Carrier 30GB Air Conditioner User Manual
Add to My manuals12 Pages
Carrier 30GB is a high-capacity liquid chiller designed for large commercial applications. It delivers 150, 175, or 200 tons of liquid chilling capacity in a single enclosure, saving space and installation time. The unit features multiple-step capacity control for precise load handling, with 6, 7, or 8 steps of control depending on the model. It also has circuited condenser coils for maximum subcooling, increasing unit capacity by 1% for each 2 degrees of subcooling.
advertisement
▼
Scroll to page 2
of
12
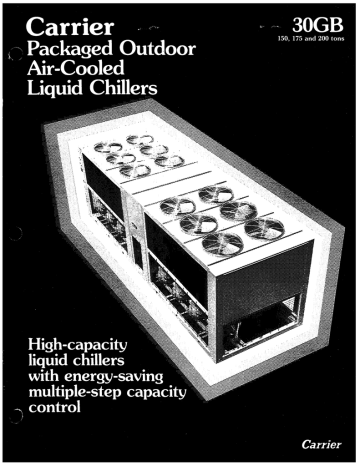
Carrier .- (176): .~ Packaged Outdoor | — Air-Cooled Liquid Chillers an | e de e, | > x Teal, vus A i A 1 pu EA o Lm) si Ea Be BC va Te я High-capacity liquid chillers with energy-saving * multiple-step capacity control a Carrier The 30GB chillers provide multiple unit capacity with single-package economy Carrier’s 30GB units deliver 150, 175 or 200 tons of liquid chilling capacity in a single enclosure. Compact size allows faster rigging, installation and setup on the ground or on the roof. Units arrive assembled and fully charged with R-22. A simple hookup to power supply and chilled water lines completes the installation. The 30GB line saves operating costs with precise multiple step capacity control. Either 6, 7 or 8 steps of control, depending on the unit, allows load handling to 12-1/2% of total capacity Condenser coils are circuited for maximum subcooling, increasing unit capacity 1% for each 2 degrees of subcooling with no increase in power input or need for larger, costlier compressors. Multiple condenser fans cycle AA tm te ry hy tt tte tata tt» automatically to maintain positive head pressure for low ambient operation down to 0°F without additional controls to purchase! The 30GB chillers perform reliably on the job, too. Com- pressors are mounted on spring-isolated rails to minimize vibration, eliminating the need for external isolation. All controls and factory wiring are protected within weather- resistant, galvanized steel enclosures. Fan guards are PVC- coated steel wire for weather resistance. Put Carrier's high capacity liquid chillers to work on your large commercial job. The cost-saving advantages of fast installation, controlled capacity operation, and low mainten- ance really add up to superior performance. TL TT TN Te Te The Carrier 30GB chillers offer more features for more cost-saving flexibility Cooler freeze-up protection Each unit is protected against cooler freeze-up by 2 methods. A low-water temperature safety thermostat stops the unit automatically if water tempera- ture drops below 36 F. By the second method, factory-installed heaters pro- tect the cooler from the effects of sub- freezing ambient temperatures. These heaters are located around the shell, be- tween the shell and a thick layer of closed-cell insulation; they are ener- gized whenever the chilled water flow stops. Compressor crankcase heaters Each compressor has an electric heater that operates only during periods of compressor shutdown to assure proper lubrication by minimizing refrigerant dilution of oil. Easy access to components All electrical components are acces- sible thru removable service panels. Cooler and compressor are protected by removable steel wire guards. Carrier also provides a handy convenience out- let (115v) for connecting lights and power tools. Standby protection Multiple compressor operation offers system reliability in case of a malfunc- tion or safety cutout. Dual, independent refrigerant circuits maintain partial unit capacity even if one circuit fails. This