- Home
- Do-It-Yourself tools
- Power tools
- Power impact wrenches
- Northern Industrial Tools
- 1981202
- User's manual
advertisement
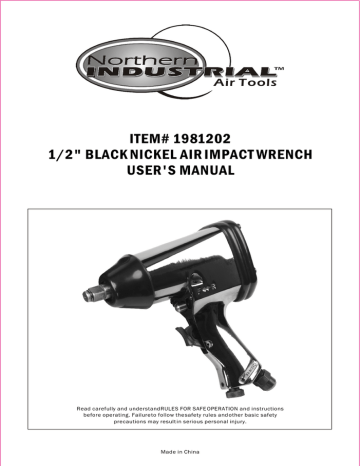
Air Tools
ITEM# 1981202
1/2" BLACK NICKEL AIR IMPACT WRENCH
USER'S MANUAL
Read carefully and understand RULES FOR SAFE OPERATION and instructions before operating. Failure to follow the safety rules and other basic safety precautions may result in serious personal injury.
Made in China
For technical questions and replacement parts, please call 1-800-222-5381.
Thank you very much for choosing a NORTHERN TOOL + EQUIPMENT CO., Product!
For future reference, please complete the owner's record below:
Model: _______________ Purchase Date: _______________
Save the receipt, warranty and these instructions. It is important that you read the entire instruction sheet to become familiar with this product before you begin using it.
This product is designed for certain applications only. Northern Tool + Equipment strongly recommends that this product is not modified and/or used for any application other than that for which it was designed. If you have any questions relative
to a particular application, DO NOT use the product until you have first contacted
Northern Tool + Equipment to determine if it can or should be performed on the product.
Before using this product, please read the following instructions carefully.
Technical Specifications
Item Description
Square Drive
Free Speed
Max. Torque
Air Consumption
1/2"
7500 RPM
230 ft-lbs
4 CFM
Item
Air Inlet Diameter
Min. Hose Size
Max. air pressure
Description
1/4"- 18NPT
3/8"
90 PSI
SAVE THIS MANUAL
You will need this manual for the safety warnings and precautions, assembly, operating, inspection, maintenance and cleaning procedures, parts list and assembly diagram.
Keep this manual and invoice in a safe and dry place for future reference.
GENERAL SAFETY RULES
Read and understand all instructions.
Failure to follow all instructions listed in the following pages may result in electric shock, fire, and/or serious injury.
Work Area
1. Keep your work area clean and well lit. Cluttered benches and dark areas invite
accidents.
2. Do not operate pneumatic tools in explosive atmospheres, such as in the presence
of flammable liquids, gases, or dust. Pneumatic tools create sparks which may ignite
flammables.
3. Keep bystanders, children, pets and onlookers away while operating a pneumatic tool.
Distractions can cause you to lose control. Protect others in the work area from debris
such as metal filings and sparks. Provide barriers or shields as needed.
Personal Safety
1. Stay alert. Watch what you are doing, and use common sense when operating a
pneumatic tool. Do not use a pneumatic tool while tired or under the influence of
drugs, alcohol, or medication. A moment of inattention while operating pneumatic
tools may result in serious personal injury.
2. Dress properly. Do not wear loose clothing or jewelry. Contain long hair. Keep your
hair, clothing, and gloves away from moving parts. Loose clothes, jewelry, or long
hair can be caught in moving parts.
1 of 5
3. Avoid accidental starting. Be sure the trigger is off before connecting to the air
supply. Carrying pneumatic tools with your finger on the trigger, or connecting
pneumatic tools to the air supply with the Trigger on, invites accidents.
4. Remove adjusting keys or wrenches before turning on the tool. A wrench or a key
that is left attached to a rotating part of the tool may result in personal injury.
5. Do not overreach. Keep proper footing and balance at all times. Proper footing
and balance enables better control of the tool in unexpected situations.
