NTI TRX Series, TRX085, TRX110C, TRX120, TRX150C Installation, Start-Up, Maintenance, Parts, Warranty
Add to my manuals
116 Pages
NTI TRX Series is a residential condensing gas boiler designed to provide efficient and reliable space heating. With its advanced features, the TRX Series offers increased energy savings, improved comfort, and peace of mind. Whether you're looking for a primary or secondary heating source, the TRX Series is an excellent choice for your home.
advertisement
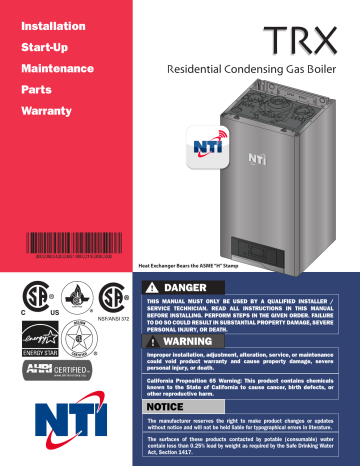
Installation
Start-Up
Maintenance
Parts
Warranty
TRX
R
esidential
C
ondensing
G
as
B
oiler
Heat Exchanger Bears the ASME “H” Stamp
DANGER
THIS MANUAL MUST ONLY BE USED BY A QUALIFIED INSTALLER /
SERVICE TECHNICIAN. READ ALL INSTRUCTIONS IN THIS MANUAL
BEFORE INSTALLING. PERFORM STEPS IN THE GIVEN ORDER. FAILURE
TO DO SO COULD RESULT IN SUBSTANTIAL PROPERTY DAMAGE, SEVERE
PERSONAL INJURY, OR DEATH.
WARNING
Improper installation, adjustment, alteration, service, or maintenance could void product warranty and cause property damage, severe personal injury, or death.
California Proposition 65 Warning: This product contains chemicals known to the State of California to cause cancer, birth defects, or other reproductive harm.
NOTICE
The manufacturer reserves the right to make product changes or updates without notice and will not be held liable for typographical errors in literature.
The surfaces of these products contacted by potable (consumable) water contain less than 0.25% lead by weight as required by the Safe Drinking Water
Act, Section 1417.
2
WARNING
WARNING: If the information in these instructions is not followed exactly, a fire or explosion may result causing property damage, personal injury or death.
• Do not store or use gasoline or other flammable vapors and liquids in the vicinity of this or any other appliance.
WHAT TO DO IF YOU SMELL GAS
• Do not try to light any appliance.
• Do not touch any electrical switch; do not use any phone in your building.
• Immediately call your gas supplier from a neighbor’s phone. Follow the gas supplier’s instructions.
• If you cannot reach your gas supplier, call the fire department.
• Installation and service must be provided by a qualified installer, service agency or the gas supplier.
Improper installation, adjustment, alteration, service, or maintenance can cause injury, property damage, or death.
Refer to this manual. Installation and service must be performed by a qualified installer, service agency, or gas supplier.
SPECIAL ATTENTION BOXES
The following defined terms are used throughout this manual to bring attention to the presence of hazards of various risk levels or to important product information.
DANGER
DANGER
indicates an imminently hazardous situation which, if not avoided, will result in serious personal injury or death.
WARNING
WARNING
indicates a potentially hazardous situation which, if not avoided, could result in personal injury or death.
CAUTION
CAUTION
indicates a potentially hazardous situation which, if not avoided, may result in moderate or minor personal injury.
CAUTION
CAUTION
used without the safety alert symbol indicates a potentially hazardous situation which, if not avoided, may result in property damage.
NOTICE
NOTICE is used to address practices not related to personal injury.
Foreword
This manual is intended to be used in conjunction with other literature provided with the boiler. This includes all related control information.
It is important that this manual, all other documents included in this system, and additional publications including the
National Fuel Gas
Code - ANSI Z223.1
in the United States and the
Natural Gas and Propane
Installation Code - B149.1
in Canada (latest versions), be reviewed in their entirety before beginning any work.
Installation should be made in accordance with the regulations of the Authority Having Jurisdiction, local code authorities, and utility companies which pertain to this type of water heating equipment.
Authority Having Jurisdiction (AHJ) – The AHJ may be a federal, state, provincial, local government, or individual such as a fire chief, fire marshal, chief of a fire prevention bureau, labor department or health department, building official or electrical inspector, or others having statutory authority. In some circumstances, the property owner or his/her agent assumes the role, and at government installations, the commanding officer or departmental official may be the AHJ.
NOTE: The manufacturer reserves the right to modify product technical specifications and components without prior notice.
For the Installer
This boiler must be installed by qualified and licensed personnel. The installer should be guided by the instructions furnished with the boiler, and by local codes and utility company requirements. In the absence of local codes, preference should be given to the
National Fuel Gas
Code - ANSI Z223.1
in the United States and the
Natural Gas and Propane
Installation Code - B149.1
in Canada (latest versions).
Installations Must Comply With:
Local, state, provincial, and national codes, laws, regulations, and ordinances.
In the United States - The latest version of the
National Fuel Gas Code,
ANSI Z223.1
, from American Gas Association Laboratories, 8501 East
Pleasant Valley Road, Cleveland, OH 44131.
The latest version of the
National Electrical Code, NFPA No. 70
.
In Canada - The latest versions of the
Natural Gas and Propane
Installation Code, CSA B149.1
, and the
Canadian Electrical Code, C22.1
, from CSA Group, 178 Rexdale Blvd, Toronto, Ontario, Canada M9W 1R3.
NOTE: The gas manifold and controls met safe lighting and other performance criteria when undergoing tests specified in
ANSI Z21.13
- latest edition.
3
4
WARNING
The hydronic supply and return connections of these products
are for installation in closed loop systems ONLY! Use of this product in any manner other than described in this manual may result in premature product failure, substantial property damage, severe personal injury, or death. Damage or failure of this product
(or the system in which it is installed) due to unauthorized use IS
NOT COVERED BY WARRANTY.
NOTICE
IMPORTANT
In accordance with Section 325 (f) (3) of the Energy Policy and
Conservation Act, NTI has provided this boiler with multiple features designed to save energy by reducing the boiler water temperature as heating load decreases.
These features include:
• A modulating combustion system that adjusts firing rate based on heat demand.
• Adjustment of boiler set point based on inferred heat load as determined by an outdoor sensor. The outdoor sensor is supplied with this boiler.
• This boiler does not include a standing pilot.
• This boiler is designed and shipped to assure the highest efficiency operation possible. Such high efficiency is achieved by limiting heating circuit water temperature to 140°F when there is no anticipated heat load, based upon the outdoor sensor and the Outdoor Reset Curve
(sensor response curve) in the boiler software.
• This feature may be over-ridden as described below in specific installations:
• The boiler control is equipped with an outdoor sensor override for use with building management systems or in cascaded systems (for systems with total input of
300,000 BTU/hr or greater).
See statement below for an important notice on the use of the override.
IMPORTANT
In accordance with Section 325 (f) (3) of the Energy Policy and Conservation Act, this boiler is equipped with a feature that saves energy by reducing the boiler water temperature as the heating load decreases. This feature is equipped with an override which is provided primarily to permit the use of an external energy management system that serves the same function. THIS OVERRIDE MUST NOT BE USED UNLESS AT
LEAST ONE OF THE FOLLOWING CONDITIONS IS TRUE:
• An external energy management system is installed that reduces the boiler water temperature as the heating load decreases.
• This boiler is not used for space heating.
• This boiler is part of a modular or multiple boiler system having a total input of 300,000 BTU/hr or greater.
NOTICE
ASME CSD-1, Section CW-400 requires the temperature controls of hot water heating boilers to a) be accepted by a nationally recognized testing agency to conform to UL 353, b) shutoff the fuel supply when the system water reaches a preset operating temperature, c) have a high temperature limit control that prevents the water temperature from exceeding the maximum allowable temperature by causing safety shutdown and lockout.
The temperature controls of this boiler have been accepted by a nationally recognized testing agency to conform to UL 353; they work to shutoff the fuel supply when the system water temperature reaches the preset operating temperature; and they cause a safety shutdown and lockout, requiring a manual reset to start, when the water temperature reaches 212°F.
Table of Contents
Part 1 - General Safety Information
A. Operation and Installation Warnings
B. Improper Combustion
C. Gas
D. When Servicing the Boiler
E. Boiler System
F. CH and DHW Loop Water Chemistry Requirements
G. Freeze Protection
H. Water Temperature Adjustment and Scalding
I. High Elevation Installations
Part 2 - Before You Start
A. What’s in the Box
B. Optional Equipment
Part 3 - Prepare the Boiler for Installation
A. Locating the Boiler
B. Leveling
C. Clearances for Service Access
D. Wall Mounting Considerations
E. Wall Mounting Instructions
1. Mounting to a Wood Studded Wall
2. Mounting to a Metal Frame
F. Residential Garage and Closet Installations
15
16
G. Exhaust Vent and Intake Pipe
1. Direct Vent of Exhaust and Intake
16
16
2. Power Venting, Indoor Combustion Air in Confined or Unconfined
17
H. Carbon Monoxide Detectors
I. Prevent Combustion Air Contamination
17
17
J. Removing a Boiler from a Common Vent System
K. Technical Specifications
Part 4 - Water Piping
A. General Plumbing Information
B. Backflow Preventer
C. Expansion Tank
D. Piping the Boiler
E. Internal Circulation Pump
F. By-Pass Valve
G. CH and DHW Pressure Relief Valves
24
24
26
26
27
18
19
24
24
24
H. Air Elimination Device
I. Applications*
H. Floor Drying Function
Part 5 - Venting
A. General
B. Approved Materials for Exhaust Vent and Intake Pipe
C. Additional Requirements for Installation in Canada
D. Exhaust Vent and Intake Pipe Location
E. Exhaust Vent and Intake Pipe Sizing
F. Tightening Boiler Collar to Exhaust Vent and Intake Pipe
G. Exhaust Vent and Intake Pipe Installation
H. Applications
1. Direct Vent Installation of Exhaust and Intake
2. Venting Through an Existing System
3. Power Venting, Indoor Combustion Air in Confined or Unconfined
37
37
38
39
39
40
42
42
48
28
28
35
36
36
12
13
13
14
14
9
10
8
9
10
14
15
15
7
7
7
7
8
6
6
Part 6 - Installing the Condensate Drain
Part 7 - Connecting Electrical Service
A. Wiring
1. Removing the Power Cord (To Hard Wire the Boiler)
2. Connecting Power (120V) for DHW and CH Circulators
3. Low Voltage Wiring Connections
4. Room Thermostat Wiring Connections
5. Outdoor Sensor Connections
6. Aquastat (Default) and Tank Sensor (Optional) Connections (Boiler
50
51
51
52
53
53
54
54
B. Internal Wiring Details 55
Part 8 - Gas Connections
A. Gas Pipe Sizing Tables
1. Gas Pipe Sizing
2. Natural Gas Pipe Sizing
3. LP (Liquid Propane) Gas Pipe Sizing
B. Gas Connection Requirements
C. Additional Precaution for Excess Flow Valve (EFV)
D. Checking Gas Pressure at the Boiler for Proper Operation 60
Part 9 - Controls 61
A. Control and Display Overview
B. Ignition Procedure
C. Central Heating (CH) Temperature Adjustment
61
62
62
D. Domestic Hot Water (DHW) Temperature Adjustment
E. User Menu
F. INFO Menu
G. Date and Time
H. Automatic CH Temperature Control (AUTO)
I. Outdoor Heating Curve Slope
J. Outdoor Heating Curve Parallel Shift
K. Room temperature Day /Night
(Only applicable when using NTI room sensor)
L. Time programs – heating schedule
62
63
64
64
65
66
66
66
59
59
59
59
59
59
60
(Only applicable when using NTI room sensor)
66
M. Automatic summer / winter changeover
N. Technical Menu
67
(Complete Programming & Troubleshooting Menus)
68
O. Boiler Control Menu Structure 69
P. Complete Menu Parameters
Part 10 - Start-Up Preparation
A. Check / Control Water Chemistry
B. Check for Gas Leaks
C. Freeze Protection (When Used)
70
78
78
78
78
D. System Water Fill, Purge, and Test
E. Purge Air from DHW System
F. Check Thermostat Circuit(s)
G. Condensate Removal
Part 11 - Start-Up
A. First Ignition
B. Combustion Checking Procedure
C. Checking Combustion Parameters
D. Converting the Appliance from Natural Gas to Propane
Operation
Part 12 - Installation Checklist
Part 13 - Troubleshooting
A. Boiler Protection Devices
1. Blocking Error
2. Lockout Error
3. Malfunction Warning
B. Boiler Error Codes
Part 14 - Maintenance
79
79
79
79
81
81
82
84
84
85
87
87
87
87
87
88
92
92
92
A. Procedures
B. Maintenance That May be Performed by the User
C. Maintenance Only to be Performed by a Qualified Service
Technician
D. Replacing Components
E. After Maintenance is Complete
Part 15 - Maintenance Report
Part 16 - Shutdown
A. Shutdown Procedure
B. Vacation Procedure
C. Failure to Operate
D. Important Notice
Part 17 - Replacement Parts
Maintenance Notes
93
97
100
100
102
102
102
102
102
103
114
5
6
Part 1 - General Safety Information
This boiler is approved for indoor installations only and is not intended for use as a pool heater. Clearance to combustible materials: 0” top, bottom, sides, and back. Boiler must have room for service: 18” front,
14” top, 12” bottom, 2” left and right sides and 0” back are minimum recommended service clearances. (A combustible door or removable panel is acceptable front clearance. A 3” minimum clearance must be provided from the boiler front cover to the removable panel or combustible door.) This boiler has been approved for closet installation and installation on combustible flooring. Do not install directly on carpeting. Install the boiler in a location where relief valve discharge or a leak will not result in damage to the surrounding area. If such a location is not available install an auxiliary catch pan.
This appliance is rated Category IV (pressurized vent, likely to form condensate in the vent) and requires a special vent system designed for pressurized venting. Use only Category IV vent systems.
WARNING
Installer -
Read all instructions in this manual before installing.
Perform steps in the given order.
User -
This manual is for use only by a qualified service technician.
Have this boiler serviced / inspected annually by a qualified service technician.
FAILURE TO ADHERE TO THE GUIDELINES ON THIS PAGE
CAN RESULT IN SUBSTANTIAL PROPERTY DAMAGE, SEVERE
PERSONAL INJURY, OR DEATH.
NOTE:
Obey all local codes. Obtain all applicable permits before installing the boiler.
NOTE:
Install all system components and piping in such a manner that does not reduce the performance of any fire rated assembly.
A. Operation and Installation Warnings
To avoid serious injury or death, read, understand, and follow all of the precautions listed here.
DANGER
Vapors from flammable liquids will explode and cause a fire, resulting in personal injury or death. The boiler has a burner that can come on at any time and ignite vapors. DO NOT use or store flammable liquids around the boiler.
Improper venting can cause a build-up of carbon monoxide.
Breathing carbon monoxide can result in brain damage or death.
DO NOT operate the boiler unless it is properly vented to the outside and has an adequate fresh air supply for safe operation.
Inspect the exterior exhaust gas outlet port and fresh air inlet port on a regular basis to ensure they are functioning properly.
A concentration of carbon monoxide as small as .04% (400 parts per million) in the air can be fatal. When making high fire or low fire adjustments, CO levels must be monitored using a calibrated combustion analyzer such that a CO level of no more than 150 ppm is exceeded at any time during operation.
Adjusting the “low fire offset” or the “main flow restrictor” in small increments can result in a significant increase in CO concentration.
To avoid serious injury or death, DO NOT make any adjustments to the gas valve without monitoring the exhaust gases with a fully functional and calibrated combustion analyzer.
Failure to follow these instructions will result in property damage, severe personal injury, or death.
WARNING
This boiler must be installed by a qualified service technician.
Improper installation and/or operation can cause a potentially hazardous situation, which if not avoided will void the warranty and could result in serious injury or death.
The manufacturer cannot anticipate every circumstance that might involve a potential hazard. Each installation has its own specialized characteristics, requirements, and possible hazards. Therefore, all possible incidents are not included in these warnings. Proper and safe installation, operation, and service are the responsibility of the qualified service technician.
Proper care of the boiler is the user’s responsibility. Ensure the user carefully reads and understands the User’s Information
Manual before operating the boiler.
Make sure the user knows the location of the gas shut-off valve and how to operate it. Immediately close the gas shut-off valve if the appliance is subjected to fire, overheating, flood, physical damage, or any other damaging condition that might affect the operation of the unit. Have the appliance checked by a qualified service technician before resuming operation.
Do not power up the unit unless the gas and water supply valves are fully opened. Make sure the fresh air intake port and exhaust gas port are open and functional.
No one but a qualified service technician should attempt to install, service, or repair this boiler. There are no serviceable parts which can be changed by the user / owner.
User / Owner: Contact the original qualified service technician if the boiler needs repair / maintenance. If the original technician is unavailable, ask your gas supplier for a list of qualified service providers.
DO NOT store or place newspapers, laundry, or other combustible items near the appliance or the exterior exhaust gas outlet and/or fresh air inlet port.
The owner should inspect the system monthly for damage, water stains, signs of rust, corrosion, and exhaust vent and air intake blockage. If inspection of the unit shows signs of damage, the boiler should be shut off until the problem is repaired by a qualified technician.
After installation, all appliance safety devices should be tested.
The boiler is certified for indoor installations only. The boiler consists of gas ignition system components which must be protected from water (dripping, spraying, etc.) during operation and service. Carefully consider installation location and the placement of critical components (circulators, condensate neutralizers, etc.) before installing the boiler.
DO NOT allow children to operate this boiler. DO NOT use this boiler if it does not appear to be operating correctly. A qualified service technician should service and inspect the boiler annually.
NOTE:
If the boiler is exposed to fire or water (or is any way damaged), do not operate. Immediately call a qualified service technician. Failure to follow this information could result in property damage, severe personal injury, or death.
WARNING
DO NOT USE THIS BOILER IF ANY PART HAS BEEN
SUBMERGED IN WATER.
Immediately call a qualified service technician. The boiler MUST BE replaced if it has been submerged.
Attempting to operate a boiler that has been submerged could create numerous harmful conditions, such as a potential gas leakage causing a fire and/or explosion, or the release of mold, bacteria, or other harmful particulates into the air. Operating a previously submerged boiler could result in property damage, severe personal injury, or death.
NOTE:
Boiler damage due to flood or submersion is considered an
Act of God, and IS NOT covered under product warranty.
WARNING
DO NOT alter or modify the appliance or appliance controls.
Altering any NTI boiler with parts not manufactured by NTI WILL
INSTANTLY VOID the boiler warranty and could result in property damage, personal injury, or death.
CAUTION
Due to the low water content of the boiler, improper sizing of the boiler with regard to heating system load will result in excessive cycling and accelerated component failure.
DO NOT
under or oversize the boiler to the system. Modular boiler installations greatly reduce the likelihood of boiler oversizing. NTI
DOES NOT
warrant failures caused by improperly sized boiler applications.
High heat sources (sources generating heat 100 o
F / 37 o
C or greater, such as stove pipes, space heaters, etc.) may damage plastic components of the boiler as well as plastic vent pipe materials. Such damages ARE NOT covered by warranty. It is recommended to keep a minimum clearance of 8” from high heat sources. Observe heat source manufacturer instructions, as well as local, state, provincial, and national codes, laws, regulations and ordinances when installing this boiler and related components near high heat sources.
Do not use this boiler for anything other than its intended purpose
(as described in this manual). Doing so could result in property damage and WILL VOID product warranty.
NOTICE
This appliance is equipped with a three prong plug. It should only be plugged directly into a properly grounded three prong receptacle.
DO NOT remove the ground plug from the plug.
This appliance provides an overheat shutdown limit. In the event the appliance water temperature exceeds the setpoint of the control limit, the cutoff will trip and the appliance will shut down. Certain local codes require additional temperature limits. In addition, certain types of systems may operate at temperatures below the minimum setpoint of the limit provided with the appliance. Contact the manufacturer for additional overheat controls.
Part 1 - General Safety Information
B. Improper Combustion
WARNING
Do not obstruct the flow of combustion and ventilating air.
Adequate air is necessary for safe operation. Failure to keep the exhaust vent and combustion air intake clear of ice, snow, or other debris could result in property damage, serious personal injury, or death.
C. Gas
Should overheating or gas supply fail to shut off, turn off the manual gas control valve to the boiler.
D. When Servicing the Boiler
WARNING
Be sure to disconnect electrical power before opening boiler cabinet or performing service. Label all wires while performing service to ensure proper re-wiring of the appliance. Wiring errors can cause improper or dangerous operation. Failure to do so could result in electrical shock, improper boiler or system operation, property damage, serious personal injury, or death.
• To avoid electric shock, disconnect electrical supply before performing maintenance.
• To avoid severe burns, allow boiler and associated equipment to cool before servicing.
• Do not use petroleum-based cleaning or sealing compounds in boiler system. Gaskets and seals in the system may be damaged, possibly resulting in substantial property damage.
• Do not use “homemade cures” or “boiler patent medicines”.
Substantial property damage, damage to boiler, and/or serious personal injury may result.
• Always verify proper operation after servicing the boiler.
NOTE: When inquiring about service or troubleshooting, reference the model and serial numbers from the boiler rating label.
E. Boiler System
• Thoroughly flush the system (without the boiler connected) to remove sediment. The high-efficiency heat exchanger can be damaged by build-up or corrosion due to sediment. The manufacturer recommends a suction strainer in this type of system.
• Do not use petroleum-based cleaning or sealing compounds in boiler system. Gaskets and seals in the system may be damaged, possibly resulting in substantial property damage.
• Do not use “homemade cures” or “boiler patent medicines”.
Substantial property damage, damage to boiler, and/or serious personal injury may result.
• Continual fresh make-up water will reduce boiler life. Mineral buildup in the heat exchanger reduces heat transfer, overheats the stainless steel heat exchanger, and causes failure. Addition of oxygen from make-up water can cause internal corrosion in system components. Leaks in the boiler or piping must be repaired at once.
NOTE: DO NOT add cold make up water to the system when the boiler is hot. Thermal shock can potentially cause cracks in the heat exchanger. Such damage IS NOT covered by warranty.
7
Part 1 - General Safety Information
F. CH and DHW Loop Water Chemistry Requirements
CAUTION
Chemical imbalance of the water supply may affect efficiency and cause severe damage to the boiler and associated equipment.
Water quality must be professionally analyzed to determine whether it is necessary to treat the water. Various solutions are available to adjust water quality. Adverse water quality will affect the reliability of the system. In addition, operating temperatures above 135 o
F will accelerate the build-up of lime scale and possibly shorten boiler service life. Failure of a boiler due to lime scale build-up, low pH, or other chemical imbalance IS NOT covered by the warranty.
The water must be potable, free of corrosive chemicals, sand, dirt, and other contaminates. It is up to the installer to ensure the water does not contain corrosive chemicals or elements that can damage the heat exchanger. Potable water is defined as drinkable water supplied from utility or well water in compliance with EPA secondary maximum contaminant levels (40 CFR Part 143.3). If the water contains contaminants higher than outlined by the EPA, water treatment is recommended and additional, more frequent maintenance may be required. See Table 1.
If you suspect that your water is contaminated in any way, discontinue use of the appliance and contact an authorized technician or licensed professional.
CH Loop Total Water Hardness Specifications
Contaminant Maximum Allowable Level
Total Hardness
120 mg/l
(7 grains/gallon)
DHW Loop Total Water Hardness Specifications
Contaminant Maximum Allowable Level
Total Hardness
(Below 140 o
F water temperature)
200 mg/l
(12 grains/gallon)
Total Hardness
(Above 140 o
F water temperature)
120 mg/l
(7 grains/gallon)
CH and DHW Loop Water Quality Specifications
Contaminant Maximum Allowable Level
Aluminum
Chloride
Copper
Iron
0.05 to 0.2 mg/l or PPM
100 mg/l or PPM
1 mg/l or PPM
0.3 mg/l or PPM
Manganese 0.05 mg/l or PPM pH
Sulfate
Total Dissolved Solids (TDS)
Zinc
Dissolved Carbon Dioxide (CO2)
6.5 - 8.5
205 mg/l or PPM
500 mg/l or PPM
5 mg/l or PPM
15 mg/l or PPM
Table 1 - Water Quality Specifications
8
G. Freeze Protection
CAUTION
Consider piping and installation when determining boiler location.
Damages resulting from incorrect installation or from use of products not approved by the manufacturer ARE NOT covered by warranty. Failure of the boiler due to freeze related damage IS NOT covered by product warranty.
WARNING
NEVER use any toxic chemical, including automotive, standard glycol antifreeze, or ethylene glycol made for hydronic (nonpotable) systems. These chemicals can attack gaskets and seals in water systems, are poisonous if consumed, and can cause personal injury or death.
NOTE: Loops Serving Indirect Water Heaters (IWHs)
Glycol used in IWH loops should be food grade propylene glycol,
FDA rated as “generally recognized as safe” (GRAS). If using a glycol / potable water mix, the water chemistry must meet the requirements in this manual. The glycol content of the liquid must not exceed 50%, unless the manufacturer specifies a different ratio. Glycol should be checked periodically to prevent it from becoming acidic. Please refer to guidelines provided by the glycol manufacturer regarding glycol maintenance.
NOTE: Glycol not recognized as GRAS may only be used in closed loop
CH applications.
NOTE: NTI DOES NOT WARRANT THE BOILER AGAINST FREEZE-RELATED
DAMAGE.
The boiler control is equipped with freeze protection that activates based on internal water temperature. See the following table for details on freeze protection operation.
NOTE: Freeze protection will not be active if the boiler loses power.
Condition
Events
Time
Condition
Events
FREEZE PROTECTION OPERATION
STAGE 1
The water temperature detected by probes NTC1 or
NTC2 ranges between 39 o
F (4 o
C) and 46 o
F (8 o
C).
• The internal pump operates at high speed.
• The 3-Way Valve alternately switches positions - 1 minute on heating mode to 1 minute on DHW mode
• The display shows the icon.
Until the NTC1 and NTC2 temperature is greater than or equal to
46°F (8°C)
If after 20 minutes the conditions described in Stage 1 are still present, the boiler proceeds to Stage 2.
STAGE 2
The water temperature detected by probes NTC1 or
NTC2 is less than 39 o
F (4 o
C).
• The burner turns on at minimum power.
• The 3-Way Valve is positioned on DHW and switches every 30 seconds between CH and DHW.
• When the temperature is greater than or equal to
104 o
F (40 o
C) the burner will turn off. The boiler will maintain the temperature between 95 and 104 o
F (40 o
C) for 45 minutes.
o
F (35 o
C)
• After 45 minutes there will be 2 minutes of post heating circulation.
• If the temperature falls below 46 o
F (8 o
C) within
150 minutes the burner will immediately power on again.
Time
• The display shows the icon.
Until the NTC1 temperature is greater than or equal to
104 o
F (40 o
C)
Table 2 - Freeze Protection Detail
CAUTION
On TRX085 / TRX120 Models ONLY
If the boiler to be used only in Heating Mode (not connected to an indirect water heater), the electrical connection of the 3-way valve motor MUST BE DISCONNECTED while the boiler is operating in central heating mode. This will lock the valve motor in central heating mode and ensure freeze protection operates properly. Failure to disconnect the valve may disable boiler freeze protection and result in property damage.
H. Water Temperature Adjustment and Scalding
This boiler can deliver scalding water. Be careful whenever using hot water to avoid scalding injury.
Certain appliances such as dishwashers and automatic clothes washers may require increased water temperatures. By setting the thermostat on this boiler to obtain the increased water temperature required by these appliances you may create the potential for scald injury.
To protect against injury, install a mixing valve in the water system. This valve will reduce point of use discharge temperatures by mixing cold and hot water in branch supply lines.
Such valves are available from your local plumbing supplier.
Table 3 details the relationship of water temperature and time with regard to scald injury and may be used as a guide in determining the safest water temperature for your applications.
Approximate Time / Temperature Relationships in Scalds
120 o F
125 o F
130 o F
135 o F
140 o F
145 o F
150 o F
More than 5 minutes
1 1/2 to 2 minutes
About 30 seconds
About 10 seconds
Less than 5 seconds
Less than 3 seconds
About 1 1/2 seconds
155 o F About 1 second
Table 3 - Time and Temperature Relationship in Scalds
Part 1 - General Safety Information
I. High Elevation Installations
WARNING
Natural gas at high elevation might contain less heating value than typical 1,000 BTU/cu ft and therefore can cause improper air / gas mix leading to improper combustion. For natural gas installations above 3,000 ft, call your gas provider to determine the heating value of the supplied natural gas.
9
Part 2 - Before You Start
NOTICE
UNCRATING THE BOILER
- Any claims for damage or shortage in shipment must be filed immediately against the transportation company by the consignee.
Remove the boiler from the packaging. Remove the accessory box from the boiler. Take care to place the boiler in a safe location prior to installation to prevent damage to the mechanical connections.
A. What’s in the Box
All models
5
5
6
2
1
13
3
14
TRX085
14a
14b
14f
12
THIS CONTROL WAS CONVERTED FOR USE WITH PROPANE GAS
This appliance has been converted for use with Propane Gas, in accordance with the instructions provided with the Natural to Propane Conversion Kit by ______________________________________ , which accepts responsibility that the conversion was performed properly.
Reference rating plate for Propane Input and Gas Pressure
420060882600
4
Connectivity
Quick Start Guide
TRX series
User’s
Information
Manual
TRX
R esidential C ondensing G as B oiler
Installation
Start-Up
Maintenance
NOTICE without notice and will not be held liable for typographical errors in literature.
Parts
The manufacturer reserves the right to make product changes or updates
Warranty
The surfaces of these products contacted by potable (consumable) water contain less than 0.25% lead by weight as required by the Safe Drinking
Water Act, Section 1417.
NOTE TO CONSUMER:
PLEASE KEEP ALL INSTRUCTIONS
FOR FUTURE REFERENCE.
R esidential
Heat Exchanger Bears the ASME “H” Stamp
C ondensing G as B oiler
TRX
NATURAL TO PROPANE
CONVERSION INSTRUCTIONS
For Qualified Technician
Installation Instructions
WARNING
IF THE INFORMATION IN THIS MANUAL IS NOT FOLLOWED EXACTLY,
A FIRE OR EXPLOSION MAY RESULT, CAUSING PROPERTY DAMAGE,
PERSONAL INJURY, OR LOSS OF LIFE. DO NOT STORE GASOLINE OR
OTHER FLAMMABLE VAPORS AND LIQUIDS IN THE VICINITY OF THIS OR
ANY OTHER BOILER.
Heat Exchanger Bears the ASME “H” Stamp
• Do not try to light any boiler.
• Do not touch any electrical switch.
DANGER
• Immediately call your gas supplier from a neighbor’s phone. Follow the
THIS MANUAL MUST ONLY BE USED BY A QUALIFIED INSTALLER /
SERVICE TECHNICIAN. READ ALL INSTRUCTIONS IN THIS MANUAL
BEFORE INSTALLING. PERFORM STEPS IN THE GIVEN ORDER. FAILURE service agency, or the gas supplier.
PERSONAL INJURY, OR DEATH.
Improper installation, adjustment, alteration, service, or maintenance could void product warranty and cause property damage, severe personal injury, or death.
WARNING
Improper installation, adjustment, alteration, service, or maintenance could void product warranty and cause property damage, severe known to the State of California to cause cancer, birth defects, or other reproductive harm.
personal injury, or death.
California Proposition 65 Warning: This product contains chemicals known to the State of California to cause cancer, birth defects, or other reproductive harm.
NOTICE
The manufacturer reserves the right to make product changes or updates without notice and will not be held liable for typographical errors in literature.
The surfaces of these products contacted by potable (consumable) water contain less than 0.25% lead by weight as required by the Safe Drinking Water
Act, Section 1417.
11
WARNING
This conversion kit shall be installed by a qualified service agency in accordance with the manufacturer’s instructions and all applicable codes and requirements of the authority having jurisdiction. If the information in these instructions is not followed exactly, a fire, an explosion or production of carbon monoxide may result causing property damage, personal injury or loss of life. The qualified service agency is responsible for the proper installation of this kit. THE INSTALLATION IS NOT
PROPER AND COMPLETE UNTIL THE OPERATION OF THE
CONVERTED APPLIANCE IS CHECKED AS SPECIFIED IN
THE MANUFACTURER’S INSTRUCTIONS SUPPLIED WITH
THE KIT, WHICH NECESSITATES THE USE OF A CALIBRATED
CO2/O2 AND CO COMBUSTION ANALYZER.
15
TRX110C
15b
14c
15c
Gas
15e
15a
14g
14d
14e
14h
ACCESSORIES BOX
BOITE ACCESSOIRES
For Qualified Technician
Installation Instructions
Pour technicien qualifié instructions d’installation
Read the code
Lire le code
code
Gas
8
15g
7
15d
ACCESSORIES BOX
BOITE ACCESSOIRES
9
0
0
20
20
40 psi
60
80
50
100
250
150
200
10
For Qualified Technician
Installation Instructions
Pour technicien qualifié instructions d’installation
Read the code
Lire le code
code
15f
Components included with the boiler:
7
8
5
6
9
3
4
1
2
10
Nr.
11
Quantity
1
1
1
1
1
1
1
1
1
1+1
1
1
1
2 + 2
1
2
1
1
1
1
Description
ALL MODELS
Condensing Gas Boiler
Condensate Drain Pipe
Bracket
Assembly Screws (Fischer Type SX )
CH Pressure Relief Valve + Connection Tube
2” CPVC Pipe, 5.5” Long
Piping Bracket
Torx screw adapter
2” Vent Screen + 3” Vent Screen
Tridicator
Installation Manual (This Document)
User’s Information Manual
Connectivity Quick Start Guide
LP Convertion Instructions
Warranty
Installation Quick Start Guide
Template
LP Gas Conversion Kit
Outdoor sensor Kit
Piping Adapter Kit
- TRX085
12
13
14
15
15-a
15-b
15-c
15-d
15-e
15-f
15-g
14-a
14-b
14-c
14-d
14-e
14-f
14-g
14-h
2
1
1
1
4
1
1
6
1
1
1
1
4
1
2
6
16 1
Cap 1/2”
Gasket (2x1/2” + 2x3/4” + 1 x 1” + 1 gas fiber)
Clamp (2x3/4” + 2x1”)
Gas Adapter 3/4”
CH supply pipe 1”
CH return pipe 1”
Tank return pipe 3/4”
Accessory box components list
Piping Adapter Kit - TRX110C
Gasket (2x1/2” + 2x3/4” + 1 x 1” + 1 gas fiber)
Clamp (2x3/4” + 2x1”)
Gas Adapter 3/4”
CH supply pipe 1”
CH return pipe 1”
DHW outlet & inlet pipes 3/4”
Accessory box components list
Piping Adapter Kit - TRX1120/ TRX150C
(see fig. 1 part b - next page)
16-a
16-b
16-c
16-d
16-e
16-f
16-g
16-h
7
4
1
1
1
1
1
1
Gasket (2x1/2” + 3x3/4” + 1 x 1” + 1 gas fiber)
Clamp (2x3/4” + 2x1”)
Gas Adapter 3/4”
CH supply pipe 1”
CH return pipe 1”
DHW outlet pipe (150C)/Tank return pipe (120) 3/4”
DHW inlet flow restrictor (150C)1/2” x 3/4”
DHW inlet pipe 3/4”
16-i
16-j
2
2
Table 4 - Included with the Boiler
Cap 1/2”
Accessory box components list
Figure 1 - Included with the Boiler - part a
10
TRX150C / TRX120
14a
16d
16b
16i
16c
16g
16f
16h
16e
16j
ACCESSORIES BOX
BOITE ACCESSOIRES
For Qualified Technician
Installation Instructions
Pour technicien qualifié instructions d’installation
Read the code
Lire le code
code
Figure 2 - Included with the Boiler - part b
or
0
50
0
20
20
100
40 psi
150
60
80
200
250
Ø 1-1/8”
View from the Front
Ø 7/8”
16” (406 mm)
Ø 7/8” Ø 1-1/8”
2-3/16” (55 mm)
6-3/8” (162 mm)
6-11/16” (169 mm)
View from the Side
Figure 3 - Adapter Kit Dimensions and
Specifications - Included with Adapter Kit
Part 2 - Before You Start
How the Boiler Operates
TRX condensing technology intelligently delivers hydronic heating while maximizing efficiency. Outlined below are system features and operation:
Stainless Steel Heat Exchanger
The highly efficient stainless steel heat exchanger is designed to extract all available heat from the supply line before it is exhausted.
Modulating Combustion System
The combustion system modulates the output of the burner during operation to match system demand and achieve the control set point while in operation. The set point can change by internal or external signals to enhance the overall performance of the system.
Control
The integrated control system monitors the system and regulates fan speed to control boiler output. This allows the boiler to deliver only the amount of heat energy required and nothing more.
The control can be set to monitor outdoor temperature through an outdoor sensor to regulate boiler set point. The system can be further enhanced by installing an indirect water heater to provide domestic hot water.
The control can regulate the output of multiple boilers through its cascade system function. The cascade system is capable of connecting up to eight boilers together in such a way that they function as one boiler system. This allows for greater turn down ratios and provides systematic control of the multiple boilers in an installation to minimize downtime and maximize efficiency.
The cascade system works by establishing one boiler as the master and the other connected boilers as followers. The master boiler requires a sensor to provide feedback on set point temperature in order to adjust heating input from the connected boilers. Each cascaded boiler will have its own pump to provide maximum flow and control heat exchanger flow rate.
Text Display and Operational Display Icons
The display allows the user to change system parameters and monitor system outputs.
Gas Valve
Senses suction from the blower, allowing gas to flow only if powered and combustion air is flowing.
Integrated Venturi
Controls air and gas flow into the burner.
Burner
The high grade stainless steel burner uses premixed air and gas to provide a wide range of firing rates.
Spark Ignition
The burner is ignited by applying high voltage through the system spark electrode. The spark from the electrode ignites mixed gas off of the burner.
Supply Water Temperature Sensor
This sensor monitors the boiler outlet water temperature (System
Supply). The control adjusts boiler firing rate so the supply temperature will match the boiler set point.
Return Water Temperature Sensor
This sensor monitors boiler return water temperature (System Return).
