- No category
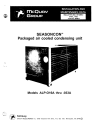
SEASONCON” Packaged air cooled condensing unit Models ALP-O16A thru -033A McQuay
Add to my manuals
24 Pages
advertisement
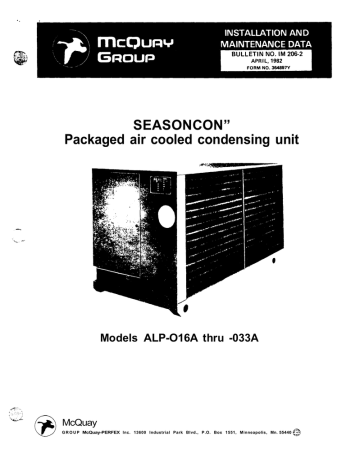
SEASONCON”
Packaged air cooled condensing unit
Models ALP-O16A thru -033A
McQuay
G R O U P McQuay-PERFEX Inc. 13600 Industrial Park Blvd., P.O. Box 1551, Minneapolis, Mn. 55440 @
.
INTRODUCTION
McQUAY type ALP SEASONCON air cooled condensing consists of an air cooled condenser with integral subcooler units are designed for outdoor installations and are section, an unloading compressor, complete discharge compatible with either air handling or chilled water piping and suction and liquid connections for connection to systems. Each unit is completely assembled and factory any air or water cooling evaporator.
wired before evacuation, charging and testing. Each unit
NOMENCLATURE
A L P - 0 3 3 A - S
Nomtnal Capacity (Tons)
INSPECTION
When the equipment is received, all items should be carefully checked against the bill of lading to insure a complete shipment. All units should be carefully inspected for damage upon arrival. All shipping damage should be reported to the carrier and a claim should be filed. The unit serial plate should be checked before unloading the unit to be sure that it agrees with the power supply available.
INSTALLATION
NOTE: Installation and maintenance are to be performed only by qualified personnel who are familiar with local codes and regulations, and experienced with this type of equipment. CAUTION: Sharp edges and coil surfaces are a potential injury hazard. Avoid contact with them.
FIGURE 1. SUGGESTED PUSHING ARRANGEMENT
H A N D L I N G
Care should be taken to avoid rough handling or shock due to dropping the unit. Do not push or pull the unit from anything other than the base, and block the pushing vehicle away from the unit to prevent damage to the sheet metal cabinet. (See Figure 1.)
To lift the unit, 2-1/2-inch diameter lifting holes are provided in the base of the unit. Spreader bars and cables should be arranged to prevent damage to the condenser coils or unit cabinet. (See Figure 2.)
LOCATION
Due to vertical condenser design, it is recommended that the unit is oriented so that prevailing winds blow parallel to the unit length, thus minimizing effects on condensing pressure. If it is not practical to orient the unit in this manner, a wind deflector should be constructed.
Units are designed for outdoor application and may be mounted on a roof or concrete slab (ground level installation). Roof-mounted units should be installed level on steel channels or an l-beam frame to support the unit above the roof. Use of vibration pads or isolators is recommended. The roof must be strong enough to support the weight of the unit. See Table 1 for unit weights.
Concrete slabs used for unit mounting should be installed level and be properly supported to prevent settling. A one-piece concrete slab with footings extended below the frost line is recommended.
TABLE 1. U N I T W E I G H T S
-?
ALP MODEL OPERATING WEIGHT (LBS.)
016A 1122
019A 1383
0 2 3 A 1471
0 2 7 A 1600
0 3 3 A 1866
GOOD PUSHING ARRANGEMENT -CABINET DAMAGE
UNLIKELY
FIGURE 2.
PAGE 3
ACCESS VIBRATION ISOLATORS
It is necessary to provide adequate clearance on all sides of the unit for service access and satisfactory performance.
Necessary clearances are shown in Figure 3.
FIGURE 3. CLEARANCE AROUND UNIT
“A-‘MIN.
CLEARANCE
FOR AIR INLET
Vibration isolators are recommended for all roof-mounted installations or wherever vibration transmission is a potential problem. Table 2 lists spring and rubber-in-shear isolators for all ALP unit sizes. Table 3 shows isolator loads and the maximum allowable load for each isolator. Figure 4 shows isolator locations in relation to the unit control panel. Figure 5 gives dimensions that are required to secure each McQUAY isolator selection to the mounting surface.
Each unit base frame is provided with the necessary holes to accept the 0.50-inch diameter positioning pin of each isolator.
-i%q Acc~~~~~N
pQ%z-
TABLE 2. ISOLATOR SELECTIONS
CLEARANCE
FOR DISCHARGE
CONTROL PANEL
A L P DIMENSIONS (IN FEET)
M O D E L A 0 C D
0 1 6 A 3 4 3 4
019A 3 4 3 4
0 2 3 A 3 5 3 4
0 2 7 A
3
5 3 4
0 3 3 A 3 6 3 4
’
ALP L O C A T I O N S 1,2.3 & 4
U N I T S P R I N G - F L E X RUBBER-IN-SHEAR
SIZE ORDERING NUMBER ORDERING NUMBER
016A
877-2164036-25 a77-216397Aal
019A
877-2164030-26
877-216397A-01
023A 877-2164030-26
877.216397AJJl
027A 877-2164030-26
877-216397Aal
033A 877-2164030-27 a77-216397A-03
FIGURE 4. ISOLATOR LOCATIONS
By removing the access screens, access can be gained to the compressor, refrigerant lines, refrigerant components, condenser fans and SPEEDTROL components. All other controls are located in the unit control panel. They are protected by a keylocked, weatherproof enclosure which contains an internal “dead front” door for protection of service personnel from high voltage starting controls while servicing low voltage operational controls.
FIGURE 5. ISOLATOR DIMENSIONS (IN.)
Spring-Flex Isolators
ADJUST MOUNTING SO UPPER
0.50 DIA. HOUSING CLEARS LOWER HOUSING
” AND NOT MORE
Rubber-In-Shear Isolators
,600
Dia.
