- Computers & electronics
- Computer components
- System components
- Internal hard drives
- Conner
- CFP2105W
- Product Manual
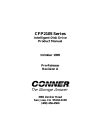
advertisement
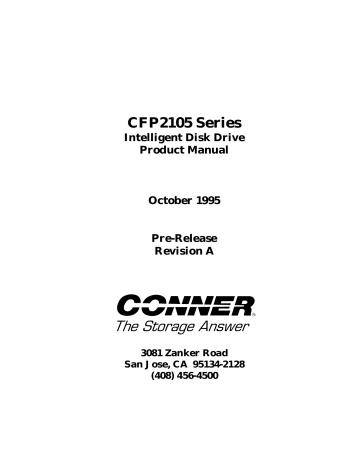
CFP2105 Series
Intelligent Disk Drive
Product Manual
October 1995
Pre-Release
Revision A
3081 Zanker Road
San Jose, CA 95134-2128
(408) 456-4500
FCC Notice
This equipment generates and uses radio frequency energy and, if not installed and used properly; that is, in strict accordance with the manufacturer's instructions, may cause interference to radio and television reception. It has been type tested and found to comply with the limits for a Class B computing device in accordance with the specifications in Part 15 of FCC Rules, which are designed to provide reasonable protection against such interference in a residential installation. However, there is no guarantee that interference will not occur in a particular installation. If this equipment does cause interference to radio or television reception, which can be determined by turning the equipment on and off, you are encouraged to try to correct the interference by one or more of the following measures:
• Reorient the receiving antenna.
• Relocate the computer with respect to the receiver.
• Move the computer into a different outlet so that the computer and receiver are on different branch circuits.
If necessary, you should consult the dealer or an experienced radio/television technician for additional suggestions. You may find the following booklet prepared by the Federal Communications Commission helpful:
How to Identify and Resolve Radio-TV Interference Problems
This booklet (Stock No. 004-000-00345-4) is available from the U.S. Government
Printing Office, Washington, DC 20402.
Warning: Changes or modifications made to this equipment which have not been expressly approved by Conner Peripherals, Inc. may cause radio and television interference problems that could void the user's authority to operate the equipment.
Further, this equipment complies with the limits for a Class B digital apparatus in accordance with Canadian Radio Interference Regulations.
Cet appareil numérique de la classe B est conforme au Règlement sur le brouillage radioélectrique, C.R.C., ch. 1374.
Conner and the Conner logo are registered trademarks of Conner Peripherals,
Inc. All other trademarks mentioned in this manual are property of their respective owners.
Copyright 1994, 1995, Conner Peripherals, Inc.
All rights reserved.
Document No. 501-072 10/95
Important Information About this Manual
All information contained in or disclosed by this document is considered proprietary by Conner Peripherals, Inc. By accepting this material, the recipient agrees that this material and the information contained therein are held in confidence and in trust and will not be used, reproduced in whole or in part, nor its contents revealed to others, except to meet the purpose for which it was delivered. It is understood that no right is conveyed to reproduce or translate any item herein disclosed without express written permission from Conner
Peripherals, Inc.
Conner Peripherals, Inc. provides this manual "as is," without warranty of any kind, either expressed or implied, including, but not limited to, the implied warranties of merchantability and fitness for a particular purpose. Conner
Peripherals, Inc. reserves the right to change, without notification, the specifications contained in this manual.
Conner Peripherals, Inc. assumes no responsibility for the accuracy, completeness, sufficiency, or usefulness of this manual, nor for any problem that might arise from the use of the information in this manual.
Table of Contents
1.
Overview of the Drives
What are the Drives?
Differences Between the Models
Features of the Drive
Drive Composition
Mechanical Design Features
Head Disk Assembly
Head Positioning Mechanism
Read/Write Heads and Disks
Data and Power Connections
Electrical Design Features
Integrated Circuit
Circuit Board
Firmware
2. Specifications
Specifications in this Chapter
Drive Capacity
Formatted Capacity*
Physical Configuration
Physical Configuration
Performance Characteristics
Seek Times (typical)*
Average Latency
Rotation Speed (+0.1%)
Controller Overhead
Start Time(Power Up)*
Stop Time at Power Down
Interleave
Read/Write Characteristics
Recording Method
Recording Density (maximum)
Flux Density (maximum)
Host Interface Characteristics
Command Set
Data Transfer Rate
Maximum Synchronous Transfer Offset:
Maximum Tagged Command Queue Depth:
Buffer Size:
Reliability
Data Reliability
Component Design Life
Start/Stop cycles
Mean Time Between Failures:
Preventive Maintenance
Power Requirements (Typical)
Minimum/Maximum Voltage:
Table of Contents
1
5
5
3
4
2
3
1
1
5
5
5
5
6
9
13
13
13
13
13
14
14
12
12
12
13
12
12
12
12
11
12
12
12
11
11
11
11
10
11
11
11
9
10
10
10
Page i
Table of Contents
Page ii
Filepro CFP2105 Series
Environmental Tolerances
Magnetic Field:
Acoustic Noise:
Safety Standards
Physical Characteristics - CFP2105E
Physical Characteristics - CFP2105S
Physical Characteristics - CFP2105W
3. Drive Operations
Functions of the Drive
Drive Operational Modes
Data Error Correction
Downloadable Microcode
Buffer Management and Command Execution
Read Look Ahead Code
Write Caching
Tagged Command Queuing
Seek Re-ordering
Buffer Management
4. Installing the Drive
Take These Precautions
Installing the Drive
Installing a CFP2105E
Setting the Drive's Jumpers - CFP2105E
Setting the SCSI Bus Address - CFP2105E
Disabling Spin-Up at Power On - CFP2105E
Delaying Spin Up at Power On - CFP2105E
Cabling the Drive - CFP2105E
Attaching Power to the Drive - CFP2105E
Mounting the Drive - CFP2105E
Mounting Screw Holes
Cooling
Installing a CFP2105S
Setting the Drive's Jumpers - CFP2105S
Setting the SCSI Bus Address - CFP2105S
Disabling Spin-Up at Power On - CFP2105S
Delaying Spin Up at Power On - CFP2105S
Disabling the SCSI Bus Parity - CFP2105S
Disabling SCSI Bus Terminator Power (TERMPWR) -
CFP2105S
Setting the Bus Termination - CFP2105S
Cabling the Drive - CFP2105S
SCSI Bus Cable
Spindle Synchronization
Attaching Power to the Drive - CFP2105S
Mounting the Drive - CFP2105S
Mounting Screw Holes
Cooling
Installing a CFP2105W
Setting the Drive’s Jumpers - CFP2105W
Setting the SCSI Bus Address - CFP2105W
Disabling Spin-Up at Power On - CFP2105W
Filepro CFP2105 Series
37
38
38
38
35
36
37
37
38
40
40
41
42
32
32
33
34
30
31
31
31
34
35
28
29
29
29
27
27
28
28
23
23
25
26
21
21
22
22
26
26
27
15
15
15
16
17
18
19
21
Filepro CFP2105 Series Table of Contents
Delaying Spin Up at Power On - CFP2105W
Disabling the SCSI Bus Parity - CFP2105W
42
43
Disabling SCSI Bus Terminator Power (TERMPWR) -
CFP2105W
Using the J5 Auxiliary Connector
- SEL0
- XTFAULT
- SEL1
- VUNIQ
- SEL2
- SPSYNC
- SEL3
- XTACTV
- GROUND
+5 Volts
- FAULT
Setting the Bus Termination - CFP2105W
Cabling the Drive - CFP2105W
SCSI Bus Cable
Mixing Wide and Narrow SCSI Devices on a SCSI Bus
Spindle Synchronization
44
44
44
45
45
45
45
45
46
46
46
46
46
47
48
48
49
Error! Bookmark not defined.
Attaching Power to the Drive - CFP2105W
Mounting the Drive - CFP2105W
Mounting Screw Holes
Cooling
47
47
47
47
5. Interface Physical Characteristics 49
Electrical Description
Output Characteristics
Input Characteristics
Model-Specific SCSI Physical Characteristics
CFP2105E (WIDE, 80-pin Single Connector Attachment [SCA])
External Terminator Power
Internal Termination
Cable Requirements
Connector Requirements
Single Connector Attachment (SCA) Signal Definitions
Power
Spindle Sync
LED Out
Motor Start Controls
SCSI ID Selection
Interface Pin Assignments
Interface Timing Requirements
Model CFP2105S (Narrow, 50-pin SCSI)
External Terminator Power
Internal Termination
Cable Requirements
Connector Requirements
Interface Pin Assignments
Interface Timing Requirements
Model CFP2105W (Wide, Unitized SCSI-3 P-Connector)
External Terminator Power
Internal Termination
56
57
58
59
54
55
55
55
60
60
60
52
52
52
53
51
51
51
52
51
51
51
51
49
49
50
50
Technical Reference Manual Page iii
Table of Contents Filepro CFP2105 Series
J5 Auxiliary Connector Signal Characteristics
Cable Requirements
Connector Requirements
Interface Pin Assignments
Interface Timing Requirements
6. SCSI Command Implementation
SCSI Command Summary
Drive Dependent SCSI Data
Error! Bookmark not defined.
Format Drive Page - 03H
Drive Geometry Page - 04H
Notch and Partition Parameters Page - 0CH
67
68
70
71
61
61
62
64
65
67
Page iv Filepro CFP2105 Series
Overview of the Drives
1
What are the Drives?
The CFP2105 series is a family of high performance 3.5-inch low-profile (1.0 inch high) 2.1GB (formatted) disk drives. They all offer 9.5 millisecond average seek time for Reading , 10.5 millisecond seek time for Writing, with an average latency of only 5.56 ms. High capacity is achieved by utilizing a zone density recording technique using 15 recording zones at an areal density of 302 Mbits per square inch. These drives feature high performance while maintaining low power consumption to reduce power supply current and system cooling requirements in disk arrays.
They are designed to operate on the Small Computer System Interface (SCSI) and are SCSI-2/3 command compatible. The mechanical and major electronic components are identical between the models and differ only in the host interface implementation:
Drive Model Form Factor
CFP2105E
CFP2105S
CFP2105W
1 inch high, 3.5 inch
1 inch high, 3.5 inch
1 inch high, 3.5 inch
Interface
80-pin Single Connector
FAST WIDE
50-pin FAST
68-pin FAST WIDE
Capacity
2147 MB
2147 MB
2147 MB
For simplicity, we often refer to these drives collectively in this manual as “the drive.”
Differences Between the Models
The three drive models differ only on the host interface implementation:
CFP2105E:
SCSI 80-pin Wide Single Connector Attachment (SCA) interface designed for applications such as Redundant Arrays in which the drives are plugged directly into a backplane. The drive also implements a Wide SCSI interface for high interface bandwidth.
CFP2105S:
SCSI 50-pin standard interface designed for applications which implement the standard SCSI-2 architecture.
CFP2105W:
SCSI 68-pin Wide interface designed for applications which require high interface bandwidth and the option of cabled interconnect. The drive utilizes the Unitized Connector defined by the Small Form Factor
Committee (refer to SFF-8009). The Unitized Connector combines the SCSI-3 Pconnector Wide interface, the standard 4-pin power and a 2mm pin pitch
Auxiliary connector into a single molded assembly.
Technical Reference Manual Page 1
Chapter 1 Overview of the Drives
Features of the Drive
The drive provides the following features:
•
512 KB segmentable cache buffer with adaptive cache management
•
Least Recently Used (LRU) Cache replacement
•
Automatic on-the-fly data error correction utilizing a 96-bit Reed-Solomon
EDAC.
•
Independent 48-bit CRC miscorrection detection.
•
On the fly header error detection and correction.
•
High performance rotary voice coil actuator with embedded servo system
•
No thermal recalibration required to maintain performance levels
•
High Shock resistance
•
Automatic actuator latch against the inner stop upon power down with dedicated landing zone
•
Active Termination with removable Resistor Packs
•
Active Negation output drivers for greater interface reliability
•
SCSI-2/3 Compatibility
•
Dual Microprocessor-controlled diagnostic routines that automatically execute at start-up
•
Sealed HDA
•
Down-loadable Code through SCSI Interface
•
1,7 run length limited code
•
Programmable Block Size (512 and 1024)
•
Tagged Command Queuing with Seek Re-ordering and Write/Read
Coalescing
Page 2 Filepro CFP2105 Series
Overview of the Drives Chapter 1
Drive Composition
The drive is composed of mechanical, electrical, and firmware elements.
Mechanical Design Features
The drive’s hardware includes the components described in the following sections. Figure 1-1 shows the drive top level assembly.
Figure 1-1
Drive Top Level Assembly
Damper
Head-Disk
Assembly
Printed Circuit
Board Assembly
Shield
Printed
Circuit
Board
Assembly
2105-1-1
Technical Reference Manual Page 3
Chapter 1 Overview of the Drives
Head Disk Assembly
The Head-Disk Assembly (HDA) consists of a die-cast aluminum base on which is mounted a die-cast aluminum cover. Both the base and the cover are made from a corrosion resistant aluminum alloy. A gasket seals the joint between the base and cover to retard the entry of moisture and environmental contaminants.
