SPX Cooling Technologies SGS FL Series User Manual
Add to My manuals20 Pages
SPX Cooling Technologies SGS FL Series is a centrifugal cooler designed for commercial and industrial applications. It is a versatile unit that can be used for a variety of cooling needs, including:
- Comfort cooling
- Process cooling
- Data center cooling
- Make-up air cooling
The SGS FL Series is available in a wide range of capacities to meet the specific needs of any application. It is also available with a variety of options and accessories, including:
- Variable speed drives
- Condenser water economizers
- Free cooling coils
- Heat recovery coils
The SGS FL Series is designed for easy installation and maintenance. It is also backed by SPX Cooling Technologies' industry-leading warranty.
advertisement
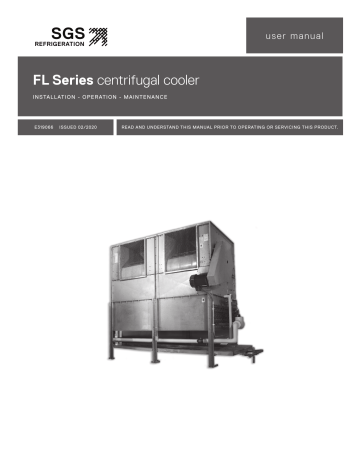
SGS
REFRIGERATION
FL Series centrifugal cooler
INSTALL ATION - OPERATION - MAINTENANCE
user manual
E319066 ISSUED 02/2020 READ AND UNDERSTAND THIS MANUAL PRIOR TO OPERATING OR SERVICING THIS PRODUCT.
contents
1 Receipt of Equipment ................................................................................................................................................... 3
1.2 Loss of Gas Holding Charge ................................................................................................................... 3
2 Assembly of Components ......................................................................................................................................... 3
2.1 Shipped Loose Parts ...................................................................................................................................... 3
2.3 Belt Attachment .................................................................................................................................................. 3
2.4 Belt Tensioning .................................................................................................................................................... 3
2.5 Belt Guard ............................................................................................................................................................... 4
2.6 Bearing Grease ................................................................................................................................................... 4
2.7 Air Directional Louvers ................................................................................................................................. 4
3 Rigging Instructions ........................................................................................................................................................ 4
4 Unit Location and Mounting .................................................................................................................................... 4
4.1 Unit Location ......................................................................................................................................................... 4
5 Refrigerant Warning ....................................................................................................................................................... 4
6 Piping Installation ............................................................................................................................................................. 4
6.1 Drain Line ................................................................................................................................................................ 4
6.2 Refrigeration Piping ........................................................................................................................................ 5
6.3 Hot Gas Interpiping ......................................................................................................................................... 5
6.4 Refrigerant Distributor Nozzle ................................................................................................................ 6
6.5 Expansion Valve (optional item) ............................................................................................................ 6
6.6 Evacuation and Leak Test .......................................................................................................................... 6
6.7 DXA and Suction Accumulators ........................................................................................................... 6
7.1 Field Wiring ............................................................................................................................................................. 7
7.2 Electrical Data ...................................................................................................................................................... 7
7.3 Suggested No Defrost Requirement Sequence of Operation ..................................12
7.4 Suggested Air Defrost Sequence of Operation ....................................................................12
7.5 Suggested Electric Defrost Sequence of Operation ........................................................12
7.6 Suggested Hot Gas Defrost Sequence of Operation ......................................................13
7.7 Suggested Water Defrost Sequence Of operation ............................................................13
8.2 Operation Checkout .....................................................................................................................................14
9.1 Drain Pan ..............................................................................................................................................................15
9.2 Coil and Cabinet ..............................................................................................................................................15
9.5 Belt Drive ..............................................................................................................................................................15
9.6 Electric Defrost Heaters ...........................................................................................................................15
9.7 Fan Shaft ...............................................................................................................................................................15
10 Replacement Parts List ............................................................................................................................................16
receiving and installation
1 RECEIPT OF EQUIPMENT
1.1 INSPECTION
All equipment should be carefully checked for damage or shortages as soon as it is received. Each shipment should be carefully checked against the bill of lading. If any damage or shortage is evident, a notation must be made on the delivery receipt before it is signed and a claim should then be filed against the freight carrier. Inspection and claims are the responsibility of the recipient.
A large multi-belt sheave should be mounted to the end of the fan shaft. Rotate fan shaft by hand to be sure the fan shaft has not bent during shipment, and that the fans do not strike the housing.
1.2 LOSS OF GAS HOLDING CHARGE
Each copper, steel, and stainless steel tube FL Series unit is leak tested, evacuated to remove moisture and then shipped with a gas holding charge. Absence of this charge may indicate a leak has developed in transit. The system should not be charged with refrigerant until it is verified that there is no leak, or the source of the leak is located. If the unit contains aluminum tubes or flanged refrigerant connections, the unit is leak tested and evacuated but a gas holding charge is not provided.
WARNING: Make sure the unit is electrically grounded. Newer drain piping and electrical conduit may not be metal, or attached to a support that is grounded.
2.3 BELT ATTACHMENT
The motor mount adjusting screw needs to be fully CLOSED. Wrap one belt around the outer most groove on the fan sheave then wrap the belt around the outer most groove of the motor sheave.
