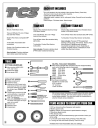
advertisement
▼
Scroll to page 2
of 27
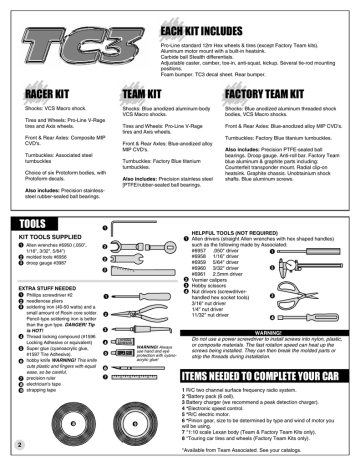
EACH KIT INCLUDES Pro-Line standard 12m Hex wheels & tires (except Factory Team kits). Aluminum motor mount with a built-in heatsink. Carbide ball Stealth differentials. Adjustable caster, camber, toe-in, anti-squat, kickup. Several tie-rod mounting positions. Foam bumper. TC3 decal sheet. Rear bumper. RACER KIT TEAM KIT FACTORY TEAM KIT Shocks: VCS Macro shock. Shocks: Blue anodized aluminum-body VCS Macro shocks. Shocks: Blue anodized aluminum threaded shock bodies, VCS Macro shocks. Tires and Wheels: Pro-Line V-Rage tires and Axis wheels. Front & Rear Axles: Blue-anodized alloy MIP CVD's. Tires and Wheels: Pro-Line V-Rage tires and Axis wheels. Front & Rear Axles: Composite MIP CVD's. Turnbuckles: Associated steel turnbuckles Choice of six Protoform bodies, with Protoform decals. Turnbuckles: Factory Blue titanium turnbuckles. Front & Rear Axles: Blue-anodized alloy MIP CVD's. Turnbuckles: Factory Blue titanium turnbuckles. Also includes: Precision stainless steel [PTFE/rubber-sealed ball bearings. Also includes: Precision PTFE-sealed ball bearings. Droop gauge. Anti-roll bar. Factory Team blue aluminum & graphite parts including: Counterfeit transponder mount. Radial clip-on heatsink. Graphite chassis. Unobtainium shock shafts. Blue aluminum screws. Also includes: Precision stainlesssteel rubber-sealed ball bearings. TOOLS HELPFUL TOOLS (NOT REQUIRED) Allen drivers (straight Allen wrenches with hex shaped handles) such as the following made by Associated: #6957 .050" driver #6958 1/16" driver #6959 5/64" driver #6960 3/32" driver #6961 2.5mm driver Vernier calipers Hobby scissors Nut drivers (screwdriverhandled hex socket tools) 3/16" nut driver 1/4" nut driver 11/32" nut driver KIT TOOLS SUPPLIED Allen wrenches #6950 (.050", 1/16", 3/32", 5/64") molded tools #6956 droop gauge #3987 8 7 6 5 4 3 2 1 0 EXTRA STUFF NEEDED Phillips screwdriver #2 needlenose pliers soldering iron (40-50 watts) and a small amount of Rosin core solder. Pencil-type soldering iron is better than the gun type. DANGER! Tip is HOT! Thread locking compound (#1596 Locking Adhesive or equivalent) Super glue (cyanoacrylic glue, #1597 Tire Adhesive). hobby knife WARNING! This knife cuts plastic and fingers with equal ease, so be careful. precision ruler electrician's tape strapping tape LOCKING ADHESIVE WARNING! Always use hand and eye protection with cyanoacrylic glue! WARNING! Do not use a power screwdriver to install screws into nylon, plastic, or composite materials. The fast rotation speed can heat up the screws being installed. They can then break the molded parts or strip the threads during installation. ITEMS NEEDED TO COMPLETE YOUR CAR 1 R/C two channel surface frequency radio system. 2 *Battery pack (6 cell). 3 Battery charger (we recommend a peak detection charger). 4 *Electronic speed control. 5 *R/C electric motor. 6 *Pinion gear, size to be determined by type and wind of motor you will be using. 7 *1:10 scale Lexan body (Team & Factory Team Kits only). 8 *Touring car tires and wheels (Factory Team Kits only). 2 *Available from Team Associated. See your catalogs. REACHING US CUSTOMER SUPPORT (714) 850-9342 Fax (714) 850-1744 http://www.rc10.com/help http://www.rc10.com/kits ASSOCIATED ELECTRICS, INC. 3585 Cadillac Ave. Costa Mesa, CA 92626-1401 USA http://www.rc10.com http://www.teamassociated.com ©2000 Associated Electrics, Inc. BEFORE BUILDING OPEN THE BAGS IN ORDER The assembly is arranged so that you will open and finish that bag before you go on to the next bag. Sometimes you will have parts remaining at the end of a bag. These will become part of the next bag. Some bags may have a large amount of small parts. To make it easier to find the parts, we recommend using a partitioned paper plate for spreading out the parts so they will be easier to find. MANUAL FORMAT The following explains the format of these instructions. The beginning of each section indicates: 1 Which bag to open ("BAG A") and which steps you'll be using those parts for ("FOR STEPS 1-3"). 2 Which parts you will use for those steps. Remove only the parts shown. "1:1" indicates an actual size drawing; place your part on top and compare it so it does not get confused with a similar part. 3 Which tools you should have handy for that section. BAG A REMOVE THESE PARTS FOR: Step 1 1:1 4449, qty 1 4-40 locknut 1:1 6918, qty 1 4-40 x 1/2 4 In some drawings, the word "REAR" with an arrow indicates which direction is the rear of the car to help keep you oriented. 5 The instructions in each step are ordered in the order you complete them, so read the words AND follow the pictures. The numbers in circles are also in the drawing to help you locate them faster. 6 When we refer to left and right sides of the car, we are referring to the driver's point of view inside the car. 7 Occasionally you will see an upside-down triangle next to a part. This indicates that more information is given about the part next to the matching triangle near the text. SUPPLEMENTAL SHEETS We are constantly developing new parts to improve our kits. These changes, if any, will be noted in supplementary sheets located in a parts bag or inside the kit box. Check the kit box before you start and each bag as it is opened. When a supplement is found, attach it to the appropriate section of the manual. 1:1 3858, qty 3 short special ball end, black 1:1 3855, qty 1 .125 x .250 rack shim, black 1:1 6587, qty 1 spring black TOOLS USED 1/16" 3855, qty 1 steering rack 3855, qty 1 steering rack arm ASTERISK ( * ) DENOTES FACTORY TEAM PART NUMBER step 1 4449 STEERING RACK ASSEMBLY Attach two #3858 short ball ends to the #3855 steering rack and one #3858 short ball end to the #3855 steering rack arm. Slide the #6587 spring and the #3855 rack shim onto the #6918 screw. Slide the screw assembly through the bottom of the steering rack. Attach the #3855 rack arm to the rack with a #4449 locknut. 4 Tighten down the spring until the screw is flush with the top of the nut. Make sure the rack arm is facing the rear when assembled on the rack: The ball end on the rack arm and the ball ends on the rack should be pointing in opposite directions. 1:1 3855, qty 2 spacer, black 3858 black Match this number to the text to find your way faster 3855 steering rack arm 3858 black 3855 steering rack 3855 See page 21 for Ackerman setup options using the spacer supplied in bag A. 6587 black 3858 black 6918 3 BAG A 1:1 1:1 TOOLS USED 1:1 6222 REMOVE THESE PARTS FOR: Step 2 3856, qty 2 rack post shim 1:1 1/16" 6291, qty 2 6222, qty 2 4-40 X 1/4 screw nylon locknut 1:1 3856 washer 3856 bushing 3971* bearing 1:1 3856 shim 3856, qty 4 washer 3856, qty 4 1/8 x 1/4 steering rack bushing FT KIT ONLY 3971*, qty 4 1/8 x 1/4 steering rack bearing 3856 bushing 3971* bearing 3856 washer 3850, 3849*, qty 1 chassis NOT IN BAG A 3856, qty 2 rack post 3856 rack post step 2 RACK TO CHASSIS ASSEMBLY Install the two #3856 rack posts to the chassis with two #6291 screws. Slide one #3856 washer, one #3856 steering rack bushing (3971* bearing), one #3856 rack post shim and one #3856 bushing (3971* bearing) onto the rack post. Repeat for the other post. Place the rack assembly over the rack posts. Add two #3856 washers, then the two #6222 nylon locknuts. 3850, 3849* Tighten each nut down until the rack does not move side-to-side freely. Then loosen the nuts 1/4 turn or until the rack moves freely. 6291 6291 BAG B REMOVE THESE PARTS FOR: Steps 1- 2 TOOLS USED 1:1 3863, qty 1, code (F) front arm rear mount 3863, qty 1, code (F+2) front arm front mount 3863, qty 1 3863, qty 1, code (R) code R+3+2 rear arm front mount rear arm rear mount 6292, 6934*, qty 9 4-40 X 3/8 screw 1/16", 3/32" 1:1 3865, qty 4 set screw step 1 3860, 3861*, qty 2 front arm 3851, qty 1 front bumper 3890, 3891*, qty 2 rear arm 3900, qty 1 rear bumper droop gauge 3866, qty 4 inner hinge pin DO NOT REMOVE!! F 3865 3860, 3861* 3863 3865 REMOVE GRAY AREAS WHERE SHOWN BE CAREFUL NOT TO REMOVE THE BALLS!! Remove flashing so balls are perfectly smooth. FRONT ARM ASSEMBLY 3863 Install a #3865 set screw into the #3860 (3861*) front arms, right and left sides. Thread the set screws into the arms until the set screws are flush with the top of the arm. We will adjust them in step 3. Attach the #3863 front arm rear mount (with the "F" molded into mount--see below for location) to the chassis with two #6292 (6934*) screws. Attach the #3863 front arm front mount (with the "F+2" molded into the mount) to the #3851 bumper with one #6292 (6934*) screw. 