Eurotech Catalyst CV Ultra Low Power and Multicore CPU Module Based on Latest Intel® Atom� N2x00 Processor Owner Manual
Add to My manuals36 Pages
advertisement
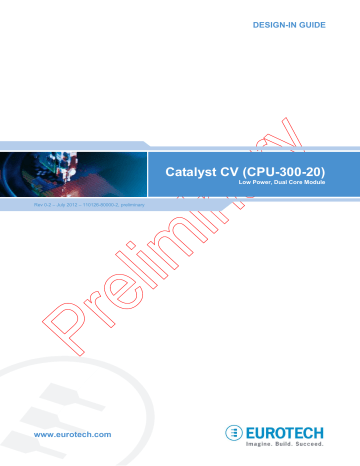
DESIGN-IN GUIDE
Rev 0-2 – July 2012 – 110126-80000-2, preliminary
Catalyst CV (CPU-300-20)
Low Power, Dual Core Module
www.eurotech.com
Trademarks
All trademarks both marked and not marked appearing in this document are the property of their respective owners.
Document Revision History
REVISION
1
DESCRIPTION
Preliminary release
DATE
July 2012
© 2012 Eurotech Inc.
Table of Contents
Table of Contents
110126-80000-2, preliminary 3
Catalyst CV (CPU-300-20) - Design-In Guide
4 110126-80000-2, preliminary
Important User Information
Important User Information
In order to lower the risk of personal injury, electric shock, fire, or equipment damage, users must observe the following precautions as well as good technical judgment, whenever this product is installed or used.
All reasonable efforts have been made to ensure the accuracy of this document; however, Eurotech assumes no liability resulting from any error/omission in this document or from the use of the information contained herein.
Eurotech reserves the right to revise this document and to change its contents at any time without obligation to notify any person of such revision or changes.
Safety Notices and Warnings
The following general safety precautions must be observed during all phases of operation, service, and repair of this equipment. Failure to comply with these precautions or with specific warnings elsewhere in this manual violates safety standards of design, manufacture, and intended use of the equipment.
Eurotech assumes no liability for the customer’s failure to comply with these requirements.
The safety precautions listed below represent warnings of certain dangers of which Eurotech is aware.
You, as the user of the product, should follow these warnings and all other safety precautions necessary for the safe operation of the equipment in your operating environment.
Installation in Enclosures
In the event that the product is placed within an enclosure, together with other heat generating equipment, ensure proper ventilation.
Do Not Operate in an Explosive Atmosphere
Do not operate the equipment in the presence of flammable gases or fumes. Operation of any electrical equipment in such an environment constitutes a definite safety hazard.
Alerts that can be found throughout this manual
The following alerts are used within this manual and indicate potentially dangerous situations.
Danger, electrical shock hazard:
Information regarding potential electrical shock hazards:
Personal injury or death could occur. Also damage to the system, connected peripheral devices, or software could occur if the warnings are not carefully followed.
Appropriate safety precautions should always be used, these should meet the requirements set out for the environment that the equipment will be deployed in.
Warning:
Information regarding potential hazards:
Personal injury or death could occur. Also damage to the system, connected peripheral devices, or software could occur if the warnings are not carefully followed.
Appropriate safety precautions should always be used, these should meet the requirements set out for the environment that the equipment will be deployed in.
Information and/or Notes:
These will highlight important features or instructions that should be observed.
110126-80000-2, preliminary 5
Catalyst CV (CPU-300-20) - Design-In Guide
Use an Appropriate Power Supply
Only start the product with a power supply that conforms to the voltage requirements as specified in
Power Supply , page 32 . In case of uncertainty about the required power supply, please contact your
local Eurotech Technical Support Team.
Use power supplies that are compliant with SELV regulation.
Avoid overcharging power-points.
Antistatic Precautions
To avoid damage caused by ESD (Electro Static Discharge), always use appropriate antistatic precautions when handing any electronic equipment.
Life Support Policy
Eurotech products are not authorized for use as critical components in life support devices or systems without the express written approval of Eurotech.
Warranty
For Warranty terms and conditions users should contact their local Eurotech Sales Office.
See Eurotech Worldwide Presence page 35 for full contact details.
WEEE
The information below is issued in compliance with the regulations as set out in the 2002/96/EC directive, subsequently superseded by 2003/108/EC. It refers to electrical and electronic equipment and the waste management of such products. When disposing of a device, including all of its components, subassemblies, and materials that are an integral part of the product, you should consider the WEEE directive.
This device is marketed after August 13, 2005 and you must separate all of its components when possible and dispose of them in accordance with local waste disposal legislations.
Because of the substances present in the equipment, improper use or disposal of the refuse can cause damage to human health and to the environment.
With reference to WEEE, it is compulsory not to dispose of the equipment with normal urban refuse and arrangements should be instigated for separate collection and disposal.
Contact your local waste collection body for more detailed recycling information.
In case of illicit disposal, sanctions will be levied on transgressors.
RoHS
This device, including all its components, subassemblies and the consumable materials that are an integral part of the product, has been manufactured in compliance with the European directive
2002/95/EC known as the RoHS directive (Restrictions on the use of certain Hazardous Substances).
This directive targets the reduction of certain hazardous substances previously used in electrical and electronic equipment (EEE).
Technical Assistance
If you have any technical questions, cannot isolate a problem with your device, or have any enquiry about repair and returns policies, contact your local Eurotech Technical Support Team.
See Eurotech Worldwide Presence page 35 for full contact details.
6 110126-80000-2, preliminary
Important User Information
Transportation
When transporting any module or system, for any reason, it should be packed using anti-static material and placed in a sturdy box with enough packing material to adequately cushion it.
Warning:
Any product returned to Eurotech that is damaged due to inappropriate packaging will not be covered by the warranty.
Conventions
The following table describes the conventions for signal names used in this document.
Convention
GND
#
_P
_N
Explanation
Digital ground plane
Active low signal
Positive signal in differential pair
Negative signal in differential pair
The following table describes the abbreviations for direction and electrical characteristics of a signal used in this document.
Type
I
O
IO
P
A
OD
CMOS
LVCMOS
LVTTL
3.3
5
HDA
LVDS
PCIe
SATA
DIFF
NC
Reserved
Explanation
Signal is an input to the system
Signal is an output from the system
Signal may be input or output
Power and ground
Analog signal
Open-drain
3.3 V CMOS
1.05 V CMOS
Low Voltage TTL
3.3 V signal level
5 V signal level
High Definition Audio, 3.3 V signal
Low Voltage Differential Signalling
PCI Express signal, not 3.3 V tolerant
SATA differential signal
Differential signal
No Connection
Use is reserved to Eurotech
Some signals include termination on the Catalyst CV. The following table describes the abbreviations that specify the signal termination.
Termination
PU
PD
R
C
Explanation
Pull-up resistor to the specified voltage
Pull-down resistor
Series resistor
Series capacitor
110126-80000-2, preliminary 7
Catalyst CV (CPU-300-20) - Design-In Guide
Product Overview
The Catalyst CV (CPU-300-20) is a high-performance, low power module based on the Intel processor N2x00 with the Intel
®
®
Atom
™
NM10 Express Chipset. The Intel Atom processor contains an integrated graphics processing engine supporting a wide range of hardware-accelerated graphics display and video processing capabilities, while the Intel NM10 Express Chipset supports extensive I/O and data storage capabilities. The Catalyst CV conforms to the same footprint as Eurotech’s
Catalyst XL, Catalyst LP, and Catalyst TC allowing existing customers to migrate to the Catalyst CV with minimal effort. The Catalyst CV allows embedded designers to offer the best graphical experience for the user with high energy efficiency.
An application-specific carrier board integrates with the Catalyst CV for a total production solution.
This flexible, modular architecture enables easy customization and quick time-to-market. A Eurotech carrier board is available that implements several industry-standard interfaces allowing development across a broad spectrum of end-use applications.
