advertisement
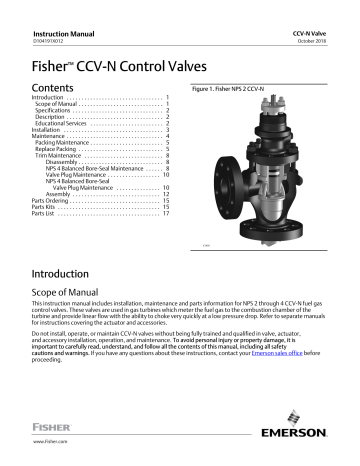
Instruction Manual
D104191X012
Fisher
™
CCV-N Control Valves
Contents
Introduction . . . . . . . . . . . . . . . . . . . . . . . . . . . . . . . . .
Scope of Manual
Specifications
. . . . . . . . . . . . . . . . . . . . . . . . . . . . .
. . . . . . . . . . . . . . . . . . . . . . . . . . . . . . .
Description . . . . . . . . . . . . . . . . . . . . . . . . . . . . . . . . .
Educational Services . . . . . . . . . . . . . . . . . . . . . . . . .
Installation
Maintenance
. . . . . . . . . . . . . . . . . . . . . . . . . . . . . . . . . .
. . . . . . . . . . . . . . . . . . . . . . . . . . . . . . . . .
Packing Maintenance
Replace Packing
. . . . . . . . . . . . . . . . . . . . . . . . .
. . . . . . . . . . . . . . . . . . . . . . . . . . . . .
Trim Maintenance . . . . . . . . . . . . . . . . . . . . . . . . . . .
Disassembly . . . . . . . . . . . . . . . . . . . . . . . . . . . . .
NPS 4 Balanced Bore-Seal Maintenance . . . . . .
Valve Plug Maintenance
NPS 4 Balanced Bore-Seal
. . . . . . . . . . . . . . . . . .
8
Valve Plug Maintenance
Assembly
. . . . . . . . . . . . . . .
. . . . . . . . . . . . . . . . . . . . . . . . . . . . . .
Parts Ordering . . . . . . . . . . . . . . . . . . . . . . . . . . . . . . .
Parts Kits
Parts List
. . . . . . . . . . . . . . . . . . . . . . . . . . . . . . . . . . .
. . . . . . . . . . . . . . . . . . . . . . . . . . . . . . . . . . .
10
Figure 1. Fisher NPS 2 CCV-N
CCV-N Valve
October 2018
X1430
Introduction
Scope of Manual
This instruction manual includes installation, maintenance and parts information for NPS 2 through 4 CCV-N fuel gas control valves. These valves are used in gas turbines which meter the fuel gas to the combustion chamber of the turbine and provide linear flow with the ability to choke very quickly at a low pressure drop. Refer to separate manuals for instructions covering the actuator and accessories.
Do not install, operate, or maintain CCV-N valves without being fully trained and qualified in valve, actuator, and accessory installation, operation, and maintenance. To avoid personal injury or property damage, it is important to carefully read, understand, and follow all the contents of this manual, including all safety cautions and warnings.
If you have any questions about these instructions, contact your Emerson sales office before proceeding.
www.Fisher.com
CCV-N Valve
October 2018
Instruction Manual
D104191X012
Table 1. Specifications
Valve Sizes
NPS 2 3 4
End Connection Style
CL300 and CL600 Raised Face (RF) Flanges per ASME
B16.5
Maximum Inlet Pressure and Temperature (1)
Consistent with CL300 pressure-temperature ratings to 316 C (600 F)
Consistent with CL600 pressure-temperature ratings to 370 C (700 F)
Maximum Pressure Drop
Consistent with pressure-temperature ratings per
ASME B16.34
Shutoff Classification
Class IV shutoff per ANSI/ FCI 70-2
Flow Direction
Flow Down
Flow Characteristic
Linear from 10% to 100% travel
Approximate Weights
RATING
CL300
CL600
1. The pressure/temperature limits in this manual and any applicable standard or code limitation for valve should not be exceeded.
VALVE SIZE,
NPS
2
3
4
2
3
4
31
51
87
Kg
31
51
77
WEIGHT lbs
68
112
168
68
112
190
Description
CCV-N valves are single port, angle-style, and balanced or unbalanced valves with metal seat, seat ring retainer guide, and push-down-to-close valve plug action.
Educational Services
For information on available courses for Fisher CCV-N fuel gas control valves, as well as a variety of other products, contact:
Emerson Automation Solutions
Educational Services - Registration
Phone: 1-641-754-3771 or 1-800-338-8158
E-mail: [email protected]
emerson.com/fishervalvetraining
2
Instruction Manual
D104191X012
CCV-N Valve
October 2018
Installation
WARNING
Always wear protective gloves, clothing, and eyewear when performing any installation operations to avoid personal injury.
Personal injury or equipment damage caused by sudden release of pressure may result if the valve assembly is installed
damage, provide a relief valve for over-pressure protection as required by government or accepted industry codes and good engineering practices.
Check with your process or safety engineer for any additional measures that must be taken to protect against process media.
If installing into an existing application, also refer to the WARNING at the beginning of the Maintenance section in this instruction manual.
CAUTION
When ordered, the valve configuration and construction materials were selected to meet particular pressure, temperature, pressure drop, and controlled fluid conditions. Since some valve body/trim material combinations are limited in their pressure drop and temperature ranges, do not apply any other conditions to the valve without first contacting your
Emerson sales office .
1. Before installing the valve, inspect the valve and associated equipment for any damage and any foreign material.
2. Make certain the valve body interior is clean, that pipelines are free of foreign material, and that the valve is oriented so that pipeline flow is in the same direction as the arrow on the side of the valve.