Pin
2 Holes
L4.12--- 1
5.50 A
Mounting Molded in
Neoorene -\1’2.5”7
ACOUSTkAL NONSKlD
NEOPRENE PAD
TABLE 3. IS0 LATO R LOADS
A L P ISOLATOR LOADS AT MAXIMUM LOADS ALLOWABLE
U N I T EACH MOUNTING LOCATION FOR EACH ISOLATOR SELECTION
S I Z E LOCATION 1.2,3 & 4 SPRING-FLEX RUBBER-IN-SHEAR
0 1 6 A 281 450
525
019A 346 600
525
0 2 3 A 368 600
0 2 7 A 400 600
525
525
0 3 3 A 467 750
750
PAGE 4
REFRIGERANT PIPING
McQUAY type ALP SEASONCON condensing units are adaptable to either chilled water or air handling air conditioning applications using refrigerant 22. Refrigerant piping to and from the unit should be sized and installed according to the latest ASHRAE Guide. The following discussion is for use as a general guide to sound, economical and trouble-free piping. The correct application of the principles discussed here is the responsibility of the installer.
EVAPORATOR ABOVE CONDENSING UNIT
Figure 6 shows an installation where the evaporator is installed above the condensing unit. It is shown for an air handling installation, but all components shown are recommended for chilled water installations except that a refrigerant distributor is not usually required for shell-and-tube evaporators.
FIGURE 6. Evaporator Above Condensing Unit
-G-AIR F L O W
EVAPORATOR BELOW CONDENSING UNIT
Figure 7 shows an installation where the evaporator is installed below the condensing unit. It is shown for an air handling installation, but all components shown are recommended for chilled water installations except that a refrigerant distributor is not usually required for shell-and-tube evaporators. Note that a double suction riser is shown for this arrangement.
Risers
“A + B” are sized so that their combined cross-sectional internal area will allow full load unit operation without excessive pressure drop (see notes, Table
4). Riser “B” is sized to provide adequate suction gas velocity for proper oil return at minimum load conditions.
This riser becomes effective only when the trap shown in riser “A” fills itself with oil. It should be emphasized that the trap shown in riser “A” should be designed to contain a minimum internal volume to keep the total system oil requirements at a minimum. Table 4 gives recommended line sizes for both single and double suction lines and for liquid lines.
FIGURE 7. Evaporator Below Condensing Unit
LEGEND a
F i l t e r d r i e r b Solenoid valve c Sightglasslmoisture indicator d Thermal expansion valve e Suction line, pitched toward compressor f Liquid line g Vibration absorber
NOTES: All piping and piping components are by others.
TABLE 4.
ALP RECOMMENDED LINE SIZE
UNIT DOUBLE
SIZE
+y;.?l
SINGLE
SUCTION
LIQUID
016A-S
1 118-l l/8 1 518 718
019A-S 1 318-l 318 2 118 718
023A-S 1 518-l 318 2 118 1 l/8
027A-S 1 518-l 318 2 118 1 l/8
033A-S 1 518-l 518 2 118 1 118
Note: Liquid and suction lines based on a recommended pressure drop of 3 PSIG 12OF) per 100 ft. equrvalent length.
e-AIR F L O W
LEGEND a F i l t e r d r i e r b Solenoid valve c Sightglass/moisture indicator d Thermal expansion valve e Suction line, pitched toward compressor f Liquid line g Vibration absorber
A+8 - Double suction riser (see note 2)
NOTES:
1. All piping and piping components are by others.
2. Trap for double suction riser should be as small in the horizontal direction as fittings will allow.
REFRIGERANT PIPING CONNECTIONS
Refrigerant piping connections should be made through the holes provided in the base frame on access screen side of the unit.
PAGE 5
LIQUID LINE COMPONENTS
McQUAY
has available a “Liquid Line Accessory Kit” for each ALP unit size. Table 5 shows the ordering number to be used for each ALP unit size. The components included in these kits are:
1.
4:
5.
Replaceable core type filter-drier.
Filter-drier core element.
Refrigerant solenoid valve.
Refrigerant sightglass/moisture indicator.
Expansion valve.
TABLE 5. LIQUID LINE ACCESSORY KITS
,
ALP LIQUID LINE CONNECTION SIZES O.D. (IN.1
U N I T ACCESSORY KIT FILTER- S O L E N O I D SIGHT- EXPANSION VALVE
SIZE ORDERING NUMBER D R I E R V A L V E G L A S S I N O U T
016A-S 886-368903641
019A-S 8 8 6 3 6 6 9 0 3 6 4 1
718
718
718
7/a
7ta
7/a
718
7/a
I
318 i
3/a
023A-S
027A-S
033A-S
8863689039-01
886-368903841 aa6-36890384x2
718
7/a
7ta
718
7/a
718
718
7/a
718
718
718
718
I
3/a i
318 i
3/a
FIGURE 8. DIMENSIONAL DRAWING
REFRIGERANT CHARGE ADDING REFRIGERANT CHARGE
Each ALP condensing unit is designed for operation using refrigerant 22. Table 6 lists refrigerant charge required for a condensing unit/cooler combination.
TABLE 6. APPROXIMATE REFRIGERANT CHARGE
O n s y s t e m s t h a t h a v e b e e n previously c h a r g e d w i t h refrigerant, an insufficient charge is indicated by bubbling in the sightglass. On uncharged systems, the system should be leak tested and evacuated before charging. Upon charging a system, the discharge and suction shut-off valves on the compressor should be open and there should be normal water flow through the cooler.
ALP ‘R-22 REFRIGERANT
M O D E L CHARGE (LBS.)
016A-S 17
019A-S 23
023A-S 32
0 2 7 A S 37
033A-S 53 l
Refrigerant
charge is for a close-coupled system. A remote cooler will require an additional charge.
CAUTION: Do not make any safety controls inoperative during the charging operation: cooler damage from freezing may result.
1. Back seat the liquid line shut-off valve and connect the charging hose to the 1/4-inch flare connectron.
2. Install pressure gauges and review start-up instructions.
3. Purge the charging hose and open the charging cylinder to allow refrigerant into the system.
PAGE 6
‘4.
Turn the liquid line shut-off valve in three turns to permit a back flow of refrigerant into the subcooler.
5.
After refrigerant stops flowing into the system, close the liquid line shut-off valve. Start the compressor to charge the system.
6.
If the amount of refrigerant has been predetermined, add this amount and check the sightglass afterward.
If the amount of charge is unknown, close the charging cylinder valve every five minutes, open the liquid line shut-off valve and check for proper charge by examining the sightglass. Continue charging and checking the sightglass until it is clear.
NOTE: Fluorocarbon refrigerants should not be released to the atmosphere. For a means of recovery, refer to the following section.
