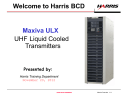
advertisement
▼
Scroll to page 2
of 182
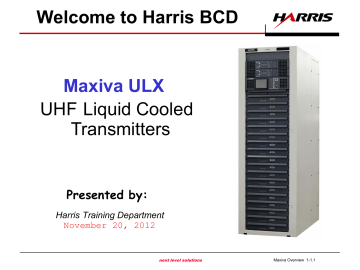
Welcome to Harris BCD Maxiva ULX UHF Liquid Cooled Transmitters Presented by: Harris Training Department November 20, 2012 next level solutions Maxiva Overview 1-1.1 Overview Maxiva™ ULX Series Liquid Cooled UHF Multimedia Transmitter ULX 25000 AN Model no. prefix Model no. suffix U = UHF L = Liquid Cooled X = Transmitter AN = analog AT=ATSC DV=DVB-T/H T2= DVB-T2 IS=ISDB-T CT= CTTB CM=CMMB FL=FLO Peak visual power for analog Average power for digital next level solutions Maxiva Overview 1-1.2 Design Considerations Software defined Capable of current/future analog & digital standards Improved efficiency Low operating cost Environmentally friendly Easy to maintain & service next level solutions Maxiva Overview 1-1.3 New Technology 50V, high power, UHF LD-MOS FET AC-DC power supply “block” M2X exciter – software definable M2X & TCU PA Module next level solutions Maxiva Overview 1-1.4 Maxiva – Liquid Cooled Transmitter • General Overview: – UHF Liquid-Cooled multi-standard transmitter – Broadband design / frequency agile for all UHF – Incorporates new PowerSmart™ technology: • First available 50 Volt UHF LDMOS Power Devices • Best in Class Power Density • Higher Efficiency ~30% better than previous designs Lower Power Consumption • Green design – RoHS compliant – Power levels per PA cabinet: • Analog: • ATSC: • COFDM: 26.2 kW pk sync 12.3 kW average 8.7 kW average (power at cabinet output) – Incorporates Apex M2X multimedia exciter – TCU (transmitter control unit) – Easy software upgradeability to new standards as they become available (e.g. DVB-T2) next level solutions Maxiva Overview 1-1.5 Maxiva – Liquid Cooled Transmitter • Additional Benefits: – RoHS compliant / CE compliant – Modular design – Simpler single gain stage PA modules • Less Complexity • Higher reliability (fewer components) • Smaller and lighter for ease of handling • Front load – hot-pluggable design • Field serviceable design with sub-assembly repair – Redundancy built into control system – All digital Real Time Adaptive Correction (RTAC) – Includes Harris web-enabled remote GUI interface next level solutions Maxiva Overview 1-1.6 Power Levels Output Power Level kW (before filter) Cabinets PA Modules ATSC 470-698 > 698 MHz MHz 470-494 MHz DVB-T 495-630 631-670 MHz MHz >670 MHz Analog 470-860 MHz 2 2.0 1.7 1.2 1.2 1.2 1.1 3.6 3 3.0 2.6 1.8 1.9 1.8 1.7 5.2 4 4.0 3.4 2.4 2.5 2.4 2.3 7.1 6 6.0 5.2 3.6 3.8 3.6 3.4 10.5 8 8.0 6.9 4.8 5.0 4.8 4.4 13.8 10 9.6 8.3 5.7 6.1 5.7 5.5 17.0 12 11.5 10.0 6.9 7.3 6.9 6.5 20.9 16 15.4 13.3 9.2 9.7 9.2 8.7 26.2 2 18 (12+6) 16.9 14.7 10.4 9.8 10.4 9.8 31.4 2 24 (12+12) 22.2 19.3 13.3 12.6 13.3 12.6 41.4 2 32 (16+16) 29.8 25.7 17.8 16.8 17.8 16.8 51.8 3 36 (12+12+12) 33.3 29.0 20.0 18.8 20.0 18.8 62.1 3 48 (16+16+16) 44.6 38.5 26.7 25.2 26.7 25.2 77.6 1 Analog power given is peak visual power. DVB-T & ATSC power given is average power. next level solutions Maxiva Overview 1-1.7 Power Levels Output Power Level kW (afterfilter) Cabinets PA Modules Analog* 470-860 MHz 2 3,200 3 5,000 4 6,800 6 10,000 8 13,000 10 16,500 12 20,000 16 25,000 2 18 (12+6) 30,000 2 24 (12+12) 40,000 2 32 (16+16) 50,000 3 36 (12+12+12) 60,000 3 48 (16+16+16) 75,000 1 Analog power given is peak visual power. DVB-T & ATSC power given is average power.* Indicates power levels used in model numbers. next level solutions Maxiva Overview 1-1.8 Apex M2X Exciter & TCU Controller RTAC Control & Status LED’s Color touch screen PC GUI Status LED’s Status LED’s next level solutions (behind cover) Ethernet RF sample port and 10MHz, 1PPS signals Control Buttons Maxiva Overview 1-1.10 Maxiva ULX Front View Apex M2X Exciters TCU System Controller B A Redundant Pre-Drivers 18 PA’s (up to 8) Slot numbers shown here. 11 Redundant Driver-PA’s 10 9 Installed PA modules vary by model. 8 PA’s (up to 8) Slots are numbered. PA’s are interchangeable. 1 next level solutions Maxiva Overview 1-1.11 Maxiva ULX Front View TM page 5-2. next level solutions Maxiva Overview 1-1.12 Cabinet Rear View TCU, PS1&2, exciter, preamps Main Circuit Breakers Temp range for inside equipment: 0 to 45o C. Temp range for outside equipment: -33 to 45o C. Control Circuit Breakers Lower PAs Upper PAs Coolant In/Out Hoses RF Output Line Upper 8-way Combiner If both fans fail transmitter will keep operating until PA modules overheat. 10 kW Final Reject Load 3dB Power Combiner Redundant Cabinet Blowers (2) Lower 8-way Combiner See Section 200 dwg. 801-0222161 control boards. AC fans. next level solutions Maxiva Overview 1-1.13 Liquid Cooled Main Cabinet Block Diagram next level solutions Maxiva Overview 1-1.14 Maxiva PA Module Key Features • Broadband, hot-pluggable design • Blind-mate control, power, RF and liquid connectors – No rear access required for hoses, as in Atlas and most other competitive transmitters • More compact PA module 22 kg (48.5 lbs) – Easier to handle than Atlas. Easier one person replacement • Simpler design, single gain stage – Less parts, less complex & more reliable • Designed for easy serviceability – Modular design with field replaceable RF pallets, LDMOS devices (pallets) and Power Supplies • 1 for 1 power supply to RF device ratio – Provides excellent redundancy and lower cost per unit next level solutions Maxiva Overview 1-1.15 Maxiva PA Module AC-DC Converters (8) Module weight < 22kg Air flow keeps PS electrolytics cool RF Pallets (4) Out Coolant blind mate connectors In Output RF Connector Power Combiner next level solutions Cold Plate Maxiva Overview 1-1.16 Maxiva PA Module User replaceable sub-assemblies shown AC-DC Converter Module Txer AC input ranges 208-240V or 380-415 -15 to 10% with AC warning at -15% TEK PS single phase 90-264VAC PN 901-0222-011G Handle RF Pallet Latch PN 901-0222-081G LDMOS Device with Heat Spreader Diagnostic Port Status LED’s LDMOS FET Copper for good heat transfer PN 943-5601-041 next level solutions Maxiva Overview 1-1.17 Maxiva PA Module 3 Power Supply 2 LDMOS 5 VSWR 1 Power On 6 Overload 4 Temperature 7 RF Input OK Index LED Color Indication Description 1 Green ON-OFF 2 Red LDMOS Failure 3 Red P.S. Failure When one or more P.S. failed. Trips when PS <40V. 4 Red Temp. Fault Temp sensors in monitor board and on pallets. Trips if pallet > 90oC or monitor board > 65oC. 5 Red VSWR Fault Reflected power overload (input and output). Trips if ref. > 100w avg. ATSC. 6 Red Power Overload Input power overdrive trips if > 55.7W peak. Output overload > 2219W trips. 