3. It is recommended the valve should be installed in the vertical orientation with the actuator vertical above the valve. Other positions may result in uneven valve plug, seal set, seat ring, seat ring retainer, packing wear and improper operation. For more information, consult your Emerson sales office.
4. It is recommended the valve upstream pipe inside diameter should match or be close to valve body inlet inside diameter to reduce valve inlet turbulence.
5. It is recommended to have a length of 6 to 12 pipe diameters of straight pipe upstream of the valve body inlet and 4 to 8 pipe diameters length downstream of the valve seat ring outlet. The straight pipe upstream and downstream of the valve body should have a smooth inside surface with no weld slag or other inside surface irregularities. It is recommended that pipe reducers not be installed in the straight pipe upstream and downstream of the valve.
6. Use a suitable gasket between valve and pipeline flanges.
7. If continuous operation is required during inspection or maintenance, install a three-valve bypass around the control valve assembly.
8. Refer to the actuator mounting procedure in the appropriate actuator instruction manual.
WARNING
Personal injury could result from packing leakage. Valve packing was tightened before shipment; however, the packing might require some readjustment to meet specific service conditions.
3
4
CCV-N Valve
October 2018
Instruction Manual
D104191X012
Valves with ENVIRO‐SEAL live‐loaded packing or HIGH‐SEAL live‐loaded packing will not require this initial re‐adjustment. See the Fisher instruction manuals, ENVIRO‐SEAL Packing System for Sliding‐Stem Valves
( D101642X012 ) or HIGH‐SEAL Live‐Loaded Packing System ( D101453X012 ) (as appropriate), for packing instructions.
If you wish to convert your present packing arrangement to ENVIRO‐SEAL packing, refer to the retrofit kits listed in the
Parts Kit sub‐section near the end of this manual.
Maintenance
Valve parts are subject to normal wear and must be inspected and replaced as necessary. Inspection and maintenance frequency depends on the severity of service conditions. This section includes instructions for packing maintenance and trim maintenance. All maintenance operations may be performed with the valve in the line.
WARNING
Avoid personal injury or property damage from sudden release of process pressure. Before performing any maintenance operations:
Do not remove the actuator from the valve while the valve is still pressurized.
Always wear protective gloves, clothing, and eyewear when performing any maintenance operations to avoid personal injury.
Disconnect any operating lines providing air pressure, electric power, or a control signal to the actuator. Be sure the actuator cannot suddenly open or close the valve.
Use bypass valves or completely shut off the process to isolate the valve from process pressure. Relieve process pressure from both sides of the valve. Drain the process media from both sides of the valve.
Release the actuator loading pressure and relieve any actuator spring pre-compression.
Use lock-out procedures to be sure that the above measures stay in effect while you work on the equipment.
The valve packing box may contain process fluids that are pressurized, even when the valve has been removed from the pipeline . Process fluids may spray out under pressure when removing the packing hardware or packing rings, or when loosening the packing box pipe plug.
Check with your process or safety engineer for any additional measures that must be taken to protect against process media.
CAUTION
Follow instructions carefully to avoid damaging the product surfaces, which could result in damage to the product. Protect all surfaces of the valve plug, valve seat ring, and seat ring retainer during maintenance to ensure control valve accuracy and choking performance is not affected.
Note
Whenever a gasket seal is disturbed by removing or shifting parts, a new gasket should be installed upon reassembly. This is necessary to ensure a good gasket seal, since the used gasket may not seal properly.
Instruction Manual
D104191X012
CCV-N Valve
October 2018
Packing Maintenance
Note
For valves with ENVIRO‐SEAL packing, see the Fisher instruction manual, ENVIRO‐SEAL Packing System for Sliding‐Stem Valves,
D101642X012 , for packing instructions.
If there is undesirable packing leakage, first try to limit the leakage and establish a stem seal by tightening the packing flange nuts.
If the packing is relatively new and tight on the stem, and if tightening the packing flange nuts does not stop the leakage, it is possible that the valve stem is worn or nicked so that a seal cannot be made. The surface finish of a new valve stem is critical for a good packing seal. If the leakage comes from the outside diameter of the packing, it is possible that the leakage is caused by nicks or scratches around the packing box wall. If performing any of the following procedures, inspect the valve stem and packing box wall for nicks and scratches.
Replace Packing
WARNING
Refer to the WARNING at the beginning of the Maintenance section in this instruction manual
1. Isolate the control valve from the line pressure, release pressure from both sides of the valve body, and drain the process media from both sides of the valve. If using a power actuator, also shut off all pressure lines to the power actuator, and releases all pressure from the actuator. Use lock-out procedures to be sure that the above measures stay in effect while you work on the equipment. Observe the Warnings at the start of the Maintenance section.
2. Disconnect the operating lines from the actuator and any leak-off piping from the bonnet. Disconnect the stem connector and remove the actuator from the valve.
valve stem threads.
WARNING
To avoid personal injury or property damage caused by uncontrolled movement of the bonnet, loosen the bonnet by following the instructions in the next step. Do not remove a stuck bonnet by pulling on it with equipment that can stretch or store energy in any other manner. The sudden release of stored energy can cause uncontrolled movement of the bonnet.
5
CCV-N Valve
October 2018
Instruction Manual
D104191X012
Figure 2. Packing Arrangements
UPPER WIPER
(KEY 12)
PACKING
FOLLOWER (KEY 13)
FEMALE
ADAPTER 1
PACKING RING
MALE
ADAPTER 1
LANTERN RING
(KEY 8)
1
PACKING BOX
RING (KEY 11)
LOWER WIPER 1
NOTE:
V-RING PACKING RINGS, MALE ADAPTER, AND LOWER WIPER RINGS.
