ProSoft Technology ILX56-PBS ProductsPROFIBUS DPV1 Slave for ControlLogix® User Manual
Add to My manuals85 Pages
advertisement
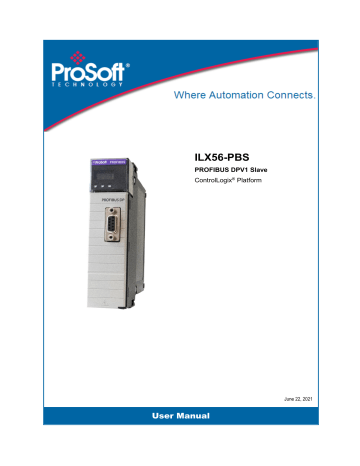
ILX56-PBS
PROFIBUS DPV1 Slave
ControlLogix ® Platform
User Manual
June 22, 2021
Your Feedback Please
We always want you to feel that you made the right decision to use our products. If you have suggestions, comments, compliments or complaints about our products, documentation, or support, please write or call us.
ProSoft Technology, Inc.
+1 (661) 716-5100
+1 (661) 716-5101 (Fax) www.prosoft-technology.com
ILX56-PBS User Manual
June 22, 2021
ProSoft Technology ® , is a registered copyright of ProSoft Technology, Inc. All other brand or product names are or may be trademarks of, and are used to identify products and services of, their respective owners.
In an effort to conserve paper, ProSoft Technology no longer includes printed manuals with our product shipments. User Manuals, Datasheets, Sample Ladder Files, and Configuration Files are provided at our website: www.prosoft-technology.com
Content Disclaimer
This documentation is not intended as a substitute for and is not to be used for determining suitability or reliability of these products for specific user applications. It is the duty of any such user or integrator to perform the appropriate and complete risk analysis, evaluation and testing of the products with respect to the relevant specific application or use thereof. Neither ProSoft Technology nor any of its affiliates or subsidiaries shall be responsible or liable for misuse of the information contained herein. Information in this document including illustrations, specifications and dimensions may contain technical inaccuracies or typographical errors. ProSoft Technology makes no warranty or representation as to its accuracy and assumes no liability for and reserves the right to correct such inaccuracies or errors at any time without notice. If you have any suggestions for improvements or amendments or have found errors in this publication, please notify us.
No part of this document may be reproduced in any form or by any means, electronic or mechanical, including photocopying, without express written permission of ProSoft Technology. All pertinent state, regional, and local safety regulations must be observed when installing and using this product. For reasons of safety and to help ensure compliance with documented system data, only the manufacturer should perform repairs to components. When devices are used for applications with technical safety requirements, the relevant instructions must be followed. Failure to use ProSoft Technology software or approved software with our hardware products may result in injury, harm, or improper operating results.
Failure to observe this information can result in injury or equipment damage.
© 2021 ProSoft Technology. All Rights Reserved.
Printed documentation is available for purchase. Contact ProSoft Technology for pricing and availability.
For professional users in the European Union
If you wish to discard electrical and electronic equipment (EEE), please contact your dealer or supplier for further information.
Warning – Cancer and Reproductive Harm – www.P65Warnings.ca.gov
ProSoft Technology, Inc. Page 2 of 85
Agency Approvals and Certifications
Please visit our website: www.prosoft-technology.com
China ROHS
有害物 质
Hazardous substances
部件名称
Component Name
鉛
Lead
(Pb)
汞
Mercury
(Hg)
鎘
Cadmium
(Cd)
六价 铬
Hexavalent
Chromium
(Cr(VI))
多溴 联苯
Polybrominated
Biphenyls
(PBB)
印刷 电路板组件
Printed Circuit
Board Assemblies
接 线和电缆
Wiring and Cable
塑料部件
Plastic
Components
X
O
O
O
O
O
O
O
O
O
O
O
O
O
O
本表格依据 SJ/T 11364 的 规定编制。
This table is made per guidance of SJ/T 11364
O: 表示 该有害物质在该部件所有均质材料中的含量均在
GB/T 26572
规定的限量要求以下。
O: Indicates that this hazardous substance contained in all of the homogeneous
materials for the part is below the limit requirement in GB/T 26572.
多溴二苯 醚
Polybrominated
Diphenyl
Ethers
(PBDE)
O
O
O
X: 表示 该有害物质至少在该部件的某一均质材料中的含量超出
GB/T 26572
规定的限量要求。
X: Indicates that this hazardous substance contained in at least one of the homogeneous
materials used for this part is above the limit requirement in GB/T 26572.
( 企 业可在此处,根据实际情况对上表中打 “X” 的技 术原因进行进一步说明。
)
(According to actual situation, extra explanations can be given here for the technical reasons of items with "X".)
ProSoft Technology, Inc. Page 3 of 85
ILX56-PBS ♦ PROFIBUS DPV1 Master/Slave
ControlLogix® Platform
Contents
User Manual
Contents
PROFIBUS DP Port (RS485) ...................................................................... 9
PROFIBUS – Slave Mode ......................................................................... 13
Adding PROFIBUS DP Devices ................................................................ 15
PROFIBUS Configuration .......................................................................... 17
Installing the Add-On Profile (AOP) ........................................................... 26
Adding a Module to I/O Configuration ....................................................... 26
PLX50 Configuration Utility Project File ..................................................... 28
Local Rack Module Location ...................................................................... 29
Remote Rack Module Location .................................................................. 30
PLX50 Configuration Utility Upload ........................................................... 38
Status and DPV0 Data Exchange ............................................................. 42
DPV1 Class 1 Messaging (MS1) ............................................................... 44
ProSoft Technology, Inc. Page 4 of 85
ILX56-PBS ♦ PROFIBUS DPV1 Master/Slave
ControlLogix® Platform
Contents
User Manual
ILX56-PBS Emulated Slave Device Status ............................................... 56
PROFIBUS Packet Capture ....................................................................... 57
PROFIBUS master and slave .................................................................... 65
PROFIBUS master class 1 (DPM1) or class 2 (DPM2) ............................. 65
PROFIBUS DP Master class 1 (DPM1) ..................................................... 65
PROFIBUS DP Master class 2 (DPM2) ..................................................... 65
Topology of PROFIBUS DP ....................................................................... 66
PROFIBUS DP cable description .............................................................. 66
PROFIBUS DP connector description ....................................................... 67
GSD File Management Tool Installation .................................................... 68
PROFIBUS Configuration .......................................................................... 70
Adding a PROFIBUS Slave ....................................................................... 71
Downloading the Configuration to the ILX56-PBS ..................................... 73
PROFIBUS Master Configuration .............................................................. 76
Contacting Technical Support .................................................................... 85
ProSoft Technology, Inc. Page 5 of 85
ILX56-PBS ♦ PROFIBUS DPV1 Master/Slave
ControlLogix® Platform
1 Preface
Preface
User Manual
1.1
Introduction to the ILX56-PBS
This manual describes the installation, operation, and diagnostics of the ProSoft
ILX56-PBS PROFIBUS DPV0/DPV1 Slave module.
The ILX56-PBS slots into a 1756 ControlLogix backplane and allows the user to interface PROFIBUS DP to a ControlLogix controller via the ControlLogix backplane.
The ILX56-PBS can operate as one or more PROFIBUS DPV0/DPV1 Slaves. This will allow a ControlLogix controller to exchange process, alarming, and diagnostic data with a PROFIBUS DP Master.
Figure 1.1
– Typical ILX56-PBS PROFIBUS Slave architecture
ProSoft Technology, Inc. Page 6 of 85
ILX56-PBS ♦ PROFIBUS DPV1 Master/Slave
ControlLogix® Platform
Preface
User Manual
1.2
Features
The ILX56-PBS will allow the user to interface PROFIBUS DPV0/DPV1 to a
ControlLogix controller via the 1756 ControlLogix backplane. The ILX56-PBS also supports an onboard non-volatile event log for improved fault finding.
PROFIBUS Slave (ILX56-PBS)
The ILX56-PBS can also be configured to emulate up to 10 PROFIBUS slave devices. Each slave device emulated by the ILX56-PBS can be configured to provide
DPV0 data exchange with a PROFIBUS Master on the network.
The data will be formatted into the engineering units for use in a ControlLogix platform by using the automatically-generated mapping imports for Logix User
Defined Data Types (UDTs).
Each emulated slave can also be configured to exchange DPV1 Class 1 data by mapping Logix tags for the relevant DPV1 data exchange. Each emulated slave will also be able to provide DPV1 alarming for the PROFIBUS Master.
1.3
Additional Information
The following documents contain additional information that can assist the user with the module installation and operation.
Table 1.1 - Additional Information
Link
Resource
PLX50 Configuration Utility
Installation
ILX56-PBS User Manual
ILX56-PBS Datasheet www.prosoft-technology.com
www.prosoft-technology.com
ProSoft Technology, Inc. Page 7 of 85
ILX56-PBS ♦ PROFIBUS DPV1 Master/Slave
ControlLogix® Platform
2 Installation
Installation
User Manual
2.1
Module Layout
The ILX56-PBS has one RS485 PROFIBUS DP port at the front of the module.
NOTE: All required power for the module is derived from the ControlLogix backplane.
The module provides 3 diagnostic LEDs and a 4-character alpha-numeric LED display that provides the mode and status of the module.
Figure 2.1 – ILX56-PBS Front View
Figure 2.2
– ILX56-PBS Bottom View
The module provides two DIP switches and a slot for a SD memory card located on the bottom of the module. These switches can only be accessed when the module is removed from the ControlLogix chassis.
ProSoft Technology, Inc. Page 8 of 85
ILX56-PBS ♦ PROFIBUS DPV1 Master/Slave
ControlLogix® Platform
DIP Switch
DIP Switch 1
DIP Switch 2
Installation
User Manual
Description
Table 2.1. - DIP Switch Settings
Used to force the module into “Safe Mode”. When in “Safe Mode” the module will not load the application firmware and will wait for new firmware to be downloaded. This should only be used in the rare occasion when a firmware update was interrupted at a critical stage.
Used to prevent changes to the configuration.
2.2 PROFIBUS DP Port (RS485)
The PROFIBUS DP port uses a female DB9 connector. This provides connection for the communication conductors, cable shielding and +5Vdc output power.
