Jacuzzi J - 325 User's Manual
Add to my manuals
62 Pages
Jacuzzi J - 325 is a technologically advanced hot tub that provides a relaxing and rejuvenating experience. With its user-friendly control panel and various customizable features, you can tailor your spa experience to your liking. The J - 325 offers a range of massage options, including adjustable jet speeds and underwater lighting, allowing you to create a personalized hydrotherapy session. Additionally, the energy-efficient design ensures optimal performance while minimizing energy consumption.
advertisement
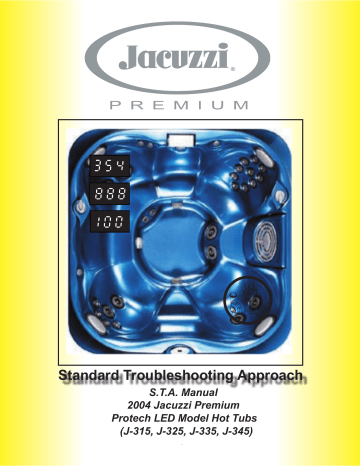
Standard Troubleshooting Approach
S.T.A. Manual
2004 Jacuzzi Premium
Protech LED Model Hot Tubs
(J-315, J-325, J-335, J-345)
1
The following symbol is placed throughout this manual for your protection. Always use extreme caution whenever performing repairs to electrical control system components of any kind!
Danger: Electrical Shock Hazard Exists!
High Voltage Present On Circuit Board. Use Extreme Caution While Servicing Circuit Board.
2
8.0
8.1
8.2
8.3
5.0
5.1
5.2
5.3
5.4
5.5
5.6
6.0
6.1
7.0
7.1
7.2
7.3
7.4
4.0
4.1
4.2
4.3
3.0
3.1
3.2
3.3
2.0
2.1
2.2
2.3
2.4
Table of Contents
1.3
1.4
1.5
1.6
Chapter
1.0
1.1
1.2
Standard Troubleshooting Approach (S.T.A.) ...............................................................
Why A Standard Troubleshooting Approach? ....................................................................
How To Use The STA .........................................................................................................
1.7
1.8
Professional Customer Service ..........................................................................................
Responding To An Incoming Service Call ..........................................................................
Preparing Foe A Service Call .............................................................................................
Before Calling Technical Support .......................................................................................
Before Leaving The Customer ..........................................................................................
Satisfying The Customer ....................................................................................................
Page
5
5
5
8
9
5
5
9
10
Electro Static Discharge (E.S.D.) ....................................................................................
ESD - What Is It? What Does It Do? ..................................................................................
Avoiding ESD Damage ......................................................................................................
What About Wrist Straps And Special Mats? .....................................................................
Must Wrist Straps And Mats Be Used When Replacing A Circuit Board? ..........................
11
11
11
11
11
Main System Specifi cations (J-345) ...............................................................................
Main System Specifi cations (J-335) ...................................................................................
Main System Specifi cations (J-325) ...................................................................................
Main System Specifi cations (J-315) ...................................................................................
12
14
16
18
Main Control Panel Functions ........................................................................................
Setting Filter Cycle Start Time ...........................................................................................
Programming Filter Cycles .................................................................................................
Aftermarket Ozone Facts ...................................................................................................
20
20
20
22
Additional Control Panel Functions ...............................................................................
Setting Water Temperature ................................................................................................
Selecting Jet Speeds .........................................................................................................
Underwater Light Operation ...............................................................................................
Lock/Unlock Control Panel .................................................................................................
Lock Out Mode ...................................................................................................................
Summer Logic ....................................................................................................................
22
22
22
22
22
23
23
Understanding Circuit Board Pin Assignments ............................................................
Circuit Board Jumpers .......................................................................................................
23
23
Troubleshooting Using The Control Panel ....................................................................
Control Panel Displays .......................................................................................................
Control Panel Default Display ............................................................................................
Control Panel Status And Error Messages ........................................................................
Testing Flow Switch ...........................................................................................................
24
24
24
24
26
Troubleshooting Without The Control Panel .................................................................
No Heat Or Not Enough Heat (Diagrams A-E) ...................................................................
Intermittent Heating ............................................................................................................
Nothing Works ....................................................................................................................
3
27
27
32
33
Chapter
8.4
Hot Tub Doesn’t Come On For Filter Cycle .......................................................................
8.5
8.6
8.7
House Breaker Trips ..........................................................................................................
Hot Tub Light Will Not Come On ........................................................................................
No Jets ...............................................................................................................................
8.8
8.9
8.10
8.11
8.12
8.13
Weak Or Surging Jets ........................................................................................................
Pump Runs And Quits During Jet Mode ............................................................................
Circulation Pump Not Working ...........................................................................................
Troubleshooting A Thermal Pump Cutout ..........................................................................
Pump Hums And Will Not Start ..........................................................................................
Ozonator Not Working .......................................................................................................
Page
33
34
38
39
40
41
42
43
43
44
A8.0
A9.0
A10.0
A11.0
A12.0
A13.0
A14.0
A15.0
A16.0
A17.0
A18.0
A19.0
A.
A1.0
A2.0
A3.0
A4.0
A5.0
A6.0
A7.0
Appendix ...........................................................................................................................
Checking Voltage To The Hot Tub .....................................................................................
Checking Voltage To Components .....................................................................................
Checking Current Consumption Of Components ...............................................................
Testing The Flow Switch ....................................................................................................
About Fuses .......................................................................................................................
The Watchdog (----) ............................................................................................................
Understanding Ozone ........................................................................................................
Understanding pH ..............................................................................................................
2004 J-315, J-325 Circuit Board Illustration (120 VAC / 3 or 4-Wire Connection) .............
2004 J-335, J345 Circuit Board Illustration ( 240 VAC / 3-Wire Connection) .....................
Load Box Connection Diagrams A-F ..................................................................................
Temperature / Hi-Limit Sensor Resistance Chart ..............................................................
Flow Switch Illustration ......................................................................................................
Sensor Harness Connector Diagram .................................................................................
Transformer Test ................................................................................................................
Troubleshooting the Optional Stereo System ....................................................................
Suggested Spare Parts ......................................................................................................
Glossary Of Terms .............................................................................................................
Sample Troubleshooting Data Collection Form .................................................................
56
56
57
58
59
49
50
51
52
55
60
61
45
46
47
47
48
48
48
49
4
1.0 Standard Troubleshooting Approach (S.T.A.)
1.1 Why A Standard Troubleshooting Approach?
Service prices are basically set by local industry and geographic region. Stiff competition in the service industry has made it diffi cult to raise the price of a service contract; or charge more for time and materials than the competetive shop down the street. If your business is to be profi table, you must control the overall
cost of service
. The total cost of service is made up of many individual factors, but three in particular are more important than the rest combined:
1.
2.
3.
Time of Repair - How long it takes to fi nd and fi x a problem.
Time Between Failures - How often are you called to repair any one particular hot tub? How many times are you called back to fi x the same problem on the same hot tub?
Parts Usage - Except in rare circumstances, only one part fails. How many parts do you replace before you fi nd the bad one.
The Jacuzzi Premium STA Manual has been designed to help you control the overall cost of service by focusing on the three important aspects of your job outlined above. The STA will help you fi x your customer’s hot tub quickly, fi x it well, and use fewer parts.
1.2 How To Use The STA
The STA was developed by the Jacuzzi Premium Technical Support
Department and is designed to be the communications link between you and your customers. If you call for help on any symptom covered in this book, you will be told to do what the STA recommends, therefore, you will save time by calling technical support after you have done what the STA tells you to do.
1.3 Professional Customer Service
Doing your job in a way that keeps cost of service low and profi t margin high also creates customer satisfaction. That’s being a professional!
1.4 Responding To An Incoming Service Call
Be
Prepared!
1.
•
Phone personnel.
Which staff member(s) takes the initial call? This person is responsible for handling the call, writing up and making sure that the service technician receives all the information the same day.
2.
•
•
Determine the customer complaint.
Determine whether this is a service call or a maintenance issue that can be handled over the phone.
Saving you (the technician) time and the company money should be a priority.
3.
•
•
Verify the model number, serial number and confi rm that this is the original owner of the spa.
The original owner is the only one covered under the terms of the warranty.
Know what components are covered under the terms of the warranty, the length of time of the warranty and then confi rm that the owner understands what will and won’t be covered in the event of a service visit.
5
4.
•
•
•
Question the homeowner to determine, if possible, what specifi c component is not functioning.
Use the map of the spa (see below); become familiar with the components and their names. This will also help when speaking to technical service.
Keep the Owner’s manuals in an accessible place.
Know the difference between the spa’s components and how they perform when utilized in the spa.
Example: An air control will induce air into the plumbing of the jet, increase the fl ow of water and make the jet more powerful.
5.
•
Ask what is showing on the control panel.
Are there any error messages? Ask the customer to specifi cally describe the topside control panel readout, if any.
6.
•
•
Determine if the error message is the result of a safety feature or if a service call needs to be set up.
“Cool” and/or “Ice” are generally the result of a spa that has just been fi lled or refi lled and doesn’t require any action on the part of the homeowner or the technician.
Know how the fi ltration system works, what its defaults are, when it comes on and if there are any automatic times that it will come on during each day.
Know the symptoms!
7.
•
•
•
Setting up the appointment.
Make sure you verify the name, address, phone number and where the customer can be reached if not at home.
Ask if there is access to the spa if the owner is not going to be present.
Ask about anything that may bar your access to the spa such as locked gates, locked electrical boxes, vicious dogs, etc.
Diverter Valve
Remote Panel
Air Controls
Waterfalls
Pillow
Topside Control Panel
Pump #2
Load Box
Jets
Filters
Fully Foamed
Wood Skirt
Spa Map
Pump #1
Circulation Pump
Removable Pan
6
8.
Make Sure there is access to the main breaker and GFCI, and ask the homeowner to disconnect if possible before you arrive at their home.
9.
Use the home service visit as an opportunity to sell aftermarket items such as chemicals, towels, etc.
10.
•
Educate your staff regarding chemicals that are important for optimal use and longevity of the spa components.
Chemical misuse is not covered under the terms of the warranty.
11.
•
Know what to recommend when the customer complains that they cannot get their chemicals properly balanced. This is not a service call covered by the warranty or a problem that involves the manufacturer.
All spas are used differently: heavy or light bather loads, adults only, the whole family, bromine or chlorine, etc.
12.
•
Does the customer know how to properly clean the fi lter and that the spa needs to be disabled when doing so?
Suggest a second fi lter to the customer if the original fi lter needs to be soaked in a cleaning solution.
Have one in your truck!
13.
Find out what chemicals the customer is using. If they have saturated the spa with different kinds of chemicals, sometimes it is best to empty the spa and start all over.
BENEFITS YOU WILL RECOGNIZE
•
A satisfi ed customer is one who will continue to call upon you for business and does not contact your competitors.
•
Educating your staff will increase their value and allow you to focus on
real
service issues.
•
Being properly prepared will increase your productivity and permit you to enjoy a weekend once in a while.
•
Bottom Line: If you change the way you approach your customer, you’ll be putting more money in your pocket.
7
1.5 Preparing For A Service Call
1.
•
•
Know what each call is asking of you; determine whether or not the extent of service can be handled with a simple phone call or if it requires a visit.
Determine whether the call is warranty or non warranty. Make sure the customer is aware that the manufacturer will not cover out-of-warranty service.
If you plan to charge the customer for travel expenses, make sure that they are aware of the costs before you show up.
2.
•
Make sure all of your testing devices are functioning properly and extra batteries are on hand.
Always bring a meter; when calling technical support, please ensure that you have all of the pertinent information, such as the spa’s serial number, model number, the system you are working on, etc.
3.
•
Prepare your route so you may complete the maximum number of service calls each day.
A map book or a large map of your service area will greatly increase your effi ciency.
4.
•
•
Bring all the tools needed to properly perform service calls.
Always have your vehicle properly stocked with replacement parts.
Have a sump pump available for draining purposes; emptying a spa from the drain line takes a lot of your time, which we know is extremely valuable.
5.
•
•
Properly prepare for the day’s service calls.
When reviewing your calls, think of every possible component and tool that you may need. For example, if there is a heating problem or the heater doesn’t come on, think of all the components that include anything to do with a heat call, such as the temperature sensor, circulation pump, main pump, fl ow or pressure switch, fi lter, circuit board, heater, etc.
Prepare for the worst possible scenario and plan to be able to satisfy the subsequent problems that may arise.
6.
•
Dress appropriately. Although this is one job where shorts are acceptable, to maintain your credibility as a professional, leave the half shirts and shirts with derogatory or obscene comments at home.
Finish your cigarette before speaking with the spa owner and remember -
no drugs or alcohol!
7.
•
Be on time for your appointments. If you are going to be late or can’t make the appointment, call the customer to inform them of what’s happening.
Call your offi ce and ask them to call the people on your schedule to tell them you are running late.
8.
•
•
Always support the product that you service.
Do not berate the product in front of the homeowner.
It is essential to maintain the integrity and reputation of the product, and berating the product may affect your credibility as an authorized service professional.
If you feel there is a problem that needs special attention, call us or complete a quality alert. Remember, this is a partnership between you and the manufacturer - we want to provide the best quality product possible, with your business providing the best service possible!
8
9.
•
•
Make professional repairs.