GRAPHITE LEAK-OFF
PACKING
FOLLOWER (KEY 13)
GRAPHITE RIBBON
PACKING RING (KEY 7)
1
W
LANTERN RING
(KEY 8)
GRAPHITE FILAMENT
PACKING RING (KEY 7) 2
W
PACKING BOX
RING (KEY 11)
12.7 mm
(1/2 INCH) STEM
NOTE: INSTALL SACRIFICAL WASHERS AT PLACES MARKED 'W'
gasketed joint by either rocking the bonnet or prying between the bonnet and valve. Work the prying tool around the bonnet until the bonnet loosens. If no fluid leaks from the joint, remove the nuts or cap screws completely and carefully lift the bonnet off the valve.
CAUTION
after being lifted partway out. When lifting the bonnet, temporarily install a valve stem locknut on the valve stem. The locknut will prevent the valve plug and stem assembly from dropping out of the bonnet.
5. Remove the locknut and separate the valve plug and stem from the bonnet. Set the parts on a protective surface to prevent damage to gasket or seating surfaces.
protect the gasket surface and prevent foreign material from getting into the valve body cavity.
CAUTION
To prevent possible product damage, cover the opening in the valve in the following procedure to prevent foreign material from getting into the valve body cavity.
7. Remove the packing flange nuts, packing flange, upper wiper, and packing follower when applicable (keys 3, 5, and
6
Instruction Manual
D104191X012
CCV-N Valve
October 2018
of the bonnet using a rounded rod or other tool that will not scratch the packing box wall. Clean the packing box and the metal packing parts.
8. Inspect the valve stem threads and packing box surfaces for any sharp edges which might cut the packing.
Scratches or burrs could cause packing box leakage or damage to the new packing. If the surface condition cannot be improved by light sanding, replace the damaged parts by following the appropriate steps in the Trim
Maintenance procedure.
stem and onto the stud bolts (key 15, figures 6, 7, 8, 12, 13, and 14.)
WARNING
Personal injury or damage to equipment could occur if improper stud and nut materials or parts are used. Do not operate or assemble this product with stud(s) and nut(s) that are not approved by Emerson/Fisher engineering and/or listed on the serial card provided with this product. Use of unapproved materials and parts could lead to stresses exceeding the design or code limits intended for this particular service. Install studs with the material grade and manufacturer's identification mark visible. Contact your Emerson sales office representative immediately if a discrepancy between actual parts and approved parts is suspected.
Make sure the nuts material matches the valve specification and set the nut surface with material specification
multistage cross pattern. Monitor the distance between the bonnet and body and keep it even to ensure that the bonnet is being torqued evenly. Use no more than 1/4 of the specified torque as indicated in table 2
.
Repeat the crisscross pattern, work up to the specified torque in 1/4 increments until the final torque is achieved. Wait a minimum of 2 minutes to allow for gasket/screw relaxation and recheck the torque, retightening as necessary. After final torquing, ensure there is an even gap and that the metal-to-metal contact between the valve body (or bonnet spacer) and bonnet is achieved around the entire circumference of the body-bonnet joint.
Table 2. Body-to-Bonnet Torque Guidelines
VALVE SIZE,
NPS
2
3
4
N m
91
122
163
SA193-B7 Studs
Lbf‐in
67
90
120
BOLT TORQUES
N m
S20910 (Nitronic 50) Studs
Lbf‐in
60
85
44
63
118 87
System for Sliding-Stem Valves Instruction Manual ( D101642X012 ) for packing arrangement and installation, complete step 11, then move to step 14. Place a smooth-edged pipe over the valve stem and gently tap each soft packing part into the packing box.
For all other packing, except Enviro-Seal packing, move to step 12.
12. Slide the packing follower, upper wiper (not applicable for graphite leak-off packing), and packing flange (keys
13. For graphite leak-off packing , tighten the packing flange nuts to the maximum recommended torque shown in table 3. Then, loosen the packing flange nuts, and retighten them to the recommended minimum torque shown in table 3.
For other packing types , tighten the packing flange of the nuts alternatively in small increments until one of the nuts reaches the minimum recommended torque shown in table 3. Then, tighten the remaining flange nut until the packing flange is level and at a 90-degree angle to the valve stem.
7
CCV-N Valve
October 2018
Instruction Manual
D104191X012
Table 3. Recommended Torque for Packing Flange Nuts
STEM SIZE
Packing Rating
PTFE Packing mm
12.7
inch
1/2
Graphite Leak-off
Packing
12.7
1/2
CL300
CL300
CL600
MINIMUM TORQUE
N m Lbf‐in
3
7
9
30
59
81
MAXIMUM TORQUE
N m Lbf‐in
5
10
14
42
88
122
14. Mount the actuator on the valve assembly and reconnect the actuator and valve stem according to the procedure in the appropriate actuator instruction manual.
Trim Maintenance
Non-Bore Seal Trim Constructions
WARNING
Refer to the WARNING at the beginning of the Maintenance section in this instruction manual.
CAUTION
Follow instructions carefully to avoid damaging the product surfaces, which could result in damage to the product. Protect all surfaces of the valve plug, valve seat ring, and seat ring retainer during maintenance to ensure control valve accuracy and choking performance is not affected.
Disassembly
1. Remove the actuator and the bonnet according to steps 1 through 6 of the Replacing Packing procedure in the
Maintenance section.
WARNING
To avoid personal injury due to leaking fluid, avoid damaging gasket sealing surfaces. The surface finish of the valve stem
reveals otherwise, assume all these parts are in good condition and protect them accordingly.
2. Remove the packing flange nuts, packing flange, upper wiper (not applicable for graphite leak-off packing), and
packing parts from the valve side of the bonnet using a rounded rod or other tool that will not scratch the packing box wall. Clean the packing box and the metal packing parts.