backup protection can help prevent costly damage in process cooling or industrial applications. Flow switch Chilled water flow switch shuts down the unit and energizes the cooler heaters in case chilled water flow stops. Units meet NEMA-MGI motor standards All compressor and fan motors meet National Electrical Manufacturer’s Association and U.S. government standards. CIRCUIT 1 14 High-pressure light Low-pressure light Discharge temperature light Oll-pressure light Valve, discharge pressure gage Discharge pressure gage Suction pressure gage Valve, suction pressure gage Control power light 3 CIRCUIT 2 980080 0000 Control power ON-OFF switch Control circuit fuse Reset button (control circuit) Reset button (low water temperature cutout) Convenience outlet (115 volts) Temperature controller Lead/lag transfer switch Demand limit light CENTER OF GRAVITY = О; RENOVABLE ACCESS Pa PANELS CIRCUIT | CIRCUIT 2 FIELD POWER SUPPLY (2 OR 3) 3" FPT STR PIPE COUPLING STEEL WIRE 2] Z FIELD SUPPLY, CONTROL С _ 98 o o SI де A © 190, 7. “RENOVABLE. ACCESS PANEL - В {EAC “END? | mes ; Teste mo Physical data (60-Hz) nn UNIT 3068. o : - 150. i и 475 on {0 2990 20 —— APPROX OPER WT (Ib) MO _ 1 14,600 asi LL _ REFRIGERANT CHARGE, R- 22 (Ib) BN 230/ckt о В 230/ ск: do 230/ckt — “ COMPRESSORS (Type. .Rpm) | Reciprocating, Semi- Hermetic 1750 обе No.) Circuit 1 | (3) 6275 | . (4) F275 (4) F275 | (No. ) Circuit 2 (3) F275 (3) F275 (4) F275 a Cap. ( Control Steps | N о 6 or у a a g 7 Circuit 1_ © BO Ш 57 RE 50 I о ее. cote es or - mans is + эн eee res sms ces et PR - pue = - ru 8 4m ww man MONO DEMAND O LAMSON — CoP Circuit 2° 07 50 A so Minimum Step Capacity (%) 167 | 43 11 = 125 CONDENSER FANS 3-Blade Propeller, Direct Drive No. . .Diameter (in ) 12 30 Rpm. .Total Kw 1140 .186 Total Airflow (cfm) } 17,600 ns "CONDENSER COILS 135 Fins/in 1/2-in OD Copper Tube Condenser | Lead | Lag Lead { Lag Ш Lead I lag No. Rows -C*t1 A A AA a Aa Face Area _Ckt 1 605 | 85 605 605 | 605 |... 605 (safe) = Ckt2 605 | 605 805 1 605 | 605 | 605 COOLER, 10HA400504 | One Direct Expansion Shell and Tube No. Refrigerant Circuits 2 Net Water Volume (gal ) 60 2 (Includes nozzles) Maximum Working Pressure (psig) _ Refrigerant Side 235, Water Side: 150 — WATER CONNECTIONS (in) Ш Ва О Inlet and Outlet 6 150-1b ASA Flat Face Flange Drain | (3/4 F 30GB150-200 TOP VIEW — FAN AND COMPRESSOR LOCATIONS; FAN OPERATION COOLER SIDE MAIN AUXILLIARY CONTROL CONTROL BOX END BOX END COMPRESSOR SIDE CIRCUIT | CIRCUIT 2 175 30GB 1200 —e | 3 5 7 8 6 4 2 le—— 306B200 3068150 — — — > | 3 5 6 4 2 *— 43068150 30GBI7 5 ~~ РАМСОМТАСТОВ №. "| CONTROLS FAN NO. CONTROLLED BY: © FC1 о 1 ALWAYS RUNS WITH COMPR NO 1 CIRCUIT FC3 | 3 0 TEMPERATURE & CHR5 (Ambient over 70 F) 1 FC5 | TA PRESSURE. Closes 260, opens 160 psig FC7 | 589 TEMPERATURE: Closes at 70 F A Оо ALWAYS RUNS WITH COMPR NO 2 { CIRCUIT FC4 4 TEMPERATURE & CHR6 (Ambient over 70 F) “а 2 FC6 DE PRESSURE: Closes at 260 psig, opens 160 psig FC8 | 5810 TEMPERATURE: Closes at 70 F S election procedure II Select unit to provide cooling load capacity. (with example) Enter Performance Ratings table at 95 F CEAT and 45 F LCWT. Under Cap., 196.7 tons is nearest to and greater than the given cooling load (190 tons). Read unit selection e I Determine job requirements. and performance data directly from table: Given: 0 A 30GB200 Cooling Load .............eeeneococorer. 190 Tons Capacity (Cap.).........ee.r.eeeeoovooo 196.7 Tons Leaving Chilled Water Temperature (LCWT)....45F Saturated Discharge Temp (SDT) ........... 1309 F Chilled Water System A T..........e.e.ereonoo 10 F Compressor Power Input (Kw). ........... 