Sommer Twist 200 Owner Manual
Add to My manuals27 Pages
Sommer Twist 200 is a radio remote control for doors and gates. It is easy to use, and the installation and operating instructions will help you to get the most out of your purchase. With its compact design and easy-to-use remote control, the Sommer Twist 200 is the perfect solution for controlling your gate or door from anywhere in your home or office.
advertisement
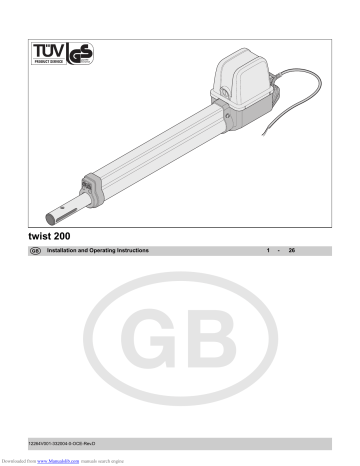
twist 200
Installation and Operating Instructions 1 26
12264V001-332004-0-OCE-Rev.D
Downloaded from www.Manualslib.com
manuals search engine
Contents
General Information. . . . . . . . . . . . . . . . . . . . . . . . . . . . . . 2
Symbols 2
Safety Instructions
Normal Use
Permitted Gate Wing Dimensions
Technical Data
Dimensions
Functions
EU-Manufacturer’s Declaration
3
3
2
2
3
3
3
Preparations of Installation . . . . . . . . . . . . . . . . . . . . . . . 4
Safety Instructions 4
Supplied Components 4
Installation . . . . . . . . . . . . . . . . . . . . . . . . . . . . . . . . . . . . . 5
Notes regarding dimensions A- / B- 5
Mounting Position of Drive
Preparation for Stop Position Settings
How can I adjust the limit switches ?
Adjusting stop position gate “OPEN”
Adjusting stop position gate “CLOSE”
A- / B-Dimension Table
Installation of Fittings
Post- / Fittings
Gate Wing Fittings
Installation of Control Unit
8
8
9
9
7
7
6
7
5
6
Commissioning . . . . . . . . . . . . . . . . . . . . . . . . . . . . . . . . 10
General Instructions 10
Preparation for Standard Operation
Activating Standard Operation
Adjusting Force Tolerance
Programming Remote Control Devices
10
10
10
10
Radio Receiver . . . . . . . . . . . . . . . . . . . . . . . . . . . . . . . . . 11
Programming Remote Control Devices 11
Operation of Gate . . . . . . . . . . . . . . . . . . . . . . . . . . . . . . 12
Opening and Closing Gate 12
Resetting Control
Emergency Release in the Event of a Power Failure
Removing the Cover
12
13
13
Additional Functions and Connections . . . . . . . . . . . . . 14
LEDs 14
DIL-Switch
Automatic Close Mode
Floating Relay Contact
Connecting Safety Devices
Connecting Safety Devices
Connecting Drives
Connecting to Power Supply (230V)
16
17
17
15
15
16
16
Accessories . . . . . . . . . . . . . . . . . . . . . . . . . . . . . . . . . . . 18
Maintenance . . . . . . . . . . . . . . . . . . . . . . . . . . . . . . . . . . 20
Regular Inspections 20
Customer Service and Warranty 20
Dismantling of Drive System . . . . . . . . . . . . . . . . . . . . . 20
Troubleshooting . . . . . . . . . . . . . . . . . . . . . . . . . . . . . . . . 21
Tips for Troubleshooting 21
Spare Parts List / Glossary . . . . . . . . . . . . . . . . . . . . . . . 23
Wiring Diagram . . . . . . . . . . . . . . . . . . . . . . . . . . . . . . . . 25
EU Conformity Declaration
Messrs
SOMMER Antriebs- und Funktechnik GmbH
Hans-Böckler-Straße 21-27
D-73230 Kirchheim/Teck declares herewith that the product designated below complies with the relevant fundamental requirements as per Article 3 of the R&TTE Directive 1999/5/EG, insofar as the product is used correctly, and that the following standards apply:
Product: RF Remote Control for doors & gates
Type: RM04-868-2, RM03-868-4, RX01-868-2/4,
RFSDT-868-1, RFSW-868-1, RM02-868-2,
RM06-868-2, RM04-868-1, RM02-868-2-TIGA,
RM08-868-2, RM01-868,
RM02-434-2, RM03-434-4, RM04-434-2
The relevant guidelines and standards are:
- ETSI EN 300220-1:09-2000, -3:09-2000
- ETSI EN 301489-1:07-2004, -3:08-2002
- DIN EN 60950-1:03-2003
Kirchheim/Teck, 04.08.2004
Frank Sommer
Managing Director
1
Downloaded from www.Manualslib.com
manuals search engine
Symbols
Indicates a potential risk.
Indicates a potential risk. Failure to comply with the instructions may result in serious injury or damage to property!
1
Information, useful advice.
General Information
(1)
Refers to the relevant illustration in the introduction or the main text of this manual.
Safety instructions
General safety instructions
• All persons in charge of the installation, maintenance or operation of the drive system must have read and fully understood these instructions.
• All instructions must be strictly adhered to. The manufacturer accepts no liability for damage or malfunction resulting from non-compliance with the instructions in this manual.
• Always comply with the statutory health and safety regulations and the applicable standards.
• The installation and operation of the drive system is governed by the following standards: EN 12 453, EN 12 604, EN 12 605, etc.
• Prior to any work at the gate or drive, disconnect drive system from the power supply and secure it against inadvertent reconnection or actuation.
• There is a risk of injury from crushing at the closing edges of the gates or near the mechanical parts.
• Never operate the drive if you suspect that is might be faulty or damaged.
• After installation and commissioning, all persons operating the drive must be instructed on its functions and proper operation.
• Use only original spare parts, accessories and fixtures supplied by the manufacturer.
Operation
• Ensure that the drive is never operated by children or persons who have not been specifically instructed.
• When operating the gate, ensure that there are no persons, especially children, animals or objects within its operating range.
• Only operate the gate with the remote control device when you have full view of the gate.
• Never reach into the gate or any of its moving parts.
• Regularly inspect the safety devices. Immediately repair damaged or defective parts. For details, see maintenance instructions.
• Only drive through the gate after it has been fully opened.
• Adjust the force tolerance to the minimum level.
• At gates with automatic closing mechanism, all edges must be secured according to the applicable regulations and standards.
• Always remove the key to prevent unauthorised operation.
Storage
• The drive mechanism may only be stored indoors, in a dry, sealed environment at an ambient temperature of between -20°C and +50°C.
• Store drives in horizontal position.
Radio remote control
• The radio remote control may only be used for equipment and systems in which defective remote operation of the transmitter or receiver does not constitute a risk to people, animals or property, or in cases where this risk is eliminated by means of additional safety facilities.
• All persons operating the gate must be instructed that systems, where there is a risk of injury or damage, may not be operated by remote control, or that such operation is only permitted, if all movements of the gate can be supervised.
• The radio remote control device may only be used, if the operator can fully supervise the movement of the device and if no persons or objects are within the movement range of the gate.
• Keep the remote control device out of reach of children or animals and prevent any inadvertent use.
• The operator of this radio-controlled equipment is not in any way protected against interference from other telecommunication systems and facilities (e.g. other radio-controlled equipment that is licensed to operate at the same frequency range). If such interference occurs, please contact the local radio and telecommunications authority requesting a radiolocation.
