Graco 312396C User's Manual
Add to my manuals12 Pages
Graco 312396C is a heated fluid regulator designed to control and regulate fluid pressure to a single spray gun, dispense valve, or atomizing head in a high-pressure system. With a maximum working pressure of 3000 psi (21 MPa, 210 bar) and a regulated fluid pressure range of 200-3000 psi (1.4-21 MPa, 14-210 bar), it ensures precise control over fluid flow. Its electrical heating system allows for maintaining consistent fluid temperature, crucial for applications requiring precise temperature control.
advertisement
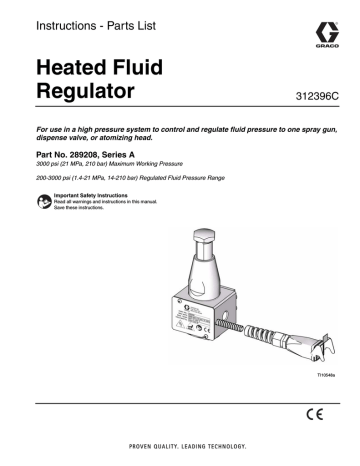
Instructions - Parts List
Heated Fluid
Regulator
312396C
For use in a high pressure system to control and regulate fluid pressure to one spray gun, dispense valve, or atomizing head.
Part No. 289208, Series A
3000 psi (21 MPa, 210 bar) Maximum Working Pressure
200-3000 psi (1.4-21 MPa, 14-210 bar) Regulated Fluid Pressure Range
Important Safety Instructions
Read all warnings and instructions in this manual.
Save these instructions.
TI10548a
2
Warnings
Contents
Warnings . . . . . . . . . . . . . . . . . . . . . . . . . . . . . . . . . 2
Installation . . . . . . . . . . . . . . . . . . . . . . . . . . . . . . . . 4
Before Installing the Fluid Regulator . . . . . . . . . . 4
Installing the Fluid Regulator . . . . . . . . . . . . . . . 4
Connect Electrical Cable . . . . . . . . . . . . . . . . . . . 4
Ground the System . . . . . . . . . . . . . . . . . . . . . . . 6
Operation . . . . . . . . . . . . . . . . . . . . . . . . . . . . . . . . . 6
Pressure Relief Procedure . . . . . . . . . . . . . . . . . 6
Adjusting the Regulator . . . . . . . . . . . . . . . . . . . . 6
Maintenance . . . . . . . . . . . . . . . . . . . . . . . . . . . . . . . 7
Flushing . . . . . . . . . . . . . . . . . . . . . . . . . . . . . . . 7
Cleaning . . . . . . . . . . . . . . . . . . . . . . . . . . . . . . . 7
Inspection Frequency . . . . . . . . . . . . . . . . . . . . . 7
Troubleshooting . . . . . . . . . . . . . . . . . . . . . . . . . . . . 8
Repair . . . . . . . . . . . . . . . . . . . . . . . . . . . . . . . . . . . . 8
Install New Heater Cartridge(s), RTD Sensor, or
Switch . . . . . . . . . . . . . . . . . . . . . . . . . . . . . . 8
Parts . . . . . . . . . . . . . . . . . . . . . . . . . . . . . . . . . . . . 10
Technical Data . . . . . . . . . . . . . . . . . . . . . . . . . . . . 11
Accessories . . . . . . . . . . . . . . . . . . . . . . . . . . . . . . 11
Dimensions . . . . . . . . . . . . . . . . . . . . . . . . . . . . . . . 11
Graco Standard Warranty . . . . . . . . . . . . . . . . . . . 12
Graco Information . . . . . . . . . . . . . . . . . . . . . . . . . 12
Warnings
The following warnings are for the setup, use, grounding, maintenance, and repair of this equipment. The exclamation point symbol alerts you to a general warning and the hazard symbol refers to procedure-specific risk. Refer back to these warnings. Additional, product-specific warnings may be found throughout the body of this manual where applicable.
WARNING
EQUIPMENT MISUSE HAZARD
Misuse can cause death or serious injury.
• Do not operate the unit when fatigued or under the influence of drugs or alcohol.
• Do not exceed the maximum working pressure or temperature rating of the lowest rated system component. See Technical Data in all equipment manuals.
• Use fluids and solvents that are compatible with equipment wetted parts. See Technical Data in all equipment manuals. Read fluid and solvent manufacturer’s warnings. For complete information about your material, request MSDS forms from distributor or retailer.
