advertisement
▼
Scroll to page 2
of
16
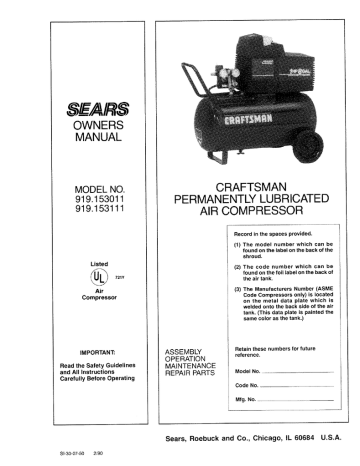
SEARS OWNERS MANUAL MODEL NO. 919.153011 919.153111 Listed Up) 721Y Air Compressor IMPORTANT: Read the Safety Guidelines and Al Instructions Carefully Before Operating CRAFTSMAN PERMANENTLY LUBRICATED AIR COMPRESSOR Record in the spaces provided. (1) The model number which can be found on the label on the back of the shroud. (2) The code number which can be found on the foil ¡abel on the back of the air tank. (3) The Manufacturers Number (ASME Code Compressors only) is located on the metal data plate which is welded onto the back side of the air tank. (This data plate is painted the same color as the tank.) Retain these numbers for future ADS RATION reference. - MAINTENANCE REPAIR PARTS Model No. — Code No. Mfg. No. 51-30-07-50 2/90 Sears, Roebuck and Co., Chicago, IL 60684 U.S.A. TABLE OF CONTENTS Page WARRANTY nan arranca. 3 SAFETY GUIDELINES... aaa, 3 WARNING CHART eno 3 SPECIFICATION CHART... 111110 a LL LL 5 GLOSSARY a a reareaeaaa 5 ACCESSORIES FOR USE WITH SEARS AIR COMPRESSORS .. 5 GENERAL INFORMATION 1111 LL LL LA 6 DESCRIPTION OF OPERATION... LL LL 6 ASSEMBLY INSTRUCTIONS... 1 LL LL Aa 7 Tools Needed for Assembly... 1111L LL LL LL LA 7 Installing Wheels, Handle, Rubberfootstrip..................... ...... 7 installing Regulator |... a aeaede e e 7 INSTALLATION AND BREAK-IN PROCEDURES. .................. 7 Location of Air Compressor. .......... LL LA LL LL LL 7 Lubricationand Oil... LL LL LL A a LL AA ALL 7 Extension Cords ..... 1120212004 aa eee La aan end a. 7 Grounding instructions. ............ aaa aaa 8 Break-in Procedures. ......... aaa a eaenaa 8 OPERATING PROCEDURES ............ LL LA 8 MAINTENANCE... ae. 9 Air FRE 2er AAA a a RAA A LL ALL 9 Check Valve — Repilacement 11111111 LL AL LL LL 9 Safety Valve — InspectionN aaa. 9 MOOT. aerea adan ona aa rana 9 STORAGE aaa aaa, 10 TROUBLESHOOTING GUIDE... LL A 10 AIR COMPRESSOR DIAGRAM... 12 Parts List anno aredocea ae 13 COMPRESSOR PUMP DIAGRAM ......... LL 14 Parts List aaa aaeaoeo o aro. 15 FULL ONE YEAR WARRANTY AIR COMPRESSORS If this air compressor fails due to a defect in material or workmanship within one year from the date of purchase, RETURN IT TO THE NEAREST SEARS SERVICE CENTER/DEPARTMENT THROUGHOUT THE UNITED STATES AND SEARS WILL REPAIR IT, FREE OF CHARGE. If this air compressor is used for commercial or rental purposes, the warranty will apply for ninety days from the date of purchase. This warranty gives you specific legal rights and you may have other rights which vary from slate to state. Sears, Roebuck and Co., Sears Tower, Dept. 698/731 CR-W, Chicago, IL. 60684 SAFETY GUIDELINES This manual contains information that is important for you to know and understand. This informa- tion relates to protecting YOUR SAFETY and PREVENTING EQUIPMENT PROBLEMS. To help you recognize this information, we use the following symbols. Please read the manual and pay attention to these sections. URGENT SAFETY INFORMATION - A HAZARD THAT WILL CAUSE SERIOUS INJURY OR LOSS OF LIFE. Be ole aie ie Ло PP PP "A WARNING | IMPORTANT SAFETY INFORMATION — A HAZARD THAT MIGHT CAUSE SERIOUS INJURY OR LOSS OF LIFE. § CAUTION $ NOTE Information for preventing damage to Information that you should pay special atten- equipment. tion to. WARNING HAZARDS CAN OCCUR IF EQUIPMENT IS NOT USED PROPERLY. PLEASE READ THE FOLLOWING CHART. WHAT TO LOOK FOR WHAT COULD HAPPEN HOW TO PREVENTIT Hot Parts The compressor head gets hot when the air Never touch the air compressor head during or compressor is running. If you touch it, you may be seriously burned. immediately after operation. Flammable Vapors it is normal for the motor's electrical contacts to spark when the compressor starts or stops. À spark can ignite flammable vapors from gasoline, flammable paints or solvents, causing an explosion or fire. Operate the compressor in well ventilated areas that are free of gasoline, flammable