• Do not use hand-held transmitters near locations or installations that are susceptible to radio interference (e.g. airports, hospitals).
Rating plate
The rating plate is located on the cover of the control unit housing.
Normal Use
After the drive system has been installed, the person responsible for the installation must complete an EU Declaration of Conformity according to Machine Directive 98/37/EU and attach a CE mark at the type plate of the drive.
This also applies in cases where the owner of the system is a private person, as well as to manually operated gates that have been upgraded with a drive. The above documents and the instructions for installation and operation must be handed over to the operator.
• The drives are exclusively designed for the opening and closing of gates.
Any other use is deemed improper. The manufacturer shall not be liable for damages resulting from improper use. The user accepts sole responsibility for any risks thereby incurred. Improper use shall void all warranty.
• Gates that are to be upgraded with an automatic drive system must comply with the applicable standards and directives as amended, e.g. EN 12 453, EN 12604, EN 12605.
• The drive system may only be operated if it is in proper working order.
Always follow standard safety procedures and adhere to the instructions in this installation and operating manual.
• Immediately eliminate any defects that might impair the safety of the equipment.
• The gate wings must only have minimum play at the hinges.
• The gate wings must be stable and warp-proof, i.e. they may not bend or warp during opening or closing operation.
• The DSTA24 control and twist 200 drive systems may only be operated in conjunction.
• The DSTA24 control and the twist 200 drives are designed for use in private premises.
• The electric drive may only be used for the opening and closing of gates with one or two wings.
Downloaded from www.Manualslib.com
manuals search engine
2
General Information
Permitted Gate Wing Dimensions
- Length:
- Height:
- Weight:
- Free surface:
- Slope: min. 0.8 m to max. 2.5 m max. 2.5 m max. 200 kg min. 50 %, irrespective of gate wing size
0 %
Technical Data
General 1 wing 2 wing
Runtime, depending on A/B approx. 10 to 22 approx. 15 ...27 sec.
Protection class
Drive
Control system housing
Rated voltage
Rated frequency
Operating temperature
Drive
Control system housing
Travel (per drive)
Max. traction force and pressure:
Operating factor:
IP 44
IP 54
220 ...240
50
-30 to +80
-20 to +70
395
2000
15
IP 44
IP 54
220 ...240 V
50 Hz
-30 to +80 °C
-20 to +70 °C
395 mm
2000
15
N
%
Stand-by
Rated current consumption 20
Rated power consumption 2,2
20
2,2
Rated operation
Motor voltage ~ 21,7
Rated current consumption: ~ 2.8
Rated power consumption: ~ 117.3
Workplace noise emission < 75 dBA - drive only
~ 20
~ 5.6
~ 234 mA
W
V
A
W
Functions
The gate wing is opened and closed by extending or retracting the push rod. When the preset stop positions are reached, the drive is automatically switched off by means of limit switches.
Locking of gate
For gates with wing lengths over 2 m and for 2-wing gates, we recommend the installation of a stop at position gate
“CLOSE”. An electric lock may be mounted for additional safety.
The gate does not require a lock to be kept closed, as the drive mechanism is self-locking(with connection to the control system). The gate can thus not be forced open by hand without damaging the drive system or fittings.
Remote control
The drive can be operated by remote control with the supplied remote control transmitter, provided that the transmitter and the radio receiver have been properly programmed.
Safety devices
The control unit is equipped with an automatic force monitoring system.
If there is more force required for opening or closing the gate as has been programmed during the programming run, the drive is set into reverse motion (gate direction “CLOSE”) or halted (direction “OPEN”).
The operator has the option to extend the control with various safety devices. For details see chapter additional functions and connections.
Examples of available accessories:
• Light barrier
• Safety contact unit with monitoring system
EU Manufacturer’s Declaration
Dimensions
All dimensions in mm.
SOMMER Antriebs- und Funktechnik GmbH
Hans-Bockler-Strasse 21-27
D-73230 Kirchheim/Teck, Germany herewith declares that its drive system:
- twist 200 complies with the following Directives:
- Machine Directive 98/37EU
- Low-Voltage Directive 73/23/EEC
- EU Directive on Electromagnetic Compatibility 89/336/EEC
The equipment fulfils the requirements of the following standards:
- DIN EN 55014-1, DIN EN 55014-2, DIN EN 55022
- DIN EN 61000-3-2, DIN EN 61000-3-3, EN 60335-1/A14,
- E DIN VDE 0700 Part 103, DIN V VDE 0801/A1, EN 12453
Note: the gate system may not be commissioned until it has been established that the system in which the above drive is to be installed fulfils all specifications of the relevant EU Directives.
Kirchheim, 01.12.2001
Uwe Sommer
Managing Director
Downloaded from www.Manualslib.com
manuals search engine
3
Preparations of Installation
Safety instructions
The power cable supplied with the control unit may only be used for the installation of the drive systems. After completion of the installation, disconnect the cable and replace it with a duct-laid cable. It is forbidden to use the supplied power cable for standard operation of the gate.
• The control unit may only be connected to the power supply by a qualified electrician.
• Always comply with the instructions in this manual.
• Locking devices (electrical keys, locking bolts, etc.) must be removed and disabled prior to installation of the dive system.
• Ensure that the gate wings are properly secured to the posts as considerable forces are applied to the devices during opening and closing of the gate.
• Prior to welding of fittings to posts or gate wings, remove or cover the drive unit to prevent damage from sparks, etc.
• If the gate is operated by means of a switch, it must be installed at a minimum height of 1.6 m above ground to prevent inadvertent activation by children.
• In public areas, use only approved fittings and securing devices (e.g.
dowels).
Supplied Components
• Prior to installation, check delivery to ensure that it contains all necessary parts.
• Depending on the design of your drive system, the delivery might deviate from the standard delivery.
kg mm
Tools required
Complete installation kit
Weight
Packaging (L x W x H):
1 wing
9.1
2 wing
13.8
800 x 200 x 220
Installation and operating instructions
Drive unit including cables
1 x
1 x
Control system, in housing 1 x
(with radio receiver, transformer and mains plug)
Remote control device including battery 1 x
Gate wing fittings 1 x
Post fittings 1 x
M10x45 stainless steel hexagon screw 2 x
M10 stainless steel locking nut 2 x
Plug 2 x
1 x
2 x
1 x
1 x
2 x
2 x
4 x
4 x
4 x
Downloaded from www.Manualslib.com
manuals search engine
4
Installation
Tips for Installation
• Consult the operator when deciding on the location for installation of the control unit.
• Do not install the housing where it is visible from the street, in order to protect it against vandalism.
• For gates with wing lengths over 2 m and for 2-wing gates, we recommend the installation of a centre respond.
The gate can be operated with a number of different control devices: Hand-held transmitter, Funkcody, interior push-button and key switch. For the hand-held transmitter, Funkcody and interior push-button, there is no need for cables as they are radio control devices. For more information, contact the supplier.
1.
Warning light
2.
Key switch (1 or 2 contact)
3.
Light barrier
4.
Connecting cables 7 m
5.
Main switch (lockable)
6.
Rod aerial (including 10 m cable)
7.
Electric lock 24V
8.
Funkcody
9.
Holder for remote control device for installation in car or on wall
10. Timber post fittings
Mounting Position of Drive
• Mount drive in horizontal position. The motor must always be at the top of the drive system.
