advertisement
▼
Scroll to page 2
of
44
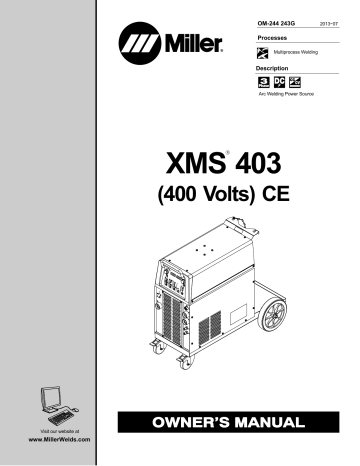
OM-244 243G Processes Multiprocess Welding Description Arc Welding Power Source R XMS 403 (400 Volts) CE Visit our website at www.MillerWelds.com 2013−07 From Miller to You Thank you and congratulations on choosing Miller. Now you can get the job done and get it done right. We know you don’t have time to do it any other way. That’s why when Niels Miller first started building arc welders in 1929, he made sure his products offered long-lasting value and superior quality. Like you, his customers couldn’t afford anything less. Miller products had to be more than the best they could be. They had to be the best you could buy. Today, the people that build and sell Miller products continue the tradition. They’re just as committed to providing equipment and service that meets the high standards of quality and value established in 1929. This Owner’s Manual is designed to help you get the most out of your Miller products. Please take time to read the Safety precautions. They will help you protect yourself against potential hazards on the worksite. We’ve made installation and operation quick and easy. With Miller you can count on years of reliable service with proper maintenance. And if for some reason the unit needs repair, there’s a Troubleshooting section that will help you figure out what the problem is. The parts list will then help you to decide which exact part you may need to fix the problem. Warranty and service information for your particular model are also provided. Miller Electric manufactures a full line of welders and welding related equipment. For information on other quality Miller products, contact your local Miller distributor to receive the latest full line catalog or individual catalog sheets. Working as hard as you do − every power source from Miller is backed by the most hassle-free warranty in the business. TABLE OF CONTENTS SECTION 1 − SAFETY PRECAUTIONS - READ BEFORE USING . . . . . . . . . . . . . . . . . . . . . . . . . . . . . . . . . . . 1-1. Symbol Usage . . . . . . . . . . . . . . . . . . . . . . . . . . . . . . . . . . . . . . . . . . . . . . . . . . . . . . . . . . . . . . . . . . . . . . . . 1-2. Arc Welding Hazards . . . . . . . . . . . . . . . . . . . . . . . . . . . . . . . . . . . . . . . . . . . . . . . . . . . . . . . . . . . . . . . . . . 1-3. Additional Symbols For Installation, Operation, And Maintenance . . . . . . . . . . . . . . . . . . . . . . . . . . . . . 1-4. California Proposition 65 Warnings . . . . . . . . . . . . . . . . . . . . . . . . . . . . . . . . . . . . . . . . . . . . . . . . . . . . . . . 1-5. Principal Safety Standards . . . . . . . . . . . . . . . . . . . . . . . . . . . . . . . . . . . . . . . . . . . . . . . . . . . . . . . . . . . . . 1-6. EMF Information . . . . . . . . . . . . . . . . . . . . . . . . . . . . . . . . . . . . . . . . . . . . . . . . . . . . . . . . . . . . . . . . . . . . . . SECTION 2 − DEFINITIONS . . . . . . . . . . . . . . . . . . . . . . . . . . . . . . . . . . . . . . . . . . . . . . . . . . . . . . . . . . . . . . . . . . . 2-1. Additional Safety Symbols And Definitions . . . . . . . . . . . . . . . . . . . . . . . . . . . . . . . . . . . . . . . . . . . . . . . . 2-2. Miscellaneous Symbols And Definitions . . . . . . . . . . . . . . . . . . . . . . . . . . . . . . . . . . . . . . . . . . . . . . . . . . . SECTION 3 − INSTALLATION . . . . . . . . . . . . . . . . . . . . . . . . . . . . . . . . . . . . . . . . . . . . . . . . . . . . . . . . . . . . . . . . . . 3-1. Important Information Regarding CE Products (Sold Within The EU) . . . . . . . . . . . . . . . . . . . . . . . . . . . 3-2. Information On Electromagnetic Compatibility (EMC) . . . . . . . . . . . . . . . . . . . . . . . . . . . . . . . . . . . . . . . . 3-3. Serial Number And Rating Label Location . . . . . . . . . . . . . . . . . . . . . . . . . . . . . . . . . . . . . . . . . . . . . . . . . 3-4. IP Rating . . . . . . . . . . . . . . . . . . . . . . . . . . . . . . . . . . . . . . . . . . . . . . . . . . . . . . . . . . . . . . . . . . . . . . . . . . . . 3-5. Specifications . . . . . . . . . . . . . . . . . . . . . . . . . . . . . . . . . . . . . . . . . . . . . . . . . . . . . . . . . . . . . . . . . . . . . . . . 3-6. Duty Cycle And Overheating . . . . . . . . . . . . . . . . . . . . . . . . . . . . . . . . . . . . . . . . . . . . . . . . . . . . . . . . . . . . 3-7. Volt-Ampere Curves . . . . . . . . . . . . . . . . . . . . . . . . . . . . . . . . . . . . . . . . . . . . . . . . . . . . . . . . . . . . . . . . . . . 3-8. Installing Turntable for Wire Feeder on Power Source (Optional) . . . . . . . . . . . . . . . . . . . . . . . . . . . . . . 3-9. Dimensions And Weight . . . . . . . . . . . . . . . . . . . . . . . . . . . . . . . . . . . . . . . . . . . . . . . . . . . . . . . . . . . . . . . . 3-10. Selecting a Location . . . . . . . . . . . . . . . . . . . . . . . . . . . . . . . . . . . . . . . . . . . . . . . . . . . . . . . . . . . . . . . . . . . 3-11. Locking Caster Operation . . . . . . . . . . . . . . . . . . . . . . . . . . . . . . . . . . . . . . . . . . . . . . . . . . . . . . . . . . . . . . 3-12. Weld Output Terminals And Selecting Cable Sizes* . . . . . . . . . . . . . . . . . . . . . . . . . . . . . . . . . . . . . . . . . 3-13. Remote 7 Receptacle Information (TIG And Stick Only) . . . . . . . . . . . . . . . . . . . . . . . . . . . . . . . . . . . . . 3-14. Circuit Breakers . . . . . . . . . . . . . . . . . . . . . . . . . . . . . . . . . . . . . . . . . . . . . . . . . . . . . . . . . . . . . . . . . . . . . . 3-15. Filling Coolant Tank . . . . . . . . . . . . . . . . . . . . . . . . . . . . . . . . . . . . . . . . . . . . . . . . . . . . . . . . . . . . . . . . . . . 3-16. Electrical Service Guide . . . . . . . . . . . . . . . . . . . . . . . . . . . . . . . . . . . . . . . . . . . . . . . . . . . . . . . . . . . . . . . . 3-17. Connecting Input Power . . . . . . . . . . . . . . . . . . . . . . . . . . . . . . . . . . . . . . . . . . . . . . . . . . . . . . . . . . . . . . . . SECTION 4 − OPERATION . . . . . . . . . . . . . . . . . . . . . . . . . . . . . . . . . . . . . . . . . . . . . . . . . . . . . . . . . . . . . . . . . . . . 4-1. Front Panel Controls . . . . . . . . . . . . . . . . . . . . . . . . . . . . . . . . . . . . . . . . . . . . . . . . . . . . . . . . . . . . . . . . . . . 4-2. Switching On the Unit and Recalling Factory Parameters . . . . . . . . . . . . . . . . . . . . . . . . . . . . . . . . . . . . 4-3. Welding Power Source Setup Menu . . . . . . . . . . . . . . . . . . . . . . . . . . . . . . . . . . . . . . . . . . . . . . . . . . . . . . 4-4. Remote Receptacle (RCTY) . . . . . . . . . . . . . . . . . . . . . . . . . . . . . . . . . . . . . . . . . . . . . . . . . . . . . . . . . . . . 4-5. Welding Process Selection . . . . . . . . . . . . . . . . . . . . . . . . . . . . . . . . . . . . . . . . . . . . . . . . . . . . . . . . . . . . . 4-6. Wire Type Selection in Synergic MIG or Synergic Pulsed MIG Welding . . . . . . . . . . . . . . . . . . . . . . . . . 4-7. Wire Diameter Selection In Synergic MIG Or Synergic Pulsed MIG Welding . . . . . . . . . . . . . . . . . . . . 4-8. Gas Selection in Synergic MIG or Synergic Pulsed MIG Welding . . . . . . . . . . . . . . . . . . . . . . . . . . . . . . 4-9. Trigger Mode Selection (L-TIG and Stick Processes) . . . . . . . . . . . . . . . . . . . . . . . . . . . . . . . . . . . . . . . . 4-10. Welding Parameter Setup Menu (Double Pulsed-MIG/L-TIG And Stick) . . . . . . . . . . . . . . . . . . . . . . . . 4-11. Preparing Power Source For MIG (GMAW) Welding Process . . . . . . . . . . . . . . . . . . . . . . . . . . . . . . . . . 4-12. Selecting Manual MIG Welding . . . . . . . . . . . . . . . . . . . . . . . . . . . . . . . . . . . . . . . . . . . . . . . . . . . . . . . . . . 4-13. Selecting Synergic MIG Welding . . . . . . . . . . . . . . . . . . . . . . . . . . . . . . . . . . . . . . . . . . . . . . . . . . . . . . . . . 4-14. Selecting Synergic Pulsed MIG Welding . . . . . . . . . . . . . . . . . . . . . . . . . . . . . . . . . . . . . . . . . . . . . . . . . . 4-15. Preparing Unit For TIG Welding . . . . . . . . . . . . . . . . . . . . . . . . . . . . . . . . . . . . . . . . . . . . . . . . . . . . . . . . . 4-16. TIG Lift-Arc Welding . . . . . . . . . . . . . . . . . . . . . . . . . . . . . . . . . . . . . . . . . . . . . . . . . . . . . . . . . . . . . . . . . . . 4-17. Preparing Unit For Stick Welding . . . . . . . . . . . . . . . . . . . . . . . . . . . . . . . . . . . . . . . . . . . . . . . . . . . . . . . . SECTION 5 − MAINTENANCE & TROUBLESHOOTING . . . . . . . . . . . . . . . . . . . . . . . . . . . . . . . . . . . . . . . . . . . 5-1. Routine Maintenance . . . . . . . . . . . . . . . . . . . . . . . . . . . . . . . . . . . . . . . . . . . . . . . . . . . . . . . . . . . . . . . . . . 5-2. Help Displays . . . . . . . . . . . . . . . . . . . . . . . . . . . . . . . . . . . . . . . . . . . . . . . . . . . . . . . . . . . . . . . . . . . . . . . . 5-3. Troubleshooting . . . . . . . . . . . . . . . . . . . . . . . . . . . . . . . . . . . . . . . . . . . . . . . . . . . . . . . . . . . . . . . . . . . . . . SECTION 6 − ELECTRICAL DIAGRAM . . . . . . . . . . . . . . . . . . . . . . . . . . . . . . . . . . . . . . . . . . . . . . . . . . . . . . . . . . SECTION 7 − PARTS LIST . . . . . . . . . . . . . . . . . . . . . . . . . . . . . . . . . . . . . . . . . . . . . . . . . . . . . . . . . . . . . . . . . . . . . WARRANTY 1 1 1 3 4 4 4 5 5 7 9 9 9 9 9 9 10 10 11 11 12 12 13 14 14 15 15 16 18 18 19 20 21 21 22 22 23 23 24 24 25 26 27 28 29 29 30 30 31 31 32 34 DECLARATION OF CONFORMITY for European Community (CE marked) products. ITW Welding Products Italy S.r.l Via Privata Iseo 6/E, 20098 San Giuliano M.se, (MI) Italy declares that the product(s) identified in this declaration conform to the essential requirements and provisions of the stated Council Directive(s) and Standard(s). Product/Apparatus Identification: Product Stock Number XMS 403 029015483 Council Directives: • 2006/95/EC Low Voltage • 2004/108/EC Electromagnetic Compatibility • 2011/65/EU Restriction of the use of certain hazardous substances in electrical and electronic equipment Standards: • IEC 60974­1 Arc Welding Equipment ­ Welding Power Sources: edition 3, 2005­07. • IEC 60974­2 Arc Welding Equipment – Liquid Cooling Systems: edition 2.0, 2007­11. • IEC 60974­10 Arc Welding Equipment ­ Electromagnetic Compatibility Requirements: edition 2.0, 2007­08. • EN 50445:2008 Product family standard to demonstrate compliance of equipment for resistance welding, arc welding and allied processes with the basic restrictions related to human exposure to electromagnetic fields (0Hz­300Hz) EU Signatory: January 2nd , 2013 ___________________________________________________________________________________ Massimigliano Lavarini Date of Declaration ELECTRONIC ENGINEER R&D TECH. SUPPORT 956 172 024 SECTION 1 − SAFETY PRECAUTIONS - READ BEFORE USING som 2011−10 7 Protect yourself and others from injury — read, follow, and save these important safety precautions and operating instructions. 1-1. Symbol Usage DANGER! − Indicates a hazardous situation which, if not avoided, will result in death or serious injury. The possible hazards are shown in the adjoining symbols or explained in the text. Indicates a hazardous situation which, if not avoided, could result in death or serious injury. The possible hazards are shown in the adjoining symbols or explained in the text. NOTICE − Indicates statements not related to personal injury. . Indicates special instructions. This group of symbols means Warning! Watch Out! ELECTRIC SHOCK, MOVING PARTS, and HOT PARTS hazards. Consult symbols and related instructions below for necessary actions to avoid the hazards. 