Belts should never be forced over sheaves. Typically a FL Series unit uses sheaves with two or more grooves, requiring that the belt be moved to the inner most groove. Move the belt on the motor sheave over one groove, then move the belt on the fan sheave over one groove. Repeat moving the belt in a similar manner until the first belt is in the inner most groove of both sheaves. Repeat the belt attachment procedure for each belt until every sheave groove contains a belt.
2.4 BELT TENSIONING
Turn the motor mount adjusting screw(s) so that the motor tilts away from the fan shaft, tightening the belts. The amount of belt
“free play” should be the distance between the sheave centers divided by 64, when the motor mount is properly adjusted.
2 ASSEMBLY OF COMPONENTS
2.1 SHIPPED LOOSE PARTS
Motor (with sheave attached), bolts, nuts, and washers (on small units the motor may be factory mounted).
Drive belts (strapped to fan sheave).
Belt guard, bolts and washers (bolts and washers are located in their final assembly holes on fan cabinet).
Fan cabinet with required assembly bolts, nuts and washers.
Optional air directional louvers with required assembly bolts, nuts,and washers.
2.2 MOTOR
If the motor is factory mounted, make sure the fan shaft contains a factory mounted sheave. If the motor is shipped loose, mount the motor onto the adjustable motor mount that is already on the fan cabinet using the provided bolts, nuts, and washers. After attachment to the unit the motor shaft should be facing away from the fan cabinet.
IMPORTANT: Make sure the motor and fan sheaves are aligned and parallel with each other (belt manufacturer recommends alignment within 0.5°). Using a long straight edge, lay the straight edge against the faces of the sheaves. If each sheave contacts the straight edge in two places the sheaves are lined up. See Figure 1.
Sheaves have 4 points aligned and parallel
Free Play
Motor
FIGURE 1
C
Sheave alignment and free play
Fan
3
receiving and installation
2.5 BELT GUARD
The belt guard attachment bolts have been shipped “in place” on the fan cabinet sheetmetal. Remove the bolts and washers before positioning the belt guard. Align the hole in one of the belt guard mounting brackets with the pre-installed nut in the fan cabinet sheetmetal. Partially screw in the bolt and washers to use as a pivot, then align the other brackets to rest of the nuts and screw in the rest of the bolts and washers. Tighten until bolts are snug.
2.6 BEARING GREASE
The fan shaft bearings are greased at the factory before shipment.
2.7 AIR DIRECTIONAL LOUVERS
The FL Series unit may have optional Air Directional Louvers supplied. The louvers for each fan outlet are assembled, but shipped loose from the unit. The installer should attach the louver assembly so that the louver direction matches the unit drawing. Bolts, nuts, and washers are supplied with the assembly.
3 RIGGING
A FL Series unit tends to be a long and heavy object. Jobsite requirements will affect the method of moving the unit into place.
Carefully consider the support that is required to lift and move the unit. Under no circumstances should the shipping skid be used for lifting the unit. To ensure that the unit is not bowed or damaged when being lifted into place from above, all of the support legs should be used as lifting points.
4.2 MOUNTING
The FL Series units should be anchored to the floor pad with ¾” diameter threaded STEEL rods (1/2” for the 1F and 2F models) or other threaded device. The rods should have double nuts for strength. Adequate support must be provided to hold the weight of the unit. Refer to the unit drawing supplied with the unit for the approximate unit weight. The unit drawing will also show leg pad hole locations. All leg pad holes should be used to support the unit.
The unit must be level in all directions to insure proper drainage of the condensate drain pan. Units must have sufficient clearance above for cleaning the top of the unit and repairing or replacing the motor and/or drive belts.
5 REFRIGERANT WARNING
The use of any refrigerant can be dangerous under certain conditions. Where people or product can be exposed to hazardous conditions, daily inspections should be made for the detection of any defect or malfunction that could cause the escape of the refrigerant and cause harm. In the case of halocarbon refrigerants, electronic detection devices are available for sensing the presence of such refrigerants in the atmosphere.
Ammonia is a “self-alarming” gas with its strong odor but detection devices are strongly recommended. People and product are a concern based on the concentration levels (ppm) of ammonia along with OSHA and EPA regulations. An ammonia gas detection device connected to an external alarm system to warn that a leak is occurring is recommended. Refer to local codes and Fire
Department for additional local regulations.
Only experienced, qualified personnel should install, operate, and maintain detection and alarm equipment.
4 UNIT LOCATION AND MOUNTING
4.1 UNIT LOCATION
Unit must be located to provide good air circulation to all areas. If an air distribution duct is not to be attached to the fan outlet(s), the unit should be positioned to blow the air away from walls and directed down an aisle, over product, or into product as the room design is specified. For best performance it is desirable to arrange the air discharge toward the door of the room to minimize the entrance of warm moist air when the door is open. Light fixtures, shelving, ceiling structures, and product boxes must be located so that they do not block the air intake or air discharge from the unit. The FL Series unit can be set against a wall so that the air enters the unit from three sides only.
On all FL Series units space should be provided for the possible future replacement of the fan shaft(s), or the electric defrost heaters if heaters have been furnished. Space equal to the overall length of the shaft(s) plus twelve inches on either side of the unit is recommended. For the electric defrost heaters Table 7 shows a recommended access dimension to remove the heater rods.
6 PIPING INSTALLATION
6.1 DRAIN LINE
The drain line should be as short and as steeply pitched as possible with a minimum of ¼” drop per running foot. The drain line should be of the same, or larger, pipe size as the drain connection. A drain line trap should be installed to prevent warm moist air from migrating through the drain line. If the temperature surrounding the drain line is below freezing (32°F) it must be wrapped with a drain line heater and insulation. Be sure to also wrap the drain pan coupling. The drain line heater must be energized continuously. Be sure to follow the manufacturer’s recommendation when installing the drain line heat tape. The drain line trap should be outside of the freezing space. See Figure 2.
