PowerTek 16-20 P Operation & Maintenance Manual
Add to My manuals22 Pages
PowerTek 16-20 SP is a powerful stump grinder designed to remove tree stumps efficiently. With its adjustable handle freight and directional control, you can easily maneuver the machine around the work area. The 16-20 SP is equipped with a hydrostatic drive belt, ensuring smooth and reliable operation. Its sturdy construction and durable cutter wheel bearings make it capable of handling even the toughest grinding jobs. Whether you're a professional landscaper or a homeowner looking to clear your property, the PowerTek 16-20 SP is an excellent choice for your stump grinding needs.
advertisement
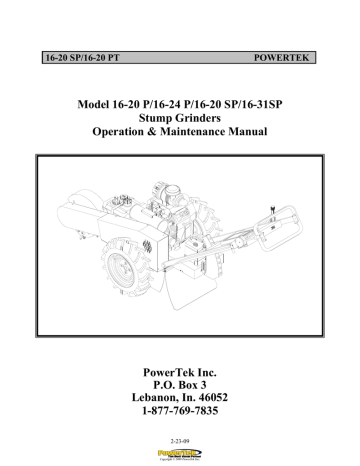
16-20 SP/16-20 PT POWERTEK
Model 16-20 P/16-24 P/16-20 SP/16-31SP
Stump Grinders
Operation & Maintenance Manual
PowerTek Inc.
P.O. Box 3
Lebanon, In. 46052
1-877-769-7835
2-23-09
TABLE OF CONTENTS POWERTEK
TABLE OF CONTENTS
WARNINGS SAFETY...........…...............................................……………………………….2-3
HOW TO USE YOUR STUMPER...........………..........................………....………………….4
WORK ZONE............................……………….……………………………….………………..5
INITIAL INSPECTION...........................................................………………………………….6
TRANSPORTATION & SET-UP......................………….………………………..................6-7
OPERATION.....................................................................…………………….….………….7-10
STARTING............................................................................……………………………………7
GRINDING STUMPS..........................................................…………………...………………..8
ADJUSTABLE HANDLE FREIGHT....................................................…………………….…8
DIRECTIONAL CONTROL…………….......................………….........................….………...9
STOPPING......................…………………………………………………….…………………10
MAINTENANCE...............................................................……………………….………...11-14
ENGINE.......................................................…………………………….………………….…...11
FUEL....................................................................................………………………………….....11
BATTERY.................................................................................……………………..……….....11
BELTS.......................................................................................…………………....…………....11
CUTTER BELT REPLACEMENT...................................................…………...…………….11
HYDROSTATIC DRIVE BELT REPLACEMENT...........................………..……………...11
HOUR METER………………………………………………………………………………....11
SHARPENING CUTTERS............................................................…………………………….12
REPLACING CUTTERS...................................................................…………….…………...13
TOOTH GAUGE......................................................……………........…………………..….…13
CUTTER WHEEL BEARINGS..........................................................…………….………….13
HYDRAULIC OIL............................................................................…………….…………….14
MAINTENANCE SCHEDULE........................................................……………………..…...14
EXPLODED VIEW 16/20 SP & 16/24 SP............................................……………………….15
PARTS LIST 16/20 SP & 16/24 SP.........................…………………………….…………......16
EXPLODED VIEW 16/20 P & 16/24 P....…....................................………………….…..…..17
PARTS LIST 16/20 P & 16/24 P.................................................………………….………......18
ELECTRICAL SCHEMATICS…………...............................................……………………..19
WARRANTY INFORMATION.............................................….……………………..…...20-21
1
WARNINGS POWERTEK
! WARNING
WARNING TO PURCHASERS OF INTERNAL COMBUSTION ENGINE EQUIPPED MACHINERY
OR DEVICES IN THE STATE OF CALIFORNIA:
The equipment that you have purchased does not have a spark arrester muffler. If this equipment is to be used on any forest or brush covered land or grass covered un-improved land in the State of California, the law requires that a spark arrester muffler be installed and be in effective working order. The spark arrester must be attached to the exhaust system and comply with Section 4442 of the California Public
Resource Code.
The engine exhaust from this equipment contains chemicals known to the State of California to cause cancer, birth defects or other reproductive harm.
! WARNING
This manual contains vital information for the safe use and efficient operation of this equipment.
Carefully read this operation maintenance manual before using this equipment, as failure to adhere to the instructions could result in death, serious bodily injury and/or property damage.
The Stump Grinder is to be used only for grinding tree stumps. Using this machinery for any other purpose may cause injury and or property damage. Improper use of the grinder will void the warranty.
2
SAFETY POWERTEK
1. Read the entire owner's manual carefully before operating the stump
grinder. Also, read the entire Engine Operator's Handbook. Familiarize
yourself with the, proper use of the Stumper. Know the controls and how to stop quickly.
2. Do not allow children to operate the stump grinder. Do not allow adults to operate the stump grinder without proper instruction- Do, not allow anyone to operate the stump grinder who is not acquainted with the Safety Instructions.
3. Be especially watchful of children and pets darting into the operating area and/or danger zone.
4. Wear protective clothing-long pants and heavy work boots as well as ear and eye protection while operating the Stumper.