1-2. Arc Welding Hazards The symbols shown below are used throughout this manual to call attention to and identify possible hazards. When you see the symbol, watch out, and follow the related instructions to avoid the hazard. The safety information given below is only a summary of the more complete safety information found in the Safety Standards listed in Section 1-5. Read and follow all Safety Standards. Only qualified persons should install, operate, maintain, and repair this unit. During operation, keep everybody, especially children, away. D Always verify the supply ground − check and be sure that input power cord ground wire is properly connected to ground terminal in disconnect box or that cord plug is connected to a properly grounded receptacle outlet. D When making input connections, attach proper grounding conductor first − double-check connections. D Keep cords dry, free of oil and grease, and protected from hot metal and sparks. D Frequently inspect input power cord for damage or bare wiring − replace cord immediately if damaged − bare wiring can kill. D Turn off all equipment when not in use. D Do not use worn, damaged, undersized, or poorly spliced cables. ELECTRIC SHOCK can kill. Touching live electrical parts can cause fatal shocks or severe burns. The electrode and work circuit is electrically live whenever the output is on. The input power circuit and machine internal circuits are also live when power is on. In semiautomatic or automatic wire welding, the wire, wire reel, drive roll housing, and all metal parts touching the welding wire are electrically live. Incorrectly installed or improperly grounded equipment is a hazard. D Do not touch live electrical parts. D Wear dry, hole-free insulating gloves and body protection. D Insulate yourself from work and ground using dry insulating mats or covers big enough to prevent any physical contact with the work or ground. D Do not use AC output in damp areas, if movement is confined, or if there is a danger of falling. D Use AC output ONLY if required for the welding process. D If AC output is required, use remote output control if present on unit. D Additional safety precautions are required when any of the following electrically hazardous conditions are present: in damp locations or while wearing wet clothing; on metal structures such as floors, gratings, or scaffolds; when in cramped positions such as sitting, kneeling, or lying; or when there is a high risk of unavoidable or accidental contact with the workpiece or ground. For these conditions, use the following equipment in order presented: 1) a semiautomatic DC constant voltage (wire) welder, 2) a DC manual (stick) welder, or 3) an AC welder with reduced open-circuit voltage. In most situations, use of a DC, constant voltage wire welder is recommended. And, do not work alone! D Disconnect input power or stop engine before installing or servicing this equipment. Lockout/tagout input power according to OSHA 29 CFR 1910.147 (see Safety Standards). D Properly install, ground, and operate this equipment according to its Owner’s Manual and national, state, and local codes. D Do not drape cables over your body. D If earth grounding of the workpiece is required, ground it directly with a separate cable. D Do not touch electrode if you are in contact with the work, ground, or another electrode from a different machine. D Do not touch electrode holders connected to two welding machines at the same time since double open-circuit voltage will be present. D Use only well-maintained equipment. Repair or replace damaged parts at once. Maintain unit according to manual. D Wear a safety harness if working above floor level. D Keep all panels and covers securely in place. D Clamp work cable with good metal-to-metal contact to workpiece or worktable as near the weld as practical. D Insulate work clamp when not connected to workpiece to prevent contact with any metal object. D Do not connect more than one electrode or work cable to any single weld output terminal. Disconnect cable for process not in use. SIGNIFICANT DC VOLTAGE exists in inverter welding power sources AFTER removal of input power. D Turn Off inverter, disconnect input power, and discharge input capacitors according to instructions in Maintenance Section before touching any parts. HOT PARTS can burn. D Do not touch hot parts bare handed. D Allow cooling period before working on equipment. D To handle hot parts, use proper tools and/or wear heavy, insulated welding gloves and clothing to prevent burns. OM-244 243 Page 1 FUMES AND GASES can be hazardous. Welding produces fumes and gases. Breathing these fumes and gases can be hazardous to your health. D Keep your head out of the fumes. Do not breathe the fumes. D If inside, ventilate the area and/or use local forced ventilation at the arc to remove welding fumes and gases. D If ventilation is poor, wear an approved air-supplied respirator. D Read and understand the Material Safety Data Sheets (MSDSs) and the manufacturer’s instructions for metals, consumables, coatings, cleaners, and degreasers. D Work in a confined space only if it is well ventilated, or while wearing an air-supplied respirator. Always have a trained watchperson nearby. Welding fumes and gases can displace air and lower the oxygen level causing injury or death. Be sure the breathing air is safe. D Do not weld in locations near degreasing, cleaning, or spraying operations. The heat and rays of the arc can react with vapors to form highly toxic and irritating gases. D Do not weld on coated metals, such as galvanized, lead, or cadmium plated steel, unless the coating is removed from the weld area, the area is well ventilated, and while wearing an air-supplied respirator. The coatings and any metals containing these elements can give off toxic fumes if welded. ARC RAYS can burn eyes and skin. Arc rays from the welding process produce intense visible and invisible (ultraviolet and infrared) rays that can burn eyes and skin. Sparks fly off from the weld. D Wear an approved welding helmet fitted with a proper shade of filter lenses to protect your face and eyes from arc rays and sparks when welding or watching (see ANSI Z49.1 and Z87.1 listed in Safety Standards). D Wear approved safety glasses with side shields under your helmet. D Use protective screens or barriers to protect others from flash, glare and sparks; warn others not to watch the arc. D Wear protective clothing made from durable, flame-resistant material (leather, heavy cotton, or wool) and foot protection. WELDING can cause fire or explosion. Welding on closed containers, such as tanks, drums, or pipes, can cause them to blow up. Sparks can fly off from the welding arc. The flying sparks, hot workpiece, and hot equipment can cause fires and burns. Accidental contact of electrode to metal objects can cause sparks, explosion, overheating, or fire. Check and be sure the area is safe before doing any welding. D Remove all flammables within 35 ft (10.7 m) of the welding arc. If this is not possible, tightly cover them with approved covers. D Do not weld where flying sparks can strike flammable material. D Protect yourself and others from flying sparks and hot metal. D Be alert that welding sparks and hot materials from welding can easily go through small cracks and openings to adjacent areas. D Watch for fire, and keep a fire extinguisher nearby. D Be aware that welding on a ceiling, floor, bulkhead, or partition can cause fire on the hidden side. D Do not weld on containers that have held combustibles, or on closed containers such as tanks, drums, or pipes unless they are properly prepared according to AWS F4.1 and AWS A6.0 (see Safety Standards). D Do not weld where the atmosphere may contain flammable dust, gas, or liquid vapors (such as gasoline). D Connect work cable to the work as close to the welding area as practical to prevent welding current from traveling long, possibly unknown paths and causing electric shock, sparks, and fire hazards. D Do not use welder to thaw frozen pipes. OM-244 243 Page 2 D Remove stick electrode from holder or cut off welding wire at contact tip when not in use. D Wear oil-free protective garments such as leather gloves, heavy shirt, cuffless trousers, high shoes, and a cap. D Remove any combustibles, such as a butane lighter or matches, from your person before doing any welding. D After completion of work, inspect area to ensure it is free of sparks, glowing embers, and flames. D Use only correct fuses or circuit breakers. Do not oversize or bypass them. D Follow requirements in OSHA 1910.252 (a) (2) (iv) and NFPA 51B for hot work and have a fire watcher and extinguisher nearby. FLYING METAL or DIRT can injure eyes. D Welding, chipping, wire brushing, and grinding cause sparks and flying metal. As welds cool, they can throw off slag. D Wear approved safety glasses with side shields even under your welding helmet. BUILDUP OF GAS can injure or kill. D Shut off compressed gas supply when not in use. D Always ventilate confined spaces or use approved air-supplied respirator. ELECTRIC AND MAGNETIC FIELDS (EMF) can affect Implanted Medical Devices. D Wearers of Pacemakers and other Implanted Medical Devices should keep away. D Implanted Medical Device wearers should consult their doctor and the device manufacturer before going near arc welding, spot welding, gouging, plasma arc cutting, or induction heating operations. NOISE can damage hearing. Noise from some processes or equipment can damage hearing. D Wear approved ear protection if noise level is high. CYLINDERS can explode if damaged. Compressed gas cylinders contain gas under high pressure. If damaged, a cylinder can explode. Since gas cylinders are normally part of the welding process, be sure to treat them carefully. D Protect compressed gas cylinders from excessive heat, mechanical shocks, physical damage, slag, open flames, sparks, and arcs. D Install cylinders in an upright position by securing to a stationary support or cylinder rack to prevent falling or tipping. D Keep cylinders away from any welding or other electrical circuits. D Never drape a welding torch over a gas cylinder. D Never allow a welding electrode to touch any cylinder. D Never weld on a pressurized cylinder − explosion will result. D Use only correct compressed gas cylinders, regulators, hoses, and fittings designed for the specific application; maintain them and associated parts in good condition. D Turn face away from valve outlet when opening cylinder valve. D Keep protective cap in place over valve except when cylinder is in use or connected for use. D Use the right equipment, correct procedures, and sufficient number of persons to lift and move cylinders. D Read and follow instructions on compressed gas cylinders, associated equipment, and Compressed Gas Association (CGA) publication P-1 listed in Safety Standards. 