The Catalyst CV is available with a variety of operating systems. Support is also available for the Java
Virtual Machine and Eurotech’s Everyware
™
Software Framework, which offers an easy-to-use, Javabased development environment that minimizes time to market and allows for easy portability for future expansion.
Block Diagram
The following diagram illustrates the system organization of the Catalyst CV. Notice that the data connector has been divided into two sections for this illustration. Dotted lines indicate options.
Catalyst CV
HDMI/DP
HDMI/DP/eDP
VGA Display
LVDS Display
BKLT Ctrl
Intel
®
Atom
™
Processor
(N2x00)
DDR-3 DRAM
DMI
PCIe0
PCIe1
PCIe2
SD/MMC
PCIe to
Expansion
Host Ctrl
PCIe3
GigE MDI
PHY
Intel
®
NM10
Express
Chipset
NAND
SSD
HD Audio
SMBus
SATA1
SATA2
USB0-7
GPIOs
BIOS
SPI LPC Bus
SPI Bus
GPIO1-2
Carrier I
2
C Bus
Sys Mgmt I/O
Embedded
Ctrl
TPM
V Reg
VBAT (RTC)
Figure 1. Catalyst CV Block Diagram
8 110126-80000-2, preliminary
Product Overview
Features
Processor
Intel
®
Atom
™
processor N2x00, up to 1.6 GHz (Contact Eurotech for availability details)
Intel
®
NM10 Express Chipset
Integrated System Functions
Embedded Controller
Optional Trusted Platform Management (Contact Eurotech for details)
Memory
Up to 4 GB DDR-3 SDRAM SODIMM
Optional on-board NAND flash SSD (Contact Eurotech for details)
Integrated system BIOS
Battery-backed real-time clock
External memory support o SATA disk drive o USB disk drive o SD/MMC card o PCI Express card o IDE/PATA disk drive (Contact Eurotech for details)
Communications
Up to four PCI Express one lane slots
Eight Universal Serial Bus 2.0 ports
10/100BASE-T Ethernet with physical layer transceiver
I
2
C bus with I
2
C master device
SPI bus
System Management Bus
User Interface and Display
Dual independent display outputs supporting o VGA o LVDS o HDMI/DisplayPort/Embedded DisplayPort
Backlight interface with control signals for intensity and power
Inputs and Outputs
Low Pin Count bus for general-purpose I/O expansion
Six general-purpose inputs and outputs
Audio Interface
Intel
®
High Definition Audio interface
Power Supply
3.3 V and 5 V main power inputs
ACPI power management
Mechanical
67 mm x 100 mm dimensions
110126-80000-2, preliminary 9
Catalyst CV (CPU-300-20) - Design-In Guide
Design Checklist
Eurotech provides a host of services to ensure that your product is up and running from the first prototype release. We recommend the following process for every Catalyst CV carrier board design:
Kickoff Stage
During the Kickoff Stage, you will develop your block diagram and identify any customizations your application may require.
Gather your reference materials
Eurotech provides several documents that include key information for designing a custom carrier board. Use the following resources and ask questions:
Catalyst CV Design-In Guide
Catalyst CV Development Kit User Manual
Carrier Board Routing Guidelines
3D CAD models
Reference Carrier Board Schematic
Reference Carrier Board Bill of Materials
Define your requirements
Define your system’s requirement. Be sure to include requirements such as the product features, the input power, the type of transient protection on the power supply, connectivity to the module, and all
I/O to your system.
Create a block diagram
Create a block diagram of your proposed design. This step helps to formulate the best way to connect different devices to the module.
Identify customizations
Identify any customizations that your application requires. Examples of customizations are custom
LCD panel timings and backlight control, custom module configurations, or supporting a device that is not included on Eurotech’s standard carrier board. Customizations may require updates to the BIOS.
Utilize the Catalyst CV Development Kit
Utilize the Catalyst CV Development Kit for validating your proposed design. For example, if a USB device is to be used on USB port 6, test that device by connecting it to USB port 6 on the Catalyst CV
Development Kit. This testing also allows you to validate your OS image with all required drivers loaded.
Kickoff review
Early in the development of your carrier board, meet with your Eurotech representative to review your block diagram and discuss customizations. Incorporate any changes into your design.
Preliminary Design Stage
During the Preliminary Design Stage, you will finalize your block diagram, agree on customizations, and begin your preliminary schematic.
Use the reference schematic
Use Eurotech’s reference carrier board schematic as a starting point for your design. This schematic includes many commonly used interfaces. Using the same connectivity to the module will minimize the time spent in debugging your design.
10 110126-80000-2, preliminary
Product Overview
Select components from the reference bill of materials
Select the same components as those used in Eurotech’s reference carrier board bill of materials.
Eurotech selects components that are optimized for embedded systems based on quality, low-power consumption, availability, reliability, and industrial temperature options. Selecting the same components also allows you to use the drivers Eurotech has already integrated with the OS builds.
Follow the design requirements and recommendations
Follow the design requirements and recommendations listed in Carrier Board Design , page 24 of this
design-in guide. This section provides details about circuitry to include on the carrier board.
Preliminary design review
Stay in contact with your Eurotech representative during your preliminary design. Together, finalize your block diagram and agree on customizations needed. Continue to ask questions as you move towards finalizing your design.
Critical Design Stage
During the Critical Design Stage, you will finalize your schematic making sure that you have met all the module’s electrical, thermal, and mechanical design requirements.
Implement power supply sequencing
Implement the exact power supply sequencing described in Power Requirements , page 21 of this
design-in guide. The module has very specific power-on sequence requirements in order to power-up and operate correctly. Power sequencing the multiple voltage rails, as described in this section, is
CRITICAL. If your design does not meet these requirements, the module will not boot.
Provide a system-level reset
all devices on the carrier board. The module controls the de-assertion of this signal with appropriate timings relative to power being stable. Timing requirements for power stable to reset de-asserted and reset de-asserted to device available are critical.
Create a power budget
Create a power budget that takes into account the current requirement of the module, as specified in
Power Supply , page 32 , and of the devices that are used with the module. Design your power supply
to handle the maximum current requirement.
Determine thermal management
Determine what type of thermal management is required for your design. Use your power budget and
the information provided in Thermal Management , page 23 of this design-in guide to design a heat
spreader, if necessary.
Follow the module’s mechanical requirements
Follow the exact mechanical requirements given in Mechanical Design , page 22 for mounting holes
placement, position of the board-to-board connectors, and stack height on your carrier board design.
Use advanced layout and high-speed routing techniques
design-in guide. Adhering to good design practices for high-speed PCB design is essential. You should have your schematic 95% complete, especially the high-speed signals and buses of the module, power sequencing, and system reset, before you start board layout. Meet with your Eurotech representative to review your schematic before you begin layout. After your layout is complete, meet again to review your complete design.
110126-80000-2, preliminary 11
Catalyst CV (CPU-300-20) - Design-In Guide
Have a strategy to debug your design
Review your strategy to bring-up and to debug your design. Ensure that you have included the necessary support in your design. The maintenance serial port is extremely important in bring-up of a new design. Eurotech highly recommends including an external connection to SMC_UART_RX
(J1 B57) and SMC_UART_TX (J1 B106) on your carrier board.
Critical design review
Do an in-depth review of your finished design, including final schematic and board layout, to ensure that you have met all the requirements described in this checklist and throughout this design-in guide.
Again, ask your Eurotech representative questions.
Prototype Bring-up Stage
Eurotech provides assistance in bringing-up your prototype at your site or ours. We have several tools that can assist the process including "stand-alone" BIOS releases, BIOS modifications to meet specific platform or test requirements, and power monitoring applications for the module. The "stand-alone"
BIOS sets up the internal functions of the module and basic I/O functions. It is not dependent on any specific carrier board, devices, or circuits. This BIOS provides "basic" level functionality and can be used as a tool in the bring-up or debug of your unique carrier board.
Begin with the basics
Begin by checking basic functionality such as power, reset, and clocks. Verify that the power sequencing is as it should be and that the voltage regulator outputs are at nominal levels. Check that the system reset signal is asserted and deasserted according to the power sequencing requirements.
