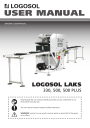
advertisement
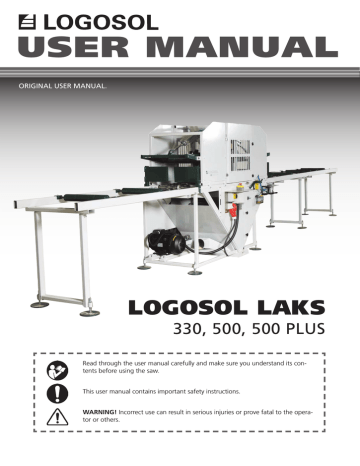
USER MANUAL
OriginaL USer manUaL.
LOGOSOL LAKS
330, 500, 500 PLUS
Read through the user manual carefully and make sure you understand its contents before using the saw.
This user manual contains important safety instructions.
Warning! Incorrect use can result in serious injuries or prove fatal to the operator or others.
2
Thanks for choosing a logosol sawmill!
Welcome! We are very pleased that you have demonstrated your confi dence in us by purchasing this sawmill and we will do our utmost to meet your expectations.
Logosol has been manufacturing sawmills since 1988, and in that time we have supplied approximately
30,000 machines to satisfi ed customers the world over.
We are concerned with your safety and ensuring that you achieve the best possible results with your bandsaw mill. We therefore recommend that you take your time in reading this supplementary user manual, as well as the standard user manual, from cover to cover in peace and quiet before you begin using the saw. Remember that the machine itself is just part of the value of the product. Much of the value is also to be found in the expertise we pass on to you in the user manuals. It would be a pity if that were not utilised.
We hope you get a lot of satisfaction from the use of your machine.
Bengt-Olov Byström
Founder and chairman,
Logosol in Härnösand
LOGOSOL undertakes continuous development of its products.
For this reason, we must reserve the right to modify the confi guration and design of our products.
Text: Kalle Låks
Document: Logosol Laks Manual
Pictures: Kalle Låks, Lars Wahlström
Revised: September 2010
Manual, part no.: 0458-395-0615
© 2011 LOGOSOL, Härnösand Sweden
Table of contents
Key to symbols
Description of machine
Pneumatic equipment
Technical data
Safety instructions
Assembly instructions
Chain tension
Controls
Starting and stopping instructions
Sawing blocks
Fitting saw blades
Care instructions
The Laks grinder
Spare parts
14
15
16
17
20
24
28
9
10
7
8
13
4
5
3
4
key to symbols
Make sure that all warning and information stickers are in place, and that they are clean and legible. Any damaged stickers must be replaced immediately.
Key To symbols
Warning! This symbol means that you have to take particular care.It is always accompanied by information on the specific risk.
For your own safety and the safety of others, do not use the bandsaw mill or handle bandsaw blades without first reading through and understanding the contents of this user manual in their entirety.
Warning! Cutting tool: Careless use of the machine can result in potentially fatal injuries. Bandsaw blades are extremely sharp and dangerous.
Always wear protective gloves when working with the bandsaw mill or handling bandsaw blades. Risk of sustaining cuts when handling bandsaw blades.
Bandsaw blades and motor parts may be hot after sawing.
Always wear approved ear protection when working with the machine. Even brief exposure to high frequency noise can damage your hearing. Always use close-fitting protective eyewear when working with the machine or handling bandsaw blades. Under certain circumstances the use of a protective mask may also be advisable. This would mainly apply if you are sawing dry wood or sawing indoors.
Always wear approved protective footwear with saw protection, steel toecaps and non-slip soles when working with the machine or handling bandsaw blades.
Always wear full-length protective trousers when working with the machine or handling bandsaw blades. Never wear loose-fitting clothing, scarves, necklaces, etc. that may get trapped in the machine during the work. Tie up long hair before working with the bandsaw mill.
description of machine - laks saw
LOGOSOL LAKS
Outfeed table Sawing section infeed table
The LAKS saw is a single-operator frame saw, intended to be used for re-sawing finished blocks into finished boards of any thickness.
The saw unit divides into three segments for easy transport.
