- Industrial & lab equipment
- Electrical equipment & supplies
- Circuit protection
- Voltage regulators
- User manual
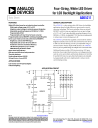
advertisement
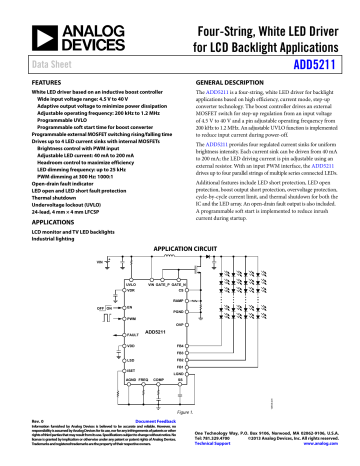
Four-String, White LED Driver for LCD Backlight Applications
ADD5211
Data Sheet
FEATURES
White LED driver based on an inductive boost controller
Wide input voltage range: 4.5 V to 40 V
Adaptive output voltage to minimize power dissipation
Adjustable operating frequency: 200 kHz to 1.2 MHz
Programmable UVLO
Programmable soft start time for boost converter
Programmable external MOSFET switching rising/falling time
Drives up to 4 LED current sinks with internal MOSFETs
Brightness control with PWM input
Adjustable LED current: 40 mA to 200 mA
Headroom control to maximize efficiency
LED dimming frequency: up to 25 kHz
PWM dimming at 300 Hz: 1000:1
Open-drain fault indicator
LED open and LED short fault protection
Thermal shutdown
Undervoltage lockout (UVLO)
24-lead, 4 mm × 4 mm LFCSP
APPLICATIONS
LCD monitor and TV LED backlights
Industrial lighting
APPLICATION CIRCUIT
GENERAL DESCRIPTION
The ADD5211 is a four-string, white LED driver for backlight applications based on high efficiency, current mode, step-up converter technology. The boost controller drives an external
MOSFET switch for step-up regulation from an input voltage of 4.5 V to 40 V and a pin adjustable operating frequency from
200 kHz to 1.2 MHz. An adjustable UVLO function is implemented to reduce input current during power-off.
The ADD5211 provides four regulated current sinks for uniform brightness intensity. Each current sink can be driven from 40 mA to 200 mA; the LED driving current is pin adjustable using an external resistor. With an input PWM interface, the ADD5211 drives up to four parallel strings of multiple series connected LEDs.
Additional features include LED short protection, LED open protection, boost output short protection, overvoltage protection, cycle-by-cycle current limit, and thermal shutdown for both the
IC and the LED array. An open-drain fault output is also included.
A programmable soft start is implemented to reduce inrush current during startup.
VIN
+
OFF ON
UVLO
VDR
VIN GATE_P GATE_N
CS
RAMP
PGND
EN
PWM
OVP
FAULT
ADD5211
VDD
LSD
ISET
AGND FREQ COMP
FB4
FB3
FB2
FB1
LGND
SS
Rev. 0 Document Feedback
Information furnished by Analog Devices is believed to be accurate and reliable. However, no responsibility is assumed by Analog Devices for its use, nor for any infringements of patents or other rights of third parties that may result from its use. Specifications subject to change without notice. No license is granted by implication or otherwise under any patent or patent rights of Analog Devices.
Trademarks and registered trademarks are the property of their respective owners.
Figure 1.
One Technology Way, P.O. Box 9106, Norwood, MA 02062-9106, U.S.A.
Tel: 781.329.4700
Technical Support
©2013 Analog Devices, Inc. All rights reserved. www.analog.com
ADD5211
TABLE OF CONTENTS
General Description ......................................................................... 1
Application Circuit ........................................................................... 1
Revision History ............................................................................... 2
Detailed Functional Block Diagram .............................................. 3
General Specifications ................................................................. 4
Step-Up Switching Controller Specifications ........................... 5
LED Current Regulation Specifications .................................... 5
Absolute Maximum Ratings ............................................................ 6
Thermal Resistance ...................................................................... 6
ESD Caution .................................................................................. 6
REVISION HISTORY
10/13—Revision 0: Initial Version
Data Sheet
Pin Configuration and Function Descriptions ..............................7
Typical Performance Characteristics ..............................................8
Theory of Operation ...................................................................... 10
Current Mode, Step-Up Switching Controller ....................... 10
LED Current Regulation ........................................................... 11
Fault Protection .......................................................................... 12
Applications Information .............................................................. 14
Layout Guidelines....................................................................... 14
Boost Component Selection ..................................................... 14
Typical Application Circuits ......................................................... 17
Outline Dimensions ....................................................................... 18
Ordering Guide .......................................................................... 18
Rev. 0 | Page 2 of 20
Data Sheet
DETAILED FUNCTIONAL BLOCK DIAGRAM
COMP
OVP
BOOST CONTROL
FB_REF
FB_MIN g m
ERROR
AMP
FREQ
PWM
COMP
OVP
OVP_REF
BOOST
SCP_REF
OVP
SCP
OSC
DCOMP
RAMP
DREF
+
+
ADD5211
OVP
POR
R
S
R
Q
VDR
SWITCH
DRIVER
STARTUP
SOFT START
CURRENT SENSE
ADD5211
GATE_P
GATE_N
PGND
SS
CS
RAMP
FAULT
FAULT
DETECTOR
VDR
VIN DEVICE
ENABLE
EN
500kΩ
AGND
UVLO
AGND
UVLO
DETECTOR
LINEAR
REGULATOR
BAND GAP
REFERENCE
VOLTAGE
REGULATOR
THERMAL
SHUTDOWN
VDD
POR
VDD
PWM
CONTROL LOGIC
500kΩ
AGND
THERMAL
SHUTDOWN
BOOST
SHORT
BOOST CONTROL
STARTUP
DIMMING CONTROL
REF
OPEN
LED
DETECTOR
SHORT
LED
DETECTOR
FB_MIN
CURRENT SOURCE 1
CURRENT SOURCE 2
CURRENT SOURCE 3
×10
UNUSED
STRING
DETECTOR
STRING
VOLTAGE
DETECTOR
CURRENT SOURCE 4
POR
LSD
FB1
FB2
FB3
FB4
DIMMING CONTROL
LGND
ISET
Figure 2.
