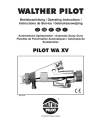
advertisement
▼
Scroll to page 2
of 12
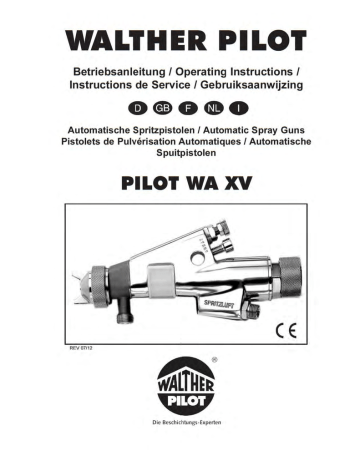
WALTHER PILOT Betriebsanleitung / Operating Instructions / Instructions de Service / Gebruiksaanwijzing O9000 Automatische Spritzpistolen / Automatic Spray Guns Pistolets de Pulvérisation Automatiques / Automatische Spuitpistolen PILOT WA XV REV 07/12 Die Beschichtungs-Experten PILOT WA XV Stand: April 2008 PILOT WA XV - HVLP Reparatursets Maintenance kits Kits de réparation Reparatiesets V 16 115 03... 3 (ММА Ху) V 16 116 03. . 3 (WA XV ziehbar, needle-pull à tirette, met trekker) V 16 117 03. . 3 (WA XV-HVLP) Listing of Contents Exploded Drawing Declaration of CE-Conformity Replacement parts 1 General 1.1 Identification of Model Version 1:2 Normal Use 1.3 Improper Use 2 Technical Description 3 Safety Instructions 3.1 Safety Warning Symbols 3.2 General Safety Instructions 4 Assembly / Installation 4.1 Mounting of Spray Gun 4.2 Connection of Input Lines 5 Operational Handling 5.1 safety Instructions 5.2 Starting / Stopping Requirements т Spray Pattern Test 54 Spray Pattern Adjustments 5.5 Retooling of Spray Gun 6 Cleaning and Maintenance 6.1 Safety Instructions 6.2 Cleaning - Complete 6.3 Cleaning - Routine 7 Repairs/Replacements 7.1 Replacement of defective Needle Seal Packings Той Replacement of Nozzles, Needles, Springs, Seals 8 Troubleshooting and Corrective Action 9 Disposal of Cleaning/Servicing Substances 10 Specification Data 24 25 27 27 27 28 28 29 29 29 30 30 30 31 31 31 31 32 34 36 36 36 37 38 38 39 39 40 40 Declaration of CE-Conformity o We, the manufacturers of the equipment, hereby declare under our sole respon- sibility that the product(s) described below conform to the essential safety requirements. This declaration will be rendered invalid if any changes are made to the equipment wit- hout prior consultation with us. Manufacturer WALTHER Spritz- und Lackiersysteme GmbH Karntner Str. 18 - 30 D - 42327 Wuppertal Tel.: +49(0)202 / 787 - 0 Fax: +49(0)202 / 787 - 2217 www.walther-pilot.de - e-mail: infor?'walther-pilot.de Type Designation Automatic Spray Gun PILOT WA XV WA XV V 20 660 WA XV needle-pull V 20 664 WA XV-HVLP V 20 672 Intended purpose Processing of sprayable media Applied Standards and Directives EU-Mechanical Engineering Directives 2006 / 42 / EC 94 / 9 EC (ATEX Directives) EN ISO 12100-1 EN ISO 12100-2 DIN EN 1953 DIN EN 1127-1 DIN EN 13463-1 Specification according 94/9 / EC Tech.File,Ref.: Category 2 Part marking N2GCTS 2411 Authorized with the compilation of the technical file: Nico Kowalski, WALTHER Spritz- und Lackiersysteme GmbH, Kárntner Str. 18 - 30 D- 42327 Wuppertal Special remarks : The named product is intended for installation in other equipment. Commissioning is prohibited until such time as the end product has been proved to conform to the pro- vision of the Directives 2006 / 42 / EC. Wuppertal, the 1st of January 2010 iv. (© [ds Name: Torsten Broker Position: Manager, Design and Development This Declaration does not give assurance of properties in the sense of product liability. The safety instructions provided in the product documentation must be observed at all times. 25 Listing of Replacement Parts for Model WA XV Item Part-No. 1 2 Y 01 101 03 000 optional V 01 10102 ..6° Description Air Cap Nut 6-Bore-Air Cap other Air Cap Versions upon request optional V 01 101 07 ..3° \ 11 301 02 000 V 20 660 02 000 V 20 661 02 000 Material Nozzle Air Distnbution Ring Gun Front Attachment Gun Front Attachment (Circulation Systems only) V 09 001 72 000 V 20 660 05 000 V 20 660 06 000 V 20 660 07 000 V 09 001 67 000 V 20 660 01 000 V 20 660 20 000 V 20 660 08 000 \ 00 101 01 000 \ 09 002 07 000 \ 20 660 04 003 V 20 201 02 000 V 09 102 02 000 V 20 660 42 000 V 20 660 32 000 V 09 102 11 000 V 20 660 33 000 V 09 102 09 000 V 20 660 31 000 V 20 651 06 000 V 20 660 34 000 optional V 20 660 51 . 3° V 10 506 02 000 V 20 651 07 000 V 20 660 36 003 V 20 606 11 000 V 20 660 35 000 V 20 660 37 000 V 20 660 38 000 V 20 660 39 120 Needle Seal Packing Mating Bush Compression Spring Compression Gland Seal Gun Body Flat-Jet Adjustment compl. Cylinder Head Screw Double Nipple Usit-Ring Hexagonal Nut Sealing Screw O-Ring Blanking Cap Sealing Collar O-Ring Screw Plug O-Ring Control Piston Sealing Collar Backup Washer Material Needle Needle Retaining Nut Needle Spring Piston End Nut Piston Spring Spring Retainer Spring Bush Spring Pin Adjustment Screw Replacement Parts - other than Replacement Parts PILOT WA XV needle-pull Type V 20 664 given values of PILOT WA XV Item Part-No. Description 27-35 Parts not applicable 36 V20664 05000 Piston End Nut 37 optional Material Needle V 2066443 .. 