Remote Automation Solutions Bristol TeleRTU PLUS 3530-25B Owner's Manual
Add to My manuals382 Pages
Remote Automation Solutions Bristol TeleRTU PLUS 3530-25B is a powerful and versatile remote terminal unit (RTU) designed to provide reliable and secure data acquisition, control, and communication in a wide range of applications. With its advanced features and robust construction, the TeleRTU PLUS 3530-25B is ideally suited for use in remote monitoring and control systems, SCADA systems, and other industrial automation applications.
advertisement
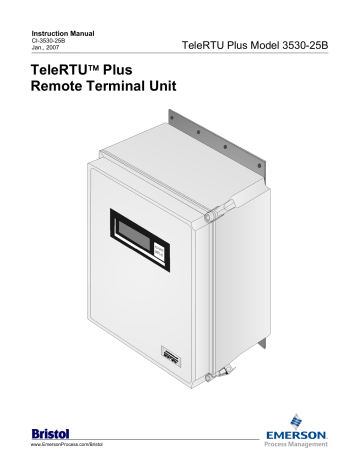
Instruction Manual
CI-3530-25B
Jan., 2007
TeleRTU
™
Plus
Remote Terminal Unit
TeleRTU Plus Model 3530-25B
www.EmersonProcess.com/Bristol
IMPORTANT! READ INSTRUCTIONS BEFORE STARTING!
Be sure that these instructions are carefully read and understood before any operation is attempted. Improper use of this device in some applications may result in damage or injury. The user is urged to keep this book filed in a convenient location for future reference.
These instructions may not cover all details or variations in equipment or cover every possible situation to be met in connection with installation, operation or maintenance.
Should problems arise that are not covered sufficiently in the text, the purchaser is advised to contact Bristol for further information.
EQUIPMENT APPLICATION WARNING
The customer should note that a failure of this instrument or system, for whatever reason, may leave an operating process without protection. Depending upon the application, this could result in possible damage to property or injury to persons. It is suggested that the purchaser review the need for additional backup equipment or provide alternate means of protection such as alarm devices, output limiting, fail-safe valves, relief valves, emergency shutoffs, emergency switches, etc. If additional in-formation is required, the purchaser is advised to contact Bristol .
RETURNED EQUIPMENT WARNING
When returning any equipment to Bristol for repairs or evaluation, please note the following: The party sending such materials is responsible to ensure that the materials returned to Bristol are clean to safe levels, as such levels are defined and/or determined by applicable federal, state and/or local law regulations or codes. Such party agrees to indemnify Bristol and save Bristol harmless from any liability or damage which Bristol may incur or suffer due to such party's failure to so act.
ELECTRICAL GROUNDING
Metal enclosures and exposed metal parts of electrical instruments must be grounded in accordance with OSHA rules and regulations pertaining to "Design Safety Standards for Electrical Systems," 29 CFR, Part 1910, Subpart S, dated: April 16, 1981 (OSHA rulings are in agreement with the National Electrical Code).
The grounding requirement is also applicable to mechanical or pneumatic instruments that include electrically-operated devices such as lights, switches, relays, alarms, or chart drives.
EQUIPMENT DAMAGE FROM ELECTROSTATIC DISCHARGE VOLTAGE
This product contains sensitive electronic components that can be damaged by exposure to an electrostatic discharge (ESD) voltage. Depending on the magnitude and duration of the ESD, this can result in erratic operation or complete failure of the equipment. Read supplemental document S14006 at the back of this manual for proper care and handling of ESD-sensitive components.
Bristol Inc.
1100 Buckingham Street, Watertown, CT 06795
Telephone (860) 945-2200
C.
D.
F.
A.
A.
B.
E.
B.
WARRANTY
Bristol warrants that goods described herein and manufactured by Bristol are free from defects in material and workmanship for one year from the date of shipment unless otherwise agreed to by Bristol in writing.
Bristol warrants that goods repaired by it pursuant to the warranty are free from defects in material and workmanship for a period to the end of the original warranty or ninety
(90) days from the date of delivery of repaired goods, whichever is longer.
Warranties on goods sold by, but not manufactured by Bristol, are expressly limited to the terms of the warranties given by the manufacturer of such goods.
All warranties are terminated in the event that the goods or systems or any part thereof are (i) misused, abused or otherwise damaged, (ii) repaired, altered or modified without
Bristol's consent, (iii) not installed, maintained and operated in strict compliance with instructions furnished by Bristol, or (iv) worn, injured or damaged from abnormal or abusive use in service time.
THESE WARRANTIES ARE EXPRESSLY IN LIEU OF ALL OTHER WARRANTIES
EXPRESS OR IMPLIED (INCLUDING WITHOUT LIMITATION WARRANTIES AS TO
MERCHANTABILITY AND FITNESS FOR A PARTICULAR PURPOSE), AND NO
WARRANTIES, EXPRESS OR IMPLIED, NOR ANY REPRESENTATIONS, PROMISES,
OR STATEMENTS HAVE BEEN MADE BY BRISTOL UNLESS ENDORSED HEREIN
IN WRITING. FURTHER, THERE ARE NO WARRANTIES WHICH EXTEND BEYOND
THE DESCRIPTION OF THE FACE HEREOF.
No agent of Bristol is authorized to assume any liability for it or to make any written or oral warranties beyond those set forth herein.
REMEDIES
Buyer's sole remedy for breach of any warranty is limited exclusively to repair or replacement without cost to Buyer of any goods or parts found by Seller to be defective if
Buyer notifies Bristol in writing of the alleged defect within ten (10) days of discovery of the alleged defect and within the warranty period stated above, and if the Buyer returns such goods to Bristol's Watertown office, unless Bristol's Water-town office designates a different location, transportation prepaid, within thirty (30) days of the sending of such notification and which upon examination by Bristol proves to be defective in material and workmanship. Bristol is not responsible for any costs of removal, dismantling or reinstalllation of allegedly defective or defective goods. If a Buyer does not wish to ship the product back to Bristol, the Buyer can arrange to have a Bristol service person come to the site. The Service person's transportation time and expenses will be for the account of the Buyer. However, labor for warranty work during normal working hours is not chargeable.
Under no circumstances will Bristol be liable for incidental or consequential damages resulting from breach of any agreement relating to items included in this quotation, from use of the information herein or from the purchase or use by Buyer, its employees or other parties of goods sold under said agreement.
How to return material for Repair or Exchange
Before a product can be returned to Bristol for repair, upgrade, exchange, or to verify proper operation, form (GBU 13.01) must be completed in order to obtain a RA (Return
Authorization) number and thus ensure an optimal lead time. Completing the form is very important since the information permits the Bristol Repair Dept. to effectively and efficiently process the repair order.
You can easily obtain a RA number by:
A. FAX
Completing the form (GBU 13.01) and faxing it to (860) 945-3875. A Bristol Repair
Dept. representative will return call (or other requested method) with a RA number.
B. E-MAIL
Accessing the form (GBU 13.01) via the Bristol Web site (www.bristolbabcock.com) and sending it via E-Mail to [email protected]
. A Bristol Repair Dept. representative will return E-Mail (or other requested method) with a RA number.
C. Mail
Mail the form (GBU 13.01) to
Bristol Inc.
Repair
1100 Buckingham Street
Watertown, CT 06795
A Bristol Repair Dept. representative will return call (or other requested method) with a RA number.
D. Phone
Calling the Bristol Repair Department at (860) 945-2442. A Bristol Repair Department representative will record a RA number on the form and complete Part I, then send the form to the Customer via fax (or other requested method) for Customer completion of Parts II & III.
A copy of the completed Repair Authorization Form with issued RA number should be included with the product being returned. This will allow us to quickly track, repair, and return your product to you.
Bristol
Repair Authorization Form
(off-line completion)
(Providing this information will permit Bristol to effectively and efficiently process your return. Completion is required to receive optimal lead time. Lack of information may result in increased lead times.)
Date___________________ RA #___________________SH
Standard Repair Practice is as follows: Variations to this is practice may be requested in the “Special Requests” section.
•
Evaluate / Test / Verify Discrepancy
•
Repair / Replace / etc. in accordance with this form
•
Return to Customer
Line No.____________
Please be aware of the Non warranty standard charge:
•
There is a $100 minimum evaluation charge, which is applied to the repair if applicable (
√
in “returned”
B,C, or D of part III below)
Part I Please complete the following information for single unit or multiple unit returns
Address No.
Bill to :
Purchase Order:
Phone:
(office use only) Address No.
Ship to:
Fax:
(office use only)
Contact Name: ____________________________________
E-Mail:
Model No./Part No. Description
Range/Calibration S/N
Reason for return : Failure Upgrade Verify Operation Other
1.
Describe the conditions of the failure (Frequency/Intermittent, Physical Damage, Environmental Conditions,
Communication, CPU watchdog, etc.)
(Attach a separate sheet if necessary)
2. Comm. interface used: Standalone RS-485 Ethernet Modem (PLM (2W or 4W) or SNW) Other: ______________
3. What is the Firmware revision? _____________________ What is the Software & version?
Part III If checking “replaced” for any question below, check an alternate option if replacement is not available
A.
If product is within the warranty time period but is excluded due to Bristol’s warranty clause, would you like the product: repaired returned replaced scrapped?
B.
If product were found to exceed the warranty period, would you like the product:
C.
If product is deemed not repairable would you like your product: repaired returned replaced scrapped? returned replaced scrapped?
D.
If Bristol is unable to verify the discrepancy, would you like the product: returned replaced *see below?
* Continue investigating by contacting the customer to learn more about the problem experienced? The person to contact that has the most knowledge of the problem is: ______________________________ phone_____________________
If we are unable to contact this person the backup person is: _________________________ phone_____________________
Special Requests: ____________________________________________________________________________________
____________________________________________________________________________________________________
Ship prepaid to: Bristol Inc., Repair Dept., 1100 Buckingham Street, Watertown, CT 06795
Phone: 860-945-2442 Fax: 860-945-2220 Form GBU 13.01 Rev. C 04/27/06
Bristol
Training
GET THE MOST FROM YOUR BRISTOL
INSTRUMENT OR SYSTEM
• Avoid Delays and problems in getting your system on-line
• Minimize installation, start-up and maintenance costs.
• Make the most effective use of our hardware and software.
• Know your system.
As you know, a well-trained staff is essential to your operation. Bristol Inc. offers a full schedule of classes conducted by full-time, professional instructors. Classes are offered throughout the year at three locations: Houston, Orlando and our Watertown, CT headquarters. By participating in our training, your personnel can learn how to install, calibrate, configure, program and maintain any and all Bristol products and realize the full potential of your system.
For information or to enroll in any class, contact our training department in Watertown at
(860) 945-2343. For Houston classes, you can also contact our Houston office, at (713) 685-
6200.
A Few Words About Bristol Inc.
For over 100 years, Bristol has been providing innovative solutions for the measurement and control industry. Our product lines range from simple analog chart recorders, to sophisticated digital remote process controllers and flow computers, all the way to turnkey
SCADA systems. Over the years, we have become a leading supplier to the electronic gas measurement, water purification, and wastewater treatment industries.
On off-shore oil platforms, on natural gas pipelines, and maybe even at your local water company, there are Bristol Inc. instruments, controllers, and systems running year-in and year-out to provide accurate and timely data to our customers.
Getting Additional Information
In addition to the information contained in this manual, you may receive additional assistance in using this product from the following sources:
Help Files / Release Notes
Many Bristol Inc. software products incorporate help screens. In addition, the software typically includes a ‘read me’ release notes file detailing new features in the product, as well as other information which was available too late for inclusion in the manual.
Contacting Bristol Inc. Directly
Bristol Inc.'s world headquarters are located at 1100 Buckingham Street, Watertown,
Connecticut 06795, U.S.A.
Our main phone numbers are:
(860) 945-2200
(860) 945-2213 (FAX)
Regular office hours are Monday through Friday, 8:00AM to 4:30PM Eastern Time, excluding holidays and scheduled factory shutdowns. During other hours, callers may leave messages using Bristol's voice mail system.
Telephone Support - Technical Questions
During regular business hours, Bristol Inc.'s Application Support Group can provide telephone support for your technical questions.
For technical questions about TeleFlow products call (860) 945-8604.
For technical questions about Control Wave call (860) 945-2394 or (860) 945-2286.
For technical questions regarding Bristol’s OpenEnterprise product, call (860) 945-3865 or e-mail: [email protected]
For technical questions regarding ACCOL products, OpenBSI Utilities , UOI and all other software except for Control Wave and OpenEnterprise products, call (860) 945-2286.
For technical questions about Network 3000 hardware, call (860) 945-2502.
You can e-mail the Application Support Group at: [email protected]
The Application Support Group maintains an area on our web site for software updates and technical information. Go to: www.bristolbabcock.com/services/techsupport/
For assistance in interfacing Bristol hardware to radios, contact Bristol’s Communication
Technology Group in Orlando, FL at (407) 629-9463 or (407) 629-9464 .
You can e-mail the Communication Technology Group at: [email protected]
Telephone Support - Non-Technical Questions, Product Orders, etc.
Questions of a non-technical nature (product orders, literature requests, price and delivery information, etc.) should be directed to the nearest sales office (listed on the rear cover of this manual) or to your Bristol-authorized sales representative.
Please call the main Bristol Inc. number (860-945-2200) if you are unsure which office covers your particular area.
Visit our Site on the World Wide Web
For general information about Bristol Inc. and its products, please visit our site on the
World Wide Web at: www.bristolbabcock.com
Training Courses
Bristol’s Training Department offers a wide variety of courses in Bristol hardware and software at our Watertown, Connecticut headquarters, and at selected Bristol regional offices, throughout the year. Contact our Training Department at (860) 945-2343 for course information, enrollment, pricing, and scheduling.
Contents
Section 1 - INTRODUCTION
Page
1.2.2 TeleRTU CPU Board ................................................................................................ 1-5
1.2.3 Internal Mounting Brackets ....................................................................................... 1-7
1.2.4 Display/Switch Panel Assembly ................................................................................ 1-7
1.2.5 Serial Communications Ports ................................................................................... 1-8
1.2.5.1 BSAP Message Support ........................................................................................... 1-8
1.3 .................................................................................................................. 1-9
1.3.1 Solar Panel Option .................................................................................................... 1-9
1.3.3 Low Power I/O Expansion Board (LPI/O EB) Option .............................................. 1-10
1.3.4 Digital To Relay I/O Option ..................................................................................... 1-11
1.3.5
Low Power Transmitter Interface Board (TIB) Option ............................................. 1-12
1.3.6 Expansion Transmitter Interface Board (ETIB) Option ........................................... 1-13
1.3.7 21V Power Supply Option ....................................................................................... 1-13
1.3.8 Expansion Communications Port RS-232 Board Option ......................................... 1-14
1.3.9 Expansion RS-485 and/or Analog Output Board Option ......................................... 1-15
1.5 MODEL NUMBER ANALYSIS ................................................................................ 1-16
Section 1A - APPLICATION SOFTWARE
1A.1 CATEGORIES OF APPLICATION SOFTWARE ....................................................1A-1
1A.2 ACCOL TOOLS SOFTWARE .................................................................................1A-2
1A.4 OPEN BSI UTILITIES SOFTWARE .......................................................................1A-4
1A.5.2 Local Area Network (LAN) ......................................................................................1A-7
1A.5.3 Wide Area Network (WAN) .....................................................................................1A-9
Section 2 - INSTALLATION
2.1 INSTALLATION IN HAZARDOUS AREAS ............................................................... 2-1
2.2 MOUNTING THE TeleRTU™ ................................................................................... 2-2
2.2.3 Opening The Instrument Front Cover ....................................................................... 2-2
2.2.4 CPU Board Configuration ......................................................................................... 2-2
2.2.4.1 JP3 - Battery Backup Enable .................................................................................... 2-2
2.2.4.2
JP4 - Security ........................................................................................................... 2-2
2.2.4.3 JP5 - Manual Reset .................................................................................................. 2-3
CI-3530-25B Contents / 0-1
Contents
Page
Section 2 - INSTALLATION (Continued)
2.3.3 Signal Shielding and Grounding ............................................................................... 2-5
2.3.4 Power
2.3.5 Optional Power Distribution Board ............................................................................ 2-6
2.4 WIRING INPUT/OUTPUT SIGNALS ........................................................................ 2-8
2.4.1 .......................................................................................................... 2-9
2.4.2 ....................................................................................................... 2-9
2.4.5.1 RS-232 Network and Local Communications Ports ................................................ 2-12
2.4.5.4 Modem or Radio On Network Port .......................................................................... 2-13
2.5 MOUNTING THE OPTIONAL SOLAR PANEL ....................................................... 2-16
2.5.1 Swivel (Directional Facing) ..................................................................................... 2-16
Tilt
2.6 TeleRTU Plus™ CONFIGURATION ....................................................................... 2-18
2.6.1 Application Software Reference Documents .......................................................... 2-18
2.6.2 Installation & Configuration of Options ................................................................... 2-19
Section 3 - SERVICE
3.2 ACCESSING PARTS FOR TESTING OR REPLACEMENT .................................... 3-1
3.3 COMPONENT REMOVAL & REPLACEMENT PROCEDURES .............................. 3-2
3.3.1 Lead Acid Battery Removal/Replacement Procedure .............................................. 3-2
3.3.2 CPU Circuit Board Removal/Replacement ............................................................... 3-4
3.3.3 Removal/Replacement of the On Board Fuse F1 ..................................................... 3-5
3.3.4 Removal/Replacement of the On Board Battery ....................................................... 3-5
3.3.5 Removal/Replacement of the Display/Switch Panel Assembly ................................ 3-6
3.3.6 Removal/Replacement of the Modem or Radio Options ........................................... 3-8
3.4 TROUBLESHOOTING TIPS ................................................................................... 3-10
3.4.1 Battery & Fuse F1 Checks (Processor not running or no power) ........................... 3-10
3.4.3 LCD Display Checks ............................................................................................... 3-11
3.4.4 Field Wiring/Signal Checks ..................................................................................... 3-12
Section 4 - SPECIFICATIONS
4.2 CPU, MEMORY & PROGRAM INTERFACE ........................................................... 4-1
4.3 CPU BOARD COMMUNICATIONS .......................................................................... 4-1
4.4 CPU BOARD DISCRETE INPUTS ........................................................................... 4-2
4.5 CPU BOARD DISCRETE OUTPUTS ....................................................................... 4-2
4.6 CPU BOARD PULSE INPUTS ................................................................................ 4-2
4.7 CPU BOARD ANALOG INPUTS .............................................................................. 4-3
0-2 / Contents CI-3530-25B
Contents
Page
Section 4 - SPECIFICATIONS (Continued)
4.10 ................................................................................................. 4-4
APPENDICES
Reserved .............................................................................................................. Appendix B
Reserved ...............................................................................................................Appendix C
Low Power I/O Expansion Board (Replaces Appendix D) ................................PIP-EXPI/OTF
Reserved ...............................................................................................................Appendix E
Reserved ............................................................................................................... Appendix F
Radio Installation Guide for MDS Model 4710A/B, 9710A/B & 9810 Radios ........Appendix H
21V Power Supply Board Option (DC/DC Converter) ...................................... PIP-353021VS
Expansion Transmitter Interface Board for 3530-XXX (392960-01-0).............. PIP-EXPTIBTF
Expansion Comm. Port RS-232 Board for Models 3530-XXX .........................PIP-EXP232TF
Expansion RS-485 and/or Analog Output Board for Model 3530-XXX ..........PIP-EXP485/AO
Care and Handling of PC Boards and ESD-Sensitive Components ...........................S14006
REFERENCED or ASSOCIATED BRISTOL DOCUMENTS
Bristol 9600 bps - PSTN Modem P/N 396039-02-2 Instruction Manual ..................... CI-9600
Bristol 9600 bps - PSTN Modem P/N 400000-01-6 Instruction Manual ................. CI-9600TF
Isolated RS-485 Interface Board ..................................................................... PIP-ISORS485
REFERENCED OEM MANUALS
MDS 4710A – Remote Data Transceiver (Radio)
MDS 4710/9710 Series 400MHz/900 MHz Remote Data Transceiver Installation and Operation Guide –
MDS Doc. 05-3305A01, Rev. B, Sept. 2000 (PDF = 3305B-710AC.pdf) for model MDS 4710A
MDS 4710B – Data Transceiver (Radio)
MDS 4710B/9710B Data Transceiver Installation and Operation Guide – MDS Doc. 05-3316A01, Rev. E,
Sept. 2000 (PDF = 3316E-x710B.pdf) for model MDS 4710B
MDS 9810 – Spread Spectrum Data Transceiver (Radio)
MDS 9810/24810 900 MHz/2.4GHz Spread Spectrum Transceivers Installation and Operation Guide –
MDS Doc. 05-3301A01, Rev. B, April 2000 (PDF = 3301B-x810.pdf) for model MDS 9810
MDS 9710A Remote Data Transceiver (Radio)
MDS 4710/9710 Series 400MHz/900 MHz Remote Data Transceiver – MDS Doc. 05-3305A01,
Rev. B, Sept. 2000 (Installation & Operation) (PDF = 3305B-710AC.pdf) for model MDS 9710A
CI-3530-25B Contents / 0-3
Contents
Page
REFERENCED OEM MANUALS (Continued)
MDS 9710B Data Transceiver (Radio)
MDS 4710B/9710B Data Transceiver Installation and Operation Guide – MDS Doc. 05-3316A01, Rev. E,
Sept. 2000 (PDF = 3316E-x710B.pdf) for model MDS 9710B
FreeWave Radio Spread Spectrum Data Transceiver Model FGRM-501X005
Contact the FreeWave Tech Support group @ 303-444-3862 or at www.freewave.com to request the latest copy of the user manual.
0-4 / Contents CI-3530-25B
Section 1
INTRODUCTION
1.1 GENERAL DESCRIPTION
TeleRTU Plus J Model 3530-25B provides a high performance and economical choice for measurement and control in the following applications:
$ SCADA RTU
$ Lift Stations
$ Metering Stations
$ Well Monitoring
$ Reservoir and Tank Monitoring
$ Pump Controller
$ Custody Transfer
$ Pressure Monitor
In addition to operation in an unprotected outdoor environment, the TeleRTU Plus J has been designed to provide the following key features:
$ Very low power consumption
$ Two independent serial ports
$ Two line alphanumeric display
$ Two discrete outputs with control capability & Two discrete inputs
$ Four analog inputs
$ Two high speed counter or two pulse inputs
$ UL approved for Class I, Division 2 Groups C & D Hazardous Locations
1.2 PHYSICAL DESCRIPTION
The TeleRTU Plus J is comprised of the following major components:
$ Enclosure
$ Circuit (CPU) Board
$ Internal mounting brackets
$ Display/Switch Panel Assembly
$ Serial communications ports
$ 12 V 40 Amp. Hour Battery
Additionally the TeleRTU Plus J has been designed to support the following options:
$ Solar Panel option
$ Communications option
$ Power Distribution Board option
$ Low Power I/O Expansion Board option
$ Digital To Relay I/O Board option
$ Expansion Transmitter Interface Board option
$ Expansion Communications Port RS-232 Board option
$ Expansion RS-485 and/or Analog Output Board option
$ Low Power Transmitter Interface Board option
$ 21V Power Supply Board option
TeleRTU Plus™ Introduction / 1-1
1.2.1 Enclosure
The enclosure is a standard Hoffman ® Enclosure. Its external dimensions (excluding the cover latches) are approximately 14.56” high by 12.97” wide by 8.31” deep. An installed
TeleCounter Assembly adds 4.36” to the height. The enclosure consists of two pieces, the body and the Instrument Front Cover. A continuous gasket seals the unit when the Instrument Front Cover is closed. A hinge on the left side (facing the front of the unit) is formed by molded channels on the Instrument Front Cover and body that capture a stainless steel pin. When closed, the Instrument Front Cover is secured by two latches on the enclosures’ right side.
1-2 / Introduction
Figure 1-1 - TeleRTU Plus J
TeleRTU Plus™
TeleRTU Plus™
Figure 1-2 - TeleRTU Plus J with Modem Option
Introduction / 1-3
1-4 / Introduction
Figure 1-3 - TeleRTU Plus J with MDS Radio Option
TeleRTU Plus™
Figure 1-4 - Inside of Instrument Front Cover
1.2.2 TeleRTU CPU Board
The TeleRTU CPU circuit board is mounted horizontally below the battery. It is stood-off from its aluminum mounting bracket by five posts. Screws secure the board to these five mounting posts. The CPU circuit board mounting bracket is mounted to an aluminum bracket, which in-turn is mounted to the bottom of the battery bracket. Two guide rails accommodate installation and removal. Two captive screws secure these brackets to one another.
TeleRTU Plus™ Introduction / 1-5
Figure 1-5 - TeleRTU™ CPU Board
The board is approximately 7.3” tall, 4.6” wide, and 0.7” deep. Both surface mount and through-hole components are located on the component side of the board, and small surface mount components are located on the solder side.
Pluggable screw terminal connectors line the front edge of the board, along with two LED indicators and a potentiometer for display contrast adjustment.
1-6 / Introduction TeleRTU Plus™
Connectors and configuration jumpers are located on the top of the board as shown in
Figures 1-5 and 1-6.
Figure 1-6 - Horizontally Mounted CPU Board
1.2.3 Internal Mounting Brackets
A large aluminum backplane bracket attached to the interior rear wall of the enclosure body provides for mounting and support of the steel battery Mounting Bracket and the aluminum Digital To Relay I/O Board Option Mounting Bracket. A steel bracket with a detachable clamping mechanism located near the top of the battery provides for removal or replacement of the battery and is used to clamp the installed battery in place. Aluminum brackets attached to the steel Battery Mounting Bracket provide for the mounting and support of the CPU Board as well as the communications and expansion options. Another bracket attaches to the inside of the Instrument Front cover to support the LCD Display and Switch Panel.
1.2.4 Display/Switch Panel Assembly
The Display/Switch Panel Assembly mounts to the inside of the Instrument Front Cover where it is visible through a window. This Assembly consists of the LCD Display
Subassembly and the Membrane Switch Assembly. A Gasket (on the inside of the cover) provides a seal between the LCD Display Subassembly and the Instrument Front Cover.
Both the LCD Display Subassembly and the Membrane Switch Panel connect to the CPU
Board through dedicated ribbon cables. The Membrane Switch is used to activate the 2 X
16 Character LCD Display.
In normal operation, the display stays off after the unit has been configured and placed into service. The operator may activate the display at any time by pressing the front panel button. When activated, the display scrolls through a list of current values. The list defaults to an appropriate set of values.
When the button is pressed (or a properly configured cable is plugged into the Local Port), the TeleRTU Plus J wakes up from sleep mode and enters calculation mode, where all circuits except the RS-232 transceiver are active. While cycling through the display list, the
TeleRTU Plus™ Introduction / 1-7
calculation interval switches to 1 second. After cycling through the list twice, the calculation interval is restored to the programmed interval and the unit returns to normal operation. Although the RS-232 transceiver is disabled while in calculation mode or sleep mode, the receiver channel dedicated to buffering Receive Data Carrier Detect (RDCD) is always active.
1.2.5 Serial Communications Ports
The TeleRTU Plus J provides two serial ports for serial communications, designated the network port (9600 bps - Default) and the local port (19200 bps - default). Both ports operate independently at rates up to 19.2 Kbps. Prior to receiving an ACCOL load, the network port is a standard BSAP slave port and the local port is a BSAP pseudo-slave port for direct connect communication with various BBI programs running on a laptop PC. It should be n oted that on the local port with a direct connect, the TeleRTU Plus J will answer to any local BSAP node address.
In a BSAP network, the TeleRTU Plus J may only be used as a ‘ Slave Node.
’ As such it is not capable of initiating a BSAP message intended for another node. The TeleRTU Plus J is always an immediate response node.
A circular plastic connector on the bottom of the enclosure body provides connection for a local communications device, typically an IBM compatible PC (personal computer). A custom cable connects the PC serial port to the TeleRTU Plus J . Internally, the circular connector is wired to field wiring terminals on the CPU circuit board.
1.2.5.1 BSAP Message Support
The TeleRTU J supports a subset of BSAP messages. Specifically, the following messages are supported:
Poll message
TS/NRT message
Alarm Acknowledge
Alarm Initialization
Peer to Peer
RDB Functions
Normal response to poll messages including alarm reporting in short, long, and extended format. If a poll is received on the network port, and the TeleRTU has no NRT, it will respond with a request for a Node Routing Table.
Normal handling.
Normal handling.
Normal handling.
Supports send and poll mode.
Supports read signal by name and address, read packed logical, read by list, read selected signal data (name match only), read array sizes, read by data array number (short form
& general form), write by name and address, write by list, and write by data array number (short form & general form).
Supports Audit Trial functions, security code functions,
EBSAP Group functions, archive data functions, read array elements, and read special information: read version, features,
PROM link. All subfunctions of these are supported.
Special RDB Functions Supports date and time requests, local BSAP address requests, and the system reset request.
1-8 / Introduction TeleRTU Plus™
1.2.6 12V Battery
The 12V Sealed Lead-Acid battery is rated for 40 Amp Hours and is secured by a steel bracket that has a detachable clamp. The battery connects to J2 on the CPU board that is situated just below the battery.
1.2.7 Field Wiring
The TeleRTU supports connection to external devices through its field wiring terminals on the CPU board and the various options. Connections to the following I/O may be provided:
$ Digital Inputs
$ Digital Outputs
$ Pulse Inputs
$ Analog Inputs
$ Analog Output
$ External Communications
$ Relays
1.3 OPTIONS
Options are introduced in sections 1.3.1 through 1.3.9 as follows:
Section 1.3.1 - Solar Panel Option
Section 1.3.2 - Comm. Options (see appropriate modem manual or Appendix H/I for Radio)
Section 1.3.3 - Low Power I/O Expansion Board (LPI/OEB) Option (see PIP-EXPI/OTF)
Section 1.3.4 - Digital To Relay I/O Option (see Appendix G)
Section 1.3.5 - Low Power Transmitter Intf. Board (LPTIB) Option (see PIP-TIBS3530)
Section 1.3.6 - Exp. Transmitter Intf. (ETIB) Option (see PIP-EXPTIBS or PIP-EXPTIBTF)
Section 1.3.7 - 21V Power Supply (DC/DC Converter) Option (see PIP-353021VS)
Section 1.3.8 - Expansion Comm. Port RS-232 Board Option (see PIP-EXP232TF)
Section 1.3.9 - Expansion RS-485 and/or Analog Output Bd. Option (see PIP-EXP485/AO)
The following options will require the use an optional Power Distribution Board (see
Section 2.3.5):
$ 21V Power Supply (DC/DC Converter) $ Low Power Transmitter Interface Board
$ Digital To Relay I/O Board $ Modem Assembly
1.3.1 Solar Panel Option
A 12V 10 watt, 30 watt or 40 watt solar panel can be used with the rechargeable battery.
Solar panels can be mounted to a 2" to 2.375” pipe. The solar panel mounts on a bracket that offers adjustable swivel and fixed tilt angles. Solar panel wires enter the TeleFlow through a liquid tight conduit fitting on the bottom of the enclosure. Internally the solar panel wires connect to the rechargeable battery via the CPU board connector J1’s PWR
(red wire) and GND (black wire) terminals.
1.3.2 Communications Option
Either a BBI PSTN modem or a radio (with integral modem) can be mounted inside the
TeleFlow Plus enclosure. The modem option will typically connect to the rechargeable bat-
TeleRTU Plus™ Introduction / 1-9
tery via CPU Board connectors J2-1 (PWR 1) and J2-8 (GND) or via the optional Power
Distribution Board connectors TB6-1 (Modem+) and TB6-2 (Modem GND). The radio is supplied power from the CPU Board connector J4’s AUX PWR and GND terminals. The modem’s communication lines are interfaced via a wiring harness connected to CPU Board
Connector J8 and the modem’s 9-pin D-type connector. The MDS radio’s communication lines are interfaced between the radio’s 25-pin D-type connector and CPU Board connectors
J7, J8 and J10. The FreeWave radio’s communication lines are interfaced between the radio’s 10-pin connector (J1) and CPU Board connector J8.
1.3.3 Low Power I/O Expansion Board (LPI/OEB) Option
The Low Power I/O Expansion Board (LPI/OEB) (see Figure 1-7) measures approximately
4” by 7.25” and mounts piggy-back to the TeleRTU CPU Board. Removable card-edge connectors are provided to accommodate field wiring. The LPI/OEB will only operate with a
Revision 3 or higher TeleRTU CPU Board.
The Low Power I/O Expansion Board provides the following additional I/O capabilities to the TeleRTU Plus:
$ 8 Discrete I/O
All 8 DI/O function as both inputs and outputs. Field terminals for each DI/O are I/O and GND. Each Discrete Input will accept signals from 0 to 16 VDC. The Discrete
Outputs utilize open drain FETs with a maximum working voltage of 16 VDC and a minimum load of 100 mA. DI/Os are not isolated.
$ 4 Analog Inputs (2 support current loop)
Two single-ended Analog Inputs are available for 4 to 20 mA or 1 to 5 V signal operation (Jumper Configurable) and two additional single-ended Analog Inputs are available for 1 to 5 V signal operation only. The two 4-20 mA Inputs will support externally powered transmitters but internally powered 4-20 mA transmitters will require an external power supply. All four channels support low power voltage output transmitters such as Rosemount and Honeywell. Resolution is 12 bits (1.42 mV) and combined error (including linearity, hysteresis and temperature effects) is £ ± 0.2%.
Each Analog Input Channel includes field wiring terminals for signal, transmitter power (+9.5V), and ground.
$ 1 Analog Output
The Analog Output can be configured for 4 to 20 mA or 1 to 5 V operation (Jumper
Configurable). Resolution is 12 bits and combined error including linearity, hysteresis and temperature effects is £ ± 0.2% after calibration.
$ 1 High Speed Counter Input
The High Speed Counter will accept pulses (with an input range from 0 to 16 VDC and up to 10KHz) from CMOS or TTL sources, including transistors, FETs, mechanical relays, or other signaling devices.
$ 1 RS-232 or RS-485 Asynchronous Serial Communication Port
The Asynchronous Serial Port will be either RS-232 or RS-485 compatible (Jumper
Configurable) and will operate at programmable speeds up to 19.2 Kbps.
1-10 / Introduction TeleRTU Plus™
Figure 1-7 - TeleFlow Plus Low Power I/O Expansion Board (LPI/OEB)
1.3.4 Digital To Relay I/O Option
The Digital To Relay I/O Board (see Figure 1-8) converts one or both TeleFlow Discrete
Output Signals from open drain MOSFET levels to Form C relay output signal using Solid
State Relay (SSR) logic.
Each TeleFlow Discrete Output can be converted to Form C relay output signals which can be configured for opposite or identical conditions, i.e., both Normally Open (NO) or
Normally Closed (NC) or one Normally Open with the other normally Closed.
TeleRTU Plus™ Introduction / 1-11
Figure 1-8 - Digital To Relay I/O Board
1.3.5 Low Power Transmitter Interface Board (TIB) Option
Low Power Transmitter Interface Boards allow up to two (2) Bristol Babcock, Series 3508C
Transmitters to communicate with an ACCOL loaded host TeleFlow 3530-20B Electronic
Gas Measurement Computer (EGMC) or 3530-25B TeleRTU Plus. The EGMC/RTU polls and stores data from each transmitter and communicates with the network. Two LEDS on the LPTI Board [CD (DS1) & RTS (DS2)] indicate the communication status.
The LPTI Board is housed in the TeleRTU Plus enclosure and is interfaced to a TeleFlow
I/O Expansion Board. LPTI Boards are powered by a 12V power supply or battery. The
LPTI Board (Figure 1) is wired to the TeleFlow I/O Expansion Board connector (TB5) and is mounted with Snap Track (holder) and Mounting Bracket.
Figure 1-9 - Low Power Transmitter Interface Board
1-12 / Introduction TeleRTU Plus™
1.3.6 Expansion Transmitter Interface Board (ETIB) Option
Expansion Transmitter Interface Boards (ETIBs) allow up to two (2) Bristol Babcock,
Series 3508C Transmitters to communicate with an ACCOL loaded host TeleFlow Plus
Electronic Gas Measurement Computer (EGMC) (3530-20B) or TeleRTU Plus (3530-25B).
The EGMC/RTU polls and stores data from each transmitter and communicates with the network. Two LEDS on the ETIB Board [CD (DS1) & RTS (DS2)] indicate the communication status.
The ETIB Board is housed in either the standard TeleFlow Plus or TeleRTU Plus enclosure and is interfaced to a TeleFlow/TeleRTU CPU Board via the CPU Board’s Expansion
Connector. Power from and communication with the host CPU Board is supplied through the Expansion Connector.
Figure 1-10 - Expansion Transmitter Interface Board
1.3.7 21V Power Supply Option
The 21V Power Supply is a continuous mode boost switching type power supply. It is based upon a low power, low noise circuit that produces 21 Volts from a 12 Volt input. Power shutdown is not an option with this unit since it employs a Boost circuit; therefore, the 21V
Power Supply must be powered continuously.
The 21V Power Supply is mainly used in conjunction with Temperature and Pressure
Transmitters which require a higher than +12V but lower than 21.4V ( ± .8V) input supply to operate.
TeleRTU Plus™ Introduction / 1-13
Figure 1-11 - 21V Power Supply (DC/DC Converter) Board
Figure 1-12 – Expansion Communications Port RS-232 Board
1.3.8 Expansion Communications Port RS-232 Board Option
The Expansion Communications Port RS-232 Board (EXPCOM232) provides a single RS-
232 asynchronous serial communications port to ACCOL-based 3530-XXX models. In addition to assignments of the resident (host) CPU’s “local” and “network” RS-232 ports,
1-14 / Introduction TeleRTU Plus™
any model 3530-XXX unit equipped with an EXPCOM232 Board can establish RS-232 communications with an external device. An EXPCOM232 Board plugs into the Expansion
Connector of the TeleFlow or TeleRTU CPU Board and is stood-off by three 15/32” long hex standoffs and is secured via three screws. The CPU Board Expansion Connector supplies power and 3530-XXX communications to the EXPCOM232 Board.
Programmable baud rates up to 19.2Kbps are supported by the EXPCOM232 Board. TXD,
RXD, RTS, CTS, DTR, CD and GND (RS-232) signals are available at TB1 of the
EXPCOM232 Board. CD (Carrier Detect) (supplied by a DCE attempting to communicate with a model 3530-XXX), will awaken the 3530-XXX CPU Board. If no activity is required, the EXPCOM232 Board’s serial communications controller (SCC) chip and RS-232 drivers can be put to sleep (low power mode) along with the host/parent 3530-XXX.
1.3.9 Expansion RS-485 and/or Analog Output Board Option
The Expansion RS-485 Comm. Port with Analog Output Board (EXP485/AO) provides a single RS-485 communications port to ACCOL-based 3530-XXX models. In addition to assignments of the resident (host) CPU’s “local” and “network” RS-232 ports, any model
3530-XXX unit equipped with a fully populated EXP485/AO Board can establish RS-485 communications with other 3530-XXX devices and/or interface to an Analog Output circuit.
The EXP485/AO Board plugs into the Expansion Connector of the TeleFlow or TeleRTU
CPU Board, is stood-off by three 15/32” long hex standoffs and is secured via three screws.
The CPU Board Expansion Connector supplies power and 3530-XXX communication to the
EXP485/AO Board.
Figure 1-13 - Expansion RS-485 and/or Analog Output Board
TeleRTU Plus™ Introduction / 1-15
Programmable baud rates up to 19.2Kbps are supported by the EXP485/AO Board.
Interface signals are available at TB1 of the EXP485/AO. The SLEEP+ and SLEEP- signals
(supplied by the Master 3530-XXX) will awaken the remote 3530-XXXCPU Boards. If no activity is required, the EXP485/AO Board’s serial communications controller (SCC) chip and RS-485 drivers can be put to sleep (low power mode) along with the host/parent 3530-
XXX.
1.4 ENVIRONMENT
The TeleRTU J operates in an unprotected outdoor environment. See Table 1-1 below for environmental specifications.
Table 1-1 - ENVIRONMENTAL SPECIFICATIONS
TOPIC
Operating Temp. Range
Operating Humidity Range
Transient Susceptibility
Vibration Effect
ESD Susceptibility
EMI Susceptibility
Hazardous Locations
SPECIFICATION
-40 E to +60 E C (-40 E to +140 E F)
15% to 90% RH Noncondensing
Field connected circuits meet the requirements of ANSI/IEEE
C37.90-1980 (formerly IEEE 472) for surge withstand capability.
Less than " 0.1% FS for (15 to 150)Hz at 2g and (150-2K)Hz at 1g on any axis per SAMA PMC.31.1.
Meets ESD withstand capability up to 10KV (No Damage).
Meets SAMA PMC 33.1-1978 from 20MHz to 500 MHz. Effect on pressure and temperature reading is less than " 0.25% FS.
Nonincendive for use in Class I, Division 2, Groups C & D hazardous locations (in certain configurations - see Section 5.1 for model numbers)(see Appendix A).
1.5 MODEL NUMBER ANALYSIS
The model number is stamped on a plate affixed to the inside of the Instrument Front
Cover. The RTU’s general features can be identified by comparing the data plate number to
Table 1-2.
1-16 / Introduction TeleRTU Plus™
Table 1-2 - MODEL NUMBER BREAKDOWN
Sample Model Number -
3530-25B-AB-CD-EFG-HJKMN ß Table Reference
3530-25B-01-02-110-14110 ß Model Number
A B = PACKAGING
0 1 BASIC PARTS
0 2 SPECIAL
C D = APPLICATION PROGRAM*
H = 21 VDC POWER SUPPLY
0 NONE
1 WITH 21 VDC POWER SUPPLY 1
K = RELAY BOARD
0 2 ACCOL
0 9 CUSTOM PROGRAM
E G = POWER SYSTEM
(* = 0 or 1)
0 NONE
1 WITH RELAY BOARD 1
J = EXPANSION BOARDS
0 * EXTERNAL
1 * 12V, 40AH LEAD ACID BATTERY
10W, SOLAR PANEL SYSTEM
2 0 12V, 40AH LEAD ACID BATTERY
30W, SOLAR PANEL SYSTEM
3 0 12V, 40AH LEAD ACID BATTERY
40W, SOLAR PANEL SYSTEM
F = COMMUNICATION
0 NONE
2 I/O EXPANSION BOARD
4 EXPANSION TIB
5 EXPANSION RS-232
6 EXPANSION RS-485
7
8
I/O EXPANSION BD; DI/DO & COMM.
I/O EXPANSION BD; DI/DO
F H K M N = POWER DIST. BOARD
(# = any No.)
0 RS-232
1 RADIO
2 MODEM
# # # 0 # NONE
# # # 1 # WITH PWR. DIST. BOARD 1
2 1 # 1 # WITH PWR. DIST. BOARD 1
2 # 1 1 # WITH PWR. DIST. BOARD 1
2 # # 1 1 WITH PWR. DIST. BOARD 1
# 1 1 1 # WITH PWR. DIST. BOARD 1
# 1 # 1 1 WITH PWR. DIST. BOARD 1
# # 1 1 1 WITH PWR. DIST. BOARD 1
1
G = CERTIFICATION J N = LOW POWER TIB
(# = any No.) (** = 2 or 5)
0 NONE
1 CLASS 1, DIV 2 (NON-INCENDIVE) # 0 NONE
** 1 WITH LOW POWER TIB 1
Mounting Kit 621475-01-7 is required. Two boards may be mounted per kit.
Proper kit quantity is determined by the configuration based on selections made.
Note: Table 1-2 is only provided for product identity and not for sales ordering purposes. Field changeable items may not match the unit’s Model
Number as shipped from the factory.
TeleRTU Plus™ Introduction / 1-17
BLANK PAGE
Section 1A
APPLICATION SOFTWARE
3530-15B
3530-20B
3530-20B
3530-20B
3530-25B
3530-25B
3530-35B
3530-35B
3530-45B
3530-45B
3530-50B
3530-50B
3530-50B
3530-55B
3530-55B
1A.1 CATEGORIES OF APPLICATION SOFTWARE
All TeleFlow GFC (Gas Flow Computer), TeleFlow Corrector, TeleRTU and TeleRecorder units have the option of running a user generated ACCOL load. In addition, Fixed ‘ C ’ application loads are available for the TeleFlow GFC and the TeleFlow Corrector, a standard
BBI ACCOL load (or a variation) is available for the TeleFlow GFC, the TeleCorrector and
TeleRecorders. Additionally, ACCOL based TeleFlow GFC, TeleFlow Corrector, TeleRTU and TeleRecorder users have the option of using UOI or TMS to view menus, and UOI configuration tools to modify menus. Units that have a Low Power I/O Expansion Board installed have the option of utilizing the 2-Run ACCOL load.
With respect to the program load, TeleRTU units that don’t contain a Low Power I/O
Expansion Board (3530-15B/25B/35B) do not have a standard BBI ACCOL load installed; the user must create and download their own ACCOL load.
Table 1A-1 provides a list of the TeleFlow GFC, TeleFlow Corrector, TeleRTU and
TeleRecorder program loads.
Table 1A-1
TeleFlow (3530-10B/20B), TeleFlow Corrector (3530-50B),
TeleRTU (3530-15B/25B/35B) & TeleRecorder (3530-45B/55B) Program Loads
Model #
3530-10B
3530-10B
3530-10B
Program Load
Fixed ‘ C ’ Program
Standard BBI ACCOL Load
User-created ACCOL load
User-created ACCOL load
Fixed ‘ C ’ Program
User-created ACCOL load
Standard BBI ACCOL Load or 2-Run ACCOL Load
User-created ACCOL load
Standard BBI ACCOL Load or 2-Run ACCOL Load
User-created ACCOL load
Standard BBI ACCOL Load or 2-Run ACCOL Load
TeleRecorder ACCOL load
User-created ACCOL load
Fixed ‘ C ’ Program
TeleCorrector ACCOL load
User-created ACCOL load
TeleRecorder ACCOL load
User-created ACCOL load
Operator Interface/Configuration
TeleFlow Menu System (TMS)
TMS or UOI Menu System Interface.
- ACCOL Workbench is used to create the load.
- Open BSI Utilities is used to download and communicate.
- User created/modified menus via UOI.
See 3530-10B with user-created ACCOL load.
TeleFlow Menu System (TMS)
See 3530-10B with user-created ACCOL load.
TMS or UOI Menu System Interface.
See 3530-10B with user-created ACCOL load.
TMS or UOI Menu System Interface.
See 3530-10B with user-created ACCOL load.
TMS or UOI Menu System Interface.
UOI Menu System Interface.
See 3530-10B with user-created ACCOL load.
TeleFlow Menu System (TMS)
TMS or UOI Menu System Interface.
See 3530-10B with user-created ACCOL load.
UOI Menu System Interface.
See 3530-10B with user-created ACCOL load.
TeleFlow 3530-XXX Application Software / 1A-1
There are basically three categories of application software used with the TeleFlow GFC,
TeleFlow Corrector, TeleRTU and TeleRecorder series:
1) ACCOL Tools and related software which are used to program your TeleFlow GFC,
TeleFlow Corrector, TeleRTU (Remote Terminal Unit) or TeleRecorder for its intended application (pump control, pipeline monitoring, etc.). In general, the System Engineer or ACCOL programmer uses this type of software.
2) Supervisory Software which is used to allow operator interaction with the controller via graphical displays, trending, and printed reports. In general, this type of software is used by the Process Operator, or Technician.
3) Open BSI Utilities Software which facilitates communication between the TeleFlow
GFC, TeleFlow Corrector, TeleRTU and/or TeleRecorder and certain types of Supervisory software. In general, the System Engineer configures this software.
Each of these application software categories will be discussed briefly in this section. Additional information on these subjects is found in documents referenced within the text.
1A.2 ACCOL TOOLS SOFTWARE
ACCOL stands for A dvanced C ommunications and C ontrolO riented L anguage, and is
Bristol Babcock's proprietary language for programming Network 3000-series controllers, such as the TeleFlow GFC, TeleFlow Corrector, the TeleRTU and the TeleRecorder. The
ACCOL compilers and related software are collectively referred to as the ACCOL Tools.
Each of these tools will be discussed later in this section.
The ACCOL language includes a large set of pre-programmed software modules and control statements which can perform various mathematical, logical, process control, or communication functions.
For example, the PID3TERM module allows proportional, integral, and derivative control over a process input value; the AGA3ITER module computes natural gas volume flow rates, and the DIFFERENTIATOR module calculates the rate of change of an input. There are over 100 different modules and control statements to choose from. For more detailed information on particular modules or statements, see the ACCOL II Reference Manual
(document # D4044).
These modules and control statements are organized by the ACCOL programmer into individual tasks . Each task is specified to execute at a specific rate, and with a specific priority, relative to other tasks. One or more tasks are then combined by the ACCOL programmer into an ACCOL program. This program must be tailored for the particular use of this controller, for example, measuring and controlling natural gas flows, monitoring pressure of a pump, etc.
Depending upon which ACCOL Tools you are using, your ACCOL program is initially created either as ASCII text in an ACCOL source file (.ACC file) or as binary data in an
ACCOL object file (.ACO file). Facilities exist for quickly translating between these two formats.
1A2 / Application Software TeleFlow 3530-XXX
When editing of the ACCOL program has been completed, it must be compiled and linked to generate an ACCOL load file . The ACCOL load file contains the original programming instructions in a machine-readable format that can be executed by the TeleFlow GFC,
TeleFlow Corrector, TeleRTU and TeleRecorder. In order to get the load file into the controller, the file is downloaded into the TeleFlow GFC, TeleFlow Corrector, TeleRTU or
TeleRecorder, which then executes the programming instructions in the load file.
The Windows Ô -based ACCOL Workbench software allows you to create, modify, compile, link, and document an ACCOL source file, all using a single integrated tool. Workbench allows direct editing of an ACCOL source file, without the need for a separate ASCII text editor, and allows the user to call up a pre-defined template of any ACCOL module or statement. The user can then edit the template to conform to the requirements of the intended application. See the ACCOL Workbench User Manual (document # D4051) for more information.
(NOTE: All workbench on-line communication and downloading is facilitated via Open
BSI Utilities software, discussed later in this chapter).
Figure 1A-1 - Files Created by Windows-based ACCOL Workbench
1A.3 SUPERVISORY SOFTWARE
Supervisory software allows operator interaction with the Bristol Babcock controllers via graphical displays, trends, and reports of historical data. Generally, the supervisory
TeleFlow 3530-XXX Application Software / 1A-3
software requires a customized communication driver in order to communicate with the
Bristol devices. In some cases this is provided via Open BSI Utilities.
Among the types of supervisory software currently supported are:
1) OpenEnterprise software is Bristol Babcock's own supervisory system. OpenEnterprise utilizes a Windows Ô NT server and one or more PC client workstations. Communication with the controller network is supported via Open BSI. OpenEnterprise provides large real time and historical data bases, which may be displayed, logged, or exported.
2) UOI or TMS are DOS-based programs, which allow an operator to view text-based menus. Operators can view process data, modify TeleFlow parameters, and collect log information, see the UOI Configuration Manual (document # D5074) and the UOI
Operators Manual (document # D5075). For information on using TMS and TeleFlow menus, see Appendix F of documents CI-3530-10B, CI-3530-20B, or CI-3530-50B.
3) Iconics Inc. Genesis software is a popular PC-based supervisory package that is suitable for systems with smaller numbers of ACCOL signals. Genesis, and the Bristol driver may be purchased from Bristol Babcock (see "Local Area Network" on page 7).
4) Intellution ® FIX ® software is a powerful PC-based graphical user interface package, suitable for high-end systems. Open BSI Utilities software is required for communications.
1A.4 OPEN BSI UTILITIES SOFTWARE
The Open Bristol System Interface (Open BSI) is a layer of communications software which provides access to a network of Bristol Babcock remote process controllers. Above this communications layer are a group of applications (programs) which are collectively known as the Open BSI Utilities . These utilities interact with the communications layer to:
$ Download ACCOL load files to 33xx controllers and/or TeleFlow GFC, TeleFlow
Corrector, TeleRTU and TeleRecorder units in the network
$ Collect and display data from the 3xxx controllers and/or TeleFlow GFC, TeleFlow
Corrector, TeleRTU and TeleRecorder units
$ Monitor and control Open BSI communications
Third-party supervisory software, such as Intellution ® FIX ® , can also use Open BSI communications, and data files generated by Open BSI utilities, to access the Bristol network in order to display and report information from field instrumentation about a running process. An operator then uses this information to monitor and/or interact with the process.
The standard set of Open BSI utilities is accessed from within a Windows program group on the PC; the major utilities are described, briefly, below. Full details on each utility are included in the Open BSI Utilities Manual (D5081).
1A4 / Application Software TeleFlow 3530-XXX
Figure 1A-2 - Open BSI Interface Diagram
NetView allows the user to define communication network characteristics, define details about individual Controllers, Correctors, RTUs and Recorders, and to change these characteristics on-line. It also allows monitoring of communication statistics from the workstation end of the communication line.
Downloader transfers a linked ACCOL load file (*.ACL) to a remote 3xxx unit.
DataView collects and displays several types of process data from a 3xxx-series controller, including signal values, data array values, signal lists, archive data, and audit trail information. In addition, it allows the user to search for signals based on various criteria.
Remote Communication Statistics Tool allows additional monitoring of Open BSI communication information. Details on buffers, communication ports, and custom protocols are accessible via this tool. Some of the information collected via this tool is primarily of interest to Bristol Babcock support personnel.
SigWrite reads ASCII files containing ACCOL signal values, and writes those values to corresponding signals or signal lists in a 3xxx controller. SigWrite scans for such files at a user-definable interval.
In addition to the standard set of Open BSI Utilities, just described, there are other utilities, available from Bristol Babcock as add-ons to the standard utilities, which provide
TeleFlow 3530-XXX Application Software / 1A-5
capabilities for scheduled data collection, and file export. These utilities include the Open
BSI Scheduler, the Open BSI DDE Server, and the Open BSI Data Collector. See the Open
BSI Scheduler Manual (document # D5082) and the Open BSI Collection & Export Utilities
Manual (document # D5083) for details.
For more information on these packages, consult the manuals accompanying them, or contact Bristol Babcock's application support group for assistance.
1A.5 SYSTEM APPLICATIONS
A TeleFlow GFC, TeleFlow Corrector, TeleRTU or TeleRecorder can operate as an independent, stand-alone unit, or as a node in a local or wide area network. These applications are described in sections 1A.5.1 through 1A.5.3.
Note: The TeleFlow GFC, TeleFlow Corrector, TeleRTU or TeleRecorder cannot serve as a serial Communications Front End (CFE) or Data Concentrator (DC).
1A.5.1 Stand-Alone Unit
Figure 1A-3 shows a TeleFlow GFC, TeleFlow Corrector, TeleRTU or TeleRecorder used as a stand-alone unit in a non-network application. This arrangement is ideal for small local systems requiring a limited number of monitoring and control points. The PC for this application runs Bristol Babcock's ACCOL Workbench Software and Open BSI Utilities.
Data stored in the TeleFlow GFC, TeleFlow Corrector, TeleRTU or TeleRecorder can be observed or edited via the PC.
Once on line, the TeleFlow GFC, TeleFlow Corrector, TeleRTU or TeleRecorder executes the
ACCOL load and performs its configured tasks. Although the PC is attached to the Model
3530-XXX in Figure 1A-3, it can be disconnected and removed once the 3530-XX-X unit has been loaded and made operational.
Figure 1A-3 - Basic Stand-Alone Application
1A6 / Application Software TeleFlow 3530-XXX
1A.5.2 Local Area Network (LAN)
LANs typically support the communications requirements of computers and equipment in one or more buildings at a site or plant complex. A local area network requires a PC with extended graphics capability. This PC will typically run a supervisory software package to display process parameters, real time or historical process data, and graphic displays, etc.
An example of a local area network is shown in Figure 1A-4. This network can communicate directly through RS-485 cable connections for short distances (1000 feet max. from master to most distant slave) or over longer distances when interconnected on RS-232 ports. For much greater distances (miles) network communications require the use of phone line modems, fiber modems or broadband/carrier band modems (on coaxial cable).
Figure 1A-4 shows a network that contains a PC as the network master and a DPC 3330 at the first level of the network hierarchy. The data concentrator, which functions as a communications traffic director, communicates upward with the PC through a slave (S) port and downward with the second level through a master (M) port. This pattern repeats through each descending level. The second level contains two controllers; one communicates with three other controllers at the third level, while the other communicates with two at the third level. Each master (configured) port has the capability of supporting up to 127 slaves.
The network communication port of each TeleFlow GFC, TeleFlow Corrector, TeleRTU or
TeleRecorder requires either TMS or ACCOL configuration to change the 9600 bps default rate. The network port operates at rates up to 19.2 Kbps. Additionally, in a BSAP network, the network communication port must be defined in the ACCOL load using Workbench
Software. The network port is a standard BSAP slave port with alarm support intended for remote communication via a BSAP network.
All TeleFlow GFCs, TeleFlow Correctors, TeleRTUs and TeleRecorders act as terminal slave nodes in the BSAP network. As such, they are not capable of initiating a BSAP message intended for another node. These units are always immediate response nodes.
The PC, which runs the supervisory software, oversees the activities of the local area network. It displays process parameters, real-time data, and historical process information in both tabular and graphic formats. Journaling and system configuration utilities can also be employed as required.
The Bristol Babcock NETWORK 3000 system supports a maximum of six levels starting with the master device at level 1. Slave nodes at each descending level communicate upward through its preceding master node. Each master node stores data from its slaves until polled.
A local area network can also include printers and/or display terminals. Figure 1A-4 shows a printer connected directly to a PC port; however, a controller port could have been configured as a logger and used in the same manner.
TeleFlow 3530-XXX Application Software / 1A-7
1A8 / Application Software
Figure 1A-4 - Local Area Network
TeleFlow 3530-XXX
1A.5.3 Wide Area Network (WAN)
WANs typically support the communications requirements of computers and equipment at numerous geographical locations and may encompass many local and remote sites. A
Network 3000 system can also be constructed as a wide area network encompassing many local area networks. This application places a dedicated “Area Operator” computer at the top of the hierarchy as shown in Figure 1A-5. The central system includes the interface, monitoring and data recording equipment necessary to operate all the subservient networks. The central system employs Open BSI software to provide the on-line network interface.
Figure 1A-5 - An Example of a Wide Area Network
The Area Operator computer running Open BSI software provides the operator with realtime communications with remotes. Depending on the associated Man Machine Interface
(MMI) software package (such as OpenEnterprise, Genesis, Winterm, moXi, FIX, etc.), various features such as real-time management, historical data, alarm logging, event journaling, color graphics, CRT trending, report logging, process modeling, supervisory control, and high-level language support may be employed. The Area Operator PC of Figure
1A-5 communicates with the local area networks and discrete remote BBI RTUs, Flow
Computers and a Smart Transmitter through a DPC 3330. Depending on the configuration
TeleFlow 3530-XXX Application Software / 1A-9
of the DPC 3330, four or more asynchronous channels for use with phone line or modem applications, as well as a single, redundant channel for data highway applications may be utilized.
1A10 / Application Software TeleFlow 3530-XXX
Section 2
INSTALLATION
2.1 INSTALLATION IN HAZARDOUS AREAS
A TeleRTU Plus J is furnished in a housing designed to meet the NEMA Type 3 specifications and to operate in a Class I, Division 2, Groups C & D environment with a nonincendive rating (see Appendix A).
Figure 2-1 - Side View of TeleRTU Plus Mounted to a 2 Inch Pipe
TeleRTU Plus ™ Installation / 2-1
2.2 MOUNTING THE TeleRTU
J
Check all clearances when choosing an installation site. Make sure that the TeleRTU Plus J
Instrument Front Cover (door - hinged on left side) can be opened for wiring and service.
Make certain that the LCD display and sensor switch is visible and accessible to the on-site operator. There should also be clearance for the optional Solar Panel (if required). The basic unit measures 14.56" in height by 12.97" in width by 8.31" in depth
The TeleRTU Plus is to be positioned vertically (base at bottom) and is to be mounted to a 2 inch pipe (clamped to the rear of the unit via two clamps and four bolts). The pipe is to be cemented into the ground deep enough to conform to local building codes associated with frost considerations (see Figure 2-1). The unit may also be mounted directly to a panel or wall.
2.2.1 Temperature Limits
The TeleRTU Plus has been designed to operate over a -40 to 140 o F (-40 to +60 o C) temperature range. Operation beyond this temperature range could cause output errors and erratic performance. Prolonged operation under extreme conditions could also result in failure of the unit.
2.2.2 Vibration Limits
Check the mounting pipe or wall for mechanical vibration. Make sure that the TeleRTU
Plus is not exposed to a level of vibration that exceeds those given in the specifications. The
TeleRTU Plus limits are 2g for 15-150 Hz & 1g for 150-2000 Hz.
2.2.3 Opening The Instrument Front Cover
The Instrument Front Cover must be opened to access the electrical wiring terminals on the
TeleRTU J CPU Board and on the various options. The Instrument Front Cover is hinged on the left side and is secured on the right side by upper and lower latches.
2.2.4 CPU Board Configuration
(see Figure 2-2)
The TeleRTU J CPU Board contains three (3) sets of User Configurable Jumpers which provide configuration selection as follows:
2.2.4.1 JP3 - Battery Backup Enable
When JP3 is open, the battery is disabled. When JP3 is installed, the battery maintains the contents of the RAM and the Real Time Clock while power is less than 3.6 VDC. When main power is connected and is greater than 3.6VDC, no current will be drawn from the backup battery regardless of the state of JP3.
2.2.4.2 JP4 - Security (Manufacturing Tests Only)
Jumper JP4 is used to prevent the occurrence of ACCOL downloads or Firmware FLASH loads.
2-2 / Installation TeleRTU Plus ™
2.2.4.3 JP5 - Manual Reset
For normal operation, JP5 is left open. When the Shunt Jumper associated with JP5 is installed, the TeleRTU J is held in a reset condition, with all processing halted. When JP5 is removed, normal operation will resume.
TeleRTU Plus ™
Figure 2-2 - TeleRTU J CPU Board
Installation / 2-3
2.3 WIRING NOTES
The field wiring terminals on the TeleRTU J CPU Board are accessed by opening the
Instrument Front Cover. The CPU Board is mounted horizontally (on edge) below the battery such that the wiring connectors on the board's card edge are facing the front of the unit. Note: Exercise care when installing a conduit fitting or field wiring to prevent damage to the CPU Board and/or other system components.
