Trane Vertical Stack WSHP Catalogue
Add to My manuals60 Pages
Trane Vertical Stack WSHP is a floor-mounted unit designed to be hidden behind drywall, providing discreet comfort for multi-story buildings. Its vertical configuration allows for stacking to minimize installation costs, while its optional ducted or free discharge design offers flexibility in air distribution. With a range of sizes from ¾ to 3 tons, it can cater to various room sizes or multiple-room dwellings.
advertisement
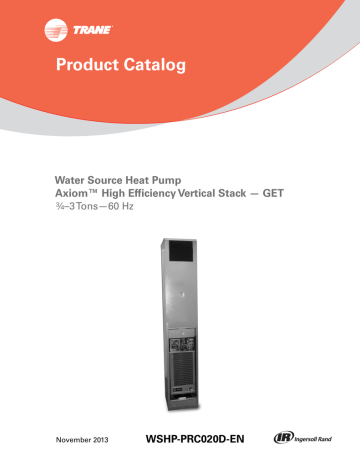
Product Catalog
Water Source Heat Pump
Axiom™ High Efficiency Vertical Stack — GET
¾–3 Tons—60 Hz
November 2013
WSHP-PRC020D-EN
Introduction
Water-Source Vertical High-Rise
The 3/4-ton through 3-ton vertical high-rise water-source heat pump is a floor mounted, “furredin” unit, designed to be hidden from view behind drywall to blend with the room’s natural decor.
In multi-story buildings, the units may be stacked one on top of the other to minimize piping and electrical costs. Supply, return and condensate riser piping may be factory mounted to simplify job site installation of the equipment.
The high-rise configuration is often used in hotels, dorms and assisted living facilities where a single unit could provide comfort to a single or multiple room dwelling. Because the units are mounted directly in the space, ductwork is optional.
All water-source heat pumps are commissioned, tested and quality certified prior to leaving the factory.This assures global quality standards from controls, water, refrigeration, and aesthetics to the building owner and installing contractor.
Key features of the water-source, vertical stack heat pump include:
1. Removable/replaceable chassis
2. Ducted and free discharge cabinet selections available
3. Factory mounted flow control with strainer and isolation valve option
4. Plug-in chassis and plug-in thermostat design
5. Factory supplied riser options
6. Maintenance accessibility for coil fin cleaning
8.
Through the front high and low pressure service ports accessible
9.
Tamper proof hinged acoustical door option
10.
Unit mounted switch and fuse option
11.
Lower height cabinet for ducted applications
12.
Auxiliary drain pan
13.
Rust resistant chassis drain pan
14.
Intelligent controls
Auxiliary
Drain Pan
Refrigeration Control
TXV
Water-Out Connection
Water-In Connection
Refrigeration Section
Completely Enclosed
Chassis Rails
Trademarks
Axiom, ReliaTel,TOPSS,Tracer,Trane, and theTrane logo are trademarks or registered trademarks of Trane in the United States and other countries. Trane is a business of Ingersoll Rand. All trademarks referenced in this document are the trademarks of their respective owners.
LonTalk is a registered trademark of Echelon Corporation.
BACnet is a registered trademarks. All trademarks referenced in this document are the trademarks of their respective owners.
Revision Summary
WSHP-PRC020D-EN (09 November 2013): Performance Data (Efficiency Upgrades); WPRD Chassis
© 2013 Trane All rights reserved WSHP-PRC020D-EN
Table of Contents
Water-Source Vertical High-Rise . . . . . . . . . . . . . . . . . . . . . . . . . . . . . . . . . 2
Deluxe 24V Electronic Controls . . . . . . . . . . . . . . . . . . . . . . . . . . . . . . . . . 51
Tracer ZN510 functions include: . . . . . . . . . . . . . . . . . . . . . . . . . . . . . . . . 53
WSHP-PRC020D-EN 3
Features and Benefits
Unit Description
The vertical high-rise water-source heat pump is a floor mounted configuration available in a ¾ ton,
1 ton, 1¼ ton, 1½ ton, 2 ton and 3 ton sizes.
The unit cabinet may be ordered for early shipment to aid in early installation of drywall, plumbing and electrical. See
“Model Number Descriptions,” p. 14 .The cabinet design is available in either an
88-inch height (free discharge) or 80-inch height (ducted) configuration. As many as 3 supply-air discharges are available for the 1¼ ton-3 ton, free discharge cabinets to provide multiple supplyair through one unit.
Air distribution is made through a rigid bar type extruded aluminum grille mounted to the sheetrock. It is both durable and attractive in design.
The return-air panel is a hinged acoustical door, see
Figure 1, p. 4 .The door allows for easy access
to the unit’s filter and for maintenance of the equipment.
The hinged acoustical panel provides greater sound attenuation, and is mounted flush to the wall.
This panel is easily removed for filter maintenance or chassis removal through the magnetic catch door. An optional tamper proof latch is available on the hinged door design to impede access if required.
Figure 1.
Return-air flush mounted hinged door
4
Blower/Motor Assembly
The unit’s blower/motor assembly includes double width, double inlet (DWDI) blower with direct drive PSC motor or optional ECM motor for improved efficiency and power factor. It may be easily removed for cleaning or service after removal of the unit chassis.The PSC motor is a multi-speed design, factory wired to high speed or low speed (order specific).The tap will be wired and capped inside the unit control box for easy field convertibility.The ECM motor is programmed to provide four constant CFM profiles and is shipped on Profile B – the rated CFM of the unit. To change the
PSC speed tap or the ECM CFM profile, see installation manual WSHP-SVX03*-EN for instructions.
Controls
Standard controls include a 24V, micro-processor Deluxe controller for a wall-mounted thermostat option. The thermostat is typically placed above the return-air door. Even though the thermostat is considered to be unit mounted, the thermostat is mounted to the dry-wall that covers the front of the unit.
WSHP-PRC020D-EN
Features and Benefits
Thermostat selections are provided in the
“Thermostats and Zone Sensors,” p. 55
section of the catalog. They are available in manual or automatic changeover options.
The deluxe controller includes relays for: anti-short cycle compressor protection, random start delay, brown-out protection low pressure time delay, compressor delay on start and night setback control. These extended control features offer greater system performance to extend the equipment’s life.
Figure 2.
Deluxe control box
The Tracer™ ZN510 controller (option) is provided on the vertical stack design for direct digital control (DDC) systems. This controller offers the building owner innovative ways to optimize heating and cooling energy for the building. Faults and sensors include: random start delay, heating/cooling status, occupied/unoccupied mode, and fan/filter status.
Figure 3.
ZN510 control box
WSHP-PRC020D-EN
The Tracer™ Loop Controller (TLC) may be added to either the Deluxe controls or the ZN510 controls to maintain system loop operation. See WMCA-IOP-1 for more information on the TLC.
The ZN510 controller may also be applied with the Tracker and Summit building management systems to further enhance system operation.
Non-fused switch and fused entrance block may be factory added to the equipment to save installation time of these components in the field where local building codes allow.
Deluxe 24V Electronic Controls
General alarm is accomplished through the lockout relay and is used to drive light emitting diodes.
This feature will drive dry contacts only, and may not be used to drive field installed control inputs.
Factory Installed Flow Control
Optional factory mounting of the isolation valve and flow control valves is available to speed field equipment installation, and help provide optimum water flow balancing support.
Refrigeration Section
The unit’s compressor is a highly efficient, hermetically sealed with internal vibration isolation.
External isolation is provided between the compressor and mounting plate to help reduce radiated noise that is typically associated with compressor start.
The air-to-refrigerant coil is easily accessible for cleaning purposes behind the unit’s removable return-air door/panel.
The water-to-refrigerant coil is a copper or cupro-nickel (option) co-axial tube-within-a-tube design.
The inner-water tube is deeply fluted to enhance heat transfer and minimize fouling and scaling.
The outer refrigerant gas tube is made from steel material. The coil is leak tested to assure there
5
Features and Benefits
is no cross leakage between the water tube and the refrigerant gas (steel tube) coil. The ½” (009/
012/015/018) and ¾”(024/036) threaded water connections to the water-coil are available on the exterior chassis top. A flexible hose connection with shut-off is typically used between the riser and water-coil in/out connections on the chassis to reduce water vibration.
The refrigerant flow metering is made through a thermal expansion valve (TXV).TheTXV allows the unit to operate with an entering fluid temperature from 25°F to 120°F, and an entering air temperature from 40°F to 90°F.The valve precisely meters refrigerant flow through the circuitry to achieve desired heating or cooling.
Unlike cap-tube assemblies, theTXV allows the exact amount of refrigerant required to meet the coil load demands. This precise metering increases the over-all efficiency of the unit.
The unit’s reversing valve is piped to be energized in the cooling mode. All vertical high-rise units ship in a heat pump configuration with a system reversing valve.
Supply/Return/Condensate Risers
Supply, return and condensate risers are available as a factory mounted and shipped option.The
risers are constructed from type L or M copper.The top of each riser is swaged to accept the same size diameter riser from above. This helps facilitate installation of the water supply, return and condensate to and from the unit. Insulation may be factory installed or field installed per order selection. The insulation helps keep moisture from forming on the pipes and damaging building construction.
The riser length may be ordered as standard in 96” to 120” lengths. See
for riser application information.
Unit Safety
All unit safety devices are provided to help prevent compressor damage. Low pressure switch and high pressure switch are added to help protect the compressor operation under a low charge (40 psig) or during high discharge (650 psig) pressures. In cases where a low charge, or excessive loss of charge occurs, each compressor comes equipped with an overload device to halt the compressor operation.
A safety lockout provides the mechanical communication of the low and high pressure switches to prevent compressor operation if the unit is under low or high refrigerant pressures, or during a condensate overflow condition.The lockout relay may be reset at the thermostat, by cycling power to the unit or through a LonTalk™ front end device (ZN510 control option).
6 WSHP-PRC020D-EN
Application Considerations
Advantages of Geothermal
The advantages of a geothermal heat pump system can literally decrease heating and cooling operating costs by 30%-40%. The units are durable, and typically last longer than conventional systems.They are protected from harsh outdoor weather conditions, because the unit is installed indoors and the loop underground. According to ASHRAE, the estimated service life for a commercial water-to-air heat pump is 19 years.
Geothermal heat pumps have fewer mechanical components, making them more reliable and less prone to failure.
Geothermal heat pumps work toward the preservation of the environment by reducing the environmental impacts of electric power generation.
Flexibility
The vertical, high-rise water-source heat pump system is versatile for installation in boiler/cooling tower applications, as well as ground-source (geothermal) applications. The system typically employs a central pumping design. The central pumping design involves a single pump design, usually located within a basement or mechanical room to fulfill pumping requirements for the entire building system. An auxiliary pump is typically applied to lessen the likelihood of system downtime if the main pump malfunctions.
Furring-In the Unit
WSHP
WSHP
WSHP
Cooling Tower
Boiler
WSHP
WSHP
WSHP
Expansion Tank
Water Storage
Tank
Central Pumps
WSHP
WSHP
WSHP
Water to Water
Heat Pump
To Fresh Air
Ventilation
System
The vertical high-rise water-source heat pump is designed to be a furred-in application. Dry-wall (sheetrock) is attached to furring studs (not unit cabinet) until the entire cabinet, except the front access panel, is enclosed. Access to the unit is made entirely through the front panel which spans approximately one-half of the unit height.
The dry-wall enclosure allows the unit to blend in with the decor of the room. If renovations are needed, the drywall portion of the unit can simply be re-papered or repainted with the remainder of the room.
With careful design, the high-riseWSHP can be incorporated into a room design, while occupying minimum floor space.
Installation Tips
When installing a high-rise water-source heat pump, there are specific installation requirements that should be taken into consideration. These include:
• Noise control
• Riser location
• Furring-in the unit
Sound Attenuation
The high-rise heat pump is better suited for acoustically sensitive water-source heat pump applications than other water-source products. Compressor and water noise are attenuated by the filter panel, sheet rock and the acoustically lined door. Air noise is silenced through the extended and insulated duct portion at the top of the vertical cabinet.
WSHP-PRC020D-EN 7
Application Considerations
Figure 4.
Installation illustration
8
Equipment Installation
The vertical high-rise unit is versatile in design to fit numerous applications. It is typically applied to dorm rooms, hotels and motels where multiple supply air configurations may be required for individual tenant heating and cooling.The equipment requires little space, and is tucked away from sight, and rough handling.The vertical stack design is economical to install, requiring no ductwork for air supply.The riser design may be stacked one on top of another for multi-story applications, or shared between two units (see example B) when architectural design permits. Because the chassis is removable, serviceability to the equipment is enhanced. If service does become a requirement, the chassis is simple to remove from the cabinet, replaced with a back-up chassis, then repaired off-site at a convenient time.
R S D
R S D
A
SINGLE SUPPLY
CORNER SET-UP C
DUAL SUPPLY
DIVIDING WALL SET-UP
B
SINGLE SUPPLY
PRIMARY/SECONDARY SET-UP
WSHP-PRC020D-EN
Application Considerations
Equipment Risers
The riser provides an easy way to facilitate the water flow through a multi-story building and the high-rise heat pump.The
high-rise heat pump is best applied to a building with identical zones on each floor, and zones that are typically small. An example building might include a hotel, dorm, condominium or assisted living facility. With these types of buildings, the riser column (external to the unit cabinet) can be stacked one on top of the other.The piping installation for the entire HVAC system becomes very simple to install because it is pre-measured, and pre-fabricated at the factory.
Factory risers are available as Type K (design special), L
(standard design), and M (standard design). The differences between these types of materials is the wall thickness of the copper.
shows the wall thickness for the most common diameters of risers. It is recommended for most jobs to use type L or M copper.Type K risers are generally not necessary for most high-rise heat pump applications.
The riser design contains threaded stubouts to facilitate connection of the supply and return risers to the hose kits.The
hose kits are then connected to the water-in/out of the unit’s chassis.
Note: Supply/return/drain risers that are ordered and supplied through the factory may be ordered as insulated.
Drain risers are generally made of type M copper. If copper, drain risers are used, the risers should be insulated since the typical temperatures of condensate may cause the riser to sweat.
Table 1.
Riser characteristics
Riser Size (in.)
1
1¼
1½
2
2½
3
1
1¼
1½
2
2½
3
Riser Size (in.)
1
1¼
I.D. (in.)
Type K (special design)
O.D. (in.)
0.995
1.245
1.481
1.959
2.435
2.907
1.125
1.375
1.625
2.125
2.625
3.125
1.025
1.265
1.505
1.985
2.465
2.945
I.D. (in.)
1.055
1.291
Type L (standard)
1.125
1.375
1.625
2.125
2.625
3.125
Type M (standard)
O.D. (in.)
1.125
1.375
Copper Wall Thickness (in.)
0.065
0.065
0.072
0.083
0.095
0.109
0.05
0.055
0.06
0.07
0.08
0.09
Copper Wall Thickness (in.)
0.035
0.042
WSHP-PRC020D-EN 9
Application Considerations
Table 1.
Riser characteristics (continued)
Riser Size (in.)
1½
2
2½
3
I.D. (in.)
1.527
2.009
2.495
2.981
Type M (standard)
O.D. (in.)
1.625
2.125
2.625
3.125
Copper Wall Thickness (in.)
0.049
0.058
0.065
0.072
Note: Pressure ratings for risers are typically greater than the maximum pressure rating of the coaxial water-to-refrigerant heat exchangers.This is true with exception ofType M copper in a 3" diameter.The maximum pressure rating forType M, 3" diameter copper is 380 psig.
All other diameters forType M copper, and all 1" through 3"Type L copper are greater than the 400 psig rating on the coaxial water-to-refrigerant heat exchanger.
Riser Sizing
The proper selection of riser diameter is critical when designing a cost effective job. If the riser diameter is too small, the flow of water to the heat pump may be restricted, making the pumping power requirement excessive. On the other hand, if the riser diameter is too large, the cost of the equipment may become unnecessarily high.
To determine the riser size, calculate the flow at a particular riser. Riser columns will begin with large diameters at the bottom of the column and decrease diameter as the water travels up toward the top floor. The GPM at the first floor is determined by totaling the GPM of all the units on the riser column. The GPM for the second floor is then determined by taking the total GPM and subtracting the flow from the first floor.
The proper size of the riser is determined by calculating the velocity of the water in the riser.The
maximum water velocity that a riser should experience is about 6 or 7 feet/second.
can be used as a quick reference chart for determining the maximum GPM allowed for a given riser size. Riser flow diagram can be found in the 2009 ASHRAE Fundamentals Handbook and may be used to calculate the precise water velocity for a given riser diameter and flow.
Table 2.
Maximum riser flow rate
Riser Size (in.)
1
1¼
1½
2
2½
3
Max. GPM
16
24
34
58
90
130
Water Velocity (ft./sec.)
6.2
6.1
6.1
6.0
6.0
6.1
Head Loss (ft.100 ft.)
15.6
11.8
9.38
6.6
5.1
4.2
Note:
is for general design calculation reference. It is not intended to take the place of an engineered piping design.
10 WSHP-PRC020D-EN
Application Considerations
Riser Size Example
Assume a six story building is served by a high-rise water-source heat pump. When referencing the catalog, determine each highrise heat pump uses 3 gallons per minute to meet the required capacity of the 1-ton unit. What is the minimum riser diameter that can be used on each floor?
With this arrangement, determine the volume of water used at each floor is 3 GPM. The top floor riser therefore only needs to be sized for 3 GPM. Referring to
Table 2, p. 10 , we know that a 1-
inch type M riser can handle up to 16 GPM, therefore the riser size is determined to be 1-inch.
The first floor will see 18 GPM through the riser. Since 18 GPM will result in more than 6 ft./second in a 1” riser, it would be advisable to move to a 1¼” riser.
WSHP-PRC020D-EN
Piping Layout of the Riser
Two methods may be used when piping a riser column. These include direct return or reverse return.
Advantages may be seen in both types of piping methods. For a direct return installation, the riser system is straightforward leaving little confusion about properly sized risers.This provides a more cost effective advantage during the installation process.
The disadvantages of this system is the pressure drop.The total pressure drop on the unit for the sixth floor is much greater than the total pressure drop on the unit for the first floor.This means that the riser column will require balancing from floor-to-floor during installation.
Piping advantages for the reverse return system include the ability to design the riser column so that the total system pressure drop through each unit is equalized. The overall pressure drop is also lower, allowing some energy savings potential. This piping method however does not eliminate the need for proper balancing at each unit.
The disadvantage of this system relates to cost and complexity.
The reverse return method typically costs more because of the additional pipe required for each riser column.
Central Plant Control
Proper central plant control is critical to the operation of a water-source heat pump system. Loss of waterflow or loop temperatures outside of the recommended range will severely impact the operation of the equipment. The following should be followed as minimum operational recommendation for the central plant:
• Heat rejector control (i.e. closed circuit cooling tower, or geothermal loop)
• Heat adder (i.e. boiler or geothermal loop)
• Circulating pumps
• Sensing elements
11
Application Considerations
12
Heat Rejection through a Closed Circuit Cooling Tower
Cooling towers serve to reject heat from the condenser water loop to the atmosphere.Two types of cooling towers are used with water-source heat pump systems: open or closed-circuit. The towers themselves are different, but when an open tower is used in conjunction with a water-towater heat exchanger, the control of the two tower types is essentially the same.
Control for the closed-circuit cooling towers may be made with aTrane®Tracer™ Loop Controller
(TLC). With the TLC, up to four stages of cooling tower control are possible.
When the loop supply temperature is 4°F below the loop supply high setpoint, the first stage of cooling is initiated by opening the closure dampers on the cooling tower.