3° 38 V2066402000 Stop Pin 39 V20 206 04000 Needle Spring 40 WV 2066404000 Adjustment Screw 41 Y 20 664 03 000 Washer 42 V206/985 000 Flat Washer 43 V 2067984 000 Serrated Lock Washer 44 2066041684 Cylinder Head Screw Replacement Parts PILOT WA XV- HVLP Type V 20 672 2 optional Air Cap for Nozzle Size V 01 101 86 086” 0.3 - 2.0 mm © V 01 101 86 256° 2.5 - 3.0 mm © 3 V 01101 85..3" Material Nozzle 11 \ 20 671 01 000 Gun Body 20 \20671 32 000 Sealing Collar 30 V20664 05000 Piston End Nut 37 optional Material Needle V 20 664 43 033 0,3 a for 0 3-Nozzle V 20 664 43 053 05 e for 0 5-Nozzle for Nozzle Size V20664 43083" 0.8 - 1.5 тт е V 20 664 43 123° 1.8 - 2.0 тт е V 20 664 43 253* 2.5 - 3.0 тит © 38 Y 20664 02 000 Stop Pin 39 V 2020604000 Needle Spring 40 V 2066404000 Adjustment Screw 41 V 20 664 03 000 Washer 42 WV 2067985000 Fat Washer 43 V2067984 000 Serrated Lock Washer 44 V 20660 41 684 Cylinder Head Screw 45 V 2067140000 Middle-Air Regulation * Please make sure to always quote the required size(s) when placing an order for Replacement Parts! We re- commend that BOLD-faced replacement parts (i.e. wearing parts) are held an stock to avoid work stoppa- ges. 26 1 General 1.1 Identification of Model Version Model: Automatic Spray Gun PILOT WA XV Type series: WA XV V 20 660 WA XV needle-pull V 20 664 WA XV-HVLP V 20 672 Manufacturer: WALTHER Spritz- und Lackiersysteme GmbH Karntner Str. 18-30 D-42327 Wuppertal Tel.: 0049 (0)202 / 787-0 Fax: OO 49 (0)202 / 787-2217 www.walther-pilot.de - Email: [email protected] 1.2 Normal Use The automatic spray guns of the WA XV type series are exclusively designed for use with sprayable material types and grades. All wetted parts are made of stainless spe- ciality steel so as to permit handling of hydrous and/or aggressive media such as, for example: = paints and lacquers = greases, oils and corrosion preventives = adhesive compounds = ceramic glazes = pickling solutions If your specific material is not listed above, please contact us for further and detailed information. Please note that sprayable material may only be applied to workpieces and/or similar items. The temperature of the spraying material shall never exceed 80 degs. C. The WA XV needle-pull gun is not designed for manual operation, but must be installed in a suitable gun mounting device. The term normal use also implies that any and all safety warnings, operational hand- ling details, etc., as contained in these Operating Instructions, are carefully read, understood and duly complied with. This equipment complies with the explosion protection requirements of Directive 94 / 9 / EC (ATEX) for the explosion group, equipment category and temperature class indicated on the type plate. When using the equipment, the requirements specified in these Operating Instructions must be observed at all times. The technical data indicated on the equipment rating plates and the specifications in the chapter "Technical Data" must be complied with at all times and must not be exceeded. An overloading of the equipment must be ruled out. The equipment may be used in potentially explosive atmospheres only with the authorisation of the relevant supervisory authority. 27 The relevant supervisory authority or the operator of the equipment are responsible for determining the explosion hazard (zone classification). The operator must check and ensure that all technical data and the marking of the equipment in accordance with ATEX are compliant with the necessary require- ments. The operator must provide corresponding safety measures for all applications in which the breakdown of the equipment might lead to danger to persons. If any irregularities are observed while the equipment is in operation, the equipment must be put out of operation immediately and WALTHER Spritz- und Lackier- systeme must be consulted. Grounding / Equipotential Bonding You must ensure that the spray gun is properly earthed (grounded) either separate- ly or in connection with the equipment with which it is being used (maximum resistance 10°Q2). 