5. Keep your mind and eyes on the machine while operating it. Do not let others distract you.
6. Check the stump grinder for any loose parts before operating.
7. Never place hands or feet anywhere near the cutter blade. The blade is larger than it appears when it is operating.
8. Make sure you are aware of the location of any pipes (water, gas, electrical, etc.) above or below the ground.
9. Clear the work area of all foreign objects such as sticks stones wires, etc.
10. Turn off clutch before moving
11. Never operate the unit without the safety guards in place and operating properly. Keep equipment in good working condition.
12. Take all possible precautions when leaving unit unattended. Stop engine and remove ignition key to prevent unauthorized use.
13. When refueling machine: shut off engine, do not smoke or allow any hot or burning material near.
14. Before removing or replacing teeth or belts, or before performing any maintenance: shut off engine and wait for all moving parts to stop, disconnect spark plug wire' and remove key.
15. Stability: The stump grinder has a narrow wheelbase and can become unstable under adverse conditions. Always go straight up or down on steep hills. Avoid steep side angles. When grinding avoid dropping one wheel into a hole to avoid a side tip of the unit.
16. When stump grinder is being transported on a trailer or in a truck make sure the machine is securely fastened to prevent property damage.
3
STUMP GRINDER USAGE POWERTEK
BEFORE YOU CUT:
Before you start to grind the stump, remove all debris-dirt, rocks, metal, and loose woodfrom around the area of the stump before the first cut. Be sure to remove any debris that may also be embedded in the tree stump itself. Debris can wear or damage the cutting teeth and can be a safety hazard. If the teeth meet these foreign objects, the stump cutter can propel these objects great distances.
Before you start the machine, become familiar with all of the controls on the stump grinder. Locate the key switch, throttle, choke, presence handle, brake and forward or reverse lever. Check to see if the debris curtains and guarding are in place to help reduce flying objects.
Take time to read all the decals and warnings that are on the machine. Read the operation and maintenance manual, it will give you information that can save you time as well as prevent serious injury.
Make sure the teeth on the cutter wheel are in good shape. Inspect them for sharpness, freedom from nicks, and damage. Teeth can wear down quickly causing performance problems as well as lost productivity.
When you are finished, lift the cutter wheel from the stump before shutting the engine off.
OPERATION:
The type of wood will determine how much to cut at one time. Softer woods such as pines or firs are easier to remove than harder woods such as elm, oak, ash or maple. For harder wood, take shallow cuts. Cutting harder woods will dull teeth faster, therefore, be prepared by having an extra set of teeth available.
If the stump is on a hill, level the area where the stump grinder will be setting. If grinding is attempted without leveling, the stumper could tip over. Also, engage the cutter wheel before allowing the cutter wheel to touch the stump.
Do not take large cuts. The recommendation is to take 1-inch deep cuts and then sweep side to side. Cuts deeper will not only slow productivity but could cause damage to the machine as well as personnel injury. Also, start at the front of the stump and work toward the center. If the stump is very large, it may be necessary to work from more than one side.
When grinding you may go as low as 12 inches below ground level. Make sure to clear away all dirt, rocks, and debris before you continue to grind.
SAFETY TIPS:
The stump grinder is a powerful machine and can throw debris. Be prepared by wearing protective clothing such as gloves, ear protection, eye protection, long pants, and heavy boots.
Never leave the operating position while the machine is engaged in a stump.
Make sure there is no one near the machine while it is in use. Use signs and/or barricades to restrict pedestrian traffic around the danger zone. Keep all children away from the stump grinder and the work area.
4
WORK ZONE POWERTEK
! WARNING
When operating grinder do not allow anyone to be in the danger zone while stump grinder is running or serious injury or death may occur.
5
INITIAL INSPECTION POWERTEK
INSPECTION
Upon receiving your stump grinder, inspect and report any shipping damage to the carrier immediately. PowerTek is not responsible for damage during transportation.
TIRES
Inflation pressure may change with temperature and or altitude. Check and adjust tire pressure to the tire manufacturer's recommended tire pressure as marked on the tire of the stump grinder.
BATTERY
As a safety precaution, the positive cable has been disconnected from the battery. Remove the unit from the shipping pallet, reconnect the cable to the terminal, and charge the battery.
ENGINE
The stump grinder engine was shipped from PowerTek with the proper amount of oil. However, you should doublecheck the level and add to or change the oil if conditions warrant. (see Engine Operators Handbook for full details).
HYDRAULIC DRIVE
The hydraulic transmission and gear reducer are shipped with the proper amount of oil. Again, double check the levels and add to the level if needed.
PRE-USE INSPECTION
Check for any loose bolts or parts before starting or first use.
PREPARATION:
Unit should not be operated until the owner's manual is read, all safety decals are noted and the user has complete knowledge of all controls.
TRANSPORTATION & SET- UP POWERTEK
TRANSPORTATION
It is the responsibility of the owner and/or operator to be aware of and abide by all applicable state and local regulations regarding transport of equipment and trailers (i.e. lights, tags, registration, etc.). Pick-up truck or similar vehicle may be used to transport the machine. The stump grinder may also be transported on any suitable trailer. Make sure it is properly secured.