The head-disk assembly, contains an integral 0.3 micron filter, which maintains a clean environment. Critical drive components are contained within this contaminant-free environment. Figure 1-2 shows the HDA and the major subassemblies contained within it:
Figure 1-2
Head-Disk Assembly
Top Cover
Disk Clamp
Disk (1 of 5)
Disk
Spacer (1 of 4)
Filter
Gasket
Preamplifier/
Flex Circuit
Assembly
Head-Stack
Assembly
Page 4
2107_1_2
Spindle Motor
Base Assembly
Actuator
Magnet
Assembly
Filepro CFP2105 Series
Overview of the Drives Chapter 1
Drive Motor and Spindle
A brushless DC direct-drive motor assembly is mounted on the drive’s base. The motor rotates the drive’s spindle at 5400 RPM. This motor/spindle assembly is dynamically balanced to provide minimal mechanical runout to the disks. A dynamic brake is used to provide a fast stop to the spindle motor and return the heads to the landing zone when power is removed.
Head Positioning Mechanism
The read/write heads are supported by a mechanism coupled to a rotary voice coil actuator.
Read/Write Heads and Disks
Data is recorded on 95mm diameter disks through 3370-type 50% nano-slider thin film heads with transverse pressure contour (TPC) air bearing surfaces.
The TPC air bearing surface allows the head to fly at a uniform height regardless of radial position. This improves data reliability and allows the aerial density to be more uniform with radius. The CFP2105 series contains five sputtered thin film disks with ten data surfaces and ten read/write heads.
At power-down, the heads are automatically retracted to the inner diameter of the disk and are latched and parked on a landing zone that is inside the data tracks.
Data and Power Connections
Data and power connections to the drive differ between the drive models. Refer to chapter 4 for information regarding a specific model's requirements.
Electrical Design Features
Integrated Circuit
A single integrated circuit (IC) is mounted within the HDA in close proximity to the read/write heads. The IC provides head selection, read pre-amplification, and write drive circuitry.
Circuit Board
The drive’s dual-microprocessor-controlled circuit board provides the remaining electronic functions, which include:
• read/write circuitry
• rotary actuator control
• interface control
• spin speed control
• auto-park
• power management
Technical Reference Manual Page 5
Chapter 1
Firmware
Page 6
Overview of the Drives
The background processor is a 16-bit Motorola 68HC16. The entire data path between the serializer-deserializer and the interface chip, including the buffer
(cache) is 16 bits wide to provide high data throughput. The SCSI interface chip manages a 16-bit to 8-bit conversion prior to transacting data over the SCSI bus for 8-bit narrow SCSI applications.
The data buffer (cache) utilizes a 256K x 16 Dynamic RAM. Data path integrity is ensured by using a 4-byte CRC which is appended to the data upon receipt by the SCSI Interface Chip. This CRC is verified by the buffer manager when the data is taken out of the buffer to be written to the disk and the CRC is written with the data. A typical sector data field consists of 512 bytes of data, 4 bytes of
CRC and 18 bytes of Error Detection And Correction (EDAC) code. The same
CRC checks are performed during an outbound process and the CRC is stripped from the data prior to sending it to the Host.
The SCSI interface functions are managed by a 8-bit Motorola 68HC11 microprocessor. Low SCSI transaction overhead is maintained by automating common SCSI bus phase sequencing using a state machine in the SCSI Interface
Chip.
Read/Write Channel
The Read/Write channel, in addition to the preamplifier discussed earlier, consists of three integrated circuits:
•
Pulse Detector
•
Data Separator
•
Time base
The drive’s firmware can be considered in two parts. The first part principally resides in the ROM for the 68HC16 background processor. This processor is responsible for:
• starting the spindle motor and maintaining precise rotational speed
• controlling track following and actuator motion during seeking
• managing background R/W activity
• power management
• monitoring the overall health of the drive.
The interface processor's control microcode resides in both ROM and RAM. The
RAM portion of the microcode can be upgraded in the field with using software.
Additional information regarding the RAM code can be found in Chapter 3, page
22. The interface processor firmware functions include:
• reporting drive status and error conditions to the host
• manage operating parameters for the drive
• parsing the Command Descriptor Block and checking for illegal fields
• converting the LBA to CHS and initiating read and write operations to the background processor
• defect management
Filepro CFP2105 Series
Overview of the Drives Chapter 1
• serial port communications
Since parsing/decoding of commands and execution of the Read/Write functions are handled by separate processors, command execution can be overlapped in multiple initiator or Tagged Command Queuing environments. Functions such as seek re-ordering and command coalescing can also be overlapped when the drive is operating with a host environment capable of supporting Tagged
Command Queuing.
For more information on the drive’s interface implementation and command set, refer to the Eleventh Generation SCSI Interface Manual.
Technical Reference Manual Page 7
Chapter 1 Overview of the Drives
Page 8 Filepro CFP2105 Series
Specifications
Specifications in this Chapter
This chapter provides the following specifications for the drive:
• drive capacity
• physical configuration
• performance characteristics
• read/write characteristics
• reliability
• power requirements
• environmental tolerances
• safety standards
• physical characteristics
2
Technical Reference Manual Page 9
Chapter 2
Drive Capacity
Formatted Capacity*
•
CFP2105 Series: 2147 MB
*1MB is equal to 10
6
or 1,000,000 bytes
Physical Configuration
Specification:
Disk Type
Head Type
Actuator Type
Number of Disks
Data Surfaces
Data Heads
Servo
Tracks per Surface
Track Density @ 0
°
Skew
Bytes per Block
Blocks per Drive (logical)
CPF2105 Series
Sputtered Thin film
Thin Film - TPC
Rotary Voice-Coil
5
10
10
Embedded
3948
4030 TPI
512
4,194,304
Specifications
Physical Configuration
Data Rate
(Mbits/sec)
Zone 0 (OD)
Zone 1
Zone 2
Zone 3
Zone 4
Zone 5
Zone 6
Zone 7
Zone 8
Zone 9
Zone 10
Zone 11
Zone 12
Zone 13
Zone 14 (ID)
68.7
65.1
62.7
60.6
57.9
54.7
53.5
50.9
48.5
45.5
43.0
41.1
37.1
35.1
33.3
Data Tracks per
Zone per Surface
356
175
228
254
266
362
433
271
244
307
222
166
360
182
114
User Sectors per Track *
111
108
103
99
92
139
132
127
122
119
87
83
79
71
67
* The physical track configuration contains one spare sector per track.
Page 10 Filepro CFP2105 Series
Specifications Chapter 2
Performance Characteristics
Seek Times (typical)*
•
Track to Track: 1.9 msec
•
Average (read/write): 9.5/10.5 msec**
•
Full Track: 21 msec
* The timing is measured from the time the last byte of the command descriptor block is written to the time seek is initiated by the drive operating at nominal DC input voltage and nominal operating temperature.
** The average seek time is determined by averaging the seek time for a minimum of
1000 seeks of random length over the surface of the disk.
Average Latency
•
5.56 milliseconds
Rotation Speed (+0.1%)
•
5400 RPM
Controller Overhead
•
700
µ sec
Start Time(Power Up)*
•
0 RPM to Ready
−
Typical: 12 seconds
* This assumes spin recovery is not invoked. If spin recovery is invoked, the maximum could be 40 seconds. Briefly removing power can lead to spin recovery being invoked.
Stop Time at Power Down
•
Typical: 7 seconds
•
Maximum: 10 seconds
Interleave
•
1:1
Technical Reference Manual Page 11
Chapter 2
Read/Write Characteristics
Recording Method
•
1,7 RLL code
Recording Density (maximum)
•
73,900 bits per inch
Flux Density (maximum)
•
55,400 flux reversals per inch
Specifications
Host Interface Characteristics
Command Set
•
SCSI-2 (refer to the Eleventh Generation SCSI Technical Reference Manual for command implementation)
Data Transfer Rate
•
To/from Buffer, synchronous narrow: 10.0 MByte/second
•
To/from Buffer, synchronous wide: 20.0 MByte/second
Maximum Synchronous Transfer Offset:
•
15 bytes/words
Maximum Tagged Command Queue Depth:
•
32 commands
Buffer Size:
•
512 KB, segmentable
Page 12 Filepro CFP2105 Series
Specifications
Reliability
Data Reliability
•
< 1 non-recoverable error in 10
14
bits read
Component Design Life
•
5 years
Start/Stop cycles
•
20,000 minimum
Mean Time Between Failures:
•
1,000,000 power-on hours*
* Projected MTBF based on comparison of similar Conner products
Preventive Maintenance
•
None
Chapter 2
Technical Reference Manual Page 13
Chapter 2 Specifications
Power Requirements (Typical)
Mode
Read/Write
Seek (100%)
Seek (40%)
Idle
Standby
Spin-up
+12V DC
(typical 1)
340 mA
760 mA
400 mA
320 mA
1 mA
1.7 A
+5V DC
(typical 2)
600 mA
470 mA
400 mA
400 mA
640 mA
700 mA
Power
(typical)
7.0 W
11.5 W
6.8 W
5.8 W
3.2 W
N/A
Power
(maximum)
7.6 W
12.2 W
7.0W
6.2 W
3.4 W
N/A
1 Typical conditions are both voltages at nominal value, room temperature (25° C) ambient to the drive without terminators installed. Maximum power is when the supply voltage is at the worst case condition.
2 Termination current of 700mA for narrow SCSI and 900 mA for wide SCSI is required for that device which is terminated.
Minimum/Maximum Voltage:
•
+5V: +5%
•
+12V: +5%
Maximum Peak-to-Peak Allowable Noise
(DC to 1 Mhz: equivalent resistive load):
•
+5V: 2%
•
+12V: 1%
Page 14 Filepro CFP2105 Series
Specifications
Environmental Tolerances
Temperature:
•
Operating: 5° to 55° C
•
Non-operating: -40° to 60° C
•
Thermal Gradient: 20° C per hour maximum
Relative Humidity (non-condensing):
•
Operating: 5 to 95%
•
Non-operating: 5 to 95%
•
Maximum Wet Bulb: 29°C
Altitude (relative to sea level):
•
Operating: -200 to 10,000 feet
•
Non-operating: 40,000 feet (maximum)
•
Altitude Gradient: 1,000 feet/minute
Shock (half-sine pulse, 11 ms duration):
•
Operating: 5G peak without non-recoverable errors
•
Non-operating: 75G without non-recoverable errors
Vibration (swept-sine, one octave per minute):
•
Operating
−
5 - 32 Hz: 0.010 inch displacement; peak to peak
−
33 - 400 Hz: 0.5G without non-recoverable errors
•
Non-operating
−
5 - 28 Hz: 0.100 inch displacement; peak to peak
−
29 - 400 Hz: 4G peak
Chapter 2
Magnetic Field:
•
The disk drive will meet its specified performance while operating in the presence of an externally-produced magnetic field under the following conditions:
Field Frequency
DC to 700 Khz
700 Khz to 1.5 Mhz
Intensity
6 gauss
7 milligauss
3 milligauss
Acoustic Noise:
•
The acoustic level will not exceed 4.3 Bels sound power in Idle Mode.
Technical Reference Manual Page 15
Chapter 2 Specifications
Safety Standards
The drive is designed to comply with relevant product safety standards, including:
•
UL 478, 5th edition, Standard for Safety of Information Processing and
Business Equipment
•
UL 1950, Standard for Safety of Information Technology Equipment
•
CSA 22.2 #220, Information Processing and Business Equipment
•
CSA 22.2 #950, Safety of Information Technology Equipment
•
IEC 380, Safety of Electrically Energized Office Machines
•
IEC 950, Safety of information Technology Equipment Including Electrical
Business Equipment
•
VDE 0805, VDE 0805 TIEL 100, and VDE 0806
•
Complies with FCC Class B, Part 15, Subpart J
Page 16 Filepro CFP2105 Series
Specifications
Physical Characteristics - CFP2105E
Height:
•
1.0 inch + .020
Width:
•
4.0 inches + .015
Depth:
•
5.75 inches +.03/
-
.01
Weight:
•
1.4 pounds
Figure 2-2
The Drive’s Physical Dimensions
0.41 [10.41]
MAXIMUM
Zone
6X
6-32 UNC-2B
.16 [4.06] MAX.
INSERTION
4.000 +0.015
[101.60 +0.38]
Chapter 2
.153 +0.016
[3.89 +0.41]
5.120
+0.032
-
0.017
+0.81
0.43
2.362
[59.99]
4.000
[101.60]
5.75
+0.03
-
0.01
+0.76
-
0.25
5.120 +0.024
[130.05 +0.61]
1.008 +0.022
[25.60 +0.56]
Pin 1 Ref.
4.00
+.00
-
.01
+0.00
[ ] w/in Zone
4X 6-32 UNC-2B
.22 [5.59] MAX. INSERTION
1.750
[44.45]
2.375 +0.015
[60.33 +0.38]
1.00 +0.02
[25.40 +0.51]
.63 [16.00]
.250 [6.36]
.125 +0.010
[3.18 +0.25]
Tolerance: .xxx +.005
.xx +.020
210X-2-2
3.750 [95.25]
2.623 +0.018
[66.62 +0.46]
.065 +0.018
[1.65 +0.46]
Technical Reference Manual Page 17
Chapter 2
Physical Characteristics - CFP2105S
Height:
•
1.0 inch + .020
Width:
•
4.0 inches + .015
Depth:
•
5.75 inches +.03/
-
.01
Weight:
•
1.4 pounds
Figure 2-3
The Drive’s Physical Dimensions
.41 [10.41]
MAXIMUM
Zone
4.000 +0.015
[101.60 +0.38]
Specifications
.140 +0.019
[3.56 +0.48]
2.734 +0.018
[69 44 +0.46]
.975 +0.005
[24.77 +0.13]
4.00
+.00
-.01
[ ]
-0.25
w/in Zone
.190 +0.016
[4.83 +0.41]
4X 6-32 UNC-2B
.22 [5.59] MAX. INSERTION
6X
6-32 UNC-2B
.16 [4.06] MAX.
