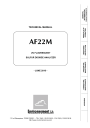
advertisement
▼
Scroll to page 2
of
134
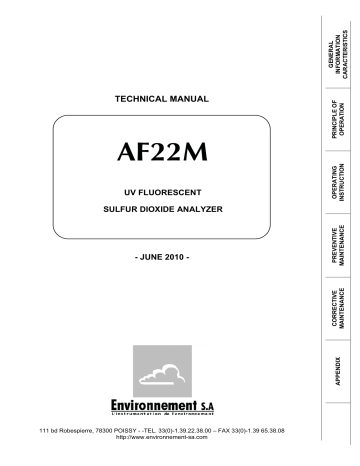
UV FLUORESCENT PRINCIPLE OF OPERATION GENERAL INFORMATION CARACTERISTICS AF22M OPERATING INSTRUCTION TECHNICAL MANUAL APPENDIX CORRECTIVE MAINTENANCE - JUNE 2010 - PREVENTIVE MAINTENANCE SULFUR DIOXIDE ANALYZER 111 bd Robespierre, 78300 POISSY - -TEL. 33(0)-1.39.22.38.00 – FAX 33(0)-1.39 65.38.08 http://www.environnement-sa.com AF22 MODULE Environnement S.A Duplication prohibited 0 WARNING The information in this documentation is subject to change without notice. Environnement S.A. all rights reserved. This document does not represent a commitment under part of Environnement S.A. 0–2 JUNE 2004 AF22 MODULE Duplication prohibited Environnement S.A SUMMARY CHAPTER 1 GENERAL INFORMATION - CHARACTERISTICS 1.1. GENERAL INFORMATION 1.2. CHARACTERISTICS 13 110 CHAPTER 2 PRINCIPLE OF OPERATION 2.1. THEORETICAL BASIS 23 2.2. PRINCIPLE OF MEASUREMENT 25 2.3. TAKING SAMPLES AND ANALYSIS 27 2.4. SIMPLIFIED FLOW CHART OF PRINCIPAL PROGRAM 29 2.5. AUTOMATIC RESPONSE TIME 210 CHAPTER 3 OPERATING INSTRUCTIONS 3.1. INITIAL START-UP 34 3.2. PROGRAMMING THE AF22M 37 3.3. DESCRIPTION OF THE DIFFERENT SCREENS 310 3.4. CALIBRATION 341 CHAPITRE 4 PREVENTIVE MAINTENANCE 4.1. SAFETY INSTRUCTIONS 42 4.2. MAINTENANCE CALENDAR 43 4.3. MAINTENANCE OPERATION SHEETS 44 4.4. AF22M MAINTENANCE KIT 411 CHAPTER 5 CORRECTIVE MAINTENANCE CHAPTER 6 APPENDIX ESTEL BOARD SOREL BOARD JUNE 2004 0–3 AF22 MODULE Environnement S.A Duplication prohibited LIST OF TABLES Table 3.1 – DB37 and DB25 connectors links Table 3.2 – MUX signals (Acceptable limit on the multiplexer 1 to 16 channels) Table 5–1– List of faults and corrective actions Table 5–2 – AF22M Module board configuration Table 5–3 – Board RS4i Configuration Table 5–4 – Keyboard Interface configuration Table 5–5 – UV lamp board configuration Table 5–6 – Configuration of UV lamp supply board Table 5–7 – Flow rate control board configuration and setting 33 337 5–4 5–9 5–10 5–11 5–12 5–13 5–14 LIST OF FIGURES Figure 1.1 – AF22M Presentation Figure 1.2 – Keyboard and display Figure 1.3 – Rear panel Figure 1.4 – Components location Figure 1.5 – Links between units Figure 1.6 – Outline dimensions Figure 2.1 – Diagram showing molecule energy levels Figure 2.2 – General principle diagram Figure 2.3 – Filtration of hydrocarbon molecules Figure 3.1 – Electrical connections Figure 3.2 – Fluid connection Figure 3.3 – Permeation tube installation Figure 3.4 – Software overview Figure 3.5 – Printout example Figure 3.6 – Pressurized gas connection example Figure 3.7 – Typical calibrator Figure 4.1 – Inlet dust filter Figure 4.2 – Zero filter cartridges position Figure 4.3 – Exploded view of the pump Figure 4.4 – Lamp/shutter assembly (front face) Figure 4.5 – Lamp/shutter assembly (rear face) Figure 5-1 – AF22M Module board Figure 5-2 – Card RS4i Configuration Figure 5-3 – Keyboard Interface board Figure 5-4 – UV lamp board Figure 5–5 – UV lamp supply board Figure 5-6 – Flow rate control board 0–4 12 13 14 15 19 110 22 26 27 33 3–4 3–5 3–9 3–34 3–42 3–45 4–4 4–7 4–9 4–10 4–10 5–8 5–10 5–11 5–12 5–13 5–14 MAY 2007 AF22 MODULE Duplication prohibited Environnement S.A INDEX OF PAGES Page Date Page Date 0-1 0-2 0-3 0-4 0-5 0-6 06.2010 07.2002 06.2004 05.2007 06.2010 06.2010 1-1 1-2 1-3 1-4 1-5 1-6 1-7 1-8 05.2007 07.2002 07.2002 05.2007 07.2002 05.2007 05.2007 07.2002 2-1 2-2 2-3 2-4 2-5 2-6 2-7 2-8 2-9 2-10 05.2007 07.2002 07.2002 07.2002 05.2007 07.2002 07.2002 07.2002 07.2002 07.2002 3-27 3-28 3-29 3-30 3-31 3-32 3-33 3-34 3-35 3-36 3-37 3-38 3-39 3-40 3-41 3-42 3-43 3-44 3-45 3-46 3-47 3-48 3-49 3-50 07.2002 07.2002 07.2002 07.2002 07.2002 07.2002 07.2002 07.2002 07.2002 05.2007 01.2008 07.2002 07.2002 07.2002 07.2002 07.2002 07.2002 07.2002 07.2002 07.2002 07.2002 07.2002 07.2002 07.2002 3-1 3-2 3-3 3-4 3-5 3-6 3-7 3-8 3-9 3-10 3-11 3-12 3-13 3-14 3-15 3-16 3-17 3-18 3-19 3-20 3-21 3-22 3-23 3-24 3-25 3-26 07.2002 05.2007 07.2002 05.2007 07.2002 05.2007 07.2002 07.2002 07.2002 07.2002 07.2002 07.2002 07.2002 05.2007 07.2002 07.2002 07.2002 07.2002 07.2002 07.2002 07.2002 05.2007 05.2007 07.2002 05.2007 07.2002 4-1 4-2 4-3 4-4 4-5 4-6 4-7 4-8 4-9 4-10 4-11 4-12 07.2002 07.2002 07.2002 07.2002 07.2002 07.2002 07.2002 07.2002 07.2002 07.2002 07.2002 07.2002 5-1 5-2 5-3 5-4 5-5 5-6 5-7 5-8 5-9 5-10 5-11 5-12 5-13 5-14 05.2007 07.2002 07.2002 07.2002 05.2007 07.2002 07.2002 07.2002 07.2002 07.2002 07.2002 07.2002 07.2007 06.2004 JUNE 2010 Page Date 6-1 6-2 06.2004 05.2007 0–5 AF22M Environnement S.A Duplication prohibited EPA EQUIVALENCY DESIGNATION Environnement S.A. Model AF22M SO2 Analyzer Automated Equivalent Method: EQSA-0802-149 “Environnement S.A Model AF22M UV Fluorescence Sulfur Dioxide Analyzer,” operated with a full scale range of 0 - 500 ppb, at any temperature in the range of 10 °C to 35 °C, with a 5-micron PTFE sample particulate filter, with a response time setting of 11 (Automatic response time), with the automatic “ZERO-REF” cycle ON and set for activation every 24 hours, and with or without either of the following options: Permeation oven, Rack mount / slides. [Federal Register: Vol. 67, page 57811, 09/12/02] 0–6 JUNE 2010 AF22 MODULE Duplication prohibited Environnement S.A CHAPTER 1 GENERAL INFORMATION - CHARACTERISTICS 1.1 GENERAL INFORMATION 1–3 1.1.1 PRESENTATION 1–3 1.1.2 DESCRIPTION 1–3 1.1.2.1 Front panel 1–3 1.1.2.2 Rear panel 1–4 1.1.2.3 Components locations 1–7 1.1.3 1.1.4 1.2 OPERATING MODES 1–8 1.1.3.1 Standard 1–8 1.1.3.2 Optional 1–8 ASSOCIATED EQUIPMENT 1–8 CHARACTERISTICS 1–9 1.2.1 TECHNICAL CHARACTERISTICS 1–9 1.2.2 OPERATING CHARACTERISTICS 1–10 1.2.3 STORAGE CHARACTERISTICS 1–10 1.2.4 INSTALLATION CHARACTERISTICS 1–10 1.2.4.1 Links between units 1–10 1.2.4.2 Dimensions and weight 1–10 1.2.4.3 Handling and storage 1–10 Figure 1-1 - AF22M Presentation Figure 1-2 - Keyboard and display Figure 1-3 – Rear panel Figure 1-4 - Components location Figure 1-5 - Links between units Figure 1-6 – Outline dimensions MAY 2007 1–2 1–3 1–4 1–6 1–10 1–11 1–1 AF22 MODULE Environnement S.A 1 Duplication prohibited GENERAL INFORMATION - CHARACTERISTICS Figure 1-1 - AF22M Presentation 1–2 JULY 2002 Duplication prohibited AF22 MODULE Environnement S.A 1.1 GENERAL INFORMATION 1.1.1 PRESENTATION The AF22M is a continuous sulfur dioxide monitor designed for use at low contents in ambient air. The detection principle is based on fluorescence in ultraviolet. The monitor provides many advantages by the use of recent advanced electronic and optical technologies and requires very limited maintenance. The sample is taken with a Teflon tube (outside diameter 6 mm) connected to the back of the unit. The measurement is indicated by a graphic display on the front panel. 1.1.2 DESCRIPTION 1.1.2.1 Front panel The front panel includes: a general switch a backlit liquid crystal display – 16 lines 40 columns (240 x 128 pixels) – the display provides the measurement values according to the selected unit, the information required for programming and testing the unit. a keyboard with 6 touch-sensitive keys The control and check functions of the unit are controlled through the keyboard. – the function of each key varies with the different screens or menus. Figure 1-2 - Keyboard and display JULY 2002 1–3 AF22 MODULE Environnement S.A 1.1.2.2 Duplication prohibited Rear panel The rear panel of the AF22M contains the electrical connectors and gas inlets/outlets. Gas inlets/outlets (right hand-side) – The inlet of sample to be analyzed is composed of a PVDF 4/6 mm fitting associated with a dust filter holder equipped with Teflon filtering membrane (1). – The "span gas" inlet (4) consists of a 4/6 mm PVDF fitting to connect an outside span gas delivered at atmospheric pressure, or span gas excess pipe when optional permeation bench is available. In case of permeation bench option, this inlet becomes an outlet of the permeation bench (certification de calibration certification by built-in permeation bench). – The "pump outlet" (3) to exhaust the analyzed sample consists of a 4/6 mm PVDF fitting. – The optional "zero air inlet" (2) allows to connect an external zero air generator. NOTE : This inlet is sealed when optional built-in zero filter is present. Optional : - optional permeation bench zero air inlet (10). Electrical Equipment Connections (left side) – The main power supply assembly consists of a 3-contact socket (5) for standard power cable connection, and general fuse: 0,6 A / 220 V or 1,2 A / 115 V (6) – 1 standard 25-pin plug (7), for serial links COM1 (RS 232C – RS 422) and COM 2 (RS232C). – 1 standard 37 pin (8) (see table 3-1 – DB37 and DB connectors links) Ventilation Ventilation is achieved by a fan (9). Figure 1-3 – Rear panel 1–4 MAY 2007 Duplication prohibited AF22 MODULE Environnement S.A Page intentionally blank JULY 2002 1–5 AF22 MODULE Environnement S.A 6 3 Duplication prohibited 2 1 17 18 19 20 7 A 20 10 14 16 15 13 7 12 11 Figure 1-4 - Components location 1–6 MAY 2007 AF22 MODULE Duplication prohibited 1.1.2.3 Environnement S.A Components locations The components inside the unit are accessed by simply unscrewing the screws at rear and lateral sides of the unit and removing the upper cover. Mechanical components This includes the following equipment: – the solenoid valves and filter assembly (1 and 2), – the internal "Zero Air" filter (activated charcoal) (6), – the carbon kicker filter (activated charcoal) (18), – the temperature controlled compartment (17), – the photo multiplier tube (15), – the UV lamp (13). After passing through the inlet dust filter (1), the sample to be analyzed is sent to a block of two 3-way solenoid valves (2). These solenoid valves are used to select: – either in "MEASUREMENT" mode, the gas sampling to be analyzed, – or in "ZERO" mode, the filtered ambient air through the activated charcoal filter (6), – or in "SPAN" mode, a span gas originating from: x the permeation oven (19) if there is one (optional), The permeation oven consists of an aluminum chamber inside which the permeation tube is placed. This chamber is regulated at a temperature of 50 °C and ventilated by an additional constant flow rate pump (20). x or an outside calibration device. The sample to be analyzed is drawn through a carbon kicker (14) aromatic hydrocarbon elimination device to the reaction chamber (16) in which the fluorescence takes place. Fluorescence is detected by a photo multiplier tube (15). The temperature of the optical block is regulated at 43 °C by the microprocessor associated with a probe and a heating resistance. Outside the compartment, the "zinc ray" type lamp (13) generating the UV radiation is powered by a stabilized voltage supply (11). The UV beam emitted is interrupted during the beginning of "ZERO REF" by a shutter (12) in order to measure the PM tube black current. The analyzed sample passes through a flow regulating restrictor and through the external tube of the carbon kicker to eliminate hydrocarbon molecules. It is then expelled by a membrane pump (3). The supply bloc 24V DC (20) enables to supply the whole necessary voltages. If the user wants to modify the original supply voltage (230 V AC to 155 V AC), 2 options are necessary : x switch the A switch to the cut-out power supply x modify value of general fuse : – from 0,6 A passes to 1,2 A for a normal analyzer, – from 1,6 A passes to 3,2 A if the CH2S option is available. MAY 2007 1–7 AF22 MODULE Environnement S.A Duplication prohibited Electronic part – The signal output by the photo multiplier tube is amplified and converted into a digital signal on the Module board (7). This board also: x supplies DC voltages at + 15 V, 15 V, + 5 V, x detects any alarms, transmits these alarms to the microprocessor board and signals them on the corresponding output connector, x performs digital/analog conversion of measurement values output by the microprocessor board. – The microprocessor (7), calculates and stores measurement values, and manages alarms and automatic cycles. – The keyboard interface board (10) controls the dialogue between the microprocessor board and the keyboard and the display unit. – The UV lamp power supply (11) provides the stabilized voltage necessary for the zinc ray lamp. The current in the zinc ray lamp is regulated. 1.1.3 OPERATING MODES 1.1.3.1 Standard – Programmable measurement range up to 10 ppm, with a minimum detectable limit of 1 ppb (typical value is below 0,5 ppb). – Remote-controlled or programmable automatic calibration and zero sequence. – Automatic control of parameters influencing metrology and tests of correct functioning. 3 – Measurement values indicated in ppb or μ/m . – Memorization of average measurements with a programmable period (capacity 5700 averages). 1.1.3.2 Optional The monitor can be equipped with the following options: – Permeation oven. – ESTEL board(s) : 1.1.4 x Analog outputs of the SO2 concentration and two of the 16 multiplexer channels. x Remote signaling of "measurement", "zero", "calibration" and "alarm" functions. ASSOCIATED EQUIPMENT – Analog recorders and data loggers. – Numerical data acquisition system – Serial printer for continuous printout of display measurements (programmable period) and configuration. 1–8 JULY 2002 Duplication prohibited AF22 MODULE 1.2 CHARACTERISTICS 1.2.1 TECHNICAL CHARACTERISTICS Environnement S.A Measurement range (programmable) : user programmable up to 10.00 ppm * Units : ppm or mg/m3 (programmable) Noise (V) : 0.0005 ppm (RT 120) Minimum detectable limit (2V) : 0.001 ppm (RT 120) Response time (0-90 %) : 20-120" fixed or automatic (programmable) Zero drift : < 1 ppb./24 hours in operation Span drift : < 1% / 24 hours Linearity : ± 1% H20 influence : Null Temperature influence : 0.3 ppb/°C Sample flow rate : about 415 cc/min (internal pump) Display : LCD 240x128 text and graphic modes Control keyboard : 6 context dependent keys Output signals : 3 analog outputs 0-1V, 0-10V, 0-20 mA or 4-20 mA Power supply : 230V-50Hz (115V-60Hz) + ground Consumption : 280 VA starting up, 110 VA normal operation Working temperature : + 10 °C to + 35 °C Memorization of measurement values : Capacity: 5700 last averages of the 3 displayed parameters Measurement values printing : By serial printer connected to COM2 Alarms checks : – Permanent – Detection and indication of functioning anomalies: optical block temperature, sample flow rate, UV energy, PM tube high voltage, SO2 measurement overthreshold, over-range, calibration fault ... Tests and diagnostics for maintenance : Selection at keyboard and display of all parameters. Backup saving time for data memorized in : > 6 months by incorporated battery. RAM and of the real-time clock. * 0.500 ppm is the only range covered under EPA equivalency designation. JULY 2002 1–9 AF22 MODULE Environnement S.A 1.2.2 OPERATING CHARACTERISTICS Not applicable. 1.2.3 STORAGE CHARACTERISTICS Duplication prohibited – Temperature: 10 ° to 60 °C. Links between units The AF22M monitor uses the external links and power supplies illustrated below: Power supplies 220V/1A or 115V/2A "Sample gas" 1.2.4.1 "Zero air" (Option) INSTALLATION CHARACTERISTICS "Span gas" 1.2.4 AF22M Serial link ESTEL Interface (option) Exhaust or pump outlet Figure 1-5 - Links between units 1.2.4.2 Dimensions and weight The analyzer is a standard 19-inch, 3-unit rack high. Length : 591 mm Width : 483 mm Height : 133 mm Weight : 9 kg 1.2.4.3 Handling and storage The AF22M monitor must be handled with care to avoid damage to the various connectors and fittings on the rear panel. Ensure the fluid inlets and outlets on the unit are protected with caps whenever storing the monitor. The unit is stored in a foam-packed case provided for this purpose. 