246.3 Kw Cooler Fouling Factor ........ _.e.eoeeecreoro 0.0005 Cooler Flow Rate (Gpm) ................. 471.0 gpm Condenser Entering Air Temperature (CEAT) ...95 F Cooler Pressure Drop (PD). ............ 12.5 ft water Performance data Ratings Cap. — Capacity The following ratings tables are based on 10 F chilled water rise, 0.0005 fouling factor in cooler, and Kw — Comer input Motor Refrigerant 22. Ratings in boldface type are in accordance with ARI Standard 590-76. Thecondi- LcwTt — Leaving Chilled tions are 95F Condenser Entering Air Temperature (dry-bulb), 44 F Leaving Chilled Water Water Temp Temperature. PD — Pressure Drop (ft water) PERFORMANCE RATINGS (10F Chilled Water Rise) SDT — Sat Disch Temp ul CONDENSER ENTERING AIR TEMPERA © Ds 95 os | Cooler inmi Cooler Ser Compr Flow Data ¿<< Ser Compr | Flow Data (F) "| брт | РБ 8 (F) | “МО | брт | РО 11147 | 1647 | 3657 76 1234 | 1735 13397 | 66 11174 | 1935 | 4144 | 97 1259 | 203.2 13857 | 85 11192, 2208 | 456 9 | 117 1276 | 2312 4251 1102 1159 | 168.7 3812 83% 11245 1778 13546 | 72 1187 | 1984 | 4321 | 105 ! 1271 | 2083 14022 92 120.5 | 226.3 | 475.7 12.7 £ 128.9 | 237.2 | 4432 111.1. 1171 1726 3971 89€ 125.7 182.2 3698 78 1199 | 2033 ; 4500 114 % 128.4 | 213.6 419.8 | 9.9 121.8 | 2319 | 494.9] 137 | 130.2 | 243.3 4616 12.0 1177 | 1746 4051 93 1262 | 184.4 | 3775 . 81 1206 | 2067 4590/118! 1290 | 2162 | 427 9 |103 1225 2347 5045 | 142 | 1309 | 2463 4710 1125 1183 | 1767 | 4133] 97% 1268 | 186.6 3854 | 84 1212 | 2082 | 467 9 | 123 1297 2189 4367 108 123.2 | 2376 | 5142 148 | 131.5 2493 | 4803 129 1195 | 1808 | 4298 104 1280 | 1910 4010 91 122 6 | 2133 | 486 7 | 133 | 1310 | 2244 | 4546 |116 124 6 | 2434 | 5341 | 159 € 132 9 | 255 6 | 4995 | 13.9 — CONDENSER ENTERING AIR TEMPERA о Cooler Cooler Сар. | SDT Compr Flow Data : SA Compr Flow Data (Fons) | (1 1 6 1 Gpm | PDS | “| брт | PD 1314 11321 1815 | 3142 57% 1407 1884 | 2885 | 48 1 1491 [1344 | 2118 | 3564 | 73€ 1430 | 2195 | 3280 | 62 1 164.7 [136.1 | 2406 | 393.7 | 88 © | 1445 | 2488 | 3623 | 75 1372 .1332| 1861 | 3282| 62 141.8 | 1935 3021 5.3 1 155.7 |135 6 | 2174 : 3724) 79 1441 | 2256 3433 67 171.9 | 137.3 2470 411.1} 9.6 ; 1457 | 2557 | 3789 | 82 1143.2 1343 1908 | 3428 6.7 11429 1987 13160 | 57 11624 1368 2230 | 3887 | 8.6 1453 | 2317 3589 | 74 ! 179.3 | 138.6 | 2537 | 429 1 | 104 1470 | 2627 {3960 | 89 _ 146.2 134.8 1932 | 3501! 70 14347 2012 13228 60 1658 1374 2259 3970 8.9 1459 | 2348 ! 3668 | 77 183.0 | 139.3 | 256.9 | 438.1 | 108 ii 1476 | 266.2 | 4046 | 93 _ 1493 | 1354 | 1956 | 35676] 73 ¢ 1440 | 2038 | 3299 | 62 169.3 | 13811 2289 | 4056] 93 Ё 146.5 | 2378 | 374.7 | 80 186 7 1399 2603 | 447.2] 113 § 1482 | 269.8 | 4133 | 97 1556 ; 1366 ; 2005 3728. 79 Ë 145.1: 209.1. 3444: 68 176.4 1394 234.7 4227, 101 147.8 | 244.1 ! 3910 | 87 194 3 | 141 2 | 2670 | 465 7 | 12 2 1495 | 2769 | 4309 | 10,5 PRESSURE DROP (FT OF WATER) 0 OOOO OO MMONLCO MDL HE TONAL 00 DF TE UAM JUDO TOTAL COOLER PRESSURE DROP 10HA400504 Cooler 100 80 AA = - = .. = <. = Киа . = a - qe m0 Fée вс EZ AT 30 25 e = x = 20 100 UNIT et ng aos -|COMERESSORS!. _ _ FANMOTORS; __|CONTROLS о Моне т | Do Оф 1 o © we ан жет | о г уре * * na РАДИО. | a RLA LRA {MTA : Total FLA | MTA Hp 30G8 : Model Name- | Supplied” | o MCA ¡MFA ICF | = (ea) | (CB) Kw PA (ea) | (FCB) | (NEC) Kw 4 1 plate | Min {Max | Start 5 _ | | 5001 208-2301 187 1253 | XL 767 1000 1136 iis 110 | 506 | 154 7 186 | 3 66 | 74 194 027 “150. ; 600 © 460 414 |508 XL 362 450 ; 550 253 | 73 [186 . 3 4 | 28 175 027 4100 575 | 518 _| 632 | XL 1 310 400 . 