Putting bondo, underwater epoxy, silicone or any other product to fi x cracked or leaking plumbing will not adequately correct the problem and will most likely result in a return visit. Replace the component or come back and do it for free!
Make repairs look as good as or better then when you started.
10.
•
Make sure you leave the customer’s home as clean as you found it.
Most customers don’t mind if you are having lunch in their backyard, as long as you remove the evidence! Make sure to pick up any trash that you may have generated through repairs as well as break times, lunch, etc.
11.
•
Leave a work order with the customer explaining what you found to be the problem and how you corrected it.
Make sure the customer understands the work order.
12.
Suggest to the customer any improvements they can make in maintaining their spa.
13.
Recommend replacement fi lters or a new cover if there is a need for one. A spa vac is an easy sell once you demonstrate it to the customer.
14.
Always carry a box of fi lters and a box of the basic chemicals; once you have fi nished the service, politely ask if they need any chemicals or a new fi lter. Drop off chemicals in a sealed box if they have ordered them when they made their service appointment.
1.6 Before Calling Technical Support
Make sure you have followed the STA and fi lled out a “Troubleshooting Data Collection Form” (see example on page 61). Have the STA manual and the Troubleshooting Data Worksheet near the telephone. Technical Support can help you best if these things become the communications tools for the phone call.
1.7 Before Leaving The Customer
Even if you don’t have to fi ll out a Troubleshooting Data Collection Form, please do so. If this is a warranty repair, the information will be needed when your offi ce fi lls out the “Returned Goods/Labor Tag”.
In any case, it will help you spot trouble before it happens. Pumps burn up if voltage at the hot tub is too low. Circuit breakers trip if heaters and motors draw too much current (Amps). Wires overheat and connections burn if wire size is too small or push-on connectors are loose.
Call backs cause cost of service to increase!
9
1.8 Satisfying The Customer
Most customers do not care what work you have done or what parts you have replaced, but they always care whether or not their problem goes away.
When you are done, show them that their problem is gone. If they ask how you did it, take a few minutes to explain. Show them the bad part(s) and explain or show why it is bad.
•
•
•
Develop
the habit of examining the hot tub’s you service. Compliment customers on the things they are doing right. Tell them how their care and attention can stop trouble before it starts.
Mention
if you noticed any adverse conditions, especially if the hot tub is under warranty or contract, that could lead to failure. Can the customer correct the problem? Would they like you to correct it? Can you recommend someone? Would they like an estimate?
Think
of yourself and the customer as a “team” trying to keep the product up and running as costeffective and time-effi cient as possible. That’s good for the customer, and it’s good for your business.
10
2.0 Electro Static Discharge
2.1 ESD - What Is It? What Does It Do?
Static electricity is always being generated around us, even at those times when we no longer get zapped after walking across a rug and touching something.
Like all state-of-the-art circuit boards, the hot tub’s circuit board can be damaged by unnoticed static electricity. Damaged is the key word. Sometimes a board which has been subjected to ESD will fail immediately upon being put back into service. Usually a board will operate for a few days, or months, then fail.
•
•
• If the hot tub runs only a few days,
the customer thinks you provided poor service.
If the hot tub runs only a few months,
the customer thinks the circuit board was a low quality product.
The customer loses
use of the hot tub.
You lose money
because you must go back to make it right. Jacuzzi Premium loses its reputation for quality.
2.2 Avoiding ESD Damage
We can’t prevent static charges from building up within us as we go about our jobs, so we must do three things to protect circuit boards from getting zapped:
1.
2.
3.
Never transport or ship circuit boards -
good boards or bad boards -
except in the static protective bags.
Never remove the board from the static protective bag unless you are ready to install it in the hot tub.
After removing the bad board from the hot tub, A) lay it on the ground, B) remove
L
L
N
Spa Light
L
N
L
Ozone
N
Circ Pump
L
N
J4
Rev. 3.53
J1
8
6
4
2
JP1
7
5
3
1 the replacement board from the static protective bag, C) lay the replacement board on the ground, D) place the bad board in the bag from which you removed the re-
N
L
Red Black
N L Heater In
N L
Heater Out
N L placement board, E) return bad board(s) to Jacuzzi Premium in undamaged sealed static protective bags.
2.3 What About Wrist Straps And Special Mats?
The purpose of these devices is to keep the technician, the work surface and the circuit board at the same electrical potential, and drain into ground any static charges which might build up. Proper use of the wrist strap and special mat guarantees maximum protection against ESD damage.
2.4 Must Wrist Straps And Mats Be Used When Replacing A Circuit Board?
No, if you keep the spare board in the protective bag during transport and you observe a few simple techniques during replacement.
The possibility of ESD damage to the circuit board during replacement will be minimal because of the hot tub’s design and the way you normally work on it. Touching the ground lug will drain all built-up static charges from your body much like a wrist strap would. Laying the bad board on the ground will tend to keep it neutral.
Touching a fi nger to the grounding lug immediately before removing the good board from the bag will drain charges built up by the rustling of your clothes. Laying the good board on the ground after removing it from the bag will tend to keep it neutral. Another quick touch of the grounding lug before picking up the bad board will drain built up charges. Slipping the bad board into the protective bag will allow it to be transported safely.
Another quick touch of the grounding lug before picking up the good board will again drain any charges built up. In the process of installing the replacement board, you and the board will be grounded to the load box or grounding lug, draining off charges you may build up during installation.
11
3.0 Main System Specifi cations J-345
Dimensions ...............................
84” x 84” x 36” (213cm x 213cm x
92cm)
Dry Weight ................................
882 lbs (400kg)
Filled Weight .............................
3,611 lbs (1,638kg)
Water Capacity (Avg. Fill) ........
336 US gallons (1,272 Liters)
Electronic Controls ..................
Solid State Electronic Controls with LED
Readout, Programmable Temperature,
Filtration, and Heat Cycles
Pump 1 ......................................
2-Speed, 4.2hp brake, 2.5hp continuous
Pump 2 ......................................
1-Speed, 4.2hp brake, 2.5hp continuous
Pump 3 ......................................
N/A
Circulation Pump ......................
Yes
Total PowerPro Jets .................
25
Maxx PowerPro (MX) ................
5
PowerPro (LX) ...........................
4
Mini PowerPro (FX) ..................
16
Micro PowerPro (SX) ................
N/A
Jet Selectors .............................
2
Air Controls ...............................
Four, On / Off Pushbutton Type
Total Foot Jet Therapy .............
2
Water Management System .....
Two 60ft
2
Filter Cartridges; Filter 1 on 24-Hour Circulation Pump; Filter 2 on 2-Speed Pump 1; Ready for optional CD Ozone Generator (Built-in
Ozone Dispersion Chamber Included in Spa)
Lighting .....................................
One Underwater with Two Colored Lenses
Cabinet ......................................
Redwood/Cedar with No Stain; Optional UV Resistant
Synthetic Plastic Cabinet with Embossed Red or Gray Wood Grain
Acrylic Colors ...........................
Textured Bluegrass, Jade, Marine, Onyx, Sahara, or Sand; Marbled
Emerald, Platinum, or Sapphire; Solid Azure or Silver
Headrests ..................................
4
Waterfall ....................................
Includes Flow Rate / On-Off Adjustment; Powered by Pump 1
Electrical Requirements ..........
North American 60Hz Models: 240 VAC @ 30A, 50A, or 60A
Export 50Hz Models: 230-240 VAC @ 35A or 40A, or suitably rated circuit breaker to comply with local electrical codes. Certain countries may require dual power inputs; two breakers are required for this confi guration.
Warranty .................................
North American 60Hz Models: 10 Years Shell, 7 Years Shell Surface,
5 Years for Plumbing Component Leaks, 5 Years Equipment &
Controls;
Export 50Hz Models: 2 Years Plumbing Component Leaks,
2 Years Equipment & Controls
Seating Capacity ....................
4 - 5
Audio System (Optional) .......
AM/FM/CD Stereo Receiver with Dual Pop-Up Speakers
Dimensions/Specifi cations are Subject to Change Without Notice
12
Jet Selector / Air Control Operation Diagram
Air Control 1:
Opens / Closes
Air Inlet to Jet
Group A
Air Control 2:
Opens / Closes
Air Inlet to Jet
Group C
Air Control 3:
Opens / Closes
Air Inlet to Jet
Group B
C
Jet Selector 2:
Directs Jet Pump 2
Output Between
Jet Groups C or D.
D
Air Control 4:
Opens / Closes
Air Inlet to Jet
Group D
D
A
B
C
D
A
B
Seat Depths
A = 25.50” (64.8cm) F = 19.75” (50.2cm) Listed Dimensions
B = 24.00” (60.1cm) G = 27.00” (58.6cm) Represent Distance from
C = 28.50” (72.4cm) H = 25.75” (65.4cm) Top of Acrylic to Lowest
D = 23.00” (58.4cm) I = 34.00” (86.4cm) Point in Seat.
E = 27.50” (69.9cm)
Jet Selector 1:
Directs Jet Pump 1
Output Between Jet
Groups A or B.
H
A
G
B
I
C
E
D
F
Dimensions/Specifi cations Subject to Change Without Notice
13
3.1 Main System Specifi cations J-335
Dimensions ...............................
84” x 84” x 36” (213cm x 213cm x
91cm)
Dry Weight ................................
781 lbs (354kg)
Filled Weight .............................
3,752 lbs (1,702kg)
Water Capacity (Avg. Fill) ........
358 US gallons (1,355 Liters)
Electronic Controls ..................
Solid State Electronic Controls with LED
Readout, Programmable Temperature,
Filtration, and Heat Cycles
Pump 1 ......................................
2-Speed, 4.2hp brake, 2.5hp continuous
Pump 2 ......................................
N/A
Pump 3 ......................................
N/A
Circulation Pump ......................
Yes
Total PowerPro Jets .................
24
Maxx PowerPro (MX) ................
N/A
PowerPro (LX) ...........................
4
Mini PowerPro (FX) ..................
18
Micro PowerPro (SX) ................
2
Jet Selectors .............................
1
Air Controls ...............................
Three, On / Off Pushbutton Type
Total Foot Jet Therapy .............
2
Water Management System .....
Two 60ft
2
Filter Cartridges; Filter 1 on 24-Hour Circulation Pump; Filter 2 on 2-Speed Pump 1; Ready for optional CD Ozone Generator (Built-in
Ozone Dispersion Chamber Included in Spa)
Lighting .....................................
One Underwater with Two Colored Lenses
Cabinet ......................................
Redwood/Cedar with No Stain; Optional UV Resistant
Synthetic Plastic Cabinet with Embossed Red or Gray Wood Grain
Acrylic Colors ...........................
Textured Bluegrass, Jade, Marine, Onyx, Sahara, or Sand; Marbled
Emerald, Platinum, or Sapphire; Solid Azure or Silver
Headrests ..................................
4
Waterfall ....................................
Includes Flow Rate / On-Off Adjustment; Powered by Pump 1
Electrical Requirements ..........
North American 60Hz Models: 240 VAC @ 30A or 50A
Export 50Hz Models: 230-240 VAC @ 35A or 40A, or suitably rated circuit breaker to comply with local electrical codes. Certain countries may require dual power inputs; two breakers are required for this confi guration.
Warranty .................................
North American 60Hz Models: 10 Years Shell, 7 Years Shell Surface,
5 Years for Plumbing Component Leaks, 5 Years Equipment &
Controls;
Export 50Hz Models: 2 Years Plumbing Component Leaks,
2 Years Equipment & Controls
Seating Capacity ....................
5
Audio System (Optional) .......
AM/FM/CD Stereo Receiver with Dual Pop-Up Speakers
Dimensions/Specifi cations are Subject to Change Without Notice
14
Jet Selector / Air Control Operation Diagram
Air Control 1:
Opens / Closes
Air Inlet to Jet
Group C
Jet Selector:
Directs Jet Pump
Output Between Jet
Groups A&B or C.
A C
A
B
Air Control 2:
Opens / Closes
Air Inlet to All
Lounge Jets A
C
B
B
Seat Depths
A = 26.50” (67.3cm) F = 19.75” (50.2cm) Listed Dimensions
B = 24.00” (60.1cm) G = 27.00” (68.6cm) Represent Distance from
C = 28.75” (73.0cm) H = 34.00” (86.4cm) Top of Acrylic to Lowest
D = 23.00” (58.4cm)
E = 27.50” (69.9cm)
Point in Seat.
Dimensions/Specifi cations Subject to Change Without Notice
Air Control 3:
Opens / Closes
Air Inlet to Jet
Group B
A
G
B
H
C
D
E
F
15
3.2 Main System Specifi cations J-325
Dimensions ...............................
84” x 76” x 34” (213cm x 193cm x
86cm)
Dry Weight ................................
738 lbs (335kg)
Filled Weight .............................
3,386 lbs (1,536kg)
Water Capacity (Avg. Fill) ........
320 US gallons (1,211 Liters)
Electronic Controls ..................
Solid State Electronic Controls with LED
Readout, Programmable Temperature,
Filtration, and Heat Cycles
Pump 1 ......................................
2-Speed, 2.0hp brake, 1.5hp continuous
Pump 2 ......................................
N/A
Pump 3 ......................................
N/A
Circulation Pump ......................
Yes
Total PowerPro Jets .................
15
Maxx PowerPro (MX) ................
N/A
PowerPro (LX) ...........................
11
Mini PowerPro (FX) ..................
