crankshaft is counterclockwise as you face the pump crankshaft. The rotation of a petrol engine varies according to manufacturer.
Check the specifications before assembling. In most cases electric motors may be operated in either direction according to the wiring. Check the manufacturer =s specifications before connection.
Minimise bends and other restrictions in hoses and other plumbing. This will ensure maximum efficiency of the motor or engine and reduce turbulence and cavitation which may damage system components.
Caution - Electrical components should only be installed by a qualified professional. Water and electricity are a dangerous combination. All electrical components should be watertight.
Never allow a spray or leak to contact any electrical component. This could cause serious injury.
It is important that the air is prevented from entering the system. Air leaks will cause a reduction in pressure, excessive noise and increased pump wear.
It is recommended that a thread sealant be used on all connections before tightening securely.
Hose clamps are not acceptable as they are susceptible to leaks and fail under pressure.
Never introduce acids, caustic substances or abrasive liquids into to pressure system. Such substances entering the system will damage pump and other components and will void any guarantee.
If necessary the pump and system should be protected from freezing.
BIG BERTIES ARE BEAUT!
PROBLEM
Pulsation
Low pressure
Pump runs extremely rough, pressure very low
Water leakage from under manifold, slight leakage
Oil leak between crankcase and pumping section
Oil leaking in the area of crankshaft
Excessive play in the end of the crankshaft pulley
Water in crankcase
Oil leaking from underside of crankcase
Oil leaking at rear portion of the crankcase
Loud knocking noise in pump
Frequent or premature failure of the packing
TROUBLESHOOTING
CAUSE
Faulty pulsation damper
Worn nozzle
Belt slippage
Air leak in inlet plumbing
Relief valve stuck, partially plugged or improperly adjusted valve seat worn
Inlet suction strainer clogged or improperly sized
Worn packing. Abrasives in pumped fluid or severe cavitation. Inadequate water
Fouled or dirty inlet or discharge valves
Worn inlet, discharge valve blocked or dirty
Leaky discharge hose
Cracked pistons as a result of dry running
Restricted inlet or air entering the inlet plumbing
Inlet restrictions and/or air leaks. Stuck inlet or discharge valve
Worn packing
Worn crankcase piston rod seals, O-rings on plunger retainer worn
Worn crankshaft seal or improperly installed oil seal o-ring
Faulty bearing
Travel plug in use on pump
Worn main bearing from excessive tension on drive belt
Humid air condensing into water inside the crankcase
Worn packing and/or piston rod sleeve. O-rings on plunger retainer worn
Worn crankcase piston rod seals
Damaged crankcase, rear cover o-ring, drain plug o-ring or sight glass o-ring
Pulley loose on crankshaft
Broken or worn bearing
Scored, damaged or worn plunger
Overpressure to inlet manifold
Abrasive material in fluid being pumped
Excessive pressure and/or temperature of fluid being pumped
Over pressure of pump
Running pump dry
REMEDY
Check precharge, if low recharge or replace
Replace nozzle
Tighten or replace
Disassemble, reseal and reassemble
Clean, adjust relief valve, check for worn and dirty valve seats. Kit available
Clean. Check more frequently
Install proper filter. Suction at inlet manifold must be limited to less than 6m lift or 8.5psi
Clean inlet and discharge valve assemblies
Replace worn valves, valve seats.
Replace worn valves, valve seats and/or discharge hose
Replace pistons
Check inlet plumbing size. Check seals are air tight
Replace worn cup or cups, clean out foreign material, replace worn valves.
Install new packing
Replace crankcase piston rod seals. Replace orings.
Remove oil seal retainer and replace damaged oring and/or seals
Replace bearing
Replace with breather plug
Replace crankcase bearing and/or tension drive belt
Change oil more frequently. Use high grade automotive 30 weight nondetergent oil
Replace packing. Replace o-rings
Replace seals
Replace cover o-ring, drain plug o-ring, or sight glass o-ring
Check key and tighten set screw
Replace bearing
Replace plungers
Reduce inlet pressure
Install proper filtration on pump inlet plumbing
Check pressures and fluid inlet temperature, ensure they are within specified range
Reduce pressure
Do not run pump without water
9
SERVICE INFORMATION
VALVE ASSEMBLIES
• All inlet and discharge valves can be serviced without disrupting the inlet or discharge plumbing.
The inlet and discharge valves are identical in all models.
• To service any valve remove valve cap and extract valve assembly.
• Examine o-rings and replace if there is any evidence of cuts, abrasions or distortion.
• Remove valve assembly (retainer, spring, valve, valve seat) from valve cavity.
