Buhler EGK 4S Installation And Operation Instructions Manual
Add to my manuals
26 Pages
Buhler EGK 4S is an industrial sample gas cooler designed to prepare gas samples for analysis in industrial gas analysis systems. It accomplishes this by removing residual moisture from the gas sample before it enters the analysis instrument, thereby protecting the instrument from damage. The device comes in different types depending on material combinations, pressure and temperature limits. It features a user-friendly menu system for easy setup, operation, and control. EGK 4S comes equipped with a heat exchanger that includes a thermoelectric element for precise temperature regulation.
advertisement
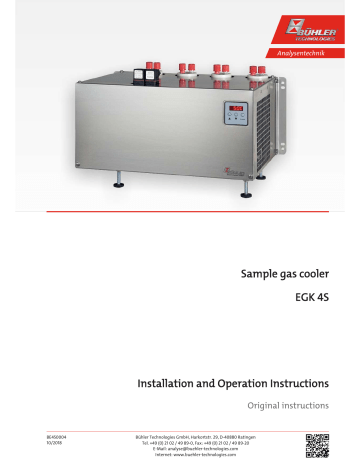
Analysentechnik
Sample gas cooler
EGK 4S
BE450004
10/2018
Installation and Operation Instructions
Original instructions
Bühler Technologies GmbH, Harkortstr. 29, D-40880 Ratingen
Tel. +49 (0) 21 02 / 49 89-0, Fax: +49 (0) 21 02 / 49 89-20
E-Mail: [email protected]
Internet: www.buehler-technologies.com
Bühler Technologies GmbH, Harkortstr. 29, D-40880 Ratingen
Tel. +49 (0) 21 02 / 49 89-0, Fax: +49 (0) 21 02 / 49 89-20
Internet: www.buehler-technologies.com
E-Mail: [email protected]
Read this instruction carefully prior to installation and/or use. Pay attention particularly to all advises and safety instructions to prevent injuries. Bühler Technologies can not be held responsible for misusing the product or unreliable function due to unauthorised modifications.
All rights reserved. Bühler Technologies GmbH 2018
Document information
Document No......................................................... BE450004
Version..........................................................................10/2018
EGK 4S
Contents
1 Introduction..................................................................................................................................................................................................................... 2
1.1
Intended use ......................................................................................................................................................................................................... 2
1.2
Types ....................................................................................................................................................................................................................... 2
1.3
Scope of delivery .................................................................................................................................................................................................. 2
1.4
Ordering instructions ........................................................................................................................................................................................ 3
2 Safety instructions......................................................................................................................................................................................................... 4
2.1
Important advice ................................................................................................................................................................................................. 4
2.2
General hazard warnings ................................................................................................................................................................................. 5
3 Transport and storage .................................................................................................................................................................................................. 6
4 Installation and connection ........................................................................................................................................................................................ 7
4.1
Installation site requirements......................................................................................................................................................................... 7
4.2
Installation ............................................................................................................................................................................................................ 7
4.2.1
Connecting the heat exchanger ...................................................................................................................................................... 8
4.3
Electrical connections ........................................................................................................................................................................................ 8
5 Operation and control ................................................................................................................................................................................................ 10
5.1
Use of menu functions .................................................................................................................................................................................... 10
5.1.1
Overview of the menu items............................................................................................................................................................ 11
5.1.2
Detailed description of the operational principle ..................................................................................................................... 11
5.2
Description of menu functions ..................................................................................................................................................................... 12
5.2.1
Main menu ........................................................................................................................................................................................... 12
5.2.2
Submenu............................................................................................................................................................................................... 12
6 Maintenance................................................................................................................................................................................................................... 13
7 Service and repair......................................................................................................................................................................................................... 14
7.1
Troubleshooting ................................................................................................................................................................................................ 14
7.2
Safety instructions ............................................................................................................................................................................................. 15
7.3
Cleaning and removal of the heat exchanger............................................................................................................................................ 15
7.4
Replacing the fuse of the cooler.................................................................................................................................................................... 16
7.5
Replacing the hoses of the peristaltic pump (option) ............................................................................................................................ 16
7.6
Spare parts and accessories ........................................................................................................................................................................... 16
7.6.1
Spare Parts and Accessories ............................................................................................................................................................ 16
8 Disposal ............................................................................................................................................................................................................................ 17
9 Appendices..................................................................................................................................................................................................................... 18
9.1
Technical Data.................................................................................................................................................................................................... 18
9.2
Performance Data ............................................................................................................................................................................................. 18
9.3
Diagram typical installation .......................................................................................................................................................................... 19
9.4
Heat exchanger.................................................................................................................................................................................................. 19
9.4.1
Heat exchanger description ............................................................................................................................................................ 19
9.4.2
Heat exchanger overview................................................................................................................................................................. 19
9.5
Dimensions (mm)............................................................................................................................................................................................. 20
10 Attached documents .................................................................................................................................................................................................... 21
BE450004 ◦ 10/2018 Bühler Technologies GmbH i
EGK 4S
1 Introduction
1.1 Intended use
This unit is intended for industrial use in gas analysis systems. It's an essential component for conditioning the sample gas to protect the analysis instrument from residual moisture in the sample gas.
