- Home
- Home security & automation
- Carbon monoxide (CO) detectors
- Carbolite Gero
- EHC 12/600 with 3216 centre zone and 3216CC end zones
- Operating manual
Carbolite Gero EHC 12/600 with 3216 centre zone and 3216CC end zones Operating Manual
Add to My manuals68 Pages
advertisement
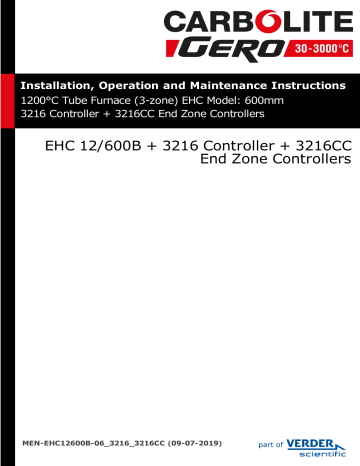
Installation, Operation and Maintenance Instructions
1200°C Tube Furnace (3-zone) EHC Model: 600mm
3216 Controller + 3216CC End Zone Controllers
EHC 12/600B + 3216 Controller + 3216CC
End Zone Controllers
MEN-EHC12600B-06_3216_3216CC ( 09-07-2019 )
2
Contents
This manual is for guidance on the use of the Carbolite Gero product specified on the front cover. This manual should be read thoroughly before unpacking and using the furnace or oven. The model details and serial number are shown on the back of this manual. Use the product for the purpose for which it is intended.
Operation as a simple controller
Digital Communications - RS232
Digital Communications - RS485
Temperature Controller Replacement
3216 Controller Navigation Diagram
Operation as a simple controller
3
4
Power Failure While Using Dwell Timer
Running Dwell Timer with Ramp Rate
Running Dwell Timer with Ramp Rate & Threshold
Running Delay Timer with Ramp Rate
Delay timer with ramp rate functions
Power Failure While Using Delay Timer
Power Failure While Using Soft Start Timer
Ramp Rate with Soft Start Timer
Digital Communications - RS232
Digital Communications - RS485
5.0 2132 Over-Temperature Controller Description (if fitted)
Resetting the Over-Temperature Alarm
Recommended Spare Parts and Spare Parts Kit
Safety Warning - Disconnection from Power Supply
Safety Warning - Refractory Fibre Insulation
Temperature Controller Replacement
5
6
1.0 Symbols and Warnings
1.0
Symbols and Warnings
1.1
Switches and Lights
Instrument switch: when the instrument switch is operated the temperature control circuit is energised.
Heat light: the adjacent light glows or flashes to indicate that power is being supplied to the elements.
Heat switch: the switch disconnects power to the heating elements; unless this switch is OFF there is a danger of electric shock when inserting objects into the product.
1.2
General Warnings
DANGER – Electric shock. Read any warning printed next to this symbol.
WARNING: Risk of fatal injury.
DANGER – Hot surface. Read any warning printed next to this symbol.
WARNING: All surfaces of a product may be hot.
DANGER – Read any warning printed next to this symbol.
1.0 Symbols and Warnings
Caution – Double Pole/Neutral Fusing
1.3
Warning Labels
On the front control panel there are 2 warning labels as shown in figure 1.3.1; they are numbered 7 and 8. These warnings must be followed for the safe operation of this furnace.
7- Warning label - Do not operate without a work tube.
The furnace must not be operated without the correctly sized work tube and correspond work tube adaptors or it could be possible for an operator to access electrically live element coils that could cause serious injury or death.
8- Warning label - Switch off the furnace before loading and unloading.
The furnace heaters must be switched OFF using the heater switch, item
2 in figure 1.3.1, when the furnace is being loaded or unloaded. The work tube can become electrically conductive at high temperatures, presenting a possible hazard to the operator. If element failure is left undetected the element could collapse onto the work tube.
7
8
1.0 Symbols and Warnings
Figure 1.3.1 - Control Box layout and warning labels.
Figure 1.3.2- Back of control box showing mains lead socket
Index to numbered items in Figure 1.3.1 and 1.3.2
1. Electrical supply switch - switches electrical power ON and OFF to the furnace.
2. Heater switch - switches electrical power ON and OFF to the furnace heating elements.
3. Heater ON light - indicates that the furnace heating elements are energized.
4. Product rating label indicating the product serial number and electrical information.
5. Access holes to front panel fixing screws.
6. Warning label - Disconnect the mains supply before removing this cover.
7. Warning label - Do not operate without a work tube.
8. Warning label - Switch OFF the furnace before loading and unloading.
9. Electrical power lead socket.
10. Back panel fixing screws.
2.0 Installation
2.0
Installation
If the product has been transported or stored in humid conditions it must be dried out completely before operating the furnace. Contact
Carbolite Gero Service for instructions.
2.1
Unpacking and Handling
When unpacking or moving the product, always lift it by its base or both ends of the main body. Never lift it by the end insulation or by a work tube. It may take 2 or 3 people to lift the furnace, depending on the size and configuration.
NOTE: This product contains Refractory Ceramic Fibre (also known as
Alumino Silicate Wool - ASW). For precautions and advice on handling
this material see section 8.2.
2.2
Siting
Place the product on a level surface in a well ventilated area.
Site away from other sources of heat and on a non-flammable surface that is resistant to accidental spillage or hot materials.
The surface on which the equipment is mounted should be stable and not subject to movement or vibrations.
The height of the mounting surface is important to avoid operator strain when loading and unloading samples.
Unless otherwise stated elsewhere in this manual, ensure that there is at least 150 mm of free space around the back and sides of the product. Clear space is required above the product to dissipate heat.
Work tubes:
It is recommended that the work tube has either insulation plugs or radiation shields fitted to minimise heat loss from both ends of the work tube. If the work tube has open ends, a significant amount of energy could be radiated from the ends of the work tube. Adjacent surfaces should always be made from a non-flammable material.
Ensure that the ends of the work tube are positioned at least 500 mm away from any adjacent surface so that any energy radiated cannot heat an adjacent surface to a dangerous temperature.
9
2.0 Installation
If the product is to be used in a process which could liberate hazardous gases, then it should be installed together with a suitable fume extraction system.
Ensure that the product is placed in such a way that it can be quickly switched off or disconnected from the electrical supply.
2.3
Setting Up
The horizontal models must have work tubes fitted before being used. The diameter of the work tube is a customer order option and therefore varies between tube furnaces.
Note: If a metal work tube is being used in the furnace, ensure that it is
Under no circumstances should any objects be placed on top of the product.
Always ensure that any vents on the top of the product are clear of any obstruction. Always ensure all cooling vents and cooling fans (if fitted) are clear of any obstruction.
Fitting the standard length work tube to furnace
Tools required: 4 mm Allen key
Fitting work tube is as follows with reference to Figure 2.3.2. Please note that standard length work tubes are also referred to as tubes suitable for working in air. They are 150
10
2.0 Installation mm longer than the heated length of the furnace (see the Specifications table at the
back of this manual). Read section 8.2 before fitting the work tube.
Figure 2.3.1 - Furnace model mounted on a control box
Figure 2.3.2 - Exploded view showing how to fit the work tube in the furnace
Index to numbered items in Figure 2.3.2
1. Tube furnace body
2. Work tube (diameter customer option)
3. Work tube adaptor (size dependent on work tube diameter)
4. Work tube adaptor fixing bracket
5. Work tube end stop (size dependent on work tube diameter)
6. Fixing screws M6 x 15
7. Washer M6
8. Tube furnace end guard l l l
Remove the work tube end guard (8) then remove the work tube adaptor fixing bracket (4) that holds in place the work tube end stop (5) and the end adaptor (3) from one side only. Note that if a different work tube with a different outer diameter is being fitted it will be necessary to fit new correctly sized work tube adaptors (3) in which case both end guards and work tube adaptor fixing brackets (4) will need removing.
Slide the work tube into the furnace through the work tube adaptor (3) until it reaches the opposite work tube end stop (5). Note that the work might be a tight fit when it is new and may need to be twisted backwards and forwards slightly as it slides in. For long work tubes it may be necessary to use a long wooden pole to support and line up the work tube as it pushed through. It may also take 2 people to perform this operation.
Reassemble the work tube end stop (5), work tube adaptor bracket (4) and tube end guard (8).
Fitting the extended work tube in the furnace
Tools required 4 mm Allen key.
Fitting of the work tube is as follows with reference to Figure 2.3.2 to 2.3.8.
11
12
2.0 Installation l l l l l l l l l
Before the extended work tube can be fitted, the work tube end stops for the standard length work tube (item 5 in figure 2.3.2 ) must be removed from both ends of the furnace. This is done by removing the furnace end guard (8) and the work tube adaptor brackets (4) to release the work tube end stop (5). The brackets should then be refitted.
Fit the tube support bracket, (5), figure 2.3.4. Use the M6 button head screws and washers supplied.
Fit the extended work tube guard, (4), figure 2.3.5. Use the M6 button head screws and washers supplied.
Re-fit furnace end guard, (3), figure 2.3.6. Use the M6 button head screws and washers supplied.
If supplied, fit the optional tube end seal assembly as shown in figures 2.3.9. and
2.3.10.
Refer to manual MEN-ENDSEALS-01 for detailed fitting instructions.
Fit the tube support bracket, (1), figure 2.3.7. Use the M6 button head screws and washers supplied.
Finally, fit tube support collar, (2) and secure figure tight using (6) until the tube is secure to be used in a vertical arrangement. The fitting arrangement is shown in figure 2.3.8.
Figure 2.3.3 - shows an exploded view of all the required parts.
Figure 2.3.8 - shows the assembled parts as they would be used.