7 Green Input Power OK OK: Green, Input Power Low: Red (<.16W) NEW ON: Green, OFF:None One or more LDMOSFET failed. Trips when LDMOS current <.5A next level solutions Maxiva Overview 1-1.18 Optional Module Test System PA Module Test System: 9810222012 (includes PA diagnostics unit) PA Diagnostics Unit: 971-00040-080 DP: 988-2765-001 TM :888-2765-001 DP: 988-2764-001 TM 888-2764-001 PA Diagnositic unit cable: 256-0346-000 USB/AB cable : 256-0346-000 Kit, PA Diagnostics Unit Cables & doc. package: 971-0040-081 Diagnostics Unit Load Pump & Heat Exchanger 6-10mW RF input 650W RF output COFDM Control Panel next level solutions Maxiva Overview 1-1.19 TCU • TCU in main cabinet contains GUI (graphical user interface panel PC). • TCU cards used may vary with model. TCU • All TCU’s contain MCM card (board). • MCM’s in each cabinet connected by system buss. • Cabinet 1 TCU is main controller in multicabinet systems. Other TCU’s are slaves. • Battery for real time clock on PCM card. Check for presence on site. • Transmitter stays on air if portions of TCU MCM or PCM card fail. • Failed cards must remain in TCU with power applied. Cards are not hot swappable. next level solutions Maxiva Overview 1-2.1 TCU – Front Panel Transmitter Control Unit GUI screen calibration can be accessed during reboot. Tap screen when “Touch screen to calibrate.” text appears. 5 point cal begins. Reboot of TCU takes about 2 minutes. Transmitter will stay on air if reset button on PCM card is used. MCM reboot takes transmitter off air for a short period. next level solutions Maxiva Overview 1-2.2 TCU – Hardware Buttons Pressing Auto turns on ALC and transmitter maintains set power level. Normal operation is in Auto mode. Switching to Manual disables ALC. Used primarily for power calibration. LED’s green for normal operation, yellow for warnings and red for faults. Manual button must be pressed for 5 seconds to actuate. LED’s and switches mounted on user interface board. Switches PDU and IPA pair. • Power Control – ALC Auto/Manual • Remote - Enable/Disable • Power - Raise/Lower • Exciter - A/B • Drive - A/B • Transmitter - On/Off next level solutions Maxiva Overview 1-2.3 TCU - with PCM-1 card Redundant PSs 1&2 PDU/IPA Switch Exciter Switch Pump Switch Flash Card (2GB,FAT 16 Format use Sandisk Ultra II) Serial Connection (use 612-1601-000 RS232-RJ45 adapter ) and TeraTerm MCM reset TCU Front Panel pull forward then down PCM-1 card Hole in each side for handles Panel PC shown here next level solutions Maxiva Overview 1-2.4 TCU – with PCM-2 card Local Ethernet Connection Fixed IP 192.168.2.100 Redundant PSs 1 & 2 PDU/IPA Switch Exciter Switch Micro SD card 2GB, 971-0039-071 Flash Card Pump Switch (2GB,FAT 16 Format use Sandisk Ultra II) Serial Connection (use 612-1601-000 ) RS232-RJ45 adapter and TeraTerm PCM reset MCM reset Hole in each side for handles PCM-2 card TCU Front Panel pull Panel PC forward then down next level solutions Maxiva Overview 1-2.5 TCU - PCM-1 & PCM-2 971-0039-056T Lithium battery, CR1025, 3V, 10mm, 660-0093-000 PCM-1 reset On-board computer PCM-2 reset • Designed for use with panel PC (not LCD) • PCM-2 upgrade is recommended. • Offers improved operation. • Replacement kit 973-4512-007 contains service bulletin, instructions and board. • Uses micro SD card, 2GB, 971-0039-071 as hard drive. Image stored on computer board too. 971-0039-156T Lithium battery, 20mm, 3V, CR2032 660-0054-000 next level solutions Maxiva Overview 1-2.6 TCU - Access Cover removed for access to cards Screw removed to allow TCU body to pivot downward TCU – front panel lowered, unit pulled out from rack. Caution ! Support unit when removing side screws. next level solutions Maxiva Overview 1-2.7 TCU - Access Depress button on both sides to slide unit into rack PCM1 card shown Be careful with ribbon cables (front and rear) TCU – Pulled out of rack and pivoted downward next level solutions Maxiva Overview 1-2.8 TCU - Components Base board PS board Behind front panel: • LCD shown here (panel PC not shown) Keep fans clean • User interface board (behind LEDs & buttons) Redundant PS1 Main Control Module MCM Redundant PS2 PA interface – 2 (if more than 8 PA’s) PA interface – 1 PS monitor Exciter Switching next level solutions Customer I/O Processor control module PCM-1 (uprocessor daughter board) RF detector (pump control daughter board) Maxiva Overview 1-2.9 TCU – PS 971-0039-008T Fan Plug 3.3, 5, +/-15 V PS 24 V PS Fan 952-9252-006 • Not hot pluggable – Turn off Control breaker before reinserting. • Individual supplies soldered onto board - difficult to change in field • Keep fan and TCU filters clean, keep spare PSs next level solutions Maxiva Overview 1-2.10 TCU - Cards • PS 1 & 2 - Redundant 24V power supplies. Operate flushing fan current monitor, produce supply voltage for external RF switch, supply boards in TCU. Turn off Control breakers before removal or replacement. • PA Interface (Digital I/O) - Provides interface between TCU, IPA (driver) and PA backplane boards. The interface features 40 digital outputs/inputs and 24 analog outputs and inputs. A fully populated cabinet will require two PA interface cards, one card per eight PA modules. The PA interface card sends the ON/OFF commands to the PA modules and receives fault information and status from them. • PS Monitor - Monitors AC lines for phase imbalance and high or low voltage, coolant inlet/outlet temperature, coolant flow, leaks, combiner temperature and cabinet fans. • Exciter Switch - Contains PWB relay, 2 RMS detectors with adjustable trips (via EPOTs) for power monitoring and a control/status interface for Exciters A and B. next level solutions Maxiva Overview 1-2.11 TCU - Cards • Customer I/O - Provides parallel remote control, status and meter outputs. Connector A has all inputs and Connector B has all outputs. • RF Detector/Pump Control/ Interlocks - Consists of a main board and a daughter card. It features 7 RMS detectors with adjustable trip points (via EPOTS). It has pump control and interlocks on one D25 pin connector and interfaces to an analog downcoverter board via another D25 connector. • Processor Control Module (PCM) - ARM based micro module running embedded Linux OS. It provides a touch screen for enhanced monitoring and control, exciter and multi-cabinet data collection, fault logs and web remote connectivity. • Standard Master Control Module (MCM) - FPGA based controller used for all critical transmitter control functions. next level solutions Maxiva Overview 1-2.12 TCU GUI Screens Original Version TCU (LCD) Control Buttons GUI Screen Status LED’s Original TCU did not have capability of displaying M2X screens. Direct connection to M2X was required to make changes to settings. Local login using username = admin and password = harris Remote login using username = admin and password = harris2009 Username and password fixed. Login on System Service Screen locally. Recommend use of Mozilla Firefox. Use zoom feature to enlarge GUI display. Ctrl + or Ctrl next level solutions Maxiva Overview 1-3.1 TCU GUI Screens Panel PC TCU – PCM1 Card Login using username = admin and password = harris2009 Username and password fixed. Login on System Service Screen locally. Remote GUI screens looks just like new style TCU. Recommend use of Mozilla Firefox, Chrome or or IE8 web browser. Use zoom feature to enlarge GUI display. Ctrl + or Ctrl Control Buttons GUI Screen Status LED’s Power Control - Auto is normal operating position. Manual is used only for calibration purposes. next level solutions Maxiva Overview 1-3.2 TCU GUI Screens Panel PC TCU – PCM 2 Card First login locally username = admin and password = admin to enter Admin screen. Use Admin screen to set usernames and passwords. Login after setup via Login button. Passwords can be changed remotely if Admin password is changed from admin. Remote GUI screens looks just like new