Flue Sensor
Monitors flue temperature and adjusts firing rate.
Temperature and Pressure Gauge
Allows the user to monitor system temperature and pressure.
Electrical field connections with terminal strips
The electrical cover allows easy access to the clearly marked line voltage and low voltage terminal strips to facilitate wiring the boiler.
11
Part 2 - Before You Start
Condensate Collection System
This boiler is a high efficiency appliance and will produce condensate.
The condensate collection system has a float switch which monitors condensate level and prevents condensate from backing up into the combustion system. Inside the collection system is a built in trap which seals the combustion system from the connected drain. This condensate should be neutralized to avoid damage to the drainage system or piping.
Outdoor Sensor
Monitors outdoor temperature and adjusts unit set point to provide greater efficiency.
0-10 Volt Input / 4-20 mA Input (with Optional Connection Card)
Allows the installer to connect a BMS (Building Management System) to control the boiler.
Condensate Trap and Air Pressure Switch
The condensate trap and air pressure switch prevent condensate and heat exchanger exhaust from backing up into the boiler.
Pump Service Mode
Allows manual operation of pumps to commission system and check pump operation.
Internal By-Pass Valve
Protects the boiler from damage in low flow conditions.
Internal ECM Pump
The internal ECM Pump uses less electricity than standard pumps, providing high performance operation.
B. Optional Equipment
Optional equipment available from NTI (and Part #):
• System Sensor (84010)
• 3” PVC Concentric Vent Kit (84634)
• 3” PVC Low Profile Vent Kit (84357)
• 2” PVC Low Profile Vent Kit (85062)
• Tank Sensor (84632)
NOTE: When using an optional system sensor, pipe insulation must be wrapped around it to improve temperature measurement accuracy and increase overall system efficiency.
12
CAUTION
COLD WEATHER HANDLING
- If the boiler has been stored in a very cold location (BELOW 0 o
F) before installation, handle with care until the components come to room temperature. Failure to do so could result in damage to the boiler.
Carefully consider installation when determining boiler location.
Please read the entire manual before attempting installation.
Failure to properly take factors such as boiler venting, piping, condensate removal, and wiring into account before installation could result in wasted time, money, and possible property damage and personal injury.
A. Locating the Boiler
WARNING
This boiler is certified for indoor use only. DO NOT INSTALL
OUTDOORS. Outdoor installations ARE NOT covered by warranty.
Failure to install the boiler indoors could result in property damage, severe personal injury, or death.
Incorrect ambient conditions can lead to damage to the heating system and put safe operation at risk. Ensure that the installation location adheres to the information included in this manual. Failure to do so could result in property damage, serious personal injury, or death. Failure of boiler or components due to incorrect operating conditions IS NOT covered by product warranty.
This boiler must be installed upright in the vertical position as described in this manual. DO NOT attempt to install this boiler in any other orientation. Doing so will result in improper boiler operation and property damage, and could result in serious personal injury or death.
1. Installation Area (Mechanical Room) Operating Conditions
• Ensure ambient temperatures are higher than 32 o
F / 0 o
C and lower than 104 o
F / 40 o
C
• Prevent the air from becoming contaminated by the products, places, and conditions listed in this manual
• Avoid continuously high levels of humidity
• Never close existing ventilation openings
• Ensure a minimum 1” clearance around hot water and exhaust vent pipes
• NOTE: To prevent condensing in the fan, it is recommended to avoid prolonged exposure to temperatures below 45 o
F
WARNING
This boiler has a condensate disposal system that may freeze if exposed to sustained temperatures below 32 o
F. Precautions should be taken to protect the condensate trap and drain lines from sustained freezing conditions.
WARNING
Circulators suitable for DHW applications must be used.
Failure to take precautions could result in property damage, severe personal injury, or death.
Part 3 - Prepare the Boiler for Installation
CAUTION
The service life of the boiler’s exposed metallic surfaces, such as the casing, as well as internal surfaces, such as the heat exchanger, are directly influenced by proximity to damp and salty marine environments. In such areas higher concentration levels of chlorides from sea spray coupled with relative humidity can lead to degradation of boiler components. In these environments, boilers must not be installed using direct vent systems which draw outdoor air for combustion. Such boilers must be installed using room air for combustion. Indoor air will have a much lower relative humidity, and hence potential corrosion will be minimized.
Failure of the boiler or components due to incorrect operating conditions IS NOT covered by product warranty.
2. Check for nearby connections to:
• System water piping
• Venting connections
• Gas supply piping
• Electrical power
• Condensate drain
3. Check area around boiler. Remove any combustible materials, gasoline, and other flammable liquids.
WARNING
Failure to keep the boiler area clear and free of combustible materials, liquids, and vapors can result in substantial property damage, severe personal injury, or death.
4. Gas control system components must be protected from dripping water during operation and service.
5. If the boiler is to replace an existing boiler, check for and correct any existing system problems, such as:
• System leaks
• Location that could cause the system and boiler to freeze and leak
• Incorrectly sized expansion tank
CAUTION
Always take future maintenance into consideration when locating the boiler. If the boiler is located in an installation location with limited clearances, it may be necessary to remove the boiler from the space to perform maintenance. Failure to consider maintenance when determining installation location could result in property damage.
6. Clean and flush system when reinstalling a boiler.
WARNING
Do not introduce toxic chemicals, such as antifreeze or appliance treatments, into any piping meant for potable water purposes.
Do not connect the appliance DHW connections to any heating systems or components that have been previously used for nonpotable applications.
Ensure that all piping and components connected to the appliance are suitable for potable water applications.
Failure to follow these instructions could result in serious personal injury or death.
13
Part 3 - Prepare the Boiler for Installation
NOTE: When installing in a zero clearance location, it may not be possible to read or view some product labeling. It is recommended to make note of the boiler model and serial number.
NOTE: A combustible door or removable panel is acceptable front clearance.
B. Leveling
CAUTION
In order for the condensate to properly flow out of the collection system, the area where you locate the boiler must be level. Failure to do so will result in improper appliance operation.
Correct installation
Figure 4 - Proper levelling
Incorrect installation
C. Clearances for Service Access
NOTE: If you do not provide the minimum clearances shown in Figure
5 and Table 5 it might not be possible to service the boiler without removing it from the space.
C
B B
Figure 5 - Minimum Clearances
Dimension
A
B
C
D
Not Displayed
Description
Top
Right or Left Side
Front
Bottom
Back
Table 5 - Minimum Installation and Service Clearances
14
Clearance
14” (355.6 mm)
2” (50.8 mm)
18” (457.2 mm)
12” (304.8 mm)
0” (0 mm)
NOTE: For closet installations, a combustible door or removable panel is acceptable front clearance. A 3” minimum clearance must be provided from the appliance front cover to the removable panel or combustible door.
Minimum Clearances from Combustible Materials
• Hot water pipes - at least 1” from combustible materials
• Exhaust vent pipe - at least 1” from combustible materials
CAUTION
All boilers eventually leak. Locate the boiler where any leakage from the relief valve, related piping, tank, or connections will not result in damage to surrounding areas or lower floors of the building. Any boiler should be installed in such a manner that if it should leak the resulting flow of water will not cause damage to the area in which it is installed. If the boiler is installed in a location where a leak could cause damage, it is required to provide containment measures. Such measures include but are not limited to: a properly sized drain pan installed beneath the boiler and piped to an open drain line, or installing the boiler on a concrete floor pitched to a free flowing drain. Failure to provide containment measures is the sole responsibility of the owner and/or installer. Leakage damages
ARE NOT covered by warranty.
In addition, water leak detection devices and automatic water shutoff valves are readily available at plumbing supply houses. IT
IS HIGHLY RECOMMENDED BY THE MANUFACTURER TO INSTALL
WATER LEAK DETECTION DEVICES AND AUTOMATIC SHUTOFF
VALVES IN ANY BOILER INSTALLATION WHERE A LEAKAGE OF
WATER COULD RESULT IN PROPERTY DAMAGES.
WARNING
The space must be provided with combustion / ventilation air openings correctly sized for all other appliances located in the same space as the boiler. The boiler cover must be securely fastened to prevent the boiler from drawing air from the boiler room. This is particularly important if the boiler is in a room with other appliances.
Failure to comply with the above warnings could result in substantial property damage, severe personal injury, or death.
D. Wall Mounting Considerations
These boilers are wall mounted. Use only the wall mounting instructions included with this boiler.
Ensure the wall that the boiler is intended to be mounted on is comprised of cement, brick, block, or wooden studs spaced 16” apart from center. Ensure the wall is capable of supporting at least 150 lbs
(68 kgs).
If flooding is possible, elevate the boiler to prevent floodwater from reaching the boiler.
Ensure the boiler is installed in a location that minimizes the risk of water damage due to leaking valves, pumps, unions, etc.
The boiler may be installed on any suitable internal wall (suitable soundproofing may be required when installing onto a stud partition wall).
WARNING
Ensure that the structure of the installation location is sufficient to support the full installed weight of the boiler, including water content of the heat exchanger and related piping and components. If the mounting location cannot support a minimum of 150 lbs. (68 kg), it is recommended to locate the boiler in a mounting location that can support the minimum weight. Failure to ensure the structure of the installation location is structurally sound before installation of the boiler and properly mount the boiler can result in structural failure, substantial property damage, severe personal injury, or death.
WARNING
Do not mount the boiler to a hollow wall.
E. Wall Mounting Instructions
WARNING
This boiler is too heavy for one person to lift. It is highly recommended to install the boiler with two people. Use caution as to not drop the boiler, which could damage the boiler and cause property damage and/or severe personal injury. Verify that the boiler is properly and securely mounted before leaving unsupervised. Failure to comply with the above and properly mount the boiler could result in substantial property damage, severe personal injury, or death.
1. Mounting to a concrete wall
Position the paper template on the concrete wall to locate the positions of the hanging bracket and piping bracket.
Drill and plug the wall and secure the hanging bracket using the screws provided (fisher S 10x50). Ensure the hanging bracket is level.
Secure the piping bracket on the concrete wall. Use suitable hardware.
Part 3 - Prepare the Boiler for Installation
2. Mounting to a Wood Studded Wall
CAUTION
If the boiler is not installed upright, vertically plumb, and level, improper and unsatisfactory operation may occur, causing excessive condensation build-up, nuisance fault codes, and unnecessary maintenance.
To install the boiler on a standard wood studded wall with 16” centers, a plywood board is required. The minimum dimensions of the plywood board are: 24” wide x 48” high x 1/2” thick.
Use at least fourteen (14) #12 x 3” (3/16” x 3”) round head tapping screws to secure the plywood board to the studded wall.
16 “
16”
(406,4 mm)
d
Ply wood boar
Dimensions:
24" wide x 48" high x 1/2" thick
STUD
4-3/4”
(120 mm)
4-3/4”
(120 mm)
boar d is minimum d to requir ed. wood ply e the
The boar
13”
To
Use
Aft ins
Loc tall er the ply ate on a standar d w wall tapping ood studded head e: 24" wide x 48" high x 1/2" thick
TO A
WOOD STUDDED (3/16"
#12 x 3" the boiler wood boar
(14)
WALL MOUNTING INSTR ack ashers f piping adapt
Moun ack et on the ply x 3") brack ack d has been installed t hanging the concr round ting d. U ood moun
(330 mm)
ete wall to loc ack et u a ply wood scr ew s to secur four teen dimensions of the ply at least the studded w
UC
TIONS of the ets the positions er br ack et and er br et. ack empla
Position ack et drilling holes
, position the paper t d. U se the har wood boar vel e le adapt dw se suitable har are deliv dw se suitable har are .
are of the brack
Drill and plug the w
Secur t the piping br
Moun
Position paper the ack templa et is le e the piping br ack te on e the han all. U ete w oncr et on the c
15-3/4”
(400 mm)
ALL
ATION
THE
AT
YOUR
CONDITIONS.
BOILER
BY
A QU
ALIFIED
APPL
OF
THE
BE
Y T
O W
T ANTICIP
ATE
ALL
INST
ALL
SECUREL
AL
CIFIC
ATIONS
Y MOUNTED
TIONS
RESUL
S MUST
PART
BE
CANNO
Y NO
PR
THE
TECHNIC
S. ALL
Y D
AMA
UC
INSTR
PERMIT
ABLE
TING
THE
INCL
THE
INST
UDED
CODE
FAIL
BUILDING
BOILER.
MUST
CONDITIONS,
BOILER
ATION
ALL
REQUIREMENT
TO
URE
INJUR
Y PR
Y, OR
ODUC
FOLL
OW
DEA
TH.
ARR
T W
THESE
AN
ANT
Y.
te on the ply the hanging wall wood moun et and brack ting and piping the ate positions scr ew s pr ovided (fisher S 10x50). Ensur
AND e
UC TIONS
LOC
TO
/
THESE
INST
INSTR
ALL
ATION
ALLER
AC
TO
CORDING
MEE
, SE
VERE
NO
T
INST , AND
IANCE
INST
Y D
AMA
ALLING
GE
ARE
OB
TAINED
T IN
PR
OPER
INST
ALL
ATION
PERSONAL
CO
VERED B
STUD
2-9/16”
(65 mm)
2-5/8”
(67 mm)
1-1/8”
2-5/8”
(67 mm)
2-9/16”
(65 mm)
50
100
150
200
250
3-7/16”
(87,2 mm)
3-7/16”
(87,6 mm)
3-7/16”
(87,6 mm)
3-7/16”
(87,2 mm)
Figure 6 - Mounting to a concrete wall
WARNING
This wall mounting system is not seismic rated and should not be applied as such. Failure to comply with the above and properly mount the boiler could result in substantial property damage, severe personal injury, or death.
Use extreme care not to drop the boiler or cause bodily injury while lifting or mounting the boiler onto the wall mount bracket.
Failure to follow these instructions could result in property damage, severe personal injury, or death.
The manufacturer cannot anticipate all installation conditions. These instructions and included parts may not apply to wall-mounting the appliance at your installation location. The appliance must be properly and securely mounted by a qualified installer according to installation conditions, the technical specifications of the appliance, and to meet AHJ / building code requirements. All applicable permits must be obtained before installing the appliance. Failure to follow these instructions could result in property damage, severe personal injury, or death. Any damages resulting from improper installation are not covered by product warranty.
Figure 7 - Mounting a playwood board
15
Part 3 - Prepare the Boiler for Installation
16 “
16”
(406,4 mm)
d
Ply wood boar
Dimensions:
24" wide x 48" high x 1/2" thick
STUD
4-3/4”
(120 mm)
4-3/4”
(120 mm)
ed.
The
13”
(330 mm)
wall a ply d is requir ply wood scr ew boar s to secur e the tapping empla wood te on the ply the moun wall minimum boar d to wood and ting
MOUNTING
To install the four teen
(14)
RUC dimensions of the ply
Use at least d ar x 3" d w e: 24" wide x 48" high x 1/2" thick
(3/16" x 3") round
, position the paper t adapt dw are deliv
. Then mark the br dw are .
TIONS brack et and ack ets ar e le vel d. U se the har ting d. U se suitable har ack ered with the boiler et and piping e brack of the hanging
Aft
Loc pipi ate pter br ng ada t the boiler br ets
WALL MOUNTING INST rack or w ood moun et on the ply ashers f et o
Moun
(fisher S 10x50) and w
Moun t the piping b templa the paper te on the wood boar concr ete to lo wall et using the scr ack dw are all. U se suitable har e the hanging br oncr ete w
15-3/4”
cat e the ew s pr ovided (fisher S 10x50). Ensur
UC
TIONS
LOC
AND
ATION. ack brack
Drill and plug the w the hanging br
Secur et is le ack
ATE
O W
ALL
(400 mm)
ALL
INST
ALL
ATION
THE
BY
A QU
OF
BE
ALIFIED
OB
THESE
INST
ALL
ALLER
AC
CORDING
TO
MEE
INST
APPLIANCE
, AND
ALL
INST
AMA
ALLING
GE
ATION
ARE
NO
T
CANNO
Y NO
PR
OPERL
THE
TECHNIC
S. ALL
AP
ABLE
PERMIT
PLIC
UC RESUL
TING
THE
INCL
THE
MANUF
UDED
BOILER
ALL
INST
G C
FAIL
BUILDIN
BOILER.
BE
REQUIREMENT
URE
Y PR
TO
FOLL
Y, OR
OW
ODE
ODUC
DEA
T W
THESE
TH.
AN
ANT
Y.
Y D
INSTR
AMA
GES
PERSONAL
CO
VERED B
STUD
F. Residential Garage and Closet Installations
CAUTION
Check with your local Authority Having Jurisdiction for requirements when installing boiler in a garage or closet. Please read the entire manual before attempting installation. Failure to properly take factors such as boiler venting, piping, condensate removal, and wiring into account before installation could result in wasted time, money, and possible property damage and personal injury.
Precautions
If the boiler is located in a residential garage, per ANSI Z223.1:
• Mount the bottom of the boiler a minimum of 18” above the floor of the garage to ensure the burner and ignition devices are well off the floor.
• Locate or protect the boiler so it cannot be damaged by a moving vehicle.
WARNING
The space must be provided with correctly sized combustion/ ventilation air openings for all other appliances located in the space with the boiler. For power venting installations using room air for combustion, refer to the boiler venting section, this manual, for descriptions of confined and unconfined spaces. Do not install the boiler in an attic. Failure to comply with these warnings could result in substantial property damage, severe personal injury, or death.
2-9/16”
(65 mm)
2-5/8”
(67 mm)
1-1/8”
2-5/8”
(67 mm)
2-9/16”
(65 mm)
20
40 60
20 psi 80
250
200
50 100
150
3-7/16”
(87,2 mm)
3-7/16”
(87,6 mm)
3-7/16”
(87,6 mm)
3-7/16”
(87,2 mm)
16 “
16 “
Figure 8 - Mounting the hanging bracket and piping bracket
After the plywood board has been installed to the studs, position the paper template on the plywood.
Locate the positions of the hanging bracket and piping adapter bracket. Position the wall mounting and piping adapter brackets.
Ensure the brackets are level. Then mark the bracket drilling holes.
Mount the boiler bracket on the plywood board. Use the hardware delivered with the boiler (fisher S 10x50) and washers for wood mounting.
Mount the piping bracket on the plywood board. Use suitable hardware .
G. Exhaust Vent and Intake Pipe
The boiler is rated ANSI Z21.13 Category IV (pressurized vent, likely to form condensate in the vent) and requires a special vent system designed for pressurized venting.
NOTE: The venting options described here (and further detailed in the Venting section, this manual) are the lone venting options approved for this boiler. Failure to vent the boiler in accordance with the provided venting instructions will void the warranty.
DANGER
Failure to vent the boiler properly will result in serious personal injury or death.
WARNING
Do not attempt to vent this boiler by any means other than those described in this manual. Doing so will void the warranty and may result in severe personal injury or death.
Vents must be properly supported. Boiler exhaust and intake connections are not designed to carry heavy weight. Vent support brackets must be within 1’ of the boiler and the balance at 4’ intervals. Boiler must be readily accessible for visual inspection for first 3’ from the boiler. Failure to properly support vents could result in property damage, severe personal injury, or death.
The exhaust discharged by this boiler may be very hot. Avoid touching or other direct contact with the exhaust gases of the vent termination assembly. Doing so could result in severe personal injury or death.
1. Direct Vent of Exhaust and Intake
If installing a direct vent option, combustion air must be drawn from the outdoors directly into the boiler intake and exhaust must terminate outdoors. There are three basic direct vent options detailed in this manual: 1. Side Wall Venting, 2. Roof Venting, and 3. Unbalanced
16
Venting.
Be sure to locate the boiler such that the exhaust vent and intake piping can be routed through the building and properly terminated.
Different vent terminals can be used to simplify and eliminate multiple penetrations in the building structure (see Optional Equipment in
Venting Section). The exhaust vent and intake piping lengths, routing, and termination methods must all comply with the methods and limits given in the Venting Section, this manual.
When installing a combustion air intake from outdoors, care must be taken to utilize uncontaminated combustion air. To prevent
combustion air contamination, see Table 6.
2. Power Venting, Indoor Combustion Air in Confined or
Unconfined Space
This boiler requires fresh, uncontaminated air for safe operation and must be installed in a mechanical room where there is adequate combustion and ventilating air. NOTE: To prevent combustion air contamination,
see Table 6.
Combustion air from the indoor space can be used if the space has adequate area or when air is provided through a duct or louver to supply sufficient combustion air based on the boiler input. Never obstruct the supply of combustion air to the boiler. If the boiler is installed in areas where indoor air is contaminated (see Table 6) it is imperative that the boiler be installed as direct vent so that all combustion air is taken directly from the outdoors into the boiler intake connection.
Unconfined space is space with volume greater than 50 cubic feet per
1,000 BTU/hr (4.8 cubic meters per kW) of the total input rating of all fuelburning appliances installed in that space. Rooms connected directly to this space through openings not furnished with doors are considered part of the space. See Venting Section for details.
Confined space is space with volume less than 50 cubic feet per 1,000
BTU/hr (4.8 cubic meters per kW) of the total input rating of all fuelburning appliances installed in that space. Rooms connected directly to this space through openings not furnished with doors are considered part of the space.
When drawing combustion air from inside a conventionally constructed building to a confined space, such space should be provided with two permanent openings: one located 6” (15 cm) below the space ceiling, the other 6” (15cm) above the space floor. Each opening should have a free area of one square inch per 1,000 BTU/hr (22cm 2 /kW) of the total input of all appliances in the space, but not less than 100 square inches (645cm 2 ).
If the confined space is within a building of tight construction, air for combustion must be obtained from the outdoors as outlined in the
Venting section of this manual.
CAUTION
When drawing combustion air from the outside into the mechanical room, care must be taken to provide adequate freeze protection.
WARNING
Failure to provide an adequate supply of fresh combustion air can cause poisonous flue gases to enter the living space, resulting in severe personal injury or death. To prevent combustion air contamination, see Table 6.
H. Carbon Monoxide Detectors
In the Commonwealth of Massachusetts and As Required by State and Local Codes:
Installation of Carbon Monoxide Detectors: At the time of installation or replacement of the vented gas fueled appliance, the installing plumber or gas fitter shall observe that a hard wired carbon monoxide detector with an alarm and battery back-up is installed on the floor level where the gas appliance is installed, unless the appliance is located in a detached, uninhabitable structure separate from the dwelling, building, or structure used in whole or in part for residential purposes.
In addition, the installing plumber or gas fitter shall observe that a hard wired carbon monoxide detector with an alarm and battery back-up is
Part 3 - Prepare the Boiler for Installation
installed on each additional level of the dwelling, building, or structure served by the vented gas appliance. It shall be the responsibility of the property owner to secure the service of qualified licensed professionals for the installation of hard wired carbon monoxide detectors.
a. In the event that the vented gas fueled appliance is installed in a crawl space or attic, the hard wired carbon monoxide detector with alarm and battery back-up shall be installed on the next adjacent floor level.
b. In the event that these requirements cannot be met at the time of completion of installation, the owner shall have a period of thirty
(30) days to comply with the above requirements; provided, however, that during said thirty (30) day period, a battery operated carbon monoxide detector with an alarm shall be installed.
WARNING
Do not attempt to vent this appliance by any means other than those described in this manual. Doing so will void the warranty and may result in severe personal injury or death.
Approved Carbon Monoxide Detectors: Each carbon monoxide detector as required in accordance with the above provisions shall comply with NFPA 70 and be ANSI/UL 2034 listed and IAS certified.
I. Prevent Combustion Air Contamination
Install intake air piping for the boiler as described in the Venting
Section, this manual. Do not terminate exhaust in locations that can allow contamination of intake air.
WARNING
Ensure that the intake air will not contain any of the contaminants in Table 6. Contaminated air will damage the boiler, resulting in possible substantial property damage, severe personal injury, or death. For example, do not pipe intake air near a swimming pool or laundry facilities. These areas always contain contaminants.
Products to Avoid
Spray cans containing fluorocarbons
Permanent wave solutions
Chlorinated waxes / cleaners
Areas Likely to H ave
Contaminants
Dry cleaning / laundry areas and establishments
Swimming pools
Metal fabrication plants chemicals
Calcium chloride used for thawing
Sodium chloride used for water softening
Refrigerant leaks
Refrigeration repair shops
Photo processing plants
Auto body shops
Paint or varnish removers
Hydrochloric or Muriatic acid
Plastic manufacturing plants
Furniture refinishing areas and establishments
New building construction Cements and glues
Antistatic fabric softeners used in clothes dryers
Remodeling areas detergents, and cleaning solvents
Adhesives used to fasten building products
Table 6 - Products and Areas Likely to Have Contaminants
NOTE: DAMAGE TO THE BOILER CAUSED BY EXPOSURE TO
CORROSIVE VAPORS IS NOT COVERED BY WARRANTY. (Refer to the limited warranty for complete terms and conditions.)
17
Part 3 - Prepare the Boiler for Installation
Figure 9 - CO Warning Label
J. Removing a Boiler from a Common Vent System
DANGER
Do not install the boiler into a common vent with any other appliance.
This will cause flue gas spillage or appliance malfunction, resulting in possible substantial property damage, severe personal injury, or death.
WARNING
Failure to follow all instructions can result in flue gas spillage and carbon monoxide emissions, causing severe personal injury or death.
When removing an existing boiler, follow the steps below.
1. Seal any unused openings in the common venting system.
2. Visually inspect the venting system for proper size and horizontal pitch to determine if there is blockage, leakage, corrosion, or other deficiencies that could cause an unsafe condition.
3. If practical, close all building doors, windows, and doors between the space in which the boiler remains connected to the common venting system and other spaces in the building. Turn on clothes dryers and any appliances not connected to the common venting system. Turn on any exhaust fans, such as range hoods and bathroom exhausts, at maximum speed. Do not operate a summer exhaust fan. Close all fireplace dampers.
4. Place in operation the appliance being inspected. Follow the lighting instructions. Adjust the thermostat so the appliance will operate continuously.
5. Test for spillage at the draft hood relief opening after 5 minutes of main burner operation. Use the flame of a match or candle or smoke from a cigarette.
6. After it has been determined that each appliance remaining connected to the common venting system properly vents when tested as outlined, return doors, windows, exhaust fans, fireplace dampers, and any other gas burning appliances to their previous condition of use.
7. Any improper operation of the common venting system should be corrected to conform to the National Fuel Gas Code, ANSI Z223.1.
When resizing any portion of the common venting system, the system should approach the minimum size as determined using the appropriate tables in Appendix G of ANSI Z223.1.
18
Part 3 - Prepare the Boiler for Installation
K. Technical Specifications
Model
Type
Installation
Space Heating
Minimum / Maximum Input (Btu/Hr)
1
Domestic Hot Water
Minimum / Maximum Input (Btu/Hr)
1
DOE AFUE
2
(%)
Heating Capacity
1, 2
(MBH)
Hot Water Capacity
35 o
F Rise
45 o
F Rise
77 o
F Rise
Flue System
Minimum - Maximum Exhaust Vent Run
3
Minimum - Maximum Intake Air Pipe Run
3
TRX085
9,400 / 85,000
TRX120 TRX110C
Boiler
Indoor, Wall Hung, Fully Condensing
13,200 / 120,000 11,200 / 106,000
Combi
TRX150C
13,200 / 120,000
N/A
96
79
N/A
N/A
N/A
N/A 11,200 / 114,000
95
111
N/A
N/A
N/A
95.5
98
6.8
5.3
3.1
Category IV, Sealed Combustion Direct Vent, Power Vent
2” (6 - 100 feet), 3” (6 - 150 feet)
2” (0 - 100 feet), 3” (0 - 150 feet)
13,200 / 150,000
95
111
8.5
6.6
3.8
Approved Exhaust Vent Materials
Gas Supply
Pressure
Shipping Weight (lbs)
NG
Power Supply
LP
General Operating Conditions
Ignition System
Burner System
Gas Valve System
Dimensions
(in Inches)
W
H
D
Approx. Full Boiler Weight (lbs)
3
78 84
PVC, CPVC, PP, Stainless Steel
83
3.5” to 10.5” WC
8” to 13” WC
120V, 60 Hz, less than 12A
Ambient Temperature Range: 33 – 104 o
F (0.6 – 40 o
C)
Product Approvals and Requirements: ANSI Z21.13 / CSA 4.9
Direct Electronic Spark Ignition / Flame Rectification
Premixed Fuel Modulation / Stainless Steel Burner
Air Ratio Valve
16” 3/64
43” 5/8
15” 1/8
88.6
91
84
88.2
92.8
Boiler Water Content (Gallons)
Boiler Setpoint Temperature Range
DHW Indirect Setpoint Temperature Range
DHW Setpoint Range (Combi Models)
Water Pressure (PSI)
Heat Exchanger MAWP
Pressure Relief Valve
DHW Max Pressure
Control Panel / Main Controller
CH Supply / Return
Connection
Sizes
DHW Inlet / Outlet
Gas Inlet
Materials
Cabinet
Heat Exchanger
Safety Devices
1.1
1.2
1.1
68 – 113 o
F Low Temperature / 95 - 179 o
F High Temperature
104 – 149 o
F
97 – 140 o
F
55
1.2
N/A
30
N/A 125
AristonThermo LCD Display / AristonThermo GALEVO2 Control
125
1” Male Sweat with Adapter
3/4” Male Sweat with Adapter
3/4” Male NPT
Painted Steel and Plastic
SA-312 Type 304L Stainless Steel Water Tube
Flame Rectifier Probe, Temperature Limit Control (190 o
F), Water Pressure Switch (Min. 8 PSI), Freeze
Protection, Blocked Condensate Pressure Switch, Condensate Trap, Flue Temperature High Limit Sensor
(210 o
F), Blocked Vent Pressure Switch
Table 7 - Technical Specifications
NOTES:
1
Listed Input and Output Ratings are at minimum vent lengths at an altitude of 0 - 2000 ft. Numbers will be lower with longer venting and/or altitudes greater than 2000 ft.
2
3
Ratings based on standard test procedures prescribed by the US Department of Energy.
The TRX requires a special venting system. Use only the vent materials and methods detailed in these installation instructions.
19
Part 3 - Prepare the Boiler for Installation
4-5/16” (110 mm)
4-3/4”
(120 mm)
4-3/4”
(120 mm)
15-3/4”
(400 mm)
2-9/16”
(65mm)
2-5/8”
(67mm)
2-5/8”
(67mm)
2-9/16”
(65mm)
A
3-7/16”
(87,2 mm)
B
3-7/16”
(87,6 mm)
C
3-7/16”
(87,6 mm)
D
3-7/16”
(87,2 mm)
E
Figure 10 - Boiler Dimensions - NOTE: All Dimensions Are Approximate
Model
A - Central Heating Supply
B - Return from Indirect Water Heater
C - Gas Inlet
D - Domestic Hot Water Inlet
E - Central Heating Return
F - Pressure Relief Valve
Table 8 - Boiler Adapter Dimensions
TRX085 TRX120
1”
3/4”
3/4”
Not Used
1”
20
15-5/16”
(390 mm)
5-7/8”
(150 mm)
2-3/16”
(55,3mm)
Model
A - Central Heating Supply
B - Domestic Hot Water Outlet
C - Gas Inlet
D - Domestic Hot Water Inlet
E - Central Heating Return
F - Pressure Relief Valve
TRX110C
1”
3/4”
3/4”
3/4”
1”
TRX150C
TRX085 - TRX120
1
11
11
12
13
2
6
7
3
4
5
8
9
Part 3 - Prepare the Boiler for Installation
21
20
19
18
17
15
14
25
24
23
22
26
5.
6.
7.
8
1.
2.
3.
4.
9.
11.
12.
13.
14.
Pressure relief valve
Air purge valve
Boiler outlet temperature sensor
Air pressure switch
Flue gas temperature sensor
Main heat exchanger
Flame detection electrode
Silencer
Junction box
Condensate trap
Gas valve
Control panel
CH circuit filter
Figure 11 - Boiler Component Locations and Descriptions
15.
17.
18.
19.
Circulation Pump with auto air vent
Water pressure switch
Modulating Fan
Boiler inlet temperature sensor
20. Frame
21. Ignition electrode
22.
23.
Spark generator
Combustion Analysis Test Point
24.
25.
26.
Air intake connection
Exhaust vent connection
Diverter valve
21
Part 3 - Prepare the Boiler for Installation
TRX110C - TRX150C
1
2
3
4
5
6
7
8
9
10
11
12
13
11
5.
6.
7.
8
1.
2.
3.
4.
9.
10.
11.
12.
13.
Pressure relief valve
Air purge valve
Boiler outlet temperature sensor
Air pressure switch
Flue gas temperature sensor
Main heat exchanger
Flame detection electrode
Silencer
Junction box
DHW heat exchanger
Condensate trap
Gas valve
Control panel
Figure 12 - Combi Boiler Component Locations and Descriptions
22
22.
23.
24.
25.
26.
14.
15.
16.
17.
CH circuit filter
Circulation Pump with auto air vent
DHW Flow switch
Water pressure switch
18.
19.
Modulating Fan
Boiler inlet temperature sensor
20. Frame
21. Ignition electrode
Spark generator
Combustion Analysis Test Point
Air intake connection
Exhaust vent connection
Diverter valve
25
24
23
22
21
20
16
15
14
19
18
17
26
TRX110C - TRX150C
1
2
6
7
19
3
12
10
28
11
29 psi
°F
9.
10.
11.
12.
13.
14.
15.
16.
5.
6.
7.
8
1.
2.
3.
4.
A
B C D E
Pressure relief valve
Air purge valve
Boiler outlet temperature sensor
Air pressure switch
Flue gas temperature sensor
Main heat exchanger
Flame detection electrode
Silencer
Junction box
DHW heat exchanger
Condensate trap
Gas valve
Control panel
CH circuit filter
Circulation Pump with auto air vent
DHW Flow switch
17.
18.
Water pressure switch
Modulating Fan
19. Boiler inlet temperature sensor
20. Frame
21.
22.
23.
24.
Ignition electrode
Spark generator
Combustion Analysis Test Point
Air intake connection
25.
26.
Exhaust vent connection
Diverter valve
27. By-pass
28. Drain valve
29. Pressure gauge
Figure 13 - Water Circuit Diagrams
15
17
26
27
16
14
214
Part 3 - Prepare the Boiler for Installation
TRX085 - TRX120
1
2
6
7
21
18
19
3
18
12
27
11
28
29 psi
°F
A
R
C
B
E
15
17
26
14
23
Part 4 - Water Piping
WARNING
Failure to follow the instructions in this section WILL VOID the warranty and may result in property damage, severe personal injury, or death.
The National Standard Plumbing Code, the National Plumbing Code of Canada, and the Uniform Plumbing Code limit heat transfer fluid pressure to less than the minimum working pressure of the potable water system up to 30 PSI maximum. In addition, the heat transfer fluid must be water or another non-toxic fluid having a toxicity of
Class 1, as listed in Clinical Toxicology of Commercial Products,
5th Edition. Failure to follow this warning could result in property damage, severe personal injury, or death.
CAUTION
Do not apply a torch within 12” of the boiler. If sweat connections are used, sweat tubing to the adapter before fitting adapter to the water connections on the boiler. Damages due to improper installation practices ARE NOT covered by warranty.
Dielectric unions or galvanized steel fittings must not be used in a system with this boiler. Doing so WILL VOID the warranty. Use only copper, brass, or stainless steel fittings. Teflon thread sealant must be used on all connections.
Plumbing of this product should only be done by a qualified, licensed plumber in accordance with all local plumbing codes. The boiler may be connected to an indirect water heater to supply domestic hot water.
NTI offers indirect water heaters in a wide range of gallon sizes in either stainless steel or glass-lined construction.
A. General Plumbing Information
CAUTION
The building piping system must meet or exceed the the piping requirements in this manual.
Use two wrenches when tightening water piping at boiler. Use one wrench to prevent the boiler return or supply line from turning.
Failure to prevent piping connections from turning could cause damage to boiler components.
The boiler control module uses temperature sensors to provide both high limit protection and modulating temperature control. The control module may also provide low water protection by sensing the water level in the heat exchanger. Some codes/jurisdictions may require additional external controls.
The water connections must be installed in accordance with all local and national plumbing codes, or any applicable standard with prevails.
• Pipe material must be suitable to meet local codes and industry standards.
• The pipe must be cleaned and without blemish before any connections are made.
• The size of the DHW pipes should be 3/4” diameter, and the CH pipes should be 1” diameter.
• Isolation (shut-off valves) should be used on both the CH and DHW loops to ease future servicing.
• All piping should be insulated.
It is recommended to install a sweat shut-off valve and a union in the return and supply piping to ease future servicing. If there is a backflow preventer or any type of a no return valve in the system, install an additional tee here suitable for an expansion tank.
NOTE: The addition of a high temperature limiting device is important if the boiler is to be connected to a domestic hot water system.
B. Backflow Preventer
Use a backflow preventer specifically designed for hydronic boiler installations. This valve should be installed on the cold water fill supply line per local codes.
C. Expansion Tank
Expansion Tank and Make-Up Water
1. Ensure that the expansion tank is designed and sized to correctly handle boiler and system water volume and temperature.
WARNING
Expansion tanks must be sized according to total system volume. This includes all length of pipe, all fixtures, boilers, etc. Failure to properly size for system expansion could result in wasted time, money, possible property damage, serious personal injury, or death.
CAUTION
Undersized expansion tanks cause system water to be lost from the relief valve, causing make-up water to be added. Eventual boiler failure can result due to excessive make-up water addition.
SUCH
FAILURE IS NOT COVERED BY WARRANTY.
DO NOT
install automatic air vents on closed type expansion tank systems. Air must remain in the system and return to the tank to provide an air cushion. An automatic air vent would cause air to leave the system, resulting in improper operation of the expansion tank.
Model
TRX085
TRX120
TRX110C
Heat Exchanger Volume (Gallons)
1.1
1.2
1.1
TRX150C
1.2
Table 9 - Heat Exchanger Water Volume (To Aid in Expansion Tank Sizing)
2. The expansion tank must be located as shown in Applications, this manual, or following recognized design methods. See expansion tank manufacturer’s instructions for details.
3. Connect the expansion tank to the air separator only if the air separator is on the suction side of the circulator. Always install the system fill connection at the same point as the expansion tank connection to the system.
4. Most chilled water systems are piped using a closed type expansion tank.
DIAPHRAGM (OR BLADDER) EXPANSION TANK
Always install an automatic air vent on top of the air separator to remove residual air from the system.