1–10 JULY 2002 AF22 MODULE Duplication prohibited Environnement S.A 430 50 125 5 54 133 14 38 483 57 7 36 Figure 1-6 – Outline dimensions JULY 2002 1–11 AF22 MODULE Environnement S.A Duplication prohibited Page intentionally blank 1–12 JULY 2002 Duplication prohibited AF22 MODULE Environnement S.A CHAPTER 2 PRINCIPLE OF OPERATION 2.1 THEORETICAL BASIS (Fig. 2.1) 2–3 2.2 PRINCIPLE OF MEASUREMENT 2–5 2.3 TAKING SAMPLES AND ANALYSIS 2–7 2.4 SIMPLIFIED FLOW CHART OF PRINCIPAL PROGRAM 2–9 2.5 AUTOMATIC RESPONSE TIME 2–10 2.5.1 SIMPLIFIED PRINCIPLE OF OPERATION 2–10 2.5.2 PROGRAMMING THE RESPONSE TIME 2–10 Figure 2-1 - Diagram showing molecule energy levels Figure 2-2 – General principle diagram Figure 2-3 – Filtration of hydrocarbon molecules MAY 2007 2–2 2–6 2–7 2–1 AF22 MODULE Environnement S.A 2 Duplication prohibited PRINCIPLE OF OPERATION Electronical Vibrational Rotational Energy levels A: Electronical spectrum (system of bands associated with an electronic transition) B: Vibration - rotation spectrum (band associated with a vibrational transition) C: Rotation spectrum (rays associated with a rotational transition) Figure 2-1 - Diagram showing molecule energy levels 2–2 JULY 2002 Duplication prohibited 2.1 AF22 MODULE Environnement S.A THEORETICAL BASIS (FIG. 2.1) Energy diagram: Many developments in quantum mechanics at the beginning of this century enabled theoretical physicists to conceptualize the processes involved in energy exchanges between a gaseous molecule such as sulfur dioxide and its environment. The diagram shown makes it easier to obtain a global understanding of the various phenomena due to absorption of a radiation by the molecule. Two essential comments clarify this diagram: Energy levels are quantified and distributed in accordance with a structure that is different for molecule electronic, vibrational and rotational levels, At the considered wavelengths, the "electronic" scale of energies only includes the energy levels of molecule valency electrons. Also, a transition from one electronic level to another by absorption of a photon is always accompanied by lower level vibrational and rotational transitions. The mathematical formulation of molecular physics associates a spatial and temporal function called a wave function to each state of the molecule, fully characterizing this state. A transition then occurs by a new spatial distribution of the wave function. Absorption and emission: In its fundamental state Ee0, the SO2 molecule can only absorb sufficient energy photons to access the first excited state on the electronic scale Ee1. The energy of a photon is given by Einstein's relation: E hv h c O where O is the radiation wavelength output from a low-pressure zinc vapor lamp, namely O = 213.9 nm, and h and c represent Plank's constant and the speed of light in a vacuum respectively. The transition is denoted in the following form: SO2 + h v o SO2* As we have already said, the molecule always reaches a vibrational and rotational sub-level of Ee1, namely higher than this sub-level. It then very quickly dissipates its vibration and rotation energy to remain on level Ee1 a little longer (a few nanoseconds). JULY 2002 2–3 AF22 MODULE Environnement S.A Duplication prohibited Starting from Ee1, it can reach any sub-level of its fundamental state along different paths: by fluorescence: Kf SO2 * o SO2 hv' Based on the above, firstly v' = c O' is less than v, therefore O' > O, secondly, O' can be equal to one of several values around an average length, since the sub-level reached can be arbitrary (statistical distribution as a function of the temperature). The monitor "observes" photons emitted through a filter centered on 350 nm. by extinction: Kq SO2 * M o SO2 M where M represents another gaseous molecule. The molecule then dissipates its energy mechanically and does not fluoresce. This is referred to as "quenching". by dissociation: SO2 * Kd o SO O The energy Ee1 is sufficient to break the SO O link. Kf, Kd, Kq denote quantum yields associated with each form of deactivation. They are related to the life of state Ee1, and express probabilities attached to each reaction type. They are determined from the integral, taken over the entire volume, of the product of wave functions of excited and fundamental states. 2–4 JULY 2002 Duplication prohibited 2.2 AF22 MODULE Environnement S.A PRINCIPLE OF MEASUREMENT The radiation intensity absorbed by sulfur dioxide in an optical chamber of length L follows the BeerLambert law: ia = i0 x (1 – e-Lc) where lo denotes the intensity at the chamber inlet, D is the characteristic SO2 absorption coefficient and c = [SO2], is the concentration of the gas to be analyzed. Also, the probability that an excited molecule will fluoresce is given by: Kf Kf Kq Kd The fluorescence intensity received by the PM is then expressed in the following form: If G la Kf Kf Kq Kd where G is a constant that depends on the illuminated part of the chamber seen by the PM. Therefore: if In our case, D L c << 1 and 1 e Gio DLc Kf x (1 e D Lc ) Kf Kq Kd can be developed to the first order as follows: 1e DLc #+DLc We then obtain: If G lo Kf D L c Kf Kq Kd E .c The radiation captured by the PM is thus directly proportional to the SO2 concentration. This result is the basis for the measurement technique used with the AF22M monitor. MAY 2007 2–5 AF22 MODULE Environnement S.A Duplication prohibited Sample inlet Span gas inlet (or span gas exess for optional permeation bench) Optional external zero air inlet (Sealed for use of built in zero filter) Exhaust Dust filter Activated charcoal filter Pump Solenoid valves assembly ~ 40 l/h Permeation bench Restrictor Pump Aromatic hydrocarbons scrubber ~ 45 l/h Activated charcoal filter Flow rate sensor Flow rate sensor Activated charcoal filter Built in optional permeation bench assembly ~25 l/h Black Stabilized power supply SO2 Reaction chamber UV UV UV UV UV UV UV UV UV UV UV UV UV UV UV UV UV UV UVUV UV UV UV UV UV UV UV UV UV UV UV UV UV UV UV UV UV UV UV UV UV UV UV UV UV UV UV UV UVUV UV UV UVUV UV UV UV UV UVUV UV UV UV UV UV UV UV UV UVUVUV UVUV UV UV UVUV UVUVUV UV UV UVUVUV UV UV UVUVUV UV UV UV UV UV UV UV UV UV UV UV UV UV UV UV UV UV UV UV UV UV UV UV Photomultiplier tube UV UV UV UV UV UV UV UV UV UV UVUV UV UV UV UVUV UV UVUV UVUV UV UV UV UV UV UV UV UV UV UV UV UV UV detector Modul board Shutter UV UV UV UV UV UVUV UV UV UVUV UV UVUV UVUV UV UV UV UV UV UV UV UV Zinc ray UV lamp Restrictor SO2 Measurements Figure 2-2 – General principle diagram 2–6 JULY 2002 AF22 MODULE Duplication prohibited 2.3 Environnement S.A TAKING SAMPLES AND ANALYSIS The sample is taken by a Teflon tube connected to the back of the monitor through a pump placed at the end of the circuit. A Teflon filter provides dust protection. Filtration of hydrocarbon molecules The sample to be analyzed is firstly filtered by an elimination device of aromatic hydrocarbon molecule. CARBON KICKER HC SAMPLE INLET HC HC HC HC HC HC HC CHAMBER HC HC HC HC HC HC HC HC Activated charcoal filter Restrictors Pump Figure 2-3 – Filtration of hydrocarbon molecules This device consists of two concentric tubes. The internal tube is made of a special polymer (silicone). The sample to be analyzed with aromatic HC molecules comes in the internal tube. Aromatic HC molecules are transferred by permeation to the external tube (silicone) with effect that the transfer is done in the direction: more HC molecules in gas to few HC molecules in gas. The pump creates a vacuum in the external tube, the partial pressure of aromatic compounds decreases due to activated charcoal filtration and molecules are evacuated to the outside of the internal tube. JULY 2002 2–7 AF22 MODULE Environnement S.A Duplication prohibited Analysis The sample to be analyzed, exempt from HC molecules, is directed to a reaction chamber in which it is irradiated by an ultraviolet radiation centered at 214 nm, the absorption wavelength of SO2 molecules. A photodiode measures the ultraviolet radiation generated by the UV lamp, through a mirror. This measurement is used during signal processing in order to compensate for any variation of the UV energy. Molecules restore a specific fluorescence in the ultraviolet, which is optically filtered between 300 and 400 nm at the outlet in order to eliminate some interfering gases. This fluorescence is visualized by the PM tube placed near the reaction chamber. At the start of each "zero-ref", a shutter is placed between the UV lamp and the reaction chamber inlet for 40 seconds. This electrical zero corresponds to the PM tube darkness current and the offset voltage of the preamplifier, incorporated into the signal processing, it eliminates the possibility of drifts with temperature and time. The PM tube signal is amplified and is converted into digital values for processing by a microprocessor that calculates the average of measurement values, checks the alarms and carries out monitor operation diagnosis. These various values and information are displayed on an alphanumeric display unit on the monitor front panel. 2–8 JULY 2002 AF22 MODULE Duplication prohibited 2.4 Environnement S.A SIMPLIFIED FLOW CHART OF PRINCIPAL PROGRAM INPUTS/OUTPUTS INITIALIZATION MEMORY TEST ALARM CHECK ALARM DISPLAY at end of warm-up REFERENCE CYCLE POSITION RANGE RELAY PM SIGNAL ACQUISITION Save this value if end od a "dark" cycle UV SIGNAL ACQUISITION Save this value if end of a "dark" cycle ENERGY CORRECTION MEAS-DARK - UV-ZERO UV-ZERO TOTAL VALUES (RT FUNCTION) MEMORIZATION OF REFERENCE REFERENCE TEMPERATURE & ENERGY CORRECTION MEASUREMENT-REFERENCE CALCULATION K SPAN + TEMPERATURE CORRECTION MEAS. SO2 = SO2 X K SPAN SCALING If mg programmed SO2(MG) = SO2(PPM) X CONV. FACT. If offset programmed ADD OFFSET ACQUISITION OF MULTIPLEXER PARAMETER AND PROCESSING CONTROL OF PROGRAMMED PLC'S RESULT DISPLAY JULY 2002 STORAGE ANALOG OUTPUTS PRINTING SERIAL LINK 2–9 AF22 MODULE Environnement S.A 2.5 Duplication prohibited AUTOMATIC RESPONSE TIME In order to optimize its metrology, the AF22M monitor is equipped with a software function called "automatic response time" which enables filtration of measurements depending on evolution of concentrations of sulfur dioxide. 2.5.1 SIMPLIFIED PRINCIPLE OF OPERATION An average of instantaneous readings is carried out corresponding to a minimum response time. >MEAS@ AVERAGE 80 ª º « ¦1 >Pm signal @ » » Reference zero = « 16 « » « ¦ >UV detector signal @ » ¬ 1 ¼ Then, a weighted average between the filtered values ( >MEAS@ FILTERED ) and the average measurements ( >MEAS@ AVERAGE ) is recursively calculated according to the formula: >MEAS@ DISPLAYED >MEAS@ FILTERED (NEW) X > MEAS@ FILTERED (OLD) Y [MEAS] AVERAGE X +Y = 1 When the difference ( >MEAS@ FILTERED (OLD) >MEAS@ AVERAGE ) exceeds a determined threshold, the value of Y is increased, up to a maximum value of 0.98 which corresponds to a fixed response time of TRMIN. When >MEAS@ 2.5.2 FILTERED (OLD) >MEAS@ AVERAGE is below the threshold, Y is progressively decreased. PROGRAMMING THE RESPONSE TIME The function of automatic response time may be activated or deactivated in the configuration Ö measurement mode menu. The minimum response time may also be modified in that menu. See chapter 3 section 3.3.4.2 to obtain more information about programming of those functions. 2–10 JULY 2002 AF22 MODULE Duplication prohibited Environnement S.A CHAPTER 3 OPERATING INSTRUCTIONS 3.1 3.2 INITIAL STARTUP 3–4 3.1.1 3.1.2 3–4 3–6 PROGRAMMING THE AF22M 3–7 3.2.1 SELECTION AND MODIFICATION OF THE PROGRAMMABLES PARAMETERS 3–7 3.2.2 3.3 PRELIMINARY OPERATIONS STARTING UP THE UNIT 3.2.1.1 Screen areas definition 3–7 3.2.1.2 Definition of the most used functions of the keyboard 3–8 PROGRAMMING THE OPERATING PARAMETERS 3–8 3.2.2.1 Programming the digital parameters 3–8 3.2.2.2 Programming the configurable parameters with toggle list 3–8 DESCRIPTION OF THE DIFFERENT SCREENS 3–10 3.3.1 MAIN MENU 3–10 3.3.2 MEASUREMENT 3–11 3.3.3 3.3.4 3.3.2.1 MEASUREMENT Ö Instantaneous 3–11 3.3.2.2 MEASUREMENT Ö Average 3–14 3.3.2.3 MEASUREMENT Ö Synoptic 3–14 3.3.2.4 MEASUREMENT Ö Graphic 3–15 3.3.2.5 MEASUREMENT Ö Printout. 3–18 3.3.2.6 MEASUREMENT Ö Alarms display 3–18 SPAN 3–19 3.3.3.1 SPAN Ö Calibration 3–19 3.3.3.2 SPAN Ö Select Gas. 3–20 3.3.3.3 SPAN Ö Cycles 3–21 3.3.3.4 SPAN Ö Pressure 3-22 3.3.3.5 SPAN Ö E2Pot 3-22 CONFIGURATION 3–23 3.3.4.1 CONFIGURATION Ö Date/time/language 3–23 3.3.4.2 CONFIGURATION Ö Measurement mode 3–24 3.3.4.3 CONFIGURATION Ö Measure channels 3–25 3.3.4.4 CONFIGURATION Ö Offsets and units 3-25 3.3.4.5 CONFIGURATION Ö Alarm limits 3–26 3.3.4.6 CONFIGURATION Ö Analog outputs 3–26 3.3.4.7 CONFIGURATION Ö Analog inputs 3–27 3.3.4.8 CONFIGURATION Ö Relay and remote control 3-28 3.3.4.9 CONFIGURATION Ö Serial link 3-29 3.3.4.10 CONFIGURATION Ö Factory settings JUNE 2004 3-29 3–1 AF22 MODULE Environnement S.A 3.3.5 STORED DATA 3–30 3.3.6 TESTS 3–35 3.3.7 3.4 Duplication prohibited 3.3.6.1 TEST Ö Optical bench 3–36 3.3.6.2 TEST Ö MUX signals 3–37 3.3.6.3 TEST Ö Other commands 3–38 3.3.6.4 TEST Ö Serial link 3–38 3.3.6.5 TEST Ö ESTEL card 3–39 STOP MODE 3-40 CALIBRATION 3–41 3.4.1 OVERVIEW OF CALIBRATION AND CONCEPTS 3–41 3.4.1.1 Zero air generation 3-42 3.4.1.2 Span gas generation 3-42 3.4.1.3 Internal solenoid valves 3-43 3.4.2 3.4.3 3.4.4 3.4.5 CHECK OF ZERO AND SPAN POINT 3–43 3.4.2.1 Facilities required 3-43 3.4.2.2 Procedure 3-43 3.4.2.3. Use of automatic cycles 3-44 SPAN ADJUSTMENT 3–44 3.4.3.1 Facilities required 3-44 3.4.3.2 Procedure 3-44 3.4.3.3 Use the AUTO-CAL automatic cycle 3-45 MULTI-POINT CALIBRATION 3–46 3.4.4.1 Overview 3-46 3.4.4.2 Equipment required 3-46 3.4.4.3 Procedure 3-46 INTERNAL PERMEATION OVEN (OPTIONAL) 3–48 Figure 3-1 - Electrical connections Figure 3-2 - Fluids connection Figure 3-3 – Permeation tube installation Figure 3-4 – Software overview Figure 3-5 - Printout example Figure 3-6 - Pressurized gas connection example Figure 3-7 - Typical calibrator 3–3 3–4 3–5 3–9 3–34 3–42 3–45 Table 3–1 - DB37 and DB25 connectors links Table 3–2 - MUX signals (Acceptable limits on the multiplexer 1 to 16 channels) 3–3 3–37 3–2 MAY 2007 AF22 MODULE Duplication prohibited 3 Environnement S.A OPERATING INSTRUCTIONS Figure 3-1 - Electrical connections Table 3-1 - DB37 and DB25 connectors links RS232 / 422 serial links COM1 2 - TX 3 - RX 4 - RTS 7 - GND 20 - DTR 21 - TX 11 - RX COM2 14 - TX 16 - RX 7 - GND ESTEL BOARD(S) PIN N° 1 2 3 4 5 6 7 8 9-28 10-29 11-30 12-31 13-32 14-33 15 16 NOTE : CONNECTION + ANA OUTPUT 1 + ANA OUTPUT 2 + ANA OUTPUT 3 + ANA OUTPUT 4 +ANA INPUT 1 +ANA INPUT 2 +ANA INPUT 3 +ANA INPUT 4 RELAY 6 CONTACT RELAY 5 CONTACT RELAY 4 CONTACT RELAY 3 CONTACT RELAY 2 CONTACT RELAY 1 CONTACT REMOTE CONTROL 1 REMOTE CONTROL 2 PIN N° 17 18 19 20 21 22 23 24 25 26 27 34 35 36 37 CONNECTION REMOTE CONTROL 3 REMOTE CONTROL 4 +5VCC ANA OUTPUT GROUND ANA OUTPUT GROUND ANA OUTPUT GROUND ANA OUTPUT GROUND ANA INPUT GROUND ANA INPUT GROUND ANA INPUT GROUND ANA INPUT GROUND REMOTE CONTROL GROUND REMOTE CONTROL GROUND REMOTE CONTROL GROUND REMOTE CONTROL GROUND Output relays contacts are normally open and potential free. Remote controls are made by closing a potential free dry contact Analog inputs accept maximum 2.5 VCC. JUNE 2004 3–3 AF22 MODULE Environnement S.A 3.1 Duplication prohibited INITIAL STARTUP The monitor is checked and calibrated in the factory before delivery. 3.1.1 PRELIMINARY OPERATIONS Start-up first consists in carrying out the following preliminary operations: – Visually examine the interior of the instrument in order to ensure that no element has been damaged during transport. – Remove the caps from the "gas" inlets and outlets on the unit (keep these aside for future storage, see Chapter 1.2.3). WARNING : Do not remove zero inlet cap if built-in zero filter is present Connect the 4/6 Teflon air sampling tube to the "sample inlet", after having checked for the presence of a Teflon filtering membrane in the inlet dust filter (fig.3-2) Connect the digital outputs to the DB25 connector (see Table. 