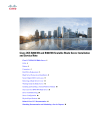
advertisement
▼
Scroll to page 2
of 40
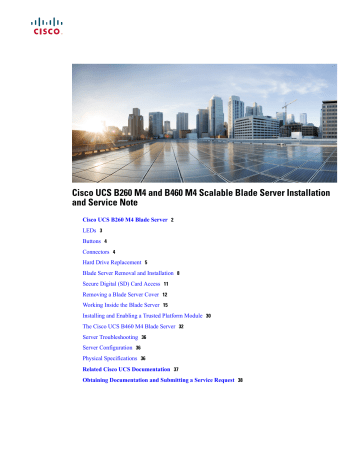
Cisco UCS B260 M4 and B460 M4 Scalable Blade Server Installation and Service Note Cisco UCS B260 M4 Blade Server 2 LEDs 3 Buttons 4 Connectors 4 Hard Drive Replacement 5 Blade Server Removal and Installation 8 Secure Digital (SD) Card Access 11 Removing a Blade Server Cover 12 Working Inside the Blade Server 15 Installing and Enabling a Trusted Platform Module 30 The Cisco UCS B460 M4 Blade Server 32 Server Troubleshooting 36 Server Configuration 36 Physical Specifications 36 Related Cisco UCS Documentation 37 Obtaining Documentation and Submitting a Service Request 38 Revised: April 17, 2015, OL-31494-01 Cisco UCS B260 M4 Blade Server This document describes how to install and service the Cisco UCS B260 M4 Blade Server (UCSB-EX-M4-1C), and how to upgrade to and install the Cisco UCS B460 M4 Blade Server (UCSB-EX-M4-1A) . The UCS B260 M4 Blade Server is an Intel-based, full-width blade that consists of the following parts: • One UCS Scalable M4 Blade Module • One UCS Scalability Terminator that is attached to the front of the blade module The UCS B260 M4 Blade Server supports these features: • Two CPU sockets that use the Intel Xeon processor E7 v2 product family • Eight scalable memory buffers that support 48 double-data-rate 3 (DDD3) DIMM slots • Two Cisco mezzanine cards • One mLOM card that supports Ethernet and Fibre Channel over Ethernet (FCoE) • An LSI3008 SAS RAID controller • Dual redundant secure digital (SD) slots • An internal USB port You can install up to four UCS B260 M4 Blade Servers in the Cisco UCS 5108 server chassis. Figure 1: Cisco UCS B260 M4 Scalable Blade Server 1 Drive bay 1 7 Network link status LED 2 Drive bay 2 8 Power button and LED 3 Reset button access 9 Right ejector handle 4 Beaconing button and LED 10 UCS Scalability Terminator 2 5 Local console connection 11 Left ejector handle 6 Blade health LED 12 Asset tag Each server has a blank plastic tag that pulls out of the front panel so you can add your own asset tracking label without interfering with the intended air flow. LEDs Server LEDs indicate whether the blade server is in active or standby mode, the status of the network link, the overall health of the blade server, and whether the server is set to give a flashing blue beaconing indication. The removable drives also have LEDs indicating hard disk access activity and disk health. Table 1: Blade Server LEDs LED Color Description Power Off Power off. Green Main power state. Power is supplied to all server components in normal operation. Amber Standby power state. Power is supplied only to the service processor (BMC) of the server so that the server can still be managed. Note Link Health If you press and release the front-panel power button, the server performs an orderly shutdown of the 12 V main power and goes to standby power state. You cannot shut down standby power from the front-panel power button. See the Cisco UCS Manager Configuration Guide for your release for information about completely powering off the server from the software interface. Off None of the network links are up. Green At least one network link is up. Off Power off. Green Normal operation. Amber Minor error. Blinking Amber Critical error. 3 LED Color Description Beaconing Off Beaconing not enabled. Blinking blue 1 Hz Beaconing to locate a selected blade—If the LED is not blinking, the blade is not selected. You can initiate beaconing in UCS Manager or by using the Locator button. Activity (Disk Drive) Health (Disk Drive) Off Inactive. Green Outstanding I/O to disk drive. Flashing Amber 4 Hz Rebuild in progress. Health LED will flash in unison. Flashing Amber 4 hz Identify drive active. Off Can mean either no fault detected or the drive is not installed. Flashing Amber 4 hz Rebuild drive active. If the Activity LED is also flashing amber, a drive rebuild is in progress. Amber Fault detected. Buttons The Reset button is just inside the chassis and must be pressed using the tip of a paper clip or a similar item. Hold the button down for five seconds, and then release it to restart the server if other methods of restarting are not working. The beaconing function for an individual server may get turned on or off by pressing the combination button and LED. The power button and LED allows you to manually take a server temporarily out of service but leave it in a state where it can be restarted quickly. If the desired power state for a service profile associated with a blade server or an integrated rack-mount server is set to "off", using the power button or Cisco UCS Manager to reset the server will cause the desired power state of the server to become out of sync with the actual power state and the server may unexpected shutdown at a later time. To safely reboot a server from a power-down state, use the Boot Server action in Cisco UCS Manager. Connectors The console port allows a direct connection to a blade server to allow operating system installation and other management tasks to be done directly rather than remotely. The port uses the KVM dongle cable (N20-BKVM) which provides a connection into a Cisco UCS blade server; it has a DB9 serial connector, a VGA connector for a monitor, and dual USB ports for a keyboard and mouse. 