SET-UP
The following procedures should be performed before each use of the stump grinder.
Check the unit for any loose parts. Tighten nuts and bolts and make sure all safety guards and devices
(Belt Guard, Brakes, Kill Switch and Clutch Switch) are securely in place and working. Please check all cutters to make sure they are tight.
Check the cutters for dulling. It is important to keep cutters sharpened by grinding or replacing them.
Dull cutters will cause excessive engine wear and poor performance. See the Maintenance Instructions for details.
Check the oil and fuel level in the engine. Follow the Engine Operators Handbook if fluid needs to be added or changed.
Check the air filter. The air filter should be cleaned of dust regularly. See the Engine Operators
Handbook for details.
Check the tension of the engine belts. The cutter wheel belts should have a deflection at the center of
3/8", under 15-lbs. deflection. Recheck belt tension after every use.
6
TRANSPORTATION & SET-UP (Cont.) POWERTEK
Check the hydraulic oil level. See the Maintenance Instructions for checking the hydraulic oil level.
Gas Tank Vent. When operating the stump grinder, make sure the gas tank vent is open. (It is threaded vent.) If the vent is not open the stump grinder will not run properly. Close Vent when transporting the stump grinder or re-fueling the gas tank (Fig. 1).
(Fig. 1)
OPERATION POWERTEK
STARTING (Fig. 2 & 3)
1. Turn the electric clutch switch off. The engine will not start if the clutch switch is on.
2. Pull the choke all the way out.
3. Slide the throttle to about 1/4 throttle.
4. Depress the operator presence control bar and turn the ignition switch until you hear the engine start.
5. Keep the control bar depressed and push the choke back in.
Important Note: The control bar is designed as a safety feature. The engine will
not start or operate without depressing the presence control bar.
(Fig. 2) (Fig. 3)
7
OPERATION POWERTEK
GRINDING STUMPS
1. Start the engine according to instructions
2. Use the throttle to gradually bring the RPM’s up to full speed.
3. To move the stump grinder, gradually push the drive handle forward. Full handle forward is walking speed. Pull back on the drive handle to travel in reverse.
4. Position the cutter wheel over the front edge of the stump and set the brake. You may need to adjust the handle position for better leverage depending on the height of the stump.
5. Once you have maneuvered the stump grinder near a stump, turn the clutch switch on to engage the cutter wheel. When the engine is cold, you may have to flip clutch switch off and on quickly to keep the engine running.
6. Slowly lower the stump grinder until the wheel comes in contact with the stump. Move the stump grinder back and forth in a long slow sweeping motion. Maintain the same elevation until a section has been removed, then lower stump grinder to take out the next section and continue until the front part of the stump is removed.
7. When the front part of the stump has been removed, release the brake and move the grinder forward to the new edge, and reset the brake.
8. Repeat Steps 6 and 7 until the stump is completely removed. Do not exceed 12" below ground level or 18" above the ground.
9. Turn the clutch switch off and wait for the cutter wheel to stop spinning before moving.
Important Note: For better performance and to avoid excessive clutch wear, run the engine at full throttle during operation.
ADJUSTABLE HANDLE HEIGHT
The handle can be raised or lowered to provide different leverages to better handle different stump heights. (Maximum stump height 18" above ground. Maximum below ground cut is 12")
! CAUTION
Shut off engine and wait for all moving parts to stop before adjusting handle.
TO ADJUST THE HEIGHT:
Holding the handle firmly, pull the handle lock pin to unlock the handle. Raise or lower the handle as needed and let the lock pin slip back into one of the holes in the bracket.
To lock the handle in the towing position:
1. Remove the handle fold-up link from the info tube.
2. Push the handle all the way forward and hold it firmly in its upright position.
3. Slide the link (hole end) onto the handle lock pin and slide the other end (peg end) into the topmost hole of the bracket.
4. Replace the hairpin cotters in the lock pin and link.
8
OPERATION POWERTEK
DIRECTIONAL CONTROL (SP)
The drive system consists of a hydrostatic transmission and differential axle assembly. The hydrostatic control lever at the handle bar, controls forward and reverse, and automatically returns to neutral or stop when released. Always 'feather" the finger control lever-easing it into the direction desired. Pushing the control lever forward propels the grinder forward, pulling the control lever back reverses the grinder (Fig. 4).
Pushing the hydrostatic lever full forward may cause stump grinder to jump forward, injury or property damage may occur. Use light pressure on hydrostatic lever to maintain proper control of stumper.
(Fig. 4)
9
OPERATION POWERTEK
BY PASS CONTROL (SP)
The hydrostatic also has a 'by-pass" control which enables the operator to manually move the machine when desired. This control is located at the rear of the main frame-lower left-hand side and is clearly identified. To put the grinder in a "free-wheeling mode" rotate the bypass handle up until it locks in place. To return it to powered travel, lower the bypass handle to original position. See Fig. 5.
! CAUTION
DO NOT start or run the engine with the “by-pass” lever in the “up” or the “freewheeling” position! DAMAGE will occur to the hydrostatic transmission. Use the “up” position ONLY when you wish to move the unit manually without the engine running.