4
5
6
7
Pin
1
2
3
8
9
Signal
-
-
RxD/TxD-P
CNTR-P
DGND
VP
-
RxD/TxD-N
-
Figure 2.3 – ILX56-PBS PROFIBUS DP (RS485) DB9 connector
Table 2.2
– DB9 Connector layout
Description
Not connected
Not connected
Data received and transmit (+)
Control signal to repeater (+)
Reference potential for +5Vdc
+5Vdc for terminating resistors (active termination)
Not connected
Data received and transmit (-)
Not connected
ProSoft Technology, Inc. Page 9 of 85
ILX56-PBS ♦ PROFIBUS DPV1 Master/Slave
ControlLogix® Platform
3 Setup
Setup
User Manual
3.1
Install Configuration Software
All the network setup and configuration of the module is achieved by means of the
ProSoft PLX50 Configuration Utility. This software can be downloaded from: http://www.prosoft-technology.com
.
Figure 3.1. - ProSoft PLX50 Configuration Utility Environment
3.2 Creating a New Project
Before the user can configure the module, a new PLX50 Configuration Utility project must be created.
1 Under the File menu, select New.
ProSoft Technology, Inc.
Figure 3.2 - Creating a new project
Page 10 of 85
ILX56-PBS ♦ PROFIBUS DPV1 Master/Slave
ControlLogix® Platform
2 A new device can now be added by selecting Add under the Device menu.
Setup
User Manual
Figure 3.3 - Adding a new device
3 In the Add New Device window select the ILX56-PBS and click the Ok button.
Figure 3.4
– ILX56-PBS
4 The device will appear in the Project Explorer tree as shown below, and its configuration window opened. The device configuration window can be reopened by either double-clicking the module in the Project Explorer tree or right-clicking the module and selecting Configuration .
ProSoft Technology, Inc.
Figure 3.5 – ILX56-PBS configuration
Page 11 of 85
ILX56-PBS ♦ PROFIBUS DPV1 Master/Slave
ControlLogix® Platform
3.3
ILX56-PBS Parameters
The ILX56-PBS parameters are configured by the PLX50 Configuration Utility.
Setup
User Manual
NOTE: Refer to the additional information section for documentation and installation links for ProSoft’s
PLX50 Configuration Utility.
3.3.1 General
The General configuration is shown in the following figure. The ILX56-PBS General configuration window is opened by either double-clicking on the module in the tree, or right-clicking the module and selecting Configuration .
Figure 3.6
– ILX56-PBS General configuration
The General configuration consists of the following parameters:
Parameter
Instance Name
Description
Mode
Table 3.1 - General configuration parameters
Description
This parameter is a user-defined name to identify between various ILX56-PBS modules.
This parameter is used to provide a more detailed description of the ILX56-
PBS.
The ILX56-PBS can operate in one of two modes:
Quiet
This mode allows the user to connect the ILX56-PBS to an active bus and run a
DP packet capture. In this mode the ILX56-PBS will not communicate on the
DP Bus, but rather only listen.
Slave
The ILX56-PBS will emulate multiple PROFIBUS Slave devices.
ProSoft Technology, Inc. Page 12 of 85
ILX56-PBS ♦ PROFIBUS DPV1 Master/Slave
ControlLogix® Platform
Setup
User Manual
3.3.2
PROFIBUS – Slave Mode
The ILX56-PBS PROFIBUS configuration is shown in the following figure. The ILX56-
PBS PROFIBUS configuration window is opened by either double-clicking on the module in the tree, or right-clicking the module and selecting Configuration .
Figure 3.7
– ILX56-PBS PROFIBUS configuration – Slave Mode
The PROFIBUS slave configuration consists of the following parameters:
Table 3.2 - PROFIBUS configuration parameters – Slave Mode
Description
Parameter
BAUD Rate Baud Rate (in Kbps) of the PROFIBUS network: 9.6, 19.2, 45.45,
93.75, 187.5, 500, 1500, 3000, 6000 or 12000 Kbps. The baud rate selected should be supported by the PROFIBUS master. The baud rate should be selected depending on the cable length, s ee chapter “ PROFIBUS
DP ”
ProSoft Technology, Inc. Page 13 of 85
ILX56-PBS ♦ PROFIBUS DPV1 Master/Slave
ControlLogix® Platform
Setup
User Manual
3.3.3
Logix
The Logix configuration is shown in the following figure. The ILX56-PBS Logix configuration window is opened by either double-clicking on the module in the tree, or right-clicking the module and selecting Configuration .
Figure 3.8 – ILX56-PBS Logix configuration
The Logix configuration consists of the following parameters:
Parameter
Logix Connections
Controller Path
Response Timeout
Logix Base Tag A/B
Table 3.3 - Logix configuration parameters
Description
The number of Logix (CIP) Connections (1 to 10) to be used in the exchange with Logix.
Each backplane connection is configured with 500 bytes output and 496 byte input and 0 byte configuration.
NOTE: This value must match the same number of connections configured in the Logix IO tree.
This is the CIP path to the Logix controller.
This path will be used for the Class 3 data exchanges for DPV1 objects and alarms.
The maximum time (ms) allowed for a Class 3 response from the Logix controller.
This is the tagname of the ILX56-PBS used for the input and output assembly. For example, if the module is in the local slot connected to a
Logix controller the base Logix tag will be local:x (where x is the slot number).
The base tagname is used when generating the Logix L5X file, which will automatically map the required data.
NOTE: Only Logix Base Tag A will be relevant.
ProSoft Technology, Inc. Page 14 of 85
ILX56-PBS ♦ PROFIBUS DPV1 Master/Slave
ControlLogix® Platform
3.4
Adding PROFIBUS DP Devices
The user will need to add each PROFIBUS device to the ILX56-PBS. Each
PROFIBUS device can then be configured. This is done by right-clicking on the
PROFIBUS Devices item in the tree and selecting Add PROFIBUS Device .
Setup
User Manual
Figure 3.9 – Adding a PROFIBUS Field Device
When adding a PROFIBUS Device in Slave Mode, the user can select any of the following devices to add:
ProSoft Technology, Inc.
Figure 3.10
– Selecting a PROFIBUS Field Device
Module
ILX56-PBS
MVI56-PDPS
Table 3.4 – Slave GSD File
GSD Filename
PSFT0EE3.GSD
PSFT098A.GSD
Page 15 of 85
ILX56-PBS ♦ PROFIBUS DPV1 Master/Slave
ControlLogix® Platform
Setup
User Manual
3.4.1
General
The General configuration is shown in the following figure. The Device General
Configuration window is opened by either double-clicking on the slave device in the tree, or right-clicking the slave device and selecting Configuration .
Figure 3.11 – Device General configuration parameters
When the module is emulating the legacy device, the General Configuration parameters will appear as follows:
Figure 3.12 – Device General configuration parameters (legacy device)
The General configuration consists of the following parameters:
Table 3.5
–Device General configuration parameters
Description
Parameter
Instance Name The device instance name which will be used to create the Tag names and UDTs in Logix.
ProSoft Technology, Inc. Page 16 of 85
ILX56-PBS ♦ PROFIBUS DPV1 Master/Slave
ControlLogix® Platform
Setup
User Manual
3.4.2
PROFIBUS Configuration
The PROFIBUS configuration is shown in the following figure. The Device
PROFIBUS configuration window is opened by either double-clicking on the slave device in the tree, or right-clicking the slave device and selecting Configuration .
Figure 3.13
– Device PROFIBUS configuration parameters
When the module is emulating the legacy device, the Profibus Configuration parameters will appear as follows:
Figure 3.14 – Device PROFIBUS configuration parameters (legacy device)
ProSoft Technology, Inc. Page 17 of 85
ILX56-PBS ♦ PROFIBUS DPV1 Master/Slave
ControlLogix® Platform
Setup
User Manual
The PROFIBUS configuration consists of the following parameters:
Table 3.6
– Field Device PROFIBUS configuration parameters
Description
Parameter
Node Address
TSDR
This is the ILX56-PBS node address on the PROFIBUS network.
Minimum Slave Interval
Watchdog Enable
Watchdog Value
N/A
N/A
N/A
Group Membership
Byte/Word Swap Option
N/A
N/A
This parameter will reformat the input and output Profibus DPV0 communication data. Below are the reformat options if the normal data format is AA BB CC DD:
None
BB AA
DD CC BB AA
CC DD AA BB
3.4.3
DPV1
The DPV1 configuration is shown in the following figure. The slave device DPV1 configuration window is opened by either double-clicking on the slave device in the tree, or right-clicking the slave device and selecting Configuration .
ProSoft Technology, Inc.
Figure 3.15 – Device DPV1 configuration parameters
Page 18 of 85
ILX56-PBS ♦ PROFIBUS DPV1 Master/Slave
ControlLogix® Platform
Setup
User Manual
When the module is emulating the legacy device, the DPV1 configuration parameters will appear as follows:
Figure 3.16
– Device DPV1 configuration parameters (legacy device)
The DPV1 configuration consists of the following parameters:
Table 3.7 – Device DPV1 configuration parameters
Description
Parameter
Enable DPV1 Enables DPV1 capabilities for the ILX56-PBS.
Note: DPV1 capabilities are not available when the module is emulating the legacy device.
Base 1ms
Enable Fail Safe
Check Config
Alarm Mode
Alarm Ack uses SAP50
Alarm Enables
N/A
N/A
N/A
N/A
This will force the DP Master to use Service Access Point
(SAP) 50 to acknowledge alarms.
N/A
ProSoft Technology, Inc. Page 19 of 85
ILX56-PBS ♦ PROFIBUS DPV1 Master/Slave
ControlLogix® Platform
3.4.4
User Parameters
Setup
User Manual
Figure 3.17
– Device User Parameter configuration parameters
The User Parameter s tab is not used for the ILX56-PBS.
ProSoft Technology, Inc. Page 20 of 85
ILX56-PBS ♦ PROFIBUS DPV1 Master/Slave
ControlLogix® Platform
3.4.5
Slot Configuration
Setup
User Manual
Figure 3.18 – Field Device Slot configuration start
The PROFIBUS Input/Output Module can be added in Slot Configuration tab. Slot data point selectable sizes are as follows: 1, 2, 4, 8 and 16 byte. Modular
Input/Output Slave supports up to 16 modules.
ProSoft Technology, Inc.
Figure 3.19
– Module Selection
Page 21 of 85
ILX56-PBS ♦ PROFIBUS DPV1 Master/Slave
ControlLogix® Platform
Setup
User Manual
When the module is emulating the legacy device, the Module Selection will appear as follows:
ProSoft Technology, Inc.
Figure 3.20 – Module Selection (legacy device)
Page 22 of 85
ILX56-PBS ♦ PROFIBUS DPV1 Master/Slave
ControlLogix® Platform
3.4.6
Start-up Parameters
Setup
User Manual
Figure 3.21 – Device Start-up Parameters
The Start-up Parameters tab is not used for the ILX56-PBS.
3.4.7
DPV1 Objects
The DPV1 Objects configuration is shown in the following figure. The slave device
DPV1 Objects configuration window is opened by either double-clicking on the slave device in the tree, or right-clicking the slave device and selecting Configuration .