Rev. 0 | Page 3 of 20
ADD5211
SPECIFICATIONS
V
IN
= 12 V, EN = 3.3 V, T
J
= −40°C to +125°C, unless otherwise noted. Typical values are at T
A
= 25°C.
GENERAL SPECIFICATIONS
Table 1.
Parameter
SUPPLY
Input Voltage Range
Quiescent Current
Shutdown Supply Current
VIN Rising Threshold
VIN Falling Threshold
VDR REGULATOR
Regulated Output
Dropout Voltage
VDD REGULATOR
Regulated Output
PWM INPUT
Input High Voltage
Input Low Voltage
PWM Input Current
PWM High to LED Turn-On Delay 1
PWM Low to LED Turn-Off Delay 1
EN CONTROL
Symbol
V
IN
I
Q
I
SD
V
UVLOR_VIN
V
UVLOF_VIN
V
VDR_REG
V
VDR_DROP
V
VDD_REG
V
PWM_HIGH
V
PWM_LOW
EN Voltage High
EN Voltage Low
EN Pin Input Current
UNDERVOLTAGE LOCKOUT
UVLO Threshold (Rising)
UVLO Hysteresis
FAULT
Sink Resistance
Fault Pin Leakage Current
LED SHORT DETECTION
EN = 5 V
LED Short Detection Enable Threshold V
LSD
LED Short Gain
LED Short Gain Control Range 1
LED Open Fault Delay
LED Short Fault Delay
OVERVOLTAGE PROTECTION
Overvoltage Threshold (Rising)
Overvoltage Hysteresis
Overvoltage Pin Leakage Current
OVP_REF
OVP_HYS
LSD = 1.0 V
Output Short-Circuit Threshold (Falling) V
SCPF
Output Short-Circuit Recovery (Rising) V
SCPR
Thermal Shutdown Threshold
Thermal Shutdown Hysteresis
1 Guaranteed by design.
T
SD
T
SDHYS
Test Conditions/Comments
EN = 0 V
Minimum V
IN
for startup
V
IN
= 4.5 V
PWM = 5 V
2.2
7.5
0.3
2.3
2.2
1.10
Min
4.5
3.2
4.75
3.0
2.2
2.5
10
5
15
2.5
100
100
150
150
25
40
13
1.19
100
Typ
2.8
4
3.65
5.1
350
11
1.6
0.8
3.3
Rev. 0 | Page 4 of 20
Data Sheet
V
V
µs
µs
V mV nA mV mV
°C
°C
Ω
µA
V
V
µA
V mV
Unit
V mA
µA
V
V
V mV
µA
µs
µs
V
V
V
VDD
13
2.0
2.7
200
17
0.8
30
1.27
100
1.5
Max
40
6
1
4.3
5.45
580
30
3.6
8
0.8
Data Sheet
STEP-UP SWITCHING CONTROLLER SPECIFICATIONS
Table 2.
ADD5211
Switching Frequency Range
Switching Frequency
PWM COMPARATOR
Leading Edge Blanking Time
CURRENT SENSE LIMIT COMPARATOR
Current-Limit Threshold f
SW
R
FREQ
= 50 kΩ
R
FREQ
= 50 kΩ
CS
LIMIT
Independent of duty cycle
200 1200 kHz
280 360 430 kHz
89 94 98 %
145 ns
275 345 400 mV
Peak Slope Compensation Ramp R
RAMP
= 5 kΩ
Transconductance g m
R
COMP Sink Current
COMP Source Current
Source Voltage
Gate On Resistance
Gate Off Resistance
Rising Time
Falling Time
Soft Start Pin Current t
R
DS_GATE_P
R
DS_GATE_N
R t
F
8 V < V
IN
< 40 V
C = 1 nF
C = 1 nF
I
SS
LED CURRENT REGULATION SPECIFICATIONS
Table 3.
45 μA
400
400
μA
μA
5.1 V
26
21 ns ns
Current Sink Range
Current Sink I
I
LED
LED100
FB100
LED100
R
SET
= 15 kΩ, T
A
= 25°C
R
SET
R
SET
= 15 kΩ, T
= 15 kΩ, T
A
A
= 25°C
= 25°C
Minimum Headroom Voltage
Off Current I
V
HR
OFF
R
V
SET
FB
= 15 kΩ, T
A
25°C
= 40 V, EN = 0 V
40
98
0.45
200
102
2.5
2.0 mA
%
%
0.4 0.55 0.85 V
Off State Clamping Current I
CLAMP
V
FB
= 55 V, EN = 0 V 4
1 String-to-string tolerance is the greatest delta between FBx currents with respect to the average of the FBx currents.
I
FB100
Max
I
FB100(MAX)
I
LED100
I
LED100
100 % :
I
FB100(MIN)
I
LED100
I
LED100
100 %
where I
FB100
is the LED current of each string.
2 Current accuracy is the delta between average current, I
LED100
,
and 100 mA with respect to 100 mA.
I
LED100
I
LED100
100 mA
100 %
100 mA where
I
LED100
I
FB1
I
FB2
I
FB3
I
FB4
4
20
1.5
80
μA
μA
Rev. 0 | Page 5 of 20
ADD5211
ABSOLUTE MAXIMUM RATINGS
T
A
= 25°C, unless otherwise noted.