• Check equipment daily. Repair or replace worn or damaged parts immediately with genuine manufacturer’s replacement parts only.
• Do not alter or modify equipment.
• Use equipment only for its intended purpose. Call your distributor for information.
• Route hoses and cables away from traffic areas, sharp edges, moving parts, and hot surfaces.
• Do not kink or over bend hoses or use hoses to pull equipment.
• Keep children and animals away from work area.
• Comply with all applicable safety regulations.
ELECTRIC SHOCK HAZARD
Improper grounding, setup, or usage of the system can cause electric shock.
• Turn off and disconnect power at main switch before disconnecting any cables and before servicing equipment.
• Connect only to grounded power source.
• All electrical wiring must be done by a qualified electrician and comply with all local codes and regulations.
312396C
312396C
Warnings
WARNING
SKIN INJECTION HAZARD
High-pressure fluid from gun, hose leaks, or ruptured components will pierce skin. This may look like just a cut, but it is a serious injury that can result in amputation. Get immediate surgical treatment.
• Do not point gun at anyone or at any part of the body.
• Do not put your hand over the spray tip.
• Do not stop or deflect leaks with your hand, body, glove, or rag.
• Do not spray without tip guard and trigger guard installed.
• Engage trigger lock when not spraying.
• Follow Pressure Relief Procedure in this manual, when you stop spraying and before cleaning, checking, or servicing equipment.
FIRE AND EXPLOSION HAZARD
Flammable fumes, such as solvent and paint fumes, in work area can ignite or explode. To help prevent fire and explosion:
• Use equipment only in well ventilated area.
• Eliminate all ignition sources; such as pilot lights, cigarettes, portable electric lamps, and plastic drop cloths (potential static arc).
• Keep work area free of debris, including solvent, rags and gasoline.
• Do not plug or unplug power cords, or turn power or light switches on or off when flammable fumes are present.
• Ground all equipment in the work area. See Grounding instructions.
• Use only grounded hoses.
• Hold gun firmly to side of grounded pail when triggering into pail.
• If there is static sparking or you feel a shock, stop operation immediately. Do not use equipment until you identify and correct the problem.
• Keep a working fire extinguisher in the work area.
TOXIC FLUID OR FUMES HAZARD
Toxic fluids or fumes can cause serious injury or death if splashed in the eyes or on skin, inhaled, or swallowed.
• Read MSDS’s to know the specific hazards of the fluids you are using.
• Store hazardous fluid in approved containers, and dispose of it according to applicable guidelines.
• Always wear impervious gloves when spraying or cleaning equipment.
BURN HAZARD
Equipment surfaces and fluid that’s heated can become very hot during operation. To avoid severe burns, do not touch hot fluid or equipment. Wait until equipment/fluid has cooled completely.
PERSONAL PROTECTIVE EQUIPMENT
You must wear appropriate protective equipment when operating, servicing, or when in the operating area of the equipment to help protect you from serious injury, including eye injury, inhalation of toxic fumes, burns, and hearing loss. This equipment includes but is not limited to:
• Protective eyewear
• Clothing and respirator as recommended by the fluid and solvent manufacturer
• Gloves
• Hearing protection
3
4
Installation
Installation
Fluid pressure regulators are used for accurate, positive control of the fluid pressure to spray guns, dispense valves, or atomizing heads.
Regulators installed at circulating line take-offs or pumps are used to reduce main line pressure and maintain the desired fluid pressure to the spray gun, dispense valve, or atomizing head.
Connect Electrical Cable
1.
Wrap hose cable around hose one time. Connect electrical cable from hose or accessory cable to regulator cable; engage metal clip on top of connector.
Before Installing the Fluid
Regulator
1.
Determine placement of the fluid regulator in system.
2.
Install a ball valve for inlet and outlet of the regulator.
3.
Install temporary plumbing between the ball valves.
4.
Thoroughly flush the system to remove metal chips and other contaminants and to check for leaks.
F
IG
. 1: Connect Electrical Cable, Step 1
2.
Place flat side of cable connection against hose, making sure metal clip faces away from hose. This will prevent damage to hose from clip rubbing against it.
Installing the Fluid Regulator
1.
Remove the temporary plumbing and install one regulator for each dispense valve. A mounting plate
(28) is provided for mounting the regulator from the side.