D. Piping the Boiler
CAUTION
Boiler Models should not be operated as a direct potable hot water heater. Only Combi Models should be used to directly heat hot water.
Use at least the MINIMUM pipe size for all appliance loop piping.
This is to avoid the possibility of inadequate flow through the appliance. Using less than the required minimum pipe size and piping could result in system problems, property damage, and premature appliance failure. Such problems ARE NOT covered by product warranty.
NOTE: Observe the minimum 1” clearance around all uninsulated hot water pipes when openings around pipes are not protected by noncombustible materials.
24
Part 4 - Water Piping
Connect the 3/4” DHW inlet and outlet pipes. A shut-off valve between the city water supply and DHW inlet is recommended for ease of service.
NTI offers threaded 3/4” DHW tankless isolation valves with a DHW pressure relief valve for ease of installation and future service.
Connect the 1” CH return and supply pipes. Isolation valves are recommended for ease of service.
TRX085 or TRX120 only Heating
TRX110C
I
L
I
L
0
0
20
20
50
40 psi
60
80
100 150
250
200
C
A
E
TRX085 or TRX120 with Indirect Water Heater
0
20
0
20
40 psi
50
60
80
250
100 150
200
C
A B
TRX150C
D E
I
L
I
L
0
0
20
20
40 psi
60
80
50
250
100 150
200
A
B
C
E
TRX085 - TRX120
A. CH Supply 1”
B. Return from Indirect Water Heater 3/4"
C. Gas Inlet 3/4"
D. Not Used
E. CH Return 1”
I. Drain Valve
L. Condensate Discharge
Figure 14 - Water / Gas Connections
0
0
20
20
40 psi
60
80
50
250
100 150
200
C
A
B
D E
TRX110C - TRX150C
A. CH Supply 1”
B. DHW Outlet 3/4"
C. Gas Inlet 3/4"
D. DHW Inlet 3/4"
E. CH Return 1”
I. Drain valve
L. Condensate discharge
25
Part 4 - Water Piping
E. Internal Circulation Pump
To calculate the size of the heating installation refer to the graph below.
Graph Representing the Available Circulation Pump Head
feet
24
20
16
12
8
4
0
0 1 2 3 4
gal/min
Table 10 - Internal Circulation Head Curve
5 6 7
F. By-Pass Valve
This boiler has a by-pass valve which requires no adjustment.
The by-pass valve protects the heat exchanger from overheating by guaranteeing a minimum flow rate of 2 gpm within the primary heat exchanger. This protects the primary heat exchanger from overheating when water circulation is insufficient or heating system load is reduced
(ex: due to the response of thermostatic valves or zone valves).
The by-pass valve is located:
- in the left hydraulic block for TRX085 and TRX120.
- in the right hydraulic block , behind the three-way valve, for
TRX110C and TRX150C.
TRX085 - TRX120
By-Pass Valve
Location
TRX110C - TRX150C
By-pass valve location
Figure 15 - Internal Circulation Pump NOTE: Ensure the Air Vent on the
Internal Circulation Pump Remains Open after Installation
Figure 16 - By-Pass Valve Location
Figure 17 - By-Pass Valve Assembly
26
G. CH and DHW Pressure Relief Valves
An external pressure relief valve must be installed on this appliance for the
CH loop. When installing, observe the following guidelines.
This boiler has a high-temperature shut-off switch built in as a standard safety feature. Therefore, a “pressure only” relief valve is required.
DO NOT operate this appliance before the supplied pressure relief valve is installed with sufficient relieving capacity in accordance with the ASME rating plate on the appliance.
WARNING
The pressure relief valve must be installed with the provided adaptor pipe in the top of the boiler as detailed in Figure 19. No other valves should be placed between the pressure relief valve and the appliance.
Failure to comply with these guidelines can result in substantial property damage, personal injury, or death.
CH Loop
This boiler is provided with a CH pressure relief valve that complies with the ANSI/ASME Boiler and Pressure Vessel Code, Section IV (Heating
Boilers). The included 30 psi CH Pressure Relief Valve must be installed at the top of the boiler, using the included pipe adapter and grommet, as illustrated below.
DO NOT install a relief valve with a pressure rating in excess of 50 psi
- the maximum allowable operating pressure of the boiler. The relief valve capacity must exceed the BTU/H input capaciy of the boiler. To install the pressure relief valve proceed as follows:
1. Remove the plastic cover on the top of the boiler.
2. Remove the nut on the flow pipe.
Figure 18 - Remove the Caps
3. Insert the pipe and gasket.
Part 4 - Water Piping
4. Connect the pressure relief valve and gasket.
NOTE: To maintain an airtight seal, ensure the gasket boot is properly fitted into the top of the boiler cabinet.
Figure 20 - Connect CH Pressure Relief Valve
DHW Loop (Combi Models)
The DHW piping must be provided with a DHW pressure relief valve that complies with local codes, but not less than valves certified as meeting the requirements of Relief Valves for Hot Water Supply Systems, ANSI
Z21.22 / CSA4.4 by a nationally recognized lab that maintains periodic inspection of production listed equipment.
A DHW pressure relief valve is not included with the boiler, and is to be field supplied and installed in the DHW piping. DO NOT install a DHW relief valve with a pressure rating greater than 125 psi - the maximum allowable operating pressure of the boiler’s DHW circuit.
After installing the relief valves and filling and pressurizing the system, test the operation of the valves by lifting the levers.
Make sure the valves discharge freely. If a valve fails to operate correctly, replace it with a new relief valve.
The relief valve capacity must exceed the BTU/H input capacity of the boiler.
Radiant heating
For appliances with underfloor heating, it is possible but not necessary to fit a safety thermostat onto the radiant heating outlet.
If the thermostat cannot be installed, the radiant heating equipment must be protected by a thermostatic valve, or by a by-pass to prevent the floor from reaching too high a temperature.
Figure 19 - Insert the Pipe
27
Part 4 - Water Piping
WARNING
To avoid water damage or scalding due to relief valve operation:
• Discharge line must be connected to relief valve outlet and run to a safe place of disposal. Terminate the discharge line in a manner that will prevent possibility of severe burns or property damage should the relief valve discharge.
• Discharge line must be as short as possible and the same size as the valve discharge connection throughout its entire length.
• Discharge line must pitch downward from the valve and terminate at least 6” above the floor drain, making discharge clearly visible.
• The discharge line shall terminate plain, not threaded, with a material serviceable for temperatures of 375 o
F or greater.
• Do not pipe discharge to any location where freezing could occur.
• No valve may be installed between the relief valve and boiler or in the discharge line. Do not plug or place any obstruction in the discharge line.
• Test the operation of the relief valve after filling and pressurizing the system by lifting the lever. Make sure the valve discharges freely. If the valve fails to operate correctly, immediately replace with a new properly rated relief valve.
• Test relief valve at least once annually to ensure the waterway is clear. If valve does not operate, turn the boiler “off” and call a plumber immediately.
• Take care whenever operating relief valve to avoid scalding injury or property damage.
FAILURE TO COMPLY WITH THE ABOVE GUIDELINES COULD
RESULT IN FAILURE OF RELIEF VALVE OPERATION, RESULTING
IN POSSIBILITY OF SUBSTANTIAL PROPERTY DAMAGE, SEVERE
PERSONAL INJURY, OR DEATH.
H. Air Elimination Device
A micro bubble air elimination device must be installed in every boiler installation. Automatic air vents alone are not an acceptable substitute for a micro bubble air elimination device. Here are a few examples of acceptable devices.
• Spirovent
• TACO 4900 Series
• Caleffi Discal
I. Applications*
CAUTION
Mixing valves are required for the protection of low temperature loops.
WARNING
Do not thread a cap or plug into the relief valve or relief valve line under any circumstances! Explosion and property damage, serious injury, or death may result.
RE-INSPECTION OF RELIEF VALVES: Relief valves should be inspected AT LEAST ONCE EVERY THREE YEARS, and replaced if necessary,
by a licensed plumbing contractor or qualified service technician to ensure that the product has not been affected by corrosive water conditions and to ensure that the valve and discharge line have not been altered or tampered with illegally. Certain naturally occuring conditions may corrode the valve and its components over time, rendering the valve inoperative. Such conditions can only be detected if the valve and its components are physically removed and inspected.
Do not attempt to conduct an inspection on your own.
Contact your plumbing contractor for a re-inspection to assure continued safety.
FAILURE TO RE-INSPECT THE RELIEF VALVE AS DIRECTED
COULD RESULT IN UNSAFE TEMPERATURE AND/OR
PRESSURE BUILD-UP WHICH CAN RESULT IN PROPERTY
DAMAGE, SERIOUS PERSONAL INJURY, OR DEATH.
Figure 21 - Piping Symbol Legend
28
Part 4 - Water Piping
Primary/Secondary Piping Shown
Cap this fitting when not in use
Figure 22 - TRX085 / TRX120 with Single Central Heating Circulator
NOTE: In piping applications utilizing a single zone, it is recommended that the installer use flow / check valves with weighted seats at or near the appliance to prevent gravity circulation.
NOTICE
Figure illustrates the basic plumbing requirements for a TRX085 /
TRX120 boiler installation utilizing Primary/Secondary piping when the boiler circulator will not provide adequate flow for the system.
Primary / Secondary is required to provide adequate flow for the secondary circuits.
CAUTION
On TRX085 / TRX120 Models Only.
If the boiler to be used only in Heating Mode (not connected to an indirect water heater), cap the fitting as indicated in the figure above and the electrical connection of the 3-way valve motor
MUST BE DISCONNECTED while the boiler is operating in central heating mode. This will lock the valve motor in central heating mode and ensure freeze protection operates properly. Failure to disconnect the valve may disable boiler freeze protection and result in property damage.
WARNING
The piping will not support the weight of the circulators. Refer to the circulator manufacturer’s instructions to properly support the circulator. Failure to comply with these instructions could result in property damage, severe personal injury, or death.
NOTES:
1. This drawing is meant to show system piping concept only.
Installer is responsible for all equipment and detailing required by local codes.
2. All closely spaced tees shall be within 4 pipe diameters center to center spacing.
3. A minimum of 6 pipe diameters of straight pipe shall be installed upstream and downstream of all closely spaced tees.
4. The minimum pipe size of DHW piping should be ¾” diameter and
CH piping should be 1” in diameter.
5. Circulators are shown with isolation flanges. The alternative is standard flanges with full port ball valves. Purge valves can be used with circulator flanges as an alternative.
6. Piping shown is Primary/Secondary.
7. Install a minimum of 12 diameters of straight pipe upstream of all circulators.
8. VERY IMPORTANT – Minimum flow rates outlined in this manual
(2 gpm) must be maintained through the heat exchanger to minimize short cycling.
9. In a valve-based system, each heating zone has a zone valve which opens when that zone calls for heat. Each zone thermostat is wired to its corresponding zone valve. Contacts in the zone valves provide a signal to the boiler to operate when there is a call for heat.
10. Unit is equipped with built-in primary pump. This pump is sized to ensure proper flow rate through the boiler heat exchanger and related piping.
11. IWH Applications - a mixing valve is recommended if the DHW temperature is set above the factory setting of 119 o
F.
29
Part 4 - Water Piping
Cap this fitting when not in use
Figure 23 - TRX085 / TRX120 without Central Heating Circulator
NOTE: In piping applications utilizing a single zone, it is recommended that the installer use flow / check valves with weighted seats at or near the appliance to prevent gravity circulation.
NOTICE
Figure illustrates the basic plumbing requirements for a TRX085
/ TRX120 boiler installation without an external Central Heating circulator; the boiler’s internal circulator delivers flow to the heating system. Application is limited to zone valve (or non-circulator) distribution systems with small flow requirements (e.g. systems requiring no more than 5 gpm at 9 ft. of head pressure)
WARNING
The piping will not support the weight of the circulators. Refer to the circulator manufacturer’s instructions to properly support the circulator. Failure to comply with these instructions could result in property damage, severe personal injury, or death.
NOTES:
1. This drawing is meant to show system piping concept only.
Installer is responsible for all equipment and detailing required by local codes.
2. The minimum pipe size of DHW piping should be ¾” diameter and
CH piping should be 1” in diameter.
3. Circulators are shown with isolation flanges. The alternative is standard flanges with full port ball valves. Purge valves can be used with circulator flanges as an alternative.
4. Install a minimum of 12 diameters of straight pipe upstream of all circulators.
5. VERY IMPORTANT – Minimum flow rates outlined in this manual
(2 gpm) must be maintained through the heat exchanger to minimize short cycling.
6. In a valve-based system, each heating zone has a zone valve which opens when that zone calls for heat. Each zone thermostat is wired to its corresponding zone valve. Contacts in the zone valves provide a signal to the boiler to operate when there is a call for heat.
7. Unit is equipped with built-in primary pump for the heating
loop. This pump is sized to ensure proper flow rate through the boiler heat exchanger and related piping.
8. IWH Applications - a mixing valve is recommended if the DHW temperature is set above the factory setting of 119 o
F.
9. In direct (not primary / secondary) piping applications, it is required to increase fill pressure to 20 psi to ensure proper system operation.
30
Part 4 - Water Piping
Cap this fitting when not in use
Primary/Secondary Piping is Required
Figure 24 - TRX085 / TRX120 with Multiple Central Heating Circulators
NOTE: In piping applications utilizing a single zone, it is recommended that the installer use flow / check valves with weighted seats at or near the appliance to prevent gravity circulation.
NOTICE
Figure illustrates the basic plumbing requirements for a TRX085 /
TRX120 boiler installation utilizing Primary/Secondary piping when the boiler circulator will not provide adequate flow for the system.
Primary / Secondary is required to provide adequate flow for the secondary circuits.
CAUTION
On TRX085 / TRX120 Models Only.
If the boiler to be used only in Heating Mode (not connected to an indirect water heater), cap the fitting as indicated in the figure above and the electrical connection of the 3-way valve motor
MUST BE DISCONNECTED while the boiler is operating in central heating mode. This will lock the valve motor in central heating mode and ensure freeze protection operates properly. Failure to disconnect the valve may disable boiler freeze protection and result in property damage.
WARNING
The piping will not support the weight of the circulators. Refer to the circulator manufacturer’s instructions to properly support the circulator. Failure to comply with these instructions could result in property damage, severe personal injury, or death.
NOTES:
1. This drawing is meant to show system piping concept only.
Installer is responsible for all equipment and detailing required by local codes.
2. All closely spaced tees shall be within 4 pipe diameters center to center spacing.
3. A minimum of 6 pipe diameters of straight pipe shall be installed upstream and downstream of all closely spaced tees.
4. The minimum pipe size of DHW piping should be ¾” diameter and
CH piping should be 1” in diameter.
5. Circulators are shown with isolation flanges. The alternative is standard flanges with full port ball valves. Purge valves can be used with circulator flanges as an alternative.
6. Piping shown is Primary/Secondary, and is mandatory.
7. Install a minimum of 12 diameters of straight pipe upstream of all circulators.
8. VERY IMPORTANT – Minimum flow rates outlined in this manual
(2 gpm) must be maintained through the heat exchanger to minimize short cycling.
9. In a valve-based system, each heating zone has a zone valve which opens when that zone calls for heat. Each zone thermostat is wired to its corresponding zone valve. Contacts in the zone valves provide a signal to the boiler to operate when there is a call for heat.
10. Unit is equipped with built-in primary pump. This pump is sized to ensure proper flow rate through the boiler heat exchanger and related piping.
11. IWH Applications - a mixing valve is recommended if the DHW temperature is set above the factory setting of 119 o
F.
31
Part 4 - Water Piping
Primary/Secondary Piping Shown
Figure 25 - TRX110C / TRX150C with Single Central Heating Circulator
NOTE: In piping applications utilizing a single zone, it is recommended that the installer use flow / check valves with weighted seats at or near the appliance to prevent gravity circulation.
NOTICE
Figure illustrates the basic plumbing requirements for a TRX110C /
TRX150C boiler installation utilizing Primary/Secondary piping when the boiler circulator will not provide adequate flow for the system.
Primary / Secondary is required to provide adequate flow for the secondary circuits.
WARNING
The piping will not support the weight of the circulators. Refer to the circulator manufacturer’s instructions to properly support the circulator. Failure to comply with these instructions could result in property damage, severe personal injury, or death.
NOTES:
1. This drawing is meant to show system piping concept only.
Installer is responsible for all equipment and detailing required by local codes.
2. All closely spaced tees shall be within 4 pipe diameters center to center spacing.
3. A minimum of 6 pipe diameters of straight pipe shall be installed upstream and downstream of all closely spaced tees.
4. The minimum pipe size of DHW piping should be ¾” diameter and
CH piping should be 1” in diameter.
5. Circulators are shown with isolation flanges. The alternative is standard flanges with full port ball valves. Purge valves can be used with circulator flanges as an alternative.
6. Install a minimum of 12 diameters of straight pipe upstream of all circulators.
7. VERY IMPORTANT – Minimum flow rates outlined in this manual
(2 gpm) must be maintained through the heat exchanger to minimize short cycling.
8. In a valve-based system, each heating zone has a zone valve which opens when that zone calls for heat. Each zone thermostat is wired to its corresponding zone valve. Contacts in the zone valves provide a signal to the boiler to operate when there is a call for heat.
9. Unit is equipped with built-in primary pump. This pump is sized to ensure proper flow rate through the boiler heat exchanger and related piping.
32
Part 4 - Water Piping
Figure 26 - TRX110C / TRX150Cwithout Central Heating Circulator
NOTE: In piping applications utilizing a single zone, it is recommended that the installer use flow / check valves with weighted seats at or near the appliance to prevent gravity circulation.
NOTICE
Figure illustrates the basic plumbing requirements for a TRX110C
/ TRX150C boiler installation without an external Central Heating circulator; the boiler’s internal circulator delivers flow to the heating system. Application is limited to zone valve (or non-circulator) distribution systems with small flow requirements (e.g. systems requiring no more than 5 gpm at 9 ft. of head pressure)
WARNING
The piping will not support the weight of the circulators. Refer to the circulator manufacturer’s instructions to properly support the circulator. Failure to comply with these instructions could result in property damage, severe personal injury, or death.
NOTES:
1. This drawing is meant to show system piping concept only.
Installer is responsible for all equipment and detailing required by local codes.
2. The minimum pipe size of DHW piping should be ¾” diameter and
CH piping should be 1” in diameter.
3. Circulators are shown with isolation flanges. The alternative is standard flanges with full port ball valves. Purge valves can be used with circulator flanges as an alternative.
4. Install a minimum of 12 diameters of straight pipe upstream of all circulators.
5. VERY IMPORTANT – Minimum flow rates outlined in this manual
(2 gpm) must be maintained through the heat exchanger to minimize short cycling.
6. In a valve-based system, each heating zone has a zone valve which opens when that zone calls for heat. Each zone thermostat is wired to its corresponding zone valve. Contacts in the zone valves provide a signal to the boiler to operate when there is a call for heat.
7. Unit is equipped with built-in primary pump for the heating
loop. This pump is sized to ensure proper flow rate through the boiler heat exchanger and related piping.
8. In direct (not primary / secondary) piping applications, it is required to increase fill pressure to 20 psi to ensure proper system operation.
33
Part 4 - Water Piping
CAUTION
Mixing valves are required for the protection of low temperature loops.
Primary/Secondary Piping is Required
Figure 27 - TRX110C / TRX150C with Multiple Central Heating Circulators
NOTE: In piping applications utilizing a single zone, it is recommended that the installer use flow / check valves with weighted seats at or near the appliance to prevent gravity circulation.
NOTICE
Figure illustrates the basic plumbing requirements for a TRX110C /
TRX150C boiler installation utilizing Primary/Secondary piping when the boiler circulator will not provide adequate flow for the system.
Primary / Secondary is required to provide adequate flow for the secondary circuits.
WARNING
The piping will not support the weight of the circulators. Refer to the circulator manufacturer’s instructions to properly support the circulator. Failure to comply with these instructions could result in property damage, severe personal injury, or death.
NOTES:
1. This drawing is meant to show system piping concept only.
Installer is responsible for all equipment and detailing required by local codes.
2. All closely spaced tees shall be within 4 pipe diameters center to center spacing.
3. A minimum of 6 pipe diameters of straight pipe shall be installed upstream and downstream of all closely spaced tees.
4. The minimum pipe size of DHW piping should be ¾” diameter and
CH piping should be 1” in diameter.
5. Circulators are shown with isolation flanges. The alternative is standard flanges with full port ball valves. Purge valves can be used with circulator flanges as an alternative.
6. Install a minimum of 12 diameters of straight pipe upstream of all circulators.
7. VERY IMPORTANT – Minimum flow rates outlined in this manual
(2 gpm) must be maintained through the heat exchanger to minimize short cycling.
8. In a valve-based system, each heating zone has a zone valve which opens when that zone calls for heat. Each zone thermostat is wired to its corresponding zone valve. Contacts in the zone valves provide a signal to the boiler to operate when there is a call for heat.
9. Unit is equipped with built-in primary pump. This pump is sized to ensure proper flow rate through the boiler heat exchanger and related piping.
34
Part 4 - Water Piping
H. Floor Drying Function
The Floor Drying Function is a special function that allows the installer, through a dedicated heating cycle, to use the boiler for drying a freshly poured radiant floor during a floor system installation.
The installer can set parameter 2.7.4 (Floor Drying Cycle) and choose the cycle‘s operation (Functional Heating, Curing Heating, a combination of Functional and Curing Heating, or Manual Heating).
This function can follow different flow temperature profiles according to the parameter 2.7.4 values:
Value
0
1
2
3
4
5
Function mode description
OFF
60
50
40
30
20
10
0
60
50
40
30
20
10
0
0 1 2 3 4 5 6 7 8
Jours
50
Jours
60
40
50
30
40
20
30
10
20
10
0
0
0 1 2 3 4 5 6 7 8 9 10 11 12 13 14 15 16 17 18
Jours
0 1 2 3 4 5 6 7 8 9 10 11 12 13 14 15 16 17 18
Jours
60
50
40
40
30
30
20
20
10
60
60
50
10
0
0
60
50
40
30
30
20
20
10
10
0
0
60
60
50
50
40
50 40
40
30
60
30
20
50
20
10
Fonction chauffage
30
20
7 jours
7 jours
0
2 jours
ARRET
2 jours
ARRET
Durcissement chauffage
18 jours
0 1 2 3 4 5 6 7 8 9 10 11 12 13 14
10
15 16 17 18 19 20 21 22 23 24 25 26 27 28
0
Jours
0 1 2 3 4 5 6 7 8
Jours
60
50
40
30
20
10
0
Durcissement chauffage
18 jours
18 jours
Jours
Jours
1 jours
ARRET
1 jours
ARRET
Fonction chauffage
Fonction chauffage
7 jours
15 16 17 18 19 20 21 22 23 24 25 26 27 28
15 16 17 18 19 20 21 22 23 24 25 26 27 28
60
50
40
30
20
10
0
0 1 2 3 4 5 6 7 8 9 10 11 12 13 14 15 16 17 18 19 20 21 22 23 24 25
Jours
Functional Heating:
The supply setpoint temperature is kept at 77°F for three (3) days, then increased to the target temperature (parameter 2.7.5 - default = 131°F) and kept at this temperature for four (4) days.
Curing Heating:
Supply setpoint temperature increases from 77°F to the target temperature (defined by parameter 2.7.5) by 5F/day, stays at target temperature for “x” days, and decreases from target temperature to 77°F by 5°F/day for a fixed total amount of days to 18.
Example 1:
Parameter 2.7.5 = 131°F; increasing phase from 77°F to 131°F = 6 days; stays at 131°F for 6 days; decreasing phase from 131°F to 77°F = 6 days.
Example 2:
Parameter 2.7.5 = 140°F; increasing phase from 77°F to 140°F = 7 days; stays at 140°F for 4 days; decreasing phase from 140°F to 77°F = 7 days.
Functional Heating + Curing Heating:
The two operation modes are executed consecutively with a stop period of two (2) days in between.
Curing Heating + Functional Heating:
The two operation modes are executed consecutively with a stop period of one (1) day in between.
Manual Heating:
The supply setpoint temperature is fixed at the value defined by the parameter 2.7.5 “Floor Drying Flow Setpoint Temperature”.
35
Part 5 - Venting
DANGER
The boiler must be vented as detailed in this section. Ensure exhaust vent and intake piping complies with these instructions regarding vent system. Inspect finished exhaust vent and intake piping thoroughly to ensure all joints are well secured, airtight, and comply with all applicable code requirements, as well as the instructions provided in this manual. Failure to properly install the vent system will result in severe personal injury or death.
A. General
DANGER
This boiler is certified as a “Category IV” appliance and requires a special venting system. The vent system will operate with a positive pressure in the pipe. Exhaust gases must be piped directly outdoors using the vent materials and rules outlined in these instructions. Do not connect vent connectors serving appliances vented by natural draft into any portion of mechanical draft systems operating under positive pressure. Follow the venting instructions carefully. Failure to do so will result in substantial property damage, severe personal injury, or death.
Exhaust and intake are to be piped separately. This boiler cannot share a common exhaust or intake with multiple appliances.
Failure to follow these instructions will result in substantial property damage, severe personal injury, or death.
1. Installation should be made in accordance with the regulations of the Authority Having Jurisdiction, local code authorities, and utility companies which pertain to this type of water heating equipment.
2. Install the venting system in accordance with these instructions and with the National Fuel Gas Code, ANSI Z223.1/NFPA 54, CAN/
CGA B149, and / or applicable provisions of local building codes.
3. This boiler must be vented with materials, components, and systems listed and approved for Category IV appliances.
NOTE: To avoid contamination often contained in indoor air, it is best to pipe all intake combustion air directly to the outdoors.
NOTE: Care must be taken to prevent condensate freezing in the exhaust vent pipe system. See local, state, provincial, and national codes for best practices to prevent condensate freezing in the exhaust vent pipe system.
WARNING
Improper seating of vent pipe gaskets can cause eventual gasket failure and exhaust gas leakage. Ensure the exhaust vent pipe is properly beveled and seated before insertion into the flue adapter.
Failure to do so could result in property damage, severe personal injury, or death.
Exhaust vent adaptors are not designed as load-bearing devices, and must not be used to support exhaust vent piping. All vent pipes must be properly connected, supported, and the exhaust vent must be pitched a minimum of 1/4” per foot back to the boiler to allow drainage of condensate. Failure to properly support vent piping and follow the information in this statement could result in product damage, severe personal injury, or death.
It is required to insert the provided exhaust and intake screens into the vent terminations to prevent blockage caused by debris or birds.
Failure to keep terminations clear could result in property damage, severe personal injury, or death.
36
DANGER
Due to the extreme flammability of most glues, cements, solvents, and primers used to join plastic exhaust vent and intake pipes, explosive solvent vapors must be cleared from all vent piping before start-up. Avoid using excess cement or primer, as this may pool in the vent pipes. Vent assemblies should be allowed to cure for a period of at least 8 hours before powering a connected appliance. Failure to follow these instructions will result in substantial property damage, severe personal injury, or death. It is the installers’ responsibility to understand the hazards associated with explosive solvents and take the necessary precautions to avoid these risks.
WARNING
• DO NOT insulate the first three (3) linear feet of the exhaust vent run.
• CPVC, Polypropylene, or Stainless
Steel pipe material MUST be used if the first three (3) linear feet of the exhaust vent run passes
Within First Three (3) Linear Feet of
Appliance Exhaust Vent Adapter
Enclosed
Space through an enclosed space greater than 6” in length, such as a wall.
NOTE:
Only Stainless Steel pipe material may be insulated.
• If CPVC is used to meet these requirements, the balance may be installed with approved PVC pipe.
• If Polypropylene or Stainless Steel
Exhaust
Length
Greater than
Six (6) Inches
LP-179-JJ
11/30/17 is used to meet these requirements, the balance of the vent run must be installed with the same material.
• Failure to comply with this warning could result in property damage, severe personal injury, or death.
Part 5 - Venting
B. Approved Materials for Exhaust Vent and Intake Pipe
Item
Pipe and Fittings Approved for Intake ONLY
Material
ABS*
Standards for Installation In:
United States Canada
ANSI/ASTM D2661 ANSI/ASTM D2661
Pipe Approved for
Intake OR Exhaust Vent
Pipe Fittings
PVC Schedule 40/80
PVC-DWV Schedule 40/80
CPVC Schedule 40/80
Polypropylene
Stainless Steel AL29-4C
PVC Schedule 40
PVC Schedule 80
CPVC Schedule 40
CPVC Schedule 80
ANSI/ASTM D1785
ANSI/ASTM D2665
ANSI/ASTM F441
UL-1738 or ULC-S636
PVC, CPVC, and PP Venting Must be ULC-S636 Certified.
Certified for Category IV and Direct Vent Appliance Venting
ANSI/ASTM D2466 or D2665
ANSI/ASTM D2467 or D2665
ANSI/ASTM F438
ANSI/ASTM F439
PVC, CPVC, and PP Venting Must be ULC-S636 Certified
ANSI/ASTM D2235
ANSI/ASTM D2564
ANSI/ASTM F493
ASTM F656
ANSI/ASTM D2235
IPEX System 636 Cements and
Primers
Pipe Cement
ABS*
PVC
CPVC
Pipe Primer
PVC / CPVC
Table 11 - Approved Materials for Exhaust Vent and Intake Pipe
DANGER
• The exhaust and intake components installed with this appliance must be used for near appliance piping BEFORE transitioning to the approved materials listed above. DO NOT REMOVE these installed components. Doing so WILL VOID appliance warranty.
• PVC / CPVC pipe and fittings of the same diameter are considered interchangeable.
• The use of cellular core PVC (ASTM F891), cellular core CPVC, or Radel
®
(polyphenolsulfone) in exhaust venting systems is prohibited.
• Covering non-metallic vent pipe and fittings with thermal insulation is prohibited.
• The boiler’s vent and air intake connections are designed to accept 2” PVC/CPVC and Polypropylene directly. DO NOT insert
PVC piping into the boiler’s exhaust connection. When venting with PVC, insert the factory supplied 5.5” length of CPVC before transitioning to PVC.
• When installing AL29-4C vent piping, install a PVC-to-stainless adapter at the boiler vent connection, and at the termination when using a PVC termination kit. DO NOT mix AL29-4C piping from different manufacturers unless using adapters specifically designed for the purpose by the manufacturer.
• DO NOT mix components from different venting systems without proper adapters. The vent system could fail, causing leakage of flue products into the living space. Use only the approved pipe and fitting materials, and primer and cement specifically designed for the material used, as listed in the above table.
• A double wall vent or insulated material may be used when using stainless steel vent material in a freezing climate.
• *ABS may be used for air intake applications ONLY.
• Contact the venting material manufacturer if there is any question about the applicability of the proposed venting material.
Failure to follow these directions will result in substantial property damage, severe personal injury, or death.
CAUTION
High heat sources (generating heat 100oF / 37oC or greater, such as boiler flue pipes, space heaters, etc.) may damage plastic components of the boiler as well as plastic vent pipe materials. Such damages ARE NOT covered by warranty. It is recommended to keep a minimum clearance of 8” from high heat sources. Observe heat source manufacturer instructions, as well as local, state, provincial, and national codes, laws, regulations, and ordinances when installing this boiler and related components near high heat sources.
NOTE: The use of double-wall vent or insulated material for the combustion air intake pipe is recommended in cold climates to prevent the condensation of airborne moisture in the incoming combustion air.
DANGER
You must not use “B” vent in an exhaust application. “B” vent is for intake applications ONLY. Using “B” vent in an exhaust application will result in serious injury or death.
C. Additional Requirements for Installation in Canada
1. Installations must be made with a vent pipe system certified to
ULC-S636.
2. The first three (3) feet of vent pipe from the boiler flue outlet must be readily accessible for visual inspection.
3. The components of the certified vent system must not be interchanged with other vent systems or unlisted pipe / fittings.
37
Part 5 - Venting
D. Exhaust Vent and Intake Pipe Location
INSIDE CORNER
DETAIL
G
E
A
H
B
B
E
OPERABLE
FIXED
CLOSED
E
C
FIXED
CLOSED
OPERABLE
E
E
D
I
E
F
M B
E
A
K
I
K
E
I
J
E
E
B
I
B
L
Area Where Intake Terminal Is Not Permitted
LP-179-CC
03/28/17
E
Exhaust Vent Terminal
I
Intake Pipe Terminal
Figure 28 - Exit Terminals for Direct Vent Systems - ANSI Z223.1 / NFPA 54 for US and CAN/CSA B149.1 for Canada
A
B
DESCRIPTION
Clearance above grade, veranda, porch, deck, or balcony
Clearance to window or door that may be opened
Direct Vent
Power Vent
US
1 foot (30 cm)
1 foot
4 ft below or to side of opening; 1 ft above opening
*
CANADA
3 feet (91 cm)
C
Clearance to permanently closed window
D
Vertical clearance to ventilated soffit located above the terminal within a horizontal distance 2 feet (61 cm) from the center line of the terminal
E
Clearance to unventilated soffit
F
Clearance to outside corner
G
Clearance to inside corner
H
Clearance to each side of center line extended above meter / regulator assembly
*
*
*
*
*
I
Clearance to service regulator vent outlet *
Above a regulator within 3 feet (91 cm) horizontally of the vertical center line of the regulator vent outlet to a maximum vertical distance of 15 ft (4.5 m)
J
K
Clearance to nonmechanical air supply inlet to building or the combustion air inlet to any other appliance
Clearance to mechanical air supply inlet
Direct Vent
Power Vent
L
Clearance above paved sidewalk or paved driveway located on public property
Direct Vent
Power Vent
M
Clearance under veranda, porch deck, or balcony
1 foot
4 ft below or to side of opening; 1 ft above opening
3 feet above if within 10 feet horizontally
*
7 feet (2.13 m)
*
3 feet (91 cm)
6 feet (1.83 m)
7 feet (2.13 m)
1 foot (30 cm)
Table 12 - Vent Termination Clearances - *NOTE: For clearances not specified in ANSI Z223.1 / NFPA 54 for US and CAN/CSA B149.1 for Canada, please use clearances in accordance with local installation codes and the requirements of the gas supplier.
WARNING
For each floor containing bedroom(s), a carbon monoxide detector and alarm shall be placed in the living area outside the bedrooms, as well as in the room that houses the heater. Detectors and alarms shall comply with NFPA 720 (latest edition). Failure to comply with these requirements could result in product damage, severe personal injury, or death.
38
WARNING
The building owner is responsible for keeping the exhaust and intake terminations free of snow, ice, or other potential blockages, as well as scheduling routing maintenance. Failure to keep the vent piping terminations clear and properly maintain the heater could result in property damage, severe personal injury, or death.
E. Exhaust Vent and Intake Pipe Sizing
1. The factory ready exhaust vent and intake air pipe diameter is 2”.
The vent diameter can be increased to 3” by installing a reducing coupling in a vertical length of pipe.
2. The total length of the intake air pipe run must not exceed one
hundred (100) feet in 2” pipe, or one hundred fifty (150) feet in
3” pipe.
NOTE: There is no minimum length for the intake air pipe run.
3. The total length of the exhaust vent pipe run must not be less
than six (6) feet.
4. The total length of the exhaust vent pipe run must not exceed
one hundred (100) feet in 2” pipe, or one hundred fifty (150)
feet in 3” pipe.
Minimum - Maximum Vent Run Lengths
Diameter
Intake Air Pipe Run
Exhaust Vent Run
2”
0 - 100 feet
6 - 100 feet
3”
0 - 150 feet
6 - 150 feet
Table 13 - Minimum - Maximum Vent Runs
5. The equivalent length of elbows, tees, and other fittings are listed in the Friction Loss Table below.
Friction Loss Equivalent in Piping and Fittings
Fittings or Piping
Equivalent Feet
2” or 3”
90 Degree Elbow*
45 Degree Elbow
Coupling
One Foot of Straight Pipe
5’
3’
0’
Concentric Kit
1’
3’
Table 14 - *Friction loss for long radius elbow is 1 foot less. NOTE: Consult
Polypropylene venting instructions for friction loss and pressure drop equivalents.
Vent Sizing Example
If the exhaust vent run has two 90 o
elbows, 10 feet of straight pipe and a concentric kit we will calculate:
Exhaust Vent Equivalent Length = (2x5) + 10 + 3 = 23 feet - Well below the maximum of 100 ft in 2” pipe, or 150 ft in 3” pipe.
If the intake air pipe run has one 90 o
elbow, two 45 o
elbows, and 14 feet of straight pipe:
Intake Air Pipe Equivalent Length = 5 + (2x3) + 14 = 25 feet - Well below the maximum of 100 ft in 2” pipe, or 150 ft in 3” pipe.
NOTE: The intake air pipe and exhaust vent do not have to be of equal length. There is no balancing requirement between intake and exhaust.
WARNING
Failure to install the boiler within the minimum and maximum vent length requirements could result in improper product operation and property damage, serious personal injury, or death.
Part 5 - Venting
When preparing pipe for installation:
• Ensure cuts are square.
• Bevel cut edges by 1/16” - 1/8”. Deburr the pipe.
• Lubricate the gasket.
1. Push the length of pipe into the connection until it touches the bottom of the fitting.
2. Tighten the clamps using a screwdriver.
3. Ensure the pipe is secure before continuing installation.
4. For 3” installations, install the reducing coupling in a vertical section of pipe.
WARNING
When venting with PVC, first install the included 5.5” length of 2” CPVC into the boiler’s exhaust connection, then adapt to PVC using approved
CPVC to PVC transition cement. Installing PVC pipe into the boiler’s exhaust connection is strictly prohibited - the strain of the gear clamp combined with heat can deform PVC over time and result in flue gas leakage causing property damage, severe personal injury, or death.
Figure 29 - Correct Installation into the Appliance Collar
NOTE: INCREASING VENT SIZE: TRANSITIONING FROM 2” TO 3” VENT
PIPE MUST ALWAYS TAKE PLACE IN A VERTICAL POSITION TO PREVENT
CONDENSATE BLOCKAGE. See Figure 30.
Figure 30 - Transitioning from 2” to 3” Vent Pipe
Follow the steps below to install air intake pipe into the boiler air intake connection. See Figure 31 for additional details.
NOTE: Clean and dry the boiler connection.
DO NOT use primer or cement on the boiler connection.
Select an air intake connection (left or right of the exhaust vent collar).
See Figure 31.