(Fig. 5)
STOPPING (SP)
1. Turn the clutch switch off.
2. Gradually reduce the throttle down idle.
3. Turn the ignition switch off.
4. Release presence control bar remember the stump grinder will not restart until clutch switch is turned off. Releasing the presence control bar will stop the stumper at anytime.
Important Note: Make sure to allow the cutter wheel to stop spinning before lowering the stump grinder nose to the ground.
10
MAINTENANCE POWERTEK
ENGINE
Follow the instructions in the Engine Operators Manual for all maintenance of the engine such as checking the oil, cleaning air filters, etc.
FUEL
Use standard unleaded gasoline in the stump grinder engine.
BELTS
Check the condition and tension of the drive belts before each operation. When properly tensioned, the belts should give a 3/8" deflection at the center span under approx. 15 lbs. of pressure.
CUTTER BELT REPLACEMENT
If the belts are excessively warm or can no longer be properly tensioned, they must be replaced. Use a 2A94 size belt when replacing the belt. To remove cutter belt, lightly loosen the tensioner bolt and the pivot bolt on the backside of the belt cover in front of the engine. Place tensioner wrench between the two tension bolts. Push the wrench handle away from the cutter wheel. Remove belt. Replace with new belt. Pull wrench handle toward cutter wheel until proper tension of 3/8" at 15 lbs. is attained. Hold wrench as you tighten the tensioner bolt and pivot bolt.
Replace belt cover. See fig. 6 & 7.
HYDROSTATIC DRIVE BELT REPLACEMENT
To remove hydrostatic drive belt, remove cutter belt as described above. Loosen the clutch bracket and remove.
Loosen idler pulley and slide forward. Remove belt. Replace with a new AX-35 belt. Replace belt over clutch pulley, hydro pulley, and idler pulley. Slide idler pulley until belt is tensioned to 3/8" at 15lbs. Tighten idler pulley.
Replace clutch bracket and re-tighten. Replace cutter drive belt as above. Replace belt cover. See fig. 7.
(Fig. 6) (Fig. 7)
HOUR METER
The meter is fully automatic with a display that may be read at all times, whether the engine is on or off. During running times, engine RPM is shown; after shut down, Accumulated Running Time is shown.
After 25 hour of running time, the meter will automatically blink as a signal for oil change. It will continue to blink for a (2) hour period of accumulated running time (ie., 25 to 27 hours). The next alert will automatically appear in
25 hours. No re-set is required.
11
MAINTENANCE POWERTEK
SHARPENING CUTTERS
The cutters should be sharpened frequently for higher performance and a longer life. It is also easier to grind them if they are ground often.
*You will need a carbide-grinding wheel (green wheel) to sharpen them. Use a coarse grinding wheel to grind the steel shank. Be sure to maintain the back grind of 15 degrees (approximately).
The cutters must be replaced when the tooth has been sharpened so that 1/4" (approximately) of the carbide is left.
(Fig. 8)
TOOTH SELECTION
WHEN ORDERING TEETH USE THIS GUIDE TO ORDER SINGLE TEETH.
16265 (L.H.) 16263 (ST.) 16264 (R.H.)
12
MAINTENANCE POWERTEK
REPLACING CUTTERS (Fig. 9)
Remember before you replace any cutters you must turn the engine off, wait for moving parts to stop, remove the key from the ignition and remove wires from spark plugs.
1. Put the handle in the transport position and tilt the Stumper all the way back until it rests firmly on the ground.
2. To make cutter replacement easier, you can slide tensioner wrench handle through the hole in the cutter guard and cutter wheel. This will prevent the wheel from turning during blade replacement.
3. Loosen the allen head bolts (16262) from each of the cutter pockets and remove the cutters.
4. Install the new cutters in pairs alternating the cutters as shown.
5. Tighten the allen head bolts only tight enough to hold the cutters in the pockets, make sure all of the cutters are extended past the cutter wheel equally. (Fig. 10)
6. Torque each allen head bolt to 175 ft. lbs. (alternating as you tighten) to lock the cutters in the
pockets.
7. Once you have installed all of the cutters, double check to make sure all the allen head
bolts have been tightened securely and make sure all the cutters are equally extended. NOTE:
cutter wheel viewed from bottom of stumper. (Fig. 9)
Important Note: Do not operate the Stumper if any of the cutters are missing. This will cause the cutter wheel to be out of balance. Also, make sure all of the pockets are the same kind.
(Fig. 9) (Fig. 10) (Fig. 11)
CUTTER WHEEL BEARINGS (Fig. 11)
Grease -cutter wheel bearing every 40 hours of operation NOTE: DO NOT OVERGREASE.
13
MAINTENANCE POWERTEK
HYDRAULIC OIL
Use- SAE 2OW Hydraulic Oil - In hydraulic Pump (16267) only. You will need to check the hydraulic oil level in both the transmission and the gear reducer. To check the transmission read the level mark located on the bottom of the fill cup. Use SAE 2OW hydraulic oil to fill the hydrostatic transmission. To check the gear reducer (16268) you will need to get, underneath the stump grinder. After removing the orange plug, you can check the level with your fingertip or use a squeeze container to fill the reducer until some oil drips out of the hole. Then re-plug the hole. Use SAE 90 weight gear lube in gear reducer, (See fig 12).