2.3.1 Wire Routing
Wiring will enter the TeleRTU Plus J through holes in the bottom of the case. Up to seven holes may be provided in the bottom of the case (in addition to the center hole that is plugged). The purpose of each of these holes (see Figure 2-3) is provided as follows:
$ (1) - A .75” hole is provided to accommodate the power input wires from the optional Solar
Panel, all DI/O, the Auxiliary Analog Input and the Pulse Input Wiring. This hole accommodates a .75” Liquid Tight Nonmetallic Conduit Fitting and is plugged when the unit is factory shipped.
$ (2) A .437" hole accommodates the local port jack.
$ (3) A .5" hole is plugged.
$ (4) A .406" hole accommodates the Battery Ventilation Assembly.
$ (5) A .5" hole is accommodates the Solar Panel wiring. When the optional Solar Panel is not installed, this hole should be plugged.
$ (6) This hole accommodates an antenna cable, or a Polyphaser, or a phone cord. If one of these items isn’t present this hole is plugged.
$ (7) Solderless Ground Lug
2-4 / Installation
Figure 2-3 - TeleRTU Plus (Bottom) Wiring Holes
TeleRTU Plus ™
2.3.2 Terminal Connections
This device uses compression-type terminals that accommodate up to #14 AWG wire. A connection is made by inserting the bared end (1/4 inch max.) into the clamp beneath the screw and securing the screw. The wire should be inserted fully to prevent short circuits.
Allow some slack in the wires when making terminal connections. Slack makes the connections more manageable and minimizes mechanical strain on the CPU Board and harnesses.
2.3.3 Signal Shielding and Grounding
TeleRTU Plus units are provided with a Ground Lug that is situated on the bottom of the enclosure. Only units equipped with a modem MUST have the Ground Lug connected to a known good earth ground using wire no larger than #4 AWG in size. A cabinet ground cable situated inside the enclosure provides the interconnection between the modem’s protective surge circuitry and the unit’s Ground Lug. The use of twisted-pair, shielded and insulated cable for I/O signal wiring will minimize signal errors caused by electromagnetic interference (EMI), radio frequency interference (RFI) and transients (see Supplement S1400A).
2.3.4 Power Connections
The unit is provided with four power connections, i.e., J1 (Solar Panel Power - PWR), J2
(Primary - PWR1), J3 (Secondary - PWR2) & J4 (Auxiliary Power - AUX PWR). Right angle
2-position harness connectors P1, P2, P3 and P4 are removable from the CPU board’s card edge to accommodate wiring when the unit is installed. Connectors J1, J2, J3 and J4 function as follows:
$ J1 - Solar Panel Power Jack
Solar power is interfaced via card edge connector J1 that utilizes a 2-connector right angle plug (P1) which can be unplugged from the edge of the PCB. This connector accommodates the input from a solar panel as follows:
J1 Pin
#
1
2
J1 Pin
Name
PWR
GND
Connection
SP Red Wire
SP Black Wire
Table 2-1 - Solar Panel Power Jack J1
$ J2 - Primary Power Jack
Primary power utilizes a 2-connector right angle plug (P2) that can be unplugged from the edge of the PCB. This connector accommodates the input from the battery and power to the optional Modem as well as the optional Relay Board as follows:
J2 Pin
#
1
2
J2 Pin
Name
Connection
PWR1 Red Wire Battery (+), Modem (TB4+) or Relay Bd.
GND Blk. Wire Battery (-), Modem (TB4-) or Relay Bd.
Table 2-2 - Primary Power Plug J2
TeleRTU Plus ™ Installation / 2-5
$ J3 - Secondary Power Jack
Secondary power utilizes a 2-connector right angle plug (P3) that can be unplugged from the card edge. This connector is used to install a temporary battery while the original battery is being replaced.
J3 Pin
#
1
2
J3 Pin
Name
Connection
PWR2 Battery (+)
GND Battery (-)
Table 2-3 - Secondary Power Jack J3
$ J4 - Auxiliary Power Output Jack
The auxiliary power output connector can be used to supply power to a communications device such as a Radio or Modem Option. This jack acts as an output supply that originates at the Primary Power Source. This output is not fused, so a fuse should be installed elsewhere in the circuitry. This fuse should not exceed a 2.5 Amp rating.
Connection to a load is accommodated as follows:
J4 Pin
#
1
2
J4 Pin
Name
Connection
AUX PWR +12 VDC
GND Ground/return
Table 2-4 - Auxiliary Power Output Jack J4
Modems are powered by the Auxiliary Power Output (Connector J4). Units shipped from the factory, with a modem installed, have the Auxiliary Power Output set ON in the standard load shipped with the product.
If you want the modem powered continuously, and
· you have since re-downloaded your standard load, or-
· you are running an ACCOL load other than the standard load shipped from the factory, or-
· you are installing a modem for a unit which originally shipped without a modem, then you MUST set the Auxiliary Power Output to ON. This can be accomplished, for standard loads, using the TeleFlow Menu System (TMS), by setting the Auxiliary Power
Output Default to ON via the Radio Communications Setup Menu (See Section F.8.5). If you are NOT using one of the standard loads, you must use the SYS_3530 Module in your
ACCOL Load to set the Auxiliary Power Default ON/OFF signal to ON. (This signal is Entry
1 in Parameter List 4 of the SYS_3530 Module, see ‘SYS_3530’ section in the ACCOL II
Reference Manual , document# D4044).
2.3.5 Optional Power Distribution Board
Because of power distribution restrictions (CPU Board connector wiring capacity), power is routed through a Power Distribution Board when an option (other than the I/O Expansion
Board, Expansion TIB or a Radio) is installed (see Figures 2-4, 2-5).
2-6 / Installation TeleRTU Plus ™
Figure 2-4 - Power Distribution Board
Figure 2-5 - Power Distribution Board Schematic/Wiring Diagram
Power Distribution Boards (Relay Boards, 21V Power Supply Boards, Low Power TIB
Boards and Modems) are mounted to the TeleRTU in question using a Snap Track and Dual
PCB Mounting Bracket (see Figure 2-6).
TeleRTU Plus ™ Installation / 2-7
Figure 2-6 - Power Distribution Board and Other Options
Snap Track Mounting Diagram
2.4 WIRING INPUT/OUTPUT SIGNALS
The TeleRTU Plus J provides I/O termination for two (2) Discrete Inputs, two (2) Discrete
Outputs, four (4) Analog Inputs and two (2) 0-16V Pulse Input. Additionally, terminations are provided for the Local and Network Communication Ports. The connections for each type
I/O and the Communication Ports are described in sections 2.4.1 through 2.4.5.4.
2-8 / Installation
Figure 2-7 - Discrete Input Wired to TeleRTU J
TeleRTU Plus ™
2.4.1 Discrete Inputs
(See Figure 2-7)
Two independent discrete input channels are available. Discrete Inputs are accepted from transistor, mechanical relays, TTL, CMOS and other devices which provide from 0 to 16
VDC. These inputs are not isolated; therefore, field input devices which are not isolated must be referenced to the TeleRTU Plus J Ground.
J5 Pin Signal
1 DIN0
2 GND
Function
Discrete Input 0
Ground
Table 2-5 - Discrete Input Connections to J5
J6 Pin Signal
1 DIN1
2 GND
Function
Discrete Input 1
Ground
Table 2-6 - Discrete Input Connections to J6
2.4.2 Discrete Outputs
(See Figure 2-8)
Two independent firmware controlled open drain discrete outputs are provided for control or signaling functions. Each output is wired to the source terminal of an N Channel MOSFET capable of switching up to 16 volts at up to 100mA. When closed, the FET shorts the output to ground with resistance of .5 ohms or less. These outputs are protected by 16V TVS diodes.
Because these outputs are not isolated, caution must be exercised to ensure that the load current does not affect operation of the TeleRTU Plus J or related devices.
TeleRTU Plus ™
Figure 2-8 - Discrete Output Wired to TeleRTU J
J5 Pin
2
3
Signal
GND
Function
Ground
DOUT 0 Discrete Output 0
Table 2-7 - Discrete Output Connections to J5
Installation / 2-9
J6 Pin
2
3
Signal
GND
Function
Ground
DOUT 1 Discrete Output 1
Table 2-8 - Discrete Output Connections to J6
2.4.3 Pulse Inputs
(See Figure 2-9)
The TeleRTU J can accept pulse inputs from TTL or CMOS outputs, transistors, mechanical relays or other signaling devices. The maximum pulse frequency input is 5KHz with low impedance sources and 200Hz with high impedance sources such as Open Collector Drive
(see Figure 2-9).
Figure 2-9 - Pulse Input Wired to TeleRTU
J9 Pin
1
2
3
4
Signal
GND
Function
Ground
PULSE1 Pulse Input 1
GND Ground
PULSE2 Pulse Input 2
Table 2-9 - Pulse Input Connections to J9
2.4.4 Analog Inputs
(See Figure 2-10)
The 1 to 5 V Auxiliary Analog Inputs AIN1 through AIN4 can be supplied source power
(nominally +9.5V) to J10 Pin 2, J11 Pin 2, J12 Pin 2 or J13 Pin 2 (Excitation), respectively, through the CPU Board’s Transmitter Excitation Regulator which has a 20mA current limit. The resolution of the analog input is nominally ±15 Bits 186 m V.
2-10 / Installation TeleRTU Plus ™
TeleRTU Plus ™
Figure 2-10 - Analog Input Wired to TeleRTU
J10 Pin
1
2
3
Signal
AIN1
EXC1
GND
Function
Analog Input 1
Excitation
Ground
Table 2-10 - Analog Input Connections to J10
J11 Pin
1
2
3
Signal
AIN2
EXC2
GND
Function
Analog Input 2
Excitation
Ground
Table 2-11 - Analog Input Connections to J11
J12 Pin
1
2
3
Signal
AIN3
EXC3
GND
Function
Analog Input 3
Excitation
Ground
Table 2-12 - Analog Input Connections to J12
Installation / 2-11
J13 Pin
1
2
3
Signal
AIN4
EXC4
GND
Function
Analog Input 4
Excitation
Ground
Table 2-13 - Analog Input Connections to J13
2.4.5 Communication Ports
2.4.5.1 RS-232 Network and Local Communications Ports
The TeleRTU provides both a network (or remote) port and customer port. Both ports provide for serial asynchronous communications compatible with RS-232 levels. These ports operate independently at baud rates up to 19.2Kbps.
Figure 2-11 - PC Connected to TeleRTU J Local Port
2.4.5.2 Local Port
D Conn. Pin #
& Wire Color
5 (Black)
3 (Red)
2 (White)
N/A
VII
Plug Pin #
6
7
2
1*
J7 Pin #
& Wire Color
1 (Black)
3 (White)
2 (Red)
4 (Green)
RTU Signal
Name
GND
LRXD
LTXD
Wake Up
N/A 4* 1 (Brown) GND
* T he green and brown wires are shorted together in the VII Plug/D Conn.
Wiring Harness. Pins 7 & 8 of the D-Type Connector are shorted together.
Table 2-14 - Local Port/PC Interconnect Cable Wiring
2-12 / Installation TeleRTU Plus ™
2.4.5.3 Network Port
The network port functions as a DTE (Data Terminal Equipment) device. The network port employs the standard RS-232 Interface signals for data transfer and handshaking.
Whenever the Carrier Detect Signal (RDCD) is active (RS-232 Mark or High Level), the
TeleRTU J exits sleep mode and stays in communication mode as long as the signal is active. The standard RS-232 signals are provided on the Network Port as follows:
CPU Pin
#
J7-4
J8-1
J8-2
J8-3
J8-4
J8-5
J8-6
Name
Modem D-Conn.
# & Wire Color
WAKEUP N/A
GND 5 (Green)
RDCD
RDTR
1 (Gray)
4 (Yellow)
RCTS
RRTS
RRXD
7 (Violet)*
7 (Orange)
2 (Blue)
Radio Conn. # &
Wire Color
MDS/FreeWave
6/N/A (Yellow)
7/6 (Black)
8/8 (Green)
N/A
5/10 (Brown)
4/9 (Blue)
3/7 (White)
TeleRTU Plus
Function
Wake Up
Ground
Data Carrier Detect Input
Data Term. Ready Output
Clear To Send Input
Request To Send Output
Receive Data Input
J8-7
J10-1
RTXD
AIN1
3 (Brown)
N/A
2/5 (Red)
21 (Orange)
Transmit Data Output
Analog Input 1
* In the case of the TeleRTU’s modem harness, a violet wire connected to CPU board connector J8-4 (RCTS) is tied to the orange wire which is connected to
CPU board connector J8-5 (RRTS).
Table 2-15 - Network Port Connections to the CPU Board
2.4.5.4 Modem or Radio On Network Port
The RS-232 signals utilized by the optional radio or BBI PSTN modem are provided in
Table 2-15 above. Table 2-16 provides the power interconnects required for optional modem or radio usage. Table 2-16 also provides the 2-wire phone connections associated with the
BBI PSTN modem.
TeleRTU
Conn.
& Sig. Name
J2-1 (PWR1)
J2-2 (GND)
-
-
Radio
Conn.
& Sig. Name
-
-
Modem
396039-02-2 Conn.
& Sig. Name
J4-1 (AUX PWR) 13.8V (+Pwr.) TB4-2 (EXTVDC)
J4-2 (GND)
J4-2 (GND) -
-
13.8V (-Pwr.) TB4-1 (GND)
TB1-1 (T/R)
TB1-2 (T/R)
Modem
400000-01-6 Conn.
& Sig. Name
-
-
TB4-1 (EXTVDC)
TB4-2 (GND)
J1-3 (T/R-1)
J1-4 (T/R-2)
Port
Usage
Power (+)
Pwr. Gnd.
Mod. Power (+)
Pwr. Gnd.
Phone Line
Phone Line
Table 2-16 - Wire Listing for Modem & Radio Power Connections
Illustrations of a radio and a modem equipped TeleRTU Plus J are provided in Figures 2-12 and 2-13 respectively. The option in question is secured to a bracket that accommodates its installation or removal. The option slides easily into or out of the horizontal guide rails on the fixed Option Mounting Bracket, which in turn is attached to the left side of the Battery
Mounting Bracket.
TeleRTU Plus ™ Installation / 2-13
2-14 / Installation
Figure 2-12 - TeleRTU Plus with MDS Radio Installed
TeleRTU Plus ™
TeleRTU Plus ™
Figure 2-13 - TeleRTU Plus with Modem Installed
Installation / 2-15
For additional information about the MDS Radio option, refer to Appendix H.
For additional information about the FreeWave Radio option, refer to Appendix I.
For additional information on the BBI PSTN Modem, see the appropriate modem instruction manual.
2.5 MOUNTING THE OPTIONAL SOLAR PANEL
The Solar Panel Systems are to be mounted to a 2” to 2-3/8” pipe as illustrated in Figures 2-
14, 2-15 & 2-16. The Muffler (Pipe) Clamps are secured via four 1/4-20 nuts and washers.
2.5.1 Swivel (Directional Facing)
Solar Panels used in the northern hemisphere should face due south (not magnetic south) while those used in the southern hemisphere should face due north (not magnetic north).
2.5.2 Tilt Angle
The 10 Watt Solar Panel Mounting Bracket provided by Bristol Babcock is designed to mount the 10 Watt Solar Panel at a fixed 45° ( ± 2 ° ) tilt angle (see Figure 2-14). The 30 Watt and 40 Watt Solar Panel Systems (Figures 2-15 & 1-16 respectively) have adjustable tilt angles.
Figure 2-14 - 10 Watt Solar Panel System Mounting Diagram
2-16 / Installation TeleRTU Plus ™
Figure 2-15 - 30 Watt Solar Panel System Mounting Diagram
Table 2-17 shows the angle (from horizontal) at which the Solar Panel should be installed in order to maximize annual energy output. At most latitudes, performance can be improved by less of an angle during the summer and more of an angle during the winter.
LATITUDE INSTALLATION ANGLE
0-4° 10° from Horizontal
5-20°
21-45°
Add 5° to the Local Latitude
Add 10° to the Local Latitude
46-65°
66-75°
Add 15° to the Local Latitude
80° from Horizontal
Table 2-17 - Solar Panel Tilt Angle for 30 Watt & 40 Watt Solar Panels
TeleRTU Plus ™ Installation / 2-17
Figure 2-16 - 40 Watt Solar Panel System Mounting Diagram
2.6 TeleRTU Plus
J
CONFIGURATION
To configure the TeleRTU Plus J follow the steps listed below:
1. Install appropriate I/O wiring to the CPU Board’s removable terminal blocks. Install the options field wiring to the appropriate removable terminal blocks (see Section
2.3, 2.3.1 through 2.3.5, 2.4, and 2.4.1 through 2.4.4).
2. Configure the Jumpers on the CPU Board (see Sections 2.2.4 through 2.2.4.3).
3. Connect DC Power to TeleRTU CPU Board (12 VDC Battery connected to P2 should be plugged into J2 on the CPU Board).
4. Connect the Local Port of the TeleRTU Plus™ to a PEI, apply power and download the ACCOL Load.
5. After receiving the ACCOL Load, the TeleRTU J should be performing its on line operation.
2.6.1 Application Software Reference Documents
Categories of application software are discussed in Chapter 1A.
The following BBI software manuals provide the information necessary to configure and operate your system:
2-18 / Installation TeleRTU Plus ™
D4044 ACCOL II Reference Manual - for information on ACCOL modules and statements
D4051 ACCOL Workbench User Manual - for information on creating an ACCOL source file
D5081 Open BSI Utilities Manual - for information on setting up communications between the
PC and the BBI controller network
D5082 Open BSI Scheduler Manual - for information on setting up scheduled data collections
D5083 Open BSI Collection & Export Utilities Manual - for information on using the Open BSI
Data Collector
D5074 UOI Configuration Manual - for information on creating and modifying menus and logs
D5075 UOI Operator Manual - for information on how to view menus and logs
2.6.2 Installation & Configuration of Options
For information on removal/replacement and service of the various options see Table 2-18.
Option
Low Power I/O Expansion Board
Low Power Transmitter Intf. Bd.
Digital To Relay I/O Board
Document
PIP-EXPI/OTF
PIP-TIBS3530
Appendix G -
Notes
for 392950-01-4
MDS Radio
FreeWave Radio
Appendix H
Appendix I
21V Pwr. Supply (DC/DC Converter) PIP-353021VS
Expansion Transmitter Intf. Bd.
PIP-EXPTIBS
Expansion Transmitter Intf. Bd.
Expansion Comm. Port RS-232 Bd.
Expansion RS-485 and/or AO Bd.
9600 bps PSTN Modem
9600 bps PSTN Modem
Isolated RS-485 Interface Bd.
PIP-EXPTIBTF
PIP-EXP232TF
PIP-EXP485/AO -
CI-9600
CI-9600TF
PIP-ISORS485
-
-
-
for 392951-01-0 for 392960-01-0 for 396039-02-2 for 400000-01-6
Externally Mounted on DIN Rail
Table 2-18 - Options Installation/Configuration Reference
TeleRTU Plus ™ Installation / 2-19
BLANK PAGE
Section 3
SERVICE
3.1 INTRODUCTION
This section provides Removal and Replacement Procedures, and Troubleshooting/Fault
Isolation information for the TeleRTU J Plus model 3530-25B.
Setup utilizes a PC running the ACCOL Workbench program or the Universal Operator
Interface (UOI) program. External test equipment such as a digital multimeter and oscilloscope will also be required to aid in isolating and troubleshooting certain problems.
Figure 3-1 - Local Port Communications Setup
3.2 ACCESSING PARTS FOR TESTING OR REPLACEMENT
In order to test or replace any major system component, it will be necessary to open the Instrument Front Cover. These operations should only be performed by technically-qualified persons having advanced mechanical and electronic skills, and possessing the proper service equipment. Any damage to the TeleRTU J Plus resulting from improper handling or incorrect service procedures will not be covered under the product warranty agreement.
If these procedures cannot be performed properly, the unit should be returned to Bristol
Babcock for factory evaluation and repairs.
TeleRTU Plus J Service / 3-1
Warning
Opening the door of a powered TeleFlow that is operating in a hazardous area exposes the electrical circuitry to the atmosphere and could result in accidental fire or explosion.
Caution
PC board components can be damaged by electrostatic discharges (ESD) during disassembly, reassembly, and test procedures. Use grounded wrist straps and surface pads when working near or handling the Main Circuit Board. See attached instruction supplement S14006 for proper grounding and handling techniques.
3.3 COMPONENT REMOVAL & REPLACEMENT PROCEDURES
The following major items are covered in this section:
$ Lead Acid Battery
$ CPU Board
$ On Board Fuse
$ On Board Battery
$ LCD Display/Switch Panel Assembly
The following options are covered in appendices:
$ Optional Low Power I/O Expansion Board (see PIP-EXPI/OTF)
$ Optional Low Transmitter Interface Board (see PIP-TIBS3530)
$ Optional Digital To Relay I/O Board (see Appendix G)
$ Optional Radio (see Appendix H for MDS or Appendix I for FreeWave)
$ Optional 21V Power Supply Board (see PIP-353021VS)
$ Optional Expansion Transmitter Interface Board (see PIP-EXPTIBS for 392951-01-0 or PIP-EXPTIBTF for 392960-01-0)
$ Optional Expansion Comm. Port RS-232 Board (see PIP-EXP232TF)
$ Optional Expansion RS-485 and Analog Output Board (see PIP-EXP485/AO)
3.3.1 Lead Acid Battery Removal/Replacement Procedure
(see Figure 3-2)
1. Push the Activate Display Button on the TeleRTU Plus's Instrument Front Cover.
2. Open the Instrument Front Cover.
3. Remove the connector P2 (Battery & Power) from J2 on the TeleRTU CPU Board.
Note: In the event the TeleRTU requires continuous operation, a small auxiliary 9V battery can be plugged into the Secondary Connector (J3).
4. Loosen the two 11/32” nuts that secure the Battery Clamp Bracket to the Battery
Bracket and carefully remove the Battery Clamp Bracket.
3-2 / Service TeleRTU Plus J
5. Remove the battery leads (wires) from the battery post and then carefully raise and remove the battery.
6. To replace the battery:
Follow steps 3 through 5 in reverse order, replacing rather than removing the item in question. Make sure that the battery is clamped in place by the Battery Clamp Bracket.
Close and secure the Instrument Front Cover.
Figure 3-2 - TeleRTU with 12V Lead Acid Battery System
TeleRTU Plus J Service / 3-3
3.3.2 CPU Circuit Board Removal/Replacement
(see Figure 3-3)
Note:
The CPU Board is not to be removed under any circumstances unless the TeleFlow has been moved to an ESD safe area (see ESDS Manual S14006). The CPU Board should typically only be removed to replace the on board Lithium Battery or Fuse
F1 or to install the optional Expansion Board.
1. Open the Instrument Front Cover.
2. Disconnect power by removing harness connector plug P2 from CPU Board edge connector J2.
Figure 3-3 - TeleRTU CPU Board - Front Edge View
3. Remove all other harnesses from the CPU Board’s front edge connectors, i.e., P1 and P3 through P13. If an optional I/O Expansion Board is installed, remove the I/O wiring connectors from its front edge
4. Remove the two screws that secure the CPU Board’s Sliding Mounting Bracket to the
Fixed Bracket on the bottom of the Battery Bracket. Carefully slide the CPU Board
(and optional I/O Expansion Board if present) toward the front of the unit and remove harness connections from J14 (Front Panel Switch), J17 (Display Module)., J15
(TeleCounter) and J16 (Wakeup Switch).
Note:
Exercise extreme care to avoid damage to surface mounted components.
5. Remove the Ground wire by loosening the CPU Board’s CPU Ground Screw.
6. Carefully remove the CPU Board from the TeleRTU Plus Enclosure. Be careful not to damage the surface mounted components. Avoid contact with the Mounting Brackets,
Wiring Harnesses, etc. Note: This operation should only be performed in an ESD safe work area. The optional Expansion Board can now be removed (5 screws) for direct replacement or the CPU Board, CPU Board Battery (see Section 3.3.4) or CPU
Board Fuse (F1) (see Section 3.3.3) can be replaced.
If you are replacing the CPU Board and an optional Expansion Board is present, remove the 5 screws that secure the Expansion Board to its 5 standoffs and then
3-4 / Service TeleRTU Plus J
remove the 5 standoffs that secure the CPU Board to its Sliding Bracket. If, however; the expansion option is not present, simply remove the 5 screws that secure the CPU
Board to its mounting standoffs.
7. To Replace the CPU Board:
Follow steps 2 through 6 in reverse order, replacing rather than removing the item in question.
8. Close and latch the Instrument Front Cover.
3.3.3 Removal/Replacement of the On Board Fuse F1
F1 is a 350mA (Schurter 3402.0043) fast acting fuse that is located on the CPU Board.
1. Open the Instrument Front Cover.
2. Follow steps 2 through 6 of section 3.3.2.
3. Remove F1 with a pair of Needle-nose Pliers or a pair of tweezers.
4. Carefully press the replacement fuse (using Tweezers or Needle-nose Pliers) into its receptacle.
5. To replace the CPU Board (with Expansion Board if present) Follow steps 2 through 6 of Section 3.3.2 in reverse order, replacing rather than removing the item in question.
6. Close and latch the Instrument Front Cover.
3.3.4 Removal/Replacement of the On Board Battery
Note:
The On Board Battery should be changed in an ESD safe area.
The On Board Lithium Thionyl Chloride Battery provides 1AH of 3.6VDC backup power for
RAM, Real Time Clock and analog switches which are powered from the V+5B Supply.
1. Open the Instrument Front Cover.
2. Remove the CPU Board (see Section 3.3.2).
3. If it is desired to save the contents of RAM, it will be necessary to install the Main
Battery Power Supply at J2 prior to removal of the Lithium Battery.
4. Cut the holddown Tie Wrap that secures the Lithium Battery and carefully pull the three pronged battery off the CPU Board.
5. Carefully install the replacement Lithium Battery onto the CPU Board making sure to install a new holddown Tie Wrap.
6. Disconnect the Main Battery Power Supply from J2.
TeleRTU Plus J Service / 3-5
7. Follow steps 2 through 6 of Section 3.3.2 in reverse order, replacing rather than removing the item in question.
3.3.5 Removal/Replacement of the Display/Switch Panel Assembly
1. Open the Instrument Front Cover.
2. Disconnect power by removing harness connector plug P2 from CPU Board edge connector J2.
3. Remove all other harnesses from the CPU Board’s front edge connectors. If an optional
I/O Expansion Board is installed, remove the I/O wiring connectors from its front edge
4. Remove the two screws that secure the CPU Board’s Sliding Mounting Bracket to the
Fixed Bracket on the bottom of the Battery Bracket. Carefully slide the CPU Board
(and optional I/O Expansion Board if present) toward the front of the unit and remove harness connections from J17 (Display Module) and J16 (Wakeup) at the rear of the board. Note: The following connectors do not require removal from the CPU Board, J15
(TeleCounter) and J14 (Front Panel).
Note:
Exercise extreme care to avoid damage to surface mounted components.
5. Carefully remove the cable assembly associated with the LCD Display/Switch Panel
Assembly’s switch. This will require opening the three (3) Flat Cable Mount clamps (2 on the door and 1 on the Fabricated Panel within the enclosure).
6. Remove the multi-color ribbon cable connector from the rear of the LCD Display Board on the inside of the Instrument Front Cover.
7. Hold (or secure with tape) the LCD Display/Switch Panel Bezel on the outside of the
Instrument Front Cover and remove the eight (8) ¼” nuts that secure the LCD
Display/Switch Panel Assembly to the Bezel and cover. Remove the LCD
Display/Switch Panel Assembly with attached Panel Switch Cable. Replace at least one of the locking nuts to temporarily secure the Bezel to the door.
8. The LCD Display/Switch Panel Assembly can be disassembled if it is desired to replace either the Membrane Switch Panel or LCD Display Sub-assembly. The LCD Display
Sub-assembly is secured to the Membrane Switch Panel via four screws (with washers).
9. To replace the LCD Display/Switch Panel assembly:
While securing the Bezel on the outside of the Instrument Front Cover (door), install the LCD Display/Switch Panel Assembly on the inside of the door via eight (8) self locking ¼” nuts.
3-6 / Service TeleRTU Plus J
Figure 3-4 - Inside View of Instrument Front Cover
Plug the multi-color ribbon cable connector into its mating Display Module connector on the top of the LCD Display Board (on the inside of the door). Note: The yellow wire should be on the right side when installed.
Additionally the cable’s connector must be centered on its mating board connector. Position the multi-colored Display Module
Cable so that it is aligned with the two Flat Cable Mounts (clamps) on the inside of the door.
TeleRTU Plus J Service / 3-7
- Carefully position and route the Switch Panel Cable so that it runs over the Display
Module Cable and along with the Display Module cable is aligned with the two Flat
Cable Mounts on the inside of the door.
- Close the 2 Flat Cable Mounts on the inside of the door.
- Install the Switch Panel cable connector into connector J17 on the CPU Board. Note:
The cable’s white conductor should be adjacent to J17 pin 1.
- Close the Flat Cable Mount on the Fabricated Panel to capture the Display/Switch
Panel Cables.
- Install the Wakeup cable connector to connector J16 on the CPU Board. Note: This cable can be plugged in either way, i.e., it is not polarity sensitive. Close the 2 Flat
Cable Mounts on the inside of the door.
10. Slide the CPU Board via its Sliding Mounting Bracket into the Fixed Bracket on the bottom of the Battery Bracket. Replace the 2 screws which secure these Sliding
Mounting Bracket to the Fixed Bracket.
11. Carefully replace all connectors to the front edge of the optional Expansion Board (if present) and then to the front edge of the CPU Board (replacing Battery Power Connector P2 last).
12.
Close and secure the Door.
3.3.6 Removal/Replacement of the Modem or Radio Options
Removal/Replacement of the 9600 bps Modem Option is covered in BBI Customer
Instruction Manuals as follows: Modem P/N 396039-02-2 (see CI-9600)
Modem P/N 400000-01-6 (see CI-9600TF)
3.4 TROUBLESHOOTING TIPS
3.4.1 Battery & Fuse F1 Checks (Processor not running or no power)
Check the output of the PWR1, PWR2 , AUX PWR (and Solar Power - PWR if present) circuits at the card edge connector.
The CPU Board requires a Supply Voltage of 5.4 to 16 (VDC) for normal operation. PWR1
(J2-1 & J2-2) and PWR2 (J3-1 & J3-2) share a single 350mA Fuse. Auxiliary Power (J4-1 &
J4-2) and Solar Power (J1-1 & J1-2) are not fused.
$ If Power is below 12 VDC at PWR1 or PWR2 (or SPWR) check the battery (and solar panel if present).
$ If no voltage is present at the PWR1 or PWR2 terminals check Fuse F1 on the CPU
Board.
3-8 / Service TeleRTU Plus J
PIN #
J4-1
J4-2
J3-1
J3-2
J2-1
J2-2
J1-1
J1-2
PIN
NAME
AUX PWR
GND
PWR 2
GND
PWR 1
GND
PWR
GND
CONNECTION
+5 to +16 (VDC)
Ground/Return
Battery +
Battery -
Battery +_
Battery -
Solar Panel +
Solar Panel -
PURPOSE
Auxiliary Power Output
Auxiliary Power Output
Secondary Power Input
Secondary Power Input
Primary Power Input
Primary Power Input
Solar Power Input
Solar Power Input
Table 3-2 - Power Plugs J6, J7 & J8
3.4.2 LED Checks:
The CPU Board contains two LEDs (D27 is green & D26 is red). These LEDs are situated between the LCD Contrast Adjuster (R18) and the AUX POWER connector (J4) on the card edge. These LEDs function as follows:
D27 - Green: This LED indicates the TeleFlow J operating mode.
Flash 5/Sec. = Communications or Calculation Mode.
Short Flash 1/Sec. = Sleep Mode.
D26 - Red:When flashing, this LED indicates a FLASH PROM download is in progress.
$ If these LEDs are inoperable, check the voltage at PWR1. Check Fuse F1.
$ These LEDs flash alternately during download to the FLASH PROM.
3.4.3 LCD Display Checks
On initial system startup, the LCD will indicate that a warm or cold start is in progress. In the case of a cold start (for new units received from the factory), the LCD Display will prompt the user as follows:
AWAITING ACCOL DOWNLOAD
The user must download an ACCOL load to continue. The display will then scroll through its list twice. Verify that the LCD displays the fol-lowing messages:
1. Date & Time
2. Local I.D. & Group I.D.
3. Network Comm. Active (Note: This message will appear intermittently when the
Carrier Detect RS-232 signal on the Network Serial Port is active.)
4. TeleFlow Version X.X
$ If the LCD Display is difficult to read, check its Contrast Adjustment on the CPU
Board. This Adjusting Pot. (R18) is situated between the Secondary Power Connector
J3 and the Green LED (D27).
$ If the LCD Display is inoperative or erratic check the cable connection at the CPU
Board and the Display Board.
TeleRTU Plus J Service / 3-9
$ If after checking the cable connections, the LCD Display is still inoperative replace the
LCD Display Module and cables with known good hardware. If the LCD Display is still inoperative, the most likely cause is a defective CPU Board.
3.4.4 Field Wiring/Signal Checks
Check Input or Output Field Wires at the Card Edge Connector and at the field device.
Check wiring for continuity, shorts & opens. Check the I/O signals at the Card Edge
Connectors (see Table 3-3). For field wiring associated with the Digital to Relay I/O Board see Appendix G. For field wiring associated with the Low Power I/O Expansion Board, the
Low Power TIB, the 21V Power Supply, the Expansion TIB, the Expansion Comm Port RS-
232 Board or the Expansion RS-485 and/or Analog Output Board see the appropriate
Product Information Packages
PIN# Signal
J5-1 DIN 0
J5-2 GND
J5-3 DOUT 0
J6-1 DIN 1
J6-2 GND
J6-3 DOUT 1
J7-1 GND
J7-2 LTXD
J7-3 LRXD
Function
Discrete Input 0
Ground
Discrete Output 0
Discrete Input 1
Ground
Discrete Output 1
Ground
Transmit Data Input
Receive Data Output
Notes
See Section 2.4.1
See Section 2.4.1 & 2.4.2
See Section 2.4.2
See Section 2.4.1
See Section 2.4.1 & 2.4.2
See Section 2.4.2
See Section 2.4.5.2
See Section 2.4.5.2
See Section 2.4.5.2
J7-4 WAKEUP Wakeup Signal
J8-1 GND Ground
J8-2 RDCD
J8-3 RDTR
Data Carrier Detect Input
Data Term Ready Output
See Section 2.4.5.2 & 2.4.5.3
See Section 2.4.5.3
See Section 2.4.5.3
See Section 2.4.5.3
J8-4 RCTS
J8-5 RRTS
J8-6 RRXD
J8-7 RTXD
Clear To Send Input
Request To Send Output
Receive Data Input
Transmit Data Output
See Section 2.4.5.3
See Section 2.4.5.3
See Section 2.4.5.3
See Section 2.4.5.3
J9-1 GND
J9-2 PULSE 1
J9-3 GND-
J9-4 PULSE 2
Ground
Pulse Input 1
Ground
Pulse Input 2
See Section 2.4.3
See Section 2.4.3
See Section 2.4.3
See Section 2.4.3
J10-1 AIN1
J10-2 EXC1
J10-3 GND
J11-1 AIN2
J11-2 EXC2
J11-3 GND
J12-1 AIN3
J12-2 EXC3
J12-3 GND
J13-1 AIN4
J13-2 EXC4
J13-3 GND
Analog Input 1
Excitation
Ground
Analog Input 2
Excitation
Ground
Analog Input 3
Excitation
Ground
Analog Input 4
Excitation
Ground
See Section 2.4.4
See Section 2.4.4
See Section 2.4.4
See Section 2.4.4
See Section 2.4.4
See Section 2.4.4
See Section 2.4.4
See Section 2.4.4
See Section 2.4.4
See Section 2.4.4
See Section 2.4.4
See Section 2.4.4
Table 3-3 - Standard Field I/O Wiring List
3-10 / Service TeleRTU Plus J
Section 4
SPECIFICATIONS
4.1 ENVIRONMENTAL CONDITIONS
Temperature:
Relative Humidity:
Vibration Effect:
Transient Susceptibility:
ESD Susceptibility:
EMI Susceptibility:
EMI Radiation:
Operating Range: -40 to +60°C (-40 to 140°F)
5% to 90% (noncondensing)
< ±0.1% FS for 10-500 Hz at 1g on any axis per
SAMA PMC 33.1-1978.
Meets the requirements of ANSI/IEEE C37.90.1-
1989 (formerly IEEE 472) for surge withstand capability.
Meets the requirement of IEC 801-2 for ESD withstand capability up to 10KV (No Damage).
Meets the requirements of IEC 801-3 level 3
(10V/M) from 500KHz to 500MHz. Effect on pressure and temperature readings is < "0.25% FS.
Computational, archival, communications, and control functions are not impaired.
Meets FCC Rules Part J, Subpart 15, Class A for radiated emissions.
Hazardous Locations: Nonincendive for use in Class I, Division 2, Groups
C & D hazardous locations (See Appendix A).
4.2 CPU, MEMORY & PROGRAM INTERFACE
Processor:
Memory:
80C188EB, 16-bit microprocessor operating at
8MHz.
- 256K bytes Flash PROM.
- 512K bytes of Battery Backed Static RAM.
RAM Battery Backup: Lithium battery (3.6V) with 5000 hours cumulative backup.
4.3 CPU BOARD COMMUNICATIONS
Communication Ports: Two asynchronous ports standard
TeleRTU Plus™ Specifications / 4-1
Signal:
Local Port:
Network Port:
Communication Rates:
Protocol:
RS-232 Levels
For configuration, data collection, etc.
For Radio or Modem
Selectable from 1200 bps to 19.2 Kbps
Bristol Standard Asynchronous Protocol (BSAP) compatible with International Standard, ISO 1745,
2111 & 2629. Interface compatible for use with
Radio Modems or Phone-line Modems (Private Line or Switched Network types).
4.4 CPU BOARD DISCRETE INPUTS
No. of Inputs:
Input Voltage Range:
Input Threshold:
2 DIs
0 to 16Vdc
High = 3.6V (Min)
Low = 0.98V (Max)
Pullup Voltage:
Input Leakage:
4.8V (Nominal) at terminal (with input open)
15uA (Max)
Sink Current (to pull input low): 100uA (Min)
Allowable Source Leakage: 7uA (Max)
4.5 CPU BOARD DISCRETE OUTPUTS
No. of Outputs:
Switched Voltage Range:
Load:
Off-state Leakage:
2 DOs
0 to 16Vdc (Transorb Clamped)
100mA Max.
8uA (Typical), 100uA (Max)
On-state Resistance (to ground): 0.29 Ohms (Typical), 0.50 Ohms (Max)
4.6 CPU BOARD PULSE INPUTS
No. of Inputs:
Voltage Range:
2
0 to 16V
4-2 / Specifications TeleRTU Plus™
Minimum Frequency:
Maximum Frequency:
(0-5V Square Wave)
Minimum Pulse Width:
Input Threshold (Low)
Input Threshold (High)
Accumulator Capacity:
DC
9kHz (Max.) (Low Impedance Source)
200 Hz (Open Collector or Dry Contact)
100 uSecs
1.95V (Typical), 1.50V (Minimum)
2.95V (Typical), 3.50V (Maximum)
65535 Pulses
4.7 CPU BOARD ANALOG INPUTS
No. of Inputs:
Input Range:
Resolution:
Accuracy (Calibrated):
4.8 POWER
4 AIs
1 to 5Vdc
±15 BITS, 186 µ V
±0.03%
Operating Voltage
Ripple Voltage Tolerance
(# 60Hz)
Operating Current
Min. = +10.8Vdc (Max. = +16Vdc)
Max. = 100mVpp
Noise Voltage Tolerance
Connector Type (J2 & J3):
Wire Size
Fuse Type & Rating
4.9 AUXILIARY POWER
Output Voltage
Typ. = 81mA Communication Mode
(Max. = 90mA)
Typ. = 63mA Calculation Mode
(Max. = 68mA)
Typ. = 0.9mA Sleep Mode
(Max. = 1.6mA)
Max. = 100mVpp
Pluggable Weidmuller
Max. = 14AWG
350mA (Schurter 3402.0043)
Equals [Vin - (Iload) x Ron)] where:
Vin = Power at the PWR Connector
Iload = Load Current
Ron = On Resistance
TeleRTU Plus™ Specifications / 4-3
Max. Load Current
On Resistance
Leakage:
4.10 BACKUP BATTERY
Type
Capacity
Voltage
Discharge Current (Backup)
1.8A Continuous (2.5A Momentary)
Typ. = 0.37 Ohms (Max. = 0.5 Ohms)
Typ> = 22 m A (Max. = 100 m A)
Tadiran TL-5134 (Lithium Thionyl Chloride)
1 Ah
3.6Vdc (Nominal)
Max. = 60uA
4-4 / Specifications TeleRTU Plus™
TeleRTU
Special Instructions for Class I, Division 2 Hazardous Locations
1. A version of the TeleRTU is available which is listed by Underwriters Laboratories (UL) as nonincendive for use in Class I, Division 2, Group C and D hazardous and non-hazardous locations.
Read this document carefully before installing a nonincendive TeleRTU. Refer to the TeleRTU User's
Manual for general information. In the event of a conflict between the TeleRTU User's Manual and this document, always follow the instructions in this document.
2. The TeleRTU includes both nonincendive and unrated field circuits. Unless a circuit is specifically identified in this document as nonincendive, the circuit is unrated. Unrated circuits must be wired using Division 2 wiring methods as specified in article 501-4(b) of the National Electrical Code (NEC),
NFPA 70 for installations within the United States, or as specified in Section 18-152 of the Canadian
Electrical Code for installation in Canada.
3. The local communications port terminates in a circular connector on the bottom of the TeleRTU enclosure. The wiring on this connector is unrated. No connections may be made to this port unless the user ensures that the area is known to be nonhazardous. Connections to this port are temporary, and must be short in duration to ensure that flammable concentrations do not accumulate while it is in use.
4. An optional power system (solar panel and battery pack) is approved for use with the nonincendive
TeleRTU as described in the Model Specification. The connection to this solar panel is approved as a nonincendive circuit, so that the use of Division 2 wiring methods is not required. The nominal panel voltage must match the nominal battery voltage (12V).
5.
WARNING: EXPLOSION HAZARD - Do Not disconnect the Solar PWR, PWR1, PWR2 or AUXPWR terminals unless the area is known to be nonhazardous.
6.
WARNING: EXPLOSION HAZARD - Substitution of components may impair suitability for use in Class I, Division 2 environments.
7.
WARNING: EXPLOSION HAZARD - The area must be known to be nonhazardous before servicing/replacing the unit and before installing or removing I/O wiring.
8.
WARNING: EXPLOSION HAZARD - Do Not disconnect equipment unless power has been disconnected and the area is known to be nonhazardous.
9. The signals available for customer wiring are available in Table A1.
10. The UL listed nonincendive TeleRTU includes radio communications (MDS Model 2310, 4310, 4710,
9710 or 9810) or (FreeWave Spread Spectrum Radio) that is used in conjunction with a 10W, 16.5V
Solar Panel System. Installation of a BBI modem in the TeleRTU housing is approved. Connection to the radio or modem is approved as a nonincendive circuit, so that the use of Division 2 wiring methods are not required.
Table A1 - CPU Board Customer Wiring Signal Names
Signal Name
SOLAR
PWR
PWR 1 & 2
AUX
POWER
DIN 0 & 1
DOUT 0 & 1
11/20/2000
Signal Description
Solar Panel inputs; 5W, 12V. Refer to ¶ 4 of this document.
Power supply inputs; maximum 16VDC. Refer to ¶ 5 of this document.
Power output to Radio or Modem; maximum 16VDC. Refer to ¶ 5 of this document.
Discrete inputs; maximum 16VDC. Use Division 2 wiring methods.
Discrete outputs; maximum 16VDC, 100mA. Use Division 2 wiring methods.
Appendix A, Document CI3530-25B Page 1 of 2
TeleRTU
Special Instructions for Class I, Division 2 Hazardous Locations
LRXD, LTXD,
& WAKEUP
RDCD, RDTR,
RCTS, RRTS,
RRXD, RTXD
Pulse 1 & 2
AI EXC &
AIN1 - 4
Local communications port; factory wired, maximum input or output is ±16VDC.
Refer to ¶ 3 of this document. Note: When WAKEUP is used with an optional radio refer to ¶ 10 of this document.
Remote communications port (for radio or modem). Refer to 3530-25B Model
Spec. and ¶ 10 of this document.
Pulse inputs; maximum 16VDC. Use Division 2 wiring methods.
Analog inputs and excitations; maximum 16VDC. Use Division 2 wiring methods.
Note: When AIN1/2/3 or 4 is used with an optional radio refer to ¶ 10 of this document.
11/20/2000 Appendix A, Document CI3530-25B Page 2 of 2
Product Information Package
PIP-EXP I/O TF
February, 2008
Low Power I/O Expansion Board
Low Power I/O Expansion Board
Part No. 392927-XX-X
(For TeleFlow Plus, TeleRTU Plus, TeleRTU Module & TeleRecorder)
For the following Instruction Manuals:
CI-3530-20B, CI-3530-25B, CI-3530-35B & CI-3530-55B
Remote Automation Solutions
www.EmersonProcess.com/Remote
IMPORTANT! READ INSTRUCTIONS BEFORE STARTING!
Be sure that these instructions are carefully read and understood before any operation is attempted. Improper use of this device in some applications may result in damage or injury. The user is urged to keep this book filed in a convenient location for future reference.
These instructions may not cover all details or variations in equipment or cover every possible situation to be met in connection with installation, operation or maintenance. Should problems arise that are not covered sufficiently in the text, the purchaser is advised to contact Emerson Process
Management, Remote Automation Solutions division (RAS) for further information.
EQUIPMENT APPLICATION WARNING
The customer should note that a failure of this instrument or system, for whatever reason, may leave an operating process without protection. Depending upon the application, this could result in possible damage to property or injury to persons. It is suggested that the purchaser review the need for additional backup equipment or provide alternate means of protection such as alarm devices, output limiting, fail-safe valves, relief valves, emergency shutoffs, emergency switches, etc. If additional information is required, the purchaser is advised to contact RAS.
RETURNED EQUIPMENT WARNING
When returning any equipment to RAS for repairs or evaluation, please note the following: The party sending such materials is responsible to ensure that the materials returned to RAS are clean to safe levels, as such levels are defined and/or determined by applicable federal, state and/or local law regulations or codes. Such party agrees to indemnify RAS and save RAS harmless from any liability or damage which RAS may incur or suffer due to such party's failure to so act.
ELECTRICAL GROUNDING
Metal enclosures and exposed metal parts of electrical instruments must be grounded in accordance with OSHA rules and regulations pertaining to "Design Safety Standards for Electrical
Systems," 29 CFR, Part 1910, Subpart S, dated: April 16, 1981 (OSHA rulings are in agreement with the National Electrical Code).
The grounding requirement is also applicable to mechanical or pneumatic instruments that include electrically operated devices such as lights, switches, relays, alarms, or chart drives.
EQUIPMENT DAMAGE FROM ELECTROSTATIC DISCHARGE VOLTAGE
This product contains sensitive electronic components that can be damaged by exposure to an electrostatic discharge (ESD) voltage. Depending on the magnitude and duration of the ESD, this can result in erratic operation or complete failure of the equipment. Read supplemental document
S14006 at the back of this manual for proper care and handling of ESD-sensitive components.
Remote Automation Solutions
A Division of Emerson Process Management
1100 Buckingham Street, Watertown, CT 06795
F.
A.
C.
D.
A.
B.
E.
B.
WARRANTY
Remote Automation Solutions (RAS) warrants that goods described herein and manufactured by RAS are free from defects in material and workmanship for one year from the date of shipment unless otherwise agreed to by RAS in writing.
RAS warrants that goods repaired by it pursuant to the warranty are free from defects in material and workmanship for a period to the end of the original warranty or ninety (90) days from the date of delivery of repaired goods, whichever is longer.
Warranties on goods sold by, but not manufactured by RAS are expressly limited to the terms of the warranties given by the manufacturer of such goods.
All warranties are terminated in the event that the goods or systems or any part thereof are (i) misused, abused or otherwise damaged, (ii) repaired, altered or modified without RAS consent, (iii) not installed, maintained and operated in strict compliance with instructions furnished by RAS or (iv) worn, injured or damaged from abnormal or abusive use in service time.
These warranties are expressly in lieu of all other warranties express or implied (including without limitation warranties as to merchantability and fitness for a particular purpose), and no warranties, express or implied, nor any representations, promises, or statements have been made by RAS unless endorsed herein in writing. Further, there are no warranties which extend beyond the description of the face hereof.
No agent of RAS is authorized to assume any liability for it or to make any written or oral warranties beyond those set forth herein.
REMEDIES
Buyer's sole remedy for breach of any warranty is limited exclusively to repair or replacement without cost to Buyer of any goods or parts found by Seller to be defective if Buyer notifies RAS in writing of the alleged defect within ten (10) days of discovery of the alleged defect and within the warranty period stated above, and if the Buyer returns such goods to the RAS Watertown office, unless the RAS Watertown office designates a different location, transportation prepaid, within thirty (30) days of the sending of such notification and which upon examination by RAS proves to be defective in material and workmanship. RAS is not responsible for any costs of removal, dismantling or reinstallation of allegedly defective or defective goods. If a Buyer does not wish to ship the product back to RAS, the Buyer can arrange to have a RAS service person come to the site. The Service person's transportation time and expenses will be for the account of the Buyer. However, labor for warranty work during normal working hours is not chargeable.
Under no circumstances will RAS be liable for incidental or consequential damages resulting from breach of any agreement relating to items included in this quotation from use of the information herein or from the purchase or use by Buyer, its employees or other parties of goods sold under said agreement.
How to return material for Repair or Exchange
Before a product can be returned to Remote Automation Solutions (RAS) for repair, upgrade, exchange, or to verify proper operation, Form (GBU 13.01) must be completed in order to obtain a RA (Return Authorization) number and thus ensure an optimal lead time. Completing the form is very important since the information permits the RAS
Watertown Repair Dept. to effectively and efficiently process the repair order.
You can easily obtain a RA number by:
A. FAX
Completing the form (GBU 13.01) and faxing it to (860) 945-2220. A RAS Repair Dept. representative will return the call (or other requested method) with a RA number.
B. E-MAIL
Accessing the form (GBU 13.01) via the RAS Web site (www.emersonprocess.com/Bristol) and sending it via E-Mail to [email protected]
. A RAS Repair Dept. representative will return E-
Mail (or other requested method) with a RA number.
C. Mail
Mail the form (GBU 13.01) to
Remote Automation Solutions
A Division of Emerson Process Management
1100 Buckingham Street
A RAS Repair Dept. representative will return call (or other requested method) with a RA number.
D. Phone
Calling the RAS Repair Department at (860) 945-2442. A RAS Repair Department representative will record a RA number on the form and complete Part I, send the form to the Customer via fax (or other requested method) for Customer completion of Parts II & III.
A copy of the completed Repair Authorization Form with issued RA number should be included with the product being returned. This will allow us to quickly track, repair, and return your product to you.
Repair Authorization Form (on-line completion)
Remote Automation Solutions (RAS)
( Providing this information will permit Bristol, also doing business as Remote Automation Solutions (RAS) to effectively and efficiently process your return. Completion is required to receive optimal lead time. Lack of information may result in increased lead times.)
Date RA SH Line No.
Standard Repair Practice is as follows: Variations to this is practice may be requested in the “Special
Requests” section.
•
Evaluate / Test / Verify Discrepancy
•
Repair / Replace / etc. in accordance with this form
•
Return to Customer
Please be aware of the Non warranty standard charge:
•
There is a $100 minimum evaluation charge, which is applied to the repair if applicable (
√
in
“returned” B,C, or D of part III below)
Part I Please complete the following information for single unit or multiple unit returns
Address No.
Bill to :
Purchase Order:
(office use only)
Ship to:
Contact Name:
Phone: Fax: E-Mail:
Part II Please complete Parts II & III for each unit returned
Model No./Part No. Description:
Range/Calibration: S/N:
Reason for return : Failure Upgrade Verify Operation Other
1. Describe the conditions of the failure (Frequency/Intermittent, Physical Damage, Environmental Conditions,
Communication, CPU watchdog, etc.) (Attach a separate sheet if necessary)
2. Comm. interface used: Standalone RS-485 Ethernet Modem (PLM (2W or 4W) or SNW) Other:
3. What is the Firmware revision? What is the Software & version?
Part III If checking “replaced” for any question below, check an alternate option if replacement is not available
A. If product is within the warranty time period but is excluded due to the terms of warranty,, would you like the product: repaired returned replaced scrapped?
B. If product were found to exceed the warranty period, would you like the product: repaired returned replaced scrapped?
C. If product is deemed not repairable would you like your product: returned replaced scrapped?
D. If RAS is unable to verify the discrepancy, would you like the product: returned replaced *see below?
* Continue investigating by contacting the customer to learn more about the problem experienced? The person to contact that has the most knowledge of the problem is: phone
If we are unable to contact this person the backup person is: phone
Special Requests:
Ship prepaid to: Remote Automation Solutions, Repair Dept., 1100 Buckingham Street, Watertown, CT 06795
Phone: 860-945-2442 Fax: 860-945-2220
Form GBU 13.01 Rev. D 12/04/07
Emerson Process Management
Training
GET THE MOST FROM YOUR EMERSON
INSTRUMENT OR SYSTEM
• Avoid Delays and problems in getting your system on-line
• Minimize installation, start-up and maintenance costs.
• Make the most effective use of our hardware and software.
• Know your system.
As you know, a well-trained staff is essential to your operation. Emerson offers a full schedule of classes conducted by full-time, professional instructors. Classes are offered throughout the year at various locations. By participating in our training, your personnel can learn how to install, calibrate, configure, program and maintain your Emerson products and realize the full potential of your system.
For information or to enroll in any class, go to http://www.EmersonProcess.com/Remote and click on “Training” or contact our training department in Watertown at (860) 945-2343.
PIP-EXPI/OTF
LOW POWER I/O EXPANSION BOARD
PT. Number 392927-XX-X
Product Information Package
TABLE OF CONTENTS
2.1
2.1.1
2.1.2
2.2
2.2.1
2.2.2
2.2.3
2.2.4
2.2.5
2.3
SECTION TITLE
1.1
1.1.1
PAGE #
GENERAL INTRODUCTION .......................................................................................... 1
Configuration Hardware ................................................................................................... 2
Section 2 - INSTALLATION & SERVICE
REMOVAL/REPLACEMENT & INSTALLATION OF THE LPI/OEB.......................... 5
Removal/Replacement of the Low Power I/O Expansion Board..................................... 5
Installation of the Low Power I/O Expansion Board....................................................... 7
I/O CONFIGURATION & WIRING ................................................................................. 9
LPI/OEB Discrete Input Wiring (TB4)............................................................................. 9
LPI/OEB Discrete Output Wiring (TB4) .......................................................................... 9
LPI/OEB Analog Input Wiring (TB2)............................................................................. 10
LPI/OEB Analog Output Wiring (TB3) .......................................................................... 12
LPI/OEB High Speed Counter Wiring (TB3) ................................................................. 13
RS-232/RS-485 COMMUNICATIONS ........................................................................... 13
3.1
FIELD WIRING SIGNAL CHECKS .............................................................................. 15
4.1
4.1.1
4.1.2
4.1.3
4.1.4
4.1.5
4.1.6
4.2
INPUT/OUTPUT SPECIFICATIONS............................................................................ 16
Discrete Inputs ................................................................................................................ 16
Discrete Outputs.............................................................................................................. 16
Analog Inputs................................................................................................................... 16
Analog Outputs................................................................................................................ 17
Communication Port........................................................................................................ 18
High Speed Counter ........................................................................................................ 18
ENVIRONMENTAL SPECIFICATIONS....................................................................... 18
Supplements
PIP-EXPI/OTF Page 0-1 Table Of Contents
Section 1
INTRODUCTION
1.1 GENERAL INTRODUCTION
The Low Power I/O Expansion Board (LPI/OEB) measures approximately 4” by 7.25” and mounts piggy-back on either the TeleFlow or TeleRTU CPU Board. Removable card-edge connectors are provided to accommodate field wiring. A 1.25” by 1.2” cutout area is incorporated into the board’s design to accommodate mounting of the Multivariable Transducer’s Wet End Connector and Balance Board onto the TeleFlow CPU Board. The
LPI/OEB operates in conjunction with Revision 3 and higher TeleFlow CPU Boards and with TeleRTU CPU Boards. Three versions of the LPI/OEB are available; fully populated version P/N 392927-01-2 (see Figure 1), depopulated version that supports DI/DO and the
Comm. Port P/N 392927-02-0 and a depopulated version that supports DI/DO only P/N
392927-03-9.
PIP-EXPI/OTF
Figure 1 - Low Power I/O Expansion Board
Page 1 Low Power I/O Expansion Board
The Low Power I/O Expansion Board provides the following additional I/O capabilities to the TeleFlow Plus EGMCs, TeleRTU Plus and TeleRTU Module RTUs and TeleRecorders:
• 8 Discrete I/O
All eight DI/O function in both input and output capacities. Field terminals for each
DI/O are I/O and GND. Each Discrete Input will accept signals from 0 to 16 VDC. The
Discrete Outputs utilize open drain FETs with a maximum working voltage of 16 VDC and a minimum load of 100 mA. DI/Os are not isolated.
• 4 Analog Inputs (available on 392927-01-2 only)
Two single-ended Analog Inputs are available for 4 to 20 mA or 1 to 5 VDC signal operation (Jumper Configurable) and two additional single-ended Analog Inputs are available for 1 to 5 VDC signal operation only. The two 4-20 mA Inputs will support externally powered transmitters; however, internally powered 4-20 mA transmitters will require an external power supply. All four channels support low power voltage output transmitters such as Rosemount and Honeywell. Resolution is 12 bits (1.42 mV) and combined error (including linearity, hysteresis and temperature effects) is ≤
± 0.2%. Each Analog Input channel includes field wiring terminals for signal, transmitter power (+9.5V), and ground. Note: Analog Inputs are designated AI5 through AI8; AI1 through AI4 are assigned to the TeleRTU CPU.
• 1 Analog Output (available on 392927-01-2 only)
The Analog Output can be configured for 4 to 20 mA or 1 to 5 VDC operation (Jumper
Configurable). Resolution is 12 bits and combined error including linearity, hysteresis and temperature effects is ≤ ± 0.2% after calibration.
• 1 High Speed Counter Input (available on 392927-01-2 only)
The High Speed Counter input will accept pulses (with an input range from 0 to 16
VDC and up to 10KHz) from CMOS or TTL sources, including transistors, FETs, mechanical relays, or other signaling devices.
• 1 RS-232 or RS-485 Asynchronous Serial Communications Port (not on 392927-03-9)
Note: Only supported by units with TeleFlow/ACCOL Firmware
The Asynchronous Serial Communications Port can be jumper configured for either
RS-232 or RS-485 operation at programmable speeds of up to 19.2 Kbps.
1.1.1 Configuration Hardware
Fully populated Low Power I/O Expansion Boards contain 8 potentiometers, 15 Jumper
Blocks and 5 removable card-edge (Terminal Blocks) connectors. Tabulated information about Terminal Block, Jumper and Potentiometer assignments are contained in Tables 1, 2 and 3 respectively.
Table 1 - Low Power I/O Exp. Board Terminal Block Assignments
TB # PIN # MNEMONIC
TB1 1
TB1 2
TB2 1
AIN5 TB2
TB2
EXC6
AIN6
TB2 6
TB2
TB2
2
TB2 3
TB2 4
5
7
8
GND
AIN7
AIN8
DESCRIPTION
+21V
-21V
EXCITATION
ANALOG IN 5
5
GROUND
EXCITATION
ANALOG IN 6
6
GROUND
ANALOG IN 7
ANLOG IN 8
Low Power I/O Expansion Board Page
2
PIP-EXPI/OTF
Table 1 - Low Power I/O Exp. Bd. Terminal Block Assignments (Continued)
TB # PIN # MNEMONIC
TB2 9
TB3 1
TB3 2
TB3
TB4
TB4
3 HSC
TB3 4
TB4
TB4
TB4
TB4
TB4 6
TB4 9
TB4
TB4
1
2
4
5
7
8
10
11
GND
DIO1
DIO2
TB4 3
DIO3
DIO4
DIO5
DIO6
GND
DIO7
DIO8
GND
TB5 2
DTR
TB5 4
RTS/TX-
TB5 6
TB5 7
DESCRIPTION
GROUND
GROUND
HIGH SPEED CNTR
GROUND
DISCRETE IN/OUT 1
DISCRETE IN/OUT 2
GROUND
DISCRETE IN/OUT 3
DISCRETE IN/OUT 4
GROUND
DISCRETE IN/OUT 5
DISCRETE IN/OUT 6
GROUND
DISCRETE IN/OUT 7
DISCRETE IN/OUT 8
GROUND
DCD
RS232
RS232/485
RTS/XMIT
REC
XMIT
Table 2 - Low Power I/O Exp. Bd. User Configurable Jumper Block Assignments
JUMPER #
JP6
JP6
JP6
JP7
JP8
JP8
JP8
JP9
POSITION
2-7 (only)
2-7 & 4-5
1-2, 3-6 & 4-5 Configuration for Internally Sourced Current Input (AIN5)
JP7 1-4
All Open
2-7 (only)
2-7 & 4-5 Configuration for Non-Isolated Current Input (AIN6)
1-2, 3-6 & 4-5 Configuration for Internally Sourced Current Input (AIN6)
JP9 1-4
All Open
PURPOSE
Configuration for 1-5V Analog Input (AIN5)
Configuration for Non-Isolated Current Input (AIN5)
Configuration for 1-5V Analog Input (AIN5)
Configuration for Non-Isolated Current Input (AIN5)
Configuration for Internally Sourced Current Input (AIN5)
Configuration for 1-5V Analog Input (AIN6)
Configuration for 1-5V Analog Input (AIN6)
Configuration for Non-Isolated Current Input (AIN6)
Configuration for Internally Sourced Current Input (AIN6)
Used in conjunction with 1-5V Analog Input - leaves 9.5V
JP10 1-2
JP10 2-3
JP11 1-2
JP11 2-3
JP17 1-2 regulated power supply ON continuously.