At 2° F below the setpoint the next stage of cooling is initiated which is the starting of the tower’s circulating pump. If the amount of heat rejected by the first two stages is not enough, the loop temperature will continue to rise.When the temperature reaches the loop supply high setpoint, the next stage of cooling is initiated. This is the first stage of cooling tower fans.
The differential between the stages now become 3°F and the temperature must remain above the differential for three minutes. Up to three individual fan stages may be sequenced or the second stage of fan can be the high speed of a multi-speed motor.
There are five different fan arrangements that theTLC supports: A single fan with a single motor, a single fan with dual motors (pony motors), a maximum of three fans with a maximum of three motors, a variable speed fan with a field supplied variable frequency drive, and a single multispeed motor.
Multiple cooling towers can be supported only if the cooling tower stages are controlled in parallel.
Boiler Operation
The TLC will operate a boiler and the mixing valve respectively. Boiler control is traditionally controlled by a separate boiler controller, provided by the boiler manufacturer.The boiler mixing valve will control the mixture of the boiler water into the main loop to achieve the desired loop supply water.
When the loop temperature falls below the low loop-supply setpoint, the TLC enables the boiler.
The ideal arrangement is for the boiler to have its own bypass loop so the boiler pump can circulate water through the heat exchanger. The boiler will maintain the temperature of the water to the desired setting in the packaged boiler control.
The three-way mixing valve is controlled by theTLC to add heat to the main loop by mixing in water from the boiler loop. A proportional-integral-derivative algorithm controls the valve.The boiler is not disable until the main loop temperature is 5°F greater than the low loop supply setpoint for more than 5 minutes.
TheTLC will also monitor the boiler loop temperature and provide an alarm if the temperature is below the boiler loop low limit after 30 minutes of run time. The TLC will provide an alarm if the boiler loop temperature exceeds the boiler loop high limit after 30 minutes continually.
Facilities Management
Water-source heat pump systems are naturally decentralized; thus they inherently provide individual zone control. Typical installations use mechanical thermostats to provide localized control. Central plant control is typically handled by a control panel located in the main mechanical room. Minimal coordination is usually required between the central plant and the individual watersource heat pumps for successful operation of the system. A direct digital control system is recommended to help support coordination efforts between the central plant and the individual water-source heat pumps. This enhanced coordination can result in reductions in operating cost of the entire system.The following items are typical of the additional coordination: Night setback and setup; After hour usage for tracking and billing; Pump cycling for occupied/unoccupied control;
Zone scheduling; Maintenance reporting for monitoring unit fault conditions;Trend logging of the system water temperatures; Monitoring of system levels for items such as waterflow, temperature, faults, heat rejector status, heat adder status and circulating pump status.
WSHP-PRC020D-EN
Selection Procedures
Model Number
Two model number designators have been defined for the cabinet configuration, and the chassis configuration. Both model numbers require input for the order to be complete and built to specification.
Typically the vertical stack equipment ships in two sections. (1)The cabinet and riser section ship first to allow the contractor to furr-in the equipment during sheetrock installation, and (2) the chassis (refrigeration/water) section ship approximately two to four weeks later eliminating storage requirements of the chassis and possible damage at the job site while waiting for installation. For this reason, there are two model number designators specific to the unit chassis, and the cabinet for the equipment.
WSHP-PRC020D-EN 13
Model Number Descriptions
Vertical High-Rise Cabinet
WSHP
Digits 1-3: Unit Configuration
GET = High Efficiency Vertical High Rise
Heat Pump
Digit 4: Development Sequence
E = R-410A
Digits 5-7: Nominal Size (Tons)
009 = ¾ Tons
012 = 1 Tons
015 = 1¼ Tons
018 = 1½ Tons
024 = 2 Tons
036 = 3 Tons
Digit 8: Voltage (Volts/Hz/Phase)
1 = 208/60/1
2 = 230/60/1
7 = 265/60/1
Digit 9: Heat Exchanger
1 = Copper Water Coil
2 = Cupro-Nickel Water Coil
3 = Copper Water Coil with Isolation
Valve and Low Flow Control
4 = Cupro- Nickel Water Coil with
Isolation Valve and Low Flow Control
5 = Copper Water Coil with Isolation
Valve and High Flow Control
6 = Cupro-Nickel Water Coil with Isolation
Valve and High Flow Control
Digit 10: Current Design
Sequence
Digit 11: Refrigeration Circuit
0 = Heating and Cooling Circuit
Digit 12: Blower Configuration
1 = Free Discharge - PSC motor
2 = Ducted Discharge - PSC motor
3 = Free Discharge w/1" Flange -
PSC motor
4 = Free Discharge w/3" Flange -
PSC motor
5 = ECM motor w/o flange
6 = ECM motor w/1" flange
7 = ECM motor w/3" flange
8 = Chassis only/No motor (ECM Control)
9 = Chassis only/No motor (PSC Control)
Digit 13: Freeze Protection
A = 20° freezestat
B = 35° freezestat
Digit 14: Open Digit
0 = Open
S = Special
Digit 15: Supply Air
Arrangement
0 = No Supply Air Arrangement
1 = Back and Front Supply Air
2 = Back and Left Supply Air
3 = Back and Right Supply Air
4 = Front and Left Supply Air
5 = Front and Right Supply Air
6 = Left and Right Supply Air
7 = Back, Front and Right Supply Air
8 = Back, Front and Left Supply Air
9 = Front, Right and Left Supply Air
B = Back Supply Air
L = Left Supply Air
R = Right Supply Air
T = Top Supply Air
F = Front Supply Air
Digit 16: Return Air
Arrangement
0 = No Return Air Door (Field Provided)
1 = Flush with Wall, Acoustic Hinged
Return Air Door with Keyless Entry
2 = Flush with Wall, Acoustic Hinged
Return Air Door with Keylock Entry
Digit 17: Control Types
D = Deluxe 24V Controls
C = Tracer™ ZN510 Controls
Digit 18: Thermostat Sensor
Location
0 = Wall Mounted Location
Digit 19: Fault Sensors
0 = No Fault Sensors
1 = Condensate Overflow Sensor
2 = Filter Maintenance Timer
3 = Condensate Overflow and Filter
Maintenance Timer
Digit 20-22: Open Digits
Digit 23: Unit Mounted
Disconnect
0 = No Unit Mounted Switch
C = Toggle Switch Only
D = Toggle Switch with Fuses
Digit 24: Filter Type
1 = 1-inch Throwaway Filter
Digit 25: Acoustic Arrangement
0 = Enhanced Sound Attenuation
1 = Deluxe Sound Attenuation
Digit 26: Factory Configuration
3 = R-410A Cabinet
Digit 27: Paint Color
8 = Polar White
Digit 28: Outside Air Option
0 = No Outside Air
Digit 29: Piping Arrangement
B = Back Riser Location
L = Left Hand Riser Location
R = Right Hand Riser Location
Digit 30: Riser Type
0 = No Riser
L = Type L Riser
M= Type M Riser
Digit 31: Supply Riser
0 = No Riser
B = 1" Dia. Riser with Insulation
C = 1¼" Dia. Riser with Insulation
D = 1½" Dia. Riser with Insulation
E = 2 Dia. Riser with Insulation
F = 2½" Dia. Riser with Insulation
G = 3" Dia. Riser with Insulation
2 = 1" Dia. Riser
3 = 1¼" Dia. Riser
4 = 1½" Dia. Riser
5 = 2" Dia. Riser
6 = 2½" Dia. Riser
7 = 3" Dia. Riser
Digit 32: Return Riser
0 = No Riser
B = 1" Dia. Riser with Insulation
C = 1¼" Dia. Riser with Insulation
D = 1½" Dia. Riser with Insulation
E = 2" Dia. Riser with Insulation
F = 2½" Dia. Riser with Insulation
G = 3" Dia. Riser with Insulation
2 = 1" Dia. Riser
3 = 1¼" Dia. Riser
4 = 1½" Dia. Riser
5 = 2" Dia. Riser
6 = 2½" Dia. Riser
7 = 3" Dia. Riser
Digit 33: Condensate Riser
0 = No Riser
B = 1" Dia. Riser with Insulation
C = 1¼" Dia. Riser with Insulation
D = 1½" Dia. Riser with Insulation
E = 2" Dia. Riser with Insulation
F = 2½" Dia. Riser with Insulation
G = 3" Dia. Riser with Insulation
2 = 1" Dia. Riser
3 = 1¼" Dia. Riser
4 = 1½" Dia. Riser
5 = 2" Dia. Riser
6 = 2½" Dia. Riser
7 = 3" Dia. Riser
14 WSHP-PRC020D-EN
Model Number Descriptions
Digit 34, 35, 36: Riser Length
000 = No Riser
096 = 96" Riser Length
097 = 97" Riser Length
098 = 98" Riser Length
099 = 99" Riser Length
100 = 100" Riser Length
101 = 101" Riser Length
102 = 102" Riser Length
103 = 103" Riser Length
104 = 104" Riser Length
105 = 105" Riser Length
106 = 106" Riser Length
107 = 107" Riser Length
108 = 108" Riser Length
109 = 109" Riser Length
110 = 110" Riser Length
111 = 111" Riser Length
112 = 112" Riser Length
113 = 113" Riser Length
114 = 114" Riser Length
115 = 115" Riser Length
116 = 116" Riser Length
117 = 117" Riser Length
118 = 118" Riser Length
119 = 119" Riser Length
120 = 120" Riser Length
Vertical High-Rise Chassis
WSHP
Digits 1-3: Unit Configuration
GET = High Efficiency Vertical High Rise
Heat Pump (cabinet with blower/motor)
Digit 4: Development Sequence
E = R-410A
Digits 5-7: Nominal Size (Tons)
009 = ¾ Tons
012 = 1 Tons
015 = 1¼ Tons
018 = 1½ Tons
024 = 2 Tons
036 = 3 Tons
Digit 8: Voltage (Volts/Hz/Phase)
1 = 208/60/1
2 = 230/60/1
7 = 265/60/1
Digit 9: Heat Exchanger
1 = Copper Water Coil
2 = Cupro-Nickel Water Coil
3 = Copper Water Coil with Isolation
Valve and Low Flow Control
4 = Cupro- Nickel Water Coil with Isolation
Valve and Low Flow Control
5 = Copper Water Coil with Isolation
Valve and High Flow Control
6 = Cupro-Nickel Water Coil with Isolation
Valve and High Flow Control
Digit 10: Current Design
Sequence
Digit 11: Refrigeration Circuit
0 = Heating and Cooling Circuit
Digit 12: Blower Configuration
1 = Free Discharge - PSC motor
2 = Ducted Discharge - PSC motor
3 = Free Discharge w/1" Flange -
PSC motor
4 = Free Discharge w/3" Flange -
PSC motor
5 = ECM motor w/o flange
6 = ECM motor w/1" flange
7 = ECM motor w/3" flange
8 = Chassis only/No motor (ECM Control)
9 = Chassis only/No motor (PSC Control)
Digit 13: Freeze Protection
0 = None or Standard
A = 20° Freezestat
B = 35° Freezestat
Digit 14: Open Digit
0 = Open
Digit 15: Supply Air
Arrangement
0 = No Supply Air Arrangement
1 = Back and Front Supply Air
2 = Back and Left Supply Air
3 = Back and Right Supply Air
4 = Front and Left Supply Air
5 = Front and Right Supply Air
6 = Left and Right Supply Air
7 = Back, Front and Right Supply Air
8 = Back, Front and Left Supply Air
9 = Front, Right and Left Supply Air
B = Back Supply Air
L = Left Supply Air
R = Right Supply Air
T = Top Supply Air
F = Front Supply Air
Digit 16: Return Air
Arrangement
0 = No Door (Chassis Only)
1 = Flush with Wall, Acoustic Hinged
Return Air Door with Keyless Entry
2 = Flush with Wall, Acoustic Hinged
Return Air Door with Keylock Entry
Digit 17: Control Types
0 = Basic Controls for WPRD Retrofit
Chassis
D = Deluxe 24V Controls
C = Tracer™ ZN510 Controls
Digit 18: Thermostat Sensor
Location
0 = Wall Mounted Location
Digit 19: Fault Sensors
0= No Fault Sensors
1 = Condensate Overflow Sensor
2 = Filter Maintenance Timer
3 = Condensate Overflow and Filter
Maintenance Timer
Digit 20-22: Open Digits
Digit 23: Unit Mounted
Disconnect
0 = No Unit Mounted Switch
C = Switch Only
D = Switch with Fuses
Digit 24: Filter Type
1 = 1-inch Throwaway Filter
Digit 25: Acoustic Arrangement
0 = Enhanced Sound Attenuation
1 = Deluxe Sound Attenuation
Digit 26: Factory Configuration
2 = R-410A Chassis
R = WPRD Retrofit Chassis
Digit 27: Paint Color
8 = Polar White
Digit 28: Outside Air Option
0 = No Outside Air
Digit 29: Piping Arrangement
B = Back Riser Location
L = Left Hand Riser Location
R = Right Hand Riser Location
Digit 30: Riser Type
0 = No Riser (Chassis Only)
Digit 31: Supply Riser
0 = No Riser (Chassis Only)
Digit 32: Return Riser
0 = No Riser (Chassis Only)
Digit 33: Condensate Riser
0 = No Riser (Chassis Only)
Digit 34, 35, 36: Riser Length
000 = No Riser (Chassis Only)
WSHP-PRC020D-EN 15
General Data
Table 3.
General Data
Model Number
Compressor Type
Cabinet Size Depth (in.)
Height (in.)
Width (in.)
Depth (mm)
Height (mm)
Width (mm)
Approximate weight cabinet
Approximate weight cabinet
Approximate weight chassis
Approximate weight chassis with Pallet (lb.) without Pallet (lb.) with Pallet (lb.)
Air-to-Refrigerant Coil without Pallet (lb.)
Face Area (ft.2)
Face Area (cm2)
Rows
Fins Per Inch
Fins Per cm.
Inches
Nominal 1”
Filter Size
Water In/Out size
Condensate
Riser Connection
PSC Ducted Discharge
PSC Free Discharge mm
NPTI
Plastic Hose ID (in)
NPTE
Blower
Motor HP
Blower
Motor HP
ECM Motor
Blower
Motor HP
Refrig. Side (PSIG)
Water-to-Refrigerant
Coil Water Side (PSIG)
Internal Volume
(gal)
009
Rotary
135
115
88
78
012
Rotary
135
115
107
97
015
Rotary
175
150
112
102
1.35 1.35 2.11
1254 1254 1959
2 4 4
14
5.5
14 x 20
356 x 508
14
5.5
14 x 20
356 x 508
14
5.5
18 x 25
457 x 635
½"
¾"
½"
90-6TDD
0.05
90-6TDD
0.05
90-6TDD
0.33
650
½"
¾"
½"
90-6TDD
0.125
90-6TDD
0.125
90-6TDD
0.33
650
½"
¾"
½"
90-6RDD
0.125
90-6RDD
0.125
100-6TDD
0.5
650
400 400
0.081 0.081
400
0.228
018
Rotary
175
150
117
107
024
Scroll
036
Scroll
16.0 16.0 18.0 18.0 24.0 24.0
88.0 88.0 88.0 88.0 88.0 88.0
16.0 16.0 20.0 20.0 24.0 24.0
406.4 406.4 457.2 457.2 609.6 609.6
2235.2 2235.2 2235.2 2235.2 2235.2 2235.2
406.4 406.4 508.0 508.0 609.6 609.6
2.11 2.88 2.88
1959 2676 2676
4 3 4
14
5.5
18 x 25
457 x 635
14
5.5
20 x 30
508 x 762
14
5.5
20 x 30
508 x 762
½"
¾"
½"
100-6TDD
0.2
100-6TDD
0.125
100-6TDD
0.5
650
¾"
¾"
¾"
100-6TDD
0.33
100-6TDD
0.33
120-8TDD11 120-8TDD11
0.5
650
¾"
¾"
¾"
120-8TDD11
0.5
120-8TDD11
0.5
0.75
650
400
0.228
225
195
174
164
400
225
195
190
180
400
0.271 0.368
16 WSHP-PRC020D-EN
Performance Data
Table 4.
AHRI-ISO performance
Unit Size
Rated
Flow
Rate
(GPM)
Rated
Air
Flow
(CFM)
340
Water Loop
Cooling
Capacity
(Mbtuh) EER
8200 12.8
Heating
Capacity
(Mbtuh) COP
10800
Ground Water
Cooling
Capacity
(Mbtuh) EER
Heating
Capacity
(Mbtuh) COP
4.6
PSC Motor
9700 18.4
8700 3.8
Ground Loop
Cooling
Capacity
(Mbtuh) EER
Heating
Capacity
(Mbtuh) COP
8800 14.9
6600 3.2
GET 009
GET 012
GET 015
GET 018
GET 024
GET 036
GET 009
GET 012
GET 015
GET 018
2.1
2.8
3.5
4.2
5.6
8.4
2.1
2.8
3.5
4.2
440
540
650
820
1170
340
440
540
650
11900
14700
18100
23300
33700
8300
12000
14900
18500
13.5
13.1
13.0
13.1
13.0
13.9
14.2
15.0
14.6
14100
17700
22900
26600
41300
10500
14300
18000
22300
4.6
4.6
4.5
4.3
13100
16600
19500
25600
4.3
37900
ECM Motor
4.6
4.8
5
4.6
9600
14100
17000
21100
18.9
20.1
18.0
18.6
18.7
21.1
23.2
23.9
22.6
11800
13700
17900
23600
34400
8500
11600
14800
18400
4.0
3.7
3.7
3.9
3.7
3.9
4.0
4.3
4.2
12300
15400
18700
24300
35100
8700
12600
15600
19500
15.1
14.8
14.3
14.9
14.6
16.2
16.5
17.5
17
9000
11800
14800
18700
27300
6500
8700
11300
14200
GET 024
GET 036
5.6
8.4
820
1170
24200
34200
16.0
15.2
26300
40200
4.8
4.6
26800
38200
24
24
23100
33500
4.4
4.1
25200
35600
18.4
17.8
17800
26300
3.5
3.3
Note:
Certified in accordance with AHRI Water to Air and Brine to Air Heat Pump Certification Program which is based on ISO Standard 13256-1: 1998.
Certified conditions are 80.6°F DB/66.2°F WB EAT in cooling and 68°F DB/59°F WB EAT in heating.
3.2
3.3
3.3
3.2
3.2
3.2
3.2
3.5
3.4
EWT
45
55
68
68
68
55
55
55
55
45
45
55
55
45
45
45
45
68
68
68
68
75
75
GPM
1.1
2.6
1.1
1.5
1.8
1.8
2.1
2.3
2.4
2.4
2.6
1.1
1.5
1.5
1.8
2.1
2.3
2.1
2.3
2.4
2.6
1.1
1.5
Table 5.