R E M O V I N G R E F R I G E R A N T C H A R G E
To prevent freeze-up when removing the refrigerant for
ALP installations on water chiller systems, either drain the water or circulate the water. If water cannot be drained, make sure the cooler heater is energized. Do not remove refrigerant rapidly since this can cause freeze-ups. Have a sufficient number of refrigerant containers and a scale for weighing them. The containers should be clean, dry and empty.
To transfer the refrigerant to a container, connect the gauge manifold from the compressor discharge valve service port to the container and purge the iines. Note the capacity of the container. Place the container in ice to cool the c o n t a i n e r s o t h e f u s i b l e p l u g d o e s n o t m e l t a s t h e refrigerant condenses. Operate the compressor normally.
Turn the discharge service valve in three turns to open the gauge manifold. Do not close off the discharge valve to the condenser. Discharge gas can enter the container and condense. Frequently weigh the container so as not to overfill. When the container is filled use additional ones.
FIELD WIRING
WARNING: USE ONLY COPPER CONDUCTORS IN MAIN TERMINAL BLOCK.
Wiring should be done in accordance with all applicable transformer is ordered, the control circuit is powered off codes and ordinances. Warranty is voided if wiring is not in the main power supply.
accordance with specifications. An open fuse indicates a Figure 9 shows typical field wiring that is required for short, ground or overload. Before replacing a fuse or unit installation. Items that require field wiring are liquid restarting a compressor or fan motor, the trouble must be line solenoid SV1, optional hot gas bypass solenoid SV5 found and corrected. and the cooling thermostat, as well as the unit power
All standard units require a 115 volt power supply for supplies.
t h e c o n t r o l c i r c u i t . I f t h e o p t i o n a l c o n t r o l c i r c u i t
FIGURE 9. TYPICAL FIELD WIRING
PB1
““ll Ml,”
,
THERMOSTAT WIRING
Since it is impossible for McQUAY to anticipate the type of to which a thermostat may be connected. These terminals installation that an ALP condensing unit may be used on, are shown and labeled “Terminals For Thermostat” on the we do not factory install a thermostat. We do, however, electrical schematics. Figure 9 shows typical field wiring for provide numbered terminals inside the unit control center a thermostat with temperature controlled unloading.
PAGE 7
FLOW SWITCH FOR CHILLED WATER APPLICATIONS
A water flow switch or pump starter interlock is required on chilled water applications to insure that there will be adequate water flow and cooling load to the evaporator switch and adaptable to any pipe size from l-inch to 6-inch nominal. Certain minimum flow rates are required to close the switch and are listed in Table 9. Installation should be before the unit can start.
This will safeguard against as shown in Figure 10.
slugging the compressors on start-up. It also serves to shut down the unit in the event that water flow is interrupted to
FIGURE 10.
guard against evaporator freeze-up.
A flow switch is available from McQUAY u n d e r ordering number 860-175033X-00. It is a “paddle” type
,/ -
FLOW DIRECTION
HARKED ON SWITCH
TABLE 9. FLOW SWITCH MINIMUM FLOW RATES
SWITCH UPRIGHT
IN A HORIZONTAL
RUN OF PIPE rJ
/
NO RESTRICTIONS NO RESTRICTIONS
5 PIPE DIAMETERS MIN. 5 PIPE DIAMETERS MIN
AFTER SWITCH BEFORE SWITCH
Electrical connections in the unit control center should be made at terminals 12 and 21. The normally open contacts of the flow switch should be wired between these two terminals. There is also a set of normally closed contacts on the switch that could be used for an indicator light or an alarm to indicate when a “no flow” condition exists.
EVAPORATOR FAN INTERLOCK FOR AIR HANDLER COIL INSTALLATIONS
It is important to interlock the air handler evaporator fan start to prevent compressor slugging. A pair of terminals is with the condensing unit control center to insure that there available in the unit control center for this purpose. These will be a cooling load on the evaporator before the unit can terminal numbers are shown in Figure 9.
ELECTRICAL
CONTROL CENTER FIGURE 11.
All electrical controls are enclosed in a weatherproof control center with a keylocked, hinged access door (see
Figure 11). The control center is composed of two sections.
The left section is the largest and contains all of the 208,
230, 380 or 460 volt compressor and fan motor starting controls. Also included in this section, but partitioned separately, are the exposed terminal type, 115 volt operational controls. A “dead front” cover over the left section protects service personnel from high voltage starting controls and exposed terminal operational controls.
The right section, not covered by the “dead front” panel, contains 115 volt adjustable or resettable controls.
Power supply conduits are intended to come into the bottom of the control center. Figure 1 1 s h o w s a recommendation for unit mounting arrangements if the disconnect is to be unit mounted.
CONTROL CENTER’
IT DISCONNECT
SkUENCE OF OPERATION
The following sequence of operation is for an ALP
SEASONCON air cooled condensing unit. With control circuit power on, control stop switch S1 closed and manual pumpdown switch PS1 closed (“auto” position), 115 volt power is applied through control circuit fuse F1 to the compressor crankcase heater HTR1 and also to the contacts of low pressure switch LPI.
When the remote time clock, ambient thermostat, manual shutdown switch and/or evaporator fan interlocks energize the thermostatic circuit and, provided that high pressure control HP1, oil pressure control OP1 (not on
ALP-016A) and compressor motor protector MP1 do not sense an alarm condition, safety relay R5 is energized closed, applying power to temperature control thermostat.
At this point the unit will operate automatically in response to the thermostat.
For ALP416 - On a call for cooling, temperature control thermostat TC1 energizes liquid line solenoid valve
SV1, opening the valve and allowing refrigerant to flow into the evaporator. As refrigerant pressure builds up, low pressure control LP1 closes, energizing low pressure relay
R9 which closes to energize time delay TD14. The closing of TD14 energizes fan motor relay Ml 1, closing its contacts and providing power to condenser fan motor contactors
M l l ,
Ml 2 and M13. At reduced load conditions, thermostat TC1, stage 2, is closed, relay R21 is energized and normally open contact R21 is closed. Relay Ml is energized and normally closed Ml AUX. contacts are open.
Compressor contactor Ml is closed and the compressor is running at slow speed.
At full load conditions, thermostat TC1, stage 2, is open, relay R21 is de-energized and normally closed contact R21 is closed. On 208 volt and 230 volt units, relay
M9 is energized and normally open contacts M9 are closed.
Compressor contactors M9 (on 208 volt and 230 volt only)
and M5 are closed and the compressor is running at fast speed.