3851 Slide the #3866 inner hinge pins through the #3860 (3861*) front arms. Slide the pins with the arms into the front arm rear mount. Align the front arm front mount and bumper with the two hinge pins and slide together. Tighten it down with two #6292 (6934*) screws. 6292, 6934* 3866 3860, 3861* F+2 3866 By changing arm mounts you can adjust for kickup and anti-dive. For more information about kickup and anti-dive settings, see the tuning section at the rear of the manual. WHERE TO FIND THE ARM MOUNT CODE (See page 20 for full explanation of arm mount codes) 4 6292, 6934* 6292, 6934* 6292, 6934* 6292, 6934* step 2 DO NOT REMOVE!! 3890, 3891* 3865 3863 R R+3+2 3865 REMOVE GRAY AREAS WHERE SHOWN BE CAREFUL NOT TO REMOVE THE BALLS!! Remove flashing so balls are perfectly smooth. 3866 REAR ARM ASSEMBLY Install a #3865 10-32 set screw into the #3890 (3891*) rear arms, right and left until the set screws are flush with the top of the arms. We will adjust them in step 3. Attach the #3863 rear arm front mount (with the "R" molded into mount--see below for location) to the chassis with two #6292 (6934*) screws. Slide the #3866 inner hinge pins through the #3890 (3891*) rear arms. Slide the pins with the arms into the #3863 rear arm front mount. Place the #3863 rear arm rear mount (with the "R+3+2" molded into the mount) on the #3900 rear bumper. Align the rear arm mount and bumper with the two hinge pins and slide together. Tighten it down with two #6292 (6934*) screws. 3890, 3891* 3866 3863 3900 By changing arm mounts you can adjust toe-in and anti-squat. For more information about the rear toe-in and anti-squat settings, see the tuning section at the rear of the manual. 6292, 6934* 6292, 6934* 6292, 6934* WHERE TO FIND THE ARM MOUNT CODE (See page 20 for full explanation of arm mount codes) 6292, 6934* step 3 SETTING DROOP Place the supplied #3987 droop gauge on a flat surface on its edge as shown. Rest the bottom of the chassis on the gauge as shown, making sure the screws are not resting on the gauge. Slide the gauge out so the front arm rests on step 6. With your 3/32" Allen wrench, adjust the set screw so the outer part of the arm just touches the step. Adjust both front arms. Slide the gauge to the rear arms and repeat, but the rear arms will rest on step 4. NOTE: 1/8 turn equals 1/2 step in change. 1/4 turn equals 1 step change. FRONT ARM SETTING REAR ARM SETTING RACER'S TIP: By using a ball end 3/32" driver it is easier to adjust the droop set screws. BAG C REMOVE THESE PARTS FOR: Steps 1- 5 1:1 1:1 1:1 1:1 TOOLS USED 1:1 6591, qty 1 Stealth diff lube 6573, qty 4 diff thrust washer 3907, qty 2 3/16 x 5/16 bushing unflanged 6575, qty 2 diff bolt 6581, qty 24 3/32 diff ball large 5/64" 6574, qty 12 5/64 thrust ball small 6588, qty 1 black grease 1:1 3904, qty 2 2-56 locknut 1:1 1:1 3908, qty 2 long outdrive 3908, qty 2 short outdrive 3906, qty 2 D-drive ring 3914, qty 2 differential ring gear 6582, qty 2 diff spring, gray 5 step 1 6573 6573 THRUST BALL ASSEMBLY 6575 Hold the #6575 diff bolt with your 5/64" Allen wrench and slide one #6573 washer onto the #6575 diff bolt. Apply a generous amount of #6588 black grease to the washer on the side facing away from the bolt head. Place six #6574 thrust balls into the grease against the #6575 bolt and washer. Add the other #6573 washer. The grease will hold the balls in place during assembly, sandwiched between the washers. 6574 5/64" Allen wrench 6588 (grease not shown) step 2 6582 6582 SPRING With a pair of pliers, compress the #6582 diff spring a few times. Slide the spring onto the bolt against the thrust assembly. thrust assembly step 3 6591 Smear a small amount of diff lube here to hold the drive ring in place LONG HUB ASSEMBLY Insert the thrust assembly into the #3908 long hub. Add a light coat of #6591 Stealth lube to the long hub face where shown. Place a #3906 diff ring on the hub, lining up the flats on the ring and hub. Insert #3907 bushing into the long hub. 3906 3908 3907 spring washer balls diff bolt washer Allen wrench CAUTION!! Make sure you line up the flats on the diff ring and hub step 4 step 5 SHORT OUTDRIVE Add a small amount of #6591Stealth diff lube to the #3904 locknut where shown to help hold it in place. Insert the #3904 2-56 locknut into the #3908 short outdrive. The nut should fit flat inside the hex shape. DIFFERENTIAL RING GEAR Trim any burrs from the inside of the gear with a hobby knife. Add a generous amount of #6591 diff lube to the #3914 ring gear ball holes and push in the twelve #6581 diff balls. Then push back in the lube that came out. 3914 6591 6591 6581 3904 3908 Trim any burrs from the inside of the gear with a hobby knife. 6 3914 BAG C 1:1 1:1 REMOVE THESE PARTS FOR: Steps 6-8 3907, qty 2 3/16 x 5/16 bushing, unflanged TOOLS USED 1:1 FACTORY TEAM ONLY 6903*, qty 4 3/8 x 5/8 bearing PTFE sealed, unflanged 1:1 1:1 3976, qty 4 3911, qty 4 3/8 x 5/8 bearing outdrive shim rubber sealed, unflanged step 6 1:1 3908, qty 2 diff cover 3906, qty 2 D-drive ring Smear a small amount of diff lube here to hold the drive ring in place 6591 SHORT HUB ASSEMBLY Add a light coat of #6591 Stealth lube to the #3908 short hub face. Place a #3906 diff ring on the hub, lining up the flats on the ring and hub. Insert one #3907 bushing onto the short hub. Push the #3908 short hub assembly into the back side of the differential ring gear assembly. 5/64 3908 3906 3907 3914 diff ring gear assembly CAUTION!! Make sure you line up the flats on the diff ring and hub step 7 DIFF ASSEMBLY Insert the long hub assembly into the short hub assembly, making sure you line up the bolt in the hub and the bolt threads into the #3904 locknut. CHECK ALIGNMENT OF THE HUBS Tighten the diff with your 5/64" Allen wrench, but not completely. Screw in the diff bolt a few turns then stop to rotate the diff hubs in opposite directions.Then screw in the bolt some more. Follow this procedure to check proper alignment of the parts. The following note clarfies this. READ THE FOLLOWING CAREFULLY. As you tighten the diff bolt, pay close attention to the feeling when the spring is fully compressed. Do not overtighten the bolt. When you feel the spring fully compressed, loosen the diff bolt 1/2 turn. No more, no less. After you have driven the car for one pack, recheck the diff adjustment as above so that when you feel the spring fully compressed, loosen the diff bolt 1/2 turn. Never adjust the diff any other way. Now assemble the second diff the same way. Rotate the hubs in opposite directions several times in between screwing in the diff bolt. 7 IT IS EXTREMELY IMPORTANT TO USE THE EXACT AMOUNT OF SHIMS SUGGESTED IN THESE STEPS. step 8 FINAL OUTDRIVE ASSEMBLY Insert the #3908 diff bolt cover into the long hub. Press two #3911 outdrive shims on the long hub. Place one #3976 bearing over each outdrive hubs. long hub 3908 1:1 1:1 3976, qty 4 3/8 x 5/8 bearing rubber sealed, unflanged BAG C 1:1 REMOVE THESE PARTS FOR: Steps 9-12 1:1 1:1 FACTORY TEAM ONLY 6903, qty 4 3/8 x 5/8 bearing PTFE sealed, unflanged 1:1 1:1 1:1 3914, qty 2 drive pinion step 9 3917, qty 2 drive cup RACER KIT ONLY 3977, qty 4 3/16 x 3/8 bearing, rubber sealed 1:1 TEAM & F.T. KITS ONLY 6288, qty 2 4-40 x 1/4 6906, qty 4 screw 3/16 x 3/8 bearing, PTFE sealed 3911, qty 1 input shaft spacer, alum. TOOLS USED 5407, qty 1 red O-ring 3915, qty 1 rear input shaft 3915, qty 1 front input shaft Slide the second #3977 or #6906 bearing onto the input shaft. Install and center the #3919 dowel pin into the input shaft. Slide a #3917 drive cup onto the end of the input shaft. Tighten it down with one #6920 screw. FRONT INPUT SHAFT ASSEMBLY Install and center the #3919 dowel pin into the #3915 front input shaft. Trim burrs from the drive pinion edge where shown above. Slide the #3914 drive pinion onto the input shaft. Make sure the dowel pin aligns perfectly with the slot in the pinion. Add the #3919 small E-clip. Slide three #3911 input shaft shims and one #3977 or #6906 bearing onto the #3915 input shaft. 6920 3917 drive cup 3919 pin 3915 input shaft 3911 shim 3919 pin 3914 drive pinion RACER KIT ONLY 3977, qty 2 3/16 x 3/8 bearing, rubber sealed step 10 REAR INPUT SHAFT ASSEMBLY Attach the #3919 C-clip to the #3915 rear input shaft. (We've included an extra C-clip in case you lose one.) Install the #3919 dowel pin into the input shaft. Slide on the #3917 gear adapter. Add the #3919 large E-clip. 8 1:1 3922, qty 1 72T Kimbrough spur gear 1:1 6920, qty 2 3919, qty 5 4-40 x 3/16 screw dowel pin Trim any burrs from this edge of the drive pinion with a hobby knife. 