GET 009 cooling performance
Total Gross
(Mbtuh)
10.3
10.1
10.2
10.2
10.2
10.3
9.4
9.5
9.6
10.4
10.5
10.6
10.8
10.8
10.8
9.8
10.0
9.6
9.6
9.7
9.7
9.2
9.3
Gross Sen
(Mbtuh)
8.0
8.0
7.7
7.7
7.7
7.9
7.9
7.9
7.9
8.1
8.1
7.8
7.9
8.0
8.0
8.1
8.1
7.7
7.8
7.8
7.8
7.6
7.6
Heat of Rej
(Mbtuh)
11.7
11.5
11.6
11.6
11.6
11.7
11.1
11.1
11.1
11.8
11.9
12.0
12.1
12.1
12.2
11.3
11.4
11.2
11.2
11.2
11.2
11.0
11.0
SHR
0.77
0.78
0.78
0.78
0.78
0.77
0.82
0.81
0.81
0.77
0.76
0.76
0.75
0.75
0.75
0.79
0.79
0.80
0.80
0.80
0.80
0.83
0.82
Comp Pwr
(kW)
0.41
0.42
0.41
0.41
0.41
0.41
0.49
0.47
0.46
0.40
0.39
0.39
0.39
0.39
0.39
0.44
0.42
0.46
0.45
0.45
0.45
0.53
0.51
LWT
65.7
67.8
66.0
65.3
64.7
63.9
87.7
82.8
80.4
60.7
58.2
56.4
55.7
55.1
54.3
75.1
70.2
78.6
77.9
77.3
76.5
94.5
89.7
WPD
(feet head)
2.1
8.7
1.9
3.1
4.3
4.5
5.9
6.7
7.5
7.8
9.1
2.0
3.3
3.4
4.7
6.2
6.9
5.6
6.4
7.1
8.3
1.8
3.1
WSHP-PRC020D-EN 17
Performance Data
EWT
75
105
105
105
105
95
105
105
105
95
95
95
95
86
86
95
95
86
86
86
86
77
77
77
86
77
77
77
77
75
75
75
75
115
115
115
120
115
115
115
115
120
120
120
Table 5.
GET 009 cooling performance (continued)
Total Gross
(Mbtuh)
9.3
8.4
8.4
8.4
8.4
8.7
8.4
8.4
8.4
8.7
8.7
8.7
8.7
9.0
9.0
8.6
8.7
8.9
9.0
9.0
9.0
9.3
9.3
9.3
8.9
9.1
9.2
9.3
9.3
9.4
9.4
9.4
9.4
8.1
8.1
8.1
8.0
8.1
8.1
8.1
8.1
8.0
8.0
8.0
GPM
1.8
2.1
2.3
2.4
2.6
2.6
1.1
1.5
1.8
1.8
2.1
2.3
2.4
2.4
2.6
1.1
1.5
1.5
1.8
2.1
2.3
2.3
2.4
2.6
1.1
1.1
1.5
1.8
2.1
2.1
2.3
2.4
2.6
2.3
2.4
2.6
1.1
1.1
1.5
1.8
2.1
1.5
1.8
2.1
Gross Sen
(Mbtuh)
7.7
7.4
7.4
7.4
7.4
7.5
7.4
7.4
7.4
7.5
7.5
7.5
7.5
7.6
7.6
7.4
7.5
7.5
7.5
7.6
7.6
7.7
7.7
7.7
7.5
7.6
7.6
7.6
7.7
7.7
7.7
7.7
7.7
7.3
7.3
7.3
7.3
7.3
7.3
7.3
7.3
7.2
7.2
7.2
18
SHR
0.82
0.86
0.88
0.88
0.88
0.88
0.88
0.88
0.88
0.84
0.84
0.86
0.86
0.86
0.86
0.86
0.86
0.82
0.82
0.82
0.85
0.84
0.84
0.84
0.84
0.82
0.82
0.82
0.82
0.83
0.83
0.82
0.82
0.90
0.90
0.90
0.90
0.90
0.90
0.90
0.91
0.91
0.91
0.91
Heat of Rej
(Mbtuh)
11.0
10.8
10.9
10.8
10.8
10.8
10.8
10.7
10.7
10.9
10.9
10.9
10.8
10.8
10.8
10.8
10.8
11.0
11.0
11.0
10.9
10.9
10.9
10.9
10.9
11.0
11.0
11.1
11.1
11.0
11.0
11.0
11.0
11.0
10.9
10.9
10.8
10.8
10.8
10.8
11.2
11.0
11.0
10.9
LWT
87.2
103.2
124.4
119.5
117.0
115.2
114.6
113.9
113.2
95.0
94.3
114.4
109.5
107.0
105.3
104.6
104.0
86.8
86.2
85.4
105.4
100.5
98.1
96.4
95.7
85.5
84.8
84.2
83.4
96.5
91.6
89.2
87.5
134.6
129.6
127.1
125.3
124.6
124.0
123.2
139.9
134.7
132.2
130.4
Comp Pwr
(kW)
0.49
0.60
0.76
0.72
0.71
0.70
0.69
0.69
0.69
0.54
0.54
0.67
0.64
0.62
0.61
0.61
0.61
0.49
0.49
0.49
0.60
0.57
0.56
0.55
0.55
0.49
0.48
0.48
0.48
0.54
0.52
0.51
0.50
0.86
0.83
0.81
0.80
0.80
0.79
0.79
0.94
0.90
0.88
0.87
WPD
(feet head)
4.2
4.9
5.5
6.2
7.3
7.5
1.6
2.7
3.7
3.8
5.1
5.7
6.4
6.7
7.9
1.7
2.8
3.0
4.1
5.3
6.0
6.2
6.9
8.1
1.8
1.8
3.0
4.2
5.5
5.5
6.2
7.0
8.2
5.4
6.1
7.1
1.6
1.6
2.6
3.6
4.8
2.6
3.6
4.7
WSHP-PRC020D-EN
Performance Data
Table 5.
GET 009 cooling performance (continued)
EWT
120
GPM
2.3
Total Gross
(Mbtuh)
8.0
Gross Sen
(Mbtuh)
7.2
SHR
0.91
Heat of Rej
(Mbtuh)
10.9
Comp Pwr
(kW)
0.86
LWT
129.7
WPD
(feet head)
5.3
120
120
2.4
2.6
7.9
7.9
7.2
7.2
0.91
0.91
10.9
10.8
0.86
0.85
129.0
128.3
6.0
7.0
Notes:
Cooling performance data is tabulated at 80.6°F DB/66.2°F WB entering air at AHRI/ISO 13256-1 rated cfm.For AHRI/ISO 13256-1 certified ratings, see
. See Performance correction tables to correct performance at conditions other than those tabulated. Interpolation of data is permissible, extrapolation is not. Rated GPM 2.1; Minimum cfm 292; Rated cfm 340; Maximum cfm 408.
EWT
25
68
68
68
68
55
55
55
68
68
68
55
55
55
55
45
45
45
45
32
45
45
45
32
32
32
32
25
25
32
32
25
25
25
25
Table 6.
GET 009 heating performance
Total Gross
(Mbtuh)
6.0
9.9
10.0
10.1
10.6
11.1
11.3
11.5
11.5
11.6
11.7
9.2
9.5
9.7
9.9
8.7
8.7
8.8
8.8
7.3
8.1
8.4
8.6
7.0
7.1
7.2
7.2
6.5
6.5
6.7
6.9
6.2
6.3
6.4
6.4
GPM
1.1
1.5
1.8
2.1
2.3
2.3
2.4
2.6
1.1
2.4
2.6
1.1
1.5
1.8
2.1
2.1
2.3
2.4
2.6
2.6
1.1
1.5
1.8
1.8
2.1
2.3
2.4
2.4
2.6
1.1
1.5
1.5
1.8
2.1
2.3
Heat of Absorb
(Mbtuh)
4.2
9.0
9.2
9.4
9.4
7.9
8.0
8.0
8.6
9.5
9.6
7.2
7.5
7.7
7.9
6.7
6.8
6.8
6.9
5.4
6.2
6.5
6.6
5.2
5.3
5.3
5.3
4.7
4.7
4.8
5.1
4.4
4.5
4.6
4.6
Compr Power
(kW)
0.52
0.59
0.59
0.59
0.60
0.61
0.61
0.61
0.61
0.61
0.61
0.57
0.57
0.57
0.57
0.58
0.58
0.59
0.59
0.54
0.54
0.54
0.54
0.54
0.56
0.57
0.57
0.52
0.53
0.53
0.53
0.53
0.53
0.53
0.54
LWT
17.5
48.0
48.4
48.9
52.8
56.0
57.8
59.1
59.6
60.1
60.7
38.6
39.0
39.3
39.8
42.2
45.0
46.4
47.5
26.2
27.0
27.3
27.6
27.9
34.0
36.4
37.6
19.1
20.0
20.6
20.9
21.1
21.4
23.4
25.3
WPD
(feet head)
2.7
3.1
4.3
5.6
6.4
6.7
7.5
8.7
1.9
7.1
8.3
2.0
3.3
4.5
5.9
6.2
6.9
7.8
9.1
11.6
2.1
3.4
4.7
6.0
7.9
8.9
9.9
10.2
11.9
2.7
4.4
4.5
6.2
8.1
9.1
WSHP-PRC020D-EN 19
Performance Data
Table 6.
GET 009 heating performance (continued)
EWT
75
GPM
1.1
Total Gross
(Mbtuh)
11.4
Heat of Absorb
(Mbtuh)
9.3
Compr Power
(kW)
0.61
LWT
58.5
WPD
(feet head)
1.8
77
86
86
86
77
77
77
77
75
75
77
77
75
75
75
75
1.5
1.8
2.1
2.3
2.4
2.6
1.1
1.5
1.8
2.1
2.3
2.4
2.6
1.1
1.5
1.8
11.9
12.2
12.4
12.5
12.5
12.6
11.6
12.1
12.4
12.6
12.7
12.8
12.9
12.7
13.3
13.5
9.8
10.0
10.2
10.3
10.4
10.5
9.5
10.0
10.3
10.5
10.5
10.6
10.7
10.5
11.1
11.3
0.62
0.62
0.63
0.63
0.63
0.63
0.62
0.62
0.63
0.63
0.63
0.63
0.63
0.63
0.64
0.65
62.0
63.9
65.3
65.8
66.4
67.0
60.1
63.7
65.6
67.0
67.6
68.2
68.9
67.3
71.3
73.4
7.0
8.2
1.8
3.0
3.1
4.2
5.5
6.2
86
86
86
86
2.1
2.3
2.4
2.6
13.8
13.8
14.0
14.0
11.6
11.6
11.7
11.8
0.65
0.65
0.66
0.65
75.0
75.7
76.2
77.0
5.3
6.0
6.7
7.9
Notes:
Heating performance data is tabulated at 68°F DB entering air at AHRI/ISO 13256-1 rated cfm. See Performance correction tables to correct performance at conditions other than those tabulated. Interpolation of data is permissible, extrapolation is not. Rated GPM 2.1; Minimum cfm
272; Rated cfm 340; Maximum cfm 408.
8.1
1.8
3.0
4.1
4.2
5.5
6.2
6.9
Table 7.
GET 012 cooling performance
EWT
45
55
68
68
68
55
55
55
55
45
45
55
55
45
45
45
45
GPM
1.5
3.5
1.5
2.0
2.4
2.4
2.8
3.0
3.2
3.2
3.5
1.5
2.0
2.0
2.4
2.8
3.0
Total Gross
(Mbtuh)
13.1
13.1
13.1
13.1
13.1
13.1
12.7
12.8
12.8
13.2
13.2
13.3
13.3
13.3
13.3
13.0
13.1
Gross Sen
(Mbtuh)
10.3
10.2
10.2
10.2
10.3
10.3
10.1
10.1
10.1
10.3
10.3
10.3
10.3
10.3
10.3
10.2
10.2
SHR
0.78
0.78
0.78
0.78
0.78
0.78
0.79
0.79
0.79
0.78
0.78
0.78
0.78
0.78
0.78
0.79
0.78
Heat of Rej
(Mbtuh)
14.7
14.7
14.7
14.7
14.7
14.7
14.8
14.8
14.7
14.7
14.7
14.7
14.7
14.7
14.7
14.8
14.7
Comp Pwr
(kW)
0.45
0.48
0.47
0.46
0.46
0.46
0.62
0.59
0.57
0.43
0.42
0.41
0.41
0.41
0.41
0.52
0.49
LWT
64.6
67.3
65.5
64.8
64.2
63.4
87.7
82.8
80.3
59.7
57.2
55.5
54.8
54.2
53.4
74.7
69.7
WPD
(feet head)
4.9
10.7
14.1
15.9
17.8
20.7
4.5
7.4
10.2
8.1
11.2
14.6
16.5
18.4
21.5
4.7
7.8
20 WSHP-PRC020D-EN
Performance Data
EWT
68
95
95
95
105
95
95
95
95
86
86
86
86
77
86
86
86
77
77
77
77
75
75
77
77
75
75
75
75
68
68
68
75
105
105
115
115
105
105
105
105
115
115
115
Table 7.
GET 012 cooling performance (continued)
Total Gross
(Mbtuh)
12.8
11.8
11.9
11.9
11.9
11.9
11.9
11.9
11.4
12.6
12.2
12.2
12.2
12.2
12.2
12.2
12.2
12.6
12.6
12.5
12.5
12.5
12.5
12.6
12.6
12.8
12.8
12.8
12.5
12.6
12.6
12.6
12.6
11.4
11.4
11.4
11.4
11.4
11.4
10.9
10.9
10.9
10.9
10.9
GPM
2.8
3.0
3.2
3.5
1.5
1.5
2.0
2.4
2.8
2.8
3.0
3.2
3.5
3.5
1.5
2.0
2.4
2.4
2.8
3.0
3.2
3.2
3.5
1.5
2.0
2.0
2.4
2.8
3.0
3.0
3.2
3.5
1.5
3.2
3.5
1.5
2.0
2.0
2.4
2.8
3.0
2.4
2.8
3.0
Gross Sen
(Mbtuh)
10.1
9.8
9.8
9.8
9.5
9.8
9.7
9.8
9.8
9.9
9.9
9.9
9.9
10.0
9.9
9.9
9.9
10.1
10.1
10.0
10.0
10.0
10.0
10.0
10.0
10.1
10.1
10.1
10.0
10.0
10.0
10.1
10.1
9.6
9.6
9.3
9.3
9.6
9.6
9.6
9.6
9.3
9.3
9.3
WSHP-PRC020D-EN
SHR
0.79
0.82
0.82
0.82
0.82
0.82
0.82
0.82
0.84
0.80
0.81
0.81
0.81
0.81
0.81
0.81
0.81
0.80
0.80
0.80
0.80
0.80
0.80
0.80
0.80
0.79
0.79
0.79
0.80
0.80
0.80
0.80
0.80
0.84
0.84
0.84
0.84
0.84
0.84
0.86
0.86
0.86
0.86
0.86
Heat of Rej
(Mbtuh)
14.7
14.9
14.8
14.7
14.6
14.6
14.6
14.6
14.9
14.7
14.9
14.8
14.7
14.7
14.7
14.7
14.6
14.7
14.7
14.8
14.8
14.7
14.7
14.7
14.7
14.7
14.7
14.7
14.8
14.8
14.7
14.7
14.7
14.7
14.7
14.6
14.6
14.6
14.6
14.8
14.7
14.6
14.6
14.5
LWT
78.5
114.8
109.8
107.2
105.5
104.8
104.1
103.3
124.8
85.4
105.8
100.8
98.3
96.5
95.8
95.2
94.4
84.2
83.4
96.8
91.8
89.3
87.5
86.8
86.2
77.8
77.2
76.4
94.8
89.8
87.3
85.5
84.8
119.7
117.2
115.4
114.7
114.1
113.3
134.8
129.7
127.2
125.4
124.7
Comp Pwr
(kW)
0.56
0.89
0.85
0.83
0.81
0.81
0.80
0.80
1.01
0.62
0.78
0.75
0.73
0.71
0.71
0.71
0.70
0.61
0.60
0.69
0.66
0.64
0.63
0.63
0.62
0.56
0.55
0.55
0.68
0.64
0.63
0.62
0.61
0.97
0.95
0.93
0.93
0.94
0.93
1.15
1.11
1.09
1.07
1.06
WPD
(feet head)
13.4
3.7
6.2
8.6
11.3
12.7
14.2
16.7
3.8
19.2
4.2
7.0
9.7
12.6
14.3
16.0
18.7
16.5
19.4
4.4
7.2
9.9
13.0
14.7
16.4
15.1
16.9
19.8
4.4
7.3
10.0
13.1
14.8
6.1
8.3
10.9
12.3
13.8
16.2
3.8
6.0
8.1
10.6
12.0
21
Performance Data
Table 7.
GET 012 cooling performance (continued)
EWT
115
GPM
3.2
Total Gross
(Mbtuh)
10.9
Gross Sen
(Mbtuh)
9.3
SHR
0.86
Heat of Rej
(Mbtuh)
14.5
Comp Pwr
(kW)
1.06
LWT
124.1
WPD
(feet head)
13.4
115
120
120
120
3.5
1.5
2.0
2.4
10.9
10.6
10.6
10.6
9.3
9.2
9.2
9.2
0.86
0.87
0.87
0.87
14.5
14.8
14.7
14.6
1.05
1.23
1.19
1.16
123.3
139.8
134.7
132.2
15.8
3.8
5.9
8.0
120
120
120
120
2.8
3.0
3.2
3.5
10.6
10.6
10.6
10.6
9.2
9.2
9.2
9.2
0.87
0.87
0.87
0.87
14.5
14.5
14.5
14.4
1.14
1.13
1.13
1.12
130.4
129.7
129.0
128.2
10.5
11.8
13.3
15.6
Notes:
Cooling performance data is tabulated at 80.6°F DB/66.2°F WB entering air at AHRI/ISO 13256-1 rated cfm.For AHRI/ISO 13256-1 certified ratings, see
. See Performance correction tables to correct performance at conditions other than those tabulated. Interpolation of data is permissible, extrapolation is not. Rated GPM 2.8; Minimum cfm 303; Rated cfm 380; Maximum cfm 456.
EWT
25
55
55
55
55
45
45
45
45
55
55
55
68
32
45
45
45
32
32
32
32
25
25
32
32
25
25
25
25
Table 8.
GET 012 heating performance
Total Gross
(Mbtuh)
7.7
10.7
10.8
10.8
10.9
11.3
11.7
11.9
12.1
12.2
12.2
12.3
13.0
9.1
10.1
10.4
10.6
8.9
9.0
9.0
9.1
8.2
8.2
8.5
8.7
7.9
8.1
8.1
8.2
GPM
1.5
1.5
2.0
2.4
2.8
2.8
3.0
3.2
3.5
3.0
3.2
3.5
1.5
3.5
1.5
2.0
2.4
2.4
2.8
3.0
3.2
3.2
3.5
1.5
2.0
2.0
2.4
2.8
3.0
Heat of Absorb
(Mbtuh)
5.4
8.9
9.2
9.4
9.6
8.3
8.3
8.4
8.4
9.7
9.7
9.7
10.5
6.8
7.7
8.0
8.2
6.5
6.6
6.7
6.7
5.9
5.8
6.1
6.4
5.6
5.7
5.8
5.8
Compr Power
(kW)
0.67
0.71
0.71
0.71
0.72
0.72
0.73
0.73
0.73
0.73
0.73
0.73
0.74
0.69
0.69
0.69
0.69
0.70
0.71
0.71
0.71
0.68
0.68
0.68
0.68
0.68
0.68
0.69
0.69
LWT
17.8
39.1
39.5
39.8
40.2
43.2
45.8
47.1
48.2
48.6
49.0
49.4
54.1
26.6
27.3
27.6
27.8
28.1
34.8
37.0
38.2
19.4
20.2
20.9
21.1
21.3
21.7
23.8
25.6
WPD
(feet head)
6.9
14.6
16.5
18.4
21.5
4.7
7.8
10.7
14.1
15.9
17.8
20.7
4.5
15.1
19.8
22.3
24.9
29.1
4.9
8.1
11.2
11.4
16.5
21.2
23.8
25.7
30.6
6.7
11.0
22 WSHP-PRC020D-EN
Performance Data
Table 8.