paint or solvent vapors. If spraying a flammable material — provide ampie ventilation. Never spray in a closed area. There must be a flow of fresh air at ail times. Do not operate the compressor while you are carrying it, or in the spray area. WHAT 70 LOOK FOR WHAT COULD HAPPEN HOW TO PREVENT IT Air Tank Modifications to the air compressor can cause the air tank to rupture or explode, Changing the air tank will cause it to weaken. The tank may rupture or explode. Do not adjust, remove or tamper with the safety valve or pressure switch. If safety valve or pressure switch replacement is necessary, a part with the same rating must be used. Never use a motor with a higher horsepower rating than the one supplied. Never replace the air tank with a different model or a larger tank. Never drill into, weld, or in any way modify the air tank. Compressed Air Compressed air can propel dust, dirt, or loose particles it comes in contact with. Too much air pressure applied to air tools or accessories can cause damage or risk of bursting. Never point any nozzle or sprayer toward a person or any part of the body. Always wear safety goggles or glasses when using the air compressor. Always turn the air compressor off before attach- ing Or removing accessories. Check the manufacturers maximum pressure rat- ing for air toois and accessories. Regulator outlet pressure must never exceed the maximum pres- sure rating, Electricity Your air compressor is powered by electricity. Like any other electrically powered device, if itis not used properly it may cause electrical shock. Always unplug the air compressor prior to mainte- nance or repair. Never use the air compressor outdoors when it is raining. Always plug the cord into an electrical outlet with the specified voltage and adequate fuse protection. Toxic Vapors It is normal for compressed air to contain toxic or irritating vapors. Such vapors are harmful if inhaled. Certain materials you are spraying (like paint, weed killer, sand or insecticide) can be harmful if you inhale them, Never directly inhale the compressed air produced by this unit. Head labels and safely data for all materials you spray. Follow all safety precautions. Use a mask or respirator if there is a chance of inhaling toxic sprayed materials. Masks and respirators have limits and will only provide protec- tion against some kinds and limited amounts of toxic material. Read mask and respirator instruc- tions carefully. Consult with a safety expert or industrial hygienist if you are not sure about the use of a certain mask or respirator. Unsuitable Solvents The solvents 1,1,1 — Trichloroethane and Methy- lene Chloride can chemically react with alumi- num used in paint spray guns, paínt pumps, etc., and cause an explosion. These solvents can also react with galvanized components and cause corrosion and weakening of parts. This does not affect your air compressor — but it may affect the equipment being used. if the material you intend to spray contains the soi- vents listed at left {read the label or data sheet), do not use accessories that contain aluminum or gal- vanized parts. You must either change the material you intend to spray, or use only stainless steel spray equipment. A e de AAA EE SPECIFICATION CHART Model No. 919153011 a18.153111 Horsepower 1 1 Displacement CFM 6.0 6.0 Bore 2%" Ye" Stroke 1.357 1.35" Voltage-Single Phase 120 120 Minimum Branch Circuit Requirement *15 amps “15 amps “Fuse Type “Fusetron” “Fusetron” Type T Type T Air Tank Capacity ~ GAL. 8 8 ASME Approximate Cut-in Pressure 80 80 Approximate Cut-out Pressure 100 100 SCFM @ 40 psig 4.5 4.5 SCFM (@ 90 psig 3.0 3.0 { CAUTION 3 As. OF FO OOO O TO OY These compressors can be operated on a 15 amp circuit if: 1. Voltage supply to circuit is normal. 2. Circuit is not used to supply any other electrical needs (lights, appliances, etc.) 3. Extension cords comply with specifications in owners manual. 