1. Using a utility knife, cut out the plastic covering the air intake connection from the side chosen. NOTE: DO NOT CUT OUT BOTH
SIDES! See Figure 31.
F. Tightening Boiler Collar to Exhaust Vent and Intake Pipe
This boiler uses 2” or 3” diameter pipe for exhaust vent and intake pipe.
In order to use 3” pipe, it is required to increase pipe size in a vertical length of pipe with a 3” x 2” reducing coupling (not included).
Follow the steps to install exhaust vent pipe into the boiler vent collar. See Figure 29 for additional details.
NOTE: Clean and dry the boiler connection.
DO NOT use primer or cement on the boiler connection.
Figure 31 - Cut Out Plastic Covering the Air Intake Connection
39
Part 5 - Venting
2. If using the right side connection, remove the gear clamp from the left side connection and install it on the right side. See Figure 32.
WARNING
You must cut out the plastic on the air intake connection being used before installing the air intake pipe. Failure to do so will result in improper boiler operation, property damage, severe personal injury, or death.
Figure 32 - Remove the Clamp
3. Insert the air intake pipe until it touches the bottom of the fitting.
4. Tighten the gear clamp using a screwdriver. See Figure 32.
Figure 33 - Air Intake Pipe Installed (Left Side Installation Demonstrated)
40
G. Exhaust Vent and Intake Pipe Installation
WARNING
All joints of positive pressure vent systems must be sealed completely to prevent leakage of flue products into the living space. Failure to do so could result in property damage, serious injury, or death.
1. Use only solid PVC, CPVC, or stainless steel pipe or a Polypropylene vent system approved for use with Category IV appliances.
ABS pipe material may be used on air inlet piping only.
2. Remove all burrs and debris from joints and fittings.
3. When using PVC or CPVC pipe, all joints must be properly cleaned, primed, and cemented. Use only cement and primer approved for use with the pipe material. Cement must conform to ASTM D2564 for PVC and ASTM F493 for CPVC pipe. NOTE: DO NOT CEMENT
POLYPROPYLENE PIPE.
4. Ensure the vent is located where it will not be exposed to prevailing winds.
5. In all roof venting applications, exhaust discharge must point away from the pitch of the roof.
6. If the exhaust vent is to be terminated in a walled off area (such as a roof with a parapet wall), ensure the exhaust vent terminates a minimum of 10’ from nearest wall and extends level with or above the top of the wall. This will ensure flue gas does does not get trapped and possibly recirculated into the intake air pipe, which could contaminate the combustion air.
7. To prevent water leakage, install adequate roof flashing where the pipe enters the roof.
8. Do not locate vent over public walkways, driveways, or parking lots. Condensate could drip and freeze, resulting in a slip hazard or damage to vehicles and machinery.
9. Due to potential moisture build-up, sidewall venting may not be the preferred venting option. To save time and cost, carefully consider venting installation and location.
10. Horizontal lengths of exhaust vent must slope back towards the boiler not less than ¼” per foot to allow condensate to drain from the vent pipe.
11. The exhaust vent must terminate where vapors cannot make accidental contact with people or pets, or damage shrubs or plants.
12. In vacant chimney applications, install and seal a rain cap over existing chimney openings.
13. All piping must be fully supported. Use pipe hangers at a minimum of 4 foot intervals to prevent sagging of the pipe where condensate may form.
14. Do not use the boiler to support any piping.
15. Ensure the outdoor exhaust vent and intake pipe terminations are screened to prevent blockage caused by debris or birds. Vent screens are included with this boiler.
instructions reference snow levels in establishing a minimum height for the installation of exhaust vent or air intake terminations.
Snow levels shall be determined as follows: a. The installation location may, by ordinance, designate how snow levels are calculated in that location; or b. In the absence of specific ordinances, snow levels shall be calculated from the average monthly maximum depth of snow accumulation as indicated by the National Weather Service’s 10 year statistics for the installation location/geographical area.
In addition:
• Total length of vent piping shall not exceed the limits specified in this manual.
• The vent piping for this direct vented appliance is approved for zero clearance to combustible construction.
• The flue products coming from the exhaust vent will create a large plume when the heater is in operation. Avoid venting in areas that will affect neighboring buildings or be considered objectionable.
• DO NOT locate exhaust vent or intake pipe in a parking area where machinery may damage the pipe.
• DO NOT vent near soffit vents, crawl space vents, or other areas where condensate or vapor could create a nuisance or hazard or cause property damage.
• DO NOT vent where condensate vapor could cause damage or could be detrimental to the operation of regulators, relief valve, or other equipment.
In the Commonwealth of Massachusetts and as Required by State and Local Codes:
• The vented gas fueled appliance shall not be installed so its combustion, ventilation, or dilution air is obtained from a bedroom or bathroom.
• Signage: Whenever any through-the-wall (horizontal or sidewall) vent is installed less than seven feet above the finished grade, a metal or plastic identification plate shall be permanently mounted to the exterior of the building at a minimum height of eight feet above grade directly in line with the exhaust vent terminal. The sign shall read, in print no less than 0.5 inches in size, “GAS VENT
DIRECTLY BELOW. KEEP CLEAR OF ALL OBSTRUCTIONS”.
Part 5 - Venting
• Marking of Exhaust Vent and Intake Pipe: Piping used for ventilation, make-up, or combustion air intake shall be labeled as follows:
a. Throughout the entire developed length:
i. Labels must be placed every ten feet for exposed/visible piping; or
ii. Labels must be placed every three feet for concealed piping.
b. At all changes of direction;
c. On each side of a penetration through a partition, wall or ceiling; and
d. The labels shall be black lettering that:
i. Indicates that the piping is used for ventilation, make-up, or combustion air intake, and
ii. The letters shall be sized equal to a minimum of the pipe inches.
The following table lists optional exhaust/intake terminations available from NTI: diameter. However, for piping with a diameter exceeding two inches, said lettering does not need to be larger than two
Description
3” PVC Concentric Termination Kit
3” PVC Low Profile Termination Kit
2” PVC Low Profile Termination Kit
Table 15 - Optional Vent Kits
Stock Code
84634
84357
85062
Description
Vent
Size
Supplier
Part Number
Figure
Vent Material
Compatibility
Vent Option Availability
Roof Wall
IPEX Low Profile
(Wall)
7
2”
3”
196984 (NTI p/n 85062)
196985 (NTI p/n 84357)
35, 39
35, 39
No Yes
IPEX Concentric
(Wall/Roof)
4, 5, 6, 7
2”
3”
196125
196116 (NTI p/n 84634)
36, 40, 45, 49
36, 40, 45, 49
PVC/CPVC
Yes Yes
196117 36, 40, 45, 49
Duravent Polypro® Concentric (Wall)
Duravent Polypro® Concentric (Roof)
2 - 3”
2 - 3”
2PPS-HK, 3PPS-HK
2PPS-VK, 3PPS-VK
37, 41
46, 50
Polypro®
Polypropylene
No
Yes
Yes
No
InnoFlue® Flush Mount (Wall)
InnoFlue® Concentric (Wall)
2 - 3” ISLPT0202, ISLPT0303
2 - 3” ICRT2439, ICTC0224
35, 39
37, 41
InnoFlue®
Polypropylene
No
No
Yes
Yes
InnoFlue® Concentric (Roof)
2 - 3” ICRT3539, ICTC0335 46, 50 Yes No
Z-DENS® Concentric (Wall)
Z-DENS® Concentric (Roof)
2 - 3”
2 - 3”
2ZDHK2, 2ZDHK3
2ZDVK2, DZDVK3
Not Shown
Not Shown
Z-DENS®
Polypropylene
No
Yes
Yes
No
NOTES:
1 Instructions included with termination kits contain detailed assembly and installation instructions.
2 Clearance requirements in this manual supersede those of the instructions included with the vent terminal.
3 Piping MUST be secured to the vent terminal during installation.
4 IPEX Concentric Terminal MUST be cemented together and to the vent pipes during installation.
5 Vent Screens provided with boiler may be used with the IPEX Concentric Vent Kits; otherwise use IPEX vent screens (2 in. vent screen p/n 196050; 3 in. vent screen p/n 196051 - each sold separately).
6 IPEX Low Profile and Concentric kits (exluding p/n 197117) are constructed out of ULC-S636 approved PVC. Check with your local authority for the acceptance of PVC as a venting material prior to use.
7 IPEX Concentric kits can be shortened to fit the requirements of the installation. See instructions included with the kit for more details.
Table 16 - Optional Vent Termination Kits
41
Part 5 - Venting
H. Applications
1. Direct Vent Installation of Exhaust and Intake
If installing a direct vent option, combustion air must be drawn from the outdoors directly into the boiler intake, and exhaust must terminate outside. There are three basic direct vent options detailed in this manual:
1. Side Wall Venting,
2. Roof Venting, and
3. Unbalanced Venting.
Be sure to locate the boiler such that the exhaust vent and intake pipe can be routed through the building and properly terminated.
Different vent terminals can be used to simplify and eliminate multiple penetrations in the building structure (see Optional Equipment in
Venting Section). The exhaust vent and intake pipe lengths, routing and termination methods must all comply with the methods and limits given in the Venting section of this manual.
When installing a combustion air intake from outdoors, care must be taken to utilize uncontaminated combustion air.
NOTE: To prevent combustion air contamination, see Table 6.
WARNING
All vent pipes must be glued, properly supported, and the exhaust pitched a minimum of 1/4” per foot back to the boiler to allow drainage of condensate. When placing support brackets on vent piping, the first bracket must be within 1 foot of the boiler and the balance of 4 foot intervals on the vent pipe. Venting must be readily accessible for visual inspection from the first three feet from the boiler.
Take extra precaution to adequately support the weight of vent pipes terminating through the roof. Failure to properly support roof terminated piping could result in property damage, serious injury, or death.
An unbalanced vent system can be installed ONLY when the exhaust is in the vertical position. Failure to do so could result in serious personal injury or death.
42
Sidewall Venting Options - Direct Vent Installation
Two Pipe Termination
WARNING
Exhaust must terminate a minimum of 18” above the air intake termination. See Figure 38 for more details.
Part 5 - Venting
Low Profile Termination
WARNING
Exhaust must terminate a minimum of 18” above the air intake termination. See Figure 39 for more details.
Figure 34 - Two Pipe Sidewall Venting
Concentric Termination
WARNING
3” IPEX Low Profile Termination illustrated. See Figure 40 for more details.
Figure 35 - Low Profile Sidewall Termination (with Optional IPEX Kit)
WARNING
3” Duravent / Innoflue Concentric Termination illustrated. See Figure 41 for more details.
Figure 36 - Sidewall Concentric Termination (with Optional IPEX kit)
Figure 37 - Sidewall Concentric Terminatio
(with Optional Duravent / Innoflue Kit)
NOTE: These drawings are meant to demonstrate system venting only. The installer is responsible for all equipment and detailing required by local codes.
43
Part 5 - Venting
Sidewall Venting Options - Direct Vent Installation
Two Pipe Termination
4 in min.
Low Profile Termination
WARNING
Refer to documentation included with termination kit for complete installation instructions.
Gas Vent Directly
Below Keep Free of
Obstructions
Gas Vent
Directly
Below Keep
Free of
Obstructions
Figure 38 - Two Pipe Sidewall Venting Detail
Concentric Termination
WARNING
Refer to documentation included with termination kit for complete installation instructions.
Figure 39 - Low Profile Sidewall Termination (with Optional IPEX Kit)
WARNING
Refer to documentation included with termination kit for complete installation instructions.
Gas Vent
Directly
Below Keep
Free of
Obstructions
Gas Vent
Directly
Below Keep
Free of
Obstructions
Figure 40 - Sidewall Concentric Termination (with Optional IPEX kit)
Figure 41 - Sidewall Concentric Termination
(with Optional Duravent / InnoFlue Kit)
NOTE: These drawings are meant to demonstrate system venting only. The installer is responsible for all equipment and detailing required by local codes.
44
Snorkel Venting (Two Pipe Sidewall Venting Terminations Beneath an Overhang)
Part 5 - Venting
Figure 42 - Two Pipe Sidewall (Horizontal Snorkel) Venting
NOTES:
A. For every 1” of overhang, the exhaust vent must be located 1” vertical below the overhang (12” minimum). Overhang means top of building structure (roof) and not two adjacent walls (corner of building).
B. Maintain minimum separation between exhaust vent and air intake sidewall terminations, as required by local codes.
C. Maintain 12” minimum clearance above highest anticipated snow level or grade (whichever is greater).
D. The exhaust vent must extend a minimum of 12” to a maximum of
24” beyond the building.
NOTE: These drawings are meant to demonstrate system venting only.
The installer is responsible for all equipment and detailing required by local codes.
45
Part 5 - Venting
Roof Venting Options - Direct Vent Installation
Two Pipe Termination
WARNING
Exhaust must terminate a minimum of 18” above the air intake termination. See Figure 47 for more details.
Unbalanced Termination (Roof Exhaust / Sidewall Intake)
WARNING
Exhaust must terminate a minimum of 12” above snow level. See Figure
48 for more details.
Figure 43 - Two Pipe Roof Venting
Concentric Termination
WARNING
3” IPEX Concentric Termination illustrated. See Figure 50 for more details.
Figure 44 - Unbalanced Venting - Roof Exhaust and Sidewall Intake
WARNING
3” Polypro / Innoflue Concentric Termination illustrated. See Figure 49 for more details.
Figure 45 - Roof Concentric Termination (with Optional IPEX kit)
Figure 46 - Roof Concentric Termination
(with Optional Duravent / InnoFlue Kit)
NOTE: These drawings are meant to demonstrate system venting only. The installer is responsible for all equipment and detailing required by local codes.
46
Roof Venting Options - Direct Vent Installation
Two Pipe Termination
Part 5 - Venting
Unbalanced Venting - Roof Exhaust Termination
WARNING
Figure illustrates two options for exhaust termination only. Neither vent pipe illustrated is intended for combustion air intake.
4 in min.
Figure 47 - Two Pipe Roof Venting Detail
Concentric Termination
WARNING
Refer to documentation included with termination kit for complete installation instructions.
Figure 48 - Unbalanced Venting - Roof Exhaust Termination Options
WARNING
Refer to documentation included with termination kit for complete installation instructions.
Figure 49 - Roof Concentric Termination (with Optional IPEX kit)
Figure 50 - Roof Concentric Termination
(with Optional Duravent / InnoFlue Kit)
NOTE: These drawings are meant to demonstrate system venting only. The installer is responsible for all equipment and detailing required by local codes.
47
Part 5 - Venting
2. Venting Through an Existing System
This boiler may be vented through an existing unused vent system.
The inner diameter of the existing vent system is utilized for the combustion air source. Two methods have been approved for such venting: Concentric Venting Through an Existing System and Venting as a Chase.
Vent / Air Inlet Size
2”
Minimum Existing Vent / Chase Size
3”
Table 17 - Minimum Existing Vent / Chase Sizing
4”
5”
DANGER
Do not install the boiler into a common existing vent with any other appliance. This will cause flue gas spillage or boiler malfunction, resulting in substantial property damage, serious personal injury, or death.
The upper and lower vent terminations as well as all joints in the venting system must be properly sealed to ensure that all combustion air is drawn properly and exhaust does not leak from the system. Failure to properly seal the venting system will result in property damage, serious personal injury, or death.
CAUTION
Contractors must check state and local codes before installing through an existing vent opening. State and local codes always take precedence over manufacturer’s instructions. Failure to check state and local codes before installing through an existing opening could result in property damage and add significantly to installation costs.
If an existing venting system is converted for use with this boiler, the installer must ensure that the existing venting system is clean and free from particulate contamination that could damage the boiler.
Failure to do so could result in property damage and boiler failure.
Such failure IS NOT covered under warranty.
Concentric Venting through an Existing System
1
SEAL
EXHAUST
Concentric Venting Through an Existing System
NOTE: The following instructions refer only to venting through an existing vent system, and not to venting with NTI’s optional concentric vent kits. Refer to Concentric Vent Kit installation manual (LP-166) for further information on venting with the optional concentric vent kits.
Concentric venting through an existing system must run vertically through the roof. See Table 17 for proper minimum vent sizing. Use only the approved venting materials specified in Table 11 for piping the system. All instructions listed in this Venting section apply. See
Figures 51-1 and 51-2 for venting demonstrations.
Chase Venting Through an Existing System
When venting as a chase, follow all instructions included in this
Venting section, including those in the previous Concentric Venting
Through an Existing System section. See Figure 51-3 for chase venting demonstration.
Concentric Venting through an Existing System
2
EXHAUST
SEAL
Chase Venting Through an Existing System
3
EXHAUST
24"
AIR INLET
COMBUSTION AIR
COMBUSTION
AIR
EXISTING
SEAL
EXISTING
EXISTING
VENT
AIR INTAKE w/SCREEN
SEAL
12" MIN.
AIR INTAKE
(w/SCREEN)
SEAL
SEALED CAP
SEAL
SEALED
CAP
SEAL
CAP
LP-700-B
03/27/19
NOTE: These drawings are meant to demonstrate system venting only. The installer is responsible for all equipment and detailing required by local codes.
48
Part 5 - Venting
3. Power Venting, Indoor Combustion Air in Confined or
Unconfined Space
This boiler requires fresh, uncontaminated air for safe operation and must be installed in a mechanical room where there is adequate combustion and ventilating air. NOTE: To prevent combustion air
contamination, see Table 6.
When the installation uses Indoor Combustion Air, provisions for combustion and ventilation air, in accordance with section “Air for
Combustion and Ventilation,” of the National Fuel Gas Code, ANSI
Z223.1/NFPA 54 (USA), or Clause 8.2, 8.3 or 8.4 of the Natural Gas and
Propane Installation Code, CAN/CSA B149.1 (Canada), or applicable provisions of the local building codes, must be adhered to.
Combustion air from the indoor space can be used if the space has adequate area or when air is provided through a duct or louver to supply sufficient combustion air based on the boiler input. Never
obstruct the supply of combustion air to the boiler. If the boiler is installed in areas where indoor air is contaminated (see Figure
52) it is imperative that the boiler be installed as direct vent so that all combustion air is taken directly from the outdoors into the boiler intake connection.
Unconfined space is space with volume greater than 50 cubic feet per
1,000 Btu/hour (4.8 cubic meters per kW) of the total input rating of all fuel-burning appliances installed in that space. Rooms connected directly to this space, through openings not furnished with doors, are considered part of the space.
Confined space is space with volume less than 50 cubic feet per
1,000 Btu/hour (4.8 cubic meters per kW) of the total input rating of all fuel-burning appliances installed in that space. Rooms connected directly to this space, through openings not furnished with doors, are considered part of the space.
When drawing combustion air from inside a conventionally constructed building to a confined space, such space should be provided with two permanent openings: one located 6” (15 cm) below the space ceiling, the other 6” (15cm) above the space floor. Each opening should have a free area of one square inch per 1,000 Btu/hr (22cm2/kW) of the total input of all appliances in the space, but not less than 100 square inches
(645cm2).
If the confined space is within a building of tight construction, air for combustion must be obtained from the outdoors as outlined in the
Venting section of this manual. See Figure 53.
Figure 53 - Indoor and Outdoor Combustion Air - Single Pipe
Figure 52 - Do Not Place Appliance Near Dryer
49
Part 6 - Installing the Condensate Drain
CAUTION
This condensing high efficiency boiler has a condensate removal system. Condensate is water vapor derived from combustion products, similar to that produced by an automobile when it is initially started. It is very important that the condensate line is sloped down away from the boiler and to a suitable drain.
The condensate line must remain unobstructed. If allowed to freeze in the line or obstructed in any other manner, condensate can exit from the boiler tee, resulting in potential water damage to property.
When installing a condensate pump, select one approved for use with condensing boilers and furnaces. The condensate pump should have an overflow switch to prevent property damage from spillage.
Condensate from the boiler will be slightly acidic (pH from 2 to 4.5).
Check with your local gas company to determine if combustion condensate disposal is permitted in your area. Install a neutralizing filter if required by local codes.
NOTES:
1. Due to its efficient design, the boiler produces condensate (water) as a normal by-product. This condensate is acidic, with a pH level between 2 and 4.5. This condensate must be drained away from the boiler and disposed in accordance with all local regulations.
2. Condensate line must be pitched at least ¼” per foot to properly drain. If this cannot be done, or a very long length of condensate hose is used, increase the condensate line to a minimum of 1” ID and place a tee in the line after the condensate neutralizer to properly reduce vacuum lock in the drain line.
3. Use corrosion-resistant materials to drain condensate. Use the included flexible plastic hose or ½” PVC and CPVC drain pipe complying with ASTM D1785, F441, or D2665 may be used. Cement must comply with ASTM D2564 for PVC pipe or F493 for CPVC pipe.
For Canadian applications, use CSA or ULC certified PVC or CPVC pipe, fittings, and cement.
4. A frozen condensate line could result in a blocked vent condition.
It is very important to protect the condensate line from freezing temperatures or any type of blockage. In installations that may encounter sustained freezing conditions, the use of heat tape is recommended to avoid freezing of the condensate line. It is also recommended to bush up the condensate line size to 1” and terminate condensate discharge as close to the unit as possible.
Longer condensate runs are more prone to freezing. Damages due to frozen or blocked condensate lines ARE NOT covered by warranty.
5. Support of the condensate line may be necessary to avoid blockage of the condensate flow.
6. Local building codes may require an in-line neutralizer to be installed
(not included) to treat the condensate. See Figure 54. If required by local authorities, a condensate filter of lime crystals, marble, or phosphate chips will neutralize slightly acidic condensate.
Follow all the installation instructions included with the neutralizer.
If a neutralizer is installed, periodic replacement of the limestone
(or neutralizing agent) will be required. The rate of depletion of the limestone varies with usage of the boiler. During the first year of boiler operation, check the neutralizer every few months for depletion.
7. Route the drain line to a nearby floor drain, laundry tub, or condensate pump. If the boiler condensate outlet is lower than the drain, you must use a condensate removal pump (kit p/n 554200 available from NTI).
NOTE: If a nearby laundry tub is used as a disposal for waste water from the washing machine, draining the condensate into this tub allows the soapy water discharge to neutralize the acidic condensate.
8. An error will appear on the boiler display if condensate line is blocked. The boiler will not operate with a blocked condensate line. It is extremely important to have this condition repaired by a qualified service technician.
WARNING
THE CONDENSATE TRAP MUST BE FILLED WITH WATER BEFORE THE
BOILER IS USED. The siphon is filled with water during the boiler and heating system purging procedure. See Purging Procedure in this manual for further instructions.
Ensure the siphon contains water. If the siphon does not contain water it must be filled. Open the manual air vent on the main heat exchanger until filling is complete. See Figure 54. Check the system pressure with a pressure gauge.
INSUFFICIENT WATER IN THE TRAP CAN CAUSE FLUE GAS TO BE
EXPELLED.
Failing to ensure the condensate trap is full of water could result in property damage, severe personal injury, or death.
Boiler Manual Air Vent
Figure 54 - Condensate Trap Filling
50
PIPE HANGERS MUST
BE USED TO SUPPORT
VERTICAL OR
HORIZONTAL PIPING
EXISTING
DRAIN
CONDENSATE
NEUTRALIZER
1” x 3/4”
PVC PIPE
REDUCER
HORIZONTAL LINES MUST
BE INSTALLED WITH A PITCH
OF 1/4” PER FOOT
TO OUTSIDE
SOURCE
PIPE HANGERS MUST
BE USED TO SUPPORT
VERTICAL OR
HORIZONTAL PIPING
PIPE HANGERS MUST
BE USED TO SUPPORT
VERTICAL OR
HORIZONTAL PIPING
CONDENSATE
HOSE (supplied)
CONDENSATE
HOSE (supplied)
Part 7 - Connecting Electrical Service
WARNING
Install wiring and electrically ground boiler in accordance with the authority having jurisdiction or, in the absence of such an authority, follow the National Electrical Code, NFPA 70, and/or CSA C22.1 Electrical
Code-Part 1 in Canada. Failure to follow all applicable local, state, and national regulations, mandates, and building supply codes for guidelines to install the electrical power supply could result in property damage, serious personal injury, or death.
ELECTRICAL SHOCK HAZARD – To ensure safety, turn off electrical power supply at service entrance panel before making any electrical connections to avoid possible electric shock hazard. Failure to do so could result in property damage, serious personal injury, or death.
Jumping out control circuits or components WILL VOID product warranty and can result in property damage, personal injury, or death.
It is of extreme importance that this unit be properly grounded. It is very important that the building system ground is inspected by a qualified electrician prior to making this connection. Electrical power must only be turned on when the boiler is completely filled with cold water. Failure to follow these instructions could result in component or product failure, serious injury, or death.
CAUTION
Label all wires prior to disconnecting when servicing the boiler. Wiring errors can cause improper and dangerous operation. Failure to follow these instructions may result in property damage or personal injury.
A. Wiring
The boiler is equipped with a three prong power cord. The boiler is limited to a maximum of 15 amps at 120 volts in use.
CONDENSATE
NEUTRALIZER
1” x 3/4”
PVC PIPE
REDUCER
Figure 55 - Condensate Piping Suggestions
HORIZONTAL LINES MUST
BE INSTALLED WITH A PITCH
OF 1/4” PER FOOT
NOTES:
1. Condensate line must be pitched at least ¼” per foot to properly drain. If this cannot be done, or a very long length of condensate hose is used, increase the condensate line to a minimum of 1” ID and place a tee in the line after the condensate neutralizer to properly reduce vacuum lock in the drain line.
2. PVC or CPVC pipe should be the only material used for condensate line. Steel, brass, copper, and other metals will be subject to corrosion or deterioration.
3. A frozen condensate line could result in a blocked vent condition.
It is very important to protect the condensate line from freezing temperatures or any type of blockage. In installations that may encounter sustained freezing conditions, the use of heat tape is recommended to avoid freezing of the condensate line. It is also recommended to bush up the condensate line size to 1” and terminate condensate discharge as close to the unit as possible.
Longer condensate runs are more prone to freezing. Damages due to frozen or blocked condensate lines ARE NOT covered by warranty.
4. Support of the condensate line may be necessary to avoid blockage of the condensate flow.
5. To allow proper drainage on longer horizontal condensate runs, tubing size may need to increase to 1” and a second line vent may be required.
NOTE: To clean out condensate trap, see Maintenance section.
Figure 56 - Proper Grounding
1. This boiler must be properly grounded. Ensure the electrical receptacle is properly grounded. Do not remove the grounding prong from the boiler plug.
2. Do not attach the ground wire to either the gas or water piping.
3. The wiring diagrams in this manual are to be used for reference purposes only.
4. Refer to these diagrams and the wiring diagrams of any external controls used with the installation when wiring the boiler. Read, understand, and follow all wiring instructions supplied with the controls.
5. Do not disconnect the power supply when the boiler is in normal operation.
51
Part 7 - Connecting Electrical Service
NOTE: For additional electrical protection, the use of a whole house surge protector is recommended. Damage caused by power surges IS
NOT covered by the warranty.
1. Removing the Power Cord (To Hard Wire the Boiler)
To remove the power cord and hard wire the boiler:
1. Shut off the power supply at the boiler and at the circuit breaker.
2. Shut off the gas at the manual shutoff.
3. Remove the boiler front cover.
4. Disconnect the three clips and open the junction box
8. Cut the cable inside the cabinet and below the plastic connector.
Remove the internal part of the cable from the junction box.
Discard the internal and external parts of the cable. Note: it may be necessary to loosen the right side panel to access the plastic cable connector.
9. Leave the plastic connection secured to ensure the cabinet remains sealed.
Figure 57 - Accessing the Junction Box
5. Unhook the power cord from the green connector CN6.
Figure 60 - Cut the power cable
10. Insert the field power cable through the hole in the side panel; use an appropriate strain relief/conduit hub to secure the cable to the side panel. Fix the wiring to the green connector at the PCB; reuse the grommet removed in step 7 to act as a strain relief at the junction box
hole Ø 7/8"
CN1
CH
PUMP
DHW
PUMP
L N
DHW PUMP
CN6
Figure 58 - Power Cord - Green Connector CN6
6. Remove the power cord and the green connector
CN1
CH
PUMP
DHW
PUMP
L N
DHW PUMP
FUSE 5AT
DHW PUMP
CN6
Figure 59 - Remove the power cord from the junction box
7. Unscrew the connector screws and remove the power cord.
Remove the grommet.
Figure 61 - Hole Position for Power Cord - Right Side of Boiler
11. Reconnect the three clips and close the Junction box.
12. Rotate and fix the control panel.
13. Reinstall the boiler front cover
14. Restore gas to the boiler.
15. Restore power to the boiler.
52
Part 7 - Connecting Electrical Service
2. Connecting Power (120V) for DHW and CH Circulators
To connect power for the CH and DHW external pump on the main
PCB:
1. Shut off the power supply at the boiler and at the circuit breaker.
2. Shut off the gas at the manual shutoff.
3. Remove the boiler front cover.
4. Disconnect the three clips and open the junction box
5. Insert the circulator power cable through the hole in the side panel; use an appropriate strain relief/conduit hub to secure the cable to the side panel.
6. Connect the cable on the connector CN5 (DHW pump) and CN4
(CH pump). See Electrical Wiring Diagram, Figure 62.
CN1
CH
PUMP
DHW
PUMP
L N
DHW PUMP
FUSE 5AT
DHW PUMP
CN6
Figure 64 - 120V Connections for DHW and CH Circulators
BUS
TT2
OD
TNK
SYS
TT1
Low Voltage Wiring Connections
Remote Control Connection
Room Thermostat 2
Outdoor Sensor
Tank Temperature Sensor (Probe / Aquastat)
System Sensor (Cascade Manager)
Room Thermostat 1
Table 18 - Low Voltage Wiring Connections
Remote Control (optional)
Outdoor
Sensor Tank temp. probe System
Sensor
OK
Room Thermostat
1 2 3 4 5 6 7
Figure 62 - 120V Connections for DHW and CH Circulators
7. Verify that the new cable is correctly positioned inside the control panel.
8. Reconnect the to cover of the junction box.
9. Reinstall the boiler front cover
10. Restore gas to the boiler.
11. Restore power to the boiler.
3. Low Voltage Wiring Connections
To access the low voltage wiring connections:
1. Shut off the power supply at the boiler and at the circuit breaker.
2. Shut off the gas at the manual shutoff.
3. Remove the boiler front cover.
4. Rotate the control panel while pulling it forwards.
5. Disconnect the two clips See Figure 63
6. Open the control panel cover to have access to the main PCB. See
Figure 64.
120V
T B
BUS
120V
TT2
120V 120V
5V IN
120V 120V
OD TNK SYS TT1
Figure 65 - Low Voltage Wiring Connections
CAUTION
DO NOT CONNECT 120V TO ANY CONTROL WIRING
CONNECTION! DOING SO WILL RESULT IN IMPROPER
OPERATION AND POSSIBLE DAMAGE TO THE BOILER. SUCH
DAMAGES ARE NOT COVERED BY PRODUCT WARRANTY!
Figure 63 - 120V Connections for DHW and CH Circulators
53
Part 7 - Connecting Electrical Service
4. Room Thermostat Wiring Connections
To connect a room thermostat:
1. Access the low voltage wiring connections by following the directions in Item 3, Low Voltage Wiring Connections.
2. Loosen the cable clamp using a screwdriver and insert the wires leading from the room thermostat.
3. Connect the room thermostat wires to the terminals indicated in
Table 18 and Figure 65.
4. Ensure that the wires are well connected and not subject to stress when the control panel or cabinet cover are closed.
CAUTION
NOTE:
Some newer thermostat models may draw too much power from the boiler and will require an additional power supply to operate properly. Review the instructions provided with the thermostat to determine if an additional power supply is needed. Failure to do so could result in improper boiler and/or thermostat operation.
5. Outdoor Sensor Connections
NOTE: WHEN CONNECTING THE BOILER TO EXTERNAL CONTROLS,
DO NOT RUN 120V CABLES AND CABLES FOR CONTROL CIRCUITS
(WHICH ARE LOW VOLTAGE) TOGETHER. USE SEPARATE CABLES TO
PREVENT INDUCED VOLTAGE ON THE LOW VOLTAGE CIRCUITS.
Outdoor Sensor
Connector OD on PCB
Figure 66 - Outdoor Sensor Connection
6. Aquastat (Default) and Tank Sensor (Optional) Connections
(non-Combi Models)
The boiler is designed for managing the production of domestic hot water via an indirect water heater (IWH) in one of two ways:
i. AQUASTAT (default) - with parameter 228 = 2, the tank temperature is managed through an ON/OFF aquastat installed in the tank.
When an aquastat is equipped, the target outlet boiler water temperature for DHW operation is 180oF.
ii. TANK SENSOR (optional) - with parameter 228 = 1, the boiler manages the IWH temperature directly via an NTC sensor installed in the tank and connected to the boiler (see electrical diagram).
The setting of the tank temperature is done through the “+” and “-” buttons on the left side of the display.
When a tank sensor is equipped, the target outlet boiler water temperature for DHW operation will be 36°F higher than the DHW setpoint.
54
Boiler Pump
Part 7 - Connecting Electrical Service
B. Internal Wiring Details
C.H. Pump
N
PUMP
DHW
N L
N
PUMP
CH
CH PUMP
FUSE 5AT
POWER-IN
DHW PUMP
FUSE 5A
1
CN2
1
CN3
Tank sensor
1
CN22
1
CN26
Bl Bl
Br Gr
CN16
1 CN19 1 CN12 1 CN20
Outlet temp
Figure 67 - Electrical Wiring Diagram
55
Part 7 - Connecting Electrical Service
56
Figure 68 - Ladder Diagram
CN1
CN2
CN3
CN8
CN4
CN7
CN9
CN26
CN20
Connector
No. of Location
POWER SUPPLY
EXTERNAL PUMP 2 / Hi-V DIVERTER VALVE
BOILER PUMP
EXTERNAL PUMP 1
FAN ON/OFF
IGNITER
GAS VALVE
POWER SUPPLY OUT
PROTECTIVE EARTH
PROTECTIVE EARTH
PROTECTIVE EARTH
NTC HEAT RETURN
NTC HEAT FLOW 1
NTC FLUE
AIR PRESSURE SWITCH
DHW FLOW SWITCH
WATER PRESSURE SWITCH
DIVERTER VALVE
5
6
3
4
1
2
1
1
2
1
6
1
4
5
2
3
7
1
5
6
3
4
1
2
Pin
1
2
3
9
10
7
8
5
6
3
4
1
2
11
12
9
10
7
8
11
Table 19 - Boiler Wiring - 1
Part 7 - Connecting Electrical Service
HT Selv Description
120 VAC LIVE INPUT
120 VAC NEUTRAL INPUT
PROTECTIVE EARTH
120 VAC EXT. PUMP2 INPUT / 120VAC LINE DIV1
120 VAC NEUTRAL
120 VAC EXT. PUMP2 (NO) / 120VAC LINE DIV2
120 VAC LIVE (NO)
120 VAC NEUTRAL
120 VAC EXT. PUMP1 INPUT
120 VAC EXT. PUMP1 (NO)
120 VAC LIVE
120 VAC NEUTRAL
120 VAC LIVE (NO)
120 VAC NEUTRAL
120 VRAC + (NO)
120 VRAC - (NO)
120 VAC LINE
120 VAC NEUTRAL
HT (120V~) AC
HT (120V~) AC
HT (120~) AC
HT (120V~) AC
+5V
CH RETURN NTC SENSOR SIGNAL
+5V
CH FLOW 1 NTC SENSOR SIGNAL
NOT USED
+5V
FLUE NTC SENSOR SIGNAL
+24V
APS DETECTION SIGNAL
NOT USED
GROUND
DHW FLOW DETECTION SIGNAL
+5V
GROUND
CH WATER PRESSURE SENSOR SIGNAL
NOT USED
STEPPER DIVERTER VALVE COIL 1 START
STEPPER DIVERTER VALVE COIL 1 END
STEPPER DIVERTER VALVE COIL 2 START
STEPPER DIVERTER VALVE COIL 2 END
SELV (5V)
SELV (24V)
SELV (5V)
57
Part 7 - Connecting Electrical Service
Connector
No. of Location
CN24
CN16
CN19
CN12
CN22
CN23
CN18
ROOM THERMOSTAT
NTC SYSTEM
NTC TANK
OUTDOOR SENSOR
ROOM THERMOSTAT 2
EBUS2
FAN MANAGEMENT
EXTERNAL CLIP-IN
HMI
PWM PUMP
FLAME
SERVICE TOOL SERIAL INTERFACE
2
3
5
1
3
4
1
2
3
4
1
2
3
4
1
2
4
5
6
2
3
1
1
9
10
11
12
7
8
5
6
Pin
1
2
3
4
Table 20 - Boiler Wiring - 2
Description
+24V
ROOM THERMOSTAT 1 SIGNAL
+5V
CASCADE NTC SENSOR SIGNAL
+5V
BOILER NTC SENSOR SIGNAL
+5V
OUTDOOR NTC SENSOR SIGNAL
+24V
ROOM THERMOSTAT 2 SIGNAL
EBUS2 SIGNAL
GROUND
GROUND
PWM FAN-DRIVER
HALL_EFFECT SENSOR
+24V
+24V
GROUND
CLIP-IN SERIAL TX SIGNAL
CLIP-IN SERIAL RX SIGNAL
+5V
GROUND
HMI SERIAL TX SIGNAL
HMI SERIAL RX SIGNAL
+24V
PWM PUMP SIGNAL
NOT USED
GROUND
FLAME SENSOR SIGNAL
+5V
GROUND
MODE
SERIAL TX SIGNAL TO PC
SERIAL RX SIGNAL FROM PC
+24V
SELV (24V - 5V)
SELV (24V)
HT (110Vrms) AC
SELV (24V - 5V)
HT Selv
SELV (24V)
SELV (5V)
SELV (24V)
SELV (24V)
SELV (24V)
SELV (24V - 5V)
58
Part 8 - Gas Connections
WARNING
FIRE AND/OR EXPLOSION HAZARD
To avoid serious injury or death, the gas line installation and the gas line inlet pressure test must be done by a licensed professional.
WARNING
Make sure the gas line pressures are within normal limits. Pressures outside normal limits can result in poor performance and hazardous operating conditions. Failure to do so could result in property damage, personal injury, or death.