Table 4.
Parameter
VIN, UVLO
FB1, FB2, FB3, FB4
EN
Rating
−0.3 V to +45 V
−0.3 V to +55 V
−0.3 V to +17 V
PWM, FAULT
VDR, GATE_N, GATE_P
−0.3 V to +8 V
−0.3 V to +7 V
COMP, CS, FREQ, ISET, LSD, OVP, RAMP −0.3 V to +3.6 V
SS −0.3 V to VDD
AGND, PGND, LGND
Maximum Junction Temperature
(T
J
max)
−0.3 V to +0.3 V
150°C
Operating Temperature Range (T
A
)
Storage Temperature Range (T
S
)
Reflow Peak Temperature
(20 sec to 40 sec)
−25°C to +85°C
−65°C to +150°C
260°C
Stresses above those listed under Absolute Maximum Ratings may cause permanent damage to the device. This is a stress rating only; functional operation of the device at these or any other conditions above those indicated in the operational section of this specification is not implied. Exposure to absolute maximum rating conditions for extended periods may affect device reliability.
Data Sheet
THERMAL RESISTANCE
θ
JA
is specified for the worst-case conditions, that is, a device soldered in a circuit board for surface-mount packages.
Table 5. Thermal Resistance
Package Type θ
JA
24-Lead LFCSP 40.5
ESD CAUTION
θ
JC
3.8
Unit
°C/W
Rev. 0 | Page 6 of 20
Data Sheet
PIN CONFIGURATION AND FUNCTION DESCRIPTIONS
ADD5211
VDR 1
UVLO
2
VIN 3
EN 4
PWM 5
FAULT 6
ADD5211
TOP VIEW
18 OVP
17 FB4
16
FB3
15 LGND
14 FB2
13 FB1
NOTES
1. CONNECT THE EXPOSED PAD TO GROUND.
Figure 3. Pin Configuration
Table 6. Pin Function Descriptions
Pin No. Mnemonic Description
1
2
9
10
11
17
18
19
20
21
22
23
24
12
13
14
15
16
3
4
5
6
7
8
VDR
UVLO
VIN
EN
PWM
FAULT
SS
COMP
FREQ
ISET
VDD
LSD
FB1
FB2
LGND
FB3
FB4
OVP
PGND
RAMP
CS
GATE_N
GATE_P
AGND
EP
Switching MOSFET Gate Driver Supply Pin. Bypass VDR to AGND with a 1 µF bypass capacitor.
Input Undervoltage Lockout. Set the start-up and shutdown input voltage level by connecting this pin to the input voltage with a resistor divider.
Supply Input Pin. Bypass VIN to AGND with a 0.1 µF bypass capacitor.
Shutdown Control Pin for PWM Input Operation Mode.
PWM Signal Input.
Open-Drain Fault Output.
Soft Start Pin.
Compensation for the Boost Converter. A capacitor and a resistor are connected in series between ground and this pin for stable operation.
Frequency Select. A resistor from this pin to ground sets the boost switching frequency from 200 kHz to 1.2 MHz.
Full-Scale LED Current Set Pin. A resistor from this pin to ground sets the LED current up to 200 mA.
Internal Linear Regulator Output. This regulator provides power to the ADD5211 . Bypass VDD to AGND with a 1 µF bypass capacitor.
LED Short Voltage Level Setting Pin. To disable LED short protection, connect this pin to VDD.
Regulated Current Sink. Connect the bottom cathode of the LED string to this pin. If unused, connect FB1 to LGND.
Regulated Current Sink. Connect the bottom cathode of the LED string to this pin. If unused, connect FB2 to LGND.
LED Current Sink Ground.
Regulated Current Sink. Connect the bottom cathode of the LED string to this pin. If unused, connect FB3 to LGND.
Regulated Current Sink. Connect the bottom cathode of the LED string to this pin. If unused, connect FB4 to LGND.
Overvoltage Protection. The boost converter output is connected to this pin with a resistor divider.
Power Ground.
Ramp Compensation Pin.
Current Sense Input. Allows the current sensing to control the boost converter and to limit the switching current.
Switching MOSFET Gate Low Driving Pin.
Switching MOSFET Gate High Driving Pin.
Analog Ground.
Exposed Pad. Connect the exposed pad to ground.