INSERTION
4.000
[101.60]
5.75
+0.03
-
0.01
+0.76
[ ]
1.750
[44.45]
2.362
[59.99]
2.375 +0.015
[60.33 +0.38]
1.00 +0.02
[25.40 +0.51]
.250 [6.36]
.63 [16.00]
.125 +0.010
[3.18 +0.25]
Tolerance: .xxx +.005
.xx +.020
3.750 [95.25]
3.413 +0.018
[86.69 +0.46]
2.623 +0.018
[66.62 +0.46]
.065 +0.018
[1.65 +0.46]
210X-2-3
Page 18 Filepro CFP2105 Series
Specifications
Physical Characteristics - CFP2105W
Height:
•
1.0 inch + .020
Width:
•
4.0 inches + .015
Depth:
•
5.75 inches +.03/
-
.01
Weight:
•
1.4 pounds
Figure 2-4
The Drive’s Physical Dimensions
4.000 +0.015
[101.60 +0.38]
0.41 [10.41]
MAXIMUM
Zone
1.977 +0.018
[50.22 +0.46]
2.720 +0.018
[69.09 +0.46]
4.00
+.00
-.01
1.610 +0.005
[40.89 +0.13] w/in Zone
Chapter 2
.190 +0.016
[4.83 +0.41]
4X 6-32 UNC-2B
.22 [5.59] MAX. INSERTION
6X
6-32 UNC-2B
.16 [4.06] MAX.
INSERTION
4.000
[101.60]
5.75
+0.03
-
0.01
2.362
[59.99]
1.00 +0.02
[25.40 +0.51]
.63 [16.00]
.250 [6.36]
.125 +0.010
[3.18 +0.25]
Tolerance: .xxx +.005
.xx +.020
210X-2-4
Technical Reference Manual
3.750 [95.25]
2.623 +0.018
[66.62 +0.46]
1.750
[44.45]
2.375 +0.015
[60.33 +0.38]
.065 +0.018
[1.65 +0.46]
Page 19
Chapter 2 Specifications
Page 20 Filepro CFP2105 Series
Drive Operations
3
Functions of the Drive
This chapter describes certain operational aspects of the drive, including discussions of:
• drive operational modes
• error correction
• read error recovery
• downloadable microcode
• buffer management
Drive Operational Modes
For the purpose of defining power requirements the following modes have been defined:
••
Read/Write Mode without seeking or head switching data is read from or written to the disk continuously.
••
Seek Mode (100%) occurs when the drive is issued continuous seek commands and the actuator is in motion
••
Seek Mode (40%) occurs when 1/3 stroke seeks are performed at a 40% seek duty cycle. While the actuator is not in motion the drive is reading or writing.
••
Idle Mode occurs when the drive is not reading, writing, or seeking. The motor is up to speed and the Drive Ready condition exists. The actuator is residing on the last-accessed track.
••
Standby Mode occurs when the motor is stopped and the actuator is latched in the landing zone. The drive will enter Standby mode after poweron reset if the Disable Spin jumper is installed or the DSPN bit in MODE
SELECT page 0 is set. A STOP UNIT command will also place a drive into
Standby Mode. The drive will spin up and go into Idle mode when a START
UNIT command is issued or on a timed basis by SCSI ID if the SDLY bit is set in MODE SELECT page 0. Refer to the MODE SELECT and MODE
SENSE commands in the Eleventh Generation SCSI Interface Manual for additional details.
••
Spin-Up Mode occurs while the drive's spindle motor is being spun up to speed after initial power on or after exiting Standby Mode.
Technical Reference Manual Page 21
Chapter 3 Drive Operations
Data Error Correction
The drive uses a three way interleaved 96-bit Reed-Solomon code to perform error correction. An additional 48-bit Cyclic Redundancy Code (CRC) provides additional miscorrection detection. For each 512-byte block, the on-the-fly error correction polynomial is capable of correcting:
• one error burst of up to 41 bits in length
• two error bursts each up to 17 bits in length
The miscorrection probability is less than 1 bit in 10
24
bits transfered.
Downloadable Microcode
The SCSI interface code is split into two parts which are designated as ROM or
RAM code. The ROM code contains the basic SCSI operating code and code to support commands such as INQUIRY, TEST UNIT READY, REQUEST SENSE,
START/STOP UNIT, etc., which may have to be responded to prior to the drive being in a ready state. The part of the interface code referred to as RAM code resides on an area of the disk which is reserved to the drive and is not directly accessible through the interface. This code is referred to as RAM code because it is read from the disk and is loaded into static RAM after power is applied to the disk, as soon as the drive is able to read from the disk.
The RAM code consists of a resident portion which is loaded after a Power On
Reset. Two different versions of RAM code overlays also reside on the disk. The read look ahead code overlay is the default and is loaded into RAM during the initial power-on. If a Queue Tag message is received by the drive, the drive will execute the command and while it is in Status Phase, will read the Queuing code overlay from the disk and load it into the RAM. This operation takes about 600 milliseconds, after which the drive will complete the command by sending the status. The drive will continue to operate with Queuing code residing in RAM until the next Power On Reset.
Refer to the next section for a discussion of the buffer management implications for the different RAM codes.
The RAM code may be upgraded on the disk via the factory serial port or through the interface using the WRITE BUFFER command. Refer to the
WRITE BUFFER command in the Eleventh Generation SCSI Interface Manual for a discussion of the procedure.
Page 22 Filepro CFP2105 Series
Drive Operations Chapter 3
Buffer Management and Command Execution
The drive contains a 512Kbyte segmentable buffer which is dynamically configured to adapt to the particular drive configuration or operating environment.
Read Look Ahead Code
The Read Retention RAM code executes commands sequentially as they are received from the initiator(s). Commands from multiple initiators may be queued and overlapped so that the subsequent command can be parsed while the current command is being executed.
The drive's 512K byte buffer is configured as four segments. These segments allow the drive to cache sequential data from four separate areas on the disk.
This can significantly improve performance in any environment in which multiple disk files are kept open simultaneously and operated upon in some interleaved fashion.
The Look-Ahead RAM code segments the 512 KB buffer into four 130,548 byte
(FD
H
blocks) segments. The remainder of the RAM is used by the microprocessor as a scratch pad area and for non read or write data information transfers. The buffer block size is equal to the data block size (typically 512 B) plus the 4 bytes of buffer CRC appended to each block. (refer to the Electrical
Design Feature section in Chapter 1 for a description of the buffer CRC).
Buffer operations default on Power-up to Read Look Ahead enabled and Write
Caching disabled. MODE SELECT page 8, byte 2, bit 0 (RCD), when set to one disables the read look-ahead cache function and bit 2 (WCE), when set to one enables write cache. In addition, MODE SELECT page 8, byte 3 contains two fields which control the retention priority for reads and writes. Refer to the
Eleventh Generation Disk Drive SCSI Interface Manual for additional details.
When a read command is received by the disk drive, the cache tables are searched to determine if the requested data is contained in any of the four cache segments (a cache hit). If there is no cache hit, the Least Recently Used (LRU) segment is selected and a read from disk is initiated into that segment which is now considered the Active Segment. The retention of data already transferred to the host and read look ahead in the Active Segment buffer is controlled by the state of the Read Retention Priority.
Technical Reference Manual Page 23
Chapter 3 Drive Operations
Read Retention On (Read Retention Priority = 0 or F):
The interface processor initiates a full segment read of 253 sectors (FD
H
blocks) to the background processor. There are three different situations which would be considered a cache hit on a subsequent read.
•
Full: All of the data requested is transferred from the buffer segment and retained.
•
Partial: Some but not all of the data is cached in a buffer segment. If the cached data is in the Active Segment and the remaining data is part of the full segment read, the drive will transfer the requested data from the buffer as the background process fills it. If the cached data is in the Active
Segment but the remaining data is not part of the full segment read, the drive will turn off read retention until the next Active Segment miss occurs and issues a new read (forever) to the background process. This allows the drive to adapt to long sequential reads even in read retention mode. If the data is part of an Inactive Segment, a new full segment read is initiated, making this the Active Segment.
•
Potential: If none of the data is in the Active Segment, but is part of the full segment read, the drive will transfer the data as it becomes available.
Read Retention Off (Read Retention Priority = 1): The interface processor initiates a "read forever" command to the background processor and the buffer segment is treated as a circular buffer which is back filled as sectors are transferred to the host. There are three different situations which would be considered a cache hit on a subsequent read.
•
Full: All of the requested data is cached in a buffer segment. If it is the
Active Segment, the data will be transferred to the host and refilled with next sequential data. If the data in an Inactive Segment, the data is transferred to the host and retained.
•
Partial: This is when some, but not all of the data is cached in a buffer segment. If the data is in the Active Segment, data is transferred to the host as the background process fills the buffer and the "read forever" is allowed to refill the buffer. If the data in an Inactive Segment, the cached data is transferred and a new read operation is initiated for the remaining data, making this the Active Segment.
•
Potential: None of the data is cached. The active segment is checked and if the requested data is within 63 sectors of being read, the drive will allow the
"read forever" operation to continue and the data is transferred to the host when it is available.
Page 24 Filepro CFP2105 Series
Drive Operations Chapter 3
Write Caching
Write Caching allows multiple write commands operating on sequential blocks to be written to the medium without losing a motor revolution between commands.
Write caching is enabled by setting the WCE bit in MODE SELECT page 8 to one. The WCE bit is only valid while the Read Look Ahead code is loaded. The
WCE bit is ignored when the Tagged Command Queuing code is in RAM because write coalescing will be active.
The drive will send good status and COMMAND COMPLETE message following the data out phase of a cached write command. The drive will cache writes when the following conditions are met:
•
Two or more write commands (Op Code 0A
H
or 2A
H
) execute consecutively without an intervening command.
•
The write commands address consecutive logical block ranges.
•
At least one logical block of data has been received in the buffer from the second write command in time to allow the medium to be written before an additional spindle revolution would be required.
•
Both writes are from the same initiator.
•
Neither write is a linked command.
If the drive encounters an error during a cached write operation, the drive will respond by:
If AWRE (MODE SELECT page 01
H
) is 0: the drive will report a CHECK
CONDITION on the next command and the response from a REQUEST SENSE will be a deferred error. (Asynchronous event notification is not supported by this drive.) Refer to the Eleventh Generation SCSI Interface Manual for additional details.
If AWRE (MODE SELECT page 01
H
) is set to 1: the drive will attempt to dynamically reassign the block of data and complete the operation. If the reassignment fails, the drive will continue to reassign the block until all the space in the grown defect list is filled (147 sectors, maximum).
Technical Reference Manual Page 25
Chapter 3 Drive Operations
Tagged Command Queuing
The drive, operating using the Tagged Command Queuing code, can queue up to
32 commands. Commands in the queue which involve seeks are re-ordered using a Scan (elevator seek methodology). Read and Write commands are coalesced (combined into a single operation to the background processor) to minimize inter processor communication overhead and reduce mechanical motion.
Seek Re-ordering
Seeks are re-ordered using the Scan or what is sometimes referred to as the elevator seek method. Seeks already in the queue are re-ordered so they can be executed sequentially on a sweep toward the inner diameter (ID) or the outer diameter (OD) of the disk. Any new seeks entering the queue ahead of the sweep is ordered for execution during the current sweep. Any new seeks entering the queue behind the current sweep are held for re-ordering during the reverse sweep. When there are no more commands in the queue ahead of the current sweep, the direction of the sweep is reversed.
Seek re-ordering is controlled by Message Code (Simple, Head of Queue or
Ordered Queue) during the Message Phase. Re-ordering of seeks issued with a
Simple Queue Tag message may also be restricted using the Queue Algorithm
Modifier bits in MODE SELECT page 0A
H
. Refer to the Eleventh Generation
SCSI Interface Manual for additional information on Messages and MODE
SELECT page 0A
H
.
Buffer Management
The 512K byte buffer is treated by the queuing code as two 240KB buffers (F0
H sectors) to maximize coalescing. Look ahead reads are performed by the drive when there are no commands in the queue awaiting execution. Look ahead reads are not performed when there are commands in the queue since another command will be waiting for execution as soon as the current command completes and because the queue affords pre-knowledge of subsequent commands instead of having to anticipate them.
Sequential read or write commands are coalesced into single commands to the background processor. On a read operation, the data associated with each queue tag is transmitted to the host as the buffer is filled by the background processor.
On write operations, the drive will connect to the initiator(s), transmit the data into the buffer and disconnect; coalescing sequential data in the buffer before initiating the write to the background processor. The drive will reconnect with each of the writes, using the queue tags, completing the command after the data has been written to the disk. This operation provides the performance of write caching without the exposure of completing the command prior to writing the data to the disk.
Page 26 Filepro CFP2105 Series
Installing the Drive
Take These Precautions
To protect your equipment from electrostatic damage, perform the installation at a static-safe workstation. If one is not available, follow these guidelines:
1. Work in an uncarpeted area.
2. Before removing the equipment from its anti-static bag,
discharge static electricity by touching your computer's
metal chassis (or any other grounded object) while
touching the anti-static bag.
3. Do not touch circuit boards unless instructed to do so.
0170
Installing the Drive
To install the drive, you must:
• set the drive’s jumpers, if desired
• attach a data cable to the drive
• attach power to the drive
• mount the drive
These procedures differ between the various drive models.
4
Technical Reference Manual Page 27
Chapter 4 Installing the Drive
Installing a CFP2105E
The following paragraphs describe the installation procedure for a 16-bit Single
Connector Attachment (SCA) interface, model CFP2105E drive.
