Emerson Process Management 3095FC Automobile Accessories Reference Manual
Add to my manuals
150 Pages
advertisement
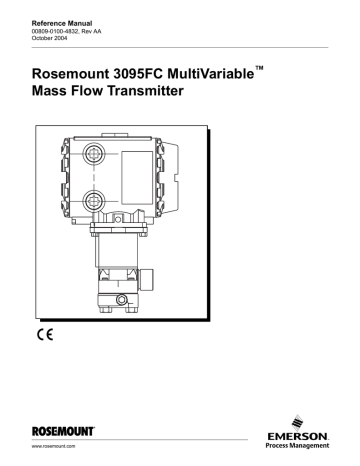
Reference Manual
00809-0100-4832, Rev AA
October 2004
Rosemount 3095FC MultiVariable
™
Mass Flow Transmitter
www.rosemount.com
Reference Manual
00809-0100-4832, Rev AA
October 2004
Rosemount 3095FC
Rosemount 3095FC MultiVariable
Mass Flow Transmitter
The products described in this document are NOT designed for nuclear-qualified applications. Using non-nuclear qualified products in applications that require nuclear-qualified hardware or products may cause inaccurate readings.
For information on Rosemount nuclear-qualified products, contact an Emerson Process
Management Sales Representative.
This device is intended for use in temperature monitoring applications and should not be used in control and safety applications.
NOTICE
Read this manual before working with the product. For personal and system safety, and for optimum product performance, make sure to thoroughly understand the contents before installing, using, or maintaining this product.
The United States has two toll-free assistance numbers and one International number.
Customer Central
1-800-999-9307 (7:00 a.m. to 7:00 P.M. CST)
International
1-(952) 906-8888
National Response Center
1-800-654-7768 (24 hours a day)
Equipment service needs www.rosemount.com
Reference Manual
00809-0100-4832, Rev AA
October 2004
SECTION 1
Introduction
SECTION 2
Installation
Rosemount 3095FC
Table of Contents
3095FC Overview . . . . . . . . . . . . . . . . . . . . . . . . . . . . . . . . . . . . . . . . 1-1
Hardware . . . . . . . . . . . . . . . . . . . . . . . . . . . . . . . . . . . . . . . . . . . . 1-2
Firmware. . . . . . . . . . . . . . . . . . . . . . . . . . . . . . . . . . . . . . . . . . . . . 1-3
Accessories . . . . . . . . . . . . . . . . . . . . . . . . . . . . . . . . . . . . . . . . . . 1-3
Automatic Tests . . . . . . . . . . . . . . . . . . . . . . . . . . . . . . . . . . . . . . . 1-3
Low Power Mode . . . . . . . . . . . . . . . . . . . . . . . . . . . . . . . . . . . . . . 1-4
3095FC Functions . . . . . . . . . . . . . . . . . . . . . . . . . . . . . . . . . . . . . 1-4
Flow Measurement . . . . . . . . . . . . . . . . . . . . . . . . . . . . . . . . . . 1-4
1992 Flow Calculations for Orifice Metering . . . . . . . . . . . . . . . 1-4
Considerations. . . . . . . . . . . . . . . . . . . . . . . . . . . . . . . . . . . . . . . . . . . 1-5
Environmental Requirements . . . . . . . . . . . . . . . . . . . . . . . . . . . . . 1-5
Enclosures . . . . . . . . . . . . . . . . . . . . . . . . . . . . . . . . . . . . . . . . . . . 1-5
Mounting. . . . . . . . . . . . . . . . . . . . . . . . . . . . . . . . . . . . . . . . . . . . . 1-5
Power Installation Requirements . . . . . . . . . . . . . . . . . . . . . . . . . . 1-5
Rosemount User Interface Software PC Requirements . . . . . . . . . 1-6
Site Requirements . . . . . . . . . . . . . . . . . . . . . . . . . . . . . . . . . . . . . 1-6
Wiring Requirements . . . . . . . . . . . . . . . . . . . . . . . . . . . . . . . . . . . 1-6
Mounting . . . . . . . . . . . . . . . . . . . . . . . . . . . . . . . . . . . . . . . . . . . . . . . 2-1
Installation . . . . . . . . . . . . . . . . . . . . . . . . . . . . . . . . . . . . . . . . . . . . . . 2-2
Rosemount 3095FC . . . . . . . . . . . . . . . . . . . . . . . . . . . . . . . . . . . . 2-2
Installing the Rosemount 3095FC on a Pipestand . . . . . . . . . . 2-2
Installing the 3095FC on an Orifice Plate (Direct Mount) . . . . . 2-2
Solar Panels . . . . . . . . . . . . . . . . . . . . . . . . . . . . . . . . . . . . . . . . . . 2-3
Solar Panel Sizing . . . . . . . . . . . . . . . . . . . . . . . . . . . . . . . . . . . 2-3
Wiring. . . . . . . . . . . . . . . . . . . . . . . . . . . . . . . . . . . . . . . . . . . . . . . . . . 2-4
Power Supply Wiring . . . . . . . . . . . . . . . . . . . . . . . . . . . . . . . . . . . 2-5
RTD Wiring . . . . . . . . . . . . . . . . . . . . . . . . . . . . . . . . . . . . . . . . . . . 2-5
Communications Wiring . . . . . . . . . . . . . . . . . . . . . . . . . . . . . . . . . 2-6
Local Operator Interface Port (LOI). . . . . . . . . . . . . . . . . . . . . . 2-6
EIA-485 (RS-485) Serial Communications - Comm 1 . . . . . . . . 2-7
EIA-232 (RS-232) Communications - Comm 2 . . . . . . . . . . . . . 2-7
Ground the Transmitter . . . . . . . . . . . . . . . . . . . . . . . . . . . . . . . . . 2-8
Earth Grounds . . . . . . . . . . . . . . . . . . . . . . . . . . . . . . . . . . . . . . 2-8
Pipelines With Cathodic Protection . . . . . . . . . . . . . . . . . . . . . . 2-8
Power Supply. . . . . . . . . . . . . . . . . . . . . . . . . . . . . . . . . . . . . . . . . . . . 2-9
Batteries . . . . . . . . . . . . . . . . . . . . . . . . . . . . . . . . . . . . . . . . . . 2-9
Apply Power. . . . . . . . . . . . . . . . . . . . . . . . . . . . . . . . . . . . . . . . . . . . 2-10
Install the Rosemount User Interface Software . . . . . . . . . . . . . . . . . 2-11
Software Overview . . . . . . . . . . . . . . . . . . . . . . . . . . . . . . . . . 2-11
Install With Autorun . . . . . . . . . . . . . . . . . . . . . . . . . . . . . . . . . . . 2-11
Install Without Autorun . . . . . . . . . . . . . . . . . . . . . . . . . . . . . . . . . 2-12
Uninstalling the Rosemount User Interface Software. . . . . . . . . . 2-12 www.rosemount.com
Rosemount 3095FC
SECTION 3
Configuration
Reference Manual
00809-0100-4832, Rev AA
October 2004
Getting Started with the Software . . . . . . . . . . . . . . . . . . . . . . . . . . . 2-12
Run the Software . . . . . . . . . . . . . . . . . . . . . . . . . . . . . . . . . . . . . 2-12
Log into the Software . . . . . . . . . . . . . . . . . . . . . . . . . . . . . . . . . . 2-12
Establishing Communication . . . . . . . . . . . . . . . . . . . . . . . . . . . . . . . 2-13
Connection Methods. . . . . . . . . . . . . . . . . . . . . . . . . . . . . . . . . . . 2-13
Direct Connect. . . . . . . . . . . . . . . . . . . . . . . . . . . . . . . . . . . . . 2-13
Connect . . . . . . . . . . . . . . . . . . . . . . . . . . . . . . . . . . . . . . . . . . 2-14
Remote Hardware Connection . . . . . . . . . . . . . . . . . . . . . . . . 2-14
Disconnect from the 3095FC. . . . . . . . . . . . . . . . . . . . . . . . . . 2-14
Configuration Tree . . . . . . . . . . . . . . . . . . . . . . . . . . . . . . . . . . . . . . . 2-14
Adding a Group . . . . . . . . . . . . . . . . . . . . . . . . . . . . . . . . . . . . 2-15
Deleting a Group . . . . . . . . . . . . . . . . . . . . . . . . . . . . . . . . . . . 2-15
Adding a 3095FC transmitter . . . . . . . . . . . . . . . . . . . . . . . . . 2-16
Deleting a 3095FC transmitter . . . . . . . . . . . . . . . . . . . . . . . . 2-16
Deleting all 3095FC transmitters . . . . . . . . . . . . . . . . . . . . . . . 2-16
Renaming a Group or 3095FC . . . . . . . . . . . . . . . . . . . . . . . . 2-16
Overview . . . . . . . . . . . . . . . . . . . . . . . . . . . . . . . . . . . . . . . . . . . . . . . 3-1
Basic Functions . . . . . . . . . . . . . . . . . . . . . . . . . . . . . . . . . . . . . . . . . . 3-1
Select TLP Options . . . . . . . . . . . . . . . . . . . . . . . . . . . . . . . . . 3-1
Display TLP Options . . . . . . . . . . . . . . . . . . . . . . . . . . . . . . . . . 3-1
Duplicating a Configuration . . . . . . . . . . . . . . . . . . . . . . . . . . . . 3-2
Using Copy and Paste. . . . . . . . . . . . . . . . . . . . . . . . . . . . . . . . 3-2
New Configuration File . . . . . . . . . . . . . . . . . . . . . . . . . . . . . . . 3-2
Open File. . . . . . . . . . . . . . . . . . . . . . . . . . . . . . . . . . . . . . . . . . 3-2
Save File . . . . . . . . . . . . . . . . . . . . . . . . . . . . . . . . . . . . . . . . . . 3-2
Download File . . . . . . . . . . . . . . . . . . . . . . . . . . . . . . . . . . . . . . 3-3
Print Configuration. . . . . . . . . . . . . . . . . . . . . . . . . . . . . . . . . . . 3-3
Configuration . . . . . . . . . . . . . . . . . . . . . . . . . . . . . . . . . . . . . . . . . . . . 3-4
Setting the Clock . . . . . . . . . . . . . . . . . . . . . . . . . . . . . . . . . . . . . . 3-4
Configuring the System Flags . . . . . . . . . . . . . . . . . . . . . . . . . . . . 3-5
General Tab . . . . . . . . . . . . . . . . . . . . . . . . . . . . . . . . . . . . . . . 3-5
Advanced Tab . . . . . . . . . . . . . . . . . . . . . . . . . . . . . . . . . . . . . . 3-7
3095FC Communications Ports Configuration . . . . . . . . . . . . . . . . 3-8
General Tab . . . . . . . . . . . . . . . . . . . . . . . . . . . . . . . . . . . . . . . 3-8
RBX Tab . . . . . . . . . . . . . . . . . . . . . . . . . . . . . . . . . . . . . . . . . . 3-9
3095FC Device Configuration / Information . . . . . . . . . . . . . . . . . 3-10
General Tab . . . . . . . . . . . . . . . . . . . . . . . . . . . . . . . . . . . . . . 3-10
Points Tab . . . . . . . . . . . . . . . . . . . . . . . . . . . . . . . . . . . . . . . . 3-11
Other Information Tab . . . . . . . . . . . . . . . . . . . . . . . . . . . . . . . 3-12
Revision Info Tab . . . . . . . . . . . . . . . . . . . . . . . . . . . . . . . . . . 3-12
Security Configuration . . . . . . . . . . . . . . . . . . . . . . . . . . . . . . . . . 3-13
Rosemount User Interface Security - Menu and Log On . . . . 3-13
3095FC Security . . . . . . . . . . . . . . . . . . . . . . . . . . . . . . . . . . . 3-14
LCD User List Configuration. . . . . . . . . . . . . . . . . . . . . . . . . . . . . 3-15
I/O Configuration . . . . . . . . . . . . . . . . . . . . . . . . . . . . . . . . . . . . . 3-15
Scanning Disabled versus Scanning Enabled. . . . . . . . . . . . . 3-15
I/O Monitor. . . . . . . . . . . . . . . . . . . . . . . . . . . . . . . . . . . . . . . . 3-15
Analog Input (AI) Configuration . . . . . . . . . . . . . . . . . . . . . . . . . . 3-16
AI General Tab . . . . . . . . . . . . . . . . . . . . . . . . . . . . . . . . . . . . 3-16
AI Advanced Tab. . . . . . . . . . . . . . . . . . . . . . . . . . . . . . . . . . . 3-17
AI Alarms Tab . . . . . . . . . . . . . . . . . . . . . . . . . . . . . . . . . . . . . 3-19
TOC-2
Reference Manual
00809-0100-4832, Rev AA
October 2004
SECTION 4
Calibration
SECTION 5
Troubleshooting and
Maintenance
Rosemount 3095FC
Soft Points Configuration . . . . . . . . . . . . . . . . . . . . . . . . . . . . . . . 3-20
Opcode . . . . . . . . . . . . . . . . . . . . . . . . . . . . . . . . . . . . . . . . . . . . . 3-21
Opcode Table Configuration . . . . . . . . . . . . . . . . . . . . . . . . . . 3-22
Radio Power Control Configuration . . . . . . . . . . . . . . . . . . . . . . . 3-23
Meter Run Configuration . . . . . . . . . . . . . . . . . . . . . . . . . . . . . . . 3-25
General Tab . . . . . . . . . . . . . . . . . . . . . . . . . . . . . . . . . . . . . . 3-26
AGA Meter Inputs Tab. . . . . . . . . . . . . . . . . . . . . . . . . . . . . . . 3-27
Gas Quality Tab . . . . . . . . . . . . . . . . . . . . . . . . . . . . . . . . . . . 3-28
Advanced Meter Setup Tab. . . . . . . . . . . . . . . . . . . . . . . . . . . 3-29
Instrument Calibration Tab . . . . . . . . . . . . . . . . . . . . . . . . . . . 3-30
Meter Setup Alarms Tab . . . . . . . . . . . . . . . . . . . . . . . . . . . . . 3-31
History Points Configuration . . . . . . . . . . . . . . . . . . . . . . . . . . . . . 3-32
Meter History . . . . . . . . . . . . . . . . . . . . . . . . . . . . . . . . . . . . . . 3-32
Averaging Technique . . . . . . . . . . . . . . . . . . . . . . . . . . . . . . . 3-33
Log Types . . . . . . . . . . . . . . . . . . . . . . . . . . . . . . . . . . . . . . . . 3-33
General History . . . . . . . . . . . . . . . . . . . . . . . . . . . . . . . . . . . . 3-35
History, Alarm, Event, and Audit Log Reports . . . . . . . . . . . . . . . 3-37
Collect Data . . . . . . . . . . . . . . . . . . . . . . . . . . . . . . . . . . . . . . . . . 3-38
Configure History for EFM Reporting . . . . . . . . . . . . . . . . . . . . . . 3-38
Electronic Flow Measurement (EFM) Reports . . . . . . . . . . . . 3-38
Modbus Configuration . . . . . . . . . . . . . . . . . . . . . . . . . . . . . . . . . 3-40
General Tab . . . . . . . . . . . . . . . . . . . . . . . . . . . . . . . . . . . . . . 3-40
Scale Values Tab . . . . . . . . . . . . . . . . . . . . . . . . . . . . . . . . . . 3-42
Modbus - History Collection . . . . . . . . . . . . . . . . . . . . . . . . . . 3-44
History Access Registers Tab . . . . . . . . . . . . . . . . . . . . . . . . . 3-44
Modbus - Events / Alarms Functionality . . . . . . . . . . . . . . . . . 3-45
Modbus - Detailed Point / Parameter Information . . . . . . . . . . 3-47
Configure Modbus Registers . . . . . . . . . . . . . . . . . . . . . . . . . . . . 3-47
Modbus Conversion . . . . . . . . . . . . . . . . . . . . . . . . . . . . . . . . . . . 3-51
Custom Displays . . . . . . . . . . . . . . . . . . . . . . . . . . . . . . . . . . . . . . . . 3-54
New Display . . . . . . . . . . . . . . . . . . . . . . . . . . . . . . . . . . . . . . . . . 3-54
Save Displays. . . . . . . . . . . . . . . . . . . . . . . . . . . . . . . . . . . . . . . . 3-55
Overview . . . . . . . . . . . . . . . . . . . . . . . . . . . . . . . . . . . . . . . . . . . . . . . 4-1
Calibrate . . . . . . . . . . . . . . . . . . . . . . . . . . . . . . . . . . . . . . . . . . . . . . . 4-1
3095FC. . . . . . . . . . . . . . . . . . . . . . . . . . . . . . . . . . . . . . . . . . . . . . 4-1
Analog Input (AI) Calibration . . . . . . . . . . . . . . . . . . . . . . . . . . . . . 4-3
Calibration Report . . . . . . . . . . . . . . . . . . . . . . . . . . . . . . . . . . . 4-5
Calibration Value . . . . . . . . . . . . . . . . . . . . . . . . . . . . . . . . . . . . 4-5
Zero Shift. . . . . . . . . . . . . . . . . . . . . . . . . . . . . . . . . . . . . . . . . . 4-5
Verify Calibration . . . . . . . . . . . . . . . . . . . . . . . . . . . . . . . . . . . . . . . . . 4-6
Backup Configuration Information . . . . . . . . . . . . . . . . . . . . . . . . . . . . 5-1
Communication Errors . . . . . . . . . . . . . . . . . . . . . . . . . . . . . . . . . . . . . 5-2
Communication Problems . . . . . . . . . . . . . . . . . . . . . . . . . . . . . 5-2
Debug Communications . . . . . . . . . . . . . . . . . . . . . . . . . . . . . . 5-2
Resetting the 3095FC . . . . . . . . . . . . . . . . . . . . . . . . . . . . . . . . . . . . . 5-3
Warm Start . . . . . . . . . . . . . . . . . . . . . . . . . . . . . . . . . . . . . . . . . . . 5-3
Cold Start . . . . . . . . . . . . . . . . . . . . . . . . . . . . . . . . . . . . . . . . . . . . 5-3
Jumper Reset . . . . . . . . . . . . . . . . . . . . . . . . . . . . . . . . . . . . . . . . . 5-3
After Installing Components. . . . . . . . . . . . . . . . . . . . . . . . . . . . . . . . . 5-4
Replacing the Batteries . . . . . . . . . . . . . . . . . . . . . . . . . . . . . . . . . . . . 5-5
TOC-3
Rosemount 3095FC
APPENDIX A
Specifications and
Reference Data
APPENDIX B
Product Certifications
APPENDIX C
Rosemount User
Interface Software
APPENDIX Glossary
Reference Manual
00809-0100-4832, Rev AA
October 2004
Changing the Plate . . . . . . . . . . . . . . . . . . . . . . . . . . . . . . . . . . . . . . . 5-5
Specifications. . . . . . . . . . . . . . . . . . . . . . . . . . . . . . . . . . . . . . . . . . . . A-1
Functional Specifications . . . . . . . . . . . . . . . . . . . . . . . . . . . . . . . . A-1
Performance Specifications . . . . . . . . . . . . . . . . . . . . . . . . . . . . . . A-3
Physical Specifications . . . . . . . . . . . . . . . . . . . . . . . . . . . . . . . . . . A-4
Memory Specifications . . . . . . . . . . . . . . . . . . . . . . . . . . . . . . . . . . A-6
Flow Specifications. . . . . . . . . . . . . . . . . . . . . . . . . . . . . . . . . . . . . A-6
Dimensional Drawings . . . . . . . . . . . . . . . . . . . . . . . . . . . . . . . . . . . . . A-7
Ordering Information . . . . . . . . . . . . . . . . . . . . . . . . . . . . . . . . . . . . . . A-9
Options . . . . . . . . . . . . . . . . . . . . . . . . . . . . . . . . . . . . . . . . . . . . . . . A-11
Standard Configuration. . . . . . . . . . . . . . . . . . . . . . . . . . . . . . . . . A-11
Custom Configuration (Option Code C1) . . . . . . . . . . . . . . . . . . . A-11
Tagging . . . . . . . . . . . . . . . . . . . . . . . . . . . . . . . . . . . . . . . . . . A-11
Optional 305 Integral Manifolds. . . . . . . . . . . . . . . . . . . . . . . . A-11
Accessories . . . . . . . . . . . . . . . . . . . . . . . . . . . . . . . . . . . . . . . . . . . . A-11
Rosemount User Interface Software Packages . . . . . . . . . . . A-11
Windows 98 or higher . . . . . . . . . . . . . . . . . . . . . . . . . . . . . . . A-11
Approved Manufacturing Locations . . . . . . . . . . . . . . . . . . . . . . . . . . . B-1
European Directive Information . . . . . . . . . . . . . . . . . . . . . . . . . . . . . . B-1
Hazardous Locations Certifications . . . . . . . . . . . . . . . . . . . . . . . . . . . B-1
North American Certifications . . . . . . . . . . . . . . . . . . . . . . . . . . B-1
. . . . . . . . . . . . . . . . . . . . . . . . . . . . . . . . . . . . . . . . . . . . . . . . . . . . . . . B-1
Overview . . . . . . . . . . . . . . . . . . . . . . . . . . . . . . . . . . . . . . . . . . . . . . .C-1
Point Type Parameter Definitions . . . . . . . . . . . . . . . . . . . . . . . . . . . .C-1
. . . . . . . . . . . . . . . . . . . . . . . . . . . . . . . . Point Type 0 InformationC-2
Device Point Types. . . . . . . . . . . . . . . . . . . . . . . . . . . . . . . . . . . . .C-3
TOC-4
Reference Manual
00809-0100-4832, Rev AA
October 2004
Section 1
3095FC OVERVIEW
Rosemount 3095FC
Introduction
3095FC Overview . . . . . . . . . . . . . . . . . . . . . . . . . . . . . . . . page 1-1
3095FC Functions . . . . . . . . . . . . . . . . . . . . . . . . . . . . . . . . page 1-4
Considerations . . . . . . . . . . . . . . . . . . . . . . . . . . . . . . . . . . page 1-5
The 3095FC is a 32-bit microprocessor-based transmitter. The device electronically measures, monitors, and manages gas flow for a single meter run using an orifice plate (DP). It reliably and accurately performs gas flow calculations, temperature measurements, and data archival.
The 3095FC performs minute, 10-minute, hourly (periodic), daily, and minimum / maximum historical data archival. It records the corrected gas flow across an orifice plate, stores the data, and has the ability to send the data to a remote host.
The 3095FC computes gas flow for both volume and energy. It provides on-site functionality and supports remote monitoring, measurement, data archival, communications, and control.
The 3095FC provides the following components and features:
• Weather-tight enclosure
• Termination Board
• 32-bit Processor Board
• Battery Charger Board
• Backplane Board
• 2 MB of flash ROM (Read Only Memory), which is field upgradeable
• 512 KB of battery backed-up RAM (Random Access Memory) storage
• Support for a three-wire 100-ohm Resistance Thermal Detector (RTD) input
• Internal lead-acid batteries (optional)
• Local Operator Interface (LOI) port - EIA-232 (RS-232)
• EIA-485 (RS-485) Comm 1 port
• Communications card using EIA-232 (RS-232) on Comm 2 port
(optional)
• Extensive applications firmware www.rosemount.com
Rosemount 3095FC
Hardware
Reference Manual
00809-0100-4832, Rev AA
October 2004
The backplane board provides the power regulation, the routing of the signals to the termination board, the processor board, the backup battery board, the optional communications board, the sensor module, and the battery charger board.
The termination board provides connections to the field wiring and is located on the terminal side of the housing. Connections include the power supply,
Local Operator Interface (LOI) communications, Comm 1 communications, optional Comm 2 communications, RTD wiring, and the I/O field wiring. The termination board provides surge and static discharge protection for the field wiring. Electronics include the RTD circuits and the final I/O drivers/receivers.
The termination board also serves as an interface to the backplane board in the electronics portion of the enclosure.
The 32-bit processor board contains the processor, memory, Local Operator
Interface (LOI) communications driver, Comm 1 communications driver, the reset controller, and the real-time clock. The functions for the I/O of analog conversion originate on the processor board. The processor board, also called the central processor unit, provides the Serial Peripheral Interface
(SPI) buss, Liquid Crystal Display drivers, and Sensor module.
The microprocessor has low-power operating modes, including inactivity and low battery condition. The 3095FC comes standard with 512 KB of built-in, static random access memory (SRAM) for storing data and history. The
3095FC also has 2 MB of flash ROM for storing operating system firmware, applications firmware, and configuration parameters.
The charger board controls the charging of the internal batteries, if installed.
Three D-size lead-acid batteries provide 2.5 Amp-hours of current at 6.2 volts nominal. The charger board also serves as the interface to the optional LCD assembly, as well as supporting the On/Off and Norm/Reset jumpers.
A backup battery provides backup power for the static RAM and the
Real-Time Clock. This battery is field replaceable. Under normal conditions, the battery has a functional life that exceeds five years.
An RTD temperature probe typically mounts in a thermowell on the meter run.
The RTD measures the flowing temperatures under a constant current drive.
The RTD wires connect directly to the RTD connector on the termination board located inside the enclosure.
The built-in inputs and outputs (I/O) on the 3095FC consist of a port for a
3-wire 100-ohm RTD input interface. Three diagnostic analog inputs (AI) monitor the battery voltage, logical voltage, and enclosure/battery temperature.
The Local Operator Interface (LOI) port provides a direct link between the
3095FC and a personal computer (PC) through a Local Operator Interface
Cable using EIA-232 (RS-232) communications. Configure the functionality of the 3095FC and monitor its operation using Rosemount User Interface
Software (see Section 3: Configuration).
The Comm 1 allows for EIA-485 (RS-485) serial communication protocols.
The EIA-232 (RS-232) activates Comm 2. “Establishing Communication” on page 2-13
The I/O parameters, Sensor inputs, flow calculations, power control, and security are configured and accessed using the configuration options available in Section 3: Configuration.
1-2
Reference Manual
00809-0100-4832, Rev AA
October 2004
Firmware
Accessories
Automatic Tests
Rosemount 3095FC
The firmware contained in flash ROM on the termination board, determines the functionality of the 3095FC and includes:
• 1992 AGA-3 flow calculations (with user-selectable AGA8 compressibility Detail, Gross I, or Gross II) for a single meter run
• Memory logging of 240 alarms and 240 events
• Archival of minute data from the last 60 minutes for 15 points
• Archival of 60 days of 10-minute data for 4 points
• Archival of 35 days of hourly data for 15 points
• Archival of 35 days of daily data for 15 points
• Archival of Min / Max historical data for today and yesterday
• Communications based on Modbus slave, (ASCII or RTU) protocol for use with EFM applications
• User level security
The 3095FC supports the following options and accessories:
• Local Operator Interface (LOI) cable
• Liquid Crystal Display (LCD) with two-line alphanumeric viewing. The
LCD automatically displays information at 3-second intervals.
• Solar panel mast assembly (installed to recharge the backup battery)
The 3095FC performs the following self-tests on a periodic basis:
• Battery low and high
• Software and hardware watchdog
• RTD automatic temperature compensation
• Sensor operation
• Memory validity
The 3095FC will operate with its internal batteries down to 5.4 VDC. The LCD becomes active when input power with the proper polarity and startup voltage
(typically set greater than 8.0 Volts) is applied to the CHG+ connector
(provided the power input fusing/protection is operational). The battery and logical voltage tests ensure that the 3095FC is operating in the optimum mode.
The software watchdog is controlled by the central processor unit (CPU). The software will arm the watchdog timer every second. If the watchdog timer is not armed for a period of 6 seconds, then the watchdog timer forces the
3095FC unit to reset. If necessary, the software automatically resets. The hardware watchdog is controlled by the CPU and monitors the power to the hardware. If the battery voltage drops below 5.4 volts, the 3095FC automatically shuts down.
The Rosemount 3095FC monitors its orifice-metering measurement for accurate and continuous operation.
1-3
Rosemount 3095FC
Low Power Mode
3095FC Functions
Reference Manual
00809-0100-4832, Rev AA
October 2004
Sleep mode is used to place the CPU in a low power mode. The battery voltage is monitored by low voltage detection circuitry and the low voltage limit value is set at 5.4 volts. During Sleep mode, sub-modules are powered down.
The 3095FC enters Sleep mode after one minute of inactivity on the communication ports.
Wake-up from Sleep occurs when the 3095FC receives a:
• Timed interrupt from the Real-Time Clock
• Signal from one of the communication ports
Most of the 3095FC functions are determined by the firmware. The features and applications provided by the firmware, which must be configured by using
Rosemount User Interface Software, include:
• Flow calculations for an orifice meter
• Extensive historical data archival
• Memory logging of 240 alarms and 240 events
• Security with local and remote password protection
Flow Measurement
The primary function of the 3095FC is to measure the flow of natural gas through an orifice in accordance with the 1992 American Petroleum Institute
(API) and American Gas Association (AGA) standards.
The primary inputs used for the orifice metering flow measurement function are DP, SP, and temperature. The DP and SP inputs are sampled once per second. The temperature input is sampled and linearized once per second from an RTD probe.
1992 Flow Calculations for Orifice Metering
The 1992 flow calculation is in accordance with ANSI/API 2530-92 (AGA
Report No. 3 1992), API Chapter 14.2 (AGA Report No. 8 1992 2nd printing
1994), and API Chapter 21.1. The 1992 flow calculation may be configured for either Metric or U.S. units.
Flow Time
The DP stored for each second is compared to the configured low flow cutoff. If the DP is less than or equal to the low flow cutoff or the converted
SP is less than or equal to zero, flow is considered to be zero for that second. Flow time for a recalculation period is defined to be the number of seconds the DP exceeded the low flow cutoff.
Input and Extension Calculation
Every second the Rosemount 3095FC stores the measured input for DP,
SP, and temperature and calculates the Integrated Value (IV) (the square root of the absolute upstream SP times the DP).
Flow time averages of the inputs and the IV over the configured calculation period are calculated, unless there is no flow for an entire calculation period. Averages of the inputs are recorded to allow monitoring during no flow periods.
1-4
Reference Manual
00809-0100-4832, Rev AA
October 2004
CONSIDERATIONS
Environmental
Requirements
Enclosures
Mounting
Power Installation
Requirements
Rosemount 3095FC
Instantaneous Rate Calculations
The instantaneous value of the IV is used with the previous calculation period of the Integral Multiplier Value (IMV) to compute the instantaneous flow rate. The IMV is defined as the value resulting from the calculation of all other factors of the flow rate equation not included in the IV. The instantaneous flow rate is used with the volumetric heating value to compute the instantaneous energy rate.
Flow and Energy Accumulation
The averages of the DP and SP, temperature, and sum of the IV are used with the flow time to compute the flow and energy over the calculation period. The flow and energy are then accumulated and stored at the top of every hour. At the configured contract hour, the flow and energy are stored to the Daily Historical Log and zeroed for the start of a new day.
The 3095FC is designed to operate between -40 to 75°C (-40 to 167°F).
When mounting, ambient temperatures may effect the operating temperature.
Operation beyond the recommended temperature range may cause measurement error and erratic performance.
The 3095FC should not be exposed to levels of vibration that exceed 2g for
15 to 150 Hz and 1g for 150 to 2000 Hz.
The 3095FC is packaged in a NEMA 4 windowed enclosure The enclosure is fabricated from die-cast aluminum alloy with iridite plating and paint. There are two ¾-in. pipe threaded holes for field conduit wiring, and communications.
Provide adequate clearance for wiring, service, and solar panel. Mount on a pipestand or to an orifice plate using a 3- or 5-valve manifold. The LCD display can be rotated 90 degrees in either direction.
For solar-powered 3095FC units orient solar panels as follows:
• Northern Hemisphere: due south (not magnetic south)
• Southern Hemisphere: and due north (not magnetic north)
• Sunlight is not blocked from 9:00 AM to 4:00 PM.
The primary power source is provided through DC voltage sources or solar power. Route power away from hazardous areas, sensitive monitoring devices, and radio equipment. Adhere to all local, company, and National
Electrical Code (NEC) requirements for power installations.
The 3095FC accepts input voltages from 8.0 volts to 28 volts at the charge
(CHG+ / CHG-) terminals on the termination board. The maximum power for
DC voltage sources is 130 mW, not including battery charging.
An external solar panel connects to the CHG+ / CHG- inputs on the termination board. Circuitry on the battery charger board monitors and regulates the charge based on battery voltage, charging voltage, and temperature. The 3095FC requires a minimum 8-volt 200 mA solar panel.
1-5
Reference Manual
00809-0100-4832, Rev AA
October 2004
Rosemount User
Interface Software PC
Requirements
Site Requirements
Wiring Requirements
Rosemount 3095FC
NOTE:
Do not allow the batteries to fully discharge. If the batteries fully discharge, the battery charger board may enter thermal limiting.
The Rosemount User Interface Software operates on any PC that meets the following requirements:
• IBM compatible
• Pentium-Class Processor (233 MHz or greater is recommended)
• CD-ROM drive
• Windows 95 (service release B), 98, ME, NT 4.0 (Service Pack 6),
2000 (Service Pack 2), or XP.
• 32 MB RAM
• 10 MB of available hard disk space
• RS-232 serial communication
• SVGA color monitor, 800 x 600 pixels
Local, state, and federal codes may restrict monitoring locations and dictate site requirements. Position the 3095FC to minimize the length of signal and power wiring.
I/O wiring requirements are site and application dependent. Local, state, or
NEC requirements determine the I/O wiring installation methods. Direct burial cable, conduit and cable, or overhead cables are options for I/O wiring installations.
1-6
Reference Manual
00809-0100-4832, Rev AA
October 2004
Section 2
MOUNTING
Rosemount 3095FC
Installation
Mounting . . . . . . . . . . . . . . . . . . . . . . . . . . . . . . . . . . . . . . . page 2-1
Installation . . . . . . . . . . . . . . . . . . . . . . . . . . . . . . . . . . . . . . page 2-2
Wiring . . . . . . . . . . . . . . . . . . . . . . . . . . . . . . . . . . . . . . . . . . page 2-4
Power Supply . . . . . . . . . . . . . . . . . . . . . . . . . . . . . . . . . . . page 2-9
Apply Power . . . . . . . . . . . . . . . . . . . . . . . . . . . . . . . . . . . . page 2-10
Install the Rosemount User Interface Software . . . . . . . . page 2-11
Getting Started with the Software . . . . . . . . . . . . . . . . . . . page 2-12
Establishing Communication . . . . . . . . . . . . . . . . . . . . . . page 2-13
Configuration Tree . . . . . . . . . . . . . . . . . . . . . . . . . . . . . . . page 2-14
Mounting the Rosemount 3095FC can be accomplished using one of the following methods:
• Pipestand mounted – The Rosemount 3095FC can mount to a 2-in. pipestand. Ensure that the pipestand meets all weight requirements and installation conforms to local building codes.
• Orifice Plate – Mount directly to an orifice plate using a 3- or 5-valve manifold.
With either mounting method, the pressure inputs must be piped to the process connections.
For solar panel mounting see “Mounting” on page 1-5. Dimensional drawings are located on page page A-7. Solar power installation is located on page page 2-3.
www.rosemount.com
Rosemount 3095FC
INSTALLATION
Rosemount 3095FC
Reference Manual
00809-0100-4832, Rev AA
October 2004
Piping from the static and DP meter runs connect to female ¼-18 NPT connections. The 3095FC is an upstream device, meaning that the SP line normally connects to the high pressure side (labeled “H” on the sensor body).
Installing the Rosemount 3095FC on a Pipestand
The following steps must be taken to install the 3095FC on a 2-in. pipestand:
1.
Install the pipestand using the pipestand documentation.
2.
Remove the orifice/meter run from service.
3.
Install the 3095FC on a pipestand using clamps or mounting brackets.
4.
Connect the impulse lines.
5.
Attach the appropriate wiring (see “Wiring” on page 2-4).
6.
Using the prefabricated operator interface cable, physically connect the 3095FC to the PC running the Rosemount User Interface
Software. One end of the cable (a 9-pin, D-shell, female connector) plugs into a serial communications port on the PC. The other end of the cable plugs into the 3095FC.
7.
Apply power to the 3095FC (see “Apply Power” on page 2-10)
8.
Log into the Rosemount User Interface Software (see page “Log into the Software” on page 2-12)
9.
Establish communication between the 3095FC and PC (see
“Establishing Communication” on page 2-13).
10. Configure the 3095FC (see “Configuration” on page 3-4)
11. Calibrate the 3095FC (see “Calibrate” on page 4-1).
12. Connect the 3095FC unit to any other external communication devices or networks.
13. Place the meter run in service and monitor with Rosemount User
Interface Software for proper operation.
Installing the 3095FC on an Orifice Plate (Direct Mount)
The following steps must be taken to install the 3095FC on an orifice plate:
1.
Remove the orifice/meter run from service.
2.
Install the 3095FC on the meter run using a manifold and hardware to secure the 3095FC to the orifice flanges.
3.
Attach the appropriate wiring (see “Wiring” on page 2-4).
4.
Using the prefabricated operator interface cable, physically connect the 3095FC to the PC running the Rosemount User Interface
Software. One end of the cable (a 9-pin, D-shell, female connector) plugs into a serial communications port on the PC. The other end of the cable plugs into the 3095FC.