Figure 2.3.3
2.0 Installation
Figure 2.3.4
Figure 2.3.5
Figure 2.3.6
Figure 2.3.7
Figure 2.3.8
13
2.0 Installation
Figure 2.3.9 - Tube support and end seal assembly
Figure 2.3.10 - Tube support and end seal assembly
Index to numbered items in figure 2.3.3 - 2.3.10
1. Tube support bracket
2. Tube support collar
14
2.0 Installation
3. End guards
4. Extended work tube guard
5. End adaptor
6. Fluted grip knob
Fitting the Optional Insulation Plugs and Radiation Shield
For optimum temperature uniformity, insulation plugs or radiation shields should be placed in the work tube ends as shown below. With a standard work tube, the insulation plug must be fitted as shown in figure A.
If a gas/vacuum end seal is fitted, either horizontally or vertically, the insulation plug hooks onto the end seal hook; see figure B.
Alignment of radiation shields is similar to that of insulation plugs, see figure C.
If a metal work tube is being used in the furnace, ensure that it is earthed. See the
safety warning in section 6.6.
Figure A- Cross-section view showing standard length work tube insulation plug fitted
Figure B- Cross-section view showing extended work tube insulation plug fitted
Figure C- Cross-section view showing an extended length work tube with a radiation shield fitted
15
2.0 Installation
2.4
Electrical Connections
Connection by a qualified electrician is recommended.
All furnaces in the range are single-phase and operate over the voltage ranges 100 to
110 volts or 200 - 240 volts. Check the rating label before connection, see "Warning
Labels" for location of rating label. To check that the OP.Hi setting is correct for the
appropriate voltage, or to change to another setting, follow the instructions in section
The electrical supply should be fused at the next standard size equal to or higher than the design current. Where a supply cable is supplied there are internal supply fuses, in
which case customer fusing is preferred but not essential. See section 11.0 for furnace
rating power, current and fusing information.
The external connection should be either a permanent connection to a fused isolator supply or to a socket on a fused isolator supply; the isolating switch must operate on both conductors. Make sure that the isolator switch is within easy reach of the furnace operator.
Terminal Connection Details
Supply
1-phase
Terminal
L
N
PE
Label
UK/ Europe
Cable Colour
Brown
Blue
Green/ Yellow
USA/
Canada
Common
Cable
Colours
Red or
Black
Live -
Neutral
To live
White To neutral
Supply Type
Reversible or
Live - Live to either power conductor to the other power conductor
Green or
Green/
Yellow
To earth
(ground) to earth (ground)
16
3.0 3216 Controller
3.0
3216 Controller
3.1
PID control
This controller uses PID (Proportional Integral Derivative) temperature control. This type of control uses a complex mathematical control system to adjust the heating power and achieve the desired temperature.
3.2
3216P1
The 3216P1 is a digital temperature controller which uses PID algorithms to give excellent temperature control. This controller can store and operate a single program of
8 ramp/ dwell segments. The 3216P1 can also be used as a simple temperature controller.
3.3
3216P5
The 3216P5 is a digital temperature controller which uses PID algorithms to give excellent temperature control. This controller can store up to 5 programs of 8 ramp/ dwell segments. The 3216P5 can also be used as a simple temperature controller.
3.4
Operation
3.4.1
Controller Layout
Key
A Power Output Indicator
B Alarm Indicator
C
Remote Indicator
(when configured)
D Page
E Scroll
F Down
G Up
H Run Indicator
J
I Hold Indicator
Setpoint Temperature
(SP)
K
Measurement Temperature
17
3.0 3216 Controller
3.4.2
Keys
Page Key
Scroll Key
Ack
Page and
Scroll
Arrow Keys
+
+
The page key is used to access level 2 when held down for 3 seconds.
The scroll key is used to scroll through parameters.
When pressed simultaneously the ACK function is used to: l l l
Return to the Home Menu
Acknowledge an alarm if activated.
Reset a program after the program has ended.
The arrow keys are used individually to adjust the selected parameters and in combinations to operate a program.
Note: If a parameter is selected and no further action is taken, the display will time out and revert back to the home display in its working level after approximately 1 minute.
3.5
Quick Start Guide
3.5.1
Operation as a simple controller
When switched on, the controller goes through a short test routine and then shows the measured temperature (PV = Process Value) in the upper part of the display and below it, the desired temperature (Setpoint).
3.5.2
Changing the Setpoint
Press Up or Down to select the required SP. If the SP is higher than the measured temperature, the OP1 indicator will illuminate in the top left corner of the display, indicating that the controller is calling for power (giving an output).
The controller will immediately attempt to reach the setpoint and then maintain it.
This will cause the product to heat as quickly as possible which may not be appropriate where the product contains sensitive ceramic components. For products with ceramic components, e.g. a tube furnaces fitted with a long ceramic work tube, use the ramp rate feature set with a low heating rate such as 5°C per minute (300°C per hour), to prevent damage.
3.5.3
Using the Controller
The parameters in the controller are first shown by a short code (mnemonic). After 5
Seconds a description of the parameter will scroll once along the display and then revert back to the mnemonic. The scrolling text can be interrupted at any time by a single press of any of the buttons, but will not scroll again until the parameter is returned to.
18
3.0 3216 Controller
In this manual the mnemonic will be shown first, followed by the scrolling text in brackets; e.g. PROG <PROGRAM NUMBER>
3.5.4
Understanding User Levels
There are two user levels in the controller; Level 1 (Operator) and Level 2 (Supervisor).
Level 1 (Operator) is for the day to day operation of the controller. These parameters are not protected by a security code.
Level 2 (Supervisor) provides access to additional parameters. Access to this level protected by a security code
To Enter Level 2
1. Press and hold the page key for 3 seconds.
2. The display will show LEu 1 GOTO
3. Release the page Key
4. Press the up or down to choose LEu 2 (level 2)
5. Press the up or down to enter the code (Level 2 Code = 9).
If the correct code is entered, PASS should momentarily be displayed and then revert to the level 2 home display.
If an incorrect code is entered the display reverts back to Level 1 home display.
When level 2 operations have been completed, the supervisor must return to Level 1 either manually or by switching the instrument off and back on. There is no time out function.
To Return to Level 1
1. Press and hold the page Key
2. Press down to select LEu 1
It is not necessary to enter a code when going from a higher level to a lower level.
When level 1 is selected, the display reverts to the home display (See Controller Layout)
Table showing parameters accessible in level 1 and Level 2
Operator LEVEL 1 home display
Programming
Program Status
Supervisor LEVEL 2 home display
Programming
Program Status
Alarms (if configured)
Current Transformer Input (if configured)
Comms (if configured)
Controller Setup
Customer Calibration
TIP
19
3.0 3216 Controller
If while navigating the controller, a parameter has been passed or you need to access parameters which would be at the end of a scroll list, press and hold scroll and use up to return to a previous parameter.
3.6
Setting up the Controller
Before using the controller (or during its lifetime) certain parameters may have to be set, depending on specific requirements. To do this the controller must be set to supervisor level (Level 2).
3.6.1
Maximum Output Power
Press scroll until the display shows OP.HI <OUTPUT HIGH>. Use the up and down keys to select the output power required as a percentage. Once the setting is made, turn the instrument switch off and on to power cycle the temperature controller.
Depending on the furnace or oven model, the maximum output power setting OP.Hi
may be accessible or locked.
For silicon carbide heated furnaces, the parameter is accessible to allow compensation for element ageing.
In many models the maximum output power setting depends on the supply voltage, see
3.6.2
Customer ID
A furnace or oven identification number can be entered if required. This maybe used to identify one of many units for production or quality control systems.
Press scroll until the display shows ID <CUSTOMER ID>. Use the up keys to enter your own identification number. This can range from 1-9999.
and down
3.6.3
Units or down Press scroll until the display shows UNITS <DISPLAY UNITS>. Use the up keys to select the required units.
Mnemonic
NONE
°C
°F
°K
PERC
Description
No units (Default °C)
Celsius
Fahrenheit
Kelvin
% (shows °C value)
3.6.4
Language
The scrolling text on the 3216 can be shown in different languages, this can only be set at the factory and therefore must be specified at the time of placing an order.
20
3.0 3216 Controller
3.6.5
Scrolling Text
If at any time the scrolling text is not required.
Press and hold the page for three seconds until “GOTO” is displayed.
Press scroll until the display shows. TEXT <ENABLE/ DISABLE SCROLLING TEXT>
Use the up and down keys to select ON or OFF.
3.6.6
Customer Calibration
The 3216 Controller series are calibrated for life at manufacture, there may however be sensor or other system errors, which affect the accuracy of the measured temperature.
Customer calibration can be used to compensate for these errors.
Dual Offset
Dual point calibration uses two offset values at two corresponding temperatures; this changes the calibration linearly as the temperature increases or decreases.
Press scroll until the display shows CAL.P (Enter Calibration Code) Use the up down keys to enter the password code. (Calibration Pass Code = 95). When the correct password has been entered the display will show PNT.LO. If the wrong pass code is entered the display will revert to zero pass code, until the correct pass code is entered.
When the correct pass code is entered and PNT.LO (Adjust Low Point) is displayed. Use the up and down keys to enter the Low Temperature Point, which you want to apply an Offset.
Press scroll until the display shows OFS.LO (Adjust Low OFFset). Use the up and down keys to enter the amount Offset you want to apply to the Low Temperature
Point.
Press scroll until the display shows PNT.HI (Adjust High Point). Use the up down and keys to enter the High Temperature Point, which you want to apply an Offset.
Press scroll until the display shows OFS.HI (Adjust High OFFset). Use the up down and keys to enter the amount Offset you want to apply the High Temperature
Point.
Once the calibration details have been entered, press scroll until the display shows the next required parameter or return to the home list. The calibration data will now be protected by the pass code. To edit the data the above procedure must be followed.
