- Computers & electronics
- Print & Scan
- Eurotherm
- 4181/4250 Chart Recorders Serial Comms
- Owner's manual
advertisement
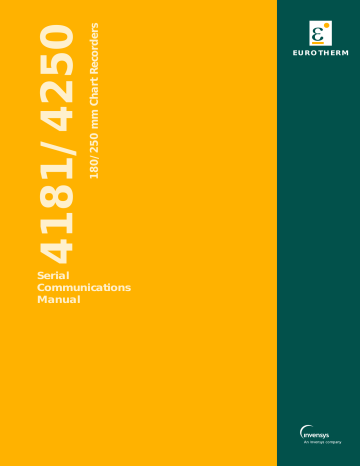
Serial
Communications
Manual
ε
E U R O T H E R M
COMMUNICATIONS MANUAL
Communications Manual
List of contents
Section Page
1 INTRODUCTION ......................................................... 3
2 INSTALLATION ........................................................... 4
2.1 INSTALLATION OF ORIGINAL VERSION
(OLDER 250mm RECORDERS ONLY) ......... 4
2.1.1 Mode selection ...................................................................... 5
2.2 ISOLATED VERSION INSTALLATION ..................................... 6
2.2.1 Installation for 250 mm recorders ............................................. 6
MULTIPOINT RECORDERS ................................................. 6
CONTINUOUS TRACE RECORDERS .................................. 6
2.2.2 Installation for 180 mm recorders ............................................ 7
2.2.3 Mode selection ...................................................................... 9
2.3 COMMUNICATIONS WIRING ............................................ 9
2.3.1 Original version .................................................................... 9
2.3.2 Isolated version ..................................................................... 9
2.3.3 Termination and biasing (not RS232) ....................................... 11
HOST COMPUTER ........................................................... 11
2.3.4 On-board links ...................................................................... 13
2.4 HARDWARE CONFIGURATION ........................................... 14
2.4.1 Communications parameters ................................................... 14
2.4.2 Handshake ........................................................................... 14
HARDWARE HANDSHAKE ............................................... 14
SOFTWARE HANDSHAKE ................................................ 14
3 MODEL 4001 COMMUNICATIONS ....................................... 15
3.1 COMMUNICATIONS PROTOCOLS ............................. 15
3.1.1 ANS I ................................................................................. 15
POLLING ......................................................................... 15
SELECTION ..................................................................... 16
3.1.2 ASCII .................................................................................. 16
3.2 PARAMETER ADDRESSING ................................................. 17
3.3 DATA FORMATS ................................................................. 17
3.3.1 Hexadecimal (Hex) ................................................................ 17
3.3.2 Decimal (Floating point) ......................................................... 17
3.3.3 Character ............................................................................. 17
Continued
© 2002 Eurotherm Limited
All rights are strictly reserved. No part of this document may be reproduced, modified, or transmitted in any form by any means, nor may it be stored in a retrieval system other than for the purpose to act as an aid in operating the equipment to which the document relates, without the prior written permission of
Eurotherm limited.
Eurotherm Limited pursues a policy of continuous development and product improvement. The specifications in this document may therefore be changed without notice. The information in this document is given in good faith, but is intended for guidance only. Eurotherm Limited will accept no responsibility for any losses arising from errors in this document.
HA246958
Issue 14 Mar 02 Page 1
Page 2
COMMUNICATIONS MANUAL
List of contents (Cont.)
Section Page
3.4 MNEMONICS ................................................................... 18
3.4.1 Channel mnemonics ............................................................... 19
INPUT CHANNELS ........................................................... 20
OUTPUT CHANNELS ........................................................ 22
DERIVED CHANNELS ....................................................... 24
3.4.2 Alarm mnemonics .................................................................. 25
ALARM BUFFER VALIDATION CHECKS. .............................. 25
3.4.3 Instrument mnemonics ............................................................ 27
3.5 COMMAND MNEMONICS ................................................ 31
3.5.1 Alarm acknowledge (AA) ....................................................... 31
3.5.2 Printer on (CG) ...................................................................... 31
3.5.3 Chart halt (CH) ...................................................................... 31
3.5.4 Printer off (CO) ...................................................................... 31
3.5.5 Chart Wind (CW) ................................................................. 31
3.5.6 Data Dump (DD) .................................................................... 31
3.5.7 Disable program mode (DP) .................................................... 31
3.5.8 Enter alarm data (EA) ............................................................. 31
3.5.9 Enter channel data (EC) .......................................................... 31
3.5.10 Enable program mode (EP) ................................................... 31
3.5.11 Get indicated alarm data (GA) .............................................. 32
NO MATHS PACK FITTED ................................................. 32
MATHS PACK FITTED ........................................................ 32
3.5.12 Get free alarm (GF) ............................................................. 32
3.5.13 Chart rewind (CR) ............................................................... 32
3.6 PARAMETER SCROLLING .................................................... 33
3.6.1 Block parameters ................................................................... 33
3.6.2 Scroll parameters .................................................................. 33
ALARM PARAMETERS ....................................................... 33
INSTRUMENT PARAMETERS .............................................. 33
3.7 CHARACTER SET ............................................................... 34
3.8 APPLICATION NOTES ........................................................ 40
3.8.1 Message timing ..................................................................... 40
3.8.2 Command mnemonics ............................................................ 40
3.8.3 Channel selection .................................................................. 40
3.8.4 Alarm selection / polling ........................................................ 40
SELECTION ..................................................................... 40
3.8.5 Printed text ........................................................................... 40
3.8.6 Special characters ................................................................. 41
ASCII MODE ................................................................... 41
ANSI MODE ................................................................... 41
3.8.7 Multi-parameter data packets .................................................. 41
3.8.8 Digital input channels ............................................................. 41
3.8.9 Floating point overflow ........................................................... 41
4 GOULD MODICON MODBUS PROTOCOL ..................... 42
4.1 CHANNEL ADDRESSING.................................................... 42
4.2 READING ANALOGUE VALUES ........................................... 42
4.2.1 16-bit format ......................................................................... 42
4.2.2 32-bit format ......................................................................... 43
EXAMPLE 1 READ CHANNEL 05 ....................................... 43
TOTALISER VALUES........................................................... 43
4.3 FUNCTION CODES ........................................................... 44
5 XMODEM TRANSFER .................................................. 46
6 LIST OF EFFECTIVE PAGES ........................................... 47
INDEX ........................................................................... 48
HA246958
Issue 14 Mar 02
COMMUNICATIONS MANUAL
COMMUNICATIONS
1 INTRODUCTION
This manual is intended as an aid to those involved in the installation and operation of a serial communications link between one or more chart recorders (or I/O racks) and a host computer.
Section 2 describes the physical installation of a communications option and its hardware set-up and wiring.
Section 3 describes host communications protocol emulation of the 4001 communications protocol allowing customers with model 4001 recorders to transfer their communications programs to more modern recorders without difficulty.
Section 4 deals with the Gould Modicon Modbus RTU protocol.
Section 5 gives a procedure for XMODEM file transfers, for saving and restoring recorder configurations.
HA246958
Issue 14 Mar 02 Page 3
COMMUNICATIONS MANUAL
2 INSTALLATION
The communications option is in two versions. The original version has a 25-way D-type connector, whilst the newer
(isolated) version has two 9-way D-type connectors - one plug; one socket. Before installation is carried out, it is recommended that the links on the circuit board be checked against figure 2.3.4 to ensure correct positioning.
2.1 INSTALLATION OF ORIGINAL VERSION (OLDER 250MM RECORDERS ONLY)
This section describes the installation of the communication option in the box located at the rear of the recorder. For those recorders already fitted with the option, this section may be ignored.
CAUTION
THE CIRCUIT BOARD INCLUDED AS A PART OF THE KIT CONTAINS COMPONENTS WHICH
ARE SENSITIVE TO STATIC ELECTRICAL DISCHARGE. ALL RELEVANT PERSONNEL SHOULD
BE AWARE OF STATIC HANDLING PROCEDURES. IF IN DOUBT, CONSULT THE RELEVANT
SECTIONS OF EITHER THE INSTALLATION AND OPERATION MANUAL OR OF THE TECHNI-
CAL MANUAL.
The communications option kit consists of a circuit board, two screws and two labels. The installation procedure is as follows. Reference should be made to figures 2.1a and 2.1b as required.
a.
Remove the battery cover, retaining it and its securing screws for later re-assembly.
b.
Remove the communications box by removing the two securing nuts. Retain these nuts and their associated shakeproof washers for use in re-assembly.
c.
Knock out the three slots in the box.
d.
Fit the labels supplied e.
After taking precautions against static discharge, screw the circuit board to the box.
f.
Plug the assembled box into the connector at the rear of the recorder.
g.
Fix the box to the recorder using the nuts and shake-proof washers previously removed.
h.
Refit the battery cover.
i.
Select RS232 or RS422/485 (section 2.1.1 below), then carry out an autoconfigure as described in the installation and operation manual supplied with the recorder.
Page 4
Figure 2.1a Battery cover and communications box location
HA246958
Issue 14 Mar 02
COMMUNICATIONS MANUAL
2.1 INSTALLATION OF ORIGINAL VERSION (Cont.)
3
Fit board to box
4
Plug box into recorder
1
Knock out holes
2
Fit labels
2.1.1 Mode selection
Set all elements left for
RS42/RS485, or right for RS232C
Tx
Rx
RTS
CTS
DTR
DSR
Figure 2.1b Communications option assembly
The communications can be set to RS232 or RS422/RS485 by sliding all the elements of the DIL switch to the right (RS232) or to the left (RS422/485).
In RS232 mode, the LEDs show their stated functions. The LEDs are off when the relevant lines are idle, and are illuminated when they are active.
In RS422/485 mode, only the transmit (Tx) and receive (Rx) LEDs are operative. These LEDs are off when the lines are at idle, and are illuminated when they are active.
The pin allocations for RS422/485 and RS232 are shown in section 2.3.1 below.
Note: Four wire (TXA/B, RXA/B) RS485 is supported; two wire RS485 is not supported.
25-Way D-type socket
Comms status
LEDs
Figure 2.1.1
Communications set-up switches
HA246958
Issue 14 Mar 02 Page 5
COMMUNICATIONS MANUAL
2.2 ISOLATED VERSION INSTALLATION
2.2.1 Installation for 250 mm recorders
MULTIPOINT RECORDERS
With the recorder isolated from hazardous voltages, remove the battery cover and dummy comms box (if fitted) as described in section 2.1 instructions 'a' and 'b'. Fit the comms module supplied with the kit, ensuring that the connector is correctly mated before tightening the fixings and replacing the battery cover.
Re-apply power to the recorder, switch on and carry out an Autoconfigure, as described in the installation and operation manual supplied with the recorder.
CONTINUOUS TRACE RECORDERS
With the recorder isolated from hazardous voltages, take the ribbon cable supplied with the kit, and plug it into the header on the comms module circuit board.
Pass the ribbon cable through the slot in the rear of the recorder, then secure the comms module to the recorder using two nuts.
Open the recorder door and release the writing system by undoing the two captive screws (fig 2.2.1a)
Pull the writing system forwards until access can be gained to the control board mounted at the rear.
Plug the free end of the ribbon cable into CON 3 on the control board (figure 2.2.1b).
Return the writing system to the case and secure it, using the two captive screws.
CON3
(Communications)
Figure 2.2.1a Writing system securing screws
Set the comms module to RS232 or RS422/
485 as described in section 2.2.3.
Re-apply power to the recorder, switch on and carry out an Autoconfigure, as described in the installation and operation manual supplied with the recorder.
Page 6
Figure 2.2.1b Communications connector location
HA246958
Issue 11 Dec 97
COMMUNICATIONS MANUAL
2.2.2 Installation for 180 mm recorders
CAUTION
THIS UPGRADE INVOLVES THE HANDLING OF COMPONENTS WHICH ARE SENSITIVE TO
STATIC ELECTRICAL DISCHARGE. ALL RELEVANT PERSONNEL MUST BE AWARE OF STATIC
HANDLING PROCEDURES. IF IN DOUBT, REFERENCE SHOULD BE MADE TO THE INSTAL-
LATION AND OPERATION MANUAL OR THE TECHNICAL MANUAL.
1.
Isolate the recorder from all high voltage sources (both supply and signal)
2.
Open the recorder door (by lifting the bottom of the catch, and then turning it clockwise) For convenience, remove the chart and print cartridge.
3.
With the cassette open, Release the writing system by undoing the captive screws (‘A’ in figure 2.2.2a)
4.
Pull the writing system forwards until it reaches its stops.
5.
Lift the writing system out of the case, releasing the various connectors as they become accessible (figure 2.2.2b).
6.
Release the Power supply unit from the front, using screws ‘B’ in figure 2.2.2b, then from the back, by removing the safety earth
(nut ‘C’ in figure 2.2.2c) and securing screw ‘D’.
A
Figure 2.2.2a
Writing system securing screws
A
B
B
B
Figure 2.2.2b Writing system removal and PSU securing screw locations
7.
Disconnect the battery pack as shown in figure 2.2.2d
8.
Rotate and lift out the power supply as shown in figure 2.2.2e, carefully avoiding damage to the battery pack connector.
C
D
Figure 2.2.2c
PSU release (rear view)
Figure 2.2.2d Battery pack disconnection
HA246958
Issue 11 Dec 97
Figure 2.2.2e PSU removal
Page 7
COMMUNICATIONS MANUAL
2.2.2 INSTALLATION FOR 180mm RECORDERS (Cont.)
9.
Fit the plastic cable clip as shown in figure 2.2.2f.