5.
Apply power to the 3095FC (see “Apply Power” on page 2-10)
6.
Log into the Rosemount User Interface Software (see page “Log into the Software” on page 2-12)
7.
Establish communication between the 3095FC and PC (see
“Establishing Communication” on page 2-13).
8.
Configure the 3095FC (see “Configuration” on page 3-4)
2-2
Reference Manual
00809-0100-4832, Rev AA
October 2004
Solar Panels
Rosemount 3095FC
9.
Calibrate the 3095FC (see “Calibrate” on page 4-1).
10. Connect the 3095FC unit to any other external communication devices or networks.
11. Place the meter run in service and monitor with Rosemount User
Interface Software for proper operation.
Solar panels generate electrical power for the 3095FC from solar radiation.
They are the optimal choice for locations where a DC voltage source is not available. The size of solar panels required for a particular installation depends on several factors, including the power consumption of all devices connected to the solar array and the geographic location of the installation. An
8-volt solar panel can provide charging power for the backup batteries (see
“Solar Panel Sizing” for information on how to determine the appropriate panel size required for an application).
An external solar panel typically mounts to the same 2-in. pipe that supports the 3095FC (see “Mounting” on page 2-1). The panel wiring terminates at the charge (CHG+ / CHG-) power terminals on the termination board.
NOTE:
Solar panel size may violate certain CSA Class I, Division 1 ratings. Use approved 3095FC enclosure connectors for routing the power wiring.
The optional solar panel is adequate for support of API Chapter 21.1 compliant measurement and the retrieval of the historical logs once a day using the internal communication methods.
Solar Panel Sizing
To determine solar panel output requirements, first determine the solar insolation for the geographic area. The map in Figure 2-1 shows solar insolation (in hours) for the United States during winter months. Contact an
Emerson Process Management representative for a map detailing a specific geographic area.
Insolation (from map) = _____ hours
Next, calculate the amount of current required from the solar array per day using the following equation. I
SF
is the system current requirement.
I array
= [I
SF
(amps) ´ 24 (hrs)]/Insolation (hrs) = _____ amps
Finally, the number of solar panels can be determined using the following equation:
Number of Panels = I array
amps/(I panel amps/panel) = _____ panels
NOTE:
The “I panel
“value varies depending on the type of solar panel installed. Refer to the vendor's specifications for the solar panel being used.
The current accepted by the Rosemount 3095FC is limited by its charging circuit to around 1 Amp. Therefore, it is not practical to install a solar array that
2-3
Rosemount 3095FC
Reference Manual
00809-0100-4832, Rev AA
October 2004 supplies significantly more than 1 Amp to the 3095FC. The maximum input is
28 volts.
Do not allow the batteries to fully discharge. If the batteries are fully discharged, the battery charger board may enter thermal limiting.
Figure 2-1. Solar Insolation in
Hours for the United States
WIRING
The field terminals are all located on a Termination Board. The input power termination (CHG+ / CHG-) uses a removable connector and accommodates wiring up to 16 AWG in size.
Use the following steps to connect wiring. See Figure 2-2 on page 2-5.
1.
Remove power from transmitter (if applicable)
2.
Strip the rubber coating from the end (
1
/
4
-in. maximum) of the wire.
3.
Insert the bared end into the clamp beneath the termination screw. To prevent short circuits, the inserted wires should have as little bare wire exposed as possible.To prevent strain, allow some slack when making connections.
4.
Tightening the screw to 0.25 N-m (2.2 lb-in.). Do not over torque the connector screws.
5.
Check the polarity before applying power.
NOTE
To avoid circuit damage, use appropriate electrostatic discharge precautions, such as wearing a grounded wrist strap.
2-4
Reference Manual
00809-0100-4832, Rev AA
October 2004
Figure 2-2. Wiring Terminals
Rosemount 3095FC
Power Supply Wiring
RTD Wiring
Table 2-1. RTD Signal Routing
The terminals are labeled CHG+ for positive power connection and CHG- for negative power connection on a label on the termination board. These connections provide the input voltage and power for the battery charging circuitry. The maximum voltage that can be applied to the CHG+ / CHG- terminals is 28 Volts dc.
Pin
1
2
Signal
CHG+
CHG–
Description
Battery 8.0 to 28 V Power
Battery Common
Temperature is input through the Resistance Temperature Detector (RTD) probe and circuitry. The 3095FC provides terminations for a 2- or 3-wire
100-ohm platinum RTD with a IEC 751 curve. The RTD has an alpha (
α) equal to 0.00385.
The RTD mounts directly to the piping using a thermowell. RTD wires should be protected by a metal sheath or by a conduit connected to a conduit wiring fitting on the enclosure. The RTD wires connect to the three screw terminals designated “RTD” on the Termination Board (see Figure 2-2).
Wiring between the RTD and 3095FC should be shielded wire, with the shield grounded only at one end to prevent ground loops. Ground loops cause RTD input signal errors.
Table 2-1 displays the RTD terminal connections for the various RTD probes.
Terminal
RTD +
RTD +
RTD RET
Designation
Signal positive input
Signal positive input
Return reference
3-Wire RTD
RTD +
RTD +
RTD RET
2-Wire RTD
RTD +
Jumper to RTD +
RTD RET
2-5
Rosemount 3095FC
Communications Wiring
Reference Manual
00809-0100-4832, Rev AA
October 2004
The communication ports located on the 3095FC provide a data link to the
Rosemount User Interface Software, other 3095FC units, and host systems.
NOTE
All communication ports for the 3095FC are located on an optional communications card or built into the termination board.
Table 2-2. Communication Ports for the 3095FC
Port
1
2
3
4
5
6
3095FC Comm
Port Location
CPU RJ-45 (top)
CPU RJ-45 (top)
CPU 5-pin (bottom)
Module Slot 1
Module Slot 2
Module Slot 3
Default Tag
Local Port
COMM1
COMM2
COMM3
COMM4
COMM5
Function/Type
LOI / RS-232D
Ethernet
Serial / EIA-232 (RS-232)
EIA-232 (RS-232), EIA-485
(RS-485), Modem, or MVS
EIA-232 (RS-232), EIA-485
(RS-485), Modem, or MVS
EIA-232 (RS-232), EIA-485
(RS-485), Modem, or MVS
Local Operator Interface Port (LOI)
The Local Operator Interface (LOI) port provides direct communications between the 3095FC and the serial port of an operator interface device, such as an IBM compatible PC using an EIA-232 (RS-232) link. The interface allows access to the 3095FC (using Rosemount User Interface Software) for configuration and transfer of stored data.
The LOI terminal on the Termination Board provides wiring access to a built-in
EIA-232 (RS-232) serial interface, which is capable of up to 19,200 bps operation. The operator interface port supports Modbus protocol communications. The LOI also supports the log-on security feature of the
3095FC if the Security on LOI is Enabled in Rosemount User Interface
Software (“Security Configuration” on page 3-13).
NOTE
By default, the LOI Port is Comm Tag Local Port in the 3095FC > Comm Port settings screen. Use the 3095FC > Direct Connect command to connect using the LOI. See “Connection Methods” on page 2-13.
To ease wiring, operator interface cable is available as an accessory (see
“Installation” on page 2-2). Refer to Figure 2-3.
Figure 2-3. Operator Interface
Wiring
6
7
8
9
1
2
3
4
5
Connection at
PC COM Port
White TX
Red TX
Black TX
To screw
Terminals
2-6
Reference Manual
00809-0100-4832, Rev AA
October 2004
Table 2-3. Local Operator
Interface Port Wiring
Rosemount 3095FC
Table 2-4. PC Comm Port
Wiring
Table 2-5. EIA-485 (RS-485)
Communications Wiring
Signal
Common
LOI Power
(1)
Common
Ready to Send
Receive (RX)
Transmit (TX)
(1) Do not use the LOI to power external devices.
Label
COM
TX + V
COM
RTS
RX
TX
Signal
Transmit (TX)
Receive (RX)
Ground (GND)
Pin
2
3
5
Label
TX
RX
COM
EIA-485 (RS-485) Serial Communications - Comm 1
Use Comm 1 to monitor or alter the 3095FC from a remote site using a host or
Rosemount User Interface Software. Comm 1 supports baud rates up to
19200 bps. Comm 1 also supports the log-on security feature of the 3095FC if the Security on Comm 1 is Enabled in Rosemount User Interface Software.
Comm 1 sends and receives messages using Modbus protocol. Comm 1 permits EIA-485 (RS-485) serial communication protocols that meet EIA-485
(RS-485) specifications for differential, asynchronous transmission of data over distances of up to 1220 m (4000 ft). The EIA-485 (RS-485) drivers are designed for true multi-point applications with multiple devices on a single bus.
The default values for the EIA-485 (RS-485) communications are: 9600 Baud
Rate, 8 Data Bits, 1 Stop Bit, No Parity, 10 millisecond Key On Delay, and 10 millisecond Key Off Delay. The maximum baud rate is 19200 bps. To enable or disable the Comm 1 port, select Configure > Radio Power Control and select the Enable (default)/Disable under Radio Power Control (see “Radio Power
Control Configuration” on page 3-23).
Wiring should be twisted-pair cable. The terminals and their functions are as follows:
Pin
1
2
Function
RS-485
RS-485
Label
B
A
EIA-232 (RS-232) Communications - Comm 2
A EIA-232 (RS-232) communications card in the Comm 2 port can switch power to an external communication devices, such as a radio, to conserve power. A label on the termination board denotes the usage of each pin on the connector.
The EIA-232 communications card meets all EIA-232 specifications for single-ended RS-232 asynchronous data transmission over distances of up to
15 m (50 ft). The EIA-232 (RS-232) communications card defaults are: 9600 baud rate, 8 data bits, 1 stop bit, no parity, 10 millisecond Key On Delay, and
10 millisecond Key Off Delay. The maximum baud rate is 19200 bps. Refer to
Table 2-6 for communication card signals.
2-7
Rosemount 3095FC
Table 2-6. Communications
Card Signals
Table 2-7. EIA-232 (RS-232)
Communications Card Wiring
Ground the Transmitter
Reference Manual
00809-0100-4832, Rev AA
October 2004
Signals
RTS
RX
TX
Action
The request to send signals that the modem is ready to transmit.
The RXD receive data signals that data is being received at the communications card.
The TXD transmit data signals that data is being transmitted from the communications card.
Signal
Signal Common Negative
Switched Power
Ground
Request to Send
Tip / Receive Data
Ring / Transmit Data
Label
COM
TX
(2)
COM
RTS
RX
TX
(3)
(1)
+ B
(1)
(1) GND at Pin 1 and Pin 3 are identical. They are separated for ease of wiring.
(2) Switched Power is used with an internal radio or cell phone. It does not power external devices.
(3) Transmit (TX) connects to the 3095FC unit's receive.
Grounding reduces the effects of electrical noise on the unit's operation and protects against lightening. The 3095FC provides lightening protection for built-in field wiring inputs and outputs. Install a surge protection device on the
DC voltage source system to protect the device against lightning and power surges.
The 3095FC has two grounding screws inside the enclosure. It is recommended that a minimum of 14 AWG wire be used for the ground wiring.
To minimize signal errors caused by EMI (electromagnetic interference), RFI
(radio frequency interference), and transients, The I/O signal wiring cable should be an insulated, shielded, twisted-pair. All grounds should terminate at a single point.
NOTE
Grounding wiring requirements for DC voltage sources equipment are governed by the National Electrical Code (NEC). When the equipment uses
DC voltage sources, the grounding system must terminate at the service disconnect. All equipment grounding conductors must provide an uninterrupted electrical path to the service disconnect.
Earth Grounds
All earth grounds must have an earth to ground rod or grid impedance of 25 ohms or less as measured with a ground system tester. The grounding conductor should have a resistance of 1 ohm or less between the 3095FC enclosure ground and the earth ground rod or grid.
Pipelines With Cathodic Protection
The 3095FC must be electrically isolated from the pipeline. Electrical isolation can be accomplished by using insulating flanges upstream and downstream on the meter run. In this case, the Rosemount 3095FC could be flange mounted or saddle-clamp mounted directly on the meter run and grounded with a ground rod or grid system (see “Earth Grounds” on page 2-8).
2-8
Reference Manual
00809-0100-4832, Rev AA
October 2004
POWER SUPPLY
Rosemount 3095FC
Pipelines Without Cathodic Protection
The pipeline may provide an adequate earth ground and the 3095FC could mount directly on the meter run using an orifice plate. Use a ground system tester to make sure the pipeline to earth impedance is less than 2 ohms. If the pipeline to earth impedance is greater than 2 ohms, the 3095FC installation should be electrically isolated and a ground rod or grid grounding system installed. If the pipeline provides an adequate ground, a separate ground rod or grid system may not need to be installed.
The 3095FC accepts input voltages from 8.0 volts to 28 volts at the power terminals (CHG+ / CHG-) with no external current limiting (internal current limit is 200 mA). The CHG+ / CHG- terminal can accommodate up to 16 AWG wire.
To adequately meet the needs of the 3095FC system, it is important to determine the total power consumption and size of solar panel requirements accordingly. To determine the total 3095FC power consumption, be sure to add the power consumption (in mW) of any other devices used with the
3095FC in the same power system. The maximum power for DC voltage sources is 130 mW not including the battery charging.
Convert the total value (in mW) to Watts by dividing it by 1000.
mW / 1000 = Watts
For selecting an adequate power supply, use a safety factor (SF) of 1.25 to account for losses and other variables not factored into the power consumption calculations. To incorporate the safety factor, multiply the total power consumption (P) by 1.25.
PSF = P x 1.25 = _____ Watts
To convert PSF to current consumption in amps (ISF), divide PSF by the system voltage (V) of 12 volts.
ISF = PSF / 12V = _____ Amps
Batteries
Batteries provide power for the 3095FC when the solar panels are not generating sufficient output. The batteries are three D-size lead-acid batteries providing 2.5 Amp-hours of current at 6.2 volts.
The batteries are connected in series by the Battery Charger Board to achieve the required capacity. The battery capacity determines the number of days of reserve (autonomy) desired.
When the 3095FC is configured as an API compliant Electric Flow
Management (EFM) and requires an internal communications card, a solar panel, and the internal batteries, the 3095FC should be able to communicate the API audit trail information once a day to a remote host using no additional battery source, no additional solar panel, and maintain a 13 day autonomy in the event that the solar panel is lost.
To determine the system capacity requirements, multiply the system current load (ISF) on the batteries by the amount of reserve time required. Compute
“ISF” as described above. The equation is as follows:
System Requirement = ISF amps x Reserve hrs = _____ amp-hrs
2-9
Reference Manual
00809-0100-4832, Rev AA
October 2004
APPLY POWER
Rosemount 3095FC
To prevent unnecessary battery drainage, the 3095FC is delivered with the reset jumper in the OFF position. To apply power to the 3095FC:
1.
Complete the necessary wiring (“Wiring” on page 2-4).
1.
Unscrew the front end cap cover (LCD end).
2.
Place the power jumper in the ON position. The jumper is located on the LCD (if installed) or at J1 on the Battery Charger Board.
3.
Screw the front-end cap cover (LCD end).
After the 3095FC completes start-up diagnostics (RAM and other internal checks), the optional LCD displays the date and time to indicate that the
3095FC completed a valid reset sequence. If the LCD does not come on, refer to Section 5: Troubleshooting and Maintenance.
2-10
Reference Manual
00809-0100-4832, Rev AA
October 2004
Rosemount 3095FC
INSTALL THE
ROSEMOUNT USER
INTERFACE SOFTWARE
Install With Autorun
If a previous version of the Rosemount User Interface Software is installed, refer to “Uninstalling the Rosemount User Interface Software” on page 2-12.
Software Overview
The Rosemount User Interface Software is used to configure the 3095FC. For
PC requirements see “I/O wiring requirements are site and application dependent. Local, state, or NEC requirements determine the I/O wiring installation methods. Direct burial cable, conduit and cable, or overhead cables are options for I/O wiring installations.” on page 1-6.
The major components of the Rosemount User Interface Software user interface are:
• Menu bar and menus
• Function screens
• Dialog boxes
• Help system, including the Status bar and message boxes
The menu bar appears on the screen after successfully logging on. From the menu bar, the user may activate a menu and select a function in that menu.
Functions may be selected using Toolbar Buttons or the Configuration Tree
Menu
Several buttons are commonly used on many Rosemount User Interface
Software screens.These buttons are:
• Update: updates content of the window.
• OK: approves and closes the window. A Confirm Save dialog box appears if there are unsaved changes.
• Cancel: cancels all changes and closes the window.
• Apply: applies changes to the window.
1.
Insert the Rosemount User Interface Software installation CD-ROM into the drive
2.
Click Next.
3.
Click Yes to agree with the Terms and Conditions
4.
Enter the users Name and the Company name. Click Next.
5.
The software is saved to the default directory
C:\Program Files\Rosemount\Rosemount 3095FC User
Interface\User Interface. If another location is desired, use to Browse button to select that location. Click Next. A warning box appears if there are incompatible files.
6.
Review the items in the list and click Next.
7.
When the installation is complete click Finish.
8.
Remove the Rosemount User Interface Software installation
CD-ROM.
2-11
Reference Manual
00809-0100-4832, Rev AA
October 2004
Install Without Autorun
Uninstalling the
Rosemount User
Interface Software
Rosemount 3095FC
1.
Insert the Rosemount User Interface Software installation CD-ROM.
2.
Click the Windows Start button.
3.
Select Run.
4.
Click the Browse button
5.
Navigate to and select the Select.exe located on the CD-ROM.
6.
Click OK in the Navigation Window.
7.
Click OK in the Run window.
8.
Continue with in “Install With Autorun" steps 2-8, located above.
1.
Click the Windows Start button.
2.
Select Settings > Control Panel.
3.
Double-click the Add/Remove Programs icon.
4.
Select Rosemount 3095FC User Interface.
5.
Click Change/Remove.
6.
Follow the instructions that appear on the screen.
GETTING STARTED
WITH THE SOFTWARE
Run the Software
Log into the Software
To run the software, perform one of the following steps
• Double-click on 3095FC User Interface located on the desktop.
• Select Start > Programs > Rosemount 3095FC User Interface >
3095FC User Interface.
• Double-click on the file 3095.exe located in C:\Program
Files\Rosemount\Rosemount 3095FC User Interface (default directory). If the program file was saved to another location in “Install
With Autorun” on page 2-11, select this location instead.
NOTE
Only one version of Rosemount User Interface Software can run at a time.
To log on to Rosemount User Interface for Windows software:
1.
Connect the 3095FC to the Local Operator Interface (LOI) port and launch Rosemount User Interface Software.
2.
Enter the factory-assigned 3-character login (username): LOI.
Enter the 4-digit password: 1000. The login is assigned using the security feature of the Rosemount User Interface Software (see
“Security Configuration” on page 3-13).
NOTE
Login is case sensitive.
If the login is not valid, a dialog box appears. Click OK and reenter the login and password. Repeat this procedure until a successful login and password is entered. To exit the login screen press >Esc> or click Cancel.
When login is successful, the Configuration Tree appears on the screen. See
“Configuration Tree” on page 2-14 for more information.
2-12
Reference Manual
00809-0100-4832, Rev AA
October 2004
ESTABLISHING
COMMUNICATION
Connection Methods
Rosemount 3095FC
When the user is logged into the Rosemount User Interface Software, the PC must connect to the 3095FC unit so communication can be accomplished.
Use one of the following connection methods:
• Direct Connect - Connect to the 3095FC using the Local Port (LOI) if the default communication parameters apply.
• 3095FC (Communications) Directory View - Double-click the Station
Name to connect to the 3095FC using the parameters currently set for that 3095FC.
NOTE
Once connected, the Configuration Tree view becomes the active screen.
Direct Connect
The Direct Connect command allows the Rosemount User Interface Software to initiate communications with the 3095FC by performing a search of the PC communication ports at various baud rates. Direct Connect “locks on” to the first Comm Port and Baud Rate (1200, 2400, 4800, 9600, 19200, 38400, and
57600 bps) that successfully communicate with a 3095FC.
If unsuccessful, the program attempts to establish communications through the remaining COM Ports of the PC, successively, until it receives a valid reply.
For the Direct Connect option to operate correctly the PC must be connected to the Local Operator (LOI) port of the 3095FC with communication settings of:
• 8 Data Bits
• 1 Stop Bit
• No Parity
To use Direct Connect:
1.
Physically connect the 3095FC (see “Installation” on page 2-2).
2.
Launch and log into Rosemount User Interface Software (see
“Getting Started with the Software” on page 2-12).
3.
Perform one of the following:
• Click on the Direct Connect icon in 3095FC Directory
(Configuration Tree.)
• Click the Direct Connect button on the toolbar.
4.
If this is the first time connecting to the 3095FC, continue with
“Setting the Clock” on page 3-4.
2-13
Reference Manual
00809-0100-4832, Rev AA
October 2004
CONFIGURATION TREE
Rosemount 3095FC
Connect
When off-line, the 3095FC menu displays Connect. To use Connect:
1.
Physically connect the 3095FC (see “Installation” on page 2-2).
2.
Launch and log into Rosemount User Interface Software (see
“Getting Started with the Software” on page 2-12).
3.
Perform one of the following:
• Select a communications port from the Device Directory and press the <Enter> key.
• Double-click on a communications port from the Device Directory.
• Click the Connect button on the toolbar.
• Select Device > Connect to connect to the 3095FC currently selected in the Device Directory. If a 3095FC is not currently selected, the error “No 3095FC is Currently Selected” appears.
Remote Hardware Connection
To connect the PC to a remote 3095FC, a serial, dial-up modem, radio, satellite, or other communications line should be installed. This connection is typically made through the host port on the 3095FC. Use the Connect command to connect to a serial or dial-up modem
Disconnect from the 3095FC
Close the screen to disconnect an on-line connection. This automatically closes the connection.
When communication is established with a 3095FC or opening a configuration file, the Configuration Tree appears on the screen. The
Configuration Tree is used to perform the following:
• Add, delete, or modify communication configurations for the 3095FC units. The communication configurations allow the Rosemount User
Interface Software to communicate to an individual 3095FC unit.
• Establish Groups of 3095FC units. A 3095FC Group is typically several units in the same geographical area or a number of units with something else in common. Each group contains a list of all the
3095FC devices contained within that group.
• Assign an address for every 3095FC within a group. Each 3095FC has a Station Name (Tag) and unique address with which to differentiate each device. The Address must be different from any other host system that may access the communications link.
• Setup the 3095FC Comm Ports
Use the “+” and “–” symbols to display or hide various options.
Toggle between the Online configuration screen and the Configuration tree/device directory using Window > >select file>.
2-14
Reference Manual
00809-0100-4832, Rev AA
October 2004
Rosemount 3095FC
NOTE
Double-click the desired communications link (3095FC name) to connect to that 3095FC. Double-clicking an icon is the same as selecting the menu bar or toolbar button Direct Connect or Connect commands.
Configuration of the PC Communication Ports to the 3095FC unit cannot be performed within the 3095FC unit configuration screen. Return to the 3095FC
Directory (Configuration Tree) screen. If the user is in a configuration, select
Window > Device Directory or View > Device Directory to view the 3095FC directory.
Figure 2-4. Configuration Tree
Screen
Adding a Group
Multiple 3095FC units can be organized to form Groups. Unit Groups are typically units in the same geographical area or units with something else in common. When a Group file is selected, a list of all 3095FC communication setups in the Group appears below the Group.
1.
Right-mouse click on the Device Root directory icon.
2.
Select Add a Group.
3.
Right-mouse click on the New Group and select Rename. Type in the new Group name.
4.
Press <Enter>.
5.
The 3095FC can now be added to the Group.
Deleting a Group
1.
Right-mouse click on the group to be deleted.
2.
Select Delete Group.
3.
Click Yes.
2-15
Reference Manual
00809-0100-4832, Rev AA
October 2004
Rosemount 3095FC
Adding a 3095FC transmitter
1.
Right-mouse click on the Device Root directory icon.
2.
Select Add a Device .
3.
Right-mouse click on the New Device and select Rename. Type in the new device name.
4.
Press <Enter>.
5.
Configure the 3095FC communication parameters.
NOTE
Place a 3095FC connection under a Group by selecting the Group before adding the 3095FC Connection.
Deleting a 3095FC transmitter
1.
Right-mouse click on the device to be deleted.
2.
Select Delete Device.
3.
Click Yes.
Deleting all 3095FC transmitters
1.
Right-mouse click on the Device Root directory icon.
2.
Select Delete All Devices.
3.
Click Yes in the Confirm Delete Message dialog box.
Renaming a Group or 3095FC
1.
Right click on the Device or Group to be renamed.
2.
Select Rename.
3.
Type the new name.
4.
Press <Enter>.
2-16
Reference Manual
00809-0100-4832, Rev AA
October 2004
Section 3
OVERVIEW
BASIC FUNCTIONS
Rosemount 3095FC
Configuration
Overview . . . . . . . . . . . . . . . . . . . . . . . . . . . . . . . . . . . . . . . page 3-1
Basic Functions . . . . . . . . . . . . . . . . . . . . . . . . . . . . . . . . . page 3-1
Configuration . . . . . . . . . . . . . . . . . . . . . . . . . . . . . . . . . . . page 3-4
Custom Displays . . . . . . . . . . . . . . . . . . . . . . . . . . . . . . . . . page 3-54
The Rosemount 3095FC has parameters that must be configured before it is calibrated and placed into operation. Configuration must be performed using
Rosemount User Interface Software. Configuration can be performed either onsite using the LOI port or off-line and later loaded into the unit.
Default values for all parameters exist in the firmware of the 3095FC. The following parameters should be verified and configured:
• “Setting the Clock” on page 3-4
• “Configuring the System Flags” on page 3-5
• “3095FC Communications Ports Configuration” on page 3-8
• “Security Configuration” on page 3-13
• “LCD User List Configuration” on page 3-15
• “Analog Input (AI) Configuration” on page 3-16
• “Meter Run Configuration” on page 3-25 and “Gas Quality Tab” on page 3-28.
• “History Points Configuration” on page 3-32
Begin the configuration process with “Setting the Clock” on page 3-4.
The following functions are used throughout the configuration process. They are provided at the beginning of the section so they can be easily referenced.
Select TLP Options
Throughout Rosemount User Interface Software, the Select TLP dialog can be accessed by clicking the browse button with three dots. The Select TLP dialog allows the user to assign specific inputs and outputs to parameters.
Rosemount User Interface Software uses Point Type (T), Logical Number (L), and Parameter (P) to define point locations.
The display field at the bottom of the Select TLP dialog displays the numeric point location of the TLP point or a text abbreviation, depending on the
Display setting (see “Display TLP Options").
Display TLP Options
Select Tools > Options to set whether the TLP displays as text or numbers in
TLP display fields throughout the Rosemount User Interface Software.
www.rosemount.com
Rosemount 3095FC
Reference Manual
00809-0100-4832, Rev AA
October 2004
Duplicating a Configuration
Duplicate the configuration of a 3095FC using these instruction.
1.
File > Save Configuration to save the configuration to a specified file.
2.
Establish Communications with the second unit (see page 2-13).
3.
File > Download loads the configuration into the unit.
4.
After loading the configuration data into the second 3095FC (Step 3), save the configuration to a unique disk file by repeating Step 1.
Using Copy and Paste
Use Copy and Paste to copy data from one configuration screen to another of the same type.
1.
Configure the point that is to be duplicated.
2.
Click Apply.
3.
Click Copy.
4.
Select the next Point Number or go to the appropriate screen.
5.
Click Paste.
6.
Click Update.
New Configuration File
Create a configuration file off-line using the following instructions.
1.
Select File > New.
2.
The Type parameter indicates the type of 3095FC unit.
3.
The number of orifice meters will be 1.
4.
Save the configuration file.
5.
Establish an on-line connection to the 3095FC unit.
6.
Configure as necessary.
Open File
The Open option opens an existing configuration file. Configuration files are created using the Save Configuration function. To open a configuration file:
1.
Establish an on-line connection to the 3095FC (see “Establishing
Communication” on page 2-13).
2.
Select File > Open.
3.
Select the configuration file name. The extension must be .800.
4.
Configure as necessary.
Once the configuration file is opened it automatically becomes active and may be edited offline. The configuration file may also be loaded into a 3095FC using the “Download File" function (see page 3-3).
Save File
The Save option saves the current configuration of a connected 3095FC to a disk file. Once a backup configuration file is created it can be loaded into a
3095FC using the “Download File" function (see page 3-3).
1.
Select File > Save Configuration. The Save As dialog box appears.
2.
Type the desired File name of the backup file or use the default.
3.
Click Save. The file is saved in the default directory C:\Program
Files\Rosemount\Rosemount 3095FC User Interface\User Interface unless another directory was selected.
3-2
Reference Manual
00809-0100-4832, Rev AA
October 2004
Rosemount 3095FC
Download File
Use this function to download a previously saved configuration to a 3095FC.
Configuration files are created using the Save Configuration function. To download a previously saved configuration:
1.
Select File > Download.
2.
Select the configuration file name with the extension .FCF
3.
Click Open.
4.
Select the Point Types to download. Use Select All or Deselect All to change multiple Point Types. Select or Deselect individual Point
Types by selecting the configuration Point Type in the left column and selecting specific Point Types in the right column.
NOTE
The Configuration Points screen changes depending on the type of device that is connected.
5.
Select only the Configuration Points to download.
6.
Click Download. Downloading automatically begins.
7.
Click OK when the download is complete.
Print Configuration
The Print Configuration option enable specifying Point Types to Print.
1.
Select File > Print Configuration.
2.
Select the Point Types to be printed. Select the All or Deselect All buttons for multiple Point Types or select/deselect individual Point
Types by using the mouse to double click on the Point Type in the left column and selecting specific Parameters in the right column.
3.
Click OK.
4.
When the Print Preview screen appears, choose one of the following buttons:
• Print to send to a local printer.
• PDF to create a .pdf (Portable Document File).
• Excel to create an .xls spreadsheet file.
• RTF to create an .rtf (Rich Text Format) file.
• HTML to create an .htm Internet browser file.
• TXT to create a .txt text file.
5.
The 3095FC Group, Address, Field, and Value information displays in the Print Configuration results window.
3-3
Rosemount 3095FC
CONFIGURATION
Setting the Clock
Reference Manual
00809-0100-4832, Rev AA
October 2004
Immediately after connecting to a 3095FC for the first time, set the
Rosemount User Interface Software Clock to ensure proper logging of history.
The internal real-time clock provides time-stamping and control of the historical databases, Event Log, Alarm Log, Audit Log, and Contract Hour.
NOTE
The time stamp reflects the time at the end of the period. Data collected from
0800 to 0900 is thus time-stamped 0900. This is used for the logging of history.
See Figure 3-1
1.
Select Device > Clock or click the Clock icon in the toolbar.
2.
The display at the bottom of the calendar is the date and time from the PC clock. Continue with Step 5 if correct.
3.
If it is not correct: a. use the arrow buttons to select the correct Month and Year b. click on the desired day of the month c. click on the time field and type in the desired value (type A or P for the AM/PM field) or use the arrows.
4.
The clock can automatically compensate for daylight savings time by enabling this feature.
5.
Click Apply and click OK.
Figure 3-1. Clock Screen
3-4
Reference Manual
00809-0100-4832, Rev AA
October 2004
Rosemount 3095FC
Configuring the System
Flags
Use System Flags to perform actions that affect the overall operation of the
3095FC. From the Flags screen, a configuration can be saved to Flash memory and the 3095FC can be re-initialized.
NOTE
Certain Flags cause data to be lost, parameter values to be changed, and configuration memory to be cleared. Confirm Flag function before changing.
General Tab
Figure 3-2 on page 3-6
After a Warm Start, the 3095FC is initialized from SRAM memory if the configuration is valid. If valid, the databases remain intact. If the memory does not have a valid configuration, the configuration that was last saved to Flash memory is used. To save a valid configuration, use the Save Configuration button.
In a Cold Start, the 3095FC is initialized from the restart configuration saved in the Flash memory. If the configuration memory does not have a valid configuration written in it, the factory defaults are used.
NOTE
Perform a Cold Start after setting the clock and BEFORE setting any other parameters to ensure the 3095FC memory is cleared before configuration begins.
Cold Start reloads all restart configuration data and may also clear logs and displays. In addition, it may cause output changes, load new accumulator values, and disable user program tasks and User Data Types. Generally, a
Cold Start should not be used on a 3095FC that is actively gathering data or performing control. Save or document all required data and parameter values that could be affected before performing the Cold Start.
The following may occur when performing a Cold Start:
• Cold Start restores a configuration from default values stored in Flash memory.
• Cold Start & Clear ALL restores a configuration from default values stored in Flash memory and clears all History, Alarm Log/Event Log, and displays.
• Cold Start & Clear Alarms/Events restores a configuration from default values stored in Flash memory and clears the Alarm Log/Event Log.
• Cold Start & Clear Displays restores a configuration from default values stored in Flash memory and clears the 3095FC Displays.
• Cold Start & Clear History Data restores a configuration from default values stored in Flash memory and clears all History database files.
3-5
Rosemount 3095FC
Reference Manual
00809-0100-4832, Rev AA
October 2004
The Clear Flash Memory procedure clears all saved restart configuration data contained in Flash memory. Only factory defaults are retained. To return the
3095FC to the original factory default settings:
1.
Select Device > Flags > General Tab
2.
Select the Clear button and click Yes.
3.
Perform a Cold Start using the Cold Start & Clear ALL button.
4.
Click Yes, Apply, and OK.
NOTE
The Status field displays the current status of the save or clear flash memory function.
To save configuration settings to Flash memory, use the Flash Memory Save
Configuration function in the 3095FC Flags screen. It is possible to backup the working configuration from SRAM to Flash memory. In the event of operating problems, the working configuration can be restored by performing a Cold Start. To save the current configuration to Flash memory:
1.
Select Device > Flags.
2.
Select Save Configuration. Click Yes, Apply, and OK.
NOTE
Depending on the communications type and speed, the user may have to reconnect to the 3095FC after this procedure.
Figure 3-2. 3095FC System
Flags General Tab
3-6
Reference Manual
00809-0100-4832, Rev AA
October 2004
Rosemount 3095FC
Advanced Tab
Use the following instructions to configure the Advanced System Flags tab.
See Figure 3-3.
1.
Select Device > Flags > Advanced Tab.
2.
Enable CRC Check to perform CRC (Cyclical Redundancy Check) check on 3095FC protocol communications.
3.
Enable I/O Scanning so the I/O is in normal scan mode. When
Disabled, all I/O scanning stops and the last values are used until scanning is resumed.
4.
Select a Pass Through Mode communications option to send Pass
Through messages. Using any of the communications ports, Pass
Through Mode allows data to be received by one unit and then passed through to other devices connected on any other communications port. For example, the host communicates using a radio on its LOI port. Other 3095FC units can then be connected to the EIA-485 (RS-485) port of the first unit. All units can use the one radio to communicate to the host.
NOTE
COM2 may only use a Dial-up modem if it is receiving Pass Through messages. It cannot transmit to other field devices via Dial-up modem.
5.
Select the respective port (LOI, COM 1, or COM 2) for the Set RTS to
High for 30 Sec option and click Apply to activate the RTS
(Request-to-Send) signal. The RTS signal turns on for 30 seconds.
Figure 3-3. 3095FC System
Flags Advanced Tab
3-7
Rosemount 3095FC
Reference Manual
00809-0100-4832, Rev AA
October 2004
3095FC Communications
Ports Configuration
The communication ports of the 3095FC provide a link to a PC, such as one running Rosemount User Interface Software or a host PC. The 3095FC can have up to three communication ports.
General Tab
See Figure 3-4.
1.
Select Device > Comm Ports > General Tab
1.
Select the Port that the 3095FC is using to communicate. Enter the
10-character Comm Tag name for identification of the communications port.
2.
Select the transmit and receive data Baud Rate in bits per second.
3.
Select the Parity radio button if checks are to be performed by the communications controller.
4.
Select the number of Data Bits contained in an asynchronous byte, or character. This number is typically 8.
5.
Select the number of Stop Bits contained in an asynchronous byte, or character. This number is typically 1.
6.
Select if the RTS/CTS Handshaking is enabled.
7.
Enter the Key On Delay to define the number of seconds to delay after turning the RTS signal on before beginning transmission. For older radios, the Key On Delay may need to be set as high as 0.2 seconds. For radios designed for data transmission, no more than
0.02 second should be required.
8.
Enter the Key Off Delay intervals defining the period to delay before turning the RTS signal off once a valid message has been sent. The default of 0.01 seconds should be sufficient for most radios.
9.
Enter the Valid Receive Ctc (Counter) to log the number of valid
OpCodes received by the device on the communication port. The value in the counter can be preset or cleared.
Figure 3-4. Device Comm Port
General Tab Screen
3-8
Reference Manual
00809-0100-4832, Rev AA
October 2004
Rosemount 3095FC
RBX Tab
To configure the RBX, a modem must be present and appropriately configured. Use the following steps to configure the RBX tab.
See Figure 3-5 on page 3-10.
1.
Configure the Device > Comm Ports > General Tab (see “General
Tab” on page 3-8).