GET 012 heating performance (continued)
EWT
68
GPM
2.0
Total Gross
(Mbtuh)
13.4
Heat of Absorb
(Mbtuh)
10.9
Compr Power
(kW)
0.75
LWT
57.1
WPD
(feet head)
7.4
77
77
77
77
75
75
75
75
68
75
75
75
68
68
68
68
1.5
2.0
2.4
2.8
2.8
3.0
3.2
3.5
3.5
1.5
2.0
2.4
2.4
2.8
3.0
3.2
14.9
15.0
15.0
15.2
14.1
14.7
14.9
15.2
13.7
13.9
14.0
14.0
14.1
13.9
14.4
14.7
12.3
12.3
12.4
12.5
11.6
12.1
12.3
12.5
11.1
11.3
11.4
11.5
11.6
11.3
11.8
12.1
0.77
0.77
0.77
0.77
0.76
0.77
0.77
0.77
0.75
0.75
0.75
0.76
0.76
0.75
0.76
0.76
66.2
66.8
67.3
67.9
61.6
64.9
66.7
68.1
58.7
59.9
60.4
60.8
61.4
59.9
63.2
65.0
86
86
86
86
77
77
77
86
3.0
3.2
3.5
1.5
2.0
2.4
2.8
3.0
15.2
15.3
15.4
15.4
15.9
16.3
16.5
16.6
12.6
12.7
12.8
12.7
13.3
13.6
13.7
13.8
0.77
0.77
0.78
0.78
0.79
0.79
0.80
0.80
68.6
69.1
69.7
69.1
72.8
74.7
76.2
76.8
14.7
16.4
19.2
4.2
7.0
9.7
12.6
14.3
86
86
3.2
3.5
16.7
16.8
13.9
14.0
0.80
0.80
77.3
78.0
16.0
18.7
Notes:
Heating performance data is tabulated at 68°F DB entering air at AHRI/ISO 13256-1 rated cfm. See Performance correction tables to correct performance at conditions other than those tabulated. Interpolation of data is permissible, extrapolation is not. Rated GPM 2.8; Minimum cfm
303; Rated cfm 380; Maximum cfm 456.
13.1
14.8
16.5
19.4
4.4
7.2
9.9
13.0
10.2
13.4
15.1
16.9
19.8
4.4
7.3
10.0
Table 9.
GET 015 cooling performance
EWT
45
45
45
55
55
45
45
45
45
55
55
GPM
1.9
4.1
4.4
1.9
2.3
2.3
2.8
3.5
3.8
2.8
3.5
Total Gross
(Mbtuh)
16.9
16.9
17.0
17.1
17.1
17.1
17.1
16.7
16.7
16.8
16.8
Gross Sen
(Mbtuh)
14.0
14.0
14.1
14.1
14.1
14.1
14.1
14.0
13.9
14.0
14.0
SHR
0.83
0.83
0.83
0.83
0.82
0.82
0.83
0.84
0.83
0.83
0.83
Heat of Rej
(Mbtuh)
18.5
18.4
18.4
18.4
18.5
18.4
18.3
18.8
18.7
18.6
18.6
Comp Pwr
(kW)
0.49
0.45
0.42
0.39
0.38
0.38
0.37
0.61
0.57
0.54
0.51
LWT
64.8
61.0
58.2
55.5
54.7
54.0
53.4
75.0
71.2
68.3
65.6
WPD
(feet head)
4.6
6.6
9.3
13.8
15.9
18.2
20.4
4.4
6.4
9.0
13.3
WSHP-PRC020D-EN 23
Performance Data
EWT
55
86
86
95
95
86
86
86
86
77
77
77
86
77
77
77
77
75
75
75
75
68
75
75
75
68
68
68
68
55
55
68
68
95
105
105
105
95
95
95
95
105
105
105
Table 9.
GET 015 cooling performance (continued)
Total Gross
(Mbtuh)
16.8
15.6
15.6
15.7
15.7
15.7
15.7
15.2
15.2
16.0
16.0
16.1
16.1
16.1
16.1
16.1
15.6
16.5
16.1
16.1
16.1
16.2
16.2
16.2
16.2
16.8
16.8
16.3
16.4
16.4
16.4
16.5
16.5
15.2
15.2
15.2
15.2
15.2
14.6
14.6
14.6
14.6
14.6
14.6
GPM
3.8
4.1
4.4
1.9
2.3
2.3
2.8
3.5
3.8
3.8
4.1
4.4
1.9
1.9
2.3
2.8
3.5
3.5
3.8
4.1
4.4
4.4
1.9
2.3
2.8
2.8
3.5
3.8
4.1
4.1
4.4
1.9
2.3
4.4
1.9
2.3
2.8
2.8
3.5
3.8
4.1
3.5
3.8
4.1
Gross Sen
(Mbtuh)
14.0
13.6
13.6
13.6
13.6
13.6
13.6
13.4
13.4
13.7
13.7
13.7
13.7
13.7
13.8
13.7
13.6
13.9
13.7
13.7
13.8
13.8
13.8
13.8
13.8
14.0
14.0
13.8
13.8
13.8
13.9
13.9
13.9
13.4
13.4
13.4
13.4
13.4
13.2
13.2
13.2
13.2
13.2
13.2
24
SHR
0.83
0.87
0.87
0.87
0.87
0.87
0.87
0.89
0.88
0.86
0.86
0.85
0.85
0.85
0.86
0.85
0.87
0.84
0.85
0.85
0.85
0.85
0.85
0.85
0.85
0.83
0.83
0.85
0.85
0.84
0.84
0.84
0.84
0.88
0.88
0.88
0.88
0.88
0.90
0.91
0.91
0.91
0.91
0.91
Heat of Rej
(Mbtuh)
18.5
18.9
18.8
18.7
18.7
18.6
18.6
19.0
18.9
19.0
18.9
18.8
18.7
18.7
18.7
18.7
19.0
18.7
18.9
18.9
18.8
18.7
18.7
18.7
18.7
18.5
18.5
18.9
18.8
18.8
18.7
18.7
18.7
18.8
18.7
18.6
18.6
18.6
19.1
18.9
18.8
18.6
18.6
18.6
LWT
64.8
102.4
99.4
96.7
95.8
95.1
94.5
115.3
111.4
97.2
93.4
90.4
87.7
86.8
86.1
85.5
106.2
76.5
95.2
91.4
88.4
85.7
84.8
84.1
83.5
64.0
63.5
88.2
84.4
81.4
78.7
77.8
77.1
108.4
105.7
104.8
104.1
103.5
125.3
121.4
118.4
115.7
114.8
114.1
Comp Pwr
(kW)
0.50
0.95
0.92
0.89
0.88
0.87
0.87
1.13
1.08
0.87
0.83
0.80
0.78
0.77
0.76
0.75
0.99
0.65
0.84
0.81
0.78
0.75
0.74
0.74
0.73
0.50
0.49
0.76
0.72
0.69
0.67
0.66
0.65
1.05
1.02
1.01
1.00
1.00
1.30
1.25
1.22
1.19
1.18
1.17
WPD
(feet head)
15.3
5.7
8.1
11.9
13.8
15.7
17.6
3.7
5.3
4.1
5.9
8.3
12.3
14.2
16.2
18.1
4.0
18.7
4.1
5.9
8.4
12.4
14.3
16.3
18.3
17.5
19.6
4.2
6.1
8.6
12.7
14.6
16.7
7.5
11.2
12.9
14.8
16.6
3.6
5.2
7.3
10.9
12.6
14.4
WSHP-PRC020D-EN
Performance Data
Table 9.
GET 015 cooling performance (continued)
EWT
105
GPM
4.4
Total Gross
(Mbtuh)
14.6
Gross Sen
(Mbtuh)
13.2
SHR
0.91
Heat of Rej
(Mbtuh)
18.5
Comp Pwr
(kW)
1.16
LWT
113.5
WPD
(feet head)
16.1
115
115
115
120
115
115
115
115
3.8
4.1
4.4
1.9
1.9
2.3
2.8
3.5
14.1
14.1
14.0
14.0
14.0
14.0
14.0
13.7
13.1
13.0
13.0
13.0
13.0
13.0
13.0
13.0
0.93
0.93
0.93
0.93
0.93
0.93
0.93
0.94
19.4
19.1
19.0
18.8
18.8
18.7
18.7
19.2
1.54
1.48
1.44
1.40
1.39
1.38
1.37
1.60
135.7
131.6
128.5
125.7
124.9
124.1
123.5
140.4
3.5
5.0
7.1
10.6
12.2
14.0
15.7
3.7
120
120
120
120
2.3
2.8
3.5
3.8
13.7
13.7
13.7
13.7
13.0
12.9
12.9
12.9
0.94
0.94
0.95
0.95
19.0
18.9
18.7
18.7
1.56
1.52
1.48
1.47
136.6
133.5
130.7
129.8
5.1
7.0
10.4
12.0
120
120
4.1
4.4
13.6
13.6
12.9
12.9
0.95
0.95
18.6
18.6
1.46
1.45
129.1
128.5
13.7
15.4
Notes:
Cooling performance data is tabulated at 80.6°F DB/66.2°F WB entering air at AHRI/ISO 13256-1 rated cfm.For AHRI/ISO 13256-1 certified ratings, see
. See Performance correction tables to correct performance at conditions other than those tabulated. Interpolation of data is permissible, extrapolation is not. Rated GPM 3.5; Minimum cfm 432; Rated cfm 540; Maximum cfm 648.
Table 10. GET 015 heating performance
EWT
25
32
45
45
45
32
32
32
32
25
25
32
32
25
25
25
25
45
45
45
45
55
55
GPM
1.9
4.4
1.9
2.3
2.8
2.8
3.5
3.8
4.1
4.1
4.4
1.9
2.3
2.3
2.8
3.5
3.8
3.5
3.8
4.1
4.4
1.9
2.3
Total Gross
(Mbtuh)
9.7
11.0
11.2
11.3
11.3
11.4
12.6
12.9
13.2
9.9
10.0
10.2
10.3
10.3
10.3
10.6
10.8
13.4
13.5
13.6
13.6
14.1
14.5
Heat of Absorb
(Mbtuh)
6.9
8.5
9.6
9.9
10.2
8.1
8.3
8.4
8.4
7.5
7.5
7.7
8.0
7.0
7.2
7.4
7.4
10.4
10.5
10.5
10.6
11.1
11.5
Compr Power
(kW)
0.82
0.85
0.85
0.85
0.85
0.85
0.87
0.87
0.88
0.83
0.83
0.83
0.83
0.83
0.83
0.84
0.84
0.88
0.88
0.88
0.88
0.89
0.89
LWT
17.7
26.2
27.3
27.6
27.9
28.1
34.7
36.4
37.7
18.9
19.9
20.8
21.1
21.4
21.6
23.8
25.1
39.1
39.5
39.9
40.2
43.2
45.0
WPD
(feet head)
6.2
12.1
17.8
20.6
23.5
26.3
4.6
6.6
9.3
8.9
12.5
18.4
21.2
24.2
27.1
6.0
8.6
13.8
15.9
18.2
20.4
4.4
6.4
WSHP-PRC020D-EN 25
Performance Data
Table 10. GET 015 heating performance (continued)
EWT
55
GPM
2.8
Total Gross
(Mbtuh)
14.8
Heat of Absorb
(Mbtuh)
11.8
Compr Power
(kW)
0.90
LWT
46.6
WPD
(feet head)
9.0
75
75
75
75
68
68
68
75
68
68
68
68
55
55
55
55
2.3
2.8
3.5
3.8
3.8
4.1
4.4
1.9
1.9
2.3
2.8
3.5
3.5
3.8
4.1
4.4
17.6
17.7
17.8
17.4
17.9
18.3
18.7
18.9
15.1
15.2
15.3
15.4
16.3
16.7
17.1
17.4
14.5
14.6
14.7
14.3
14.8
15.2
15.6
15.8
12.1
12.2
12.2
12.3
13.2
13.6
14.0
14.4
0.91
0.91
0.91
0.91
0.91
0.91
0.91
0.91
0.90
0.90
0.90
0.90
0.91
0.90
0.91
0.91
60.4
60.9
61.3
59.7
62.1
64.1
66.1
66.7
48.1
48.6
49.0
49.4
54.0
56.2
58.0
59.8
77
77
77
77
75
75
77
77
2.8
3.5
3.8
4.1
4.1
4.4
1.9
2.3
19.0
19.1
17.7
18.3
18.7
19.1
19.2
19.4
15.9
16.0
14.6
15.2
15.6
16.0
16.1
16.3
0.91
0.91
0.91
0.91
0.91
0.91
0.91
0.91
67.3
67.7
61.4
63.8
65.9
67.9
68.5
69.1
16.3
18.3
4.1
5.9
8.3
12.3
14.2
16.2
77
86
86
86
4.4
1.9
2.3
2.8
19.5
19.3
19.8
20.3
16.4
16.2
16.7
17.2
0.91
0.91
0.91
0.91
69.5
68.8
71.4
73.7
18.1
4.0
5.7
8.1
86
86
86
86
3.5
3.8
4.1
4.4
20.8
20.9
21.1
21.2
17.7
17.9
18.1
18.1
0.90
0.90
0.90
0.90
75.9
76.6
77.2
77.7
11.9
13.8
15.7
17.6
Notes:
Heating performance data is tabulated at 68°F DB entering air at AHRI/ISO 13256-1 rated cfm. See Performance correction tables to correct performance at conditions other than those tabulated. Interpolation of data is permissible, extrapolation is not. Rated GPM 3.5; Minimum cfm
432; Rated cfm 540; Maximum cfm 648.
14.6
16.7
18.7
4.1
5.9
8.4
12.4
14.3
13.3
15.3
17.5
19.6
4.2
6.1
8.6
12.7
Table 11. GET 018 cooling performance
EWT
45
45
45
45
45
GPM
2.3
2.9
3.6
4.2
4.6
Total Gross
(Mbtuh)
20.1
19.9
19.8
19.7
19.7
Gross Sen
(Mbtuh)
15.9
15.8
15.8
15.8
15.7
SHR
0.79
0.79
0.80
0.80
0.80
Heat of Rej
(Mbtuh)
22.5
22.2
22.0
21.8
21.8
Comp Pwr
(kW)
0.72
0.67
0.64
0.62
0.61
LWT
65.0
60.3
57.2
55.4
54.5
WPD
(feet head)
3.8
6.0
8.7
11.4
13.4
26 WSHP-PRC020D-EN
Performance Data
EWT
45
77
86
86
86
77
77
77
77
75
75
77
77
75
75
75
75
68
68
68
75
68
68
68
68
55
55
55
55
45
55
55
55
95
95
95
95
86
86
86
86
95
95
95
Table 11. GET 018 cooling performance (continued)
Total Gross
(Mbtuh)
19.6
19.2
19.2
19.2
19.2
19.2
18.6
18.6
18.6
19.3
19.3
19.3
19.3
19.3
19.3
19.1
19.2
19.6
19.6
19.6
19.6
19.6
19.6
19.6
19.2
19.6
20.0
20.0
19.9
19.9
19.9
19.9
19.9
18.6
18.7
18.7
18.7
17.9
18.0
18.0
18.0
18.0
18.0
18.0
GPM
5.0
5.3
2.3
2.9
3.6
3.6
4.2
4.6
5.0
5.0
5.3
2.3
2.9
2.9
3.6
4.2
4.6
4.6
5.0
5.3
2.3
2.3
2.9
3.6
4.2
4.2
4.6
5.0
5.3
5.3
2.3
2.9
3.6
2.3
2.9
3.6
4.2
4.2
4.6
5.0
5.3
4.6
5.0
5.3
Gross Sen
(Mbtuh)
15.6
15.6
15.6
15.6
15.6
15.6
15.3
15.4
15.4
15.6
15.6
15.6
15.6
15.6
15.6
15.5
15.6
15.7
15.7
15.7
15.7
15.7
15.7
15.7
15.6
15.7
15.9
15.8
15.8
15.8
15.8
15.8
15.8
15.4
15.4
15.4
15.4
15.1
15.1
15.1
15.2
15.2
15.2
15.2
WSHP-PRC020D-EN
SHR
0.80
0.81
0.81
0.81
0.81
0.81
0.83
0.83
0.82
0.81
0.81
0.81
0.81
0.81
0.81
0.81
0.81
0.80
0.80
0.80
0.80
0.80
0.80
0.80
0.81
0.80
0.79
0.79
0.79
0.79
0.79
0.80
0.80
0.82
0.82
0.82
0.82
0.84
0.84
0.84
0.84
0.84
0.84
0.84
Heat of Rej
(Mbtuh)
21.6
22.8
22.7
22.7
22.6
22.6
22.9
22.7
22.6
22.8
22.8
22.7
22.7
22.7
22.6
23.0
22.8
23.0
22.9
22.8
22.7
22.7
22.6
22.6
23.0
21.6
22.9
22.7
22.5
22.4
22.4
22.4
22.3
22.6
22.6
22.5
22.5
22.7
22.6
22.5
22.4
22.4
22.4
22.4
LWT
53.6
89.6
87.8
86.9
86.1
85.6
106.3
101.7
98.6
90.8
87.6
85.8
84.9
84.1
83.6
97.4
92.7
88.4
83.8
80.6
78.8
77.9
77.1
76.6
95.4
53.2
75.3
70.6
67.5
65.7
64.7
63.9
63.5
96.7
95.8
95.0
94.6
115.2
110.6
107.5
105.7
104.7
104.0
103.5
Comp Pwr
(kW)
0.60
1.04
1.03
1.02
1.01
1.00
1.26
1.21
1.17
1.05
1.02
1.00
0.99
0.98
0.98
1.13
1.08
1.01
0.96
0.92
0.90
0.90
0.89
0.88
1.10
0.60
0.84
0.79
0.76
0.74
0.73
0.73
0.72
1.15
1.14
1.13
1.13
1.41
1.35
1.32
1.30
1.28
1.28
1.27
WPD
(feet head)
15.5
7.8
10.2
11.9
13.8
15.0
3.3
5.2
7.5
5.4
7.8
10.2
12.0
13.9
15.1
3.4
5.3
3.5
5.5
8.0
10.5
12.3
14.2
15.5
3.4
16.9
3.7
5.7
8.4
11.0
12.9
14.9
16.2
3.0
4.8
7.0
9.1
9.9
11.6
13.4
14.6
10.7
12.4
13.6
27
Performance Data
Table 11. GET 018 cooling performance (continued)
EWT
105
GPM
2.3
Total Gross
(Mbtuh)
17.2
Gross Sen
(Mbtuh)
14.9
SHR
0.86
Heat of Rej
(Mbtuh)
22.7
Comp Pwr
(kW)
1.60
LWT
125.2
WPD
(feet head)
2.9
115
120
120
120
115
115
115
115
105
105
115
115
105
105
105
105
2.9
3.6
4.2
4.6
5.0
5.3
2.3
2.9
3.6
4.2
4.6
5.0
5.3
2.3
2.9
3.6
17.2
17.3
17.3
17.3
17.3
17.3
16.5
16.5
16.5
16.5
16.5
16.5
16.5
15.7
15.8
15.8
14.9
14.9
14.9
14.9
14.9
14.9
14.6
14.6
14.6
14.6
14.6
14.6
14.6
14.2
14.3
14.3
0.86
0.86
0.86
0.86
0.86
0.86
0.89
0.88
0.89
0.89
0.89
0.89
0.89
0.90
0.90
0.90
22.5
22.4
22.3
22.3
22.2
22.2
22.7
22.5
22.3
22.2
22.2
22.2
22.1
22.2
22.1
22.0
1.54
1.50
1.47
1.46
1.45
1.45
1.83
1.76
1.72
1.69
1.68
1.67
1.66
1.90
1.85
1.81
120.5
117.4
115.6
114.7
113.9
113.5
135.2
130.5
127.4
125.6
124.6
123.9
123.4
139.8
135.2
132.2
4.6
6.8
8.9
10.4
12.1
13.2
2.9
4.5
6.6
8.7
10.2
11.8
12.8
3.0
4.5
6.5
120
120
120
120
4.2
4.6
5.0
5.3
15.9
15.9
15.9
15.9
14.3
14.3
14.3
14.4
0.90
0.90
0.90
0.90
21.9
21.9
21.9
21.9
1.78
1.76
1.75
1.75
130.4
129.5
128.8
128.3
8.5
10.0
11.6
12.7
Notes:
Cooling performance data is tabulated at 80.6°F DB/66.2°F WB entering air at AHRI/ISO 13256-1 rated cfm.For AHRI/ISO 13256-1 certified ratings, see
. See Performance correction tables to correct performance at conditions other than those tabulated. Interpolation of data is permissible, extrapolation is not. Rated GPM 4.2; Minimum cfm 501; Rated cfm 650; Maximum cfm 780.