Ensure all clocks necessary for bring-up are running properly.
Start with minimal devices
Minimize the number of devices required for bringup. Using Eurotech’s "debug" set of firmware is a good start. This firmware can be used (on case-by-case) basis as a debug and bring-up tool for your specific design prototyping or in the debugging phases of your development. It disables all NON-
Critical-to-BOOT functions to simplify the system functionality to base level. After you have verified this base level, enable each subsystem as needed. Adding one device at a time will help determine which subsystem, if any, is having problems.
Utilize the maintenance port
Utilize the maintenance port output to identify problems during bring-up. This port provides important debug information including BIOS POST codes and error messages that enable you to monitor the operation of the module.
Use your Catalyst CV Development Kit
Use your Catalyst CV Development Kit to isolate problems. If a problem occurs during bring-up of your carrier board, try to duplicate the problem on the development kit.
Prototype bring-up review
Review your bring-up process and share lessons learned with your Eurotech representative.
Acceptance of Customizations
Eurotech is committed to your design success. Using our support services throughout the development cycle ensures a complete and robust solution with which to move forward.
Customization Acceptance
Meet with your Eurotech representative to discuss acceptance of any customizations and to plan the steps toward production of your Catalyst CV design.
12 110126-80000-2, preliminary
Product Overview
Development Kit
The Catalyst CV Development Kit is designed to get the developer up and running quickly. The development kit includes the Catalyst CV, a standard development kit carrier board, and supporting peripheral devices. To provide flexibility and allow development across a broad spectrum of end-use applications, the carrier board maximizes the Catalyst CV functionality and implements many industrystandard interfaces. This configuration allows you to become familiar with the Catalyst CV functionality prior to customization for your specific application. In addition, the standard development kit carrier board provides a reference for custom carrier board design.
Related Documents
This guide provides details about the various features of the Catalyst CV and about how it creates a system that meets your application needs. Design details are provided as guidelines for custom carrier board design.
Check the Eurotech support site ( http://support.eurotech-inc.com/ ) or contact your local Eurotech representative for additional resources for the Catalyst CV.
110126-80000-2, preliminary 13
Catalyst CV (CPU-300-20) - Design-In Guide
Software Specification
Eurotech provides an application-ready platform including BIOS, operating system, and development environment. This section gives a brief description of the software support available for the
Catalyst CV. For additional details, contact your local Eurotech representative.
Operating System Support
The Catalyst CV is compatible with the following operating systems:
Windows
®
7
Windows Embedded Compact
Windows Embedded Standard
Wind River Linux
Select real-time operating systems
For details about available support of each operating system, contact your local Eurotech representative.
BIOS
The Catalyst CV incorporates a custom system BIOS developed by Eurotech.
Everyware
™
Software Framework
Everyware Software Framework (ESF) is an inclusive software framework that puts a middleware layer between the operating system and the OEM application. It provides industry-standard interfaces that shorten development time, simplify coding, and allow software to be ported from one Eurotech hardware platform to another. The Catalyst CV supports ESF. If your application requires ESF, contact your local Eurotech representative.
Information about ESF is available at http://esf.eurotech.com
.
14 110126-80000-2, preliminary
Hardware Specification
Hardware Specification
Core Processor
The Catalyst CV bases its architecture on an integrated two-chip solution comprised of the Intel Atom processor N2x00 and Intel NM10 Express Chipset. In addition, the Catalyst CV fully integrates system functions that include system management and control implemented by an advanced chip level solution, tightly integrated power management controls, system BIOS firmware memory, and optional
Trusted Platform Management (TPM) for industry-standard secure data encryption. This fully integrated and flexible feature set increases product readiness and compliance. The following sections describe the functionality and feature set of this processor technology as it relates to the
Catalyst CV architecture.
Intel Atom Processor
At the core of the Catalyst CV is the Intel Atom processor N2x00. This processor’s architecture offers an integrated graphics processing engine supporting a wide range of hardware-accelerated graphics
External Interrupts
(This section to be determined.)
Intel NM10 Express Chipset
The Intel Atom processor operates in conjunction with the Intel NM10 Express Chipset. This companion device supports extensive I/O and data storage capabilities that include USB, SATA, Intel
High Definition Audio, PCI Express, Ethernet, GPIO, SMBus, and LPC bus. Subsequent sections describe each capability.
Embedded Controller
An embedded controller included on the Catalyst CV performs two main functions: ACPI power management and hardware monitoring. It connects to the Intel NM10 Express Chipset using the LPC bus. Combined with the on-module power switch, the embedded controller supports ACPI power management. It ensures proper start-up, shutdown, and power saving transitions by sequencing the voltages and monitoring the input power and on-module voltage regulators. For further details about power management, see
Power Requirements , page 21 . As a second function, the embedded
controller performs temperature monitoring, measuring the temperatures on the Intel Atom processor die and near the memory. You can also monitor temperatures on your carrier board by connecting an external temperature sensor to the embedded controller I
2
C bus provided on connector J1.
Trusted Platform Management (option)
The optional on-module TPM function is compliant with the Trusted Computer Group specification version 1.2. This function provides public key generation, public key storage encryption/decryption, storage of hashes, key endorsement, and TPM initialization. As an option, the TPM is included on the
LPC bus.
110126-80000-2, preliminary 15
Catalyst CV (CPU-300-20) - Design-In Guide
Memory
The Catalyst CV combined with a carrier board provides a variety of storage capabilities. The following sections describe the different types of memory supported and provide details about implementation.
Synchronous DRAM
A Double Data Rate Synchronous DRAM (DDR-3) small outline dual in-line memory module
(SODIMM) is used on the Catalyst CV for system main memory and frame buffer memory. The
module is installed in J5 : SODIMM, page 31 . Options up to 4 GB are available.
Non-Volatile Memory
The Catalyst CV includes non-volatile memory for system BIOS storage and a real-time clock (RCV) functionality.
BIOS and Configuration Data
A serial interface flash memory device stores the BIOS boot firmware, BIOS Setup settings, and module configuration data on the Catalyst CV. Standard configuration is 2 MB. The flash device performs logically as a firmware hub (FWH) and connects to the Intel NM10 Express Chipset using a serial peripheral interface (SPI).
Real-Time Clock
The Intel NM10 Express Chipset includes a RTC function. It retains the system date and time when the system is powered down as long as the 3.3 V “always” power or backup power is provided to the chip.
Flash SSD (option)
The Catalyst CV supports an optional on-module NAND flash SSD. An 8 GB option is available in the standard module configuration.
Notes:
If populated, the flash SSD connects to the SATA1 port on the module. For additional details, contact your local Eurotech representative.
External Memory Interfaces
Four types of external memory interfaces provide mass storage options on a carrier board. The
Catalyst CV supplies the signals for up to two SATA ports, eight USB ports, a SD/MMC interface, and up to four PCIe slots that can connect external memory to the module. Connector J1 provides the signals for each option. Include support circuitry and connectors on your carrier board. The highspeed differential and single-ended signals associated with these external memory interfaces require strict routing constraints on the carrier board.
Notes:
As an optional configuration, the Catalyst CV can provide an IDE/PATA interface. In this configuration, the IDE/PATA signals replace DDI Port 0 and DDI Port 1 on connector J1.
For additional details, contact your local Eurotech representative.
16
SATA Disk Drive
The Catalyst CV provides up to two serial ATA (SATA) buses externally allowing connection to a highcapacity, removable storage SATA disk drive. These buses support the Serial ATA Specification,
Revision 1.0a with data transfer rates of up to 3.0 Gb/s.
USB Mass Storage Device
A USB mass storage device can connect to one of eight USB ports on the Catalyst CV. Any USB device that has USB drivers installed on the Catalyst CV can connect to the USB host ports. For a
description of these ports, see Universal Serial Bus , page 17 .