2.
Select Device > Comm Ports > RBX Tab.
3.
Enable RBX Mode. The RBX (Report-by-Exception) feature allows the 3095FC to call in to a host PC when a configured alarm occurs.
4.
Enter the RBX Host Address and Group number. The defaults of “1” and “0” are used by most host driver software.
5.
Set the Delay to define the time, in seconds, between attempts to transmit an RBX message. There is a Delay parameter associated with each Retry Count parameter, allowing the user to identify different length delays for each entry.
6.
The RBX Attempts #1 - 3 (Retry Count) is the number of attempts a message is repeated if a valid response is not obtained on the first attempt. Attempts include the initial message plus the retries. The three Retry Count parameters each have an associated Delay parameter. Selecting Fixed Number allows the user to enter a value for how many times a message is retried after the first unsuccessful attempt. Note that a “0” entry causes no retries. Selecting Continuous causes continuous retries that can only be stopped when the host clears the RBX alarm.
For example: If setting the Retry Count #1 to “2”, Delay #1 to “10”,
Retry Count #2 to “1” and Delay #2 to “20”, then after the first unsuccessful attempt to communicate with the host, the 3095FC tries two more times after waiting 10 seconds each time, and once more after waiting 20 seconds.
7.
Enabling the Extra Key On Delay to add an additional amount of time to delay transmitting an RBX message after turning the RTS signal on. The amount of time is fixed. This parameter is used for radio communications.
8.
RBX ACK Timeout - This is a message from the Device. If the ACK fails to be received within the timeout period the 3095FC retries the
RBX.
NOTE
The RBX Alarm Index indicates alarms currently being reported through the
RBX. The RBX Status parameter indicates the status of RBX messaging, either Active or Inactive. Active indicates that an SRBX alarm is being processed.
9.
After configuring the RBX function, use Device > Flags > Flash
Memory Save Configuration to save the configuration to the Flash
Memory in case a Cold Start must be performed.
3-9
Rosemount 3095FC
Figure 3-5. Device Comm Port
RBX Tab Screen
Reference Manual
00809-0100-4832, Rev AA
October 2004
3095FC Device
Configuration /
Information
This step establishes the Station Name, Address, Group, and other global variables that differentiate a 3095FC. Other system variables set in the information screen must be established for a particular application.
General Tab
See Figure 3-6 on page 3-11.
Use the following instructions to configure the Device Information General tab.
1.
Select Device > Information > General Tab.
2.
Enter the Station Name to be logged with the historical database for site identification.
3.
Enter a unique Address to differentiate each device in a communications group. The Address can be assigned a value from 1 to 255. The System Default Address of 240 should not be used.
4.
Enter a Group to identify a set of 3095FC units for communication purposes, typically to a host that polls the 3095FC. The station Group can be assigned a value from 1 to 255. All of the 3095FCs addressed as an area in the host have the same station Group.
5.
Set the Contract Hour to indicate when the values are totaled for a single day of production, accumulators are cleared, and data is logged to the Daily History database. The Contract Hour is based on a 24-hour clock with midnight as the “0” hour.
6.
Select Force End of Day to reset the daily and hourly accumulators.
Click Apply to cause the daily and hourly values to be logged into memory for all historical data totals.
7.
Select either U.S. or Metric Units for calculations. All calculations will be performed to reflect the selected preference.
8.
Use Device > Flags > Flash Memory Save Configuration to save the configuration to the Flash Memory in case a Cold Start must be performed.
NOTE
The Device Type field displays the type of 3095FC being configured.
3-10
Reference Manual
00809-0100-4832, Rev AA
October 2004
Figure 3-6. 3095FC
Differentiation / Information
General Screen
Rosemount 3095FC
Figure 3-7. 3095FC
Differentiation / Information point
Tab Screen
Points Tab
The Points screen allows the user to change the number of certain points that will be active.
1.
Select Device > Information > Points Tab
3-11
Rosemount 3095FC
Reference Manual
00809-0100-4832, Rev AA
October 2004
Other Information Tab
This tab displays information about the firmware (Version Name, Part
Number, ID, and Time Created), the boot firmware (Version Name, Part
Number, and Time Created), the processor (loading), amount of RAM installed, and the ROM (customer name and serial number).
Figure 3-8. 3095FC
Differentiation / Information
Other Information Screen
Figure 3-9. 3095FC
Differentiation / Information
Revision Info Screen
Revision Info Tab
This screen displays information about the firmware or accessory software installed in the 3095FC. The first field displays the name of an accessory if one is installed. For example, this field may say I/O Expansion Board or
Turbine Interface. When the field displays Not Used, there are no additional accessories installed. The part number and version control number may also be displayed.
3-12
Reference Manual
00809-0100-4832, Rev AA
October 2004
Security Configuration
Rosemount 3095FC
The 3095FC has two types of security.
• Rosemount User Interface Security - Enables access to the
Rosemount User Interface Software and what menu items the user can access.
• 3095FC Security - Enables communication to the transmitter.
Rosemount User Interface Security - Menu and Log On
See Figure 3-10 on page 3-14.
Use Operator ID and Password controls who can log on to Rosemount User
Interface Software and the Access Level controls access to menus and screens. Up to 21 different users are permitted.
1.
Select Utilities > 3095FC User Interface Security.
2.
Enter the 3 alphanumeric characters for each operator I.D. (login).
Each operator I.D. must be unique. The I.D.is case sensitive. The default is LOI.
3.
Assign the four numeric characters between 0000 and 9999 to define the password for each operator I.D (login). Users can have the same password. The default is 1000.
4.
Assign an access level for each user
• Level 0: only allows access to several options in the File and
Display menus, plus all options in the Help menu.
• Level 1: allows access to the menu options of Level 0 and several options in the View menu.
• Level 2: allows access the menu options of all lower level options,
Collect Data, EFM reports, and Meter menu.
• Level 3: allows access the menu options of all lower level options, several options in the Device and File menu, and the
Configuration menu.
• Level 4: allows access the menu options of all lower level options and several options in the Utilities menu.
• Level 5 (system administrator level: allows access to all menus and options.
NOTE
To prevent unauthorized users from accessing the software, delete the default factory-assigned login (username) LOI and the password 1000 after the security parameters are established.
Ensure that someone has Level 5 Access prior to deleting LOI 1000.
3-13
Rosemount 3095FC
Figure 3-10. Security Access
Level Screen
Reference Manual
00809-0100-4832, Rev AA
October 2004
Figure 3-11. Security Enable
Screen
3095FC Security
See Figure 3-11.
The 3095FC Security controls access to the device Comm Ports. When enabled, login is required to use the communication ports. Each communication port can be enabled or disabled separately.
The Access Level provides security for the 3095FC communication ports depending on the value of the Comm Port Security parameter as defined by the Comm Ports screen.
• Disabled - All login requested accepted. Access Level is ignored.
• Enabled - Login required (setup Operator ID and Password in
“Rosemount User Interface Security - Menu and Log On” on page 3-13). Upon successful login, full read and write access is allowed. Access Level is ignored.
• User Access Level Enabled - Login required (setup Operator ID and
Password in “Rosemount User Interface Security - Menu and Log On” on page 3-13). Rejects a login request when the Access Level is greater than the Access Level stored in the Utilities > 3095FC Security
Interface Security screen. This ensures the user is limited to the
Access Level configured in Rosemount User Interface.
3-14
Reference Manual
00809-0100-4832, Rev AA
October 2004
LCD User List
Configuration
I/O Configuration
Rosemount 3095FC
LCD User List Setup allows the user to assign up to 16 parameters to be displayed on the LCD. Each parameter is displayed for three seconds before continuing to the next.
1.
Select Configure > LCD User List Setup.
2.
Use the drop-down list box to select the desired LCD User List
Number (List No.) to configure.
3.
Click the Point Definition TLP button to define the desired point parameters to view on the LCD display. “Undefined” indicates that no parameter has been specified.
4.
Define up to 16 Data Point definitions to be displayed in the User List.
Enter the 10-character Description (Text) of the parameter.
Configuring the 3095FC is a matter of establishing points and then configuring various parameters. Each input and output has a unique Point Number to identify the input or output. Each I/O point parameter must be individually configured. The point number indicates the location of the point on the termination board. It is automatically assigned and cannot be edited.
Each Point Number is given a Tag, which includes up to 10 characters to identify the Point Number being defined in the I/O screen. Any alphanumeric characters, including spaces, may be used.
NOTE
Units is a user-defined 10-character description for the engineering units assigned to the I/O. For example: PSIG, MCF, degrees F, mA, or volts.
The I/O can be configured through either the Configure > I/O menu or the I/O list on the Configuration Tree.
A1 - DP
A2 - SP
A3 - RTD
B1 - Aux AI
E1 - Logic Voltage
E2 - Bat Voltage
E3 - Spare
E4 - Spare
E5 - Brd Temp
Scanning Disabled versus Scanning Enabled
If scanning is set to disabled, the transmitter stops updating values for each point number and values may be manually entered. Scanning Enabled allows the transmitter to continuously update the parameters.
I/O Monitor
I/O Monitor displays all installed and active I/O points and flow calculation information. The I/O Monitor screen shows the requested point information, such as field I/O values or calculated flow values. These on-screen values are automatically updated by Rosemount User Interface Software.
3-15
Rosemount 3095FC
Analog Input (AI)
Configuration
Reference Manual
00809-0100-4832, Rev AA
October 2004
Analog Inputs are analog signals generated by measurement devices, such as pressure and temperature transmitters, including RTD probes.
The following tabs are available as part of the AI configuration:
• AI General tab
• AI Advanced tab
• AI Calibration tab (see “Analog Input (AI) Calibration” on page 4-3)
• AI Alarms tab
AI General Tab
The AI General Table sets the basic parameters for the Analog Input point.
Use the following steps to configure the AI General Tab.
See Figure 3-12
1.
Select Device > I/O > AI Points > General Tab
2.
Select the Analog Input.
3.
Enter a 10-character Tag for identification of this Point Number.
4.
Enter the Value and Units.
5.
Select the Scanning option.
• When Scanning is set to Enabled, Value automatically displays the last Analog Input scan in engineering units.
• When Scanning is set to Disabled (manual mode), the value is no longer updated by the 3095FC. If Scanning is set to Disabled, enter a value to override the input. If Alarming is Enabled, an alarm generates when Scanning is set to Disabled.
6.
Set the Alarming option. The Active Alarms field indicates any alarms that are active for this point. For example, when Alarming is Enabled, the limit alarms (such as Low Alarm and Rate Alarm) that are active appear. Even if Alarming is Disabled, the Point Fail (hardware reports a malfunction) alarm and Manual (Scanning Disabled) indicators can still appear.
7.
Enter the Scan Period as the amount of time between updates of the filter value. All Analog Inputs are updated based on their individual
Scan Periods. The default value is 1 second. The minimum Scan
Period allowed is 50 msec.
8.
Enter the Low Reading EU (engineering unit) corresponding to 0% input. Enter the High Reading EU corresponding to 100% input.
For example: If a temperature transmitter is connected to the Analog
Input with a range of -40 °F to 212 °F, the Low Reading EU would be set to -40 and the High Reading EU would be set to 212.
9.
To complete point configuration click Apply.
10. Use Device > Flags > Flash Memory Save Configuration to save the configuration to the Flash Memory in case a Cold Start must be performed.
3-16
Reference Manual
00809-0100-4832, Rev AA
October 2004
Figure 3-12. AI General Tab
Screen
Rosemount 3095FC
AI Advanced Tab
The AI Advanced tab enables the user to configure features, such as filtering,
A/D conversions, and clipping for the selected Analog Input. Use the following steps to configure the AI Advanced Tab.
See Figure 3-13 on page 3-18.
1.
Select Device > I/O > AI Points > Advanced
2.
Enter a Filter value, which is a weighted sample using a percentage of the last value plus a percentage of the new value. The entered data is the percentage of the last value used. The Filter is calculated every
Scan Period by the formula:
(Last Value × Entered %) + (New Value × (100 - Entered %)) = Filtered Value
3.
Enter the Adjusted A/D 0%, which is the calibrated Analog-to-Digital
(A/D) reading that corresponds to 0%input. In the Calibrate function, this value is altered to set the 0% input exactly at the Low Reading
EU value to eliminate transmitter and system errors.
4.
Enter the Adjusted A/D 100%, which is the calibrated A/D reading corresponding to 100% input. This value is used to convert the input to engineering units. In the Calibrate function, this value is altered to set the 100% input exactly at the High Reading EU value.
NOTE
Raw A/D Input displays the current reading directly from the analog-to-digital converter. Actual Scan displays the actual amount of time in seconds that passes between scans. This number should be the same as shown for the
Scan Period parameter if the system is not overloaded.
5.
The Enable Average Raw Values calculates and averages the raw readings during the Scan Period. Use the outcome as the Raw A/D
Input during calculations. For example: When Enabled, an Analog
Input point configured with a Scan Period of 1.0 seconds obtains a new value from the A/D every 50 milliseconds. During the Scan
Period, 20 values are obtained from the A/D and summed together. At
EU Value calculation, the values summed are divided by the number of samples taken during the scan period and are used as the Raw
A/D Input. Disable this function to acquire instantaneous values.
3-17
Rosemount 3095FC
Reference Manual
00809-0100-4832, Rev AA
October 2004
6.
When Temp Compensation is Enabled, a temperature compensation curve is applied to the Analog Input using the board temperature of the 3095FC as a reference. Use this feature to improve the A/D conversion accuracy at temperature extremes for modular Analog
Inputs only; built-in Analog Inputs already have temperature compensation. When using this feature, be sure to perform a calibration after it is Enabled.
7.
When Clipping is Enabled, the 3095FC forces the Filtered EUs to stay within the range defined by the cut off limits. Set the cut off limits by using the LoLo Alarm and HiHi Alarm parameters (see “AI Alarms
Tab” on page 3-19).
8.
To complete point configuration click Apply.
9.
Use Device > Flags > Flash Memory Save Configuration to save the configuration to the Flash Memory in case a Cold Start must be performed.
Figure 3-13. AI Advanced Tab
Screen
3-18
Reference Manual
00809-0100-4832, Rev AA
October 2004
Rosemount 3095FC
AI Alarms Tab
See Figure 3-14 on page 3-20.
The AI Alarms tab sets the alarm parameters for the AI point.
1.
Select Device > I/O > AI Points > Alarms
2.
Set the values for the different alarms. There are six different alarms:
• Low Alarm: The limit value, in engineering units, to which the I/O must fall to generate a Low Alarm.
• High Alarm: The limit value, in engineering units, to which the I/O must rise to generate a High Alarm.
• LoLo Alarm: The limit value, in engineering units, to which the I/O must fall to generate a LoLo Alarm. The value is set lower than the
Low Alarm.
• HiHi Alarm: The limit value, in engineering units, to which the I/O must rise to generate a HiHi Alarm. The value is set higher than the High Alarm.
• Rate Alarm: The value, in engineering units, that represents the maximum amount of change permitted between updates. If the change is equal to, or greater than this value, an alarm is generated. To disable the Rate Alarm without disabling the other alarms, the Rate Alarm value must be set greater than the Span of the Analog Input or TDI.
• Alarm Deadband - The value, in engineering units, is an inactive zone above the Low Alarm limits and below the High Alarm limits.
The purpose of the Alarm Deadband is to prevent the alarm from being continuously set and cleared when the input value is oscillating around the alarm limit. This prevents the Alarm Log from being over-filled with data.
3.
Select RBX Alarming
• Disabled if limit alarms are not necessary for this point. Even if
Alarming is Disabled, the Point Fail (hardware reports a malfunction) alarm and Manual (Scanning Disabled) indicators can still occur. To conserve Alarm Log space, only Enable
Alarming when necessary.
• If the host PC is configured to receive field-initiated calls, a
Report-by-Exception (RBX) option is available.
• On Alarm Set - When the point enters an alarm condition, the
3095FC generates a RBX message.
• On Alarm Clear - When the point leaves an alarm condition, the 3095FC generates a RBX message.
• On Alarm Set and Clear - When point enters and leaves an alarm condition, the 3095FC generates a RBX message.
4.
To complete point configuration click Apply.
5.
Use Device > Flags > Flash Memory Save Configuration to save the configuration to the Flash Memory in case a Cold Start must be performed.
3-19
Rosemount 3095FC
Figure 3-14. AI Alarms Tab
Screen
Reference Manual
00809-0100-4832, Rev AA
October 2004
Soft Points Configuration
Softpoints are data storage areas that can be used by any 3095FC application. Softpoints consist of a Tag identifier, one integer value, and twenty floating values. Softpoints consist of:
• tag identifier (10 character string)
• 20 floats (floating point values)
• 1 integer value (16 bit)
• 2 longs (32-bit)
• 10 shorts (16-bit)
• 10 bytes (8-bit). Select:
Use the following steps to configure the soft points
See Figure 3-15.
1.
Select Configure > I/O > Soft Points.
2.
Select the Softpoint to be configured or viewed.
3.
Enter the Tag identification name (10-character).
4.
The Integer Flag is a 16-bit unsigned integer value used as a flag to denote the validity of the floating point data or as a counter.
5.
Enter the Float number (1 - 20 parameters). These parameters provide storage for IEEE floating point values.
6.
To complete point configuration click Apply.
7.
Use Device > Flags > Flash Memory Save Configuration to save the configuration to the Flash Memory in case a Cold Start must be performed.
3-20
Reference Manual
00809-0100-4832, Rev AA
October 2004
Figure 3-15. Soft Point Screen
Rosemount 3095FC
Opcode
Table 3-1. Summary of
Opcodes
Opcode (operation code) is an instruction from a host system that informs a slave device what actions to take. Table 3-1 contains a summary and brief description of each Opcode. In some cases the number of data bytes returned for an Opcode varies. For example, Opcode 0, a full update, always returns certain input/output (I/O) information along with optionally specified data.
Opcode Description
105
107
120
121
122
123
124
126
128
130
8
10
11
17
0
6
7
18
24
80
103
131
132
133
148
149
160
Send general update such as I/O update, gas flows, and control loop status.
Send device configuration with 20 data bytes defining device configuration.
Send current time and date
Set new time and date
Send data from configurable Opcode tables.
Set data in configuration Opcode tables
Set operator identification
Log event.
Store and forward
Reserved
Send system information such as on/off times, manual/alarm status, firmware version, and current time and date.
Send history point definition, min/max data, and current values for specified history point.
Send tag and current history period for specified history points.
Send pointer for alarm, even, and history logs
Send specified number of alarms starting at specified alarm pointer
Send specified number of events starting at specified event pointer
Read user template data
Read user Program Memory Allocation Information
Send last 60 minutes of data for specified history point.
Send archived daily and hourly data for the currently selected day and month
Send archived hourly and daily data for specified history point starting at specified history pointer
Send specified number of event sequence numbers starting at specified pointer
(1)
Clear specified number of event sequence number starting at specified pointer
(1)
Send number of writable events
(1)
Reads 240 bytes of data from a specified judgment: offset address
Reserved
Sends the entire structure for a specified Function Sequence Table (FST)
3-21
Rosemount 3095FC
Reference Manual
00809-0100-4832, Rev AA
October 2004
Opcode Description
162
165
166
167
180
181
Sets a single parameter
Set or send current configurable historical data
Set specified contiguous block of parameters
Send specified contiguous block of parameters
Send specified parameters
Set specified parameters
190/195 Reserved
224 Send Spontaneous Report-by-Exception (SRBX or RBX) message to host
225
255
Acknowledge Spontaneous Report-by-Exception message from device
Error messages transmitted by device in response to a request with invalid parameters or format.
(1) Industry Canada
Certain Opcodes only send data and do not receive data from the device. For example, Opcode 8 requests the device to set the time and date. The device resets the time and date and sends back an acknowledgement in which the
Opcode is repeated, but no data bytes are transmitted back. All acknowledgements are 8-byte messages that repeat the Opcode received, but do not transmit any data bytes.
Opcode 255 is an error message indicator. This is also an 8-byte message with no data bytes included. The Opcode is set to 255 to indicate the message received by the device had Cyclical Redundancy Error, but contained invalid parameters. For example, if a request was made for the information on Analog input #9, but the device only has 8 Analog inputs (0–7), the device would respond back with the 8-byte message with the opcode equal to 255 (error).
Opcode Table Configuration
Use the Opcode Table to group data for more efficient communication.
Parameters from different point types can be assigned to the Opcode table data points, substantially reducing the number of polls from a host PC.
See Figure 3-16 on page 3-23
1.
Select Configure > Opcode Table.
2.
Select the Table Number for the Opcode Screen.
3.
If the configuration has changed, update the version number. The version number field attaches a version number to an Opcode table configuration. It is a floating point number.
NOTE
Each Opcode Data point has a TLP box for mapping TLP values into the
Opcode Table Data point. If a host PC asks for a specific Opcode Data point, the 3095FC returns the value that is referred by the mapped TLP.
Once the parameters have been configured in the Opcode Table:
1.
Opcodes 10 and 11 can be used to read and write data directly without specifying the Point Type, Logical Number, or Parameter
Number (TLP).
2.
Opcodes 180 and 181 can be used to read and write the parameter data and do not include the parameter definition.
3-22
Reference Manual
00809-0100-4832, Rev AA
October 2004
Figure 3-16. Opcode Table
Screen
Rosemount 3095FC
Radio Power Control
Configuration
Figure 3-17. Radio Power
Control Timing
Radio Power Control conserves battery power to a radio or any other communicating device. Radio power is controlled either by the DTR signal or by a Discrete Output (DO). Because there are separate Radio Control points for COM1 and COM2, radio power cycling for COM1 can be configured differently from that for COM2, including independent timer values and separate output controls using the Output Definitions options.
For each Radio Power Control point, the power cycling can be configured to automatically change three times a day. During each of these three periods
(Zone 1, Zone 2, and Zone 3), the ON and OFF times can be setup to operate at various intervals. Figure 3-17 is a graphical depiction of how the power control operates within each time “zone.”
Time = N
Time = N
Zone 1
Zone 2 Zone 3
On Time Off Time On Time Hold Time Off Time On Time
Host Communication Detected
During the ON time:
• The DO is switched to ON.
• Communication may occur.
During the OFF time:
• The DO is set to OFF.
• Communication does not occur.
If communications occur during the ON time, the time is extended by the Hold
Time. The DO remains ON and receives interrupts remain enabled for the duration of the Hold Time. When the Radio Power Control parameter is
Enabled, radio power cycling is activated. The Low Battery Shutoff parameter allows power cycling to be automatically disabled whenever the input voltage to the 3095FC falls below the specified threshold.
See Figure 3-18 on page 3-25.
1.
Select Configure > Control > Radio Power Control.
2.
Select the Radio Power Control point to be configured. Enter the Tag
(10-character) to identify this point.
3-23
Rosemount 3095FC
Reference Manual
00809-0100-4832, Rev AA
October 2004
3.
Enter the The Radio Power Status, which indicates the current status of the Power Control function of ON, OFF, or RBX. The Active Zone indicates which zone is currently activated for determining the Start
Time, On Time, and Off Time. Some of the On Time is also used by the radio during power-up initialization of the receiver, causing part of the On Time to be unavailable for receiving requests.
4.
Select Radio Power Control Enabled to activate the Radio Power
Control function.
5.
Use the radio buttons to select Seconds and Minutes. In Seconds mode, the time base for the timers is in 0.1 second increments, primarily used with radios. In Minutes mode, the time base for the timers is in one-minute increments, primarily used with cellular telephones.
6.
Enter the Zone parameters to indicate when Radio Power Control is active/inactive.
• Start Time that the respective Zone begins, in hours and minutes
(HHMM). Time is expressed in local time, 24-hour clock. For example: “1500” under Zone 2 means that the associated On
Time and Off Time are used beginning at 3:00 p.m.
• On Time during a power cycle when the output is in the ON state.
• Off Time during a power cycle that the output is in the OFF state.
7.
Enter the Hold Time that the output remains ON after detection of communications activity (in seconds, unless the Minutes mode has been enabled). This value applies to all Zones. When communications occur during the On Time, the On Time is extended by the Hold Time.
8.
Enter the Low Battery Deadband. The Low Battery Deadband value is added to the Low Battery Shutoff to determine when the Radio
Power Control function is enabled and allows the DO to turn ON as needed.
9.
Enter a Low Battery Shutoff value that specifies the voltage at which
Power Control is automatically disabled. The voltage being sensed is the System AI Battery Input voltage (0-1). The Low Battery Shutoff parameter allows power cycling to be automatically disabled whenever the input voltage to the 3095FC falls below the specified threshold. The default value is 11 Volts.
10. Select the Power Timer, which counts down the amount of time (On
Time, Off Time, or Hold Time) that the Radio Control is currently using. The value is the number of seconds remaining.
11. Select which DO point the signal will send along.
12. Enter the On Counter, which indicates the cumulative time that the
Power Control has been in the ON state. The Off Counter value indicates the cumulative time that the Power Control has been in the
OFF state.
3-24
Reference Manual
00809-0100-4832, Rev AA
October 2004
Rosemount 3095FC
NOTE
If a Report By Exception (RBX) message needs to be sent to the host PC, the radio power on DO will come on and allow the message to be sent. The hold time should be long enough to allow the 3095FC to receive a response back from the host.
13. Click Apply when configuration is complete. Save the configuration using Device > Flags > Flash Configuration Memory Save.
Figure 3-18. Radio Power
Control Screen
Meter Run Configuration
The Meter Setup screens allows configuring the AGA calculation point for the connected 3095FC. The Meter Setup screens are used to configure the computation of gas flow through a meter (Orifice AGA3)
Each meter run must be uniquely identified to ensure proper configuration and allows the host to acquire the required data.
Each meter run Point Number is given a unique Meter ID of up to 10 characters to label the meter run for which this flow calculation is performed.
Use the Meter Description field to enter up to 30 characters to further identify this meter run or provide information about the run.
The 3095FC uses AGA3 (1992) for flow calculation in orifice metering.
Additionally, the AGA8 compressibility method is used as well. The AGA8 method calculates the compressibility factor based on the physical chemistry of the gasses at specified temperatures and pressures. The AGA8 method provides extended capabilities for accurate computation of compressibility factors beyond the temperature, pressure, and composition ranges of NX19.
3-25
Rosemount 3095FC
Reference Manual
00809-0100-4832, Rev AA
October 2004
General Tab
The General tab sets the basic parameters for the meter.
See Figure 3-19 on page 3-26
1.
Select Meter > Setup.
2.
Select the Point number to be configured. Enter the meter tag. Enter a unique Meter Description for the meter.
3.
Select the Meter Type. Orifice is the default.
4.
Select the Calculation Standard and Edition.
5.
Select if Alarming is enabled or disabled.
6.
Enter the inside Pipe Diameter (orifice) of the pipe, The U.S. units are inches and the Metric units are millimeters.
7.
Enter the Orifice Diameter (orifice) of the orifice. The U.S. units are inches and the Metric units are millimeters.
8.
Enter the Low Flow Cutoff (orifice) when the DP value of the metering device is less than the Low Flow Cutoff value, the calculated flow is set equal to zero. No Flow is recorded in the Alarm Log if Alarming is
Enabled. For the Orifice AGA3 calculation method, this value is in inH
2
O (U.S.) or kPa (Metric).
9.
Enter the Integral Multiplier Period (IMP) to indicate the frequency of calculation in minutes of the Integral Multiplier Value (IMV) to be used in the flow equation. The Integral Value (IV) portion of the flow equation is calculated once per second. The value must be an integer divider of 60, such as 1, 2, 3, 4, 5, 6, 10, 12, 15, 20, 30, or 60.
Figure 3-19. Meter Setup
General Tab Screen
3-26
Reference Manual
00809-0100-4832, Rev AA
October 2004
Figure 3-20. Meter Setup Inputs
Tab Screen
Rosemount 3095FC
AGA Meter Inputs Tab
See Figure 3-20 on page 3-27.
The Inputs tab screen defines the field inputs, including DP and SP to be used in the flow calculation.
To setup the meter inputs used in the flow calculation:
1.
Select Meter > Setup >Input tab.
2.
Click the Differential Pressure TLP button to assign the input that senses the DP (high DP, if Stacked Dp is Enabled). The input units are inH
2
O (U.S.) or kPa (Metric).
NOTE
If Manual appears, the Values field can be used to enter a value for the meter input. Otherwise, the Values field indicates the current input value.
3.
Click the Static Pressure TLP button to assign the input that senses the SP. The input units are psig (U.S.) or kPa (Metric).
4.
Click the Temperature TLP button to assign the input that senses the temperature of the flowing gas. The input units are degrees
Fahrenheit (U.S.) or degrees Celsius (Metric).
3-27
Rosemount 3095FC
Reference Manual
00809-0100-4832, Rev AA
October 2004
Gas Quality Tab
See Figure 3-21 on page 3-28
Gas Quality defines the mole percentage of twenty gas components, the
Heating Value Basis, the Heating Value, and the Specific Gravity.
NOTE
Entering Hexane+ (C
6
+) and the mole percent of hexane+ will automatically distribute among hexane, heptane, octane, nonane, and decane as specified by the heavy gas distribution parameters under the Advanced tab (“Advanced
Meter Setup Tab” on page 3-29.
1.
Select Meter > Setup > Gas Quality tab.
2.
Enter the mole percent of each Gas Component, or use the default values of 96% methane, 3% ethane, and 1% nitrogen. The Total Mole
% should equal 100%. If changes are applied to the device when the
Total Mole % does not equal 100%, the composition will be adjusted based on the Normalization Type selected.
3.
Select Log Methane Adjust Enabled if the percentages are automatically adjusted to total 100.
4.
Select the Heating Value Basis. If Dry or Wet is selected, select
Calculate for the Heating Value parameter (the heating value is always calculated on a dry basis). If As Delivered is selected, select
Enter for the Heating Value parameter and provide the value.
5.
Select either Calculate or Enter for the capacity Heating Value of a specified quantity of gas. If Calculate is chosen, the Heating Value is calculated from the gas composition data. If Enter is chosen, the value entered will be used in the heating value calculation. Use the units button to toggle between volume or mass measurement U.S units are BTU/Cf or BTU/Lb and the metric unit are MJ/m3 or MJ/Kg.
6.
Select either Calculate or Enter for the Specific Gravity to specify the ratio of the molar mass of the gas to the molar mass of air. If
Calculate is selected, the specific gravity is calculated from the gas composition data at standard conditions of 14.73 PSIA and 60 °F. If
Enter is selected, the value entered for standard conditions is used.
Figure 3-21. Meter Setup Gas
Quality Tab Screen
3-28
Reference Manual
00809-0100-4832, Rev AA
October 2004
Rosemount 3095FC
Advanced Meter Setup Tab
See Figure 3-22 on page 3-30
The Meter Setup advanced tab contains a number of additional parameters that affect the flow calculation.
1.
Select Meter > Setup > Advanced tab.
2.
Select the FPV Method of calculating the compressibility factor under the 1992 AGA scheme. The three methods are:
• Detailed - Requires the natural gas composition in mole percent to be entered.
• Gross I - Uses the density of the natural gas, its heating value, and the quantity of non-hydrocarbon components as follows:
• Specific Gravity
• Real gas gross heating value per unit volume
• The mole % of CO
2
• Gross II - Uses the density of the natural gas as well as the quantity of non-hydrocarbon components as follows:
• Specific Gravity
• The mole % of CO
2
• The mole % of N
2
NOTE
If either Gross Method is chosen, manually enter the Specific Gravity and
Heating Value in the Gas Quality screen. For Gross Method II, the heating value is required only for calculating the gas energy flow.
3.
Select the units (U.S. or metric)
4.
Select either Calculate or Enter Atmospheric Pressure for the value of the atmospheric pressure (absolute) at the metering location. If
Calculate is selected, the value is calculated from other parameters. If
Enter is selected, type a value greater than zero for the pressure. The units of measurement are in psia (U.S.) or kPa (metric).
5.
Enter the flow measurement Base Pressure specified in the gas contract. The pressure units are in psia (U.S.) or kPa (metric).
6.
Enter the flow measurement Base Temperature specified in the gas contract. The temperature units are in degrees Fahrenheit (U.S.), or degrees Celsius (metric).
7.
Enter the Elevation or altitude of the metering location. The units are in feet (U.S.) or meters (metric) is selected.
8.
Enter the geographic Latitude of the metering location. The units are in degrees (U.S.) and minutes separated by a decimal point (metric).
For example: 46.15.
9.
Select the Pressure Tap used in the meter run.
• Select Gauge or Absolute as the way of measuring pressure at the
SP tap. The selection must be consistent with the type of pressure measured by the sensor (absolute or gauge).
10. Select the Force Recalculation Set and click Apply to cause a full recalculation of the flow without waiting for the next normal recalculation.
3-29
Rosemount 3095FC
Reference Manual
00809-0100-4832, Rev AA
October 2004
NOTE
Normal recalculation periods are established in Meter Set-up screen using
Integral Multiplier period or the Base Multiplier Period. Upon forcing a recalculation, the accumulations are zeroed and the flow value is logged as a new entry. The Force Recalculation parameter is automatically set to Clear after the recalculation.
Figure 3-22. Meter Setup
Advanced Tab Screen
Figure 3-23. Meter Setup
Instrument Calibration Tab
Screen
Instrument Calibration Tab
See Figure 3-23 on page 3-30.
The 3095FC Instrument Calibration options allow setting the calibration parameters for the Analog Inputs of the flow calculation.
1.
Select Meter > Setup > Instrument Calib tab.
2.
Dead Weight Calibration - If a deadweight tester is used to calibrate the DP or the SP, select the respective Yes option. Enter the
Calibrated Grav. Accel. value.
3.
Enter the User Correction Factor value that is multiplied by the base volume flow equation, allowing the user to make any desired adjustment to the flow. When using the default value 1, no correction is applied.
3-30
Reference Manual
00809-0100-4832, Rev AA
October 2004
Rosemount 3095FC
Meter Setup Alarms Tab
See Figure 3-24 on page 3-32.
Meter Setup Alarms allows setting the alarm limits, configure RBX Alarming, and view active alarms for the selected meter run. Alarms can be configured for the individual meter runs and/or the stations, generating meter-specific and /or station-wide alarm conditions.
For enable alarms, the alarms can be configured using the Alarms tab in the
Meter Set-up screen and are logged to the Alarm Log. To conserve log space, alarms should be enabled only when necessary. For alarm disable, no alarm is generated for a point, regardless of the Alarm configuration. Alarm conditions display in the Active Alarm fields located in the Meter Configuration screen.
NOTE
Even if alarms are not used, check and adjust the alarm value to prevent false alarms.
Use the following steps to set the alarm values.
1.
Go to Select Meter > Setup > General tab. Set the Alarming to Enable
(see “General Tab” on page 3-26).
2.
Go to Select Meter > Setup > Alarms tab.
3.
Enter the Low Alarm limit value, in engineering units, within the calculated flow value resides to generate a Low Alarm. The default value is 1000 MCF/day (U.S.) or km
3
/day (metric).
4.
Enter the High Alarm limit value, in engineering units, within the calculated flow value resides to generate a High Alarm. The input units are 10000 MCF/day (U.S.) or km
3
/day (metric). The Active
Alarms field on the General tab indicates any alarm currently activated. For example, Low indicates that the calculated flow is below the Low Alarm limit.
5.
Select the RBX Alarming option.
• On Alarm Set - When the point enters an alarm condition, the
3095FC generates a RBX message.
• On Alarm Clear - When the point leaves an alarm condition, the
3095FC generates a RBX message.
• On Alarm Set and Clear - When point enters and leaves an alarm condition, the 3095FC generates a RBX message.
NOTE
RBX Alarming requires the communications port to be properly configured.
3-31
Rosemount 3095FC
Figure 3-24. Meter Setup Alarms
Tab Screen
Reference Manual
00809-0100-4832, Rev AA
October 2004
History Points
Configuration
The History option allows data stored in the current value database to be copied and stored for up to a month in the historical database. The historical database can be configured to log only the values that need to be logged. The values are logged in the standard (minute-hourly-daily) time base.
NOTE
The time stamp used for standard logging reflects the time at the end of the period, not at the beginning. For example: Data collected from 8:00 to 9:00 is stamped 9:00.
The 3095FC also maintains a 10-minute historical database.
Four types of historical databases are maintained:
• Min/Max Database (see “Meter History")
• Minute Database (see “General History")
• Hourly Database (see “General History")
• Daily Database (see “General History")
Meter History
The Min/Max Database is for viewing only and cannot be saved to a disk file.
A total of fifteen history points may be accessed. For an AGA3 meter run, the first eight (out of fifteen) history points are pre-configured for flow metering history and cannot be changed. They are configured as follows:
1.
Flowing Minutes Today (Accumulate archive type)
2.
DP (Average)
3.
Static or Line Pressure (Average)
4.
Flowing Temperature (Average)
5.
C´ or Integral Multiplier Value (IMV)
6.
Pressure Extension or Integral Value (IV) (Average)
7.
Instantaneous Flow (Accumulate)
8.
