King Canada KWL-1218VS 12" X 18" VARIABLE SPEED WOOD LATHE Instruction Manual
Add to my manuals
11 Pages
King Canada KWL-1218VS is a versatile and powerful 2-speed wood lathe that is perfect for a wide range of woodworking projects, from simple spindle turning to complex bowl turning. With its variable speed motor, digital readout, and sturdy construction, the KWL-1218VS is a great choice for both beginners and experienced woodworkers. It features a 12" swing over the bed, an 18" distance between centers, and a 1" x 8 TPI spindle. The KWL-1218VS also comes with a number of accessories, including a spur center, a faceplate, a live center, and two tool rests.
advertisement
▼
Scroll to page 2
of 11
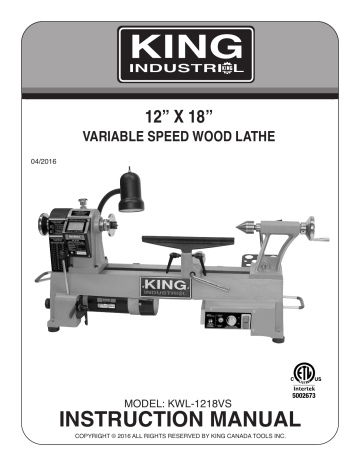
12” x 18” 04/2016 variable speed wood lathe iNstrUCtioN MaNUal MODEL: KWL-1218VS COPYRIGHT © 2016 ALL RIGHTS RESERVED BY KING CANADA TOOLS INC. warraNtY iNForMatioN 2-Year liMited warraNtY For this 12” x 18” wood lathe prooF oF pUrChase kiNG CaNada tools oFFers a 2-Year liMited warraNtY iNteNded For CoMMerCial Use Please keep your dated proof of purchase for warranty and servicing purposes. replaCeMeNt parts Replacement parts for this product are available at our authorized King Canada service centres across Canada. liMited tool warraNtY King Canada makes every effort to ensure that this product meets high quality and durability standards. King Canada warrants to the original retail consumer a 2-year limited warranty as of the date the product was purchased at retail and that each product is free from defects in materials. Warranty does not apply to defects due directly or indirectly to misuse, abuse, normal wear and tear, negligence or accidents, repairs done by an unauthorized service centre, alterations and lack of maintenance. King Canada shall in no event be liable for death, injuries to persons or property or for incidental, special or consequential damages arising from the use of our products. To take advantage of this limited warranty, return the product at your expense together with your dated proof of purshase to an authorized King Canada service centre. Contact your retailer or visit our web site at www.kingcanada.com for an updated listing of our authorized service centres. In cooperation with our authorized serviced centre, King Canada will either repair or replace the product if any part or parts covered under this warranty which examination proves to be defective in workmanship or material during the warranty period. Note to User This instruction manual is meant to serve as a guide only. Specifications and references are subject to change without prior notice. parts diaGraM & parts lists Refer to the Parts section of the King Canada web site for the most updated parts diagram and parts list. kiNG CaNada iNC. dorval, qUÉbeC, CaNada h9p 2Y4 www.kingcanada.com GeNeral & speCiFiC saFetY rUles 1. keep GUards iN plaCe and in working order. 2. keep work area CleaN. Cluttered areas and benches invite accidents. 3. doN’t Use iN daNGeroUs eNviroNMeNt. Don’t use power tools in damp or wet locations, or expose them to rain. Keep work area well lighted. 4. keep ChildreN awaY. All visitors should be kept safe distance from work area. 5. Make workshop kid prooF removing starter keys. 6. doN’t ForCe tool. It will do the job better and safer at the rate for which it was designed. 7. Use riGht tool. Don’t force tool or attachment to do a job for which it was not designed. 8. Use proper exteNsioN Cord. Make sure your extension cord is in good condition. When using an extension cord, be sure to use one heavy enough to carry the current your product will draw. An undersized cord will cause a drop in line voltage resulting in loss of power and overheating. Table shows the correct size to use depending on cord length and nameplate ampere rating. If in doubt, use the next heavier gage. The smaller the gage number, the heavier the cord. 9. wear proper apparel. Do not wear loose clothing, gloves, neckties, rings, bracelets, or other jewelry which may get caught in moving parts. Nonslip footwear is recommended. Wear protective hair covering to contain long hair. 10. alwaYs Use saFetY Glasses. Also use face or dust mask if cutting operation is dusty. Everyday eyeglasses only have impact resistant lenses, they are NOT safety glasses. 