4 With this cable, you can create a direct connection to the operating system and the BIOS running on a blade server. A KVM cable ships standard with each blade chassis accessory kit. Figure 2: KVM Cable for Blade Servers 1 Connector to blade server slot 3 VGA connection for a monitor 2 DB9 serial connector 4 2-port USB connector for a mouse and keyboard Hard Drive Replacement You can remove and install blade server hard drives without removing the blade server from the chassis. The drives supported in this blade server come with the drive sled attached. Spare drive sleds are not available. A list of currently supported drives is in the specification sheets at: http://www.cisco.com/en/US/products/ps10280/products_data_sheets_list.html Before upgrading or adding an HDD to a running system, check the service profile in Cisco UCS Manager and make sure the new hardware configuration will be within the parameters allowed by the service profile. Caution To prevent ESD damage, wear grounding wrist straps during these procedures and handle modules by the carrier edges only. RAID Considerations If the drive being replaced was part of a RAID array, Cisco recommends using a new drive of identical size, model, and manufacturer to replace the failed drive. This recommendation comes from the industry standard practice of using drives of the same capacity when creating RAID volumes. If drives of different capacities are used, the useable portion of the smallest drive will be used on all drives that make up the RAID volume. For hard disk and RAID troubleshooting information, see the Cisco UCS Manager B-Series Troubleshooting Guide. 5 Removing a Blade Server Drive Procedure Step 1 Push the button to release the ejector, and then pull the hard drive from its slot. Figure 3: Removing and Installing a Server Drive Step 2 Step 3 6 Place the hard drive on an antistatic mat or antistatic foam if you are not immediately reinstalling it in another blade server. Install a blank faceplate (N20-BBLKD) to keep dust out of the blade server if the slot will remain empty. Installing a Blade Server Drive Procedure Step 1 Place the hard drive lever into the open position by pushing the release button. Figure 4: Removing and Installing a Drive Step 2 Step 3 Gently slide the hard drive into the opening in the blade server until it seats into place. Push the hard drive lever into the closed position. You can use Cisco UCS Manager to format and configure RAID services. See the UCS Manager configuration guide for your software release for details on RAID configuration. If you need to move a RAID cluster from one server to another, refer to the "Moving a RAID Cluster" section of the "Troubleshooting Server Hardware" chapter of the Cisco UCS Troubleshooting Guide. 7 Blade Server Removal and Installation Before performing any internal operations on this blade server, you must remove it from the chassis. To prevent ESD damage, wear grounding wrist straps during these procedures and handle modules by the carrier edges only. Caution Powering Off Blade Servers Using the Power Button Tip You can also shut the server down remotely using Cisco UCS Manager. For details, see the Configuration Guide for the version of Cisco UCS Manager that you are using. The configuration guides are available at the following URL: http://www.cisco.com/en/US/products/ps10281/products_installation_and_ configuration_guides_list.html Procedure Step 1 For each server in the chassis that you want to power off, check the color of the Power Status LED. • Green indicates that the server is running and must be shut down before it can be safely powered off. Go to Step 2. • Amber indicates that the server is already in standby mode and can be safely powered off. Go to Step 3. Step 2 Press and release the Power button, then wait until the Power Status LED changes to amber. The operating system performs a graceful shutdown and the server goes to standby mode. To avoid data loss or damage to your operating system, you should always invoke a graceful shutdown of the operating system. (Optional) If you are shutting down all blade servers in a chassis, disconnect the power cords from the chassis to completely power off the servers. Remove the appropriate servers from the chassis. Caution Step 3 Step 4 Removing a Blade Server You must decommission the server using Cisco UCS Manager before physically removing the blade server. 8 Procedure Step 1 Step 2 Step 3 Step 4 Step 5 Step 6 Turn off the blade server using either Cisco UCS Manager or the power button. Completely loosen the captive screws on the front of the blade. Remove the blade from the chassis by pulling the ejector levers on the blade until it unseats the blade server. Slide the blade part of the way out of the chassis, and place your other hand under the blade to support its weight. Once removed, place the blade on an antistatic mat or antistatic foam if you are not immediately reinstalling it into another slot. If the slot is to remain empty, reinstall the slot divider (N20-CDIVV) and install two blank faceplates (N20-CBLKB1) to keep assure proper ventilation and cooling. Installing a Blade Server Full-width Blade Servers are intended to run in the upper slots of the chassis, if the chassis will house both full-width and half-width servers. A chassis with four full width servers is fully supported. Procedure Step 1 If necessary, remove the slot divider (N20-CDIVV) from the chassis. a) Simultaneously pull up on the left side catch and push down on the right side catch as shown in callout 1 of the following figure. 