2.
Put sealer on threaded connections, except on swivel unions as it interferes with the swivel action.
3.
See F IG . 4. Connect the fluid supply line to the 3/8
npt(f) inlet (B) of the fluid regulator (A). Connect the fluid line between the dispense valve (D) and the regulator's 3/8 npt(f) outlet (C). Make sure that the direction of fluid flow agrees with the IN and OUT markings on the regulator body.
4.
Flush and test the entire system.
F
IG
. 2: Connect Electrical Cable, Step 2
3.
Fasten Velcro insulation wrap (198422) snugly around hose. Secure wrap with two Velcro straps
(198442) on ends of wrap.
F IG . 3: Connect Electrical Cable, Step 3
312396C
Installation
D
C A
B
E
F
IG
. 4: Typical Installation
Key:
A Heated Fluid Pressure Regulator
B 3/8 npt(f) Regulator Fluid Inlet
C 3/8 npt(f) Regulator Fluid Outlet
D Dispense Valve
E Electrical Cable
TI10640a
312396C 5
6
Operation
Ground the System Operation
Pressure Relief Procedure
The following grounding instructions are minimum requirements for a basic dispensing system. Your system may include other equipment or objects that must be grounded. Check your local electrical code for detailed grounding instructions for your area and type of equipment. Your system must be connected to a true earth ground.
• Fluid regulator: ground by connecting to a properly grounded fluid hose and by a ground wire in the cable. Check ground continuity between the regulator body and the heat control ground lug.
• Fluid hoses: use only grounded fluid hoses. Check electrical resistance of your fluid hoses at least once a week. If the hose resistance exceeds 25 megohms, replace it immediately. If your hose does not have a tag on it that specifies the maximum electrical resistance, contact the hose supplier or manufacturer for the maximum resistance limits.
• Dispense valve: ground by connecting to a properly grounded fluid hose and by a ground wire in the cable. Check ground continuity between the valve body and the heat control ground lug.
• Fluid supply container: ground according to the local code.
• Flammable liquids in the dispense area: must be kept in approved, grounded containers. Do not store more than the quantity needed for one shift.
• All solvent pails used when flushing: ground according to local code. Use only metal pails, which are conductive. Do not place the pail on a non-conductive surface, such as paper or cardboard, which interrupts the grounding continuity.
To maintain grounding continuity when flushing or relieving pressure: hold a metal part of the gun firmly to the side of a grounded metal pail, then trigger the gun. To reduce the risk of static sparking, ground the pump, object being dispensed to, and all other spraying/dispensing equipment used or located in the spraying/dispensing area. Check your local electrical code for detailed grounding instructions for your area and type of equipment.
1.
Shut off the fluid supply pump.
2.
Open the dispense valve, having a waste container ready to catch drainage.
3.
If you suspect the dispense valve or hose is clogged or that pressure has not been fully relieved after following the steps above, VERY SLOWLY loosen hose end coupling to relieve pressure gradually, then loosen completely. Clear hose or valve obstruction.
Adjusting the Regulator
The fluid pressure regulator controls pressure downstream from its outlet.
To adjust the fluid regulator, first, back the adjusting screw (16) out until there is no spring pressure. Then, turn the screw clockwise to increase pressure.
NOTE: If you are using an accessory fluid pressure gauge, relieve the dispense valve line when reducing pressure to ensure a correct gauge reading.
Adjust the pump air pressure and the fluid regulator for the best dispensing combination. Record all the settings for future reference. The adjusting screw (16) has exterior markings (set points 1 to 5) for repeat settings.
312396C
Maintenance
Maintenance
Flushing
Trapped air can cause the pump to cycle unexpectedly, which could result in serious injury from splashing or moving parts.
NOTE:
• Flush before changing materials, before fluid can dry in the equipment, at the end of the day, before storing, and before repairing equipment.
• Flush at the lowest pressure possible. Check connectors for leaks and tighten as necessary.
• Flush with a fluid that is compatible with the fluid being dispensed and the equipment wetted parts.
Cleaning
When changing materials, the regulator should be disassembled and cleaned. Regular cleaning and inspection, and lubrication of the piston (7) and piston packing
(12) are necessary to keep the fluid regulator working properly.
1.
Relieve all the air and fluid pressure in the system.
2.
Remove the regulator from the system.