Please note the specifications in the data sheet on the specific intended use, existing material combinations, as well as pressure and temperature limits.
1.2 Types
The device is delivered with different configurations. The part number given on the type plate informs you about the specific configuration of your device.
1.3 Scope of delivery
– Cooler
– Product documentation
– Connection-/mounting accessories (optional)
2 Bühler Technologies GmbH BE450004 ◦ 10/2018
EGK 4S
1.4 Ordering instructions
The item number is a code for the configuration of your unit. Please use the following model key:
457
0
1
X X X X X 0 0 0 X Product Characteristics
Gas cooler models
Wall mounting
19" rack installation
Supply voltage
3
4
1
2
115 V metric screw connections
230 V metric screw connections
115 V US screw connections
230 V US screw connections
Gas paths 1)
2
3
0
1
4
0 0
1 0
2 0
3 0
0 without heat exchanger
1 gas path
2 gas paths
3 gas paths
4 gas paths
Heat exchanger without heat exchanger
Single stainless steel heat exchanger/ (TS or TS-I)
Single glass heat exchanger/ (TG)
Single PVDF heat exchanger/ (TV or TV-I)
Condensate drain 2) without condensate drain
Mounting Accessories
0 without mounting accessories
1 with mounting brackets
2 with feet
3 with mounting brackets and feet
4 with handles
5 with mounting brackets and handles
6 with feet and handles
7 with all mounting accessories
1) up to 8 gas paths upon request.
2) Peristaltic pumps must be installed separately or can be mounted to the cooler using a mounting angle. The supply voltage corresponds with that of the main unit. Automatic condensate drains are installed separately.
BE450004 ◦ 10/2018 Bühler Technologies GmbH 3
EGK 4S
2 Safety instructions
2.1 Important advice
Operation of the device is only valid if:
– the product is used under the conditions described in the installation- and operation instruction, the intended application according to the type plate and the intended use. In case of unauthorized modifications done by the user Bühler Technologies GmbH can not be held responsible for any damage,
– when complying with the specifications and markings on the nameplates.
– the performance limits given in the datasheets and in the installation- and operation instruction are obeyed,
– monitoring devices and safety devices are installed properly,
– service and repair is carried out by Bühler Technologies GmbH,
– only original spare parts are used.
This manual is part of the equipment. The manufacturer keeps the right to modify specifications without advanced notice. Keep this manual for later use.
Signal words for warnings
Signal word for an imminent danger with high risk, resulting in severe injuries or death if not avoided.
DANGER
WARNING
CAUTION
Signal word for a hazardous situation with medium risk, possibly resulting in severe injuries or death if not avoided.
Signal word for a hazardous situation with low risk, resulting in damaged to the device or the property or minor or medium injuries if not avoided.
Signal word for important information to the product.
NOTICE
Warning signs
These instructions use the following warning signs:
Warns of a general hazard General information
Warns of voltage
Warns not to inhale toxic gasses
Warns of corrosive liquids
Warns of explosive areas
Unplug from mains
Wear respiratory equipment
Wear a safety mask
Wear gloves
4 Bühler Technologies GmbH BE450004 ◦ 10/2018
EGK 4S
2.2 General hazard warnings
The equipment must be installed by a professional familiar with the safety requirements and risks.