4
Micro PowerPro (SX) ................
N/A
Jet Selectors .............................
1
Air Controls ...............................
Three, On / Off Pushbutton Type
Total Foot Jet Therapy .............
2
Water Management System .....
Two 60ft
2
Filter Cartridges; Filter 1 on 24-Hour Circulation Pump; Filter 2 on 2-Speed Pump 1; Ready for optional CD Ozone Generator (Built-in
Ozone Dispersion Chamber Included in Spa)
Lighting .....................................
One Underwater with Two Colored Lenses
Cabinet ......................................
Redwood/Cedar with No Stain; Optional UV Resistant
Synthetic Plastic Cabinet with Embossed Red or Gray Wood Grain
Acrylic Colors ...........................
Textured Bluegrass, Jade, Marine, Onyx, Sahara, or Sand; Marbled
Emerald, Platinum, or Sapphire; Solid Azure or Silver
Headrests ..................................
4
Waterfall ....................................
Includes Flow Rate / On-Off Adjustment; Powered by Pump 1
Electrical Requirements ..........
North American 60Hz Models: 120 VAC @ 15A or 240 VAC @ 30A or
40A,
Export 50Hz Models: 230-240 VAC @ 35A or 40A, or suitably rated circuit breaker to comply with local electrical codes. Certain countries may require dual power inputs; two breakers are required for this confi guration.
Warranty .................................
North American 60Hz Models: 10 Years Shell, 7 Years Shell Surface,
5 Years for Plumbing Component Leaks, 5 Years Equipment &
Controls;
Export 50Hz Models: 2 Years Plumbing Component Leaks,
2 Years Equipment & Controls
Seating Capacity ....................
4
Audio System (Optional) .......
N/A
Dimensions/Specifi cations are Subject to Change Without Notice
16
Jet Selector / Air Control Operation Diagram
Air Control 1:
Opens / Closes
Air Inlet to Jet
Group A
Jet Selector:
Directs Jet Pump
Output Between
Jet Groups A or
B&C
A
B C
A
B
Air Control 3:
Opens / Closes
Air Inlet to Jet
Group C
C B
Seat Depths
A = 27.00” (68.6cm) F = 31.25” (79.4cm) Listed Dimensions
B = 27.25” (69.2cm) Represent Distance from
C = 25.75” (65.4cm)
D = 21.50” (54.6cm)
E = 28.00” (71.1cm)
Top of Acrylic to Lowest
Point in Seat.
Dimensions/Specifi cations Subject to Change Without Notice
Air Control 2:
Opens / Closes
Air Inlet to Jet
Group B
A B
E
F
D
C
17
3.3 Main System Specifi cations J-315
Dimensions ...............................
76” x 66” x 32” (193cm x 168cm x
81cm)
Dry Weight ................................
640 lbs (290kg)
Filled Weight .............................
2,283 lbs (1036kg)
Water Capacity (Avg. Fill) ........
200 US gallons (757 Liters)
Electronic Controls ..................
Solid State Electronic Controls with LED
Readout, Programmable Temperature,
Filtration, and Heat Cycles
Pump 1 ......................................
2-Speed, 2.0hp brake, 1.5hp continuous
Pump 2 ......................................
N/A
Pump 3 ......................................
N/A
Circulation Pump ......................
Yes
Total PowerPro Jets .................
13
Maxx PowerPro (MX) ................
N/A
PowerPro (LX) ...........................
7
Mini PowerPro (FX) ..................
6
Micro PowerPro (SX) ................
N/A
Jet Selectors .............................
1
Air Controls ...............................
Two, On / Off Pushbutton Type
Total Foot Jet Therapy .............
2
Water Management System .....
Two 60ft
2
Filter Cartridges; Filter 1 on 24-Hour Circulation Pump; Filter 2 on 2-Speed Pump 1; Ready for optional CD Ozone Generator (Built-in
Ozone Dispersion Chamber Included in Spa)
Lighting .....................................
One Underwater with Two Colored Lenses
Cabinet ......................................
Redwood/Cedar with No Stain; Optional UV Resistant
Synthetic Plastic Cabinet with Embossed Red or Gray Wood Grain
Acrylic Colors ...........................
Textured Bluegrass, Jade, Marine, Onyx, Sahara, or Sand; Marbled
Emerald, Platinum, or Sapphire; Solid Azure or Silver
Headrests ..................................
3
Waterfall ....................................
Includes Flow Rate / On-Off Adjustment; Powered by Pump 1
Electrical Requirements ..........
North American 60Hz Models: 120 VAC @ 15A or 240 VAC @ 30A or
40A,
Export 50Hz Models: 230-240 VAC @ 35A or 40A, or suitably rated circuit breaker to comply with local electrical codes. Certain countries may require dual power inputs; two breakers are required for this confi guration.
Warranty .................................
North American 60Hz Models: 10 Years Shell, 7 Years Shell Surface,
5 Years for Plumbing Component Leaks, 5 Years Equipment &
Controls;
Export 50Hz Models: 2 Years Plumbing Component Leaks,
2 Years Equipment & Controls
Seating Capacity ....................
3
Audio System (Optional) .......
N/A
Dimensions/Specifi cations are Subject to Change Without Notice
18
Jet Selector / Air Control Operation Diagram
Jet Selector:
Directs Jet Pump
Output Between
Jet Groups A or B
Air Control 1:
Opens / Closes
Air Inlet to Jet
Group A
A
B
A
B
Air Control 2:
Opens / Closes
Air Inlet to Jet
Group B
A = 26.50” (67.3cm)
B = 28.00” (71.1cm)
C = 27.00” (68.6cm)
D = 28.00” (71.1cm)
E = 27.75” (70.5cm)
Seat Depths
Listed Dimensions
Represent Distance from
Top of Acrylic to Lowest
Point in Seat.
Dimensions/Specifi cations Subject to Change Without Notice
A B
E
D
C
19
4.0 Main Control Panel Functions
Panel Functions:
A.
Heat Indicator:
Lit when heater is on.
B.
Warmer Button:
ture setpoint.
Increases water tempera-
C.
D.
D
Cooler Button:
Decreases water temperature setpoint.
LED Display:
Can display current water
C
B
temperature (default display*), water temperature setpoint, selected fi ltration mode,
E.
F.
G.
104
A
G
F
and error messages.
Light Button:
Turns underwater light on and off.
*Disply shown for example purposes only, actual water temperature display will vary..
E
Jets 1 Button:
Turns pump 1 on and off as follows: Press once for low speed; a second time for high speed; a third time to turn off.
Jets 2 Button (J-345 only):
turns pump 2 on and off as follows: Press once for high speed; a second time to turn off.
Operation Details:
•
Temperature Adjustment: 65 to 104ºF (18 to 40ºC). Factory setting is 100ºF (38ºC).
•
Underwater Light Operation: The light runs for 1 hour, then shuts off for increased bulb life.
•
Jet Buttons Operations: The jets run for 20 minutes after activated then turn off automatically to conserve energy. Simply press a Jet Button to continue operation for an additional 20 minutes.
4.1 Setting Filter Cycle Start Time
Two methods for setting the fi lter cycle start time are possible:
•
Turn power on to the hot tub two minutes prior to the desired fi lter cycle start time, or
•
Press and hold both the Warmer and Cooler Buttons at the same time, then press and hold the Jet 1
Button to reset the control panel and start the power up sequence. During the power up sequence, the previously set fi lter cycle setting and temperature setpoint will be maintained. To select another fi lter cycle at this time, see section 4.2 below. The selected fi lter cycle will start approximately two minutes after the power up sequence ends.
Example: If you desire your fi rst fi lter cycle to begin at 10:00am, perform either of the above steps at 9:
58am. Filter cycle start time may vary slightly from the setpoint.
4.2 Programming Filter Cycles
Proper fi ltration is an important key to maintaining the clarity of your hot tubs water. The hot tubs fi ltration system is designed for unsurpassed effectiveness at removing debris and suspended particles from the water anytime the water is circulated by the pump.
To select a pre-programmed fi lter cycle or lockout mode, press and hold both the Warmer and Cooler
Buttons at the same time, then release. Then press either the Warmer or Cooler Buttons to select either fi lter mode FØ through L2.
20
FØ
F1
F2
F3
Standard Filtration Modes FØ - F3
Heating in either of these modes (FØ - F3) is automatically controlled by the water temperature. If the hot tub water drops 2ºF (1.2ºC) below the temperature setpoint, the heater will turn on with the circulation pump. Both remain on until the water temperature rises to the temperature setpoint, then the heater will turn off. Refer to the options below:
3.53 Revision
No fi lter cycles.
4 hours of fi ltration a day (2 hour cycle every 12 hours)
6 hours of fi ltration a day (2 hour cycle every 8 hours)
8 hours of fi ltration a day (2 hour cycle every 6 hours)
3.54+ Revision
FØ
F1
F2
F3
No fi lter cycles, 5 minute blowout cycle once a day, every 24 hours from the time of power up.
1 hour of fi ltration a day (1/2 hour cycle every 12 hours)
1 1/2 hours of fi ltration a day (1/2 hour cycle every 8 hours)
2 hours of fi ltration a day (1/2 hour cycle every 6 hours)
Economy Filtration Modes F4 - F6
In any economy mode (F4 - F6), the control panel’s digital timer circuit determines when each fi lter cycle takes place. The heater will only operate while a fi lter cycle is running. The heater will not operate when either Jets button is pressed to manually cancel an active fi lter cycle or to activate the main jet pump between fi lter cycles. Refer to the options below:
3.53 Revision
F4
F5
F6
4 hours of fi ltration a day (2 hour cycle every 12 hours)
6 hours of fi ltration a day (2 hour cycle every 8 hours)
8 hours of fi ltration a day (2 hour cycle every 6 hours)
3.54+ Revision
F4
F5
F6
1 hour of fi ltration a day (1/2 hour cycle every 12 hours)
1 1/2 hours of fi ltration a day (1/2 hour cycle every 8 hours)
2 hours of fi ltration a day (1/2 hour cycle every 6 hours)
Lockout Modes L1 - L2
Additional modes (L1 - L2) are special modes designed for servicing/cleaning. Refer to the options below:
L1
L2
Lock Out (disables all hot tub functions to permit fi lter cleaning or other maintenance) - If the hot tub is heating when the system is put into lockout mode, the heater will immediately shut off and the circulation pump will cycle water for 30 seconds to cool the heater element, then shut off.
Lock Mode (disables the jets and light buttons to prevent unauthorized use of the hot tub) - The fi lter cycles and heater will continue to operate as programmed in this mode.
Example: The “F3” fi lter cycle was enabled prior to choosing the lock mode. The hot tub continues to perform fi lter cycle “F3” until lock mode is cancelled, allowing another fi lter cycle to be selected.
The temperature display fl ashes when either Lock Out Mode is enabled.
21
4.3 Aftermarket Ozone Facts
An aftermarket ozonator can be installed on all 2002+ models. A mazzei injector is required on all models.
Ozone System Specifi cations
•
Circulation pump runs 24 hours
•
Ozonator runs 24 hours
•
The ozonator shuts off when a Jets Button is pressed. The ozonator will resume operation approximately 5 minutes after the jets are turned off intentionally or automatically. The ozonator also shuts off if the hot tub goes into “Summer Logic.” See section 5.6 (page 23).
Refer to section 8.13 (page 44) for troubleshooting details.
5.0 Additional Control Panel Functions
5.1 Temperature Setting
To enable the set temperature display:
1.
2.
3.
Press WARMER or COOLER button while the current water temperature is displayed. The current temperature setpoint appears.
Press WARMER or COOLER button within 3 seconds to increase or decrease set
Use Warmer/
Cooler Buttons temperature by 1º per button press.
After 3 seconds of keypad inactivity the display will return to the actual water temperature and the new temperature setting will be maintained.
5.2 Selecting Jets Speed
To select jet speeds:
1.
Press JET 1 button once for low speed; a second time for high speed; a third time
2.
to turn off.
J-345 only; Press JET 2 button once for high speed; a second time to turn off.
Use JET 1/
JET 2 Buttons
Note: Anytime a pump has been manually turned on by selecting either JET button, it will automatically turn off after approximately 20 minutes. If at this time you desire more jet operation, simply turn the jet pump back on.
5.3 Underwater Light Operation
Press the LIGHT Button once to turn on; a second time to turn off.
Note: Anytime the light has been manually turned on, it will automatically turn off after approximately 1 hour to maximize bulb life. If at this time you desire more light operation, simply turn the light back on.
5.4 Lock/Unlock Control Panel
The control panel temperature display fl ashes when Lock Mode is active. Lock Mode disables the jets and underwater light to prevent unauthorized use of the hot tub. This mode is selected in the fi lter cycle selection menu. When selected, both fi lter cycles and heater will operate as programmed.
See sections 4.2 (page 20).
Use Light
Button
Display is
Flashing
22
5.5 Lock Out Mode
The control panel temperature display fl ashes when the Lock Out Mode is active. Lock
Out Mode disables all hot tub functions to permit fi lter cleaning. If the hot tub is heating when lockout mode is selected, the heater will immediately turn off and the circulation pump will cycle water for 30 seconds to cool the heater element, then turn off.
See section 4.2 (page 20).