Single Offset
If a constant offset is required across the temperature range, set the required “High
Point” (PNT.HI) and “Low Point” (PNT.LO) to the required values (not the same), then set the “low Offset” (OFS.LO) and “High Offset” (OFS.HI) to the same value.
21
3.0 3216 Controller
Caution! - Do not make PNT.LO and PNT.HI the same value as the controller will not work correctly and could cause the product to overheat.
3.6.7
Holdback
If the temperature ramp rate of the program is quicker than the product can achieve, the program will wait until the temperature of the product catches up.
e.g. If a holdback value of 10 is set and the program is set to ramp to a setpoint of 600
°C, the program will reach 600 °C, then go into a hold state; the hold indicator will light until the product temperature reaches 590 °C, the program will then continue to control again.
The holdback will only apply once per segment, therefore when control has been reestablished, the holdback will not apply again to that segment, even if the product temperature goes outside the holdback band.
Holdback can only be accessed in supervisor level (level 2) by scrolling with the scroll until the display shows H.BACK <PROGRAM HOLDBACK>: Use the up keys to select the required Holdback value.
and down
If a multi programmer is used, each program can have its own holdback value assigned to it.
Note: When a holdback is set, each segment used must have a Ramp Rate assigned to it, in order for it to be recognised by the program.
22
3.0 3216 Controller
3.7
Programming
3.7.1
Creating a Program
Programs can be created in level 1 or level 2 of the 3216P1 and 3216P5. Each program contains 8 Ramp/ Dwell pairs.
Note: A currently active program cannot be altered. Go into 'Reset' mode before starting to create or modify a program
3.7.2
Program Number (3216P5 Only)
Press scroll until the display shows PROG <PROGRAM NUMBER.> Select the program number.
3.7.3
Ramp Units
Press scroll until the display shows RAMP.U <Ramp Units>: Use the up select the Ramp Units of Hour, Min or Seconds.
3.7.4
Dwell Units down to
Press scroll until the display shows DWEL.U <Dwell Units>: Use the up select the Dwell Units of Hour or Min.
3.7.5
Holdback down to
until the display shows H.BACK <Program Holdback>: If a holdback value is required, use the up select “OFF” if no holdback is required.
down to enter the required value or
3.7.6
Ramp Rate
Press scroll until the display shows RMP.1 <Ramp Rate 1>: Using the up down enter the value for the first ramp rate depending on the Ramp Units selected. If the
Ramp segment is not required select “OFF”.
3.7.7
Target Setpoint
Press scroll until the display shows T.SP 1 <Target SP 1>: Enter the temperature that you want the product to ramp up to using “Ramp rate 1”.
If “Ramp Rate 1” has been set to “OFF”. The product will Heat/ Cool directly to the
Target SP.
3.7.8
Dwell Time
Press scroll until the display shows DWELL. 1 <DWELL TIME 1>: Enter the time to dwell at “Target SP 1”. If the dwell segment is not required, use the down to select
OFF, which is below the Zero value.
This Process is repeated for each of the 8 segments of the program.
23
3.0 3216 Controller
If not all the segments are used for a program, the Ramp & Dwell of each of the subsequent segments should be set to OFF.
A program will end in one of two ways, either revert to the control setpoint or dwell at the temperature set in the last segment used. When a program finishes on a dwell and the dwell time expires the temperature will revert to the control setpoint.
Note: Before operating a program ensure that the control setpoint is set to Zero to avoid unexpected heating at the end of the program.
3.7.9
Running a Program
If using the 3216P5 controller press scroll to display PROG <PROGRAM NUMBER>.
Select the required Program Number before operating a Program.
Table below shows the key presses to operate a program.
Operation Action
To RUN a program
Press and quickly release
+
Indication
Indicator – RUN = ON
Scrolling Display – Current
Program state
To HOLD a program
Press and quickly release
+
To RESET a program Press and hold
Program Ended
+ more than 1 second for
Indicator – RUN = Flashing
Scrolling Display – Program Hold
Indicator – RUN = OFF
Scrolling Display - None
Indicator – RUN = OFF
Scrolling Text – Program End
To RESET a program after it has completed
Press and hold + for more than 1 second or press and quickly release Ack
Indicator – RUN = OFF
Scrolling Display - None
3.7.10
Program Status
While the program is operating in level 1 or level 2, the home display shows two values at any one time:
3.7.11
Process Value
The upper display shows the current temperature of the product.
3.7.12
PSP, Segment Type and Number
The lower display continually alternates between the programs current set value
(Program SP = PSP) and scrolling text, indicating the current status of the program whether RAMP or DWELLING followed by the segment number.
Additional information can be obtained using the scroll key while the program is operating.
24
3.0 3216 Controller
Working Output Power
From the home display, press scroll until the display shows WRK.OP <WORKING
OUTPUT POWER>. This shows the power being used as a percentage.
Time Remaining
Press scroll until the display shows T.REMN <TIME REMAINING>. This shows the dwell time remaining for the current segment. There is no value for “Ramp Time
Remaining” therefore when the program is ramping the dwell time set will be shown and will only begin to count down when the ramp has finished.
Program Review
Further presses of scroll will reveal the settings of the current program operating.
These parameters are locked, while the program is operating.
Program Hold with Holdback
If a holdback value has been set (see section 3.6) and the program goes into a hold
state, the red “HLD” indicator will light, until the current temperature catches up.
If while in this condition the program itself is put into “Hold” by pressing the up , down together, the “HLD” indicator will turn off and the “Run” indicator will flash, indicating the program is on hold. When the program is started again by pressing the up , down together, the “Run“ indicator will stop flashing and show continually and the “HLD” indicator will light, if the current temperature has not caught up with the program.
Power Failure
If there is a power failure while the program is operating and the power is subsequently restored, the scrolling text will read <POWER FAIL - PROGRAM RESET>.
Press the “ACK” function to acknowledge this message, press the “ACK” function again to reset the program.
Alarms
Alarms are used to alert the operator when a pre-set level has been exceeded or a function error has occurred such as a sensor break. They are indicated by a scrolling message on the display and a flashing red ALM (Alarm) indicator. The alarm may also switch an output – usually a relay to allow external devices to be operated when an alarm occurs. Alarms only operate if they have been configured and are dependent on customer requirements.
How to acknowledge an alarm will depend on the type of latching which has been configured. A non-latched alarm will reset itself when the alarm condition is removed. A latched alarm requires acknowledgement with the “ACK” function before it is reset.
If an alarm has been activated the red “ALM” indicator will light and the scrolling text will indicate the type of alarm.
To acknowledge an alarm and cancel the “ALM” indicator, press “ACK” function.
Note: The alarm indicator may seem to be permanently on when viewed from above.
When an alarm is active the indicator should only be flashing, to confirm this, the controller must be viewed directly from the front.
25
26
3.0 3216 Controller
Program Example
The following sequence of entries creates and runs the program shown graphically below.
1. Press scroll until the display shows RAMP.U <SP RAMP UNITS>. Select MIN.
2. Press scroll until the display shows DWELL.U <DWELL UNITS>. Select MIN.
3. Press scroll until the display shows RMP.1 <RAMP RATE 1>. Select 5
4. Press scroll until the display shows T.SP1 <TARGET SP 1>. Select 600
5. Press scroll until the display shows DWEL.1 <DWELL TIME 1>. Select 30
6. Press scroll until the display shows RMP.2 <RAMP RATE 2>. Select 4
7. Press scroll until the display shows T.SP2 <TARGET SP 2>. Select 400
8. Press scroll until the display shows DWEL.2 <DWELL TIME 2>. Select 30
9. Press scroll until the display shows RMP.3 <RAMP RATE 3>. Select OFF
10. Press scroll until the display shows T.SP3 <TARGET SP 3>. Select 600
11. Press scroll until the display shows DWEL.3 <DWELL TIME 3>. Select 60
12. Press scroll until the display shows RMP.4 <RAMP RATE 4>. Select 3
13. Press scroll until the display shows T.SP4 <TARGET SP 4>. Select 800
14. Press scroll until the display shows DWEL.4 <DWELL TIME 4>. Select OFF
15. Press scroll until the display shows RMP.5 <RAMP RATE 5>. Select 5
16. Press scroll until the display shows T.SP5 <TARGET SP 5>. Select 400
17. Press scroll until the display shows DWEL.5 <DWELL TIME 5>. Select 480
18. Press the ACK function to return to the home display.
19. Press the up and down keys together, to operate the program.
Segment
3.0 3216 Controller
1
RMP.1= 5°C/Min
T.SP1= 600°C
Dwel.1= 30 Min
2
RMP.1= 4°C/Min
T.SP1= 400°C
Dwel.1= 30 Min
3
RMP.1= OFF
T.SP1= 600°C
Dwel.1= 60 Min
4
RMP.1= 3°C/Min
T.SP1= 800°C
Dwel.1= OFF
5
RMP.1=5°C
T.SP1= 400°C
Dwel.1= 480 Min
3.8
Controller Options
As options can be ordered in a variety of combinations and for a variety of purposes, exact instructions are not given here. The full Eurotherm manual may be required to determine customer parameter settings. To reveal or hide parameters in the controllers it is necessary to go into configuration mode, a security code is needed. Please consult
Carbolite Gero.
3.8.1
Digital Communications - RS232
If the RS232 option is supplied, the furnace is fitted with one sub-miniature Dsocket connected to the controller comms module. RS232 is suitable for direct connection to a personal computer (PC) using a “straight through” cable as follows
(the linked pins at the computer end are recommended but may not be necessary).
The cable is usually 9-pin at the furnace end and 9-pin at the computer, but other alternatives are shown in parentheses.