9 b) Pull the slot divider out of the chassis as shown in callout 2 of the following figure. Keep the slot divider in case it is needed at another time. Figure 5: Removing a Slot Divider Tip 10 To reinstall the slot divider, align it with the dimples in the slot top and bottom and slide it back in until it clicks into place. Step 2 Grasp the front of the blade server and place your other hand under the blade to support it. Figure 6: Positioning a Blade Server in the Chassis Step 3 Step 4 Step 5 Step 6 Open the ejector levers in the front of the blade server. Gently slide the blade into the opening until you cannot push it any farther. Press the ejector levers so that they catch the edge of the chassis and press the blade server all the way in. Tighten the captive screw on the front of the blade to no more than 3 in-lbs. Tightening with bare fingers only is unlikely to lead to stripped or damaged captive screws. Secure Digital (SD) Card Access SD card slots are provided and one or two SD cards can be populated. If two SD cards are populated, they can be used in a mirrored mode (Cisco UCS Manager 2.2.x and later required). 11 Note Do not mix 16 GB and 32 GB SD cards in the same server. Figure 7: SD Card Slot Locations Removing a Blade Server Cover Replacing the cover is the reverse of removing the cover. Procedure Step 1 Step 2 Press and hold the button down as shown in the figure below. While holding the back end of the cover, pull the cover back and then up. Figure 8: Opening a B260 M4 Blade Server 12 Internal Components Figure 9: Inside View of the Blade Server 1 Hard drive bay 1 15 Memory Buffer for channel G and channel H 2 Drive bay 2 16 Memory Buffer for channel I and channel J 3 UCS Scalability Terminator 17 DIMM slots I1-I3 and J1-J3 4 CMOS battery 18 DIMM slots N1-N3 and M1-M3 13 5 CPU 1 under heat sink 19 Memory Buffer for channel M and channel N 6 CPU 2 under heat sink 20 Memory Buffer for channel K and channel L 7 Trusted Platform Module (TPM) 21 DIMM slots K1-K3 and L1-L3 8 Memory Buffer for channel A and channel B 22 DIMM slots O1-O3 and P1-P3 9 DIMM slots A1-A3 and B1-B3 23 Memory Buffer for channel O and channel P 10 DIMM slots C1-C3 and D1-D3 24 mLOM card This slot is shown in Cisco UCS Manager as “Adapter 1” but the BIOS lists it as “mLOM.” The VIC 1240 is a type of adapter with a specific footprint that can only be used in this slot. 11 Memory Buffer for channel C and channel D 25 Adapter card This slot is shown in Cisco UCS Manager as “Adapter 2,” but is shown in the BIOS as “Mezz 1.” Mixing adapter types is supported. 12 Memory Buffer for channel E and channel F 26 Adapter card This slot is shown in Cisco UCS Manager as “Adapter 3,” but it is shown in the BIOS as “Mezz 2.” Mixing adapter types is supported. 13 DIMM slots E1-E3 and F1-F3 27 Internal USB connector Cisco UCS-USBFLSH-S-4GB= is recommended, but if you use another USB drive it must be no wider than 0.8 inches (20 mm), and no more than 1.345 inches (34 mm) long in order to provide needed clearances to install or remove the USB drive. USB flash memory from sources other than Cisco is allowed, but is not supported by Cisco and is used at the user’s risk. 14 14 DIMM slots G1-G3 and H1-H3 Note • A squeeze-to-remove retaining clip is provided to secure the internal USB flash memory, the clip must always be securely fastened when the flash memory is in use. Memory that does not fit in the clip should not be used. • Use of this server may require an upgrade to the FEX in the chassis. The 2104XP fabric extender is not compatible when any Cisco-certified adapter is installed in slot 1 or slot 2. If a VIC 1240 modular LOM card is installed, you will have connectivity through the mLOM but other adapters will not be recognized. Diagnostics Button and LEDs At blade start-up, POST diagnostics test the CPUs, DIMMs, HDDs, and adapter cards, and any failure notifications are sent to UCS Manager. You can view these notifications in the System Error Log or in the output of the show tech-support command. If errors are found, an amber diagnostic LED also lights up next to the failed component. During run time, the blade BIOS, component drivers, and OS all monitor for hardware faults and will light up the amber diagnostic LED for a component if an uncorrectable error or correctable errors (such as a host ECC error) over the allowed threshold occur. LED states are saved, and if you remove the blade from the chassis the LED values will persist for up to 10 minutes. Pressing the LED diagnostics button on the motherboard causes the LEDs that currently show a component fault to light for up to 30 seconds for easier component identification. LED fault values are reset when the blade is reinserted into the chassis and booted, and the process begins from its start. If DIMM insertion errors are detected, they may cause the blade discovery to fail and errors will be reported in the server POST information, which is viewable using the UCS Manager GUI or CLI. UCS blade servers require specific rules to be followed when populating DIMMs in a blade server, and the rules depend on the blade server model. Refer to the documentation for a specific blade server for those rules. HDD status LEDs are on the front face of the HDD. Faults on the CPU, DIMMs, or adapter cards also cause the server health LED to light solid amber for minor error conditions or blinking amber for critical error conditions. Working Inside the Blade Server Installing a Motherboard CMOS Battery All Cisco UCS blade servers use a CR2032 battery (Cisco PID N20-MBLIBATT=) to preserve BIOS settings while the server is powered down. Warning There is danger of explosion if the battery is replaced incorrectly. Replace the battery only with the same or equivalent type recommended