3-1). Connect the analog inputs / outputs to the DB37 connector(s) (see Table 3-1). – Connect the mains power supply cable to a socket: 230 V, 50 Hz + ground or 115 V, 60 Hz + ground depending on the voltage specified on order. Zero air inlet of the permeation bench (option) Figure 3-2 - Fluids connection 3–4 MAY 2007 AF22 MODULE Duplication prohibited 3.1.2 Environnement S.A PERMEATION TUBE INSTALLATION (WHEN OPTION AVAILABLE) 2 3 1 Figure 3-3 – Permeation tube installation Pull the Teflon tap (1) of permeation oven inlet (2). After putting it out of its housing, insert permeation tube (3) in permeation oven, with porous diaphragm faced to the bottom. NOTE : It is essential to NOT OPEN permeation tube and to NOT PERFORATE the porous diaphragm. If analyzer has to be kept switched off for a while, it is necessary to remove tube from permeation oven, place it in its delivery box with drying bags, and store it in a cool place. JUNE 2004 3–5 AF22 MODULE Environnement S.A 3.1.3 Duplication prohibited STARTING UP THE UNIT Press the ON/OFF switch located on the front panel. The monitor goes into the "warm-up" cycle. The duration of this cycle is a function of the time elapsed since the last switch off. The warm-up cycle is terminated when the two following conditions are satisfied: – All metrological parameters are within operational limits, – The analyzer has made 10 consistent measurements within ± 4 ppb. Display at start-up: the WARM UP message appears in the top right corner. Display after warm-up : the measurement display mode can be chosen in CONFIGURATION Ö Measurement mode. Example given here below: Synoptic screen. STOP After some time (programmable in CONFIGURATION Ö Measurement mode) without action on any key, the screen passes in stand-by mode. Pressing down any key makes it going back to display mode. 3–6 MAY 2007 AF22 MODULE Duplication prohibited Environnement S.A 3.2 PROGRAMMING THE AF22M 3.2.1 SELECTION AND MODIFICATION OF THE PROGRAMMABLE PARAMETERS The keyboard is located under the LCD. The bottom line gives the function of each key for the current screen. The title of the menus and the selected fields are displayed in reverse video. By default the first line of the menus is selected. In the next paragraphs, the selected fields are symbolized in white on black background. 3.2.1.1 Screen areas definition 1 2 3 Information area: displays the date and time in the top left corner. In the top right corner, the WARM UP, REFERENCE or SPAN messages blinks. The ALARM message appears if an operating fault is detected within the instrument operating parameters. 1 2 Measurement or configuration area: displays the measurement parameters (gas, value, units ...) or the programmable parameters according to the selected menu. 3 Status areas and keys functions: displays the keys functions, the analyzer operating mode and the SO2 inlet ("sample" in the example above). NOTE : In the next paragraphs, the keys are symbolized by the icon or function displayed inside a rectangle. JUNE 2004 3–7 AF22 MODULE Environnement S.A 3.2.1.2 Duplication prohibited Definition of the most used functions of the keyboard (The availability of these functions is context dependent) Used to display the previous menu or to abort the current operation (parameter programming, etc.) Used to select the required sub-menu and the parameter to be modified. It is also used to increase the digit whose modification is in progress. Used to select the required sub-menu and the parameter to be modified. It is also used to decrease the digit whose modification is in progress. Moves the cursor to the left (only available during numerical parameters modifications). Moves the cursor to the right (only available during numerical parameters modifications). Authorizes the selected parameter modification. Used to valid the selection or the parameter value whose modification is in progress. Print It is used to print out the current screen. >> Used to display the next page. When there are several parameters, pressing down this key allows to display the next parameters. 3.2.2 PROGRAMMING THE OPERATING PARAMETERS 3.2.2.1 Programming the digital parameters Select the parameter with the key in the appropriate menu, press down the or key to st access to the modification of the parameter, the 1 digit blinks. Select the digit to be modified with the or key then increase it with the key or decrease it with the validates the modifications of the selected field, the key. The key key cancels the modifications of the selected field. 3.2.2.2 Programming the configurable parameters with toggle list Select the parameter with the or key in the appropriate menu, press down the access to the modification of the parameter, the field blinks. Select with the wanted value in the toggle list. The or key to key the key validates the modifications of the selected field, the key cancels the modifications of the selected field. 3–8 JUNE 2004 AF22 MODULE Duplication prohibited Environnement S.A MAIN MENU Measurement Span Configuration Stored Data Tests Instantaneous Calibration Date/Time/ Language Selection Optical bench Select gas Measurement Mode Tablular MUX signals Cycles Measure channels Histogram Other commands Pressure Offsets and units Printer output Serial link Stop Mode Cycle Average Cycle Synoptic Cycle Graphic Alarm limits Menu Speed Base Scale Printout Alarm display Estel card * Analog output * Analog input * Relays and remote control Serial link Factory settings Figure 3-4 – Software overview *: appears in the menu when option present JUNE 2004 3–9 AF22 MODULE Environnement S.A 3.3 DESCRIPTION OF THE DIFFERENT SCREENS 3.3.1 MAIN MENU Duplication prohibited This screen is used to choose the menus giving access to the analyzer operating parameters Select the menu with the Example: ACTION or key, validates the selection with the DISPLAY key. REMARKS – Displays the main menu, the 1ST item is selected by default. – Selects the next item. – Selects the next item. – Validates the selection (Configuration menu) and displays the sub-menu. – Goes back to the previous menu. NOTE : To make the reading easier, when a sub menu is quoted in the text, the corresponding menu is reminded before (ex. CONFIGURATION Ö Date / time / language). 3–10 JUNE 2004 AF22 MODULE Duplication prohibited 3.3.2 Environnement S.A MEASUREMENT This screen is used to choose the measurement display mode: instantaneous, average, synoptic (diagram) or graphic, to activate the real-time printout and to display possible alarms. 3.3.2.1 MEASUREMENT Ö Instantaneous Definition of the specific keys to this screen Sample Zero Selects the sample gas inlet. The gas is continuously sampled through the inlet dust filter. The measurement mode, the unit and the range are those chosen in the Configuration menu and in the corresponding sub-menus. This mode can be interrupted at any time by starting an automatic cycle or by manual selection of another mode or gas inlet (zero or span). Selects the zero gas inlet. Allows manual control of the zero on the built in zero filter or on the optional external zero gas inlet. The analyzer gives its reading on zero gas (possibly increased by a programmed offset). This operation allows to check the stability and the drift of the zero reading of the analyzer to determine the necessity to launch a reference cycle or to program its repetition period. JUNE 2004 3–11 AF22 MODULE Environnement S.A Span Duplication prohibited Selects the span gas inlet. Allows manual control of the span. The analyzer gives its reading on span gas (possibly increased by a programmed offset). This operation allows to check the stability and the drift of the span reading of the analyzer to determine the necessity to launch an auto-span cycle or to program its repetition period. >> Cycle Used to display the next page. When there are several parameters, pressing down this key allows to display the next parameters. Gives access to the screen allowing manual launching of cycles. Definition of the specific keys to this screen Z.ref Escape End Allows to manually launch an automatic corrective cycle in case of electrical zero and zero gas difference. At the top right corner, zero reference and the gas inlet on which the cycle is conducted are displayed. Allows to skip the current cycle without computing the new Zero-reference. Allows to manually shorten the cycle duration. Be careful : the new zero-reference displayed value is computed, this could occur a wrong zero reference value. 3–12 JUNE 2004 AF22 MODULE Duplication prohibited Auto Environnement S.A Allows to launch manually an automatic span cycle. The analyzer adjusts automatically its span factor K in order to equal its reading value (minus the programmed offset) and span gas concentrations. The span gas concentrations are programmable in the SPAN Ö Select gas menu, the concentration programmed for the gas inlet used for calibration is reminded in the top right corner of the screen (CAL=XXXX). The adjustment takes place for the duration programmed in the SPAN Ö Cycles menu. The cycle time duration countdown is displayed in the right top corner of the screen, the cycle is achieved when count is 0000 sec. Cycle can be shorten pressing down the Auto key. The new span factor is then memorized if reading value equals + 5 % span concentration. Escape End Allows to skip the current cycle without computing the new K-Span. Allows to manually shorten the cycle duration. Be careful : the span factor is computed even if the read and the target values are not equal. This could occur a wrong span factor. This function launches the auto-span using the gas inlet selected before pressing STOP down the Auto key, select the correct gas inlet before executing an auto span To go back to normal measurement after manual auto-span, press down the Sample key to select the sample inlet again. JUNE 2004 3–13 AF22 MODULE Environnement S.A 3.3.2.2 Duplication prohibited MEASUREMENT Ö Average Definition of the specific keys to this screen Sample 3.3.2.3 Zero Span Cycle have the same function as the screen MEASUREMENT Ö Instantaneous. MEASUREMENT Ö Synoptic This screen represents the flow circuit and displays significant operation parameter values: Gas, concentration and unit (1), PM high voltage (2), PM signal (3), optical bench temperature (4), Gas pressure (5), internal temperature (6), UV detector signal (7), voltage proportional to UV lamp current (8). 6 5 7 4 8 2 3 1 Definition of the specific keys of this screen Sample Zero Span 3–14 Cycle Have the same function than the screen MEASUREMENT Ö Instantaneous. MAY 2007 AF22 MODULE Duplication prohibited 3.3.2.4 Environnement S.A MEASUREMENT Ö Graphic This screen is used for graphic plotting of the measurement values on sample or zero/span gas inlet. The vertical line shows the current position: The refreshed measurements are given on the left side of this line. The vertical full scale of the graphic is the one programmed for the analog outputs. Definition of the specific keys to this screen Sample Zero Span have the same function as the screen MEASUREMENT Ö Instantaneous. When sample inlet is already active, pressing down the Sample key refreshes the graph. Press down the >> key to select the parameter to display. 3.3.2.4.1 Graphic Ö "Menu" screen Pressing down the Menu x Plotting speed x Base line x Full scale The R.S.T key gives access to the following graphic adjustments: key is used to reset the graph to zero. Plotting speed Current scale Graphic base JUNE 2004 3–15 AF22 MODULE Environnement S.A 3.3.2.4.2 Duplication prohibited Graphic Ö screen "Base" Pressing down the Base key allows to adjust the value of the graph base line (the minimum value is zero, the maximum value is just inferior to the full scale). __ _ Selects the inferior base line among 5000, 2000, 1000, 500, 200, 100, 50, 20, 10, 5, 2, 1, 0. + Selects the superior base line among 0, 1, 2, 5, 10, 20, 100, 200, 500, 1000, 2000, 5000. ++ 3.3.2.4.3 Divides 10 times the current base line (when the base line is 5, it resets to zero) Multiplies 10 times the current base line. Graphic Ö screen "Speed" Pressing down the Speed. key allows to adjust the plotting speed on the screen (the minimum value is 1 second, the maximum value is 60 seconds). 3–16 JUNE 2004 AF22 MODULE Duplication prohibited - 10s Decreases 10 seconds to the current plotting speed - 1s Decreases 1 second to the current plotting speed. +1s Increases 1 second to the current plotting speed. +10s Environnement S.A Increases 10 seconds to the current plotting speed. The programmed time is the interval duration between 2 points of the graph E.g.: when the plotting speed is 10 seconds, the graphic screen lasts for 240 x 10 = 2400 seconds. 3.3.2.4.4 Graphic Ö screen "Scale" Pressing down the Scale key allows to adjust the full scale of the graph (the minimum value is just superior to the base line, the maximum value 10000) This screen allows to adjust the full scale of the graphic (minimum not exceeding the basis line, maximum value reaching 1000). __ Selects the current scale among 5000, 2000, 1000, 500, 200, 100, 50, 20, 10, 5, 2, 1, 0. + Selects the current scale among 0, 1, 2, 5, 10, 20, 50, 100, 200, 500, 1000, 2000, 5000. ++ JUNE 2004 Divides 10 times the current scale (when the scale is 5, it reset to zero.) _ Multiplies 10 times the current scale. 3–17 AF22 MODULE Environnement S.A 3.3.2.5 Duplication prohibited MEASUREMENT Ö Printout. This menu is used to start real time printout on a serial printer connected to the COM2 serial port. It is also used to define measurement average calculation period and printing rate from (0001 to 9999mn). 3.3.2.6 MEASUREMENT Ö Alarms display This screen displays the operating faults in case of alarm. Possible corrective actions for these faults are given in chapter 5. 3–18 JUNE 2004 AF22 MODULE Duplication prohibited 3.3.3 Environnement S.A SPAN This menu gives access to the followings functions: x Programming the calibration factors K. x Programming the span gas values. x Gas inlet selection for span cycles. x Programming the period and duration of the automatic cycles. x Pressure sensors calibration Programmable digital potentiometer (E2Pot) allows to: 3.3.3.1 x Adjust mercury lamp current and consequently measurements and reference signal amplitude; x Adjust flow rate control point. SPAN Ö Coefficients This screen is used to modify manually calibration factors. The factors variations after a new auto-cal cycle are displayed in the "Delta %" fields. To reset manually the Delta % in case of calibration alarm due to a wrong use of the auto-cal function, select the Factor field of the gas whose the Delta % is greater than 5.0, press down the key and press down the key and the key. Exit the screen by pressing down the key to select again the SPAN Ö Calibration screen in order to refresh the Delta % display. JUNE 2004 3–19 AF22 MODULE Environnement S.A 3.3.3.2 Duplication prohibited SPAN Ö Select Gas. This screen is used to associate a span gas concentration to each gas inlet. These concentrations are the reference values for manual or automatic auto-calibration cycles. 