4
installation
Evaporator
Drain pan
Heating cable power line
Union
Insulated
Wall
Slope drain pipe down and away from evaporator
(1/4" per foot of pipe)
Vapor seal the pipe penetration
Drain line wrapped with insulating material
Thermostatically controlled heating cable
Condensate drain line
4" to 6" drain trap with access
FIGURE 2 Drain Line
FIGURE 3 Pipe Joining
A union at the drain connection in the drain pan is recommended for ease of installation and future servicing. Two unions may be required so that a length of drain pipe can be removed and be out of the way if a pan must be removed. Use two wrenches when tightening to prevent the drain fitting from twisting and damaging the drain pan. See Figure 3.
Long runs of drain line, i.e. more than a few feet, should be supported to avoid damage to the drain pan.
6.2 REFRIGERATION PIPING
Installation design must conform to all local and national codes, laws and regulations applying to the site of installation. In addition the safety code for mechanical refrigeration, ASME B31.5, should be followed as a guide to safe installation and operation practice.
Refrigerant line sizes, piping support, and piping techniques should be obtained from published recognized refrigeration standards.
Under no circumstances should the refrigerant connection size of the unit be used as the basis for sizing the lines.
For aluminum flange union connections see Figure 4 for final assembly drawing.
IMPORTANT —The FL Series units have not been designed to carry the weight of any external piping or valves. Improper support of external piping and valves may result in unit breakage and refrigerant spillage.
The horizontal suction line should slope away from the unit. Vertical suction risers on halocarbon systems require a properly sized “P” trap at the foot of the riser for proper oil return.
6.3 HOT GAS INTERPIPING
If the unit was ordered with hot gas defrost the drawing shipped with the unit will contain the piping connection locations for the hot gas inlet and the condensate relief. The interpiping supplied may be shipped loose to avoid damage during transportation, and will need to be installed after delivery. The hand valve needs to be adjusted for site conditions so that the drain pans receive enough hot gas to defrost, but not too much so that the coil is short of hot gas.
5
installation
Coil
Hex head bolt with isolation sleeve
SAE flat washer
Fiber isolation washer
System
Flange fiber gasket
Hex nut
SAE flat washer
Steel socket-weld male flange
Aluminum female flange
FIGURE 4 Aluminum Flange Assembly
6.4 REFRIGERANT DISTRIBUTOR NOZZLE
For a direct expansion system, the FL Series units already have the distributor nozzle installed. As a check, see that the nozzle is in the distributor, or the auxiliary hot gas tee for direct expansion halocarbon with hot has defrost, before installing the thermal expansion valve to the distributor or auxiliary hot gas tee.
6.5 EXPANSION VALVE (optional item)
The expansion valve should be installed directly to the distributor body or as close as possible with no elbows or bends. Steel expansion valves for direct expansion ammonia requires the removal of the discharge tube. Locate the expansion valve bulb on a horizontal length of suction line as close to the suction header as possible. Position the bulb in a 3, 4, 8, or 9 o’clock position. Do not position the bulb on the top or the bottom of the pipe. Clamp the bulb down flush and tightly against the pipe and insulate. Never locate the bulb on a trap or downstream from a trap.
Expansion valves are NOT adjusted at the factory prior to shipment.
It is important that the operation of the expansion valve be checked after the system has balanced out at the desired room temperature.
If the coil is being starved it is necessary to reduce the superheat setting of the valve by turning the adjusting stem counter-clockwise.
If the superheat is too low it is necessary to increase the superheat setting of the valve by turning the adjusting stem clockwise. It is recommended that for a 10°F to 12°F T.D. system, the valve be adjusted to maintain 5°F to 6°F of superheat.
6.6 EVACUATION AND LEAK TEST
When all refrigeration connections have been completed, the entire system must be tested for leaks and then evacuated.
6.7 DXA AND SUCTION ACCUMULATORS
Do not use units with Direct Expansion Ammonia (DXA) feed below
0°F evaporating temperatures unless the compressor system is designed and protected to handle the overfed liquid by use of a suction accumulator.
6
installation
7 ELECTRICAL
If the FL Series unit is equipped with an electrical power disconnect switch make sure the switch is in the “OFF” position, preferably locked in this position.
7.1 FIELD WIRING
Field wiring should comply with NEC and local codes. The power supply voltage, phase and frequency must match what is shown on the unit data plate. Wire motor so that the exposed part of the fan wheel(s) turns toward the air discharge opening of the unit.
Wiring for a unit with Air, Hot Gas, or Water Defrost, without a SGS mounted electrical panel, requires power to the fan motor only.
If the unit is supplied with Electric Defrost, but no control panel, wiring will be required to the mounted terminal blocks for the defrost heaters and also directly to the motor. See Figure 5 for typical unit wiring with 230/3/60 power or Figure 6 for 460/3/60 power. If a SGS mounted control panel is provided, wiring to only one set of terminal blocks is required. See wiring diagram supplied with unit.
A motor in a cold room may draw greater than nameplate amperage due to denser, colder air flowing through the unit. For a motor requiring external overload protection, measure motor amps after pulldown and select correct motor overloads for the measured amperage. Also compensate for the variance in ambients between motor and overload locations. Motor overload protection is recommended for all phase legs. All wiring must be in accordance with the governing electrical code.