3919 small E-clip 1:1 1/16" 3919, qty 1 3911, qty 6 3919, qty 2 3919, qty 1 C-clip input shaft small E-clip large E-clip shim 1:1 3917, qty 1 spur gear adapter 3911 1:1 1:1 TEAM & F.T. KITS ONLY 6906, qty 2 3/16 x 3/8 bearing, PTFE-sealed 3919 large E-clip 3917 3915 rear input shaft 3919 C-clip 3919 pin front input shaft assembled PLEASE COMPARE YOUR ASSEMBLY CAREFULLY step 11 6920 REAR INPUT SHAFT ASSEMBLY Slide one #3977 or #6906 bearing and one #3911 input shaft spacer onto the #3915 rear input shaft. Install and center one #3919 dowel pin into the input shaft. Slide a #3917 drive cup onto the input shaft. Tighten it down with one #6920 screw. Slide in a #5407 O-ring into the #3917 drive cup. 3911 spacer 3917 drive cup 5407 3915 rear input shaft 3919 pin Slide one #3977 or #6906 bearing and three #3911 input shaft shims onto the #3915 rear input shaft. Install and center a #3919 dowel pin into the input shaft. Slide a #3914 drive pinion onto the end of the input shaft. Make sure the dowel pin aligns perfectly with the slot in the pinion. Add a #3919 small E-clip. 1:1 1:1 3914 drive pinion 3915 rear input shaft 3911 shims 3919 RACER KIT ONLY 3977, qty 2 3/16 x 3/8 bearing, rubber sealed 3919 pin TEAM & F.T. KITS ONLY 6906, qty 2 3/16 x 3/8 bearing, PTFE sealed step 12 REAR INPUT SHAFT ASSEMBLY Slide the #3922 spur gear over the drive cup and align it on the #3917 gear adapter. Tighten down the spur gear with two #6288 screws. 6288 3922 spur gear 6288 assembled PLEASE COMPARE YOUR ASSEMBLY CAREFULLY BAG C TOOLS USED 1/16, 3/32 3910, qty 2 lower transmission case 1:1 6292, 6934*, qty 8 4-40 x 3/8 screw step 13 3910 REMOVE THESE PARTS FOR: Steps 13-15 FRONT TRANSMISSION ASSEMBLY, LOWER HALF Attach the #3910 lower transmission case to the chassis with four #6292 screws. 3910, qty 1 upper transmission case 1:1 6924, 6860*, qty 6 4-40 x 3/8 screw 6591, qty 1 Stealth diff lube 6292, 6934* 6292, 6934* 6292, 6934* 6292, 6934* 9 step 15 step 14 FRONT TRANSMISSION ASSEMBLY Install the diff assembly and front input shaft assembly into the lower transmission case. Add a small amount of #6591 diff lube to the front side of the ring rear and pinion gear. Attach the #3910 upper transmission case to the lower case with six #6924 (6860*) screws. 6924, 6860* 3910 REAR TRANSMISSION ASSEMBLY, LOWER HALF Attach the #3910 lower transmission case to the chassis with four #6292 (6934*) screws. 3910 6591 6292, 6934* 6292, 6934* 6292, 6934* 6292, 6934* BAG C REMOVE THESE PARTS FOR: Steps 16-18 TOOLS USED 1:1 3/32 6924, 6860*, qty 8 4-40 x 3/8 screw 3924, qty 1 driveshaft 3910, qty 1 upper transmission case 3917, qty 1 drive bearing cap 6591, qty 1 Stealth diff lube step 16 REAR TRANSMISSION ASSEMBLY Install the diff assembly into the lower transmission case. Place one end of the #3924 drive shaft into the drive cup on the rear input shaft assembly. Install the opposite end of the drive shaft into the front drive cup. Set the rear input shaft into place. Add a small amount of #6591 diff lube to the front side of the ring gear and pinion 10 rear input shaft 3924 drive shaft drive cup 6591 front side of gear step 17 step 18 DRIVE BEARING CAP Align the #3917 drive bearing cap over the bearing and attach with two #6924 (6860*) screws where shown. REAR TRANSMISSION CASE Attach the #3910 upper transmission case to the lower case with six #6924 (6860*) screws. Do not overtighten the #6924 (6860*) bearing cap screws. 6924, 6860* 3917 6924, 6860* BAG D REMOVE THESE PARTS FOR: Steps 1-4 1:1 6924, 6860* 1:1 1:1 TOOLS USED 1:1 1/16", 3/32" 3858, qty 4 long special ball end, black 6272, qty 4 6924, 6860*, qty 6 7260, qty 8 ball end dust cover 4-40 x 3/8 screw 4-40 plain nut 3881, 3882*, qty 1 front shock tower 7413, qty 4 4-40 x 3/4 screw 3895, 3896*, qty 1 rear shock tower step 1 step 2 FRONT SHOCK TOWER ASSEMBLY Install the two #7413 screws through the outer holes on the #3881 (3882*) front shock tower. Then thread on the #7260 nuts. Attach the #3858 ball ends and #7260 nuts through the lower inner holes on the shock tower. Add a #6272 dust cover to the ball ends. 3881, 3882* 1:1 FRONT SHOCK TOWER ASSEMBLY Attach the #3881 (3882*) front shock tower to the upper transmission case with three #6924 (6860*) screws. 6924, 6860* 3881, 3882* 7413 6272 7260 3858 7413 7260 6272 7260 7260 3858 11 step 3 step 4 REAR SHOCK TOWER ASSEMBLY Install the two #7413 screws through the outer holes on the #3895 (3896*) rear shock tower. Then thread on the #7260 nuts. Attach the #3858 ball ends and #7260 nuts through the lower inner holes on the shock tower. Add a #6272 dust cover to 7413 the ball ends. 6924, 6860* 3895, 3896* REAR SHOCK TOWER ASSEMBLY Attach the #3895 (3896*) rear shock tower to the upper transmission case with three #6924 (6860*) screws. 3895, 3896* 6272 7260 3858 7413 7260 6272 3858 7260 7260 BAG E REMOVE THESE PARTS FOR: Steps 1-4 1:1 7381, qty 4 CVD coupling 1:1 1:1 1:1 3868, 3869*, qty 2 3876, 3877*, qty 2 front block carrier front steering (0° caster block) block 1:1 1:1 1:1 TEAM & F.T. KITS ONLY 6273, qty 2 6906, qty 4 long ball end 3/16 x 3/8 natural color PTFE sealed bearing 3887 or 3888, qty 4 CVD bone 3858, qty 2 long special ball end, black 6588, qty 1 black grease 3886, qty 4 CVD axle 12 6588 3887 or 3888 dogbone 7260 3886 axle 3876, 3877* 7381 set screw 7381 coupling 3965 7368 7369 thread lock RACER KIT ONLY 3977, qty 4 3/16 x 3/8 rubber sealed bearing LONG NATURAL COLOR BALL END. DO NOT USE THE BLACK BALL END HERE!! 1:1 3875, qty 2 4-40 x 11/32 screw with shoulder 3866, qty 2 front outer hinge pin step 2 7381 cross pin 1:1 1:1 step 1 MIP CVD ASSEMBLY Spread some Associated #6588 black grease inside the axle hole where shown, then on the coupling and insert the coupling into the axle. Slide the axle into the dogbone, aligning the cross holes. Insert the cross pin, making sure it is evenly spaced on both sides of the bone. Add the MIP thread lock to the set screw. Angle and turn the CVD so the set screw can be screwed in with the Allen wrench. 5 Repeat steps for the three remaining CVD's. 3965, qty 2 bearing spacer 10 6273 10 6272 1:1 1/16", .050" 7368, qty 2 shim 1:1 1:1 TOOLS USED 1:1 1:1 7260, qty 2 7381, qty 4 6272, qty 2 7369, qty 2 CVD set screw 4-40 plain nut ball end dust cover CVD roll pin 7381, qty 4 CVD cross pin RACER KIT ONLY 3977, qty 4 3/16 x 3/8 rubber sealed bearing 1:1 1:1 3862, qty 2 5-40 set screw gold 1:1 3874, qty 4 block carrier bushings STEERING BLOCK ASSEMBLY Install one #3977 or #6906 bearing on the axle. Slide the axle assembly into the back of the #3876 (3877*) steering block. Slide in a #3965 bearing spacer. Install the second #3977 or #6906 bearing into the steering block and on the axle, followed by one #7368 thin spacer. Insert the #7369 roll pin into the axle. 10 Thread the natural color #6273 ball end into the bottom of the #3876 steering block and add the #7260 plain nut. Add a #6272 dust cover over ball the end. 11 Repeat steps for the right side, installing the steering block ball end in the opposite way: TEAM & F.T. KITS ONLY 6906, qty 4 3/16 x 3/8 PTFE-sealed bearing step 4 step 3 LEFT BLOCK CARRIER ASSEMBLY Break through and push out the 6272 thin webbing in the holes with 3868, your 2mm Allen wrench before 3869* assembly. Insert two #3874 steering block 3858 bushings and steering block assembly into the #3868 (3869*) block carrier as shown. Make sure the CVD dogbone goes through the hole of the block carrier as shown. Align the steering block and block carrier and thread a #3858 long special ball end on top, and a #3875 screw on the bottom. Add a #6272 dust cover 3862 over the ball end. Insert the 3862 5-40 set screw 3875 into the bottom of the block carrier. Do not thread it all the way in. We will tighten it in the next step. 6 Repeat steps for the right side. ATTACH BLOCK CARRIER ASSEMBLY Place the left block carrier assembly between the arm holes. Insert the #3866 front outer hinge pin through the arm holes. Tighten the set screw of step 3, #5, locking the hinge pin in place. DO NOT OVERTIGHTEN! Insert the univeral dogbone into the slots of the outdrive hub. 4 Now install the block carrier for the other side. 3874 3874 3866 BAG E REMOVE THESE PARTS FOR: Steps 5-6 1:1 1:1 1:1 1:1 1:1 TOOLS USED 1/16" RACER KIT ONLY 3977, qty 4 3/16 x 3/8 rubber sealed bearing 7260, qty 2 6272, qty 2 3858, qty 2 F.T. & TEAM KITS 4-40 plain nut ball end dust cover long special 6906, qty 4 ball end, black 3/16 x 3/8 PTFE sealed bearing 1:1 3876, 3977*, qty 2 rear hub carrier 1:1 7369, qty 2 CVD roll pin 1:1 1:1 3862, qty 2 4187, qty 4 5-40 set screw, gold washers, plastic 7368, qty 2 3/16 axle shim 1:1 3866, qty 2 rear outer hinge pin step 5 1:1 3965, qty 2 bearing spacer LEFT REAR HUB CARRIER SHOWN REAR HUB CARRIER ASSEMBLY Break through and push out the thin webbing in the holes of both hub carriers with your 2mm Allen wrench (as shown above). Install one #3977 or #6906 bearing onto the axle. Slide the axle assembly into the back of the #3876 (3877*) rear hub carrier. Slide in the #3965 bearing spacer. Install the second #3977 or #6906 bearing into the hub carrier and onto the axle followed by one #7368 axle shim. Insert the #7369 roll pin into the axle. Thread on the #3858 long special ball end into the front of the hub carrier as shown and add the #7260 plain nut. Add a #6272 dust cover over the ball end. 6 Repeat steps for the right side. See assembly picture at right. 