1. Sawing section
2. infeed table
3. Outfeed table
The Laks frame saw is a resawing machine for finished blocks and produces up to 2-3 m
3
of sawn timber (depending on model) per hour
(20 cuts per sawing operation), with minimal cutting loss (saw kerf 2.3 mm) and a surface finish and dimensional accuracy that minimise demanding finishing work.
The saw is powered by an electric motor of 7.5 or 11 kW. (Can be supplied with a more powerful motor of up to 15 kW if required). This drives a crankshaft, by means of gear reduction, with a connecting rod drawing a saw frame up and down along vertically-positioned guides.
The sawmill is supplied complete with all necessary equipment.
5
6
8 7 6
18
9
1
2
4
3
17
18
5
11
10
8
Saw unit viewed from operating side
1. Distribution box
2. On switch
3. Power plug in
4. Main switch
5. Control lever for feeding
6. Clamp roller, infeed
7. Clamp roller, outfeed
8. Lever for clamp rollers
9. Emergency stop button
10. Control panel for compressed air
11. Oil pump, central lubrication
Saw unit viewed from work side
12. Electric motor
13. Pulley wheel for gear reduction
14. Pulley wheel for crankshaft
15. Crankshaft with balancer
16. Feeder mechanism
17. Saw frame with saw blade cartridge
18. Air cylinders for press rollers
19. Backing plate
16
15
14
13
19
12
nOTE! The pictures on this page show the LAKS saw with cover plates removed.
These must be fi tted for all sawing work!
pneUmatic eQUipment
LOGOSOL LAKS
The Laks saw is equipped with an air cylinder, the purpose of which is to press the clamp rollers on the infeed side against the timber for sawing.
The air pressure can be adjusted to a suitable level
(6 bar) by means of a regulator.
The cylinders are operated by levers.
Up and Down
7
8
technical data
Length, standard*
Width
Height
Max. block size
Min. feed rate
Max. feed rate
LAKS 330
6,600 mm
1,000 mm
1,650 mm
W 330 mm H 180 mm
30 m/hour
60 m/hour
LAKS 500
8,000 mm
1,350 mm
2,200 mm
W 490 mm H 260 mm
24 m/hour
42 m/hour
LAKS 500 PLUS
8,000 mm
1,350 mm
2,200 mm
W 490 mm H 260 mm
0.1 m/hour
120 m/hour
Electric motor
Power requirements
7.5 kW
16 A
7.5 kW or 11 kW
16 A or 25 A
11 kW
25 A
*) The length of the saw chassis can be extended as required. Consult the manufacturer Låks Sågen when ordering.
We reserve the right to make changes to the specifications.
safety instrUctions
LOGOSOL LAKS
PoinTs To noTe beFore using your lAKs sAW!
1. Read through the instruction manual and familiarise yourself with the functions of the saw.
2. Take careful note of the location of the emergency stop button and how best to reach it.
3. All cover plates must be in place.
4. The cover plates (A) are permanently fi tted with screw joints. The hood (B) is on hinges and can be opened. The hood must be closed when starting the saw!
5. Wear ear protection during sawing work.
The noise level of the saw can exceed 85 dB.
6. The power cable MUST ALWAYS be unplugged and the air hose disconnected for all servicing work or repairs. This is to prevent unintentional start-up or the risk of crushing.
9
assembly instrUctions
PrerequisiTe
Look for a spot with solid ground that is as flat and even as possible. We recommend a concrete slab as a base and having a simple roof over the work station. Operation of the saw will not be affected by a slight slope along its length. However, it must be absolutely level laterally. Similarly, there must be no difference in the angle of the infeed table and sawing section. This can cause problems of crooked sawing.
Adjust the height of the sawing section in relation to the infeed section using the adjustment screws on the support leg as shown in the picture. This may be necessary to line up the joints on the sawing section and infeed section.
A correctly-set sawmill will ensure no vibrations.
10
Screw together the infeed section and sawing section using two screws.
LOGOSOL LAKS
Attach the distribution box and screw it into place. Connect the power cable to the plug (A).
(This must only be done once the entire saw has been assembled.)
