MacDon 960 Harvest Draper Headers and Adapters for Combine Operators Manual
Add to My manuals64 Pages
MacDon 960 Harvest is a combine header designed for efficient grain harvesting. It seamlessly integrates with a variety of combine models, maximizing productivity and simplifying operations. Its self-tracking draper system ensures smooth grain flow, while its adjustable header angle and float optimize cutting height and ground engagement. You can rely on this header to reliably handle a wide range of crops and conditions.
advertisement
▼
Scroll to page 2
of
64
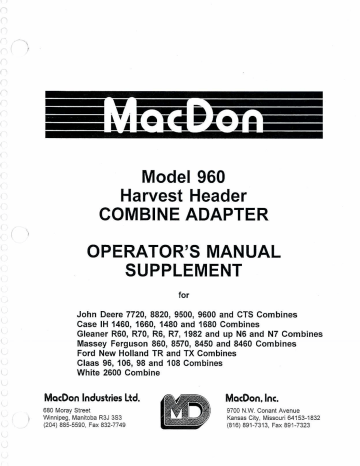
Î У i _ al I a TA AN à 7 A A A Model 960 Harvest Header COMBINE ADAPTER OPERATOR’S MANUAL SUPPLEMENT for John Deere 7720, 8820, 9500, 9600 and CTS Combines Case IH 1460, 1660, 1480 and 1680 Combines Gleaner R60, R70, R6, R7, 1982 and up N6 and N7 Combines Massey Ferguson 860, 8570, 8450 and 8460 Combines Ford New Holland TR and TX Combines Claas 96, 106, 98 and 108 Combines White 2600 Combine MacDon Industries Ltd. 680 Moray Street Winnipeg, Manitoba R3J 383 (204) 885-5590, Fax 832-7749 MacDon, Inc. 9700 N.W. Conant Avenue Kansas City, Missouri 64153-1832 (816) 891-7313, Fax 891-7323 ДЕ К) К A IQ 02220539 —_ Ca a= — —_ ней + E » | E gm" mi (D pu INTRODUCTION This Manual Supplement contains information on the adapter which is required to allow attachment of the MacDon Model 960 Harvest Header to the various models of combines (see list on cover). NOTE: This supplement does not provide all the information required to operate the header. It must be used in conjunction with your Harvest Header and Combine Operator's Manuals. CAREFULLY READ ALL MANUALS TO BECOME FAMILIAR WITH RECOMMENDED PROCEDURES BEFORE ATTEMPTING TO UNLOAD, ASSEMBLE OR USE THE MACHINE. This manual is divided into sections on: Safety, Attaching and Detaching the Header, Operation and Maintenance/Service. In addition, Assembly and Adapter Mounting Instructions for each type of combine are found at the back of this book. Use the Table of Contents and the Index to guide you to specific areas. Study the Table of Contents to familiarize yourself with how the material is organized. Keep this manual handy for frequent reference and to pass on to new operators or owners. Call your dealer if you need assistance, information or additional copies of the manual. NOTE: Right hand (R/H), and Left hand (L/H) designations are determined from the operators position, facing forward. TABLE OF CONTENTS INTRODUCTION: sua us urea ys y das ESE-1% NES El MEN Dl ZU ENS de Hex EN $ LN tax à dau: 1 SERIAL NUMBER LOCATION & SPECIFICATIONS ........ 2.2.0... ea A ea a aa a au ee 3 SAFETY Safety Alert Symbol .....2242 420114424444 4 A 4 A 44 A4 A4 4 A 4 A4 4 A 4 4 a a a ea a 20 4 Signal Words ..........o.e_eexerredre vere rre dae nde reraCrvearercererarcorcea 4 Safety Signs ........ _—.o_eéesxredderere ae rece noernoaeriano ne noe adoererorarora 5 HEADER ATTACHING & DETACHING Attaching Header to Combine and Adapter . . ..... 2... area. 6,7 Detaching Header from Combine and Adapter . . . ..... inn 8 Detaching Header and Adapter from Combine . . . .... 001110100444 4 24 4 4 a a a eee 9 Attachinga Header and Adapter to COMDINÉ . .. «civ viv inv ve cov vs mn wns on bas on woes 10 OPERATION Break-In Period . . . oe ee eee 11 Draper Seal GONG] + =— vaz a Es da Ea 06 de me a H6 RET Beal La MG Se ws diss ses nié à 11 Header FIot@HON wu iv oon vam in i ses wie die WE BE EWR WE Ke ES SNA Dl GAN 4 12 ACA ANDO: === yu vim pain ¿a 5d Sp SE GE BR de HR sa DE SAG Wh WEE EEN OF BEE ge yas i 13 alge Whee] BOSIIOR © as mu se wex Ma WS on wes Ra ALE Se de Ma de € Dn Nue Va EM 13 MAINTENANCE/SERVICE Service Procedures . coreana rnne a 14 Recommended Lubricants ...........eeeeeeosrererrecreaonenereroansoerearonarea, 15 Enclosed Drive Lubricant Capacities . . . . .. eee 15 Sealed Bearing Installation... ...... eee 15 Greasing the Adapter пол Кале сот 238 sti Háb el Sane 5b Edi LA Hd 1% Ha abera Gia xo ea ma » 16,17 Feeder DIEDSI" ow oi vos von ds КБ БП dl Ka 07 A NN 995 599 EN SAN E ВО Vox à 567 à 18 Hydraulic System ERIGE SUStOM: Dele «ox oo кс: gas a de GEES de ROS wn was mens ФО: ВИЖ ARE SA MOMIA SA YO GU à 18 Fosas ana LINES su aa uc om im a EA DA Rom avd SEs wi SWS WR CUA SENDA SN E WORE UH Rem 3 18 НОНО СЛЕ RESENVON + aaa es va ea ra na wm НИЕ НОВОЕ ЖИМ ЖЕЛЕ SN or sie Fos: qUe GUN ВОВ wo 6 i 19 Hydraulic Oil Filter .. .... ve= ex ova vea вла am Rea ER KR acme CUA a NENE NU NOM à 19 Flow Control Relief Pressure ............o.eeÑceee20e0eZsirerere 4 4 4 0 4 44 4 44 4 140 20 Hydraulic Schematic . . . . . .. 2410414 4 L 444 4e reee Aecem ener 0 20 Combine Adapter Chain Case RR ee eee ee eee 21 Fesder Draper Diivelite Sip:CIULel <= vis 07 57% 1% Web El DEE PEA 05 dE Tel dl Hd UA E AE: 21 Maintenance Schell Lov iv ii Bod Shs i Be oe HSE PA ECS TE Ц ШО; VER DA TUE UA Y En A 22 mamtenarice Record : « oo vin pr oo wim sui so asta EN DÍ: E DOE NES ZN SAG SEN Sa GM AA ONES 23 TROUBLESHOOTING FILER + == comes wi swam ax de Bis Sms Mone iw WDE de BINGE i Bich Ho КОВ ОНЧНО ЧКЗОКО КОР НТИ BER MU y 24 FT 24,25 1 [o)é=1i[e) PP ee. 25 ASSEMBLY Frepanno Tor Combine USe + si Бо коб бал ей 744 9h RER E E EE E Pan Pau oh nah vas 26-30 ADAPTER MOUNTING INSTRUCTIONS JONT-MRBIO o uma ves a ANA RED GEN SCAN ESS UE PEE OV RR BN NE GORE A WANE SNR BN НЙ ВИНО 31-34 ASE sos zu sas FE HE HUN КИ EEE EEE WERE BEE WE RER 6 RO RE BUCH BEE WE 35-37 De a WINE AA BR Se SED 38-40 He cn ue 2 MEE E ED NRO me DD a WE SEG eH EDO EZ DECIDE SEA 41-44 Claas & MF 8450/8460 ...............e_exesmenecara dere rda ra venecorre rara 45-47 ME BBO Le ee ee ee ee eee ea 48-50 MF 8570: Modification fo Case Adapter ........... eee 51-54 NE 0870 su e SN ma REX 5h NA a RÚ dlrs eli Mani Un cha Ned A Tal DN huía Creme E meme aes 55-58 INDEX = yu as eu en eS Es EG (4 UA 0% GEN El SUN IS VAR dd EA TN 54 DAN Dels EIN БОБЫ Ц: 59 SERIAL NUMBER LOCATION Record the serial number in the space provided. Combine Adapter: Plate is located on left side of adapter frame. no RE Tee ui ae = LE sa i iris edn A es NENE "En a E Е y E Er COMBINE ADAPTER SERIAL PLATE NOTE: When ordering parts and service, be sure to give your dealer the complete and proper serial number. SPECIFICATIONS FEED DRAPER DRIVE: Mechanical TYPE: Self-tracking rubber coated polyester fabric with rubber slats WIDTH: 37.4" (950 mm) or 54.9" (1395 mm), depending on combine SPEED: 560 ft/min. (170 m/min.) FEED AUGER DRIVE: Hydraulic SIZE: 16" (400 mm) diameter SPEED: Varies with side drapers (0 to 400 RPM) HEADER FLOTATION 8" (200 mm) vertical and 5° lateral SAFETY SAFETY ALERT SYMBOL This safety alert symbol indicates important safety messages in this manual and on safety signs on the machine. This symbol means: ATTENTION ! BECOME ALERT ! YOUR SAFETY IS INVOLVED ! Carefully read and follow the safety message accompanying this symbol. Why is SAFETY important to you? + ACCIDENTS DISABLE AND KILL 3 BIG REASONS « ACCIDENTS COST « ACCIDENTS CAN BE AVOIDED SIGNAL WORDS Note the use of the signal words DANGER, WARNING, and CAUTION with safety messages. The appropriate signal word for each message has been selected using the following guidelines: « an immediate and specific hazard or forbidden practice D AN e = R which WILL result in severe personal injury or death if the message is not followed. a specific or unsafe practice which COULD result in severe personal injury or death if the message is not followed. A WARNING + unsafe practice which could result in personal injury if the | message is not followed, or a reminder of good safety CAUTION practices. SAFETY SAFETY SIGNS The safety signs below appear on the combine adapter. Keep safety signs clean and legible at all times Replace safety signs that are missing or become illegible. If original parts on which a safety sign was installed are replaced, be sure the repair part also bears the current safety sign. Safety signs are available from your Dealer Parts Department. To install safety signs: Te 0 A тн Be sure the installation area is clean and dry. Decide on the exact location before you remove the decal backing paper. Remove the smaller portion of the split backing paper. Place the sign in position and slowly peel back the remaining paper, smoothing the sign as it is applied. Small air pockets can be smoothed out or pricked with a pin. A DANGER| ul > Rest header on ground or engage mechanical locks before going under unit. See Operator's Manual. " 44611 A DANGER Entanglement in rotating driveline can cause serious injury or death. Keep all shields in place. Avoid contact with rotating parts. * 30479 HEADER ATTACHING & DETACHING ATTACHING HEADER TO COMBINE AND ADAPTER 1. Attach adapter to combine feeder housing. See "Adapter Mounting Instruction" at back of book. NOTE: If header has been previously attached to windrower, remove linkage supports from header lower legs. Connector shaft on header back tube may remain installed. 2. Choose an area that is as level as possible, and support both ends of cutterbar 6" (150 mm) off ground (A). 3. For headers with gauge wheels, block both wheels front and rear, and be sure gauge wheel pins are in stand position (L), both sides, to support rear of header. For headers without gauge wheels, be sure header stand is secure in the down position (B). CAUTION: Be sure area is clear of bystanders before starting engine. 4. Slowly drive combine forward and engage adapter legs (C) in header legs (D). Continue forward until lip of adapter (E) is under cutterbar and catch (F) engages under stop in header lea. se I 5 Ho 3 Ti e e IMPORTANT: Take care not to crush EEES COTA да Ls hydraulic hoses when driving into header. ALIGN MOUNTING LEGS 5. Raise header, stop engine and remove key. \ DANGER: To avoid bodily injury from fall of raised header, engage header lift cylinder stops when H G working on or around raised header. See your Combine Operator's Manual for details. 