7.2 ELECTRICAL DATA
Table 1 — Motor Amps (approximate)
Motor hp 208/3/60 230/3/60
5
7.5
10
15
1
1.5
2
3
20
25
13.4
20.4
28.4
38.8
3.4
4.2
6.0
8.2
48.0
60.0
6.7
10.2
14.2
19.4
1.7
2.1
2.8
4.1
24.0
30.0
460/3/60
5.4
8.2
11.4
15.5
1.2
1.7
2.2
3.4
19.1
24.2
380/3/50
7.0
10.4
13.5
21.0
1.7
2.2
3.0
3.9
28.0
34.0
7
installation
HEADER END
FAN MOTOR
ADJUSTABLE
DEFROST CONTROL
MOUNTED ON UNIT
4Y
1R
2B
1R 4Y 2B L1 L2 L3 L4 L5 L6
MOTOR
CIRCUIT
TO MOTOR
STARTER
DEFROST
CONTROL
UNIT
HEATER
CIRCUIT #1
HEATER
CIRCUIT #2
FIGURE 5 Electric Defrost Wiring 230/3/60
TERMINAL BLOCKS
MOUNTED INSIDE
ELECTRICAL BOX ON UNIT
FACTORY WIRING
FIELD WIRING
8
installation
HEADER END
FAN MOTOR
ADJUSTABLE
DEFROST CONTROL
MOUNTED ON UNIT
4Y
1R
2B
1R 4Y 2B L1 L2 L3
MOTOR
CIRCUIT
TO MOTOR
STARTER
DEFROST
CONTROL
UNIT
HEATER
CIRCUIT #1
FIGURE 6 Electric Defrost Wiring 460/3/60
TERMINAL BLOCKS
MOUNTED INSIDE
ELECTRICAL BOX ON UNIT
FACTORY WIRING
FIELD WIRING
9
installation
Table 2 – Coil (ED) Heater Amps
Unit Model 208/3/60
2H-546
2H-548
2D-566
2D-568
3C-596
3C-598
2A-646
2A-648
3H-696
3H-698
2G-406
2G-408
2H-466
2H-468
2C-486
2C-488
3G-506
3G-508
1D-286
1D-288
1A-326
1A-328
2G-336
2G-338
2C-396
2C-398
1F-096
1F-098
2F-186
2F-188
1G-206
1G-208
1C-246
1C-248
95.3
109.0
81.7
98.1
81.7
102.2
114.4
130.8
102.2
122.6
49.0
65.4
68.1
81.7
65.4
81.7
61.3
81.7
40.9
49.0
57.2
65.4
40.9
54.5
54.5
68.1
10.9
16.3
21.8
32.7
24.5
32.7
32.7
40.9
230/3/60
105.4
120.5
90.4
108.4
90.4
113.0
126.5
144.6
113.0
135.6
54.2
72.3
75.3
90.4
72.3
90.4
67.8
90.4
45.2
54.2
63.3
72.3
45.2
60.2
60.2
75.3
12.0
18.1
24.1
36.1
27.1
36.1
36.1
45.2
*Heater removal is required at the refrigerant connection end of the unit
**Heater removal is required at both ends of the unit
460/3/60
52.7
60.2
45.2
54.2
45.2
56.5
63.3
72.3
56.5
67.8
27.1
36.1
37.7
45.2
36.1
45.2
33.9
45.2
22.6
27.1
31.6
36.1
22.6
30.1
30.1
37.7
6.0
9.0
12.0
18.1
13.6
18.1
18.1
22.6
575/3/60
42.2
48.2
36.1
43.4
36.1
45.2
50.6
57.8
45.2
54.2
21.7
28.9
30.1
36.1
28.9
36.1
27.1
36.1
18.1
21.7
25.3
28.9
18.1
24.1
24.1
30.1
4.8
7.2
9.6
14.5
10.8
14.5
14.5
18.1
380/3/50
58.1
66.4
49.8
59.7
49.8
62.2
69.7
79.6
62.2
74.7
29.9
39.8
41.5
49.8
39.8
49.8
37.3
49.8
24.9
29.9
34.8
39.8
24.9
33.2
33.2
41.5
6.6
10.0
13.3
19.9
14.9
19.9
19.9
24.9
64**
80**
52**
64**
52**
52**
64**
52**
Heater Access in
41*
41**
64*
64*
64*
64*
80**
64**
80**
10
installation
Table 3 – Coil and Drain Pan (EDL) Heater Amps
Unit Model 208/3/60 230/3/60
2H-546
2H-548
2D-566
2D-568
3C-596
3C-598
2A-646
2A-648
3H-696
3H-698
2G-406
2G-408
2H-466
2H-468
2C-486
2C-488
3G-506
3G-508
1D-286
1D-288
1A-326
1A-328
2G-336
2G-338
2C-396
2C-398
1F-096
1F-098
2F-186
2F-188
1G-206
1G-208
1C-246
1C-248
114.6
141.8
104.9
137.5
110.1
151.0
137.5
170.2
130.6
171.4
72.2
88.5
87.3
114.6
88.5
121.2
89.7
110.1
53.0
69.3
69.3
85.6
60.1
73.7
73.7
100.9
18.4
23.8
36.8
47.7
36.6
44.8
44.8
61.1
126.7
156.8
115.9
152.1
121.8
167.0
152.1
188.2
144.4
189.5
79.8
97.9
96.6
126.7
97.9
134.0
99.2
121.8
58.6
76.6
76.6
94.7
66.4
81.5
81.5
111.6
20.3
26.4
40.7
52.7
40.5
49.5
49.5
67.6
575/3/60
50.7
62.7
46.4
60.8
48.7
66.8
60.8
75.3
57.7
75.8
31.9
39.1
38.6
50.7
39.1
53.6
39.7
48.7
23.4
30.6
30.6
37.9
26.6
32.6
32.6
44.6
8.1
10.5
16.3
21.1
16.2
19.8
19.8
27.0
460/3/60
63.3
78.4
58.0
76.0
60.9
83.5
76.0
94.1
72.2
94.8
39.9
48.9
48.3
63.3
48.9
67.0
49.6
60.9
29.3
38.3
38.3
47.3
33.2
40.7
40.7
55.8
10.2
13.2
20.3
26.4
20.2
24.8
24.8
33.8
*Heater removal is required at the refrigerant connection end of the unit
**Heater removal is required at both ends of the unit
380/3/50
69.8
86.4
63.9
83.8
67.1
92.0
83.8
103.7
79.5
104.4
43.9
53.9
53.2
69.8
53.9
73.8
54.6
67.1
32.2
42.2
42.2
52.2
36.6
44.9
44.9
61.5
11.2
14.5
22.4
29.0
22.3
27.3
27.3
37.2
64**
80**
52**
64**
52**
52**
64**
52**
Heater Access in
41*
41**
64*
64*
64*
64*
80**
64**
80**
11
installation
7.3 SUGGESTED NO DEFROST REQUIREMENT
SEQUENCE OF OPERATION
Used for units with a suction temperature above freezing.
A. When the room thermostat calls for cooling, refrigerant begins flowing to the unit.