Rev. 0 | Page 7 of 20
ADD5211
TYPICAL PERFORMANCE CHARACTERISTICS
112
110
108
106
104
102
100
98
96
94
92
90
88
–35 –25 –15 –5 5 15 25 35 45
TEMPERATURE (°C)
55
Figure 4. I
LED100
vs. Temperature
65 75 85 95
10
8
6
4
2
0
22
20
18
16
14
12
T
A
= –25°C
T
A
= +85°C
0 5 10 15 20 25 30 35 40
FB VOLTAGE (V)
45
Figure 5. FB Leakage Current vs. FB Voltage
50 55
Data Sheet
1.0
0.8
0.6
1.8
1.6
1.4
1.2
0.4
0.2
0
–35 –25 –15 –5 5 15 25 35 45
TEMPERATURE (°C)
55 65 75 85 95
Figure 7. ΔI
FB100
vs. Temperature
4.5
4.0
3.5
3.0
2.5
6.0
5.5
5.0
2.0
1.5
0 5 10 15 20 25
INPUT VOLTAGE (V)
30 35
Figure 8. VDR Voltage vs. Input Voltage
40
1
2
3
4
V
SW
30V/DIV
V
FB
20V/DIV
PWM
3V/DIV
I
FB
100mA/DIV
1ms/DIV
Figure 6. PWM Dimming Waveform, PWM Duty Cycle = 50%
1
2
3
4
V
FB1
20V/DIV
V
FB2
20V/DIV
V
FB3
20V/DIV
V
FB4
20V/DIV
1ms/DIV
Figure 9. FB1 to FB4 Waveforms, PWM Duty Cycle = 50%
Rev. 0 | Page 8 of 20
Data Sheet
1
2
3
4
20ms/DIV
Figure 10. Startup (Brightness = 100%, EN Is High,
V
IN
Goes from Low to High)
V
SW
30V/DIV
V
FB
20V/DIV
EN
3V/DIV
V
IN
20V/DIV
ADD5211
1
2
3
4
20ms/DIV
Figure 13. Startup (Brightness = 100%, V
IN
Is High,
EN Goes from Low to High
V
SW
30V/DIV
V
FB
20V/DIV
EN
3V/DIV
V
IN
20V/DIV
3
4
1
2
20ms/DIV
Figure 11. Startup (Brightness = 10%, EN Is High,
V
IN
Goes from Low to High)
V
SW
30V/DIV
V
FB
20V/DIV
EN
3V/DIV
V
IN
20V/DIV
3
4
1
2
20ms/DIV
Figure 14. Startup (Brightness = 10%, V
IN
Is High,
EN Goes from Low to High
V
SW
30V/DIV
V
FB
20V/DIV
EN
3V/DIV
V
IN
20V/DIV
2
3
4
V
FB1
30V/DIV
PWM
3V/DIV
I
FB1
100mA/DIV
5µs/DIV
Figure 12. LED Current Rising and Falling Waveform
3
4
1
2
1ms/DIV
Figure 15. LED Open Protection (Open LED on FB2)
V
OUT
50V/DIV
V
FB2
20V/DIV
FAULT
3V/DIV
I
FB1
100mA/DIV
Rev. 0 | Page 9 of 20
ADD5211
THEORY OF OPERATION
The ADD5211 uses a PWM boost controller to generate the minimum output voltage required to drive the LED string at the programmed LED current. The current mode control architecture allows a fast transient response while maintaining a stable output voltage. The boost converter provides power to the LED strings, and the four current sinks control the LED current with dynamic headroom control to improve efficiency.
CURRENT MODE, STEP-UP SWITCHING
CONTROLLER
The ADD5211 is a current mode, PWM boost controller that operates at a fixed switching frequency from 200 kHz to
1.2 MHz. The switching frequency is set by an external resistor connected from the FREQ pin to AGND. The minimum headroom voltage—which is monitored at the FB1, FB2, FB3, and
FB4 pins—is compared with the internal reference voltage by the internal transconductance error amplifier to create an error current at COMP. A resistor and capacitor connected from the
COMP pin to AGND convert the error current to an error voltage.
At the beginning of the switching cycle, the MOSFET is turned on and the inductor current ramps up. The MOSFET current is measured and converted to a voltage using the current sense resistor (R
CS
) and is added to the stabilizing slope compensation ramp from the ramp resistor (R
RAMP
). The resulting voltage sum passes through the current sense amplifier to generate the current sense voltage. Under light loads, the converter can also operate in discontinuous mode with pulse skip modulation to maintain output voltage regulation.
The current mode regulation system of the ADD5211 allows fast transient responses while maintaining a stable output voltage. By selecting the proper resistor-capacitor network from
COMP to AGND, the regulator response can be optimized for a wide range of input voltages, output voltages, and load currents.
Input Voltage
The ADD5211 can be powered directly from the VIN pin, which accepts a voltage from 4.5 V to 40 V. The voltage on the
VIN pin must exceed V
UVLOR_VIN
(4.0 V typical) for startup. The
ADD5211 has two linear regulators: a 3.3 V linear regulator
(VDD), which supplies power to the internal control circuitry, and a 5.1 V linear regulator (VDR), which supplies power to the internal GATE_P and GATE_N drivers.
Data Sheet
UVLO Pin
The UVLO pin is used to control the VIN voltage at which the ADD5211 starts up. This function is accomplished using a resistor divider between the input voltage and the UVLO pin,
VIN
R
UVLO1
UVLO_REF
R
UVLO2
UVLO
PIN
Figure 16. Undervoltage Lockout Circuit
The startup voltage, as determined by the resistor divider to the
UVLO pin, can be calculated using the following equation:
V
IN(START)
= (1.19 V/R
UVLO2
) × (R
UVLO1
+ R
UVLO2
)
To start the device at the lowest possible VIN level, select an
R
UVLO1
value of 100 kΩ (or greater) and do not connect R
UVLO2
.
If UVLO is controlled from a separate voltage source, make sure that a 100 kΩ (or greater) resistor is in series between the voltage source and the UVLO pin.
Enable and Disable
To enable the ADD5211 , the voltage at the EN pin must be higher than 2.2 V. To disable the ADD5211 , the voltage at the
EN pin must be lower than 0.8 V. An internal 500 kΩ resistor is connected between EN and AGND.
Internal 3.3 V Regulator (VDD)
The ADD5211 contains a 3.3 V linear regulator (VDD) that is used to bias the internal control circuitry. The VDD regulator requires a 1 µF bypass capacitor. Place this bypass capacitor between VDD and AGND, as close as possible to the VDD pin.
Internal 5.1 V Regulator (VDR)
The ADD5211 contains a 5.1 V linear regulator (VDR) that is used to supply the MOSFET gate driver. The VDR regulator requires a 1 µF bypass capacitor. Place this bypass capacitor between VDR and AGND, as close as possible to the VDR pin.