Setting the Drive's Jumpers - CFP2105E
There are no jumpers to set on the model CFP2105E and CFP1007E drives since all the necessary control signals are on the SCA connector. This drive is intended for applications where the drive is configured at the interface when the drive is plugged into the interface connector.
Setting the SCSI Bus Address - CFP2105E
The SCSI bus ID of the drive is set by grounding the Interface bus signals shown below in Table 4-4.
Table 4-4
Setting the SCSI ID
SCSI ID SCSI ID(0) SCSI ID(1) SCSI ID(2) SCSI ID(3)
11
12
13
14
15
7
8
9
10
5
6
3
4
0
1
2
Open
Ground
Open
Ground
Open
Ground
Open
Ground
Open
Ground
Open
Ground
Open
Ground
Open
Ground
Open
Open
Ground
Ground
Open
Open
Ground
Ground
Open
Open
Ground
Ground
Open
Open
Ground
Ground
Open
Open
Open
Open
Ground
Ground
Ground
Ground
Open
Open
Open
Open
Ground
Ground
Ground
Ground
Ground
Ground
Ground
Ground
Ground
Ground
Ground
Ground
Open
Open
Open
Open
Open
Open
Open
Open
Page 28 Filepro CFP2105 Series
Installing the Drive Chapter 4
Disabling Spin-Up at Power On - CFP2105E
Spin up upon application of power to the drive can be disabled by grounding the
RMT_START line on the interface. Disabling spin up on application of power can also be enabled by setting the DSPN bit in MODE SELECT page 00
H
(Vendor Specific Parameters). The Host must issue a START UNIT command to cause the drive to spin up. Refer to the Eleventh Generation SCSI Technical
Reference Manual for additional information regarding the MODE SELECT and
START/STOP UNIT commands.
Table 4-5
Disabling Spin Up at Power On
RMT_START
Ground
Ground
Open
Open
DSPN
0
1
0
1
Result
Spin Disabled
Spin Disabled
Spin up on Power On
Spin Disabled
Delaying Spin Up at Power On - CFP2105E
Grounding the DLYD_START signal on the interface delays spin up on power-up by the value of the drive's SCSI ID multiplied by 4 seconds (i.e. SCSI ID 4 will delay 16 seconds). Delaying spin up on application of power can also be enabled by setting the SDLY bit in MODE SELECT page 00
H
(Vendor Specific
Parameters). Refer to the Eleventh Generation SCSI Technical Reference
Manual for additional information regarding the MODE SELECT command.
Table 4-6
Delaying Spin Up at Power On
DLYD_START
Ground
Ground
Open
Open
SDLY
0
1
0
1
Result
Spin Delayed
Spin Delayed
Spin up on Power On
Spin Delayed
Cabling the Drive - CFP2105E
The drive may be connected to the host SCSI interface directly through a backplane SCA connector or through cabling. Both the connector and cabling is described in Chapter 5.
Technical Reference Manual Page 29
Chapter 4 Installing the Drive
The design of the SCSI bus interconnect system should meet the following guidelines, particularly with FAST SCSI-2 systems:
•
Do not route the data signals next to any high frequency or large current switching signals. Unreliable drive operation can result from improper signal routing.
•
Signal line stubs should not exceed 0.1 meter (4 inches).
•
There should be 0.3 meters (12 inches) of transmission line between drives.
•
The total length of any signal line should not exceed 6 meters (20 feet) and may have to be reduced if excessive impedance discontinuities exist on the bus.
•
Maintain a minimum of 0.050 inches (1.27mm) gap between adjacent signal.runs to control crosstalk between signal lines.
•
Signals routed over a ground plane or between ground planes have different characteristic impedance. Signals with critical timing like REQ, ACK and
Data should be routed similarly.
The signal length between devices should either be spaced shorter than the stub length, which treats a group of devices as a lumped element, or far enough apart that a transmission line exists (0.3 meters or 12 inches). These signal length considerations should include the length of signal traces and connectors on the printed circuit board. The diagram below shows how it is possible to interconnect six 1-inch height drives over a relatively short length of interconnect.
3" [0.08m] maximum
12" [0.3m] minimum
These guidelines apply to both cabled and backplane implementations.
Guidelines specifically for cabled implementations can be found on page Error!
Bookmark not defined.. While it is possible to connect SCA drives using a cable, users should be aware that the mating connector is designed for 0.025 inch
(0.63 mm) pitch 30 AWG wire. There are four +12 volt and three +5 volt line pairs carrying power to the drive on the SCA so spin up must be staggered to connect two drives on the same cable and the cable length kept to a minimum.
Otherwise, there should only be one drive per cable.
Attaching Power to the Drive - CFP2105E
The drive is powered through the SCA connector.
Page 30 Filepro CFP2105 Series
Installing the Drive Chapter 4
Mounting the Drive - CFP2105E
The drive is designed to be used in applications where the unit may experience shock and vibrations at greater levels than larger and heavier disk drives will tolerate.
The design features which allow greater shock tolerance are the use of rugged heads and media, a dedicated landing zone, closed loop servo positioning and specially designed motor and actuator assemblies.
Mounting Screw Holes
Six side, or four bottom base mounting points are provided to the customer. The drive is mounted using 6-32 UNC -2B X 0.16 maximum insertion length screws.
Refer to Figure 2-2 in Chapter 2 for the location of the mounting holes. The drive may be mounted in any orientation.
Cooling
The enclosure design for the drive must provide adequate provision for removing heat generated by the drive via conduction or air flow convection cooling. The maximum operating temperature for the drive is 55°C. A temperature sensor mounted on the drive at the location shown below should remain at or below
55°C while the drive(s) are operated at the worst case condition.
Recommended
Themocouple location
The enclosure design should allow air flow above and below the drive to cool both the
HDA and printed circuit board assembly.
The drive(s) should be positioned in the path of least resistance to the flow of air so that the flow is not routed around the drive. Placing the drive at the source of the shortest air flow path helps to ensure adequate air flow and avoids pre-heating of the air by other heat generating sources.
Technical Reference Manual Page 31
Chapter 4 Installing the Drive
Installing a CFP2105S
The following paragraphs describe the installation procedure for a 8-bit, 50-pin
SCSI-2 interface, model CFP2105S drive.
Setting the Drive's Jumpers - CFP2105S
Figure 4-3 shows you where the drive’s jumpers are located.
Figure 4-3
Jumper Locations
J1
OE1
:
OE3
OE5, Disable
Spin
J3
SS
LED
J6
LED
E8
F1
J2 pin 1
J7
E1..E3
E7 (Disable Parity)
E6 (Delay Spin)
E5 (Disable Spin)
E4: Reserved
J4
2107_4_3
Page 32 Filepro CFP2105 Series
Installing the Drive Chapter 4
Setting the SCSI Bus Address - CFP2105S
There are three jumpers available for configuration of the SCSI ID: E1, E2, and
E3.
An optional 2mm pin pitch right angle header is located on the front of the
PCBA (opposite the SCSI interface connector) which allows changing the SCSI
IDs while the drive is mounted in the system. The header includes three pins,
0E1, 0E2 and 0E3 which can alternatively be used to select the SCSI Bus address. This connector may also be used to cable the SCSI ID select to a remote switch. A receptacle connector Amp P/N 111622-1 or equivalent can be used to connect a ribbon cable to this header.
Table 4-6 defines the relationship between the jumpers and the SCSI ID:
Table 4-7
Setting the SCSI ID
Optional header
Standard
0E1
E1
Out
In
Out
In
Out
In
Out
In
0E2
E2
Out
Out
In
In
Out
Out
In
In
0E3
E3
In
In
In
In
Out
Out
Out
Out
SCSI ID
6
7
4
5
2
3
0
1
Note: When controlling the SCSI ID remotely, In = Ground or TTL
Low and Out = Open or TTL High. The odd numbered pins (lower row) are grounded and the even numbered pins carry the signal.
Technical Reference Manual Page 33
Chapter 4 Installing the Drive
Disabling Spin-Up at Power On - CFP2105S
A jumper in the E5 location, disables spin up after power-on for applications where spin up sequencing is necessary. Disabling spin up on application of power can also be enabled by setting the DSPN bit in MODE SELECT page 00
H
(Vendor Specific Parameters). The Host must issue a START UNIT command to cause the drive to spin up. Refer to the Eleventh Generation SCSI Technical
Reference Manual for additional information regarding the MODE SELECT and
START/STOP UNIT commands. Refer to Figure 4-3 for the location of the
Disable Spin jumper, E5.
Table 4-8
Disabling Spin Up at Power-On
E5
In
In
Out
Out
DSPN
0
1
0
1
Result
Spin Disabled
Spin Disabled
Spin up on Power On
Spin Disabled
Note: In = Ground or TTL Low and Out = Open or TTL High. The odd numbered pin is grounded and the even numbered pin carries the signal.
Delaying Spin Up at Power On - CFP2105S
A jumper in the E6 location, delays spin up on power-up by the value of the drive's SCSI ID multiplied by 4 seconds (i.e. SCSI ID 4 will delay 16 seconds).
Delaying spin up on application of power can also be enabled by setting the
SDLY bit in MODE SELECT page 00
H
(Vendor Specific Parameters). Refer to the Eleventh Generation SCSI Technical Reference Manual for additional information regarding the MODE SELECT command. Refer to Figure 4-3 for the location of the Delayed Spin jumper, E6.
Table 4-9
Delaying Spin Up at Power On
E6 SDLY Result
In
In
Out
Out
0
1
0
1
Spin Delayed
Spin Delayed
Spin up on Power On
Spin Delayed
Note: In = Ground or TTL Low and Out = Open or TTL High. The odd numbered pin is grounded and the even numbered pin carries the signal.
Page 34 Filepro CFP2105 Series
Installing the Drive Chapter 4
Disabling the SCSI Bus Parity - CFP2105S
SCSI parity is always enabled in both directions, unless the E7 Parity disable jumper is installed. Installing the jumper will cause the drive to ignore SCSI bus Parity In but it will continue to generate SCSI bus Parity Out.
Disabling SCSI Bus Terminator Power (TERMPWR) - CFP2105S
Power to the on-board terminators is provided by the higher of the voltage supplied at Pin #26, J2 or the voltage level at the 5 Volt power input to the drive minus one diode drop. Termination Power to external terminators can be supplied by the drive through Pin #26, J2. The signal output characteristics are described in chapter 5. The TERMPWR line can be disconnected from the drive by removing Jumper E8.
Table 4-10
Disabling SCSI Bus TERMPWR
Jumper E8
In
Out
Result
TERMPWR (J2, Pin #26) connected to the drive's internal termination power.
TERMPWR (J2, Pin #26) open circuit.
Technical Reference Manual Page 35
Chapter 4 Installing the Drive
Setting the Bus Termination - CFP2105S
This drive provides on-board Alternative 2 active termination for the SCSI bus.
The termination resistors, which are contained in two Single Inline Packs (SIPs) should be removed from the drive unless it is a SCSI device at the physical end of the bus. Figure 4-4 shows the location of the terminator resistors.
Figure 4-4
Terminator Resistor Locations
SCSI Terminators.
Remove in all but the last drive in the chain
Remove to
Disable TERMPWR
Input/Output
J1
E8
F1
J2
J3
SS
LED
J7
J5
J4
2107_4_4
TERMPWR
Fuse
NOTE: The TERMPWR output of the drive is protected by a 1 Ampere fuse. If external terminators are being powered from the drive and SCSI bus problems are suspected, verify that the fuse is still operational using a meter.
Page 36 Filepro CFP2105 Series
Installing the Drive Chapter 4
Cabling the Drive - CFP2105S
Connect the SCSI interface cable and the spindle synchronization cable (when needed) as shown in Figure 4-5.
Figure 4-5
Connecting the cabling
J1
E8
F1
J2
50-pin SCSI
Interface
Spindle
Synchronization
Connection
Key
J3
SS
LED
J7
LED
Connection
Pin 1 (typically indicated by a colored stripe on the cable
J4
J6
LED
Pin 1
2107_4_5
4-pin Power
Connector
OE6, LED Connection
SCSI Bus Cable
The cable and mating connector required to connect the drive to the SCSI bus are described in Chapter 5. In addition, the cable should meet the following guidelines, particularly with FAST SCSI-2 systems:
•
Do not route the data cable next to the drive PCB or any other high frequency or large current switching signals. Improper drive operation can result from improper cable routing.
•
Cable stubs should not exceed 0.1 meter (4 inches).
•
There should be 0.3 meters (12 inches) of cable between drives.
•
The total cable length should not exceed 6 meters (20 feet) and may have to be reduced if a mixture of round and flat cable are used.
•
Do not tightly bundle excess flat cable against each other since this promotes cross coupling of signals on the cable. Use spacers to maintain a minimum of
0.050 inches (1.27mm) gap between cable runs.
•
Do not clamp the cable tightly against a metal chassis since this will degrade the signal. Use spacers or a non-flammable insulation material to maintain a gap between the chassis and the cable.
Spindle Synchronization
The spindle rotation of up to 35 drives may be synchronized together by daisy chaining pin 1 to pin 1 and pin 2 to pin 2 on connector J3. Spindle
Synchronization is enabled by setting the appropriate bits in the RPL field of
Mode Select page 04. Refer to the Eleventh Generation Disk Drive SCSI-2
Interface Manual for a description of the command implementation. The synchronization tolerance is 1%.
Technical Reference Manual Page 37
Chapter 4 Installing the Drive
Attaching Power to the Drive - CFP2105S
The drive has a 4-pin DC power connector, J4 mounted on the PCB. The recommended mating connector is AMP part number 1-480424-0 utilizing AMP pins, part number 350078-4 or equivalent.
Connect the DC Power cable to the drive as shown in Figure 4-5.
