- Home
- Do-It-Yourself tools
- Garden tools
- Lawnmowers
- Toro
- Commercial Walk-Behind Mower, Fixed Deck, Pistol Grip, Hydro Drive
- User manual
Toro Commercial Walk-Behind Mower, Fixed Deck, Pistol Grip, Hydro Drive Walk Behind Mower Operator's Manual
Add to my manuals
56 Pages
advertisement
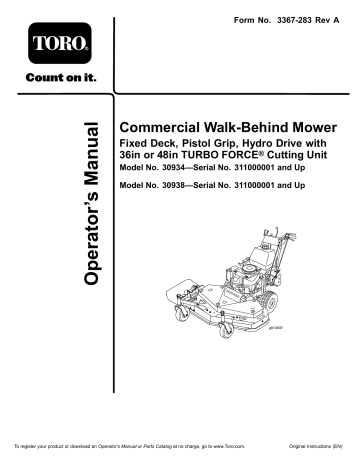
Form No. 3367-283 Rev A
Commercial Walk-Behind Mower
Fixed Deck, Pistol Grip, Hydro Drive with
36in or 48in TURBO FORCE ® Cutting Unit
Model No. 30934—Serial No. 311000001 and Up
Model No. 30938—Serial No. 311000001 and Up
g014937
To register your product or download an Operator's Manual or Parts Catalog at no charge, go to www.Toro.com.
Original Instructions (EN)
WARNING
CALIFORNIA
Proposition 65 Warning
The engine exhaust from this product contains chemicals known to the State of
California to cause cancer, birth defects, or other reproductive harm.
This spark ignition system complies with Canadian
ICES-002.
Important: This engine is not equipped with a spark arrester muffler. It is a violation of California
Public Resource Code Section 4442 to use or operate the engine on any forest-covered, brush-covered, or grass-covered land. Other states or federal areas may have similar laws.
WARNING
Removing standard original equipment parts and accessories may alter the warranty, traction, and safety of the machine. Failure to use original Toro parts could cause serious injury or death. Making unauthorized changes to the engine, fuel or venting system, may violate EPA and CARB regulations.
Replace all parts including, but not limited to, tires, belts, blades, and fuel system components with original Toro parts.
The enclosed
Engine Owner’s Manual
is supplied for information regarding the US Environmental
Protection Agency (EPA) and the California
Emission Control Regulation of emission systems, maintenance, and warranty. Replacements may be ordered through the engine manufacturer.
You may contact Toro directly at www.Toro.com for product and accessory information, help finding a dealer, or to register your product.
Whenever you need service, genuine Toro parts, or additional information, contact an Authorized Service
Dealer or Toro Customer Service and have the model
and serial numbers of your product ready. Figure 1
identifies the location of the model and serial numbers on the product. Write the numbers in the space provided.
Figure 1
1.
Model and serial number location
Model No.
Serial No.
This manual identifies potential hazards and has safety messages identified by the safety alert symbol
(Figure 2), which signals a hazard that may cause serious
injury or death if you do not follow the recommended precautions.
Introduction
This rotary-blade, lawn mower is intended to be used by residential homeowners or professional, hired operators. It is designed primarily for cutting grass on well-maintained lawns on residential or commercial properties. It is not designed for cutting brush or for agricultural uses.
Read this information carefully to learn how to operate and maintain your product properly and to avoid injury and product damage. You are responsible for operating the product properly and safely.
1.
Safety alert symbol
Figure 2
This manual uses 2 other words to highlight information.
Important calls attention to special mechanical information and Note emphasizes general information worthy of special attention.
© 2010—The Toro® Company
8111 Lyndale Avenue South
Bloomington, MN 55420
2
Contact us at www.Toro.com.
Printed in the USA.
All Rights Reserved
Contents
Introduction................................................................. 2
Safety ........................................................................... 4
Safe Operating Practices ....................................... 4
Toro Mower Safety ............................................... 5
Slope Indicator..................................................... 7
Safety and Instructional Decals ............................. 8
Product Overview ...................................................... 12
Controls ............................................................. 12
Specifications ..................................................... 13
Attachments/Accessories................................... 13
Operation................................................................... 14
Adding Fuel ....................................................... 14
Think Safety First ............................................... 15
Operating the Parking Brake ............................... 15
Starting and Stopping the Engine ........................ 15
Operating the Neutral Locks............................... 16
Operating the Mower Blade Control Knob
(PTO) ............................................................ 17
The Safety Interlock System................................ 17
Driving the Machine Forward and
Backward ....................................................... 18
Bringing the Machine to Neutral Position ............ 19
Stopping the Machine......................................... 19
Pushing the Machine by Hand............................. 19
Adjusting the Flow Baffle ................................... 19
Positioning the Flow Baffle................................. 20
Transporting Machines ....................................... 21
Side Discharging or Mulching the Grass .............. 22
Adjusting the Height-of-Cut ............................... 22
Adjusting the Caster Position .............................. 23
Adjusting the Handle Height .............................. 23
Height of Cut Chart............................................ 25
Maintenance............................................................... 26
Recommended Maintenance Schedule(s) ................ 26
Lubrication............................................................. 27
How to Grease ................................................... 27
Lubricating the Caster and Wheel
Bearings ......................................................... 27
Greasing the Mower Belt Idler ............................ 27
Greasing the Pump Control and Bell
Crank ............................................................. 27
Engine Maintenance............................................... 28
Servicing the Air Cleaner .................................... 28
Servicing the Engine Oil ..................................... 29
Servicing the Spark Plugs.................................... 30
Fuel System Maintenance ....................................... 31
Servicing the Fuel Tank ...................................... 31
Servicing the Fuel Filter ...................................... 32
Servicing the Fuel Vent System ........................... 32
Drive System Maintenance ..................................... 33
Adjusting the Speed Control Linkage .................. 33
Adjusting the Neutral Control Linkages .............. 33
Adjusting the Hydro Control Linkages ................ 34
Adjusting the Control Rod.................................. 36
Adjusting the Tracking ....................................... 37
Adjusting the Spring Anchor Links ..................... 37
Checking the Tire Pressure ................................. 37
Cooling System Maintenance .................................. 38
Cleaning the Air Intake Screen ............................ 38
Cleaning the Cooling System............................... 38
Brake Maintenance ................................................. 39
Servicing the Brake............................................. 39
Belt Maintenance.................................................... 40
Checking the Belts.............................................. 40
Replacing the Mower Belt ................................... 40
Adjusting the Mower Belt Tension ...................... 41
Hydraulic System Maintenance ............................... 45
Servicing the Hydraulic System ........................... 45
Mower Deck Maintenance ...................................... 47
Servicing the Cutting Blades ............................... 47
Adjusting the Blade Brake................................... 49
Replacing the Grass Deflector............................. 49
Storage ....................................................................... 50
Troubleshooting......................................................... 52
Schematics ................................................................. 54
3
Safety
Note: The addition of attachments made by other manufacturers that do not meet American
National Standards Institute certification will cause noncompliance of this machine.
Improper use or maintenance by the operator or owner can result in injury. To reduce the potential for injury, comply with these safety instructions and always pay attention to the safety alert symbol , which means
CAUTION, WARNING, or DANGER-“personal safety instruction." Failure to comply with the instruction may result in personal injury or death.
Safe Operating Practices
The following instructions are from ANSI standard
B71.4-2004.
Training
• Read the Operator’s Manual and other training material. If the operator(s) or mechanic(s) can not read English it is the owner’s responsibility to explain this material to them.
• Become familiar with the safe operation of the equipment, operator controls, and safety signs.
• All operators and mechanics should be trained. The owner is responsible for training the users.
• Never let children or untrained people operate or service the equipment. Local regulations may restrict the age of the operator.
• The owner/user can prevent and is responsible for accidents or injuries occurring to himself or herself, other people or property.
Preparation
• Evaluate the terrain to determine what accessories and attachments are needed to properly and safely perform the job. Only use accessories and attachments approved by the manufacturer.
• Wear appropriate clothing including hard hat, safety glasses and hearing protection. Long hair, loose clothing or jewelry may get tangled in moving parts.
• Inspect the area where the equipment is to be used and remove all objects such as rocks, toys and wire which can be thrown by the machine.
• Use extra care when handling gasoline and other fuels. They are flammable and vapors are explosive.
– Use only an approved container
– Never remove gas cap or add fuel with engine running. Allow engine to cool before refueling.
Do not smoke.
– Never refuel or drain the machine indoors.
• Check that operator’s presence controls, safety switches and shields are attached and functioning properly. Do not operate unless they are functioning properly.
Operation
• Lightning can cause severe injury or death. If lightning is seen or thunder is heard in the area, do not operate the machine; seek shelter.
• Never run an engine in an enclosed area.
• Only operate in good light, keeping away from holes and hidden hazards.
• Be sure all drives are in neutral and parking brake is engaged before starting engine. Only start engine from the operator’s position.
• Be sure of your footing while using this machine, especially when backing up. Walk, don’t run. Never operate on wet grass. Reduced footing could cause slipping.
• Slow down and use extra care on hillsides. Be sure to travel side to side on hillsides. Turf conditions can affect the machine’s stability. Use caution while operating near drop-offs.
• Slow down and use caution when making turns and when changing directions on slopes.
• Never raise deck with the blades running.
• Never operate with the PTO shield, or other guards not securely in place. Be sure all interlocks are attached, adjusted properly, and functioning properly.
• Never operate with the discharge deflector raised, removed or altered, unless using a grass catcher.
• Do not change the engine governor setting or overspeed the engine.
• Stop on level ground, disengage drives, engage parking brake, shut off engine before leaving the operator’s position for any reason including emptying the catchers or unclogging the chute.
• Stop equipment and inspect blades after striking objects or if an abnormal vibration occurs. Make necessary repairs before resuming operations.
• Keep hands and feet away from the cutting unit.
• Look behind and down before backing up to be sure of a clear path.
4
• Keep pets and bystanders away.
• Slow down and use caution when making turns and crossing roads and sidewalks. Stop blades if not mowing.
• Be aware of the mower discharge direction and do not point it at anyone.
• Do not operate the mower under the influence of alcohol or drugs.
• Use care when loading or unloading the machine into or from a trailer or truck.
• Use care when approaching blind corners, shrubs, trees, or other objects that may obscure vision.
Maintenance and storage
• Disengage drives, set parking brake, stop engine and remove key or disconnect spark plug wire. Wait for all movement to stop before adjusting, cleaning or repairing.
• Clean grass and debris from cutting unit, drives, mufflers, and engine to help prevent fires. Clean up oil or fuel spillage.
• Let engine cool before storing and do not store near flame.
• Shut off fuel while storing or transporting. Do not store fuel near flames or drain indoors.
• Park machine on level ground. Set parking brake.
Never allow untrained personnel to service machine.
• Use jack stands to support components when required.
• Carefully release pressure from components with stored energy.
• Disconnect the battery or remove spark plug wire before making any repairs. Disconnect the negative terminal first and the positive last. Reconnect the positive first and negative last.
• Use care when checking blades. Wrap the blade(s) or wear gloves, and use caution when servicing them.
Only replace blades. Never straighten or weld them.
• Keep hands and feet away from moving parts. If possible, do not make adjustments with the engine running.
• Keep all parts in good working condition and all hardware tightened. Replace all worn or damaged decals.
Toro Mower Safety
The following list contains safety information specific to Toro products and other safety information you must know.
This product is capable of amputating hands and feet and throwing objects. Always follow all safety instructions to avoid serious injury or death.
This product is designed for cutting and recycling grass or, when equipped with a grass bagger, for catching cut grass. Any use for purposes other than these could prove dangerous to user and bystanders.
General Operation
• Be sure the area is clear of other people before mowing. Stop the machine if anyone enters the area.
• Do not touch equipment or attachment parts which may be hot from operation. Allow to cool before attempting to maintain, adjust or service.
• Use only Toro approved attachments. Warranty may be voided if used with unapproved attachments.
• Check carefully for overhead clearances (i.e.
branches, doorways, electrical wires) before operating under any objects and do not contact them.
Slope Operation
All slopes and ramps require extra caution. If you feel uneasy on a slope, do not mow it.