Be sure to observe the safety regulations and generally applicable rules of technology relevant for the installation site. Prevent malfunctions and avoid personal injuries and property damage.
The operator of the system must ensure:
– Safety notices and operating instructions are available and observed,
– The respective national accident prevention regulations are observed,
– The permissible data and operational conditions are maintained,
– Safety guards are used and mandatory maintenance is performed,
– Legal regulations are observed during disposal.
– the device is protected from mechanical loads.
Maintenance, Repair
Please note during maintenance and repairs:
– Repairs to the unit must be performed by Bühler authorised personnel.
– Only perform conversion-, maintenance or installation work described in these operating and installation instructions.
– Always use genuine spare parts.
Always observe the applicable safety and operating regulations in the respective country of use when performing any type of maintenance.
DANGER Electrical voltage
Electrocution hazard.
a) Disconnect the device from power supply.
b) Make sure that the equipment cannot be reconnected to mains unintentionally.
c) The device must be opened by trained staff only.
d) Regard correct mains voltage.
DANGER Toxic, corrosive gas/condensate
Sample gas/condensate may be hazardous to health.
a) If necessary, ensure a safe gas/condensate discharge.
b) Always disconnect the gas supply when performing maintenance or repairs.
c) Protect yourself from toxic/corrosive gasses/condensate when performing maintenance. Wear appropriate protective equipment.
DANGER Potentially explosive atmosphere
Explosion hazard if used in hazardous areas.
The device is not suitable for operation in hazardous areas with potentially explosive atmospheres.
Do not expose the device to combustible or explosive gas mixtures.
BE450004 ◦ 10/2018 Bühler Technologies GmbH 5
EGK 4S
3 Transport and storage
Only transport the product inside the original packaging or a suitable alternative.
The equipment must be protected from moisture and heat when not in use. It must be stored in a covered, dry and dust-free room at a temperature of -20 °C to 60 °C (-4 °F to 140 °F).
6 Bühler Technologies GmbH BE450004 ◦ 10/2018
EGK 4S
4 Installation and connection
4.1 Installation site requirements
The unit is intended for use in enclosed areas in a 19” rack, wall-mounting, or as a table-top unit. Adequate protection from the weather must be provided when used outdoors.
Install the unit leaving enough room below the cooler to discharge the condensate. Leave room above for the gas supply.
Be sure to maintain the approved ambient temperature. Do not obstruct the convection of the cooler. The vents must have enough room to the next obstacle. The distance must especially be a minimum of 10 cm on the air outlet side.
Ensure adequate ventilation when installing in enclosed housings, e.g. analyser cabinets. If the convection is inadequate, we recommend aerating the cabinet or installing a fan to lower the inside temperature.
4.2 Installation
Run the gas supply to the cooler with a downward slope. The gas inputs are marked in red and additionally labelled "IN".
If a large amount of condensate accumulates, we recommend using a condensate trap with automatic condensate drain. Our condensate drains, 11 LD spec., AK 20 V, or model 165 SS, are suitable.
Glass vessels and automatic condensate drains are available for draining condensate for external mounting below the unit.
When using automatic condensate drains, the sample gas pump must be installed upstream of the cooler (pressure operation) to ensure proper function of the condensate drain.
If the sample gas pump is located at the cooler outlet (suction operation), we recommend using glass condensate traps or peristaltic pumps.
Connecting the condensate drains
Depending on the material, build a connecting line with fittings and tubing or hose between the heat exchanger and condensate drain. For stainless steel the condensate drain can be suspended directly to the connecting tube, for hoses the condensate drain must be secured separately using a clamp.
The condensate drain can be mounted directly to the heat exchanger.
Condensate lines must always be installed with a slope and a minimum inside diameter of DN 8/10 (5/16”).
The DTV heat exchanger cannot be operated in conjunction with an automatic condensate drain.
Peristaltic pump (optional)
A peristaltic pump may also be installed a little away from the cooler. A mounting angle is available for installing up to 4 pumps directly below the cooler. Two M8 rivet nuts in the cooler bottom are designated for mounting the angle.