by the manufacturer. Dispose of used batteries according to the manufacturer’s instructions. To install or replace a motherboard complementary metal-oxide semiconductor (CMOS) battery, follow these steps: 15 Procedure Step 1 Remove the old CMOS battery: a) Power off the blade, remove it from the chassis, and remove the top cover. b) Push the battery socket retaining clip away from the battery. c) Lift the battery from the socket. Use needle-nose pliers to grasp the battery if there is not enough clearance for your fingers. Step 2 Install a motherboard CMOS battery: a) Push the battery socket retaining clip away from where the battery fits in the housing. b) Insert the new battery into the socket with the battery’s positive (+) marking facing away from the retaining clip. Ensure that the retaining clip can click over the top of the battery to secure it in the housing. c) Replace the top cover. d) Replace the server in the chassis and power on the blade by pressing the Power button. Removing a CPU and Heat Sink You will use these procedures to move a CPU from one server to another, to replace a faulty CPU, or to upgrade from one CPU to another. Note The CPU pick and place tool is required to prevent damage to the connection pins between the motherboard and the CPU. Do not attempt this procedure without the required tool, which is included with each CPU option kit. Procedure Step 1 Unscrew the four captive screws securing the heat sink to the motherboard. Loosen one screw by a quarter turn, then move to the next screw. Continue loosening until the heat sink can be lifted off. Step 2 Remove the heat sink. Remove the existing thermal compound from the bottom of the heat sink using the cleaning kit (UCSX-HSCK= ) included with each CPU option kit. Follow the instructions on the two bottles of cleaning solvent. Step 3 Unhook the first socket hook, which has the following icon: Step 4 Unhook the second socket hook, which has the following icon: Open the socket latch. See callout 5 in the following figure. Step 5 16 See callout 3 in the following figure. See callout 4 in the following figure. Step 6 Press the central button on the provided CPU pick and place tool (UCS-CPU-EP-PNP=) to release the catch. The CPU pick and place tool is included with each CPU option kit, or the tool may be purchased separately. Step 7 Remove an old CPU as follows: a) Place the CPU pick and place tool on the CPU socket aligned with the arrow pointing to the CPU registration mark. b) Press the button/handle on the tool to grasp the installed CPU. c) Lift the tool and CPU straight up. Installing a New CPU and Heat Sink Before installing a new CPU in a server, verify the following: • The CPU is supported for that given server model. This may be verified via the server's Technical Specifications ordering guides or by the relevant release of the Cisco UCS Capability Catalog. • A BIOS update is available and installed that supports the CPU and the given server configuration. 17 • If the server will be managed by Cisco UCS Manager, the service profile for this server in Cisco UCS Manager will recognize and allow the new CPU. The Pick-and-Place tools used in this procedure are required to prevent damage to the contact pins between the motherboard and the CPU. Do not attempt this procedure without the required tools, which are included with each CPU option kit. If you do not have the tool, you can order a spare: Cisco PID UCS-CPU-EP-PNP= for 10-, 8-, 6-, 4-, or 2-core CPUs (green); UCS-CPU-EP2-PNP= for v2 12-core CPUs (purple). Caution Procedure Step 1 (Optional) If you are installing a CPU in a socket that had been shipped empty, there will be a protective cap intended to prevent bent or touched contact pins. The pick and pull cap tool provided can be used in a manner similar to a pair of tweezers. Grasp the protective cap and pivot as shown. Step 2 Step 3 Release the catch on the pick and place tool by pressing the handle/button. Remove the new CPU from the packaging, and load it into the pick and place tool as follows: a) Confirm that the pedestal is set up correctly for your processor. The pedestal ships configured with the markings “LGA2011-R1” facing upward, and this is the correct orientation. b) Place the CPU on the pedestal. The CPU corners should fit snugly at the pedestal corners and the notches should meet the pegs perfectly. c) Place the CPU pick and place tool on the CPU pedestal aligned with the A1 arrow pointing to the A1 registration mark on the pedestal. d) Press the button/handle on the tool to grasp the CPU. 18 e) Lift the tool and CPU straight up off of the pedestal. Figure 10: Loading the Pick and Place Tool 1 Alignment mark on the pick and place tool, CPU and pedestal 19 Step 4 Step 5 Place the CPU and tool on the CPU socket with the registration marks aligned as shown. Press the button/handle on the pick and place tool to release the CPU into the socket. Figure 11: Using the CPU Pick and Place Tool to Insert the CPU 1 Alignment mark on the tool button/handle 2 Step 6 Step 7 Close the socket latch. See callout 1 in the following figure. Step 8 Secure the second hook, which has the following icon: 20 Secure the first hook, which has the following icon: Alignment mark on the CPU socket See callout 2 in the following figure. See callout 3 in the following figure. Step 9 Using the syringe of thermal grease provided with replacement CPUs and servers (UCS-CPU-GREASE=), add 2 cubic centimeters of thermal grease to the top of the CPU where it will contact the heat sink. Use the pattern shown. This should require half the contents of the syringe. Caution The thermal grease has very specific thermal properties, and thermal grease from other sources should not be substituted. Using other thermal grease may lead to damage. Note CPU spares come with two syringes of thermal grease; one with a blue cap and one with a red cap. The syringe with the blue cap is UCS-CPU-GREASE=, which is used with this server Figure 12: Thermal Grease Application Pattern Step 10 Replace the heat sink. See callout 4. 