4. Circuit is equipped with 15 amp circuit breaker or 15 amp Fusetron Type “T” time delay fuse. If any of the above conditions cannot be met, or if operation of the compressor repeatedly causes interruption of the power it may be necessary to operate it from a 20 amp circuit. it is not necessary to change the cord set. A circuit breaker is preferred. Use only a fuse or circuit breaker that is the same rating as the branch circuit the air compressor is operated on. !f the air compressor is connected to a circuit protected by fuses, use dual element time delay fuses (Buss Fusetron Type “T” oniy). CFM: Cubic feet per minute. GLOSSARY SCFM: Standard cubic feet per minute; a unit of meas- ure of air delivery. PSIG: Pounds per square inch gauge; a unit of meas- ure of pressure. ASME: American Society of Mechanical Engineers; made, tested, inspected and registered to meet the standards of the ASME. U.L. LISTED: Samples of compressor outfits, taken from production, were submitted to U.L. and found to Cut-In Pressure: While the motor is off, air tank pres- sure drops as you continue to use your accessory. When the tank pressure drops to a certain iow level the motor will re-start automatically. The low pressure at which the motor automatically re-starts is called “cut-in pressure”, Cut-Qut Pressures: When you turn on your air com- pressor and it begins to run, air pressure in the air tank begins to build. ti builds to a certain high pressure before the motor automatically shuts off — protecting your air tank from pressure higher than its capacity. The high pressure at which the motor shuts off is called “cut-out pressure’. comply with their requirements for design and performance. ACCESSORIES FOR USE WITH SEARS AIR COMPRESSORS The following accessories are available through the current general sales catalog or at full-line. Sears stores. « SPRAY GUNS « PAINT TANKS * AIR TOOLS: « BLOW GUNS * AIR TANKS Sanders > AIR CAULKING GUNS * INFLATER KITS Drills » AIR POWERED WASHER GUNS + QUICK CONNECTOR SETS impact wrenches + SANDBLASTERS (various sizes) Hammers * AIR BRUSHES * VISCOSIMETER + AIR HOSE: » AIR PRESSURE REGULATORS - OIL FOG LUBRICATORS Ма”, Зе” ОГ Зв” В). in various iengths + AIR LINE FILTERS » TIRE AIR CHUCKS You have purchased an air compressor unit consisting of a 1 cylinder, single-stage air compressor pump, an air tank, air hose, wheels, handle, and associated controls. You will also find an air chuck. This air compressor requires no oil. Now you can enioy all the benefits of having an air compressor without ever having to purchase, add or change oil. REGULATOR AIR OUTLET REGULATED PRESSURE GAUGE PRESSURE SWITCH TANK PRESSURE GAUGE SAFETY VALVE Air Compressor Pump: To compress air, the piston moves up and down in the cylinder. On the downstroke, air is drawn in through the air intake valves. The exhaust valve remains closed. On the upstroke of the piston, air is compressed. The intake valves close and compressed alr is forced out through the exhaust valve, through the outlet tube, through the check valve and into the air tank. Working air is not available until the compressor has raised the air tank pressure above that required at the air outlet. Check Valve: When the air compressor is operating, the check vaive is “open”, allowing compressed air to enter the air tank. When the air compressor reaches “cut-out” pressure, the check valve “cioses”, allowing air pressure to remain inside the air tank. Pressure Release Valve: The pressure release valve located on the side of the pressure switch, is designed to automatically release compressed air from the com- pressor nead and the outlet tube when the air compres- sor reaches “cut-out” pressure or is shut off. if the air is not released, the motor will try to start, but will be unable to. The pressure release valve allows the motor to restar! freely. When the motor stops running, air will be heard escaping from the valve for a few seconds. No air should be heard leaking when the motor is