5
Downloaded from www.Manualslib.com
manuals search engine
Installation
Preparation for Stop Position Settings
Never adjust limit switches with a power drill or similar tool, as the switches could thereby be pulled from the holders.
Never connect drive to 230V power, as this would immediately destroy the motor.
How can I adjust the limit switches?
First install and adjust the limit switches for “gate OPEN” and
“gate CLOSE”. Ensure that the gate wing does not touch the housing to prevent damage to the drive.
Always tighten the limit switch cables to prevent jamming within the protective tube.
Gate wing closes less
• Upon the first command, the drives must move the gate in direction
“OPEN”. If this is not the case, exchange the connecting cables of the drive at the control unit.
Gate wing closes more
• Mount hood.
• Engage drive (1) and lock it (2).
Gate wing opens more
1. Pull out push rod to a length of C1 = 270 mm.
2. Measure dimensions A and B, look up dimensions C1 and C2 in the A/B dimension table.
3. Connect drive to control unit.
- First connect and adjust drive at the wing with stop (M1), then install drive for pedestrian wing (M2).
1-wing gate
(M2) pedestrian wing
Terminals 7 + 8
Connection of drive systems
2-wing gate
(M1) wing with stop
Terminals 5 + 6
(M2) pedestrian wing
Terminals 7 + 8
4. Set all DIL switches to OFF.
5. Set jumpers: single-wing or double-wing gate
6. Connect control system to power supply.
LED for power supply is on and “WL” LED flashes.
Gate wing opens less
6
Downloaded from www.Manualslib.com
manuals search engine
Installation
A/B Dimension Table
Prior to installation, define dimensions A/B. Without knowing these dimensions, it is not possible to properly install and operate the drive system.
• The greater dimension B, the more sensitive the power cut-off function.
• If possible, ensure that dimensions A/B are corresponding (max. permissible deviation: 40 mm).
• Pay attention to different post dimensions.
Note
Select dimensions that allow for the desired opening angle.
Please note that the values in this table are standard values only. For gate wing lengths of more than 1.5 m, dimension B must be at least 140 mm.
A
B
80
C C1
D C2
C
D
100
C1
C2
C
D
120
C1
C2
C
D
140
C1
C2
C
D
160
C1
C2
C
D
180
C1
C2
C
D
200
C1
C2
C
D
220
C1
C2
C
D
240
C1
C2
C
D
94° 84 103° 84 110° 84 116° 84 122° 84 117° 84 108° 84 102° 84 97° 84 93°
140 893 312 924 343 959 377 992 411 1028 447 1035 454 1035 454 1035 454 1035 454
93° 84 101° 84 108° 84 114° 84 119° 84 109° 84 101° 84 96° 84 92° 84
260
C1
C2
100 854 272 889 308 925 344 963 382 1001 420 1035 454 1035 454 1035 454 1035 454 1035 454
95° 84 105° 84 113° 84 120° 84 126° 84 129° 84 115° 84 107° 84 102° 84 98° 84
120 873 291 908 326 941 360 976 395 1014 433 1035 454 1035 454 1035 454 1035 454 1035 454
84
160 915 334 946 365 976 396 1010 428 1035 454 1035 454 1035 454 1035 454
93° 84 100° 84 106° 84 112° 84 110° 84 101° 84 95° 84 91° 84
180 937 356 966 385 997 416 1029 447 1035 454 1035 454 1035 454
94° 84 90° 84 93° 84 99° 84 104° 84 109° 84 100° 84
200 959 377 988 406 1017 436 1035 454 1035 454
92° 84 98° 84 103° 84 100° 84 93° 84
Dimensions A, B, C, C1, C2 in mm
D = widest possible opening angle
1 rotation = 1.25 mm setting step 220 982 400 1010 428 1035 454 1035 454
92° 84 97° 84 100° 84 90° 84
240 1005 424 1031 449
92° 84
260 1028 447
92° 84
96° 84
Recommended range
Adjusting stop position gate “OPEN” Adjusting stop position gate “CLOSE”
Factory settings for gate “OPEN”: approx. C2 = 84 mm.
1. Press key (Imp). Gate moves to end position gate “OPEN”.
Hold push rod to prevent it from rotating, as it would otherwise not be retracted.
2. When the end position is reached, measure dimension C2.
3. Set limit switch for gate “OPEN” to respective dimension C2. Prior to adjusting the end switch, move gate slightly in direction gate “CLOSE”.
4. Press key (Imp). Gate moves to end position gate “OPEN”.
5. Repeat steps 1 to 4 until the desired value for dimension C2 is reached.
Factory settings for gate “CLOSE”: approx. C1 = 455 mm.
1. Press key (Imp). Gate moves to end position gate “CLOSE”.
Hold push rod to prevent it from rotating, as it would otherwise not be retracted.
2. When the end position is reached, measure dimension C1.
3. Set limit switch for gate “CLOSE” to respective dimension C1. Prior to adjusting the end switch, move gate slightly in direction gate “OPEN”.
4. Press key (Imp). Gate moves to end position gate “CLOSE”.
5. Repeat steps 1 to 4 until the desired value for dimension C1 is reached.
After the end positions for gate “OPEN” and “CLOSE” have been adjusted, mount the post fittings.
7
Downloaded from www.Manualslib.com
manuals search engine
Installation
Installation of Fittings
The strength of the supplied fittings has been specifically chosen to suit the supplied drive system (twist 200). The manufacturer shall not be held liable for damages, if fittings other than those supplied are used.
If dimension B is smaller than the smallest value in the above table, install a spacer plate below the post fittings to ensure that dimension B is at least 100 mm.
• Prior to welding of fittings to posts or gate wings, remove or cover the drive unit to prevent damage from sparks, etc.
• At solid stone and concrete posts, mount fittings in such a way that the plugs cannot loosen during operation. Instead of steel or plastic straddling dowels, we recommend using adhesive bond anchors that allow for the tension-free adhesion of the threaded pin in the post.
• Ensure that the distances between the gate wing and the post, and the gate wing and the drive system conform with the applicable standards.
Steel posts
Take into account wall thickness of post!
The fittings can be welded directly to the post or fixed by means of screws.
Stone and concrete posts
When mounting fittings onto stone posts, ensure that the boreholes for the screws are not too close to the edge of the post. The distance to be maintained may vary, depending on the dowel used. Please follow the instructions of the dowel producer.
Timber posts
As no additional forces are applied, you can use the supplied fittings.
If the supplied fittings do not fit your posts, contact a specialised dealer for special fittings (e.g. timber post fittings).
After installation of the fittings, do not carry out any welding or grinding work, as residues resulting from such work lead to accelerated corrosion at the fittings.
3. Inside hinge /fittings
Dimensions:
Post 195 mm x 100 mm
Desired opening angle: min. 100°
Length of gate wing: 1 m
Measurements:
A = 100 mm
B = 75 mm
Post Fittings
As dimension B is 75 mm, insert a spacer plate below the fittings. This ensures that dimension B is increased to minimum 100 mm.