Product end of cable female (25-pin) 9-pin
RS232 Cable: product to PC
Computer end of cable
9-pin (25-pin) male
Rx
Tx
Com
(2)
(3)
(7)
3
2
5
_________________
_________________
_________________
3
2
(2)
(3)
Tx
Rx
5 (7) Com
7,8 (4,5) Link together
1,4,6 (6,8,20) Link together
3.8.2
Digital Communications - RS485
If an RS485 option is supplied, the furnace is fitted with two D-sockets. Connection between products is by “straight” cable as follows:
Product end of cable female (25-pin) 9-pin
-
+
Com
(2)
(3)
(7)
3
2
5
RS485 Cable: product to PC
_________________
Computer end of cable
9-pin (25-pin) female
3
2
5
(2)
(3)
(7)
Tx
Rx
Com
3.8.3
Comms Address
Typically the comms address is set to 1, but this can be changed. In the case of RS485 and multiple instruments it is necessary to set different addresses. To change the
27
3.0 3216 Controller address value, access the level 2 list. In level 2 press the page key until the COMMS parameter is displayed. Press up down to select the address value.
3.8.4
Alarm Option
When an alarm board is fitted, which consists of a relay with voltage free contacts, for operator use, the contacts are taken to a panel plug on the control panel, wired as indicated:
Key
C Temperature Controller
F Fuse (2A)
S Supply
L Load
*
Normally open relay contacts
RO
Relay Output 240V 2A
MAX
The purpose of the 2 amp fuse is to break the circuit to prevent overloading on the circuit due to high voltage.
The instrument configuration and parameters available to the operator depend on the customer requirements.
3.9
Temperature Controller Replacement
Before handling the controller: wear an anti-static wrist strap or otherwise avoid any possibility of damage to the unit by static electricity.
Refer to the detailed instructions supplied with the replacement controller.
Ease apart the two lugs at the side; grip the instrument and withdraw it from its sleeve; push in the replacement.
3.10
3216 Controller Navigation Diagram
The following diagram details how to navigate to the various menu options within the
3216 Controller. At each option, values can be set using the arrow keys.
28
3.0 3216 Controller
L1 Level 1 Press the Scroll Key
L2 Level 2
Press the Scroll Key multiple times
*
If configured A Access
**
Do not raise the power limit (if accessible) above the design level for the product
~
Multiple Program Only
Hold the Page key for 3 seconds
Locked - password required
Unlocked
Black = Progress
Dashed = Through multiple menus
White = Return
29
4.0 3216CC Controller
4.0
3216CC Controller
4.1
3216CC
This section should be disregarded unless the controller is used as an independent end zone controller.
The 3216CC Controller is a digital temperature controller which uses PID algorithms to give excellent temperature control when properly set. This controller can only be used as a simple temperature controller, it cannot be programmed.
4.2
PID control
This controller uses PID (Proportional Integral Derivative) temperature control. This type of control uses a complex mathematical control system to adjust the heating power and achieve the desired temperature.
4.3
Operation
4.3.1
Controller Layout
Key
A Power Output Indicator
B Alarm Indicator
C
Remote Indicator
(when configured)
D Page
E Scroll
F Down
G Up
H Run Indicator
I Hold Indicator
J
Setpoint Temperature
(SP)
K
Measurement Temperature
30
4.0 3216CC Controller
4.3.2
Keys
Page Key
Scroll Key
Ack
Page and
Scroll
Arrow Keys
+
+
The page key is used to access level 2 when held down for 3 seconds.
The scroll key is used to scroll through parameters.
When pressed simultaneously the ACK function is used to: l l l
Return to the Home Menu
Acknowledge an alarm if activated.
Reset a program after the program has ended.
The arrow keys are used individually to adjust the selected parameters and in combinations to operate a program.
Note: If a parameter is selected and no further action is taken, the display will time out and revert back to the home display in its working level after approximately 1 minute.
4.4
Quick Start Guide
4.4.1
Operation as a simple controller
When switched on, the controller goes through a short test routine and then shows the measured temperature (PV = Process Value) in the upper part of the display and below it, the desired temperature (Setpoint).
4.4.2
Changing the Setpoint
Press Up or Down to select the required SP. If the SP is higher than the measured temperature, the OP1 indicator will illuminate in the top left corner of the display, indicating that the controller is calling for power (giving an output).
The controller will immediately attempt to reach the setpoint and then maintain it.
This will cause the product to heat as quickly as possible which may not be appropriate where the product contains sensitive ceramic components. For products with ceramic components, e.g. a tube furnaces fitted with a long ceramic work tube, use the ramp rate feature set with a low heating rate such as 5°C per minute (300°C per hour), to prevent damage.
4.4.3
Using the Controller
The parameters in the controller are first shown by a short code (mnemonic). After 5
Seconds a description of the parameter will scroll once along the display and then revert back to the mnemonic. The scrolling text can be interrupted at any time by a single press of any of the buttons, but will not scroll again until the parameter is returned to.
In this manual the mnemonic will be shown first, followed by the scrolling text in brackets; e.g. PROG <PROGRAM NUMBER>
31
4.0 3216CC Controller
4.4.4
Understanding User Levels
There are two user levels in the controller; Level 1 (Operator) and Level 2 (Supervisor).
Level 1 (Operator) is for the day to day operation of the controller. These parameters are not protected by a security code.
Level 2 (Supervisor) provides access to additional parameters. Access to this level protected by a security code
To Enter Level 2
1. Press and hold the page key for 3 seconds.
2. The display will show LEu 1 GOTO
3. Release the page Key
4. Press the up or down to choose LEu 2 (level 2)
5. Press the up or down to enter the code (Level 2 Code = 9).
If the correct code is entered, PASS should momentarily be displayed and then revert to the level 2 home display.
If an incorrect code is entered the display reverts back to Level 1 home display.
When level 2 operations have been completed, the supervisor must return to Level 1 either manually or by switching the instrument off and back on. There is no time out function.
To Return to Level 1
1. Press and hold the page Key
2. Press down to select LEu 1
It is not necessary to enter a code when going from a higher level to a lower level.
When level 1 is selected, the display reverts to the home display (See Controller Layout)
Table showing parameters accessible in level 1 and Level 2
Operator LEVEL 1 home display
Supervisor LEVEL 2 home display
Programming
Program Status
Alarms (if configured)
Current Transformer Input (if configured)
Comms (if configured)
Controller set up (if configured)
Customer Calibration (if configured)
TIP
32
4.0 3216CC Controller
If while navigating the controller, a parameter has been passed or you need to access parameters which would be at the end of a scroll list, press and hold scroll and use up to return to a previous parameter.
4.5
Setting up the Controller
Before using the controller (or during its lifetime) certain parameters may have to be set, depending on specific requirements. To do this the controller must be set to supervisor level (Level 2).
4.5.1
Setpoint Ramp Rate
To control the rate at which the temperature rises to setpoint, the SP.RATE function is used.
Before setting the ramp rate, it is advisable to set the setpoint to a low value,
preferably 0 °C (see section 4.4). Once the ramp rate has been set, the required
setpoint can be entered from the home menu. Doing so will activate the ramp rate, which can be identified with the run indicator showing on the bottom of the display.
While the ramp rate is active the working setpoint will be shown on the lower temperature display (this is the setpoint, set by the ramp rate).
When the process temperature has reached the setpoint value at the given ramp rate, the run indicator will turn off and the instrument will control at the required setpoint temperature.
Any further modifications to setpoint will cause the ramp rate to be activated and the instrument to control as described above.
NOTE: Ensure timer configuration is set to ‘none’ (see section 4.6) to use the setpoint
ramp rate feature without any timer functions.
4.5.1.1
Setting Setpoint Ramp Rate
In supervisor level (level 2).
Press scroll until the display shows SP.Rate <setpoint rate limit>. Using up down select the ramp rate required, in °C/ Min.
4.5.1.2
Running with Ramp Rate and
Press the up and down keys at the same time to activate the ramp rate. The
"Run" indicator will illuminate and the scrolling text will read <RAMPING> to show the ramp rate is active. The ramp rate will then start from the current process temperature.
When the ramp reaches the setpoint temperature, the "Run" indicator will turn off and the instrument will maintain control at the setpoint.
To put the ramp rate into a hold condition, press the up and down keys and release. The "Run" indicator will flash and the scrolling text will read <HOLD> to show the ramp rate is on hold.
33
4.0 3216CC Controller
To cancel the ramp rate, press and hold the up indicator turns off.
4.5.2
Maximum Output Power and down keys until the "Run"
Press scroll until the display shows OP.HI <OUTPUT HIGH>. Use the up and down keys to select the output power required as a percentage. Once the setting is made, turn the instrument switch off and on to power cycle the temperature controller.
Depending on the furnace or oven model, the maximum output power setting OP.Hi
may be accessible or locked.
For silicon carbide heated furnaces, the parameter is accessible to allow compensation for element ageing.
In many models the maximum output power setting depends on the supply voltage, see
4.5.3
Customer ID
A furnace or oven identification number can be entered if required. This maybe used to identify one of many units for production or quality control systems.
Press scroll until the display shows ID <CUSTOMER ID>. Use the up keys to enter your own identification number. This can range from 1-9999.
and down
4.5.4
Units or down Press scroll until the display shows UNITS <DISPLAY UNITS>. Use the up keys to select the required units.
Mnemonic
NONE
°C
°F
°K
PERC
Celsius
Kelvin
Description
No units (Default °C)
Fahrenheit
% (shows °C value)
4.5.5
Language
The scrolling text on the 3216 can be shown in different languages, this can only be set at the factory and therefore must be specified at the time of placing an order.
4.6
Timer
4.6.1
Setting the Timer
A timer can be configured to operate in four different modes. These can be selected in level 2 (supervisor level) using the TM.CFG parameter as:-
• None
• Dwell Timer
34
4.0 3216CC Controller
• Delayed switch on timer
• Soft start timer
None
The timer is turned off, no timer configurations are available, the instrument works as a simple setpoint controller.