running. Pressure Switch: The pressure switch automatically starts the motor when the alr tank pressure drops below N OF OPER Your air compressor can be used for operating paint spray guns, air tools, caulking guns, grease guns, air brushes, sandblasters, or inflating tires and plastic toys, spraying weed Killers, insecticides, etc. Separate air transformers which combine the functions of air regulation and/or moisture and dirt removal should be used where applicable. AIR FILTER (NOT SHOWN) DRAIN COCK the factory set “cut-in” pressure. It stops the motor when the air tank pressure reaches the factory set “cut-out” pressure. Safety Valve: if the pressure switch does not shut off the alr compressor at its cut-out pressure setting, the safety valve will protect against high pressure by “popping out” at its pre-set pressure. Regulator: The air pressure coming from the air tank is controlled by the regulator knob. Turn the knob clockwise to increase pressure and counter-clockwise to decrease pressure, To avoid minor readiustment after making a change in pressure setting, always approach the desired pressure from a lower pressure. When reducing from a higher to a lower setting, first reduce to some pressure less than that desired, then bring up to the desired pressure. Depending on the air requirements of each particular accessory, the outlet regulated air pressure may have 10 be adjusted while operating the accessory. Outlet Pressure Gauge: The outlet pressure gauge indicates the air pressure available ai the outlet side of the regulator. This pressure is controlled by the regulator and is always less or equal to the tank pressure. See “Operating Procedures.” Tank Pressure Gauge: The tank pressure gauge indi- cates the reserve air pressure in the tank. ASSEMBLY INSTRUCTIONS Tools Needed for Assembly < pipe thread sealant (not included) - an adjustable wrench for attaching the pressure regulator a %s” socket or open end wrench for attaching the wheels and hose adapter. ° a 7/6" open end wrench for attaching the air pressure gauges « a 346” hex key for installing the plug in the reguiator * a ¥%" open end wrench to tighten handie screws installing Wheels, Handle, Rubber Foot Strip | WARNING THE WHEELS AND HANDLE DO NOT PRO- VIDE ADEQUATE CLEARANCE, STABILITY OR SUPPORT FOR PULLING THE UNIT UP AND DOWN STAIRS OR STEPS. THE UNIT MUST BE LIFTED, OR PUSHED UP A RAMP. 1. Attach the handle to the inside of the compressor sad- dle by pushing the handle in, until the slotin the handie engages with the tabs in the saddle. Puli the handle back and install the two screws, one on each side of the saddle. Tighten securely. a a a aie i ah an a a ai oe Pe Te PE nal Sul gl gl Ng a ag ug ag CE OR ONE EW ply i hy Ww Fa gig gl a a ag al NEE EAE It may be necessary to brace or supportone end of the outfit when attaching the wheels and the rubber foot strip, because the air compressor will have a tendency to tip. 2 Remove the protective paper strip from the adhesive backed rubber foot strip. Attach the rubber foot strip to the bottom of the air tank leg. Press firmiy into piace. 3, Attach one wheel! to each side of the air compressor. Use one shoulder bolt and one nut for each wheel. Tighten securely. installing Regulator Use a small amount of pipe thread sealant on ali pipe thread joints. Install the regulator on the end of the manifold using the short pipe nipple. The arrow on the botiom of the regulator must point away from the manifold in order for the regulator to function properly. Install the adapter and plug in the regulator. The piug is supplied with the regulator. Install the gauges. See dia- gram below. PLUG PIPE MANIFOLD NIPPLE REGULATOR / ADAPTER 7 A REGULATED TANK PRESSURE GAUGE PRESSURE GAUGE INSTALLATION PROCEDURES Location of the Air Compressor { ocaie the air compressor in a clean, dry and well venti- lated area. The air filter must be kept clear of obstruc- tions which could reduce air delivery of the