Check
Hydraulic Oil
CheckGear
Reducer Oil
(Fig. 12)
MAINTENANCE SCHEDULE
Check engine oil
Check Machine Tire Pressure
Inspect/Check Engine Cooling Fins
Check for Loose Bolts
Check Hitch and Safety Chains (PT only)
Check Stump Grinder Teeth
Check Air Cleaner
Grease Bearings
Check Belts for Proper Tension
Check Hyd. Transmission Oil Level (SPH)
Check that Clutch is Working Properly
Check Rubber Guards
Check and Gap Spark Plugs
Daily Weekly Monthly Yearly/as
X
X
X
X
X
X
X
X
X
X
X
X
X
Change Engine Oil as Indicated in Engine Manufacturers Owners Manual
14
PARTS BREAKDOWN 16/20 SP POWERTEK
4 1
15
30
31
32
33
34
35
36
37
38
39
20
21
22
23
24
25
26
27
28
29
40
41
42
43
44
45
46
47
48
49
50
9
10
11
12
13
14
15
16
17
18
19
Key
1
2
3
4
5
6
7
8
63
64
65
66
67
68
69
70
71
72
73
74
51
52
53
54
55
56
57
58
59
60
61
62
16243
16244
16245
16246
16247
16249
16250
16251
16252
16253
16365
16354
16255
16256
16257
16258
16356
16260
16261
16262
16263
16265
16264
16266
16267
16268
16269
16270
16271
16272
16273
16275
16276
16281
16284
16285
16233
16234
16235
16236
16237
16238
16239
16240
16241
16242
16223
16224
16225
16226
16227
16228
16229
16230
16231
16232
16353
16211
16212
16213
16215
72646
16216
16217
16219
16220
16221
16222
Part No. Qty
16200 1
16201
16202
16203
1
1
1
16209
16205
16207
16208
2
1
1
1
1
1
1
1
1
1
2
1
1
1
1
1
3
1
1
1
1
1
1
1
1
1
2
2
1
1
1
1
1
1
1
1
1
1
2
1
1
1
1
1
1
1
1
1
1
1
1
1
1
6
6
12
6
3
3
1
1
2
1
1
1
2
3
1
1
1
2
1
PARTS LIST 16/20 SP POWERTEK
Description
Main Frame. 1620
Taper Bushing, 1.18
Cutting Wheel Pulley
Idler, Main Drive
Main drive Belt, Single
Electric Clutch, 1.437
Clutch Bracket
Idler Pulley, 3”
Frame Control Handle
J-Bolt, Battery Hold Down
Red, Positive Cable
Black, Negative Cable
Tach/Hour Meter thru S/N
Tach/Hour Meter S/N 61497/up
Gas Cap
Gas Tank, Includes Cap
Adjustment Tool
Inner Belt Guard
Curtain Mount, Left
Curtain, Left
90
91
83
84
85
86
87
88
89
Key
75
76
77
78
79
80
81
82
16295
16296
16297
16298
16299
18105
18123
20118
16336
72673
20119
16337
Part No. Qty
16286 1
16287
16288
16289
2
1
2
16291
16292
16293
16294
1
1
1
1
1
1
1
1
1
2
1
1
1
1
1
1
Description
Dump Valve Knob
Presence Handle Spacer
Info Tube Pad thru S/N 61496 only
Info Tube End Caps thru S/N 61496 only
3/8” Clutch Bushing
LH Wheel Spacer, Short
RH Wheel Spacer, Long
Adj. Pin Handle Grip
Tension Adj. Spacers
Transmission Gear Spacer
Retaining Ring, M17
Pin, Handle Lock
Idler Spacer
Belt, AX-35
Battery
Engine, 20HP Kohler (1620 SP)
Engine, 24HP Honda (1624 SP)
Engine 31HP Briggs Van. (1631 SP)
Muffler Kit, 20HP Kohller (1620 SP)
Muffler Kit, 24HP Honda (1624 SP)
Curtain Mount, Rear
Curtain, Rear
Rt. Curtain Mnt, Long
Rt. Curtain Mnt, Short
Right Curtain
Rear Side Curt. Mount
Rear Side Curtain
Outer Rear Belt Guard
Outer Front belt Guard
Battery Hold Down (2)
Gas Tank Strap
92
93
94
95
96
97
98
99
100
16359
28801
28839
16310
16313
16314
16316
16318
1
2
2
5001002 8
5001225 8
1
2
1
1
1
Muffler w/Shield 31HP Va. (1631 SP)
1” x 4” Clevis Pin
Fuel Line Clamp
½” Lug Nuts
½” Wheel Hub Stud
Fuel Line, 48”
Wire Stop
Ball Joint
Handle Fold-Up Link
Shield, Right Curtain
Tube Strap thru S/N 61496 only
Male Fuel Coupling
Female Fuel Coupling
Spring, Kill Switch
Dump Valve Handle
Presence Handle
Clutch Switch
Brake Handle
Brake Cable
Kill Switch
Shut Off Rod
Spring, Handle Lock