Used in conjunction with 1-5V Analog Input - shuts down the
9.5V power supply during TeleFlow CPU SLEEP Mode.
Used in conjunction with an internally sourced 4-20 mA Current
Loop Analog Input - leaves current loop powered continuously.
Used in conjunction with an internally sourced 4-20 mA Current
Loop Analog Input - shuts down the internal current loop when the TeleFlow CPU is in SLEEP Mode.
JP13, 14, 16 JP13 to JP16 RS-232 Signals present at TB5 - RS-485 Converter asleep.
JP13, 14, 16 JP14 to JP16 RS-485 Signals present at TB5 - RS-232 Converter asleep.
JP15 1-2
Used in conjunction with RS-485 Communications
Installed = Transmit End Node (120-Ohm) Termination
Used in conjunction with RS-485 Communications
Installed = Receive End Node (120-Ohm) Termination
PIP-EXPI/OTF Page 3 Low Power I/O Expansion Board
Table 2 - Low Power I/O Exp. Bd. User Configurable Jumper Block Assignments
(Continued)
JUMPER # POSITION
JP19 1-2
JP19 2-3
JP20 1-2
JP21 1-2
JP22 1-2
JP22 2-3
PURPOSE
Used in conjunction with Analog Output - Current Loop output configuration.
Used in conjunction with Analog Output - Voltage output configuration.
Used with RS-485 Communications for RX Pull-up.
Install at End Node with (120-Ohm) RX Termination Installed.
Used with RS-485 Communications for RX Pull-down.
Install at End Node with (120-Ohm) RX Termination Installed.
RS-232 - RTS to CTS Loopback
RS-232 - Use External CTS
Table 3 - Low Power I/O Board Potentiometer Assignments
POT. #
R29
R30
R33
R36
R37
R45
R48
R49
POTENTIOMETER USAGE
Analog Input #7 circuitry offset calibration
Analog Input #8 circuitry offset calibration
1-5V Analog Output Adjustment - 1V point
Analog Input #5 circuitry offset calibration
Analog Input #6 circuitry offset calibration
1-5V Analog Output Adjustment - 5V point
4-20mA Analog Output Adjustment - 4mA point
4-20mA Analog Output Adjustment - 20mA point
Note All potentiometer adjustments require the use of TeleFlow Diagnostics
Low Power I/O Expansion Board Page
4
PIP-EXPI/OTF
Section 2
INSTALLATION & SERVICE
2.1 REMOVAL/REPLACEMENT & INSTALLATION OF THE LPI/OEB
2.1.1 Removal/Replacement of the Low Power I/O Expansion Board
Low Power I/O Expansion Board Field Upgrade Kits contain the following major parts:
1. Low Power I/O Expansion Board
2.
Five #4-40 - .188” x .469” Standoffs & Five #4-40 - .408” x .469” Standoffs*
* Use these Standoffs (BBI P/N SK100210M) if the others are insufficient!
3.
Five #4-40 x 3/16” Pan Head Screws - (May be required in lieu of original screws).
To remove an installed Low Power I/O Expansion Board, follow steps 1 through 7 below. To replace the Low Power I/O Expansion Board, follow steps 2 through 6 below in reverse order, installing rather than removing the item in question and then perform step 7.
1. Open the Instrument Front Cover.
2. Disconnect the wiring harness connectors associated with power, i.e., P10, P8, P7 and
P6 from the TeleFlow CPU Board or P1, P2, P3 and P4 from the TeleRTU CPU Board.
3. Disconnect I/O connectors P5, P13 and P14 from the TeleFlow CPU Board or P5, P6, P7,
P8, P9, P10, P11, P12 and P13 from the TeleRTU CPU Board.
4. Disconnect I/O connectors TB1, TB2, TB3, TB4 and TB5 from the Low Power I/O
Expansion Board.
5. Remove the two screws that secure the sliding bracket to the fixed bracket and carefully slide the CPU Board (with non-removed cabling) and I/O Expansion Board toward the front of the unit until the sliding bracket is free of the fixed bracket. In the case of
Model 3530-35B, skip this step. In the case of the TeleRecorder (3530-55B) remove the four screws that secure the Blank Plate or Display Mounting Plate to the four long standoffs.
6.
Remove the five screws that secure the Low Power I/O Expansion Board to its mounting stand-offs and unplug I/O Expansion Board (Connector P1) from CPU Board (Connector
J2).
Note: If a replacement LPI/OEB is available follow steps 2 through 6 in reverse order (after configuring the LPI/OEB), installing rather than removing the item in question If a replacement I/O Expansion Board is not immediately available and the unit must be placed back into operation
(without expanded I/O) follow steps 2 through 5 in reverse order, installing rather than removing the item in question. Then go to step 7.
7. Close and secure the Door.
PIP-EXPI/OTF Page 5 Low Power I/O Expansion Board
Figure 2A - I/O Expansion Board Mounted to TeleFlow Plus CPU Board
Figure 2B - I/O Expansion Board Mounted to TeleRTU Plus CPU Board
Figure 2C - I/O Expansion Board Mounted to TeleRTU Module CPU Board
Figure 2D - I/O Expansion Board Mounted to TeleRecorder CPU Board
Low Power I/O Expansion Board Page
6
PIP-EXPI/OTF
2.1.2 Installation of the Low Power I/O Expansion Board
1. Open the Instrument Front Cover.
2. Disconnect the wiring harness connectors associated with power, i.e., P10, P8, P7 and
P6 from the TeleFlow CPU Board or P1, P2, P3 and P4 from the TeleRTU CPU Board.
3. Disconnect I/O connectors P5, P13 and P14 from the TeleFlow CPU Board or P5 through
P13 from the TeleRTU CPU Board.
4. For Models 3530-20B & 3530-25B remove the two screws that secure the sliding bracket to the fixed bracket and carefully slide the CPU Board (with non-removed cabling toward the front of the unit until the sliding bracket is free of the fixed bracket. In the case of Model 3530-35B, skip this step. In the case of the TeleRecorder (3530-55B) remove the four screws that secure the Blank Plate or Display Mounting Plate to the four long standoffs.
5.
Remove the five screws that secure the CPU Board to its standoffs.
6. Install the appropriate five standoffs supplied with the I/O Expansion Option in place of the five screws removed in step 5. In the case of the TeleRecorder, replace the
BlankPlate or Display Mounting Plate that was removed in step 4.
7. Route field wiring cable(s) associated with the I/O Expansion Board into the TeleFlow
Plus, TeleRTU Plus or TeleRecorder through a ¾” conduit fitting (user installed) (see
Figure 3A, 3B or 3C) on the bottom of the enclosure. Configure the LPI/OEB Jumpers
(see Table 2 and Section 2.2).
PIP-EXPI/OTF
Figure 3A - Bottom View of TeleFlow Plus
Page 7 Low Power I/O Expansion Board
Figure 3B - Bottom View of TeleRTU Plus
Figure 3C - Bottom View of TeleRecorder
8 Install the I/O Expansion Board by aligning its connector P1 with CPU Board Connector J2 and then securing the boards with either the five screws removed in step 5, or the five screws supplied with the kit. Connect I/O Wiring to the appropriate removable
I/O Expansion Board Connectors (TB1, TB2, TB3, TB4 and TB5) (see Section 2.2).
Connect the wiring harness connectors associated with power, i.e., P10, P8, P7 and P6 on the TeleFlow CPU Board or P1, P2, P3 and P4 on the TeleRTU CPU Board. Connect
I/O connectors P5, P13 and P14 to the TeleFlow CPU Board or P5, P6, P7, P8, P9, P10,
P11, P12 and P13 to the TeleRTU CPU Board.
9. Close and secure the Instrument front Cover.
Low Power I/O Expansion Board Page
8
PIP-EXPI/OTF
2.2 I/O CONFIGURATION & WIRING
Figure 4 - LPI/OEB Discrete Input Configuration
2.2.1
LPI/OEB Discrete Input Wiring (TB4)
(see Figure 4 and Table 4)
Discrete Inputs have a range of 0-16 Vdc ± 10% and have surge suppression but are not isolated. A Discrete Input is activated by closing the connection between DI/On and Ground
(GND) with a Dry Contact (such as a transistor, mechanical relay, TTL, CMOS and other devices which provide from 0-16 Vdc). The Discrete Input (DI) is lightly pulled up to 5V.
2.2.2 LPI/OEB Discrete Output Wiring (TB4)
(see Figure 5 and Table 4)
Each Discrete Output is wired to an open drain capable of switching up to +16 Vdc at
100mA. Surge suppression is provided via 16V bi-directional Transorbs across each out-put; however, since these outputs are not isolated, caution must be exercised to ensure that the load current does not adversely affect operation of the TeleFlow Plus or related devices.
Table 4 - Low Power I/O Expansion Board Discrete I/O Terminal Designations
TB4 Pin # Pneumonic
1 DIO1
2 DIO2
Description
Discrete In/Out 1
Discrete In/Out 2
4
5
7
8
10
11
DIO3
DIO4
DIO5
DIO6
DIO7
DIO8
Discrete In/Out 3
Discrete In/Out 4
Discrete In/Out 5
Discrete In/Out 6
Discrete In/Out 7
Discrete In/Out 8
PIP-EXPI/OTF Page 9 Low Power I/O Expansion Board
Figure 5 - LPI/OEB Discrete Output Configuration
2.2.3 LPI/OEB Analog Input Wiring (TB2)
(see Figures 6 through 8 and Table 5)
Up to 4 single ended analog inputs can be wired to the I/O Expansion Board. Analog Inputs
5 and 6 can be configured as 1-5 V non-isolated inputs, 4-20 mA non-isolated inputs, or 4-20 mA loops powered internally and referenced to the board’s analog ground (AGND). When configured for internally powered current loop operation (which can be turned off when the
CPU Board is in SLEEP mode), an external 21V power supply is required. Analog Inputs 7 and 8 can only be configured for 1-5 V non-isolated input operation
Figure 6 - LPI/OEB Non-Isolated 4-20mA Current Source AI Configuration
Low Power I/O Expansion Board Page
10
PIP-EXPI/OTF
Figure 7 - LPI/OEB 1-5V Non-Isolated Voltage Analog Input Configuration
Figure 8 - LPI/OEB 4-20 mA Internally Sourced Analog Input Configuration
PIP-EXPI/OTF Page 11 Low Power I/O Expansion Board
Table 5 - LPI/OEB Analog Input Terminal Designations
TB# Pin # Pneumonic
TB1-1
TB1-2
+21VEXT
21VGND
Description
External +21VDC
External 21V Gnd.
TB2-2 AIN5 Analog Input #5
TB2-3 GND Ground
TB2-5 AIN6 Analog Input #6
TB2-6 GND Ground
TB2-7
TB2-8
AIN7
AIN8
Analog Input #7
Analog Input #8
TB2-9 GND Ground
2.2.4 LPI/OEB Analog Output Wiring (TB3)
(see Figure 9 and Table 1)
Figure 9 - LPI/OEB Analog Output Configuration
Low Power I/O Expansion Board Page
12
PIP-EXPI/OTF
The single analog output can be configured for 4 to 20 mA or 1 to 5 V operation. The analog output section of the LPI/OEB consists of a bus interface, a one channel Digital to Analog
Converter (DAC) and signal conditioning circuitry designed to generate a 4-20 mA output or a 1-5 V output. Jumper JP19 controls selection. When set in position 1-2, JP19 configures the analog output for current loop operation. When set in position 2-3, Jumper JP19 configures the analog output for 1 to 5 V operation.
2.2.5 LPI/OEB High Speed Counter Wiring (TB3)
(see Figure 10 & Table 1)
The High Speed Counter input circuitry is powered from the 5V power source on the
LPI/OEB. The HSC Input is configured as a dry contact input with filtering and surge protection. Field connections are HSC and GND. The frequency range of the HSC is DC to
10KHz. Field devices can be open collector transistors, open drain FETs or dry contacts.
Figure 10 - LPI/OEB High Speed Counter Configuration
2.3
RS-232/RS-485 COMMUNICATIONS
Terminal Block TB5 can be configured to support RS-232 or RS-485 communications (see
Figure 11).
For RS-232 operation the following configuration jumpers must be set:
JP13 Jumper to JP16
JP22 Pin-1 to Pin-2 for RTS to CTS Loopback or Pin-2 to Pin-3 for use with an external
CTS
For RS-485 operation the following configuration jumpers must be set:
JP14 Jumper to JP16
JP15 - 120 Ohm TX Termination (at end nodes ONLY)
JP17 - 120 Ohm RX Termination (at end nodes ONLY)
JP20 - RX Pull-up (Install at end node with RX Term. Installed)
JP21 - TX Pull-up (Install at end node with TX Term. Installed)
PIP-EXPI/OTF Page 13 Low Power I/O Expansion Board
Figure 11 - RS-232/485 Communication Configuration Diagram
Low Power I/O Expansion Board Page
14
PIP-EXPI/OTF
Section 3
TROUBLESHOOTING
3.1 FIELD WIRING SIGNAL CHECKS
Check Input or Output Field Wires at the Card Edge Connector and at the field device.
Check wiring for continuity, shorts & opens. Check the I/O signals at the card-edge connectors (see Figures 4 through 10 as follows):
Figure 4 - LPI/OEB Discrete Input Configuration
Figure 5 - LPI/OEB Discrete Output Configuration
Figure 6 - LPI/OEB Non-Isolated 4-20 mA Current Source Analog Input Configuration
Figure 7 - LPI/OEB 1-5V Non-Isolated Voltage Analog Input Configuration
Figure 8 - LPI/OEB 4-20 mA Internally Sourced Analog Input Configuration
Figure 9 - LPI/PEB Analog Output Configuration
Figure 10 - LPI/OEB High Speed Counter Configuration
If RS-232 or RS-485 communications problems are encountered, check Low Power I/O
Expansion Board Configuration Jumpers for proper configuration (see Table 2). Check communication signals at card-edge Connector TB5 (see Table 1 and Figure 11 - RS-232/485
Communication Configuration Diagram).
PIP-EXPI/OTF Page 15 Low Power I/O Expansion Board
Section 4
SPECIFICATIONS
4.1 INPUT/OUTPUT SPECIFICATIONS
4.1.1 Discrete Inputs
Number of DIs: 8 selectable non-isolated DI Max. (Note: Any DI/O configured for DO operation diminishes the number of DIs, i.e., if 6 DI/O are configured for DO operation, only 2 DI/O can be configured for DI operation)
Input Type:
Input Current:
Surge Suppression/protection:
0 - 16 Vdc
5mA ± 10% (Contact Closure)
16V Bi-directional Transient Absorption Zeners
Across input
4.1.2 Discrete Outputs
Number of DOs: 8 selectable non-isolated DO Max. (Note: Any DI/O configured for DI operation diminishes the number of DOs, e.g., if 6 DI/O are configured as DI operation, only 2 DI/O can be configured for DO operation)
Output Type:
Surge Suppression/Protection:
Open Drain 16Vdc @ 100mA
16V Bi-directional Transient Absorption
Zeners across output
4.1.3 Analog Inputs
Number of Inputs: 2 Analog Single Ended Inputs (Selectable Current
Input or Voltage Input operation)
Input Type:
2 Analog Single Ended Inputs (Voltage Input only)
1-5 Volt dc or
4-20 mA Current Loop (Externally Sourced)
Accuracy: or
4-20 mA Current Loop (Internally Sourced)
(Requires external 21V Power Supply)
At room temperature +25 ° C (77 ° F)
V/I
Low Power I/O Expansion Board Page
16
PIP-EXPI/OTF
-20 ° C to +70 ° C (-4 ° F to +158 ° F)
V/I
-40 ° C to +70 ° C (-40 ° F to +158 ° F)
V/I
Input Filtering: Single Pole (50 msec time constant) 300 msec to
± 0.1% of input value
Settling time of any selected AI is 18 μ sec to .01%
Input Impedance:
Common Mode Range:
Surge Suppression/Protection:
Common Mode Rejection Ratio 47 to 63 Hz is 90dB
Normal Mode Rejection at 60 Hz is 26dB
1-5 V Input - 195 kohms
4-20 mA Input - 250 ohms
0V to +5V
4.1.4 Analog Outputs
Number of Outputs:
Accuracy:
22V Bi-directional Transient Absorption Zeners across input
Output Range:
1
4-20 mA into a 250 ohm load or
1-5 VDC @ 5mA Max.
At room temperature +25
± 0.1% of Span
° C (77 ° F)
At
± 0.2% of Span
At
± 0.3% of Span
° C (-40 ° F to +158 ° F)
Setting Time:
Isolation:
100 msec to .1%
Surge Suppression: 16V Unidirectional Transient Absorption Zeners output
Outputs are not isolated and are referenced to
Analog Ground
4.1.5 Communication Port
Configuration: RS-232 or RS-485 (Jumper Selectable)
PIP-EXPI/OTF Page 17 Low Power I/O Expansion Board
ESD: RS-232 - 16V Bi-directional Transient Absorption
Zeners across output
RS-485 - 5V Bi-directional Transient Absorption
Zeners across output
4.1.6 High Speed Counter
Number of Inputs:
Input Type:
Input Current:
Input Frequency:
Input Impedance:
Surge Suppression:
1
Voltage
5mA ± 10% (open collector/contact closure)
DC to 10kHz
4.7 kohms ± 10% for 16V input range
16V Bi-directional Transient Absorption Zeners across input
4.2 ENVIRONMENTAL SPECIFICATIONS
Temperature: Operating: -40 ° C to +70 ° C (-40 ° F to +158 ° F)
-40 ° C to +85 ° C (-40 ° F to +185 ° F)
Relative Humidity:
Vibration:
15-95% RH Non-condensing
10 to 500 Hz at 1g on axis per SAMA PMC-31-1 without damage or impairment
ESD Susceptibility: Field connected circuits are designed to meet the requirements of IEC 801-2 for ESD withstand capability up to 10KV
EMI Capability: Designed to coexist inside a shielded enclosure with the TeleFlow or TeleRTU electronics. EMI radiation is insignificant and susceptibility is comparable or superior to associated electronics
Transient Susceptibility: Field connected circuits are designed to meet the requirements of ANSI/IEEEC37.90.1-1989 (Formerly IEEE 472) for surge withstand capability.
Part Numbers: 392927-01-2 - Fully Populated LPI/OEB
392927-02-0 - Depopulated has DI/DO and Comm.
392927-03-9 - Depopulated has DI/DO only
Low Power I/O Expansion Board Page
18
PIP-EXPI/OTF
Low Power I/O Expansion Board
Special Instructions for Class I, Division 2 Hazardous Locations
1. The BBI Low Power I/O Expansion Board (LPI/OEB) is listed by Underwriters
Laboratories (UL) as nonincendive and is suitable for use in Class I, Division 2, Groups
A, B, C and D hazardous locations or non-hazardous locations only. Read this document carefully before installing a nonincendive BBI LPI/OEB Board. In the event of a conflict between the LPI/OEB Board User Manual (PIP-EXPI/OTF) and this document, always follow the instructions in this document.
2. Wiring must be performed in accordance with Class I, Division 2 wiring methods as defined in Article 501-4 (b) of the National Electrical Code, NFPA 70 for installations within the United States, or as specified in Section 18-152 of the Canadian Electrical
Code for installation in Canada.
3. WARNING: EXPLOSION HAZARD - Substitution of components may impair suitability for use in Class I, Division 2 environments.
4. WARNING: EXPLOSION HAZARD - When situated in a hazardous location, turn off power before servicing/replacing the unit and before installing or removing I/O wiring.
5. WARNING: EXPLOSION HAZARD - Do Not disconnect equipment unless the power has been switched off or the area is known to be nonhazardous.
07/21/2000 Appendix A of PIP-EXPI/OTF - LPI/OEB Board Page 1 of 1
BLANK PAGE
Low Power I/O Expansion Board
Product Information Package
PIP-EXPI/OTF
February, 2008
Emerson Process Management
Remote Automation Solutions
1100 Buckingham Street
Watertown, CT 06795
Phone: +1 (860) 945-2262
Fax: +1 (860) 945-2525 www.EmersonProcess.com/Remote
Emerson Process Management
Remote Automation Solutions
6338 Viscount Rd.
Mississauga, Ont. L4V 1H3
Canada
Phone: 905-362-0880
Fax: 905-362-0882 www.EmersonProcess.com/Remote
Emerson Process Management Mexico
Viveros de la Colina No 238
Col. Viveros de la Loma
Tlalnepantla, Mexico 54080 www.EmersonProcess.com/Remote
Emerson Process Management
Bristol Babcock, Ltd.
Blackpole Road
Worcester, WR3 8YB
United Kingdom
Phone: +44 1905 856950
Fax: +44 1905 856969 www.EmersonProcess.com/Remote
Emerson Process Management
Bristol Digital Systems Australasia
22 Portofino Crescent,
Grand Canals Bunbury, Western Australia 6230
Mail to: PO Box 1987 (zip 6231)
Phone: +61 (8) 9725-2355
Fax: +61 (8) 8 9725-2955 www.EmersonProcess.com/Remote
NOTICE
“Remote Automation Solutions (“RAS”), division of Emerson Process
Management shall not be liable for technical or editorial errors in this manual or omissions from this manual. RAS MAKES NO WARRANTIES,
EXPRESSED OR IMPLIED, INCLUDING THE IMPLIED WARRANTIES OF
MERCHANTABILITY AND FITNESS FOR A PARTICULAR PURPOSE WITH
RESPECT TO THIS MANUAL AND, IN NO EVENT SHALL RAS BE LIABLE
FOR ANY INCIDENTAL, PUNITIVE, SPECIAL OR CONSEQUENTIAL
DAMAGES INCLUDING, BUT NOT LIMITED TO, LOSS OF PRODUCTION,
LOSS OF PROFITS, LOSS OF REVENUE OR USE AND COSTS
INCURRED INCLUDING WITHOUT LIMITATION FOR CAPITAL, FUEL AND
POWER, AND CLAIMS OF THIRD PARTIES.
Bristol, Inc., Bristol Babcock Ltd, Bristol Canada, BBI SA de CV and the Flow
Computer Division are wholly owned subsidiaries of Emerson Electric Co. doing business as Remote Automation Solutions (“RAS”), a division of
Emerson Process Management. FloBoss, ROCLINK, Bristol, Bristol
Babcock, ControlWave, TeleFlow and Helicoid are trademarks of RAS. AMS,
PlantWeb and the PlantWeb logo are marks of Emerson Electric Co. The
Emerson logo is a trademark and service mark of the Emerson Electric Co.
All other trademarks are property of their respective owners.
The contents of this publication are presented for informational purposes only. While every effort has been made to ensure informational accuracy, they are not to be construed as warranties or guarantees, express or implied, regarding the products or services described herein or their use or applicability. RAS reserves the right to modify or improve the designs or specifications of such products at any time without notice. All sales are governed by RAS’ terms and conditions which are available upon request.
© 2008 Remote Automation Solutions, division of Emerson Process
Management. All rights reserved.
Instruction Manual
CI-3530-25B
Jan., 2007
DIGITAL TO RELAY I/O BOARD
TeleRTU Plus
Appendix G
www.EmersonProcess.com/Bristol
Appendix G
DIGITAL TO RELAY I/O BOARD
TABLE OF CONTENTS
SECTION TITLE
1.1
1.1.1
1.1.2
2.1
2.1.1
2.1.2
2.2
2.2.1
3.1
3.1.1
3.1.2
PAGE #
GENERAL INTRODUCTION...........................................................................................1
Configuration Hardware ...................................................................................................1
Jumper Settings.................................................................................................................2
Section 2 - INSTALLATION & SERVICE
REMOVAL/REPLACEMENT & INSTALLATION OF THE DTRI/OB..........................3
Removal/Replacement of the Digital to Relay I/O Board ................................................3
Installation of the Digital to Relay I/O Board Option .....................................................4
FIELD WIRING .................................................................................................................6
Terminal Connections........................................................................................................6
DIGITAL TO RELAY I/O BOARD SPECIFICATIONS...................................................8
Input Requirements...........................................................................................................8
Output Requirements ........................................................................................................8
CI-3530-25B Appendix G Page 0-1 Table Of Contents
Section 1
INTRODUCTION
1.1 GENERAL INTRODUCTION
The Digital to Relay I/O Board accepts up to two discrete input signals from an open drain
SFET device (TeleRTU DOs) and convert them to Form C relay output signals using Solid
State Relay (SSR) logic. The minimum current load will be 100mA. Figure 1 provides a component view of the Digital to Relay I/O Board.
Each of the TeleRTU's Discrete Outputs is converted to Form C relay output signals which can be configured for opposite or identical state conditions, i.e., both Normally Open (NO) or Normally Closed (NC) or one Normally open with the other Normally Closed.
1.1.1 Configuration Hardware
The Digital to Relay I/O Board contains ten (10) Jumpers which allow the user to configure contacts for Normally Open/Normally Closed states. Contacts associated with each of the
Form C Relays may be configured for identical or opposite states. Note: Jumper Pairs
W3/W5, W4/W6, W7/W9 and W8/W10 must be set in opposite states.
CI-3530-25B Appendix G
Figure 1 - Digital to Relay I/O Board
Page 1 Digital to Relay I/O Board
1.1.2 Jumper Settings
The commons associated with each form C Relay (R0COM and R1COM) have the option of being tied to the TeleFlow Power Ground or to a floating Ground. Jumper W1 is associated with Outputs R0A and R0B and W2 is associated with outputs R1A and R1B. When Jumper
W1 is installed the common (C) associated with Outputs R0A and R0B is tied to TeleRTU
Power ground; when Jumper W1 is not installed, the common will be floating. When
Jumper W2 is installed the common (C) associated with Outputs R1A and R1B is tied to
TeleFlow Power ground; when Jumper W2 is not installed, the common will be floating.
Table 1 - Jumper Settings versus Form C Relay Output States
JUMPERS
W3/W5
R0A
STATE
JUMPERS
W4/W6
R0B
STATE
JUMPERS
W7/W9
R1A
STATE
JUMPERS
W8/W10
R1B
STATE
IN/OUT NO IN/OUT NO IN/OUT NO IN/OUT NO
OUT/IN NC OUT/IN NC OUT/IN NC OUT/IN NC
Table 1 provides the relationship between Jumper settings and Form C Relay Outputs.
CI-3530-25B Appendix G Page 2 Digital to Relay I/O Board
Section 2
INSTALLATION & SERVICE
2.1 REMOVAL/REPLACEMENT & INSTALLATION OF THE DTRI/OB
2.1.1 Removal/Replacement of the Digital to Relay I/O Board
An installed Digital to Relay I/O Board option will contain the following parts:
1. Digital To Relay I/O Board (with removable 12 Position Terminal Block)
2. Relay Board Bracket
3. Snap Track
4. Relay Board Cable
5. Two #8-32 x 1/4” SEM Screws
6. Two #10-32 x 3/8” SEM Screws
Figure 2 - Digital to Relay I/O Board Mounting Diagram with
Power Distribution Board, Low Power TIB Board & 21V Power Supply Board
CI-3530-25B Appendix G Page 3 Digital to Relay I/O Board
To remove an optional Digital to Relay I/O Board, follow steps 1 through 4 below. To replace the Digital to Relay I/O Board follow steps 2 and 3 below in reverse order, installing rather than removing the item in question and then perform step 4.
1. Open the Instrument Front Cover (Door).
2. Unplug the removable Terminal Block (with wiring harness installed) from the optional
Digital to Relay I/O Board.
3. Slide the Digital to Relay I/O Board toward the front of the unit and out of the Snap
Track.
Note: If a replacement Digital to Relay I/O Board is available follow steps 2 through 3 in reverse order (after configuring the DTRI/OB - see Section 1.1) installing rather than removing the item in question. If a replacement Digital to
Relay I/O board is not immediately available the TeleRTU Plus may be placed back into operation without the use of DO1 and DO2.
4. Close and Secure the Door.
Figure 3 - Bottom View of TeleRTU Plus
2.1.2 Installation of the Digital to Relay I/O Board Option
1. Open the Instrument Front Cover.
2. Install the Snap Track onto the appropriate Dual PCB Mounting Bracket (if not already mounted) using the two (2) #8-32 x 1/4” SEM Screws (see Figure 2).
3. Configure the Digital to Relay I/O Board Jumpers (see Section 1.1).
CI-3530-25B Appendix G Page 4 Digital to Relay I/O Board
4. Install the Dual PCB Mounting Bracket (with Snap Track) onto the TeleRTU Plus
Fabricated Panel (lower right corner) using the two (2) #10-32 x 3/8” SEM Screws (see
Figure 2).
5. Connect one end of the four-wire Relay Board Cable to the Digital to Relay I/O Board
Connector P1 and the other end to the CPU Board (J2 and J5 - see Figure 5). Note:
Power to the Digital to Relay I/O Board may be provided by the CPU Bd. or a Power
Distribution Board (if present) (see Table 2 and Figures 4 & 5).
6. Route field wiring cable(s) associated with the Digital to Relay I/O Board into the
TeleRTU Plus through a 3/4” conduit fitting (user installed) (see Figure 3) on the bottom of the enclosure. Connect I/O Wiring to the Digital to Relay Board Terminal Block J1
(see Section 2.2.1, Table 2 & Figure 5).
7. Close and Secure the Instrument Front Cover.
Figure 4 - Power Distribution Board Schematic/Wiring Diagram
CI-3530-25B Appendix G Page 5 Digital to Relay I/O Board
2.2 FIELD WIRING
2.2.1 Terminal Connections
The device uses compression-type terminals that accommodate up to #14 AWG wire. A connection is made by inserting the bared end (1/4 inch Max.) into the clamp beneath the screw and then securing the screw. Insert the bared end fully to prevent short circuits.
Table 2 - Digital To Relay I/O Board Connections to J1/P1
J1 Pin Signal Function Wiring Connections
1 R1B Relay 1 Output B To Field
2
3
4
R1A
R1COM
Relay 1 Output A
Relay 1 Common
CHASSIS GND Chassis Ground
To Field
To Field (See W2)
CPU Bd. Gnd Lug
5
6
R0COM
ROB
Relay 0 Common To Field (See W1 - Section 1.1.1)
Relay 0 Output B To Field
7
9
10
11
12
ROA Relay 0 Output A To Field
8 - - -
POWER GND Power Ground CPU Bd. J2 Pin 2 or Pwr. Dist. Bd.
TB4 Pin 2 (Black Wire)
POWER - DC Power - 6/12 Vdc CPU Bd. J2 Pin 1 or Pwr. Dist. Bd.
TB4 Pin 1 (Red Wire)
DOUT0 Discrete Output 0 CPU Bd. J5 Pin 3 (Yellow Wire)
DOUT1 Discrete Output 1 CPU Bd. J6 Pin 3 (Orange Wire)
The TeleRTU CPU Board provides two independent firmware controlled open drain outputs which can be used for control or signaling functions. Each output is wired to the source terminal of an N Channel MOSFET capable of switching up to 16 Volts at up to 100mA.
When closed, the FET shorts the output to ground with resistance of .5 Ohms or less. These outputs are protected by 16V Transorbs. Since these outputs are not isolated, caution must be exercised to ensure that the load current does not affect operation of the TeleRTU or related devices.
These outputs may be wired directly to field circuitry or to field circuitry via the Digital to
Relay I/O Board (see Figure 5). Table 2 provides the wiring connections for the TeleRTU
CPU Board and the Digital to Relay I/O Board.
Allow some slack in the wires when making terminal connections. The slack makes the connections more manageable and minimizes mechanical strain on the CPU Board and harness.
CI-3530-25B Appendix G Page 6 Digital to Relay I/O Board
Figure 5 - TeleRTU Discrete Outputs Wired Through Digital to Relay I/O Board
CI-3530-25B Appendix G Page 7 Digital to Relay I/O Board
Section 3
SPECIFICATIONS
3.1 DIGITAL TO RELAY I/O BOARD SPECIFICATIONS
3.1.1 Input Requirements
Power Source Range:
SSR
Maximum MOSFET Sink Current:
3 to 15 Vdc
20 mA (both SSRs in Normally Closed mode)
3.1.2 Output Requirements
Contact
Maximum Current:
Maximum
Minimum
3 Amps at 25°C (1.5 Amps @ 70°C)
CI-3530-25B Appendix G Page 8 Digital to Relay I/O Board
Instruction Manual
CI-3530-25B
May, 2006
TeleRTU Plus Model 3530-25B
RADIO INSTALLATION GUIDE for MDS
Model 4710A/B, 9710A/B & 9810 Radios
Appendix H
www.EmersonProcess.com/Bristol
Appendix H
RADIO INSTALLATION GUIDE
For MDS Model 4710A/B, 9710A/B & 9810 Radios
TABLE OF CONTENTS
SECTION TITLE
1.2 LEDs ................................................................................................................................... 1
Section 2 - INSTALLATION & SERVICE
3.1
3.1.1
3.1.2
3.1.3
3.2
3.2.1
3.2.2
3.2.3
3.3
3.3.1
3.3.2
3.3.3
3.4
2.1.1 Radio
2.1.2
Installation of the Radio Option into a Radio Ready TeleRTU Plus ................................... 4
2.1.3
2.2
Installation of the Radio Option into a Non-Radio Ready TeleRTU Plus ........................... 5
WIRING LISTS.................................................................................................................... 6
GENERAL SPECIFICATIONS............................................................................................ 8
Model 4710 General Specs ................................................................................................ 8
Model 9710 General Specs. ............................................................................................... 8
Model 9810 General Specs. ............................................................................................... 9
TRANSMITTER SPECIFICATIONS ................................................................................... 9
Model 4710 Transmitter Specs. .......................................................................................... 9
Model 9710 Transmitter Specs. ........................................................................................ 10
Model 9810 Transmitter Specs. ........................................................................................ 10
RECEIVER SPECIFICATIONS......................................................................................... 10
Model 4710 Receiver Specs. ............................................................................................ 10
Model 9710 Receiver Specs. ............................................................................................ 11
Model 9810 Receiver Specs. ............................................................................................ 11
ENVIRONMENTAL SPECIFICATIONS............................................................................ 12
REFERENCED OEM MANUALS
MDS 4710A – Remote Data Transceiver (Radio)
MDS 4710/9710 Series 400MHz/900 MHz Remote Data Transceiver Installation and Operation Guide –
MDS Doc. 05-3305A01, Rev. B, Sept. 2000 (PDF = 3305B-710AC.pdf) for model MDS 4710A
MDS 4710B – Data Transceiver (Radio)
MDS 4710B/9710B Data Transceiver Installation and Operation Guide – MDS Doc. 05-3316A01, Rev. E,
Sept. 2000 (PDF = 3316E-x710B.pdf) for model MDS 4710B
MDS 9810 – Spread Spectrum Data Transceiver (Radio)
MDS 9810/24810 900 MHz/2.4GHz Spread Spectrum Transceivers Installation and Operation Guide –
MDS Doc. 05-3301A01, Rev. B, April 2000 (PDF = 3301B-x810.pdf) for model MDS 9810
CI-3530-25B Appendix H Page 0-1 Table Of Contents
Appendix H
RADIO INSTALLATION GUIDE
For MDS Model 4710A/B, 9710A/B & 9810 Radios
TABLE OF CONTENTS
REFERENCED OEM MANUALS (Continued)
MDS 9710A Remote Data Transceiver (Radio)
MDS 4710/9710 Series 400MHz/900 MHz Remote Data Transceiver – MDS Doc. 05-3305A01,
Rev. B, Sept. 2000 (Installation & Operation) (PDF = 3305B-710AC.pdf) for model MDS 9710A
MDS 9710B Data Transceiver (Radio)
MDS 4710B/9710B Data Transceiver Installation and Operation Guide – MDS Doc. 05-3316A01, Rev. E,
Sept. 2000 (PDF = 3316E-x710B.pdf) for model MDS 9710B
CI-3530-25B Appendix H Page 0-2 Table Of Contents
BLANK PAGE
Appendix H
RADIO INSTALLATION GUIDE for MDS Model 4710A/B, 9710A/B & 9810 Radios
Section 1 - INTRODUCTION
1.1 GENERAL INTRODUCTION
Each TeleRTU J Plus
may be ordered with an MDS Radio Installed, i.e., "Radio Equipped," or as a
"Radio Ready" unit. Radio Ready units contain all hardware required to field install a Bristol provided
MDS Radio, except the radio, mounting screws, radio power cable, antenna, and the external antenna cable. Radio Ready units can be ordered with or without an optional Polyphaser (Lightning/Impulse
Suppresser) (see Figures 1, 2 & 5).
A Bristol supplied MDS Data Transceiver (Radio) Option mounts inside the TeleRTU Plus Enclosure and is secured to a Sliding Bracket by four screws.
TeleRTU Plus units equipped with the MDS Radio Option discussed herein utilize the following additional hardware:
1.
MDS Radio Transceiver (Choice of five models):
Model 4710A/B (9600 Baud/330-512 MHz)
Model 9710A/B (9600 Baud/800-960 MHz)
Model 9810 (900MHz -Spread Spectrum)
2.
Fixed Mounting Bracket (with (2) PC Card Guides, (2) ¼ Turn Clip-On Receptacles, and (2) Push-On
Retainers).
3.
Sliding Mounting Bracket (with (2) studs, (2) washers and (2) stud ejector springs
4.
TeleRTU Plus/Radio Interface Cable (392635-01-1) - Radio 12 Conductor Plug (P2) to CPU Board
Connectors P5 & P13 (see Table 2).
5.
2-Wire Radio Power Cable (392638-01-0) - Connects to the Radio Power Connector and J6 of
TeleFlow) (see Table 1).
6.
(4) #6-32 x ¼” SEM Screws (for securing Radio to Sliding Bracket)
7.
(4) #6-32 x 3/8” Flat Head Screws (for securing Fixed Mounting Bracket to Battery Bracket).
8.
Internal Coaxial Antenna Cable or Polyphaser and Polyphaser Cable.
1.2 LEDs
MDS Radio model 9810 is supplied with six (6) LEDs that function as follows:
TR - Terminal Ready RTS (Request To Send) has been received by the internal modem from the TeleFlow.
MR - Modem Ready CTS (Clear To Send) time has elapsed and the radio is ready to transmit data from the TeleFlow.
CD - Carrier Detect The radio senses an RF signal from the master station.
TD - Transmit Data Reflects the current state of the Transmit Data (TXD) line from the
TeleFlow. LED ON = 0 Bit, LED OFF = 1 Bit.
IN - Radio Inhibited/Disabled A ground on Pin 12 of the INTERFACE connector disables all radio functions. This LED is dimly lit when Pin 12 of the INTERFACE connector is grounded and power is applied to the radio.
RD - Receive Data Reflects the current state of the Receive Data line from the transceiver's internal modem. LED ON = 0 Bit, LED OFF = 1 Bit.
CI-3530-25B Appendix H – MDS 4710A/B, 9710A/B & 9810 Radio Installation Guide Page 1
Figure 1 - TeleRTU Plus with Radio and optional Polyphaser
MDS Radios models 4710 & 9710 are supplied with four (4) LEDs that function as follows:
Moderate
Off = No power applied to radio or radio is in sleep mode.
Page 2 Appendix H – MDS 4710A/B, 9710A/B & 9810 Radio Installation Guide CI-3530-25B
DCD - Carrier Detect Flashing = Radio is receiving valid data frames.
Continuous = Radio is receiving a data signal from a continuously keyed radio.
TXD - Transmit Data A mark signal is being received at the Data Interface.
RXD - Receive Data A mark signal is being sent out from the Data Interface.
Section 2 – INSTALLATION & SERVICE
2.1 RADIO REMOVAL/REPLACEMENT & INSTALLATION
DANGER
MDS Radio 4710A/B, 9710A/B & 9810 provided by Bristol are approved for use in
Class I, Groups C & D, Division 2, Hazardous Locations. The installer must be familiar with hazardous location installation guidelines before installation or maintenance is undertaken. Do not begin radio installation or service to the
TeleRTU Plus unless the area is known to be non-hazardous. Refer to the apropriate appendix of the MDS Installation, Operation & Field Maintenance Manual applicable to the radio in question, for approved conditions under which the
MDS radio can be installed in hazardous locations.
AVOID OPERATING EQUIPMENT DURING AN ELECTRICAL STORM. THE
IMPULSE SUPPRESSOR MAY SAVE EQUIPMENT FROM DANGER, BUT SHOULD
NOT BE CONSIDERED AS BEING SAFE FOR PERSONNEL.
2.1.1 Radio Removal/Replacement Procedure
To remove the Radio Transceiver follow steps 1 through 6 below. To replace the Radio Transceiver follow steps 2 through 5 below in reverse order, installing rather than removing the item in question and then perform step 6.
1. Open the Instrument Front Cover.
2.
Remove the Internal Antenna Cable or Polyphaser Cable from the bottom of the radio.
3.
Remove the Power Harness from the bottom of the radio. The radio’s Power Harness is secured by a built-in screw-in/out type fastener.
4.
Using a screwdriver, turn counterclockwise the Slotted Studs which secure the radio’s Sliding Bracket to the radio’s Fixed Bracket. Slide the radio toward the front of the unit and out of the Fixed Bracket.
Remove the Radio Interface Cable from the bottom of the radio by unscrewing the 25-pin D-type connector mounting screws.
5.
If replacing the radio, remove the four #6-32 x ¼” SEM Screws that secure the radio to the Sliding
Bracket.
6. Close and secure the Door.
CI-3530-25B Appendix H – MDS 4710A/B, 9710A/B & 9810 Radio Installation Guide Page 3
Figure 2 - MDS Radio Option Mounting Diagram
2.1.2 Installation of the Radio Option into a Radio Ready TeleRTU Plus
Radio Ready TeleRTU Plus units contain all the hardware required (except the radio, radio power cable, mounting screws, external antenna cable and antenna) to accommodate installation and operation of the radio option.
1.
Open the Instrument Front Cover.
2.
Using a screwdriver, turn counterclockwise the Slotted Studs which secure the radio’s Sliding Bracket to the radio’s Fixed Bracket on the left side of the Battery Bracket and remove the Sliding Bracket.
3.
Secure the radio to the Sliding Bracket via four #6-32 x ¼” SEM Screws.
4.
Install the Radio Interface Cable into the radio’s 25-pin D-type connector on the bottom of the radio and tighten the harness connector mounting screws.
Page 4 Appendix H – MDS 4710A/B, 9710A/B & 9810 Radio Installation Guide CI-3530-25B
5.
Slide the radio and Sliding Bracket into the radio’s Fixed Bracket and turn the Slotted Studs clockwise to lock the radio in place.
6.
Insert the Power Cable into the bottom of the radio. The radio’s Power Cable is secured by a built-in screw-in/out type fastener.
7.
Install the Internal Antenna Cable or Polyphaser Cable into the bottom of the radio.
8.
Close and secure the Door.
9. Connect the user supplied antenna cable to the polyphaser or antenna cable connection on the bottom of the TeleRTU Plus.
Figure 3 - Bottom View of MDS Radios
2.1.3 Installation of the Radio Option into a Non-Radio Ready TeleRTU Plus
1.
Open the Instrument Front Cover.
2.
Remove the Lead Acid Battery (see Section 3.3.1).
3.
Install the Fixed Mounting Bracket (with (2) PC Card Guides) to the left side of the Battery Mounting
Bracket via four #6-32 x 3/8” Flat Head Screws.
4.
Mount the radio onto the Sliding Mounting Bracket via four #6-32 x 1/4" SEM Screws.
5.
Connect the Radio Interface Cable to the 25-pin D-Type Connector on the bottom of the radio.
6.
Connect the Radio Power Cable to the 13.8 VDC Power Connector on the bottom of the radio.
CI-3530-25B Appendix H – MDS 4710A/B, 9710A/B & 9810 Radio Installation Guide Page 5
7.
Install the radio mounted on the Sliding Bracket assembly into the Fixed Mounting Bracket and secure the brackets by turning the two fastening Studs (on the Sliding Bracket) clockwise.
8.
Install the battery (see Section 3.3.1).
9.
Remove the Seal plug from the bottom of the enclosure. If a Polyphaser is not present, connect the
Antenna Cable’s Right Angle N-Type Male Coaxial Connector to the Female N-Type Coaxial Antenna
Connector on the bottom of the radio. Install the other end of this cable (N-Type Female Coaxial
Bulkhead Jack to the bottom of the enclosure (see Figure 6).
If a Polyphaser is utilized, connect one end of the Radio to Polyphaser Cable to the radio and the other end to the Polyphaser. Note; Both ends of this cable have N-Type Male Coaxial Cable
Connectors.
10.
Referring to Table 1, connect the other end of the Radio Interface Cable to the CPU Board.
11. Connect the bare wire end of the Radio Power Cable to J6 as follows:
Red Wire = J6-1 = PWR 1
Blk Wire = J6-2 = GND
12.
Connect the user supplied antenna cable to the Polyphaser or Antenna Cable connection on the bottom of the TeleFlow Plus.
13. Close and secure the Door.
2.2 WIRING LISTS
TeleFlow/Radio Interface Cable (392635-01-1)
CPU Pin #
CPU Board
Sig. Name
Radio D-Conn. #
& Wire Color
Radio D-Conn.
Signal Name
Function
J13-2
J13-3
J13-4
J13-5
J13-6
J13-7
RDCD
RDTR
RCTS
RRTS
RRXD
RTXD
8 (Green)
N/A
5 (Brown)
4 (Blue)
3 (White)
2 (Red)
DCD (Out)
CTS (Out)
RTS (In)
RXD (Out)
TXD (In)
J14-8 AI 21 RSSI
Ground
Data Carrier Detect Input
Data Term. Ready Output
Clear To Send Input
Request To Send Output
Receive Data Input
Transmit Data Output
Receive Signal Strength
Indicator/Analog Input
Table 1- TeleRTU Plus/Radio Interface Cable (392635-01-1) Wire List
(MDS Radio Interface Cable)
Radio Power Cable (392638-01-0)
RADIO
Pwr. Conn.
COLOR
TeleFlow CPU
SIGNAL
+ RED 1
− BLK 2
16.5 V Max
13.8 V Typ.
GND
Table 2- Radio Power Cable (392638-01-0) Wire List
Page 6 Appendix H – MDS 4710A/B, 9710A/B & 9810 Radio Installation Guide CI-3530-25B
Figure 4 - Radio Power Cable 392638-01-0
Figure 5 – TeleRTU Plus/Radio Interface Cable 392635-01-1
Note:
The orange RRSI conductor (Receive Strength Signal Indicator) can be used to monitor the receiver's signal strength when a volt meter is placed across RRSI (Orange) and Ground (CPU Connector J13-1).
Figure 6 - Mounting Diagram for Internal & External Coaxial Antenna Cable
CI-3530-25B Appendix H – MDS 4710A/B, 9710A/B & 9810 Radio Installation Guide Page 7
Figure 7 - Mounting Diagram for Polyphaser/Polyphaser Cable
& External Coaxial Antenna Cable
Section 3 - SPECIFICATIONS
3.1 GENERAL SPECIFICATIONS
3.1.1 Model 4710 General Specs.
Frequency Band:
Frequency Increments:
Frequency Stability:
380-512 MHz
6.25 kHz or 5 kHz (factory configurable)
1.5 PPM, -30
°
C to +60
°
C,
(-22
°
F to +140
°
F)
Primary Power:
Voltage: 13.8 Vdc nominal
(10.5 - 16 Vdc Operating Range)
1.8 A nominal, 2.5 A maximum TX Supply Current:
RX Supply Current:
Reverse Polarity Protection:
3.1.2 Model 9710 General Specs.
Frequency Band:
Frequency Increments:
Frequency Stability:
150 mA (< 16 mA in Sleep Mode)
Diode across primary input
800-960 MHz
6.25 kHz or 5 kHz (factory configurable)
1.5 PPM, -30
°
C to +60
°
C,
(-22
°
F to +140
°
F)
Page 8 Appendix H – MDS 4710A/B, 9710A/B & 9810 Radio Installation Guide CI-3530-25B
Primary Power:
Voltage:
TX Supply Current:
RX Supply Current:
Reverse Polarity Protection:
3.1.3 Model 9810 General Specs.
Frequency Band:
Frequency Hopping Range:
Frequency Stability:
Primary Power:
Voltage:
TX Supply Current:
RX Supply Current:
Standby Current (Sleep Mode):
Reverse Polarity Protection:
3.2 TRANSMITTER SPECIFICATIONS
3.2.1 Model 4710 Transmitter Specs.
Frequency Range:
Power Output:
Duty Cycle:
Output Impedance:
Frequency Stability:
RF Channel Bandwidth:
Spurious & Harmonic Emissions:
Response Time:
13.8 Vdc nominal
(10.5- 16 Vdc Operating Range)
1.8 A nominal, 2.5 A maximum
150 mA (< 16 mA in Sleep Mode)
Diode across primary input
902-928 MHz part 15 Spread Spectrum Band
8 selectable zones each containing 128 frequencies for a total of 1019 frequencies
±
0.00015% (1.5 PPM), -30
°
C to +60
°
C,
(-22
°
F to +140
°
F) For all Models
13.8 Vdc nominal
(10.5- 26.0 Vdc Operating Range)
<400 mA
<125 mA
<30 mA
Diode across primary input
380-512 MHz, Programmable in 6.25 kHz or 5 kHz increments (factory configurable) to any channel pair in radio operating sub-band.
5 Watts/+37 dBm (maximum) at the Antenna
Connector
Continuous
50 Ohms
1.5 PPM, -30
°
C to +60
°
C,
(-22
°
F to +140
°
F)
12.5 kHz
-65 dBc
5 ms
CI-3530-25B Appendix H – MDS 4710A/B, 9710A/B & 9810 Radio Installation Guide Page 9
Time-out Timer:
3.2.2 Model 9710 Transmitter Specs.
Frequency Range:
Power Output:
Duty Cycle:
Output Impedance:
Frequency Stability:
RF Channel Bandwidth:
Spurious & Harmonic Emissions:
Response Time:
Time-out Timer:
3.2.3 Model 9810 Transmitter Specs.
Frequency Band:
Power Output:
Duty Cycle:
Output Impedance:
Frequency Stability:
Spurious Emissions:
Harmonic Emissions:
Transmitter Keying:
3.3 RECEIVER SPECIFICATIONS
3.3.1 Model 4710 Receiver Specs.
Frequency Range:
Page 10
Internal; programmable from 1-255 seconds in
1-second increments
800-960 MHz, Programmable in 6.25 kHz or 5 kHz increments (factory configurable) to any channel pair in radio operating sub-band.
5 Watts/+37 dBm (maximum) at the Antenna
Connector
Continuous
50 Ohms
1.5 PPM, -30
°
C to +60
°
C,
(-22
°
F to +140
°
F)
12.5 kHz
-65 dBc
5 ms
Internal; programmable from 1-255 seconds in
1-second increments
902-928 MHz Part 15 Spread Spectrum Band.
.1 to 1 Watt (20-30 dBm ± 1dB)
Continuous
50 Ohms
±
0.00015% (1.5 PPM), -30
°
C to +60
°
C,
(-22
°
F to +140
°
F) For all Models
-60 dBc
-80 dBc
Data activated
380-512 MHz Programmable in 6.25 kHz increments to any channel pair in radio operating sub-band.
Appendix H – MDS 4710A/B, 9710A/B & 9810 Radio Installation Guide CI-3530-25B
Frequency Stability:
Intermodulation:
IF Selectivity:
Desensitization:
Spurious and Image Rejection:
RF Channel Bandwidth:
Sensitivity:
Squelch Opening Time:
3.3.2 Model 9710 Receiver Specs.
Frequency Range:
Frequency Stability:
Intermodulation:
IF Selectivity:
Desensitization:
Spurious and Image Rejection:
RF Channel Bandwidth:
Sensitivity:
Squelch Opening Time:
3.3.3 Model 9810 Receiver Specs.
Frequency Band:
Frequency Stability:
Intermodulation:
Desensitization:
Spurious and Image Rejection:
CI-3530-25B
1.5 PPM, -30
°
C to +60
°
C,
(-22
°
F to +140
°
F)
75 dB minimum (EIA)
65 dB minimum at adjacent Channel
65 dB minimum on 12.5 kHz Channel
85 dB minimum
12.5 kHz
12 dB SINAD at -110 dBm
2 ms
800-960 MHz Programmable in 6.25 kHz increments to any channel pair in radio operating sub-band.
1.5 PPM, -30
°
C to +60
°
C,
(-22
°
F to +140
°
F)
75 dB minimum (EIA)
65 dB minimum at adjacent Channel
65 dB minimum on 12.5 kHz Channel
85 dB minimum
12.5 kHz
12 dB SINAD at -110 dBm
2 ms
902-928 MHz Part 15 Spread Spectrum Band.
±0.00015% (1.5 PPM), -30
°
C to +60
°
C,
(-22
°
F to +140
°
F) For all Models
75 dB minimum (EIA)
65 dB minimum (EIA) on 12.5 kHz Channels
70 dB minimum
Appendix H – MDS 4710A/B, 9710A/B & 9810 Radio Installation Guide Page 11
Bit Error Rate:
3.4 ENVIRONMENTAL SPECIFICATIONS
3.4.1 MDS Models 4710, 9710 & 9810
Temperature Range:
Humidity:
Less than 10
-6
at -110 dBm
Full Performance -30
°
C to +60
°
C,
(-22
°
F to +140
°
F)
95% at +40
°
C (104
° F)
Page 12 Appendix H – MDS 4710A/B, 9710A/B & 9810 Radio Installation Guide CI-3530-25B
Appendix I
FreeWave RADIO OPTION
For Instruction Manual
CI-3530-25B
Issue: 04/2002
FREE
W AVE
Model Number: DGRO9RFS
RS232
6V
Serial Number: XXX-XXXX
FCC ID: KNY-205-108213
Canada: 2329 102 336A
FreeWavw Technologies, Inc.
Boulder, CO 80301. This device complies with
Part 15 of the FCC Rules. Operation is subject to the following two conditions: 1) This device may not cause harmful interference, and 2) this device must accept any interference received, including interferences that may cause undesired operation.
1
Bristol Babcock
Appendix I
FreeWave RADIO OPTION
TABLE OF CONTENTS
SECTION TITLE
1.1
1.2
2.1
2.1.1
2.1.2
2.1.3
2.2
2.3
3.1
3.2
3.3
3.4
PAGE #
GENERAL INTRODUCTION .......................................................................................... 1
LEDs................................................................................................................................... 1
Section 2 - INSTALLATION & SERVICE
RADIO REMOVAL/REPLACEMENT & INSTALLATION ............................................ 4
Radio Removal/Replacement Procedure .......................................................................... 4
Installation of the Radio Option into a Radio Ready TeleFlow Plus.............................. 7
Installation of the Radio Option into a Non-Radio Ready TeleFlow Plus...................... 8
WIRING LISTS................................................................................................................ 10
ADDITIONAL FreeWave INFORMATION ................................................................... 10
GENERAL SPECIFICATIONS ...................................................................................... 11
TRANSMITTER SPECIFICATIONS ............................................................................. 11
RECEIVER SPECIFICATIONS ..................................................................................... 11
ENVIRONMENTAL SPECIFICATIONS....................................................................... 12
Reference Document
FreeWave Spread Spectrum Wireless Data Transceiver User Manual
FreeWave Technologies, Inc.
1880 South Flatiron Court
Boulder, CO 80301
CI-3530-25B Appendix I Page 0-1 Table Of Contents
Section 1
INTRODUCTION
1.1 GENERAL INTRODUCTION
The TeleRTU J Plus may be ordered with a FreeWave Radio installed, i.e., "Radio
Equipped," or as a “ Radio Ready ” unit. Radio Ready units contain all hardware required to field install a BBI provided FreeWave Radio except the radio, antenna and external antenna cable. The FreeWave Radio option can be used with or without an optional
Polyphaser (Lightning/Impulse Suppresser). Radio Ready units can be ordered with or without an optional Polyphaser (see Figures 1 through 7).
The BBI supplied FreeWave Wireless Data Transceiver (Radio) Option mounts inside the
TeleRTU J Plus Enclosure and is secured to sliding bracket via (4) 4-40 x 1/4 pan head screws.
TeleRTUs (model 3530-25B) equipped with the FreeWave Radio Option utilize the following additional hardware:
1. FreeWave Wireless Data Transceiver
2. Fixed Mounting Bracket (with (2) PC Card Guides, (2) ¼ Turn Clip-On Receptacles, and (2) Push-On Retainers).
3. Sliding Mounting Bracket (with (2) studs, (2) washers and (2) stud ejector springs
4.
Radio/TeleRTU Interface Cable (396369-01-4) - 10-Pin Jack Connector (MTA-100) connects to the radio while the eight (8) open-ended wires (see Table 4) are connected to
CPU Board Connectors J4/P4 (Power) and J8/P8 (Network).
5.
(4) #4-40 x 1/4 Pan Head Screws (for securing radio to Sliding Bracket)
6.
(4) #6-32 x 5/16 Flat Head Screws (for securing Fixed Mounting Bracket to Battery
Bracket).
7.
Internal Coaxial Antenna Cable or Polyphaser and Polyphaser Cable.
1.2 LEDs
The FreeWave Radio is supplied with three (3) visible LEDs that provide important information on the operation of the transceiver. Compare the status of radio’s LEDs with
Tables 1 and 2 to aid you in the troubleshooting process.
CD - Carrier Detect LED
TX Transmit LED
CTS - Clear To Send LED
CI-3530-25B Appendix I Page 1 FreeWave Radio Option
Table 1 - LED Status in Point to Point Communications
Condition
Power Disconnected
Connected, no repeater, sending sparse data
Master calling slave through repeater
Master connected to
Repeater, not to slave
Repeater connected to slave
Mode 6, disconnected
Setup Mode
Master Slave Repeater
CD TX CTS CD TX CTS CD TX CTS
SR SR SR SR O BR SR O BR
SG IF IF SG IF IF
SR SD
FO SD
SG
SR
IF
O
SG SG
SR
SR
IF
BR
SG
SR
SR
SG
SR
SG
O
O
IF
O
SG
BR
BR
IF
SG
SR
SR
SG
SG
O
SD
IF
SG
BR
SR
IF
SG
Table 1 & Table 2 Legend:
BR
FO
IF
O
SD
SG
SR
Blinking Red
Flashing Orange
Intermittent Flash Red
Off
Solid Red, Dim
Solid Green
Solid Red, Bright
Table 2 - LED Status in Multipoint Communications
Condition
Power Disconnected
Repeater & slave connected to master, no data
Repeater & slave connected to master, master sending data to slave
Repeater & slave connected to master, slave sending data to master
Master Slave Repeater
CD TX CTS CD TX CTS CD TX CTS
SR SD O SR O BR SR O BR
SR
SR
SG-
SR
SD
SD
SD
O
O
IF
SG
SG
SG
O
O
IF
SR*
SR*
SR*
SG
SG
SG
SD
SD
SR
SR*
SR*
SR*
* = CTS will be Solid Red with a solid link, as the link weakens the CTS LED on the repeater and slave radios will begin to flash.
FreeWave Radio Option Page 2 CI-3530-25B Appendix I
Figure 1 - FreeWave Radio
Figure 2 - Sliding Mounting Bracket installation Diagram
CI-3530-25B Appendix I Page 3 FreeWave Radio Option
Section 2
INSTALLATION & SERVICE
2.1 RADIO REMOVAL/REPLACEMENT & INSTALLATION
DANGER
The FreeWave Wireless Data Transceiver (Radio) model DGRO-115 provided by Bristol Babcock is approved for use in Class I, Division 2,
Groups A, B, C & D or non-hazardous locations. The installer must be familiar with hazardous location installation guidelines before installation or maintenance is undertaken. Do not begin radio installation or service to the TeleFlow J unless the area is known to be non-hazardous.
AVOID OPERATING EQUIPMENT DURING AN ELECTRICAL STORM. THE
IMPULSE SUPPRESSOR MAY SAVE EQUIPMENT FROM DANGER, BUT
SHOULD NOT BE CONSIDERED AS BEING SAFE FOR PERSONNEL.
2.1.1 Radio Removal/Replacement Procedure
To remove the Radio follow steps 1 through 6 below. To replace the Radio perform step 5 of section 2.1.2 and the follow steps 2 through 6 below in reverse order, installing rather than removing the item in question and then perform step 7.
1. Open the Instrument Front Cover.
2. Remove the Internal Antenna Cable or Polyphaser Cable from the top of the radio.
3. Disconnect power from the radio by removing the two-wire auxiliary power jack from the TeleRTU CPU Board connector P4.
4. Using a screwdriver, turn counter-clockwise the Slotted Studs which secure the radio’s
Sliding Mounting Bracket to the radio’s Fixed Mounting Bracket. Slide the radio toward the front of the unit and out of the Fixed Mounting Bracket.
5. Disconnect the Radio/TeleFlow Interface Cable (396369-01-4) from the lower edge of the radio and remove the FreeWave Radio (installed on the Sliding Mounting Bracket).
6. If replacing the radio, remove the four screws that secure the radio to the Sliding
Mounting Bracket and remove the FreeWave Radio.
7. Close and secure the Door.
FreeWave Radio Option Page 4 CI-3530-25B Appendix I
Figure 3 - FreeWave Radio Option Installed in TeleRTU Plus
(without Polyphaser Option) - Front View
CI-3530-25B Appendix I Page 5 FreeWave Radio Option
Figure 4 - FreeWave Radio Option Installed in TeleRTU Plus
(without Polyphaser Option) - Side View
FreeWave Radio Option Page 6 CI-3530-25B Appendix I
2.1.2 Installation of the Radio Option into a Radio Ready TeleRTU Plus
Radio Ready TeleRTUs contain all the hardware required (except the radio, internal and external antenna cables and antenna) to accommodate installation and operation of the radio option.
1. Open the Instrument Front Cover.
2. Using a screwdriver, turn counterclockwise the Slotted Studs which secure the radio’s
Sliding Bracket to the radio’s Fixed Bracket on the left side of the Battery Bracket and remove the Sliding Bracket.
3. Secure the radio to the Sliding Mounting Bracket via four #4-40 x 1/4 Pan Head Screws
(see Figures 2 & 6).