10. At the rear of the recorder, remove the blanking plate, and fit the communications module (figure 2.2.2g).
11. Feed the communications module ribbon cable across the inside back of the recorder, secure it with the clip, then fold the cable back on itself and make a right angle turn upwards (figure 2.2.2f).
12. Re-fit the power supply unit, and ensuring that the battery pack connector is passed through its aperture, secure it at the front and at the back, using the four screws and safety earth nut previously removed. ENSURE THAT
THE SAFETY EARTH IS SECURELY TERMINATED.
13. Return the writing system to the case, ensuring all the connectors are re-made.
14. Re-apply power to the recorder, and carryout an Autoconfigure as described in the Installation and Operation manual suppled with the recorder.
To comms module
To control board
Cable cl ip
65 mm View on inside of case; bottom left-hand corner
Figure 2.2.2f Cable clip location Figure 2.2.2g Comms module fitting
Page 8
Figure 2.2.2h Routing cables and returning the PSU Figure 2.2.2i Communications connector location
HA246958
Issue 11 Dec 97
COMMUNICATIONS MANUAL
2.2.3 Mode selection
Once physical installation is complete, the communications mode should be set up as RS232 (Single drop) or RS422/
RS485 (Multiple drop) before electrical connections are made.
The selection of communications mode is made by setting ALL of the switches located between the two 9-way D-types up for RS232 or down for RS422/485*, as shown on the communications module label.
* The module is mounted ‘sideways’ on Graphics Display Units. The switches should be set left for RS232 or right for
RS422/485.
Set all switches up for RS232.
Set all switches down for RS422/485.
9-way socket
9-way plug
Figure 2.2.3 Set-up switch locations (isolated version)
2.3 COMMUNICATIONS WIRING
2.3.1 Original version
The serial link is implemented using a 25-way D-type (fixed socket) connector. Table 2.3 gives pin-out information for
RS232C and for RS422/485. Recorder Tx should be connected to the host Rx and vice-versa.
2.3.2 Isolated version
Tx should be connected to Rx at the host and vice-versa.
The serial link is implemented using two 9-way D-type connectors. For non-graphics instruments set to RS422/485, the two connectors are wired in parallel for easy ‘daisy-chaining’ in multi-drop applications. For non-graphics instruments set to RS232, and for all data acquisition racks, only the ‘male’ connector (plug) is to be used.
See the graphics unit manual for graphics recorders/display units details.
Note: The signal ground MUST be earthed at one point (only) in the link.
HA246958
Issue 11 Dec 97 Page 9
COMMUNICATIONS MANUAL
2.3 COMMUNICATIONS WIRING (Cont.)
Isolated Comms
(2 x 9-way D-types)
Pin Function
4
5
6
1
2
3
7
8
9
RX
TX
1k0
DTR
Signal ground
DSR
RTS
CTS
5V
Not connected
RS232 Pin out
(Switches up)
(Fixed plug only)
Pin Function
4
5
6
1
2
3
7
8
9
TXA
1k0
TXB
5V
Not connected
Signal ground
Not connected
RXB
RXA
Not connected
RS422/485 Pin out
(Switches down)
(Plug or socket)
Comms pinouts for current recorders and I/O (data acquisition) racks.
(I/O racks may use only the fixed male connector (plug) for the serial link)
Page 10
RS232 Terminations RS422/485 Terminations
5v* Rx Tx DTR 0V DSR RTS CTS
RS232 available with upper connector only (all switches left)
5v* TxA TxB NC 0V NC RxB RxA
Lower connector always RS422/485.
Upper connector selectable RS232
(all switches left) or RS424/485
(all switches right)
Comms pinouts for Graphics Display Units
Pin Function
6
7
19
20
1
2
3
4
5
Protective ground
TX
RX
RTS
CTS
DSR
Signal ground
5V
DTR
1k0
RS232 Pin out
(Switches right)
Non-Isolated Comms
(25-way D-type)
Pin Function
6
7
19
20
1
2
3
4
5
Protective ground
TXB
TXA
RXB
RXA
Not connected
Signal ground
5V
1k0
Not connected
RS422/485 Pin out
(Switches left)
Comms pinouts for previous recorder versions
Table 2.3 Communications module pinouts
HA246958
Issue 11 Dec 97
COMMUNICATIONS MANUAL
2.3.3 Termination and biasing (not RS232)
If the communications line is left open-ended, the end of the cable acts as a reflector, returning what can appear to be
‘true’ data signals back down the line. A receiver cannot distinguish between ‘true’ and reflected data, with the result that the ‘true’ data is corrupted.
In order to avoid this, a termination resistor is fitted across the line at the final instrument. If the value of this resistor is equal to the characteristic impedance of the cable (120 Ohms in this case), then the line appears to be of infinite length and no reflections occur. Such a value however, does not give the best signal-to-noise ratio, so a compromise value (220 Ohms) is chosen to give the optimum performance in reducing unwanted reflections and in improving the signal-to-noise ratio.
The recorder communications port is terminated as shown in figure 2.3.3a, below. In a single point-to-point application, it may be necessary to terminate the instrument with a 220
Ω
resistor. In multi-drop systems, only the final unit should be terminated in this way, otherwise the transmitted signal levels may be reduced to an unacceptable level.
TxB
Transmit lines from host
TxA
RxA
100k
Ω
RxB
5 Volts
100k
Ω
RxB
220
Ω
RxA
5 Volts
100k
Ω
Receiver device
100k
Ω
0 Volts
Recorder B (Final recorder)
0 Volts
Receiver device
Recorder A
Figure 2.3.3a System termination and biasing
HOST COMPUTER
When not communicating, the instrument outputs go to a high-impedance state to allow multi-drop connection. This will cause a problem if the host computer is not fitted with biasing resistors to pull these essentially open circuit lines to their idle states as defined for the RS422/RS485 standards. To overcome such problems, external biasing resistors can be fitted as shown in figure 2.3.3b (a) below.
With long cable runs it may also be necessary to terminate the transmission line. Figure 2.3.3b (b) shows how this may be done using external biasing resistors. Such a circuit is for use where the host receiver does not have its own internal biasing arrangements. Where the host does have its own internal biasing, the fitting of a 220
Ω
resistor across the receive inputs (figure 2.3.3b (c)) will terminate the line correctly.
HA246958
Issue 14 Mar 02 Page 11
COMMUNICATIONS MANUAL
2.3.3 TERMINATION AND BIASSING (Cont.)
Host receiver device
5 Volts
4k7
TxB
Transmit lines from recorder*
TxA
4k7
Host receiver device
5 Volts
470R
TxB
Transmit lines from recorder*
TxA
470R
0 Volts a. Host with external bias resist ors
0 Volts b. Host with external bias resistors providing termination.
5 Volts
4k7 min.
* For 'recorder' read 'Graphics unit',
'Data acquisition unit' etc. as appropriate
Host receiver device
TxB
220R
Transmit lines from recorder*
TxA 4k7 min.
0 Volts c. Host with internal bias resistors and ext ernal termination.
Figure 2.3.3b Host computer termination and biasing
Page 12
HA246958
Issue 14 Mar 02
COMMUNICATIONS MANUAL
2.3.4 On-board links
When retro-fitting or replacing a communications board, a number of links need to be correctly set. The positions of these links depends on the model as shown in the sketches below. The sketches show an issue 2 board. Issue 1 boards are similar, but do not have links at 'A'. This is important only for I/O rack users.
The communications link is set to RS232 by setting all the toggle switches up (as shown in the figures) or to RS422/
485 by setting all the switches down.
A A
180mm graphics recorder (U100)
250mm graphics recorder (U200)
180/250mm continuous trace recorder (U100)
180mm multipoint recorder (U100)
250mm Multipoint recorder (U200)
A A
HA246958
Issue 14 Mar 02
Graphics display unit (U200) I/O (Data acquisition) rack (U200)
Figure 2.3.4 Communications board link positions
Page 13
COMMUNICATIONS MANUAL
2.4 HARDWARE CONFIGURATION
Configuration : Select a category
MEMORY COMMS TRANSFER DIAGS MORE>
Top level configuration menu
Protocol 4001 ANSI Baud Rate BBBBB
Parity Even Seven data bits
One stop bits Hardware handshake off
Group address 0
Figure 2.4 Communications configuration
2.4.1 Communications parameters
Protocol
Baud Rate
Parity
Data Bits
4001 ANSI*
4001 ASCII*
MODBUS
110 to 19,200
Odd, even, none
7, 8
Stop bits 1, 2
H/W Handshake On/Off
Group Address
Address
0 to 7
1 to 247
Uses ASCII codes, including control codes (e.g. STX)
Uses ASCII codes, but control codes are replaced by printing characters
(See section 3.1.2 below).
RTU protocol. Fixed data bits = 8; No handshake.
Scrollable 19,200, 9,600, 4,800, 2,400 1,200, 600, 300, 110
Allows parity to be set.
Eight bits required for ‘special’ characters Hex 80 to E2 in table 3.7.
Allows the number of stop bits to be set.
Enables / Disables handshake.
Group address (G) used as a part of the 4001 channel address.
Gould Modicon address
* 4001 ASCII and 4001 ANSI protocols may not be applicable to all recorder models.
2.4.2 Handshake
Handshake is not applicable to MODBUS protocol.
HARDWARE HANDSHAKE
Hardware handshake operates with three signals CTS, RTS and DTR. DSR is ignored by the recorder.
When hardware handshake is ‘ON’, DTR and RTS outputs are set to their ‘ON’ condition (voltage +’ve) when the instrument is capable of communication. These signals will therefore be off during power up / initialisation etc. The
CTS input high to the instrument enables its transmitter.
When hardware handshake is set ‘OFF’ DTR and RTS are set to their OFF states (voltage -’ve). The CTS input is ignored.
SOFTWARE HANDSHAKE
XON/XOFF handshaking is implemented in ASCII mode only (section 3.1.2). On receipt of XOFF (ASCII hex 13) the recorder will stop transmitting at the end of the current character, and will not re-start transmission until it receives
XON (ASCII hex 11). All bytes received between XOFF and XON are ignored. Multiple XONs are ignored. The instrument does not generate XON or XOFF.
Page 14
HA246958
Issue 14 Mar 02
COMMUNICATIONS MANUAL
3 MODEL 4001 COMMUNICATIONS
Note: 4001 communications protocols may not be available on all Models.
3.1 COMMUNICATIONS PROTOCOLS
3.1.1 ANSI
This is an implementation of the ANSI standard ANSI - X3.28 - 2.5 - A4 and specifies two modes: POLLING (for reading values from an instrument), and SELECTING (for writing values to an instrument).
POLLING
The sequence of bytes sent to the instrument in order to read a value is:
<EOT>[G][G][U][U][CA][C1][C2]<ENQ>
Where:
G
U is the Group Address set up in the communications configuration.
is a ‘Logical Unit’ number, associated with up to eight channel addresses.
CA is a channel address within the logical unit.
C1C2 is the two character mnemonic which defines the parameter to be read.
See table 3.2 for U and CA allocations, and tables 3.4.1, 3.4.2 and 3.4.3 for a mnemonic / parameter cross reference.
In response to such a polling message, the instrument will reply with one of the following:
POLL COMPLETE MESSAGE
<STX>[CA][C1][C2][D1][D2.......DN]<ETX>[BCC]
Where D1 to DN is the N byte value of the polled parameter. The number of bytes required is a function of the particular parameter polled. BCC is a block check control character which is the result of exclusive ORing bytes [CA] to
<ETX> inclusive. After a POLL COMPLETE message, the host can respond with <NAK> (which causes re-transmission of the parameter previously polled), <ACK> (which polls the next parameter in the poll list (see section 3.6)), or with a complete new polling message.
POLL INCOMPLETE MESSAGE
<STX>[CA][C1][C2]<EOT>
This indicates that there was an error in the polling message. The host must send a complete new polling message in order to access the parameter (i.e. sending <ACK> or <NAK> does not have any effect).
NO RESPONSE
The polling message was not recognised.
HA246958
Issue 14 Mar 02 Page 15
COMMUNICATIONS MANUAL
3.1 COMMUNICATIONS PROTOCOL (Cont.)
SELECTION
The sequence of bytes sent to the instrument in order to write a value to a parameter is:
<EOT>[G][G][U][U]<STX>[CA][C1][C2][D1][D2.....DN]<ETX><BCC>
Where:
G
U
CA
C1C2 is the Group Address set up in the communications configuration.
is a ‘Logical Unit’ number, associated with up to eight channel addresses.
is a channel address within the logical unit.
is the two character mnemonic which defines the parameter to be read.
D1 to DN is the N-byte value to be written to the parameter.
BCC is a block check character calculated by exclusive ORing bytes CA to ETX inclusive.
See table 3.2 for U and CA allocations for current recorders and tables 3.4.1, 3.4.2 and 3.4.3 for a mnemonic / parameter cross reference.
In response to such a selection message, the instrument will reply with one of the following:
SELECTION COMPLETE MESSAGE
The instrument responds with a single <ACK>. The host may now re-enter the selection procedure after <STX> and write a new [CA] to <BCC> message, providing that the new parameter is in the same logical unit as the last one (i.e.
[G] and [U] are the same). Alternatively, the host can send a complete new selection message.
SELECTION INCOMPLETE MESSAGE
The instrument responds with a single <NAK>, indicating that there was an error in the selection message. The host must send a complete new selection message (i.e. it may not re-enter after STX)
NO RESPONSE
The selection message was not recognised.