430 J 4 1176 | 63 18.6 | 3 22 1175 027 15.500 1208-230 | 187 253 | XL | 877 |1000 |1246 | 10 506 |154 ¡186 | 3 5 6” 74 ¡194 | 027 175.1 690 | 460 ; 414 508 | XL 414 500 | 602 32 253 73 {186 | 3 + 30 28 | 1.75 | 027 Li. 190: 575 1518 632 | XL | 355 | 400 | 475 | 4 0 1176 | 63 186 3 |24 | 22 |. 0.27 1 500 | 208-230 187 1253 | XL | 987 | 1200 11356 E 506 :154 186 | 3 | 66 | 74 | 194 | 027 “200 ; 600 | 460 | 414 508 XL | 466 | 600 A 52 |253 | 73 186 3 30 28 175 | 0.27 4.300 | 575 | 518 632 | XL | 400 450 | 520 45 176 | 63 186 13 | 24 | 22 175 | 027 CB — Circuit Breaker MTA — Must Trip Amps (Circuit Breaker) FCB — Fan Circuit Breaker NEC — National Electrical Code FLA — Full Load Amps (Fan Motors) Ph — Phase Hp — Horsepower RLA — Rated Load Amps (Compressors) ICF — Maximum Instantaneous Current Flow during starting (the XL — Across-the-Line point in the starting sequence where the sum of the LRA for the starting compressor, plus the total RLA for all running compressors, plus the total FLA for all running fan motors *Units are suitable for use on electrical systems where voltage \ is maximum) supplied to the unit terminals is not below or above the listed + Kw — Total condenser fan motor power input minimum and maximum limits LRA — Locked Rotor Amps T30GB150 has 6 compressors; 30GB175 has 7 compressors; MCA — Minimum Circuit Amps (for wire sizing) Complies with NEC 30GB200 has 8 compressors Section 430-24 tEach unit has 12 fans MFA — Maximum Fuse Amps (Maximum overcurrent protective **Each unit has 2 fan circuit breakers; 6 fans are protected by each device amps) 200 250 300 400 500 600. COOLER WATER FLOW (GPM) Electrical data (60-Hz) HATE NORRATH Зимние COE EHH rT Ha erat ос MORON Ii кони 1000 900 HL GUNS OOOO Ce Ha HEMER DOOR Bl FCB Electrical data (60-Hz) (cont) General electrical notes 1. The 115-1-60 control circuit power must be supplied from a separate source, thru a field-supplied 30-amp fused disconnect. 2. Crankcase and cooler heaters are wired into the control circuit so they are always operable as long as the control circuit power supply disconnect is on, even if any safety device is open or the unit ON-OFF switch is off. 3. Heaters are wired ahead of the control circuit fuse; thus, they are protected by the 30-amp overcurrent protective device in the control circuit power supply. Start-up sequence The control power switch is off and all crankcase heaters and cooler heaters are energized. The chilled water pump (CWP) must be turned on before the control circuit can be energized. When the chilled water begins circulating, the flow switch (CWFS) closes. The cooler heater cable (CHC) is de- energized and the flow relay is energized. When the control circuit switch is turned on, the 115-volt control circuit and parts of the 24-volt circuit are energized. The SC cycles back to the completely unloaded position and unit start-up can proceed. 4 All units have single-point power connection to simplify field-power wiring. 5. The 208-230/3/60 units have 3 terminal blocks and require 9 parallel conductors from the disconnect 6 The 460 and 575/3/60 units have 2 terminal blocks and require 6 parallel conductors from the disconnect. 7 Maximum incoming wire size for each terminal block is 500 MCM. 8 The 208-230-volt 30GB200 units must have copper main power conductors to meet NEC requirements. Circuit no. 1 (start-up of lead compressor) — With the temperature controller (TC) calling for cooling, SW1 in the SC makes and no. 1 condenser fan starts. If the ambient is over 70 F, fans no. 5 and 9 start; fans no. 7 and 11 start after compressor no. 1 starts and the discharge pressure exceeds 260 psig. Relay no. 1 (R1) and the rest of the 24-volt circuit are energized. The start-up function continues as