6. Attach adapter to header with pin (G), both sides. Note that pin (G) has a spring pin installed near the bend. Position hair pin (H) to capture spring pin between header leg and hair pin. K 7. Disengage float lock-out by lowering retainers | S'en De INSTALL PINS & DISENGAGE FLOAT LOCK HEADER ATTACHING & DETACHING ATTACHING HEADER TO COMBINE AND ADAPTER (continued) 8. Install driveline on chain case shaft (J). Pull back spring-loaded collar on driveline yoke and slide yoke onto chain case top shaft. Release collar, ensuring yoke locks in position on shaft. NOTE: For 21° Header on some combine models, it will be necessary to modify driveline. See Mounting Instructions at back of this book. 9. Make the hydraulic line connections: EE Reel drive pressure and return lines: For Bs we им ЗО John Deere, Massey Ferguson and Claas ATTACH DRIVELINE combine adapters, connect hoses from header to the appropriate couplers on the combine. For Case, Gleaner, and New Holland combine adapters, connect hoses from header to couplers on adapter, then complete the connections from adapter to combine. Reel lift line: Connect hose from header to reel lift coupler on combine. | Draper drive pressure and return lines: : Connect hoses from header to appropriate couplers on adapter. NOTE: As an aid in connecting hydraulics, the following colour coding has been used: RED - Draper Drive Pressure BLUE - Draper Drive Return YELLOW - Reel Drive Return 10. For headers with gauge wheels, remove pins at gauge wheels and place in field position (F). (For headers with gauge wheel/transport option, gauge wheel support is not exactly as illustrated. See decal at support.) NOTE: Rotate pin to align roll pin with key slot for removal and installation. Roll pin locks inside to secure the position. 11. For headers without gauge wheels, raise header stand to storage position (G). 12. Disengage header lift cylinder stops and lower header. HEADER STAND - STORAGE POSITION HEADER ATTACHING & DETACHING DETACHING HEADER FROM COMBINE AND ADAPTER Using this procedure, adapter will remain attached to the combine. This would be appropriate when header is to be used as a windrower. Instructions for detaching both header and adapter from combine are given on the next page. 1. Choose a level area. Lower the reel and raise the header. Stop engine and remove key. DANGER: To avoid bodily injury from A fall of raised header, engage header lift cylinder stops when working on or around raised header. See your Com- bine Operator's Manual for details. DANGER: Wait for all movement to stop. A rotating driveline can cause entanglement resulting in serious personal injury or death. 2. Disconnect driveline from chain case shaft and store on welded pin (A) on header tube. 3. Disconnect five hydraulic lines: - Reel lift at combine quick coupler. - Reel drive pressure and reel return at header hose quick couplers. - Draper return (blue) and auger/draper drive pressure (red) at adapter quick couplers. IMPORTANT: Couple or cap all lines to prevent hydraulic system contamination. Be sure header stored hoses and combine stored hoses are not entangled. 4. Set 6" (150 mm) blocks beneath the cutterbar, approximately 18 inches (450 mm) from each end of header. 5. For headers with gauge wheels, remove pins at gauge wheels and place in stand position (B). Block both gauge wheels. For headers without gauge wheels, lower header stand into position (E). 6. Move float lock-out retainers to engaged position (C). 7. Remove pins (D) securing adapter legs to header legs. 8. Disengage header lift cylinder stops, start engine and lower header onto blocks. LOCK OUT FLOAT AND REMOVE 9. Slowly back away from header. HEADER PINS - BOTH SIDES HEADER ATTACHING & DETACHING DETACHING HEADER AND ADAPTER FROM COMBINE Using this procedure, adapter will remain attached to the header. This would be appropriate when detaching header for transport. Instructions for detaching header only from adapter and combine are given on the previous page. 1. Choose a level area. Lower the reel and raise the header. Stop engine and remove key. DANGER: To avoid bodily injury from fall of raised header, engage header lift cylinder stops when working on or around raised header. See your Combine Operators Manual for details. 2. Move float lock-out retainers to engaged position (A). LOCK OUT FLOAT LINK - BOTH SIDES 3. Disconnect hydraulic lines at combine quick couplers: * Reel drive pressure line. * Reel lift line, * Flow return line. * Reel hydraulic fore-aft hoses (if applicable) Couple or cap all lines to prevent hydraulic system contamination. IMPORTANT: Be sure header stored hoses and combine stored hoses are not entangled. DANGER: Wait for all movement to stop before approaching driveline. A rotating driveline can cause entanglement resulting in serious personal injury or death. 4. Disconnect driveline from combine feeder | / house output shaft. See Mounting Instruction С at back of book. = 5. Disengage the header lock system. See | / Mounting Instruction at back of book. / 6. Disengage header lift cylinder stops, start a fn engine and lower header to ground. C24 7. Slowly back combine away from header. NOTE: Where it is necessary to reduce the \ / transport width of the header/combine adapter N O package, remove chain case pivot bolt (5), swing Sa WM chain case in to transport position, align slot (C) with hole and reinstall bolt. CHAIN CASE PIVOT HEADER ATTACHING & DETACHING ATTACHING HEADER AND ADAPTER TO COMBINE 1. If applicable, block both gauge wheels front and rear (B). NOTE: Choose an area that is as level as possible. CAUTION: Be sure area is clear of bystanders before starting engine. 2. Drive combine slowly forward and engage feeder house lifting device in adapter top BLOCK GAUGE WHEELS cross member. See Mounting Instruction at back of book for details. 3. Raise header, stop engine and remove key. DANGER: To avoid bodily injury from fall of raised header, engage A header lift cylinder stops when | working on or around raised PN / header. See your Combine Operator's Manual for details. 4. Connect feeder house lock system at bottom of adapter. See Mounting Instruction at back of book. 5. If adapter chain case has been pivoted to transport position, remove pivot bolt (A) and swing chain case out to working position. O Replace bolt (A). PIVOT CHAIN CASE TO WORKING POSITION 6. Connect driveline to feeder house output shaft. See Mounting Instruction at back of book. 7. Connect three hydraulic lines at combine quick couplers: * Reel drive pressure line. * Reel lift line. * Reel drive return line. CEE 8. Disengage float lock-out by lowering retainers to position (K). 9. Disengage header lift cylinder stops and 200 of, lower header. | a DISENGAGE FLOAT LOCK-OUT QU 10 OPERATION BREAK-IN PERIOD 1. Run drapers slowly for 5 minutes to fill hydraulic lines, then check oil level at (A). Maintain level between LOW and FULL. 2. Check tension of drive chain (C) on combine adapter after 10 hours operation and every 50 hours thereafter. See Maintenance/Service section. 3. Change the hydraulic oil filter (D) on combine adapter after 100 hours operation and every 250 hours thereafter. See "Break-In Period" in Header Operator's Manual for further information on break-in maintenance. y ha e ZH CHECK HYDRAULIC OIL LEVEL CHECK DRIVE CHAIN TENSION - 10 HOURS CHANGE OIL FILTER - 100 HOURS DRAPER SPEED CONTROL Draper speed is adjusted at the flow control on the combine adapter. Move flow control lever (B) clockwise to increase draper speed and counter- clockwise to decrease. Range is 0 to 800 roller RPM, or 0 to 470 ft. /minute (145 m/min.). A mid- range setting (5 to 6 on flow control indicator) is suggested. NOTE: If sufficient draper speed cannot be achieved, a possible cause is low relief pressure. See "Flow Control Relief Pressure" in Maintenance/Service section. 11 OPERATION HEADER FLOTATION IMPORTANT: To avoid: - frequent breakage of sickle components - scooping soil - soil build-up at cutterbar in wet conditions, set header float as light as possible without causing excessive bouncing. Under normal conditions, adjust float spring tension so 50 to 70 Ibs. force (220 to 300 N) is required to lift cutterbar off ground at each end. To adjust header float at combine adapter: 1. Raise header fully. DANGER: To avoid bodily injury or A death from unexpected start-up or fall of raised header; stop engine, remove key and engage header lift cylinder stops before going under header to adjust float (or for any reason). 2. Turn bolts (E) at each side of adapter clock- wise to increase float (which makes header lighter when lowered to ground). Turn bolts counter-clockwise to decrease float (which makes header heavier when lowered). NOTE: With header raised off the ground, float link should contact stop at (A). A gap between link and stop with header off the ground is an indication that float is set too light. 3. Disengage lift cylinder stops and lower header. Check float at both ends of cutterbar. Force required to lift cutterbar should be approx- imately the same at both ends. 12 FLOAT ADJUSTMENT - COMBINE OPERATION HEADER ANGLE The header (or guard) angle can be set at between 13° and 16° below horizontal. (Actual range may vary with combine set-up.) See Combine Operator's Manual for header levelling and additional header angle adjustments. IMPORTANT: The flattest header angle (13°) is recommended for normal conditions and is the factory set position. A flatter header angle reduces sickle section breakage and reduces soil scooping or build-up at the cutterbar in wet conditions. Use a steeper angle to cut very close to the ground, or in down crop for better lifting action. To adjust header angle: 1. Rest header on 6 inch (150 mm) blocks. 