3.1.2 ASCII
This mode is intended for use with simple micros, or ‘dumb’ terminals, which are unable to transmit ASCII control characters and / or having no hardware handshake. The non-printing control codes are replaced with ‘printing’ characters as shown in table 3.1.2 below. BCC is omitted, since it might easily be one of the control codes 22 to 26 or 28.
XON/XOFF handshaking is supported. In all other respects, the protocol is the same as the ANSI mode, described above.
Control character definition
Start of text
End of text
End of transmission
Enquiry
Acknowledge
Negative acknowledge
ANSI standard character
STX
ETX
EO T
ENQ
ACK
NAK
Hex code
4
5
2
3
6
15
Printing character
Hex code
"
#
$
%
&
(
22
23
24
25
26
28
Table 3.1.2 Printing and non-printing codes
Page 16
HA246958
Issue 14 Mar 02
COMMUNICATIONS MANUAL
3.2 PARAMETER ADDRESSING
The protocol uses a three element address: Group Address (G) (0 to 7), set up in the communications configuration to identify one of up to eight recorders on a multi-drop link; Logical Unit Address (U) and Channel Address (CA). The recorder can have up to 16 logical units (LUs) associated with it according to the model number. LU 0 is used to access instrument, alarm and control mnemonics. In such cases, the channel address is irrelevant, but a valid CA (0 to
F) must still be included in the polling/selecting messages.
As can be seen from table 3.2 below, logical units can have up to 16 associated channel addresses (CAs). For example, to access Measuring Channel 28, the logical unit address (U) would be 7, and CA would be 3. To access Derived Channel 28, the LU address would be ‘C’ and the CA would be 3.
LOGICAL UNIT ADDRESS (U)
1 2 3 4 5 6 7 8 9 A B C D E F
7 57 66 75 84 93 D8 D16 D24 D32 D72 D80 D88
8 58 67 76 85 94
9 59 68 77 86 95
D33 D41 D49 D57 D89 D97
D34 D42 D50 D58 D90 D98
A 60 69 78 87 96 D35 D43 D51 D59 D91 D99
B 61 70 79 88 D36
C 62 71 80 89 D37
D 63 72 81 90 D38
E 64 73 82 91 D39
F 65 74 83 92 D40 D56
Table 3.2 Logical unit and channel addresses
3.3 DATA FORMATS
Current recorder protocol specifies a variable number of data bytes, according to the parameter being accessed. Three basic formats are used:
3.3.1 Hexadecimal (Hex)
Five data bytes are transmitted in the form >HHHH where > must always be present, followed by four hex bytes (H in the example). The data transferred may represent a single parameter, or a group of parameter values packed into a 16bit word and then Hex encoded.
3.3.2 Decimal (Floating point)
Five data bytes are transmitted in on of the following formats according to decimal point position and whether the value is positive (use decimal point) or negative (use – sign).
DDDD.
DDD.D
DD.DD
D.DDD
.DDDD
DDDD–
DDD–D
DD–DD
D–DDD
–DDDD
3.3.3 Character
A string of hex data bytes, the number of bytes being defined for each relevant parameter.
HA246958
Issue 14 Mar 02 Page 17
COMMUNICATIONS MANUAL
IH
LG
LN
MV
NA
OC
OF
OH
OL
OS
PV
SH
ST
EU
FH
FL
IL
CF
CJ
DH
DL
3.4 MNEMONICS
The tables which follow, give an alphabetic list of mnemonics with definitions, formats etc. in the following groups.
All mnemonics must be in CAPITAL letters. 4001 mnemonics which are not emulated are not included in the tables.
In such cases, selection will be ignored, and polling will always return the value 0.
A1
A2
A3
A4
Channel mnemonics (see table 3.4.1)
Channel flags *
External CJ temperature.
Output signal high value.
Output signal low value.
Engineering units and print zone.
Function high value.
Function low value.
Input signal low value.
Input signal high value.
Legend string.
Legend number.
Measured value in hex.
Number of alarms assigned.
Constant output value
Offset value
Scale high value.
Scale low value.
Output source configuration †
CJ type
Function engineering units
Interpolation enable
Linearisation (function) type
Error drive
Source type
†
* Channel Flags are:
Scale print enable
Scale type
Trace skip
Output type
Output source configuration contents:
Process variable (Measured value scaled to engineering units).
Shunt value.
Channel status.
Source Channel number
Value format
Alarm mnemonics (see table 3.4.2)
Alarm type, hysteresis, average.
Alarm sense, alarm status, rate-of-change alarm period.
Set point as a proportion of channel scale.
Deviation, rate-of-change change value.
HR
IF
II
IS
BN
CS
DY
ER
L1/2/3
MI
MO
M2/3
PM
Instrument mnemonics (see table 3.4.3)
Batch number
Chart speeds A and B (See also IF)
Day number
Serial link communications errors
Hours
Instrument flags (Current chart speed, Date format, Internal CJ units)
Instrument identifier
Instrument alarm and printer on/off-line flags
User linearisation tables
(Not M1) Minutes
Month number
Mode 2(3) log interval A
Print mode
(Continued)
Page 18
HA246958
Issue 14 Mar 02
COMMUNICATIONS MANUAL
Instrument mnemonics (continued)
PT
RJ
SC
SE
T0
T1 to Tn
VN
XT
XE
YR
Text string to be printed
Remote CJ mode (Software versions 3.12 onwards)
Slot configuration
Seconds
Single Remote CJ configuration (Software versions 3.12 onwards)
Multiple remote CJ configurations for input boards 1 to n (Software versions 3.12 onwards)
Communications software version number
Enter XModem mode
Modem error code
Year
3.4.1 Channel mnemonics a) b) c)
NOTES:
1) Channel parameter updates are loaded into a buffer, until an EC mnemonic is received. The checks a) b) listed below are then carried out, and if the update is valid, it is loaded into the recorder’s data base and an ACK is returned. If the update is not valid, the buffer content is discarded and a NAK is returned.
OL
≠
OH
IL < IH c) d)
FL < FH
Linearisation type is valid for the input type.
e) Output channel is fitted f) Output channel source exists.
g) 4-digit value format selected for constant output channel h) DL < DH i) Output channel constant
≥
0
2) Further checks are carried out as a background task. This means that an ‘ACK’ may be returned, as described above, even if one of these checks (listed below) fails, causing the channel not to measure. It is recommended therefore, that a read of channel status (ST -ref. table 3.4.1) is made, 10 seconds (minimum) after an EC has been written, to establish that all the checks have passed. The background checks are as follows:
Linearisation limits are not exceeded .
External cold-junction lies within the linearisation limits.
Maximum input range is not exceeded.
HA246958
Issue 14 Mar 02 Page 19
COMMUNICATIONS MANUAL
3.4.1 CHANNEL MNEMONICS (Cont.)
Input channels
Mnemonic Format
CF Hex
CJ
EU
Page 20
Hex
Hex
Bits
0
1
2
3
4 & 5
6 & 7
8 to 11
12 & 13
14 & 15
0 TO 15
0 to 3
4 to 7
8 to 11
12 to 15
Definition Permission wrt host
CHANNEL FLAGS
SCALE PRINT FLAG ........................................................................... R/W
Select: Sets scale type A off (0) or automatic (1)
Poll: 0 = Scale type A off; 1 = Auto or customised
Not used
TRACE SKIP FLAG .............................................................................. R/W
Select: 0 = Trace on; 1 = Trace off
Poll: 0 = Trace on or conditional; 1 = Trace off
INTERPOLATION ENABLE (1 = on; 0 = off) .................................... R/W
Not used
COLD JUNCTION TYPE ..................................................................... R/W
0 = Off
For software versions prior to 3.12, Bits 6/7 are defined as follows:
1 = Internal
0 = Off, 1 = Internal,
2 = External
2 = External (if polling, 2 = External or Remote)
3 = Remote
LINEARISATION TYPE ....................................................................... R/W
0 = Thermocouple type B
1 = Thermocouple type E
2 = Thermocouple type J
3 = Thermocouple type K
4 = Thermocouple type R
5 = Thermocouple type S
6 = Thermocouple type T
7 = Pt100 (100
Ω
platinum resistance thermometer)
8 = mV (Square root extraction)
9 = Volts / linear
A = mv (linear)
B = Input type = comms.
C = Input type = Off
D to F = User linearisation tables 1 to 3 respectively
LINEARISATION TYPE ENGINEERING UNITS ............................. R/W
0 = Degrees Celsius (ËšC displayed)
1 = Degrees Fahrenheit (ËšF displayed)
2 = Kelvins (K displayed)
3 = Rankine (R displayed)
Not used
COLD JUNCTION TEMPERATURE
CONTROL TEMPERATURE ............................................................... R/W
Integer 0 to 999 (Hex 0000 to 03E7)
ENGINEERING UNITS AND PRINT ZONE
PRINT ZONE A Integer 0 to 9. When polled, returns 0.
0 = 0 to 100% 5 = 50 to 100%
Software version 3.17 onwards.
1 = 0 to 75%
2 = 25 to 100%
6 = 0 to 25%
7 = 25 to 50%
Should the print area be more than 1% different from any of these zone limits, zone 0 is returned.
3 = 0 to 50%
4 = 25 to 75%
8 = 50 to 75%
9 = 75 to 100%
E.G. 24 to 76% would be returned as zone 4, but 23 to
76% would be returned as zone 0.
INPUT SIGNAL UNITS ....................................................................... R/W
Select: Ignored
Poll: Returns 0
SCALE UNITS ...................................................................................... R/W
Ignored unless value is hex C, in which case the units string is cleared. Always returns 0.
Not used. Always returns 8
Table 3.4.1a Input channel mnemonics (sheet 1)
HA246958
Issue 14 Mar 02
COMMUNICATIONS MANUAL
3.4.1 CHANNEL MNEMONICS (Cont.)
Mnemonic
FH
FL
IH
IL
LG
LN
MV*
NA
OH
OL
PV*
SA
SH
ST
Format
Decimal
Decimal
Decimal
Decimal
Character
Hex
Hex
Hex
Decimal
Decimal
Decimal
Hex
Hex
Hex
Bits
N/A
N/A
N/A
N/A
N/A
0 to 15
0 to 15
N/A
N/A
N/A
0 to 15
0 to 15
0 to 15
Definition Permission wrt host
FUNCTION HIGH VALUE ................................................................... R/W
FUNCTION LOW VALUE ................................................................... R/W
INPUT HIGH VALUE ........................................................................... R/W
INPUT LOW VALUE ............................................................................ R/W
CHANNEL LEGEND ............................................................................ R/W
18–character string = 1st 18 characters of channel descriptor.
When selected, original characters 19 and 20 left unchanged;
When polled, characters 19 and 20 are truncated.
LEGEND NUMBER .............................................................................. R/W
Two digit number 0 to 99 (decimal) written to the last two characters of the descriptor.
Numbers greater than 99 give two spaces. When polled, returns zero if final two characters are non-numeric.
MEASURED VALUE ............................................................................ R/W
Integer F99A to 4665 (-10 to +110% of span)
0000 = Scale zero
3FFF = Full scale
A000 = Invalid data
9FFF = Over range data
A001 = Under range data
NUMBER OF ALARMS ................................................................... Read only
Always returns 4
SCALE HIGH VALUE AND CHART SPAN HIGH ............................ R/W
SCALE LOW VALUE AND CHART SPAN LOW .............................. R/W
PROCESS VARIABLE .......................................................................... R/W
Measured value scaled in engineering units.
Poll: -9999. = Under range or invalid
9999. = Over range
Select: Values outside the current range by more than 10% which are sent to the recorder are represented as being over or under range as appropriate.
SPAN ADJUST POINT ......................................................................... R/W
Select: ignored; Poll: always returns 3FFF
SHUNT VALUE ..................................................................................... R/W
Shunt value in Ohms between 1 and 65535 (Hex 0001 to FFFF)
Values > 65535 = 0
CHANNEL STATUS ......................................................................... Read only
0 = Configured and measuring analogue input
1 = Configured and reading comms input
2 = Channel off
5 = Input hardware capabilities exceeded
9 = Channel under range
A = Channel over range
B = Channel invalid
3, 4, 6, 7, 8 and C to F not used
* MV and PV may be written-to only when linearisation type (CF bits 8 to 11) is set to COMMS
Table 3.4.1a (cont.) Input channel mnemonics (sheet 2)
HA246958
Issue 14 Mar 02 Page 21
COMMUNICATIONS MANUAL
3.4.1 CHANNEL MNEMONICS (Cont.)
Output channels
Mnemonic Format
CF Hex
DH
DL
EU
LG
LN
MV
Decimal
Decimal
Hex
Character
Hex
Hex
Bits
0
1
2
3
4 to 13
14 & 15
N/A
N/A
0 to 3
4 to 11
12 to 15
0 to 15
0 to 15
Definition Permission wrt host
CHANNEL FLAGS
SCALE PRINT FLAG ........................................................................... R/W
Select: Set scale type A to off (=0) or Automatic (=1)
Poll: 0 = Scale type A off; 1 = Automatic or customised
Not used
TRACE SKIP FLAG .............................................................................. R/W
Select: 0 = trace on; 1 = trace off
Poll: 0 = trace on or conditional; 1 = trace off
INTERPOLATION ENABLE (1 = on; 0 = off) .................................... R/W
Not used. Always return 0
OUTPUT TYPE ..................................................................................... R/W
0 = Off; 1 = Voltage o/p; 2 = Current o/p
OUTPUT LOW LIMIT (in engineering units) ...................................... R/W
For constant channel, also sets chart span low to this value
OUTPUT HIGH LIMIT (in engineering units) ..................................... R/W
For constant channel, also sets chart span high to this value
PRINT ZONE
Selects print zone A Integer 0 to 9. When polled, returns 0.