1-3. Additional Symbols For Installation, Operation, And Maintenance FIRE OR EXPLOSION hazard. BATTERY EXPLOSION can injure. D Do not install or place unit on, over, or near combustible surfaces. D Do not install unit near flammables. D Do not overload building wiring − be sure power supply system is properly sized, rated, and protected to handle this unit. D Do not use welder to charge batteries or jump start vehicles unless it has a battery charging feature designed for this purpose. MOVING PARTS can injure. D Keep away from moving parts such as fans. D Keep all doors, panels, covers, and guards closed and securely in place. FALLING EQUIPMENT can injure. D Use lifting eye to lift unit only, NOT running gear, gas cylinders, or any other accessories. D Use equipment of adequate capacity to lift and support unit. D If using lift forks to move unit, be sure forks are long enough to extend beyond opposite side of unit. D Keep equipment (cables and cords) away from moving vehicles when working from an aerial location. D Follow the guidelines in the Applications Manual for the Revised NIOSH Lifting Equation (Publication No. 94−110) when manually lifting heavy parts or equipment. OVERUSE can cause OVERHEATING D Allow cooling period; follow rated duty cycle. D Reduce current or reduce duty cycle before starting to weld again. D Do not block or filter airflow to unit. D Have only qualified persons remove doors, panels, covers, or guards for maintenance and troubleshooting as necessary. D Reinstall doors, panels, covers, or guards when maintenance is finished and before reconnecting input power. READ INSTRUCTIONS. D Read and follow all labels and the Owner’s Manual carefully before installing, operating, or servicing unit. Read the safety information at the beginning of the manual and in each section. D Use only genuine replacement parts from the manufacturer. D Perform maintenance and service according to the Owner’s Manuals, industry standards, and national, state, and local codes. H.F. RADIATION can cause interference. FLYING SPARKS can injure. D Wear a face shield to protect eyes and face. D Shape tungsten electrode only on grinder with proper guards in a safe location wearing proper face, hand, and body protection. D Sparks can cause fires — keep flammables away. STATIC (ESD) can damage PC boards. D D D D D Put on grounded wrist strap BEFORE handling boards or parts. D Use proper static-proof bags and boxes to store, move, or ship PC boards. ARC WELDING can cause interference. MOVING PARTS can injure. D Keep away from moving parts. D Keep away from pinch points such as drive rolls. D WELDING WIRE can injure. D Do not press gun trigger until instructed to do so. D Do not point gun toward any part of the body, other people, or any metal when threading welding wire. D High-frequency (H.F.) can interfere with radio navigation, safety services, computers, and communications equipment. D Have only qualified persons familiar with electronic equipment perform this installation. The user is responsible for having a qualified electrician promptly correct any interference problem resulting from the installation. If notified by the FCC about interference, stop using the equipment at once. Have the installation regularly checked and maintained. Keep high-frequency source doors and panels tightly shut, keep spark gaps at correct setting, and use grounding and shielding to minimize the possibility of interference. D D D D Electromagnetic energy can interfere with sensitive electronic equipment such as computers and computer-driven equipment such as robots. D Be sure all equipment in the welding area is electromagnetically compatible. To reduce possible interference, keep weld cables as short as possible, close together, and down low, such as on the floor. Locate welding operation 100 meters from any sensitive electronic equipment. Be sure this welding machine is installed and grounded according to this manual. If interference still occurs, the user must take extra measures such as moving the welding machine, using shielded cables, using line filters, or shielding the work area. OM-244 243 Page 3 1-4. California Proposition 65 Warnings Welding or cutting equipment produces fumes or gases which contain chemicals known to the State of California to cause birth defects and, in some cases, cancer. (California Health & Safety Code Section 25249.5 et seq.) This product contains chemicals, including lead, known to the state of California to cause cancer, birth defects, or other reproductive harm. Wash hands after use. 1-5. Principal Safety Standards Safety in Welding, Cutting, and Allied Processes, ANSI Standard Z49.1, is available as a free download from the American Welding Society at http://www.aws.org or purchased from Global Engineering Documents (phone: 1-877-413-5184, website: www.global.ihs.com). Safe Practices for the Preparation of Containers and Piping for Welding and Cutting, American Welding Society Standard AWS F4.1, from Global Engineering Documents (phone: 1-877-413-5184, website: www.global.ihs.com). Safe Practices for Welding and Cutting Containers that have Held Combustibles, American Welding Society Standard AWS A6.0, from Global Engineering Documents (phone: 1-877-413-5184, website: www.global.ihs.com). National Electrical Code, NFPA Standard 70, from National Fire Protection Association, Quincy, MA 02269 (phone: 1-800-344-3555, website: www.nfpa.org and www. sparky.org). Safe Handling of Compressed Gases in Cylinders, CGA Pamphlet P-1, from Compressed Gas Association, 14501 George Carter Way, Suite 103, Chantilly, VA 20151 (phone: 703-788-2700, website:www.cganet.com). Safety in Welding, Cutting, and Allied Processes, CSA Standard W117.2, from Canadian Standards Association, Standards Sales, 5060 Spectrum Way, Suite 100, Ontario, Canada L4W 5NS (phone: 800-463-6727, website: www.csa-international.org). Safe Practice For Occupational And Educational Eye And Face Protection, ANSI Standard Z87.1, from American National Standards Institute, 25 West 43rd Street, New York, NY 10036 (phone: 212-642-4900, website: www.ansi.org). Standard for Fire Prevention During Welding, Cutting, and Other Hot Work, NFPA Standard 51B, from National Fire Protection Association, Quincy, MA 02269 (phone: 1-800-344-3555, website: www.nfpa.org. OSHA, Occupational Safety and Health Standards for General Industry, Title 29, Code of Federal Regulations (CFR), Part 1910, Subpart Q, and Part 1926, Subpart J, from U.S. Government Printing Office, Superintendent of Documents, P.O. Box 371954, Pittsburgh, PA 15250-7954 (phone: 1-866-512-1800) (there are 10 OSHA Regional Offices— phone for Region 5, Chicago, is 312-353-2220, website: www.osha.gov). Applications Manual for the Revised NIOSH Lifting Equation, The National Institute for Occupational Safety and Health (NIOSH), 1600 Clifton Rd, Atlanta, GA 30333 (phone: 1-800-232-4636, website: www.cdc.gov/NIOSH). 1-6. EMF Information Electric current flowing through any conductor causes localized electric and magnetic fields (EMF). Welding current creates an EMF field around the welding circuit and welding equipment. EMF fields may interfere with some medical implants, e.g. pacemakers. Protective measures for persons wearing medical implants have to be taken. For example, restrict access for passers−by or conduct individual risk assessment for welders. All welders should use the following procedures in order to minimize exposure to EMF fields from the welding circuit: 1. Keep cables close together by twisting or taping them, or using a cable cover. 2. Do not place your body between welding cables. Arrange cables to one side and away from the operator. 3. Do not coil or drape cables around your body. OM-244 243 Page 4 4. Keep head and trunk as far away from the equipment in the welding circuit as possible. 5. Connect work clamp to workpiece as close to the weld as possible. 6. Do not work next to, sit or lean on the welding power source. 7. Do not weld whilst carrying the welding power source or wire feeder. About Implanted Medical Devices: Implanted Medical Device wearers should consult their doctor and the device manufacturer before performing or going near arc welding, spot welding, gouging, plasma arc cutting, or induction heating operations. If cleared by your doctor, then following the above procedures is recommended. SECTION 2 − DEFINITIONS 2-1. Additional Safety Symbols And Definitions . Some symbols are found only on CE products. Warning! Watch Out! There are possible hazards as shown by the symbols. Safe1 2012−05 Do not discard product (where applicable) with general waste. Reuse or recycle Waste Electrical and Electronic Equipment (WEEE) by disposing at a designated collection facility. Contact your local recycling office or your local distributor for further information. Safe37 2012−05 Wear dry insulating gloves. Do not touch electrode (wire) with bare hand. Do not wear wet or damaged gloves. Safe57 2012−05 Protect yourself from electric shock by insulating yourself from work and ground. Safe3 2012−05 Disconnect input plug or power before working on machine. Safe5 2012−05 Keep your head out of the fumes. Safe59 2012−05 Use forced ventilation or local exhaust to remove the fumes. Safe60 2012−06 Use ventilating fan to remove fumes. Safe61 2012−06 Keep flammables away from welding. Do not weld near flammables. Safe62 2012−06 Welding sparks can cause fires. Have a fire extinguisher nearby, and have a watchperson ready to use it. Safe63 2012−06 OM-244 243 Page 5 Do not weld on drums or any closed containers. ? Safe64 2012−06 Do not remove or paint over (cover) the label. Safe20 2012−05 Disconnect input plug or power before working on machine. Safe30 2012−05 When power is applied failed parts can explode or cause other parts to explode. Safe26 2012−05 Flying pieces of parts can cause injury. Always wear a face shield when servicing unit. Safe27 2012−05 Always wear long sleeves and button your collar when servicing unit. Safe28 2012−05 After taking proper precautions as shown, connect power to unit. Safe29 2012−05 ? ? V A Consult rating label for input power requirements. Safe34 2012−05 ÍÍ Read Owner’s Manual and inside labels for connection points and procedures. Safe67 2012−06 Use coolant suggested by the manufacturer. XXXXX Safe52 2012−05 OM-244 243 Page 6 <10° Falling unit can cause injury. Do not move or operate unit where it could tip. Safe53 2012−05 Become trained and read the instructions before working on the machine or welding. Safe65 2012−06 Wear hat and safety glasses. Use ear protection and button shirt collar. Use welding helmet with correct shade of filter. Wear complete body protection. Safe66 2012−06 V V >5min 3 Hazardous voltage remains on input capacitors after power is turned off. Do not touch fully charged capacitors. Always wait 5 minutes after power is turned off before working on unit, OR check input capacitor voltage, and be sure it is near 0 before touching any parts. V Safe43 2012−05 Move jumper links as shown on inside label to match input voltage at job site. Include extra length in grounding conductor and connect grounding conductor first. Connect line input conductors as shown on inside label. Double-check all connections, jumper link positions, and input voltage before applying power. 