Figure 3.22 – Device DPV1 Objects configuration parameters – Logix
The DPV1 configuration consists of the following parameters:
Table 3.8
– Device DPV1 Objects configuration parameters
Description
Parameter
Slot
Index
Size
Functions
Tagname
The Slot number to which the PROFIBUS DP transaction will be directed.
The Index number to which the PROFIBUS DP transaction will be directed.
The size (bytes) of the transaction.
The Functions supported for this object:
Read
Write
Read/Write
The Logix Tagname where the data will be read / written.
The Logix Tagname can be either entered manually or selected using the Logix
Tag Browser by clicking on the Browse button (…) adjacent to the Tagname.
ProSoft Technology, Inc. Page 23 of 85
ILX56-PBS ♦ PROFIBUS DPV1 Master/Slave
ControlLogix® Platform
Setup
User Manual
NOTE: The list of Logix tags will not be available if the Logix controller path has not first been correctly configured.
Figure 3.23 – Device DPV1 Objects Tag Browsing
3.4.8
DPV1 Alarms
The DPV1 Alarms configuration is shown in the following figure. The slave device
DPV1 Alarms configuration window is opened by either double-clicking on the slave device in the tree, or right-clicking the slave device and selecting Configuration .
Important: The Size of the DPV1 Alarm must be greater than 4 or the alarm triggering will not execute.
Figure 3.24
– Device DPV1 Alarms configuration parameters (Logix)
The DPV1 configuration consists of the following parameters:
Table 3.9 – Device DPV1 Alarms configuration parameters
Parameter
Size
Tagname
Description
The size (bytes) of the Alarm object.
The Logix Tagname from where the alarm data will be read.
(Logix Only)
NOTE: The PROFIBUS DP Master connected to the ILX56-PBS will be able to configure the following alarms: Diagnostic Alarm, Process Alarm, Pull Plug Alarm, Status Alarm, Update Alarm, and Manufacturer
Specific Alarm.
ProSoft Technology, Inc. Page 24 of 85
ILX56-PBS ♦ PROFIBUS DPV1 Master/Slave
ControlLogix® Platform
Setup
User Manual
3.5
Module Download
Once the ILX56-PBS configuration has been completed, it must be downloaded to the module. The configured IP address of the Logix Controller or the 1756 Ethernet card will be used to connect to the module, as set in the “Connection Path”.
1 To initiate the download, right-click on the module and select the Download option.
Figure 3.25 - Selecting Download
2 Once complete, the user will be notified that the download was successful.
Figure 3.26 - Successful download
3 Within the PLX50 Configuration Utility, the module will be in the Online state. This is indicated by the green circle around the module. The module is now configured and in an operational state.
Figure 3.27 - Module online
ProSoft Technology, Inc. Page 25 of 85
ILX56-PBS ♦ PROFIBUS DPV1 Master/Slave
ControlLogix® Platform
3.6
Studio 5000 Configuration
Setup
User Manual
NOTE: The minimum Studio 5000 version that can be used is v21. The ILX56-PBS uses an Add-On
Profile (AOP) for the 1756 Backplane.
The ILX56-PBS can be easily integrated with Allen-Bradley Logix family of controllers. Integration with the Logix family in Studio5000 makes use of the Add-On-
Profile (AOP).
3.6.1 Installing the Add-On Profile (AOP)
The user will first need to install the ILX56-PBS AOP before the module can be added to the Logix I/O tree. Download the AOP from www.prosoft-technology.com
.
Once downloaded, extract the zip file and run the MPSetup.exe
file.
3.6.2
Adding a Module to I/O Configuration
1 Under the 1756 Backplane, right-click and select the New Module option.
Figure 3.28 – Adding a module
2 The Select Module Type dialog will open. To easily find the module, use the
Vendor filter to select the ProSoft modules as shown in the following figure.
Locate and select the ILX56-PBS and select the Create option.
ProSoft Technology, Inc.
Figure 3.29 – Selecting the module
Page 26 of 85
ILX56-PBS ♦ PROFIBUS DPV1 Master/Slave
ControlLogix® Platform
Setup
User Manual
3 The module configuration dialog will open, specify the Name and Slot to complete the instantiation.
Figure 3.30
– Module instantiation
4 Once the instantiation is complete, the ILX56-PBS module will appear in the
Logix IO tree.
Figure 3.31 – Logix IO tree
5 The Module Defined Data Types will automatically be created during the instantiation process.
ProSoft Technology, Inc. Page 27 of 85
ILX56-PBS ♦ PROFIBUS DPV1 Master/Slave
ControlLogix® Platform
Setup
User Manual
3.6.3
PLX50 Configuration Utility Project File
The ILX56-PBS AOP allows the user to save the PLX50 Configuration Utility project file in the AOP, as well as launch the PLX50 Configuration Utility from the AOP.
Figure 3.32
– AOP - PLX50 Configuration Utility
When no PLX50 Configuration Utility project has been defined, the user can Browse for an existing PLX50 Configuration Utility project. If no PLX50 Configuration Utility project has been defined, the user can enter the project file name in the PLX50
Configuration Utility Project File textbox and select Launch PLX50 Configuration
Utility.
NOTE: Once the file name has been entered, the user will first need to click Apply before the Launch
PLX50 Configuration Utility button will become available.
ProSoft Technology, Inc.
Figure 3.33 – AOP – Launch PLX50 Configuration Utility
Page 28 of 85
ILX56-PBS ♦ PROFIBUS DPV1 Master/Slave
ControlLogix® Platform
Setup
User Manual
3.7
Generating a Logix .L5X File
The PLX50 Configuration Utility will generate the required UDTs and Routines
(based on the ILX56-PBS configuration) to map the required PROFIBUS Slave input and output data.
The user will need to generate the required Logix and UDTs by right-clicking on the module in the PLX50 Configuration Utility and selecting the Generate Logix L5X option.
Important: The user will need to ensure that the Logix Base Tag is correct for the generated Logix L5X code to work. The base tag will be the tag name for the module input and output assemblies in the Logix controller owning the module.
3.7.1 Local Rack Module Location
If the ILX56-PBS is in the same local rack as the Logix controller owning it, the Logix
Base Tag will be Local:xx (where xx is the slot number of the module). Below is an example where the ILX56-PBS is in slot 1 of the local rack.
Figure 3.34
– Logix Base tag assignment in PLX50CU
ProSoft Technology, Inc.
Figure 3.35 – Logix Base tag assignment in Studio 5000
Page 29 of 85
ILX56-PBS ♦ PROFIBUS DPV1 Master/Slave
ControlLogix® Platform
Setup
User Manual
3.7.2
Remote Rack Module Location
If the module is in a remote rack, the user will need to enter the Logix Base Tag based on the name of the remote rack (see the example below):
Figure 3.36
– Logix Base tag assignment in PLX50CU
ProSoft Technology, Inc.
Figure 3.37 – Logix Base tag assignment in Studio 5000
Page 30 of 85
ILX56-PBS ♦ PROFIBUS DPV1 Master/Slave
ControlLogix® Platform
3.7.3
Generating the L5X File
Setup
User Manual
1 In the PLX50 Configuration Utility, right-click on the ILX56-PBS item in the tree and select Generate Logix L5X .
Figure 3.38
– Selecting Generate Logix L5X
2 The user will then be prompted to select a suitable file name and path for the L5X file.
ProSoft Technology, Inc.
Figure 3.39
– Selecting the Logix L5X file name
Page 31 of 85
ILX56-PBS ♦ PROFIBUS DPV1 Master/Slave
ControlLogix® Platform
Setup
User Manual
3 This L5X file can now be imported into the Studio 5000 project by right-clicking on a suitable Program and selecting Add , and then Import Routine .
Figure 3.40
– Importing the L5X file into Studio 5000
4 In the file open dialog, select the newly-created L5X file and click OK .
The import will create the following:
Mapping Routine
Multiple UDT (User-Defined Data Types)
Multiple Controller Tags
5 Since the imported mapping routine is not a Main Routine, it will need to be called from the current Main Routine.
Figure 3.41
– Calling the mapping routine
ProSoft Technology, Inc. Page 32 of 85
ILX56-PBS ♦ PROFIBUS DPV1 Master/Slave
ControlLogix® Platform
Setup
User Manual
Figure 3.42
– Imported Logix Objects
6 Tags are created for each emulated slave device. The structure of which comprises the following:
Input Status - Status related to slave device
Input Data – As specified in the Input Data Points in the Slot configuration
Output Control
Output Data
– Used to trigger alarms
– As specified in the Output Data Points in the Slot configuration
ProSoft Technology, Inc. Page 33 of 85
ILX56-PBS ♦ PROFIBUS DPV1 Master/Slave
ControlLogix® Platform
Setup
User Manual
Figure 3.43 – Slave Device-Specific tag
ProSoft Technology, Inc. Page 34 of 85
ILX56-PBS ♦ PROFIBUS DPV1 Master/Slave
ControlLogix® Platform
Setup
User Manual
3.8
SD Card
The ILX56-PBS supports an SD Card that can be used for disaster recovery. It can be pre-loaded with the required firmware and/or application configuration.
Figure 3.44 – Module Bottom View – SD Card Slot
Important: The user will need to ensure that the SD Card has been formatted for FAT32.
Important: All needed files must be copied into the root directory of the SD Card.
3.9 Firmware
The user can copy the required firmware (which can be downloaded from www.prosoft-technology.com
) onto the root directory of the SD Card.
Figure 3.45
– SD Card – Firmware file
Important: If more than one firmware file, with different firmware revisions, is on the SD Card, it can cause the module to constantly firmware upgrade the module.
If a faulty module is replaced the user can insert the SD Card with the firmware file on into the new module. While the module is booting it can detect if the firmware on the new module is different from that on the SD Card. If yes, the firmware will either be upgraded or downgraded to the firmware revision on the SD Card.
ProSoft Technology, Inc. Page 35 of 85
ILX56-PBS ♦ PROFIBUS DPV1 Master/Slave
ControlLogix® Platform
Setup
User Manual
3.10
Configuration
The user can add the PLX50CU configuration file to the SD Card root directory in one of two ways.
Figure 3.46
– SD Card – Configuration file
3.10.1 Manual Copy
Once the user has created the needed application configuration in the PLX50CU, the configuration can be exported to a file that can be copied into the root directory of the
SD Card.
ProSoft Technology, Inc.
Figure 3.47
– Configuration Export for SD Card
Page 36 of 85
ILX56-PBS ♦ PROFIBUS DPV1 Master/Slave
ControlLogix® Platform
Setup
User Manual
Figure 3.48 – Configuration Export for SD Card
Important: The filename of the configuration file must not be changed.