• Only one Aussie Pumps valve kit is required to repair all valves in the pump. The kit contains orings, valve seats, poppets, springs and retainers.
• Install new o-ring in valve cavity.
• Insert assembly into valve cavity.
• Replace valve cap and torque to specifications.
REMOVING MANIFOLD HEAD
• Remove the fasteners retaining head
• Separate head from crankcase. It may be necessary to tap head lightly with soft mallet to loosed. Care should be taken not to damage plungers when sliding head from crankcase.
• The V-packing assemblies may come off with the head. Examine plungers. The surface should be smooth and free from scoring and pitting. If not, replace.
• Replace manifold head and torque to specifications using the sequence shown below:
TORQUE SEQUENCE FOR TIGHTENING HEAD
Install all head bolts fingertight. Torque to 14 Nm in sequence as shown, then retorque to specifications following the same sequence
10
SERVICE INFORMATION
REPLACING PLUNGERS
•Remove stainless steel piston nut and copper washer from piston rod
• If slinger washer comes off with plunger ensure this is replaced before the new plunger is installed.
• Separate piston from plunger
• Install new o-ring and teflon backup ring on
plunger.
• A thin film of grease on the outside of the o-rings
will ensure a better seal.
• Carefully press piston over plunger
• Fit new copper washer to the piston guides and torque to specifications
TYPICAL PACKING ASSEMBLY
Unique Bertolini
Double Seal
O-ring
Female adaptor
V-packing
Male adaptor head ring
Intermediate ring
Long life ring
V-packing
Head ring
11
SERVICE INFORMATION
REPLACING V-PACKINGS
• Remove manifold from crankcase
• Insert proper extractor collet through main seal
retainer. Tighten collet and extract retainers,
v-packings and head rings.
• Place correct insertion tool in cylinder and install front head ring, v-packing and long life ring and press firmly into cylinder until they will go no further.
• Insert intermediate seal retainer pressing it
firmly into cylinder until it will go no further
using proper insertion tool.
• Install rear head ring v-packing and main seal retainer into cylinder in order shown and
press firmly into cylinder
• Repeat this sequence for each cylinder
• Coat each plunger with grease and carefully remount manifold. Torque head to specifications.
12 Aussie Pumps Bertolini Pumps Service Guidelines – July 2011
AUSSIE WATER BLASTERS RECOMMENDED PUMP OILS
It is recommended that the following oils be used:
APPLICATION
Axial style wobble-plate pumps
AUSSIE BLASTER
H101
H110
H120
H130
F140
F150
F180
Panther
Cougar
Tiger MkII
RECOMMENDED OIL
Renolin 100B non-foaming oil
Triplex style crankshaft/piston pumps
Pressure cleaner gear boxes
Monsoon Series
AB Series
BB Series
Super Indy Series
Top Pro (TK) Series
Admiral
Terminator
Predator
Slow speed machines
SAE 75W/90 gear oil
SAE 75W/90 gear oil
AUSSIE PRESSURE CLEANER TEST SET
Everybody knows that professional pressure cleaners occasionally need to have their pressure tested and sometimes reset. Doing this efficiently, and in line with our professional recommendations (see pages 13 and 14) is not easy unless you have the right equipment.
Checking pressure regularly will tell you if nozzles are worn, if the pressure regulator is worn, if there are leaks in the system, if the valves are sticking and signal other problems that can manifest themselves in low pressure operation.
The new Aussie “Part number ATESTSET/Aussie test set up” will solve those problems. Consisting of a convenient brass T with M22 quick coupler and 6000 psi pressure gauge you can check to make sure everything is operating as it should.
Detailed instructions are included with each kit.
13
AUSSIE BLASTER PRESSURE SETTING INSTRUCTIONS
Engine drive blasters
NOTE: These instructions are intended for the use of Authorised Aussie Eco-Clean service centres only
1. Connect machine to mains pressure water supply, ensuring that water is passing freely through the pump at the correct flow rate for specified pump by holding the gun trigger open.
2. Check gun nozzle size with gauge to ensure correct nozzle size (see chart). Replace nozzle if worn.
3. Ensure machine is set up correctly for testing with two gauges, as shown above. Pressure gauge ‘A’ to be installed on top central valve cap. This gauge will measure the pump pressure.
Pressure gauge ‘B’ is to be installed at the pump outlet on the delivery hose. This gauge will measure the in-line pressure when gun is shut off. This pressure must not exceed 20%
increase on operating pump pressure. Example: 2000psi pump pressure on gauge ‘A’ with gun open: when gun is shut off gauge ‘B’ must not exceed 2400psi.