1.3 Improper Use This spray gun shall not be used for purposes other than set forth in the above Chapter Normal! Use. Any other form of use and/or application is prohibited and considered as improper use in contrast to the original engineering design concept. The term improper use also includes such operations as may be: = spraying of material onto persons and animals » spraying of liquid nitrogen, etc. 2 Technical Description Spray guns of the WALTHER PILOT Type Series WA XV are allautomatic air-con- trolled guns operating in combination with a 3/2-way control valve in the form of hand-, foot- or solenoid-actuated valves. Actuation of the 3/2-way valve directs control air into the cylinder inside the gun so as to open - in sequence - the atomizing air and the material input. Closing of the 3/2-way valve is followed by the control air escaping from the cylin- der inside the gun, upon which the spring-loaded material control needle returns to its initial position, where it shuts the material and atomizing air Input off. The material flow rate and the spray jet contour (i.e. flat, wide or round) are adju- sted at the gun by way of regulating screws. The material inlet duct of the WA XV needle-pull can be opened by hand so as to permit, for example, cleaning of a clogged material nozzle. The model PILOT WA XV-HVLP is a low pressure spray gun and operate with a spraying pressure of 0.7 bar using an inlet pressure of 3.5 bar. The gun front attachment with twin connector for material input permits inclusion of the PILOT spray gun in a circulation system the closed loop layout of which is desi- gned to operate several spray guns. This spray gun can be connected to material pressure tanks, pumping and circula- tion systems. 28 3 Safety Instructions 3.1 Safety Warning Symbols Warning This pictograph and the accompanying warning note "Warning" indicates possible risks and dangers for yourself and others, likely to result in injuries of any descripti- on. Caution This pictograph and the accompanying Warning note "Caution"-indicates possible damage to equipment, workpieces, etc. Notice This pictograph and the accompanying note "Notice"indicates additional and useful information to help you handling the spray gun with even greater confidence and efficiency. 3.2 General Safety Instructions = All applicable accident prevention rules and regulations as well as other recognised industrial safety and health rules and regulations must be observed at all times. - Use the spray gun only in well-ventilated rooms. Fire, naked flames and smoking are strictly prohibited within the working area. WARNING — during the spraying of flammable matenals (e.g. lacquers, adhesives, cleaning agents, etc.), there is an increased risk to health as well as an increased risk of explosion and fire. = You must ensure that the spray gun is properly earthed (grounded) either separate- М or in connection with the equipment with which it is being used (max. resistance 1050). . Before carrying out maintenance or servicing work, always ensure that the air and matenal feed to the spray gun have been depressunsed. Risk of injury! . When spraying materials, do not place your hands or other parts of the body in front of he pressurised nozzle or the spray gun. Risk of injury! . Never point the spray gun at persons or animals. Risk of injury! . Always observe the spraying and safety instructions given by the manufacturers of the spraying material and the cleaning agent. Aggressive and corrosive materials in particular can be harmful to health. : Exhaust air containing particles (overspray) must be kept away from the working area and personnel. In spite of these measures, always wear the regulation brea- thing masks and protective overalls when using the gun. Airborne particles repre- sent a serious health hazard! = Always wear hearing protection when using the gun or when in the vicinity of a gun that is in use. The noise level generated by the spray gun is approx. 86 dB (A). . After camying out assembly or maintenance work, always ensure that all nuts, bolts and screw connections have been fully tightened before the gun is used. . Use only original replacement parts, since WALTHER can only quarantee safe and fault-free operation for original parts. For further information on the safe use of the spray qun and the spraying matenals, ple- ase contact WALTHER Spntz- und Lackiersysteme GmbH, D-42327 Wuppertal, Germany. 