Important: If more than one configuration file, with different configuration signatures, of the same product is on the SD Card, only the last configuration will be used.
ProSoft Technology, Inc. Page 37 of 85
ILX56-PBS ♦ PROFIBUS DPV1 Master/Slave
ControlLogix® Platform
Setup
User Manual
3.10.2
PLX50 Configuration Utility Upload
When the SD Card has been inserted into the module, the user has the option to directly upload the configuration onto the SD Card using the Save Configuration to
SD Card option in PLX50CU. This will copy the module’s current configuration directly to the SD Card without the need to remove it from the module and inserted into a PC.
Important: All other configuration files in the SD Card root directory will be deleted when the upload is complete.
ProSoft Technology, Inc.
Figure 3.49
– Save Configuration to SD Card
Page 38 of 85
ILX56-PBS ♦ PROFIBUS DPV1 Master/Slave
ControlLogix® Platform
4 Operation
Operation
User Manual
4.1
Logix Operation
The ILX56-PBS will exchange data with a ControlLogix® controller by establishing a
Class 1 I/O connection with the ILX56-PBS.
4.1.1 PROFIBUS DP - Slave
Important: The module input and output assembly of each connection will be an undecorated array of data. The imported Logix routine (generated by PLX50CU) will copy this data to the constructed input and output assemblies.
General Status
Below are the definitions for the tags in the General Status UDT created by the
PLX50CU.
Tag
ConnectionFaulted
ModuleStatus
ConfigValid
Owned
DuplicateDPStation
ProSoft Technology, Inc.
Figure 4.1
– Logix General Status tags
Table 4.1 – Logix General Status tags
Description
Indication of backplane connection fault. Each backplane connection will have this indication
Indication of the module status on all Bool data type below this Controller
Tag.
Configuration has been downloaded to the ILX56-PBS and is being executed.
1
– ILX56-PBS has been successfully configured.
0
– ILX56-PBS is not configured.
Indicates if the ILX56-PBS is owned by a Logix Controller with a connection count similar to what has been configured in PLX50CU.
1
– ILX56-PBS is connected.
0 – ILX56-PBS is not connected.
Indicates that the ILX56-PBS has detected another PROFIBUS DP station with the same station address as itself and has entered a temporary Backoff mode.
1 – Duplicate detected (Back-off mode active).
0
– Normal (No duplicate detected).
Page 39 of 85
ILX56-PBS ♦ PROFIBUS DPV1 Master/Slave
ControlLogix® Platform
Operation
User Manual
NOTE: In this condition the ILX56-PBS will not communicate on the PROFIBUS DP network. Although the back-off time is approximately 5 seconds, should the conflicting DP master remain active on the PROFIBUS network, the ILX56-PBS will continuously re-enter the back-off mode.
PROFIBUSFieldbusError
PROFIBUSDeviceError
PROFIBUSOffline
PROFIBUSStopped
PROFIBUSClear
PROFIBUSOperational
SlaveMode
ControllerRun
ModuleRedundancyEnabled
ModuleRedundancyStatus
ConfigCRC
ActiveNodeCount
SwitchOverTimeOut
DeviceLiveList
DeviceDataExchangeActive
DeviceAlarmPendingFlags
There is a PROFIBUS network issues (e.g. cable unplugged, under/over terminated, etc.).
1 – Fieldbus error detected.
0
– Normal (No errors detected).
At least one slave device has a communication issue (e.g. offline, not exchanging process data, etc.)
1 – Device error detected.
0
– Normal (No errors detected).
For ILX56-PBM only.
For ILX56-PBM only.
For ILX56-PBM only.
For ILX56-PBM only.
This tag was designed for ILX56-PBM to decipher between ILX56-PBM in master mode or slave mode.
1 – The ILX56-PBS will always have this bit on.
0 – The ILX56-PBS should never be in state where this bit is 0.
The connected Logix controller is in RUN mode. 1
– RUN mode 0 –
PROGRAM / FAULT mode
For ILX56-PBM only (Currently not implemented)
For ILX56-PBM only (Currently not implemented)
The signature of the configuration currently executing on the module.
The number of active and online PROFIBUS devices exchanging data with the master.
For ILX56-PBM only (Currently not implemented)
Indicates the nodes that are online on the local PROFIBUS network. Each bit represents a node. When the specific bit is set ‘1’ then the device is online and when the bit is off ‘0’ the device is not on the PROFIBUS network.
Bit 0
– Node 0 Online
Bit 1 – Node 1 Online
……….
Bit 126 – Node 126 Online
Indicates the nodes that are online and exchanging DPV0 data on the local
PROFIBUS network. Each bit represents a node. When the specific bit is set ‘1’ then the device is online and exchanging data and when the bit is off
‘0’ the device is not exchanging data on the PROFIBUS network.
Bit 0
– Node 0 Exchanging DPV0 Data
Bit 1 – Node 1 Exchanging DPV0 Data
……….
Bit 126 – Node 126 Exchanging DPV0 Data
Indicates the nodes that have an alarm pending on the local PROFIBUS network. Each bit represents a node. When the specific bit is set ‘1’ then the device has an alarm pending that must be unloaded and when the bit is off ‘0’ the device does not have an alarm pending.
Bit 0
– Node 0 has an alarm pending
Bit 1 – Node 1 has an alarm pending
……….
Bit 126
– Node 126 has an alarm pending
DeviceDiagnosticPendingFlags Indicates the nodes that have diagnostics pending on the local PROFIBUS network. Each bit represents a node. When the specific bit is set ‘1’ then
ProSoft Technology, Inc. Page 40 of 85
ILX56-PBS ♦ PROFIBUS DPV1 Master/Slave
ControlLogix® Platform
Operation
User Manual the device has diagnostics pending that must be unloaded and when the bit is off ‘0’ the device does not have any diagnostics pending.
Bit 0 – Node 0 has diagnostics pending
Bit 1
– Node 1 has diagnostics pending
……….
Bit 126 – Node 126 has diagnostics pending
Table 4.2
– Logix General Status tags
General Control
The emulated ILX56-PBS slave devices will be enabled by setting the correct enable bit in the Logix output assembly. Once the respective bit has been set in the
DeviceEnable array, the ILX56-PBS will become active on the PROFIBUS network and will start responding to a PROFIBUS DP Master.
Figure 4.2 – General Control tags
Tag
MasterControl
DeviceEnable
Table 4.3
– General Control tags
Description
For ILX56-PBM only.
These bits enable nodes on the PROFIBUS network for data exchange. Each bit represents a node. When the specific bit is set ‘1’, then the device (if configured) will exchange data with the PROFIBUS master. When the bit is off ‘0’, the device does exchange data with the PROFIBUS master.
Bit 0
– Node 0 is enabled for data exchange
Bit 1 – Node 1 is enabled for data exchange
……….
Bit 126 – Node 126 is enabled for data exchange
The user will be able to see if there are any faults (e.g. configured device not found) by:
Viewing the LEDs of the ILX56-PBS (see the Diagnostics section for more details)
Going online with the module in the PLX50 Configuration Utility and viewing the
ILX56-PBS Slave and Device Diagnostics
Viewing the input assembly of the ILX56-PBS in Logix.
ProSoft Technology, Inc. Page 41 of 85
ILX56-PBS ♦ PROFIBUS DPV1 Master/Slave
ControlLogix® Platform
Operation
User Manual
Status and DPV0 Data Exchange
The DPV0 data is exchanged with Logix using the Class 1 Logix connection. The device-specific tag contains all the input and output data fields, as well as important control and status information.
Tag
Status
Online
DataExchangeActive
IdentMismatch
DeviceError
Figure 4.3
– ILX56-PBS Slave Device-Specific tag
Table 4.4 – Device Input tags
Description
DisabledByOutputAssembly
This bit indicates if the device is online on the PROFIBUS network.
1
– Device is online
0 – Device is not online
This bit indicates if the device is configured and exchanging data on the PROFIBUS network.
1
– Device is active and exchanging data
0 – Device is not exchanging data
The user must ensure that all application code making use of data from a slave device first checks that the DataExchangeActive bit is 1.
The device configured in the PLX50CU and the device at the configured node address do not match because they have different ident numbers.
1 – Online device Ident does not match configured device
0
– Online device and configured device ident match
This bit indicates if the device has not been enabled for data exchange in the ILX56-PBS device enable control bits.
1
– Device has not been enabled for data exchange
0
– Device has been enabled for data exchange
This bit indicates an error with the device.
1 – Device has an error.
0
– Device has no error.
The error flag will be set when one of the following conditions occur:
If there is an ident mismatch during slave parameterization,
When receiving any form of FDL fault (data link layer fault). For example: SAP Not Activated or Resource Not Available.
When the data size of the DPV0 data exchange does not match what has been configured in the PLX50CU.
ProSoft Technology, Inc. Page 42 of 85
ILX56-PBS ♦ PROFIBUS DPV1 Master/Slave
ControlLogix® Platform
Operation
User Manual
AlarmPending
DiagnosticsPending
OutputAssemblyNodeAddrMismatch This bit indicates that there is a mismatch between the actual device station address and the expected Logix mapping station address.
0 – Station address matches
1
– Station address mismatch
MappingCRCMismatch
Indicates the device has diagnostics pending on the local PROFIBUS network. When the specific bit is set ‘1’ then the device has diagnostics pending that must be unloaded and when the bit is off ‘0’ the device does not have any diagnostics pending.
0 – The node has no diagnostics pending
1
– The node has diagnostics pending
If there is a mismatch in the mapping between Logix and the ILX56-
PBS it can result in data appearing in the incorrect location which means the user can be sending incorrect data to a device which can have unpredicted results.
0 – The mapping for the output data is correct.
1
– There is a mapping mismatch in the output data.
SlaveClearOpMode
This Error flag is transient and will clear once a valid response is received.
Indicates the device has an alarm pending on the local PROFIBUS network. Wh en the specific bit is set ‘1’ then the device has an alarm pending that must be unloaded and when the bit is off ‘0’ the device does not have an alarm pending.
0 – The node has no alarm pending
1
– The node has an alarm pending
SlaveAlarmAck
This will indicate that the respective slave is in fieldbus CLEAR mode
(received from the DP Master on the network).
0
– Slave Station is in CLEAR fieldbus mode.
1 – Slave Station is not in CLEAR fieldbus mode.
This will indicate that the respective emulated slave has received an acknowledgement for the pending alarm.
0
– Slave Station has received an Alarm Acknowledgement for last pending alarm.
1 – No Alarm Acknowledgement have been received for a pending alarm or there is no alarm pending.
StationNumber
DeviceMappingCRC
DeviceSpecificInputDataFields
The station number of the specific slave device.
The checksum of the Mapping for the specific slave device.
