advertisement
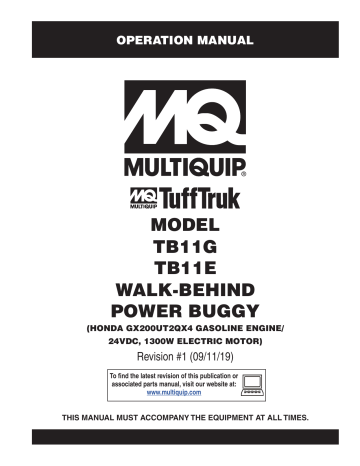
OPERATION MANUAL
MODEL
TB11G
TB11E
WALK-BEHIND
POWER BUGGY
(HONDA GX200UT2QX4 GASOLINE ENGINE/
24VDC, 1300W ELECTRIC MOTOR)
Revision #1 (09/11/19)
To find the latest revision of this publication or associated parts manual, visit our website at:
www.multiquip.com
THIS MANUAL MUST ACCOMPANY THE EQUIPMENT AT ALL TIMES.
PROPOSITION 65 WARNING
TB11G/TB11E
POWER BUGGY
PAGE 2 — TB11G/E TUFFTRUK • OPERATION MANUAL — REV. #1 (09/11/19)
TB11G/E TuffTruk
Walk-Behind Power Buggy
Proposition 65 Warning ........................................... 2
Table of Contents ..................................................... 3
Safety Information ............................................. 4–10
Specifications (Buggy) ........................................... 11
Specifications (Engine) .......................................... 12
Noise and Vibration Emissions .............................. 13
Dimensions ............................................................ 14
General Information ............................................... 15
Components .................................................... 16–17
Engine Components .............................................. 18
Inspection ........................................................ 19–21
Operation (Gasoline) ...................................... 22–23
Operation (Electric) ........................................ 24–25
Operation (Gas/Electric) ................................. 26–28
Maintenance .......................................................... 29
Maintenance (Gasoline) .................................. 30–36
Maintenance (Electric) ..................................... 37–39
Maintenance (Gas/Electric) ............................. 40–44
Troubleshooting (Engine) ................................. 45–46
Troubleshooting (Gas) ........................................... 47
Troubleshooting (Electric) ...................................... 48
Error Codes ........................................................... 49
Electronic Component Locator ............................. 50
Wiring Diagram ...................................................... 51
TABLE OF CONTENTS
TB11G/E TUFFTRUK• OPERATION MANUAL — REV. #1 (09/11/19) — PAGE 3
DO NOT
operate or service the equipment before reading the entire manual. Safety precautions should be followed at all times when operating this equipment.
Failure to read and understand the safety messages and operating instructions could result in injury to yourself and others.
SAFETY MESSAGES
The four safety messages shown below will inform you about potential hazards that could injure you or others. The safety messages specifi cally address the level of exposure to the operator and are preceded by one of four words:
DANGER, WARNING, CAUTION
or
NOTICE.
SAFETY SYMBOLS
DANGER
Indicates a hazardous situation which, if not avoided,
WILL
result in
DEATH
or
SERIOUS INJURY.
WARNING
Indicates a hazardous situation which, if not avoided,
COULD
result in
DEATH
or
SERIOUS INJURY.
CAUTION
Indicates a hazardous situation which, if not avoided,
COULD
result in
MINOR
or
MODERATE INJURY.
NOTICE
Addresses practices not related to personal injury.
SAFETY INFORMATION
Potential hazards associated with the operation of this equipment will be referenced with hazard symbols which may appear throughout this manual in conjunction with safety messages.
Symbol Safety Hazard
Lethal exhaust gas hazards
Explosive fuel hazards
Burn hazards
Rotating parts hazards (V-belt)
Rotating parts hazards (Chain)
Hydraulic fluid hazards
PAGE 4 — TB11G/E TUFFTRUK • OPERATION MANUAL — REV. #1 (09/11/19)
GENERAL SAFETY
CAUTION
NEVER
operate this equipment without proper protective clothing, shatterproof glasses, respiratory protection, hearing protection, steel-toed boots and other protective devices required by the job or city and state regulations.
Avoid wearing jewelry or loose fi tting clothes that may snag on the controls or moving parts as this can cause serious injury.
NEVER
operate this equipment when not feeling well due to fatigue, illness or when under medication.
NEVER
operate this equipment under the infl uence of drugs or alcohol.
SAFETY INFORMATION
NOTICE
This equipment should only be operated by trained and qualifi ed personnel 18 years of age and older.
Whenever necessary, replace nameplate, operation and safety decals when they become diffi cult read.
Manufacturer does not assume responsibility for any accident due to equipment modifi cations. Unauthorized equipment modifi cation will void all warranties.
NEVER
use accessories or attachments that are not recommended by Multiquip for this equipment. Damage to the equipment and/or injury to user may result.
ALWAYS
know the location of the nearest
fi re extinguisher.
ALWAYS
know the location of the nearest
fi rst aid kit.
ALWAYS
know the location of the nearest phone or
keep a phone on the job site.
Also, know the phone numbers of the nearest
ambulance, doctor
and
fi re department.
This information will be invaluable in the case of an emergency.
ALWAYS
clear the work area of any debris, tools, etc. that would constitute a hazard while the equipment is in operation.
No one other than the operator is to be in the working area when the equipment is in operation.
DO NOT
use the equipment for any purpose other than its intended purposes or applications.
TB11G/E TUFFTRUK• OPERATION MANUAL — REV. #1 (09/11/19) — PAGE 5
TUFFTRUK SAFETY
DANGER
Engine fuel exhaust gases contain poisonous carbon monoxide. This gas is colorless and odorless, and can cause death if inhaled.
The engine of this equipment requires an adequate free fl ow of cooling air.
NEVER
operate this equipment in any enclosed or narrow area where free fl ow of the air is restricted. If the air fl ow is restricted it will cause injury to people and property and serious damage to the equipment or engine.
DANGEROUS
GAS FUMES
NEVER
operate the equipment in an explosive atmosphere or near combustible materials. An explosion or fi re could result causing severe
bodily harm or even death.
WARNING
NEVER
use your hand to fi nd hydraulic leaks.
Use a piece of wood or cardboard. Hydraulic fl uid injected into the skin must be treated by a knowledgeable physician immediately or severe injury or death can occur.
Accidental starting can cause severe injury or death.
ALWAYS
place the ON/OFF switch in the OFF position.
NEVER
disconnect any
emergency or safety devices.
These devices are intended for operator safety.
Disconnection of these devices can cause severe injury, bodily harm or even death. Disconnection of any of these devices will void all warranties.
NEVER
approach power lines with any part of the
TuffTruk unless all local, state/provincial and federal
(OSHA) required safety precautions have been taken.
Use extreme caution when approaching high voltage power lines.
SAFETY INFORMATION
CAUTION
ALWAYS
inspect the surface over which you will travel.
Look for holes, drop-offs and obstacles. Look for rough and weak spots on docks, ramps or fl oor.
ALWAYS
Look for oil spills, wet spots and slippery surfaces. Look for soft soil, deep mud and standing water.
Watch for anything that might make you lose control or cause the TuffTruk to tip over.
ALWAYS
clear away trash and debris. Pick up anything that might puncture the tires.
ALWAYS
make sure aisles, ramps, doorways and passages are clear.
ALWAYS
plan your work. Make sure you know where you will make your pickups, dumps and turns. Before you take a load, know where you will place it.
NEVER
travel down a slope with a
full load
. The possibility exists of tipping.
DO NOT
operate the TuffTruk on unsafe haul roads, load areas, and dump areas.
WARNING
TIPPING OF BUGGY
CAN OCCUR
DO NOT
operate TuffTruk on excessive slopes with a grade higher than 25° (45%), forward and backward.
DO NOT
operate TuffTruk on extremely uneven surfaces.
NEVER
allow people to ride inside the tub/bucket.
DO NOT
operate the TuffTruk at excessive speeds.
Reckless operation may cause accidents and severe injury. Slow down when approaching people, wet areas, and going up and down grades. It is the responsibility of the operator to adjust speed, as necessary, depending on the conditions of the road or path.
Forward travel speed should not exceed 4 mph
(6.44 km/h). Reverse travel speed should not exceed
1.5 mph (2.42 km/h).
ALLOW
extra time to stop when operating the TuffTruk on wet surfaces or loosely graded materials.
DO NOT
dump materials from bucket/tub while the
TuffTruk is moving.
PAGE 6 — TB11G/E TUFFTRUK • OPERATION MANUAL — REV. #1 (09/11/19)
NOTICE
ALWAYS
ensure TuffTruk is
securely
placed on appropriate blocks or jackstands when performing maintenance.
When parking on a slope, position the TuffTruk at a right angle to a slope.
When filling or dumping capacity of TuffTruk.
DO NOT
exceed payload
ALWAYS
be aware of traveling conditions. Reduce load if necessary.
DO NOT
activate dump mechanism (tub/bucket) if
TuffTruk is facing a down hill slope.
DO NOT
stand in front or along side the TuffTruk when discharging a load.
ALWAYS
block the TuffTruk with appropriate blocks when leaving the TuffTruk parked on a slope.
To prevent unexpected loss of control, engine on a sloping surface.
DO NOT
start
Ensure that the speed control levers works freely and returns to the stop position.
DO NOT
start engine unless speed control linkage is working properly.
Make sure that the tires are infl ated to the manufacturer’s recommended tire pressure.
NEVER
operate the TuffTruk with bad or worn tires.
ALWAYS
replace defective tires with new ones.
Avoid sudden stops and starts and changes in direction.
Operate the controls smoothly.
DO NOT
jerk the steering or any other controls.
NEVER
attempt to engage the controls except from the operator’s position.
NEVER
roads.
operate or tow the TuffTruk in traffi c or on public
ALWAYS
keep the machine in proper running condition.
Fix damage to machine and replace any broken parts immediately.
SAFETY INFORMATION
The entire TuffTruk (tub, shroud, wheels, etc.) should be cleaned after every use. Make sure there is no buildup of concrete, grease, oil or debris on the machine.
ALWAYS
store equipment properly when it is not being used. Equipment should be stored in a clean, dry location out of the reach of children and unauthorized personnel.
ALWAYS
place the fuel valve lever in the when the equipment is not in use.
OFF
position
ENGINE SAFETY
WARNING
DO NOT
place hands or fingers inside engine compartment when engine is running.
NEVER
operate the engine with heat shields or guards removed.
Keep fi ngers, hands hair and clothing away from all moving parts to prevent injury.
ALWAYS
shut down the engine before performing service or maintenance.
DO NOT
remove the engine oil drain plug while the engine is hot. Hot oil will gush out and severely scald any persons in the general area of the TuffTruk.
CAUTION
NEVER
touch the hot exhaust manifold, muffl er or cylinder. Allow these parts to cool before servicing equipment.
Make certain the operator knows how to and is capable of turning the engine
OFF
in case of an emergency.
NOTICE
NEVER
run engine without an air fi lter or with a dirty air fi lter. Severe engine damage may occur. Service air fi lter frequently to prevent engine malfunction.
NEVER
tamper with the factory settings of the engine or engine governor. Damage to the engine or equipment can result if operating in speed ranges above the maximum allowable.
TB11G/E TUFFTRUK• OPERATION MANUAL — REV. #1 (09/11/19) — PAGE 7
FUEL SAFETY
DANGER
DO NOT
start the engine near spilled fuel or combustible fl uids. Fuel is extremely fl ammable and its vapors can cause an explosion if ignited.
ALWAYS
refuel in a well-ventilated area, away from sparks and open fl ames.
ALWAYS
use extreme caution when working with
fl ammable
liquids.
DO NOT
or hot.
fi ll the fuel tank while the engine is running
DO NOT
overfi ll tank and tighten fuel cap until you hear
"clicking", since spilled fuel could ignite if it comes into contact with hot engine parts or sparks from the ignition system.