air compressor. The air compressor should be located at least 12" away from the wall or other obstructions that will interfere with the flow of air. The air compressor head and shroud are designed to allow for proper cooling. If humidity is high a Sears air filter can be installed to remove excessive moisture. Follow the instructions packaged with the air filter for proper installation. Lubrication and Oil This unit needs no additional lubrication or oiling. Extension Cords Use extra air hose instead of an extension cord to avoid voltage drop and power loss to the motor. If an extension cord must be used, be sure it is! о а 3-wire extension cord that has a 3-blade grounding plug, and a 3-slot receptacie that will accept the plug on the product. in good condition. » no longer than 50 feet. - 12 gauge (AWG) or larger. (Wire size increases as gauge number decreases. 10 AWG and 8 AWG may also be used. DO NOT USE 14 or 16 AWG.) Grounding Instructions WARNING IMPROPER GROUNDING CAN RESULT IN ELECTRICAL SHOCK. IN THE EVENT OF A SHORT CIRCUIT, GROUNDING REDUCES THE RISK OF SHOCK BY PROVIDING AN ESCAPE WIRE FOR THE ELECTRIC CUR- RENT. THIS AIR COMPRESSOR MUST BE PROPERLY GROUNDED. 1. The air compressor is equipped with a cord having a grounding wire with an appropriate grounding plug. The plug must be used with an outlet that has been installed and grounded in accordance with all local codes and ordinances. The outlet must have the same configuration as the plug. DO NOT USE AN ADAPTER. 2. Do not modify the plug that has been provided. H it does not fit the available outlet, the correct outlet should be installed by a qualified electrician. 3. Inspect the plug and cord before each use. Do not use if there are signs of damage. A DANGER RISK OF ELECTRICAL SHOCK. IF REPAIR- ING OR REPLACING CORD OR PLUG, THE GROUNDING WIRE MUST BE KEPT SEPA- RATE FROM THE CURRENT-CARRYING WIRES. NEVER CONNECT THE GROUND- ING WIRE TO A FLAT BLADE PLUG TER- MINAL. (THE GROUNDING WIRE HAS INSULATION WITH AN OUTER SURFACE THAT IS GREEN — WITH OR WITHOUT YEL- LOW STRIPES.) if these grounding instructions are not completely under- * stood, or if in doubt as to whether the compressor is properly grounded, have the installation checked by a qualified electrician, OUTLET PLUG Grounding > Pin L White Wire Terminal Grounding Pin Break-in Procedures This procedure is required only once, before the air com- pressor is pui into service. 1. Set the pressure switch OFF/AUTO lever to the “OFF” position. 2. Piug the power cord into the correct branch circuit receptacle. 3. Turn the regulator clockwise, opening it fully, to pre- vent air pressure build-up in the tank. 4. Move the OFF/AUTO lever to “AUTO”. The compres- sor will start, 5. Bun the compressor for 15 minutes. Make sure the regulator is open and there is no tank pressure build- up. 6. After 15 minutes, close the regulator by turning it counter-clockwise. The air tank will fill to cut-out prés- sure and then the motor will stop. Refer to Operating Procedures, OPERATING PROCEDURES 1. Before attaching air hose or accessories, make sure the OFF/AUTO lever is set to “OFF” and the air regulator is closed. (Close it by turning it counter- clockwise.) 2. Attach hose and accessories. WARNING TOO MUCH AIR PRESSURE CREATES A HAZARDOUS RISK OF BURSTING. CARE- FULLY FOLLOW STEPS 3 AND 5 EACH TIME THE COMPRESSOR IS USED. 3. Check the manufacturer's maximum pressure rating for air tools and accessories. The regulator outlet pressure must never exceed the maximum pressure rating. 4. Turn the OFF/AUTO lever to “AUTO” and allow tank pressure to build. Motor will stop when tank pressure reaches “cut-out” pressure. 5. Open the regulator by turning it clockwise, Adjust the regulator to the correct pressure setting. Your com- pressor is ready for use. 6. Always operate the air compressor in well-ventilated areas; free of gasoline or other solvent vapors. Do not operate the compressor near the spray area. * When you are finished: 7, Set the “OFF-AUTO" lever to “OFF”. 