3. Inspect the valve stem threads and packing box surfaces for any sharp edges which might cut the packing.
Scratches or burrs could cause packing box leakage or damage to the new packing. If the surface condition cannot be improved by light sanding, replace the damaged parts.
8
Instruction Manual
D104191X012
CCV-N Valve
October 2018
(key 10, 12, figures 6, 7, 8, 12, and 13).
assembly through the bottom of seat ring retainer.
8. For all constructions, inspect parts for wear or damage which would prevent proper operation of the valve. Replace or repair trim parts according to the following procedure for plug maintenance procedure.
NPS 4 Balanced Bore-Seal Trim Maintenance
WARNING
Refer to the WARNING at the beginning of the Maintenance section in this instruction manual.
1. Remove the actuator and the bonnet according to steps 1 through 6 of the Replacing Packing procedure in the
Maintenance section.
WARNING
To avoid personal injury due to leaking fluid, avoid damaging gasket sealing surfaces. The surface finish of the valve stem
and protect them accordingly.
Carefully push out all the remaining packing parts from the valve side of the bonnet using a rounded rod or other tool that will not scratch the packing box wall. Clean the packing box and the metal packing parts.
3. Inspect the valve stem threads and packing box surfaces for any sharp edges which might cut the packing.
Scratches or burrs could cause packing box leakage or damage to the new packing. If the surface condition cannot be improved by light sanding, replace the damaged parts.
10 and 12, figure 14) without rotating the seat ring retainer (key 3, figure 14).
assembly contains sensitive guiding and sealing surfaces on its outside diameter and care must be taken in its handling.
by holding the valve stem and seat ring retainer. Using an appropriate tool such as a flat‐blade screwdriver, carefully pry out the piston rings from the grooves in the Bore Seal retainer.
8. By holding both valve stem and seat ring retainer, place the whole valve plug and stem assembly, seat ring retainer,
Bore-seal trim set on a soft surface such as clean cloth, which will not damage the trim. The valve plug and stem assembly, seat ring retainer and Bore-seal will remain as a whole trim set. Do not rotate the valve plug and stem assembly within seat ring retainer. Do not apply any axial force into valve stem which might damage the Bore-seal.
9
CCV-N Valve
October 2018
Instruction Manual
D104191X012
9. Remove the seat ring (key 9, figure 14) and seat ring gasket (key 13, figure 14).
10. Inspect parts for wear or damage which would prevent proper operation of the valve. Replace or repair trim parts according to the following procedure for NPS 4 Bore-seal plug maintenance procedure.
Valve Plug Maintenance (Except NPS 4 Balanced Bore-seal Plug)
figure 7 or 13, and NPS 4 key numbers are referenced in figure 8.
Note
Due to the design requirement of this product, the valve and stem are precision-matched and the stem is not replaceable. If damaged, the valve plug and stem must be replaced as an assembly. Contact your Emerson sales office for parts replacement.
CAUTION
To avoid the valve plug seal ring (key 24) not sealing properly, be careful not to scratch the surfaces of the ring groove in the valve plug or any of the surfaces of the replacement ring.
Do not remove the valve stem from the plug/retainer assembly unless you are planning to replace the valve stem. Never reuse an old valve stem with a new plug or reinstall a valve stem after it has been removed. Replacing a valve stem requires drilling a new pin hole in the stem. This drilling weakens the stem and damage may result in service.
1. With the valve plug (key 2) removed according to the Disassembly portion of the Trim Maintenance procedure, proceed as appropriate:
2. NPS 2 design for application up to and including 316 _ C (600 _
: Mark the orientation between valve plug
(key 2) and seal retainer (key 4). Punch out the pin (key 8) that connects the valve plug (key 2), stem (key 7) and seal retainer (key 4). Remove the seal retainer (key 4) with a spanner wrench or strap wrench while counter-holding the valve plug (key 2) with a second strap wrench, or other suitable tool, to prevent rotation of the valve plug on the valve stem (key 7). Slide the upper anti-extrusion ring, seal ring, bi-directional back up ring, seal ring, and anti-extrusion ring (key 63, 24, and 33) off the plug.
Inspect all parts for defects and cleanliness and replace the damaged parts. The removed seal set soft parts should not be reused. To install the new seal parts, slide the lower anti-extrusion ring, seal ring, bi-directional back up ring,
lubricant (key 45) to the thread of the seal retainer and flat mating surfaces between the seal retainer and plug (key
2 and 4). Then, install the seal retainer (key 4) into the plug (key 2) and tighten it with a spanner wrench or strap wrench until the pin holes and previous mark are aligned. Once the holes are aligned, secure the seal retainer (key
4) to the plug stem assembly with a new pin (key 8). Make sure the pin is inserted completely into the assembly with
0.025” depth from the radial surface.
CAUTION
To avoid damaging the seal ring, slowly and gently stretch it for the following procedure. Avoid jerking sharply on the ring.
NPS 3 design for application up to and including 316 _ C (600 _ F) (figure
Remove the retainer ring (key 26) off the groove, and slide the back up ring, upper anti-extrusion ring, seal ring, bidirectional back up ring, seal ring, and anti-extrusion ring (key 63, 24, 25, and 33) off the plug.
Inspect all parts for defects and cleanliness and replace the damaged parts. The removed seal set soft parts should not be reused. To install the new seal parts, slide the lower anti-extrusion ring, seal ring, bi-directional back up ring,
10
Instruction Manual
D104191X012
CCV-N Valve
October 2018
view B. Then install the retaining ring (key 26) by inserting one end in the groove and pressing the ring into the groove while turning the plug. Again, be careful not to scratch any surfaces of the ring or plug.