29 4 Assembly / Installation This WALTHER PILOT spray gun is delivered in completely assembled condition - but requires the following preparations before it can be taken into operation: 4.1 Mounting of Spray Gun Install the gun in a suitable and stable mounting device as shown in the following example: 4.2 Connection of Input Lines Warning 1. Slide the gun with its 12 mm @ mounting bore ® onto the rod @ of the mounting device. . Adjust the gun an the mounting rod to point at the workpiece. Point the gun an the mounting rod - by sliding and turning it up or down - at the workpiece. Lock the gun in the desired position by tightening the cap screw @ with a Size 8 mm hex. hd. socket wrench. Make sure not to confuse the control and atomizing air connections - Risk of Injury. PILOT WA XV -HVLP . Connect the Input line for = Atomizing air to the "SPRITZLUFT" inlet fitting (G 1/4") of the gun. = Control air to the "STEUERLUFT" inlet fitting (G 1/4") of the gun. - Material to inlet Fitting @ (G 3/8") of the gun. . Use the tool wrench to tighten the three hex. nuts @. The spray gun is now properly installed and connected and ready for operation. 30 5 Operational Handling 5.1 Safety Instructions Your special attention is drawn to the following Safety Warnings prior to taking this spray gun into operation! = Make sure to wear proper respiratory protection masks and protective Overalls whenever you are operating this spray gun. Remember: Air-Borne particles represent a health hazard. = Make sure to wear suitable Kearing protectors. Remember: Spray guns pro- duce sound levels of up to about 86 dB (A), which are highly likely to cause hearing defects. = Make sure your working area is absolutely free from open fires and naked lights -and anybody smoking. Remember: Spraying of readily flammable media such as, for example, paints, adhesive compounds, cleaning solutions, etc., is always accompanied by the risk of fire and explosion. 5.2 Starting / Stopping Requirements The following requirements must be met before this spray gun can be taken into operation: = atomizing air must be available at the gun. » material pressure must be available at the gun. = control air must be avaiable at the gun. Caution The material pressure shall not exceed = 10 bar in the WA XV * 15 bar in the WA XV needle-pull / WA XV-HVLP as, otherwise, the functional reliability of the spray gun will suffer. Adjust the control air pressure to * 8 bar maximal in order to operate the spray gun. The operation of the spray gun can be started/stopped by way of the 3/2-way con- trol valve (see the Operating Instructions of the plant systems manufacturer). Warning lt is important to remember that the spray gun must be relieved of all pressures whenever work is terminated - lines left in pressurized condition could burst, with their contents likely to injure anybody present nearby. 5.3 Spray Pattern Test Spray pattern tests should be performed whenever: * the spray gun is taken into operation for the first time. » the spraying medium is changed. » the spray gun was taken apart for servicing or repairs. The spray pattern is best tested using a workpiece sample, a sheet of metal, card- board or paper. 31 Warning Keep away from the front of the spray gun - imminent Risk of Injury. Warning Make sure that nobody is present in the spraying zone when the gun is started - imminent Risk of Injury. 1. Start the gun to produce a spray pattern sample (see 5.2 Starting / Stopping Requirements). 2. Inspect the sample and readjust the settings of the gun as may be required (see 5.4 Spray Pattern Adjustments). 5.4 Spray Pattern Adjustments The spray pattern of the PILOT WA XV / WA XV needle-pull / WA XV-HVLP can be adjusted as follows. Wide and / or Flat Jet Pattern . Loosen the knurled air cap retaining ring O slightly. Rotate the air cap @ horns into = a vertical position = flat jet pattern = a horizontal position = wide jet pattern Tighten the air cap retaining ring ®. Wide / Flat and / or Round Jet Pattern ao 4. 5. Loosen the lock nut @ using a Size 11 mm wrench. Turn the fine-adjusting screw @ in * - direction = increase roundness of spray jet contour « + direction = increase wideness/ flatness of spray jet contour Once the desired spray jet contour is adjusted tighten the lock nut @. 