5.6 Summer Logic
When the water temperature in the hot tub rises 2ºF (1ºC) above the set temperature setpoint. the hot tub goes into “Summer Logic.” When this happens, the circulation pump automatically turns off to prevent additional heat build up from the pump that would eventually create an overheat condition. The circulation pump, main pump and aftermarket ozone (when installed) will remain off until the water temperature cools to the set temperature, then reactivate as programmed.
This setting is not user-programmable.
Display is
Flashing
Display is
Flashing
Note: Summer Logic does not take effect until the hot tub’s water reaches 95ºF (35ºC) or higher.
6.0 Understanding Circuit Board Pin Assignments
6.1 Circuit Board Jumpers
All ProTech LED circuit boards can be confi gured for either 15/30A or 50A 240 VAC operation (J-340 can be confi gured for 60A with 3.54 Revision Chip). Refer to the jumper pin table and circuit board diagram below for specifi c details:
2002+ ProTech LED Circuit Boards
Pins 1-2:
Jumper OFF - Enables 50A Logic; Allows heater to run with 1 pump in high speed.
Pins 1-2:
Jumper ON - Enables 15/30A Logic; Forces heater off when any jet pump is in high
speed.
Overrides 50 or 60A Logic.
Pins 3-4:
Pins 3-4:
Pins 5-6:
Jumper OFF
Jumper ON
Jumper OFF
- Enables 1 Pump Logic.
- Enables 2 Pump Logic; J-340 only.
-
Revision 3.53 Circuit Boards;
Not used at this time.
Pins 5-6:
Pins 5-6:
Pins 7-8:
Pins 7-8:
Jumper OFF
Jumper ON
Jumper OFF
Jumper ON
-
Revision 3.54+ Circuit Boards;
Enables 50A Logic.
-
Revision 3.54+ Circuit Boards;
Enables 60A Logic, J-345 only.
- Enables Fahrenheit (ºF) temperature display.
- Enables Celsius (ºC) temperature display.
N
Spa Light
L
N
L
Ozone
N
Circ Pump
L
N
Rev. 3.53
J1
4
2
8
6
JP1
7
5
3
1
L
L
N
L
J4
8
6
4
2
JP1
7
5
3
1
N
Red Black
L
Heater In
N
L
Heater Out
N L
23
7.0 Troubleshooting Using The Control Panel
7.1 Control Panel Displays
Complete operating instructions for the control panel can be found in the owner’s manual. The hot tub’s self-diagnostic control system constantly monitors the hot tub for proper operation. When anything goes wrong, the control panel displays a message for the user which may result in a service call. Refer to section 7.3 below for a listing of error messages and probable causes.
•
7.2 Control Panel Default Display
The control Panel displays the following information during initial start up:
1.
2.
3.
The control panel displays the current software eprom revision, then
The control panel displays “888” and all of the indicator LED’s are lit, permitting visual inspection of all display segments and indicator lights for proper operation.
After the initial start up sequence ends, the actual water temperature is displayed. If the water temperature at this time is less than the factory preset temperature setting of 100ºF (38ºC):
The circulation pump and heater will turn on and run until the temperature rises to the factory preset temperature setting. The heater shuts off and the circulation pump remains on for 24 hour operation.
Approximately two minutes after initial start up, the fi rst fi lter cycle begins to operate.
The fi ltration cycle can be modifi ed any time after the start up sequence ends. You will be able to select a preprogrammed fi lter cycle and reset your temperature setpoint at this time (see page 20). Press either the COOLER or WARMER buttons once at this time to display the current temperature setpoint. You can change the setpoint by pressing either the COOLER or WARMER buttons within 3 seconds. Each button press increases or decreases the temperature setpoint by 1º. Three seconds after the setpoint is set, the display defaults back to the actual water temperature.
7.3 Control Panel Status And Error Messages
Sn1 Nonfunctional Hi-Limit Sensor
Open or shorted hi-limit sensor. Heater is deactivated. Refer to test steps 1-2 below:
1.
2.
Turn off the main breaker to the hot tub. Refer to appendix page 55 for expected hi-limit sensor resistance/water temperature values.
Remove the hi-limit sensor connector from the circuit board test point 10. Refer to pages 50-51 for your circuit board confi guration. Set your ohmmeter to 100-200k range, then measure resistance across the hi-limit sensor wires (see page 56). If the sensor tests OK, check the sensor connections.
If the connections are OK, replace the circuit board. If the sensor resistance is incorrect, replace the hi-limit sensor.
Sn2 Nonfunctional Temperature Sensor
Open or shorted temperature sensor. Heater is deactivated. Refer to test steps 1-2 below:
1.
2.
Turn off the main breaker to the hot tub. Refer to appendix page 55 for expected temperature sensor resistance/water temperature values.
Remove the temperature sensor connector from the circuit board test point 10. Refer to pages
50-51 for your circuit board confi guration. Set your ohmmeter to 100-200k range, then measure resistance across the temperature sensor wires (see page 56). If the sensor tests OK, check the sensor connections. If the connections are OK, replace the circuit board. If the sensor resistance is incorrect, replace the temperature sensor.
24
FL1 And FL2 Water Flow Problem
• FL1:
The fl ow switch
is not
closed when the circulation pump
is
running. The heater is deactivated. Proper water fl ow is inhibited or the fl ow switch may be obstructed, misaligned or defective. Refer to troubleshooting steps 1-4 below:
1.
Remove the fi lter and allow the air to bleed out of the cartridge. Check the fi lter for trapped air.
2.
Check for the proper water level.
3.
4.
Check for a clogged fi lter cartridge.
If the problem persists, refer to section 7.4 (page 26) for fl ow switch testing instructions.
• FL2:
The fl ow switch
is
closed when the circulation pump
is not
running. The heater is deactivated and the pump may or may not turn on. The fl ow switch is usually defective.
Refer to section 7.4 (page 26) for fl ow switch testing instructions.
COL Cool Condition
If the water temperature drops 20ºF (11ºC) below the set temperature, the heater will activate to raise the water temperature to within 15ºF (8ºC) of the set temperature. No corrective action is necessary.
ICE Freeze Condition
A potential water freeze condition of 55ºF (13ºC) has been detected. No action is required.
The heater will activate and raise the water temperature to approximately 65ºF (18ºC), cancelling the “ICE” error message. After the error message is cancelled, the heater will turn off.
OH High Temperature Condition
The water temperature is above acceptable limits. DO NOT ENTER THE HOT TUB
WATER. The water temperature has reached 112ºF (44ºC) and the low speed pump has activated to circulate water through the hot tub to cool it down. Refer to test steps 1-4 below:
1.
Verify the actual water temperature with an accurate thermometer. If the actual water temperature is less than 112ºF (44ºC), proceed to steps 2-4.
2.
3.
Turn off the main breaker to the hot tub. Refer to appendix page 55 for expected hi-limit/temperature sensor resistance/water temperature values.
Remove the hi-limit sensor connector from the circuit board points 10. Refer to pages 50-51 for your circuit board confi guration. Set your ohmmeter to the 100-200k range, then measure resistance across the sensor wires (see page 56). If the resistance tests OK, check the wiring harness connec-
4.
tions. If the wiring harness connections test OK, replace the circuit board. If the sensor resistance is incorrect, replace the hi-limit sensor.
Set your ohmmeter to the 100-200k range, then measure resistance across the temperature sensor wires (see page 56). If the resistance tests Ok, replace the circuit board. If the temperature sensor resistance is incorrect, replace the temperature sensor.
--- Watchdog
The water temperature has reached 118ºF (48ºC). DO NOT ENTER THE HOT TUB WA-
TER. The entire system is disabled. Refer to test steps 1-4 below:
1. Check the hi-limit and temperature sensor resistance values. Both sensors should measure close in resistance to each other (e.g. one may be defective and way out of range). Refer to appendix page
55 for expected hi-limit/temperature sensor resistance/water temperature values. If either sensor is faulty, replace it and recheck the system. If the problem persists, proceed to step 2.
25
2.
3.
4.
Plug in a new control panel. If the problem is corrected, replace the control panel. If the problem persists, proceed to step 3.
Check the voltage at the transformer secondary. See section A15, page 57, for transformer testing instructions. If the voltage is bad, replace the transformer. If the voltage is good, proceed to step 4.
Check the circuit board transformer connections. If the connections are loose or oxidized, repair the connections and retest the system. If the problem persists, replace the circuit board.
7.4 Testing Flow Switch
1.
2.
3.
Verify the fl ow switch directional arrow is pointing in the direction of fl ow towards the heater return fi tting outlet. If the fl ow switch orientation is incorrect, loosen or tighten the switch no more than 1/2 turn, being careful not to bottom out the switch in the fi tting. The switch’s fl ow arrow must be parallel to the tee fi tting as shown (fi g. A). Test the system operation. If the condition persists, proceed to step 2.
Remove the switch from the fi tting making note of the number of turns (revolutions) it takes to do so.
Visually inspect the switch for debris interference or damage. If debris is present, remove the debris, then reinstall the switch with the same number of turns as originally installed. Test the sytem. If the switch is damaged, replace the switch and retest the system. If the condition persists, proceed to step 3.
Test the switch operation with an ohmmeter (set to 1000-2000k range) for continuity across the switch terminals. Measure resistance across the switch terminals for infi nite resistance with the magnet arm
not
touching the switch body (fi g. B), and for continuity (Ø ohms) with the magnet arm touching the switch body (fi g. B). If the fl ow switch tests OK, check the wiring harness. If the wiring harness tests OK, replace the circuit board.
fig. A
FLOW
Incorrect
Orientation
Arrows not aligned
fig. B
FLOW
Correct
Orientation
Arrows aligned
Open
‰
Infinite ‰
(Pump OFF)
26
‰
Closed
Continuity 0 ‰
(Pump ON)
8.0 Troubleshooting Without The Control Panel
• Diagnostic Tools for Sections 8.1A - 8.1D:
Clamp-on ammeter, voltmeter and ohmmeter.
• Suggested Spare Parts for Sections 8.1A - 8.1D:
Circuit board, control panel, temperature sensor, fl ow switch, heater assembly, hi-limit, circulation pump. Refer to page 59 for additional information.
8.1A No Heat Or Not Enough Heat
• Symptoms:
Circulation pump (heating pump) is moving water, panel heat indicator is lit.
water is not getting hot.
• Confi guration:
Protech LED system heaters will not operate with both jet pumps (J-345 only) running in high speed if the circuit board is confi gured for 30 or 50 Amp operation. See section 6.1, page 23.
Standard Troubleshooting Approach
Turn up temperature setpoint to initiate a heat call (must be in "standard mode" F0-F3; see page 21). Is voltage present at the heater output? Test points 6 and 7.
No
Is voltage present at heater input? Test points 4 and 5.
Yes
Replace circuit board.
No
Replace or reconnect wires between heater input relay and TB1 (main power terminal block).
Yes
Is voltage present at heater element? Test points 8 and 9.
No
Yes
Is there current draw? Refer to section A3 (page 47) for expected heater current consumption values.
Check heater element with clamp-on ammeter around one of the heater element wires.
No
Is the heater element’s current draw within –10% of its listed value?
Yes
Current draw is proof that heater element is working.
Make sure customer knows how to use control panel and heater. Ask about any possible error messages.
Locate thermal switch inside heater box. Set voltage meter to
500-1000 VAC range. Test thermal switch by connecting voltage meter across the terminals with a heat call present
(see fig. C). If 120 VAC* or 240
VAC exists, the switch is open. If no voltage exists, the switch is closed. Is the switch open?
*Convertible J315 and J325 models only.
No
Replace or reconnect wires between heater output and heater element.
Replace Thermal Switch
fig. C
Thermal Switch
Bad
Thermal Switch
Good
Yes
Place thermometer against heater housing and verify temperature.
Is temperature above 130 F?
Yes
**Call Technical Support
No
Replace heater.
VAC VAC
Optional Test Method:
you can also remove one wire from either side of switch and test across its terminals for continuity.
Infinite =bad switch; 0 =good switch
Circuit Board Illustrations
A. 2002+ Protech LED Models (Page 50-51)
Danger: Electrical Shock Hazard Exists!
High Voltage Present On Circuit Board. Use Extreme Caution While Servicing Circuit Board.
**Warning: heater temperature may have exceeded 130ºF (54ºC). Inspect heater. Call technical support if visible damage is apparent.
27
8.1B No Heat Or Not Enough Heat
• Symptoms:
Circulation pump (heating pump) not turning, panel heat indicator not lit,
panel is fl ashing FL2.
Standard Troubleshooting Approach
Pull wire off flow switch. Does the
FL2 error message go away?
No
Is wire shorted?
Yes
Replace wire.
No
Replace circuit board.
Yes
Turn off power to hot tub. Test flow switch with ohmmeter for continuity across switch terminals (fig.
D-E). Does meter read continuity
(0)?
No
Yes
Remove flow switch and inspect for debris interference.
Remove debris if present. Test switch for continuity (0) when closed and for infinite when open
(fig. E). Does switch operate correctly?
No
Make sure wire is not shorted when installed on switch.
Replace flow switch.
Yes
Install switch making sure flow arrow points in direction of flow and switch doesn’t bottom in fitting (fig. F). Retest system.
Fig. D
Pump off
Infinite
Pump on
Continuity 0
Fig. E
Open
Infinite
Fig. F
Closed
Continuity 0
FLOW
Arrows not aligned
Orientation
FLOW
Arrows aligned
Orientation
OK
Pipe End
View
28
8.1C No Heat Or Not Enough Heat
• Symptoms:
Circulation pump (heating pump) not turning, panel heat indicator not lit,
panel is fl ashing FL1.