2. Remove lock (D), both sides of adapter. 3. Turn nut (E) clockwise to flatten header angle, or counter-clockwise to steepen angle. IMPORTANT: Adjust both sides to the same position. 4. Replace lock (D). 5. IMPORTANT: Header flotation is changed when header angle is changed, and must be readjusted. See "Header Flotation”, one page back. 13 HEADER ANGLE ADJUST. - COMBINE MAINTENANCE/SERVICE SERVICE PROCEDURES CAUTION: To avoid personal injury, before servicing machine or opening drive covers: 1. Fully lower header and reel. If it is necessary to service in the raised position, first engage header lift cylinder stops and reel props. 2. Disengage header drive clutch. 3. Stop engine and remove key. 4. Engage park brake. 5. Wait for all moving parts to stop. Park on level surface when possible. Block wheels securely. Follow all recommendations in your Combine Operator's Manual. Wear close-fitting clothing and cover long hair. Never wear dangling items such as scarves or bracelets. Wear protective shoes with slip resistant soles, a hard hat, protective glasses or goggles and heavy gloves. Be prepared if an accident should occur. Know where the first aid kit and fire extinguisher are located and how to use them. Keep the service area clean and dry. Wet or oily floors are slippery. Wet spots can be dangerous when working with electrical equipment. Be sure all electrical outlets and tools are properly grounded. Use adequate light for the job at hand. Replace all shields removed or opened for service. Use only service and repair parts made or approved by the equipment manufacturer. Substituted parts may not meet strength, design or safety requirements. Keep the machine clean. Never use gasoline, naphtha or any volatile material for cleaning purposes. These materials may be toxic and/or flammable. 14 MAINTENANCE/SERVICE RECOMMENDED LUBRICANTS GREASE Use an SAE Multi-Purpose High Temperature Grease with Extreme Pressure (EP) Performance and containing at least 1.5% molybdenum disulphide. Also acceptable is an SAE Multi-Purpose Lithium Base Grease. HYDRAULIC OIL Use SAE 10W30 Class SF or CC engine oil. CAPACITIES Adapter Chain Case - 2000 grams (70 oz.) SAE Multi Purpose Grease Adapter Hydraulic System (Draper Drive) - 28 litres (7.4 U.S. gals.) Tank only - 25 litres (6.6 U.S. gals.) STORING AND HANDLING LUBRICANTS Your machine can operate at top efficiency only if clean lubricants are used. Contaminant in lubricants is the most likely cause of bearing and hydraulic system failure. Use clean containers to handle all lubricants. Store lubricants in an area protected from dust, moisture and other contaminants. Keep hydraulic couplers and connectors clean. SEALED BEARING INSTALLATION 1. Clean shaft and coat with rust preventative. 2. Install flangette, bearing, flangette and lock collar. The locking cam is only on one side of the bearing. 3. Install and tighten the flangette bolts. 4. When the shaft is located correctly, lock the lock collar with a punch. The collar should be locked in the same direction the shaft rotates. Tighten the set screw in the collar. 5. Loosen the flangette bolts on the mating bearing one turn and re-tighten. this will allow the bearing to line up. TIGHTEN COLLAR IN DIRECTION SHAFT ROTATES 15 MAINTENANCE/SERVICE GREASING THE ADAPTER See "Recommended Lubricants" in this section for recommended greases. The following greasing points are marked on the adapter by decals showing a grease gun (A), and grease interval (B) in hours of operation. Use the hour meter in the combine cab and the "Maintenance Checklist" provided to keep a record of scheduled maintenance. Procedure: 1. Wipe grease fitting with a clean cloth before greasing, to avoid injecting dirt and grit. 2. Inject grease through fitting with grease gun until grease overflows fitting. 3. Leave excess grease on fitting to keep out dirt. 4. Replace any loose or broken fittings immedi- ately. 5. If fitting will not take grease, remove and clean thoroughly. Also clean lubricant passageway. Replace fitting if necessary. 10 Hours or Daily DANGER: Stay clear of drivelines until all movement has stopped. Entanglement with rotating driveline will cause serious personal injury or death. Avoid loose fitting or dangling clothing. 1. Chain Case Input Driveline (A) - one or two fittings depending on make of combine. 2. Feeder Draper Driveline (B) - three fittings NOTE: Do not grease slip clutch daily. Daily remove packed dirt and chaff from around feeder draper driveline and feeder draper drive roller bearings (both sides of deck). COMBINE ADA lam 108 SAMPLE GREASE DECAL ad НЫ Es GA a EA PTER DRIVELINES at nd o ACE ооо un Te S = rt A AA =. MAINTENANCE/SERVICE GREASING THE ADAPTER (continued) 100 Hours or Annuall Ings ix fitt 5 Case Bearings (C) - ain 1. Ch Tn CHAIN CASE BEARINGS 2. Cross Auger Bearing (D) - one fitting LE: Mg pa es ты Eee CROSS AUGER BEARING ings (E) - Roller Bear Ive Feeder Draper Dr two fittings 3 ing seal, To avoid damage to beari NOTE a En 3 un D) = ler bear ive ro le slow stroke of grease gun when greasing dr sing FEEDER DRAPER DRIVE ROLLER BEARING (BOTH ENDS) 17 MAINTENANCE/SERVICE FEEDER DRAPER To adjust draper tension: IMPORTANT: Do not turn nut (X) to adjust draper tension. 1. Loosen nut (N). 2. Turn bolt (B) counter-clockwise to tighten draper until outside of bolt head lines up with edge of decal. (Dimensions are shown for adapters without decal.) Tighten nut (N). Repeat at other side. o replace feeder draper tension spring: Remove nut (N). Remove cotter pin and loosen nut (X). While holding nut (X) with a wrench, remove bolt (B). Replace spring and reassemble. Adjust spring length to 4 7/8 in. (125 mm) and lock the position with nut (X) and cotter pin. 5. Adjust tension as above. A ONAY DO Change draper roller bearings every 500 hours REPLACING TENSION SPRING or annually. NOTE: When tightening locknuts on end of idler roller, torque to 30-45 ft.Ibs. (40-60 N-m) only. HYDRAULIC SYSTEM Hydraulic Hoses and Lines Check hydraulic hoses and lines daily for signs of leaks. WARNING: Avoid high-pressure fluids. Escaping fluid can penetrate the skin causing serious injury. Relieve pressure before disconnecting hydraulic lines. Tighten all connections before applying pressure. Keep hands and body away from pin-holes and nozzles which eject fluids under high pressure. Use a piece of cardboard or paper to search for leaks. IF ANY fluid is injected into the skin, it must be surgically removed within a few hours by a doctor familiar with this type of injury or gangrene may result. AVOID HIGH PRESSURE FLUIDS IMPORTANT: » Ensure all hydraulic couplings are fully engaged before operating header. * Keep hydraulic coupler tips and connectors clean. Dust, dirt, water and foreign material are the major causes of hydraulic system damage. + To prevent improper mixing of oils: If header is to be switched back and forth from combine to windrower, change oil in windrower tractor (or Bi-Directional Tractor) hydraulic system and in combine adapter hydraulic reservoir to match combine hydraulic system. CHECK PROPERLY FOR LEAKS 18 MAINTENANCE/SERVICE HYDRAULIC SYSTEM (continued) Hydraulic Oil Reservoir The combine adapter's hydraulic oil reservoir provides oil for the draper (and cross auger) drives. Check oil level daily (before start-up) at dipstick (A) . Maintain level between "LOW" and "FULL" marks. Tank Capacity - 25 litres (6.6 U.S. gallons), 3 additional litres (0.8 U.S. gallons) to fill filter, hoses, etc. Type - SAE 10W30 Class SF or CC Engine Oil Change hydraulic oil every 600 hours or 3 years. To drain the reservoir: 1. Remove dipstick cap (A). 2. Remove plug (B). NOTE: A drain pan with a capacity of 30 litres (8 U.S. gallons) will be required. Replace the hydraulic oil filter. See below. Replace plug (B) and fill the reservoir through filler neck. 5. Replace cap (A). > 9 Hydraulic Oil Filter Change hydraulic oil filter (C) after the first 100 hours operation and every 250 hours thereafter. To change: 1. Clean around the filter head. 2. Remove the filter and clean the gasket surface of the filter head. 3. Apply a thin film of clean oil to the gasket on the new filter. 4. Install the new filter. Turn the filter onto the mount until the gasket contacts the filter head. tighten the filter an additional 1/2 to 3/4 turn by hand. , IMPORTANT: Do not use a filter wrench to OIL FILTER install the filter. Over-tightening can damage gasket and filter. = 19 MAINTENANCE/SERVICE HYDRAULIC SYSTEM (continued) Flow Control Relief Pressure A possible cause of insufficient draper speed is low relief pressure. To check relief pressure: 1. Attach a 3000 psi (20 MPa) pressure gauge at red-coded male coupler (A) on combine adapter. Set flow control lever (B) to 6. Run combine engine at operating speed. Engage header drive. Pressure reading should be 2000 psi (13.7 Mpa) at 6 gallons/minute flow. п в оо ю If relief pressure requires adjustment: о о 1. Remove cap nut (С). He a 2. Turn relief screw until relief pressure is correct. FLOW CONTROL RELIEF ADJUSTME 6 a 10 “ha te EE Rr 3. Replace cap nut. A COMBINE ADAPTER FLOW CONTROL | a | | 7 GPM [ J 1 | PUMP | | а ——— 0-7GPM BLUE = mss | | 600 - 2000 PSI COUPLER id | COUPLER COUPLER M | MiF Ea — a SOF RELIEF VALVE SETTING: ha AUGER MOTOR A ones: J | 2000 PSI о ~— FILTER | | | | — TANK | | | | Y =o RIGHT DRAPER COMBINE ADAPTER HYDRAULIC SCHEMATIC LEFT DRAPER MOTOR MOTOR 20 MAINTENANCE/SERVICE CHAIN CASE Chain Tension Check chain tension after the first 10 hours operation and every 50 hours thereafter, as follows: 1. Remove rubber plug at (A). 