NPS 4 design for application up to and including 316 _ C (600 _
Using a punch, drive the pin (key 5)
spanner wrench to unthread the seal retainer (key 4) from the plug (key 2) using the pin holes on the top surface of
ring, bi-directional back up ring, seal ring, and anti-extrusion ring (key 63, 24, and 33) off the plug.
Inspect all parts for defects and cleanliness and replace the damaged parts. The removed seal set soft parts should not be reused. To install the new seal parts, slide the lower anti-extrusion ring, seal ring, bi-directional back up ring,
anti-seize lubricant (key 45) to the seal retainer threads and flat mating surfaces between the seal retainer and plug
(key 2 and 4). Install the seal retainer into the plug (key 2 and 4) and tighten it with a spanner wrench until the pin holes are aligned. Retain the seal retainer (key 4) to the plug (key 2) by pinning a new pin (key 5) into one of the remaining pin holes with 0.025” depth from the surface. Do not insert the pin into a pin hole that was previously
NPS 2 and 3 unbalanced design for application above 316 _ C (600°F)
(figure 12 and 13): No seal is required for the
unbalanced design. Inspect all parts for defects and cleanliness and replace the damaged parts.
NPS 4 Balanced Bore-seal Valve Plug Maintenance
Emerson sales office for Bore Seal trim replacement.
Note
Due to the design requirement of this product, the valve and stem are precision-matched and the stem is not replaceable. If damaged, the valve plug and stem must be replaced as an assembly. The set of valve plug and stem assembly, seat ring retainer and Bore-seal is designed as a whole assembly trim set, which might need special tool and fixture to remove and install. Contact your Emerson sales office for parts replacement.
CAUTION
To avoid leakage when the valve is returned to service, use appropriate methods and materials to protect all sealing surfaces of the trim parts during maintenance. Use caution when removing piston ring(s) and the Bore Seal plug seal to avoid scratching any sealing surface.
Do not remove the valve stem from the plug/retainer assembly unless you are planning to replace the valve stem. Never reuse an old valve stem with a new plug or reinstall a valve stem after it has been removed. Replacing a valve stem requires drilling a new pin hole in the stem. This drilling weakens the stem and may cause failure in service.
Follow instructions carefully to avoid damaging the product surfaces, which could result in damage to the product. Protect all surfaces of the valve plug, valve seat ring, and seat ring retainer during maintenance to ensure control valve accuracy and choking performance is not affected.
1. With the whole valve plug and stem assembly, seat ring retainer and Bore-seal set (key 2, 4, 7, 8, 17 ) removed from valve body (key 1), pull the valve stem (key 7) to the top end of seat ring retainer (key 3) as shown in figure 15.
Remove the two graphite piston rings (key18, figure 14). To remove plug retainer for maintenance purpose, locate the staked thread on top of the valve plug (key 2) between the valve plug and plug retainer. The staked thread secures the retainer. Use a drill with a 1/8 inch bit to drill out the staked area of the thread. Drill approximately 1/8
11
CCV-N Valve
October 2018
Instruction Manual
D104191X012 inch into the metal to remove the staking. The seat ring retainer and valve plug should be protected during processing.
2. Loosen the plug retainer (key 4) with strap wrench or spanner wrench and remove plug retainer from the valve plug
(key 2). Pull the plug retainer out of valve stem (key 7).
3. Remove the Bore-seal (key 17) without damaging the Bore-seal sealing surface and plug sealing surface.
4. Gently slide or push the plug and stem assembly (key 2, 7) into seat ring retainer (key 3) to move out from the seat ring retainer bottom end.
5. Inspect plug sealing surface. Replace valve plug and stem assembly, and seat ring retainer if wear or damage is found on the sealing, guiding and seat ring retainer window surfaces. Clean all parts if necessary to remove any buildup especially on the sealing, guiding and seat ring retainer window surfaces.
6. Gently slide the plug and stem assembly (key 7) back into seat ring retainer (key 3) from the seat ring retainer bottom end. Hold the seat ring retainer (key 3) and pull the valve stem (key 7) all the way up until there is metal to metal contact between valve plug and seat ring retainer. The two piston ring grooves on top of the plug retainer should stick out of the top of seat ring retainer. Coat new Bore-seal sealing surface and valve plug bore-seal groove sealing surface with high temperature grease. Place the new Bore-Seal plug seal over the top of the valve plug by hand. The Bore-seal opening should be oriented down into the valve plug as shown in view B on figure 14. Do not use uneven force to push the Bore-seal into the valve plug groove.
7. Coat thread of plug retainer (key 4) or valve plug (key 2) with anti-seize lubricant. Hand tighten the plug retainer into valve plug, which might push the Bore-seal into plug sealing groove. Use strap wrench to overcome extra thread friction to tighten plug retainer into valve plug until metal-to-metal contact between them. The Bore-seal will be pushed into the plug Bore-seal groove. To avoid leakage when the valve is returned to service, use appropriate methods and materials to protect all sealing surfaces of the trim parts during maintenance.
8. Pull the valve plug and stem assembly all the way to the top end of the seat ring retainer (key 3) and hold the valve plug and stem assembly so that the plug retainer (key 4) and bore seal are above the top of the seat ring retainer (as shown in Figure 15). Make sure the plug retainer is fully tightened onto the valve plug to ensure a metal-to-metal contact with the valve plug. Stake the thread between the valve plug and plug retainer in one place to deform the thread to secure the plug retainer to the valve plug.
9. The replacement piston rings will arrive in one piece. Use a vise with smooth or taped jaws to break this replacement piston rings into halves. Coat new piston ring surface and plug retainer grooves sealing surface with high temperature grease. Place piston rings into plug retainer therefore the openings of one piston ring would be
90° away from the other piston ring.