0 = 0 to 100%
1 = 0 to 75%
2 = 25 to 100%
3 = 0 to 50%
4 = 25 to 75%
Not used.
5 = 50 to 100%
6 = 0 to 25%
7 = 25 to 50%
8 = 50 to 75%
9 = 75 to 100%
Should the print area be more than 1% different from any of these zone limits, zone 0 is returned.
E.G. 24 to 76% would be returned as zone 4, but 23 to
76% would be returned as zone 0.
Not used. Always returns 8
LEGEND STRING ................................................................................ R/W
18-character string mapped onto the first 18 characters of the channel descriptor. When selected, the last two characters of the descriptor remain unchanged. When polled they are removed.
LEGEND NUMBER .............................................................................. R/W
When selected,a two digit number 0 to 99 (decimal) written to the
last two characters of the descriptor.
Numbers greater than 99 give two spaces. When polled, returns zero if final two characters are non-numeric.
MEASURED OUTPUT VALUE ...................................................... Read only
Integer F99A to 4665 (-10 to +110% of span)
0000 = Scale zero
3FFF = Full scale
A000 = Invalid data
9FFF = Over range data
A001 = Under range data
Table 3.4.1b Output channel mnemonics (sheet 1)
Page 22
HA246958
Issue 14 Mar 02
COMMUNICATIONS MANUAL
3.4.1 CHANNEL MNEMONICS (Cont.)
Mnemonic
NA
OC
OF
OH
OL
OS
PV
SA
ST
ZA
Format
Hex
Decimal
Decimal
Decimal
Decimal
Hex
Decimal
Hex
Hex
Hex
Bits
N/A
N/A
N/A
N/A
0 & 1
2 to 8
9 to 12
Definition Permission wrt host
NUMBER OF ALARMS ................................................................... Read only
Always returns 4
CONSTANT OUTPUT VALUE (in engineering units) ....................... R/W
OFFSET VALUE ................................................................................... R/W
SOURCE SPAN HIGH VALUE (in engineering units) ........................ R/W
Also sets chart span high to the same value.
Ignored and returns 0 for constant channels.
SOURCE SPAN LOW VALUE (in engineering units) ......................... R/W
Also sets chart span low to the same value.
Ignored and returns 0 for constant channels.
OUTPUT SOURCE CONFIGURATION
SOURCE TYPE. .................................................................................... R/W
0 = Input channel; 1 = Derived channel; 2 = Constant
SOURCE CHANNEL NUMBER .......................................................... R/W
Integer 1 to 96 (Hex 0001 TO 0060)
Ignored and returns 0 if Constant.
OUTPUT CHANNEL DECIMAL PLACE ........................................... R/W
0 to F valid for source channel. Only 0 to 4 valid for constant
0 = XXXXX.
1 = XXXX.X
2 = XXX.XX
3 = XX.XXX
4 = X.XXXX 8 = XXXXX.XXX C = Scientific
5 = XXXXXXXX. 9 = XXXX.XXXX D = Time
6 = XXXXXXX.X A = XXX.XXXXX E = Date
7 = XXXXXX.XX B = XX.XXXXXX F = Elapsed time
13 & 14
15
N/A
0 to 15
0 to 15
ERROR DRIVE ..................................................................................... R/W
0 = Drive off; 1 = Drive high; 2 = Drive low
Not used
PROCESS VARIABLE (OUTPUT VALUE) .................................... Read only
Measured output value scaled in engineering units.
Poll: -9999. = Under range or invalid
9999. = Over range
SPAN ADJUST POINT ......................................................................... R/W
Ignored; Always returns 3FFF
CHANNEL STATUS ......................................................................... Read only
0 = Configured and operating analogue output
2 = Channel off
5 = Output hardware capabilities exceeded
9 = Under range
A = Over range
1, 3, 4, 6 to 8 and B to F not used.
ZERO ADJUST POINT ......................................................................... R/W
Ignored; Always returns 0 0 to 15
Table 3.4.1b (cont.) Output channel mnemonics (sheet 2)
HA246958
Issue 14 Mar 02 Page 23
COMMUNICATIONS MANUAL
3.4.1 CHANNEL MNEMONICS (Cont.)
Derived channels
Mnemonic Format
CF Hex
Bits
EU
LN
MV
NA
OH
OL
PV*
ST
Hex
Hex
Hex
Hex
Decimal
Decimal
Decimal
Hex
0
1
2
3
4 to 15
0 to 3
4 to 7
8 to 11
12 to 15
0 to 15
0 to 15
N/A
N/A
N/A
0 to 15
Definition Permission wrt host
CHANNEL FLAGS
SCALE PRINT FLAG ........................................................................... R/W
Select: Set scale type A to off (=0) or Automatic (=1)
Poll: 0 = Scale type A off; 1 = Automatic or customised
LEGEND PRINT ENABLE FLAG ....................................................... R/W
Select: ignored
Poll: Scale type is off (=0) or Automatic or customised (=1)
TRACE SKIP FLAG .............................................................................. R/W
Select: 0 = trace on; 1 = trace off
Poll: 0 = trace on or conditional; 1 = trace off
INTERPOLATION ENABLE (1 = on; 0 = off) .................................... R/W
Not used
ENGINEERING UNITS AND PRINT ZONE
PRINT ZONE A Integer 0 to 9. When polled, returns 0.
0 = 0 to 100%
1 = 0 to 75%
5 = 50 to 100%
6 = 0 to 25%
Software version 3.17 onwards.
Should the print area be more than 1% different from
2 = 25 to 100%
3 = 0 to 50%
7 = 25 to 50%
8 = 50 to 75% any of these zone limits, zone 0 is returned.
E.G. 24 to 76% would be returned as zone 4, but 23 to
4 = 25 to 75%
Not used
9 = 75 to 100% 76% would be returned as zone 0.
CHANNEL ENGINEERING UNITS .................................................... R/W
Ignored unless value is hex C, in which case the units string is cleared. Always returns 0.
Not used. Always returns 0
LEGEND NUMBER .............................................................................. R/W
Two digit number 0 to 99 (decimal) written to the last two characters of the descriptor.
Numbers greater than 99 give two spaces. When polled, returns zero if final two characters are non-numeric.
MEASURED VALUE ............................................................................ R/W
Integer F99A to 4665 (-10 to +110% of span)
0000 = Scale zero
3FFF = Full scale
A000 = Invalid data
9FFF = Over range data
A001 = Under range data
NUMBER OF ALARMS ................................................................... Read only
Always returns 4
SCALE HIGH VALUE AND CHART SPAN HIGH ............................ R/W
SCALE LOW VALUE AND CHART SPAN LOW .............................. R/W
PROCESS VARIABLE ...................................................................... Read only
Measured value scaled in engineering units.
Poll: -9999. = Under range or invalid
9999. = Over range
CHANNEL STATUS ......................................................................... Read only
2 = Channel off
7 = Configured and recording derived function
8 = Derived function becoming erroneous in real time
0, 1, 3 to 6 and 9 to F not used.
Table 3.4.1c Derived channel parameters
Page 24
HA246958
Issue 14 Mar 02
COMMUNICATIONS MANUAL
3.4.2 Alarm mnemonics
NOTES...
1. Alarm parameters are accessible only with a logical unit address (U) of zero.
2. Before a new alarm can be set-up a “get alarm” mnemonic (GA) must be transmitted. Refer to section
3.5.11 for GA definition.
3. After all the data for the alarm has been set-up, an “enter alarm” mnemonic (EA) must be transmitted to cause the data to be written into the recorder’s data base.
4. When an EA is received the checks listed below are carried out, and if the update is valid, the data is loaded into the recorder’s data base and an ACK is returned. If the update is not valid, the buffer content is discarded and a NAK is returned.
5. In order to access current alarms, a ‘get alarm’ command (GA) must be transmitted in order to copy the relevant alarm’s parameters into the alarm buffer. Refer to section 3.5.11 for GA definition. After any update to the alarm an EA must be transmitted, to write the new data to the recorder’s data base
6. When using inverted scales it is important to note that the alarm sense (e.g. rising or falling) is related to the input signal, but the alarm setpoints are related to the scale.
ALARM BUFFER VALIDATION CHECKS.
a) Deviation out alarms Hysteresis < twice deviation value
HA246958
Issue 14 Mar 02 Page 25
COMMUNICATIONS MANUAL
3.4.2 ALARM MNEMONICS (Cont.)
Mnemonic
A1
A2
A3
A4
Format
Hex
Hex
Hex
Hex
Bits
0 to 7
8 to 9
10 to 14
0
1
2 to 7
8
9
10
11 to 13
14 to 15
0 to 15
0 to 15
Definition Permission wrt host
ALARM PACKET 1
Not used; always return 0 ..................................................................... R/W
ALARM TYPE ...................................................................................... R/W
0 = Not used
1 = Absolute
2 = Deviation
3 = Rate-of-change
HYSTERESIS (Absolute and deviation alarms only) ........................... R/W
(Fixed point 0.0 to 9.5% span)
{Bit 14 is a binary fraction (logic 1
≡
1/2)}
ALARM PACKET 2
SKIP FLAG ............................................................................................ R/W
Poll: 0 = Alarm latched, unlatched or process;
1 = Alarm off
SENSE FLAG ........................................................................................ R/W
For absolute alarms, 1 = high; 0 = low
For deviation alarms, 1 = in; 0 = out
For rate-of-change alarms, 1 = rise; 0 = fall
Not used - always return 0 when polled ................................................ R./W
ALARM FLAG (1 = alarm; 0 = no alarm) ........................................ Read only
ACKNOWLEDGE FLAG ................................................................. Read only
0 = not acknowledged; 1 = acknowledged
NEEDS ACKNOWLEDGE FLAG ................................................... Read only
0 = Does not need acknowledgement;
1 = Needs acknowledgement
RATE-OF-CHANGE ALARM PERIOD .............................................. R/W
0 = 1 second 4 = 10 minutes
1 = 10 seconds
2 = 30 seconds
5 = 30 minutes
6 = 1 hour
3 = 1 minute
Not used - always return 0 when polled ................................................ R/W
ALARM PACKET 3 (Absolute and Deviation alarms only)
SET POINT as a proportion of channel scale ........................................ R/W
Scale low = 0000; scale high = 3FFF
ALARM PACKET 4 (Deviation and Rate-of-change alarms)
DEVIATION VALUE OR CHANGE VALUE ...................................... R/W
(as a proportion of channel scale)
0000 =0.0; 3FFF = |Scale high - Scale low|
Table 3.4.2 Alarm mnemonics
Note: Because the setpoint is a proportion of full scale, any change in scale will result in a change in the absolute value of any setpoints, deviation values or rates-of-change set up in A3 and A4 above
Page 26
HA246958
Issue 14 Mar 02
COMMUNICATIONS MANUAL
3.4.3 Instrument mnemonics
DY
ER
Notes
1. Access to instrument parameters may be gained only through the use of logical unit address 0
2. A valid (0 to F) channel address must be present, even though it is not used when accessing instrument parameters.
Bits Mnemonic Format
BN Character
CD
CE
CS
Character
Character
Hex
Hex
Hex
0 to 7
8 to 15
0 to 15
0 to 15
Definition Permission wrt host
Poll: First eight characters of operator message 1. ................................ R/W
Select: Sends eight characters (pads with spaces)
Not used - returns eight strings of 18 spaces each ................................. R/W
Not used - returns 13 strings of five spaces ........................................... R/W
CHART SPEED
Chart speed A. Integer 0 to B ................................................................ R/W
Chart speed B. Integer 0 to B ................................................................ R/W
Integer
0
1
2
3
4
5
6
7
8
9
A
B mm/hr
Off
5
10
20
30
60
120
300
600
1200
1500
User
2
4
6
10
25 in/hr
Off
0.25
0.5
1
50
5
User
DAY NUMBER
Integer 1 to 31 (Hex 0001 to 001F) ....................................................... R./W
COMMS ERROR STATUS
(Cleared by reading. ER holds only the last comms. error code.)
Integer 0 to 43 (Hex 0 to 2B) ............................................................. Read only
00 No error
01 Invalid mnemonic
02 Checksum error
03 Read attempted on write-only parameter
04 Write attempted on read-only parameter
05 Invalid unit/channel address combination
06 No free alarms available
07 Access attempted on invalid alarm record.
08 Invalid alarm number for this channel.
09 Printer buffer not empty
0A Invalid time parameter
0B Invalid instrument ID string length.
0C Invalid batch number string length.
0D Invalid channel parameter buffer
0E Invalid channel descriptor string length.
0F Invalid channel engineering units string length
Table 3.4.3a Instrument mnemonics (sheet 1)
HA246958
Issue 14 Mar 02 Page 27
COMMUNICATIONS MANUAL
3.4.3 INSTRUMENT MNEMONICS (Cont.)
Mnemonic
ER
HR
ID
IF
II
IS
L1 to L3
Format
Hex
Hex
Character
Hex
Hex
Hex
Character
Bits
0 to 15
0
1
2
3
4 to 15
0 to 15
0
1
2 to 15
Definition Permission wrt host
COMMS ERROR STATUS (Cont.)