B. The fan motor is energized.
C. When the thermostat is satisfied, refrigerant stops flowing to the unit.
D. The fan motor continues to run until the refrigerant is completely boiled out of the tubes, then the fan motor is de-energized.
7.4 SUGGESTED AIR DEFROST SEQUENCE OF
OPERATION
Used for units with a suction temperature below freezing, but a room temperature above 36°F.
A. A defrost timer is wired into the fan motor controls.
B. The timer turns off the liquid line solenoid valve at a predetermined time.
C. The refrigerant in the unit boils off, continuing the cooling cycle.
D. When the refrigerant is completely boiled out of the unit, the fan motor continues to operate so that the room air temperature melts the coil frost.
E. At a second predetermined time the timer energizes the liquid line solenoid valve.
The timer settings are to be programmed per the need of the job site.
7.5 SUGGESTED ELECTRIC DEFROST SEQUENCE OF
OPERATION
Used for units with a suction temperature below freezing. The
Electric Defrost cycle is time clock initiated and temperature terminated. Two to three defrost cycles per 24 hour period are typical. The following sequence is based on the Paragon 8145 or equal time clock.
A. Power is supplied to the defrost timer.
B. The defrost termination thermostat is off and the defrost heaters are off.
C. The unit operates in cooling mode.
D. Upon initiation of the defrost cycle the time clock turns off the liquid line solenoid valve.
E. After a site determined time period the timer de-energizes the fan motor and energizes the defrost heaters.
F. The heaters, positioned within the coil turbo spacers in the fin pack, heat up the fins directly to melt the accumulated frost.
G. When the coil reaches the temperature setting of the defrost termination thermostat the thermostat closes, telling the defrost timer to cut off power to the heaters.
H. The defrost timer energizes the liquid line solenoid valve, allowing refrigerant to flow into the unit, cooling the coil and refreezing any remaining condensate drops that are still present.
I. The fan motor is started through the fan delay thermostat temperature setting, putting the unit in the cooling cycle.
The timer settings and the adjustable defrost termination fan delay thermostat settings are to be programmed per the need of the job site.
12
installation
7.6 SUGGESTED HOT GAS DEFROST SEQUENCE OF
OPERATION
Used for units with a suction temperature below freezing. The
Hot Gas Defrost cycle is time clock initiated and terminated. The following sequence is based on the Hansen Frost Master or equal time clock.
A. Power is supplied to the defrost timer.
B. The unit operates in the cooling cycle.
C. Upon initiation of the defrost cycle, the defrost time clock turns off the liquid line solenoid valve. The fan motor continues to operate to boil off the remaining refrigerant in the coil tubes.
D. After a predetermined time period the defrost timer deenergizes the fan motor and energizes the hot gas supply solenoid valve.
E. Hot gas flows into the unit and warms up the tubes and fins
(and drain pan if an HGU unit), melting the accumulated frost.
F. Approximately ten minutes after starting the hot gas defrost cycle the defrost time clock should de-energize the hot gas supply solenoid valve. If the unit is in defrost for a much longer period of time the condensate on the tubes and fins could “steam” and refreeze on the fan cabinet, fan(s), or shaft causing maintenance problems.
G. The defrost time clock should allow the coil to vent, allowing any remaining gas to escape the coil.
H. The defrost timer energizes the liquid line solenoid valve allowing refrigerant to flow into the unit, cooling the coil and refreezing any remaining condensate drops that are still present.
I. The fan motor is energized after a preset fan delay in the time clock and the unit is in the cooling cycle.
The timer settings are to be programmed per the need of the job site.