4. Install Radio Cable (396306-01-2) between the radio’s RF connector and the bottom of the TeleRTU Plus enclosure (see Figures 3, 4 & 7) (also see Section 2.3.1 of CI-3530-
25B). Note: If an optional Polyphaser is used install Radio Cable (396306-02-0) between the radio’s RF connector and the top of the Polyphaser (within the enclosure) (see Figure 7). TeleFlow enclosures that support a Polyphaser have a
.625” diameter mounting hole while those that support a radio (without Polyphaser
Option) have a .580” diameter mounting hole.
5.
Follow the “Tuning Transceiver Performance” section of the FreeWave Technologies,
Inc. FreeWave Spread Spectrum Wireless Data Transceiver User Manual to configure the radio.
Note: The setup program is invoked by connecting the radio to any PC equipped with a terminal program (such as Hyperterminal), setting the parameters for that terminal to those of Table 3, and putting the radio into setup mode.
Connection to the PC requires a special RS-232 cable with a 9-pin Female D-
Type connector on the PC side and a 10-pin Female MTA-100 Connector assembly on the radio side. A cable can be constructed as illustrated in Figure
5. The terminal program must be running before invoking the setup program.
The setup program is invoked by shorting MTA-100 Connector pins 4 (GND) and 2 (MENU) together.
Table 3 - Setup Menu Terminal Settings
PARAMETER
Baud Rate
Data Rate
Parity
Stop Bits
Parity Check
Carrier Detect
SETTING
19,200
8
None
1
None/Off
None/Off
CI-3530-25B Appendix I Page 7 FreeWave Radio Option
Figure 5 - Cable Diagram for Radio to PC Interface
6. Install the TeleFlow Radio Interface Cable (396369-01-4) onto Radio Connector J1. (see
Figures 1 & 4).
7. Slide the radio and Sliding Mounting Bracket into the radio’s Fixed Mounting Bracket and turn the Slotted Studs clockwise to lock the radio in place (see Figures 3 & 6).
8. Install the TeleFlow Radio Interface Cable (396369-01-4) between Radio Connector J1 and TeleRTU CPU Board Connectors J4 & J8 (see Table 4). Make sure that the cable connector’s red wire aligns with FreeWave Radio connector Pin 1 (see Figures 1, 3 & 4).
9. Connect the user supplied antenna cable to the polyphaser or antenna cable connection on the bottom of the TeleRTU (see Figures 3, 4 & 7).
10. Close and secure the Door.
2.1.3 Installation of the Radio Option into a Non-Radio Ready TeleRTU Plus
1. Open the Instrument Front Cover.
2. Remove the Lead Acid Battery (see Section 3.3.1 of CI-3530-25B).
3. Install the Fixed Mounting Bracket (with (2) PC Card Guides) to the left side of the
Battery Mounting Bracket via four #6-32 x 5/16” Flat Head Screws.
4. Mount the radio onto the Sliding Mounting Bracket via four #4-40 x 1/4 Pan Head
Screws (see Figures 2 & 5).
5. Perform step 5 of section 2.1.2.
6. Install Radio Cable (396306-01-2) between the radio’s RF connector and the bottom of the TeleRTU Plus enclosure (see Figures 3, 4 & 7) (also see Section 2.3.1 of CI-3530-
25B). Note: If an optional Polyphaser is used install Radio Cable (396306-02-0)
FreeWave Radio Option Page 8 CI-3530-25B Appendix I
between the radio’s RF connector and the top of the Polyphaser (within the enclosure) (see Figure 7). TeleFlow enclosures that support a Polyphaser have a
.625” diameter mounting hole while those that support a radio (without Polyphaser
Option) have a .580” diameter mounting hole.
7. Install the TeleFlow Radio Interface Cable (396369-01-4) onto Radio Connector J1. (see
Figures 1 & 4).
8. Slide the radio and Sliding Bracket into the radio’s Fixed Bracket and turn the Slotted
Studs clockwise to lock the radio in place.
9. Install the TeleFlow Radio Interface Cable (396369-01-4) between Radio Connector J1 and TeleRTU CPU Board Connectors J4 & J8 (see Table 4). Make sure that the cable connector’s red wire aligns with FreeWave Radio connector Pin 1 (see Figures 1, 3 & 4).
10. Connect the user supplied antenna cable to the polyphaser or antenna cable connection on the bottom of the TeleRTU Plus (see Figures 3, 4 & 7).
11. Close and secure the Door.
Figure 6 - FreeWave Radio Mounted on Sliding Mounting Bracket
CI-3530-25B Appendix I Page 9 FreeWave Radio Option
Figure 7 - Partial View - TeleRTU Plus with Polyphaser Installed
2.2 WIRING LISTS
Radio/TeleRTU Interface Cable (396369-01-4)
CPU Pin #
J4-1
J4-2
J8-1
CPU Board
Sig. Name
AUX PWR
GND
GND
Wire Pin. #
& Color
01 (Red)
04 (Black)
06 (Black)
J8-2
J8-4
J8-5
J8-6
J8-7
RDCD
RCTS
RRTS
RRXD
RTXD
Note: Pins 2 & 3 are not used.
08 (Green)
10 (Brown)
09 (Blue)
05 (Red)
07 (White)
Radio
Signal Name
B+
GND
GND
DCD (Out)
CTS (Out)
RTS (In)
TXD (Out)
RXD (In)
Function
DC Power (+)
DC Power (-) Ground
Ground
Data Carrier Detect Output
Clear To Send Output
Request To Send Input
Transmit Data Output
Receive Data Input
Table 4 - Radio/TeleRTU Interface Cable (396369-01-4) Wire List
2.3 ADDITIONAL FreeWave INFORMATION
The FreeWave Spread Spectrum Wireless Data Transceiver User Manual contains indepth details on modem parameters, operation, installation, tuning transceiver performance, and more. Copies of the FreeWave Spread Spectrum Wireless Data Transceiver User Manual can be obtained from FreeWave Technologies, Inc. (electronically) by contacting their Technical Support Group.
FreeWave Tech. Support can be reached at 303-444-3862 or 303-786-9948.
Online information about Spread Spectrum Modem (Model DRG09RFS) can be obtained at www.freewave.com or www.freewave.com/ProductInformation/products.htm.
FreeWave Radio Option Page 10 CI-3530-25B Appendix I
Section 3
SPECIFICATIONS
3.1 GENERAL SPECIFICATIONS
Frequency:
Power Requirements:
Transmit Current:
Receive Cuurrent:
Idle Current:
Operating Modes:
3.3 RECEIVER SPECIFICATIONS
Sensitivity:
902 - 928 MHz
650 mA at 12V for 1W
600 mA at 8.5V for 400mW
100 mA at 12V
65 mA at 12V
Point-to-Point
Point-to-Multipoint
Peer-to-Peer
Store and Forward Repeater
Data Transmission:
Error Detection:
Data Encryption:
Link Throughput:
Interface:
32 Bit CRC, resend on error
Substitution, dynamic key
115 Kbaud
RS-232, 1200 Baud to 115.2 Kbaud,
Async., full duplex
3.2 TRANSMITTER SPECIFICATIONS
Output Power:
Range:
Modulation:
Occupied Bandwidth:
1W (+30 dBm) at 9.5V to 18.0V
400mW (+25 dBm) at 7.5V to 9.5V
20 Miles - Line of sight distance with unity gain antenna at 900 MHz.
GFSK, 120 kBs - 170 kBs
230 kHz
-108 dB at 10 -6 raw BER
CI-3530-25B Appendix I Page 11 FreeWave Radio Option
Selectivity: 40 dB at fc ±230kHz
60 dB at fc ±460 kHz
3.4 ENVIRONMENTAL SPECIFICATIONS
Temperature Range:
Humidity:
Full Performance -40 ° C to +60 ° C,
(-40 ° F to +140 ° F)
5% to 90% (noncondensing)
FreeWave Radio Option Page 12 CI-3530-25B Appendix I
21 Volt Power Supply
Board
Part No. 392947-01-3
(For TeleFlow Plus & TeleRTU Plus)
For The Following BBI Instruction Manuals:
CI-3530-20B & CI-3530-25B
Product Information Package
Bristol Babcock
PIP-353021VS
- January 2003
NOTICE
Copyright Notice
The information in this document is subject to change without notice. Every effort has been made to supply complete and accurate information. However, Bristol Babcock assumes no responsibility for any errors that may appear in this document.
Request for Additional Instructions
Additional copies of instruction manuals may be ordered from the address below per attention of the Sales Order Processing Department. List the instruction book numbers or give complete model number, serial or software version number. Furnish a return address that includes the name of the person who will receive the material. Billing for extra copies will be according to current pricing schedules.
TeleFlow TM and TeleRTU TM are trademarks of Bristol Babcock. Other trademarks or copyrighted products mentioned in this document are for information only, and belong to their respective companies, or trademark holders.
Copyright (c) 2003 Bristol Babcock, 1100 Buckingham St., Watertown, CT 06795. No part of this manual may be reproduced in any form without the express written permission of
Bristol Babcock.
IMPORTANT! READ INSTRUCTIONS BEFORE STARTING!
Be sure that these instructions are carefully read and understood before any operation is attempted. Improper use of this device in some applications may result in damage or injury. The user is urged to keep this book filed in a convenient location for future reference.
These instructions may not cover all details or variations in equipment or cover every possible situation to be met in connection with installation, operation or maintenance. Should problems arise that are not covered sufficiently in the text, the purchaser is advised to contact Bristol Babcock for further information.
EQUIPMENT APPLICATION WARNING
The customer should note that a failure of this instrument or system, for whatever reason, may leave an operating process without protection. Depending upon the application, this could result in possible damage to property or injury to persons. It is suggested that the purchaser review the need for additional backup equipment or provide alternate means of protection such as alarm devices, output limiting, fail-safe valves, relief valves, emergency shutoffs, emergency switches, etc.
If additional information is required, the purchaser is advised to contact Bristol
Babcock.
RETURNED EQUIPMENT WARNING
When returning any equipment to Bristol Babcock for repairs or evaluation, please note the following: The party sending such materials is responsible to ensure that the materials returned to Bristol Babcock are clean to safe levels, as such levels are defined and/or determined by applicable federal, state and/or local law regulations or codes. Such party agrees to indemnify Bristol Babcock and save Bristol
Babcock harmless from any liability or damage which Bristol Babcock may incur or suffer due to such party's failure to so act.
ELECTRICAL GROUNDING
Metal enclosures and exposed metal parts of electrical instruments must be grounded in accordance with OSHA rules and regulations pertaining to "Design
Safety Standards for Electrical Systems," 29 CFR, Part 1910, Subpart S, dated: April
16, 1981 (OSHA rulings are in agreement with the National Electrical Code).
The grounding requirement is also applicable to mechanical or pneumatic instruments that include electrically-operated devices such as lights, switches, relays, alarms, or chart drives.
EQUIPMENT DAMAGE FROM ELECTROSTATIC DISCHARGE VOLTAGE
This product contains sensitive electronic components that can be damaged by exposure to an electrostatic discharge (ESD) voltage. Depending on the magnitude and duration of the ESD, this can result in erratic operation or complete failure of the equipment. Read supplemental document S14006 for proper care and handling of
ESD-sensitive components.
Bristol Babcock 1100 Buckingham Street, Watertown, CT 06795
Telephone (860) 945-2200
A.
B.
C.
D.
E.
F.
A.
B.
WARRANTY
Bristol warrants that goods described herein and manufactured by Bristol are free from defects in material and workmanship for one year from the date of shipment unless otherwise agreed to by Bristol in writing.
Bristol warrants that goods repaired by it pursuant to the warranty are free from defects in material and workmanship for a period to the end of the original warranty or ninety (90) days from the date of delivery of repaired goods, whichever is longer.
Warranties on goods sold by, but not manufactured by Bristol are expressly limited to the terms of the warranties given by the manufacturer of such goods.
All warranties are terminated in the event that the goods or systems or any part thereof are
(i) misused, abused or otherwise damaged, (ii) repaired, altered or modified without Bristol's consent, (iii) not installed, maintained and operated in strict compliance with instructions furnished by Bristol, or (iv) worn, injured or damaged from abnormal or abusive use in service time.
THESE WARRANTIES ARE EXPRESSLY IN LIEU OF ALL OTHER WARRANTIES
EXPRESS OR IMPLIED (INCLUDING WITHOUT LIMITATION WARRANTIES AS TO
MERCHANTABILITY AND FITNESS FOR A PARTICULAR PURPOSE), AND NO
WARRANTIES, EXPRESS OR IMPLIED, NOR ANY REPRESENTATIONS, PROMISES, OR
STATEMENTS HAVE BEEN MADE BY BRISTOL UNLESS ENDORSED HEREIN IN
WRITING. FURTHER, THERE ARE NO WARRANTIES THAT EXTEND BEYOND THE
DESCRIPTION OF THE FACE HEREOF.
No agent of Bristol is authorized to assume any liability for it or to make any written or oral warranties beyond those set forth herein.
REMEDIES
Buyer's sole remedy for breach of any warranty is limited exclusively to repair or replacement without cost to Buyer of any goods or parts found by Seller to be defective if
Buyer notifies Bristol in writing of the alleged defect within ten (10) days of discovery of the alleged defect and within the warranty period stated above, and if the Buyer returns such goods to Bristol's Watertown office, unless Bristol's Watertown office designates a different location, trans-portation prepaid, within thirty (30) days of the sending of such notification and which upon examination by Bristol proves to be defective in material and workmanship.
Bristol is not responsible for any costs of removal, dismantling or reinstallation of allegedly defective or defective goods. If a Buyer does not wish to ship the product back to Bristol, the
Buyer can ar-range to have a Bristol service person come to the site. The Service person's transportation time and expenses will be for the account of the Buyer. However, labor for warranty work during normal working hours is not chargeable.
Under no circumstances will Bristol be liable for incidental or consequential damages resulting from breach of any agreement relating to items included in this quotation from use of the information herein or from the purchase or use by Buyer, its employees or other parties of goods sold under said agreement.
How to return material for Repair or Exchange
Before a product can be returned to Bristol Babcock for repair, upgrade, exchange, or to verify proper operation, form (GBU 13.01) must be completed in order to obtain a RA
(Return Authorization) number and thus ensure an optimal lead time. Completing the form is very important since the information permits the Bristol Babcock Repair Dept. to effectively and efficiently process the repair order.
You can easily obtain a RA number by:
A. FAX
Completing the form (GBU 13.01) and faxing it to (860) 945-3875. A BBI Repair
Dept. representative will return call (or other requested method) with a RA number.
B. E-MAIL
Accessing the form (GBU 13.01) via the Bristol Babcock Web site
(www.bristolbabcock.com) and sending it via E-Mail to [email protected]
.
A BBI Repair Dept. representative will return E-Mail (or other requested method) with a RA number.
C. Mail
Mail the form (GBU 13.01) to
Bristol Babcock Inc.
Repair Dept.
1100 Buckingham Street
Watertown, CT 06795
A BBI Repair Dept. representative will return call (or other requested method) with a RA number.
D. Phone
Calling the BBI Repair Department at (860) 945-2442. A BBI Repair Department representative will record a RA number on the form and complete Part I, then send the form to the Customer via fax (or other requested method) for Customer completion of Parts II & III.
A copy of the completed Repair Authorization Form with issued RA number should be included with the product being returned. This will allow us to quickly track, repair, and return your product to you.
&VMWXSP &EFGSGO -RG 6ITEMV %YXLSVM^EXMSR *SVQ
(Providing this information will permit BBI to effectively and efficiently process your return. Completion is required to receive optimal lead time. Lack of information may result in increased lead times.)
Date___________________ RA #___________________SH_ Line No.____________
Standard Repair Practice is as follows: Variations to this is practice may be requested in the “Special Requests” section.
•
Evaluate / Test / Verify Discrepancy
•
Repair / Replace / etc. in accordance with this form
•
Return to Customer
Part I
Please be aware of the Non warranty standard charge:
•
There is a $100 minimum evaluation charge, which is applied to the repair if applicable (
B,C, or D of part III below)
Please complete the following information for single unit or multiple unit returns
√
in “returned”
Address No.
Bill to :
(office use only) Address No.
Ship to:
(office use only)
Purchase Order:
Phone: Fax:
Contact Name:____________________________________
E-Mail:
Part II Please complete Parts II & III for each unit returned
Model No./Part No.
Range/Calibration
Description
S/N
Reason for return : Failure Upgrade Verify Operation Other
1. Describe the conditions of the failure (Frequency/Intermittent, Physical Damage, Environmental Conditions,
Communication, CPU watchdog, etc.)
(Attach a separate sheet if necessary)
2. Comm. interface used: Standalone RS-485 Ethernet Modem (PLM (2W or 4W) or SNW) Other: ______________
3.
What is the Firmware revision? _____________________ What is the Software &version?
Part III If checking “replaced” for any question below, check an alternate option if replacement is not available
A. If product is within the warranty time period but is excluded due to BBI’s warranty clause, would you like the product: repaired returned replaced scrapped?
B. If product were found to exceed the warranty period, would you like the product:
C. If product is deemed not repairable would you like your product:
D. If BBI is unable to verify the discrepancy, would you like the product: repaired returned replaced scrapped?
returned replaced scrapped?
returned replaced *see below?
* Continue investigating by contacting the customer to learn more about the problem experienced? The person to contact that has the most knowledge of the problem is: _______________________________ phone
If we are unable to contact this person the backup person is: _________________________ phone
Special Requests:
Ship prepaid to: Bristol Babcock Inc., Repair Dept., 1100 Buckingham Street, Watertown, CT 06795
Phone: 860-945-2442 Fax: 860-945-3875
Form GBU 13.01
Rev. A
Bristol Babcock
Training
GET THE MOST FROM YOUR BRISTOL
BABCOCK INSTRUMENT OR SYSTEM
● Avoid Delays and problems in getting your system on-line
● Minimize installation, start-up and maintenance costs.
● Make the most effective use of our hardware and software.
● Know your system.
As you know, a well-trained staff is essential to your operation. Bristol Babcock offers a full schedule of classes conducted by full-time, professional instructors. Classes are offered throughout the year at four locations: Houston, Birmingham, Orlando and our Watertown,
CT headquarters. By participating in our training, your personnel can learn how to install, calibrate, configure, program and maintain any and all Bristol Babcock products and realize the full potential of your system.
For information or to enroll in any class, contact our training department in Watertown at
(860) 945-2269. For Houston classes, you can also contact our Houston office, at (713) 685-
6200.
BLANK PAGE
A Few Words About Bristol Babcock
For over 100 years, Bristol 7 has been providing innovative solutions for the measurement and control industry. Our product lines range from simple analog chart recorders, to sophisticated digital remote process controllers and flow computers, all the way to turnkey
SCADA systems. Over the years, we have become a leading supplier to the electronic gas measurement, water purification, and wastewater treatment industries.
On off-shore oil platforms, on natural gas pipelines, and maybe even at your local water company, there are Bristol Babcock instruments, controllers, and systems running year-in and year-out to provide accurate and timely data to our customers.
Getting Additional Information
In addition to the information contained in this manual, you may receive additional assistance in using this product from the following sources:
Contacting Bristol Babcock Directly
Bristol Babcock's world headquarters are located at 1100 Buckingham Street, Watertown,
Connecticut 06795, U.S.A.
Our main phone numbers are:
(860) 945-2200
(860) 945-2213 (FAX)
Regular office hours are Monday through Friday, 8:00AM to 4:30PM Eastern Time, excluding holidays and scheduled factory shutdowns. During other hours, callers may leave messages using Bristol's voice mail system.
Telephone Support - Technical Questions
During regular business hours, Bristol Babcock's Application Support Group can provide telephone support for your technical questions.
For technical questions about TeleFlow Ô products call (860) 945-8604.
For technical questions about Control Wave call (860) 945-2244 or (860) 945-2286.
For technical questions regarding Bristol’s OpenEnterprise product, call (860) 945-2501 or e-mail: [email protected]
For technical questions regarding ACCOL products, Open BSI Utilities , as well as
Bristol's Enterprise Server 7 / Enterprise Workstation 7 products, call (860) 945-2286.
For technical questions about Network 3000 hardware, call (860) 945-2502.
You can e-mail the Application Support Group at: [email protected]
The Application Support Group maintains an area on our web site for software updates and technical information. Go to: www.bristolbabcock.com/services/techsupport/
For assistance in interfacing Bristol Babcock hardware to radios, contact Bristol Babcock’s
Communication Technology Group in Orlando, FL at (407) 629-9463 or (407) 629-
9464 .
Telephone Support - Non-Technical Questions, Product Orders, etc.
Questions of a non-technical nature (product orders, literature requests, price and delivery information, etc.) should be directed to the nearest sales office (listed on the rear cover) or to your Bristol-authorized sales representative. A list of
Please call the main Bristol Babcock number (860-945-2200) if you are unsure which office covers your particular area.
Visit our Site on the World Wide Web
For general information about Bristol Babcock and its products, please visit our site on the
World Wide Web at: www.bristolbabcock.com
Training Courses
Bristol Babcock’s Training Department offers a wide variety of courses in Bristol hardware and software at our Watertown, Connecticut headquarters, and at selected Bristol regional offices, throughout the year. Contact our Training Department at (860) 945-2269 for course information, enrollment, pricing, and scheduling.
PIP-353021VS
21V POWER SUPPLY BOARD OPTION
TABLE OF CONTENTS
SECTION TITLE
1.1
DESCRIPTION................................................................................................................... 1
2.1
2.1.1
2.1.2
2.2
2.2.1
Section 2 - INSTALLATION & SERVICE
REMOVAL/REPLACEMENT & INSTALLATION OF THE 21V
POWER SUPPLY OPTION ............................................................................................... 2
Removal/Replacement of the 21V Power Supply Option .................................................. 2
Installation of the 21V Power Supply Option .................................................................... 3
FIELD WIIRING ................................................................................................................ 4
Terminal Connections......................................................................................................... 4
3.1
3.2
3.3
GENERAL SPECIFICATIONS ......................................................................................... 6
PERFORMANCE SPECIFICATIONS .............................................................................. 6
ENVIRONMENTAL SPECIFICATIONS ......................................................................... 6
Supplements
Reference Documents
Low Power I/O Expansion Board Product Information Package....................................... PIP-EXPI/OTF
TeleFlow Plus - Electronic Gas Measurement Computer (3530-20B) Instruction Manual CI-3530-20B
TeleRTU Plus - Remote Terminal Unit (3530-25B) Instruction Manual ............................. CI-3530-25B
PIP-353021VS Page 0-1 Table Of Contents
BLANK PAGE
Section 1
INTRODUCTION
1.1 DESCRIPTION
The 21V Power Supply is a continuous mode boost switching type power supply. It is based upon a low power, low noise circuit that produces 21 Volts from a 12 Volt input. Fuse F1
(500 mA Slow Blow) is provided to protect the TeleFlow/TeleRTU power source from failures within 21V Power Supply. Fuse F2 (350 mA Fast Blow) is provided to protect the 21V Power
Supply circuitry from short circuits on an output.
Power shutdown is not an option with this unit since it employs a Boost circuit; therefore, the 21V Power Supply must be powered continuously. 21V Power Supplies receive input power (12V) from connector TB3 of the Power Distribution Board. The Power Distribution
Board is required because of CPU Board connector wiring capacity restrictions, i.e., the connectors only accommodate up to #14 AWG wire.
Four (4) mounting holes (one in each corner) are provided to accommodate a #4 mounting screw. However, these units are typically Snap Track mounted on a Dual PCB Mounting
Bracket (see Figure 2)).
The 21V Power Supply is mainly used in conjunction with Temperature and Pressure
Transmitters which require a higher than +12V but lower than 21.4V ( ± .8V) input supply to operate.
PIP-353021VS
Figure 1 - 21V Power Supply Board
Page 1 21V Power Supply Board
Section 2
INSTALLATION & SERVICE
2.1 REMOVAL/REPLACEMENT & INSTALLATION OF THE
21V POWER SUPPLY OPTION
2.1.1 Removal/Replacement of the 21V Power Supply Option
An installed 21V Power Supply option will contain the following parts:
1. 21V Power Supply Board (with removable Terminal Blocks)
2. Dual PCB Mounting Bracket
3. 2 Snap Tracks
4. Power Distribution Board (with removable Terminal Blocks)
5. Two #8-32 x ¼” SEM Screws
6. Two #8-32 x 3/8” Pan Head Screws and Two #7-32 Elastic Locking Nuts
Figure 2 - 21V Power Supply Option Major Components
TeleFlow Plus or TeleRTU Plus with Power Distribution Board
PIP-353021VS Page 2 21V Power Supply Board
To remove the optional 21V Power Supply, follow steps 1 through 4 below. To replace the
21V Power Supply follow steps 2 and 3 below in reverse order, installing rather than removing the item in question and then perform step 4.
1. Open the Instrument Front Cover (Door).
2. Unplug the removable Terminal Blocks (with wiring harnesses installed) from the optional 21V Power Supply Board.
3. Slide the 21V Power Supply Board toward the front of the unit and out of the Snap
Track.
Note: If a replacement 21V Power Supply Board is available follow steps 2 through 3 in reverse order, installing rather than removing the item in question.
4. Close and secure the Door.
Figure 3 - Bottom View of TeleRTU Plus (Similar to TeleFlow Plus)
2.1.2 Installation of the 21V Power Supply Option
1. Open the Instrument Front Cover.
2. If the unit in question already contains a Power Distribution Board, but only has one
Snap Track, the other Snap Track will have to be installed. This will require removal of the two (2) #8-32x3/8” Pan Head Screws and the two (2) #8-32 Elastic locking Nuts which secure the Power Distribution Board’s Snap Track to the Dual PCB Mounting
Bracket. Secure the second Snap Track to the Dual PCB Mounting Bracket as shown in
Figure 2 using two (2) #8-32 x 3/8” Pan Head Screws and two (2) #8-32 Elastic Locking
Nuts. Slide the Power Distribution Board into the Snap Track as illustrated in Figure 2.
PIP-353021VS Page 3 21V Power Supply Board
3. Connect power wiring (14 AWG) between the Power Distribution Board (PDB) and the
21V Power Supply Board’s input terminals and between the 21V Power Supply’s output terminals and the appropriate terminals on the Low Power I/O Expansion Board
(LPI/OEB) (see Table 1 and Figure 4). Route field wiring cable(s) (14 AWG) associated with the item to be powered, e.g., a 3508B Transmitter into the TeleFlow Plus or
TeleRTU Plus through a ¾” conduit fitting (user supplied) on the bottom of the enclosure
(see Figure 3). Connect Transmitter wiring to the appropriate LPI/OEB terminals (see
Figure 4).
4. Close and Secure the Instrument Front Cover.
2.2 FIELD WIRING
The device uses compression-type terminals that accommodate up to #14 AWG wire. A connection is made by inserting the bared end (1/4 inch Max.) into the clamp beneath the screw and then securing the screw. Insert the bared end fully to prevent short circuits.
Allow some slack in the wires when making terminal connections. The slack makes the connections more manageable and minimizes mechanical strain on the printed circuit boards and harnesses.
2.2.1 Terminal Connections
21V Power Supply Boards contain two terminal blocks that accommodate interface connections to the 3530-20B or 3530-25B, power and field wiring connections. TB1 is a threeposition terminal block that provides input power connection from the Power Distribution
Board. Four-position Terminal Block (TB2) provides +21V power and ground to the Low
Power I/O Expansion Board (LPI/OEB) (see PIP-EXPI/OTF) which will power external devices requiring 21V power such as 3508B Transmitters.
TABLE 1 - 21V POWER SUPPLY BOARD TERMINAL DESIGNATIONS
21VPS
TB#
TB1-1
TB1-2
TB1-3
TB2-1
TB2-2
TB2-3
TB2-4
TB
ASSIGNMENT
+12VIN
12VGND
CONNECTION to PDB.
TB3-1
TB3-2
CHASSISGND N/A
+21V N/A
21VGND
+21V
21VGND
N/A
N/A
N/A
CONNECTION to LPI/OEB
N/A
N/A
N/A
TB1-1
TB1-2
N/A
N/A
21V Power Supply Boards may be connected to transmitters that require a higher than +12V but lower than 21.4V ( ± .8V) input supply to operate. The supply is wired across the +12VIN and 12VGND terminals of the 21V Power Supply Board. The input voltage range is
+10.8Vdcc to +16Vdc.
The +21V Power Supply Option is typically powered from the 3530’s power source (battery).
Because of power distribution restrictions (CPU Board connector wiring capacity), power must be routed through a Power Distribution Board (see Figures 2 & 4). Power Distribution
Boards are mounted to the 3530 in question using a Snap Track and Dual PCB Mounting
PIP-353021VS Page 4 21V Power Supply Board
Bracket identical to the ones used for the LPTIB Board and the Digital to Relay I/O Board options.
PIP-353021VS
Figure 4 - 21V Power Supply Board Field Wiring
Page 5 21V Power Supply Board
Section 3
SPECIFICATIONS
3.1 GENERAL SPECIFICATIONS
ESD Susceptibility:
EMI Compatibility:
Transient Susceptibility:
Field connected circuits are designed to meet the requirements of IEC 801-2 for ESD withstand capability up to 10KV.
Designed to coexist within a shielded enclosure with the TeleFlow (3530-20B) or the TeleRTU
(3530-25B) electronics. EMI radiation is insignificant and susceptibility is comparable or superior to associated electronics.
Field connected circuits are designed to meet the requirements of ANSI/IEEEC37.90-1998
(Formerly IEEE 472) for surge withstand capability.
3.2 PERFORMANCE SPECIFICATIONS
Input Voltage (Vin):
Input Current (Iin):
Output Voltage (Vout):
Output Current (Iout):
Ripple/Noise:
Efficiency:
Short Circuit Protection Fuses:
10.8V to 16V (dc)
100 mA (Typ. @ 12V & 50mA load)
140 mA (Max. over Temp. @ 50 mA load)
21.4V ± 0.8V
50 mA (Max.)
20mV (Max. P-P)
88% (Typ.)
F1 = 500 mA (Slow Blow)
F2 = 350 mA (Fast Blow)
3.3 ENVIRONMENTAL SPECIFICATIONS
Operating Temperature:
Storage Temperature:
Relative Humidity:
Vibration:
-40°C to +60°C (-40°F to +140°F)
-40°C to +85°C (-40°F to +185°C)
15% - 95% Non-condensing
1G for 10Hz to 500Hz per PMC-31-1
(without damage or impairment)
PIP-353021VS Page 6 21V Power Supply Board
21 Volt Power Supply Board
Special Instructions for Class I, Division 2 Hazardous Locations
1. The BBI 21 Volt Power Supply Board is listed by Underwriters Laboratories (UL) as nonincendive and is suitable for use in Class I, Division 2, Groups A, B, C and D hazardous locations and non-hazardous locations only. Read this document carefully before installing a nonincendive BBI 21 Volt Power Supply Board. In the event of a conflict between the BBI 21 Volt Power Supply Board User Manual (PIP-353021VS) and this document, always follow the instructions in this document.
2. All power and I/O wiring must be performed in accordance with Class I, Division 2 wiring methods as defined in Article 501-4 (b) of the National Electrical Code, NFPA 70 for installations within the United States, or as specified in Section 18-152 of the
Canadian Electrical Code for installation in Canada.
3. WARNING: EXPLOSION HAZARD - Substitution of components may impair suitability for use in Class I, Division 2 environments.
4. WARNING: EXPLOSION HAZARD - When situated in a hazardous location, turn off power before servicing/replacing the unit and before installing or removing I/O wiring.
5. WARNING: EXPLOSION HAZARD - Do Not disconnect equipment unless the power has been switched off or the area is known to be nonhazardous.
07/21/00 Appendix A, Document PIP-353021VS Page 1 of 1
BLANK PAGE
READER RESPONSE FORM
Please help us make our documentation more useful to you! If you have a complaint, a suggestion, or a correction regarding this manual, please tell us by mailing this page with your comments. It's the only way we know we're doing our job by giving you correct, complete, and useful documentation.
DOCUMENT NUMBER: PIP-353021VS
TITLE:
21V Power Supply Board Option Product Information Package
ISSUE DATE: JAN., 2003
COMMENT/COMPLAINT:
______________________________________________________________________________
______________________________________________________________________________
______________________________________________________________________________
______________________________________________________________________________
______________________________________________________________________________
______________________________________________________________________________
______________________________________________________________________________
______________________________________________________________________________
______________________________________________________________________________
______________________________________________________________________________
______________________________________________________________________________
______________________________________________________________________________
______________________________________________________________________________
Mail this page to:
Bristol Babcock Inc.
1100 Buckingham Street
Watertown, CT 06795
Attn: Technical Publications Group, Dept. 315
Bristol Babcock
1100 Buckingham Street
Watertown, CT 06795
Phone: (860) 945-2200
Fax: (860) 945-2213
Website: www.bristolbabcock.com
U.S.A. Locations:
Northern Region
Bristol Babcock Inc.
1100 Buckingham Street
Watertown, CT 06795
Phone: (860) 945-2381
Fax: (860) 945-2525
Southwest Region
Bristol Babcock Inc.
2000 Governor's Circle
Suite F
Houston, TX 77092-8731
Phone: (713) 685-6200
Fax: (713) 681-7331
Western Region
Bristol Babcock Inc.
1609 South Grove Avenue
Suites 106 & 107
Ontario, CA 91761
Phone: (909) 923-8488
Fax: (909) 923-8988
Southeast Region
Bristol Babcock Inc.
317 S. North Lake Blvd.
Suite 1016
Altamonte Springs, FL 32701
Phone: (407) 740-7084
Fax: (407) 629-2106
Helicoid Instruments
1100 Buckingham Street
Watertown, CT 06795
Phone: (860) 945-2218
Fax: (860) 945-2213 [email protected]
Dallas District Office
Bristol Babcock Inc.
777 South Central
Expressway
Suite 1-C
Richardson, TX 75080
Phone: (972) 238-8197
Fax: (972) 238-8198 [email protected]
International Affiliates :
Canada
Bristol Babcock, Canada
234 Attwell Drive
Toronto, Ont. M9W 5B3
Canada
PH: 416-675-3820
FAX: 416-674-5129 [email protected]
Mexico
BBI, S.A. de C.V.
Ejercito Nacional No. 718, 4
Piso
Colonia Polanco
Mexico, D.F. 11560
Mexico
PH: 52-555-254-5281
FAX: 52-555-254-3408
Sales Office New Mexico
Bristol Babcock Inc.
906 San Juan Blvd., Suite A
Farmington, NM 87401
Phone: (505) 320-5046
Fax: (505) 327-3273
Communications
Technology Group
Bristol Babcock Inc.
317 S. North Lake Blvd.
Suite 1016
Altamonte Springs, FL 32701
Phone: (407) 629-9464
Fax: (407) 629-2106 [email protected]
United Kingdom
Bristol Babcock Ltd.
Vale Industrial Estate
Stourport Road
Kidderminster
Worcestershire DY11 7QU
United Kingdom
PH: +44 (0) 1562 820001
FAX: +44 (0) 1562 746721 [email protected]
Australia
Bristol Babcock, Inc.
22 Hastie St.
PO Box 1987
Banbury, Western Australia
6230
PH: 61 (0)8 9791 3654
FAX: 61 (0)8 9791 3173 [email protected]
Calgary Office
Bristol Babcock, Canada
3812 Edmonton Trail N.E.
Calgary, Alberta T2E 5T6
Canada
PH: 403-265-4808
FAX: 403-233-2914 [email protected]
Villahermosa Office
BBI, S.A. de C.V.
Av. Plomo No.2
Bodega No. 1 - Ciudad
Industrial
Villahermosa, Tabasco 86010
Mexico
PH: 52-993-353-3142
FAX: 52-993-353-3145 [email protected]
Middle East
Bristol Babcock Ltd.
Vale Industrial Estate
Stourport Road
Kidderminster
Worcestershire DY11 7QU
United Kingdom
PH: +44 (0) 1562 820001
FAX: +44 (0) 1562 746721 [email protected]
Product Information Package
PIP-TIBS3530
Mar., 2007 TeleFlow Plus & TeleRTU Plus
Low Power Transmitter Interface
Board Part No. 392950-01-4
For The Following Bristol Instruction Manuals:
CI-3530-20B & CI-3530-25B
www.EmersonProcess.com/Bristol
IMPORTANT! READ INSTRUCTIONS BEFORE STARTING!
Be sure that these instructions are carefully read and understood before any operation is attempted. Improper use of this device in some applications may result in damage or injury. The user is urged to keep this book filed in a convenient location for future reference.
These instructions may not cover all details or variations in equipment or cover every possible situation to be met in connection with installation, operation or maintenance. Should problems arise that are not covered sufficiently in the text, the purchaser is advised to contact Bristol for further information.
EQUIPMENT APPLICATION WARNING
The customer should note that a failure of this instrument or system, for whatever reason, may leave an operating process without protection. Depending upon the application, this could result in possible damage to property or injury to persons.
It is suggested that the purchaser review the need for additional backup equipment or provide alternate means of protection such as alarm devices, output limiting, failsafe valves, relief valves, emergency shutoffs, emergency switches, etc. If additional in-formation is required, the purchaser is advised to contact Bristol .
RETURNED EQUIPMENT WARNING
When returning any equipment to Bristol for repairs or evaluation, please note the following: The party sending such materials is responsible to ensure that the materials returned to Bristol are clean to safe levels, as such levels are defined and/or determined by applicable federal, state and/or local law regulations or codes. Such party agrees to indemnify Bristol and save Bristol harmless from any liability or damage which Bristol may incur or suffer due to such party's failure to so act.
ELECTRICAL GROUNDING
Metal enclosures and exposed metal parts of electrical instruments must be grounded in accordance with OSHA rules and regulations pertaining to "Design
Safety Standards for Electrical Systems," 29 CFR, Part 1910, Subpart S, dated: April
16, 1981 (OSHA rulings are in agreement with the National Electrical Code).
The grounding requirement is also applicable to mechanical or pneumatic instruments that include electrically-operated devices such as lights, switches, relays, alarms, or chart drives.
EQUIPMENT DAMAGE FROM ELECTROSTATIC DISCHARGE VOLTAGE
This product contains sensitive electronic components that can be damaged by exposure to an electrostatic discharge (ESD) voltage. Depending on the magnitude and duration of the ESD, this can result in erratic operation or complete failure of the equipment. Read supplemental document S14006 at the back of this manual for proper care and handling of ESD-sensitive components.
Bristol 1100 Buckingham Street, Watertown, CT 06795
Telephone (860) 945-2200
WARRANTY
A. Bristol warrants that goods described herein and manufactured by Bristol are free from defects in material and workmanship for one year from the date of shipment unless otherwise agreed to by Bristol in writing.
B. Bristol warrants that goods repaired by it pursuant to the warranty are free from defects in material and workmanship for a period to the end of the original warranty or ninety (90) days from the date of delivery of repaired goods, whichever is longer.
C. Warranties on goods sold by, but not manufactured by Bristol, are expressly limited to the terms of the warranties given by the manufacturer of such goods.
D. All warranties are terminated in the event that the goods or systems or any part thereof are (i) misused, abused or otherwise damaged, (ii) repaired, altered or modified without Bristol's consent, (iii) not installed, maintained and operated in strict compliance with instructions furnished by Bristol, or (iv) worn, injured or damaged from abnormal or abusive use in service time.
E. THESE WARRANTIES ARE EXPRESSLY IN LIEU OF ALL OTHER
WARRANTIES EXPRESS OR IMPLIED (INCLUDING WITHOUT LIMITATION
WARRANTIES AS TO MERCHANTABILITY AND FITNESS FOR A PARTICULAR
PURPOSE), AND NO WARRANTIES, EXPRESS OR IMPLIED, NOR ANY
REPRESENTATIONS, PROMISES, OR STATEMENTS HAVE BEEN MADE BY
BRISTOL UNLESS ENDORSED HEREIN IN WRITING. FURTHER, THERE ARE
NO WARRANTIES WHICH EXTEND BEYOND THE DESCRIPTION OF THE
FACE HEREOF.
F. No agent of Bristol is authorized to assume any liability for it or to make any written or oral warranties beyond those set forth herein.
REMEDIES
A. Buyer's sole remedy for breach of any warranty is limited exclusively to repair or replacement without cost to Buyer of any goods or parts found by Seller to be defective if Buyer notifies Bristol in writing of the alleged defect within ten (10) days of discovery of the alleged defect and within the warranty period stated above, and if the Buyer returns such goods to Bristol's Watertown office, unless Bristol's Watertown office designates a different location, transportation prepaid, within thirty (30) days of the sending of such notification and which upon examination by Bristol proves to be defective in material and workmanship. Bristol is not responsible for any costs of removal, dismantling or reinstallation of allegedly defective or defective goods. If a Buyer does not wish to ship the product back to Bristol, the Buyer can arrange to have a Bristol service person come to the site. The Service person's transportation time and expenses will be for the account of the Buyer. However, labor for warranty work during normal working hours is not chargeable.
B. Under no circumstances will Bristol be liable for incidental or consequential damages resulting from breach of any agreement relating to items included in this quotation, from use of the information herein or from the purchase or use by Buyer, its em-ployees or other parties of goods sold under said agreement.
How to return material for Repair or Exchange
Before a product can be returned to Bristol for repair, upgrade, exchange, or to verify proper operation, form (GBU 13.01) must be completed in order to obtain a RA (Return
Authorization) number and thus ensure an optimal lead time. Completing the form is very important since the information permits the Bristol Repair Dept. to effectively and efficiently process the repair order.
You can easily obtain a RA number by:
A. FAX
Completing the form (GBU 13.01) and faxing it to (860) 945-3875. A Bristol Repair
Dept. representative will return call (or other requested method) with a RA number.
B. E-MAIL
Accessing the form (GBU 13.01) via the Bristol Web site (www.bristolbabcock.com) and sending it via E-Mail to [email protected]
. A Bristol Repair Dept. representative will return E-Mail (or other requested method) with a RA number.
C. Mail
Mail the form (GBU 13.01) to
Bristol Inc.
Repair
1100 Buckingham Street
Watertown, CT 06795
A Bristol Repair Dept. representative will return call (or other requested method) with a RA number.
D. Phone
Calling the Bristol Repair Department at (860) 945-2442. A Bristol Repair Department representative will record a RA number on the form and complete Part I, then send the form to the Customer via fax (or other requested method) for Customer completion of Parts II & III.
A copy of the completed Repair Authorization Form with issued RA number should be included with the product being returned. This will allow us to quickly track, repair, and return your product to you.
Bristol
Repair Authorization Form
(off-line completion)
(Providing this information will permit Bristol to effectively and efficiently process your return. Completion is required to receive optimal lead time. Lack of information may result in increased lead times.)
Date___________________ RA #___________________SH
Standard Repair Practice is as follows: Variations to this is practice may be requested in the “Special Requests” section.
•
Evaluate / Test / Verify Discrepancy
•
Repair / Replace / etc. in accordance with this form
•
Return to Customer
Line No.____________
Please be aware of the Non warranty standard charge:
•
There is a $100 minimum evaluation charge, which is applied to the repair if applicable (
√
in “returned”
B,C, or D of part III below)
Part I Please complete the following information for single unit or multiple unit returns
Address No.
Bill to :
Purchase Order:
Phone:
(office use only) Address No.
Ship to:
Fax:
(office use only)
Contact Name: ____________________________________
E-Mail:
Model No./Part No. Description
Range/Calibration S/N
Reason for return : Failure Upgrade Verify Operation Other
1.
Describe the conditions of the failure (Frequency/Intermittent, Physical Damage, Environmental Conditions,
Communication, CPU watchdog, etc.)
(Attach a separate sheet if necessary)
2. Comm. interface used: Standalone RS-485 Ethernet Modem (PLM (2W or 4W) or SNW) Other: ______________
3. What is the Firmware revision? _____________________ What is the Software & version?
Part III If checking “replaced” for any question below, check an alternate option if replacement is not available
A.
If product is within the warranty time period but is excluded due to Bristol’s warranty clause, would you like the product: repaired returned replaced scrapped?
B.
If product were found to exceed the warranty period, would you like the product:
C.
If product is deemed not repairable would you like your product: repaired returned replaced scrapped? returned replaced scrapped?
D.
If Bristol is unable to verify the discrepancy, would you like the product: returned replaced *see below?
* Continue investigating by contacting the customer to learn more about the problem experienced? The person to contact that has the most knowledge of the problem is: ______________________________ phone_____________________
If we are unable to contact this person the backup person is: _________________________ phone_____________________
Special Requests: ____________________________________________________________________________________
____________________________________________________________________________________________________
Ship prepaid to: Bristol Inc., Repair Dept., 1100 Buckingham Street, Watertown, CT 06795
Phone: 860-945-2442 Fax: 860-945-2220 Form GBU 13.01 Rev. C 04/27/06
Bristol
Training
GET THE MOST FROM YOUR BRISTOL
BABCOCK INSTRUMENT OR SYSTEM
• Avoid Delays and problems in getting your system on-line
• Minimize installation, start-up and maintenance costs.
• Make the most effective use of our hardware and software.
• Know your system.
As you know, a well-trained staff is essential to your operation. Bristol Inc. offers a full schedule of classes conducted by full-time, professional instructors. Classes are offered throughout the year at three locations: Houston, Orlando and our Watertown, CT headquarters. By participating in our training, your personnel can learn how to install, calibrate, configure, program and maintain any and all Bristol products and realize the full potential of your system.
For information or to enroll in any class, contact our training department in Watertown at
(860) 945-2343. For Houston classes, you can also contact our Houston office, at (713) 685-
6200.
A Few Words About Bristol Inc.
For over 100 years, Bristol ® has been providing innovative solutions for the measurement and control industry. Our product lines range from simple analog chart recorders, to sophisticated digital remote process controllers and flow computers, all the way to turnkey
SCADA systems. Over the years, we have become a leading supplier to the electronic gas measurement, water purification, and wastewater treatment industries.
On off-shore oil platforms, on natural gas pipelines, and maybe even at your local water company, there are Bristol Inc. instruments, controllers, and systems running year-in and year-out to provide accurate and timely data to our customers.
Getting Additional Information
In addition to the information contained in this manual, you may receive additional assistance in using this product from the following sources:
Help Files / Release Notes
Many Bristol software products incorporate help screens. In addition, the software typically includes a ‘read me’ release notes file detailing new features in the product, as well as other information which was available too late for inclusion in the manual.
Contacting Bristol Inc. Directly
Bristol's world headquarters is located at 1100 Buckingham Street, Watertown,
Connecticut 06795, U.S.A.
Our main phone numbers are:
(860) 945-2200
(860) 945-2213 (FAX)
Regular office hours are Monday through Friday, 8:00AM to 4:30PM Eastern Time, excluding holidays and scheduled factory shutdowns. During other hours, callers may leave messages using Bristol's voice mail system.
Telephone Support - Technical Questions
During regular business hours, Bristol's Application Support Group can provide telephone support for your technical questions.
For technical questions about TeleFlow products call (860) 945-8604.
For technical questions about Control Wave call (860) 945-2394 or (860) 945-2286.
For technical questions regarding Bristol’s OpenEnterprise product, call (860) 945-3865 or e-mail: [email protected]
For technical questions regarding ACCOL products, OpenBSI Utilities , UOI and all other software except for Control Wave and OpenEnterprise products, call (860) 945-2286.
For technical questions about Network 3000 hardware, call (860) 945-2502.
You can e-mail the Application Support Group at: [email protected]
The Application Support Group maintains an area on our web site for software updates and technical information. Go to: www.bristolbabcock.com/services/techsupport/
For assistance in interfacing Bristol hardware to radios, contact Bristol’s Communication
Technology Group in Orlando, FL at (407) 629-9463 or (407) 629-9464 .
You can e-mail the Communication Technology Group at: [email protected]
Telephone Support - Non-Technical Questions, Product Orders, etc.
Questions of a non-technical nature (product orders, literature requests, price and delivery information, etc.) should be directed to the nearest sales office (listed on the rear cover of this manual) or to your Bristol-authorized sales representative.
Please call the main Bristol Inc. number (860-945-2200) if you are unsure which office covers your particular area.
Visit our Site on the World Wide Web
For general information about Bristol Inc. and its products, please visit our site on the
World Wide Web at: www.bristolbabcock.com
Training Courses
Bristol’s Training Department offers a wide variety of courses in Bristol hardware and software at our Watertown, Connecticut headquarters, and at selected Bristol regional offices, throughout the year. Contact our Training Department at (860) 945-2343 for course information, enrollment, pricing, and scheduling.
PIP-TIBS3530
LOW POWER TRANSMITTER INTERFACE BOARD
PT. NO. 392950-01-4
TABLE OF CONTENTS
SECTION TITLE
1.1
1.1.1
1.2
1.3
DESCRIPTION ...................................................................................................................1
Transmitter Operation .........................................................................................................1
LED INDICATORS ............................................................................................................2
JUMPER JP1.......................................................................................................................2
2.1
2.1.1
2.1.2
2.2
2.2.1
3.1
3.2
Section 2 - INSTALLATION & SERVICE
REMOVAL/REPLACEMENT & INSTALLATION OF THE LPTIB..............................3
Removal/Replacement of the Low Power Transmitter Interface Bd. .................................3
Installation of the Low Power Transmitter Interface Board Option ...................................4
FIELD WIIRING.................................................................................................................5
Terminal Connections .........................................................................................................5
GENERAL SPECIFICATIONS..........................................................................................8
ENVIRONMENTAL SPECIFICATIONS..........................................................................8
SUPPLEMENTS
PIP-TIBS3530 Page 0-1 Table Of Contents
BLANK PAGE
Section 1
INTRODUCTION
1.1 DESCRIPTION
Low Power Transmitter Interface Boards allow up to two (2) Bristol, Series 3508 or Series
3808 Transmitters to communicate with an ACCOL loaded host TeleFlow 3530-20B
Electronic Gas Measurement Computer (EGMC) or 3530-25B TeleRTU. The EGMC/RTU polls and stores data from each transmitter and communicates with the network. Two
LEDS on the LPTI Board [CD (DS1) & RTS (DS2)] indicate the communication status.
The LPTI Board is housed in the TeleFlow Plus or TeleRTU Plus enclosure and is interfaced to a TeleFlow I/O Expansion Board. LPTI Boards are powered by a 12V power supply or battery. LPTI Boards contain one jumper (JP1) for configuration purposes.
The LPTI Board (Figure 1) is wired to the TeleFlow I/O Expansion Board connector (TB5) and is mounted with Snap Track (holder) and Mounting Bracket as illustrated in Figure 2.
1.1.1 Transmitter Operation
3508 Series
Each Transmitter must be assigned a unique address via the SMARTKIT program as described in Section 4.2 PROGRAM LOADING AND STARTUP of the appropriate 3508
Transmitter manual. Additionally, all Transmitters wired to the TI Board must be operated in the minimum current mode (3.8 mA). This mode is selected via the SMARTKIT program as described in Section 4.7 TRANSMITTER OPERATING MODES of the appropriate 3508
Transmitter manual, i.e., CI-3508-10C, CI-3508-30C or CI-3508-99C.
Figure 1 - Transmitter Interface Board P/N 392950-01-4
PIP-TIBS3530 Page
3808 MVT Series
Each Model 3808 MVT Transmitter must be assigned a unique address via the WebBSI
Sign On/Off Menu (see Section 3 of Customer Instruction Manual CI-3808). Additionally, only analog versions of the 3808 MVT can be interfaced to a Transmitter Interface Board.
1.2 LED INDICATORS
The LPTIB contains two LEDs which have the following functions: Carrier Detect (CD) and
Request to Send (RTS). When the board is sending a Request To Send, LED DS2 (RTS) will be ON and LED DS1 (CD) will be OFF. Conversely, when the LPTIB is receiving data from a 3508/3808 Transmitter, LED DS2 (RTS) will be OFF and LED DS1 - Carrier Detect (CD) will be ON.
1.3 JUMPER JP1
Jumper JP1 is used to configure the LPTIB for operation with one or two 3508/3808
Transmitters. If only one 3508/3808 Transmitter is to be connected to the LPTIB, Jumper
JP1 must be installed across JP1-1 and JP1-2. Additionally, when only one 3508/3808
Transmitter is to be connected to the LPTIB, it must be connected to connector TB1. When two 3508/3808 Transmitters are connected to the LPTIB, Jumper JP1 must be removed and stored in either JP1-1 or JP1-2.
PIP-TIBS3530 Page
Section 2
INSTALLATION & SERVICE
2.1 REMOVAL/REPLACEMENT & INSTALLATION OF THE LPTIB
2.1.1 Removal/Replacement of the Low Power Transmitter Interface Bd.
An installed LPTI Board option will contain the following parts:
1. LPTI Board (with removable Terminal Blocks
2. Dual PCB Mounting Bracket
3. Snap Track
4. LPTI Board Cables (Power & RS-232 Intf.)
5. Two #8-32 x ¼” SEM Screws
6. Two #8-32 x 3/8” Pan Head Screws and Two #7-32 Elastic Locking Nuts
Figure 2 - Low Power Transmitter Interface Board Mounting Diagram
TeleFlow Plus or TeleRTU with Power Distribution Board, 21V Power Supply
Board & Digital To Relay I/O Board
PIP-TIBS3530 Page
To remove the optional Low Power Transmitter Interface Board follow steps 1 through 4 below. To replace the Low Power Transmitter Interface Board follow steps 2 and 3 below in reverse order, installing rather than removing the item in question and then perform step
4.
1. Open the Instrument Front Cover (Door).
2. Unplug the removable Terminal Blocks (with wiring harnesses installed) from the optional Low Power Transmitter Interface Board.
3. Slide the Low Power Transmitter Interface Board toward the front of the unit and out of the Snap Track.
Note: If a replacement Low Power Transmitter Interface Board is available follow steps 2 through 3 in reverse order (after configuring Jumper JP1
(see Section 1.3), installing rather than removing the item in question.
4. Close and Secure the Door.
Figure 3 - Bottom View of TeleRTU Plus (Similar to TeleFlow Plus)
2.1.2 Installation of the Low Power Transmitter Interface Board Option
1. Open the Instrument Front Cover.
2. If the unit in question already contains a Power Distribution Board, but only has one
Snap Track, the other Snap Track will have to be installed. This will require removal of the two (2) #8-32x3/8” Pan Head Screws and the two (2) #8-32 Elastic locking Nuts which secure the Power Distribution Board’s Snap Track to the Dual PCB Mounting
Bracket. Secure the second Snap Track to the Dual PCB Mounting Bracket as shown in
Figure 2 using two (2) #8-32 x 3/8” Pan Head Screws and two (2) #8-32 Elastic Locking
PIP-TIBS3530 Page
Nuts. Configure the LPTIB for operation with one or two 3508/3808 Transmitters. If only one 3508/3808 Transmitter is to be connected to the LPTIB, Jumper JP1 must be installed across JP1-1 and JP1-2. Additionally, when only one 3508/3808 Transmitter is to be connected to the LPTIB, it must be connected to connector TB1. When two
3508/3808 Transmitters are connected to the LPTIB, Jumper JP1 must be removed and installed in JP1-1 or JP1-2. Slide the LPTI Board into the Snap Track (see Figure 2).
3. Connect power wiring (14 AWG) and RS-232 Interface wiring (20 to 14 AWG) to LPTIB.
Route field wiring cable(s) (20 to 14 AWG) associated with the LPTI Board into the
TeleFlow Plus or TeleRTU Plus through a ¾” conduit fitting (user installed) on the bottom of the enclosure (see Figure 3). Connect Transmitter wiring to the appropriate
LPTI Board Terminal Connectors (TB1 and TB2) (see Section 2.2.1, Table 1 & Figure 4).
5. Close and Secure the Instrument Front Cover.
2.2 FIELD WIRING
The device uses compression-type terminals that accommodate up to #14 AWG wire. A connection is made by inserting the bared end (1/4 inch Max.) into the clamp beneath the screw and then securing the screw. Insert the bared end fully to prevent short circuits.
Allow some slack in the wires when making terminal connections. The slack makes the connections more manageable and minimizes mechanical strain on the printed circuit boards and harnesses.
2.2.1 Terminal Connections
LPTI Boards contain four terminal blocks that accommodate interface connections to the
3530-20B or 3530-25B, power and field wiring connections. TB1 & TB2 are two-position
Terminal Blocks, which connect to the signal/power inputs of the transmitters. Threeposition Terminal Block (TB3) connects to the 3530-20B or 3530-25B power source. Fiveposition Terminal Block TB4 provides an RS-232 interface with the host 3530-20B/25B.
TABLE 1 - LPTI BOARD TERMINAL DESIGNATIONS
LPTIB
TB#
LPTIB
TB NAME
TB1-1 XMTR1-
CONNECTION if PDB.
Is Present
3508/3808-
3530-20B
CONNECTION
If no PDB.
3508/3808-
3530-25B
CONNECTION
If no PDB.
3508/3808-
TB1-2 XMTR1+ 3508/3808+ 3508/3808+
TB2-1 XMTR2- 3508/3808- 3508/3808- 3508/3808-
TB2-2 XMTR2+ 3508/3808+ 3508/3808+
TB3-1 SHUTDOWN N/A
TB3-2 +12VIN TB5-1 of PDB.
TB3-3 +12VRET
TB4-1 GND
TB5-2 of PDB.
N/A N/A
CPUB J8-1 or J6-1 CPUB J2-1 or J4-1
CPUB J8-2 or J6-2 CPUB J2-2 or J4-2
GND of LPI/OB TB5-1 LPI/OB TB5-1 LPI/OB TB5-1
TB4-2 CTS
TB4-3 RTS
TB4-4 RXD
TB4-5 TXD
RTS of LPI/OB TB5-5
CTS of LPI/OB TB5-4
TXD of LPI/OB TB5-7
RXD of LPI/OB TB5-6
LPI/OB TB5-5
LPI/OB TB5-4
LPI/OB TB5-7
LPI/OB TB5-6
LPI/OB TB5-5
LPI/OB TB5-4
LPI/OB TB5-7
LPI/OB TB5-6
Note: PDB = Power Distribution Board
PIP-TIBS3530 Page
LPTI Boards may be connected to internally powered transmitters (see Figure 4). In the case of an Internally Powered Transmitter (powered from LPTIB’s on-board +12V Supply/Regulator) an external +12 Vdc power supply is wired to LPTI Board connector TB3 as shown in Figure 4. The supply is wired across the +12VIN and +12VRET terminals. The input voltage range is +10.8Vdcc to +16Vdc.
LPTIB’s are typically powered from the 3530’s power source (battery). Because of power distribution restrictions (CPU Board connector wiring capacity), power is typically routed through a Power Distribution Board (see Figures 5 & 6). Power Distribution Boards are mounted to the 3530 in question using a Snap Track and Dual PCB Mounting Bracket identical to the ones used for the LPTI Board and the Digital to Relay I/O Board options.
Figure 4 - Internally Powered Transmitter Field Wiring
PIP-TIBS3530 Page
Figure 5 - Mounted Power Distribution Board
Figure 6 - Power Distribution Board Schematic/Wiring Diagram
PIP-TIBS3530 Page
Section 3
SPECIFICATIONS
3.1 GENERAL SPECIFICATIONS
Communication Interface:
3508/3808 Interface:
ESD Susceptibility:
RS-232 ( ± 3V minimum)
FSK Modem - Bell 202 Compatible
(1200 Hz/2200 Hz modulation)
Baud Rate is 1200
Field connected circuits are designed to meet the requirements of IEC 801-2 for ESD withstand capability up to 10KV.
EMI Compatibility: Designed to coexist within a shielded enclosure with the TeleFlow (3530-20B) or the TeleRTU (3530-25B) electronics. EMI radiation is insignificant and susceptibility is comparable or superior to associated electronics.
Transient Susceptibility: Field connected circuits are designed to meet the requirements of ANSI/-
IEEEC37.90-1998 (Formerly IEEE 472) for surge withstand capability.
3.2 ENVIRONMENTAL SPECIFICATIONS
Operating Temperature:
Storage Temperature:
Relative Humidity:
Vibration:
-40°C to +60°C (-40°F to +140°F)
-40°C to +85°C (-40°F to +185°C)
15% - 95% Non-condensing
1G for 10Hz to 500Hz per PMC-31-1 (without damage or impairment)
PIP-TIBS3530 Page
Low Power Transmitter Interface Board
Special Instructions for Class I, Division 2 Hazardous Locations
1. The Bristol Low Power Transmitter Interface Board (LPTIB) is listed by Underwriters
Laboratories (UL) as nonincendive and is suitable for use in Class I, Division 2, Groups
A, B, C and D hazardous locations or non-hazardous locations only. Read this document carefully before installing a nonincendive Bristol LPTIB Board. In the event of a conflict between the LPTIB Board User Manual (PIP-TIBS3530) and this document, always follow the instructions in this document.
2. Wiring must be performed in accordance with Class I, Division 2 wiring methods as defined in Article 501-4 (b) of the National Electrical Code, NFPA 70 for installations within the United States, or as specified in Section 18-152 of the Canadian Electrical
Code for installation in Canada.
3. WARNING: EXPLOSION HAZARD - Substitution of components may impair suitability for use in Class I, Division 2 environments.
4. WARNING: EXPLOSION HAZARD - When situated in a hazardous location, turn off power before servicing/replacing the unit and before installing or removing I/O wiring.
5. WARNING: EXPLOSION HAZARD - Do Not disconnect equipment unless the power has been switched off or the area is known to be nonhazardous.
03/24/2007 Appendix A of PIP-TIBS3530 - LPTIB Board Page 1 of 1
BLANK PAGE
BLANK PAGE
Product Information Package
Low Power Transmitter Interface Board Part No. 392950-01-4
PIP-TIBS3530
Mar., 2007
Emerson Process Management
Bristol, Inc.
1100 Buckingham Street
Watertown, CT 06795
Phone: +1 (860) 945-2262
Fax: +1 (860) 945-2525 www.EmersonProcess.com/Bristol
Emerson Electric Canada, Ltd.
Bristol Canada
6338 Viscount Rd.
Mississauga, Ont. L4V 1H3
Canada
Phone: 905-362-0880
Fax: 905-362-0882 www.EmersonProcess.com/Bristol
Emerson Process Management
BBI, S.A. de C.V.
Homero No. 1343, 3er Piso
Col. Morales Polanco
11540 Mexico, D.F.
Mexico
Phone: (52-55)-52-81-81-12
Fax: (52-55)-52-81-81-09 www.EmersonProcess.com/Bristol
Emerson Process Management
Bristol Babcock, Ltd.
Blackpole Road
Worcester, WR3 8YB
United Kingdom
Phone: +44 1905 856950
Fax: +44 1905 856969 www.EmersonProcess.com/Bristol
Emerson Process Management
Bristol, Inc.
