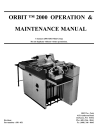
advertisement
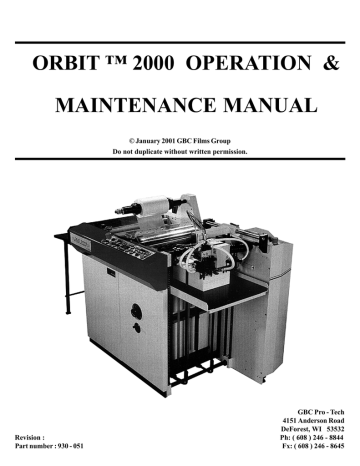
ORBIT ™ 2000 OPERATION &
MAINTENANCE MANUAL
© January 2001 GBC Films Group
Do not duplicate without written permission.
GBC Pro - Tech
4151 Anderson Road
DeForest, WI 53532
Revision : Ph: ( 608 ) 246 - 8844
Part number : 930 - 051 Fx: ( 608 ) 246 - 8645
Orbit™ 2000 Operation and Maintenance Manual Read me file
Read Me File . . . . . . . . .
The information in this publication is provided for reference and is believed to be accurate and complete. GBC Films Group is not liable for errors in this publication or for incidental or consequential damage in connection with the furnishing or use of the information in this publication, including, but not limited to, any implied warranty of fitness or merchantability for any particular use.
GBC Films Group reserves the right to make changes to this publication and to the products described in it without notice. All specifications and information concerning products are subject to change without notice.
Reference in this publication to information or products protected by copyright or patent does not convey any license under the rights of GBC Films Group or others. GBC Films
Group assumes no liability arising from infringements of patents or any other rights of third parties.
This publication is copyrighted © 2000 by GBC Films Group. All rights reserved. The information contained in this publication is proprietary and may not be reproduced, stored, transmitted, or transferred, in whole or in part, in any form without the prior and express written permission of GBC Films Group.
The following information will explain how to move around within the electronic version of this publication. The hand will change to a pointer finger identifying hyperlinked areas. When moving from page to page, use to return to the first PAGE, use to advance to the last
PAGE, use to go back one PAGE and use to advance one PAGE. When moving from view to view, use to return to a previous VIEW and use to advance to the next
VIEW.
Should you find an error within this publication or would like to make a suggestion, please utilize the fax correspondence sheet following this read me file and fax it to the number provided. Your comments and help will ensure up to date information. Thank you.
© GBC Films Group January 2001
Read me file
This page intentionally left blank.
Orbit™ 2000 Operation and Maintenance Manual
© GBC Films Group January 2001
Orbit™ 2000 Operation and Maintenance Manual
Fax Correspondence
Fax number : ( 608 ) 246 - 8645 Date :
To : Sean Flood at GBC Pro-Tech
4151 Anderson Road
DeForest, WI 53532
From :
Company :
Address :
Phone number : ( ) Fax number : ( )
Re : Orbit™ 2000 Operations and Maintenance Manual ( 930051 )
Section #: Page #:
Correction (s):
Read me file
Additional comments:
© GBC Films Group January 2001
Read me file
This page intentionally left blank.
Orbit™ 2000 Operation and Maintenance Manual
© GBC Films Group January 2001
Orbit™ 2000 Operation and Maintenance Manual
Table of Contents
Section 1: Safety
Table of Contents
1.3 Safety - Rules for handling the feeding head ..............................................1 - 5
1.4 Safety - Rules for setting up the rollers and the hinged stops .....................1 - 7
1.5 Safety - Rules for set-up of the adjustable guide plates ..............................1 - 9
1.6 Safety - Rules for the chrome and pressure rollers ..................................1 - 10
1.9 Safety - Rules for the position adjustment of the decurling bar ................1 - 19
1.12 Safety - Rules for machine maintenance and adjustments .....................1 - 24
© GBC Films Group January 2001 Page I
Table of Contents Orbit™ 2000 Operation and Maintenance Manual
1.14 Safety - Rules for the central drive maintenance ....................................1 - 27
1.15 Safety - Rules for snapping assembly/ chain/ belt drive maintnenance ..1 - 28
1.16 Safety - Rules for maintenance/ replacement of the twin knife ..............1 - 29
Section 2: Warranty
Section 3: Specifications
3.0 Specific dimensions and weight of the equipment illustration ...................3 - 1
3.1 Dimensions and weight of the equipment ....................................................3 -1
Page II © GBC Films Group January 2001
Orbit™ 2000 Operation and Maintenance Manual
Section 4: Installation
Table of Contents
4.6 Becker T4.25 DSK compressor installation ..............................................4 - 8
Section 5: Operations
5.1.1 Main and secondary operator position ..........................................5 - 2
© GBC Films Group January 2001 Page III
Table of Contents Orbit™ 2000 Operation and Maintenance Manual
Original overlay illustration ..........................................................5 - 4
New overlay illustration ................................................................5 - 5
5.2.2 Feeder table positioning ................................................................5 - 9
5.2.7 Adjustable guide plates ................................................................5 - 22
Page IV
© GBC Films Group January 2001
Orbit™ 2000 Operation and Maintenance Manual Table of Contents
5.3.4 Spreader roller ( option ) .............................................................5 - 32
Section 6: Applications
© GBC Films Group January 2001 Page V
Table of Contents
Section 7: Troubleshooting
Orbit™ 2000 Operation and Maintenance Manual
Section 8: Maintenance
8.2.1 Safety - Rules for machine cleaning ...............................................8 - 5
Page VI
8.2.2 Safety - Rules for maintenance/ replacement of the twin knife ......8 - 7
8.2.3 Feed table chain tensioning ...........................................................8 - 9
© GBC Films Group January 2001
Orbit™ 2000 Operation and Maintenance Manual
1.0 Safety regulations
1.1 Safety - Complete equipment
1/
ATTENTION
Do not operate this equipment unless you have read and understand this operator manual and have been fully trained in its operation by a qualified GBC service technician.
2/
ATTENTION
The operator may use the Orbit 2000 only for the lamination of paper sheets.
The equipment may not be used for any other type of work. The type of paper and film must comply with conditions of Section 2 of the Technical Specifications.
The equipment is provided with means to control lamination functions. The controls as set up by the factory may not be modified or altered.
Safety
3/
ATTENTION
Do not operate , adjust, service or repair the Orbit 2000 if you are under the influence of alcohol, drugs, or medication.
4/
ATTENTION
Do not operate the Orbit 2000 if you are ill or tired.
© GBC Films Group January 2001 Page 1 - 1
Safety Orbit™ 2000 Operation and Maintenance Manual
5/
ATTENTION
All safety covers must be in place during operation. The equipment must not be started and used, if all covers are not in place, and safety switches are not operational.
6/
A T T E N T IO N
T est all three interlocked safety guards each day ( the chrom e roller guard, snap roller guard and the guard under the lam inating and snap A R G A s ) and the tw o em ergency stop sw itches ( one on the control p anel and one on the drive sid e of the feeder ) and the pile u p safety sw itch ( on the feeder table guide rails )to ensure th at they function properly.
7/
ATTENTION
Exercise extreme caution when working with sheets to avoid paper cuts.
8/
ATTENTION
Never clean any rollers while the equipment is running. If needed, turn the rollers for cleaning or testing by using the slow forward or slow reverse push buttons.
9/
Page 1 - 2
ATTENTION
When using the slow forward and slow reverse push buttons, push and release the buttons and wait for the machine to stop before cleaning the exposed area of the rollers.
© GBC Films Group January 2001
Orbit™ 2000 Operation and Maintenance Manual
10/
A T T E N T IO N
N ever p erform adjustm ents w hile the m achine is runn ing. T he m achin e m ust first be stopped , adjusted and then restarted. ( E xcept W hen A djusting L ap F or Sheet Size ! )
Safety
11/
ATTENTION
Excercise caution when working around the feeder table, control panel and stacking tray to avoid bumping you head.
12/
ATTENTION
The equipment must be fixed/ positioned on a firm and even floor. The working station of the operator must be at the same level.
13/
ATTENTION
The operator shall provide adequate lighting suitable for the given task.
14/
ELECTRICAL
S H O C K
Do not remove or modify any guards, covers or enclosures. Contact with any moving parts or/ and electrical voltage can result in injury or death!
© GBC Films Group January 2001 Page 1 - 3
Safety Orbit™ 2000 Operation and Maintenance Manual
1.2 Safety - Rules for loading paper
The normal function of the equipment is to insert paper and laminate it. For a safe loading of paper it is necessary to follow these safety rules:
1/
ATTENTION
Do not attempt to load paper while the machine is running. Your fingers couldbe hurt during the automatic insertion of paper.
2/
W A R N I N G
Ensure the feeder stack/ pile is in the bottom position before loading paper. To move into that position, press the Pile/ Stack down push button.
C A U T I O N : A v o i d b u m p i n g y o u r h e a d o n t h e f e e d e r w h e n l o a d i n g p a p e r .
3/
W A R N I N G
Do not touch the stack/ pile, table or chains with your fingers or other body parts when the table is moving or the laminator is running.
Feeder Stack/ Pile
Feeder Table
Page 1 - 4
Chains
© GBC Films Group January 2001
Orbit™ 2000 Operation and Maintenance Manual
1.3 Safety - Rules for handling the feeding head
Safety
The feeding head grabs the paper sheet and inserts it into the pull rollers. When changing paper size, the position of the feeding head must also be changed. For safe adjustments, the following safety rules apply:
1/
W A R N I N G
Do not touch the feeder head while the machine is running. The moving suction cups may hurt your hands or fingers.
2/
ATTENTION
Do not adjust the feeding head while the machine is running with the exception of the control buttons described in Section 5.0
3/
ATTENTION
To move the head, loosen the clamp on the locating bar, then slide the head by grabbing the upper handle bar and gently pull or push.
Handle bar
Locating bar
Clamp
© GBC Films Group January 2001 Page 1 - 5
Safety
4/
Orbit™ 2000 Operation and Maintenance Manual
A T T E N T IO N
D o not p lace any objects on the upper surface of the feeding head or feeder table.
5/
ATTENTION
Do not remove covers, fixed cover of the feeding head and/ or the protective rubber cover.
6/
A T T E N T IO N
O perate the turning kn obs carefully an d w ith only one hand w hile the m achine is running. O n ly trained operators m ay use th e m achine. D o not w ear ties, loose fit clothing or dangling jew elry w hile operating the m achine.
Page 1 - 6
T u rn in g k n o b s
© GBC Films Group January 2001
Orbit™ 2000 Operation and Maintenance Manual Safety
1.4 Safety - Rules for setting up the rollers and the hinged stops
1/
ATTENTION
Do not touch the rollers or hinged stops while the machine is running.
2/
W A R N I N G
WARNING: The chrome roller may be hot. Contact will result in severe burns!
3/
ATTENTION
The insertion or removal of any weights is permissable only when the machine is idle.
Counter weights
© GBC Films Group January 2001 Page 1 - 7
Safety
4/
Orbit™ 2000 Operation and Maintenance Manual
W A R N I N G
Caution: Excercise extreme caution when adjusting the rollers to avoid pinching by the loading roller.
5/
A T T E N T IO N
H andle the rollers only w hen the Plexi-glass cover of the chrom e roller is closed.
6/
ATTENTION
Keep fingers, hands and clothing clear away from the rollers while the machine is in operation.
7/
W A R N IN G
W A R N IN G : D o not be startled by the pressure roller dropping approxim ately tw o m in utes after the lam inator has been stopped.
Page 1 - 8 © GBC Films Group January 2001
Orbit™ 2000 Operation and Maintenance Manual Safety
1.5 Safety - Rules for setup of the adjustable guide plates
The guiding plates form paper before it enters into the chrome roller. Their position must be adjusted for different paper weights. For a safe adjustment of plates follow these safety rules:
1/
ATTENTION
The plate's position may be adjusted while the equipment is running by using the set-up screw. This may only be performed by a trained operator.
2/
W A R N I N G
CAUTION: Do not wear ties, loose fit clothing or dangling jewelry. These items can get caught by the hinged stops or the feed rollers.
3/
A T T E N T IO N
T he ch rom e roller guard m ust be in the fully closed position .
S e t-u p s c re w
C h ro m e ro lle r g u a rd
C h ro m e ro lle r
P a p e r & film s to c k
P re s s u re ro lle r
© GBC Films Group January 2001 Page 1 - 9
Safety Orbit™ 2000 Operation and Maintenance Manual
1.6 Safety - Rules for the chrome and pressure rollers
The working temperature of the chrome roller is 120 to 135 deg C. Because of the machine function it is not possible to cover the area around the chrome and pressure rollers completely. Near the contact area of the rollers, there is a very dangerous zone. Because of that and the high temperature, the following safety rules must be complied with:
1/
W A R N I N G
WARNING: The chrome roller may be hot. Contact will result in severe burns!
2/
W A R N I N G
WARNING: Keep fingers, hands and other body parts away from the rollers.
3/
W A R N I N G
CAUTION: Never clean the surface of the rollers while the machine is running.