10 Program mode active - cannot disable
11 Print line too long
12 Invalid colour select code
13 Linearisation table too long
14 Linearisation table too short
15 Invalid slot configuration string length
16 Invalid slot configuration
17 Invalid print mode
18 Invalid paper divisions
19 Invalid chart speed parameter
1A Invalid log interval - mode 2
1B Invalid log interval - mode 3
1C Parity error
1D Receive overrun error
1E Framing error
1F Invalid data format
20 Channel number out of range
21 Alarm number out of range
22 Channel not configured for external input
23 Data base update pending
24 Protected area of RAM is not write enabled
25 Printer off line
26 Printer on line
27 Printer busy
28 No log in mode 1
2A No resettable channels
2B Input not defined for current function
HOURS .................................................................................................. R/W
Integer 0 to 23 (Hex 0000 to 0017)
INSTRUMENT DESCRIPTOR ............................................................. R/W
Not used - always returns 24 spaces if polled
INSTRUMENT FLAGS
Not used - always returns 0 if polled
CURRENT CHART SPEED FLAG (Ref. CS) ...................................... R/W
0 = Speed A; 1 = Speed B
CHART SPEED UNITS FLAG (0 = mm/hr; 1 = in/hr) ....................... R/W
DATE FORMAT (0 = dd/mm/yy; 1 = mm/dd/yy) ................................. R/W
Not used - always return 0 when polled ................................................ R/W
INSTRUMENT IDENTIFIER ........................................................... Read only
Always returns >4001
INSTRUMENT STATUS
INSTRUMENT ALARM FLAG (1 = active) .................................... Read only
PRINTER ON/OFF LINE (1 = Off; 0 = On) ..................................... Read only
Not used - always return 0 ................................................................. Read only
LINEARISATION TABLES .................................................................. R/W
Not used. Return ‘Empty’ when polled.
Table 3.4.3a (Cont.) Instrument mnemonics (sheet 2)
Page 28
HA246958
Issue 14 Mar 02
COMMUNICATIONS MANUAL
3.4.3 INSTRUMENT MNEMONICS (Cont.)
Mnemonic
MI
MO
(Not M 0 )
M2
M3
PM
PT
RJ
SC
SE
T0
(T zero)
Format
Hex
Hex
Hex
Hex
Hex
Character
Hex
Character
Hex
Hex
Bits
0 to 15
0 to 15
0 to 15
0 to 15
0 to 1
2 to 15
0
1 to 15
Definition Permission wrt host
MINUTES
Integer 0 to 59 (Hex 0000 to 003B) ....................................................... R/W
MONTH
Integer 0 to 12 (Hex 0000 to 000C) ....................................................... R/W
MODE 2 LOG INTERVAL (0 = Off) .................................................... R/W
Interval in minutes between timed logs (log interval A)
Integer 0 to 6039 (Hex 0000 to 1797)
MODE 3 LOG INTERVAL (0 = Off) .................................................... R/W
Integer 0 to 36234 (Hex 0000 to 8D8A)
Poll: Log interval A in 10s of seconds
Select: Truncates to a multiple of minutes
PRINT MODE ........................................................................................ R/W
Print mode (1 = trend; 2 = Text; 3 = Text only)
Not used - always return 0 when polled.
TEXT TO BE PRINTED .................................................................. Write only
Up to 100 printable characters printed in black.
Colour underlining is possible using ‘!n’ embedded in the text string, to select colour n (see table below). Up to 10 colour selections can be embedded in one string.
USE OF THE EXCLAMATION MARK (!) IS NOT ALLOWED IN
A TEXT STRING EXCEPT TO DEFINE THE UNDERLINE COL-
OUR n Underline colour n Underline colour
1
2
3
Red
Orange
Green
4
5
6
Purple
Blue
None
REMOTE CJ (Software versions 3.12 onwards) ................................... R/W
REMOTE CJ MODE
0 = Single remote CJ used for all channels (see 'T0' below)
1 = Remote CJ channel for each input board (see 'T1 to TC' below)
Not used
0 to 15
0
1 to 2
3
4 to 10
11 to 15
SLOT CONFIGURATION ................................................................ Read only
When polled, gives the type of board fitted at each address as:
0 (8 or 16 channel input), 6 (Relay output), D (8-channel output),
E (4-channel output) or F (Empty)
Byte 1 contains the type for address 1; byte 2 the type for address 2 etc. Byte 8 always returns ‘F’ (Empty)
SECONDS
Integer 0 to 59 (Hex 0000 to 003B) ................................................... Read only
MAY NOT BE WRITTEN TO
SINGLE REMOTE CJ CONFIG (Software versions 3.12 onwards) ... R/W
Used only when RJ above is set to 0
REMOTE CJ ENABLE
0 = Disable remote CJ channel
1 = Enable remote CJ channel
REMOTE CJ UNITS
0 = Degrees Celsius 1 = Degrees Fahrenheit
2 = Kelvins 3 = Rankine
CHANNEL TYPE
0 Input channel; 1 = Derived channel
REMOTE CJ CHANNEL ADDRESS
See table 3.4.3b
Not used
Table 3.4.3a (Cont.) Instrument mnemonics (sheet 3)
HA246958
Issue 14 Mar 02 Page 29
COMMUNICATIONS MANUAL
3.4.3 INSTRUMENT MNEMONICS (Cont.)
Mnemonic
T1 to TC
VN
XE
XT
YR
Format
Hex
Character
Hex
Hex
Hex
Bits
0 to 15
0 to 3
0 to 1
2 to 15
0 to 15
Definition Permission wrt host
MULTIPLE REMOTE CJ CONFIG (S/W versions 3.12 onwards) ..... R/W
Used only when RJ above is set to 1
Note Tn = Remote CJ config. for input board with address n where n = 1 to C for 250mm recorders n = 1 to 6 for 180mm multipoint recorders n = 1 to 4 for 180/250 mm continuous recorders.
As for T0 above
VERSION NUMBER OF EMULATED 4001 SOFTWARE ............ Read only
Returns:
7.1LE0 (no maths pack)
7.1LE2 (Maths pack level 1 fitted)
7.1LE3 (Maths pack level 2 fitted)
XMODEM ERROR REPORTING .................................................... Read only
0 Transfer OK, no errors
1 Restore failed completely. File incompatible or comms transfer failure. Previous configuration unaffected.
2 Restore failed on data. Some records ignored, but restore operation mostly successful.
3 Restore failed on transfer - new configuration undefined.
16 Save operation had no reply from comms and timed out
32 Save operation failed before transfer was completed.
ENTER XMODEM MODE .............................................................. Write only
0 = as standby; 1 = as receiver; 2 = as sender
Not used
YEAR ..................................................................................................... R/W
Offset from year 1900
Integer 88 to 188 (Hex 0058 to 00BC)
Table 3.4.3a (Cont.) Instrument mnemonics (sheet 3)
All recorders
00 Reserved
01 = Channel 1
02 = Channel 2
03 = Channel 3
04 = Channel 4
05 = Channel 5
06 = Channel 6
07 = Channel 7
08 = Channel 8
09 = Channel 9
0A = Channel 10
0B = Channel 11
0C = Channel 12
0D = Channel 13
0E = Channel 14
0F = Channel 15
10 = Channel 16
11 = Channel 17
12 = Channel 18
13 = Channel 19
14 = Channel 20
15 = Channel 21
16 = Channel 22
17 = Channel 23
18 = Channel 24
19 = Channel 25
1A = Channel 26
1B = Channel 27
1C = Channel 28
1D = Channel 29
1E = Channel 30
1F = Channel 31
20 = Channel 32
21 = Channel 33
22 = Channel 34
23 = Channel 35
24 = Channel 36
25 = Channel 37
26 = Channel 38
27 = Channel 39
28 = Channel 40
29 = Channel 41
2A = Channel 42
2B = Channel 43
2C = Channel 44
2D = Channel 45
2E = Channel 46
2F = Channel 47
30 = Channel 48
Input channel addresses
Multipoint recorders only
250 mm multipoint recorders only
31 = Channel 49
32 = Channel 50
33 = Channel 51
34 = Channel 52
35 = Channel 53
36 = Channel 54
37 = Channel 55
38 = Channel 56
39 = Channel 57
3A = Channel 58
3B = Channel 59
3C = Channel 60
3D = Channel 61
3E = Channel 62
3F = Channel 63
40 = Channel 64
41 = Channel 65
42 = Channel 66
43 = Channel 67
44 = Channel 68
45 = Channel 69
46 = Channel 70
47 = Channel 71
48 = Channel 72
49 = Channel 73
4A = Channel 74
4B = Channel 75
4C = Channel 76
4D = Channel 77
4E = Channel 78
4F = Channel 79
50 = Channel 80
51 = Channel 81
52 = Channel 82
53 = Channel 83
54 = Channel 84
55 = Channel 85
56 = Channel 86
57 = Channel 87
58 = Channel 88
59 = Channel 89
5A = Channel 90
5B = Channel 91
5C = Channel 92
5D = Channel 93
5E = Channel 94
5F = Channel 95
60 = Channel 96
Table 3.4.3b Remote CJ Channel addressing (Mnemonics T0 and T1 to TC - table 3.4.3a)
Page 30
HA246958
Issue 14 Mar 02
COMMUNICATIONS MANUAL
3.5 COMMAND MNEMONICS
There are a number of mnemonics that do not directly access parameters, but which cause the serial link to perform some action. These mnemonics are write-only i.e. they must be sent as a selection message and cannot be polled.
3.5.1 Alarm acknowledge (AA)
On receipt of this mnemonic, all alarms requiring acknowledgement are acknowledged.
3.5.2 Printer on (CG)
If the printer is off line receipt of this mnemonic will turn it on and return an ACK. If the printer is already on, a NAK is returned.
3.5.3 Chart halt (CH)
No action taken. Always returns ACK
3.5.4 Printer off (CO)
If the printer is on-line, then receipt of this mnemonic causes the it to be switched off-line and an ACK is returned. If the printer is already off, a NAK is returned.
3.5.5 Chart Wind (CW)
Receipt of this command whilst the printer is off-line, causes the chart to wind forward 16 cm. at maximum speed.
CW commands received whilst the printer is on-line return a NAK.
3.5.6 Data Dump (DD)
If the printer is on-line, then receipt of this command causes log1 to be printed on the chart and an ACK to be returned. If the printer is off-line then no action is taken and a NAK is returned.
3.5.7 Disable program mode (DP)
If the recorder is not in configuration mode, then the sending of ‘DP’ causes entry to the configuration mode to be inhibited and an ACK to be returned. If the recorder is in configuration mode, then no action is taken and a NAK is returned. Should the operator attempt to enter configuration, when it has thus been disabled, the message “Configuration access disabled by comms” will appear.
3.5.8 Enter alarm data (EA)
When alarm data is being written to the recorder, the new data is held in a temporary storage area (buffer), which is reinitialised each time new alarm data is entered. On receipt of the ‘EA’ mnemonic, the data in the buffer is checked, and if valid, it is written to the recorder’s data base and an ACK is returned. If the data is not valid, then the buffer content is discarded and a NAK is returned.
3.5.9 Enter channel data (EC)
When channel parameters are being written to (selected), the new data is held in a temporary storage area (buffer), which is re-initialised each time a new channel is written to. On receipt of the ‘EC’ mnemonic, the data in the buffer is checked, and if valid, it is written to the recorder’s data base and an ACK is returned. If the data is not valid, then the buffer content is discarded and a NAK is returned.
3.5.10 Enable program mode (EP)
The sending of ‘EP’ causes the configuration menu to be enabled regardless of its existing state. ACK is always returned.
HA246958
Issue 14 Mar 02 Page 31
COMMUNICATIONS MANUAL
3.5.11 Get indicated alarm data (GA)
Allows the channel number and alarm number required to be defined, as follows:
NO MATHS PACK FITTED
Bits
0 to 5
Definition
Alarm number (integer 1 to 4)
6 to 7 Not used
8 to 15 Channel number
Integer 1 to 30 (Hex 0001 to 001E) = channels 1 to 30 respectively
Integer 63 to 131 (Hex 003F to 0083) = channels 31 to 99 respectively
MATHS PACK FITTED
Bits
0 to 5
Definition
Alarm number (integer 1 to 4)
6 to 7 Not used
8 to 15 Channel number
Integer 1 to 30 (Hex 0001 to 001E) = Measuring channels 1 to 30 respectively
Integer 31 to 62 (Hex 001F to 003E) = Derived channels 1 to 32 respectively
Integer 63 to 131 (Hex 003F to 0083) = Measuring channels 31 to 99 respectively
Integer 132 to 198 (Hex 0084 to 00C6) = Derived channels 33 to 99 respectively
3.5.12 Get free alarm (GF)
Implemented only on model 4001
3.5.13 Chart rewind (CR)
Implemented only on model 4001
Page 32
HA246958
Issue 14 Mar 02
COMMUNICATIONS MANUAL
3.6 PARAMETER SCROLLING
This is a feature which allows a number of parameters to be read one after the other on receipt of an ACK after each poll. The parameters are divided into two types: Block Command and Scroll List.
3.6.1 Block parameters
If the previous command parameter was a Block Command Parameter, the recorder automatically increments the channel address within the logical unit, and transmits the value of the same mnemonic as last time, but for the new channel. The channel address is continuously incremented until it reaches its maximum value for the particular LU / CA entry combination, and is then reset to the minimum, and so on, as follows:
LU CA sequence LU CA sequence
1 0, 1, 2, 3, 0, 1, 2, ....
1 4, 5, 6, 4, 5, 6, ....
1 7, 8, 9, A, B, C, D, E, F, 7, 8, 9,....
8 0, 1, 0, 1, 0.......
8 2, 3, 4, 5, 6, 2, 3, 4,....
9 0, 1, 2, 3, 4, 5, 6, 7, 0, 1, 2, ......
2 0, 1, 2, 3, 0, 1, 2, ....
2 4, 5, 6, 4, 5, 6, ....
9 8, 9, A, B, C, D, E, F, 8, 9, A, ....