22 Portofino Crescent,
Grand Canals Bunbury, Western Australia 6230
Mail to: PO Box 1987 (zip 6231)
Phone: +61 (8) 9725-2355
Fax: +61 (8) 8 9725-2955 www.EmersonProcess.com/Bristol
The information in this document is subject to change without notice. Every effort has been made to supply complete and accurate information. However, Bristol, Inc. assumes no responsibility for any errors that may appear in this document.
If you have comments or questions regarding this manual, please direct them to your local Bristol sales representative, or direct them to one of the addresses listed at left.
Bristol, Inc. does not guarantee the accuracy, sufficiency or suitability of the software delivered herewith. The Customer shall inspect and test such software and other materials to his/her satisfaction before using them with important data.
There are no warranties, expressed or implied, including those of merchantability and fitness for a particular purpose, concerning the software and other materials delivered herewith.
TeleFlow
™
is a trademark of Bristol, Inc. The Emerson logo is a trade mark and service mark of Emerson Electric Co. Other trademarks or copyrighted products mentioned in this document are for information only, and belong to their respective companies, or trademark holders.
Copyright (c) 2007, Bristol, Inc., 1100 Buckingham St., Watertown, CT 06795. No part of this manual may be reproduced in any form without the express written permission of
Bristol, Inc.
Product Information Package
PIP-EXPTIBS
Mar., 2007 TeleFlow Plus & TeleRTU Plus
Expansion Transmitter Interface
Board Part No. 392951-01-0
For The Following Bristol Instruction Manuals:
CI-3530-20B & CI-3530-25B
www.EmersonProcess.com/Bristol
IMPORTANT! READ INSTRUCTIONS BEFORE STARTING!
Be sure that these instructions are carefully read and understood before any operation is attempted. Improper use of this device in some applications may result in damage or injury. The user is urged to keep this book filed in a convenient location for future reference.
These instructions may not cover all details or variations in equipment or cover every possible situation to be met in connection with installation, operation or maintenance. Should problems arise that are not covered sufficiently in the text, the purchaser is advised to contact Bristol for further information.
EQUIPMENT APPLICATION WARNING
The customer should note that a failure of this instrument or system, for whatever reason, may leave an operating process without protection. Depending upon the application, this could result in possible damage to property or injury to persons.
It is suggested that the purchaser review the need for additional backup equipment or provide alternate means of protection such as alarm devices, output limiting, failsafe valves, relief valves, emergency shutoffs, emergency switches, etc. If additional in-formation is required, the purchaser is advised to contact Bristol .
RETURNED EQUIPMENT WARNING
When returning any equipment to Bristol for repairs or evaluation, please note the following: The party sending such materials is responsible to ensure that the materials returned to Bristol are clean to safe levels, as such levels are defined and/or determined by applicable federal, state and/or local law regulations or codes. Such party agrees to indemnify Bristol and save Bristol harmless from any liability or damage which Bristol may incur or suffer due to such party's failure to so act.
ELECTRICAL GROUNDING
Metal enclosures and exposed metal parts of electrical instruments must be grounded in accordance with OSHA rules and regulations pertaining to "Design
Safety Standards for Electrical Systems," 29 CFR, Part 1910, Subpart S, dated: April
16, 1981 (OSHA rulings are in agreement with the National Electrical Code).
The grounding requirement is also applicable to mechanical or pneumatic instruments that include electrically-operated devices such as lights, switches, relays, alarms, or chart drives.
EQUIPMENT DAMAGE FROM ELECTROSTATIC DISCHARGE VOLTAGE
This product contains sensitive electronic components that can be damaged by exposure to an electrostatic discharge (ESD) voltage. Depending on the magnitude and duration of the ESD, this can result in erratic operation or complete failure of the equipment. Read supplemental document S14006 at the back of this manual for proper care and handling of ESD-sensitive components.
Bristol 1100 Buckingham Street, Watertown, CT 06795
Telephone (860) 945-2200
WARRANTY
A. Bristol warrants that goods described herein and manufactured by Bristol are free from defects in material and workmanship for one year from the date of shipment unless otherwise agreed to by Bristol in writing.
B. Bristol warrants that goods repaired by it pursuant to the warranty are free from defects in material and workmanship for a period to the end of the original warranty or ninety (90) days from the date of delivery of repaired goods, whichever is longer.
C. Warranties on goods sold by, but not manufactured by Bristol, are expressly limited to the terms of the warranties given by the manufacturer of such goods.
D. All warranties are terminated in the event that the goods or systems or any part thereof are (i) misused, abused or otherwise damaged, (ii) repaired, altered or modified without Bristol's consent, (iii) not installed, maintained and operated in strict compliance with instructions furnished by Bristol, or (iv) worn, injured or damaged from abnormal or abusive use in service time.
E. THESE WARRANTIES ARE EXPRESSLY IN LIEU OF ALL OTHER
WARRANTIES EXPRESS OR IMPLIED (INCLUDING WITHOUT LIMITATION
WARRANTIES AS TO MERCHANTABILITY AND FITNESS FOR A PARTICULAR
PURPOSE), AND NO WARRANTIES, EXPRESS OR IMPLIED, NOR ANY
REPRESENTATIONS, PROMISES, OR STATEMENTS HAVE BEEN MADE BY
BRISTOL UNLESS ENDORSED HEREIN IN WRITING. FURTHER, THERE ARE
NO WARRANTIES WHICH EXTEND BEYOND THE DESCRIPTION OF THE
FACE HEREOF.
F. No agent of Bristol is authorized to assume any liability for it or to make any written or oral warranties beyond those set forth herein.
REMEDIES
A. Buyer's sole remedy for breach of any warranty is limited exclusively to repair or replacement without cost to Buyer of any goods or parts found by Seller to be defective if Buyer notifies Bristol in writing of the alleged defect within ten (10) days of discovery of the alleged defect and within the warranty period stated above, and if the Buyer returns such goods to Bristol's Watertown office, unless Bristol's Watertown office designates a different location, transportation prepaid, within thirty (30) days of the sending of such notification and which upon examination by Bristol proves to be defective in material and workmanship. Bristol is not responsible for any costs of removal, dismantling or reinstallation of allegedly defective or defective goods. If a Buyer does not wish to ship the product back to Bristol, the Buyer can arrange to have a Bristol service person come to the site. The Service person's transportation time and expenses will be for the account of the Buyer. However, labor for warranty work during normal working hours is not chargeable.
B. Under no circumstances will Bristol be liable for incidental or consequential damages resulting from breach of any agreement relating to items included in this quotation, from use of the information herein or from the purchase or use by Buyer, its em-ployees or other parties of goods sold under said agreement.
How to return material for Repair or Exchange
Before a product can be returned to Bristol for repair, upgrade, exchange, or to verify proper operation, form (GBU 13.01) must be completed in order to obtain a RA (Return
Authorization) number and thus ensure an optimal lead time. Completing the form is very important since the information permits the Bristol Repair Dept. to effectively and efficiently process the repair order.
You can easily obtain a RA number by:
A. FAX
Completing the form (GBU 13.01) and faxing it to (860) 945-3875. A Bristol Repair
Dept. representative will return call (or other requested method) with a RA number.
B. E-MAIL
Accessing the form (GBU 13.01) via the Bristol Web site (www.bristolbabcock.com) and sending it via E-Mail to [email protected]
. A Bristol Repair Dept. representative will return E-Mail (or other requested method) with a RA number.
C. Mail
Mail the form (GBU 13.01) to
Bristol Inc.
Repair
1100 Buckingham Street
Watertown, CT 06795
A Bristol Repair Dept. representative will return call (or other requested method) with a RA number.
D. Phone
Calling the Bristol Repair Department at (860) 945-2442. A Bristol Repair Department representative will record a RA number on the form and complete Part I, then send the form to the Customer via fax (or other requested method) for Customer completion of Parts II & III.
A copy of the completed Repair Authorization Form with issued RA number should be included with the product being returned. This will allow us to quickly track, repair, and return your product to you.
Bristol
Repair Authorization Form
(off-line completion)
(Providing this information will permit Bristol to effectively and efficiently process your return. Completion is required to receive optimal lead time. Lack of information may result in increased lead times.)
Date___________________ RA #___________________SH
Standard Repair Practice is as follows: Variations to this is practice may be requested in the “Special Requests” section.
•
Evaluate / Test / Verify Discrepancy
•
Repair / Replace / etc. in accordance with this form
•
Return to Customer
Line No.____________
Please be aware of the Non warranty standard charge:
•
There is a $100 minimum evaluation charge, which is applied to the repair if applicable (
√
in “returned”
B,C, or D of part III below)
Part I Please complete the following information for single unit or multiple unit returns
Address No.
Bill to :
Purchase Order:
Phone:
(office use only) Address No.
Ship to:
Fax:
(office use only)
Contact Name: ____________________________________
E-Mail:
Model No./Part No. Description
Range/Calibration S/N
Reason for return : Failure Upgrade Verify Operation Other
1.
Describe the conditions of the failure (Frequency/Intermittent, Physical Damage, Environmental Conditions,
Communication, CPU watchdog, etc.)
(Attach a separate sheet if necessary)
2. Comm. interface used: Standalone RS-485 Ethernet Modem (PLM (2W or 4W) or SNW) Other: ______________
3. What is the Firmware revision? _____________________ What is the Software & version?
Part III If checking “replaced” for any question below, check an alternate option if replacement is not available
A.
If product is within the warranty time period but is excluded due to Bristol’s warranty clause, would you like the product: repaired returned replaced scrapped?
B.
If product were found to exceed the warranty period, would you like the product:
C.
If product is deemed not repairable would you like your product: repaired returned replaced scrapped? returned replaced scrapped?
D.
If Bristol is unable to verify the discrepancy, would you like the product: returned replaced *see below?
* Continue investigating by contacting the customer to learn more about the problem experienced? The person to contact that has the most knowledge of the problem is: ______________________________ phone_____________________
If we are unable to contact this person the backup person is: _________________________ phone_____________________
Special Requests: ____________________________________________________________________________________
____________________________________________________________________________________________________
Ship prepaid to: Bristol Inc., Repair Dept., 1100 Buckingham Street, Watertown, CT 06795
Phone: 860-945-2442 Fax: 860-945-2220 Form GBU 13.01 Rev. C 04/27/06
Bristol
Training
GET THE MOST FROM YOUR BRISTOL
BABCOCK INSTRUMENT OR SYSTEM
• Avoid Delays and problems in getting your system on-line
• Minimize installation, start-up and maintenance costs.
• Make the most effective use of our hardware and software.
• Know your system.
As you know, a well-trained staff is essential to your operation. Bristol Inc. offers a full schedule of classes conducted by full-time, professional instructors. Classes are offered throughout the year at three locations: Houston, Orlando and our Watertown, CT headquarters. By participating in our training, your personnel can learn how to install, calibrate, configure, program and maintain any and all Bristol products and realize the full potential of your system.
For information or to enroll in any class, contact our training department in Watertown at
(860) 945-2343. For Houston classes, you can also contact our Houston office, at (713) 685-
6200.
A Few Words About Bristol Inc.
For over 100 years, Bristol ® has been providing innovative solutions for the measurement and control industry. Our product lines range from simple analog chart recorders, to sophisticated digital remote process controllers and flow computers, all the way to turnkey
SCADA systems. Over the years, we have become a leading supplier to the electronic gas measurement, water purification, and wastewater treatment industries.
On off-shore oil platforms, on natural gas pipelines, and maybe even at your local water company, there are Bristol Inc. instruments, controllers, and systems running year-in and year-out to provide accurate and timely data to our customers.
Getting Additional Information
In addition to the information contained in this manual, you may receive additional assistance in using this product from the following sources:
Help Files / Release Notes
Many Bristol software products incorporate help screens. In addition, the software typically includes a ‘read me’ release notes file detailing new features in the product, as well as other information which was available too late for inclusion in the manual.
Contacting Bristol Inc. Directly
Bristol's world headquarters is located at 1100 Buckingham Street, Watertown,
Connecticut 06795, U.S.A.
Our main phone numbers are:
(860) 945-2200
(860) 945-2213 (FAX)
Regular office hours are Monday through Friday, 8:00AM to 4:30PM Eastern Time, excluding holidays and scheduled factory shutdowns. During other hours, callers may leave messages using Bristol's voice mail system.
Telephone Support - Technical Questions
During regular business hours, Bristol's Application Support Group can provide telephone support for your technical questions.
For technical questions about TeleFlow products call (860) 945-8604.
For technical questions about Control Wave call (860) 945-2394 or (860) 945-2286.
For technical questions regarding Bristol’s OpenEnterprise product, call (860) 945-3865 or e-mail: [email protected]
For technical questions regarding ACCOL products, OpenBSI Utilities , UOI and all other software except for Control Wave and OpenEnterprise products, call (860) 945-2286.
For technical questions about Network 3000 hardware, call (860) 945-2502.
You can e-mail the Application Support Group at: [email protected]
The Application Support Group maintains an area on our web site for software updates and technical information. Go to: www.bristolbabcock.com/services/techsupport/
For assistance in interfacing Bristol hardware to radios, contact Bristol’s Communication
Technology Group in Orlando, FL at (407) 629-9463 or (407) 629-9464 .
You can e-mail the Communication Technology Group at: [email protected]
Telephone Support - Non-Technical Questions, Product Orders, etc.
Questions of a non-technical nature (product orders, literature requests, price and delivery information, etc.) should be directed to the nearest sales office (listed on the rear cover of this manual) or to your Bristol-authorized sales representative.
Please call the main Bristol Inc. number (860-945-2200) if you are unsure which office covers your particular area.
Visit our Site on the World Wide Web
For general information about Bristol Inc. and its products, please visit our site on the
World Wide Web at: www.bristolbabcock.com
Training Courses
Bristol’s Training Department offers a wide variety of courses in Bristol hardware and software at our Watertown, Connecticut headquarters, and at selected Bristol regional offices, throughout the year. Contact our Training Department at (860) 945-2343 for course information, enrollment, pricing, and scheduling.
PIP-EXPTIBS
EXPANSION TRANSMITTER INTERFACE BOARD
PT. Number 392951-01-0
Product Information Package
TABLE OF CONTENTS
SECTION TITLE
1.1
1.1.1
1.2
1.3
PAGE #
DESCRIPTION................................................................................................................... 1
Transmitter Operation......................................................................................................... 1
LED INDICATORS............................................................................................................ 2
JUMPER JP1 ...................................................................................................................... 2
2.1
2.1.1
2.1.2
2.2
2.2.1
Section 2 – INSTALLATION & SERVICE
REMOVAL/REPLACEMENT & INSTALLATION OF THE ETIB................................ 3
Removal/Replacement of the Expansion Transmitter Interface Board .............................. 3
Installation of the Expansion Transmitter Interface Board Option .................................... 6
FIELD WIRING ................................................................................................................. 7
Terminal Connections......................................................................................................... 7
3.1
3.2
GENERAL SPECIFICATION............................................................................................ 9
ENVIRONMENTAL SPECIFICATIONS ......................................................................... 9
SUPPLEMENTS
PIP-EXPTIBS Page 0-1 Table Of Contents
BLANK PAGE
Section 1
INTRODUCTION
1.1 DESCRIPTION
Expansion Transmitter Interface Boards (ETIBs) allow up to two (2) Bristol, Series 3508C
Transmitters to communicate with an ACCOL loaded host TeleFlow Plus Electronic Gas
Measurement Computer (EGMC) (3530-20B) or TeleRTU Plus (3530-25B). The EGMC/RTU polls and stores data from each transmitter and communicates with the network. Two
LEDS on the ETIB Board [CD (DS1) & RTS (DS2)] indicate the communication status.
The ETIB Board is housed in either the standard TeleFlow Plus or TeleRTU Plus enclosure and is interfaced to a TeleFlow/TeleRTU CPU Board via the CPU Board’s Expansion Connector. Power from and communication with the host CPU Board is supplied through the
Expansion Connector. ETIB Boards contain one jumper (JP1) for configuration purposes.
1.1.1 Transmitter Operation
Each Transmitter must be assigned a unique address via the SMARTKIT program as described in Section 4.2 PROGRAM LOADING AND STARTUP of the appropriate 3508
Transmitter manual. Additionally, all Transmitters wired to the TI Board must be operated in the minimum current mode (3.8 mA). This mode is selected via the SMARTKIT program as described in Section 4.7 TRANSMITTER OPERATING MODES of the appropriate 3508
Transmitter manual, i.e., CI-3508-10C, CI-3508-30C or CI-3508-99C.
Figure 1 - Transmitter Interface Board P/N 392951-01-0
PIP-EXPTIBS Page
1.2 LED INDICATORS
The ETIB contains two LEDs which have the following functions: Carrier Detect (CD) and
Request to Send (RTS). When the board is sending a Request To Send, LED DS2 (RTS) will be ON and LED DS1 (CD) will be OFF. Conversely, when the ETIB is receiving data from a
3508 Transmitter, LED DS2 (RTS) will be OFF and LED DS1 - Carrier Detect (CD) will be
ON.
1.3 JUMPER JP1
Jumper JP1 is used to configure the ETIB for operation with one or two 3508 Transmitters.
If only one 3508 Transmitter is to be connected to the ETIB, Jumper JP1 must be installed across JP1-1 and JP1-2. Additionally, when only one 3508 Transmitter is to be connected to the ETIB, it must be connected to connector TB1. When two 3508 Transmitters are connected to the ETIB, Jumper JP1 must be removed and stored in either JP1-1 or JP1-2.
PIP-EXPTIBS Page
Section 2
INSTALLATION & SERVICE
2.1 REMOVAL/REPLACEMENT & INSTALLATION OF THE ETIB
2.1.1 Removal/Replacement of the Expansion Transmitter Interface Bd.
An installed ETIB option will contain the following parts:
1. Expansion Transmitter Interface Board (ETIB) (with removable Terminal Blocks)
2. Three #8-32 x 1/4
”
SEM Screws
3. Three #4-40 x 15/32
”
Standoffs
Figure 2 - Expansion Transmitter Interface Bd. Mounted on TeleFlow CPU Board
PIP-EXPTIBS Page
Figure 3 - Expansion TIB Mounted on TeleRTU CPU Board
To remove the optional Expansion Transmitter Interface Board, follow steps 1 through 7 below. To replace the ETIB Board follow steps 2 and 6 below in reverse order, installing rather than removing the item in question and then perform step 7 (see Figures 4 & 5).
Note:
Any PC Board is not to be removed under any circumstances unless the
TeleFlow/TeleRTU has been moved to an ESD safe area (see ESDS Manual S14006).
The CPU Board should typically only be removed to replace the on board Lithium
Battery or Fuse F1 or to install an optional I/O Expansion Board or an Expansion
TIB Board.
PIP-EXPTIBS Page
1. Open the Instrument Front Cover (Door).
2. Disconnect power by removing harness connector plug (P8 for TeleFlow - P2 for
TeleRTU) from the CPU Board edge connector (J8 for TeleFlow - J2 for TeleRTU).
3. Unplug the remaining removable Terminal Blocks (with wiring harnesses installed) from the CPU Board’s front edge connectors.
4. Unplug the removable Terminal Blocks (with wiring harnesses installed) from the optional ETIB Board.
Figure 4 - Horizontally Mounted TeleFlow CPU & Expansion ETIB
5. Remove the two screws that secure the CPU Board’s Sliding Mounting Bracket to the
Fixed Bracket on the bottom of the Battery Bracket. Carefully slide the CPU Board (and optional ETIB Board) toward the front of the unit and remove harness connections from the Front Panel Switch (J12 on TeleFlow CPU - J14 on TeleRTU CPU), the Display
Module (J2 on TeleFlow CPU - J17 on TeleRTU CPU), the Wakeup Switch (J3 on
TeleFlow CPU - J16 on TeleRTU CPU), and for TeleFlow CPU Boards connector J1 associated with the Multivariable Transducer.
Figure 5 - Horizontally Mounted TeleRTU CPU & Expansion ETIB
6. Remove the 3 screws that secure the ETIB Board to the standoffs and carefully remove the ETIB Board toward the front of the unit.
PIP-EXPTIBS Page
Note: If a replacement Expansion Transmitter Interface Board is available follow steps 2 through 6 in reverse order (after configuring Jumper JP1
(see Section 1.3), installing rather than removing the item in question.
7. Close and Secure the Door.
Figure 6 - Bottom View of TeleRTU Plus (Similar to TeleFlow Plus)
2.1.2 Installation of the Expansion Transmitter Interface Board Option
1. Open the Instrument Front Cover and remove the CPU Board (see Section 2.1.1 - steps
2 through 5).
2. Replace the three screws that secure the CPU Board to the Mounting standoffs with #4-
40 x 15/32
”
Standoffs (see Section 2.1.1 - Figures 4 & 5).
3. Install the ETIB Board onto the CPU Board in question making sure that the
Expansion Connectors properly mate. Secure the ETIB Board to the three mounting standoffs with three #8-32 x 1/4
”
screws.
4. Reinstall the CPU Board (with ETIB) into the TeleFlow or TeleRTU (see Section 2.1.1).
5. Install 3508 Transmitter wiring to the ETIB Board (see Section 2.2.1). Wiring should be routed through a 3/4
”
conduit fitting (user installed) on the bottom of the enclosure (see
Figure 6).
6. Close and Secure the Instrument Front Cover.
PIP-EXPTIBS Page
2.2 FIELD WIRING
The device uses compression-type terminals that accommodate up to #14 AWG wire. A connection is made by inserting the bared end (1/4 inch Max.) into the clamp beneath the screw and then securing the screw. Insert the bared end fully to prevent short circuits.
Allow some slack in the wires when making terminal connections. The slack makes the connections more manageable and minimizes mechanical strain on the printed circuit boards and harnesses.
2.2.1 Terminal Connections
ETIB Boards contain two terminal blocks that field wiring connections to the transmitter(s). TB1 & TB2 are two-position Terminal Blocks which connect to the signal/power inputs of the transmitters.
Figure 7 - Internally Powered Transmitter Field Wiring
PIP-EXPTIBS Page
TABLE 1 - ETIB BOARD TERMINAL DESIGNATIONS
LPTIB
TB#
LPTIB
TB NAME
CONNECTION if PDB.
Is Present
TB1-1 XMTR1- 3508-
TB1-2 XMTR1+ 3508+
TB2-1 XMTR2- 3508-
3530-20B
CONNECTION
If no PDB.
3508-
3508+
3508-
3530-25B
CONNECTION
If no PDB.
3508-
3508+
3508-
TB2-2 XMTR2+ 3508+ 3508+ 3508+
ETIB Boards may be connected to internally powered transmitters. Connection to internally powered transmitters (powered from ETIB’s on-board +12V Supply/Regulator) is illustrated in Figure 7.
PIP-EXPTIBS Page
Section 3
SPECIFICATIONS
3.1 GENERAL SPECIFICATIONS
Communication Interface:
3508-10C/30C Interface:
ESD Susceptibility:
EMI Compatibility: comparable or superior to associated electronics.
Transient Susceptibility:
RS-232 ( ± 3V minimum)
FSK Modem - Bell 202 Compatible
(1200 Hz/2200 Hz modulation)
Field connected circuits are designed to meet the requirements of IEC 801-2 for ESD withstand capability up to 10KV.
Designed to coexist within a shielded enclosure with the TeleFlow (3530-20B) or the TeleRTU (3530-25B) electronics. EMI radiation is insignificant and susceptibility is
Field connected circuits are designed to meet the requirements of ANSI/-
IEEEC37.90-1998 (Formerly IEEE 472) for surge withstand capability.
3.2 ENVIRONMENTAL SPECIFICATIONS
Operating Temperature:
Storage Temperature:
Relative Humidity:
Vibration:
-40°C to +60°C (-40°F to +140°F)
-40°C to +85°C (-40°F to +185°C)
15% - 95% Non-condensing
1G for 10Hz to 500Hz per SAMA PMC-31-1
(without damage or impairment)
PIP-EXPTIBS Page
BLANK PAGE
Expansion Transmitter Interface Board
Special Instructions for Class I, Division 2 Hazardous Locations
1. The Bristol Expansion Transmitter Interface Board (ETIB) is listed by Underwriters
Laboratories (UL) as nonincendive and is suitable for use in Class I, Division 2, Groups
A, B, C and D hazardous locations or non-hazardous locations only. Read this document carefully before installing a nonincendive Bristol ETIB Board. In the event of a conflict between the ETIB Board User Manual (PIP-EXPTIBS) and this document, always follow the instructions in this document.
2. Wiring must be performed in accordance with Class I, Division 2 wiring methods as defined in Article 501-4 (b) of the National Electrical Code, NFPA 70 for installations within the United States, or as specified in Section 18-152 of the Canadian Electrical
Code for installation in Canada.
3. WARNING: EXPLOSION HAZARD - Substitution of components may impair suitability for use in Class I, Division 2 environments.
4. WARNING: EXPLOSION HAZARD - When situated in a hazardous location, turnoff power before servicing/replacing the unit and before installing or removing I/O wiring.
5. WARNING: EXPLOSION HAZARD - Do Not disconnect equipment unless the power has been switched off or the area is known to be nonhazardous.
03/14/2007 Appendix A of PIP-EXPTIBS - ETIB Board Page 1 of 1
BLANK PAGE
BLANK PAGE
Product Information Package
Expansion Transmitter Interface Board Part No. 392951-01-0
PIP-EXPTIBS
Mar., 2007
Emerson Process Management
Bristol, Inc.
1100 Buckingham Street
Watertown, CT 06795
Phone: +1 (860) 945-2262
Fax: +1 (860) 945-2525 www.EmersonProcess.com/Bristol
Emerson Electric Canada, Ltd.
Bristol Canada
6338 Viscount Rd.
Mississauga, Ont. L4V 1H3
Canada
Phone: 905-362-0880
Fax: 905-362-0882 www.EmersonProcess.com/Bristol
Emerson Process Management
BBI, S.A. de C.V.
Homero No. 1343, 3er Piso
Col. Morales Polanco
11540 Mexico, D.F.
Mexico
Phone: (52-55)-52-81-81-12
Fax: (52-55)-52-81-81-09 www.EmersonProcess.com/Bristol
Emerson Process Management
Bristol Babcock, Ltd.
Blackpole Road
Worcester, WR3 8YB
United Kingdom
Phone: +44 1905 856950
Fax: +44 1905 856969 www.EmersonProcess.com/Bristol
Emerson Process Management
Bristol, Inc.
22 Portofino Crescent,
Grand Canals Bunbury, Western Australia 6230
Mail to: PO Box 1987 (zip 6231)
Phone: +61 (8) 9725-2355
Fax: +61 (8) 8 9725-2955 www.EmersonProcess.com/Bristol
The information in this document is subject to change without notice. Every effort has been made to supply complete and accurate information. However, Bristol, Inc. assumes no responsibility for any errors that may appear in this document.
If you have comments or questions regarding this manual, please direct them to your local Bristol sales representative, or direct them to one of the addresses listed at left.
Bristol, Inc. does not guarantee the accuracy, sufficiency or suitability of the software delivered herewith. The Customer shall inspect and test such software and other materials to his/her satisfaction before using them with important data.
There are no warranties, expressed or implied, including those of merchantability and fitness for a particular purpose, concerning the software and other materials delivered herewith.
TeleFlow
™
is a trademark of Bristol, Inc. The Emerson logo is a trade mark and service mark of Emerson Electric Co. Other trademarks or copyrighted products mentioned in this document are for information only, and belong to their respective companies, or trademark holders.
Copyright (c) 2007, Bristol, Inc., 1100 Buckingham St., Watertown, CT 06795. No part of this manual may be reproduced in any form without the express written permission of
Bristol, Inc.
Product Information Package
PIP-EXPTIBTF
Mar., 2007 TeleFlow Series 3530-10B/15B/20B/25B/35B/50B
Expansion Transmitter Interface
Board Part No. 392960-01-0
For The Following Bristol Instruction Manuals:
CI-3530-10B, CI-3530-15B, CI-3530-20B,
CI-3530-25B, CI-3530-35B & CI-3530-50B
www.EmersonProcess.com/Bristol
IMPORTANT! READ INSTRUCTIONS BEFORE STARTING!
Be sure that these instructions are carefully read and understood before any operation is attempted. Improper use of this device in some applications may result in damage or injury. The user is urged to keep this book filed in a convenient location for future reference.
These instructions may not cover all details or variations in equipment or cover every possible situation to be met in connection with installation, operation or maintenance. Should problems arise that are not covered sufficiently in the text, the purchaser is advised to contact Bristol for further information.
EQUIPMENT APPLICATION WARNING
The customer should note that a failure of this instrument or system, for whatever reason, may leave an operating process without protection. Depending upon the application, this could result in possible damage to property or injury to persons.
It is suggested that the purchaser review the need for additional backup equipment or provide alternate means of protection such as alarm devices, output limiting, failsafe valves, relief valves, emergency shutoffs, emergency switches, etc. If additional in-formation is required, the purchaser is advised to contact Bristol .
RETURNED EQUIPMENT WARNING
When returning any equipment to Bristol for repairs or evaluation, please note the following: The party sending such materials is responsible to ensure that the materials returned to Bristol are clean to safe levels, as such levels are defined and/or determined by applicable federal, state and/or local law regulations or codes. Such party agrees to indemnify Bristol and save Bristol harmless from any liability or damage which Bristol may incur or suffer due to such party's failure to so act.
ELECTRICAL GROUNDING
Metal enclosures and exposed metal parts of electrical instruments must be grounded in accordance with OSHA rules and regulations pertaining to "Design
Safety Standards for Electrical Systems," 29 CFR, Part 1910, Subpart S, dated: April
16, 1981 (OSHA rulings are in agreement with the National Electrical Code).
The grounding requirement is also applicable to mechanical or pneumatic instruments that include electrically-operated devices such as lights, switches, relays, alarms, or chart drives.
EQUIPMENT DAMAGE FROM ELECTROSTATIC DISCHARGE VOLTAGE
This product contains sensitive electronic components that can be damaged by exposure to an electrostatic discharge (ESD) voltage. Depending on the magnitude and duration of the ESD, this can result in erratic operation or complete failure of the equipment. Read supplemental document S14006 at the back of this manual for proper care and handling of ESD-sensitive components.
Bristol 1100 Buckingham Street, Watertown, CT 06795
Telephone (860) 945-2200
WARRANTY
A. Bristol warrants that goods described herein and manufactured by Bristol are free from defects in material and workmanship for one year from the date of shipment unless otherwise agreed to by Bristol in writing.
B. Bristol warrants that goods repaired by it pursuant to the warranty are free from defects in material and workmanship for a period to the end of the original warranty or ninety (90) days from the date of delivery of repaired goods, whichever is longer.
C. Warranties on goods sold by, but not manufactured by Bristol, are expressly limited to the terms of the warranties given by the manufacturer of such goods.
D. All warranties are terminated in the event that the goods or systems or any part thereof are (i) misused, abused or otherwise damaged, (ii) repaired, altered or modified without Bristol's consent, (iii) not installed, maintained and operated in strict compliance with instructions furnished by Bristol, or (iv) worn, injured or damaged from abnormal or abusive use in service time.
E. THESE WARRANTIES ARE EXPRESSLY IN LIEU OF ALL OTHER
WARRANTIES EXPRESS OR IMPLIED (INCLUDING WITHOUT LIMITATION
WARRANTIES AS TO MERCHANTABILITY AND FITNESS FOR A PARTICULAR
PURPOSE), AND NO WARRANTIES, EXPRESS OR IMPLIED, NOR ANY
REPRESENTATIONS, PROMISES, OR STATEMENTS HAVE BEEN MADE BY
BRISTOL UNLESS ENDORSED HEREIN IN WRITING. FURTHER, THERE ARE
NO WARRANTIES WHICH EXTEND BEYOND THE DESCRIPTION OF THE
FACE HEREOF.
F. No agent of Bristol is authorized to assume any liability for it or to make any written or oral warranties beyond those set forth herein.
REMEDIES
A. Buyer's sole remedy for breach of any warranty is limited exclusively to repair or replacement without cost to Buyer of any goods or parts found by Seller to be defective if Buyer notifies Bristol in writing of the alleged defect within ten (10) days of discovery of the alleged defect and within the warranty period stated above, and if the Buyer returns such goods to Bristol's Watertown office, unless Bristol's Watertown office designates a different location, transportation prepaid, within thirty (30) days of the sending of such notification and which upon examination by Bristol proves to be defective in material and workmanship. Bristol is not responsible for any costs of removal, dismantling or reinstallation of allegedly defective or defective goods. If a Buyer does not wish to ship the product back to Bristol, the Buyer can arrange to have a Bristol service person come to the site. The Service person's transportation time and expenses will be for the account of the Buyer. However, labor for warranty work during normal working hours is not chargeable.
B. Under no circumstances will Bristol be liable for incidental or consequential damages resulting from breach of any agreement relating to items included in this quotation, from use of the information herein or from the purchase or use by Buyer, its em-ployees or other parties of goods sold under said agreement.
How to return material for Repair or Exchange
Before a product can be returned to Bristol for repair, upgrade, exchange, or to verify proper operation, form (GBU 13.01) must be completed in order to obtain a RA (Return
Authorization) number and thus ensure an optimal lead time. Completing the form is very important since the information permits the Bristol Repair Dept. to effectively and efficiently process the repair order.
You can easily obtain a RA number by:
A. FAX
Completing the form (GBU 13.01) and faxing it to (860) 945-3875. A Bristol Repair
Dept. representative will return call (or other requested method) with a RA number.
B. E-MAIL
Accessing the form (GBU 13.01) via the Bristol Web site (www.bristolbabcock.com) and sending it via E-Mail to [email protected]
. A Bristol Repair Dept. representative will return E-Mail (or other requested method) with a RA number.
C. Mail
Mail the form (GBU 13.01) to
Bristol Inc.
Repair
1100 Buckingham Street
Watertown, CT 06795
A Bristol Repair Dept. representative will return call (or other requested method) with a RA number.
D. Phone
Calling the Bristol Repair Department at (860) 945-2442. A Bristol Repair Department representative will record a RA number on the form and complete Part I, then send the form to the Customer via fax (or other requested method) for Customer completion of Parts II & III.
A copy of the completed Repair Authorization Form with issued RA number should be included with the product being returned. This will allow us to quickly track, repair, and return your product to you.
Bristol
Repair Authorization Form
(off-line completion)
(Providing this information will permit Bristol to effectively and efficiently process your return. Completion is required to receive optimal lead time. Lack of information may result in increased lead times.)
Date___________________ RA #___________________SH
Standard Repair Practice is as follows: Variations to this is practice may be requested in the “Special Requests” section.
•
Evaluate / Test / Verify Discrepancy
•
Repair / Replace / etc. in accordance with this form
•
Return to Customer
Line No.____________
Please be aware of the Non warranty standard charge:
•
There is a $100 minimum evaluation charge, which is applied to the repair if applicable (
√
in “returned”
B,C, or D of part III below)
Part I Please complete the following information for single unit or multiple unit returns
Address No.
Bill to :
Purchase Order:
Phone:
(office use only) Address No.
Ship to:
Fax:
(office use only)
Contact Name: ____________________________________
E-Mail:
Model No./Part No. Description
Range/Calibration S/N
Reason for return : Failure Upgrade Verify Operation Other
1.
Describe the conditions of the failure (Frequency/Intermittent, Physical Damage, Environmental Conditions,
Communication, CPU watchdog, etc.)
(Attach a separate sheet if necessary)
2. Comm. interface used: Standalone RS-485 Ethernet Modem (PLM (2W or 4W) or SNW) Other: ______________
3. What is the Firmware revision? _____________________ What is the Software & version?
Part III If checking “replaced” for any question below, check an alternate option if replacement is not available
A.
If product is within the warranty time period but is excluded due to Bristol’s warranty clause, would you like the product: repaired returned replaced scrapped?
B.
If product were found to exceed the warranty period, would you like the product:
C.
If product is deemed not repairable would you like your product: repaired returned replaced scrapped? returned replaced scrapped?
D.
If Bristol is unable to verify the discrepancy, would you like the product: returned replaced *see below?
* Continue investigating by contacting the customer to learn more about the problem experienced? The person to contact that has the most knowledge of the problem is: ______________________________ phone_____________________
If we are unable to contact this person the backup person is: _________________________ phone_____________________
Special Requests: ____________________________________________________________________________________
____________________________________________________________________________________________________
Ship prepaid to: Bristol Inc., Repair Dept., 1100 Buckingham Street, Watertown, CT 06795
Phone: 860-945-2442 Fax: 860-945-2220 Form GBU 13.01 Rev. C 04/27/06
Bristol
Training
GET THE MOST FROM YOUR BRISTOL
BABCOCK INSTRUMENT OR SYSTEM
• Avoid Delays and problems in getting your system on-line
• Minimize installation, start-up and maintenance costs.
• Make the most effective use of our hardware and software.
• Know your system.
As you know, a well-trained staff is essential to your operation. Bristol Inc. offers a full schedule of classes conducted by full-time, professional instructors. Classes are offered throughout the year at three locations: Houston, Orlando and our Watertown, CT headquarters. By participating in our training, your personnel can learn how to install, calibrate, configure, program and maintain any and all Bristol products and realize the full potential of your system.
For information or to enroll in any class, contact our training department in Watertown at
(860) 945-2343. For Houston classes, you can also contact our Houston office, at (713) 685-
6200.
A Few Words About Bristol Inc.
For over 100 years, Bristol ® has been providing innovative solutions for the measurement and control industry. Our product lines range from simple analog chart recorders, to sophisticated digital remote process controllers and flow computers, all the way to turnkey
SCADA systems. Over the years, we have become a leading supplier to the electronic gas measurement, water purification, and wastewater treatment industries.
On off-shore oil platforms, on natural gas pipelines, and maybe even at your local water company, there are Bristol Inc. instruments, controllers, and systems running year-in and year-out to provide accurate and timely data to our customers.
Getting Additional Information
In addition to the information contained in this manual, you may receive additional assistance in using this product from the following sources:
Help Files / Release Notes
Many Bristol software products incorporate help screens. In addition, the software typically includes a ‘read me’ release notes file detailing new features in the product, as well as other information which was available too late for inclusion in the manual.
Contacting Bristol Inc. Directly
Bristol's world headquarters is located at 1100 Buckingham Street, Watertown,
Connecticut 06795, U.S.A.
Our main phone numbers are:
(860) 945-2200
(860) 945-2213 (FAX)
Regular office hours are Monday through Friday, 8:00AM to 4:30PM Eastern Time, excluding holidays and scheduled factory shutdowns. During other hours, callers may leave messages using Bristol's voice mail system.
Telephone Support - Technical Questions
During regular business hours, Bristol's Application Support Group can provide telephone support for your technical questions.
For technical questions about TeleFlow products call (860) 945-8604.
For technical questions about Control Wave call (860) 945-2394 or (860) 945-2286.
For technical questions regarding Bristol’s OpenEnterprise product, call (860) 945-3865 or e-mail: [email protected]
For technical questions regarding ACCOL products, OpenBSI Utilities , UOI and all other software except for Control Wave and OpenEnterprise products, call (860) 945-2286.
For technical questions about Network 3000 hardware, call (860) 945-2502.
You can e-mail the Application Support Group at: [email protected]
The Application Support Group maintains an area on our web site for software updates and technical information. Go to: www.bristolbabcock.com/services/techsupport/
For assistance in interfacing Bristol hardware to radios, contact Bristol’s Communication
Technology Group in Orlando, FL at (407) 629-9463 or (407) 629-9464 .
You can e-mail the Communication Technology Group at: [email protected]
Telephone Support - Non-Technical Questions, Product Orders, etc.
Questions of a non-technical nature (product orders, literature requests, price and delivery information, etc.) should be directed to the nearest sales office (listed on the rear cover of this manual) or to your Bristol-authorized sales representative.
Please call the main Bristol Inc. number (860-945-2200) if you are unsure which office covers your particular area.
Visit our Site on the World Wide Web
For general information about Bristol Inc. and its products, please visit our site on the
World Wide Web at: www.bristolbabcock.com
Training Courses
Bristol’s Training Department offers a wide variety of courses in Bristol hardware and software at our Watertown, Connecticut headquarters, and at selected Bristol regional offices, throughout the year. Contact our Training Department at (860) 945-2343 for course information, enrollment, pricing, and scheduling.
PIP-EXPTIBTF
EXPANSION TRANSMITTER INTERFACE
BOARD
PT. Number 392960-01-0
Product Information Package
TABLE OF CONTENTS
SECTION TITLE
1.1 DESCRIPTION .................................................................................................... 1
Operation ........................................................................................ 1
1.2 Features................................................................................................................ 2
1.3 JUMPER
Section 2 – INSTALLATION & SERVICE
REMOVAL/REPLACEMENT & INSTALLATION OF THE ETIB................... 3
Removal/Replacement of the Expansion Transmitter Interface Board ............ 3
2.1
2.1.1
2.1.1.1
2.1.1.2
Installation/Removal for Models 3530-10B, -15B & -50B.................................. 3
Installation/Removal for Models 353-20B & -25B............................................ 10
2.1.1.3 Installation/Removal for Model 3530-35B........................................................ 12
2.2 FIELD
2.2.1.1
2.2.1.2
2.2.1.3
WIRING ................................................................................................. 13
2.2.1 Terminal
Terminal Connections for Model 3808 Transmitters....................................... 14
Terminal Connections for a single Model 3508 Transmitter........................... 14
Trminal Connections for two Model 3508 Transmitters.................................. 15
3.1 GENERAL
SPECIFICATIONS ......................................................... 17
SPECIFICATION ........................................................................... 17
3.2 ENVIRONMENTAL
SUPPLEMENTS
PIP-EXPTIBTF Page 0-1 Table Of Contents
BLANK PAGE
Section 1
1.1 DESCRIPTION
INTRODUCTION
Expansion Transmitter Interface Boards (ETIBs) allow up to two (2) Bristol, Series 3508 or
Series 3808 Transmitters to communicate with an ACCOL loaded host TeleFlow or
TeleFlow Plus Electronic Gas Measurement Computer (EGMC) (3530-10B/20B), a
TeleRTU, TeleRTU Plus or TeleRTU Module (3530-15B/25B/35B) or a TeleFlow Corrector
(3530-50B). The TeleFlow EGMC/RTU/Corrector polls and stores data from each transmitter and communicates with the network.
The ETIB Board interfaced to a TeleFlow/TeleRTU CPU Board via the CPU Board’s
Expansion Connector. Power from and communication with the host CPU Board is supplied through the Expansion Connector. ETIB Boards contain one jumper (JP1) for configuration.
1.1.1 Transmitter Operation
3508 Series
Each Model 3508 Transmitter must be assigned a unique address via the SMARTKIT program as described in Section 4.2 PROGRAM LOADING AND STARTUP of the appropriate 3508 Transmitter manual. Additionally, all Model 3508 Transmitters wired to the TI Board must be operated in the minimum current mode (3.8 mA). This mode is selected via the SMARTKIT program as described in Section 4.7 TRANSMITTER
OPERATING MODES of the appropriate 3508 Transmitter manual, i.e., CI-3508-10C, CI-
3508-30C or CI-3508-99C.
PIP-EXPTIBTF
Figure 1 - Transmitter Interface Board P/N 392960-01-0
Page 1 Expansion TIB Option
3808 MVT Series
Each Model 3808 MVT Transmitter must be assigned a unique address via the WebBSI
Sign On/Off Menu (see Section 3 of Customer Instruction Manual CI-3808). Additionally, only analog versions of the 3808 MVT can be interfaced to a Transmitter Interface Board.
1.1.2 Features
• ESD & Transient Susceptibility
Field connected circuitry has been designed to meet the requirements of IEC 801-2 for ESD withstand capability up to 10KV and the requirements of ANSI/IEEE
C37.90.1-1989 (formerly IEE 472) for surge withstand capability.
• EMI Compatibility
ETIB Boards have been designed to coexist inside a shielded enclosure with the
TeleFlow ™ electronics. EMI radiation is insignificant and susceptibility is comparable or superior to associated electronics.
• Mounting
The ETIB Board measures 3.75” (9.525cm) in width x 4.0” (10.160cm) in height and mounts piggy-back on a TeleFlow or TeleRTU CPU Board.
1.2 JUMPER JP1
Jumper JP1 is used to configure the ETIB for operation with one or two 3508/3808 Transmitters. If only one 3508/3808 Transmitter is to be connected to the ETIB, Jumper JP1 must be installed across JP1-1 and JP1-2. Additionally, when only one 3508/3808
Transmitter is to be connected to the ETIB, it must be connected to connector TB1. When two 3508/3808 Transmitters are connected to the ETIB, Jumper JP1 must be removed and stored in either JP1-1 or JP1-2.
Expansion TIB Option Page 2 PIP-EXPTIBTF
Section 2
INSTALLATION & SERVICE
2.1 REMOVAL/REPLACEMENT & INSTALLATION OF THE ETIB
2.1.1 Removal/Replacement of the Expansion Transmitter Interface Bd.
An installed ETIB option will contain the following parts:
1. Expansion Transmitter Interface Board (ETIB) (with removable Terminal Blocks)
2. Three #4-40 x 15/32” Standoffs (Note: Models 3530-10B, -15B & -50B will also contain
Three (3) #4-40 x .188” Standoffs & Two (2) #4-40 x 1/8” SEM Screws)
3. Modified PC Shield Assembly (for models 3530-10B, -15B & -50B)
WARNING
Never attempt to service a TeleFlow or TeleRTU while it is powered and operating in a hazardous environment.
Either the area must be made safe or the unit must be powered down, unwired, unmounted, and taken to a safe, non-hazardous area.
WARNING
Never attempt to install or remove any components
(PCBs, Field Wiring, Transducers, etc.) while the unit is powered and running. Doing so can cause sudden electrical transients or imbalances that are capable of causing damage to the module or component in question, as well as other associated circuit boards. Always turn off the external/internal power source, including any additional supply sources used for externally-powered
I/O circuits, before changing or adding any components.
CAUTION
Place any related critical processes under manual or auxiliary control prior to shutting down or performing any of the steps discussed herein.
2.1.1.1 Installation/Removal for Models 3530-10B, -15B & -50B
To install the optional ETIB option into a model 3530-10B, -15B or -50B, follow steps 1 through 13 below. To remove the optional ETIB Board, see step 14. Note: The Instrument
Front Cover must be open.
1.
To open the Instrument Front Cover, remove the lock if present and turn each of the three captive screws a quarter (1/4) turn counterclockwise.
PIP-EXPTIBTF Page 3 Expansion TIB Option
Note:
The CPU Board is not to be removed under any circumstances unless the unit has been moved to an ESD safe area (see ESDS Manual - S14006).
2.
Remove the Power Plug(s), Solar Panel Power Plug, and the Auxiliary Power Plug as required, from the CPU Board in question.
3.
Remove the optional radio or modem if installed.
To remove an optional modem :
Disconnect the phone wires. Loosen the four (4) screws that secure the Modem/Radio
Mounting Plate (with modem) to the Battery Mounting Bracket. Slide the modem to the left and remove it and then disconnect the D-Type connector from the modem.
To remove an optional radio :
Disconnect the Radio/TeleFlow Interface Cable from the bottom of the Radio. Unplug the 2-wire power connector associated with the 2-wire Radio Power Interface Cable from the bottom of the Radio. Loosen the four (4) screws that secure the Modem/Radio
Mounting Plate (with radio) to the Battery Mounting Bracket. Slide the radio to the left and remove it.
4.
Remove the Battery(s) (if present).
To remove the battery(s) from units without an optional modem or radio :
Hold the battery securely and remove the Left Battery Mounting Bracket (secured with 2 screws. Loosen the screws which secure the Right Battery Mounting Bracket
(Carefully remove the battery (with wiring harness). Remove the Right Battery
Mounting Bracket.
To remove the battery(s) from units with an optional modem or radio :
Carefully remove the battery (with wiring harness). Note: You may have to loosen the two left 1/4-20 x 3/8” screws that secure the left side of the Battery Mounting Bracket and the Main Mounting Bracket to the rear of the unit.
While holding the Main
Mounting Bracket, remove the four (4) 1/4-20 x 3/8” screws and lock washers that secure the Battery Mounting Bracket and Main Mounting Bracket to the rear of the unit. Remove the Battery Mounting Bracket and temporarily reinstall the four screws to secure the Main Mounting Bracket to the 3530-10B or 3530-15B.
5.
Disconnect the Local Port, Network Port, RTD, and Field I/O wires from the CPU
Board connectors by unplugging their associated Terminal Plugs (front edge of CPU).
6. Carefully remove the PC Shield which is secured to the Main Mounting Bracket by 2
(#4-40 x 1/4”) screws and to the CPU Board by 2 (#4-40 x 1/4”) screws.
7. Remove the screw (location ‘A’ in Figures 2 & 3) and the two (2) #4-40 x 5/8” Standoffs
(location ‘B’ in Figures 2 & 3) which secure the CPU Board to the Main Mounting
Bracket. Replace these items with the three new #4-40 x 15/32” Standoffs.
Note:
This operation should only be performed in an ESD safe area.
8.
Align the ETIB Board Connector P1 with CPU Board Connector J4 (for 3530-10B) or
J18 (for 3530-15B). Push the EXPCOM232 Board toward the CPU Board until
Connector P1 is fully seated.
Expansion TIB Option Page 4 PIP-EXPTIBTF
Figure 2 - TeleFlow CPU Board – Installation Drawing #1
9.
Secure the ETIB Board to the CPU Board by installing three (3) #4-40 x .188”
Standoffs at Locations ‘A’ & ‘B’ (see Figures 2 & 3).
10. Carefully install the Modified PC Shield, securing it to the Main Mounting Bracket (at locations ‘C’) with two (2) #4-40 x 1/4” screws and to the CPU Board (at locations ‘B’) with two (2) #4-40 x 1/8” SEM screws (see Figures 4, 5, 6 & 7).
11. Follow steps 2 through 6 in reverse order, replacing rather than removing the item in question.
PIP-EXPTIBTF Page 5 Expansion TIB Option
12.
Install 3508/3808 Transmitter wiring to the ETIB Board (see Section 2.2.1). Wiring should be routed through a ¾” conduit fitting (user installed) on the bottom of the enclosure.
Figure 3 - TeleRTU CPU Board – Installation Drawing #1
13.
Close and secure the Instrument Front Cover.
14. To remove an optional ETIB Board, follow steps 1 through 6 (unplug the Field Wiring
Terminals during step 5). Remove the PC Shield along with the three Standoffs that
Expansion TIB Option Page 6 PIP-EXPTIBTF
secure the ETIB Board to the CPU Board. Then unplug the ETIB Board from the CPU
Board in question.
PIP-EXPTIBTF
Figure 4 - TeleFlow CPU Board (with ETIB Installed)
Installation Drawing #2
Page 7 Expansion TIB Option
Figure 5 - TeleRTU CPU Board (with ETIB Installed)
Expansion TIB Option
Installation Drawing #2
Page 8 PIP-EXPTIBTF
Figure 6 - 3530-10B & 3530-50B (with ETIB Installed)
PIP-EXPTIBTF
Figure 7 - 3530-15B (with ETIB Installed)
Page 9 Expansion TIB Option
2.1.1.2 Installation/Removal for Models 3530-20B & -25B
To install the optional ETIB Board into a model 3530-20B or 3530-25B, follow steps 1 through 10 below. To remove the optional ETIB Board, perform steps 1 and 2 and then follow steps 4 through 9 in reverse order, removing rather than installing the item in question after the system has been shut down. Note: The Instrument Front Cover must be open.
1.
Open the Instrument Front Cover
2.
Disconnect power by removing harness connector plug (P8 for TeleFlow - P2 for
TeleRTU) from the CPU Board edge connector (J8 for TeleFlow - J2 for TeleRTU).
Expansion TIB Option
Figure 8 - 3530-20B CPU (with ETIB Installed)
Page 10 PIP-EXPTIBTF
3.
Unplug the remaining removable Terminal Blocks (with wiring harnesses installed) from the CPU Board’s front edge connectors.
4.
Remove the two screws that secure the CPU Board’s Sliding Mounting Bracket to the
Fixed Bracket on the bottom of the Battery Bracket. Carefully slide the CPU Board
(and optional ETIB Board) toward the front of the unit. Remove harness connections from the Front Panel Switch (J12 on the TeleFlow CPU - J14 on TeleRTU CPU), the
Display Module (J2 on TeleFlow CPU - J16 on TeleRTU CPU), the Wakeup Switch (J3 on TeleFlow CPU - J16 on TeleRTU CPU), and for TeleFlow CPU Boards connector J1
(associated with the Multivariable Transducer).
Figure 9 - 3530-25B CPU (with ETIB Installed)
5.
Remove the three screws (of five) that secure the CPU Board to the Sliding Mounting
Bracket (locations ‘A’ & ‘B’ in Figures 2 & 3) and replace these items with the three new #4-40 x 15/32” Standoffs.
PIP-EXPTIBTF Page 11 Expansion TIB Option
Note:
This operation should only be performed in an ESD safe area.
6.
Align the ETIB Board Connector P1 with CPU Board Connector J4 (for 3530-20B) or
J18 (for 3530-25B). Push the ETIB Board toward the CPU Board until Connector P1 is fully seated.
7.
Secure the ETIB Board to the CPU Board by installing three (3) #4-40 x 1/4” SEM screws as illustrated in Figures 8 & 9.
8.
Install 3508/3808 Transmitter wiring to the ETIB Board (see Section 2.2.1). Wiring should be routed through a ¾” conduit fitting (user installed) on the bottom of the enclosure.
9. Close and secure the Instrument Front Cover.
2.1.1.3 Installation/Removal for Models 3530-35B
To install the optional ETIB Board into a model 3530-35B, follow steps 1 through 7 below.
To remove the optional ETIB Board, perform step 1 and then follow steps 5 through 7 in reverse order, removing rather than installing the item in question after the system has been shut down.
1.
Disconnect power by removing harness connector plug P2 from the CPU Board edge connector J2.
2. Unplug the remaining removable Terminal Blocks (with wiring harnesses installed) from the CPU Board’s front edge connectors.
3. Remove harness connections from the Front Panel Switch (J14), the Display Module
(J16) and the Wakeup Switch (J16).
4. Remove the three screws (of five) that secure the CPU Board to the RTU Mounting
Bracket (locations ‘A’ & ‘B’ in Figures 2 & 3) and replace these items with the three new #4-40 x 15/32” Standoffs.
Note:
This operation should only be performed in an ESD safe area.
5. Align the ETIB Board Connector P1 with CPU Board Connector J18. Push the ETIB
Board toward the CPU Board until Connector P1 is fully seated.
6.
Secure the ETIB Board to the CPU Board by installing three (3) #4-40 x 1/4” SEM screws as illustrated in Figure 10.
7.
Install 3508/3808 Transmitter wiring to the ETIB Board (see Section 2.2.1).
Expansion TIB Option Page 12 PIP-EXPTIBTF
Figure 10 - 3530-35B (with ETIB Installed)
2.2 FIELD WIRING
The device uses compression-type terminals that accommodate up to #14 AWG wire. A connection is made by inserting the bared end (1/4 inch Max.) into the clamp beneath the screw and then securing the screw. Insert the bared end fully to prevent short circuits.
Allow some slack in the wires when making terminal connections. The slack makes the connections more manageable and minimizes mechanical strain on the printed circuit boards and harnesses.
PIP-EXPTIBTF Page 13 Expansion TIB Option
2.2.1 Terminal Connections
2.2.1.1 Terminal Connections for Model 3808 Transmitters
ETIB Boards contain two terminal blocks that are used to provide field wiring connections to up to two Model 3808 Transmitters. TB1 & TB2 are two-position Terminal Blocks which connect to the signal/power inputs of the Transmitters.
JP1 Note:
If only one Transmitter is connected to the ETIB,
Jumper JP1 must be INSTALLED across JP1-1 & JP1-2.
When two Transmitters are connected to the ETIB,
Jumper JP1 must be REMOVED. Store the Jumper on
Jumper Post JP1-1 or JP1-2.
Note:
When only one Transmitter is connected to the ETIB, it
MUST BE connected to TB1.
Figure 11 - Internally Powered Model 3808 Transmitters - Field Wiring Diagram
ETIB Boards may be connected to up to two internally powered Model 3808 Transmitters.
Connection to internally powered Model 3808 Transmitters (powered from ETIB’s on-board
+12V Supply/Regulator) is illustrated in Figure 11.
2.2.1.2 Terminal Connections for a single Model 3508 Transmitter
The two-position Terminal Block TB1 is utilized to provide field wiring connections to an internally powered Model 3508 Transmitter.
Expansion TIB Option Page 14 PIP-EXPTIBTF
JP1 Note:
Jumper JP1 must be INSTALLED across JP1-1 & JP1-2.
Figure 12 - Internally Powered Model 3508 Transmitter - Field Wiring Diagram
Connection to an internally powered Model 3508 Transmitter (powered from the ETIB’s onboard Supply/Regulator) is illustrated in Figure 12.
2.2.1.3 Terminal Connections for two Model 3508 Transmitters
ETIB Boards contain two terminal blocks that are used to provide field wiring connections for up to two Model 3508 Transmitters. TB1 & TB2 are two-position Terminal Blocks which connect to the signal/power inputs of the Transmitters. When using two Model 3508
Transmitters, an external 21 Volt (dc) power supply must be utilized (see Figure 13).
PIP-EXPTIBTF Page 15 Expansion TIB Option
JP1 Note:
Jumper JP1 must be REMOVED. Store the Jumper on
Jumper Post JP1-1 or JP1-2.
TeleFlow CPU Connector J5-5
TeleRTU CPU Connector J6-2
GND
External 21V
Power Supply
Figure 13 - Externally Powered Model 3508 Transmitters - Field Wiring Diagram
Expansion TIB Option Page 16 PIP-EXPTIBTF
Section 3
SPECIFICATIONS
3.1 GENERAL SPECIFICATIONS
Communication Interface:
3508/3808 Interface:
ESD Susceptibility:
EMI Compatibility:
RS-232 ( ± 3V minimum)
FSK Modem - Bell 202 Compatible
(1200 Hz/2200 Hz modulation)
Baud rate is 1200
Field connected circuits are designed to meet the requirements of IEC 801-2 for ESD withstand capability up to 10KV.
Designed to coexist within a shielded enclosure with the TeleFlow (3530-10/20B) or the TeleRTU (3530-15B/25B) electronics. EMI radiation is insignificant and susceptibility is comparable or superior to associated electronics.
Transient Susceptibility: Field connected circuits are designed to meet the requirements of ANSI/-
IEEEC37.90-1998 (Formerly IEEE 472) for surge withstand capability.
3.2 ENVIRONMENTAL SPECIFICATIONS
Operating Temperature:
Storage Temperature:
Relative Humidity:
Vibration:
-40°C to +60°C (-40°F to +140°F)
-40°C to +85°C (-40°F to +185°C)
15% - 90% Non-condensing
1G for 10Hz to 500Hz per SAMA PMC-31-1
(without damage or impairment)
PIP-EXPTIBTF Page 17 Expansion TIB Option
BLANK PAGE
Expansion Transmitter Interface Board
Special Instructions for Class I, Division 2 Hazardous Locations
1. The Bristol Expansion Transmitter Interface Board (ETIB) is listed by Underwriters
Laboratories (UL) as nonincendive and is suitable for use in Class I, Division 2, Groups
A, B, C and D hazardous locations or non-hazardous locations only. Read this document carefully before installing a nonincendive Britol ETIB Board. In the event of a conflict between the ETIB Board User Manual (PIP-EXPTIBTF) and this document, always follow the instructions in this document.
2. Wiring must be performed in accordance with Class I, Division 2 wiring methods as defined in Article 501-4 (b) of the National Electrical Code, NFPA 70 for installations within the United States, or as specified in Section 18-152 of the Canadian Electrical
Code for installation in Canada.
3. WARNING: EXPLOSION HAZARD - Substitution of components may impair suitability for use in Class I, Division 2 environments.
4. WARNING: EXPLOSION HAZARD - When situated in a hazardous location, turn off power before servicing/replacing the unit and before installing or removing I/O wiring.
5. WARNING: EXPLOSION HAZARD - Do Not disconnect equipment unless the power has been switched off or the area is known to be nonhazardous.
03/14/2007 Appendix A of PIP-EXPTIBTF - ETIB Board Page 1 of 1
Product Information Package
Expansion Transmitter Interface Board Part No. 392960-01-0
PIP-EXPTIBTF
Mar., 2007
Emerson Process Management
Bristol, Inc.
1100 Buckingham Street
Watertown, CT 06795
Phone: +1 (860) 945-2262
Fax: +1 (860) 945-2525 www.EmersonProcess.com/Bristol
Emerson Electric Canada, Ltd.
Bristol Canada
6338 Viscount Rd.
Mississauga, Ont. L4V 1H3
Canada
Phone: 905-362-0880
Fax: 905-362-0882 www.EmersonProcess.com/Bristol
Emerson Process Management
BBI, S.A. de C.V.
Homero No. 1343, 3er Piso
Col. Morales Polanco
11540 Mexico, D.F.
Mexico
Phone: (52-55)-52-81-81-12
Fax: (52-55)-52-81-81-09 www.EmersonProcess.com/Bristol
Emerson Process Management
Bristol Babcock, Ltd.
Blackpole Road
Worcester, WR3 8YB
United Kingdom
Phone: +44 1905 856950
Fax: +44 1905 856969 www.EmersonProcess.com/Bristol
Emerson Process Management
Bristol, Inc.
22 Portofino Crescent,
Grand Canals Bunbury, Western Australia 6230
Mail to: PO Box 1987 (zip 6231)
Phone: +61 (8) 9725-2355
Fax: +61 (8) 8 9725-2955 www.EmersonProcess.com/Bristol
The information in this document is subject to change without notice. Every effort has been made to supply complete and accurate information. However, Bristol, Inc. assumes no responsibility for any errors that may appear in this document.
If you have comments or questions regarding this manual, please direct them to your local Bristol sales representative, or direct them to one of the addresses listed at left.
Bristol, Inc. does not guarantee the accuracy, sufficiency or suitability of the software delivered herewith. The Customer shall inspect and test such software and other materials to his/her satisfaction before using them with important data.
There are no warranties, expressed or implied, including those of merchantability and fitness for a particular purpose, concerning the software and other materials delivered herewith.