6. Use safety equipment. Always wear ANSI-approved safety glasses underneath a
full face shield, and hearing protection.
Use and Care
1. Use clamps or other practical ways to secure and support the work piece to a stable
platform. Holding the work by hand is unstable and may lead to loss of control. Only
work on a workpiece that is properly secured.
2. Do not force the tool. Use the correct tool for your application. The correct tool will
do the job better and safer at the rate for which it is designed.
3. Do not use the power tool if the trigger does not turn it on or off. Any tool that cannot
be controlled with the Trigger is dangerous and must be replaced.
4. Disconnect the air hose from the tool before making any adjustments, changing
accessories, or storing the tool. Such preventive safety measures reduce the risk
of starting the tool accidentally.
5. Store idle tools out of reach of children and other untrained persons. Tools are
dangerous in the hands of untrained users.
until repaired.
7. Check for misalignment or binding of moving parts, breakages of parts, damaged air
hose (not included), and any other condition that may affect the tool's operation. If
damaged, have the tool serviced before using. Many accidents are caused by poorly
maintained tools.
8. Use only accessories that are recommended by the manufacturer for your model.
Accessories that may be suitable for one tool may become hazardous when used on
another tool.
Service
1. Tool service must be performed only by qualified repair personnel. Service or
maintenance performed by unqualified personnel could result in a risk of injury.
2. When servicing a tool, use only identical replacement parts. Follow instructions in
the Inspection, Maintenance and Cleaning section of this manual. Use of
unauthorized parts or failure to follow maintenance instructions may create a risk
of injury.
SPECIFIC SAFETY RULES
1. To avoid accidental injury, always wear ANSI-approved safety glasses, a full face
shield, and hearing protection when operating the tool.
2. Use clean, dry, regulated, compressed air at 90 PSI. Do not exceed the
recommended 90 PSI. Never use oxygen, carbon dioxide, combustible gases, or
any other bottled gas as a power source for this tool.
3. When connecting to the air supply: Prior to each use, if an automatic oiler is not
used, add two drops of air tool oil (not included) into the air inlet fitting of the tool.
4. Always disconnect the tool from its compressed air supply source, and squeeze the
Trigger to release all compressed air in the tool before performing any maintenance
or service.
2 of 5
5. The warnings, precautions, and instructions discussed in this manual can not cover
all possible conditions and situations that may occur. The operator must understand
that common sense and caution are factors which cannot be built into this product,
but must be supplied by the operator.
ASSEMBLY AND OPERATING INSTRUCTIONS
To attach a quick connector
!
WARNING
Prior to performing any assembly and/or adjustment procedures, make sure the air supply hose (not included) is disconnected from the impact wrench.
1.Prior to use, the impact wrench requires the attachment of a quick-connector into its air inlet. To do so, wrap approximately 3" of pipe thread sealer tape (not included) around the male threads of a quick-connector. Then, firmly tighten the quick-connector into the air inlet.
Fig. 1
Loosening
1.Attach the correct size socket to the anvil.
2.Set the compressor's pressure regulator to 90 PSI. Do not set the compressor's outlet regulator above 90PSI.
3.Connect the tool to the air compressor's hose. If leakage is detected, disconnect the air hose and fix it correct before use.
4.Place the socket over the nut to loosen.
5.Grip the tool firmly. Press the REVERSE valve in from the area above the trigger so that the REVERSE valve protrudes out the back of the housing. Press the trigger
to start the tool.
Caution:
Make sure the nut or bolt can withstand the impact wrench's working torque.
NOTE:
ØIf the tool cannot loosen the nut, DO NOT raise the outlet pressure of the air compressor.
ØWhen the nut is moved, stop the tool by releasing the trigger and remove the tool
from the nut. Remove the nut from the socket if needed.
Tightening
The working torque of the impact wrench is 230 ft.-lbs. Make sure that the nut or bolt you are using the tool to tighten can withstand the rated torque.