Standard Troubleshooting Approach
Is there correct voltage coming to the hot tub at
TB1?
No
240 VAC, +/-10%, or
(120/240 VAC, +/-10% for J315/J325 models).
Yes
Put hot tub in standard filtration mode (page
21). Set temperature high enough to initiate a heat call. Is voltage ok from circuit board to circulation pump?
No
Call an electrician.
Replace circuit board.
Test points 16 and 17 for circulation pump.
Circuit Board Illustrations
A. 2002+ Protech LED Models (Page 50-51)
Yes
Is connection OK from circuit board to pump?
No
Repair connection.
Yes
Replace pump.
Note: Refer to the voltage and current charts on appendix page 46-47 for expected voltage/current readings.
Danger: Electrical Shock Hazard Exists!
High Voltage Present On Circuit Board. Use Extreme Caution While Servicing Circuit Board.
29
8.1D No Heat Or Not Enough Heat
• Symptoms:
Circulation pump (heating pump) is turning, panel heat indicator not lit,
panel is fl ashing FL1.
Standard Troubleshooting Approach
Is the circulation pump
(Heat Pump) moving water?
Yes
No
1. Remove filter and allow air to bleed out of cartridge.
2. Check for proper water level.
3. Check for clogged / excessively dirty filter.
4. Is pump moving water?
Verify hot tub is in standard filtration mode
(page 21). Remove flow wires from switch.
Increase set temperature to Initiate a heat call, then jumper flow switch wires together (see fig. G).
Does heat indicator appear and FL1 error message disappear?
Yes
No
No
Remove flow switch connector from circuit board at point 11 (fig. H).
Place jumper across exposed connector pins*.
Does heat indicator appear and FL1 error message disappear?
No
Yes
Yes
Repair or replace flow sensor cable.
Test flow switch with ohmmeter for continuity (0) across switch terminals
(fig. I). Does meter read continuity
(0) with pump on?
Yes
No
Remove flow switch and inspect for debris blockage. Remove blockage or replace switch. Install flow switch with arrow pointing in direction of flow. Make sure magnet arm doesn’t bottom out in fitting (fig. J).
Clean connectors between flow cable and switch.
*Lightly scrape contact pins at point 11 with a razor blade or sandpaper to remove conformal coating or oxidation from contact surface.
Danger: Electrical Shock Hazard Exists!
High Voltage Present On Circuit Board. Use Extreme Caution While Servicing Circuit Board.
See section 8.10 (pg. 42)
Replace circuit board.
Jumper
Temporarily
Short Pins with Jumper
#6560-864
Open
Pump off
Infinite
FLOW
Arrows not aligned
Incorrect
Orientation fig. G
Temporarily Jumper
Flow Switch Cable
Wires Together as Shown.
fig. H fig. I fig. J
22
23
FLOW
Arrows aligned correct
Correct
Orientation
Flow
Cable
Closed
Pump on
Continuity 0
incorrect
Pipe
End View
30
8.1E No Heat Or Not Enough Heat
• Symptoms:
Circulation pump (heating pump) is turning, panel heat indicator not lit,
panel is not fl ashing FL1.
Standard Troubleshooting Approach
Put hot tub in standard filtration mode (page 21).
Set temperature high enough to initiate a heat call. Remove power to hot tub then plug in a spare control panel. Turn power on. Does indicator work now?
No
Call Jacuzzi Premium
Technical Support.
Yes
Replace control panel.
31
8.2 Intermittent Heating
As with all intermittent problems, routine measurements and display panel error messages are not trustworthy. The following procedure will eliminate the most probable causes.
It is important to explain to the customer how diffi cult intermittent problems are to locate. You will be doing a series of things to eliminate the problem. Ask the customer to be patient and please cooperate by calling you back to inform you of the hot tub’s status until the problem is corrected. It might be a good idea to review this STA with the customer. It may help he or she understand why it might take several callbacks to effect a repair.
Suspects: circuit board, temperature sensor, control panel, wiring connections, and partial water fl ow obstructions.
Diagnostic Tools:
Voltmeter, ohmmeter and ammeter.
Suggested Spare Parts (Page 59):
Heater, circuit board, temperature sensors, fl ow switch, control panel, circulation pump, hi-limit.
Standard Troubleshooting Approach
1.
2.
3.
4.
5.
6.
7.
Check the crimped wire connections to the heater. If burned, replace the heater. Verify that the heater connections are good on the circuit board. Check the heater resistance, see the current chart on page 47 for expected heater resistance values.
Check the connections labeled “heater out” on the circuit board (test points 6 & 7). Refer to pages
50-51 for your circuit board confi guration. If possible, clean and renew the connections. If a relay is physically burned at the connections, replace the circuit board.
Check the fl ow switch for proper and consistant mechanical operation. Observe the mechanical action of the switch.
Refer to page 26 for the fl ow switch testing procedure.
Clean the connections where the panel plugs into the circuit board.
If all of the above items check out, ask the customer if the Sn2 error has ever displayed. If the Sn2 error message has displayed, replace the temperature sensor.
Tell the customer what you have done, that you are not sure that the problem has been fi xed, and that you want to be called immediately if the problem returns. Explain what you will do if the problem returns. Check back with the customer in a few days if you haven’t been contacted.
If the customer calls back, call Jacuzzi Premium Technical Support.
Note: All models use a ‘magnetic reed switch” type of fl ow switch that can remain closed or open from debris interference. Removal of the fl ow switch for cleaning and inspection will correct most problems. Record the number of turns it takes to remove the switch from the fi tting. After cleaning, use the same number of turns to reinstall the switch. DO NOT thread the switch further than originally installed, or the paddle may stick on the bottom of the fi tting.
correct incorrect
32
8.3 Nothing Works
Things to remember: when a system fails, there is probably one, and only one problem. Verify power to the hot tub by observing the control panel’s LED display. The control panel will usually display something as long as there is proper power to the hot tub. Check for error messages. Displayed error messages usually indicate the problem.
Diagnostic Tools:
Voltmeter.
Suggested Spare Parts (Page 59):
Fuses (see appendix page 48), control panel, circuit board.
Nothing Works (Panel Indicator Lit):
1.
2.
3.
4.
Plug in a spare control panel. If it works, replace the control panel.
Remove power from the hot tub. Check the connections on the sensor harness and verify proper resistance of the temperature and hi-limit sensors (see appendix page 55). Replace the defective temperature or hi-limit sensor, then test the system.
Check the transformer. See section A15, page 57.
Still no operation? Replace the circuit board.
Nothing Works (Panel Dead):
1.
2.
3.
4.
Check for proper power to the hot tub (see appendix page 46). Check for 240 VAC (120 or 240
VAC for J-315, J-325) at TB1 on the main terminal block. See pages 50-51 for your circuit board confi guration. If the voltage is not 240 VAC (120 or 240 VAC for J-315/J-325) ±10%, consult an electrician.
Check for power at the transformer secondary.
Refer to appendix page 57.
If power exists on the transformer secondary, plug in a spare control panel. Still nothing? Replace the circuit board.
If no power exists at the transformer secondary, check for voltage at the transformer primary.
Refer to appendix page 57.
If voltage exists on the primary but is missing on the secondary, replace the transformer.
No power at the transformer primary indicates either an open 1.5 Amp fuse, 20/30 Amp fuse, or a loose or disconnected wire. If voltage exists on the primary but is missing from the secondary, replace the transformer. See section A5 (page 48) for specifi c fuse details.
8.4 Hot Tub Doesn’t Come On For Filter Cycle
Turn power to the hot tub off and then on to restart the fi lter cycle program. Does the fi lter cycle start approximately two minutes after applying power?
• If yes:
the hot tub is functioning properly. Refer to sections 4.1 - 4.2 (page 20) for fi lter cycle setup details. Take time to explain the fi lter cycle selection and operation to your customer. Make sure your customer understands the fi lter cycles are selectable, not programmable.
• If no:
select an appropriate fi lter cycle mode within two minutes after applying power. Refer to sections 4.1 - 4.2 (page 20). If the fi lter cycle starts within two minutes after setting, no corrective action is required. If the fi lter cycle does not start two minutes after setting, replace the circuit board.
33
8.5 House Breaker Trips
The hot tub’s current draw will vary depending on how it’s circuit board is jumpered. Jumper options determine whether multiple functions can operate together.
If the house breaker trips, check the hot tub’s current draw. If the jumpers are properly set and the current draw is within expected limits, the house breaker or wiring may be defective and need to be replaced or repaired. The hot tub’s current draw at the breaker represents the sum of all enabled components.
Refer to appendix page 47.
If the hot tub’s current draw is high, individual component current measurements must be made to determine which component is pulling excessive current.
Refer to appendix page 47.
Repair or replace the component which is drawing excessive current.
8.5A GFCI Tripping
If the GFCI trips, try disconnecting the heater and the pumps from the circuit board one at a time to fi nd which component may be causing the GFCI to trip.
When a customer complains of intermittent GFCI tripping, these questions need to be answered before we start replacing components on the hot tub. 90% of a GFCI’s tripping problems are the direct result of improper wiring or installation.
1.
Has the GFCI always tripped or has it just recently started tripping?
•
Has the hot tub just been installed?
•
Electricians are not as smart as they think they are and the owner’s cousin’s nephew who’s a painter really isn’t a licensed electrician.
•
New deliveries cause 90% of all GFCI tripping problems.
•
Know what to look for when you approach this problem.
Refer to section A9-A11 (pages 50-52).
2.
How was the hot tub delivered?
• Check for visible damage to all hot tub components.
3.
What Brand of GFCI was installed?
•
Some brands are known to be more sensitive than others which can cause nuisance tripping.
4.
When does it trip? At the start of a fi ltration cycle, etc., be specifi c.
•
The customer needs to provide you with this information. Have them takes notes on when the hot tub trips. How often does it trip? Be specifi c. Intermittent tripping of the GFCI is very hard to pinpoint if you can’t get specifi c information.
5.
What size is the GFCI? 30, 50 or 60 Amp?
6.
What size is the wiring? 8-10 gauge for 30 Amp, 8-6 gauge for 50 Amp, 6 gauge for 60 Amp. All wiring must be done to Local and NEC code.
7.
What kind of wire are they using, copper or aluminum?
•
Aluminum wire is not recommended.
34
8.
Is the GFCI utilized at the main panel?
•
Verify how it is hooked up.
•
If you are not licensed to properly change the wiring, show the customer how it should be hooked up and have them call the electrician.
(Improper installation is not a warranty call which once corrected may involve you coming back to replace a component.)
If there is a problem with the electrician understanding the correct hook up of the hot tub, have the electrician contact Jacuzzi
Premium Technical Support.
9.
Is the GFCI and wiring dedicated only to the hot tub?
10.
Are there any other devices hooked up to the hot tub; a light, extra outlet, etc.?
11.
How long is the run from the main panel to the hot tub?
•
Longer runs require a wire size compatible to that length of the run.
12.
Is there a disconnect or sub-panel in the run?
13.
How is the disconnect hooked up? Be specifi c.
•
There needs to be FOUR wires (two hots, a neutral, and a ground) at the disconnect for the GFCI to properly function.
14.
Is this a 3-wire or a 4-wire hook up?
•
The J-335, J-345 are all 240 VAC, 3-wire hook ups.
•
The J-315, J-325 is a 3-wire when hooked up to 120 VAC, and a 4-wire when hooked up to 240
VAC.
15.
Is there 240 VAC (120 or 240 VAC on J-315-J-325) at the hot tub?
•
Refer to the model the customer has purchased and then confi rm the hook up using the diagrams provided in sections A9-A11 on pages 50-52.
16.
How are the wires connected at the GFCI?
•
3-wire, 240 VAC hook ups
DO NOT USE A LOAD NEUTRAL OUT OF THE GFCI TO THE HOT
TUB.
17.
Is the neutral wire hooked up on the GFCI?
•
In a 240 VAC only hook up, this will cause the GFCI to trip.
18.
Where is the neutral wire hooked up at the GFCI?
•
The neutral “Pigtail” should go directly to the neutral bar.
19.
Is the load neutral wire capped off or taped at the spa?
•
This will cause the breaker to nuisance trip; the wires can act like an antenna and pick up stray or inductive current.
35
20.
What is the model and serial number of the hot tub?
•
This will help determine how the hot tub should be hooked up.
21.
Did a licensed electrician hook up the hot tub?
• See question number one!
22.
What is the voltage at the hot tub?
• Always have your meter with you!
23.
What is voltage between the neutral wire and the ground?
• There should not be a neutral wire! (Except on J-315, J-325 models.)
24.
What is the voltage between the two hot leads?
•
This should be 240 VAC (120 or 240 VAC on J-315, J-325), ±10%. If there is no voltage, then you have lost a hot leg or the GFCI has tripped. Verify voltage at the GFCI, if the GFCI is not tripped and you don’t have 240 VAC (120 or 240 VAC on J-315, J-325) at the hot tub, then the problem is between the GFCI and the hot tub. A licensed electrician should be called at this time.
25.
What is the voltage between one hot lead to ground, and the other hot lead to ground?
•
This should be 120 VAC.
26.
What is the voltage between one hot lead and the neutral?
• There should not be a neutral wire! (Except on J-315, J-325).
27.
Are the wires connected to the proper position inside the hot tub load box? Verifi y and be specifi c.