Instantaneous Energy (Accumulate)
3-32
Reference Manual
00809-0100-4832, Rev AA
October 2004
Rosemount 3095FC
History Point 2, History Point 3, History Point 4, and History Point 6 are all setup as an Average Archive Type that employs one of the following techniques:
• Flow dependent time-weighted linear averaging (default)
• Flow dependent time-weighted formulaic averaging
• Flow-weighted linear averaging
• Flow-weighted formulaic averaging
Averaging Technique
The averaging technique is selected using Rosemount User Interface
Software. The user-configurable history points, 9-15, may be configured using
Rosemount User Interface Software. In the Meter > Setup > Inputs tab, select the desired Averaging Technique. The selected Averaging Technique is applied to the meter inputs.
History point archival includes:
• Archival of minute data from the last 60 minutes for 15 points.
• Archival of 60 days of 10-minute data for 4 points.
• Archival of 35 days of hourly data for 15 points.
• Archival of 35 days of daily data for 15 points.
• Archival of minimum / maximum historical data for today and yesterday.
Log Types
The following are logs that are available through the History Points data.
• Minute Historical Log: The 3095FC has a 60-minute historical log for each history point. The Minute Historical Log stores the last 60 minutes of data from the current minute. Each history point has Minute
Historical Log entries.
• 10-Minute Historical Log: The 3095FC has a 10-minute historical log for up to four (4) history points that stores 60 days of 10-minute data.
The four (4) 10-Minute history points include DP, SP, flowing temperature, and an auxiliary Analog Input.
• Hourly Historical Log: The 3095FC has a total of 35 days of hourly historical logs available for every history point. The Hourly Historical
Log is also called the Periodic database. Normally, the Hourly Log is recorded at the beginning of every hour. The time stamp for periodic logging consists of the month, day, hour, and minute.
• Daily Historical Log: The 3095FC has a total of 35 daily historical logs for every history point. The Daily Log is recorded at the configured contract hour every day with a time stamp that is the same as the
Hourly Log. Each history point has daily historical log entries.
• Min / Max Historical Log: The Min / Max database displays the minimum and the maximum values for the database points over a
24-hour period for today and yesterday. The Min / Max historical log can be viewed, but not saved to disk.
3-33
Rosemount 3095FC
Reference Manual
00809-0100-4832, Rev AA
October 2004
• Alarm Log: The Alarm Log contains the change in the state of any alarm signal that has been enabled for alarms. The system Alarm Log has the capacity to maintain and store up to 240 alarms in a “circular” log. The Alarm Log has information fields that include time and date stamp, alarm clear or set indicator, and either the Tag name or a
14-byte detail string in ASCII format.
In addition to providing functionality for appending new alarms to the log, the Alarm Log allows host packages to request the index of the most recently logged alarm entry. Alarm Logs are not stored to the flash
ROM during the Save Configuration function in Rosemount User
Interface Software.
The Alarm Log operates in a circular fashion with new entries overwriting the oldest entry when the buffer is full. The Alarm Log provides an audit history trail of past alarms. The Alarm Log is stored separately to prevent recurring alarms from overwriting configuration audit data.
• Event Log: The Event Log contains changes to any parameter within the 3095FC made through the protocol. This Event Log also contains other 3095FC events, such as power cycles, cold starts, and disk configuration downloads. The Event Log provides an audit history trail of past operation and changes.
The system Event Log has the capacity to maintain and store up to 240 events in a circular log. The Event Log has information fields that includes point type, parameter number, time and date stamp, point number if applicable, the operator identification, and either the previous, current parameter values, and either the Tag name or a
14-byte detail string in ASCII format.
In addition to providing functionality for appending new events to the log, the Event Log allows host packages to request the index of the most recently logged event entry.
Event Logs are not stored to Flash memory when Save Configuration is issued in Rosemount User Interface Software. The Event Log operates in a circular fashion with new entries overwriting the oldest entry when the buffer is full. The Event Log provides an audit trail history of past operation and changes. The Event Log is stored separately to prevent recurring alarms from overwriting configuration audit data.
3-34
Reference Manual
00809-0100-4832, Rev AA
October 2004
Rosemount 3095FC
General History
The Configure > History option allows data to be stored in the historical database. Hourly and daily values are stored for up to 35 days. The historical database can be configured to log only the values that need to be logged.
NOTE
History points setup in the Meter > History screen override history points setup in the Configure > History screen. When configuring history points ensure that the point is not already defined in Meter History.
1.
Select Configure > History Points.
2.
Select the desired history point to be configured in Select History
Point. The parameter currently configured (if any) for this history point appears in the Value to Archive field.
NOTE
The first eight history points are reserved for use as Meter History; begin selecting history points with History Pt. #9.
3.
Click the TLP Value to Archive label to specify a point type and parameter to be archived.
4.
Select the Point Type to archive. To prevent this history point from logging values, select Undefined as the Point Type.
5.
Select the Logical Number. For example, select Analog Input AIN A 2.
6.
Select the specific Parameter to log.
7.
Click OK.
8.
Choose the Select Archive Type to specify the exact archive type of the history point. The archive type affects how the logged value is calculated.
• Undefined – Point not configured
• Disabled - Point not configured
• Average - Minute values are averaged to compute the hourly value. The flow inputs (such as DP) allow the user to select among four types of averaging for calculating flow quantities or for providing values. Refer to the Select Average Type parameter.
• Accumulate - The flow, energy, or uncorrected flow values are summed over a specified time period to compute the value based on what is selected in the Select Accumulation Time Basis. The accumulation technique is used to acquire accurate accumulated counts from an input for a specified time period.
• Current Value - Current sampled value is used for the hourly value.
3-35
Rosemount 3095FC
Reference Manual
00809-0100-4832, Rev AA
October 2004
• Totalize - The difference between the current value and last hour's current value is used for point values polled or received as accumulated values. The Totalization technique assumes that the value being archived is zeroed out by something else at Contract
Hour and that no rollover of the value occurs. Totalization occurs at the Minute Historical Log and is summed up for the Hourly and
Daily Historical Logs. A minute after Contract Hour, the current value is archived. All other minutes are the difference between the current value and the previous minute's archived value.
• Select Average Type -The Select Average Type parameter is set to Average, this list appears at the bottom of the screen. Choose one of the following options to determine how the average value is calculated.
• Flow Dependant Linear - This is the default method for calculating the average for the flow input. It is the simplest and most commonly used method. This method discards samples for periods when there is no measurable flow and performs a straightforward (linear) average of the remaining samples to compute the minute and hour values. The value specified in the Low Flow Cutoff of the Meter setup determines the values.
When no flow occurs, all values are sampled.
• Flow Dependant Formulaic - Like the Flow-Dependent Linear method, this method discards samples for periods when there is no flow. However, in calculating the average, this method typically takes the square root of each sample before averaging the samples together and then squares the result.
This formulaic method produces a slightly lower value than the linear method.
• Flow Weighted Linear - This method does not discard any samples. Instead, it “weights” each sample by multiplying it by a flow value (square root of the DP measured during the sample period), and then performs a linear average by dividing the sum of the flow-weighted sample by the sum of the flow values. This results in minute and hourly values that are more reflective of short periods of high flow.
• Flow Weighted Formulaic - This method combines the flow-weighting action with the formulaic averaging technique, both of which were described previously.
9.
Select Accumulation Time Basis - When the Selected Archive Type is
Accumulate, this list appears at the bottom of the screen. Choose one of the following options to determine how the accumulated values are computed:
• Per Sec - Values summed to compute the second value.
• Per Min - Values summed to compute the minute value.
• Per Hour - Values summed to compute the hourly value.
• Per Day - Values summed to compute the daily value.
3-36
Reference Manual
00809-0100-4832, Rev AA
October 2004
History, Alarm, Event, and Audit Log Reports
Rosemount 3095FC
History, Alarm, Event, and Audit Log can be viewed from the View menu.
History can viewed from an on-line Rosemount User Interface Software,
3095FC, or from a disk file. History and log files work in a circular fashion; the newest data overrides the oldest data when the log is full.
Once a selected history log has been displayed, the following options are available:
• Select New - Return to the Select History points screen and make a new selection.
• Save - Save the history archives to a file.
• Print Preview - Show a preview of what will be sent to the printer and allow printing of the history log.
• Close - Close the screen. View the History Logs from the View menu.
Once the alarms are displayed the following options are available:
• Save - Save the alarm log to a file.
• Print Preview - Show a preview of what will be sent to the printer and allow printing of the alarm log.
• Close - Close the screen. View the Alarm Logs from the View menu.
Once the events are displayed the following options are available:
• Save - Save the event log to a file.
• Print Preview - Show a preview of what will be sent to the printer and allow printing of the event log.
• Close - Close the screen. View the Event Logs from the View menu.
A report is generated based on the Search Criteria from the 3095FC.
1.
Select View menu > History, Alarm, or Event > From 3095FC.
2.
Select the History Points in the Search Criteria field (History only).
Select, Deselect All, and Select All allow the user to mass select or deselect History Points. The Search Criteria selections change depending on the Frequency.
3.
Select the Frequency to be viewed (History only). The Minute, Hourly
(Hour), Daily (Day), or Minimum and Maximum (Min/Max) values can be view.
4.
Click Upload.
A report is generated based on the Search Criteria from a disk file.
1.
Select View menu > History, Alarm, or Event Log > From File.
2.
Select the file and click Open.
3.
Perform one of the following:
• Select New - Return to the Select History points to be shown screen and perform a new search.
• Invert - View the log in reverse order (default is newest to oldest).
This changes the time order of the Alarm, or Event Log.
• Save - Save the report to a file.
• Print Preview - Print the report.
• Close - Close the screen.
3-37
Rosemount 3095FC
Reference Manual
00809-0100-4832, Rev AA
October 2004
Collect Data
Select 3095FC > Collect Data to save various 3095FC data to disk files.
Select the values to be saved for later generating into a report(s). This screen may only be accessed when the user is on-line with the already configured
3095FC from which data will be gathered.
Use Save As and the Browse button to either accept the default File name or enter a new File name. The files are saved in the default directory C:/Program
Files/Rosemount User Interface for Windows/Data unless another directory was selected. When selecting EFM Report Data, the Collect Data function saves all the values for EFM parameters. The files has the .efm extension.
The EFM Reports utility uses the flow data that was gathered using either the
“EFM Report Data” or the “All” option. The “All” function retrieves Rosemount
User Interface Software data including the EFM Report Data and stores it in disk files identified with various extensions. The “EFM Report” function retrieves just the detailed flow data needed for an EFM report and stores it in disk files with an .AGA extension.
NOTE
EFM Reports can be created, using this data, by selecting View >EFM Report.
Configure History for
EFM Reporting
Electronic Flow Measurement (EFM) Reports
The Rosemount User Interface Software has the ability to create an EFM report file that contains all the configuration, alarms, events, and history logs associated with the stations and meter runs. This file becomes the custody transfer audit trail. To collect the periodic and daily history logs required for the
EFM report file, a specific list of station and meter run parameters must be configured for historical archiving.
For Orifice meters, the following history points must be configured for EMF reports.
Table 3-2. Orifice Meter Run History Points
Description
Flowing Minutes
DP
SP
Temperature
Pressure Extension
Multiplier Value
Volume
Energy
Archive Type
Totalize
Avg (Flow Dependent Linear)
Avg (Flow Dependent Formulaic)
Avg (Flow Weighted Linear)
Avg (Flow Weighted Formulaic)
Avg (Flow Dependent Linear)
Avg (Flow Dependent Formulaic)
Avg (Flow Weighted Linear)
Avg (Flow Weighted Formulaic)
Avg (Flow Dependent Linear)
Avg (Flow Dependent Formulaic)
Avg (Flow Weighted Linear)
Avg (Flow Weighted Formulaic)
Avg (Flow Dependent Linear)
Avg (Flow Dependent Formulaic)
Avg (Flow Weighted Linear)
Avg (Flow Weighted Formulaic)
Avg (Flow Dependent Linear)
Avg (Flow Dependent Formulaic)
Avg (Flow Weighted Linear)
Avg (Flow Weighted Formulaic)
Totalize
Totalize
Point Type
Orifice Meter Run Values
Orifice Meter Run Configuration
Orifice Meter Run Configuration
Orifice Meter Run Configuration
Orifice Meter Run Configuration
Orifice Meter Run Configuration
Orifice Meter Run Configuration
Orifice Meter Run Configuration
Parameter
Minutes Accumulated
DP
SP
TMP
Pressure Extension
Multiplier Value
Flow Accumulated
Energy Accumulated
3-38
Reference Manual
00809-0100-4832, Rev AA
October 2004
Rosemount 3095FC
Selecting View > EFM Reports opens the initial screen. The utility program is used in conjunction with the AGA flow calculation capabilities of the 3095FC to display or print previously collected flow data. EFM Reports generate printed and on-screen reports of the historical flow data for a meter point.
Selecting EFM Reports causes the Rosemount User Interface Software to suspend operation and load the EFM Reports Utility.
The flow data is contained in an EFM Report file, which includes the operational characteristics of all the meter runs configured in the 3095FC. The operational characteristics consist of Configuration Parameters, Hourly and
Daily History, Events, and Alarms associated with each measured meter run.
The Audit Log events are also included for Industry Canada custody transfer.
To create the EFM Report disk file, use Device > Collect Data and select either the “EFM Report” or “All” option (“Configure History for EFM Reporting” on page 3-38). Once the disk file is created, a report can be generated anytime thereafter and connection/communication with the Rosemount User
Interface Software is no longer necessary. The EFM Reports utility formats this report for a single meter run covering a specified period of time. The user can choose to view the report or print the report.
NOTE
In order for the EFM Reports utility to work, the historical database in the
Rosemount User Interface Software or 3095FC must be configured so that certain flow calculation values can be retrieved from memory.
1.
Select View > EFM Reports.
2.
Click the EFM Report File button to display a lists the names of all the files that have the .AGA extension previously created by using the
Collect Data function (see “Configure History for EFM Reporting” on page 3-38).
3.
Select the desired file and click Open.
4.
Use the Enter meter run drop-down list box to select the meter run for which to create a report.
5.
Enter the Start date and End date. Any alarms, events, hourly history, and daily history records that occur between these dates will be included in the report. Click Next.
6.
Under the Available sections list select the Data files to be included in the report. Use the arrows to scroll through the selections.
7.
Click Next.
8.
Select the Available Subsections to include in the report. Use the arrows to scroll through the selections.
9.
Click Next.
10. Select the Point Types and Fields to include in the report.
11. Click Finish. The EFM Report displays.
3-39
Rosemount 3095FC
Modbus Configuration
Table 3-3. Modbus Function
Codes
Reference Manual
00809-0100-4832, Rev AA
October 2004
The 3095FC has the ability to communicate using Modbus protocol. This makes it possible to integrate with Modbus devices into the same Host/Slave system. The 3095FC can act as a Slave device.
The LOI, Comm 1, and Comm 2 ports all support Modbus communications.
The Modbus mapping on the Modbus Registers screen and Modbus History
Access Registers screen will affect Modbus communication on all of the
3095FC comm ports.
The 3095FC point types and parameters for Function Codes 1, 2, 3, 4, 5, 6,
15, and 16 are configured using the Rosemount User Interface Software.
Table 3-3 provides details of the Function Codes supported by the 3095FC.
Code Meaning
01
02
03
04
05
06
15
16
Read Logic Coil Status
Read Discrete Input Status
Read Output Registers (Holding)
Read Input Registers
Force Single Logic Coil
Preset Single Holding Register
Action
Obtain current status (ON/OFF) of a group of logic coils (outputs)
Obtain current status (ON/OFF) of a groups of
Discrete Inputs
Obtain current binary value in one or more holding requests
Obtain current binary value in one or more binary registers
Force logic coil to a state of ON or OFF.
Acknowledge Alarm or Event request
Place a specific binary value into a holding register
Force Multiple Logic Coils Force a series of consecutive logic output coils to defined ON or OFF states.
Preset Multiple Holding Registers Place specific binary values into a series of consecutive holding registers.
General Tab
The General tab sets the basic communication parameters.
See Figure 3-25 on page 3-42
1.
Select Configure > Modbus > Configuration > General tab
2.
Select the Modbus Type. The Modbus protocol supports two modes of transmission ASCII and RTU. All devices in the same communications must be configured with the same mode of transmission.
• American Standard Code for Information Interchange (ASCII) – allows additional time intervals of up to one second to occur between characters without causing an error. This allows the messages to be read with the use of a dumb terminal. Each character is divided into two 4-bit parts that are represented by their hexadecimal equivalent. The ASCII mode uses twice as many characters as the RTU mode. Each character sent is composed of a Start bit, 8 or 7 Data bits, and one or two Stop bits with Even, Odd, or No parity. ASCII mode uses Longitudinal
Redundancy Checking (LRC) error checking
3-40
Reference Manual
00809-0100-4832, Rev AA
October 2004
Table 3-4. Message Framing
Rosemount 3095FC
• Remote Terminal Unit (RTU)– Allows for greater character density and better data throughput than ASCII for the same baud rate.
Each message is transmitted in a continuous stream. Data is sent in 8-bit binary characters. In the ASCII mode, each RTU character is divided into two 4-bit parts that are represented by their hexadecimal equivalent. RTU mode uses Cyclic Redundancy
Check (CRC) error checking. By default, RTU is enabled.
In either mode, ASCII or RTU, a Modbus message is placed by the transmitting device into a frame that has a known beginning and ending point.
ASCII Message Framing
Begin of
Frame
:
Address Function Data
LRC Error
Check End
2 characters 2 characters N characters 2 Characters CRLF
RTU Message Framing
Begin of
Frame Address
T1-T2-T3-T4 1 Byte
Function Data
1 Byte
CRC Error
Check
N * 1 Byte 2 Bytes
End
T1-T2-T3-T4
3.
Select Log Modbus Events Enabled to log all Modbus parameter changes to the Event Log or select Disabled to allow Modbus parameter changes to occur without being logged. By default, Log
Modbus Events is Enabled.
4.
Select the Byte Order of data bytes in a transmission or request can be reversed by the selection made in these check boxes. This only affects the Data field of a Modbus message, has no effect on the data for Function Codes 01, 02, and 05, and only applies to floating points.
• Least Significant Byte First - Selecting this check box places the least significant byte first. This is the default value.
• Most Significant Byte First - Selecting this check box places the most significant byte first.
5.
Select EFM Modbus Enable to use an implementation of Modbus protocol with EFM extensions. This causes the Hourly (Periodic) and
Daily indices to be returned as floating point values instead of the standard integer and character values. In addition, the history index is adjusted to accommodate a one-based index (1 to 840), and the date stamp (MMDDYY) is returned before the time stamp (HHMM), which does not include seconds.
6.
The “status” field displays the status codes returned from the modem.
3-41
Rosemount 3095FC
Figure 3-25. Configure Modbus
General Tab Screen
Reference Manual
00809-0100-4832, Rev AA
October 2004
Scale Values Tab
The Scale Value tab allows the user to enter low and high floating point and integer values for converting between integer and floating point numbers.
See Figure 3-26 on page 3-43
1.
Select Configure > Modbus > Configuration > Scale Values tab.
2.
Enter the Integer Scale values. In the 3095FC, the endpoints of the
Analog Inputs and the Analog Outputs are used to scale or calibrate the range of the input or output signal. Because each I/O point can have different scaling, the raw values from the Analog I/O points are normalized to the values defined by the Integer Scale Low Value and
Integer Scale High Value fields.
3.
Enter the Low Value that contains the 0% value for all analog data
(Type 3, Parameter 17 and Type 4, Parameter 9) registers. Enter the
High Value that contains the 100% value for all analog data (Type 3,
Parameter 17 and Type 4, Parameter 9) registers.
NOTE
The High and Low Value fields are signed integers, so they can range from zero to 32767. These data fields can also be used to scale the Analog I/O to integer values with an implied decimal point. For example: All Analog I/O Raw values can be transmitted with 0 to 1000 values (0 to 100.0, decimal point implied) by setting the values in this field to 0 for the Integer Scale Low Value and 1000 for the Integer Scale High Value.
3-42
Reference Manual
00809-0100-4832, Rev AA
October 2004
Figure 3-26. Configure Modbus
Scaled Values Tab Screen
Rosemount 3095FC
4.
Enter the Float Scale # in the Low Value Float Scale and High Value
Float Scale fields used when the Host is not able to process floating point numbers.
In Host systems that do not accept floating point numbers, eight sets of floating point ranges for values can be specified. This allows floating point values, such as PID Setpoints, to be read and set by the
Host as integer values. The 3095FC floating point values are converted to integers by configuring a register or range of registers with the Conversion field set in the Modbus Registers Definition configuration.
The equations used to convert floating point values to integer values to enable the reading of floating point values are:
• Float Range = High Value Float Scale - Low Value Float Scale
• Integer Range = High Value Integer Scale - Low Value Integer Scale
• Adjusted Reading = Float Reading - Low Value Float Scale
• Integer = (Integer Range × Adjusted Reading)/(Float Range) + Low Value
Integer Scale
The equations used to convert integers to floating point values are:
• Float Range = High Value Float Scale - Low Value Float Scale
• Integer Range = High Value Integer Scale - Low Value Integer Scale
• Adjusted Integer = Integer Sent - Low Value Integer Scale
• Float Value = (Adjusted Integer × Float Range)/(Integer Range) + Low
Value Float Scale
3-43
Rosemount 3095FC
Reference Manual
00809-0100-4832, Rev AA
October 2004
Modbus - History Collection
The Modbus protocol sends the Hourly (periodic) and Daily History. Refer to
“History Access Registers Tab” on page 3-44. Each record contains a time and date stamp and all of the history archives for which the Register Number is configured. The Modbus Function Code 03 and the History Archive
Register are used to collect the archived data. Two Modbus registers indicate the current Hourly and Daily history index as selected in the Archive Type field. These can be configured in the Hourly History Index Register and the
Daily History Index Register. These indexes identify the current history archive at which data was last logged.
To collect the Hourly and Daily history a standard Modbus Function Code 03 is used. The Register Number field is used to address the individual History
Archive Register. The Daily Index, Hourly Index, and Event/Alarm data fields are used to address a history index number. The response message contains two floating point values for the time and date stamp of the history archive
(time stamp = HHMMSS and date stamp = MMDDYY) and floating point values for each of the defined history points for that History Archive Register.
The date stamp for history uses the current year and does not figure the number of years since 1980.
NOTE
When in Modbus with EFM extensions mode, the time stamp is in the HHMM format. In addition, the date time stamp is returned before the time stamp.
History Access Registers Tab
See Figure 3-27 on page 3-45
The History Archive Register is a single register that can contain one or more history points for retrieval of the Event Log, Alarm Log, and Historical
Archives. Historical data is contained in Point Type 55 up to 35 days of hourly data for each of its history points can be stored. The points mapped on the history tab are configured on the Configure > History Points screen.
1.
Enter Configure > Modbus > Configuration > History Access
Registers tab.
2.
Enter the modbus Register Number used to acquire the Daily Index values.
3.
Enter the Modbus Register Number used to acquire the Hourly Index values.
4.
Enter the Modbus Register Number used to acquire the Events/Alarm logs.
5.
Enter the Modbus Register Number used to acquire the group of history points defined in the Starting History Point and Ending History
Point fields without having to define each history point separately.
6.
Enter the Starting History Point to acquire a group of history points without having to define each history point separately, enter values in the Starting History Point and Ending History Point fields. The Starting
History Point value is the first history point to be retrieved.
7.
Enter the Ending History Point to acquire a group of history points without having to define each history point separately, enter values in the Starting History Point and Ending History Point fields. Then
Ending History Point is the last history point to be retrieved.
3-44
Reference Manual
00809-0100-4832, Rev AA
October 2004
Figure 3-27. Modbus History
Access Registers Screen
Rosemount 3095FC
NOTE
The Starting History Point and Ending History Point values must be different with the Starting History Point value being the smaller of the two. The group of history points is specified by the Modbus register value set in the Register
Number field.
8.
Enter the Archive Type to archive either Hourly or Daily values.
9.
Enter the Conversion field to specify the type of conversion required, if any, on the data before it is sent to the Host or before it is written to the 3095FC. The conversions are used to allow integer values instead of floating point values to be transmitted and received.
Table 3-5 summarizes the applicable function calls and their associated register and data fields.
Modbus - Events / Alarms Functionality
The record formats for the Event log and Alarm log are the same size and have similar contents. The first word in a record is a bit map in which bit 9 indicates if the log record is an Event (1) or an Alarm (0). The meanings of the other bits are specific to either the event or the alarm log records. The Event and Alarm log record consists of the bytes shown in Table 3-6. A breakdown of the bit map in the first byte is given in the table immediately after the record table.
3-45
Rosemount 3095FC
Reference Manual
00809-0100-4832, Rev AA
October 2004
Table 3-5. History, Event, and
Alarm Functionality
Function
Code Register Field
3
3
3
5
3
3
7160 – Daily Index
7161 – Hourly Index
32 – Event/Alarm Register
32 – Event/Alarm Register
703 – 7160 – Daily History
704 – Hourly Index
Data Field
Ignored
Ignored
Ignored
Ignored
History Archive
Register (0 to 34)
History Archive
Register (0 to
8.39)
Description
Response contains current daily index
Response contains current hourly index
Response contains Events and Alarm records. Maximum number of bytes returned is 240 (12 records of 20 bytes each). Events are returned before
Alarms are returned. The format is displayed in Table 3-6.
After Events and Alarms have been returned, there must e an acknowledgement made so that the same Events and Alarms are not returned on the next request.
Response contains two floating point values for the time and date stamp of the history archive (time stamp = HHMMSS and date stamp = MMDDYY) and floating point values for each of the defined history point for that History Archive
Register.
Response contains two floating point values for the time and date stamp of the history archive (time stamp = HHMMSS and date stamp = MMDDYY) and floating point values for each of the defined history point for that History Archive
Register.
The 3095FC supports the Modbus with EFM extensions method for retrieving alarms, events, and history. When a Function code 3 request referencing defined Events/Alarms Register (usually 32) is received, it begins to collect records from first the Event Log and then the Alarm Log, starting where the last poll left off. The 3095FC will collect records until either there are not any more new events/alarms or the maximum of twelve records have been collected. The 3095FC sends the information back to the host, which in return replies with Function Code 5, referencing the same Events/Alarms Register, indicating that the points have been received and that the host is ready for the next twelve records.
When the 3095FC receives a Function Code 3 request referencing one of the user-defined Periodic History Registers or Daily History Registers, the number of registers field is interrupted as an index into the specific history log.
The reply message contains the date and time stamp and historical values configured for the specified for that index.
Reading Events / Alarms Register
The Modbus request to read the Event/Alarm log (see Table 3-6) uses the standard read Function Code 03 and the Event/Alarm Register (parameter
#0) in the Modbus Special Function Table (point type 39). In this request, the number of registers is included to maintain format compatibility but is ignored by the receiving 3095FC unit. For the date stamp in the events and alarms returned, the year (YY) is really the number of years since
1980 (for example, the current year is 1997, so the year (YY) for the date stamp would be 17).
Acknowledging Events / Alarms
The Modbus request to acknowledge the event/alarm log uses Function
Code 05 and the Event/Alarm Register (parameter #0) in the Modbus
Special Function Table (point type 39). In this request, the number of registers is always one (1).
3-46
Reference Manual
00809-0100-4832, Rev AA
October 2004
Rosemount 3095FC
Table 3-6. Modbus Events and
Alarms Log Content
Byte Content of Event Log Record
1 – 2
3 – 4
5 –8
9 – 12
13 – 16
17 – 20
Operator change bit map (16-bit)
Modbus register number of variable (16-bit integer)
Time Stamp (HHMMSS; 32-bit floating point)
Date Stamp (HHMMSS; 32-bit floating point)
Previous value of variable (32-bit floating point)
Current (new) value of variable ((32-bit floating point
Contents of Alarm Log Record
Alarm change bit map (16-bit integer)
Modbus register number of variable (16-bit integer)
Time Stamp (HHMMSS; 32-bit floating point)
Date Stamp (HHMMSS; 32-bit floating point)
Current (alarmed) value of variable (32-bit floating point)
Unused at the current time (zero filled when transmitted to the master)
Bit
12
13
14
15
8
9
10
11
6
7
3
5
0
1
2
Operator Change Bit Map
Fixed value - change to an EU value on an I/O point in Manual mode
Zero scale - change to the 0% Adjusted on an AI
Full scale - change to the 100% Adjusted on an AI
Operator entry work value - change to any parameter other than those described
Fixed / variable flag - change to manual mode for an I/O point
Table entry change - change to Modbus Function Tables
System command change - events logged by system (power up)
Not used
Operator change event identifier bit
LoLo Limit - change to LoLo alarm parameter
Low Limit - change to Low alarm parameter
HiHi Limit - change to HiHi alarm parameter
High Limit - change to High alarm parameter
Rate of change limit - change to Rate Alarm parameter
Not used
Alarm Changed Bit Map
Not used
Not used
Not used
Not used
Manual alarm
Status change alarm
No flow alarm
Point fail alarm
Operator change even identifier bit
LoLo Alarm
Low Alarm
HiHi Alarm
High Alarm
Rate Alarm
Set/clear alarm (1=set, 0=clear)
Modbus - Detailed Point / Parameter Information
The Modbus Special Function Table (point type 39) returns the Event Log,
Alarm Log, and the Historical Archives. The Event/Alarm Register (parameter
#0), Hourly (periodic) History Index Register (parameter #1), and the Daily
History Index Register (parameter #2) can be configured to the desired
Register Number. The History Archive Register is a single register, which can contain one or more history points for retrieval. The Starting History Point field contains the Starting History Point for the History Archive Register, while the
Ending History Point is the last history point to be included in the History
Archive Register. All history points in between the Starting History Point and the Ending History Point are included in the History Archive Register. The
Type of History Archive can only be one of two choices: Hourly or Daily. The
Conversion Code can be used to convert the history values. However, the
Conversion Code does not affect the time and date stamp.
Configure Modbus
Registers
The Modbus register configuration tables are used to associate Modbus register numbers with 3095FC point data. When a Modbus request is received, the Modbus user program searches the function table for the
Modbus function requested, starting with the first table entry down to the last.
If a register number match is found, it builds a response based on the point type and parameter configured in the table. If no register number match is located, an error message is returned. The user program locates a register as long as it matches the Starting Register number, the Ending Register number, or any number in between for that particular entry in the table.
3-47
Rosemount 3095FC
Reference Manual
00809-0100-4832, Rev AA
October 2004
Register numbers should be unique for a given communication port.
Registers may be duplicated as long as they are assigned to separate port or located in a separate Modbus configuration table. If a register number is duplicated within the same Modbus function table, the first occurrence is used. In addition, it is best to number the table from the smallest register number to the largest register number, especially when using two table entries to configure a continuous group of registers. Up to fifteen different lines can be configured for Modbus Functions 4 and 16. Up to thirty different lines can be configured for Modbus Function 3, split into tables 3A and 3B. By making the registers continuous, meaning the Starting Register address of a new line is one greater than the Ending Register address of the previous line, a continuous data table can be created up for Modbus Function 3, 4, or 16 up to the limit of 240 bytes. This type of data table allows access to all its data with one request.
Up to fifteen different lines can also be configured for Modbus Function Codes
1, 2, 5, 6, and 15. For Function Codes 1, 2, 5, and 15, the parameter specified should be a single-byte parameter type, preferably a status parameter (only bit 0 is used), because this function packs the data into a binary format for transmission. Each address span must be unique within the function for proper operation. If not, the first valid address is used.
Modbus Register tables allow the user to map Modbus Registers to 3095FC
Point Type, Logical, and Parameter (TLP) numbers. One line in the Modbus
Register table can be used to map more than one register-TLP pair by using either Point Indexing or Parameter Indexing.
Point Indexing means that the Start Register is mapped to the selected TLP.
Subsequent registers, through the End Register, are mapped to the same point type and parameter and increment as the point logical number.
Parameter Indexing means that the Start Register is mapped to the selected
TLP. Subsequent registered, through the End Register, are mapped to the same point type and point logical number, and increment the parameter number.
Once a register is mapped, it can be referenced by any Modbus request, providing the data type of the TLP is appropriate for the Function Code. If the native 3095FC data type does not me the requirements of the Modbus host device, conversion codes are available to convert data to the required data type. The user can select to have the mapping apply to all 3095FC communication ports or on a selected port only.
Use the following steps to Configure the Modbus Registers.
See Figure 3-28 on page 3-51.
1.
Select Configure > Modbus > Modbus Registers. (See Table 3-7 on page 3-49).
2.
Select the Function Index to which the maps are to be registered.
There are 9 function indexes available, each corresponding to a
Function Code displayed in the Function name field. Refer to Table
3-2 on page 3-38 for a detailed description of supported Modbus
Function Codes.
3.
Enter a Function Name up to 20 characters to distinguish between the different Modbus Register tables.
3-48
Reference Manual
00809-0100-4832, Rev AA
October 2004
Rosemount 3095FC
Table 3-7. Modbus Registers
Function
Code Row
Starting
Register
Ending
Register Device Parameter (s)
15
16
4
5
6
1
2
3
3
4
1
2
1
1
5
2
3
4
1
1
1
5
0
1
2
7262
0
1070
7052
7100
7103
7108
1070
0
7052
7100
7103
7108
7262
0
8000
8054
0
1070
7059
7102
7107
7127
1070
0
7059
7102
7107
7127
7288
7288
0
8053
8063
N/A
N/A
Filtered EUs (Analog Inputs 1-8)
DP, P, Temp
Meter Flow Values - Starting with “Flow Rate/Day,” Ending with “hwPf”
Meter Flow Values - Starting with “Flow Today,” Ending with
“Uncorrected Accumulated”
Meter Config Parameters - Starting with “Atmospheric Pressure,”
Ending with “Carbon Monoxide”
N/A
N/A
Filtered EUs (Analog Inputs 1-8)
DP, P, Temp
Meter Flow Values - Starting with “Flow Rate/Day,” Ending with “hwPf”
Meter Flow Values - Starting with “Flow Today,” Ending with
“Uncorrected Accumulated”
Meter Config Parameters - Starting with “Atmospheric Pressure,”
Ending with “Carbon Monoxide”
N/A
Meter Config Parameters - Starting with “Point Tag ID,” Ending with
“Low Flow Cutoff”
All Meter Calibration Parameters - Starting with “Calibration Options)
Indexing Conversion
Point
Point
Point
Param
Param
Param
0
0
0
0
0
0
Param
Point
Point
Point
Param
Param
Param
Param
Point
Param
0
0
0
0
0
0
0
0
0
0
Param 0
4.
Enter a Starting Register to represent the first data register in the address span. Any number from 0 to 65535 is valid. Register numbers can be duplicated as long as they are in separate Modbus
Function configuration tables. The tables should be numbered from smallest to largest. For example, the Host device requests the
Starting Register 500 through Ending Register 700. The Starting
Register is 400 and the Ending Register is 700. All register numbers requested by the Host (500 through 700) are valid and would be responded because the requested register numbers fall between the
Start and Ending Register numbers (400 through 700).
5.
Specify that the Ending Register address is a number representing the last location of a point's data. The value for this number is computed by: Ending Register address = (Starting Register address +
Number of Functions) - 1
6.
The Device Parameter field denotes the type of data associated with an address (Starting through Ending Register). When the Host requests a valid range of register numbers, the Function Code tells the Slave what to do and between which registers (Starting Register through Ending Register). The Rosemount User Interface Software
Parameter defines what data is collected or which parameter is set.
3-49
Rosemount 3095FC
Reference Manual
00809-0100-4832, Rev AA
October 2004
For example: When using Point Indexing the configuration of:
Starting
Register
Ending
Register
Device
Parameter(s) Indexing Conversion
100 103 AIN, 4-1, EU Point 0
Specifies four Registers (100, 101, 102, and 104) that are mapped to a group of Analog Input (AIN) values in engineering units (EU) starting at the Analog Input in the forth module location, first position
(4-1).
• Register 100 - EU of AIN point in location 4-1
• Register 101 - EU of AIN point in location 4-2
• Register 102 - EU of AIN point in location 4-3
• Register 103 - EU of AIN point in location 4-4
For example: When using Parameter Indexing the configuration of:
Starting
Register
Ending
Register
Device
Parameter(s) Indexing Conversion
7100 7102 AGANEW1,
CUR DP
Parameter 0
Specifies three Registers (7100, 7101, and 7102) that are mapped to a group of AGA parameters starting at CUR DP.
• Register 7100 - CUR DP (hw - differential pressure)
• Register 7101 - CUR SP (Pf - static pressure)
• Register 7102 - CUR TP (Tf - temperature)
7.
Select the type of Indexing to define the block of Register values for the Point Types or the Parameters without having to define each separately.
• Select Point to define the Register values as Point Types. If multiple Registers are used (Starting and Ending Register values are different), each successive Register increments to the next logical point number of the same Point Type.
• Select Param to define the Register values as Parameters. If multiple Registers are used (Starting and Ending Register values are different), each successive Register increments to the next logical Parameter of the Point Types to be set or acquire data. Be aware of the different data types (Character, Integer, Long, Float) and the size of the data types. Use the TLP button to select parameters.
8.
Specify the type of Conversion required, if any, on the data before it is sent to the host or written to the 3095FC. The conversions are used to allow integer values to be transmitted and received instead of floating point values. Table 3-8 lists the Convert Codes used with the
Modbus Protocol Emulation program. Conversion codes affect
Function Codes 3, 4, 6, 8, and 16.