1 Safe49 2012−05 Plugged filter or hoses can cause overheating to the power source and torch. Safe50 2012−05 100 h. Std. Every 100 hours, check and clean filter and check condition of hoses. Safe51 2012−05 2-2. Miscellaneous Symbols And Definitions A U1 V Hz Voltage Alternating Current (AC) Remote On Off Protective Earth (Ground) Line connection Three Phase Direct Current (DC) Increase Constant Voltage Constant Current Lift-Arc Operation (GTAW) Gas Tungsten Arc Welding Three Phase Static Frequency ConverterTransformerRectifier Gas Metal Arc Welding (GMAW) Shielded Metal Arc Welding (SMAW) Recycle or dispose of used coolant in an environmentally safe way Maximum Effective Supply Current Wire Feed Speed Amperage Primary Voltage I1max Rated Maximum Supply Current I1eff Hertz OM-244 243 Page 7 U2 U0 Conventional Load Voltage Rated No Load Voltage (Average) I2 IP Rated Welding Current X Duty Cycle % Percent Degree Of Protection Purge Wire ’Jog’ Set-Up MIG Synergic MIG Pulsed Synergic Welding MIG Double Pulsed Synergic Welding Circuit Breaker 2T Trigger Mode Memory Store 4T Trigger Mode Material Thickness Mini-Logic Trigger Mode Arc Length (Trim) Read Instructions OM-244 243 Page 8 SECTION 3 − INSTALLATION 3-1. Important Information Regarding CE Products (Sold Within The EU) ! This equipment shall not be used by the general public as the EMF limits for the general public might be exceeded during welding. This equipment is built in accordance with EN 60974−1 and is intended to be used only in an occupational environment (where the general public access is prohibited or regulated in such a way as to be similar to occupational use) by an expert or an instructed person. Wire feeders and ancillary equipment (such as torches, liquid cooling systems and arc striking and stabilizing devices) as part of the welding circuit may not be a major contributor to the EMF. See the Owner’s Manuals for all components of the welding circuit for additional EMF exposure information. S S The EMF assessment on this equipment was conducted at 0.5 meter. At a distance of 1 meter the EMF exposure values were less than 20% of the permissible values. ce-emf 1 2010-10 3-2. Information On Electromagnetic Compatibility (EMC) ! This Class A equipment is not intended for use in residential locations where the electrical power is provided by the public low voltage supply system. There can be potential difficulties in ensuring electromagnetic compatibility in those locations, due to conducted as well as radiated disturbances. ! This equipment does not comply with IEC 61000−3−12. If it is connected to a public low voltage system, it is the responsibility of the installer or user of the equipment to ensure, by consultation with the distribution network operator if necessary, that the equipment can be connected. ce-emc 2 2011-09 3-3. Serial Number And Rating Label Location The serial number and rating information for this product is located on the back panel. Use rating label to determine input power requirements and/or rated output. For future reference, write serial number in space provided on back cover of this manual. 3-4. IP Rating IP Rating Operating Temperature Range IP23S −10 to 40 °C (14 to 104 °F) This equipment is designed for outdoor use. It may be stored, but is not intended to be used outside during precipitation unless sheltered. 3-5. Specifications Rated Welding Output 300 A @ 32 Volts DC, 60% Duty Cycle Voltage Range 10 − 35 V Amperage Range 5 − 400 A Maximum Open-Circuit Voltage DC 90 Amperes Input at Rated Load Output 50/60 Hz 400 V KVA KW 17.0 (0,15*) 12.4 (0,09*) 11.5 (0,04*) *While idling OM-244 243 Page 9 3-6. Duty Cycle And Overheating Duty Cycle is percentage of 10 minutes that unit can weld at rated load without overheating. If unit overheats, output stops, a Help message is displayed, and cooling fan runs. Wait fifteen minutes for unit to cool. Reduce amperage or duty cycle before welding. NOTICE − Exceeding duty cycle can damage unit and void warranty. 60% Duty Cycle 6 Minutes Welding 4 Minutes Resting Overheating A 0 15 Minutes OR Reduce Duty Cycle Ref. SA-178 651 3-7. Volt-Ampere Curves Volt-ampere curves show minimum and maximum voltage and amperage output capabilities of unit. Curves of other settings fall between curves shown. A. CC Mode B. CV Mode ARC CONTROL va_curve1 4/95 − SA-178 652 / SA-178 653 OM-244 243 Page 10 3-8. Installing Turntable for Wire Feeder on Power Source (Optional) ! Turn off welding power source and disconnect input power before proceeding. Remove wire spool. 1 2 1 Turntable Screw Remove the 4 screws and the plastic cap on the power source upper cover and keep them for future use. 2 Insert the turntable in the upper hole and secure with 4 screws. Be sure screws are tight. If desired, install the wire feeder on the turntable using the hole in the bottom of the feeder. Ref. 956142645-5-A 3-9. Dimensions And Weight Dimensions 1010 mm (39.7 in.) Weight 90 kg (198 lb) 860 mm (33.8 in.) 490 mm (19.3 in.) Ref. 956142645-3-B OM-244 243 Page 11 3-10. Selecting a Location Location ! Special installation may be required where gasoline or volatile liquids are present − see NEC Article 511 or CEC Section 20. 1 Handle Do not use handle to lift unit. 2 Line Disconnect Device Locate unit near correct input power supply. 2 500 mm (19.7 in.) 500 mm (19.7 in.) 1 Movement ! Do not move or operate unit where it could tip. 500 mm (19.7 in.) 500 mm (19.7 in.) Ref. 956142645-3-B 3-11. Locking Caster Operation 1 2 3 Caster With Brake Off Brake Caster With Brake On To lock caster, push brake down. To release (unlock) caster, push brake up and back. Lock casters to prevent unwanted movement of power source. 3 1 2 Ref. 956142645_6-A OM-244 243 Page 12 3-12. Weld Output Terminals And Selecting Cable Sizes* NOTICE − The Total Cable Length in Weld Circuit (see table below) is the combined length of both weld cables. For example, if the power source is 100 ft (30 m) from the workpiece, the total cable length in the weld circuit is 200 ft (2 cables x 100 ft). Use the 200 ft (60 m) column to determine cable size. Weld Cable Size** and Total Cable (Copper) Length in Weld Circuit Not Exceeding*** Weld Output Terminals ! Turn off power before connecting to weld output terminals. ! Do not use worn, damaged, undersized, or poorly spliced cables. 30 m (100 ft) or Less Positive receptacle MIG * This 70 m (250 ft) 90 m (300 ft) 105 m (350 ft) 120 m (400 ft) 60 − 100% Duty Cycle mm2 (AWG) mm2 (AWG) 100 20 (4) 20 (4) 20 (4) 30 (3) 35 (2) 50 (1) 60 (1/0) 60 (1/0) 150 30 (3) 30 (3) 35 (2) 50 (1) 60 (1/0) 70 (2/0) 95 (3/0) 95 (3/0) 200 30 (3) 35 (2) 50 (1) 60 (1/0) 70 (2/0) 95 (3/0) 120 (4/0) 120 (4/0) 250 35 (2) 50 (1) 60 (1/0) 70 (2/0) 95 (3/0) 120 (4/0) 2x70 (2x2/0) 2x70 (2x2/0) 300 50 (1) 60 (1/0) 70 (2/0) 95 (3/0) 120 (4/0) 2x70 (2x2/0) 2x95 (2x3/0) 2x95 (2x3/0) 350 60 (1/0) 70 (2/0) 95 (3/0) 120 (4/0) 2x70 (2x2/0) 2x95 (2x3/0) 2x95 (2x3/0) 2x120 (2x4/0) 400 60 (1/0) 70 (2/0) 95 (3/0) 120 (4/0) 2x70 (2x2/0) 2x95 (2x3/0) 2x120 (2x4/0) 2x120 (2x4/0) 500 70 (2/0) 95 (3/0) 120 (4/0) 2x70 (2x2/0) 2x95 (2x3/0) 2x120 (2x4/0) 3x95 (3x3/0) 3x95 (3x3/0) 600 95 (3/0) 120 (4/0) 2x70 (2x2/0) 2x95 (2x3/0) 2x120 (2x4/0) 3x95 (3x3/0) 3x120 (3x4/0) 3x120 (3x4/0) 10 − 100% Duty Cycle mm2 (AWG) Gas Negative receptacle MIG/TIG/Stick 60 m (200 ft) 10 − 60% Duty Cycle Welding Amperes Positive receptacle TIG/Stick 45 m (150 ft) chart is a general guideline and may not suit all applications. If cable overheats, use next size larger cable. **Weld cable size is based on either a 4 volts or less drop or a current density of at least 300 circular mils per ampere. ***For distances longer than those shown in this guide, call a factory applications representative. Milan Ref. S-0007-J 2011−07 OM-244 243 Page 13 3-13. Remote 7 Receptacle Information (TIG And Stick Only) Socket 7-Pin Remote Receptacle Socket Information 1 +10 volts DC supply voltage to remote 2 GND Remote control circuit common 3 IREF 0 to 10 current control signal 4 Not used. 5 UP 0V/10V digital signal 6 Not used. 7 TYPE 0V/10V digital signal . This remote receptacle cannot be used with a standard Miller remote control. A customer supplied remote control is required to use the remote receptacle. Some signals can be enabled when TIG or Stick welding. Contact Factory Authorized Service Agent for confirmation. 3-14. Circuit Breakers Circuit breakers with numbers 7 and 10 are placed on the rear panel of the welder as shown. 1 1 2 Circuit Breaker 7 Protects the auxiliary 115 volt AC output from overload. The 115 volt AC output powers the water cooling unit inside the power source. 2 Circuit Breaker 10 Protects the auxiliary 24 volt AC output from overload. The 24 volt AC output powers the wire feeder inside the power source. Ref. 956142645-4-A OM-244 243 Page 14 3-15. Filling Coolant Tank . Operating cooler when coolant is low can damage cooler and torch components. Always have proper amount of coolant in tank and use coolant recommended by the manufacturer. 1 2 Coolant Tank Cap Coolant Level Indicator . Remove shielding gas cylinder 1 from rear of unit to fill coolant tank. 2 Unscrew cap from tank. Use table to select proper coolant, and fill tank until coolant appears in upper half of indicator. Check coolant level after attaching torch coolant hoses and running cooler. Be sure coolant appears in upper half of indicator. Add coolant if necessary. Rear View GTAW Or Where HF* Is Used GMAW Or Where HF* Is Not Used Where Coolant Contacts Aluminum Parts MILLER Low Conductivity Coolant No. 043 810**; Distilled Or Deionized Water OK Above 32° F (0° C) MILLER Low Conductivity Coolant No. 043 810**; Or MILLER Aluminum Protecting Coolant No. 043 809**; Distilled Or Deionized Water OK Above 32° F (0° C) MILLER Aluminum Protecting Coolant No. 043 809** Application Coolant *HF: High Frequency Current **MILLER coolants protect to -37° F (-38°C) and resist algae growth. NOTICE − Use of any coolant other than those listed in the table voids the warranty on any parts that come in contact with the coolant (pump, radiator, etc.). Ref. 956142645-4-A 3-16. Electrical Service Guide . Actual input voltage should not exceed ± 10% of indicated required input voltage. If actual input voltage is outside of this range, output may not be available. Failure to follow these electrical service guide recommendations could create an electric shock or fire hazard. These recommendations are for a dedicated circuit sized for the rated output and duty cycle of the welding power source. In dedicated circuit installations, the National Electrical Code (NEC) allows the receptacle or conductor rating to be less than the rating of the circuit protection device. All components of the circuit must be physically compatible. See NEC articles 210.21, 630.11, and 630.12. 50/60 Hz Three Phase Input Voltage (V) 400 Input Amperes (A) At Rated Output 17 Max Recommended Standard Fuse Rating In Amperes 1 Time-Delay Fuses 2 Normal Operating Fuses 3 20 25 Min Input Conductor Size In mm2, 4 2.5 Max Recommended Input Conductor Length In Meters 41 mm2, 4 Min Grounding Conductor Size In 2.5 Reference: 2011 National Electrical Code (NEC) (including article 630) 1 If a circuit breaker is used in place of a fuse, choose a circuit breaker with time-current curves comparable to the recommended fuse. 2 “Time-Delay” fuses are UL class “RK5” . See UL 248. 3 “Normal Operating” (general purpose - no intentional delay) fuses are UL class “K5” (up to and including 60 amps), and UL class “H” ( 65 amps and above). 4 Conductor data in this section specifies conductor size (excluding flexible cord or cable) between the panelboard and the equipment per NEC Table 310.15(B)(16). If a flexible cord or cable is used, minimum conductor size may increase. See NEC Table 400.5(A) for flexible cord and cable requirements. OM-244 243 Page 15 3-17. Connecting Input Power 3 = GND/PE Earth Ground 4 7 2 L1 3 L2 5 L3 6 1 Tools Needed: 5/16 in. Input2 2012−05 / Ref. 803 766-C / 956142645-3-B 956142645-3-A OM-244 243 Page 16 3-17. Connecting Input Power (Continued) ! Installation must meet all National and Local Codes − have only qualified persons make this installation. See rating label on unit and check input voltage available at site. ! Disconnect and lockout/tagout input power before connecting input conductors from unit. Follow established procedures regarding the installation and removal of lockout/ tagout devices. 1 Input Power Cord Connect input conductors L1, L2, and L3 to disconnect device line terminals. 