10. Gently slide the valve plug, plug retainer, stem, Bore-seal and piston rings assembly into seat ring retainer. Do not try to push the valve plug, plug retainer, stem, Bore-seal and piston rings assembly into seat ring retainer Bore-seal sealing surface, which might require extra actuator force. Do not rotate the valve stem end when the whole assembly is inside seat ring retainer. Set the whole trim set of valve plug, plug retainer, stem, seat ring retainer,
Bore-seal and piston rings on a soft surface such as clean cloth, without any movement.
Assembly
Except where indicated, key numbers are referenced in figure 6, 7, 8, 12, 13, and 14.
1. Inspect all parts for damage and cleanliness; remove any burrs on metal valve components.
2. Place a gasket (key 13) into the valve body (key 1) where the seat ring flange seats. Then, insert the seat ring
(key 9) into the valve body (key 1). The seat ring (key 9) end will protrude out from the valve body (key 1).
3. Assemble the plug stem assembly of each size into the valve body (key 1) as the following:
4. Inspect the sealing surface of the plug, stem, and seal assembly for nicks and scratches. Then, apply high temperature grease (key 46) sparingly around the spring-loaded seal ring (key 24) or piston rings. For unbalanced design, there is no seal in the valve plug (key 2). Apply high temperature grease (key 46) sparingly around the unbalanced plug guiding surface only.
No lubricant (key 46) should be applied on the balanced or unbalanced plug surfaces which would contact the flow fluid.
12
Instruction Manual
D104191X012
CCV-N Valve
October 2018
5. For NPS 2 and 3 balanced design , carefully insert the bottom end of plug stem seal assembly into the top of the seat
Slide the plug stem seal assembly into the seat ring retainer (key 3) until the top of the plug stem seal assembly is even with the top of the seat ring retainer (key 3). At this point, the plug (key 2) should have a snug fit with the seal ring retainer (key 3).
For NPS 2 and 3 unbalanced design , carefully insert the bottom end of plug stem assembly into the top of the seat ring retainer (key 3) through the inner bore. Make sure there is no damage done to the seals. Slide the plug stem assembly into the seat ring retainer (key 3) until the top of the plug stem seal assembly is even with the top of the seat ring retainer (key 3).
For NPS 4 balanced design , except Bore-seal trim , carefully insert the top end of the plug stem seal assembly into the bottom of the seat ring retainer (key 3) through the inner bore. Ensure no damage is done to the seals, as shown
assembly is even with the top of the seat ring retainer (key 3). At this point, the plug (key 2) should have a snug fit with the seat ring retainer (key 3).
For NPS 4 balanced design Bore-seal trim , the valve plug, stem, plug retainer, Bore-seal, piston rings assembly is in a whole trim set with seat ring retainer, which is ready for step 6. See the NPS 4 Balanced Bore-seal Valve Plug
Maintenance section.
6. Hold on to the end of the stem (key 7) and seat ring retainer (key 3) and slowly insert them into the valve body
retainer (key 3) may fall off. At the same time, ensure that the seat ring retainer (key 3) bottom diameter is guided properly to the seat ring (key 9) when installed into the valve body (key 1).
1), ensure one of the seat ring retainer legs centerline aligns with the valve body inlet centerline and the previous
surface against the seat ring (key 9). Note the plug stem assembly is symmetrical, so no orientation is necessary.
For NPS 4 balanced design Bore-seal trim , do not try to push the valve plug, plug retainer, stem, Bore-seal and piston rings assembly very hard into seat ring retainer Bore-seal sealing surface might require extra actuator force.
Wait until the valve stem is attached to actuator therefore the actuator could push the Bore-seal plug into Bore-seal sealing surface.
quantity1 flat sheet gasket (key 10) over the seat ring retainer (key 3). Make sure the bottom of the gasket is flush with the mating surface on the seat ring retainer shoulder.
9. Coat the bonnet studs (key 15) with anti-seize lubricant (key 45) up to the deformed thread. Thread the studs into the valve body (key 1) by hand until the deformed thread prevents further insertion.
(key 32) onto the flat sheet gasket (key 10) over the seat ring retainer (key 3). Then, slide another flat sheet gasket
(key 10) onto the bonnet spacer (key 32) over the seat ring retainer (key 3).
replacement procedure.
and connecting valve stem to actuator stem connector per actuator instruction manual. Make sure the actuator stem and the valve stem are aligned with each other before connecting.
13
CCV-N Valve
October 2018
Instruction Manual
D104191X012
CAUTION
Do not force the actuator to stroke the valve stem if actuator stem and valve stem are misaligned with each other, which might damage the valve trim and packing. Contact your Emerson sales office for further troubleshooting assistance.
14
Instruction Manual
D104191X012
CCV-N Valve
October 2018
Parts Ordering
Each body ‐ bonnet assembly is assigned a serial number which can be found on the valve body. This same number also appears on the actuator nameplate when the valve is shipped from the factory as part of a control valve assembly.
Refer to the serial number when contacting your Emerson sales office for technical assistance. When ordering replacement parts, refer to the serial number and to the eleven ‐ character part number for each part required from the following parts kit or parts list information.
CAUTION
Use only genuine Fisher replacement parts. Components that are not supplied by Emerson should not, under any circumstances, be used in any Fisher valve, because they may void your warranty, might adversely affect the performance of the valve, and could cause personal injury and property damage.