8. Turn the regulator counter-clockwise and set the out- let pressure to zero. 9. Remove the air tool or accessory. 10. Open the regulator and allow the air to slowly bleed from the tank. Close the regulator when tank pres- sure is approximately 20 psi. 11. Drain water from air tank. WARNING WATER WILL CONDENSE IN THE AIR TANK. IF NOT DRAINED, WATER WiLL CORRODE AND WEAKEN THE AIR TANK CAUSING A RISK OF AIR TANK RUPTURE. With tank pressure at approximately 20 psi, open the drain cock and allow moisture to drain. NOTE If drain cock valve is plugged, release ali air pres- sure. The valve can then be removed, cleaned, then reinstalled. 12. After the water has been drained, close the drain cock. The air compressor can now be stored. MAINTENANCE WARNING | UNIT CYCLES AUTOMATICALLY WHEN POWER IS ON. WHEN DOING MAINTENANCE, YOU MAY BE EXPOSED TO VOLTAGE SOURCES, COMPRESSED AIR OR MOVING PARTS. PERSONAL INJURIES CAN OCCUR. BEFORE PERFORMING ANY MAINTENANCE OR REPAIR, UNPLUG THE COMPRESSOR AND BLEED OFF ALL AIR PRESSURE. Air Filter — Inspection NOTE Keep the air filter clean at all times. Do not oper- ate the compressor with the air filter removed. A dirty air filter will not allow the compressor {o operate at full capacity. Before you use the compressor, check the air filter to be sure it is clean. If it is dirty, simply pull it out. You may wash it with a mild detergent and warm water, or replace it. Check Valve — Replacement 1. Release all air pressure from air tank and unplug outfit. . Remove shroud. . Loosen the top and bottom nuts and remove the outlet tube. . Remove the pressure release tube and fitting. . Unscrew the check valve (turn counterclockwise) using a socket wrench. , Check that the valve disc moves freely inside the check valve and that the spring holds the disc in the upper, closed position. The check valve may be cleaned with a solvent, such as paint and varnish remover. 7. Apply sealant to the check valve threads. Reinstall the check valve {turn clockwise}. 8. Replace the pressure release tube and fitting. 9. Replace the outlet tube and tighten top and bottom nuts, 10. Replace the shroud. on & со Ро с Safety Valve — inspection WARNING IF THE SAFETY VALVE DOES NOT WORK PROPERLY, OVER-PRESSURIZATION MAY OCCUR, CAUSING AIR TANK RUPTURE OR AN EXPLOSION. OCCASIONALLY PULL THE RING ON THE SAFETY VALVE TO MAKE SURE THAT THE SAFETY VALVE OPERATES FREELY. IF THE VALVE 15 STUCK OR DOES NOT OPERATE SMOOTHLY, IT MUST BE REPLACED WITH THE SAME TYPE OF VALVE. Motor The motor has an automatic reset thermal overioad pro- tector. If the motor overheats for any reason, the over- load protector will shut off the motor. The motor must be aliowed to cool down before restarting. The compressor will automatically re-start after the motor cools. If the overload protector shuts the motor off frequently, check for a possible voltage problem. Low voltage can also be suspected when: 1. the motor does not get up to full power or speed; 2 fuses blow out when starting the motor; lights dim and remain dim when motor is started and is running. Before you store the air compressor, make sure you do the following: STORAGE 1. Review the “Maintenance” section on the preceeding pages and perform maintenance as necessary. Be sure to drain water from the air tank. TROUBLESHOOTING GUIDE WARNING | PERFORMING REPAIRS MAY EXPOSE VOLTAGE SOURCES, MOVING PARTS, OR COM- PRESSED AIR SOURCES. PERSONAL INJURY MAY OCCUR. PRIOR TO ATTEMPTING ANY REPAIRS UNPLUG THE COMPRESSOR AND BLEED OFF TANK AIR PRESSURE. 