7.7 SUGGESTED WATER DEFROST SEQUENCE OF
OPERATION
Used for units with a suction temperature below freezing. The
Water Defrost cycle is time clock initiated and terminated.
A. Power is supplied to the defrost timer.
B. The unit operates in the cooling cycle.
C. Upon initiation of the defrost cycle, the defrost time clock turns off the liquid line solenoid valve. The fan motor continues to operate to boil off the remaining refrigerant in the coil tubes.
D. After a predetermined time period the defrost timer deenergizes the fan motor and energizes the water supply solenoid valve.
E. Water flows onto the unit and warms up the tubes, fins, and drain pan, melting the accumulated frost.
F. Approximately ten minutes after starting the water defrost cycle the defrost time clock should de-energize the water supply solenoid valve.
G. The defrost time clock should allow the remaining water to drip off of the coil surface.
H. The defrost timer energizes the liquid line solenoid valve allowing refrigerant to flow into the unit, cooling the coil and refreezing any remaining condensate drops that are still present.
I. The fan motor is energized after a preset fan delay in the time clock and the unit is in the cooling cycle. The timer settings are to be programmed per the need of the job site.
The timer settings are to be programmed per the need of the job site.
13
operation
8.0 OPERATION
8.1 PRE-STARTUP
After the installation is completed, a review of the following items should be preformed before the system is placed into operation:
AA. Check electrical connections, sheave bushing set screws, motor mount bolts, belt guard, flange bolts, and all other fasteners for tightness. If required, be sure the thermostatic expansion valve bulb is properly located, strapped, and insulated.
B. For systems with a defrost time clock check the timer to see that it is set for the correct time of day and the starting pins have been installed (normally two or three sets per day).
Defrost should be scheduled when the freezer doors are not likely to be open.
C. When the unit is first started the room temperature is typically above the opening temperature of the fan delay thermostat, if a fan delay thermostat is provided for Electric Defrost units
(see that particular unit electrical diagram). The fans may remain off for a lengthy period of time. To prevent this delay it is permissible to install a temporary jumper wire between terminals that contain the Red and Blue wires from the fan delay thermostat. Once the room temperature is below +25°F the jumper wire should be removed.
D. Make sure that the grease lines to the bearings are filled with grease. See the Maintenance section for recommended grease types.
8.2 OPERATION CHECKOUT
With the system operating, check the supply voltage. The voltage must be within +/- 10% of the voltage marked on the unit nameplate and the phase to phase unbalance should be 2% or less.
Check the room THERMOSTAT setting. Be sure it functions properly.
For RECIRCULATED refrigeration systems the hand expansion valve should be opened slowly until either condensate or frost forms on the return bends from the bottom to the top of the coil.
For FLOODED refrigeration systems check to make sure the float valve is working properly and fills the surge drum to the appropriate level and will allow refrigerant into the drum when the liquid level is sufficiently low.
For DIRECT EXPANSION systems let the system balance out at the desired room temperature and check the operation of the expansion valve by properly measuring the superheat at the sensing bulb. As much as thirty minutes may be required for the new balance to take place after an adjustment is made.
For BRINE or WATER COOLING systems keep the closest vent open while the fluid fills the coil to allow trapped air to escape.
Close the valve once fluid flows out of the valve and check for water hammer in the coil.
With HOT GAS DEFROST systems allow the coil to frost, then manually advance the defrost timer to initiate a defrost cycle.
Observe the defrost cycle to see if all controls are functioning properly and that the coil is clear of all frost before the system returns to refrigeration. Adjust the time clock pins if necessary.
Reset the defrost timer to the correct time of day. A defrost cycle is only needed with the frost build up is such that it impedes the airflow through the coil. The defrost requirements will vary on each installation and may change depending on the time of the year and other conditions.
With ELECTRIC DEFROST systems allow the coil to frost then manually advance the defrost timer to initiate a defrost. Observe the defrost cycle to see if all controls are functioning properly and that the coil is clear of all frost before the system returns to refrigeration.
Adjust the time clock pins if necessary. Reset the defrost timer to the correct time of day. A defrost cycle is only needed with the frost build up is such that it impedes the airflow through the coil.
The defrost requirements will vary on each installation and may change depending on the time of the year and other conditions.
With WATER DEFROST systems allow the coil to frost then manually advance the defrost timer to initiate a defrost cycle. Observe the defrost cycle to see if all controls are functioning properly and that the coil is clear of all frost before the system returns to refrigeration.
Adjust the time clock pins if necessary. Reset the defrost timer to the correct time of day. A defrost cycle is only needed with the frost build up is such that it impedes the airflow through the coil.
The defrost requirements will vary on each installation and may change depending on the time of the year and other conditions.
LISTEN CAREFULLY to the unit to make sure there are no unusual sounds. Sounds such as the belts squealing, the bearings running dry, the fan(s) scraping on the housing, the sheaves scraping against the belt guard, or loose fasteners allowing parts to rattle need to be addressed immediately before continued unit operation.
14
maintenance
9 MAINTENANCE
A preventive maintenance schedule should be set up as soon as the FL Series unit is installed. The unit should be inspected periodically for proper operation and build up of soil.
WARNING: All power must be off before cleaning or maintenance is performed.
9.1 DRAIN PAN
Inspect and clean the drain pan to insure free drainage of condensate. The drain pan should be cleaned regularly with warm water and soap.