style TCU. Recommend use of Mozilla Firefox, Chrome or or IE8 web browser. Use zoom feature to enlarge GUI display. Ctrl + or Ctrl Login GUI Screen Control Buttons Status LED’s Power Control - Auto is normal operating position. Manual is used only for calibration purposes. next level solutions Maxiva Overview 1-3.3 TCU – Admin Login - PCM-2 • Initially passwords must be set locally (not via remote web session). • Remote login as administrator allows all passwords to be viewed. • If admin password has been changed then remote setting of passwords is allowed. Factory defaults Must be set up prior to remote web use Sets timeout of TCU password. Navigation to exciter screens and back to TCU requires new TCU login. next level solutions Maxiva Overview 1-3.4 TCU HOME GUI Screen via Web Browser Press Exciter buttonsee next slide. TCU Home Icon Remote GUI screens and control panel buttons. Use zoom (Ctrl +/_) feature to enlarge GUI display. Power Control - Auto is normal operating position. Manual is used only for calibration purposes. next level solutions Maxiva Overview 1-3.5 Exciter access via TCU GUI Exciter screens accessible from TCU GUI. Use web browser zoom feature to enlarge GUI display. Buttons on exciter section work via software. next level solutions Maxiva Overview 1-3.6 TCU – System Home Screen - PCM-2 Select Cab 1, 2 or 3 to go to TCU Home screens. This is Home screen for multiple cabinet transmitters. next level solutions Maxiva Overview 1-3.7 TCU – Home Screen - PCM-2 Sound in analog models. Log in as Eng to make changes. Next page. Red background indicates a fault Active Exciter Sub-Menus Follow Active Drive Chain Inactive Drive Chain - Yellow Note: If exciter GUI screens are accessed locally you must log into the TCU each time you return. next level solutions Maxiva Overview 1-3.8 TCU – Event Log – PCM-2 Save to .txt file on computer Print log Clear Log Date and time set. Slide down for additional entries (up to 1000). Date and time cleared. next level solutions Maxiva Overview 1-3.9 TCU - Drive Chain - PCM-2 next level solutions Maxiva Overview 1-3.10 TCU - Power Amps - PCM-2 • Approximate 1 amp per FET PA module idle current • Use scroll bars and next cabinet buttons to access additional data • FET current, temps and voltages available via PA diagnostics unit. next level solutions Maxiva Overview 1-3.11 TCU – Output - PCM-2 (single cabinet) ALC 3.2V-3.6V nominal at factory. V increases as PA modules warm up. Saturation is 4V. V adjusted by changing attenuator at PDU splitter input while in manual mode. Change power here for single cabinet systems. RF switch selection (Ant/Load) displays here if status is present. Transmitter will mute while switch moves. Power Out (kW) = Normal Power x (# of good modules/total # of modules)2 next level solutions Maxiva Overview 1-3.12 TCU – Output - PCM-2 (multiple cabinet) ALC 3.2V-3.6V nominal at factory. V increases as PA modules warm up. Saturation is 4V. V adjusted by changing attenuator at PDU splitter input while in manual mode. Change power here for multiple cabinet systems. ALC Setup instructions given in Section 5 of technical manual 888-2628-300 (Rev C). Power Out (kW) = Normal Power x (# of good modules/total # of modules)2 next level solutions Maxiva Overview 1-3.13 TCU - Power Supply - PCM-2 • AC Mains High >10% gives Warning From PS in TCU • AC Mains Low < -15% gives Warning • AC Phase Imbalance & MOV Fuse # give Warning but do not turn off Txer • AC Phase Sequence gives RF mute, pumps and heat exchanger off, goes back to on when fault clears. next level solutions Maxiva Overview 1-3.14 TCU – System - PCM-2 Temperature in TCU Coolant Temps Flow in liters per minute. Varies with model and installation. Mutes RF when open resumes when interlock closed. Faults off when open. Needs reset to resume operation. next level solutions Maxiva Overview 1-3.15 TCU – System> Service - PCM-2 All user settable Submenus follow Time/dates automatically set if NTP ON & TCU connected to network. next level solutions Maxiva Overview 1-3.16 TCU -System >Service>System Setup - PCM-2 Sets 100% bar. Sets exciter frequency Effects screens in analog 0-8 used settings can be stored. CAL & MCM settings saved to Eprom for N+1 uses. 0-8 settings used for N+1 cases to store CAL & MCM settings to Eprom. Current changes stored to value entered here. Saves CAL & MCM settings to compact flash card. 0-8 setups can be recalled for N+1 cases. Frequency, CAL and settings can all be recalled. next level solutions Maxiva Overview 1-3.17 TCU-System >Service>Network - PCM-2 Identifies transmitter IP on network by this name. Can be Enabled or Disabled. If Enabled IP address set by network. If Manual IP set set by user. next level solutions Maxiva Overview 1-3.18 TCU – System>Service>Software Update - PCM-2 PCM version running PCM version (old). Press Activate to load old program. Press View MCM version running MCM version (old). Press Activate to load old program. Press View This page used to upload software files for PCM & MCM. Once uploaded they can be activated on the PCM and MCM Software Management screens. next level solutions Maxiva Overview 1-3.19 TCU – System>Service>Cab Setup - PCM-2 Sets nominal cabinet power for ALC. Max power limit is 10% over this value See next slide Set these values for each cabinet. next level solutions Maxiva Overview 1-3.20 TCU - System/Service/Cabinet Setup/Service Mode - PCM-2 The cabinet flow meter sends out a frequency sample based on the flow rate. The transmitter RF is MUTED if there is insufficient flow (<50% of recommended). When flow is restored and the flow meter frequency is above the threshold, the transmitter automatically UNMUTES. Service Mode screen allows three faults to be disabled. These faults cause the transmitter to MUTE: Coolant Flow, Inlet/Outlet Temperatures and Coolant Leak. If for any reason any of these sensor devices are faulty, and there is no evidence of a real problem, customers can remain on-air. For example if the flow meter becomes defective but in fact there is sufficient flow, then the customer can put the transmitter in the Service Mode of operation while a replacement is sent. next level solutions Maxiva Overview 1-3.21 TCU – System>Service>System Setup> System Threshold - PCM-2 2.8% of nominal is maximum. Power bar turns red here. Set to 100 mV less than detector voltage during system reflected power calibration. Power bar turns yellow here. Power bar turns red here. Warnings and faults are logged when levels reached. next level solutions Maxiva Overview 1-3.22 TCU – System>Service>System Setup>System Calibrate - PCM-2 3.0-3.2 V nominal. 3.6V saturated. Calibrations done here control foldback operation and VSWR fault events. Nominal 2V during cal. In multi-cabinet transmitters the reject load calibration shows up here. Set to approximately 3V at 100% reject power. Enter cal value measured on power meter in W. Press to disable VSWR protection for 5 minutes. Use during reflected cal. next level solutions Maxiva Overview 1-3.23 TCU – System>Service>Cab Setup>Cab Pwr Calibrate - PCM-2 3.0-3.2 V nominal. 