Transmission Gasket
101
102
103
104
105
106
107
108
109
110
111
16320
16325
16326
72522
72523
16338
16339
16355
16357
1
1
1
1
1
1
1
1
1
5000408 1
5000406 1
Main Idler Bushing
1/8” Clutch Bushing
Guard Lock Tab
Clutch Retainer
Retainer Bolt
Cover Plate S/N 61497/up only
Manual Pack S/N 61497/up only
Axle curtain, RH
Wheel Slot Cover
½-12 x 1” Shoulder Bolt
½-12 x ¾ Shoulder Bolt
Forward/Reverse Cable
Hydro Control Arm
Pillow Block Bearing
Cable Support
Clutch Stabilizer
Clutch Stabilizer (1624 only)
Idler Arm
Belt Tensioner Bracket
Cutter Shaft
Hydro Brake Bracket
Shut Off Rod
Cutter Wheel
Threaded Tooth Pocket
Counter Bore Tooth Pocket
162171 Float Assembly, 3&6 gal. tank
120
121
123
Optional Accessories
16300
16301
16303
124 16304
125 16305
16327
128 16327A
45060A
Counter Bore Mnt.,Std Angle
Counter Bore Mnt., Straight
Tooth, Deep Dish, Hard Carbide
Threaded Mnt., Std. Angle
Threaded Mnt., Straight
Caster Tube, Transport Wheel
Pocket Bolt
Straight Tooth
Left Hand Tooth
Right Hand Tooth
1 ½” Muffler Clamp
68050
45061
132 16218
7500802
Clevis Pin, 3/8” s 2 ¼”
Eaton Hydro Transmission
Peerless Transaxle
12 Tooth Gear
Wheel Hub
Wheel Assembly, RH
134
135
16328
16328A
136
137
16328B
16328C
Adjustment arm, Gauge Wheel
Wheel Spacer, Gauge Wheel
Wheel
Wheel Assembly, LH
Snap Ring
Pulley, 3” x 1.437 Bore
140
85226
500126
Pulley, 3” x 17MM Bore
Hydro Valve Control Lever
Woodruff Key, Axle
Woodruff Key, Transmission
16
141
16352B
143
16352A
16352
Gauge Wheel Assembly
Mount Arm, Gauge Wheel
Bolt, ½” -13 x 3 ¼”
Mirror Mount Arm
Sight Mirror Assembly 3-31-09
PARTS BREAKDOWN 16/20 P POWERTEK
17
PARTS LIST 16/20 P POWERTEK
Part No. Qty Description
Part No. Qty
Description
48
49
50
51
52
43
44
45
46
47
38
39
40
41
42
31
32
33
34
35
36
37
58
59
60
61
62
63
64
65
66
53
54
55
56
57
14
15
16
17
18
10
11
12
13
5
6
7
8
9
Key
1
2
3
4
24
25
26
27
28
29
30
19
20
21
22
23
16201
16202
16209
16205
16353
16211
16212
16213
16215
72646
16217
16220
16221
16223
16225
16226
16228
16229
16230
16231
16232
16233
16234
16235
16236
16237
16238
16245
16246
16251
16255
16256
16260
16261
16287
16288
16289
16294
16295
16298
16307
1
1
2
1
1
1
1
1
1
1
1
1
1
1
2
2
1
1
1
1
1
1
2
1
1
1
1
1
1
2
1
1
6
6
1
2
1
2
1
2
1
Taper Bushing, 1.187
Cutting Wheel Pulley
Main Drive Belt, Single
Electric Clutch, 1.437
Frame Control Handle
J-Bolt, Battery Hold Down
Red, Positive Cable
Black, Negative Cable
Tach/Hour Meter thru S/N 61496
Tach/Hour Meter S/N 61497/up
Gas Tank, Includes Cap
Inner Belt Guard
Curtain Mount, Left
Curtain Mount, Rear
Rt. Curtain Mnt, Long
Rt. Curtain Mnt, Short
Rear Side Curt. Mount
Rear Side Curtain
Outter Rear Belt Guard
Outter Front Belt Guard
Batter Hold Down (2)
Gas Tank Strap
Info Tube thru S/N 61496 only
Tube Strap thru S/N 61496 only
Male Fuel Coupling
Female Fuel Coupling
Spring Kill Switch
Shut Off Rod
Spring, Handle Lock
Pillow Block Bearing
Belt Tensioner Bracket
Cutter Shaft
Threaded Tooth Pocket
Counter Bore Tooth Pocket
16264
16265
3
3
Right Hand Tooth
Left Hand Tooth
16266 1 1 1/2" Muffler Clamp
16321 1 Wheel PT
16279 1 Wheel Hub w/ Brake Drum
Presence Handle Spacer
Info Tube Pad thru S/N 61496 only
Tube End Caps thru S/N 61496 only
Adj. Pin Handle Grip
Tension Adj. Spacers
Pin, Handle Lock
Brake Bracket Ass'y
113
114
115
116
117
118
119
120
121
122
123
124
125
126
127
128
100
101
103