Dimensions according to table
A = 100 mm
B = 100 mm
Max. opening angle = 105°
Examples of dimensions A / B
1. Short post
Dimensions:
Steel column 100 mm x 100 mm
Desired opening angle: min. 90°
Length of gate wing: 1.5 m
Measurements:
A = 80 mm
B = 110 mm
Dimensions according to table
A = 80 mm
B = 120 mm
Max. opening angle = 94°
2. Long post
Dimensions:
Concrete column 215 mm x 100 mm
Desired opening angle: min. 95°
Length of gate wing: 2.5 m
Measurements:
A = 225 mm
B = 165 mm
Dimensions according to table
A = 220 mm
B = 160 mm
Max. opening angle = 91°
1. Minimum distance between ground and bottom edge of hinge plate: 50 mm. However, ensure that the drive can be properly mounted onto the gate wing.
2. Tighten nut at screw, ensuring that the drive can still be easily moved.
8
Downloaded from www.Manualslib.com
manuals search engine
Gate Wing Fittings
Installation
Installation of Control Unit
The power cable supplied with the control unit may only be used for the installation of the drive systems. After completion of the installation, disconnect the cable and replace it with a duct-laid cable. It is forbidden to use the supplied power cable for standard operation of the gate.
Establish power connection according to EN 12453 (all-pole disconnecting switch).
1. Close gate.
2. Mount hinge plate at the push rod of the drive.
Insert screws but do not tighten.
3. Clamp the hinge plate to the gate wing and complete a programming run to ensure that the limit switch settings are correct.
4. At three different positions, inspect drive and ensure that it is in a horizontal position:
A. Gate “CLOSE”
B. Gate “OPEN”
C. Gate at 45° angle
5. Check position of hinge plate; if ok, secure hinge plate to wing.
6. Tighten nut at screw, ensuring that the drive can still be easily moved.
Timber post fittings
Available as optional accessories.
Downloaded from www.Manualslib.com
manuals search engine
9
• Prior to carrying out any work at the control unit, disconnect it from the power supply.
• If there is humidity inside the housing, dry it with a blower.
• The control unit may only be connected to the power supply by a qualified electrician.
• Install control unit in upright position (cable ducts at base) and without applying any strain. The cover must fully close to prevent water from penetrating the housing.
• The cable ducts are designed for 1.5 mm² to 2.5 mm² cables.
Do not use any other cables.
• Attach the housing at the intended fixing points; do not drill through the rear wall of the housing, as it might otherwise not be waterproof.
Commissioning
General Instructions
All programming runs must be supervised, as the drives operate at full force and at half the normal speed. Ensure that no persons or objects are located within the operating range of the gate.
• During the programming run, the “WL” LED or the connected warning lamp are flashing, irrespective of position of DIL switch 4.
• During the commissioning runs, the force necessary to properly open and close the gate, the runtime and the delay upon closing are evaluated and stored by the control system.
• If a programming run is interrupted before it is completed (“WL” LED is on during opening or closing), all previously saved values are deleted.
Preparation for Standard Operation
Caution!
Risk of short circuit! Prior to adjusting the DILswitch settings, disconnect control unit from power supply.
1. Select 1 or 2 wing option, connect desired components and complete settings (see additional functions and connections).
2. Connect control unit to power supply (230V) (“Power” LED is on).
3. Tighten all screws at the fittings so that the drives can easily be moved.
4. Replace cover and snap on.
5. Engage emergency release and secure with lock.
6. Close gate.
Activating Standard Operation
“WL” LED flashes, until the values for force, runtime and closing delay have been registered and stored.
2 wing gate!
Wing 1 (M1 wing with stop) is closed first, followed by wing 2 (M2 pedestrian wing). This prevents that gates with different runtimes are closed in the wrong sequence.
• Check end switch settings. Open and close the door. If the drive switches off when an end position is reached, complete a teaching-in process.
Complete at least 2 programming runs:
Set DIL switch 8 to ON and leave it in this position.
Adjusting Force Tolerance
After the drive system has been installed, the person responsible for the installation must complete an EU Declaration of Conformity according to Machine Directive 98/37/EU and attach a CE mark at the type plate of the drive.
This also applies in cases where the owner of the system is a private person, as well as to manually operated gates that have been upgraded with a drive. The above documents and the instructions for installation and operation must be handed over to the operator.
The force settings are relevant for the system’s safety and must therefore be adjusted with due care and attention. If the force tolerance is outside the permitted range, there is a serious risk of injury and damage.
Select the lowest possible force tolerance in order to ensure that obstacles are immediately and reliably detected.
• Maximum force = programmed force + force tolerance
(adjustable at potentiometer)
• If the set force is not sufficient to fully open or close the gate, increase the force tolerance by turning the potentiometer clockwise.
• Adjust value while the gate is in operation; the new values are subsequently stored upon the next opening operation of the gate.
• After the adjustment of the force tolerance is completed, check the end positions and readjust, if necessary.
Inspection of force tolerance settings
For detailed instructions, see chapter Maintenance / Regular Inspections.
1. Potentiometer set to left stop (0): smallest tolerance value; potentiometer set to right stop (9): largest tolerance value
2. When both end positions are adjusted correctly, insert the plug.
It prevents dirt penetrating the openings.
1. Press key (Imp). Gate moves to end position gate “OPEN”.
- “Power” LED is on, “WL” LED flashes.
2. Press key (Imp). Gate moves to end position gate “CLOSE”.
- “Power” LED is on, “WL” LED flashes.
When the “WL” LED stops flashing, all values have been registered and stored.
Upon the next command, the gates are started and stopped in soft run. The control system thereby checks the force, runtime and closing delay during every opening and closing procedure and gradually adjusts the settings each time the end position is reached.
If a programming run could not be properly completed (drives not in soft run mode, LED "WL" flashes), the control system is reset (all stored values are deleted, see control reset). Start a new programming run.
Programming Remote Control
Prior to teaching in the hand transmitter, clear the radio receiver memory.
Gate system with 1 wing:
- Key 1 to radio channel 1
Gate system with 2 wing:
- Key 1 to radio channel 1
- Key 2 to radio channel 2
Check
Press key 2. The pedestrian gate wing opens.
Press key 1. Both wings open.
10
Downloaded from www.Manualslib.com
manuals search engine
Radio Receiver
Safety instructions
• The operator of this radio-controlled equipment is not in any way protected against interference from other telecommunications systems and facilities (e.g. other radio-controlled equipment that is licensed to operate at the same frequency range).
• In the event of poor reception, replace the battery of the remote control.
Display and keys
1
Programming key
2 internal aerial
3
4
5
LEDs: indicate the selected channel.
K1 = radio channel 1 -> same function as Imp key
K2 = radio channel 2 -> same function as pedestrian gate key
! K3 = radio channel 3 -> no function assigned
! K4 = radio channel 4 -> no function assigned
Connection for external aerial (6)
If the internal aerial does not have the necessary reach, connect an external aerial to the device. For details, see accessories.
Remote control transmission key
6 External aerial
Programming of Remote Control Device
Prior to teaching in the hand transmitter, clear the radio receiver memory.
• Press programming key (1) once for channel 1; LED (K1) is on twice for channel 2; LED (K2) is on
- If no code is transmitted within the next 10 seconds, the radio receiver is reset to standard mode.
- Aborting programming: repeatedly press programming key (1) until all LEDs are off.
• Press desired remote control key (5) until the LED at the receiver is off; the programming procedure.
Programme all other remote control devices by repeating the above steps.
The max. number of memory blocks is 112.
Disabling Remote Control Key at
Receiver
If, for instance, a user of a parking facility is moving house and wishes to keep his remote control device, all radio codes of this device must be disabled at the receiver.