3–20 JUNE 2004 Duplication prohibited 3.3.3.3 AF22 MODULE Environnement S.A SPAN Ö Cycles This screen is used to program the period and the duration of the automatic cycles, the durations programmed here are also those of the manually launched cycles. The possible automatic cycles are: ZERO : zero air check SPAN : span gas check. Z.Ref : automatic zero adjust correction AUTO : automatic span factor correction The “Remote” fields are used to configure the cycles remote controls (ESTEL board option), ZERO, ZERO REFERENCE, AUTO or SPAN. The status programmed in the “Cyclical” fields (ON = active, OFF = inactive) governs the analyzer reaction when a dry contact is closed on the remote controls inputs (see Table 3.1). The “Inlet” fields allow to select gas inlets used during the automatic sequences. The reference concentrations for automatic calibration are those programmed in the previous menu. The “Starting time” field is used to program the hour when the cycles are launched. If a 24 h ZERO cycle, a 24 h AUTO cycle, and a 24 h SPAN cycle are programmed, the sequence is launched at starting time according to the following priority: Z.Ref., ZERO, AUTO, then SPAN. To inhibit an automatic cycle, program 0000h in the “Period” field. To inhibit both an automatic and a manual cycle, program 0000s in the “Timing” field. JUNE 2004 3–21 AF22 MODULE Environnement S.A 3.3.3.4 Duplication prohibited SPAN Ö Pressure This screen is used to program the calibration curve of the pressure sensors. Pressure sensors calibration: Connect a reference pressure sensor in parallel to the pressure sensor to be calibrated. Enter the slope value (A) and its intercept (B) in the pressure calibration window fields. 3.3.3.5 SPAN Ö E2Pot This screen allows to adjust, in a digital way, electric gains on measurement signals. + Pressing down this key increase the signal - Pressing down this key decrease the signal 3–22 MAY 2007 Duplication prohibited 3.3.4 3.3.4.1 AF22 MODULE Environnement S.A CONFIGURATION This menu gives access to the following functions: x Response time programming. x Dilution function programming. x Analog outputs configuration. x Unit change and offset adjustment x Alarm thresholds, activation and assignment of the alarm relays. x Serial link programming. x Reset of the main programmable parameters. CONFIGURATION Ö Date/time/language This screen is used to set the internal clock of the analyzer, as well as to choose the displayed language among French, English, German, Italian and Spanish. It also shows the software version number to remind in case of software dysfunction. MAY 2007 3–23 AF22 MODULE Environnement S.A 3.3.4.2 Duplication prohibited CONFIGURATION Ö Measurement mode This screen is used to program the response time from about 20 sec. to 120 sec. The first digit of the programmed number activates (1) or de-activates (0) the automatic response time function, the second item divides the basic electronic integration time (120 sec.) Examples: Response time = 13 gives an automatic response time with a minimum of 40 sec. Response time = 03 gives an integration time fixed to 40 sec. The advised value is; Response time =11 (see chapter 2, automatic response time) This screen gives also access to the dilution function: to measure very high concentrations (i.e. founded in industrial environment), it is necessary to bring them to values corresponding to the range of analyzer by inserting a dilution system in the sampling line to get: C analyser inlet C sample Kdilution The real concentration display is obtained by applying a K Dilution multiplying factor to the measured concentration. "Latch DAC" field: when this field is ON, it latches the analog outputs to the last measurement values during the zero or span cycles in order not to perturb eventual data loggers. "Maintenance" field: when this field is on, it allows to trigger one of the alarm relays (see section 3.3.4.5 and table 3.1). The maintenance mode condition is reminded on the MEASUREMENT screens. "Starting screen" field allows to choose the screen displayed after warm-up when starting on the analyzer. 4 choices are offered: Instantaneous, Synoptic, Average, Graphic, corresponding to the menu MEASUREMENT. Screen std –by delay" field allows to program the time delay after which, without any action on keyboard, the screen passes in stand-by mode. "Zero filter life time" field allows to program a day down-counter which triggers, when zero, a filter alarm message. The setting value depends on the analyzer using conditions. The factory setting value, 365 days, corresponds to the advised maintenance frequency. 3–24 JUNE 2004 Duplication prohibited 3.3.4.3 AF22 MODULE Environnement S.A CONFIGURATION Ö Measure channels This screen is used to select the parameter, the display format and the unit for each measure channel. The measure channels programming allows to display (MEASUREMENT Ö Instantaneous screen or MEASUREMENT Ö Average screen) and to store (STORED DATA menu) other parameters than the one displayed by default (SO2). It allows to store MUX channels and analog inputs (ESTEL option). x The 8 "Channels" fields are used to choose the parameter among: SO2, H2S (if H2S rack option available), TRS (if TRS rack option available), GND, Int.t°, Opt.t°, Aux.t°, Flow r., Pressure, +15V, -15V, I.Pbse, I.IR, Signal. x The "Formats" fields are used to choose the display format among 4 possibilities (X.XXX, XX.XX, XXXX.X, XXXX). "Auto" manages the comma in order to display the best resolution at any time. The "Units" fields refer to the units programmed in screen CONFIGURATION Ö Offsets and units, or CONFIGURATION Ö Analog inputs. 3.3.4.4 CONFIGURATION ÖOffsets and units This screen is used to program the offset. This value is added to the measurements. It is also used to program the conversion factors from ppm to mg/m3, when the mg/m3 unit is selected. The conversion factor of 2,660 is applied for normal conditions of temperature and pressure, as follow : (20°C and 101,3 kPa). MAY 2007 3–25 AF22 MODULE Environnement S.A 3.3.4.5 Duplication prohibited CONFIGURATION Ö Alarm limits 2 limits are programmable for the programmed parameter: Threshold 1 and Threshold 2, allowing to activate relays and alarm messages. When the "Alarms display" field is “OFF”, displays and alarm relays are inhibited. 3.3.4.6 CONFIGURATION Ö Analog outputs This screen allows to choose the analog outputs parameters (only when ESTEL board option is available) among: x The SO2 concentration, the H2S concentration (optional), the TRS concentration (optional). x From MX01 to MX16, the 16 channels multiplexer x The external inputs. The chosen parameters correspond to the analog outputs. This screen is used to program the ranges for each displayed parameter. The ranges correspond to the analog output full scale. Scale 1 corresponds to the analyzer standard range. The analyzer switches to scale 2 when scale 1 is exceeded. It switches again to scale 1 when measurement decreases below 85 % of the full scale 1. This screen is also used to choose the parameters units among ppb, mg/m3, mV, °C or hPa. 3–26 JUNE 2004 Duplication prohibited 3.3.4.7 AF22 MODULE Environnement S.A CONFIGURATION Ö Analog inputs This screen is used to program the analog inputs characteristics. JUNE 2004 x "ESTEL card" field allows to select the board to be programmed: each ESTEL board has 4 analog inputs. x "Name" fields allow to enter 8 alphanumeric digits. x "Unit" fields allow to choose a unit among : none, ppt, ppb, ppm, μg/m3, mg/m3, gr/m3, μg/Nm3, mg/Nm3, gr/Nm3, μg/Sm3, mg/Sm3, gr/Sm3, %, μgr, mgr, gr, mV, U, °C, °K, hPa, mb, b,l, Nl, Sl, m3, l/min, NI/min, Sl/min, m3/h, Nm3/h, Sm3/h, m/s or km/h, in a scrolling menu. x "aX + b" fields allow to enter the calibration curve for each parameter. x "Meteo" fields allow to assign the channel where meteorological parameters are connected in order to apply a trigonometric treatment to those data. 3–27 AF22 MODULE Environnement S.A 3.3.4.8 Duplication prohibited CONFIGURATION Ö Relays and remote control This screen allows to configure the function of each input / output of the Estel board(s). x "Estel card Nb" field allows to choose what board to configure. x "Relays" fields allow to control the relays according to the following situations : Disable Ö Relay not assigned General alarm Ö Any operating fault triggers the relay Ch.1 > Thrs.1 Ö Limit 1 channel 1 exceedance triggers the relay Ch.1 > Thrs.2 Ö Limit 2 channel 1 exceedance triggers the relay Ch.2 > Thrs.1 Ö Limit 1 channel 2 exceedance triggers the relay Ch.2 > Thrs.2 Ö Limit 2 channel 2 exceedance triggers the relay Ch.3 > Thrs.1 Ö Limit 1 channel 3 exceedance triggers the relay Ch.3 > Thrs.2 Ö Limit 3 channel 3 exceedance triggers the relay Over range Ö Range 2 exceedance triggers the relay Flow rate Ö Abnormal flow rate triggers the relay Temperature Ö Abnormal temperature in the analyzer triggers the relay Pressure Ö Barometric pressure in chamber Null gas Ö On zero, relay is triggered Span Ö On span, relay is triggered Ref-Zero Ö On Ref-Zero, relay is triggered Auto Span Ö On Auto Span, relay is triggered Warm-up Ö On Warm-up, relay is triggered Stand-by Ö On Stand-by, relay is triggered Maintenance Ö Relay triggered when the analyzer is in maintenance mode x "Type" fields allow to control (NC) or not (NO) the relays when alarm OFF. x "Mode" field allows to configure working remote controls mode. Two different modes are possible: "State" mode: control is activated as long as remote control is active. When remote control falls down, control is no more active. "Rise" mode: control is activated when remote control activation is detected. When it is down, control remains active. It is necessary to re-activate the same remote control to make down the previous remote control. 3–28 JUNE 2004 Duplication prohibited 3.3.4.9 AF22 MODULE Environnement S.A CONFIGURATION Ö Serial link This screen is used to configure the Serial links (COM 1 and 2). The baud rate, format and communication mode of the 2 channels are programmable among: 3.3.4.10 x Baud rate: 1200, 2400, 4800, 9600, 19200, 38400 (limited to 19200 bds at present time) x Format : 7n1, 7o1, 7e1, 7n2, 7o2, 7e2, 8n1, 8o1, 8e1, 8n2, 8o2, 8e2 x Communication mode: Mode 4, impress. to send measurements to printer in real time, Jbus, Special1, and Special2. CONFIGURATION Ö Factory settings When this item is selected, pressing down the JUNE 2004 key displays the screen shown here below: 3–29 AF22 MODULE Environnement S.A 3.3.5 Duplication prohibited STORED DATA The access to stored data management is directly done from Main Menu. The stored data consists in the average of analyzer measurements within a defined time interval. 1 This screen allows to parameter data recording period from 1 to 1440 min (i.e. 24 hours) and informs about memory status: Free memory: from 80 Ko in standard operation, it can be increased to 464 Ko in adding a 384 Ko memory board (optional). This board is automatically detected when switching on the analyzer and it is indicated on the screen (1). Storage : it is the possible records number, it depends on free memory Autonomy: it is the duration (days, months, years, hours, minutes) while memory can store data, considering free space and data recording period. In the here-above example: 4 days, 0 month, 17 hours, 46 minutes. Data can be edited in the form as table or histogram: this screen allows to program date and hour of edition beginning, date and hour of edition end, histogram column width. Menu key gives access to table or histogram data display, printing functions, and memory reset-to-zero. 3–30 JUNE 2004 AF22 MODULE Duplication prohibited Environnement S.A Stored data edition in the form as tabular This screen presents stored data list according to parameters defined in the screen before. The running mode (measurement, zero, calibration…), during a memorization period, is coded in the status column. The status codes meaning are: 00 Measurement valid 01 Range 2 over shooting 02 General alarm 04 Calibration fault 08 Zero measurement 10 Span measurement 20 Maintenance 40 Less than 2/3 of valid measurements during the average period 80 Power supply failure FF Configuration modification The displayed status code corresponds to the summation of the status codes (hexadecimal numbers) that occurs during the memorization period. Example: with an average period of 20 min: 5 min zero and 15 min measurement give the 00 status code and the displayed average is the 15 min. measurement average. 11 min. zero and 9 min. measurement give the 08 status code and the displayed average is the 11 min. zero average. Definition of the specific keys to this screen: Select the previous or the next page. < Select stored data beginning or end. Display the other measure channels if more than 3 channels are programmed in CONFIGURATION Ö Measure channels screen JUNE 2004 3–31 AF22 MODULE Environnement S.A Duplication prohibited Stored data edition in the form as histogram This screen displays records in the form as columns; each column corresponds to the measurements average within the data-recording period as defined in STORED DATA screen. Only one channel is displayed at once. The information line gives first record date and hour, the channel name, and, alternatively blinking, full scale with unit, and data recording period. This area corresponds to no stored data. Definition of the specific keys to this screen Return to previous menu. Display previous stored data plotting. Display next stored data plotting. X 2 zoom in 1/2 zoom out. >> Select the next measure channel, when more than one measure channel is programmed. 3–32 JUNE 2004 Duplication prohibited AF22 MODULE Environnement S.A Stored data printing To print data, press down the Print key found in "Menu" function of "Memorized data" screen. The blinking message "Printing…" indicates printed data output. Data printing can be suspend at any time, pressing down F1 key. When printing is finished, the screen displays the message "Printing finished". When none communication port is programmed on printer output (serial port), the error message "Printing not set" is displayed. JUNE 2004 3–33 AF22 MODULE Environnement S.A Duplication prohibited AF22M[3.1] 11-10-2001 SO2 HH:MM status PPB 10:15 00 14.7 10:30 00 21.7 10:45 00 21.4 11:00 00 17.9 11:15 00 16.0 11:30 00 14.7 11:45 00 13.9 12:00 00 13.5 12:15 08 1.0 12:30 00 12.9 12:45 00 12.7 13:00 00 12.3 13:15 00 11.8 13:30 00 10.6 13:45 00 9.2 14:00 00 8.5 14:15 00 8.0 14:30 00 7.7 14:45 00 6.8 15:00 00 7.6 15:15 00 7.5 EXT1 hPa 1001.7 1001.4 1002.1 1002.6 1002.4 1000.7 1001.4 1002.1 1001.8 1001.6 1001.1 1000.8 1001.0 1001.3 1001.5 1001.8 1002.1 1002.3 1002.5 1002.6 1002.4 MX13 ºC 39.4 39.5 39.4 39.4 39.4 39.4 39.4 39.5 39.4 39.3 39.2 39.1 39.0 38.9 38.7 38.7 38.5 38.3 38.2 38.1 38.0 15:45 16:00 16:15 16:30 16:45 17:00 17:15 17:30 17:45 1002.4 1002.3 1002.6 1002.6 1002.5 1001.8 1002.4 1002.2 1002 0 37.9 37.5 37.5 37.7 37.8 37.9 38.0 37.9 37 9 00 00 00 00 00 00 00 00 00 8.1 8.5 8.5 8.7 9.1 9.2 9.2 9.0 9 1 Figure 3-5 - Printout example Memory reset to zero Pressing down the Reset key allows to empty storage memory. This action is irreversible: before to do it, the software asks you to confirm. If your answer is "YES", the software resets end edition dates and hours to the current dates and hours. 3–34 JUNE 2004 AF22 MODULE Duplication prohibited 3.3.6 Environnement S.A TESTS This screen gives access to the following functions: JUNE 2004 x Optical and flow parameters checking when maintenance operations occurs. x Serial link checking. x Checking of the ESTEL board working (when option available) 3–35 AF22 MODULE Environnement S.A 3.3.6.1 Duplication prohibited TESTS Ö Optical bench This screen is used to follow-up the measurement parameters periodically or occasionally. x Pm = instantaneous amplified PM signal x Pm0 = PM black signal (shutter closed) memorized during the last reference cycle x UV = Instantaneous amplified UV detector signal x uv0 = UV detector black signal (shutter closed) memorized during the last reference cycle x brut = UV energy compensated raw measurement x REFER = "brut" memorized during the last reference cycle x inst = instantaneous measurement in ppb x moy = last memorized measurement average x Optical T° = optical bench temperature x Internal T° = internal temperature of the analyzer x B. Perm. T° = Permeation bench temperature (optional) x Flow rate = Voltage proportional to flow rate x Pressure = vacuum pressure in the chamber. x Lamp I = lamp current Definition of the specific keys of this screen Sample Zero Span have the same function as the screen Measurement Ö Instantaneous. 