TeleFlow
™
is a trademark of Bristol, Inc. The Emerson logo is a trade mark and service mark of Emerson Electric Co. Other trademarks or copyrighted products mentioned in this document are for information only, and belong to their respective companies, or trademark holders.
Copyright (c) 2007, Bristol, Inc., 1100 Buckingham St., Watertown, CT 06795. No part of this manual may be reproduced in any form without the express written permission of
Bristol, Inc.
EXPANSION COMMUNICATIONS
PORT RS-232 BOARD
Part No. 392970-01-5
(For Models 3530-XXX)
For The Following BBI Instruction Manuals:
CI-3530-10B, CI-3530-15B, CI-3530-20B, CI-3530-25B,
CI-3530-35B, CI-3530-40B, CI-3530-45B & CI-3530-50B
Product Information Package
Bristol Babcock
PIP-EXP232TF
– December, 2003
NOTICE
Copyright Notice
The information in this document is subject to change without notice. Every effort has been made to supply complete and accurate information. However, Bristol Babcock assumes no responsibility for any errors that may appear in this document.
Request for Additional Instructions
Additional copies of instruction manuals may be ordered from the address below per attention of the Sales Order Processing Department. List the instruction book numbers or give complete model number, serial or software version number. Furnish a return address that includes the name of the person who will receive the material. Billing for extra copies will be according to current pricing schedules.
TeleFlow TM , TeleRTU TM and TeleRecorder TM are trademarks of Bristol Babcock. Other trademarks or copy-righted products mentioned in this document are for information only, and belong to their respective companies, or trademark holders.
Copyright (c) 2003 Bristol Babcock, 1100 Buckingham St., Watertown, CT 06795. No part of this manual may be reproduced in any form without the express written permission of
Bristol Babcock.
IMPORTANT! READ INSTRUCTIONS BEFORE STARTING!
Be sure that these instructions are carefully read and understood before any operation is attempted. Improper use of this device in some applications may result in damage or injury. The user is urged to keep this book filed in a convenient location for future reference.
These instructions may not cover all details or variations in equipment or cover every possible situation to be met in connection with installation, operation or maintenance. Should problems arise that are not covered sufficiently in the text, the purchaser is advised to contact Bristol Babcock for further information.
EQUIPMENT APPLICATION WARNING
The customer should note that a failure of this instrument or system, for whatever reason, may leave an operating process without protection. Depending upon the application, this could result in possible damage to property or injury to persons. It is suggested that the purchaser review the need for additional backup equipment or provide alternate means of protection such as alarm devices, output limiting, fail-safe valves, relief valves, emergency shutoffs, emergency switches, etc.
If additional information is required, the purchaser is advised to contact Bristol
Babcock.
RETURNED EQUIPMENT WARNING
When returning any equipment to Bristol Babcock for repairs or evaluation, please note the following: The party sending such materials is responsible to ensure that the materials returned to Bristol Babcock are clean to safe levels, as such levels are defined and/or determined by applicable federal, state and/or local law regulations or codes. Such party agrees to indemnify Bristol Babcock and save Bristol Babcock harmless from any liability or damage which Bristol Babcock may incur or suffer due to such party’s failure to so act.
ELECTRICAL GROUNDING
Metal enclosures and exposed metal parts of electrical instruments must be grounded in accordance with OSHA rules and regulations pertaining to "Design
Safety Standards for Electrical Systems," 29 CFR, Part 1910, Subpart S, dated: April
16, 1981 (OSHA rulings are in agreement with the National Electrical Code).
The grounding requirement is also applicable to mechanical or pneumatic instruments that include electrically-operated devices such as lights, switches, relays, alarms, or chart drives.
EQUIPMENT DAMAGE FROM ELECTROSTATIC DISCHARGE VOLTAGE
This product contains sensitive electronic components that can be damaged by exposure to an electrostatic discharge (ESD) voltage. Depending on the magnitude and duration of the ESD, this can result in erratic operation or complete failure of the equipment. Read BBI supplemental document S14006 for proper care and handling of ESD-sensitive components.
Bristol Babcock 1100 Buckingham Street, Watertown, CT 06795
Telephone (860) 945-2200
A.
B.
C.
D.
E.
F.
A.
B.
WARRANTY
Bristol warrants that goods described herein and manufactured by Bristol are free from defects in material and workmanship for one year from the date of shipment unless otherwise agreed to by Bristol in writing.
Bristol warrants that goods repaired by it pursuant to the warranty are free from defects in material and workmanship for a period to the end of the original warranty or ninety (90) days from the date of delivery of repaired goods, whichever is longer.
Warranties on goods sold by, but not manufactured by Bristol are expressly limited to the terms of the warranties given by the manufacturer of such goods.
All warranties are terminated in the event that the goods or systems or any part thereof are (i) misused, abused or otherwise damaged, (ii) repaired, altered or modified without Bristol’s consent, (iii) not installed, maintained and operated in strict compliance with instructions furnished by Bristol, or (iv) worn, injured or damaged from abnormal or abusive use in service time.
THESE WARRANTIES ARE EXPRESSLY IN LIEU OF ALL OTHER
WARRANTIES EXPRESS OR IMPLIED (INCLUDING WITHOUT LIMITATION
WARRANTIES AS TO MERCHANTABILITY AND FITNESS FOR A PARTICULAR
PURPOSE), AND NO WARRANTIES, EXPRESS OR IMPLIED, NOR ANY
REPRESENTATIONS, PROMISES, OR STATEMENTS HAVE BEEN MADE BY
BRISTOL UNLESS ENDORSED HEREIN IN WRITING. FURTHER, THERE ARE
NO WARRANTIES WHICH EXTEND BEYOND THE DESCRIPTION OF THE
FACE HEREOF.
No agent of Bristol is authorized to assume any liability for it or to make any written or oral warranties beyond those set forth herein.
REMEDIES
Buyer’s sole remedy for breach of any warranty is limited exclusively to repair or replacement without cost to Buyer of any goods or parts found by Seller to be defective if Buyer notifies Bristol in writing of the alleged defect within ten (10) days of discovery of the alleged defect and within the warranty period stated above, and if the Buyer returns such goods to Bristol’s Watertown office, unless Bristol’s Watertown office designates a different location, transportation prepaid, within thirty (30) days of the sending of such notification and which upon examination by Bristol proves to be defective in material and workmanship. Bristol is not responsible for any costs of removal, dismantling or reinstallation of allegedly defective or defective goods. If a Buyer does not wish to ship the product back to Bristol, the Buyer can arrange to have a Bristol service person come to the site. The Service person’s transportation time and expenses will be for the account of the Buyer. However, labor for warranty work during normal working hours is not chargeable.
Under no circumstances will Bristol be liable for incidental or consequential damages resulting from breach of any agreement relating to items included in this quotation from use of the information herein or from the purchase or use by Buyer, its employees or other parties of goods sold under said agreement.
How to return material for Repair or Exchange
Before a product can be returned to Bristol Babcock for repair, upgrade, exchange, or to verify proper operation, form (GBU 13.01) must be completed in order to obtain a RA
(Return Authorization) number and thus ensure an optimal lead time. Completing the form is very important since the information permits the Bristol Babcock Repair Dept. to effectively and efficiently process the repair order.
You can easily obtain a RA number by:
A. FAX
Completing the form (GBU 13.01) and faxing it to (860) 945-3875. A BBI Repair
Dept. representative will return call (or other requested method) with a RA number.
B. E-MAIL
Accessing the form (GBU 13.01) via the Bristol Babcock Web site
(www.bristolbabcock.com) and sending it via E-Mail to [email protected]
.
A BBI Repair Dept. representative will return E-Mail (or other requested method) with a RA number.
C. Mail
Mail the form (GBU 13.01) to
Bristol Babcock Inc.
Repair Dept.
1100 Buckingham Street
Watertown, CT 06795
A BBI Repair Dept. representative will return call (or other requested method) with a RA number.
D. Phone
Calling the BBI Repair Department at (860) 945-2442. A BBI Repair Department representative will record a RA number on the form and complete Part I, then send the form to the Customer via fax (or other requested method) for Customer completion of Parts II & III.
A copy of the completed Repair Authorization Form with issued RA number should be included with the product being returned. This will allow us to quickly track, repair, and return your product to you.
&VMWXSP&EFGSGO-RG6ITEMV%YXLSVM^EXMSR*SVQ
(Providing this information will permit BBI to effectively and efficiently process your return. Completion is required to receive optimal lead time. Lack of information may result in increased lead times.)
Date___________________ RA #___________________SH_ Line No.____________
Standard Repair Practice is as follows: Variations to this is practice may be requested in the “Special Requests” section.
•
Evaluate / Test / Verify Discrepancy
•
Repair / Replace / etc. in accordance with this form
•
Return to Customer
Part I
Please be aware of the Non warranty standard charge:
•
There is a $100 minimum evaluation charge, which is applied to the repair if applicable (
√
in “returned” B,C, or D of part III below)
Please complete the following information for single unit or multiple unit returns
Address No.
Bill to :
(office use only) Address No.
Ship to:
(office use only)
Purchase Order:
Phone: Fax:
Contact Name:____________________________________
E-Mail:
Part II Please complete Parts II & III for each unit returned
Model No./Part No.
Description
Range/Calibration
Reason for return : Failure Upgrade
S/N
Verify Operation Other
1.
Describe the conditions of the failure (Frequency/Intermittent, Physical Damage, Environmental Conditions,
Communication, CPU watchdog, etc.)
(Attach a separate sheet if necessary)
2. Comm. interface used: Standalone RS-485 Ethernet Modem (PLM (2W or 4W) or SNW) Other: ______________
3.
What is the Firmware revision? _____________________ What is the Software &version?
Part III If checking “replaced” for any question below, check an alternate option if replacement is not available
A.
If product is within the warranty time period but is excluded due to BBI’s warranty clause, would you like the product: repaired returned replaced scrapped?
B.
If product were found to exceed the warranty period, would you like the product:
C.
If product is deemed not repairable would you like your product:
D.
If BBI is unable to verify the discrepancy, would you like the product: repaired returned replaced scrapped?
returned replaced scrapped?
returned replaced *see below?
* Continue investigating by contacting the customer to learn more about the problem experienced? The person to contact that has the most knowledge of the problem is: _______________________________ phone
If we are unable to contact this person the backup person is: _________________________ phone
Special Requests:
Ship prepaid to: Bristol Babcock Inc., Repair Dept., 1100 Buckingham Street, Watertown, CT 06795
Phone: 860-945-2442 Fax: 860-945-3875
Form GBU 13.01
Rev. A
Bristol Babcock
Training
GET THE MOST FROM YOUR BRISTOL
BABCOCK INSTRUMENT OR SYSTEM
● Avoid Delays and problems in getting your system on-line
● Minimize installation, start-up and maintenance costs.
● Make the most effective use of our hardware and software.
● Know your system.
As you know, a well-trained staff is essential to your operation. Bristol Babcock offers a full schedule of classes conducted by full-time, professional instructors. Classes are offered throughout the year at three locations: Houston, Orlando and our Watertown, CT headquarters. By participating in our training, your personnel can learn how to install, calibrate, configure, program and maintain any and all Bristol Babcock products and realize the full potential of your system.
For information or to enroll in any class, contact our training department in Watertown at
(860) 945-2269. For Houston classes, you can also contact our Houston office, at (713) 685-
6200.
BLANK PAGE
A Few Words About Bristol Babcock
For over 100 years, Bristol 7 has been providing innovative solutions for the measurement and control industry. Our product lines range from simple analog chart recorders, to sophisticated digital remote process controllers and flow computers, all the way to turnkey
SCADA systems. Over the years, we have become a leading supplier to the electronic gas measurement, water purification, and wastewater treatment industries.
On off-shore oil platforms, on natural gas pipelines, and maybe even at your local water company, there are Bristol Babcock instruments, controllers, and systems running year-in and year-out to provide accurate and timely data to our customers.
Getting Additional Information
In addition to the information contained in this manual, you may receive additional assistance in using this product from the following sources:
Contacting Bristol Babcock Directly
Bristol Babcock's world headquarters are located at 1100 Buckingham Street, Watertown,
Connecticut 06795, U.S.A.
Our main phone numbers are:
(860) 945-2200
(860) 945-2213 (FAX)
Regular office hours are Monday through Friday, 8:00AM to 4:30PM Eastern Time, excluding holidays and scheduled factory shutdowns. During other hours, callers may leave messages using Bristol's voice mail system.
Telephone Support - Technical Questions
During regular business hours, Bristol Babcock's Application Support Group can provide telephone support for your technical questions.
For technical questions about TeleFlow Ô products call (860) 945-8604.
For technical questions about Control Wave call (860) 945-2244 or (860) 945-2286.
For technical questions regarding Bristol’s OpenEnterprise product, call (860) 945-3865 or e-mail: [email protected]
For technical questions regarding ACCOL products, Open BSI Utilities , as well as
Bristol's Enterprise Server 7 / Enterprise Workstation 7 products, call (860) 945-2286.
For technical questions about Network 3000 hardware, call (860) 945-2502.
You can e-mail the Application Support Group at: [email protected]
The Application Support Group maintains an area on our web site for software updates and technical information. Go to: www.bristolbabcock.com/services/techsupport/
For assistance in interfacing Bristol Babcock hardware to radios, contact Bristol Babcock’s
Communication Technology Group in Orlando, FL at (407) 629-9463 or (407) 629-
9464 .
Telephone Support - Non-Technical Questions, Product Orders, etc.
Questions of a non-technical nature (product orders, literature requests, price and delivery information, etc.) should be directed to the nearest sales office (listed on the rear cover) or to your Bristol-authorized sales representative.
Please call the main Bristol Babcock number (860-945-2200) if you are unsure which office covers your particular area.
Visit our Site on the World Wide Web
For general information about Bristol Babcock and its products, please visit our site on the
World Wide Web at: www.bristolbabcock.com
Training Courses
Bristol Babcock’s Training Department offers a wide variety of courses in Bristol hardware and software at our Watertown, Connecticut headquarters, and at selected Bristol regional offices, throughout the year. Contact our Training Department at (860) 945-2269 for course information, enrollment, pricing, and scheduling.
PIP-EXP232TF
EXPANSION COMMUNICATIONS PORT
RS-232 BOARD
PT. Number 392970-01-5
Product Information Package
TABLE OF CONTENTS
1.1
1.1.1
1.1.2
1.2
1.3
1.3.1
SECTION TITLE PAGE #
DESCRIPTION................................................................................................................... 1
Function .............................................................................................................................. 1
Features............................................................................................................................... 2
COMPONENT IDENTIFICATION................................................................................... 2
INSTALLATION COMPATIBILITY................................................................................ 2
Restrictions ......................................................................................................................... 2
2.1
2.1.1
2.1.1.1
2.1.1.2
2.1.1.3
2.2
Section 2 - INSTALLATION & SERVICE
EXPCOM232 REMOVAL/REPLACEMENT & INSTALLATION................................. 3
Installation/Removal of the EXPCOM232 Board .............................................................. 3
Installation/Removal for Models 3530-10B, -15B, -40B, -45B & -50B ............................ 3
Installation/Removal for Models 3530-20B & -25B ........................................................ 10
Installation/Removal for Models 3530-35B ..................................................................... 11
RS-232 WIRING............................................................................................................... 12
3.1
3.2
PERFORMANCE SPECIFICATIONS ............................................................................ 15
ENVIRONMENTAL SPECIFICATIONS ....................................................................... 15
SUPPLEMENTS
PIP-EXP232TF Page 0-1 Table Of Contents
BLANK PAGE
Section 1
INTRODUCTION
1.1 DESCRIPTION
1.1.1 Function
The Expansion Communications Port RS-232 Board (EXPCOM232) provides a single RS-
232 asynchronous serial communications port to ACCOL-based 3530-XXX models. In addition to assignments of the resident (host) CPU’s “local” and “network” RS-232 ports, any model 3530-XXX unit equipped with an EXPCOM232 Board can establish RS-232 communications with an external device. An EXPCOM232 Board plugs into the Expansion
Connector of the TeleFlow or TeleRTU CPU Board and is stood-off by three 15/32” long hex standoffs and is secured via three screws. The CPU Board Expansion Connector supplies power and 3530-XXX communication to the EXPCOM232 Board.
EXPCOM232 Boards measure 4.0” by 3.75” and utilizes a 7-position Industrial 3.5mm pitch plugable connector to interface with an external RS-232 device. 16V bi-directional
Transient Absorption Zener Diodes are placed across all RS-232 outputs.
Programmable baud rates up to 19.2Kbps are supported by the EXPCOM232 Board. TXD,
RXD, RTS, CTS, DTR, CD and GND (RS-232) signals are available at TB1 of the
EXPCOM232 Board. CD (Carrier Detect) (supplied by a DCE attempting to communicate with a model 3530-XXX), will awaken the 3530-XXX CPU Board. If no activity is required, the EXPCOM232 Board‘s serial communications controller (SCC) chip and RS-232 drivers can be put to sleep (low power mode) along with the host/parent 3530-XXX.
PIP-EXP232TF
Figure 1 - Expansion Communications Port RS-232 Board
Page 1 EXPCOM232 Option
1.1.2 Features
· Low Power
+5V @ 20mA (Max) regulated power is supplied by the host/parent 3530-XXX via the
40-pin Expansion Interface Connector P1.
· ESD & Transient Susceptibility
The RS-232 I/O circuitry has been designed to meet the requirements of IEC 801-2 for ESD withstand capability up to 10KV and the requirements of ANSI/IEEE
C37.90.1-1989 (formerly IEE 472) for surge withstand capability.
· EMI Compatibility
EXPCOM232 Boards have been designed to coexist inside a shielded enclosure with the TeleFlow ä electronics. EMI radiation is insignificant and susceptibility is comparable or superior to associated electronics.
· Mounting
The EXPCOM232 Board measures 3.75” (9.525cm) in width x 4.0” (10.160cm) in height and mounts piggy-back on a TeleFlow or TeleRTU CPU Board.
· RS-232 Serial Port
EXPCOM232 Boards provide an additional RS-232 serial port that is programmable for rates up to 19.2Kbps. 3530-XXX units equipped with the EXPCOM232 Board can communicate with a local RS-232 device even though a radio or modem may be installed on the CPU Board’s network port.
1.2 COMPONENT IDENTIFICATION
EXPCOM232 Boards do not contain LEDs, switches or configuration jumpers. Two connectors are provided; 40-pin connector P1 mates with the host 3530-XX-X (connector J4 -
TeleFlow CPU or J18 - TeleRTU CPU) and accommodates the TTL interface between the two entities, while 7-pin connector TB1 mates with the RS-232 device that is being interfaced to the 3530-XXX. Additionally, the 3.5mm pitch plugable connector TB1 is removable from its mating EXPCOM232 Board socket.
1.3 INSTALLATION COMPATIBILITY
An EXPCOM232 Board can be installed into any of the following 3530-XXX models:
3530-10B - TeleFlow
3530-15B - TeleRTU
3530-35B - TeleRTU Module
3530-40B - TeleFlow ECR
3530-20B - TeleFlow Plus 3530-45B - TeleRecorder
3530-25B - TeleRTU Plus 3530-50B - TeleFlow Corrector
1.3.1 Restrictions
The 3530-XXX in question must be equipped with ACCOL application software. 3530-XXX units support installation of only one optional piggyback mounted Expansion Board (I/O,
Comm. or TIB).
EXPCOM232 Option Page 2 PIP-EXP232TF
Section 2
INSTALLATION & SERVICE
2.1 EXPCOM232 REMOVAL/REPLACEMENT & INSTALLATION
2.1.1 Installation/Removal of the
EXPCOM232 Board
In addition to hardware normally contained within the 3530-XXX in question, units with an installed EXPCOM232 Option will contain the following major parts.
1.
Expanded Communications Port RS-232 Board (EXPCOM232)
2.
Three #4-40 x 15/32” Standoffs (Note: Models 3530-10B, - 15B, -40B, -45B & -50B will also contain Three (3) #4-40 x .188” Standoffs & Two (2) #4-40 x 1/8” SEM Screws)
3.
Modified PC Shield Assembly (for models 3530-10B, -15B, -40B, -45B & -50B)
WARNING
Never attempt to service a TeleFlow, TeleRTU,
TeleRecorder or TeleFlow Corrector while it is powered and operating in a hazardous environment. Either the area must be made safe or the unit must be powered down, unwired, unmounted, and taken to a safe, nonhazardous area.
WARNING
Never attempt to install or remove any components
(PCBs, Field Wiring, Transducers, etc.) while the unit is powered and running. Doing so can cause sudden electrical transients or imbalances that are capable of causing damage to the module or component in question, as well as other associated circuit boards. Always turn off the external/internal power source, including any additional supply sources used for externally-powered
I/O circuits, before changing or adding any components.
CAUTION
Place any related critical processes under manual or auxiliary control prior to shutting down or performing any of the steps discussed herein.
2.1.1.1 Installation/Removal for Models 3530-10B, -15B, -40B, -45B & -50B
To install the optional EXPCOM232 Board into a model 3530-10B, -15B, -40B, -45B or -
50B, follow steps 1 through 14 below. To remove the optional EXPCOM232 Board, see step
15. Note: The Instrument Front Cover must be open.
1.
To open the Instrument Front Cover, remove the lock if present and turn each of the three captive screws a quarter (1/4) turn counterclockwise.
PIP-EXP232TF Page 3 EXPCOM232 Option
Note:
The CPU Board is not to be removed under any circumstances unless the unit has been moved to an ESD safe area (see ESDS Manual - S14006).
2.
Remove the Power Plug(s), Solar Panel Power Plug, and the Auxiliary Power Plug as required, from the CPU Board in question.
3.
Remove the optional radio or modem if installed.
To remove an optional modem :
Disconnect the phone wires. Loosen the four (4) screws that secure the Modem/Radio
Mounting Plate (with modem) to the Battery Mounting Bracket. Slide the modem to the left and remove it and then disconnect the D-Type connector from the modem.
To remove an optional radio :
Disconnect the Radio/TeleFlow Interface Cable from the bottom of the Radio. Unplug the 2-wire power connector associated with the 2-wire Radio Power Interface Cable from the bottom of the Radio. Loosen the four (4) screws that secure the Modem/Radio
Mounting Plate (with radio) to the Battery Mounting Bracket. Slide the radio to the left and remove it.
4.
Remove the Battery(s) (if present).
To remove the battery(s) from units without an optional modem or radio :
Hold the battery securely and remove the Left Battery Mounting Bracket (secured with 2 screws. Loosen the screws which secure the Right Battery Mounting Bracket
(Carefully remove the battery (with wiring harness). Remove the Right Battery
Mounting Bracket.
To remove the battery(s) from units with an optional modem or radio :
Carefully remove the battery (with wiring harness). Note: You may have to loosen the two left 1/4-20 x 3/8” screws that secure the left side of the Battery Mounting Bracket and the Main Mounting Bracket to the rear of the unit.
While holding the Main
Mounting Bracket, remove the four (4) 1/4-20 x 3/8” screws and lock washers that secure the Battery Mounting Bracket and Main Mounting Bracket to the rear of the unit. Remove the Battery Mounting Bracket and temporarily reinstall the four screws to secure the Main Mounting Bracket to the 3530-10B, 15B, -45B or -50B.
5.
Disconnect the Local Port, Network Port, RTD, and Field I/O wires from the CPU Bd.
connectors by unplugging their associated Term. Plugs on the front edge of the CPU.
6. Carefully remove the PC Shield which is secured to the Main Mounting Bracket by 2
(#4-40 x 1/4”) screws and to the CPU Board by 2 (#4-40 x 1/4”) screws.
7. Remove the screw (location ‘A’ in Figures 2 & 3) and the two (2) #4-40 x 5/8” Standoffs
(location ‘B’ in Figures 2 & 3) which secure the CPU Board to the Main Mounting
Bracket. Replace these items with the three new #4-40 x 15/32” Standoffs.
Note:
This operation should only be performed in an ESD safe area.
8.
Align the EXPCOM232 Board Connector P1 with CPU Board Connector J4 (for 3530-
10B, 40B or -50B) or J18 (for 3530-15B & -45B). Push the EXPCOM232 Board toward the CPU Board until Connector P1 is fully seated.
EXPCOM232 Option Page 4 PIP-EXP232TF
Figure 2 - TeleFlow CPU Board – Installation Drawing #1
9.
Secure the EXPCOM232 Board to the CPU Board by installing three (3) #4-40 x .188”
Standoffs at locations ‘A’ and ‘B’ (see Figures 2 & 3).
10. Carefully install the Modified PC Shield, securing it to the Main Mounting Bracket (at locations ‘C’) with two #4-40 x 1/4” screws and to the CPU Board (at locations ‘B’) with two (2) #4-40 x 1/8” SEM screws (see Figures 4, 5, 6 & 7).
11. Follow steps 2 through 6 in reverse order, replacing rather than removing the item in question.
PIP-EXP232TF Page 5 EXPCOM232 Option
12.
Connect wiring between the EXPCOM232 Board and the DTE/DCE device to which it is to be interfaced (see Section 2.2).
13.
Configure the new network port in the ACCOL Load resident in the host 3530-XXX device.
Figure 3 - TeleRTU CPU Board – Installation Drawing #1
14.
Close and secure the Instrument Front Cover.
15. To remove an optional EXPCOM232 Board, follow steps 1 through 6 (unplug the RS-
232 cable during step 5). Remove the PC Shield along with the three Standoffs that
EXPCOM232 Option Page 6 PIP-EXP232TF
secure the EXPCOM232 Board to the CPU Board. Then unplug the EXPCOM232
Board from the CPU Board in question.
Figure 4 - TeleFlow CPU Board (with EXPCOM232 Installed)
Installation Drawing #2
PIP-EXP232TF Page 7 EXPCOM232 Option
Figure 5 - TeleRTU CPU Board (with EXPCOM232 Installed)
Installation Drawing #2
EXPCOM232 Option Page 8 PIP-EXP232TF
Figure 6 - 3530-10B, 3530-40B & 3530-50B (with EXPCOM232 Installed)
Figure 7 - 3530-15B & 3530-45B (with EXPCOM232 Installed)
PIP-EXP232TF Page 9 EXPCOM232 Option
2.1.1.2 Installation/Removal for Models 3530-20B & -25B
To install the optional EXPCOM232 Board into a model 3530-20B or 3530-25B, follow steps
1 through 11 below. To remove the optional EXPCOM232 Board, perform steps 1 and 2 and then follow steps 4 through 9 in reverse order, removing rather than installing the item in question after the system has been shut down. Note: The Instrument Front Cover must be open.
1.
Open the Instrument Front Cover
2.
Disconnect power by removing harness connector plug (P8 for TeleFlow - P2 for
TeleRTU) from the CPU Board edge connector (J8 for TeleFlow – J2 for TeleRTU).
Figure 8 - 3530-20B CPU (with EXPCOM232 Installed)
3.
Unplug the remaining removable Terminal Blocks (with wiring harnesses installed) from the CPU Board’s front edge connectors.
4.
Remove the two screws that secure the CPU Board’s Sliding Mounting Bracket to the
Fixed Bracket on the bottom of the Battery Bracket. Carefully slide the CPU Board
(and optional EXPCOM232 Board) toward the front of the unit. Remove harness connections from the Front Panel Switch (J12 on the TeleFlow CPU - J14 on TeleRTU
CPU), the Display Module (J2 on TeleFlow CPU - J16 on TeleRTU CPU), the Wakeup
Switch (J3 on TeleFlow CPU - J16 on TeleRTU CPU), and for TeleFlow CPU Boards connector J1 (associated with the Multivariable Transducer).
5.
Remove the three screws (of five) that secure the CPU Board to the Sliding Mounting
Bracket (locations ‘A’ & ‘B’ in Figures 2 & 3) and replace these items with the three new #4-40 x 15/32” Standoffs.
Note:
This operation should only be performed in an ESD safe area.
6.
Align the EXPCOM232 Board Connector P1 with CPU Board Connector J4 (for 3530-
20B) or J18 (for 3530-25B). Push the EXPCOM232 Board toward the CPU Board until
Connector P1 is fully seated.
7.
Secure the EXPCOM232 Board to the CPU Board by installing three (3) #4-40 x 1/4”
SEM screws as illustrated in Figures 8 & 9.
EXPCOM232 Option Page 10 PIP-EXP232TF
Figure 9 - 3530-25B CPU (with EXPCOM232 Installed)
8.
Route the RS-232 cable through a ¾” conduit fitting (user installed) on the bottom of the enclosure.
9.
Connect wiring between the EXPCOM232 Board and the DTE/DCE device to which it is to be interfaced (see Section 2.2).
10.
Configure the new network port in the ACCOL Load resident in the host 3530-XXX device.
11. Close and secure the Instrument Front Cover.
2.1.1.3 Installation/Removal for Models 3530-35B
To install the optional EXPCOM232 Board into a model 3530-35B, follow steps 1 through 8 below. To remove the optional EXPCOM232 Board, perform step 1 and then follow steps 5 through 7 in reverse order, removing rather than installing the item in question after the system has been shut down.
1.
Disconnect power by removing harness connector plug P2 from the CPU Board edge connector J2.
2. Unplug the remaining removable Terminal Blocks (with wiring harnesses installed) from the CPU Board’s front edge connectors.
3. Remove harness connections from the Front Panel Switch (J14), the Display Module
(J16) and the Wakeup Switch (J16).
4.
Remove the three screws (of five) that secure the CPU Board to the RTU Mounting
Bracket (locations ‘A’ & ‘B’ in Figures 2 & 3) and replace these items with the three new #4-40 x 15/32” Standoffs.
Note:
This operation should only be performed in an ESD safe area.
5.
Align the EXPCOM232 Board Connector P1 with CPU Board Connector J18. Push the
EXPCOM232 Board toward the CPU Board until Connector P1 is fully seated.
PIP-EXP232TF Page 11 EXPCOM232 Option
6.
Secure the EXPCOM232 Board to the CPU Board by installing three (3) #4-40 x 1/4”
SEM screws as illustrated in Figure 10.
7.
Connect wiring between the EXPCOM232 Board and the DTE/DCE device to which it is to be interfaced (see Section 2.2).
8.
Configure the new network port in the ACCOL Load resident in the host 3530-XXX device.
Figure 10 - 3530-35B (with EXPCOM232 Installed)
2.2 RS-232 WIRING
Table 2-1 and Figure 11 must be referenced to configure the RS-232 cable. Pin 2 of TB1 =
DCD (Data Carrier Detect - DCD). DCD can be used to awaken the 3530-XXX in question from power conservation (sleep) mode. This signal is not supplied by DTE equipment.
EXPCOM232 Option Page 12 PIP-EXP232TF
PIP-EXP232TF
Figure 11 - EXPCOM232 Wiring Diagrams
Page 13 EXPCOM232 Option
Either an RS-232 level control signal (high) can be supplied to TB1-2, or TB1-2 may be connected to the EXC signal on the CPU Board. It must be noted that as long as TB1-2
(DCD) remains HIGH, the 3530-XXX in question will remain awake. Therefore, if TB1-2 is connected to an EXC signal on the resident CPU Board, power conservation will be defeated, thus reducing the battery back-up time.
RS-232 cables are typically short (20’ or less in length). When significant distances are a factor (i.e., between an EXPCOM232 Board and the remote Data Terminal Device (DTE) to which it is desired to communicate), the RS-232 Port (TB1) cable can be connected to the
RS-232 Port of a modem or that of a BBI Isolated RS-485 Board (see Table 2-1).
Table 2-1
EXPCOM232 Board (DTE) & DCE/DTE - RS-232 Port Pin Assignments
EXPCOM232
RS-232 – TB1
DTE
2 - DCD (In)
6 - RXD (In)
7 - TXD (Out)
3 - DTR (Out)
1 - GND
-
5 - RTS (Out)
4 - CTS (In)
-
EXPCOM232
RS-232 TB1 or
3530 Network
Port J13/J8
DTE
-
7 - TXD (Out)
6 - RXD (In)
-
1 - GND
-
4 - CTS (In)
5 - RTS (Out)
-
Modem
9-Pin – J4
DCE
1 - DCD (Out)
2 - RXD (Out)
3 - TXD (In)
4 - DTR (In)
5 - GND
6 - DSR (Out)
7 - RTS (In)
8 - CTS (Out)
9 - N/A
PC
(RS-232)
3310/30/35
3305
3332
Notes 1 & 2
BBI
Isolated RS-485
Board Option
J1
DTE
-
DTE
-
DTE
-
3 - TXD (Out) 2 - TXD (Out) 7 - TXD (Out)
2 - RXD (In)
-
4 - RXD (In)
-
6 - RXD (In)
-
5 - GND
-
8 - CTS (In)
7 - RTS (Out)
-
9 - GND
-
6 - CTS (In)
5 - RTS (Out)
-
1 - GND
-
4 - CTS (In)
5 - RTS (Out)
-
Note 1: Ports BIP1 & BIP2
BIP1 and BIP2 are RS-562 Ports (RS-232 compatible.
Note 2: 3310 Ports A & C (MFIB Board)
A & C are RS-423 Ports (RS-232 compatible).
3330 Ports A, B, C, D, G, H, I & J (Enhanced Comm. Boards)
ECB’s 392587-01-7, 392587-02-5, 392587-03-3 & 392903-01-6
A, B, C, D, G, H, I & J are RS-562 Ports (RS-232 compatible).
3335 Ports A, B, C, D, I & J (Enhanced Comm. Boards)
ECB’s 392589-01-0 & 392589-02-8
A, B, C, D, I & J are RS-232 Ports
3335 Ports A, B, C & D (Comm. Engine Boards)
CEB’s 392043-01-7 & 392058-01-4
A, B, C & D are RS-423 Ports (RS-232 compatible)
The device uses compression-type terminals that accommodate up to #14 AWG wire. A connection is made by inserting the bared end (1/4 inch Max.) into the clamp beneath the screw and then securing the screw. Insert the bared end fully to prevent short circuits.
Allow some slack in the wires when making terminal connections. The slack makes the connections more manageable and minimizes mechanical strain on the printed circuit boards and harnesses.
EXPCOM232 Option Page 14 PIP-EXP232TF
Section 3
SPECIFICATIONS
3.1 PERFORMANCE SPECIFICATIONS
Baud Rate (Max.):
Power Requirements:
Transient Protection:
RS-232 Outputs:
RS-232 Inputs:
RS-232 Ground:
RS-232 Interface Connector:
19.2K Asynchronous
+5Vdc @ 20mA Max. (Regulated)
16V Bi-directional Transient Absorption Zeners across all
RS-232 outputs
TXD (TB1-7)
DTR (TB1-3)
RTS (TB1-5)
DCD (TB1-2)
RXD (TB1-6)
CTS (TB1-4)
GND (TB1-1)
7-Pin Industrial 3.5mm Pitch Plugable Connector
3.2 ENVIRONMENTAL SPECIFICATIONS
Operating Temperature:
Storage Temperature:
Humidity:
ESD Susceptibility:
EMI Compatibility:
Transient Susceptibility:
-40 ° to +60 ° (C) [-40 ° to 140 ° (F)]
-40 ° to +85 ° (C) [-40 ° to 185 ° (F)]
15% to 90% RH (Non-Condensing)
Meets the requirement of IEC 801-2 for ESD withstand
Capability up to 10KV.
Designed to coexist inside a shielded enclosure with the
TeleFlow electronics. EMI radiation is insignificant and
Susceptibility is comparable or superior to associated
Electronics.
Designed to meet the requirements of ANSI/IEEE
C37.90.1-1989 (Formerly IEEE 472) for surge withstand
Capability.
PIP-EXP232TF Page 15 EXPCOM232 Option
BLANK PAGE
Expansion Communications Port RS-232 Board
Special Instructions for Class I, Division 2 Hazardous Locations
1. The BBI Expansion Communications Port RS-232 Board is listed by Underwriters
Laboratories (UL) as nonincendive and is suitable for use in Class I, Division 2, Groups
A, B, C and D hazardous locations or non-hazardous locations only. Read this document carefully before installing a nonincendive BBI Expansion Communications Port RS-232
Board. In the event of a conflict between the Expansion Communications Port RS-232
Board User Manual (PIP-EXP232TF) and this document, always follow the instructions in this document.
2. Wiring must be performed in accordance with Class I, Division 2 wiring methods as defined in Article 501-4 (b) of the National Electrical Code, NFPA 70 for installations within the United States, or as specified in Section 18-152 of the Canadian Electrical
Code for installation in Canada.
3. WARNING: EXPLOSION HAZARD - Substitution of components may impair suitability for use in Class I, Division 2 environments.
4. WARNING: EXPLOSION HAZARD - When situated in a hazardous location, turn off power before servicing/replacing the unit and before installing or removing I/O wiring.
5. WARNING: EXPLOSION HAZARD - Do Not disconnect equipment unless the power has been switched off or the area is known to be nonhazardous.
07/17/2000 Appendix A of PIP-EXP232TF - EXPCOM232 Board Page 1 of 1
BLANK PAGE
Expansion Communications Port RS-232 Board for 3530-XXX
Special Instructions for Class I, Division 1 Hazardous Locations
1.
A version of the Expansion Communications Port RS-232 Board is available that is listed by Underwriters Laboratories (UL) as intrinsically safe for use in Class I, Division
1, Groups C and D hazardous locations. Read this document carefully before installing an intrinsically safe Expansion Communications Port RS-232 Board. Refer to the
Expansion Communications Port RS-232 Board User’s Manual (PIP-EXP232TF) for general information. In the event of a conflict between the Expansion Communications
Port RS-232 Board User’s Manual and this document, always follow the instructions in this document.
2.
Unless the Expansion Communications Port RS-232 Board is used in conjunction with an IStran Communications Interface Assembly (see CI-3530-Istran) it may not be used in a Class I, Division 1 hazardous location.
3.
When a TeleFlow equipped with an Expansion Communications Port RS-232 Board is used in a Class I, Division 1 location, it must be used in conjunction with a BBI IStran
Communications Interface and installed per instruction manual CI-3530-IStran and
PIP-EXP232TF.
4.
The IStran and Expansion Communications Port RS-232 Board can be located in a nonhazardous or Division 2 rated area, while the TeleFlow can reside in a Division 1, 2 or nonhazardous area.
A suitable enclosure must be provided for the IStran. When the IStran is mounted in a
Division 2 area, the nonhazardous interface connections shall be made in accordance with Article 501-4(b) of the National Electrical Code NFPA 70.
CAUTION
When connecting the IStran and Expansion Communications
Port RS-232 Board to a TeleFlow that is mounted in a Division
1 area, wire all circuits using wiring methods specified in article 504 of the National Electrical Code NFPA 70. Contact your IStran supplier for assistance.
When installing an Expansion Communications Port RS-232
Board in a TeleFlow that is mounted in a Division 2 area, ensure that the area is nonhazardous before connecting or disconnecting the nonhazardous interface.
5.
Figures B1 through B4 show variations of approved connections to the Expansion
Communications Port RS-232 Board via a BBI IStran Communications Interface
Assembly.
12/12/03 Appendix B - Document PIP-EXP232TF Page 1 of 3
Expansion Communications Port RS-232 Board for 3530-XXX
Special Instructions for Class I, Division 1 Hazardous Locations
Figure B1 - Intrinsically Safe System with Radio and EXPCOM232 Board
(with Single Power Source)
Figure B2 - Intrinsically Safe System with Modem and EXPCOM232 Board
(with Single Power Source)
12/12/03 Appendix B - Document PIP-EXP232TF Page 2 of 3
Expansion Communications Port RS-232 Board for 3530-XXX
Special Instructions for Class I, Division 1 Hazardous Locations
Figure B3 - Intrinsically Safe System with Modem and EXPCOM232 Board
(with Independent Power Sources)
Figure B4 - Intrinsically Safe System with Radio and EXPCOM232 Board
(with Independent Power Sources)
12/12/03 Appendix B - Document PIP-EXP232TF Page 3 of 3
BLANK PAGE
READER RESPONSE FORM
Please help us make our documentation more useful to you! If you have a complaint, a suggestion, or a correction regarding this manual, please tell us by mailing this page with your comments. It's the only way we know we're doing our job by giving you correct, complete, and useful documentation.
DOCUMENT NUMBER: PIP-EXP232TF
TITLE:
EXPANSION COMMUNICATIONS PORT RS-232 BOARD (for Models 3530-XXX)
Product Information Package
ISSUE DATE: DEC., 2003
COMMENT/COMPLAINT:
______________________________________________________________________________
______________________________________________________________________________
______________________________________________________________________________
______________________________________________________________________________
______________________________________________________________________________
______________________________________________________________________________
______________________________________________________________________________
______________________________________________________________________________
______________________________________________________________________________
______________________________________________________________________________
______________________________________________________________________________
______________________________________________________________________________
______________________________________________________________________________
Mail this page to:
Bristol Babcock Inc.
1100 Buckingham Street
Watertown, CT 06795
Attn: Technical Publications Group, Dept. 315
Bristol Babcock
1100 Buckingham Street
Watertown, CT 06795
Phone: +1 (860) 945-2200
Fax: +1 (860) 945-2213
Website: www.bristolbabcock.com
U.S.A. Locations:
Northern Region
Bristol Babcock Inc.
1100 Buckingham Street
Watertown, CT 06795
Phone: +1 (860) 945-2381
Fax: +1 (860) 945-2525
Gulf Coast Region
Bristol Babcock Inc.
2000 Governor's Circle
Suite F
Houston, TX 77092-8731
Phone: +1 (713) 685-6200
Fax: +1 (713) 681-7331
Western Region
Bristol Babcock Inc.
1609 South Grove Avenue
Suites 106 & 107
Ontario, CA 91761
Phone: +1 (909) 923-8488
Fax: +1 (909) 923-8988
Southeast Region
Bristol Babcock Inc.
317 S. North Lake Blvd.
Suite 1016
Altamonte Springs, FL 32701
Phone: +1 (407) 740-7084
Fax: +1 (407) 629-2106
Helicoid Instruments
1100 Buckingham Street
Watertown, CT 06795
Phone: +1 (860) 945-2218
Fax: +1 (860) 945-2213 [email protected]
Central Region
Bristol Babcock Inc.
777 South Central
Expressway
Suite 1-C
Richardson, TX 75080
Phone: +1 (972) 238-8197
Fax: +1 (972) 238-8198 [email protected]
International Affiliates:
Canada
Bristol Babcock, Canada
234 Attwell Drive
Toronto, Ont. M9W 5B3
Canada
PH: 416-675-3820
FAX: 416-674-5129 [email protected]
Mexico
BBI, S.A. de C.V.
Homero No. 1343, 3er Piso
Col. Morales Polanco
11540 Mexico, D.F.
Mexico
PH: (52-55)-52-81-81-12
FAX: (52-55)-52-81-81-09
Rocky Mountain Region
Bristol Babcock Inc.
906 San Juan Blvd., Suite A
Farmington, NM 87401
Phone: +1 (505) 320-5046
Fax: +1 (505) 327-3273
Communications
Technology Group
Bristol Babcock Inc.
317 S. North Lake Blvd.
Suite 1016
Altamonte Springs, FL 32701
Phone: +1 (407) 629-9464
Fax: +1 (407) 629-2106 [email protected]
United Kingdom
Bristol Babcock Ltd.
Blackpole Road
Worcester, WR3 8YB
United Kingdom
PH: +44 (0) 1905 856950
FAX: +44 (0) 1905 856969 [email protected]
Asia Pacific
Bristol Babcock, Inc.
PO Box 1987
Bunbury, Western Australia
6231
PH: +61 (0) 8 9791 3654
FAX: +61 (0) 8 9791 3173 [email protected]
Victoria, Australia
PH: +61 (0) 3 9384 2171
FAX: +61 (0) 3 8660 2501
Calgary Office
Bristol Babcock, Canada
3812 Edmonton Trail N.E.
Calgary, Alberta T2E 5T6
Canada
PH: 403-265-4808
FAX: 403-233-2914 [email protected]
Villahermosa Office
BBI, S.A. de C.V.
Av. Plomo No.2
Bodega No. 1 - Ciudad
Industrial
Villahermosa, Tabasco 86010
Mexico
PH: 52-993-353-3142
FAX: 52-993-353-3145 [email protected]
Middle East
Bristol Babcock Ltd.
Blackpole Road
Worcester, WR3 8YB
United Kingdom
PH: +44 (0) 1905 856950
FAX: +44 (0) 1905 856969 [email protected]
RC Rev: 13-Jun-03
EXPANSION RS-485 and/or
ANALOG OUTPUT BOARD
Series No. 392971-XX-X
(For Models 3530-XXX)
For The Following BBI Instruction Manuals:
CI-3530-10B, CI-3530-15B, CI-3530-20B, CI-3530-25B,
CI-3530-35B, CI-3530-40B & CI-3530-50B
Product Information Package
Bristol Babcock
PIP-EXP485/AO
- January 2003
NOTICE
Copyright Notice
The information in this document is subject to change without notice. Every effort has been made to supply complete and accurate information. However, Bristol Babcock assumes no responsibility for any errors that may appear in this document.
Request for Additional Instructions
Additional copies of instruction manuals may be ordered from the address below per attention of the Sales Order Processing Department. List the instruction book numbers or give complete model number, serial or software version number. Furnish a return address that includes the name of the person who will receive the material. Billing for extra copies will be according to current pricing schedules.
TeleFlow TM and TeleRTU TM are trademarks of Bristol Babcock. Other trademarks or copyrighted products mentioned in this document are for information only, and belong to their respective companies, or trademark holders.
Copyright (c) 2003 Bristol Babcock, 1100 Buckingham St., Watertown, CT 06795. No part of this manual may be reproduced in any form without the express written permission of
Bristol Babcock.
IMPORTANT! READ INSTRUCTIONS BEFORE STARTING!
Be sure that these instructions are carefully read and understood before any operation is attempted. Improper use of this device in some applications may result in damage or injury. The user is urged to keep this book filed in a convenient location for future reference.
These instructions may not cover all details or variations in equipment or cover every possible situation to be met in connection with installation, operation or maintenance. Should problems arise that are not covered sufficiently in the text, the purchaser is advised to contact Bristol Babcock for further information.
EQUIPMENT APPLICATION WARNING
The customer should note that a failure of this instrument or system, for whatever reason, may leave an operating process without protection. Depending upon the application, this could result in possible damage to property or injury to persons. It is suggested that the purchaser review the need for additional backup equipment or provide alternate means of protection such as alarm devices, output limiting, fail-safe valves, relief valves, emergency shutoffs, emergency switches, etc.
If additional in-formation is required, the purchaser is advised to contact Bristol
Babcock.
RETURNED EQUIPMENT WARNING
When returning any equipment to Bristol Babcock for repairs or evaluation, please note the following: The party sending such materials is responsible to ensure that the materials returned to Bristol Babcock are clean to safe levels, as such levels are defined and/or determined by applicable federal, state and/or local law regulations or codes. Such party agrees to indemnify Bristol Babcock and save Bristol
Babcock harmless from any liability or damage, which Bristol Babcock may incur or suffer due to such party's failure to so act.
ELECTRICAL GROUNDING
Metal enclosures and exposed metal parts of electrical instruments must be grounded in accordance with OSHA rules and regulations pertaining to "Design
Safety Standards for Electrical Systems," 29 CFR, Part 1910, Subpart S, dated: April
16, 1981 (OSHA rulings are in agreement with the National Electrical Code).
The grounding requirement is also applicable to mechanical or pneumatic instruments that include electrically-operated devices such as lights, switches, relays, alarms, or chart drives.
EQUIPMENT DAMAGE FROM ELECTROSTATIC DISCHARGE VOLTAGE
This product contains sensitive electronic components that can be damaged by exposure to an electrostatic discharge (ESD) voltage. Depending on the magnitude and duration of the ESD, this can result in erratic operation or complete failure of the equipment. Read BBI document S14006 for proper care and handling of ESDsensitive components.
Bristol Babcock 1100 Buckingham Street, Watertown, CT 06795
Telephone (860) 945-2200
A.
B.
C.
D.
E.
F.
A.
B.
WARRANTY
Bristol warrants that goods described herein and manufactured by Bristol are free from defects in material and workmanship for one year from the date of shipment unless otherwise agreed to by Bristol in writing.
Bristol warrants that goods repaired by it pursuant to the warranty are free from defects in material and workmanship for a period to the end of the original warranty or ninety (90) days from the date of delivery of repaired goods, whichever is longer.
Warranties on goods sold by, but not manufactured by Bristol are expressly limited to the terms of the warranties given by the manufacturer of such goods.
All warranties are terminated in the event that the goods or systems or any part thereof are (i) misused, abused or otherwise damaged, (ii) repaired, altered or modified without Bristol's consent, (iii) not installed, maintained and operated in strict compliance with instructions furnished by Bristol, or (iv) worn, injured or damaged from abnormal or abusive use in service time.
THESE WARRANTIES ARE EXPRESSLY IN LIEU OF ALL OTHER
WARRANTIES EXPRESS OR IMPLIED (INCLUDING WITHOUT LIMITATION
WARRANTIES AS TO MERCHANTABILITY AND FITNESS FOR A PARTICULAR
PURPOSE), AND NO WARRANTIES, EXPRESS OR IMPLIED, NOR ANY
REPRESENTATIONS, PROMISES, OR STATEMENTS HAVE BEEN MADE BY
BRISTOL UNLESS ENDORSED HEREIN IN WRITING. FURTHER, THERE ARE
NO WARRANTIES WHICH EXTEND BEYOND THE DESCRIPTION OF THE
FACE HEREOF.
No agent of Bristol is authorized to assume any liability for it or to make any written or oral warranties beyond those set forth herein.
REMEDIES
Buyer's sole remedy for breach of any warranty is limited exclusively to repair or replacement without cost to Buyer of any goods or parts found by Seller to be defective if Buyer notifies Bristol in writing of the alleged defect within ten (10) days of discovery of the alleged defect and within the warranty period stated above, and if the Buyer returns such goods to Bristol's Watertown office, unless Bristol's Watertown office designates a different location, transportation prepaid, within thirty (30) days of the sending of such notification and which upon examination by Bristol proves to be defective in material and workmanship. Bristol is not responsible for any costs of removal, dismantling or reinstallation of allegedly defective or defective goods. If a Buyer does not wish to ship the product back to Bristol, the Buyer can arrange to have a Bristol service person come to the site. The Service person's transportation time and expenses will be for the account of the Buyer. However, labor for warranty work during normal working hours is not chargeable.
Under no circumstances will Bristol be liable for incidental or consequential damages resulting from breach of any agreement relating to items included in this quotation from use of the information herein or from the purchase or use by Buyer, its employees or other parties of goods sold under said agreement.
How to return material for Repair or Exchange
Before a product can be returned to Bristol Babcock for repair, upgrade, exchange, or to verify proper operation, form (GBU 13.01) must be completed in order to obtain a RA
(Return Authorization) number and thus ensure an optimal lead time. Completing the form is very important since the information permits the Bristol Babcock Repair Dept.to effectively and efficiently process the repair order.
You can easily obtain a RA number by:
A. FAX
Completing the form (GBU 13.01) and faxing it to (860) 945-3875. A BBI Repair
Dept. representative will return call (or other requested method) with a RA number.
B. E-MAIL
Accessing the form (GBU 13.01) via the Bristol Babcock Web site
(www.bristolbabcock.com) and sending it via E-Mail to [email protected]
.
A BBI Repair Dept. representative will return E-Mail (or other requested method) with a RA number.
C. Mail
Mail the form (GBU 13.01) to
Bristol Babcock Inc.
Repair Dept.
1100 Buckingham Street
Watertown, CT 06795
A BBI Repair Dept. representative will return call (or other requested method) with a RA number.
D. Phone
Calling the BBI Repair Department at (860) 945-2442. A BBI Repair Department representative will record a RA number on the form and complete Part I, then send the form to the Customer via fax (or other requested method) for Customer completion of Parts II & III.
A copy of the completed Repair Authorization Form with issued RA number should be included with the product being returned. This will allow us to quickly track, repair, and return your product to you.
Bristol Babcock Inc. Repair Authorization Form
(Providing this information will permit BBI to effectively and efficiently process your return. Completion is required to receive optimal lead time. Lack of information may result in increased lead times.)
Date___________________ RA #___________________SH_ Line No.____________
Standard Repair Practice is as follows: Variations to this is practice may be requested in the “Special Requests” section.
· Evaluate / Test / Verify Discrepancy
· Repair / Replace / etc. in accordance with this form
· Return to Customer
Part I
Please be aware of the
·
Non warranty standard charge:
There is a $100 minimum evaluation charge, which is applied to the repair if applicable ( or D of part III below)
Please complete the following information for single unit or multiple unit returns
Ö in “returned” B,C,
Address No.
Bill to :
(office use only) Address No.
Ship to:
(office use only)
Purchase Order:
Phone: Fax:
Contact Name: ____________________________________
E-Mail:
Part II Please complete Parts II & III for each unit returned
Model No./Part No.
Description
Range/Calibration
Reason for return : Failure Upgrade
S/N
Verify Operation Other
1.
Describe the conditions of the failure (Frequency/Intermittent, Physical Damage, Environmental Conditions,
Communication, CPU watchdog, etc.)
(Attach a separate sheet if necessary)
2. Comm. interface used: Standalone RS-485 Ethernet Modem (PLM (2W or 4W) or SNW) Other: ______________
3. What is the Firmware revision? _____________________ What is the Software &version?
Part III If checking “replaced” for any question below, check an alternate option if replacement is not available
A.
If product is within the warranty time period but is excluded due to BBI’s warranty clause, would you like the product: repaired returned replaced scrapped?
B.
If product were found to exceed the warranty period, would you like the product:
C.
If product is deemed not repairable would you like your product:
D.
If BBI is unable to verify the discrepancy, would you like the product: repaired returned replaced scrapped?
returned replaced scrapped?
returned replaced *see below?
* Continue investigating by contacting the customer to learn more about the problem experienced? The person to contact that has the most knowledge of the problem is: _______________________________ phone
If we are unable to contact this person the backup person is: _________________________ phone
Special Requests:
Ship prepaid to: Bristol Babcock Inc., Repair Dept., 1100 Buckingham Street, Watertown, CT 06795
Phone: 860-945-2442 Fax: 860-945-3875
Form GBU 13.01
Rev. A
Bristol Babcock
Training
GET THE MOST FROM YOUR BRISTOL
BABCOCK INSTRUMENT OR SYSTEM
● Avoid Delays and problems in getting your system on-line
● Minimize installation, start-up and maintenance costs.
● Make the most effective use of our hardware and software.
● Know your system.
As you know, a well-trained staff is essential to your operation. Bristol Babcock offers a full schedule of classes conducted by full-time, professional instructors. Classes are offered throughout the year at four locations: Houston, Birmingham, Orlando and our Watertown,
CT headquarters. By participating in our training, your personnel can learn how to install, calibrate, configure, program and maintain any and all Bristol Babcock products and realize the full potential of your system.
For information or to enroll in any class, contact our training department in Watertown at
(860) 945-2269. For Houston classes, you can also contact our Houston office, at (713) 685-
6200.
BLANK PAGE
A Few Words About Bristol Babcock
For over 100 years, Bristol 7 has been providing innovative solutions for the measurement and control industry. Our product lines range from simple analog chart recorders, to sophisticated digital remote process controllers and flow computers, all the way to turnkey
SCADA systems. Over the years, we have become a leading supplier to the electronic gas measurement, water purification, and wastewater treatment industries.
On off-shore oil platforms, on natural gas pipelines, and maybe even at your local water company, there are Bristol Babcock instruments, controllers, and systems running year-in and year-out to provide accurate and timely data to our customers.
Getting Additional Information
In addition to the information contained in this manual, you may receive additional assistance in using this product from the following sources:
Contacting Bristol Babcock Directly
Bristol Babcock's world headquarters are located at 1100 Buckingham Street, Watertown,
Connecticut 06795, U.S.A.
Our main phone numbers are:
(860) 945-2200
(860) 945-2213 (FAX)
Regular office hours are Monday through Friday, 8:00AM to 4:30PM Eastern Time, excluding holidays and scheduled factory shutdowns. During other hours, callers may leave messages using Bristol's voice mail system.
Telephone Support - Technical Questions
During regular business hours, Bristol Babcock's Application Support Group can provide telephone support for your technical questions.
For technical questions about TeleFlow Ô products call (860) 945-8604.
For technical questions about Control Wave call (860) 945-2244 or (860) 945-2286.
For technical questions regarding Bristol’s OpenEnterprise product, call (860) 945-2501 or e-mail: [email protected]
For technical questions regarding ACCOL products, Open BSI Utilities , as well as
Bristol's Enterprise Server 7 / Enterprise Workstation 7 products, call (860) 945-2286.
For technical questions about Network 3000 hardware, call (860) 945-2502.
You can e-mail the Application Support Group at: [email protected]
The Application Support Group maintains an area on our web site for software updates and technical information. Go to: www.bristolbabcock.com/services/techsupport/
For assistance in interfacing Bristol Babcock hardware to radios, contact Bristol Babcock’s
Communication Technology Group in Orlando, FL at (407) 629-9463 or (407) 629-
9464 .
Telephone Support - Non-Technical Questions, Product Orders, etc.
Questions of a non-technical nature (product orders, literature requests, price and delivery information, etc.) should be directed to the nearest sales office (listed on the rear cover) or to your Bristol-authorized sales representative. A list of
Please call the main Bristol Babcock number (860-945-2200) if you are unsure which office covers your particular area.
Visit our Site on the World Wide Web
For general information about Bristol Babcock and its products, please visit our site on the
World Wide Web at: www.bristolbabcock.com
Training Courses
Bristol Babcock’s Training Department offers a wide variety of courses in Bristol hardware and software at our Watertown, Connecticut headquarters, and at selected Bristol regional offices, throughout the year. Contact our Training Department at (860) 945-2269 for course information, enrollment, pricing, and scheduling.
PIP-EXP485/AO
EXPANSION RS-485 COMMUNICATIONS and/or ANALOG OUTPUT BOARD
PT. Number 392971-XX-X
Product Information Package
TABLE OF CONTENTS
1.1
1.1.1
1.1.2
1.2
1.3
1.3.1
SECTION TITLE PAGE #
DESCRIPTION................................................................................................................... 1
Function .............................................................................................................................. 1
Features............................................................................................................................... 2
COMPONENT IDENTIFICATION................................................................................... 3
INSTALLATION COMPATIBILITY................................................................................ 3
Restrictions ......................................................................................................................... 3
2.1
2.1.1
2.1.1.1
2.1.1.2
2.1.1.3
2.2
Section 2 – INSTALLATION & SERVICE
EXP485/AO REMOVAL/REPLACEMENT & INSTALLATION ................................... 4
Installation/Removal of the EXP485/AO Board ................................................................ 4
Installation/Removal for Models 3530-10B, -15B, -40B & -50B ...................................... 4
Installation/Removal for Models 3530-20B & -25B ........................................................ 11
Installation/Removal for Models 3530-35B ..................................................................... 13
RS-485 and AO WIRING ................................................................................................. 14
3.1
3.2
3.3
PERFORMANCE SPECIFICATIONS ............................................................................ 16
ENVIRONMENTAL SPECIFICATIONS ....................................................................... 16
ENTITY PARAMETERS (INTRINSICALLY SAFE EXPAO Bd.) ............................... 17
SUPPLEMENTS
PIP-EXP485/AO Page 0-1 Table Of Contents
BLANK PAGE
Section 1
INTRODUCTION
1.1 DESCRIPTION
1.1.1 Function
The Expansion RS-485 Comm. Port with Analog Output Board (EXP485/AO) provides a single RS-485 communications port to ACCOL-based 3530-XXX models. In addition to assignments of the resident (host) CPU’s “local” and “network” RS-232 ports, any model
3530-XXX unit equipped with a fully populated EXP485/AO Board can establish RS-485 asynchronous communications with other 3530-XXX devices and/or can interface to an
Analog Output circuit. The EXP485/AO Board plugs into the Expansion Connector of the
TeleFlow or TeleRTU CPU Board, is stood-off by three 15/32” long hex standoffs and is secured via three screws or standoffs depending on the model. The CPU Board Expansion
Connector supplies power and 3530-XXX communication to the EXP485/AO Board.
EXP485/AO Boards measure 4.25” by 3.75” and utilizes a 9-position Industrial 3.5mm pitch plugable connector to interface (RS-485) to a series of remote 3530-XXX devices and or a single 1-5Vdc or 4-20mA AO device.
Programmable baud rates up to 19.2Kbps are supported by the EXP485/AO Board.
Interface signals are available at TB1 of the EXP485/AO. When the SLEEP+ & SLEEPsignals (supplied by the Master 3530-XXX) are Low and High respectively, the remote
3530-XXX CPU Boards will be awakened. If no activity is required, the EXP485/AO Board‘s serial communications controller (SCC) chip and RS-485 drivers can be put to sleep (low power mode) along with the host/parent 3530-XXX and the SLEEP+ and SLEEP- signals will be set High and Low respectively.
Figure 1 - EXP485/AO Board (with RS-485 & Configurable AO)
PIP-EXP485/AO Page 1 EXP485/AO Option
Figure 2 - EXPAO Board (with 1-5Vdc AO and without RS-485)
1.1.2 Features
· Low Power
+5Vdc @ 20mA (Max) regulated power and 5.8Vdc to 16Vdc @ 50mA (Max) unregulated power are supplied by the host/parent 3530-XXX via the 40-pin
Expansion Interface Connector P1.
· ESD & Transient Susceptibility
The RS-485 I/O circuitry has been designed to meet the requirements of IEC 801-2 for ESD withstand capability up to 10KV and the requirements of ANSI/IEEE
C37.90.1-1989 (formerly IEE 472) for surge withstand capability.
· EMI Compatibility
EXP485/AO Boards have been designed to coexist inside a shielded enclosure with the TeleFlow ä electronics. EMI radiation is insignificant and susceptibility is comparable or superior to associated electronics.
· Mounting
The EXP485/AO Board measures 3.75” (9.525cm) in width x 4.25” (10.795cm) in height and mounts piggy-back on a TeleFlow or TeleRTU CPU Board.
· RS-485 Comm. Port
EXP485/AO Boards provide an RS-485 communications port that is programmable for asynchronous rates up to 19.2Kbps. 3530-XXX units equipped with the
EXP485/AO Board can communicate with a network of 3530-XXX units (equipped
EXP485/AO Option Page 2 PIP-EXP485/AO
with EXP485/AO Boards), even though a radio or modem may be installed on the
CPU Board’s network port.