NOTICE
Do not operate the boiler on Natural Gas or LP gas with average sulfur rates greater than 30 mg/m3. Doing so could result in improper product operation and failure, and WILL VOID the boiler warranty.
Ensure the gas on which the boiler will operate is the same type specified on the rating plate (natural gas or LP gas). This boiler must be converted into propane operation. Follow Gas Conversion Manual instructions
(separate document). Failure to follow these instructions could result in property damage, personal injury, or death.
A. Gas Pipe Sizing Tables
1. Gas Pipe Sizing
This information is for reference use only. Refer to gas pipe manufacturer specifications for actual delivery capacity. The DOE standard for Natural
Gas is 1100 BTU/ft
3
. Contact the local gas supplier for actual BTU/ft
3 rating.
2. Natural Gas Pipe Sizing
The following tables list maximum capacity of pipe in cubic feet of gas per hour for gas pressures of 14” or less and a pressure drop of 0.5 inches water column, based on a 0.60 specific gravity for natural gas.
Pipe Size (in.)
10 20 30 40
Length of Pipe (Feet)
50 60 80 100 150 200
BTU’s Per Hour x
1,000
3/4
360 247 199 170 151 137 117 104 83 71
1
678 466 374 320 284 257 220 195 157 134
Schedule 40
Metallic Pipe
1 1/4
1390 957 768 657 583 528 452 400 322 275
1 1/2
2
3
2090
4020
11300
1430
2760
7780
1150
2220
6250
985
1900
5350
873
1680
4740
791
1520
4290
677
1300
3670
600
1160
3260
482
928
2610
412
794
2240
(0.60 Specific
Gravity,
0.5 WC Pressure
Drop)
4
23100 15900 12700 10900 9660 8760 7490 6640
Table 21 - Natural Gas Delivery Capacity - Refer to ANSI Z223.1 - National Fuel Gas Code, Latest Edition
3. LP (Liquid Propane) Gas Pipe Sizing
Contact gas supplier to size pipes, tanks, and 100% lockup gas pressure regulator. Adjust propane supply regulator provided by the gas supplier for 14 inches w.c. maximum pressure.
5330 4560 subject to freezing conditions. See Figure 69.
5. A manual gas shut-off valve should be installed in the gas supply line close to the boiler. See Figure 69.
6. To facilitate any future maintenance, it is also recommended that an approved gas union fitting be installed in the supply line between the shut-off valve and the ¾” NPT connection on the boiler.
B. Gas Connection Requirements
1. The gas connection fitting on the boiler when the supplied adapter is installed is ¾” NPT.
NOTE: The pipe size must not be less than ¾”.
NOTE: DO NOT USE 1/2” quick flex gas lines! Doing so will result in improper appliance operation.
2. The supply line must be sized for the maximum input of the boiler being installed. If there are additional gas appliances on the main supply line, measure the size of the supply line according to the
COMBINED total maximum BTUH draw for the appliances as if they were operating at the same time.
3. Measure the length of the gas supply line from the gas meter to the boiler. The boiler must be installed downstream of the gas meter to ensure adequate gas supply. Use the tables in this manual or refer to the gas line manufacturer’s sizing information to determine the correct supply pipe size.
4. The National Fuel Gas Code (NFPA 54) requires that a sediment trap
(drip leg) be installed in the gas line on boilers not so equipped.
The drip leg must be accessible, a minimum of 3” in length, and not
Manual Gas
Shut-off
Valve
Sediment trap
Union Adapter
Figure 69 - Gas Line with Shut-Off and Sediment Trap Detail
59
Part 8 - Gas Connections
1. Use a manometer to test the gas pressure to make sure it meets the minimum standards and does not exceed the maximum standards of the boiler.
2. Leak test the gas line pipe before placing the boiler in operation.
Only use approved leak detector liquid solutions to check for leaks.
3. Do not operate the boiler until all connections have been completed and the heat exchanger is filled with water.
C. Additional Precaution for Excess Flow Valve (EFV)
If an excess flow valve (EFV) is in the gas line, check the manufacturer’s minimum and maximum flow capacity ratings. An improperly sized
EFV will not allow for a full flow of gas to the boiler and will cause the boiler to malfunction. See Figure 70.
WARNING
DO NOT REMOVE OR ATTEMPT TO MAKE AN
ADJUSTMENT TO SCREWS 2 and 4 WITHOUT A
CALIBRATED COMBUSTION ANALYZER. DOING SO
COULD RESULT IN FIRE, PROPERTY DAMAGE, SERIOUS
PERSONAL INJURY, OR DEATH.
4
2
1
Figure 70 - Excess Flow Valve (EFV)
WARNING
When performing a pressure test on the gas line pipng, be sure the boiler is disconnected or isolated if the test pressure is expected to exceed 1/2
PSI (14” WC), as damage to the gas valve could occur. Such damage could result in fire, property damage, serious personal injury, or death.
D. Checking Gas Pressure at the Boiler for Proper
Operation
NOTE: Refer to Figure 71 when checking gas pressure. Loosen the bolts before checking the gas inlet pressure.
1. The boiler and its individual shutoff valve must be disconnected from the gas supply piping system during any pressure testing of the system at test pressures greater than ½ psi (3.5 kPa).
2. The boiler must be isolated from the gas supply piping system by closing its individual manual shutoff valve during any pressure testing of the gas supply piping system at test pressures equal to or less than ½ psi (3.5 kPa).
The minimum and maximum inlet gas line pressures must meet the requirements shown in Table 22.
Natural Gas
Minimum Pressure
Maximum Pressure
LP Gas
Minimum Pressure
Maximum Pressure
Table 22 - Gas Pressure Requirements
3.5” WC
10.5”WC
8” WC
13”WC
NOTICE
Do not fire (operate) the boiler until all connections have been completed and the heat exchanger is filled with water. Doing so will damage the boiler and void the warranty.
60
1. Line pressure Test point
2. OFFSET Adjustment Screw
4. Throttle Adjustment Screw
Figure 71 - Gas Valve Detail
Gas Inlet
Part 9 - Controls
A. Control and Display Overview
SRA
1 2 3 4
Figure 72 - Control and Display Overview
5 6
7 8 9
Item #
1
2
3
Description
ON / OFF Button (see NOTICE below)
Domestic Hot Water Adjustment Button +/-
MENU
(short press = User Menu); (long press = Info Menu)
4
5
8
9
6
7
HISTORY Button - view last 10 errors
RESET Button (see NOTICE below)
OK – confirms menu selection
ESC – exits menu selection
Heating Temperature Adjustment Button +/-
Table 23 - Control Descriptions
Display
NOTICE
Operating Description
On / Off Button
The button lights (white) when the boiler is electrically powered.
On / Off Button
The button is not lit in the event of an error or power failure.
RESET BUTTON
The button lights (red) in the event of a lockout error.
After pressing the Reset button to clear an error condition, the button will flash for five (5) seconds.
COMFORT
ON OFF
MENU PAR CODE
0
AUTO
Display Icon Description
Digits Indicating:
• Boiler Status
• Temperature indication ( level o
F) with bar
• Error Codes (ERROR)
• Press Reset Button Request (RESET)
(boiler lockout)
• Menu Settings
Technical assistance request
AUTO
Flame detected with indication of power level
CH Heating Operation Set
CH Heating Operation Active
DHW Operation Set
DHW Operation Active
Hot Water Comfort Activated (Combi Only)
Boiler off with Antifreeze Function Active
Antifreeze Function Active
Automatic Temperature Control activated
High Efficiency Operation
(Low CH flow temperature)
Solar inlet temperature probe connected -
Optional
Error signal - Display will also show a code and description
Outdoor Sensor Connected - Optional
WiFi Active
Table 24 - Display Icon Descriptions
61
Part 9 - Controls
B. Ignition Procedure
Press the ON/OFF button on the control panel to power on the boiler.
The display shows the current operating mode.
C. Central Heating (CH) Temperature Adjustment
It is possible to set the central heating (CH) temperature by pressing the buttons described in Figure 72, Item 8.
The CH temperature range is 68 - 122 o
F (low temperature) and 96 -
179 o
F (high temperature).
Figure 73 - Powering On the Boiler
Operating Mode
Description
Stand-by
CH request supply temperature displayed
DHW request
DHW setpoint displayed
Purging Cycle
Central Heating Post Circulation
DHW Circuit Post Circulation
Display
Figure 74 - Central Heating (CH) Temperature Adjustment
NOTE: The CH Setpoint cannot be changed by pressing the CH +/- buttons if an outdoor sensor is connected to the boiler and AUTO is active. When using an outdoor sensor, the boiler will automatically change the CH target temperature based on the Outdoor Heating
Curve
D. Domestic Hot Water (DHW) Temperature Adjustment
Not for non-COMBI using Aquastat
It is possible to set the domestic hot water (DHW) temperature by pressing the buttons described in Figure 72, Item 2.
The DHW temperature range is 97 - 140 o
F. The previously set value will flash on the display.
Figure 75 - Domestic Hot Water (DHW) Temperature Adjustment
DANGER
Hotter water increases the risk of scald injury. Scalding may occur within five (5) seconds at a setting of 140°F. Water temperature over 125°F can instantly cause severe burns or death from scalds.
Children, disabled, and elderly persons are at the highest risk of being scalded. See instruction manual before setting temperature at the appliance. Feel water before bathing or showering.
62
Approximate Time / Temperature Relationships in Scalds
120 o F
125 o F
130 o F
135 o F
140 o F
145 o F
150 o F
More than 5 minutes
1 1/2 to 2 minutes
About 30 seconds
About 10 seconds
Less than 5 seconds
Less than 3 seconds
About 1 1/2 seconds
155 o F About 1 second
Table 25 - Time and Temperature Relationship in Scalds
Part 9 - Controls
WARNING
An ASSE 1017 or ASSE 1070 temperature limiting or mixing valve is recommended in installations servicing disabled or elderly persons, or children. Mixing valves do not eliminate the risk of scalding.
To avoid scalding:
• Set the water heater set point temperature as low as possible.
• Feel water before bathing or showering.
• If thermostatic valves are required, use devices specifically designed for such purpose. Install these devices in accordance with instructions provided by the manufacturer.
Failure to install a temperature limiting or mixing valve and follow these instructions could result in property damage, severe personal injury, or death due to scalds.
E. User Menu
Press the MENU button to open the user menu.
To navigate within the menu or parameters, press the + and - buttons ( or ).
To change a parameter, select it by pressing the OK button.
To change the set value, press the + and - buttons ( or ).
Press the OK button to save.
To exit without savin the changes, press the
ESC button.
Figure 76 - Access user menu
For parameters 5 to 12 it is also possible to set / change the heating zone 2 (if available).
By pressing the HISTORY button after accessing the parameter, the number 1 or
2 of the selected zone appears next to the heating symbol: / .
Continue to change the setting as described above.
Activate change with OK button, + / - buttons change the value, OK button for confirmation,
ESC to return without change.
1.
NTI Wi-Fi
WIFI
AP
SN
RESET
ON/OFF Wi-Fi
Access point open for 10 minutes
Shows Wi-Fi serial number (Not Appliance)
ITEMP
2.
Date and Time
Delete Wi-Fi settings Disconnect user account
Set Internet weather (only without outdoor sensor)
The following values are displayed in a sequence. For setting, select OK and +/-.
Day (1-31)
Month (1-12)
Year (year)
Time (hh: mm) (*)
(*) Press
+/- button for setting hours
Press +/- button for setting the minutes)
Press OK to confirm the entered data.
5.
Automatic C.H. temperature control / AUTO function
OFF AUTO function deactivated
ON AUTO function Active (AUTO appears on the display)
6.
Room temperature Day / only applicable if using NTI room sensor(s)
7.
Room temperature Night / only applicable if using NTI room sensor(s)
8.
Time programs – heating schedule / only applicable if using NTI room sensor(s)
0+24 h
Always active
P1
P2
P3
06-22 h
P EXT
Family program
Program no lunch
Program with lunch
C.H. active from 06:00 to 22:00
Time program defined by REMOCON room unit or NTI NET app.
9.
Outdoor Heating Curve Slope (only with AUTO function active)
/
10. Outdoor Heating Curve Parallel Shift (only with AUTO function active)
/
Setting range + -7 at low temperature and + -14 at high temperature range (each step + or - 1.8°C)
11.
Automatic summer / winter changeover /
ON
OFF
Active
Function deactivated
12. Summer / winter changeover temperature
/
Table 2 - User menu
63
Part 9 - Controls
F. INFO Menu
Press the MENU button for 5 seconds to access the INFO menu, navigate within the INFO menu with + and - (both possible, or ).
Attention:
No values can be changed here, only information can be read! Changes can only be made in the user menu or in the specialist area.
Figure 77 - Access Info menu
MENU INFO
FLOOR Drying function remaining days (with Floor Drying function active)
Heating supply temperature [°F]
Heating return temperature [°F]
D.H.W. temperature [°F]
(for boilers connected to an external storage with NTC probe)
Outdoor temperature (only with external sensor connected) [°F]
Room temperature (only with NTI room sensor connected) [°F] (Zone1 / 2)
Fan speed (%)
Heating outlet setpoint temperature [°F]
Exhaust flue temperature [°F]
Boiler power level [%]
Table 3 - Info menu
PARAMETER
857
831
832
840
835
430/530
822
830
834
878
G . Date and Time
The control unit is equipped with a 365-day clock that displays the day, month, year and time.
In order to ensure correct operation of the boiler when using time programs, the date and time must be set correctly. If the boiler is connected to the Wifi application, the Internet time is automatically taken into account. Manual entry:
Day (1-31)
Months (1-12)
Year (2019)
Time (00:00)
Buttons
/
for the hour setting
(item 2 - Figure 72)
Buttons
/
for setting minutes
(item 8 - Figure 72)
64
Part 9 - Controls
H. Automatic CH Temperature Control (AUTO)
Automatic Temperature Control (AUTO) function allows the boiler to adapt to outdoor temperature conditions and the type of system in which it is installed.
Contact a qualified service technician to inform you about the device and program the system to suit your needs.
If a room sensor (NTI accessory) is used, the boiler switches on / off according to the current measured room temperature.
To activate the AUTO Function, set to “ON” via the User Menu, or via technical menu parameter 2.2.4.
°F
194
1.3
176
3.5 3.0
2.5
2.0 1.8
1.5
1.0
158
0.8
140
0.6
122
0.4
104
1.0
0.8
0.6
0.4
86
73
70
66
°C
77
50
73
Setpoint of the room temperature
0.2
32
77 68 59 50 41 32 23
Outdoor temperature
Figure 78 - Heating curves
14 5 -4 -13 °F
179 °F
NOTICE
To detect changes in room temperature it is necessary to install an NTI Room Sensor. Other thermostats (not
NTI) can only switch the boiler ON and OFF.
120 °F
20 °F 65 °F
Outdoor temperature
Figure 79 - Default value (HT)
Default Parameters of Automatic Temperature Control
4
4.2
Zone 1
Parameter
Zone 1 Parameter
4.2.0
Zone 1 Temperature Range
4.7.5
Automatic Slope Adaptation
179 °F
Notes
0 = Low Temperature (LT 68-113°F)
4.2.1
4.2.2
Type of Temperature Control
Outdoor Heating Curve Slope
4.2.3
Heating Curve Offset
4.2.5
Setting the Maximum Heating Temperature
Zone 1
4.2.6
Zone 1 heating MINIMUM temperature setting
0 Fixed Outlet Temperature
1 Auto. Outlet Temp Adaptation
2 Only Room Sensor
3 Only Outdoor Sensor
4 Room Sensor and Outdoor Sensor
Low Temp Range: 0.2-0.8 (0.6 LT)
High Temp Range: 0.4-3.5
from -25 to +25 (high temperature) from -12 to +12 (low temperature)
Low Temp Range: 68-122°F (120°F LT)
High Temp Range: 86-179°F
0 = OFF
1 = ON
Outdoor temperature
Outdoor temperature
80 °F
0,4 1,3 3,5
Factory Settings
Default
1 (HT)
3
1.3 (HT)
0
120 (HT)
0
Table 26 - Default Parameters for the Heating System zone 1
65
+25°F
0 °F Default
-25°F
Part 9 - Controls
I. Outdoor Heating Curve Slope
The Outdoor Heating Curve represents the operation of the boiler when using an outdoor sensor.
The boiler control adjusts the supply temperature according to the outdoor temperature.
The lower the outdoor temperature, the higher the boiler supply
The User may also modify the heating curve shift by pressing the CH + and – buttons.
NOTE: This is only possible when parameter
4.7.5 is set to 0 (OFF).
Upon pressing the CH + or – buttons, the display shows the current CH target temperature for 5 seconds.
The supply temperature needed to efficiently satisfy a call for heat from a thermostat depends on the heating system and building conditions
(building materials, insulation, etc.)
The slope of the Outdoor Heating Curve may be adjusted using the
“CH curves Slope” parameter from the User Menu, in order to adapt the boiler supply temperature to the installation conditions. A higher slope means that the maximum supply temperature is achieved a
65 °F
Outdoor temperature
80 °F
NOTE: The boiler supply temperature is limited upwards by the fixed high limit (4.2.5).
Access parameter 4.2.2 to modify the Outdoor Heating Curve.
After 5 seconds the display shows the amount of shift, and allows the user to modify it by further presses of the CH + or – buttons.
After few seconds the display shows the new
CH target and come back to the homescreen.
AUTO
1
179 °F 0,4 1,3 3,5
K. Room temperature Day /Night
(Only applicable when using NTI room sensor)
179 °F
120 °F
Default
The room temperatures (both zones 1/2) can be set to different setpoints. These setpoints become effective with the selected operating mode and the time program, so that different temperature levels can occur in each zone. The range of adjustable target values is limited by their interdependence, which can be seen in the accompanying graph.
Daily setpoint (comfort), factory setting 70°F
Night setpoint (reduced), factory setting 61 °F
Outdoor temperature
120 °F
Figure 80 - Outdoor Heating Curve adjustment
20 °F 65 °F 80 °F
J. Outdoor Heating Curve Parallel Shift
179 °F
If the ambient temperature is too hot or cold, regardless of the outdoor temperature, use parallel shift to adjust the curve.
Depending on system conditions (settings on the boiler during
+25°F
0 °F
120 °F
Decrease parallel shift
The boiler will automatically shift the Outdoor Heating Curve
-25°F
Default to 1 = ON (factory setting).
Figure 82 - Day and Night setpoint
4.2.3 from the technical menu.
179 °F
Increase parallel shift
Decrease parallel shift
120 °F
Outdoor temperature
Figure 81 - Outdoor Heating Curve parallel shift
+25°F
0 °F Default
-25°F
66
L. Time programs – heating schedule
(Only applicable when using NTI room sensor)
The end user can choose from five predefined time programs to heat according to his wishes. When a time program is activated, the boiler will operate in the desired time periods to maintain the room temperature at comfort temperature level. Outside these periods, the boiler operates at a reduced temperature level.
0-24h
P1
Family
Program
Mo-Su 00:00 – 24:00
Mo-Th 06:00 – 22:00
Fr-Sa 06:00 – 23:00
P2
Program without lunch
P3
Program with lunch
Su 07:00 – 22:00
Mo-Th 06:00 – 08:00 16:00 – 22:00
Fr 06:00 – 08:00 15:00 – 23:00
Sa
Su
07:00 – 23:00
08:00 – 22:00
Mo-Th 06:00 – 08:00 11:30 – 13:00 16:00 – 22:00
Fr 06:00 – 08:00 11:30 – 23:00
Sa 06:00 – 23:00
Su 07:00 – 22:00
Mo-Su 06:00 – 22:00
6-22h
EXT
Time program defined by external source (app or room unit). The details can not be displayed on the boiler display.
Time program defined by external source (app or room unit).
The details can not be displayed on the boiler display.
Table 4 - Time programs heating
NOTICE
Time programs heating are active only with NTI Room
Thermostat or Sensor
M. Automatic summer / winter changeover
When this function is activated, the boiler automatically switches from “winter” mode ( + ) to “summer” mode
( ), based on outdoor temperature conditions.
This means that the appliance can independently activate or deactivate the heating mode.
The criteria for the change are:
If the outdoor temperature is more than 1°F above the desired summer / winter switchover temperature during 5h (delay time), the boiler goes from winter to summer mode.
If the outdoor temperature is more than 1°F lower than the desired summer / winter switchover temperature during 5h
(delay time), the boiler will go from summer to winter mode.
Summer / winter changeover temperature
External temperature criterion to switch from winter operation to summer operation, factory setting is 68 °F.
Part 9 - Controls
67
Part 9 - Controls
N. Technical Menu
(Complete Programming & Troubleshooting Menus)
The boiler control can manage the entire heating and domestic hot water system. The boiler control menu enables the system and connected components to be customized for maximum comfort and efficiency. The control also provides important information relating to boiler operation and offers some “quick settings” that can be accessed without entering the access code. To see all available parameters, see
K. Complete Menu Parameters.
See J. Boiler Control Menu Structure, for an overview of the menus.
Instructions on how to access and change the menus is provided below.
The various parameters can be activated and changed using the buttons shown below:
The menu and parameter numbers are shown on the display.
CAUTION! THE MENUS RESERVED FOR QUALIFIED TECHNICIANS MAY
ONLY BE ACCESSED AFTER ENTERING THE ACCESS CODE.
To access the Menus, open the cover and proceed as follows (in this example: Parameter
2.3.1)
1.
Simultaneously press the
OK and ESC buttons for 5 seconds.
The display shows 222.
CODE
AUTO
CODE
AUTO
2. Press the “+” button to select 234, the service code.
3. Press the OK button.
The display shows
MENU.
MENU
AUTO
OK and ESC buttons together for 5 seconds to access the technical menu. CH + and – buttons to scroll through the menus and adjust settings. OK button to select parameters and save settings. ESC button to exit menu level / parameter without saving.
MENU
AUTO
4. Press the OK button.T
he display shows menu
0.
AUTO
MENU
AUTO
5. Press the “+” button to select
menu 2
.
MENU
AUTO
6. Press the OK button t o access the menu
. The display shows sub-menu 20.
Figure 83 - Access to the Techical Area
7. Press the “+” button to select the sub-menu 23.
MENU
AUTO
PAR
AUTO
9. Press
OK t o access the sub-menu
. T he display shows the parameter 231.
PAR
AUTO
10. Press OK to access the parameter.
T he display shows the current parameter value. In this example,
100
.
PAR
AUTO
11. Press the “+” or “-” buttons to select a new value.
In this example, 96.
12. Press OK to save the change, or press the
ESC button to exit without saving.
In this example press OK.
After making changes, press the ESC button until the normal display screen is restored.
68
O. Boiler Control Menu Structure
AccessCode
COMPLETE MENU
The parameters of each menu are listed on the following pages.
ERR - Fault
The display shows the last 10 errors with information on the code, description, and date.
Press “+” (2) to scrool the error
PCB
Direct Access to the Parameters:
214 - 220 -226 (not active) 228 - 229 - 230 (not active)
- 231- 232- 233 - 234 - 247 - 250 - 253 - 247 (only with parameter 228=1)
DHW - Domestic Hot Water settings
Direct Access to the Parameters:
200 - 228
CH1 - Heating
Zone 1 settings
Direct Access to the Parameters:
402 - 420 - 425 - 426
CH2- Heating
Zone 2 settings
Direct Access to the Parameters:
223 - 502 - 520 - 525 - 526
CH3- Heating
Zone 3 settings
Direct Access to the Parameters:
602 - 620 - 625 - 626
MODE - Boiler working MODE
Press “+” (2) to select:
(Only DHW)
(CH + DHW)
(Only CH)
Figure 84 - Menu Structure
Part 9 - Controls
0 NETWORK
0 4 User Interface
2
Boiler Parameters
2 0 General
2 1 Free Parameters
2 2 Settings
2 3 Central Heating-1
2 4 Central Heating-2
2 5 Domestic Hot Water
2 6 Boiler Manual Settings
2 7 Test & Utilities
2 8 Reset Factory Settings
4 Zone1 Parameters
4 0 Setpoint
4 1 S/W Changeover
4 2 Z1 Settings
4 3 Z1 Diagnostics
4 7 Z1 Regulation parameters
5 Zone2 Parameters
5 0 Setpoint
5 1 S/W Changeover
5 2 Z2 Settings
5 3 Z2 Diagnostics
5 7 Z2 Regulation parameters
6 Zone3 Parameters
6 0 Setpoint
6 1 S/W Changeover
6 2 Z3 Settings
6 3 Z3 Diagnostics
6 7 Z3 Regulation parameters
8 Service Parameters
8 0 Boiler Statistics -1
8 1 Boiler Statistics -2
8 2 Boiler
8 3 Boiler Temperature
8 4 Storage
8 5 Service
8 6 Error History
8 7 Free parameters
69
Part 9 - Controls
P. Complete Menu Parameters
Description Value
Default S
ACCESS to the complete MENU
1.
Simultaneously press the the
OK and ESC buttons for 5 seconds. T he display shows
222.
2. Press the “+” button to select 234 , the service code.
3. Press the OK button. until the display shows
MENU.
4. Press the OK button to enter the complete menu, see instructions on page 68, and complete menu list below
0 NETWORK
0 4 USER INTERFACE
0 4
0 Zone to be set by display
1 = 1 Zone
2 = 2 Zones
3 = 3 Zones from 1 to 10 minutes or 24 hours
1
10
0 4
1 Backlight timing
2 BOILER PARAMETERS
2 0 GENERAL
DHW Setpoint Temperature TRX COMBI
2 0 0
DHW Setpoint Temperature TRX non-COMBI
2 1 FREE PARAMETERS (DO NOT USE)
2 1
1 DO NOT USE
2 1
2 DO NOT USE
2 1
3 DO NOT USE
2 1
5 DO NOT USE
2 1
6 DO NOT USE
2 2 BOILER GENERAL SETTINGS
2 2
0 Ignition Power
2 2 3
Room (Floor thermostat or Room thermostat zone
2 selection)
2 2
4 Automatic CH Temperature Control
Heating ignition delay
2 2 5
2 2 8
Boiler Version - TRX C
CANNOT BE MODIFIED
Boiler Version - TRX
CANNOT BE MODIFIED ATTENTION!
Only change from 1 to 2 when external storage with an ON / OFF thermostat is connected.
from 97 to 140 (°F) from 104 to 149 (°F) from 0 to 100
0 = Floor safety thermostat
1 = Room thermostat zone 2
0 = Absent, 1 = Present
0 = Disabled,
1 = 10 seconds,
2 = 90 seconds,
3 = 210 seconds from 0 to 5
0 = Combi from 0 to 5
0 = NOT USED
1 = Storage with NTC
2 = Storage with thermostat
3 - 5 = NOT USED from 0 to 200
124 Set by pressing DHW buttons
124
Must be set in accordance with Table 29.
1
0
0
0
2 item 2 - Figure 72
RESERVED FOR TECHNICAL
ASSISTANCE
Only if the PCB is changed
2 2
9 Set boiler heating power
2 3 BOILER CH PARAMETERS - 1
2 3 1
Max CH Power
(limitation, in% of the maximum heat output,
Parameter 234)
2
2
2
3
3
3
2
3
4
Max DHW percentage
CANNOT BE MODIFIED
Min percentage
CANNOT BE MODIFIED
Max CH percentage
CANNOT BE MODIFIED
2 3
5 CH Anti-cycling time mode from 0 to 100 from 0 to 100 from 0 to 100 from 0 to 100
0 = Manual
1 = Automatic
1
See the table 29, Information on
Starting
RESERVED FOR TECHNICAL
ASSISTANCE
Only if the gas or PCB is changed see table 29.
70
Part 9 - Controls
Description Value
Default S
2 3
6 Anti-cycling Ignition Time Delay
2 3
7 CH Post Pump Cycle Time
2 4 BOILER PARAMETER - PART 2
2
2
4
4
3 CH Fan Post-Purge
4
0 = OFF
1 = ON
0
CH Boost Delay Period Time from 0 to 60 (minutes) 16
Activated only with thermostat
This parameter allows a time delay to be set before the automatic increase of the outlet
On/Off and heating control temperature calculated in increments of 39.2°F (max 53.6°F). If this parameter retains the value activated
00, this function is not active.
(parameter 421 - 521 - 621 = 01)
2
2
4
4
7 CH Pressure Safety
9 Outdoor Temperature Reading Correction
0 = temperature sensor only
1 = pressure switch at minimum
2 = pressure sensor from -5 to +5 (°F)
1
0
RESERVED FOR TECHNICAL
ASSISTANCE
Only if the PCB is changed
Only active with outdoor sensor connected
2 5 DOMESTIC HOT WATER PARAMETER
from 0 to 7 (minutes) from 0 to 15 minutes or OC (AC)
3
3
COMFORT function
0 = deactivated
1 = timed
2 = always on
0
2 5 0
Timed
(
TRX models
with external storage with NTC sensor)
=
according to time program.
Allows hourly / weekly management for maintaining the temperature of the hot water tank. The DHW flow function remains active. Read the description in this manual.
Timed
(
TRX C models)
activated for 30 minutes after domestic hot water draw-off.
The appliance allows the hot water heating comfort to be increased via the “COMFORT” function.
This function keeps the secondary heat exchanger temperature stable when the boiler is not in use. COMFORT will be displayed when the function is active.
NOTE: This function can be activated and deactivated by pressing the COMFORT button.
2 5
1 DHW Comfort Anti-cycling Time from 0 to 120 (minutes) 0
2 5
2 DHW Start Delay 5 Anti “water hammering”
2 5
3 DHW Switch Off Logic from 5 to 200 (0.5 to 20 seconds)
0 = anti-scale (stop at > 144°F)
1 = + 7 °F /setting
0
2 5 4
DHW Post Purge and Pump Cycle
0 = OFF
1 = ON
0
OFF = 3 minutes post-circulation and post-ventilation after DHW draw-off if the boiler temperature requires it.
ON = Always on for 3 minutes post-circulation and post-ventilation after DHW draw-off.
2 5
5 DHW timer from 0 to 30 (minutes) 0
2
2
5
5
7
Anti-legionella Function
0 = OFF
1 = ON
0
TRX = Activated when the boiler is connected to a tank by an NTC sensor.
(Parameter 228 = 1)
This function prevents the formation of Legionnaire’s disease bacteria which may develop in piping and indirect water heaters
(IWH) at temperatures between 68°F and 104°F. When activated, if the IWH temperature stays below 138°F for over 100 hours, the boiler will heat the water in the IWH until it reaches 149°F for 30 minutes.
8 Antilegionella frequency from 24 to 720 (Hours) or 30 days
30 days
TRX = Activated when the boiler is connected to a tank by an NTC sensor.
(Parameter 228 = 1)
Only to test components
2 6 BOILER MANUAL SETTINGS
2 6
0 Manual mode activation
2 6
1 Boiler pump control
2 6
2 Fan control
2 6
3 3 way valve control
2 7 TEST & UTILITIES
0 = OFF, 1 = ON
0 = OFF, 1 = ON
0 = OFF, 1 = ON
0 = DHW, 1 = Heating
0
0 Set parameter 260=1
0 Set parameter 260=1
0 Set parameter 260=1
71
72
Part 9 - Controls
Description Value
Default S
2 7
0 Test Mode
TEST+ = Max Heating power
TEST+ = Max DHW power
TEST+ = Minimum power.
TEST Mode can also be activated by pressing the Reset button for 10 seconds. The function is deactivated after 30 minutes or by pressing Reset.
See First Ignition section.
2 7
1 Air-purge cycle
2 7 4
Floor drying cycle
0 = OFF
1 = ON
0 = OFF
1 = Functional Heating
2 = Curing Heating
3 = Functional Heating + Curing
Heating
4 = Curing Heating + Functional
Heating
5 = Manual fromm 77 to 140 °F
0
131
2 7 5
Floor dry Supply setpoint temperature
2 8 RESET FACTORY SETTINGS
2 8 0
Automatically resets all parameter settings to the factory defaults.
4 ZONE 1 PARAMETERS
4 0 ZONE 1 TEMPERATURE SETTINGS
4 0
0 Temperature Day
4 0
1 Temperature Night
4 0
2 Zone 1 Fixed Temperature
4 0
3 Zone Freeze Protection Temperature
4 1 SUMMER/WINTER CHANGEOVER
4 1
0 S/W function activation
4 1
1 S/W temperature threshold
4 1
2 S/W delay time
4 2 ZONE 1 SETTINGS
Reset: OK = yes, ESC = no from 50 to 86 °F from 32 to 86 °F from 86 to 179 °F from 68 to 122 °F from 36 to 59 °F
0 = OFF, 1 = ON from 50 to 86 °F from 0 to 300 minutes
0
68
60
To reset all parameter settings, press the OK button.
66
61
179 Parameter 420 = 1
120 Parameter 420 = 0
41 Changes all zones
4 2
0 Zone temperature range
4 2
1 Temperature Control Mode
0 = from 68 to 113°F
(low temperature)
1 = from 95 to 179°F
(high temperature)
0 = Fixed outlet temperature
1 = Basic On/Off
2 = Room Sensor Only
3 = Outdoor Sensor Only
4 = Room and Outdoor Sensors
1 select in the appliance type base
3
Part 9 - Controls
Description Value
Default S
4 2 2
Outdoor Heating Curve Slope from 0.2 to 0.8
from 0.4 to 3.5
°F
194
3.5 3.0
2.5
2.0 1.8
1.5
1.3
176
158
1.0
0.8
140
122
0.6
0.4
104
1.0
0.8
0.6
86
73
70
66
°C
77
50
73
Setpoint of the room temperature
32
77 68 59
Heating Curve Offset
0.4
0.2
50 41 32 23
Outside temperature
14 5 -4 -13 °F from -12 to +12 (low temperature) from -25 to +25 (high temperature)
4 2 3
To adapt the heating curve to installation requirements, it is possible to perform a parallel shift of the curve in order to alter the calculated outlet temperature and therefore the ambient temperature.
The value is indicated on the display:
- from -12 to +12 (low temperature)
- from -25 to +25 (high temperature)
Each step represents an outlet temperature increase/decrease of 1°F in relation to the setpoint value.
For the User, it’s possible to modify the heating curve offset by pressing the CH buttons
“+” and “-” (8).
0.6
(low temperature)
1.3
(high temperature)
0
If an outdoor temperature sensor is used, the boiler calculates the most suitable heating outlet temperature, taking the outdoor temperature and type of appliance into account.
The type of curve must be chosen according to the type of appliance radiator and the heat losses present in the building.
Press the Ch buttons “+” or “-” (8), the display shows the current CH target temperature:
After 5 seconds the display allows the users to modify the offset.
The User could modify this value by pressing CH buttons “+” and “-” (8).
AUTO
1
After few seconds the display shows the new CH target and come back to the homescreen.
4
4
2
2
4
Room Sensor Impact
If setting = 0, the temperature taken from the room sensor does not affect the calculation of the setting. If setting = 20, the temperature taken has the maximum influence on the setting.
5 Zone 1 heating MAXIMUM temperature setting from 0 to 20 from 4 to 20 from 86 to 179 °F from 68 to 122 °F
2 if parameter 420 = 0
4 if parameter 420 = 1
179 if parameter 420 = 1
120 if parameter 420 = 0
4 2
6 Zone 1 heating MINIMUM temperature setting from 86 to 179 °F from 68 to 122 °F
120 if parameter 420 = 1
80 if parameter 420 = 0
73
74
Part 9 - Controls
Description Value
Default S
4 3 ZONE 1 DIAGNOSTICS
4 3
0 Room Temperature
4 3
1 Room Temperature Setpoint
4 3
4 Zone 1 Heat Call
0 = OFF
1 = ON
4 7 ZONE REGULATION PARAMETERS
4 7
5 Auto Slope Adaptation
0 = OFF
1 = ON
0
5 ZONE 2 PARAMETERS
5 0 ZONE 2 TEMPERATURE SETTINGS
5
5
5
0
0
0
0 Temperature Day
1 Temperature Night
2 Zone 2 Fixed Temperature from 50 to 86 °F from 32 to 86 °F from 86 to 179 °F from 68 to 122 °F from 36 to 59 °F
66
61
179 Parameter 420 = 1
120 Parameter 420 = 0
41 Changes all zones
5 0
3 Zone Freeze Protection Temperature
5 1 SUMMER/WINTER CHANGEOVER
5 1
0 S/W function activation
5 1
1 S/W temperature threshold
0 = OFF, 1 = ON from 50 to 86 °F
0
68
5 1
2 S/W delay time from 0 to 300 minutes 60
5 2 ZONE 2 SETTINGS
5
5
5
2
2
2
0 Zone temperature range
1 Temperature Control Mode
2
0 = from 68 to 113°F
(low temperature)
1 = from 95 to 179°F
(high temperature)
0 = Fixed outlet temperature
1 = Basic On/Off
2 = Room Sensor Only
3 = Outdoor Sensor Only
4 = Room and Outdoor Sensors from 0.2 to 0.8
from 0.4 to 3.5
1
1 select in the appliance type base
Outdoor Heating Curve Slope
0.6
(low temperature)
1.3
(high temperature)
See graph on the previous page.
If an outdoor sensor is used, the boiler calculates the most suitable heating outlet temperature taking the external temperature and the type of appliance into account.
The type of curve must be chosen according to the type of appliance radiator and the heat losses present in the building.
from -12 to +12 (low temperature)
Heating Curve Offset from -25 to +25 (high temperature)
0
5 2 3
To adapt the heating curve to installation requirements, it is possible to perform a parallel shift of the curve in order to alter the calculated outlet temperature and therefore the ambient temperature.
The value is indicated on the display:
- from -12 to +12 (low temperature)
- from -25 to +25 (high temperature)
Each step represents an outlet temperature increase/decrease of 1°F in relation to the setpoint value.
See note on parameter 423.
Room Sensor Impact from 0 to 20 from 4 to 20
2 if parameter 420 = 0
4 if parameter 420 = 1
5 2 4
5 2
If setting = 0, the temperature taken from the room sensor does not affect the calculation of the setting. If setting = 20, the temperature taken has the maximum influence on the setting.