For reasons of safety, we recommend to disable every single key and possible key combination!
• Press programming key (1) and hold for 5 seconds until one of the
LEDs is flashing.
• Release programming key (1) - the radio receiver is no in delete mode.
• Press key to be disabled at the remote control. The LED is switched off when the deletion is successfully completed.
11
Downloaded from www.Manualslib.com
manuals search engine
Operation of Gate
Safety instructions
• Never operate the drive if you suspect that is might be faulty or damaged.
• Before opening or closing the gate, ensure that no persons, especially children, animals or objects are within the opening range of the gate.
• Never use remote control device at locations where it might interfere with other important radio systems (e.g. airports, hospitals).
• Only operate the gate with the remote control when you have full view of the gate.
• Keep the remote control device out of reach of children or animals and prevent any inadvertent use.
• Use remote control device only, if the force tolerance is set to a permitted value. Select the lowest possible force tolerance to reduce the risk of injury.
Opening and Closing Gate
• DIL switch 8 set to ON and programming run completed.
• Remote control programmed (key 1 to channel K1, key 2 to channel K2).
Standard Operation
Damage to the gate, humidity, subsidence, extreme temperature, etc. may affect the force that is required to open and close the gate.
If the force required to open or close the gate is increased within the tolerance range set at the potentiometer, the force settings are automatically adjusted accordingly. In the same way, the drive adjusts the settings, if less force is required.
Operation in summer/winter
Due to the temperature variations between summer and winter, the forces required to operate the gate might vary considerably. If the gate cannot be opened or closed, reset the control system and complete a programming run.
The temperature difference might also affect the end position of the wings.
If necessary, adjust positions at the limit switch.
Intermediate stop
2 wing gate system
If the wing is opened by means of the pulse command and stopped with the stop command, before wing 1 is opened, the pedestrian gate wing can only be closed with the pedestrian gate command.
Obstacle detection:
The obstacle detection function is only working properly after the programming runs are completed and the force tolerance is set.
If the moving gate wing touches an obstacle, it is identified as such.
Depending on the actual movement and DIL switch settings, the gate wing responds in different ways. The first subsequent gate movement is always away from the obstacle.
Procedure for single-wing gates
1. Press key (Imp) or key 1 at remote control.
2. Gate opens until end position “OPEN” is reached.
- LEDs “OPEN”+ “WL” are on.
- When end position “OPEN” is reached, the LEDs “OPEN” + “WL” are switched off.
Procedure for double-wing gates - operation of both wings
1. Press key (Imp) or key 1 at remote control.
- Wing 2 (M2/pedestrian wing) opens first. After 3 seconds, wing 1 (M1) opens - LEDs “OPEN” + “WL” are on.
- When end position “OPEN” is reached, the LEDs “OPEN” + “WL” are switched off.
2. Press key (Imp) or key 1 at remote control.
- Wing 1 (M1) closes first. After 5 seconds, wing 2 (M2/pedestrian wing) closes - LEDs “CLOSE” + “WL” are on.
- When end position “CLOSE” is reached, the LEDs “CLOSE” + “WL” are switched off.
Procedure for double-wing gates - operation of pedestrian gate only
1. Press key (Geh) or key 2 at remote control.
- Wing opens until end position “OPEN” is reached - LEDs “OPEN” +
“WL” are on.
- When end position “OPEN” is reached, the LEDs “OPEN” + “WL” are switched off.
2. Press key (Geh) or key 2 at remote control.
- Gate closes until end position “CLOSE” is reached - LEDs “CLOSE” +
“WL” are on.
- When end position “CLOSE” is reached, the LEDs “CLOSE” + “WL” are switched off.
Resetting Control
When the control system is reset, all programmed values (e.g. force settings: drive force required to open/close the gate, delay settings) are deleted. Under certain circumstances, it might be necessary to delete all stored values and reprogramme the system.
Downloaded from www.Manualslib.com
manuals search engine
12
1. Press keys (Imp. + Geh) and hold until LED “WL” begins to flash.
2. LED “WL” is off - all data is deleted. Release keys.
3. LED “WL” flashes.
4. Complete programming run, see chapter “Activating Standard Operation”.
Operation of Gate
Emergency Release in the Event of a
Power Failure
This procedure should only be applied if the control system is not powered and is secured against inadvertent activation.
In the event of a power failure, the gate can be manually opened or closed, irrespective of its initial position.
1. Turn key (6) 90° to the right - emergency release lever is released.
2. Pull emergency release lever (11) from the housing (12); the motor (7) is removed from the threaded spindle (13).
The springs (36) push the motor (7) from the threaded spindle (13).
To make opening easier: move gate wing manually.
Engaging of drive system
Complete above steps in reverse order.
The emergency release lever (11) must be firmly pressed against the housing (12).
If the drive is not properly engaged, the motor might be damaged (7).
Removing the Cover
The cover may only be removed, if the control system is not powered and is secured against inadvertent activation.
Downloaded from www.Manualslib.com
manuals search engine
13
Additional Functions and Connections
Jumpers
Selection of gate system (single-wing or double-wing)
After changing the jumper settings, reset the control system and complete a new programming run.
LEDs
The LEDs indicate the control system status.
Label double-wing / single-wing
Function
Jumper at upper pins = double-wing
Jumper at lower pins = single-wing
Jumper not set = single-wing
Potentiometer for force tolerance settings
Adjustment of force tolerance to programmed value. The potentiometer data is read every time the system is started.
If the potentiometer is set to the left stop (0), the force tolerance is minimal, if set to the right stop (9), the force tolerance is set to the highest value.
Control panel keys
Label Colour Status
Power green OFF = no power
ON = power in low-voltage range (24V) of teh control
If the mains fuse is blown, this LED is off; terminals 1, 2 19 or 21 might however be powered with mains voltge (230 V AC).
OPEN yellow
CLOSE
SH
WL
Imp.
Geh yellow red yellow yellow yellow
OFF = idle
ON = gate is opening
OFF = idle
ON = gate is closing
OFF = idle
ON = signal at safety input
(light barrier triggered)
OFF = idle, with programmed force values flashing = test mode, where DIL switch 8 is set to OFF.
- During programming run, where
DIL switch 8 is set to ON.
- The gate is opened and closed, whereby the programmed force values are applied and DIL switch 4 is set to
ON.
ON = gate is opening or closing with the programmed force values, and DIL switch
4 is set to OFF.
OFF = idle
ON = pulse key or radio channel 1 activated.
OFF = idle
ON = pedestrian gate key or radio channel 2 activated.
Label
Imp.
Geh.
Function
Pulse key: opens both gate wings
If the Imp key is pressed while a pedestrian gate wing is in motion, the wing is stopped. If the pedes trian wing is fully opened, wing 1 can be opened by pressing the Imp key.
Sequence: open - stop - close - stop - open ...
Pedestrian gate key: Open only the pedestrian gate
In a double-wing gate, this key opens only gate wing 2. In gates where the stop bar is on the outside, wing 2 always opens before wing 1.
Sequence: open - stop - close - stop - open ...
Key (Geh) is only enabled, if wing 1 is fully closed.
Reset of control:
To reset the control, press both keys together for minimum 5 seconds until LED (WL) is switched off.
14
Downloaded from www.Manualslib.com
manuals search engine
Additional Functions and Connections
DIL switch
Factory settings: OFF
Prior to adjusting the DIL switch settings, disconnect the control unit from the power supply.