6272 3858 7260 3876, 3877* axle 3965 7368 left hub carriers assembled 7369 Break through and push out the thin webbing in the holes with your 2mm Allen wrench before assembly. RACER KIT ONLY 3977, qty 4 3/16 x 3/8 bearing right 1:1 1:1 TEAM & F.T. KITS ONLY 6906, qty 4 3/16 x 3/8 PTFE-sealed bearing 13 step 6 ATTACH REAR HUB CARRIER ASSEMBLY Place the left hub carrier between the arm holes as shown and add two #4187 spacers where shown. Insert the #3866 rear outer hinge pin through the arm and hub carrier. Thread in the #3862 5-40 set screw into the hub carrier. Tighten down the set screw, locking the hinge pin in place. DO NOT OVERTIGHTEN! Insert the universal dogbone into the slots of the outdrive hub. 4 Now install the hub carrier assembly for the right side. BAG F 3866 4187 4187 4187 LEFT REAR HUB CARRIER SHOWN 3862 4187 1:1 1:1 1:1 1:1 TOOLS USED 1:1 REMOVE THESE PARTS FOR: Steps 1-2 1/16", 3/32" TEAM & F.T. KITS ONLY 1356, qty 6 blue titanium turnbuckle 3879, 3880*, qty 2 rear chassis brace step 1 REAR RACER KIT ONLY 3867, qty 6 steel turnbuckle 6923, qty 4 4-40 x 3/4 screw 6924, 6860*, qty 8 4-40 x 3/8 screw 6274, qty 12 ball cup 3879, 3880*, qty 2 front chassis brace TURNBUCKLE ASSEMBLY 1 Twist the #6274 ball cups onto the #1356 blue titanium turnbuckle or #3867 steel turnbuckle until you get the dimension shown for each part. Assemble all six turnbuckles. 2 Snap all six turnbuckles into place where shown, making sure that all the universal bones are in the slots of the outdrive hubs. 1.72 in 43.7 mm FRONT front camber (2 sets) 6274 6274 1356 or 3867 1.53 in 38.8 mm steering (2 sets) 6274 rear camber link (2 sets) 1.72 in 6274 14 1356 or 3867 43.7 mm 1356 or 3867 6274 6274 step 2 INSTALLING CHASSIS BRACE Mount the #3879 (3880*) left front and left rear chassis braces with two #6924 (6860*) screws and one #6923 screw for each brace as shown. 2 Repeat step for the right side. FRONT 6924, 6860* WHERE TO FIND THE CHASSIS BRACE I.D. Each chassis brace has a molded identification that indicates where it goes on the car, as shown below. 6924, 6860* 6923 3879, 3880* 6924, 6860* 6924, 6860* right front left front REAR 6923 LF 3879, 3880* LR (car shown fully assembled) right rear left rear BAG G REMOVE THESE PARTS FOR: Steps 1-4 8844, 3964*, qty 4 shock shaft 1:1 1:1 5407, qty 8 red O-ring 6299, qty 8 E-clip 1:1 1:1 8456, qty 4 VC foam FACTORY TEAM KIT ONLY 3963*, qty 4 threaded macro shock body blue 6428, qty 4 shock cap RACER KIT ONLY 8458, qty 4 macro shock composite body 7217, qty 4 shock pivot ball TEAM KIT ONLY 8450B, qty 4 macro shock body blue step 1 1:1 1:1 6465, qty 4 shock piston #2 5423, qty 1 7217, qty 4 40 wt shock eyelet silicone oil 6469, qty 4 large O-ring 8456, qty 4 VC bobbin wrong VC FOAM AND BOBBIN Soak the #8456 VC foam with #5423 40wt shock oil and install it onto the #8456 VC bobbin. L OI step 2 right TRIM SHOCK PISTON Burrs on the #6465 shock piston interfere with smooth shock action within the shock body. To remove from tree without creating burrs, twist up, not down. Remove four #2 shock pistons. Remove remaining burrs carefully with a hobby knife. TOOLS USED 5423 8456 foam burr 6464 assembled 8456 bobbin 15 step 3 On the #8844 (3964*) shock shaft, install a #6299 E-clip on both sides of a #6465 (#2) piston from step #1. INTERNAL SHOCK ASSEMBLY (Assemble all four shocks at once.) Install the #6469 O-ring over the threads of the shock body. Slide the VC foam/ bobbin assembly over the #8844 (3964*) shaft and then two #5407 O-rings. Place a couple drops of oil on the O-rings. Insert the assembly into the shock body and pull the shaft through firmly to seat the VC bobbin at the base of the shock bore. Push the #7217 pivot ball and eyelet together. As you hold the shaft with a rag and needlenose pliers next to threads, screw the eyelets onto the end of the shock shaft. 6299 TIP: Use a permanent marker to mark your shocks with an F and R to designate front and rear. 6299 5423 OI L 6469 8844, 3964* 6465 (#2) 7217 pivot ball 8844, 3964* RACER KIT ONLY: 8458 TEAM KIT ONLY: 8450B 5407 FACTORY TEAM KIT: 3963* 7217 eyelet step 4 Holding the shock upright, fill with oil to the top of the body. Refill with oil to the top of the body. Push the shaft up until the piston is level with the top of the body. The oil will bulge up above the shock body. OI OI Slowly move the shaft up and down several times to allow air bubbles to escape to the top. L L Fill The #6428 shock cap about halfway with oil and install onto the body. Try to retain as much oil as possible during assembly. The shaft will extend out as you tighten the cap down. OI L 6428 9 If the shock rebounds too fast, or you cannot push the shaft in until the eyelet hits the body, there is too much oil. Loosen the cap about a full turn and pump out a small amount of oil by pushing the shaft in. Retighten the cap and try steps 6-7 again. Too much oil in the shock will result in leakage. TOOLS USED 1:1 3/32" 6925, qty 4 4-40 x 1/2 screw 16 1:1 1:1 REMOVE THESE PARTS FOR: Steps 5-8 If the shock does not push out this far there is not enough oil in it. Add just a little oil and try steps 6-7 again. L BAG G Then the shaft should push itself out to its full length very slowly. OI SETTING THE REBOUND Move the shock shaft in and out a few times an then push it all the way in. It should be easy to push the shaft in until the eyelet hits the body 6473, qty 4 shock bushing 8846, spring preload spacer qty 4 ea. 1/8" qty 2 ea. 1/16" 6475, qty 4 spring collar 6475, qty 4 spring cup 6472, qty 4 shock nut, small FACTORY TEAM ONLY 3963*, qty 4 collar O-ring 3944, qty 2 spring, gold, front 3942, qty 2 spring, silver, rear FACTORY TEAM ONLY 3963*, qty 4 shock collar Use one drop of oil on the O-ring before you thread on the shock collar. Slide one black O-ring into the groove in the threaded shock collar. FACTORY TEAM ONLY, STEP 5 Thread on the shock collar. Make sure that the shoulder is facing down when threaded on the body. OI L step 5 shoulder faces down step 6 step 7 FINAL SHOCK ASSEMBLY Slide the 1/8" #8846 preload spacer onto the body of the two front shocks. Slide the 1/8" and 1/16" preload spacers onto the rear shocks. Slide on the #6475 spring collar, then #3944 gold spring on the front shocks, and #3942 silver spring on the rear shocks. Compress the spring to add the #6475 spring cup. step 8 FRONT SHOCK MOUNTING Add the #6473 shock bushing to the shock tower. Push the shock cap over the bushing and add the #6472 nut. Do not overtighten or the shock will bind. Fasten the lower shock into the arm with the #6925 screw. 4 Do the other front shock. REAR SHOCK MOUNTING Add the #6473 shock bushing to the rear shock tower. Push the shock cap over the bushing and add the #6472 nut. Do not overtighten or the shock will bind. Fasten the lower shock into the arm with the #6925 screw. 4 Do the other rear shock. 6473 FRONT: 1/8" REAR: 1/8" and 1/16" 6473 8846 6472 6472 6475 6475 NOT USED IN FACTORY TEAM KITS ON THREADED SHOCK BODIES 6925 6925 FRONT: 3944 gold REAR: 3942 silver See page 25 to set ride height for your kit. BAG H 1:1 REMOVE THESE PARTS FOR: Steps 1-6 3858, qty 1 short special ball end, black 1:1 7337, qty 4 steel washer 1:1 3934, qty 2 4449, qty 2 3mm motor screw 4-40 locknut 1:1 1:1 RACER & TEAM 6917, qty 4 4-40 x 3/8 screw 1:1 6928, qty 1 4-40 x 1 screw TOOLS USED 1:1 1/16" 5/64" 3/32" 6916, qty 2 4-40 x 1/2 screw with hole 1:1 7673, 6934*, qty 2 4-40 x 5/16 screw 6272, qty 4 3848 qty 1 ball end dust cover foam spacer 1:1 F.T. & TEAM KIT ONLY 1356, qty 1 blue titanium turnbuckle 1:1 3930, 3932*, qty 1 motor cam 3931, 3933*, qty 1 motor clamp (with heatsink) 9180, qty 4 servo horn 7336, offset spacer qty 2, thin qty 2, thick 1:1 RACER KIT ONLY 3867, qty 1 steel turnbuckle 6332, qty 3 battery clip 3853, 3974*, qty 1 battery brace 6727, qty 1 servo tape 3902, qty 1 transponder mount 1:1 1:1 3929, qty 1 4-40 x 1.25 screw 3929, qty 1 motor clamp spring 6338, qty 1 antenna tube and cap 7336, qty 2 servo mount F.T.KIT ONLY 6860*, qty 4 4-40 x 3/8 screw blue aluminum F.T. KIT ONLY 3968*, qty 1 counterfeit transponder F.T. KIT ONLY 3927*, qty 1 clip-on radial heatsink 17 step 1 ADD MOUNTS TO THE SERVO Find the appropriate #9180 servo horn for your servo from the chart at right. Install the #3858 ball end into the servo horn. Add the #6272 dust cover. Remove the servo horn from your servo and replace it with the #9180 horn that you selected, then fasten with the stock mounting screw that came with your servo in the position shown below. DO NOT POINT IT STRAIGHT UP! See drawing for correct dimension. Find the appropriate #7336 offset spacer for your servo from the chart at right. Attach the spacer, if any, in between the #7336 mount and the servo with the #7337 washers and #6917 (6860*) screws. 