NOTICE
Installing peristaltic pumps CPsingle / CPdouble limits the maximum permissible operating pressure in the system!
Operating pressure ≤ 1 bar
BE450004 ◦ 10/2018 Bühler Technologies GmbH 7
EGK 4S
4.2.1 Connecting the heat exchanger
The gas inputs are marked in red.
On glass heat exchangers the correct position of the seal is important when connecting the gas lines (see image). The seal consists of a silicone ring with a PTFE sleeve. The PTFE side must face the glass thread.
Glass
PTFE
4.3 Electrical connections
The operator must install an external separator for the device which is clearly assigned to this device.
This separator
– must be located near the device,
– must be easy for the operator to reach,
– must comply with IEC 60947-1 and IEC 60947-3,
– must separate all live conductors and the status output, and
– must not be attached to the power feed.
WARNING Hazardous electrical voltage
The device must be installed by trained staff only.
CAUTION Wrong mains voltage
Wrong mains voltage may damage the device.
Regard the correct mains voltage as given on the type plate.
WARNING High voltage
Damage to the device in case of insulation testing
Do not proceed insulation tests with high voltage to the device as a whole!
Insulation test
The device is equipped with extensive EMC protection. If insulation tests are carried out the electronic filter devices will be damaged. All necessary tests have been carried out for all concerned groups of components at the factory (test voltage 1 kV or 1.5 kV respectively, depending on the device).
If you wish to carry out the insulation test by yourself, please test only separate groups of components.
Disconnect the compressor, the fan, the heating or the peristaltic pumps, respectively, and then carry out the insulation tests.
8 Bühler Technologies GmbH BE450004 ◦ 10/2018
EGK 4S
Connection via plug
The device is equipped with connectors according to EN 175301-803 for mains and status output. If the cables are mounted properly, they cannot be interchanged. Please make sure that the connectors are remounted correctly after connecting the cable. The following figures show the pin assignment with respect to the numbers printed on the connector.
The supply line cross-sections must be suitable for the rated current. Use a maximum line cross-section of 1.5 mm² (AWG 16) and a cable diameter of 8 - 10 mm (0.31 - 0.39 inch).
pin assignment power supply status output function ok alarm
Fig. 1: A05-100002 Cooler electric supply
The mains supply must be protected with 10 A. The clamping area has a diameter of 8-10 mm. If the unit features a peristaltic pump, it must be connected to a power source separately.
BE450004 ◦ 10/2018 Bühler Technologies GmbH 9
EGK 4S
5 Operation and control
NOTICE
The device must not be operated beyond its specifications.
After switching on the cooler the block temperature will be displayed. The display will flash until the block temperature has reached the preset target value (± adjustable alarm range). The status contact is in the Alarm position.
Once the target temperature range has been reached, the temperature will continuously be displayed and the status contact switches over.
If the display flashes during operation or an error message appears, please refer to bullet “Troubleshooting”.
Please refer to the data sheet for performance data and maximum ratings.
5.1 Use of menu functions
Overview of the operational principal:
Use this short description if you have experience with the device.
Operation is carried out by only the keys with the following functions:
Key Function
– Switch from measurement display to main menu
– Selection of the display menu item
– Accepting the changed value or selection
– Switch to the upper menu item
– Increase of the value of switching the selection
– Temporary display of the alternative measurement display (if option is installed)
– Switch to lower menu item
– Decrease of the value of switching the selection
– Temporary display of the alternative measurement display (if option is installed)
10 Bühler Technologies GmbH BE450004 ◦ 10/2018
EGK 4S
5.1.1 Overview of the menu items
Display of current temperature and operating state
Display
Current temperature
Displayed is the block temperature with a resolution of 0,5°C/0.75 °F. By pressing the Enter button brings the display to the Main Menu. The unit of temperature is adjustable in the menu Global Settings (Celsius or Fahrenheit).