F o r ALP-019, 023, 027 and 033 - On a call for cooling, temperature control thermostat TC1 energizes liquid line solenoid valve SV1, opening the valve and allowing refrigerant to flow into the evaporator. A s refrigerant pressure builds up, low pressure control LP1 closes, energizing low pressure relay R9 which closes to energize compressor contactor Ml, starting the compressor.
Closing relay R9 contacts also energizes condenser fan relay
Ml 1, closing its contacts and providing power to condenser fan motor contactors Ml 1, Ml2 and M13. At reduced load conditions, thermostat TC1, stage 2, is closed, unloader U1 is energized and the compressor is unloaded. At full load conditions, thermostat TC1, stage 2, is open, unloader U1 is de-energized and the compressor is loaded.
I
PUMPDOWN CYCLE
As the temperature control thermostat is satisfied, it opens its contacts, de-energizing liquid line solenoid valve SV1, causing the valve to close. When the compressor has pumped most of the refrigerant from the evaporator to the condenser, the low pressure control LP1 opens, shutting down the compressor and condenser fan motors.
Should a closed solenoid valve allow refrigerant to leak to the low side of the refrigerant circuit during unit “off” time, the buildup in pressure will cause the low pressure control to close, energizing the low pressure relay and starting the compressor for pumpdown.
MAJOR COMPONENT LOCATIONS
TABLE 10.
MODEL
NOTE: Condenser
REAR VIEW OF UNIT
COIL ON
OPPOSITE SIDE
Fan
11 is
location of optional
SPEEDTROL motor.
COh4PRESSOR
PAGE
11
START-UP & SHUT-DOWN
PRE START-UP
1.
2.
With electrical disconnects open, check all screw or lug type electrical connections to be sure they are tight for good electrical contact. Check all compressor valve connections for tightness to avoid refrigerant loss at startup. Although all factory connections are tight before shipment, some loosening may have resulted from shipping vibration.
A. On chilled water installations, check to see that all water piping is properly connected.
off the chilled water pump or evaporator fan.
NOTE: With the unit left in this condition, it is capable of recycling pumpdown operation. To defeat this mode of operation, move the control stop switch S1 to the “off” position.
It is especially important on chilled water installations that the compressors pump down before the water flow to the evaporator is interrupted to avoid freeze-up.
START-UP AFTER TEMPORARY SHUT-DOWN
B. Open all water flow valves and start the chilled water pump. Check all piping for leaks and vent the air from the evaporator and system piping. Flush the evaporator and system piping to obtain clean, non-corrosive water in the evaporator circuit.
Start the chilled water pump or evaporator fan.
With control stop switch S1 in the “on” position, move pumpdown switch PS1 to the “auto. pumpdown” position.
3.
Check the compressor oil level. Prior to start-up, the oil level should cover at least 1/2 of the oil sightglass.
Observe the unit operation for a short time to be sure that the compressors do not cut out on low oil pressure.
4.
Check the voltage of the unit power supply and see that it is within the RIO% tolerance that is allowed. Phase voltage unbalance must be within &2%.
EXTENDED SHUT-DOWN
1.
Close the manual liquid line shut-off valve.
5.
Check the unit power supply wiring for adequate ampacity and a minimum insulation temperature rating of 75c.
2.
6.
Verify that all mechanical and electrical inspections have been completed per local codes.
3.
After the compressor has pumped down, turn off the chilled water pump or evaporator fan.
Turn off all power to the unit and to the auxiliary equipment.
7.
See that all auxiliary control equipment is operative and that an adequate cooling load is available for initial start-up.
4.
5.
6.
Move the control stop switch S1 to the “off” position.
Close the compressor suction and discharge valves.
INITIAL START-UP
Tag all opened disconnect switches to warn against start-up before opening the compressor suction and discharge valves.
1. Open the compressor suction and discharge shut-off valves until back seated. Always replace valve seal caps.
START-UP AFTER EXTENDED SHUT-DOWN
2. Open the manual liquid line shut-off valve at the outlet of the subcooler.
1.
inspect all auxiliary equipment (pumps, fans, etc.) to see that each device is in satisfactory operating condition.
3. Allow the crankcase heater to operate for at least eight hours prior to start-up.
2.
Remove all debris that has collected on the surface of the condenser coils.
4. Check to see that pumpdown switch PS1 is in the
“manual pumpdown” position and the control switch
S1 is in the “on” position.
3.
4.
Open the compressor suction and discharge valves.
Open the manual liquid line shut-off valve.
5. Adjust the dial on the temperature controller to the desired chilled water or leaving air temperature.
CAUTION: Most relays and terminals in the unit control canter are hot with S1 and the control circuit disconnect on.
6.
Throw the main power and control circuit disconnects to the “on” position.
5.
6.
Check to see that pumpdown switch PS1 is in the
“manual pumpdown” position.
Turn on the electric power to the unit and other parts of the system.
Allow the crankcase heaters to operate for at least eight hours prior to start-up.
7.
8.
Start the auxiliary equipment for the installation.
Start the system by moving pumpdown switch PS1 to the “auto. pumpdown” position.
On chilled water installations, start the chilled water pump and purge the water piping as well as the evaporator.
9.
Check to see that the control stop switch S1 is in the
“on” position.
After system performance has stabilized, it is necessary that the “Compressorized Equipment Warranty Form”
(Form No. 206036A) be completed to obtain full warranty benefits. This form is shipped with the unit and after completion should be returned to McQUAY’s
Service Department through your sales representative.
CAUTION: Most relays and terminals in the unit control center are hot with S1 and the control circuit disconnect on.
10.
Start the unit by moving pumpdown switch PS1 to the
“auto. pumpdown” position.
TEMPORARY SHUT-DOWN
Move pumpdown switch PS1 to the “manual pumpdown” position. After the compressors have pumped down, turn
11.
After running the unit tor a short time, check the oil level in the compressor crankcase and check for flashing in the refrigerant sightglass.
PAGE 17
C O N T R O L S
OIL PRESSURE SAFETY CONTROL
ALP-OlSA, 023A, 027A, 033A (NOT ON ALP-OlGAI
The oil pressure safety control is a manually resettable device which senses the differential between oil pressure at the discharge of the compressor oil pump and suction pressure inside the compressor crankcase. When the oil pressure reaches approximately 15 PSI above the crankcase suction pressure, the pressure actuated contact of the control opens from its normally closed position. If this pressure differential cannot be developed, the contact will remain closed and energize a heater element within the control. The heater element warms a normally closed bimetallic contact and causes the contact to open, de-energizing a safety relay and breaking power to the compressor.