•
Wires incorrectly hooked up to the main terminal block will cause the GFCI to trip or the hot tub will not function properly.
28.
What is the voltage at the hot tub when all of the components are energized?
•
Voltage to the hot tub should stay consistent with or without the components energized.
29.
Are all of the connections tightened down properly?
•
Loose wires will cause them to get hot. Look for melted wire coverings or burnt connections.
30.
Are there frayed or loose wires touching metal?
•
Any wires that are hot and are touching metal will trip the GFCI immediately.
36
31.
Are there any sprinklers that will hit the equipment bay of the hot tub?
Eliminate The Components
32.
Does the hot tub have an ozone unit attached to it or any type of sanitizing device?
•
Unplug or disconnect the unit and see if the GFCI will hold.
33.
Does the hot tub have a blower in it?
(2001 and previous models only.)
•
Disconnect the blower and see if the GFCI will hold. 2002+ models do not have blowers.
34.
Check the heater fi rst before you check any of the pumps.
•
The heater will be energized if there is a heat call. Disconnect
both legs
fi rst before you try the pumps.
35.
Is the hot tub equipped with a circulation pump?
(All 2002+ models are equipped this way.)
•
Unplug or disconnect the circulation pump and see if the GFCI will hold.
36.
If the GFCI still trips, disconnect the main, two speed pump fi rst, then the secondary, single speed pump if the hot tub has one.
37.
Do you notice any water deposits near any of the motors or any other electrical devices?
•
Look at the area around the air controls. If water is backing up into the control, it will leak out, possibly onto an electrical component.
38.
Is the control panel properly sealed as to not allow water to leak down onto the load box?
39.
Are there any components, specifi cally the pumps, heater, ozone, etc., leaking?
40.
Do you notice any corrosion around any of the components, specifi cally the heater, pumps, circulation pump, ozone, etc.?
41.
What is the amperage draw of the hot tub with everything energized. Be specifi c.
•
Use a clamp on ammeter to determine the amperage draw.
42.
What is the amperage draw of each individual component? Be specifi c.
•
Again, use a clamp on ammeter to determine each components amperage draw.
•
If a component has excessive amperage draw, replace that component.
If you should need to contact Jacuzzi Premium Technical Support, these are questions that will be asked of you. It is also a good idea to have the “Troubleshooting Data Collection Form” (see example on page 61) fi lled out.
37
North American 60Hz Installations:
As of January 1, 1994, the National Electrical Code (NEC) requires a Ground Fault Circuit Interrupter (GFCI) on all hot tub installations in the US. A GFCI must be wired correctly or it will trip. Make sure the electrician has wired the GFCI according to the diagrams on page 52.
8.6 Hot Tub Light Will Not Come On
Diagnostic Tools:
Voltmeter.
Suggested Spare Parts (Page 59):
Control panel, circuit board, light bulb, light harness.
Standard Troubleshooting Approach
Press Light Button on control panel.
Do you hear a relay click on the circuit board?
No
Plug in spare control panel then press Light
Button.
Did you hear a relay click on the circuit board?
No
Replace circuit board.
Yes Yes
Replace control panel.
Is there 12 VAC at test points 12 and 13?
No
Replace circuit board.
Yes
Is connection between circuit board and light
OK?
No
Correct connection.
Yes
Change light bulb.
Circuit Board Illustrations
A. 2002+ Protech LED Models (Page 50-51)
Danger: Electrical Shock Hazard Exists!
High Voltage Present On Circuit Board. Use Extreme Caution While Servicing Circuit Board.
38
8.7 No Jets
This is a condition of constant zero water pressure. The fi rst step in diagnosing the problem is to determine if the pump is actually turning. Once this determination is made, follow the appropriate portion of this S.T.A.
Diagnostic Tools:
Voltmeter, spare control panel.
Suggested Spare Parts (Page 59):
Control panel, circuit board, pump.
Pump Is Turning - Checking For A Flow Problem
1.
2.
3.
Is the fi lter clogged?
Is there an obstruction in the plumbing line?
Check for an air lock (clear the air lock by opening the pump union on the discharge side or loosening the diverter cap, with the pump off).
Pump Not Turning;
Standard Troubleshooting Approach
Press JETS Button to turn on jets pump.
Do you hear a relay click on the circuit board?
No Plug in spare control panel then press
JETS Button.
Do you hear a relay click on the circuit board?
No
Replace circuit board.
Yes
Is voltage from circuit board to main pump correct? Check for
240 VAC (120 VAC for J315,
J325 models) at recommended test points. See table at right for a listing of recommended test points.
No
Replace circuit board.
Yes
Replace control panel.
Yes
Is connection between circuit board and pump OK?
No
Repair wiring.
Yes
Circuit Board Illustrations
Recommended Test Points
1. Low Speed Pump 1 - test points 18 & 19
2. High Speed Pump 1 - test points 18 & 20
3. Pump 2 - test points 21 & 22
A. 2002+ Protech LED Models (Page 50-51)
Replace pump.
Danger: Electrical Shock Hazard Exists!
High Voltage Present On Circuit Board. Use Extreme Caution While Servicing Circuit Board.
39
8.8 Weak Or Surging Jets
Weak or surging jets are usually caused by an insuffi cient water supply to the pump or a clogged or broken impeller. The water level may simply be too low, or there may be an obstruction in the water fl ow path to the pump or in the pump’s impeller.
Before making a service call, ask the customer to verify that all jets are open and that there is suffi cient water in the hot tub.
Suggested Spare Parts (Page 59):
Filter, pump.
Standard Troubleshooting Approach
Is water level
OK?
No
Adjust water level.
Yes
Are filter cartridges clogged or dirty?
No
Are the filters installed correctly?
No
Fix filter installation problem.
Yes
Yes
Clean or replace filter cartridges.
Take pump housing apart. Is debris present in pump impeller? Is the impeller broken?
No
Is there debris or a loose foreign object between the filters and pump input?
Yes Yes
No
If pump suction line is clear, check for blockage in plumbing on the return side of pump. Call Jacuzzi
Premium Technical
Support for assistance in performing this verification step.
Remove debris or replace broken impeller
Remove debris or loose foreign object.
40
8.9 Pump Runs And Quits During Jet Mode
This is usually a problem of the pump overheating. The pump motor incorporates a thermal cutout that triggers when the motor gets too hot. There is no reset for this condition.
When the motor cools, the thermal switch resets automatically. In some cases, a faulty circuit can also cause this problem.
Diagnostic Tools:
Clamp-on ammeter, voltmeter.
Suggested Spare Parts (Page 59):
Circuit board, pump.
Standard Troubleshooting Approach
Press JETS 1 button. Does pump make a "laboring" sound?
Yes
No
Is voltage from circuit board to pump correct after pump quits? Check for 240 VAC
(120 VAC for J315, J325 models) at recommended test points. See table at right for a listing of recommended test points.
No
Replace circuit board.
Yes
Pump has thermally shut down. See page 43.
Recommended Test Points
1. Low Speed Pump 1 - test points 18 & 19
2. High Speed Pump 1 - test points 18 & 20
3. Pump 2 - test points 21 & 22
Is there sufficient voltage connected to hot tub. Check for
240 VAC –10% (or
120 VAC –10% for
J315, J325 Models) at TB1 test points 1 and 2.
No
Call an electrician to fix problem.
Yes
Check voltage with pump running. Is the voltage 240 VAC
–10 % (or 120 VAC
–10% for J315, J325 models) at test points 1 and 2.
Yes
No
Replace pump.
This is caused by insufficient wiring or the pump drawing too much current.
Contact Jacuzzi
Premium Technical
Support.
Danger: Electrical Shock Hazard Exists!
High Voltage Present On Circuit Board. Use Extreme Caution While Servicing Circuit Board.
Circuit Board Illustrations
A. 2002+ Protech LED Models (Page 50-
51)
41
8.10 Circulation Pump Not Working
The circulation pump should be on for the programmed duration each day and for a heat call unless “Summer Logic” is activated. Verify the pump should be on before troubleshooting. Check the circulation pump start time and duration setting.
Refer to section
5.6C (page 23).
Diagnostic Tools:
Clamp-on ammeter, voltmeter.
Suggested Spare Parts (Page 59):
Circuit board, circulation pump.
Standard Troubleshooting Approach
Is 240 VAC (120 VAC for
J315, J325 models) present at pump output?
Circuit board test points
16 and 17
Yes
No
Make sure circulation pump should be on. If pump should be on and there is no voltage at test points 16 and 17 change circuit board.
Is there current draw
(0.5 Amp)? Check with clamp-on ammeter.
No
Check connection between circuit board and circulation pump. If connection is OK, replace pump.
Yes
Current draw is proof that circulation pump is working. Read steps above to make sure circulation pump should be on*.
Circuit Board Illustrations
A. 2002+ Protech LED Models (Page 50-51)
*Note: If the circulation pump is running, but there is no water fl ow, check for an air lock, a blockage in the plumbing, debris in the pump or a broken pump impeller.
Danger: Electrical Shock Hazard Exists!
High Voltage Present On Circuit Board. Use Extreme Caution While Servicing Circuit Board.
42
8.11 Troubleshooting A Thermal Pump Cutout
1.
2.
3.
4.
Verify that the voltage to the hot tub is 240 VAC (120 or 240 VAC for J-315, J-325)
±10%. An insuffi cient voltage supply can cause the motor to pull too much current and to overheat. This situation must be corrected.
Check the voltage to the hot tub. Remember, the power company is required by law to provide the correct voltage to the customer. They will come out and check suspected problems (in most cases, free of charge).
If the voltage is OK, examine the environment in which the hot tub is installed. Hot sun, hot weather, and the lack of a breeze can cause heat buildup in the equipment bay in addition to the normal heat produced by the pump. This can raise the temperature high enough to cause the thermal cutout to trip. There are two possible solutions to thermal cutout problems which are not due to low line voltage. One is to change the fi lter cycle periods so that they do not coincide with the hottest time of the day and peak power consumption hours. Another is to ventilate the equipment bay. Call Jacuzzi
Premium Technical Support for advice on this matter.
If there seems to be no overheating problem, yet the motor keeps cutting out, the pump’s thermal switch may be bad. In this case the pump should be replaced.
8.12 Pump Hums And Will Not Start
If the pump impeller is not “frozen”, this condition almost always indicates a bad start capacitor. This component is inside the motor housing.
Diagnostic Tools:
Voltmeter.
Suggested Spare Parts (Page 59):
Pump and motor, circuit board.
mmm......
Standard Troubleshooting Approach
1.
Press the Jets 1 button.
2.
Check voltage at pump 1 (low speed) test points 18 and 19 for 240 VAC (120 VAC for J-315, J-325).
If there is no voltage, replace the circuit board. If voltage is present, the pump needs to be repaired or replaced.
If pump 1 runs in low speed but hums in high speed, make sure the circuit board is not sending voltage to both speeds at the same time. When voltage exists while in low speed at test points 18 and 19, there should be no voltage at test points 18 and 20. Conversely, when voltage exists while in high speed at test points 18 and 20, there should be no voltage at test points 18 and 19. If voltage is present across both sets of test points at the same time, replace the circuit board. Refer to pages 50 and 51 for the circuit board layout.
Recommended Test Points (Pages 50 and 51):
•
Pump 1 - Low speed test points 18 and 19; high speed test points 18 and 20.
•
Pump 2 - High speed test points 21 and 22.
43
8.13 Ozone not working
Diagnostic Tools:
Clamp-on ammeter and voltmeter.
Suggested Spare Parts (Page 59):
Ozonator, circuit board, control panel.
Standard Troubleshooting Approach
Turn power to hot tub off and on.
Wait approximately two minutes for filter cycle to begin and turn on ozonator and circulation pump.
DO NOT press either JETS button at this time or ozonator will shut off!
No
Turn power off, plug in spare control panel, then turn power on. Wait approximately 2 minutes for filter cycle to begin. Is filter cycle running?
No
Yes
Replace control panel.
Yes
Replace circuit board.
Is 240 VAC (120 or 240 VAC*) present at circuit board ozone outputs? Test points 14 and 15.
*J315/J325 models only.
No Replace circuit board.
Yes
CD Ozonator:
is there a faint buzzing sound coming from the ozonator’s internal high voltage arching chamber? Or is there current draw from the ozonator (0.1 Amp)?
Check with clamp-on ammeter.
No Replace ozonator.
O
3
Yes
CD Ozonator:
a faint buzzing sound and/or current draw is proof that the ozonator is working.
Read steps outlined above to ensure customer understands ozone logic.
Circuit Board Illustrations
A. 2002+ Protech LED Models (Page 50-51)
Danger: Electrical Shock Hazard Exists!
High Voltage Present On Circuit Board. Use Extreme Caution While Servicing Circuit Board.
44
Appendix
45
A1.0 Checking Voltage To Hot Tub
Correct supply voltage wiring to the hot tub is essential for safe/proper operation. The fi rst step in troubleshooting a new installation should be to take voltage readings at the terminal block TB1.
Do not trust wire colors. Electricians make mistakes and electrons are colorblind.
A low line voltage or incorrectly wired hot tub will result in either of the following symptoms: A) Strange or intermitent symptoms, B) Displays with indications that simply cannot be correct.
Many of the most perplexing problems in the past have been errors and voltage drops.