3.6V saturated. Nominal 2V during cal. Nominal 1- 3.2V at full power out. Enter value in micro W. Disables VSWR for 5 minutes. Used during reflected cal. next level solutions Maxiva Overview 1-3.24 Outline Drawing, 1 Cabinet 843-5601-279 Sh 1 Section 100 Drawing Title Box Revision History Drawing number Revision number 1 of 2 next level solutions Maxiva System Drawings 2-1.1 Outline Drawing, 1 Cabinet 843-5601-279 Sh 1 Section 100 Drawing notes may be numbered inside a triangle on the drawing. 1 of 2 Latest revision next level solutions Previous revision Maxiva System Drawings 2-1.2 Wiring Diagram, PA Cabinet 843-5601-001 Sh 1 Section 200 Wire number (159) Number of conductors (8) Continues on sheet 3 section B8 Signal name EXC B CTL 1 of 10 next level solutions Maxiva System Drawings 2-1.3 Wiring Diagram, PA Cabinet 843-5601-001 Section 200 Continues on 1/A1 & 2/A1 Vertical ID Signal name EXC B CTL Board number Horizontal ID 3 of 10 next level solutions Maxiva System Drawings 2-1.4 Outline Drawing, 1 Cabinet 843-5601-279 Sh 1 Section 100 1 of 2 next level solutions Maxiva System Drawings 2-1.5 Outline Drawing, 1 Cabinet 843-5601-279 Sh 2 Section 100 Both versions of heat exchanger have two fans Internal pump module (future) 25 kW cooling system 50 kW cooling system 2 of 2 next level solutions Maxiva System Drawings 2-1.6 Block Diagram, 1 Cabinet 843-5601-284 Sh 1 Section 100 1 of 2 next level solutions Maxiva System Drawings 2-1.7 Block Diagram, 1 Cabinet 843-5601-284 Sh 2 Section 100 2 of 2 next level solutions Maxiva System Drawings 2-1.8 Wiring Interconnect, 1 Cabinet 843-5601-705 (was 282) Section 100 1 of 1 next level solutions Maxiva System Drawings 2-1.9 AC Power Flow, 1 Cabinet 843-5601-583 Sh 1 (was 283) Section 100 1 of 2 next level solutions Maxiva System Drawings 2-1.10 AC Power Flow, 1 Cabinet 843-5601-583 Sh 2 (was 283) Section 100 2 of 2 next level solutions Maxiva System Drawings 2-1.11 Layout, RF System 1 Cabinet 843-5601-281 Section 100 1 of 4 next level solutions Maxiva System Drawings 2-1.12 Layout, RF System 1 Cabinet 843-5601-281 Section 100 2 of 4 next level solutions Maxiva System Drawings 2-1.13 Layout, RF System 1 Cabinet 843-5601-281 Section 100 3 of 4 next level solutions Maxiva System Drawings 2-1.14 Layout, RF System 1 Cabinet 843-5601-281 Section 100 4 of 4 next level solutions Maxiva System Drawings 2-1.15 Layout, Plumbing, 1 Cabinet 843-5601-562 Section 100 1 of 6 next level solutions Maxiva System Drawings 2-1.16 Layout, Plumbing, 1 Cabinet 843-5601-562 Section 100 2 of 6 next level solutions Maxiva System Drawings 2-1.17 Layout, Plumbing, 1 Cabinet 843-5601-562 Section 100 3 of 6 next level solutions Maxiva System Drawings 2-1.18 Layout, Plumbing, 1 Cabinet 843-5601-562 Section 100 4 of 6 next level solutions Maxiva System Drawings 2-1.19 Layout, Plumbing, 1 Cabinet 843-5601-562 Section 100 5 of 6 next level solutions Maxiva System Drawings 2-1.20 Layout, Plumbing, 1 Cabinet 843-5601-562 Section 100 6 of 6 next level solutions Maxiva System Drawings 2-1.21 Wiring Diagram, PA Main 843-5601-001 Section 200 Customer I/O Panel Exc. A Exc. B 1 of 10 next level solutions Amplifier Cabinet Drawings 2-2.1 Wiring Diagram, PA Main 843-5601-001 Section 200 2 of 10 next level solutions Amplifier Cabinet Drawings 2-2.2 Wiring Diagram, PA Main 843-5601-001 Section 200 11-18 1-8 IPAs 3 of 10 next level solutions Amplifier Cabinet Drawings 2-2.3 Wiring Diagram, PA Main 843-5601-001 Section 200 Cab Buss pin 7 used Predriver & IPA control lines 801-0222-131 IPA Backplane RF Drive Adjusts drive to preamp 801-0222-101 843-5601-062 4 way 3 way 2way 6 way 8 way 4 of 10 next level solutions Amplifier Cabinet Drawings 2-2.4 Wiring Diagram, PA Main 843-5601-001 Section 200 Upper splitter RF drive from IPA switch Upper cabinet PA backplanes ¼ wave hybrid Control buss Lower cabinet Lower splitter 5 of 10 next level solutions Amplifier Cabinet Drawings 2-2.5 Wiring Diagram, PA Main 843-5601-001 Section 200 6 of 10 next level solutions Amplifier Cabinet Drawings 2-2.6 Wiring Diagram, PA Main 843-5601-001 Section 200 7 of 10 next level solutions Amplifier Cabinet Drawings 2-2.7 Wiring Diagram, PA Main 843-5601-001 Section 200 8 of 10 next level solutions Amplifier Cabinet Drawings 2-2.8 Wiring Diagram, PA Main 843-5601-001 Section 200 9 of 10 next level solutions Amplifier Cabinet Drawings 2-2.9 Wiring Diagram, PA Main 843-5601-001 Section 200 AT2 – forward power sample. Change value to set detector voltage during forward cabinet cal. 10 of 10 AT1 – reflected power sample. Change value to set detector voltage during reflected cabinet cal. next level solutions Amplifier Cabinet Drawings 2-2.10 SCH, 4 PA Backplane 801-0222-101 Section 200 Jumper 2&3 for 208-240 1&2 for 380-415 AC-DC Converter AC-DC Converter AC-DC Converter 1 of 5 next level solutions Amplifier Cabinet Drawings 2-2.11 SCH, 4 PA Backplane 801-0222-101 Section 200 2 of 5 next level solutions Amplifier Cabinet Drawings 2-2.12 SCH, 4 PA Backplane 801-0222-101 Section 200 3 of 5 next level solutions Amplifier Cabinet Drawings 2-2.13 SCH, 4 PA Backplane 801-0222-101 Section 200 4 of 5 next level solutions Amplifier Cabinet Drawings 2-2.14 SCH, 4 PA Backplane 801-0222-101 Section 200 5 of 5 next level solutions Amplifier Cabinet Drawings 2-2.15 SCH, IPA Backplane 801-0222-131 Section 200 1 of 3 next level solutions Amplifier Cabinet Drawings 2-2.16 SCH, IPA Backplane 801-0222-131 Section 200 2 of 3 next level solutions Amplifier Cabinet Drawings 2-2.17 SCH, IPA Backplane 801-0222-131 Section 200 3 of 3 next level solutions Amplifier Cabinet Drawings 2-2.18 ULX-25000AN N or Stages 4 Splitter/Combin er Loss/Gain -0.50 Device Losses Combiner Unbalance Loss -0.50 Total Gain (Loss) -6 -3 -1.2 -1.2 -7.22 -4.21 32.0 0 19 16 4 -12.04 12.04 0.00 -1 -1.2 -0.6 0 -0.05 -0.15 1.00 -13.24 11.44 0 -0.05 -0.15 19 Peak Sync 0.082 Power (Watts) 0.073 0.014 0.0052 8.31 659.9 524.18 24.9 1879 26178 26178 25879 25000 Back Porch 0.049 Power (Watts) 0.043 0.008 0.003 4.95 393 312 15 1118 15582 15582 15404 14881 Peak Power (Watts) 0.135 0.120 0.023 0.00086 13.71 1088.7 864.82 41.00 3257 45386 45386 44867 43344 Peak RF Voltage (Volts) 4 3 2 1 37 330 294 64 571 2130 2130 2118 2082 Peak Power (dBm) 21.30 20.80 13.58 9.37 41.37 60.37 59.37 46.13 65.13 76.57 76.57 76.52 76.37 Average Power 0.054 (Watts) 0.048 0.009 0.003 5.49 436.4 346.7 16.4 1306 18194 18194 17986 17375 16.83 9.61 5.40 37.40 56.40 55.40 42.16 61.16 72.60 72.60 72.55 72.40 3.97 3.97 3.97 3.97 3.97 3.97 3.97 3.97 3.97 3.97 3.97 3.97 Average Power 17.33 (dBm) Peak/Average 3.97 Ratio (dB) Hybrid Loss -0.15 Block Diagram ULX-5000AN 16 Analog Modules/1 Cabinet Power Budgets 3-1.1 ULX-12300AT N or Stages 4 Splitter/Combi ner Loss/Gain -0.50 Device Losses -6.02 -3 -1.2 -1.2 -7.22 4.2 1 16 4 -12.04 12.04 0.00 -1 -1.2 -0.6 0 -0.05 -0.15 -1.00 -13.24 11.44 0 -0.05 -0.15 Combiner Unbalance Loss Total Gain (Loss) Peak Power (Watts) Peak RF Voltage (Volts) Peak Power (dBm) Average Power (Watts) Average Power (dBm) Peak/Average Ratio (dB) Hybrid Loss -0.50 0.289 0.258 5 5 24.61 24.11 32.0 0 19 19 0.04 9 0.019 29.389 1 2334 1854 87.92 3500 48774 48774 48215 46579 2 1 54 483 431 94 592 2208 2208 2196 2158 12.68 44.68 63.68 62.68 49.44 65.44 76.88 76.88 76.83 76.68 0.002 3 3.6999 293.9 233.4 11.1 879 12251 12251 12111 11700 