Use the Slow FWD and Slow Reverse to change the exposed area for cleaning.
4/
Page 1 - 10
W A R N I N G
CAUTION: Do not wear ties, loose fit clothing or dangling jewelry. These items can get caught the rollers while working around or loading film.
© GBC Films Group January 2001
Orbit™ 2000 Operation and Maintenance Manual
5/
W A R N I N G
CAUTION: Do not use any tools for cleaning or removing remnants of films from the rollers while the machine is in operation.
Safety
6/
ELECTRICAL
S H O C K
Do not remove or modify any guards, covers or enclosures. Contact with any moving parts or/ and electrical voltage can result in injury or death!
7/
W A R N I N G
CAUTION: Do not cover the chrome roller guard ventilation holes.
8/
ATTENTION
When cleaning, follow the rules for Safety - Rules for cleaning in Section 3.10
9/
W A R N I N G
WARNING: Keep hands and fingers away from the pressure/ chrome roller when using Pressure Roll Up/ Close and Down/ Open push buttons.
© GBC Films Group January 2001 Page 1 - 11
Safety
10/
Orbit™ 2000 Operation and Maintenance Manual
W A R N IN G
W A R N IN G : D epress the lam inator Stop button before attem pting to perform any w eb up procedure on the lam inator.
11/
A T T E N T IO N
A lw ays ensure the adhesive is facing aw ay from the chrom e roller w hen loading film .
12/
W A R N IN G
C A U T IO N : O pen the plastic chrom e roller guard fully to prevent to accidental closing onto your hands and fingers.
13/
W A R N I N G
WARNING: Hot surface. Ensure the chrome roller is below 122
O
F ( 50
O
C ) before servicing or adjusting. Check the temperature on the temperature control display or by using an external temperature sensor or wait
60 minutes from the time the machine has been turned off.
Page 1 - 12 © GBC Films Group January 2001
Orbit™ 2000 Operation and Maintenance Manual
14/
W A R N IN G
W A R N IN G : A void m ak ing contact w ith any of the hot surface areas. A void all pinch points and crush hazard areas as illustrated below .
Safety
Side view
a - DANGER: High temperature roller surface area.
b - DANGER: Pinch/ Crush point area.
a b
Rear view
WARNING: Hot surface area
© GBC Films Group January 2001
WARNING: Crush hazard area
Page 1 - 13
Safety Orbit™ 2000 Operation and Maintenance Manual
1.7 Safety - Rules for the snap roller area
It is not possible to cover the entire zone around the snapping roller because of the operation of the machine. It is therefore necessary to observe the following safety rules:
1/
W A R N IN G
C A U T IO N : D o not adju st the regulatin g screw s of the snapping roller w hile the lam inator is in operation. D uring operation the regulating screw hand le is m oving an d your fin gers m ay be cru shed betw een the regulating screw s and the P lexi-G lass cover.
2/
W A R N I N G
CAUTION: Do not place your fingers or any other part of your body near the contact point between the upper and lower snap rollers.
3/
A T T E N T IO N
D u rin g o p era tio n , th e p la stic co v er m u st rem a in in th e fu lly closed p o sitio n .
4/
Page 1 - 14
W A R N I N G
CAUTION: Open the plastic snap roller guard fully to prevent accidental closing onto your hands or fingers.
© GBC Films Group January 2001
Orbit™ 2000 Operation and Maintenance Manual
5/
W A R N I N G
CAUTION: Do not place any objects on the plastic snap roller guard.
Safety
6/
ELECTRICAL
S H O C K
Do not remove or modify any guards, covers or enclosures. Contact with any moving parts or/ and electrical voltage can result in injury or death!
The snap roller side view
C AU T IO N : K e e p fin g e rs c le a r d u rin g m a c h in e o p e ra tio n
Ad ju s tin g re g u la tin g s c re w s
W AR N IN G : P in c h h a z a rd a re a
T o p
D AN G E R : C ru s h p o in t b y
R e g u la tin g S c re w s
B o tto m
© GBC Films Group January 2001 Page 1 - 15
Safety Orbit™ 2000 Operation and Maintenance Manual
Regulating screw view from the stacking table
CAUTION: Finger Crush hazard area
Rear view of the Snap Roller Guard Cover
Page 1 - 16 © GBC Films Group January 2001
Orbit™ 2000 Operation and Maintenance Manual
1.8 Safety - Rules for the use of the twin knife
Safety
The cutting knives are covered by plastic guards from the top and side. Because of the sharpness and speed with which the knives move it is necessary to observe the following safety rules:
1/
W A R N I N G
CAUTION: Do not place your fingers or any other part of your body near the plastic guard while the machine is running.
2/
W A R N I N G
WARNING: Do not place your fingers or objects under the plastic guard, unless the equipment is disconnected from the power supply and the emergency stop switch is depressed.
WARNING: Sharp knife can cut you!
Remove power and depress emergency stop switch before woking in this vicinity.
© GBC Films Group January 2001 Page 1 - 17
Safety
3/
Orbit™ 2000 Operation and Maintenance Manual
W A R N I N G
WARNING: For safe knife adjustment, use a 4 mm allen wrench only. The allen wrench can be inserted through the oval shaped openings in the upper section of the plastic guard of the twin knife.
4/
W A R N I N G
WARNING: Disconnect power to the equipment before performing any task in the vicinity of the twin knife requiring the removal of the cover
5/
A T T E N T IO N
D o n o t o p era te th e la m in a to r u n less th e p lastic g u a rd is in p la ce a b o v e th e tw in k n ife.
6/
W A R N I N G
CAUTION: Do not place any objects on the plastic knife guard.
7/
Page 1 - 18
ELECTRICAL
S H O C K
Do not remove or modify any guards, covers or enclosures. Contact with any moving parts or/ and electrical voltage can result in injury or death!
© GBC Films Group January 2001
Orbit™ 2000 Operation and Maintenance Manual Safety
1.9 Safety - Rules for the position adjustment of the decurling bar
During lamination internal stress develops between paper and the chrome roller. The decurling bar straightens the sheets before they exit the lamination section. During adjustment of the bar, the following safety rules must be observed:
1/
W A R N I N G
CAUTION: Exercise caution while loosening the decurling bar handle.
The securing screw and the edge of the groove on the regulating wheel may collide during sudden loosening.
2/
W A R N I N G
CAUTION: Exercise caution while adjusting the control lever position.
During sudden change in the position of the control lever, the set-up lever of the decurling bar may be hit.
3/
W A R N I N G
CAUTION: Do not place your fingers near the groove on the regulating wheel while changing the position of the decurling bar.
4/
W A R N IN G
C A U T IO N : D ue to heat em inating from the chrom e roller and pressu re
roller area, avoid con tact w ith the decurling bar.
© GBC Films Group January 2001 Page 1 - 19
Safety Orbit™ 2000 Operation and Maintenance Manual
1.10 Safety - Rules for electrical installation
1/
W A R N I N G
CAUTION: Repairs, adjustments and/ or maintenance may be performed by a qualified technician ( excludes any operator maintenance and operator adjustments ). The word "qualified" is decribed below.
Qualified
• Any engineer that has experience with electrical and mechanical design of lamination equipment.
The engineers should be fully aware of all aspects of safety with regards to lamination equipment.
• Any commissioning or service engineer must be of competent nature, trained and qualified to GBC
Pro-Tech standards to fulfill that job. This person will have completed and passed the full service training course from GBC Pro-Tech.
• Any GBC Technician, GBC Specialist, and / or GBC Pro-Tech Technician that has been through the GBC Pro-Tech service training course.
2/
W A R N I N G
W A R N I N G : O p e r a t o r m a i n t e n a n c e a n d o p e r a t o r a d j u s t m e n t s m a y b e p e r f o r m e d only by person(s) trained in all aspects of the equipment.
Page 1 - 20 © GBC Films Group January 2001
Orbit™ 2000 Operation and Maintenance Manual
3/
W A R N I N G
WARNING: At no time should you attempt to overide/ by pass and safety shield, safety switches or safety device located on this equipment.
Safety
4/
ELECTRICAL
S H O C K
WARNING: Do not modify any part of the circuitry at any time or for any reason!
5/
W A R N I N G
WARNING: All guards and covers must be returned to their original position after any repairs, adjustments and/ or maintenance has been completed.
6/
W A R N I N G
WARNING: At least 1 ft. ( 1 meter ) of free space is required in front of the machine to allow for safe access for work on the machine electrical system.
7/
ELECTRICAL
S H O C K
Do not remove or modify any guards, covers or enclosures. Contact with any moving parts or/ and electrical voltage can result in injury or death!
© GBC Films Group January 2001 Page 1 - 21
Safety Orbit™ 2000 Operation and Maintenance Manual
1.11 Safety - Rules for machine cleaning
1/
W A R N I N G
WARNING: Do not clean any part of the machine while the laminator is in operation.
2/
W A R N I N G
CAUTION: Never clean the surface of the rollers while the machine is running.
Use the Slow FWD and Slow Reverse to change the exposed area for cleaning.
Use the sequence described below.
a/ Press and hold the Inch/ Slow FWD or Reverse/ Slow Reverse push button.
b/ Release the perspective push button and wait for the machine to stop.
W A R N I N G
WARNING: The chrome roller is hot. Contact will result in severe burns!
c/ Clean the exposed area of the rollers.
d/ Repeat as necessary.
Page 1 - 22 © GBC Films Group January 2001
Orbit™ 2000 Operation and Maintenance Manual
3/
W A R N I N G
WARNING: Hot surface. Exercise extreme caution when cleaning the chrome roller.
Surface temperatures may be upwards of 248
O
F to 275
O
F ( 120 - 135
O
C ).
Safety
ATTENTION
4/
5/
W A R N I N G
CAUTION: Do not use aggressive solvents that could cause damage to the rubber rollers. Use only Mineral Spirits.
6/
W A R N I N G
WARNING: Crush hazard exists near any rollers. Do not press Pressure Up/ Pressure
Roll Close switch when your hands or fingers are near the pressure roller arms.
7/
ELECTRICAL
S H O C K
Do not remove or modify any guards, covers or enclosures. Contact with any moving parts or/ and electrical voltage can result in injury or death!
© GBC Films Group January 2001 Page 1 - 23
Safety Orbit™ 2000 Operation and Maintenance Manual
1.12 Safety - Rules for machine maintenance and adjustments
1/
W A R N I N G
WARNING: Do not remove any covers or guards while the machine is in operation.
2/
W A R N I N G
WARNING: Do not start the machine with the guards or covers removed.
3/
W A R N I N G
WARNING: Shut off and lock the electric supply circuit breaker before performing any operator maintenance or operator adjustments.
4/
Page 1 - 24
W A R N I N G
WARNING: Hot surface! Ensure the chrome roller temperature is below
122
O
F ( 50
O
C ) before servicing or adjusting.
© GBC Films Group January 2001
Orbit™ 2000 Operation and Maintenance Manual
5/
W A R N I N G
W A R N I N G : Check the temperature on the temperature control display if power is "ON" or by using an external temperature sensor or wait 60 minutes from the time the machine has been turned off before performing any operator maintenance, operator adjustments or set-up.
Safety
6/
W A R N I N G
CAUTION: Do not wear ties, loose fit clothing or dangling jewelry. These items can get caught by moving parts while performing tasks.
7/
W A R N I N G
CAUTION: Always wear safety glasses when changing the springs.
Uncontrolled springs can damage your eyes.
8/
W A R N I N G
W A R N I N G : O p e r a t o r m a i n t e n a n c e a n d o p e r a t o r a d j u s t m e n t s m a y b e p e r f o r m e d only by person(s) trained in all aspects of the equipment.
9/
ELECTRICAL
S H O C K
Do not remove or modify any guards, covers or enclosures. Contact with any moving parts or/ and electrical voltage can result in injury or death!
© GBC Films Group January 2001 Page 1 - 25
Safety Orbit™ 2000 Operation and Maintenance Manual
1.13 Safety - Rules for the feeder table
During the automated run the feeder table moves upward in steps. When a new ream of paper is loaded, the table must be moved down. To ensure your safety, the following safety rules should be followed:
1/
W A R N I N G
WARNING: Operation of the feeder table may be performed only by person(s) trained in all aspects of the equipment.
2/
A T T E N T IO N
U se th e P ile/ S ta ck U p or P ile/ S ta ck D o w n p u sh b u tto n s to m o ve th e feed er ta b le.
3/
ELECTRICAL
S H O C K
Do not remove or modify any guards, covers or enclosures. Contact with any moving parts or/ and electrical voltage can result in injury or death!
Page 1 - 26 © GBC Films Group January 2001
Orbit™ 2000 Operation and Maintenance Manual
1.14 Safety - Rules for the central drive maintenance
Safety
The main motor drives the feeding head, the feeding roller, and the chrome roller. It is located on the opposite side from the operator, and protected by a fixed cover. For safe work, the following safety rules should be followed:
1/
W A R N I N G
WARNING: Shut off the compressed air intake before setting up the second hinged end-stops and pressure rollers.
2/
W A R N I N G
WARNING: Only person(s) trained in all aspects of the equipment may operate the central drive.
