advertisement
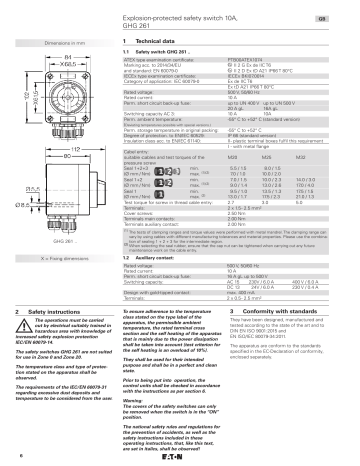
Dimensions in mm
GHG 261 ..
X = Fixing dimensions
2 Safety instructions
a The operations must be carried out by electrical suitably trained in hazardous area with knowledge of increased safety explosion protection
IEC/EN 60079-14.
The safety switches GHG 261 are not suited for use in Zone 0 and Zone 20.
The temperature class and type of protection stated on the apparatus shall be observed.
The requirements of the IEC/EN 60079-31 regarding excessive dust deposits and temperature to be considered from the user.
Explosion-protected safety switch 10A,
GHG 261
GB
1 Technical data
1.1 Safety switch GHG 261 ..
ATEX type examination certificate:
Marking acc. to 2014/34/EU and standard: EN 60079-0
IECEx type examination certificate:
Category of application: IEC 60079-0
Rated voltage:
Rated current:
Perm. short circuit back-up fuse:
Switching capacity AC 3:
Perm. ambient temperature:
Degree of protection. to EN/IEC 60529:
Insulation class acc. to EN/IEC 61140:
Cabel entry: suitable cables and test torques of the pressure screw
Seal 1+2+3
(Ø mm / Nm)
1
2 3 min. max. (1)(2)
PTB00ATEX1074
D II 2 G Ex de IIC T6
D II 2 D Ex tD A21 IP66 T 80°C
IECEx BKI07.0014
Ex de IIC T6
Ex tD A21 IP66 T 80°C
500 V, 50/60 Hz
10 A up to UN 400 V up to UN 500 V
20 A gL
10 A
M20
16A gL
10A
-55° C to +52° C (standard version)
(
Deviating temperatures possible with special versions.)
Perm. storage temperature in original packing: -55° C to +52° C
IP 66 (standard version)
II - plastic terminal boxes fulfil this requirement
I - with metal flange
5.5 / 1.5
7.0 / 1.0
M25
8.0 / 1.5
10.0 / 2.0
M32
Seal 1+2
(Ø mm / Nm)
Seal 1
(Ø mm / Nm)
1
1
2
2
3
3 min. max. min. max.
(1)(2)
(2)
Test torque for screw in thread cable entry:
Terminals:
Cover screws:
Terminals main contacts:
Terminals auxiliary contact:
7.0 / 1.5
9.0 / 1.4
9.5 / 1.0
13.0 / 1.7
2.7
2 x 1.5 - 2.5 mm²
2.50 Nm
2.00 Nm
2.00 Nm
10.0 / 2.3
13.0 / 2.6
13.5 / 1.3
17.5 / 2.3
3.0
14.0 / 3.0
17.0 / 4.0
17.5 / 1.5
21.0 / 1.3
5.0
(1)
The tests of clamping ranges and torque values were performed with metal mandrel. The clamping range can vary by using cables with different manufacturing tolerances and material properties. Please use the combination of sealing 1 + 2 + 3 for the intermediate region.
(2)
When selecting the seal rubber, ensure that the cap nut can be tightened when carrying out any future maintenance work on the cable entry.
1.2 Auxiliary contact:
Rated voltage:
Rated current:
Perm. short circuit back-up fuse:
Switching capacity: 400 V / 6.0 A
230 V / 0.4 A
Design with gold-tipped contact:
Terminals:
500 V, 50/60 Hz
10 A
16 A gL up to 500 V
AC 15 230V / 6.0 A
DC 13 24V / 6.0 A max. 400 mA
2 x 0.5 - 2.5 mm²
To ensure adherence to the temperature class stated on the type label of the apparatus, the permissible ambient temperature, the rated terminal cross section and the self heating of the apparatus that is mainly due to the power dissipation shall be taken into account (test criterion for the self heating is an overload of 10%).
They shall be used for their intended purpose and shall be in a perfect and clean state.
Prior to being put into operation, the control units shall be checked in accordance with the instructions as per section 6.
Warning:
The covers of the safety switches can only be removed when the switch is in the “ON” position.
The national safety rules and regulations for the prevention of accidents, as well as the safety instructions included in these operating instructions, that, like this text, are set in italics, shall be observed!