____
Main Menu
____
Submenu Setting range adjust value store value wait 5s: no storage
Display
Cooler display tEMP
Set temperature
Parameter
Cooler temperature
Adjust the set point:
2°C...20°C / 35.6°F...68°F
Alarm high A Hi
Alarm hysteresis
Parameter
Upper alarm
Set the upper alarm threshold above setpoint: tEMP 1°C...7°C / 1.8°F...12.6°F
Parameter
Lower alarm
Set the lower alarm threshold below setpoint: tEMP -1°C...-3°C / -1.8...-5.4F
Alarm Low
Alarm hysteresis
Exit
Exit Submenu
Top Settings toP
Global Settings
Exit
Exit Main Menu
Parameter
C - F
Set unit Celsius or Fahrenheit
5.1.2 Detailed description of the operational principle
The detailed description will guide you through the menu step by step.
Connect the unit to the power supply and wait for the startup procedure to complete. At first the software version implemented on the unit will be displayed for a brief period. The unit will then switch directly into measured value display.
Pressing the button will take you from display mode to the main menu. (The control will continue running whilst in menu mode.)
Use these buttons to navigate the main menu.
After confirming a main menu item the associated submenu will open
Here you can configure operating parameters:
Cycle through the submenu to configure the parameters, then confirm the menu item to be changed.
E
You can now set values within specific limits.
After confirming the value the system will save it. This will automatically return you to the submenu.
If no button is pushed for approx. 5 s, the unit will automatically return to the submenu. Changes to values will not be saved.
The same applies to the sub- and main menu. The system will automatically return to display mode without saving the (last) value changed. Parameters which were previously changed and saved will be retained and not reset.
NOTICE! After saving values with the Enter key they will be applied to the control.
To exit the main or submenu, select menu item E (Exit).
BE450004 ◦ 10/2018 Bühler Technologies GmbH 11
EGK 4S
5.2 Description of menu functions
5.2.1 Main menu
Cooler
From here you will be able to access to all relevant cooler settings. The related submenu allows you to select the target temperature and alarm thresholds.
Globale settings (ToP Settings)
Selection of the global temperature unit, either degree Celsius (C) or degree Fahrenheit (F).
Note:
Exit main menu
Display → E
This menu item has no sub-item. The temperature unit is directly selected.
Selecting this will return you to display mode.
5.2.2 Submenu
Cooler -> nominal temperature (temperature)
Note:
This setting determines the nominal temperature for the cooler temperature. The value can be set to a range from 2 °C (35.6 °F) to 20 °C (68 °F).
The standard value at delivery is 5 °C (41 °F) (unless otherwise agreed). If the temperature is changed the indicator may blink, until the new operating range has been reached.
Cooler -> upper alarm limit (alarm high)
Note:
Here you can set the upper threshold for the visual signal and the alarm relay. The alarm limit is set to a range from 1 °C (1.8 °F) to 7 °C (12.6 °F) in relation to the cooler temperature setting.
The standard value at delivery is 3 °C (5.4 °F) (unless otherwise agreed).
Cooler -> lower alarm limit (alarm low)
Note:
Here you can set the lower threshold for the visual signal and the alarm relay. The alarm limit is set to a range from -1 °C (-1.8 °F) to -3 °C (-5.4 °F) in relation to the cooler temperature setting.
The standard value at delivery is -3 °C (-5.4 °F) (unless otherwise agreed).
Exit submenu
Selecting this item returns to the main menu.
12 Bühler Technologies GmbH BE450004 ◦ 10/2018
EGK 4S
6 Maintenance
The basic version of the cooler requires no special maintenance.
However, it may have different options depending on the cooler model. In this case the following maintenance must be performed regularly:
– Optional peristaltic pump: Check hoses
During maintenance, remember:
– The equipment must be maintained by a professional familiar with the safety requirements and risks.
– Only perform maintenance work described in these operating and installation instructions.
– When performing maintenance of any type, observe the respective safety and operation regulations.
DANGER Electrical voltage
Electrocution hazard.
a) Disconnect the device from power supply.
b) Make sure that the equipment cannot be reconnected to mains unintentionally.
c) The device must be opened by trained staff only.
d) Regard correct mains voltage.
DANGER Toxic, corrosive gas/condensate
Sample gas/condensate may be hazardous to health.
a) If necessary, ensure a safe gas/condensate discharge.
b) Always disconnect the gas supply when performing maintenance or repairs.
c) Protect yourself from toxic/corrosive gasses/condensate when performing maintenance. Wear appropriate protective equipment.