3/
ELECTRICAL
S H O C K
Do not remove or modify any guards, covers or enclosures. Contact with any moving parts or/ and electrical voltage can result in injury or death!
© GBC Films Group January 2001 Page 1 - 27
Safety Orbit™ 2000 Operation and Maintenance Manual
1.15 Safety - Rules for Snapping assembly/ chain/ belt drive
maintenance
The chain and belt drives are protected by a fixed cover and is located on the opposite side from the operator. For safe work, the following safety rules should be followed:
1/
W A R N I N G
WARNING: Turn power off at the main breaker before tentioning the chains or belts.
2/
A T T E N T IO N
O p erator m ain ten an ce for th e ch ain s an d b elts are lim ited to lu b rication an d ten tion in g. A ll oth er w ork m u st b e p erform ed b y a q u alified tech n ician .
3/
ELECTRICAL
S H O C K
Do not modify any guards, covers or enclosures. Contact with any moving parts or/ and electrical voltage can result in injury or death!
Page 1 - 28 © GBC Films Group January 2001
Orbit™ 2000 Operation and Maintenance Manual Safety
1.16 Safety - Rules for maintenance/ replacement of the twin
knife
The twin knife is very sharp and extreme caution should be exercised when working in its vicinity.
For safe work, the following safety rules should be followed:
1/
W A R N I N G
WARNING: Knife has sharp edges! Do not touch the sharp edges of the knives.
2/
W A R N I N G
WARNING: For safe knife adjustment, use a 4 mm allen wrench only. The allen wrench can be inserted through the oval shaped openings in the upper section of the plastic guard of the twin knife.
3/
W A R N I N G
WARNING: Do not place your fingers or objects under the plastic guard, unless the equipment is disconnected from the power supply and the emergency stop switch is depressed.
4/
ELECTRICAL
S H O C K
Do not remove or modify any guards, covers or enclosures. Contact with any moving parts or/ and electrical voltage can result in injury or death!
© GBC Films Group January 2001 Page 1 - 29
Safety
This page intentionally left blank.
Orbit™ 2000 Operation and Maintenance Manual
Page 1 - 30 © GBC Films Group January 2001
Orbit™ 2000 Operation and Maintenance Manual
2.0 Warranty
Warranty
GBC Films Group’s sole and exclusive liability and the customer’s sole and exclusive remedy under this warranty shall be, at GBC Films Group’s option, to repair or replace any such defective part or product.
These remedies are only available if GBC Films Group’s examination of the product discloses to GBC
Films Group’s satisfaction that such defects actually exist and were not caused by misuse, neglect, attempt to repair, unauthorized alteration or modification, incorrect line voltage, fire, accident, flood or other hazards.
2.1 Terms and conditions
2.1.1
GBC Films Group warrants that the laminating machine ORBIT™ 2000, except as noted below, is free from defects in material and workmanship for a period of ( 3 ) three months from the date of installation.
2.1.2
The warranty shall be limited to repairs, adjustments and/ or replacement as deemed necessary by GBC Films Group.
2.1.3
THE WARRANTY MADE HEREIN IS IN LIEU OF ALL OTHER WARRANTIES,
EXPRESS OR IMPLIED, INCLUDING ANY WARRANTY OR MERCHANTABILITY OR FITNESS
FOR A PARTICULAR PURPOSE. GBC FILMS GROUP WILL NOT BE LIABLE FOR PROPERTY
DAMAGE OR PERSONAL INJURY ( UNLESS PRIMARILY CAUSED BY ITS NEGLIGENCE ), LOSS
OF PROFIT OR OTHER INCIDENTAL OR CONSEQUENTIAL DAMAGES ARISING OUT OF THE
USE OR INABILITY TO USE THE EQUIPMENT.
© GBC Films Group January 2001 Page 2 - 1
Warranty Orbit™ 2000 Operation and Maintenance Manual
2.2 Limited period of warranty
Consumption replacement parts are warranted to be free from defects and workmanship for a period of ( 60 ) sixty days from date of installation and include:
• Nip rollers, Snapping rollers and Pull rollers
• All rubber made rollers
• All belts
• Feeder suction cups
Warranty repair or replacement does not extend the warranty beyond the initial ( 60 ) day period from the date of installation.
2.3 Limited warranty conditions
The warranty becomes void in the event of mishandling, tampering, incorrect use of films not compatible with our equipment or use contrary to the applicable instruction materials, shipping damage or repair performed by other than a qualified service personnel authorized by GBC. Routine maintenance, cleaning, adjustments, normal cosmetic and mechanical wear or deterioration due to extreme conditions are not covered by this warranty.
Page 2 - 2 © GBC Films Group January 2001
Orbit™ 2000 Operation and Maintenance Manual
Warranty
2.3.1 Warranty is not applicable to the following conditions:
1/ Damage to the chrome laminating roller, rubberized feeding rollers, pressure rollers, pull rollers and snapping rollers if caused by knives, razor blades or any other type of sharp tool.
2/ Damage to the chrome laminating roller, rubberized feeding rollers, pressure rollers, pull rollers and snapping rollers if caused by:
– any object falling into the working area of the machine.
– cleaning the rollers using solutions or material that could harm the surface. Refer to Section 8
Maintenance under cleaning the rollers for suitable cleaners.
3/ Damage to the Plexi-Glass panels or air regulator glass caused:
– mechanically
– by using cleaners that would harm the Plexi-Glass covers
4/ Damage to the exterior finish caused:
– mechanically
– by using cleaning solvents that would harm the finish. Refer to Section 8 Maintenance under
cleaning the exterior for suitable cleaners.
5/ Damage to the feeding head by incompetent handling or adjusting.
6/ Damage to the machine caused by:
– moving
– installation performed by any person other than a qualified GBC service technician
– Operation of the equipment by person(s) not fully trained in all aspects of the machine.
© GBC Films Group January 2001 Page 2 - 3
Warranty
This page intentionally left blank.
Orbit™ 2000 Operation and Maintenance Manual
Page 2 - 4 © GBC Films Group January 2001
Orbit™ 2000 Operation and Maintenance Manual Specifications
3.0 Specific dimensions and weight of the equipment
1956 mm
1325 mm
1010 mm
1010 mm
3.1 DIMENSIONS AND WEIGHT OF THE EQUIPMENT
Machine dimensions
Base dimensions
Floor area
Weight of the Machine
© GBC Films Group January 2001
US VERSION
77" x 39.76" x 47.64"
(length x width x height)
3.3' x 6.4'
21.3 ft
2
1543 Ib
EU VERSION
1956 x 1010 x 1210 mm
(length x width x height)
1.01 x 1.96 m
1.98 m
2
700 kg
Page 3 - 1
Specifications Orbit™ 2000 Operation and Maintenance Manual
3.2 SHIPPING CRATE DIMENSIONS AND WEIGHT
Dimensions of the crate with machine
Weight of the Machine with the crate
US VERSION
59.1" x 47.3" x 56.7"
(length x width x height)
1676 lb
EU VERSION
1500 x 1200 x 1440 mm
(length x width x height)
760 kg
3.3 BASIC TECHNICAL DATA
1.
PAPER SPECIFICATION
Max. paper size
Min. paper size
Smallest paper size
US VERSION
14" x 20"
8" x 8"
70 lb - 24 pt
2.
FILM SPECIFICATIONS
Types of useable films
Film gauge
Inside film roll diameter
Outside film roll diameter
Length of rolled film 1700 ft 520 m
3.
MACHINE PARAMETER
Speed
Feeder pile height
4.
ACOUSTIC NOISE DATA
Equivalent noise level L AEG
Maximum noise level L Aeg (max)
Level of the acoustic output L WA
Page 3 - 2
65 ft/min.
25"
EU VERSION
360 x 520 mm
200 x 200 mm
115 - 350 g/m
2
Polypropylene, Polyester, Nylon film
1.0 - 1.7 mil.
1.0 - 1.7 mil.
21/4" - 3"
7.4"
57 - 77 mm
190 mm
20 m/min.
635 mm
75.3 dB (A)
79.8 dB (A)
87.7 dB (A)
75.3 dB (A)
79.8 dB (A)
87.7 dB (A)
© GBC Films Group January 2001
Orbit™ 2000 Operation and Maintenance Manual
US VERSION
5.
ELECTRICAL CIRCUIT
Power input
Basic voltage requirements
Nominal current
5 kVA +/- 10 %
3 phase 230 V 60 Hz with ground
30 A
Specifications
EU VERSION
5 kVA +/- 10 %
3 phase 400 V 50
Hz with ground
30 A
6.
PNEUMATIC CIRCUIT
Pressure in the machine circuit
The feeder pneumatic circuit
- vacuum
- pressure
7.
MIN/ MAX
Slow Forward
Slow Reverse
90 psi @ 4 CFM
- 0.6 Bar
+0.6 Bar
0,6 MPa @ 113 l/min.
- 0.6 Bar
+0.6 Bar
1ft./ min / 65 ft./ min .3 m/ min. / 20 m./ min
Variable speed
Variable speed
Variable speed
Variable speed
© GBC Films Group January 2001 Page 3 - 3
Specifications
This page intentionally left blank.
Orbit™ 2000 Operation and Maintenance Manual
Page 3 - 4 © GBC Films Group January 2001
Orbit™ 2000 Operation and Maintenance Manual
4.0 Installation Precautions
W A R N I N G
WARNING: To avoid injury to yourself or damage to the equipment, please read and understand the instructions in this manual before you attempt to install, operate or service the laminator!
Installation
1. The GBC Orbit™ 2000 System may be installed only by a qualified ( as defined below ) GBC employed technician.
2. Any moving or un-installing of the equipment may also, only be done by a qualified ( as defined below ) GBC employed technician.
3. Once the machine is installed, all cables remaining on the floor from the electrical cabinet to the machine must be covered, to avoid any accidents.
Qualified
• Any engineer that has experience with electrical and mechanical design of lamination equipment. The engineers should be fully aware of all aspects of safety with regards to lamination equipment.
• Any commissioning or service engineer must be of competent nature, trained and qualified to GBC Pro-Tech standards to fulfill that job. This person will have completed and passed the full service training course from GBC Pro-
Tech.
• Any GBC Technician, GBC Specialist, and / or GBC Pro-Tech Technician that has been through the GBC
Pro-Tech service training course.
© GBC Films Group January 2001 Page 4 - 1
Installation Orbit™ 2000 Operation and Maintenance Manual
4.1 Pre-installation checklist
The installation of the machine, the start-up of operation, and training must be provided by a qualified
GBC Films Group service technician, or another authorized organization.
Prior to the machine installation it is necessary to provide:
– an even floor of 2500 kg/ sq. meter minimal load factor ( 36.165 lb/ sq.ft ).
– a connection to air pressure of 0.6 Mpa @ 113L/ min. ( 90 PSI @ 4 CFM ) for the pneumatic
circuit.
– a fused dicconnect
– a connection of 3 phase with ground, 400/ 230VAC+/- 10 %, 50 Hz, 30 amps ( EU Version )
for the electrical circuit.
– a connection of 3 phase with ground 230VAC +/- 10 %, 60Hz, 30 amps ( US Version ) for
the electrical circuit.
Becker Compressor
The Becker compressor supplies air to the feeding assembly, and is connected by means of a plug to the machine.
Machine position
The machine must be placed so that
– space of at least 40 cm (1.3 ft) is available between the stacking table and the wall or any
other fixed object
– space of at least 80 cm (2.6 ft) is available on the drive side between the covers and the wall
or any other fixed object (another machine, etc.)
Page 4 - 2 © GBC Films Group January 2001
Orbit™ 2000 Operation and Maintenance Manual Installation
The Floor
The machine must be placed on a firm and reasonably even floor capable of supporting a load of 2500 kg/ square meter ( 36165 lb/ sq.ft. ).
Note
The machine is also provided with a terminal to connect an additional conductor for the interconnection, since the value of leakage currents from noise suppression elements is higher than 3.5
mA AC. This terminal for the additional interconnection can be located on the bar between the side plates, when the lower cover on the operator's side has been opened. The additional interconnecting conductor is to be attached to this terminal.
ELECTRICAL
S H O C K
Only a qualified electrician should connect power to the laminator. You can be severely shocked, electrocuted or cause a fire if power is improperly applied.
ELECTRICAL
S H O C K
Do not allow anything to rest on the power cord. Do not locate the cord where people can walk on it. You or others can be severely shocked, electrocuted or cause a fire.
© GBC Films Group January 2001 Page 4 - 3
Installation
4.2 Suggested floor layout
Orbit™ 2000 Operation and Maintenance Manual
Page 4 - 4 © GBC Films Group January 2001
Orbit™ 2000 Operation and Maintenance Manual
4.3 Shipping damage inspection
Installation
INFORMATION
Before signing the Bill of Lading, youshould inspect the crate and / or palletfor signs of damage or missing items; ifapplicable, make note of this on theBill of Lading.
INFORMATION
A L L S H I P M E N T S A R E E X - W O R K S . A t o u r d o c k , t i t l e p a s s e s t o t h e b u y e r . P l e a s e review your insurance coverage prior to shipment, as you are responsible for all subsequent freight charges and risks.