Table 12. GET 018 heating performance
EWT
32
32
45
45
32
32
32
32
25
25
25
32
25
25
25
25
GPM
5.0
5.3
2.3
2.9
2.9
3.6
4.2
4.6
4.6
5.0
5.3
2.3
2.3
2.9
3.6
4.2
Total Gross
(Mbtuh)
13.9
14.1
14.4
14.4
14.5
14.6
16.3
16.8
12.3
12.6
12.8
12.9
12.9
12.9
12.9
13.5
Heat of Absorb
(Mbtuh)
10.3
10.5
10.7
10.8
10.9
10.9
12.5
13.0
9.4
9.4
9.3
9.9
8.8
9.1
9.3
9.3
Compr Power
(kW)
1.06
1.06
1.07
1.07
1.07
1.07
1.11
1.12
1.03
1.03
1.04
1.04
1.04
1.04
1.04
1.05
LWT
24.9
26.2
26.9
27.3
27.7
27.9
33.9
36.1
17.2
18.7
19.8
20.6
20.9
21.3
21.5
23.2
WPD
(feet head)
7.8
11.4
14.9
17.5
20.2
22.0
3.8
6.0
5.2
8.1
11.7
15.8
18.3
21.0
22.7
5.0
28 WSHP-PRC020D-EN
Performance Data
Table 12. GET 018 heating performance (continued)
EWT
45
GPM
3.6
Total Gross
(Mbtuh)
17.2
Heat of Absorb
(Mbtuh)
13.3
Compr Power
(kW)
1.13
LWT
37.6
WPD
(feet head)
8.7
77
77
77
77
75
77
77
77
75
75
75
75
68
68
75
75
68
68
68
68
55
55
55
68
55
55
55
55
45
45
45
45
4.2
4.6
5.0
5.3
2.3
2.9
3.6
4.2
4.6
5.0
5.3
2.3
2.9
3.6
4.2
4.6
5.0
5.3
2.3
2.9
3.6
4.2
4.6
5.0
5.3
2.3
2.9
3.6
4.2
4.6
5.0
5.3
17.4
17.6
17.7
17.7
18.5
19.1
19.6
19.9
20.0
20.1
20.2
21.3
22.2
22.6
22.9
23.0
23.2
23.3
22.9
23.7
24.2
24.5
24.6
24.8
24.9
23.4
24.2
24.6
25.0
25.1
25.2
25.3
13.6
13.7
13.8
13.9
14.5
15.1
15.6
15.8
15.9
16.1
16.1
17.2
18.0
18.5
18.7
18.8
19.0
19.1
18.7
19.5
20.0
20.3
20.4
20.6
20.7
19.1
19.9
20.4
20.7
20.9
21.0
21.0
1.13
1.14
1.14
1.14
1.16
1.17
1.18
1.18
1.18
1.19
1.19
1.21
1.22
1.22
1.23
1.22
1.23
1.23
1.23
1.24
1.24
1.24
1.24
1.24
1.24
1.24
1.25
1.24
1.25
1.24
1.24
1.24
38.5
39.1
39.5
39.7
42.1
44.6
46.4
47.5
48.1
48.6
48.9
52.7
55.6
57.7
59.1
59.8
60.4
60.7
58.4
61.6
63.9
65.4
66.1
66.8
67.1
60.0
63.3
65.7
67.1
67.9
68.6
69.0
86
86
86
86
2.3
2.9
3.6
4.2
25.2
26.0
26.4
26.7
20.9
21.7
22.2
22.5
1.26
1.25
1.25
1.24
67.4
71.0
73.7
75.3
3.3
5.2
7.5
9.9
86
86
4.6
5.0
26.8
26.9
22.6
22.7
1.24
1.24
76.2
76.9
11.6
13.4
86 5.3
27.0
22.8
1.23
77.3
14.6
Notes: Heating performance data is tabulated at 68°F DB entering air at AHRI/ISO 13256-1 rated cfm. See Performance correction tables to correct performance at conditions other than those tabulated. Interpolation of data is permissible, extrapolation is not. Rated GPM 4.2; Minimum cfm
501; Rated cfm 650; Maximum cfm 780.
12.9
14.9
16.2
3.5
5.5
8.0
10.5
12.3
11.4
13.4
15.5
16.9
3.7
5.7
8.4
11.0
15.1
3.4
5.3
7.8
10.2
11.9
13.8
15.0
14.2
15.5
3.4
5.4
7.8
10.2
12.0
13.9
WSHP-PRC020D-EN 29
Performance Data
Table 13. GET 024 cooling performance
Total Gross
(Mbtuh)
25.5
25.6
25.6
25.6
24.8
25.1
25.2
25.3
26.0
26.1
26.2
26.2
26.3
25.0
25.3
25.4
26.9
27.1
27.2
27.3
27.4
27.4
25.6
25.9
27.4
27.8
28.0
28.2
28.3
28.4
28.3
26.6
25.4
25.4
25.5
24.0
24.2
24.3
24.5
24.5
24.6
24.6
23.0
EWT
77
77
77
77
75
75
75
75
68
75
75
75
68
68
68
68
55
55
68
68
55
55
55
55
45
45
45
55
45
45
45
45
86
86
86
86
77
77
77
86
86
86
95
GPM
3.0
3.9
4.7
5.6
5.6
6.1
6.5
7.0
7.0
3.0
3.9
4.7
4.7
5.6
6.1
6.5
6.5
7.0
3.0
3.9
3.9
4.7
5.6
6.1
6.1
6.5
7.0
3.0
3.0
3.9
4.7
5.6
3.9
4.7
5.6
6.1
6.1
6.5
7.0
3.0
6.5
7.0
3.0
Gross Sen
(Mbtuh)
20.1
20.1
20.2
20.2
19.9
19.9
20.0
20.1
20.3
20.4
20.4
20.4
20.4
19.9
20.0
20.1
20.7
20.7
20.7
20.8
20.8
20.8
20.2
20.3
20.9
21.0
21.1
21.1
21.2
21.2
21.2
20.5
20.1
20.1
20.1
19.5
19.6
19.7
19.7
19.7
19.8
19.8
19.2
SHR
0.79
0.79
0.79
0.79
0.80
0.80
0.79
0.79
0.78
0.78
0.78
0.78
0.78
0.80
0.79
0.79
0.77
0.76
0.76
0.76
0.76
0.76
0.79
0.78
0.76
0.76
0.75
0.75
0.75
0.75
0.75
0.77
0.79
0.79
0.79
0.81
0.81
0.81
0.81
0.81
0.80
0.80
0.83
Heat of Rej
(Mbtuh)
29.7
29.7
29.7
29.7
29.6
29.6
29.6
29.7
29.9
29.9
29.9
29.9
29.9
29.6
29.7
29.7
30.1
30.2
30.2
30.3
30.3
30.3
29.8
29.9
30.3
30.4
30.5
30.6
30.6
30.7
30.6
30.0
29.7
29.7
29.7
29.3
29.3
29.4
29.4
29.4
29.4
29.4
29.1
LWT
85.6
84.7
84.1
83.5
96.7
92.2
89.6
87.6
80.7
78.7
77.8
77.2
76.6
94.8
90.2
87.6
70.4
67.8
65.8
64.9
64.3
63.7
87.9
83.3
65.2
60.6
58.0
55.9
55.0
54.4
53.7
75.0
86.7
86.1
85.5
105.6
101.0
98.5
96.5
95.6
95.0
94.4
114.4
Comp Pwr
(kW)
1.23
1.22
1.21
1.20
1.40
1.33
1.30
1.27
1.13
1.10
1.09
1.08
1.07
1.36
1.30
1.26
0.94
0.91
0.87
0.86
0.85
0.84
1.23
1.17
0.84
0.77
0.73
0.70
0.69
0.68
0.67
1.01
1.25
1.25
1.24
1.57
1.50
1.47
1.44
1.43
1.42
1.41
1.77
WPD
(feet head)
3.1
4.9
6.7
9.2
9.2
10.7
12.0
13.6
6.9
9.4
11.0
12.3
14.0
3.1
4.9
6.8
5.2
7.3
9.9
11.5
12.9
14.6
3.2
5.0
3.4
5.5
7.6
10.3
12.0
13.4
15.2
3.3
10.6
11.9
13.5
3.0
4.7
6.6
8.9
10.3
11.6
13.2
2.7
30 WSHP-PRC020D-EN
Performance Data
Table 13. GET 024 cooling performance (continued)
EWT
95
GPM
3.9
Total Gross
(Mbtuh)
23.3
Gross Sen
(Mbtuh)
19.3
SHR
0.83
Heat of Rej
(Mbtuh)
29.1
Comp Pwr
(kW)
1.70
LWT
109.9
WPD
(feet head)
4.3
115
115
115
115
105
105
105
105
95
105
105
105
95
95
95
95
3.0
3.9
4.7
5.6
5.6
6.1
6.5
7.0
7.0
3.0
3.9
4.7
4.7
5.6
6.1
6.5
22.4
22.4
22.4
22.5
20.7
20.9
21.0
21.1
23.4
23.5
23.6
23.6
23.6
21.9
22.2
22.3
18.9
18.9
19.0
19.0
18.3
18.4
18.4
18.4
19.3
19.3
19.3
19.4
19.4
18.7
18.8
18.9
0.85
0.84
0.84
0.84
0.88
0.88
0.88
0.87
0.82
0.82
0.82
0.82
0.82
0.86
0.85
0.85
28.7
28.7
28.7
28.7
28.4
28.4
28.4
28.3
29.1
29.1
29.1
29.1
29.1
28.8
28.8
28.7
1.86
1.84
1.84
1.83
2.28
2.20
2.15
2.12
1.66
1.63
1.61
1.60
1.59
2.01
1.93
1.89
115.3
114.4
113.8
113.2
134.0
129.6
127.1
125.1
107.4
105.4
104.5
103.9
103.3
124.2
119.7
117.2
120
120
120
120
115
115
115
120
6.1
6.5
7.0
3.0
3.9
4.7
5.6
6.1
21.1
21.2
21.2
20.1
20.3
20.4
20.5
20.6
18.5
18.5
18.5
18.0
18.1
18.1
18.2
18.2
0.87
0.87
0.87
0.89
0.89
0.89
0.89
0.88
28.3
28.3
28.3
28.3
28.2
28.2
28.2
28.1
2.11
2.09
2.08
2.39
2.32
2.27
2.24
2.22
124.3
123.7
123.1
138.8
134.5
132.0
130.1
129.2
9.0
10.1
11.5
2.7
4.1
5.6
7.6
8.9
120
120
6.5
7.0
20.6
20.6
18.2
18.2
0.88
0.88
28.1
28.1
2.21
2.20
128.6
128.0
9.9
11.3
Notes:
Cooling performance data is tabulated at 80.6°F DB/66.2°F WB entering air at AHRI/ISO 13256-1 rated cfm.For AHRI/ISO 13256-1 certified ratings, see
. See Performance correction tables to correct performance at conditions other than those tabulated. Interpolation of data is permissible, extrapolation is not. Rated GPM 5.6; Minimum cfm 656; Rated cfm 820; Maximum cfm 984.
2.6
4.1
5.7
7.7
7.9
9.2
10.3
11.8
6.0
8.2
9.5
10.6
12.1
2.6
4.2
5.8
Table 14. GET 024 heating performance
EWT
25
25
25
32
32
25
25
25
25
32
32
GPM
3.0
6.5
7.0
3.0
3.9
3.9
4.7
5.6
6.1
4.7
5.6
Total Gross
(Mbtuh)
14.8
15.3
15.5
15.8
15.9
15.9
16.0
16.4
17.0
17.3
17.6
Heat of Absorb
(Mbtuh)
10.4
10.8
11.1
11.3
11.4
11.5
11.6
12.0
12.5
12.8
13.1
Compr Power
(kW)
1.30
1.30
1.31
1.30
1.31
1.31
1.31
1.31
1.32
1.32
1.32
LWT
18.1
19.5
20.3
21.0
21.3
21.5
21.7
24.0
25.6
26.6
27.3
WPD
(feet head)
4.7
7.4
10.3
14.0
16.2
18.1
20.6
4.6
7.2
10.0
13.5
WSHP-PRC020D-EN 31
Performance Data
EWT
32
75
75
77
77
75
75
75
75
68
68
68
75
68
68
68
68
55
55
55
55
45
55
55
55
45
45
45
45
32
32
45
45
77
86
86
86
77
77
77
77
86
86
86
Table 14. GET 024 heating performance (continued)
Total Gross
(Mbtuh)
17.7
28.8
29.4
29.8
30.0
30.1
30.3
28.4
29.3
26.0
26.8
27.4
27.8
28.0
28.1
28.3
27.8
21.6
22.5
23.3
23.7
24.1
24.3
24.4
24.5
17.8
17.9
19.9
20.6
20.9
21.3
21.4
21.5
29.9
30.3
30.5
30.7
30.9
30.7
31.8
32.4
32.8
33.0
33.1
GPM
6.1
6.5
7.0
3.0
3.9
3.9
4.7
5.6
6.1
6.1
6.5
7.0
3.0
3.0
3.9
4.7
5.6
5.6
6.1
6.5
7.0
7.0
3.0
3.9
4.7
4.7
5.6
6.1
6.5
6.5
7.0
3.0
3.9
7.0
3.0
3.9
4.7
4.7
5.6
6.1
6.5
5.6
6.1
6.5
Heat of Absorb
(Mbtuh)
13.2
23.8
24.3
24.7
24.9
25.0
25.1
23.4
24.3
21.1
21.9
22.4
22.9
23.0
23.1
23.3
22.9
17.0
17.8
18.5
19.0
19.3
19.5
19.6
19.7
13.3
13.3
15.3
15.9
16.3
16.6
16.8
16.8
24.8
25.2
25.4
25.6
25.7
25.6
26.6
27.1
27.5
27.7
27.8
32
Compr Power
(kW)
1.33
1.48
1.49
1.49
1.49
1.49
1.50
1.47
1.49
1.43
1.44
1.45
1.46
1.46
1.46
1.46
1.46
1.37
1.38
1.39
1.40
1.40
1.40
1.40
1.41
1.33
1.33
1.35
1.36
1.36
1.37
1.37
1.37
1.49
1.50
1.50
1.51
1.51
1.51
1.53
1.54
1.56
1.56
1.56
WPD
(feet head)
15.7
4.9
6.8
9.2
10.7
12.0
13.6
3.1
4.9
11.0
12.3
14.0
3.1
3.2
5.0
6.9
9.4
15.2
3.3
5.2
7.3
9.9
11.5
12.9
14.6
17.5
20.0
3.4
5.5
7.6
10.3
12.0
13.4
6.7
9.2
10.6
11.9
13.5
3.0
4.7
6.6
8.9
10.3
11.6
WSHP-PRC020D-EN
LWT
27.7
62.8
64.7
66.2
66.8
67.3
67.8
61.4
64.6
53.9
56.8
58.5
59.8
60.5
60.9
61.4
59.8
40.2
43.1
45.5
46.9
48.1
48.6
49.0
49.4
27.9
28.2
34.8
36.8
38.1
39.1
39.5
39.8
66.4
68.0
68.7
69.1
69.7
69.0
72.4
74.5
76.2
76.9
77.5
Performance Data
Table 14. GET 024 heating performance (continued)
EWT
86
GPM
7.0
Total Gross
(Mbtuh)
33.3
Heat of Absorb
(Mbtuh)
27.9
Compr Power
(kW)
1.57
LWT
78.0
WPD
(feet head)
13.2
Notes:
Heating performance data is tabulated at 68°F DB entering air at AHRI/ISO 13256-1 rated cfm. See Performance correction tables to correct performance at conditions other than those tabulated. Interpolation of data is permissible, extrapolation is not. Rated GPM 5.6; Minimum cfm
656; Rated cfm 820; Maximum cfm 984.