3.
Disassemble the regulator, referring to Parts on page 10. Clean and inspect all parts.
NOTICE
Use special care when handling the piston (7) and seat
(5). Damage will cause poor operation and leakage.
1.
Record the pressure adjustment setting of the regulator before flushing.
2.
Shut off the pump and relieve fluid pressure in the system by triggering the dispense valve.
3.
Never exceed the maximum working pressure of the lowest rated system component.
4.
Open the fluid regulator by turning the adjusting screw (16) fully clockwise.
5.
Supply flushing material to the system. Set pump to the lowest possible pressure, and start pump.
6.
Flush until thoroughly clean.
7.
Adjust the fluid regulator to return to the desired fluid pressure setting.
NOTE: Do not allow material or flushing material to set in the system for a long time. Fluid could dry on the piston, causing leakage at the piston packing. If leakage occurs, disassemble and clean the regulator.
Inspection Frequency
Heater
Every two weeks, check heater for proper resistance.
Resistance should be approximately 262 ohms, + 26/-13 ohms for the 240V valves. Replace heater if necessary.
Also inspect heater when performing regular maintenance procedures.
Sensor
Every two weeks, check sensor resistance. Resistance should be 108 ohms at 70° F (21° C). Replace sensor if necessary.
Also inspect sensor when performing regular maintenance procedures.
312396C 7
Troubleshooting
Troubleshooting
8
Some solutions require disassembling fluid regulator.
Always relieve system pressure and disconnect electrical cable before performing these procedures.
Problem
Regulator does not heat material
Cause(s)
Loose heater wires.
Loose sensor wires.
Heater cartridge failed.
Sensor failed.
Temperature controller failed.
No power to heating circuitry.
Solution(s)
Check and reconnect wire connections.
Check and reconnect wire connections.
Replace failed heater.
Replace failed sensor.
Refer to Therm-O-Flow
®
manual.
Refer to Therm-O-Flow
®
manual.
Repair
Normally, only the ball support/seat (5) and piston packing (12) will ever need replacement. Repair Kit 225474
is available to replace these parts. See page 10.
1.
Lubricate the piston packing (12), piston (7), and spring guide (15) with lithium base grease.
2.
Place the washer (13) over the pointed end of the piston (7).
3.
Place the packing (12), with its lips facing down, over the pointed end of the piston (7) and against the washer (13).
4.
Insert the piston (7) into the bottom of the cylinder
(3) and gently work it into place.
5.
Reassemble the remaining parts in reverse order of disassembly. Torque the valve seat (5) into the housing to 175 to 200 in-lb (20 to 22 N•m). Overtightening could break off the hex portion of the seat.
Install New Heater Cartridge(s),
RTD Sensor, or Switch
1.
Remove cover (25).
2.
Remove and disconnect lead wires of failed components.
3.
Gently slide new heater(s) or sensor into appropriate hole.
4.
Feed new wires through conduit to connector (38) and crimp after cutting to length and stripping.
5.
Use an ohmmeter to check: a.
Heater pins 1 to 2, 262 ohms, + 26/-13 ohms.
b.
RTD sensor pin 3 to 4, 108 ohms, +/-1 ohm at
70°F (21°C).
c.
Continuity to regulator body from pin 8.
d.
No continuity from pins 1-7 to regulator body or connector shell, or ground pin 8.
312396C
Repair
F IG . 5: 8 Pin, 240 Volt Shown
312396C 9
Parts
Parts
30
20
11
37, 38, 39
5* 4*
29
28
36
1 17
10
9
8
*2
19
18
21
22
23
26
18
2
7*
14
13*
12*
15
27
3
16
25
Ref.
Part Description
4*
5*
7*
8
1
2*
3
9
10
11 n/a n/a n/a n/a n/a n/a n/a n/a n/a n/a
HOUSING, heated regulator
PACKING, o ring; ptfe
CYLINDER, valve
GASKET; copper
SEAT, valve, support, ball
PISTON, regulator
BAR, piston
SPACER
BAR, support
SCREW, cap socket-hd; 1/4-20 x
18
19
20
21
22
12* n/a
1-3/4 in. (44 mm)
SEAL, u-cup
13* n/a
14
WASHER, ptfe
101954 RING, retaining
15
16
17
166988 GUIDE, spring n/a n/a
SCREW, adjusting, knob
CONDUIT, flexible; 1/4 in. (6 mm)
ID x 18 in. (0.46 m)
121205 HEATER, cartridge, 240V
119711 SENSOR, temperature n/a CAP, end n/a n/a
TERMINAL
WASHER, lock; #6
Qty
1
1
1
1
1
2
1
2
1
2
1
1
1
1
1
1
2
1
1
1
1
24
TI10548a
30
36
37
38
39
Ref.