5 Zone 2 heating MAXIMUM temperature setting from 86 to 179 °F from 68 to 122 °F
179 if parameter 420 = 1
120 if parameter 420 = 0
5 2
6 Zone 2 heating MINIMUM temperature setting from 86 to 179 °F from 68 to 122 °F
120 if parameter 420 = 1
80 if parameter 420 = 0
Part 9 - Controls
Description Value
Default S
5 3 ZONE 2 DIAGNOSTICS
5 3
0 Room Temperature
5 3
1 Room Temperature Setpoint
5 3
4 Zone 2 Heat Call
0 = OFF
1 = ON
5 7 ZONE REGULATION PARAMETERS
5 7
5 Auto Slope Adaptation
0 = OFF
1 = ON
0
6 ZONE 3 PARAMETERS
6 0 ZONE 2 TEMPERATURE SETTINGS
6
6
6
0
0
0
0 Temperature Day
1 Temperature Night
2 Zone 3 Fixed Temperature from 50 to 86 °F from 32 to 86 °F from 86 to 179 °F from 68 to 122 °F from 36 to 59 °F
66
61
179 Parameter 420 = 1
120 Parameter 420 = 0
41 Changes all zones
6 0
3 Zone Freeze Protection Temperature
6 1 SUMMER/WINTER CHANGEOVER
6 1
0 S/W function activation
6 1
1 S/W temperature threshold
0 = OFF, 1 = ON from 50 to 86 °F
1
68
6 1
2 S/W delay time from 0 to 300 minutes 60
6 2 ZONE 3 SETTINGS
6 2
0 Zone temperature range
0 = from 68 to 113°F
(low temperature)
1 = from 95 to 179°F
(high temperature)
1 select in the appliance type base
6
6
2
2
1 Temperature Control Mode
2
Outdoor Heating Curve Slope
0 = Fixed outlet temperature
1 = Basic On/Off
2 = Room Sensor Only
3 = Outdoor Sensor Only
4 = Room and Outdoor Sensors from 0.2 to 0.8
from 0.4 to 3.5
1
0.6
1.3
(low temperature)
(high temperature)
See graph on the previous page.
If an outdoor sensor is used, the boiler calculates the most suitable heating outlet temperature taking the external temperature and the type of appliance into account.
The type of curve must be chosen according to the type of appliance radiator and the heat losses present in the building.
6 2 3
from -12 to +12 (low temperature)
Heating Curve Offset from -25 to +25 (high temperature)
0
To adapt the heating curve to the installation requirements, it is possible to perform a parallel shift of the curve in order to alter the calculated outlet temperature and therefore the ambient temperature.
The value is indicated on the display:
- from -12 to +12 (low temperature)
- from -25 to +25 (high temperature)
Each step represents an outlet temperature increase/decrease of 1°F in relation to the setpoint value.
See note on parameter 423.
6
6
2
2
4
Room Sensor Impact
If setting = 0, the temperature taken from the room sensor does not affect the calculation of the setting. If setting = 20, the temperature taken has the maximum influence on the setting.
5 Zone 3 heating MAXIMUM temperature setting from 0 to 20 from 4 to 20 from 86 to 179 °F from 68 to 122 °F
2 if parameter 420 = 0
4 if parameter 420 = 1
179 if parameter 420 = 1
120 if parameter 420 = 0
6 2
6 Zone 3 heating MINIMUM temperature setting from 86 to 179 °F from 68 to 122 °F
120 if parameter 420 = 1
80 if parameter 420 = 0
75
76
Part 9 - Controls
Description Value
Default S
6 3 DIAGNOSTICS
6
6
3
3
0 S/W function activation
1 S/W temperature threshold
0 = OFF, 1 = ON from 50 to 86 °F
0
68
6 3
4 S/W delay time from 0 to 300 minutes 60
6 7 ZONE REGULATION PARAMETERS
6 7
5 Auto Slope Adaptation
0 = OFF
1 = ON
0
8 SERVICE PARAMETERS
8 0 BOILER STATISTICS-1
8 0 0
3 way valve cycles No. (n x10)
8 0 1
Pump Power on (h x10)
8 0 2
Boiler pump cycles No. (n x10)
8 0 3
Boiler Power On Time (h x10)
8 0
4 Fan cycles No. (n x10)
8 0
5 Number of fan cycles (n x10)
8 0
6 CH flame detection No. (n x10)
8 0
7 DHW flame detection No. (n x10)
8 1 BOILER STATISTICS-2
8 1
0 CH Burner On Hours (h x10)
8 1
1 DHW Burner On Hours (h x10)
8 1
2 Number Of Flame Faults (n x10)
8 1
3 Number Of Ignition Cycles (n x10)
8 1
4 Average CH Cycle Length (min)
8 2 Boiler Current Status
8 2
1 Fan Status
8 2
2 Fan Speed (x100) RPM
8 2
4 3 Way Valve Position
0 = OFF, 1 = ON
8 2
6 APS Status
0 = DHW, 1 = Central Heating
0 = Open
1 = Closed
8 2
8 Gas Power (kW)
8 3 BOILER CURRENT TEMPERATURES
8 3
0 CH Supply Setpoint (in °F)
8 3
1 CH Supply Temperature (in °F)
8 3
2 CH Return Temperature (in °F)
8 3
4 Exhausts Flue Temperature
8 3
5 Outdoor Temperature (in °F)
8 5 SERVICE
8
8 5
1 Enable Maintenance advice
8
5
5
0
2
Months to next maintenance from 0 to 60 (months)
If set the boiler will display when it is time to call the installer for maintenance
Maintenance Warning Reset
To erase the advice for maintenance
0 = OFF, 1 = ON
Reset? OK= Yes , Esc = No
8 5
4 SW Version Interface
8 5
5 SW Version Main
8 6 Error History
12
0
8 6 0
10 last errors from ERROR 0 to ERROR 9
This parameter allows the last 10 boiler errors to be displayed, indicating the day, month and year.
When the parameter is accessed, the errors are displayed listed from ERROR 0 to ERROR 9.
8 6
1 Error list reset Reset? OK = y es, ESC = no
Only with outdoor sensor connected
8 7 FREE PARAMETERS
8 7
0 NOT USED
8 7
1 NOT USED
8 7
2 NOT USED
8 7
3 NOT USED
8 7
4 Boiler flow switch
8 7
6 Safety flame sensor
8 7
8 Boiler power level
Table 27 - Complete Parameters List
Description Value
Default S
0= OFF, 1= ON
0= OFF, 1= ON from 0 to 100
(0 = minimum power
100 = maximum power)
Part 9 - Controls
77
Part 10 - Start-Up Preparation
WARNING
Thoroughly clean and flush any system that has used glycol before installing the boiler. Provide the customer with a material safety data sheet (MSDS) on the fluid used.
A. Check / Control Water Chemistry
CAUTION
Chemical imbalance of the water supply may affect efficiency and cause severe damage to the appliance and associated equipment. It is important that the water chemistry on both the domestic hot water and central heating sides are checked before installing the appliance. Water quality must be professionally analyzed to determine whether it is necessary to treat the water. Various solutions are available to adjust water quality. Adverse water quality will affect the reliability of the system. In addition, operating temperatures above
135oF will accelerate the build-up of lime scale and possibly shorten appliance service life. Failure of an appliance due to lime scale build-up, low pH, or other chemical imbalance IS
NOT covered by the warranty.
To ensure extended service life, it is recommended to test water quality prior to installation. Listed below are some guidelines.
CAUTION
Do not use petroleum-based cleaning or sealing compounds in the boiler system. Damage to elastomer seals and gaskets in the system could occur, resulting in substantial property damage.
The water must be potable, free of corrosive chemicals, sand, dirt, and other contaminants. It is up to the installer to ensure the water does not contain corrosive chemicals or elements that can damage the heat exchanger. Potable water is defined as drinkable water supplied from utility or well water in compliance with EPA secondary maximum contaminant levels (40 CFR Part 143.3). If the water contains contaminants higher than outlined by the EPA, water treatment is recommended and additional, more frequent maintenance may be required. See Table 1.
If you suspect that your water is contaminated in any way, discontinue use of the appliance and contact an authorized technician or licensed professional.
Clean system to remove sediment*
1. You must thoroughly flush the system (without boiler connected) to remove sediment. The high-efficiency heat exchanger can be damaged by buildup or corrosion due to sediment.
2. For zoned systems, flush each zone separately through a purge valve. (If purge valves and isolation valves are not already installed, install them to properly clean the system.)
3. Check the return Y strainer (if installed). Remove and clean sediment and debris if necessary.
4. Flush system until water runs clean and you are sure piping is free of sediment.
*NOTE: Boiler failure due to improper water chemistry is not covered by warranty.
NOTE: Combi Models: It is recommended to clean the DHW side of the heat exchanger at least once a year to prevent lime scale buildup. Follow the maintenance procedure to clean the heat exchanger in the Maintenance Section of this manual.
78
B. Check for Gas Leaks
WARNING
Before starting the boiler, and during initial operation, smell near the floor and around the boiler for gas odorant or any unusual odor. Remove boiler front door and smell interior of boiler enclosure. Do not proceed with startup if there is any indication of a gas leak. Repair any leaks at once.
PROPANE BOILERS ONLY – The propane supplier mixes an odorant with the propane to make its presence detectable.
In some instances the odorant can fade, and the gas may no longer have an odor. Before startup (and periodically thereafter), have the propane supplier verify the correct odorant level in the gas.
If you discover any evidence of a gas leak shut down the boiler at once. Find the leak source with a bubble test and repair immediately. Do not start the appliance again until the leak is repaired. Failure to comply could result in substantial property damage, severe personal injury, or death.
C. Freeze Protection (When Used)
WARNING
NEVER use automotive or standard glycol antifreeze. Do not use ethylene glycol made for hydronic systems. Use only freeze-protection fluids certified by fluid manufacturer as suitable for use with stainless steel boilers, verified in the fluid manufacturer’s literature. Thoroughly clean and flush any system that has used glycol before installing the new boiler. Provide the boiler owner with a material safety data sheet (MSDS) on the fluid used.
NOTE: Loops Serving Indirect Water Heaters (IWHs)
Glycol used in IWH loops should be food grade propylene glycol,
FDA rated as “generally recognized as safe” (GRAS). If using a glycol / potable water mix, the water chemistry must meet the requirements in this manual. The glycol content of the liquid must not exceed 50%, unless the manufacturer specifies a different ratio. Glycol should be checked periodically to prevent it from becoming acidic. Please refer to guidelines provided by the glycol manufacturer regarding glycol maintenance.
NOTE: Glycol not recognized as GRAS may only be used in closed loop
CH applications.
1. Determine the freeze protection fluid quantity using total system water content following the fluid manufacturer’s instructions.
Remember to include expansion tank water content.
2. Local codes may require back flow preventer or actual disconnect from city water supply.
3. When using freeze protection fluid with automatic fill, install a water meter to monitor water makeup. Freeze protection fluid may leak before the water begins to leak, causing concentration to drop, reducing the freeze protection level.
4. Glycol in hydronic applications should include inhibitors that prevent the glycol from attacking metallic system components.
Make certain that the system fluid is checked for the correct glycol concentration and inhibitor level.
5. The glycol solution should be tested at least once a year or as recommended by the glycol manufacturer.
6. Anti-freeze solutions expand more than water. For example: A 50% by volume solution expands 4.8% in volume for a temperature increase from 32 - 80 o
F, while water expands 3% over the same temperature rise. Allowances must be made in system design for expansion.
7. A 30% mixture of glycol will result in a BTU output loss of 15% with a 5% increase in head against the system circulator.
8. A 50% mixture of glycol will result in a BTU output loss of 30% with a 50% increase in head against the system circulator.
NOTE: BTU losses apply to both CH and DHW.
CAUTION
It is highly recommended to carefully follow the glycol manufacturer’s recommended concentrations, expansion requirements, and maintenance recommendations (pH additive breakdown, inhibitor reduction, etc.) You must carefully calculate the additional friction loss in the system as well as the reduction in heat transfer coefficients.
D. System Water Fill, Purge, and Test
WARNING
Ensure the boiler is full of water before firing the burner.
Failure to do so will damage the boiler. Such damage IS NOT covered by warranty, and could result in property damage, severe personal injury, or death.
CAUTION
Connect the condensate discharge pipe before filling and purging the heating circuit.
It is important to purge the system of air to avoid damage to the boiler.
The boiler and heating system must be thoroughly purged of air during the initial installation or system maintenance. Proceed as follows to purge the boiler and heating system:
1. Open the manual air vent positioned on the side of the primary exchanger.
The valve is already connected to a discharge hose routed to the condensate trap.
2. Lift the cap on the automatic air release valve on the pump. Leave open permanently.
3. Gradually open the main water valve until water flows. Do not open fully.
4. Thoroughly purge each zone starting with the lowest point and close them only when clear water free of air is visible.
5. Close the manual air vent when clear water free of air is visible.
6. Continue filling the system until at least 12 psi registers on the pressure gauge.
Boiler Manual Air
Vent
Figure 85 - Manual Air Vent
Position
Part 10 - Start-Up Preparation
WARNING
Eliminate all system leaks. Continual fresh make-up water will reduce boiler life. Minerals can build up in the heat exchanger, reducing heat transfer, overheating the heat exchanger and causing heat exchanger failure.
Check if the condensate trap contains water. If not, it must be refilled. Open the manual air vent on the main exchanger until completely filled. Check the system pressure on the pressure gauge again.
E. Purge Air from DHW System
1. Make sure the CH and DHW lines are open and full of water. Turn on all electric power to boiler.
WARNING
Ensure the boiler is full of water before firing the burner.
Failure to do so will damage the boiler. Such damage IS NOT covered by warranty, and could result in property damage, severe personal injury, or death.
2. Open hot water faucets in the DHW system. Start with the faucets nearest the boiler.
3. Keep faucets open until water runs freely and all air is purged. Then move on to faucets further away from the boiler in the system.
4. When water flows freely from all hot water faucets, DHW purging is complete.
F. Check Thermostat Circuit(s)
1. Disconnect the two external wires connected to the boiler thermostat terminals TT1/TT2 (low voltage terminal strip).
2. Connect a voltmeter across these two incoming wires with power supplied to the thermostat circuits. Close each thermostat, zone valve and relay in the external circuit one at a time and check the voltmeter reading across the incoming wires.
3. There should NEVER be a voltage reading.
4. If a voltage reading does occur under any condition, check and correct the external wiring. (This is a common problem when using
3-wire zone valves.)
5. Once the external thermostat circuit wiring is checked and corrected if necessary, reconnect the external thermostat circuit wires to the boiler low voltage terminal strip. Allow the boiler to cycle.
G. Condensate Removal
1. The boiler is a high efficiency condensing appliance. Therefore, the unit has a condensate drain. Condensate fluid is nothing more than water vapor, derived from combustion products, similar to that produced by an automobile when it is initially started.
Condensation is slightly acidic (typically with a pH of 3 to 5) and must be piped with the correct materials. Never pipe the condensate using steel, copper, brass or other materials that will be subject to corrosion. Plastic PVC or CPVC pipe are the only approved materials.
A condensate neutralizer, if required by local authorities, can be made up of lime crystals, marble or phosphate chips that will neutralize the condensate. This may be done by the installer or you may purchase a condensate neutralizer from NTI (7450P-212).
2. The boiler is equipped with a barbed outlet fitting, to which the supplied hose must be installed and routed to a local drain. It is very important that the condensate line is sloped downward away from the boiler to a suitable indoor drain.
79
Part 10 - Start-Up Preparation
Figure 86 - Condensate Discharge
If the condensate outlet on the boiler is lower than the drain, you must use a condensate removal pump, available from NTI (554200).
This pump is equipped with two leads that can be connected to an alarm or another type of warning device to alert the user of a condensate overflow, which, if not corrected, could cause property damage.
3. If a long horizontal run is used, it may be necessary to create a vent in the horizontal run to prevent a vacuum lock in the condensate line.
4. Do not expose the condensate to freezing temperatures.
5. It is very important you support the condensation line to assure proper drainage.
80
WARNING
FOR YOUR OWN SAFETY READ BEFORE OPERATING
1. This boiler does not have a pilot. It is equipped with an ignition device which automatically lights the burner. Do not try to light the burner by hand.
2. BEFORE OPERATING: Smell all around the boiler area for gas.
Be sure to smell next to the floor because some gas is heavier than air and will settle on the floor.
3. WHAT TO DO IF YOU SMELL GAS
• Do not try to light any boiler.
• Do not touch any electric switch, do not use any phone in your building.
• Immediately call your gas supplier from a neighbor’s phone. Follow the gas suppliers’ instructions.
• If you cannot reach your gas supplier, call the fire department.
• Turn off the gas shutoff valve (located outside the boiler) so that the handle is crosswise to the gas pipe. If the handle will not turn by hand, don’t try to force or repair it, call a qualified service technician. Force or attempted repair may result in a fire or explosion.
4. Do not use this boiler if any part has been under water.
Immediately call a qualified service technician to inspect the boiler and to replace any part of the control system and any gas control that has been damaged.
5. The boiler shall be installed so the gas ignition system components are protected from water (dripping, spraying, rain, etc.) during boiler operation and service (circulator replacement, condensate trap, control replacement, etc.)
Failure to follow these instructions could result in property damage, serious personal injury, or death.
If you discover any evidence of a gas leak, shut down the boiler at once. Find the leak source with a bubble test and repair immediately. Do not start the boiler again until the leak is repaired. Failure to comply could result in substantial property damage, severe personal injury, or death.
A. First Ignition
1. Make sure that the gas valve is closed and the electrical connection has been properly wired. Ensure the green grounding wire is connected to a sufficient earth ground.
2. Unscrew the cap on the automatic air relief valve on the pump.
3. Ensure that the system pressure is at least 12 psi on the tridicator and no hot water or heating requests will be made.
4. Power on the boiler (press the ON/OFF button).
Part 11 - Start-Up
9. The exhaust vent piping for combustion products should be suitable and free from any obstructions.
10. Any necessary ventilation inlets in the room should be open
(power vent installation).
11. Verify the condensate trap contains water. If not, it must be filled.
If necessary, open the manual air vent on the main exchanger until completely filled.
WARNING
If the boiler has not been used for a long period of time the condensate trap may need to be refilled. Failure to do so could result in flue gases being released into the boiler room, property damage, serious personal injury, or death.
12.
Set the room thermostat to the highest setting to start the boiler and test Lockout Error 501.
consecutive failed ignition attempt.
- The combustion fan will pre-purge for a short time before activating the igniter.
- Ensure the combustion fan post-purges for at least 5 seconds before reactivating the igniter.
- After the boiler displays Error 501, set the room thermostat to the normal setting to start the boiler.
13. Open the gas valve and check the connection seals, including the boiler connection seals. Check for and eliminate any leaks.
14. Press the RESET button to clear Error 501. The display will show
OK.
15. Start the boiler by selecting CH or DHW operation.
16. Proceed with Combustion Checking Procedure.
5. The air purge function
starts automatically.
6. During the air purge cycle open the manual air vent on the primary heat exchanger. Close the air vent when clear water free of air is visible.
7. Ensure the system is completely purged of air after the purging cycle has ended. If not, repeat the procedure. Press the Auto button for 5 seconds.
8. Purge air from the CH and DHW systems. After CH system purging is complete, verify that system pressure is at least 12 psi on the pressure gauge.
NOTE: The water pressure switch safety is set at 8 psi to protect the boiler.
81
Part 11 - Start-Up
B. Combustion Checking Procedure
The order of operations for this procedure must always be respected.
Operation 1
-
Gas inlet pressure check
Loosen screw 1 (Torx 10 - Line Pressure Test
Port) and connect a manometer to the port using applicable tubing.
Ensure the boiler is powered on. Then enable Test Mode by pressing the RESET button for 10 seconds. The display will show
2
1
4
and the icon .
The gas line pressure must remain within the
Figure 87 - Gas Valve
range provided in Table 29 for the gas type during all operating conditions. Upon completion of the combustion analysis and adjustment (Operations 2 through 5), remove the pressure gauge and tighten screw 1. Verify and repair any gas leaks.
Operation 2 - Combustion Analysis
Remove the combustion test port plug as illustrated, and insert a calibrated combustion analyzer.
Figure 88 - Combustion Test Port
WARNING
Make sure the calibrated combustion analyzer is set to the appropriate gas type. Failure to do so could result in serious personal injury or death.
It is required to use a calibrated combustion analyzer to verify final adjustment according to the combustion chart (Table 27).
Failure to do so could result in serious personal injury or death.
It is very important that the combustion system be set within the recommended CO measurements listed in Table 27. Visually looking at the burner does not determine combustion quality.
Failure to measure combustion with a calibrated combustion analyzer and set the throttle within the recommended CO measurements could result in property damage, severe personal injury, or death.
Operation 3 - Adjusting the CO2 at Maximum Gas Flow Rate (High
Fan Speed)
Set the thermostat at the highest possible setting or draw off the domestic hot water at the maximum water flow rate to create a thermostatic valves present in the CH circuit.
2
Select the TEST Function by pressing and holding the RESET button for
10 seconds.
WARNING! When the Test Function is activated the temperature of the water coming out of the boiler may be more than 150°F.
1
and the icon will appear on the display when Test Function is active. The boiler will operate at maximum heating power.
Press the button to operate the boiler at the maximum power. The icon will display.
0
Wait 1 minute for the boiler to stabilize before carrying out the combustion analyses.
Read the CO2 value (%) and compare it with the values given in the table below:
Fan Speed
CO PPM
CO
2
(%)
Natural Gas
Low
<175
8.5 - 9.7
High Low
LP Gas
<175
High
9.5 - 10.5
ATTENTION: The CO
2
at minimum gas flow must not be set higher than the CO
2
reading at maximum gas flow. It may be set lower by as much as 0.3%
For Example: If CO
2
at Max. = 9.2%, CO
2
at Min. = 8.9-9.2%
Table 28 - Combustion Settings
ATTENTION!! Obtain all values with the front cover installed.
If the CO2 (%) reading differs from the values given in the table, adjust the gas valve following the instructions below. Otherwise move directly to Operation 4.
Adjusting the Gas Valve at Maximum
Gas Flow
Adjust the gas valve by turning setting screw 4 clockwise to increase the CO2 level; counterclockwise to reduce the
4
CO2 level (1 turn adjusts the CO2 level by approximately 0.3%). Wait 1 minute after each change in setting for the CO2 value to stabilize.
If the value measured corresponds to the
Figure 89 - Max CO2
Adjustment
value given in the Table 28, max adjustment is complete. Otherwise continue the setting procedure.
ATTENTION!! The Test Function will automatically deactivate after 30 minutes, or Test Function can be turned off manually by pressing the
RESET button.
4
82
Part 11 - Start-Up
Operation 4 - Checking the CO2 at Minimum Gas Flow (Low Fan
Speed)
With the Test Function active, press the button to operate the boiler at minimum
DHW power. The and icons will display.
Wait 1 minute for the boiler to stabilize before carrying out the combustion analyses.
If the CO2 (%) reading at min gas flow is greater than the
CO2 (%) reading at max flow, or if it is less than the reading at max flow by more than 0.3%, adjust the gas valve following the instructions below. Otherwise move directly to
Operation 5.
Adjusting the Gas Valve at Minimum
Gas Flow
Remove cap and adjust screw 2 by turning counter-clockwise to reduce the CO2 level; clockwise to increase the CO2 level. Wait 1 minute after each adjustment for the CO2 value to stabilize.
WARNING! Minimum Gas Flow
Adjustment is very sensitive.
2
If the value measured corresponds to the value given in Table 28 adjustment is complete. Otherwise continue the setting procedure.
Figure 90 - Min CO2
Adjustment
Attention!! If the value of the CO2 at minimum power has been changed, it is necessary repeat the adjusting at maximum gas flow.
Operation 5 - Ending Adjustment
1. Exit Test Mode by pressing RESET.
2. Turn down the thermostat and / or stop the DHW draw-off. For Only
Heating Boiler applications reset all thermostatic valves.
3. Check for and repair any leaks of gas.
4. Reinstall the front cover.
5. Reinstall the combustion test port - see Figure 88.
2
83
Part 11 - Start-Up
Inlet Gas Pressure Nominal (Inches WC)
Inlet Gas Pressure Min/Max (Inches WC)
Ignition Power
Maximum CH Power Adjustable (%)
Minimum Power (%)
Max CH Power (%)
Max DHW Power (%)
Gas Orifice (
Ø)
Gas Inlet (MBH)
Max DHW
Max CH
Min
Table 29 - Table Summarizing Powers
Parameter
220
231
233
234
232 mm
TRX085 TRX120 TRX110C TRX150C
Natural Propane Natural Propane Natural Propane Natural Propane
7 11
3.5 - 10.5
8 - 13
7
3.5 - 10.5
11
8 - 13
7
3.5 - 10.5
11
8 - 13
7
3.5 - 10.5
11
8 - 13
53
100
3
61
61
43
100
2
73
73
40
100
3
71
77
34
100
2
73
93
6.4
5.5
8.5
6.0
6.9
5.5
8.5
6.0
85
85
9,400
120
120
13,200
114
106
11,200
150
120
13,200
C. Checking Combustion Parameters
Menu 2. - Boiler Parameters
Submenu 3. - Parameter 1 Maximum Heating Power Adjustment
Submenu 2. - Parameter 0 Ignition Power
Submenu 3. - Parameter 5 Heating Ignition Delay
Maximum Heating Power Adjustment 2.3.1
The maximum heating power can be adjusted to between the maximum and minimum power allowed by the boiler.
The display shows the heating power value between 100% (“100” on the display) and 0% (“0”) of this interval.
To check the maximum heating power, access menu 2/sub menu 3/ parameter1 (231) - see page 60.
Check the value. If necessary, modify it as indicated in Table 29.
ATTENTION:
LIQUEFIED PETROLEUM (LP) PROPANE
Liquefied Petroleum (LP) propane gas is heavier than air; therefore, it is imperative that your boiler is not installed in a pit or similar location that will permit heavier than air gas to collect.
Local Codes may require appliances fueled with LP gas be provided with an alarm or an approved means of removing unburned gases from the room. Check your local codes for this requirement.
Checking Ignition Power 2.2.0
To check the Ignition power access menu 2/sub menu 2/parameter 0
(220) - see page 60.
If necessary, modify it as indicated in Table 29.
TRX
NATURAL TO PROPANE
CONVERSION INSTRUCTIONS
For Qualified Technician
Installation Instructions
Heating Ignition Delay Adjustment 2.3.5
This parameter is used to manually (0) or automatically (1) set the heating ignition delay time. This is the time the boiler delays igniting the burner after it has met the central heating mode setpoint and switched off.
To change this parameter, access menu 2/sub menu 3/parameter 5
(2.3.5)- see page 60.
After selecting manual, access the successive parameter 2.3. 6 to set the delay between 0 and 7 minutes.
Automatic selection means that the boiler will establish the delay time based on the set-point temperature.
WARNING
This conversion kit shall be installed by a qualified service agency in accordance with the manufacturer’s instructions and all applicable codes and requirements of the authority having jurisdiction. If the information in these instructions is not followed exactly, a fire, an explosion or production of carbon monoxide may result causing property damage, personal injury or loss of life. The qualified service agency is responsible for the proper installation of this kit. THE INSTALLATION IS NOT
PROPER AND COMPLETE UNTIL THE OPERATION OF THE
CONVERTED APPLIANCE IS CHECKED AS SPECIFIED IN
THE MANUFACTURER’S INSTRUCTIONS SUPPLIED WITH
THE KIT, WHICH NECESSITATES THE USE OF A CALIBRATED
CO2/O2 AND CO COMBUSTION ANALYZER.
Figure 91 - Conversion Kit
Instruction Cover
D. Converting the Appliance from Natural Gas to
Propane Operation
NTI boilers are factory set to operate on Natural Gas. BEFORE
OPERATING ON PROPANE the boiler must be converted to Propane using the included conversion kit specific to the boiler model.
WARNING
These instructions CANNOT be used to convert NTI appliance models not referenced within these instructions. Contact NTI for the availability of conversion kits and instructions for other models.
84
Failure to apply these instructions properly may result in dangerous Carbon Monoxide levels, fire, or explosion, leading to property damage, serious personal injury, or death.
Part 12 - Installation Checklist
Yes Note Before Installing
Is there enough space to ensure proper installation?
Does installation location allow for proper service clearances?
Are water and gas lines properly sized and set at proper pressures for the installation?
Is boiler location as near the exhaust vent / intake pipe terminations as possible?
Have combustible materials been cleared from the installation location?
Is there a drain close to the boiler?
Water Piping
Does boiler loop piping meet the minimum sizing requirements listed?
NOTE: Smaller piping will cause performance problems.
Does the system have an adequate air removal / CH Air separator?
Has water chemistry been checked?
Does water chemistry meet requirements?
If water chemistry does not meet requirements, have treatment measures been put in place?
Has the system been cleaned and flushed?
Install Exhaust Vent and Intake Piping
Has the boiler been vented with the approved materials listed in this manual or to meet local codes?
Is air supply sufficient for proper boiler operation?
Is total vent piping length within the maximum vent length restriction listed in this manual?
Have venting lengths been minimized?
Are terminations properly spaced from windows, doors, and other intake vents?
Have all vent terminations been installed at least one foot above exterior grade and one foot above maximum snow accumulation level?
Is vent piping properly supported?
Has vent piping been checked for leaks?
Has the exhaust vent line been pitched back to the boiler at a rate of 1/4” per foot?
Have the exhaust vent and intake pipes been properly installed to the boiler?
Is the condensate drain supported so as to not place strain on the boiler’s condensate outlet fitting?
Install Condensate Piping / Tubing and Components
Have all condensate components included with the boiler been installed?
Is the condensate line piped with the approved materials listed in this manual?
Has the condensate line been routed to a laundry tub or other drain?
Install Gas Piping
If operating on Propane, has the appropriate LP Conversion Kit been installed and the LP Conversion
Instructions been followed?
Is the gas supply line a minimum of 3/4” in diameter?
Is the gas supply line length and diameter adequate to deliver the required BTUs?
When operating at maximum and minimum gas input rates, does the gas line pressure remain between
3.5 and 14” WC for Natural Gas, or between 8 and 13” WC for Propane?
Does the gas type match the type indicated on the boiler rating plate? If converted to Propane, has the LP
Conversion Label been affixed adjacent to the boiler’s rating plate label?
Has a union and shut-off valve been installed?
Relief Valve
Is the CH Pressure Relief Valve rated to 30 psi properly installed and the at least 3/4” discharge line run to an open drain and protected from freezing?
Is the DHW Pressure Relief Valve rated to 125 psi properly installed and the at least 3/4” discharge line run to an open drain and protected from freezing?
Yes
Yes
Yes
Yes
Yes
Note
Note
Note
Note
Note
85
Part 12 - Installation Checklist
Wiring
Has the power and control been wired per boiler wiring diagram, this manual?
Is the main electrical connection polarity within boiler requirements?
Does the power supply voltage agree with the boiler rating plate? 120V AC?
Start-Up, Adjust, and Test
Has the boiler been started?
If necessary, has the boiler gas valve been adjusted?
Has the installation been customized per installation location requirements?
Have all customized system parameters been tested?
Has proper boiler operation been confirmed?
Burner Flame
Has the burner flame been checked?
Have combustion values been verified with a calibrated combustion analyzer?
If the flame does not appear normal, it may need to be cleaned by a qualified service technician. See flame sight glass window location.
Final Installation Approvals
Signed by Technician
Yes
Yes
Yes
Table 30 - Installation Checklist
Note
Note
Note
Date
86
A. Boiler Protection Devices
The boiler is protected from malfunctioning by means of internal checks performed by the electronic microprocessor PCB, which stops the boiler from operating if necessary. In the event of the boiler being shut off in this manner, a code appears on the display which refers to the type of shut-off and the reason behind it.
There are two types of shut-off:
1. Blocking Error
A blocking error means the boiler will restart automatically as soon as the problem which caused the error clears or is removed; the error is indicated by the « » symbol which appears on the display followed by the error code.
For example, if the boiler indicates a 110 error code, the error will clear automatically when the CH temperature decreases. The boiler will restart and operate normally.
Figure 92 - Blocking
Error Example
NOTE: Contact a qualified service technician if the error continues to occur.
In the event of Error 108 - Shut-off due
to insufficient water pressure inside the
heating circuit - Pressure can be increased by filling the heating circuit. See filling and purging procedures, this manual.
Figure 93 - Shut-Off
Error for Low Water
Pressure
If Error 108 occurs frequently and system needs repeated refilling, turn the boiler off. Turn the external electric power to the OFF position. Shut off the main gas valve. Contact a qualified service technician to check for any leaks of water.
2. Lockout Error
A lockout error means the boiler does not return to operation after the error condition goes away. The button must be pressed on the control panel to restore boiler operation.
If the error condition occurs often contact a qualified service technician.
Part 13 - Troubleshooting
3. Malfunction Warning
This warning is shown by the display in the following format:
5 P1 = FIRST IGNITION ATTEMPT UNSUCCESSFUL
The first part of the error code (e.g. 1 01) indicates the affected operational assembly.
1 - Primary Circuit
2 - Domestic Hot Water Circuit
3 - Internal Electronic Part
4 - External Electronic Part
5 - Ignition and Detection
6 - Air inlet - flue gas outlet
7 - Multi-zone Heating
Figure 94 - Lockout Error Example
WARNING
Important
Contact a qualified service technician for assistance if a
Lockout Error occurs frequently. For safety reasons, the boiler will permit a maximum of five (5) resets in 15 minutes
(five [5] presses of the RESET button). A sixth (6th) attempt within this 15 minute period will lock out the boiler. The boiler will only operate again after the electrical supply has been disconnected and reconnected.
Repeated Lockout Error conditions could indicate a serious error with the boiler or installation. Failure to contact a qualified service technician to troubleshoot the error could result in substantial property damage, serious personal injury, or death.
87
Part 13 - Troubleshooting
B. Boiler Error Codes
Display
CH Circuit
Description Possible Remedies
1 01
1 03
Overheat
Insufficient circulation or low water pressure:
Gradient T supply> 44.6 °F / sec, three times
Press the Reset button to clear the Error Code.
If Error happens again:
1. Check for the correct functioning and positioning of the supply and return temperature probes.
2. Check for the correct functioning and positioning of the circulation pump.
3. Check the water pressure on the pressure gauge.
Press the Reset button to clear the Error Code.
If Error happens again:
1. Check the water pressure on the pressure gauge.
2. Purge the air from the central heating circuit.
3. Check for the correct functioning and positioning of the supply and return temperature probes.
4. Check for the correct functioning and positioning of the circulation pump.
1 04
Insufficient circulation or low water pressure:
Gradient T supply> 68 °F / sec. or gradient T return> 68 °F / sec.
Press the Reset button to clear the Error Code.
If Error happens again:
1. Check the water pressure on the pressure gauge.
2. Purge the air from the central heating circuit.
3. Check for the correct functioning and positioning of the supply and return temperature probes.
4. Check for the correct functioning and positioning of the circulation pump.
1 05
Insufficient circulation or low water pressure:
T supply - T Return> 131 °F, three times
Press the Reset button to clear the Error Code.
If Error happens again:
1. Check the water pressure on the pressure gauge.
2. Purge the air from the central heating circuit.
3. Check for the correct functioning and positioning of the supply and return temperature probes.
4. Check for the correct functioning and positioning of the circulation pump.
1 06
Insufficient circulation or low water pressure:
Gradient T flow + 50 °F, three times
Press the Reset button to clear the Error Code.
If Error happens again:
1. Check the water pressure on the pressure gauge.
2. Purge the air from the central heating circuit.
3. Check for the correct functioning and positioning of the supply and return temperature probes.
4. Check for the correct functioning and positioning of the circulation pump.
1 07
1 08
Insufficient circulation or water:
T Return> T supply + 86 °F
Fill system: No water in the primary circuit
(P <Pmin).
Reset?
Reset
Reset
Press the Reset button to clear the Error Code.
If Error happens again:
1. Check the water pressure on the pressure gauge.
2. Purge the air from the central heating circuit.
3. Check for the correct functioning and positioning of the supply and return temperature probes.
4. Check for the correct functioning and positioning of the circulation pump.
This Error Code will go away when the condition is remedied.
If Error happens again:
1. Ensure the system is filled with water. Ensure all valves are open to the appliance and there are no leaks.
2. Check wiring connections to low water pressure switch. Ensure all are secure.
3. Check low water pressure switch resistance. If resistance is not zero, replace the sensor.
4. If the problem persists, replace the main control.
No Reset
88
Display
1 10
1 12
Description
CH Flow temp. probe circuit open / short circuit
CH Return temp. probe circuit open / short circuit
1 14
External sensor circuit open / short circuit
Part 13 - Troubleshooting
Reset?
If Error happens again:
1. Check CH temperature sensor. Ensure connections are secure.
2. Check sensor resistance. If resistance is zero, replace the sensor.
3. If the problem persists, replace the main control.
No Reset
This Error Code will go away when operating temperature decreases. If
Error happens again:
1. Check return temperature sensor. Ensure connections are secure.
2. Check return sensor resistance. If resistance does not match Table 33 –
Sensor Temperature Resistance
3. If the problem persists, replace the main control.
The Error Code will go away when the condition is remedied.
If Error happens again:
1. Check outdoor sensor. Ensure all wiring connections are intact and secure. If the sensor wires were secured to the wall with staples, the wires may have been damaged.
2. Check outdoor sensor resistance. If resistance does not match Table 33
– Sensor Temperature Resistance
3. If the problem persists, replace the outdoor sensor.
NOTE: When this error occurs, the appliance will still operate at the max setting of the Outdoor Heating Curve.
No Reset
No Reset
1 16
Floor Thermostat contact open
1. If parameter 223 is set to 1 and floor safety thermostat is not present, set the parameter 223 to 0 or connect a floor safety thermostat.
2. If parameter 223 is set to 1 and floor safety thermostat is present reduce the CH set-point.
No Reset
1 P1
Insufficient circulation or missing water: Gradient T supply> 44.6 °F / sec
1 P2
Insufficient circulation or missing water: T supply - T return> 131 °F
1 P3
Inadequate circulation or missing water: Gradient T supply + 50 °F
DHW Circuit
2 03
Storage temp. probe circuit open / short circuit
2 05
DHW In Probe Open Circuit (Solar temp. probe)
2 09
Storage overheating
(> 176 °F = on; <175 °F; off)
Check storage sensor and wiring. Replace if damaged.
1 P2
Anti - Legionella function not completely finished
Internal PCB’s
3 01
3 02
3 03
3 04
Display error Eeprom
Communication error GP - GIU
PCB internal error
Too many (> 5) resets in 15 minutes
(1) Turn Off the Power to the Boiler
Switch OFF and ON the boiler at the main electrical power supply. If the problem happens again replace the main PCB.