Store fuel in appropriate containers, in well-ventilated areas and away from sparks and fl ames.
NEVER
use fuel as a cleaning agent.
DO NOT
smoke around or near the equipment.
Fire or explosion could result from fuel vapors or if fuel is spilled on a hot engine.
DO NOT
leave the TuffTruk in the vicinity of ovens, furnaces or radiant heaters. Heat could raise the pressure of the fuel so that vented gas could ignite.
BATTERY SAFETY (ELECTRIC START ONLY)
DANGER
DO NOT
drop the battery. There is a possibility that the battery will explode.
DO NOT
expose the battery to open fl ames, sparks, cigarettes, etc. The battery contains combustible gases and liquids. If these gases and liquids come into contact with a fl ame or spark, an explosion could occur.
SAFETY INFORMATION
WARNING
ALWAYS
wear safety glasses when handling the battery to avoid eye irritation.
The battery contains acids that can cause injury to the eyes and skin.
Use well-insulated gloves when picking up the battery.
ALWAYS
keep the battery charged. If the battery is not charged, combustible gas will build up.
DO NOT
charge battery if frozen. Battery can explode.
When frozen, warm the battery to at least 61°F (16°C).
ALWAYS
recharge the battery in a well-ventilated environment to avoid the risk of a dangerous concentration of combustible gases.
If the battery liquid (dilute sulfuric acid) comes into contact with
clothing or skin
, rinse skin or clothing immediately with plenty of water.
If the battery liquid (dilute sulfuric acid) comes into contact with
eyes
, rinse eyes immediately with plenty of water and contact the nearest doctor or hospital to seek medical attention.
CAUTION
ALWAYS
disconnect the
NEGATIVE battery terminal
before performing service on the equipment.
ALWAYS
keep battery cables in good working condition.
Repair or replace all worn cables.
ALWAYS
use proper lifting procedures when removing the batteries from the machine. Batteries are quite heavy.
Bodily injury may result if proper lifting procedures are not employed.
PAGE 8 — TB11G/E TUFFTRUK • OPERATION MANUAL — REV. #1 (09/11/19)
LIFTING SAFETY
CAUTION
NEVER
allow any person or animal to stand underneath the equipment while lifting.
NOTICE
When lifting of the TuffTruk is required, attach lifting straps or chains to designated lifting points only.
Use lifting straps or chains of adequate lifting capacity.
NEVER
tip the engine to extreme angles during lifting as it may cause oil to gravitate into the cylinder head, making the engine start diffi cult.
DO NOT
lift machine to unnecessary heights.
NEVER
lift the equipment while the engine is running.
ALWAYS
use ramps capable of supporting the weight of the TuffTruk and the operator to load and unload the
TuffTruk.
SAFETY INFORMATION
TRANSPORTING SAFETY
NOTICE
ALWAYS
shutdown engine before transporting.
Tighten fuel tank cap securely and close fuel cock to prevent fuel from spilling.
When transporting of the TuffTruk is required, place the
TuffTruk on a fl at bed truck or equivalent and tie down securely.
ALWAYS
make sure all tie-downs are in place and the tub/bucket is completely lowered in the fl at (horizontal) position and securely latched.
Place
chock blocks
underneath wheel to prevent rolling.
DO NOT
use the TuffTruk to transport people.
When transporting the TuffTruk on a truck or trailer, know the overall height to avoid contacting overhead obstructions such as bridges and power lines. Check the truck and ramp capacities.
ALWAYS
place the fuel valve lever in the before transporting.
OFF
position
TB11G/E TUFFTRUK• OPERATION MANUAL — REV. #1 (09/11/19) — PAGE 9
ENVIRONMENTAL SAFETY/DECOMMISSIONING
NOTICE
Decommissioning is a controlled process used to safely retire a piece of equipment that is no longer serviceable.
If the equipment poses an unacceptable and unrepairable safety risk due to wear or damage or is no longer cost effective to maintain (beyond life-cycle reliability) and is to be decommissioned (demolition and dismantlement),be sure to follow rules below.
DO NOT
pour waste or oil directly onto the ground, down a drain or into any water source.
Contact your country's Department of
Public Works or recycling agency in your area and arrange for proper disposal of any electrical components, waste or oil associated with this equipment.
When the life cycle of this equipment is over, remove battery (if equipped) and bring to appropriate facility for lead reclamation. Use safety precautions when handling batteries that contain sulfuric acid.
When the life cycle of this equipment is over, it is recommended that the unit frame and all other metal parts be sent to a recycling center.
Metal recycling involves the collection of metal from discarded products and its transformation into raw materials to use in manufacturing a new product.
Recyclers and manufacturers alike promote the process of recycling metal. Using a metal recycling center promotes energy cost savings.
SAFETY INFORMATION
EMISSIONS INFORMATION
NOTICE
This equipment conforms with applicable Environmental
Protection Agency (EPA) and California Air Resources
Board (CARB) emission regulations.
The gasoline engine used in this equipment has been designed to reduce harmful levels of carbon monoxide
(CO), hydrocarbons (HC) and nitrogen oxides (NOx) contained in gasoline exhaust emissions.
Mandated Emission Components:
Engine, EPA certifi ed
Fuel cap, EPA certifi ed
Fuel and vapor recovery hoses, EPA certifi ed SAE J30R7 or SAE J30R14T2
Charcoal canister, EPA certifi ed
Miscellaneous Parts Associated with Emission System:
Hose clamps and retainer brackets
Roll over valve vapor recovery valve
Steel fuel tank
Tampering with or altering the emission control system may increase emissions beyond the legal limit. Do not remove or alter any part of the system.
Additionally, modifying the fuel system may adversely affect evaporative emissions, resulting in fi nes or other penalties.
The Emission control system is valid only for the United
States, its territories and commonwealths to include
Canada.
Emission Control Label
The emission control label is an integral part of the emission system and is strictly controlled by regulation(s).
The label must remain with the engine for its entire life.
If a replacement emission label is needed, please contact your authorized engine distributor.
PAGE 10 — TB11G/E TUFFTRUK • OPERATION MANUAL — REV. #1 (09/11/19)
SPECIFICATIONS (BUGGY)
Model
Maximum Weight Capacity
Maximum Payload Weight
Bucket/Tub Capacity
Bucket/Tub Capacity (Option)
Bucket/Tub Material
Drive and Controls
Speed Forward
Speed Reverse
Steering Radius Outside Dia.
Hydraulic Pump Capacity
Hydraulic Oil Tank Capacity
Hydraulic Oil Type
Brake System
Dump Control
Discharge Height
Gradeability Slope (Up/Down)
Gradeability Lateral (Side-Side)
Battery (LxWxH)
Battery Weight
Pneumatic Tires
Pneumatic Tire Pressure
Table 1. Specifications (TuffTruk)
TB11G
374 lbs. (170 kg)
990 lbs. (450 kg.)
10.6 cu. ft. Water Level (.40 cu. yd.)
7.0 cu. ft. Water Level (.26 cu. yd.)
Steel
Hydrostatic System
Up to 4.0 mph. (6.4 km/h)
Up to 1.5 mph. (2.42 km/h)
58 in. (1,473 mm)
77.23 fl. oz. (2.28 liters)
16.90 fl. oz. (.5 liters)
20W-50 Motor Oil
Hydrostatic/Dead Man Handle
TB11E
561 lbs. (255 kg)
990 lbs. (450 kg.)
10.6 cu. ft. Water Level (.40 cu. yd.)
7.0 cu. ft. Water Level (.26 cu. yd.)
Steel
24 VDC Electric Motor Gearbox
Up to 3.5 mph. (5.63 km/h)
Up to 1.5 mph. (2.42 km/h)
58 in. (1,473 mm)
N/A
N/A
N/A
Hydrostatic/Dead Man Handle
Mechanical Dump and Manual Return Mechanical Dump and Manual Return
2.0 in. (50.8 mm) 2.0 in. (50.8 mm)
25°
6°
25°
6°
N/A
N/A
16 x 6.50 x 8
(406 x 165 x 203 mm)
28 PSI (193 kPa)
12V BCI Group 27 550 CCA @ 0°F
12.05 x 6.84 x 9.32 in.
(306 x 174 x 237 mm)
64 lbs (29 kg)
16 x 6.50 x 8
(406 x 165 x 203 mm)
28 PSI (193 Kpa)
TB11G/E TUFFTRUK• OPERATION MANUAL — REV. #1 (09/11/19) — PAGE 11
SPECIFICATIONS (ENGINE)
Table 2. Gasoline Engine Specifications
Model HONDA GX200UT2QX4
Type
Bore X Stroke
Air-cooled 4 stroke, Single Cylinder,
OHV, Horizontal Shaft Gasoline Engine
2.7 in. X 2.1 in.
(68 mm x 54 mm)
Displacement
Max Output
Fuel Tank Capacity
Fuel
12.0 cu. in. (196 cc)
5.8 H.P./3,600 rpm
0.95 U.S. Gallons (3.6 Liters)
Unleaded Automobile Gasoline
Lube Oil Capacity
Speed Control Method
Starting Method
Dimension Approx.
(L x W x H)
Dry Net Weight
0.63 qt. (0.6 liter)
Centrifugal Fly-Weight Type
Recoil Start
12.6 X 14.8 X 13.6 in.
(321 X 376 X 346 mm)
35.2 lbs. (16.0 Kg)
Model
Table 3. Electric Motor Specifications
AMER
Type
Speed Control Method
Starting Method
Max RPM (No Load)
Input Voltage
Wattage
Poles
Protection Class
Insulation Class
IEC Duty Cycle
Dimension Approx.
(L x W x H)
Dry Net Weight Approx.
Permanent Magnet DC Electric Motor
Curtis 1228 Controller
Electric
2900
24 VDC
1300W
4
IP: 44
F
S3 15%
6.4 X 7.81 X 5.7 in.
(164 X 200 X 145 mm)
22 lbs. (10 kg)
PAGE 12 — TB11G/E TUFFTRUK • OPERATION MANUAL — REV. #1 (09/11/19)
NOISE AND VIBRATION EMISSIONS
Model
Table 4. Noise and Vibration Emissions
TB11G
Guaranteed ISO 11201:2010 Based Sound Pressure Level at Operator Station in dB(A) a
82
Guaranteed ISO 3744:2010 Based Sound Power Level in dB(A) b 96
TB11E
56
69
Hand-Arm Vibration Per ISO 5349-1:2001 in m/s
2
∑
A(8)
4.6
a. With an uncertainty factor K of 2.5 dB (A) included per Note 1 in section 7.2.1 of EN 12649::2008+A1:2011 b. With an uncertainty factor K of 1.5 dB (A) included per Note 1 in section 7.2.1 of EN 12649::2008+A1:2011
2.5
NOTES:
1.
Sound pressure and power levels are “A” weighted measures per ISO 3744:2010. They are measured with the operating condition of the machine which generates the most repeatable but highest values of the sound levels. Under normal circumstances, the sound level will vary depending on the condition of the material being worked upon.
2.
The vibration level indicated is the vector sum of the RMS (root mean Ssquare) values of amplitudes on each axis, standardized to an 8-hour exposure period, and obtained using the operating condition of the machine that generates the most repeatable but highest values in accordance with the applicable standards for the machine.
3.
Per EU Directive 2002/44/EC, the daily exposure action value for hand/arm vibration is 2.5 m/s
2
∑
A(8). The daily exposure limit value is 5 m/s
2
∑
A(8).