follows (refer to LEGEND for identification of components): LEGEND CH — Crankcase Heater DTR — Discharge Temperature Relay OPR Oil-Pressure Relay CHC — Cooler Heater Cable FLR — Flow Relay OPS Oil-Pressure Switch CHR — Crankcase Heater Relay HPR — High-Pressure Relay R Relay - CLO — Compressor Lockout HPS — High-Pressure Switch sc Step Controller CR — Control Relay LLS — Liquid Line Solenoid Valve SW Switch CWFS — Chilled Water Flow Switch LOR — Lock-Out Relay TC Temperature Controller CWP — Chilled Water Pump LPR — Low-Pressure Relay TD Time Delay DGT — Discharge Gas Thermostat LPS — Low-Pressure Switch ® ery COMPRESSOR ee Cr SHUTS NOT a = ЗУМОМ ‘OFF. RI TE = ; ; ия est & OPS? Les Is - CLOSED. (e Circuit no. 2 (start-up of lead compressor) Circuit no. 2 shuts down 4 As the TC continues to call for cooling, SW2 in the SC As cooling load continues to decrease: makes. As in circuit no. 1, circuit no. 2 is energized and compressor no 2 starts thru a sequence of electrical functions which are a duplication of circuit no. 1. Also, : 14 : condenser fans no 2, 6, 10, 8 and 12 start | SCBREAKS With the lead compressor in each circuit running, and the TC still calling for cooling, the start-up continues: COMPRESSOR. | al Va Ma En at. NO. 3 STARTS. e TT a a Ta Tae a aa AT aa Tata a a a Dn us opens a uo Ш When compressor no. 5 starts, condenser fan no. 3 EET OR = UA ; starts, if ambient is over 70F; when compressor no. 6 starts, condenser fan no 4 starts, if ambient is over 70F. 1 The unit is now running at full load with all compressoss FT TT TT me and fans operating. compressor NO. 2 STOPS НЕ Operation as load is decreased As the demand for cooling decreases, the unit shuts down Circuit no. 1 shuts down thru the following steps: Cooling load continues to decrease: be MEN LG COMPRESSOR | Sn | ENERGIZED. |) SC BREAKS: [7H “NO. © STOPS- 5 Le | MON COMPRESSOR ENERGIZED BEET ome “scsreacs TP} No.7 STOPS y The unit is now cycled off, ready to restart under TC В ВЕ control when additional cooling is needed. © CONTINUES UNTIL 5 COMPRESSOR NO. 3 STOPS © a When compressor no. 6 stops, condenser fan no. 4 stops and when compressor no. 5 stops, condenser fan no 3 stops. Application data Unit performance with external static on condenser fans Every effort should be made to install unit where the condenser airflow above the unit is unrestricted. If this is not possible, unit performance is affected and data must be corrected as follows: EXTERNAL STATIC CORRECTION FACTORS EXTERNAL | % СЕМ CAPACITY | — KW ‘ DECREASE | MULTIPLIER | MULTIPLIER (in. wg) | | 0.10 85 0 986 1014 T7020 |! 175 0 968 | 1.031 Cooler fouling factor correction FOULING CAPACITY KW FACTOR MULTIPLIER MULTIPLIER _... 00005 | ___ 100 110 10 9.001 „097 _ 09% __—__ 0.002 091 0 94 Corrected Cap. = Rated Cap. x Cap. Corr Factor Corrected Kw = Rated Kw x Kw Corr Factor _ Corrected Cap. (tons) x 24 À T (F) Corrected Gpm Low-ambient operation — The minimum ambient tem- perature at which the unit will start and build up head pressure on the first and second steps of capacity 15 20 Е. After operation is established, the minimum operating tem- perature is approximately 0°F. Field-installed chilled water piping may be protected at lower ambients by wrapping with field-supplied heating cable and covered with 2-in. thick closed cell insulation. It is strongly recommended that ethylene glycol be used in installations where sub-freezing temperatures are expected. Unit performance data must be corrected as shown in the following example: I Determine concentration of ethylene glycol re- quired to protect system to -10F (at zero flow). Given: Unit .......e.ecreoaarororarocacrorecrao 30GB200 Condenser Entering Air Temperature (CEAT) ..95 F Leaving Chilled Water Temperature (LCWT) ...45 F Chilled Water System A T.........e.eeeeese.. 