Switch Position OFF
1
2
3
4
5
6 *
7 *
8
Position ON
No response to signal at the safety input upon opening of gate.
Gate movement reversed, when safety input is triggered while the gate is closing.
Switch 2 OFF: reversion
Gate is stopped, when the safety input is triggered while the gate is opening.
Gate is stopped, when the safety input is triggered while the gate is closing.
Switch 2 OFF: gate is fully opened
Warning lamp is on
Early warning OFF
Manual mode
No function assigned
Warning lamp flashes
Early warning period approx. 3 seconds. Lamp is on or flashes, before the gate is started, depending on position of switch
4.
Automatic close mode:
Gate is automatically closed after 60 seconds.
Switch 6 ON, gate closes automatically 5 seconds afterthe light barrier has been triggered
Standard mode: Test mode:
Drive can be operated while no force values are programmed.
Use test mode to adjust end position settings.
- After switching from OFF to
ON; the force values, run times, and delays for closing/opening are programmed in the course of programming runs..
- The gate opens or closes.
Automatic close mode, option 1
Automatic closing is activated as soon as the end position gate OPEN is reached; at this moment, the GATE CLOSE time set at the potentiometer is started.
If a command is issued during the GATE CLOSE period, this period is restarted.
Settings:
- set potentiometer to the desired time (5 to 255 seconds)
- DIL switch 7 OFF
- DIL switch 8 ON
- Other DIL switches set as required
Automatic close mode + light barrier, option 2
Hint
This option allows for the manual interruption of the automatic closing motion.
Similar to the option described above; the gate is however automatically closed 5 seconds after the light barrier has been triggered.
Settings:
- set potentiometer to the desired time (5 to 255 seconds)
- DIL switch 7 ON
- DIL switch 8 ON
- Other DIL switches set as required
Slot for radio receiver
The radio receiver is inserted here (factory-installed).
* See TorMinal manual
Operate gate only with full view of the gate’s operating range.
After programming, leave DIL switch
8 in position ON.
Automatic close mode
For operation with automatic close mode, comply with EN 12453
(e.g. installation of light barrier 1).
The gate closes automatically after the time for GATE OPEN set at the potentiometer has lapsed. The gate can only be opened by means of a command issued via a push-button or manual remote control. When the gate is opening, no command issued can stop it from doing so.
When it is closing automatically and a further command is given, the gate opens fully. If a command is issued during the GATE OPEN period, this period is restarted.
The GATE OPEN time can be adjusted at DIL switch 6:
- Time (adjustable in TorMinal): 5 to 255 seconds
Behaviour of the drive system when a signal is received at the safety input
While gate is closing: drive behaves according to the settings of DIL switch 2.
While gate is opening: drive behaves according to the settings of DIL switch 1.
15
Downloaded from www.Manualslib.com
manuals search engine
Fuses
Additional Functions and Connections
Connect keys
Label
Mains
24 V
Warning light
Capacity
1.6 A, slow
1 A, slow
1 A, slow
Description
Power supply line 230V AC
Power output 24V DC
Terminals 9 + 10
Warning light output 24V DC
Terminals 11 + 12
Terminal
13 + 14
15 + 16
Label
Impuls
Gehtur
Function
Connection for pulse key used to operate one or both gate wings.
Connection for pulse key used to operate one gate wing.
Use contact only for potential-free normally closed contacts.
External voltage may damage the control system.
Admissible cable diameters for all terminals: 1 mm² - 2.5 mm²
potential-free relay contact
A 2-contact key is only required for double-wing gates, and if the pedestrian gate function is to be used.
In single-wing gates, the pulse and the pedestrian gate key are assigned identical functions.
Connection Key 1 Contact: single-wing gate system Key to terminals 13 + 14 or 15 + 16 double-wing gate system Key to terminals 13 + 14
Connection Key 2 Contact
Pedestrian gate terminals 15 + 16
Both wings terminals 13 + 14 Terminal
25 + 26
Description Function
Special funct.
Connection for electric lock, etc.
max. 8A, 24V DC at ohmic load
Connecting Safety Devices
Connecting warning lamp
Available as optional accessories.
For operation with automatic close mode, comply with EN 12453
(e.g. installation of light barrier).
Factory settings: Bridge between terminals 17 + 18.
Terminal
17 + 18
Label
Sicherh.
Function
Connection for safety devices, e.g.
- Light barrier
- Contact strip
If the connected safety device is not triggered, the contact must be closed.
If the contact is not used, mount a bridge between the terminals (factory settings).
Use contact only for potential-free normally closed contacts.
External voltage may damage the control system.
For function settings, see DIL switches 4 + 5
Terminal Label Function
11 + 12 24V Warning lamp Connection for 24 V warning lamp , fused with 1A at max. 20W.
Rectified, not stabilised transformer voltage, fluctuating between 22V and 27V at full load.
Downloaded from www.Manualslib.com
manuals search engine
16
Additional Functions and Connections
Connecting external device Connecting to Power Supply (230V)
Terminal
9
10
Label
0 V
24 V
Function
24V output, fused with 1A max. 20W
Rectified, not stabilised transformer voltage, fluctuating between 22V and 27V at full load.
Connecting Drives
Terminal
1
2
3 + 4
Label
L
N
PE
Function
Power conductor 230V AC
Neutral conductor
Earth conductor
The connection to the power supply must be carried out by a qualified electrician.
Connection of transformer
Terminal
5 + 6
7 + 8
Label
M1
M2
Function single-wing gate: no function assigned double-wing gate: connection for motor-1
The motor must be mounted on the wing that opens as the second wing, or that is equipped with a stop bar at the outside.
Terminal 5: Motor cable, brown
Terminal 6: Motor cable, blue single-wing gate: connection for motor double-wing gate: connection for motor-2
The motor must be mounted on the wing that opens as the first wing, or that is not equipped with a stop bar at the outside.
Terminal 7 Motor cable, brown
Terminal 8: Motor cable, blue
Terminal
19 + 21
23 + 24
Label
230V AC
24V AC
Function
Power supply (primary winding), brown
24V output (secondary winding), power supply line to control unit, mauve
Motor circuit board
Terminal
1
2
3
4
5
6
7
8
Function / cable colour
24V supply line from control unit, blue
Limit switch gate “CLOSE”, blue
Limit switch gate “CLOSE”, blue
Motor, blue
24V supply line from control unit, brown
Limit switch gate “OPEN”, yellow
Limit switch gate “OPEN”, yellow
Motor, black
Downloaded from www.Manualslib.com
manuals search engine
17
Accessories
Safety instructions
Caution!
Prior to any work at the gate or drive, disconnect control unit from the power supply and secure it against inadvertent reconnection or actuation.
1. Warning lamp
3. Light barrier
2. Key switch
Position the key switch box in such a way that the operator can see the gate, while he/she is not inside the operating area of the gate.
• Never lead the key switch cable along the power line, as this could lead to interference in the control system.
• Use a separate conduit for the key switch line.
4. Connecting cables
• Secure distribution box with screws at the provided eyelets.
Installation
Only connect cables that have the same colour, i.e.:
- blue to blue
- brown to brown
Secure screws tightly to prevent moisture from penetrating the distribution box. After installation, connect distribution box to power supply.
Wiring diagram:
• Install key switch box at a suitable location where it can be easily accessed.