W A R N I N G
The Orbit™ 2000 is a large and heavy piece of equipment. It is necessary to e m p l o y L I C E N S E D R I G G E R S O N L Y t o m o v e t h e m a c h i n e . T h e m a c h i n e i s n o t designed to be tipped up or sideways in any way. Such action disturbs the exact alignment of moving parts on the machine and requires extensive realignment.
You can be crushedor seriously injured.
W A R N I N G
GBC Pro-Tech's warranty does not cover malfunction of the equipment due to mishandling and / or tipping. GBC Films Group bears no responsibility for personal injury or damage due to moving the machine improperly.
© GBC Films Group January 2001 Page 4 - 5
Installation Orbit™ 2000 Operation and Maintenance Manual
4.4 Transporting of the machine
The machine is shipped from the factory bolted to a wooden shipping pallet/ frame.
Note the position of the machine on the pallet/ frame as illustrated to the right.
Moving the machine on the pallet/ frame can only be accomplished with a lift truck or a pallet wagon.
The forks of the lift truck/ pallet wagon must be long enough to reach past the transport supports on the farthest side from the lift truck/ pallet wagon.
To remove the machine from the pallet/ frame:
– remove the shipping bolts
– drive the lift truck/ pallet wagon between the
pallet/ frame and the machine frame
– slowly raise the machine from the pallet/ frame
– Replace the shipping angle irons with the leveling
feet before final placement.
The shift of the machine from the frame to the floor is shown on the picture.
Page 4 - 6 © GBC Films Group January 2001
Orbit™ 2000 Operation and Maintenance Manual
4.5 Electrical installation
Installation
The main plug may be inserted only into a fixed electrical distribution socket, regularly inspected according to appropriate national standards. Prior to the start-up, the initial inspection of the machine electrical equipment must be done according to IEC 364-6-61 standard, which includes the fixed power input if the machine is not connected by a flexible cable. The machine may be started only when all electrical requirements have been complied with according to appropriate national standards for printing machines.
During the entire time of operation the user is obligated to comply with the requirements of applicable national standards for printing machines, and their electrical wiring.
Nominal voltage
Operating voltage
Power input
Nominal current
Recommended fuses
EU VERSION
3 NPE 400 V/230 V 50 Hz
24 VDC
5 kVA
30 Amps
25 A gTF 500V
US VERSION
3 Phase with ground
230+/- 10% VAC 60 Hz
24 VDC
5 kVA
30 Amps
25 A gTF 500V
Electrical installation has been designed, manufactured and tested according to EN 60204-1, 1992
Standard, and is shown on electrical installation schematic diagram BJ-41-110 to BJ-41-118, description
BJ-41-211 to BJ-41-212, and lay-out BJ-41-200- to BJ-41-203.
The manufacturer of ORBIT 2000 guarantees that the machine complies with interference elimination to a level specified by EN 500081-1 part 1, in residential, business, and light industry zones.
Repairs, setup, and maintenance may be performed by a technically trained or sufficiently experienced person, who knows how to avoid dangers involved in manipulations with electricity, as stated in EN 60204-
1, article 3.55.
© GBC Films Group January 2001 Page 4 - 7
Installation Orbit™ 2000 Operation and Maintenance Manual
4.6 Becker T4.25 DSK Compressor installation
W A R N I N G
WARNING: Do not place the compressor near machines that have exhaust air containing oil.
The machine includes a compressor with its own original technical description. It is the rotary wing type Becker T4.25 DSK compressor, operating without the use of oil. It may not suck in any moisture, oil, or any other fluid.
When the compressor has been attached to the machine, check the vacuum, which should be 0.4 Bar
( 11.81 inHg ). Adjust the compressor for correct vacuum gauge ( a ) indication. The compressor may be switched on and off by means of the switch ( b ), while the machine is being adjusted.
a b
The pressure and the vacuum valves are adjusted as needed for the operation. When the valves are completely closed, the compressor has the highest output, electric power is unnecessarily wasted, and wear and tear are increased.
Page 4 - 8 © GBC Films Group January 2001
Orbit™ 2000 Operation and Maintenance Manual
4.7 Initial inspection
Installation
ELECTRICAL
S H O C K
Remove power to the laminator before performing step ( a ) below. Contact with electrical components while power is supplied can result in injury or death!
a/
Electrical assembly inspection
– Component mounting
– Terminal security
– Wire tightness
– Circuit breaker wires
ELECTRICAL
S H O C K
Electrical troubleshooting should be left to qualified GBC service technicians!
Electrical shock hazard!
b/
Protective circuit inspection
– The safety of protective circuits may be checked by feeding a current of at least 10 A (50
Hz) from the PELV source for at least 10 seconds. The test is done between the PE terminal
and various points that are part of the protective circuit. See EN 60204-1, article 20.2.
© GBC Films Group January 2001 Page 4 - 9
Installation Orbit™ 2000 Operation and Maintenance Manual
– The voltage measured between the terminal PE and the test points may not exceed
U =3.3V
U = 2.6V
U = 1.9V
for for for
S= 1.0 square millimeters
S= 1.5 sq. millimeters
S = 2.5 sq. millimeters
( U ) is the largest drop in voltage and ( S ) is the smallest effective diameter of the protective conductor in the tested branch of the protective circuit.
c/
Voltage checks
– from fused disconnect - 240 VAC +/- 10% 3 phase with ground.
– Check each leg, A,B nad C, to ground for proper voltage drop.
– Check main line voltage to locking plug connection on the Orbit™2000.
– Connect plug from Orbit™2000 to electrical supply.
d/
Perform a safety check of all emergency stops, safety latches and lockouts.
– Emergency stop buttons
– Safety shields
– Power on/ off lockout
– Table limit switches
– Feeder head protect from pile-up table e/
Power-up the Orbit™2000 and confirm that the temperature contoller is illuminated.
If the temperature controller is not illuminated, check the E-Stops, safety latches or lockouts for activation.
f/
Check all roatations of motors: Feeder Pile-up, Feeder pile-down, main drive and compressor/ feeder
Page 4 - 10 © GBC Films Group January 2001
Orbit™ 2000 Operation and Maintenance Manual g/
Perform a function check of the control panel switches.
h/
Ensure all guides move correctly.
i/
Install the stacking table.
Installation
© GBC Films Group January 2001 Page 4 - 11
Installation
This page intentionally left blank.
Orbit™ 2000 Operation and Maintenance Manual
Page 4 - 12 © GBC Films Group January 2001
Orbit™ 2000 Operation and Maintenance Manual
5.0 Operation
W A R N I N G
WARNING: Only person(s) trained in all aspects of safety and operations may use this equipment.
Operations
W A R N I N G
CAUTION: Do not wear ties, loose fit clothing or dangling jewelry. These items can get caught by the hinged stops or the feed rollers.
This section describes in detail each part of the four areas on the Orbit™ 2000. The four areas consist of;
( 1 ) 5.1 General information
( 2 ) 5.2 The Feeder Section
( 3 ) 5.3 The Lamination Section
( 4 ) 5.4 The Separator Section.
A T T E N T IO N
D o not operate this equ ipm ent unless you have read an d understand this operator m anual and h ave been fully trained in its operation by a qualified G B C service technician.
© GBC Films Group January 2001 Page 5 - 1
Operations
5.1 General information
Orbit™ 2000 Operation and Maintenance Manual
Under this section you will find an illustration of the main and secondary operator positions, the control panel legend and an illustration of the control panel (with the original overlay and the new overlay).
5.1.1 The main and secondary operator positions
Becker Compressor
T4.25DSK
Secondary
Operation
Page 5 - 2
Secondary
Operation
Main
Operation
© GBC Films Group January 2001
Orbit™ 2000 Operation and Maintenance Manual
5.1.2 The control panel
Legend
1.
2.
3.
4.
5.
6.
Push button - start
Push button - stop
Speed indicator
Potentiometer - speed adjustment by means of the main motor
Push button - feeder table UP
Push button - feeder table DOWN
7.
8.
9.
Push button - pressure roller UP
Push button - pressure roller DOWN
Laminated sheets counter
10.
Temperature regulator of the chrome roller deg C/ deg. F
11.
Indicator of missing sheets
12.
Switch for changing heating zones on the chrome roller
13.
The pulling roller switch, UP/DOWN
14.
The cutter drive switch ON/OFF
15.
Push button for pulsing the snapping assembly
16.
Snapping drive switch
17.
Potentiometer - snapping drive speed adjustment
18.
Push button - reverse drive
19.
Push button - emergency stop
20.
Push button - stepping run (slow drive for equipment cleaning)
Operations
Please refer to the control panel diagram that resembles your machine on pages 4 and 5.
INFORMATION
The overlay has changed but the functions have remain the same.
© GBC Films Group January 2001 Page 5 - 3
Operations
Original overlay
Orbit™ 2000 Operation and Maintenance Manual
Page 5 - 4 © GBC Films Group January 2001
Orbit™ 2000 Operation and Maintenance Manual
New overlay
Operations
© GBC Films Group January 2001 Page 5 - 5
Operations
5.2 Feeder Section
Orbit™ 2000 Operation and Maintenance Manual
The feeding mechanism consists mainly of the assembly for the lowering and lifting of the feeding table. In addition, there are the feeding table, the feeding head, fixed face stops, first gate, side stackers, feeding roller, and the second gate.
The feeder serves the purpose of stacking paper sheets, and is operated by roller chains guided by two leading spindles. The sheets are taken from the table and inserted into the machine by means of the feeding head. During lamination the paper is removed from the pile.
The feeding head feeler controls the height of the pile and the lifting of the table. The feed table is lifted automatically as the paper is removed. One step of lift equals 2 to 3 mm, independently of the amount of paper. The table lift is either automatically controlled by the feeding head feeler, or manually by means of push buttons on the control panel.
"PILE UP” (5) the table lifts
"PILE DOWN” (6) the table lowers
New overlay Oroginal overlay
5
6
Page 5 - 6 © GBC Films Group January 2001
Orbit™ 2000 Operation and Maintenance Manual
5.2.1 Sheet stacking
Face stacking
Operations
The correct face position of the paper stack on the feeding table is provided by the face stackers
( a ), and the first gate ( b ). The sheets must be pushed tight against the surface of the face stackers. One should make sure that the paper doesn't bend, which can cause problems in the feeding process.
b a
© GBC Films Group January 2001 Page 5 - 7
Operations
Side stacking
Orbit™ 2000 Operation and Maintenance Manual
The collation of paper pile on the sides is done by side stackers ( c ), which are placed symmetrically.
A slight play must be allowed between the ledges and the paper pile to prevent damage to the paper and improper feeding. The side stackers are controlled by the knob ( d ) on the operator's side. The arrow indicates ( e ) the direction of turning for the changing of sheet size. Smaller size in the “ - “ direction, larger size in the “ + “ direction.
e d
W A R N I N G
CAUTION: Ensure the path of the side stackers are clear before making any adjustments.
Page 5 - 8 c
© GBC Films Group January 2001
Orbit™ 2000 Operation and Maintenance Manual
5.2.2 Feeder table positioning
Operations
When the paper pile has been loaded, press the “ FEEDER STACK/ PILE UP ” button. The table
( f) starts lifting, and its top position is determined by the Paper Pile Height Sensor ( g ), adjust so that the first gate exceeds the height of the paper by 6 mm.
ATTENTION
The capacity sensor may be adjusted by a qualified service technician only.
g
First gate
© GBC Films Group January 2001 f
Page 5 - 9
Operations
5.2.3 The feeding head
Orbit™ 2000 Operation and Maintenance Manual
W A R N I N G
WARNING: Press the stop button before performing the following set-up procedure!
Feeding head setup
Loosen the clamp ( a ) using the handle bar ( b ). Push the head to its back position, away from the machine. Press the button FEEDER STACK/ PILE UP until the paper pile stops at the Paper Pile Height
Sensor ( d ). The feeder foot ( e ) now assumes control and lift the table with paper stack on to its working position. Move the head so that the rear stops ( c ) touch gently the rear side of the paper stack, and tighten the clamp.
b
Page 5 - 10 c a
© GBC Films Group January 2001
Orbit™ 2000 Operation and Maintenance Manual
The separating elements setup
Operations
1/
The foot of the ( d ) feeler touches the top of the paper stack. Move the strip ( e ) to the stack so that its front edge is 5 to 7 mm within the paper and 4 to 6 mm above it. For various paper weights ( e ) must be set to provide for correct paper sheets separation.
e
5 - 7 mm d
2/
Brushes ( f ) should overlap the paper edge by 2 to 3 mm, and touch the paper very lightly, and not interfere with paper sheets feathering. For heavier paper use only brushes instead of strips.
f
© GBC Films Group January 2001 f
Page 5 - 11
Operations Orbit™ 2000 Operation and Maintenance Manual
3/
Set up the center suction cups ( g ) by adjusting strips ( e ) so the paper sheets between the cups are tight.
g g e
4/
Depending on the paper type, adjust vacuum as needed to lift the sheets via the transport suction cups by turning the regulator on the Becker compressor. The amount of vacuum can be observed on the manometer ( h ).
h
5/
The proper air pressure required to feather the paper is set up by means of regulators ( i ) and
( j ).
i
Page 5 - 12 j
© GBC Films Group January 2001
Orbit™ 2000 Operation and Maintenance Manual Operations
6/
Adjust air blowing tubes ( k ) by turning the nut ( l ) so that 10 - 20 sheets at the top of the stack are feathered.
k l
7/
Regulator ( m ) sets up the stack height.
m
© GBC Films Group January 2001 Page 5 - 13
Operations
Feeding small sheet sizes
Orbit™ 2000 Operation and Maintenance Manual
W A R N I N G
WARNING: Press the stop button before performing the following set-up procedure!