EWT
45
77
77
77
77
75
75
75
77
77
77
86
86
75
75
75
75
68
68
68
68
55
68
68
68
55
55
55
55
45
45
55
55
45
45
45
45
Table 15. GET 036 cooling performance
Total Gross
(Mbtuh)
41.9
38.4
38.4
38.4
37.6
37.8
38.0
38.1
38.1
39.4
39.4
39.4
39.5
37.9
38.1
38.3
38.3
38.1
38.1
36.2
36.4
41.1
41.2
41.2
41.2
41.3
38.9
39.1
39.3
42.1
42.3
42.4
42.5
42.6
42.6
40.6
40.9
GPM
4.5
5.8
7.1
8.4
9.1
9.1
9.8
10.5
4.5
4.5
5.8
7.1
8.4
8.4
9.1
9.8
10.5
9.8
10.5
4.5
5.8
10.5
4.5
5.8
7.1
7.1
8.4
9.1
9.8
9.8
10.5
4.5
5.8
5.8
7.1
8.4
9.1
Heat of Rej
(Mbtuh)
46.1
44.3
44.2
44.2
44.3
44.2
44.2
44.1
44.1
44.7
44.7
44.7
44.7
44.4
44.4
44.3
44.3
44.1
44.1
43.7
43.6
45.5
45.5
45.5
45.5
45.5
44.9
44.8
44.7
46.0
46.0
46.0
46.0
46.0
46.0
45.6
45.6
SHR
0.75
0.79
0.78
0.78
0.80
0.79
0.79
0.79
0.79
0.78
0.77
0.78
0.78
0.79
0.79
0.79
0.78
0.79
0.79
0.81
0.81
0.76
0.76
0.76
0.76
0.76
0.78
0.78
0.78
0.75
0.75
0.75
0.75
0.75
0.75
0.76
0.76
Gross Sen
(Mbtuh)
31.5
30.1
30.2
30.2
29.9
30.0
30.0
30.1
30.1
30.6
30.5
30.6
30.6
30.0
30.1
30.1
30.1
30.1
30.1
29.3
29.4
31.2
31.2
31.3
31.3
31.3
30.4
30.5
30.5
31.7
31.7
31.8
31.9
31.9
31.9
31.0
31.2
Comp Pwr
(kW)
1.23
1.72
1.71
1.70
1.96
1.87
1.82
1.78
1.77
1.57
1.55
1.54
1.53
1.91
1.82
1.77
1.74
1.76
1.75
2.19
2.10
1.31
1.27
1.26
1.25
1.23
1.74
1.66
1.60
1.14
1.08
1.04
1.02
1.01
0.99
1.45
1.36
LWT
65.5
84.7
84.0
83.4
96.7
92.2
89.4
87.5
86.7
78.6
77.8
77.1
76.5
94.7
90.3
87.5
85.5
86.0
85.4
105.4
101.0
67.8
65.8
65.0
64.3
63.7
87.9
83.4
80.6
60.9
57.9
55.9
55.1
54.4
53.8
75.2
70.7
WPD
(feet head)
5.6
17.3
19.7
22.2
5.0
7.8
11.1
14.9
17.2
15.4
17.7
20.1
22.7
5.0
7.9
11.2
15.0
19.5
22.0
4.9
7.6
12.0
16.1
18.5
21.1
23.8
5.2
8.0
11.5
8.8
12.5
16.8
19.3
22.0
24.8
5.4
8.4
WSHP-PRC020D-EN 33
Performance Data
Table 15. GET 036 cooling performance (continued)
EWT
86
GPM
7.1
Total Gross
(Mbtuh)
36.5
Gross Sen
(Mbtuh)
29.4
SHR
0.80
Heat of Rej
(Mbtuh)
43.5
Comp Pwr
(kW)
2.05
LWT
98.3
WPD
(feet head)
10.8
105
105
105
105
95
95
95
105
95
95
95
95
86
86
86
86
5.8
7.1
8.4
9.1
9.1
9.8
10.5
4.5
4.5
5.8
7.1
8.4
8.4
9.1
9.8
10.5
35.2
35.2
35.2
32.9
33.1
33.2
33.3
33.4
36.6
36.7
36.7
36.7
34.7
34.9
35.0
35.1
28.9
29.0
29.0
28.1
28.2
28.2
28.2
28.2
29.5
29.5
29.6
29.5
28.8
28.9
28.9
28.9
0.82
0.82
0.82
0.85
0.85
0.85
0.85
0.85
0.80
0.80
0.81
0.80
0.83
0.83
0.82
0.82
42.8
42.8
42.8
42.4
42.3
42.2
42.1
42.1
43.5
43.5
43.5
43.5
43.1
43.0
42.9
42.9
2.24
2.23
2.22
2.79
2.68
2.62
2.58
2.56
2.01
1.99
1.98
1.97
2.46
2.36
2.30
2.27
104.4
103.7
103.1
123.9
119.6
116.9
115.0
114.2
96.4
95.5
94.9
94.3
114.2
109.8
107.1
105.2
115
115
115
115
105
105
115
115
7.1
8.4
9.1
9.8
9.8
10.5
4.5
5.8
33.4
33.4
31.0
31.2
31.3
31.4
31.4
31.4
28.3
28.3
27.3
27.4
27.5
27.5
27.5
27.5
0.85
0.85
0.88
0.88
0.88
0.88
0.88
0.87
42.1
42.0
41.8
41.6
41.5
41.4
41.4
41.3
2.54
2.53
3.16
3.05
2.98
2.94
2.92
2.90
113.6
113.0
133.6
129.3
126.7
124.9
124.1
123.4
17.2
19.4
4.2
6.6
9.5
12.8
14.7
16.7
115
120
120
120
10.5
4.5
5.8
7.1
31.5
30.0
30.2
30.3
27.5
26.9
26.9
27.0
0.87
0.89
0.89
0.89
41.3
41.3
41.2
41.1
2.89
3.30
3.21
3.15
122.9
138.4
134.2
131.6
18.9
4.4
6.7
9.4
120
120
120
120
8.4
9.1
9.8
10.5
30.4
30.4
30.4
30.4
27.0
27.0
27.0
27.0
0.89
0.89
0.89
0.89
41.0
40.9
40.9
40.9
3.10
3.08
3.06
3.05
129.8
129.0
128.3
127.8
12.5
14.4
16.5
18.7
Notes:
Cooling performance data is tabulated at 80.6°F DB/66.2°F WB entering air at AHRI/ISO 13256-1 rated cfm.For AHRI/ISO 13256-1 certified ratings, see
. See Performance correction tables to correct performance at conditions other than those tabulated. Interpolation of data is permissible, extrapolation is not. Rated GPM 8.4; Minimum cfm 936; Rated cfm 1170; Maximum cfm 1404.
15.5
17.7
20.0
4.3
6.8
9.7
13.1
15.1
14.5
16.7
19.0
21.4
4.5
7.0
10.0
13.5
Table 16. GET 036 heating performance
EWT
25
25
25
25
GPM
4.5
5.8
7.1
8.4
Total Gross
(Mbtuh)
23.4
23.9
24.3
24.6
Heat of Absorb
(Mbtuh)
16.9
17.4
17.8
18.1
Compr Power
(kW)
1.90
1.90
1.90
1.90
LWT
17.5
19.0
20.0
20.7
WPD
(feet head)
7.6
11.8
16.8
22.5
34 WSHP-PRC020D-EN
Performance Data
EWT
25
68
68
75
75
68
68
68
68
55
55
55
68
55
55
55
55
45
45
45
45
32
45
45
45
32
32
32
32
25
25
32
32
75
77
77
77
75
75
75
75
77
77
77
Table 16. GET 036 heating performance (continued)
Total Gross
(Mbtuh)
24.6
41.2
41.8
42.2
42.3
42.5
42.6
42.9
44.2
34.7
35.7
36.2
36.6
36.7
36.8
36.9
40.1
27.3
30.9
31.6
32.1
32.4
32.5
32.6
32.7
24.7
24.8
25.7
26.4
26.8
27.0
27.2
27.3
44.9
45.4
45.5
45.6
45.7
43.8
45.1
45.8
46.2
46.4
46.5
GPM
9.1
9.8
10.5
4.5
5.8
5.8
7.1
8.4
9.1
9.1
9.8
10.5
4.5
4.5
5.8
7.1
8.4
10.5
4.5
5.8
7.1
8.4
9.1
9.8
10.5
7.1
8.4
9.1
9.8
9.8
10.5
4.5
5.8
10.5
4.5
5.8
7.1
7.1
8.4
9.1
9.8
8.4
9.1
9.8
Heat of Absorb
(Mbtuh)
18.1
33.9
34.5
34.9
35.0
35.2
35.3
35.5
36.8
27.7
28.7
29.2
29.6
29.7
29.8
29.9
32.8
20.8
24.0
24.8
25.3
25.6
25.7
25.8
25.9
18.2
18.3
19.1
19.8
20.2
20.5
20.6
20.7
37.5
37.9
38.0
38.1
38.2
36.3
37.6
38.3
38.7
38.8
38.9
WSHP-PRC020D-EN
Compr Power
(kW)
1.90
2.14
2.13
2.13
2.13
2.13
2.13
2.17
2.19
2.05
2.05
2.05
2.05
2.05
2.05
2.05
2.13
1.92
2.00
1.99
1.99
1.99
1.99
1.99
1.98
1.90
1.90
1.92
1.93
1.93
1.92
1.92
1.92
2.19
2.19
2.18
2.19
2.18
2.19
2.20
2.21
2.20
2.20
2.20
WPD
(feet head)
25.8
8.0
11.5
15.4
17.7
20.1
22.7
5.0
7.9
5.4
8.4
12.0
16.1
18.5
21.1
23.8
5.2
32.2
5.6
8.8
12.5
16.8
19.3
22.0
24.8
29.4
33.2
7.4
11.5
16.3
21.8
25.1
28.5
11.2
15.0
17.3
19.7
22.2
5.0
7.8
11.1
14.9
17.2
19.5
35
LWT
21.0
56.3
58.3
59.7
60.3
60.8
61.3
59.2
62.3
42.7
45.1
46.8
48.0
48.5
48.9
49.3
53.4
28.0
34.3
36.5
37.9
38.9
39.4
39.7
40.1
21.3
21.5
23.5
25.2
26.3
27.1
27.5
27.8
64.5
66.0
66.6
67.2
67.7
60.9
64.0
66.2
67.8
68.5
69.1
Performance Data
Table 16. GET 036 heating performance (continued)
EWT
77
GPM
10.5
Total Gross
(Mbtuh)
46.6
Heat of Absorb
(Mbtuh)
39.0
Compr Power
(kW)
2.20
LWT
69.6
WPD
(feet head)
22.0
86
86
86
86
4.5
5.8
7.1
8.4
47.7
49.1
49.9
50.3
39.9
41.3
42.1
42.5
2.27
2.29
2.30
2.30
68.3
71.8
74.2
75.9
4.9
7.6
10.8
14.5
86
86
9.1
9.8
50.5
50.6
42.6
42.7
2.30
2.30
76.6
77.3
16.7
19.0
86 10.5
50.6
42.8
2.30
77.9
21.4
Notes: Heating performance data is tabulated at 68°F DB entering air at AHRI/ISO 13256-1 rated cfm. See Performance correction tables to correct performance at conditions other than those tabulated. Interpolation of data is permissible, extrapolation is not. Rated GPM 8.4; Minimum cfm
936; Rated cfm 1170; Maximum cfm 1404.
Table 17. Correction factors for variation in entering air temperature
Cooling
Entering
Air WB°F
Cooling
Capacity
Cooling
Input
Watts
Sensible vs. Entering Dry Bulb Multipliers
65.6
70.6
75.6
80.6
49.4 0.954 1.005 0.995 1.059 1.123 *
85.6
*
56.3 0.953 1.005 0.816 1.036 1.122 *
60.3 0.952 1.006 0.612 0.846 1.070 *
*
*
63.2 0.963 1.004 0.466 0.700 0.926 1.150 *
66.2 1.000 1.000 — 0.545 0.773 1.000 1.221
72.1 1.087 0.992 —
77.1 1.166 0.983 —
—
—
0.464 0.696 0.920
— 0.431 0.653
Heating
Entering
Air DB°F
Heating
Capacity
Heating
Input
Watts
53.0 1.025 0.853
58.0 1.017 0.899
63.0 1.012 0.950
68.0 1.000 1.000
73.0 0.992 1.055
78.0 0.984 1.116
83.0 0.975 1.179
Table 18. Correction factors for variation in air flow
Model
GET 012
Entering CFM Cooling Capacity
Sensible
Capacity
Cooling Input
Watts
Heating
Capacity
Heating Input
Watts
272 0.961 0.868 1.004 0.989 1.098
289 0.972 0.902 1.003 0.993 1.068
306 0.982 0.934 1.002 0.996 1.043
323 0.991 0.967 1.001 0.998 1.020
340 1.000 1.000 1.000 1.000 1.000
357 1.009 1.032 0.999 1.003 0.984
374 1.017 1.064 0.998 1.004 0.968
391 1.024 1.094 0.998 1.006 0.954
408 1.031 1.124 0.997 1.008 0.942
303 0.961 0.879 1.006 0.975 1.086
323 0.972 0.910 1.004 0.984 1.061
342 0.982 0.940 1.003 0.991 1.038
361 0.991 0.970 1.001 0.996 1.018
380 1.000 1.000 1.000 1.000 1.000
399 1.009 1.032 0.999 1.004 0.984
418 1.016 1.061 0.998 1.009 0.970
437 1.023 1.090 0.997 1.013 0.958
487 1.035
1.162
0.994
1.025
0.929
36 WSHP-PRC020D-EN
Performance Data
Table 18. Correction factors for variation in air flow (continued)
Model
GET 018
Entering CFM Cooling Capacity
Sensible
Capacity
Cooling Input
Watts
Heating
Capacity
Heating Input
Watts
432 0.961 0.865 1.010 0.975 1.082
459 0.972 0.899 1.007 0.982 1.057
486 0.982 0.933 1.006 0.989 1.036
513 0.990 0.968 1.003 0.995 1.017
540 1.000 1.000 1.000 1.000 1.000
567 1.008 1.034 0.997 1.005 0.984
594 1.015 1.067 0.995 1.009 0.971
621 1.022 1.098 0.993 1.013 0.958
648 1.029 1.125 0.991 1.017 0.947
501 0.954
0.866
1.015
0.994
1.074
553 0.973 0.907 1.003 0.995 1.061
585 0.983 0.939 1.002 0.997 1.038
618 0.992 0.970 1.001 0.998 1.018
650 1.000 1.000 1.000 1.000 1.000
683 1.008 1.030 0.999 1.002 0.985
715 1.015 1.060 0.998 1.001 0.969
748 1.022 1.087 0.997 1.003 0.956
780 1.028 1.117 0.996 1.002 0.944
656 0.962 0.877 1.003 0.974 1.079
697 0.973 0.910 1.002 0.981 1.055
738 0.983 0.940 1.000 0.988 1.034
779 0.992 0.970 1.001 0.995 1.016
820 1.000 1.000 1.000 1.000 1.000
861 1.008 1.029 0.999 1.005 0.985
902 1.014 1.058 0.998 1.010 0.972
943 1.022 1.088 0.997 1.014 0.961
984 1.028 1.117 0.996 1.018 0.950
936 0.957 0.876 1.002 0.974 1.077
995 0.969 0.907 1.001 0.981 1.052
1053 0.980 0.939 1.001 0.989 1.033
1112 0.990 0.970 1.000 0.994 1.015
1170 1.000 1.000 1.000 1.000 1.000
1229 1.009 1.032 1.000 1.005 0.987
1287 1.017 1.062 0.999 1.010 0.974
1346 1.024 1.090 0.999 1.014 0.963
1404 1.033 1.121 0.999 1.018 0.953
WSHP-PRC020D-EN 37
Unit Fan Performance
Table 19. PSC blower motor external static pressure without return air door (RAD) with filter
External Static Pressure (in. of wg)
(a) The NO “Ducted” option is for non-ducted (free return) units. Units specified as “non-ducted” (free return) are factory wired to low-speed. Units specified as “ducted” are factory wired to high-speed.
38 WSHP-PRC020D-EN
Unit Fan Performance
Table 20. ECM Blower motor external static pressure without return air door (RAD) with filter
Model
No.
External Static Pressure (in. of wg)
Speed
Profile
0.00 0.05 0.10 0.15 0.20 0.25 0.30 0.35 0.40 0.45 0.50 0.55 0.60 0.65 0.70
CFM kW kW kW kW kW kW kW kW kW kW kW kW kW kW kW
A 374 0.025 0.037 0.050 0.062 0.075 0.087 0.098 0.110 0.121 0.133 0.144 0.155 0.165 0.176 0.176
GET 009
GET 012
GET 015
GET 018
D
A
B
C
D
A
B
C
D
A
B
C
D
A
B
C
344 0.023 0.035 0.046 0.057 0.068 0.079 0.090 0.100 0.110 0.120 0.130 0.140 0.149 0.159 0.159
313 0.021 0.032 0.042 0.052 0.062 0.071 0.081 0.090 0.099 0.108 0.117 0.126 0.134 0.143 0.143
285 0.017 0.027 0.036 0.045 0.054 0.063 0.071 0.080 0.088 0.096 0.104 0.112 0.120 0.127 0.127
487 0.027 0.042 0.057 0.071 0.086 0.100 0.114 0.128 0.142 0.155 0.168 0.181 0.193 0.206 0.206
442 0.025 0.038 0.052 0.065 0.077 0.090 0.103 0.115 0.127 0.139 0.151 0.162 0.173 0.184 0.184
403 0.023 0.034 0.046 0.057 0.069 0.080 0.091 0.102 0.112 0.122 0.133 0.142 0.152 0.161 0.161
368 0.019 0.029 0.039 0.049 0.059 0.068 0.078 0.087 0.096 0.105 0.114 0.123 0.131 0.139 0.139
594 0.062 0.072 0.081 0.090 0.100 0.109 0.119 0.128 0.138 0.148 0.158 0.168 0.179 0.191 0.202
540 0.044 0.054 0.064 0.073 0.083 0.092 0.101 0.111 0.121 0.131 0.141 0.151 0.162 0.173 0.185
486 0.032 0.042 0.051 0.060 0.069 0.079 0.088 0.097 0.106 0.116 0.126 0.136 0.146 0.157 0.168
432 0.025 0.034 0.042 0.051 0.059 0.068 0.076 0.085 0.093 0.102 0.111 0.120 0.130 0.140 0.150
712 0.097 0.109 0.121 0.134 0.148 0.163 0.178 0.193 0.208 0.223 0.239 0.253 0.268 0.282 0.282
648 0.077 0.087 0.098 0.110 0.123 0.136 0.150 0.163 0.177 0.191 0.205 0.218 0.230 0.242 0.242
584 0.056 0.066 0.076 0.087 0.099 0.111 0.123 0.135 0.148 0.160 0.172 0.183 0.194 0.204 0.204
522 0.039 0.048 0.058 0.069 0.080 0.091 0.102 0.114 0.125 0.136 0.147 0.157 0.166 0.175 0.175
903 0.100 0.118 0.135 0.152 0.168 0.185 0.201 0.216 0.232 0.247 0.261 0.276 0.290 0.303 0.303
GET 024
D
A
B
C
827 0.081 0.096 0.111 0.125 0.140 0.154 0.168 0.182 0.196 0.209 0.222 0.236 0.248 0.261 0.261
746 0.060 0.073 0.085 0.098 0.110 0.123 0.136 0.148 0.161 0.173 0.185 0.198 0.210 0.222 0.222
659 0.041 0.052 0.063 0.074 0.085 0.097 0.109 0.121 0.133 0.145 0.157 0.169 0.182 0.194 0.194
1293 0.285 0.306 0.328 0.349 0.370 0.392 0.413 0.433 0.454 0.475 0.496 0.516 0.537 0.557 0.557
GET 036
B
C
1178 0.214 0.233 0.253 0.272 0.292 0.311 0.330 0.349 0.369 0.388 0.406 0.425 0.444 0.463 0.463
1063 0.158 0.175 0.193 0.210 0.227 0.245 0.262 0.279 0.296 0.313 0.331 0.348 0.365 0.382 0.382
D 950 0.117 0.133 0.148 0.163 0.178 0.193 0.208 0.223 0.238 0.254 0.269 0.284 0.299 0.314 0.314
Note:
The ECM motor is programmed for constant CFM. The CFM is factory set on Profile B. The ECM motor will reduce airflow to 50% in fan only mode for additional energy savings.
Figure 5.
ECM control board and dip switch setting
Dip switch to select profile
WSHP-PRC020D-EN 39
Unit Fan Performance
Table 21. Pressure drop due to return air door (RAD)
Model No.
GET 009
CFM
272
DP
0.04
CFM
340
DP
0.05
CFM
408
DP
0.08
GET 012
GET 015
GET 018
GET 024
303
432
520
656
0.04
0.06
0.08
0.06
380
540
650
820
0.07
0.09
0.12
0.08
456
648
780
984
0.11
0.12
0.16
0.12
GET 036 936 0.10
1170 0.16
1404 0.23
Note:
The pressure drop across the RAD door should be included in the TOTAL ESP when determining airflow and fan motor power usage. If the door is supplied by another vendor, the pressure drop across that door must be included in the TOTAL ESP when determining airflow and fan motor power usage.
Table 22. Antifreeze correction factors
Item
Item
Item
Item
Methanol
0% 10%
Concentration by Volume
20% 30% 40% 50%
1.000 0.998 0.997 0.995 0.993 0.992
1.000 0.995 0.990 0.985 0.979 0.974
1.000 1.023 1.057 1.091 1.122 1.160
Ethylene Glycol
Concentration by Volume
20% 30% 0% 10% 40% 50%
1.000 0.996 0.991 0.987 0.983 0.979
1.000 0.993 0.985 0.977 0.969 0.961
1.000 1.024 1.068 1.124 1.188 1.263
Propylene Glycol
0% 10%
Concentration by Volume
20% 30% 40% 50%
1.000 0.993 0.987 0.980 0.974 0.968
1.000 0.986 0.973 0.960 0.948 0.935
1.000 1.040 1.098 1.174 1.273 1.405
Brine (NaCL)
Concentration by Volume
0% 10% 20% 30% 40% 50%
1.000 0.994 0.987 0.979 0.971 0.963
1.000 0.993 0.987 0.982 0.978 0.976
1.000 1.154 1.325 1.497 1.669 1.841
40 WSHP-PRC020D-EN
Unit Fan Performance
Figure 6.