3–36 MAY 2007 AF22 MODULE Duplication prohibited 3.3.6.2 Environnement S.A TESTS Ö MUX signals This screen is used to check the multiplexer signals. NOTE : The "XXXX mV" displayed value will be checked according to the acceptable limits in next table. Table 3–2 - MUX signals (Acceptable limits on the multiplexer 1 to 16 channels) Channel 1 Display GND Parameters Analog ground Lower Limit 0 mV 2 Int. T° Internal temperature of the analyzer 3 Opt. T° Temperature of optical chamber 4 PM HV 5 Flow r. Voltage proportional to high voltage applied to photo multiplier tube (***) Flow rate sensor voltage. 6 Pressure 7 100 mV Normal 0 mV Upper limit 50 mV 300 mV 600 mV 450 mV 500 mV 2400 mV 3000 mV 1000 mV 2800 mV 3500 mV 3300 mV 3200 mV 4000 mV 5000 mV Pressure of measurement chamber (*) 1200 mV 4000 mV 5000 mV -15V Test point of power supply voltage 1200 mV 1500 mV 1600 mV 8 +15V Test point of power supply voltage 1200 mV 1500 mV 1600 mV 9 UV Sig 7000 mV 9000 mV 10 ------- Measurement of UV lamp signal used to 1000 mV compensate for any possible drift. Not used – 11 PM sig. Measurement signal at PM amplifier 12 UV cur. 13 H2S T° TRS T° 14 B.P. T° 15 O2 Voltage proportional to temperature of 2200 mV built-in permeation oven (**) _ O2 sensor (**) 16 2.5 V ref. Reference voltage of analog / digital converter – Embase HAMA SDS – – 0 mV – 9900 mV Lamp current 250 mV 380 mV 440 mV Thermocouple probe temperature (***) 14 mV 0 mV 17 mV 100 mV 22 mV 500 mV 2234 mV 2260 mV 2480 mV _ _ 2500 mV 2520 mV (*) These values are given as information and they depends on the A and B linearization coefficients (SPAN Ö Pressure screen) (**) Only when the corresponding options are available in the analyzer. (***) According to the PM embase (HAMA. or SDS) specified in the Check List attached to the analyzer. JANUARY 2008 3–37 AF22 MODULE Environnement S.A 3.3.6.3 Duplication prohibited TESTS Ö Other commands STOP The selection of this menu makes ineffective some commands and regulations. When the instrument is again in measurement mode, some alarms could occur. This screen is used to check that the MODULE board is working correctly. Jxx refers to the connector command, SV refers to solenoid valve. 3.3.6.4 TESTS Ö Serial link This screen allows to check the serial link and shows the inputs / outputs which have to be strapped when the serial link is not connected and you still want to check it are: 2-3: Emission/Reception, 4-6 and 7-8: modem signals. 3–38 JUNE 2004 AF22 MODULE Duplication prohibited 3.3.6.5 Environnement S.A TESTS Ö ESTEL card This screen is only displayed when the option is available. It is used to set the analog outputs and to monitor the working state of the remote controls and analog inputs. The “Estel card Nb:” field is used to select the board to be tested. The “DA.C” (digital to analog converter) fields are used to program the number of points generated at analog output. The “Ax + B” fields are used to program the span factors of each output. These factors are calculated according to the value measured at the output. The “Out” fields are used to control the relays manually. The "AD.C" & "Rem" fields are used to read the status of these inputs. Definition of this screen specific keys: The sixth key is a toggle key, its function toggles from 0/OFF 4000/ON JUNE 2004 0/OFF to 4000/ON Gives 0 pt on all analog outputs and opens all relays contacts. Gives the full scale (4000 pts) on all analog outputs and closes all relays contacts. 3–39 AF22 MODULE Environnement S.A 3.3.7 Duplication prohibited STOP MODE This screen is used to activate the "Stop mode". To return to measurement mode, it is necessary to press down the "Sample" key in any screen of Measurement Menu (see Chapter 3.3.2). Stop mode is used to turn pumping unit off, all the other regulations keep on operation. 3–40 JUNE 2004 Duplication prohibited AF22 MODULE 3.4 CALIBRATION 3.4.1 OVERVIEW OF CALIBRATION AND CONCEPTS Environnement S.A To ensure the accuracy of the measurements performed using the AF22M monitor, the unit must be regularly checked, calibrated and adjusted, following the quality assurance plan of the user. – Check of zero and span point: This operation consists of comparing the monitor response, for zero air and a span point of the range used, to the gas standards used. This check is used to measure the monitor drift in time without modifying the adjustment coefficient. This check can be performed using the internal zero air and span. Frequency: generally 24 hours in automatic cycle mode. – 2-point calibration: This is a procedure for checking and correcting the response of the monitor at zero and at a span point located at approximately 80 % of the full scale of the measurement range used. Frequency: monthly, or more frequently if the monitor requires it. – Span (multi-point calibration): This involves a complete check up of the monitor performance characteristics (linearity). Frequency: quarterly, or following out-of-tolerance calibration check results requiring an intervention on the monitor. Note about gas generation devices: For devices providing pressurized gas, it is necessary to provide an excess system to deliver the gas at atmospheric pressure to the monitor inlet. The materials making up this device should be neutral for the gas used. When used in an automatic cycle with a cylinder, provide a shut-off solenoid valve that can be remotecontrolled by the monitor (see figure 3.6). Note about gas cylinders connections: When the analyzer is equipped with the internal zero filter and/or the internal permeation bench, these respective inlets are no more available (see figure 2-2), therefore during the calibration procedures the calibration gas cylinders will be connected to the sample inlet JUNE 2004 3–41 AF22 MODULE Environnement S.A Needle valve Duplication prohibited Solenoid valve Double pressure regulator Vent Gas cylinder Manifold External solenoid valve control SPAN INLET ANALYZER Figure 3-6 - Pressurized gas connection example 3.4.1.1 Zero air generation – Check: internal zero filter. – Calibration: cylinder of reconstituted air or zero air generator. The zero air should be free of any constituent likely to be measured by the monitor and should not contain more than 0.0005 ppm of SO2. 3.4.1.2 Span gas generation (SO2) SO2 calibration gas source standards used for adjustments should be traceable to a National Institute of Standard & Technology (NIST), Standard reference Material (SRM) or Certified Reference Material (CRM) in accordance with EPA's Protocol n° 2. If a permeation device calibration system is used, be sure to allow 24 hours for warm-up. Zero air used for the dilution of standard gas concentration and for zeroing the analyzer should be the same and contain less than 0.0005 ppm of SO2. All fittings, valves, pneumatic lines and other components that may contact span test gas must be fabricated with highly cleaned inert to SO2 material (i.e. stainless steel). – Calibration check: xCylinder of SO2 (1 % accuracy) with a concentration of approximately 80 % of the upper range limit. The cylinder used should be regularly certified in accordance with the user's quality assurance plan. xOptional built in permeation oven with an SO2 wafer device. The concentration generated by the permeation oven is recorded on the check sheet (only for span check). xExternal permeation device equipped with an SO2 permeation tube and able to generate a concentration of approximately 80 % of the upper range limit. 3–42 JUNE 2004 Duplication prohibited AF22 MODULE Environnement S.A – 2-point and multi-point calibration: xCylinder of SO2 (1 % accuracy) associated to a calibrator allowing the generation of 6 concentrations, including zero, up to 80 % of the upper range limit. The cylinder used should be regularly certified in accordance with the user's quality assurance plan. xExternal permeation device equipped with an SO2 permeation tube and able to generate 6 concentrations, including zero, up to 80 % of the upper range limit (refer to section Section10.3 of Appendix A to 40CFR50). NOTE : 3.4.1.3 The devices used to generate the span gases should deliver 700 cc/min. minimum and 2500 cc/min. maximum. All fittings, valves, pneumatic lines and other components that may contact span gases must be fabricated or coated with cleaned PTFE, glass or stainless steel. Internal solenoid valves During multipoint calibration the gas sources will be connected to the sample inlet of the monitor. After this calibration operation, the gas sources will be connected to their respective inlets and a check will be made to see that the monitor's response is identical on any inlet used. The various gas inlets can therefore be used for zero and span point checks and for 2-point calibration of the monitor. Otherwise, the solenoid valves must be cleaned or replaced. 3.4.2 CHECK OF ZERO AND SPAN POINT 3.4.2.1 Facilities required – "Zero" air: a sufficient quality of "zero" air is obtained using the monitor "ZERO AIR" filter (Purafil/activated vegetable charcoal). – Span point: x SO2 gas cylinder, which concentration is below 1 PPM and connected to the monitor "span gas" inlet. x Or internal permeation oven with SO2 tube (connected to monitor "span gas" inlet). The concentration generated by the oven is recorded on the check sheet. x Or portable calibrator (type VE3M) equipped with an SO2 tube and connected to the monitor "span gas" inlet. NOTE : If the analyzer is equipped with an internal permeation oven, the sampling input must be used to connect the reference cylinder or the portable calibrator. 3.4.2.2 Procedure – Zero check: Select the monitor "zero air" inlet using the Zero key or appropriate inlet if required and wait for the measurement to stabilize. The reading should be less than + 2 ppb. If this is not the case, a zero adjustment is necessary. – Check of scale point: Select the gas inlet where the span gas is connected using the Span key or the Sample key, as per the above note, and wait for the measurement to stabilize. The result will be compared to the concentration generated by the device used, taking into account its accuracy. If the difference between span gas and reading is more than + 10 %, a span adjustment is necessary. JUNE 2004 3–43 AF22 MODULE Environnement S.A 3.4.2.3 Duplication prohibited Use of automatic cycles To program the cycles, see section 3.3.3.3 Span Ö Cycles menu. – Zero cycle: The "zero" air generator is permanently connected to the monitor "zero air" inlet. The minimum recommended duration of the zero check is 10 minutes. – Calibration cycle: The scale point generator (the internal permeation oven if option is present) is permanently connected to the monitor "span gas" inlet, it can be the internal permeation oven . The SO2 concentration must be below the full scale of the range used for the measurement. The minimum recommended duration of the check is 10 minutes. 3.4.3 SPAN ADJUSTMENT 3.4.3.1 Facilities required – "Zero" air: See section 3.4.1.1. – Span point: See section 3.4.1.2. 3.4.3.2 Procedure – Zero reference: x Start by doing a reference cycle (minimum of 600 seconds). Feed zero air to the desired inlet (or span) and press the Cycle key in one of the Measurement screen, then the Z.Ref key of the cycle screen, the cycle duration countdown is displayed in the top right corner of the screen. – Span adjustment: x automatic: Select the measurement range (Configuration Ö Signals/Ranges/Units menu) corresponding to the concentration (Span Ö Select gas menu) of the standard gas and the inlet used. Press the Cycle key, then the Auto key of the cycle screen. The analyzer automatically changes its calibration factor as a function of the concentration programmed. It is advisable that the AUTOCAL lasts 600 seconds, the cycle duration countdown and the concentration of the span gas are displayed in the top right corner. NOTE : During the cycle, the SO2 displayed measurement uses the former K span, it is updated when the AUTO-CAL cycle is achieved. If the new K span is out of the bounds K(former) r 50 %, the analyzer gives a calibration alarm, in that case check: – the calibration pneumatic circuit – the generated concentration of the gas source used – the programmed span gas concentration – the programmed gas inlet If one of the above points is wrong, correct it and repeat the AUTO-CAL cycle. If nothing is wrong, proceed to a manual adjustment of the span factor as described after. 3–44 JUNE 2004 AF22 MODULE Duplication prohibited Environnement S.A x manual: Select the inlet to which the gas is connected by means of the Sample or Span keys. Wait for the measurement to stabilize. Program the new K (span) in the Span Ö factors mode menu. Calculation of new coefficient: K new = K (former) x span gas value read value (without offset) CAUTION: It is advisable to note K (former) before changing it, since it will be deleted when you enter K (new). 3.4.3.3 Use the AUTO-CAL automatic cycle To program this cycle, see paragraph 3.3.3.3 Span Ö Cycles menu. To configure the concentration, see paragraph 3.3.3.2, Span Ö Select gas menu. The gas generation system is connected permanently to the monitor "span gas" inlet. The recommended time for automatic calibration is 600 seconds. If the span gas meets the requirements described in § 3.4.2.1,this feature could be covered under US EPA designation. Flow controler Flow rate measurement Dilution air cylinder or zero air generator Flow controler Flow rate measurement Mixing chamber Doublepressure reducing valve Gas cylinder Vent Manifold To monitor Figure 3-7 - Typical calibrator JUNE 2004 3–45 AF22 MODULE Environnement S.A 3.4.4 MULTIPOINT CALIBRATION 3.4.4.1 Overview Duplication prohibited The minimum device will be made up of a diluter, a certified cylinder of SO2 (1 % accuracy), the calibration of which can be traced to reference materials from the National Institute of Standards (NIST) for calibration in the framework of measurements according to the US EPA, and a zero air generator. Figure 3.7 shows an example of a typical calibrator. The gases will be applied to the sample inlet of the monitor at atmospheric pressure. Calibration of the monitor requires generation, in addition to the zero, of 6 gas concentrations (for example, 15 %, 30 %, 45 %, 60 %, 75 % and 90 % of full scale of range used). The dilution air must be the same as the zero air. It is advisable to connect the analog output of the monitor to a strip chart recorder for acquisition and processing of the data. 3.4.4.2 Equipment Required – Diluter: x flow regulators: they must regulate flow rates to the nearest r 1 %. x flow meters: they must read and record flow rates to the nearest r 2 %. x mixing chamber: its shape and volume should allow a homogeneous mixture of SO2 and dilution air. – Manifold: The manifold must include at least one outlet for the monitor and one outlet for the excess flow meter. The outlet must have a sufficient diameter so as not to create any load losses at the inlet of the monitor. The outlet of the excess flow (at least 20 % of the total flow rate) will be designed so that the pressure in the manifold is quite near the atmospheric pressure (no overpressure), but so that the ambient air cannot be back scattered. – Dilution air (zero air): Zero air generator or cylinder of reconstituted air free of any contaminants likely to be measured by monitor and of which the SO2 concentration does not exceed 0.0005 ppm. – Span gas (SO2): Certified cylinder of SO2 in air at 1 % of which the concentration will allow generation of 6 ranges between 15 % and 90 % of the full scale of the measurement range used. 3.4.4.3 Procedure x Switch on monitor at least 6 hours before making the calibration. x Configure monitor as follows (advised configuration): Span ÖCycles menu REFER. time ................... 