Rev. 0 | Page 10 of 20
Data Sheet
Frequency
The ADD5211 boost converter switching frequency (f
SW
) is user adjustable from 200 kHz to 1.2 MHz using an external resistor,
R
FREQ
1200
1000
800
600
400
200
0
0 10 20 30 40 50
R
FREQ
(kΩ)
60 70 80
Figure 17. Switching Frequency vs. R
FREQ
90 100
The following equation can also be used to calculate the typical switching frequency:
f
SW
(kHz)
=
19 , 000
R
FREQ
(k
Ω
)
−
30
(
R
FREQ
, 000
(k
Ω
))
2
Soft Start
At startup, the voltage at the SS pin ramps up slowly by charging the soft start capacitor (C
SS
) from an internal 2.1 μA (typical) current source. The peak inductor current follows the SS pin ramp to provide a controlled start-up profile. The soft start cycle is complete when the SS pin reaches its final value of 1.19 V (typical).
A capacitor must always be connected to the SS pin. The soft start time can be calculated as follows:
t
SS
= (C
SS
× 1.19 V)/2.1 µA
For a typical setup, a 27 nF soft start capacitor results in negligible input current overshoot at startup, making it suitable for most applications. However, if an unusually large output capacitor is used, a longer soft start period is required to prevent input inrush current and output voltage overshoot of the boost switching regulator. Conversely, if fast startup is required, the value of the soft start capacitor can be reduced to allow the boost output to start quickly, but allow greater peak switch current during startup and larger boost output overshoot.
CURRENT CONTROL
DIMMING CONTROL
ADD5211
LED CURRENT REGULATION
Current Sink
The ADD5211 contains four current sinks to provide accurate current sinking for each LED string. The current for each LED string is adjusted from 40 mA to 200 mA using an external resistor. Connect any unused FBx pins to LGND.
If the ADD5211 current sink voltage is greater than 45 V, a
Zener diode and a 410 kΩ resistor in parallel with the current
sink are activated (see Figure 18).
Programming the LED Current
ADD5211 has an LED current set pin
(ISET). A resistor (R
SET
) from the ISET pin to AGND adjusts the
LED current from 40 mA to 200 mA. The LED current level can be set using the following equation:
I
LED
(mA) = 1500/R
SET
(kΩ)
The resulting minimum current sink voltage (FB_REF) is given by
FB_REF = 0.23 + 0.0041 × I
LED
(mA) where 40 mA < I
LED
< 200 mA.
If only one or two LED strings are used, it is most efficient to connect the FBx pins in parallel and adjust R
SET
accordingly.
This configuration gives the lowest V
FB
operating voltage and improves efficiency. For example, to drive two LED strings at
100 mA, connect FB1 and FB2 together for one LED string, and connect FB3 and FB4 together for the other LED string. Then, set R
SET
to 30.1 kΩ (50 mA). The minimum FBx voltage is now
0.44 V (typical) instead of 0.64 V (typical). See Figure 23 for an
example of a two-string application.
PWM Dimming Control
The ADD5211 features LED brightness control using an external
PWM signal applied at the PWM pin. A logic high signal on the
PWM input enables the LED current sinks; a logic low signal disables them. If the PWM input remains low for 50 ms, the
ADD5211 stops boost regulation and enters shutdown mode. If the PWM input returns high after the ADD5211 enters shutdown, the device initiates a new soft start sequence.
FBx
410kΩ
V
Z
= 45V
LGND
Figure 18. Current Sink Circuit
Rev. 0 | Page 11 of 20
ADD5211
FAULT PROTECTION
Fault protections in the ADD5211 include boost output overvoltage protection, LED short protection, LED open protection, boost output short-circuit protection, and thermal shutdown.
The FAULT pin provides an alert for some of these conditions
Boost Output Overvoltage Protection (OVP)
The ADD5211 contains an overvoltage protection (OVP) circuit to prevent potential damage if the output voltage becomes excessive for any reason. OVP is implemented with a resistor divider from the boost output to the OVP pin. When the OVP pin voltage reaches 2.5 V (typical), the boost controller stops switching, which causes the output voltage and the OVP pin voltage to decrease. When the OVP pin voltage decreases below the OVP falling threshold (2.4 V typical), the boost converter resumes switching.
BOOST OUTPUT
R
OVP1
OVP_REF
OVP
R
OVP2
OVP
Figure 19. Boost Output Overvoltage Protection Circuit
The OVP threshold can be calculated using the following equation:
V
OUT_OVP
= (2.5 V/R
OVP2
) × (R
OVP1
+ R
OVP2
)
LED Short Protection
If an LED in one of the LED strings is shorted, the voltage of the
FBx pin that is connected to the faulty LED string increases to regulate the LED current. If this FBx pin reaches the LED short protection threshold (10× the voltage at the LSD pin) during normal operation, the ADD5211 disables the FBx pin that is connected to the shorted LED string and pulls down the FAULT pin.
VDD
R
LSD1
LSD_REF LSD ENABLE
R
LSD2
×10
SHORT
STRING
DETECTOR
LSD
FBx
Figure 20. LED Short Protection Circuit
Data Sheet
The LED short protection threshold can be calculated using the following equations:
V
LSD
= (3.3 V/(R
LSD1
+ R
LSD2
)) × R
LSD2
V
LED_SHORT_THRESHOLD
= 10 × V
LSD
To disable LED short protection, set the voltage of the LSD pin to a value greater than 3 V, or connect the pin to the VDD pin.
LED Open Protection
The ADD5211 contains a headroom control circuit to minimize power loss at each current sink. Therefore, the minimum feedback voltage is achieved by regulating the output voltage of the boost converter. If any LED string is open circuit during normal operation, the current sink voltage (V
FBx
) will be near 0 V. LED open protection is activated if V
FBx
is less than 100 mV (typical) and the boost converter output voltage reaches V
OUT_OVP
. The ADD5211 then disables the open LED string and pulls the open-drain fault indicator low. The remaining LED strings continue to operate normally. If all LED strings are open, the ADD5211 shuts down.