If the drain pan section of the unit needs to be replaced note that there are two separate pans on each FL Series unit. If the drain pan uses hot gas defrost make sure the unit is completely pumped out and isolated with hand valves to prevent refrigerant from escaping to the atmosphere. Remove the hot gas piping or electric wires if the unit has a hot gas or an electric defrost drain pan. Remove the drain line(s) so that they are out of the way of the pan(s) when the pan(s) are being removed. Remove the drain pan attachment bolts from the support legs, the screws attaching the center “V” shaped cap, and the cap. Slowly slide one pan out from the unit, then the other if required. Support the pan from underneath with a minimum of two 4x4s for one and two fan units or two 6x6s for three and four fan units so that the outer sheetmetal skin does not buckle and become damaged. Assemble pan(s) in reverse order.
Replace hot gas interpiping gaskets before tightening flange bolts.
9.2 COIL AND CABINET
Clean the coil, fan cabinet, fan(s), and belt guard with warm water and soap.
The evaporator coil should be checked once a month for proper defrosting. Many variables affect coil frosting such as room temperature, type of product being stored or processed, how often new product is brought in, and the length of time the door to the room remains open. Summer conditions of high humidity can cause heavier frost loads and it may be necessary to change the number of defrost cycles seasonally.
9.3 BEARINGS
The use of ball bearings to support the fan shaft will require periodic greasing of the bearings. Greasing should take place between 6 to
12 months for normal duty service and 1 to 6 months for severe duty service, according to site conditions. When greasing use
Chevron RRM Arctic, Esso Beacon #325 or equivalent grease.
Use a low pressure, not high pressure, gun to avoid over lubrication or destruction of the bearing seals.
9.4 MOTOR
If it becomes necessary to add lubricant to the factory furnished motor, follow the motor manufacturers lubrication instructions.
9.5 BELT DRIVE
Inspect motor driven belts for normal wear pattern. If necessary adjust the motor mount to provide approximately one inch of belt
“free-play”. If replacing a belt is necessary, all belts on the same FL
Series unit must be replaced. Remove the belt guard and adjust the motor mount to allow the belt enough “free-play” to be easily removed. Install the new belts as described in section 2.4. Replace the belt guard. After 24 to 48 hours of operation, again check the belt “free-play” and adjust the motor mount as necessary.
9.6 ELECTRIC DEFROST HEATERS
Inspect the electric defrost heater ends to determine if they are operating. A heater will be operating properly when the heater is observed to be glowing during the defrost cycle. If a heater rod is cold during the defrost cycle it will need to be replaced.
Coil heaters require horizontal removal from one end of the unit.
On two or three fan units heater rods are on both ends of the unit.
Remove heater wire from terminal block and note where original wires were located. Rotate the heater rod so that the heater and retainer clip can be slid through the coil endplate slot. Remove clip from the old heater rod and install on the new heater rod in approximately the same location as the original heater. Install new heater rod in the coil original coil slot, rotate the rod 90°, and replace the wires in the positions of the original wires in the terminal block.
Drain pan heaters do not require the drain pan to be removed.
Remove the heater wires from the terminal block(s). Remove the nuts from the heater hold down brackets and remove the brackets.
Replace the heater then replace the hold down brackets. Rewire the heaters in the original terminal block(s).
9.7 FAN SHAFT
The fan shaft usually does not require any maintenance. If a shaft is determined to be damaged and needs to be replaced, remove the belt guard, belts, and sheave. After any safety collar, bushing, or setscrew is loosened from the shaft removal process file any metal burr that may be present on the shaft. Burr removal prevents damage to the bearing bore surface as the shaft is removed from the bearing. Remove the small curved deflector plate from in front of the blower wheel and place a support between the blower wheel and the coil, so the coil will support the wheel when the shaft is removed. Remove bearings and bearing support plates. Remove shaft horizontally from unit. Install new shaft in the reverse order.
➠
15
maintenance
10 REPLACEMENT PARTS LIST
Listed below are the major replacement parts of the standard FL
Series units. The sheaves, bushings, and belts are sized per project, requiring the specific unit model number and serial number for proper replacement part selection. Call sales representative or factory to identify replacement parts.
5
7.5
10
15
1
1.5
2
3
20
25
Table 4 – Standard Motor
Motor hp
230/460V
E314167
E311896
11517
11519
11520
11092T
E311619
E312051
E312696
E312664
Part Number
575V call call call
E315514
E311765
E311388
E313891
E312564 call call
380V call call
E315714
E314373
E313616
E313212
E312978
E313211 call
E313653
Table 5 – Fan Wheels and Housings
Part Number
Fan Number
Wheel
G
H
E
F
C
D
A
B
E312163
E312370
E311189
E311964
E312368
11286
E312288
E312372
Housing
E312164
E312371
E311188
E311963
Table 6 – Fan Shaft and Bearing
Unit Size
1 Fan ( 09 )
1 Fan ( 20, 24, 28, 32 )
2 Fan ( 18 )
2 Fan (31, 33, 39, 46, 54 )
2 Fan ( 40, 48, 56, 64, 67 )
3 Fan ( 47, 50, 59, 69, 81 )
3 Fan ( 60, 72, 85, 96, 99 )
4 Fan ( 62, 77, 93, 109 )
Shaft
E315682
E312304
E315683
E312011
E312012
E312252 and E312343
E312344 and E312251
(2)E312343
Part Number
Motor End Bearing
10509
Opposite End Bearing
10509
10510
10509
10510
10510
10177
10509
10177
10177
E312297
E312297
E312297
10177
10177
E312297
Internal Bearing
E312608
E312608
E312608
E312369
11287
E312289
E312373
16
maintenance
Table 7 – 230 and 460 Volt Electric Defrost Heaters
Unit Size
Coil Heater ED Unit quantity
Coil Heater EDL Unit quantity
09 6 ROW
09 8 ROW
18 6 ROW
6
9
12
9
12
18
18 8 ROW
20 6 ROW
20 8 ROW
24 6 ROW
24 8 ROW
28 6 ROW
28 8 ROW
32 6 ROW
32 8 ROW
33 6 ROW
33 8 ROW
39 6 ROW
39 8 ROW
40 6 ROW
40 8 ROW
46 6 ROW
46 8 ROW
48 6 ROW
48 8 ROW
50 6 ROW
18
9
12
12
15
15
18
21
24
18
24
24
30
18
24
30
36
24
30
18
24
12
15
15
21
18
50 8 ROW
54 6 ROW
54 8 ROW
56 6 ROW
56 8 ROW
59 6 ROW
59 8 ROW
64 6 ROW
36
24
30
42
24
42
48
30
48
30
42
48
30
48
60
36
64 8 ROW
69 6 ROW
69 8 ROW
48
30
36
60
36
48
Consult factory for heaters with voltages other than 230 or 460 volt.