3-50
Reference Manual
00809-0100-4832, Rev AA
October 2004
Figure 3-28. Modbus Registers
Configuration Screen
Rosemount 3095FC
Modbus Conversion
Conversion codes convert the data into a format that is compatible to a
Modbus device.
Select the Conversion field, on the Modbus Registers or Modbus History screen, (Configure > Modbus > Modbus Register) to specify the type of conversion required, if any, on the data before it is sent to the host or before it is written to the 3095FC. The conversions are used to account for differences in data types between the master and slave devices. Table 3-8 lists the
Convert Codes used.
Conversion Codes 65 to 72 allows a four-byte IEEE formatted floating point number to be sent or received in two Modbus registers with the byte orders configurable. A check is made to ensure that an even number of registers is requested, that the Start Register number does not begin in the middle of a register pair, and that the number of registers does not exceed the number of registers configured.
3-51
Rosemount 3095FC
Reference Manual
00809-0100-4832, Rev AA
October 2004
46
47
44
45
48
42
43
40
41
36
39
34
35
Table 3-8. Modbus Conversion
Codes
Convert
Code Description
19
20
21
22
8
9 to 16
17
18
6
7
4
5
2
3
0
1
23
24
30 to 32
33
No Conversion
Float to Integer, Float Scale 1
Float to Integer, Float Scale 2
Float to Integer, Float Scale 3
Float to Integer, Float Scale 4
Float to Integer, Float Scale 5
Float to Integer, Float Scale 6
Float to Integer, Float Scale 7
Float to Integer, Float Scale 8
No Conversion
Integer to Float, Float Scale 1
Integer to Float, Float Scale 2
Integer to Float, Float Scale 3
Integer to Float, Float Scale 4
Integer to Float, Float Scale 5
Integer to Float, Float Scale 6
Integer to Float, Float Scale 7
Integer to Float, Float Scale 8
No Conversion
Character to Integer
Integer to Character
Long to Integer
Integer to Long
Float to Integer, No Scaling
Integer to Float, No Scaling
Float to Byte, No Scaling
Byte to Float, No Scaling
Float to Long, No Scaling
Long to Float, No Scaling
Float to Byte
Float to Unsigned Integer
Float to Unsigned Long
No Conversion
3, 4, 6, 16
3, 4
3, 4, 6, 16
3, 4
3, 4, 6, 16
6, 16
6, 16
6, 16
–
Slave
Function
3, 4
6, 16
6, 16
6, 16
6, 16
6, 16
6, 16
6, 16
–
3, 4
3, 4
3, 4
3, 4
3, 4
3, 4
3, 4
6, 16
6, 16
–
3, 4
6, 16
3, 4
6, 16
3, 4
Definition
–
The Float to Integer conversion changes floating point data to an integer for transmission to the host. The number of the Convert Code specifies which floating point scaling value is to be used for the conversion
–
The Integer to Float conversion changes a transmitted integer value to a floating point value. The number of the Convert Code specifies which floating point scaling value is to be used for the conversion. If no fractional part is coming through on conversion from integer to float, use a float conversion that more closely fits the range of integer to be converted, such as float range 0 to
10 instead of 0 to 1000.
–
The Character to Integer conversion changes a character data type to an integer for transmitter to the host.
The Integer to Character conversion changes a transmitted integer value to a character data type.
The Long to Integer conversion changes a long data type to an integer for transmission to the host.
The Integer to Long conversion changes a transmitter integer value to a long data type.
The Float to Integer conversion changes a floating point data type to an integer for transmitter to the host.
The Integer to Float conversion changes a transmitted integer value to a floating point data type.
The Float to Byte conversion changes a floating point data type to a byte for transmission to the host.
The Byte to Float conversion changes a transmitted byte value to a floating point data type
The Float to Long conversion changes a floating point data type to a Long
Integer for transmission to the host.
The Long to Float conversion changes a transmitted Long Integer value to a floating point data type.
he Float to Byte Unsigned Character conversion changes a transmitted floating point value to an unsigned character data type.
The Float to Unsigned Integer conversion changes a transmitted floating point value to an unsigned integer data type.
The Float to Unsigned Long conversion changes a transmitted floating point value to an unsigned long data type.
–
3-52
Rosemount 3095FC
Reference Manual
00809-0100-4832, Rev AA
October 2004
Convert
Code
49
50
51
52
53
54
55
56
57 to 64
65
66
67
68
69
70
71
72
73
74
75 to 255
Description
Deadband, Float Scale 1
Deadband, Float Scale 2
Deadband, Float Scale 3
Deadband, Float Scale 4
Deadband, Float Scale 5
Deadband, Float Scale 6
Deadband, Float Scale 7
Deadband, Float Scale 8
No Conversion
IEEE Floating Point Number
IEEE Floating Point Number
IEEE Floating Point Number
IEEE Floating Point Number
IEEE Floating Point Number
IEEE Floating Point Number
IEEE Floating Point Number
IEEE Floating Point Number
IEEE Floating Point Number
IEEE Floating Point Number
No Conversion
Slave
Function
3, 4, 6, 16
3, 4, 6, 16
3, 4, 6, 16
3, 4, 6, 16
3, 4, 6, 16
3, 4, 6, 16
3, 4, 6, 16
3, 4, 6, 16
–
3, 4, 16
3, 4, 16
Definition
The Deadband to Float Scale conversion changes the Deadband pint data to an integer for transmission to the host. The number of the Convert Code specifies which floating point scaling value is to be used for the conversion.
3, 4, 16
3, 4, 16
3, 4, 16
3, 4, 16
3, 4, 16
3, 4, 16
3, 4, 6, 16
3, 4, 6, 16
–
–
Places byte 0 an byte 1 in register xxxxx; bye 2 and bye 3 are placed in register xxxxx + 1. this places a 4-byte floating point value into two, 2-byte registers to allow integer values to be transmitted. Code 66 does the same as
Coded 65 regardless of the Byte Order field in the Modbus Configuration screen. Register xxxxx byte 0, byte 1 register xxxxx + 1 byte 2, byte 3.
Code 67 reverses byte 0 and byte 1 order in register xxxxx; reverses byte 2 and byte 3 order in register xxxxx + 1. This places a 4-byte floating point value into two, 2-byte registers to allow integer values to be transmitter. Code 68 does the same as Code 67 regardless of the Byte Order field in the Modbus
Configuration screen. Register xxxxx byte 1, byte 0 Register xxxxx + 1 byte 3, byte 2.
Code 69 places byte 2 and byte 3 in register xxxxx; byte 0 and byte 1 are placed in register xxxxx + 1. This places a 4-byte floating point value into two,
2-byte registers to allow integer values to be transmitted. Code 70 does the same as Code 69 regardless of the Byte Order field in the Modbus
Configuration screen. Register xxxxx byte 2, byte 3 Register xxxxx + 1 byte 0, byte 1.
Code 67 reverses byte 2 and byte 3 order in register xxxxx; reverses byte 0 and byte 1 order in register xxxxx + 1. This places a 4-byte floating point value into two, 2-byte registers to allow integer values to be transmitter. Code 72 does the same as Code 71 regardless of the Byte Order field in the Modbus
Configuration screen. Register xxxxx + 1byte 1, byte 0.
Convert Codes 73 and 74 send the IEEE formatted floating point number as four bytes with a single register request. Only the byte order is changed:
Function Code 73 loads register xxxxx in byte 2, byte 3, byte 0, byte 1 order.
Function code 74 does the same as Function Code 73 regardless of the Byte
Order field in the Modbus Configuration screen.
–
3-53
Rosemount 3095FC
CUSTOM DISPLAYS
New Display
Reference Manual
00809-0100-4832, Rev AA
October 2004
This section describes the Custom Display option. The Custom Display option allows the creation of customized “live” displays, loading a display from a disk file, and monitoring flow and I/O points. Display options are located under the
View menu. The 3095FC stores displays to disk.
A new display must be created while connected to the 3095FC and then saved either to a disk file or to display memory in the 3095FC. The display can incorporate “live” data, as well as other information to be conveyed. One example is a graphical representation of the application that a 3095FC is monitoring and controlling.
Use the following instructions to create a new display.
1.
Select View > Display > New.
2.
If the Properties box does not appear, select the Properties button from the toolbar.
3.
Enter the name of the display in the Properties: Form Display Name field.
4.
Select to Enable or Disable the Logical Point Number Selection List.
• When Enabled, enter a Point Type. When selecting a TLP, the
Logical Number (L) comes from the logical listing selection box for those parameters that have the Point Type (T) match the Point
Type entered in this screen.
• When Disabled, the display is in What You See Is What You Get
(WYSIWYG) mode and the user selects the TLP to view.
5.
Place the cursor where the display element is to appear. Right-click on the mouse and select an element.
• Add Frame - Place like elements in a Frame to group user selections. Once Frame is in place, drag and drop elements onto the Frame.
• Add Label - Use labels to mark other elements.
• Add Text Box - Data entry fields.
• Add Check Box - Multiple selection box.
• Add Option Button - Radio button to limit input to a single selection.
NOTE
Create elements in the main Form before dragging and dropping them into a
Frame.
6.
Enter or select the desired data in the Properties Form. The items in the Properties box depend on the added object.
7.
Many elements can be created and placed anywhere on the edit screen. Option buttons should be placed within a frame. Element properties can be edited at any time.
8.
After creating elements to display, click Save to save the display to a disk file located on the PC or floppy drive. Enter the desired File name of the disk file, or use the default. The .DSP extension will automatically be added.
3-54
Rosemount 3095FC
Save Displays
Reference Manual
00809-0100-4832, Rev AA
October 2004
9.
Press the Test button to display the screen as it will appear in use.
Use the Update, Autoscan, Stop Scan, Edit, Save, and Close buttons at the bottom of the screen to perform the following functions:
• Update - Use this button to update all TLP (live data) information with the current reading from the 3095FC. The message “Reading
Data” appears in the Status Line.
• Apply - Applies changes made to fields in display which display is not in Autoscan.
• Autoscan - Provides an automatic update on intervals lasting one to three seconds.
• Stop Scan - Stops Autoscan.
• Edit Display - Change currently selected display.
• Character Set - Show the Character Set currently selected for building the display. This button toggles between viewing and not viewing Character Sets. Eight different character sets are supported: two for upper and lower case alphabetical characters, and six for various types of graphical characters.
• TLP Box - Enter live data from the Rosemount User Interface
Software or 3095FC. To use the TLP Box, first determine the Point
Type to use as a flow input by highlighting it. Next, select the exact
Logical Number. For example, an Analog Input Point Type that the user might select is AIN A 2. Finally, select the specific Parameter to use. For example, an Analog Input is typically Filtered EUs.
Save - If the display is new, this push button saves the current display to a disk file located on the PC. If the display already exists, this saves the display back to where it had been saved before. The extension .DSP (display) is added to the specified file name. Refer to “Save Displays” on page 3-55.
• Save As - Saves the current display to a disk file under a different name to a file or to internal Display1 or Display2. The extension.DSP (display) is applied to the name of the file.
• Close - Close the selected display screen with option to save.
NOTE
Use the mouse or >Alt+F6> keys to move between the buttons. Cut, Copy, and Paste can also be used when creating custom Displays.
After creating a display, store the current display to:
• Disk file located on the PC or floppy drive.
• Display1.
• Display2 (if available in the device).
To save a Display:
1.
Click Save and proceed to Step 4. Click Save As to save either to a file or to display memory.
2.
Click To Rosemount User Interface Software or To File.
3.
If To Rosemount User Interface Software is selected, select Display1 or Display2.
4.
If To File is selected, enter the desired File name of the disk file, or use the default. The .DSP extension will automatically be added.
3-55
Rosemount 3095FC
Reference Manual
00809-0100-4832, Rev AA
October 2004
3-56
Reference Manual
00809-0100-4832, Rev AA
October 2004
Section 4
OVERVIEW
Rosemount 3095FC
Calibration
Overview . . . . . . . . . . . . . . . . . . . . . . . . . . . . . . . . . . . . . . . page 4-1
Calibrate . . . . . . . . . . . . . . . . . . . . . . . . . . . . . . . . . . . . . . . page 4-1
Verify Calibration . . . . . . . . . . . . . . . . . . . . . . . . . . . . . . . . page 4-6
Once startup is successful and configuration is complete, it is necessary to calibrate the 3095FC to meet the requirements of the application. The following section details the procedure for calibrating the 3095FC and the I/O.
Once calibration is complete the 3095FC can be placed into operation.
NOTE
When the enclosure end caps are unscrewed, local calibration or monitoring of the 3095FC through its LOI port must be performed in a non-hazardous area. Performance of these procedures in a hazardous area could result in personal injury or property damage.
CALIBRATE
3095FC
Use the Rosemount User Interface Software to calibrate as follows:
1.
Launch the Rosemount User Interface Software and connect to the
3095FC.
2.
Select the Meter > Calibration. The current reading displays under each meter input as the Freeze Value. The 3095FC uses these values in the flow calculations while calibrating the points.
3.
Click Freeze. If necessary, create a calibration file.
4.
Isolate the device from the process by opening the by-pass valve on the valve manifold prior to isolating the device from the process (to protect the sensor module). This keeps one side of the differential sensor from being subjected to high pressure while the other side has no pressure applied. This is required when calibrating either DP or
SP. See Figure 4-1.
5.
To calibrate the pressure input, setup the pressure calibrator and make the necessary connections to the device.
6.
To calibrate the temperature input, disconnect the RTD sensor and connect a decade box (or comparable equipment) to the RTD terminals of the 3095FC.
7.
Click Calibrate under the desired input to calibrate DP, SP, or
Temperature. This displays the Set Zero calibration window.
www.rosemount.com
Rosemount 3095FC
Figure 4-1. Removing the
Device from Service
Reference Manual
00809-0100-4832, Rev AA
October 2004
Bleed Bleed
High
Pressure
Remains
1
2
3
Operating
Shutdown Sequence
8.
Apply the low (zero) value. For a pressure input, this would typically be open to atmosphere.
9.
Enter the applied value in the Dead Weight / Tester Value field of the
Set Zero dialog. For SP on an absolute-pressure device, enter the actual current atmospheric pressure.
NOTE
Apply pressure to both the high and low sides of the transmitter when calibrating SP.
10. When the displayed Live Reading is stable, click Set Zero to calibrate the zero reading. The Set Span window then appears
11. Apply the desired high value to the input (the top end of the expected operating range).
12. Enter the applied value in the Dead Weight / Tester Value field of the
Set Span dialog.
• For SP on an absolute-pressure device, add the actual atmospheric pressure, such as 300 + 14.73.
13. When the Live Reading is stable, click Set Span to calibrate the high reading. The window advances to the Set Midpoint 1 window.
14. To perform a two-point calibration, click Done to complete calibration.
15. To calibrate midpoints, apply the desired pressure or temperature and enter the applied value in the Dead Weight / Tester Value field.
Midpoint can be calibrated in any order.
16. When the Live Reading is stable, click Set Mid 1 to calibrate the reading. The display advances to the Set Midpoint 2 window.
17. To perform a three-point calibration, click Done to complete calibration.
18. To calibrate additional midpoints, apply the desired pressure or temperature and enter the applied value in the Dead Weight / Tester
Value field.
19. When the Live Reading is stable, click Set Mid 2 to calibrate this reading. The display advances to the Set Midpoint 3 window.
20. To perform a four-point calibration, click Done to complete calibration.
21. To calibrate a third midpoint, apply the desired pressure or temperature and enter the applied value in the Dead Weight / Tester
Value field.
4-2
Reference Manual
00809-0100-4832, Rev AA
October 2004
Figure 4-2. Returning the
Sensor Module to Service
Analog Input (AI)
Calibration
Rosemount 3095FC
22. When the Live Reading is stable, click Set Mid 3 to calibrate the reading. The display returns to the Meter Calibration window.
23. When the calibration for a selected point is complete, another input can be calibrated or complete the calibration. If calibration is complete return the device to service.
NOTE
Do NOT close the by-pass valve on the valve manifold until after process pressure has been reapplied, to protect the sensor module. This keeps one side of the differential sensor from being subjected to high pressure while the other side has no pressure applied. See Figure 4-2.
1a 1b
4
3
2
Pre-Startup
Shutdown Sequence
NOTE:
If calibrating the DP input, refer to “Zero Shift” on page 4-5 before completing the last step.
24. Finally, click Done to cause the calibration window to close, cancel freeze values (unfrozen), and enable live readings for use in the flow calculations. The Event Log records all calibration settings that were changed.
Select Utilities > AI Calibration Value to view the calibration values for a specific Analog Input point.
NOTE
Deadweight calibration may be performed from the Calibration tab in the AI
Configuration screen. The Calibration Freeze Value field displays the value received from the AI when the Update button was last pressed.
Use the drop-down list box to select the AI Point to be viewed. The Tag for that point displays. Not all of the following parameters apply to each point.
• Raw Value #1 to 5 - Raw Value 1 is the lowest calibrated Raw A/D input, Raw Value 5 is the highest calibrated Raw A/D input.
• EU Value #1 to 5 - The five calibration settings in Engineering Units
Values, converted from the Raw Values, based on the Low Reading EU and High Reading EU defined for the point. EU Value 1 is the Zero value, EU Value 5 is the Span value, and the rest are Midpoint values.
4-3
Reference Manual
00809-0100-4832, Rev AA
October 2004
Figure 4-3. AI Calibration Values
Screen
Rosemount 3095FC
• Press Effect is the Zero Shift adjustment value; it is used as an offset to the calibrated EU Values to compensate for the working SP effect on a
DP transmitter that was calibrated at atmospheric pressure.
• Set EU Value is the Tester Value specified for the last calibration value that was set. Manual EU is the Live Reading for the last calibration value that was set.
• The Timer field shows the last inactivity count-down in seconds
(starting from 3600 seconds) that occurred during the last calibration session. Had the countdown reached 0, time-out would have taken place, causing the calibration mode to end.
• Mode indicates:
• 0 = Use Current Calibration
• 1 = Start Calibration
• 2 = Calibrate
• 3 = Restore Previous Calibration
• 4 = Stop Calibration.
NOTE
No event is logged for the Mode Read-Only parameter.
• Type indicates which calibration value is currently being set:
• 0 = Inactive (no value)
• 1 = Zero
• 2 = Span
• 3 = Midpoint 1
• 4 = Midpoint 2
• 5 = Midpoint 3
• 6 = Zero Shift
4-4
Reference Manual
00809-0100-4832, Rev AA
October 2004
Rosemount 3095FC
Calibration Report
The Calibration Report details which parameters were set during calibration.
1.
Select View > Calibration Report.
2.
Select the Calibration Report to be viewed. The file has the extension
*.800 and is located in the default directory C:/Program
Files/Rosemount User Interface for Windows/Data directory unless the directory location was changed when the Calibration Report was created.
3.
Click Open.
Calibration Value
Select Utilities > Calibration Value to view the calibration values for a specific analog input point.
NOTE
Remove/restore the device from/to working pressure during calibration.
Failure to follow recommendations may cause sensor damage.
Zero Shift
To check or adjust for Zero Shift, leave the sensor by-pass valve open (to simulate a no-flow condition), with either line pressure or a normal operating
SP from the calibrator applied to the sensor. This applies the same pressure to both sides of the DP diaphragm to give a zero DP reading.
Perform the following steps:
1.
Connect the Rosemount User Interface Software to the 3095FC and run the calibration procedure.
2.
Select Meter > Calibration > Freeze.
3.
Under the Diff Press input, click Zero Shift to open the Set Zero Shift window.
4.
Verify Reading to determine if a Zero Shift correction is required.
5.
If the reading is not zero, click Set Zero Shift to adjust the Zero and click Done. If the reading is zero, click Done.
6.
Click Done to close the calibration window and cancel the freeze values to begin using live readings for the flow calculations.
4-5
Reference Manual
00809-0100-4832, Rev AA
October 2004
VERIFY CALIBRATION
Rosemount 3095FC
Rosemount User Interface Software can verify the calibration to check if the device requires re-calibration. To verify, perform the following steps:
1.
Launch the Rosemount User Interface Software. Connect the
3095FC.
2.
Select the Meter > Calibration.
3.
Click Freeze. This opens the Meter Calibration window. The current reading displays under each meter input as the Freeze Value. The
3095FC uses these values in the flow calculations while verifying the points.
NOTE
Open the by-pass valve on the valve manifold prior to isolating the device from the process, to protect the sensor module. This keeps one side of the sensor from being subjected to high pressure while the other side has no pressure applied. This is required when calibrating either DP or SP.
4.
While observing the previous Note, apply the desired pressure setting to the input.
NOTE
Apply pressure to both the high and low sides of the transmitter when verifying SP.
5.
Click Verify listed under the input to be calibrated.
6.
To log the Tester Value and the Live Reading to the Event Log as a record of the verification, click Log Verify.
7.
Click Done.
8.
Continue to verify all required pressures/values.
9.
When complete, connect the 3095FC back to the process.
NOTE
Do NOT close the by-pass valve on the valve manifold until after process pressure has been reapplied, to protect the device. This keeps one side of the differential sensor from being subjected to high pressure while the other side has no pressure applied.
10. Click Done to close the calibration window, to cancel the freeze values, and to begin using live readings for the flow calculations.
Figure 4-4. Meter Calibration
Screen
4-6
Reference Manual
00809-0100-4832, Rev AA
October 2004
Section 5
BACKUP
CONFIGURATION
INFORMATION
Rosemount 3095FC
Troubleshooting and
Maintenance
Backup Configuration Information . . . . . . . . . . . . . . . . . . page 5-1
Communication Errors . . . . . . . . . . . . . . . . . . . . . . . . . . . . page 5-2
Resetting the 3095FC . . . . . . . . . . . . . . . . . . . . . . . . . . . . . page 5-3
After Installing Components . . . . . . . . . . . . . . . . . . . . . . . page 5-4
Replacing the Batteries . . . . . . . . . . . . . . . . . . . . . . . . . . . page 5-5
Changing the Plate . . . . . . . . . . . . . . . . . . . . . . . . . . . . . . . page 5-5
The following tools are required for troubleshooting:
• IBM-compatible PC
• Rosemount User Interface Software
Perform backup procedure before removing power to the 3095FC for repairs, troubleshooting, removing or adding components, or upgrades. This procedure preserves the current flow PC configuration and log data held in
RAM.
NOTE
When installing equipment in a hazardous area, ensure that all components are approved for use in such areas. Check the product labels. Change components only in an area known to be non-hazardous. Performing these procedures in a hazardous area could result in personal injury or property damage.
To avoid circuit damage when working inside the unit, use appropriate electrostatic discharge precautions, such as wearing a grounded wrist strap.
1.
Log into the Rosemount User Interface Software.
2.
Save the configuration in flash memory Click Device > Flags > Save
Flash Memory Configuration. This saves all configuration settings, including the current states of the flags and calibration values.
3.
Select Device > Collect Data. Click OK to save event logs (.evt), alarm logs (.alm), report data (.det), hourly logs (.pdb), and daily
(.day) logs. Specify the desired file name and path.
4.
Backup the 10-minute history file.
5.
Select File > Save.
6.
Type the desired File name for the backup file.
7.
Click Save. The file is saved in the default directory C:/Program
Files/Rosemount/Rosemount User Interface Data, unless the directory has been changed.
www.rosemount.com
Rosemount 3095FC
COMMUNICATION
ERRORS
Reference Manual
00809-0100-4832, Rev AA
October 2004
Several events can cause a connection failure:
• If the Direct Connect communication link fails, use the Connect feature to establish a connection to the 3095FC. The Configuration Tree option allows the user to change the communications port, time-out settings, and other variables used when establishing a communications link to the PC.
• A communications failure can also occur if Rosemount User Interface
Software stands idle for too long and exceeds the timeout value for a device. In this case, simply log back into Rosemount User Interface
Software using Direct Connect or the Configuration Tree connect feature.
• Enter an Operator and Password for each user who connects to a
3095FC in the 3095FC security options located under the 3095FC menu.
Communication Problems
The PC communications options may need to be altered if communicating problems occur.
1.
If not currently active, select 3095FC Directory from the View or
Window menu.
2.
Select the desired Station Name of the 3095FC device.
3.
Right-mouse click and select Properties.
4.
Specified the correct 3095FC Address and 3095FC Group of the
3095FC with which communicate is being established. If communicating through the LOI port of the device, set the 3095FC
Address to 240 and Group Address to 240, which is the universal address.
5.
Click the Advanced tab.
6.
Try increasing the Time Out and/or Tx Delay.
7.
Click Apply, and then OK.
8.
Click the General tab, and click Connect.
9.
If communication problems still occur, try increasing the Number of
Retries field in the Advanced tab screen. Contact an Emerson
Process Management representative for additional assistance.
Debug Communications
Select Utilities > Debug Communications to open a Diagnostics window, which displays the data bytes (in hex format) sent and received from the
3095FC during any operation. Bytes sent are shown in black; bytes received are shown in red. Right-click on the display to Copy highlighted data, Clear All data, or Unselect. Copied data can be pasted in a file for analyzing.
5-2
Reference Manual
00809-0100-4832, Rev AA
October 2004
Rosemount 3095FC
RESETTING THE 3095FC
If problems occur that appear to be software related, try resetting with a Warm
Start, Cold Start, or Jumper Reset.
Warm Start
The re-initialization is performed by setting a parameter in the Rosemount
User Interface Software Flags. The re-initialization includes the Tasks,
Database, Communication Ports, sensor module, and I/O. It does not change the current configuration of any parameters.
1.
Log into the Rosemount User Interface Software.
2.
Connect the PC to the 3095FC.
3.
Perform “Backup Configuration Information” on page 5-1.
4.
Select 3095FC > Flags
5.
Click on Warm Start
6.
Apply to save the change.
Cold Start
The re-initialization is performed by setting a parameter in the Rosemount
User Interface Software Flags, called Cold Start. The re-initialization includes the Tasks, Database, Communication Ports, Sensor, I/O, and restoring the saved configuration, if there is one. It also includes resetting or clearing other items, based upon the selection made in the Options screen.
1.
Log into the Rosemount User Interface Software.
2.
Connect the PC to the 3095FC.
3.
Perform “Backup Configuration Information” on page 5-1.
4.
Select 3095FC > Flags.
5.
Click on Cold Start.
6.
Apply to save the change.
Jumper Reset
The Reset jumper located on the LCD (if installed) or on the Battery Charger
Board can be used to perform a special type of cold start. The jumper permits a power-up reset to re-establish a known operating point. It includes re-initializing the Communication Ports to the factory default configuration.
The cold start does not include any of the clearing options available in a Cold
Start performed using Rosemount User Interface Software.
NOTE:
This type of reset restores the communications ports to the factory configuration defaults. Some user-entered configuration parameters may be lost. Therefore, back up any required data before performing the reset.
1.
Perform “Backup Configuration Information” on page 5-1.
2.
Unscrew the front end cap cover (LCD end).
3.
Place the reset jumper (located on the LCD if installed or on the
Battery Charger Board at J2) in the Reset position.
4.
Cycle the power.
5.
Remove the reset jumper and install it in the normal (NORM) position.
6.
Replace the front end cap cover (LCD end).
7.
Perform the “After Installing Components” on page 5-4.
The reset procedure loads the factory default values into the communication ports.
5-3
Reference Manual
00809-0100-4832, Rev AA
October 2004
AFTER INSTALLING
COMPONENTS
Rosemount 3095FC
After removing power to the 3095FC and installing components as needed, perform the following steps to start the 3095FC and reconfigure the data.
NOTE
Ensure all input devices, output devices, and processes remain in a safe state upon restoring power. An unsafe state could result in property damage.
When installing equipment in a hazardous area, ensure that all components are approved for use in such areas. Check the product labels. Change components only in an area known to be non-hazardous. Performing these procedures in a hazardous area could result in personal injury or property damage.
1.
Reconnect power to the 3095FC by inserting the CHG+ / CHG- power terminal.
2.
Launch Rosemount User Interface Software, log in, and connect to the 3095FC.
3.
Verify that the configuration is correct. If it is not, continue by configuring the required items. If major portions or the entire configuration needs to be reloaded, perform the remaining steps.
4.
Select File > Download.
5.
From the Open dialog box, select the backup configuration file (has extension *.800).
6.
Select the portions of the configuration to download (restore).
7.
Click Download to restore the configuration.
5-4
Reference Manual
00809-0100-4832, Rev AA
October 2004
REPLACING THE
BATTERIES
CHANGING THE PLATE
Rosemount 3095FC
The battery pack contains three D-size lead-acid batteries providing 2.5
Amp-hours of current at 6.2 volts nominal.
NOTE
When installing equipment in a hazardous area, ensure that all components are approved for use in such areas. Check the product labels. Change components only in an area known to be non-hazardous. Performing these procedures in a hazardous area could result in personal injury or property damage. To avoid circuit damage when working inside the unit, use appropriate electrostatic discharge precautions, such as wearing a grounded wrist strap.
To replace the battery pack.
1.
Unscrew the front end cap cover.
2.
Remove the LCD display (if applicable).
3.
Place the power jumper (located at J1 on the Battery Charger Board) in the OFF position.
4.
Remove the four screws from the Battery Charger Board.
5.
Remove the ribbon cable from the Battery Charger Board to the
Backplane Board.
6.
Remove the Battery Charger Board.
7.
Replace the Battery Charger Board.
8.
Replace the ribbon cable from the Backplane Board to the Battery
Charger Board.
9.
Replace the four screws from the Battery Charger Board.
10. Reinstall the LCD display (if applicable).
11. Place the power jumper in the ON position.
12. Replace the front end cap cover.
The Plate Change option allows the user to change the size of an orifice plate.
1.
Select Plate Change from the Meter menu to record an orifice plate change.
2.
Select Yes if the plate change occurs during flowing conditions. Click
No for non-flowing conditions.
3.
After selecting the appropriate Meter ID, click Freeze. If performing the Plate Change under flowing conditions, the dialog box shows the
Freeze Value of each meter input (for purposes of data logging) while the change is being made. All I/O values are held in Manual mode at the current value. The values are returned to an active state after clicking OK in the Plate Change dialog box.
4.
Enter the new exact size for the Orifice Diameter (Inches or
Millimeters) in the new plate.
5.
Click Apply to record the change creating a record in the Event Log and restarts the flow calculation using the new orifice size data.
6.
Click OK.
5-5
Reference Manual
00809-0100-4832, Rev AA
October 2004
Rosemount 3095FC
5-6
Reference Manual
00809-0100-4832, Rev AA
October 2004
Rosemount 3095FC
Appendix A Specifications and Reference
Data
Specifications . . . . . . . . . . . . . . . . . . . . . . . . . . . . . . . . . . . page A-1
Dimensional Drawings . . . . . . . . . . . . . . . . . . . . . . . . . . . . page A-7
Ordering Information . . . . . . . . . . . . . . . . . . . . . . . . . . . . . page A-9
Options . . . . . . . . . . . . . . . . . . . . . . . . . . . . . . . . . . . . . . . . page A-11
Accessories . . . . . . . . . . . . . . . . . . . . . . . . . . . . . . . . . . . . . page A-11
SPECIFICATIONS
Functional
Specifications
Service
Gas or liquid
Input
Single input for a 2- or 3-wire RTD
Differential Sensor
Limits
• Code 2: –250 to 250 inH
2
O (-622,70 to 622,7mbar)
• Code 3: –1000 to 1000 inH
2
O (-2,49 to 2,49 bar)
Absolute Sensor
Limits
• Code 3: 0 to 800 psia (0 to 55158,1 mbar)
• Code 4: 0 to 3,626 psia (0 to 250,0 bar)
Gage Sensor
Limits
• Code C: 0 to 800 psig (0 to 55158,1 bar)
• Code D: 0 to 3,626 psig (0 to 250,0 bar)
Over Pressure Limit
0 psia to two times the absolute pressure sensor range with a maximum of
3,626 psia.
Static Pressure Limit
Operates within specifications between static line pressures of 0.5 psia and the URL of the absolute pressure sensor. www.rosemount.com
Rosemount 3095FC
Reference Manual
00809-0100-4832, Rev AA
October 2004
Power
• Transmitter: operates on terminal voltage of 8 - 28 Vdc
• Input current: 5mA nominal, 9.5 mA at 100% duty cycle (battery charging not included)
• Internal battery: rechargeable, Nominal 6.2 Vdc (2.5 Amp/hr)
• Maximum power consumption: 19 watts
• Solar panel input: nominal 8 V to 200 mA
• Solar panel output: 2 watts, 9 V nominal
• External charging input: 12 Vdc max (8 - 10 Vdc nominal)
RS-485 Signal Wiring
2-wire half-duplex RS-485 MODBUS with 8 data bits, 1 stop bit, and no parity
Bus Terminations
Standard RS-485 bus terminations required per EIA-485.
Failure Mode Alarm
If self-diagnostics detect a gross transmitter failure, non-latched status bits are set in the transmitter alarm registers.
Humidity Limits
0–95%, non condensing
Communications
User Interface: EIA-232 (RS-232C) format
Baud Rate: 600 to 19200 bps User selectable
Host: RS-485 / RS-232
Rosemount User Interface Software and Hardware Requirements:
• IBM-compatible PC
• 1 MB of RAM
• Pentium-grade processor: 233 MHz or faster
• Microsoft Windows 98 or higher operating system
• CD-ROM drive
Temperature Limits
Process (at transmitter isolator flange for atmospheric pressures and above):
• –40 to 212 °F (–40 to 100 °C)
• Inert fill sensor: 0 to 185 °F (-18 to 85 °C).
• Process temperatures above 185 °F (85 °C) requires derating the ambient limits by a 1.5:1 ratio.
Ambient:
• –40 to 167 °F (–40 to 75 °C)
• with integral meter: -4 to 167 °F (-20 to 75 °C)
Storage:
• –50 to 185 °F (–46 to 85 °C)
• with integral meter: -40 to 185 °F (-40 to 85 °C)
A-2
Reference Manual
00809-0100-4832, Rev AA
October 2004
Performance
Specifications
Rosemount 3095FC
Turn-on Time
Process variables will be within specifications less than 4 seconds after power is applied to transmitter.
Real Time Clock
• Year /month / day / hour / minute / second
• Battery Packed
Serial Card – EIA-232D Card
Standards
• Meets EIA-232 standard for single-ended data transmission over distances of up to 50 ft (15 m).
Data Rate
• Selectable from 1200 to 19200 bps
Format
• Asynchronous, 7 or 8-bit (software selectable with full handshaking)
Parity
• None, odd, or even (software selectable)
(Zero-based spans, reference conditions, silicone oil fill, 316 SST isolating diaphragms, and digital trim values equal to the span end points.)
Differential Pressure
Range 2
• 0–2.5 to 0–250 inH
2
O (0–6,2 to 0–622,7 mbar)
(100:1 rangeability is allowed)
Range 3
• 0–10 to 0–1000 inH
2
O(0–0,025 to 0–2,49 bar)
(100:1 rangeability is allowed)
Accuracy (including Linearity, Hysteresis, Repeatability)
• ±0.075% of span for spans from 1:1 to 10:1 URL for spans less than 10:1 rangedown
Accuracy =
--------------
% of span
Ambient Temperature Effect per 50 °F (28 °C)
• ±(0.025% URL + 0.125% span) spans from 1:1 to 30:1
• ±(0.035% URL + 0.175% span) spans from 30:1 to 100:1
Static Pressure Effects
• Zero error = ±0.05% of URL per 1,000 psi (68.9 bar)
• Span error = ±0.20% of reading per 1,000 psi (68.9 bar)
Stability
• ±0.125% URL for five years for ±50 °F (28 °C) ambient temperature changes, and up to 1000 psi (6,9MPa) line pressure.
Absolute/Gage Pressure (AP)(GP)
Range 3 (absolute), Range C (gage)
• 0–8 to 0–800 psi (0–0,55 to 0–55,2 bar)
(100:1 rangeability is allowed)
A-3
Rosemount 3095FC
Physical Specifications
Reference Manual
00809-0100-4832, Rev AA
October 2004
Range 4 (absolute)/ Range D (gage)
• 0–36.26 to 0–3,626 psi (0–2,5 to 0–250,0 bar)
(100:1 rangeability is allowed)
Accuracy (including Linearity, Hysteresis, Repeatability)
• ±0.075% of span for spans from 1:1 to 6:1 of URL
• For spans less than 6:1 rangedown,
Accuracy =
--------------
% of span
Ambient Temperature Effect per 50 °F (28 °C)
• ±(0.05% URL + 0.125% of span) spans from 1:1 to 30:1
±(0.06% URL – 0.175% of span) spans from 30:1 to 100:1
Stability
• ±0.125% URL for five years for ±50 °F (28 °C) ambient temperature changes, and up to 1000 psi (6,9MPa) line pressure.
Process Temperature (RTD)
Specification for process temperature is for the transmitter portion only.
Sensor errors caused by the RTD are not included. The transmitter is compatible with any PT100 RTD conforming to IEC 751 Class B, which has a nominal resistance of 100 ohms at 0 °C and ∝ = 0.00385. Examples of compatible RTDs include the Rosemount Series 68 and 78 RTD Temperature
Sensors.