Boost Output Short-Circuit Protection (SCP)
The ADD5211 contains an SCP circuit to prevent boost converter damage if the Schottky diode becomes open or the boost converter output is shorted to ground for any reason. When the voltage on the OVP pin falls below 100 mV (typical), the boost converter stops switching until the OVP voltage rises to 150 mV (typical).
The SCP function is disabled during boost converter soft start.
BOOST OUTPUT
R
OVP1
SCP_REF
SCP
R
OVP2
OVP
Figure 21. Boost Output Short-Circuit Protection Circuit
The boost output short-circuit protection threshold can be calculated using the following equation:
V
OUT_SCP
= (0.15 V/R
OVP2
) × (R
OVP1
+ R
OVP2
)
Thermal Shutdown (TSD)
Thermal overload protection prevents excessive power dissipation from overheating and damaging the ADD5211 . When the junction temperature (T
J
) exceeds 150°C (typical), a thermal sensor immediately activates the fault protection, which shuts down the device and allows it to cool. The device restarts when the junction temperature (T
J
) of the die falls below 125°C (typical).
Rev. 0 | Page 12 of 20
Data Sheet
Table 7. Fault Protection
Fault
LED string short
LED string open
R
SET
short to AGND
Boost output short
Thermal shutdown
Description
Boost output overvoltage V
OVP
> OVP_REF
Boost Regulation Response
Stop switching until V
OVP
< 2.4 V (typical)
V
FBx
> 10 × V
LSD
; PWM pin is high
V
FBx
< 0.1 V; V
OVP
> OVP_REF; PWM pin is high Open LED string disabled; other LED strings operate normally
R
SET
is shorted to AGND
Shorted LED string disabled; other LED strings operate normally
V
OVP
< 100 mV (typical) after soft start
ADD5211 shuts down; automatic restart if
R
SET
returns to normal resistance range
ADD5211 shuts down; automatic restart if
V
OVP
rises above 150 mV (typical)
T
J
> 150°C (typical) ADD5211 shuts down; automatic restart after T
J
falls below 125°C (typical)
ADD5211
FAULT Pin State
Open
Pulled down
Pulled down
Open
Pulled down
Pulled down
Rev. 0 | Page 13 of 20
ADD5211
Data Sheet
APPLICATIONS INFORMATION
LAYOUT GUIDELINES
To achieve high efficiency, good regulation, and stability, a good
PCB layout is required. Use the following general guidelines when designing PCBs:
Ensure that the high current loop from C
IN
to L1 to Q1 to
R
CS
then back to the ground of C
IN
is as short as possible.
Ensure that the high current loop from C
IN
to L1 to D1 to
C
OUT
then back to the ground of C
IN
is as short as possible.
Make high current traces as short and wide as possible.
Keep nodes that are connected to L1, Q1, and D1 away from sensitive traces, such as COMP, to prevent coupling of the traces. If such traces must be run near each other, place a ground trace between the two as a shield.
Place the compensation components as close as possible to the COMP pin.
Use thermal vias and a thermal pad with the same dimensions as the exposed pad on the bottom of the package.
Heat Sinking
When using a surface-mount power IC or external power switches, the PCB can often be used as the heat sink. This is achieved by using the copper area of the PCB to transfer heat from the device; maximizing this area optimizes thermal performance.
BOOST COMPONENT SELECTION
Calculating the Peak Inductor Current and Duty Cycle
To select the optimal external components, the first step is to calculate the peak inductor current and maximum duty cycle. The peak inductor current is given by
I
PK
= I
L (AVG)
+ (ΔI
L
/2) where:
ΔI
L
= (V
IN
× D)/(L × f
SW
)
I
L (AVG)
= (4 × I
LED
)/(η × (1 − D))
I
LED
is the LED current per string.
D is the duty cycle (D = (V
OUT
− V
IN
)/V
OUT
).
Rev. 0 | Page 14 of 20
Verify that the worst-case duty cycle does not exceed the maxi-
mum allowed value (89%) given in Table 2. For the worst-case
duty cycle, use the minimum V
IN
and the maximum V
OUT
. The maximum V
OUT
is given by
V
OUT_MAX
= N × V
F MAX
+ 1 V where:
N is the number of LEDs per string.
V
F MAX
is the maximum LED forward voltage.
Selecting the Inductor
When selecting the inductor, consider these inductor properties: inductance, maximum saturation current, resistance (DCR), and physical size.
Choose an inductance such that ΔI
L
is 20% to 40% of I
L (AVG)
.
L =
V
IN
0 .
3
D f
SW
( 1
D
I
OUT
) where I
OUT
is the total LED current through all the strings.
The saturation current is generally listed as the current at which the inductance is reduced by 30%. Ensure that this current is greater than the calculated peak inductor current.
Of the inductors that meet the required inductance and saturation current, choose one that provides the best trade-off between DCR and layout footprint for your application. The power dissipation due to the DCR of the inductor is given by
P
L
= DCR × I
L (AVG)
2
Selecting the Current Sense (CS) Resistor
To calculate the worst-case inductor peak current, use the maximum duty cycle, minimum inductance, and minimum switching frequency. Then select the current sense resistor (R
CS
) as follows:
R
CS
= CS
LIMIT (MIN)
/I
PK (MAX)
Ensure that the selected inductor can tolerate the maximum peak current given by this current sense resistor.