16.8 9 0.00 6 0.036 0.032 15.61 15.11 7.89 3.68 35.68 54.68 53.68 40.44 59.44 70.88 70.88 70.83 70.68 9 9 9 9 9 9 9 9 6 6 6 6 6 -0.15 Block Diagram ULX-12300AT 16 ATSC Digital Modules/1 Cabinet Power Budgets 3-1.2 ULX-8700DV N or Stages 4 Splitter/Combi ner Loss/Gain -0.50 Device Losses Combiner Unbalance Loss Total Gain (Loss) Peak Power (Watts) Peak RF Voltage (Volts) Peak Power (dBm) Average Power (Watts) Average Power (dBm) Peak/Average Ratio (dB) Hybrid Loss -0.50 -6.02 -3 -1.2 -1.2 -7.22 -4.21 32.0 0 19 16 4 -12.04 12.04 0.00 -1 -1.2 -0.6 0 -0.05 -0.15 1.00 -13.24 11.44 0 -0.05 -0.15 18 0.843 0.752 0.143 0.05 4 85.705 2710 2153 102.07 4354 60674 60674 59980 57944 9 9 4 2 93 521 464 101 660 2463 2463 2449 2407 29.26 28.76 21.54 49.33 64.33 63.33 50.09 66.39 77.83 77.83 77.78 77.63 0.034 0.030 0.006 3.412 271.0 215.3 10.2 644 8974 8974 8872 8570 15.26 14.76 7.54 3.33 35.33 54.33 53.33 40.09 58.09 69.53 69.53 69.48 69.33 14 14 14 14 14 10 10 10 8.3 8.3 8.3 8.3 8.3 17.3 3 0.00 22 -0.15 Block Diagram ULX-8700DV 16 DVB-T Modules/1 Cabinet Power Budgets 3-1.3 ULX-8700IS N or Stages 4 Splitter/Combi ner Loss/Gain -0.50 Device Losses Combiner Unbalance Loss Total Gain (Loss) Peak Power (Watts) Peak RF Voltage (Volts) Peak Power (dBm) Average Power (Watts) Average Power (dBm) Peak/Average Ratio (dB) Hybrid Loss -0.50 -6.02 -3 -1.2 -1.2 -7.22 -4.21 32.0 0 19 16 4 -12.04 12.04 0.00 -1 -1.2 -0.6 0 -0.05 -0.15 1.00 -13.24 11.44 0 -0.05 -0.15 18 0.843 0.752 0.143 0.05 4 85.705 2710 2153 102.07 4354 60674 60674 59980 57944 9 9 4 2 93 521 464 101 660 2463 2463 2449 2407 29.26 28.76 21.54 49.33 64.33 63.33 50.09 66.39 77.83 77.83 77.78 77.63 0.034 0.030 0.006 3.412 271.0 215.3 10.2 644 8974 8974 8872 8570 15.26 14.76 7.54 3.33 35.33 54.33 53.33 40.09 58.09 69.53 69.53 69.48 69.33 14 14 14 14 14 10 10 10 8.3 8.3 8.3 8.3 8.3 17.3 3 0.00 22 -0.15 Block Diagram ULX-8700IS 16 ISDB-T Modules/1 Cabinet Power Budgets 3-1.4 ULX ALC LOOP The ALC (automatic level control) in the ULX transmitter regulates the power output of the transmitter as amplifier gains vary. ALC provides the only output regulation for the ULX transmitter system. The PA modules do not have a automatic power control. PA module gain drops as they warm up. ALC increases the RF drive level to modules maintaining the desired power output. ALC is based on cabinet forward power. It uses the forward cabinet power sample for regulation. System forward power is not used for output power regulation. next level solutions Maxiva Overview 3-2.1 ULX ALC LOOP Components 1. 2. 3. 4. Cabinet forward power RF detector is in the TCU RF Monitor card The TCU MCM (main controller module) card generates the ALC voltage Pre-Driver Unit (PDU) contains the variable attenuator that adjusts the drive level Cabinet directional coupler provides the RF forward sample Predriver Chassis Predriver A (PDU-A) 16 PAs IPA-A Internal Cabinet Coupler AT8 AT1 RF Drive From Exciter RF Splitter IPA-B ÷ Σ AT2 Predriver B (PDU-B) TCU 12-Bit 0 to 4 V D/A 0 to 3.6 V A/D 12-Bit Cabinet ALC Voltage from MCM Card Cabinet Forward Power Sample to TCU RF Monitor Card next level solutions Maxiva Overview 3-2.2 Cabinet ALC Voltage Two voltages are key to ALC operation: • Cabinet ALC voltage • RF cabinet forward sample detected voltage Cabinet ALC Voltage adjusts the electronic attenuator in each PDU (predriver unit) to raise the power up or down. 4V gives maximum power (minimum attenuation) and 0V gives the lowest power (maximum attenuation). The ALC voltage needs to be between 3.2 to 3.6 Volts. 3.6 is best. As the amplifiers heat up their gain decreases and the ALC will increase the ALC voltage to a higher level. If ALC of 4V is reached, the loop is maxed out and there is no way to increase the power further. The ALC voltage must be lowered. next level solutions Maxiva Overview 3-2.3 Cabinet ALC Voltage Adjustment Adjust ALC voltage with power control set to Auto as long as calibration has been performed . Turn Tx off when changing attenuators. Change attenuator AT8 between the exciter and the PDU until ALC voltage is 3.2 to 3.6 V . The attenuator AT8 is shown on the previous diagram. ALC Voltage. Must be between 3.2 to 3.6 V at nominal power next level solutions Maxiva Overview 3-2.4 Cabinet Forward Sample Detected Voltage The cabinet detected voltage, shown on the Cab Pwr Calibrate screen (next page) is developed from the forward power sample on the cabinet internal coupler. The detection takes place in the RF Monitor card in the TCU. The RF detector has a voltage range of 0 to 3.6V. Therefore, careful attention must be paid to ensure the detector is not saturated. If when doing a power calibration the detected voltage reads above 3.6 volts, the detector is saturated and the ALC loop will not work. next level solutions Maxiva Overview 3-2.5 Cabinet Forward Sample Detected Voltage The forward voltage needs to be between 3.0 to 3.2 V at nominal power. When doing a power calibration, maintaining this voltage within this range is critical for correct operation of the control loop. The forward power detected voltage can be read from the Cab Calibration page. Cabinet Forward Voltage. Must be between 3.0 to 3.2 V at nominal power next level solutions Maxiva Overview 3-2.6 Cabinet Forward Sample Detected Voltage Adjustment Set the transmitter POWER CONTROL to MANUAL The only way to adjust the forward power detector voltage is to change the attenuator connected to the internal cabinet coupler forward sample. This is shown as AT2 in the diagram. Since the drive chain PDU-A + IPA-A may have slightly different combined gain than the PDU-B + IPA-B path, both drive chains must be checked. The ALC voltage may be slightly different between the two paths. But as long as it falls within the limits (3.2 to 3.6 V), the performance will not suffer. next level solutions Maxiva Overview 3-2.7 Power Calibration When both the ALC voltage and the cabinet forward detected voltage are within range, a cabinet power calibration must be performed so that the ALC routine can store all references. Perform the cabinet forward power calibration in POWER CONTROL MANUAL mode. Once the calibration is done, go to the Output page and enter the transmitter nominal power in the Cab Fwd Pwr Reference box. Enter the transmitter nominal power next level solutions Maxiva Overview 3-2.8 Power Calibration Set the POWER CONTROL to AUTO. The AUTO button may flash for a few seconds and then should stay solidly lit. Try entering different Cab Fwd Pwr Reference values to make sure the ALC loop commands the transmitter properly to the exact power entered. Once the calibration is done, go to the Output page and enter the transmitter nominal power in the Cab Fwd Pwr Reference box. Enter the transmitter nominal power. This value will set the transmitter output power. The Raise/Lower buttons on the TCU will also change this value. next level solutions Maxiva Overview 3-2.9 ULX PA Module – Component ID AC Distribution Monitor I/O Connector 4-Way Splitter PA AC-DC Power Supply Signal Distribution Coolant In/Out PA Pallet 4 –Way Combiner RF Out PA Module Cover Removed next level solutions Maxiva PA Module 4-1.1 PA/IPA Module – Simplified Block Diagram 200 to 240 