2. Protect the electrical cord and air hose from damage {such as being stepped on or run over). Wind them loosely around the compressor handle. Store the air compressor in a clean and dry location. PROBLEM CAUSE CORRECTION Excessive Tank pressure — safety valve pops off. Pressure switch does not shut off motor when compressor reaches “cut-out” pressure. Pressure switch “cut-out” too high. Move the pressure switch lever to the “OFF” posi- tion. if the outfit doesn’t shut off, and the electrical contacts are welded together, replace the pressure switch. It the contacts are good, check to see if the pin in the bottom of the pressure release valve is stuck. if it does not move freely, replace the valve. Return the outfit to Sears Service Center to check and adjust, or replace switch. Air leaks at fittings Tube fittings are not tight enough. Tighten fittings where air can be heard escaping. Check fittings with soapy water solution. DO NOT OVER-TIGHTEN. Air leaks at check valve. Defective or dirty check valve. A defective check valve results in a constant air leak at the pressure release valve when there is pressure in the tank and the compressor is shut off. Remove and clean or replace check valve. DO NOT OVER-TIGHTEN. Air leaks at pressure switch release valve Defective pressure switch release valve. Defective check valve. Remove and replace the release valve. A defective CHECK valve results in a constant air leak at the pressure release valve when there is pressure in the tank and the compressor is shut off. Remove and clean or replace check vaive. DO NOT OVER-TIGHTEN, Air leaks in air tank. Defective air tank. Air tank must be replaced. Do not repair the leak. WARNING DO NOT DRILL INTO, WELD, OR OTHERWISE MODIFY AIR TANK OR IT WILL WEAKEN. Pressure reading on the regulated pressure gauge drops when an accessory is used. It is normal for “some” pressure drop to occur. if there is an excessive amount of pressure drop when the accessory is used, adjust the regulator following the instructions on pg. 6. Note Adjust the regulated pressure under flow conditions (while accessory is being used.) TROUBLESHOOTING GUIDE (Continued) PROBLEM CAUSE CORRECTION Air leak from Safety Vaive Possible defect in Safety Valve. Operate safety valve manually by pulling on ring. В valve still leaks, it should be replaced. Knocking Noise Defective Check Valve. Remove and clean or replace. Compressor is not supply- ing enough air 10 operate accessories. Prolonged excessive use of air. Compressor is not large enough for air requirement. Restricied air intake filter. Hole in hose. Check Valve restricted. Air leaks. Decrease amount of air usage. Check the accessory air requirement. if it is higher than the SCFM or pressure supplied by your air compressor, you need a larger compressor. Clean or replace air intake filter. Do not operate the air compressor in the paint spray area. Check and replace if required. Remove and clean or replace. Tighten fittings. (See Air Leaks Section of Troubleshooting Guide.) Motor Will Not Run Motor overload protection switch has tripped. Tank pressure exceeds pressure switch “cut-in” pressure. Wrong gauge wire or length of extension cord. Check Valve stuck open. Loose electrical connections. Paint spray on internal motor paris. Possible defective motor. Fuse blown, circuit breaker tripped. Pressure release valve on pres- sure switch has not unloaded head pressure. Let motor cool off and overicad switch will auto- matically reset. Motor will start automatically when tank pressure drops below “cut-in” pressure of pressure switch. Check for proper gauge wire and cord length. Remove and clean or replace. Check wiring connection inside pressure switch and terminal box area. Have checked at Sears Service Center. Do not operate the compressor in the paint spray area. See flammable vapor warning on page 3. Have checked at a local Sears Service Center. 1. Check fuse box for blown fuse and replace if necessary. Re-set circuit breaker. Do not use a fuse or circuit breaker with higher rating than that specified for your particular branch circuit. 2. Check for proper fuse; only “Fusetron” type T fuses are acceptable. 