Press scroll until the display shows TM.CFG <TIMER CONFIGURATION>. Using the up down select NONE.
4.6.2
Dwell Timer
A dwell timer is used to control a process at a fixed temperature for a defined period. At the end of the time period the controller will switch off the output power to the elements.
Press scroll until the display shows TM.CFG <TIMER CONFIGURATION>. Using the up down select Dwell.
When Dwell parameter is selected, the Timer resolution (TM.RES), Time duration
(DWELL) and Timer Threshold (THRES) functions become available.
Press scroll until the display shows TM.RES < Time resolution >. Use the up to select the timer units in Min or Hours.
down
Press scroll until the display shows DWELL < SET TIME DURATION >. Use the up down to enter the time duration required.
Press scroll until the display shows THres < TIMER THRESHOLD >. Use the up down to select the temperature threshold that you require the timer to start at.
The threshold value is ±n around the setpoint (n=threshold value).
Example: If the setpoint is set to 800 °C and the timer threshold is set to 2, after the timer is activated it will not start until the process value reaches 798 °C if ramping up or
802 °C if it is cooling.
Note: If the threshold is set to OFF, the timer will either; start to count down as soon
as it is activated with the mode keys or if a ramp rate has been set (see section 4.5.1
), the timer will start as soon as the ramp reaches the setpoint. (see section 4.7.1)
4.6.3
Delayed Switch On Timer
The delayed switch on timer is used to switch on the output power to the elements after a set time period.
Press scroll until the display shows TM.CFG <TIMER CONFIGURATION>. Using the up down select dELY.
When delay parameter is selected, the Timer Resolution (TM.RES) and Time Duration
(DWELL) functions become available.
Press scroll until the display shows TM.RES < Time Resolution >. Use the up to select the timer units in Min or Hours.
down
35
4.0 3216CC Controller
Press scroll until the display shows DWELL < SET TIME DURATION >. Use the up down to enter the time duration required before the output power switches on.
4.6.4
Soft Start Timer
The Soft Start Timer is used to start a process at a reduced setpoint and power. The
Soft Start Setpoint is used as a threshold only and is not a control point.
Example: Main Setpoint = 800 °C
Max power limit = 75 % (This may be set at the factory)
Soft Start Setpoint = 600 °C (Threshold)
Soft Start Power Limit = 50% (Cannot be set above max power Limit)
When the timer is running, the maximum power is controlled by the Soft Start Setpoint of 600 °C and the Soft Start Power limit of 50%. This will continue until the timer ends or the current temperature exceeds the Soft Start Setpoint.
When the timer ends or the current temperature exceeds the Soft Start Setpoint, the instrument will start to control using the main setpoint of 800 °C and the Max Power
Limit of 75%.
Press scroll until the display shows TM.CFG <TIMER CONFIGURATION>. Using the up down select SF.st.
When Soft Start parameter is selected, the Timer Resolution (TM.RES), Time Duration
(DWELL), Soft Start Setpoint (SS.SP) and Soft Start Power Limit (SS.PWR) functions become available.
Press scroll until the display shows TM.RES < Time resolution >. Use the up to select the timer units in minutes or hours.
down
Press scroll until the display shows DWELL < SET TIME DURATION >. Use the up down to enter the time duration required, before the instrument starts to control using the main setpoint and max power.
Press scroll until the display shows SS.SP < Soft Start Setpoint >. Use the up down to enter the Soft Start Setpoint.
Press scroll until the display shows SS.PWR < Soft Start Power Limit >. Use the up down to enter the Soft Start Power Limit.
4.7
Running a Timer
l l l l
Run . This starts the timer.
Hold . This stops the timer at the elapsed time. It will start again from the elapsed time when Run is selected again.
Reset . This sets the timer back to zero. It can be operated again from this state.
End cannot be set – it occurs automatically when the timer has counted down to zero.
36
4.0 3216CC Controller l
Acknowledge any timer after a timer has timed out using ACK function (see section
and simultaneously.
4.7.1
Dwell Timer
Operation
To RUN Timer
To HOLD timer
To switch off Timer / Cancel
Action
Press and quickly release
+
Press and quickly release
+
Press and hold + for more than 1 second
To return to home after reset Press and hold
+ for more than 1 second
Indication
Indicator – RUN = ON
Scrolling Display – Timer
Running
Indicator – RUN = Flashing
Scrolling Display – Timer
Hold
Indicator – RUN = OFF
Scrolling Display – None
Static Text - OFF
Indicator – RUN = OFF
Display – A-M <LOOP
MODE- AUTO MANUAL
OFF>
To re-RUN Timer
To RESET timer and return to home menu after timer end
Timer Ended
Press and quickly release
Ack
+
Press and quickly release
+
Press and hold + for more than 1 second
Use the up or down to select AUTO
Indicator – RUN = OFF
Scrolling Text – Timer End
Static Text - OFF
Indicator – RUN = ON
Scrolling Display – Timer
Running
Indicator – RUN = OFF
Scrolling Display - None
Indicator – RUN = OFF
Display – A-M <LOOP
MODE- AUTO MANUAL
OFF>
Use the up down to select
4.7.2
Power Failure While Using Dwell Timer
If there is a power failure while the timer is operating and the power is subsequently restored, the timer will reset and the static text will display “OFF“ until the are pressed to re-run the timer.
+ keys
37
4.0 3216CC Controller
4.7.3
Running Dwell Timer with Ramp Rate
Set the ramp rate as outlined in section 4.5.1
Set the dwell time as outlined in section 4.6.2.
When the timer is set to operate with a set ramp rate, the timer will not start to count down until the setpoint has been reached with the ramp, at which time the timer will begin time count down.
The scrolling display will indicate “timer running” and the run indicator will be illuminated while the ramp rate is active and during the timer count down, after which the display
will indicate the instrument has switched off power to the elements (see section 4.7.7),
and the run indicator will switch off.
4.7.4
Running Dwell Timer with Ramp Rate & Threshold
Set the ramp rate as outlined in section 4.5.1.
Set the dwell time as outlined in section 4.6.2.
Set the threshold as outlined in section 4.6.3.
When the timer is set to operate with a set ramp rate and threshold, the timer will not start to count down until the process temperature has reached the threshold value (see
The scrolling display will indicate “timer running” and the run indicator will be illuminated while the ramp rate is active, while the process value is reaching the threshold value and during the timer count down, after which the display will indicate the instrument has
switched off power to the elements (see section 4.7.1).
4.7.5
Delayed Switch on Timer
Operation Action
To RUN Timer
To HOLD timer
Press and quickly release
Press and quickly release
+
+
Indication
Indicator – RUN = ON
Scrolling Display – Timer
Running
Static Text - OFF
Indicator – RUN = Flashing
Scrolling Display – Timer
Hold
Static Text - OFF
To switch off Timer /
Cancel
To return to home menu. After Resetting timer
Press and hold + for more than 1 second Indicator –
RUN = Off
Scrolling Display – None
Static Text - OFF
Press and hold + more than 1 second for
Indicator – RUN = Off
Display – A-M <LOOP MODE-
AUTO MANUAL OFF>
Use the up select or down to
38
4.0 3216CC Controller
To re-RUN Timer
Timer Ended
Press and quickly release +
Indicator – RUN = OFF
Scrolling Text – Timer End
Indicator – RUN = ON
Scrolling Display – Timer
Running
Static Text – OFF
4.7.6
Running Delay Timer with Ramp Rate
Set the ramp rate as outlined in section 4.5.1.
Set the delay time as outlined in section 4.6.3.
When ramp rate is active with a delay timer the run indicator serves two functions:
• Indicates timer is running
• Indicates ramp rate is active
This means that when the timer has timed out the run indicator will still be illuminated if the ramp rate is still active and will continue to be illuminated until the ramp reaches setpoint, at which time it will switch off.
A characteristic of these combinations of parameters is that the scrolling text will continue to indicate timer running when the timer has timed out. Checking whether the
timer has timed out or not can be done with the 'T.REMN' function. (see section 4.7.12)
The delay timer with ramp rate will function as outlined in the table above with the addition of the functions in the following table.
4.7.7
Delay timer with ramp rate functions
Timer Ended
When ramp rate active
Indicator – RUN = ON - if ramp rate active
Scrolling Text – Timer Running
To
HOLD timer
Press and quickly release +
Indicator – RUN = Flashing
Scrolling Display – Timer Hold
Static Text - OFF
To switch off
Timer /
Cancel
Press and hold
+ for more than 1 second
To re-
RUN
Timer Press and quickly release +
Indicator – RUN = ON - if ramp rate active
Scrolling Display – None
Static Text - OFF
Indicator – RUN = ON
Scrolling Display – Timer Running
Static Text – OFF
39
4.0 3216CC Controller
4.7.8
Power Failure While Using Delay Timer
If there is a power failure while the timer is operating and the power is subsequently restored, the timer will reset and will re-run from the power on time.
4.7.9
Soft start Timer
Operation
To RUN
Timer
To HOLD timer
To switch off
Timer/
Cancel
Action
Press and quickly release
Press and quickly release
Press and hold second
Timer Ended
+
+
+ for more than 1
Indication
Indicator – RUN = ON
Scrolling Display – Timer
Running
Static Text - OFF
Indicator – RUN = Flashing
Scrolling Display – Timer Hold
Static Text - OFF
Indicator – RUN = OFF
Scrolling Display – None
Static Text - OFF
Indicator – RUN = OFF
Scrolling Text – Timer End
Running Soft Start Timer
When the soft start timer is set to operate, the scrolling display will indicate “timer running” and the setpoint temperature, not the soft start setpoint.
4.7.10
Power Failure While Using Soft Start Timer
If there is a power failure while the timer is operating and the power is subsequently restored, the timer will reset and will re-run from the power on time.