• Remove obstacles such as rocks, tree limbs, etc. from the mowing area.
• Watch for holes, ruts or bumps. Tall grass can hide obstacles.
• Use caution near drop-offs, ditches, or embankments.
The machine could suddenly turn over if a wheel goes over the edge of a cliff or ditch, or if an edge caves in.
• Use extra care with grass catchers or other attachments. These can change the stability of the machine.
• Keep all movement on slopes slow and gradual. Do not make sudden changes in speed or direction.
• Mow slopes side to side.
• Do not mow slopes greater than 20 degrees.
Service
• Never store the machine or fuel container inside where there is an open flame, such as near a water heater or furnace.
• Keep nuts and bolts tight, especially the blade attachment bolts. Keep equipment in good condition.
• Never tamper with safety devices. Check safety systems for proper operation before each use.
5
• Use only genuine replacement parts to ensure that original standards are maintained.
• Check brake operation frequently. Adjust and service as required.
6
Slope Indicator
G01 1841
Figure 3
This page may be copied for personal use.
1.
The maximum slope you can safely operate the machine on is 20 degrees . Use the slope chart to determine the degree of slope of hills before operating.
Do not operate this machine on a slope greater than 20 degrees.
Fold along the appropriate line to match the recommended slope.
2.
Align this edge with a vertical surface, a tree, building, fence pole, etc.
3.
Example of how to compare slope with folded edge.
7
Safety and Instructional
Decals
Safety decals and instructions are easily visible to the operator and are located near any area of potential danger. Replace any decal that is damaged or lost.
98-0776
43-8480
98-3296
For Models with 36 Inch Mower Decks
66-1340
95-5537
1.
Read the Operator’s
Manual for instructions on operating the cutting blade
2.
Push forward to engage
3.
Pull back to disengage
98-5130
1.
Warning—read the Operator’s Manual for instructions on torquing the blade bolt/nut to 75-80 ft-lb (102-106 N ⋅ m).
98-5954
8
Battery Symbols
Some or all of these symbols are on your battery
1.
Explosion hazard
2.
No fire, open flame, or smoking.
3.
Caustic liquid/chemical burn hazard
4.
Wear eye protection
5.
Read the Operator’s
Manual.
6.
Keep bystandersa safe distance from the battery.
7.
Wear eye protection; explosive gases can cause blindness and other injuries
8.
Battery acid can cause blindness or severe burns.
9.
Flush eyes immediately with water and get medical help fast.
10.
Contains lead; do not discard.
104-8569
105-4109
105-4110
99-3943
For Models with 48 Inch Mower Decks
1.
Engine
1.
Fast
2.
Continuous variable setting
106-2733
3.
Slow
103-2103
9
106-2743
Manufacturer’s Mark
1.
Indicates the blade is identified as a part from the original machine manufacturer.
1.
Hydraulic oil level
2.
Read the Operator’s
Manual .
115-4212
3.
Warning—do not touch the hot surface.
110-2067
106-0699
110-2068
1.
Read the Operator’s Manual .
10
1.
Park
2.
Drive
3.
Neutral
4.
Engine—stop
5.
Engine—run
6.
Warning—wear ear protection.
106-2738
7.
Fast
8.
Continuous variable setting
9.
Slow
10.
Neutral
11
Product Overview
1.
Side discharge
2.
Mower deck
3.
Recoil starter
4.
Gas tank g014938
Figure 4
5.
Controls
6.
Handle
7.
Caster wheel
Controls
Become familiar with all the controls (Figure 5) before
you start the engine and operate the machine.
1.
Throttle control
2.
Speed control lever
3.
Ignition switch
4.
Neutral lock
5.
Operator Presence
Control levers (OPC)
Figure 5
6.
Handle
7.
Drive Lever
8.
Blade control knob (PTO)
9.
Choke
10.
Fuel shut-off valve
Throttle Control
The throttle control has two positions: Fast and Slow .
Operator Presence Control (OPC)
Levers
When you squeeze the OPC levers against the handles, the OPC system senses that the operator is in the normal operating position. When you release the OPC levers, the OPC system senses that the operator has left the normal operating position, and the system will stop the engine if either the speed control lever is not in the neutral position or the blade control (PTO) knob is engaged.
Blade Control Knob (PTO)
The blade control knob (PTO) is used to engage and disengage the drive belt to drive the mower blades with the OPC levers pressed against the handles. Pull the knob up to engage the blades and down to disengage the blades.
12
Ignition Switch
This switch is used in conjunction with recoil starter and has two positions: Run and Off .
Speed Control Lever
This machine has a variable speed control with a neutral position. This controls how fast the machine will travel forward.
Drive Levers
Release drive levers to engage forward traction operation and squeeze the levers until an increase in force is felt to go into neutral position and continue to squeeze to go in reverse. Squeeze right side of drive lever to turn right and left side to turn left.
Neutral Lock
Squeeze drive levers back until an increase in force is felt and move locks to the rear for neutral lock.
Recoil Starter
Pull the recoil starter handle to start engine (Figure 4).
Fuel Shut-off Valve
Close the fuel shut-off valve when transporting or storing mower.
Choke
Use the choke to start a cold engine.
Specifications
Note: Specifications and design are subject to change without notice.
36 inch mowers:
Width with deflector down
Length
Height
Weight
46.6 inches (118.4 cm)
80 inches (203.2 cm)
44 inches (111.8 cm)
532 lb (241 kg)
Attachments/Accessories
A selection of Toro approved attachments and accessories are available for use with the machine to enhance and expand its capabilities. Contact your
Authorized Service Dealer or Distributor or go to www.Toro.com for a list of all approved attachments and accessories.
48 inch mowers:
Width with deflector down
Length
Height
Weight
63–1/2 inches (161.3 cm)
78–3/8 inches (198.9 cm)
44 inches (111.8 cm)
570 lb (259 kg)
13
Operation
Adding Fuel
Use Unleaded Regular Gasoline suitable for automotive use (85 pump octane minimum). Leaded regular gasoline may be used if unleaded regular is not available.
Important: Never use methanol, gasoline containing methanol, or gasohol containing more than 10% ethanol because the fuel system could be damaged. Do not mix oil with gasoline.
DANGER
In certain conditions, gasoline is extremely flammable and highly explosive. A fire or explosion from gasoline can burn you and others and can damage property.
• Fill the fuel tank outdoors, in an open area, when the engine is cold. Wipe up any gasoline that spills.
• Never fill the fuel tank inside an enclosed trailer.
• Do not fill the fuel tank completely full. Add gasoline to the fuel tank until the level is 1/4 to
1/2 inch (6 to 13 mm) below the bottom of the filler neck. This empty space in the tank allows gasoline to expand.
• Never smoke when handling gasoline, and stay away from an open flame or where gasoline fumes may be ignited by a spark.
• Store gasoline in an approved container and keep it out of the reach of children. Never buy more than a 30-day supply of gasoline.
• Do not operate without entire exhaust system in place and in proper working condition.
DANGER
In certain conditions during fueling, static electricity can be released causing a spark which can ignite the gasoline vapors. A fire or explosion from gasoline can burn you and others and can damage property.
• Always place gasoline containers on the ground away from your vehicle before filling.
• Do not fill gasoline containers inside a vehicle or on a truck or trailer bed because interior carpets or plastic truck bed liners may insulate the container and slow the loss of any static charge.
• When practical, remove gas-powered equipment from the truck or trailer and refuel the equipment with its wheels on the ground.
• If this is not possible, then refuel such equipment on a truck or trailer from a portable container, rather than from a gasoline dispenser nozzle.
• If a gasoline dispenser nozzle must be used, keep the nozzle in contact with the rim of the fuel tank or container opening at all times until fueling is complete.
WARNING
Gasoline is harmful or fatal if swallowed.
Long-term exposure to vapors can cause serious injury and illness.
• Avoid prolonged breathing of vapors.
• Keep face away from nozzle and gas tank or conditioner bottle opening.
• Keep gas away from eyes and skin.
Using Stabilizer/Conditioner
Use a fuel stabilizer/conditioner in the machine to provide the following benefits:
• Keeps gasoline fresh during storage of 90 days or less. For longer storage it is recommended that the fuel tank be drained.
• Cleans the engine while it runs
• Eliminates gum-like varnish buildup in the fuel system, which causes hard starting
Important: Do not use fuel additives containing methanol or ethanol.
Add the correct amount of gas stabilizer/conditioner to the gas.
14
Note: A fuel stabilizer/conditioner is most effective when mixed with fresh gasoline. To minimize the chance of varnish deposits in the fuel system, use fuel stabilizer at all times.
Filling the Fuel Tank
1. Shut the engine off and set the parking brake.
2. Clean around fuel tank cap and remove the cap.
Add unleaded regular gasoline to fuel tank, until the level is 1/4 to 1/2 inch (6 to 13 mm) below the bottom of the filler neck. This space in the tank allows gasoline to expand. Do not fill the fuel tank completely full.
3. Install fuel tank cap securely. Wipe up any gasoline that may have spilled.
Think Safety First
Carefully read all the safety instructions and decals in the safety section. Knowing this information could help you or any bystanders avoid injury.
The use of protective equipment for eyes, hearing, feet and head is recommended.
CAUTION
This machine produces sound levels in excess of
85 dBA at the operator’s ear and can cause hearing loss through extended periods of exposure.
Wear hearing protection when operating this machine.
Figure 6
1.
Warning—wear hearing protection.
Operating the Parking Brake
Always set the parking brake when you stop the machine or leave it unattended. Before each use, check the parking brake for proper operation.
If the parking brake does not hold securely, adjust it.
Refer to Servicing the Parking Brake.
CAUTION
Children or bystanders may be injured if they move or attempt to operate the machine while it is unattended.
Always remove the ignition key and set the parking brake when leaving the machine unattended, even if just for a few minutes.
Setting the Parking Brake
Pull the parking brake lever rearward (Figure 7).
Figure 7
1.
Parking brake lever (in the released position)
Releasing the Parking Brake
Push the parking brake lever forward.
Starting and Stopping the
Engine
Starting the Engine
1. Connect the wires to the spark plugs.
2. Open the fuel valve.
Note: A cold weather staring kit has been incorporated to assist engine starting in cold weather or when the unit has not been run for a period of time.
To use the cold start kit:
•
Grasp split ring (Figure 8) on right side of
machine, pull ring and chain straight out from side of machine and hook ring over control shield bolt.
15
4. Let engine idle for 30 to 60 seconds before turning the engine off.
5. To stop the engine, turn the ignition key to off.
1.
Split ring
Figure 8
2.
Control shield bolt
• After the engine is started, pull the chain straight out from side of machine until ring can be removed from shield bolt. Slowly release tension on chain.
3. Disengage the blade control knob (PTO) and move the speed control lever to neutral.
4. Move the drive levers to neutral and set the neutral locks.
5. Set the parking brake.
6. Turn the ignition key to the run
7. To start a cold engine, move the throttle control midway between the fast and slow positions.
8. To start a warm engine, move the throttle control to the fast position.
9. Pull the choke knob if the engine is cold (Figure 5).
Note: A warm or hot engine usually does not require any choking.
10. Grasp the recoil starter handle firmly and pull it out until positive engagement results; then pull the handle vigorously to start the engine. Allow the rope to recoil slowly.
11. Push the choke to off as the engine warms up
12. If the engine is cold, allow it to warm up and then move the throttle control to the fast position.
Stopping the Engine
1. Move the throttle lever to slow (Figure 9).
2. Move drive levers to neutral and set neutral locks.
3. Disengage the blade control knob (PTO) and move the speed control lever to neutral.
1.
Throttle lever
2.
Ignition switch
Figure 9
3.
Choke
Important: Make sure fuel shut off valve is closed before transporting or storing machine, as fuel leakage may occur. Before storing machine, pull wire off spark plug(s) to prevent possibility of accidental starting.
Operating the Neutral Locks
Always set the neutral lock when you stop the machine.
Set the parking brake if it is left unattended.
Setting the Neutral Lock
1. Squeeze the drive levers back until an increase in force is felt.
2. Place thumbs on the upper part of the locks and
16
2. Pull blade control knob (PTO) up. Hold the OPC levers against handle grip.
Note: The engine will kill if the OPC levers are released with the mower running and the speed control lever is not in neutral.