Part
23
24
25
26
27
28
29 n/a n/a
Description
SCREW, machine; 6-32 x 1/4 in. (6 mm)
SCREW, cap, hex, button-head;
Qty
1
2 n/a n/a
166986 SPRING, helical n/a n/a
6-32 x 3/8 in. (10 mm)
COVER, plate
SCREW, set, socket-head; 8-32 x
3/8 in. (10 mm)
BLOCK, mounting
SCREW, cap, socket-head; 1/4-20 n/a n/a x 3/4 in. (19 mm)
PLUG, 1/4 npt
BUSHING, strain relief n/a CONNECTOR, cable coupler hood 1
115862 CONNECTOR, male 1 n/a INSERT, male
1
1
1
1
1
4
1
1
* Parts included in Kit 255474 (purchase separately).
Parts designated n/a are not available separately.
10 312396C
Technical Data
Technical Data
Maximum Fluid Working Pressure
Regulated Fluid Pressure Range
Maximum Flow Rate
Maximum Fluid Temperature
Voltage
Wattage
Maximum Current
Resistance temperature detector
(platinum RTD; 0.00385 ohm/ohm/°C)
Heater resistance
Fluid Inlet
Fluid Outlet
Optional Fluid Outlet
Weight
Wetted Parts
Accessories
3000 psi (21 MPa, 210 bar)
200-3000 psi (1.4-21 MPa, 14-210 bar)
1.2 gpm (4.56 liter/min) with 7000 centipoise fluid at 350°F (176°C)
400°F (204°C)
230/240 Vac
220 W
1 A
108.2 ohms @ 70°F
individually: 524 ohms, + 53/- 26 ohms
wired in parallel: 262 ohms, + 26/- 13 ohms
3/8 npt(f)
3/8 npt(f)
1/4 npt(f)
6.5 lb (2.9 kg)
Tungsten Carbide, Copper, Cadmium and Zinc-Plated Steel, PTFE,
Chrome-Plated Stainless Steel
Dimensions
Part Description
C34137 Fitting insulation, 1/8 in. (3 mm) thick x 2 in.
(51 mm) wide. Sold by the foot.
C33049 Adhesive tape, high temp for securing insulation (C34137), 1 in. (25 mm) x 108 ft (33 m).
198422 Wrap, velcro, 10 in. x 10 in. (250 mm x 250 mm). Covers electrical connection on heated hose.
198442 Strap, velcro. Use two around ends of wrap
(198422) for security.
113654 Fluid pressure gauge; 0-5000 psi (0-35 MPa,
0-350 bar); 1/4 npt(m); sst.
196315 Cable, electrical; 16 x 8; 15 ft (4.57 m) long.
196316 Cable, electrical; 16 x 8; 25 ft (7.62 m) long.
501511 Spring, compression. Recommended for low pressure, low viscosity applications.
A
C
Key:
A
B
C
6.9 in. (175 mm)
3.1 in. (80 mm)
3.0 in. (77 mm)
B
TI10659a
312396C 11
Graco Standard Warranty
Graco warrants all equipment referenced in this document which is manufactured by Graco and bearing its name to be free from defects in material and workmanship on the date of sale to the original purchaser for use. With the exception of any special, extended, or limited warranty published by Graco, Graco will, for a period of twelve months from the date of sale, repair or replace any part of the equipment determined by
Graco to be defective. This warranty applies only when the equipment is installed, operated and maintained in accordance with Graco’s written recommendations.
This warranty does not cover, and Graco shall not be liable for general wear and tear, or any malfunction, damage or wear caused by faulty installation, misapplication, abrasion, corrosion, inadequate or improper maintenance, negligence, accident, tampering, or substitution of non-Graco component parts. Nor shall Graco be liable for malfunction, damage or wear caused by the incompatibility of Graco equipment with structures, accessories, equipment or materials not supplied by Graco, or the improper design, manufacture, installation, operation or maintenance of structures, accessories, equipment or materials not supplied by Graco.