6272 7336 servo mount SERVO TYPE SPACER Airtronics 94102 no spacer A Airtronics 94155, 94156, 94157, 94158, 94257, 94258, 94737, 94738, 94741, 94452 thick spacer A Futaba S3003, S9404, S9402, S9303, S3401, S9101, S9202 no spacer F Hitec S-300, HS-303, HS-525BB, HS-545BB, HS-422, HS-425, HS-605BB, HS-615MG, HS-925MG, HS-945MG 3858 no spacer SERVO ARM H 7337 6917, 6860* 6917, 6860* 6917, 6860* 9180 7336 offset spacer trim edges so servo will fit no spacer J JR Z250, Z550, Z2750 thin spacer J no spacer J KO PS-1012 FET, PS-2000 FET, PS-2001 FET, PS-2004 FET, PS-2015 FET 7337 6917, 6860* 1/16" (1.5mm) JR Z8450, Z8550, NES-4721, NES-4735, Z4750 See page 19, Radio Adjustments, for more info on correctly setting steering linkage. little On Futaba servo S3003 and on all KO servos you will need to trim a off the sides of the servo ears. We have not tested any servos that were released after mid-1999. trim edges so servo will fit 1.56 in step 2 6274 39.6 mm See page 19, Radio Adjustments, for more info on correctly setting steering linkage. 1356 or 3867 6274 MOUNT THE SERVO Mount the servo to the chassis with two #7673 (6934*) screws. Twist #6274 ball cups onto #1356 blue turnbuckle or #3867 steel turnbuckle until you get the dimension shown. Use needle-nose pliers to attach the link to the ball ends. 7673, 6934* step 3 INSTALL YOUR MOTOR Attach the #3930 (3932*) motor cam to the optional motor with two #3934 button head motor screws. Install the optional pinion gear of your choice. (Refer to the gearing chart on page 19.) Install the two #4449 locknuts to the underside of the chassis. These fit tight, so be sure to put them in straight and all the way in. Slide the motor and cam down into the groove of the chassis. 18 Motor not included in kit. Pinion gear not included in kit. 6928 3929 3930, 3932* 3929 3934 3931, 3933* the screw and spring. Now tighten the screw 2 to 3 turns. No more. It is normal to have an approximately .040"-.050" (1 to 1.2mm) gap remain between the clamp and the bulkhead, as shown. About .220"-.250" (5.5-6.5mm) when correctly tightened 3934 Screw down the #6928 inner screw first until the #3931 (3932*) motor clamp just touches the chassis bulkhead. 6 Set your gear mesh. Slide the #3929 spring onto the #3929 screw and thread in only until there is no free play between No gap 4449 4449 Small gap, .040-.050" (1-1.2mm) step 4 step 5 RADIO AND RECEIVER INSTALLATION Cut a piece of #6727 servo tape and use it to attach your optional ESC and switch where shown. Cut a piece of #6727 servo tape and use it to attach your optional receiver where shown. 3 Connect the ESC and steering servo to your receiver according to your radio or ESC instructions. Then connect the motor to your ESC. Push your receiver wire through the built-in antenna mount. Slide the wire through the #6338 antenna and push the antenna firmly into the chassis antenna mount hole. Cap the other end of the antenna tube and wire with the black rubber cap. FACTORY TEAM KITS ONLY: Push the #3927* radial heatsink onto the motor. 3927* 6338 3968* 6332 TRANSPONDER MOUNT If needed, remove the transponder mount and cut away all the areas shown in gray as shown in illustration. Attach the mount to the servo where shown with servo tape. FACTORY TEAM KIT ONLY: Push the #3968* counterfeit transponder peg up through the hole in the mount and slide a #6332 body clip through the small hole on top of the mount. switch 6338 receiver 3902 cut out gray areas ESC attach mount here step 6 6916 BATTERY INSTALLATION Install your battery pack. See which figure, at left or right, best represents your battery orientation. Thread on the two #6916 screws. Aim the body clip hole across the chassis. Add the #3848 foam spacer. Add the #3853 (3974*) battery hold down strap, orienting it up or down according to your battery pack design. Adjust the screws so the batteries are held tight, but you are still able to push the #6332 body clips through the screws. 6332 3853, 3974* 6332 6916 3848 BAG I 1:1 REMOVE THESE PARTS FOR: Steps 1-2 6332, qty 8 body clip 7874, 7873*, qty 2 4-40 x 7/16 screw 3852, qty 1 foam bumper 8874, qty 2 rear body post 1:1 6922, qty 2 4-40 x 1/2 screw 3897, qty 4 pivoting body mount 8818, qty 2 front body post TOOLS USED 1/16" 6916 6332 6332 3853, 3974* 6916 3848 step 1 8818 8818 FRONT BODY POSTS Attach each #8818 front body post to the front bumper with one #6922 screw. 6922 6922 19 step 2 REAR BODY POSTS Place the rear #8874 body post to the front side of the rear shock tower. Align the tab and hole and attach it with a #7874 (7873*) screw. Slide the #3897 pivoting body mount over the body post so its holes line up with the fifth hole from the top. (Adjust for proper hole later when you fit your body.) Slide the #6332 body clip into the body post and pivoting body mount. (You'll add another body clip after you install your body.) 8 Repeat on the other rear body post. 3897 FOAM BUMPER Place the #3852 foam bumper over the front body posts. (You will trim it later to fit your body.) Slide the #3897 pivoting body mount over the body post so its holes line up with the fourth hole from the top. (Adjust for proper hole later when you fit your body.) Slide the #6332 body clip into the body post and pivoting body mount. (You'll add another body clip after you 4 install your body.) Do both front posts. 6332 3897 Line up the pivoting body mount with the post holes 7874, 7873* 8874 3852 (after trimming) 6332 BAG J TOOLS USED REMOVE THESE PARTS FOR: Steps 1-2 6943, qty 4 8-32 locknut 3950, 3972*, qty 4 wheel hex adator 3951, qty 4 TC3 wheel 3955, qty 4 foam wheel insert 3955, qty 4 TC3 tire step 1 step 2 TIRE ASSSEMBLY Make a 1/8" hole in the #3951 TC3 wheel. Insert the #3955 foam insert into the #3955 tire. Make sure the insert is centered in the tire. Install the #3955 tire and insert onto the #3951 wheel. Glue the tire to the wheel with super glue (cyanoacrylic glue #1597 Tire Adhesive) in four equally-spaced spots around the tire on both sides. WARNING! Follow the adhesive manufacturer's instructions for proper use and safety. Wear eye and hand protection. TIP: Place a rubber band around the tire to hold it tight to the wheel while gluing. 5 Repeat steps for the three remaining tires. MOUNT TIRES Install the #3950 (3972*) wheel hex adaptor to the axle, lining up the roll pin with the slot in the hex adapter. Slide the wheels over the axle and tighten it down with a #6943 lock nut. 3 Install the remaining tires. 3951 3955 3955 3950, 3972* 6943 Wheels and tires are not included in Factory Team kits. 20 TOOLS USED REMOVE THESE PARTS FOR: Steps 1-4 8828*, qty 4 8828*, qty 4 open cup closed cup 8828*, qty 4 3960*, qty 2 5/16" set screw anti-roll bar WHAT ARE ANTI-ROLL BARS? Anti-roll bars (also known as sway bars) are used to stabilize a car from excessive chassis roll (which occurs when your car leans outward through the turns by centrifugal force). Anti-roll bars are generally used on smooth, high traction track conditions. If the conditions are very bumpy, then anti-roll bars are probably not necessary. step 1 ROLL BAR LINKS Thread one #8828 open cup and one closed cup onto each 5/16" set screw to the dimension shown at right. 8830*, qty 4 6951*, qty 4 pivot set screw 9146*, qty 4 screw WHEN ARE ANTI-ROLL BARS NEEDED? If you are driving on a high traction surface and your car wants to oversteer, then use the bar on the front only. This will decrease the front chassis roll and decrease steering through the corner. This has the feeling of increasing rear traction. If your car is understeering, then try the anti-roll bar kit on the rear only. The rear anti-roll bar will decrease rear traction. This has the feeling of increasing steering. 8828 open cup 8828 open cup 8828 5/16" set screw 8828 5/16" set screw 1.01 or 25.6mm) 8828 closed cup 8828 closed cup step 2 8830 8830 ADD PIVOTS Place the aluminum #8830 anti-roll bar pivots over the ends of the anti-roll bar according to the dimension shown, and tighten down with the #6951 set screw. 