Attaching a Remote LED - CFP2107S
J3, pin 3 or J6 pin 10
J3, pin 4 or J6, pin 9
A remote LED can be attached using a 0.1
inch center, 2-pin connector to pins 3 and 4 of
J3. The anode of the LED should be connected to pin 3 and the cathode to pin 4.
An external LED can optionally be attached using a 2mm center connector on J6, pins 9 and 10 (location OE6). The anode of the LED should be connected to pin 10 and the cathode to pin 9.
The external LED is connected in parallel to the on board LED and is powered through a
200 ohm current limiting resistor to the +5 volt power.
Mounting the Drive - CFP2105S
The drive is designed to be used in applications where the unit may experience shock and vibrations at greater levels than larger and heavier disk drives will tolerate.
The design features which allow greater shock tolerance are the use of rugged heads and media, a dedicated landing zone, closed loop servo positioning and specially designed motor and actuator assemblies.
Mounting Screw Holes
Six side, or four bottom base mounting points are provided to the customer. The drive is mounted using 6-32 UNC -2B X 0.16 maximum insertion length screws.
Refer to Figure 2-3 in Chapter 2 for the location of the mounting holes. The drive may be mounted in any orientation.
Cooling
The enclosure design for the drive must provide adequate provision for removing heat generated by the drive via conduction or air flow convection cooling. The maximum operating temperature for the drive is 55°C. A temperature sensor
Page 38 Filepro CFP2105 Series
Installing the Drive Chapter 4 mounted on the drive at the location shown below should remain at or below
55°C while the drive(s) are operated at the worst case condition.
Recommended
Themocouple location
The enclosure design should allow air flow above and below the drive to cool both the
HDA and printed circuit board assembly.
The drive(s) should be positioned in the path of least resistance to the flow of air so that the flow is not routed around the drive. Placing the drive at the source of the shortest air flow path helps to ensure adequate air flow and avoids pre-heating of the air by other heat generating sources.
Technical Reference Manual Page 39
Chapter 4
Installing a CFP2105W
Setting the Drive’s Jumpers - CFP2105W
Figure 4-6 shows you where to access the drive’s jumpers.
Figure 4-6
Jumper Locations
Installing the Drive
J1
J3
SS
LED
OE1
:
OE3
OE5, Disable
Spin
J6
LED
E8
J2
J5
J4
E7 (Disable Parity)
E1. . .E4
E6 (Delay Spin)
E5 (Disable Spin)
2107_4_6
Page 40 Filepro CFP2105 Series
Installing the Drive Chapter 4
Setting the SCSI Bus Address - CFP2105W
There are four jumpers available for configuration of the SCSI ID: E1, E2, E3 and E4.
The 68-pin unified connector includes a standard 2mm pitch auxiliary header which includes pins to allow remote selection of SCSI IDs. A receptacle connector Amp P/N 1-111623-7 or equivalent can be used to connect a ribbon cable to this header.
Table 4-11 defines the relationship between the jumpers or the pins on J5 and the SCSI ID:
Table 4-11
Setting the SCSI ID
SCSI ID
11
12
13
14
15
7
8
9
10
5
6
3
4
0
1
2
E1 / Pin 1
Out/Open
In/Ground
Out/Open
In/Ground
Out/Open
In/Ground
Out/Open
In/Ground
Out/Open
In/Ground
Out/Open
In/Ground
Out/Open
In/Ground
Out/Open
In/Ground
E2 / Pin 3
Out/Open
Out/Open
In/Ground
In/Ground
Out/Open
Out/Open
In/Ground
In/Ground
Out/Open
Out/Open
In/Ground
In/Ground
Out/Open
Out/Open
In/Ground
In/Ground
E3 / Pin 5
Out/Open
Out/Open
Out/Open
Out/Open
In/Ground
In/Ground
In/Ground
In/Ground
Out/Open
Out/Open
Out/Open
Out/Open
In/Ground
In/Ground
In/Ground
In/Ground
Note: Open means open circuit or high impedance. Ground means
TTL logic low or logic ground. The odd numbered pins (lower row) are grounded and the even numbered pins carry the signal.
E4 / Pin 7
Out/Open
Out/Open
Out/Open
Out/Open
Out/Open
Out/Open
Out/Open
Out/Open
In/Ground
In/Ground
In/Ground
In/Ground
In/Ground
In/Ground
In/Ground
In/Ground
Technical Reference Manual Page 41
Chapter 4 Installing the Drive
Disabling Spin-Up at Power On - CFP2105W
A jumper in the E5 location, disables spin up on power-on for applications where spin up sequencing is necessary. Disabling spin up on application of power can also be enabled by setting the DSPN bit in MODE SELECT page 00
H
(Vendor
Specific Parameters). The Host must issue a START UNIT command to cause the drive to spin up. Refer to the Eleventh Generation SCSI Technical
Reference Manual for additional information regarding the MODE SELECT and
START/STOP UNIT commands. Refer to Figure 4-6 for the location of the
Disable Spin jumper E5 and the option header.
Table 4-12
Disabling Spin Up at Power On
E5 DSPN Result
In
In
Out
Out
0
1
0
1
Spin Disabled
Spin Disabled
Spin up on Power On
Spin Disabled
Note: In = Ground or TTL Low and Out = Open or TTL High. The odd numbered pin is grounded and the even numbered pin carries the signal.
Delaying Spin Up at Power On - CFP2105W
A jumper in the E6 location, delays spin up on power-up by the value of the drive's SCSI ID multiplied by 4 seconds (i.e. SCSI ID 4 will delay 16 seconds).
Delaying spin up on application of power can also be enabled by setting the
SDLY bit in MODE SELECT page 00
H
(Vendor Specific Parameters). Refer to the Eleventh Generation SCSI Technical Reference Manual for additional information regarding the MODE SELECT command. Refer to Figure 4-6 for the location of the Delayed Spin jumper, E6.
Table 4-13
Delaying Spin Up at Power On
E6 SDLY Result
In
In
Out
Out
0
1
0
1
Spin Delayed
Spin Delayed
Spin up on Power On
Spin Delayed
Note: In = Ground or TTL Low and Out = Open or TTL High. The odd numbered pin is grounded and the even numbered pin carries the signal.
Page 42 Filepro CFP2105 Series
Installing the Drive Chapter 4
Disabling the SCSI Bus Parity - CFP2105W
SCSI parity is always enabled in both directions, unless the E7 Parity disable jumper is installed. Setting the jumper will cause the drive to ignore SCSI bus parity in but it will continue to generate SCSI bus parity out.
Technical Reference Manual Page 43
Chapter 4 Installing the Drive
Disabling SCSI Bus Terminator Power (TERMPWR) - CFP2105W
Power to the on-board terminators is provided by the higher of the voltage supplied at Pins #17, 18, 51 & 52, J2 or the voltage level at the 5 Volt power input to the drive minus one diode drop. Termination Power to external terminators can be supplied by the drive through Pins #17, 18, 51 & 52, J2. The signal output characteristics are described in chapter 5. The TERMPWR line can be disconnected from the drive by removing Jumper E8.
Table 4-14
Disabling SCSI Bus TERMPWR
Jumper E8
In
Out
Result
TERMPWR (J2, Pins #17, 18, 51 & 52) connected to the drive's internal termination power.
TERMPWR (J2, Pins #17, 18, 51 & 52) open circuit.
Using the J5 Auxiliary Connector
External logic cabled to the J5 connector may be used to control certain characteristics of the drive or access signals.
Table 5-15
J5 Auxiliary Connector Signal Definitions
Pin Number Signal Name
5
7
1
3
9
11
- SEL0
- SEL1
- SEL2
- SEL3
- ENTERM
+5V
Pin Number Signal Name
6
8
2
4
10
12
- XTFALT
- VUNIQ
- SPSYNC
- XTACTV
- GROUND
- FAULT
- SEL0
Bit 0 of the binary coded SCSI ID selection input. This signal has a value of 0 when it is negated and a value of 1 when it is asserted for the purpose of selection or arbitration.
This signal is latched within 250 msec of the application of valid power to the drive or optionally the negation of -RST.
If SCSI ID SEL0 is intended to be selected, the host must provide a low impedance connection from - SEL (0) to - XTFALT or to ground, while the ID is being latched, through an appropriate means. Refer to chapter 5 for specific electrical characteristics of these signals.
Page 44 Filepro CFP2105 Series
Installing the Drive Chapter 4
- XTFAULT
This signal is intended to drive an LED to indicate an external fault condition has occurred. This signal is held asserted following the application of power or optionally the negation of -RST during initialization while the SCSI ID is being read. This signal is not supported but meets the requirement of negating the signal while the ID is being read.
- SEL1
Bit 1 of the binary coded SCSI ID selection input. This signal has a value of 0 when it is negated and a value of 2 when it is asserted for the purpose of selection or arbitration.
This signal is latched within 250 msec of the application of valid power to the drive or optionally the negation of -RST.
If SCSI ID SEL 1 is intended to be selected, the host must provide a low impedance connection from - SEL1 to - VUNIQ or to ground, while the ID is being latched, through an appropriate means. Refer to chapter 5 for specific electrical characteristics of these signals.
- VUNIQ
This signal is an open-collector output available for Vendor Unique usage. This signal is not supported but meets the requirement of negating the signal while the ID is being read.
- SEL2
Bit 2 of the binary coded SCSI ID selection input. This signal has a value of 0 when it is negated and a value of 4 when it is asserted for the purpose of selection or arbitration.
This signal is latched within 250 msec of the application of valid power to the drive or optionally the negation of -RST.
If SCSI ID SEL2 is intended, to be selected, the host must provide a low impedance connection from - SEL2 to - SPSYNC or to ground, while the ID is being latched, through an appropriate means. Refer to chapter 5 for specific electrical characteristics of these signals.
- SPSYNC
This signal used to provide a spindle rotation synchronization reference. The pins for all of the drives which are to be synchronized must be connected together. The drives must be of like model to operate. The spindles are synchronized using a "floating master" concept, where the drives will synchronize to the first drive to reach full speed. The synchronization tolerance is 1%.
This signal meets the requirement of negating the signal while the ID is being read.
Technical Reference Manual Page 45
Chapter 4 Installing the Drive
- SEL3
Bit 3 of the binary coded SCSI ID selection input. This signal has a value of 0 when it is negated and a value of 8 when it is asserted for the purpose of selection or arbitration.
This signal is latched within 250 msec of the application of valid power to the drive or optionally the negation of -RST.
If SCSI ID SEL3 is intended, to be selected, the host must provide a low impedance connection from - SEL3 to - XTACTV or to ground, while the ID is being latched, through an appropriate means. Refer to chapter 5 for specific electrical characteristics of these signals.
- XTACTV
This signal is an open collector output intended to drive an LED to indicate the device is active. This signal is negated while the SCSI ID is being read.
- GROUND
This signal is connected to the drive's logic ground.
+5 Volts
This signal provides 5 volts of DC power to drive LEDs and is current limited by a 120 ohm resistor.
- FAULT
The assertion of this signal will cause the drive to stop any media-altering activity, which may result in the drive asserting -XTFALT or -VUNIQ, or both.
This signal is intended to be used as a power failure warning and/or as a write protect input. This signal is not supported by this drive.
Page 46 Filepro CFP2105 Series
Installing the Drive Chapter 4
Setting the Bus Termination - CFP2105W
This drive provides on board Alternative 2 active termination for the SCSI bus.
The termination resistors, which are contained in three Single Inline Packs
(SIPs) should be removed from the drive unless it is a SCSI device at the physical end of the bus. Figure 4-7 shows the location of the terminator resistors.
Figure 4-7
Terminator Resistor Locations
SCSI Terminators.
Remove in all but the last drive in the chain
Remove E8 to
Disable TERMPWR
Input/Output
J1
J3
SS
LED
J6
LED
E8
F1
J2
J5
J4
2107_4_7
TERMPWR
Fuse
Technical Reference Manual Page 47
Chapter 4 Installing the Drive
Cabling the Drive - CFP2105W
Connect the SCSI interface cable and the spindle synchronization cable (when needed) as shown in Figure 4-8.
Figure 4-8
Connecting the cabling
J1
Spindle
Synchronization
Connection
LED
Connection
J3
SS
LED
E8
J2
J5
J4
68-pin
SCSI
Interface
Connection
Pin 1 (typically indicated by a colored stripe on the cable
Pin 1
2-mm Auxiliary
Connector
Pin 1
4-pin Power
Connection
J6
LED
2107_4_8
OE6, LED Connection
SCSI Bus Cable
The cable and mating connector required to connect the drive to the SCSI bus are described in Chapter 5. In addition, the cable should meet the following guidelines, particularly with FAST SCSI-2 systems:
•
Do not route the data cable next to the drive PCB or any other high frequency or large current switching signals. Improper drive operation can result from improper cable routing.
•
Cable stubs should not exceed 0.1 meter (4 inches).
•
There should be 0.3 meters (12 inches) of cable between drives.
•
The total cable length should not exceed 3 meters (10 feet) and may have to be reduced if a mixture of round and flat cable are used.
•
Do not tightly bundle excess flat cable against each other since this promotes cross coupling of signals on the cable. Use spacers to maintain a minimum of
0.050 inches (1.27mm) gap between cable runs.
•
Do not clamp the cable tightly against a metal chassis since this will degrade the signal. Use spacers or a non-flammable insulation material to maintain a gap between the chassis and the cable.