3 Conformity with standards
They have been designed, manufactured and tested according to the state of the art and to
DIN EN ISO 9001:2015 and
EN ISO/IEC 80079-34:2011.
The apparatus are conform to the standards specified in the EC-Declaration of conformity, enclosed separately.
6
Fig. 2
Apparatus holder size 1 for wall and trellis fixing
C
C
Fig. 1
Apparatus holder size 1 for pipe fixing
C = screw fixing points for safety switch
GHG 261, 10A
Fig. 3
Wiring diagram
Explosion-protected safety switch 10A,
GHG 261
GB
4 Field of application
The safety switches GHG 261 are intended for use in potentially explosive atmospheres in
Zones 1 and 2 as well as in Zones 21 and 22 in accordance with IEC/EN 60079-10-1 and
IEC/EN 60079-10-2.
The enclosure materials used, including any external metal parts, are high quality materials that ensure a corrosion resistance and resistance to chemical substances according to the requirements for use in a ”normal industrial atmosphere”:
– impact resistant polyamide
– special steel AISI 316 L.
For use in an extremely aggressive atmosphere, please contact your Cooper Crouse-
Hinds agent for additional information on the chemical stability of the plastics used.
5 Application / Properties
The safety switches are designed for the safe isolation of the electrical energy at all poles while maintenance, cleaning and repair work is being carried out on equipment, machinery and drives in potentially explosive atmospheres.
See technical data, page 6, for the temperature class, explosion group and permissible ambient temperature.
Due to the AC 3 motor switching capacity of the safety switches, reliable isolation
(switching) is also possible during operation.
In addition to this, the safety switches are so designed, that they also switch off the drive, e.g. via the contactor that precedes the auxiliary contact. In relation to the main contacts, this auxiliary contact is lagging while making and leading while breaking.
Versions with gold-tipped auxiliary contacts are suited for switching extra-low voltage circuits.
Special attention shall be paid to the maximum current load (see technical data, page 6). The contact chamber of the gold-tipped version is marked with the letter ”G” or colour-coded.
Due to the mechanical design of the safety switch, compulsory opening of the contacts is possible.
The safety switches fulfil the isolating properties according to IEC/EN 60947-3.
The ”EMERGENCY-STOP“ version conforms to the requirements of IEC/EN 60204-1.
To prevent unauthorized switching, the switches can be locked in the ”OFF“ position by means of 3 padlocks, see fig. 1, (shackle diameter of the padlocks up to 4 to 6 mm).
A built-in locking device prevents the opening of the enclosure in the ”OFF“ position.
The data according to sections 3 and 4 shall be taken into account during use.
Applications other than those described are not permissible without a written declaration of consent from Messrs. COOPER
Crouse-Hinds.
During operation the instructions stated in section 7 of the operating instructions shall be observed.
The sole responsibility with respect to the suitability and proper use of the control switches with regard to the basic requirements of these instructions (see technical data) lies with the operator.
6 Installation
The relevant national regulations(e.g. Elex V, the equipment safety law for Germany) and the generally recognized rules of engineering apply for the installation and operation
(IEC/EN 60079-14).
The improper installation and operation of safety switches may result in the invalidation of the guarantee.
6.1 Mounting
Before mounting the safety switch, the cover has to be removed from the enclosure base.
For this, the switch has to be set to the ”ON“ position.
When the safety switches are mounted directly onto the wall, they shall rest evenly only on the fastening points provided for this purpose.
The screw chosen shall fit the fixing hole (see dimensional drawings, page 6) and shall not damage the hole (e.g. use of a washer).
The apparatus shall be fixed diagonally with a minimum of 2 screws.
If the screws are overtightened, the apparatus may be damaged.
The safety switches GHG 261 are suited for mounting on CEAG apparatus holders size 1 by means of self-cutting screws (see fig. 2).
See the respective mounting instructions.
6.2 Opening apparatus /
Electrical connection
The electrical connection of the apparatus may only be carried out by specialists
(IEC/EN 60079-14).
Before opening the apparatus, ensure that it has been isolated from the voltage supply or to take suitable protective measures.
Before opening, set the switch to the ”ON“ position.
7
Explosion-protected safety switch 10A,
GHG 261
GB
Fig. 4
External earth connection
Inner wall of the enclosure
Internal earth plate
Internal earth connection
The properly bared conductors of cables shall be connected with due regard to the respective regulations.
To maintain the explosion protection, conductors shall be connected with special care.
The insulation shall reach up to the terminal.