1.2 COMPONENT IDENTIFICATION
EXP485/AO Boards do not contain LEDs or switches. Fully populated EXP485/AO Boards
(P/N 392971-01-0) are provided with seven (7) configuration jumpers (see Figures 1 & 11).
Depopulated EXPAO Boards (P/N 392971-02-0) are factory set for 1-5Vdc AO operation and don’t have configuration jumpers (see Figure 2). Two connectors are provided; 40-pin connector P1 mates with the host 3530-XX-X (connector J4 - TeleFlow CPU or J18 - TeleRTU
CPU) and accommodates the TTL interface between the two entities, while 9-pin connector
TB1 mates with the RS-485 device that is being interfaced to the 3530-XXX and/or an analog output device. Additionally, the 3.5mm pitch plugable connector TB1 is removable from its mating EXP485/AO Board socket.
1.3 INSTALLATION COMPATIBILITY
An EXP485/AO Board can be installed into any of the following 3530-XXX models:
3530-10B - TeleFlow
3530-15B - TeleRTU
3530-35B - TeleRTU Module
3530-40B - TeleFlow ECR
3530-20B - TeleFlow Plus 3530-50B - TeleFlow Corrector
3530-25B - TeleRTU Plus
1.3.1 Restrictions
The 3530-XXX in question must be equipped with ACCOL application software. The
TeleFlow Plus (3530-20B), TeleRTU Plus (3530-25B) and the TeleRTU Module (3530-35B) support installation of either a Low Power I/O Expansion Board (LPI/OEB), an
EXPCOM232 Board, or the EXP485/AO Board discussed herein, i.e., YOU CAN ONLY
INSTALL ONE (1) OF THESE ITEMS .
EXP485/AO Board (P/N 392971-01-0) is fully populated and supports RS-485 network communications and interface to either a 1-5Vdc or a 4-20mA analog output device.
P/N 392971-02-0 is a depopulated version of the EXP485/AO Board and only supports interface to a 1-5Vdc analog output device. Connector TB1 has two usable pins (08 = AO and 09 = AOGND). This version is designed for use in a Class I, Division 2, Groups C and D nonincendive environment or a Class I, Division 1, Groups C and D intrinsically safe environment.
Intrinsically safe EXPAO Boards can be installed in 3530-XXX units with 6V Lead Acid or
7.2V Lithium battery systems.
PIP-EXP485/AO Page 3 EXP485/AO Option
Section 2
INSTALLATION & SERVICE
2.1 EXP485/AO REMOVAL/REPLACEMENT & INSTALLATION
2.1.1 Installation/Removal of the
EXP485/AO Board
In addition to hardware normally contained within the 3530-XXX in question, units with an installed EXP485/AO Option will contain the following major parts.
1.
Expanded Comm. Port RS-485/AO Board (EXP485/AO)
2.
Three (3) #4-40 x 15/32” Standoffs (Note: Models 3530-10B, -15B, -40B & -50B will also contain Three (3) #4-40 x .188” Standoffs & Two (2) #4-40 x 1/8” SEM Screws)
3.
Modified PC Shield Assembly (for models 3530-10B, -15B, -40B & -50B)
WARNING
Never attempt to service a TeleFlow, TeleFlow ECR, TeleRTU or
TeleFlow Corrector while it is powered and operating in a hazardous environment. Either the area must be made safe or the unit must be powered down, unwired, unmounted, and taken to a safe, nonhazardous area.
WARNING
Never attempt to install or remove any components (PCBs, Field
Wiring, Transducers, etc.) while the unit is powered and running.
Doing so can cause sudden electrical transients or imbalances that are capable of causing damage to the module or component in question, as well as other associated circuit boards. Always turn off the external/internal power source, including any additional supply sources used for externally-powered I/O circuits, before changing or adding any components.
CAUTION
Place any related critical processes under manual or auxiliary control prior to shutting down or performing any of the steps discussed herein.
2.1.1.1 Installation/Removal for Models 3530-10B, -15B, -40B & -50B
To install the optional EXP485/AO Board into a model 3530-10B, -15B, -40B or -50B, follow steps 1 through 14 below. To remove the optional EXP485/AO Board, see step 15. Note: The
Instrument Front Cover must be open.
1.
To open the Instrument Front Cover, remove the lock if present and turn each of the three captive screws a quarter (1/4) turn counterclockwise.
EXP485/AO Option Page 4 PIP-EXP485/AO
Note:
The CPU Board is not to be removed under any circumstances unless the unit has been moved to an ESD safe area (see ESDS Manual - S14006).
2.
Remove the Power Plug(s), Solar Panel Power Plug, and the Auxiliary Power Plug as required, from the CPU Board in question.
3.
Remove the optional radio or modem if installed.
To remove an optional modem :
Disconnect the phone wires. Loosen the four (4) screws that secure the Modem/Radio
Mounting Plate (with modem) to the Battery Mounting Bracket. Slide the modem to the left and remove it and then disconnect the D-Type connector from the modem.
To remove an optional radio :
Disconnect the Radio/TeleFlow Interface Cable from the bottom of the Radio. Unplug the 2-wire power connector associated with the 2-wire Radio Power Interface Cable from the bottom of the Radio. Loosen the four (4) screws that secure the Modem/Radio
Mounting Plate (with radio) to the Battery Mounting Bracket. Slide the radio to the left and remove it.
4.
Remove the Battery(s) (if present).
To remove the battery(s) from units without an optional modem or radio :
Hold the battery securely and remove the Left Battery Mounting Bracket (secured with 2 screws. Loosen the screws which secure the Right Battery Mounting Bracket
(Carefully remove the battery (with wiring harness). Remove the Right Battery
Mounting Bracket.
To remove the battery(s) from units with an optional modem or radio :
Carefully remove the battery (with wiring harness). Note: You may have to loosen the two left 1/4-20 x 3/8” screws that secure the left side of the Battery Mounting Bracket and the Main Mounting Bracket to the rear of the unit.
While holding the Main
Mounting Bracket, remove the four (4) 1/4-20 x 3/8” screws and lock washers that secure the Battery Mounting Bracket and Main Mounting Bracket to the rear of the unit. Remove the Battery Mounting Bracket and temporarily reinstall the four screws to secure the Main Mounting Bracket to the 3530-10B, 15B, -45B or -50B.
5.
Disconnect the Local Port, Network Port, RTD, and Field I/O wires from the CPU
Board connectors by unplugging their associated Terminal Plugs on the front edge of the CPU.
6. Carefully remove the PC Shield which is secured to the Main Mounting Bracket by 2
(#4-40 x 1/4”) screws and to the CPU Board by 2 (#4-40 x 1/4”) screws.
7. Remove the screw (location ‘A’ in Figures 3 & 4) and the two (2) #4-40 x 5/8” Standoffs
(location ‘B’ in Figures 2 & 3) which secure the CPU Board to the Main Mounting
Bracket. Replace these items with the three new #4-40 x 15/32” Standoffs.
Note:
This operation should only be performed in an ESD safe area.
8.
Align the EXP485/AO Board Connector P1 with CPU Board Connector J4 (for 3530-
10B or -50B) or J18 (for 3530-15B). Push the EXP485/AO Board toward the CPU
Board until Connector P1 is fully seated.
PIP-EXP485/AO Page 5 EXP485/AO Option
Figure 3 - TeleFlow CPU Board – Installation Drawing #1
9.
Secure the EXP485/AO Board to the CPU Board by installing three (3) #4-40 x .188”
Standoffs at locations ‘A’ and ‘B’ (see Figures 3 & 4).
10. Carefully install the Modified PC Shield, securing it to the Main Mounting Bracket (at locations ‘C’) with two #4-40 x 1/4” screws and to the CPU Board (at location ‘B’) with two (2) #4-40 x 1/8” SEM screws (see Figures 5, 6, 7 & 8).
11.
Follow steps 2 through 6 in reverse order, replacing rather than removing the item in question.
EXP485/AO Option Page 6 PIP-EXP485/AO
12.
Connect wiring between the EXP485/AO Board and the remote 3530-XXX units to which it is to be interfaced (see Section 2.2).
13.
Configure the new network port in the ACCOL Load resident in the host 3530-XXX device.
Figure 4 - TeleRTU CPU Board – Installation Drawing #1
14.
Close and secure the Instrument Front Cover.
15. To remove an optional EXP485/AO Board, follow steps 1 through 6 (unplug the RS-485 cable during step 5). Remove the PC Shield along with the three Standoffs that secure
PIP-EXP485/AO Page 7 EXP485/AO Option
the EXP485/AO Board to the CPU Board. Then unplug the EXP485/AO Board from the CPU Board in question.
Figure 5 - TeleFlow CPU Board (with EXP485/AO Installed)
Installation Drawing #2
EXP485/AO Option Page 8 PIP-EXP485/AO
Figure 6 - TeleRTU CPU Board (with EXP485/AO Installed)
Installation Drawing #2
PIP-EXP485/AO Page 9 EXP485/AO Option
Figure 7 - 3530-10B, 3530-40B & 3530-50B (with EXP485/AO Installed)
EXP485/AO Option
Figure 8 - 3530-15B (with EXP485/AO Installed)
Page 10 PIP-EXP485/AO
2.1.1.2 Installation/Removal for Models 3530-20B & -25B
To install the optional EXP485/AO Board into a model 3530-20B or 3530-25B, follow steps 1 through 11 below. To remove the optional EXP485/AO Board, perform steps 1 and 2 and then follow steps 4 through 9 in reverse order, removing rather than installing the item in question after the system has been shut down. Note: The Instrument Front Cover must be open.
1.
Open the Instrument Front Cover
2.
Disconnect power by removing harness connector plug (P8 for TeleFlow - P2 for
TeleRTU) from the CPU Board edge connector (J8 for TeleFlow - J2 for TeleRTU).
PIP-EXP485/AO
Figure 9 - 3530-20B CPU (with EXP485/AO Installed)
Page 11 EXP485/AO Option
3.
Unplug the remaining removable Terminal Blocks (with wiring harnesses installed) from the CPU Board’s front edge connectors.
4.
Remove the two screws that secure the CPU Board’s Sliding Mounting Bracket to the
Fixed Bracket on the bottom of the Battery Bracket. Carefully slide the CPU Board
(and optional EXP485/AO Board) toward the front of the unit. Remove harness connections from the Front Panel Switch (J12 on the TeleFlow CPU - J14 on TeleRTU
CPU), the Display Module (J2 on TeleFlow CPU - J16 on TeleRTU CPU), the Wakeup
Switch (J3 on TeleFlow CPU - J16 on TeleRTU CPU), and for TeleFlow CPU Boards connector J1 (associated with the Multivariable Transducer).
Figure 10 - 3530-25B CPU (with EXP485/AO Installed)
5.
Remove the three screws (of five) that secure the CPU Board to the Sliding Mounting
Bracket (locations ‘A’ & ‘B’ in Figures 3 & 4) and replace these items with the three new #4-40 x 15/32” Standoffs.
EXP485/AO Option Page 12 PIP-EXP485/AO
Note:
This operation should only be performed in an ESD safe area.
6.
Align the EXP485/AO Board Connector P1 with CPU Board Connector J4 (for 3530-
20B) or J18 (for 3530-25B). Push the EXP485/AO Board toward the CPU Board until
Connector P1 is fully seated.
7.
Secure the EXP485/AO Board to the CPU Board by installing three (3) #4-40 x 1/4”
SEM screws as illustrated in Figures 9 & 10.
8.
Route the RS-485 and AO cables through a ¾” conduit fitting (user installed) on the bottom of the enclosure.
9.
Connect wiring between the EXP485/AO Board and the remote 3530-XXX units to which it is to be interfaced (see Section 2.2).
10.
Configure the new network port in the ACCOL Load resident in the host 3530-XXX device.
11. Close and secure the Instrument Front Cover.
2.1.1.3 Installation/Removal for Models 3530-35B
To install the optional EXP485/AO Board into a model 3530-35B, follow steps 1 through 8 below. To remove the optional EXP485/AO Board, perform step 1 and then follow steps 5 through 7 in reverse order, removing rather than installing the item in question after the system has been shut down.
1.
Disconnect power by removing harness connector plug P2 from the CPU Board edge connector J2.
2. Unplug the remaining removable Terminal Blocks (with wiring harnesses installed) from the CPU Board’s front edge connectors.
3. Remove harness connections from the Front Panel Switch (J14), the Display Module
(J16) and the Wakeup Switch (J16).
4.
Remove the three screws (of five) that secure the CPU Board to the RTU Mounting
Bracket (locations ‘A’ & ‘B’ in Figures 2 & 3) and replace these items with the three new #4-40 x 15/32” Standoffs.
Note:
This operation should only be performed in an ESD safe area.
5.
Align the EXP485/AO Board Connector P1 with CPU Board Connector J18. Push the
EXP485/AO Board toward the CPU Board until Connector P1 is fully seated.
6.
Secure the EXP485/AO Board to the CPU Board by installing three (3) #4-40 x 1/4”
SEM screws as illustrated in Figure 11.
7.
Connect wiring between the EXP485/AO Board and the remote 3530-XXX units to which it is to be interfaced (see Section 2.2).
PIP-EXP485/AO Page 13 EXP485/AO Option
8.
Configure the new network port in the ACCOL Load resident in the host 3530-XXX device.
Figure 11 - 3530-35B (with EXP485/AO Installed)
2.2 RS-485 and AO WIRING
Figure 12 must be referenced to configure the RS-485 cable. It is recommended that a low capacitance 24-gauge communications grade 2-twisted pair cable such as Belden 9842 be used for RS-485 networking.
EXP485/AO Option Page 14 PIP-EXP485/AO
Figure 12 - EXP485/AO Wiring Diagrams
The device uses compression-type terminals that accommodate up to #14 AWG wire. A connection is made by inserting the bared end (1/4 inch Max.) into the clamp beneath the screw and then securing the screw. Insert the bared end fully to prevent short circuits.
Allow some slack in the wires when making terminal connections. The slack makes the connections more manageable and minimizes mechanical strain on the printed circuit boards and harnesses.
PIP-EXP485/AO Page 15 EXP485/AO Option
Section 3
SPECIFICATIONS
3.1 PERFORMANCE SPECIFICATIONS
Baud Rate (Max.):
Power Requirements:
Transient Protection:
RS-485 Inputs/Outputs:
Analog Output Pins:
Interface Connector:
19.2K Asynchronous
+5Vdc @ 20mA Max. (Regulated)
+5.8Vdc to +16Vdc @ 50mA Max. (Unregulated)
5V Bi-directional Transient Absorption Zeners across all
RS-485 communication points
12V Bi-directional Transient Absorption Zeners across the
AO points (when configured for 1-5Vdc operation)
16V Bi-directional Transient Absorption Zeners across the
AO points (when configured for 4-20mA operation)
TXD/RDX+ (TB1-3)
TXD/RXD- (TB1-4)
SLEEP+ (TB1-5)
SLEEP(TB1-6)
AO (TB1-8) - 1-5Vdc @ 5mA Max. ONLY on
392971-02-0
(TB1-8) - 1-5Vdc @ 5mA Max. or 4-20mA on
392971-01-0
AOGND (TB1-9) - Analog Output Ground/Return
9-Pin Industrial 3.5mm Pitch Plugable Connector
3.2 ENVIRONMENTAL SPECIFICATIONS
Operating Temperature:
Storage Temperature:
Humidity:
Vibration:
RFI Susceptibility:
EMI Compatibility:
-40 ° to +60 ° (C) [-40 ° to 140 ° (F)]
-40 ° to +85 ° (C) [-40 ° to 185 ° (F)]
15% to 90% RH (Non-Condensing)
10 to 500 Hz at 1g on any axis per SAMA PMC-31-1 without damage or impairment.
Meets the requirement of IEC 1000-4-6 level 2 (3V/M) from 150kHz to 80MHz.
Designed to coexist inside a shielded enclosure with the
TeleFlow electronics. EMI radiation is insignificant and
Susceptibility is comparable or superior to associated
Electronics.
EXP485/AO Option Page 16 PIP-EXP485/AO
Surge Susceptibility:
EMI Radiated:
Designed to meet the requirements of ANSI/IEEE
C37.90.1-1989 (Formerly IEEE 472) for surge withstand capability.
Designed to meet the requirements of IEC 1004-4-3 for radiated emissions.
3.3 ENTITY PARAMETERS (INTRISICALLY SAFE EXPAO Bd.)
F1: .125A
R66:
D20/D21:
Voc:
Vmax:
Isc:
Imax:
Ca:
Ci:
La:
Li:
200 Ohms ±5%, .5W
6.2V ±5%
6.51V
15V
34.3mA
150mA
400µF
0µF
80mH
0mH
PIP-EXP485/AO Page 17 EXP485/AO Option
BLANK PAGE
Expansion RS-485 and/or Analog Output Board
Special Instructions for Class I, Division 2 Hazardous Locations
1. The BBI Expansion RS-485 and/or Analog Output (EXP485/AO) Board is listed by
Underwriters Laboratories (UL) as nonincendive and is suitable for use in Class I,
Division 2, Groups C and D hazardous locations or non-hazardous locations only. Read this document carefully before installing a nonincendive BBI Expansion RS-485 and/or
Analog Output Board. In the event of a conflict between the Expansion RS-485 and/or
Analog Output Board User Manual (PIP-EXP485/AO) and this document, always follow the instructions in this document.
2. Wiring must be performed in accordance with Class I, Division 2 wiring methods as defined in Article 501-4 (b) of the National Electrical Code, NFPA 70 for installations within the United States, or as specified in Section 18-152 of the Canadian Electrical
Code for installation in Canada.
3. WARNING: EXPLOSION HAZARD - Substitution of components may impair suitability for use in Class I, Division 2 environments.
4. WARNING: EXPLOSION HAZARD - When situated in a hazardous location, turn off power before servicing/replacing the unit and before installing or removing I/O wiring.
5. WARNING: EXPLOSION HAZARD - Do Not disconnect equipment unless the power has been switched off or the area is known to be nonhazardous.
12/14/2001 Appendix A of PIP-EXP485/AO - EXP485/AO Board Page 1 of 1
Expansion RS-485 and/or Analog Output Board for 3530-XXX
Special Instructions for Class I, Division 1 Hazardous Locations
1.
A version of the Expansion RS-485 and/or Analog Output (EXP485/AO) Board is available that is listed by Underwriters Laboratories (UL) as intrinsically safe for use in
Class I, Division 1, Groups C and D hazardous locations. Read this document carefully before installing an intrinsically safe Expansion RS-485 and/or Analog Output Board.
Refer to the Expansion RS-485 and/or Analog Output Board User’s Manual (PIP-
EXP485/AO) for general information. In the event of a conflict between the Expansion
RS-485 and or Analog Output User’s Manual and this document, always follow the instructions in this document.
2.
Only the depopulated version of the Expansion RS-485 and/or Analog Output Board
(EXP485/AO) (P/N 392971-02-0) may be used in a Class I, Division 1 hazardous location.
3.
TeleFlow models 3530-10B, 3530-40B and 3530-50B approved for use in Class I,
Division 1, Groups C and D hazardous locations and equipped with the EXP485/AO
Board option may reside in a Division 1, 2 or nonhazardous area. 3530-XXX units not approved for use in a Class I, Division 1 environment may contain an EXP485/AO Board but can only reside in a Class I, Division 2 or nonhazardous area.
CAUTION
When connecting the Expansion Analog Output Board to a
TeleFlow that is mounted in a Division 1 area, wire all circuits using wiring methods specified in article 501-4(A) of the
National Electrical Code NFPA 70.
When installing an Expansion RS-485 and/or Analog Output
Board (EXP485/AO) into a TeleFlow that is mounted in a
Division 2 area, ensure that the area is nonhazardous before connecting or disconnecting the nonhazardous interface.
4.
Intrinsically safe TeleFlows equipped with an intrinsically safe EXPAO Board (P/N
392971-02-0) do not include any internal communications options.
01/11/02 Appendix B - Document PIP-EXP485/AO Page 1 of 1
READER RESPONSE FORM
Please help us make our documentation more useful to you! If you have a complaint, a suggestion, or a correction regarding this manual, please tell us by mailing this page with your comments. It's the only way we know we're doing our job by giving you correct, complete, and useful documentation.
DOCUMENT NUMBER: PIP-EXP485/AO
TITLE:
EXPANSION RS-485 and/or ANALOG OUTPUT BOARD (for Models 3530-XXX)
Product Information Package
ISSUE DATE: JAN., 2003
COMMENT/COMPLAINT:
______________________________________________________________________________
______________________________________________________________________________
______________________________________________________________________________
______________________________________________________________________________
______________________________________________________________________________
______________________________________________________________________________
______________________________________________________________________________
______________________________________________________________________________
______________________________________________________________________________
______________________________________________________________________________
______________________________________________________________________________
______________________________________________________________________________
______________________________________________________________________________
Mail this page to:
Bristol Babcock Inc.
1100 Buckingham Street
Watertown, CT 06795
Attn: Technical Publications Group, Dept. 315
Bristol Babcock
1100 Buckingham Street
Watertown, CT 06795
Phone: (860) 945-2200
Fax: (860) 945-2213
Website: www.bristolbabcock.com
U.S.A. Locations:
Northern Region
Bristol Babcock Inc.
1100 Buckingham Street
Watertown, CT 06795
Phone: (860) 945-2381
Fax: (860) 945-2525
Southwest Region
Bristol Babcock Inc.
2000 Governor's Circle
Suite F
Houston, TX 77092-8731
Phone: (713) 685-6200
Fax: (713) 681-7331
Western Region
Bristol Babcock Inc.
1609 South Grove Avenue
Suites 106 & 107
Ontario, CA 91761
Phone: (909) 923-8488
Fax: (909) 923-8988
Southeast Region
Bristol Babcock Inc.
317 S. North Lake Blvd.
Suite 1016
Altamonte Springs, FL 32701
Phone: (407) 740-7084
Fax: (407) 629-2106
Helicoid Instruments
1100 Buckingham Street
Watertown, CT 06795
Phone: (860) 945-2218
Fax: (860) 945-2213 [email protected]
Dallas District Office
Bristol Babcock Inc.
777 South Central
Expressway
Suite 1-C
Richardson, TX 75080
Phone: (972) 238-8197
Fax: (972) 238-8198 [email protected]
International Affiliates :
Canada
Bristol Babcock, Canada
234 Attwell Drive
Toronto, Ont. M9W 5B3
Canada
PH: 416-675-3820
FAX: 416-674-5129 [email protected]
Mexico
BBI, S.A. de C.V.
Ejercito Nacional No. 718, 4
Piso
Colonia Polanco
Mexico, D.F. 11560
Mexico
PH: 52-555-254-5281
FAX: 52-555-254-3408
Sales Office New Mexico
Bristol Babcock Inc.
906 San Juan Blvd., Suite A
Farmington, NM 87401
Phone: (505) 320-5046
Fax: (505) 327-3273
Communications
Technology Group
Bristol Babcock Inc.
317 S. North Lake Blvd.
Suite 1016
Altamonte Springs, FL 32701
Phone: (407) 629-9464
Fax: (407) 629-2106 [email protected]
United Kingdom
Bristol Babcock Ltd.
Vale Industrial Estate
Stourport Road
Kidderminster
Worcestershire DY11 7QU
United Kingdom
PH: +44 (0) 1562 820001
FAX: +44 (0) 1562 746721 [email protected]
Australia
Bristol Babcock, Inc.
22 Hastie St.
PO Box 1987
Banbury, Western Australia
6230
PH: 61 (0)8 9791 3654
FAX: 61 (0)8 9791 3173 [email protected]
Calgary Office
Bristol Babcock, Canada
3812 Edmonton Trail N.E.
Calgary, Alberta T2E 5T6
Canada
PH: 403-265-4808
FAX: 403-233-2914 [email protected]
Villahermosa Office
BBI, S.A. de C.V.
Av. Plomo No.2
Bodega No. 1 - Ciudad
Industrial
Villahermosa, Tabasco 86010
Mexico
PH: 52-993-353-3142
FAX: 52-993-353-3145 [email protected]
Middle East
Bristol Babcock Ltd.
Vale Industrial Estate
Stourport Road
Kidderminster
Worcestershire DY11 7QU
United Kingdom
PH: +44 (0) 1562 820001
FAX: +44 (0) 1562 746721 [email protected]
Supplement Guide - S1400A
Issue: 04/03
TeleFlow
TM
SITE CONSIDERATIONS
For
EQUIPMENT INSTALLATION,
GROUNDING
&
WIRING
A Guide for the Protection of
Site Equipment & Personnel
In the Installation of
Series 3530-XX-X Instrumentation
Bristol Babcock
NOTICE
Copyright Notice
The information in this document is subject to change without notice. Every effort has been made to supply complete and accurate information. However, Bristol Babcock assumes no responsibility for any errors that may appear in this document.
Request for Additional Instructions
Additional copies of instruction manuals may be ordered from the address below per attention of the Sales Order Processing Department. List the instruction book numbers or give complete model number, serial or software version number. Furnish a return address that includes the name of the person who will receive the material. Billing for extra copies will be according to current pricing schedules.
TeleFlow TM and TeleRTU TM are trademarks of Bristol Babcock. Other trademarks or copyrighted products mentioned in this document are for information only, and belong to their respective companies, or trademark holders.
Copyright (c) 2003 Bristol Babcock, 1100 Buckingham St., Watertown, CT 06795. No part of this manual may be reproduced in any form without the express written permission of
Bristol Babcock.
Supplement Guide S1400A
SITE CONSIDERATIONS FOR EQUIPMENT
INSTALLATION, GROUNDING & WIRING
TABLE OF CONTENTS
4.1
4.1.1
4.1.2
4.1.3
4.1.4
4.1.5
4.2
3.1
3.1.1
3.2
3.3
3.3.1
3.3.1.1
3.3.1.2
3.3.1.3
3.3.2
3.3.2.1
3.3.3
3.4
3.4.1
3.4.2
SECTION TITLE
1.1
1.2
2.1
2.1.1
2.2
2.2.1
2.2.2
2.3
PAGE #
GENERAL INTRODUCTION .......................................................................................1-1
MAJOR TOPICS.............................................................................................................1-1
PROTECTING INSTRUMENT SYSTEMS...................................................................2-1
Quality Is Conformance To Requirements....................................................................2-1
PROTECTING EQUIPMENT & PERSONNEL ...........................................................2-1
Considerations For The Protection of Personnel.......................................................... 2-2
Considerations For The Protection of Equipment........................................................2-2
OTHER SITE SAFETY CONSIDERATIONS...............................................................2-3
Section 3 - GROUNDING & ISOLATION
POWER & GROUND SYSTEMS...................................................................................3-1
Modem Grounding Kit 621495-01-8. ............................................................................. 3-1
IMPORTANCE OF GOOD GROUNDS.........................................................................3-2
EARTH GROUND CONNECTIONS.............................................................................3-2
Establishing a Good Earth Ground. ..............................................................................3-2
Soil Conditions................................................................................................................3-3
Soil Types ........................................................................................................................3-3
Dry, Sandy or Rocky Soil................................................................................................3-5
Ground Wire Considerations. ........................................................................................3-6
Modem Ground Wiring Diagrams .................................................................................3-7
Other Grounding Considerations. ...............................................................................3-20
ISOLATING EQUIPMENT FROM THE PIPELINE .................................................3-21
Meter Runs Without Cathodic Protection...................................................................3-21
Meter Runs With Cathodic Protection ........................................................................3-22
Section 4 - LIGHTNING ARRESTERS & SURGE PROTECTORS
STROKES & STRIKES ..................................................................................................4-1
Chance of Being Struck by Lightning. ..........................................................................4-1
Antenna Caution ............................................................................................................4-3
Ground Propagation .......................................................................................................4-5
Tying it all Together.......................................................................................................4-5
Impulse Protection Summary ........................................................................................4-5
USE OF LIGHTNING ARRESTERS & SURGE PROTECTORS................................4-6
Supplement S1400A Page 0-1 Table Of Contents
Supplement Guide S1400A
SITE CONSIDERATIONS FOR EQUIPMENT
INSTALLATION, GROUNDING & WIRING
TABLE OF CONTENTS
5.1
5.2
5.2.1
5.2.2
5.2.3
5.2.4
5.2.5
5.2.6
5.2.7
5.2.8
5.2.9
5.2.10
SECTION TITLE PAGE #
OVERVIEW ....................................................................................................................5-1
INSTRUMENT WIRING. ..............................................................................................5-1
Common Returns............................................................................................................5-1
Use of Twisted Shielded Pair Wiring (with Overall Insulation)..................................5-2
Grounding of Cable Shields. ..........................................................................................5-3
Use of Known Good Earth Grounds ..............................................................................5-3
Earth Ground Wires .......................................................................................................5-3
Working Neatly & Professionally ..................................................................................5-3
High Power Conductors and Signal Wiring ..................................................................5-4
Use of Proper Wire Size ................................................................................................. 5-4
Lightning Arresters & Surge Protectors .......................................................................5-4
Secure Wiring Connections............................................................................................5-5
REFERENCE DOCUMENTS
1. IEEE Recommended Practice for Grounding of Industrial and Commercial Power Systems - ANSI/IEEE Std
142-1982
2. IEEE Guide for the Installation of Electrical Equipment to Minimize Electrical Noise inputs to Controllers from External Sources - IEE Std 518-1982
3.
Lightning Strike Protect; Roy B. Carpenter, Jr. & Mark N. Drabkin, Ph.D.; Lightning Eliminators &
Consultant, Inc., 6687 Arapahoe Road, Boulder Colorado
4.
Lightning Protection Manual for Rural Electric Systems, NRECA Research Project 82-5, Washington DC,
1983
5.
Grounding for the Control of EMI; Hugh W. Denny; Don White Consultants, Inc., 1983, 1 st Edition
6.
Fundamentals of EGM - Electrical Installations; Michael D. Price; NorAm Gas Transmission, 525 Milam
Street, Shreveport, Louisiana 71151
7.
TeleFlow Modem Grounding Kit 621495-01-8 Installation Instructions - PIP-3530MGKI; Bristol Babcock,
Watertown, CT 06795
Supplement S1400A Page 0-2 Table Of Contents
Section 1 - Overview
1.1 INTRODUCTION
This document provides information pertaining to the installation of TeleFlow systems; more specifically, information covering reasons, theory and techniques for protecting your personnel and equipment from electrical damage. Your instrument system affects the quality of service provided by your company and many aspects of its operational safety.
Loss of instruments means lost production and profits as well as increased expenses.
Information contained in this document is for educational purposes. Bristol Babcock makes no warranties or guarantees on the effectiveness or the safety of techniques described herein.
Where the safety of installations and personnel is concerned, refer to the National Electrical
Code Rules and rules of local regulatory agencies.
1.2
MAJOR TOPICS
Topics are covered in seven sections designed to pinpoint major areas of concern for the protection of site equipment and personnel. The following overview is provided for each of the major sections.
· Section 2 - Protection
This section provides the reasons for protecting instrument systems. An overview of the definition of quality and what we are trying to accomplish in the protection of site installations and how to satisfy the defined requirements is presented. Additionally, this section provides considerations for the protection of personnel and equipment.
· Section 3 - Grounding & Isolation
Construction of the TeleFlow with respect to grounds, isolation and electrical considerations is discussed. Information pertaining to what constitutes a good earth ground, how to test and establish such grounds, as well as when and how to connect equipment to earth grounds is provided
· Section 4 - Lightning Arresters & Surge Protectors
Some interesting information dealing with Lightning strikes and strokes is presented in technical and statistical form along with a discussion of how to determine the likelyhood of a lightning strike.
Protecting equipment and personnel during the installation of radios and antenna is discussed in a review of the dangers to equipment and personnel when working with antennas. Reasons for the use of lightning arresters and surge protectors are presented along with overviews of how each device protects site equipment.
· Section 5 - Wiring Techniques
Installation of Power and “Measurement & Control” wiring is discussed. Information on obscure problems, circulating ground and power loops, bad relays, etc. is presented.
Good wire preparation and connection techniques along with problems to avoid are discussed. This sections list the ten rules of instrument wiring.”
Section 1 - Overview Page 1-1 S1400A
Section 2 - Protection
2.1 PROTECTING INSTRUMENT SYSTEMS
Electrical instrumentation is susceptible to damage from a variety of natural and man made phenomena. In addition to wind, rain and fire, the most common types of system and equipment damaging phenomena are lightning, power faults, communication surges & noise and other electrical interference’s caused by devices such as radios, welders, switching gear, automobiles, etc. Additionally there are problems induced by geophysical electrical potential & noise plus things that are often beyond our wildest imagination.
2.1.1 Quality Is Conformance To Requirements
A quality instrumentation system is one that works reliably, safely and as purported by the equipment manufacturer (and in some cases by the system integrator) as a result of good equipment design and well defined and followed installation practices. If we except the general definition of quality to be, “quality is conformance to requirements,” we must also except the premise that a condition of “quality” can’t exist where requirements for such an end have not been evolved. In other words, you can’t have quality unless you have requirements that have been followed. By understanding the requirements for a safe, sound and reliable instrumentation system, and by following good installation practices (as associated with the personnel and equipment in question), the operational integrity of the equipment and system will be enhanced.
Understanding what is required to properly install BBI equipment in various environments, safely, and in accordance with good grounding, isolating and equipment protection practices goes a long way toward maintaining a system which is healthy to the owner and customer alike. Properly installed equipment is easier to maintain and operate, and is more efficient and as such more profitable to our customers. Following good installation practices will minimize injury, equipment failure and the customer frustrations that accompany failing and poorly operating equipment (of even the finest design). Additionally, personnel involved in the installation of a piece of equipment add to or subtract from the reliability of a system by a degree which is commensurate with their technical prowess, i.e., their understanding of the equipment, site conditions and the requirements for a quality installation.
2.2
PROTECTING EQUIPMENT & PERSONNEL
TeleFlow installations must be performed in accordance with National Electrical Code
Rules, electrical rules set by local regulatory agencies, and depending on the customer environment (gas, water, etc), other national, state and local agencies such as the American
Water Works Association (AWWA). Additionally, installation at various customer sites may be performed in conjunction with a “safety manager” or utility personnel with HAZMAT
(hazardous material) training on materials present (or potentially present) as required by
OSHA, the customer, etc.
Section 2 - Protection Page 2-1 S1400A
2.2.1
Considerations For The Protection of Personnel
Always evaluate the site environment as if your life depended on it. Make sure that you understand the physical nature of the location where you will be working. Table 2-1 provides a general guideline for evaluating an installation site.
Table 2-1 - Installation Site Safety Evaluation Guide
#
1 Indoor or outdoor – Dress Appropriately
Guide
2 If outdoor, what kind of environment, terrain, etc. Watch out for local varmint (bees, spiders, snakes, etc.)
3 If indoor or outdoor – determine if there are any pieces of dangerous equipment or any processes which might be a risk to your safety
4 If in a tunnel, bunker, etc. watch out for a build up of toxic or flammable gases. Make sure the air is good. Watch out for local varmint (bees, spiders, snakes, etc.)
5 Hazardous or Non-Hazardous Environment – Wear appropriate safety equipment and perform all necessary safety measures.
6 Before installing any equipment or power or ground wiring, make sure that there are no lethal (life threatening) voltages between the site where the instrument will be installed and other equipment, pipes, cabinets, etc. or to earth itself.
7 Never assume that adjacent or peripheral equipment has been properly installed and grounded. Determine if this equipment and a TeleFlow can be touched simultaneously without hazard to personnel and/or equipment?
8 Before embarking to remote locations where there are few or no human inhabitants ask a few simple questions like, should I bring water, food, hygienic materials, first aid kit, etc?
Be Prepared!
9 Observe the work habits of those around you – for your own safety!
Some of the items that a service person should consider before ever going on site can be ascertained by simply asking questions of the appropriate individual. Obviously other safety considerations can only be established at the installation site.
2.2.2
Considerations For The Protection of Equipment
Always evaluate the site installation/service environment and equipment. Understand the various physical interfaces you will be dealing with such as TeleFlow mounting and supporting, transducer mechanical and electrical connections, TeleFlow analog and digital circuits, power circuits, communication circuits and various electrical grounds. Table 2-2 provides a general guideline for evaluating the equipment protection requirements of an installation site.
Table 2-2 – Equipment Protection Site Safety Evaluation Guide
# Guide
1 Environment - Class I, Division 2 - Nonincendive
Environment - Class I, Division 1 - Intrinsically Safe
Other – Safe or unrated area
2 Earth Ground - Established by mechanical/electrical or
(both) or not at all.
3 Is the area prone to lightning strikes?
4 Are there surge suppressors installed or to be installed?
5 Are there overhead or underground power or communication cables in the immediate area?
Reference Section
See Appendix A of CI-3530-XX-X
See Appendix B of CI-3530-XX-X
See Section 3
See Section 4
See Section 4
See Section 2.3
S1400A Page 2-2 Section 2 - Protection
Table 2-2 –Equipment Protection Site Safety Evaluation Guide (Continued)
# Guide
6 Is there an antenna in the immediate area?
7 If pipe mounted, is a cathodic charge present on the pipe? Should the
TeleFlow be isolated?
8 How close is other equipment? Can someone safely touch this equipment and a TeleFlow simultaneously?
9 Determine equipment ground requirements. How will the TeleFlow and its related wiring be grounded? Consider Earth Ground, Circuit
Ground, Conduit Ground, Site Grounds, Manifold grounded or not?
10 Are there any obviously faulty or questionable power or ground circuits?
Reference Section
See Section 4.1.2
See Section 3.4
See Section 2.3
See Section 3
See Section 2.3
2.3
OTHER SITE SAFETY CONSIDERATIONS
Overhead or underground power or communication cables must be identified prior to installing a new unit. Accidentally cutting, shorting or simply just contacting power, ground, communication or process control I/O wiring can have potentially devastating effects on site equipment, the process system and or personnel.
Don’t assume that it is safe to touch adjacent equipment, machinery, pipes, cabinets or even the earth itself. Adjacent equipment may not have been properly wired or grounded, may be defective or may have one or more loose system grounds. Measure between the case of a questionable piece of equipment and its earth ground for voltage. If a voltage is present, something is wrong.
AC powered equipment with a conductive case should have the case grounded. If you don’t see a chassis ground wire, don’t assume that it is safe to touch this equipment. If you notice that equipment has been grounded to pipes, conduit, structural steel, etc., you should be leery. Note: AWWA’s policy on grounding of electric circuits on water pipes states,
“The American Water Works Association (AWWA) opposes the grounding of electrical systems to pipe systems conveying water to the customer’s premises….”
Be sure that the voltage between any two points in the instrument system is less than the stand-off voltage. Exceeding the stand-off voltage will cause damage to the instrument and will cause the instrument to fail.
Section 2 - Protection Page 2-3 S1400A
Section 3 - Grounding & Isolation
3.1 POWER & GROUND SYSTEMS
TeleFlow GFCs, TeleFlow ECRs, TeleFlow Correctors, TeleRTUs and TeleRecorders are similar in that they all have basically two system grounds, i.e., Chassis Gnd and
CPU/Circuit Ground. Chassis Ground is galvanically isolated from CPU/Circuit Ground by
500V (ac/dc). A jumper on the CPU Board would (if installed) place these two ground systems at the same potential and thus eliminate the 500V galvanic isolation. Installation of this jumper is not recommended. CPU/Circuit Ground consists of Power, Analog, Digital, and Comm. Grounds (all common).
Teleflows are DC (+6V or +12V) systems. AC power supplies are not provided with
TeleFlows. The TeleFlow’s Electronics are galvanically isolated from the case and should not be affected by cathodic protection or other EMF on the pipeline. Grounding to the pipeline, i.e., completing a connection between the 3530-XXX Ground Lug and the mounting media (valve, manifold, pipeline, etc.) is not recommended even if the media in question is earth grounded. When grounding a TeleFlow, always connect directly to a known good Earth Ground.
NOTE
Never connect the CPU Board’s Ground Lug to Earth Ground. The
CPU Board’s CPU/Circuit Ground must always be isolated from the case. The TeleFlow/TeleRTU/TeleRecorder case is to be connected to
Earth Ground.
NOTE
Some 3530-20Bs and 3530-25Bs have been factory shipped with the
Cabinet Ground Cable connected to the CPU Board’s Ground Ring.
Remove this ground connection from the CPU Board. This cable should be removed (or electrically isolated) if a modem is not present. If a modem is present, the Cabinet Ground Cable should be connected to the modem.
3.1.1 Modem Grounding Kit 621495-01-8
Some TeleFlows (3530-10B), TeleRTUs (3530-15B), TeleRecorders (3530-45B) and TeleFlow
Correctors (3530-50B) have been shipped without a system Ground Lug. These units must be modified before they can be properly connected to earth ground. Product Information
Package PIP-3530-MGKI provides the information required to properly install the TeleFlow
Modem Grounding Kit (621495-01-8). This kit may also be used to support a TeleRTU
Module (3530-35B).
The TeleFlow Modem Grounding Kit consists of the following items: i Hex Nut - #10-32 i Cabinet Ground Cable i Self-Locking Nut - #10-32 UNF i Flat Washer - #10 i Ground Lug
Section 3 - Grounding & Isolation Page 3-1 S1400A
i Pan Head Screw - #10-32 x 3/4”) i Pan Head Screw - - #4-40 x 3/8” i Self-Locking Nut - #4-40 UNC i Hex Nut - #4-40
3.2 IMPORTANCE OF GOOD GROUNDS
Model 3530-XXXs are utilized in instrument and control systems that must operate continually and within their stated accuracy over long periods of time with minimum attention. Since many system sites are unmanned and located in remote areas, failures resulting from an improperly grounded system can become costly in terms of lost time and disrupted processes. A properly grounded system will help prevent electrical shock hazards resulting from contact with live metal surfaces, provide additional protection of equipment from lightning strikes and power surges, minimize the effects of electrical noise and power transients, and reduce signal errors caused by ground wiring loops. Conversely, an improperly grounded system may exhibit a host of problems that appear to have no relationship to grounding. It is essential that the reader (service technician) have a good understanding of this subject to prevent needless troubleshooting procedures.
WARNING
This device must be installed in accordance with the National
Electrical Code (NEC) ANSI/NEPA-70. Installation in hazardous locations must also comply with Article 500 of the code. For information on the usage of Model 3530-XXX units in Class I, Division
2, Groups C & D Hazardous and Nonhazardous locations, see appendix A of the applicable CI-3530-XXX manual. For information on the usage of Models 3530-10B, 3530-40B & 3530-50B in Class I,
Division 1, Groups C & D Hazardous locations, see appendix B of CI-
3530-10B, CI-3530-40B or CI-3530-50B.
3.3
EARTH GROUND CONNECTIONS
To properly ground a TeleFlow (3530-10B/20B/40B), TeleRTU (3530-15B/25B),
TeleRecorder (3530-45B/55B) or TeleFlow Corrector (3530-50B), connect the Earth Ground wire between the Ground Lug on the bottom of the case and a known good Earth Ground.
Observe recommendations provided in topics Establishing a Good Earth Ground and
Ground Wire Considerations. Note: In the case of the TeleRecorder (3530-55B), connection to a known good Earth Ground is only required when a BBI 9600 PSTN modem is installed.
3.3.1 Establishing a Good Earth Ground
A common misconception of a ground is that it consists of nothing more than a metal pipe driven into the soil. While such a ground may function for some applications, it will often not be suitable for a complex system of sophisticated electronic equipment. Conditions such as soil type, composition and moisture will all have a bearing on ground reliability.
A basic ground consists of a 3/4-inch diameter rod with a minimum 8-foot length driven into conductive earth to a depth of about 7-feet as shown in Figure 3-1. Number 3 or 4 AWG solid copper wire should be used for the ground wire. The end of the wire should be clean,
S1400A Page 3-2 Section 3 - Grounding & Isolation
free of any coating and fastened to the rod with a clamp. This ground connection should be covered or coated to protect it from the weather and the environment.
Figure 3-1 - Basic Ground Rod Installation
3.3.1.1 Soil Conditions
Before installing a ground rod, the soil type and moisture content should be analyzed.
Ideally, the soil should be moist and moderately packed throughout to the depth of the ground rod. However, some soils will exhibit less than ideal conditions and will require extra attention.
Soil types can be placed into two general categories with respect to establishing and maintaining a good earth ground, i.e., ‘Good Soil’ and ‘Poor Soil.’
To be a good conductor, soil must contain some moisture and free ions (from salts in the soil). In very rainy areas, the salts may be washed out of the soil. In very sandy or arid area the soil may be to dry and/or salt free to a good conductor. If salt is lacking add rock salt
(NaCl); if the soil is dry add calcium chloride (CaCl
2
).
3.3.1.2 Soil Types: Good
Damp Loam
Salty Soil or Sand
Farm Land
Poor
Back Fill
Dry Soil
Sand Washed by a Lot of Rain
Dry Sand (Desert)
Rocky Soil
Ground Beds must always be tested for conductivity prior to being placed into service. A brief description of ground bed testing in ‘Good Soil’ and ‘Poor Soil’ is provided herein.
Details on this test are described in the National Electrical Code Handbook. Once a reliable
Section 3 - Grounding & Isolation Page 3-3 S1400A
ground has been established, it should be tested on a regular basis to preserve system integrity.
Figure 3-2 - Basic Ground Bed Soil Test Setup
Figure 3-3 - Basic Ground Bed Soil Test Setup with Additional Ground Rods
Figure 3-2 shows the test setup for ‘Good Soil’ conditions. If the Megger* reads less than 5 ohms, the ground is good. The lower the resistance, the better the earth ground. If the
S1400A Page 3-4 Section 3 - Grounding & Isolation
Megger reads more than 10 ohms, the ground is considered ‘poor.’ If a poor ground is indicated, one or more additional ground rods connected 10 feet from the main ground rod should be driven into the soil and interconnected via bare AWG 0000 copper wire and 1” x
¼-20 cable clamps as illustrated in Figure 3-3). * Note: Megger is a Trademark of the
Biddle Instrument Co. (now owned by AVO International). Other devices that may be used to test ground resistance are “Viboground”; Associated Research,
Inc., “Groundmeter”; Industrial Instruments, Inc., and “Ground-ohmer”; Herman
H. Sticht Co., Inc.
If the Megger still reads more than 10 ohms, mix a generous amount of cooking salt, ice cream salt or rock salt with water and then pour about 2.5 to 5 gallons of this solution around each rod (including the test rods). Wait 15 minutes and re-test the soil. If the test fails, the soil is poor and a ‘Poor Soil Ground Bed’ will have to be constructed.
Figure 3-4 shows a typical Poor Soil Ground Bed Electrode. A Poor Soil Ground Bed will typically consists of four or more 10-foot long electrodes stacked vertically and separated by earth. Figure 3-5 shows the construction of a Poor Soil Ground Bed. For some poor soil sites, the ground bed will be constructed of many layers of ‘Capacitive Couplings’ as illustrated. In extremely poor soil sites one or more 3’ by 3’ copper plates (12 gauge or 1/16” thick) will have to be buried in place of the electrodes.
Figure 3-4 - Ground Electrode Construction for Poor Soil Conditions
3.3.1.3 Dry, Sandy or Rocky Soil
Very dry soil will not provide enough free ions for good conductance and a single ground rod will not be effective. A buried counterpoise or copper screen is recommended for these situations. It will be necessary to keep the soil moist through regular applications of water.
Sandy soil, either wet or dry, may have had its soluble salts leached out by rain water, thereby reducing conductivity of the ground. High currents from lightning strikes could also melt sand and cause glass to form around the ground rod, rendering it ineffective. A buried counterpoise or copper screen is preferred for these installations along with regular applications of salt water.
Rocky soil can pose many grounding problems. A counterpoise or copper plate will probably be required. Constructing a trench at the grounding site and mixing the fill with a hygroscopic salt such as calcium chloride may help for a time. Soaking the trench with water on a regular basis will maintain conductivity.
Any TeleFlow, TeleRTU, TeleRecorder or TeleFlow Corrector, may be connected to Earth
Ground via its Ground Lug; however, units equipped with a BBI 9600 bps PSTN modem must be connected to Earth Ground. Units with phone modems require the use of a
Section 3 - Grounding & Isolation Page 3-5 S1400A
lightning arrestor. The lightning arrestor must be situated at the point where the communication line enters the building.
Figure 3-5 - Poor Soil Ground Bed Construction Diagram
3.3.2 Ground Wire Considerations
i Ground wire size should be AWG 4. It is recommended that stranded copper wire is used for this application and that the length should be as short as possible.
i This ground wire should be clamped or brazed to the Ground Bed Conductor (that is typically a stranded copper AWG 0000 cable installed vertically or horizontally).
i The wire ends should be tinned with solder prior to insertion into the TeleFlow
Ground Lug.
i The ground wire should be run such that any routing bend in the cable has a minimum radius of 12-inches below ground and 8-inches above ground.
S1400A Page 3-6 Section 3 - Grounding & Isolation
3.3.2.1 Modem Ground Wiring Diagrams
Figure 3-6A/B - TeleFlow Modem Ground Wiring - for 3530-10B, -15B, 45B & -50B
Figure 3-7A/B - TeleFlow/TeleRTU Plus Modem Ground Wiring - for 3530-20B & -25B
Figure 3-8A/B - TeleFlow Plus Modem Ground Wiring - for 3530-20B
Figure 3-9A/B - TeleRTU Plus Modem Ground Wiring - for 3530-25B
Figure 3-10A/B - TeleFlow/Corrector/TeleRTU Modem Ground Wiring (Side View)
Figure 3-11A/B - TeleRecorder (3530-45B) Modem Ground Wiring (Front View)
Figure 3-12
Figure 3-13
- TeleRecorder (3530-55B) Modem Ground Wiring (Front View)
- Earth Grounding Of TeleFlow Modem & Case
Figure 3-6A - TeleFlow Modem (396039-02-2) Ground Wiring
Section 3 - Grounding & Isolation Page 3-7 S1400A
S1400A
Figure 3-6B - TeleFlow Modem (400000-01-6) Ground Wiring
Page 3-8 Section 3 - Grounding & Isolation
Figure 3-7A - TeleFlow/TeleRTU Plus Modem (396039-02-2)
Ground Wiring
(Side View)
Section 3 - Grounding & Isolation Page 3-9 S1400A
S1400A
Figure 3-7B - TeleFlow/TeleRTU Plus Modem (400000-01-6)
Ground Wiring
(Side View)
Page 3-10 Section 3 - Grounding & Isolation
Figure 3-8A - TeleFlow Plus Modem (396039-02-2) Ground Wiring
(Front View)
Section 3 - Grounding & Isolation Page 3-11 S1400A
S1400A
Figure 3-8B - TeleFlow Plus Modem (400000-01-6) Ground Wiring
(Front View)
Page 3-12 Section 3 - Grounding & Isolation
Figure 3-9A - TeleRTU Plus Modem (396039-02-2)
Ground Wiring
(Front View)
Section 3 - Grounding & Isolation Page 3-13 S1400A
S1400A
Figure 3-9B - TeleRTU Plus Modem (400000-01-6)
Ground Wiring
(Front View)
Page 3-14 Section 3 - Grounding & Isolation
Figure 3-10A - 3530-10B/15B/50B Modem (396039-02-2) Ground Wiring (Side View)
Figure 3-10B - 3530-10B/15B/50B Modem (400000-01-6) Ground Wiring (Side View)
Section 3 - Grounding & Isolation Page 3-15 S1400A
Figure 3-11A - 3530-45B Modem (396039-02-2) Ground Wiring (Front View)
S1400A Page 3-16 Section 3 - Grounding & Isolation
Figure 3-11B - 3530-45B Modem (400000-01-6) Ground Wiring
(Front View)
Section 3 - Grounding & Isolation Page 3-17 S1400A
Figure 3-12 - 3530-55B Modem (400000-01-6) Ground Wiring
(Front View)
Figure 3-13 shows a model 3530-10B (TeleFlow) installation. An AWG 4 solid copper ground wire has been connected to the Ground Lug on the bottom of the enclosure and to
Earth Ground. The units Earth Ground Cable should be clamped to an exposed Ground Rod or to an AWG 0000 stranded copper Ground Cable that in turn should be connected to either an Earth Ground Rod or Earth Ground Bed. Both ends of the units Earth Ground
Cable must be free of any coating such as paint or insulated covering as well as any oxidation. The connecting point of the Ground Rod or AWG 0000 Ground Cable must also be free of any coating and free of oxidation. Once the ground connection has been established (at either the Ground Rod or Ground Cable) it should be covered or coated to protect it from the environment.
S1400A Page 3-18 Section 3 - Grounding & Isolation
Note:
3530-40B not shown but similar to 3530-10B/15B/50B without modem.
3530-55B not shown (see Figure 3-12). Connect AWG 4 Earth Ground
Cable to Ground Lug when a BBI 9600 bps PSTN Modem is installed.
Figure 3-13
- Earth Grounding Of TeleFlow Modem & Case
Note that the recommended grounding convention for a model 3530-XXX is to install the specified AWG 4 Earth Ground Cable between the Ground Lug (on the bottom of the unit in
Section 3 - Grounding & Isolation Page 3-19 S1400A
question) and a known good Earth Ground. Some models may be equipped with an optional radio. Units equipped with the radio option (not shown) may have an optional polyphaser
(lightning arrester) installed. Regardless of the 3530-XXX configuration, an Earth Ground
Cable should always be installed between the units Ground Lug and a known good Earth
Ground.
3.3.3 Other Grounding Considerations
For applications employing equipment that communicates over telephone lines, a lightning arrester Must Be provided. For indoor equipment the lightning arrester must be installed at the point where the communication line enters the building as shown in Figure 3-14. The ground terminal of this arrester must connect to a ground rod and/or a buried ground bed.
For units that are installed outdoors, it is recommended that the lightning arrester be installed to an Earth Ground (Bed) that is not common to the one used by the associated
3530-XXX.
Figure 3-14 - Grounding of Phone Line
Gas lines also require special grounding considerations. If a gas meter run includes a thermocouple or RTD sensor installed in a thermowell, the well (not the sensor) must be connected to a gas discharge-type lightning arrestor as shown in Figure 3-15. A copper braid, brazed to the thermal well, is dressed into a smooth curve and connected to the
S1400A Page 3-20 Section 3 - Grounding & Isolation
arrestor as shown. The curve is necessary to minimize arcing caused by lightning strikes or high static surges. The path from the lightning arrestor to the ground bed should also be smooth and free from sharp bends for the same reason.
Figure 3-15 - Grounding of Thermometer Well in Gas Line
Remove this ground connection from the CPU Board. This cable should be removed (or electrically isolated) if a modem is not present. If a modem is present, the Cabinet Ground Cable should be connected to the modem.
3.4 ISOLATING EQUIPMENT FROM THE PIPELINE
3.4.1 Meter Runs Without Cathodic Protection
TeleFlows (3530-10B, 3530-20B & 3530-40B) may be mounted directly on the pipeline or remotely on a vertical stand-alone two-inch stand-pipe (see Figure 3-16). The Earth Ground
Cable is to run between the TeleFlow’s Ground Lug and Earth Ground (Rod or Bed) even though the TeleFlow'’s Multivariable Transducer may be grounded to the pipeline.
TeleFlow Correctors (3530-50B) are typically mounted directly to a Turbine Meter. The
Earth Ground Cable is to run between the TeleFlow Corrector’s Ground Lug and Earth
Ground (Rod or Bed). If any pressure transmitters or pulse transducers are remotely mounted, connect their chassis grounds to the pipeline or earth ground.
Section 3 - Grounding & Isolation Page 3-21 S1400A
Figure 3-16 - 3530-10B/20B/40B Remote Installation without Cathodic Protection
3.4.2 Meter Runs With Cathodic Protection
Dielectric isolators are available from Bristol Babcock and are always recommended as an added measure in isolating the TeleFlow (3530-10B or 3530-20B) from the pipeline even though the TeleFlow does provide 500V galvanic isolation from the pipeline and should not be affected by cathodic protection or other EMF on the pipeline. TeleFlows (3530-10B, 3530-
20B & 3530-40B) may be mounted directly on the pipeline (see Figure 3-17) or remotely on a vertical stand-alone two-inch stand-pipe (see Figure 3-18). It is recommended that isolation fitting always be used in remotely mounted meter systems. An isolation fittings or gasket should be installed between the following connections: i all conductive tubing that runs between the pipeline and mounting valve manifold and/or the units miltivariable pressure transducer i all conductive connections or tubing runs between the GFC and turbine meter, pulse transducer, or any input other device that is mounted on the pipeline i any Temperature Transducer, Pressure Transmitter, etc. and their mount/interface to the pipeline.
S1400A Page 3-22 Section 3 - Grounding & Isolation
Mount the GFC (3530-10B/20B) or ECR (3530-40B) on a stand-alone vertical 2-inch pipe.
The ground conductor connects between the GFC/ECR’s Ground Lug and a known good earth ground. Connect the cases of Temperature Transducers, Pressure Transmitters, etc., to the known good earth ground. If the mounting 2-inch pipe is in continuity with the pipeline it will have to be electrically isolated from the GFC/ECR. Use a strong heat-shrink material such as RAYCHEM WCSM 68/22 EU 3140. This black tubing will easily slip over the 2-inch pipe and then after uniform heating (e.g., with a rose-bud torch) it electrically insulates and increases the strength of the pipe stand.
See BBI Specification Summary F1670SS-0a for information on PGI Direct Mount Systems and Manifolds.
Figure 3-17 - 3530-10B/20B/40B Direct Mount Installation
(with Cathodic Protection)
Section 3 - Grounding & Isolation Page 3-23 S1400A
Figure 3-18 - 3530-10B/20B/40B Remote Installation
(with Cathodic Protection)
S1400A Page 3-24 Section 3 - Grounding & Isolation
Section 4 - Lightning Arresters & Surge Protectors
4.1 STROKES & STRIKES
Lightning takes the form of a pulse that typically has a 2 µS rise and a 10 µS to 40 µS decay to a 50% level. The IEEE standard is an 8 µS by 20 µS waveform. The peak current will average 18 KA for the first impulse and about half of that for the second and third impulses. Three strokes (impulses) is the average per lightning strike. The number of visible flashes that may be seen is not necessarily the number of electrical strokes.
A lightning strike acts like a constant current source. Once ionization occurs, the air becomes a luminous conductive plasma reaching up to 60,000° F. The resistance of a struck object is of little consequence except for the power dissipation on the object (I 2 x R). Fifty percent of all lightning strikes will have a first impulse of at least 18 KA, ten percent will exceed the 60 KA level, and only about one percent will exceed 120 KA.
4.1.1 Chance of Being Struck by Lightning
The map of Figure 4-1 shows the average annual number of thunderstorm days
(Isokeraunic level) for the various regions within the continental U.S.A. This map is not representative of the severity of the storm or the number of lightning strikes since it does not take into account more than one lightning strike in a thunderstorm day. The
Isokeraunic or Isoceraunic number provides a meteorological indication of the frequency of thunderstorm activity; the higher the Isokeraunic number the greater the lightning strike activity for a given area. These levels vary across the world from a low of 1 to a high of 300.
Within the United States the Isokeraunic level various from a low of 1 to a high of 100.
Figure 4-1 - Average Thunderstorm Days of the Year (for Continental USA)
Section 4 - Lightning & Surge Page 4-1 S1400A
Thunderstorms are cloud formations that produce lightning strikes (or strokes). Across the
United States there is an average of 30 thunderstorm days per year. Any given storm may produce from one to several strokes. Data on the subject indicates that for an average area within the United States there can be eight to eleven strokes to each square mile per year.
The risk of stroke activity is increased for various areas such central Florida where up to 38 strokes to each square mile per year are likely to occur.
To determine the probability of a given structure (tower, building, etc.) (within your location) being struck, perform the following computation:
1.
Using the map of Figure 4-1 (or a comparable meteorological map for your local), find the Isokeraunic level (I) for your area. Then using Chart 1, find “ A ” for your area.
2.
Refer to Figure 4-1 to find the latitude. Then using Chart 2, find “ B ” for your latitude
(Lat.°).
3.
Multiply “ A ” x “ B ” to get “ C ” .
4.
To calculate the number of lightning strikes per year that are likely to strike a given object (tower, mast, etc.), use the equation that follows (where “ C ” was calculated in step 3 and “ H ” is equal to the height of the object.
Strikes Per Year = ( “ C ” x H 2 ) ÷ (.57 x 10 6 )
Chart 1
I “ A ”
5
10
20
30
40
50
60
70
80
90
100
26
8
85
169
275
402
548
712
893
1069
1306
25
30
35
40
45
Chart 2
LAT.° “ B ”
.170
.200
.236
.280
.325
Note for these charts:
I = Thunderstorm Days Per Year (Isokeraunic Number)
A= Stroke activity for associated Isokeraunic Area
B= Height/Stroke coefficient for associated latitude
For Example: On Long Island, New York (Isokeraunic number 20), Chart 1 gives “A” to equal 85. The latitude is approximately 40°. Referring to Chart 2, “B” is found to be equal to
.28. “C” for this example is equal to 23.80. Using the equation for strikes per year, it is determined that a 100-foot tower has .4 chances per year of being struck by lightning.
Assuming that no other structures are nearby, the tower will more than likely be struck by lightning at least once in three years.
Note: The Isokeraunic activity numbers connoted as I, “A” and “B” in Charts 1 and 2 above are provided for the continental United States. Isokeraunic data for various countries is available from various federal or state Civil Engineering or Meterorelogical organizations. This information is typically available from manufacturers of lightning strike protection equipment (such as Lightning Arresters).
Since TeleFlow (3530-XXX) units are battery operated systems that are isolated from AC grids (as they don’t draw power from them), they are typically immune to lightning strikes to power lines or power equipment (except for inductive flashover due to close installation proximity). However, once a radio or modem has been installed into a model 3530-XXX, the
S1400A Page 4-2 Section 4 - Lightning & Surge
possibility of damage due to a lightning strike on power or telephone lines or to a radio antenna or the antenna’s tower must be considered. Model 3530-XXX’s equipped with a radio may have an optional BBI supplied lightning arrester installed. Units equipped with modems have built in Surge Protection circuitry. It is recommended that the additional lightning protection considerations listed below be followed for units installed in areas with a high possibility or history of stroke activity.
Units equipped with a modem : In series with the phone line (as far away as possible from the equipment) – for indoor installations the lightning arrester should typically be located at the point where the line enters the structure.
Units equipped with a radio : Mount antenna discharge unit (lightning arrester) as close as possible to where the lead in wire enters the structure. For an exposed (outdoor)
3530-XXX, in the proximity of the unit. See Antenna Caution below.