3. Restart the engine and repeat the procedure to engage the mower blades if the operator presence control (OPC) levers are released.
1.
Handle
2.
Neutral lock
3.
Neutral position
Figure 10
4.
Drive lever
5.
Full speed forward
6.
Reverse position
Releasing the Neutral Lock
1. Squeeze the drive levers back until an increase in force is felt.
2. Place thumbs on the upper part of locks and move them forward until the pins are in the forward slot
1.
Throttle lever
2.
Operator Presence
Control levers (OPC)
3.
Handle
Figure 12
4.
Drive Lever
5.
Blade control knob (PTO)
1.
Handle
2.
Neutral lock
3.
Drive lever
Figure 11
4.
Pin in full speed forward
5.
Handle
6.
Forward slot
Operating the Mower Blade
Control Knob (PTO)
The blade control knob (PTO) is used in conjunction with the Operator Presence Control (OPC) levers to engage and disengage the mower blades.
Engaging the Mower Blades (PTO)
1. To engage blades, squeeze the Operator Presence
Control (OPC) levers against handle grips
Disengaging the Mower Blades (PTO)
The mower blades can be disengaged by one of the following steps.
1. Push the blade control knob (PTO) down to off
2. Releasing the Operator Presence Control (OPC) levers will kill the engine and stop the blades
(Figure 12) with the blade control lever engaged.
The Safety Interlock System
CAUTION
If safety interlock switches are disconnected or damaged the machine could operate unexpectedly causing personal injury.
• Do not tamper with the interlock switches.
• Check the operation of the interlock switches daily and replace any damaged switches before operating the machine.
17
Understanding the Safety Interlock
System
The safety interlock system is designed to prevent the mower from starting unless:
• The blade control knob (PTO) is pushed off.
• The speed control lever is in neutral.
The safety interlock system is designed to kill the engine when:
• The Operator Presence Control (OPC) levers are released with the mower engaged and/or the speed control is out of neutral.
• The speed control lever is shifted out of neutral without holding OPC levers or with the brake engaged.
• The blade control knob (PTO) is pulled up without holding the OPC levers.
Testing the Safety Interlock System
Service Interval: Before each use or daily
Test the safety interlock system before you use the machine each time. If the safety system does not operate as described, have an Authorized Service
Dealer repair the safety system immediately.
WARNING
While testing the safety interlock system, the machine may move forward and cause personal injury or property damage.
• Perform the safety interlock test in an open area.
• Ensure no one is standing in front of the machine while performing the safety interlock test.
1. Set the neutral locks and place speed control lever in neutral.
2. Start the engine; refer to Starting and Stopping the
Engine.
3. Without holding the Operator Presence Control
(OPC) levers, pull the blade control knob (PTO) up.
The engine should kill.
4. Push the blade control knob down to off.
5. With engine running, hold down the OPC levers.
Pull the blade control knob (PTO) up. The drive belt should engage and the mower blades begin rotating.
6. With engine running, release the OPC levers. The engine should kill.
7. With the engine running, move the speed control lever forward slightly. Release the OPC levers. The engine should kill.
8. If all the above conditions are not met have an
Authorized Service Dealer repair the safety system immediately.
Driving the Machine Forward and Backward
The throttle control regulates the engine speed as measured in RPM (revolutions per minute). Place the throttle control in the fast position for best mowing performance.
Driving Forward
1. Release the parking brake.
2. To go forward, move the speed control lever to desired speed.
3. Release the neutral lock. Refer to Releasing the
Neutral Lock.
4. Slowly release the drive levers to move forward
To go straight, release drive levers equally
To turn, squeeze the drive lever on the side and
direction you want to turn (Figure 13).
1.
Drive lever
Figure 13
2.
Speed control lever
Driving Backward
From neutral, slowly squeeze the drive levers to move
18
Bringing the Machine to
Neutral Position
Always set the neutral lock and parking brake when you stop the machine.
1. Squeeze the drive levers to neutral position.
2. Set the neutral locks. Refer to Operating Neutral
Locks.
3. Move speed control lever to neutral position.
Note: The speed control lever can also be used to bring the mower to neutral position and then set the neutral locks.
Stopping the Machine
1. To stop the machine, squeeze the drive levers to neutral position and engage neutral locks.
2. Move speed control lever into neutral.
3. Stop the engine; refer to Stopping the Engine.
4. Wait for all moving parts to stop before leaving the operating position. Set the parking brake.
CAUTION
Children or bystanders may be injured if they move or attempt to operate the machine while it is unattended.
Always remove the ignition key and set the parking brake when leaving the machine unattended, even if just for a few minutes.
Pushing the Machine by Hand
The by-pass valves allow the machine to be pushed by hand without the engine running.
Important: Always push the machine by hand.
Never tow the machine because hydraulic damage may occur.
To Push the Machine
1. Disengage the PTO, move the motion control levers to the neutral locked position and set the parking brake.
2. Open the by-pass valves by turning them counter clockwise 1 to 2 turns. This allows hydraulic fluid to by-pass the pumps and the wheels to turn
3. Release the parking brake.
4. Push the machine to the desired location.
5. Set the parking brake.
6. Close the by-pass valves, but do not overtighten them.
Note: Rotate the by-pass valves a maximum of 2 turns so the valve does not come out of the body causing fluid to run out.
Important: Do not start or operate the machine with the by-pass valves open. Damage to system may occur.
1.
By-pass valve
Figure 14
Adjusting the Flow Baffle
The mower discharge flow can be adjusted for different types of mowing conditions. Position the cam lock and baffle to give the best quality of cut.
1. Disengage the PTO, move the motion control levers to the neutral locked position and set the parking brake.
2. Stop the engine, remove the key, and wait for all moving parts to stop before leaving the operating position.
3. To adjust the cam lock, swing the lever up to loosen
4. Adjust the baffle and cam lock in the slot to the desired discharge flow.
5. Swing the lever back over to tighten the baffle and
6. If the cam does not lock the baffle into place or it is too tight, loosen the lever and then rotate the cam lock. Adjust the cam lock until the desired locking pressure is achieved.
19
1.
Cam lock
2.
Lever
Figure 15
3.
Rotate cam to increase or decrease locking pressure
4.
Slot
Positioning the Flow Baffle
The following figures are only recommendations for use. Adjustments will vary by grass type, moisture content, and height of grass.
Note: If the engine power draws down and the mower ground speed is the same, open up the baffle.
Position A
This is the full rear position (see Figure 16). The
suggested use for this position is a follows.
• Use for short, light grass mowing conditions.
• Use in dry conditions.
• For smaller grass clippings.
• Propels grass clippings farther away from the mower.
Figure 16
Position B
Use this position when bagging (Figure 17).
20
Figure 17 Figure 18
Position C
This is the full open position. The suggested use for
this position is as follows (Figure 18).
• Use in tall, dense grass mowing conditions.
• Use in wet conditions.
• Lowers the engine power consumption.
• Allows increased ground speed in heavy conditions.
• This position is similar to the benefits of the Toro
SFS mower.
Transporting Machines
Use a heavy-duty trailer or truck to transport the machine. Ensure that the trailer or truck has all necessary lighting and marking as required by law.
Please carefully read all the safety instructions.
Knowing this information could help you, your family, pets or bystanders avoid injury.
To transport the machine:
1. Stop the engine, remove the key, set the brake, and close the fuel valve.
2. Securely fasten the machine to the trailer or truck with straps, chains, cable, or ropes.
3. Secure a trailer to towing vehicle with safety chains.
4. If applicable, connect the trailer brakes.
21
Side Discharging or Mulching the Grass
This mower has a hinged grass deflector that disperses clippings to the side and down toward the turf.
DANGER
Without the grass deflector, discharge cover, or complete grass catcher assembly mounted in place, you and others are exposed to blade contact and thrown debris. Contact with rotating mower blade(s) and thrown debris will cause injury or death.
• Never remove the grass deflector from the mower because the grass deflector routes material down toward the turf. If the grass deflector is ever damaged, replace it immediately.
• Never put your hands or feet under the mower.
• Never try to clear discharge area or mower blades unless you release the bail and the power take off (PTO) is off. Rotate the ignition key to
Off. Also remove the key and pull the wire off the spark plug(s).
Adjusting the Height-of-Cut
This machine has a 1 to 4-1/4 inch (26 to 108 mm) range for height-of-cut. This can be achieved by adjusting blade spacers, rear axle height and front caster spacers. Use the Height-of-Cut chart to select the combination of adjustments required
Adjusting the Blade Height
Adjust the Blades by using the 4 spacers (1/4 inch) spacers on the blade spindle bolts. This allows for a
1-inch (25 mm) adjustment range of cutting height, in 1/4 inch (6 mm) increments, in any axle position.
Use the same number of blade spacers on all blades to achieve a level cut (2 above and 2 below, 1 above and 3 below, etc.).
1. Disengage the PTO and pull the throttle to the slow position.
2. Turn the ignition switch to off.
3. Wait for all moving parts to stop before leaving the operating position. Set the parking brake.
4. Hold the blade bolt and remove the nut. Slide the bolt down through the spindle, and change the
spacers as needed (Figure 19).
1.
Blade
2.
Blade bolt
3.
Curved washer
Figure 19
4.
Spacer
5.
Thin washer
6.
Nut
5. Install the bolt, curved washer, blade, add extra spacers, and secure them with a thin washer and a
6. Torque the blade bolt to 75-80 ft.-lb. (101-108 N-m).
Adjusting the Axle Height
Adjust the axle position to the selected height-of-cut setting.
1. Disengage the PTO and pull the throttle to the stop position.
2. Wait for all moving parts to stop before leaving the operating position and then set the parking brake.
3. Place a jack under the rear center of the engine frame. Raise the back end of the engine frame up enough to remove the drive wheels.
4. Remove the drive wheels.
5. Loosen, but do not remove, the 2 top axle bolts
22
6. Remove the 2 lower axle bolts (Figure 20).
Adjusting the Handle Height
The handle position can be adjusted to match the operator’s height preference.
1. Remove the hairpin cotter pins and clevis pins from
the drive levers and neutral locks (Figure 22).
1.
Top axle bolt
Figure 20
2.
Lower axle bolt
7. Raise or lower the mounting bracket, so that you can install the 2 axle adjustment bolts in the desired
hole location (Figure 20). A tapered punch can be
used to help align the holes.
8. Tighten all 4 bolts.
9. Install drive wheels and lower the mower.
Adjusting the Caster Position
1. Using the Height-of-Cut Chart, adjust the caster spacers to match with the axle hole selected
1.
Control rod
2.
Clevis pin
3.
Drive lever
4.
Operator Presence
Control lever (OPC)
Figure 22
5.
Left handle shown
6.
Neutral lock
7.
Hairpin cotter pin
2. Loosen the upper flange bolts (3/8 x 1-1/4 inch) and flange nut securing handle to rear frame
3. Remove the lower flange bolts (3/8 x 1 inch) and flange nuts securing handle to rear frame
4. Pivot handle to desired operating position and install lower flange bolts (3/8 x 1 inch)and flange nuts into mounting holes. Tighten all flange bolts.
Figure 21
1.
Latch pin
2.
Spacer, 3/16 inch (5 mm)
3.
Spacer, 1/2 inch (13 mm)
2. Remove the latch pin, slide the caster from the
support, and change the spacers (Figure 21).
3. Install the caster in the support and insert the latch
23
Figure 23
1.
Control rod fitting
2.
Lower mounting holes
3.
Rear frame
4.
Lower flange bolt (3/8 x 1 inch)
5.
Upper flange bolt (3/8 x
1-1/4 inches)
6.
High position
7.
Lower position
8.
Upper mounting hole
9.
Handle
10.
Flange nut (3/8 inch)
11.
5. Adjust the control rod length by rotating the control rod in the rod fitting (Fig. 8).
6. Install hairpin cotter between drive levers and neutral locks and into clevis pins (Fig. 25).
Note: Make sure the clevis pins are inserted into the neutral locks.
7. Perform the hydraulic linkage adjustments when the handle height is changed; refer Hydraulic Linkage
Adjustments.