A 0, 1, 2, 3, 4, 5, 6, 7, 0, 1, 2, ....
2 7, 8, 9, A, B, C, D, E, F, 7, 8, 9, .... A 8, 9, A, B, C, D, E, F, 8, 9, A, ....
3 0, 1, 2, 3, 0, 1, 2, .... B 0, 1, 2, 3, 4, 5, 6, 7, 0, 1, 2, ....
3 4, 5, 6, 4, 5, 6, .... B 8, 9, A, B, C, D, E, F, 8, 9, A, ....
3 7, 8, 9, A, B, C, D, E, F, 7, 8, 9, .... C 0, 1, 2, 3, 4, 5, 0, 1, 2, ....
4 0, 1, 2, 3, 0, 1, 2, ....
4 4, 5, 6, 4, 5, 6, ....
C
C
6, 7, 6, 7, 6, .....
8, 9, A, B, C, D, E, F, 8, 9, A, ....
4 7, 8, 9, A, B, C, D, E, F, 7, 8, 9, .... D 0, 1, 2, 3, 4, 5, 6, 7, 0, 1, 2, ....
5 0, 1, 2, 3, 0, 1, 2, .... D 8, 9, A, B, C, D, E, F, 8, 9, A, ....
5 4, 5, 6, 4, 5, 6, .... E 0, 1, 2, 3, 4, 5, 6, 7, 0, 1, 2, ....
5 7, 8, 9, A, B, C, D, E, F, 7, 8, 9, .... E 8, 9, A, 8, 9, A, ....
6 0, 1, 2, 3, 0, 1, 2, ....
6 4, 5, 6, 4, 5, 6, ....
F 0, 1, 2, 3, 4, 5, 6, 7, 0, 1, 2, ....
7 0, 1, 2, 3, 0, 1, 2, ....
7 4, 5, 6, 4, 5, 6, ....
Table 3.6.1 Block parameter scroll sequences
3.6.2 Scroll parameters
Alarm and Instrument parameters are all scroll parameters. This means that when an ACK is received, the next parameter in the lists below is accessed.
ALARM PARAMETERS
The alarms are scrolled in order A1, A2, A3, A4, ,A1, A2 —etc
INSTRUMENT PARAMETERS
The instrument parameters are scrolled in order:
SC, IF, PM, PD * , IS, ER, HR, MI, SE, DY, MO, YR, BN, CD*, CE*, II, VN, ID, CS, M2, M3, L1 to L3, J1 * to J5 * ,
RJ † , T0 † , T1 † to Tn † , SC, IF, ... , etc.
* These parameters are not emulated by the recorder. If selected, they are ignored, if polled, they return zero.
† These parameters appear only with software versions 3.12 onwards.
In 'Tn' n = Hex C for 250mm multipoint recorders, n = 6 for 180mm recorders and n = 4 for continuous recorders.
HA246958
Issue 14 Mar 02 Page 33
COMMUNICATIONS MANUAL
3.7 CHARACTER SET
CHARACTER
NUL
SOH (Start of heading)
STX (Start of text) *
ETX (End of text) *
EOT (End of transmission) *
BEL (Bell)
BS (Backspace)
CONTROL
KEY
I
J
E
F
G
H
A
B
C
D
K
L
M
N
O
BINARY
CODE
000 0000
000 0001
000 0010
000 0011
000 0100
000 0101
000 0110
000 0111
000 1000
000 1001
000 1010
000 1011
000 1100
000 1101
000 1101
000 1111
HEX
CODE
04
05
06
07
00
01
02
03
08
09
0A
0B
0C
0D
0E
0F
DECIMAL
CODE
DLE (Data link escape)
DC1 {Device control 1 (XON)} *
DC2 (Device control 2)
DC3 {Device control 3 (XOFF)} *
DC4 {Device control 4 (stop)}
NAK (Negative acknowledge) *
ETB (End of transmission block)
CAN (Cancel)
EM (End of medium)
SUB (Substitute)
ESC (Escape)
T
U
V
W
P
Q
R
S
X
Y
Z
001 0000
001 0001
001 0010
001 0011
001 0100
001 0101
001 0110
001 0111
001 1000
001 1001
001 1010
001 1011
001 1100
001 1101
001 1110
001 1111
18
19
1A
1B
1C
1D
1E
1F
14
15
16
17
10
11
12
13
24
25
26
27
28
29
30
31
20
21
22
23
16
17
18
19
(Space)
#
$
(Hash) (£ sign - ISO 7)
{Dollar (or £ sign)}
(
)
& (Ampersand)
` (Closing single quote)
(Opening round bracket)
(Closing round bracket)
* (Asterisk)
, (Comma)
. {Full stop (period)}
/ (Oblique)
010 0000
010 0001
010 0010
010 0011
010 0100
010 0101
010 0110
010 0111
010 1000
010 1001
010 1010
010 1011
010 1100
010 1101
001 1110
010 1111
2C
2D
2E
2F
28
29
2A
2B
24
25
26
27
20
21
22
23
36
37
38
39
40
32
33
34
35
41
42
43
44
45
46
47
* Only those control characters marked with an asterisk are correctly interpreted by the instrument. The use of other control codes may lead to unrecoverable errors.
Table 3.7 Character set: Sheet 1 Hex 00 to 2F
Page 34
HA246958
Issue 14 Mar 02
COMMUNICATIONS MANUAL
3.7 CHARACTER SET (Cont.)
6
7
4
5
0
1
2
3
8
9
: (colon)
; semi-colon)
= (equals)
CHARACTER
I
J
K
L
E
F
G
H
M
N
O
@
A
B
C
D
T
U
V
W
P
Q
R
S
Z
[
X
Y
]
(opening square bracket)
(closing square bracket)
^ (circumflex)
_ (Underline)
101 0000
101 0001
101 0010
101 0011
101 0100
101 0101
101 0110
101 0111
101 1000
101 1001
101 1010
101 1011
101 1100
101 1101
101 1110
101 1111
Table 3.7 (cont.) Sheet 2: Hex 30 to 5F
100 0000
100 0001
100 0010
100 0011
100 0100
100 0101
100 0110
100 0111
100 1000
100 1001
100 1010
100 1011
100 1100
100 1101
100 1110
100 1111
BINARY
CODE
011 0000
011 0001
011 0010
011 0011
011 0100
011 0101
011 0110
011 0111
011 1000
011 1001
011 1010
011 1011
011 1100
011 1101
011 1110
011 1111
91
92
93
94
95
87
88
89
90
80
81
82
83
84
85
86
74
75
76
77
78
79
70
71
72
73
64
65
66
67
68
69
DECIMAL
CODE
48
49
50
51
52
53
54
55
56
57
58
59
60
61
62
63
5B
5C
5D
5E
5F
57
58
59
5A
50
51
52
53
54
55
56
4A
4B
4C
4D
4E
4F
46
47
48
49
40
41
42
43
44
45
HEX
CODE
30
31
32
33
34
35
36
37
38
39
3A
3B
3C
3D
3E
3F
HA246958
Issue 14 Mar 02 Page 35
COMMUNICATIONS MANUAL
3.7 CHARACTER SET (Cont.) g h f e i j k c d a b n o l m
CHARACTER z
{ x y v w r s t u p q
}
(opening curly bracket)
(closing curly bracket)
~ (tilde)
Not printed
111 0000
111 0001
111 0010
111 0011
111 0100
111 0101
111 0110
111 0111
111 1000
111 1001
111 1010
111 1011
111 1100
111 1101
111 1110
111 1111
Table 3.7 (Cont.) Sheet 3: Hex 60 to 7F.
BINARY
CODE
110 0000
110 0001
110 0010
110 0011
110 0100
110 0101
110 0110
110 0111
110 1000
110 1001
110 1010
110 1011
110 1100
110 1101
110 1110
110 1111
HEX
CODE
6C
6D
6E
6F
68
69
6A
6B
64
65
66
67
60
61
62
63
79
7A
7B
7C
75
76
77
78
7D
7E
7F
70
71
72
73
74
DECIMAL
CODE
104
105
106
107
108
109
110
111
96
97
98
99
100
101
102
103
120
121
122
123
124
125
126
127
112
113
114
115
116
117
118
119
Page 36
HA246958
Issue 14 Mar 02
COMMUNICATIONS MANUAL
3.7 CHARACTER SET (Cont.)
CHARACTER
ö
ü
ù
ÿ
¢
£
¥
ô
ö
ò
û
É
æ
Æ
ç
ê
à
å
ë
ï
è
ì
î
Ä
Å
é
â
ä
Ç
ü o
¿
ú
ñ
Ñ a
á
í
ó
DECIMAL
CODE
134
135
136
137
138
139
128
129
130
131
132
133
140
141
142
143
152
153
154
155
156
157
158
159
144
145
146
147
148
149
150
151
160
161
162
163
164
165
166
167
168
169
170
171
172
173
174
175
HEX
CODE
8B
8C
8D
8E
8F
85
86
87
88
89
8A
80
81
82
83
84
97
98
99
9A
9B
9C
9D
9E
9F
90
91
92
93
94
95
96
A7
A8
A9
AA
AB
AC
AD
AE
AF
A0
A1
A2
A3
A4
A5
A6
BINARY
CODE
1000 0000
1000 0001
1000 0010
1000 0011
1000 0100
1000 0101
1000 0110
1000 0111
1000 1000
1000 1001
1000 1010
1000 1011
1000 1100
1000 1101
1000 1110
1000 1111
1001 0000
1001 0001
1001 0010
1001 0011
1001 0100
1001 0101
1001 0110
1001 0111
1001 1000
1001 1001
1001 1010
1001 1011
1001 1100
1001 1101
1001 1110
1001 1111
1010 0000
1010 0001
1010 0010
1010 0011
1010 0100
1010 0101
1010 0110
1010 0111
1010 1000
1010 1001
1010 1010
1010 1011
1010 1100
1010 1101
1010 1110
1010 1111
Table 3.7 (Cont.) Sheet 4: Hex 80 to AF
HA246958
Issue 14 Mar 02 Page 37
COMMUNICATIONS MANUAL
3.7 CHARACTER SET (Cont.)
5
6
3
4
0
1
2
7
8
9
2
3
0
1
4
5
6
7
8
9
0
1
2
7
8
9
5
6
3
4
(Subscript)
(Subscript)
(Subscript)
(Subscript)
Not printed
Not printed
(Superscript)
(Superscript)
(Superscript)
(Superscript)
(Superscript)
(Superscript)
(Superscript)
(Superscript)
(Superscript)
(Superscript)
(Subscript)
(Subscript)
(Subscript)
(Subscript)
(Subscript)
(Subscript)
Not printed
Not printed
Not printed
Not printed
Not printed
Not printed
Not printed
Not printed
Not printed
∫
{Bell (alarm) symbol}
CHARACTER
C8
C9
CA
CB
CC
CD
CE
CF
C4
C5
C6
C7
C0
C1
C2
C3
D5
D6
D7
D8
D9
DA
DB
DC
D0
D1
D2
D3
D4
DD
DE
DF
HEX
CODE
BC
BD
BE
BF
B7
B8
B9
BA
BB
B0
B1
B2
B3
B4
B5
B6
200
201
202
203
204
205
206
207
192
193
194
195
196
197
198
199
213
214
215
216
217
218
219
220
208
209
210
211
212
221
222
223
DECIMAL
CODE
183
184
185
186
187
188
189
190
191
176
177
178
179
180
181
182
1101 0000
1101 0001
1101 0010
1101 0011
1101 0100
1101 0101
1101 0110
1101 0111
1101 1000
1101 1001
1101 1010
1101 1011
1101 1100
1101 1110
1101 1101
1101 1111
1100 0000
1100 0001
1100 0010
1100 0011
1100 0100
1100 0101
1100 0110
1100 0111
1100 1000
1100 1001
1100 1010
1100 1011
1100 1100
1100 1101
1100 1110
1100 1111
BINARY
CODE
1011 0000
1011 0001
1011 0010
1011 0011
1011 0100
1011 0101
1011 0110
1011 0111
1011 1000
1011 1001
1011 1010
1011 1011
1011 1100
1011 1101
1011 1110
1011 1111
Table 3.7 (Cont.) Sheet 5: Hex B0 to E2
Page 38
HA246958
Issue 14 Mar 02
COMMUNICATIONS MANUAL
3.7 CHARACTER SET (Cont.)
µ
τ
Σ
σ
Γ
π
α
β
φ
θ
Ω
δ
∞
∩
≥
≤
≡
±
÷
≈
(Minus)
(Plus)
(Divide)
Not printed
CHARACTER
BINARY
CODE
1110 0000
1110 0001
1110 0010
1110 0011
1110 0100
1110 0101
1110 0110
1110 0111
1110 1000
1110 1001
1110 1010
1110 1011
1110 1100
1110 1101
1110 1110
1110 1111
1111 0000
1111 0001
1111 0010
1111 0011
1111 0100
1111 0101
1111 0110
1111 0111
1111 1000
1111 1001
1111 1010
1111 1011
1111 1100
1111 1101
1111 1110
1111 1111
HEX
CODE
E0
E1
E2
E3
E4
E5
E6
E7
E8
E9
EA
EB
EC
ED
EE
EF
F7
F8
F9
FA
F0
F1
F2
F3
F4
F5
F6
FB
FC
FD
FE
FF
DECIMAL
CODE
224
225
226
227
228
229
230
231
232
233
234
235
236
237
238
239
240
241
242
243
244
245
246
247
248
249
250
251
252
253
254
255
Table 3.7 (Concluded) Sheet 6: Hex E0 to FF
HA246958
Issue 14 Mar 02 Page 39
COMMUNICATIONS MANUAL
3.8 APPLICATION NOTES
3.8.1 Message timing
The recorder can receive a message as a continuous byte stream (i.e. the bytes in a message may be end to end).