2 Disconnect Device (switch shown in the OFF position) 7 3 Green Or Green/Yellow Grounding Conductor Select type and size of over-current protection using Section 3-16 (fused disconnect switch shown). ! Always connect green or green/yellow conductor to supply grounding terminal first, and never to a line terminal. For Three-Phase Operation 4 Disconnect Device Grounding Terminal 5 Input Conductors L1, L2, L3 6 Disconnect Device Line Terminals Connect green or green/yellow grounding conductor to disconnect device grounding terminal first. Over-Current Protection Close and secure door on disconnect device. Follow established lockout/tagout procedures to put unit in service. Input2 2012−05 Notes Work like a Pro! Pros weld and cut safely. Read the safety rules at the beginning of this manual. OM-244 243 Page 17 SECTION 4 − OPERATION 4-1. Front Panel Controls 8 10 11 12 13 14 15 9 18 19 20 17 16 4 1 5 3 2 7 6 Ref. 956142645-5-A 1 ON/OFF Switch (I/O) Use switch to turn unit On/Off. . The power source cooling fan is thermally controlled running only as required (Fan On Demand). . Water cooling unit operation can be set to function as required (auto) (Cooling On Demand) “ON or OFF”. 2 Positive Power Connection for TIG and Stick Welding. . Do not use for MIG welding. 3 4 5 6 Negative Power Connection for all welding processes. Remote Control Receptacle for TIG and Stick welding Gas Connector (TIG Process) Red Quick Connect Fitting Coolant return from torch. 7 Blue Quick Connect Fitting OM-244 243 Page 18 Coolant output to torch. 15 P2 (Setup Push Button) 8 Handle 9 Control Panel 10 D1 (Display 1) Allows selecting setup or advanced programming menus. Displays values and parameters for selected welding process. During welding it displays actual arc voltage. Allows selecting welding process. 11 D2 (Display 2) Displays values and parameters for selected welding process. During welding it shows measured welding current. 12 E1 (Encoder Control 1) Use control to change values and parameters that appear on display D1. 13 E2 (Encoder Control 2) Use control to change values and parameters that appear on display D2. 14 P1 (Memory Push Button) Permits storage of welding parameters into 4 locations (TIG and Stick only). 16 P3 (Process Push Button) 17 P4 (Material Push Button) Allows selecting material type for synergic MIG and synergic pulsed MIG processes. 18 P5 (Wire Diameter Push Button) Selects desired welding wire diameter for synergic MIG and synergic pulsed MIG processes. 19 P6 (Gas Selection Push Button) Selects desired welding gas type for synergic MIG and synergic pulsed MIG processes. 20 P7 (Trigger Selection Push Button) Selects desired trigger mode in TIG welding and enables weld output for Stick welding (Default = OFF). 4-2. Switching On the Unit and Recalling Factory Parameters . Write down any parameters that need to be restored before performing this procedure. 1 Power Switch Use power switch to turn unit On. When XMS 403 appears on D1 and D2, press P3 and P8 simultaneously. When MEMO CLEAR appears on D1 and D2, release P3 and P7. Wait until DONE appears on D1, and turn unit Off. The next time unit is turned On, all parameters will return factory default settings. 1 P3 P7 Ref. 956142645-5-A OM-244 243 Page 19 4-3. Welding Power Source Setup Menu P1 - Welding Parameter Setup Button. P2 - Power Source Setup Button. Press and hold P1 and P2. XMS 403 appears on D1 and D2 followed by UNIT - IPM. Wire feed speed is displayed as (IPM) inches per minute. Rotating knob P2 scrolls through the following options: UNIT MPM - Wire feed speed is displayed in Meters Per Minute. UNIT CUR - Power source will display welding current. P1 P2 UNIT THCK - Power source welding parameters will be chosen according to the gauge (thickness) of material to be welded. Rotating knob P1 scrolls through the following options: W-UN AUTO - Rotate P2 to select water cooling unit mode. AUTO (Default) ON (Continuous) or OFF (Water cooling not required) RCTY 1 - Selects function mode for remote receptacle (TIG). Rotating P2 selects the following: RCTY 2 - Selects function mode for remote receptacle (For future applications) RCTY 3 - Selects function mode for remote receptacle (For future applications) RCTY 4 - Selects function mode for remote receptacle (For future applications) LANG ENG - Selects language ENG = English (Default) Rotating P2 selects the following: LANG FRA - Selects language FRA = French LANG ITA - Selects language ITA = Italian LANG GER - Selects language GER = German LANG SPA - Selects language SPA = Spanish Ref. 956142645-5-A OM-244 243 Page 20 4-4. Remote Receptacle (RCTY) 1 7 Pin Remote Receptacle 1 4-5. Welding Process Selection L1 L2 L3 L4 P3 Ref. 956142645-5-A L1 LED L2 LED L3 LED L4 LED P3 Push Button Press P3 until desired process LED illuminates. Values and parameters that appear on D1 and D2 are either factory default settings or last settings entered for the selected process. L1 selection is Manual MIG welding. D1 value is welding voltage, default is 18.5V (range is 10 V to 50 V). D2 value is wire feed speed, default is 5.0 m/min (range is 1 m/min to 20 m/min). See Section 4-11. L2 Synergic MIG welding (non-pulsed). D1 value is welding voltage, default is 16.5 V (range is −10 V to 50 V). D2 value is the unit of measure as determined in the setup menu. (IPM, MPM, Current and Thickness) . When L2 LED is stable the welding arc is in a Short Circuit or Spray Arc transfer. If L2 is flashing this indicates that the welding parameters are outside of the specific setting required for either arc transfer to exist. This process is known as Globular Arc transfer. This process produces considerable undesirable welding spatter. It may be desirable to switch to a Pulsed-MIG Arc transfer to reduce/eliminate welding spatter. L3 Synergic Pulsed MIG welding. D1 value is welding voltage, default is 20 V (range is −10 V to 50 V). D2 value is the unit of measure as determined in the setup menu. (IPM, MPM, Current and Thickness) L4 Lift-TIG process (see Section 4-16) or Stick process (see Section 4-17). If selected process is TIG: D1 displays TIG, and D2 value is welding current, default is 220 A (range is 10 A to 400 A). If selected process is Stick: D1 displays Stick welding. Output is not enabled until button P7 is set to Output enabled mode. Display D1 displays open circuit voltage (OCV) at approximately 85 VDC. Display D2 displays welding current, default is 220 A (range is 10 A to 400 A). OM-244 243 Page 21 4-6. Wire Type Selection in Synergic MIG or Synergic Pulsed MIG Welding L5 L6 L7 Ref. 956142645-5-A L8 P4 L5 LED is no program for the process, material, wire diameter, and shielding gas combination. L6 LED L7 LED L8 LED L5 selection is for carbon steel. P4 Push Button Press P4 until desired material LED illuminates. D1 and D2 will show material name only momentarily, and then return to the main display. . D1 and D2 will show NO PROG or a selection will not be allowed when there L6 selection is for stainless steel. L7 selection is for aluminum. L8 selection is for other wire types not provided by standard selection. Pressing P2 push button after a selection is made to allow choosing other wire types within the main selection. SG2/3 allows selecting SG2 or SG3. CrNi allows selecting 308L, 309L, or 316L. Al allows selecting AlMg (AlMg5) or AlSi (AlSi5). Special permits selection of cored wire or special wire types. (Abbreviations for the different wire types appear in displays D1 and D2). . Wire type selection is retained in the welding process memory until a new selection is made. 4-7. Wire Diameter Selection In Synergic MIG Or Synergic Pulsed MIG Welding L9 L10 L11 L12 P5 Ref. 956142645-5-A L9 LED L10 LED L11 LED L12 LED P5 Push Button Press P5 until desired wire diameter LED illuminates. OM-244 243 Page 22 . D1 and D2 will show NO PROG or a selection will not be allowed when there is no program for the process, material, wire diameter, and shielding gas combination. L9 selection is for 0.8 mm diameter wire. L10 selection is for 1.0 mm diameter wire. L11 selection is for 1.2 mm diameter wire. L12 selection is for other wire diameters not provided by standard selection. Pressing P2 push button after the special selection is made to allow choosing other wire diameters not available by standard selection. 4-8. Gas Selection in Synergic MIG or Synergic Pulsed MIG Welding L13 Ref. 956142645-5-A Gas P6 L13 LED P6 Push Button Press P6 until gas LED illuminates. D1 and D2 will show gas name momentarily. Rotate E2 encoder to select desired gas type. After a brief moment the the displays will return to the main parameters. . Displays D1 and D2 will display NO PROG or alternate selection will not be possible when either process, material, wire diameter, and shielding gas combination is not permitted. 4-9. Trigger Mode Selection (L-TIG and Stick Processes) L14 L15 L16 L17 P7 . Always check and set a trigger mode. If trigger mode is undefined for a welding process, select the desired mode. L14 LED L15 LED L16LED L17 LED Ref. 956142645-5-A al welding current. If welding output is disabled welding (L17 OFF, D1 displays STICK and D2 displays set current). Press P7 to select the desired trigger mode: L14 ON selects 2T trigger mode. When trigger is pressed, welding starts. When trigger is released, welding stops. When trigger is pressed, welding starts with initial level of welding current (Level 1). When trigger is released, welding current increases to the set current level (Level 2). When trigger is pressed a second time, weld current decreases to the set current level (Level 3) arc extinguishes. Trigger mode can be set for TIG only. When trigger is pressed, welding starts at initial current level (IN). During level 2 mode if the torch trigger is pressed and held, welding current decreases to the set final-current level (FI-A). Releasing trigger extinguishes welding arc. In TIG welding, pressing P7 will change the trigger mode, but D1 and D2 will not change values. When trigger is released, welding current increases to the set current level. . L16 trigger mode is useful for thin mate- In Stick welding, pressing P7 will enable welding (L17 ON, D1 shows open circuit voltage (OCV) or weld voltage. When trigger is pressed and held, welding current decreases to the set final current (FI-A) is achieved. Releasing trigger extinguishes welding arc. D2 displays pre-set welding current or actu- L16 ON selects 3 levels trigger function. L17 ON: Weld output power is enabled welding terminals are electrically live. Stick/ TIG process requires LED L17 to be enabled. LED L17 will illuminate when welding output power is enabling MIG mode. P7 Push Button L15 ON selects 4T trigger mode. rials and for a crater fill sequence. OM-244 243 Page 23 4-10. Welding Parameter Setup Menu (Double Pulsed-MIG/L-TIG And Stick) Press P2 to enter SET UP menu. SET UP will appear on D1 and D2 momentarily changing to the selected process parameter values. Setup permits the viewing and changing of default parameters for each process mode. Double Pulsed-MIG (DP) Mode D1 displays DP. D2 displays ON/OFF. E1 changes the mode of D2. L-TIG/STICK Mode D1 displays the welding parameter. P2 D2 displays the parameter value. E1 changes the welding parameter. E2 changes the parameter value. . Incorrect settings in any process can result in a program with undesirable weld characteristics. Setup should only be used by operators familiar with various welding processes and parameters. Ref. 956142645-5-A 4-11. Preparing Power Source For MIG (GMAW) Welding Process Ref. 956142645-5-A To select MIG welding process, proceed as follows: . Follow safety precautions according to Section 1. Prepare unit according to Section 3. Use the correct interconnecting cable to connect power source unit to the wire feeder (see Wire Feeder manual). Use a cable with a correct adapter, connect gun to the MIG gun connector on wire feeder (see Wire Feeder manual). OM-244 243 Page 24 Connect work clamp cable to the WORK connector. If using a water-cooled gun, connect input coolant hose to blue quick connect fitting and return coolant hose to red quick connect fitting. . Check coolant level after attaching torch coolant hoses and running cooler. Be sure coolant appears in upper half of indicator. Add coolant if necessary (see Section 3-15). Setting Cooler Status (see Section 4-3) . To prevent damage to water-cooled torch and components, be sure that coolant is turned on. If a remote control is desired, connect it to the Remote Control receptacle on the wire feeder (see Wire Feeder manual). Turn unit On. Allow time for unit to complete its start up cycle. Set MIG welding process using P3 push button. 