24
Height of Cut Chart
Number of spacers below caster
1/2 inch
(13mm)
3/16 inch (5 mm)
Axle Position
A 0 0
A
A
B
B
B
B
C
C
C
C
D
D
D
D
E
E
E
0
1
0
1
1
2
1
2
2
3
2
3
3
4
3
4
4
1
0
1
0
1
0
1
0
1
0
1
0
1
0
1
0
1
4
Number of 1/4 inch blade spacers below spindle
3
1–1/4 inch
(32 mm)
1–3/8 inch
(35 mm)
1–5/8 inch
(41 mm)
1–5/8 inch
(41 mm)
1–7/8 inch
(48 mm)
2 inch (51 mm)
2–1/4 inch
(57 mm)
2–1/8 inch
(54 mm)
2–3/8 inch
(60 mm)
2–1/2 inch
(64 mm)
2–3/4 inch
(70 mm)
2–5/8 inch
(67 mm)
2–3/4 inch
(70 mm)
3 inch (76 mm)
3–1/4 inch
(82 mm)
3–1/8 inch
(79 mm)
3–3/8 inch
(86 mm)
3–1/2 inch
(89 mm)
1 inch (26 mm)
1–1/8 inch
(29 mm)
1–3/8 inch
(35 mm)
1–3/8 inch
(35 mm)
1–5/8 inch
(41 mm)
1–3/4 inch
(45 mm)
2 inch (51 mm)
1–7/8 inch
(48 mm)
2–1/8 inch
(55 mm)
2–1/4 inch
(57 mm)
2–1/2 inch
(64 mm)
2–3/8 inch
(61 mm)
2–1/2 inch
(64 mm)
2–3/4 inch
(70 mm)
3 inch (76 mm)
2–7/8 inch
(73 mm)
3–1/8 inch
(79 mm)
3–1/4 inch
(82 mm)
2 1 0
1–1/2 inch
(38 mm)
1–5/8 inch
(41 mm)
1–7/8 inch
(48 mm)
1–7/8 inch
(48 mm)
2–1/8 inch
(54 mm)
2–1/4 inch
(57 mm)
2–1/2 inch
(64 mm)
2–3/8 inch
(60 mm)
2–5/8 inch
(67 mm)
2–3/4 inch
(70 mm)
3 inch (76 mm)
2–7/8 inch
(73 mm)
3 inch (76 mm)
3–1/4 inch
(82 mm)
3–1/2 inch
(89 mm)
3–3/8 inch
(86 mm)
3–5/8 inch
(92 mm)
3–3/4 inch
(95 mm)
2 inch (51 mm)
2–1/8 inch
(54 mm)
2–3/8 inch
(60 mm)
2–3/8 inch
(60 mm)
2–5/8 inch
(67 mm)
2–3/4 inch
(70 mm)
3 inch (76 mm)
2–7/8 inch
(73 mm)
3–1/8 inch
(79 mm)
3–1/4 inch
(83 mm)
3–1/2 inch
(89 mm)
3–3/8 inch
(86 mm)
3–1/2 inch
(89 mm)
3–3/4 inch
(95 mm)
4 inch (102 mm)
3–7/8 inch
(98 mm)
4–1/8 inch
(105 mm)
4–1/4 inch
(108 mm)
1–3/4 inch
(45 mm)
1–7/8 inch
(48 mm)
2–1/8 inch
(54 mm)
2–1/8 inch
(54 mm)
2–3/8 inch
(60 mm)
2–1/2 inch
(64 mm)
2–3/4 inch
(70 mm)
2–5/8 inch
(67 mm)
2–7/8 inch
(73 mm)
3 inch (76 mm)
3–1/4 inch
(83 mm)
3–1/8 inch
(79 mm)
3–1/4 inch
(82 mm)
3–1/2 inch
(89 mm)
3–3/4 inch
(95 mm)
3–5/8 inch
(92 mm)
3–7/8 inch
(98 mm)
4 inch (102 mm)
25
Maintenance
Note: Determine the left and right sides of the machine from the normal operating position.
Recommended Maintenance Schedule(s)
Maintenance Service
Interval
After the first 8 hours
After the first 25 hours
Before each use or daily
Every 25 hours
Every 50 hours
Every 100 hours
Every 200 hours
Every 400 hours
Before storage
Maintenance Procedure
• Change the engine oil.
• Check the mower belt tension.
• Check the hydraulic fluid level.
• Change the hydraulic filter.
• Check the mower belt tension.
• Check the safety system.
• Grease the caster wheels and caster pivot.
• Check the engine oil level.
• Clean the air intake screen.
• Inspect the blades.
• Clean the mower deck.
• Clean foam air cleaner element.
• Check the hydraulic fluid level.
• Grease the mower belt idler.
• Grease the pump drive idler pivot.
• Grease the pump control.
• Check the paper air cleaner element.
• Check the tire pressure.
• Check the belts.
• Check the mower belt tension.
• Grease the blade engagement bellcrank.
• Change the engine oil.
• Check the spark plugs.
• Check and clean engine cooling fins and shrouds.
• Check the hydraulic hoses.
• Replace the paper air cleaner element.
• Change the oil filter.
• Replace the fuel filter.
• Replace the fuel vent filter.
• Change the hydraulic filter.
• Lubricate cam lock with Never-Seez®.
• Paint chipped surfaces.
• Perform all maintenance procedures listed above before storage.
Important: Refer to your engine operator’s manual for additional maintenance procedures.
CAUTION
If you leave the key in the ignition switch, someone could accidently start the engine and seriously injure you or other bystanders.
Remove the key from the ignition and disconnect the spark plug wire from the spark plug(s) before you do any maintenance. Set the wire aside so that it does not accidentally contact the spark plug.
26
Lubrication
Use Figure 24 for locating the grease points on the
machine.
Grease with No. 2 general purpose lithium base or molybdenum base grease.
How to Grease
1. Disengage the PTO and set the parking brake.
2. Stop the engine, remove the key, and wait for all moving parts to stop before leaving the operating position.
3. Clean the grease fittings with a rag. Make sure to scrape any paint off the front of the fitting(s).
4. Connect a grease gun to the fitting. Pump grease into the fittings until grease begins to ooze out of the bearings.
5. Wipe up any excess grease.
Lubricating the Caster and
Wheel Bearings
Service Interval: Before each use or daily—Grease the caster wheels and caster pivot.
Lubricate the front wheel bearings and front spindles
Greasing the Mower Belt Idler
Service Interval: Every 50 hours—Grease the mower belt idler.
Grease the fitting on the mower belt idler arm pivot
Note: Remove the mower deck cover to access the grease fitting for the mower belt idler arm.
Greasing the Pump Control and Bell Crank
Service Interval: Every 50 hours—Grease the pump drive idler pivot.
Every 50 hours—Grease the pump control.
Every 100 hours—Grease the blade engagement bellcrank.
Every 400 hours—Lubricate cam lock with Never-Seez®.
Grease the fitting on the pump drive idler pivot and the pump control.
Grease the blade engagement (PTO) bellcrank
1.
Pump drive idler arm
2.
Pump control arm
3.
Bellcrank
Figure 24
4.
Mower belt idler arm
5.
Caster wheel bearing
6.
Caster pivot
27
Engine Maintenance
Servicing the Air Cleaner
Service Interval/Specification
Service Interval: Every 25 hours—Clean foam air cleaner element.
Every 50 hours—Check the paper air cleaner element.
Every 200 hours—Replace the paper air cleaner element.
Note: Service the air cleaner more frequently (every few operating hours) if the operating conditions are extremely dusty or sandy.
Important: Do not oil the foam or paper element.
Removing the Foam and Paper
Elements
1. Disengage the PTO and set the parking brake.
2. Stop the engine, remove the key, and wait for all moving parts to stop before leaving the operating position.
3. Clean around the air cleaner to prevent dirt from getting into the engine and causing damage
4. Unscrew the cover knobs and remove the air cleaner
5. Unscrew the hose clamp and remove the air cleaner
6. Carefully pull the foam element off the paper
1.
Cover
2.
Hose clamp
Figure 25
3.
Paper element
4.
Foam element
Cleaning the Foam Air Cleaner Element
1. Wash the foam element in liquid soap and warm water. When the element is clean, rinse it thoroughly.
2. Dry the element by squeezing it in a clean cloth.
Important: Replace the foam element if it is torn or worn.
Servicing the Paper Air Cleaner
Element
1. Do not clean the paper filter, replace it (Figure 25).
2. Inspect the element for tears, an oily film, or damage to the rubber seal.
3. Replace the paper element if it is damaged.
Installing the Foam and Paper Elements
Important: To prevent engine damage, always operate the engine with the complete foam and paper air cleaner assembly installed.
1. Carefully slide the foam element onto the paper air
2. Place the air cleaner assembly onto the air cleaner
base and secure it with the 2 wing nuts (Figure 25).
3. Place the air cleaner cover into position and tighten
28
Servicing the Engine Oil
Service Interval/Specification
Service Interval: Before each use or daily—Check the engine oil level.
After the first 8 hours—Change the engine oil.
Every 100 hours—Change the engine oil.
Every 200 hours—Change the oil filter.
Note: Change the oil more frequently when the operating conditions are extremely dusty or sandy.
Oil Type: Detergent oil (API service SF, SG, SH, SJ or SL)
Crankcase Capacity: 58 ounces (1.7 liter) with the filter removed; 51 ounces (1.5 liter) without the filter removed
Viscosity:
Refer to the table (Figure 26).
1.
Oil dipstick
Figure 27
2.
Filler tube
5. Unscrew the oil dipstick and wipe the end clean
6. Slide the oil dipstick fully into the filler tube, but do
not thread onto tube (Figure 27).
7. Pull the dipstick out and look at the end. If the oil level is low, slowly pour only enough oil into the filler tube to raise the level to the Full mark.
Important: Do not overfill the crankcase with oil and run the engine; engine damage can result.
Figure 26
Checking the Engine Oil Level
1. Park the machine on a level surface.
2. Disengage the PTO and set the parking brake.
3. Stop the engine, remove the key, and wait for all moving parts to stop before leaving the operating position.
4. Clean around the oil dipstick (Figure 27) so that dirt
cannot fall into the filler hole and damage the engine.
Changing the Engine Oil
1. Start the engine and let it run five minutes. This warms the oil so it drains better.
2. Park the machine so that the drain side is slightly lower than the opposite side to assure the oil drains completely.
3. Disengage the PTO and set the parking brake.
4. Stop the engine, remove the key, and wait for all moving parts to stop before leaving the operating position.
5. Slide the drain hose over the oil drain valve.
6. Place a pan below the drain hose. Rotate oil drain
valve to allow oil to drain (Figure 28).
7. When oil has drained completely, close the drain valve.
8. Remove the drain hose (Figure 28).
Note: Dispose of the used oil at a recycling center.
29
1.
Oil drain valve
Figure 28
2.
Oil drain hose
9. Slowly pour approximately 80% of the specified oil
into the filler tube (Figure 27).
10. Check the oil level; refer to Checking the Engine Oil
Level.
11. Slowly add the additional oil to bring it to the Full mark.
Changing the Oil Filter
Note: Change the oil filter more frequently when the operating conditions are extremely dusty or sandy.
1. Drain the oil from the engine; refer to Changing the
Engine Oil.
2. Remove the old filter (Figure 29).
4. Install the replacement oil filter to the filter adapter, turn the oil filter clockwise until the rubber gasket contacts the filter adapter, then tighten the filter an
additional 3/4 turn (Figure 29).
5. Fill the crankcase with the proper type of new oil; refer to Servicing the Engine Oil.
6. Run the engine for about 3 minutes, stop the engine, and check for oil leaks around the oil filter and drain valve.
7. Check the engine oil level and add oil if needed.
8. Wipe up any spilled oil.
Servicing the Spark Plugs
Service Interval: Every 100 hours
Ensure that the air gap between the center and side electrodes is correct before installing the spark plug.
Use a spark plug wrench for removing and installing the spark plugs and a gapping tool/feeler gauge to check and adjust the air gap. Install a new spark plugs if necessary.