Cooling capacity correction factor
Figure 7.
Heating capacity correction factor
Figure 8. Water pressure drop correction factor
WSHP-PRC020D-EN
Example 1 (Ethylene Glycol):
The antifreeze solution is 20% by volume of Ethylene Glycol.
Determine the corrected cooling capacity and waterside pressure drop for a GET009 when the EWT is 86°F and the GPM is 2.3.
From the catalog data, the cooling capacity at these conditions with 100% water is 8.3 Mbtuh, and the waterside pressure drop is 9.1 feet of head. At 20% Ethylene Glycol, the correction factor for cool capacity is 0.9912 and the pressure drop is 1.068.
The corrected cooling capacity (Mbtuh) = 8.50* 0.9912 = 8.43. The corrected water side pressure drop (Ft. head) = 9.1 * 1.068 = 9.72.
Example 2 (Propylene Glycol):
The antifreeze solution is 30% by volume of Propylene Glycol.
Determine the corrected heating capacity and waterside pressure drop for a GET009 when the EWT is 45°F and the GPM is 2.3.
From the catalog data, the heating capacity at these conditions with 100% water is 8.3 Mbtuh, and the waterside pressure drop is 11.1 feet of head. At 30% Propylene Glycol, the correction factor for heat capacity is 0.9603 and the pressure drop is 1.174.
The corrected heating capacity (Mbtuh) = 8.3 * 0.9603 = 7.97.The corrected water side pressure drop
(Ft. head) = 11.1 * 1.174 = 13.03.
41
Electrical Data
Table 23. Electrical performance
Model No.
GET 009
GET 012
GET 015
GET 018
GET 024
GET 036
Motor
Option
PSC Motor
ECM Motor
PSC Motor
ECM Motor
PSC Motor
ECM Motor
Free
Discharge
PSC Motor
ECM Motor
Ducted
PSC Motor
PSC Motor
ECM Motor
PSC Motor
ECM Motor
Unit Volts
208/60/1
265/60/1
208/60/1
230/60/1
265/60/1
208/60/1
230/60/1
265/60/1
208/60/1
230/60/1
265/60/1
208/60/1
230/60/1
265/60/1
208/60/1
230/60/1
265/60/1
230/60/1
265/60/1
208/60/1
230/60/1
265/60/1
208/60/1
230/60/1
265/60/1
208/60/1
230/60/1
265/60/1
208/60/1
230/60/1
265/60/1
208/60/1
230/60/1
208/60/1
230/60/1
265/60/1
208/60/1
230/60/1
265/60/1
Comp RLA
(ea)
3.7
9.6
7.7
13.5
13.5
9.0
13.5
13.5
9.0
9.6
9.6
7.7
9.6
6.4
9.6
9.6
7.7
14.1
14.1
12.2
14.1
14.1
12.2
7.9
6.4
7.9
7.9
6.3
6.3
5.0
7.9
2.8
6.3
6.3
5.0
3.5
2.8
3.7
3.5
Total
FLA
4.3
11.3
8.8
15.7
15.7
10.8
14.5
14.5
10.0
7.0
10.3
10.3
8.3
10.2
10.2
8.3
11.3
17.7
17.7
15.0
16.1
16.1
14.2
8.6
7.0
8.5
8.5
6.9
6.9
5.6
8.6
3.4
7.0
7.0
5.6
4.1
3.3
4.3
4.1
Blower
Motor FLA
0.60
1.70
1.10
2.20
2.20
1.80
0.95
0.95
0.95
0.60
0.70
0.70
0.60
0.60
0.60
0.60
1.70
3.60
3.60
2.77
2.00
2.00
2.00
0.60
0.60
0.60
0.70
0.70
0.60
0.60
0.60
0.60
0.50
0.55
0.55
0.55
0.70
0.70
0.60
Comp
LRA
16.0
42.0
35.0
58.3
58.3
54.0
58.3
58.3
54.0
30.0
42.0
42.0
35.0
42.0
42.0
35.0
42.0
77.0
77.0
72.0
77.0
77.0
72.0
30.0
30.0
23.0
36.0
36.0
30.0
36.0
36.0
17.0
13.0
16.0
17.0
13.0
30.0
30.0
23.0
Blower
Motor HP
1/20
1/5
1/5
1/3
1/3
1/3
1/2
1/2
1/2
1/2
1/8
1/8
1/8
1/2
1/2
1/2
1/5
1/2
1/2
1/2
3/4
3/4
3/4
1/3
1/3
1/3
1/8
1/8
1/8
1/2
1/2
1/20
1/20
1/3
1/3
1/3
0.13
0.13
0.13
Minimum
Circuit
Ampacity
5.23
13.70
10.73
19.08
19.08
13.05
17.83
17.83
12.20
8.60
12.70
12.70
10.23
12.60
12.60
10.23
13.70
21.23
21.23
18.02
19.63
19.63
17.25
8.48
8.48
6.85
10.58
10.58
8.60
10.48
10.48
4.98
4.00
5.18
4.93
4.05
8.58
8.58
6.85
Maximum
Overcurrent
Protective
Device
15
20
30
30
20
20
15
30
30
20
20
15
20
15
20
20
15
35
35
30
30
30
25
15
15
15
15
15
15
15
15
15
15
15
15
15
15
15
15
42 WSHP-PRC020D-EN
Dimensional Data
Figure 9.
Unit cabinet/riser
TOP
12 1/2"
(318)
8" (203)
3 3/4"
(95) R S D
VARIES DEPENDENT
ON RISER O.D.
OPTIONAL
DUCT OPENING
1" (12.7) DUCT
COLLAR
B
SWAGE 3" (76)
RETURN
SUPPLY
G
DRAIN
H
1/2" (12.7) O.D.
ELECTRIC CONDUIT
1" (25.4)
J
11" (279) FOR 80" (2032) CABINET HEIGHT
3" (76) FOR 88" (2235) CABINET HEIGHT
SUPPLY-AIR OPENINGS AND RISER LOCATIONS CANNOT
BE ON THE SAME SIDE OF THE UNIT.
K
RISER LOCATION CAN BE ON ANY SIDE EXCEPT FRONT,
AND MAY BE SUPPLIED BY TRANE OR BY OTHERS.
OPTIONNAL 1” or 3” DISCHARGE FLANGE (NOT SHOWN)
A
G
SUPPLY-AIR
OPENING
K
LOW VOLTAGE
CONNECTION BOX
FOR THERMOSTAT
C
CONTROL BOX
THROWAWAY
FILTER
D
Table 24. Unit cabinet/riser
GET
009, 012
015-018
024-036
A
16¼" (413)
18" (457)
24" (610)
CHASSIS
ACCESS
PANEL
4 3/4"
(121)
F
FRONT
DRAIN
CONNECTION
3/4" (19) O.D.
E
B
16¼" (413)
20" (508)
24" (610)
RISER CONNECTION
1/2” (13) NPTE = 009-018
3/4” (19) NPTE = 024,036
NOTE:
RIGHT RISER
LOCATION SHOWN
IN FRONT AND RIGHT
VIEWS.
RIGHT SIDE
C
8 1/8" (206)
10" (254)
12" (305)
D
39 1/8" (994)
40 5/8" (1032)
49 5/8" (1260)
E
14¾" (375)
18¾" (476)
22 5/8" (575)
F
¾" (19)
¾" (19)
¾" (19
WSHP-PRC020D-EN 43
Dimensional Data
Figure 10. Unit cabinet/riser
WATER OUT
1/2" (13) NPTI = GET 009-018
3/4" (19) NPTI = GET 024-036
7/8" (22 mm) O.D.
FOR FIELD ELECTRIC
CONDUIT
A
3 3/4"
(95)
8"
(203)
R
E
T
U
R
N
S
U
P
P
L
Y
D
R
A
I N
12 1/2"
(318)
B
C
1"
(24.4)
LOW VOLTAGE
CONNECTION BOX
FOR UNIT MTD
THERMOSTAT
1/2" (12.7) O.D.
FACTORY
ELECTRIC CONDUIT
K
60"
(1524)
D
J
E
H
F
G
NOTE: REAR RISER
LOCATION SHOWN.
Table 25. Dimensional data - unit cabinet/riser
Unit Size
009
012
015-018
024-036
A
16¼"
(413)
16¼"
(413)
18"
(457)
24"
(610)
B
16¼"
(413)
16¼"
(413)
20"
(508)
24"
(610)
C
8 1/8"
(206)
8 1/8"
(206)
10"
(254)
12"
(305)
D
43 7/8"
(1114)
43 7/8"
(1114)
45 3/8"
(1153)
54 3/8"
(1381)
E
32½"
(826)
32½"
(826)
34 8/9"
(886)
41"
(1041)
F
13 5/8"
(346)
13 5/8"
(346)
17 3/8"
(441)
21 3/8"
(543)
G
14"
(356)
14"
(356)
16 1/8"
(410)
22"
(559)
H
16 7/8"
(429)
16 3/8"
(416)
18½"
(470)
21¾"
(552)
J
4 3/8"
(111)
4 3/8"
(111)
5¾"
(146)
4"
(102)
K
6¾"
(171)
6¾"
(171)
4¾"
(121)
6"
(152)
44 WSHP-PRC020D-EN
Water Flow Control
The factory installed water flow control option is hard piped to the copper or cupro-nickel water coil. The selection is available in a high or low flow option. An isolation valve and strainer are standard when the factory flow device is selected.
Two foot hose and ball valves are recommended for these units. The hoses and ball valves are optional and can be selected with the chassis portion of the order, or can be field provided.These items are shipped separate from the chassis.
Dimensional Data
Water In
Strainer
Isolation Valve
Water Out
Flow
Control
Table 26. Factory hose kit flow options
Unit Size
009
012
015
018
024
036
Low Flow
Digit 9 = 3,4
1.5 GPM
2.0 GPM
2.5 GPM
3.0 GPM
4.0 GPM
6.0 GPM
High Flow
Digit 9 = 5,6
2.0 GPM
2.5 GPM
3.5 GPM
4.0 GPM
6.0 GPM
8.0 GPM
WSHP-PRC020D-EN 45
Dimensional Data
Figure 11. Riser to unit connection
RISER ARRANGEMENTS
SYSTEM SUPPLY IS FROM THE BOTTOM.
- ALL RISERS ARE CAPPED AT THE CABINET
RUN OUTS.
SYSTEM SUPPLY IS FROM THE TOP OR BOTTOM.
- DRAIN RISER IS CAPPED AT THE CABINET
RUN OUT.
- BOTTOM SUPPLY AND RETURN RISERS
ARE PIPED WITH OPEN TOP FOR VENTING
OR FLUSHING.
- TOP SUPPLY AND RETURN RISERS.
SYSTEM SUPPLY IS FROM THE TOP OR BOTTOM.
- TOP OR BOTTOM SUPPLY AND RETURN
RISERS ARE OPEN AT THE TOP FOR
SUPPLYING WATER TO OTHER UNITS.
- BOTTOM SUPPLY TO UNITS OPEN AT THE
TOP FOR VENTING OR FLUSHING OF THE SYSTEM.
SYSTEM SUPPLY IS FROM THE BOTTOM.
- CAPPED SUPPLY AND RETURN PIPING.
- OPEN DRAIN FOR VENTING TO ROOF
OR CONDENSATE REMOVAL FROM OTHER
EQUIPMENT.
SUPPLY, RETURN AND DRAIN RISER
CONNECTIONS TO THE UNIT
BACK OR RIGHT VIEW SHOWN
IN FIGURE A
SYSTEM SUPPLY IS FROM THE TOP/BOTTOM.
OR, SYSTEM RETURN IS FROM THE TOP/
BOTTOM.
- SUPPLY OR RETURN CAPPED AT THE
CABINET.
SYSTEM SUPPLY IS FROM THE TOP.
- CAPPED SUPPLY AND RETURN PIPING.
Note: This page may be used in riser schedule preparation for field installed risers.
Factory installed risers are only available as shown in
.
Modification to the factory riser may be required in the field to fit the contractor’s riser schedule.
Riser location and appropriate hose length for ease of service is an important factor during unit installation.
Recommended hose length per riser location includes:
• 2” hose = All riser locations.
Trapping the main condensate riser is recommended but not mandatory as the unit condensate line is trapped internal to the equipment.
46 WSHP-PRC020D-EN
Dimensional Data
Figure 12. Supply-air arrangements
R S D
R
S
D
DIGIT 15 - 0
R
S
D
R
S
D
DIGIT 15 - 1
R
S
D
DIGIT 15 - 2
R
S
D
R
S
D
DIGIT 15 - 3
FIELD CUT SUPPLY-AIR
R S D
DIGIT 15 - 4
R
S
D
FRONT/BACK SUPPLY-AIR
009,012 = 10"W X 6"H
015-024 = 14"W X 12"H
036 = 16"W X 14" H
R S D
R
S
D
DIGIT 15 - 5
BACK/LEFT SUPPLY-AIR
009,012 = 10"W X 6"H
015-024 = 14"W X 12"H
036 = 16"W X 14" H
R S D
DIGIT 15 - 6
R
S
D
BACK/RIGHT SUPPLY-AIR
009,012 = 10"W X 6"H
015-024 = 14"W X 12"H
036 = 16"W X 14" H
DIGIT 15 - 7
FRONT/LEFT SUPPLY-AIR
009,012 = 10"W X 6"H
015-024 = 14"W X 12"H
036 = 16"W X 14" H
DIGIT 15 - 8
R
S
D
FRONT/RIGHT SUPPLY-AIR
009,012 = 10"W X 6"H
015-024 = 14"W X 12"H
036 = 16"W X 14" H
R S D
DIGIT 15 - 9
R
S
D
LEFT/RIGHT SUPPLY-AIR
009,012 = 10"W X 6"H
015-024 = 14"W X 12"H
036 = 16"W X 14" H
DIGIT 15 - B
R
S
D
BACK/FRONT/RIGHT SUPPLY-AIR
009,012 = Not Recommended
015-024 = 12"W X 8"H
036 = 14"W X 12" H
R S D
DIGIT 15 - L
R
S
D
LEFT SUPPLY-AIR
009, 012 = 14"W X 14"H
015, 018 = 16"W X 12"H
024 = 14”W x 16”H
036 = Not Recommended
R
S
D
BACK/FRONT/LEFT SUPPLY-AIR
009,012 = Not Recommended
015-024 = 12"W X 8"H
036 = 14"W X 12" H
FRONT/RIGHT/LEFT SUPPLY-AIR
009,012 = Not Recommended
015-024 = 12"W X 8"H
036 = 14"W X 12" H
R S D
DIGIT 21 - R
R
S
D
R S D
DIGIT 15 - T
R
S
D
R
S
D
BACK SUPPLY-AIR
009, 012 = 14"W X 14"H
015, 018 = 16"W X 12"H
024 = 14”W x 16”H
036 = Not Recommended
R S D
DIGIT 15 - F
R
S
D
RIGHT SUPPLY-AIR
009, 012 = 14"W X 14"H
015, 018 = 16"W X 12"H
024 = 14”W x 16”H
036 = Not Recommended
TOP SUPPLY-AIR
009, 012 = 14" X 10"
015-024 = 16" X 14"
036 = 17" x 17"
FRONT SUPPLY-AIR
009, 012 = 14"W X 14"H
015, 018 = 16"W X 12"H
024 = 14”W x 16”H
036 = Not Recommended
WSHP-PRC020D-EN 47
Dimensional Data
Figure 13. Riser extensions
11"
(279)
24"
(610)
11"
(279)
80"
(2032)
120"
(3048)
29"
(737)
4"
(102)
80"
(2032)
120"
(3048)
136"
(3454)
24"
(610)
88"
(2235)
120"
(3048)
29"
(330)
4"
(102)
88"
(2235)
120"
(3048)
136"
(3454)
29"
(737)
29"
(737)
80" UNIT HEIGHT FOR TOP SUPPLY-AIR 88" UNIT HEIGHT FOR FRONT, BACK, SIDE SUPPLY-AIR
Riser Extensions are field provided and installed.
Note: Riser expansion must be considered when calculating total riser length.
48 WSHP-PRC020D-EN
Dimensional Data
Figure 14. Hinged acoustical door
SHEETROCK
3 1/2” ±3/8”
2“ X 4” STUD
A
1“ X 1” CLOSED
CELL INSULATION
RETURN AIR OPENING
FLANGE ON CABINET
B
SHEET ROCK
OPENING
RETURN AIR OPENING
FLANGE ON CABINET
1“ X 1” CLOSED
CELL INSULATION
SHEETROCK
2“ X 4”
STUD
Note:
Finished wall and framing should not touch the unit cabinetry.
TOP VIEW
CABINET
3 1/2” ±3/8”
A
RETURN AIR
DOOR FRAME
1“ X 1” CLOSED
CELL INSULATION
2 X 4 STUD
RETURN-AIR OPENING
FLANGE ON CABINET
B
RETURN-AIR OPENING
FLANGE ON CABINET
1“ X 1” CLOSED
CELL INSULATION
RETURN AIR
DOOR FRAME
SHEETROCK
FLOOR
1 1/2” X 2 3/8”
3 1/2” ±3/8”
2 1/4“
4 5/8“
5“
CABINET
SIDE VIEW
WSHP-PRC020D-EN 49
Dimensional Data
Table 27. Return air hinged acoustical door
Unit Size
009
012
015
018
024
036
A
19¼”
(489)
23¼”
(591)
27 1/8”
(689)
B
44 1/8”
(1121)
45¼”
(1149)
54 5/8”
(1387)
Return Air (hinged) Acoustical Door
The hinged acoustical door is recessed into the wall so that the door is flush with the surface of the wall.
The opening through the wall for the door assembly must be centered with the return-air opening of the unit cabinet. For full installing instructions of the return-air acoustical door, see WSHP-
SVN08*-EN.
The dimensional data shown is based on Trane’s factory supplied return air door.
Figure 15. Single deflection grille
Blades are adjustable for controlling horizontal discharge path.
Figure 16. Double deflection grille
50
Blades are adjustable for controlling discharge path in both horizontal and vertical paths.
Table 28. Supply air opening size
GET
009, 012
015, 018
024
036
Single Grille
100% CFM
14”W x 14”H
16”Wx12”H
22”Wx18”H
Not Recommended
Two Grille
50% CFM
10”W x 6”H
14”Wx12”H
14”Wx12”H
16”Wx14”H
Three Grille
33% CFM
Not Recommended
12”Wx8”H
12”Wx8”H
14”Wx12”H
Top Discharge up to 100% CFM
14”W x 10”H
16”Wx14”H
16”Wx14”H
17”Wx17”H
WSHP-PRC020D-EN
Controls
Deluxe 24V Electronic Controls
The 24V deluxe design is a microprocessor-based control board conveniently located in the control box.The board is unique toTrane water-source products and is designed to control the unit as well as provide outputs for unit status and fault detection.
The board is factory wired to a terminal strip to provide all necessary terminals for field connections.
The deluxe 24V electronic unit control contains upgraded features to maximize system performance to extend the system life. Each device, is factory mounted, wired, and tested in the unit. Other features include compressor contactor, compressor lockout function, anti-short cycle compressor protection, random start delay, brown-out protection, low pressure time delay, low pressure switch, condensate overflow, freeze protection, high pressure switch, compressor delay on start, reversing valve coil (for heating and cooling units), multi-speed fan motor, soft lockout mode.
Note: Electric heat is optional.