110126-80000-2, preliminary
Hardware Specification
SD Cards
The Catalyst CV includes a Secure Digital and MultiMediaCard (SD/MMC) interface for memory and
I/O expansion. You can use this interface to implement a SD/MMC socket on a carrier board providing mass storage or to develop custom unique add-in cards. In addition to the SD/MMC signals, connector J1 includes signals to control SD/MMC support circuitry on the carrier board. The interface includes signals to control a power FET and to drive a LED.
Notes:
The Host Controller for the SD/MMC interface connects to PCIe slot 2 on the module. If this device is used, PCIe slot 2 is not available on connector J1. For additional details, contact your local Eurotech representative.
PCIe Memory Card
A PCIe x1 memory card can connect to one of four PCIe x1 slots available on the Catalyst CV. For a
description of the PCI Express capability, see PCI Express , page 17 .
Communications
The Catalyst CV supports several industry-standard channels for communication with peripheral and peer devices on the carrier board. These include PCI Express, USB, Ethernet, I
2
C bus, SPI bus, and
SMBus. The Catalyst CV does not limit flexibility by integrating fixed function I/O components. All communication signals are available on connector J1 providing flexibility and ease of implementation on the carrier board. This allows development of a unique carrier board optimized for your requirements.
PCI Express
A key capability of the Catalyst CV is its PCI Express (PCIe) support. Up to four PCIe one lane
(PCIe x1) slots are available on connector J1. These high-speed differential pairs require strict routing constraints on the carrier board and AC coupling. An on-module clock buffer supplies the PCIe clocks for the four ports. Additional input signals to the module, CLK_SLOTx_OE#, control each reference clock. On a carrier board, these signals connect to the PCIe sockets indicating the presence of a PCIe device. When activated, this signal enables the PCIe clock for the device.
Notes:
On the module, PCIe slot 2 connects to the Host Controller for the SD/MMC interface. In addition, the reference clock shares pins on connector J1 with the SD/MMC interface. If
SD/MMC is used, PCIe slot 2 is not available on connector J1.
On the module, PCIe slot 3 connects to the Ethernet Physical Layer Transceiver. In addition, the reference clock shares pins on connector J1 with the MDI. If Ethernet is used,
PCIe slot 3 is not available on connector J1.
For additional details, contact your local Eurotech representative.
Universal Serial Bus
The Catalyst CV provides eight general-purpose Universal Serial Bus (USB) host ports. These USB host ports support the USB 2.0 specification operating at low (1.5 Mbps), full (12 Mbps) speeds, and high speed (480 Mbps). USB0-5 include the associated over-current detection inputs. Use these USB host ports to connect to devices external to the carrier board. USB mouse and keyboard are the most common client devices, but you can connect any USB device that has USB drivers installed on the
Catalyst CV. USB6 and USB7 do not include the associated over-current detection signals. When possible, connect these ports to devices on the carrier board.
In order to create a fully functioning USB host port, include the host power supply, current limiter circuits, EMI chokes, and over-voltage protection on your carrier board. The USB protocol allows client devices to negotiate the power they need from 100 mA to 500 mA in 100 mA increments. The carrier board must supply the 5 V power required by client devices. Use a power switch with the corresponding over-current detection for each port.
110126-80000-2, preliminary 17
Catalyst CV (CPU-300-20) - Design-In Guide
Ethernet
The Intel NM10 Express Chipset includes an integrated LAN Controller that conforms to the IEEE
802.3 standard. This device connects to an Intel
®
82574 Gigabit Ethernet Physical Layer Transceiver located on the module, supporting a Media Dependent Interface (MDI) for 10Base-T and 100Base-TX applications. For information about this device, refer to www.intel.com
. In addition, the transceiver drives three programmable LED control signals which are available on connector J1. Include magnetics, termination, and an RJ-socket on your carrier board to complete the connection to your network. Contact your local Eurotech representative for additional information about the magnetics recommended for use on the carrier board.
Notes:
The Intel 82574 connects to PCIe slot 3 on the module. If this device is used, PCIe slot 3 is not available on connector J1. For additional details, contact your local Eurotech representative.
Carrier I
2
C Bus
I
2
C (Inter-IC) bus is a multi-master, "two-wire" synchronous serial bus for communications between integrated circuits (ICs) and for addressing peripherals in a system. The Catalyst CV provides an
2 external connection to its carrier I C bus with the embedded controller acting as the bus master. When this bus is used on your carrier board, power all devices connected to it using the 3.3 V “Always”
(V3.3A) power or isolate the devices from the bus when powered off. Notice that the module does not include termination on this I
2
C bus. Include 10k pull-up resistors to V3.3A on the carrier board.
I
When possible, use the SMBus to communicate with devices on the carrier board instead of the carrier
2
C bus.
SPI Bus
The Serial Peripheral Interface (SPI) is a synchronous serial port that consists of a clock, transmit, receive, ground, and one or more device selects. Each device on the bus requires its own select line.
Buses may be full or half duplex, clocking data one or both directions at the same time, respectively.
The Catalyst CV provides an external connection on connector J1 to a SPI bus with the embedded controller acting as the bus master.
System Management Bus
System Management Bus (SMBus) follows the same operating principles as I
2
C. Similar to I
2
C,
SMB us is a “two-wire” interface allowing multiple devices to communicate with each other. Devices function as bus masters and bus slaves. SMBus enables communication between devices and allows connection of devices that require legacy software accessibility thru standard SMB addressing. The
Catalyst CV provides an external connection on connector J1 to its SMBus with the Intel NM10
Express Chipset acting as bus master. This bus supports the SMBus Specification, Version 2.0. In addition, the module supports hardware alerting on the SMBus using the I/O signal SMB_ALERT#.
Consider this capability when you are selecting between connectivity to this bus or the carrier I
2
C bus.
Notes:
SMBus is not compatible with all I
2
C devices. Review the device data sheet carefully before connecting an I
2
C device to the SMBus.
Notice that the module includes pull-up resistors to V3.3S on the SMBus. On your carrier board, power all devices connected to this bus using the V3.3S power or isolate the devices from the bus when powered off.
18 110126-80000-2, preliminary
Hardware Specification
Display and User Interface
The Intel Atom processor includes an integrated 2D/3D graphics engine supporting a wide range of hardware-accelerated graphics display and video processing capabilities. The processor provides two independent display outputs supporting HDMI, DisplayPort, Embedded DisplayPort, LVDS, and analog
VGA outputs. In addition, the processor provides discrete backlight control signals. This section summarizes the Catalyst CV graphics display and video processing capabilities.
VGA Display
The Catalyst CV drives an analog RGB output. This output provides red, green, and blue data, as well as horizontal sync and vertical sync signals. To connect to a VGA display, add termination, output filters, and buffers on your carrier board. In addition, the module provides a Display Data Channel
(DDC) serial bus (VGA_DDC_DATA on J1 pin A30, VGA_DDC_CLK on J1 pin B30) for monitor Plug and Play capability with various computer displays.
LVDS Display and Backlight Control
The Catalyst CV supplies a LVDS output consisting of four LVDS data pairs, as well as a LVDS pixel clock, supporting 24-bit color. If your application requires transmission over a long display cable, include an LVDS buffer/repeater on your carrier board to boost the data and pixel clock signals.
Cables should not introduce major impedance discontinuities that cause signal reflections. The differential pairs also require strict routing constraints on the carrier board. Additional capabilities include the discrete signal L_VDDEN (J1 pin A32) that controls power to the display and an I
2
C interface (L_DDC_DATA on J1 pin B28, L_DDC_CLK on J1 pin A29) for communication with the LCD
Display Data Channel (DDC).
Backlight
Most LCDs include one or more cold-cathode fluorescent lamp (CCFL) tubes to backlight the displays.
Backlight inverters drive the panel backlights. These circuits are typically external to the display and generate the several hundred volts required to drive the CCFL tubes. Backlights can easily become the greatest source of power consumption in a portable system. To reduce power consumption, most backlight inverters include control signals to dim and turn off the backlight. To support these features, the Catalyst CV supplies three backlight control signals and an I
2
C bus (L_CTLB_DATA on J1 pin B25,
L_CTLA_CLK on J1 pin B29) for communication with the backlight. The following table describes the three backlight control signals.