1.Tighten the nut as far as you can by hand.
2.Place the socket on the nut. Press the REVERSE valve forward so it protrudes
out the front of the Housing. Press the trigger to start the tool.
3 of 5
NOTE:
ØIf the tool stalls while tightening, DO NOT raise the outlet pressure of the air
compressor above 90 PSI.
ØWhen the nut has been tightened, remove the tool and socket.
Do not over-tighten.
ØIf available, check the recommended torque specifications for the nut.
You should use a torque wrench to torque the nut after using the impact wrench.
INSPECTION, MAINTENANCE AND CLEANING
its compressed air supply before performing any inspection, adjustments,
maintenance, or cleaning.
2. Before each use, inspect the general condition of the tool. Check for loose screws,
misalignment or binding of moving parts, cracked or broken parts, damaged air hose,
and any other condition that may affect its safe operation. If abnormal noise or
vibration occurs, have the problem corrected before further use. Do not use
damaged equipment.
3. Daily: With a clean cloth, remove all dirt, oil, and grease from the tool. If necessary,
you may use a mild detergent. Do not use solvents, as damaged to the tool may occur.
Do not immerse the tool in any liquids.
GENERAL TOUBLE SHOOTING
TROUBLES
ØTool does not run at a normal speed or at a variable speed.
ØThe motor blocks.
ØAutomatic start when connected to compressed air.
ØTorque reduces
ØAbnormal vibrating Easy hot rising at the housing.
CAUSES
ØAir supply is not enough (air pressure not in a required standard)
ØSpeed controller/switch breaks down
ØRotor blades break or wear out
ØDust gets into the motor
ØThrottle lever or starting trigger malfunctions
ØAir leakage at the inlet or somewhere else
ØBearing damages
ØCorrespondent O-rings wear out or out of position
ØLack of lubricating
TROUBLE SHOOTING
ØCheck the air hose to see whether it is blocked or twisted for less air supply
ØCheck the air compressor to gain the correct air pressure required
ØReplace rotor blades
ØDisassemble the tool and clean the inner structure under proper instructions
ØCheck and fix the throttle lever or starting trigger for accurate operation
ØCheck the air leakage and fix it under proper instruction
ØReplace new bearing
ØReplace the damaged O-ring or put it back in correct position
ØOil/Lubricate the tool consistently until it gains the right speed and torque.
NOTE: For any other special troubles which cannot be settled down by the operator,
please contact the selling agent from whom you purchased the tool.
4 of 5
Diagram
12
13
14
15
8
9
10
11
Part No.
1
2
3
6
7
4
5
20
21
22
16
17
18
19
Description
Housing
Valve Sleeve
Reverse valve
Trigger
Spring Pin
Valve Stem
Valve seat
Steel Ball
Spring
Air Inlet
Air Regulator
O-ring
Set Screw
Spring
Anvil Bushing
Anvil collar
O-ring
Standard Anvil
Hammer Cage
Hammer Pin
Hammer Dog
Drive Cam
Qty.
1
1
1
1
1
1
1
1
1
1
1
1
1
1
1
1
1
1
1
1
1
2
5 of 5
32
33
34
35
28
29
30
31
Part No.
23
24
25
26
27
40
41
42
43
36
37
38
39
Description
Ball Bearing
Cylinder
Rotor
Rotor Blade
Front End Blade
Front Dowel Pin
Rear end Plate
Rear Dowel Pin
Rear Gasket
Back Cover
Spring Washer
Cap Screw
Stop Pin
Spring Pin
Set Screw
Exhaust Deflect
Tapping Screw
Plug
Nose Rubber
Protect Ring
O-ring
Qty.
1
1
4
1
1
4
1
1
1
1
6
1
2
1
1
1
1
1
2
1
1
advertisement
* Your assessment is very important for improving the workof artificial intelligence, which forms the content of this project
Related manuals
advertisement