4.7.11
Ramp Rate with Soft Start Timer
It is not recommended that the ramp rate function be used with a soft start timer.
Note: If the temperature is already above the threshold when the timer is set to operate, the timer will time out immediately.
4.7.12
Time Remaining
The time remaining of any 'Timer' mode can be checked at any time while a timer is active.
To view the time remaining, press scroll until the display shows T.REMN <TIME
REMAINING>.
Note: The time remaining can be modified at any time while the count down timer is operating by pressing the up active.
or down key while the time remaining function is
40
4.0 3216CC Controller
4.7.13
Alarms
Alarms are used to alert the operator when a pre-set level has been exceeded or a function error has occurred such as a sensor break. They are indicated by a scrolling message on the display and a flashing red ALM (Alarm) indicator. The alarm may also switch an output – usually a relay to allow external devices to be operated when an alarm occurs. Alarms only operate if they have been configured and are dependant on customer requirements.
How to acknowledge an alarm will depend on the type of latching which has been configured. A non-latched alarm will reset itself when the alarm condition is removed. A
latched alarm requires acknowledgement with the “ACK” Function (see section4.3.2)
before it is reset.
If an alarm has been activated the red “ALM” indicator will illuminate and the scrolling text will indicate the type of alarm.
To Acknowledge an alarm and cancel the “ALM” indicator, press ACK function.
Note: The alarm indicator may seem to be permanently on when viewed from above.
When an alarm is active the indicator should only be flashing, to confirm this, the controller must be viewed directly from the front.
4.8
Controller Options
As options can be ordered in a variety of combinations and for a variety of purposes, exact instructions are not given here. The full Eurotherm manual may be required to determine customer parameter settings. To reveal or hide parameters in the controllers it is necessary to go into configuration mode, a security code is needed. Please consult
Carbolite Gero.
4.8.1
Digital Communications - RS232
If the RS232 option is supplied, the furnace is fitted with one sub-miniature Dsocket connected to the controller comms module. RS232 is suitable for direct connection to a personal computer (PC) using a “straight through” cable as follows
(the linked pins at the computer end are recommended but may not be necessary).
The cable is usually 9-pin at the furnace end and 9-pin at the computer, but other alternatives are shown in parentheses.
Product end of cable female (25-pin) 9-pin
Computer end of cable
9-pin (25-pin) male
Rx
Tx
Com
(2)
(3)
(7)
3
2
5
RS232 Cable: product to PC
_________________
_________________
_________________
3 (2) Tx
2 (3) Rx
5 (7) Com
7,8 (4,5) Link together
1,4,6 (6,8,20) Link together
41
4.0 3216CC Controller
4.8.2
Digital Communications - RS485
If an RS485 option is supplied, the furnace is fitted with two D-sockets. Connection between products is by “straight” cable as follows:
Product end of cable female (25-pin) 9-pin
-
+
Com
(2)
(3)
(7)
3
2
5
RS485 Cable: product to PC
_________________
Computer end of cable
9-pin (25-pin) female
3
2
5
(2)
(3)
(7)
Tx
Rx
Com
4.8.3
Comms Address
Typically the comms address is set to 1, but this can be changed. In the case of RS485 and multiple instruments it is necessary to set different addresses. To change the address value, access the level 2 list. In level 2 press the page key until the COMMS parameter is displayed. Press up down to select the address value.
4.8.4
Alarm Option
When an alarm board is fitted, which consists of a relay with voltage free contacts, for operator use, the contacts are taken to a panel plug on the control panel, wired as indicated:
Key
C Temperature Controller
F Fuse (2A)
S Supply
L Load
*
Normally open relay contacts
RO
Relay Output 240V 2A
MAX
The purpose of the 2 amp fuse is to break the circuit to prevent overloading on the circuit due to high voltage.
The instrument configuration and parameters available to the operator depend on the customer requirements.
Before handling the controller: wear an anti-static wrist strap or otherwise avoid any possibility of damage to the unit by static electricity.
Refer to the detailed instructions supplied with the replacement controller.
42
4.0 3216CC Controller
Ease apart the two lugs at the side; grip the instrument and withdraw it from its sleeve; push in the replacement.
4.9
3216CC Navigation Diagram
43
5.0 2132 Over-Temperature
5.0
2132 Over-Temperature Controller Description (if fitted)
5.1
Description
Key
A Alarm Light
B Page
C Scroll
D Down
E Up
F Display
This over-temperature controller is fitted and supplied ready to use by Carbolite Gero.
It is a digital instrument with a latching alarm, requiring no additional panel controls.
The controller features easy setting of over-temperature setpoint and reading of current temperature by the over-temperature sensor.
5.2
Operation
5.2.1
Controls
Most Carbolite Gero products are fitted with an instrument switch which cuts off power to the controller and other parts of the control circuit.
To operate the controller, power must be supplied to the product and the instrument switch must be on. If a time switch is included in the product circuit, this must be in the
'ON' position.
When an over-temperature condition occurs, the controller cuts the power to a contactor, which in turn cuts power to the heating elements. Power is not restored until the controller is 'reset'.
Some components will operate after the over-temperature feature isolates the power supply e.g. cooling fans will continue to operate, provided that there is a power supply to the product. In some cases the product may not do so, if other options (such as a door switch) are fitted.
44
5.0 2132 Over-Temperature
5.2.2
Operation
When switched on, the controller lights up, goes through a short test routine and then displays the measured temperature or the over-temperature setpoint.
The page key allows access to parameter lists within the controller.
A single press of the page key displays the temperature units, normally set to °C; further presses reveal the lists indicated in the navigation diagram.
The scroll key allows access to the parameters within a list. Some parameters are display-only; others may be altered by the operator.
A single press of the scroll key in the 'Home' list displays the temperature units; further presses reveal the parameters in the current list indicated in the navigation diagram.
To return to the 'Home' list at any time, press page and scroll together, or wait for 45 seconds.
The down and up keys are used to alter the setpoint or other parameter values.
5.2.3
Over-Temperature Operation
Use down and up to alter the over-temperature setpoint. This should normally be set a little above the working temperature (for example 15 °C above). The product is supplied with the over-temperature set at 15 °C above the furnace or oven maximum working temperature.
Press scroll twice view the present temperature as measured by the overtemperature controller. Press it twice, the first press shows the temperature units (°C).
5.2.4
Over-Temperature Alarm
If an over-temperature condition occurs, the OP2 indicator flashes and an alarm message 2FSH also flashes, alternating with the setpoint. Power to the heating elements is disconnected.
5.2.5
Resetting the Over-Temperature Alarm
To acknowledge the alarm press scroll and page together.
If the alarm is acknowledged while there is still an over-temperature condition, the OP2 indicator stops flashing but continues to glow. The 2FSH alarm continues to flash until the over-temperature condition is cleared (by the temperature falling), when normal operation resumes.
If the alarm is acknowledged when the temperature has dropped (or after the overtemperature setpoint has been raised) so that the over-temperature condition no longer exists, then the furnace or oven immediately resumes normal operation.
5.2.6
Sensor Break
The over-temperature cut-out system also operates if the over-temperature control thermocouple breaks or becomes disconnected. The message S.br flashes where the measured temperature is normally displayed.
45
5.0 2132 Over-Temperature
5.3
Audible Alarm
If an audible alarm is supplied for use with the over-temperature controller, it is normally configured to sound on over-temperature condition and to stop sounding when
the alarm is acknowledged as given in section 5.2.
Note: the alarm may sound during controller start-up.
5.4
Navigation Diagram
HL Home List
OTSP
Over-Temperature
Setpoint
AL Access List
Page Key
Scroll Key
For factory access to list and parameters not available to the operator.
Black = Progress
Dashed = Through to other options
46
6.0 Operation
6.0
Operation
6.1
Operating Cycle
This product is fitted with an instrument switch which cuts off power to the control circuit.
Connect the product to the electrical supply.
Turn on the instrument switch to activate the temperature controllers. The controllers illuminate and go through a short test cycle.
Over-Temperature option only . If the digital over-temperature option has not yet been set as required, set and activate it according to the over-temperature controller instructions.
Switch on the heater switch, located on the instrument panel. Unless a time switch is fitted and is switched off, the product will start to heat up. The Heat light(s) glow steadily at first and then flash as the product approaches the desired temperature or a program setpoint.
Over-Temperature option only.
If the over-temperature circuit has tripped, an indicator on the over-temperature controller flashes and the heating elements are isolated. Find and correct the cause before resetting the over-temperature controller according to the instructions supplied.
To switch off power to the heating elements, use the heater switch. To switch the product off, use both the heater switch and the instrument switch. If the product is to be left switched off and unattended, isolate it from the electrical supply.
6.2
Control Method
Set the three temperature controllers to the desired setpoints. The setting and operation of the end zone controllers depends on the 3-zone control options selected when the product was ordered. These options are described in the 3-zone control methods section.
Note: Despite its vertical orientation, the heated zones of the KVZ model are labelled to correspond with the relevant control module on the CC-T1 touchscreen controller display (Left, Main, Right).
6.3
Safe Operation of the Furnace
For the safe operation of this furnace the following warnings must be followed:
47
6.0 Operation
Explosive Materials
The furnace must not be used to heat materials which could explode, or which could emit gases that could form explosive mixtures. If the safe heating of a material is dependent on its temperature, only heat these type of materials if the furnace has the optional over-temperature protection device fitted. Ensure that the over-temperature device is calibrated and set to an over-temperature safety limit that is sufficiently large as to avoid any hazards. If in doubt, seek expert advice before proceeding. Customers are responsible for carrying out their own risk assessments on the heating of materials.
Do not operate without a work tube . The furnace must not be operated without the correctly sized work tube and correspond work tube adaptor. Otherwise, an operator can access electrically live element coils that could cause serious injury of death.
Switch off the furnace before loading and unloading.