2. Chain should deflect maximum 1 inch (25 mm). 3. If adjustment is required: a. Turn driveline by hand until chain is at its tightest. b. Loosen three bolts at top bearing flanges (B) (three per side). c. Adjust chain tension with bolts (C) to 1/4" (6 mm) deflection. IMPORTANT: To maintain proper alignment, turn both bolts (C) the number of turns when adjusting. 4. Replace plug (A). chain same Chain Lubrication Check chain lubrication every 100 hours or annually: 1. Remove rubber plug at (A). 2. Chain should be coated with a thin film of grease. 3. If required, add one 400 gram tube (14 oz.) of SAE Multi-Purpose Grease to the chain case. Case capacity is 2000 grams (five tubes). 4. Replace plug (A). Feeder Draper Driveline Slip Clutch An overhaul kit is available from your dealer for repair of slip clutch (D) on feeder draper driveline. NOTE: This repair Kit includes: * 8 cams * 8 springs * 1 seal ring Adjust the torque at which the clutch slips by adding or deleting springs. Add (or remove) springs in sets of two, across from each other. 8 springs should produce the recommended slip torque of 40-55 ftibs. (60-74 N-m) in the direction of rotation. Measure torque after clutch has slipped a minimum of 30 revolutions. IMPORTANT: Damage to feed draper may occur if 55 ft.Ibs. (74 N-m) is exceeded. 21 à a Page ie er en Lt Ha fe pc se ace 2 ED я Tee = a, а Te ETA = ле ЗН ran AER E RE Tes o Lo “он a o me net eg Feu ЕО O Rd AE ro Epa ie CHAIN TENSION & LUBRICATION ea . 3 HA ile 1 os Ea ee ES TE ES Mc TA 2 in mh fm mie dE Spa A ee E = =: = = ds E a Br RAPER SLIP CLUTCH MAINTENANCE/SERVICE MAINTENANCE SCHEDULE The following maintenance schedule is a listing of periodic maintenance procedures, organized by service intervals. For detailed instructions, see the specific headings in Maintenance/Service section. Use "Recommended Lubricants" as specified under that heading. Service Intervals The recommended service intervals are in hours of operation. Use the hour meter in the combine to indicate when the next service interval has been reached. IMPORTANT: Recommended intervals are for average conditions. Service the adapter more often if operated under adverse conditions (severe dust, extra heavy loads, etc.). Regular maintenance is the best insurance against early wear and untimely breakdowns. Following this schedule will increase machine life. Where a service interval is given in more than one time frame, eg. "100 hours or Annually”, service the machine at whichever interval is reached first. A CAUTION: Carefully follow safety messages given under "Service Procedures”. AT FIRST USE: See "Break-In Period" in Operation section. 10 HOURS OR DAILY 1. Grease chain case input driveline 2. Grease feeder draper driveline 3. Check hydraulic hoses, lines and components for leaks 4. Check hydraulic oil level at reservoir 50 HOURS 1. Check chain tension at chain case 100 HOURS OR ANNUALLY * . Grease chain case bearings 2. Grease cross auger bearing 3. Grease feeder draper drive roller Dearings 4, Lubricate chain at chain case * It is recommended that Annual Maintenance be done prior to start of operating season. ck, 250 HOURS 1. Change hydraulic oil filter 500 HOURS OR ANNUALLY 1. Change draper roller bearings. 600 HOURS OR 3 YEARS 1. Change hydraulic oil in reservoir 22 MAINTENANCE RECORD Adapter Serial No. Combine this record with the record in the Harvest Header Operator's Manual. See Maintenance/Service section for details on each procedure. Copy this page to continue record. ACTION: v - Check © - Lubricate Hour Meter Reading / Maintenance Serviced Procedure By: BREAK-IN See "Break-In Period" in Operation section for checklist. 10 HOURS or DAILY Chain Case Input Driveline Feeder Draper Driveline Hydraulic Hoses and Lines Hydraulic Oil Level 50 HOURS Adapter Chain Tension 100 HOURS OR ANNUALLY Chain Case Bearings Cross Auger Bearing Feed Draper Drive Roller Brgs Adapter Chain 250 HOURS Hydraulic Oil Filter 500 HOURS OR ANNUALLY Draper Roller Bearings 600 HOURS OR 3 YEARS raulic Oil 23 SYMPTOM HYDRAULICS Insufficient draper speed. FEEDING Cross auger back-feeds. Cross auger too high above feeder draper. TROUBLESHOOTING PROBLEM Speed control set too low. Relief pressure too low. Side drapers running too fast, piling material in center of feeder draper. Cross auger improperly positioned. Front drum of feeder housing improperly positioned. Build-up of material in corners due to slow draper speed. Dust shield on front of feeder house. Delivery opening panels on header do not align with feeder house opening. John Deere: Feeder chain running too slow. John Deere: Equipped with feeder chain with 4 pitches per bar. Case IH : Stone retarding drum installed. NH-TR: Stone ejection roll set too low. When cutting low, gauge wheel springs raise header with respect to feeder draper. * See your Combine Operator's Manual ** See your Combine Dealer *** See your Header Operators Manual 24 SOLUTION Increase contro! setting. Increase relief pressure to 2000 psi. Reduce draper speed. Position auger to clear backsheet extensions by 1/2 inch (13 mm). Move front drum forward and down. Increase draper speed Remove dust shield Install proper panels. Run feeder chain at high speed. Replace with 6 pitch per bar feeder chain, or remove every other bar. Install standard drum or fill slots in stone retard. drum. Adjust roll position. Remove one spring at each gauge wheel support. (Move remaining spring to center notch on clevis.) REF. 11 20 11 27 11 27 ЖЖ SYMPTOM FEEDING (continued) Cross auger blocks flow of bulky crop. Side drapers back-feed. Crop is thrown across opening and under opposite side draper. FLOTATION Combine feeder housing pushes dirt when trying to pick up down crop. Cutterbar does not float or pushes dirt. TROUBLESHOOTING PROBLEM Header angle too flat. Reel too far back. Cross auger too far forward. Side drapers running too slow in heavy crop. Side drapers improperly set with respect to feed draper. Side drapers running too fast in light crop. Excessive overlap of feeder draper. Feeder housing lowered too far, eliminating header float. Float too light, float links do not rest on stops. Float set too heavy. Float lock-out not disengaged. *** See your Header Operators Manual. 25 SOLUTION Steepen header angle. Move reel forward on support arms. Move auger back. Increase draper speed. Center side draper idler rollers over feed draper side deflectors. Reduce draper speed. Align side drapers with feeder house opening. Raise feeder housing until float linkage bottoms, change header to steeper angle to pick up down crop. Adjust to heavier float. Adjust to lighter float. Raise header, disengage float lock-out. REF. 12 Ed 27 11 26 11 26 13 12 12 ASSEMBLY Preparing for Combine Use IMPORTANT: To prevent damage to the combine and/or header hydraulic system: If combine adapter serial number 81800 or higher is to be used with header serial number 77400 or lower, the conveyor hydraulics on the header must be modified with the following parts: Header Size Case Drain Kit # Hydraulic Line 25 B 2369 37828 30 B 2369 37829 36 B 2369 — INSTALL HEADER SIDE DRAPERS 1. Connect side drapers. See the Adapter Mounting Instructions for your make of combine at the back of this book. See "Delivery Opening Width" In Header Operator's Manual for idler roller position adjustment procedure. IMPORTANT: Cut off any excess flap only after drapers have been connected and tensioned and overlap at sides of feed draper (A) deck has been checked (Step 2). 6 2. When properly installed, the header side draper idler rollers (R) should be centered 1 $ over the feed draper side deflectors (D) as shown. To check this, place a square on draper and measure dimension (X). It should be between 1 and 2 % inches (25 to 64 mm), DELIVERY OPENING both sides. NOTE: This is the setting for standing grain. For rice, set dimension (X) to between 3 and 4 inches (75 to 100 mm). RE-ROUTE HEADER SIDE DRAPER HOSES: 962 HEADERS ONLY 1. Loosen hose clamp (A) and remove hose (B) (with female coupler) from clamp. Position hose (C) (with male coupler) in clamp as shown. Tighten clamp (A). 2. For hose storage, pass hose (B) behind hoses routed along header back sheet as shown. Route hose from cross auger with male coupler through loop (E) and connect to hose (B). lee RE-ROUTE DRAPER HOSES: 962 HEADER 26 ASSEMBLY Preparing for Combine Use INSTALL DELIVERY OPENING PANELS (shipped with combine adapter) Install panels (C) both sides of delivery opening with 3/8 x 3/4 carriage bolts and nuts (2 per panel). NOTE: The purpose of the panels is to align header opening with the opening in combine feeder. For the following models, to achieve this it will be necessary to remove panel extensions from their storage position on panels (C) and reinstall in position (D) to provide narrower opening: John Deere 9500 , 7720 and CTS Case IH 1460 and 1660 Massey 860, 8570, and 8450 255 Ford New Holland TR INSTALL DELIVERY OPENING PANELS Claas 96 and 98 INSTALL TERRACE SKID PLATE (Rice Special Headers) Mount skid under chain case on the left hand side of the adapter with the hardware supplied. > de co CHAIN CASE | COMBINE ADAPTER LOWER BEAM ) REAR VIEW TERRACE SKID PLATE 27 ASSEMBLY Preparing for Combine Use INSTALL CROSS AUGER 1. Install lower mounting bolts for cross auger in left and right header legs. Left leg: (1) 1/2 x 1" hex head bolt (1) 3/16" thick flat washer (2) 1/2" lock washers Tighten bolt. Right leg: (1) 1/2 x 1" hex head bolt (1) 1/2" lock washer Leave bolt a few turns loose. Position auger in delivery opening and engage open-ended slots in auger supports on lower mounting bolts. NOTE: When completely installed, auger flighting should clear delivery opening panels by 1/2 inch (13 mm). See illustration (lower right) for proper slot in auger support to achieve this clearance. For most rearward position (Case, Gleaner, etc.) it may be necessary to loosen and reposition hoses to auger motor. Route hoses from auger motor through hole in back panel. Swing auger supports into place and install top mounting bolts. Left leq: same hardware as above. Right leq: same hardware as above. Use the hole which corresponds to the slot used at the bottom. Tighten both top bolts and R/H lower bolt. IMPORTANT: Left auger support is not clamped tightly to header leg (even when hardware is tight). This prevents a thrust load which could damage auger motor bearings. If left auger support is bearing on either of the 3/16" thick flat washers on the mounting bolts, a thrust load is indicated. If this is the case, install additional lock washers until there is a gap between the support and flat washer. Connect auger hose male coupler to female coupler at left header leg (orange to orange). Blue coupler (from header) and red coupler (from auger) will be connected to combine adapter, but can be coupled for storage. 