Switch OFF and ON the boiler at the main electrical power supply. If the problem happens again:
1. Check the connection between the main PCB and the HMI
2. Replace the main PCB.
Switch OFF and ON the boiler at the main electrical power supply. If the problem happens again replace the main PCB.
Switch OFF and ON the boiler at the main electrical power supply.
3 05
3 06
3 07
3 09
3 P9
PCB internal error
PCB internal error
PCB internal error
Gas relay check failed
Sched. Maintenance-Call for Service
Switch OFF and ON the boiler at the main electrical power supply. If the problem happens again replace the main PCB.
Switch OFF and ON the boiler at the main electrical power supply. If the problem happens again replace the main PCB.
Switch OFF and ON the boiler at the main electrical power supply. If the problem happens again replace the main PCB.
Switch OFF and ON the boiler at the main electrical power supply. If the problem happens again replace the main PCB.
Reset the error with the parameter 852
Warning
Warning
Warning
No Reset
No Reset
No Reset
Warning
Reset?
No Reset
No Reset
No Reset
No Reset(1)
Reset
Reset
Reset
Reset
89
Part 13 - Troubleshooting
Display
5 04
5 P1
5 P2
Detection of 10 flame lifts in one operating cycle
Description
1st Ignition Failed
2nd Ignition Failed
Possible Remedies
External P.C.B.’s
4 11
Room sensor circuit open or short circuit Zone 1
4 12
Room sensor circuit open or short circuit Zone 2
4 13
Room sensor circuit open or short circuit Zone 3
Ignition and Detection
5 01
5 02
No flame detected (3 times)
Flame detected with gas valve closed
Press the Power button to clear the Error Code.
If Error happens again:
1. Monitor the gas pressure to the appliance while in operation. Ensure pressure is between 3.5 and 10.5” WC (Natural Gas), or between 8 and
13” WC for boilers converted to Propane (LP) operation.
2. Check gas valve wire. Ensure connection is secure.
3. Check flame detection sensor. Ensure connections are secure. Normal operating settings are more than 2.5DC before ignition; less than 2.5DC after ignition.
4. Check igniter transformer for proper connection.
5. Clean the spark igniter with steel wool to remove oxides. Ensure proper separation (3-4 mm).
6. Replace the spark igniter if damaged.
7. Assure that the flame is stable when lit.
8. If the problem persists, replace the main control.
Press the Reset button to clear the Error Code.
1. If Error happens again disconnect the flame detection electrode.
Then press Reset.
2. If the error does not happen again replace the flame detection
electrode.
3. If the error happens again replace the main PCB.
Press the Power button to clear the Error Code.
If Error happens again:
1. Monitor the gas pressure to the appliance while in operation. Ensure pressure is between 3.5 and 10.5” WC.
2. Check gas valve wire. Ensure connection is secure.
3. Check flame detection sensor. Ensure connections are secure. Normal operating settings are more than 2.5DC before ignition, less than 2.5DC after ignition.
4. Check vent terminations. Ensure there are no blockages.
5. Ensure that the flame is stable when lit.
6. If the problem persists, replace the main control.
1. Monitor the gas pressure to the appliance while in operation. Ensure pressure is between 3.5 and 10.5” WC (Natural Gas), or between 8 and 13” WC for boilers converted to Propane (LP) operation.
2. Check gas valve wire. Ensure connection is secure.
3. Check flame detection sensor. Ensure connections are secure.
Normal operating settings are more than 2.5DC before ignition;
less than 2.5DC after ignition.
4. Check igniter transformer for proper connection.
5. Clean the spark igniter with steel wool to remove oxides. Ensure
proper separation (2/16”-3/16”).
6. Replace the spark igniter if damaged.
7. Ensure that the flame is stable when lit.
8. If the problem persists, replace the main control.
1. Monitor the gas pressure to the appliance while in operation. Ensure pressure is between 3.5 and 10.5” WC (Natural Gas), or between 8 and 13” WC for boilers converted to Propane (LP) operation.
2. Check gas valve wire. Ensure connection is secure.
3. Check flame detection sensor. Ensure connections are secure.
Normal operating settings are more than 2.5DC before ignition;
less than 2.5DC after ignition.
4. Check igniter transformer for proper connection.
5. Clean the spark igniter with steel wool to remove oxides. Ensure
proper separation (2/16”-3/16”).
6. Replace the spark igniter if damaged.
7. Ensure that the flame is stable when lit.
8. If the problem persists, replace the main control.
Reset?
No Reset
No Reset
No Reset
Reset
No Reset
Reset
Warning
Warning
90
Part 13 - Troubleshooting
Display
5 P3
5 P6
Description
Detection of 9 Flame cut-off
3rd and 4th Ignition Failed
Possible Remedies
1. Monitor the gas pressure to the appliance while in operation.
Ensure pressure is between 3.5 and 10.5” WC.
2. Check gas valve wire. Ensure connection is secure.
3. Check flame detection sensor. Ensure connections are secure.
Normal operating settings are more than 2.5DC before ignition,
less than 2.5DC after ignition.
4. Check vent terminations. Ensure there are no blockages.
5. Ensure that the flame is stable when lit.
6. If the problem persists, replace the main control.
1. Monitor the gas pressure to the appliance while in operation. Ensure pressure is between 3.5 and 10.5” WC (Natural Gas), or between 8 and
13” WC for boilers converted to Propane (LP) operation.
2. Check gas valve wire. Ensure connection is secure.
3. Check flame detection sensor. Ensure connections are secure.
Normal operating settings are more than 2.5DC before ignition;
less than 2.5DC after ignition.
4. Check igniter transformer for proper connection.
5. Clean the spark igniter with steel wool to remove oxides. Ensure
proper separation (2/16”-3/16”).
6. Replace the spark igniter if damaged.
7. Ensure that the flame is stable when lit.
8. If the problem persists, replace the main control.
Air Intake / Exhaust Gas Outlet
6 02
6 03
6 12
Exhaust NTC detects Vent Temperature is greater than 204°F (96°C)
This Error Code will go away when the condition is remedied.
If Error happens again:
1. Check exhaust temperature sensor. Ensure connections are secure.
2. Check sensor resistance. If resistance is zero, replace the sensor.
3. Check exhaust vent for blockage.
4. If the problem persists, replace the control.
5. If the problem persists, replace the heat exchanger.
Exhaust NTC circuit open or short circuit
Press the Power button to clear the Error Code.
1. Check APS and main controller connections. Ensure all are secure.
2. Check APS resistance. If resistance is not zero, replace the switch.
3. Check APS hose. Ensure it is connected and in good condition.
4. Check condensate line and termination for blockages.
5. Check exhaust vent for blockages.
6. If the problem persists, replace the main control.
APS Open
Insufficient fan speed
(<500 for 3 seconds or RPM min -300 for 3 minutes)
Press the Power button to clear the Error Code.
1. Check APS and main controller connections. Ensure all are secure.
2. Check APS resistance. If resistance is not zero, replace the switch.
3. Check APS hose. Ensure it is connected and in good condition.
4. Check condensate line and termination for blockages.
5. Check exhaust vent for blockages.
6. If the problem persists, replace the main control.
This Error Code will go away when the condition is remedied.
If Error happens again:
1. Check the connections to the fan. Ensure all are secure.
2. If the fan does not rotate during the ignition sequence, check for 8Vac
26.5VDC power at the fan connection.
If 8Vac 26.5VDC power is present at the control, replace the fan. If the blower does not have 8Vac 26.5VDC power, check power at the control.
If 8Vac 26.5VDC power is not present at the control, replace the control.
3. If the problem persists, replace the main control.
Reset?
Warning
Reset
No Reset
No Reset
Reset
Table 31 - Boiler Error Codes
Important
Contact a qualified service technician for assistance if a Lockout Error occurs frequently. For safety reasons, the boiler will permit a maximum of five (5) resets in 15 minutes (five [5] presses of the RESET button). A sixth (6th) attempt within this 15 minute period will lock out the boiler permanently. The boiler will only operate again after the electrical supply has been disconnected and reconnected.
Repeated Lockout Error conditions could indicate a serious error with the boiler or installation. Failure to contact a qualified service technician to troubleshoot the error could result in substantial property damage, serious personal injury, or death.
91
Part 14 - Maintenance
DANGER
The boiler must be inspected and serviced annually, preferably at the start of the heating season, by a qualified service technician. In addition, the maintenance and care of the boiler as outlined in this manual must be performed by the user/owner to assure maximum efficiency and reliability.
Follow the maintenance procedures given throughout this manual. Failure to perform the service and maintenance or follow the directions in this manual could damage the boiler or system components, resulting in substantial property damage, severe personal injury, or death.
A. Procedures
Periodic maintenance should be performed once a year by a qualified service technician to ensure that all the equipment is operating safely and efficiently. The owner should make necessary arrangements with a qualified heating contractor for periodic maintenance of the boiler.
The installer must also inform the owner that a lack of proper care and maintenance of the boiler may result in a hazardous condition.
B. Maintenance That May be Performed by the User
Check the Surrounding Area
DANGER
To prevent the potential of substantial property damage, severe personal injury, or death, eliminate all the materials listed in
Table 6 from the area surrounding the boiler and the vicinity of the combustion air intake. If contaminants are found:
• Remove products immediately from area.
• If contaminants have been there for an extended period, call a qualified service technician to inspect the boiler for possible damage from acid corrosion.
If products cannot be removed, immediately call a qualified service technician to re-pipe the combustion air intake piping away from the contaminated areas.
Ensure the Cabinet is Closed When the Boiler is Operating
The boiler cabinet must be closed when the boiler is operating.
Combustible/Flammable Materials
Do not store combustible materials, gasoline, or other flammable vapors or liquids near the boiler. If found, remove these materials immediately.
Air Contaminants
If allowed to contaminate combustion air, products containing chlorine or fluorine will produce acidic condensate that will cause significant damage to the boiler. Read the list of potential contaminants and areas likely to have these contaminants in Table 6. If any of these contaminants are in the room where the boiler is located, or combustion air is taken from one of the areas listed, the contaminants must be removed immediately or the intake pipe must be relocated to another area.
Check the Power Source
Make sure the power cord and the main power line are properly connected to the manual switch box inside the boiler.
Check the Status of the Control Panel
Observe the Control Panel to ensure the boiler is powered on and to check for any error codes. Clear any debris from the panel.
Check CH Pressure Gauge
Ensure the pressure reading on the CH gauge does not exceed 30 psig.
Higher pressure readings may indicate a problem with the expansion tank. Immediately contact a qualified service technician to inspect the boiler and system.
Check Exhaust Vent and Intake Pipe Terminations
Verify that the boiler exhaust vent and intake pipe terminations are clean and free of obstructions. Remove any debris from the exhaust vent or intake pipe openings. If removing the debris does not allow the boiler to operate correctly, contact your qualified service technician to inspect the boiler and the vent system.
Check Exhaust Vent and Intake Piping
Visually inspect the exhaust vent for any signs of blockage, leakage, or deterioration of the piping. Inspect the exhaust vent bracing. Ensure bracing is undamaged and in good condition. Notify a qualified service technician immediately if any problems are found.
WARNING
Failure to inspect the venting system and have it repaired by a qualified service technician can result in vent system failure, causing severe personal injury or death.
Check Pressure Relief Valve
1. Visually inspect the primary pressure relief valve and discharge pipe for signs of weeping or leakage.
2. If the pressure relief valve often weeps, the expansion tank may not be operating properly. Immediately contact a qualified service technician to inspect the boiler and system.
Operate Pressure Relief Valve
1. Before proceeding, verify that the relief valve outlet has been piped to a safe place of discharge, avoiding any possibility of scalding from hot water.
2. Shut power off to the boiler. To avoid scalding, wait for boiler to cool before operating the relief valve.
WARNING
To avoid water damage or scalding due to relief valve operation, a discharge line must be connected to the valve outlet and directed to a safe place of disposal. This discharge line must be installed by a qualified service technician in accordance with the boiler installation manual.
The discharge line must be terminated so as to eliminate possibility of severe burns or property damage should the valve discharge.
3. Lift the relief valve lever. If water flows freely, release the lever and allow the valve to seat. Watch the end of the relief valve discharge pipe to ensure that the valve does not weep after the line has had time to drain. If the valve weeps, lift the lever again to attempt to clean the valve seat. If the valve does not properly seat and continues to weep, contact a qualified service technician to inspect the valve and system.
4. If water does not flow from the valve when you completely lift the lever, the valve or discharge line may be blocked. Immediately shut the boiler down per instructions on page 2 and call a qualified service technician to inspect the valve and system.
5. If relief valve seats properly, restore power to the boiler. Observe operation for five minutes and ensure it operates properly.
Check the Condensate Drain System
1. While the boiler is running, check the discharge end of the condensate drain tubing. Ensure no flue gas is leaking from the condensate drain tubing by holding your fingers near the opening.
2. If you notice flue gas leaking from the opening, this indicates a dry condensate drain trap. If problem persists, contact a qualified service technician to inspect the boiler and condensate line and refill the condensate trap.
92
3. If applicable, check the condensate neutralizer and ensure it is full of condensate neutralizing marble chips.
C. Maintenance Only to be Performed by a Qualified
Service Technician
Removing the Cabinet Cover and Inspecting the Boiler
Before carrying out any work on the boiler, switch off the power supply at the external power switch and circuit breaker. Close the external gas shutoff.
DANGER
Ensure power and gas to the appliance are shut off before performing the following operations. Failure to do so will result in substantial property damage, severe personal injury, or death.
See Figure 95 to access the interior of the boiler:
1. Unscrew the two screws from the front panel (a).
2. Pull the panel forwards and uncouple it from the upper pins (b).
3. Pivot the electronic housing by pushing in tabs (c).
(a)
(c)
Figure 95 - Removing Housing
(b)
Part 14 - Maintenance
Check the Air Vent
Loosen cap one counterclockwise turn to allow air vent to operate. If the air vent works freely without leaking, close the valve by turning clockwise. If vent does not operate correctly, contact a qualified service technician to replace the vent.
Check Primary and Gas Piping
1. Remove the boiler cover and perform a gas leak inspection following Operating Instructions, page 2, this manual. If gas odor or leak is detected, follow procedures on page 2. Call a qualified service technician.
2. Visually inspect for leaks around the boiler water connections and around the heat exchanger. Visually inspect the external system piping, circulators, and system components and fittings.
Immediately call a qualified service technician to repair any leaks.
WARNING
Have leaks fixed at once by a qualified service technician.
Failure to comply could result in substantial property damage, severe personal injury, or death.
Before Starting Maintenance:
1. Ensure the power and gas remain off.
2. Close the valves of heating and hot water circuit.
3. Remove the front panel as shown in Figure 95.
4. If necessary, empty the appliance on the water side.
Draining Procedure
To drain the heating system:
1. Ensure the boiler power and gas remain off.
2. Loosen the automatic air relief valve.
3. Open the system drain valve and collect the escaping water in a container.
4. Drain the water from the lowest points of the system (where applicable).
If the system is to be inactive in areas where the room temperature may fall below 0°C during winter, it is recommended that anti-freeze liquid be added to the heating system in order to avoid the need for repeated draining. Ensure the antifreeze used is compatible with the stainless steel boiler heat exchanger.
WARNING
NEVER use any toxic chemical, including automotive, standard glycol antifreeze, or ethylene glycol made for hydronic (non-potable) systems. These chemicals can attack gaskets and seals in water systems, are poisonous if consumed, and can cause personal injury or death.
It is recommended to use antifreeze which contains PROPYLENE
GLYCOLS as these inhibit corrosion. Use the quantities and formulation suggested by the antifreeze manufacturer to protect against freezing in your region and prevent scaling and corrosion.
Regularly check the pH level of the water/anti-freeze mix in the boiler circuit and replace it when the value measured is lower than the limit prescribed by the manufacturer.
DO NOT MIX DIFFERENT TYPES OF ANTI-FREEZE.
The manufacturer will not be held liable for any damage caused by the appliance or the system due to the use of inappropriate antifreeze substances or additives.
Draining the DHW System and Indirect Water Heater
Every time there is a danger of freezing, the domestic hot water system must be drained as follows:
1. Shut off the main water inlet valve.
2. Open all the hot and cold water taps.
3. Drain the water from the lowest points of the system.
93
Part 14 - Maintenance
WARNING
Water drained from the boiler could be scalding hot. Wait for the boiler to cool before draining water, and take precautions when draining water. Failure to do so could result in property damage, personal injury, or death.
WARNING
Allowing the boiler to operate with a dirty combustion chamber will hurt operation. Failure to clean the heat exchanger as needed by the installation location could result in boiler failure, property damage, personal injury, or death.
Such product failures ARE NOT covered under warranty.
The combustion chamber insulation in this product contains ceramic fiber material. Ceramic fibers can be converted to cristobalite in very high temperature applications. The
International Agency for Research on Cancer (IARC) has concluded, “Crystalline silica inhaled in the form of quartz or cristobalite from occupational sources is carcinogenic to humans
(Group 1).”
• Avoid breathing dust and contact with skin and eyes.
• Use a NIOSH certified dust respirator (N95). This type of respirator is based on the OSHA requirements for cristobalite at the time this document was written. Other types of respirators may be needed depending on job site conditions. Current
NIOSH recommendations can be found on the NIOSH website: http://www.cdc.gov/niosh/homepage.html. NIOSH approved respirators, manufacturers, and phone numbers are also listed on this website.
• Wear long-sleeved, loose fitting clothing, gloves, and eye protection.
• Apply enough water to the combustion chamber lining to prevent dust.
• Wash potentially contaminated clothes separately from other clothing. Rinse clothes washer thoroughly.
NIOSH stated First Aid.
• Eye: Irrigate immediately.
• Breathing: Fresh air.
Cleaning the Heat Exchanger Combustion Chamber
*Before beginning this procedure, have on hand the following items:
• a nylon or other non-metallic brush
• an FDA approved liquid lime scale remover in a spray bottle
• gloves and eye protection
1. Unhook the junction box
2. Unhook the junction box support from the fan and silencer
Figure 97 - Unhook the junction box support
3. Remove the silencer
Figure 98 - Remove the silencer
4. Unscrew the two nuts and remove the gas pipe.
Figure 99 - Remove the gas pipe
Figure 96 - Removing the Junction box
94
5. Remove the gas orifice.
6. Remove the electrical connection of the electrode.
7. Remove the electrical connection to the igniter.
8. Loosen the four screws and remove the burner unit.
Part 14 - Maintenance
13. After all maintenance is complete, reinstall the combustion assembly. Ensure all gaskets are installed and all components are tightened properly.
14. Restore power and gas to the boiler. Restart the boiler. Check for leaks in the combustion system. Observe operation for 5 to 10 minutes.
If boiler is operating properly, condensate is flowing normally, and no gas leaks are detected, combustion coil cleaning is complete.
Checking the Burner
While the combustion assembly is removed from the heat exchanger, inspect the burner. Proceed as follows:
1. Unscrew the four screws securing the two electrodes to the burner plate.
Figure 100 - Remove the Combustion Assembly 1
9. Pull the assembly towards you.
Figure 101 - Remove the Combustion Assembly 2
10. Check the back wall insulation and replace if necessary.
WARNING
Protect the back wall insulation from water before performing any cleaning. Failure to do so could result in damage to the insulation, improper boiler operation, personal injury, or death.
11. Disconnect the condensate hose and siphon cap from the boiler.
12. Clean the combustion chamber by spraying water or solution into the combustion assembly and monitor the flow through the combustion system. Liquid should flow freely through each tube.
If there is an obstruction, increase the flow on the tube to force blockage out.
WARNING
Do not use solvents to clean any of the boiler components.
The components could be damaged, resulting in unreliable or unsafe boiler operation, substantial property damage, severe personal injury, or death.
Figure 102 - Remove the Electrodes
2. Remove the ceramic fiber.
3. Remove the four screws and pull the burner toward you.
NOTE: Whenever replacing the burner, ALWAYS replace the burner gasket.
Figure 103 - Disassembled Burner Assembly
95
Part 14 - Maintenance
4. Verify and replace the other gaskets if they are damaged or showing signs of deterioration.
5. Make sure that the burner is not damaged. Replace if necessary.
6. Reassemble the burner assembly.
7. Ensure the combustion assembly sealing ring is not damaged.
Replace if necessary.
DANGER
Failure to replace a damaged sealing ring will result in exhaust gas leaks, substantial property damage, severe personal injury, or death.
8. Reinstall the two removed electrodes with the four removed screws.
9. Reassemble the combustion assembly and tighten the four screws.
10. Reconnect the gas line. Replace the sealing ring.
11. Reconnect the electrode electrical connections.
12. Reinstall the support bracket of the air pressure switch.
13. Reinstall the silencer.
14. Reinstall the air pressure switch.
15. Reconnect the air pressure switch electrical connection.
Clean the Condensate Trap
WARNING
Take care when opening the condensate trap cap, as condensate may escape. Failure to do so could result in property damage due to leaks, personal injury, or death.
DANGER
When servicing is complete, make sure the condensate collector cap is replaced securely. The condensate trap assembly MUST
BE PROPERLY INSTALLED according to these instructions when operating the boiler. Operating the boiler without the condensate trap assembly will cause flue gases to leak and result in serious personal injury or death.
the entire condensate trap assembly.
3. Refill the condensate trap with fresh water prior to operating the boiler.
4. If a condensate neutralizer kit is installed, check the assembly when cleaning the condensate trap, and replenish the limestone chips if necessary. When replacing the limestone chips, take care to ensure chips are no smaller than ½” to avoid blockage in condensate piping. See Figure 55 for piping details.
5. Check condensate piping for sagging and/or leakage. Repair any sags or leaks before restoring power to the boiler.
6. If the boiler has a condensate pump, ensure the pump operates
CAUTION
It is very important that the condensate piping be no smaller than ¾”. To prevent sagging and maintain pitch, condensate piping should be supported with pipe supports, and pitched
¼” per foot to allow for proper drainage.
The condensate line must remain unobstructed, allowing free flow of condensate. If condensate freezes in the line, or if line is obstructed in any other manner, condensate can exit from the tee, resulting in potential water damage to property.
properly before considering maintenance complete.
WARNING
Ensure the boiler and CH and DHW heating systems have been drained following the instructions in this manual BEFORE attempting to remove the CH or DHW filters. Failure to do so could result in property damage, serious personal injury, or death.
Cleaning the CH and DHW Inlet Filters
1. Remove the clip and remove the CH filter.
Figure 104 - Clean the Condensate Trap
1. Remove the condensate hose and open the siphon cap.
2. When the condensate trap is sufficiently clean, reassemble in the reverse order.
boiler. If any parts are missing DO NOT operate the boiler. Replace
WARNING
Do not install the condensate assembly if a component is lost or missing. Replace the entire assembly. Failure to follow this warning could result in property damage, serious personal injury, or death.
Do not operate the appliance without the clear hose attached from the hose barb to the pressure switch. Failure to do so could result in property damage, serious personal injury, or death.
96
Figure 105 - Removing the CH Filter
WARNING
Water drained from the boiler could be scalding hot. Wait for the boiler to cool before draining water, and take precautions when draining water. Failure to do so could result in property damage, personal injury, or death.
2. Clean the filter with a toothbrush and clean running water.
3. Reinstall the CH Filter.
4. Remove the DHW flow switch to have access to the DHW inlet filter. Remove the clip and pull the flow switch assembly upward.
Part 14 - Maintenance
DANGER
Failure to replace a damaged sealing ring will result in exhaust gas leaks, substantial property damage, severe personal injury, or death.
5. Proceed in the reverse order to reinstall the components.
Replacing the Fan
1. Remove the combustion assembly as described in Cleaning the
Heat Exchanger Combustion Chamber and Checking the Burner.
2. Remove the three nuts and bolts to disconnect the fan from the air inlet assembly.
Figure 107 - Removing the Fan
DHW Filter
Figure 106 - Removing the DHW Filter
5. Clean the filter with a toothbrush and clean running water.
6. Reinstall the DHW inlet filter.
7. Refill the DHW circuit following the filling and purging instructions in this manual.
8. Refill the CH circuit following the filling and purging instructions in this manual.
9. Restore gas and power to the boiler.
D. Replacing Components
At any point in time over the boiler’s service life it may be necessary to replace boiler components. If the boiler displays an error message, determine its cause and possible remedies.
If the remedy is replacement of a component, ensure:
1. That the boiler is powered OFF. Press the ON/OFF button to turn the boiler off. Then turn the main electrical power to the boiler off at the circuit breaker.
2. The boiler electrical connection is connected properly. A loose electrical connection could the root cause of problems.
3. The front cover has been removed.
4. The main shutoff gas valve is closed.
5. All water valves to and from the boiler (supply, return, inlet, outlet) are closed.
6. If necessary, the water has been drained from the boiler and/or appropriate circuit.
7. No water can get into the display / control panel.
Replacing the Burner
1. Remove the front cover and pivot the electronic housing following the instructions described in Removing the Cabinet Cover and
Inspecting the Boiler.
2. Remove the combustion assembly as described in Cleaning the
Heat Exchanger Combustion Chamber.
3. Remove, inspect, and replace the burner as described in Checking
the Burner.
4. Replace all damaged seals that are damaged or showing signs of wear.
1 2 3 4 5 6
Figure 108 - Removed Fan, Bi-Venturi, and Components
Legend:
1 - Bi-Venturi Tube
(Replace with the Bi-Venturi for Gas Propane present in the Convertion Kit delivered with the boiler - See Fuel
Conversion Kit Instructions)
2 - Gas Orifice (Replace with the
Gas Orifice for Gas Propane present in the Convertion
Kit delivered with the boiler
- See Fuel Conversion Kit
Instructions)
3 - Gas Seal
4 - O-Ring
5 - Fan
6- Fan to Air Inlet Channel
Gasket
3. Inspect the fan to air inlet channel gasket. Ensure it is not damaged or deteriorating.
DANGER
Ensure that the correct gas orifice and bi-venturi are used for the correct fuel type for the boiler - Natural Gas or Propane. See
Conversion Kit Instructions. Failure to do so will result in substantial property damage, severe personal injury, or death.
97
Part 14 - Maintenance
4. Loosen the three screws to release the bi-venturi from the fan.
Ensure the O-Ring is not damaged or deteriorating.
5. Reassemble the bi-venturi and fan assembly in the reverse order.
Ensure the O-Ring is installed between the bi-venturi and fan.
DANGER
Failure to replace damaged or deteriorating gaskets or O-Rings will result in exhaust gas leaks, substantial property damage, severe personal injury, or death.
6. Reinstall the fan to the air inlet channel. Ensure the gasket is assembled between the fan and air inlet channel.
7. Reconnect the gas line. Replace the sealing ring.
8. Restore the electrical connections of the electrodes.
9. Reinstall the support bracket of the pressure switch.
10. Reinstall the silencer.
11. Reinstall the air pressure switch.
12. Reconnect the electrical connection of the air pressure switch.
Removing the By-Pass Valve
TRX085 and TRX120
The by-pass valve is located in the left hydraulic block. To remove it:
1. Ensure the boiler is drained of water.
2. Remove the securing clip from the valve.
3. Pull the by-pass valve assembly upwards.
CAUTION
It is possible to block the overflow valve insert. To do this, remove the overflow valve insert and refit it again.
Removing the By-Pass Valve
TRX110C and TRX150C
The by-pass valve is located in the right hydraulic block. To remove it:
1. Ensure the boiler is drained of water.
2. Rotate clockvise to unhook the locking ring of the diverter valve.
3. Remove the securing clip from the valve.
4. Pull the by-pass valve assembly upwards.
Figure 112 - Remove the locking ring of the diverter valve
Figure 109 - Remove the Clip
Figure 110 - Remove the By-Pass Valve
Figure 111 - By-Pass Valve Assembly
98
Figure 113 - Remove the clip and pull the assembly
Figure 114 - By-Pass Valve Assembly
CAUTION
It is possible to block the overflow valve insert. To do this, remove the overflow valve insert and refit it again.
Part 14 - Maintenance
Replacing the Main Heat Exchanger
1. Remove the combustion assembly as described in Cleaning the
Heat Exchanger Combustion Chamber.
2. Loosen and remove the CH relief valve.
3. Loosen and remove the CH relief valve pipe and gasket.
4. Remove the securing clips from positions a and b.
Figure 115 - Remove the locking ring of the diverter valve
5. Disconnect the plastic pipes from the manual breather.
a b
Figure 116 - Remove the CH Outlet Pipe
6. Disconnect the heating supply pipe.
7. Disconnect the condensate line.
8. Remove the clip and disconnect the connection line from the heating return pipe.
Figure 118 - Remove the Heat Exchanger
Replacing the Gas Valve
1. Remove the electrical connections from the gas valve.
2. Remove the two screws under the combustion assembly and disconnect the gas line from the gas valve.
3. Remove the gas valve.
4. Reinstall the new gas valve in reverse order.
Figure 117 - Remove the Condensate Pipe and CH Return Pipe
9. Remove the four screws to remove the heat exchanger.
10. Proceed in reverse order to install the new device.
Figure 119 - Disconnect the Gas Line
5. BE SURE TO USE NEW SEALING RINGS.
6. Ensure there are no gas leaks.
99
Part 14 - Maintenance
Replace the Main PCB
1. Fold down the electronics box.
2. Unlock the two clips and open the electronics box cover.
DANGER
Failure to replace the sealing rings will result in exhaust gas leaks, substantial property damage, severe personal injury, or death.
3. Disconnect the electrical connections.
4. Unhook the controller board and remove it.
5. Proceed in reverse order to install the new PCB.
6. Follow the instructions provided with the replacement PCB kit for setting all necessary parameters.
Part 15 - Maintenance Report
CAUTION
In unusually dirty or dusty conditions, care must be taken to keep boiler cabinet door in place at all times. Failure to do so VOIDS WARRANTY!
WARNING
Allowing the boiler to operate with a dirty combustion chamber will hurt operation. Failure to clean the heat exchanger as needed by the installation location could result in boiler failure, property damage, personal injury, or death. Such product failures ARE NOT covered under warranty.
The combustion chamber insulation in this product contains ceramic fiber material. Ceramic fibers can be converted to cristobalite in very high temperature applications. The
International Agency for Research on Cancer (IARC) has concluded, “Crystalline silica inhaled in the form of quartz or cristobalite from occupational sources is carcinogenic to humans
(Group 1).”
• Avoid breathing dust and contact with skin and eyes.
• Use a NIOSH certified dust respirator (N95). This type of respirator is based on the OSHA requirements for cristobalite at the time this document was written. Other types of respirators may be needed depending on job site conditions.
Current NIOSH recommendations can be found on the NIOSH website: http://www.cdc.gov/niosh/homepage.html. NIOSH approved respirators, manufacturers, and phone numbers are also listed on this website.
• Wear long-sleeved, loose fitting clothing, gloves, and eye protection.
• Apply enough water to the combustion chamber lining to prevent dust.
• Wash potentially contaminated clothes separately from other clothing. Rinse clothes washer thoroughly.
NIOSH stated First Aid.
• Eye: Irrigate immediately.
• Breathing: Fresh air.
Figure 120 - Disconnect the Main PCB
E. After Maintenance is Complete
Functional Test
After maintenance is complete, ensure the CH circuit is filled and purged with a pressure of 12 psi. Ensure the DHW circuit is filled and purged.
1. Power the boiler on.
2. If necessary, purge air again from the CH and DHW circuits.
3. Check the boiler and system settings and components. Ensure all adjustments are working properly.
4. Ensure the exhaust pipe is connected properly.
5. Reinstall the boiler front cover.
6. If necessary, set the maintenance interval.
Inform the User
1. Inform the user of any changes / adjustments / replacements in the system.
2. Ensure the user understands how the system works.
3. Hand the instructions to the user. Ensure the instructions will be kept close to the unit.
4. Have the user perform these regular tasks:
• Check the system water pressure regularly.
• If necessary, restore pressure and vent the system.
• Set the setpoints and control systems to ensure correct and economical control of the system.
• Have the system serviced in accordance with regulations at regular intervals.
• NEVER attempt to service the boiler or adjust the combustion system.
The boiler requires minimal periodic maintenance under normal conditions. However, in unusually dirty or dusty conditions, periodic vacuuming of the cover to maintain visibility of the display and indicators is recommended.
Periodic maintenance should be performed once a year by a qualified service technician to ensure that all the equipment is operating safely and efficiently. The owner should make necessary arrangements with a qualified heating contractor for periodic maintenance of the boiler.
Installer must also inform the owner that the lack of proper care and maintenance of the boiler may result in a hazardous condition.
100
Part 15 - Maintenance Report
INSPECTION ACTIVITIES
PIPING
Near boiler piping Check boiler and system piping for any sign of leakage. Leaking pipes could cause property damage. Make sure all piping is properly supported. See
User’s Information manual for instructions.
DATE LAST COMPLETED
1st YEAR 2nd YEAR 3rd YEAR 4th YEAR*
Vent
Gas
Check condition of all vent pipes and joints. Ensure all vent piping is properly supported. Check for obstructions at exhaust and intake termination points.
Check Gas piping, test for leaks and signs of aging. Make sure all pipes are properly supported.
SYSTEM
Visual
Functional
Temperatures
Temperatures
Do a full visual inspection of all system components.
Test all functions of the system (central heat, water heating, Safeties)
Verify safe settings on boiler or Anti-Scald Valve
Verify programmed temperature settings
ELECTRICAL
Connections
Smoke and CO detector
Circuit Breakers
Switch and Plug
Check wire connections. Make sure they are tight.
Verify devices are installed and working properly. Change batteries if necessary.
Ensure the circuit breaker is clearly labeled. Exercise circuit breaker.
Verify ON/OFF switch and convenience plug are both functional
CHAMBER/BURNER
Combustion Chamber Check burner tube and combustion chamber coils. Clean according to maintenance section of manual. Vacuum combustion chamber.
Spark Electrode
CONDENSATE
Clean. Set gap at 1/8”.
Condensate Trap
Neutralizer
Condensate hose
Clean debris from the condensate trap. Fill with clean water.
Check condensate neutralizer. Replace if necessary.
Disconnect condensate hose. Clean out dirt and re-install. (NOTE: Verify the flow of condensate, making sure that the hose is properly connected during final inspection.)
GAS
Pressure
Pressure Drop
Measure incoming gas pressure (3.5 to 10.5” W.C. NG, 8 to 13” W.C. LP)
Measure drop in pressure on light off (no more than 1” W.C.)
Check gas piping for leaks. Verify that all are properly supported.
Check for leaks
COMBUSTION
CO/CO2 Levels Check CO and CO2 levels in Exhaust. Record at high and low fire.
SAFETIES
ECO (Energy Cut Out) Check continuity on flue temperature sensor. Replace the flue gas temperature sensor if corroded.
Check continuity on Water ECO. Check position and sensor resistance.
Ensure air pressure switch is properly connected (electrical connections and silicone pipe).
DHW LOOP - Combi Models
It is recommended to flush the DHW heat exchanger annually if water hardness exceeds 12 grains per gallon (considered extremely hard water). If water hardness falls below 12 grains per gallon it is recommended to flush the heat exchanger every two to three years.
It is also recommended to clean the CH and DHW inlet filters annually.
FINAL INSPECTION
Check list
Homeowner
TECH SIGN OFF
Verify that you have completed entire check list. WARNING: FAILURE TO DO
SO COULD RESULT IN SERIOUS INJURY OR DEATH.
Review what you have done with the homeowner.
Table 32 - *Continue annual maintenance beyond the 4th year as required.
101
Part 16 - Shutdown
A. Shutdown Procedure
If the burner is not operating, disconnect the electrical supply.
If the burner is operating, lower the set point value to 86 o
F(for high temperature system) or 68°F (for low temperature system) and wait for the burner to shut off. Continue to wait for the combustion blower to stop, so all latent combustion gases are purged from the system. This should take a maximum of 40 to 90 seconds.
B. Vacation Procedure
If there is danger of freezing, change the set point to 86 o
F(for high temperature system) or 68°F (for low temperature system). DO NOT turn off electrical power. If there is no danger of freezing, follow
“Shutdown Procedure”.
C. Failure to Operate
Should the burner fail to light, the control will perform four more ignition trials prior to entering a lockout state. Note that each subsequent ignition trial will not occur immediately. After a failed ignition trial, the blower must run for approximately 5 seconds to purge the system.
If the burner lights during any one of these five ignition trails, normal operation will resume.
If the burner does not light after the fifth ignition trial, the control will enter a lockout state.
This lockout state indicates that a problem exists with the boiler, the controls, or the gas supply.
Under such circumstances, a qualified service technician should be contacted immediately to properly service the boiler and correct the problem. If a technician is not available, depressing and holding the
RESET button for more than 1 second will remove the lockout state so additional trials for ignition can be performed.
If the RESET key is not pressed (error code 501 or 503), the boiler will reset automatically after an hour.
Outdoor Sensor
(7250P-319)
Outside
Temperature
( o
F)
-22
-13
-4
5
14
23
32
41
86
95
104
113
50
59
68
77
Resistance
(ohms)
178605
132045
98438
73995
56079
42846
32997
25609
20027
15777
12517
10000
8042
6510
5302
4343
176
185
194
202
Table 33 - Sensor Temperature Resistance
212
140
149
158
167
104
113
122
131
Supply Temperature Sensor
(7250P-324)
Boiler Sensor
(7250P-667)
Indirect Sensor
(7350P-325)
High / Low
Temp Sensor
Temp. ( o
F)
Resistance
(Ohms)
68
77
86
95
32
41
50
59
27219
22021
17926
14674
12081
10000
8315
6948
5834
4917
4161
3535
3014
2586
2228
1925
1669
1452
1268
1110
974
D. Important Notice
NOTICE
It is extremely important that whenever work is performed on the plumbing system that either:
• The appliance is powered off, or,
• The appliance is valved off and isolated from the plumbing system.
Failure to take these measures could result in a dry-firing condition.