Sensing Range
• –40 to 212 °F (–40 to 100 °C)
Accuracy (including Linearity, Hysteresis, Repeatability)
• ±1.0 °F (0.56 °C)
Ambient Temperature Effects per 50 °F (28 °C)
• ±0.90 °F (0.50 °C) for process temperatures from –40 to 212 °F (–40 to
100°C)
Stability
• ±1.0 °F (0.56 °C) for one year
Electrical Connections
½–14 NPT
3
/
4
-14 NPT, CM 20, PG-13.5
RTD Process Temperature Input:
100-ohm platinum RTD per IEC-751 Class B
Process Connections
• Transmitter: ¼–18 NPT on 2
1
/
8
-in. centers
• RTD: RTD dependent (see ordering information)
Battery
Lead-acid
A-4
Reference Manual
00809-0100-4832, Rev AA
October 2004
Rosemount 3095FC
Process Wetted Parts
Isolating Diaphragms
• 316L SST or Hastelloy C-276
®
Drain/Vent Valves
• 316 SST or Hastelloy C
®
Flanges
• Plated carbon steel, 316 SST, or Hastelloy C
Wetted O-rings
• Glass-Filled TFE
Non-Wetted Parts
Electronics Housing
• Low copper aluminum
Bolts
• Plated carbon steel per ASTM A449, Grade 5; or austenitic 316 SST
Fill Fluid
• Silicone oil
• Inert oil (available for gage pressure ranges only)
Paint
• Polyurethane
O-rings
• Buna-N
Weight
Components
3095 Transmitter
LCD Meter
SST Mounting Bracket
Battery / Solar Panel
Battery Backup
Weight in lb. (kg)
3095FC
12.4 (5.6)
0.5 (0.2)
1.0 (0.5)
2.0 (0.9)
1.3 (0.6)
A-5
Rosemount 3095FC
Memory Specifications
Flow Specifications
Reference Manual
00809-0100-4832, Rev AA
October 2004
Programmable Memory
2 MB x 8 flash EPROM
Data Memory
512 kB 5 RAM
Boot Memory
128 kB flash EPROM
Data Logging
Archival
• 60 days of 10 minutes data
• 35 days of hourly data
• 35 days of daily data
• minimum/maximum values for a single data
Memory Logging
• 240 alarms before rollover
• 240 events before rollover
Flow Calculation:
• Computed in accordance with ANSI/API 2530-92 (AGA 3, 1992), API 14.2
(AGA 8, 1992), and API 21.1. Detail Gross I, Gross II.
A-6
Reference Manual
00809-0100-4832, Rev AA
October 2004
DIMENSIONAL DRAWINGS
Side View
7.50 (191)
10.71 (272)
Terminal
Block
3095FC
Meter Cover
Optional
1.2 (30.5)
Clearance
Required to remove cover
3
/
4
-in.–14 NPT
Conduit Plug
17 (732)
Rosemount 3095FC
Front View
6.4 (163)
Dimensions are in inches (millimeters)
Side View
3095FC with Solar Panel Assembly
Front View
6.24 (159)
Solar Panel
Assembly
(optional)
4.48 (114)
10.71 (272)
Dimensions are in inches (millimeters)
A-7
Rosemount 3095FC
Reference Manual
00809-0100-4832, Rev AA
October 2004
2.0 (51)
Panel Mount
Mounting Configurations for 3095FC Transmitter
Pipe Mount
10.25
(260)
3
/
4
–14 NPT
Conduit Plug
Terminal Block
7.50 (191)
6.40
(163)
2.81 (71)
1.10 (28)
5.26 (134)
6.40 (163)
Dimensions are in inches (millimeters)
3.70
(93)
A-8
Reference Manual
00809-0100-4832, Rev AA
October 2004
ORDERING INFORMATION
Rosemount 3095FC
Code
3095F
Code
3
4
C
D
Code
A
B
(1)
J
(2)
K
(1)(2)
Code
B
C
Code
2
3
Code
A
B
C
0
Code
4
7
2
3
0
1
B
C
8
A
Code
A
C
J
E
B
K
L
A
C
(1)
0
Code
1
Code
Product Description
MultiVariable Transmitter
Output
Process Variable Measurement: Modbus RS-485
Process Variable Measurement: Mass Flow and Data Logging: Modbus RS-485
Differential Pressure Range
0 – 2.5 to 0 – 250 inH
2
O (0 – 6,23 to 0 – 623 mbar)
0 – 10 to 0 – 1000 inH
2
O (0 – 0,025 to 0 – 2,49 bar)
Absolute/Gage Pressure Ranges
0–8 to 0–800 psia (0–0,55 to 0–55,1 bar)
0–36.26 to 0–3,626 psia (0–2,5 to 0–250 bar)
0–8 to 0–800 psig (0–0,55 to 0–55,1 bar)
0–36.26 to 0–3,626 psig (0–2,5 to 0–250 bar)
Isolator Material
316L Stainless Steel (SST)
Hastelloy C-276
316L SST
Hastelloy C-276
Flange Style
Fill Fluid
Silicone
Silicone
Inert
Inert
Material
CS
SST
Hastelloy C
(2)
SST
Coplanar
Coplanar
Coplanar
None (Required for Option Codes S3 or S5)
Drain/Vent Material
SST
Hastelloy C
None (Required for Option Codes S3 or S5)
O-ring
Glass-filled TFE
Process Temperature Input (RTD ordered separately)
No RTD Cable
(3)
RTD Input with 12 ft. (3.66 m) of Shielded Cable
RTD Input with 24 ft. (7.32 m) of Shielded Cable
RTD Input with 12 ft. (3.66 m) of Armored, Shielded Cable
RTD Input with 24 ft. (7.32 m) of Armored, Shielded Cable
RTD Input with 75 ft. (22.86 m) of Shielded Cable
RTD Input with 75 ft. (22.86 m) of Armored, Shielded Cable
RTD Input with 12 ft. (3.66 m) of CENELEC Flameproof Cable
RTD Input with 24 ft. (7.32 m) of CENELEC Flameproof Cable
RTD Input with 75 ft. (22.86 m) of CENELEC Flameproof Cable
Transmitter Housing Material
Polyurethane-covered Aluminum
Polyurethane-covered Aluminum
Polyurethane-covered Aluminum
Polyurethane-covered Aluminum
SST
SST
SST
Conduit Entry Size
1
/
2
–14 NPT
3
/
4
–14 NPT
M20 x 1.5 (CM20)
PG 13.5
1
/
2
–14 NPT
M20 x 1.5 (CM20)
PG 13.5
•
•
•
•
•
•
•
•
•
•
•
•
•
•
•
•
•
•
•
•
•
•
•
•
•
•
•
•
•
•
•
—
•
• Available
— Not available
3095FB 3095FC
• •
•
•
•
—
—
•
•
•
—
—
—
—
•
—
—
—
—
—
Adapter
•
Adapter
Adapter
—
—
—
•
•
•
•
•
•
•
•
•
•
•
•
•
•
•
•
A-9
Rosemount 3095FC
Reference Manual
00809-0100-4832, Rev AA
October 2004
• Available
— Not available
3095FB 3095FC
Code
A
B
C
Code
0
1
Code
6
7
4
5
2
3
0
1
8
9
Code
Terminal Block
Standard
With Integral Transient Protection
CE MARK / Compliant with EMC – Transient Protection Included
Meter
None
LCD Meter
Bracket
None
Coplanar SST Flange Bracket for 2-in. Pipe or Panel Mount, SST Bolts
Traditional Flange Bracket for 2-in. Pipe Mounting, CS Bolts
Traditional Flange Bracket for panel Mounting, CS Bolts
Traditional Flange Flat Bracket for 2-in. Pipe Mounting, CS Bolts
Traditional Flange Bracket for 2-in. Pipe Mounting, SST Bolts
Traditional Flange Bracket for panel Mounting, SST Bolts
Traditional Flange Flat Bracket for 2-in. Pipe Mounting, SST Bolts
SST Traditional Flange Bracket for 2-in. Pipe Mounting, SST Bolts
SST Traditional Flange Flat Bracket for 2-in. Pipe Mounting, SST Bolts
Bolts
0
1
N
Code
0
H
M
A
C
Code
Carbon Steel bolts
Austenitic 316 SST bolts
None (required for Options code S5)
Product Certifications
None
Factory Mutual (FM) Explosion-Proof
Canadian Standards Associate (CSA) Explosion Proof
ATEX Flame-proof
Canadian Standards Association (CSA) U.S. and Canada Explosion-Proof
Engineered Measurement Solution (EMS)
N
C
(3)
Code
Process Variable Measurement: MODBUS
Mass Flow with Process Variable Measurement and Data Logging: MODBUS
Options
S5
C1
A3
P1
Assemble to 305 Integral Manifold (requires integral manifold model number)
Custom Flow Configuration (requires completed Configuration Data Sheet (see document number
00813-0100-4716))
Mast with Solar Panel Assembly: includes 12 Vdc Batteries
Hydrostatic Testing
Cleaning for Special Services
P2
Q4
Q8
DF
(4)
Calibration Certificate
Material Traceability Certification per EN 10204 3.1B
1
/
2
–14 NPT Flange Adapter, Carbon Steel, Stainless Steel, Hastelloy C
Additional RS-232 Communication Board
A1
A2 12 Vdc System with Batteries
Typical Model Number: 3095F B 2 3 A B A 1 1 A B 0 1 0 A N
•
•
•
•
•
•
•
•
•
•
•
•
•
•
•
•
•
•
•
•
•
•
—
•
—
•
•
—
•
•
•
•
•
—
—
•
•
•
•
•
•
•
•
•
—
—
—
•
•
•
•
•
•
—
•
—
—
•
(1) Materials of Construction meet NACE material recommendation per MR 01-75. Environmental limits apply to certain materials. Consult standard for details.
(2) Only available with C or D Gage Sensor Modules.
(3) Required for 3095FC.
(4) Material determined by Flange Style material selection.
•
•
•
•
•
•
•
•
•
•
•
•
A-10
Reference Manual
00809-0100-4832, Rev AA
October 2004
OPTIONS
Standard Configuration
Custom Configuration
(Option Code C1)
ACCESSORIES
Rosemount 3095FC
Unless otherwise specified, the transmitter is shipped as follows:
Engineering units:
Differential
Absolute/gage
Output:
Flange type:
Flange material:
O-ring material:
Drain/vent:
Flow Configuration Parameters:
Software tag: inH
2
O psi (all ranges)
Modbus RTU protocol signal
Specified model code option
Specified model code option
Specified model code option
Specified model code option
Factory default
(Blank)
If Option Code C1 is ordered, the user-specified information for the 3095F
Modbus Transmitter in addition to the standard configuration parameters are factory configured.
Message, descriptor, slave address, baud rate, upper and lower trim points for each process variable, damping for each process variable, units for each process variable, upper and lower operation limits. Unspecified parameters will remain at the factory default settings.
Tagging
Three customer tagging options are available:
• Standard SST tag is wired to the transmitter. Tag character height is 0.125 in. (3,18 mm),
85 characters maximum.
• Tag may be permanently stamped on transmitter nameplate upon request.
Tag character height is 0.0625 in. (1,59 mm),
65 characters maximum.
• Tag may be stored in transmitter memory. Software tag is left blank unless specified
.
• Software tag is left blank unless specified.
Optional 305 Integral Manifolds
The Rosemount 3095FC Transmitter with 305RC (or 305AC, 305BC) Integral
Manifold are fully assembled, calibrated, and seal tested by the factory. Refer to PDS 00813-0100-4733 for additional information.
Rosemount User Interface Software Packages
The Rosemount User Interface Software package is available with or without the converter and connecting cables. All configurations are packaged separately.
Windows 98 or higher
3095FC
• Part Number 03095-5136-0001: Windows User Interface Software–Single
PC License, and Cable.
• Part Number 03095-5135-0001: Windows User Interface Software–Single
PC License.
• Part Number 03095-5135-0002: Windows User Interface Software– Site
License.
• Part Number 03095-5106-0003: 10 foot (3.05 m) 9-pin Serial Cable
A-11
Rosemount 3095FC
Reference Manual
00809-0100-4832, Rev AA
October 2004
A-12
Reference Manual
00809-0100-4832, Rev AA
October 2004
Rosemount 3095FC
Appendix B Product Certifications
Approved Manufacturing Locations . . . . . . . . . . . . . . . . . page B-1
European Directive Information . . . . . . . . . . . . . . . . . . . . page B-1
Hazardous Locations Certifications . . . . . . . . . . . . . . . . . page B-1
Rosemount Inc. — Chanhassen, Minnesota USA
APPROVED
MANUFACTURING
LOCATIONS
EUROPEAN DIRECTIVE
INFORMATION
HAZARDOUS
LOCATIONS
CERTIFICATIONS
The EC declaration of conformity for all applicable European directives for this product can be found on the Rosemount website at www.rosemount.com. A hard copy may be obtained by contacting our local sales office.
ATEX Directive (94/9/EC)
Emerson Process Management complies with the ATEX Directive.
European Pressure Equipment Directive (PED) (97/23/EC)
3095F_2/3,4/D Flow Transmitters — QS Certificate of Assessment - EC
No. PED-H-20 Module H Conformity Assessment
All other 3095_ Transmitters/Level Controller — Sound Engineering
Practice
Transmitter Attachments: Process Flange - Manifold — Sound
Engineering Practice
Electro Magnetic Compatibility (EMC) (89/336/EEC)
3095F Flow Transmitters — EN 50081-1: 1992; EN 50082-2:1995; EN
61326-1:1997 – Industrial
North American Certifications
2, Groups A, B, C, and D. Install per Rosemount drawing 03095-1025.
Canadian Standards Association (CSA) Approvals
M
Explosion-Proof for Class I, Division 1, Groups C and D. Optional solar panel: mast option: Explosion-Proof for Class I, Division 2, Groups A, B,
C, D, and T3. CSA Enclosure Type 4.
ISSeP www.rosemount.com
Rosemount 3095FC
Reference Manual
00809-0100-4832, Rev AA
October 2004
B-2
Reference Manual
00809-0100-4832, Rev AA
March 2004
Rosemount 3095FC
Appendix C Rosemount User
Interface Software
Overview . . . . . . . . . . . . . . . . . . . . . . . . . . . . . . . . . . . . . . . page C-1
Point Type Parameter Definitions . . . . . . . . . . . . . . . . . . . page C-1
OVERVIEW
POINT TYPE
PARAMETER
DEFINITIONS
Table C-1. Data Types
To configure the 3095FC, you must be familiar with the structure of the database. The database is broken into individual parameters and each database parameter is uniquesly associated by Parameter Number and Point
Type.
A list of all Point Types is provided in Table 3 1 on page 3-1. For each of the configurable point types (0 through 59), a parameter table is given in Table 3 5 through Table 3 48. Note that the parameter tables each have a point type name and five columns:
Parameter # - Identifies the specific parameter associated with the Point
Type.
Read-Write - Indicates if the parameter can be read and written to (R/W) or if the parameter is read-only (R/O).
Data Type - Table C-1 defines the Data Types found in the parameters table.
Data Type Definition
AC
BIN
ASCII character (groups of 10, 20, or 30 characters)
Binary
FLP Floating Point - IEEE Format
INT 8, 16, 32 Signed Integer - number of bits follows
N/A Not applicable
TLP Point Type, Logical or Point Number, and Parameter
Number
UINT 8, 16, 32 Unsigned Integer - number of bits follows
Byte Length
1 per character
1
4
1, 2, or 4
–
3
1, 2, or 4
Length - The byte length of the parameter is indicated in this column.
Description - A brief description of each parameter is provided in this column.
www.rosemount.com
Rosemount 3095FC
Reference Manual
00809-0100-4832, Rev AA
March 2004
Point Type 0 Information
Table 3 5 lists the parameters for the Configurable Opcode Point Type found in the 3095FC. The parameters for this Point Type consist of a sequence number and 44 device parameter identifications (Point Type, Logical Number, and Parameter Number - TLP). After the TLPs have been configured in Point
Type 0:
• Opcodes 10 and 11 can be used to read and write data directly without specifying the Point Type, Logical Number, or Parameter Number.
• Opcodes 180 and 181 can be used to read and write the parameter data and do not include the parameter definition.
Table C-2. Point Type 0 - Configurable Opcode
Parameter
Number
27
28
29
30
23
24
25
26
19
20
21
22
15
16
17
18
35
36
37
38
31
32
33
34
11
12
13
14
7
8
9
10
5
6
3
4
0
1
2
Read-Write
R/W
R/W
R/W
R/W
R/W
R/W
R/W
R/W
R/W
R/W
R/W
R/W
R/W
R/W
R/W
R/W
R/W
R/W
R/W
R/W
R/W
R/W
R/W
R/W
R/W
R/W
R/W
R/W
R/W
R/W
R/W
R/W
R/W
R/W
R/W
R/W
R/W
R/W
R/W
Data Type
TLP
TLP
TLP
TLP
TLP
TLP
TLP
TLP
TLP
TLP
TLP
TLP
TLP
TLP
TLP
TLP
TLP
TLP
TLP
TLP
TLP
TLP
TLP
TLP
TLP
TLP
TLP
TLP
TLP
TLP
TLP
TLP
FLP
TLP
TLP
TLP
TLP
TLP
TLP
Length
3
3
3
3
3
3
3
3
3
3
3
3
3
3
3
3
3
3
3
3
3
3
3
3
3
3
3
3
3
3
3
3
3
3
3
3
4
3
3
Description
Data 15
Data 16
Data 17
Data 18
Data 19
Data 20
Data 21
Data 22
Data 23
Data 24
Data 25
Data 26
Data 27
Data 28
Data 29
Data 30
Sequence / Revision Number
Data 1
Data 2
Data 3
Data 4
Data 5
Data 6
Data 7
Data 8
Data 9
Data 10
Data 11
Data 12
Data 13
Data 14
Data 31
Data 32
Data 33
Data 34
Data 35
Data 36
Data 37
Data 38
C-2
Reference Manual
00809-0100-4832, Rev AA
March 2004
Rosemount 3095FC
Parameter
Number
39
40
41
42
43
44
Read-Write
R/W
R/W
R/W
R/W
R/W
R/W
Device Point Types
Table C-3. Point Type 3 - Analog Input
Parameter
Number
9
10
11
12
7
8
5
6
13
14
15
0
3
4
1
2
Read-
Write
R/W
R/W
R/W
R/W
R/W
R/W
R/W
R/W
R/W
R/W
R/W
R/W
R/W
R/W
R/W
R/W
Data Type
AC
AC
UINT 16
UINT 16
INT 16
INT 16
FLP
FLP
FLP
FLP
FLP
FLP
FLP
FLP
FLP
BIN
Data Type
TLP
TLP
TLP
TLP
TLP
TLP
Length
3
3
3
3
3
3
Description
Data 39
Data 40
Data 41
Data 42
Data 43
Data 44
The tables in the rest of this section list the parameters for each of the Point
Types.
Length
4
4
4
4
4
4
2
4
4
4
1
10
10
2
2
2
Description
Point Tag Identification
Units
Scan Period (50 millisecond intervals)
Filter (50 millisecond intervals)
Adjusted A/D 0%
Adjusted A/D 100%
Low Reading EU
High Reading EU
Low Alarm EU
High Alarm EU
Low Low Alarm EU
Hi Hi Alarm EU
Rate Alarm EU
Alarm Deadband
Filtered EUs
Mode:
Bit 7 – Manual Mode
0 = Normal Scan
1 = Manual Scan
Bit 6 – RBX on Set
0 = Disabled
1 = Active
Bit 5 – RBX on Clear
0 = Disabled
1 = Active
Bit 4 – Alarm Enable
0 = Disabled
1 = Log Alarm
Bit 3 – Not Used
Bit 2 – Not Used
Bit 1 – Clipping
0 = Disable
1 = Clipping Enable
Bit 0 – Fault Handling
0 = Retain Last EU Value
1 = Set EU Value to Fault EU Value (Parameter 19)
Abbr.
TAG
UNITS
SCANPR
FILTER
MINRAW
MAXRAW
MINEU
MAXEU
LOAL
HIAL
LOLOAL
HIHIAL
RATEAL
ALDBND
EU
BIN
C-3
Rosemount 3095FC
Parameter
Number
16
Read-
Write
R/O
Data Type
BIN
17
18
19
R/O
R/O
R/W
INT 16
UINT 16
FLP
Table C-4. Point Type – AGA Flow Parameters
Parameter
Number
0
1
2
3
Read-
Write
R/W
R/W
R/W
R/W
Data Type
AC
FLP
FLP
BIN
Length
10
4
4
1
Length
1
2
2
4
Description
Alarm Code:
Bit 7 – Manual Mode
Bit 6 – Point Fail
Bit 5 – Not Used
Bit 4 – Rate Alarm
Bit 3 – High High Alarm
Bit 2 – High Alarm
Bit 1 – Low Low Alarm
Bit 0 – Low Alarm
Raw A/D Input
Actual Scan Time
Fault EU Value
Description
Point Tag Identification
Latitude
Elevation
Calculation Method:
Bit 7 – Manual Mode
0 = Normal
1 = Manual
Bit 6 – RBX Set
0 = Disabled
1 = Active
Bit 5 – RBX on Clear
0 = Disabled
1 = Active
Bit 4 – ALM Enable
0 = Disabled
1 = Log Alarms
Bit 3 – US or Metric
0 = US Units
1 = Metric Units
Bit 2 – AGA3 Algorithm
1 = 1992 Algorithm
Bit 1 – Flow Calculation Method
0 = AGA3
Bit 0 – Compressibility Method
1 = AGA8
Reference Manual
00809-0100-4832, Rev AA
March 2004
Abbr.
ALARM
CURRAW
SCAN
FAULTVAL
Abbr.
TAG
LAT
ELAVTN
METHOD
C-4
Reference Manual
00809-0100-4832, Rev AA
March 2004
Rosemount 3095FC
Parameter
Number
4
Read-
Write
R/W
26
27
28
29
22
23
24
25
30
31
18
19
20
21
15
16
17
10
11
12
13
14
5
8
9
6
7
R/W
R/W
R/W
R/O
R/W
R/W
R/W
R/W
R/W
R/O
R/W
R/W
R/W
R/W
R/W
R/W
R/W
R/W
R/W
R/W
R/W
R/W
R/W
R/W
R/W
R/W
R/W
FLP
FLP
FLP
FLP
FLP
FLP
FLP
FLP
FLP
FLP
FLP
FLP
FLP
FLP
FLP
FLP
FLP
Data Type
BIN
FLP
FLP
FLP
UINT 16
FLP
FLP
FLP
UINT 8
AC
BIN
1
30
4
4
1
4
2
4
4
4
4
4
4
4
4
4
4
4
4
4
4
4
4
4
4
4
4
Length
1
Description
AGA Configuration – Options:
Bit 7 – Log Methane Adjustment
0 = Yes
1 = No
Bit 6 – Heating Value
0 = Mass
1 = Volume Basis
Bit 5 – Gravitational Acceleration
0 = Calculate
1 = Enter Acceleration
Bit 4 – Heating Capacity
0 = Calculate
1 = Enter Heating Value
Bit 3 – Static Pressure Value
0 = Gauge
1 = Absolute Static Press
Bit 2 – Static Pressure Value
0 = Downstream
1 = Upstream Static Press
Bit 1 – Specific Gravity
0 = Calculate
1 = Enter Specific Gravity
Bit 0 – Tap
0 = Flange Tap
Specific Gravity
Heating Value
Gravity Acceleration Correction
Scan Period
Pipe Diameter
Orifice Diameter
Orifice Measured (Reference) Temperature
Orifice Material
Meter Run (Point) Identification
Alarm Code:
Bit 7 – Manual Mode
Bit 6 – No Flow
Bit 2 – High Alarm
Bit 0 – Low Alarm
Bits 5, 4, 3, and 1 – Not Used
Low Alarm EU – Flow
High Alarm EU – Flow
Viscosity
Specific Heat Ratio
BBase Pressure
Base Temperature
Low Differential Pressure (hw) Cutoff
Fpwl – Gravitational User Correction Factor
N
2
– Nitrogen
CO
2
– Carbon Dioxide
H
2
S – Hydrogen Sulfide
H
2
O – Water
He – Helium
CH
4
– Methane
C
2
C
3
H
H
6 –
8
Ethane
– Propane
C
4
H
10
– n-Butane
Abbr.
OPTION
LOAL
HIAL
VISCOS
SPHTRA
BASEPR
BASETP
MINDP
FPWL
NITROG
CARBDI
HYDSUL
WATER
HELIUM
METHAN
ETHANE
PROPAN
NBUTAN
SPGR
GASHV
GRAVIT
SCANPR
PIPDIA
ORFDIA
TMEAS
OR_MAT
DESC
ALARM
C-5
Rosemount 3095FC
Reference Manual
00809-0100-4832, Rev AA
March 2004
Parameter
Number
38
39
40
41
42
43
32
33
34
35
36
37
Read-
Write
R/W
R/W
R/W
R/W
R/W
R/W
R/W
R/W
R/W
R/W
R/W
R/W
Data Type
FLP
FLP
FLP
FLP
FLP
FLP
FLP
FLP
FLP
FLP
FLP
UINT 8
44
45
46
47
48
49
50
51
52
53
R/W
R/W
R/W
R/W
R/W
R/W
R/W
R/W
R/W
R/W
UINT 8
TLP
TLP
TLP
TLP
FLP
FLP
FLP
FLP
FLP
Table C-5. Point Type 8 – History Parameters
Parameter
Number
11
12
13
14
9
10
7
8
5
6
3
4
0
1
2
19
20
21
15
16
17
18
Read-
Write
R/O
R/O
R/O
R/O
R/O
R/O
R/O
R/O
R/O
R/O
R/O
R/O
R/O
R/O
R/O
R/O
R/O
R/O
R/O
R/O
R/O
R/O
Data Type
TLP
TLP
UINT 8
UINT 8
TLP
TLP
UINT 8
UINT 8
TLP
TLP
UINT 8
UINT 8
TLP
TLP
UINT 8
UINT 8
TLP
TLP
UINT 8
UINT 8
TLP
TLP
Length
3
1
1
3
3
1
1
3
3
1
1
3
3
3
1
1
3
3
3
1
1
3
3
4
3
3
1
3
4
4
4
4
Length
4
4
4
4
4
1
4
4
4
4
4
4
Description
C
4
C
5
C
5
C
6
H
10
– i-Butane
H
12
– n-Pentane
H
12 –
i-Pentane
H
14
– n-Hexane
C
7
C
8
H
16
– n-Heptane
H
18
– n-Octane
C
9
H
20
– n-Nonane
C
10
H
22
– n-Decane
O
2
– Oxygen
CO – Carbon Monoxide
H
2
– Hydrogen
Calculation Units (
0 = MCF (km
3
) / MMBTU (GJoules)
1 = CCF (100 m3) / MBTU (MJoules)
2 = 10 MCF (10 km
3
) / MMMBTU (TJoules)
Enable Stacked Differential Pressure (hw)
Low Differential Pressure (hw) Input
Differential Pressure (hw) Input
Static Pressure Input – Pf
Temperature Input – Tf
Low Differential Pressure (hw) Setpoint
High Differential Pressure (hw) Setpoint
Meter Value Differential Pressure (hw)
Static Flowing Pressure Value – Pf
Flowing Temperature Value – Tf
Description
Point Tag Identification TLP
History Log Point Number 1
Archive Type
Averaging or Rate Type
Point Tag Identification TLP
History Log Point Number 2
Archive Type
Averaging or Rate Type
Point Tag Identification TLP
History Log Point Number 3
Archive Type
Averaging or Rate Type
Point Tag Identification TLP
History Log Point Number 4
Archive Type
Averaging or Rate Type
Point Tag Identification TLP
History Log Point Number 5
Archive Type
Averaging or Rate Type
Point Tag Identification TLP
History Log Point Number 6
Abbr.
IBUTAN
NPENTA
IPENTA
NHEXAN
NHEPTA
NOCTAN
NNONAN
NDECAN
OXYGEN
CARBMO
HYDROG
FLOUNITS
DPSTEN
LO_TYP
DP_TYP
FP_TYP
TP-TYP
LODPSP
HIDPSP
CURDP
CURFP
CURMP
Abbr.
TAG
HST#1
ARCH1
AVG#1
TAG#2
HIST#2
ARCH2
AVG#2
TAG#3
HIST#3
ARCH3
AVG#3
TAG#4
HIST#4
ARCH4
AVG#4
TAG#5
HIST#5
ARCH5
AVG#5
TAG#6
HIST#6
C-6
Reference Manual
00809-0100-4832, Rev AA
March 2004
Rosemount 3095FC
Parameter
Number
48
49
50
51
44
45
46
47
40
41
42
43
36
37
38
39
56
57
58
59
52
53
54
55
32
33
34
35
28
29
30
31
22
23
24
25
26
27
Read-
Write
R/O
R/W
R/W
R/W
R/O
R/W
R/W
R/W
R/O
R/W
R/W
R/W
R/O
R/W
R/W
R/W
R/O
R/W
R/W
R/W
R/O
R/W
R/W
R/W
R/O
R/O
R/O
R/O
R/O
R/W
R/W
R/W
R/O
R/O
R/O
R/O
R/O
R/O
Data Type
TLP
TLP
UINT 8
UINT 8
TLP
TLP
UINT 8
UINT 8
TLP
TLP
UINT 8
UINT 8
TLP
TLP
UINT 8
UINT 8
TLP
TLP
UINT 8
UINT 8
TLP
TLP
UINT 8
UINT 8
UINT 8
UINT 8
TLP
TLP
UINT 8
UINT 8
TLP
TLP
UINT 8
UINT 8
TLP
TLP
UINT 8
UINT 8
Length
1
1
3
3
1
1
3
3
1
1
3
3
1
1
3
3
1
1
3
3
1
1
3
3
1
1
3
3
1
1
3
3
1
1
3
3
1
1
Description
Archive Type
Averaging or Rate Type
Point Tag Identification TLP
History Log Point Number 7
Archive Type
Averaging or Rate Type
Point Tag Identification TLP
History Log Point Number 8
Archive Type
Averaging or Rate Type
Point Tag Identification TLP
History Log Point Number 9
Archive Type
Averaging or Rate Type
Point Tag Identification TLP
History Log Point Number 10
Archive Type
Averaging or Rate Type
Point Tag Identification TLP
History Log Point Number 11
Archive Type
Averaging or Rate Type
Point Tag Identification TLP
History Log Point Number 12
Archive Type
Averaging or Rate Type
Point Tag Identification TLP
History Log Point Number 13
Archive Type
Averaging or Rate Type
Point Tag Identification TLP
History Log Point Number 14
Archive Type
Averaging or Rate Type
Point Tag Identification TLP
History Log Point Number 15
Archive Type
Averaging or Rate Type
Table C-6. Point Type 10 – AGA Flow Calculation Values
Parameter
Number
0
1
2
3
4
5
6
Read-
Write
R/O
R/O
R/O
R/O
R/O
R/O
R/O
Data Type
FLP
FLP
FLP
FLP
FLP
FLP
FLP
Length
4
4
4
4
4
4
4
Description
hw – Meter Differential Pressure Value (Inches H
2
O or kPa)
Pf – Static Flowing Pressure Value (psi or kPa)
Tf – Flowing Temperature Value (°F or °C)
Instantaneous Flow (Flow rate per Day) – MCF/Day or km
3
/Day
Instantaneous Energy (Energy rate per Day) –
MMBTU/Day or GJ/Day
Flow Today – MCF or km
3
Energy Today – MMBTU or GJ
Abbr.
CURDP
CURFP
CURTMP
CURFLO
ENERGY
TDYFLO
TDYENG
Abbr.
TAG#10
HIST#10
ARCH10
AVG#10
TAG#11
HIST#11
ARCH11
AVG#11
TAG#12
HIST#12
ARCH12
AVG#12
TAG#13
HIST#13
ARCH13
AVG#13
ARCH6
AVG#6
TAG#7
HIST#7
ARCH7
AVG#7
TAG8
HIST#8
ARCH
AVG#8
TAG#9
HIST#9
ARCH9
AVG#9
TAG#14
HIST#14
ARCH14
AVG#14
TAG#15
HIST#15
ARCH15
AVG#15
C-7
Rosemount 3095FC
Reference Manual
00809-0100-4832, Rev AA
March 2004
Parameter
Number
7
8
9
10
11
12
13
14
15
16
17
18
19
20
Read-
Write
R/O
R/O
R/O
R/O
R/O
R/O
R/O
R/O
R/O
R/O
R/O
R/O
R/O
R/O
Data Type
FLP
FLP
FLP
FLP
FLP
FLP
FLP
FLP
FLP
FLP
FLP
FLP
FLP
FLP
Table C-7. Point Type 12 – Clock
Parameter
Number
5
6
3
4
0
1
2
7
8
9
10
Read-
Write
R/W
R/W
R/W
R/W
R/W
R/W
R/O
R/O
R/O
R/W
R/W
Data Type
UINT 8
UINT 8
UINT 8
UINT 8
UINT 8
UINT 8
UINT 8
UINT 8
UNIT 8
UINT 8
UINT 8
Length
1
1
1
1
1
1
1
1
1
1
6
Table C-8. Point Type 13 – System Flags
Parameter
Number
0
1
Read-
Write
R/W
R/W
Data Type
UINT 8
UINT 8
Length
1
1
6
7
8
9
2
3
4
5
R/W
R/W
R/W
R/W
R/W
R/W
R/W
R/W
UINT 8
UINT 8
UINT 8
UINT 8
UINT 8
UINT 8
UINT 8
UINT 8
1
1
1
1
1
1
1
1
Length
4
4
4
4
4
4
4
4
4
4
4
4
4
4
Description
Flow Yesterday – MCF or km
3
Energy Yesterday – MMBTU or GJ
Pressure Extension – hwPf
IMV (Integral Multiplier Value) – called C prime (C') in
AGA3 1985
Sample Time
Orifice: Expansion Factor (Y)
Fr – AGA 1992
Ftf
Fpv – Compressibility
Fgr
Cd – Orifice AGA 1992 (Coefficient of discharge)
Fpb
Ftb
Fa – AGA 1985
Ev – AGA 1992
Description
Seconds
Minutes
Hours
Day
Month
Year
Leap Year
Day of Week
Time: Seconds, Minutes, Hour, Day, Month, and Year
Century
Daylight Savings Enable
Description
CRC Check
System Mode Flag :
Bit 0 to 6 = Not Used
Bit 7:
0 = Lowest Power Mode
1 = No sleep – Communications Always On
User Calc Program 1 Enable (FloBoss 100-Series)
User Operator Port Enable
FST / Display Clear
User COM1 Enable
Flag 5 (RegFlo)
User COM2 Enable
User Calc Program 1 Enable
RTS Operator Interface (LOI) Port
RTS Communications Port 1
C-8
Abbr.
SECOND
MINUTE
HOUR
DAY
MONTH
YEAR
LEAPYR
DAYOWK
TIME
CENT
DLSTEN
Abbr.
CRCCHK
FLAG1
FLAG2
FLAG3
FLAG4
COM1EN
COM2EN
USRCEN
RTSROI
RTSCM1
Abbr.
YDYFLO
YDYENG
HWPF
IMV
SAMPLE
EXPFTR
FR
FTF
FPV
FGR
FB
FPB
FTB
FA
Reference Manual
00809-0100-4832, Rev AA
March 2004
Rosemount 3095FC
Parameter
Number
10
11
12
13
14
15
Read-
Write
R/W
R/W
R/W
R/W
R/W
R/W
16
17
18
19
20
21
22
23
24
25
26
27
28
29
R/W
R/W
R/W
R/W
R/W
R/W
R/W
R/W
R/W
R/W
R/W
R/W
R/W
R/W
Data Type
UINT 8
UINT 8
UINT 8
UINT 8
UINT 8
UINT 8
UINT 8
UINT 8
UINT 8
UINT 8
UINT 8
UINT 8
UINT 8
UINT 8
UINT 8
UINT 8
UINT 8
UINT 8
UINT 8
UINT 8
1
1
1
1
1
Length
1
1
1
1
1
1
1
1
1
1
1
1
1
1
1
Description
RTS Communications Port 2
Clear Config Memory
I/O Scan Enable
Auxiliary Output 2 On
Auxiliary Output 1 On
Cold (Hard) Start options:
0 = None
1 = Restore config from flash / defaults
2 = Restore config and clear alarm / event logs
3 = Restore config and clear ROC displays
4 = Restore config and clear FSTs
5 = Restore config and clear history
6 = Restore config and clear all of above
Warm Start
Read I/O
Write to Config Memory
Config Memory Write Complete
Event Log Flag (FloBoss 100-series and FloBoss
500-series)
Init History (FloBoss 407 and ROC300-series with a
FlashPAC)
LOI Security On
Comm Port 1 Security On
Comm Port 2 Security On
Termination Type Installed:
1 = 4 point I/O – DI, DO, AI, AO Installed
2 = 4 point I/O – No I/O Installed
3 = 6 point I/O – I/O Installed
4 = 6 point I/O – No I/O Installed
Comm Port Pass Through Mode:
0 = No Pass Through.