The tags created for the input data will be slave specific.
Table 4.5
– Device Output tags
Description
Tag
Control
StationNumber
AlarmTrigger
DeviceMappingCRC
DeviceSpecificOutputDataFields
The station number entered by the Logix mapping code of the specific slave device.
When this bit is transitioned from 0 to 1, it will trigger an alarm notification to the DP Master.
The checksum of the mapping that was applied by the generated Logix code used to verify if the mapping being used is valid.
The tags created for the output data will be slave which has been emulated in the configuration manager.
ProSoft Technology, Inc. Page 43 of 85
ILX56-PBS ♦ PROFIBUS DPV1 Master/Slave
ControlLogix® Platform
Operation
User Manual
DPV1 Class 1 Messaging (MS1)
The ILX56-PBS supports DPV1 Class 1 (MS1) messaging. See the DPV1 Objects in the PLX50 Configuration Utility device configuration section for more information regarding the configuration of the DPV1 Objects. The user can configure several slot and index combinations for DPV1 Class 1 communication (for each added
PROFIBUS Slave device).
When the PROFIBUS Master sends a DPV1 read/write command for the configured slot and index, the ILX56-PBS will access the configured Logix tag to provide the required data. The data that will be written or read will be extracted from the Logix
SINT array configured in the DPV1 objects of the device configuration window. The following is an example of the DPV1 operation.
Figure 4.4
– ILX56-PBS DPV1 Object exchange
Alarming
The ILX56-PBS supports DPV1 Alarming. The user can trigger an alarm from the
Logix device output assembly which will notify the PROFIBUS Master that a new alarm has been generated. When the PROFIBUS Master sends a DPV1 alarm read command, the ILX56-PBS will access the configured Logix tag to provide the required data for the specific alarm.
NOTE: The ILX56-PBS can only allow one alarm to be triggered at a time.
To trigger an alarm notification for the PROFIBUS Master, the user will need to toggle (from 0 to 1) the AlarmTrigger tag as shown below:
Figure 4.5 – ILX56-PBS Slave Alarm Trigger
Once the alarm has been triggered, the ILX56-PBS will read the alarm data from the
Logix tag and add it to the PROFIBUS diagnostics (which will then be read by the
PROFIBUS Master).
When the PROFIBUS Master acknowledges the alarm, the SlaveAlarmAck bit in the input assembly for the field device will be set indicating to the Logix controller that the next alarm can be triggered.
ProSoft Technology, Inc. Page 44 of 85
ILX56-PBS ♦ PROFIBUS DPV1 Master/Slave
ControlLogix® Platform
Operation
User Manual
Figure 4.6
– ILX56-PBS Alarm Acknowledge
NOTE: An alarm will only be triggered when the AlarmTrigger tag is toggled from 0 to 1.
The format of the DPV1 Alarm data in the Logix SINT array is shown below:
Description
Alarm Parameter
Alarm Length
Byte
Offset
0
Byte
Size
1
This is the length of the Alarm data at the bottom of the table.
Alarm Type
Alarm Slot
1
2
1
1
Refer to the PROFIBUS Specification EN 50170 for information regarding the diagnostics.
Examples:
1 - Diagnosis_Alarm
3 - Pull_Alarm
4 - Plug_Alarm
Refer to the PROFIBUS Specification EN 50170 for information regarding the diagnostics.
Alarm Specifier
Alarm data
3
4
1
Alarm
Length
Refer to the PROFIBUS Specification EN 50170 for information regarding the diagnostics.
Examples:
0 - No further differentiation
1 - Incident appeared
2 - Incident disappeared and slot is ok
3 - One incident disappeared, others remain
Refer to the PROFIBUS Specification EN 50170 for information regarding the diagnostics.
Table 4.6
– Slave Alarm Data Format
ProSoft Technology, Inc. Page 45 of 85
ILX56-PBS ♦ PROFIBUS DPV1 Master/Slave
ControlLogix® Platform
An example of the Alarm Data is shown below:
Operation
User Manual
Figure 4.7 –DPV1 Alarm Data Example
ProSoft Technology, Inc. Page 46 of 85
ILX56-PBS ♦ PROFIBUS DPV1 Master/Slave
ControlLogix® Platform
Operation
User Manual
4.2
Firmware Upgrade
The PLX50 Configuration Utility allows the user to upgrade the module firmware in the field.
1 In the PLX50 Configuration Utility, go to the Tool menu and select the
DeviceFlash option.
Figure 4.8 - DeviceFlash Tool
2 The user will need to select the appropriate AFB binary file and click Open .
ProSoft Technology, Inc.
Figure 4.9 - Select the AFB binary
Page 47 of 85
ILX56-PBS ♦ PROFIBUS DPV1 Master/Slave
ControlLogix® Platform
Operation
User Manual
3 The user will need to select the ILX56-PBS module in the Target Browser dialog.
Figure 4.10 - Select the ILX56-PBS module
4 Once firmware upgrade is complete, the Device Flash tool will provide the details of the updated module.
Figure 4.11
– ILX56-PBS successfully updated
Important: The ILX56-PBS firmware is digitally signed so the user will only be able to flash the ILX56-
PBS with authorized firmware.
ProSoft Technology, Inc. Page 48 of 85
ILX56-PBS ♦ PROFIBUS DPV1 Master/Slave
ControlLogix® Platform
5 Diagnostics
Diagnostics
User Manual
5.1
LEDs
The ILX56-PBS provides 3 diagnostic LEDs and a 4-character alpha-numeric LED display for diagnostics purposes.
Figure 5.1 - ILX56-PBS LEDs
The ILX56-PBS LEDs indicate the module status as follows:
LED
Table 5.1 – ILX56-PBS Module LED operation
Description
SF
BF
Ok
This LED indicates the System Fault status.
Off
– ControlLogix Class 1 Connection Ok
Flashing Red – ControlLogix Class 1 Connection not established.
This LED indicates the status of the configured field devices.
Solid Red – There are bus communication errors (if no valid packet has been received by any configured slave for more than 1s).
Flashing Red – There are slave errors (at least one slave has not been configured properly and is not exchanging DPV0 data).
Flashing Green – All slaves are successfully exchanging DPV0 data and the
DP network operational state is CLEAR .
Solid Green – All slaves are successfully exchanging DPV0 data and the DP network operational state is OPERATE .
The module LED will provide information regarding the system-level operation of the module. Thus, if the LED is red then the module is not operating correctly. For example, if the module application firmware has been corrupted or there is a hardware fault the module will have a red Module LED.
If the LED is green (flashing), then the module has booted and is running correctly without any application configuration loaded.
If the LED is green (solid), then the module has booted and is running correctly with application configuration loaded.
ProSoft Technology, Inc. Page 49 of 85
ILX56-PBS ♦ PROFIBUS DPV1 Master/Slave
ControlLogix® Platform
Diagnostics
User Manual
The alphanumeric LED display may display the following messages:
Table 5.2
– ILX56-PBS LED Display operation
Description
LED Text
TEST
OK
OPERATE mode
The module is busy testing all hardware during bootup.
The module has successfully booted, and all hardware testing has passed.
The PROFIBUS network is in OPERATE operational mode.
The PROFIBUS network is in CLEAR operational mode. CLEAR mode
Device Fault
Comms Fault
PROFIBUS Slave
At least one slave device is not operating correctly.
Communication fault (e.g. bus cable has been unplugged).
The module is operating as a PROFIBUS Slave.
Duplicate Station
No Config Loaded
A PROFIBUS station with a duplicate node has been detected.
No configuration has been loaded onto the ILX56-PBS.
The module LED display will also show the instance name of the module configured in PLX50CU.
ProSoft Technology, Inc. Page 50 of 85
ILX56-PBS ♦ PROFIBUS DPV1 Master/Slave
ControlLogix® Platform
Diagnostics
User Manual
5.2
Module Status Monitoring
The ILX56-PBS provides a range of statistics including module operation, maintenance, and fault finding. The statistics can be accessed in full by the PLX50
Configuration Utility.
To view the mod ule’s status in the PLX50 Configuration Utility environment, the
ILX56-PBS must be online. If the module is not already online (following a recent configuration download), then right-click on the module and select the Go Online option.
Figure 5.2 - Selecting to Go Online
The Online mode is indicated by the green circle behind the module in the Project
Explorer tree.
Figure 5.3 – Module online
ProSoft Technology, Inc. Page 51 of 85
ILX56-PBS ♦ PROFIBUS DPV1 Master/Slave
ControlLogix® Platform
Diagnostics
User Manual
5.2.1
ILX56-PBS Status
The Status monitoring window of the ILX56-PBS can be opened by either doubleclicking on the Status item in the Project Explorer tree, or by right-clicking on the module and selecting Status .
Figure 5.4 - Selecting ILX56-PBS online Status
General
The General tab displays the following general parameters:
ProSoft Technology, Inc.
Figure 5.5 – ILX56-PBS Status monitoring – General
Page 52 of 85
ILX56-PBS ♦ PROFIBUS DPV1 Master/Slave
ControlLogix® Platform
Diagnostics
User Manual
Parameter
Table 5.3 - Parameters displayed in the Status Monitoring
– General Tab
Description
Configuration Indicates if the downloaded configuration is valid and executing.
Owned
Redundancy State
Logix State
Indicates whether or not the module is currently owned (Class 1) by a Logix
Controller.
N/A
Indicates the state of the connected Logix controller:
Run – Controller is in RUN mode
Program
– Controller is in PROGRAM or FAULT mode or TEST mode.
Mode
PROFIBUS Operation
Profibus Status
This is the mode of operation of the module.
Quiet
This mode allows the user to connect the ILX56-PBS to an active bus and run a DP packet capture. In this mode the ILX56-PBS will not communicate on the DP Bus but rather only listen.
Slave
In this mode the ILX56-PBS will emulate multiple PROFIBUS Slave devices.
N/A
Status of the PROFIBUS network:
Ok – No PROFIBUS errors
Fieldbus Error
– PROFIBUS network issue detected (e.g. cable fault)
Device Error
– One or more PROFIBUS devices not communicating.
N/A
The BAUD Rate of the PROFIBUS network.
Master Node
BAUD Rate
IO bytes/second The number of process variable bytes being exchanged between the ILX56-
PBS and PROFIBUS Master device every second.
Acyclic Requests Pending The number of acyclic requests (DPV1 Class 1 and Class 2 requests) pending.
Up Time Indicates the elapsed time since the module was powered-up.
Firmware Revision
Boot Revision
Configuration Signature
Serial Number
Logix Slot
Temperature
Processor Scan
DIP Switch Position
SD Card
The application firmware revision currently executing.
The bootloader firmware revision.
The signature of the configuration currently executing on the module.