21 On certain models, heat sinks are keyed to fit into the plastic baffle extending from the motherboard. Do not force a heat sink if it is not fitting well, rotate it and re-orient the heat sink. Secure the heat sink to the motherboard by tightening the four captive screws a quarter turn at a time in an X pattern as shown in the upper right. Caution Step 11 Installing Memory To install a DIMM into the blade server, follow these steps: Procedure Step 1 Press the DIMM into its slot evenly on both ends until it clicks into place. DIMMs are keyed. If a gentle force is not sufficient, make sure the notch on the DIMM is correctly aligned. Be sure that the notch in the DIMM aligns with the slot. If the notch is misaligned you may damage the DIMM, the slot, or both. Press the DIMM connector latches inward slightly to seat them fully. Note Step 2 Supported DIMMs The DIMMs supported in this blade server are constantly being updated. A list of currently supported and available DIMMs is in the specification sheets at: http://www.cisco.com/en/US/products/ps10280/products_data_sheets_list.html Do not use any memory DIMMs other than those listed in the specification sheet. Doing so may irreparably damage the server and require an RMA and down time. Memory Arrangement The Cisco UCS B260 M4 Blade Server contains 48 slots for installing DIMMs—24 for each CPU. Each CPU has 24 DIMM slots spread over 8 channels. This blade server needs at least one DIMM attached to all populated CPUs. DIMMs installed in slots for an 22 absent CPU will not be recognized. For optimal performance, distribute DIMMs evenly across all CPUs. DIMM connector latches are color coded blue, black, and white/ivory, and we recommend that you install memory in roughly that order. Figure 13: Memory Slots Within the Blade Server 1 DIMMs for CPU 1 2 DIMMs for CPU 2 Channels Each CPU has 8 channels, consisting of 3 DIMMs. Each channel is identified by a letter. Each channel member is identified by numbers, 1, 2, or 3. Install DIMMs according to the configuration in the following table. 23 CPU 1 DIMMs, Channels A Through H CPU 2 DIMMs, Channels I Through P A1 (blue slot), A2 (black slot), A3 (white/ivory slot) I1 (blue slot), I2 (black slot), I3 (ivory slot) B1 (blue slot), B2 (black slot), B3 (white/ivory slot) J1 (blue slot), J2 (black slot), J3 (ivory slot) C1 (blue slot), C2 (black slot), C3 (ivory slot) K1 (blue slot), K2 (black slot), K3 (ivory slot) D1 (blue slot), D2 (black slot), D3 (ivory slot) L1 (blue slot), L2 (black slot), L3 (ivory slot) E1 (blue slot), E2 (black slot), E3 (ivory slot) M1 (blue slot), M2 (black slot), M3 (ivory slot) F1 (blue slot), F2 (black slot), F3 (ivory slot) N1 (blue slot), N2 (black slot), N3 (ivory slot) G1 (blue slot), G2 (black slot), G3 (ivory slot) O1 (blue slot), O2 (black slot), O3 (white/ivory slot) H1 (blue slot), H2 (black slot), H3 (ivory slot) P1 (blue slot), P2 (black slot), P3 (white/ivory slot) 24 The following figure shows the physical representation of DIMMs and CPUs. Figure 14: Physical Representation of DIMMs and CPUs 25 The following figure shows the logical representation of the channels. Figure 15: Logical Representation of Channels Memory Performance When configuring your server, consider the following: • DIMMs within the blade server can be of a different size, but mixing speeds causes the faster DIMMs to run at the speed of the slower DIMMs. • No mixing of DIMM type (LRDIMM, RDIMM) is allowed. • Your selected CPU(s) can have some affect on performance. CPUs used must be of the same type. Bandwidth and Performance You can achieve maximum bandwidth, performance, and system memory by using the following configuration: • DDR3, 1600 millions of transfers per second (MT/s) across four Channels • 12 DIMMs per CPU (48 DIMMs total) • Maximum capacity of 1536 GB (using 32-GB DIMMs) Performance is less than optimal if the following memory configurations are used: • Mixing DIMM sizes and densities 26 • Unevenly populating DIMMs between CPUs Depending on the application needed, performance loss might or might not be noticeable or measurable. Installing a mLOM Adapter Note You must remove the adapter card to service the mLOM. To install an mLOM on the blade server, follow these steps: Procedure Step 1 Position the mLOM’s board connector above the motherboard connector and align the captive screw to the standoff post on the motherboard. Step 2 Firmly press the mLOM’s board connector into the motherboard connector. Tighten the captive screw. Tip To remove an mLOM, reverse the above procedure. You might find it helpful when removing the connector from the motherboard to gently rock the board along the length of the connector until it loosens. Step 3 Figure 16: Installing an mLOM 27 Installing an Adapter Card The network adapters and interface cards all have a shared installation process and are constantly being updated. A list of currently supported and available models for this server is in the specification sheets at this URL: http://www.cisco.com/en/US/products/ps10280/products_data_sheets_list.html