Type: Champion® RCJ8Y or equivalent Air Gap:
0.030 inch (0.75 mm)
Removing the Spark Plugs
1. Disengage the PTO and set the parking brake.
2. Stop the engine, remove the key, and wait for all moving parts to stop before leaving the operating position.
3. Disconnect the wires from the spark plugs
1
Figure 30
1.
Spark-plug wire/spark plug
1.
Oil filter
Figure 29
2.
Adapter
3. Apply a thin coat of new oil to the rubber gasket on
the replacement filter (Figure 29).
4. Clean around the spark plugs to prevent dirt from falling into the engine and potentially causing damage.
5. Remove the spark plugs and the metal washers.
30
Checking the Spark Plugs
1. Look at the center of the spark plugs (Figure 31).
If you see light brown or gray on the insulator, the engine is operating properly. A black coating on the insulator usually means that the air cleaner is dirty.
2. If needed, clean the spark plug with a wire brush to remove carbon deposits.
Figure 31
1.
Center electrode insulator 3.
Air gap (not to scale)
2.
Side electrode
Important: Always replace the spark plugs when it has worn electrodes, an oily film on it, or has cracks in the porcelain.
3. Check the gap between the center and side electrodes
(Figure 31). Bend the side electrode (Figure 31) if
the gap is not correct.
Installing the Spark Plugs
1. Install the spark plugs and the metal washer. Ensure that the air gap is set correctly.
2. Tighten the spark plugs to 16 ft-lb (22 N-m).
3. Connect the wires to the spark plugs (Figure 31).
Fuel System
Maintenance
Servicing the Fuel Tank
DANGER
In certain conditions, gasoline is extremely flammable and highly explosive. A fire or explosion from gasoline can burn you and others and can damage property.
• Drain gasoline from the fuel tank when the engine is cold. Do this outdoors in an open area.
Wipe up any gasoline that spills.
• Never smoke when draining gasoline, and stay away from an open flame or where a spark may ignite the gasoline fumes.
Draining the Fuel Tank
1. Park the machine on a level surface, to assure fuel tank drains completely. Then disengage the power take off (PTO), set the parking brake, and turn the ignition key to off . Remove the key.
2. Close the fuel shut-off valve at the fuel tank
3. Squeeze the ends of the hose clamp together and slide it up the fuel line away from fuel filter
4. Pull the fuel line off the fuel filter (Figure 32). Open
the fuel shut-off valve and allow the gasoline to drain into a gas can or drain pan.
Note: Now is the best time to install a new fuel filter because the fuel tank is empty. Refer to Replacing the Fuel Filter.
5. Install the fuel line onto the fuel filter. Slide the hose clamp close to the valve to secure the fuel line.
31
1.
Fuel shut-off valve
Figure 32
2.
Clamp
Servicing the Fuel Filter
Service Interval: Every 200 hours/Yearly (whichever comes first)
Replacing the Fuel Filter
Never install a dirty filter if it is removed from the fuel line.
Note: Note how the fuel filter is installed in order to install the new filter correctly.
Note: Wipe up any spilled fuel.
1. Disengage the PTO and set the parking brake.
2. Stop the engine, remove the key, and wait for all moving parts to stop before leaving the operating position.
3. Close fuel shut-off valve at the fuel tank (Figure 32).
4. Squeeze the ends of the hose clamps together and
slide them away from the filter (Figure 33).
5. Remove the filter from the fuel lines.
6. Install a new filter and move the hose clamps close to the filter.
7. Open fuel shut-off valve at fuel tank (Figure 32).
8. Check for fuel leaks and repair if needed.
9. Wipe up any spilled fuel.
Servicing the Fuel Vent System
Service Interval: Every 200 hours/Yearly (whichever comes first)
1. Disengage the PTO and set the parking brake.
2. Stop the engine, remove the key, and wait for all moving parts to stop before leaving the operating position.
3. Remove the existing fuel vent filter (Figure 34).
4. Install a new filter.
1 2
1.
Fuel vent filter g014686
Figure 34
2.
Right side of motor
1.
Hose clamp
2.
Fuel line
Figure 33
3.
Filter
32
Drive System
Maintenance
Perform the following linkage adjustments when the machine needs maintenance. Perform steps Adjust the
Speed Control Linkage through Adjusting the Tracking.
If and adjustment is needed , do them in the order that they are listed.
Adjusting the Speed Control
Linkage
1. Disengage the PTO and set the parking brake.
2. Stop the engine and wait for all moving parts to stop before leaving the operating position.
3. Move the speed control lever (located on the console) to the full forward position.
4. Check the orientation of the tabs on the ends of the speed control crank. These tabs should be pointing straight down at the 6 o’clock position approximately
5. Adjust the threaded yoke at the bottom of the speed control linkage until the tabs are at the 6 o’clock
7. Check to make sure the safety switch is depressed and there is a 5/16 inch (8 mm) space between the
actuating tab and the switch. (Figure 36).
8. If needed, adjust switch location to create the
5/16 inch (8 mm) space (Figure 36).
Figure 36
1.
Actuating tab
2.
5/16 inch (8 mm) space
3.
Safety switch
1.
Speed control rod
2.
Yoke
3.
Speed control crank
Figure 35
4.
Tabs, 6 o’clock position
5.
Jam nut
6. Pull the speed control lever back to neutral.
33
Adjusting the Neutral Control
Linkages
WARNING
Engine must be running so control linkage adjustments can be performed. Contact with moving parts or hot surfaces may cause personal injury.
Keep hands, feet, face, clothing and other body parts away from rotating parts, muffler and other hot surfaces.
WARNING
Mechanical or hydraulic jacks may fail to support machine and cause a serious injury.
• Use jack stands when supporting machine.
• Do not use hydraulic jacks.
1. Disengage the PTO and set the parking brake.
2. Stop the engine and wait for all moving parts to stop before leaving the operating position.
3. Raise the rear of the machine onto jack stands to raise the drive wheels off the ground.
4. Disengage the parking brake.
5. Start the engine and move the throttle ahead to the full throttle position.
6. Place the neutral locks in the full forward position and move the speed control lever to the medium speed position.
7. Hold OPC levers down.
Note: The OPC levers must be held down whenever the speed control lever is out of the neutral position or the engine will kill.
WARNING
Electrical system will not perform proper safety shut off with Operator Presence Control (OPC) levers held down in place.
• Make sure Operator Presence Control (OPC) levers are working when adjustment is completed.
• Never operate this unit with Operator
Presence Control (OPC) levers held down in place.
8. Squeeze one drive lever until an increased resistance is felt. This is where neutral should be.
Note: Make sure you have not reached the end of the neutral lock slot. If you have, shorten the control lever linkage. Refer to Adjusting the Control Rod.
9. If the wheel turns while holding the drive lever in neutral, the neutral control linkages need to be
adjusted (Figure 37). If wheel stops then go to step
12.
10. Loosen the nut against the neutral control linkage
11. Adjust the neutral control linkage until the respective drive wheel stops while the drive lever is pulled against the neutral spring (neutral position)
12. Turn the adjusting bolt approximately 1/4 turn clockwise if the wheel is turning in reverse or turn the bolt approximately 1/4 turn counter-clockwise if
the wheel is turning forward (Figure 37).
13. Release the drive lever to the forward drive position and squeeze back into the neutral position. Check to see if the wheel stops. If not, repeat the above adjustment procedure.
14. After adjustments are made, tighten the nuts against the yokes.
15. Repeat this procedure for the opposite side.
Figure 37
1.
Neutral control linkage
2.
Yoke
3.
Adjusting bolt
4.
Nut
Adjusting the Hydro Control
Linkages
WARNING
Engine must be running so control linkage adjustments can be performed. Contact with moving parts or hot surfaces may cause personal injury.
Keep hands, feet, face, clothing and other body parts away from rotating parts, muffler and other hot surfaces.
WARNING
Mechanical or hydraulic jacks may fail to support machine and cause a serious injury.
• Use jack stands when supporting machine.
• Do not use hydraulic jacks.
Adjusting the Left Side Linkage
1. Disengage the PTO and set the parking brake.
2. Stop the engine and wait for all moving parts to stop before leaving the operating position.
3. Raise the rear of the machine onto jack stands high enough to raise the drive wheels off of the ground.
4. Disengage the parking brake.
5. Start the engine and move the throttle ahead to the full throttle position.
34
6. Place the left drive lever in the full forward position.
7. Place the speed control lever in the neutral position.
WARNING
Electrical system will not perform proper safety shut off with Operator Presence Control (OPC) levers held in place.
• Make sure Operator Presence Control (OPC) levers are working when adjustment is completed.
• Never operate this unit with Operator
Presence Control (OPC) levers held in place.
8. Loosen the front adjusting nut on left hydro control
linkage as shown in Figure 39.
9. Turn the left rear adjusting nut counter-clockwise
until wheel rotates forward (Figure 39).
10. Turn the rear adjusting nut clockwise 1/4 of a turn at a time. Then move the speed control lever forward and back to neutral. Repeat this until left wheel stops
11. Turn the rear nut an additional 1/2 turn and tighten the front adjusting nut.
Note: Make sure flat part of linkage is perpendicular to pin part of swivel.
14. Make sure the speed control lever is in the neutral position and the tire does not rotate.
15. Repeat the adjustment if needed.
1.
Hydro control linkage
2.
Front adjustingnut
Figure 39
3.
Rear adjusting nut
4.
Control arm
Note: If inconsistent neutral occurs, check to be sure both springs are properly tightened on the speed control lever under the console, especially the rear pivot spring. Repeat above adjustments if necessary
1.
Speed control lever
2.
Rear pivot spring
Figure 40
3.
spring
Figure 38
12. After adjusting the left hydro control linkage, move the speed control lever forward and then back to the neutral position.
13. Hold the OPC levers down.
Note: The OPC levers must be held down whenever the speed control lever is out of the neutral position or the engine will kill.
Adjusting the Right Side Linkage
1. Place the speed control lever in the neutral position.
2. Place the right drive lever in the full forward position.
3. Adjust the right side linkage by turning the quick track knob counterclockwise until the tire begins to
4. Turn the knob clockwise 1/4 of a turn at a time.
Then move the speed control forward and back to neutral. Repeat this until right wheel stops rotating
35
5. Hold the OPC levers down.
Note: The OPC levers must be held down whenever the speed control lever is out of the neutral position or the engine will kill.
6. The spring that keeps tension on the knob should normally not need adjustment. However if an adjustment is needed, adjust the length of spring to
1 inch (26 mm) between the washers (Figure 41).
7. Adjust spring length by turning nut at front of spring
2. Lengthen the control rod if the tire is turning in reverse and shorten the rod if the tire is turning forward.
3. Rotate the rod several turns if the tire is rotating fast.
Then, adjust the rod in 1/2 turn increments.
4. Place the clevis pin into the drive lever (Figure 42).
1.
Control rod
2.
Clevis pin
3.
Drive lever
4.
Operator Presence
Control lever (OPC)
Figure 42
5.
Left handle shown
6.
Neutral lock
7.
Hairpin cotter pin
1.
Hydro control linkage
2.
Quick track knob
Figure 41
3.
Spring
4.
1 inch (26 mm)
Adjusting the Control Rod
Checking the Control Rod
1. With rear of machine still on jack stands and engine running at full throttle, move the speed control lever to the medium speed position.
Note: The OPC levers must be held down whenever the speed control lever is out of the neutral position or the engine will kill.
2. Move the respective drive lever upward until it reaches the neutral position and engage neutral locks.
3. If the tire rotates in either direction, the length of the control rod will need to be adjusted.
Adjusting the Control Rod
1. Adjust the rod length by releasing the drive lever and removing the hairpin cotter pin and clevis pin.
Rotate the rod in the rod fitting (Figure 42).
5. Release and engage neutral lock checking that the tire
does not rotate (Figure 43). Continue this process
until the tire does not rotate.
6. Install the hairpin cotter pin between the drive levers and the neutral locks and into the clevis pins
7. Repeat this adjustment for the opposite side.
36
2. Stop the engine and wait for all moving parts to stop before leaving the operating position.
3. For a heavier drive setting, relocate the spring anchor links to either the medium or heavy duty positions
(Figure 45). The spring anchor links are attached to
the upper rear corner of the hydro drive shields on the left and right sides of the machine.