4-12. Selecting Manual MIG Welding D1 D2 P3 Ref. 956142645-5-A Set Manual MIG welding process using P3 push button. In Manual MIG mode, the operator may need to adjust main welding parameters for specific arc characteristics. Wire feed speed and arc voltage will appear on D1 and D2. During Setting : D1 value is default voltage setting of 18.5 V (range is 10.0 V to 50.0 V). D2 value is default wire feed speed setting of 5.0 m/min (range is 1.0 m/min to 20.0 m/min). During MIG Welding: D1 value is Measured Welding Voltage in Volts. D2 value is Measured Welding Amperage in Amperes. See Wire Feeder manual for remaining manual MIG settings. OM-244 243 Page 25 4-13. Selecting Synergic MIG Welding E1 P3 P4 D1 P5 D2 P6 E2 P7 Ref. 956142645-5-A Set Synergic MIG welding process using P3 push button. In Synergic MIG mode, the operator may need to adjust welding data (wire type, wire diameter, and gas type) and only one weld parameter. Generally, wire feed speed is adjusted and the synergic process automatically sets appropriate weld voltage. Synergic welding also sets many secondary welding parameters automatically for improved weld quality. D1 value is default voltage setting (range is OM-244 243 Page 26 defined by wire type, wire diameter and gas type selection). D2 value is the default current setting (range is defined by wire type, wire diameter and gas type selection). During Synergic MIG Welding: D1 value is Measured Welding Voltage in Volts. D2 value is Measured Welding Amperage in Amperes. See Wire Feeder manual for all remaining Synergic MIG settings. Select wire type using P4 push button. Select wire diameter using P5 push button. Select gas using P6 push button. Select trigger mode using P7 push button. See Wire Feeder manual for remaining Synergic MIG settings. Setting Cooler Status (see Section 4-3 ) . To prevent damage to water-cooled torch and components, be sure that coolant is turned on. 4-14. Selecting Synergic Pulsed MIG Welding E1 P3 P4 D1 P5 D2 P6 E2 P7 Ref. 956142645-5-A Set Synergic Pulsed MIG welding process using P3 push button. Synergic Pulsed MIG welding is a high quality welding process that produces very little spatter. This process works well on thin metals such as stainless steel and aluminum. During Synergic MIG Welding: D1 value is Measured Welding Voltage in Volts. D2 Value is Measured Welding Amperage in Amperes. Select wire type using P4 push button. Select wire diameter using P5 push button. In Synergic Pulsed MIG mode, the operator may need to adjust welding data (wire type, wire diameter, and gas type) and only one weld parameter. Generally, wire feed speed is adjusted and the synergic process automatically sets appropriate weld voltage. Synergic welding also sets many secondary welding parameters automatically for improved weld quality. During Setting: D1 value is the default voltage setting (range is defined by wire type, wire diameter and gas type selection). D2 value is the default current setting (range is defined by wire type, wire diameter and gas type selection). . Incorrect settings in Synergic Double Pulsed Welding process can result in a program with undesirable weld characteristics. Setup should only be used by operators familiar with various welding processes and parameters. In certain applications standard Pulsed MIG welding may be preferred. Select gas using P6 push button. Press P2 to enter setup menu. Select trigger mode using P7 push button. D1 displays DP. See wire feeder manual for all the remaining Synergic MIG settings. D2 default setting is OFF. Setting Cooler Status (see Section 4-3) Use E2 to change D2 value to ON. This setting will enable or disable Double Pulsed MIG Synergic welding. Setting Synergic Double Pulsed MIG Welding Some metals weld better using the Synergic Double Pulsed Welding process due to the unique pulsing of the welding arc. Heat generated in the workpiece is generally lower and the arc characteristics produce a better weld bead appearance especially on aluminum. The Synergic Double Pulsed MIG process allows control all parameters to produce high quality welds on aluminum. . On power source, only Double pulse enabling and disabling is possible. All the remaining Double Pulse settings are made on the wire feeder (see Wire Feeder manual). From the wire feeder it is possible to recall Synergic MIG, Synergic Pulsed MIG and Synergic Double Pulsed MIG programs (see Wire Feeder manuals). OM-244 243 Page 27 4-15. Preparing Unit For TIG Welding E1 D1 D2 E2 P2 P3 P7 Ref. 956142645-5-A To prepare unit for TIG welding, proceed as follows: . If D1 does not display TIG proceed as Follow safety precautions according to Section 1. Press P2 setup button. D1 will display STK. Rotating E2 encoder changes process to TIG mode. Use E1 to change D1 to SLUP. Purge air from torch gas hose using Torch Trigger (Manual Purge). Setting Slope-Down Time Prepare unit according Section 3. Connect torch to the WORK connector 3 and the gas pipe to the gas connector 5. Using a cable with a proper adapter, connect work clamp cable to the MIG gun connector. If using a water-cooled torch, connect input coolant hose to blue quick connect fitting and return coolant hose to red quick connect fitting. . Check coolant level after attaching torch coolant hoses and running cooler. Be sure coolant appears in upper half of indicator. Add coolant if necessary (see Section 3-15). Turn unit On. Allow time for unit to complete its start up cycle. Set TIG welding process using P3 push button. OM-244 243 Page 28 follows: Select trigger mode using P7 push button (see Section 4-9). Setting Slope-Up Time Press P2 to enter SET UP menu. D2 default setting is 0.1 second (range is 0.0 seconds to 10.0 A). Press P2 to enter SET UP menu. Use E1 to change D1 to SLDW. Setting Initial And Final Current D2 value is default setting of 0.1 second (range is 0.0 seconds to 10.0 A). Use E1 to change D1 to IN−A (Initial Current). Setting Postflow D2 value is default setting of 20 A (range is 5 A to 400 A). Use E2 to change D2 value. This parameter allows starting the welding process at a lower initial amperage setting. Use E1 to change D1 to FI−A (Final Current). D2 value is default setting of 20 A (range is 5 A to 400 A). Use E2 to change D2 value. This parameter allows finishing the welding process at a lower final amperage setting. Press P2 to enter SET UP menu. Use E1 to change D1 to POSG. D2 value is default setting of 5.0 second (range is 0.0 seconds to 50.0 seconds). Use E2 to change D2 value. Setting Cooler Status (see Section 4-3) . To prevent damage to water-cooled torch and components, be sure that coolant is turned on. Purge air from torch gas hose using Torch Trigger (Manual Purge). Select trigger mode using P7 push button. 4-16. TIG Lift-Arc Welding Lift-Arc Start When process selector LED 4 is illuminated in TIG mode Lift-Arc TIG is enabled. 1 “Touch” 2 1−2 Seconds 1 TIG Electrode 2 Workpiece Touch tungsten electrode to workpiece at weld start point, enable output and shielding gas with torch trigger, foot control, or hand control. Hold electrode to workpiece for 1-2 seconds, and slowly lift electrode. Arc is formed when electrode is lifted. Normal open-circuit voltage is not present before tungsten electrode touches workpiece; only a low sensing voltage is present between electrode and workpiece. The solid-state output contactor does not energize until after electrode is touching workpiece. This allows electrode to touch workpiece without overheating, sticking, or getting contaminated. Application: Do NOT Strike Like A Match! Lift-Arc is used for the DCEN or AC GTAW process when HF Start method is not permitted, or to replace the scratch method. Ref. S-156 279 4-17. Preparing Unit For Stick Welding To select Stick welding process, proceed as follows: Follow safety precautions according to Section 1. Prepare unit according to Section 3. Connect electrode holder to the Positive power connector 2. Connect work clamp cable to the negative connector 3. If a remote control is desired, connect it to the Remote Control receptacle 4. Turn unit On. Allow time for unit to complete its start up cycle. Set Stick welding process using P3 push button. . If D1 does not display STK proceed as follows: Press P2 setup button. D1 will display TIG. Rotating E2 encoder changes process to STK mode. HOT START Setting To change HOT START setting, proceed as follows: Press P2 to enter SET UP menu. Use E1 to change D1 to HOT. D2 value is default setting of 20% (range is 0% to 100%). Use E2 to change D2 value. This parameter increases output amperage at the start of a weld to eliminate electrode sticking. ARC FORCE Setting To change ARC FORCE setting, proceed as follows: Press P2 to enter SET UP menu. Use E1 to change D1 to ARC. D2 value is default setting of 0% (range is 0% to 100%). Use E2 to change D2 value. When setting is increased, short-circuit amperage at low arc voltage increases. STUCK Setting To change STUCK ON/OFF setting, proceed as follows: Press P2 to enter SET UP menu. Use E1 to change D1 to STUK. D2 default setting is OFF Use E2 to change D2 to ON. This parameter prevents the wire from sticking at the start of the weld . STICK welding can be enabled (L20 ON) or disabled (L20 OFF) using P7 push button, and this status is retained in the STICK welding process memory. OM-244 243 Page 29 SECTION 5 − MAINTENANCE & TROUBLESHOOTING 5-1. Routine Maintenance ! . Maintain more often Disconnect power before maintaining. during severe conditions. 3 Months Repair Or Replace Cracked Cables Replace Damaged Or Unreadable Labels Replace Cracked Torch Body Repair Or Replace Cracked Cables And Cords Clean And Tighten Weld Connections 6 Months Blow Out Inside Replace Cracked Hoses Change Coolant (If Using Water) Blow Out Heat Exchanger Fins 12 Months Change Coolant (If Using MILLER Coolant) OM-244 243 Page 30 5-2. Help Displays . All directions are in reference to the front of the unit. All circuitry referred to is located inside the unit. Help 0 Help 4 Help 8 Indicates a malfunction in the thermal protection circuitry on right side of unit. Contact a Factory Authorized Service Agent. Help 5 Indicates shorted thermistor RT2 on left side of unit. Contact a Factory Authorized Service Agent. Help 1 Indicates overheating on right side of unit. Unit will shutdown and fan will run until internal temperature drops within operational range. Help 6 Indicates a malfunction in the primary power circuit. Contact a Factory Authorized Service Agent. Help 2 Indicates a malfunction in the thermal protection circuitry on left side of unit. Contact a Factory Authorized Service Agent. Help 3 Indicates overheating on left side of unit. Unit will shutdown and fan will run until internal temperature drops within operational range. Indicates input voltage is too low and unit has automatically shut down. Operation will continue when voltage is within an acceptable lower range limit (15% below acceptable input voltage). Contact an electrician to check input line voltage. Help 7 Indicates input voltage is too high and unit has automatically shut down. Operation will continue when voltage is within an acceptable upper range limit (15% above acceptable input voltage). Contact an electrician to check input line voltage. HELP 7 may also indicate a bus voltage imbalance. Indicates a malfunction in the secondary power circuit of the unit. Contact a Factory Authorized Service Agent. Help 9 Indicates a shorted thermistor RT1 on right side of unit. Contact a Factory Authorized Service Agent. Help 15 Indicates a malfunctioning cooling unit. Unit will shut down immediately. Turn off primary power. Check and repair cooling unit components as necessary. Unit will operate when power to unit is turned off and back on. Help 50 Indicates an overload at the power module. Reduce weld parameter settings and/or duty cycle. If error continues, contact a Factory Authorized Service Agent. 