10 Е Capacity ..........eseorcorerererere.. 196.7 Tons Chilled Water Flow Rate ................ 471.0 gpm Cooler Pressure Огор ................ 12.5 ft water Compressor Power Input............_.... 246.3 Kw From curve, read 40% concentration is required for solution crystallization at -10F. II Correct unit capacity. From curve, read 0.983 capacity correction at 40% concentration. Corrected Capacity 0.983 x Given Capacity 0.983 x 196 7 Tons 193.4 Tons il 10 II Correct chilled water flow rate. From curve, read 1.097 gpm correction at 40% concentration. Chilled Water Flow _ Tons x 24 _ 193.4 x 24 (at corrected Cap.) AT a 10 = 464.2 gpm Ethylene Glycol Flow = water flow x 1.097 (40% solution) = 464.2 x 1.097 = 509.2 gpm IV Correct cooler pressure drop. From curve, read 1.185 cooler pressure drop correction at 40% concentration. From cooler pressure drop curve, for 509.2 gpm of water, pressure drop = 14.7 ft water. PD for 40% ethylene glycol solution = 1.185 x 14.7 = 17.4 ft water. V Reduction in compressor power input (Kw) is insignificant. ETHYLENE GLYCOL PERFORMANCE CORRECTION FACTORS AND SOLUTION CRYSTALLIZATION POINTS 1.20 1.15 i 10 CORRECTION FACTOR 100 mena -40 Na = am alae Te ee FE a’ “a ... = -; - 095 E ow ERT ее . —20 TEMPERATURE (F) +20 % CONCENTRATION (BY WEIGHT) ETHYLENE GLYCOL A A EA CA D tr We WI pe a Rh my Am A yn ee pe af PR PES Cate rere re eT nT Te ret a a ARAL Ad ES Crema à мне Fx". - vw ee wn rn mom AE sm ne. Te Guide specifications Furnish and install factory-assembled, one-piece Carrier 30GB packaged air-cooled liquid chiller(s). Unit(s) shall be completely factory charged with Refrigerant 22. All factory wiring and piping shall be contained within the unit enclosure. All electrical components shall be mounted in a rain-tight enclosure. The exterior sheet metal shall be galvanized steel, zinc phosphatized, with an electro- statically applied, high solids polyester, baked enamel finish. Capacity of unit(s) shall be not less than tons, cooling gpm of water from F to F, air entering the condenser at F. Cooling fouling factor shall be . Unit power input shall not exceed kw. Unit electrical power shall be volts, 3-phase, 60-Hz. Unit shall be capable of operating within line voltage limits of to volts. Control power shall be provided by a separate 115-volt, single-phase, 60-Hz source. Construction and ratings shall be in accordance with ARI Standard 590-76 and shall comply with ANSI B9.1 Safety Code, National Electrical Code (NEC) and ASME Code. Each compressor shall be reciprocating, serviceable hermetic type and shall have an automatically reversible oil pump, complete with operating oil charge Compressors shall be equipped with suction and discharge shut-off valves and shall be mounted on spring-isolated rails. Motors shall be cooled by suction gas passing around the windings and shall have overtemperature protection Manual restart of unit shall be required after motor stoppage due to thermal overload. Each compressor shall be equipped with an insert-type crankcase heater to minimize oil dilution during shutdown periods Each compressor motor shall be operated and protected against overload by means of definite-purpose contactors and calibrated, ambient-compensated, magnetic-trip circuit breakers. The circuit breakers shall open all (3) phases in the event of overload in any one phase and shall be manual reset. Cooler shall be covered by 2 layers of 3/4-in. closed cell, vapor barrier, expanded