The conductor itself shall not be damaged.
The minimum and maximum conductor cross sections that can be connected shall be observed (see technical data).
All screws and / or nuts of connection terminals, including those not in use, shall be tightened down securely.
Excessive tightening may affect or damage the connection.
The standard terminals are designed for the direct connection of conductors with copper wires.
If multi- or fine-wire connection cables are used, the wire ends shall be handled according to the applicable national and international regulations (e.g. use of multicore cable ends).
The position of the connection terminals is shown in the wiring diagrams on the switch base and in fig. 3 on page 7 of the operating instructions.
To ensure that the safety switch closes correctly, switching at the switch shaft of the switch insert is not permitted when the apparatus is open.
If, to facilitate the feeding of conductors into the enclosure, the switch insert is removed from the enclosure base, it shall be put back correctly before the electrical connection is made.
6.3 Cable entries (KLE); blanking plugs
Generally only certified cable entries and blanking plugs may be used.
Flexible cables shall be used with trumpetshaped cable glands or other suitable entries with additional pull relief.
When using cable entries with a degree of protection that is lower than the IP protection of the apparatus (see page 6), the degree of IP protection for the complete unit is reduced.
The relevant mounting directives for cables entries being used shall be observed.
In order to ensure the minimum degree of protection, any unused entry holes shall be sealed with certified blanking plugs.
When fitting cable entries, care has to be taken that the sealing inserts are suitable for the cable diameter. In the case of sealing inserts that are cut out, it is necessary to ensure that the insert is properly adapted to the cable diameter.
In order to ensure the required minimum degree of protection, the cable entries shall be tightened down securely.
Overtightening can impair the degree of protection.
Warning: When tightening the cap nut of the metal cable entry (e.g. type ADL/ADE),a suitable tool shall be used to safeguard the gland against twisting.
Any unused metric CEAG cable entries shall be sealed with the blanking plug certified for these metric cable entries.
6.4 Metal plates and external earth connection
In case an external earth connection is mounted on the plastic enclosure, it should be connected with a max. 25mm² wire.
This earth connection is inserted through a M6 drill in the inner wall of the enclosure (see fig. 4).
The standard terminals are designed for the direct connection of conductors with copper wires.
Warning: Metal plates and metal glands shall be incorporated in the potential equalization.
6.5 Closing apparatus
Any foreign matter shall be removed from the apparatus.
The switch handle on the cover of the switch is to be set to the "ON" position.
When fitting the apparatus cover, care shall be taken to ensure that the switch shaft of the switch insert engages correctly in the carrier hole of the switch handle.
To ensure the required minimum degree of protection, the cover screws shall be tightened down.
Overtightening may impair the degree of protection.
6.6 Putting into operation
Before putting the apparatus into operation, the tests specified in the individual national regulations shall be performed.
In addition to this, before being put into operation, the correct functioning of the apparatus and installation of the apparatus shall be checked in accordance with these operating instructions and other applicable regulations.
The improper operation of safety switches may result in the invalidation of the guarantee.
7 Maintenance / Servicing
The valid national regulations for the servicing / maintenance of electrical apparatus for use in potentially explosive atmospheres shall be observed
(IEC/EN 60079-17).
Prior to opening the enclosure, it is necessary to ensure that the voltage supply has been isolated or to take suitable protective measures.
The necessary intervals between servicing depend upon the specific application and shall be stipulated by the operator according to the respective operating conditions.
During servicing, special attention shall be given to checking the parts on which the explosion protection depends (e.g. intactness of the flameproof components, the enclosure, the seals and cable entries).
If, in the course of servicing, it is ascertained, that repairs are necessary, section 8 of these operating instructions shall be observed.
8 Repairs / Overhaul /
Modifications
Only original COOPER Crouse-Hinds parts shall be used for carrying out repairs.
In the event of damage to the flameproof encapsulation, replacement of these components is mandatory. In case of doubt, the respective apparatus shall be sent to
COOPER Crouse-Hinds for repair.
Repairs that affect the explosion protection may only be carried out by COOPER
Crouse-Hinds or by a qualified electrician in compliance with the respective national regulations (IEC/EN 60079-19).
Modifications or changes to the safety switches are not permitted.
9 Disposal / Recycling
The respective valid national regulations for waste disposal shall be observed when disposing of apparatus.
To facilitate the recycling of individual parts, parts made of moulded plastic shall bear the marking for the type of plastic used.
The product range is subject to changes and additions.
8
advertisement
* Your assessment is very important for improving the workof artificial intelligence, which forms the content of this project
Related manuals
advertisement