32 Middle-air adjustment (only PILOT WA XV-HVLP) The adjusting screw © is used to adjusted the middle- air. Adjustment of the Material Flow Rate 1. Turn the material Input regulating screw © from its normal position (= notch mark an the matrial needle adjuster) in » —direction = decrease of flow rate. « + direction = increase of flow rate. Adjustment of the Material Pressure This adjustment can only be made at the controls of the pumping or circulation system or material pressure tank. Please comply with the Operating Instructions and Safety Warnings issued by the manufacturers concerned. Adjustment of the Atomisation Air Pressure The atomizing air Pressure is to be adjusted at the air Pressure reducing valve of the compressor system. Please comply with the Operating Instructions and Safety War- nings issued by the manufacturer. If you wish to change the spraying Pattern beyond the adjustments outlined so far, you must retool the spray gun (see 5.5 Retooling of Spray Gun). WALTHER offer a great variety of air cap/material nozzle/-needle combinations for this purpose. Correcting of Spray Pattern Imperfections The table below shows what to do to correct a spray pattem. CC. desired spray pattern Spray pattern test Fault Required adjustment TE > Spray pattern is split in the | * setting a wider spray pattem “E | centre = Spray pattern is too thick at | = Setting a more rounded spray pattern = the ends Een The spray pattern shows » Increase the atomising air pressure rather large droplets Maternal application in the * Decrease the atomising air pressure centre of the spray pattem Is very thin a Sora Нет is split in * Increase the nozzle diameter > @ pray pa « Reduce atomising air pressure a the centre A « Increase material pressure Spray pattem is very spher- | = Reduce matenal pressure nn ical « Increase atomising air pressure 33 5.5 Retooling of Spray Gun 8. Remove the piston © very carefully from the gun body (use a suitable pair of pliers). Combinations of air cap, material nozzle + needle, designed to match specific spraying media types and grades, form a unit - namely the nozzle insert assembly, which must always be interchanged as a complete assembly to maintain the desi- red spray- finish quality standard. 9. Remove the piston end nute from the con- trol piston @ (use Size 13 mm and 22 mm wrenches). The material needle © is now freely accessible and can be pulled out. Warning Prior to retooling: make sure that the spray gun is in unpressurized condition, i.e. all air and material inputs must be shut off - if not, imminent Risk of Injury. 10. Unscrew the two needle retaining nuts &. Replacement of Air Cap 1. Unscrew the knurled air cap retaining ring O. Installation of the new nozzle insert assembly and of the remaining parts in reverse 2. Pull the air cap @ off the gun front order. attachment. 3. Position the required air cap an the gun WA XV needle-pull / WA XV-HVLP: front attachment. 1. Remove all pressures from the gun (see 4. Screw the air cap retaining ring @ onto 5.2 Starting / Stopping Requirements). the gun front attachment. 2. Remove the air control head (see 5.5 Replacement of Air Cap). 3. Unscrew the material nozzle from the gun Replacement of Material Nozzle and Needle front attachment (12 mm wrench). WA XV / WA XV-HVLP: 4. Remove the cap screw and pull the was- her off. 1. Remove all Pressures from the gun (see TEATRE AQUA 5. Remove the material input regulating screw. 2. Remove the air control head (see 5.5 Replacement of Air Cap). 6. Pull the needle spring @ out. . Unscrew the material nozzle © from the 7. Pull the stop piston @ plus material need- gun front attachment (use a Size 12 mm le @ out. wrench). : 8. Unscrew the material needle @ from the . Unscrew the material Input regulating screw @. . Pull the two spring pins @ off. . Unscrew the spring retaining bush © (use a Size 27 mm wrench). . Remove the compression spring © from the gun body. stop pin @. Installation of the new nozzle insert assembly and of the remaining parts in reverse order. 35 6 Cleaning and Maintenance 3. Use a suitable cloth with a compatible cleaning solution to clean the gun body 6.1 Safety Instructions and all remaining parts. 