polyvinyl chloride (PVC) insula- tion, with a maximum “K” factor of 0.28. Heaters along the shell, under the insulation, shall protect the cooler against freeze-up. 11 Refrigerant circuit components shall include hot-gas muffler; highside pressure relief device; liquid line shut-off valve; replaceable-core filter-drier; moisture-indicating sight glass; liquid line solenoid valve; maximum operating pres- sure limiting thermal expansion valve. Air-cooled condensers shall be circuited to provide sub- cooling. Condensers shall be constructed of 1/2-in. OD seamless copper tubes with mechanically-bonded alumi- num fins, leak tested at 150 psig and pressure tested at 450 psig. Condenser fans and motors — The condenser section of each unit shall have direct-drive, propeller type fans, with steel wire safety guards. Fan motors shall be 3-phase, permanently lubricated and inherently protected with corrosion-resistant fan shaft. Head pressure control — Each unit shall be equipped with a head pressure control system. Condenser fans shall be cycled by a combination of discharge pressure and ambient temperature to permit unit operation to 0°F out- door ambient at full load. Each unit shall contain an electrically operated multiple- step capacity controller with a minimum of 6 steps of capacity reduction (30GB150); the 30GB175 unit shall have 7 steps and the 30GB200 shall have 8 steps. Unit capacity shall be controlled by starting and stopping compressors. The unit can be field modified for use of hot gas bypass. Controls shall be factory mounted and wired in a weather- proof enclosure. It shall include a low-pressure switch for each refrigerant circuit; an electronic ground current sensing refrigerant circuit protection device for each com- pressor; lead-lag switch; suction and discharge pressure gages, with shut-off valves; chilled water safety thermostat; field power and control circuit terminal blocks; compressor motor and fan motor circuit breakers; motor contactors; control relays; control circuit ON-OFF switch; energy management system interface for demand-limit control. A high-pressure switch shall be factory mounted on each compressor; on the lead compressor in each circuit an oil- pressure safety switch shall be factory mounted. A chilled water flow switch shall be factory mounted on the chilled water inlet nozzle. Number One Air Conditioning Maker © Division of à Carrier Corporation Carrier Parkway + Syracuse N'Y 13221 Manufacturer reserves the right to discontinue, or change at any time, specifications or designs without notice and without incurring obligations. Book |2 Form 30GB-1P New PrintedinUS A 8-81 PC 111 CatalogNo 523-030 Tab |5c
advertisement
Key Features
- High capacity
- Multiple-step capacity control
- Energy-saving
- Reliable operation
- Easy access to componets
- Cooler freeze-up protection
- Compressor crankcase heater
- Standby protection
- Flow switch
- NEMA-MGI motor standards
Related manuals
Frequently Answers and Questions
What is the capacity range of the Carrier 30GB chillers?
The Carrier 30GB chillers provide 150, 175, or 200 tons of liquid chilling capacity in a single enclosure.
How does the 30GB chiller save energy?
The 30GB chiller utilizes a precise multiple-step capacity control system to match the cooling load, reducing energy consumption.
What type of compressors are used in the 30GB chiller?
The 30GB chillers feature reciprocating, semi-hermetic compressors mounted on spring-isolated rails to minimize vibration.
What is the minimum operating temperature for the 30GB chiller?
The 30GB chiller can operate down to 0°F outdoor ambient temperature.
advertisement