Signal
L_BKLTCTL
L_BKLTEN
L_BKLTSEL0_GPIO#
J1 Pin
B33
B32
B58
Type
O
O
O
Description
Controls the intensity of the backlight
Turns power to the backlight on or off
Selects backlight control (PWM vs. I
2
C)
Table 1. Backlight Control Signals
HDMI, DisplayPort, and Embedded Display Port
The Catalyst CV provides two digital display interfaces, DDI Port 0 and DDI Port 1, that support High-
Definition Multimedia Interface (HDMI), DisplayPort (DP), and Embedded DisplayPort (eDP). The following table describes the configuration options for each port.
DDI Port
0
1
Capability
HDMI or DP
HDMI or DP/eDP
Table 2. Configuration Options
Each DDI port consists of four differential data pairs, as well as a bidirectional auxiliary channel for command/control functions when configured for DP. These high-speed differential pairs require strict routing constraints on the carrier board and AC coupling. Additional signals provided with each port include an I
2
C interface (DDIx_SDA, DDIx_SCL) for communication with the display and DDIx_HPD for hot plug detect.
110126-80000-2, preliminary 19
Catalyst CV (CPU-300-20) - Design-In Guide
Inputs and Outputs
Several signals on the Catalyst CV support I/O expansion and system management. The module includes a Low Pin Count bus supporting legacy I/O capabilities and multiple discrete I/O signals performing system reset, power control, and general-purpose input and output. Connector J1 includes all I/O signals.
Low Pin Count Bus
In response to the transition from ISA-based systems, the Low Pin Count (LPC) bus provides a migration path for legacy I/O capabilities. This interface enables general-purpose I/O expansion and provides communication to low-bandwidth devices. For this purpose, the Intel NM10 Express Chipset supplies a LPC bus supporting the Low Pin Count Interface Specification, Revision 1.1. On the
Catalyst CV, the LPC bus connects to the Intel NM10 Express Chipset, the embedded controller, and an optional TPM. Externally, the LPC bus provides general-purpose expansion. A common application on the carrier board includes a Super I/O Controller that provides I/O capabilities such as additional serial ports, keyboard, mouse, IrDA, and general-purpose I/O. Ensure that the LPC signals are routed as critical nets on your carrier board and include 10k pull-up resistors to V3.3S on the
LPC_ADx signals.
Reset Signals
One of two signals resets the circuitry on the module and carrier board. One signal originates from the module, while the second signal originates from the carrier board. The output signal RST# drives multiple loads on the module. Include additional buffering on the carrier board to drive multiple devices. The following table compares the reset signals.
Signal
RST#
FP_RESET#
J1 Pin Type Description
B56
A59
O
I
Use as a power-on reset to reset all devices on the carrier board.
Output is driven by the module, forces complete system hardware reset, and is used for proper reset timing and logic synchronization.
Do not use this signal as a power-on reset. FP_RESET# will not be detected until RST# is de-asserted.
Input initiates a hardware reset including the Intel Atom processor and
Intel NM10 Express Chipset.
Table 3. Reset Signals
In addition to the hardware resets, the input signal H_INIT# (J1 pin B3) initiates a soft reset of the module.
General-Purpose Input and Output
The Catalyst CV provides six general-purpose input and output (GPIO) signals, as described in the following table.
Signal
GPIO1
GPIO2
GPIO3
GPIO5
FWH_WP#
SCH_GPIOSUS_3
J1 Pin
A108
A3
B92
B54
A2
B53
Description
Embedded controller GPIO
Embedded controller GPIO
Intel NM10 Express Chipset GPIO24
Intel NM10 Express Chipset GPIO26
Intel NM10 Express Chipset GPIO8
Intel NM10 Express Chipset GPIO15
Table 4. GPIO Signals
Intel High Definition Audio
The Intel High Definition Audio (Intel HD Audio) Specification implements high quality audio in a PC environment. The specification defines a uniform interface between a host computer and audio codec specifying register control, physical connectivity, programming model, and codec architectural components. The Intel NM10 Express Chipset provides an Intel HD Audio interface capable of supporting up to two external audio codecs. All Intel HD Audio signals are available on connector J1.
The Intel NM10 Express Chipset supports only 3.3 V signalling levels. Include audio codecs along with amplifiers, switches, and connectors on your carrier board.
20 110126-80000-2, preliminary
Power Requirements
(This section is to be determined.)
Hardware Specification
110126-80000-2, preliminary 21
Catalyst CV (CPU-300-20) - Design-In Guide
Mechanical Specifications
This section describes mechanical and thermal design guidelines for the Catalyst CV.
Mechanical Design
Mechanical Drawing
The following mechanical drawing specifies the dimensions of the Catalyst CV, as well as locations of key components on the board. All dimensions are in millimeters.
22
Figure 2. Catalyst CV, Top View
Figure 3. Catalyst CV, Side View
110126-80000-2, preliminary
Mechanical Specifications
Figure 4. Catalyst CV, Bottom View
Thermal Management
(This section is to be determined.)
110126-80000-2, preliminary 23
Catalyst CV (CPU-300-20) - Design-In Guide
Carrier Board Design
An application-specific carrier board integrates with the Catalyst CV to meet various system requirements. The Catalyst CV Development Kit includes a carrier board designed to maximize the
Catalyst CV functionality. This carrier board implements many industry-standard interfaces and provides a reference for custom carrier boards optimized for your requirements. This section includes many of the considerations followed in the design of the Catalyst CV Development Kit carrier board.
Design Guidelines
(This section is to be determined.)
Test and Debug
The maintenance serial port is extremely important in bring-up of a new carrier board design.
Eurotech highly recommends including an external connection to SMC_UART_RX (J1 B57) and
SMC_UART_TX (J1 B106) on your carrier board.
The IEEE1149.1 JTAG port, provided on connector J1, is available for programming the CPLD on the module, factory test, and software debugging. Otherwise, this port is not supported for application use.
Eurotech highly recommends including an external connection to this JTAG port on your carrier board.
To ensure correct operation of the JTAG interface, include a 10k pull-up resistor to V3.3S on the
TDO signal on the carrier board.
An additional ITP debug port, connector J3, provides full access to the XDP debugger port using a
SFF style connector. Eurotech highly recommends allowing for access to this connector, in the event you are directed to use this port when working with Eurotech staff. Allow for the size of the mating connector and bend radius of the cable.
24 110126-80000-2, preliminary
Connectors
Connectors
Identifying Connectors
The following diagrams illustrate the location and numbering of the connectors on the Catalyst CV.
When viewing the module from the component side, connector J1 and connector J3 lie under the module.
J3
J5
Figure 5. Connector Location, Top View
110126-80000-2, preliminary
J1
Figure 6. Connector Location, Bottom View
J2
25
Catalyst CV (CPU-300-20) - Design-In Guide
Signal Headers
The following tables describe the electrical signals available on the connectors of the module. Each section provides relevant details about the connector including part numbers, mating connectors, and connector pinout. The pinout table includes signal type, termination included on the module, and a signal description.
26 110126-80000-2, preliminary
Connectors
J1: Docking Connector: Data
Board connector: 220-pin, stacking board-to-board receptacle, 0.5 mm, Tyco Electronics 3-6318490-6
Carrier board connector: Tyco Electronics 3-1827253-6, 5 mm stacking height
Tyco Electronics 3-6318491-6, 8 mm stacking height
The Catalyst CV connector J1 mates to the carrier board. Most data signals are provided on this docking connector.