Page 48 Filepro CFP2105 Series
Installing the Drive Chapter 4
Mixing Wide and Narrow SCSI Devices on a SCSI Bus
It may sometimes be desirable to attach Narrow SCSI devices such as tape backup devices or CDROMs to the same SCSI Host Bus Adapter being used to control Wide SCSI devices, such as the CFP2105W. Intermixing of both Wide and Narrow SCSI devices on the same bus requires special considerations:
•
The Narrow SCSI devices must be placed at the physical end of the bus
•
The high byte of the SCSI data bus must be terminated at the transition adapter from the 34-pair wire to the 25-pair wire. Figure 4-9 shows the interconnection.
•
The cable impedance of the 34-pair wire and the 25-pair wire should be as closely matched as possible.
•
The 68-pair cable with 30 AWG wire uses four wires to carry TERMPWR, which must be joined to wire 26 of the 25-pair wire, if terminator power has to be carried over the cable.
Figure 4-9
Wide-to-Narrow Adapter
P Cable
Ground
TERMPWR
TERMPWR
TERMPWR
TERMPWR
Reserved
Reserved
-I/O
Ground
-DB(8)
Ground
-DB(9)
Ground
-DB(10)
Ground
-DB(11)
Ground
-DB (12)
Ground
-DB (13)
Ground
-DB (14)
Ground
-DB (15)
Ground
-DB(P1)
Ground
-DB (0)
Ground
64
65
66
67
68
60
61
62
63
36
37
38
32
33
34
35
7
8
5
6
9
10
11
12
13
1
2
3
4
I
N
A
T
O
R
R
M
T
E
M
I
N
A
T
E
R
T
O
R
A Cable
26
27
28
22
23
24
25
50
1
2
3
Ground
-DB (0)
Ground
Ground
Reserved
Reserved
Open
TERMPWR
Reserved
Reserved
-I/O
Spindle Synchronization
The spindle rotation of up to 35 drives may be synchronized together by daisy chaining pin 1 to pin 1 and pin 2 to pin 2 on connector J3. Spindle
Synchronization is enabled by setting the appropriate bits in the RPL field of
Mode Select page 04. Refer to the Eleventh Generation Disk Drive SCSI-2
Interface Manual for a description of the command implementation. The synchronization tolerance is 1%.
Technical Reference Manual Page 49
Chapter 4 Installing the Drive
Attaching Power to the Drive - CFP2105W
The drive has a 4-pin DC power connector, J4, which is part of the Unified
Connector, mounted on the PCB. The recommended mating connector is AMP part number 1-480424-0 utilizing AMP pins, part number 350078-4 or equivalent.
Attaching a Remote LED - CFP2107W
J3, pin 3 or J6, pin 10 or J5, pin 11
A remote LED can be attached using a 0.1
inch center, 2-pin connector to pins 3 and 4 of
J3. The anode of the LED should be connected to pin 3 and the cathode to pin 4.
An external LED can optionally be attached using a 2mm center connector on J6, pins 9 and 10 (location OE6). The anode of the LED should be connected to pin 10 and the cathode to pin 9.
J3, pin 4 or J6, pin 9 or J5, pin 8
A external LED on J3 or J6 is connected in parallel to the on board LED and is powered through a 200 ohm current limiting resistor to the +5 volt power.
A third option is available on J5, which is between the 68-pin SCSI interface and the 4-pin power input on the unified connector. The anode can be connected to pin 11, which is connected to +5 volts through a 120 ohm current limiting resistor or an external current limited voltage source. The cathode is connected to pin 8.
Mounting the Drive - CFP2105W
The drive is designed to be used in applications where the unit may experience shock and vibrations at greater levels than larger and heavier disk drives will tolerate.
The design features which allow greater shock tolerance are the use of rugged heads and media, a dedicated landing zone, closed loop servo positioning and specially designed motor and actuator assemblies.
Mounting Screw Holes
Six side, or four bottom base mounting points are provided to the customer. The drive is mounted using 6-32 UNC -2B X 0.16 maximum insertion length screws.
Refer to Figure 2-4 in Chapter 2 for the location of the mounting holes. The drive may be mounted in any orientation.
Page 50 Filepro CFP2105 Series
Installing the Drive Chapter 4
Cooling
The enclosure design for the drive must provide adequate provision for removing heat generated by the drive via conduction or air flow convection cooling. The maximum operating temperature for the drive is 55°C. A temperature sensor mounted on the drive at the location shown below should remain at or below
55°C while the drive(s) are operated at the worst case condition.
Recommended
Themocouple location
The enclosure design should allow air flow above and below the drive to cool both the
HDA and printed circuit board assembly.
The drive(s) should be positioned in the path of least resistance to the flow of air so that the flow is not routed around the drive. Placing the drive at the source of the shortest air flow path helps to ensure adequate air flow and avoids pre-heating of the air by other heat generating sources.
Technical Reference Manual Page 51
Chapter 4 Installing the Drive
Page 52 Filepro CFP2105 Series
Interface Physical Characteristics
5
Electrical Description
The paragraphs which follow describe the input and output electrical characteristics of the drive.
Output Characteristics
The output drivers for Data, Parity, REQ and ACK are optionally active negation. When they are set for active negation, they have three states: asserted, negated and high impedance. The remainder of the signals have open collector (drain) outputs. The drivers maintain a high impedance state during power-on and power-off cycles. The driven signals have the following output characteristics when measured at the drive connector:
Table 5-1
Active Negation Driver Output Signal Characteristics
Signal Characteristic
Signal Assertion
Minimum Driver Output Capability
Signal Negation
Value
0.1 VDC to 0.5 VDC at 48 mA
48 mA (sinking) at 0.5 VDC
2.0 VDC to 3.24 VDC at 7 mA
3.0 VDC at 20 mA
Table 5-2
Open Collector Driver Output Signal Characteristics
Signal Characteristic
Signal Assertion
Minimum Driver Output Capability
Signal Negation
Value
0.0 VDC to 0.5 VDC at 48 mA
48 mA (sinking) at 0.5 VDC
2.5 VDC to 5.25 VDC
Technical Reference Manual Page 53
Chapter 5 SCSI Physical Characteristics
Input Characteristics
The characteristics of the input receivers and the requirements for each signal received by the drive as measured at the drive connector are shown in table 5-3:
Table 5-3
Drive Input Signal Characteristics
Signal Characteristic
Signal Assertion
Signal Negation
Input Load (low level)
Input Load (high level)
Value
0.0 VDC to 0.8 VDC
2.0 VDC to 5.25 VDC
-20
µ
A to 0.0 mA at 0.5 VDC
0.0 mA to 20
µ
A at 2.7 VDC
Model-Specific SCSI Physical Characteristics
The sections which follow describe, for each of the drive models, those SCSI characteristics which vary from model to model. These characteristics include:
•
Termination
•
Cable requirements
•
Connector requirements
•
Connector Pin assignments
•
Interface Timing requirements
Page 54 Filepro CFP2105 Series
SCSI Physical Characteristics Chapter 5
CFP2105E (WIDE, 80-pin Single Connector Attachment [SCA])
External Terminator Power
The interface connector carries both power and ground so a separate TERMPWR interface line is not provided.
Internal Termination
This version of the drive has no on-board termination so the drive must be externally terminated. Alternative 2 active termination is recommended.
Alternative 1 passive termination is not suitable for this application.
Cable Requirements
This version of the drive is designed to facilitate interfacing directly to a mating connector which is on a passive back plane or directly into a motherboard.
The design of the SCSI bus interconnect system should meet the following guidelines, particularly with FAST SCSI-2 systems:
•
Do not route the data signals next to any high frequency or large current switching signals. Unreliable drive operation can result from improper signal routing.
•
Signal line stubs should not exceed 0.1 meter (4 inches).
•
There should be 0.3 meters (12 inches) of transmission line between drives.
•
The total length of any signal line should not exceed 6 meters (20 feet) and may have to be reduced if excessive impedance discontinuities exist on the bus.
•
Maintain a minimum of 0.050 inches (1.27mm) gap between adjacent signal.runs to control crosstalk between signal lines.
•
Signals routed over a ground plane or between ground planes have different characteristic impedance. Signals with critical timing like REQ, ACK and
Data should be routed similarly.
The signal length between devices should either be spaced shorter than the stub length, which treats a group of devices as a lumped element, or far enough apart that a transmission line exists (0.3 meters or 12 inches). These signal length considerations should include the length of signal traces and connectors on the printed circuit board. The diagram below shows how it is possible to interconnect six 1-inch height drives over a relatively short length of interconnect.
3" [0.08m] maximum
12" [0.3m] minimum
Technical Reference Manual Page 55
Chapter 5 SCSI Physical Characteristics
Connector Requirements
The drive's connector will mate with a AMP Champ 2-557103-1 vertical receptacle or the AMP Champ 2-557101-1 right angle receptacle. A mating connector which is compatible with 0.025 inch (0.63 mm) centerline #30 AWG solid PVC insulation cabling is AMP Camp 1-557089-3. Refer to figure 2-1 for the location of the connector on the drive.
Single Connector Attachment (SCA) Signal Definitions
Power
Four +12 Volt signals provide the +12 volt power to the drive. The current return for the +12 volt power is through the +12 Volt Ground signals. The maximum current that can be provided to the drive through the +12 Volt signal pins is 3 Amperes. The supply current and return current must be distributed as evenly as possible among the pins. The maximum current is required while the drive motor is starting.
Three +5 Volt signal pins provide +5 volt power to the drive. The current return for the +5 volt power is through the +5 Volt Ground pins. It is expected that the
+5 Volt Ground will also establish the digital logic ground for the drive. The maximum current that can be provided to the drive through the +5 Volt signal pins is 2 Amperes. The supply current and return current must be distributed as evenly as possible among the pins.
These specifications refer to the connector's characteristics. Refer to Chapter 2 for the drive's power requirements.
Spindle Sync
The spindle rotation of up to 35 drives may be synchronized together by daisy chaining pin 1 to pin 1 and pin 2 to pin 2 of each drive on connector J3. The synchronization tolerance is 1%.
Table 5-4
Electrical Characteristics for the Spindle Sync Signal
STATE
High
Low
Current
0 < I
IH
< 20
µ
A
0 < I
OH
< -48 mA
Voltage
2.5 V < V
IH
< V
CC
-0.1 V < V
IL
+ 0.3 V
< 0.4 V
Page 56 Filepro CFP2105 Series
SCSI Physical Characteristics Chapter 5
LED Out
The LED out signal is driven by the drive when the drive is performing a SCSI operation. The LED out signal is designed to pull down the cathode of an LED.
The anode is attached to the proper +5 volt supply through an appropriate current limiting resistor. The LED and the current limiting resistor are external to the drive.
Table 5-5
Output Characteristics of the LED Driver Signal
Output Voltage State
Drive LED Off
Drive LED On
Current Drive Available
0 < I
OH
< 100
µ
A
I
OL
< -30 mA 0 < V
OL
< 0.8 Volts
Motor Start Controls
Table 5-6
Electrical Characteristics for RMT_START and DLYD_START
State
Open
Ground
Current
0 < I
IH
< +100
µ
A
0 < I
OH
< -3 mA
Voltage
2.4 V < V
IH
< V
CC
+ 0.5 V
-0.5 V < V
IL
< 0.4 V
SCSI ID Selection
Table 5-7
Electrical Characteristics for the SCSI ID Signals SCSI ID (0) - (3)
State
Open
Ground
Current
0 < I
IH
< +100
µ
A
0 < I
OH
< -3 mA
Voltage
2.4 V < V
IH
< V
CC
+ 0.5 V
-0.5 V < V
IL
< 0.4 V
Technical Reference Manual Page 57
Chapter 5 SCSI Physical Characteristics
Interface Pin Assignments
The pin assignments for the interface connector are shown below:
Table 5-8
Interface Signal Definitions
Pin
29
30
31
32
25
26
27
28
21
22
23
24
17
18
19
20
37
38
39
40
33
34
35
36
13
14
15
16
9
10
11
12
7
8
5
6
3
4
1
2
Notes:
1. The minus sign (-) indicates active low.
2. Pins marked Reserved are not connected.
Signal
-ACK
-BSY
-ATN
-DB(P0)
-DB(7)
-DB(6)
-DB(5)
-DB(4)
-DB(3)
-DB(2)
-DB(1)
-DB(0)
-DB(P1)
-DB(15)
-DB(14)
-DB(13)
+12 Volt
+12 Volt
+12 Volt
+12 Volt
Reserved / NC
Reserved / NC
-DB(11)
-DB(10)
-DB(9)
-DB(8)
-I/O
-REQ
-C/D
-SEL
-MSG
-RST
-DB(12)
+5 Volt
+5 Volt
+5 Volt
SYNC
RMT_START
SCSI ID (0)
SCSI ID (2)
Pin
69
70
71
72
65
66
67
68
61
62
63
64
57
58
59
60
77
78
79
80
73
74
75
76
53
54
55
56
49
50
51
52
45
46
47
48
41
42
43
44
Signal
Ground
Ground
Ground
Ground
Ground
Ground
Ground
Ground
Ground
Ground
Ground
Ground
Ground
Ground
Ground
Ground
+12 Volt Ground
+12 Volt Ground
+12 Volt Ground
+12 Volt Ground
Reserved / NC
Reserved / NC
Ground
Ground
Ground
Ground
Ground
Ground
Ground
Ground
Ground
Ground
Ground
+5 Volt Ground
+5 Volt Ground
+5 Volt Ground
LED
DLYD_START
SCSI ID (1)
SCSI ID (3)
Page 58 Filepro CFP2105 Series
SCSI Physical Characteristics Chapter 5
Interface Timing Requirements
Unless otherwise noted, the delay-time measurements are calculated from signal conditions existing at the drive's own SCSI bus connector. Normally these measurements (except cable skew delay) can be made without considering delays in the inter-connect system.