Displays the module’s serial number.
The current slot in which the module resides of the ControlLogix rack.
The internal temperature of the module.
The amount of time (microseconds) taken by the module’s processor in the last scan.
The status of the DIP switches when the module booted.
Indicates if a SD Card has been inserted into the module.
ProSoft Technology, Inc. Page 53 of 85
ILX56-PBS ♦ PROFIBUS DPV1 Master/Slave
ControlLogix® Platform
Slave Status
The Slave mode diagnostics tab displays the following parameters:
Diagnostics
User Manual
Figure 5.6 – ILX56-PBS Status monitoring – Slave Status
Table 5.4 - Parameters displayed in the Status Monitoring
– Slave Status Tab
Parameter
Description
BAUD Rate Current BAUD rate of the PROFIBUS Network
Auto-BAUD
CLEAR Op-Mode
Comms State
If the BAUD rate for the PROFIBUS Network will be automatically detected
If the operational state of the PROFIBUS Network is CLEAR
Slave Count
OK
All configured slaves are operating correctly.
Failure
At least one of the configured devices are not operating correctly.
Number of slaves configured
Last Response Time
Max Response Time
Min Response Time
The time it took (in microseconds) to respond to the last request from a DP
Master.
The maximum time it took (in microseconds) to respond to a request from a
DP Master.
The minimum time it took (in microseconds) to respond to a request from a DP
Master.
ProSoft Technology, Inc. Page 54 of 85
ILX56-PBS ♦ PROFIBUS DPV1 Master/Slave
ControlLogix® Platform
Diagnostics
User Manual
Logix Statistics
The Logix statistics are the statistics for connections and messages from the ILX56-
PBS to the Logix Controller. These are used when DPV1 messaging and alarming are mapped to Logix tags.
Figure 5.7 – Status Monitoring – Logix Statistics Tab
Table 5.5 - Parameters displayed in the Status Monitoring
– Logix Statistics Tab
Parameter
Description
Connection Failures The number of failed attempts at establishing a class 3 connections with a Logix controller.
Tag Not Exist Errors
Privilege Violation Errors
General Access Error
The number of tag read and tag write transactions that failed due to the destination tag not existing.
The number of tag read and tag write transactions that failed due to a privilege violation error.
This may be caused by the External Access property of the Logix tag being set to either None or Read Only.
This statistic is used to indicate that the tag could not be accessed due to a general error (eg. writing to a tag more data than the actual array size).
Message Retries
Message Failures
This count increases when no response was received from the Logix
Controller by the time the Message timeout is reached.
This count increases when the Message Retry Limit is reached and no response has been received from the Logix Controller.
ProSoft Technology, Inc. Page 55 of 85
ILX56-PBS ♦ PROFIBUS DPV1 Master/Slave
ControlLogix® Platform
Diagnostics
User Manual
5.2.2
ILX56-PBS Emulated Slave Device Status
The Status monitoring window of each PROFIBUS slave device connected to the
ILX56-PBS can be opened by right-clicking on the specific slave device in the PLX50
Configuration Utility tree, and selecting Status .
Figure 5.8 - Selecting slave device online Status
The device status window contains multiple tabs to display the current status of the specific slave device.
ProSoft Technology, Inc. Page 56 of 85
ILX56-PBS ♦ PROFIBUS DPV1 Master/Slave
ControlLogix® Platform
Diagnostics
User Manual
5.3
PROFIBUS Packet Capture
The ILX56-PBS provides the capability to capture the PROFIBUS traffic for analysis.
To invoke the capture, double-click on the module in the Project Explorer tree, or right-clicking the module and selecting DP Packet Capture.
Figure 5.9 - Selecting PROFIBUS Packet Capture
The DP Packet Capture window will open and automatically start capturing all
PROFIBUS packets.
Figure 5.10 - PROFIBUS packet capture
NOTE: The module will capture packets until the user presses Stop or when 10,000 packets have been reached.
ProSoft Technology, Inc. Page 57 of 85
ILX56-PBS ♦ PROFIBUS DPV1 Master/Slave
ControlLogix® Platform
Example PROFIBUS capture:
Diagnostics
User Manual
Figure 5.11 - PROFIBUS Packet Capture complete
The captured PROFIBUS packets are tabulated as follows:
Statistic
Index
Time
Dirn.
Status
Frame
Src
Dest
Function
Details
Src SAP
Dest SAP
Description
PDU
Data
Table 5.6 - PROFIBUS Packet Capture fields
Description
The packet index incremented for each packet sent or received.
The time is measured in microseconds (us) and is started at a fraction of a second and continued until the packet capture is done.
The direction of the packet, either transmitted (Tx) or received (Rx).
The status of the packet. Received packets are checked for valid
PROFIBUS constructs and valid checksums.
PROFIBUS Frame type. (e.g. SD1, SD2, SD3 etc)
PROFIBUS node address of the message source.
PROFIBUS node address of the message destination.
The PROFIBUS function (e.g. Token, Request, etc.)
Additional details associated with the PROFIBUS command/function.
The source Service Access Point (SAP) when used.
The destination Service Access Point (SAP) when used.
A more detailed description of the packet payload. Only applicable to specific packet types.
The PROFIBUS packet payload.
The packet’s raw data displayed in space delimited hex.
ProSoft Technology, Inc. Page 58 of 85
ILX56-PBS ♦ PROFIBUS DPV1 Master/Slave
ControlLogix® Platform
Diagnostics
User Manual
5.3.1
Packet Details
Additional detail about specific packets can be viewed by either double-clicking or right-clicking on the packet and selecting the Show Detail option.
Figure 5.12 - PROFIBUS Packet Capture - Show Detail
A Packet Window will display the details of the selected packet.
Figure 5.13 - PROFIBUS Packet Capture - Detail Example
ProSoft Technology, Inc. Page 59 of 85
ILX56-PBS ♦ PROFIBUS DPV1 Master/Slave
ControlLogix® Platform
Diagnostics
User Manual
5.3.2
Packet Filter
The packet filter can be used to hide certain packet types. To open the packet filter, click on the Filter icon in the toolbar.
Figure 5.14 - PROFIBUS Packet Filter
Figure 5.15 - PROFIBUS Packet Filter Options
PROFIBUS packets can be filtered on the following criteria:
Station Address
Telegram (Frame) Type
Function
Service Access Point
ProSoft Technology, Inc. Page 60 of 85
ILX56-PBS ♦ PROFIBUS DPV1 Master/Slave
ControlLogix® Platform
5.3.3
Saving Packet Filter Options
The selected Filter options can also be saved and re-opened for future use.
Diagnostics
User Manual
Figure 5.16 - PROFIBUS Packet Filter Options
– Save / Open
The packet capture can be saved to a file for further analysis, by selecting the Save button on the toolbar. Previously saved PROFIBUS Packet Capture files can be viewed by selecting the PROFIBUS Packet Capture Viewer option in the tools menu.
Figure 5.17 - Selecting the PROFIBUS Packet Capture Viewer
ProSoft Technology, Inc. Page 61 of 85
ILX56-PBS ♦ PROFIBUS DPV1 Master/Slave
ControlLogix® Platform
Diagnostics
User Manual
5.4
Module Event Log
The ILX56-PBS module logs various diagnostic records to an internal event log.
These logs are stored in non-volatile memory and can be displayed using the PLX50
Configuration Utility.
To view the logs, select the Event Viewer option in the Project Explorer tree.
Figure 5.18. - Selecting the module Event Log
The Event Viewer window will open and display all the events from the module. The log entries are sorted with the latest record at the top.
Figure 5.19. – Module Event Log
The log can also be stored to a file by selecting the Save button in the tool menu.
To view previously saved files, use the Event Log Viewer option under the Tools menu.
ProSoft Technology, Inc. Page 62 of 85
ILX56-PBS ♦ PROFIBUS DPV1 Master/Slave
ControlLogix® Platform
6 Technical Specifications
6.1
Electrical
Specification
Backplane Current Load
Enclosure rating
Temperature
Earth connection
Emissions
ESD Immunity
Radiated RF Immunity
EFT/B Immunity
Surge Immunity
Conducted RF Immunity
Table 6.1 - Electrical specification
Rating
450 mA @ 5 VDC
2 mA @ 24 VDC
IP20, NEMA/UL Open Type
-20 to 70 °C
Yes, terminal based
IEC61000-6-4
EN 61000-4-2
IEC 61000-4-3
EFT: IEC 61000-4-4
Surge: IEC 61000-4-5
IEC 61000-4-6
Technical Specifications
User Manual
6.2
PROFIBUS DP
Specification
Connector
Conductor
DP Master Mode Support
DP Slave Mode Support
Isolated
BAUD Rate supported
Table 6.2
– PROFIBUS DP specification
Rating
Female DB9 connector
See PROFIBUS DP Section.
DPV0 Data Exchange
DPV1 Class 1 Messaging
DPV1 Class 2 Messaging
DPV1 Alarming
DPV0 Data Exchange
DPV1 Class 1 Messaging
DPV1 Alarming
Yes
9.6 kbps, 19.2 kbps, 45.45 kbps, 93.75 kbps, 187.5 kbps, 500 kbps,
1.5 Mbps, 3 Mbps, 6 Mbps, 12 Mbps,
6.3 Certifications
Please visit our website: www.prosoft-technology.com
ProSoft Technology, Inc. Page 63 of 85
ILX56-PBS ♦ PROFIBUS DPV1 Master/Slave
ControlLogix® Platform
7 PROFIBUS DP
PROFIBUS DP
User Manual
7.1
Introduction
PROFIBUS is a vendor-independent, open Fieldbus standard for a wide range of applications in manufacturing, process and building automation. Vendor independence and openness are guaranteed by the PROFIBUS standard EN 50 170.
With PROFIBUS, devices of different manufacturers can communicate without special interface adjustments. PROFIBUS can be used for both high-speed time critical data transmission and extensive complex communication tasks. The
PROFIBUS family consists of three compatible versions.
7.1.1 PROFIBUS DP
Optimized for high speed and inexpensive hookup, this PROFIBUS version is designed especially for communication between automation control systems and distributed I/O at the device level. PROFIBUS-DP can be used to replace parallel signal transmission with 24 V or 4-20 mA.