TB11G/E TUFFTRUK• OPERATION MANUAL — REV. #1 (09/11/19) — PAGE 13
C
DIMENSIONS
REAR VIEW
K
L
A B
D
SIDE VIEW
G
P
OUTSIDE DIAMETER
TURNING RADIUS
F
H
J
TOP VIEW
P
E
I
M
N
O
K
L
J
I
G
H
E
F
Table 5. Dimensions
Reference
Letter
Dimension in. (mm)
C
D
A
B
43.34 (1,101)
34.68 (881)
70.98 (1,803)
31.10 (790)
O
P
M
N
16.73 (425)
9.37 (238)
6.18 (157)
29.52 (750)
7.71 (196)
60.11 (1,527)
33.46 (850)
23.62 (600)
5.55 (141)
6.37 (162)
33.46 (850)
57.67 (1,465)
Figure 1. TB11G/E Dimensions
PAGE 14 — TB11G/E TUFFTRUK • OPERATION MANUAL — REV. #1 (09/11/19)
The Multiquip Walk-Behind Series TuffTruk Power Buggies are available in two versions, gas (Model TB11G) or electric
(Model TB11E). Both modes are intended for job site cleanup and material transport.
The buggy is equipped with a 2.0 in. (50.8 mm) dump height which provides clearance and enables the operator to maneuver over any form height.
A low center of gravity has been incorporated into the design which provides added safety when maneuvering the buggy in tight areas.
Maximum
forward
speed for the
gasoline
driven TuffTruk buggy is rated at 4.0 mph. (6.4 km/h). The maximum
forward
speed of the
electric
driven buggy is rated at 3.5 mph. (5.63 km/h). Maximum
reverse
speed for both models is 1.5 mph. (2.42 km/h).
For ease of dumping, a manual hand lever control is provided. Maximum weight capacity (payload) is 990 lbs.
(450 kg). Multiple lift points have been provided to allow for easy access of a forklift when lifting is required.
POWER PLANT (ELECTRIC)
The electric model (TB11E) is powered by a 24 VDC, 1300 watt permanent magnet DC electric motor. The output shaft of the electric motor is connected to a gearbox reduction unit which drives the front and rear wheels. For additional
information, reference Table 3.
POWER PLANT (GASOLINE)
The gas model (TB11G) is powered by a Honda 5.8 HP,
GX200 air cooled, 4-cycle gasoline engine. Power is transferred from the output shaft of the engine to the V-belt pulley drive system which drives the front and rear wheels.
Reference Table 2 for complete engine specifications. In addition, refer to the engine owner’s manual for instructions regarding the operation and maintenance of your engine.
If the original manual is lost or damaged, please contact your nearest Multiquip dealer for a replacement.
GENERAL INFORMATION
MOTOR CONTROLLER (TB11E MODEL ONLY)
The TB11E is equipped with a sealed heavy-duty permanent motor controller, Curtis Model 1229 Speed
Controller (ECU). This controller provides functional and directional control of the TuffTruk buggy. It allows the buggy to start and stop or move in a forward or reverse direction.
This controller can detect a wide variety of faults or error conditions. Diagnostic information can be obtained by interfacing with the Curtis Model 3100R Gauge Display.
This gauge will display error codes as referenced in the maintenance section of this manual.
In addition, this controller has the capability of interfacing with Controller Area Network (CAN bus) applications.
DIAGNOSTIC GAUGE (TB11E MODEL ONLY)
TB11E is equipped with a diagnostic gauge. This gauge will display system error codes. Reference maintenance section in this manual for further details.
WARNING
All operators must have training before operating the
TuffTruk buggy. For your safety, warnings are on the machine and in this manual. Failure to obey these warnings can cause severe injury or even death.
CAUTION
DO NOT
attempt to operate the TuffTruk buggy until the Safety Information, General
Information, and Inspection sections of this manual have been
read and thoroughly understood.
TB11G/E TUFFTRUK• OPERATION MANUAL — REV. #1 (09/11/19) — PAGE 15
1
2
8
9
7
3
6
23
GASOLINE
COMPONENTS
10
4
5
13
14
12
11
15
27
26
24
25
22
21
20
16
17
ELECTRIC
19
18
Figure 2. TuffTruk Walk-Behind Power Buggy Components
PAGE 16 — TB11G/E TUFFTRUK • OPERATION MANUAL — REV. #1 (09/11/19)
1.
Deadman Control Lever
—
Yellow
handle lever, when engaged (closed) allows the buggy to travel in either a forward or reverse direction. Works in conjunction with forward and reverse control levers. In addition, this lever when engaged releases the brake.
2.
Reverse Control Lever Signal Cable (TB11E)
— This lever/cable is a 2-wire cable (switch) that when activated sends a +12 VDC signal (J1-10) to the motor controller indicating that the reverse travel function has been selected.
3.
Handle Bar (Steering)
— This handle bar is used to steer the buggy. When steering the buggy, use both hands and hold onto both handle bar grips.
4.
Tub or Bucket
— Used for the transportation of material. Tub holds approximately 10.6 cubic feet
(0.40 cubic yards) of water.
5.
Tires
— Unit uses pneumatic tires. Reference
6.
Lifting Point
— Attach a suitable lifting strap to these points when lifting of the buggy is required.
7.
Battery (TB11E)
— Uses two 12 volt batteries connected in series (24 volts). Always use gloves and eye protection when handling the batteries.
8.
Battery Charger Receptacle (TB11E)
— Plug the battery charger cable into this receptacle, then connect the free-end of the cable to a 120 VAC power source.
9.
Forward/Reverse Speed Control Lever
— When fully engaged, the buggy will travel at
FULL
speed in either the forward or reverse direction. When released, the buggy will
STOP
. This feature is only on the
TB11E
model.
10.
Dump Control Lever
— Push the lever forward to place the tub in the dump position (vertical).
11.
Component Fuse (TB11E)
— 10 amp fuse that provides protection for the Curtis Model 3100R
Diagnostic Display and other electronic components.
12.
Ignition/Key (TB11E)
— When activated allows the unit to be started.
13.
Emergency Stop Switch (TB11E)
— In the event of an emergency,
push
this button to shutdown the electric motor.
COMPONENTS
14.
Battery/Diagnostic Gauge (TB11E)
— Uses a Curtis
Model 3100R Gauge Display. Displays battery voltage and fault codes. CAN bus compatible.
15.
Free-Wheel Brake Lever (TB11E)
— Two position lever. When placed in the up position (OFF) and held allows the buggy to be moved with the electric motor disengaged (
OFF
).
16.
Contactor Solenoid (TB11E)
— When energized provides +12 VDC power to motor controller.
17.
5K OHM Potentiometer (TB11E)
— Provides signal for speed sensor.
18.
Deadman Microswitch (TB11E)
— When activated sends a +12 VDC signal (J1-3) to the motor controller to release the brake.
19.
Motor Speed Controller (TB11E)
— Unit uses a
Curtis Model 1229 Controller. Requires a 24 VDC input.
Interfaces with CAN bus applications.
20.
Electric Motor (TB11E)
— Uses a 24 VDC, 1300 watt electric motor.
21.
Contactor Fuse (TB11E)
— 125 amp fuse that provides protection for the electric motor.
22.
Battery Charger (TB11E)
— When activated, charges both 12-volt batteries. This feature is only on the
TB11E
model.
23.
Hydraulic Tank/Cap (TB11G)
— Remove this cap to add hydraulic oil. Tank holds approximately 16.90 fl. oz.
(.5 liters).
DO NOT
over fill. Reference Table 1 for
hydraulic pump oil capacity.
24.
Forward Speed Control Lever (TB11G)
— When fully engaged, the buggy will travel at
FULL
speed in the forward direction. When released, the buggy will
STOP.
25.
Reverse Speed Control Lever (TB11G)
— When fully engaged, the buggy will travel at
FULL
speed in the reverse direction. When released, the buggy will
STOP
.
26.
Engine (TB11G Model Only)
— Uses a recoil start
Honda 5.8 HP, GX200 air cooled, 4-cycle gasoline engine.
27.
Free-Wheel Brake Lever (TB11G)
— Two position lever. When placed in the up position (OFF) and held allows the buggy to be moved with the gasoline engine disengaged.
TB11G/E TUFFTRUK• OPERATION MANUAL — REV. #1 (09/11/19) — PAGE 17
9
8
7
6
10
11
1
2
5
4
3
Figure 3. Engine Components
INITIAL SERVICING
The engine (Figure 3) must be checked for proper
lubrication and filled with fuel prior to operation. Refer to the manufacturer's engine manual for instructions and details of operation and servicing.
1.
Throttle Lever
– Used to adjust engine RPM speed.
2.
Fuel Filler Cap/Fuel Tank
– Remove this cap to add unleaded gasoline to the fuel tank. Fill with unleaded
gasoline. Refer to Table 2 for fuel tank capacity. Make
sure cap is tightened securely.
DO NOT
over fill. For additional information, refer to Honda engine owner's manual.
DANGER
Add fuel to the tank only when the engine is stopped and has had an opportunity to cool down. In the event of a fuel spill,
DO
NOT
attempt to start the engine until the fuel residue has been completely wiped up and the area surrounding the engine is dry.
ENGINE COMPONENTS
3.
Engine On/Off Switch
–
ON
position permits engine starting,
OFF
position stops engine operation.
4.
Recoil Starter (pull rope)
– Manual-starting method.
Pull the starter grip until resistance is felt, then pull briskly and smoothly.
5.
Fuel Valve Lever
–
OPEN
to let fuel flow,
CLOSE
to stop the flow of fuel.
6.
Oil Drain Plug
– Remove this plug to remove oil from the engine's crankcase.
7.
Dipstick/Oil Filler Cap
– Remove this cap to determine if the engine oil is low. Add oil through this filler port as
8.
Choke Lever
– Used in the starting of a cold engine, or in cold weather conditions. The choke enriches the fuel mixture.
9.
Spark Plug
– Provides spark to the ignition system.
Set spark plug gap according to engine manufacturer's instructions. Clean spark plug once a week.
10.
Muffler
– Used to reduce noise and emissions.
NEVER
touch when
hot!
CAUTION
Engine components can generate extreme heat. To prevent burns,
DO NOT
touch these areas while the engine is running or immediately after operating.
NEVER
operate the engine with the muffler removed.
11.
Air Cleaner
– Prevents dirt and other debris from entering the fuel system. Remove wing-nut on top of air filter canister to gain access to filter element.
NOTICE
Operating the engine without an air filter, with a damaged air filter or a filter in need of replacement, will allow dirt to enter the engine, causing rapid engine wear.
PAGE 18 — TB11G/E TUFFTRUK • OPERATION MANUAL — REV. #1 (09/11/19)
BEFORE STARTING
CAUTION
NEVER
disable or disconnect the
start/stop switch
.
It is provided for operator safety. Injury may result if it is disabled, disconnected or improperly maintained.
1. Read all safety instructions at the beginning of manual.
2. Clean the unit, removing dirt and dust, particularly the engine cooling air inlet, carburetor and air cleaner.
3. Check the air filter for dirt and dust. If air filter is dirty, replace air filter with a new one as required.
4. Check carburetor for external dirt and dust. Clean with dry compressed air.
5. Check fastening nuts and bolts for tightness.
CAUTION
ALWAYS
wear approved eye and hearing protection while operating the buggy.
CAUTION
NEVER
place hands or feet inside the engine guard cover while the engine is running.
ALWAYS
shut the engine down before performing any kind of maintenance service on the buggy.
INSPECTION
ENGINE OIL CHECK
1. To check the engine oil level, place the unit on secure level ground with the engine stopped.
2. Remove the filler dipstick from the engine oil filler hole
DIPSTICK
Figure 4. Engine Oil Dipstick (Removal)
3. Insert and remove the dipstick without screwing it into the filler neck. Check the oil level shown on the dipstick.
Maximum oil capacity is 0.63 quarts (0.6 liters).
Reference engine manufacturer’s manual for specific servicing instructions.