3. Check for low voltage conditions and/or proper extension cord. 4. Disconnect the other electical appliances from circuit or operate the compessor on its own branch circuit. Bieed the line by pushing the lever on the pressure switch to the “Off” position; if the valve does not open, replace it. Regulator knob - continu- ous air leak. Regulator will not shut-off at air outlet. Dirty or damaged regulator inter- nal paris. Clean or replace regulator, or internal parts. 11 AIR COMPRESSOR DIAGRAM See page 14 and 15 for compressor/motor parts breakdown. KEY NO. tele A» O do tin PART NUMBER LA-1995 LA-1997 LA-2015 LA-1779 САС-1140 LA-1996 SS-655-ZN CAC-4300 CAC-1121 LA-1994-1 SSF-928 TA-4138-1 TA-4137-1 STD541437 CAC-1106 CAC-60 SSF-981-ZN LA-1810-1 SUDL-6-1 LA-1978 CAC-1087 LA-1535 CAC-4290 SSP-7813 CAC-333-1 SEN-8001 CAC-1120 SSP-7821 CAC-1083-1 C-GA-345 55-2072 SS-2071 H-2099 CAC-4296 SS-3222-CD CAC-365 TIA-4125 SUDL-403-1 CAC-4220-1 LA-1531-1 CAC-1085 STD575025 STD575026 SSP-9013 SSP-6088 CAC-4215-1 SSW-7367 KK-4315 PARTS LIST DESCRIPTION Model No. Label (Model No. 919.153111) Model No. Label (Model No. 919.153011) Maintenance Label Hot Surface Label Shroud — front Performance Label Hex Nut 74-20 (2 used) Rear shroud assembly (includes 2 ea. #7A) Shroud Bracket (2 used) Advanced tech. Label Screw (2 used) Air Tank (Model No. 919.153011) Air Tank ASME (Model! No. 919.153111) Nut 34"-16 (2 used) Wheel (2 used) Shoulder bolt 3-16 x 214" (2 used) Screw Ya" AB x 34" long (2 used) Sears Craftsman Label Rubber foot strip Drain Tank Label Handie (black finish) Warning Label Check valve Nut sleeve assembly (for % O.D. Tube) Shroud Plate Ratchet Fastener (2 used) Silicone sleeve Nut (torque 60-70 in. Ibs.) Qutlet tube Pressure Gauge (2 used) Nipple (% NPT x 172" long) Nipple (44" NPT x 112" long Adapter Regulator Pipe plug 74” NPT Manifold Safety valve Cord assembly — line Pressure switch On-Off Label Pressure relief tube (warm tube before installing on #42.) Nut (For 117 O.D. Tube) Ferrule (For 4" O.D. Tube) Tube insert Barbed fitting Cord assembly — motor Strain relief (2 used) Pressure release vaive and mounting nut (included with #36) 13 COMPRESSOR PUMP DIAGRAM POSITION LOCATING MARK TOWARDS MOTOR. 55 14 PARTS LIST KEY NO. PART NUMBER DESCRIPTION 46 CAC-260-2 Air Filter 47 CAC-1046 intake muffler 48 SSF-990 Screw 14” - 20 x 171” (2 used, torque 7-10 ft. 165.) 49 CAC-1067-U-1 Head 50 SSF-6640 Stud 14-20 x 171” (2 used, torque 7-10 ft. ibs.) 51 CAC-1066 Gasket 52 CAC-4281-1 Valve plate assembly (includes valves, restrictors & screws) 53 SSG-8156 O-ring y 54 — Connecting rod assembly (torque screw 30-35 in. Ibs.) Y 55 — Cylinder sleeve (position locating mark towards motor) 56 C-MO-3005 Motor 1 HP 57 CAC-1023 Eccentric/Fiywheel 58 SSF-2043 Screw (eccentric/flywheel, torque 50-60 in. ibs.) 59 CAC-1055 Fan 60 SSF-3101 Screw #10-24 x 3" long (torque 30-35 in. ibs.) 61 SST-3025 Bearing (eccentric) NOT ILLUSTRATED H-5796 Air Hose assembly (44"I.D. x 15") 9-16269 Air Chuck S1-30-07-50 Owners Manual y Key 54 855 Can only be purchased as part of KK-4835 connecting rod kit 15 SEARS OWNERS MANUAL SERVICE MODEL NO. 919.153011 919.153111 HOW TO ORDER REPAIR PARTS S1-30-07-50 2/90 CRAFTSMAN PERMANENTLY LUBRICATED AIR COMPRESSOR Now that you have purchased your Sears Air Compressor, should a need ever exist for repair parts or service, simply contact any Sears Service Center and most Sears, Roebuck and Co. stores. Be sure to provide all pertinent facts when you call or visit. The model number of your Sears Air Compressoris 919. … This number can be found on the label which is located on the back of the shroud. WHEN ORDERING REPAIR PARTS, ALWAYS GIVE THE FOLLOWING INFORMATION: * PART NUMBER « PART DESCRIPTION » MODEL NUMBER * NAME OF ITEM All parts listed may be ordered from any Sears Service Center and most Sears stores. If the parts you need are not stocked locally, your order will be elec- tronically transmitted to a Sears Repair Parts Distribution Center for handling. Sears, Roebuck and Co., Chicago, IL 60684 U.S.A. Printed in U.S.A.
advertisement
Related manuals
advertisement