Table 5-9
SCSI Bus Timing Values
Timing Description
Arbitration Delay
Bus Clear Delay
Bus Free Delay
Bus Set Delay
Bus Settle Delay
Cable Skew Delay
1
Data Release Delay
Receive Assertion Period
Receive Hold Time
Receive Negation Period
Receive Setup Time
Reset Hold Time
Selection Abort Time
Selection Time-out Delay
2
System Deskew Delay
Transmit Assertion Period
Transmit Hold Time
Transmit Negation Period
Transmit Setup Time
fast
2.4
µ s
800 ns
800 ns
1.8
µ s
400 ns
4 ns
400 ns
22 ns
25 ns
22 ns
15 ns
25
µ s
200
µ s
250 ms
20 ns
30 ns
33 ns
30 ns
23 ns
Timing Value slow
2.4
µ s
800 ns
800 ns
1.8
µ s
400 ns
4 ns
400 ns
70 ns
25 ns
70 ns
15 ns
25
µ s
200
µ s
250 ms
45 ns
80 ns
53 ns
80 ns
23 ns
asynch
2.4
µ s
800 ns
800 ns
1.8
µ s
400 ns
4 ns
400 ns n/a n/a n/a n/a
25
µ s
200
µ s
250 ms
45 ns n/a n/a n/a n/a
Notes:
1
This time does not apply at the SCSI connector of the drive.
2
This is a recommended time. It is not mandatory.
Technical Reference Manual Page 59
Chapter 5 SCSI Physical Characteristics
Model CFP2105S (Narrow, 50-pin SCSI)
External Terminator Power
Power to the on-board terminators is provided by the higher of the voltage supplied at Pin #26, J2 or the voltage level at the 5 Volt power input to the drive minus one diode drop. The diode prevents back flow of current to the drive.
Termination Power to external terminators can be supplied by the drive through
Pin #26, J2. The TERMPWR line can be disconnected from the drive by removing Jumper E8. Table 5-10 describes the electrical characteristics of the
TERMPWR line when it is used to supply power to an external terminator.
Table 5-11 describes the required electrical characteristics for any external source of termination power.
Table 5-10
TERMPWR Output Electrical Characteristics
Signal Characteristic
Supply voltage
Minimum source capability:
Value
4.06 VDC to 4.56 VDC
800 mA (fused at 1000 mA)
Table 5-11
TERMPWR Input Electrical Characteristics
Signal Characteristic
Input voltage
Minimum source capability:
Sink current:
Value
4.00 VDC to 5.25 VDC
1000 mA (fused at 1000 mA)
1.0 mA maximum, excluding power to the internal terminator.
Internal Termination
This drive provides on-board Alternative 2 active termination for the SCSI bus.
The termination resistors, which are contained in two Single Inline Packs (SIPs) should be removed from the drive unless it is a SCSI device at a physical end of the bus. The terminator equivalent circuit is shown below for reference:
Figure 5-1
Terminator Equivalent Circuit
+5V
TERMPWR
E8
F1
Voltage
Regulator
2.5K
10K
110
-DB0
-DB1
-DB2
: :
: :
: :
-REQ
-I/O
Page 60 Filepro CFP2105 Series
SCSI Physical Characteristics Chapter 5
Cable Requirements
A 50 conductor cable no more than 6 meters (19.68 feet) cumulative length with at least 28 AWG wire size and a characteristic impedance of 70 to 100 ohms (84 ohms nominal) is required. In systems which use the fast synchronous transfer option, the cable should meet the following additional requirements:
Table 5-12
Interface Cable Electrical Characteristics
Specification
Signal Attenuation
Pair-to-Pair Propagation Delay Delta
DC Resistance
Value
0.095dB maximum per meter at 5 Mhz
0.20 ns maximum per meter
0.230 ohms maximum per meter at 20
°
C
Technical Reference Manual Page 61
Chapter 5 SCSI Physical Characteristics
Connector Requirements
The connector on the drive is a 50-position header which consists of 2 rows of 25 male pins on 0.100 inch centers. The mating connector is a SCSI-2 Non-shielded
Alternative 1, A-cable connector which is shown below:
Figure 5-2
A-Cable Connector
Contact 50
C1
Back view
C4
Contact 1
C3
C2
See Note 1
Contacts for even wires are not shown.
Side view
C5
C6
Socket 1
Socket 49
C7
Front view
C8
Socket 2
Socket 50
Dimensions Millimeters Inches
C5
C6
C7
C8
C1
C2
C3
C4
2.540
60.960
2.540
3.302
32.385
68.072
6.096
7.620
0.100
2.400
0.100
0.130
1.275
2.680
0.240
0.300
Notes:
(1) Fifty contacts on 1.27mm (0.05
inch) staggered spacing =
62.23mm (2.450 inch) [ref.]
(2) Tolerances +0.127mm (0.005
inch) noncumulative unless specified otherwise.
(3) Connector cover and strain relief are optional
Page 62 Filepro CFP2105 Series
SCSI Physical Characteristics
Interface Pin Assignments
The pin assignments for the interface connector are shown below:
Pin
09
11
13
15
17
01
03
05
07
19
21
23
25
27
29
31
41
43
45
47
49
33
35
37
39
Table 5-13
Interface Signal Definitions
Signal
GND
GND
GND
GND
GND
GND
GND
GND
GND
GND
GND
RESERVED
OPEN
RESERVED
GND
GND
GND
GND
GND
GND
GND
GND
GND
GND
GND
Pin
10
12
14
16
18
02
04
06
08
20
22
24
26
28
30
32
42
44
46
48
50
34
36
38
40
Signal
-DB0
-DB1
-DB2
-DB3
-DB4
-DB5
-DB6
-DB7
-DBP
GND
GND
RESERVED
TERMPWR
RESERVED
GND
-ATN
GND
-BSY
-ACK
-RST
-MSG
-SEL
-C/D
-REQ
-I/O
Notes:
1. The minus sign (-) indicates active low.
2. All odd pins except pin 25 must be connected to ground. Pin 25 is left open.
3. Pins marked Reserved are connected to ground.
Chapter 5
Technical Reference Manual Page 63
Chapter 5 SCSI Physical Characteristics
Interface Timing Requirements
Unless otherwise noted, the delay-time measurements are calculated from signal conditions existing at the drive's own SCSI bus connector. Normally these measurements (except cable skew delay) can be made without considering delays in the cable.
Table 5-14
SCSI Bus Timing Values
Timing Description
Arbitration Delay
Bus Clear Delay
Bus Free Delay
Bus Set Delay
Bus Settle Delay
Cable Skew Delay
1
Data Release Delay
Receive Assertion Period
Receive Hold Time
Receive Negation Period
Receive Setup Time
Reset Hold Time
Selection Abort Time
Selection Time-out Delay
2
System Deskew Delay
Transmit Assertion Period
Transmit Hold Time
Transmit Negation Period
Transmit Setup Time
fast
2.4
µ s
800 ns
800 ns
1.8
µ s
400 ns
4 ns
400 ns
22 ns
25 ns
22 ns
15 ns
25
µ s
200
µ s
250 ms
20 ns
30 ns
33 ns
30 ns
23 ns
Timing Value slow
2.4
µ s
800 ns
800 ns
1.8
µ s
400 ns
4 ns
400 ns
70 ns
25 ns
70 ns
15 ns
25
µ s
200
µ s
250 ms
45 ns
80 ns
53 ns
80 ns
23 ns
asynch
2.4
µ s
800 ns
800 ns
1.8
µ s
400 ns
4 ns
400 ns n/a n/a n/a n/a
25
µ s
200
µ s
250 ms
45 ns n/a n/a n/a n/a
Notes:
1
This time does not apply at the SCSI connector of the drive.
2
This is a recommended time. It is not mandatory.
Page 64 Filepro CFP2105 Series
SCSI Physical Characteristics Chapter 5
Model CFP2105W (Wide, Unitized SCSI-3 P-Connector)
External Terminator Power
Power to the on-board terminators is provided by the higher of the voltage supplied at Pin #17, 18, 51, & 52, J2 or the voltage level at the 5 Volt power input to the drive minus one diode drop. The diode prevents back flow of current to the drive. Termination Power to external terminators can be supplied by the drive through Pin #17, 18, 51, & 52, J2. The TERMPWR line can be disconnected from the drive by removing Jumper E8. Table 5-11 describes the electrical characteristics of the TERMPWR line when it is used to supply power to an external terminator.
Table 5-15
TERMPWR Electrical Output Characteristics
Signal Characteristic
Supply voltage
Minimum source capability:
Value
4.06 VDC to 4.56 VDC
(dependent on power supplied to the drive)
1500 mA
Table 5-16
TERMPWR Input Electrical Characteristics
Signal Characteristic
Input voltage
Minimum source capability:
Sink current:
Value
4.00 VDC to 5.25 VDC
1500 mA (fused at 1500 mA)
1.0 mA maximum, excluding power to the internal terminator.
Internal Termination
This drive provides on-board Alternative 2 active termination for the SCSI bus.
The termination resistors, which are contained in three Single Inline Packs
(SIPs) should be removed from the drive unless it is a SCSI device at a physical end of the bus. The terminator equivalent circuit is shown below for reference:
Figure 5-2
Terminator Equivalent Circuit
+5V
TERMPWR
E8
F1
Voltage
Regulator
2.5K
10K
110
-DB0
-DB1
-DB2
: :
: :
: :
-REQ
-I/O
Technical Reference Manual Page 65
Chapter 5 SCSI Physical Characteristics
J5 Auxiliary Connector Signal Characteristics
Table 5-17
J5 Auxiliary Interface Electrical Characteristics
High
Low
State Current
0 < I
IH
< 20
µ
A
0 < I
OH
< -48 mA
Voltage
2.5 V < V
IH
< V
CC
+ 0.3 V
-0.1 V < V
IL
< 0.4 V
Cable Requirements
A 68 conductor cable no more than 3 meters (9.84 feet) cumulative length with at least 30 AWG wire size and a characteristic impedance of 70 to 100 ohms (84 ohms nominal) is required. In systems which use the fast synchronous transfer option, the cable should meet the following additional requirements:
Table 5-18
Interface Cable Electrical Characteristics
Specification
Signal Attenuation
Pair-to-Pair Propagation Delay Delta
DC Resistance
Value
0.095dB maximum per meter at 5 Mhz
0.20 ns maximum per meter
0.230 ohms maximum per meter at 20
°
C
Page 66 Filepro CFP2105 Series
SCSI Physical Characteristics Chapter 5
Connector Requirements
The connector on the drive is a 68-pin . The mating connector is a SCSI 3 Nonshielded P-cable connector which is shown below:
Figure 5-4
P-Cable Connector
T
A13
A16 R
A8
A14 A15
A9
M
T V S W S
A10
A11
M T V S W S
PIN 1
A1
W
A12
PIN 68
A6
PIN 34
A3
A2
V
DIMENSIONS
A1
A2
A3
A4
A5
A6
A7
A8
A9
A10
A11
A12
A13
A14
Technical Reference Manual
PIN 35
A7
Millimeters
46.28
5.69
2.54
1.27
41.91
15°
1.04 R
0.396 + 0.010
0.23
0.60 + 0.03
0.23
0.05
5.15 + 0.15
4.39 MAX
A4
A5
Inches
1.822
0.224
0.100
0.050
1.650
15°
0.041 R
0.0156 + 0.0004
0.009
0.024 + 0.001
0.009
0.002
0.203 + 0.006
0.173 MAX
Page 67
Chapter 5
A15
A16
3.02 MIN
1.02 + 0.25
0.119 MIN
0.040 + 0.010
SCSI Physical Characteristics
Page 68 Filepro CFP2105 Series
SCSI Physical Characteristics
Interface Pin Assignments
The pin assignments for the interface connector are shown below:
Table 5-19
Interface Signal Definitions
Pin
21
22
23
24
25
17
18
19
20
26
27
28
29
30
31
32
33
34
7
8
9
5
6
3
4
1
2
10
11
12
13
14
15
16
Signal
Ground
Ground
Ground
Ground
Ground
Ground
Ground
Ground
Ground
Ground
Ground
Ground
Ground
Ground
Ground
Ground
Ground
Ground
Ground
Ground
Ground
Ground
Ground
Ground
Ground
Ground
Ground
Ground
Ground
TERMPWR
TERMPWR
Reserved
Ground
Ground
Notes:
1. The minus sign (-) indicates active low.
2. Pins marked Reserved are not connected.
Pin
55
56
57
58
59
51
52
53
54
60
61
62
63
64
65
66
67
68
39
40
41
42
43
35
36
37
38
44
45
46
47
48
49
50
Signal
-DB(12)
-DB(13)
-DB(14)
-DB(15)
-DB(P1)
-DB(0)
-DB(1)
-DB(2)
-DB(3)
Ground
-BSY
-ACK
-RST
-MSG
-SEL
-C/D
-REQ
-I/O
-DB(8)
-DB(9)
-DB(10)
-DB(11)
-DB(4)
-DB(5)
-DB(6)
-DB(7)
-DB(P)
Ground
Ground
TERMPWR
TERMPWR
Reserved
Ground
--ATN
Chapter 5
Technical Reference Manual Page 69
Chapter 5 SCSI Physical Characteristics
Interface Timing Requirements
Unless otherwise noted, the delay-time measurements are calculated from signal conditions existing at the drive's own SCSI bus connector. Normally these measurements (except cable skew delay) can be made without considering delays in the cable.