28 A ao CROSS AUGER INSTALLATION - LEFT SIDE (PANELS REMOVED FOR PHOTO CLARITY) fa pu pe Нй : La == E CROSS AUGER INSTALLATION - RIGHT SIDE (PANELS REMOVED FOR PHOTO CLARITY) \ CASE À NC NH - TR & TX MF 6570 MF 8450 JOHN DEERE MF 460 ME 8&0 CLAAS MH with dust shield removed) GLEANER CHOOSE APPROPRIATE SLOT ASSEMBLY Preparing for Combine Use POSITION CHAIN CASE ON COMBINE ADAPTER 1. Remove pivot bolt (A) and swing chain case ; out to working position. Replace bolt (A). / PIVOT CHAIN CASE TO WORKING POSITION INSTALL FEEDER DRAPER ON COMBINE ADAPTER 1. Slide feeder draper in from rear of adapter, (2 D) ensuring belt on underside seats properly on — # à left side of both rollers. NX Вт Y 2. Position connector slats (D) as shown. Install ua | in screws (F) with heads leading in direction of `` - travel. L — — |] DIRECTION OF TRAVEL FEEDER DRAPER CONNECTION 3. Apply draper tension as follows: IMPORTANT: Do not turn nut (X) to adjust draper tension. | a. Loosen nut (N). oo 3/8 b. Turn bolt (B) counter-clockwise to tighten e 4 1/27 1] 10 mm draper until outside of bolt head lines up with dr === а —] Fe d f decal. (Di ions are shown for | | РА LA E IAN . Tighten nut (N). LO e- с Я. Repeat at other side. FEEDER DRAPER TENSION NOTE: If idler roller does not slide freely, loosen nut (P). 29 ASSEMBLY Preparing for Combine Use ATTACH ELECTRICAL HARNESS Attach electrical harness extension, (shipped with adapter) to your combine wiring harness. This allows connection to header harness for operation of amber lights on header. Dark Blue Wire: to L/H turn signal circuit Light Blue Wire: to R/H turn signal circuit Black Wire: to Ground NOTE: If combine will be used with Triple Delivery Header for end delivery windrowing, order B-2407 Harness and Support for deck shift switch. Installation instructions are included with the package. The deck shift switch is supplied with the Triple Delivery Header. ATTACH ADAPTER TO COMBINE IMPORTANT: For proper feeding: 1. Move combine feeder drum down and forward. 2. Remove feeder house dust shields if adapter feed deck is wider than feeder house opening. Attach combine adapter to feeder housing of combine. See Mounting Instructions for your particular make of combine on the following pages: John Deere - page 31 Claas & MF 8450/8460 - page 45 Case IH - page 35 MF 860 - page 48 Gleaner & White - page 38 MF 8570 Adapter Modification - page 51 New Holland - page 41 MF 8570 Adapter Mounting - page 55 ATTACH HEADER CAUTION: Read the Operator's Manuals carefully to familiarize yourself with procedures and controls before attaching header to combine. NOTE: Hydraulic hose lengths and couplings are provided based on the latest available information from combine manufacturers. Should these not be suitable for a particular model or production series, modify or purchase the necessary components. See page 6 for "Attaching Header to Combing”. See Harvest Header Operator's Manual for assembly instructions not related to the adapter. ADJUSTMENTS & CHECKS 1. Be sure header delivery opening is adjusted to align with combine feeder house opening width. 2. Check that rear of feeder deck moves up and down freely. 3. Run drapers slowly for 5 minutes to fill hydraulic lines, then check oil level at adapter reservoir. Perform final adjustments and checks as listed on the "Pre-Delivery Checklist” (yellow insert) in the Header Operator's Manual to ensure the machine is field-ready. Use the Operator's Manual for directions. 30 Adapter Mounting Instructions for John Deere Combines PREPARING THE COMBINE 1. For 7720, 9500 and CTS combines, check with Combine dealer to ensure combine is equipped with tire size, rear ballast etc. to carry larger headers. 2. Remove dust shield and optional feeder house closure strips (A) if installed. 3. Lock pin (B) both sides must be in retracted position before attaching adapter. E mE a RI 4. If combine is equipped with variable speed o uu. header drive, set header drive speed to 520 Gea NN sa RPM. REMOVE FEEDER HOUSE CLOSURE STRIPS ATTACHING ADAPTER TO COMBINE 1. Slowly drive combine up to adapter until lift lugs (C) are directly under lift pockets in adapter top cross member. NOTE: Shims can be added or removed under lugs (C) to level header. 2. Raise feeder house to lift adapter, ensuring lift lugs are properly engaged. Raise adapter fully. WARNING: To avoid bodily injury or death from unexpected start-up or fall of raised attachment; stop engine, remove key and engage lift cylinder stop before proceeding with hook-up. 3. Engage lock pins (E) in adapter brackets, both sides. ENGAGE LOCK PINS - BOTH SIDES 31 Adapter Mounting Instructions for John Deere Combines ATTACHING ADAPTER TO COMBINE (continued) 4. Attach driveline to feeder house output drive: 7720, 9500 & CTS a. Push shield (A) back to retracted position. Install chain (B) on both sprockets. c. Pull shield (A) forward to secure the chain in position. = 8820 & 9600 a. Remove snap ring and sprocket from adapter driveline. b. Attach telescoping coupler provided with feeder house. c. Install chain and secure with shield as above. NOTE: For 8820 and 9600 combines with wide feeder house, rubber shield attached to adapter cover may be removed. DANGER: Entanglement with rotating driveline will cause serious personal injury or death. Close adapter cover and keep all shields in place. 5. Adjust chain case height with three drawbolts (E) to level the driveline. 32 = 720 , 9500 & CTS ATTACH DRIVELINE © 8820 & 9600 ATTACH DRIVELINE ADJUST CHA mo 7 E IN CASE TO LEV E =; fes gt L do ret te DRIVELINE Adapter Mounting Instructions for John Deere Combines PREPARING THE HEADER 1. Attach reel lift hose (from adapter kit) to header hose (L) at left of delivery opening. Route reel lift hose behind reel drive hoses as shown. NOTE: 36' header is shown. For 21’, 25" & 30' headers the reel lift hose connects to hydraulic line at (D). Mount reel lift coupler support (F) to bracket on header frame tube with 3/8 NC x 3/4 carriage bolts and flange nuts as shown. 36' Header (with Ser. No. 108199 and below) on 9600 Combine only: Install hose extensions (and hose holder) from adapter package to reel drive pressure and return hoses as follows: Remove reel drive coupler support from frame tube. Detach couplers from reel drive pressure and return hoses. NOTE: Male coupler is on reel drive pressure line. Label hoses so couplers are not switched when extensions are installed. Attach hose extensions (G) to reel drive pressure and return hoses and route along frame tube to R/H header leg. Install hose holder (H). . Attach reel drive coupler support (J) at side of header R/H leg. Be sure male coupler is on reel drive pressure line. See step 2 b. NOTE: For other combinations of header size and combine model, hose extensions in adapter package are not used. . 21 ft. Header Only: Shorten header driveline before attaching to the combine adapter. To shorten: Separate the driveline. Male Shaft Half: Cut plastic shield tube at 590 mm (23-1/4") from center of cross and bearing. Cut steel shaft at 600 mm (23-5/8") from center of cross and bearing. Female Tube Half: Replace with shorter drive- line half, Part No. 40495, available from your MacDon dealer. Join the driveline. Collapsed length (center of cross to center of cross) should be 650 mm (25-21/32"). . Cut hole in plastic shield to expose grease fitting. a 5 E т aa ere Se За: EE F = or i a di - En er +. no : x ea REEL DRIVE HOSE EX one Ue Pra O Fite Hs E a о . В Le 36' HEADER ON 9600 COMBINE ONLY HEADER DRIVELINE ADAPTER DRIVE CASE FEEDER HOUSE le MODIFY HEADER DRIVELINE -21" ONLY Adapter Mounting Instructions for John Deere Combines PREPARING THE HEADER (continued) 4. Connect header side drapers as shown in the illustration below. Trim front corners at 45° as described in 960 Header Operator's Manual, Unloading & Assembly section. ) | | > 2 = \ \ ‘ JD MODELS 9600, 9500 8820, 7720, CIS SIDE DRAPER CONNECTION 34 Adapter Mounting Instructions for Case IH Combines PREPARING THE COMBINE 1. For 1460, 1660 and 1480 combines, check with Combine dealer to ensure combine is equipped with tire size, rear ballast etc. to carry larger headers. 2. For 36 foot header, install optional third feeder house lift cylinder. Order numbers: Feeder House Lift Cylinder Kit: Kind - 172, Code - 1092 Accumulator Kit: Kind - 172, Gode - 1084 3. Remove rubber dust shield in front of feeder housing. 