1 = LOI to COM1
2 = COM1 to LOI
3 = LOI to COM2
4 = COM2 to LOI
5 = COM1 to COM2
6 = COM2 to COM1
6 Point I/O Setup Flag:
Bit 0:
0 = AI1
1 = DI1
Bit 1:
0 = AI2
1 = DI2
Bit 2:
0 = AO
1 = DO1
Bit 4:
0 = PI1
1 = DI3
Bit 5:
0 = PI2
1 = DI4
Bits 3, 6 and 7 – Not Used
Flag 27
Flag 28
Flag 29
Abbr.
RTSCM2
CLREEP
IOSCAN
AUX2
AUX1
COLD
WARM
IOREAD
WRITE
COMPLT
EVTFLAG
LOISEC
COM1SEC
COM2SEC
FLAG24
FLAG25
FLAGE26
FLAG27
FLAGE28
FLAG29
C-9
Rosemount 3095FC
Reference Manual
00809-0100-4832, Rev AA
March 2004
Table C-9. Point Type 14 – Communication Ports
Parameter
Number
2
3
0
1
4
Read-
Write
R/W
R/W
R/W
R/W
R/W
Data Type
AC
UINT 16
UINT 8
UINT 8
UINT 8
Length
10
2
1
1
1
5
6
10
11
12
13
14
15
16
17
18
19
7
8
9
R/O
R/W
R/W
R/W
R/W
R/W
R/O
R/O
R/O
R/W
R/O
R/W
R/W
R/W
R/W
BIN
BIN
UINT 8
UINT 8
UINT 8
UINT 16
UINT 16
UINT 16
UINT 16
UINT 16
UINT 8
UINT 8
FLP
AC
AC
1
1
2
1
2
2
2
2
1
4
40
40
1
1
1
Description
Tag Identification
Baud Rate
Stop Bits
Data Bits
Parity:
0 = None
1 = Odd
2 = Even
Status:
Bit 7 – User Status Bits 6 through 2 – Not Used
Bit 1 – RBX Status
0 = RBX Inactive
1 = RBX Active for this port
Bit 0 – No Port Installed
0 = Comm Board Present
1 = No Comm Cards Installed
Mode:
Bit 7 – User Flag
0 = Reset
1 = Set
Bit 6 – User Flag
0 = Reset
1 = Set
Bit 5 – Store and Forward Port
0 = Same
1 = Opposite
Bit 4 – Not Used
Bit 3 – Enable RTS / CTS
0 = Disabled
1 = Enabled
Bit 2 – Enable Extra Key-On
0 = Disabled
1 = Enabled
Bit 1 = Enable RBX
0 = RBX Disabled
1 = RBX Enabled
Bit 0 – Not Used
Key On Delay
Key Off Delay – Turnaround
Optional Interface Board Type:
Bit 5 through 7 – Not Used
Bit 4 – Radio Logic
Bit 3 – Reserved
Bit 2 – Dial-up Modem
Bit 1 – EIA-232 (RS-232)
Bit 0 – None
Host Retry Time
Alarm Pointer
Receive Counter Copy
Retry Counter
Valid Receive Counter
Modem Status
Modem Type
Connect Time
Configuration Command
Connect Command
C-10
Abbr.
TAG
BAUD
SBITS
DBITS
PARITY
STATUS
MODE
KEY
TURN
RCOUNT
XKEYON
ALMPTR
COPY
RCNTR
VALRCV
MDMSTS
MDMTYP
CONNTM
CFGCMD
CONNCMD
Reference Manual
00809-0100-4832, Rev AA
March 2004
Rosemount 3095FC
Parameter
Number
30
31
32
33
26
27
28
29
34
35
20
21
22
23
24
25
Read-
Write
R/W
R/W
R/W
R/W
R/W
R/W
R/W
R/W
R/W
R/W
R/W
R/W
R/W
R/W
R/W
R/W
Data Type
FLP
FLP
FLP
UINT 8
FLP
UINT 8
FLP
UINT 8
UINT 8
UINT 8
UINT 8
UINT 8
UINT 8
UINT 8
UINT 8
UINT 8
Length
1
1
1
1
1
1
1
1
4
1
4
1
4
1
4
4
Description
Disconnect Time
Inactivity Time
RBX Time Base #1
RBX Retry Count #1
RBX Time Base #2
RBX Retry Count #2
RBX Time Base #3
RBX Retry Count #3
RBX Address
RBX Group
Store and Forward Address #1 (Not Used for RegFlo)
Store and Forward Group #1 (Not Used for RegFlo)
Store and Forward Address #2 (Not Used for RegFlo)
Store and Forward Group #2 (Not Used for RegFlo)
Store and Forward Address #3 (Not Used for RegFlo)
Store and Forward Group #3 (Not Used for RegFlo)
Table C-10. Point Type 15 – System Variables (Device Information)
Parameter
Number
9
10
11
12
7
8
5
6
0
3
4
1
2
17
18
19
20
13
14
15
16
Read-
Write
R/W
R/W
R/W
R/W
R/W
R/W
R/O
R/O
R/W
R/W
R/W
R/W
R/W
R/O
R/O
R/O
R/O
R/O
R/O
R/O
R/O
Data Type
UINT 8
UINT 8
AC
UINT 8
UINT 8
UINT 8
UINT 8
UINT 8
UINT 8
UINT 8
UINT 8
AC
AC
AC
AC
AC
UINT 8
UINT 8
UINT 8
UINT 8
BIN
Length
1
1
20
20
1
1
1
1
1
1
20
1
1
1
1
1
1
20
12
20
1
Description
Device Address
Device Group
Station Name
Active PIDs
Active AGA Meter Runs
Not used
Number of Standard History Points
Number of Extended History Points
Number of RAM2 Database Points
Force End of Day
Contract Hour
Version Name – Part Number
Hardware Identification Number
Time Created
ROM Serial Number
Customer Name
Maximum PIDs
Maximum AGA Meter Runs
Maximum Tanks
FSTs Possible
RAM Installed – Memory Assignments:
Bit 7 – E0000-FFFFF
Bit 6 – C0000-DFFFF
Bit 5 – A0000-BFFFF
Bit 4 – 80000-9FFFF
Bit 3 – 60000-7FFFF
Bit 2 – 40000-5FFFF
Bit 1 – 20000-3FFFF
Bit 0 – 00000-1FFFF
Abbr.
ROCADR
ROCGRP
STNNAME
#PIDS
#AGAS
FSTINST
#RAM0
#RAM1
#RAM2
FORCE
CONTRC
VERSION
VENDORID
CREATETM
ROMSN
CUSTNAME
MAXPIDS
MAXAGAS
MAXTANKS
MAXFSTS
RAM
Abbr.
DISCTM
INACTM
RBXTB#1
RBXRC#1
RBXTB#2
RBXRC#2
RBXTB#3
RBXRC#4
RBXADR
RBXGRP
SFADR#1
SFG#1
SFADR#2
SFG#2
SFADR#3
SFG#4
C-11
Rosemount 3095FC
Reference Manual
00809-0100-4832, Rev AA
March 2004
Parameter
Number
21
22
23
24
25
Read-
Write
R/O
R/O
R/O
R/O
R/W
Data Type
BIN
FLP
BIN
UINT 16
UINT 8
Length
1
2
1
4
1
Description
ROM Installed – Memory Assignments:
Bit 7 – E0000-FFFFF
Bit 6 – C0000-DFFFF
Bit 5 – A0000-BFFFF
Bit 4 – 80000-9FFFF
Bit 3 – 60000-7FFFF
Bit 2 – 40000-5FFFF
Bit 1 – 20000-3FFFF
Bit 0 – 00000-1FFFF
MPU Loading
Utilities:
Bit 7 – Industry Canada Unit
Bit 6 – Not Used
Bit 5 – Not Used
Bit 4 – User Calculation Program Allowed
Bit 3 – COM2 User Program Allowed
Bit 2 – COM1 User Program Allowed
Bit 1 – LCD Installed
Bit 0 – AGA Data archived
Type of device:
3095 = Rosemount 3095
Units Flag
0 = English
1 = Metric (kPa)
2 = Metric (bar)
Table C-11. Point Type 17 – Soft Point Parameters
Parameter
Number
12
13
14
15
8
9
10
11
6
7
4
5
2
3
0
1
16
17
18
19
20
21
Read-
Write
R/W
R/W
R/W
R/W
R/W
R/W
R/W
R/W
R/W
R/W
R/W
R/W
R/W
R/W
R/W
R/W
R/W
R/W
R/W
R/W
R/W
R/W
Data Type
FLP
FLP
FLP
FLP
FLP
FLP
FLP
FLP
AC
UINT 16
FLP
FLP
FLP
FLP
FLP
FLP
FLP
FLP
FLP
FLP
FLP
FLP
Length
4
4
4
4
4
4
4
4
4
4
4
4
10
2
4
4
4
4
4
4
4
4
Description
Point Tag Identification
Integer Flag
Data #1
Data #2
Data #3
Data #4
Data #5
Data #6
Data #7
Data #8
Data #9
Data #10
Data #11
Data #12
Data #13
Data #14
Data #15
Data #16
Data #17
Data #18
Data #19
Data #20
Abbr.
ROM
MPU
UTIL
ROCTYPE
UNITS
Abbr.
TAG
INT1
DATA1
DATA2
DATA3
DATA4
DATA5
DATA6
DATA7
DATA8
DATA9
DATA10
DATA11
DATA12
DATA13
DATA14
DATA15
DATA16
DATA17
DATA18
DATA19
DATA20
C-12
Reference Manual
00809-0100-4832, Rev AA
March 2004
Rosemount 3095FC
Table C-12. Point Type 19 – Database Parameters
NOTE
Point Type 19 is used by Opcode 165 to configure history points and create events.
9
10
11
12
13
14
6
7
8
Parameter
Number
2
3
0
1
4
5
Read-
Write
R/O
R/O
R/O
R/O
R/O
R/O
Data Type
FLP
UINT 8
UINT 8
UINT 8
UINT 8
FLP
Length
1
1
4
1
1
4
Table C-13. Point Type 41 – Run Parameters
Parameter
Number
0
1
2
Read-
Write
R/W
R/W
R/W
Data Type
AC
FLP
BIN
Length
10
4
1
3
4
5
R/O
R/W
R/W
R/O
R/O
R/O
R/O
R/O
R/O
R/O
R/O
R/O
TLP
FLP
UINT 8
UINT 8
FLP
FLP
FLP
FLP
FLP
FLP
FLP
FLP
4
4
4
4
4
4
1
4
4
3
4
1
Description
Pointer to Tag
Archive Type
Point Type
Point / Logical Number
Parameter Number
Yesterday’s Total
Description
Point Tag Identification
Atmospheric Pressure
Calculation Method II:
Bits 7 through 5 – Not Used
Bit 4 – BTU Dry or Wet Override
0 = See Bit 3
1 = BTU as Delivered
Bit 3 – BTU Dry or Wet
0 = BTU Dry
1 = BTU Wet
Bit 2 – Calculated or Manual Value
0 = Calculated
1 = Enter Atmospheric Pressure – AGA 1992
Bit 1 – Gross Method
0 = Gross Method II
1 = Gross Method I
Bit 0 – Detail Level
0 = Detailed Method
1 = Gross Method
Not Used
Pipe Reference Temperature – AGA1992
Pipe Material – AGA1992:
0 = SS (Stainless Steal)
1 = Monel
2 = Carbon steel
Not Used
Cd – AGA 1992
Fr – AGA 1985
Reynolds Number – AGA 1992
Y – Expansion Factor – Orifice
Fpm – Turbine
Fpb Factor
Ftb Factor
Ftf Factor
Fgr Factor
Fpv – Super-compressibility Factor
Abbr.
TAGPNTR
ARCHTYPE
TYPE
LOGICAL
PARAM
YDYTOTAL
Abbr.
TAG
ATMPRS
METHOD
PIPEREFT
PIPEMAT
FB
FR
FY
FPB
FTB
FPB
FTB
FTF
FGR
FPV
C-13
Rosemount 3095FC
Read-
Write
R/W
R/W
R/W
R/W
R/W
R/W
R/W
R/W
R/W
R/W
R/W
R/W
R/W
R/W
R/W
R/W
R/W
R/W
R/W
R/W
R/W
R/W
R/W
R/W
R/W
R/W
R/W
R/W
R/W
R/W
R/W
R/W
R/W
R/W
R/W
R/W
R/W
R/W
R/W
Parameter
Number
41
42
43
44
37
38
39
40
33
34
35
36
29
30
31
32
49
50
51
52
45
46
47
48
53
54
25
26
27
28
21
22
23
24
15
16
17
18
19
20
Data Type
TLP
FLP
UINT 8
UINT 8
TLP
FLP
UINT 8
UINT 8
TLP
FLP
UINT 8
UINT 8
TLP
FLP
UINT 8
UINT 8
UINT 8
UINT 8
TLP
FLP
UINT 8
UINT 8
TLP
FLP
UINT 8
UINT 8
TLP
FLP
UINT 8
UINT 8
TLP
FLP
UINT 8
UINT 8
TLP
FLP
UINT 8
TLP
FLP
Reference Manual
00809-0100-4832, Rev AA
March 2004
Length
1
1
3
4
1
1
3
4
1
1
3
4
1
1
3
4
1
1
3
4
3
4
1
1
3
4
1
1
3
4
1
1
3
4
1
1
3
4
1
1
Description Abbr.
History Point 1
RollUp
HISTPT1
ROLLUP1
TLP TLP1
Conversion CONV1
History Point 2
RollUp
HISTPT2
ROLLUP2
TLP TLP2
Conversion CONV2
History Point 3
RollUp
HISTPT3
ROLLUP3
TLP TLP3
Conversion CONV3
History Point 4
RollUp
HISTPT4
ROLLUP4
TLP TLP4
Conversion CONV4
History Point 5
RollUp
HISTPT5
ROLLUP5
TLP TLP5
Conversion CONV5
History Point 6
RollUp
HISTPT6
ROLLUP6
TLP TLP6
Conversion CONV6
History Point 7
RollUp
HISTPT7
ROLLUP7
TLP TLP7
Conversion CONV7
History Point 8
RollUp
HISTPT8
ROLLUP8
TLP TLP8
Conversion CONV8
History Point 9
RollUp
HISTPT9
ROLLUP9
TLP TLP9
Conversion CONV9
History Point 10
RollUp
HISTPT10
ROLLUP10
TLP TLP10
Conversion CONV10
C-14
Reference Manual
00809-0100-4832, Rev AA
March 2004
Rosemount 3095FC
Table C-14. Point Type 42 – Extra Run Parameters
Parameter
Number
24
25
26
27
28
20
21
22
23
16
17
18
19
12
13
14
15
8
9
10
11
6
7
4
5
2
3
0
1
Read-
Write Data Type
R/O
R/O
R/O
R/O
R/O
R/W
R/W
R/W
R/W
R/W
R/O
R/O
R/O
R/W
R/W
R/W
R/W
R/W
R/W
R/W
R/W
R/W FLP
R/W FLP
R/W
R/W
FLP
FLP
R/W
R/W
R/W
R/W
FLP
FLP
FLP
FLP
AC
FLP
FLP
FLP
FLP
FLP
FLP
FLP
FLP
FLP
FLP
FLP
FLP
FLP
FLP
FLP
FLP
FLP
FLP
FLP
FLP
Length
4
4
4
4
4
4
4
4
4
4
4
4
4
4
4
4
4
4
4
4
4
4
4
4
4
10
4
4
4
Description Abbr.
Point Tag Identification
Flow Today – MCF (km
3
)
TAG
FLOTDY
Flow Yesterday – MCF (km
3
) FLODY
Flow Month – MCF (km
3
)
Flow Previous Month – MCF (km
3
)
Flow Accumulated – MCF (km
3
)
FLOMTH
FLOPRV
FLOACC
Minutes Today
Minutes Yesterday
MINTDY
MINYDY
Minutes Previous Month
Minutes Accumulated
Energy Today – MMBTU (GJ)
MINMTH
MINPRV
MINACC
ENGTDY
Energy Yesterday – MMBTU (GJ)
Energy Month – MMBTU (GJ)
ENGYDY
ENGMTH
Energy Previous Month – MMBTU (GJ) ENGPRV
Energy Accumulated – MMBTU (GJ) ENGACC
Uncorrected Today – MCF (km
3
) UCCTDY
Uncorrected Yesterday – MCF (km
3
) UCCYDY
Uncorrected Month – MCF (km
3
) UCCMTH
Uncorrected Previous Month – MCF (km
3
) UCCPRV
Uncorrected Accumulated – MCF (km
3
) UCCACC
Orifice Plate Bore Diameter – d
Meter Tube (Pipe) Internal Diameter – D
Beta – Diameter Ratio
ORIF_D
PIPE_D
BETA
Ev (Velocity of approach) – AGA 1992
Cd (Coefficient of discharge) – AGA 1992
Reynolds Number
Upstream Static Pressure
Molecular Weight
EV
CDISCH
REYNLD
U_PRSR
MLWGHT
Table C-15. Point Type 43 – User List Parameters
Parameter Number
10
11
12
13
8
9
6
7
14
15
4
5
2
3
0
1
Read-
Write
R/W
R/W
R/W
R/W
R/W
R/W
R/W
R/W
R/W
R/W
R/W
R/W
R/W
R/W
R/W
R/W
Data Type
AC
AC
AC
AC
AC
AC
AC
AC
AC
AC
AC
AC
AC
AC
AC
AC
Length
10
10
10
10
10
10
10
10
10
10
10
10
10
10
10
10
Description
Text 1
Text 2
Text 3
Text 4
Text 5
Text 6
Text 7
Text 8
Text 9
Text 10
Text 11
Text 12
Text 13
Text 14
Text 15
Text 16
C-15
Rosemount 3095FC
Reference Manual
00809-0100-4832, Rev AA
March 2004
Parameter Number
26
27
28
29
22
23
24
25
30
31
16
17
18
19
20
21
Read-
Write
R/W
R/W
R/W
R/W
R/W
R/W
R/W
R/W
R/W
R/W
R/W
R/W
R/W
R/W
R/W
R/W
Data Type
TLP
TLP
TLP
TLP
TLP
TLP
TLP
TLP
TLP
TLP
TLP
TLP
TLP
TLP
TLP
TLP
Length
3
3
3
3
3
3
3
3
3
3
3
3
3
3
3
3
Table C-16. Point Type 44 – Power Control Parameters
Parameter
Number
0
1
Read-
Write
R/W
R/O
Data Type
AC
INT 16
Length
10
2
2
13
14
15
16
9
10
11
12
17
18
19
7
8
5
6
3
4
R/W
R/W
R/W
R/W
R/W
R/W
R/W
R/O
R/W
R/W
R/W
R/W
R/W
R/W
R/W
R/W
R/W
R/W
INT 16
INT 16
INT 16
INT 16
INT 16
INT 16
INT 16
INT 16
INT 16
INT 16
INT 16
INT 16
INT 16
INT 16
INT 16
FLP
UINT 32
UINT 32
2
2
2
2
2
2
2
2
2
4
4
4
2
2
2
2
2
2
Description
Point Tag Identification
Status:
0 = Power off
1 = Power on
Enable:
0 = Disabled
1 = Second mode
2 = Minute mode
Valid RX (Receive)
Start Time #1
Start Time #2
Start Time #3
On Time #1
On Time #2
On Time #3
Off Time #1
Off Time #2
Off Time #3
Active Time Zone
Hold Time (100 millisecond intervals)
Power Timer (100 millisecond intervals)
Discrete Output Number
Low Battery
On Counter
Off Counter
Description
Data 1
Data 2
Data 3
Data 4
Data 5
Data 6
Data 7
Data 8
Data 9
Data 10
Data 11
Data 12
Data 13
Data 14
Data 15
Data 16
Abbr.
TAG
STATUS
ENABLE
VALRX
STTM1
STTM2
STTM3
ONTM1
ONTM2
ONTM3
OFFTM1
OFFTM2
OFFTM3
AZONE
HLDTM
PWRTMR
LOGDO
LOBAT
ONCNT
OFFCNT
C-16
Reference Manual
00809-0100-4832, Rev AA
March 2004
Rosemount 3095FC
Table C-17. Point Type 45 – Meter Calibration and Sampler
Parameter
Number
0
1
4
5
2
3
8
9
6
7
Read-
Write
R/W
R/W
R/W
R/W
R/W
R/W
R/W
R/W
R/W
R/W
Data Type
BIN
FLP
FLP
FLP
FLP
FLP
FLP
UINT 8
FLP
FLP
Length
1
4
4
4
4
4
4
4
4
1
Description
Calibration Options:
Bit 5 through 7 – Not Used
Bit 4 – Orifice Thermal Expansion Factor – 1985
Requires Parameters 11 and 12 of Point Type
46 be set.
Bit 3 – Differential Pressure Water Manometer
Calibrator, Requires Parameters 4 and 5 of
Point Type 45 and Parameters 20, 21, and 22 of Point Type 46 be set.
Bit 2 – Differential Pressure Deadweight Calibrator
Requires Parameter 3 of Point Type 45 and
Parameters 20, 21, and 22 of Point Type 46 be set.
Bit 1 – Static Pressure Deadweight Calibrator
Requires Parameter 3 of Point Type 45 and
Parameters 20, 21, and 22 of Point Type 46 be set.
Bit 0 – Mercury Manometer
Requires Parameters 1 and 2 of Point Type 45 be set.
Note: Either Bit 2 or Bit 3 can be set, but not both. If both bits are set, Bit 3 is cleared and Bit 2 is used.
Ambient Temperature of Mercury
Temperature of Mercury when Calibrated
Calculated Weights Gravitational Acceleration
Water Temperature when Calibrated
Air Temperature when Calibrating
User Correction Factor
Sampler Enable
Sampler Volume Accumulation
Sampler Duration
Abbr.
OPTION
AMBTMP
MTPCAL
CALWGT
WTPCAL
ATPCAL
CORFAC
SPLENA
VOLACC
SPLDUR
Table C-18. Point Type 46 – Meter Configuration Parameters
C-17
Rosemount 3095FC
Parameter
Number
0
1
2
Read-
Write
R/W
R/W
R/W
Data Type
AC
AC
BIN
3 R/W BIN
Length
10
30
1
1
Description
Point Tag Identification
Point Description
Calculation Method:
Bit 7 – Manual Mode
0 = Normal
1 = Manual Calculation Standard
0 = AGA
1 = ISO
Bit 6 – RBX on Set
0 = Disable RBX on Set
1 = Enable RBX on Set
Bit 5 – RBX on Clear
0 = Disable RBX on Clear
1 = Enable RBX on Clear
Bit 4 – Alarming
0 = Disabled
1 = Enabled
Bit 3 – Units of Measurement
0 = English Units
1 = Metric Units
Bit 2 – Calculation Version
0 = 1985
1 = 1992
Bit 2 – AGA Limits Events
0 = Disable
1 = Enable
Bit 1 – Calculation Type
0 = Orifice
Bit 0 – Fpv Method
1 = AGA8
Calculation Method II:
Bit 7 – Not Used
Bit 6 – Reserved
Bit 5 – Gas Quality
0 = Constant
1 = Live Data (Not Logged)
Bit 4 – Heating Value Basis
0 = Ignore
1 = Heating Value as Delivered
Bit 3 – Heating Value Basis
0 = Heating Value Dry
1 = Heating Value Wet
Bit 2 – Atmospheric Press
0 = Calculate Atmospheric Pressure
1 = Enter Atmospheric Pressure
Bit 1 – Fpv Method
0 = AGA8 Gross Method II
1 = AGA Gross Method I
Bit 0 – Fpv Method
0 = AGA8 Detail / ISO 12213-2
1 = AGA8 Gross (1992)
Reference Manual
00809-0100-4832, Rev AA
March 2004
Abbr.
TAG
DESC
CMTHI
CMTHII
C-18
Reference Manual
00809-0100-4832, Rev AA
March 2004
Rosemount 3095FC
Parameter
Number
4
Read-
Write
R/W
5
8
9
6
7
10
11
12
22
23
24
25
18
19
20
21
13
14
15
16
17
26
27
28
29
30
31
R/W
R/W
R/W
R/W
R/W
R/W
R/W
R/W
R/W
R/W
R/W
R/W
R/W
R/W
R/W
R/W
R/W
R/W
R/W
R/W
R/W
R/W
R/W
R/W
R/W
R/W
R/W
FLP
FLP
FLP
FLP
FLP
FLP
FLP
FLP
FLP
FLP
FLP
FLP
FLP
FLP
FLP
FLP
FLP
FLP
FLP
Data Type
BIN
UINT 8
FLP
FLP
FLP
UINT 8
FLP
FLP
UINT 8
1
4
1
4
4
4
4
4
4
4
4
4
4
4
4
4
4
4
4
4
4
4
4
4
Length
1
4
4
1
Description
Options:
Bit 7 – Log Methane Adjust
0 = Log Normalization
1 = Do Not Log Normalization
Bit 6 – Heating Value Basis
0 = Mass Basis Heating Value
1 = Volume Basis Heating Value
Bit 5 – Gravitational Acceleration
0 = Calculate Gravity
1 = Enter Gravity
Bit 4 – Heating Value
0 = Calculate Heating Value
1 = Enter Heating Value
Bit 3 – Press Tap
0 = Gauge Static Pressure
1 = Absolute Static Pressure
Bit 2 – Press Tap
0 = Downstream Static Pressure
1 = Upstream Static Pressure
Bit 1 – Gravitational Acceleration
0 = Calculate Specific Gravity
1 = Enter Specific Gravity
Bit 0 – Press Tap
0 = Flange Tap
Contract Hour
Integral Multiplier Period
Pipe Diameter (In. or mm)
Pipe Reference Temperature – AGA 1992
Pipe Material – AGA 1992:
0 = SS (Stainless Steel)
1 = Monel
2 = Carbon steel
Orifice Diameter (inches or millimeters)
Orifice Reference Temperature
Orifice Material:
0 = SS (Stainless Steel)
1 = Monel
2 = Carbon steel
Base or Contract Pressure (psia or kPa)
Base or Contract Temperature (degrees F or C)
Atmospheric Pressure (psia or kPa)
Specific Gravity
Heating Value
Viscosity (lbm/ft-sec or cP)
Specific Heat Ratio
Elevation (ft or m)
Latitude
Local Gravitational Acceleration (ft/sec
2
or M/sec
2
)
N
2
Nitrogen
CO
2
Carbon Dioxide
H
2
S Hydrogen Sulfide
H
2
O Water
He Helium
CH
4
Methane
C
2
H
6
Ethane
C
3
H
8
Propane
C
4
H
10
n-Butane
Abbr.
AGACFG
CTHOUR
IMP
PIPDIA
PIPERT
ALPH
ORFDIA
TMEAS
ORMAT
PBASE
TBASE
ATMPRS
SPGR
GASHV
VISCOS
SPHTRA
ELEVAT
LATUDE
GRAVIT
NITROG
CARBDI
HYDSUL
WATER
HELIUM
METHAN
ETHANE
PROPAN
NBUTAN
C-19
Rosemount 3095FC
Parameter
Number
42
43
44
45
38
39
40
41
32
33
34
35
36
37
50
51
52
53
46
47
48
49
54
Read-
Write
R/W
R/W
R/W
R/W
R/W
R/W
R/W
R/W
R/W
R/W
R/W
R/W
R/W
R/W
R/W
R/W
R/W
R/W
R/W
R/W
R/W
R/W
R/O
Data Type
FLP
FLP
FLP
FLP
FLP
FLP
FLP
FLP
FLP
FLP
FLP
FLP
FLP
FLP
UINT 8
TLP
TLP
TLP
TLP
FLP
FLP
FLP
BIN
55
56
57
58
R/W
R/W
R/W
R/W
FLP
FLP
UINT 8
UINT 8
Length
4
4
4
4
4
4
4
4
4
4
4
4
4
4
4
4
3
4
3
3
1
3
1
4
4
1
1
Description
C
4
C
5
C
5
C
6
H
10
i-Butane
H
12
n-Pentane
H
12
i-Pentane
H
14
n-Hexane
C
7
C
8
H
16
n-Heptane
H
18
n-Octane
C
9
H
20
n-Nonane
C
10
H
22
n-Decane
O
2
Oxygen
CO Carbon Monoxide
H
2
Hydrogen
Low hw Cutoff
High hw Setpoint – Differential Pressure
Low hw Setpoint – Differential Pressure
Enable Stacked hw – Differential Pressure
Low hw TLP – Differential Pressure hw TLP
Pf TLP
Tf TLP hw – Orifice Differential Pressure
Pf – Flowing Pressure
Tf – Flowing Temperature (degrees F or C)
Alarm Code:
Bit 7 – Manual Mode
0 = No Alarm Present
1 = Alarm Present
Bit 6 – No Flow
0 = No Alarm Present
1 = Alarm Present
Bit 5 – Flow Rate Register Discrepancy
0 = No Alarm Present
1 = Alarm Present
Bit 4 – Total Counts Register Discrepancy
0 = No Alarm Present
1 = Alarm Present
Bit 3 – Not Used
Bit 2 – High Alarm
0 = No Alarm Present
1 = Alarm Present
Bit 1 – Not Used
Bit 0 – Low Alarm
0 = No Alarm Present
1 = Alarm Present
Low Alarm Flow (1000 ft
3
/day or m
3
/day)
High Alarm Flow (1000 ft
3
/day or m
3
/day)
Averaging Technique
Full Recalculation Flag
Reference Manual
00809-0100-4832, Rev AA
March 2004
LOALM
HIALM
AVGTYP
FUCALL
Abbr.
IBUTAN
NPENTA
IPENTA
NHEXAN
NHEPTA
NOCTAN
NNONAN
NDECAN
OXYGEN
CARBMO
HYDROG
LOFLOW
LODPSP
HIDPSP
STDPEN
LO_TYP
DP_TYP
FP_TYP
TP_TYP
CURDP
CURSP
CURTP
ALARM
C-20
Reference Manual
00809-0100-4832, Rev AA
March 2004
Rosemount 3095FC
Table C-19. Point Type 47 – Meter Flow Values
Parameter
Number
6
7
4
5
2
3
0
1
36
37
38
39
32
33
34
35
28
29
30
31
24
25
26
27
44
45
46
47
40
41
42
43
48
49
20
21
22
23
16
17
18
19
12
13
14
15
8
9
10
11
Read-
Write
R/O
R/O
R/O
R/O
R/O
R/O
R/O
R/O
R/O
R/O
R/O
R/O
R/O
R/O
R/O
R/O
R/O
R/O
R/O
R/O
R/O
R/O
R/O
R/O
R/O
R/O
R/O
R/O
R/O
R/O
R/O
R/O
R/O
R/O
R/O
R/O
R/O
R/O
R/O
R/O
R/O
R/O
R/O
R/O
R/O
R/O
R/O
R/O
R/O
R/O
Data Type
FLP
FLP
FLP
FLP
FLP
FLP
FLP
FLP
FLP
FLP
FLP
FLP
FLP
FLP
FLP
FLP
FLP
FLP
FLP
FLP
FLP
FLP
FLP
FLP
FLP
FLP
FLP
FLP
FLP
FLP
FLP
FLP
FLP
FLP
FLP
FLP
FLP
FLP
FLP
FLP
FLP
FLP
FLP
FLP
FLP
FLP
FLP
FLP
FLP
FLP
Length
4
4
4
4
4
4
4
4
4
4
4
4
4
4
4
4
4
4
4
4
4
4
4
4
4
4
4
4
4
4
4
4
4
4
4
4
4
4
4
4
4
4
4
4
4
4
4
4
4
4
Description Abbr.
Flow rate per day (MCF or km
3
)
Energy rate per day (MMBTU or GJoules)
Flow rate per hour (CF or M3)
Energy rate per hour (BTU or MJoules)
Pressure Extension (hwPf)
Expansion Factor – Orifice
CdFT – AGA 1992
Fn – Orifice AGA 1992 (FloBoss 100-series and FloBoss
500-series Backward Compatibility)
FLOWDY
ENGDAY
FLOWHR
ENGHR
HWPF
EXPFTR
FR
FB
Fpb
Ftb
Ftf
Fgr
FPB
FTB
FTF
FGR
Fpv
Zs – AGA 1992
FPV
FA
Zb ZB
Zf1 – AGA 1992 ZF
IMV – AGA 1992
Orifice Plate Bore Diameter (d) (inches or millimeter)
Meter Tube Internal Diameter (D) (inches or millimeter)
Diameter Ratio (Beta)
Velocity of Approach (Ev) – AGA 1992
Average hw\
Average Pf – used during IMV calculation in psia
Average Tf – used during IMV calculation in Rankin
IMV
BORIDA
TUBDIA
BETA
VELAPP
AVGDP
AVGAP
AVGTP
Density
Base Density
Reynolds Number
Upstream Static Pressure (PSIG, psia or kPa)
Molecular Weight
Fam
Fwt
Fwl
Fpwl (Static)
Fpwl (Differential)
Fhgm
Fhgt
Flow Today (MCF or km
3
)
Flow Yesterday (MCF or km
3
)
Flow Month (MCF or km
3
)
Flow Previous Month (MCF or km
3
)
Flow Accumulated (MCF or km
3
)
Minutes Today
Minutes Yesterday
Minutes Month
Minutes Previous Month
Minutes Accumulated
Energy Today (MMBTU or GJoules)
Energy Yesterday (MMBTU or GJoules)
Energy Month (MMBTU or GJoules)
Energy Previous Month (MMBTU or GJoules)
DENS
BASDEN
REYNLD
UPSPR
MOLWGT
FAM
FWT
FWL
FPWLSP
FPWLDP
FHGM
FHGT
FLOTDY
FLOOYDY
FLOMTH
FLOPRV
FLOACC
MINTDY
MINYDY
MINMTH
MINPRV
MINACC
ENGTDY
ENGYDY
ENGMTH
ENGPRV
C-21
Rosemount 3095FC
Parameter
Number
50
51
52
53
54
55
56
Read-
Write
R/O
R/O
R/O
R/O
R/O
R/O
R/O
Data Type
FLP
FLP
FLP
FLP
FLP
FLP
UINT 8
Length
4
4
4
4
4
4
1
Description
Energy Accumulated (MMBTU or GJoules)
Uncorrected Today (MCF or km
3
)
Uncorrected Yesterday (MCF or km
3
)
Uncorrected Month (MCF or km
3
)
Uncorrected Previous Month (MCF or km
3
)
Uncorrected Accumulated (MCF or km
3
)
Partial Recalculation Flag
Table C-20. Point Type 53 – Modbus Configuration Parameters
Parameter
Number
0
10
11
12
13
8
9
6
7
1
4
5
2
3
14
15
16
17
18
19
Read-
Write
R/W
R/W
R/W
R/W
R/W
R/W
R/W
R/W
R/W
R/O
R/W
R/W
R/W
R/W
R/W
R/W
R/W
R/W
R/W
R/W
Data Type
BIN
UINT 8
INT 16
INT 16
FLP
FLP
FLP
FLP
FLP
FLP
FLP
FLP
FLP
FLP
FLP
FLP
FLP
FLP
FLP
FLP
Length
1
4
4
4
4
4
4
4
4
1
4
4
2
2
4
4
4
4
4
4
Description
Options:
Bits 4 through 7 – Not Used
Bit 3 – Modbus Type
0 = Standard
1 = Modbus with EFM Extensions
Bit 2 – Byte Order
0 = Least Significant Byte (LSB)
1 = Most Significant Byte (MSB)
Bit 1 – Log Modbus Events
0 = Log to Event Log
1 = No Logging
Bit 0 – Modbus Type
0 = RTU
1 = ASCII
Status
High Integer Scale
Low Integer Scale
High Float Scale #1
Low Float Scale #1
High Float Scale #2
Low Float Scale #2
High Float Scale #3
Low Float Scale #3
High Float Scale #4
Low Float Scale #4
High Float Scale #5
Low Float Scale #5
High Float Scale #6
Low Float Scale #6
High Float Scale #7
Low Float Scale #7
High Float Scale #8
Low Float Scale #8
Reference Manual
00809-0100-4832, Rev AA
March 2004
Abbr.
ENGACC
UCCTDY
UCCYDY
UCCMTH
UCCPRV
UCCACC
PACALC
Abbr.