Table 9.1 – PROFIBUS Protocol (OSI model)
OSI Layer
7 Application
6 Presentation
5
Session
4
Transport
3 Network
2 Data Link
1
Physical
PROFIBUS
DPV0
FDL
EIA-485
DPV1
Optical
DPV2
MBP
To utilize these functions, various service levels of the DP protocol were defined:
DP-V0 provides the basic functionality of DP, including o cyclic data exchange, o station, module and channel-specific diagnostics
DP-V1 contains enhancements geared towards process automation, in particular o acyclic data communication for parameter assignment o alarm handling
DP-V2 for isochronous mode and data exchange broadcast (slave-to-slave communication)
7.1.2 PROFIBUS PA
PROFIBUS PA is designed especially for process automation. It permits sensors and actuators to be connected on one common bus line through a dedicated DP/PA gateway or link between the PROFIBUS DP and PROFIBUS PA networks, even in intrinsically-safe areas. PROFIBUS PA permits data communication and power over the bus using a 2-wire technology according to the international standard IEC 1158-
2.
ProSoft Technology, Inc. Page 64 of 85
ILX56-PBS ♦ PROFIBUS DPV1 Master/Slave
ControlLogix® Platform
PROFIBUS DP
User Manual
7.1.3
PROFIBUS FMS
PROFIBUS FMS is the general-purpose solution for communication tasks at the cell level. Powerful FMS services open up a wide range of applications and provide great flexibility. PROFIBUS FMS can also be used for extensive and complex communication tasks. This protocol is the first developed for PROFIBUS, but it is no longer currently used.
PROFIBUS specifies the technical and functional characteristics of a serial fieldbus system with which decentralized digital controllers can be networked together from the field level to the cell level.
7.2 PROFIBUS master and slave
PROFIBUS distinguishes between master devices and slave devices.
Master devices determine the data communication on the bus. A master can send messages without an external request when it holds the bus access rights (the token). Masters are also called ' active stations ' in the PROFIBUS protocol.
Slave devices are peripheral devices. Typical slave devices include input/output devices, valves, drives and measuring transmitters. They do not have bus access rights and they can only acknowledge received messages or send messages to the master when requested to do so. Slaves are also called ' passive stations '
7.3
PROFIBUS master class 1 (DPM1) or class 2 (DPM2)
7.3.1 PROFIBUS DP Master class 1 (DPM1)
A class 1 master handles the normal communication or exchange of data with the slaves assigned to it. This is typically a PLC.
It uses cyclic communication to exchange process data with its associated slaves.
The class 1 mast er sets the baud rate and the slave’s auto-detect this rate. Each slave device is assigned to one master and only that master may write output data to that slave. Other masters may read information from any slave but can only write output data to their own assigned slaves.
7.3.2
PROFIBUS DP Master class 2 (DPM2)
A class 2 master is a special device primarily used for commissioning slaves and for diagnostic purposes. This is typically a Supervisor. It uses acyclic communication over what is known as the MS2 channel . A DPM2 does not have to be permanently connected to the bus system.
7.4
Cyclic communication
The DP master class 1 cyclically exchanges data with all of the slaves assigned to it.
This service is configured. During the configuration process, master and slave addresses are assigned, the bus parameters are defined, the types and numbers of modules (in the case of modular slaves) are specified, user-selectable parameter choices are made, etc.
Before data exchange can take place, the master will send parameterization and configuration telegrams to all of its assigned slaves. These parameters and configuration data are checked by the slaves. If both are valid, the master will initiate cyclic I/O data communication with the slave devices.
ProSoft Technology, Inc. Page 65 of 85
ILX56-PBS ♦ PROFIBUS DPV1 Master/Slave
ControlLogix® Platform
PROFIBUS DP
User Manual
7.5
Acyclic communication
In addition to the cyclic data exchange, the PROFIBUS protocol has the option of acyclic communication. This service is not configured. There are 2 different communication channels possible between the requested master and the slave:
MS1 channel (MS1 connection): can only be established if cyclic data exchange is taking place between that master (DPM1) and the slave
MS2 channel (MS2 connection): is possible with several masters simultaneously, but the connection must be established explicitly by the master.
Acyclic reading and writing of data requires an established MS1 or MS2 connection.
For the MS1 channel, 3 conditions must be satisfied:
The slave device must support the MS1 channel (key C1_Read_Write_supp at 1 in the GSD file)
The DPV1_enable bit must be set during the parameter assignment
Data exchange is taking place
For the MS2 channel, the connection must be explicitly initiated by the master. The maximum number of possible MS2 connections to the slave must not be reached.
The connection can be closed by either the master or the slave device.
7.6 Topology of PROFIBUS DP
PROFIBUS devices are connected in a bus structure. Up to 32 stations (master or slaves) can be connected in one segment. The bus is terminated by an active bus terminator at the beginning and end of each segment. Both bus terminations must always be powered. When more than 32 stations are used, repeaters (line amplifiers) must be used to connect the individual bus segments.
7.7 PROFIBUS DP cable description
Only one type of cable can be used for PROFIBUS network:
Parameter
Table 9.2 – PROFIBUS DP network cable
Type A
Surge Impedance
135…165Ω
(3 to 20 MHz)
Capacity
Loop Resistance
Wire gauge
Conductor area
<30 pF/m
<110 Ω/km
>0.64 mm
>0.34 mm²
The maximum cable length depends on the transmission speed and cable type. The specified cable length can be increased using the repeaters. The use of more than 3 repeaters in series is not recommended.
Table 9.3
– PROFIBUS DP cable length
Baudrate (kbps) 9.6
Length A (m) 1200
19.2
1200
93.75
1200
187.5
1000
500
400
1500
200
3000-
12000
100
ProSoft Technology, Inc. Page 66 of 85
ILX56-PBS ♦ PROFIBUS DPV1 Master/Slave
ControlLogix® Platform
PROFIBUS DP
User Manual
7.8
PROFIBUS DP connector description
Table 9.4
– PROFIBUS DP connector
DB9 Pin# DB9 Termination with ILX56-PBS
DB9 Pin Description
Chassis ground 1
Reserved
Data+ / B
2
3
Tx enable
Isolated ground
Voltage plus
Reserved
Data- / A
Reserved
4
5
6
7
8
9
In case of termination connect this pin to Pin 8
(Data - / A) with 220 ohm resistor
Connect this pin to Pin 8 (Data - / A) with 390 ohm resistor
Connect this pin to Pin 3 (Data + / B) with 390 ohm resistor
ProSoft Technology, Inc. Page 67 of 85
ILX56-PBS ♦ PROFIBUS DPV1 Master/Slave
ControlLogix® Platform
8 ILX56-PBS Quickstart
ILX56-PBS Quickstart
User Manual
This chapter covers the configuration of the ILX56-PBS to communicate with a
Siemens CPU 315-2PN/DP PROFIBUS Master using the Siemens TIA Portal v15 software.
8.1
GSD File Management Tool Installation
1 Download the ProSoft PLX50 Configuration Utility from http://www.prosofttechnology.com
.
2 Run the PLX50 Configuration Utility Setup.msi to install the software.
3
Follow the Setup Wizard to complete the installation process.
Figure 8.1
– PLX50 Configuration Utility Setup Wizard
ProSoft Technology, Inc. Page 68 of 85
ILX56-PBS ♦ PROFIBUS DPV1 Master/Slave
ControlLogix® Platform
8.2
Creating a New Project
ILX56-PBS Quickstart
User Manual
Note: If project was started from a Studio 5000 Add-On Profile (AOP), the following step (creating a new project) can be skipped.
Before configuring the module, a new PLX50 Configuration Utility project must be created.
1 Under the File menu, select New.
Figure 8.2 – Creating a new project
2 A PLX50 Configuration Utility Design Tool project will be created, showing the
Project Explorer tree view. A new device can now be added by selecting Add under the Device menu.
Figure 8.3
– Adding a new device
3 In the Add New Device window, select the ILX56-PBS and click the Ok button.
Figure 8.4 – Adding a new ILX56-PBS device
4 The device will appear in the Project Explorer tree with its configuration window opened.
ProSoft Technology, Inc. Page 69 of 85
ILX56-PBS ♦ PROFIBUS DPV1 Master/Slave
ControlLogix® Platform
8.2.1
PROFIBUS Configuration
Navigate to the Profibus tab to update the Basic Settings .
ILX56-PBS Quickstart
User Manual
Figure 8.5 – Profibus tab
8.2.2
Logix Configuration
Under the Logix tab, configure the Logix Connections and Logix Base Tag A to reflect ILX56-PBS position in ControlLogix Rack. Click Apply and then the Ok button.
ProSoft Technology, Inc.
Figure 8.6
– Logix tab
Page 70 of 85
ILX56-PBS ♦ PROFIBUS DPV1 Master/Slave
ControlLogix® Platform
ILX56-PBS Quickstart
User Manual
8.3
Adding a PROFIBUS Slave
You will need to add each PROFIBUS device to the ILX56-PBS project tree, depending on how many PROFIBUS slaves you need to emulate (up to 10). In this example, 1 slave PROFIBUS slave will be added and configured.
1 Right-click on the PROFIBUS Devices icon in the tree and select Add
PROFIBUS Device .
Figure 8.7 – Adding a PROFIBUS device
2 Once the device has been added, the General Configuration dialog opens and the device is added at the first open PROFIBUS Station Address.
Figure 8.8
–PROFIBUS configuration
3 Navigate to Profibus Configuration tab to assign the Node Address.
4 Navigate to Slot Configuration tab, and click on the Add Module button.
ProSoft Technology, Inc.
Figure 8.9 – Add Module
Page 71 of 85
ILX56-PBS ♦ PROFIBUS DPV1 Master/Slave
ControlLogix® Platform
5 Add the appropriate modules and click the Ok button.
ILX56-PBS Quickstart
User Manual
Figure 8.10 – Added modules
The ILX56-PBS is now configured in the ProSoft PLX50 Configuration Utility.
ProSoft Technology, Inc. Page 72 of 85
ILX56-PBS ♦ PROFIBUS DPV1 Master/Slave
ControlLogix® Platform
8.4
Downloading the Configuration to the ILX56-PBS
1 Establish a connection path for each module.
2 Right-click on the ILX56-PBS icon and select Connection Path .
ILX56-PBS Quickstart
User Manual
Figure 8.11 – Connection Path option
3 Click on the Browse button to launch the target browser. Navigate to the module, and press Ok .
Figure 8.12 – Connection Path
4 Download device configuration by right-clicking on the ILX56-PBS icon and selecting Download.
Figure 8.13
– Downloading the device configuration
5 Upon successful download, the PLX50 Configuration Utility device configuration is now complete.
ProSoft Technology, Inc. Page 73 of 85
ILX56-PBS ♦ PROFIBUS DPV1 Master/Slave
ControlLogix® Platform
8.5
ControlLogix Configuration
ILX56-PBS Quickstart
User Manual
1 Generate the required Logix and UDTs in the PLX50 Configuration Utility by rightclicking on the ILX56-PBS icon and selecting Generate Logix L5X .
Figure 8.14
– Generate Logix L5X option
2 Select a suitable file name and path for the L5X file, then click the Save button.
ProSoft Technology, Inc.