It takes about 120 seconds to warm the heater element enough to open the bimetallic contact, thus allowing time for the pressure differential to develop.
If during operation the differential drops below 10 PSI, the heater element will be energized and the compressor will stop. The control can be reset by pushing the reset button on the control. If the compressor does not restart, allow a few minutes for the heater element and bimetallic contacts to cool and reset the control again.
To check the control, pump down and shut off all power to the unit. Remove the compressor relay wiring at terminals 2 and 8, and install a voltmeter between terminals
L and M of the oil pressure control. Turn on power to the unit control circuit (separate disconnect or main unit disconnect, depending on the type of installation). Check to see that the control stop switch S1 is in the “on” position. The control circuit should now be energized, but with the absence of the compressor running, no oil pressure differential can develop and thus the pressure actuated contacts of the control will energize the heater element and open the bimetallic contacts of the control within 120 seconds. When this happens the safety relay is de-energized, the voltmeter reading will rise to 115V and the compressor contactor should open. Repeated operations of the control will cause a slight heat build-up in the bimetallic contacts resulting in a slightly longer time for reset with each successive operation.
LINE (SEE NOTE
1)
1
I
I t
y HEATER ELEMENT
N E U T R A L
C O N T A C T
LINE (SEE NOTE 2)
L M
41
I
N E U T R A L
BIMETALLIC CONTACTS SAFETY RELAY
NOTES: 1. Hot only when the unit thermostat calls for compressor to run.
2. Hot only when other safety control contacts are closed.
NOTE: PERFORM AN OPERATIONAL CHECK ON ALL UNIT SAFETY CONTROLS ONCE PER YEAR.
interchangeable.
SOLID STATE COMPRESSOR MOTOR PROTECTION
All air cooled condensing units have compressors with solid state motor protection. Both Robertshaw and Texas
Instruments systems are used and their components are not
There are two major components in a protection system. First, the protector sensors are mounted internally in the motor windings. The sensors monitor winding temperature. A change in temperature causes a change in sensor resistance. Sensor resistance is monitored by the second component of the system - the control module which is a sealed enclosure containing a relay, transformer and other electronic components. Leads from the sensors are connected to the module. Sensor resistance triggers the control module relay at definite opening and closing settings.
The module voltage will always be 120V and will be so marked. When the control module needs repair no attempt should be made to repair it. It should be returned intact for replacement . If the module is opened or physically damaged the warranty is void.
The control module and solid state sensor can be damaged by high voltage. A high potential test should never be made to the module or sensors.
If the compressor motor is not operating properly, the following procedure may be used to check the solid state motor control circuit.
1.
2.
If the compressor has been operating and has been stopped by the motor protector, allow one hour for the compressor to cool and the motor protector to reset.
If reset does not occur, connect a jumper wire across the motor protector from terminal 30 to 36. If the compressor does not operate with the jumper installed, the problem is not within the solid state protector system. If the compressor operates with the jumper installed and does not operate without the jumper, the control circuit relay in the module is open for some reason.
CAUTION: Only check compressor operation with jumper installed. Do not continue operation.
A possible cause of the open relay is the motor sensors.
They may be checked by first removing the connections to the terminal board. Use an ohmmeter of 3 volt maximum voltage to check resistance from each sensor terminal to the common terminal. No voltage or current should be applied to the sensors to check continuity. The resistance across each motor sensor should be approximately 500 to 2400 ohms with a motor temperature below 1400F. If the resistance is zero, there is a short. If the resistance is infinity, there is an open connection.
PAGE 18
O n reset the resistance of the sensors must be below the reset point before the relay contacts will close. The reset resistance is 2700 to 4500 ohms.
If the sensor resistance has been checked and found to be satisfactory and the compressor will run with the control bypassed but will not run with the control wired properly, the control module is defective and must be replaced.
In case the resistance across a sensor is infinity, the module will prevent compressor operation. As an emergency means of obtaining compressor operation until the compressor can be replaced, a resistor may be added between the terminal of the open sensor and the common terminal in the terminal box. The control module then
“sees” an acceptable resistance and compressor operation will be restored. The emergency resistor should be 1 watt,
2200 ohms L 10% resistor. The emergency resistor will not provide the same degree of protection, but it provides a reasonable measure of safety.
RESIS
OPEN l
L--L-
L-J
SENSORS
SOLID STATE MODULE
1
. .
HIGH PRESSURE CONTROL
The high pressure control is a single pole pressure activated condenser pressure rise. The highest point reached before switch that opens on a pressure rise to de-energize the cut-out is the cut-out setting of the control.
entire control circuit except for compressor crankcase heater. It senses condenser pressure and is factory set to CAUTION: Although there is an additional pressure open at 380 PSIG and can be manually reset closed at 315 relief device in the system set at 425 PSIG, it is highly
PSIG. To check the control, block off condenser surface recommended that the control stop switch S1 be close at and observe the cut-out point of the control by watching hand in case the high pressure control should malfunction.
LOW PRESSURE CONTROL
The low pressure control is a single pole pressure switch that closes on a pressure rise. It senses evaporator pressure and is factory set to close at 60 PSIG and automatically open at 25 PSIG. The control has an adjustable range of 20 rn. of Hg. to 100 PSIG and an adjustable differential of 6 to
40 PSIG. To check the control (unit must be running), m o v e t h e pumpdown s w i t c h PS1 t o t h e “ m a n u a l pumpdown” position.
As the compressor pumps down, condenser pressure will rise and evaporator pressure will drop. The lowest evaporator pressure reached before cut-out is the cut-out setting of the control. By moving the pumpdown switch PS1 to the “auto. pumpdown” position, evaporator pressure will rise. The highest evaporator pressure reached before compressor restart is the cut-in setting of the control.
FANTROL - HEAD
PRESSURE CONTROL
FANTROL is a system for progressively turning on or off condenser fans when they are no longer required. This is done to reduce condenser capacity (typically in low outdoor ambient temperatures) and is accomplished by a combination of pressure and temperature actuated controls.
The first fan (No. 11) is started by its contactor when the compressor in the unit starts. The second fan (No. 12) is controlled by a pressure switch which senses condenser pressure. The third fan (No. 13) is controlled by a temperature switch which senses condenser air inlet temperature. Pressure and temperature control setpoints are indicated below.