4. Set feeder house face plate to mid-position. ATTACHING ADAPTER TO COMBINE 1. Slowly drive combine up to adapter until feeder saddle (C) is directly under adapter top cross member (D). 2. Raise feeder house to lift adapter, ensuring feeder saddle is properly engaged in adapter frame. Raise adapter fully. WARNING: To avoid bodily injury or death from unexpected start-up or fall of raised attachment; stop da engine, remove key and engage lift le 70208 et EG cylinder stop before proceeding ALIGN FEEDER SADDLE UNDER with hook-up. ADAPTER FRAME 3. Lower latch handle (E) (one each side of feeder house) to hook pivot bar (F). Lift handle to over-center position to lock. It should take 40 to 50 lbs. force (180 to 220 N) to move handle over-center. Adjusting the torque of bolts (G) will vary the handle force required. When handle force is correct, tighten jam nuts (K). 4. Install pin (H) as shown to secure the latch handle in locked position. ENGAGE LOCKS - BOTH SIDES 35 Adapter Mounting Instructions for Case IH Combines ATTACHING ADAPTER TO COMBINE (continued) 5. Remove driveline from storage bolt and attach to feeder house output shaft: a. Pull back spring-loaded collar on driveline yoke and slide yoke onto shaft. b. Release collar, ensuring yoke locks in position on shaft. DANGER: Entanglement with vs rotating driveline will cause serious х personal injury or death. Replace shield (A) over driveline and close ps gg Q OO. Ei adapter cover. SS OO nn se pea Y: + ATTACH DRIVELINE NOTE: For driveline storage, align cross as ET i A , E и : shown, pull back spring-loaded collar and store я on bolt (B). = rane 4 DRIVELINE STORAG PREPARING THE HEADER 1. 21, 25 & 30 ft. Headers: Reposition the reel drive couplers mounting plate (C) by rotating it up to align upper corner of plate with rear edge of R/H header leg within § mm (3/16"). R/H HEADER LEG — REPOSITION COUPLER MOUNTING PLATE 21", 25 E 30" HEADERS 36 Adapter Mounting Instructions for Case IH Combines PREPARING THE HEADER (continued) _ CUTTERBAR 2. Attach idler bar supports (F) to left and right = header decks with 3/8 x 3/4 carriage bolts si p-- (2-1/8") | | I | and nuts as shown. NOTE: If holes are not provided in deck support angle, drill 3/8 diameter holes at dimensions shown. If holes are field drilled, reverse hardware so square of carriage bolt Is properly seated. - ATTACH IDLER BAR SUPPORTS Position the support to keep idler bar parallel TO HEADER DECKS (R/H SHOWN) to, but not touching cutterbar. 3. Attach support (G) to left and right idler bar (H) (at front of long deck idler rollers) using 3/8 x 1 inch carriage bolt and nut as shown. NOTE: For Triple Delivery Headers, install support (G) after deck stop (J). These supports prevent the idler roller from lowering, which can cause draper damage. ATTACH SUPPORTS TO IDLER BARS (L/H SHOWN) 4. Connect header side drapers as shown in the illustration below. Trim front corners at 45° as described in 960 Header Operator's Manual, Unloading & Assembly section. CASE MODELS 2166, 1660, 1460— ——— Ш № / 1 14 Ч I 22 | & 1 \\ A \ А CASE MODELS 2188, 1680, 1480—— SIDE DRAPER CONNECTION 37 Adapter Mounting Instructions for Gleaner & White Combines PREPARING THE COMBINE 1. For K6, R60, and N6 combines, check with Combine dealer to ensure combine is equipped with tire size, rear ballast etc. to carry larger headers. 2. Rotate feeder house latches back into the feeder house. 3. Set feeder house face plate to mid-position. ATTACHING ADAPTER TO COMBINE 1. A Slowly drive combine up to adapter until feeder housing truss hooks (C) are directly under adapter top cross member. Raise feeder house to lift adapter, ensuring truss hooks are properly engaged in adapter frame. Raise adapter fully, allowing the lower pins to penetrate the holes in the adapter back. WARNING: To avoid bodily injury or death from unexpected start-up or fall of raised attachment; stop engine, remove key and engage lift cylinder stop before proceeding with hook-up. Insert concave door tool (E) in the latch socket (F) and rotate the latch clockwise to lock the hooks into the adapter frame (both sides). MAKE CERTAIN that the latch is rotated over-center to securely lock the hooks. If it does not latch, check to determine if the lower pins are seated in the adapter back. If not, place a block under the left end of the header and lower the header to reseat the pins. Relatch the hooks. Raise the adapter and lower it against the ground a few times to settle the adapter on the feeder housing. Remove driveline from storage pin and attach to feeder house output shaft: Pull back spring loaded collar on driveline yoke and slide yoke onto shaft (G) (above). Release collar, ensuring yoke locks in position on shaft. DANGER: Entanglement with rotating driveline will cause serious personal injury or death. Close adapter cover and keep all shields in place. NOTE: For driveline storage, pull back spring loaded collar and store on pin (B). Le Eat ER. Hr i wr - "= № - и bar wl ha EC Le Le, mn НЕ MRE SEE TAC lr A de Mad A a rico y ue Ca г Jn Cc all ALIGN TRUSS HOOKS DRIVELINE STORAGE 38 Adapter Mounting Instructions for Gleaner & White Combines PREPARING THE HEADER 1. 21, 25 € 30 ft. Headers: Reposition the reel drive couplers mounting plate (C) by rotating it up to align upper corner of plate with rear edge of R/H header leg within 5 mm (3/16. R/H HEADER LEG REPOSITION COUPLER MOUNTING PLATE 21', 25, 6 30 HEADERS (36) 2. Attach reel lift hose assembly (from adapter > = ; kit) to header as follows: a. Bolt coupler support (H) to angle on back of © header tube at location shown with 3/8 x 3/4 = 0 © carriage bolt and flange nut. b. 21, 25 & 30 ft. Headers: Attach other end of hose to reel lift line (D) at left of delivery | do DELIVERY opening. c. 36 ft. Header: Attach other end of hose to OPENING reel lift hose (E) at left of delivery opening. (21°, 25" & 30) ATTACH REEL LIFT HOSE ASSEMBLY 3. Attach idler bar supports (F) to left and right CUTTERBAR header decks with 3/8 x 3/4 carriage bolts К and nuts as shown. NOTE: If holes are not provided in deck support angle, drill 3/8 dia. holes at dimensions shown. If holes are field drilled, reverse hardware so square of carriage bolt is properly seated. Position the support to keep idler bar parallel to, but not touching cutterbar. ATTACH IDLER BAR SUPPORTS TO HEADER DECKS (R/H SHOWN) 4. Attach support (G) to left and right idler bar (H) (at front of long deck idler rollers) using 3/8 x 1 inch carriage bolt and nut as shown. NOTE: For Triple Delivery Headers, install support (G) after deck stop (J). These supports prevent the idler roller from lowering, which can cause draper damage. ATTACH SUPPORTS TO IDLER BARS (L/H SHOWN) 39 Adapter Mounting Instructions for Gleaner & White Combines PREPARING THE HEADER (continued) 5. Connect header side drapers as shown in the illustration below. Trim front corners at 45° as described in 860 Header Operator's Manual, Unloading & Assembly section. WHITE MODEL 2100 - fo / / \ “on \ —— GLEANER MODELS R72, R62, R70, R60 E R7, R6, N7, N6 SIDE DRAPER CONNECTION 40 Adapter Mounting Instructions for New Holland Combines PREPARING THE COMBINE 1. For TR86, TR87, TR88 and all TX model 3. Adjust to flattest table angle. combines, check with combine dealer to ensure combine is equipped with tire size, 4. Remove dust shields from front of feeder rear ballast etc. to carry larger headers. house. On TR combines, also remove feeder house closure strips. 2. For TR model combines, if equipped with variable speed header drive, set header drive speed to 580 RPM. PREPARING THE ADAPTER Swing chain case out to working position (P). If chain case has been removed, attach front bolt at (R) for TR combines and at (X) for TX combines. IMPORTANT: Damage to housing or drivelines may occur if housing is incorrectly mounted. ATTACHING ADAPTER TO COMBINE 1. Slowiy drive combine up to adapter until feeder saddle (C) is directly under adapter top cross-member (D). 2. Raise feeder house to lift adapter, ensuring feeder saddle is properly engaged in adapter frame. Raise adapter fully. WARNING: To avoid bodily injury or death from unexpected start-up or fall of raised attachment; stop engine, remove key and engage lift cylinder stop before proceeding ALIGN FEEDER SADDLE UNDE with hook-up. ADAPTER FRAME DE ; can 41 Adapter Mounting Instructions for New Holland Combines ATTACHING ADAPTER TO COMBINE (continued) 3. Raise eye bolt (E) up to feeder house. Turn eye bolt (E) until pin (F) on feeder house lines up with hole in eye bolt (E). 4, Install pin (F) through feeder house frame and eye bolt (E). Lock with hair pin (G). ; > i оо я : а as y я а $ 5 ENGAGE LOCK PINS - - BOTH SIDES (TX) ENGAGE LOCK PINS - BOTH SIDES TR) 5. Remove driveline from storage bolt (A) and attach to feeder house output shaft: a. Push button on driveline yoke and slide yoke onto shaft. b. Be sure yoke locks in position on shaft. NOTE: The button on the driveline must be aligned with the groove in the shaft. DANGER: Entanglement with rotating driveline will cause serious personal injury or death. Close driveline cover on adapter. ATTACH DRIVELINE 42 Adapter Mounting Instructions for New Holland Combines PREPARING THE HEADER HEADER DRIVELINE Se ADAPTER 1. 21 ft. Header Only: Shorten header driveline / DRIVE CASE before attaching fo the combine adapter. / FEEDER HOUSE To shorten: / a. Separate the driveline. b. Male Shaft Half: Cut plastic shield tube at 590 mm (23-1/4") from center of cross and bearing. Cut steel shaft at 600 mm (23-5/8") from center of cross and bearing. c. Female Tube Half: Replace with shorter drive- MODIFY HEADER DRIVELINE - line half, Part No. 40495, available from your 21" HEADER ONLY MacDon dealer. d. Join the driveline. Collapsed length (center of cross to center of cross) should be 650 mm (25-21/32"). e. Cut hole in plastic shield to expose grease fitting. — Ee —————— 2. 