Deluxe 24V features include:
Anti-short Cycle Timer
The anti-short cycle timer provides a three minute time delay between compressor stop and compressor restart. Once thermostat is enabled, an automatic 3 minute delay is provided for compressor protection.
Brown-out Protection
The brown-out protection function measures the input voltage to the controller and halts the compressor operation. Once a brown-out situation has occurred, the anti-short cycle timer will become energized.The general fault contact will not be affected by this condition.The voltage will continue to be monitored until the voltage increases.The compressors will be enabled at this time if all start-up time delays have expired, and all safeties have been satisfied.
Compressor Disable
The compressor disable relay provides a temporary disable in compressor operation. The signal would be provided from a water loop controller in the system. It would disable the compressor because of low water flow, peak limiting or if the unit goes into an unoccupied state. Once the compressor has been disabled, the anti-short cycle time period will begin. Once the compressor disable signal is no longer present, and all safeties are satisfied, the control will allow the compressor to restart.
Diagnostics
Three LEDs (light emitting diodes) are provided for indicating the operating mode of the controller.
See the unit IOM for diagnostics or troubleshooting through the use of the LEDs.
Random Start
The random start relay provides a time delay start-up of the compressor when cycling in the occupied mode. A new start delay time between 3 and 10 seconds is applied each time power is enabled to the unit.
Safety Control
The deluxe microprocessor receives separate input signals from the refrigerant high pressure switch, low suction pressure switch and condensate overflow.
WSHP-PRC020D-EN 51
Controls
In a high pressure situation, the compressor contactor is de-energized, which suspends compressor operation. The control will go into soft lockout mode initializing a three minute time delay and a random start of 3 to 10 second time delays. Once these delays have expired, the unit will be allowed to run. If a high pressure situation occurs within one hour of the first situation, the control will be placed into a manual lockout mode, halting compressor operation, and initiating the general alarm.
In a low temperature situation, the low pressure switch will transition open after the compressor starts. If the switch is open for 45 seconds during compressor start, the unit will go into soft lockout mode initializing a three minute time delay and a random start of 3 to 10 second time delays. Once these delays have expired, the unit will be allowed to run. If the low pressure situation occurs again within 30 minutes, and the device is open for more than 45 seconds, the control will be placed into a manual lockout mode, halting compressor operation, and initiating the general alarm.
In a condensate overflow situation, the control will go into manual lockout mode, halting compressor operation, and initiating the general alarm.
The general alarm is initiated when the control goes into a manual lockout mode for either high pressure, low pressure or condensate overflow conditions. The alarm can be reset at the thermostat or by cycling power to the unit.
Small Building Control
The deluxe 24V electro-mechanical design may be applied as a stand-alone control system or as a multi-unit installation system.With a stand-alone design, units run independently of one another with an electronic digital thermostat.
With a multiple unit installation, the units may be daisy-chained directly to the Trane Tracer loop controller (TLC), pump(s), boiler, and tower for a complete net worked water-source system.
Direct Digital Controls
When the ZN510 controller is linked directly to theTracer
Summit, each Tracer Summit building automation system can connect a maximum of 120 Tracer ZN510 controllers.
52
Tracer ZN510 Controls
The Tracer ZN510 direct digital control (DDC) system is specifically designed for single watersource equipment to provide control of the entire unit, as well as outputs for unit status and fault detection.This device is factory installed, commissioned, and tested to ensure the highest level of quality in unit design.
Each of the controller's features and options were selected to coordinate with the unit hardware to provide greater energy efficiency and equipment safety to prolong the equipment life.
Because the ZN510 is LonTalk certified, it is capable of working with, and talking to other LonTalk certified controllers providing the building owner more choices, and the design engineers more flexibility to meet the challenges of building automation. Features include 75 VA transformer, compressor contactor, compressor lockout relay, compressor run capacitor, random start delay, heating/cooling status, occupied/unoccupied mode, low pressure switch, high pressure switch, fan
WSHP-PRC020D-EN
Controls
and filter status, reversing valve coil, two-speed fan motor and water isolation valve support (for variable speed pumping).
Note: Optional: condensate overflow
Tracer ZN510 functions include:
Building Control Advantages
The Tracer ZN510 controller has the ability to share information with one or several units on the same communication link.This sharing of information is made possible via a twisted pair of wire and a building automation system or through Trane's Rover™ service tool.
An advantage of installing a ZN510 is its capability to work with other LonTalk™ certified controllers. This provides greater flexibility to the building owner, as well as greater flexibility in design.
Integrating the ZN510 on water-source equipment, and tying it to aTracer Summit system provides a complete building management system. EachTracer Summit can connect to a maximum of 120 controllers. With the ICS system, the Tracer can initiate an alarm on a loss of performance on equipment malfunctions; allowing problems to be handled in a timely manner before compromising comfort.
This type of application would most commonly be used for a large space(s) that may require more than one unit. In addition to this application design, theTracer ZN510 controller provides a way for units located within the same space to share the same zone sensor to prevent units from simultaneously heating and cooling in the same space.
Compressor Operation
The compressor is cycled on and off to meet heating or cooling zone demands.The control of the unit uses the units’ capacity and pulse width modulation (PWM) logic along with minimum on/off timers to determine the compressor's operation. The compressor is controlled ON for longer periods as capacity increases and shorter periods as capacity decreases.
Condensate Overflow
When condensate reaches the trip point, a condensate overflow signal generates a diagnostic which disables the fan, unit water valves (if present), and compressor. The unit will remain in a halted state until the condensation returns to a normal level. At this time, the switch in the drain pan will automatically reset. However, the controller's condensate overflow diagnostic must be manually reset to clear the diagnostic and restart the unit.
Data Sharing
TheTracer ZN510 controller is capable of sending or receiving data (setpoints, fan request, or space temperature) to and from other controllers on the communication link.This allows multiple units to share a common space temperature sensor in both stand-alone and building automation applications.
Fan Operation
The supply air fan operates at the factory wired speed in the occupied or occupied standby mode.
When switch is set to AUTO, the fan is configured for cycling ON with heating or cooling. In heat mode, the fan will run for 30 seconds beyond compressor shutdown in both occupied and unoccupied mode.
Fan Run Timer
The controller's filter status is based on the unit fan's cumulative run hours. The controller compares the fan run time against an adjustable fan run hours limit and recommends unit maintenance as required.
WSHP-PRC020D-EN 53
Controls
High and Low Pressure Safety Controls
TheTracer ZN510 controller detects the state of the high pressure or low pressure switches. When a fault is sensed by one of these switches, the corresponding message is sent to the controller to be logged into the fault log. When the circuit returns to normal, the high pressure control and low pressure control automatically reset. If a second fault is detected within a thirty-minute time span, the unit must be manually reset.
Random Start
To prevent all of the units in a building from energizing major loads at the same time, the controller observes a random start from 0 to 25 seconds.This timer halts the controller until the random start time expires.
Reversing Valve Operation
For cooling, the reversing valve output is energized simultaneously with the compressor. It will remain energized until the controller turns on the compressor for heating. At this time, the reversing valve moves to a de-energized state. In the event of a power failure or controller OFF situation, the reversing valve output will default to the heating (de-energized) state.
54 WSHP-PRC020D-EN
Thermostats and Zone Sensors
Table 29. Thermostat/sensor selection
Thermostat/Sensor Part Number
X13511211010
X13511212010
X13511213010
X13511214010
X13651467020
Description
3 Heat/2 Cool Digital Display Thermostat
• 3 H/2 C
• Non Programmable
2 Heat/2 Cool Digital Display Programmable Thermostat
• 2 H/2 C
• 7-Day Programmable
2 Heat/2 Cool Digital Display Programmable Thermostat with
Touch Screen
• 2 H/2 C
• 7-Day Programmable with Touch Screen
3 Heat/2 Cool Digital Display Programmable Thermostat with
Relative Humidity Sensing Built-in
• 3 H/2 C
• 7-Day Programmable
• Humidity Sensing
Communication Module
• Sold in packs of 12
• Compatible with X1351529010 and X13511527010
X13511529010
X13511527010
X1379084501
Zone Sensor
• Tracer ZN510 and ZN524 compatible
• External setpoint adjustment wheel
Zone Sensor
• Tracer ZN510 and ZN524 compatible
• External setpoint adjustment wheel
• ON and CANCEL buttons
Zone Sensor
• Tracer ZN510 and ZN524 compatible
• External setpoint adjustment wheel
• ON and CANCEL buttons
• Fan switch AUTO-OFF
WSHP-PRC020D-EN 55
Accessories
System balancing hose kit
For automatic system balancing of a water source heat pump, the Mesurflo® self-balancing hose kit provides a constant flow rate over the pressure differential rage of 2 to 80 psid. As system pressure changes (through further addition of heat pumps, for example) each individual flow control valve will automatically adjust to the new system conditions. In variable water volume applications, a self-balancing hose kit can provide continuous balancing because of its ability to automatically adjust to the varying system conditions.
Note: At low differential pressure the flow area required to achieve higher flow can exceed the flow area available for the respective series.Therefore, the minimum pressure differential requirement is increased for the higher flow ranges of each series Mesurflo valve.
Figure 17.
Ball valve kit (manual)/MeasurfloVac kit (automatic)
Optional Isolation Valve
2-Position Valve
Optional Isolation Valve
2-Position Valve
Mesurmeter w/PT’s
AUTOMATIC
TEMPERATURE
CONTROL
VALVE
2510 Mesurflo w/PT’s
AUTOMATIC
TEMPERATURE
CONTROL
VALVE
Ball Valve Ball Valve
Flex Hose Flex Hose
Optional Yball Strainer w/Blowdown Valve &
Hose Connector
FLOW
PT
Optional Yball Strainer w/Blowdown Valve &
Hose Connector
FLOW
PT
Tracer Loop Controller
Trane’sTracer Loop Controller (TLC) is a cost effective way of controlling the WSHP equipment, as well as the mechanical components of the system. Fluid coolers, boilers, pumps and water-source heat pump units can be connected and controlled by the loop controller for total system optimization. The Tracer loop control panel has the ability to lower or raise the water loop temperature during low energy use hours (typically during the night time hours) to provide a greater optimization during the time of day where energy consumption may be at it’s greatest.
Using the loop controller as a means of coordinating cooling or heating storage, the building owner can expect better efficiencies from the WSHP equipment.
56 WSHP-PRC020D-EN
Mechanical Specifications
General
Equipment is factory assembled, piped, internally wired, fully charged with R-410A refrigerant and oil. Units are tested at the factory.
Products are certified in accordance with AHRIWater to Air and Brine to Air Heat Pump Certification
Program which is based ISO Standard 13256-1: 1998. All units have an ETL label that meets USA
(UL std) and Canadian (CSA std).
Casing
The cabinet assembly is constructed of heavy-gauge galvanized steel. It houses the blower, fan and control hook-up to the unit thermostat or zone sensor. A basepan with condensate hose is included with the cabinet design. Base rails allow ease of chassis installation/removal for service or maintenance. One, two or three supply air openings shall are factory provided. Optional one or three inch flanges are provided on all free discharge openings.
The chassis is constructed of heavy-gauge galvanized steel. The chassis houses the compressor, reversing valve, water-to-refrigerant heat exchanger, air-to-refrigerant heat exchanger, thermal expansion valve, corrosive resistant condensate pan, and water inlet/outlet connections. The chassis is installed into the cabinet by sliding it in place on the locating rails within the cabinet design.
The insulation contains a flame spread rating of less than 25 and smoke density rating of less than
50 (as tested in accordance with ASTM-85). The elastomer insulation has a UL 94-5V rating.
Sound Attenuation
Sound attenuation is applied as a standard feature in the product design.The enhanced reduction package includes a heavy gage base plate, and gasket/insulation around the compressor enclosure.
An optional deluxe sound reduction package is also available. It includes a heavy gage base plate, gasket and insulation around the compressor enclosure, and vibration isolation between the chassis and cabinet. An additional dampening treatment is applied around the compressor enclosure to achieve greater acoustical reductions.
Filters
One inch, throwaway filters are standard and factory installed. The filters have an average resistance of 76% and dust holding capacity of 26-grams per square foot.
Compressors
All units have direct-drive, hermetic, rotary (unit sizes 009-018) and scroll (unit sizes 024 and 036) type compressors. The compressor contains rubber isolation to aid in noise reduction during compressor start/stop.
Internal thermal overload protection and compressor anti-short cycle timers are also provided.
Protection against excessive discharge pressure is provided by means of a high pressure switch.
Loss of charge protection is provided by a low pressure switch.
Refrigerant Circuits
The refrigerant circuit contains a thermal expansion device, service pressure ports, and system safety devices factory-installed as standard.
Air-to-Refrigerant Coil
Internally finned, 3/8” copper tubes mechanically bonded to a configured aluminum plate fin are standard. Coils are leak tested at the factory to ensure the pressure integrity.The coil is leak tested to 200 psig and pressure tested to 650 psig.
WSHP-PRC020D-EN 57
Mechanical Specifications
58
Drain Pan
The condensate pan is constructed of corrosive resistant material.The bottom of the drain pan is sloped in two planes to pitch the condensate towards the drain connection. Condensate is piped to a lower base pan through condensate hose for ease of chassis removal. A clear drain hose is factory clamped onto the drain connection for field hook-up.
Water-to-Refrigerant Heat Exchanger
The water-to-refrigerant heat exchanger is of a high quality co-axial coil for maximum heat transfer.
The copper or optional cupro-nickel coil is deeply fluted to enhance heat transfer and minimize fouling and scaling.The coil has a working pressure of 650 psig on the refrigerant side and 400 psig on the water side.
Indoor Fan
The blower is a double width, double inlet (DWDI) forward curved wheel. The blower is a direct drive PSC or optional ECM fractional horsepower motor.The blower/motor assembly is designed for efficient and quiet operation. The PSC motor is multi-speed and is wired for a HIGH or LOW setting. The ECM motor is programmed to provide four constant CFM profiles and is shipped on
Profile B – the rated CFM of the unit.The motor is also factory programmed to provide 50% airflow in the fan only mode for additional energy savings. Service or maintenance to the blower/motor is easily achieved by removal of a single bracket.
Risers
Factory provided supply and return risers are Type L copper. The drain riser is Type M copper.
Swages from one diameter to another are performed as specified by the engineer in the field.
Diameters and length are specified by the equipment model number. Riser insulation (optional) contains a flame rating per UL94-5V with flame spread rate of no more than 25.
Controls
The unit control box contains all necessary devices to allow heating and cooling operation to occur from a unit mounted, plug-in thermostat or sensor. The devices are as follows:
• 24 VAC energy limiting class II 75 VA breaker type transformer.
• 24 VAC blower motor relay
• 24 VAC compressor contactor for compressor control
• Lockout relay which controls cycling of the compressor is provided to protect the compressor during adverse operating conditions. The device may be reset by interrupting the 24 VAC control circuit. Reset may be done either at the thermostat or by momentary main power interruption.
• A high pressure switch protects the compressor against operation at refrigerant system pressures exceeding 650 psig.
• A low pressure switch is provides that trips at 40 psig. A freezestat is provided - tripping at either
35° or 20°F.
• Factory installed wire harness is available for the Deluxe and ZN510 control packages.
• Power connections are made through a factory installed conduit located at the top of the unit’s cabinet. An optional disconnect is provided. The conduit grants access directly to the control box.
Nameplate information is given for the application of either time-delay fuses or HACR circuit breakers for branch circuit protection from the primary source of power.
Single phase, single voltage rated equipment is designed to operate between plus or minus 10% of nameplate utilization voltage.
Operation outside of this range may adversely effect the service life of the equipment.
WSHP-PRC020D-EN
WSHP-PRC020D-EN
Mechanical Specifications
Deluxe Controls (option)
The deluxe control package provides a 75VA transformer with circuit breaker.The Micro-processor based controller is designed to include a lockout relay, anti-short cycle compressor protection, random start delay, brown-out protection, low pressure time delay, compressor delay on start and an open relay for night setback or pump request. Optional wiring from the factory for condensate overflow and compressor enable are also supplied. LEDs (light emitting diodes) are included for diagnostics of the equipment. The deluxe controller accepts a standard 24V digital thermostat.
ZN510 Controller (option)
This system utilizes factory furnished and mounted DDC controls for operation on a COMM 5
(LonMark) link. The Tracer™ ZN510 control package includes a 75 VA transformer. The controller provides random start delay, heating/cooling status, occupied/unoccupied mode, fan status and filter maintenance options. Optional wiring from the factory for condensate overflow is also available. Three LEDs (light emitting diodes) are included for diagnostics of the equipment.
Return-Air Hinged Acoustical Door (option)
A frame mounted acoustical door is provided to attenuate noise. The door is hinged to the wall frame, and contains magnetic latches to keep the door aesthetically in place. It is flush mounted to the wall as to not protrude into the owner space.The door allows access to the unit for ease of filter replacement
The door is constructed from heavy-gauge formed galvanized steel and painted Polar white. It is made available in a keylock design and a keyless design to fit several design applications.
Supply-Air Grilles (option)
Supply air grilles are available for air discharge from the unit. The grilles are made in either a vertical louver, or a bi-directional louver option. The grilles are painted the Polar White to match the door assembly.
Ball Valves (option)
Ball valves are field installed between the riser stub out and the flexible hose.
Hoses (option)
Hoses shall consist of a stainless steel outer braid with an inner core of tube made of a nontoxic synthetic polymar material.The hoses shall be suitable for water temperatures ranging between
33°F and 211°F without the use of glycol.
Automatic Flow Devices (option)
The automatic self-balancing device shall automatically limit the rate of flow to within 10-percent of the specified amount, over a 40 to 1 differential pressure operating range of 2 to 80 PSID. The operational temperature shall be rated from fluid freezing, to 225°F.
The valve body shall be suited for working pressures of 400 PSIG. The valve internal core shall consist of one or more high temperature elastomeric diaphragms and precision orifice with sculptured orifice seat.
Dual pressure/temperature test ports shall be standard for verifying the pressure differential and system temperature.
59
Trane optimizes the performance of homes and buildings around the world. A business of Ingersoll Rand, the leader in creating and sustaining safe, comfortable and energy efficient environments, Trane offers a broad portfolio of advanced controls and HVAC systems, comprehensive building services, and parts. For more information, visit www.Trane.com.
Trane has a policy of continuous product and product data improvement and reserves the right to change design and specifications without notice.
© 2013 Trane All rights reserved
WSHP-PRC020D-EN 09 Nov 2013
Supersedes WSHP-PRC020-EN (23 Apr 2013)
We are committed to using environmentally conscious print practices that reduce waste.
advertisement
Key Features
- Vertical stack design for efficient installation in high-rise buildings
- Concealed behind drywall for a seamless blend with room decor
- Optional ducted or free discharge design for customized air distribution
- Multiple supply-air discharges (for larger units) for versatile airflow
- Hinged acoustical door for easy maintenance and enhanced sound attenuation
- Tamper-proof latch option for added security (on hinged door design)
Related manuals
Frequently Answers and Questions
What are the size options available for this unit?
Can I use this unit in a ducted or non-ducted setup?
How do I access the unit for maintenance or filter changes?
advertisement
Table of contents
- 2 Introduction
- 2 Water-Source Vertical High-Rise
- 4 Features and Benefits
- 7 Application Considerations
- 13 Selection Procedures
- 14 Model Number Descriptions
- 16 General Data
- 17 Performance Data
- 38 Unit Fan Performance
- 42 Electrical Data
- 43 Dimensional Data
- 51 Controls
- 51 Deluxe 24V Electronic Controls
- 51 Deluxe 24V features include:
- 53 Tracer ZN510 functions include:
- 55 Thermostats and Zone Sensors
- 56 Accessories
- 57 Mechanical Specifications