Pin Name
A1 GND
A2 FWH_WP#
A3 GPIO2
A4 HDA_SYNC
A5 HDA_RST#
A6 HDA_SDATAIN0
A7 HDA_SDATAIN1
A8 SLOT0_DATA4
A9 SLOT0_DATA3
A10 SLOT0_DATA1
A11 GND
A12 SLOT0_LED
A13 SLOT0_CLK
A14 LDRQ0#
A15 SLOT0_DATA7
A16 SLOT0_PWR#
A17 SATA1_TX_P
A18 SATA1_TX_N
A19 SATA1_RX_P
A20 SATA1_RX_N
A21 GND
A22 MDI0_P
A23 MDI0_N
A24 LAN_LED0
A25 MDI2_P
A26 MDI2_N
A27 MDI3_P
A28 MDI3_N
A29 L_DDC_CLK
A30 VGA_DDC_SDA
A31 GND
A32 L_VDDEN
A33 SMB_ALERT#
A34 SPKR
A35 ICH_CLKRUN#
A36 CLK_LPC_FWH
A37 DDI1_SDA
A38 SMB_CLK
A39 INT_SERIRQ
A40 LPC_FRAME#
A41 GND
A42 DDI1_TX0_D_P
A43 DDI1_TX0_D_N
A44 DDI1_TX1_D_P
A45 DDI1_TX1_D_N
A46 DDI1_SCL
A47 DDI0_TX0_D_P
A48 DDI0_TX0_D_N
A49 DDI0_TX1_D_P
A50 DDI0_TX1_D_N
A51 GND
O-3.3
P
O-DIFF
O-DIFF
O-DIFF
O-DIFF
O-3.3
O-DIFF
O-DIFF
O-DIFF
O-DIFF
P
Type On Module Termination Description
P
IO-LVTTL PU 10k V3.3A
IO-CMOS
O-HDA
O-HDA
I-HDA
I-HDA
IO-3.3
IO-3.3
IO-3.3
P
Ground
Intel NM10 Express Chipset GPIO8
Embedded controller GPIO
Intel HD Audio frame sync
Intel HD Audio reset
Intel HD Audio serial data input 0
Intel HD Audio serial data input 1
SD/MMC 0 data 4
SD/MMC 0 data 3
SD/MMC 0 data 1
Ground
O-3.3 SD/MMC 0 LED
O-3.3
IO-3.3
IO-3.3
O-3.3
O-SATA
O-SATA
I-SATA
I-SATA
P
IO-A
IO-A
O-3.3
IO-A
IO-A
IO-A
IO-A
O-OD
IO-3.3
P
O-CMOS
O-3.3
O-3.3
O-LVTTL
PU 2.2k V3.3S
IO-LVTTL PU 2.21k V3.3S
O-LVTTL
IO-3.3
PU 4.7k V3.3S_PRIME
PU 8.25k V3.3S_PRIME
SD/MMC 0 clock
LPC bus encoded DMA request
(Contact Eurotech for details)
SD/MMC 0 data 7
SD/MMC 0 power control
SATA1 transmit, positive signal
SATA1 transmit, negative signal
SATA1 receive, positive signal
SATA1 receive, negative signal
Ground
Ethernet, positive signal
Ethernet, negative signal
Ethernet LED 0
Ethernet, positive signal
Ethernet, negative signal
Ethernet, positive signal
Ethernet, negative signal
LCD DDC I
2
C clock
CRT DDC I
2
C data
Ground
LCD power enable
SMBus activity alert
Intel HD Audio speaker
Initiates active clock output from
LPC bus master
LPC bus clock
DDI Port 1, I
2
C data
SMBus clock
IO-3.3
R33
PU 2.2k V3.3S
PU 2.21k V3.3S
PU 4.7k V3.3S_PRIME
PU 10k V3.3S
PU 2.2k V3.3S
LPC bus interrupt
LPC bus frame sync
Ground
DDI Port 1, Transmit 0, positive
DDI Port 1, Transmit 0, negative
DDI Port 1, Transmit 1, positive
DDI Port 1, Transmit 1, negative
DDI Port 1, I
2
C clock
DDI Port 0, Transmit 0, positive
DDI Port 0, Transmit 0, negative
DDI Port 0, Transmit 1, positive
DDI Port 0, Transmit 1, negative
Ground
110126-80000-2, preliminary 27
Catalyst CV (CPU-300-20) - Design-In Guide
28
Pin Name
A52 DDI0_HPD
A53 DDI0_TX2_D_P
A54 DDI0_TX2_D_N
A55 DDI0_TX3_D_P
A56 DDI0_TX3_D_N
A57 HDA_DOCK_EN#
A58 HDA_DOCK_RST#
A59 FP_RESET#
A60 GND
A61 USB_OC5#
A62 USB6_P
A63 USB6_N
A64 GND
A65 USB4_P
A66 USB4_N
A67 GND
A68 USB2_P
A69 USB2_N
A70 GND
A71 USB0_P
A72 USB0_N
A73 GND
A74 LA_CLK_P
A75 LA_CLK_N
A76 GND
A77 LA_DATA2_P
A78 LA_DATA2_N
A79 USB_OC2#
A80 GND
A81 LA_DATA1_P
A82 LA_DATA1_N
A83 GND
A84 PCIE_TX_SLOT2_P
A85 PCIE_TX_SLOT2_N
A86 GND
A87 PCIE_RX_SLOT2_P
A88 PCIE_RX_SLOT2_N
A89 USB_OC3#
A90 GND
A91 VGA_R
A92 VGA_G
A93 GND
A94 PCIE_RX_SLOT1_N
A95 PCIE_RX_SLOT1_P
A96 GND
A97 CLK_SLOT0_OE#
A98 PCIE_TX_SLOT0_N
A99 PCIE_TX_SLOT0_P
A100 GND
A101 CLK_PCIE_SLOT0_P
A102 CLK_PCIE_SLOT0_N
A103 GND
A104 JTAG_TMS
A105 JTAG_TCK
A106 JTAG_TDO
A107 JTAG_TDI
A108 GPIO1
A109 THERM_ALERT
A110 GND
B1 GND
B2 ICH_SUS_STAT#
B3 H_INIT#
B4 HDA_BITCLK
B5 HDA_SDATAOUT
B6 SLOT0_CMD
Type
I
O-DIFF
O-DIFF
O-DIFF
O-DIFF
O-3.3
O-3.3
I-3.3
P
I-3.3
IO
P
IO
IO
IO
IO
P
IO
P
IO
IO
P
O-LVDS
O-LVDS
P
O-LVDS
O-LVDS
I-3.3
P
O-LVDS
O-LVDS
P
O-PCIe
O-PCIe
P
I-PCIe
I-PCIe
I-3.3
P
O-A
O-A
P
I-PCIe
I-PCIe
P
I-3.3
On Module Termination Description
PD 100k
PU 10k V3.3A
DDI Port 0, Hot plug detect
DDI Port 0, Transmit 2, positive
DDI Port 0, Transmit 2, negative
DDI Port 0, Transmit 3, positive
DDI Port 0, Transmit 3, negative
Signal is pulled up on module
Signal is pulled up on module PU 10k V3.3A
PU 10k V3.3S Front panel reset
Ground
USB5 over current PU 8.25k V3.3A
PU 8.25k V3.3A
USB 6, positive signal
USB 6, negative signal
Ground
USB 4, positive signal
USB 4, negative signal
Ground
USB 2, positive signal
USB 2, negative signal
Ground
USB 0, positive signal
USB 0, negative signal
Ground
LVDS clock, positive signal
LVDS clock, negative signal
Ground
LVDS data 2, positive signal
LVDS data 2, negative signal
USB2 over current
Ground
LVDS data 1, positive signal
LVDS data 1, negative signal
Ground
PCIe 2 Transmit, positive signal C 0.1 F
C 0.1 F
PU 8.25k V3.3A
PCIe 2 Transmit, negative signal
Ground
PCIe 2 Receive, positive signal
PCIe 2 Receive, negative signal
USB 3 over current
Ground
PD 150
PD 150
O-PCIe
O-PCIe
P
PU 10k V3.3S
C 0.1 F
C 0.1 F
O
O
P
R 33
R 33
O
I
PU 10k V3.3S
PD 1k
O
I
IO-CMOS
PU 10k V3.3S
VGA, Red data
VGA, Green data
Ground
PCIe 1 Receive, negative signal
PCIe 1 Receive, positive signal
Ground
PCIe 0 clock enable
PCIe 0 Transmit, negative signal
PCIe 0 Transmit, positive signal
Ground
PCIe 0 Clock, positive signal
PCIe 0 Clock, negative signal
Ground
JTAG
JTAG
O-3.3
P
P
O-3.3
I-LVCMOS PU 1k 1.05V
O-HDA
O-HDA
IO-3.3
PU 10k V3.3S
PU 10k V3.3S
PU 40.2k V3.3S
JTAG
JTAG
Embedded controller GPIO
Thermal alert
Ground
Ground
(For details, contact Eurotech)
Soft reset for host processor
Intel HD Audio bit clock
Intel HD Audio data out
SD/MMC 0 command
110126-80000-2, preliminary
Connectors
Pin Name
B7 SLOT0_DATA0
B8 SLOT0_DATA6
B9 SLOT0_DATA5
B10 SLOT0_DATA2
B11 GND
B12 SLOT0_WP
B13 SLOT0_CD#
B14 CP_SCK
B15 CP_SSEL
B16 PCIE_TX_SLOT3_P
B17 PCIE_TX_SLOT3_N
B18 PCIE_RX_SLOT3_P
B19 PCIE_RX_SLOT3_N