11. doN’t overreaCh. Keep proper footing and balance at all times. 12. MaiNtaiN tools with Care. Keep tools sharp and clean for best and safest performance. Follow instructions for lubricating and changing accessories. 13. disCoNNeCt tools before servicing; when changing accessories, such as blades, bits, cutters, and the like. 14. redUCe the risk oF UNiNteNtioNal startiNG. Make sure switch is in off position before plugging in. 15. Use reCoMMeNded aCCessories. Consult the owner’s manual for recommended accessories. The use of improper accessories may cause risk of injury to persons. 16. Never staNd oN tool. Serious injury could occur if the tool is tipped or if the cutting tool is unintentionally contacted. 17. CheCk daMaGed parts. Before further use of the tool, a guard or other part that is damaged should be carefully checked to determine that it will operate properly and perform its intended function – check for alignment of moving parts, binding of moving parts, breakage of parts, mounting, and any other conditions that may affect its operation. A guard or other part that is damaged should be properly repaired or replaced. 18. Never leave tool rUNNiNG UNatteNded. tUrN power oFF. Don’t leave tool until it comes to a complete stop. speCiFiC saFetY rUles For wood lathes additioNal saFetY rUles For wood lathes warNiNG - No adjustment should be made until the tool has been stopped. 1. Do not allow the turning tools to bite into the wood. The wood could split or be thrown from the lathe. warNiNG For Your Own Safety Read Instruction Manual Before Operating Lathe. 3. Do not operate the lathe if it is rotating in the wrong direction. The workpiece must always be rotating toward you. warNiNG - Risk of injury due to accidental starting. Do not use in an area where children may be present. a) Wear eye protection. b) Do not wear gloves, necktie, or loose clothing. c) Tighten all locks before operating. d) Rotate workpiece by hand before applying power. e) Rough out workpiece before installing on faceplate. f) Do not mount split workpiece or one containing knot. g) Use lowest speed when starting new workpiece. warNiNG: DO NOT EXPOSE TO RAIN OR USE IN DAMP LOCATIONS. 2. Always position the tool rest above the centreline of the lathe when shaping a piece of stock. 4. Before attaching a workpiece to the faceplate, always rough it out to make it as round as possible, this minimizes the vibrations while the piece is being turned. Always fasten the workpiece securely to the faceplate, failure to do this could result in the workpiece being thrown away from the lathe. 5. Position your hands so that they will not slip onto the workpiece. GettiNG to kNow YoUr wood lathe Getting to know your wood lathe 1) Spindle handwheel 2) Belt and pulley cover 3) Digital readout 4) Spindle lock 5) Headstock 6) Work light (Max. 40W) 7) Spur centre 8) Faceplate 9) Bed 10) 12” Tool rest (6” tool rest not shown) 11) Tool rest locking handles 12) Tool storage rack 13) Live centre 14) Tailstock quill locking handle 15) Tailstock 16) Tailstock quill adjusting handwheel 17) Tailstock locking lever 18) Carry handle 12” x 18” varibale speed wood lathe specifications Model Swing over bed Distance between centres Spindle size Spindle bore Spindle speeds Headstock and tailstock taper Gap in bed DC motor Voltage Ass. dimensions (LxWxH)/weight Pkg dimensions (LxWxH)/weight 19) On/Off switch 20) Variable speed selector dial 21) Foward/reverse switch 22) Tool rest base locking lever 23) Motor tension