Note If a VIC 1240 mLOM is not installed, you must have an adapter card installed. Note Use of the adapters available for this server might require an upgrade to the FEX in the chassis. The 2104XP FEX is not compatible with any Cisco-certified adapter. If a VIC 1240 mLOM card is installed, you will have connectivity through the mLOM but other adapters will not be recognized. Use of all slots requires Cisco UCS 2200 series FEXes. If you are switching from one type of adapter card to another, before you physically perform the switch make sure that you download the latest device drivers and load them into the server’s operating system. For more information, see the firmware management chapter of one of the Cisco UCS Manager software configuration guides. The Cisco UCS 785GB or 365GB MLC Fusion-io Drive and LSI 400GB SLC WarpDrive have the same form factor as M3 adapter cards and can be installed and removed using the same procedures. Using these drives in a B200 M3, or B22 M3 blade server requires the presence of a VIC 1240 mLOM to provide blade I/O. They will not work in M1 and M2 generation Cisco UCS servers. These drives appear in Cisco UCS Manager as regular SSDs. Procedure Step 1 Step 2 Step 3 28 Position the adapter board connector above the motherboard connector and align the two adapter captive screws to the standoff posts (see callout 1) on the motherboard. Firmly press the adapter connector into the motherboard connector (see callout 2). Tighten the two captive screws (see callout 3). Tip Removing an adapter card is the reverse of installing it. You might find it helpful when removing the connector from the motherboard to gently rock the board along the length of the connector until it loosens. Figure 17: Installing an Adapter Card Figure 18: Installing an Adapter Card 29 Installing and Enabling a Trusted Platform Module The Trusted Platform Module (TPM, Cisco Product ID UCSX-TPM2-001) is a component that can securely store artifacts used to authenticate the server. These artifacts can include passwords, certificates, or encryption keys. A TPM can also be used to store platform measurements that help ensure that the platform remains trustworthy. Authentication (ensuring that the platform can prove that it is what it claims to be) and attestation (a process helping to prove that a platform is trustworthy and has not been breached) are necessary steps to ensure safer computing in all environments. It is a requirement for the Intel Trusted Execution Technology (TXT) security feature, which must be enabled in the BIOS settings for a server equipped with a TPM. Intel Trusted Execution Technology (TXT) provides greater protection for information that is used and stored on the business server. A key aspect of that protection is the provision of an isolated execution environment and associated sections of memory where operations can be conducted on sensitive data, invisibly to the rest of the system. Intel TXT provides for a sealed portion of storage where sensitive data such as encryption keys can be kept, helping to shield them from being compromised during an attack by malicious code. Note TPM installation is supported after-factory. However, a TPM installs with a one-way screw and cannot be replaced or moved to another server. If a server with a TPM is returned, the replacement server must be ordered with a new TPM. Procedure Step 1 30 Install the TPM hardware. a) Power off, decommission, and remove the blade server from the chassis. b) Remove the blade server cover. c) Install the TPM to the TPM socket on the server motherboard and secure it using the one-way screw that is provided. See the figure below for the location of the TPM socket. d) Return the blade server to the chassis, power it on, and allow it to be automatically reacknowledged, reassociated, and recommissioned. e) Continue with enabling TPM support in the server BIOS in the next step. Figure 19: TPM Socket Location 1 Front of server 2 TPM socket on motherboard Step 2 Enable TPM Support in the BIOS. a) Enable Quiet Mode in the BIOS policy of the server’s service profile. b) Establish a direct connection to the server, either by connecting a keyboard, monitor, and mouse to the front panel using a KVM dongle (N20-BKVM) or by other means. c) Reboot the server. d) Press F2 during reboot to enter the BIOS setup screens. e) On the Advanced tab, select Trusted Computing and press Enter to open the TPM Security Device Configuration window. f) Set the TPM Support option to Enabled. g) Press F10 to save and exit. Allow the server to reboot, but watch for the prompt to press F2 in the next step. Step 3 Enable TPM State in the BIOS. a) Press F2 during reboot to enter the BIOS setup screens. 