4. Apply a thin film of the appropriate grease type/grade to the: = Prior to any servicing and repair work: Make sure that the spray gun is in + sealing collar of the piston unpressurised condition, i.e. all air and material inputs must be shut off - if not, » O-ring of the piston imminent Risk of Injury . - material control needle = No open fires and naked lights as well as smoking are allowed in the work - needle spring area. This is a major requirement to prevent the euer present risk of fire and » inside of the gun body explosion, particularly when spraying readily flammable media such as, for Make sure to use a non-acidic, non-resinogenic grease type/ grade and apply example cleaning solutions, etc. same with a soft brush. Assemble the spray gun in reverse order. » ltis important that all processing specifications and safety warnings issued by the manufacturer of cleaning media are duly complied with. Remember: Aggressive and corrosive media represents risks and hazards to personal health. 6.3 Cleaning - Routine The spray gun need not necessarily be dismantled for cleaning if and when the spraying medium is changed in regular intervals or upon termination of work 6.2 Cleaning - Complete (depending, of course, an the material used). The spray gun should be frequently cleaned and lubricated so as to ensure a long service life and functional reliability. Cleaning of the gun only with cleaning solutions recommended by the manufacturer of the spraying material used at the time. It is im-portant to make sure that cleaning solutions do not contain any of the following Notice It is recommended practice to clean and lubricate the spray gun frequently in accordance with Chapter 6.2 Cleaning - Complete, as this will greatly help towards ensuring a Jong service life and functional reliability. constituents: = halogenated hydrocarbons (e.g. 1,1,1-trichloroethane; methylene chloride, etc.) The following requirements must be met before the routine cleaning work can be = acids and acidiferous cleaning solutions performed: = regenerated solvents (so-called cleaning dilutions) = the material tank must be clean and then filled with a compatible cleaning = paint removers solution. = cleaning solution should neuer be sprayed - yet the material pressure must be The above constituents cause chemical reactions with electroplated components available at the gun. resulting in corrosion damage. WALTHER Spritz- und Lackiersysteme is not liable for any damages resulting from The spraying system must be in Operation if a spray gun is to be cleaned. improper treatement of the gun. 1. Take the spray gun into Operation (see 5.2 Starting / Stopping Requirements). 2. Do not stop the spray gun until clear cleaning solution emerges from the nozz- Clean the spray gun le. = prior to each change of the spraying medium. = atleast once a week. Only WA XV needle-pull / WA XV-HVLP » as often as may be required by the spraying medium handled and the resultant The material Input can be released by hand so that the complete spraying system degree of fouling. must not be taken into operation. 1. Pull the disk © at the end of the spray gun back. The material inlet is now open and both the material duct and the material needle will be washed clean. Caution Never immerse the spray gun in solvent or any other cleaning solution as such measure is highly likely to affect the functional reliability and efficiency of the gun. A Caution 2. Do not let go of the disk @ until clear cleaning Do not use any hard, pointed or sharp-edged objects when cleaning the spray gun. solution emerges from the nozzle. Any damage of the precision-made parts are likely to affect your spraying results. All pressures should now be removed from the complete spraying system - which should be left in this condition until it is taken into operation again. 1. Dismantle the spray gun (see 5.5 Retooling the Spray Gun). 2. Use a soft brush together with a compatible cleaning solution to clean the air cap and nozzle. 36 37 A 7 Repairs / Replacements Warning Prior to any repairs/replacements: Make sure that the spray gun is in unpressurised condition, i.e. all air and material inputs must be shut off - if not, imminent Risk of Injury. 7.1 Replacement of defective Needle Seal Packings 1. Remove all pressures from the gun -see 5.2 Starting / Stopping Requirements. 2. Pull the white protective cover © off the gun body. 3. Unscrew the hex. nut @ with a Size 17 mm wrench. 