30
36
48
30
42
24
30
30
42
24
24
24
30
24
230/3/60
Coil Heater part number
E312491
E312491
E312491
E312491
E311562
E311562
E311562
E311562
E311562
E311562
E311562
E311562
17784
17784
17784
17784
E311562
E311562
17784
17784
E311562
E311562
17785
17785
17784
17784
E311562
E311562
17785
17785
E311562
E311562
17785
17785
Defrost Termination Thermostat: Part Number E205004
Table 8 – Drain Pan – call
460/3/60
Coil Heater part number
E313973
E313973
E313973
E313973
E311099
E311099
E311099
E311099
E311099
E311099
E311099
E311099
17781
17781
17781
17781
E311099
E311099
17781
17781
E311099
E311099
17782
17782
17781
17781
E311099
E311099
17782
17782
E311099
E311099
17782
17782
Drain Pan Heater quantity
230/3/60
Drain Pan Heater part number
460/3/60
Drain Pan Heater part number
6
6
6
6
6
6
6
6
6
6
3
6
3
3
3
3
3
3
6
3
6
6
6
6
6
6
6
6
6
6
6
3
3
6
21756
21756
21756
21756
E312205
E312205
E312205
E312205
E312205
E312205
E312205
E312205
21759
21759
21759
21759
21760
21760
21759
21759
21760
21760
21761
21761
21759
21759
21760
21760
21761
21761
21760
21760
21761
21761
21762
21762
21762
21762
E312206
E312206
E312206
E312206
E312206
E312206
E312206
E312206
21765
21765
21765
21765
21766
21766
21765
21765
21766
21766
21767
21767
21765
21765
21766
21766
21767
21767
21766
21766
21767
21767
17
maintenance
MAINTENANCE TABLE
Date Performed
Drain Pan
Inspection and
Cleaning
Cabinet and
Coil Inspection and Cleaning
Motor Inspection
Fan Inspection
Electric Heater
Inspection
Water Defrost
Pan Inspection
18
19
SPX COOLING TECHNOLOGIES, INC.
827 WEST PROGRESS DRIVE
DIXON, IL 61021 USA
815 284 2700 | [email protected]
spxcooling.com
E319066 | ISSUED 02/2020
©2020 SPX COOLING TECHNOLOGIES, INC | ALL RIGHTS RESERVED
In the interest of technological progress, all products are subject to design and/or material change without notice.
FL Series
U S E R MAN UAL
advertisement
Related manuals
advertisement
Table of contents
- 3 1 Receipt of Equipment
- 3 1.2 Loss of Gas Holding Charge
- 3 2 Assembly of Components
- 3 2.1 Shipped Loose Parts
- 3 2.3 Belt Attachment
- 3 2.4 Belt Tensioning
- 4 2.5 Belt Guard
- 4 2.6 Bearing Grease
- 4 2.7 Air Directional Louvers
- 4 3 Rigging Instructions
- 4 4 Unit Location and Mounting
- 4 4.1 Unit Location
- 4 5 Refrigerant Warning
- 4 6 Piping Installation
- 4 6.1 Drain Line
- 5 6.2 Refrigeration Piping
- 5 6.3 Hot Gas Interpiping
- 6 6.4 Refrigerant Distributor Nozzle
- 6 6.5 Expansion Valve (optional item)
- 6 6.6 Evacuation and Leak Test
- 6 6.7 DXA and Suction Accumulators
- 7 7.1 Field Wiring
- 7 7.2 Electrical Data
- 12 7.3 Suggested No Defrost Requirement Sequence of Operation
- 12 7.4 Suggested Air Defrost Sequence of Operation
- 12 7.5 Suggested Electric Defrost Sequence of Operation
- 13 7.6 Suggested Hot Gas Defrost Sequence of Operation
- 13 7.7 Suggested Water Defrost Sequence Of operation
- 14 8.2 Operation Checkout
- 15 9.1 Drain Pan
- 15 9.2 Coil and Cabinet
- 15 9.5 Belt Drive
- 15 9.6 Electric Defrost Heaters
- 15 9.7 Fan Shaft
- 16 10 Replacement Parts List