1 3/8" (1.38 or 35mm) 6951 6951 Bar shown right side up step 3 Place the anti-roll bar into the grooves of the lower transmission case and secure using two #9146 2-56 x 3/16" screws. Do not overtighten; the roll bar should move up and down freely. Front Rear step 4 Attach the open cup side of the linkages to the antiroll bar. Make sure your car is ready to run without the body installed. Drop your car from about 2" high onto a flat surface. Without moving the suspension, adjust the link so it aligns with the balls exactly, then snap it onto the balls with your needle nose pliers. This ensures that the anti-roll bar is not under tension when your vehicle is at ride height. Front Rear 21 FINAL ADJUSTMENTS FINISHING THE BODY Before you start to mask and paint the inside of your TC3’s body, wash it out with soap and water to remove any mold release residue or dirt that may show up in your paint. 1. Mark the body post holes and rear wheel cutout Make these adjustments before racing with a marker on the outside of the body. 2. Each body comes with pre-cut self-adhesive window masks for your convenience. 3. Be sure to use a paint that is specifically formulated to adhere to Lexan. Spray several thin coats (instead of one thick coat) to avoid runs. If possible, spray your darker colors first. 4. After painting, trim the wheel wells with curved scissors or a sharp hobby knife. 5. Trim out the rear wing and mount it to the body with the supplied 4-40 button head screws and nylon nuts. 6. Finish by applying decals. RADIO ADJUSTMENTS Use the following steps to make the final adjustments on your car. 1. Turn the transmitter on. 2. Make sure the motor is disconnected. 3. Connect your battery pack. 4. Turn the power switch on. 5. Move the steering control on the transmitter to the right and left. Do the wheels move in the correct direction? If not, you must reverse the steering servo direction on your transmitter (see radio manual.) 6. Look at the servo horn mounted on the servo. It should lean toward the centerline of the chassis about 1/8” (3mm). 7. Adjust the servo turnbuckle so that the steering rack arm is EXACTLY in the center of the car. 8. Using the two steering turnbuckles, adjust the front wheels so they are pointed straight ahead. 9. Adjust the ESC (electronic speed control) according to the speed control manufacturer’s instructions. Note: Some manufacturers have the motor connected during adjustment and some do not. Now turn the power switch off. 10. Connect the motor. Place your car on a block or car stand so that all four wheels cannot touch anything. Turn the power switch on again. Check the ESC and steering settings you have made and then turn the power switch back off. 10. Remember this! The transmitter is always the FIRST TO BE TURNED ON and THE LAST TURNED OFF. CONGRATULATIONS!YOUR CAR IS NOW READY TO RUN! MOTOR GEARING To get the most from your motor, proper gearing is important. The gear ratios listed in the chart are recommended starting gear ratios. Ratios can vary from track to track, but you should not change the pinion size more than one tooth from the recommended ratio. CAUTION! Increasing the pinion size by more than one tooth can damage your motor from excess heat. MAINTENANCE MOTOR 24° ROAR stock motor 36° stock motor 16 turn modified motor 15 turn modified motor 14 turn modified motor 13 turn modified motor 12 turn modified motor 11 turn modified motor 10 turn modified motor 9 turn modified motor PINION 28 26 26 25 24 23 22 21 20 19 FINAL SPUR DRIVE RATIO 72 2.5:1 72 2.5:1 72 2.5:1 72 2.5:1 72 2.5:1 72 2.5:1 72 2.5:1 72 2.5:1 72 2.5:1 72 2.5:1 OVERALL RATIO 6.43 6.92 6.92 7.2 7.5 7.83 8.18 8.57 9.00 9.47 Follow these steps to keep your car in shape for racing CHECK FOR FIT You should periodically check all the moving parts: front and rear end, suspension arms, steering blocks, steering linkage, shocks, and so on. If any of these should get dirty or bind then your car’s performance will suffer. MOTOR MAINTENANCE Between runs, inspect the brushes to ensure they are moving freely in the brush holder. This is done by 22 carefully removing the spring and sliding the brush in and out of the holder. If there is any resistance or rough spots, remove the brush and carefully wipe the brush clean. This will clean off any buildup and lubricate the brush so it slides smoothly in the brush holder. After every 3 to 5 runs, remove the brushes from the holders and inspect the tips for wear and/or burning. If there is a noticeable amount of wear, replace the brush with a new pair. If the tip is a burnt blue color, then the lubricant in the brush has been burned away and new brushes should be installed. After every other battery charge you should carefully clean the motor. One recommended method is to spray motor cleaner directly on the brush and commutator area. Run the motor for approximately 15 seconds. Disconnect the motor and spray it again, making sure the runoff is clear and clean. If the runoff is still dirty, repeat the spraying action until clean. After completing the cleaning, apply a small amount of lightweight oil to each bushing or bearing for lubrication. Be careful not to apply too much oil, for this will pick up dirt and contaminate the commutator and brushes. DIFFERENTIAL MAINTENANCE You should rebuild the differentials when the action gets somewhat “gritty” feeling. Usually cleaning the diff parts and applying new lube per the instructions will bring it back to new condition again. The standard 3/32” carbide balls rarely need replacing. Normally, as the parts seat, the diff will get smoother. If the diff still feels gritty after carefully cleaning and re-lubing the diff parts, the thrust balls, thrust washers, and drive rings should be checked and possibly replaced. TUNING & SETUP TIPS The parts will normally wear out in the following order: 1. #6575 5/64” diff thrust balls (qty 6). 2. #6573 diff thrust washers (2). 3. #3906 D-drive rings (2). Refer to the differential section to correctly assemble the diff. These tips prepare your car for maximum performance Your car is one of the most tunable on road cars on the market. This section will try to explain the parts and adjustments you can use to tune your car for different track conditions. Positive caster means the kingpin leans rearward at the top. FRONT CASTER describes the angle of the kingpin from vertical when looked at from the side of the car. Positive caster means the kingpin leans rearward at the top. Negative caster should never be used. 0° block carrier, #3868 2° block carrier, #3870 4° block carrier, #3872 KICKUP refers to the angle at which the front suspension is mounted in EFFECTS OF ARM MOUNT/BLOCK CARRIER COMBINATIONS relation to horizontal when looked from the side of the car. Kickup is adjusted by changing the suspension arm mounts, which have molded codes to help you tell them apart. The two front arm mount combinations are as follows: RECOMMENDED ARM MOUNT/BLOCK CARRIER COMBINATIONS FOR THIS SETUP: USE THESE PARTS: Arm Mounts Block Carrier A 2° 2° 0° 0° 0° kickup, kickup, kickup, kickup, kickup, A B 2° 4° 0° 2° 4° caster caster caster caster caster F F F F F B F+2 F+2 F-0 F-0 F-0 The kit setting of 2° kickup will work best in most conditions, especially in bumpy conditions. 1 FRONT C 0° 2° 0° 2° 4° C F F+2 A B 0° kickup will have a more aggressive steering feeling but will not absorb bumps as well as 2°. 2 ARM MOUNT PART NUMBERS Associated makes block carriers for the TC3 with 0° (kit standard), 2°, and 4° of caster. Increasing caster in the TC3 (with 2° or 4° block carriers) will give your car more steering entering corners but less steering exiting corners. It will also be more stable in bumpy conditions. Note: When figuring total caster in your car, add the amount in the block carrier to the amount of kickup. Example: 2° of kickup (kit standard) and 0° block carrier equals total of 2° of caster. F F-0 A B BLOCK CARRIER PART NUMBERS A code F F+2 F-0 effect +2° kickup 0° kickup part # #3863 (std) #3863 (std) #3864 (optional) B effect 0° caster 2° caster 4° caster part # #3868 (std) #3870 (optional) #3872 (optional) C FRONT TOE-IN AND TOE-OUT is adjusted by turning the steering turnbuckles. Toe-in will make your car easier to drive by improving stability during acceleration. Toe-out will increase steering when entering corners but will be slightly more difficult to drive. We suggest using 0° to 1° toe-out on the TC3. Toe-in: Easier to drive. Improves stability during acceleration. Toe-out: Harder to drive. Increases steering entering corners. 