lever lock handle 24) Knock-out rod 25) Reset kwl-1218vs 12” 18” 1” x 8 TPI 3/8” 2 (450-1800, 950-3800 RPM) MT # 2 1 1/4” 1 HP, 7 Amp. 110V, 1 phase, 60 Hz 39" x 15” x 18” / 105 lbs 36" x 14-1/2” x 18-3/8” / 110 lbs eleCtriCal iNForMatioN warNiNG! ALL ELECTRICAL CONNECTIONS MUST BE DONE BY A QUALIFIED ELECTRICIAN. FAILURE TO COMPLY MAY RESULT IN SERIOUS INJURY! ALL ADJUSTMENTS OR REPAIRS MUST BE DONE WITH THE MACHINE DISCONNECTED FROM THE POWER SOURCE. FAILURE TO COMPLY MAY RESULT IN SERIOUS INJURY! power sUpplY warNiNG: YOUR WOOD LATHE MUST BE CONNECTED TO A 110V120V, 15-AMP CIRCUIT BREAKER. FAILURE TO CONNECT IN THIS WAY CAN RESULT IN INJURY FROM SHOCK OR FIRE. properlY GroUNded oUtlet CUrreNt CarrYiNG proNGs GroUNdiNG This wood lathe must be grounded. In the event of a malfunction or breakdown, grounding provides a path of least resistance for electric current to reduce the risk of electric shock. This tool is equipped with an electric cord having an equipment-grounding conductor and a grounding plug. The plug must be plugged into a matching outlet that is properly installed and grounded in accordance with all local codes and ordinances. Do not modify the plug provided – if it will not fit the outlet, have the proper outlet installed by a qualified electrician. Improper connection of the equipment-grounding conductor can result in a risk of electric shock. The conductor with insulation having an outer surface that is green with or without yellow stripes is the equipmentgrounding conductor. If repair or replacement of the electric cord or plug is necessary, do not connect the equipment-grounding conductor to a live terminal. Check with a qualified electrician or service personnel if the grounding instructions are not completely understood, or if in doubt as to whether the tool is properly grounded. Use only 3-wire extension cords that have 3-prong grounding plugs and 3-pole receptacles that accept the tool’s plug. Repair or replace damaged or worn cord immediately. 110v-120v operatioN This tool is intended for use on a circuit that has an outlet that looks like the one illustrated in Fig. 1. The tool has a grounding plug that looks like the plug illustrated in Fig.1. A temporary adapter, which looks like the adapter illustrated in Fig.1A, may be used to connect this plug to a 2pole receptacle as shown if a properly grounded outlet is not available. The temporary adapter should be used only until a properly grounded outlet can be installed by a qualified electrician. The green-colored rigid ear, lug, and the like, extending from the adapter must be connected to a permanent ground such as a properly grounded outlet box. exteNsioN Cords GroUNdiNG proNG FiGUre 1 properlY GroUNded oUtlet GroUNdiNG proNG adapter Metal sCrew FiGUre 1a FiGUre 2 The use of any extension cord will cause some loss of power. Use the chart in Fig.2 to determine the minimum wire size (A.W.G-American Wire Gauge) extension cord. Use only 3-wire extension cords which have 3prong grounding type plugs and 3-hole receptacles which accept the tool’s plug. For circuits that are further away from the electrical circuit box, the wire size must be increased proportionately in order to deliver ample voltage to the wood lathe motor. Refer to Fig.2 for wire length and size. reset bUttoN (overload proteCtor) This wood lathe comes with an overload reset button (A) Fig.3. If the motor overheats or there is low voltage, a safety mechanism stops the motor. Press the reset button and restart the wood lathe. If the wood lathe does not restart, wait 5 minutes before restarting. FiGUre 3 asseMblY & operatioN warNiNG! IF ANY PART IS MISSING OR DAMAGED, DO NOT PLUG THE WOOD LATHE IN UNTIL YOU HAVE REPLACED THE MISSING OR DAMAGED PART. For your safety, complete the assembly of the wood lathe before plugging it into the power supply. iNstalliNG headstoCk with diGital readoUt 1. Install the headstock (A) Fig.4 on the top of the wood lathe bed (B) using 4 cap screws, washers and spring washers (C). Do not completely tighten the cap screws, an alignment adjustment will be needed later on to make sure the spindle is in perfect alignment with the tailstock. iNstalliNG FaCeplate 1. The faceplate (D) Fig.4 gets installed to the outside thread of the headstock spindle. Screw the faceplate onto the headstock spindle. 