To check the cut-in points of the controls, the unit must initially be off. With the unit prepared for start-up according to the procedures outlined in this bulletin, move pumpdown switch PS1 to the “auto. pumpdown” position.
Evaporator pressure will begin to rise and the compressor should start with Fan 11 starting immediately. After the compressor starts, observe condenser pressure as it rises.
When the condenser pressure reaches approximately 270
PSIG, contactor Ml2 should pull in to start Fan 12. On three-fan units Fan 13 should start via contactor Ml3 whenever the ambient air at the condenser inlet reaches
8OF.
It may be difficult to check the cut-out point of Fan 13
(on three-fan units) at the instant it happens, but it should be off whenever the ambient air at the condenser inlet is below 70F. To check the cut-out point of Fan 12, some means of reducing the load on the unit must be available or the fan operation and condenser pressure must be observed as the load drops off naturally. When the condenser pressure drops to approximately 170 PSIG, contactor Ml2 should drop out to turn off Fan 12.
PAGE
19
OPTIONAL CONTROLS
SPEEDTROL (OPTIONAL)
McQUAY’s solid state SPEEDTROL, located on the backside of the control center, continuously varies No. 11 condenser fan motor speed on air cooled condensers by sensing changes in refrigerant head pressure. SPEEDTROL makes possible unit operation in lower ambient temperatures.
With an increase in refrigerant head pressure SPEED-
TROL increases fan motor speed. With a decrease in pressure fan motor speed is decreased.
The pressure connection of the transducer is made to the high pressure side of the refrigeration system at the purge valve connection on the condenser coil header. This transducer coupled with a solid stage unit modulates the phase conduction angle of the AC sine wave supplied to the fan motor. The fan motor is a special 208/230V SPEEDTAOL motor. For 460 volt units a transformer is supplied to decrease line voltage to 230 volt motor voltage. The
SPEEDTROL controller is calibrated to deliver 90% of line voltage at the setpoint pressure of 230 PSIG. It has an effective throttling range of 60 PSIG which is the decrease in pressure below the calibration setpoint where 45% of supply voltage is transmitted to the motor. When 45% of supply voltage is transmitted to the motor, minimum motor speed is reached; below this point there is no change in speed.
PART WINDING START (OPTIONAL)
Part winding start consists of a solid state time delay wired is energized instantly, while that for the second motor in series with the contactor that energizes the second winding is delayed for one second.
winding of each compressor motor. Its purpose is to limit Control checkout is best accomplished by observation current in-rush to the compressors upon start-up. As each as each contactor is pulled in to see that the one-second compressor starts, the contactor for the first motor winding delay occurs before the second contactor pulls in.
LINE NEUTRAL
PART WINDING
TIME DELAY 1
COMPRESSOR CONTACTOR
(1st MOTOR WINDING)
LINE +
NEUTRAL
COMPRESSOR CONTACTOR
(2nd MOTOR WINDING)
LOW AMBIENT START (OPTIONAL)
Low ambient start is available on all units as an option with
F ANTROL and included automatically with optional
SPEEDTROL. It consists of a solid state normally closed time delay wired in series with a relay. These are both wired in parallel to the liquid line solenoid valve so that when the solenoid valve is energized by the unit thermostat, the low ambient start relay is
also
energized through the time delay.
The relay has contacts that essentially short circuit the low pressure control and allow the compressor to start with the low pressure control open.
After about 2-3/4 minutes, the time delay will open and de-energize the relay. If the system has not built up enough evaporator pressure to close the low pressure control, the compressor will stop. The time delay can be reset to its original normally closed position by moving the pumpdown switch PS1 to the “manual pumpdown” position. Moving the pumpdown switch PS1 back to the “auto. pumpdown” position will again energize the relay for another attempt at start-up. If the system has built up enough evaporator pressure, the compressor will continue to run.
To check the control, turn off all power to the unit and remove the wire leading to the low pressure control LP1 from terminal 11 in the unit control center. Remove the wires leading from the contactors to the compressor and jumper across terminals L and M of the oil pressure safety control. Energize the control circuit by turning on the control circuit disconnect or main power disconnect
(depending on the installation) and the control stop switch
S1. The compressor contactors should pull in instantly.
NOTE : Line is only hot when the unit thermostat calls for compressor to run
PAGE
20
COMPRESSOR
LOCKOUT
(OPT
I
ONAL)
Compressor lockout consists of a solid state time delay wired in series with the compressor contactor( Its purpose is to prevent rapid compressor cycling when cooling demands are erratic.
When the unit thermostat no longer calls for cooling initially.
Move pumpdown” the pumpdown switch PS1 to the “manual position. immediately after the compressor has stopped running, move the pumpdown switch back to the “auto. pumpdown” position.
The compressor should
not restart for five minutes.
and the compressor contactor(s) have opened, the lockout time delay breaks open the circuit preventing compressor restart.
LINE
(SEE NOTE)
The circuit remains open for a period of five minutes so that if the unit thermostat should call for cooling before the delay period has expired, the compressor will not restart. After five minutes, the time delay will close its contacts to complete the circuit and be ready for start-up.
The time delay opens its contacts whenever there is power to the terminals of the compressor relay and resets closed automatically after the time delay period.
To check the control, the compressor must be running
NOTE: Hot whenever freeze cc,n,r~, and hqh ,xessure contrd permt safe ~,xtatcr
A
L A
R M B
E
L
L (
O
P T
I O N A L
)
It is expected
that the customer will want to locate the alarm bell where it will be heard in the event of a safety circuit it will sound whenever there is a failure due to low oil pressure (not on ALP-OlGAI, motor overload, or failure. After mounting, the bell should be wired to excessive condenser pressure.
transformer T4. When the bell is wired into the control
HOT
GAS BYPASS (OPTIONAL)
Hot gas bypass is a system for maintaining evaporator pressure at or above a minimum value. The purpose for doing this is to keep the velocity of the refrigerant as it passes through the evaporator high enough for proper oil return to the compressor when cooling load conditions are light.
The system usually consists of a solenoid valve piped in series with a pressure regulating valve as shown. Provisions are provided for installing the hot gas bypass kit.