23 REAR ANTI-SQUAT describes the angle at which the rear suspension is mounted in relation to horizontal when looked at from the side of the car. The TC3 comes standard with 2° of rear anti-squat. This provides good rear traction. Installing the #3864 (R3+0) rear arm mount reduces anti-squat to 0° and will reduce rear traction. However, it will improve acceleration in bumpy conditions and increase steering slightly. code R R+3+2 R+3+0 R+2+0 R+2+2 REAR ARM MOUNT INFORMATION effect part # #3863 (std) 3° toe-in & 2° anti-squat #3863 (std) 3° toe-in & 0° anti-squat #3864 (optional) 2° toe-in & 0° anti-squat #3864 (optional) 2° toe-in & 2° anti-squat #3864 (optional) FRONT 2° of anti-squat is kit standard. 0° anti-squat will reduce rear traction, but improve steering slightly. REARTOE-IN is adjusted by changing the rear WHEELBASE ADJUSTMENT can be arm mounts. The TC3 comes standard with 3° of toein on each side. This setting should work best in any condition. However, if less toe-in is desired, install the #3864 (R+2+2) or #3864 (R+2+0) rear arm mounts. These mounts have 2° of toe-in and will decrease rear traction and add steering. (See rear antisquat details above for more info on the mounts.) made to the TC3 by moving the two #4187 1/32” plastic spacers on the outer rear hinge pins (next to the hub carrier). Moving the spacers to the front of the hub carrier will lengthen the wheelbase and decrease rear traction. Moving the spacers to the rear of the hub carrier will shorten the wheelbase and increase rear traction. FRONT Spacers to rear shorten your wheelbase. RIDE HEIGHT describes the height of the chassis in relation to the surface it is sitting on. This adjustment must be made with the chassis ready-torun but with no body. The #8846 shock preload spacers are used for raising and lowering the ride height. We suggest starting with about 1/4” (6.0mm) clearance between the chassis and ground. Try using a slightly lower right height for high traction conditions such as carpet racing. Do not use a ride height lower than 5/32” (4mm). For more tips on setting ride height, see next page. Spacers to front lengthen your wheelbase. Adjust preload spacers to change your ride height. Ideal ride height is between 1/4” (6.3mm) and 5/32” (4mm). CAMBER LINK LOCATIONS on the TC3 have been thoroughly tested to find the best all around positions. We suggest using the standard setting for all conditions. However, if you must make adjustments, the following guidelines should help you: The longer or higher the link, the more traction and less stability. The shorter or lower the link, the less traction and greater stability. Camber link possibilities for the rear tower and hub carrier. Standard setup shown. ACKERMAN is a term describing the effect of the inside front wheel turning tighter than the outside front wheel. The standard setup works best in most conditions and is preferred by most of our Team drivers. By adding two .100” (2.5mm) spacers and the longer #3858 ball ends to the steering rack, a more aggressive steering feeling can be achieved. This is because there will be less ackerman. CAMBER describes the angle the wheels ride relative to the ground when looked at from the front or back. Negative camber means that the tire leans inward at the top. Positive camber means just the opposite, and should not be used. 24 Standard ackerman. For a neutral steering feeling. Camber link possibilities for the front tower. Standard setup shown. Optional ackerman. For a more aggressive steering feeling. #3858 black long ball end used #3858 black #3855 short ball end used We suggest using 2° of negative camber to start with. For tips on setting camber, see next page. Negative camber means that the tire leans inward at the top. Change camber by turning the camber link. SETTING CAMBER 1° negative camber 2° (recommended) Setting camber is one of the tuning options that the TC3 offers. To set the camber we recommend using a camber gauge, 3x5” card or just a square piece of cardboard. When adjusting camber you need to have the car ready to run with no body. 1. Set the car on a flat surface. 2. Take your 3x5 card and push it against the tire as shown in fig. 1. 3. Use your supplied molded turnbuckle wrench to adjust the camber link to 1°, 2° or 3° by either eyeball the gap between the card and the top of the tire (fig. 2), or place a ruler across the top of the tires and measure from the card to the tire. (If you really want to know exact figures, 1° produces a .045” (1.1mm) gap, 2° produces a .088” (2.2mm) gap, and 3° produces a .130” (3.3mm) gap. But it’s hard to measure!) We recommend using 2° of negative camber. On high traction tracks 2° to 3° negative camber would be used, 1° to 2° would be used in low traction conditions. We don’t recommend using positive camber under any circumstances. 3° negative camber Fig. 1 Fig. 2 Push a 3x5 card against the tire. Arrow is pointing to the negative camber gap at the top. SETTING RIDE HEIGHT Setting the ride height is another adjustment of the TC3. The ride height is easily adjusted by the #8846 shock preload spacers, shown in fig. 1, used for the non-threaded shocks. The suggested preload for the TC3 is one 1/8” preload for the front shocks and one 1/8” and one 1/16” spacers for the rear shocks. (See page 17, step 6 for more about the preload spacers.) These preload spacers set the ride height at ¼” (6.0mm). The Factory Team Kit shocks are adjusted by the collar on the bodies, shown in fig. 2A. The spacing between the collars on the threaded shocks is 7/64” (2.78mm) for the front shocks (fig. 2B). The spacing for the rear shocks is 9/64” (3.58mm) (fig. 2C). This also sets the ride height at ¼” (6.0mm). For adjusting the ride height we recommend using Associated ride height gauge #1450 (fig. 3). The ride height gauge is stepped every ½mm and every every 1mm step is numbered. 1. When adjusting the ride height you need to have Eyeball or measure the gap for camber. We recommend 2° negative camber to start with. the car ready to run with no body. 2. Set the car on a flat surface. 3. Slide the ride height gauge underneath the chassis, as shown in fig. 4A, until the gauge just touches the chassis. To get a measurement on the chassis and not the bumper, you might need to slide the gauge in the corner of the car as shown in fig. 4A. Check both corners of the front. 4. Slide the gauge underneath the back of the car. Check both corners of the rear (fig. 4B). Fig. 1 Fig. 2A Fig. 2B, front Fig. 2C, rear Shock pre-load spacer inserted on non-threaded shock. Adjusting collar on threaded shock. Front shock spacing: 7/64” (2.78mm) Rear shock spacing: 9/64” (3.58mm) Fig. 3 Measure your ride height quickly and easily with Associated’s Ride Height Gauge #1450 (not included in kits). Fig. 4A, front Fig. 4B, rear Slide your Ride Height Gauge under the chassis so you don’t measure the bumper. Slide your Ride Height Gauge under the chassis so you don’t measure the bumper. 25 SHOCKTRAVEL can be adjusted on the TC3 SHOCK SPRINGS try to keep your car level to help speed up or slow down how fast the car changes direction when cornering. The TC3 standard setup is setting 6 on your droop gauge in the front and 4 on the rear. This setup will work best in almost any condition. If your track is bumpy, you may want to add droop to your car by going to a lower droop gauge step. If your track has very high traction, such as occurs with carpet, then you may want to take droop out of your car by going higher on the droop gauge. Too little droop will cause a loss of traction. during acceleration, deceleration, and cornering. Stiffer springs will help your suspension respond more quickly, but because of their stiffness will not absorb bumps as well. Use stiffer springs in high traction conditions such as carpet racing. Softer springs are best for slippery or bumpy conditions. ANTI-ROLL BARS are used to stabilize a higher traction less droop droop gauge more bumps more droop car from excessive chassis roll (which occurs when your car leans through the turns by centrifugal force). Anti-roll bars are generally used on smooth, high traction track conditions. If the conditions are very bumpy, then anti-roll bars are probably not necessary. If you are driving on a high traction surface and your car wants to oversteer, then use the optional #3960 anti-roll bar kit on the front only. This will decrease the front chassis roll and decrease steering throughout the corner. This has the feeling of increasing rear traction. #3941 #3942 #3943 #3944 #3945 #3946 #3952 #3953 #3954 Green Silver Blue Gold Red Copper Purple Yellow White 12 lbs/in softer 14.5 lbs/in (std rear) 17 lbs/in 19.5 lbs/in (std front) 22 lbs/in 25 lbs/in 30 lbs/in 35 lbs/in 40 lbs/in stiffer If your car is understeering, then try the optional #3960 anti-roll bar kit on the rear only. The rear antiroll bar will decrease rear chassis roll and