VAC 2 ea. 50 Vdc via steering diodes Pallet 2 ea. * Combiner * Pallet +12 V 2 ea. * Pallet Splitter 2 ea. * * Pallet 19-20 dB gain typ. Indicates Pallets and PSs removed from IPAs in Txers with 8 or less PA modules. Modified IPAs can’t be used as PAs. PAs can be used as IPAs. next level solutions Maxiva PA Module 4-1.2 PA/IPA Module – Board ID Note: These ID numbers follow the GUI error messages. See TM page 5-9. PS1 Out P4 Coolant PS2 * PS3 * PS4 P3* PS5 PS6 * PS7 * PS8 * P2 P1 In RF Out PS = Power Supply P = Pallet Indicates Pallets and PSs removed from IPAs in Txers with 8 or less PA modules. * Modified IPAs can’t be used as PAs. PAs can be used as IPAs. next level solutions Maxiva PA Module 4-1.3 PA Module – Monitor Board Monitor Pin in modified IPA module. next level solutions Maxiva PA Module 4-1.4 PA Module – AC Distribution Board PA Module Cover Removed Signal distribution board (extends under splitter board) AC Distribution Board PS Connects Here next level solutions Maxiva PA Module 4-1.5 PA Module – AC-DC Power Supply PA Module Cover Removed PA AC-DC Power Supply PA or IPA Modules (systems with more than 8 PAs) Module Part No.: 971-0040-004 without RF monitor port in front. 971-0040-003 with RF monitor port in front. IPA Module (systems with 8 PAs or less) Part No.: 971-0040-011 without RF monitor port in front. 971-0040-006 with RF monitor port in front. next level solutions Maxiva PA Module 4-1.6 PA Module – AC-DC Power Supply Interface Connector Under Board Fuse F1 Part no. 398-0777-001 Fuse 8A 250V Fast 5mm x20mm Output Adjustment Pot Output Wire 48V PS Module Part no. 901-0222-011GT Pad, Thermal Part no. 411-0126-000 next level solutions Maxiva PA Module 4-1.7 PA Module – AC-DC Power Supply AC/DC CONVERTER INTERFACE BLOCK DIAGRAM PFE500-48 5A AC1 AC(L) AC2 AC(N) R -BC 5.755V ---- 44V Rtrim1 Vout +S Rext TRIM JP1 +BC Vtrim Levels 4.122 V --- 46V +V Setting AC to DC output voltage: -V -S 1. Remove JP1 Vtrim 2.49V 2.490V ---- 48V 2. Set Vout to 48V 3. Replace JP1 0.875V ---- 50V next level solutions Maxiva PA Module 4-1.8 Wiring Diagram, PA Module 843-5601-012 Section 600 208-240VAC 6 5 TB1 J9 pins 2 & 3 +12V from AC distribution board TB3 TB2 801-0222-021 56 pins, AC and Gnd Sync, status, monitoring 24 pins 1 3 2 J3 pins 6 & 8 +12V out to test box 5 4 6 8 7 801-0222-011 RF input Port 4 360o Port 3 270o 801-0222-071 Port 180o J1-21 & 22 +12V out to test box. J1-36 +3.3V Port 1 90o J1 J4 801-0222-061 J7 J6 J5 8010222051 J2 801-0222-041 4 3 2 1 J4-3 & 4 +12V out 801-0222-081 801-0222-091 Port 4 Port 3 Port 2 Port 1 J1 J2 1 of 1 next level solutions Maxiva PA Module Drawings 4-2.1 SCH, I/O Connector 801-0222-041 Section 600 J1-A thru D, 4 rows of 6 pins each. 24 pins. J1-E thru H J1-J thru L 7 rows of 8 pins each. 56 pins. 1 of 1 TB1 thru TB3 AC distribution board TB1 thru TB3 respectively. next level solutions Maxiva PA Module Drawings 4-2.2 SCH, AC Distribution 801-0222-021 Section 600 R6-R8 allows limited operation of AC/DC converter so they can power +12V relays. Feeds 3 PS. Feeds 3 PS. Feeds 2PS. 1 of 2 next level solutions Maxiva PA Module Drawings 4-2.3 SCH, AC Distribution 801-0222-021 Section 600 Votage is approx. 50V from PS1-8 via steering diodes. 2 of 2 next level solutions Maxiva PA Module Drawings 4-2.4 SCH, PA Pallet 801-0222-081 Section 600 Differential amp. From Sheet 2 Bias adjust. Bias temp adjust. Source Q4 Thermistor for PA module temp. Zener diode regulator. 1 of 2 next level solutions Maxiva PA Module Drawings 4-2.5 SCH, PA Pallet 801-0222-081 Section 600 Bias for Q1 1a idle current 0o Bias for Q2 -90 o 2 of 2 To sh. 1 1a idle current next level solutions Maxiva PA Module Drawings 4-2.6 SCH, 4 Way Splitter 801-0222-071 Section 600 1/4 power 1/4 power 1/4 power 1/4 power 70.7 ohm lines -270O -90O -360O -180O -180O Grounds 1/2 power ¼ wave hybrid 0O Wilkinson Splitter -90O Input from IPA 1/2 power -90O Used as phase shifter. Zs = ZO2/ZL Zo = SQRT(ZS x ZL) Pout = Pnorm (# good amps/total amps)2 1 of 2 next level solutions Maxiva PA Module Drawings 4-2.7 SCH, 4 Way Splitter 801-0222-071 Section 600 2 of 2 next level solutions Maxiva PA Module Drawings 4-2.8 SCH, 4 Way Combiner 801-0222-091 Section 600 2X Watts 3 dB Hybrid 1:1 Combiner -90O X Watts -180O X Watts 1 of 2 4X Watts 3X Watts 4.77 dB Hybrid 2:1 Combiner -270O X Watts next level solutions 6 dB Hybrid 3:1 Combiner -360O X Watts Maxiva PA Module Drawings 4-2.9 SCH, 4 Way Combiner 801-0222-091 Section 600 2 of 2 next level solutions Maxiva PA Module Drawings 4-2.10 Wiring Diagram, Pre-driver 843-5601-062 Section 500 DC to phase & gain board. Output amp. RF from exciter switcher 1 of 1 next level solutions Pre-driver Drawings 4-3.1 SCH, Phase & Gain 801-0222-221 Section 500 1 of 5 next level solutions Pre-driver Drawings 4-3.2 SCH, Phase & Gain 801-0222-221 Section 500 2 of 5 next level solutions Pre-driver Drawings 4-3.3 SCH, Phase & Gain 801-0222-221 Section 500 Hybrid RF in. Mute opens or closes this switch. Varying bias values changes phase 0-90o for each hybrid. 3 of 5 next level solutions Pre-driver Drawings 4-3.4 SCH, Phase & Gain 801-0222-221 Section 500 4 of 5 next level solutions Pre-driver Drawings 4-3.5 SCH, Phase & Gain 801-0222-221 Section 500 5 of 5 next level solutions Pre-driver Drawings 4-3.6 SCH, Pre Driver Module Interface 801-0222-261 Section 500 1 of 2 next level solutions Pre-driver Drawings 4-3.7 SCH, Pre Driver Module Interface 801-0222-261 Section 500 2 of 2 next level solutions Pre-driver Drawings 4-3.8 SCH, Pre Driver Signal Interface 801-0222-271 Section 500 1 of 1 next level solutions Pre-driver Drawings 4-3.9 SCH, Down Converter 801-0222-241 Section 400 1 of 9 next level solutions Downconverter Drawings 4-4.1 SCH, Down Converter 801-0222-241 Section 400 2 of 9 next level solutions Downconverter Drawings 4-4.2 SCH, Down Converter 801-0222-241 Section 400 3 of 9 next level solutions Downconverter Drawings 4-4.3 SCH, Down Converter 801-0222-241 Section 400 4 of 9 next level solutions Downconverter Drawings 4-4.4 SCH, Down Converter 801-0222-241 Section 400 5 of 9 next level solutions Downconverter Drawings 4-4.5 SCH, Down Converter 801-0222-241 Section 400 6 of 9 next level solutions Downconverter Drawings 4-4.6 SCH, Down Converter 801-0222-241 Section 400 7 of 9 next level solutions Downconverter Drawings 4-4.7 SCH, Down Converter 801-0222-241 Section 400 8 of 9 next level solutions Downconverter Drawings 4-4.8 SCH, Down Converter 801-0222-241 Section 400 9 of 9 next level solutions Downconverter Drawings 4-4.9 PA/IPA Module – Pallet Replacement PA Pallet PA Module Cover Removed 4 6 & 11 1. 2. 3. 4. 5. 6. 7. Turn off PA module breaker. Unscrew hold down screws and remove PA module. Remove PA module cover. Remove 4 center pallet hold down screws. Remove 5 additional pallet hold down screws (circled). De-solder two jumpers and the blue & gray DC supply wires. Remove board and cleanup heat transfer compound. 8. 9. 10. 11. 12. 13. 14. 