B20 CP_MISO
B21 GND
B22 MDI1_P
B23 MDI1_N
B24 LAN_LED2
B25 L_CTLB_DATA
B26 CP_MOSI
B27 LAN_LED1
B28 L_DDC_DATA
B29 L_CTLA_CLK
B30 VGA_DDC_CLK
B31 GND
B32 L_BKLTEN
B33 L_BKLTCTL
B34 LPC_AD2
B35 SMB_DATA
B36 LPC_AD0
B37 CLK_LPC_SIO
B38 LPC_AD3
B39 LPC_AD1
B40 DDI0_SDA
B41 GND
B42 DDI0_AUX_P
B43 DDI0_AUX_N
B44 DDI1_AUX_P
B45 DDI1_AUX_N
B46 DDI1_TX2_D_P
B47 DDI1_TX2_D_N
B48 DDI1_TX3_D_P
B49 DDI1_TX3_D_N
B50 DDI0_SCL
B51 GND
B52 DDI1_HPD
B53 SCH_GPIOSUS_3
B54 GPIO5
B55 PCIE_WAKE#
B56 RST#
B57 SMC_UART_RX
B58 L_BKLTSEL0_GPIO#
B59 BTN_ONOFF#
B60 GND
B61 USB7_P
B62 USB7_N
B63 GND
B64 USB5_P
B65 USB5_N
B66 GND
B67 USB3_P
B68 USB3_N
B69 USB_OC0#
B70 GND
O-LVTTL
I-5
P
IO
IO
P
IO
IO
P
IO
IO
I-3.3
P
Type
IO-3.3
IO-3.3
IO-3.3
IO-3.3
P
I-3.3
I-3.3
O-CMOS
IO-CMOS
On Module Termination Description
PU 10k V3.3S
SD/MMC 0 data 0
SD/MMC 0 data 6
SD/MMC 0 data 5
SD/MMC 0 data 2
Ground
SD/MMC 0 write protect
SD/MMC 0 card detection
SPI bus, Clock signal
SPI bus, Chip select signal
PCIE 3 transmit, positive signal
PCIE 3 transmit, negative signal
O-PCIe
O-PCIe
I-PCIe
I-PCIe
I-CMOS
P
IO-A
IO-A
O-3.3
IO-OD
C 0.1 F
C 0.1 F
O-CMOS
O-3.3
IO-OD
O-OD
O-3.3
P
O-CMOS
O-CMOS
PU 2.2k V3.3S
IO-3.3
IO-LVTTL PU 2.21k V3.3S
IO-3.3
PCIE 3 receive, positive signal
PCIE 3 receive, negative signal
SPI bus, Data input
Ground
Ethernet, positive signal
Ethernet, negative signal
Ethernet LED 2
Backlight I
2
C data
SPI bus, Data output
Ethernet LED 1
LCD DDC I
2
C data
Backlight I
2
C clock
CRT DDC I
2
C clock
Ground
Turns power to the backlight on/off
Controls intensity of the backlight
LPC bus address/data 2
SMBus data
LPC bus address/data 0
O-3.3
IO-3.3
IO-3.3
O-3.3
P
IO-DIFF
IO-DIFF
IO-DIFF
IO-DIFF
O-DIFF
R 33
PU 2.2k V3.3S
O-DIFF
O-DIFF
O-DIFF
O-3.3 PU 2.2k V3.3S
P
I PD 100k
IO-LVTTL PU 10k V3.3A
IO-LVTTL
I-LVTTL PU 10k VBATA
O-LVTTL
I-3.3
LPC bus clock
LPC bus address/data 3
LPC bus address/data 1
DDI Port 0, I
2
C data
Ground
DDI Port 0 auxiliary, positive
DDI Port 0 auxiliary, negative
DDI Port 1 auxiliary, positive
DDI Port 1 auxiliary, negative
DDI Port 1, Transmit 2, positive
DDI Port 1, Transmit 2, negative
DDI Port 1, Transmit 3, positive
DDI Port 1, Transmit 3, negative
DDI Port 0, I
2
C clock
Ground
DDI Port 1, Hot plug detect
Intel NM10 Express Chipset GPIO15
PU 10k V3.3A
PU 10k V5A
PU 8.25k V3.3A
Intel NM10 Express Chipset GPIO26
Standard I/O device wake event
System reset
Maintenance port Receive
Selects backlight control
(PWM vs. I
2
C)
Power button input
Ground
USB 7, positive signal
USB 7, negative signal
Ground
USB 5, positive signal
USB 5, negative signal
Ground
USB 3, positive signal
USB 3, negative signal
USB 0 over current
Ground
110126-80000-2, preliminary 29
Catalyst CV (CPU-300-20) - Design-In Guide
Pin Name
B71 USB1_P
B72 USB1_N
B73 GND
B74 LA_DATA3_P
B75 LA_DATA3_N
B76 GND
B77 LA_DATA0_P
B78 LA_DATA0_N
B79 USB_OC4#
B80 GND
B81 SATA2_TX_P
B82 SATA2_TX_N
B83 GND
B84 SATA2_RX_P
B85 SATA2_RX_N
B86 GND
B87 VGA_HS
B88 VGA_VS
B89 USB_OC1#
B90 GND
B91 VGA_B
B92 GPIO3
B93 GND
B94 PCIE_RX_SLOT0_N
B95 PCIE_RX_SLOT0_P
B96 GND
B97 CLK_SLOT1_OE#
B98 PCIE_TX_SLOT1_N
B99 PCIE_TX_SLOT1_P
B100 GND
B101 CLK_PCIE_SLOT1_P
B102 CLK_PCIE_SLOT1_N
B103 Cat_CV Detect
B104 PM_EN_S0#
B105 PM_EN_PWR
B106 SMC_UART_TX
B107 PM_EN_S3#
B108 CARRIER_I2C_SDA
B109 CARRIER_I2C_SCL
B110 GND
Type
IO
IO
P
O-LVDS
O-LVDS
P
O-LVDS
O-LVDS
I-3.3
P
O-SATA
O-SATA
P
I-SATA
I-SATA
P
O-CMOS
O-CMOS
I-3.3
P
PU 8.25k V3.3A
PU 8.25k V3.3A
O-A
IO-LVTTL
PD 150
P
I-PCIe
I-PCIe
P
On Module Termination Description
USB 1, positive signal
USB 1, negative signal
Ground
LVDS data 3, positive signal
LVDS data 3, negative signal
Ground
LVDS data 0, positive signal
LVDS data 0, negative signal
USB 4 over current
Ground
SATA2 transmit, positive signal
SATA2 transmit, negative signal
Ground
SATA2 receive, positive signal
SATA2 receive, negative signal
Ground
VGA, Horizontal sync
VGA, Vertical sync
USB 1 over current
Ground
VGA, Blue data
Intel NM10 Express Chipset GPIO24
Ground
PCIe 0 receive, negative signal
PCIe 0 receive, positive signal
Ground
I-3.3
O-PCIe
O-PCIe
P
O
O
I-3.3
O-3.3
O-3.3
O-3.3
O-3.3
IO-OD
O-OD
P
PU 10k V3.3S
C 0.1 F
C 0.1 F
R 33
R 33
PU 10k V3.3A
PCIe 1 clock enable
PCIe 1 transmit, negative signal
PCIe 1 transmit, positive signal
Ground
PCIe 1 clock, positive signal
PCIe 1 clock, negative signal
Indicates Catalyst CV mode
Power state indicator
Power state indicator
Maintenance port Transmit
Power state indicator
I
2
C bus data
I
2
C bus clock
Ground
30 110126-80000-2, preliminary
Connectors
J2: Docking Connector: Power
Board connector: 2x7 socket, 1 mm, Samtec CLM-107-02-LM-D
Carrier board connector: Samtec MW-07-03-G-D-095-085, 5 mm stacking height
Samtec MW-07-03-G-D-226-065, 8 mm stacking height
The Catalyst CV receives the power input and controls for interfacing with an external power supply on
Pin Name
1
2
V3.3
PM_CARRIER_PWRGD
3
4
V3.3
V_BATTERY
V3.3 5
6
7
8
V5A
V5S
V3.3A
9 V5S
10 GND
11 V3.3S
12 GND
13 V3.3S
14 GND
Type
PI
PI
P
PI
P
PI
P
PI
I-3.3
PI
PI
PI
PI
PI
Description
3.3 V primary supply voltage
Indicator for input power voltages
3.3 V primary supply voltage
RCV backup power
3.3 V primary supply voltage
5 V “always” power
5 V normal operating power
3.3 V “always” power
5 V normal operating power
Ground
3.3 V normal operating power
Ground
3.3 V normal operating power
Ground
Warning:
Disconnect the power input before removing the Catalyst CV. Removing the module from a powered carrier board may result in damage to both the carrier board and to the module.