To feed small sizes of paper sheets, less than the distance between the outside suction cups ( n ), you must loosen the screw ( o ) and rotate the two outside suction cups ( n ) 90 degrees forward then secure in place by tightening the screws ( o ). This is necessary to prevent the outside suction cups ( n ) from colliding with the side stacker guides and to not waste vacuum power on suction cups not in contact with the paper pile.
o n n
Page 5 - 14
90
o
© GBC Films Group January 2001
Orbit™ 2000 Operation and Maintenance Manual
5.2.4 First gate
W A R N I N G
CAUTION: Only a qualified service technician may adjust the first gate.
Operations
The first gate assembly is calibrated at the factory and may be field calibrated by a qualified service technician only. Refer to Section 8 Maintenance.
Function of the first gate
The first gate ( a ) positions the paper ream so that the front is always vertical. While the head is moving forward, the first gate will tip so as to not interfere with the paper feeding.
© GBC Films Group January 2001 a
Page 5 - 15
Operations
5.2.5 Feed roller assembly
Orbit™ 2000 Operation and Maintenance Manual
The assembly consists of gravity rollers ( a), accelerating rollers ( b ), plate holders ( c ) and the sheet overlap sensor ( d ).
d a c c a b b
Gravity rollers
The gravity rollers are always touching the paper pressing it against the feed rollers. The position is factory set, and remains unchanged for all sizes of paper. For higher paper weights the pressure has to be increased. For this purpose, a set of weights ( e ) is supplied as accessories. The weight is simply pulled out or inserted.
Page 5 - 16 e
© GBC Films Group January 2001
Orbit™ 2000 Operation and Maintenance Manual
Accelerating rollers
W A R N I N G
CAUTION: The position of the rollers are set at the factory and does not require changing, regardless of sheet size.
Operations
Accelerating rollers increase the pressure on the feeding roller at the moment the second gate drops out of the way. Allowing equal pressure to feed paper stock evenly to the chrome roller and pressure roller area. The moment of pressure is controlled by the control system and has been factory set. The spring ( g) determines the pressure.
g
© GBC Films Group January 2001 Page 5 - 17
Operations
Plate holders
Orbit™ 2000 Operation and Maintenance Manual
The plate holders keeps the paper sheet on the lower guiding plate to prevent it from jumping over the second gate.
Positioning: The machine has three hold-down fingers in total. The position of the middle one does not change and is factory set. The position of the extreme two change with respect to the size of sheet, and is adjusted to be about 10 mm distant from the edge of paper, after the screw ( h ) has been loosened. Be sure to tighten the screw ( h ) after positioning the hold down fingers.
10 10
Adjusting: Pressure is adjusted by moving the holder ( i ) , which is held by screw ( j ). Follow the procedure below.
j
1/
Loosen the screw ( h ).
2/
Insert one sheet of paper ( of the same specific weight ) to be laminated.
3/
Adjust the holders so the finger ( k )
touches the paper without bending.
4/
Tighten the screw ( h ).
Page 5 - 18
P re s s u re a re a k h
F e e d e r i
© GBC Films Group January 2001
Orbit™ 2000 Operation and Maintenance Manual
Sheet misfeed sensor
Operations
The sheet misfeed sensor protects the supporting laminating roller from the laminating adhesive.
Check its function daily.
To check the sensor, follow the procedure below.
1/
Take a single sheet of paper, insert it under the sensor ( l ).
2/
Block the sensor repeatedly by sliding the sheet of paper in and out from under the sensor.
3/
The proper function is signaled by the sensor LED, which lights up accordingly.
l
W A R N I N G
CAUTION: Only a qualified service technician may repair the sheet overlap sensor.
© GBC Films Group January 2001 Page 5 - 19
Operations
Overlap adjustment
Orbit™ 2000 Operation and Maintenance Manual
W A R N I N G
WARNING: Only person(s) trained in all aspects of the equipment may perform any operator adjustments.
W A R N I N G
C A U T I O N : N E V E R T U R N T H E D I A L ( t ) W H E N T H E M A C H I N E I S S T O P P E D !
For each paper size, the speed of the feeding head must be adjusted. This is done by manually turning the dial pointer ( u ) located below the control panel.
Steps
1/
Set the machine to its lowest running speed.
2/
Start the machine.
u
3/
Set the dial pointer ( u ) to a value
just short of the sheet length. ( ie. a 17 in.
sheet, set the dial to 16.5 in. )
4/
Check the overlap.
5/
Should you require a shorter overlap, turn the dial pointer ( u ) slightly toward the “larger sheet size” direction.
6/
Should you require a longer overlap, turn the dial pointer ( u ) slightly toward the “shorter sheet size” direction.
7/
After turning the dial pointer ( u ), always wait for 2 to 4 sheets, before continuing with the adjustments. The variator has a slight delay.
Page 5 - 20 © GBC Films Group January 2001
Orbit™ 2000 Operation and Maintenance Manual
5.2.6 Second gate
W A R N I N G
CAUTION: Only a qualified service technician may adjust the second gate.
Operations
The second gate ( a ) rigisters the sheet and drops out of the way releasing the sheet so that the overlap of the individual sheets are within the required limits of +/- 1.5 mm.
Position of the second gate
mm.
The top edge of the second gate ( a ) must exceed the height of the guide plate ( b ) by 2.3 to 2.7
2.3 - 2.7
m m a b
© GBC Films Group January 2001 Page 5 - 21
Operations Orbit™ 2000 Operation and Maintenance Manual
5.2.7 Adjustable guide plates
Sliding plates ( a ) guide the sheets into the pressure area helping to minimize wrinkles of the sheets. They form the sheet before it enters the laminating rollers. The plates position is adjusted by turning screw ( b ) and nut ( c ).
When working with heavy paper, adjust the plates so the sheet is guided into roller 1/8 in. ( 3.17 mm ) below chrome roller and pressure roller nip.
b c a
When working with light paper,adjust the plates so the sheet is guided into roller 1/4 in. ( 6.35 mm ) below chrome roller and pressure roller nip.
b c a
Page 5 - 22 © GBC Films Group January 2001
Orbit™ 2000 Operation and Maintenance Manual
5.3 Lamination section
Operations
The lamination section consists mainly of the spool arbor, heating controls, laminating rollers and the spreader roller.
The laminator serves the purpose of unwind the spool of film via the spool arbor, activating the thermal adhesive via the chrome roller, laying it on the fed sheets via the laminating rollers and decurling the sheets for flat separation via the decurling bar.
5.3.1 Film roll positioning
W A R N I N G
CAUTION: Do not wear ties, loose fit clothing or dangling jewelry. These items can get caught the rollers while working around or loading film.
Use the following instructions to load a roll of film and to properly position it:
1/
Set the lateral film adjust nut ( a ) so that the face is in line with the marker ( b ) on the thread of the spool arbor ( c ). This provides acenter point in which you can adjust the film shaft left or right to fine tune the film lay down on the sheets.
a b c
© GBC Films Group January 2001 Page 5 - 23
Operations Orbit™ 2000 Operation and Maintenance Manual
2/
Lower the spool arbor support arm ( d ) by pressing down on the latch ( e ) and pull towards you from the control side.
e d
*
YOUR MACHINE MAY OR
MAY NOT HAVE A
SUPPORT ARM.
3/
Loosen the 8 mm screw to the control side conical cone ( f ) and slide it off of the spool arbor
( c ).
c f
4/
Loosen the nut ( g ) on the drive side conical cone ( h ) and leave loose measurement purposes.
g h
Page 5 - 24 © GBC Films Group January 2001
Orbit™ 2000 Operation and Maintenance Manual Operations
5/
Position the roll of film on the spool arbor ( c ) with respect to the adhesive side (Poly-in or Polyout). Refer to Section 6 Applications.
c f
6/
Replace the control side conical cone ( f ) on the operator’s side and leave the 8 mm screw loose for movemt.
7/
Measure from operators side/ side frame to paper pile left margin ( a ). Always add 1/8 in.
( 3.17 mm ) to this measurement. Use the measurement just obtained, with the 1/8 in ( 3.17 mm ) addition, to measure the edge of the film ( b ) on the spool arbor to the operators side/ side frame.
X
X + 1 0 m m
X + 3 /8 in .
© GBC Films Group January 2001 b a
5 m m
Page 5 - 25
Operations Orbit™ 2000 Operation and Maintenance Manual
8/
Tighten the 8 mm screws on both conical cones and tighten the nut ( g ) on the drive side conical cone ( h ) to secure the roll of film to the spool arbor ( c ).
g h c
9/
Use the lateral film adjust nut ( a ) to fine tune the positioning of the spool arbor with respect to the pile stack and use the unwind brake nut ( i ) to apply tension to film roll on shaft.
Page 5 - 26 i a
© GBC Films Group January 2001
Orbit™ 2000 Operation and Maintenance Manual
5.3.2 Heating
W A R N I N G
WARNING: The chrome roller can become extremely hot.
Contact will result in severe burns!
Operations
W A R N I N G
WARNING: Keep fingers, hands and other body parts away from the rollers.
Heating is controlled by two means. ( 1 ) by using the temperature controller and ( 2 ) by using the heat width selection. Heat is delivered from the chrome roll of the laminating rollers.
Temperature adjustment
Adjust the chrome roller temperature for good lamination by pressing
or on the
temperature controller.
Actual temperature
( Green numbers )
Decrease set point
© GBC Films Group January 2001
120.0
120.0
Set temperature
( Red numbers )
Increase set point
Page 5 - 27
Operations
Heat width selection
Orbit™ 2000 Operation and Maintenance Manual
For sheet width size between 8 - 11 in. ( 200-280 mm ), set the heater switch ( a ) to 8-11”.
H E A T E R S
S T O P
N e w overlay a
8"-11"
H E A T E R
O F F
12"-14"
Original overlay
C h r o m e roller
12-14 in.
( 305-356 mm )
For sheet width size between 12 - 14 in. ( 305-356 mm ), set the heater switch ( a ) to 12-14”.
H E A T E R S
S T O P
N e w overlay a
8"-11"
H E A T E R
OFF
12"-14"
Original overlay
Chrome roller
8-11 in.
( 200-280 mm )
Page 5 - 28 © GBC Films Group January 2001
Orbit™ 2000 Operation and Maintenance Manual
5.3.3 Laminating rollers
W A R N I N G
WARNING: Keep fingers, hands and other body parts away from the rollers.
Operations
The upper chrome roller combined with the lower pressure roller make up the laminating rollers. The laminating rollers function is to press the adhesive and the film onto the surface of the sheets. Pressure is regulated by turning the right side regulator ( a ) and/or left side regulator ( b ).
a b
Independent control of the left and right side pressure enables the operator to control the amount of pressure applied to the sheets. Equal pressure should be applied for good, clear lamination with no wrinkling on the paper. Off setting pressures on controls can help with minor wrinkling problems.
© GBC Films Group January 2001 Page 5 - 29
Operations
Adjusting pressure
Orbit™ 2000 Operation and Maintenance Manual
W A R N IN G
W A R N IN G : D o not rem ove any covers or guards w hile the m achine is in operation.
Pressure may be adjusted by two air regulators. One for each side of the pull rollers. To adjust, follow the procedure below.
1/
Pull up on the outer part of the regulator knob to unlock.
2/
Turn clockwise to increase pressure and/or counterclockwise to decrease pressure.
3/
Push the outer part of the regulator knob down to lock.
L o c k e d
U n lo c k
Page 5 - 30 © GBC Films Group January 2001
Orbit™ 2000 Operation and Maintenance Manual
Automatic pressure cancellation
Operations
The closure of the pressure rollers is controlled by the PLC. The PLC will open the pressure rollers two minutes after the laminator stops to prevent damage to the rubber roller surface.
Automatic pressure cancellation occurs when:
– two ( 2 ) minutes has expired after the machine has been switched off.
– two ( 2 ) minutes has expired form an idle state.
( You can reengage the pressure rollers by pressing the pressure roller selector switch to
Close/ Up position. )
U P
P R E S S U R E R O L L
U P
N e w o ve rla y
D O W N
O rig in a l o ve rla y
( The up indicator is illuminated when the pressure roller is up )
D O W N
– immediately after an emergency stop push button has been depressed.
– immediately after power has been removed or turned off.