5-3. Troubleshooting Trouble Remedy No weld output: unit completely inopera- Place line disconnect switch in On position (see Section 3-17). tive. Check and replace line fuse(s), if necessary, or reset circuit breaker (see Section 3-17). Check for proper input power connections (see Section 3-17). No weld output; meter display On. Verify welding parameter settings. Verify Help messages and correction procedures as necessary. Check, repair, or replace remote control. Unit overheated. Allow fan to run and unit cool (see Section 3-6). Erratic or improper weld output. Use proper size and type of weld cable (see Section 3-12). Clean and tighten all weld connections. Coolant system not working (HELP 15 is displayed). Check and secure coolant hose connectors. Reset circuit breaker CB7 (see Section 3-14). Motor overheated. Allow motor to cool and restart operation. Have Factory Authorized Service Agent check cooling unit. Reduced or no coolant flow from cooling unit (HELP 15 can be displayed). Add coolant. Check for blockage at hoses. Control panel not functioning properly. Software problems. Switch unit off and back on again to verify LEDs and display status. Reinstall factory parameters (see Section 4-2). Contact a Factory Authorized Service Agent. OM-244 243 Page 31 SECTION 6 − ELECTRICAL DIAGRAM Figure 6-1. Circuit Diagram For XMS 403 OM-244 243 Page 32 956142623-C OM-244 243 Page 33 SECTION 7 − PARTS LIST 8 . Hardware is common and 9 7 12 17 18 16 15 1 2 14 3 4 13 12 11 5 6 19 10 23 22 21 20 not available unless listed. 956142645-1-B Figure 7-1. Unit Outer Assembly OM-244 243 Page 34 Item No. Dia. Mkgs. Part No. Description Quantity Figure 7-1. Unit Outer Assembly ... ... ... ... ... ... ... ... ... ... ... ... ... ... ... ... ... ... ... ... ... ... ... 1 2 3 4 5 6 7 8 9 10 11 12 13 14 15 16 17 18 19 20 21 22 23 . . . . . . . . . . . . . . . . . +V17031284 . . . . . . . . . . . . . . . . . . . 156012136 . . . . . . . . . . . . . . . . . . . . . . 207235 . . . . . . . . . . . . . . . . . +156005098 . . . . . . . . . . . . . . . . . . . 956142616 . . . . . . . . . . . . . . . . . . . 956142617 . . . . . . . . . . . . . . . . . . . 956142621 . . . . . . . . . . . . . . . . . . . 156087017 . . . . . . . . . . . . . . . . . . . 156009067 . . . . . . . . . . . . . . . . . . . 056054075 . . . . . . . . . . . . . . . . . . . 156012119 . . . . . . . . . . . . . . . . . . . . . . 207233 . . . . . . . . . . . . . . . . . +V16122287 . . . . . . . . . . . . . . . . . . V56142305 . . . . . . . . . . . . . . . . . . . 056054092 . . . . . . . . . . . . . . . . . . V56142303 . . . . . . . . . . . . . . . . . . . . . . 207291 . . . . . . . . . . . . . . . . . +V16122288 . . . . . . . . . . . . . . . . . . . 156018115 . . . . . . . . . . . . . . . . . . . 057052044 . . . . . . . . . . . . . . . . . . . 057052045 . . . . . . . . . . . . . . . . . . . 057052043 . . . . . . . . . . . . . . . . . . . 058066057 ... ... ... ... ... ... ... ... ... ... ... ... ... ... ... ... ... ... ... ... ... ... ... Wrapper . . . . . . . . . . . . . . . . . . . . . . . . . . . . . . . . . . . . . . . . . . . . . . . Turntable . . . . . . . . . . . . . . . . . . . . . . . . . . . . . . . . . . . . . . . . . . . . . . Label, Warning, Tilting . . . . . . . . . . . . . . . . . . . . . . . . . . . . . . . . . . . Cylinder Rack, Upper Support . . . . . . . . . . . . . . . . . . . . . . . . . . . . Nameplate, Rear, Gas, 14 Pin & Fuse Terminals . . . . . . . . . . . . Nameplate, Rear, Water & Dinse . . . . . . . . . . . . . . . . . . . . . . . . . . Nameplate, Coolant Level . . . . . . . . . . . . . . . . . . . . . . . . . . . . . . . . Pin, Split . . . . . . . . . . . . . . . . . . . . . . . . . . . . . . . . . . . . . . . . . . . . . . . Washer . . . . . . . . . . . . . . . . . . . . . . . . . . . . . . . . . . . . . . . . . . . . . . . . Wheel, Rear, 250 o.d. . . . . . . . . . . . . . . . . . . . . . . . . . . . . . . . . . . . Axle, Rear Wheels . . . . . . . . . . . . . . . . . . . . . . . . . . . . . . . . . . . . . . Label, General Precautionary . . . . . . . . . . . . . . . . . . . . . . . . . . . . . Side Panel, R . . . . . . . . . . . . . . . . . . . . . . . . . . . . . . . . . . . . . . . . . . . Nameplate, Front, Dinse Negativ . . . . . . . . . . . . . . . . . . . . . . . . . . Wheel/Caster Wheel w/Brake, Front . . . . . . . . . . . . . . . . . . . . . . . Nameplate, Front, Dinse Positiv . . . . . . . . . . . . . . . . . . . . . . . . . . . Label, Primary Power Connections . . . . . . . . . . . . . . . . . . . . . . . . Side Panel, L . . . . . . . . . . . . . . . . . . . . . . . . . . . . . . . . . . . . . . . . . . . Nut 5/8 . . . . . . . . . . . . . . . . . . . . . . . . . . . . . . . . . . . . . . . . . . . . . . . . Fitting, Hose Brs Barbed M 1/4Tbg x 5/8−18 SAE . . . . . . . . . . . Fitting, Quick Connector . . . . . . . . . . . . . . . . . . . . . . . . . . . . . . . . . Adapter 5/8 UNC−3/8 BSP . . . . . . . . . . . . . . . . . . . . . . . . . . . . . . . Gas, Connection Kit . . . . . . . . . . . . . . . . . . . . . . . . . . . . . . . . . . . . . 1 1 1 1 1 1 1 2 4 2 1 2 1 1 2 1 1 1 1 1 1 1 1 +When ordering a component originally displaying a precautionary label, the label should also be ordered. To maintain the factory original performance of your equipment, use only Manufacturer’s Suggested Replacement Parts. Model and serial number required when ordering parts from your local distributor. OM-244 243 Page 35 2 3 1 4 5 OM-244 243 Page 36 18 6 19 20 12 13 8 7 21 9 22 Figure 7-2. Unit Main Assembly 36 32 6 35 10 34 25 26 24 27 23 11 33 32 31 30 29 28 39 38 37 15 14 41 40 48 46 47 16 17 50 42 51 49 52 60 43 44 53 54 45 33 32 31 59 58 55 61 48 56 57 62 63 64 65 . Hardware is common and not available unless listed. 956142645-2-B Item No. Dia. Mkgs. Part No. Description Quantity Figure 7-2. Unit Main Assembly ... ... ... ... ... ... ... ... ... ... ... ... ... ... ... ... ... ... ... ... ... ... ... ... ... ... ... ... ... ... ... ... ... ... ... ... ... ... ... ... ... ... ... ... ... ... ... ... ... ... ... ... ... ... ... ... ... ... ... ... ... ... 1 2 3 4 5 6 7 8 9 10 11 12 13 14 15 16 17 18 19 20 21 22 23 24 25 26 27 28 29 30 31 32 33 34 35 36 37 38 39 40 41 42 43 44 45 46 47 48 49 50 51 52 53 54 55 56 57 58 59 60 61 62 . . . . . . . . . . . . . . . . . . . 316005010 . . . . . . . . . . . . . . . . . . . . . . 201531 . . . . . . . . . . . . . . . . . . . . . . 199840 . . . . . . PC6 . . . . . . . . . . . 229967 . . . . . . HD1 . . . . . . . . . . . 182918 . . . . . . RT2 . . . . . . . . . . . 173632 . . . . . . PC1 . . . . . . . . . . . 229959 . . . . . . . T1 . . . . . . . . . . . . 179616 . . . . . . . L1 . . . . . . . . . . . . 173563 . . . . . . . Z1 . . . . . . . . . . . . 173570 . . . . . . . T2 . . . . . . . . . . . . 195829 . . . . . PM1,2 . . . . . . . . . . 233043 . . . . . . SR1 . . . . . . . . . . . 179629 . . . . . . C1 . . . . . . . . . . . 188446 . . . . . . C3,4 . . . . . . . . . . . 192935 . . . . . . . . . . . . . . . . . . V16117300 . . . . . . . . . . . . . . . . . . V16117360 . . . . . . . . . . . . . . . . . . . 156002045 . . . . . . . . . . . . . . . . . . . . . . 213051 . . . . . . . . . . . . . . . . . . . . . . 193919 . . . . . . . . . . . . . . . . . . . 156118056 . . . . . . . S1 . . . . . . . . . . . 176226 . . . . . . PC2 . . . . . . . . . . . 212210 . . . . . . PC3 . . . . . . . . 057084139 . . . . . . . . . . . . . . . . . . . 116118180 . . . . . . . . . . . . . . . . . . . 057028110 . . . . . . . . . . . . . . . . . . . 656026097 . . . . . . . . . . . . . . . . . . . 656026099 . . . . . . . . . . . . . . . . . . . 656026102 . . . . . . . . . . . . . . . . . . . . . . 188192 . . . . . . . . . . . . . . . . . . . . . . 208967 . . . . . . . . . . . . . . . . . . . 556049402 . . . . . . . . . . . . . . . . . . . 556049401 . . . . . . FM . . . . . . . V56126046 . . . . . . . . . . . . . . . . . . V56005296 . . . . . . . . . . . . . . . . . . V16039294 . . . . . . . . . . . . . . . . . . . 056082099 . . . . . . . . . . . . . . . . . . . 656026100 . . . . . . . . . . . . . . . . . . . 116117082 . . . . . . . . . . . . . . . . . . . 156005141 . . . . . . . . . . . . . . . . . . . 056061070 . . . . . . . . . . . . . . . . . . . 656026111 . . . . . . . . . . . . . . . . . . V56031377 . . . . . . . . . . . . . . . . . . . 556049411 . . . . . . . . . . . . . . . . . . V16006289 . . . . . . . . . . . . . . . . . . . . . . 176106 . . . . . . . . . . . . . . . . . . . 116122306 . . . . . . . . . . . . . . . . . . . 656026098 . . . . . . . . . . . . . . . . . . . 027042002 . . . . . . . . . . . . . . . . . . . . . . 166564 . . . . . . . . . . . . . . . . . . V57011071 . . . . . . . . . . . . . . . . . . . 656026092 . . . . . WCP . . . . . . . 057010059 . . . . . . . . . . . . . . . . . . V56118293 . . . . . . CB2 . . . . . . . . . . . 083423 . . . . . . CB1 . . . . . . . . . . . 161078 . . . . . . . . . . . . . . . . . . V56091091 . . . . . . GSV . . . . . . . . . . . 228036 . . . . . . . . . . . . . . . . . . . 156076085 . . . . . WCF . . . . . . . . . . 213072 . . . . . . . . . . . . . . . . . . . 