UPPER LIMIT
LOWER LIMIT
Figure 5. Engine Oil Dipstick (Oil Level)
Season
Summer
Spring/Fall
Winter
Table 6. Engine Oil Type
Temperature
25°C or Higher
25°C ~ 10°C
0°C or Lower
Oil Type
SAE 10W-30
SAE 10W-30/20
SAE 10W-10
TB11G/E TUFFTRUK• OPERATION MANUAL — REV. #1 (09/11/19) — PAGE 19
FUEL CHECK
DANGER
If your TuffTruk buggy has a gasoline engine, determine if the engine fuel is low. If fuel is low, remove the fuel filler cap and fill it with
unleaded
gasoline.
Motor fuels are
highly flammable
and can be dangerous if mishandled.
DO NOT
smoke while refueling.
DO NOT
attempt to refuel the mixer if the engine is
hot
or
running.
1. Remove the fuel cap (Figure 6) located on top of fuel
tank.
2. Visually inspect to see if fuel level is low. If fuel is low, replenish with unleaded fuel.
INSPECTION
TIRES
Check for
worn
or
defective
defective or worn tires immediately.
FUEL
CAP
V-BELT CHECK
Figure 7. Tire Wear
Visually examine the V-belt (Figure 8) and determine if it
is full of tiny cracks, frayed, has pieces of rubber missing, is peeling or otherwise damaged.
Also, examine the belt and determine if it is
oil soaked
or
"
glazed
" (hard shiny appearance on the sides of the belt).
Either of these two conditions can cause the belt to run hot, which can weaken it and increase the danger of it breaking.
If the V-belt exhibits any of the above wear conditions replace the V-belt immediately.
OIL SOAKED
Figure 6. Fuel Check
3. When refueling, be sure to use a strainer for filtration.
DO NOT
top-off fuel. Wipe up any spilled fuel immediately.
GLAZED
CORD FAILURE
WORN BACK
COVER
BROKEN
MISSING RUBBER
CRACKS
SIDEWALL
WEAR
Figure 8. V-Belt Inspection
PAGE 20 — TB11G/E TUFFTRUK • OPERATION MANUAL — REV. #1 (09/11/19)
BATTERY (ELECTRIC MODEL ONLY)
This unit is of negative ground
DO NOT
connect in reverse.
ALWAYS
maintain battery fluid level between the specified marks. Battery life will be shortened, if the fluid levels are not properly maintained. Add only distilled water when replenishment is necessary.
DO NOT
over fill. Check to see whether the battery cables are loose. Poor contact may result in poor starting or malfunctions.
ALWAYS
keep the terminals firmly tightened and coat the terminals with an approved battery terminal treatment compound. Replace battery with only recommended type battery. The battery type used in this power buggy is BCI
Group 27.
The battery is sufficiently charged if the specific gravity of the battery fluid is 1.28 (at 68° F). If the specific gravity should fall to 1.245 or lower, it indicates that the battery is dead and needs to be recharged or replaced.
Before charging the battery with an external electric source, be sure to disconnect the battery cables.
CAUTION
ALWAYS
disconnect the negative terminal
FIRST
and reconnect the negative terminal
LAST
.
Battery Cable Installation
ALWAYS
be sure the battery cables (Figure 9) are properly
connected to the battery terminals as shown below. The batteries are connected in series.
JUMPER
24 VDC TOTAL
SERIES CONNECTION
POSITIVE
NEGATIVE
RED
BLACK
Y 1
T
INSPECTION
When connecting battery do the following:
1.
NEVER
connect the battery cables to the battery terminals when the ignition is in the
ON
position (start).
2. Place a small amount of battery terminal treatment compound around both battery terminals. This will ensure a good connection and will help prevent corrosion around the battery terminals.
NOTICE
If the battery cable is connected incorrectly, electrical damage to the power buggy will occur. Pay close attention to the polarity of the battery when connecting the battery.
CAUTION
Inadequate battery connections may cause poor starting of the TuffTruk buggy, and create other malfunctions.
TIRE PRESSURE CHECK
The wheels and tires of the power buggy are very important in its effective operation.
1. Check the tires regularly to make certain the lug nuts are tight.
2. Make sure tires are inflated to manufacturer's suggested tire pressure.
DO NOT
operate the buggy with bad or worn tires.
LINKAGE CHECK
Check and make sure that
all
linkages within the TuffTruk buggy are functioning correctly.
STEERING CHECK
1. Check and make sure that the power buggy's steering turns freely and that there is no binding.
BA
TTER
12 VOL
Y 2
T
Figure 9. Battery Series Connections
TB11G/E TUFFTRUK• OPERATION MANUAL — REV. #1 (09/11/19) — PAGE 21
OPERATION (GASOLINE)
This section is intended to assist the operator with the initial start-up of the unit. It is extremely important that this section be read carefully before attempting to use the TuffTruk walk-behind power buggy in the field.
DO NOT
use your buggy until the
General Information, and Inspection sections of this manual have been
read and thoroughly understood
.
WARNING
Failure to understand the operation of the buggy could result in severe damage to the buggy or personal injury.
Reference Figure 2 and Figure 3 for the location of any
components referenced in this manual.
CAUTION
NEVER
operate the TuffTruk walk-behind power buggy in a confined area or enclosed area structure that does not provide ample free flow of air. Gasoline models only.
STARTING THE BUGGY (GASOLINE MODEL)
The following steps outline the procedure for starting the gasoline TuffTruk buggy.
1. Place the fuel shut-off lever (Figure 10) in the
ON
position.
CHOKE LEVER
CLOSE
OPEN
Figure 11. Choke Lever (Closed)
NOTICE
The
CLOSED
position of the choke lever enriches the fuel mixture for starting a cold engine. The
OPEN
position provides the correct fuel mixture for normal operation after starting, and for restarting a warm engine.
3. If starting a warm engine or the temperature is warm, move the
choke lever (Figure 12) to the
OPEN
position.
CHOKE LEVER
FUEL VALVE
LEVER
OFF
ON
Figure 10. Fuel Shut-Off Lever (ON)
2. To start a cold engine, move the choke lever (Figure 11)
to the
CLOSED
position.
CLOSE
OPEN
Figure 12. Choke Lever (Open)
4. Move the throttle lever (Figure 13) away from the slow
position, about 1/3 of the way toward the fast position.
THROTTLE
LEVER
FAST SLOW
Figure 13. Throttle Lever
PAGE 22 — TB11G/E TUFFTRUK • OPERATION MANUAL — REV. #1 (09/11/19)
OPERATION (GASOLINE)
5. Place the engine ON/OFF switch (Figure 14) in the
ON
position.
PUSH
DOWN
OFF
ON
TRANSMISSION
BYPASS LEVER
(SET/ENGAGED)
ENGINE SWITCH
Figure 14. Engine On/Off Switch (ON)
6. Pull the
starter grip
(Figure 15) lightly until you feel
resistance, then pull briskly. Return the starter grip gently.
Figure 16. Transmission Bypass Lever (Engaged)
NOTICE
NEVER
activate (pull upwards) the transmission bypass lever with the engine running. Serious damage to the unit could occur.
2. With the engine running, fully squeeze the
YELLOW
deadman lever (Figure 16) and hold down. Transmission
is now active (unlocked).
NOTICE
The transmission bypass lever when
pushed down
works in conjunction with the deadman lever. With the deadman lever in the upright position, the transmission is
locked
. When the
YELLOW
deadman lever is engaged (fully squeezed), the transmission will automatically be unlocked.
STARTER GRIP
Figure 15. Starter Grip
NOTICE
DO NOT
pull the starter rope all the way to the end.
DO NOT
release the starter rope after pulling. Allow it to rewind as soon as possible.
TRAVELING
1. Make sure the transmission bypass lever (Figure 16)
is engaged (down position). To engage, push lever downward and move to the left.
NOTICE
If the transmission bypass lever is placed in the
UP
position (free-wheel) the buggy will not move when the forward or reverse speed control levers are activated.
For normal operation this lever should always be placed in the down position.
“DEADMAN” LEVER
HOLD DOWN
Figure 17. Deadman Lever (Gas)
TB11G/E TUFFTRUK• OPERATION MANUAL — REV. #1 (09/11/19) — PAGE 23
3. Located underneath the
YELLOW
deadman lever is the forward speed control lever.
4. Slightly squeeze the
forward
speed control lever
(Figure 18) until the buggy begins to move in a forward
direction.
OPERATION (ELECTRIC)
STARTING THE BUGGY (ELECTRIC MODEL)
NOTICE
The travel function (forward/reverse) for the electric model is different from the gasoline version.
The following steps outline the procedure for starting the electric model power buggy.
1. Located on the control panel of the buggy, is the
start/ stop
button (Figure 20). Pull this button outward to start
the electric motor.
EMERGENCY
STOP SWITCH
FORWARD SPEED
CONTROL LEVER
Figure 18. Forward Speed Control Lever (Gas)
5. Walk slowly behind the buggy to get a feel for the buggy.
For maximum speed,
fully squeeze
the forward speed control lever.
6. To stop, release the forward speed control lever.
7. On the opposite side of the handle bar is the
reverse
speed control lever (Figure 19). Repeat the above steps
for traveling in the reverse direction.
PULL
Figure 20. Emergency Stop Switch (Closed)
2. Place the ignition key (Figure 21) in the
START
position.
Verify that all segments of the diagnostic gauge illuminate for 1 second and then turn off. In addition, check battery voltage level. If low, recharge batteries.
DIAGNOSTIC
GAUGE
IGNITION
SWITCH
BATTERY
GAUGE
START
REVERSE SPEED
CONTROL LEVER
Figure 19. Reverse Speed Control Lever (Gas)
NOTICE
NEVER
squeeze both speed control levers at the same time, as this will cause damage to the unit.
LOW
BATTERY
LEVEL
Figure 21. Ignition Key (Start)
PAGE 24 — TB11G/E TUFFTRUK • OPERATION MANUAL — REV. #1 (09/11/19)
TRAVELING
1. Place the brake bypass lever (Figure 22) in the
AUTO
position. If the lever is left in the
ON
(free-wheel) position, the buggy will not move when the forward/ reverse speed control lever is activated.
NOTICE
The brake bypass lever when placed in the
AUTO
position works inconjunction with the deadman lever.
With the deadman lever in the upright position, the brake is set (engaged). When the
YELLOW
deadman lever is engaged (fully squeezed), the brake will automaticlly be released (disengaged).
BRAKE BYPASS
LEVER (
AUTO
)
OFF
AUTO
OPERATION (ELECTRIC)
3. Slightly squeeze the
forward/reverse
speed control
lever (Figure 24) until the buggy begins to move in a
forward
direction.
FORWARD/REVERSE
SPEED CONTROL LEVER
Figure 24. Forward/Reverse Speed
Control Lever (Electric)
4. On the opposite side of the handle bar is the
reverse
control lever
signal cable
. This cable is a 2-wire cable that sends a signal via a switch to the motor controller
(J1-10) indicating that the
reverse
travel function has been selected.
5. Squeeze the
reverse
control lever signal cable
Figure 22. Brake Bypass Lever (Auto)
2. With the electric motor running, fully squeeze the
YELLOW
deadman lever (Figure 23) and hold down.
When the lever is held down, a signal is sent via a microswitch to the motor controller (J1-3) to release the brake.
“DEADMAN” LEVER
SIGNAL
CABLE
Avoid sudden and quick turns. When steering, turn the handle bar slowly.
ALWAYS
face the controls when traveling.
REVERSE SPEED
CONTROL LEVER
Figure 25. Reverse Control Lever Signal Cable
6. Slightly squeeze the
forward/reverse
speed control
lever (Figure 24) until the buggy begins to move in a
reverse
direction.
CAUTION
HOLD DOWN
Figure 23. Deadman Lever (Electric)
TB11G/E TUFFTRUK• OPERATION MANUAL — REV. #1 (09/11/19) — PAGE 25
STEERING (GAS/ELECTRIC)
To steer the buggy, use the handle bar in front of the unit.
1. To turn left (Figure 26) when traveling in the forward
direction, turn the handle bar clockwise.