15. Reapply heat transfer compound. Use a small roller to apply even, thin coat. Install pallet and all hold down screws. Torque 4 allen screws to 30 in lbs. Solder two jumpers and blue & gray wires. Replace PA module cover. Replace PA module in rack. Tighten module hold down screws. Turn on PA module breaker. Press ON button to reset all modules. next level solutions Maxiva Maintenance Overview 5-1.1 PA/IPA Module – Pallet Replacement Soldered Jumper Module Repair Kit: Part no. 990-0160-002 Includes: Pallet Heat transfer Compound Buss wire (for UAX) Ribbon Wire (jumpers) Circled allen screws to be torqued Soldered Jumper next level solutions Maxiva Maintenance Overview 5-1.2 PA Module – PS Replacement PA AC-DC Power Supply PA Module Cover Removed 5 & 10 4 1. Turn off PA module breaker. 2. Unscrew hold down screws and remove PA module. 3. Remove PA module cover. 4. Remove 4 PS hold down screws. 5. Remove supply wire from WAGO block. 6. Remove board from connector and cleanup heat transfer compound. 7. Reapply heat transfer compound. Use a small roller to apply thin coat evenly. 8. 9. 10. 11. 12. Install new PS. Install PS hold down screws. Reconnect supply wire to WAGO. Replace PA module cover. Replace PA module in rack. Tighten module hold down screws. 13. Turn on PA module breaker. 14. Press ON button to reset all modules. next level solutions Maxiva Maintenance Overview 5-1.3 PA Module – PS Replacement Interface Connector under board Fuse F1 Part no. 398-0777-001 Fuse 8A 250V Fast 5mm x20mm Supply Wire PS Module Part no. 901-0222-011GT Pad, Thermal Part no. 411-0126-000 next level solutions Maxiva Maintenance Overview 5-1.4 PA Module – Power Supply Voltage Adjust AC/DC CONVERTER INTERFACE BLOCK DIAGRAM PFE500-48 5A AC1 AC(L) AC2 AC(N) R -BC 5.755V ---- 44V Rtrim1 Vout +S Rext TRIM JP1 +BC Vtrim Levels 4.122 V --- 46V +V -V -S Setting AC to DC output voltage: 1. Remove JP1 Vtrim 2. Set Vout to 48V 2.490V ---- 48V 3. Replace JP1 0.875V ---- 50V next level solutions Maxiva Maintenance Overview 5-1.5 PA Module – Board ID Note: PS numbers are numbered in reverse order of Pallets. PS1 PS2 PS3 PS4 PS5 PS6 PS7 PS8 Out P4 Coolant P3 P2 P1 In RF Out PS = Power Supply next level solutions P = Pallet Maxiva Maintenance Overview 5-1.6 PA Module – PS Troubleshooting SCH, PA Monitor 801-0222-051 Sheet 14 of 14 1 3 ……………….. ..…………….. 4 2 Front Connector on PA Module next level solutions Maxiva Maintenance Overview 5-1.7 PA Module – Test Connector Pin out Pin Signal Pin 1 /ON-OFF STATUS (0V -4.9V) 2 PS8 VOLTAGE (3.8V) 27 P3 FET 1 CURRENT (.3V) 28 GND 3 PS VOLT SEL-TB (44=5.15V, 4 GND 29 P3 FET 2 CURRENT (.3V) 30 CANH (3.2V) 5 AVG INPUT POWER (.012V) 6 +12V (11.9V) 31 P4 FET 1 CURRENT (.3V) 32 CANL 7 GND 8 +12V (11.9V) 33 P4 FET 2 CURRENT (.3V) 34 GND 9 OUTPUT POWER (.023V) 10 PALLET 1 TEMP (2.0V) 35 PA SUM CURRENT (.3V) 36 /SPI-CS(TMS) (3.2V) 11 REFLECTED POWER (.022V) 12 PALLET 2 TEMP (2.0V) 37 PS1 VOLTAGE (3.8V) 38 SP1-SCK(TCK) (3.2V) 13 FAULT STATUS 3 (4.95V) 14 PALLET 3 TEMP (2.0V) 39 PS2 VOLTAGE (3.8V) 40 SPI-MOSI(TDI) (3.2V) 15 FAULT STATUS 2 (4.95 V) 16 PALLET 4 TEMP (2.0V) 41 PS3 VOLTAGE (3.8V) 42 SPI-MISO (TDI) (3.2V) 17 FAULT STATUS 1 (0V) 18 AMBIENT TEMP (2.0V) 43 PS4 VOLTAGE (3.8V) 44 SPI-JTAG-SEL (3.2V) 19 P1 FET 1 CURRENT (.3V) 20 ON/OFF FROM TB (0 V) 45 PS5 VOLTAGE (3.8V) 46 GND 21 P1 FET 2 CURRENT (.3V) 22 PSV TB SEL (0 V) 47 PS6 VOLTAGE (3.8V) 48 BP SYNC PRESENT (4.9V) 23 P2 FET 1 CURRENT (.3V) 24 GND 49 PS7 VOLTAGE (3.8V) 50 GND 25 P2 FET 2 CURRENT (.3V) 26 GND 46=4.12V, 48=2.49V, 50= .87V) Signal Voltages taken with module enabled and no RF applied. Pin next level solutions Signal Pin (0V) Maxiva Maintenance Overview 5-1.8 Optional Module Test System next level solutions Maxiva Maintenance Overview 5-1.9 Optional Module Test System Front Connection on PA Modules Handheld Analyzer next level solutions Maxiva Maintenance Overview 5-1.10 Optional Module Test System FROM TRANSMITTER CABINET DEDICATED PA FIXTURE HOSE AND CABLE CONNECTIONS PA Cable Harness EXTENSION HOSES TEST FIXTURE • The select buttons toggles through the meter choices. • For troubleshooting on the bench, a test fixture is available. The PA plugs into the test fixture. next level solutions Multimeter 2 10.3 Pallet Current PS Voltage Temperature Text Driver Current Select Faults Select PS Overtemp Pallet Fwd Power Refled Power Other PA ON ON/OFF Overdrive Underdrive Drive Stage Maxiva Maintenance Overview 5-1.11 Optional Module Test System next level solutions Maxiva Maintenance Overview 5-1.12 Transmitter Fuses – Have Spares OPA Module Power Supply (901-0222-011G): F1 - 3980777001 • FUSE 8A 250V FAST 5MM X 20MM MOV / AC Sample (901-0222-361G): F1 to F4 – 3980586000 • FUSE, FAST 600VAC/500VDC 12A Contactor Control Board (901-0222-601G): F1 to F8 – 3980489000 • FUSE, CART 5X20MM 2A SLOW next level solutions Maxiva Maintenance Overview 5-1.13 Transmitter Internal Liquid Cooling System Layout • 16 PA module 2 IPA module system shown. • Combiners and splitters liquid cooled. • 55o C. coolant inlet temp. warning. @ 65o C. RF faults off. Turns on automatically when cooled. • Typically 3 degs C difference in temperature between inlet and outlet of Txer. Delta not limited however. • In Manual pump mode - Low flow will cause an RF mute. - No flow will switch off pump and transmitter. • In Auto pump mode - Low flow or no flow causes a pump switch. - If flow is not restored after four pump switches in a 5 minute period pumps and Txer go off. • Coolant leak causes fault OFF. Manual turn ON is required to re-start. next level solutions Maxiva Maintenance Overview 6-1.1 Low Flow Fault Levels A pump switch (in auto mode on dual pump models) or an RF mute will occur (in manual mode or in single pump models) when levels below these flow values are reached. Number of PA Minimum Flow Modules Liters/Minute 1 11.36 2 15.14 3 18.93 4 22.71 5 26.50 6 30.28 7 34.07 8 37.85 9 41.64 10 45.42 11 49.21 12 53.00 13 56.78 14 60.57 15 64.35 16 68.14 next level solutions Maxiva Maintenance Overview 6-1.2 Cooling System Block Diagram Hose Hose Bucket Closed Loop (pressurized) Cooling System next level solutions Maxiva Maintenance Overview 6-1.3 HE Pump Module Outlet Inlet Temperature Probe Vent Air Separator Relief Valve Pump B Pump A next level solutions 12 psi Pre-charged Bladder Tank (reservoir) Maxiva Maintenance Overview 6-1.4 Pump Module and Control Panel • Indoor use only • Requires Phillips screwdriver to open. • Inverters control AC supply frequency and motor speed. • Loss of flow for 5 sec. causes pump switch. • Loss of flow that causes 4 pump switches in 5 minutes turns off pumps. Pump Module Rear View Pump Module & Control Panel Front View next level solutions Maxiva Maintenance Overview 6-1.5 Cooling Control Panel Pump B Inverter Fan A Inverter Pump A Inverter Fan B Inverter System Control LOCALREMOTE Pump & Fan Breakers Pump Switches ON/OFF next level solutions Maxiva Maintenance Overview 6-1.6 Inside Cooling Control Panel AC to Fans Status & Control FAN and Pump Breakers 3 Phase AC Input Inverters maintain output phases with loss of input phase. next level solutions Maxiva Maintenance Overview 6-1.7 Inside Cooling Control Panel Control lines to Tx AC to Fans See Wiring Diagram or TM 888-2625-001 for connection details. next level solutions Maxiva Maintenance Overview 6-1.8 Cooling Control & Interlock Connections on Tx Interlock Jumpers Cabinet Safety 8-9 Control lines to Pump Module System RF Mute 5-6 Cab