Table 5-20
SCSI Bus Timing Values
Timing Description
Arbitration Delay
Bus Clear Delay
Bus Free Delay
Bus Set Delay
Bus Settle Delay
Cable Skew Delay
1
Data Release Delay
Receive Assertion Period
Receive Hold Time
Receive Negation Period
Receive Setup Time
Reset Hold Time
Selection Abort Time
Selection Time-out Delay
2
System Deskew Delay
Transmit Assertion Period
Transmit Hold Time
Transmit Negation Period
Transmit Setup Time
fast
2.4
µ s
800 ns
800 ns
1.8
µ s
400 ns
4 ns
400 ns
22 ns
25 ns
22 ns
15 ns
25
µ s
200
µ s
250 ms
20 ns
30 ns
33 ns
30 ns
23 ns
Timing Value slow
2.4
µ s
800 ns
800 ns
1.8
µ s
400 ns
4 ns
400 ns
70 ns
25 ns
70 ns
15 ns
25
µ s
200
µ s
250 ms
45 ns
80 ns
53 ns
80 ns
23 ns
asynch
2.4
µ s
800 ns
800 ns
1.8
µ s
400 ns
4 ns
400 ns n/a n/a n/a n/a
25
µ s
200
µ s
250 ms
45 ns n/a n/a n/a n/a
Notes:
1
This time does not apply at the SCSI connector of the drive.
2
This is a recommended time. It is not mandatory.
Page 70 Filepro CFP2105 Series
SCSI Physical Characteristics Chapter 5
Technical Reference Manual Page 71
SCSI Command Implementation
6
This section contains a brief summary of the SCSI Interface implemented in the drive. For additional details regarding command descriptions, please refer to the Eleventh Generation SCSI Interface Manual.
SCSI Command Summary
Following is a list of commands that the drive supports:
Format Unit
Inquiry
Mode Select
Mode Sense
Read (6)
Read Buffer
Read Capacity
Read Defect Data
Read Extended (10)
Read Long
Reassign Blocks
Receive Diagnostics
Release
Request Sense
Reserve
Re-zero Unit
Seek (6)
Seek Extended (10)
Send Diagnostic
Start/Stop Unit
Test Unit Ready
Verify
Write (6)
Write Extended (10)
Write and Verify
Write Buffer
Write Long
1DH
1BH
00H
2FH
0AH
2AH
2EH
3BH
3FH
1CH
17H
03H
16H
01H
0BH
2BH
04H
12H
15H
1AH
08H
3CH
25H
37H
28H
3EH
07H
Drive Dependent SCSI Mode Sense Data
The following pages show the drive dependent Mode Sense information for this drive. The default values are noted in parenthesis (). Parameters not specified are 00
H
.
Technical Reference Manual Page 73
Chapter 6
Page 74
SCSI Command Implementation
Vendor Specific Parameters Page - 00
H
The Vendor Specific Parameters Page contains options that allow the drive's power-on reset sequences to be modified. Only one copy of this page is maintained, thus modifications to this page affects all initiators.
Table 7-12
Vendor Specific Parameters Page Format
Bit
Byte
7 6 5 4
0
Reserved Page Code = 00
H
3
1
2
3
Page Length = 2
H
DINR
(0)
DSPN
(0)
Delay Time
(00)
DAD
(0)
DUA
(0)
Rsvd
(0)
2
Rsvd
(0)
1 0
TSYN
(0)
SDLY
(0)
DINR (Disable Immediate Not Ready): When this bit is zero, any command received by the drive while it is spinning up returns a CHECK CONDITION status to the host. A subsequent REQUEST SENSE command will return a
NOT READY.
When this bit is a one, a TEST UNIT READY command reports GOOD status.
Any other command will cause the drive to accept the command, disconnect, wait until the drive is up to speed and ready, then execute the command, re-connect and complete the command.
DSPN (Disable Motor Spin-Up): When set to zero, it indicates that motor spin-up at power-on is enabled. When set to one, it indicates that motor spin-up at power-on is disabled.
DAD (Disable Automatic Disconnects): This bit has impact only when the drive is operating in its READ-AHEAD mode of operation. When set to zero, the drive will automatically disconnect from the SCSI bus when receiving a WRITE command. When DAD is set to one and WCE is set to zero, the drive will immediately start to accept write data without first disconnecting from the SCSI bus. When DAD is set to one, WCE is set to one, and a previous write command’s data has been accepted and GOOD status reported, the drive will immediately accept write data if the request is perfectly sequential to the previous WRITE.
DUA (Disable Unit Attention): When set to zero, a CHECK CONDITION status with a sense key of UNIT ATTENTION occurs for each initiator following a bus reset, a BUS DEVICE RESET message or a power-on reset. When set to one, presentation of a CHECK CONDITION status for the UNIT ATTENTION condition is disabled.
TSYN (Target Initiate Synchronous Negotiation): When set to zero, the drive cannot initiate synchronous transfer negotiations. When set to one, the drive can initiate synchronous transfer negotiation, if necessary.
Filepro CFP2105 Series
SCSI Command Implementation Chapter 6
SDLY (Spin Up Delay): When set to zero, the spin up occurs when power is applied to the drive. When set to one, the spin up is delayed at power-on by the value of the drive's SCSI ID times 4 seconds (i.e., SCSI ID 4 will delay 16 seconds).
Delay Time: When set to a value other than zero, specifies the spin up delay constant used to multiply with the SCSI ID to determine the spin up delay when
SDLY is set to one. A value of 40H is equal to 4 seconds, which is also the default value if Delay Time is set to zero.
Technical Reference Manual Page 75
Chapter 6
Page 76
SCSI Command Implementation
Format Drive Page - 03H
The Format Drive page contains parameters which specify the medium format.
Table 6-1
Format Drive Page Format
Byte
Bit
7 6 5 4 3 2 1
8
9
6
7
10
0
1
2
3
4
5
11
12
13
14
15
16
17
18
19
20
21-23
Rsvd Rsvd Page Code = 03
H
Page Length = 16
H
Tracks per Zone (MSB)
(00
H
)
Tracks per Zone (LSB)
(01
H
)
Alternate Sectors per Zone (MSB)
(00
H
)
Alternate Sectors per Zone (LSB)
(01
H
)
Alternate Tracks per Zone (MSB)
Alternate Tracks per Zone (LSB)
Alternate Tracks per Logical Unit (MSB)
Alternate Tracks per Logical Unit (LSB)
SSEC HSEC
(1)
Sectors per Track (MSB)
(00
H
)
Sectors per Track (LSB)
(8C*
H
)
Data Bytes per Physical Sector (MSB)
(02
H
)
Data Bytes per Physical Sector (LSB)
(00
H
)
Interleave (MSB)
(00
H
)
Interleave (LSB)
(01
H
)
Track Skew Factor (MSB)
(00
H
)
Track Skew Factor (LSB)
(05
H
)
Cylinder Skew Factor (MSB)
(00
H
)
Cylinder Skew Factor (LSB)
(45
H
)
RMB SURF Reserved
Reserved
* Varies depending on active notch.
0
Tracks Per Zone: Defines the number of tracks per zone to use in dividing the capacity of the drive for the purpose of allocating alternate sectors. A value of zero means that one zone is defined for the entire drive.
Filepro CFP2105 Series
SCSI Command Implementation Chapter 6
Alternate Sectors Per Zone: Defines the number of spare sectors per zone the drive reserves for defect handling. Not supported. Must be set to zero.
Alternate Tracks Per Logical Unit: Not supported. Must be set to zero.
Sectors Per Track: Defines the number of physical sectors per track. The number includes the one alternate sector per track the drive allocates. The value reported for the number of sectors per track is dependent on the active notch value.
Data Bytes Per Physical Sector: Defines the number of data bytes per physical sector.
Interleave: Defines the interleave value used by the drive.
Track Skew Factor: Defines the number of physical sectors between the last logical block of one track, and the first logical block on the next sequential track of the same cylinder.
Cylinder Skew Factor: Specifies the number of physical sectors between the last logical block of one cylinder and the first logical block on the next sequential cylinder.
SSEC (Soft Sector Format): Set to zero to indicate the drive does not support a soft sector format.
HSEC (Hard Sector Format): Set to one to indicate the drive supports a hard sector format.
RMB (Removable Media): Set to zero to indicate the drive does not have removable media.
SURF (Surface Format): The SURF bit is set to zero, meaning the drive allocates progressive addresses to all logical blocks within a cylinder prior to allocating addresses on the next cylinder.
Technical Reference Manual Page 77
Chapter 6 SCSI Command Implementation
Drive Geometry Page - 04
H
Table 6-2
Drive Geometry Page
Bit
Byte
7 6 5
9
10
11
0
1
2
3
4
5
6
7
8
4 3 2 1
Rsvd Rsvd Page Code = 04H
Page Length = 16
H
Number of Cylinders (MSB)
(00
H
)
Number of Cylinders
(0F
H
)
Number of Cylinders (LSB)
(64
H
)
Number of Heads
(0A
H
)
Starting Cylinder - Write Precompensation (MSB)
(00
H
)
Starting Cylinder - Write Precompensation
(00
H
)
Starting Cylinder - Write Precompensation (LSB)
(00
H
)
Starting Cylinder - Reduced Write Current (MSB)
Starting Cylinder - Reduced Write Current
Starting Cylinder - Reduced Write Current (LSB)
15
16
17
12
13
14
Drive Step Rate (MSB)
Drive Step Rate (LSB)
Landing Zone Cylinder (MSB)
Landing Zone Cylinder
Landing Zone Cylinder (LSB)
Reserved
0
RPL
(0
H
)
18
19
Rotational Offset
Reserved
20
21
22-23
Medium Rotation Rate (MSB)
(15
H
)
Medium Rotation Rate (LSB)
(18
H
)
Reserved
* Varies depending on active notch.
Only one copy of this page is maintained. There is only one changeable field,
RPL. All other fields are described in the MODE SENSE Command.
Page 78 Filepro CFP2105 Series
SCSI Command Implementation Chapter 6
RPL (Rotational Position Locking): Enables spindle synchronization.
Setting either bit 0 or 1, or both, causes multiple drives which have their spindle synchronization (SS) pins daisy chained together to synchronize their spindles.
Notch and Partition Parameters Page - 0C
H
The Notch and Partition Parameters Page contains information which pertains to each notch of the drive. Each section of the drive with a different number of logical blocks per cylinder is referred to as a notch or zone. Only one copy of this page is maintained. The only changeable field in this page is Active Notch.
Technical Reference Manual Page 79
Chapter 6
Page 80
SCSI Command Implementation
Table 6-3
Notch and Partition Parameters Page Format
Bit
Byte
7 6 5 4 3
Rsvd Rsvd
0
1
2
ND
(1)
LPN
2
Page Code - OCH
Page Length = 16H
Reserved
1
3
Reserved
4
5
6
7
(0
Maximum Number of Notches (MSB)
(00
H
)
Maximum Number of Notches (LSB)
(0F
H
)
H
)
Active Notch (MSB)
(00
H
)
Active Notch (LSB)
(1*
H
)
8
9
10
11
12
13
14
15
Starting Boundary (MSB)
(00*
H
)
Starting Boundary
(00*
H
)
Starting Boundary
(08*
H
)
Starting Boundary (LSB)
(00*
H
)
Ending Boundary (MSB)
(00*
H
)
Ending Boundary
(01*
H
)
Ending Boundary
(71*
H
)
Ending Boundary (LSB)
(00*
H
)
Pages Notched (MSB)
Pages Notched
16
17
18
19
20
3F
37
2F
27
1F
Pages Notched
Pages Notched
Pages Notched
21
17 Pages Notched
22
0F
Pages Notched
(10
H
)
23
07
Pages Notched (LSB)
(08
H
)
* Varies depending on active notch.
0
38
30
28
20
18
10
08
00
Filepro CFP2105 Series
SCSI Command Implementation Chapter 6
ND (Notched Drive): If set to zero, the drive is not notched and all other parameters in this page are returned as zeros. If set to one, the drive is notched and this page defines the starting and ending boundaries for each active notch.
This parameter is always set to one.
LPN (Logical or Physical Notch): When set to zero, indicates the notch boundaries are physical addresses (i.e., cylinder and head). An LPN bit of one is not supported.
The Maximum Number of Notches field indicates the maximum number of notches supported by the drive.
The Active Notch field indicates which notch is being referred to by this and subsequent MODE SELECT and MODE SENSE commands, until changed by a later MODE SELECT command. Active notches are numbered beginning from one up to the maximum number of notches.
The Starting Boundary field indicates the beginning of the active notch; the three most significant bytes represent the cylinder number and the least significant byte represents the head number.
The Ending Boundary field indicates the ending of the active notch; the three most significant bytes represent the cylinder and the least significant byte represents the head number.
The Pages Notched field is a bit map of the MODE SELECT page codes which indicates the pages containing parameters that are changed for different notches. The most significant bit of this field corresponds to page code 3F and the least significant bit represents page code 0. If a bit is a one, the corresponding MODE SELECT page contains parameters that are changed for different notches. If a bit is a zero, the corresponding MODE SELECT page parameters are constant for all notches.
Technical Reference Manual Page 81
Previous
Pre-Release
Revision A
October 1994
Revision
Current
Revision A
June 1995
Description
• deleted reference to spindle synchronization
• changed sector sizes supported to 512 & 1024
• eliminated reference to e-coating on page 4.
• corrected controller overhead definition
• updated power consumption specification per DVT.
• updated drawings and dimensions of drive to match
23311-001 rev Y5.
Date
6/95
Technical Reference Manual Page 82
advertisement
* Your assessment is very important for improving the workof artificial intelligence, which forms the content of this project
Related manuals
advertisement