Human safety depends on proper hot tub grounding. It is essential that the voltage readings described below are as indicated. The ground connection must be heavy duty wiring.
•
All models (except J-315, J-325 convertible models) are exclusively powered by 240 VAC. The J-315,
J-325 models are convertible for either 120 VAC 3-wire or 120/240 VAC 4-wire operation. The 4-wire power confi guration powers the heater only with 240 VAC for increased performance while powering all other components with 120 VAC.
Verify Power Connections As Follows:
Danger: Electrical Shock Hazard Exists!
High Voltage Present On Circuit Board. Use Extreme Caution While Servicing Circuit Board.
US/Canada J-315, J-325 Model (120 VAC/60Hz, fi g. K)
•
Hot to Neutral: Measure across test points 1 and 23 with voltmeter for 120 VAC.
•
Hot to Ground: Measure across test points 1 and 3 for 120 VAC.
US/Canada J-315, J-325 Model (240 VAC/60Hz, fi g. L)
•
Hot to Neutral: Measure across test points 1 and 23 for 120 VAC; then across test points 2 and 23
for 120 VAC.
•
Hot to Ground: Measure across test points 1 and 3 for 120 VAC; then across test points 2 and 3 for
120 VAC.
•
Hot to Hot: Measure across test points 1 and 2 for 240 VAC,
US/Canada J-335, J-345 Models (240 VAC/60Hz, fi g. M)
•
Hot to Hot: Measure across test points 1 and 2 for 240 VAC.
•
Hot to Ground: Measure across test points 1 and 3 for 120 VAC; then across test points 2 and 3 for
120 VAC.
fig. L fig. M fig. K
WHT
1
BLK
2
TB1
23
1
3
2
3
GRN
US/Canada (60 Hz)
120 VAC 3-Wire
J315, J325
WHT
RED
BLK
BLK to Circuit
Board
WHT
1
TB1
23
WHT
BLK
2
1
RED
3
3
GRN
2
US/Canada (60 Hz)
240 VAC 4-Wire
J315, J325
BLK
BLK
RED to Circuit
Board
RED
1
TB1
2
BLK
2
1
3
GRN
HOT
HOT
HOT
HOT to Circuit Board
US/Canada (60 Hz)
240 VAC 3-Wire
J335, J345
46
A2.0 Checking Voltages To Devices
Device voltages are often measured at the circuit board to determine whether the board or the device is bad. If the circuit board delivers voltage when the device operation is called, the circuit board is probably good and the problem lies with the device or the wiring to the device. The following voltage chart shows operating voltages for all major hot tub components. Voltage is considered good if it is within
±10% of the listed value. Refer to appendix pages 50-51 for your specifi c circuit boards test point locations.
• 2004 ProTech LED J-315, J-325 Models (US/Canada 60Hz)
Device
Pump (Low Speed)
Pump (High Speed)
Circulation Pump
Test Points
18 and 19
18 and 20
16 and 17
Voltage ±10%
120 VAC
120 VAC
120 VAC
Heater
Ozone Generator
6 and 7
14 and 15
120 VAC or 240 VAC*
* Depends whether hot tub is connected to 120 VAC or 240 VAC supply
120 VAC
• 2004 ProTech LED J-335, J-345 (US/Canada/Export 50/60Hz)
Device
Pump 1 (Low Speed)
Pump 1 (High Speed)
Pump 2 (J-340 Only)
Circulation Pump
Heater
Ozone Generator
Test points
18 and 19
18 and 20
21 and 22
16 and 17
6 and 7
14 and 15
Voltage ±10%
240 VAC
240 VAC
240 VAC
240 VAC
240 VAC
240 VAC
A3.0 Checking Current Consumption Of Devices
This table lists the current draw for most major hot tub components.
J-315, J-325 Model (US/ Canada 60Hz)
Device
Pump High/Low
Current Consumption ±10%
10.6 - 13.6A / 2.6 - 3.9A
Heater
Circulation Pump
Ozone Generator
16.6A (240 VAC) / 8.3A (120 VAC) 14.5 Ohms
0.5A
0.1A
J-335, J-345 Models (US/Canada 60Hz)
Device
Pump 1 High/Low
Pump 2 High
Heater
Circulation Pump
Ozone Generator
Current Consumption ±10%
7.0A - 9.5A / 2.5A - 3.2A
6.8A - 9.3A
22A - 25A
0.5A
0.1A
10.5 Ohms
47
A4.0 Testing The Flow Switch
When the “FL1” or “FL2” message appears, it means the fl ow switch contacts have failed to close when the circulation pump was on, or failed to open when the circulation pump was off. This could be caused by an obstruction in the fl ow path or by a bad switch. The fi rst thing to look for is an obvious obstruction, remembering (while not likely) that it is possible for a small object to work its way into the plumbing where it will not be obvious. After verifying no obvious blockage exists, the fl ow switch can be tested. Refer to page 26 for fl ow switch testing instructions.
A5.0 About Fuses
When current passes through a conductor the conductor heats up. If the conductor is a heavy piece of wire or a strip of metal, it will pass large currents and generate very little heat. If a wire is fi ne, or a strip of metal is thin, it will heat up at lower current levels. Fuses rely on this principle to protect circuits from massive current fl ows by simply melting if their current rating is exceeded. By selecting different alloys for the fuse element, fuses can be made to have their current rating exceeded for a short period of time.
Such slow-blow fuses are excellent for protecting motor circuits where start up currents (surge currents) are higher than running currents.
Fuse
Main Power, 20A
Main Power, 30A
Transformer Primary, 1.5A
Part Number
6660-106
6660-105
6760-120
J-315, J-325
X
X
J-335, J-345
X
X
Testing Fuses
A good fuse should read continuity (Ø ohms); a blown fuse will read no continuity (infi nite ohms).
Caution:
Make sure replacement fuses are exactly those listed above. Never test a fuse for continuity while it is installed in the fuse holder.
A6.0 The Watchdog (---)
Three horizontal dashes with no other control panel indicators illuminated is a result of the
Watchdog circuitry detecting a potential destructive condition within the hot tub.
Before making the service call, have the customer turn off power to the hot tub, then turn it back on. If this corrects the problem, have the customer monitor the hot tub and call if it occurs again.
There are many conditions that can cause a Watchdog error message. Except for a runaway heat condition, most are caused by a faulty circuit board, bad hi-limit or temperature sensor. On rare occasions a control panel or a bad transformer will cause Watchdog. Confi rm this by using a test panel and testing the transformer connections on the circuit board,
refer to appendix page 57.
1.
2.
3.
4.
Turn the power to the hot tub off. Verify proper resistance of the hi-limit and temperature sensors (see appendix page 55). Replace the defective temperature or hi-limit sensor, then re-stest the system. If the
Watchdog error goes away, skip steps 2-4.
If the heater is not overly hot to the touch and the Watchdog displays an immediate dashed line error, the circuit board is probably bad. Check the transformer primary and secondary voltages (page 57) before changing the circuit board.
The temperature in the heater may have reached 118ºF (48ºC). If the heater got too hot, check for fl ow restrictions and correct the problem.
If you cannot reproduce the Watchdog error and the hi-limit and temperature sensors check out OK, tell the customer to call you if the Watchdog display reappears.
48
A7.0 Understanding Ozone
Oxygen is an element, and like other gaseous elements, normally exists as a pair of atoms bonded together to make a whole molecule. Chemists therefore use the symbol O
2 ecules” rather than oxygen atoms.
to speak of “oxygen mol-
In the presence of an electric discharge like lightning or a strong source of ultraviolet light, three molecules of O
2
can combine to form two molecules of O
3
known as Ozone. While oxygen has no smell, ozone has a very pronounced smell in large concentrations. In small quantities, it causes the pleasant
“fresh air” smell that laundry has when dried on an outdoor clothesline. Some clothing dryer manufacturers have installed an ultraviolet light inside their machines to give clothes that “fresh-as-all-outdoors” smell. Jacuzzi Premium offers a type of ozone system, the corona discharge (CD). The corona discharge (CD) uses a highly effi cient low current/high voltage arching chamber to generate ozone. The
CD ozone introduces ozone into the hot tub water through a “Mazzei” venturi fi tting.
The technician must understand three things about ozone:
•
Ozone (O
3
) breaks down quickly into plain oxygen (O
2
).
•
Ozone kills germs.
•
Ozone is a strong oxidizer.
Because ozone breaks down quickly into oxygen, the hot tub would have to run 24 hours a day with the ozone generator operating to insure constant disinfecting. Even then, a residual sanitizer must be used.
There are two choices, chlorine or bromine. While chlorine is oxidized by ozone just as quickly as bromine, the resulting bromine compounds are a much better disinfectant than the resulting chlorine compounds. Therefore, ozone and bromine team up better to do the overall job than ozone and chlorine.
A8.0 Understanding pH
Keeping the hot tub water clean and clear involves a very complex set of chemical reactions. Most importantly, the hot tub must be sanitized. Bacteria, algae and other single-cell life forms that may fi nd their way into the hot tub must be killed. Three chemical elements, chlorine, bromine and ozone are all good sanitizing agents. When any of these elements come into contact with bacteria or algae, these single-cell organisms die. Therefore, to keep the water germfree, we must simply keep a residual of the sanitizing agent in the water.
Making germs dead is only half the objective, however. The dead cells of the bacteria and algae we have killed, and the organic “stuff” (dandruff, persperation, dead skin cells, etc.) that our bodies deposit in the hot tub, will make the water cloudy and univiting as they decompose. These microscopic contaminants must be “burned out” or oxidized. These oxidation reactions occur simultaneously with reactions known as reduction reactions. The balance of these chemical reactions is quite critical and can occur properly only if pH levels are maintained from 7.2 to 7.8 pH. If the pH is out of range, the sanitizing agent itself will be oxidized or reduced and in effect be “used up” before it has a chance to do it’s job.
pH is critical for maximum disinfection, sanitizing and cleaning results with the least amount of chemical addition. Make sure your customer understands the importance of regular water test intervals and the proper use of chemicals. Both are necessary to ensure maximum water quality and to maintain a healthy and fun hot tub environment.
49
A9.0 2004 J-315, J-325 Circuit Board Wiring Diagram (US/Canada 60Hz)
US/Canada 60Hz Model
•
Circuit Board Type: ProTech LED, 6600-086.
Heater 1.0 kW @ 120
F1 20A 250V SC-20
50
A10.0 2004 ProTech LED Circuit Board Wiring Diagram (US/Canada 60Hz)
J-335, J-345 US/Canada 60Hz Models
•
Circuit Board Type: ProTech LED, 6600-088.
Circ. Pump
51
A11.0 Load Box Connection Diagram For J-335, J-345 (240 VAC only, 60Hz)
A
J-335, J-345 (240 VAC Only)
2-Pole Circuit Breaker with 2-Wire Grounded Load Connection
(3 Wires to Hot Tub, 2-Hot, 1-Ground)
240 VAC/120 VAC
White
Black
Red 2-Pole
GFCI
Breaker
R
TB1
B
Hot Tub
Load Box
Main
Service
Panel with
GFCI
White (Neutral)
Green (Ground)
*GFCI Sub Panel commonly used when recommended GFCI does not install in Main Panel.
Red
Black
Green
TB2
No Load Neutral Wire
Pigtail
Neutral Bus
Ground
Ground
Note: service disconnect not shown in this diagram.
B
J-335, J-345 (240 VAC Only)
Main Panel with Secondary GFCI Sub-Panel Using a
2-Pole GFCI Breaker with 2-Wire Grounded Connection
(3 Wires to Hot Tub, 2-Hot, 1-Ground)
Hot Tub Load Box
Main Panel*
GFCI Sub Panel*
Red (Hot)
Black (Hot)
2-Pole
GFCI
Breaker
R
TB1
B
Red
Black
Green
TB2
Ground
Pigtail
Neutral Bus
Ground
No Load Neutral Wire
Note: service disconnect not shown in this diagram.
52
Load Box Connection Diagram For J-315, J-325 (120/240 VAC, 60Hz)
C
J-315, J-325 (240 VAC)
2-Pole Circuit Breaker with 3-Wire Grounded Load Connection
(4 Wires to Hot Tub, 2-Hot, 1-Neutral, 1-Ground)
240 VAC/120 VAC
White
Black
Red 2-Pole
GFCI
Breaker
R B
TB1
W
Hot Tub
Load Box
Main
Service
Panel with
GFCI
Red
Black
White
Green
TB2
Ground
Pigtail
Neutral Bus
Ground
Note: service disconnect not shown in this diagram.
D
J-315, J-325 (240 VAC)
Main Panel with Secondary GFCI Sub-Panel Using a
2-Pole GFCI Breaker with 3-Wire Grounded Connection
(4 Wires to Hot Tub, 2-Hot, 1-Neutral, 1-Ground)
Hot Tub Load Box
Main Panel*
GFCI Sub Panel*
Red (Hot)
Black (Hot)
2-Pole
GFCI
Breaker
R B
TB1
W
TB2
Red
Black
White
Green
Ground
White (Neutral)
Green (Ground)
*GFCI Sub Panel commonly used when recommended GFCI does not install in Main Panel.
Pigtail
Neutral Bus
Ground
Note: service disconnect not shown in this diagram.