I
PK (CS)
= CS
LIMIT (MAX)
/R
CS (MIN)
The power dissipation from the sense resistor is given by
P
RCS
= D × R
CS
× I
L (AVG)
2
Data Sheet
Selecting the NMOS Switch
The external NMOS switch must have an adequate drain-tosource breakdown voltage (BV
DSS
) and rms current rating. The breakdown voltage rating should be at least
BV
DSS
> V
OUT (MAX)
+ 10 V
The rms current rating should exceed the following:
I
NMOS (RMS)
= I
L (AVG)
× √D
The power dissipation from the NMOS switch arises from two components: RDS
ON
losses and switching losses. These losses can be calculated as follows:
P
NMOS (RDSON)
= D × RDS
ON
× I
L (AVG)
2
P
NMOS (SW)
= 0.5 × V
OUT
× I
L (AVG)
× (t
R
+ t
F
) × f
SW
The rise and fall times (t
R
and t
F
) are a function of the strength of the ADD5211 gate drivers and the gate capacitance of the
NMOS. Typical values are given in Table 2, but these times vary
substantially for various power FETs. Therefore, t
R
and t
F
are best measured in the application.
Selecting the Diode
The diode must be selected for a low forward voltage (V
F
) and fast switching times. Generally, a fast Schottky diode provides the best performance for the cost. Ensure that the breakdown voltage (V
D
) is greater than the maximum V
OUT
plus some margin.
Also ensure that the rated current of the diode is greater than the output current (total LED current). The power dissipation of the diode is as follows:
P
DIODE
= V
F
× I
OUT
Selecting C
OUT
To provide stability and reduce the output voltage ripple, particularly when PWM dimming of the LED currents is in effect, the output capacitance should be in the range of 4.7 µF to 22 µF.
Boost Converter Loop Gain Calculations
The total closed-loop gain is given by G
EA
× G
P
(s). G
EA
is the compensation gain. G
P
(s) is the control to output gain. G
P
(s) is the gain of the power stage and includes L, C
OUT
, and the PWM modulator. The G
P
(s) gain is
G
P
(s) =
A
PS
×
1
+
2
×
π
1
s
×
+
f
2
LFP
×
π
×
s
×
f
ZESR
1
+
Q n
×
×
1
2
s
×
−
π
2
×
×
f
π
n s
×
+
f
(
RHP
2
×
π
s
2
×
f n
where A
PS
is the dc gain and includes the PWM modulator gain, as follows:
)
2
A
PS
=
( 1
−
2
×
D
)
×
V
OUT
R
CS
×
4
×
×
G
I
LED
CS
ADD5211
The equation for G
P
(s) shows that there are two zeros (f
ZESR
and f
RHP
). The f
ZESR
zero is formed by the ESR of the output capacitance.
Because ceramic capacitors are used in this application, this value should be small and can usually be ignored. The zero is given by
f
ZESR
=
1
2
× π ×
ESR
×
C
OUT
The right half plane zero (f
RHP
) is given by
f
RHP
=
2
× π ×
V
OUT
L
×
4
×
I
LED
×
V
IN
V
OUT
2
This RHP zero results in a gain boost, but a phase drop. Because of its dependence on so many variables, f
RHP
is extremely difficult to compensate for. Therefore, it is best to choose a loop crossover frequency well before the phase drop of this RHP zero is seen.
Typically, this is an order of magnitude less than the frequency of the RHP zero.
G
P
(s) also gives two poles at f
LFP
and f n
. The low frequency pole
(f
LFP
) is formed by the output capacitance and is found at
f
LFP
=
4
×
I
LED
π ×
V
OUT
×
C
OUT
f n
is the double pole formed by the current sense sampling action.
It is always located at half the switching frequency.
The f n
double pole becomes unstable if Q n
(the quality factor) is not sufficiently damped. Q n
is damped by adding external ramp compensation (S e
).
Q n
=
1
π ×
−
D
+
0 .
5
+
( 1
−
D
)
×
S e
S n
where:
S e
is the external ramp compensation = 75% × ((V
OUT
− V
IN
)/L).
S n
is the inductor up slope = V
IN
/L.
The external ramp compensation slope is usually set to a value from 50% to 75% of the inductor down slope as reflected across the sense resistor. Given the wide variation in parameters, it is best to stay closer to 75%.
R
RAMP
(
Ω
)
=
3
4
×
R
CS
45
×
µ
(
V
A
OUT
×
f
SW
−
V
IN
×
L
)
Rev. 0 | Page 15 of 20
ADD5211
Compensation Component Selection
To increase the crossover frequency (beyond the LFP frequency), some kind of phase boost is required. Because the ADD5211 operates in current mode, only one zero is needed to counteract f
LFP
. Therefore, a Type II compensator should be sufficient. This
compensator (see Figure 2) has a gain, G
EA
, that is expressed as follows:
G
EA
=
V
FB
V
OUT
×
g m
×
s
×
R
C s
×
C
C
×
C
C
+
1
G
EA
gives one zero and one pole at the origin, as follows:
f zEA
= 1/(2π × R
C
× C
C
)
f pEA
= 1/(2π × R
O
× C
C
) where R
O
is the output impedance of the error amplifier.
Data Sheet
To boost the phase and increase the crossover frequency, place the compensation zero (f zEA
) at or near the LFP pole. This placement gives the following equation for C
C
:
C
C
=
V
OUT
2
×
R
C
×
C
OUT
×
I
OUT
These values may need to be adjusted experimentally to achieve satisfactory phase margin over all operating conditions and toler-
ances. Table 8 provides recommended values for switching
frequencies of 360 kHz and 1 MHz.