4. Pull the "USIT" ring © off. 5. Pull the gun front attachment @ carefully off the gun body. 6. Remove the gasket @ - and replace same if damaged. 7. Unscrew the packing seal @ with a Size 11 mm from the gun front attachment. 8. Remove the compression spring @ (re- place if damaged) and the counter bush @ from the threaded socket. 9. Remove the needle seal packing @ from its seat - use a strong wire with one end bent to form a small hook. 10. Lubricate the new needle seal packing with a non-acidic, non-resinogenic grease type / grade. 11. Install the new needle seal packing in the gun body. Installation of the remaining parts in reverse order. Caution Never reinstall a used needle seal packing as, otherwise, the functional sealing reliability of the spray gun will suffer. 38 7.2 Replacement of Nozzles, Needles, Springs and Seals For replacement of any of the following parts dismantle the spray gun in accor- dance with 5.5 Replacement of Material Nozzle and Needle: + Material Nozzle = Piston Spring + Material Needle” + Needle Spring” «= Piston Sealing Collar « Piston O-Ring” Caution Parts marked * must be lubricated with a non-acidic, non-resinogenic grease type / grade prior to installation. WALTHER Repair kits are also available for WA XV, WA XV needle-pull and WA XV-HVLP spray guns. Wearing parts are also shown (in boldface) in the Listing of Replacement Parts. Repair kit-material side: WA XV: Art. No.: V 16 115 03..3 WA XV needle pull: Art. No.: V 16 116 03..3 WA XV-HVLP: Art. No.: V 16 117 03..3 8 Troubleshooting and Corrective Action Warning Prior to any servicing and repair work: Make sure that the spray gun is in unpressuri- zed condition, i.e. all air and material inputs must be shut off - if not, imminent Risk of Injury. Fault Cause Remedy Material nozzle or needle fou- | Remove see 5.5 Matenal Nozzle or led or damaged Needle and clean or replace Gun is dripping Packing gland too tight Loosen packing gland shightly use a Size 11 wrench Increase control air pressure to max. & bar (see operating Instructions of plant systems manuf- acturer) Gun fails to open | Control air pressure too low Top-up material level (see operating Spray jet pulsa- Level in matenal tank too low Instructions of plant systems manuf- ting or unsteady acturer) Material leaks Needle seal packing leaks Te see /.1 Needle Seal pak- пи Packing gland to loose Tighten packing gland slightly use a Size 11 mm wrench 39 9 Disposal of Cleaning / Servicing Substances Disposal of any such substances must be in accordance with all applicable local and national regulations, directives and laws. Warning Particular attention is drawn to all processing specifications and safety wamings issued by the manufacturers of spraying and cleaning media. Remember: The improper disposal of any toxic waste material represents a serious threat to the environment, i.e. to the health of mankind and animal life. 10 Specification Data Weight: 920 g Connections: Atomizing Air G 1/4" Control Air С 1/4" Material Inlet G 3/8" Pressure Ranges: Control Air Pressure max. 8 bar Material Pressure max. 10 bar (WA XV) max. 15 bar (WA XV needle-pull / WA XV-HVLP) Atomising Air Pressure see table max. Operating Temperature of Spray Gun 80 °C Sound Level (measured at a distance of 1 m from the spray gun) 86 dB (A) Air consumption (six-bore air cap): 1.0 bar Atomizing Air Input 8.2 m*/h 2.0 bar Atomizing Air Input 12.1 m*/h 3.0 bar Atomizing Air Input 16.0 m?/h 4.0 bar Atomizing Air Input 20.1 m*/h 5.0 bar Atomizing Air Input 24.0 m*/h 6.0 bar Atomizing Air Input 28.0 m*/h Right to effect technical changes reserved. 40 uapadx3-sguniyaiyosag aig эрдона-лецуем@©оуи :неш-Э 1122-1481 1 2020 Xed « 0-28. / 2070 :'I8L jemnoddnm 2¿2€7Zv-Q + 0€£-81 NS JOUJWEM 43 № Hawo awajsAsiaoe] pun -zjuds YIHL VM wo loyaqnz pun awa)sASzINyoswaly + ewsjsÁS-Uninz + 19UYIO | + punpirsyosqgesseN Ji swejsÁsBnesqgy + Punpisyosqgeuayool | LU eWajsÁSsBnesqgy e uexoqueyoo! | pun -Z.ds eeluiquoy + owejSsÁs nejunjemnajen + ueduwndsayDissn|4 pun aje199-ssaIy + aW8]SÄAS-MIOMIUNH e 19yeU9g esojyan.g + 19 EU9QyonNIPIENSIEN » (dT1AH WelsAs) usjoj)sidz)11.ds-yonipi1apaiN - uej0jSIdZz.ds-ynewony « U9|O]SIdZ}11dS-pue}H - wwe.iboid-1071ld HAHLIVM Sed
advertisement
* Your assessment is very important for improving the workof artificial intelligence, which forms the content of this project
Related manuals
advertisement