© GBC Films Group January 2001 Page 5 - 31
Operations Orbit™ 2000 Operation and Maintenance Manual
5.3.4 Spreader roller ( option )
IN F O R M A T IO N
T he follow ing inform ation is for those m achines that are euipped w ith the optional spreader roller.
The spreader roller ( a ) is designed to adjust so the laminate is evenly applied across the chrome roller. The adjustment is located on the operator side of the machine. Follow the steps below to adjust the spreader roller: a
1/
Loosen the lock nut ( b ).
2/
Turn the adjustment knob ( c ).
– Clockwise to raise the control side of
the spreader roller.
– Counterclockwise to lower the control
side of the spreader roller.
3/
Tighten the lock nut ( b ).
c b
Page 5 - 32 © GBC Films Group January 2001
Orbit™ 2000 Operation and Maintenance Manual
5.4 Separator section
Operations
This section consists of the decurling bar, pull roller, twin knives, snapping assembly and the stacking table. The separator section runs in conjunction with the laminator and feeder sections.
W A R N IN G
C A U T IO N : D o not w ear ties, loose fit clothing or dangling jew elry. T hese item s can get caught the rollers w hile w orkin g around or loading film .
5.4.1 The decurling bar
W A R N I N G
CAUTION: Do not wear ties, loose fit clothing or dangling jewelry. These items can get caught the rollers while working around or loading film.
The decurling bar applies or removes curl from the paper sheet following the lamination of film on the paper by the chrome roller.
W A R N I N G
WARNING: The chrome roller may be hot. Contact will result in severe burns!
© GBC Films Group January 2001 Page 5 - 33
Operations
Position of the decurling bar
Orbit™ 2000 Operation and Maintenance Manual
The position of the decurling bar is dependent of the paper thickness. For thin paper, 60 lb. to
100 lb., the decurling bar effects the web path.
Thin paper
Chrome roller
Decurling bar
For thicker papers, 12 pt. to 18 pt., the decurling bar should not effect the web path.
Thick paper
Chrome roller
Decurling bar
Page 5 - 34 © GBC Films Group January 2001
Orbit™ 2000 Operation and Maintenance Manual
Adjusting the decurling bar
W A R N IN G
W A R N IN G : K eep fingers, hands and other body parts aw ay from the rollers.
Operations
Follow the steps below to adjust the decurling bar:
1/
Loosen the locking lever ( b ).
2/
Turn the decurling bar adjustment lever ( a ) with respect to the paper thickness.
3/
Secure the decurling bar in position by tightening the locking lever ( b ).
a b
For thin paper, radius R3 ( c ) may required if a line is caused by the decurling bar on the laminated sheets.
© GBC Films Group January 2001 Page 5 - 35
Operations
To change the from R2 to R3 and vice versa, follow the steps below:
Orbit™ 2000 Operation and Maintenance Manual
1/
Remove the four 8 mm bolts ( a ).
R2
R3
2/
Turn the decurling bar ( b ) with the
desired radius up.
b
3/
Replace the four 8 mm bolts ( a ).
a
Effects of the decurling bar
table.
The sheets should lay flat when exiting the snapping rollers and are collected on the stacking
Correctly decurled sheets Incorrectly decurled sheets
Stacking table
Page 5 - 36
Stacking table
© GBC Films Group January 2001
Orbit™ 2000 Operation and Maintenance Manual
5.4.2 Pull rollers
W A R N I N G
WARNING: Keep fingers, hands and other body parts away from the rollers.
Operations
W A R N IN G
C A U T IO N : D o not w ear ties, loose fit clothing or dangling jew elry. T hese item s can get caught the rollers w hile w orkin g around or loading film .
The pull rollers ( a ) provide pull on the paper between the laminating section and the snapping rollers to achieve straight sheets on the decurling bar.
a
© GBC Films Group January 2001 Page 5 - 37
Operations Orbit™ 2000 Operation and Maintenance Manual
PAPER PULL ADJUSTMENT
To adjust the paper pull force use the following steps:
1/
Loosen the locking nut ( b ).
2/
Turn the regulating bolt ( c ).
3/
The setting is indicated by the white marker of the control device ( d ) with respect to the upper roller position scale ( e ).
4/
Tighten the locking nut ( b ) to secure the regulating bolt ( c ).
c
Page 5 - 38 e b d
© GBC Films Group January 2001
Orbit™ 2000 Operation and Maintenance Manual
Paper pull adjustment with regards to sheet weight.
Operations
L ig h t p u ll
© GBC Films Group January 2001
H e a v y p u ll
Page 5 - 39
Operations
5.4.3 Twin knives
Orbit™ 2000 Operation and Maintenance Manual
A T T E N T IO N
D o not operate the lam inator unless th e plastic guard is in place above the tw in knife.
W A R N IN G
C A U T IO N : D o not place your fingers or any other part of your body near the plastic guard w hile the m achine is running.
The twin knives slit the web of sheets for separation by the snapping assembly. Due to the machines capability of operating at high speeds, an oscillating knife assembly is used to maintain a consistant film cut.
Positioning of the knife assembly with respect to sheet width
P o s itio n fix in g b o lt P o s itio n fix in g b o lt
Page 5 - 40
S lid in g p in S lid in g p in
© GBC Films Group January 2001
Orbit™ 2000 Operation and Maintenance Manual Operations
Positioning of the knife assembly with respect to sheet edge
K n ife 1 K n ife 2
5 - 6 m m w e b
Positioning of the knife assembly with respect to sheet weight
Heavier paper may require shims under the twin knifes to achieve a clean cut of the film. To add shims, remove the four screws from the knife cover. Remove the the four metric allen screws fro mthe twin knifes and insert one shim under each knife. Reassemble the twin knife assembly and adjust the position of the knives.
T h in p a p e r
H e a vie r p a p e r a b
Face ( a ) of knife close to guide bar ( b ).
© GBC Films Group January 2001 a b
Face ( a ) of knife open to guide bar ( b ).
Page 5 - 41
Operations
5.4.4 Snapping assembly
Orbit™ 2000 Operation and Maintenance Manual
W A R N I N G
WARNING: Keep fingers, hands and other body parts away from the rollers.
W A R N IN G
C A U T IO N : D o not w ear ties, loose fit clothing or dangling jew elry. T hese item s can get caught the rollers w hile w orkin g around or loading film .
The snapping assembly separates webbed overlapped sheets after the overlap has been knicked by the twin knives. The snapping roller ( a ) separates the sheets from the web by moving downward toward the idler roller underneath. The sheets pass between the snapping rollers and idler roller and at a set separation position are burst from the web into single sheets.
a
Page 5 - 42 © GBC Films Group January 2001
Orbit™ 2000 Operation and Maintenance Manual Operations
Upper snap roller positioning with respect to sheet weight
With respect to the type of laminating film and paper weight, adjusting of the upper snap roller ( a ) angle may be necessary. The idler roller ( b ) is not adjustable.
3 - 5 o
T h in p a p e r
( O P P F ilm )
a
5 - 10 o
H e a v y p a p e r
( P o ly e s te r, N y lo n F ilm )
a b b
© GBC Films Group January 2001 Page 5 - 43
Operations Orbit™ 2000 Operation and Maintenance Manual
Adjusting the upper snap roller
Angling of the upper snap roller is achieved by turning the regulating bolts ( b ). To adjust the angle of the upper snap roller, use the following steps: d c b
1/ Loosen the locking nut ( c ).
2/ Turn the regulating bolt ( d )
3/ Tighten the locking nut ( c ).
D ire c tio n o f th e re g u la tin g b o lt
D ire c tio n o f th e ro lle r
D ire c tio n o f th e re g u la tin g b o lt
D ire c tio n o f th e ro lle r
Page 5 - 44 © GBC Films Group January 2001
Orbit™ 2000 Operation and Maintenance Manual
5.4.5 Stacking table
M AX .
M IN .
The stacking table stacks the laminated sheets once the snap rollers have separated them.
The stacking table guides ( a ) should be adjusted
to accommodate the sheet size.
a
Operations
Table slope adjustment
The table slope may be adjusted by changing the length of the adjustable legs. There are six possible positions. Both sides must be in the same position when adjusting.
L a rg e s t s lo p e S m a lle s t s lo p e
© GBC Films Group January 2001 Page 5 - 45
Operations
Blower angle adjustment
Orbit™ 2000 Operation and Maintenance Manual
The blower angle may be adjusted to assist the sheet for stacking. Turn the blower angle handle ( a ) to the desired position.
a
Blower pressure adjustment
The blower pressure can be adjusted with respect to the paper weight. To adjust the amount of air flow follow the procedure below.
1/
Loosen the locking nut ( b ).
2/
Turn the regulating dial ( c ) clockwise or counterclockwise.
c
3/
Tighten the locking nut ( b ).
Page 5 - 46 b
© GBC Films Group January 2001
Orbit™ 2000 Operation and Maintenance Manual
6.0 Applications
A T T E N T IO N
D o not operate this equ ipm ent unless you have read an d understand this operator m anual and h ave been fully trained in its operation by a qualified G B C service technician.
Applications
This section will illustrate the recommended types of films, general threading procedure and film threading diagram.
6.1 Recommended types of film for your Obit™ 2000 machine
Polyester - PET
1.7 mil
8200 clear
1.7 mil
43u
30u
43u
Polypropylene - OPP
8300 clear
1.2 mil
33u
47u
GBC Lay-Flat® film ( nylon )
1.7 mil
8500
43u
30u
© GBC Films Group January 2001
Hi-Tac™ film
1.2 mil film
Nap-Lam II film
1.3 mil film
Nap-Lam III film
Aggressive adhesive
EVA adhesive
EVA adhesive
EVA adhesive
EVA adhesive
Hi-Tac™ Lay-Flat®
1.2 mil Lay-Flat®
Aggressive adhesive
EVA adhesive
Page 6 - 1
Applications Orbit™ 2000 Operation and Maintenance Manual
6.2 General threading procedure
W A R N IN G
C A U T IO N : D o not w ear ties, loose fit clothing or dangling jew elry. T hese item s can get caught the rollers w hile w orkin g around or loading film .
W A R N IN G
W A R N IN G : K eep fingers, hands and other body parts aw ay from the rollers.
W A R N IN G
W A R N IN G : T he chrom e roller m ay be hot. C ontact w ill result in severe burns!
Once you have become trained in all aspects of the Orbit™ 2000 explained in Section 5
Operations and the safety rules explained in Section 1 Safety, you may use this general threading procedure to web your machine.
1/
Set the heat required for the type of film being used. ( Described in Section 5 )
2/
Load the roll of film onto the film unwind arbor with respect to the adhesive side. ( Described in
Section 5 )
Page 6 - 2 © GBC Films Group January 2001
Orbit™ 2000 Operation and Maintenance Manual
3/
Load the sheet stack on the feed table. ( Described in Section 5 )
Applications
4/
Adhere one sheet of the same width as the sheets in the feeder to start the film web.
5/
Switch the compressor on and push the start button at it’s slowest speed.
6/
Stop the machine at the instant the first sheet passes under the chrome roller and the leading edge of the paper appears to be at least 8 in. ( 200 mm ) past the contact area between the laminating rollers.
7/
Press the pressure up button.
8/
At the slowest speed of the machine, allow 2-3 sheets pass through the laminating rollers so you can thread the web through the snapping section.
9/
Feed the web through the decurling bar.
10/
Feed the web through the pull rollers. ( Described in Section 5 )
11/
Feed the web through the twin knife assembly. ( Described in Section 5 )
12/
Feed the web through the snap rollers. ( Described in Section 5 )
© GBC Films Group January 2001 Page 6 - 3
Applications Orbit™ 2000 Operation and Maintenance Manual
13/
Grab the web beyond the snapping rollers and pull straight and tight ensuring the web is properly under the twin knives for knicking.
14/
Apply air to the pull roller so that the web is held tightly.
15/
Adjust the stack table guides and slope as necessary. ( Described in Section 5 )
IN F O R M A T IO N
Y ou m ay use an alternate m ethod for w ebbing that is m ore com foratable to you. It is strongly advised that all safety rules ap ply to your alternate m ethod at all tim es.
Page 6 - 4 © GBC Films Group January 2001
Orbit™ 2000 Operation and Maintenance Manual
6.3 Film threading diagram
F ilm a rb o r
S n a p ro lle rs
Applications
F ilm ro ll
C h ro m e ro lle r
S ta c k ta b le
P u ll ro lle rs
D e c u rlin g b a r
S h e e ts
Poly-in / Poly-out webbing diagram
P o ly - o u t
F ilm ro ll F ilm ro ll
P o ly - in
C h ro m e ro lle r
© GBC Films Group January 2001
C h ro m e ro lle r
Page 6 - 5
Applications
This page intentionally left blank.
Orbit™ 2000 Operation and Maintenance Manual
Page 6 - 6 © GBC Films Group January 2001
Obit™ 2000 Operation and Maintenance Manual
7.0 Troubleshooting
Troubleshooting
W A R N IN G
C A U T IO N : D o not w ear ties, loose fit clothing or dangling jew elry. T hese item s can get caught the rollers w hile w orkin g around or loading film .