Table 8. Recommended Values for Compensation Components f
SW
(kHz) L (µH) C
OUT
(µF) R
RAMP
(kΩ) R
C
(Ω) C
C
(µF)
360
1000
33
22
10
4.7
6.81
6.81
100
100
2.2
1.0
Rev. 0 | Page 16 of 20
Data Sheet
TYPICAL APPLICATION CIRCUITS
VIN
+
C
IN
10µF
C
IN2
0.1µF
L1
33µH
Q1
D1
C
OUT
10µF
22 LEDs/CH, 100mA/CH
C
VDR
1µF
OFF ON
UVLO
VDR
EN
VIN GATE_P GATE_N
CS
R
RAMP
6.8k
Ω
RAMP
R
CS
0.1
Ω
PGND
PWM
VDD
R
FLT
100k
Ω
FAULT
ADD5211
OVP
R
LSD1
24k
Ω
R
LSD2
4.7k
Ω
C
VDD
1µF
R
SET
15k
Ω
R
OVP1
560k
Ω
R
OVP2
16k
Ω
VDD
LSD
ISET
FB4
FB3
FB2
FB1
LGND
SS AGND FREQ COMP
R
FREQ
49.9k
Ω
R
C
100Ω
C
C
2.2µF
C
SS
30nF
Figure 22. Typical Four-String Application Circuit
L1
33µH
D1
VIN
+
C
IN
10µF
C
OUT
10µF
22 LEDs/CH, 100mA/CH
C
IN2
0.1µF
Q1
C
VDR
1µF
OFF ON
UVLO
VDR
EN
VIN GATE_P GATE_N
CS
RAMP
R
RAMP
6.8k
Ω
R
CS
0.1
Ω
PGND
PWM
VDD
R
FLT
100k
Ω
FAULT
ADD5211
OVP
R
LSD1
24k
Ω
R
LSD2
4.7k
Ω
C
VDD
1µF
R
SET
30.1k
Ω
R
OVP1
560k
Ω
R
OVP2
16k
Ω
VDD
LSD
ISET
FREQ COMP
FB4
FB3
FB2
FB1
LGND
SS AGND
R
FREQ
49.9k
Ω
R
C
100Ω
C
C
2.2µF
C
SS
30nF
Figure 23. Typical Two-String Application Circuit
ADD5211
Rev. 0 | Page 17 of 20
ADD5211
OUTLINE DIMENSIONS
PIN 1
INDICATOR
0.80
0.75
0.70
SEATING
PLANE
4.10
4.00 SQ
3.90
TOP VIEW
0.30
0.25
0.18
18
19 24
1
PIN 1
INDICATOR
0.50
BSC
EXPOSED
PAD
2.65
2.50 SQ
2.45
0.50
0.40
0.30
0.05 MAX
0.20 REF
13
12
BOTTOM VIEW
7
6
0.25 MIN
FOR PROPER CONNECTION OF
THE EXPOSED PAD, REFER TO
THE PIN CONFIGURATION AND
FUNCTION DESCRIPTIONS
SECTION OF THIS DATA SHEET.
0.02 NOM
COPLANARITY
0.08
COMPLIANT TO JEDEC STANDARDS MO-220-WGGD.
Figure 24. 24-Lead Lead Frame Chip Scale Package [LFCSP_WQ]
4 mm × 4 mm Body, Very Very Thin Quad
(CP-24-7)
Dimensions shown in millimeters
ORDERING GUIDE
ADD5211ACPZ-R7
ADD5211ACPZ-RL
ADD5211CP-EVALZ
1 Z = RoHS Compliant Part.
Temperature Range
−40°C to +125°C
−40°C to +125°C
Package Description
24-Lead LFCSP_WQ, 7” Tape and Reel
24-Lead LFCSP_WQ, 13” Tape and Reel
Evaluation Board and LED Array
Data Sheet
Package Option
CP-24-7
CP-24-7
Rev. 0 | Page 18 of 20
Data Sheet
NOTES
ADD5211
Rev. 0 | Page 19 of 20
ADD5211
NOTES
Data Sheet
©2013 Analog Devices, Inc. All rights reserved. Trademarks and
registered trademarks are the property of their respective owners.
D10555-0-10/13(0)
Rev. 0 | Page 20 of 20
Mouser Electronics
Authorized Distributor
Click to View Pricing, Inventory, Delivery & Lifecycle Information:
Analog Devices Inc.
:
ADD5211ACPZ-R7 ADD5211ACPZ-RL ADD5211EB-EVALZ ADD5211CP-EVALZ
advertisement
Related manuals
advertisement
Table of contents
- 1 Features
- 1 Applications
- 1 General Description
- 1 Application Circuit
- 2 Table of Contents
- 2 Revision History
- 3 Detailed Functional Block Diagram
- 4 Specifications
- 4 General Specifications
- 5 Step-Up Switching Controller Specifications
- 5 LED Current Regulation Specifications
- 6 Absolute Maximum Ratings
- 6 Thermal Resistance
- 6 ESD Caution
- 7 Pin Configuration and Function Descriptions
- 8 Typical Performance Characteristics
- 10 Theory of Operation
- 10 Current Mode, Step-Up Switching Controller
- 10 Input Voltage
- 10 UVLO Pin
- 10 Enable and Disable
- 10 Internal 3.3 V Regulator (VDD)
- 10 Internal 5.1 V Regulator (VDR)
- 11 Frequency
- 11 Soft Start
- 11 LED Current Regulation
- 11 Current Sink
- 11 Programming the LED Current
- 11 PWM Dimming Control
- 12 Fault Protection
- 12 Boost Output Overvoltage Protection (OVP)
- 12 LED Short Protection
- 12 LED Open Protection
- 12 Boost Output Short-Circuit Protection (SCP)
- 12 Thermal Shutdown (TSD)
- 14 Applications Information
- 14 Layout Guidelines
- 14 Heat Sinking
- 14 Boost Component Selection
- 14 Calculating the Peak Inductor Current and Duty Cycle
- 14 Selecting the Inductor
- 14 Selecting the Current Sense (CS) Resistor
- 15 Selecting the NMOS Switch
- 15 Selecting the Diode
- 15 Selecting COUT
- 15 Boost Converter Loop Gain Calculations
- 16 Compensation Component Selection
- 17 Typical Application Circuits
- 18 Outline Dimensions
- 18 Ordering Guide