The solenoid valve should be wired to operate as close to the unit’s maximum unloaded state as possible. The pressure regulating valve that McQuay offers is factory set to being opening at 58 PSIG (32F for R-22) when the air charged bulb is in an 80F ambient temperature. The bulb can be mounted anywhere as long as it senses a fairly constant temperature at various load conditions. The compressor suction line is one such mounting location. It is generally in the 50F to 60F range. The chart below indicates that when the bulb is sensing 50F to 60F temperatures, the valve will begin opening at 54 to 56
PSIG. This setting can be changed, as indicated above, by changing the pressure of the air charge in the adjustable bulb. To raise the pressure setting, remove the cap on the bulb and turn the adjustment screw clockwise. To lower the setting, turn the screw counter-clockwise. Do not force the adjustment beyond the range it is designed for as this will damage the adjustment assembly.
The regulating valve opening point can be determined by slowly reducing the system load while observing the suction pressure. When the bypass valve starts to open, the refrigerant line on the evaporator side of the valve will begin to feel warm to the touch.
CAUTION: The
hot gas line may become hot enough to cause injury in a very short time, so care should be taken during valve checkout.
On installations
where the condensing unit is remote from the evaporator, it is recommended that the hot gas bypass valve be mounted near the condensing unit to minimize the amounts of refrigerant that will condense in the hot gas line during periods when hot gas bypass is not required.
HOT GAS BYPASS PIPING DIAGRAM
80
3 0
3 0
r
40
Hot
Gas Bypass
Solenoid Valve
y-
Surt1on Line
External Equalizer in ALP Unit
Bypass Valve Expansion Valve with Factory (On DX Coil with
Capped Tee for Distributor, use
Connection. A
Sporlan Auxiliary manual shut-off
Sideport Connector valve between the or Equivalent.) bypass tee and solenoid valve is recommended.
HOT GAS BYPASS ADJUSTMENT RANGE
RE
M
OTE BULB ADJUSTMENT RANGE
52 60 70 80 90
TEuP f0F1
A
T BULB LOCATION
100 1,:
PAGE 21
MAINTENANCE PROCEDURES
NOTE: Service on
this equipment is to he performed by qualified refrigeration service personnel. Causes for repeated tripping of Safety controls
must be
investigated and corrected. CAUTION: Disconnect all power before doing any service inside the unit.
On Initial start-up and periodically during operation it will be necessary to perform certain routine service checks,
Among these are checking the compressor o i l level and taking condensing, suction and oil pressure readings. During operation the oil level should be visible in the oil sightglass with the compressor running. On units ordered with gauges, condensing, suction and o i l pressures can be read from the gauges. Oil pressure gauge is not available on ALP-OIGA.
The gauges are installed with a manual shut-off valve on each gauge line. The valves should be closed at all times except when gauge readings are being taken.
R E F R I G E R A N T S I G H T G L A S S
The refrigerant sightglass should be observed periodically. o r d e r e d f r o m McQUAY as part of the "Liquid L i n e
(A monthly observation should be adequate.) A clear glass Accessory Kits”, an element Inside the sightglass indicates of liquid indicates that there is adequate refrigerant charge what moisture condition corresponds to a given element in the system to insure proper feed through the expansion color. If the sightglass does not indicate a dry condition valve. Bubbling refrigerant in the srghtglass indicates that after a few hours of operation, the unit should be pumped the system is short of refrigerant charge. On sightglasses down and the cores in the filter-driers changed.
FILTER-DRIERS
To change the filter-drier core, pump the unit down by position. T h i s will close the liquid line solenoid valve and moving pumpdown switch PS1 to the “manual pumpdown” isolate the short section of refrigerant piping containing the position. Turn off all power to the unit and install a jumper filter-drier. Remove the cover plate from the filter-drier from terminal 31 to 34. Turn power to the unit back on shell and replace the core.
and restart the unit by moving pumpdown switch PS1 to After core replacement, replace the cover plate. A leak the “auto. pumpdown” position. Close the manual liquid c h e c k a r o u n d t h e f l a n g e o f t h e f i l t e r - d r i e r s h e l l i s line shut-off valve and when evaporator pressure reaches 0 recommended after the core has been changed.
PSIG. m o v e t h e c o n t r o l s t o p s w i t c h S1 t o t h e “ o f f ”
LIQUID LINE SOLENOID VALVE
T h e liquid line solenoid valve, which is responsible for by simply removing a nut or snap ring located at the top of automatic pumpdown during normal unit operation, does the coil. The coil can then be slipped off its mounting stud not normally require any maintenance. It may, however, for replacement. Be sure to replace the c o i l on its mounting require replacement of the solenoid coil or of the entire stud before returning pumpdown switch PS1 to the “auto.
valve assembly. pumpdown” position.
The solenoid c o i l may be removed from the valve body
To replace the entire solenoid valve, the unit must be without o p e n i n g t h e r e f r i g e r a n t piping b y m o v i n g pumped down by use of the manual liquid line shut-off pumpdown s w i t c h PS1 t o t h e “ m a n u a l p u m p d o w n ” valve.
position. The c o i l can then be removed from the valve bodv
CONDENSERS
Condensers are air cooled and constructed with 3 / 8 O.D.
copper tubes bonded in a staggered pattern into rippled a l u m i n u m f i n s . N o m a i n t e n a n c e
IS
ordinarily r e q u i r e d except the occasional removal of dirt and debris from the outside surface of the fins. Care should be taken not to damage the fins during cleaning. Periodic use of the Purge valve on the condenser will prevent the build-up of non-condensables.
COMPRESSOR OIL LEVEL
Because of the large refrigerant charge required in an air At the present time, Suniso 3GS o i l is the only oil cooled condensing unit it
IS
u s u a l l y n e c e s s a r y t o p u t approved by Copeland and Sundstrand for use in these a d d i t i o n a l o i l into the system. The oil level should be compressors. The oil level should be maintained at about watched carefully upon initial start-up and for sometime the midpoint of the sightglass on the compressor body. The thereafter. use of a light may be required for proper o i l level reading.
ADDING OIL TO COMPRESSOR
Oil may be added to the Copeland compressor through the Stop the compressor and close the discharge valve.
011 1111 h o l e i n t h e c r a n k c a s e and t o t h e S u n d s t r a n d Add the requrred amount of
011. Durirrg the perrod the compressor through the 3/8-Inch process tube on the side compressor
IS exposed to the atmosphere the refrigerant of the compressor. To add 011, Isolate the crankcase and pour or pump the necessary
011 in. If the system contains w i l l qeneratc a vapor pressure, retarding the entrance Of contamrnants. Before resealing the compressor purge the no rcfrrgerant. no special precautrons are necessary other crdnkcasr! by openrnq the suctrorr valve slightly for 1 or 2 than keeping the o i l clean and dry.
seconds. Close the o i l port,
open the compressor valves and
If the system contains a refrigerant charge, close the restore the system to operation.
suction valve and reduce crankcase pressure to 1 to 2 PSIG.