J3: ITP Debug Port
Board connector: 26-pin FFC/FPC connector, 0.5 mm, OMRON XF2L-2625-1A
Connector J3 provides an In-Target Probe (ITP) debug port for the Catalyst CV. For additional details,
see Test and Debug , page 24 .
J5: SODIMM
Board connector: 204-pin SODIMM socket, 0.6 mm, Tyco Electronics 2013289-2
Mating device: SODIMM
Socket J5 supports a 204-pin DDR3 SODIMM. For further details about the system memory, see
110126-80000-2, preliminary 31
Catalyst CV (CPU-300-20) - Design-In Guide
System Specifications
Power Supply
(This section is to be determined.)
Performance
(This section is to be determined.)
Electrical
(This section is to be determined.)
General
(This section is to be determined.)
Environmental
(This section is to be determined.)
32 110126-80000-2, preliminary
Appendix A – Reference Information
Appendix A – Reference Information
Product Information
Product notices, updated drivers, support material: www.eurotech.com
Intel
Information about the Intel products, High Definition Audio specification, and
LPC bus specification: www.intel.com
Trusted Computing Group
Trusted Computer Group specification: www.trustedcomputinggroup.org
SATA
Serial ATA specification: www.sata-io.org
USB
Universal Serial Bus specification: www.usb.org
SDIO Card
SD Card Association and SDIO specification: www.sdcard.org
MMC Card
MultiMediaCard specification: www.jedec.org
PCI SIG
PCI Express specification: www.pcisig.com
I
2
C Bus
I
2
C bus specification: www.nxp.com
SMBus
SMBus specification: www.smbus.org
ACPI Specification
ACPI specification: www.acpi.info/spec.htm
110126-80000-2, preliminary 33
Catalyst CV (CPU-300-20) - Design-In Guide
Appendix B – Board Revision
This guide applies to the current revision of the module as given in the following section.
Identifying the Board Revision
(This section is to be determined.)
Board Revision History
(This section is to be determined.)
34 110126-80000-2, preliminary
Eurotech Worldwide Presence
AMERICAS
USA
EUROTECH
Toll free +1 800.541.2003
Tel. +1 301.490.4007
Fax +1 301.490.4582
E-mail: [email protected]
E-mail: [email protected]
Web: www.eurotech-inc.com
PARVUS
Tel. +1 800.483.3152
Fax +1 801.483.1523
E-mail: [email protected]
E-mail: [email protected]
Web: www.parvus.com
DYNATEM
Tel. +1 800.543.3830
Fax +1 949.770.3481
E-mail: [email protected]
E-mail: [email protected]
Web: www.dynatem.com
EUROPE
Italy
EUROTECH
Tel.
Fax
+39 0433.485.411
+39 0433.485.499
E-mail: [email protected]
E-mail: [email protected]
Web: www.eurotech.com
United Kingdom
EUROTECH
Tel. +44 (0) 1223.403410
Fax +44 (0) 1223.410457
E-mail: [email protected]
E-mail: [email protected]
Web: www.eurotech-ltd.com
France
EUROTECH
Tel.
Fax
+33 04.72.89.00.90
+33 04.78.70.08.24
E-mail: [email protected]
E-mail: [email protected]
Web: www.eurotech.com
ASIA
Japan
ADVANET
Tel.
Fax
+81 86.245.2861
+81 86.245.2860
E-mail: [email protected]
E-mail: [email protected]
Web: www.advanet.co.jp
India
EUROTECH
Tel. +91 80.43.35.71.17
E-mail: [email protected]
E-mail: [email protected]
Web: www.eurotech.com
To find your nearest contact refer to: www.eurotech.com/contacts
EUROTECH HEADQUARTERS
Via Fratelli Solari 3/a
33020 Amaro (Udine) – ITALY
Phone: +39 0433.485.411
Fax: +39 0433.485.499
For full contact details go to: www.eurotech.com/contacts
www.eurotech.com
advertisement
Related manuals
advertisement
Table of contents
- 1 Trademarks
- 2 Document Revision History
- 3 Table of Contents
- 5 Important User Information
- 5 Safety Notices and Warnings
- 6 Life Support Policy
- 6 Warranty
- 6 Technical Assistance
- 7 Conventions
- 8 Product Overview
- 8 Block Diagram
- 9 Features
- 10 Design Checklist
- 13 Development Kit
- 13 Related Documents
- 14 Software Specification
- 14 Operating System Support
- 14 Software Framework
- 15 Hardware Specification
- 15 Core Processor
- 15 Intel Atom Processor
- 15 Intel NM10 Express Chipset
- 15 Embedded Controller
- 15 Trusted Platform Management (option)
- 16 Memory
- 16 Synchronous DRAM
- 16 Non-Volatile Memory
- 16 Flash SSD (option)
- 16 External Memory Interfaces
- 17 Communications
- 17 PCI Express
- 17 Universal Serial Bus
- 18 Ethernet
- 18 C Bus
- 18 SPI Bus
- 18 System Management Bus
- 19 Display and User Interface
- 19 VGA Display
- 19 LVDS Display and Backlight Control
- 19 HDMI, DisplayPort, and Embedded Display Port
- 20 Inputs and Outputs
- 20 Low Pin Count Bus
- 20 Reset Signals
- 20 General-Purpose Input and Output
- 20 Intel High Definition Audio
- 21 Power Requirements
- 22 Mechanical Specifications
- 22 Mechanical Design
- 22 Mechanical Drawing
- 23 Thermal Management
- 24 Carrier Board Design
- 24 Design Guidelines
- 24 Test and Debug
- 25 Connectors
- 25 Identifying Connectors
- 26 Signal Headers
- 27 J1: Docking Connector: Data
- 31 J2: Docking Connector: Power
- 31 J3: ITP Debug Port
- 31 J5: SODIMM
- 32 System Specifications
- 32 Power Supply
- 32 Performance
- 32 Electrical
- 32 General
- 32 Environmental
- 33 – Reference Information
- 34 – Board Revision
- 35 Eurotech Worldwide Presence