decrease rear traction (this has the feeling of increasing steering). Antiroll bar (sway bar) kit #3960. BATTERY PLACEMENT in the TC3 al- TIRES & INSERTS are two of the most in- STANDARD SETTINGS of the TC3 are lows you to slide your batteries forward or back to change the handling characteristics of your car. There are many combinations, but here are three we suggest trying. presented below. FRONT Foam spacers fluential changes you can make to your car. The TC3 comes standard with Pro-Line S-2 compound V-Rage tires. This is a good traction, long-wearing tire for all around use. If you would like more traction, try the Pro-Line #1091 S-3 compound tires with Pro-Line tire inserts. For racing conditions, try the Pro-Line #1089S2 S-2 slicks or #1089S3 S-3 racing slicks. These optional tires are available from Pro-Line. SETUP SHEET for the TC3 is included. Set Batteries to rear: More traction. Less steering. Foam spacers Batteries to front: Less traction. More steering. Foam spacers 26 Batteries separated: Slightly more steering than full rear. Slightly less rear traction than full front. Easy to drive. up your TC3 with the standard settings at right, then deviate from them in response to your track conditions and driving style, as noted below. Tips for beginners: For best results, make only one setup change at a time, testing it before making another change. Make a copy of the setup sheet included in this manual to help keep track of your changes. Before you make any changes to the standard settings, make sure you can get around the track without crashing. None of your setup changes will work if you cannot stay on the track. Your goal is consistent lap times. Inconsistent lap times may indicate poor control. When you have consistent lap times, then make changes to your car. If the change results in a faster lap, then mark the change in your setup sheet. If performance is worse, then revert back to the previous setup and try another change. Fill out your setup sheet thoroughly when you are satisfied with it and file it away. It can be a practical guide for future track layouts and conditions you encounter. 1. Front camber: -2°. 2. Front camber link: inside lower hole on tower. 3. Front block carrier: 0°. 4. Front toe: 0° to 1° toe-out. 5. Front ride height: 1/4” (6.3mm). 6. Kickup: +2°. 7. Bump steer spacers: none. 8. Ackerman: #3858 ball ends, no spacers. 9. Front anti-roll bar: none. 10. Rear camber: 1° to 2° negative. 11. Rear camber link: tower: inside lower hole. Hub carrier: outside hole. 12. Rear toe-in: 3°. 13. Rear ride height: 1/4” (6.3mm). 14. Rear Anti-squat: 2°. 15. Rear anti-roll bar: none. 16. Driveshafts: MIP CVD’s. 17. Wheelbase: hub carriers centered. 18. Shock body: macro shock. 19. Shock oil: front, 40wt. Rear, 40wt. 20. Shock shaft: front, #8844. Rear, #8844. 21. Shock pistons: front, #2. Rear, #2. 22. Shock springs: front, Gold. Rear, Silver. 23. Shock limiters: front, 4. Rear, 2. 24. Shock mounting, front tower, outside hole. 25. Shock mounting, rear tower, outside hole. 26. Batteries: 6-cell. 27. Battery placement: rear. 28. Motor: varies. 29. Speed control: varies. 30. Radio: varies. 31. One way, front diff: none. 32. Tires, front: Pro-Line V-Rage S-2 compound. 33. Tires, rear: Pro-Line V-Rage S-2 compound. 34. Tire additive: none. 35. Inserts: incl. with tires. 36. Wheels: Pro-Line. 37 Spur gear: 72 (from Kimbrough) 38. Pinion gear: varies. 39. Lead weights: none. 40. Chassis: Composite. 41. Body: varies. 42. Wing: varies with body. RECOMMENDED SETTINGS Use these settings to start off with BUMPY TRACK SETTING CARPET WITH FOAM TIRES Front Suspension: 1. Block carriers: 0° 2. Kickup: 2° 3. Toe-in: 0° 4. Toe-out: 0° 5. Camber: -1.5° 6. Ride height: 6mm 7. Anti-roll bar: none 8. Ackerman setting: std 9. Shock bodies: VCS 10. Shock piston: #2 11. Shock oil: 30wt 12. Spring: silver 13. Droop setting: 5 14. Camber link postion: std 15. Shock mounting: middle hole Front Suspension: 1. Block carriers: 4° 2. Kickup: 2° 3. Toe-in: 0° 4. Toe-out: 0° 5. Camber: -1.5° 6. Ride height: 4mm 7. Anti-roll bar: std 8. Ackerman setting: std 9. Shock bodies: VCS 10. Shock piston: #2 11. Shock oil: 70wt 12. Spring: white 13. Droop setting: 6 14. Camber link postion: std 15. Shock mounting: middle hole 16. Tires: Jaco orange purple Rear Suspension: 1. Toe-in: 2° 2. Anti-squat: 2° 3. Camber: -1.5° 4. Wheelbase: middle 5. Ride height: 6mm 6. Anti-roll bar: none 7. Shock bodies: VCS 8. Shock piston: #2 9. Shock oil: 25wt 10. Spring: green 11. Droop setting: 3 12. Camber link postion Tower: std Hub: std 13. Shock mounting: middle hole General: 1. Battery postion: rear 2. One-way or Diff: diff 3. Drive shafts: alum CVD’s 4. Body: varies 5. Spur: 72 Rear Suspension: 1. Toe-in: 3° 2. Anti-squat: ° 3. Camber: -2° 4. Wheelbase: middle 5. Ride height: 4mm 6. Anti-roll bar: std 7. Shock bodies: VCS 8. Shock piston: #2 9. Shock oil: 50wt 10. Spring: red 11. Droop setting: 4 12. Camber link postion: Tower: upper inner hoe Hub: std 13. Shock mounting- middle hole 14. Tires: Jaco purple General: 1. Battery postion: rear 2. One-way or Diff: diff 3. Drive shafts: alum CVD’s 4. Body: varies 5. Spur: 72 ONE-WAY FRONT DIFF (Worlds 2000) Front Suspension: 1. Block carriers: 4° 2. Kickup: 2° 3. Toe-in: 0° 4. Toe-out: 0° 5. Camber: -2° 6. Ride height: 4.5mm 7. Anti-roll bar: std 8. Ackerman setting: std 9. Shock bodies: VCS 10. Shock piston: #2 11. Shock oil: 40wt 12. Spring: gold 13. Droop setting: 5.5 14. Camber link postion: upper inner hole 15. Shock mounting: inner hole Rear Suspension: 1. Toe-in: 3° 2. Anti-squat: 0° 3. Camber: -2° 4. Wheelbase: middle 5. Ride height: 4.5mm 6. Anti-roll bar: std 7. Shock bodies: VCS 8. Shock piston: #2 9. Shock oil: 30wt 10. Spring: silver 11. Droop setting: 4 12. Camber link postion: Tower: upper inner hole Hub: std 13. Shock mounting: inner hole General: 1. Battery postion: rear 2. One-way or Diff: one-way 3. Drive shafts: alum CVD’s 4. Body: varies 27 Driver: ________________________________________ Track/City: _____________________________________ 5 - 6 7 2 5 0 - - 6 Team Associated RC10TC3 4WD Touring Car Event: ___________________________ Date: ________ FRONT SUSPENSION FRONT SHOCKS CASTER 0° 2° 4° ANTI-ROLL BAR: KICKUP 0° 2° -2° BODY Size: ______ SHAFT ACKERMAN SETTING Std Other: Ball end: ___________ Spacer: ____________ TOE-IN _____° TOE-OUT _____° CAMBER _____° None Std Alum. Other: ____________________ LIMITERS: Inside: ________ Outside: _______ BUMP STEER ________ RIDE HEIGHT Composite SHOCK MOUNT & CAMBER LINK Fill in holes used DROOP GAUGE #: ____ PISTON # ___ OIL _____ WT SPRING ___________ REAR SUSPENSION ANTI-SQUAT REAR SHOCKS 0° 2° ANTI-ROLL BAR: TOE-IN 3° RIDE HEIGHT None BODY Size: _____ Other: ______ SHAFT CAMBER: ______° Composite Std Other: ____________________ LIMITERS: Inside: ________ Outside: _______ DROOP GAUGE #: ____ WHEELBASE ADJUSTMENT Alum. SHOCK MOUNT & CAMBER LINK Fill in holes used PISTON # ___ FRONT Short Medium Long OIL _____ WT SPRING ___________ OTHER FRONT TIRES: ____________________________ Compound: __________________ Insert: _________________ Wheel: __________________________ REAR TIRES: ____________________________ Compound: __________________ Insert: _________________ Wheel: __________________________ BATTERY PLACEMENT CHASSIS Std Back Carbon Fiber Front Other: _____________________ BATTERY TYPE: _________________________________________ FRONT/REAR DRIVE Std One-way SPUR/PINION ______ T / ______T MOTOR ______________________________ BRUSH _______________________ SPRING _______________ RADIO _______________________________ SERVO ______________________ ESC ___________________ BODY ________________________________ WING ________________________ TIRE ADDITIVE ____________________________ LEAD WEIGHTS _______(oz/gm) Indicate location: None None SPONSORED BY: ___________________________________________________________________________ RACE COMMENTS TRACK CONDITIONS SURFACE: Smooth TRACTION: Low Bumpy Med. COMPOSITION: Concrete Asphalt MAIN ______ FINISH ______ QUALIFYING. POS. _______ High NOTES: __________________________________________________ _________________________________________________________ Carpet Other: ____________________________ NOTES: _____________________________________________________________ CAR COMMENTS ____________________________________________________________________ NOTES: _________________________________________________ ____________________________________________________________________ ________________________________________________________
advertisement
* Your assessment is very important for improving the workof artificial intelligence, which forms the content of this project