2. To secure the faceplate, lock the spindle using the spindle lock (E) Fig.4. Pull the spindle lock upwards and turn it so the “locked” arrow faces the front of the machine. Tighten the faceplate to the spindle, then secure it to the spindle by tightening both sets screws (F) on the faceplate collar (only one is shown). FiGUre 4 iNstalliNG/reMoviNG spUr CeNtre Before installing spur centre, make sure it is thoroughly cleaned. 1. The spur centre (G) Fig.4 gets installed inside the headstock spindle, simply push the spur centre quickly and firmly into the spindle. A properly installed spur centre will not pull out by hand. 2. To remove the spur centre from the headstock spindle, insert the knock-out rod into the opposite end of the headstock spindle and knock the spur centre out of the spindle. iNstalliNG belt, belt Cover aNd spiNdle haNdwheel FiGUre 5 The drive belt (A) Fig.6 gets installed on one of the 2 steps of the spindle and motor pulleys, the position of the belt on the pulleys will determine if you get the low range or high range variable speeds. 1. Loosen lock handle (A) Fig.5 and lift the motor/belt tension lever, retighten the lock handle. 2. Position the belt (A) Fig.6 on step 1 or 2 of the pulleys (B), refer to illustration below for belt positioning and speed range selection. BELT POSITION AND SPEED RANGE POSITION DE LA COURROIE ET GAMME DE VITESSE VARIABLE SPEED/VITESSE VARIABLE SPINDLE PULLEY POULIE DE L’ARBRE 1 MOTOR PULLEY POULIE DU MOTEUR 2 1 450-1800 RPM/tr/min. 2 950-3800 RPM/tr/min. FiGUre 6 WARNING! AVERTISSEMENT! TO REDUCE THE RISK OF SERIOUS INJURY, DO NOT REMOVE THIS PULLEY COVER WHILE OPERATING! A FIN DE RÉDUIRE LE RISQUE DE BLESSURES, NE RETIRER PAS CE COUVERCLE DES POULIES LORSQUE LA MACHINE EST EN MARCHE! 3. Once the belt is installed, loosen lock handle (A) Fig.5 and lower the motor/belt tension lever (B) Fig.5 to tension the belt, retighten the lock handle. 4. Position the belt cover (A) Fig.7 over the spindle pulley and belt and lock it in place using the side plate (B) and lock knob (C). 5. Install handwheel (D) Fig.7 to spindle by tightening the 2 set screws (E). FiGUre 7 asseMblY & operatioN Motor aNd CirCUit board wire CoNNeCtioNs 1. Make sure the motor cord (A) Fig.8 is connected to the switch box motor cord connector (1). 2. Make sure the power cord (B) Fig.8 is connected to the switch box power cord connector (2). 3. Make sure the variable speed input connector (C) is connected to the switch box speed input connector (3). 4. Connect the variable speed input connector (C) Fig.8 and (A) Fig.9 to the connector (B) Fig.9 found inside the headstock. iNstalliNG tool rest (6” or 12”) oN wood lathe bed 1. Slide the tool rest base (A) Fig.10 onto the lathe bed using the provided slotted clamp and large hex. nut, to allow for adjustment, do not fully tighten hex. nut. FiGUre 8 2. Secure the tool rest base by turning the tool rest base lock lever (B). If the lock lever will not lock the tool rest base down onto the bed, loosen or tighten the hex. nut (located on the underside of the tool rest base) in small increments to achieve proper clamping pressure. 