0600 AUTO-CAL time .............. 0600 (deactivate all cycles or check that no one of them will be triggered during calibration). Configuration Ö Measurement mode menu Resp. time ...................... 01 Configuration Ö Ranges / Units menu Range 1 - Range 2.....range currently used in measurement Configuration Ö Offset / Conversion menu SO2 offset ....................... 10.00 ppb (at least or 5% of full scale of the range used). 3–46 JUNE 2004 AF22 MODULE Duplication prohibited Environnement S.A – Connect analog output (see table 3-1) of monitor to recorder. Use response from recorder to calibrate device as described below. – Connect sample inlet of monitor to dilution system manifold. – Adjust dilution system so that it generates a total zero air flow rate that is more than 20 % greater than the sample flow rate of the monitor. – Generate zero air. Wait for reading to stabilize (recommended duration: 600 sec). Note value of ZSO2, expressed in percentage of maximum recorder response (for example, 400 mV / 10 V = 4 %). – Follow steps in section 3.4.3.2. ("span point correction" section) to adjust calibration coefficient. Use formula below to calculate value of span generated: [SO2] generated [SO2] Cylinder u FSO2 FD FSO2 where: [SO2]Generated is the concentration of SO2 in the gas generated at the outlet of the manifold, [SO2]Cylinder is the concentration of SO2 in the certified cylinder, FSO2 is the flow rate of SO2 in NI/min, FD is the dilution air flow rate in NI/min. Use formula below to calculate the reading value in ppm from the value in % full scale to be taken into account: [SO2] read § Srecord ZSO2 · ¨ ¸ u ECH © ¹ 100 where: S record is the value noted on the recorder, expressed in percentage of the full scale of the recorder, ECH is the full scale of the monitor, ZSO2 was measured previously. – Then generate the other five SO2 concentrations between 15 and 90 % of the full scale, varying the flow rates FSO2 and/or FD. – Plot the [SO2]read values as a function of the [SO2]generated values, including the zero air point. Check linearity. – Plot or calculate, using the formula for least error squares below, the straight line that will constitute the straight calibration line for the monitor. [SO2] read a x [SO2] generated b where: a ; is the linear regression coefficient (slope), and is calculated as follows: a n x ¦ [SO2] generated x [SO2] read ¦ [SO2] generated x ¦ [SO] read n x ¦ [SO2] 2generated ¦ [SO2] generated 2 b ; is the constant linear regression term (intercept) ; it is calculated as follows: b JUNE 2004 ¦ [SO2] read a x ¦ [SO2] generated n n is the number of items of data. 3–47 AF22 MODULE Environnement S.A 3.4.5 Duplication prohibited INTERNAL PERMEATION OVEN (OPTIONAL) The scale point check can be performed using a permeation oven equipped with a SO2 source. – Principle: The SO2 used is maintained in a state of liquid/vapor phase equilibrium in a closed cylindrical tube fitted with a polymer diaphragm. Due to the differential partial pressure of the gas on either side of the diaphragm and the diaphragm "permeability", gas is diffused toward the outside of the tube. The weight of the gas diffused by unit of time, called "permeation rate", depends on several parameters: type of gas, thickness, surface and nature of diaphragm, partial gas pressures on either side of diaphragm, temperature. – Setup: The permeation tube is placed in a block which is thermostat-controlled to 50 °C (± 0,1 °C) and continuously ventilated with a scavenging gas whose flow is regulated to about 45 l/h. The rinsing gas is filtered by an active charcoal filter located at the rear of the analyzer and directly connected to the inlet of the permeation oven. The outlet of the permeation oven (PTFE plug) is connected to the "span gas" inlet of the analyzer. When this inlet is selected, the monitor samples a part of the generated gas and thus measures the concentration of this gas. – Procedure: x The internal oven is selected using the "span" key, or automatically on a calibration cycle. Once stabilized, the SO2 measured by the monitor must be compared to the concentration recorded on the check sheet. x Since SO2 permeation is very sensitive to the quality of the rinsing air, the condition of the activated vegetable charcoal filter should be checked periodically. x The oven temperature is set using the Tests Ö Mux signals function on channel No. 14 (see Table 3.3). x The system operating temperature range is 10 to 35 °C (ambient temperature). x When setting into service or following an extended shutdown period, the stabilization time is about 24 hours. x The permeation source supplied with the monitor has an autonomy of about 16 months. If the monitor is not used, the source should be removed from the oven, and placed in its original package with the desiccant and absorbent bags, then stored in a cool, ventilated location. 3–48 JUNE 2004 Duplication prohibited AF22 MODULE Environnement S.A – To maintain the best precision, the following characteristics should be checked regularly: x flow rate of oven diluent air, x permeation tube rate (theoretically constant). A differential weighing using an accurate balance should be performed to the 10 th, or better to the 100 th of mg. Calculation of permeation (P) and (CG) concentration rates generated by oven: m0 = Initial weight of tube (ng) m1 = Final weight of tube (ng) m0 m1 = Weight of SO2 diffused (ng) t = Time between two weighings (min) P = (m0 m1) / t = Tube permeation rate (ng/min.) F = Real total air flow rate passing through the oven (CC/min.) Km = Molar coefficient, for SO2 = 0.382 CG = Km x P / F = Concentration of span gas generated (ppm) NOTE : These calculations must be repeated each time a permeation tube is changed, or, more simply, the concentration generated by the new tube can be determined by reading the concentration on the oven just after calibration of the analyzer (see section on calibration). JUNE 2004 3–49 AF22 MODULE Environnement S.A Duplication prohibited Page intentionally left blank 3–50 JUNE 2004 AF22 MODULE Duplication prohibited Environnement S.A CHAPTER 4 PREVENTIVE MAINTENANCE 4.1 SAFETY INSTRUCTIONS 4–2 4.2 MAINTENANCE CALENDAR 4–3 4.3 MAINTENANCE OPERATION SHEETS 4–4 4.4 AF22M MAINTENANCE KIT FOR 1 YEAR JULY 2002 4–11 4–1 AF22 MODULE Environnement S.A 4 PREVENTIVE MAINTENANCE 4.1 SAFETY INSTRUCTIONS Duplication prohibited The safety instructions must be observed at any time by the user. Whenever possible, cut off the power supplies when performing any work on the monitor. Only qualified personnel should intervene on the monitor. As concerns safety, the manufacturer shall not be responsible for any consequences resulting from: use of the monitor by non-qualified people, use of the monitor under conditions other than those specified in this document, modification of the monitor by the user, no-maintenance of the monitor. A systematic periodic inspection is required. 4–2 JULY 2002 AF22 MODULE Duplication prohibited 4.2 Environnement S.A MAINTENANCE CALENDAR By its design, the AF22M requires very limited maintenance. However, to ensure the monitor's performance characteristics over time, the unit must be serviced regularly. The periodicities indicated below are given as an example and can vary according to operating conditions. Operation – Sample inlet PTFE filter – Check of electrical parameters – Check of zero and calibration – Replacement of activated charcoal (internal zero filter) and kicker zero filter cartridge – Inspection of pump valves and diaphragms – Replacement of UV lamp Periodicity Sheet No. 15 days 4.3.1 1 month 4.3.2 1 month 4.3.3 One year 4.3.4 Six months 4.3.5 2 years 4.3.6 Annual check The monitor must be returned to laboratory for complete cleaning (measurement chambers, restrictors, flow circuit, etc.) and check of all metrological parameters. JULY 2002 4–3 AF22 MODULE Environnement S.A 4.3 Duplication prohibited MAINTENANCE OPERATION SHEETS MAINTENANCE SHEET MONITOR Serial No.: Scope: Replacement of filters OPERATION SHEET: 4.3.1 PAGE: 1/1 Periodicity: 15 days Sample inlet PTFE filter: "MITEX" Teflon filter - 5 μm porosity - 47 mm dia. Ref.: F05-11-842 Date a) Unlock the filter cover (2) by rotating the locking spring (1) b) Remove the dirty filter (3) c) Place the new filter (4) by slipping it slightly from its paper protection(5) onto the filter holder (6). 2 1 3 5 4 6 Figure 4-1 – Inlet dust filter Tools required x none 4–4 JULY 2002 AF22 MODULE Duplication prohibited Environnement S.A MAINTENANCE SHEET MONITOR Serial No.: Scope: Check of electrical parameters OPERATION SHEET: 4.3.2 PAGE: 1/1 Periodicity: 1 month – Electrical values are checked using the Tests Ö Mux signals (see Chapter 3, paragraph 3.3.6.2). – Compare the voltage values at each input of the multiplexer to the values given for the same inputs on the test sheet provided with the monitor. Mux Reading Dates 2 6 7 8 9 10 11 12 14 – Tools required x None. JULY 2002 4–5 16 AF22 MODULE Environnement S.A Duplication prohibited MAINTENANCE SHEET MONITOR Serial No.: Scope: Checks of zero and calibration OPERATION SHEET: 4.3.3 PAGE: 1/1 Periodicity: 1 month ZERO Span reading reading Dates – Check of zero (see section 3.4.2) Zero checking operations can be carried out: x Either using a pressure-packed, synthetic air cylinder guaranteed to be free of any trace of SO2, and injected in the analyzer sample inlet at atmospheric pressure. x or using a zero air provided by the pure-air generator, for example of the AADCO type, and injected under the same conditions as the previous example. x or using the internal zero filter, by actuating the Zero key, which controls the internal solenoid valve. – Manual calibration of monitor (see section 3.4.3). It is highly advisable to carry out this operation on site, under regular operating conditions. Once the calibration is made, the connections of the analyzer must not be handled. This operation requires the use of a SO2 in synthetic air gas cylinder for calibration (this cylinder should be fitted with a double pressure relief valve) or the use of a calibration device (portable calibrator). The gas used for calibration should be delivered at atmospheric pressure (for example, through a manifold at the "span gas" inlet of the analyzer). – Tools required x None 4–6 JULY 2002 Duplication prohibited AF22 MODULE Environnement S.A MAINTENANCE SHEET MONITOR Serial No.: Scope: Replacement activated charcoal (internal zero filter) and kicker zero filter cartridge. OPERATION SHEET: 4.3.4 PAGE: 1/1 Periodicity: Six months Date – Disconnect and remove used cartridge. – Connect the tube to the fitting provided for this purpose on the Zero solenoid valve. – Position cartridge. 1 2 Figure 4-2 – Zero filter cartridges position NOTE : The built-in zero filter (1) lifetime is 1 year. The hydrocarbon elimination device scavenging air zero filter (2) is 6 months (double flow rate than filter (1) and continuous working) – Tools required x None JULY 2002 4–7 AF22 MODULE Environnement S.A Duplication prohibited MAINTENANCE SHEET MONITOR serial No.: OPERATION SHEET: 4.3.5 Scope: Check of pump valves and diaphragm PAGE: 1/1 – Check condition of diaphragm and pump valves. Replace them if necessary. Frequency: Yearly Type of operation Date Replacement of diaphragm and valves – The diaphragms and valves are parts that wear out; these parts are replaced very easily. Replacement of diaphragm and pump valves – Power instrument off, unplug the power cord a) Disconnect supply connector. b) Disconnect gas flow connections. c) Loose the 3 screws (1) fastening pump assembly to frame in order to release the 3 pump holder slots. d) Unscrew the 2 screws (3) fastening pump on its holder. e) Draw a permanent mark (13) on the pump body (8) for reassembling purpose. f) Remove the nut (5) fastening pump body (8) on the vibrating blade (6). g) Unscrew the 2 screws (7) fastening pump body to pump housing (9). h) Remove pump body. i) Separate the various parts.. j) Clean diaphragm (10), the two valves (11) and the gasket (12). k) Dust off or clean the different parts with alcohol (dismount valves if only necessary) l) Check diaphragm, change it if necessary. m) Reassemble, repeating steps above in reverse order. – Tools required x Dia. 4 mm cross-tip screwdriver, x Dia. 5 mm flat screwdriver, x Combination pliers x Alcohol solution Type of operation: D: Replacement of diaphragm 4–8 V: Replacement of valves JULY 2002 AF22 MODULE Duplication prohibited Environnement S.A MAINTENANCE SHEET MONITOR serial No.: OPERATION SHEET: 4.3.5 Scope: Check of pump valves and diaphragm PAGE: 2/2 Frequency: Yearly 1 10 2 3 11 4 12 5 6 13 7 8 9 Figure 4-3 – Exploded view of the pump. JULY 2002 4–9 AF22 MODULE Environnement S.A Duplication prohibited MAINTENANCE SHEET MONITOR Serial No.: Scope: Replacement of UV lamp OPERATION SHEET: 4.3.6 PAGE: 1/1 Periodicity: 2 years WARNING: Do not touch the glass part of the lamp. a) Switch off the monitor. b) Disconnect the 2 supply wires of the lamp, loosening them from the UV supply board. c) Unscrew the 2 screws (1) to remove the lamp / shutter assembly. d) Loose off 3 mm the 2 screws (2) to release the UV lamp. e) Replace the UV lamp. f) Align mechanically the new lamp, taking into account the MAX OUTPUT PORT mark (3). This window must face the hole (4). g) Remount the lamp assembly. h) Select the Tests Ö MUX signals screen: x Check the voltage and current of the UV lamp. I-UV supply: 350-450 mV adjusted on UV lamp supply board x Adjust the position of the lamp by rotating and translating it so as to have the maximum UV signal (channel 9 of MUX) voltage. Adjust to approximately 4300 mV. i) Tighten the 2 screws (2) when maximum signal is obtained to fix the UV lamp. j) After stabilization of the UV power, run a reference cycle, and then calibrate the analyzer. 