This warranty is conditioned upon the prepaid return of the equipment claimed to be defective to an authorized Graco distributor for verification of the claimed defect. If the claimed defect is verified, Graco will repair or replace free of charge any defective parts. The equipment will be returned to the original purchaser transportation prepaid. If inspection of the equipment does not disclose any defect in material or workmanship, repairs will be made at a reasonable charge, which charges may include the costs of parts, labor, and transportation.
THIS WARRANTY IS EXCLUSIVE, AND IS IN LIEU OF ANY OTHER WARRANTIES, EXPRESS OR IMPLIED, INCLUDING BUT NOT LIMITED
TO WARRANTY OF MERCHANTABILITY OR WARRANTY OF FITNESS FOR A PARTICULAR PURPOSE.
Graco’s sole obligation and buyer’s sole remedy for any breach of warranty shall be as set forth above. The buyer agrees that no other remedy
(including, but not limited to, incidental or consequential damages for lost profits, lost sales, injury to person or property, or any other incidental or consequential loss) shall be available. Any action for breach of warranty must be brought within two (2) years of the date of sale.
GRACO MAKES NO WARRANTY, AND DISCLAIMS ALL IMPLIED WARRANTIES OF MERCHANTABILITY AND FITNESS FOR A
PARTICULAR PURPOSE, IN CONNECTION WITH ACCESSORIES, EQUIPMENT, MATERIALS OR COMPONENTS SOLD BUT NOT
MANUFACTURED BY GRACO. These items sold, but not manufactured by Graco (such as electric motors, switches, hose, etc.), are subject to the warranty, if any, of their manufacturer. Graco will provide purchaser with reasonable assistance in making any claim for breach of these warranties.
In no event will Graco be liable for indirect, incidental, special or consequential damages resulting from Graco supplying equipment hereunder, or the furnishing, performance, or use of any products or other goods sold hereto, whether due to a breach of contract, breach of warranty, the negligence of Graco, or otherwise.
FOR GRACO CANADA CUSTOMERS
The Parties acknowledge that they have required that the present document, as well as all documents, notices and legal proceedings entered into, given or instituted pursuant hereto or relating directly or indirectly hereto, be drawn up in English. Les parties reconnaissent avoir convenu que la rédaction du présente document sera en Anglais, ainsi que tous documents, avis et procédures judiciaires exécutés, donnés ou intentés, à la suite de ou en rapport, directement ou indirectement, avec les procédures concernées.
Graco Information
TO PLACE AN ORDER, contact your Graco distributor or call to identify the nearest distributor.
Phone: 612-623-6921 or Toll Free: 1-800-328-0211 Fax: 612-378-3505
For the latest information about Graco products, visit www.graco.com.
All written and visual data contained in this document reflects the latest product information available at the time of publication.
Graco reserves the right to make changes at any time without notice.
This manual contains English. MM 312396
Graco Headquarters: Minneapolis
International Offices: Belgium, China, Japan, Korea
GRACO INC. P.O. BOX 1441 MINNEAPOLIS, MN 55440-1441
Copyright 2007, Graco Inc. is registered to ISO 9001 www.graco.com
7/2007 Revised 4/2009
advertisement
* Your assessment is very important for improving the workof artificial intelligence, which forms the content of this project
Related manuals
Frequently Answers and Questions
What is the maximum working pressure of the Graco 312396C fluid regulator?
What is the regulated fluid pressure range for this regulator?
How do I install the fluid regulator?
How do I connect the electrical cable?
What is the purpose of the heated fluid pressure regulator?
How do I ground the system?
What is the pressure relief procedure for this regulator?
advertisement
Table of contents
- 2 Warnings
- 4 Installation
- 4 Before Installing the Fluid Regulator
- 4 Installing the Fluid Regulator
- 4 Connect Electrical Cable
- 6 Ground the System
- 6 Operation
- 6 Pressure Relief Procedure
- 6 Adjusting the Regulator
- 7 Maintenance
- 7 Flushing
- 7 Cleaning
- 7 Inspection Frequency
- 8 Troubleshooting
- 8 Repair
- 8 Install New Heater Cartridge(s), RTD Sensor, or Switch
- 10 Parts
- 11 Technical Data
- 11 Accessories
- 11 Dimensions
- 12 Graco Standard Warranty
- 12 Graco Information