TURN HANDLE BAR
CLOCKWISE TO STEER
BUGGY TO THE LEFT
LEFT
Figure 26. Steering the Buggy (CW-Left)
2. To turn right (Figure 27) when traveling in the forward
direction, turn the handle bar in the counterclockwise direction.
RIGHT
TURN HANDLE BAR
COUNTERCLOCKWISE TO STEER
BUGGY TO THE RIGHT
OPERATION (GAS/ELECTRIC)
TRAVELING ON A SLOPE
1. When traveling on a slope, it is necessary to determine the grade of the path. The TB11G/E buggies can travel
up or down slopes not exceeding 25° (Figure 28) .
DO
NOT
travel on steeper slopes.
To determine the % grade of your path of travel, use
the formula and graph in Figure 28.
.
2. Lateral side to side travel cannot exceed 6°.
100
95
90
85
80
75
70
65
60
40
35
30
25
20
15
10
5
0
55
50
45
100
95
90
85
80
75
70
65
60
35
30
25
20
15
10
5
0
55
50
45
40
100%
45°
70%
35°
45%
25°
MAX
10%
6°
10
15
20
25
30
35
40
45
50
55
60
65
70
GRADE (DEGREES)
75
80
85 90
DIRECTION OF TRAVEL
DISTANCE (D)
% GRADE = 100 (H ¸ D)
LEVEL BASE LINE
10%
6°
MAX
70%
35°
100%
45°
15
35
30
20
25
OF TRAVEL
40
45
50
55
60
65
70
GRADE (DEGREES)
75
80
10
85 90
DISTANCE (D)
% GRADE = 100 (H ¸ D)
LEVEL BASE LINE
HEIGHT (H)
HEIGHT (H)
Figure 28. Determining Grade of Slope
Figure 27. Steering the Buggy (CCW-Right)
CAUTION
DO NOT
steer the buggy left or right when traveling up or down on a grade. Travel in a straight path.
PAGE 26 — TB11G/E TUFFTRUK • OPERATION MANUAL — REV. #1 (09/11/19)
NOTICE
The possibility of
tipping
A
) exist when transporting heavy loads.
ALWAYS
transport heavy loads as shown in Figure 29
B
.
OPERATION (GAS/ELECTRIC)
A
DUMP
LEVER
WARNING
TIPPING OF BUGGY
CAN OCCUR
B
CORRECT DIRECTION
FOR TRAVELING UP OR
DOWN A SLOPE
25° MAX.
Figure 29. Slope Travel Direction
TUB (BUCKET) DUMPING
1. To place the tub in the dump position (Figure 30)
pull back on the dump lever and release. The tub will automatically rotate to the vertical position and dump its contents.
Figure 30. Tub Vertical Position
NOTICE
If the buggy is on a incline, it might be necessary to slightly push the tub upward in a forward direction so the tub can be placed in the dump position.
2. To return the tub back to the horizontal position, grab
hold of the tub (Figure 31) and push down.
Figure 31. Tub Horizontal Position
TB11G/E TUFFTRUK• OPERATION MANUAL — REV. #1 (09/11/19) — PAGE 27
NORMAL SHUTDOWN (GASOLINE)
Correct shutdown is important for safe operation. Follow these general steps:
1. Release the
YELLOW
deadman lever and come to a complete stop. Brake is now set.
2. Let the engine idle for 3-5 minutes for gradual cooling.
3. Place the engine ON/OFF switch in the
OFF
position.
4. Place the fuel valve lever in the
OFF
position.
5. Block wheels if on a slope or incline.
EMERGENCY SHUTDOWN (GASOLINE)
1. Place the engine ON/OFF switch (Figure 32) in the
OFF
position.
OPERATION (GAS/ELECTRIC)
NORMAL SHUTDOWN (ELECTRIC)
1. Release the
YELLOW
deadman lever and come to a complete stop. Brake is now set.
2. Place the ignition switch in the
OFF
position.
3. Block wheels if on a slope or incline.
EMERGENCY SHUTDOWN (ELECTRIC)
1. Push the
EMERGENCY STOP
EMERGENCY
STOP SWITCH
START
OFF
ON
ENGINE SWITCH
Figure 32. Engine ON/OFF Switch (OFF)
PUSH
Figure 33. Emergency Stop Switch (Push)
PAGE 28 — TB11G/E TUFFTRUK • OPERATION MANUAL — REV. #1 (09/11/19)
MAINTENANCE
DESCRIPTION
(3)
OPERATION
Table 7. Engine Maintenance Schedule
BEFORE
EACH
USE
FIRST
MONTH OR
25 HRS.
EVERY 6
MONTHS
OR 100
HRS.
X
Engine Oil
Check
Change
Engine Oil Filter Replace
Check
Air Cleaner Clean
Change
X
X
X (1)
X
Every 100 Hrs.
X
Spark Plugs
Check/Adjust
Cooling Fins
Fuel Filter
Fuel Tube
Replace
Clean
Replace
Check
* - Replace the paper filter element only.
(1) Service more frequently when used in
DUSTY
areas.
X
EVERY
YEAR
OR 300
HRS.
X
X
X (2)
Every 2 years (replace if necessary) (2)
EVERY 2
YEARS OR
500 HRS.
X (*)
(2) These items should be serviced by your service dealer, unless you have the proper tools and are mechanically proficient.
Refer to the Briggs & Stratton, Vanguard Shop Manual for service procedures.
(3) For commercial use, log hours of operation to determine proper maintenance intervals.
Check Item
Tub
Tub For Cracks/Deformations
Tires For Severe Cuts/Wear
Hydraulic Oil Level (TB11G)
Hydraulic Oil (TB11G)
Hydraulic Oil System (TB11G)
Drive Chains
V-Belt (TB11G)
Bearing (TB11E)
Fastners
Table 8. Power Buggy Maintenance Schedule
OPERATION DAILY
X
Every
25 Hrs
Periodic Maintenance Interval
Every
50 Hrs
Every
100-125
Hrs
X
Every 200 Hrs
X
Clean
Check
Check
Check
Replace
Check
Clean/Lube
Check
Lube
Check
X
X
X
X
X
X
1st time
X
X
X
Once a Year
TB11G/E TUFFTRUK• OPERATION MANUAL — REV. #1 (09/11/19) — PAGE 29
MAINTENANCE (GASOLINE)
MAINTENANCE
When performing any maintenance on the power buggy engine or electric motor, follow all safety messages and rules for safe operation stated at the beginning of this manual.
WARNING
Accidental starts can cause severe injury or death.
ALWAYS
place the ON/OFF switch in the
OFF position.
Disconnect and ground spark plug leads and disconnect negative battery cable from battery before servicing.
WARNING
Some maintenance operations may require the engine to be run. Ensure that the maintenance area is well ventilated. Exhaust contains poisonous carbon monoxide gas that can cause unconsciousness and may result in
DEATH
CAUTION
ALWAYS
allow the engine to cool before servicing.
NEVER
attempt any maintenance work on a hot engine.
NOTICE
See the engine manual supplied with your machine for appropriate engine maintenance schedule and troubleshooting guide for problems.
Perform the scheduled maintenance procedures as defined
DAILY
Thoroughly remove dirt and oil from the engine and control area. Clean or replace the air cleaner elements as necessary. Check and retighten all fasteners as necessary.
WIRING
Inspect the entire buggy for bad or worn electrical wiring or connections. If any wiring or connections are exposed
(insulation missing) replace wiring immediately.
PIPING AND HOSE CONNECTION
Inspect all piping, oil hose, hydraulic hose and fuel hose connections for wear and tightness. Tighten all hose clamps and check for leaks. If any hose lines are defective replace them immediately.
FUEL STRAINER (IF EQUIPPED)
1. Thoroughly clean the area around the fuel cap.
2. Remove the fuel cap from the fuel tank.
3. Next, remove, inspect and clean the fuel filter
FUEL
CAP
GASKET
FUEL
FILTER
DANGER
DO NOT
use gasoline as a cleaning solvent to avoid creating the risk of fire or an explosion.
NOTICE
Operating the engine with loose or damaged air cleaner components could allow unfiltered air into the engine causing premature wear and failure to the engine. In addition, plugged cooling fins, and/or cooling shrouds removed will cause engine damage due to overheating.
FUEL
TANK
Figure 34. Fuel Strainer
PAGE 30 — TB11G/E TUFFTRUK • OPERATION MANUAL — REV. #1 (09/11/19)
SPARK PLUG
1. Remove and clean the spark plug (Figure 35), then
adjust the spark gap to 0.024~0.028 inch (0.6~0.7 mm).
This unit has electronic ignition, which requires no adjustments.
MAINTENANCE (GASOLINE)
ENGINE AIR CLEANER
1. Remove the air cleaner cover and foam filter element
2. Tap the paper filter element (Figure 37) several times
on a hard surface to remove dirt, or blow compressed air [not exceeding 30 psi (207 kPa, 2.1 kgf/cm2)] through the filter element from the air cleaner case side.
NEVER
brush off dirt. Brushing will force dirt into the fibers. Replace the paper filter element if it is excessively dirty.
3. Clean foam element in warm, soapy water or nonflammable solvent. Rinse and dry thoroughly. Dip the element in clean engine oil and completely squeeze out the excess oil from the element before installing.
DANGER
DO NOT
use gasoline as a cleaning solvent to avoid creating the risk of fire or an explosion.
GAP
:
0.024 - 0.028 in.
(0.6 - 0.7 mm.)
Figure 35. Spark Plug Gap
ENGINE OIL
1. Drain the engine oil when the oil is warm as shown in
2. Unscrew the oil filler dipstick from its holder.
3. Next, remove oil drain bolt and sealing washer and allow the oil to drain into a suitable container.
4. Replace engine oil with recommended type oil as
listed in Table 6. For engine oil capacity, see Table 2
(Engine Specifications).
DO NOT
overfill.
5. Install drain bolt with sealing washer and tighten securely.
OIL FILLER
DIPSTICK
WING NUT
AIR CLEANER
COVER
FOAM FILTER
ELEMENT
BLOW COMPRESSED
AIR FROM THE
INSIDE OUT
PAPER FILTER
ELEMENT
GASKET
Figure 37. Engine Air Cleaner
DRAIN
BOLT
SEALING
WASHER
Figure 36. Draining Engine Oil
TB11G/E TUFFTRUK• OPERATION MANUAL — REV. #1 (09/11/19) — PAGE 31
SPARK ARRESTER CLEANING (OPTIONAL)
Clean the spark arrester (Figure 38) every 6 months or
100 hours.
1. Remove the 4 mm screw (3) from the exhaust deflector
(Figure 38), then remove the deflector.
4 MM
SCREW
PROTECTOR
4 MM
SCREW
5 MM
SCREW
MAINTENANCE (GASOLINE)
ADDING HYDRAULIC OIL
1. Replace hydraulic oil after every 200 hours of operation.
The reservoir tank capacity is 16.90 fl. oz. (.5 liters).
2. Visually inspect the hydraulic oil level by reading the
hydraulic oil level (Figure 40) indicated on the hydraulic
oil tank.
MOT
20W
MUFFLER
5 MM
SCREW
HYDRAULIC OIL
RESERVOIR TANK
SPARK
ARRESTOR
Figure 38. Spark Arrester
2. Remove the 5 mm screw (4) from the muffler protector, then remove the muffler protector.
3. Carefully remove carbon deposits from the spark
arrester screen (Figure 39) with a wire brush
WIRE BRUSH
FULL
COLD
Figure 40. Hydraulic Oil Reservoir Tank
3. If the hydraulic oil level is low, fill to the proper level with
20W-50 motor oil or equivalent as indicated on the tank.
4. Start the engine and read the oil level on the tank again.
If oil level is still low, add motor oil as required.