656026101 . . . . . . . . . . . . . . . . . +V16118292 ... ... ... ... ... ... ... ... ... ... ... ... ... ... ... ... ... ... ... ... ... ... ... ... ... ... ... ... ... ... ... ... ... ... ... ... ... ... ... ... ... ... ... ... ... ... ... ... ... ... ... ... ... ... ... ... ... ... ... ... ... ... LEM, Support . . . . . . . . . . . . . . . . . . . . . . . . . . . . . . . . . . . . . . . . . . . Kit Diode, Power Module . . . . . . . . . . . . . . . . . . . . . . . . . . . . . . . . . Bus Bar, Diode . . . . . . . . . . . . . . . . . . . . . . . . . . . . . . . . . . . . . . . . . Circuit Card, Filter Board . . . . . . . . . . . . . . . . . . . . . . . . . . . . . . . . . Transducer, Current 400A Module Supply V +/− 15V . . . . . . . . . Thermistor, NTC 30K ohms . . . . . . . . . . . . . . . . . . . . . . . . . . . . . . . Circuit Card, Control . . . . . . . . . . . . . . . . . . . . . . . . . . . . . . . . . . . . . Transformer, HF . . . . . . . . . . . . . . . . . . . . . . . . . . . . . . . . . . . . . . . . Inductor, Input . . . . . . . . . . . . . . . . . . . . . . . . . . . . . . . . . . . . . . . . . . Stabilizer . . . . . . . . . . . . . . . . . . . . . . . . . . . . . . . . . . . . . . . . . . . . . . . Transformer, Control . . . . . . . . . . . . . . . . . . . . . . . . . . . . . . . . . . . . . Kit, Transistor IGBT Module . . . . . . . . . . . . . . . . . . . . . . . . . . . . . . Kit Diode, Power Module . . . . . . . . . . . . . . . . . . . . . . . . . . . . . . . . . Capacitor, Polyp Film .5Uf 900VDC . . . . . . . . . . . . . . . . . . . . . . . . Capacitor, Elctlt 2700Uf 450VDC . . . . . . . . . . . . . . . . . . . . . . . . . . Wind Tunnel Extension, Front . . . . . . . . . . . . . . . . . . . . . . . . . . . . . Wind Tunnel Extension, Rear . . . . . . . . . . . . . . . . . . . . . . . . . . . . . Handle . . . . . . . . . . . . . . . . . . . . . . . . . . . . . . . . . . . . . . . . . . . . . . . . Plastic, Upper . . . . . . . . . . . . . . . . . . . . . . . . . . . . . . . . . . . . . . . . . . Knob, Pointer . . . . . . . . . . . . . . . . . . . . . . . . . . . . . . . . . . . . . . . . . . . Front Panel, Membrane . . . . . . . . . . . . . . . . . . . . . . . . . . . . . . . . . . Switch, Power ON/OFF . . . . . . . . . . . . . . . . . . . . . . . . . . . . . . . . . . Circuit Card, Interconnect . . . . . . . . . . . . . . . . . . . . . . . . . . . . . . . . Circuit Card, Control . . . . . . . . . . . . . . . . . . . . . . . . . . . . . . . . . . . . . Panel, Front . . . . . . . . . . . . . . . . . . . . . . . . . . . . . . . . . . . . . . . . . . . . Remote Control 14 Pin . . . . . . . . . . . . . . . . . . . . . . . . . . . . . . . . . . . Hose, 5x8,5x940 Black Gas . . . . . . . . . . . . . . . . . . . . . . . . . . . . . . Hose, 6x11x470 Blu Water . . . . . . . . . . . . . . . . . . . . . . . . . . . . . . . Hose, 6x11x270 Red Water . . . . . . . . . . . . . . . . . . . . . . . . . . . . . . . Receptacle, Gas . . . . . . . . . . . . . . . . . . . . . . . . . . . . . . . . . . . . . . . . Receptacle, Dinse . . . . . . . . . . . . . . . . . . . . . . . . . . . . . . . . . . . . . . . Water Connection, Quick Connect . . . . . . . . . . . . . . . . . . . . . . . . . Water Connection, Quick Connect . . . . . . . . . . . . . . . . . . . . . . . . . Fan Assy . . . . . . . . . . . . . . . . . . . . . . . . . . . . . . . . . . . . . . . . . . . . . . Support, Module, Fan . . . . . . . . . . . . . . . . . . . . . . . . . . . . . . . . . . . . Box Louver . . . . . . . . . . . . . . . . . . . . . . . . . . . . . . . . . . . . . . . . . . . . . Radiator Assy . . . . . . . . . . . . . . . . . . . . . . . . . . . . . . . . . . . . . . . . . . Hose, 6x11x780 Blu Water . . . . . . . . . . . . . . . . . . . . . . . . . . . . . . . Plenum, Fan . . . . . . . . . . . . . . . . . . . . . . . . . . . . . . . . . . . . . . . . . . . Support, Radiator . . . . . . . . . . . . . . . . . . . . . . . . . . . . . . . . . . . . . . . Flow-Meter . . . . . . . . . . . . . . . . . . . . . . . . . . . . . . . . . . . . . . . . . . . . . Hose, 6x11x160 Red Water . . . . . . . . . . . . . . . . . . . . . . . . . . . . . . . Support Switch, Pressure . . . . . . . . . . . . . . . . . . . . . . . . . . . . . . . . Header, 3 Way . . . . . . . . . . . . . . . . . . . . . . . . . . . . . . . . . . . . . . . . . . Base . . . . . . . . . . . . . . . . . . . . . . . . . . . . . . . . . . . . . . . . . . . . . . . . . . Label, Fan Warning . . . . . . . . . . . . . . . . . . . . . . . . . . . . . . . . . . . . . Mounting Bracket, Tank Assy . . . . . . . . . . . . . . . . . . . . . . . . . . . . . Hose, 6x11x250 Blu Water . . . . . . . . . . . . . . . . . . . . . . . . . . . . . . . Tank, Water 8 Liter . . . . . . . . . . . . . . . . . . . . . . . . . . . . . . . . . . . . . . Filter, In−line Assy . . . . . . . . . . . . . . . . . . . . . . . . . . . . . . . . . . . . . . . Pump Assy . . . . . . . . . . . . . . . . . . . . . . . . . . . . . . . . . . . . . . . . . . . . . Hose, 6x11x350 Blu Water . . . . . . . . . . . . . . . . . . . . . . . . . . . . . . . Motor, 170W, 115 VAC . . . . . . . . . . . . . . . . . . . . . . . . . . . . . . . . . . . Panel, Intermediate . . . . . . . . . . . . . . . . . . . . . . . . . . . . . . . . . . . . . Circuit Breaker, Man Reset 1P 10A 250VAC . . . . . . . . . . . . . . . . Circuit Breaker, Man Reset 1P 7A 250VAC . . . . . . . . . . . . . . . . . Strain Relief, Primary Cord . . . . . . . . . . . . . . . . . . . . . . . . . . . . . . . Valve, 24VAC 1 Way . . . . . . . . . . . . . . . . . . . . . . . . . . . . . . . . . . . . Receptacle, 14 Pin . . . . . . . . . . . . . . . . . . . . . . . . . . . . . . . . . . . . . . Fan Assy, Radiator Cooling 115 V . . . . . . . . . . . . . . . . . . . . . . . . . Hose, 6x11x590 Red Water . . . . . . . . . . . . . . . . . . . . . . . . . . . . . . . Panel, Rear . . . . . . . . . . . . . . . . . . . . . . . . . . . . . . . . . . . . . . . . . . . . 1 1 2 1 1 2 1 1 1 1 1 1 1 1 2 1 1 1 1 2 1 1 1 1 1 1 1 1 1 1 3 2 2 1 1 1 1 1 1 1 1 2 1 1 1 1 1 2 1 1 1 1 1 1 1 1 1 1 1 1 1 1 OM-244 243 Page 37 Item No. Dia. Mkgs. Part No. Description Quantity Figure 7-2. Unit Main Assembly (Continued) . . . 63 . . . . . . . T4 . . . . . . . . V58021080 . . . Transformer, 400VAC . . . . . . . . . . . . . . . . . . . . . . . . . . . . . . . . . . . . 1 . . . 64 . . . . . . . . . . . . . . . . . . . . . . 220805 . . . Nut . . . . . . . . . . . . . . . . . . . . . . . . . . . . . . . . . . . . . . . . . . . . . . . . . . . . 1 . . . 65 . . . . . . . . . . . . . . . . . . V57014066 . . . Primary Cable, 4 Core 6,0 Mq . . . . . . . . . . . . . . . . . . . . . . . . . . . . 1 +When ordering a component originally displaying a precautionary label, the label should also be ordered. To maintain the factory original performance of your equipment, use only Manufacturer’s Suggested Replacement Parts. Model and serial number required when ordering parts from your local distributor. Notes OM-244 243 Page 38 Effective January 1, 2013 (Equipment with a serial number preface of MD or newer) This limited warranty supersedes all previous Miller warranties and is exclusive with no other guarantees or warranties expressed or implied. LIMITED WARRANTY − Subject to the terms and conditions below, ITW Welding Products Italy warrants to its original retail purchaser that new Miller equipment sold after the effective date of this limited warranty is free of defects in material and workmanship at the time it is shipped by Miller. THIS WARRANTY IS EXPRESSLY IN LIEU OF ALL OTHER WARRANTIES, EXPRESS OR IMPLIED, INCLUDING THE WARRANTIES OF MERCHANTABILITY AND FITNESS. Within the warranty periods listed below, Miller will repair or replace any warranted parts or components that fail due to such defects in material or workmanship. Miller must be notified in writing within thirty (30) days of such defect or failure, at which time Miller will provide instructions on the warranty claim procedures to be followed. Miller shall honor warranty claims on warranted equipment listed below in the event of such a failure within the warranty time periods. All warranty time periods start on the date the equipment was delivered to the original retail purchaser or one year after the equipment is shipped to a European distributor or eighteen months after the equipment is shipped to an International distributor. 1. 3 Years — Parts and Labor * * * * * * 3. Auto-Darkening Helmet Lenses (No Labor) Migmatic 175 HF Units Water Coolant Systems (EU Models, Non-Integrated) 1 Year — Parts and Labor Unless Specified * * * * * * * * * * * 5. Engine Driven Welding Generators (NOTE: Engines are warranted separately by the engine manufacturer.) Inverter Power Sources (Unless Otherwise Stated) Process Controllers Semi-Automatic and Automatic Wire Feeders Transformer/Rectifier Power Sources Water Coolant System (Integrated) 2 Years — Parts * * * * 4. Original main power rectifiers only to include SCRs, diodes, and discrete rectifier modules with exclusion of STR, Si, STi, STH and MPi series. Automatic Motion Devices Field Options (NOTE: Field options are covered under True Blue® for the remaining warranty period of the product they are installed in, or for a minimum of one year — whichever is greater.) Induction Heating Power Sources, Coolers, and Electronic Controls/Recorders Motor Driven Guns (w/exception of Spoolmate Spoolguns) Positioners and Controllers Powered Air Purifying Respirator (PAPR) Blower Unit (No Labor) Racks Running Gear and Trailers Subarc Wire Drive Assemblies Water Coolant Systems (USA Models, Non-Integrated) Work Stations/Weld Tables (No Labor) 6 Months — Parts * Batteries 90 Days — Parts * Accessory (Kits) * Canvas Covers * Induction Heating Coils and Blankets * MIG Guns * Remote Controls * Replacement Parts (No Labor) * Spoolmate Spoolguns * Cables and Non-Electronic Controls Miller’s True Blue® Limited Warranty shall not apply to: 1. Consumable components; such as contact tips, cutting nozzles, contactors, brushes, switches, slip rings, relays or parts that fail due to normal wear. 2. Items furnished by Miller, but manufactured by others, such as engines or trade accessories. These items are covered by the manufacturer’s warranty, if any. 3. Equipment that has been modified by any party other than Miller, or equipment that has been improperly installed, improperly operated or misused based upon industry standards, or equipment which has not had reasonable and necessary maintenance, or equipment which has been used for operation outside of the specifications for the equipment. 5 Years Parts — 3 Years Labor * 2. 6. MILLER PRODUCTS ARE INTENDED FOR PURCHASE AND USE BY COMMERCIAL/INDUSTRIAL USERS AND PERSONS TRAINED AND EXPERIENCED IN THE USE AND MAINTENANCE OF WELDING EQUIPMENT. In the event of a warranty claim covered by this warranty, the exclusive remedies shall be, at Miller’s option: (1) repair; or (2) replacement; or, where authorized in writing by Miller in appropriate cases, (3) the reasonable cost of repair or replacement at an authorized Miller service station; or (4) payment of or credit for the purchase price (less reasonable depreciation based upon actual use) upon return of the goods at customer’s risk and expense. Miller’s option of repair or replacement will be F.O.B., Factory at ITW Welding Products Group Europe or F.O.B. at a Miller authorized service facility as determined by Miller. Therefore no compensation or reimbursement for transportation costs of any kind will be allowed. TO THE EXTENT PERMITTED BY LAW, THE REMEDIES PROVIDED HEREIN ARE THE SOLE AND EXCLUSIVE REMEDIES. IN NO EVENT SHALL MILLER BE LIABLE FOR DIRECT, INDIRECT, SPECIAL, INCIDENTAL OR CONSEQUENTIAL DAMAGES (INCLUDING LOSS OF PROFIT), WHETHER BASED ON CONTRACT, TORT OR ANY OTHER LEGAL THEORY. ANY EXPRESS WARRANTY NOT PROVIDED HEREIN AND ANY IMPLIED WARRANTY, GUARANTY OR REPRESENTATION AS TO PERFORMANCE, AND ANY REMEDY FOR BREACH OF CONTRACT TORT OR ANY OTHER LEGAL THEORY WHICH, BUT FOR THIS PROVISION, MIGHT ARISE BY IMPLICATION, OPERATION OF LAW, CUSTOM OF TRADE OR COURSE OF DEALING, INCLUDING ANY IMPLIED WARRANTY OF MERCHANTABILITY OR FITNESS FOR PARTICULAR PURPOSE, WITH RESPECT TO ANY AND ALL EQUIPMENT FURNISHED BY MILLER IS EXCLUDED AND DISCLAIMED BY MILLER. milan_warr 2013−01 Owner’s Record Please complete and retain with your personal records. Model Name Serial/Style Number Purchase Date (Date which equipment was delivered to original customer.) Distributor Address Country Zip/Postal Code For Service Contact a DISTRIBUTOR or SERVICE AGENCY near you. Always provide Model Name and Serial/Style Number. Contact your Distributor for: Welding Supplies and Consumables Options and Accessories Service and Repair Replacement Parts Owner’s Manuals ITW Welding Italy S.r.l. Contact the Delivering Carrier to: File a claim for loss or damage during shipment. For assistance in filing or settling claims, contact your distributor and/or equipment manufacturer’s Transportation Department. ORIGINAL INSTRUCTIONS − PRINTED IN USA © 2013 Miller Electric Mfg. Co. 2013−01 Via Privata Iseo, 6/E 20098 San Giuliano Milanese, Italy Phone: 39 (0) 2982901 Fax: 39 (0) 298290-203 email: miller@itw−welding.it
advertisement