3. Insert the desired tool rest (C) into the tool rest base and fix it in place using the lock handles (D). Caution: Make sure there is adaquate clearance between the workpiece and the tool rest assembly before turning on the wood lathe. Turn your workpiece by hand to check clearance. Normally the tool rest is positioned as close as possible to the workpiece in between the headstock and the tailstock. iNstalliNG/adjUstiNG tailstoCk FiGUre 9 1. Slide the tailstock base (A) Fig.11 onto the lathe bed using the provided slotted clamp and large hex. nut, to allow for adjustment, do not fully tighten hex. nut. 2. The tailstock can be moved to any position on the wood lathe bed by loosening the tailstock lock lever (B) and pushing the tailstock to the desired position on the bed. Tighten tailstock lock lever (B) once the adjustment is made. 3. Install the handwheel (C) and handle (D) to the tailstock, tighten set screw (E). 4. The tailstock quill (F) can extend up to 1-5/8” from the tailstock housing. To move the tailstock quill, loosen the lock handle (G) and turn the tailstock handwheel (C). Retighten lock handle once the adjustment is made. 5. Before using the wood lathe, make sure the lock handle (G) firmly locks the quill in position, the lock handle must be aligned and must engage the quill keyway or else the quill will just spin. FiGUre 10 warNiNG: The tailstock quill must always be locked with lock handle (G) before and during operation of the wood lathe. If this warning is not respected, the workpiece can be thrown from the wood lathe. Also, the tailstock quill should not protrude past the tailstock housing by more than 1-5/8” or the quill will not be supported adequately. FiGUre 11 asseMblY & operatioN iNstalliNG/reMoviNG live CeNtre Before installing live centre, make sure it is thoroughly cleaned. 1. The live centre (A) Fig.12 gets installed inside the tailstock quill (B), simply push the live centre quickly and firmly into the quill. A properly installed live centre will not pull out by hand. 2. To remove the live centre from the tailstock quill, insert the knock-out rod (C) into the opposite end of the tailstock quill (through the centre of the handwheel) and knock the live centre out of the quill or turn the handwheel (D) counterclockwise until the tailstock quill bottoms out causing the live centre to be forced out of the quill. iNstalliNG tool storaGe raCk aNd Cord wrap posts FiGUre 12 This wood lathe comes with a convenient tool storage rack (A) Fig.13, which can be installed to either the right side or left side, at the rear of the lathe bed. Install it to the bed using the supplied screwdriver and 2 pan hd. screws. This wood lathe also comes with convenient power cord wrap posts (B) Fig.13 which get installed to the rear of the lathe bed using 2 pan hd. screws. Wrap the power cord around these posts during storage. aliGNiNG spUr CeNtre with live CeNtre It is extremely important that the spur centre (A) Fig.14 installed in the headstock spindle be perfectly aligned with the live centre (B) installed in the tailstock. The headstock was not securely bolted up to now to allow this adjustment. FiGUre 13 1. Position the live centre in the tailstock as close as possible to the spur centre in the headstock. 2. Check to see if they are perfectly aligned, if they are not aligned, move the headstock into alignment and then tighten the 4 cap screws which secure the headstock. work liGht (40w Max) This wood lathe comes with a work light, only use 40 Watt max. light bulb or smaller light bulb. Light bulb not included. tUrNiNG wood lathe oN/oFF FiGUre 14 1. Your wood lathe is equipped with an On/Off switch (A) Fig.15. To turn the machine on, push the “On” button (A), to turn it off, push the “Off” button (B). 2. It is always recommended to keep your hand close to the switch when starting an operation, just in case you need to turn the wood lathe off quickly. FiGUre 15 operatioN UsiNG the variable speed dial aNd diGital readoUt The variable speed dial (A) Fig.16 determines the speed in RPM’s at which the spindle will turn, this speed is indicated on the digital readout screen (B). 