3.8.2 Command mnemonics
These mnemonics cause the serial link to perform some action. Command mnemonics which control the chart have the same priority as the operator (i.e. last input from either source overrides previous inputs).
3.8.3 Channel selection
It is not possible to write directly to the recorder data base because of the interdependence of parameters. For this reason, the characters are held in a buffer until an ‘EC’ command mnemonic is received.
As each parameter is received it is checked, and if it is valid, an ACK is returned and the data is stored in the buffer.
(If the data is not valid, a NAK is returned and the data is discarded.) When the EC mnemonic is received the contents of the buffer are checked, and if the data is all valid, the contents of the buffer are stored in the recorder data base, and an ACK is returned. If the data is not valid, a NAK is returned, the data is discarded and an error flag set in ‘ER’ (See Instrument Mnemonics in section 3.4.3, above).
Note: It is not possible for the user to read the buffer, either before or after the EC mnemonic.
3.8.4 Alarm selection / polling
There is a single buffer through which alarms can be accessed. The relevant alarm is read into the buffer from the data base as the result of a command mnemonic ‘GA’. This buffer can then be written to or read, via the instrument address (U = 0). When writing to the buffer, the data is stored until a command mnemonic (EA) is received, as described below.
SELECTION
As each parameter is received it is checked, and if it is valid, an ACK is returned and the data is stored in the buffer.
(If the data is not valid, a NAK is returned and the data is discarded.) When the EA mnemonic is received the contents of the buffer are checked, and if the data is all valid, the contents of the buffer are stored in the recorder data base, and an ACK is returned. If the data is not valid, a NAK is returned and the data is discarded. The alarm buffer is marked as ‘invalid’ and must be refilled before it can again be accessed. A NAK is returned if an attempt is made to read or write to the buffer before it is refilled.
3.8.5 Printed text
If text to be printed is sent via the ‘PT’ mnemonic (section 3.4.3) it is placed in the instrument’s demand message queue, and treated as a standard demand message. If there is insufficient space in the queue, a NAK is returned.
Page 40
HA246958
Issue 14 Mar 02
COMMUNICATIONS MANUAL
3.8.6 Special characters
ASCII MODE
The printing control characters (table 3.1.2) may be used only as control characters (i.e. they may not be used as a part of a text string). The ASCII control characters (e.g. STX) may not be used at all in ASCII mode.
ANSI MODE
The ASCII control characters may be used only in their correct positions (i.e. they may not be used as a part of a text string).
Notes
1. The special characters shown in table 3.7 sheets 3, 4 and 5, above, require the use of eight data bits, and both the recorder and the host must be configured as such.
2. Model 4001 characters which are not available with curent recorders and vice-versa, are treated as an underline symbol (_).
3.8.7 Multi-parameter data packets
When a parameter which contains a number of different individual items (e.g. channel flags CF - see table 3.4.1) then it is not possible to change only a single item within the parameter; the whole word must be written with the required data for each bit.
When one or more bits in a multi-parameter mnemonic are READ-ONLY, or not used, those bits are ignored. No error flag is set in ‘ER’.
3.8.8 Digital input channels
These types of channel cannot be written to using this communications protocol. If an attempt is made to do so, a
NAK is returned and code 05 is set into ‘ER’.
The process value (PV) for digital channels may be polled (read), with the response 0.0 if the input is open and 1.0 if the input is closed.
The measured value (MV) for digital channels may also be polled (read), with the response 0000 if the input is open and 0001 if the input is closed.
3.8.9 Floating point overflow
Maths channel PVs, scales, alarm setpoints etc. may exceed the floating point range ( 9999) of the 4001 emulation protocol. In such a case, the value 9999 (with appropriate sign) is returned.
HA246958
Issue 14 Mar 02 Page 41
COMMUNICATIONS MANUAL
4 GOULD MODICON MODBUS PROTOCOL
When connected to a host computer the recorder acts as a slave Modbus device. The unit address (1 to 247) being set up as a part of the recorder’s communications configuration. Only a limited number of function codes have been implemented (ref. Modbus protocol manual) and these are listed in section 4.3
4.1 CHANNEL ADDRESSING
The channel 1 address listed in table 4.3 is the base address at which channel 1 may be accessed.
Note: Addressing starts at zero, whilst channel numbers start at 1
Example: to read a digital input at channel 23, the required address passed with the code 01 would be 22
If an alarm is set for an input or derived channel, the associated alarm parameters can be read using code 03
Example: To read the set point of absolute alarm 1 on channel 8, the required address passed with code 03 should be
1257 (1250 = channel 1; 1251 = channel 2 etc.).
The interpretation of alarm parameters (A1 to A4 and SP1 to SP4 in table 4.3) depends on alarm type as follows:
ALARM TYPE PARAMETER
Absolute
Absolute
Deviation
Deviation
Rate
Rate
Digital
Digital
A1 to A4
SP1 to SP4
A1 to A4
SP1 to SP4
A1 to A4
SP1 to SP4
A1 to A4
SP1 to SP4
DEFINITION
Not used
Setpoint values
Deviation values
Setpoint values
Rate value
Period value (secs)
Not used
0000 = Open; FFFF = closed
Table 4.1 Alarm paramteter interpretation
Note: Any request to read a nonexistent setpoint value will result in the value 0000 being returned. This should not be taken to mean that the setpoint is at 0.000
4.2 READING ANALOGUE VALUES
4.2.1 16-bit format
The values read are in the range 0000 to FFFF. To obtain the scaled relative value, the following calculation must be carried out:
Scaled value =

ï£ï£¬
High range - Low range
FFFF
x Analogue measurement


+ low range where the analogue measurement is in hex.
In the event of a hardware error or under-range value, the value is forced to scale zero. Should the analogue value be over range, the scaled value is forced to scale high.
Page 42
HA246958
Issue 14 Mar 02
COMMUNICATIONS MANUAL
4.2 READING ANALOGUE VALUES (Cont.)
4.2.2 32-bit format
Values read from service code 03 addresses based at:
7250 (Analogue channel scale low value)
7750 (Analogue channel scale high value)
8250 (Derived channel scale low value)
8750 (Derived channel scale high value) and values read from service code 04 addresses based at:
1500 (Analogue channel value)
2000 (Derived channel value) are in 32-bit IEEE floating point format. Each value resides in two consecutive 16-bit registers transmitted most significant byte first. Two registers per channel must be requested, and the required address increases by two per channel number, for example:
Analogue channel 1: Code04; address 1500
Analogue channel 2: Code 04; address 1502 or generally:
Analogue channel N: code 04; address 1500 + 2(N-1)
Example 1 Read channel 05
( 0x- means the two characters following the 'x' are in hexadecimal)
<slave address><code><register addr high><register addr low><nº of registers high>
<nº of registers low><CRC high><CRC low>
Specifically, to read analogue channel 05 from slave address 2:
<0x02><0x04><0x05><0xE4><0x00><0x02><CRC high><CRC low>
To which the reply should be:
<slave address><code><byte count><most significant byte><next byte><next byte>
<least significant byte>
Specifically for channel 5 having a value of 1.123 (0x3F8FBE76 in 32-bit IEEE format)
<0x02><0x04><0x04><0x3F><0x8F><0xBE><0x76>
TOTALISER VALUES
To read a totaliser value, use the derived channel copy facility to import the totaliser value into a derived channel, and read this derived channel using service code 04 (base address 2000). The returned value will be in 32-bit IEEE float as described above.
HA246958
Issue 14 Mar 02 Page 43
COMMUNICATIONS MANUAL
4.3 FUNCTION CODES
CODE
01
02
03
FUNCTION RECORDER ACTION CHANNEL 1
ADDRESS (DECIMAL)
Read coil status Digital input state (true = >0.5) ................................................ 0
Digital read input status Digital input state (true = < 0.5) ............................................... 0
I/O alarm 1 status .................................................................... 250
Read holding register
I/O alarm 2 status .................................................................... 500
I/O alarm 3 status .................................................................... 750
I/O alarm 4 status ................................................................... 1000
Derived alarm 1 status ............................................................ 1250
Derived alarm 2 status ............................................................ 1500
Derived alarm 3 status ............................................................ 1750
Derived alarm 4 status ............................................................ 2000
I/O channel value ...................................................................... 0
I/O channel A1 (Table 4.1) ...................................................... 250
I/O channel A2 (Table 4.1) ...................................................... 500
I/O channel A3 (Table 4.1) ...................................................... 750
I/O channel A4 (Table 4.1) ..................................................... 1000
I/O channel SP1 (Table 4.1) ................................................... 1250
I/O channel SP2 (Table 4.1) ................................................... 1500
I/O channel SP3 (Table 4.1) ................................................... 1750
I/O channel SP4 (Table 4.1) ................................................... 2000
Derived channel A1 (Table 4.1) ............................................. 2250
Reserved (always returns 0000) ............................................. 2500
Derived channel A2 (Table 4.1) ............................................. 2750
Reserved (always returns 0000) ............................................. 3000
Derived channel A3 (Table 4.1) ............................................. 3250
Reserved (always returns 0000) ............................................. 3500
Derived channel A4 (Table 4.1) ............................................. 3750
Reserved (always returns 0000) ............................................. 4000
Derived channel SP1 (Table 4.1) ........................................... 4250
Reserved (always returns 0000) ............................................. 4500
Derived channel SP2 (Table 4.1) ........................................... 4750
Reserved (always returns 0000) ............................................. 5000
Derived channel SP3 (Table 4.1) ........................................... 5250
Reserved (always returns 0000) ............................................. 5500
Derived channel SP4 (Table 4.1) ........................................... 5750
Reserved (always returns 0000) ............................................. 6000
I/O channel status (read only) (flags - see code 04) .............. 6250
Derived channel status (read only) (flags - see code 04) ...... 6500
Instrument status (read only) (flags - see code 07) ................ 6750
Analogue real channel scale low value (32-bit) .................... 7250
Analogue real channel scale high value (32-bit) ................... 7750
Derived channel scale low value (32-bit) .............................. 8250
Derived channel scale high value (32-bit) ............................. 8750
Table 4.3 Modbus implementation channel addresses (Sheet 1: codes 01 to 03)
Page 44
HA246958
Issue 14 Mar 02
COMMUNICATIONS MANUAL
4.3 FUNCTION CODES (Cont.)
CODE
04
05
06
07
08
15
16
65
66
FUNCTION
Read input register
Force single coil
Preset single register
Read exception status
Loopback test
Force multiple coil
Preset multiple registers
Enter XMODEM mode
Report XMODEM error
RECORDER ACTION CHANNEL 1
ADDRESS (DECIMAL)
Analogue input/output value ................................................................. 0
I/O channel status ................................................................................ 250
No bits set: Channel OK
Bit 0 set:
Bit 1 set:
Bit 2 set:
Bit 3 set:
Channel off
Over range
Under range
Hardware error / bad PV
Bit 4 set:
Bit 5 set:
Ranging error / no data
Overflow
Bits 6 to 15: Always 0.
Derived channel value ......................................................................... 500
Reserved (returns 0000) ...................................................................... 750
Derived channel status ...................................................................... 1000
(Bits 0 to 15 as for I/O channel status above)
Instrument status (flags - code 7) ...................................................... 1250
Analogue real channel value (32-bit) ............................................... 1500
Derived channel value (32-bit) ......................................................... 2000
Sets digital input state for comms channel ........................................... 0
0 = 0.000; 1 = 1.000
Preset holding register .................................................................. As code 03
(Presets values for comms channels only)
(Base addresses 7250, 7750, 8250 and 8750 cannot be preset)
Read instrument status
Bit 0:
Bit 1:
System error
Writing system failure
Bit 2: Paper out (250 mm non-graphics recorders only)
Bits 3 to 7 Always 0
Diagnostic code 0 (Echoes message as sent)
Sets digital input code for comms channels in address range. ............. 0
0 = 0.000
1 = 1.000
Preset holding register for each channel in address range. .......... As code 03
(Presets values for comms channels only)
(Base addresses 7250, 7750, 8250 and 8750 cannot be preset)
Holds 1 byte of data specifying which mode to enter
0 = standby; 1 = Receiver; 2 = Sender
Returns 1 byte of data as follows:
0: Transfer OK - no errors
1: Restore failed completely
File was incompatible or comms failed
2: to transfer the file,
Original configuration unchanged.
Restore failed on data.
Some records ignored, but transfer mostly successful.
3: Restore failed on transfer
Some config. transferred before failure.
New configuration undefined
16: Save had no reply from comms and timed out
32: Save failed before transfer completed
Table 4.3 Modbus implementation channel addresses (Sheet 2)
HA246958
Issue 14 Mar 02 Page 45
COMMUNICATIONS MANUAL
4.3 FUNCTION CODES (Cont.)
CODE
01
02
03
06
FUNCTION RECORDER ACTION CHANNEL 1
ADDRESS (DECIMAL)
Illegal function
Illegal data address
Illegal data
Illegal busy
EXCEPTION RESPONSES
Unsupported or illegal Modbus function .............................................. 0
Data address out of range for instrument config .................................. 0
Attempt to preset input value of non comms channel
Invalid configuration data
Data value out of range for function
Configuration transfer in progress via another port so unable to action function
Table 4.3 Modbus implementation channel addresses (Sheet 3)
5 XMODEM TRANSFER
XMODEM transfers take place between a host computer and a single instrument using MODBUS or 4001 protocol.