1 3 4 2 2 1 Figure 4-5 – Lamp / shutter assembly (rear face) Figure 4-4 – Lamp / shutter assembly (front face) – Tools required x 3.5 x 75 mm - 2.5 x 50 mm screwdrivers 4–10 JULY 2002 Duplication prohibited 4.4 AF22 MODULE Environnement S.A AF22M MAINTENANCE KIT FOR 1 YEAR Kit reference : AF22-K This kit consists in: 1 box of 25 filtering membranes for sample inlet particulate filter SAV-K-000042-A 3 filtering cartridges F05-0128-1 1 maintenance kit for internal pump V02-K-0041-A JULY 2002 4–11 AF22 MODULE Environnement S.A Duplication prohibited Page intentionally left blank 4–12 JULY 2002 AF22 MODULE Duplication prohibited Environnement S.A CHAPTER 5 CORRECTIVE MAINTENANCE Table 5–1– List of faults and corrective actions Table 5–2 – AF22M Module board configuration Table 5–3 – Board RS4i Configuration Table 5–4 – Keyboard Interface configuration Table 5–5 – UV lamp board configuration Table 5–6 – Configuration of UV lamp supply board Table 5–7 – Flow rate control board configuration and setting 5–4 5–9 5–10 5–11 5–12 5–13 5–14 Figure 5-1 – AF22M Module board Figure 5-2 – Card RS4i Configuration Figure 5-3 – Keyboard Interface board Figure 5-4 – UV lamp board Figure 5–5 – UV lamp supply board Figure 5-6 – Flow rate control board 5–8 5–10 5–11 5–12 5–13 5–14 MAY 2007 5–1 AF22 MODULE Environnement S.A Duplication prohibited Page intentionally left blank 5–2 JUNE 2004 Duplication prohibited 5. AF22 MODULE Environnement S.A CORRECTIVE MAINTENANCE Corrective maintenance of the monitor should only be performed by qualified people using the information provided in this document. The monitor automatically and continuously self-tests its main components. Any malfunction detected is indicated by a clear message on the display and a buzzer. Table 5.1 summarizes the main faults indicated by the unit with corresponding corrective possible actions. In case of operating fault, the ALARM message blinks in the top right corner. To check which operating fault is present select the menu Measurement Ö Alarms display. JUNE 2004 5–3 AF22 MODULE Environnement S.A Duplication prohibited Table 5-1– List of faults and corrective actions ALARM MESSAGE CHOPPER FAULT OVERRANGE Optical T°C FAULT Flow rate Fault CAUSE POSSIBLE ACTION – The shutter does not cut off the UV beam. – Check that connector J9 is indeed inserted. – Check that the shutter is not blocked by its supply cable. – Check the solenoid control. x To do this: start a Zero Ref. cycle. x Put a multimeter between the two terminals of the connector. For the first 40 seconds of the cycle, the multimeter should give a voltage reading of 24 V. x If it does not, disconnect J9. Check the electrical continuity of the coil of the solenoid (between end terminals of J1). Replace solenoid if necessary. Otherwise, check mechanical positioning of the shutter. If you still do not locate the problem, contact us. x If this is not the case: check that the 5 V is available in the control transistor emitter, located on the motherboard, throughout the duration of the control. If the voltage is indeed available, check the availability of the D.C. power supply. If you still do not locate the problem, contact us. – The measurement value exceeds the range 2. – Change ranges. – The temperature of the optical – Check that connector J17 is correctly bench does not fall within the inserted. boundary values for correct Run a warm up of the monitor by stopping it operation for a few seconds, then switching it back on. (38 °C < T < 48 °C) Check the availability of the 24 V voltage at both end terminals on J17. – The temperature probe is defective. – Contact us. – The Module board is defective. – Replace board or contact us. – Incorrect flow rate in measurement chamber; the pump is not working. – Check connection. If everything is OK, overhaul pump completely. – Leak in fluid circuit. – Check all connections. – Place a flow meter at the outlet of the monitor. Plug the sample or calibration inlet, according to the case. The ball in the flow meter should drop to zero. If it does not, there is a leak. 5–4 JUNE 2004 Duplication prohibited ALARM MESSAGE Calibration fault UV Power FAULT AF22 MODULE CAUSE Environnement S.A POSSIBLE ACTION – Span gas source – Check the availability of the span gas at atmospheric pressure on the selected inlet. – Following a manual reset of the span K factor – Run a manual calibration. – The control voltage of the UV power does not fall in the boundary values for correct operation 2,500 mV < UV voltage < 4,500 mV. – Check that connector J7 is correctly inserted. Check the stability of the regulated voltage between the right-hand end point of connector J7 and the ground. If one of these voltages is off, contact us. – The voltage function of lamp current does not fall in the boundary values 80 < UV cur < 440 Set voltage between 350 mV and 450 mV using potentiometer P (MUX 12) I. UV. x move the lamp to adjust maximum UV energy. If it is still not possible: x increase the UV lamp supply current using SPAN Ö E2Pot screen, I (mA) lamp function. If it is still impossible to make the setting, or if the voltage is regulated but the failure persists, contact us. – After stabilization of the UV power, run a Zero Ref. cycle, then calibrate the analyzer. UV SOURCE FAULT Pressure Fault Permeation T° Fault ZERO filter life time MAY 2007 – The UV signal does not fall in the boundary values for correct operation 1000 mV < UV signal < 9800 mV. – The signal given by the pressure sensor (optional) doesn't fall in the limits 500 < Pressure < 1050 – Refer to possible actions described for UV power fault – Adjust the SPAN Ö E2Pot, UV signal function. – Check that sample is indeed at atmospheric pressure. – Check that there is no clogging. – Disconnect the tube on pressure sensor. Check that measurement corresponds to the ambient barometric pressure. – Ambient working temperature out of bounds – Permeation oven temperature – +15V permeation oven pcb's fault. regulation fault – The zero filter life time down – Replace the filter (see maintenance sheet counter has reached 0. 4.3.4) – Reset the zero filter life time down counter (ConfigurationÖMeasurement mode screen). 5–5 AF22 MODULE Environnement S.A Duplication prohibited Table 5-1– List of faults and corrective actions SYMPTOM (no fault indication) Monitor does not react when switched on. POSSIBLE CAUSES – Mains fault – Check for presence of mains power supply. – Faulty mains cable – Test continuity of mains cable. – Connector plugged in – Check fuse in connector assembly. – Mains Monitor remains in preheating status ACTIONS incorrectly fuse blown – Module board faulty. – Check that display flashes. – Reset circuit blocked Micro 5 V faulty. – If not flashing, check if the microprocessor board is in place. – Replace if necessary. – If flashing, wait for 15 min. and possible fault indication. Switching power supply is protected from short circuits. In such case, it is necessary to disconnect / re-connect the power cord to reset STOP 5–6 JUNE 2004 Duplication prohibited AF22 MODULE Environnement S.A Page intentionally left blank JUNE 2004 5–7 AF22 MODULE Environnement S.A Duplication prohibited J1 J2 PT4 J3 PT5 PT3 PT2 J4 J5 PT4 PT1 J6 J35 ST3 J7 ST1 J8 PT16 PT17 PT7 J9 ST2 J10 PT9 SW4 J11 SW3 J12 Pt 14 J13 J14 J19 J15 PT11 J16 J17 J18 PT8 Pt 13 Pt 12 Figure 5-1 – AF22M Module board 5–8 JUNE 2004 AF22 MODULE Duplication prohibited Environnement S.A Table 5-2 – AF22M Module board configuration Type of signal Test points. Connection Connector PT1 Flow rate J1 PT2 Chamber pressure J2 O2 option UV detector PT3 PM signal J3 PM preamplifier PT4 Gas temperature J4 Gas temperature PT5 A/D RUN J5 Chamber temperature PT6 A/D STATUS J6 Flow rate sensor PT7 Permeation bench J7 UV lamp supply PT8 0 V (GND) J8 Permeation bench PT9 H2S converter J9 Chopper PT10 MUX output J10 H2S/TRS converter PT11 +24VCC J11 Fan PT12 +5VCC J12 Zero SV PT13 +15 VCC J13 Span SV PT14 -15VCC J14 H2S SV PT15 Not used J15 Pump 2 (permeation) PT16 I off+ J16 Flow rate PT17 I off - J17 Chamber heating J18 +24VCC supply J19 +24VCC on/off switch J20 Estel board I2C bus J21 Synchro bus J22 RAM extention option J23 RS4i board I2C bus J24 Not used J25 Not used J26 Not used J27 Not used Nature of operation Jumpers SW1 EPROM Configuration SW3 Power supply SW4 Internal clock ST1 ST2 Watch dog JUNE 2004 1 2 3 Selects 27C20 (2 Mbytes) 1 2 3 Selects 27C40 (4 Mbytes) 1 2 3 5V I2C Bus J28 Not used 1 2 3 24V I2C Bus J29 Not used 1 2 3 =CLK/2 J30 Not used 1 2 3 = CLK (default position) J31 Not used (default position) J32 Not used Resets microprocessor J33 Not used Inactive J34 Stand by LED option Active (default position) J35 Maintenance switch option 5–9 AF22 MODULE Environnement S.A Duplication prohibited Table 5-3 – Board RS4i Configuration Jumpers references SW1, SW2 SW3 Nature of operation Channel 1 on RS422 standard Channel 1 on RS232 standard Load RX bus RS422 active ST1 Load RX bus RS422 inactive Load TX bus RS422 active ST2 Load TX bus RS422 inactive Not used ST3 NOTE : Symbols Channel 2 is on the RS232 standard. ST3 SW2 SW3 SW1 ST2 ST1 Figure 5-2 – Card RS4i Configuration 5–10 JUNE 2004 AF22 MODULE Duplication prohibited Environnement S.A Table 5-4 – Keyboard Interface configuration Jumpers references Symbols Nature of operation Keyboard inhibited ST1 Keyboard active P1 LCD contrast adjustment potentiometer P1 ST1 Figure 5-3 – Keyboard Interface board JUNE 2004 5–11 AF22 MODULE Environnement S.A Duplication prohibited Table 5-5 – UV lamp board configuration References P1 Nature of operation Lamp current pre-adjustment PT1 GND PT2 LM2596 output (SV) PT3 Frequency (25 kHz) PT4 V. f(I) PT5 I lamp adjust PT6 I lamp UV lamp supply PT4 PT5 P1 PT6 PT2 PT1 PT3 Figure 5-4 – UV lamp board 5–12 JUNE 2004 Duplication prohibited AF22 MODULE Environnement S.A Table 5–6 – Configuration of UV lamp supply board Jumpers SW1 Nature of operations 3 2 1 AF22M Measure lamp (2-3 are linked) ST1 ON ST2 OFF Figure 5–5 – UV lamp supply board MAY 2007 5–13 AF22 MODULE Environnement S.A Duplication prohibited Table 5-6 – Flow rate control board configuration and setting Designation Nature of operations Ground referenced to Module Board ST1 Direct ground (default position) P1 Flow rate adjustment P2 Pump frequency adjustment PT0 Ground PT1 Flow rate signal PT2 Pump supply voltage P2 PT2 PT2 ST1 P1 PT0 Figure 5-5 – Flow rate control board 5–14 JUNE 2004 Duplication prohibited AF22M Environnement S.A 6 CHAPTER 6 APPENDIX ESTEL board SOREL board JUNE 2004 6–1 AF22 MODULE Environnement S.A Duplication prohibited Page intentionally left blank 6–2 MAY 2007 ESTEL Board INPUTS / OUTPUTS BOARD OPTION OF 2M ANALYZERS - June 2009 - WARNING Information contained in this document are likely to be modified without notice. The designer reserves the right to modify the equipment without improving this document, therefore, information of this document does not represent a commitment under ENVIRONNEMENT S.A. ENVIRONNEMENT S.A. all right reserved. 111 bd Robespierre, 78300 POISSY - -TEL. 33(0)-1.39.22.38.00 – FAX 33(0)-1.39 65.38.08 http://www.environnement-sa.com ESTEL Board Environnement S.A Duplication prohibited ESTEL BOARD 1.1 FUNCTION AND USE 3 1.2 TECHNICAL CHARACTERISTICS 3 1.3 CONFIGURATION 4 1.4 PROGRAMMATION 8 1.5 1.6 1.4.1 ESTEL CARD(S) Ö Analog output 1.4.2 ESTEL CARD(S) Ö Analog input 11 1.4.3 ESTEL CARD(S) Ö Relay 12 1.4.4 ESTEL CARD(S) Ö Remote controls 13 9 INSTALLATION AND REPLACEMENT OF ESTEL BOARD 14 1.5.1 Switch off the analyzer 14 1.5.2 Unplug the mains cable 14 1.5.3 Put off the cover 14 1.5.4 Dismount ESTEL board 15 1.5.5 Unrivet the back plate (6) of rear panel of analyzer 15 1.5.6 Installation of board inside the analyzer 16 OPTION OF EXTERNAL CONNECTION 17 Figure 1 - ESTEL board_index A Figure 2 – ESTEL board-index B Figure 3 – Option of external connection P10-1337-A Figure 4 – Option of external connection + 4 insulated outputs P10-1338-A 5 6 18 18 Table 1 - Configuration of ESTEL board_index A Table 2 - Configuration of ESTEL board_index B 5 6 Up-to-date: Pages Up-to-date Pages Up-to-date 1 05-2004 9 06-2009 17 06-2009 2 05-2004 10 06-2009 18 06-2009 3 05-2004 11 06-2009 4 05-2004 12 06-2009 5 05-2004 13 06-2009 6 05-2004 14 06-2009 7 05-2004 15 06-2009 8 06-2009 16 06-2009 2 Pages Up-to-date JUNE 2009 ESTEL Board Duplication prohibited 1. Environnement S.A ESTEL BOARD ESTEL board is a universal board of logic and analog inputs/outputs for the 2M series analyzers. It is optional: it is possible to install up to 2 ESTEL boards in an analyzer. 1.1 FUNCTION AND USE The ESTEL board has 4 functions: x 4 Analog inputs, x 4 Analog outputs, x 6 Relays, x 4 Remote controls. The ESTEL board enables dialog with the measurement module and relieves it of the Inputs/Outputs functions. It enables remote control and/or remote signalling of certain functions as: "measurement", "zero", "calibration", "alarm". The analog inputs are used to connect independent monitors in order to follow-up, for example, weather parameters. The analog outputs enable to send numeric parameters (gas concentration to be analyzed, MUX channels) to analog independent peripherals in order, for example, to store and process several data of several months. Equipped with an ESTEL board, the analyzer can work as an autonomous unit of analysis. 1.2 TECHNICAL CHARACTERISTICS Management by specialized micro controller: x 4 analog inputs of 12 bits, 0-2,5 volts full scale, x 4 not-insulated analog outputs, configurable into: 0-1 volts, 0-10 volts, 0-20 mA, 4-20 mA (maximum load of 1000 Ohm). x 4 insulated by optocoupler logic inputs, x 6 potential-free contacts for remote signalling, x only one power supply of 8 to 24 volts, x i2C communication visualization using a LED. Electric connection: x 4-point connector for link with Module boards of 2M series, x Inputs / Outputs centralized on only one female connector SUB D 37 points. This connector is screwed on the rear panel of the analyzer. x Option of external connection, see paragraph 1.6 Voltage and current on relays: x Maximum voltage by relay contact : 50 volts x Maximum current by relay contact : 1 Ampere at 24 V D.C. (resistive load) Remote controls: x MAY 2004 By dry contact between (1-4) Remote control and ground Remote control. 3 ESTEL Board Environnement S.A 1.3 CONFIGURATION PIN N° CONNECTION 1+ 20 GND Analog output 1 2+ 21 GND Analog output 2 3+ 22 GND Analog output 3 4+ 23 GND Analog output 4 5+ 24 GND 6+ 25 GND 7+ 26 GND 8+ 27 GND Duplication prohibited PIN N° CONNECTION 14-33 Relay contact 1 13-32 Relay contact 2 12-31 Relay contact 3 11-30 Relay contact 4 10-29 Relay contact 5 9-28 Relay contact 6 15 + 34 GNDI Remote control 1 16 + 35 GNDI Remote control 2 17 + 36 GNDI Remote control 3 18 + 37 GNDI Remote control 4 19 5 VCC or + 24 VCC Analog input 1 Analog input 2 Analog input 3 Analog input 4 (*) according to SW5 jumper position GND: ground GNDI: insulated ground 4 MAY 2004 ESTEL Board Duplication prohibited Environnement S.A Table 1 - Configuration of ESTEL board_index A Jumpers mark Symbols Nature of operations ESTEL selection, board N° 1 ESTEL selection, board N° 2 ST1, ST2, ST8 ESTEL selection, board N° 3 ESTEL selection, board N° 4 ST3 0 V to ground (default) Floating 0 V 0-1 V, idem for the 4 DAC. DAC1 DAC2 DAC3 DAC4 0-10 V, idem for the 4 DAC. 0-20 mA, idem for the 4 DAC. 4-20 mA, idem for the 4 DAC. P1, P2, P3, P4 4 mA adjustment in 4-20 mA mode Figure 1 - ESTEL board_index A MAY 2004 5 ESTEL Board Environnement S.A Duplication prohibited Table 2 - Configuration of ESTEL board_index B Jumpers mark Symbols Nature of operations ESTEL selection, if 1 board ESTEL selection, if 2 boards ST7, ST6, ST5 ESTEL selection , if 3 boards ESTEL selection, if 4 boards ST8 0 V to ground (default) Floating 0V DAC 1 0-1 V (or optional 2,5 V and 10 V) idem for the 4 DAC DAC 2 0-10 V, idem for the 4 DAC DAC 3 0-20 mA, idem for the 4 DAC DAC 4 4-20 mA, idem for the 4 DAC SW5 Output 5 V Output 24 V on pin 19 Figure 2 – ESTEL board-index B 6 MAY 2004 ESTEL Board Duplication prohibited Environnement S.A Specific configuration of output 0-5 volts instead of 0-10 volts There are 4 possible configurations for 0-5 volts output: x Board configured into 0-10 volts with addition of a by-2 divider bridge : The user (customer) carries out himself the operation at input of his acquisition system. Operating mode: Connect each analog output, previously configured into 0-10 volts, to ground through 2 resistances of equal value within 500 and 1000 ohms. Take off the divided-by-2 signal at terminals of the resistance that is connected to the ground. 0-10 V R 0-5 V R Ground x R = 500 ohms Board configured into 0-10 Volts with adjustment of half gain : In menu Tests Ö ESTEL boards, adjust the A and B coefficients of each channel in order to obtain 0-5V at analog output for 0-4000 pts resolution of analog-to-digital converter. x Board configured into 0-20 MA The user (customer) carries out himself the operation at output of his acquisition system. Operating mode: Connect each analog output, previously configured into 0-20 mA, to ground using a 250 0hms resistance, tolerance 1 %. Voltage, thus generated, is equal to UmV = 250 x ImA, that is to say 5 V for I = 20 mA. Note: place resistance the nearest possible of receiver equipment. x Modification of gain resistance on ESTEL board We carry it out if the user (customer) does not accept the other solutions. MAY 2004 7 ESTEL Board Environnement S.A 1.4 Duplication prohibited PROGRAMMATION The ESTEL board programmation is carried out from the « ESTEL board » menu of the « Carte(s) I2C » screen. This menu enables to visualize the effective communications of the various modules and to configure the various ESTEL boards. The analyzer automatically detects the presence of one or several ESTEL boards and offers menus enabling the user to adjust and configure each board. 