1. Turn the variable speed dial (A) clockwise to increase the spindle speed and counterclockwise to decrease spindle speed. UsiNG the Forward/reverse switCh This wood lathe comes with a 3 position forward/reverse switch (C) Fig.16 which sets the direction of rotation of the spindle. Move the switch to the up position for forward rotation. To set the rotation in the reserve direction, lower the switch to the centre position, then lower it again to the down position. If the direction of rotation is changed while the spindle is turning, the wood lathe will automatically turn off and it will be necessary to turn the wood lathe back on. FiGUre 16 iNdexiNG The spindle lock knob, also known as the indexing knob (A) Fig.17 allows the user to make evenly spaced cuts on a workpiece while keeping the headstock spindle locked. The spindle index indicator (B) contains 24 grooves so the turning sections can be made in multiples of 24, 12, 8, 6, 4, 3 and 2. For example, to make 8 equal sections, mark your work at 1, 4, 7, 10, 13, 16, 19 and 22 as shown below. FiGUre 17 MAX SPEED FOR BALANCED TURNINGS VITESSE MAXIMALE POUR TOURNAGE ÉQUILIBRÉ 1. Pull the index knob (A) Fig.17 upwards and turn it clockwise to lock the spindle. 2. Make your first indexing operation. 3. Then unlock the spindle by pulling upwards on the index knob and turn it counterclockwise, the spindle will now turn freely. 4. Rotate the spindle to the next index indicator position, continue until all operations are done. FaCeplate If using the faceplate to mount your workpiece to the spindle, use brass wood screw to secure your workpiece (brass wood screws not supplied). To remove the faceplate, hold the spindle handwheel and unscrew the faceplate. ChoosiNG the riGht spiNdle speed For instructions on how to change the spindle speed range, refer to previous section named “INSTALLING BELT, BELT COVER AND SPINDLE HANDWHEEL” (Fig.5 and 6). It is very important to set the spindle speed to the recommended RPM to obtain balanced turning operations. Turning too fast for the size of your workpiece may result in injury or damage to the lathe. Follow the recommended maximum spindle speed based on your workpiece diameter as shown in chart Fig.18. DIAMETER DIAMÈTRE MAX RPM- ROUGHING MAX TR/MIN- RUDE MAX RPM- FINISHING MAX TR/MIN- FINITION 1” 3800 3800 2” 3000 3500 3” 2000 2600 4” 1500 2000 5” 1200 1600 6” 1000 1330 7” 850 1100 8” 750 1000 9” 660 900 10” 600 800 11” 540 725 12” 500 660 FiGUre 18 operatioN spiNdle tUrNiNG Spindle turning operations are performed when a workpiece is mounted between the headstock (spur centre) and the tailstock (live centre). 1. Mark the centre of both ends of your workpiece, this is easily done by drawing diagonal lines from corner to corner. The intersection of these two lines will indicate the centre point of your workpiece. 2. Drive the spur centre approximately 1/4” into the centre of your workpiece, then install the spur centre into the headstock spindle (with workpiece still attached). 3. Install the live centre into the tailstock quill, reposition the tailstock towards the other end of the workpiece until the live centre touches the centre point of the workpiece, lock the tailstock. 4. Unlock the tailstock quill, using the handwheel, push the live centre approximately 1/4” into the centre of your workpiece. 5. Position the tool rest approximately 1/4” away from your workpiece and 1/8” above the centre line. Make sure there is sufficient clearance before starting the wood lathe motor. FaCeplate tUrNiNG Faceplate turning operations are performed when a workpiece is mounted to the faceplate, which is mounted to the headstock spindle. This type of turning is ideal for open-faced workpieces such as bowls. 1. Mark the centre point at the back of your workpiece, this is easily done by drawing diagonal lines from corner to corner. The intersection of these two lines will indicate the centre point of your workpiece. 