104
105
107
108
109
110
111
112
79
80
81
82
83
74
75
76
77
78
71
72
73
Key
67
68
69
70
89
84
85
86
87
88
16311 1 Brake Band Lock Pin
18123 1 Battery
20118
16336
20119
16337
1
1
1
1
Engine, 20HP Kohler (1620 P)
Engine, 24HP Honda (1624 P)
Muffler Kit, 20HP Kohler (1620 P)
Muffler Kit, 24HP Honda (1624 P)
28801
28839
2
2
1" x 4" Clevis Pin
Fuel Line Clamps
5001002 10 Lug Nut, 1/2"
51611 2 Wheel/Tire
51667 2 Wheel Bearing Kit
16310 1 Fuel Line, 48”
16316
16318
16320
16326
16338
16339
16355
16357
16290
16290A
16290B
16290C
16290D
16290E
16290F
162171
162172
1
1
1
1
Cover Plate S/N 61497/up only
Manual Pack S/N 61497/up only
Axle Curtain, RH
Wheel Slot Cover
Complete Decal Set 1620
Decal, Clutch Switch
Decal, Transmission Valve
Decal, Caution Stumps Only
Decal, Warning Don't Move
Decal, Belt Tension
Decal, Danger Cutter Wheel
Float Assembly, 3 & 6 gal. tank
Pick-Up Assembly, 3 & 6gal. tank
Optional Accessories
16300 Counter Bore Mnt., Std Angle
16301
16303
16304
16305
16-20PTB
162801
Counter Bore Mnt., Straight
Tooth, Deep Dish, Hard Carbide
Threaded Mnt., Std. Angle
Threaded Mnt., Straight
Tow Bar Assembly, P1621
Tow Bar, P1621
51625
51601
16327
16327A
46218
16328
16328A
16328B
16328C
5000126
16352A
1
1
1
1
Handle Fold-Up Link
Shield, Right Curtain
Main Idler Bushing
Guard Lock Tab
Safety Chain Spacer
2" Coupler
Transport Wheel Ass’y
Caster Tube, Transport Wheel
Clevis Pin, 3/8” x 2 ¼”
Gauge Wheel Assembly
Mount Arm, Gauge Wheel
Adjustment Arm, Gauge Wheel
Wheel Spacer, Gauge Wheel
Bolt, ½”-13 x 3 ¼”
Mirror Mount Arm
16352 Sight Mirror Assembly
11-13-07
18
ELECTRICAL SCHEMATICS POWERTEK
20HP Kohler
BL
UE
BL
UE
ON
SO
TO
LE
IN
NO
ICE
TO
ID
IN
BL
E
TO
KE
BL
YS
UE
W
UE
W
IRE
W
ITC
IRE
H
CLUTCH
WRAP RED
LEAD AROUND
PLUG WIRE
GR
EE
N
BL
AC
K
HOUR-METER
W
HIT
W
E O
HIT
N E
E
IN
TO
NG
INE
BLUE
BLUE
ON
N
OFF
CLUTCH SWITCH
BL
AC
K
YELLOW
)
YE
LL
CO
NN
EC
T T
ON
EN
GI
NE
OW
O
(1
YE
2V
LL
A
OW
UX
PO
W
ER
OPERATOR PRESENCE
KILL SWITCH
GR
EE
N
W
HIT
E
24HP Honda
BL
UE
BL
UE
W
SPL
IRE
ICE
ON
TO
ST
AR
TE
IN
TO
SO
LE
NO
AC
ID
CLUTCH
R S
OL
ON
OID
K/W
HIT
E
GR
EE
N
BL
AC
K
BLUE
BLUE
ON
N
OFF
CLUTCH SWITCH
BL
AC
K
YELLOW
K/
YE
LL
W
OW
ER
)
CO
NN
YE
LL
EC
T T
ON
EN
GI
NE
OW
O
BL
(1
2V
AC
A
UX
PO
OPERATOR PRESENCE
KILL SWITCH
GR
EE
N
W
HIT
E
31HP VANGUARD
BL
UE
BL
UE
SPL
YE
LL
SPL
M
ICE
OV
ICE
OW
IN
ED
CLUTCH
ON
W
TO
FR
TO
AS
YE
OM
TE
ON
LL
RM
AT
OW
INA
SO
L T
LE
SO
LE
W
NO
IRE
ID
HA
NO
T
ID
EE
N
GR
BL
AC
K
BLUE
BLUE
ON
N
OFF
CLUTCH SWITCH
BL
AC
K
YELLOW
PO
W
ER
)
NN
YE
EC
CO
ON
EN
GI
LL
T T
OW
NE
O
GR
(1
2V
EY
A
UX
OPERATOR PRESENCE
KILL SWITCH
GR
EE
N
W
HIT
E
HOUR-METER
BL
SP
AC
W
LIC
K O
HIT
E
E IN
TO
INE
19
WRAP RED
LEAD AROUND
PLUG WIRE
WRAP
LEAD AROUND
PLUG WIRE
HOUR-METER
BL
AC
SPL
W
ED
HIT
E
IN
ON
TO
EN
GIN
E
WARRANTY POWERTEK
WARRANTY INFORMATION
Each new product is warranted against manufacturing defects in workmanship and/or materials under normal use and service for a period of 12 months from the date of delivery of the product to the original purchaser. PowerTek, Inc.'s obligation under this warranty shall be limited to the replacement to the original purchaser of any part which, as delivered to the original purchaser, and upon PowerTek, Inc.'s examination, is shown to PowerTek, Inc.'s satisfaction, to be defective due to faulty workmanship or materials at the factory.