102
2
100
200
300
400
Part 17 - Replacement Parts
TRX - TRXC
402
415
312
417 210
282
214
282
201
425
426
551
152
405
*116
152
317
403
316
404
372
123
152
178
111
105
271
213
211
151
180
171
316
152
114
151
117
202
423
190
150
102
172
173
183
371
310
315
415
*116
101
172
110
271
Table 34 - Replacement Parts List
103
Part 17 - Replacement Parts
104
Description
0100 BURNER ASSEMBLY
0101 IGNITION ELECTRODE
0102 ELECTRODE (DETECTION)
0105 FLUE PROBE 10K D4X39
0110 INSULATION (BURNER DOOR)
0111 HEAT EXCHANGER 120/150C
HEAT EXCHANGER 85/110C
0114 BURNER 24KW
BURNER 30kW
BURNER 35KW
0116 DOOR ASSY
0117 CONDENSATE TRAP
0123 AIR VENT
0150 CONDENSATE DRAIN HOSE D:19 L:500
0151 CONDENSATE COLLECTION PIPE
0152 CONNECTION Y +TUBES
0171 GASKET (BURNER)
0172 GASKET (IGNITION ELECTRODE)
0173 DOOR GASKET
0178 O-RING 17.86X2.62
0180 SPARK GENERATOR
0183 PLASTIC PIPE 2" CPVC L=5,5''
0190 O-RING 41.6X2.4
0200 GAS SECTION
0201 GAS VALVE
0202 FAN
0210 GAS RESTRICTOR D: 5,5
GAS RESTRICTOR D: 6
GAS RESTRICTOR D: 6.40
GAS RESTRICTOR D: 6.90
GAS RESTRICTOR D: 8.5
0211 MIXER 085/85WBN LP
MIXER 085/85WBN NG
MIXER 110C120WCN NG
MIXER 120-150C/120 WBN-WCN LP
MIXER 120-150C/120 WBN-WCN NG
MIXER 85/120WCN LP
0213 SILENCER
0214 GAS PIPE
GAS PIPE
0271 FAN GASKET
0282 SHEET GASKET D: 24-18.2-1.5
0300 TOP PANEL ASSEMBLY
0310 CASE COVER ASSY
0312 FLUE TEST PORT PLUG
0315 SPLASH PREVENTER
0316 AIR PRESSURE SWITCH
0317 PIPE (CONDENSATE AIR PRESSURE SWITCH)
0371 COLLAR GASKET
0372 SUPPORT (AIR PRESSURE SWITCH)
0400 SEALED CASE
0402 PRESSURE RELIEF VALVE
0403 PIPE (PRESSURE RELIEF VALVE)
0404 GASKET 1Z
0405 SILICONE PIPE D:8 L:330
0415 SIDE PANELS LEFT + RIGHT
0417 CASE PANEL (FRONT)
0423 BOTTOM PANEL
0425 GAS ADAPTER (3/4” NPT)”
0426 SHEET GASKET D: 24-17-1.5
65118645
65118672
65118689
65118718
60001923
60001924
65118713
65118688
65118669
65118722
65118717
65118712
65118724
65113062
65118668
65118714
65116530
60022835-01
65118673
65118674
65118667
65118694
65118715
65118671
65116596
65116603
65116604
65118690
65117391
65119079
60000976
65118670
65119326
65116521
65116263
65105788
61308091
65119323
65119324
65118686
Manf. Pt. N Type
65119579
65104295
65116536
65118678
65119086
65118682
65118680
65118683
65119083
569387
65116520
65119081
65119080
65119082
65119084
60061855-19
10C.
1 2
TRX085.
....
. .
....
....
....
....
....
....
.
.
.
.
....
....
....
....
....
....
....
....
....
....
From to
3
4
500
570
571
521
563
514
590
123
582
565
576
551
501
562
507
568
519 562
Part 17 - Replacement Parts
585 562 557
556
555
585
519
558
556
555
TRX082.-TRX120.
111
105
106
Part 17 - Replacement Parts
Description
0500 FLOW GROUP
0501 FLOW GROUP
FLOW GROUP
0507 SANITARY HEAT EXCHANGER (16 P.)
0514 BY-PASS VALVE
0519 INTERFACE 'System +' Open
0521 HYDRAULIC GROUP SUPPORT
0551 PIPE (CH OUTLET)
PIPE (CH OUTLET)
0555 CLIP D10
0556 O-RING 8.9X2.7
0557 PIPE (D.H.W.RETURN)
0558 BY-PASS PIPE
0562 CLIP D18
0563 CLIP D:12
0565 CLIP
0568 EXCHANGER GASKET
0570 CH ADAPTER (3/4”)”
0571 DHW ADAPTER (1/2”)”
0576 TEMPERATURE PROBE + CLIP
0582 O-RING 17.86X2.62
0585 O-RING 17.04X3.53
0590 O-RING 11.91X2.62
65118664
65118720
65116537
65117089
60001365
65119440
65116569
65116578
65104260
60002398
65115935
65116210
65104259
65114932
60000309
65114928
65114929
65114930
990686-01
61308091
65104262
65114940
Manf. Pt. N Type
10C.
1 2
TRX085.
..
. .
..
....
....
....
From to
5
6
Part 17 - Replacement Parts
600
123
BN
672
606
693
672
610
605
608
607
693
660
681
612
683
694 665
671
602
664
622
692
614
691
603
660
692
616
687
689
667
615
601
682
666
688
681
612
670
604
111
107
108
Part 17 - Replacement Parts
Description
0600 RETURN GROUP
0601 RETURN GROUP
RETURN GROUP
0602 LOW PRESSURE SWITCH
0603 CLIP
0604 TACO PUMP HIGH EFFICIENCY
0605 MOTOR (3-WAY VALVE)
0606 SENSOR (REED)
0607 FLOW METER
0608 CLIP
0610 MOTOR + SPRING 3 WAY VALVE KIT
0612 PLUG
0614 AUTO AIR VENT - TACO ENER+
0615 DRAIN COCK
0616 WATER FILTER
0622 BY-PASS VALVE
0651 PIPE (C.H. RETURN)
0660 CLIP D:10
0664 CLIP
0665 CLIP D:12
0666 CLIP
0667 CLIP D:6
0670 TEMPERATURE PROBE + CLIP
0671 CLIP
0672 CLIP
0681 O-RING 9.9X2.62
0682 O-RING 17.04X3.53
0683 O-RING 23.47X2.62
0687 O-RING 5.7X1.9
0688 O-RING 21.89X2.62
0689 PLUG
0691 O-RING 17.86X2.62
0692 O-RING 11.91X2.62
0693 O-RING 17.13X2.62
0694 O-RING 15,88X2,62
65116543
65114933
65104322
65114932
60000309
65100680
990686-01
65114926
65114931
65114937
65104262
65114939
61009834-10
65104320
65119580
61308091
65114940
65114938
65114941
65118665
65118721
65118663
61307589
65118666
65114936
65114921-01
65114919
65114927
65114924
65114920
65112086
65114922
65114923
65117089
Manf. Pt. N Type
10C.
1 2
TRX085.
....
....
....
....
....
....
....
....
....
....
From to
7
800
814
851
825
900
910
8
5000
Transf. gaz
Conv. gas
Trasf. gas
Transf. gas
5001
Options
Accessories
Opzioni
Accessorio
5020
816
886
889
888
Part 17 - Replacement Parts
885
881
842
824
815
801
880
109
110
Part 17 - Replacement Parts
Description
0800 ELECTRICAL BOX
0801 GROMMET (PCD TOOL ACCESS)
0814 CONTROL PANEL BASE
0815 P.C.B. (MAIN)
0816 P.C.B. (DISPLAY)
0824 CONTROL PANEL COVER
0825 PRESSURE/TEMPERATURE GAUGE
0842 CONTROL PANEL HINGE
0851 CONTROL PANEL
0880 3-WAY VALVE CABLE
3-WAY VALVE CABLE
CABLE (DETECTION ELECTRODE)
CABLE (FAN-POWER SUPPLY)
CABLE (FUME PROBE-EXTENSION)
CABLE (POWER SUPPLY)
CABLE (PUMP 5M PWM TACO)
CABLE (PWM)
CABLE (SPARK GENERATOR)
DISPLAY WIRING - 5 WIRES BLUES
998382
65118650
65118648
65117700
65118651
65118685
65116548
65119087
65118657
65118719
65118654
65118655
65119085
65118675
65118695
65118658
65118653
60000746
GAS VALVE CABLE
NTC CABLE
65118652
65118681
WIRING (AIR PRESSURE SWITCH AND PROBES) 65118656
WIRING (PUMP+JUN.BOX+MAIN BOARD) 65118659
WIRING (WI-FI BOARD)
0881 CONNECTOR 2P
0885 JUNCTION BOX BASE
0886 JUNCTION BOX COVER
0888 P.C.B. (JUNCTION BOX)
0889 P.C.B. (WIFI-REM3)
65115826
65111933
65118661
65118662
65118660
65118649
0900 JIG PLATE & PIPE FITTING
0910 WALL HOOK
5000 ACCESSORIES
5001 LP CONVERTION KIT 120C
LP CONVERTION KIT 150C & 110S
LP CONVERTION KIT 85S
5020 KIT AIR VENT
OUTDOOR SENSOR
RIDUCTORS (KIT)
Manf. Pt. N Type
60000625
65118723
65118716
65118687
65118684
65112215
65116836
10C.
1 2
TRX085.
....
..
....
....
....
....
....
....
....
....
. .
..
From to
9
10
6XXXXXXX
0101
0102
0105
0110
0111
0114
0211
0213
65119324
65118686
65118645
65118672
60001923
60001924
65118689
65118713
65118670
65119326
65116521
65116263
65105788
61308091
65119323
65118718
65118669
65118688
65118712
65118717
65118722
65118724
65113062
65118673
65118674
65118667
65118694
65118671
65118715
65116596
65116603
65116604
65118690
65117391
65119079
60000976
0151
0152
0171
0172
0116
0117
0123
0150
0173
0178
0180
0183
0190
0201
0202
0210
EN
FR
DE
ES
6XXXXXXX
6XXXXXXX
EN
FR
DE
ES
DE
ES
6XXXXXXX
NL
IT
Part 17 - Replacement Parts
DE
ES
NL
IT
IGNITION ELECTRODE
ELECTRODE ALLUMAGE
ELECTRODE (DETECTION)
ELECTRODE IONISATION
FLUE PROBE 10K D4X39
SONDE FUMÉE 10K D4X39
INSULATION (BURNER DOOR)
PANNEAU ISOLEMENT
HEAT EXCHANGER 85/110C
ECHANGEUR 85/110C
HEAT EXCHANGER 120/150C
ECHANGEUR 120/150C
BURNER 24KW
BRULEUR 24KW
65118673
65118674
65118667
65118694
65118671
65118668
65118714
65116530
60022835-01
65119579
GAS PIPE
TUBE GAZ
GAS PIPE
TUBE GAZ
FAN GASKET
JOINT VENTILATEUR
SHEET GASKET D: 24-18.2-1.5
JOINT PLAT D: 24-18.2-1.5
CASE COVER ASSY
COUVERCLE CAISSON EQUIPE
0214
0271
0282
0310
AUSTAUSCHER 120/150C
BRENNER 24KW
0114
65118715
65104295
FLUE TEST PORT PLUG
BOUCHON DE PRISE FUMEE
0312
65116596
65116536
1
0315
65118668
65118714
65116530
60022835-01
65119579
65104295
65116536
GASBUIS
TUBO GAS
GASBUIS
TUBO GAS
DICHTING VENTILATOR
GUARNIZIONE VENTILATORE
DICHTING VLAK D. 24-18.2-1.5
GUARNI. PIANA D: 24-18.2-1.5
ABDECK. BRENNERG. KOMPLETT
COPERCHIO TELAIO
STOP ROOKGASMEETNIPPELS
TAPPO ANALISI FUMI + O-RING
BESCHERMING WATERTOEVOER
PARASPRUZZI
1
1
1
1
1
1
1
GASBUIS
TUBO GAS
GASBUIS
TUBO GAS
DICHTING VENTILATOR
GUARNIZIONE VENTILATORE
DICHTING VLAK D. 24-18.2-1.5
GUARNI. PIANA D: 24-18.2-1.5
ABDECK. BRENNERG. KOMPLETT
COPERCHIO TELAIO
STOP ROOKGASMEETNIPPELS
TAPPO ANALISI FUMI + O-RING
BESCHERMING WATERTOEVOER
PARASPRUZZI
BURNER 30kW
BRULEUR 30kW
BURNER 35KW
BRULEUR 35KW
BRENNER 30kW
QUEMADOR 30kW
BRENNER 35KW
QUEMADOR 35KW
65116603
65118678
AIR PRESSURE SWITCH
PRESSOSTAT AIR
0316 65118678
DRUKSCHAKELAAR LUCHT
PRESSOSTATO ARIA
1
DRUKSCHAKELAAR LUCHT
PRESSOSTATO ARIA
65116604
65119086
1
0317 65119086
1
1
BUIS (LUCHTDRUKSCHAKELAAR COND.)
TUYAU CONDENS.COMMUT..PRES.AIR TUBO CONDENS.INTER.PRESIÓN AIRE TUBO CONDENSA PRESSOSTATO
DOOR ASSY
PORTE EQUIPEE
CONDENSATE TRAP
SIPHON
AIR VENT
PURGEUR D'AIR
SIPHON
0117
65118690
65118682
COLLAR GASKET
JOINT COLLIER
65119079
65118683
PRESSURE RELIEF VALVE
SOUPAPE DE SECURITE
0371
0402
65118682
65118683
DICHTING KLEMRING
GUARNIZIONE USCITA FUMI
VEILIGHEIDSGROEP
VALVOLA DI SICUREZZA
1
65117391
65118680
SUPPORT PRESSOSTAT D'AIR
1
0372 65118680
1
1
1
DICHTING KLEMRING
GUARNIZIONE USCITA FUMI
SUPPORTO PRESSOSTATO ARIA
VEILIGHEIDSGROEP
VALVOLA DI SICUREZZA
CONDENSATE DRAIN HOSE D:19 L:500
TUBE PVC D:19 L:500
60000976
65119083
PIPE (PRESSURE RELIEF VALVE)
TUBE SOUPAPE DE SECURITE
0403 65119083
BUIS VEILIGHEIDSKLEP
TUBO VALVOLA DI SICUREZZA
1
BUIS VEILIGHEIDSKLEP
TUBO VALVOLA DI SICUREZZA
CONDENSATE COLLECTION PIPE
TUBE FLEXIBLE
SCHLAUCH
0151
569387
GASKET 1Z
JOINT 1Z
1
0404 569387
AFDICHTING WATER/GAS 1Z
GUARNIZIONE ACQUA-GAS 1Z
1
AFDICHTING WATER/GAS 1Z
GUARNIZIONE ACQUA-GAS 1Z
CONNECTION Y +TUBES
RACCORD Y + TUBES
GASKET (BURNER)
JOINT DE FORME
FORMDICHTUNG
JUNTA
0171
65119326
65116520
SILICONE PIPE D:8 L:330
RACCORDO Y + TUBI
0405 65116520
SILICONESLANG D:8 L:330
TUBE SILICONE D:8 L:330
1
65116521
65119081
1
0415 65119081
ZIJPANEEL RECHTS + LINKS
PANNELLI LATERALI DX + SX
1
1
SILICONESLANG D:8 L:330
TUBO SILICONE D:8 L:330
ZIJPANEEL RECHTS + LINKS
PANNELLI LATERALI DX + SX
GASKET (IGNITION ELECTRODE)
JOINT ELECTRODE
65116263
65119080
CASE PANEL (FRONT)
PANNEAU FRONTAL
0417 65119080
VOORPANEEL
MANTELLO FRONTALE
1
VOORPANEEL
MANTELLO FRONTALE
DOOR GASKET
JOINT DE PORTE
TUERDICHTUNG
0173 65105788
65119082
BOTTOM PANEL
FOND 18-24 KW
0423 65119082
PLATE WIRE BOX
FONDO 18-24 KW
1
PLATE WIRE BOX
FONDO 18-24 KW
O-RING 17.86X2.62
JOINT TORIQUE D: 17.86-2.62
61308091
65119084
GAS ADAPTER (3/4” NPT)”
RACCORD 3/4
0425 65119084
VERBINDINGSSTUK 3/4"
RACCORDO 3/4
5
VERBINDINGSSTUK 3/4"
RACCORDO 3/4
SPARK GENERATOR
TRANSFORMATEUR D'ALLUMAGE
ZUNDTRAFO
ENCENDEDOR
0180 65119323
60061855-19
SHEET GASKET D: 24-17-1.5
JOINT PLAT D: 24-17-1.5
0426 60061855-19
DICHTING VLAK D. 24-17-1.5
GUARNI. PIANA D: 24-17-1.5
1
DICHTING VLAK D. 24-17-1.5
GUARNI. PIANA D: 24-17-1.5
PLASTIC PIPE 2" CPVC L=5,5''
0183 65119324
65118664
FLOW GROUP
GROUPE DEPART CHAUFFAGE
1
0501
O-RING 41.6X2.4
JOINT TORIQUE D: 41.6X2.4
GAS VALVE
VALVE GAZ
GASVENTIL
VALVULA GAS
0201
65118686
65118720
FLOW GROUP
GROUPE DEPART CHAUFFAGE
65118645
65116537 0507
FAN
VENTILATEUR
GAS RESTRICTOR D: 6.40
DIAPHRAGME GAZ D: 6.40
GAS RESTRICTOR D: 6.90
DIAPHRAGME GAZ D: 6.90
GAS RESTRICTOR D: 5,5
DIAPHRAGME GAZ D: 5,5
65118664
65118720
FLOW GROUP
GROUPE DEPART CHAUFFAGE
GROEP AANVOER VERWARMING
GRUPPO MANDATA
1
1
65116537
SCAMBIATORE SANITARIO 16
1
1
LAUFRAD
0202 65118672
65117089
BY-PASS VALVE
BY-PASS
60001923
60001365
1
0519 60001365
INTERFACCIA RISCALDAMENTO
1
PLATTENVENTIL GAS D: 6.90
DIAFRAGMA GAS D: 6.90
60001924
65119440
HYDRAULIC GROUP SUPPORT
SUPPORT HYDRAULIQUE
1
BY-PASS
0514
0521
65117089
65119440
BY-PASS
BY-PASS
HYDRAULIC SUPPORT BRACKET
STAFFA SUPPORTO IDRAULICO
1
1
PLATTENVENTIL GAS D: 5,5
DIAFRAGMA GAS D: 5,5
65118689
65116569
PIPE (CH OUTLET)
TUBE DEPART CHAUFFAGE
0551 65116569
BUIS VERTREK VERWARMING
TUBO MANDATA
1
GROEP AANVOER VERWARMING
GRUPPO MANDATA
GROEP AANVOER VERWARMING
GRUPPO MANDATA
WARMTEWISSELAAR SANITAIR 16 PLATEN
SCAMBIATORE SANITARIO 16
BY-PASS
BY-PASS
1
INTERFACCIA RISCALDAMENTO
HYDRAULIC SUPPORT BRACKET
STAFFA SUPPORTO IDRAULICO
BUIS VERTREK VERWARMING
TUBO MANDATA
GAS RESTRICTOR D: 8.5
DIAPHRAGME GAZ D: 8,5
GAS RESTRICTOR D: 6
DIAPHRAGME GAZ D: 6
PLATTENVENTIL GAS D: 8,5
DIAFRAGMA GAS D: 8,5
65118713
65116578
PLATTENVENTIL GAS D: 6
DIAFRAGMA GAS D: 6
65118718
65104260
PIPE (CH OUTLET)
TUBE DEPART CHAUFFAGE
CLIP D10
CLIP D10
0555
65116578
65104260
BUIS VERTREK VERWARMING
TUBO MANDATA
CLIP D10
CLIP D10
1
1
BUIS VERTREK VERWARMING
TUBO MANDATA
CLIP D10
CLIP D10
MIXER 085/85WBN NG
MIXER 085/85WBN NG
MIXER 085/85WBN LP
MIXER 085/85WBN LP
MIXER 085/85WBN LP
MIXER 085/85WBN LP
65118669
65118688
60002398
65115935
O-RING 8.9X2.7
JOINT TORIQUE D: 8.9-2.7
PIPE (D.H.W.RETURN)
TUBE RETOUR EAU SANITAIRE
1
1
0556
0557
60002398
65115935
DICHTINGSRING D: 8.9-2.7
ANELLO OR D: 8.9-2.7
TUBE RETOUR EAU SANITAIRE
1
1
DICHTINGSRING D: 8.9-2.7
ANELLO OR D: 8.9-2.7
BUIS (GEZONDHEID WATER RETOUR)
TUBO RITORNO ACQUA CALDA
MIXER 120-150C/120 WBN-WCN NG
MIXER 120-150C/120 WBN-WCN NG
MIXER 120-150C/120 WBN-WCN LP
MIXER 120-150C/120 WBN-WCN LP
65118712
65118717
65116210
65104259
BY-PASS PIPE
TUBE BY-PASS
CLIP D18
CLIP D18
0558
0562
65116210
65104259
BUIS BY-PASS
TUBO BY-PASS
KLEM D18
CLIP D18
1
1
BUIS BY-PASS
TUBO BY-PASS
KLEM D18
CLIP D18
MIXER 110C120WCN NG
MIXER 110C120WCN NG
MIXER 85/120WCN LP
MIXER 85/120WCN LP
SILENCER
SILENCIEUX
MIXER 110C120WCN NG
MIXER 110C120WCN NG
65118722
65114932
MIXER 85/120WCN LP
MIXER 85/120WCN LP
SCHALLDAMPFE
SILENCIADOR
0213
65118724
65113062
60000309
65114928
CLIP D:12
CLIP D:12
CLIP
CLIP
EXCHANGER GASKET
JOINT ECHANGEUR
0563
0565
0568
65114932
KLEM D:12
CLIP D:12
60000309
65114928
KLEM
CLIP
SILENCER
DICHTING WISSELAAR
GUARNIZIONE SCAMBIATORE
1
1
1
KLEM D:12
CLIP D:12
KLEM
CLIP
DICHTING WISSELAAR
GUARNIZIONE SCAMBIATORE
111
10
11
1
1
1
10
1
1
1
1
1
1
1
1
1
10
1
1
1
1
1
10
1
1
1
1
1
1
1
1
1
1
1
1
1
5
1
5
11
12
0570
0571
0576
0582
0585
0590
0601
0672
0681
0682
0683
0666
0667
0670
0671
0651
0660
0664
0665
0614
0615
0616
0622
0687
0688
0689
0606
0607
0608
0610
0612
0602
0603
0604
0605
6XXXXXXX
65118663
61307589
65118666
65114936
65114921-01
65114919
65114927
65114924
65114920
65114929
65114930
990686-01
61308091
65104262
65114940
65118665
65118721
60000309
65100680
990686-01
65114926
65114931
65114937
65104262
65114939
65112086
65114922
65114923
65117089
65116543
65114933
65104322
65114932
61009834-10
65104320
65119580
EN
FR
DE
ES
Part 17 - Replacement Parts
EN
FR
DE
ES
DE
ES
6XXXXXXX
NL
IT
DE
ES
NL
IT
CH ADAPTER (3/4”)”
RACCORD 3/4
DHW ADAPTER (1/2”)”
RACCORD 1/2
ANSCHLUSS, 3/4
RACOR 3/4
ANSCHLUSS, 1/2
RACOR 1/2
0570
0691
0571
0692
TEMPERATURE PROBE + CLIP
SONDE NTC + CLIPS KIT
O-RING 17.86X2.62
JOINT TORIQUE D: 17.86-2.62
O-RING 17.04X3.53
JOINT TORIQUE 3,53X17,04
O-RING 11.91X2.62
JOINT TORIQUE D: 11.91-2.62
0576
0582
0585
0590
0693
0694
0801
0814
RETURN GROUP
GROUPE RETOUR (REMPL. MANUEL)
0601
0815
RETURN GROUP
GROUPE RETOUR
RUCKLAUFGRUPPE
GRUPO RETORNO
0816
O-RING 17.86X2.62
JOINT TORIQUE D: 17.86-2.62
O-RING 11.91X2.62
JOINT TORIQUE D: 11.91-2.62
O-RING 17.13X2.62
JOINT TORIQUE D: 17.13-2.62
O-RING 15,88X2,62
JOINT TORIQUE D: 15.88-2.62
GROMMET (PCD TOOL ACCESS)
JOINT ENTREE REGULATION
CONTROL PANEL BASE
PORTE INSTRUMENTS
0691
0692
0693
0694
0801
0814
P.C.B. (MAIN)
CIRCUIT IMPRIME PRINCIPAL
1
0815
P.C.B. (DISPLAY)
CIRCUIT IMPRIME D'AFFICHAGE
0816
61308091
65114940
65114938
65114941
998382
65118650
65118648
65117700
DICHTINGSRING D: 17.86-2.62
ANELLO OR D: 17.86-2.62
DICHTINGSRING D: 11.91-2.62
ANELLO OR D: 11.91-2.62
DICHTINGSRING D: 17.13-2.62
ANELLO OR D: 17.13-2.62
DICHTINGSRING D: 15.88-2.62
ANELLO OR D: 15.88-2.62
BEHUIZING BEDIENINGSPANEEL
PORTASTRUMENTI
PRINTKAART
SCHEDA PRINCIPALE
PRINT DISPLAY
SCHEDA DISPLAY
1
1
1
5
DICHTING
GOMMINO ACCESSO REGOLAZIONE
10
5
1
1
DICHTINGSRING D: 17.86-2.62
ANELLO OR D: 17.86-2.62
DICHTINGSRING D: 11.91-2.62
ANELLO OR D: 11.91-2.62
DICHTINGSRING D: 17.13-2.62
ANELLO OR D: 17.13-2.62
DICHTINGSRING D: 15.88-2.62
ANELLO OR D: 15.88-2.62
DICHTING
GOMMINO ACCESSO REGOLAZIONE
BEHUIZING BEDIENINGSPANEEL
PORTASTRUMENTI
PRINTKAART
SCHEDA PRINCIPALE
PRINT DISPLAY
SCHEDA DISPLAY
LOW PRESSURE SWITCH
DETECTEUR DE PRESSION
CLIP
CLIP
TACO PUMP HIGH EFFICIENCY
POMPE TACO
CLIP
CLIP
PUMPE TACO
0602
0603
0604
0824
0825
0842
LOW PRESSURE SWITCH
DETECTEUR DE PRESSION
1
CLIP
CLIP
PRESSURE/TEMPERATURE GAUGE
MANOMETRE / THERMOMETRE
CONTROL PANEL HINGE
SUPPORT
1
0824
0825
0842
65118651
65118685
65116548
DRUKSCHAKELAAR MINIMUM
COPERCHIO BOX
KLEM
CLIP
MANOMETER - THERMOMETER
TERMOIDROMETRO
SUPPORT
SUPPORTO
1
1
1
1
COPERCHIO BOX
MANOMETER - THERMOMETER
TERMOIDROMETRO
SUPPORT
SUPPORTO
MOTOR (3-WAY VALVE)
MOTEUR VANNE 3 VOIES
0605
0851
CONTROL PANEL
TABLEAU DE COMMANDE
0851 65119087
BEDIENINGSPANEEL
FRONTALINO
1
BEDIENINGSPANEEL
FRONTALINO
SENSOR (REED)
AMPOULE REED
FLOW METER
CARTOUCHE DEBIMETRE
PLUG
BOUCHON
AUTO AIR VENT - TACO ENER+
DEGAZEUR - TACO ENER+
REEDKONTAKT
STOPFEN
TAPON
0606
0880
SENSOR (REED)
AMPOULE REED
1
0880 60000746
SENSOR (REED)
SENSORE REED
1
1
BEDRADING DISPLAY
CABLAGE AFFICHEUR - 5 FILS BLEUS CABLEADO DISPLAY - 5 cables azules CABLAGGIO DISPLAY - 5 cavi azzurri
WIRING (WI-FI BOARD)
CABLAGE (CIRCUIT WIFI)
65115826
ELEKTRISCHE BEDRADING (PRINT WIFI)
CABLAGGIO SCHEDA WIFI
1
CLIP
CLIP
CLIP
CLIP
0608
CLIP
CLIP
GAS VALVE CABLE
CABLAGE VANNE GAZ
1
KABEL ZUNDER
65118652
KLEM
CLIP
BEDRADING GASBLOK
CABLAGGIO VALVOLA GAS
1
MOTOR + SPRING 3 WAY VALVE KIT
0610
CABLE (SPARK GENERATOR)
KIT MOTORE+OTTURAT.VALV.3 VIE
1
KABEL (ZUNDTRAFO)
65118653
CABLE (SPARK GENERATOR)
KIT MOTORE+OTTURAT.VALV.3 VIE
1
1
ELEKTRISCHE BEDRADING (PRINT WIFI)
CABLAGGIO SCHEDA WIFI
BEDRADING GASBLOK
CABLAGGIO VALVOLA GAS
KABEL (VONKENGENERATOR)
CABLAGGIO ACCENDITORE
0612
PLUG
CABLE (DETECTION ELECTRODE)
CABLAGE ELECTRODE IONISATION
1 65118654
STOPPEN
TAPPO
1
0614
CABLE (FAN-POWER SUPPLY)
DEGAZEUR - TACO ENER+
1
65118655
ONTLUCHTINGSKLEP - TACO ENER+
VALVOLA SFOGO ARIA - TACO ENER+
1
1
1
CABLE (DETECTION ELECTRODE)
CABLE ELECTRODO DE DETECCION CAVO ELETTRODO RILEVAZIONE
DRAIN COCK
ROBINET EVACUATION INSTALLA.
WATER FILTER
FILTRE EAU
BY-PASS VALVE
BY-PASS
PIPE (C.H. RETURN)
TUBE RETOUR CHAUFFAGE
CLIP D:10
CLIP D:10
WASSERSIEB
BY-PASS
BY-PASS
0622
RUCKLAUFROHR
0651
CLIP D:10
CLIP D:10
0616
0660
DRAIN COCK
ROBINET EVACUATION INSTALLA.
1 65118656
LEEGLAATKRAAN
RUBINETTO SVUOTAMENTO
1 1
BEDRADING (LUCHTDRUKSCHAKEL.EN VOELERS)
CÂBLAGE COMMUT.DE PRESS.D'AIR ET SONDES CABLEADO INTER.DE PRES.AIRE Y SONDAS CABLAGGIO PRESS.TO ARIA E SONDE
3-WAY VALVE CABLE
CABLAGE VANNE 3 VOIES
65118657
BEDRADING DRIEWEG KLEP
CABLAGGIO VALVOLA A 3 VIE
1
BEDRADING DRIEWEG KLEP
CABLAGGIO VALVOLA A 3 VIE
CABLE (PWM)
CABLAGE PWM
PIPE (C.H. RETURN)
TUBE RETOUR CHAUFFAGE
1
65118658
65118659
Cablage PWM
CABLAGGIO PWM
BUIS RETOUR VERWARMING
TUBO RITORNO
1
1
1
Cablage PWM
CABLAGGIO PWM
CLIP
CLIP
CLIP D:12
CLIP D:12
CLIP
CLIP
CLIP D:6
CLIP D:6
TEMPERATURE PROBE + CLIP
SONDE NTC + CLIPS KIT
CLIP
CLIP
CLIP
CLIP
O-RING 9.9X2.62
JOINT TORIQUE D: 9.9-2.62
O-RING 17.04X3.53
JOINT TORIQUE 3,53X17,04
O-RING 23.47X2.62
JOINT TORIQUE D: 23.47-2.62
O-RING 5.7X1.9
JOINT TORIQUE D: 5.7-1.9
O-RING 21.89X2.62
JOINT TORIQUE 21.89X2.62
PLUG
BOUCHON
KLAMMER PUMPE
CLIP
CLIP D:12
CLIP D:12
CLIP
CLIP
CLIP D:6
CLIP D:6
CLIP
CLIP
CLIP
CLIP
STOPFEN
TAPON
0665
0666
0667
0670
0671
0672
0681
0682
0683
0687
0689
0881
0885
0886
0888
0889
0910
5001
CABLE (POWER SUPPLY)
CABLAGE D'ALIMENTATION
CLIP
CLIP
NTC CABLE
CABLAGE NTC
CABLE (PUMP 5M PWM TACO)
CABLE POMPE 5M PWM TACO
CLIP
CLIP
3-WAY VALVE CABLE
CABLAGE VANNE 3 VOIES
CONNECTOR 2P
CONNECTEUR 2 POLES
1
NTC CABLE
CABL. NTC
65118675
65118681
65118695
BEDRADING ONTSTEKING
CABLAGGIO ALIMENTAZIONE
KLEM
CLIP
BEDRADING NTC
CABLAGGIO NTC
BEDRADING POMP 5M PWM TACO
CAVO POMPA 5M PWM TACO
1
KABEL 3-WEGEVENTIL
65118719
KLEM
CLIP
BEDRADING DRIEWEG KLEP
CABLAGGIO VALVOLA A 3 VIE
0881 65111933
STEKKER 2-POLIG
CONNETTORE 2 POLI
5
1
5
1
BEDRADING ONTSTEKING
CABLAGGIO ALIMENTAZIONE
BEDRADING NTC
CABLAGGIO NTC
BEDRADING POMP 5M PWM TACO
CAVO POMPA 5M PWM TACO
BEDRADING DRIEWEG KLEP
CABLAGGIO VALVOLA A 3 VIE
CLIP D:6
CLIP D:6
1 65119085
KLEM D:6
CLIP D:6
1 1
VERLENGINGSKABEL ROOK SONDE
CABLE D'EXTENS.SONDE D'ECHAPPEM. CABLE DE EXTENS.SONDA DE HUMO CAVO PROLUNGA SONDA FUMI
1
STEKKER 2-POLIG
CONNETTORE 2 POLI
CLIP
CLIP
JUNCTION BOX BASE
CLIP
CLIP
JUNCTION BOX COVER
COUVERCLE (BOITE DE JONCTION)
P.C.B. (JUNCTION BOX)
CIRCUIT CLIP-IN LOADS NA
P.C.B. (WIFI-REM3)
CIRCUIT IMPRIME REM 3
WALL HOOK
PLATINE SUPPORT MURAL
LP CONVERTION KIT 85S
EQT TRANSF. G31 85S
LP CONVERTION KIT 150C & 110S
EQT TRANSF. G31 40 KW
PLUG
LP CONVERTION KIT 120C
EQT TRANSF. G31 30KW COMBI
1
5
0885
0886 65118662
KLEM
CLIP
DEKKING (JUNCTION BOX)
COPERCHIO JUNCTION BOX
5 0888 65118660
DICHTINGSRING D: 9.9-2.62
ANELLO OR D: 9.9-2.62
0889
0910
5001
65118661
65118649
60000625
65118687
65118716
65118723
CLIP FONDO JUNCTION BOX
PRINTKAART REM3
SCHEDA REM3
WANDBEVESTIGING
STAFFA D'AGGANCIO SUPERIORE
OMBOUWSET G31 85S
TRASFORMAZIONE G31 85S
OMBOUWSET G31 40 KW
TRASFORMAZIONE G31 40 KW
STOPPEN
TAPPO
1
5
5
10
5
10
1
1
1
FONDO JUNCTION BOX
DEKKING (JUNCTION BOX)
COPERCHIO JUNCTION BOX
1
PRINTKAART (CLIP IN LOADS NA)
CIRCUITO ELECTR.CLIP-IN LOADS NA SCHEDA CLIP-IN LOADS NA
PRINTKAART REM3
SCHEDA REM3
WANDBEVESTIGING
STAFFA D'AGGANCIO SUPERIORE
OMBOUWSET G31 85S
TRASFORMAZIONE G31 85S
OMBOUWSET G31 40 KW
TRASFORMAZIONE G31 40 KW
112
12 13
5
5
5
5
5
1
1
1
1
1
1
1
1
1
1
1
1
1
1
1
1
1
1
1
1
1
1
5
1
1
1
1
1
1
1
1
13
6XXXXXXX
5020 65112215
65116836
65118684
EN
FR
OUTDOOR SENSOR
SONDE EXTERIEURE FILAIRE
RIDUCTORS (KIT)
LIMITEURS DE DEBIT KIT
KIT AIR VENT
KIT AIR VENT
DE
ES
TUELLESET
REDUCTOR (KIT)
KIT AIR VENT
KIT AIR VENT
6XXXXXXX
65112215
65116836
65118684
OUTDOOR SENSOR
SONDE EXTERIEURE FILAIRE
RIDUCTORS (KIT)
LIMITEURS DE DEBIT KIT
KIT AIR VENT
KIT AIR VENT
DE
ES
Part 17 - Replacement Parts
NL
IT
BUITENVOELER
SONDA ESTERNA CON CAVI
DEBIETBEGRENZER (KIT)
LIMITATORI DI PORTATA (KIT)
KIT AIR VENT
KIT PROTEZIONE SCARICO FUMI
1
1
1
14 14
113
Part 17 - Replacement Parts
Maintenance Notes
114
Part 17 - Replacement Parts
Customer Installation Record Form
The following form should be completed by the qualified installer / service technician for you to keep as a record of the installation in case of a warranty claim. After reading the important notes at the bottom of the page, please also sign this document.
Customer’s Name
Date of Installation
Installation Address
Product Name / Serial Number(s)
Comments
Installer’s Code / Name
Installers Phone Number
Signed by Installer
Signed by Customer
Installation Notes
IMPORTANT
Customer: Please only sign after the qualified installer / service technician has fully reviewed the installation, safety, proper operation, and maintenance of the system. If the system has any problems please call the qualified installer / service technician. If you are unable to make contact, please call your sales representative.
Distributor / Dealer: Please insert contact details.
115
Visit us online
NTI Boilers Inc.
30 Stonegate Drive Saint John,
NB E2H 0A4 Canada
Technical Assistance: 1-800-688-2575
Website: www.ntiboilers.com
Fax: 1-506-432-1135
420010970800
advertisement
* Your assessment is very important for improving the workof artificial intelligence, which forms the content of this project
Key Features
- Condensing technology for high-efficiency operation
- Modulating combustion system for precise temperature control
- Stainless steel heat exchanger for durability and longevity
- Quiet operation for a comfortable living environment
- Compact design for easy installation in tight spaces
- Electronic ignition for reliable and safe operation
- Built-in freeze protection for added safety
- Limited lifetime warranty for peace of mind
Related manuals
Frequently Answers and Questions
What is the efficiency rating of the TRX Series boiler?
What size home is the TRX Series boiler suitable for?
What type of gas does the TRX Series boiler use?
How long is the warranty on the TRX Series boiler?
Is the TRX Series boiler compatible with a smart thermostat?
What is the minimum clearance required around the TRX Series boiler?
Can the TRX Series boiler be installed outdoors?
advertisement