BE450004 ◦ 10/2018 Bühler Technologies GmbH 13
EGK 4S
7 Service and repair
This chapter contains information on troubleshooting and correction should an error occur during operation.
Repairs to the unit must be performed by Bühler authorised personnel.
Please contact our Service Department with any questions:
Tel.: +49-(0)2102-498955 or your agent
If the equipment is not functioning properly after correcting any malfunctions and switching on the power, it must be inspected by the manufacturer. Please send the equipment inside suitable packaging to:
Bühler Technologies GmbH
- Reparatur/Service -
Harkortstraße 29
40880 Ratingen
Germany
Please also attach the completed and signed RMA decontamination statement to the packaging. We will otherwise be unable to process your repair order.
You will find the form in the appendix of these instructions, or simply request it by e-mail: [email protected]
.
7.1 Troubleshooting
Problem / Malfunction
No display
Cooler doesn’t start up
Possible cause
– Mains voltage interrupted
Action
– Connect to mains; verify
– the plug is inserted correctly
– Fuse defective – Check fuse and replace, if necessary
– Compressor housing temperature too high – Allow to cool down and ensure adequate ventilation
Display flashes due to:
– Excess temperature
– Temperature low
Condensate inside the gas output
Reduced gas flow rate
No cooling
Fuse is triggering
– Operating point not yet reached
– Cooling output too low despite the cooler running
– Flow rate / dew point / gas temperature too high
– Built-in fan stopped
– Control unit failure
– Condensate trap full
– Valve inside the automatic condensate drain may be stuck
– Cooler overload
– Gas circuit clogged
– Condensate output iced over
– Compressor doesn’t start up
– Increased compressor current consumption due to faulty compressor start-up
– Wait (max. 20 min)
– Ensure the vents are not covered (heat buildup)
– Maintain limits / install pre-separator
– Check and replace if necessary
– Send in cooler
– Empty condensate trap
– Flush in both directions
– Maintain limits
– Remove and clean heat exchanger
– Send in cooler
– Compressor PTC not cooled down sufficiently.
Wait 5 minutes and try again.
– Compressor PTC not cooled down sufficiently.
Wait 5 minutes and try again.
Error Messages in the Display
The display alternates between the temperature and error message,
Problem / Malfunction
Error 01 – Interruption
Possible cause Action
– Temperature sensor failure: Send in cooler
Error 02 – Short circuit – Temperature sensor failure: Send in cooler
14 Bühler Technologies GmbH BE450004 ◦ 10/2018
EGK 4S
7.2 Safety instructions
– The device must be operated within its specifications.
– All repairs must be carried out by Bühler authorised personnel only.
– Only perform modifications, servicing or mounting described in this manual.
– Only use original spare parts.
DANGER Electrical voltage
Electrocution hazard.
a) Disconnect the device from power supply.
b) Make sure that the equipment cannot be reconnected to mains unintentionally.
c) The device must be opened by trained staff only.
d) Regard correct mains voltage.
DANGER Toxic, corrosive gas/condensate
Sample gas/condensate may be hazardous to health.
a) If necessary, ensure a safe gas/condensate discharge.
b) Always disconnect the gas supply when performing maintenance or repairs.
c) Protect yourself from toxic/corrosive gasses/condensate when performing maintenance. Wear appropriate protective equipment.
CAUTION Health hazard in case of leaking cooling circuit / heat exchanger
The cooling circuit is filled with coolant R134a.
The heat exchanger is filled with a coolant based on glycol.
In case of leaking / broken cooling circuit / heat exchanger: a) Avoid contact with skin or eyes.
b) Do not ingest or inhale coolant.
ð Due to the small amount of coolant no health hazards need be feared.
ð Do not put the device back to operation if leakage of the cooling circuit happend.
7.3 Cleaning and removal of the heat exchanger
Heat exchangers only need to be replaced or maintained if clogged or damaged. If they are clogged, we recommend checking if using a filter will avoid future occurrences.
– Close gas supply.
– Switch off device and disconnect all plugs (e.g. connector plug alarm output, supply input, etc.).
– Disconnect gas connections and condensate drain.
– Pull the heat exchanger up and out.