PAGE 22
.I.
I
ELECTRICAL TERMINALS
CAUTION: ELECTRIC
SHOCK HAZARD -TURN OFF ALL POWER BEFORE CONTINUING WITH
FOLLOWING SERVICE.
All
power electrical terminals should be retightened every six months, as they tend to loosen in service due to normal heating and cooling of the wire.
FAN MOTOR BEARINGS
All
fan motors are pre-lubricated and do not require the addition of grease.
THERMOSTATIC EXPANSION VALVE
The expansion valve is responsible for allowing the proper amount of refrigerant to enter the evaporator, regardless of cooling load. It does this by maintaining a constant superheat. (Superheat is the difference between refrigerant temperature as it leaves the evaporator and the saturation temperature corresponding to the evaporator pressure.)
Typically, superheat should run in the range of 10F to 15F.
On valves purchased through McQUAY, the superheat setting can be adjusted by removing a cap at the bottom of the valve to expose the adjustment screw. Turn the screw clockwise (when viewed from the adjustment screw end) to increase the superheat setting and counter-clockwise to reduce superheat. Allow time for system rebalance after each superheat adjustment.
The expansion valve, like the solenoid valve, should not normally require replacement, but if it does, the unit must be pumped down by using the manual liquid line shut-off valve. If the problem can be traced to the power element only, it can be unscrewed from the valve body without removing the valve, but only after pumping the unit down with the manual liquid line shut-off valve.
IN1
.ET
‘POWER ELEMENT
(CONTAINS DIAPHRAGM)
OUTLET
SPRING
ADJUSTMENT SCREW
CAP
IN-WARRANTY RETURN MATERIAL PROCEDURE
COMPRESSOR
Bristol Corporation [compressor used in the ALP-0161, and
Copeland Corporation [all other units], have stocking wholesalers who maintain a stock of replacement compressors and service parts to service refrigeration contractors and servicemen.
When a compressor fails in warranty, contact your local sales representative or McQuay Warranty Claims Department at the address on the cover of this bulletin. You will be authorized to exchange the defective compressor locally
(an advance replacement can be obtained), or we will ship you a replacement from our stock. A salvage credit is issued to you by the wholesaler on the returned compressor after
Bristol or Copeland factory inspection of the inoperative compressor. Provide McQuay with full details and invoices and we will reimburse the difference. In this transaction, be certain that the compressor is definitely defective. If a compressor is received from the field that tests satisfactorily, a service charge plus a transportation charge will be charged against its original credit value.
On all out-of-warranty compressor failures, Bristol and
Copeland offer the same field facilities for service and/or replacement as described above. The credit issued by Bristol or Copeland on the returned compressor will be determined by the repair charge established for that particular unit.
COMPONENTS OTHER THAN COMPRESSORS
Material may not be returned except by permission of should include part name, part number, model number and authorized factory service personnel of McQUAY Inc. at serial number of the unit involved.
Minneapolis, Minnesota. A “Return Goods” tag will be sent Following our personal inspection of the returned part, to be included with the returned material. Enter the and if it is determined that the failure is due to faulty information as called for on the tag in order to expedite material or workmanship and in warranty, credit will be handling at our factories and prompt issuance of credits. Issued on customer’s purchase order.
The return of the part does not constitute an order for All parts shall be returned to the pre-designated replacement. Therefore, a purchase order must be entered McQUAY factory, transportation charges prepaid.
through your nearest McQUAY Representative. The order
PAGE 23
advertisement
* Your assessment is very important for improving the workof artificial intelligence, which forms the content of this project
Related manuals
advertisement
Table of contents
- 2 Table of Contents
- 3 Introduction
- 3 Nomenclature
- 3 Inspection
- 3 Installation
- 3 Handling
- 3 Location
- 4 Access
- 4 Vibration Isolators
- 5 Refrigerant Piping
- 5 General
- 5 Evaporator Above Condensing Unit
- 5 Evaporator Below Condensing Unit
- 5 Refrigerant piping Connections
- 6 Liquid Line Components
- 6 Adding Refrigerant Charge
- 7 Removing Regrigerant Charge
- 7 Field Wiring
- 7 Thermostat Wiring
- 8 Wire Sizing Ampacities
- 8 Compressor and Condenser Fan Motors
- 9 Flow Switch for Chilled Water Applications
- 9 Evaporator Fan Interlock
- 9 Electrical
- 9 Control Center
- 10 Control Panel Layouts
- 10 Electrical Legend
- 11 Sequence of Operation
- 11 Major Component Locations
- 12 Wiring Diagrams
- 12 Power Schematics - Compressors and Fan Motors
- 12 Model ALP-016A-S (208/230V)
- 12 Model ALP-016A-S (460V)
- 13 Models ALP-019A-S,023A-S,027A-S,033A-S (208/230V & 380/460V)
- 14 Compressor Control Schematic
- 14 Model ALP-016A-S (208/230V)
- 15 Model ALP-016A-S (308/460V)
- 16 Models ALP-019A-S,023A-S,027A-S,033A-S (208/230V & 380/460V)
- 17 Start-Up and Shut-Down
- 17 Pre Start-Up
- 17 Initial Start-Up
- 17 Temporary Shut-Down
- 17 Start-Up afetr Temporary Shut-Down
- 17 Extended Shut-Down
- 17 Start-Up After Extended Shut-Down
- 18 Controls
- 18 Oil Pressure Safety Controls
- 18 Solid State Compressor Motor Protection
- 19 High Pressure Control
- 19 Low Pressure Control
- 19 FANTROL -Head Pressure Control
- 20 Optional Controls
- 20 SPEEDTROL
- 20 Part Winding Start
- 20 Low Ambient Start
- 21 Compressor Lockout
- 21 Alarm Bell
- 21 Hot Gas Bypass
- 22 Unit Maintenance
- 22 Refrigerant Sightglass
- 22 Filter-Driers
- 22 Liquid Line Solenoid Valve
- 22 Condensers
- 22 Compressor Oil Level
- 22 Adding Oil to Compressor
- 23 Electrical Terminals
- 23 Fan Motor Bearings
- 23 Thermostatic Expansion Valve
- 23 In-Warranty Return Material Procedure
- 23 Compressor
- 23 Components Other Than Compressor
- 24 Trouble Shooting Chart