The transfer is used to save or restore recorder configurations. The transfer procedure is as follows
1. Place any other instruments on the communications link into standby mode.
2. Set the required recorder to sender or receiver mode as appropriate.
3. Send or receive file at host.
4. 10 seconds after completion, host communications is restored to normal use.
Notes:
1. 10 seconds of inactivity on the communications link, at any point in the procedure, will cause the host communications to return to normal use for instruments in standby mode.
2. XMODEM transfer is not possible with graphics recorders or graphics display units.
Page 46
HA246958
Issue 14 Mar 02
COMMUNICATIONS MANUAL
6 LIST OF EFFECTIVE PAGES
This (issue 14) manual consists of the following pages at their stated issues:
Page 1
Page 2
Page 3
Page 4
Page 5
Page 6
Page 7
Page 8
Page 9
Page 10
Page 11
Page 12
Page 13
Page 14
Page 15
Page 16
Page 17
Page 18
Page 19
Page 20
Page 21
Page 22
Page 23
Page 24
Issue 14 Mar 02
Issue 14 Mar 02
Issue 14 Mar 02
Issue 14 Mar 02
Issue 14 Mar 02
Issue 11 Dec 97
Issue 11 Dec 97
Issue 11 Dec 97
Issue 11 Dec 97
Issue 11 Dec 97
Issue 14 Mar 02
Issue 14 Mar 02
Issue 14 Mar 02
Issue 14 Mar 02
Issue 14 Mar 02
Issue 14 Mar 02
Issue 14 Mar 02
Issue 14 Mar 02
Issue 14 Mar 02
Issue 14 Mar 02
Issue 14 Mar 02
Issue 14 Mar 02
Issue 14 Mar 02
Issue 14 Mar 02
Page 25
Page 26
Page 27
Page 28
Page 29
Page 30
Page 31
Page 32
Page 33
Page 34
Page 35
Page 36
Page 37
Page 38
Page 39
Page 40
Page 41
Page 42
Page 43
Page 44
Page 45
Page 46
Page 47
Page 48
Issue 14 Mar 02
Issue 14 Mar 02
Issue 14 Mar 02
Issue 14 Mar 02
Issue 14 Mar 02
Issue 14 Mar 02
Issue 14 Mar 02
Issue 14 Mar 02
Issue 14 Mar 02
Issue 14 Mar 02
Issue 14 Mar 02
Issue 14 Mar 02
Issue 14 Mar 02
Issue 14 Mar 02
Issue 14 Mar 02
Issue 14 Mar 02
Issue 14 Mar 02
Issue 14 Mar 02
Issue 14 Mar 02
Issue 14 Mar 02
Issue 14 Mar 02
Issue 14 Mar 02
Issue 14 Mar 02
Issue 14 Mar 02
HA246958
Issue 14 Mar 02 Page 47
COMMUNICATIONS MANUAL
Symbols
4001 ANSI protocol
Description ................................................. 15
Selection .................................................... 14
4001 ASCII protocol
Description ................................................. 16
Selection .................................................... 14
A
Alarm mnemonics ........................................... 25
Application notes ............................................ 40
B
Baud rate setting............................................. 14
C
Channel mnemonics
Derived channels ......................................... 24
Input channels ............................................. 20
Output channels .......................................... 22
Character set ................................................. 34
Circuit board links .......................................... 13
Command mnemonics ..................................... 31
Configuration
Circuit board links ....................................... 13
Hardware ................................................... 14
Software..................................................... 14
D
Data bits ........................................................ 14
Data formats .................................................. 17
F
Function codes ...................................... 44 to 46
H
Hardware handshake ...................................... 14
Index
I
Installation
Electrical ...................................................... 9
Mechanical .................................................. 4
180 mm recorders...................................... 7
250mm continuous-trace recorders ............... 6
Instrument mnemonics ...................................... 27
M
Modbus protocol ............................................ 42
P
Parameter
Addressing ................................................. 17
Alarm ........................................................ 25
Derived channel .......................................... 24
Input channel .............................................. 20
Instrument ................................................... 27
Mnemonics overview ................................... 18
Output channel ........................................... 22
Scrolling order ............................................ 33
Parity setting .................................................. 14
Protocol selection ............................................ 14
R
Reading analogue values
16-bit ......................................................... 42
32-bit ......................................................... 43
Reading totaliser values ................................... 43
RS232/RS422/RS485 selection
Isolated version ............................................. 9
Original version ............................................ 5
S
Software Handshake ....................................... 14
Stop bits ........................................................ 14
T
Termination and biasing .................................. 11
X
XMODEM transfer .......................................... 46
XON-XOFF .................................................... 14
Page 48
HA246958
Issue 14 Mar 02
Inter-Company sales and service locations
Australia
Eurotherm Pty. Limited.
Unit 10.
40 Brookhollow Avenue,
Baulkham Hills,
NSW 2153
Telephone: 61 2 9634 8444
Fax: 61 2 9634 8555 e-mail: [email protected]
http://www.eurotherm.com.au
Austria
Eurotherm GmbH
Geiereckstraße 18/1,
A1110 Wien,
Telephone: 43 1 798 76 01
Fax: 43 1 798 76 05 e-mail:[email protected]
http://www.eurotherm.at
Belgium
Eurotherm BV,
Kontichsesteenweg 54
2630 Aartselaar
Antwerpen
Telephone: 32 3 320 8550
Fax: 32 3 321 7363
Denmark
Eurotherm Danmark A/S
Finsensvej 86,
DK 2000 Fredriksberg,
Telephone: +45 (38) 871622
Fax: +45 (38) 872124 e-mail: [email protected]
Finland
Eurotherm Finland,
Aurakatu 12A,
FIN-20100 Turku
Telephone: 358 2 25 06 030
Fax: 358 2 25 03 201
France
Eurotherm Automation Division Chessell
Parc d'Affaires,
6, Chemin des Joncs,
BP55
F - 69574 Dardilly, CEDEX
Telephone: 33 0 4 78 66 55 20
Fax: 33 0 4 78 66 55 35
Germany
Eurotherm Deutschland GmbH
Ottostraße 1,
65549 Limburg
Tel: +49 (0) 64 31/2 98 - 0
Fax: +49 (0) 64 31/2 98 - 1 19 e-mail:[email protected]
http://www.eurotherm-deutschland.de
Great Britain
Eurotherm Limited,
Faraday Close,
Worthing,
West Sussex BN13 3PL
Telephone: +44 (0)1903 695888
Fax: +44 (0)1903 695666 e-mail:[email protected]
http://www.eurotherm.co.uk
Hong Kong
Eurotherm Limited,
Unit D, 18/F Gee Chang Hong Centre,
65, Wong Chuk Hang Road,
Aberdeen.
Telephone: 852 2873 3826
Fax: 852 2870 0148 e-mail:[email protected]
India
Eurotherm DEL India Limited,
152, Developed Plots Estate,
Perungudi,
Chennai 600 096,
Telephone: 91 44 4961129
Fax: 91 44 4961831 e-mail: [email protected]
http://www.eurothermdel.com
Italy
Eurotherm SpA,
Via XXIV Maggio,
I-22070 Guanzate,
Como.
Telephone: 39 031 975111
Fax: 39 031 977512 e-mail:[email protected]
http://www.eurotherm.it
Japan
Densei Lambda K.K.,
Strategic Products Dept.
5F Nissay Aroma Square,
37-1, Kamata, 5-Chome,
Ohta-ku,
Tokyo 144-8721
Telephone: 81 3 5714 0620
Fax: 81 3 5714 0621 e-mail (Sales): [email protected]
e-mail (Technical): [email protected]
http://www.densei-lambda.com
Korea
Eurotherm Korea Limited,
J- Building
402-3
Poongnab-Dong,
Songpa-Ku
Seoul, 138-040
Telephone: 82 2 478 8507
Fax: 82 2 488 8508
Netherlands
Eurotherm BV,
Genielaan 4,
2404CH Alphen aan den Rijn,
The Netherlands
Telephone: 31 172 411 752
Fax: 31 172 417 260 e-mail: [email protected]
http://www.eurotherm.nl
Norway
Eurotherm A/S,
Vollsveien 13D
1366 Lysaker,
Postboks 227
NO-1326 Lysaker
Norway,
Telephone: 47 67 592170
Fax: 47 67 118301 http://www.eurotherm.no
Spain
Eurotherm España SA,
Pol. Ind. De Alcobendas,
Calle de la Granja 74,
28108 Alcobendas,
Madrid.
Telephone: 34 91 661 60 01
Fax: 34 91 661 90 93 http://www.eurotherm.es
Sweden
Eurotherm AB,
Lundavägen 143,
S-21224 Malmö.
Telephone: 46 40 38 45 00
Fax: 46 40 38 45 45 e-mail:[email protected]
http://www.eurotherm.se
Switzerland
Eurotherm Produkte (Schweiz) AG,
Schwerzistraße, 20,
CH-8807 Freienbach.
Telephone: 41 55 415 44 00
Fax: 41 55 415 44 15 e-mail:[email protected]
http://www.eurotherm.ch
United States of America
Eurotherm Recorders Inc.
741-F Miller Drive
Leesburg
VA 20175-8993
Telephone: 1 703 669 1342
Fax: 1 703 669 1307 e-mail (Sales): [email protected]
e-mail (Technical): [email protected]
http://www.chessell.com
ε
E U R O T H E R M
EUROTHERM LIMITED
Faraday Close, Durrington, Worthing, West Sussex, BN13 3PL
Telephone: 01903 695888 Facsimile: 01903 695666 e-mail: [email protected]
Website: http://www.eurotherm.co.uk
Specification subject to change without notice. ©Eurotherm Limited.
HA246958/14 (CN13655)
advertisement
Related manuals
advertisement
Table of contents
- 3 CONTENTS
- 5 1 INTRODUCTION
- 6 2 INSTALLATION
- 6 2.1 INSTALLATION OF ORIGINAL VERSION
- 7 2.1.1 Mode selection
- 8 2.2 ISOLATED VERSION INSTALLATION
- 8 2.2.1 Installation for 250 mm recorders
- 8 Multipoint recorders
- 8 Continuous trace recorders
- 9 2.2.2 Installation for 180 mm recorders
- 11 2.2.3 Mode selection
- 11 2.3 COMMUNICATIONS WIRING
- 11 2.3.1 Original version
- 11 2.3.2 Isolated version
- 13 2.3.3 Termination and biasing (not RS232)
- 13 HOST COMPUTER
- 15 2.3.4 On-board links
- 16 2.4 HARDWARE CONFIGURATION
- 16 2.4.1 Communications parameters
- 16 2.4.2 Handshake
- 16 HARDWARE HANDSHAKE
- 16 SOFTWARE HANDSHAKE
- 17 3 MODEL 4001 COMMUNICATIONS
- 17 3.1 COMMUNICATIONS PROTOCOLS
- 17 3.1.1 ANS I
- 17 POLLING
- 18 SELECTION
- 18 3.1.2 ASCII
- 19 3.2 PARAMETER ADDRESSING
- 19 3.3 DATA FORMATS
- 19 3.3.1 Hexadecimal (Hex)
- 19 3.3.2 Decimal (Floating point)
- 19 3.3.3 Character
- 20 3.4 MNEMONICS
- 21 3.4.1 Channel mnemonics
- 22 Input channels
- 24 Output channels
- 26 Derived channels
- 27 3.4.2 Alarm mnemonics
- 27 ALARM BUFFER VALIDATION CHECKS.
- 29 3.4.3 Instrument mnemonics
- 33 3.5 COMMAND MNEMONICS
- 33 3.5.1 Alarm acknowledge (AA)
- 33 3.5.2 Printer on (CG)
- 33 3.5.3 Chart halt (CH)
- 33 3.5.4 Printer off (CO)
- 33 3.5.5 Chart Wind (CW)
- 33 3.5.6 Data Dump (DD)
- 33 3.5.7 Disable program mode (DP)
- 33 3.5.8 Enter alarm data (EA)
- 33 3.5.9 Enter channel data (EC)
- 33 3.5.10 Enable program mode (EP)
- 34 3.5.11 Get indicated alarm data (GA)
- 34 NO MATHS PACK FITTED
- 34 MATHS PACK FITTED
- 34 3.5.12 Get free alarm (GF)
- 34 3.5.13 Chart rewind (CR)
- 35 3.6 PARAMETER SCROLLING
- 35 3.6.1 Block parameters
- 35 3.6.2 Scroll parameters
- 35 ALARM PARAMETERS
- 35 INSTRUMENT PARAMETERS
- 36 3.7 CHARACTER SET
- 42 3.8 APPLICATION NOTES
- 42 3.8.1 Message timing
- 42 3.8.2 Command mnemonics
- 42 3.8.3 Channel selection
- 42 3.8.4 Alarm selection / polling
- 42 SELECTION
- 42 3.8.5 Printed text
- 43 3.8.6 Special characters
- 43 ASCII MODE
- 43 ANSI MODE
- 43 3.8.7 Multi-parameter data packets
- 43 3.8.8 Digital input channels
- 43 3.8.9 Floating point overflow
- 44 4 GOULD MODICON MODBUS PROTOCOL
- 44 4.1 Channel addressing
- 44 4.2 Reading analogue values
- 44 4.2.1 16-bit format
- 45 4.2.2 32-bit format
- 45 Example 1 Read channel 05
- 45 TOTALISER VALUES
- 46 4.3 FUNCTION CODES
- 48 5 XMODEM TRANSFER
- 49 6 LIST OF EFFECTIVE PAGES
- 50 INDEX