A
nOTE! Before starting and stopping the saw frame, the control for feeding must be in the OFF position.
11
12
Fit the cover plates on both sides of the saw.
Connect the power cable and test the saw to check that the electric motor runs in the right direction (according to the arrow on the motor). If not, this is probably due to the poles of the connection cable being reversed. Change this by switching the poles around.
Adjust and test again!
nOTE! When testing, always make sure that no one is in the vicinity of the sawmill and likely to be in danger. Before starting, make sure you know where the emergency stop button is located!
checking chain tension
LOGOSOL LAKS
F
1. Check that the runners under the chains are
OK (wear, etc.)
2. Tension the chains using the screws (F). Make sure that they are equally taut on both sides.
Lift the runner approximately 10 mm at one end for correct tension. Fig. 9
3. Wind the infeed track several turns using the hand crank to make sure that everything goes round without anything catching.
F
cirka 10 mm
13
14
controls
1
2
3
Emergency stop button
1. Cuts off all current feed to the electric motor, which means both feeding and the saw frame stop immediately.
Controls on distribution box
2. Power switch for electric motor (on and off, YD-coupled).
3. Main switch.
Controls for feeding
4. Manual feeding crank with which trunks can be fed to their start position.
5. Start or shut-off of automatic infeed when sawing.
Controls for feeding
4. Manual feeding crank with which trunks can be fed to their start position.
5. Start or shut-off of automatic infeed when sawing.
4
5
LOGOSOL LAKS
starting and stopping instrUctions
5
sTArTing The mAchine
1. Make sure that the control for feeding is in the OFF position (
pos 5).
2 The power cable must be connected to enable starting ( pos 1).
3. Turn the main switch to the ON position (
pos 2).
4. To start the machine, turn the switch
( pos 3) towards ON in two stages (Y and
D).
5. If the electric motor has been overloaded, a protective motor switch will be triggered. This switch will be automatically reset after approximately 1 min.
3
2
4
1
sToPPing The mAchine
6. The control for feeding must be in the
OFF position ( pos 5).
7. To stop the machine, turn the switch
(
pos 3) to the OFF position.
8. In the event of an emergency, stop the machine using the emergency stop button
( pos 4).
15
16
sawing blocks
One or more blocks can be sawn at the same time.
When arranging the saw block on the infeed table, it is very important to ensure that the block is directed in a straight line towards the saw frame.
When sawing several blocks, place them on top of one another.
Please note that the maximum height must never exceed 250 mm.
If the block height is too great, then the saw frame will hit the block, resulting in damage and jamming.
LOGOSOL LAKS
removing/fitting saw blades remoVAl
1. When replacing individual saw blades
(max. 2), loosen them with the aid of an
Allen key as per fig. Undo the screw fully and remove.
2. When replacing or removing three or more blades, the tension in all blades must be released. This is done by screwing up the clamping screws a ¼ turn on each blade alternately until all the blades are loosened. When re-assembling the same thing applies, i.e. alternately tightening until all blades are under tension again.
The screws for the blades in the bottom of the saw frame must also be removed.
The saw blade can then be removed.
Undo the power cable from the distribution box and the air hose to avoid unintentional start-up and the risk of crushing.
Remove the cover plates on both sides of the saw and over the frame drive.
If necessary, turn the electric motor by hand to move the saw frame to its bottom position.
17
18
A
A
re-Assembly
c:a 5 mm
Regardless of whether it's a matter of replacing damaged individual blades or resetting the entire saw frame, the following must be observed:
approx.
5 mm
With the aid of the lower screws (A) the saw blades should be adjusted leaving a gap of around 5 mm between blade and saw frame. Check that the screws in the saw blade's bracket are tightened and that the bracket is secure and stable on the saw blade.
When resetting it is possible to use different "comb-shaped holders” and corresponding spacers adapted to the pre-determined dimensions of the sawn timber.
The comb-shaped holders can be custommade to suit any timber dimensions.
A comb-shaped holder at each end of the saw frame determines the dimensions of the sawn timber.
b b b
LOGOSOL LAKS
Great accuracy is required during assembly to ensure the spacer is secured in the correct position, thus ensuring the correct position of the saw blades. Correctly adjust the spacer, so that the bolts (by the arrows) end up the right way.