31 b) On the Advanced tab, select Trusted Computing and press Enter to open the TPM Security Device Configuration window. c) Set the TPM State option to Enabled. d) Press F10 to save and exit. Allow the server to reboot, but watch for the prompt to press F2 in the next step. Step 4 Verify that TPM Support and TPM State are enabled. a) Press F2 during reboot to enter the BIOS setup screens. b) On the Advanced tab, select Trusted Computing and press Enter to open the TPM Security Device Configuration window. c) Verify that TPM Support and TPM State are set to Enabled. d) Continue with enabling the Intel TXT feature in the next step. Step 5 Enable the Intel TXT feature in the BIOS. a) Choose the Advanced tab. b) Choose Intel TXT (LT-SX) Configuration to open the Intel TXT (LT-SX) Hardware Support window. c) Set TXT Support to Enabled. d) Verify that the following items are listed as Enabled: • VT Support (default is Enabled) • VT-d Support (default is Enabled) • TPM Support • TPM State If VT Support and VT-d Support are not enabled, return to the Advanced tab, select Processor Configuration, and then set Intel (R) VT and Intel (R) VT-d to Enabled. e) Press F10 to save and exit. The Cisco UCS B460 M4 Blade Server The UCS B460 M4 Blade Server is a four-socket blade server that consists of two UCS Scalable M4 Blade Modules that are attached together with the UCS Scalability Connector. An upgrade kit is available to upgrade the Cisco UCS B260 Blade Server to the UCS B460 M4 Blade Server. The upgrade kits includes the following parts: • One UCS Scalable M4 Blade Module • One UCS Scalability Connector that attaches to the front of the blade modules and connects them to form the four-socket blade server. 32 The two UCS Scalable M4 Blade Modules in the UCS B460 M4 Blade Server are in a master-slave relationship. The lower module is the master. Figure 20: Cisco UCS B460 M4 Blade Server 1 Drive bay 1 4 UCS Scalability Connector 2 Drive bay 2 5 Drive bay 4 3 Drive bay 3 Installing a Cisco UCS B460 M4 Blade Server A Cisco UCS B460 M4 Blade Server is created when you use a scalability connector to connect two Cisco UCS B260 M4 servers. To install the UCS B460 M4 Blade Server, perform the following tasks: 1 Install a UCS B260 M4 Blade Server in slot 7 (the lowest slot) in the chassis. 2 Remove the UCS Scalability Terminator from the UCS B260 M4 server that is installed in slot 7. Once the terminator is removed, you have a UCS Scalable M4 Blade Module. 3 Install the second UCS Scalable M4 Blade Module (the second B260 M4 server) from the upgrade kit in slot 5. 4 Connect the two UCS Scalable M4 Blade Modules together with the UCS Scalability Connector. Note The KVM cable, USB flash drive, and the SD card must be configured on the bottom (master) blade in the UCS B460 M4 Blade Server. 33 Removing the Scalability Terminator Upgrading to the UCS B460 M4 Blade Server requires that you remove the UCS Scalability Terminator from a UCS B260 M4 Blade Server. If you do not plan to upgrade to a UCS B460 M4 Blade Server, you should not need to remove the UCS Scalability Terminator from the UCS B260 M4 Blade Serve. To remove the UCS Scalability Terminator, follow these steps: Procedure Step 1 Step 2 Step 3 Step 4 Step 5 34 Decommission the blade server using Cisco UCS Manager to take the server offline. Completely loosen the captive screws on the front of the terminator. Open both ejector levers on the front of the terminator. While holding the ejector levers open, pull the terminator away from the bracket to separate it from the blade server. Once removed, place the terminator on an antistatic mat or antistatic foam Installing a Scalability Connector Install a UCS Scalability Connector to two UCS Scalable M4 Blade Modules and form the UCS B460 M4 Blade Server. Figure 21: Installing the UCS Scalability Connector Before You Begin • Ensure that the original UCS M4 Scalable Blade module, without the UCS Scalability Terminator, is in slot 7 in the chassis. This module will be the master in the UCS B460 M4 Blade Server. • Ensure that the UCS Scalable M4 Blade Module from the upgrade kit in slot 5 in the chassis. Procedure Step 1 Step 2 Step 3 Step 4 Step 5 Open the ejector levers on the front of the connector. While holding the ejector levers open, line up the four guide posts with the holes on the bracket and push the connector into place until it engages. Close the ejector levers. Tighten the captive screws on the front of the connector. Use Cisco UCS Manager to power on the blade server and reconfigure it. 35 Server Troubleshooting For general troubleshooting information, see the see the Cisco UCS Manager B-Series Troubleshooting Guide. Server Configuration Cisco UCS blade servers are intended to be configured and managed using Cisco UCS Manager. For details, see the Configuration Guide for the version of Cisco UCS Manager that you are using. The configuration guides are available at the following URL: http:/ /www.cisco.com/en/US/products/ps10281/products_installation_and_configuration_guides_list.html Physical Specifications Table 2: Cisco UCS B260 M4 Blade Server Specification Value Height 1.95 inches (49.5 mm) Width 16.50 inches (419.1 mm) Depth 25.5 inches (647.7mm) Weight 34.5 lbs (15.65 kg) The system weight listed here is an estimate for a fully configured system and will vary depending on peripheral devices installed. Table 3: Cisco UCS B460 M4 Blade Server Specification Value Height 4.04 inches (102.6 mm) Width 16.50 inches (419.1 mm) Depth 25.5 inches (647.7 mm) Weight 67.4 lbs (30.5 kg) The system weight listed here is an estimate for a fully configured system and will vary depending on peripheral devices installed. 36 Revised: April 17, 2015, OL-31494-01 Related Cisco UCS Documentation Documentation Roadmaps For a complete list of all B-Series documentation, see the Cisco UCS B-Series Servers Documentation Roadmap available at the following URL: http://www.cisco.com/go/unifiedcomputing/b-series-doc. For a complete list of all C-Series documentation, see the Cisco UCS C-Series Servers Documentation Roadmap available at the following URL: http://www.cisco.com/go/unifiedcomputing/c-series-doc. Other Documentation Resources Follow Cisco UCS Docs on Twitter to receive document update notifications. Revised: April 17, 2015, OL-31494-01 Obtaining Documentation and Submitting a Service Request For information on obtaining documentation, submitting a service request, and gathering additional information, see the monthly What's New in Cisco Product Documentation, which also lists all new and revised Cisco technical documentation. Subscribe to the What's New in Cisco Product Documentation as a Really Simple Syndication (RSS) feed and set content to be delivered directly to your desktop using a reader application. The RSS feeds are a free service and Cisco currently supports RSS version 2.0. Follow Cisco UCS Docs on Twitter to receive document update notifications. 