NOTICE
If adding oil to an
empty
hydraulic drive pump, oil capacity is 77.23 fl. oz. (2.28 liters)
SPARK ARRESTOR
SCREEN
Figure 39. Cleaning The Spark Arrester
4. If the spark arrester is damaged and has breaks or holes, replace with a new one.
5. Reinstall the spark arrester and muffler protector in reverse order of disassembly.
PAGE 32 — TB11G/E TUFFTRUK • OPERATION MANUAL — REV. #1 (09/11/19)
DEADMAN CONTROL CABLE ADJUSTMENT
The
deadman
cable may require adjustment at some point in time. This cable is responsible for the dis-engagement of the safety pin, the setting and releasing of the brake. To gain access to the safety pin, the access panel
must
be removed.
1. Remove the four screws (Figure 41) that secure the
rear access panel to the frame.
MAINTENANCE (GASOLINE)
3. Verify that the safety pin (Figure 43) has been released
from the
pump direction bracket slot
.
PUMP
DIRECTION
BRACKET
SAFETY PIN
(RELEASED)
SLOT
1
REMOVE (2)
ACCESS P
ANEL
REMOVE (2)
Figure 41. Rear Access Panel Removal
2. With the engine
OFF
, push down on the
YELLOW
deadman lever (Figure 42) about 10~20°.
Figure 43. Safety Pin Released
4. If the safety pin has not been released from the pump
direction bracket slot, adjust the nut (Figure 44) on the
deadman lever until the safety pin clears the pump direction bracket slot.
DEADMAN LEVER
ADJUSTMENT NUT
10°~20°
DEADMAN
LEVER
10°~20°
Figure 44. Deadman Lever Adjustment Nut
Figure 42. Deadman Lever Engaged (10°~20°)
TB11G/E TUFFTRUK• OPERATION MANUAL — REV. #1 (09/11/19) — PAGE 33
5. Release the deadman lever (Figure 45).
DEADMAN
LEVER
RELEASED
MAINTENANCE (GASOLINE)
DIRECTION CONTROL CABLE ADJUSTMENTS
After some use, it may become necessary to adjust the tension on the forward and reverse control cables. Please use the following procedure to make the adjustments.
Forward/Reverse Control Cables Adjustment
1. Fully engage the deadman control lever (Figure 47).
Secure lever with a cable-tie in the closed position.
DEADMAN
LEVER
Figure 45. Deadman Lever Released (Disengaged)
6. Verify that the safety pin (Figure 46) has been properly
seated back into the pump direction bracket slot.
PUMP
DIRECTION
BRACKET
SAFETY PIN
(SET/LOCKED)
CABLE TIE
Figure 47. Securing Deadman Lever
2. Verify that the safety pin (Figure 43) has cleared the
pump direction bracket slot.
3. Fully squeeze the
forward
control lever and verify
that a 0.12~0.20 inch (3~5 mm) gap (Figure 48) exists
between the control lever and the handle bar/hand grip.
Figure 46. Safety Pin Engaged (Locked)
HAND
GRIP
0.12~0.20 IN.
(3~5 MM) GAP
FORWARD
CONTROL LEVER
Figure 48. Forward Control Lever Gap
4. If the correct gap has not been achieved, adjust the
nut (Figure 49) on the cable of the
forward lever
until the correct gap has been achieved.
PAGE 34 — TB11G/E TUFFTRUK • OPERATION MANUAL — REV. #1 (09/11/19)
MAINTENANCE (GASOLINE)
5° CW
PUMP
DIRECTION
BRACKET
FORWARD CONTROL
LEVER ADJUSTMENT NUT
Figure 49. Forward Control Lever Adj. Nut
5. Once the correct gap has been established and the forward control lever is fully engaged, verify that the
pump direction bracket
15° CCW.
PUMP
DIRECTION
BRACKET
15° CCW
FORWARD
CONTROL
CABLE
REVERSE
CONTROL
CABLE
Figure 51. Pump Direction Bracket (CW 5°)
PUMP NEUTRAL SETTING
NOTICE
Lifting of the buggy will be required when making the pump neutral setting adjustments. Use two people to lift the TuffTruk buggy.
If the unit tends to creep while in the
neutral
position, adjustment of the pump neutral setting will be required.
The pump neutral setting requires that the buggy be placed on wooden blocks.
1. Lift the buggy and place wooden blocks (Figure 52) at
the front and rear of the buggy. Place blocks so that the front and rear wheels can rotate freely just above the ground.
Figure 50. Pump Direction Bracket (CCW15°)
6. If the correct bracket rotation (15°) has not been
achieved, adjust the nut (Figure 49) on the cable of
the
forward control lever
until the correct rotation has been achieved.
7. Recheck forward lever control lever gap (0.12~0.20 inch/3~5 mm).
8. Repeat the same procedure for the
reverse control lever
using 5° rotation for the pump direction bracket
FRONT
REAR
WOODEN
BLOCK
Figure 52. Wood Block Placement
TB11G/E TUFFTRUK• OPERATION MANUAL — REV. #1 (09/11/19) — PAGE 35
NOTICE
Disconnection of the forward and reverse control cables from the cable support bracket may not be required. If the cables have
sufficient slack
, then disconnection will not be required. Disconnect these cables only if necessary.
2. If necessary, disconnect both the forward and reverse control cables from the cable support bracket as shown
MAINTENANCE (GASOLINE)
5. Using a 3/16-inch allen wrench, loosen the pump
neutral setting screw (Figure 54).
PUMP DIRECTION
CONTROL BRACKET
PUMP
NEUTRAL
SCREW
(LOOSEN)
CCW CW
JAM NUT
(LOOSEN)
CABLE
SUPPORT
BRACKET
JAM NUT
(LOOSEN)
Figure 53. FWD/REV Cable Support Bracket
3. Start the engine and let idle.
4. Next, fully engage the
YELLOW
deadman control lever
(Figure 47). Secure lever with tape or rubber band in
the
closed
position.
CAUTION
When loosening the pump neutral screw or rotating the pump direction control bracket, be sure to keep
hands clear
of the V-belt and pulley. Possibility exists of entaglement.
Figure 54. Pump Neutral Setting Screw
6. Slightly move the
pump direction control bracket
(Figure 54) either CW or CCW. Tighten pump neutral
setting screw.
7. Verify if the front or rear wheels are rotating (creeping).
If buggy still creeps, repeat steps 5 and 6.
8. If the forward and reverse control cables were disconnected, reconnect to the cables to the support bracket.
9. Fully engage the forward control lever and verify that the wheels rotate between 74~78 rpm's in the forward direction.
10. Fully engage the reverse control lever and verify that the wheels rotate between 28~32 rpm's in the reverse direction.
11. Turn off engine.
PAGE 36 — TB11G/E TUFFTRUK • OPERATION MANUAL — REV. #1 (09/11/19)
FREE-WHEEL
In the event the buggy loses power a free-wheel feature has been built into the buggy so that the unit can be moved due to loss of power.
Gas Version
1.
Pull up
on the transmission bypass lever (Figure 55).
GAS
PULL
UP
MAINTENANCE (ELECTRIC)
BATTERY CHARGER
The TB11E buggy has a built-in 24 VDC battery charger.
When charging of the battery is required, perfom the following:
NOTICE
The battery charger installed on the TB11E is a Smart
Charger, it can be left connected to the batteries after full charge (green light on) without harming batteries.
The charger uses minimum power in this stand-by mode
(battery fully charged) and maintains the batteries at full charge and extends battery life.
1. Place the ignition switch key (Figure 57) on the
OFF
position.
OFF
IGNITION
SWITCH
TRANSMISSION
BYPASS LEVER
(FREE-WHEEL)
Figure 55. Transmission Bypass
Lever (Free-Wheel)
2. Next, fully squeeze the
YELLOW
deadman lever.
3. The buggy can now be moved.
Electric Version
1.
Push
and
hold
the brake bypass lever (Figure 56).
BRAKE BYPASS
LEVER (OFF)
FREE-WHEEL
PUSH AND
HOLD
OFF
AUTO
ELECTRIC
Figure 57. Ignition Switch (OFF)
2. Push the
EMERGENCY STOP
PUSH
EMERGENCY
STOP SWITCH
Figure 58. Emergency Stop Switch (Push)
Figure 56. Brake Bypass Lever
2. The buggy can now be moved.
TB11G/E TUFFTRUK• OPERATION MANUAL — REV. #1 (09/11/19) — PAGE 37
3. Insert the 3-pronged blue and white battery charger power cable plug into the battery charger receptacle
BATTERY CHARGER
RECEPTACLE
BATTERY CHARGER
3-PRONGED PLUG
CONNECT TO
120 VAC POWER
SOURCE
BATTERY CHARGER
POWER CABLE
Figure 59. Battery Charger Power Cable
4. Next, connect the other end of the battery charger power cable to a 120 VAC voltage source.
5. Charging of the batteries can be observed by viewing
the small window (Figure 60) on the left-hand side of
the battery box.
CHARGE
LAMP
Figure 60. Charging Light
6. The charging light is normally
orange
which changes to
green
when the battery is fully charged.
MAINTENANCE (ELECTRIC)
5K OHM POTENTIOMETER REPLACEMENT
The speed on the the electric buggy is controlled by a 5K ohm potentiometer. This potentiometer provides a 0~5 VDC input signal to the motor controller via pin-13. Reference wiring diagram.
Use the following procedure when installing a replacement
potentiometer. ReferenceFigure 61.
1. Lift the buggy and place wooden blocks at the front and rear of the buggy. Place blocks so that the front and rear wheels can rotate freely just above the ground
2. Remove the four screws that secure the control panel to the frame.
3. Carefully set control panel down.
4. Loosen the nut on the
deadman clevis
A
) that secures the deadman cable to the throttle bracket upper spring.
5. Remove bolt, black rubber spacer and
upper
spring
) from the deadman clevis.
6. Position deadman cable (Figure 61
C
) away from throttle bracket.
7. Unhook the clip attached to the FWD/REV clevis
). Position the clip downward.
8. Next, remove the
lower
E
) from the
FWD/REV clevis.
9. Remove the FWD/REV clevis (Figure 61
) from the throttle arm.
10. Position the FWD/REV cable (Figure 61
) away from throttle bracket.
11. Remove the four bolts (Figure 61
) that secure the throttle bracket to the frame.
I
) that secures the potentiometer to the throttle arm.
13. Slide the throttle arm (Figure 61
J
) off the output shaft of the potentiometer.
14. Remove the nut that secures the potentiometer to the
.
15. Next, unsolder the
WHITE
,
BLACK
and
BLUE
wires
connected to the potentiometer (Figure 61
L
). Mark orientation.
16. Solder the
WHITE
,
BLACK
and
BLUE
wires removed in step 15 back onto the 5K ohm replacement potentiometer in the same orientation.
PAGE 38 — TB11G/E TUFFTRUK • OPERATION MANUAL — REV. #1 (09/11/19)
MAINTENANCE (ELECTRIC)
5K OHM
L
POTENTIOMETER
UNSOLDER (3)
C
DEADMAN
CABLE
C
NUT
G
FWD/REV
CABLE
CLIP
D
I
NUT
CLEVIS
DEADMAN
A
UPPER
SPRING
B
THROTTLE
BRACKET
BOLT
H
NUT
THROTTLE
ARM
LOWER
SPRING
E
K
POTENTIOMETER
J
FWD/REV
CLEVIS
F
THROTTLE ADJUSTMENT
Figure 61. 5K Ohm Potentiometer Replacement
17. Install new 5K ohm potentiometer back onto throttle bracket and secure with retaining nut.
18. Reinstall throttle arm back onto output shaft of potentiometer. Do not tighten retaining nut at this time.
19. Reconnect deadman and FWD/REV cables and associated hardware back onto throttle bracket.
1. Using a small flat blade screw driver, rotate the shaft on the potentiometer
fully
counterclockwise.