2. Centre the faceplate on the workpiece and fix the workpiece to the faceplate by drilling wood screws through the mounting holes. Make note of the lenght of the screws used as to not hit them when gouging out the centre of the workpiece. If screws can’t be drilled into your workpiece, glue a backing block to your workpiece, make sure the glue has completely cured before attempting to mount it to the faceplate and turning wood lathe On. 3. Install the faceplate and workpiece onto the headstock spindle. 4. Position the tool rest on the outside or inside of your workpiece depending on the operation, again 1/8” above the centre line of your workpiece. Make sure there is sufficient clearance before starting the wood lathe motor. tUrNiNG tips 1. Start and stop the wood lathe in the lowest speed setting. Use the lowest speed when doing rough cutting. 2. Select the right speed for the size of workpiece you are turning. Use lower speeds for large diameter workpieces (over 4”), use mid range speeds for medium diameter workpieces (2-4”) and use the higher speeds for small diameter workpieces (under 2”). See Fig.18. 3. When turning the lathe On, do not stand in front of the spinning workpiece, stand to the side until the wood lathe has reached full speed, this way if the workpiece is thrown from the wood lathe due to incorrect mounting, possible risk of injury is reduced. 4. The cutting tool must be in contact with the tool rest the entire time that it is in contact with the workpiece. 5. In order to produce quality work, good quality chisels designed for your specific turning operation are required. MaiNteNaNCe & troUbleshootiNG warNiNG! FOR YOUR OWN SAFETY, TURN THE SWITCH OFF AND REMOVE THE PLUG FROM THE POWER SOURCE BEFORE PERFORMING MAINTENANCE, CLEANING OR LUBRICATION WORK ON THE LATHE. CleaNiNG / lUbriCatiNG 1. Blow out dust accumulation and wood chips inside the motor, housing, and bed assembly frequently. 2. A coat of automotive wax applied to the bed will help keep the surface clean and keep the movement of the tool rest and tailstock smooth. It will also ensure that moisture from the wood does not remain on bare metal surfaces which can cause rust. 3. Periodic lubrication of spring loaded handles and threaded parts will make these parts easier to operate. troUbleshootiNG probleM The motor will not start or starts very slowly. solUtioN 1. Always start the wood lathe with the speed dial in the lowest speed setting. 2. Disconnect power cord, inspect electrical circuit for shorts. Replace circuit breaker if it has tripped repeatedly. 3. Inspect motor fan and cover, replace or repair if damaged. 4. Faulty motor, replace. Vibration noise during operation. 1. Tighten the pulley cover knob. 2. Inspect the pulley cover for signs of rubbing. 3. Spindle bearing(s) damaged, replace. Unsatifactory surface finish. Inaccurate turning results one end of the workpiece to the other. Tailstock quill will not move forward when handwheel is turned. 1. Incorrect speed. Adjust speed depending on workpiece diameter. 2. Use sharper or different chisel. 1. Realign the tailstock to the headstock. Both centres must be aligned. 1. Align the quill keyway with the quill lock handle.
advertisement
* Your assessment is very important for improving the workof artificial intelligence, which forms the content of this project
Key Features
- 12” x 18” swing capacity
- Variable speed control (0-3000 RPM)
- Powerful 1.5 HP motor
- Spindle lock for easy workpiece changes
- Key switch for added safety
- Cast iron bed for stability
- Adjustable tool rest for precise control
Related manuals
Frequently Answers and Questions
What is the maximum swing capacity of the KWL-1218VS?
12” x 18”
What is the variable speed range of the KWL-1218VS?
0-3000 RPM
What is the motor power of the KWL-1218VS?
1.5 HP
Does the KWL-1218VS have a spindle lock?
Yes
Does the KWL-1218VS have a key switch?
Yes
What type of bed does the KWL-1218VS have?
Cast iron
Is the tool rest of the KWL-1218VS adjustable?
Yes
advertisement