The torque of the saw blades must finally be adjusted to achieve correct clamping.
The correct tightening torque is 15 Nm.
During torque tightening, the combshaped holders' fixing screws (B) must not be tightened (this applies to both upper and lower holder).
When torque tightening of all saw blades is complete, tighten the screws (B).
19
care instrUctions
Inspection and lubrication of certain parts must be carried out daily. However, many bearings are fully enclosed and thus maintenance-free. The following instructions should be observed to ensure problem-free operation.
1 2
20
4
5
5
3
1. Infeed table with sliding shelf.
2. Saw frame.
3. Electric motor, pulleys and belts.
4. Feeder mechanism.
5. Bearing housing (lubrication with grease).
LOGOSOL LAKS
saw frame
4
A
C
3
1
1
3
2
B
4
D
lubricATion
Friction between the saw frame and chassis should be minimised as much as possible.
1. The roller bearings (1) are lubricationfree. With continuous sawing, the friction surfaces must be lubricated several times per day using the central lubrication device installed. Pumping the handle (2) several times will cause lubricating oil to emerge at the top and bottom (3) of the saw frame. Check that the oil holes (x 4) have not got clogged up. Use motor-oiltype liquid lubricating oil, saw chain oil or similar with good adhesion.
2. The slide/support lugs (4) must be kept set close to the chassis, to counteract sawdust on the sliding surfaces. When adjusting, the safety nut should be loosened, which allows the adjusting screw to be screwed in by hand very easily.
3. The slide/support lugs are also intended as a guide for the saw frame in the chassis. It is essential for the saw frame to be parallel in the chassis and not as shown in fig. (excessively crooked track). The frame is correctly set up when delivered from the factory, but this can be disturbed when replacing the frame or dismantling for other reasons. For adjusting and measuring, position some kind of measuring tool against the lateral surface of the saw blade (not teeth) to check that the blade is running completely parallel with the chassis when the frame is guided up and down (by hand).
Lateral displacement of the blade must be minimised to +/- 0 mm for good sawing results.
nOTE! For any work on and around the saw frame, the saw must be shut off and the power cable unplugged.
21
22
electric motor, pUlleys and belts
b
A
1. Keep a close check on whether much sawdust has collected around pulleys and the electric motor. Daily removal of sawdust is essential.
If sawdust becomes trapped between belt and pulley, there is a great risk of the pulley breaking.
lubricATion
The middle pulley shaft has 2 bearings
(by arrow A), and the bearing housing
(by arrow B) has bearings that must be lubricated very lightly (single spray with a grease gun) once a week. NOTE! The bearings are enclosed and require very sparing lubrication.
Pulley rePlAcemenT
Unscrew both socket head cap screws, screw one into the empty hole. Screw until it divides. Re-assemble in reverse order.
nOTE! Make sure that the pulley is at an angle to the others.
nOTE! When removing the protective cover over the pulleys, shut off the power supply to the electric motor. This is to prevent unintentional start-up of the saw. Test runs or similar with the cover removed may only be carried out by service personnel from the manufacturer.
1
A
feeder mechanism
b
2
3
LOGOSOL LAKS
Adjustment screws for the feeder mechanism are indicated by arrows A and B.
The notches will alternately move the cog wheel clockwise.
lubricATion
The mechanism has joints with teflon bushings at arrows 1, 2 and 3. These must be lubricated with an oil can once a week or more as required.
belT Tension
The belt tension can be adjusted by moving the wheel bearing or electric motor with the aid of the adjusting screws (approximately 20 mm depression of the belts indicates normal tension). See picture.
23
24
the laks grinder
The Laks grinder is a grinder designed to be used for sharpening saw blades for the Laks frame saw. The grinder is electric.