2. Fully engage the deadman control lever, then fully squeeze the forward speed control lever.
3. Verify that a 4mm gap () exist between the throttle arm and the stop screw. Adjust if necessary.
4. With the deadman lever held down and the forward speed lever still fully engaged, turn the potentiometer adjustment screw slowly clockwise until the motor
clicks
. Verify that the wheels rotate forward. slowly
I
) that secures the output shaft of the potentiometer to the throttle arm.
6. Remove support blocks, and reinstall control panel.
NOTICE
Ensure when the forward speed lever is released the motor dis-engages the drive before the potentiometer arm makes contact with the stop screw.
THROTTLE
ARM
THROTTLE
BRACKET
STOP
SCREW
4 MM
GAP
Figure 62. Throttle Arm Gap (4 MM)
TB11G/E TUFFTRUK• OPERATION MANUAL — REV. #1 (09/11/19) — PAGE 39
DRIVE CHAIN LUBRICATION
There are
three
drive chains that require lubrication at least once a year. Follow the procedure below when lubrication of the drive chains are required.
Drive Chains Lubrication
NOTICE
Lifting of the buggy will be required when lubrication of the three drive chains is required. Use two people to lift the TuffTruk buggy.
1. Pull back on the dump lever and place the tub in the dump position.
2. Next, remove the
six
bolts that secure the front drive
chain access panel (Figure 63) to the frame. Set the
bolts aside and remove access panel.
MAINTENANCE (GAS/ELECTRIC)
3. Next, remove the
four
bolts that secure the rear drive chains access panel to the frame. Set the bolts aside and remove access panel.
GAS
REAR ACCESS
PANEL
ELECTRIC
FRONT ACCESS
PANEL
Figure 64. Rear Access Panel Removal
4. Lift the buggy and place wooden blocks at the front and
rear of the buggy as shown in Figure 52. Place blocks
so that the front and rear wheels can rotate freely just above the ground.
5. Start the engine and let idle.
6. Fully squeeze the
YELLOW
deadman lever and hold down.
7. Next, slightly squeeze the
forward
speed control lever and verify that all three chains are rotating.
8. Using chain lube lubricant (Figure 65), lubricate each
rotating chain.
Figure 63. Front Access Panel Removal
PAGE 40 — TB11G/E TUFFTRUK • OPERATION MANUAL — REV. #1 (09/11/19)
FRONT
REAR
MAINTENANCE (GAS/ELECTRIC)
TIRES/WHEELS/LUG NUTS
Tires and wheels are very important and critical components of the buggy. When specifying or replacing the wheels, it is important that the wheels, tires, and axle are properly matched.
CAUTION
DO NOT
attempt to repair or modify a wheel. If the rim is cracked, replace the rim immediately and inspect the tire for cuts, wear, and deformations.
TIRE WEAR
The tires (Figure 67) used on the power buggy are
pnuematic. Proper inflation is 28 PSI (193 kPa). In addition, inspect the tires for cuts, wear and deformity.
CHAIN
LUBRICANT
Figure 65. Lubricating Drive Chains
9. Reinstall
all
access panels. Tighen bolts securely.
Zerk Fitting Lubrication
1. Lubricate the zerk fitting as shown in Figure 66 using
lithium base grease, grade N0.1 once a year. Apply two shots. of grease
Figure 67. Tire Inspection
2 SHOTS
Figure 66. Zerk Fitting Lubrication
TB11G/E TUFFTRUK• OPERATION MANUAL — REV. #1 (09/11/19) — PAGE 41
LUG NUT TORQUE REQUIREMENTS
It is extremely important to apply and maintain proper wheel mounting torque on the TuffTruk. Be sure to use only the fasteners matched to the cone angle of the wheel. Proper procedure for attachment of the wheels is as follows:
1. Start all wheel lug nuts by hand.
2. Torque all lug nuts (Figure 68) in sequence.
DO NOT
torque the wheel lug nuts all the way down. Tighten
each lug nut in 3 separate passes as defined by Table 9.
Table 9. Tire Torque Requirements
480 x 8 in.
20-25
Second Pass
FT-LBS
35-40
Third Pass
FT-LBS
50-65
MAINTENANCE (GAS/ELECTRIC)
TUB REMOVAL/PLACEMENT
1. Place both locking levers in the
unlock
position
LOCKING LEVERS
3. After first road use, retorque all lug nuts in sequence
Check all wheel lug nuts periodically.
4
1
2
3
4
2
1
5
3
Figure 69. Locking Levers (Unlock)
2. With
two people
, lift and remove the tub (Figure 70).
Place the tub onto its side away from the unit.
CAUTION
DO NOT
attempt to lift or move the tub by yourself.
4-LUG NUTS 5-LUG NUTS
6
4
1
2
3
5
8
6
4
1
2
3
5
7
6-LUG NUTS 8-LUG NUTS
LUG NUT
TORQUE
WRENCH
PNEUMATIC
AIRGUN
Figure 68. Lug Nut Torque Sequence
Figure 70. Tub Removal
PAGE 42 — TB11G/E TUFFTRUK • OPERATION MANUAL — REV. #1 (09/11/19)
MAINTENANCE (GAS/ELECTRIC)
3. Orient the tub tipping bracket to the base of the tub as
5. Tilt the tub into its discharge position and place both locking levers in the
lock
TUB TIPPING
BRACKET
Figure 71. Tipping Bracket Orientation
4. With
two people
, lift the tub and tipping bracket onto
the chassis (Figure 72). Make sure the tipping bracket
pivot bar rests within the tipping slots.
CAUTION
DO NOT
attempt to lift or move the tub by yourself.
LOCKING
LEVER
Figure 73. Locking Levers (Lock)
6. Place the tub in the forward position and make sure it is
secured firmly under the tub catch (Figure 74). Adjust
the tub catch if necessary.
TUB
LATCH
TIPPING BRACKET
PIVOT BAR
TIPPING
BRACKET
TIPPING SLOTS
Figure 72. Tub Placement
Figure 74. Tub Latch
TB11G/E TUFFTRUK• OPERATION MANUAL — REV. #1 (09/11/19) — PAGE 43
TUFFTRUK BUGGY STORAGE
CAUTION
NEVER
store the power buggy with fuel in the tank for any extended period of time.
ALWAYS
clean up spilled fuel immediately.
MAINTENANCE (GAS/ELECTRIC)
For storage of the buggy for over 30 days, the following is recommended:
Run the engine until the gasoline in the carburetor is completely consumed.
Drain the fuel tank completely, or add STA-BIL to the fuel.
Completely drain the oil from the crankcase and refill with fresh oil.
Remove the spark plug, pour 2 or 3 cc of SAE 30 oil into the cylinder and crank slowly to distribute the oil.
Slowly rotate the engine a few times with the starter rope and install a new plug.
Pull out the starter rope slowly and stop at the compression point.
Clean the entire buggy and engine compartment.
Clean drum of all debris and foreign matter.
Cover the buggy with a plastic sheet in a moisture and dust-free location out of direct sunlight.
PAGE 44 — TB11G/E TUFFTRUK • OPERATION MANUAL — REV. #1 (09/11/19)
TROUBLESHOOTING (ENGINE)
Symptom
Diffi cult to start, fuel is available, but no spark at spark plug.
Diffi cult to start, fuel is available, and spark is present at the spark plug.
Diffi cult to start, fuel is available, spark is present and compression is normal.
Diffi cult to start, fuel is available, spark is present and compression is low.
No fuel present at carburetor.
Troubleshooting (Engine)
Possible Problem
Spark plug bridging?
Carbon deposit on spark plug?
Short circuit due to defi cient spark plug insulation?
Improper spark plug gap?
Spark plug is red?
Solution
Check gap, insulation or replace spark plug.
Clean or replace spark plug.
Check spark plug insulation, replace if worn.
Spark plug is bluish white?
No spark present at tip of spark plug?
No oil?
Oil pressure alarm lamp blinks upon starting? (if applicable)
If insuffi cient compression, repair or replace engine. If injected air leaking, correct leak. If carburetor jets clogged, clean carburetor.
Check if transistor ignition unit is broken, and replace defective unit. Check if voltage cord cracked or broken and replace. Check if spark plug if fouled and replace.
Add oil as required.
Check automatic shutdown circuit, "oil sensor".
(if applicable)
ON/OFF switch is shorted?
Ignition coil defective?
Improper spark gap, points dirty?
Set correct spark gap and clean points.
Condenser insulation worn or short circuiting?
Replace condenser.
Spark plug wire broken or short circuiting?
Check switch wiring, replace switch.
Replace ignition coil.
Wrong fuel type?
Replace defective spark plug wiring.
Flush fuel system, replace with correct type of fuel.
Water or dust in fuel system?
Air cleaner dirty?
Choke open?
Suction/exhaust valve stuck or protruded?
Piston ring and/or cylinder worn?
Cylinder head and/or spark plug not tightened properly?
Head gasket and/or spark plug gasket damaged?
No fuel in fuel tank?
Set to proper gap.
Check transistor ignition unit.
Flush fuel system.
Clean or replace air cleaner.
Close choke.
Reseat valves.
Replace piston rings and/or piston.
Torque cylinder head bolts and spark plug.
Fuel cock does not open properly?
Fuel fi lter/lines clogged?
Fuel tank cap breather hole clogged?
Air in fuel line?
Replace head and spark plug gaskets.
Fill with correct type of fuel.
Apply lubricant to loosen fuel cock lever, replace if necessary.
Replace fuel fi lter.
Clean or replace fuel tank cap.
Bleed fuel line.
TB11G/E TUFFTRUK• OPERATION MANUAL — REV. #1 (09/11/19) — PAGE 45
TROUBLESHOOTING (ENGINE)
Weak in power, compression is proper but misfi res.
Engine overheats
Will not start, no power with key "ON". (if applicable)
Symptom
Weak in power, compression is proper and does not misfi re.
Rotational speed fl uctuates.
Recoil starter malfunctions. (if applicable)
Starter malfunctions.
Burns too much fuel.
Exhaust color is continuously "white".
Exhaust color is continuously "black".
Troubleshooting (Engine) - continued
Possible Problem
Air cleaner dirty?
Improper level in carburetor?
Defective spark plug?
Improper spark plug?
Water in fuel system?
Solution
Clean or replace air cleaner.
Check fl oat adjustment, rebuild carburetor.
Clean or replace spark plug.
Set to proper gap.
Flush fuel system and replace with correct type of fuel.
Clean or replace spark plug.
Dirty spark plug?
Ignition coil defective?
Wrong type of fuel?
Cooling fi ns dirty?
Intake air restricted?
Oil level too low or too high?
Governor adjusted incorrectly?
Governor spring defective?
Over-accumulation of exhaust products?
Wrong spark plug?
Replace ignition coil.
Replace with correct type of fuel.
Clean cooling fi ns.
Clear intake of dirt and debris. Replace air cleaner elements as necessary.
Fuel fl ow restricted?
Check entire fuel system for leaks or clogs.
Recoil mechanism clogged with dust and dirt?
Clean recoil assembly with soap and water.
Spiral spring loose?
Loose, damaged wiring?
Battery insuffi ciently charged?
Starter damaged or internally shorted?
Replace spiral spring.
Ensure tight, clean connections on battery and starter.
Recharge or replace battery.
Replace starter.
Lubricating oil is wrong viscosity?
Worn rings?
Air cleaner clogged?
Choke valve set to incorrect position?
Adjust oil to proper level.
Adjust governor.
Replace governor spring.
Check and clean valves. Check muffl er and replace if necessary.
Replace spark plug with manufacturer's suggested type.
Replace lubricating oil with correct viscosity.
Replace rings.
Clean or replace air cleaner.
Adjust choke valve to correct position.
Carburetor defective, seal on carburetor broken?
Poor carburetor adjustment, engine runs too rich?
ON/OFF device not activated ON?
Replace carburetor or seal.
Adjust carburetor.