Downloaded from www.Manualslib.com
manuals search engine
18
Accessories
5. External aerial
• If the built-in aerial is not sufficient for the proper operation of the gate, you have the option to connect an external aerial to the system.
• Ensure that the aerial cable is laid in such a way that there is no physical impact to the radio transmitter. Install tension protection, if necessary.
• Consult the operator/owner of the system in order to find a suitable location for the external aerial.
Electric lock 24V
Installation:
• Reset the control system.
• After completion of the installation adjust end position gate “CLOSE”.
• Mount the lock horizontally, as it might otherwise be jammed when the gate is operated.
• Distance between lock and closing plate: min. 4 mm, max. 6 mm.
Connecting 24V electric lock
This diagram is only applicable to 24V electric locks. If you wish to install a 12V electric lock, you must first contact the manufacturer.
• Connect external aerial to the respective adapter.
6. Main switch
Downloaded from www.Manualslib.com
manuals search engine
19
Maintenance
Safety instructions
Never clean drive system or control unit with a water hose or power washer.
• Never clean the drive with alkaline or acidic solutions.
• Carefully remove dirt from drive system and clean push rod from time to time with a dry cloth.
• If necessary, clean and/or dry.
• Regularly inspect all screws at the fittings and retighten, if necessary.
• Inspect the cover of control unit and readjust, if necessary, to ensure that it is watertight.
Regular Inspections
• Regularly, at least annually, inspect all safety devices and test their function (see for example ZH 1/494 April 2002, valid only in Germany).
• Safety devices that are sensitive to pressure (e.g. safety switch unit) should be checked every 4 weeks to ensure proper functioning, see EN
60335-2-95.
Service and Warranty
The warranty granted complies with statutory requirements. In the event of a repair that is covered by warranty, please contact your dealer/specialist stockist. Warranty entitlements only apply to the country in which the product has been purchased.
Batteries, fuses and light bulbs are not covered by warranty.
Replaced parts remain the property of the service agent.
If you require after-sales service, spare parts or accessories, please contact your dealer/specialist stockist.
We have made every effort to ensure that these instructions are as clear and concise as possible. However, if you have any queries or wish to comment on this document, please contact us with your suggestions:
Fax: 0049 / 7021 / 8001-53
E-mail: [email protected]
Disassembly
Observe safety instructions!
To dismantle the unit, complete the respective steps described in chapter
“Installation” in reverse order. There is of course no need to adjust settings.
Test Behaviour
Force cut-off
While the wing isclosing, try to stop it by hand. Do not try to hold the wing.
Does gate stop and move in opposite direction after it has been halted?
yes/no yes
Possible cause Remedy
• Force cut-off works properly • Do not change settings.
no • Potentiometer at right stop.
Force tolerance set too high.
• Control system defective
• Set force tolerance to lower value by turning the potentiometer in anticlockwise direction until the test is successful. Prior to test, open and close the gate twice watching its operation.
• Shut down the gate and secure against switching on.
Contact customer service!
Emergency release system
Proceed as described in section “Emergency
Release”.
It must be possible to open/close the gate by hand without special effort.
Can the motor be removed from the shaft?
yes no
• Everything OK!
• Gate fittings rusty • Lubricate gate fittings
Safety contact unit (optional)
Open/close gate and interrupt motion by triggering the safety contact strip.
Gate behaviour according to settings of DIL switches
1, 2 and 3.
yes • Everything OK!
no • Cable defective, terminal screw loose •
• DIL switch settings changed
• Contact strip defective
• Inspect wiring, retighten terminal screws
• Check DIL switch settings and adjust
• Shut down gate system and secure against inadvertent switching on. Contact customer service!
Light barrier (optional)
Open/close gate and interrupt motion by triggering the light barrier.
Gate behaviour according to settings of DIL switches
1, 2 and 3. Is the LED “SH” on?
yes • Everything OK!
no • Cable defective, terminal screw loose •
• DIL switch settings changed
• Light barrier dirty
• Light barrier defective
• Inspect wiring, retighten terminal screws
• Check DIL switch settings and adjust
• Clean light barrier
• Shut down gate system and secure against inadvertent switching on. Contact customer service!
20
Downloaded from www.Manualslib.com
manuals search engine
Troubleshooting
Tips for Troubleshooting
Should you be unable to identify and eliminate a fault using this table, please take the following steps:
• Carry out a reset of the control system (deletion of set force values).
• Disconnect any accessories (e.g. light barrier) connected to your system.
• Reset all DIL switches to the default settings.
• Reset potentiometer to the default settings.
• If settings have been changed with TorMinal, reset the control system with the TorMinal software.
Fault Check
Gate cannot be opened or closed with the switch or the
Is “Power” LED on?
remote control.
yes/no no
Possible cause
• No mains power
• Mains fuse blown
Remedy
• Check power line and reconnect, if necessary.
• Check fuse and replace, if necessary.
yes • Gate jammed
• Motor makes a sound but does not move
• Drive disengaged
• Cable insulation too long, preventing contact
• Gate frozen to ground/posts
• Gate obstructed by snow
• Cable disconnected from motor board
• A gate wing has been pushed down or has warped due to high temperature differences.
• Shut down unit. Possible motor and/or control system failure. Contact customer service.
• Engage drive.
• Disconnect cable, remove insulation and reconnect again.
• Remove ice and snow from gate and hinges.
• Remove snow.
• Reconnect cable to motor board
Is LED at the remote control device on?
no • Battery empty
• Battery incorrectly inserted
• Remote control defective
• Replace battery
• Insert battery correctly
• Replace remote control device
Is at least one LED at the receiver on when a remote control key is pressed?
Are LEDs “Power” +
“OPEN/CLOSE” on?
yes • Remote control battery nearly empty; resulting in limited
• Replace battery radio range
• Radio receiver defective
• Remote control not programmed
• Replace radio receiver
• Programme remote control device
• Poor reception
• Wrong frequency
• Install external aerial, see section “Accessories”
• Check frequency; remote control and radio receiver must be set to the same frequency.
no • Radio receiver not properly mounted
• Radio receiver not powered, or defective
• Remote control not programmed
• Battery of remote control empty
• Battery incorrectly inserted
• Remote control defective
• Check and readjust radio receiver
• Replace radio receiver
• Programme remote control device
• Replace battery
• Insert battery correctly
• Replace remote control device yes • Permanent signal • Pulser defective; disconnect all pulsers
Are LEDs “Power” + “SH” on?
yes • Light barrier triggered • Remove object triggering the barrier
Disruption occurs only from time to time or temporarily yes • Powerful radio transmitters
(pager systems) of hospitals or industrial plants might interfere with your gate system.
• Change radio frequency.
• Contact telecommunication authority.
21
Downloaded from www.Manualslib.com
manuals search engine
Troubleshooting
Fault
Gate cannot be opened/closed with a key switch.
Check
LEDs “Power” + “Imp./Geh” on?
yes/no no
Possible cause
• Cable connections loose
• Key switch defective
• Cable defective
• Retighten terminals
• Replace key switch
• Replace cable
Remedy yes • Pulser (key switch, remote control) defective
• Check pulser and replace, if defective.
Gate is stopped or continues in reverse motion.
Obstacle in operating range?
no • Hinges too stiff
• Post has moved
• Lubricate hinges
• Contact specialist
• Limit switch settings incorrect • Readjust limit switch yes • Force cut-off triggered yes • Wing not stable
• Remove obstacle
• Reinforce wing Is gate wing hopping at start?