E L E C T R IC A L
S H O C K
D o not rem ove or m odify any guards, covers or enclosures. C ontact w ith any m oving parts or/ and electrical voltage can result in in jury or death!
W A R N IN G
W A R N IN G : A lw ays exercise L ock out/ T ag out proced ures w hen perform ing any type of troubleshooting to avoid injury to yourself, oth ers and to the equipm ent.
As an operator, you may correct minor problems by performing some simple checks. At no time should you attempt to remove or bypass and safety device on the machine. Always pay careful attention to warnings placed throughout this section. All safety rules from Section 1 apply.
Within this section, you will find Lamination troubleshooting, Wave pattern troubleshooting, Feeder troubleshooting, Misfeed troubleshooting, Web troubleshooting and Machine troubleshooting.
© GBC Films Group January 2001 Page 7 - 1
Troubleshooting Orbit™ 2000 Operation and Maintenance Manual
7.1 Lamination troubleshooting
Blistering
Cause:
A condition where the paper coating is bubbled up from the image paper causing a “blister”.
It is created by using excessive heat during the lamination process. Blistering is most commonly found with photographic and ink jet media.
Solution:
Blistering can be avoided by ensuring you are using the correct operating parameters for the media type and film type being used.
Bond strength
Cause:
Refers to one of three conditions; 1) the anchor strength of adhesive to laminate substrate,
2) the anchor strength of the laminating film to the product that has been laminated, or 3) when two layers of film are laminated together, the strength of the adhesive to adhesive bond.
Solution:
Bond strength can be ensured by using the correct amount of air pressure on the pressure roller as well correct chrome roller temperature and machine speed.
Coiling / curling
Cause:
The finished image curls or rolls up on itself. This is generally caused by improper decurling
bar adjustment and/ or improper setting/ braking of film tension.
Solution:
Adjust the decurling bar properly as described in Section 5. Adjust braking if film tension is
tight.
Page 7 - 2 © GBC Films Group January 2001
Obit™ 2000 Operation and Maintenance Manual
Delamination
Troubleshooting
Cause:
Refers to either one of two conditions; 1) the adhesive separating from the laminate substrate, or 2) the laminate separating from the product being laminated.
Solution:
Delamination is eliminated by using the correct type of film for the type of media being used and setting the machine to the optimal operating parameters.
Out gassing
Cause:
The term that describes the phenomenon where the heat from the laminating process turns components of the printed media into a gas. This is seen as a cloudy or murky finished image. It can also be caused by a chemical incompatibility between the overlaminate’s adhesive and the printed media.
Solution:
Heat related out gassing may be eliminated by reducing the operating temperature or increasing the speed. If out gassing is due to incompatibility, it will be necessary to change film or media.
Silvering
Cause:
A term used to describe one of two occurrences; 1) air bubbles trapped between the product and a thermal laminate, generally caused by insufficient heat being applied to the laminator or 2) the adhesive not fully activated in a pressure sensitive film, which will disappear once the adhesive is fully activated. This activation process can be sped up if a small amount of heat is applied during the application.
Solution:
Ensure your set point for the type of film being used is correct. You may also decrease the speed which will increase the dwell ( time in the laminating rollers nip ) time which allows the film more time to absorb the heat to activate the adhesive.
© GBC Films Group January 2001 Page 7 - 3
Troubleshooting Orbit™ 2000 Operation and Maintenance Manual
7.2 Wave pattern troubleshooting
Waves or ripples in laminated images can be caused by; paper tension, laminating temperature, incorrect nip, clutch tension, binding of film core on brakes or core ends, and cooling. Below is a description of some common waves. Please refer to the wave illustration associated with each description.
Paper tension ( Wave 1 )
Cause:
These waves, visible in the finished image, are caused by uneven paper tension across the width of the image, often called D-Waves. This can occur due to improper handling of the paper at the laminator. Prior to entering the nip, the middle of the image becomes baggy and eventually folds on itself.
Solution:
To remove these waves, check that the feed head is feeding the images smoothly and/or check the nip pressure of the laminating rollers.
Laminating temperature ( Wave 2 )
Cause:
These are caused by the different rates of expansion and contraction of laminates and papers
( specifically coated ink-jet and photographic papers ) during lamination. The waves are induced when the laminate and paper are both heated and then cooled, causing stress due to different rates of cooling between the film and the paper.
Solution:
To eliminate the waves, you may either decrease the laminating temperature or increase the speed.
Nip ( Wave 3 )
Cause:
These waves are seen on one side or the other of the laminated image. They are generally caused by uneven settings of either the laminating rollers or the pull rollers, causing uneven tension between the laminating rollers and the pull rollers.
Solution:
Check the paper pull adjustment, laminating roller pressure and/or the spreader roller ( if equipped ) adjustment.
Page 7 - 4 © GBC Films Group January 2001
Obit™ 2000 Operation and Maintenance Manual Troubleshooting
Paper pull tension ( Wave 2 & 4 )
Cause:
These patterns are caused by too little ( Wave 2 ) or too much ( Wave 4 ) tension of the laminated material between the laminating rollers and the pull rollers.
Solution:
To remove these waves, adjust the paper pull adjustment and/or laminating roller pressure.
Brake tension ( Wave 5 )
Cause:
These are straight bands across the image, usually at uneven intervals and are usually minimal to excessive. This intermittent tension is caused by binding of the film core on the brake or core end inserts.
Solution:
Ream out the core.
Cooling / brake tension ( Wave 6 )
Cause:
These waves may have no particular pattern and may manifest themselves in a wavy ( rather than flat ) finished product. They are caused by stresses or unevenness in the laminate or the image.
Solution:
To prevent this type of waving, reduce the tension on the film. If this proves to be ineffective, check for gauging ( uneven thickness across the width ) in the laminate.
Wrinkles on both edges after the pressure roller ( Wave 7 )
Cause:
Excessive film tension may be applied to the roll of film.
Solution:
To prevent this type of waving, check the film tension as film rides around the chrome roller.
Minimum film tesion should be achieved. Adjusting the spreader roller may also assist with this type of wave form.
Wrinkles from center to edge after pressure roller ( Wave 8 )
Cause:
Pressure roller air pressure may be to great or moisture in the paper may contribute to this type of wrinkle.
Solution:
To prevent this type of waving, adjust the amount of air pressure applied tothe pressure
roller. It may be necessary to set the air pressure below 20 psi. Store paper in a dry enviroment.
© GBC Films Group January 2001 Page 7 - 5
Troubleshooting Orbit™ 2000 Operation and Maintenance Manual
Wrinkles on either edge after the pressure roller ( Wave 9 )
Cause:
Air pressure on the pressure roller from side to side may require off setting.
Solution:
To prevent this type of waving, off set the pressure roller by adjusting the air regulators on
the pressure rollers.
No pattern wrinkles after the pressure roller ( Wave 10 )
Cause:
Excessive film tension may be applied to the web of film traveling around the chrome roller.
Solution:
To prevent this type of waving, check the film tension as film rides around the chrome roller.
Minimum film tesion should be achieved. Adjusting the spreader roller may also assist with this type of wave form.
Wrinkles appear after the pull roller ( Wave 11 )
Cause:
Overlap may be set incorrectly for the weight of paper being used. Pull roller tension may
require adjustments.
Solution:
To prevent this type of waving, check the overlap setting for the sheets. Thinner ( 60 lb. to
80 lb. ) weighted sheets bend under the decurling bar and can cause wrinkles after the pull
roller. Shorten overlap to 1/8 in. ( 3.17 mm ) if possible. You may also have to adjust the pull
roller tension as well.
Wrinkles appear after the snapping roller ( Wave 12 )
Cause:
Incorrect angle may be set on the snapping roller.
Solution:
To prevent this type of waving, adjust the angle of the snapping roller. Ensure that proper
angle is maintained.
All wave patterns are illustrated on page 7-7 and 7-8.
Page 7 - 6 © GBC Films Group January 2001
Obit™ 2000 Operation and Maintenance Manual
Wave patterns 1 - 6
Troubleshooting
W a v e 1 W a v e 2
W a v e 3 W a v e 4
W a v e 5
© GBC Films Group January 2001
W a v e 6
Page 7 - 7
Troubleshooting
Wave patterns 7 - 12
Orbit™ 2000 Operation and Maintenance Manual
( s heet
)
W a ve 7 W a ve 8
W a ve 9 W a ve 1 0
Page 7 - 8
W a ve 1 1 W a ve 1 2
© GBC Films Group January 2001
Obit™ 2000 Operation and Maintenance Manual
7.3 Feeder troubleshooting
Troubleshooting
W A R N I N G
W A R N I N G : O p e r a t o r m a i n t e n a n c e a n d o p e r a t o r a d j u s t m e n t s m a y b e p e r f o r m e d only by person(s) trained in all aspects of the equipment.
1.
The table move is sluggish even without paper load.
W A R N I N G
CAUTION: Depress the emergency stop button before checking for chain tension!
W A R N I N G
CAUTION: Do not wear ties, loose fit clothing or dangling jewelry. These items can get caught by moving parts while performing tasks.
Check the tension of each chain, and adjust properly. Clean or lubricate leading spindles.
2.
The automatic operation is not consistent.
W A R N I N G
CAUTION: Only a qualified service technician may correct this fault.
Check the micro switch inside the feeder, check for loose wires and the contactor in the electrical cabinet.
© GBC Films Group January 2001 Page 7 - 9
Troubleshooting Orbit™ 2000 Operation and Maintenance Manual
7.4 Misfed sheets troubleshooting
W A R N I N G
WARNING: Only person(s) trained in all aspects of the equipment may perform any troubleshooting procedures.
PROBLEM
• Paper is not acclimatized
• Incorrect vacuum or pressure
FIX
– Feed at lower speed
– Adjust vacuum &/ or pressure
W A R N I N G
WARNING: Press the stop button before performing any troubleshooting!
PROBLEM
• Sheets are sticking
• Side stacker plates are tight
• Suctions cups are plugged
• Suction cups are not picking up
the sheets
Page 7 - 10
FIX
– Ream needs fanning
– Adjust for a slight gap
– Clean the suction cups
– Replace the dry or worn
suction cup(s)
© GBC Films Group January 2001
Obit™ 2000 Operation and Maintenance Manual
7.5 Web troubleshooting
Troubleshooting
A stripe appears across the laminated paper sheets
Cause:
The stripe is caused by the decurling bar.
Solution:
This may be corrected by turning the bar over to a larger radius ( described in Section 5 ) and/or increasing pressure on the pull rollers ( described in Section 5 ).
When using polypropylene film ( GBC 8300,....), the sheets separate between the laminating section and the separator
Cause:
The tension between the laminating rollers and the pull rollers is too great for the film.
Solution:
Decrease the paper pull adjustment on the pull rollers ( described in Section 5 ).
The sheets are cut from the side by the twin knives.
Cause:
The gap between the knife’s sharp edge and the leading pin is too small.
W A R N IN G
W A R N IN G : D o not place your fingers or objects under the plastic gu ard, unless th e equipm ent is disconnected from the pow er supply and the em ergen cy stop sw itch is depressed.
Solution:
Turn the knife farther away from the pin and/or insert the shims.
© GBC Films Group January 2001 Page 7 - 11
Troubleshooting Orbit™ 2000 Operation and Maintenance Manual
7.6 Machine troubleshooting
A T T E N T IO N
A t no tim e should a guard, panel, cabin et, door or cover be rem oved b y an operator for troubleshooting purpose ( not even trained operators ). O nly qualified G B C service technicians m ay perform any troubleshooting w here in ternal com pon ents m ust be ch ecked.
W A R N IN G
W A R N IN G : A lw ays exercise L ock out/ T ag out proced ures w hen perform ing any type of troubleshooting to avoid injury to yourself, oth ers and to the equipm ent.
E L E C T R IC A L
S H O C K
D o not rem ove or m odify any guards, covers or enclosures. C ontact w ith any m oving parts or/ and electrical voltage can result in in jury or death!
(1) Symptom: The machine cannot be started with the START button
Possible causes: – Check whether the main switch is in the “ON” position on the distributor.
– Check for red and green digits on the temperature regulator indicating correct
power.
– Check for a green light in the start button.
Page 7 - 12 © GBC Films Group January 2001
Obit™ 2000 Operation and Maintenance Manual
(2) Symptom: The light in the start button is off.
Troubleshooting
Possible causes: – Check the Lucite cover over the chrome roller is closed.
– Check the Lucite cover over the separator is closed.
– Check the side door under the control panel is closed.
– Check all emergency push buttons are in the released ( up ) position.
– Check that the paper in the feeder is not too high where the microswitch is pressed.
(3) Symptom: The machine is running, then suddenly stops.
Possible causes: – Check for a green light in the start button. ( if not start at that symptom )
– A sheet of paper switched off the microswitch on the feeding head.
(4) Symptom: The machine was running, suddenly stopped and cannot be restarted again. The red LED located in the electrical cabinet is not illuminated.
Possible causes: – The paper pile moved upwards causing the emergency microswitch on the feeding
head to be depressed.