– Clean the heat exchanger hole (hole inside the cooler block), as the heat exchangers are installed with silicone grease.
– Flush the heat exchanger until all contaminants have been removed.
– Grease the cooled outside surface external surface with silicone grease.
– Reinsert the heat exchanger into the cooling nest with a rotating movement.
– Reconnect the gas supply and condensate drain. The gas inlet is marked red.
– Restore power/gas supply and wait for unit to be ready for operation.
– Open gas supply.
BE450004 ◦ 10/2018 Bühler Technologies GmbH 15
EGK 4S
7.4 Replacing the fuse of the cooler
– Turn off gas supply.
– Switch the device off and disconnect power supply.
– Loosen the screws of the cover.
– Remove the cover carefully.
– The fuse is placed on the PBC beneath a plastic cap. Replace the fuse and push down the plastic cap. Regard the supply voltage for selecting the correct value of the fuse.
– Fix the cover. Fasten the screws.
– Reconnect power supply.
7.5 Replacing the hoses of the peristaltic pump (option)
– Turn off gas supply.
– Switch the device off and disconnect power supply.
– Remove the supplying and draining hoses from the pump ( Take care of the safety instructions!
).
– Loosen the centre knurled screw but do not remove it. Push the screw downwards.
– Pull off the cover.
– Pull the connections sidewards and remove the hose.
– Replace the hose and remount the pump in reverse order.
– Reconnect power supply.
7.6 Spare parts and accessories
Please also specify the model and serial number when ordering parts.
Upgrade and expansion parts can be found in our catalog.
Available spare parts:
Item no.
44 10 030
44 00 030
91 000 10 133
91 000 10 134
91 000 10 124
91 000 10 125
91 100 00 001
Description
230 V Fan
115 V Fan
230 V power and controller board
115 V power and controller board
Display ABT 400
Controller Board MCP 1
Sample gas cooler micro-fuse, 230 V / 115 V, 5 x 20 mm, 800 mA delayed action
7.6.1 Spare Parts and Accessories
Item no.
44 10 00 1
44 10 00 4
44 10 00 5
44 10 01 9 see data sheet 450020
45 70 00 8
Description
Automatic condensate drain 11 LD V 38
Automatic condensate drain AK 20, PVDF
Condensate trap GL 1; glass, 0.4 L
Condensate trap GL 2; glass, 1 L
Peristaltic Pump CPsingle, CPdouble
Mounting angles for up to 4 peristaltic pumps
16 Bühler Technologies GmbH BE450004 ◦ 10/2018
EGK 4S
8 Disposal
The refrigerant circuit of the cooler contains R134a refrigerant. The heat exchanger is charged with glycol-based coolant.
Dispose of parts so as not to endanger the health or environment. Follow the laws in the country of use for disposing of electronic components and devices as well as hazardous materials during disposal.
BE450004 ◦ 10/2018 Bühler Technologies GmbH 17
EGK 4S
9 Appendices
9.1 Technical Data
Gas Cooler Technical Data
Ready for operation
Rated cooling capacity (at 25 °C)
Ambient temperature
Gas output dew temperature, preset:
Dew point fluctuations static: in the entire specification range:
IP rating
Housing
Packaging dimensions
Weight incl. 4 heat exchangers
Electric supply
Status output switching capacity
Electrical data
Starting current
Status output switching capacity after max. 15 minutes
800 kJ/h
5 °C to 50 °C
5 °C
± 0.2 K
± 2 °C
IP 20
Stainless steel approx. 510 x 355 x 450 mm max. 32 kg
115 V, 60 Hz or 230 V, 50 Hz
250 VAC/ 150 VDC
Changeover contact 2 A, 30 VA
Typical power input: max. operating current:
10 A
250 VAC/ 150 VDC
Changeover contact 2 A, 30 VA
9.2 Performance Data
230 V
240 VA
2.5 A
115 V
215 VA
4.6 A
Ambient temperature (°C)
Note: The limit curves for the heat exchangers exchanger apply to a dew point of 65 °C.
18 Bühler Technologies GmbH BE450004 ◦ 10/2018
EGK 4S
9.3 Diagram typical installation
Test gas
Sample gas
1 Sample gas probe
3 Reversing tap
5 Sample gas cooler
7 Fine mesh filter
9 Flow meter
See data sheets for individual component models and data.