Battery disconnected or discharged?
Ignition switch/wiring defective?
Turn on ON/OFF device.
Check cable connections. Charge or replace battery
Replace ignition switch. Check wiring.
PAGE 46 — TB11G/E TUFFTRUK • OPERATION MANUAL — REV. #1 (09/11/19)
TROUBLESHOOTING (GAS)
Symptom
Loss of Power.
Troubleshooting (Power Buggy Gas)
Possible Problem
FWD/REV speed cables out of adjustment?
Solution
Adjust FWD/REV speed control cables. Replace cables if necessary
Hydraulic drive pump defective?
Hydraulic oil level low?
Low engine RPM?
Defective V-belt?
Check or replace hydraulic drive pump.
Check hydraulic oil level. Add oil if necessary.
Check engine speed.
Check or replace V-belt.
FWD/REV speed cables out of adjustment?
Adjust FWD/REV speed control cables.
Loss of Travel Speed.
Parking brake in free-wheel position?
Hydraulic drive pump defective?
Place parking brake lever in set (down) position
Check or replace hydraulic drive pump.
System Operating Hot.
Hydraulic oil level low?
System jerky when started.
Diffi cult to steer.
Defective hydraulic drive pump?
Low tire pressure?
Parking brake will not hold. Pump neutral setting incorrect?
Check hydraulic oil level add hydraulic oil if necessary.
Defective cooling fan?
Inspect cooling fan, replace if necessary.
FWD/REV speed cables out of adjustment?
Adjust FWD/REV speed control cables.
Check drive pump, replace if necessary.
Check tire pressure.
Adjust pump neutral setting.
Diffi culty in stopping
Engine will not start.
.
Deadman lever out of adjustment?
Pump neutral setting incorrect?
Low on fuel or fuel tank empty?
Engine ON/OFF switch in OFF position?
Fuel Shut-off valve CLOSED?
Adjust deadman lever.
Adjust pump neutral setting.
Add fuel.
Set engine ON/OFF switch to ON position.
Open Fuel shut-off valve.
TB11G/E TUFFTRUK• OPERATION MANUAL — REV. #1 (09/11/19) — PAGE 47
TROUBLESHOOTING (ELECTRIC)
Symptom
Loss of Power.
Loss of Travel Speed.
System jerky when started.
Diffi cult to steer.
Parking brake will not hold.
Diffi culty in stopping
.
Electric motor will not start.
Troubleshooting (Power Buggy Electric)
Possible Problem
Defective motor controller?
Solution
Check or replace motor controller.
125A main fuse blown?
Check or replace fuse.
10A ignition fuse blown?
Emergency Stop Switch open?
Low electric motor RPM?
Defective batteries?
Check or replace fuse.
CLOSE
switch. Pull to close.
Check electric motor voltage.
Defective contactor?
FWD/REV speed cable signal not present?
REV speed switch signal not present?
Parking brake in free-wheel position?
Defective motor controller?
Check or replace batteries.
Check or replace contactor.
Check or replace 5K ohm potentiometer.
Check or replace switch inside reverse lever.
Place parking brake lever in set (AUTO) position.
Check or replace motor controller/software.
FWD/REV speed signal intermittent?
Low tire pressure?
Defective damper or steering rod?
Defective electric motor?
Defective motor controller?
Defective deadman microswitch?
Defective brake motor?
Defective motor controller?
Check or replace 5K ohm potentiometer.
Check tire pressure.
Check or replace damper or steering rod.
Check or replace electric motor.
Check or replace motor controller/software.
Check or replace microswitch.
Check or replace electric motor.
Check or replace motor controller/software.
Defective motor controller?
125A main fuse blown?
10A ignition fuse blown?
Emergency Stop Switch open?
Defective batteries?
Defective contactor?
Defective ignition switch?
Check or replace motor controller.
Check or replace fuse.
Check or replace fuse.
Close switch. Pull to close.
Check or replace batteries.
Check or replace contactor.
Check or replace ignition switch.
PAGE 48 — TB11G/E TUFFTRUK • OPERATION MANUAL — REV. #1 (09/11/19)
ERROR CODES
DIAGNOSTICS
NOTICE
The Curtis 1229 controller is not repairable in the field.
Please contact your nearest Multiquip Authorized
Service Center (ASC) for repair or replacement.
ERROR
CODE
The Curtis1229 controller detects a wide variety of faults or error conditions. Diagnostic information will be shown
on the Curtis 3100R diagnostic display (Figure 75). Error
or faults will be displayed in the format “Er ##”.
The error code shown in Figure 75 is an
encoder
failure
(Er 18). Reference the error code table shown below for additional codes.
Some errors may be corrected by simply turning the ignition key off, then back on and see if the fault clears. If that does not work turn the ignition to the off position and remove the
35-pin connector from the controller.
Figure 75. Curtis 3100 Diagnostic Gauge
Check the connector for corresion or damage, clean if necessary and reinsert. If that does not correct the problem, please contact your nearest Multiquip Authorized Service
Center (ASC) for repair or replacement.
Error Codes
1 HW Failsafe
2 PLD Clock Fail
29 Supervisor SW 4 Fault
30 Supervisor SW 5 Fault
76 Driver 5 Overcurrent
77 Driver 6 Fault
9 Calibration Reset 31 Supervisor KSI Voltage Fault 78 Driver 6 Overcurrent
10 Main Brake Driver Overcurrent 32 Supervisor Motor Speed Fault 79 Correlation Fault
11 Main Driver Open Drain
12 EMR Redundancy
13 EEPROM Failure
15 Main Contactor Dropped
16 Current Sensor
17 Main Contactor Welded
33 Supervisor Dir Check Fault
34 External Supply Fault
36 EM Brake Driver Open Drain
37 EM Brake Driver On
41 Pot 1
42 Pot 2
80 HPD Sequencing
81 Parameter Change
82 NV Memory Fault
90 Motor Temp Hot Cutback
92 Motor Open
93 Controller Overcurrent
18 Encoder
19 PDO Timeout
20 Supervisor Comms
21 Supervisor Watchdog
22 Supervisor Pot 1 Fault
23 Supervisor Pot 2 Fault
24 Supervisor Pot 3 Fault
25 Supervisor Pot H Fault
26 Supervisor SW1 Fault
43 Pot 3
50 Severe Undervoltage
54 Precharge Failed
70 Driver Shorted
71 Driver 3 Fault
72 Driver 3 Overcurrent
73 Driver 4 Fault
94 VBAT Too High
95 Controller Undertemp Cutback
52 Controller Severe Undertemp 96 Stall Detected
53 Controller Severe Overtemp 97 Controller Overtemp Cutback
98 Overvoltage Cutback
99 Undervoltage Cutback
101 User Fault Estop
102 User Fault Severe
27 Supervisor SW2 Fault
28 Supervisor SW3 Fault
74 Driver 4 Overcurrent
75 Driver 5 Fault
TB11G/E TUFFTRUK• OPERATION MANUAL — REV. #1 (09/11/19) — PAGE 49
A
B
C D
ELECTRONIC COMPONENT LOCATOR
TB11E
ELECTRIC BUGGY
O
M
L
K
J
E
F
J1
N
H
G
I
P
PAGE 50 — TB11G/E TUFFTRUK • OPERATION MANUAL — REV. #1 (09/11/19)
WIRING DIAGRAM
12 VDC PWR
DIAGNOSTIC
GAUGE
2
4
A
1
3
GND.
D
EMERGENCY
STOP SWITCH
RED
A
1
10A FUSE
RED
IGNITION
SWITCH
C
30
75
15
B
D
2
RED
CAN LO
RED/YEL
9
SPEED CONTROLLER
CONNECTOR J1
YEL/PURPLE
1
12
YEL
2
16
17
BLUE/YEL
2
4
GRN/YEL
1
3
3
4
5
SERIAL
PORT
CABLE
6
8
10
B
13
18
20
CONTACTOR
SOLENOID
RED
K1-1
RED
K1-2
RED
I
GRN
BRN
PURPLE
GRAY
ORANGE
WHT
F
RED
BLK/WHT
BLK
C
RED
B
12 VDC PWR
CONTACTOR
COIL
K1
12 VDC
SPLICE
E
PINK (COIL RETURN)
ORANGE
M
RED
M
BLK/WHT
F
RED
F
A2
A1
F
F
BLUE
MOTOR
BRAKE
K
B+
M1
B-
M2
D
BLK/YEL
6-PIN
MOLEX
CONNECTOR
BLK
M
1
F
1
N
BLUE
2 2
WHT
NC
GRAY
3
5
4
6
3
4
5
6
NC
GRAY
F
BROWN
REVERSE
SWITCH
NC
O
BLUE
M
NO COM
M
BROWN
DEADMAN
BRAKE MICROSWITCH
NC
G
COM
NO
RED
J1
J
24 VDC
ELECTRIC
MOTOR
1300W
I
CURTIS 1229 MOTOR
CONTROLLER
POS
WHT
NEG
P
12V BATTERY #1
H
BLK
BLK
A
FUSE
125A
BLK
L
SERIES
CONNECTION
POS
NEG
P
12V BATTERY #2
RED/YEL
F
ANALOG GND.
WHT
3-WIRE 5K OHM
POTENTIOMETER
1
F
0~5V IN
BLK
2
5V OUT BLUE
3
BLK
GND
M
C
CONNECT
TO 120 VAC
POWER SOURCE
GRN
BATTERY
CHARGER
M
NOTES:
1
BLUE SQUARE
WHITE LETTERING DENOTES INTER-CONNECTIONS POINTS
2
BLACK CIRCLE
WHITE LETTERING DENOTES COMPONENT LOCATION.
REFERENCE COMPONENT LOCATOR OPPOSITE PAGE.
TB11G/E TUFFTRUK• OPERATION MANUAL — REV. #1 (09/11/19) — PAGE 51
OPERATION MANUAL
UNITED STATES
Multiquip Inc.
(310) 537- 3700
6141 Katella Avenue Suite 200
Cypress, CA 90630
E-MAIL: [email protected]
WEBSITE: www.multiquip.com
HERE’S HOW TO GET HELP
PLEASE HAVE THE MODEL AND SERIAL
NUMBER ON-HAND WHEN CALLING
CANADA
Multiquip
(450) 625-2244
4110 Industriel Boul.
Laval, Quebec, Canada H7L 6V3
E-MAIL : [email protected]
© COPYRIGHT 2019, MULTIQUIP INC.
Multiquip Inc , the MQ logo are registered trademarks of Multiquip Inc. and may not be used, reproduced, or altered without written permission. All other trademarks are the property of their respective owners and used with permission.
This manual MUST accompany the equipment at all times. This manual is considered a permanent part of the equipment and should remain with the unit if resold.
The information and specifi cations included in this publication were in effect at the time of approval for printing. Illustrations, descriptions, references and technical data contained in this manual are for guidance only and may not be considered as binding. Multiquip Inc. reserves the right to discontinue or change specifi cations, design or the information published in this publication at any time without notice and without incurring any obligations.
Your Local Dealer is:
advertisement
Related manuals
advertisement
Table of contents
- 2 Proposition 65 Warning
- 3 Table of Contents
- 10 Safety Information
- 11 Specifications (Buggy)
- 12 Specifications (Engine)
- 13 Noise and Vibration Emissions
- 14 Dimensions
- 15 General Information
- 17 Components
- 18 Engine Components
- 21 Inspection
- 23 Operation (Gasoline)
- 25 Operation (Electric)
- 28 Operation (Gas/Electric)
- 29 Maintenance
- 36 Maintenance (Gasoline)
- 39 Maintenance (Electric)
- 44 Maintenance (Gas/Electric)
- 46 Troubleshooting (Engine)
- 47 Troubleshooting (Gas)
- 48 Troubleshooting (Electric)
- 49 Error Codes
- 50 Electronic Component Locator
- 51 Wiring Diagram