Is there strong wind?
yes • Wind pressure too high • Simply open and close gate again
Gate does not fully open or close.
Does gate stop before it has reach its end position?
no yes
• Wing hinge incorrectly mounted
• Change fittings at wing
• Limit switch settings incorrect • Readjust limit switch
Incorrect closing sequence
Drive cannot be properly programmed
Gate is not stopped by an obstacle
• Drive wires incorrectly connected at terminals
• DIL switch 8 is in position
OFF
• End switch set incorrectly.
• Read the instructions and reconnect drives to the the control system
• Set switch to position ON
• Adjust end switch settings.
• Gate is completing a programming run
• Force tolerance set too high
• After the programming is completed, the force cut-off is operational
• Readjust force tolerance
Drive touches the post Have dimensions A/B been remeasured?
no • Incorrect dimension A or B • Readjust connection of drive at the post
Irregular gate movement
Pedestrian wing cannot be opened with remote control device
Drive cannot be started Is LED “SH” flashing rapidly?
yes • Limit switch settings incorrect • Readjust limit switch
• Incorrect dimensions A/B • Adjust dimensions, if possible
• Remote control key not programmed
• Programme key, see section “Programming Remote
Control Devices” yes • Position of jumper with programmed force values has been changed
• 1. Reset jumper to previous position
2. Reset control system
3. Position jumper as desired
4. Complete programming runs
Downloaded from www.Manualslib.com
manuals search engine
22
Spare Parts List / Glossary
1.5
1.4
1.6
1.7
1.8
1.10
close open
1.14
1.4
1.3
1.2/3.3
1.1
1.22 1.21 1.20
close open
1.19
1.18
1.17
1.16
1.15
1.14
1.11
1.12
1.13
1.28
1.29
1.30
1.31
1.32
1.33
2.5
2.1
5
1.34
1.24
1.23
1
2
3
4
5
6
7
8
1.14
1.20
2.3
2.2
1.24/3.1
2.8
2.7
2.6
2.9
2.4
2.6
1.23/3.2
4 1.27
1.26
Downloaded from www.Manualslib.com
manuals search engine
1.25
23
1.40
1.39
1.38
1.37
1.36
1.35
1.25
1.26
1.27
1.28
1.29
1.30
1.31
1.32
1.17
1.18
1.19
1.20
1.21
1.22
1.23/3.2
1.24/3.1
1.33
1.34
1.35
1.36
1.37
1.38
1.39
1.40
2.1
-
-
4
2.6
2.7
2.8
2.9
-
-
2.4
2.5
2.2
-
-
2.3
5
Item no.
1.1
1.2/3.3
1.3
1.4
1.5
1.6
1.7
1.8
1.9
1.10
1.11
1.12
1.13
1.14
1.15
1.16
Name
Use
Plug
Cover
Holder
Limit switch spindle
Lock
Motor
Cover
-
Connecting cable
Emergency release lever
Housing
Threaded spindle
Screw
Limit switch / “open”
Switching nut
Protective tube
Limit switch / “close”
Push rod, complete
Seal
Sliding ring
Scraper
Hexagon nut
Screw
Motor circuit board
Inlay
Flange sleeve
Inlay with sleeve
Fuse
Washer
Inlay
O-ring
Seal
Spring
Circlip
Stop disk
Flange sleeve
Friction bearing
Stop disk
Stop disk
Housing
Cable threaded coupling M20
Threaded coupling M20
Counter nut M20
Cable threaded coupling M16
Threaded coupling M16
Counter nut M16
Control (TorMinal connection)
Holding plate for transformer
Screw 3.5 x 9.5
Annular transformer core
Screw 5.5 x 50
868 MHz radio receiver module
434 MHz radio receiver module
40 MHz radio receiver module
Fittings / post
Fittings / gate wing
Remote control transmitter
Operating range
Main closing edge
Other closing edges
Force tolerance
Soft run
Intermediate stop
12206
12265
12223
12202
12222
12244
12243
12242
12270
12200
12239
3207
12218
12217
12216
12221
32046
12227
12220V001
12226
12205
12231
12225
12204
12224
-
30016
30018
-
30015
30017
12269V000
12232
20064
12219V000
12240
7000V000
7080V000
12247V000
32063
32065
Product no.
12211
12230
12215
12213
12212
12228
359V000
12207
-
12220V001
12203
12201
12208
12229
12214
-
4020
Spare Parts List / Glossary
4
2
1
2
2
1
1
1
1
1
2
2
1
2
1
1
1
1
1
1
1
1
1
1
2
1
1
1
1
1
8
1
1
1
1
1
1
3
1
1
Quantity
1
1
-
2
1
1
2
1
2
5
1
-
1
1
1
1
Details
Plastic insert. Only supplied in conjunction with push rod (1.19) and switch nut (1.16)
Plug to protect for end switch spindle (1.5)
Protects limit switch spindles (1.5) and threaded spindle (1.13)
Holder for limit switches (1.15 + 1.18)
These spindles are used for the adjustment of the limit switches (1.15 + 1.18)
Locking device for cover (8) and emergency release lever (1.11)
Covers and protects motor and motor board
Length 1 m
Used to pull the motor from the threaded spindle, thus releasing the gate
Secures cover (3) and protective tube (1.17)
Limit switch for gate position “OPEN”; determines the max. opening angle.
Actuates the limit switches (1.15 + 1.18).
Only supplied in conjunction with push rod (1.19) and insert (1.1)
Protects the drive mechanism and holds the switching nut.
Limit switch for gate position “CLOSE”, determines closing angle of gate.
Factory-mounted, with insert (1.1) and switching nut (1.16)
1
Front bearing of push rod (1.19)
Cleans push rod (1.19), removes deposits
For insertion in inlay (1.27)
Seal of cover (8) from serial no. SRL-3003574
Friction bearing with flange
Friction bearing for forces in direction gate “CLOSE” no picture no picture
Secure drive mechanism to post.
The fittings can be welded or fixed with screws.
Secure drive mechanism to gate wing.
The fittings can be welded or fixed with screws.
Transmits pulse to open or close the gate
Area travelled by the gate during operation (opening/closing)
Bottom edge of the gate and edge at the hinged side
Upon certain signals, the gate is stopped (during both closing and opening).
Upon the next signal, the gate moves in reverse direction.
24
Downloaded from www.Manualslib.com
manuals search engine
Wiring Diagram
Downloaded from www.Manualslib.com
manuals search engine
25
Gate operators
Garage door operators marathon / sprint ...
... garage door operator duo …
Operators for roller shutters and awnings
... tube motors
(electronic and mechanical) ...
... control system …
... sliding gate operator starglider 300 ...
Radio technology
... wall-mounting bracket, removable …
Accessories
... light barriers …
... Funkcody ...
... Hand transmitter holder ...
... radio plug key ...
... electric lock ...
... warning lamp, 24 V …
... aerial
... and much more.
26
Downloaded from www.Manualslib.com
manuals search engine
advertisement
Key Features
- Compact design
- Easy-to-use remote control
- Programmable remote control devices
- Automatic close mode
- Floating relay contact
- Safety devices can be connected
- Easy to install and operate
- Complies with all relevant EU directives
Related manuals
Frequently Answers and Questions
What is the maximum permissible gate wing dimension?
How do I adjust the limit switches?
How do I program the remote control devices?
advertisement