38 THE SPECIFICATIONS AND INFORMATION REGARDING THE PRODUCTS IN THIS MANUAL ARE SUBJECT TO CHANGE WITHOUT NOTICE. ALL STATEMENTS, INFORMATION, AND RECOMMENDATIONS IN THIS MANUAL ARE BELIEVED TO BE ACCURATE BUT ARE PRESENTED WITHOUT WARRANTY OF ANY KIND, EXPRESS OR IMPLIED. USERS MUST TAKE FULL RESPONSIBILITY FOR THEIR APPLICATION OF ANY PRODUCTS. THE SOFTWARE LICENSE AND LIMITED WARRANTY FOR THE ACCOMPANYING PRODUCT ARE SET FORTH IN THE INFORMATION PACKET THAT SHIPPED WITH THE PRODUCT AND ARE INCORPORATED HEREIN BY THIS REFERENCE. IF YOU ARE UNABLE TO LOCATE THE SOFTWARE LICENSE OR LIMITED WARRANTY, CONTACT YOUR CISCO REPRESENTATIVE FOR A COPY. The following information is for FCC compliance of Class A devices: This equipment has been tested and found to comply with the limits for a Class A digital device, pursuant to part 15 of the FCC rules. These limits are designed to provide reasonable protection against harmful interference when the equipment is operated in a commercial environment. This equipment generates, uses, and can radiate radio-frequency energy and, if not installed and used in accordance with the instruction manual, may cause harmful interference to radio communications. Operation of this equipment in a residential area is likely to cause harmful interference, in which case users will be required to correct the interference at their own expense. The following information is for FCC compliance of Class B devices: This equipment has been tested and found to comply with the limits for a Class B digital device, pursuant to part 15 of the FCC rules. These limits are designed to provide reasonable protection against harmful interference in a residential installation. This equipment generates, uses and can radiate radio frequency energy and, if not installed and used in accordance with the instructions, may cause harmful interference to radio communications. However, there is no guarantee that interference will not occur in a particular installation. If the equipment causes interference to radio or television reception, which can be determined by turning the equipment off and on, users are encouraged to try to correct the interference by using one or more of the following measures: • Reorient or relocate the receiving antenna. • Increase the separation between the equipment and receiver. • Connect the equipment into an outlet on a circuit different from that to which the receiver is connected. • Consult the dealer or an experienced radio/TV technician for help. Modifications to this product not authorized by Cisco could void the FCC approval and negate your authority to operate the product The Cisco implementation of TCP header compression is an adaptation of a program developed by the University of California, Berkeley (UCB) as part of UCB’s public domain version of the UNIX operating system. All rights reserved. Copyright © 1981, Regents of the University of California. NOTWITHSTANDING ANY OTHER WARRANTY HEREIN, ALL DOCUMENT FILES AND SOFTWARE OF THESE SUPPLIERS ARE PROVIDED "AS IS" WITH ALL FAULTS. CISCO AND THE ABOVE-NAMED SUPPLIERS DISCLAIM ALL WARRANTIES, EXPRESSED OR IMPLIED, INCLUDING, WITHOUT LIMITATION, THOSE OF MERCHANTABILITY, FITNESS FOR A PARTICULAR PURPOSE AND NONINFRINGEMENT OR ARISING FROM A COURSE OF DEALING, USAGE, OR TRADE PRACTICE. IN NO EVENT SHALL CISCO OR ITS SUPPLIERS BE LIABLE FOR ANY INDIRECT, SPECIAL, CONSEQUENTIAL, OR INCIDENTAL DAMAGES, INCLUDING, WITHOUT LIMITATION, LOST PROFITS OR LOSS OR DAMAGE TO DATA ARISING OUT OF THE USE OR INABILITY TO USE THIS MANUAL, EVEN IF CISCO OR ITS SUPPLIERS HAVE BEEN ADVISED OF THE POSSIBILITY OF SUCH DAMAGES. Any Internet Protocol (IP) addresses and phone numbers used in this document are not intended to be actual addresses and phone numbers. Any examples, command display output, network topology diagrams, and other figures included in the document are shown for illustrative purposes only. Any use of actual IP addresses or phone numbers in illustrative content is unintentional and coincidental. Cisco and the Cisco logo are trademarks or registered trademarks of Cisco and/or its affiliates in the U.S. and other countries. To view a list of Cisco trademarks, go to this URL: http:// www.cisco.com/go/trademarks. Third-party trademarks mentioned are the property of their respective owners. The use of the word partner does not imply a partnership relationship between Cisco and any other company. (1110R) © 2014 Cisco Systems, Inc. All rights reserved. Americas Headquarters Cisco Systems, Inc. San Jose, CA 95134-1706 USA Asia Pacific Headquarters Cisco Systems (USA) Pte. Ltd. Singapore Europe Headquarters Cisco Systems International BV Amsterdam, The Netherlands Cisco has more than 200 offices worldwide. Addresses, phone numbers, and fax numbers are listed on the Cisco Website at www.cisco.com/go/offices.
advertisement
* Your assessment is very important for improving the workof artificial intelligence, which forms the content of this project
Related manuals
advertisement