21, 25 & 30 ft. Headers: Reposition the reel drive couplers mounting plate (C) by rotating it up to align upper corner of plate with rear edge of R/H header leg within 5 mm (3/16"). REPOSITION COUPLER MOUNTING PLATE 21", 25 € 30 HEADERS 3. TR Combine: Attach reel lift hose from adapter package to hydraulic line (D) or hose (E) at left of delivery opening. TX Combine: Attach reel lift hose and coupler support from adapter package to header as follows: a. Bolt coupler support (H) to angle on back of header tube at location shown with 3/8 x 3/4 carriage bolt and flange nut. b. Mount coupling (A), supplied with TX Combine, onto support. c. Attach reel lift hose to coupling (A). ATTACH COUPLER SUPPORT TO HEADER | TX COMBINE ONLY A (367 d. 21, 25 & 30 ft. Headers: Attach other end of 5 hose to reel lift line (D) at left of delivery = © opening. © e. 36 ft. Header: Attach other end of hose to ® reel lift hose (E) at left of delivery opening. d DELIVERY : OPENING (21', 25' & 30) ATTACH REEL LIFT HOSE TO HEADER —. 43 Adapter Mounting Instructions for New Holland Combines PREPARING THE HEADER (continued) —_— 4. TR Combine: Attach idler bar supports (F) to left and right header decks with 3/8 x 3/4 carriage bolts and nuts as shown. NOTE: If holes are not provided in deck support angle, drill 3/8 diam. holes at dimensions shown. If holes are field drilled, reverse hardware so square of carriage bolt is properly seated. Position the support to keep idler bar parallel ATTACH IDLER BAR SUPPORTS to, but not touching cutterbar. TO HEADER DECKS (R/H SHOWN) TR COMBINE ONLY 5. TR Combine: Attach support (G) to left and & Va right idler bar (H) (at front of long deck idler | AT: rollers) using 3/8 x 1 inch carriage bolt and а nut as shown. SA NOTE: For Triple Delivery Headers, install (A) : = support (G) after deck stop (J). These supports prevent the idler roller from lowering, which can cause draper damage. 6. Connect header side drapers as shown in the illustration below. Trim front corners at 45° as described in 960 Header Operator's Manual, Unloading & Assembly section. S) ATTACH SUPPORTS TO IDLER BARS (L/H SHOWN) - TR COMBINE ONLY NH MODELS TRS7, TR87/ - TR96 & TR86 (1991 and after) | NH MODELS TR96, TR86 - (1990 and prior) # f as | | = i 4 + A Л NH MODELS TX68, TX36 — TX66, TX34 44 Adapter Mounting Instructions for Claas and MF 8450/8460 Combines PREPARING THE COMBINE 1. For Claas 98, 96 and MF 8450 combines, check with Combine dealer to ensure combine is equipped with tire size, rear ballast etc. to carry larger headers. 2. Add third header lift cylinder, if required. ATTACHING ADAPTER TO COMBINE 1. Slowly drive combine up to adapter until lift lugs on combine are directly under lift pockets (A) in adapter top cross member, e 3 ives в Fels an SE 8 о — o i E = Tn Frans о Но ЗЫ Eo o Te o to AE Ne o o "ALIGN LIFT LUGS UNDER ADAPTER FRAME. 2. Raise feeder house to lift adapter, ensuring lift lugs are properly engaged. Raise adapter fully. “e SE To ue me ep poe TEE A E o Tu eo rs WARNING: To avoid bodily injury or death from unexpected start-up or fall of raised attachment; stop engine, remove key and engage lift cylinder stop before proceeding with hook-up. o iene tin == me BOLO RE ARE SE Ж2 5 3. Engage lock pins (B) in adapter brackets, and install hair pin (C), both sides. ENGAGE LOCK PINS - BOTH SIDES 45 Adapter Mounting Instructions for Claas and MF 8450/8460 Combines ATTACHING ADAPTER TO COMBINE (continued) 4. Attach driveline (D) to feeder house output shaft: Push button on driveline yoke and slide yoke onto shaft. Be sure yoke locks in position on shaft. DANGER: Entanglement with rotating driveline will cause serious personal injury or death. Close driveline cover on adapter. ATTACH DRIVELINE PREPARING THE HEADER 1. Attach reel lift hose from adapter package to hydraulic line at left of delivery opening. Install hose extensions from adapter package to reel drive pressure and return hose quick couplers at header R/H leg. 21 ft. Header Only: Shorten header driveline before attaching to the combine adapter. To shorten: Separate the driveline. Male Shaft Half: Cut plastic shield tube at 590 mm (23-1/4") from center of cross and bearing. Cut steel shaft at 600 mm (23-5/8") from center of cross and bearing. Female Tube Half: Replace with shorter drive- line half, Part No. 40495, available from your MacDon dealer. . Join the driveline. Collapsed length (center of cross to center of cross) should be 650 mm (25-21/32"). Cut hole in plastic shield to expose grease fitting. 46 HEADER DRIVELINE ADAPTER DRIVE CASE FEEDER HOUSE 7 e MODIFY HEADER DRIVELINE - 21 HEADER ONLY Adapter Mounting Instructions for Claas and MF 8450/8460 Combines PREPARING THE HEADER (continued) 4. Connect header side drapers as shown in the illustration below. Trim front corners at 45° as described in 960 Header Operator's Manual, Unloading & Assembly section. CLAAS MODELS 108, 98 106, 96 Fo b E E a ее Il r a a E 6 Bo oD | E = Mi -— MASSEY MODELS 5460, 8450 —— SIDE DRAPER CONNECTION MAINTENANCE Adapter drive chain tension adjustment is different than as shown in Adapter Operator's Manual. Inspect chain by removing rubber plug in drive case. Maximum chain deflection is 1 in. (25 mm). To adjust chain tension: 1. Loosen nut on idler mounting bolt (A). 2. Turn nut (B) clockwise to increase chain tension. 3. Tighten nut on bolt (A) to secure the position. ADAPTER CHAIN TENSION ADJUSTMENT 47 Adapter Mounting Instructions for Massey Ferguson 860 Combine ATTACHING ADAPTER TO COMBINE 1. Slowly drive combine up to adapter until lift lugs (C) are directly under notched lift brackets on adapter top cross member. 2. Raise feeder house to lift adapter, ensuring lift lugs are properly engaged. Raise adapter fully. WARNING: To avoid bodily injury or death from unexpected start-up or fall of raised attachment; stop engine, remove key and engage lift cylinder stop before proceeding with hook-up. [EL ОР == A a raiz ALIGN LUGS UNDER ADAPT Ea PF Ci ER E PA FRAME 3, Position bottom lock pins (E) in adapter frame and raise handle (F) to lock in position, Install retaining pin (G). 4. Attach driveline, with adapter (H), to feeder house output shaft. Be sure spring loaded pin (J) engages groove In driveline shaft. DANGER: Entanglement with rotating driveline will cause serious personal injury or death. Close adapter cover and keep all shields in place. ATTACH DRIVELINE 48 Adapter Mounting Instructions for Massey Ferguson 860 Combine PREPARING THE HEADER 1. Attach reel lift hose from adapter package to hydraulic line at left of delivery opening. 21 ft. Header Only: Shorten header driveline before attaching to the combine adapter. To shorten: Separate the driveline. Male Shaft Half: Cut plastic shield tube at 590 mm (23-1/4") from center of cross and bearing. Cut steel shaft at 600 mm (23-5/8") from center of cross and bearing. Female Tube Half: Replace with shorter drive- line half, Part No. 40495, available from your MacDon dealer. . Join the driveline. Collapsed length (center of cross to center of cross) should be 650 mm (25-21/32"). Cut hole in plastic shield to expose grease fitting. HEADER DRIVELINE ADAPTER DRIVE CASE FEEDER HOUSE MODIFY HEADER DRIVELINE - 21 HEADER ONLY . Connect header side drapers as shown in the illustration below. Trim front corners at 45° as described in 960 Header Operater's Manual, Unloading & Assembly section. / ( MASSEY MODEL 860 SIDE DRAPER CONNECTION Adapter Mounting Instructions for Massey Ferguson 860 Combine MAINTENANCE Adapter drive chain tension adjustment is different than as shown in Adapter Operators Manual, Inspect chain by removing rubber plug in drive case. Maximum chain deflection is 1 in. (25 mm). To adjust chain tension: 1. Loosen nut on idler mounting bolt (A). 2. Turn nut (B) clockwise to increase chain tension. 3. Tighten nut on bolt (A) to secure the position. 50 Modification to Case Adapter to fit Massey 8570 Combine NOTE: Steps 1 and 2 are required for Case adapters with serial numbers below 78150. For adapters with serial numbers above 78150, go to step 3. la DRILL 0.53" DIA. a. Remove bolt (J) and pivot chain case forward to expose left end of adapter frame. b. Drill a 0.53 inch hole in left end of adapter frame, located as shown. c. Cut away sufficient material from chain case at (L) and from left end of adapter frame at (M) to allow chain case to be pivoted enough to install bolt (J) in new hole. INSTALL CHAIN CASE IN NEW POSITION a. Remove feeder draper deck. b. Remove sheet metal plugs over U-bolts (D). Remove U-bolts (D) from adapter frame. c. Salvage pivot bar (K) from U-bolts. Discard the U-bolts and nuts. d. Replace feeder draper deck. NOTE: Step 3 is required for Case adapters with serial numbers above 78150. For adapters with serial numbers below 78150, go to step 4. e EE EE Е 3. Salvage pivot bar (K) and 5/8 NC jam nuts Eno. ee, from 5/8 NC x 4 1/2 long bolts. Discard bolts. REMOVE BOLTS AND PIVOT BAR 51 Modification to Case Adapter to fit Massey 8570 Combine . Clamp adapter mounting bracket (B) and deflector (C) from kit to top of adapter frame (A). Drill holes as shown. . Install deflector (C) with 3/8 NC x 3/4 long carriage bolts and flange nuts. . Install L-bolts (E) from modification kit onto sub-frame. Install 5/8 jam nuts and pivot bar (K) (salvaged previously) and secure with 5/8 nuts and lock washers from modification kit. . Install 5/8 NC x 1-1/2 long carriage bolt, flat washer, lock washer and hex nut in the two new holes drilled In step 4a. DRILL Ye — 7 HOLES (4) INSTALL BOLTS THIS SIDE DRILL MOUNTING HOLES IN CASE ADAPTER TO, IE a 7 TR ee A mr A ee a dono en pi PE Ea ses 6% Fine Hee EE г a an wa e e ни BOLT SUB-FRAME TO CASE ADAPTER FRAME INSTALL L-BOLTS AND PIVOT BAR 52 5. Modification to Case Adapter to fit Massey 8570 Combine NOTE: Depending on the serial number of your Case adapter, complete the following steps: Serial numbers below 78150: Steps a., b., and c. a. Remove and salvage male quick coupler and cap (J) on the end of return hose (F). Remove and discard hose (F) from chain case, . Attach longer hose (F) complete with coupler and cap from 8570 adapter bag. Install male coupler and cap (salvaged in step a) on reel pressure hose (see Header Manual). NOTE: Go to Step i. Serial numbers 78150 to 82855: Steps d. and e. d. Remove and salvage male quick coupler from hose in Case adapter bag. Install this coupler on reel return hose (see Header Manual). Remove and salvage male coupler and cap from hose in 8570 adapter bag. Install on reel pressure hose (see Header Manual). NOTE: Go to Step i). Serial numbers above 82885: see page 54. 