8 JUNE 2009 ESTEL Board Duplication prohibited 1.4.1 Environnement S.A ESTEL CARD(S) Ö Analog output To access the various screens of the ESTEL board, select the current function and choose the wanted function using the [ K ], [ L ] keys. « Analog output » Function This screen enables to assign the parameters to the analog outputs for the ESTEL board whose n° indicated in the field « No » is highlighted. These parameters are: x Concentration of the analyzed gases, x Auxiliary channels (multiplexer), x Analog inlets. REMINDER : On an ESTEL board, analog outputs can be configured into: 0–1 Volt, 0–10 Volt, 0-20 mA, 4–20 mA. Four ranges are available and correspond to the full scale of the analog output, units are those of the parameters displayed in the « Signal » column. When signal value is higher than the full scale of the current range, the analyzer switches to the next higher range. It switches again to the lower range when measurement again passes under 85%. JUNE 2009 9 ESTEL Board Environnement S.A Duplication prohibited When the user assigns several measurement ranges to only one analog output, he can change the metrological resolution as the here-below curve shows it. OUTPUT SIGNAL 1V 0 1 10 2 100 3 1000 4 10000 MEASUREMENT RANGES (PPM) To avoid the ranges switching, the user must assign the same value to the 4 ranges of the parameter he will send to an analog output. The Ax+B calibration curve is used to adjust the mV signal of the taken-into-account analog output. The « Test » column is used to test the 5 analog outputs and to adjust the points number. For a range 1 : – 0 point (lower scale of output) @ 0 volt obtained at output, – 4000 points (higher scale of output) @ 1 volt obtained at output. F6 key [ Points 4000 ] enables to force the full scale on the whole analog outputs. 10 JUNE 2009 Duplication prohibited 1.4.2 ESTEL Board Environnement S.A ESTEL CARD(S) Ö Analog input Each ESTEL board has 4 analog inputs : this screen is used to program characteritics of these analog inputs. JUNE 2009 x "Name" fields are used to enter a name of 8 alphanumeric digits. x "Unit" fields are used to select the unit by : none, ppt, ppb, ppm, μg/m3, mg/m3, gr/m3, μg/Nm3, mg/Nm3, gr/Nm3, μg/Sm3, mg/Sm3, gr/Sm3, %, μgr, mgr, gr, mV, U, °C, °K, hPa, mb, b,l, Nl, Sl, m3, l/min, NI/min, Sl/min, m3/h, Nm3/h, Sm3/h, m/s ou km/h, in the toggle menu. x The "Ax + B" fields enable to adjust the calibration curve of each parameter. 11 ESTEL Board Environnement S.A 1.4.3 Duplication prohibited ESTEL CARD(S) Ö Relay "Relays" fields are used to control relays according to the following conditions: Disable Ö Relay not assigned General alarm Ö Any operating fault triggers the relay Range over-range Ö Scale 2 over range triggers the relay Flow rate Ö Abnormal flow rate triggers the relays Temperature Ö Abnormal temperature in the analyzer triggers the relay Pressure Ö Barometric pressure in chamber Zero Air Ö On Zero, relay is triggered Span Ö On Span, relay is triggered Zero-Ref Ö On Zero-Ref, relay is triggered Auto Span Ö On Auto-Span, relay is triggered Warm-Up Ö On Warm-up, relay is triggered Stop mode Ö In Stop mode, relay is triggered Alarm control Ö Control detection during threshold over range, relay is triggered. Alarm or Control Ö Relay triggered Module alarm Ö Alarm detected on module, relay triggered Measure Ö Relay triggered Maintenance Ö In Maintenance mode, relay is triggered x The "Type" fields are used to control (NC) or not (NO) the relays when alarms are OFF. x "Test" fields are used to manually control these relays. 12 JUNE 2009 Duplication prohibited 1.4.4 ESTEL Board Environnement S.A ESTEL CARD(S) Ö Remote controls This screen displays the assignment of remote control inlets. The available assignment choice are : « Inactive», « Stop mode », « Zero Ref. », « Zero », « Span », « Auto span». «Test» column is used to display the value read at remote control inlet, for the selected assignment. JUNE 2009 13 ESTEL Board Environnement S.A 1.5 1.5.1 1.5.3 Duplication prohibited INSTALLATION AND REPLACEMENT OF ESTEL BOARD x Switch off the analyzer and unplug the mains cable before any maintenance work of the analyzer, x Respect connection of ESTEL board / MODULE board at J20 when reassembling. Switch off the analyzer 1.5.2 Unplug the mains cable Put off the cover (2) Unscrew the screws located on lateral sides (1) Unscrew the screws located on the rear panel of the analyzer (3) Lift up the cover (4) Remove the cover by pulling it backward 14 JUNE 2009 Duplication prohibited ESTEL Board Environnement S.A If the analyzer is already equipped with an ESTEL board, follow step 1.5.4. If the analyzer is not equipped with ESTEL board, follow step 1.5.5. 1.5.4 Dismount ESTEL board (1) Module board (2) ESTEL board (3) J20 connector on Module board (4) (5) Connecting cable between Estel board / Module board Fixing screw of Estel board on rear panel of the analyzer Disconnect the connecting cable between ESTEL board (4) / Module board (3). Unscrew the fixing screws (5) of ESTEL board on rear panel of the analyzer. Remove ESTEL board. Configure jumpers of the new board making functionality correspondences according to Table 1 or Table 2. Re-assemble the board. 1.5.5 Unrivet the back plate (6) of rear panel of analyzer Then, install at the same place, the new plate (7) delivered with the board (7) JUNE 2009 15 ESTEL Board Environnement S.A 1.5.6 Duplication prohibited Installation of board inside the analyzer ANALYZER SWITCHED OFF (1) Vertically insert the board inside its slot. (2) Re-screw the board on the slot (3) Fit again connector on ESTEL board (4) Then, re-connect on Module board at J20 (5) Replace cover on the analyzer. See 1.5.3 . (6) Connect mains cable and switch on the analyzer. See 1.5.2 and 1.5.1. 16 JUNE 2009 Duplication prohibited 1.6 ESTEL Board Environnement S.A OPTION OF EXTERNAL CONNECTION Five different options of ESTEL external connection are available: DESIGNATION REFERENCE Option of external Estel connection P10-1337-A MARK Figure 3 x Cable x D02-INF-37-37M-M-A (1) x Tie-point block interface board x C10-0012-A (2) x DIN track x G13-IB-18066 (3) DESIGNATION Option of external Estel connection + 4 insulated outputs. REFERENCE P10-1338-A MARK Figure 4 x Cable x D02-INF-37-37M-M-A (1) x Tie-point block interface board x C10-0012-A (2) x Symmetrical DIN track Limit stop x G13-IB-18066 D03-103-002-26 (3) x 2-way galvanic insulator x I11-Jk2000-2 (4) DESIGNATION REFERENCE Option of external Estel connection + 1 insulated output P10-1350-A MARK Figure 4 x Cable x D02-INF-37-37M-M-A (1) x Tie-point block interface board x C10-0012-A (2) x Symmetrical DIN track Limit stop x G13-IB-18066 D03-103-002-26 (3) x 1-way galvanic insulator x I11-Jk2000-1 (4) DESIGNATION Option of external Estel connection + 2 insulated outputs REFERENCE P10-1351-A MARK Figure 4 x Cable x D02-INF-37-37M-M-A (1) x Tie-point block interface board x (2) 10-0012-A x Symmetrical DIN track Limit stop x G13-IB-18066 D03-103-002-26 (3) x 2-way galvanic insulator x I11-Jk2000-2 (4) DESIGNATION Option of external Estel connection + 3 insulated outputs REFERENCE P10-1352-A MARK Figure 4 x Cable x D02-INF-37-37M-M-A (1) x Tie-point block interface board x C10-0012-A (2) x Symmetrical DIN track Limit stop x G13-IB-18066 D03-103-002-26 (3) x 2-way galvanic insulator 1-way galvanic insulator x I11-Jk2000-2 I11-JK2000-1 (4) JUNE 2009 17 ESTEL Board Environnement S.A Duplication prohibited Figure 3 – Option of external connection P10-1337-A Figure 4 – Option of external connection + 4 insulated outputs P10-1338-A 18 JUNE 2009 SOREL Board BOARD OF LOGIC INPUTS / OUTPUTS OPTION OF 2M ANALYZERS - April 2010 - WARNING Information contained in this document are likely to be modified without notice. The designer reserves the right to modify the equipment without improving this document, therefore, information of this document does not represent a commitment under ENVIRONNEMENT S.A. ENVIRONNEMENT S.A. all right reserved. 111 bd Robespierre, 78300 POISSY - -TEL. 33(0)-1.39.22.38.00 – FAX 33(0)-1.39 65.38.08 http://www.environnement-sa.com SOREL Board Environnement S.A Duplication prohibited SOREL BOARD 1.1 FUNCTION AND USE 3 1.2 TECHNICAL CHARACTERISTICS 3 1.3 CONFIGURATION 4 1.3.1 Programmation 5 1.3.2 CONFIGURATION Ö Relays and remote controls 6 1.3.3 TESTS Ö ESTEL card 7 1.4 INSTALLATION OR REPLACEMENT OF SOREL BOARD 8 1.4.1 Switch off the analyzer 8 1.4.2 Unplug the mains cable 8 1.4.3 Put off the cover 8 1.4.4 Dismount SOREL board 9 1.4.5 Unrivet the back plate (6) of rear panel of analyzer 9 1.4.6 Installation of board inside the analyzer 10 Table 1 - Configuration of SOREL board 4 Figure 1 – SOREL board 4 Up-to-date: Pages Up-to-date : 1 10-04 2 10-04 3 05-04 4 10-04 5 05-04 6 05-04 7 05-04 8 05-04 9 05-04 10 05-04 2 APRIL 2010 SOREL Board Duplication prohibited 1. Environnement S.A SOREL BOARD SOREL board is a universal board of logic inputs/outputs for the 2M analyzers. It is optional. It is possible to install up to 2 SOREL boards in an analyzer. 1.1 FUNCTION AND USE SOREL board has 2 functions: x Relays control ( 4 in all ) x Remote controls ( 4 inputs ) SOREL board communicates with measurement module through Bus i2C and relieves it of the Inputs/Outputs functions. It enables the remote control and/or the remote signaling of certain functions as: "measurement", "zero", "calibration" and "alarm". 1.2 TECHNICAL CHARACTERISTICS Management by specialized micro controller: x only one power supply of 24 volts, x 4 logic inputs, x 4 contacts for remote signaling, potential configurable by the user, x Visualization of i2C communication using a LED. Electric connection: x 4-point connector for link with module boards of 2M series, x Inputs / Outputs centralized on plug-in connector. This connector in screwed on the rear panel of the analyzer using a back-plate. Voltage and current on relays: x Maximum voltage by relay contact: 50 volts D.C. x Maximum current by relay contact : 1 Ampere at 24 V D.C. (resistive load) Voltage at logic inputs: x MAY 2004 Maximum voltage 24 V D.C. 3 SOREL Board Environnement S.A 1.3 Duplication prohibited CONFIGURATION Table 1 - Configuration of SOREL board JUMPERS MARK SYMBOLS NATURE OF OPERATIONS SOREL selection, board N° 1 SOREL selection, board N° 2 SOREL selection, board N° 3 SOREL selection, board N° 4 ST1, ST2, ST3 SOREL selection, board N° 5 SOREL selection, board N° 6 SOREL selection, board N° 7 SOREL selection, board N° 8 0 V to ground (default) ST4 Floating 0 V SW1 Relay nb 1 SW2 Relay nb 2 SW3 Relay nb 3 SW4 Relay nb 4 Potential free contact Referenced contact to 0 V and 24V 18 17 16 15 14 13 12 11 10 9 8 7 6 5 4 3 2 1 3 Remote control 1 1 +24 V 4 GND (2) 5 to 24V D.C. 2 (1) Relay contact #4 (-) Relay contact #4 (+) Relay contact #3 (-) Relay contact #3 (+) Relay contact #2 (-) Relay contact #2 (+) Relay contact #1 (-) Relay contact #1 (+) GND Remote control #4 GND Remote control #3 GND Remote control #2 GND Remote control #1 +15V +24V 3 Remote control 1 + Figure 1 – SOREL board NOTE: Output relay contacts are normally open when analyzer is switched off. 4 APRIL 2010 SOREL Board Duplication prohibited 1.3.1 Environnement S.A Programmation The hereafter screens (§ 1.3.1 à § 1.3.3) are given as example. Refer to technical manual of the analyzer in which SOREL board is installed. The analyzer automatically detects the presence of one or several SOREL and/or ESTEL boards and offers menus enabling the user to adjust and configure each board. x In CONFIGURATION menu of main software program, the "Analog outputs", "Analog inputs", "Relays and remote controls" items are only displayed if the SOREL and/or ESTEL board option is available. Only, the sub-menu "Relay and remote controls is necessary to program the SOREL board. x In the TESTS menu of the main program, the item "ESTEL card" is displayed if one SOREL board at least is detected. The same screen as for ESTEL board must be used, but it is necessary not to take into account of data about analog inputs and outputs. MAY 2004 5 SOREL Board Environnement S.A 1.3.2 Duplication prohibited CONFIGURATION Ö Relays and remote controls This screen enables to configure function of each input / output of SOREL and/or ESTEL board(s). x SOREL board is displayed as an ESTEL board, x The "ESTEL card Nb: " is used to select what board to configure. x "Relays" fields are used to control the relays according to each analyzer: refer to CONFIGURATION Ö Relays and remote controls paragraph of the technical manual of your analyzer. x The "Type" fields are used to program relays into "normally closed" (NC) or "normally open" (NO) when alarms are OFF. x The "Mode" field is used to configure the working mode of remote controls. Two different modes are possible: "State" mode: control is activated as long as remote control is active (closed contact). "Rise" mode: control is activated when state modification of remote control is detected. When it is down, control remains active. A new modification of state de-activates control. 6 MAY 2004 SOREL Board Duplication prohibited 1.3.3 Environnement S.A TESTS Ö ESTEL card This screen is used to check operation of remote controls and relays. Analog functionalities are not active for SOREL board. The “Estel card Nb:” field is used to select the board to be tested. The “Out” fields are used to control the relays manually. The "Rem." fields are used to know state of these logic inputs. Definition of the specific keys of this screen: MAY 2004 0/OFF Opens all the relay contacts. 4000/ON Closes all the relay contacts. 7 SOREL Board Environnement S.A 1.4 1.4.1 1.4.3 Duplication prohibited INSTALLATION OR REPLACEMENT OF SOREL BOARD x Switch off the analyzer and unplug the mains cable before any maintenance work in the analyzer, x Respect connection of SOREL board / MODULE board at J20 when reassembling. Switch off the analyzer 1.4.2 Unplug the mains cable Put off the cover (2) Unscrew the screws located on lateral sides (1) Unscrew the screws located on the rear panel of the analyzer (3) Lift up the cover (4) Remove the cover by pulling it backward 8 MAY 2004 Duplication prohibited SOREL Board Environnement S.A If the analyzer is already equipped with a SOREL board, follow step 1.4.4 If the analyzer is not equipped with ESTEL board, follow step 1.4.5 1.4.4 Dismount SOREL board (1) Module board (2) SOREL board (3) Connector J20 on Module board (4) (5) Connecting cable between Sorel board / Module board Fixing screw of Sorel board on rear panel of the analyzer Disconnect the connecting cable between SOREL board (4) / Module (3) board. Unscrew the fixing screws (5) of SOREL board on rear panel of the analyzer. Remove SOREL board. Configure jumpers of the new board carrying out correspondence of functionalities according to Table 1. Re-assemble the board. 1.4.5 Unrivet the back plate (6) of rear panel of analyzer Then, install at the same place the new plate (7) delivered with the board (7) MAY 2004 9 SOREL Board Environnement S.A 1.4.6 Duplication prohibited Installation of board inside the analyzer ANALYZER SWITCHED OFF (2) Re-screw the board on back plate (1) Vertically insert the board inside its slot. (3) Fit again connector on SOREL board (4) Then, re-connect on Module board at J20 (5) Replace cover on the analyzer. See 1.4.3. (6) Connect mains cable and switch on the analyzer. See 1.4.2 and 1.4.1. 10 MAY 2004
advertisement