Parts Kits
Standard Packing Repair/Retrofit Kits
Table 4. Standard Packing Repair/Retrofit Kits
Stem Diameter mm (Inches)
Yoke Boss Diameter, mm (Inches)
Double PTFE (Contains keys 12, 6, 8, 11, and 218)
Graphite Leak-off Packing (Contains keys 7, 8, and 11)
Graphite Leak-off Packing
(Contains keys 4, 5, 7, 8, 11, and 13)
ENVIRO-SEAL Graphite ULF
(Contains keys 207, 208, 209, 210, 211, 214, and
217)
ENVIRO-SEAL Graphite ULF
(Contains keys 200, 201, 207, 208, 209, 210, 211,
212, 214, and 217)
12.7 (1/2)
71 (2-13/16)
RPACKX00662
RPACKX00722
RPACKXRTA22
RPACKXRTA32
RPACKXRTA42
Gasket Kits
Table 5. Gasket Kits
Valve Size, NPS
2
3
4
Application
<600 ° F
>600 ° F
<600 ° F
>600 ° F
<600 ° F
>600 ° F
Table 6. Gasket Descriptions
Key Number
10
12
13
Description
Bonnet Gasket
Spiral-Wound Gasket
Seat Ring Gasket
Key Numbers
10, 12, 13
10, 12, 13
10, 12, 13
10, 12, 13
10, 12, 13
10, 12, 13
Kits
RGASKETXF82
RGASKETXG82
RGASKETXF92
RGASKETXG92
RGASKETXG12
RGASKETXH02
Materials
Graphite/ S31600
N06600/ Graphite
Graphite/ S31600
15
CCV-N Valve
October 2018
Seal Ring Kits
Table 7. Seal Ring Kits
Valve Size
NPS 2
NPS 3
NPS 4
Port Size
1.50
1.00
1.60
2.25
2.25
3.10
3.10
Design
Balanced
Unbalanced
Unbalanced
Balanced
Unbalanced
Balanced, PTFE seal ring with anti-extrusion ring
Balanced, Bore-Seal
Application
≤ 600 ° F
>600 ° F
>600 ° F
≤ 600 ° F
>600 ° F
≤ 600 ° F
>600 ° F
Instruction Manual
D104191X012
Key Numbers
8, 63, 24, 33
Not Applicable
Not Applicable
26, 25, 63, 24, 33
Not Applicable
5, 63, 24, 33
17, 18
Kits
RSEALX00262
Not Applicable
Not Applicable
RSEALX00272
Not Applicable
RSEALX00282
RSEALX00292
16
Instruction Manual
D104191X012
Parts List
Note
Contact your Emerson sales office for Part Ordering information.
Bonnet Assembly
(figures 3, 4 and 5)
Key Description
6
7
4
5
8
1
3
11
12
13
14
15
34
Bonnet
Packing Flange
Packing Stud
Packing Nut
Packing Set
Packing Ring
Lantern Ring
Packing Box Ring
Upper Wiper
Packing Follower
Pipe Plug
Yoke Locknut
Lubricant, anti-seize
37 Warning tag
200 Packing Studs
201 Packing Flange
207 Guide Bushing
208 Guide Bushing
209 Packing Ring (qty 2 req'd)
210 Packing Ring (qty 2 req'd)
211 Packing Box Ring
214 Packing Washer
217 Spring Pack Assembly
218 Lower Wiper
See Parts Kits
See Parts Kits
See Parts Kits
See Parts Kits
See Parts Kits
12B5799X012
14B7498X012
See Parts Kits
Recommended Spare Trim Parts
All designs except NPS 4 Bore-Seal design: Seat Ring Retainer (key 3) and
Seat Ring (key 9)
NPS 4 Bore-Seal design: Seat Ring (key 9)
Recommended Spare Trim Parts Assembly
Balanced Plug/Stem/Seal Assembly for Applications Up to and Including
316°C (600°F)
NPS 2: Includes key 2, 4, 7, 8, 24 (qty 2), 63 (qty 2), and 33
NPS 3: Includes key 2, 7, 8, 24 (qty 2), 63 (qty 2), 33, 25, and 26
NPS 4: Includes key 2, 4, 5, 7, 8, 24 (qty 2), 63 (qty 2), and 33
CCV-N Valve
October 2018
13
14
15
16
17
8
9
10
11
12
5
6
3
4
7
1
2
18
24
25
26
32
33
45
46
63
Valve Assembly
(figures 6, 7, 8, 12, 13, and 14)
Key Description
Valve Body
Plug
Seat Ring Retainer
Plug Retainer
Groove Pin, Nameplate
Flow Direction Arrow
Valve Stem
Groove pin
Seat Ring
Bonnet Gasket
Drive Screw
Spiral-wound Gasket
Seat Ring Gasket
Lead Seal and Wire
Bonnet Stud
Bonnet Nut
Bore-seal
Piston Ring
Spring Load Seal Ring
Backup Ring
Retaining Ring
Bonnet Spacer
Bi-directional Ring
Lubricant, anti-seize
High temperature grease
PEEK Anti-extrusion Ring
See Parts Kits
See Parts Kits
See Parts Kits
See Parts Kits
See Parts Kits
See Parts Kits
See Parts Kits
See Parts Kits
Recommended Spare Packing, Gasket and
Seal Ring Kits
See table 4, 5, and 7
Un-Balanced Plug/Stem Assembly for
Applications Above 316°C (600°F)
NPS 2: Includes key 2, 7, and 8
NPS 3: Includes key 2, 7, and 8
Balanced NPS 4 Bore-Seal Plug/Plug
Retainer/Stem Assembly, Seat Ring
Retainer and Seal set for Applications
Above 316°C (600°F)
NPS 4: Includes key 2, 3, 4, 7, 8, 17, and 18 (qty 2)
17
CCV-N Valve
October 2018
Figure 3. Bonnet and Single PTFE Packing Arrangements with Key Numbers
Instruction Manual
D104191X012
APPLY LUB/SEALANT
NOTE: KEY 14 PIPE PLUG IS NOT APPLICABLE FOR OPTIONAL NON-TAPPED BONNET.