53 REPLACE HOSE (SERIAL NUMBERS BELOW 78150) Modification to Case Adapter to fit Massey 8570 Combine 5. (continued) Serial numbers above 82885: Steps f., g., and h. f. Install reel lift hose (A) from Case adapter bag onto reel lift line at left of delivery opening on header. . Remove three hoses from lines on back of Case adapter. Install long hose (B) at right end of line (D). This will now become part of the reel lift circuit. . Install two male quick couplers (C) from 8570 adapter bag on the two short hoses removed in step g). (To match 8570 combine colour coding, install the quick coupler with blue cable tie on the hose with the male coupler at the opposite end.) Connect these hoses to header reel drive pressure and return lines as shown. NOTE: Go to step |i. REEL PRESSURE — ~~ REEL RETURN HEADER g | | ADAPTER В НОЗЕ (В — — — »E HOSE (8) FROM / HERE LINE NOT USED — HYDRAULICS MODIFICATIONS: SERIAL NO. ABOVE 82885 COMBINE veLLow— | ый BLUE All serial Numbers: Steps 1. and ]. Replace 1-1/8" hex feeder house driveline yoke (H) on chain case drive shaft with 1-1/4" hex yoke from modification Kit. Shorten driveline (H) to dimensions shown so it can be installed with chain case in field position. NOTE: Following items from Adapter bags are not required for 8570: Below S.N. 78150 - female coupler in Case Adapter bag. S.N. 78150 to 82885 - Hose (from step 5d) and female coupler in Case Adapter bag. - Hose (from step 5e) in 8570 Adapter bag. Above S.N. 82885 - Hose in 8570 Adapter bag and one hydraulic line on back of Case Adapter. clamp yoke — >| 4-3/4 on chain case + 6-7/8" (175 mm * (feeder house end) SHORTEN DRIVELINE SEE PAGE 55 FOR HOOK-UP 54 Adapter Mounting Instructions for MF 8570 Combines PREPARING THE COMBINE 1. Check with Combine dealer to ensure combine is equipped with tire size, rear ballast etc. to carry larger headers. 2. For 36 foot header, install optional third feeder house lift cylinder. See Combine dealer for kit. 3. Remove rubber dust shield in front of feeder housing. ATTACHING ADAPTER TO COMBINE 1. Modify adapter according to Instruction beginning on page 51. 2. Slowly drive combine up to adapter until feeder saddle (C) is directly under adapter top О cross member (D). fil 3. Raise feeder house to lift adapter, ensuring feeder saddle is properly engaged in adapter frame. Raise adapter fully. WARNING: To avoid bodily injury of = An" discus death from unexpected start-up or fall of raised attachment; stop engine, remove key and engage lift a > ss cylinder stop before proceeding ALIGN FEEDER SADDLE UNDER with hook-up. ADAPTER FRAME A ; = e. = * 4. Engage pivot bar on adapter frame into latch at (E), both sides. Pull up on latch lever and / | lock over-center. / ENGAGE LATCH - BOTH SIDES 55 Adapter Mounting Instructions for MF 8570 Combines ATTACHING ADAPTER TO COMBINE (continued) a Attach driveline to feeder house output shaft: a. Align hole in shaft with hole in yoke and slide yoke onto shaft. b. Install 5/16 NC x 3 bolt (F) supplied with modification kit. DANGER: Entanglement with rotating driveline will cause serious personal injury or death. Close adapter cover. EA OE ea E. За ee по. eee crc RE egy EE gra ATTACH DRIVELINE (SERIAL # BELOW 78150 - ATTACH HOSE TO COMBINE RETURN) NOTE: Step 6 applies only to adapters with serial number below 78150. 6. Connect the non colour-coded hydraulic hose (G) (from tee fitting at flow control on adapter) to blue colour-coded combine return coupler (H) on right hand side of feeder. IMPORTANT: This coupler must be fully connected before engaging drive. FAILURE TO DO SO MAY DAMAGE MOTOR AND PUMP SEALS. NOTE: The rest of the hydraulic connections are header to combine or header to adapter. See 7 ENT EN "Attaching Header to Combine and Adapter" in . NS the Operator's Manual and use the hose colour- as ai coding as a guide. SERIAL # BELOW 78150 - ATTACH HOSE TO COMBINE RETURN H this adapter is being used with a fixed center- delivery Harvest Header (no shiftable decks), remove hose clamp from the yellow coded hose on adapter to provide adequate length for attachment to hose on header. NOTE: Hydraulic hose lengths and couplings are provided based on the latest available information from combine manufacturers. Should these not be suitable for a particular model or production series, modify or purchase the necessary components. 56 Adapter Mounting Instructions for MF 8570 Combines PREPARING THE HEADER 1. 21. 25 & 30 ft. Headers: Reposition the reel drive couplers mounting plate (C) by rotating it up to align upper corner of plate with rear „” edge of R/H header leg within 5 mm (3/16"). sd R/H HEADER LEG REPOSITION COUPLER MOUNTING PLATE 21,25 E 30 HEADERS CUTTERBAR 2. Attach idler bar supports (F) to left and right — a E: | | header decks with 3/8 x 3/4 carriage bolts o] | and nuts as shown. NOTE: If holes are not provided in deck support angle, drill 3/8 diam. holes at dimensions shown, If holes are field drilled, reverse hardware so square of carriage bolt Is properly seated. Position the support to keep idler bar parallel to, but not touching cutterbar. ATTACH IDLER BAR SUPPORTS TO HEADER DECKS (R/H SHOWN) 3. Attach support (G) to left and right idler bar (H) (at front of long deck idler rollers) using 3/8 x 1 inch carriage bolt and nut as shown. NOTE: For Triple Delivery Headers, install support (G) after deck stop (J). These supports prevent the idler roller from lowering, which can cause draper damage. A ATTACH SUPPORTS TO IDLER BARS (L/H SHOWN) 57 Adapter Mounting Instructions for MF 8570 Combines PREPARING THE HEADER (continued) 4. Connect header side drapers as shown in the illustration below. Trim front corners at 45° as described in 960 Header Operator's Manual, Unloading & Assembly section. N | = MASSEY MODEL 8570 1 SIDE DRAPER CONNECTION 58 A PAGE Adapter Mounting Instructions: BABE lA. y as ea ys gua da Gu mae os 35 CLAAS € MF 8450/8460 .......... 45 GLEANER ........e.ereseoei o 38 JOFIN DEERE .. i: aca me ca aaa a 31 МЕ 860 ...................... 48 MF 8570. Adapter Modification . . . . .. 51 MF 8570: Adapter Mounting . . ...... 55 NEWHOLLAND ................ 41 WHITE ......... ... remera 38 Assembly ............. 2... . 0 26 Attaching Header and Adapter to Combine 10 Attaching Header to Combine and Adapter 6 B Bearing Installation ................ 15 Break-In Period - 10 ox wan on à va voi #б 11 с Capacities, Enclosed Drive . . . ........ 15 Chain Case Maintenance ............ 21 D Delivery Opening Width ............. 26 Detaching Header and Adapter fromCombine................... 9 Detaching Header from Combine and Adapter ........... o ee.ee... 8 Draper Speed Control .............. 11 Draper Speed Flow Control Relief Pressure . . ............... 20 F Feeder Draper ................... 18 Feeder Draper Driveline Slip Clutch ной | G Gauge Wheel Position .............. 13 Greasing the Adapter ............... 16 59 H Header Angle Control .............. 13 Header Flotation .................. 12 Hydraulic Hoses and Lines . .......... 18 Aydranie: OUFIÉSE.. 5. x x » on mmo scans ws 19 Hydraulic Oil Reservoir ............—. 19 Hydraulic Schematic ............... 20 Hydraulic System Safety ............ 18 L Lubricants, recommended ........... 15 M Maintenance Record . .............. 23 Maintenance Schedule .............. 22 P Preparing for Combine Use ......... . 26 5 Safety Alert Symbol... ................ 4 Hydraulic System ............... 18 Service Procedures , . ............ 14 SignalWords .................. 4 Signs . Lo... в квн квн) 5 Serial Number Location ............. 3 Service Procedures ............... . 14 Specifications ................... i 9 x Terrace Skid Plate (Rice Header) ...... 27 Trouble Shooting Feel 2-17 sun oven so ME BE БИЯ . 24 Flotation. « += mess mans où © 08 fr NO 25 HydreulS = cies sam suv ox came owns 24 EN Macdon The Quiet Leader 46050 Issue 9/97 Sugg. Retail: $10.00 Printed in Canada
advertisement
Key Features
- Self-tracking draper
- Adjustable header angle
- Combine compatibility
- Hydraulic drive
- Heavy-duty construction
Related manuals
Frequently Answers and Questions
How do I adjust header float?
You can adjust the header float using bolts on the combine adapter. Turning them clockwise increases float, making the header lighter, while turning them counter-clockwise decreases float, making it heavier.
What is the recommended header angle?
The flattest header angle (13°) is recommended for most conditions. However, you can adjust the angle to between 13° and 16° depending on the crop and terrain.
How do I change the draper speed?
Draper speed is adjusted using the flow control lever on the combine adapter. Move the lever clockwise to increase speed and counter-clockwise to decrease speed.