4.1.2 Antenna Caution
Each year hundreds of people are killed, mutilated, or receive severe permanent injuries when attempting to install or remove an antenna or antenna lead. In many cases, the victim was aware of the danger of electrocution but failed to take adequate steps to avoid the hazard. For your safety, and for proper installation maintenance, please read and follow the safety precautions that follow - they may save your life .
i When installing or servicing an antenna:
DO NOT use a metal ladder. DO NOT step onto or touch an antenna mast while power is applied to an associated radio unless the radio is a low power (low current) type.
DO NOT work on a wet or windy day, especially during a thunderstorm or when there is lightning or thunder in your area. Dress properly; shoes with rubber soles and heels, rubber gloves, long sleeve shirt or jacket.
i The safe distance from power lines should be at least twice the height of the antenna and mast combination.
i Antenna Grounding per National Electrical Code Instructions:
A.
Use AWG 10 or 8 aluminum or AWG 1 copper-clad steel or bronze wire, or larger as ground wires for both the mast and lead-in. Securely clamp the wire to the bottom of the mast.
B.
Secure lead-in wire from antenna to antenna discharge (lightning arrester) unit and the mast ground wire to the structure (building, shed, etc.) with stand-off insulators spaced from 4 feet (1.22 meters) to 6 feet (1.83 meters) apart.
C.
Mount antenna discharge unit as close as possible to where the lead-in wire enters the structure.
D.
The hole drilled through the wall for the lead-in wire should be just large enough to accommodate the cable. Before drilling this hole, make sure there are no wires or pipes, etc. in the wall.
E.
Push the cable through the hole and form a rain drip loop close to where the wire enters the exterior of the structure.
F.
Caulk around the lead-in wire (where it enters the structure) to keep out drafts.
G.
Install lightning arresters (antenna discharge units). The grounding conductor should be run in as straight a line as practicable from the antenna mast and/or the antenna discharge units to grounding electrode(s).
H.
Only connect the antenna cable to the radio after the mast has been properly grounded and the lead-in cable has been properly connected to lightning arresters which in turn have each been properly connected to a known good earth ground.
Section 4 - Lightning & Surge Page 4-3 S1400A
Figure 4-2 - Radio Antenna Field Installation Site Grounding Diagram
For all systems it is best to have all communication equipment input/output grounds tied together. In the case of TeleFlow (3530-XXX) this is accomplished via the unit’s Ground
Lug. However additional communication equipment lightning arresters and surge suppres-
S1400A Page 4-4 Section 4 - Lightning & Surge
sors should be tied to the same system ground. System ground consists of the tower leg grounds utility ground and bulkhead-equipment ground-stakes that are tied together via bare copper wire.
4.1.3 Ground Propagation
As in any medium, a dynamic pulse, like R.F., will take time to propagate. This propagation time will cause a differential step voltage to exist in time between any two ground rods that are of different radial distances from the strike. With a ground rod tied to a struck tower, the impulse will propagate its step voltage outwardly from this rod in ever-expanding circles, like a pebble thrown into a pond. If the equipment house has a separate ground rod and the power company and/or telephone company grounds are also separate, the dynamic step voltage will cause currents to flow to equalize these separate ground voltages. Then if the coax cable (associated with a radio) is the only path linking the equipment chassis with the tower ground, the surge can destroy circuitry.
4.1.4 Tying it all Together
To prevent this disaster from occurring, a grounding system must be formed which interconnects all grounds together. This will equalize and distribute the surge charge to all grounds, and at the same time, it will make for a lower surge impedance ground system.
This interconnection can be done as a grid, where each ground has a separate line to each other ground, or by using a “rat Race” ring which forms a closed loop (not necessarily a perfect circle) which surrounds the equipment house completely.
By making this interconnection, it will be necessary to use proper I/O protectors for the equipment. Of course, these should be a requirement regardless of whether this grounding technique is used. I/O protectors are used for power lines (even those these don’t feed into a
TeleFlow unit), telephone lines, and also to minimize EMI pick-up from a strike. Ideally it is best to place all I/O protectors on a common panel that has a low inductance path to the ground system. The Teleflow (3530-XXX) would then have a single ground point from its
Ground Lug to this panel. In lieu of this, the 3530-XXX in question should be tied to a ground rod that in turn is connected to the Earth/System Ground created for the site.
Your protected equipment connected to a common single ground system will now be just like a bird sitting on a high tension wire. When lightning strikes, even with a 50 ohm surge impedance ground system, the entire system consisting of equipment, ground system, building, etc., will all rise together to the one million volt peak level (for example) and will all decay back down together. So long as there is no voltage differential (taken care of by protectors and ground interconnections, there will be no current flow through the equipment and therefore no resulting equipment damage.
4.1.5 Impulse Protection Summary
i Use more than one ground rod.
i Place multi-ground stakes more than their length apart.
i Tie Power, Telco, Tower, Bulkhead and equipment ground together.
i Make all ground interconnect runs that are above ground with minimum radius bends of eight inches and run them away from other conductors and use large solid wire or a solid strap.
i Watch out for dissimilar metals connections and coat accordingly.
Section 4 - Lightning & Surge Page 4-5 S1400A
i Use bare wire radials together where possible with ground stakes to reduce ground system impedance.
i Use I/O protectors (Phone line, Radio) with a low inductance path to the ground system.
i Ground the Coaxial Cable Shield (or use an impulse suppressor) at the bottom of the tower just above the tower leg ground connection.
4.2 USE OF LIGHTNING ARRESTERS & SURGE PROTECTORS
Units equipped with radios or modems use lightning arresters and surge protectors to protect equipment from lightning strikes, power surges and from damaging currents that have been induced onto communication lines.
The first line of defense is the Lightning Arrester. These devices typically use gas discharge bulbs that can shunt high currents and voltages to earth ground when they fire. The high current, high voltage gas discharge bulb has a relatively slow response time and only fire when their gas has been ionized by high voltage.
The second line of defense is the Surge Protector, which is made of solid state devices, fires very quickly and conducts low voltages and currents to ground. Surge protectors are built into BBI 9600 bps modems.
Lightning Arresters are applied to circuits as follows: i Equipment or circuits that can be exposed to lightning strikes, falling power lines, high ground currents caused by power system faults, by operational problems on electric railways, etc.
i Equipment installed in dry, windy areas, such as the Great Plains and the
Southwaset Desert in the United States. Wind and wind blown dust can cause high voltages (static) to appear on overhead wires, fences, and metal buildings.
Note: Lightning Arresters may explode if lightning strike is very close. Mount lightning arresters where flying parts won't cause injury to equipment or personnel.
S1400A Page 4-6 Section 4 - Lightning & Surge
Section 5 - Wiring Techniques
5.1 OVERVIEW
This section provides information pertaining to good wiring practices. Installation of Power and “Measurement & Control” wiring is discussed. Information on obscure problems, circulating ground and power loops, bad relays, etc. is presented. Good wire preparation and connection techniques along with problems to avoid are discussed.
5.2 INSTRUMENT WIRING
Each of the rules listed below is briefly discussed; the emphasis herein is placed on the avoidance of problems as well as equipment safety.
Rule 1 - Never utilize common returns.
Rule 2 - Use twisted shielded pairs (with overall insulation) on all Signal/Control circuits.
Rule 3 - Ground cable shields at one end only.
Rule 4 - Use known good earth grounds (Rod, Bed, System) and test them periodically,
Rule 5 - Earth connections must utilize smoothly dressed large wire.
Rule 6 - Perform all work neatly and professionally.
Rule 7 - Route high power conductors away from signal wiring according to NEC Rules.
Rule 8 - Use appropriately sized wires as required by the load.
Rule 9 - Use lightning arresters and surge protectors.
Rule 10 - Make sure all wiring connections are secure.
5.2.1 Common Returns
Use of common returns on I/O wiring is one of the most common causes of obscure and difficult to troubleshoot control signal problems. Since all wires and connections have distributed resistance, inductance and capacitance, the chances of a achieving a balanced system when common returns are present is very remote. Balanced systems (or circuits) are only achieved when all currents and voltages developed in association with each of the common returns are equal. In a balanced system (or circuit) there are no noise or measurment errors introduced due to by “sneak circuits.”
The illustration of Figure 5-1 shows the difference between testing an I/O circuit that is discrete and has no sneak circuits and one that utilizes common returns. Common sense tells us that it is tough to mix up connections to a twisted shielded pair (with overall vinyl covering) to every end device. Do yourself a favor; to make start up easier, DON’T USE
COMMON RETURNS!
Section 5 - Wiring Techniques Page 5-1 S1400A
Figure 5-1 - Field Wired Circuits With & Without A Common Return
5.2.2 Use of Twisted Shielded Pair Wiring (with Overall Insulation)
For all field I/O wiring the use of twisted shielded pairs with overall insulation is highly recommended. This type of cable provides discrete insulation for each of the wires and an additional overall insulated covering that provides greater E.M.I. immunity and protection to the shield as well.
S1400A Page 5-2 Section 5 - Wiring Techniques
5.2.3 Grounding of Cable Shields
DO NOT connect the cable shield to more than one ground point; it should only be grounded at one end. Cable shields that are grounded at more than one point or at both ends may have a tendency to induce circulating currents or sneak circuits that raise havoc with I/O signals. This will occur when the ground systems associated with multipoint connections to a cable shield have a high resistance or impedance between them and a ground induced voltage is developed (for what ever reason, i.e., man made error or nature produced phenomena).
5.2.4 Use of Known Good Earth Grounds
TeleFlow (models 3530-XXX) should only have one connection to earth ground. This connection is provided via the Ground Lug that is situated on the bottom of the unit. Some older units will require the installation of this ground lug when a connection to earth ground becomes absolutely necessary, i.e., when a radio or modem is added to the unit.
Since model 3530-XXX’s are DC-based systems, grounding does not take into account AC power grounding considerations. Earth grounding the 3530-XXX unit (case) is absolutely necessary when the unit is equipped with a radio or modem. Additionally these units should be connected to earth ground when they are installed in areas that have frequent lightning strikes or are located near or used in conjunction with equipment that is likely to be struck by lightning or if struck by lightning may cause equipment or associated system failure. Earth Grounds must be tested and must be known to be good before connecting the
TeleFlow. Earth grounds must be periodically tested and maintained (see Section 4).
5.2.5 Earth Ground Wires
Earth connections must utilize smoothly dressed large wire. Use AWG 3 or 4 stranded copper wire with as short a length as possible. Exercise care when trimming the insulation from the wire ends. Twists the strands tightly, trim off any frizzes and tin the ends with solder. The earth ground wire should be clamped or brazed to the Ground Bed Conductor
(that is typically a standard AWG 0000 copper cable. The earth ground wire should be run such that any routing bend in the cable is a minimum 8-inch radius above ground or a minimum 12-inch radius below ground. The only earth ground connection permitted to the
TeleFlow must be made via the unit’s Ground Lug. Make sure that the connection at the
TeleFlow’s Ground Lug is secure.
5.2.6 Working Neatly & Professionally
Take pride in your work and observe all site and maintenance safety precautions. After properly trimming the stranded pair wire ends, twist them in the same direction as their manufacturer did and then tin them with solder. Install the tinned wire end into it’s connector and then secure the associated connector’s clamping screw. Remember to check these connections for tightness from time to time. If solid copper wire is used (in conjunction with the DC Power System or for Earth Ground) make sure that the conductor is not nicked when trimming off the insulation. Nicked conductors are potential disasters waiting to happen. Neatly trim shields and whenever possible, coat them to protect them and prevent shorts and water entry.
Section 5 - Wiring Techniques Page 5-3 S1400A
Remember loose connections, bad connections, intermittent connections, corroded connections, etc., are hard to find, waste time, create system problems and confusion in addition to being costly.
5.2.7 High Power Conductors and Signal Wiring
When routing wires, keep high power conductors away from signal conductors. Space wires appropriately to vent high voltage inductance. Refer to the National Electrical Code
Handbook for regulatory and technical requirements.
5.2.8 Use of Proper Wire Size
TeleFlows utilize compression-type terminals that accommodate up to AWG 14 gauge wire.
A connection is made by inserting the bared end (1/4 inch max.) into the clamp beneath the screw and securing the screw.
Allow some slack in the wires when making terminal connections. Slack makes the connections more manageable and minimizes mechanical strain on the PCB connectors.
Provide external strain relief (utilizing Tie Wrap, etc.) to prevent the loose of slack at the
TeleFlow.
Be careful to use wire that is appropriately sized for the load. Refer to equipment manufacturer’s Specs. and the National Electrical Code Handbook for information on wire size and wire resistance. After installing the field wiring, test each load to determine if the correct voltage or current is present at the load. If you know the resistance of the field wires
(Circular Mills x Length) you should be able to calculate the load voltage. Conversely, if you know the minimum load voltage and current, you should be able to derive the maximum voltage loss that is allowable due to line resistance and then the correct wire size.
Referring to Figure 5-2, a relay that is picked by 100 mA, with a loop supply voltage of 24V and a total line resistance of 20 ohms, the load voltage (voltage across the relay) should be:
V
L
= V
S
- (V
22 = 24 - 2
C
+ V
C
)
where
V
C where 2V
+ V
C
= (R
C
+ R
= (20 Ω
C
) I
) x 0.1 A
Figure 5-2 - Calculating Load Voltage due to Line Resistance
5.2.9 Lightning Arresters & Surge Protectors
Use lightning arresters in association with any radio or modem equipped unit. BBI 9600 bps modems are equipped with surge protection circuitry. Lightning arresters or Antenna
S1400A Page 5-4 Section 5 - Wiring Techniques
Discharge Units should be placed on the base of the antenna and at the point where the antenna lead (typically coax) enters the site equipment building. When a modem is used, a lightning arrester should be placed at the point where the phone line enters the site equipment building. If you use a modem (manufactured by other than BBI) it is recommended that you also install a surge suppressors or lightning arrester on the phone line as close to the modem as possible. Any unit equipped with a radio or modem must be connected to a known good earth ground via the units Ground Lug.
5.2.10 Secure Wiring Connections
Make sure that all wiring connections are secure. In time wires that were once round will become flattened due to the pressure applied by screw compression type terminals and site vibrations. After a while these compression screws have a tendency to become loose. Part of a good maintenance routine should be to check and tighten all screws associated with wiring terminal connections. Avoid nicking the wire(s) when stripping insulation.
Remember, nicked conductors will lead to future problems. Also remember to provide some cabling slack and strain relief.
If installing stranded or braided wiring that has not been tinned, be sure to tightly twist the end (in the same direction as manufactured) and then trim off any frizzed wires.
Section 5 - Wiring Techniques Page 5-5 S1400A
BLANK PAGE
READER RESPONSE FORM
Please help us make our documentation more useful to you! If you have a complaint, a suggestion, or a correction regarding this manual, please tell us by mailing this page with your comments. It's the only way we know we're doing our job by giving you correct, complete, and useful documentation.
DOCUMENT NUMBER: S1400A
TITLE:
TeleFlow
TM
SITE CONSIDERATIONS For EQUIPMENT INSTALLATION,
GROUNDING & WIRING
ISSUE DATE: APRIL, 2003
COMMENT/COMPLAINT:
______________________________________________________________________________
______________________________________________________________________________
______________________________________________________________________________
______________________________________________________________________________
______________________________________________________________________________
______________________________________________________________________________
______________________________________________________________________________
______________________________________________________________________________
______________________________________________________________________________
______________________________________________________________________________
______________________________________________________________________________
______________________________________________________________________________
______________________________________________________________________________
Mail this page to:
Bristol Babcock Inc.
1100 Buckingham Street
Watertown, CT 06795
Attn: Technical Publications Group, Dept. 315
Bristol Babcock
1100 Buckingham Street
Watertown, CT 06795
Phone: +1 (860) 945-2200
Fax: +1 (860) 945-2213
Website: www.bristolbabcock.com
U.S.A. Locations:
Northern Region
Bristol Babcock Inc.
1100 Buckingham Street
Watertown, CT 06795
Phone: +1 (860) 945-2381
Fax: +1 (860) 945-2525
Gulf Coast Region
Bristol Babcock Inc.
2000 Governor's Circle
Suite F
Houston, TX 77092-8731
Phone: +1 (713) 685-6200
Fax: +1 (713) 681-7331
Western Region
Bristol Babcock Inc.
1609 South Grove Avenue
Suites 106 & 107
Ontario, CA 91761
Phone: +1 (909) 923-8488
Fax: +1 (909) 923-8988
Southeast Region
Bristol Babcock Inc.
317 S. North Lake Blvd.
Suite 1016
Altamonte Springs, FL 32701
Phone: +1 (407) 740-7084
Fax: +1 (407) 629-2106
Helicoid Instruments
1100 Buckingham Street
Watertown, CT 06795
Phone: +1 (860) 945-2218
Fax: +1 (860) 945-2213 [email protected]
Central Region
Bristol Babcock Inc.
777 South Central
Expressway
Suite 1-C
Richardson, TX 75080
Phone: +1 (972) 238-8197
Fax: +1 (972) 238-8198 [email protected]
International Affiliates:
Canada
Bristol Babcock, Canada
234 Attwell Drive
Toronto, Ont. M9W 5B3
Canada
PH: 416-675-3820
FAX: 416-674-5129 [email protected]
Mexico
BBI, S.A. de C.V.
Homero No. 1343, 3er Piso
Col. Morales Polanco
11540 Mexico, D.F.
Mexico
PH: (52-55)-52-81-81-12
FAX: (52-55)-52-81-81-09
Rocky Mountain Region
Bristol Babcock Inc.
906 San Juan Blvd., Suite A
Farmington, NM 87401
Phone: +1 (505) 320-5046
Fax: +1 (505) 327-3273
Communications
Technology Group
Bristol Babcock Inc.
317 S. North Lake Blvd.
Suite 1016
Altamonte Springs, FL 32701
Phone: +1 (407) 629-9464
Fax: +1 (407) 629-2106 [email protected]
United Kingdom
Bristol Babcock Ltd.
Vale Industrial Estate
Stourport Road
Kidderminster
Worcestershire DY11 7QU
United Kingdom
PH: +44 (0) 1562 820001
FAX: +44 (0) 1562 746721 [email protected]
Asia Pacific
Bristol Babcock, Inc.
PO Box 1987
Bunbury, Western Australia
6231
PH: +61 (0) 8 9791 3654
FAX: +61 (0) 8 9791 3173 [email protected]
Victoria, Australia
PH: +61 (0) 3 9384 2171
FAX: +61 (0) 3 8660 2501
Calgary Office
Bristol Babcock, Canada
3812 Edmonton Trail N.E.
Calgary, Alberta T2E 5T6
Canada
PH: 403-265-4808
FAX: 403-233-2914 [email protected]
Villahermosa Office
BBI, S.A. de C.V.
Av. Plomo No.2
Bodega No. 1 - Ciudad
Industrial
Villahermosa, Tabasco 86010
Mexico
PH: 52-993-353-3142
FAX: 52-993-353-3145 [email protected]
Middle East
Bristol Babcock Ltd.
Vale Industrial Estate
Stourport Road
Kidderminster
Worcestershire DY11 7QU
United Kingdom
PH: +44 (0) 1562 820001
FAX: +44 (0) 1562 746721 [email protected]
RC Rev: 27-Mar-03
ESDS Manual
S14006
4/15/92
CARE AND HANDLING
OF
PC BOARDS
AND
E SD-SENSITIVE
COMPONENTS
BRISTOL BABCOCK
BLANK PAGE
ESDS Manual
S14006
4/15/92
TABLE OF CONTENTS
PAGE
TOOLS AND MATERIALS REQUIRED 1
ESD-SENSITIVE COMPONENT HANDLING PROCEDURE 2
1. Introduction 2
2. General Rules 3
3. Protecting ESD-Sensitive Components 5
4. Static-Safe Field Procedure 6
5. Cleaning and Lubricating 8
6. Completion 10
TOOLS AND MATERIALS REQUIRED
1. Tools
Anti-Static Field kit. It is recommended that an anti-static field kit be kept on any site where solid-state printed circuit boards and other ESD-sensitive components are handled. These kits are designed to remove any existing static charge and to prevent the build-up of a static charge that could damage a PC board or
ESD-sensitive components. The typical anti-static field kit consists of the following components:
1. A work surface (10mm conductive plastic sheet with a female snap fastener in one corner for ground cord attachment).
2. A 15-foot long ground cord for grounding the work surface.
3. Wrist strap (available in two sizes, large and small, for proper fit and comfort) with a female snap fastener for ground cord attachment.
4. A coiled ground cord with a practical extension length of 10 feet for attachment to the wrist strap.
Toothbrush (any standard one will do)
1
ESDS Manual
#S14006
4/15/92
2.
Materials
Inhibitor (Texwipe Gold Mist ; Chemtronics Gold Guard, or equivalent)
Cleaner (Chemtronics Electro-Wash; Freon TF, or equivalent)
Wiping cloth (Kimberly-Clark Kim Wipes, or equivalent)
1.
ESD-SENSITIVE COMPONENT HANDLING PROCEDURE
Introduction
Microelectronic devices such as PC boards, chips and other components are electrostatic-sensitive. Electrostatic discharge (ESD) of as few as 110 volts can damage or disrupt the functioning of such devices. Imagine the damage possible from the 35,000 volts (or more) that you can generate on a dry winter day by simply walking across a carpet. In fact, you can generate as much as 6,000 volts just working at a bench.
There are two kinds of damage that can be caused by the static charge. The more severe kind results in complete failure of the PC board or component. This kind of damage is relatively simple, although often expensive, to remedy by replacing the affected item(s). The second kind of damage results in a degradation or weakening which does not result in an outright failure of the component. This kind of damage is difficult to detect and often results in faulty performance, intermittent failures, and service calls.
Minimize the risk of ESD-sensitive component damage by preventing static build-up and by promptly removing any existing charge. Grounding is effective, if the carrier of the static charge is conductive such as a human body. To protect components from
nonconductive carriers of static charges such as plastic boxes, place the component
in static-shielding bags.
This manual contains general rules to be followed while handling ESD-sensitive components. Use of the anti-static field kit to properly ground the human body as well as the work surface is also discussed.
2
ESDS Manual
S14006
4/15/92
Table 1
Typical Electrostatic Voltages
Electrostatic Voltages
10-20 Percent
Relative Humidity
65-90 Percent
Relative Humidity
Means of Static
Generation
Walking across carpet
Walking over vinyl floor
Worker at bench
Vinyl envelopes for work instructions
Poly bag picked up from bench
Work chair padded with poly foam
35,000
12,000
6,000
7,000
20,000
18,000
1,500
250
100
600
1,200
1,500
2.
General Rules
(1) ESD-sensitive components shall only be removed from their static-shielding bags by a person who is properly grounded.
(2) When taken out of their static-shielding bags, ESD-sensitive components shall
never be placed over, or on, a surface which has not been properly grounded.
(3) ESD-sensitive components shall be handled in such a way that the body does not come in contact with the conductor paths and board components. Handle
ESD-sensitive components in such a way that they will not suffer damage from physical abuse or from electric shock.
(4) EPROMS/PROMS shall be kept in anti-static tubes until they are ready to use and shall be removed only by a person who is properly grounded.
(5) When inserting and removing EPROMS/PROMS from PC boards, use a chip removal tool similar to the one shown in the figure following. Remember, all work should be performed on a properly grounded surface by a properly-grounded person.
3
ESDS Manual
#S14006
4/15/92
4
Typical Chip Removal Tool
(6) It is important to note when inserting EPROMS/PROMS, that the index notch on the PROM must be matched with the index notch on the socket. Before pushing the chip into the socket, make sure all the pins are aligned with the respective socket-holes. Take special care not to crush any of the pins as this could destroy the chip.
(7) Power the system down before removing or inserting comb connectors/plugs or removing and reinstalling PC boards or ESD-sensitive components from card files or mounting hardware. Follow the power-down procedure applicable to the system being serviced.
(8) Handle all defective boards or components with the same care as new components. This helps eliminate damage caused by mishandling. Do not strip used PC boards for parts. Ship defective boards promptly to Bristol Babcock in a staticshielding bag placed inside static-shielding foam and a box to avoid damage during shipment.
ESDS Manual
S14006
4/15/92
CAUTION
Don't place ESD-sensitive components and paperwork in the same bag.
The static caused by sliding the paper into the bag could develop a charge and damage the component(s).
(9) Include a note, which describes the malfunction, in a separate bag along with each component being shipped. The repair facility will service the component and promptly return it to the field.
3.
Protecting ESD-Sensitive Components
(1) As stated previously, it is recommended that an electrically-conductive anti-static field kit be kept on any site where ESD-sensitive components are handled. A recommended ESD-protective workplace arrangement is shown on page 7. The anti-static safety kit serves to protect the equipment as well as the worker. As a safety feature, a resistor (usually of the one-megohm, 1/2-watt, current-limiting type) has been installed in the molded caps of the wrist strap cord and the ground cord. This resistor limits current should a worker accidently come in contact with a power source. Do not remove the molded caps from grounded cords. If a cord is damaged, replace it immediately.
(2) Be sure to position the work surface so that it does not touch grounded conductive objects. The protective resistor is there to limit the current which can flow through the strap. When the work surface touches a grounded conductive object, a short is created which draws the current flow and defeats the purpose of the current-limiting resistor.
(3) Check resistivity of wrist strap periodically using a commercially-available system tester similar to the one shown in the figure below:
5
ESDS Manual
#S14006
4/15/92
Note: If a system checker is not available, use an ohmmeter connected to the cable
ends to measure its resistance. The ohmmeter reading should be 1 megohm +/-
15%. Be sure that the calibration date of the ohmmeter has not expired. If the
ohmmeter reading exceeds 1 megohm by +/- 15%, replace the ground cord with a new one.
4.
Static-safe Field Procedure
(1) On reaching the work location, unfold and lay out the work surface on a convenient surface (table or floor). Omit this step if the table or floor has a built-in ESD-safe work surface.
(2) Attach the ground cord to the work surface via the snap fasteners and attach the other end of the ground cord to a reliable ground using an alligator clip.
(3) Note which boards or components are to be inserted or replaced.
(4) Power-down the system following the recommended power-down procedure.
(5) Slip on a known-good wristband, which should fit snugly; an extremely loose fit is not desirable.
(6) Snap the ground cord to the wristband. Attach the other end of the ground cord to a reliable ground using the alligator clip.
6
ESDS Manual
S14006
4/15/92
(7) The components can now be handled following the general rules as described in the instruction manual for the component.
(8) Place the component in a static-shielding bag before the ground cord is disconnected. This assures protection from electrostatic charge in case the work surface is located beyond the reach of the extended ground cord.
A
C
✰
R
R
D
E F
R
R
EARTH GROUND
B
G
FLOOR OF BUILDING
LEGEND
A - Chair with ground (optional)
B - ESD protective floor mat (optional)
C - Wrist strap
D - ESD protective trays, etc.
E - Ionizer
F - Other electrical equipment
G - Workbench with ESD protective table top
✰
NOTE: ALL RESISTORS 1M
Ω
+/-10% 1/2W
7
ESDS Manual
#S14006
4/15/92
(9) If a component is to undergo on-site testing, it may be safely placed on the grounded work surface for that purpose.
(10) After all component work is accomplished, remove the wrist straps and ground wire and place in the pouch of the work surface for future use.
5.
Cleaning And Lubricating
The following procedure should be performed periodically for all PC boards and when a PC board is being replaced.
CAUTION
Many PC board connectors are covered with a very fine gold-plate.
Do not use any abrasive cleaning substance or object such as a pencil eraser to clean connectors.
Use only the approved cleaner/lubricants specified in the procedure following.
WARNING
Aerosol cans and products are extremely combustible.
Contact with a live circuit, or extreme heat can cause an explosion.
Turn OFF all power and find an isolated, and ventilated area to use any aerosol products specified in this procedure.
(1) Turn the main line power OFF. Blow or vacuum out the component. This should remove potential sources of dust or dirt contamination during the remainder of this procedure.
8
ESDS Manual
S14006
4/15/92
(2) Clean PC board connectors as follows: a.
Review the static-safe field procedure detailed earlier.
b.
c.
Following the ESD-sensitive component handling procedures, remove the connectors from the boards and remove the PC boards from their holders.
Use cleaner to remove excessive dust build-up from comb connectors and other connectors. This cleaner is especially useful for removing dust.
d.
Liberally spray all PC board contacts with Inhibitor. The inhibitor:
Provides a long lasting lubricant and leaves a protective film to guard against corrosion e.
f.
Improves performance and reliability
Extends the life of the contacts
Is nonconductive, and is safe for use on most plastics
Clean the comb contacts using a lint-free wiping cloth.
Lightly mist all comb contacts again with Inhibitor.
NOTE: Do not use so much Inhibitor that it drips.
g.
Repeat the above procedure for the other PC boards from the device.
(3) Cleaning PC edge connectors a.
Use cleaner to remove excessive dust build-up from connectors. This cleaner is especially useful for removing dust.
b.
c.
Liberally spray the outboard connector with Inhibitor.
Lightly brush the outboard connector with a soft, non-metallic, bristle brush such as a toothbrush.
9
ESDS Manual
#S14006
4/15/92 d.
e.
Spray the connector liberally to flush out any contaminants.
Remove any excess spray by shaking the connector or wiping with either a toothbrush, or a lint-free wiping cloth.
6.
Completion
(1) Replace any parts that were removed.
(2) Make sure that the component cover is secure.
(3) Return the system to normal operation.
(4) Check that the component operates normally.
10
TeleFlow
Material Safety Data Sheets
Material Safety Data Sheets are provided herein to comply with OSHA’s Hazard
Communication Standard, 29 CFR 1910.1200. This standard must be consulted for specific requirements.
Material Safety Data Sheets are provided in the order listed in Table Z-1 below.
TABLE Z-1 MSDS for TeleFlow Instruction Manual CI-3530-25B
Manufacturer
Power-Sonic
Corp.
Tadiran
Electronics
General Description
Bristol Babcock Part Number or Media Notes
Sealed Lead-Acid Battery 395407-04-4 (12V - 40AH)
Lithium/Thionyl Chloride
Battery
390618-03-9 (3.6V - On-board)
04/01/98 Appendix Z - CI-3530-25B MSDS
BLANK PAGE
MATERIAL SAFETY DATA SHEET
Product Name: Sealed Maintenance Free Lead-Acid Batteries
DATE:
COMPONENTS
Lead (Pb, Pb0
2
, PBSO
4
)
Sulfuric Acid
Fiberglass Separator
ABS Plastic
COMPONENTS
Lead
Lead Sulfate
Lead Dioxide
Sulfuric Acid
Fiberglass Separator
ABS Plastic
COMPONENTS
Lead
Sulfuric Acid
Hydrogen
Fiberglass Separator
ABS Plastic
Skin Contact:
Eye Contact:
Ingestion:
10/1/2003
WEIGHT %
6.2
9.4
about 1.3
N/A
ISSUED BY ENGINEERING
HAZARDOUS COMPONENTS
LD50
TLV
N/A
1mg/m 3
ORAL
(500) mg/kg
(2,140) mg/kg about 70% about 20% about 5% about 5%
DENSITY
11.34
N/A
N/A
N/A
N/A
PHYSICAL DATA
MELTING POINTS
SOLLUBILITY
(H
2
O)
327.4º C (Boiling)
1070º C (Boiling)
None
40 mg/l(15 0 C)
290º C (Boiling) about 114º C (Boiling)
N/A
None
100%
Slight
N/A N/A None
FLAMMABILITY DATA
FLASHPOINT EXPLOSIVE LIMIT
None
None
None
None
N/A
None
4% - 72.4%
N/A
N/A
TELEPHONE NO.
LC50
INHALATION
N/A
N/A
N/A
N/A
ODOR
None
None
None
Acidic
Toxic
No Odor
COMMENTS
(619) 661-2030
LC50
CONTACT
N/A
N/A
N/A
N/A
APPEARANCE
Silver-Gray Metal
White Powder
Brown Powder
Clear Colorless Liquid
White Fibrous Glass
Solid
Sealed batteries can emit hydrogen if over charged
(float voltage > 2.40 VPC).
Toxic vapors may be released. In case of fire, wear self-contained breathing apparatus.
Temp. over 300º C (572º F) may release combustible gases. In case of fire: wear positive pressure self-contained breathing apparatus.
FIRST AID
SULFURIC ACID PRECAUTIONS
Flush with water, see physician if contact area is large or if blisters form.
Call physician immediately and flush with water until physician arrives.
Call physician. If patient is conscious, flush mouth with water, have patient drink milk or sodium bicarbonate solution.
Continued on Page 2
MATERIAL SAFETY DATA SHEET
(PAGE 2 OF 2)
C O M P O N E N T
S T A B I L I T Y
C O L Y M E R I Z A T I O N
I N C O M P A T I B I L I T Y
D E C O M P O S I T I O N P R O D U C T S
C O N D I T I O N S T O A V O I D
R E A C T I V I T Y D A T A
S u l f u r i c A cid
S t a b l e a t a l l t e m p e r a t u r es
W i l l n o t p o l y m e r i ze
R e a c t i v e m e t a l s , s t r o n g b a s e s , m o s t o r g a n i c c o m p o u n d s
S u l f u r i c d i o x i d e , t r i o x i d e , h y d r o g e n s u l f i d e , h y d r o g e n
P r o h i b i t s m o k i n g , s p a r k s , e t c .
f r o m b a t t e r y c h a r g i n g a r e a .
A v o i d m i x i n g a c i d w i t h o t h e r c h e m i c a l s
S t
W e a p s t s e t o t d i s a k e p o s a i l n c a m e t s e h o o f d : l e a k o r s p i l l :
S P I L L O R L E A K P R O C E D U R E S
I f s u l f u r i c a c i d i s s p i l l e d f r o m a b a t t e r y , n e u t c a r b o n s y s t e m .
( s o
D o d a n o a s h ) , t o a l l o w r c a l c i u m u n n e u t r a l o x i d e i z e d
( l i m e ) .
a c i d i n t o r i l i z e a c i d
F l u s h a r e a s e w a g e s w i t h b i c a r b o n a t e w y s i t h t e m .
w a t e r a n d d
( b a k i n g i s c a r d t s o o d a t h e
) , s o d i u m s e w a g e
N e u w a s t t r i l e i z e d a n d a c i d d i s p o m a y s e d b o f e f l u s h a c c o r e d d i d o n g t w o n t h e l o c a ,l s e w e r .
s t a t e ,
S p a n d e f n t e d b a t t e r i e s e r a l g u i d e m l i u s t n e s .
b e
A t r e a t e d c o p y o f a s h t h i s a z a r
M S d o u s
D S m u s t b e s u p p l i e d t o a n y s c r a p d e a l e r o r s e c o n d a r y l e a d s m e l t e r w i t h b a t t e r y .
P R O T E C T I O N
S
R
E
K
E
Y
I
S P
E
N
S
I R
E
A T
X P
O R
O S
Y
U R E S I T E P R O T E C T I ON C O M M E N TS
R u b b e r g l o v e s , A p r on
R e s p i r a t o r ( f o r l e a d)
P r o t e c t i v e e q u i p m e n t o t h e r w i s e d a m a g e d .
A m u r e s t b s p i r e a t w o o r r n i f t h s h o u l d e b b a t t e r y i s e c r a c k e d o r w o r n d u r i n g r e c l a i m o p e r a t i o n s i f t h e T L V i s e x c e e d e d .
S a f e t y g o g g l e s , F a c e S h i e ld
E L E C T R I C A L S A F E T Y
D u e t o t h e b a t t e r y ' s l o w i n t e r n a l r e s i s t a n c e a n d h i g h p o w e r d e n s i t y , h i g h l e v e l s o f s h o r t c i r c u i t c u r r e n t c a n b e d e v e l o p e d a c r o s s t h e b a t t e r y t e r m i n a l s .
D o n o t r e s t t o o l s m a i n t a i n i n g b a t t e r y s y s t e m s .
o r c a b l e s o n t h e b a t t e r y .
U s e i n s u l a t e d t o o l s o n l y .
F o l l o w a l l i n s t a l l a t i o n i n s t r u c t i o n s a n d d i a g r a m s w h e n i n s t a l l i n g o r
H E A L T H H A Z A R D D A T A
L E A D : T h e t o x i c e f f e c t s o f l e a d a r e a c c u m u l a t i v e a n d s l o w t o a p p e a r .
I t a f f e c t s t h e k i d n e y s , r e p r o d u c t i v e , a n d c e n t r a l n e r v o u s s y s t e m s .
T h e s y m p p a i n .
t o m s
E x p o o f s u r l e e a d t o o v e r l e a d e x p o f r o m s u a r e a b a t r e t e r a n e m i a , y m o s t v o m o f t e r n i t i n g o c
, c h u r e a s d a c h e d u r i n g
, l s t o m a c h e a d r e c l a i p a i n ( l e a d m o p e r a t i c o l o n s i c ) , t h r o d i z z i n e s s , u g h t h e l o s s b r e a t h o f i n g a p p o r e t i t e , a n d m u s c l e a n d i n g e s t i o n o f l e a d d u s t j o i n t o r f u m e s .
S U L a c i d
F U w i l l
R c
I C a u s
A e
C I D : S u l f u r i c
G I t r a c t b u r n s .
a c i d
A c i d i s a c a n s t r o n g b e r e l c o e a r r o s s e d i v i f e t
.
h
C o n t a c t w i t h a c i d e b a t t e r y c a s e i s d c a n a m a c g a s e d u e s e v e r e o r i f v e n t s b u r n s a r e o n t h e s t a m p e r e d k i n w i t a n d h .
i n e y e s .
I n g e s t i o n o f s u l f u r i c
F I B E R G L A S S S E P A R A T O R :
C o m f o l l w i t h t y p e H f i l t e r .
A b o v e
N T P o r O S H A .
F i b r o u r g l a s s
1 0 F / C C u p t o i s a n i r r i t a
5 0 F / C C n t u s o f t h e e U l t r u a p p e r
T w i n r e p i r a t o r y w i t h t y p e t r a c t ,
H f i l s t e r .
k i n
T h a n d i s p e r o y e s .
d u c t
F o r e x p o s u r e i s n o t c o n s i d u p e r e d t o 1 0 F / C C u c a r c i n o g e n i c s e M b y
S A
A L L D A T A M U S T B E P A S S E D T O A N Y S C R A P D E A L E R O R S M E L T E R W H E N B A T T E R Y I S R E S O L D .
Power-Sonic Corporation
9163 Siempre Viva Road, San Diego, CA 92154 Tel (619) 661-2020 Fax (619) 661-3650
Website: www.power-sonic.com E-Mail: [email protected]
B
MSDS No.- T-36-01 (Revision. -G)
Q u a l i t y F i r s t
MATERIAL SAFETY DATA SHEET
SECTION 1- CHEMICAL PRODUCT AND COMPANY IDENTIFICATION
Manufacturer Name- Tadiran Batteries Ltd., P. O. Box 1, Kiryat Ekron, Israel 70500.
US office address- 2 Seaview Blvd. Port Washington NY 11050
Emergency Telephone No. – CHEMTREC: 1-800-424-9300
Tel. for information: 1-516-621-4980
Tel. for information 972-8-944-4503
Products Name: Primary Lithium Thionyl Chloride (Li/SOCl
2
) cells and batteries, Nonrechargeable. Cells include the models of TL, TLH, and TLL, 3.6V series.
SECTION 2- COMPOSITION, INFORMATION ON INGREDIENTS
Ingredient Name
Lithium Metal (Li)
CAS # % ACGIH (TLV) OHSA
(PEL)
7439-93-2 <5% Not Established None
CHIP
Classification
F: R14/15
C: R34
Thionyl Chloride (SOCl
Lithium Chloride (LiCl)
2
) 7719-09-7 <47
7447-41-8
%
1 ppm
(5 mg/M 3 )
<2% Not Established
R: 14/15, 34
S: (1/2), 8,43,45
5 mg/m 3 R: 14,20/22,29,
35.
S: (1/2),26,36/
37/39, 45
Carbon (C)
Aluminum Chloride (AlCl
3
1333-86-4 <6% 3.5 mg/m
) 7446-70-0 <5% 2 mg/m 3
3 3.5
(Al salt, soluble)
R:
S:
45
34
(1/2),7/8,28,
SECTION 3 - HAZARD IDENTIFICATION
The lithium Thionyl chloride batteries described in this MSDS are hermetically sealed units, which are not hazardous when used according to the recommendations of the manufacturer.
Under normal condition of use of the batteries, the electrode materials and the liquid electrolyte they contained are non-reactive provided the battery integrity is maintained. Risk of exposure exists only in case of mechanical, electrical or thermal abuse. Thus the batteries should not short circuit, recharge, puncture, incinerate, crush, immerse in water, force discharge, or expose to temperatures above the temperature range of the cell or battery. In these cases there is risk of fire or explosion
MSDS SOCl2 G rev GB.doc
1/6
Revised-
22/9/2004
B
SECTION 4- FIRST AID MEASURES
Q u a l i t y F i r s t
In case of battery rupture, explosion, or major leakage, evacuate personnel from contaminated area and provide good ventilation to clear out corrosive fumes, gases or the pungent odor. Seek immediate medical attention.
Eyes -
First rinse with plenty of water for 15 minutes (remove contact lenses if easily possible), and then seek medical attention.
Skin -
Remove contaminated clothes and rinse skin with plenty of water or shower for
15 min. Refer to medical attention.
Inhalation -
Remove to fresh air, rest, and half-upright position, use artificial respiration if needed, and refer to medical attention.
Ingestion -
rinse mouth,
DO NOT
induce vomiting, give plenty of water to drink, and refer to medical attention.
SECTION 5- FIRE FIGHTING MEASURES
FLAMMABLE LIMIT IN AIR: NA
EXTINGUISHING MEDIA:
1. Lith- X (Class D extinguishing media) is the
only
effective on fires involving a few lithium batteries. If the cells are directly involved in a fire
DO NOT USE:
WATER,
SAND, CO
2
, HALON, and DRY POWDER OR SODA ASH EXTINGUISHERS.
2. If the fire is in adjacent area and the cells that are either packed in their original containers or unpacked, the fire can be fought based on fueling material, e.g., paper and plastic products. In these cases the use of copious amounts of
cold
water is effective extinguishing media. Storage area may employ sprinkler system with cold water.
AUTO-IGNITION: NA
SPECIAL FIRE FIGHTING PROCEDURES: Wear self-contained breathing apparatus to avoid breathing of irritant fumes (NIOSH approved SCBA & full protective equipment). Wear protective clothing and equipment to prevent body contact with electrolyte solution.
Fire may be fought, but only from safe fire-fighting distance. Evacuate all persons from immediate area of fire.
UNUSUAL EXPLOSION AND FIRE EXPLOSION: Battery may explode when subject to: excessive heat (above 150ºC), recharged, over-discharged (discharge below 0V), punctured and crushed. During thermal decomposition generation of chlorine (Cl
2
), hydrogen chloride (HCl), and sulfur dioxide (SO
2
) can be formed.
SECTION 6- SPILL OR LEAKAGE PROCEDURES
PROCEDURES TO CONTAIN AND CLEAN UP LEAKS OR SPILLS: The material contained within the battery would only be released under abusive conditions.
In the event of battery rapture and leakage: contain the spill while wearing proper protective clothing and ventilate the area. Than, cover with sodium carbonate
MSDS SOCl2 G rev GB.doc
2/6
Revised-
22/9/2004
B
Q u a l i t y F i r s t
(Na
2
CO
3
) or 1:1 mixture of soda ash and slaked slime. Keep away from water, rain, and snow. Placed in approved container (after cooling if necessary) and disposed according to the local regulations.
NEUTRALIZING AGENT: Sodium carbonate (Na
2 and slaked slime.
CO
3
) or 1:1 mixture of soda ash
WASTE DISPOSAL METHOD: Product decomposed by water must be neutralized.
May be added to waste water in sufficiently diluted form.
PRECAUTIONS IN HANDLING AND STORING; Avoid short-circuiting, overcharging and heating to high temperatures. Store the batteries in dry and cool area and keep container dry and tightly closed in well-ventilated area. Store away from food and drink.
OTHER PRECAUTIONS; Never attempt to disassemble, machine, or otherwise modify batteries or injury may result.
SECTION 7- HANDLING AND STORAGE
The batteries should not be opened, destroyed or incinerate, since they may leak or rupture and release to the environment the ingredients that they normally contained in the hermetically sealed container.
HANDLING-
Do not short circuit terminals, or expose to temperatures above the temperature rating of the battery, over charge the battery, forced over-discharge
(voltage below 0.0V), throw to fire.
Do not crush or puncture the battery, or immerse in liquids.
STORAGE-
Storage preferably in cool (below 30ºC), dry and ventilated area, which is subject to little temperature change.
Do not place the battery near heating equipment, nor expose to direct sunlight for long periods. Elevated temperatures can result in shortened battery life and degrade performance.
Keep batteries in original packaging until use and do not jumble them.
Do not store batteries in high humidity environment for long periods.
OTHER-
the cells and the batteries are not rechargeable batteries and should not be charged.
Applying pressure and deforming the battery may lead to disassembly followed by eye skin and throat irritation.
Follow manufacturers recommendations regarding maximum recommended current and operating temperature range.
SECTION 8 - EXPOSURE CONTROLS & PERSONAL PROTECTION
RESPIRATORY PROTECTION: None necessary under normal use. In case of abuse and leak of liquid or fumes, use NIOSH approved Acid Gas Filter Mask or Self-
Contained Breathing Apparatus.
VENTILATION: Not necessary under normal use. In case of abuse, use adequate mechanical ventilation (local exhaust) for battery that vent gas or fumes.
PROTECTIVE GLOVES: None under normal use. In case of spill use PVC or Nitrile gloves of 15 mils (0.015 inch) or thicker.
MSDS SOCl2 G rev GB.doc
3/6
Revised-
22/9/2004
B
Q u a l i t y F i r s t
EYE PROTECTION: Use ANSI approved chemical worker safety goggles or face shield.
OTHER PROTECTIVE EQUIPMENT: Chemical resistance clothing is recommended along with eye wash station and safety shower should be available meeting ANSI design criteria.
WORK HYGIENIC PRACTICES: Use good chemical hygiene practice. Wash hands after use and before drinking, eating or smoking. Launder contaminated cloth before reuse.
SUPPLEMENTARY SAFETY AND HEALTH DATA: If the battery is broken or leaked the main hazard is the electrolyte. The electrolyte is mainly solution of Lithium chloride (LiCl), and aluminum chloride (AlCl
3
) in Thionyl chloride (SOCl
2
).
Fires may be fought but only from safe fire fighting distance, evacuate all persons from immediate area of fire.
Prevent heating of the battery, charging the battery, discharge to predetermined limit, do not crush, disassemble, incinerate or short circuit.
SECTION 9- PHYSICAL DATA
BOILING POINT (760 mm Hg)
VAPOR PRESSURE (mm Hg, 25ºC)
VAPOR DENSITY (air=1)
NA, unless individual components exposed
NA, unless individual components exposed
NA, unless individual components exposed
DENSITY (gr/cc)
VOLATILE BY VOLUME (%)
> 1 gr/cc
NA
EVAPORATION RATE (butyl acetate=1) NA, unless individual components exposed
PHYSICAL STATE Solid
SOLUBILITY IN WATER (% by weight) NA, unless individual components exposed
PH
APPEARANCE
ODOR
NA, unless individual components exposed
Geometric Solid Object
If leaking, gives off pungent corrosive odor
SECTION 10- STABILITY AND REACTIVITY
STABLE OR NOT STABLE Stable
INCOMPATIBILITY (MATERIAL TO AVOID) Strong mineral acids, water and alkali solutions.
HAZARDOUS
DECOMPOSITION
PRODUCTS
1. Reaction of lithium with water: Hydrogen (H
2 hydroxide (LiOH).
), Lithium
2. Thermal decomposition over 150ºC: Sulfur oxides, (SO
2
SO
3
), Sulfur chorides (SCl
2
, S
2
Cl
2
), Chlorine (Cl
2 oxide (Li
2
O).
,
), Lithium
3. Electrolyte with water: Hydrogen Chloride (HCl) and SO
2
DECOMPOSITION TEMPERATURE (ºF)
NA
HAZARDOUS POLYMERIZATION: May Occur____ Will Not Occur __X__
CONDITIONS TO AVOID Avoid mechanical abuse, and electrical abuse such as short-circuiting, overcharge, over-discharge,
(voltage reversal) and heating.
MSDS SOCl2 G rev GB.doc
4/6
Revised-
22/9/2004
B
SECTION 11- TOXICOLOGICAL INFORMATION
Q u a l i t y F i r s t
THRESHOLD LIMIT VALUE (TLV) AND SOURCE: NA
HEALTH HAZARD ACUTE AND CHRONIC: Inhalation, skin contact, eye contact and ingestion are not likely by exposure to sealed battery.
Inhalation, skin contact and eye contact are possible when the battery is opened.
Exposure to internal contents, the corrosive fumes will be very irritating to skin, eyes and mucous membranes. Overexposure can cause symptoms of non-fibrotic lung injury and membrane irritation.
Carcinogenicity- NTP: No
Carcinogenicity- IARC: No
Carcinogenicity- OSHA: No
Explanation of Carcinogenicity- No ingredient of a concentration of 0.1% or greater is listed as a carcinogen or suspected carcinogen.
SIGNS AND SYMPTOMS OF OVEREXPOSURE: Exposure to leaking electrolyte from ruptured or leaking battery can cause:
Inhalation
- Burns and irritation of the respiratory system, coughing, wheezing, and shortness of breath.
Eyes
- Redness, tearing, burns. The electrolyte is corrosive to all ocular tissues.
Skin
- The electrolyte is corrosive and causes skin irritation and burns.
Ingestion
- The electrolyte solution causes tissue damage to throat and gastro/ respiratory track.
MEDICAL CONDITION AGGRAVATED BY EXPOSURE: Preexisting skin, asthma and respiratory diseases are generally aggravated by exposure to liquid electrolyte vapors or liquid. For further information refer to section 4.
SECTION 12- ECOLOGICAL INFORMATION
1. When properly used and disposed the battery does not present environmental hazard.
2. The battery does not contain mercury, cadmium, or lead.
3. Do not let internal components enter marine environment. Avoid release to waterways, wastewater or ground water.
SECTION 13- DISPOSAL CONSIDERATIONS
1. Disposal must be in accordance with the applicable regulations in every country and state.
2. Disposal of the Lithium batteries should be performed by permitted, professional disposal firms knowledgeable in Federal, State or Local requirements of hazardous waste treatment and hazardous waste transportation.
3. Incineration should never be performed by battery users, but eventually by trained professional in authorized facility with proper gas and fume treatment.
4. Recycling of battery can be done in authorized facility, through licensed waste carrier.
MSDS SOCl2 G rev GB.doc
5/6
Revised-
22/9/2004
B
SECTION 14- TRANSPORTATION /SHIPPING
Q u a l i t y F i r s t
Lithium batteries UN number 3090, class 9 (miscellaneous)
Lithium batteries contained in equipment, UN number 3091, class 9 (miscellaneous).
Packing instructions for 3090- ICAO 903 for air transport
IMDG 903 for sea transport
ADR/RID 903 and 903a for road /rail transport
Packing instructions for 3091- ICAO 912/918 for air transport
IMDG 903 for sea transport
ADR/RID 903 and 903a for road /rail transport
In the USA transportation is according to Code of Federal Regulations (CFR 49
Chapter 1, paragraph 173.185)
A list of Tadiran batteries and cells that are subject to transport regulations and those that are exempted can be obtained from Tadiran Batteries Ltd.
Identification and labeling in compliance with the product drawing should include the battery title, nominal voltage, lot number and warning.
SECTION 15- REGULATORY INFORMATION
1. The transport of the lithium batteries is regulated by the United Nations, “Model
Regulations on Transport of Dangerous Goods”, 13 revised edition-2003 (special provisions 188, 230, and 310).
2. Within the US the lithium batteries and cells are subject to shipping requirements under 49 CFRCh. 1, paragraph 173.185, “lithium batteries”.
3. Shipping of lithium batteries in aircrafts are regulated by the International Civil
Aviation Organization (ICAO) and the International Air Transport Association
(IATA) 2003 requirements in Special Provisions A45, A88 and A99.
4. Shipping of lithium batteries on sea are regulated the International Maritime
Dangerous Goods (IMDG) 2002 requirements in special provisions 188, 230 and 310.
5. Shipping of lithium batteries on Road and Rail, 2002 requirements in special provisions 188, 230 and 310.
6. The internal component (thionyl chloride) is hazardous under the criteria of the
Federal OHSA Hazard Communication Standard 29 CFR 1920.1200.
SECTION 16- OTHER INFORMATION/DISCLAIMER
The information and the recommendations set forth are made in good faith and believed to be accurate at the date of preparation. The present file refers to normal use of the product in question. Tadiran Batteries makes no warranty expressed or implied.
MSDS SOCl2 G rev GB.doc
6/6
Revised-
22/9/2004
BLANK PAGE
TeleRTU Plus Model 3530-25B
Customer Instruction Manual
CI-3530-25B
Jan., 2007
Emerson Process Management
Bristol, Inc.
1100 Buckingham Street
Watertown, CT 06795
Phone: +1 (860) 945-2262
Fax: +1 (860) 945-2525 www.EmersonProcess.com/Bristol
Emerson Electric Canada, Ltd.
Bristol Canada
6338 Viscount Rd.
Mississauga, Ont. L4V 1H3
Canada
Phone: 905-362-0880
Fax: 905-362-0882 www.EmersonProcess.com/Bristol
Emerson Process Management
BBI, S.A. de C.V.
Homero No. 1343, 3er Piso
Col. Morales Polanco
11540 Mexico, D.F.
Mexico
Phone: (52-55)-52-81-81-12
Fax: (52-55)-52-81-81-09 www.EmersonProcess.com/Bristol
Emerson Process Management
Bristol Babcock, Ltd.
Blackpole Road
Worcester, WR3 8YB
United Kingdom
Phone: +44 1905 856950
Fax: +44 1905 856969 www.EmersonProcess.com/Bristol
Emerson Process Management
Bristol, Inc.
22 Portofino Crescent,
Grand Canals Bunbury, Western Australia 6230
Mail to: PO Box 1987 (zip 6231)
Phone: +61 (8) 9725-2355
Fax: +61 (8) 8 9725-2955 www.EmersonProcess.com/Bristol
The information in this document is subject to change without notice. Every effort has been made to supply complete and accurate information. However, Bristol, Inc. assumes no responsibility for any errors that may appear in this document.
If you have comments or questions regarding this manual, please direct them to your local Bristol sales representative, or direct them to one of the addresses listed at left.
Bristol, Inc. does not guarantee the accuracy, sufficiency or suitability of the software delivered herewith. The Customer shall inspect and test such software and other materials to his/her satisfaction before using them with important data.
There are no warranties, expressed or implied, including those of merchantability and fitness for a particular purpose, concerning the software and other materials delivered herewith.
TeleFlow
™
is a trademark of Bristol, Inc. The Emerson logo is a trade mark and service mark of Emerson Electric Co. Other trademarks or copyrighted products mentioned in this document are for information only, and belong to their respective companies, or trademark holders.
Copyright (c) 2006, Bristol, Inc., 1100 Buckingham St., Watertown, CT 06795. No part of this manual may be reproduced in any form without the express written permission of
Bristol Inc.
advertisement
Key Features
- Supports多种 communication protocols, including DNP3, Modbus, and IEC 60870-5-104
- Provides a wide range of I/O options, including digital inputs and outputs, analog inputs and outputs, and pulse inputs
- Offers a variety of mounting options, including DIN rail, panel mount, and rack mount
Related manuals
Frequently Answers and Questions
What is the operating temperature range for the TeleRTU PLUS 3530-25B?
What is the power consumption of the TeleRTU PLUS 3530-25B?
What is the warranty period for the TeleRTU PLUS 3530-25B?
advertisement
Table of contents
- 84 GENERAL INTRODUCTION
- 85 Configuration Hardware
- 88 REMOVAL/REPLACEMENT & INSTALLATION OF THE LPI/OEB
- 88 Removal/Replacement of the Low Power I/O Expansion Board
- 90 Installation of the Low Power I/O Expansion Board
- 92 I/O CONFIGURATION & WIRING
- 92 LPI/OEB Discrete Input Wiring (TB4)
- 92 LPI/OEB Discrete Output Wiring (TB4)
- 93 LPI/OEB Analog Input Wiring (TB2)
- 95 LPI/OEB Analog Output Wiring (TB3)
- 96 LPI/OEB High Speed Counter Wiring (TB3)
- 96 RS-232/RS-485 COMMUNICATIONS
- 98 FIELD WIRING SIGNAL CHECKS
- 99 INPUT/OUTPUT SPECIFICATIONS
- 99 Discrete Inputs
- 99 Discrete Outputs
- 99 Analog Inputs
- 100 Analog Outputs
- 101 Communication Port
- 101 High Speed Counter
- 101 ENVIRONMENTAL SPECIFICATIONS
- 107 GENERAL INTRODUCTION
- 107 Configuration Hardware
- 108 Jumper Settings
- 109 REMOVAL/REPLACEMENT & INSTALLATION OF THE DTRI/OB
- 109 Removal/Replacement of the Digital to Relay I/O Board
- 110 Installation of the Digital to Relay I/O Board Option
- 112 FIELD WIRING
- 112 Terminal Connections
- 114 DIGITAL TO RELAY I/O BOARD SPECIFICATIONS
- 114 Input Requirements
- 114 Output Requirements
- 133 GENERAL INTRODUCTION
- 136 RADIO REMOVAL/REPLACEMENT & INSTALLATION
- 136 Radio Removal/Replacement Procedure
- 139 Installation of the Radio Option into a Radio Ready TeleFlow Plus
- 140 Installation of the Radio Option into a Non-Radio Ready TeleFlow Plus
- 142 WIRING LISTS
- 142 ADDITIONAL FreeWave INFORMATION
- 143 GENERAL SPECIFICATIONS
- 143 TRANSMITTER SPECIFICATIONS
- 143 RECEIVER SPECIFICATIONS
- 144 ENVIRONMENTAL SPECIFICATIONS
- 157 DESCRIPTION
- 158 POWER SUPPLY OPTION
- 158 Removal/Replacement of the 21V Power Supply Option
- 159 Installation of the 21V Power Supply Option
- 160 FIELD WIIRING
- 160 Terminal Connections
- 162 GENERAL SPECIFICATIONS
- 162 PERFORMANCE SPECIFICATIONS
- 162 ENVIRONMENTAL SPECIFICATIONS
- 177 PT. NO
- 177 DESCRIPTION
- 177 Transmitter Operation
- 178 LED INDICATORS
- 178 JUMPER JP
- 179 REMOVAL/REPLACEMENT & INSTALLATION OF THE LPTIB
- 179 Removal/Replacement of the Low Power Transmitter Interface Bd
- 180 Installation of the Low Power Transmitter Interface Board Option
- 181 FIELD WIIRING
- 181 Terminal Connections
- 184 GENERAL SPECIFICATIONS
- 184 ENVIRONMENTAL SPECIFICATIONS
- 199 PT. Number
- 199 DESCRIPTION
- 199 Transmitter Operation
- 200 LED INDICATORS
- 200 JUMPER JP
- 201 REMOVAL/REPLACEMENT & INSTALLATION OF THE ETIB
- 201 Removal/Replacement of the Expansion Transmitter Interface Board
- 204 Installation of the Expansion Transmitter Interface Board Option
- 205 FIELD WIRING
- 205 Terminal Connections
- 207 GENERAL SPECIFICATION
- 207 ENVIRONMENTAL SPECIFICATIONS
- 255 PT. Number
- 255 DESCRIPTION
- 255 Function
- 256 Features
- 256 COMPONENT IDENTIFICATION
- 256 INSTALLATION COMPATIBILITY
- 256 Restrictions
- 257 EXPCOM232 REMOVAL/REPLACEMENT & INSTALLATION
- 257 Installation/Removal of the EXPCOM232 Board
- 257 Installation/Removal for Models 3530-10B, -15B, -40B, -45B & -50B
- 264 Installation/Removal for Models 3530-20B & -25B
- 265 Installation/Removal for Models 3530-35B
- 266 RS-232 WIRING
- 269 PERFORMANCE SPECIFICATIONS
- 269 ENVIRONMENTAL SPECIFICATIONS
- 291 DESCRIPTION
- 291 Function
- 292 Features
- 293 COMPONENT IDENTIFICATION
- 293 INSTALLATION COMPATIBILITY
- 293 Restrictions
- 294 EXP485/AO REMOVAL/REPLACEMENT & INSTALLATION
- 294 Installation/Removal of the EXP485/AO Board
- 294 Installation/Removal for Models 3530-10B, -15B, -40B & -50B
- 301 Installation/Removal for Models 3530-20B & -25B
- 303 Installation/Removal for Models 3530-35B
- 304 RS-485 and AO WIRING
- 306 PERFORMANCE SPECIFICATIONS
- 306 ENVIRONMENTAL SPECIFICATIONS
- 307 ENTITY PARAMETERS (INTRINSICALLY SAFE EXPAO Bd.)
- 317 GENERAL INTRODUCTION
- 317 MAJOR TOPICS
- 318 PROTECTING INSTRUMENT SYSTEMS
- 318 Quality Is Conformance To Requirements
- 318 PROTECTING EQUIPMENT & PERSONNEL
- 318 Considerations For The Protection of Personnel
- 318 Considerations For The Protection of Equipment
- 318 OTHER SITE SAFETY CONSIDERATIONS
- 319 POWER & GROUND SYSTEMS
- 319 Modem Grounding Kit
- 319 IMPORTANCE OF GOOD GROUNDS
- 319 EARTH GROUND CONNECTIONS
- 319 Establishing a Good Earth Ground
- 319 Soil Conditions
- 319 Soil Types
- 319 Dry, Sandy or Rocky Soil
- 319 Ground Wire Considerations
- 319 Modem Ground Wiring Diagrams
- 319 Other Grounding Considerations
- 319 ISOLATING EQUIPMENT FROM THE PIPELINE
- 319 Meter Runs Without Cathodic Protection
- 319 Meter Runs With Cathodic Protection
- 320 STROKES & STRIKES
- 320 Chance of Being Struck by Lightning
- 320 Antenna Caution
- 320 Ground Propagation
- 320 Tying it all Together
- 320 Impulse Protection Summary
- 320 USE OF LIGHTNING ARRESTERS & SURGE PROTECTORS