Note: In the medium or heavy duty positions, the drive lever forces at the upper handle will also be increased
1.
Handle
2.
Neutral lock
3.
Handle
4.
Neutral lock slot
Figure 43
5.
Neutral position
6.
Drive lever
7.
Full speed forward
8.
Control rod
Adjusting the Tracking
1. Remove machine from any jack stands.
2. Check the rear tire pressure. Refer to Checking the
Tire Pressure.
3. Run the unit and observe the tracking on a level, smooth, hard surface such as concrete or asphalt.
4. If the unit tracks to one side or the other, turn the quick track knob. Turn the knob right to steer right
and turn the knob left to steer left (Figure 44).
Figure 44
1.
Spring anchor
2.
Standard setting
Figure 45
3.
Medium setting
4.
Heavy duty setting
Checking the Tire Pressure
Service Interval: Every 50 hours/Monthly (whichever comes first)—Check the tire pressure.
Check the pressure at the valve stem (Figure 46).
Maintain the air pressure in the rear tires at 12-14 psi
(83-97 kPa). Uneven tire pressure can cause an uneven cut.
Note: The front tires are semi-pneumatic tires and do not require air pressure maintenance.
1.
Quick track knob
Adjusting the Spring Anchor
Links
For medium or heavy duty drive conditions, such as operating with a sulky on steep slopes, a higher spring force may be required on the hydro pump control arms to prevent the drive system from stalling.
1. Disengage the PTO and set the parking brake.
37
Figure 46
Cooling System
Maintenance
Cleaning the Air Intake Screen
Service Interval: Before each use or daily—Clean the air intake screen.
Before each use remove any build-up of grass, dirt or other debris from the cylinder and cylinder head cooling fins, air intake screen on flywheel end, and carburetor-governor levers and linkage. This will help insure adequate cooling and correct engine speed and will reduce the possibility of overheating and mechanical damage to the engine.
Cleaning the Cooling System
Service Interval: Every 100 hours/Yearly (whichever comes first)—Check and clean engine cooling fins and shrouds.
1. Disengage the PTO and set the parking brake.
2. Stop the engine, remove the key, and wait for all moving parts to stop before leaving the operating position.
3. Remove the air intake screen, recoil starter and fan
4. Clean the debris and grass from the engine parts.
5. Install air intake screen, recoil starter and fan housing
38
1.
Air intake screen
2.
Fan housing
3.
Recoil starter
Figure 47
4.
Bolt
5.
Nut
Brake Maintenance
Servicing the Brake
Before each use, check the parking brake for proper operation.
Always set the parking brake when you stop the machine or leave it unattended. If the parking brake does not hold securely, adjust it.
Checking the Parking Brake
1. Move the machine onto a level surface.
2. Disengage the power take off (PTO) and stop the engine.
3. Set the parking brake.
Note: Setting the parking brake should take a reasonable amount of force. If it engages too hard or too easily, an adjustment is required. Refer to
Adjusting the Parking Brake.
Adjusting the Parking Brake
The parking brake lever is on the right side of the
machine (Figure 45). If the parking brake does not hold
securely, adjust it.
1. Check the parking brake before you adjust it; refer to
Checking the Parking Brake.
2. Release the parking brake; refer to Releasing the
Parking Brake.
3. Remove the spring hair pin from the lower brake
39
1.
Brake linkage yoke
2.
Lower brake lever
3.
Spring clevis pin
Figure 48
4.
Lower brake link
5.
1/4 inch (6 mm)
6.
Hair pin
4. Rotate the lower brake link yoke clockwise into the yoke to tighten the parking brake; rotate the brake link yoke counterclockwise out of the yoke out to
loosen the parking brake (Figure 48).
Note: There should be approximately 1/4 inch clearance between the tire and the flat bar when the
parking brake in the released position (Figure 48).
5. Secure the lower link to the lower brake lever with
the hair pin cotter and the clevis pin (Figure 48).
6. Check the brake operation again; refer to Checking the Parking Brake.
Belt Maintenance
Checking the Belts
Service Interval: Every 50 hours/Monthly (whichever comes first)—Check the belts.
Check belts for cracks, frayed edges, burn marks, wear, signs of overheating or any other damage. Replace damaged belts.
Replacing the Mower Belt
Important: The brake needs to be adjusted when the belt tension or the brake linkage is adjusted.
1. Disengage the blade control (PTO) lever and set the parking brakes.
2. Stop the engine and wait for all moving parts to stop before leaving the operating position.
3. Remove the knobs and the belt cover on the mower.
4. Remove the idler pulley and the worn belt.
5. Install the new mower belt.
6. Install the idler pulley.
7. Engage the blade control (PTO) lever and check the belt tension. Refer to Adjusting the Mower Belt
Tension.
Note: The proper mower belt tension is 10-15 lbf.
(44-67 N) with the belt deflected 1/2 inch (13 mm)
halfway between the pulleys (Figure 52 or Figure 53).
8. Engage the blade control (PTO) lever.
9. Check the clearance between the bell crank and the
transmission output shaft (Figure 49).
40
Figure 49
1.
1/16-1/8 inch (2-3 mm)
2.
Bell crank
4.
Hairpin cotter
5.
Clevis pin
3.
Transmission output shaft 6.
Clevis
Note: The clearance should be 1/16-1/8 inch
(2-3 mm).
10. Remove the hairpin cotter pin and the clevis pin from the bell crank.
11. Rotate the clevis clockwise on the rod to increase the clearance; rotate it counterclockwise to decrease
12. Disengage the blade control (PTO) lever.
Note: If the assist arm does not contact the front
stop on the mower deck (Figure 50 or Figure 51),
adjust the clevis to bring the bell crank closer to the
transmission output shaft (Figure 49).
Figure 50
36in Mower Deck
1.
1/2 inch (13 mm) deflection here
2.
Assist arm
3.
Front stop
4.
Locknut
5.
Turnbuckle
Figure 51
48in Mower Deck
41
13. Check the belt guide under the engine frame for the proper adjustment.
Note: The distance between the belt guide and the mower belt should be 1-1/4 inch (32 mm) when you engage the mower belt. Adjust the mower belt as necessary. The disengaged belt should not drag or fall off the pulley when the guides are properly adjusted.
Adjusting the Mower Belt
Tension
Adjusting the Tension for 36in Mower
Decks
Service Interval: After the first 8 hours—Check the mower belt tension.
After the first 25 hours—Check the mower belt tension.
Every 50 hours—Check the mower belt tension.
Important: The brake needs to be adjusted when the belt tension or the brake linkage is adjusted.
Important: The belt must be tight enough to not slip during heavy loads while cutting grass. Over tensioning the belt will reduce the spindle bearing life, the belt life and the idler pulley life.
The belt must be tight enough so it does not slip during heavy loads while cutting grass and over-tensioning will reduce belt and spindle bearing life.
1. Disengage the blade control (PTO) lever and set the parking brakes.
2. Stop the engine and wait for all moving parts to stop before leaving the operating position.
3. Loosen the locknut on the turnbuckle (Figure 52).
4. Rotate the turnbuckle toward the rear of the mower to increase the tension on the belt. Rotate the turnbuckle toward the front of the mower to
decrease the tension on the belt (Figure 52).
Note: The eyebolt threads on both ends of the turnbuckle should be engaged a minimum of
5/16 inch (8 mm).
5. Engage the bladed control lever (PTO) and check the belt tension. Adjust tension until it is correct.
Note: The proper mower belt tension is 10-15 lbf.
(44-67 N) with the belt deflected 1/2 inch (13 mm)
halfway between the pulleys (Figure 52).
1. Disengage the blade control (PTO) lever and set the parking brakes.
2. Stop the engine and wait for all moving parts to stop before leaving the operating position.
3. Loosen the locknut on the turnbuckle (Figure 54).
4. Rotate the turnbuckle toward the rear of the mower to increase the tension on the belt. Rotate the turnbuckle toward the front of the mower to
decrease the tension on the belt (Figure 54).
Note: The proper mower belt tension is 10-15 lbf.
(44-67 N) with the belt deflected 1/2 inch (13 mm)
halfway between the pulleys (Figure 53).
Figure 52
36in Mower Deck
1.
Mower belt with 1/2 inch
(13mm) deflection
2.
Idler pulley
6. Tighten the locknut on the turnbuckle.
7. Check the blade brake adjustment; refer to Adjusting the Blade Brake.
Adjusting the Tension for 48in Mower
Decks
Important: The belt must be tight enough to not slip during heavy loads while cutting grass. Over tensioning the belt will reduce the spindle bearing life, the belt life and the idler pulley life.
Important: The brake needs to be adjusted when the belt tension or the brake linkage is adjusted.
Figure 53
48in Mower Deck
1.
Mower belt with 1/2 inch
(13mm) deflection
2.
Idler pulley
Note: The eyebolt threads on both ends of the turnbuckle should be engaged a minimum of
5/16 inch (8 mm).
42
Note: The distance between the belt guide and the mower belt should be 3/4 inch (19 mm) when
you engage the mower belt (Figure 56). Adjust the
mower belt as necessary. The disengaged belt should not drag or fall off the pulley when the guides and belt tension are properly adjusted.
9. Check the blade brake adjustment; refer to Adjusting the Blade Brake.
Figure 54
1.
1/2 inch (13 mm) deflection here
2.
Assist arm
3.
Front stop
4.
Locknut
5.
Turnbuckle
Figure 56
5. Engage the bladed control lever (PTO) and check the belt tension.
6. If there is no adjustment left in the turnbuckle and the belt is still loose, the rear idler pulley needs to be
positioned to the middle or front hole (Figure 55).
Use the hole that will give the correct adjustment.
7.
When the idler pulley is moved the belt guide must be moved. Move the belt guide to the front position
1.
Belt guide
Adjusting the PTO Engagement
Linkage
The PTO engagement linkage adjustment is located beneath the front left hand corner of the engine deck.
1. Disengage the blade control (PTO) lever and set the parking brakes.
2. Stop the engine and wait for all moving parts to stop before leaving the operating position.
3. Engage the blade control lever (PTO).
4. Adjust the linkage length to where the lower end of the bellcrank just clears the axle support gusset
1.
Rear idler pulley
2.
Middle hole
3.
Front hole
Figure 55
4.
Belt guide in back position
5.
Front idler pulley
8. Check the belt guide under the engine frame for
proper adjustment (Figure 56).
43
1.
Bellcrank
2.
Safety switch located under engine deck
3.
Bellcrank just clears the gusset with the PTO engageded
Figure 57
4.
Yoke
5.
Nut
6.
Assist arm link
5. Make sure the assist arm is against the rear assist arm
6. Push the blade control lever (PTO) down to the disengaged position.
7. The assist arm should contact the front assist arm stop on the deck. If it does not contact, adjust the
bellcrank so it is closer to the gusset (Figure 58).
10. Remove the assist arm link from the assist arm and rotate the link to adjust the length.
11. Install the assist arm link into the assist arm and
secure it with the hairpin cotter pin (Figure 58).
12. Check if the assist arm hits against the stops correctly.
Adjusting the PTO Safety Switch
1. Disengage the blade control (PTO) lever and set the parking brakes.
2. Stop the engine and wait for all moving parts to stop before leaving the operating position.
3. Disengage the blade control lever (PTO). Make sure the assist arm is against the front assist stop arm.
4. If needed, adjust the blade safety switch by loosening
the bolts holding the switch bracket (Figure 59).
5. Move the mounting bracket until the bellcrank depresses the plunger by a 1/4 inch (6 mm).
6.
Note: Make sure the bellcrank does not touch the switch body or damage to the switch could occur
Tighten the switch mounting bracket.
1.
Yoke
2.
Nut
3.
Rear assist arm stop
4.
Front assist arm stop
Figure 58
5.
Assist arm link
6.
Assist arm
7.
Turnbuckle
8. To adjust the assist arm link, remove the hairpin
cotter pin from the assist arm (Figure 58).
9. Loosen the nut against the yoke (Figure 57).
1.
Bellcrank
2.
Bolts and nuts
Figure 59
3.
Switch mounting bracket
4.