The furnace elements must be switched off using the heater switch, item 2 in
"Warning Labels", when the furnace is being loaded or unloaded. The
work tube can become electrically conductive at high temperatures. If an element has failed and collapsed onto the work tube, the work tube will become live causing serious injury or death.
6.4
3-Zone Control Methods
There are three different control options (A, B & C).
(A) Back to back thermocouples
(B) Retransmission of Setpoint
(C) Independent control
The models listed in this manual are designed to achieve an extended uniform temperature zone, through use of three control zones, rather than achieving different temperatures in each zone.
For A & B, the control zones are linked so that they all follow the centre zone controller in a master-slave approach
Note: l l
Option A is NOT applicable when using the CC-T1 controller
Option B is NOT applicable when using the Eurotherm 2132 End Zone Controller
48
6.0 Operation
A. Back-to-Back Thermocouples
This is the most commonly supplied option. The centre zone of the tube furnace is controlled directly by the centre zone temperature controller. The two end zone thermocouples are wired in opposition to the centre zone reference thermocouple. If the temperatures of the centre and end zones are the same then 0°C will be displayed on the end zone controllers. If the end zone temperatures are either higher or lower than the centre zone, the end zone controller will display the difference in temperature
(higher = positive value, lower = negative value).
It is best practice to set the setpoint of the two end zone controllers to zero.
Alternatively, a small temperature difference (offset) can be created by setting a nonzero value, for example to compensate for heat losses at the end or where using a gas flow. However, the sum of the centre zone controller setpoint and the end zone controller offset MUST NOT exceed the furnace maximum temperature.
To alter the setpoint with the display showing the Home screen, press Down or Up once to display the setpoint and then press again or hold down to adjust it. The display returns to the measured temperature when no key is pressed for a short period of time.
Sometimes a furnace using this type of control does not cool down because the end zones lose heat first and therefore the end zone controllers try to compensate for this by switching on the end zone elements, preventing the furnace from cooling.
B. Retransmission of Setpoint
Three independent thermocouples are connected to three controllers. The three controllers are linked together and the centre zone controller communicates the desired setpoint to the end zone controllers. If the centre zone controller is set to a setpoint or is running a program, the end zone controllers will automatically follow.
For products with the CC-T1 controller, please refer to the separate CC-T1 controller manual for details on enabling and disabling setpoint retransmission.
For other products, additional communication modules are fitted in the controllers. The communication between the controllers of the Eurotherm 3000 series is known as
Broadcast communications. It is possible to switch off the linked control and allow the controllers to work independently. In the level 2 menu of the end zone controllers (see controller operating instruction), scroll to L-r. Where the end zone controller is a 3216 use the up down buttons and select NO. Where the end zone controller is a 3508 use the up down buttons to select SP1, (SP1 = Local, and SP2 = Remote). There is no need to alter the centre zone controller.
It is possible to set an offset (local trim) between the centre and end zone controllers.
This can be either a positive or negative difference from the centre zone temperature.
Once entered, this offset will always be added to, or subtracted from, the retransmitted setpoint temperature.
49
6.0 Operation
For products with the CC-T1 controller, please refer to the separate CC-T1 controller manual for details on how to set an offset trim.
To make this adjustment on other controllers, enter thelevel 2 menu of the end zone controllers (see controller operating instruction), scroll to LOC.T (local trim) and use the up down buttons to enter the desired positive or negative value. This will then be added to, or subtract from, the end zone set temperature. There is no need to alter the centre zone controller.
C. Independent Control
The three controllers are completely independent. Note that it is not possible to maintain very different temperatures in the three zones because of heat transfer between the zones. The models listed in this manual are designed to achieve an extended uniform temperature zone by the use of three control zones rather than achieving different temperatures in each zone.
6.5
General Operating Advice
Heating element life is shortened by overheating. Do not leave the product at high temperature when it is not required. The maximum
temperature is shown on the product rating label and in section 12.0
towards the back of this manual.
Lightweight ceramic fibre insulation can easily be marked by accidental contact. Some fine cracks may develop in the surface of the insulation due to the progressive shrinkage of the insulation materials. Cracks are not usually detrimental to the functioning or the safety of the product.
Clean up any spillages in the insulation, as these can increase the rate of degradation of the insulation material.
6.6
Operator Safety
The ceramic materials used in the product manufacture become electrically conductive to some extent at high temperatures. DO NOT use any conductive tools within the product without isolating it. If a metal work tube is used, it must be earthed (grounded).
Switch off the heater switch whenever loading or unloading the product.
The elements are isolated when the heater switch is OFF. This switch cuts both sides of the circuit via a contactor.
50
6.0 Operation
6.7
Tube Life
A ceramic work tube may crack if work pieces are inserted too quickly or at temperatures below 900 °C (when the tube is more brittle). Large work pieces should also be heated slowly to ensure that large temperature differences do not arise.
Poor thermal contact should be encouraged between the work piece and the tube; crucibles or boats should be of low thermal mass and should have feet to reduce the contact with the tube (fig. 4).
Key
A Tube
B Crucible
Fig 4 - Avoidance of thermal contact
Do not set too high a heating or cooling rate. As tubes are susceptible to thermal shock and may break. Tubes which extend beyond the heated part of the furnace are more at risk. A general rule for maximum heating or cooling rate is 400 ÷ internal diameter in mm to give (°C/ min); for 75 mm i/ d tubes this comes to 5 °C per minute. The controller can be set to limit both the heating and cooling rate.
6.8
Pressure
Work tubes are not able to accept high internal pressure. When gas seals or similar fittings are in use, the gas pressure should be restricted to a maximum of 0.2 bar (3 psi). A pressure of approximately half of that should normally be sufficient to achieve the desired flow rate. The operator must ensure that the exhaust path from the tube is not blocked, so that excess pressure does not occur.
A suitably regulated gas supply should always be used.
It is recommended that a pressure relief system should be used to avoid an over pressurisation of the work tube.
Please note: A product should not be heated up if any valves that have been fitted are closed to create a sealed volume. A sealed work tube should not be heated from cold due to the pressure increase caused by the trapped air or gas expanding during the heating process.
6.9
Gas Tightness
Work tubes of IAP material are impervious. Sillimanite may look similar but is porous.
Ensure that the correct tube material is in use before connecting and using gases other
51
6.0 Operation than inert gases, such as nitrogen.
52
7.0 Maintenance
7.0
Maintenance
7.1
General Maintenance
Preventive rather than reactive maintenance is recommended. The type and frequency depends on the product use; the following are recommended.
7.2
Maintenance Schedule
CUSTOMER
QUALIFIED PERSONNEL
DANGER! ELECTRIC SHOCK . Risk of fatal injury. Only electrically qualified personnel should attempt these maintenance procedures.
Safety
Maintenance
Procedure
Over-Temperature Safety Circuit
(if fitted)
Method
Set an over-temperature setpoint lower than the displayed temperature and check for an over-temperature alarm as detailed in this manual
Over-Temperature Safety Circuit
(if fitted)
Safety Switch Function
(split models only)
Safety Switch Function
(split models only)
Electrical Safety (external)
Electrical Safety (internal)
Electrical measurement
Set a safe temperature above ambient, and open the furnace to see if the heater light goes out
Electrical measurement
Visual check of external cables and plugs
Physically check all connections and cleaning of the power plate area
Frequency
Daily Weekly Monthly
Bi-
Annually
Annually
Function
Temperature Calibration
Operational Check
Operational Check
Work Tube Position
End Plugs / Radiation Shields
Tested using certified equipment, frequency dependent on the standard required
Check that all functions are working normally
Thorough inspection and report incorporating a test of all functions
Visually check that the tube is central to the heated zone (horizontally / vertically)
Visual check for damage or wear, and correct positioning
53
7.0 Maintenance
Seals (if fitted)
Performance
Element Circuit
Power Consumption
Cooling Fans (if fitted)
Check all seals and O-rings and clamps
Electrical measurement
Measure the current drawn on each phase / circuit
Check whether the cooling fans are working
54
7.0 Maintenance
7.2.1
Cleaning
Soot deposits may form inside the furnace, depending on the process. At appropriate intervals remove these by heating as indicated in the General Operation Notes.
The product's outer surface may be cleaned with a damp cloth. Do not allow water to enter the interior of the case or chamber. Do not clean with organic solvents.
7.3
Calibration
After prolonged use, the controller and/or thermocouple may require recalibration. This is important for processes that require accurate temperature readings or for those that use the product close to its maximum temperature. A quick check using an independent thermocouple and temperature indicator should be made from time to time to determine whether full calibration is required. Carbolite Gero can supply these items.
Depending on the controller fitted, the controller instructions may contain calibration instructions.
7.4
After-Sales Service
Carbolite Gero Service has a team of Service Engineers who can offer repair, calibration and preventive maintenance of furnace and oven products both at the Carbolite Gero factory and at customers’ premises throughout the world. A telephone call or email often enables a fault to be diagnosed and the necessary parts to be despatched.
In all correspondence please quote the serial number and model type given on the rating label of the product. The serial number and model type are also given on the back of this manual when supplied with the product.
Carbolite Gero Service and Carbolite Gero contact information can be found on the back page of this manual.
7.5
Recommended Spare Parts and Spare Parts Kit
Carbolite Gero can supply individual spare parts or a kit of the items most likely to be required. Ordering a kit in advance can save time in the event of a breakdown.
Each kit consists of two thermocouples of different lengths, one solid state relay and one complete tube body element set. When ordering spare parts please quote the model details i.e. model type and serial number as stated on the rating label.
55
8.0 Repairs and Replacements
8.0
Repairs and Replacements
8.1
Safety Warning - Disconnection from Power Supply
Immediately switch the product off in the event of unforeseen circumstances (e.g. large amount of smoke). Allow the product to return to room temperature before inspection.