OPTIONS
STATUS
HIGHINT
LOINT
HFLT1
LFLT1
HFLT2
LFLT2
HFLT3
LFLT3
HFLT4
LFLT4
HFLT5
LFLT5
HFLT6
LFLT6
HFLT7
LFLT7
HFLT8
LFLT8
C-22
Reference Manual
00809-0100-4832, Rev AA
March 2004
Table C-21. Point Type 54 – Modbus Function Table
Parameter
Number
28
29
30
31
24
25
26
27
20
21
22
23
16
17
18
19
12
13
14
15
8
9
10
11
6
7
4
5
2
3
0
1
44
45
46
47
40
41
42
43
48
49
50
36
37
38
39
32
33
34
35
Read-
Write
R/W
R/W
R/W
R/W
R/W
R/W
R/W
R/W
R/W
R/W
R/W
R/W
R/W
R/W
R/W
R/W
R/W
R/W
R/W
R/W
R/W
R/W
R/W
R/W
R/W
R/W
R/W
R/W
R/W
R/W
R/W
R/W
R/W
R/W
R/W
R/W
R/W
R/W
R/W
R/W
R/W
R/W
R/W
R/W
R/W
R/W
R/W
R/W
R/W
R/W
R/W
Data Type
UINT 8
UINT 16
UINT 16
TLP
UINT 8
UINT 16
UINT 16
TLP
UINT 8
UINT 16
UINT 16
TLP
UINT 8
UINT 16
UINT 16
TLP
AC
UINT 16
UINT 16
TLP
UINT 8
UINT 16
UINT 16
TLP
UINT 8
UINT 16
UINT 16
TLP
UINT 8
UINT 16
UINT 16
TLP
UINT 8
UINT 16
UINT 16
TLP
UINT 8
UINT 16
UINT 16
TLP
UINT 8
UINT 16
UINT 16
TLP
UINT 8
UINT 16
UINT 16
TLP
UINT 8
UINT 16
UINT 16
Length
2
3
1
2
2
3
1
2
2
3
1
2
2
3
1
2
2
3
1
2
2
3
1
2
2
3
1
2
20
2
2
3
2
3
1
2
2
3
1
2
1
2
2
2
3
1
2
2
3
1
2
Description
Conversion Code
Start Register #9
End Register #9
Parameter(s)
Conversion Code
Start Register #10
End Register #10
Parameter(s)
Conversion Code
Start Register #11
End Register #11
Parameter(s)
Conversion Code
Start Register #12
End Register #12
Parameter(s)
Conversion Code
Start Register #13
End Register #13
Point Tag Identification
Start Register #1
End Register #1
Parameter(s)
Conversion Code
Start Register #2
End Register #2
Parameter(s)
Conversion Code
Start Register #3
End Register #3
Parameter(s)
Conversion Code
Start Register #4
End Register #4
Parameter(s)
Conversion Code
Start Register #5
End Register #5
Parameter(s)
Conversion Code
Start Register #6
End Register #6
Parameter(s)
Conversion Code
Start Register #7
End Register #7
Parameter(s)
Conversion Code
Start Register #8
End Register #8
Parameter(s)
Rosemount 3095FC
Abbr.
CONV4
START5
END5
PARA5
CONV5
START6
END6
PARA6
CONV6
START7
END7
PARA7
CONV7
START8
END8
PARA8
TAG
START1
END1
PARA1
CONV1
START2
END2
PARA2
CONV2
START3
END3
PARA3
CONV3
START4
END4
PARA4
CONV8
START9
END9
PARA9
CONV9
START10
END10
PARA10
CONV10
START11
END11
PARA11
CONV11
START12
END12
PARA12
CONV12
START13
END13
C-23
Rosemount 3095FC
Parameter
Number
51
52
53
54
55
56
57
58
59
60
Read-
Write
R/W
R/W
R/W
R/W
R/W
R/W
R/W
R/W
R/W
R/W
Data Type
TLP
UINT 8
UINT 16
UINT 16
TLP
UINT 8
UINT 16
UINT 16
TLP
UINT 8
Length
3
1
2
2
3
1
3
1
2
2
Description
Parameter(s)
Conversion Code
Start Register #14
End Register #14
Parameter(s)
Conversion Code
Start Register #15
End Register #15
Parameter(s)
Conversion Code
Table C-22. Point Type 55 – Modbus Special Function Table
Read-
Write
R/W
R/W
R/W
R/W
R/W
R/W
R/W
R/W
R/W
R/W
R/W
R/W
R/W
R/W
R/W
R/W
R/W
R/W
R/W
R/W
R/W
R/W
R/W
R/W
R/W
R/W
R/W
R/W
R/W
R/W
R/W
R/W
R/W
R/O
R/O
R/W
R/W
Parameter
Number
27
28
29
30
23
24
25
26
19
20
21
22
15
16
17
18
31
32
33
34
35
36
11
12
13
14
7
8
9
10
5
6
3
4
0
1
2
Data Type
UINT 16
UINT 8
UINT 8
UINT 8
UINT 8
UINT 16
UINT 8
UINT 8
UINT 8
UINT 8
UINT 16
UINT 8
UINT 8
UINT 8
UINT 8
UINT 16
UINT 16
UINT 16
UINT 16
UINT 16
UINT 8
UINT 16
UINT 8
UINT 8
UINT 8
UINT 8
UINT 16
UINT 8
UINT 8
UINT 8
UINT 8
UINT 8
UINT 8
UINT 8
UINT 8
UINT 16
UINT 8
Length
1
2
1
1
2
1
1
1
1
1
1
2
1
1
2
1
1
1
1
1
2
1
1
1
1
1
1
2
1
1
2
1
2
1
2
2
2
Description
Event / Alarm Register
Periodic History Index Register
Daily History Index Register
Spare
History Format
History Archive Register #1
Start History Point
End History Point
Type of History Archive
Conversion Code
History Archive Register #2
Start History Point
End History Point
Type of History Archive
Conversion Code
History Archive Register #3
Start History Point
End History Point
Type of History Archive
Conversion Code
History Archive Register #4
Start History Point
End History Point
Type of History Archive
Conversion Code
History Archive Register #5
Start History Point
End History Point
Type of History Archive
Conversion Code
History Archive Register #6
Start History Point
End History Point
Type of History Archive
Conversion Code
History Archive Register #7
Start History Point
C-24
Reference Manual
00809-0100-4832, Rev AA
March 2004
Abbr.
PARA13
CONV13
START14
END14
PARA14
CONV14
START15
END15
PARA15
CONV15
Abbr.
ARCREG3
START3
END3
TYPE3
CONV3
ARCREG4
START4
END4
TYPE4
CONV4
ARCREG5
START5
END5
TYPE5
CONV5
ARCREG6
EVTALRM
PERIODIC
DAILY
SPARE
FORMAT
ARCREG1
START1
END1
TYPE1
CONV1
ARCREG2
START2
END2
TYPE2
CONV2
START6
END6
TYPE6
CONV6
ARCREG7
START7
Reference Manual
00809-0100-4832, Rev AA
March 2004
Parameter
Number
47
48
49
50
43
44
45
46
51
52
53
54
37
38
39
40
41
42
Read-
Write
R/W
R/W
R/W
R/W
R/W
R/W
R/W
R/W
R/W
R/W
R/W
R/W
R/W
R/W
R/W
R/W
R/W
R/W
Data Type
UINT 8
UINT 8
UINT 8
UINT 16
UINT 8
UINT 8
UINT 8
UINT 8
UINT 16
UINT 8
UINT 8
UINT 8
UINT 8
UINT 16
UINT 8
UINT 8
UINT 8
UINT 8
Length
1
2
1
1
2
1
1
1
1
1
1
1
1
1
1
2
1
1
Description
End History Point
Type of History Archive
Conversion Code
History Archive Register #8
Start History Point
End History Point
Type of History Archive
Conversion Code
History Archive Register #9
Start History Point
End History Point
Type of History Archive
Conversion Code
History Archive Register #10
Start History Point
End History Point
Type of History Archive
Conversion Code
Table C-23. Point Type 56 – Analog Input Calibration Parameters
Parameter
Number
11
12
13
14
7
8
9
10
15
16
5
6
3
4
0
1
2
Read-
Write
R/W
R/W
R/W
R/W
R/O
R/W
R/O
R/O
R/W
R/W
R/W
R/W
R/W
R/W
R/W
R/W
R/W
Data Type
AC
INT 16
INT 16
INT 16
INT 16
INT 16
FLP
FLP
FLP
FLP
FLP
FLP
FLP
FLP
UINT 16
UINT 8
UINT 8
Length
4
2
4
4
1
1
4
4
4
4
2
4
2
2
10
2
2
Description
Point Tag Identification
Raw Value 1
Raw Value 2
Raw Value 3
Raw Value 4
Raw Value 5
EU Value 1
EU Value 2
EU Value 3
EU Value 4
EU Value 5
Press Effect
Set EU Value
Manual EU
Timer
Mode
Type
Rosemount 3095FC
Abbr.
END7
TYPE7
CONV7
ARCREG8
START8
END8
TYPE8
CONV8
ARCREG9
START9
END9
TYPE9
CONV9
ARCREG10
START10
END10
TYPE10
CONV10
Abbr.
TAG
RAW1
RAW2
RAW3
RAW4
RAW5
EU1
EU2
EU3
EU4
EU5
PRESSEFF
SETVAL
MANUAL
TIMER
MODE
TYPE
C-25
Rosemount 3095FC
Reference Manual
00809-0100-4832, Rev AA
March 2004
Table C-24. Point Type 58 – Revision Information
Parameter
Number
2
3
0
1
Read-
Write
R/O
R/O
R/O
R/O
Data Type
AC
AC
AC
UINT 8
Length
20
10
10
1
Description
Device Firmware Description
Part Number
Version
Information Present Flag
Read-
Write
R/W
R/W
R/W
R/W
R/W
R/W
R/W
R/W
R/W
R/W
R/W
R/W
R/W
R/W
R/W
R/W
R/W
R/W
R/W
R/W
R/W
R/W
R/W
R/W
R/W
R/W
R/W
R/W
R/W
R/W
R/W
R/W
R/W
R/W
R/O
R/W
R/W
R/W
R/W
R/W
R/W
Table C-25. Point Type 86 – Extended History Parameters
Parameter
Number
27
28
29
30
23
24
25
26
19
20
21
22
15
16
17
18
35
36
37
38
31
32
33
34
39
40
11
12
13
14
7
8
9
10
5
6
3
4
0
1
2
Data Type
TLP
UINT 8
UINT 8
TLP
TLP
UINT 8
UINT 8
TLP
TLP
UINT 8
UINT 8
TLP
TLP
UINT 8
UINT 8
TLP
TLP
UINT 8
UINT 8
TLP
TLP
UINT 8
UINT 8
TLP
TLP
UINT 8
UINT 8
UINT 8
TLP
TLP
UINT 8
UINT 8
TLP
TLP
UINT 8
UINT 8
TLP
TLP
UINT 8
UINT 8
TLP
Length
1
3
3
1
1
3
3
1
1
3
3
1
1
3
3
1
1
3
3
1
3
1
1
3
3
1
1
3
3
1
1
3
3
1
1
3
3
1
1
1
3
Description
Maximum number of Extended History Points
Sample Log Interval – Units in Minutes
Point Tag Identification TLP
Extended History Log Point #1
Archive Type
Averaging or Rate Type
Point Tag Identification TLP
History Log Point #2
Archive Type
Averaging or Rate Type
Point Tag Identification TLP
History Log Point #3
Archive Type
Averaging or Rate Type
Point Tag Identification TLP
History Log Point #4
Archive Type
Averaging or Rate Type
Point Tag Identification TLP
History Log Point #5
Archive Type
Averaging or Rate Type
Point Tag Identification TLP
History Log Point #6
Archive Type
Averaging or Rate Type
Point Tag Identification TLP
History Log Point #7
Archive Type
Averaging or Rate Type
Point Tag Identification TLP
History Log Point #8
Archive Type
Averaging or Rate Type
Point Tag Identification TLP
History Log Point #9
Archive Type
Averaging or Rate Type
Point Tag Identification TLP
History Log Point #10
Archive Type
Abbr.
DESC
PART#
VERSION
PRESENT
Abbr.
HST#4
ARCH4
AVG#4
TAG#5
HST#5
ARCH5
AVG#5
TAG#6
HST#6
ARCH6
AVG#6
TAG#7
HST#7
ARCH7
AVG#7
TAG#8
MAXPTS
INTERVAL
TAG#1
HST#1
ARCH1
AVG#1
TAG#2
HST#2
ARCH2
AVG#2
TAG#3
HST#3
ARCH3
AVG#3
TAG#4
HST#8
ARCH8
AVG#8
TAG#9
HST#9
ARCH9
AVG#9
TAG#10
HST#10
ARCH10
C-26
Reference Manual
00809-0100-4832, Rev AA
March 2004
Parameter
Number
51
52
53
54
47
48
49
50
41
42
43
44
45
46
59
60
61
55
56
57
58
Read-
Write
R/W
R/W
R/W
R/W
R/W
R/W
R/W
R/W
R/W
R/W
R/W
R/W
R/W
R/W
R/W
R/W
R/W
R/W
R/W
R/W
R/W
Data Type
UINT 8
TLP
TLP
UINT 8
UINT 8
TLP
TLP
UINT 8
UINT 8
TLP
TLP
UINT 8
UINT 8
TLP
TLP
UINT 8
UINT 8
TLP
TLP
UINT 8
UINT 8
Length
1
3
3
1
1
3
3
1
1
3
3
1
1
3
3
1
1
1
3
3
1
Description
Averaging or Rate Type
Point Tag Identification TLP
History Log Point #11
Archive Type
Averaging or Rate Type
Point Tag Identification TLP
History Log Point #12
Archive Type
Averaging or Rate Type
Point Tag Identification TLP
History Log Point #13
Archive Type
Averaging or Rate Type
Point Tag Identification TLP
History Log Point #14
Archive Type
Averaging or Rate Type
Point Tag Identification TLP
History Log Point #15
Archive Type
Averaging or Rate Type
Rosemount 3095FC
Abbr.
AVG#10
TAG#11
HST#11
ARCH11
AVG#11
TAG#12
HST#12
ARCH12
AVG#12
TAG#13
HST#13
ARCH13
AVG#13
TAG#14
HST#14
ARCH14
AVG#14
TAG#15
HST#15
ARCH15
AVG#15
C-27
Rosemount 3095FC
Reference Manual
00809-0100-4832, Rev AA
March 2004
C-28
Reference Manual
00809-0100-4832, Rev AA
October 2004
Glossary
Rosemount 3095FC
A
A/D - Analog to Digital
AGA - American Gas Association.
AI - Analog Input.
AO - Analog Output.
Analog - Analog data is represented by a continuous variable, such as an electrical current signal.
AP - Absolute Pressure.
ASCII - American (National) Standard Code for Information Interchange.
Attribute - A parameter that provides information about an aspect of a database point. For example, the alarm attribute is an attribute that uniquely identifies the configured value of an alarm.
B
Built-in I/O - I/O channels that are fabricated into the 3095FC and do not require a separate option. Also called
“on-board” I/O.
C
COMM - Abbreviation for communications. Most commonly used as comm port, referring to the communication port of the 3095FC.
Configuration - Typically, the software setup of a device, such as a 3095FC, that can often be defined and changed by the user. Can also mean the hardware assembly scheme.
Configuration Tree - When a configuration file is open in Rosemount User Interface Software, the Configuration
Tree View menu appears.
CRC - Cyclical Redundancy Check
CSA - Canadian Standards Association.
CTS - Clear To Send modem communications signal.
D
DB - Database.
dB - Decibel. A unit for expressing the ratio of the magnitudes of two electric signals on a logarithmic scale.
DCD - Data Carrier Detect modem communications signal.
Deadband - A value that is an inactive zone above the low limits and below the high limits. The purpose of the deadband is to prevent a value such as an alarm from being set and cleared continuously when the input value is oscillating around the specified limit. This also prevents the logs or data storage location from being overfilled with data.
Directory View - The Communication Directory tree provides a tree style means of navigating through the PC
Comm Ports and the 3095FC Comm Ports setup screens.
www.rosemount.com
Rosemount 3095FC
Reference Manual
00809-0100-4832, Rev AA
October 2004
Discrete - Input or output that is non-continuous, typically representing two levels such as on/off.
DP - Differential Pressure.
DSR - Data Set Ready modem communications signal.
DTR - Data Terminal Ready modem communications signal.
Duty Cycle - Proportion of time during a cycle that a device is activated. A short duty cycle conserves power for I/O channels, radios, and such.
DVM - Digital voltmeter.
Sensor Module - Dual-Variable Sensor. Provides static and DP inputs to a 3095FC.
E
EFM - Electronic Flow Metering or Measurement./
EIA-232 - Serial Communications Protocol using three or more signal lines, intended for short distances. Also referred to as RS-232.
EIA-422 - Serial Communication Protocol using four signal lines. Also referred to as the RS-422 standard.
EIA-485 - Serial Communications Protocol requiring only two signal lines. Can allow up to 32 devices to be connected together in a daisy-chained fashion. Also referred to as RS-485.
EMI - Electro-magnetic interference.
ESD - Electronic Static Discharge.
EU - Engineering Units.
F
Firmware - Internal software that is factory-loaded into a form of ROM. In the 3095FC, the firmware supplies the software used for gathering input data, converting raw input data calculated values, storing values, and providing control signals.
Flash ROM - A type of read-only memory that can be electrically re-programmed. It is a form of permanent memory and requires no backup power.
FSK - Frequency shift keyed.
G
GFA - Ground fault analysis.
GND - Electrical ground, such as used by the 3095FC power supply.
GP - Gauge Pressure.
H
HistoryLink Utility - HistoryLink utility allows the user to access and retrieve the 10-Minute History from the
3095FC. The HistoryLink utility supplements Rosemount User Interface for Windows Software.
Holding Register - Analog output number value to be read.
hw - DP.
Glossary-2
Reference Manual
00809-0100-4832, Rev AA
October 2004
Rosemount 3095FC
I, J
IC - Industry Canada, more recently know an Measurement Canada, which grants custody transfer approvals on certain 3095FC units. IC can also mean integrated circuit.
ID - Identification
IEC - Industrial Electrical Code.
IEEE - Institute of Electrical and Electronic Engineers. the Open System Interconnection (OSI) reference model and an international standard for the organization of local area networks (LANs) established by the INternational
Standards Organization (ISO) and the IEEE.
IMV - Integral Multiplier Value.
Input - Digital input, a bit to be read.
Input Register - Input numeric value to be read.
I/O - Input/Output.
IRQ - Interrupt Request. Hardware address oriented.
ISO - Organization internationale de normalisation (International Standards Organization)
IV - Integral Value
K
KB - Kilobytes.
kHz - Kilohertz.
L
LCD - Liquid Crystal Display. Display only device used for reading data.
LED - Light-emitting diode.
LOI - Local Operator Interface. Refers to the serial (RS-232) port on the 3095FC through which local communications are established, typically for configuration software running on a PC.
LRC - Longitudinal Redundancy Checking error checking.
M
mA - Milliamp(s); one thousandth of an ampere.
Manual Mode - Scanning is disabled.
Modbus - A device communications protocol developed by Gould-Modicon.
mW - Milliwatts, or 0.001 watt.
mV - Millivolts, or 0.001 volt.
N
NEC - National Electrical Code.
NEMA - National Electrical Manufacturer's Association.
O
OH - Off-Hook modem communications signal.
Off-line - Accomplished while the target device is not connected (by a communications link). For example, off-line configuration is configuring a 3095FC in an electronic file that is later loaded into the 3095FC.
Ohms - Units of electrical resistance.
Glossary-3
Rosemount 3095FC
Reference Manual
00809-0100-4832, Rev AA
October 2004
On-line - Accomplished while connected (by a communications link) to the target device. For example, on-line configuration is configuring a Rosemount User Interface Software while connected to it, so that current parameter values are viewed and new values can be loaded immediately.
OP - Operator Port; see LOI.
Opcode - Type of message protocol used by the 3095FC to communicate with Rosemount User Interface
Software, as well as host PC with Rosemount User Interface Software driver software.
P, Q
Parameter - A property of a point that typically can be configured or set by the user. For example, the Point Tag ID is a parameter of an Analog Input point. Parameters are normally edited by using configuration software running on a PC.
Pf - Flowing pressure.
PC - Personal computer.
P/PD - Pressure / DP
PI - Pulse Input. Also referred to as PIN.
Point - Software-oriented term for an I/O channel or some other function, such as a flow calculation. Points are defined by a collection of parameters.
Point Number - The number of an I/O point as installed in the 3095FC system.
Point Type - The point type attribute defines the database point to have one of the possible types of pints available to the system. The point type determines the basic functions of a point.
Preset - Number value previously determined for a register.
PRI - Primary PID control loop.
Protocol - A set of standards that enables communication or file transfers between two PCs. Parameters include baud rate, parity, data bits, stop bit, and the type of duplex.
PSTN - Public Switched Telephone Network.
PT - Process Temperature.
PTI - Periodic Timer Interrupt
PTC - Positive Temperature Coefficient.
PTT - Push-to-Talk signal.
Pulse - Transient variation of a signal whose value is normally constant.
PV - Process variable or process value.
R
RAM - Random Access Memory. In a 3095FC, it is used to store history, data, most user programs, and additional configuration data.
RBX - Report-by-exception. In a 3095FC, it always refers to spontaneous RBX, in which the 3095FC contacts the host to report an alarm condition.
RFI - Radio frequency interference.
RI - Ring Indicator modem communications signal.
User Interface Software - Remote Operations Controller is a microprocessor-based unit that provides remote monitoring and control.
Rosemount User Interface Software - Configuration software used to configure 3095FC units.
Glossary-4
Reference Manual
00809-0100-4832, Rev AA
October 2004
Rosemount 3095FC
ROM - Read-only memory. Typically used to store firmware.
RTC - Real-time clock.
RTD - Resistance Temperature Detector.
RTS - Ready to Send modem communications signal.
RTU - Remote Terminal Unit.
RXD - Received Data communications signal.
S
Script - An uncompiled text file (such as keystrokes for a macro) that is interpreted by a program to perform certain functions. Typically, scripts can be easily created or edited by the end-user to customize the software.
Soft Points - A type of point with generic parameters that can be configured to hold data as desired by the user.
SP - Setpoint, or Static Pressure.
SPI - Slow Pulse Input.
SPK - Speaker.
SRAM - Static Random Access Memory. Stores data as long as power is applied; typically backed up by a lithium battery or super capacitor.
SRBX - Spontaneous Report-by-Execution. Refer to RBX.
SVA - Signal Value Analog. Stored in the Results Register.
SVD - Signal Value Discrete. Stored in the Compare Flag.
T-Z
Tf - Flowing temperature.
TLP - Type (of point), Logical (or point) number, and Parameter number.
TXD - Transmitted Data communications signal.
Glossary-5
Rosemount 3095FC
Reference Manual
00809-0100-4832, Rev AA
October 2004
Glossary-6
Reference Manual
00809-0100-4832, Rev AA
October 2004
Index
Rosemount 3095FC
A
Accessories
. . . . . . . . . . . 1-3
,
A-11
After Installing Components
. . . . 5-4
Apply Power
. . . . . . . . . . . . . 2-10
Approved Manufacturing Locations
.
B-1
Automatic Tests
. . . . . . . . . . . . 1-3
B
Backup Configuration Information
Basic Functions
5-1
. . . . . . . . . . . . 3-1
Display TLP
. . . . . . . . . . . 3-1
Download File
. . . . . . . . . . 3-3
Duplicating a Configuration
New Configuration File
Open File
. 3-2
. . . . 3-2
. . . . . . . . . . . . . 3-2
Print Configuration
Save File
. . . . . . . 3-3
. . . . . . . . . . . . . 3-2
Select TLP
. . . . . . . . . . . . 3-1
Using Copy and Paste
. . . . 3-2
C
Calibrate
3095FC
. . . . . . . . . . . . . . 4-1
Analog Input (AI)
. . . . . . . . 4-3
Calibration Report
Calibration Value
. . . . 4-5
. . . . . 4-5
Zero Shift
Verify
. . . . . . . . . . 4-5
. . . . . . . . . . . . . . . . 4-6
Changing the Plate
. . . . . . . . . . 5-5
Communication Errors
. . . . . . . 5-2
Communication Problems
Debug Communications
. . 5-2
. . . 5-2
Configuration
Analog Input
AI Advanced Tab
CD User List
Collect Data
. . . . . . . . . . .3-16
AI Alarms Tab
AI General Tab
. . . .3-17
. . . . . .3-19
. . . . . .3-16
. . . . . . . . . . .3-15
. . . . . . . . . . .3-38
Communications Ports
Configuration
General Tab
RBX Tab
. . . . .3-8
. . . . . . . . .3-8
. . . . . . . . . . .3-9
Configure History for EFM
Reporting
EFM Reports
. . . . . .3-38
. . . . . . .3-38
Device Configuration / Information
3-10
General Tab
Points Tab
. . . . . . . .3-10
Other Information Tab
.3-12
. . . . . . . . . 3-11
Revision Info Tab
. . . .3-12
History Points
. . . . . . . . . .3-32
Averaging Technique
General History
Log Types
.3-33
. . . . .3-35
. . . . . . . . .3-33
Meter History
. . . . . . .3-32
History, Alarm, Event, and Audit
I/O
Log Reports
. . . . .3-37
. . . . . . . . . . . . . . . . . .3-15
I/O Monitor
. . . . . . . . .3-15
Scanning Disabled vs
Meter Run
Enabled
. . . .3-15
. . . . . . . . . . . .3-25
Advanced Meter Setup Tab
3-29
AGA Meter Inputs Tab
Gas Quality Tab
General Tab
3-27
. . . . .3-28
. . . . . . . .3-26
Instrument Calibration Tab
.
3-30
Meter Setup Alarms Tab
Modbus
3-31
. . . . . . . . . . . . . .3-40
Detailed Point
. . . . . . .3-47
General Tab
. . . . . . . .3-40
History Access Registers Tab
3-44
Modbus - Events / Alarms
Functionality
.3-45
Modbus - History Collection
.
3-44
Parameter Information
Scale Values Tab
Modbus Conversion
Modbus Registers
Opcode
3-47
. . . . 3-42
. . . . . 3-51
. . . . . . 3-47
. . . . . . . . . . . . . . 3-21
Opcode Table Configuration
Overview
3-22
. . . . . . . . . . . . . . 3-1
Radio Power Control
Security
. . . . . 3-23
. . . . . . . . . . . . . . 3-13
3095FC
. . . . . . . . . . . 3-14
Menu and Log On
. . . 3-13
. . . . . . . . 3-4
Setting the Clock
Soft Points
. . . . . . . . . . . . 3-20
System Flags
. . . . . . . . . . . 3-5
Advanced Tab
General Tab
. . . . . . . 3-7
. . . . . . . . 3-5
Considerations
Enclosure
Environmental
Mounting
Power
. . . . . . . . . . . . . 1-5
. . . . . . . . . . 1-5
. . . . . . . . . . . . . . 1-5
. . . . . . . . . . . . . . . . 1-5
Rosemount User Interface
Software
. . . . . . . . 1-6
Site
. . . . . . . . . . . . . . . . . . 1-6
Wiring
. . . . . . . . . . . . . . . . 1-6
Custom Displays
. . . . . . . . . . . 3-54
New Display
. . . . . . . . . . . 3-54
Save Displays
. . . . . . . . . 3-55
D
Dimensional Drawings
. . . . . . . . A-7
E
Enclosure Considerations
. . . . . 1-5
Environmental Considerations
European Directive Information
. . 1-5
. B-1
F
Firmware
. . . . . . . . . . . . . . . . . 1-3
Functions
. . . . . . . . . . . . . . . . . 1-4 www.rosemount.com
Rosemount 3095FC
Reference Manual
00809-0100-4832, Rev AA
October 2004
G
Glossary
Earth
. . . . . . . . . . . Glossary-1
Grounding
. . . . . . . . . . . . . . . . 2-8
. . . . . . . . . . . . . . . . 2-8
Pipelines With Cathodic Protection
. . . . . . . . . . . . . . 2-8
Pipelines Without Cathodic
Protection
. . . . . . 2-9
H
Hardware
. . . . . . . . . . . . . . . . 1-2
Hazardous Locations Certifications
B-1
.
North American Certifications
B-1
I
Installation
. . . . . . . . . . . . . . . . 2-2
Rosemount 3095FC
Orifice Plate
Pipestand
. . . . . . 2-2
. . . . . . . . 2-2
. . . . . . . . . . 2-2
Rosemount User Interface
Software
. . . . . . 2-11
With Autorun
Without Autorun
Solar Panels
Sizing
. . . . . . . 2-11
. . . . 2-12
. . . . . . . . . . . 2-3
. . . . . . . . . . . . 2-3
L
Low Power Mode
. . . . . . . . . . . 1-4
M
Modbus
Configuration
. . . . . . . . . . 3-40
Conversion
Mounting
. . . . . . . . . . . 3-51
Register Configuration
. . . . . . . . . . . . . . . . . 2-1
Mounting Considerations
. . . 3-47
. . . . . 1-5
O
Options
. . . . . . . . . . . . . . . . . A-11
Custom Configuration
. . . A-11
Standard Configuration
. . . A-11
Ordering Information
. . . . . . . . . A-9
Overview
. . . . . . . . . . . . . . . . . 1-1
3095FC
. . . . . . . . . . . . . . 1-1
3095FC Functions
Accessories
. . . . . . . 1-4
. . . . . . . . . . . 1-3
Automatic Tests
. . . . . . . . . 1-3
Calibration
. . . . . . . . . . . . 4-1
Configuration
. . . . . . . . . . . 3-1
Firmware
Hardware
. . . . . . . . . . . . . 1-3
. . . . . . . . . . . . . 1-2
Low Power Mode
. . . . . . . . 1-4
P
Power Considerations
Power Supply
. . . . . . . .1-5
. . . . . . . . . . . . . .2-9
Applying
Batteries
. . . . . . . . . . . . . .2-10
. . . . . . . . . . . . . .2-9
R
Replacing the Batteries
Resetting the 3095FC
Cold Start
. . . . . . .5-5
. . . . . . . .5-3
. . . . . . . . . . . . . .5-3
Jumper Reset
Warm Start
. . . . . . . . . . .5-3
. . . . . . . . . . . . .5-3
Rosemount User Interface Software
Adding a 3095FC transmitter
2-16
Adding a Group
. . . . . . . .2-15
.
Deleting a 3095FC transmitter
2-16
Deleting a Group
. . . . . . . .2-15
Deleting all 3095FC transmitters
2-16
Device Point Types
. . . . . . C-3
Establishing Communication
Configuration Tree
. . .2-14
Connection
Installation
. . . . . . . .2-13
. . . . . . . . . . . . 2-11 with Autorun
. . . . . . . . 2-11
. . . . .2-12
Without Autorun
Log in
. . . . . . . . . . . . . . .2-12
Overview
. . . . . . . . . . . . . 2-11
Point Type 0
. . . . . . . . . . . C-2
Point Type Parameter Definitions
C-1
Renaming a Group or 3095FC
.
2-16
Requirements
. . . . . . . . . . .1-6
Run the Software
. . . . . . .2-12 stall
Uninstalling
. . . . . . . .2-12
S
Site Considerations
Sizing
. . . . . . . . . .1-6
Solar Panels
. . . . . . . . . . . . . . . .2-3
Specifications
Flow
. . . . . . . . . . . . . . . . A-6
Functional
Memory
. . . . . . . . . . . . A-1
. . . . . . . . . . . . . . A-6
Performance
. . . . . . . . . . . A-3
Physical
. . . . . . . . . . . . . . A-4
W
Wiring
. . . . . . . . . . . . . . . . . . . 2-4
Communications
EIA-232
. . . . . . . . 2-6
. . . . . . . . . . . 2-7
EIA-485
. . . . . . . . . . . 2-7
Local Operator Interface
2-6
Ground the Transmitter
Power Supply
. . . . 2-8
. . . . . . . . . . . 2-5
RTD
. . . . . . . . . . . . . . . . . 2-5
Wiring Considerations
. . . . . . . . 1-6
Index-2
Reference Manual
00809-0100-4832, Rev AA
October 2004
This product powers
PlantWeb through diagnostics including device temperature limit and low battery voltage.
Rosemount and the Rosemount logotype are registered trademarks of Rosemount Inc.
PlantWeb is a registered trademark of one of the Emerson Process Management group of companies.
All other marks are the property of their respective owners.
Emerson Process Management
Rosemount Inc.
8200 Market Boulevard
Chanhassen, MN 55317 USA
T (U.S.) 1 800 999 9307
T (International) (952) 906 8888
F (952) 949 7001
Fisher-Rosemount GmbH & Co.
Argelsrieder Feld 3
82234 Wessling
Germany
Tel 49 (8153) 9390
Fax 49 (8153) 939172
Emerson Process Management Asia
Pacific Private Limited
1 Pandan Crescent
Singapore 128461
T (65) 6777 8211
F (65) 6777 0947
www.rosemount.com
Beijing Rosemount Far East
Instrument Co., Limited
No. 6 North Street,
Hepingli, Dong Cheng District
Beijing 100013, China
T (86) (10) 6428 2233
F (86) (10) 6422 8586
00809-0100-4832
© 2004 Rosemount Inc. All rights reserved.
advertisement
* Your assessment is very important for improving the workof artificial intelligence, which forms the content of this project
Related manuals
advertisement
Table of contents
- 14 3095FC Overview
- 14 Hardware
- 14 Firmware
- 14 Accessories
- 14 Automatic Tests
- 14 Low Power Mode
- 14 3095FC Functions
- 14 Flow Measurement
- 14 1992 Flow Calculations for Orifice Metering
- 14 Considerations
- 14 Environmental Requirements
- 14 Enclosures
- 14 Mounting
- 14 Power Installation Requirements
- 14 Rosemount User Interface Software PC Requirements
- 14 Site Requirements
- 14 Wiring Requirements
- 15 Mounting
- 15 Installation
- 15 Rosemount 3095FC
- 15 Installing the Rosemount 3095FC on a Pipestand
- 15 Installing the 3095FC on an Orifice Plate (Direct Mount)
- 15 Solar Panels
- 15 Solar Panel Sizing
- 15 Wiring
- 15 Power Supply Wiring
- 15 RTD Wiring
- 15 Communications Wiring
- 15 Local Operator Interface Port (LOI)
- 15 EIA-485 (RS-485) Serial Communications - Comm
- 15 EIA-232 (RS-232) Communications - Comm
- 15 Ground the Transmitter
- 15 Earth Grounds
- 15 Pipelines With Cathodic Protection
- 15 Power Supply
- 15 Batteries
- 15 Apply Power
- 15 Install the Rosemount User Interface Software
- 15 Software Overview
- 15 Install With Autorun
- 15 Install Without Autorun
- 15 Uninstalling the Rosemount User Interface Software
- 30 Getting Started with the Software
- 30 Run the Software
- 30 Log into the Software
- 30 Establishing Communication
- 30 Connection Methods
- 30 Direct Connect
- 30 Connect
- 30 Remote Hardware Connection
- 30 Disconnect from the 3095FC
- 30 Configuration Tree
- 30 Adding a Group
- 30 Deleting a Group
- 30 Adding a 3095FC transmitter
- 30 Deleting a 3095FC transmitter
- 30 Deleting all 3095FC transmitters
- 30 Renaming a Group or 3095FC
- 31 Overview
- 31 Basic Functions
- 31 Select TLP Options
- 31 Display TLP Options
- 31 Duplicating a Configuration
- 31 Using Copy and Paste
- 31 New Configuration File
- 31 Open File
- 31 Save File
- 31 Download File
- 31 Print Configuration
- 31 Configuration
- 31 Setting the Clock
- 31 Configuring the System Flags
- 31 General Tab
- 31 Advanced Tab
- 31 3095FC Communications Ports Configuration
- 31 General Tab
- 31 RBX Tab
- 31 3095FC Device Configuration / Information
- 31 General Tab
- 31 Points Tab
- 31 Other Information Tab
- 31 Revision Info Tab
- 31 Security Configuration
- 31 Rosemount User Interface Security - Menu and Log On
- 31 3095FC Security
- 31 LCD User List Configuration
- 31 I/O Configuration
- 31 Scanning Disabled versus Scanning Enabled
- 31 I/O Monitor
- 31 Analog Input (AI) Configuration
- 31 AI General Tab
- 31 AI Advanced Tab
- 31 AI Alarms Tab
- 91 Soft Points Configuration
- 91 Opcode
- 91 Opcode Table Configuration
- 91 Radio Power Control Configuration
- 91 Meter Run Configuration
- 91 General Tab
- 91 AGA Meter Inputs Tab
- 91 Gas Quality Tab
- 91 Advanced Meter Setup Tab
- 91 Instrument Calibration Tab
- 91 Meter Setup Alarms Tab
- 91 History Points Configuration
- 91 Meter History
- 91 Averaging Technique
- 91 Log Types
- 91 General History
- 91 History, Alarm, Event, and Audit Log Reports
- 91 Collect Data
- 91 Configure History for EFM Reporting
- 91 Electronic Flow Measurement (EFM) Reports
- 91 Modbus Configuration
- 91 General Tab
- 91 Scale Values Tab
- 91 Modbus - History Collection
- 91 History Access Registers Tab
- 91 Modbus - Events / Alarms Functionality
- 91 Modbus - Detailed Point / Parameter Information
- 91 Configure Modbus Registers
- 91 Modbus Conversion
- 91 Custom Displays
- 91 New Display
- 91 Save Displays
- 92 Overview
- 92 Calibrate
- 92 3095FC
- 92 Analog Input (AI) Calibration
- 92 Calibration Report
- 92 Calibration Value
- 92 Zero Shift
- 92 Verify Calibration
- 93 Backup Configuration Information
- 93 Communication Errors
- 93 Communication Problems
- 93 Debug Communications
- 93 Resetting the 3095FC
- 93 Warm Start
- 93 Cold Start
- 93 Jumper Reset
- 93 After Installing Components
- 93 Replacing the Batteries