Switch body
44
Hydraulic System
Maintenance
Servicing the Hydraulic
System
Checking the Hydraulic Fluid
Service Interval: After the first 8 hours
Every 25 hours
Hydraulic Oil Type: Toro® HYPR-OIL™ 500 hydraulic oil or Mobil® 1 15W-50
Hydraulic System Oil Capacity: 77 oz. (2.3 l)
Important: Use oil specified. Other fluids could cause system damage.
Note: There are two ways of checking the hydraulic oil.
One is when the oil is warm and one is when the oil is cold. The baffle inside the tank has two levels depending if the oil is warm or cold.
1. Position machine on a level surface.
2. Disengage the power take off (PTO) and shut off the engine.
3. Wait for all moving parts to stop before leaving the operating position and then set the parking brake.
4. Clean area around cap and filler neck of hydraulic
1.
Cap
2.
Baffle
Figure 60
3.
Cold fluid level-full
4.
Hot fluid level-full
5. Remove cap from filler neck. Look inside to check if
there is fluid in the reservoir. (Figure 60).
6. If there is no fluid, add fluid to the reservoir until it reaches the cold level of the baffle.
7. Run the machine at low idle for 15 minutes to allow any air to purge out of the system and warm fluid.
Refer to Starting and Stopping the Engine.
8. Recheck the fluid level while the fluid is warm. If required, add fluid to the reservoir until it reaches the hot level of the baffle.
Note: The fluid level should be to the top of the hot
level of the baffle, when the fluid is warm (Figure 60).
9. Install cap on filler neck.
WARNING
Hydraulic fluid escaping under pressure can penetrate skin and cause injury.
• If hydraulic fluid is injected into the skin it must be surgically removed within a few hours by a doctor familiar with this type of injury. Gangrene may result if this is not done.
• Keep body and hands away from pin hole leaks or nozzles that eject high pressure hydraulic fluid.
• Use cardboard or paper to find hydraulic leaks.
• Safely relieve all pressure in the hydraulic system before performing any work on the hydraulic system.
• Make sure all hydraulic fluid hoses and lines are in good condition and all hydraulic connections and fittings are tight before applying pressure to hydraulic system.
Replacing the Hydraulic Filter
Service Interval: After the first 8 hours
Every 200 hours
1. Disengage the PTO and set the parking brake.
2. Stop the engine and wait for all moving parts to stop before leaving the operating position.
Important: Do not substitute automotive oil filter or severe hydraulic system damage may result.
3. Remove hydraulic reservoir cap and temporarily cover opening with a plastic bag and rubber band to prevent all hydro fluid from draining out.
4. Locate filter under engine base and place drain pan
5. Remove the old filter and wipe the filter adapter
gasket surface clean (Figure 61).
45
1.
Hydraulic filter
2.
Gasket
Figure 61
3.
Adapter
6. Apply a thin coat hydro fluid to the rubber gasket on the replacement filter.
7. Install replacement hydraulic filter onto the filter adapter. Do not tighten.
8. Remove plastic bag from reservoir opening and allow filter to fill with hydraulic fluid.
9. When the hydraulic filter is full, turn the oil filter clockwise until the rubber gasket contacts the filter adapter, then tighten the filter an additional 1/2 turn
10. Clean up any spilled fluid.
11. If there is no fluid, add Mobil 1 15W-50 synthetic motor oil or equivalent synthetic oil to approximately
1/4 inch (6 mm) below the top of reservoir baffle.
Important: Use oil specified or equivalent.
Other fluids could cause system damage.
12. Start engine and let run for about two minutes to purge air from the system. Stop the engine and check for leaks. If one or both wheels will not drive, refer to Bleeding Hydraulic System.
13. Recheck level and add fluid, if required. Do not overfill.
Bleeding the Hydraulic System
The traction system is self bleeding, however, it may be necessary to bleed the system if fluid is changed or after work is performed on the system.
Air must be purged from the hydraulic system when any hydraulic components, including oil filter, are removed or any of the hydraulic lines are disconnected. The critical area for purging air from the hydraulic system is between the oil reservoir and each charge pump located on the top of each variable displacement pump. Air in other parts of the hydraulic system will be purged through normal operation once the charge pump is primed.
1. Disengage the PTO and set the parking brake.
2. Stop the engine and wait for all moving parts to stop before leaving the operating position.
3. Raise the rear of the machine up onto jack stands high enough to raise the drive wheels off the ground.
4. Check the hydraulic fluid level.
5. Start the engine and move the throttle control to the full throttle position. Move the speed control lever to the middle speed position and place the drive levers into the drive position.
If either drive wheel does not rotate, it is possible to assist the purging of the charge pump by carefully rotating the tire in the forward direction.
Note: It is necessary to lightly touch the charge pump cap with your hand to check the pump temperature. If the cap is too hot to touch, turn off engine. The pumps may be damaged if the pump becomes too hot. If either drive wheel still does not rotate continue to next step.
1.
Charge pump cap
Figure 62
2.
Socket head screw
6. Thoroughly clean the area around each of the charge pump housings.
7. To prime the charge pump, loosen two hex socket
head capscrews (Figure 62) 1-1/2 turns only. Make
sure engine is not running. Lift charge pump housing upward and wait for a steady flow of oil to flow out from under housing. Retighten capscrews. Do this for both pumps.
Note: Hydraulic reservoir can be pressurized to up to 5 psi to speed this process.
8. If either drive wheel still does not rotate, stop and repeat steps 4 and 5 on the respective pump. If wheels rotate slowly, the system may prime after additional running. Recheck hydraulic fluid level.
46
9. Allow unit to run several minutes after the charge pumps are primed with drive system in the full speed position.
10. Check the hydro control linkage adjustment. Refer to Adjusting the Hydro Control Linkages.
Mower Deck
Maintenance
Checking the Hydraulic Hoses
Service Interval: Every 100 hours
Check hydraulic hoses for leaks, loose fittings, kinked lines, loose mounting supports, wear, weather and chemical deterioration. Make necessary repairs before operating.
Note: Keep areas around hydraulic system clean from grass and debris build up.
WARNING
Hydraulic fluid escaping under pressure can penetrate skin and cause injury.
• If hydraulic fluid is injected into the skin it must be surgically removed within a few hours by a doctor familiar with this type of injury.
Gangrene may result if this is not done.
• Keep body and hands away from pin hole leaks or nozzles that eject high pressure hydraulic fluid.
• Use cardboard or paper to find hydraulic leaks.
• Safely relieve all pressure in the hydraulic system before performing any work on the hydraulic system.
• Make sure all hydraulic fluid hoses and lines are in good condition and all hydraulic connections and fittings are tight before applying pressure to hydraulic system.
Servicing the Cutting Blades
To ensure a superior quality of cut, keep the blades sharp. For convenient sharpening and replacement, you may want to keep extra blades on hand.
WARNING
A worn or damaged blade can break, and a piece of the blade could be thrown into the operator’s or bystander’s area, resulting in serious personal injury or death.
• Inspect the blade periodically for wear or damage.
• Replace a worn or damaged blade.
Before Inspecting or Servicing the
Blades
Park the machine on a level surface, disengage the blade control bail and set the parking brake. Turn the ignition key to off. Remove the key and disconnect the spark plug wire(s) from the spark plug(s).
Inspecting the Blades
Service Interval: Before each use or daily
1. Inspect the cutting edges (Figure 63). If the edges
are not sharp or have nicks, remove and sharpen the blades. Refer to Sharpening the Blades.
47
1.
Cutting Edge
2.
Sail
Figure 63
3.
Wear/slot forming in curved area
4.
Crack in the curved area
2. Inspect the blades, especially the curved area
(Figure 63). If you notice any damage, wear, or a slot forming in this area (item 3 in Figure 63),
immediately install a new blade.
Checking for Bent Blades
1. Rotate the blades until the ends face forward and
the machine, use genuine Toro replacement blades.
Replacement blades made by other manufacturers may result in non-conformance with safety standards.
1. Hold the blade bolt with a wrench.
2. Remove the nut, blade bolt, curved washer, blade,
spacers, and thin washer from the spindle (Figure 66).
Figure 64
Figure 65
1.
Measure from cutting edge to a level surface
2. Measure from a level surface to the cutting edge,
position A, of the blades (Figure 65). Note this
dimension.
3. Rotate the opposite ends of the blades forward.
4. Measure from a level surface to the cutting edge of
the blades at the same position as in step 1. The
difference between the dimensions obtained in steps
1 and 2 must not exceed 1/8 inch (3 mm). If this
dimension exceeds 1/8 inch (3 mm), the blade is bent and must be replaced. Refer to Removing the
Blades and Installing the Blades.
WARNING
A blade that is bent or damaged could break apart and could seriously injure or kill you or bystanders.
• Always replace bent or damaged blade with a new blade.
• Never file or create sharp notches in the edges or surfaces of blade.
Removing the Blades
Replace the blades if you hit a solid object or if the blades are out of balance or bent. To ensure optimum performance and continued safety conformance of
1.
Blade
2.
Blade bolt
3.
Curved washer
Figure 66
4.
Spacer
5.
Thin washer
6.
Nut
Sharpening the Blades
1. Use a file to sharpen the cutting edge at both ends
of the blade (Figure 67). Maintain the original angle.
The blade retains its balance if the same amount of material is removed from both cutting edges.
48
Figure 67
1.
Sharpen at original angle
2. Check the balance of the blade by putting it on a
blade balancer (Figure 68). If the blade stays in a
horizontal position, the blade is balanced and can be used. If the blade is not balanced, file some metal off
the end of the sail area only (Figure 68). Repeat this
procedure until the blade is balanced.
1.
Spring mounting bolts
2.
Blade brake pad
Figure 69
3.
1/8-3/16 inch (3mm-5mm)
1.
Blade
Figure 68
2.
Balancer
Installing the Blades
1. Install the bolt, curved washer, and blade. Select the proper number of spacer(s) for the height-of- cut,
and slide the bolt into the spindle (Figure 66).
Important: The curved part of the blade must point upward toward the inside of the mower to ensure proper cutting.
2. Install the remaining spacer(s) and secure them with
a thin washer and a nut (Figure 66).
3. Torque the blade bolt to 75-80 ft-lb (101-108 N-m).
Adjusting the Blade Brake
1. Disengage the PTO, turn the ignition key to off, and remove the key.
2. Wait for all moving parts to stop before leaving the operating position and then set the parking brakes.
3. If necessary, adjust the spring mounting bolts so that the blade brake pad rubs against both sides of the
4. Adjust the nut at the end of the blade brake rod until there is 1/8-3/16 inch (3 mm -5 mm) between the
5. Engage the blades. Ensure the blade brake pad no longer contacts the pulley groove.
Replacing the Grass Deflector
WARNING
An uncovered discharge opening could allow the lawn mower to throw objects in the operator’s or bystander’s direction and result in serious injury or death. Also, contact with the blade could occur.
Never operate the lawn mower with the grass deflector removed unless you install a cover plate, a mulch plate, or a grass chute and catcher.
1. Remove the locknut, bolt, spring and spacer holding
the deflector to the pivot brackets (Figure 70).
Remove damaged or worn grass deflector.
49
1.
Bolt
2.
Spacer
3.
Locknut
4.
Spring
Figure 70
5.
Spring installed
6.
Grass Deflector
7.
L end of spring, place behind deck edge before installing bolt
8.
J hook end of spring
2. Place spacer and spring onto grass deflector. Place the L end of spring behind deck edge.
Note: Make sure the L end of spring is installed behind deck edge before installing the bolt as shown
3. Install bolt and nut. Place the J hook end of spring
around grass deflector (Figure 70).
Important: The grass deflector must be free to rotate. Lift the deflector up to the full open position and ensure that it rotates freely without binding into the full down position.
Storage
1. Disengage the power take off (PTO), set the parking brake, and turn the ignition key to off. Remove the key.
2. Remove grass clippings, dirt, and grime from the external parts of the entire machine, especially the engine. Clean dirt and chaff from the outside of the engine’s cylinder head fins and blower housing.
Important: You can wash the machine with mild detergent and water. Do not pressure wash the machine. Avoid excessive use of water, especially near the shift lever plate, and engine.
3. Check the brake; refer to Servicing the Brake in
4. Service the air cleaner; refer to Servicing the Air
Cleaner.