9.4 Heat exchanger
2 Sample gas line
4 Sample gas pump
6 Automatic condensate drain
8 Moisture detector
10 Analyser
9.4.1 Heat exchanger description
The energy content of the sample gas and the required cooling capacity of the gas cooler is determined by three parameters: gas temperature ϑ
G
, (inlet) dew point τ e
(moisture content) and volume flow v. The outlet dew point rises with increasing energy content of the gas. The approved energy load from the gas is therefore determined by the tolerated rise in the dew point.
The following limits are specified for a normal standard operating point of τ e
= 65 °C and ϑ
G
= 90 °C. The maximum volume flow v max
in Nl/h of cooled air is indicated, so after moisture has condensed.
If the values fall below τ e
and ϑ
G
, the flow v max
may be increased. For example, on the TG heat exchanger the parameter triple
τ e
= 65 °C, ϑ
G
= 90 °C and v = 280 Nl/h may also be used in place of τ e
= 50 °C, ϑ
G
= 80 °C and v = 380 Nl/h
Please contact our experts for clarification or refer to our design program.
9.4.2 Heat exchanger overview
Heat exchanger
Version / Material
Flow v max
1)
Inlet dew point τ e,max
1)
Gas inlet temperature ϑ
G,max
1)
Max. Cooling capacity Q max
Gas pressure p max
Pressure drop Δp (v=150 L/h)
Dead volume V tot
Gas connections (metric)
Gas connections (US)
Condensate out connections (metric)
Condensate out connections (US)
TS
TS-I 2)
Stainless steel
530 L/h
80 °C
180 °C
450 kJ/h
160 bar
8 mbar
69 ml
G1/4
NPT 1/4”
G3/8
NPT 3/8"
1) Max. cooling capacity of the cooler must be considered
2) Models marked I have NPT threads or US tubes, respectively.
3) Gasket inside diameter
TG
TG
Glass
280 L/h
80 °C
140 °C
230 kJ/h
3 bar
8 mbar
48 ml
GL 14 (6 mm) 3)
GL 14 (1/4") 3)
GL 25 (12 mm) 3)
GL 25 (1/2") 3)
TV
TV-I 2)
PVDF
150 L/h
65 °C
140 °C
120 kJ/h
3 bar
8 mbar
129 ml
DN 4/6
1/4"-1/6"
G3/8
NPT 3/8"
BE450004 ◦ 10/2018 Bühler Technologies GmbH 19
EGK 4S
9.5 Dimensions (mm)
20 Bühler Technologies GmbH BE450004 ◦ 10/2018
EGK 4S
10 Attached documents
– Declaration of conformity KX450001
– RMA - Decontamination Statement
BE450004 ◦ 10/2018 Bühler Technologies GmbH 21
advertisement
* Your assessment is very important for improving the workof artificial intelligence, which forms the content of this project
Related manuals
advertisement
Table of contents
- 4 Introduction
- 4 Intended use
- 4 Types
- 4 Scope of delivery
- 5 Ordering instructions
- 6 Safety instructions
- 6 Important advice
- 7 General hazard warnings
- 8 Transport and storage
- 9 Installation and connection
- 9 Installation site requirements
- 9 Installation
- 10 Connecting the heat exchanger
- 10 Electrical connections
- 12 Operation and control
- 12 Use of menu functions
- 13 Overview of the menu items
- 13 Detailed description of the operational principle
- 14 Description of menu functions
- 14 Main menu
- 14 Submenu
- 15 Maintenance
- 16 Service and repair
- 16 Troubleshooting
- 17 Safety instructions
- 17 Cleaning and removal of the heat exchanger
- 18 Replacing the fuse of the cooler
- 18 Replacing the hoses of the peristaltic pump (option)
- 18 Spare parts and accessories
- 18 Spare Parts and Accessories
- 19 Disposal
- 20 Appendices
- 20 Technical Data
- 20 Performance Data
- 21 Diagram typical installation
- 21 Heat exchanger
- 21 Heat exchanger description
- 21 Heat exchanger overview
- 22 Dimensions (mm)
- 23 10 Attached documents