18
Instruction Manual
D104191X012
Figure 4. Bonnet and Graphite Leak-Off Packing Arrangements with Key Numbers
CCV-N Valve
October 2018
APPLY LUB/SEALANT
NOTE: KEY 14 PIPE PLUG IS NOT APPLICABLE FOR OPTIONAL NON-TAPPED BONNET.
19
CCV-N Valve
October 2018
Figure 5. Bonnet and Enviro-Seal Graphite ULF Packing Arrangement with Key Numbers
Instruction Manual
D104191X012
APPLY LUB/SEALANT
NOTE: PARTS SHOULD BE IDENTIFIED BY PART NUMBER OR SHAPE AS SHOWN BEFORE INSTALLATION. KEY
210 SHOULD BE INSTLALED WITH ITS CONCAVE SURFACE FACING TO THE HIGH PRESSURE SIDE AS SHOWN.
KEY 14 PIPE PLUG IS NOT APPLICABLE FOR OPTIONAL NON-TAPPED BONNET.
20
LOW PRESSURE SIDE
HIGH PRESSURE SIDE
Instruction Manual
D104191X012
Figure 6. NPS 2 Balanced CCV-N Valve Assembly with Key Numbers for Application
Up to and Including 316 _ C (600 _ F)
CCV-N Valve
October 2018
VIEW B
VIEW A
VIEW A
APPLY LUB/SEALANT
VIEW B
21
CCV-N Valve
October 2018
Figure 7. NPS 3 Balanced CCV-N Valve Assembly with Key Numbers for Applications
Up to and Including 316 _ C (600 _ F)
Instruction Manual
D104191X012
VIEW B
VIEW A
VIEW A
22
APPLY LUB/SEALANT
VIEW B
Instruction Manual
D104191X012
Figure 8. NPS 4 Balanced CCV-N Valve Assembly with Key Numbers for Applications
Up to and Including 316 _ C (600 _ F)
VIEW B
CCV-N Valve
October 2018
VIEW A
VIEW A
APPLY LUB/SEALANT
VIEW B
23
CCV-N Valve
October 2018
Figure 9. Non-Bore-Seal NPS 4 CCV-N Maintenance for Application
Up to and Including 316 _ C (600 _ F)
USED
PIN HOLE
NEW PIN
IN NEW
PIN HOLE
Instruction Manual
D104191X012
Figure 10. CCV-N NPS 2 and 3 Assembly —
Insert of Plug Stem Seal Assembly through the Top of the Seat Ring Retainer
PLUG STEM
SEAL ASSEMBLY
SEAT RING
RETAINER
24
Instruction Manual
D104191X012
CCV-N Valve
October 2018
Figure 11. CCV-N NPS 4 Assembly for Application Up to and Including 316 _ C (600 _ F) (Except Bore-Seal Trim) —
Insert of Plug Stem Seal Assembly through the Bottom of the Seat Ring Retainer
SEAT RING
RETAINER
PLUG STEM
SEAL ASSEMBLY
25
CCV-N Valve
October 2018
Instruction Manual
D104191X012
Figure 12. NPS 2 Unbalanced CCV-N Valve Assembly with Key Numbers for Applications Above 316 _ C (600 _ F)
VIEW A
VIEW A
26
APPLY LUB/SEALANT
Instruction Manual
D104191X012
CCV-N Valve
October 2018
Figure 13. NPS 3 Unbalanced CCV-N Valve Assembly with Key Numbers for Applications Above 316 _ C (600 _ F)
VIEW A
VIEW A
APPLY LUB/SEALANT
27
CCV-N Valve
October 2018
Figure 14. NPS 4 Balanced Bore-Seal Design CCV-N Valve Assembly with Key Numbers for Applications Above 316 _ C (600 _ F)
Instruction Manual
D104191X012
VIEW B
VIEW A
VIEW A
VIEW B
28
APPLY LUB/SEALANT
Instruction Manual
D104191X012
Figure 15. NPS 4 Balanced Bore-Seal CCV-N Trim Maintenance —
Pull the Valve Plug and Stem Assembly to the Top of the Seat Ring Retainer
VALVE STEM
PLUG
STAKED THREAD BETWEEN
PLUG AND PLUG RETAINER
PLUG RETAINER
BORE-SEAL
SEAT RING RETAINER
CCV-N Valve
October 2018
PLUG
29
CCV-N Valve
October 2018
Instruction Manual
D104191X012
30
Instruction Manual
D104191X012
CCV-N Valve
October 2018
31
CCV-N Valve
October 2018
Instruction Manual
D104191X012
Neither Emerson, Emerson Automation Solutions, nor any of their affiliated entities assumes responsibility for the selection, use or maintenance of any product. Responsibility for proper selection, use, and maintenance of any product remains solely with the purchaser and end user.
Fisher is a mark owned by one of the companies in the Emerson Automation Solutions business unit of Emerson Electric Co. Emerson Automation Solutions,
Emerson, and the Emerson logo are trademarks and service marks of Emerson Electric Co. All other marks are the property of their respective owners.
The contents of this publication are presented for informational purposes only, and while every effort has been made to ensure their accuracy, they are not to be construed as warranties or guarantees, express or implied, regarding the products or services described herein or their use or applicability. All sales are governed by our terms and conditions, which are available upon request. We reserve the right to modify or improve the designs or specifications of such products at any time without notice.
Emerson Automation Solutions
Marshalltown, Iowa 50158 USA
Sorocaba, 18087 Brazil
Cernay, 68700 France
Dubai, United Arab Emirates
Singapore 128461 Singapore www.Fisher.com
advertisement
Related manuals
advertisement