6
4
5
3
7
2
9
1
8
1. Chassis
2. Centreless grinding work support
3. Electric motor 380 V (0.55 Kv 2,800 rpm B3)
4. Distribution box
5. ON button
6. OFF button
7. Power plug
8. Grinding disc
9. Saw blade holder
fig. A fig. A
20°
15°
20° fig. B fig. B
20°
20°
15° fig. A fig. A
20°
20° fig. B fig. B
LOGOSOL LAKS
insTAlling And AdjusTmenT
The grinder is supplied with the grinding work support separate, so step 1 is to install the support as per fig. A, with washer and nut.
The machine's electric motor is mounted on the chassis and set by the manufacturer, and the grinding disc is set for the correct grinding result.
The grinding angle is adjusted by turning the grinding work support to the correct angle as per fig. B. Once the correct angle is achieved, tighten the nut.
To set the correct grinding depth, insert the grinding work support into the oblong hole in the chassis, in connection with angle adjustment. Fig. A.
20°
20°
The sketch shows the standard grinding angle used in normal conditions (20°).
15°
15°
The sketch shows an example of how grinding should be performed in extreme conditions, e.g. frozen timber. The tooth is ground to a slightly sharper angle at the outer tip for less aggressive feeding.
nOTE! Only around 1.5-2.0 mm of the hard metal tip should be ground to the sharper angle (15°).
25
26
grinding
Place the saw blade on the blade holder and tighten gently (by hand is sufficient).
Set the grinding depth (if this has not already been done as per 2.4). The grinding depth depends on how much the saw blade is worn.
Applying very light and sparing pressure against the grinding disc, grind each tooth carefully until all teeth are exactly the same height.
It is very important to check that grinding is at right angles to the saw blade, Fig. C.
Sågblad
disc
90° fig. C
FEL!
90°
RÄTT!
fig. D
One simple method for verifying that grinding is being performed correctly is to check the appearance of the saw teeth in profile as per fig. D. The hard metal section should have sharp corners and a 90° angle to the blade. To adjust the grinding angle, screw on the electric motor's fixing screws (x 4).
Normally this should not be necessary, but if the motor or grinding work support have been removed, the basic setting may have changed.
nOTE! Always wear gloves and protective goggles for grinding work!
90° fig. F
LOGOSOL LAKS
90°
90°
1
fig. E
1
1
mAinTenAnce/AdjusTmenTs
In all instances where the electric motor has been removed from its attachment plate, a careful check must be performed to ascertain that the 90° angle between grinding disc and grinding work support has not been disturbed. Adjustments can be made using the 4 screws indicated by the arrow (1).
If the grinding disc has been replaced, it must be checked carefully so that it does not "warp" or run defectively in any other way. This can be due to incorrect installation or the grinding disc having a manufacturing defect.
Small defects can be remedied using a grinding disc dresser.
In the event of major irregularities, fit a
fig. E
Any new grinding disc must also be adjusted using a dresser, so that it suits the configuration of the saw teeth as per fig. F.
27
28
spare parts for laks saw 330, 500, 500 plUs
When ordering spare parts, indicate the page number together with the position number of the relevant spare part.
22
20
19
17
11
9
10
18
21
2
3
4 5
16
15
6
1
27
14
7
26
13
8
24
23
25
12
14
LOGOSOL LAKS
45
27
44
43
42
29
30
31
32
38
23
28
34
33
35
36
37
39
24
25
19
18
20
40
41
21
17
14
26
22
13
11
12
15
16
10
9
8
7
6
4
5
1
2
3
4
29
14
4
5
3
3
8
7
6
4
5
1
10
9
7
6
15
6
7
6
7
12
13
12
13
6
7
11
2
12 13
6
7
14
15
12
13
19
18
17
16
20
7
6
11
30
5
LOGOSOL LAKS
1
3
4
5*
16
14
2
11
Notera / Note
*) Metervara / on the metre
6
15
13
12
9
8
7
10
20
21
19
28
27
22
17 18
23
29*
30*
24
25
26
31
LOgOSOL SWEdEn
Industrigatan 13, SE-871 53 Härnösand, Sweden
Tel. +46 (0)611-18285 | Fax +46 (0)611-182 89 [email protected] | www.logosol.se
advertisement
* Your assessment is very important for improving the workof artificial intelligence, which forms the content of this project