4. To obtain correct pressure at pre-determined rpm:
1. Remove grub screw in unloader lock ring;
2. Wind down unloader until required pressure is achieved. Governor setting on engine will increase engine rpm automatically once the engine comes under load. This will increase engine rpm to approximately 3000rpm for Honda GX160.
5. Release trigger on gun to shut off water flow and read gauge ‘B’ to determine the increase in line pressure (20% increase limit).
6. If test proves OK, repeat procedure for final check.
7. Unwind unloader by half a turn to ensure no pressure loss is indicated on gauge ‘A’ in pump.
8. Apply Loctite 243 Super Thread to grub screw in unloader lock ring and tighten with 1.5mm allen key.
9. Apply paint seal to grub screw head and thread below unloader lock ring.
10. Check engine rpm and adjust throttle. Do not set engine speed higher than 3200 rpm.
11. Use a 6mm nut to screw onto the throttle adjusting screw and lock tightly against the bracket.
12. Apply paint seal to screw head of engine throttle adjustment screw and protruding thread behind throttle bracket.
14 Aussie Pumps Bertolini Pumps Service Guidelines – July 2011
AUSSIE BLASTER PRESSURE SETTING INSTRUCTIONS
Electric drive blasters
NOTE: These instructions are intended for the use of Authorised Aussie Eco-Clean service centres only
1. Connect machine to mains pressure water supply, ensuring that water is passing freely through the pump at the correct flow rate for specified pump by holding the gun trigger open.
2. Check gun nozzle size with gauge to ensure correct nozzle size (see chart). Replace nozzle if worn.
3. Ensure machine is set up correctly for testing with two gauges, as shown above. Pressure gauge ‘A’ to be installed on top central valve cap. This gauge will measure the pump pressure.Pressure gauge ‘B’ is to be installed at the pump outlet on the delivery hose. This gauge will measure the in-line pressure when gun is shut off. This pressure must not exceed
20% increase on operating pump pressure. Example: 2000psi pump pressure on gauge ‘A’ with gun open: when gun is shut off gauge ‘B’ must not exceed 2400psi.
Measure amps on power supply cable to make sure amps are running at acceptable levels when desired pump performance is obtained.
4. To obtain correct pressure at pre-determined rpm:
1. Remove grub screw in unloader lock ring;
2. Wind down unloader until required pressure is achieved. Check amp meter to ensure electrical characteristics are within acceptable parameters.
5. Release trigger on gun to shut off water flow and read gauge ‘B’ to determine the increase in line pressure (20% increase limit).
6. If test proves OK, repeat procedure for final check.
7. Unwind unloader by half a turn to ensure no pressure loss is indicated on gauge ‘A’ in pump.
8. Apply Loctite 243 Super Thread to grub screw in unloader lock ring and tighten with 1.5mm allen key.
9. Apply paint seal to grub screw head and thread below unloader lock ring.
15
PREVENTATIVE MAINTENANCE
)Prevent pump failure
)Avoid costly repairs
)Minimise downtime
Simple steps in preventative maintenance will allow you to get the best out of your machinery:
DAILY CHECK LIST
1.
4.
Check pump and gearbox oil level
2. Check engine oil level
3. Check nozzle wear
Check all high pressure components for leaks: a) gun/lance b) high pressure hose c) all fittings.
5.
6.
Check water filter and clean if necessary
Check unloader, safety valve and thermal dump for leaks.
THREE MONTHLY REGULAR SERVICE
All professional machines need to be thoroughly serviced every three months. The service involved should include the engine manufacturer’s recommendations, where applicable, (see separate Engine
Manual) and the following:
1. Change pump oil
2. Change gearbox oil
3.
4.
5.
Check filter for foreign debris
Check unloader, safety valve and thermal dump for leaks
Check all high pressure components for leaks: a) gun/lance b) high pressure hose c) all fittings
7. Check gearbox to engine key for wear. If the key is worn, see your local Aussie Eco-Clean service agent for instructions on rectification or contact Aussie Eco-Clean Service Department.
LOOK AFTER YOUR MACHINE AND IT WILL LOOK AFTER YOU!
AND REMEMBER . . .
Always wear protective clothing, including boots and goggles!
RELIABLE PRODUCTS . . . RELIABLE PEOPLE
AUSTRALIAN PUMP INDUSTRIES PTY LTD
ACN 061 619 234
7 Gladstone Rd, Castle Hill NSW 2154. PO Box 6164, BHBC NSW 2153
Ph 02 9894 4144 Fx 02 9894 4240 email: [email protected] www.aussiepumps.com.au
16 Aussie Pumps Bertolini Pumps Service Guidelines – July 2011
advertisement
* Your assessment is very important for improving the workof artificial intelligence, which forms the content of this project
Related manuals
advertisement