Figure 8.15
– File name and path for the L5X file
Page 74 of 85
ILX56-PBS ♦ PROFIBUS DPV1 Master/Slave
ControlLogix® Platform
ILX56-PBS Quickstart
User Manual
3 The L5X file can now be imported into the Studio 5000 project. Right-click on a suitable Program task and select Add > Import Routine .
Figure 8.16
– Import Routine option
4 In the File Open dialog, select the L5X file and accept the import by pressing Ok .
The import will create the following:
Mapping Routine
Multiple UDT (User-Defined Data Types)
Multiple Controller Tags
5 Since the imported mapping routine is not a Main Routine, it will need to be called from the current Main Routine.
Figure 8.17 – Imported mapping routine
6 To enable the ILX56PBS PROFIBUS slave, place a value of ‘1’ in the appropriate slave ID Controller Tag(s) Local:1:O1.DeviceEnable.SlaveID_xxx.
ProSoft Technology, Inc.
Figure 8.18
– Setting the value of the slave ID Controller Tag
Page 75 of 85
ILX56-PBS ♦ PROFIBUS DPV1 Master/Slave
ControlLogix® Platform
ILX56-PBS Quickstart
User Manual
8.6
PROFIBUS Master Configuration
The Siemens 315-2PN/DP Processor will be used as a PROFIBUS Master to the
ILX56-PBS slave.
1 Open the Total Integrated Automation Portal V15 software and create a new project.
Figure 8.19
– Creating a new project
2 Add the Siemens CPU 315-2 PN/DP processor as a new device.
ProSoft Technology, Inc.
Figure 8.20
– Adding the processor as a new device
Page 76 of 85
ILX56-PBS ♦ PROFIBUS DPV1 Master/Slave
ControlLogix® Platform
ILX56-PBS Quickstart
User Manual
3 Add the ILX56-PBS GSD by selecting Option at the menu bar then selecting
Manage general station description files (GSD)
Figure 8.21
– Manage general station description files
4 *In this example, ILX56-PBS GSD has already been installed in this computer but this may not be the case for new users.
5 Configure the device’s IP Address appropriately.
Figure 8.22 – Configuring the device’s IP address
ProSoft Technology, Inc. Page 77 of 85
ILX56-PBS ♦ PROFIBUS DPV1 Master/Slave
ControlLogix® Platform
ILX56-PBS Quickstart
User Manual
6 Configure MP/DP interface [X1] as PROFIBUS DP master with appropriate address.
Figure 8.23
– Configuring the MP/DP interface
7 Add ILX56-PBS as PROFIBUS slave by choosing ILX56-PBS in the catalog list from the right and dragging the ILX56-PBS module in the Network window.
Figure 8.24 – Adding the ILX56-PBS as PROFIBUS slave
ProSoft Technology, Inc. Page 78 of 85
ILX56-PBS ♦ PROFIBUS DPV1 Master/Slave
ControlLogix® Platform
ILX56-PBS Quickstart
User Manual
8 Connect the two purple box icons to assign the PLC_1 CPU 315-2PN/DP
PROFIBUS Master to Slave_1 ILX56-PBS PROFIBUS Slave.
Figure 8.25 – Connecting the purple box icons
9 Double click on Slave_1 ILX56-PBS icon to configure the input/output bytes of
ILX56-PBS.
ProSoft Technology, Inc.
Figure 8.26 – Configuring the input/output bytes
Page 79 of 85
ILX56-PBS ♦ PROFIBUS DPV1 Master/Slave
ControlLogix® Platform
10 Change the address of I address and Q address if so desire.
ILX56-PBS Quickstart
User Manual
Figure 8.27
– Changing the I address and Q address
11 Add Watch Table to modify the output and monitor the input. Add desired QB and IB address to modify and monitor.
ProSoft Technology, Inc.
Figure 8.28 – Changing the I address and Q address
Page 80 of 85
ILX56-PBS ♦ PROFIBUS DPV1 Master/Slave
ControlLogix® Platform
12 Compile and download the TIA V15 file to the 315-2PN/DP CPU.
ILX56-PBS Quickstart
User Manual
Figure 8.29
– Compiling the TIA V15 file
ProSoft Technology, Inc.
Figure 8.30 – Downloading the TIA V15 file
Page 81 of 85
ILX56-PBS ♦ PROFIBUS DPV1 Master/Slave
ControlLogix® Platform
13 Click the Load button.
ILX56-PBS Quickstart
User Manual
14 Click the Finish button.
Figure 8.31
– Load preview
Figure 8.32 – Load results
ProSoft Technology, Inc. Page 82 of 85
ILX56-PBS ♦ PROFIBUS DPV1 Master/Slave
ControlLogix® Platform
15 Go Online with the Siemens processor.
ILX56-PBS Quickstart
User Manual
Figure 8.33 – Going online with the Siemens processor
16 To modify and monitor the PROFIBUS Output/Input data, open the Watch table and click the Monitor All button.
Figure 8.34
– Monitor All button
17 To modify the PROFIBUS Output data, enter modify values in Modify value column and click Modify all selected values once and now button.
ProSoft Technology, Inc.
Figure 8.35 – Monitor All button
Page 83 of 85
ILX56-PBS ♦ PROFIBUS DPV1 Master/Slave
ControlLogix® Platform
ILX56-PBS Quickstart
User Manual
18 To verify the data was sent and received by the ILX56-PBS, Open Studio 5000 and check the appropriate Controller Tags while being online with the Rockwell
Processor.
Figure 8.36
– Checking the Controller Tags
19 To monitor the PROFIBUS Input data, enter values in the appropriate Controller
Tags in Studio 5000 while being online with Rockwell Processor.
Figure 8.37 – Entering values in the Controller Tags
20 Verify the data was received in Siemens 315-2PN/DP Processor by monitoring the appropriate tags in the Watch Table.
Figure 8.38 – Monitoring the tags
ProSoft Technology, Inc. Page 84 of 85
ILX56-PBS ♦ PROFIBUS DPV1 Master/Slave
ControlLogix® Platform
9 Support, Service & Warranty
Support, Service & Warranty
User Manual
9.1
Contacting Technical Support
ProSoft Technology, Inc. is committed to providing the most efficient and effective support possible. Before calling, please gather the following information to assist in expediting this process:
Product Version Number
System architecture
Network details
If the issue is hardware related, we will also need information regarding:
Module configuration and associated ladder files, if any
Module operation and any unusual behavior
Configuration/Debug status information
LED patterns
Details about the interfaced serial, Ethernet or Fieldbus devices
Note: For technical support calls within the United States, ProSoft’s 24/7 after-hours phone support is available for urgent plant-down issues.
North America (Corporate Location)
Phone: +1.661.716.5100 [email protected]
Languages spoken: English, Spanish
REGIONAL TECH SUPPORT [email protected]
Latin America Regional Office
Phone: +52.222.264.1814 [email protected]
Languages spoken: Spanish, English
REGIONAL TECH SUPPORT [email protected]
Europe / Middle East / Africa Regional Office
Phone: +33.(0)5.34.36.87.20 [email protected]
Languages spoken: French, English
REGIONAL TECH SUPPORT [email protected]
Asia Pacific Regional Office
Phone: +60.3.2247.1898 [email protected]
Languages spoken: Bahasa, Chinese, English,
Japanese, Korean
REGIONAL TECH SUPPORT [email protected]
For additional ProSoft Technology contacts in your area, please visit: https://www.prosoft-technology.com/About-Us/Contact-Us .
9.2
Warranty Information
For complete details regarding ProSoft Technology’s TERMS & CONDITIONS OF
SALE, WARRANTY, SUPPORT, SERVICE AND RETURN MATERIAL
AUTHORIZATION INSTRUCTIONS, please see the documents at: www.prosofttechnology/legal
ProSoft Technology, Inc. Page 85 of 85
advertisement
Related manuals
advertisement
Table of contents
- 2 Your Feedback Please
- 2 Content Disclaimer
- 6 Introduction to the ILX56-PBS
- 7 Features
- 7 Additional Information
- 8 Module Layout
- 9 PROFIBUS DP Port (RS485)
- 10 Install Configuration Software
- 10 Creating a New Project
- 12 ILX56-PBS Parameters
- 12 General
- 13 – Slave Mode
- 14 Logix
- 15 Adding PROFIBUS DP Devices
- 16 General
- 17 PROFIBUS Configuration
- 20 User Parameters
- 21 Slot Configuration
- 23 Start-up Parameters
- 23 DPV1 Objects
- 24 DPV1 Alarms
- 25 Module Download
- 26 Studio 5000 Configuration
- 26 Installing the Add-On Profile (AOP)
- 26 Adding a Module to I/O Configuration
- 28 PLX50 Configuration Utility Project File
- 29 Generating a Logix .L5X File
- 29 Local Rack Module Location
- 30 Remote Rack Module Location
- 31 Generating the L5X File
- 35 SD Card
- 35 Firmware
- 36 Configuration
- 36 Manual Copy
- 38 PLX50 Configuration Utility Upload
- 39 Logix Operation
- 39 PROFIBUS DP - Slave
- 39 General Status
- 41 General Control
- 42 Status and DPV0 Data Exchange
- 44 DPV1 Class 1 Messaging (MS1)
- 44 Alarming
- 47 Firmware Upgrade
- 51 Module Status Monitoring
- 52 ILX56-PBS Status
- 52 General
- 54 Slave Status
- 55 Logix Statistics
- 56 ILX56-PBS Emulated Slave Device Status
- 57 PROFIBUS Packet Capture
- 59 Packet Details
- 60 Packet Filter
- 61 Saving Packet Filter Options
- 62 Module Event Log
- 63 Electrical
- 63 PROFIBUS DP
- 63 Certifications
- 64 Introduction
- 64 PROFIBUS DP
- 64 PROFIBUS PA
- 65 PROFIBUS FMS
- 65 PROFIBUS master and slave
- 65 PROFIBUS master class 1 (DPM1) or class 2 (DPM2)
- 65 PROFIBUS DP Master class 1 (DPM1)
- 65 PROFIBUS DP Master class 2 (DPM2)
- 65 Cyclic communication
- 66 Acyclic communication
- 66 Topology of PROFIBUS DP
- 66 PROFIBUS DP cable description
- 67 PROFIBUS DP connector description
- 68 GSD File Management Tool Installation
- 69 Creating a New Project
- 70 PROFIBUS Configuration
- 70 Logix Configuration
- 71 Adding a PROFIBUS Slave
- 73 Downloading the Configuration to the ILX56-PBS
- 74 ControlLogix Configuration
- 76 PROFIBUS Master Configuration
- 85 Contacting Technical Support
- 85 Warranty Information