RF Mute 11-12 System Safety 2-3 AC to Fans See Wiring Diagram for connection details. next level solutions Maxiva Maintenance Overview 6-1.9 Inverter Controller • Set up of Controller for pumps and fans is described in the HE Pump Module technical manual 888-2625-001 Section 3. • Controllers differ for pumps (2HP) and fans (1HP). • Controllers differ for supply volatges 3 phase 208 to 240 VAC or 380-415 VAC (determined at time of order) • Specify voltage when placing order. next level solutions Maxiva Maintenance Overview 6-1.10 Inverter Controller • Pump potentiometers only active when pump module set to LOCAL mode. • Pump inverter settings LL (pump lower limit Hz) = recommended flow rate) and F202 (set to same value as LL) need to be set on site. next level solutions Maxiva Maintenance Overview 6-1.11 Inverter Controller • Allows operation with loss of phase. • Voltage and frequency supplied to pumps and fans changes with cooling requirements. • Specify voltage when placing order. next level solutions Maxiva Maintenance Overview 6-1.12 Heat Exchanger • Heat exchanger designed for outdoor use. • 3 phase 208 to 240 VAC or 380415 VAC (determined at time of order). Air Flow • Specify voltage when placing order. • One heat exchanger & pump module unit is required for each PA cabinet. • 50 kW heat exchanger can be mounted vertically or horizontally. • 25kW heat exchanger mounts vertical only. Closed Loop System Heat Exchanger (top) next level solutions Maxiva Maintenance Overview 6-1.13 Heat Exchanger Conduit and emergency cut off by Customer Inlet Air Flow Heat Exchanger Exhaust (fan side) Outlet Heat Exchanger Intake (fin side) 50 kW vertical heat exchanger shown. next level solutions Maxiva Maintenance Overview 6-1.14 Valve ID Globe or ball valves used in supply line for filters or test loads. Gate Valve (use in return lines only) Globe Valve Ball Valves (use in supply line) (90o on/off) next level solutions Maxiva Maintenance Overview 6-1.15 Cooling System Installation • Route RF system first to minimize use of elbows. • Install pipe or hose so coolant can be fully drained from all parts of system. • Avoid sharp bends in hoses. • Install drain valves in system low points and vents in system high points. • Install heat exchanger outside & protect from falling ice. • Need 2 M clearance on exhaust side of vertical heat exchanger. 10 M on horizontal units. • Need 1 M clearance on intake side of heat exchangers. • Some models won’t support a water cooled test load. Air cooled load may be needed. next level solutions Maxiva Maintenance Overview 6-1.16 Cooling System Installation • Hoses must be supported every few feet using padded clamps. Padded Clamps Vent • Static pressure (pumps off) of 10 psi is required before turn on. • Flush cooling system prior to first use (bypass Tx cabinet). Sight glass • 50/50 glycol/water mixture • Initial PH > 8.0 • System air purger and sight glass need to be located at the highest point in the system. Bypass Manifold Assy. Purger See section 2 in Technical Manual for installation instructions. • Sight glass used to check fluid level, flow and for presence of air bubbles. • Low fluid level or presence of bubbles indicates that system needs to be charged with more coolant. next level solutions Maxiva Maintenance Overview 6-1.17 Cooling System Installation Supply Return next level solutions Maxiva Maintenance Overview 6-1.18 Cooling System Maintenance • Check coolant level monthly. Check for bubbles, level of coolant in sight tube and static pressure of 10 psi. • Operate valves monthly to insure continued trouble free operation. • Check glycol/water ratio regularly (quarterly). Use a float hydrometer or digital refractometer with ethylene glycol. Use a digital refractometer with propylene (hydrometers not accurate with propylene). Note: Hydrometers only work for ethylene glycol-based coolants/antifreeze. Propylene glycol should not be read with a hydrometer due to the fact that up to 70 percent concentration specific gravity increases, but above 70 percent specific gravity decreases. A 100 percent solution reads identical to a 40 percent solution. next level solutions Maxiva Maintenance Overview 6-1.19 Cooling System Maintenance • Check coolant PH regularly (quarterly) PH > 8.0 is ok. • PH < 8.0 indicates additives or coolant change needed. • Alternate pumps monthly. Use GUI In Local. Pumps switch when turned ON/OFF. • Check and clean strainer regularly (quarterly at first then yearly). Pumps must be off to clean the strainer. • Check and clean heat exchanger fins frequently (quarterly or more often in dirty locations). next level solutions Maxiva Maintenance Overview 6-1.20 Pump Module Pressures Return (10psi) Supply (40-50psi) These pressures will vary from system to system depending on no. of elbows, hose size and length, transmitter model etc. next level solutions Maxiva Maintenance Overview 6-1.21 Pump Module Strainer Assembly • Pump must be off to clean screen. • Strainer screen is removed with adjustable wrench. Strainer Screen • Clean after initial system flushes. Top of Pump Module next level solutions Maxiva Maintenance Overview 6-1.22 Cooling System Maintenance "Inhibitor Additions” Over time, the corrosion inhibitors in heat transfer fluids may become depleted. UCAR HTF Inhibitors can be added to replace those lost and restore anti-corrosion properties. Union Carbide inhibitor packages replenish corrosion inhibitors while adjusting the fluid’s pH and reserve alkalinity. If the analytical report suggests the need for additional corrosion inhibitors, it will also recommend the best UCAR Inhibitor package for your system." Above from: http://www.dow.com/PublishedLiterature/dh_0035/0901b80380035962.pdf ?filepath=/heattrans/pdfs/noreg/180-01442.pdf&fromPage=GetDoc General Dow Chemical information at: http://www.dow.com/PublishedLiterature/dh_0034/0901b80380034ba4.pdf ?filepath=/heattrans/pdfs/noreg/180-01463.pdf&fromPage=GetDoc next level solutions Maxiva Maintenance Overview 6-1.23 Broadcast Customer Portal (eCustomer Home Page) • Got to http://support.broadcast.harris.com/ next level solutions Customer Portal 7-1.1 Customer Portal - Login Window Apply for User ID and Password MUST use OK button to submit User ID & Password • If you are a new user select “New User” and then specify a user ID and a password. • Log in using your new User ID and Password. • Note: You must use the OK button to submit your Log In/Password. Using the enter key will not work. next level solutions Customer Portal 7-1.2 Customer Portal – Access Summary •Go to this link and create an account (or login if you already have an account) http://support.broadcast.harris.com •Logon to the site and click on “Review Documentation” •Select “Television Transmission” •Select “UHF Digital” •Select “Maxiva-ULX” •Click “Manual, Technical-Maxiva ULX TM (Dry Cooler or HE)” •File Download page will display, select “Open” or “Save” next level solutions Customer Portal 7-1.3 Customer Portal – Opening Page next level solutions Customer Portal 7-1.4
advertisement
* Your assessment is very important for improving the workof artificial intelligence, which forms the content of this project
Related manuals
advertisement