5. Grease the machine; refer to Greasing and
Lubrication in Lubrication (page 27).
6. Change the crankcase oil; refer to Servicing the
Engine in.
7. Check the tire pressure; refer to Checking the Tire
Pressure in Drive System Maintenance (page 33).
8. For long-term storage:
A. Add stabilizer/conditioner additive to fuel in the tank.
B. Run engine to distribute conditioned fuel through the fuel system (5 minutes).
C. Stop engine, allow to cool and drain the fuel tank; refer to Servicing the Fuel Tank in
Fuel System Maintenance (page 31), or operate
engine until it stops.
D. Restart engine and run until it stops. Repeat, on
Choke until engine will not restart.
E. Dispose of fuel properly. Recycle as per local codes.
Note: Do not store stabilizer/conditioned gasoline over 90 days.
9. Remove the spark plug(s) and check its condition; refer to Servicing the Spark Plug. With the spark plug(s) removed from the engine, pour two tablespoons of engine oil into the spark plug hole. Now use the starter to crank the engine and distribute the oil inside the cylinder. Install the spark plug(s). Do not install the wire on the spark plug(s).
10. Check and tighten all bolts, nuts, and screws. Repair or replace any part that is damaged or defective.
50
11. Paint all scratched or bare metal surfaces. Paint is available from your Authorized Service Dealer.
12. Store the machine in a clean, dry garage or storage area. Remove the key from the ignition switch and keep it in a memorable place. Cover the machine to protect it and keep it clean.
51
Troubleshooting
Problem
Engine will not start, starts hard, or fails to keep running.
Engine loses power.
Engine overheats.
Machine does not drive.
Abnormal vibration.
Uneven cutting height.
Possible Cause
1. Fuel tank is empty.
2. Fuel shut off valve is closed.
3. Choke is not on.
4. Air cleaner is dirty.
5. Spark plug wire is loose or disconnected.
6. Spark plug is pitted, fouled, or the gap is incorrect.
7. Dirt in the fuel filter.
8. Dirt, water, or stale fuel is in the fuel system.
1. Engine load is excessive.
2. Air cleaner is dirty.
3. Oil level in the crankcase is low.
4. Cooling fins and air passages under the engine blower housing are plugged.
5. Spark plug is pitted, fouled, or the gap is incorrect.
6. Vent hole in the fuel cap is plugged.
7. Dirt in the fuel filter.
8. Dirt, water, or stale fuel is in the fuel system.
1. Engine load is excessive.
2. Oil level in the crankcase is low.
3. Cooling fins and air passages under the engine blower housing are plugged.
1. Shift lever is in neutral.
Corrective Action
1. Fill fuel tank with gasoline.
2. Open the fuel shut off valve.
3. Move the throttle lever to choke position.
4. Clean or replace the air cleaner element.
5. Install wire on spark plug.
6. Install a new, correctly gapped spark plug.
7. Replace the fuel filter.
8. Contact an Authorized Service Dealer.
1. Reduce the ground speed.
2. Clean the air cleaner element.
3. Add oil to the crankcase.
4. Remove the obstruction from the cooling fins and air passages.
5. Install a new, correctly gapped spark plug.
6. Clean or replace the fuel cap.
7. Replace the fuel filter.
8. Contact an Authorized Service Dealer.
1. Reduce the ground speed.
2. Add oil to the crankcase.
3. Remove the obstruction from the cooling fins and air passages.
1. Move the shift lever to a drive gear position.
2. Change the belt.
3. Change the belt.
4. Replace the spring.
1. Install new cutting blade(s).
2. Traction belt is worn, loose or broken.
3. Traction belt is off a pulley.
4. Broken or missing idler spring.
1. Cutting blade(s) is/are bent or unbalanced.
2. Blade mounting bolt is loose.
3. Engine mounting bolts are loose.
4. Loose engine pulley, idler pulley, or blade pulley.
5. Engine pulley is damaged.
6. Blade spindle is bent.
1. Blade(s) not sharp.
2. Cutting blade(s) is/are bent.
3. Mower is not level.
4. Underside of mower is dirty.
5. Tire pressure is not correct.
6. Blade spindle bent.
2. Tighten the blade mounting bolt.
3. Tighten the engine mounting bolts.
4. Tighten the appropriate pulley.
5. Contact an Authorized Service Dealer.
6. Contact an Authorized Service Dealer.
1. Sharpen the blade(s).
2. Install new cutting blade(s).
3. Level the mower from side-to-side and front-to-rear.
4. Clean the underside of the mower.
5. Adjust the tire pressure.
6. Contact an Authorized Service Dealer.
52
Problem
Blades do not rotate.
Possible Cause
1. Mower deck belt is worn or loose.
2. Mower deck belt is broken.
3. Mower deck belt is off pulley.
4. Broken or missing idler spring.
Corrective Action
1. Check the belt tension.
2. Install new deck belt.
3. Inspect the belt and replace if damaged.
Check the pulleys and idlers and adjust the belt tension.
4. Replace the spring.
53
Schematics
Electrical Schematic (Rev. -)
Hydraulic Schematic (Rev. -)
54
Notes:
55
The Toro Total Coverage Warranty
A Limited Warranty (see warranty periods below)
Landscape
Contractor
Equipment (LCE)
Conditions and Products Covered
The Toro Company and its affiliate, Toro Warranty Company, pursuant to an agreement between them, jointly promise to the original purchaser to repair the Toro Products listed below if defective in materials or workmanship.
The following time periods apply from the date of purchase by the original owner:
Warranty Period Products
All Mowers
• Engine
• Battery
•
•
Belts and Tires
Attachments
21 in. Heavy Duty Mowers
Mid-Size Walk-Behind Mowers
Grand Stand TM Mowers
• Frame
Z Master ® Z400, Z500 Mowers
• Frame
Z Master ® G3 Mowers
• Frame
See engine manufacturer’s warranty 1
90 days Parts and Labor
1 year Parts only
90 days
1 year
1 year Commercial Use
2 years Residential Use 2
2 years
5 years or 1,200 hours 3
Lifetime (original owner only) 4
4 years or 1,200 hours 3
Lifetime (original owner only) 4
5 years or 1,200 hours 3
Lifetime (original owner only) 4
1 Some engines used on Toro LCE Products are warranted by the engine manufacturer.
2 Residential use means use of the product on the same lot as your home. Use at more than one location is considered commercial use and the commercial use warranty would apply.
3 Whichever occurs first.
4 Lifetime Frame Warranty - If the main frame, consisting of the parts welded together to form the tractor structure that other components such as the engine are secured to, cracks or breaks in normal use, it will be repaired or replaced, at Toro’s option, under warranty at no cost for parts and labor. Frame failure due to misuse or abuse and failure or repair required due to rust or corrosion are not covered.
This warranty includes the cost of parts and labor, but you must pay transportation costs.
Instructions for Obtaining Warranty Service
If you think that your Toro Product contains a defect in materials or workmanship, follow this procedure:
1.
Contact any Authorized Toro Service Dealer to arrange service at their dealership. To locate a dealer convenient to you, refer to the Yellow
Pages of your telephone directory (look under “Lawn Mowers”) or access our web site at www.Toro.com. You may also call the numbers listed in item #3 to use the 24-hour Toro Dealer locator system.
2.
Bring the product and your proof of purchase (sales receipt) to the
Service Dealer. The dealer will diagnose the problem and determine if it is covered under warranty.
3.
If for any reason you are dissatisfied with the Service Dealer’s analysis or with the assistance provided, contact us at:
RLC Customer Care Department
Toro Warranty Company
8111 Lyndale Avenue South
Bloomington, MN 55420-1196
888-865-5676 (U.S. Customers)
888-865-5691 (Canada customers)
Owner Responsibilities
You must maintain your Toro Product by following the maintenance procedures described in the Operator’s Manual . Such routine maintenance, whether performed by a dealer or by you, is at your expense.
Items and Conditions Not Covered
There is no other express warranty except for special emission system and engine warranty coverage on some products.
This express warranty does not cover the following:
•
Cost of regular maintenance service or wear parts, such as filters, fuel, lubricants, tune-up parts, blade sharpening, brake and clutch adjustments.
•
Any product or part which has been altered or misused and requires replacement or repair due to normal wear, accidents, or lack of proper maintenance.
•
Repairs necessary due to improper fuel, contaminants in the fuel system, or failure to properly prepare the fuel system prior to any period of non-use over three months.
•
Pickup and delivery charges.
General Conditions
All repairs covered by these warranties must be performed by an
Authorized Toro Service Dealer using Toro approved replacement parts.
Neither The Toro Company nor Toro Warranty Company is liable for indirect, incidental or consequential damages in connection with the use of the Toro Products covered by this warranty, including any cost or expense of providing substitute equipment or service during reasonable periods of malfunction or non-use pending completion of repairs under this warranty.
All implied warranties of merchantability (that the product is fit for ordinary use) and fitness for use (that the product is fit for a particular purpose) are limited to the duration of the express warranty
Some states do not allow exclusions of incidental or consequential damages, or limitations on how long an implied warranty lasts, so the above exclusions and limitations may not apply to you.
This warranty gives you specific legal rights, and you may also have other rights which vary from state to state.
Countries Other than the United States or Canada
Customers who have purchased Toro products outside the United States or Canada should contact their Toro Distributor (Dealer) to obtain guarantee policies for your country, province, or state. If for any reason you are dissatisfied with your Distributor’s service or have difficulty obtaining guarantee information, contact the Toro importer. If all other remedies fail, you may contact us at Toro Warranty Company.
374-0252 Rev B
advertisement
* Your assessment is very important for improving the workof artificial intelligence, which forms the content of this project
Related manuals
advertisement
Table of contents
- 2 Introduction
- 4 Safety
- 4 Safe Operating Practices
- 5 Toro Mower Safety
- 7 Slope Indicator
- 8 Safety and Instructional Decals
- 12 Product Overview
- 12 Controls
- 13 Specifications
- 13 Attachments/Accessories
- 14 Operation
- 14 Adding Fuel
- 15 Think Safety First
- 15 Operating the Parking Brake
- 15 Starting and Stopping the Engine
- 16 Operating the Neutral Locks
- 17 (PTO)
- 17 The Safety Interlock System
- 18 Backward
- 19 Bringing the Machine to Neutral Position
- 19 Stopping the Machine
- 19 Pushing the Machine by Hand
- 19 Adjusting the Flow Baffle
- 20 Positioning the Flow Baffle
- 21 Transporting Machines
- 22 Side Discharging or Mulching the Grass
- 22 Adjusting the Height-of-Cut
- 23 Adjusting the Caster Position
- 23 Adjusting the Handle Height
- 25 Height of Cut Chart
- 26 Maintenance
- 26 Recommended Maintenance Schedule(s)
- 27 Lubrication
- 27 How to Grease
- 27 Bearings
- 27 Greasing the Mower Belt Idler
- 27 Crank
- 28 Engine Maintenance
- 28 Servicing the Air Cleaner
- 29 Servicing the Engine Oil
- 30 Servicing the Spark Plugs
- 31 Fuel System Maintenance
- 31 Servicing the Fuel Tank
- 32 Servicing the Fuel Filter
- 32 Servicing the Fuel Vent System
- 33 Drive System Maintenance
- 33 Adjusting the Speed Control Linkage
- 33 Adjusting the Neutral Control Linkages
- 34 Adjusting the Hydro Control Linkages
- 36 Adjusting the Control Rod
- 37 Adjusting the Tracking
- 37 Adjusting the Spring Anchor Links
- 37 Checking the Tire Pressure
- 38 Cooling System Maintenance
- 38 Cleaning the Air Intake Screen
- 38 Cleaning the Cooling System
- 39 Brake Maintenance
- 39 Servicing the Brake
- 40 Belt Maintenance
- 40 Checking the Belts
- 40 Replacing the Mower Belt
- 41 Adjusting the Mower Belt Tension
- 45 Hydraulic System Maintenance
- 45 Servicing the Hydraulic System
- 47 Mower Deck Maintenance
- 47 Servicing the Cutting Blades
- 49 Adjusting the Blade Brake
- 49 Replacing the Grass Deflector
- 50 Storage
- 52 Troubleshooting
- 54 Schematics