Always ensure that the product is disconnected from the electrical supply before repair work is carried out.
Caution : Double pole/neutral fusing may be used in this product.
8.2
Safety Warning - Refractory Fibre Insulation
Insulation made from High Temperature Insulation Wool
Refractory Ceramic Fibre, better known as (Alumina silicate wool - ASW).
This product contains alumino silicate wool products in its thermal insulation. These materials may be in the form of blanket or felt, formed board or shapes, slab or loose fill wool.
Typical use does not result in any significant level of airborne dust from these materials, but much higher levels may be encountered during maintenance or repair.
Whilst there is no evidence of any long term health hazards, it is strongly recommended that safety precautions are taken whenever the materials are handled.
Exposure to fibre dust may cause respiratory disease.
When handling the material, always use approved respiratory protection equipment (RPE-eg. FFP3), eye protection, gloves and long sleeved clothing.
Avoid breaking up waste material. Dispose of waste in sealed containers.
After handling, rinse exposed skin with water before washing gently with soap
(not detergent). Wash work clothing separately.
Before commencing any major repairs it is recommended to make reference to the
European Association representing the High Temperature Insulation Wool industry
(www.ecfia.eu).
Further information can be provided on request. Alternatively, Carbolite Gero Service can quote for any repairs to be carried out either on site or at the Carbolite Gero factory.
8.3
Temperature Controller Replacement
Refer to the controller instructions for more information on how to replace the temperature controller.
56
8.0 Repairs and Replacements
8.4
Solid-state Relay Replacement
Disconnect the product from the power supply and remove the appropriate cover as given above.
Make a note of the wire connections to the solid state relay and disconnect them.
Remove the solid state relay from the base panel or aluminium plate.
Replace and reconnect the solid state relay ensuring that the bottom of it has good thermal contact with the base panel or aluminium plate.
Replace the access panel.
8.5
Thermocouple Replacement
For vertical models it may be necessary to dismount the furnace from its stand and remove the terminal cover.
Disconnect the product from the power supply. Remove terminal cover to gain access to the thermocouple connections. Make a note of the thermocouple connections.
Thermocouple cable colour codings are: thermocouple leg colour positive (type N) negative pink white
Disconnect the thermocouple from its terminal block.
Carefully withdraw the thermocouple from the product and remove any broken bits of thermocouple.
Bend the new thermocouple carefully to match the shape of the original (working from the terminal end). Should the length differ from that of the original this is usually not important provided that the thermocouple tip is within a work tube diameter's distance from the furnace centre.
Insert the new thermocouple into position, restoring any removed porcelain spacers and ensuring correct polarity.
Re-assemble the furnace.
8.6
Element Replacement
Individual elements are not available for this model of product, if an element fails then a complete element assembly is required. For details and fitting instructions contact
Carbolite Gero Service, see the back page of this manual for contact information.
57
8.0 Repairs and Replacements
8.7
Fuse Replacement
Fuses are marked on the wiring diagram with type codes, e.g. F1, F2. For more
information on fuses refer to section 11.0.
Depending on model and voltage, the different fuse types may or may not be fitted.
If any fuse has failed, it is advisable for an electrician to check the internal circuits.
Replace any failed fuses with the correct type. For safety reasons do not fit larger capacity fuses without first consulting Carbolite Gero.
The fuses are located at the cable entry point. Remove the back panel or control box back panel to gain access to the fuses.
58
9.0 Fault Analysis
9.0
Fault Analysis
A.
Furnace Does Not Heat Up
1.
The HEAT light is ON
The heating element has failed
2.
The HEAT light is OFF
The controller shows a very high temperature or code such as S.br
The controller shows a low temperature
There are no lights glowing on the controller
Check also that the SSR is working correctly
The thermocouple has broken or has a wiring fault
The door switch(es) (if fitted) may be faulty or need adjustment
The contactor/relay (if fitted) may be faulty
The heater switch (if fitted) may be faulty or need adjustment
The SSR could be failing to switch on due to internal failure, faulty logic wiring from the controller, or faulty controller
Check the supply fuses and any fuses in the furnace control compartment
The controller may be faulty or not receiving a supply due to a faulty switch or a wiring fault.
59
9.0 Fault Analysis
B.
Product Overheats
1.
Product only heats up when the instrument switch is ON
2.
Product heats up when the instrument switch is OFF
The controller shows a very high temperature
The controller shows a low temperature
The SSR has failed
"ON"
The controller is faulty
The thermocouple may be faulty or may have been removed out of the heating chamber
The thermocouple may be connected the wrong way around
The controller may be faulty
Check for an accidental wiring fault that could have overloaded the SSR
60
10.0
Wiring Diagrams
10.1
WC-13-30
10.0 Wiring Diagrams
10.2
WC-13-31
Connections below show single phase with indirect safety switches and overtemperature control.
61
11.0 Fuses and Power Settings
11.0
Fuses and Power Settings
11.1
Fuses
F1 - F2: Refer to the circuit diagrams.
F1
Internal
Supply
Fuses
F2
Auxiliary
Circuit Fuses
Customer
Fuses
Fitted if supply cable fitted.
Fitted on board to some types of EMC filter.
GEC Safeclip of the type shown
(glass type F up to 16 A)
38 mm x 10 mm type F fitted on
EMC filter circuit board(s)
Fitted on board to some types of EMC filter.
May be omitted up to 25 Amp/ phase supply rating.
Required if no supply cable fitted.
Recommended if cable fitted.
2 Amps glass type F
On board: 20 mm x 5 mm
Other: 32 mm x 6 mm
See rating label for current;
See table below for fuse rating.
Model
EHC 12/600B
EHC 12/600B
Phases
1-phase
1-phase
Volts
200-208
220-240
Supply Fuse Rating (Amps)
F1
16 A
16 A
62
11.0 Fuses and Power Settings
11.2 Power Settings
The power limit settings (OP.Hi) for this model is as follows. The figures represent the maximum percentage of time that controlled power is supplied to the elements. Do not attempt to "improve performance" by setting a value higher than the one from the table. To adjust the parameter refer to the "Changing the Maximum Output Power" of the control section of the manual.
All standard models covered by this manual are fitted with elements designed for use over the range of voltages 100 V-120 V and 200 V-240 V; the power limit parameter is set according to the table below.
The power limit depends on the voltages follows:
Voltage
Percentage (%)
100 V 120 V 200 V 208 V 220 V 230 V 240 V
100 100 89 81 75
Please refer to the rating label for product specific information.
63
12.0 Specifications
12.0
Specifications
Carbolite Gero reserves the right to change the specification without notice.
All models have cylindrical elements with wire mounted in the surface of the insulation material.
All models can accept work tubes up to a maximum outside diameter of 60 mm.
All models have a maximum operation temperature of 1200°C (1100°C continuous).
Model
Max Temp
(°C)
Max Power
(kW)
Minimum
Work
Tube
Length
(mm)
Tube length for use with modified atmosphere
(mm)
Heated
Length
(mm)
Weight
(kg)
EHC 12/600B 1200
Horizontal 3-zone tube furnaces.
2.52
750 1050 600 25
Work tube adaptors, extended work tube supports, insulation plugs and gas/ vacuum end seals are available from Carbolite Gero for work tubes with outside diameters of 32 mm, 46 mm and 60 mm.
12.1
Environment
The furnaces contain electrical parts and should be stored and used in indoor conditions as follows:
Ambient temperature working range
Temperature: 5 °C to 40 °C
Note: when operating the furnace at temperatures close to the maximum and the ambient temperature is above 30 °C, the allowed external temperature defined in EN
61010-1:2010 may be exceeded.
Relative humidity
Maximum 80% up to 31 °C, decreasing linearly to 50% at 40 °C.
Important safety notice:
After transportation or storage in humid conditions, the furnace could fail to meet all the safety requirements of BSEN 61010-2-010 until it has completed the drying out process to restore its normal condition.
Warning:
It cannot be assumed that the furnace will meet all the safety requirements of BSEN
61010-2-010 during the drying out process.
64
12.0 Specifications
Furnace drying out process
Step 1. Before the furnace is connected to the electrical supply, remove the back panel and check for signs of moisture on the electrical circuits. If visible signs of moisture are present then allow it to dry out in ambient temperature for at least 24 hours. If the problem persists ensure that the furnace is isolated and contact Carbolite Gero Service for more information.
Step 2. Complete the Installation procedure (see section 2.1
Step 3. After reading the controller operation instructions, heat the furnace following the temperature profile given below. This will need to be done manually on furnaces with basic control option or programmed into the controller if an advanced control option is fitted: l l l l l
Ramp the setpoint temperature @ 2 °C/ minute to 100 °C and dwell for 2 hours.
Ramp the setpoint temperature @ 2 °C/ minute to 300 °C and dwell for 3 hours.
Ramp the setpoint temperature @ 3 °C/ minute to 1100 °C and dwell for 1 hour.
Cool naturally to ambient temperature.
Furnace drying out process is complete.
65
Notes
Engineer Name Date
Service Record
Record of Work
The products covered in this manual are only a small part of the wide range of ovens, chamber furnaces and tube furnaces manufactured by Carbolite Gero for laboratory and industrial use. For further details of our standard or custom built products please contact us at the address below, or ask your nearest stockist.
For preventive maintenance, repair and calibration of all furnace and oven products, please contact:
Carbolite Gero Service
Telephone: + 44 (0) 1433 624242
Fax: +44 (0) 1433 624243
Email: [email protected]
Carbolite Gero Ltd,
Parsons Lane, Hope, Hope Valley,
S33 6RB, England.
Telephone: + 44 (0) 1433 620011
Fax: + 44 (0) 1433 621198
Email: [email protected]
www.carbolite-gero.com
Copyright © 2019 Carbolite Gero Limited
advertisement
Related manuals
advertisement