(5) Symptom: When the sheet size is changed, the feeding head feeds the sheets irregularly or the sheet stays on the paper pile
Possible cause: – The reason for this may be the suction cups that overlap the paper width and suck
air from where there is no paper. By turning the cup the suction orifice in the
suction bar is closed.
– Check vacuum on the manometer above the feeding head.
© GBC Films Group January 2001 Page 7 - 13
Troubleshooting Orbit™ 2000 Operation and Maintenance Manual
(6) Symptom: Large variations in the sheet overlap
Possible causes: – The sheets may slip under the rolls during feeding of heavy paper without weights
in the gravity rollers. Add weights to the gravity rollers.
– The sheets are pressed excessively against the gates during feeding of very light
paper if the weights in the gravity rollers are to large. Remove the weights.
(7) Symptom: The upper snapping roller was turning and stopped suddenly while the machine was running
Possible cause: – The reasons may be too small of a gap between the upper snapping roller
– Because of the roller friction against paper, the motor overheated and the fuse
tripped. Reset the fuse in the distributor. ( Service technician repair only)
(8) Symptom: The feeding table does not rise automatically.
Possible causes: – The reason may be, while the paper pile was moved into its working position, the
table rise wasn't switched off by the sensor, which is located on the roll bar in the
center of the machine.
– The sensor in the feeding head didn’t switch on due to the adjustment knob on the
feeding head was turned completely to the right.
(9) Symptom: The snapping assembly operates correctly at low speeds but loses its efficiency at higher speeds
Possible causes:
Page 7 - 14
– Low air pressure and flow in the pneumatic circuit of the laminator. Ensure the air
pressure source is adequate.
– Increase the air hose diameter from the air source.
© GBC Films Group January 2001
Obit™ 2000 Operation and Maintenance Manual
(9) Symptom: continued
Troubleshooting
Possible causes: – Adjust for snapping ( separation ) moves under actual snapping roller.
– Adjust snapping position backward towards tension roller.
(10) Symptom: The upper snapping roller doesn’t move up or down.
Possible causes: – Check main air to machine.
– The snapping roller ON/OFF switch is not functioning. ( Service technician repair
only )
– Check air cylinder/ solenoid.
(11) Symptom: The snapping roller moves up and down only when the snapping roller drive motor is in the “ON” position.
Possible causes: – The snap roller push button was not pushed enough to engage the relay. If the
button is not illuminated, the relay is not engaged. Push the snap roller push
button again.
(12) Symptom: The machine doesn’t run when the main breaker is switched to “ON”.
The machine doesn’t run after it was stopped by the emergency push button and the emergency push button was released.
Possible causes: – The “START” button has not been pushed to activate the control system. Push
the “Start” button.
© GBC Films Group January 2001 Page 7 - 15
Troubleshooting
This page intentionally left blank.
Orbit™ 2000 Operation and Maintenance Manual
Page 7 - 16 © GBC Films Group January 2001
Orbit™ 2000 Operation and Maintenance Manual
8.0 Maintenance
W A R N I N G
WARNING: To avoid injury to yourself or damage to the equipment, please read and understand the instructions in this manual before you attempt to install, operate or service the laminator!
Maintenance
This section explains maintenance for operator and service:
Operator Maintenance –
Operator maintenance is limited to that described in this manual. Operator maintenance may only be performed by person(s) fully trained in all aspects of the equipment.
Service maintenance –
Service maintenance may only be performed by a qualified GBC service technician. Described in the Orbit™ 2000 Service
Manual.
ELECTRICAL
S H O C K
Do not modify any guards, covers or enclosures. Contact with any moving parts or/ and electrical voltage can result in injury or death!
W A R N I N G
W A R N I N G : A l w a y s e x e r c i s e L o c k o u t / T a g o u t p r o c e d u r e s w h e n p e r f o r m i n g a n y type of maintenance to avoid injury to yourself, others and to the equipment.
© GBC Films Group January 2001 Page 8 - 1
Maintenance
8.1 Maintenance schedule
Orbit™ 2000 Operation and Maintenance Manual
It is necessary to lubricate and inspect individual parts at regular intervals to prolong the life and ensure the correct functioning of the machine. Safety as described in Section 1 of this manual must be followed when performing any type of maintenance.
DAILY
– Check the quantity of condensed water in the air treatment unit.
If the amount in the vessel is higher than 20 mm, release the fluid.
– Check the presence of covers and bolts
– Check the correct function of sensors
– end switches of the feeding table
– capacity sensor
– sensor protecting the feeding head
– control sensors of removable covers
– emergency stop push button
– Cleaning of the rollers and machine.
EVERY TWO WEEKS
– Lubricate and grease with oil or spray all sliders and leading spindles
– Clean the cam and grease
– Clean and grease guiding rollers
Page 8 - 2 © GBC Films Group January 2001
Orbit™ 2000 Operation and Maintenance Manual
MONTHLY
– Tighten and grease all roller chains
Maintenance
ANNUALLY
– Cleaning of the electrical assembly
E L E C T R IC A L
S H O C K
W A R N IN G : Pow er m u st be disconnected to m achine at fused disconn ect!
– Dust can be removed by vacuuming the cabinet with a soft brush wand.
W A R N IN G
W A R N IN G : N ever use com pressed air to rem ove dust from the inside of the electrical cabinet.
– Inspection of the electrical assembly.
– Tightness of terminals
– Circuit breaker wires
– Loose wires
– Protective Circuit inspection
– Check whether protective connectors are tight. Tighten loose connections. The safety of
protective circuits may be checked by feeding a current of at least 10 A (50 Hz) from the
PELV source for at least 10 seconds. The test is done between the PE terminal and
various points that are part of the protective circuit. See EN 60204-1, article 20.2.
© GBC Films Group January 2001 Page 8 - 3
Maintenance Orbit™ 2000 Operation and Maintenance Manual
– The voltage measured between the terminal PE and the test points may not exceed
U =3.3V
U = 2.6V
U = 1.9V
for for for
S= 1.o square millimeters
S= 1.5 sq. millimeters
S = 2.5 sq. millimeters
Where U
S is the largest drop in voltage and is the smallest effective diameter of the protective conductor in the tested branch of the protective circuit.
– The number of measurements of the protective circuit link is given by the requirements
of particular regulations and standards valid in the user’s country.
– MAIN DRIVE AND FEED TABLE GEAR DRIVE
– Running in - 300 hrs
– Normal operation - 400 hrs
-oil PP 90 H
-oil PP 90 H
In case of higher demands the ecologically acceptable oil TOP-BLEND may be used. TOP-BLEND allows for up to 10.000 operation hours between changes.
– VARIATOR
– Running in - 10.000 hrs - oil OTK 8 to 10
– Normal operation - 10.000 hrs - oil OTK 8 to 10
Page 8 - 4 © GBC Films Group January 2001
Orbit™ 2000 Operation and Maintenance Manual
8.2 Operators Maintenance
Maintenance
W A R N I N G
W A R N I N G : A l w a y s e x e r c i s e L o c k o u t / T a g o u t p r o c e d u r e s w h e n p e r f o r m i n g a n y type of maintenance to avoid injury to yourself, others and to the equipment.
8.2.1 Safety - Rules for machine cleaning
1/
W A R N I N G
WARNING: Do not clean any part of the machine while the laminator is in operation.
2/
W A R N I N G
CAUTION: Never clean the surface of the rollers while the machine is running.
Use the Slow FWD and Slow Reverse to change the exposed area for cleaning.
Use the sequence described below.
a/ Press the Inch/ Slow FWD or Reverse/ Slow Reverse b/ Release the perspective push button and wait for the machine to stop.
3/
W A R N I N G
WARNING: The chrome roller is hot. Contact will result in severe burns!
© GBC Films Group January 2001 Page 8 - 5
Maintenance Orbit™ 2000 Operation and Maintenance Manual c/ Clean the exposed area of the rollers.
d/ Repeat as necessary.
4/
W A R N I N G
WARNING: Hot surface. Exercise extreme caution when cleaning the chrome roller.
Surface temperatures may be upwards of 248
O
F to 275
O
F ( 120 - 135
O
C ).
ATTENTION
5/
6/
W A R N I N G
CAUTION: Do not use aggressive solvents that could cause damage to the rubber rollers. Use only Mineral Spirits.
7/
W A R N I N G
WARNING: Crush hazard exists near any rollers. Do not press Pressure Up/ Pressure
Roll Close switch when your hands or fingers are near the pressure roller arms.
8/
Page 8 - 6
ELECTRICAL
S H O C K
Do not remove or modify any guards, covers or enclosures. Contact with any moving parts or/ and electrical voltage can result in injury or death!
© GBC Films Group January 2001
Orbit™ 2000 Operation and Maintenance Manual Maintenance
8.2.2 Safety - Rules for maintenance/ replacement of the twin
knife
The twin knife is very sharp and extreme caution should be exercised when working in its vicinity.
For safe work, the following safety rules should be followed:
1/
W A R N I N G
WARNING: Knife has sharp edges! Do not touch the sharp edges of the knives.
2/
W A R N I N G
WARNING: For safe knife adjustment, use a 4 mm allen wrench only. The allen wrench can be inserted through the oval shaped openings in the upper section of the plastic guard of the twin knife.
3/
W A R N I N G
WARNING: Do not place your fingers or objects under the plastic guard, unless the equipment is disconnected from the power supply and the emergency stop switch is depressed.
4/
ELECTRICAL
S H O C K
Do not remove or modify any guards, covers or enclosures. Contact with any moving parts or/ and electrical voltage can result in injury or death!
© GBC Films Group January 2001 Page 8 - 7
Maintenance
4/
Orbit™ 2000 Operation and Maintenance Manual
W A R N I N G
W A R N I N G : A l w a y s e x e r c i s e L o c k o u t / T a g o u t p r o c e d u r e s w h e n p e r f o r m i n g a n y type of maintenance to avoid injury to yourself, others and to the equipment.
a/
Raise the snapping section safety shield.
b/
Remove the lock down thumb screw.
c/
With a #3 flat tip screwdriver, remove the four flat head shoulder bolts securing the twin knife safety cover.
d/
Replace the lock down thumb screw. This will prevent the twin knife assembly from sliding.
e/
Use a 4 mm allen wrench to remove the two hex bolts securing the blade you are replacing.
f/
Replace the knife.
g/
Secure the knife reusing the same bolts and a 4 mm allen wrench.
h/
Remove the lock down thumb screw.
i/
Replace the twin knife safety cover and secure in place using the same flat head shoulder bolts and a #3 flat tip screwdriver.
j/
Replace the lock down thumb screw.
Page 8 - 8 © GBC Films Group January 2001
Orbit™ 2000 Operation and Maintenance Manual
8.2.3 Feed table chain tensioning
Maintenance a
/ Tensioning is done by means of turning the bolts where the chain connects to the feeding table.
Tentioning bolt
W A R N I N G
WARNING: Overturning of the bolt can result in disconnection of the chain to the feeding table.
© GBC Films Group January 2001 Page 8 - 9
Maintenance Orbit™ 2000 Operation and Maintenance Manual
8.2.4 Paper release adjustment
W A R N I N G
CAUTION: Only a qualified service technician may perform this set-up.
W A R N I N G
WARNING: Press the stop button before performing the following set-up procedure!
Proper feeding is obtained by setting the lift and release of the paper for correct timing. For correct feeding, the instant of paper release and the instant of suction must be adjusted precisely. The adjustment is done by turning the slide valve ( p ).
q
The instant of release must be 1.5 to 2 mm before top dead center; suction is adjusted simultaneously.
At the moment of suction, the cups are in the rear position and start dropping. The correct position of the slide valve ( q ) is factory adjusted, and is marked by a paint filled drilled hole.
Page 8 - 10 © GBC Films Group January 2001
advertisement
Related manuals
advertisement
Table of contents
- 12 1.1 Safety - Complete equipment
- 15 1.2 Safety - Rules for loading paper
- 16 1.3 Safety - Rules for handling the feeding head
- 18 1.4 Safety - Rules for setting up the rollers and the hinged stops
- 20 1.5 Safety - Rules for set-up of the adjustable guide plates
- 21 1.6 Safety - Rules for the chrome and pressure rollers
- 25 1.7 Safety - Rules for the snap roller area
- 28 1.8 Safety - Rules for the use of the twin knife
- 30 1.9 Safety - Rules for the position adjustment of the decurling bar
- 31 1.10 Safety - Rules for electrical installation
- 33 1.11 Safety - Rules for machine cleaning
- 35 1.12 Safety - Rules for machine maintenance and adjustments
- 37 1.13 Safety - Rules for the feeder table
- 64 5.1.2 The control panel
- 65 Original overlay illustration
- 66 New overlay illustration
- 67 5.2 Feeder section
- 68 5.2.1 Sheet stacking
- 70 5.2.2 Feeder table positioning
- 71 5.2.3 The feeding head
- 76 5.2.4 First Gate
- 77 5.2.5 Feed roller assembly
- 82 5.2.6 Second gate
- 83 5.2.7 Adjustable guide plates
- 84 5.3 Lamination section
- 84 5.3.1 Film roll positioning
- 88 5.3.2 Heating