53
Load Box Connection Diagram For J-315, J-325 (120 VAC only, 60Hz)
E
J-315, J-325 (120 VAC)
2-Pole Circuit Breaker with 2-Wire Grounded Load Connection
(3 Wires to Hot Tub, 1-Hot, 1-Neutral, 1-Ground)
240 VAC/120 VAC
White
Black
Red 2-Pole
GFCI
Breaker
B
TB1
W
Hot Tub
Load Box
Main
Service
Panel with
GFCI
Black
White
Green
TB2
Ground
Pigtail
Neutral Bus
Ground
Note: service disconnect not shown in this diagram.
F
J-315, J-325 (120 VAC)
Main Panel with Secondary GFCI Sub-Panel Using a
2-Pole GFCI Breaker with 2-Wire Grounded Connection
(3 Wires to Hot Tub, 1-Hot, 1-Neutral, 1-Ground)
Hot Tub Load Box
Main Panel*
GFCI Sub Panel*
Red (Hot)
Black (Hot)
2-Pole
GFCI
Breaker
B
TB1
W
TB2
Black
White
Green
Ground
White (Neutral)
Green (Ground)
*GFCI Sub Panel commonly used when recommended GFCI does not install in Main Panel.
Pigtail
Neutral Bus
Ground
Note: service disconnect not shown in this diagram.
54
A12.0 Temperature / Hi-Limit Sensor Resistance Chart
Fahrenheit (ºF)
59.0 ........................
60.8 ........................
62.6 ........................
64.4 ........................
66.2 ........................
68.0 ........................
69.8 ........................
71.6 ........................
73.4 ........................
75.2 ........................
77.0 ........................
78.8 ........................
80.6 ........................
82.4 ........................
84.2 ........................
86.0 ........................
87.8 ........................
89.0 ........................
91.4 ........................
93.2 ........................
95.0 ........................
96.8 ........................
98.6 ........................
100.4 ......................
102.2 ......................
104.0 ......................
105.8 ......................
107.6 ......................
109.4 ......................
111.2 ......................
113.0 ......................
Celcius (ºC)
15 ...........................
16 ...........................
17 ...........................
18 ...........................
19 ...........................
20 ...........................
21 ...........................
22 ...........................
23 ...........................
24 ...........................
25 ...........................
26 ...........................
27 ...........................
28 ...........................
29 ...........................
30 ...........................
31 ...........................
32 ...........................
33 ...........................
34 ...........................
35 ...........................
36 ...........................
37 ...........................
38 ...........................
39 ...........................
40 ...........................
41 ...........................
42 ...........................
43 ...........................
44 ...........................
45 ...........................
Ohms (Ω)
............................................................................... 48840
............................................................................... 46680
............................................................................... 44610
............................................................................... 42630
............................................................................... 40770
............................................................................... 39000
............................................................................... 37290
............................................................................... 35700
............................................................................... 34170
............................................................................... 32700
............................................................................... 30000
............................................................................... 28740
............................................................................... 27540
............................................................................... 26400
............................................................................... 25311
............................................................................... 24270
............................................................................... 23280
............................................................................... 22329
............................................................................... 21429
............................................................................... 20571
............................................................................... 19740
............................................................................... 18960
............................................................................... 18210
............................................................................... 17490
............................................................................... 16800
............................................................................... 16149
............................................................................... 15519
............................................................................... 14919
............................................................................... 14349
............................................................................... 13800
............................................................................... 13281
55
A13.0 Flow Switch Illustration
Flow Switch #6560-852
Compatibility: All 2004 J-315, J-325 Models
Connection: This fl ow switch style has spade connectors at the top for easy cable removal for electronic troubleshooting.
Flow Switch #6560-860
Compatibility:
Connection:
All 2004 J-335, J-345 Models
This fl ow switch style has connectors that are potted into the top and cannot be removed at the fl ow switch.
6560-860
6560-852
FLOW
A14.0 ProTech LED Sensor Harness Diagram
J2 Connector (Cable Side)
Shown While Plugged Into The Circuit Board
J2 Connector Flow Switch (Cable Side)
Shown While Plugged Into The Circuit Board
Temperature
Sensor Wires
PIN
TINE
Hi-limit Sensor, Temperature Sensor,
And Flow Switch Wires
Connector
(Side View)
Hi-Limit
Sensor Wires
PAPER CLIP
To remove a sensor/fl ow switch wire from either the J2 or J3 connectors, insert the end of a paper clip or similar device into the slot corresponding with the wire to be removed.
This will depress the tine on the pin, allowing the wire to be pulled from the harness.
Important!
When reinstalling the sensor/fl ow switch wire, make sure the tine on the pin is lifted so the sensor wire will lock into the connector body.
56
A15.0 Transformer Test
To Test The Transformer:
1.
2.
3.
Leave the transformer connector J4 plugged into the circuit board.
Set your voltmeter to the highest VAC range.
Place the voltmeter probes directly into the backside (wire side) of the J4 connector and test as follows:
US/Canada 60Hz
J-315, J-325 (120 VAC or 240 VAC Powered*)
Connector J4
Black to White
Voltage
120 VAC*
Yellow to Yellow
US/Canada 60Hz
J-335, J-345 (240 VAC Powered)
Connector J4
Black to Red
Yellow to Yellow
12-14 VAC
Voltage
240 VAC
12-14 VAC
120 VAC/240 VAC
J-315, J-325 Model
(Wire Side View)
B
W
Y
Y
240 VAC
J-335, J-345
(Wire Side View)
B
R
Y
Y
*Special Instructions For All 120 VAC/240 VAC Convertible Models (J-315, J-325)
120 VAC Power Confi guration:
Convertible models include a factory installed 15 foot GFCI cord rated at 15A/120 VAC. To use the cord, the hot tub must be installed within 10 feet of a dedicated, grounded type electrical outlet.
Do not use an extension cord of any type!
If the hot tub is more than 10 feet from such an outlet, it must be hard wired to a single pole 15A GFCI breaker. Refer to pages 50-51 for your specifi c circuit board confi guration.
240 VAC Power Confi guration:
Convertible models can be hard wired for 4-wire 120/240 VAC power. This confi guration powers the heater with 240 VAC while powering all other components with 120
VAC. An external 30 or 50A dual pole GFCI breaker is required. Refer to pages 50-51 for your specifi c circuit board confi guration.
57
A16.0 Troubleshooting the Optional Stereo System (J-335 and J-345 only)
The optional stereo system provides a marine AM/FM/CD stereo receiver with two “pop-up” speaker towers for superior sound quality. If the stereo deck does not turn on, refer to the following test procedure.
A. Testing the Power Supply
1. Check for 240 VAC from the
TB1 terminal block to the stereo power supply by measuring across test points
18 and 19 as shown.
2. Check the inline fuses at the back of the stereo deck for continuity. The fuse in the red
ANTENNA
IR SENSORS
SPEAKERS
wire is an 8 amp fuse that supplies power to the deck.
The fuse on the yellow wire is a 0.5 amp fuse that supplies power for the deck’s memory
REMOTE
INTERFACE
Fuses
STEREO
DECK
15
VDC
(Spade
Conn.)
POWER
SUPPLY
MAIN LOAD BOX
TERMINAL BLOCK
TB1
18
240 VAC
circuit.
3. Test the mating spade connectors (while connected) between the stereo power supply and the deck for 12-15 volts DC. If voltage is unstable (fl uctuating) or inadequate, replace the power supply.
4. If the power supply and the fuses all test properly in steps 1-3, and the deck does not turn on, replace the deck. If the deck does turn on but is malfunctioning, replace the deck.
19
B. Testing the Wireless Remote Control (Purchased Separately)
1. Power up the spa.
2. Point the wireless remote at the speakers and try to activate the stereo. Do the infra-red (IR)
LED’s (lights) on the speakers fl icker? If so, proceed to step 3, if not, try another wireless remote.
The fi rst remote may be defective or have a dead battery.
3. Unplug the IR Remote Interface from the stereo deck and try to activate the stereo system. Does it work? If so, replace the module, if not, replace the stereo deck.
58
A17.0 Suggested Spare Parts
(ProTech LED)
Circuit Boards
•
6600-088: J-335, J-345, 50/60Hz
•
6600-088: All Export Models
•
6600-086: J-315, J-325 Domestic Only
Control Panels
•
2600-301: One Pump Control Panel, 50/60Hz
•
2600-302: Two Pump Control Panel, 50/60Hz
Filter Cartridges
•
6540-476: 60 sq. ft., All Models
Flow Switch
•
2560-040: J-335, J-345
•
6560-852: J-315, J-325 Models Only
Fuses
•
6660-105: 30A, Main Power
•
6660-112: 1.5A, Transformer
•
6660-106: 20A, Main Pwr, J-315, J-325 Only
•
2000-081: 10A, Stereo(Opt.J-335 J-345 Only)
•
6660-106: 20A, Export, Main Power, All
Models
Heater Assembly
•
6500-063: 1kW/4kW, J-315, J-325 Only
•
6500-062: 2.7kW, J-315, J-325 Export Only
•
6500-402: 5.5kW Tube Heater
•
6500-401: Export, 2.7kW Tube Heater
Hi-Limit Sensor
•
6600-068: Curled fi nger Connectors, All
Mazzei Kit
•
6472-486: Includes Hose Clamps, All Models
Light Bulb
•
6560-246: Underwater Light, All Models
•
6560-247: Light Harness, All Models
Owner’s Manual
•
6530-225: All Domestic and Export Models
Ozone Generator
•
6472-685: 240 VAC, 60Hz, J-335, J-345
•
6472-685E: Export, 230 VAC, 50Hz, All
Models
•
2472-650: 120 VAC, 60Hz, J-315, J-325
Main Jet Pumps
•
6500-254: Pump #1, J-335, J-345
•
6500-263: Pump #2, J-345
•
6500-258: Pump #1, J-315
• 6500-259: Pump #1, J-325
•
6500-299: Pump #1, Exp. J-315, J-335, J-345
• 6500-291: Pump #1, Export J-325
•
6500-239: Pump #2, Export, J-345
Circulation Pump
•
6500-035: 240 VAC J-335, J-345
•
6500-023: Export, 230VAC All Models
•
6500-038: 120 VAC, J-315, J-325 Only
Temperature Sensor
•
6600-070: Box End Connectors, All Models
Transformer
•
6560-274: 240 VAC, All Models
•
6660-039: Export, 230 VAC, All Models
Note: You must reuse the old plugs when ever replacing any transformer. A new replacement transformer will not come in with any plugs.
59
A18.0 Glossary Of Terms
Circuit Board:
Control Panel:
Ammeter:
Device which measures electrical current conducted through a wire or electrical device.
Chip on the circuit board that stores hot tub software.
Eprom:
Flow Switch:
Switch that informs circuit board there is suffi cient water movement to activate heater. This switch identifi es water fl ow.
Hi-Limit Sensor:
Sensor that monitors water temperature inside heater.
Jumper:
Ohmmeter:
Printed circuit board assembly that distributes voltage to selected components.
Component that allows user to access functions provided by the circuit board.
Ozonator:
ProClear:
Device on circuit board that mechanically connects (bridges) two points together.
Device that measures the resistance in ohms (Ω) of a component or temperature sensitive device (e.g. temperature sensor, heater element, etc.).
A device that produces ozone gas by passing air by a UV light source or through
Corona Discharge (high voltage arc) methods.
A 24-hour ozone fi ltration system added to a hot tub’s circulation pump line which introduces Ozone while circulating the water.
Pin Assignments:
Locations identifi ed by numbers on circuit board.
Sensor Harness:
Plug in connector containing the temperature sensor, hi-limit sensor, fl ow switch and interlock jumper device connections.
Summer Logic:
Temp. Sensor:
Transformer:
Voltage Meter:
Deactivates circulation pump and ozone when hot tub water reaches 2ºF (1ºC) above the set temperature. Hot tub water must be 95ºF (35ºC) or higher for summer logic to activate.
Sensor that monitors hot tub water temperature.
Device that converts primary high voltage AC signal to a secondary low voltage AC signal.
Device that measures AC or DC voltage potentials across components or from a specifi c test point to ground.
60
Troubleshooting Data Collection Form
Protech LED Models
Customer Name
Address
Phone ( )
Before troubleshooting, collect the following:
1.
Model # of Hot Tub
2.
Serial Number
3.
Operating Voltage
Input Voltage
Before calling Jacuzzi Premium, collect the following:
4.
Low Speed Pump 1 Amps
5.
Circ Pump with Heater Amps
6.
High Speed Pump 1 Amps
7.
Pump 2 Amps
8.
High Speed Pump 1, Pump 2, and Heater Amps
9.
Circuit Board Eprom Revision
Jacuzzi Premium Technical Support (866) 234-7727
61
Jacuzzi Premium
14525 Monte Vista Avenue, Chino, CA, 91710, U.S.A.; Phone (909) 606-1416; Fax (909) 393-1583,
Website: http://www.jacuzzipremium-dealers.com/
Revision B: 06/04 © 2004 Jacuzzi Premium Created in the U.S.A.
62
advertisement
* Your assessment is very important for improving the workof artificial intelligence, which forms the content of this project
Key Features
- Adjustable jet speeds for a customized massage experience
- Underwater lighting for ambiance and relaxation
- Energy-efficient design for reduced operating costs
- User-friendly control panel for easy operation
- Durable construction for long-lasting enjoyment
Related manuals
Frequently Answers and Questions
How do I set the water temperature?
How do I turn on the underwater light?
How do I lock the control panel?
What is the default filter cycle time?
How do I reset the control panel?
advertisement