This warranty does not apply to damage in transit, damage caused by user misuse, negligence, accident, normal wear, or alterations or repairs done outside the factory and/or authorized service stations as determined by PowerTek, Inc. This warranty does not apply to any labor charges in connection with the replacement parts claimed to be defective.
All parts claimed to be defective must be returned to PowerTek, Inc.'s factory for inspection, repair or replacement, with all transportation or mailing charges prepaid. It is the exclusive responsibility of the purchaser to bear the transportation or mailing charges in any warranty claim.
This warranty specifically excludes engines or batteries, which are warranted separately by their respective manufacturers, all claims for defective batteries; engines or engine parts must be made in accordance with the battery and/or engine manufacturers warranty. This warranty also specifically excludes costs of regular maintenance and replacement of service items such as belts, hoses, blades, and similar items.
PowerTek, Inc. reserves the right to make changes upon PowerTek, Inc., products without imposing any obligation upon PowerTek, Inc. to install the same on a product manufactured prior to the change. PowerTek, Inc. makes no other warranties, representations or promises other than those set forth herein. POWERTEK, INC. SPECIFICALLY DISCLAIMS ANY AND ALL IMPLIED
WARRANTIES OF FITNESS FOR PARTICULAR PURPOSE AND MERCHANTABILITY.
The remedies available to a distributor, dealer, and/or purchaser in connection with PowerTek,
Inc.'s warranty set forth above. In no event will PowerTek, Inc. be liable for special, incidental or consequential damages.
POWERTEK, INC. WARRANTY PROCEDURE
A. All requests for warranty must have approval from PowerTek, Inc. before work starts, or the warranty
claim will be denied.
B. All requests for warranty must be made on an O.P.E. warranty claim form. This is available
from an authorized distributor or dealer on a no charge basis.
C. It is the responsibility of the distributor; dealer and/or purchaser to complete the form warranty claim
and submit it to PowerTek, Inc.
1. The form must be filled out completely. It is the sole responsibility of the purchaser to obtain the proper and correct information for the warranty claim. Claims received without serial numbers, model numbers, replacement part numbers, purchase dates, repair dates, purchasers correct address, signature or other information requested by PowerTek, Inc. shall be returned without service.
2. Warranty claims that are illegible will be returned without service. Please type or print in black ink.
3. PowerTek, Inc. warranty makes no allowance for the time spent to fill out the
warranty claim, any such claim will be denied.
20
WARRANTY INFORMATION POWERTEK
4. All parts shall be retained and tagged for a period of sixty (60) days or until credit is
issued.
5. The factory may request parts to be returned for examination or analysis. These parts
shall be sent by prepaid freight to the PowerTek, Inc. Returns sent freight collect,
without the express, written permission of PowerTek, Inc, shall not be accepted by
PowerTek, Inc.
6. It is the responsibility of the dealer to review the claim and to comply fully with all
procedures set forth herein. Failure to do so shall result in the denial of the warranty
claims.
A. Any warranty payments by PowerTek, Inc. will be -paid by credit memo to the distributor,
dealer, rental store or purchaser.
B. All warranty claims, which are denied, will be returned with a reason for denial.
C. Labor Allowance.
1. The warranty labor rate is $40.00 per hour.
2. The actual time is divided into tenths of an hour. The warranty form should show the
time to the nearest tenth of an hour.
3. Labor credit is based on the actual time required only to make the repair.
Items not covered by warranty.
1. Mileage and transportation costs of any kind. All warranty is "Bench Work"only. The warranty specifically states that any transportation charges in connection with a warranty repair is the exclusive responsibility of the purchaser.
2. Postage, delivery, telephone calls or similar communication.
3. Normal maintenance or adjustments. This includes set up and service.
4. Battery, engines or engine parts. Warranty on batteries, engines, engine parts or other vendor parts that are covered by the component manufacturers warranty and must be handled by that component manufacturers representative.
5. Failure caused by neglect, normal wear, or abuse. PowerTek, Inc. depends on its dealer network to accurately determine when such conditions occur.
6. Any alteration of the original design of the unit, or the use of unauthorized or non-PowerTek, Inc. parts. Any claim submitted containing such unauthorized alteration repairs shall be rejected.
7. Freight or transportation –damage. All such damage is the responsibility of the carrier and any
claim for damages must be made with the carrier.
8. Parts or labor supplied by unauthorized repair facility.
9. Compound or repeat warranties caused by negligent/improper repair.
10.Any claim for warranty where the date of repair -exceeds thirty (30) days from the submission of the warranty claim.
11.Any claim for warranty on the entire unit.
12.Warranty claim involving oils or fluids of any kind.
13.Any warranty claims for leaking, punctured, blown, flat, or otherwise damaged tires on units that have been placed in service.
14.Lost time, lost rental, lost profits, or other economic loss due to warranty work.
Voluntary cooperation with the entire warranty procedure will make the program work better for both the purchaser and PowerTek, Inc.
21
advertisement
Related manuals
advertisement